Analyzing McDonald's Operations: Capacity, Performance, and Challenges
VerifiedAdded on 2022/12/29
|8
|2071
|52
Report
AI Summary
This report provides a comprehensive analysis of McDonald's operations management. It begins with an introduction to operations management and its importance, followed by an examination of capacity management strategies employed by McDonald's to reconcile capacity and demand, including the use of Just-in-Time (JIT) and demand management techniques. The report then delves into the implementation of the four Ds (Design, Direct, Develop, and Deliver) within the company. Furthermore, it analyzes McDonald's performance objectives, such as customer satisfaction, quality, speed, cost, and technology adoption. The report includes a calculation of average customer waiting time and concludes with a summary of key findings and recommendations for improving delivery time. It also includes a list of references used in the report.
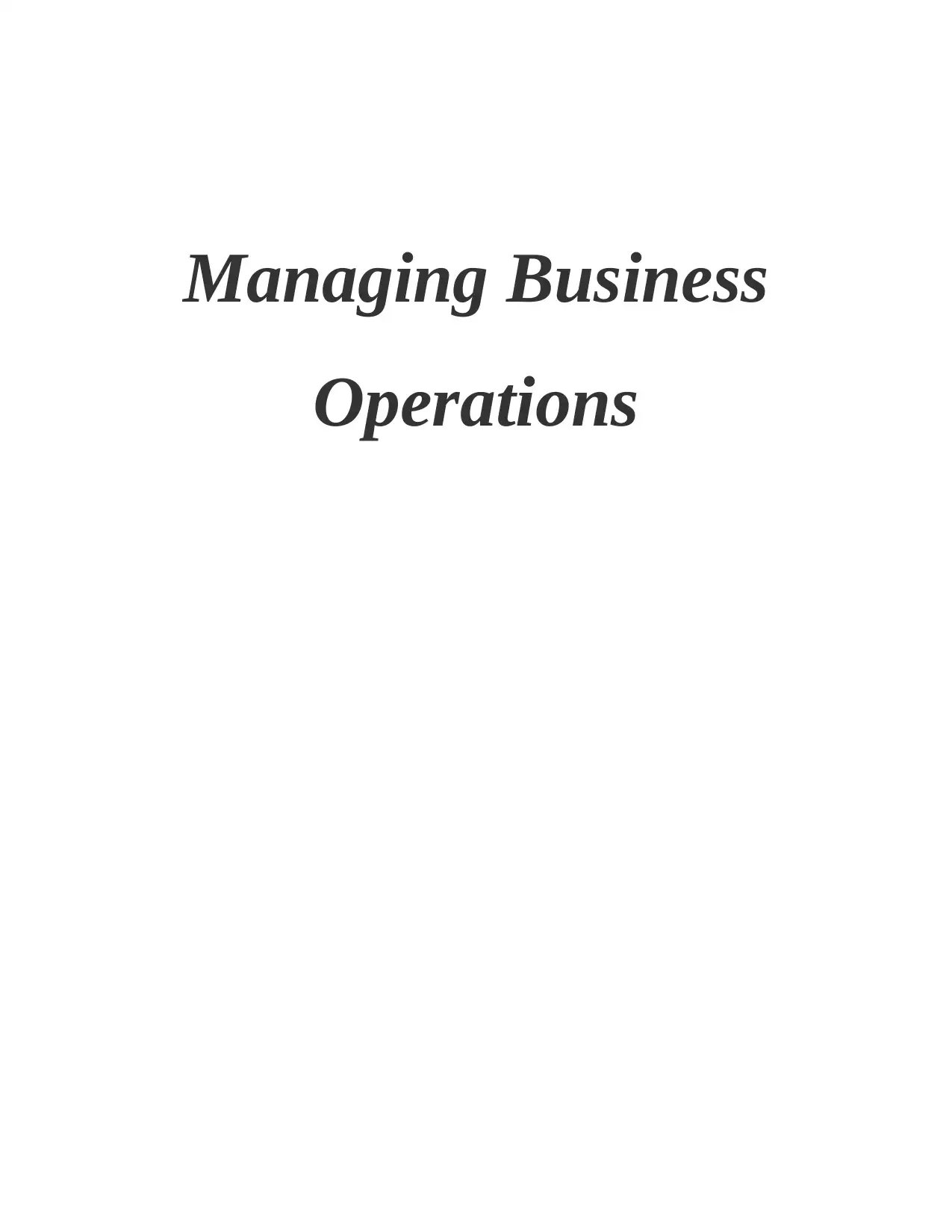
Managing Business
Operations
Operations
Paraphrase This Document
Need a fresh take? Get an instant paraphrase of this document with our AI Paraphraser
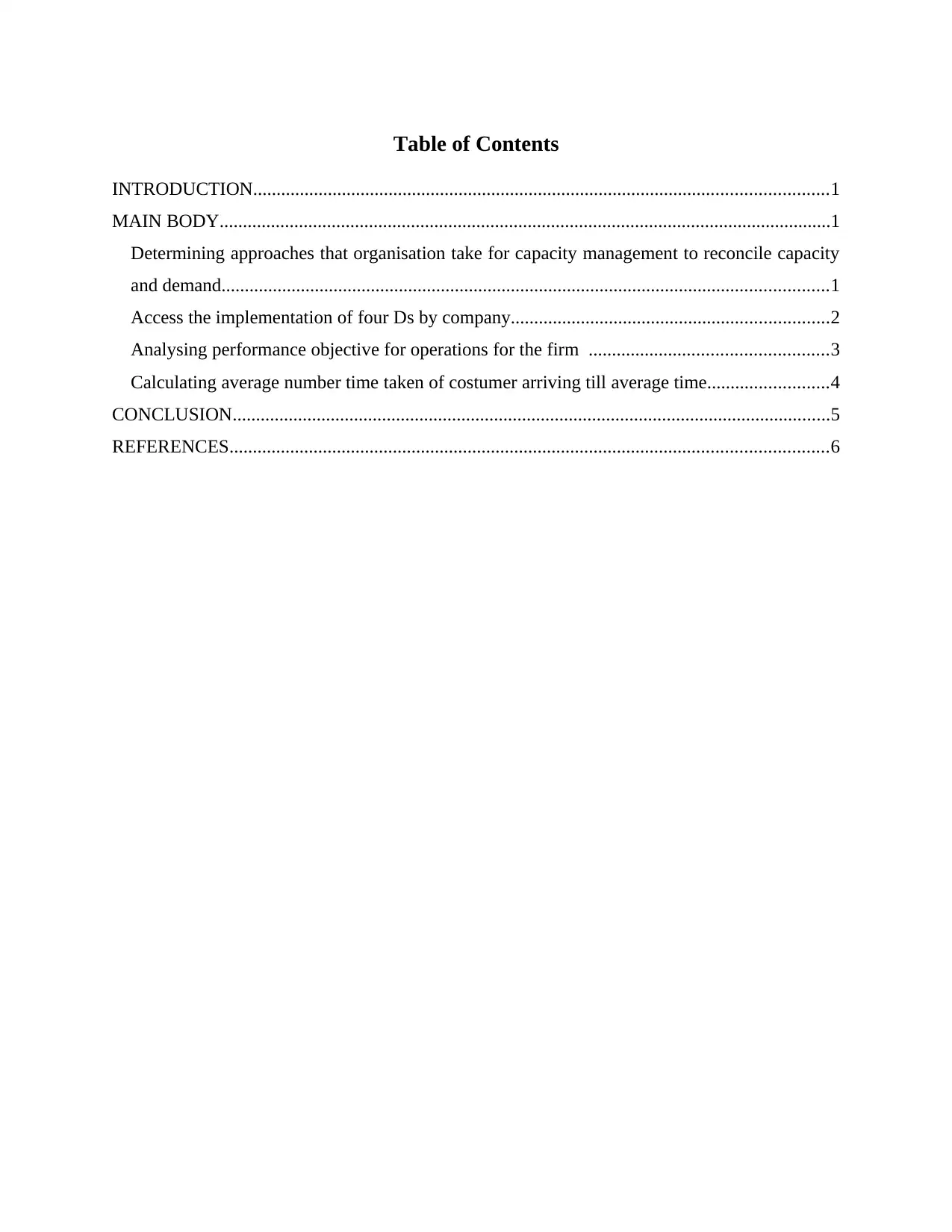
Table of Contents
INTRODUCTION...........................................................................................................................1
MAIN BODY...................................................................................................................................1
Determining approaches that organisation take for capacity management to reconcile capacity
and demand..................................................................................................................................1
Access the implementation of four Ds by company....................................................................2
Analysing performance objective for operations for the firm ...................................................3
Calculating average number time taken of costumer arriving till average time..........................4
CONCLUSION................................................................................................................................5
REFERENCES................................................................................................................................6
INTRODUCTION...........................................................................................................................1
MAIN BODY...................................................................................................................................1
Determining approaches that organisation take for capacity management to reconcile capacity
and demand..................................................................................................................................1
Access the implementation of four Ds by company....................................................................2
Analysing performance objective for operations for the firm ...................................................3
Calculating average number time taken of costumer arriving till average time..........................4
CONCLUSION................................................................................................................................5
REFERENCES................................................................................................................................6
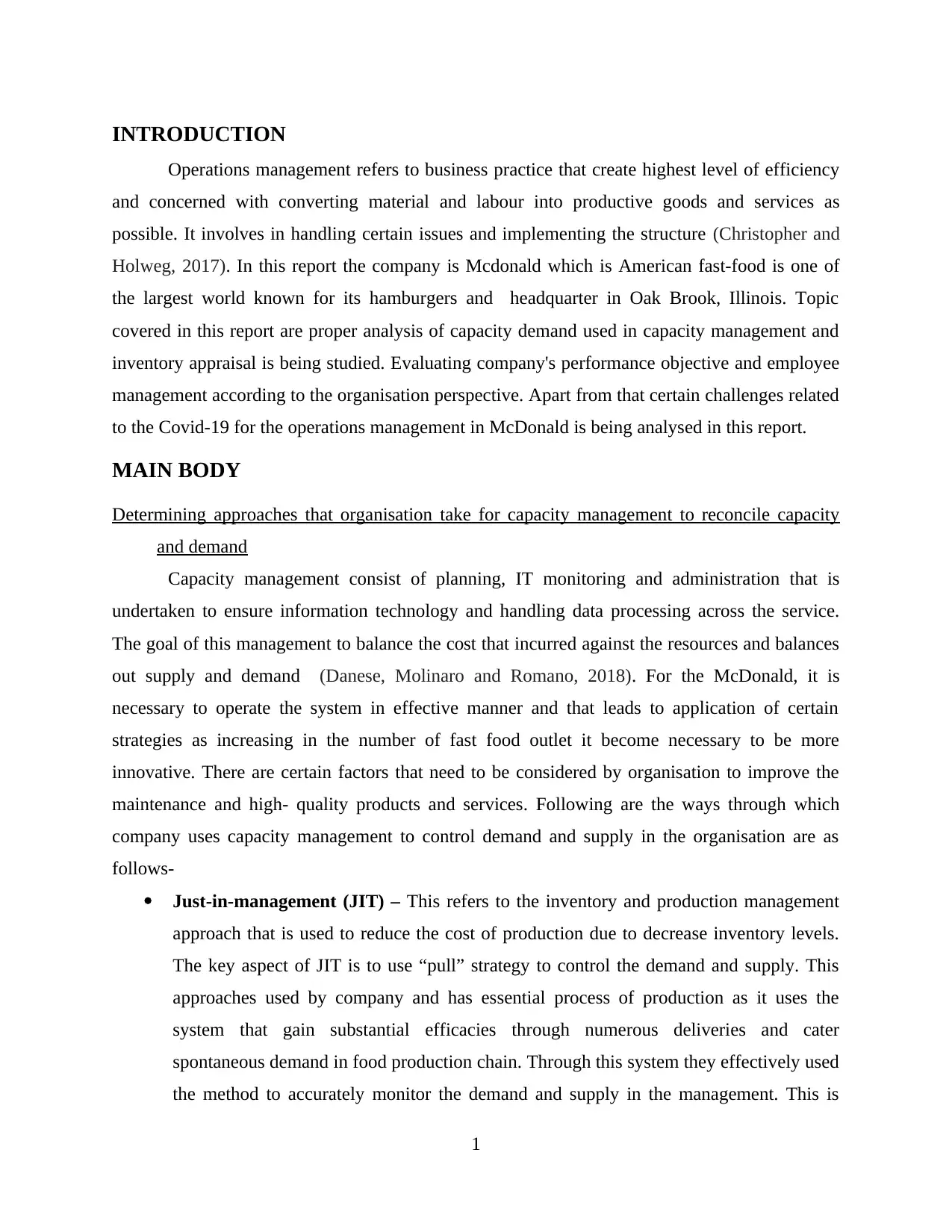
INTRODUCTION
Operations management refers to business practice that create highest level of efficiency
and concerned with converting material and labour into productive goods and services as
possible. It involves in handling certain issues and implementing the structure (Christopher and
Holweg, 2017). In this report the company is Mcdonald which is American fast-food is one of
the largest world known for its hamburgers and headquarter in Oak Brook, Illinois. Topic
covered in this report are proper analysis of capacity demand used in capacity management and
inventory appraisal is being studied. Evaluating company's performance objective and employee
management according to the organisation perspective. Apart from that certain challenges related
to the Covid-19 for the operations management in McDonald is being analysed in this report.
MAIN BODY
Determining approaches that organisation take for capacity management to reconcile capacity
and demand
Capacity management consist of planning, IT monitoring and administration that is
undertaken to ensure information technology and handling data processing across the service.
The goal of this management to balance the cost that incurred against the resources and balances
out supply and demand (Danese, Molinaro and Romano, 2018). For the McDonald, it is
necessary to operate the system in effective manner and that leads to application of certain
strategies as increasing in the number of fast food outlet it become necessary to be more
innovative. There are certain factors that need to be considered by organisation to improve the
maintenance and high- quality products and services. Following are the ways through which
company uses capacity management to control demand and supply in the organisation are as
follows-
Just-in-management (JIT) – This refers to the inventory and production management
approach that is used to reduce the cost of production due to decrease inventory levels.
The key aspect of JIT is to use “pull” strategy to control the demand and supply. This
approaches used by company and has essential process of production as it uses the
system that gain substantial efficacies through numerous deliveries and cater
spontaneous demand in food production chain. Through this system they effectively used
the method to accurately monitor the demand and supply in the management. This is
1
Operations management refers to business practice that create highest level of efficiency
and concerned with converting material and labour into productive goods and services as
possible. It involves in handling certain issues and implementing the structure (Christopher and
Holweg, 2017). In this report the company is Mcdonald which is American fast-food is one of
the largest world known for its hamburgers and headquarter in Oak Brook, Illinois. Topic
covered in this report are proper analysis of capacity demand used in capacity management and
inventory appraisal is being studied. Evaluating company's performance objective and employee
management according to the organisation perspective. Apart from that certain challenges related
to the Covid-19 for the operations management in McDonald is being analysed in this report.
MAIN BODY
Determining approaches that organisation take for capacity management to reconcile capacity
and demand
Capacity management consist of planning, IT monitoring and administration that is
undertaken to ensure information technology and handling data processing across the service.
The goal of this management to balance the cost that incurred against the resources and balances
out supply and demand (Danese, Molinaro and Romano, 2018). For the McDonald, it is
necessary to operate the system in effective manner and that leads to application of certain
strategies as increasing in the number of fast food outlet it become necessary to be more
innovative. There are certain factors that need to be considered by organisation to improve the
maintenance and high- quality products and services. Following are the ways through which
company uses capacity management to control demand and supply in the organisation are as
follows-
Just-in-management (JIT) – This refers to the inventory and production management
approach that is used to reduce the cost of production due to decrease inventory levels.
The key aspect of JIT is to use “pull” strategy to control the demand and supply. This
approaches used by company and has essential process of production as it uses the
system that gain substantial efficacies through numerous deliveries and cater
spontaneous demand in food production chain. Through this system they effectively used
the method to accurately monitor the demand and supply in the management. This is
1
⊘ This is a preview!⊘
Do you want full access?
Subscribe today to unlock all pages.

Trusted by 1+ million students worldwide

appropriate way to use and it also consider as beneficial for the organisation as this
facilitates in proper supply of food to right place with the use of this approach (Exler,
Mendling and Taudes, 2019). Some important steps that need to be taken to resolve the
issue of meeting current demand with forecasted and projected supply of food items.
McDonald is offering the services and it is essential to deliver the goods and services
accordingly and satisfy the goods and services to cater the needs of costumer.
Demand management- In McDonald they were using this strategy to create an
appropriate demand that need to have the stock of such product and link directly to the
costumer. In this strategy it create the high profit and high level of production in food
management of company and helps in the growth of company (Zhang and et.al., 2020).
McDonald is usually able to fulfil the demand with the help of supply chain management
and will facilitates in executing the plan and satisfy the needs of supply and demand for
the company.
Access the implementation of four Ds by company
For every company the need to consider these factors is essential to study and to meet the
following demand of costumer and maintaining the efficiency in the management is also
important. For the company McDonald the four Ds are discussed below-
Design- This is part of product that is consider to attract the costumer and every
organisation is try to build best design for their respective goods and service (Gupta and
Singh, 2020). In this they used to maintain the design process and it require lots of
reteach and efforts to decide catchy design. For the McDonald, this is important decision
while deciding appropriate design and getting the cost optimization in the management
process.
Direct- This concern with guiding the employees to direct the process ad ensuring that
everything is done as per the direction. In the McDonald there are many system that uses
to consider the different processes and responsible for delivery to its costumer and
regulating that everything is happening as per the standards. For such big organisation
this is core system to control all system and make sure that everything is successful in
achieving the desired objectives.
Develop- It consist of developing the effective strategies and concept to provide better
services to costumer and giving best product to meet the demands of costumer. This is
2
facilitates in proper supply of food to right place with the use of this approach (Exler,
Mendling and Taudes, 2019). Some important steps that need to be taken to resolve the
issue of meeting current demand with forecasted and projected supply of food items.
McDonald is offering the services and it is essential to deliver the goods and services
accordingly and satisfy the goods and services to cater the needs of costumer.
Demand management- In McDonald they were using this strategy to create an
appropriate demand that need to have the stock of such product and link directly to the
costumer. In this strategy it create the high profit and high level of production in food
management of company and helps in the growth of company (Zhang and et.al., 2020).
McDonald is usually able to fulfil the demand with the help of supply chain management
and will facilitates in executing the plan and satisfy the needs of supply and demand for
the company.
Access the implementation of four Ds by company
For every company the need to consider these factors is essential to study and to meet the
following demand of costumer and maintaining the efficiency in the management is also
important. For the company McDonald the four Ds are discussed below-
Design- This is part of product that is consider to attract the costumer and every
organisation is try to build best design for their respective goods and service (Gupta and
Singh, 2020). In this they used to maintain the design process and it require lots of
reteach and efforts to decide catchy design. For the McDonald, this is important decision
while deciding appropriate design and getting the cost optimization in the management
process.
Direct- This concern with guiding the employees to direct the process ad ensuring that
everything is done as per the direction. In the McDonald there are many system that uses
to consider the different processes and responsible for delivery to its costumer and
regulating that everything is happening as per the standards. For such big organisation
this is core system to control all system and make sure that everything is successful in
achieving the desired objectives.
Develop- It consist of developing the effective strategies and concept to provide better
services to costumer and giving best product to meet the demands of costumer. This is
2
Paraphrase This Document
Need a fresh take? Get an instant paraphrase of this document with our AI Paraphraser
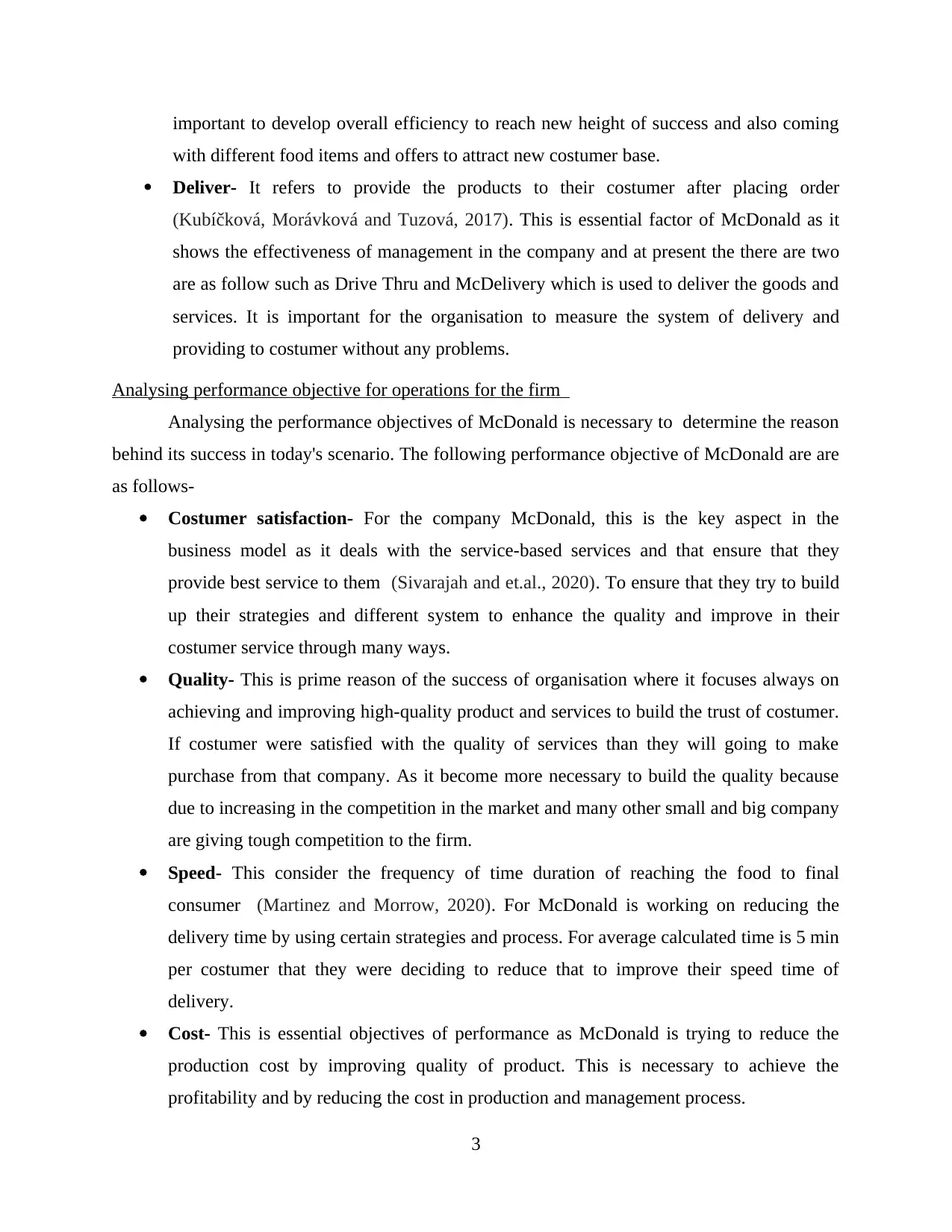
important to develop overall efficiency to reach new height of success and also coming
with different food items and offers to attract new costumer base.
Deliver- It refers to provide the products to their costumer after placing order
(Kubíčková, Morávková and Tuzová, 2017). This is essential factor of McDonald as it
shows the effectiveness of management in the company and at present the there are two
are as follow such as Drive Thru and McDelivery which is used to deliver the goods and
services. It is important for the organisation to measure the system of delivery and
providing to costumer without any problems.
Analysing performance objective for operations for the firm
Analysing the performance objectives of McDonald is necessary to determine the reason
behind its success in today's scenario. The following performance objective of McDonald are are
as follows-
Costumer satisfaction- For the company McDonald, this is the key aspect in the
business model as it deals with the service-based services and that ensure that they
provide best service to them (Sivarajah and et.al., 2020). To ensure that they try to build
up their strategies and different system to enhance the quality and improve in their
costumer service through many ways.
Quality- This is prime reason of the success of organisation where it focuses always on
achieving and improving high-quality product and services to build the trust of costumer.
If costumer were satisfied with the quality of services than they will going to make
purchase from that company. As it become more necessary to build the quality because
due to increasing in the competition in the market and many other small and big company
are giving tough competition to the firm.
Speed- This consider the frequency of time duration of reaching the food to final
consumer (Martinez and Morrow, 2020). For McDonald is working on reducing the
delivery time by using certain strategies and process. For average calculated time is 5 min
per costumer that they were deciding to reduce that to improve their speed time of
delivery.
Cost- This is essential objectives of performance as McDonald is trying to reduce the
production cost by improving quality of product. This is necessary to achieve the
profitability and by reducing the cost in production and management process.
3
with different food items and offers to attract new costumer base.
Deliver- It refers to provide the products to their costumer after placing order
(Kubíčková, Morávková and Tuzová, 2017). This is essential factor of McDonald as it
shows the effectiveness of management in the company and at present the there are two
are as follow such as Drive Thru and McDelivery which is used to deliver the goods and
services. It is important for the organisation to measure the system of delivery and
providing to costumer without any problems.
Analysing performance objective for operations for the firm
Analysing the performance objectives of McDonald is necessary to determine the reason
behind its success in today's scenario. The following performance objective of McDonald are are
as follows-
Costumer satisfaction- For the company McDonald, this is the key aspect in the
business model as it deals with the service-based services and that ensure that they
provide best service to them (Sivarajah and et.al., 2020). To ensure that they try to build
up their strategies and different system to enhance the quality and improve in their
costumer service through many ways.
Quality- This is prime reason of the success of organisation where it focuses always on
achieving and improving high-quality product and services to build the trust of costumer.
If costumer were satisfied with the quality of services than they will going to make
purchase from that company. As it become more necessary to build the quality because
due to increasing in the competition in the market and many other small and big company
are giving tough competition to the firm.
Speed- This consider the frequency of time duration of reaching the food to final
consumer (Martinez and Morrow, 2020). For McDonald is working on reducing the
delivery time by using certain strategies and process. For average calculated time is 5 min
per costumer that they were deciding to reduce that to improve their speed time of
delivery.
Cost- This is essential objectives of performance as McDonald is trying to reduce the
production cost by improving quality of product. This is necessary to achieve the
profitability and by reducing the cost in production and management process.
3
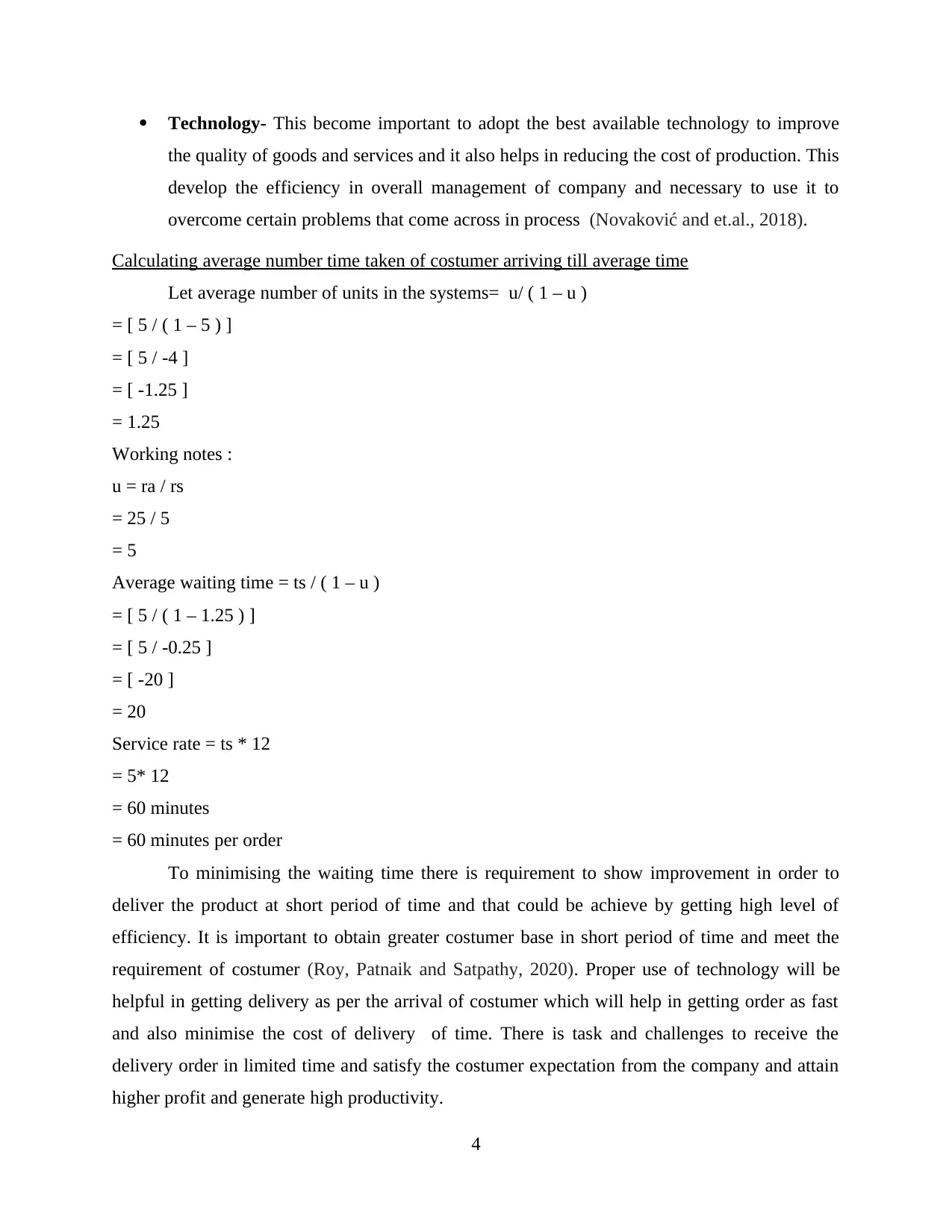
Technology- This become important to adopt the best available technology to improve
the quality of goods and services and it also helps in reducing the cost of production. This
develop the efficiency in overall management of company and necessary to use it to
overcome certain problems that come across in process (Novaković and et.al., 2018).
Calculating average number time taken of costumer arriving till average time
Let average number of units in the systems= u/ ( 1 – u )
= [ 5 / ( 1 – 5 ) ]
= [ 5 / -4 ]
= [ -1.25 ]
= 1.25
Working notes :
u = ra / rs
= 25 / 5
= 5
Average waiting time = ts / ( 1 – u )
= [ 5 / ( 1 – 1.25 ) ]
= [ 5 / -0.25 ]
= [ -20 ]
= 20
Service rate = ts * 12
= 5* 12
= 60 minutes
= 60 minutes per order
To minimising the waiting time there is requirement to show improvement in order to
deliver the product at short period of time and that could be achieve by getting high level of
efficiency. It is important to obtain greater costumer base in short period of time and meet the
requirement of costumer (Roy, Patnaik and Satpathy, 2020). Proper use of technology will be
helpful in getting delivery as per the arrival of costumer which will help in getting order as fast
and also minimise the cost of delivery of time. There is task and challenges to receive the
delivery order in limited time and satisfy the costumer expectation from the company and attain
higher profit and generate high productivity.
4
the quality of goods and services and it also helps in reducing the cost of production. This
develop the efficiency in overall management of company and necessary to use it to
overcome certain problems that come across in process (Novaković and et.al., 2018).
Calculating average number time taken of costumer arriving till average time
Let average number of units in the systems= u/ ( 1 – u )
= [ 5 / ( 1 – 5 ) ]
= [ 5 / -4 ]
= [ -1.25 ]
= 1.25
Working notes :
u = ra / rs
= 25 / 5
= 5
Average waiting time = ts / ( 1 – u )
= [ 5 / ( 1 – 1.25 ) ]
= [ 5 / -0.25 ]
= [ -20 ]
= 20
Service rate = ts * 12
= 5* 12
= 60 minutes
= 60 minutes per order
To minimising the waiting time there is requirement to show improvement in order to
deliver the product at short period of time and that could be achieve by getting high level of
efficiency. It is important to obtain greater costumer base in short period of time and meet the
requirement of costumer (Roy, Patnaik and Satpathy, 2020). Proper use of technology will be
helpful in getting delivery as per the arrival of costumer which will help in getting order as fast
and also minimise the cost of delivery of time. There is task and challenges to receive the
delivery order in limited time and satisfy the costumer expectation from the company and attain
higher profit and generate high productivity.
4
⊘ This is a preview!⊘
Do you want full access?
Subscribe today to unlock all pages.

Trusted by 1+ million students worldwide
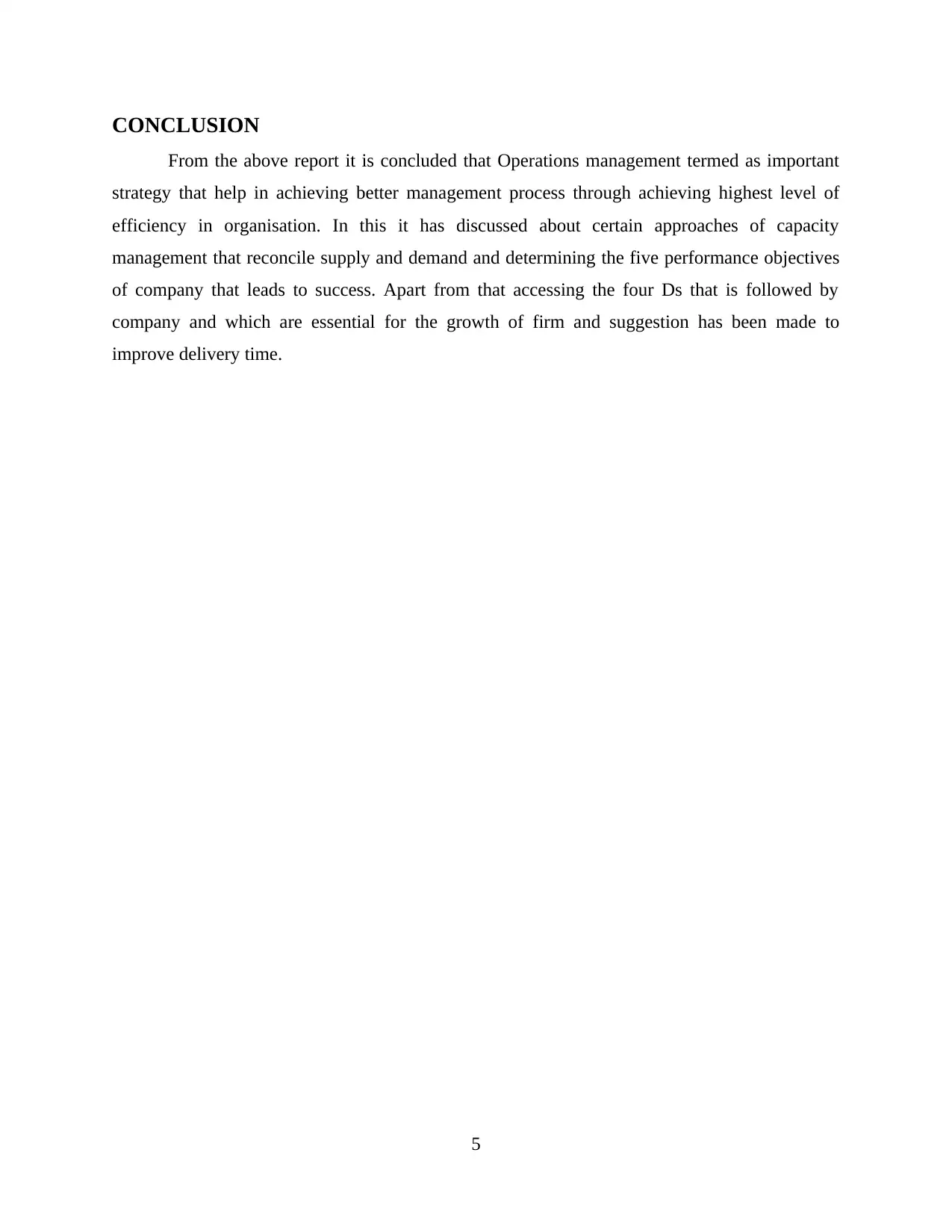
CONCLUSION
From the above report it is concluded that Operations management termed as important
strategy that help in achieving better management process through achieving highest level of
efficiency in organisation. In this it has discussed about certain approaches of capacity
management that reconcile supply and demand and determining the five performance objectives
of company that leads to success. Apart from that accessing the four Ds that is followed by
company and which are essential for the growth of firm and suggestion has been made to
improve delivery time.
5
From the above report it is concluded that Operations management termed as important
strategy that help in achieving better management process through achieving highest level of
efficiency in organisation. In this it has discussed about certain approaches of capacity
management that reconcile supply and demand and determining the five performance objectives
of company that leads to success. Apart from that accessing the four Ds that is followed by
company and which are essential for the growth of firm and suggestion has been made to
improve delivery time.
5
Paraphrase This Document
Need a fresh take? Get an instant paraphrase of this document with our AI Paraphraser
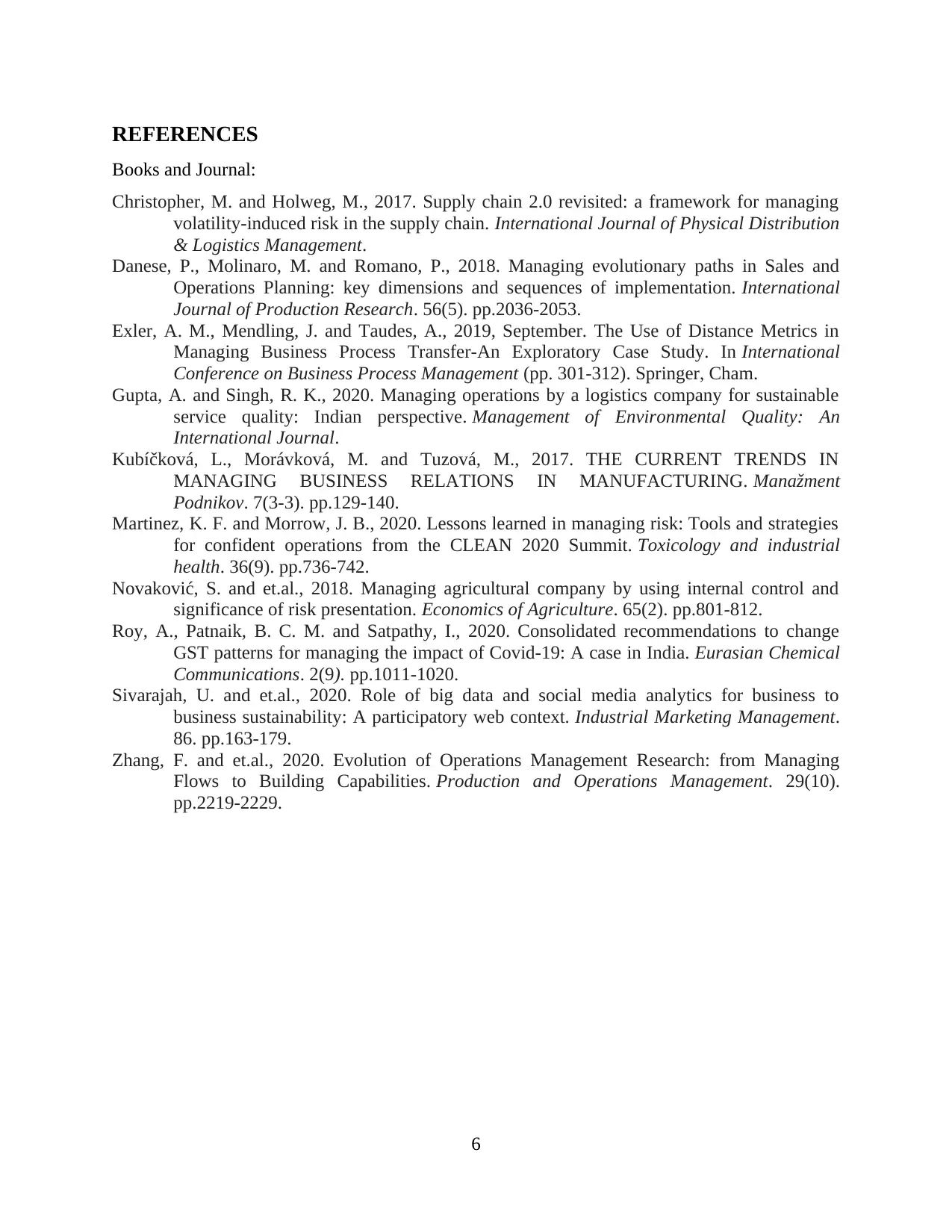
REFERENCES
Books and Journal:
Christopher, M. and Holweg, M., 2017. Supply chain 2.0 revisited: a framework for managing
volatility-induced risk in the supply chain. International Journal of Physical Distribution
& Logistics Management.
Danese, P., Molinaro, M. and Romano, P., 2018. Managing evolutionary paths in Sales and
Operations Planning: key dimensions and sequences of implementation. International
Journal of Production Research. 56(5). pp.2036-2053.
Exler, A. M., Mendling, J. and Taudes, A., 2019, September. The Use of Distance Metrics in
Managing Business Process Transfer-An Exploratory Case Study. In International
Conference on Business Process Management (pp. 301-312). Springer, Cham.
Gupta, A. and Singh, R. K., 2020. Managing operations by a logistics company for sustainable
service quality: Indian perspective. Management of Environmental Quality: An
International Journal.
Kubíčková, L., Morávková, M. and Tuzová, M., 2017. THE CURRENT TRENDS IN
MANAGING BUSINESS RELATIONS IN MANUFACTURING. Manažment
Podnikov. 7(3-3). pp.129-140.
Martinez, K. F. and Morrow, J. B., 2020. Lessons learned in managing risk: Tools and strategies
for confident operations from the CLEAN 2020 Summit. Toxicology and industrial
health. 36(9). pp.736-742.
Novaković, S. and et.al., 2018. Managing agricultural company by using internal control and
significance of risk presentation. Economics of Agriculture. 65(2). pp.801-812.
Roy, A., Patnaik, B. C. M. and Satpathy, I., 2020. Consolidated recommendations to change
GST patterns for managing the impact of Covid-19: A case in India. Eurasian Chemical
Communications. 2(9). pp.1011-1020.
Sivarajah, U. and et.al., 2020. Role of big data and social media analytics for business to
business sustainability: A participatory web context. Industrial Marketing Management.
86. pp.163-179.
Zhang, F. and et.al., 2020. Evolution of Operations Management Research: from Managing
Flows to Building Capabilities. Production and Operations Management. 29(10).
pp.2219-2229.
6
Books and Journal:
Christopher, M. and Holweg, M., 2017. Supply chain 2.0 revisited: a framework for managing
volatility-induced risk in the supply chain. International Journal of Physical Distribution
& Logistics Management.
Danese, P., Molinaro, M. and Romano, P., 2018. Managing evolutionary paths in Sales and
Operations Planning: key dimensions and sequences of implementation. International
Journal of Production Research. 56(5). pp.2036-2053.
Exler, A. M., Mendling, J. and Taudes, A., 2019, September. The Use of Distance Metrics in
Managing Business Process Transfer-An Exploratory Case Study. In International
Conference on Business Process Management (pp. 301-312). Springer, Cham.
Gupta, A. and Singh, R. K., 2020. Managing operations by a logistics company for sustainable
service quality: Indian perspective. Management of Environmental Quality: An
International Journal.
Kubíčková, L., Morávková, M. and Tuzová, M., 2017. THE CURRENT TRENDS IN
MANAGING BUSINESS RELATIONS IN MANUFACTURING. Manažment
Podnikov. 7(3-3). pp.129-140.
Martinez, K. F. and Morrow, J. B., 2020. Lessons learned in managing risk: Tools and strategies
for confident operations from the CLEAN 2020 Summit. Toxicology and industrial
health. 36(9). pp.736-742.
Novaković, S. and et.al., 2018. Managing agricultural company by using internal control and
significance of risk presentation. Economics of Agriculture. 65(2). pp.801-812.
Roy, A., Patnaik, B. C. M. and Satpathy, I., 2020. Consolidated recommendations to change
GST patterns for managing the impact of Covid-19: A case in India. Eurasian Chemical
Communications. 2(9). pp.1011-1020.
Sivarajah, U. and et.al., 2020. Role of big data and social media analytics for business to
business sustainability: A participatory web context. Industrial Marketing Management.
86. pp.163-179.
Zhang, F. and et.al., 2020. Evolution of Operations Management Research: from Managing
Flows to Building Capabilities. Production and Operations Management. 29(10).
pp.2219-2229.
6
1 out of 8
Related Documents

Your All-in-One AI-Powered Toolkit for Academic Success.
+13062052269
info@desklib.com
Available 24*7 on WhatsApp / Email
Unlock your academic potential
© 2024 | Zucol Services PVT LTD | All rights reserved.