Operations Management of TESLA Inc.
VerifiedAdded on  2023/01/12
|10
|3209
|39
AI Summary
This report explores the operations management of TESLA Inc., focusing on quality management and lean production. It also discusses the application of the triple bottom line framework for TESLA Inc., evaluating its financial, social, and environmental impact.
Contribute Materials
Your contribution can guide someone’s learning journey. Share your
documents today.
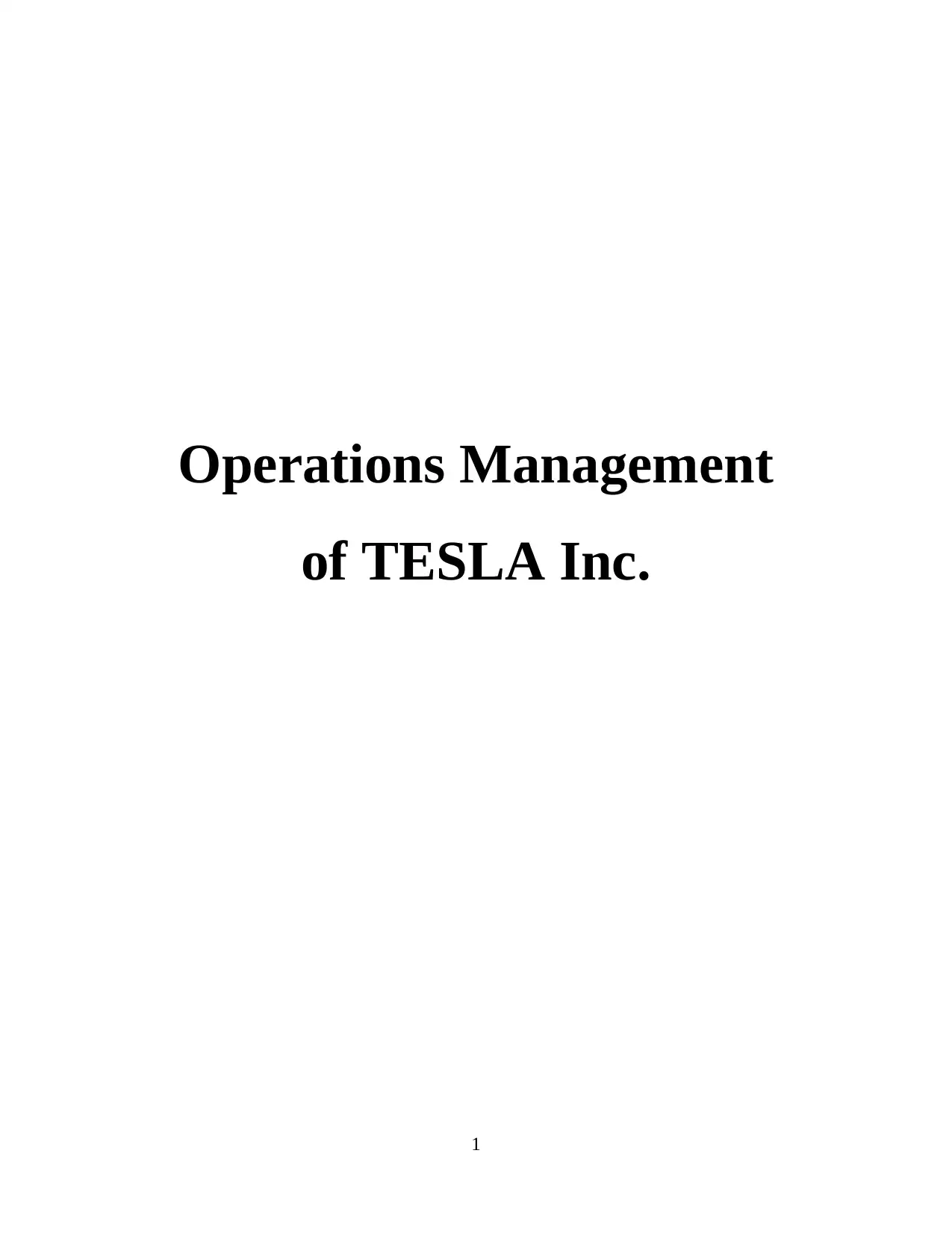
Operations Management
of TESLA Inc.
1
of TESLA Inc.
1
Secure Best Marks with AI Grader
Need help grading? Try our AI Grader for instant feedback on your assignments.
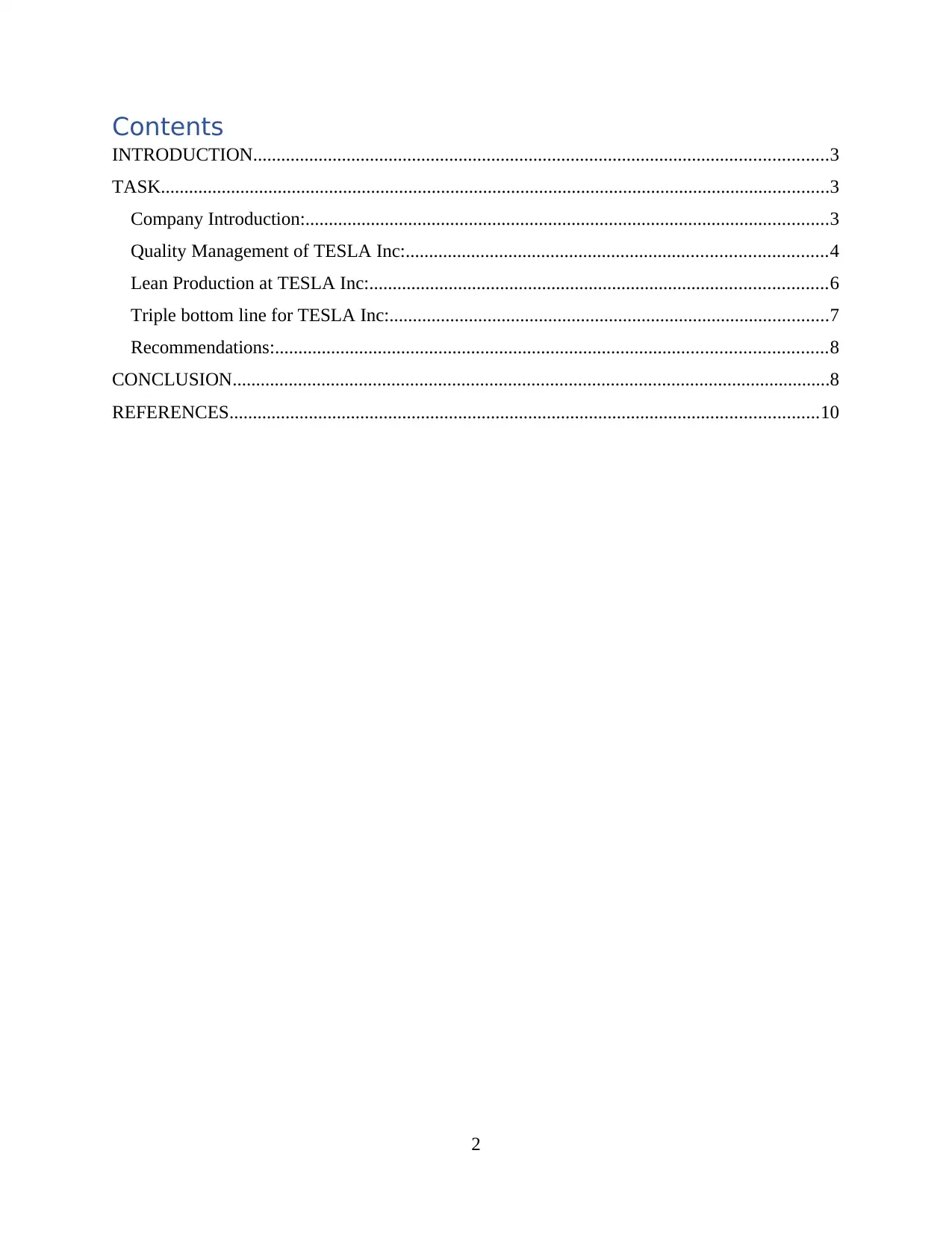
Contents
INTRODUCTION...........................................................................................................................3
TASK...............................................................................................................................................3
Company Introduction:................................................................................................................3
Quality Management of TESLA Inc:..........................................................................................4
Lean Production at TESLA Inc:..................................................................................................6
Triple bottom line for TESLA Inc:..............................................................................................7
Recommendations:......................................................................................................................8
CONCLUSION................................................................................................................................8
REFERENCES..............................................................................................................................10
2
INTRODUCTION...........................................................................................................................3
TASK...............................................................................................................................................3
Company Introduction:................................................................................................................3
Quality Management of TESLA Inc:..........................................................................................4
Lean Production at TESLA Inc:..................................................................................................6
Triple bottom line for TESLA Inc:..............................................................................................7
Recommendations:......................................................................................................................8
CONCLUSION................................................................................................................................8
REFERENCES..............................................................................................................................10
2
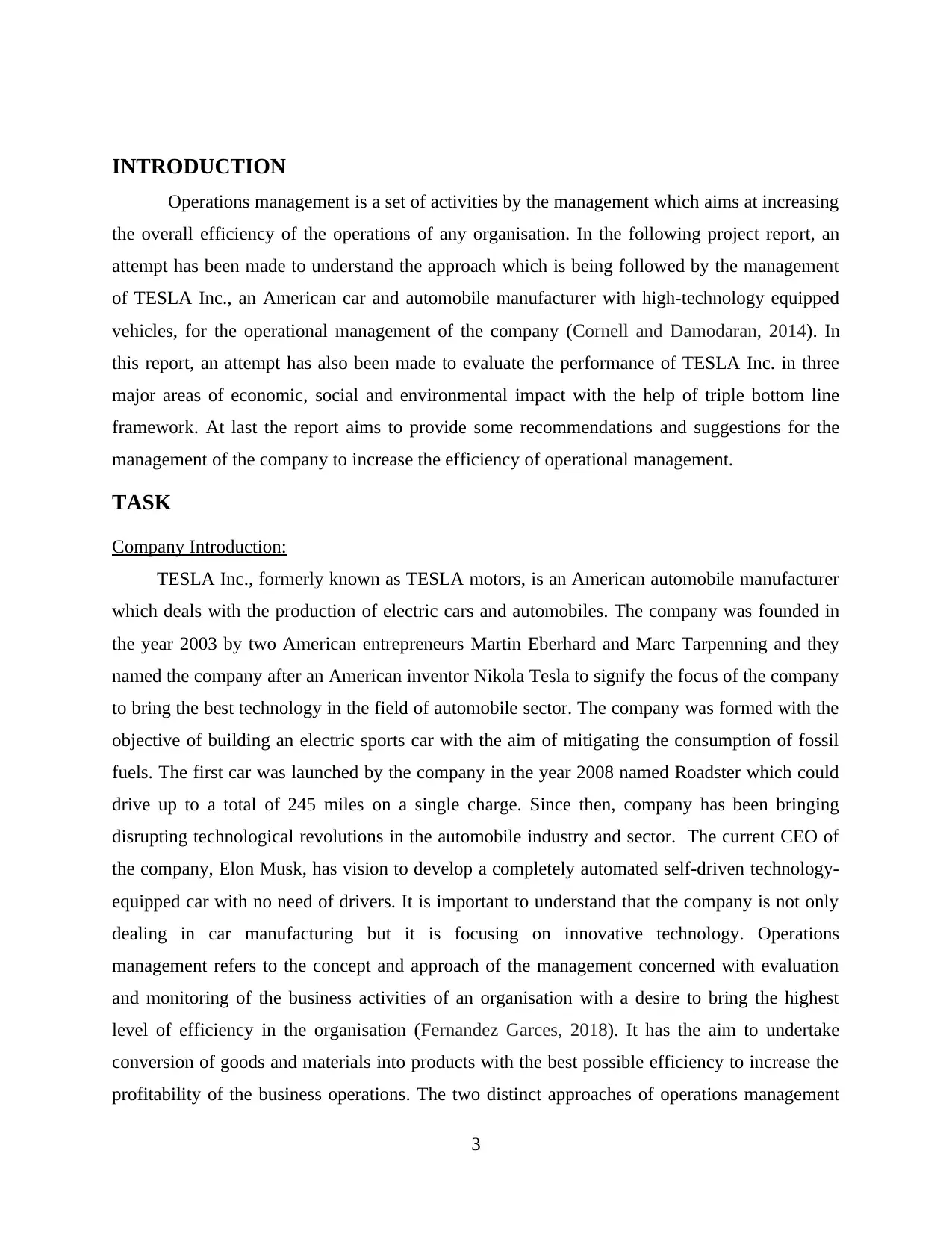
INTRODUCTION
Operations management is a set of activities by the management which aims at increasing
the overall efficiency of the operations of any organisation. In the following project report, an
attempt has been made to understand the approach which is being followed by the management
of TESLA Inc., an American car and automobile manufacturer with high-technology equipped
vehicles, for the operational management of the company (Cornell and Damodaran, 2014). In
this report, an attempt has also been made to evaluate the performance of TESLA Inc. in three
major areas of economic, social and environmental impact with the help of triple bottom line
framework. At last the report aims to provide some recommendations and suggestions for the
management of the company to increase the efficiency of operational management.
TASK
Company Introduction:
TESLA Inc., formerly known as TESLA motors, is an American automobile manufacturer
which deals with the production of electric cars and automobiles. The company was founded in
the year 2003 by two American entrepreneurs Martin Eberhard and Marc Tarpenning and they
named the company after an American inventor Nikola Tesla to signify the focus of the company
to bring the best technology in the field of automobile sector. The company was formed with the
objective of building an electric sports car with the aim of mitigating the consumption of fossil
fuels. The first car was launched by the company in the year 2008 named Roadster which could
drive up to a total of 245 miles on a single charge. Since then, company has been bringing
disrupting technological revolutions in the automobile industry and sector. The current CEO of
the company, Elon Musk, has vision to develop a completely automated self-driven technology-
equipped car with no need of drivers. It is important to understand that the company is not only
dealing in car manufacturing but it is focusing on innovative technology. Operations
management refers to the concept and approach of the management concerned with evaluation
and monitoring of the business activities of an organisation with a desire to bring the highest
level of efficiency in the organisation (Fernandez Garces, 2018). It has the aim to undertake
conversion of goods and materials into products with the best possible efficiency to increase the
profitability of the business operations. The two distinct approaches of operations management
3
Operations management is a set of activities by the management which aims at increasing
the overall efficiency of the operations of any organisation. In the following project report, an
attempt has been made to understand the approach which is being followed by the management
of TESLA Inc., an American car and automobile manufacturer with high-technology equipped
vehicles, for the operational management of the company (Cornell and Damodaran, 2014). In
this report, an attempt has also been made to evaluate the performance of TESLA Inc. in three
major areas of economic, social and environmental impact with the help of triple bottom line
framework. At last the report aims to provide some recommendations and suggestions for the
management of the company to increase the efficiency of operational management.
TASK
Company Introduction:
TESLA Inc., formerly known as TESLA motors, is an American automobile manufacturer
which deals with the production of electric cars and automobiles. The company was founded in
the year 2003 by two American entrepreneurs Martin Eberhard and Marc Tarpenning and they
named the company after an American inventor Nikola Tesla to signify the focus of the company
to bring the best technology in the field of automobile sector. The company was formed with the
objective of building an electric sports car with the aim of mitigating the consumption of fossil
fuels. The first car was launched by the company in the year 2008 named Roadster which could
drive up to a total of 245 miles on a single charge. Since then, company has been bringing
disrupting technological revolutions in the automobile industry and sector. The current CEO of
the company, Elon Musk, has vision to develop a completely automated self-driven technology-
equipped car with no need of drivers. It is important to understand that the company is not only
dealing in car manufacturing but it is focusing on innovative technology. Operations
management refers to the concept and approach of the management concerned with evaluation
and monitoring of the business activities of an organisation with a desire to bring the highest
level of efficiency in the organisation (Fernandez Garces, 2018). It has the aim to undertake
conversion of goods and materials into products with the best possible efficiency to increase the
profitability of the business operations. The two distinct approaches of operations management
3
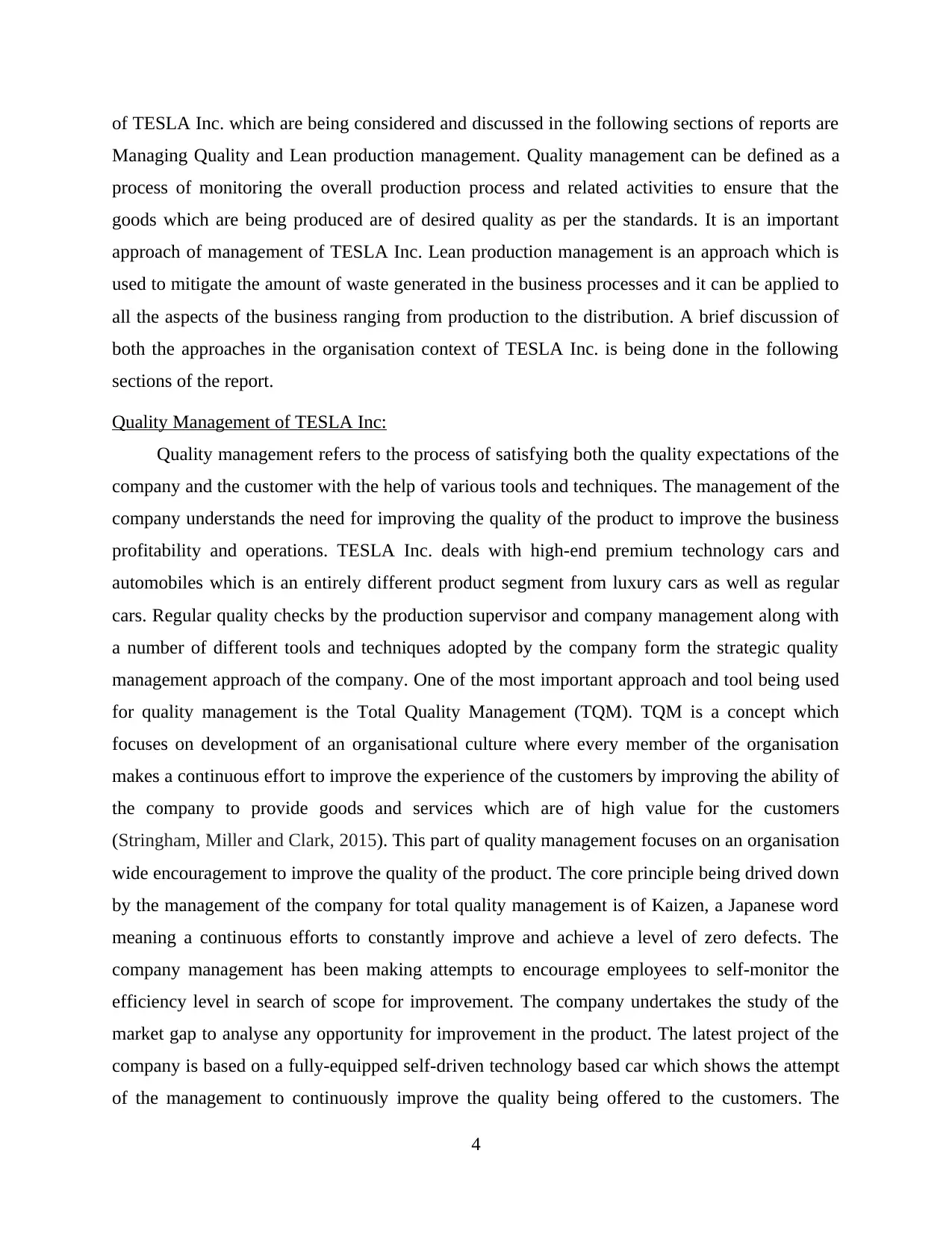
of TESLA Inc. which are being considered and discussed in the following sections of reports are
Managing Quality and Lean production management. Quality management can be defined as a
process of monitoring the overall production process and related activities to ensure that the
goods which are being produced are of desired quality as per the standards. It is an important
approach of management of TESLA Inc. Lean production management is an approach which is
used to mitigate the amount of waste generated in the business processes and it can be applied to
all the aspects of the business ranging from production to the distribution. A brief discussion of
both the approaches in the organisation context of TESLA Inc. is being done in the following
sections of the report.
Quality Management of TESLA Inc:
Quality management refers to the process of satisfying both the quality expectations of the
company and the customer with the help of various tools and techniques. The management of the
company understands the need for improving the quality of the product to improve the business
profitability and operations. TESLA Inc. deals with high-end premium technology cars and
automobiles which is an entirely different product segment from luxury cars as well as regular
cars. Regular quality checks by the production supervisor and company management along with
a number of different tools and techniques adopted by the company form the strategic quality
management approach of the company. One of the most important approach and tool being used
for quality management is the Total Quality Management (TQM). TQM is a concept which
focuses on development of an organisational culture where every member of the organisation
makes a continuous effort to improve the experience of the customers by improving the ability of
the company to provide goods and services which are of high value for the customers
(Stringham, Miller and Clark, 2015). This part of quality management focuses on an organisation
wide encouragement to improve the quality of the product. The core principle being drived down
by the management of the company for total quality management is of Kaizen, a Japanese word
meaning a continuous efforts to constantly improve and achieve a level of zero defects. The
company management has been making attempts to encourage employees to self-monitor the
efficiency level in search of scope for improvement. The company undertakes the study of the
market gap to analyse any opportunity for improvement in the product. The latest project of the
company is based on a fully-equipped self-driven technology based car which shows the attempt
of the management to continuously improve the quality being offered to the customers. The
4
Managing Quality and Lean production management. Quality management can be defined as a
process of monitoring the overall production process and related activities to ensure that the
goods which are being produced are of desired quality as per the standards. It is an important
approach of management of TESLA Inc. Lean production management is an approach which is
used to mitigate the amount of waste generated in the business processes and it can be applied to
all the aspects of the business ranging from production to the distribution. A brief discussion of
both the approaches in the organisation context of TESLA Inc. is being done in the following
sections of the report.
Quality Management of TESLA Inc:
Quality management refers to the process of satisfying both the quality expectations of the
company and the customer with the help of various tools and techniques. The management of the
company understands the need for improving the quality of the product to improve the business
profitability and operations. TESLA Inc. deals with high-end premium technology cars and
automobiles which is an entirely different product segment from luxury cars as well as regular
cars. Regular quality checks by the production supervisor and company management along with
a number of different tools and techniques adopted by the company form the strategic quality
management approach of the company. One of the most important approach and tool being used
for quality management is the Total Quality Management (TQM). TQM is a concept which
focuses on development of an organisational culture where every member of the organisation
makes a continuous effort to improve the experience of the customers by improving the ability of
the company to provide goods and services which are of high value for the customers
(Stringham, Miller and Clark, 2015). This part of quality management focuses on an organisation
wide encouragement to improve the quality of the product. The core principle being drived down
by the management of the company for total quality management is of Kaizen, a Japanese word
meaning a continuous efforts to constantly improve and achieve a level of zero defects. The
company management has been making attempts to encourage employees to self-monitor the
efficiency level in search of scope for improvement. The company undertakes the study of the
market gap to analyse any opportunity for improvement in the product. The latest project of the
company is based on a fully-equipped self-driven technology based car which shows the attempt
of the management to continuously improve the quality being offered to the customers. The
4
Secure Best Marks with AI Grader
Need help grading? Try our AI Grader for instant feedback on your assignments.
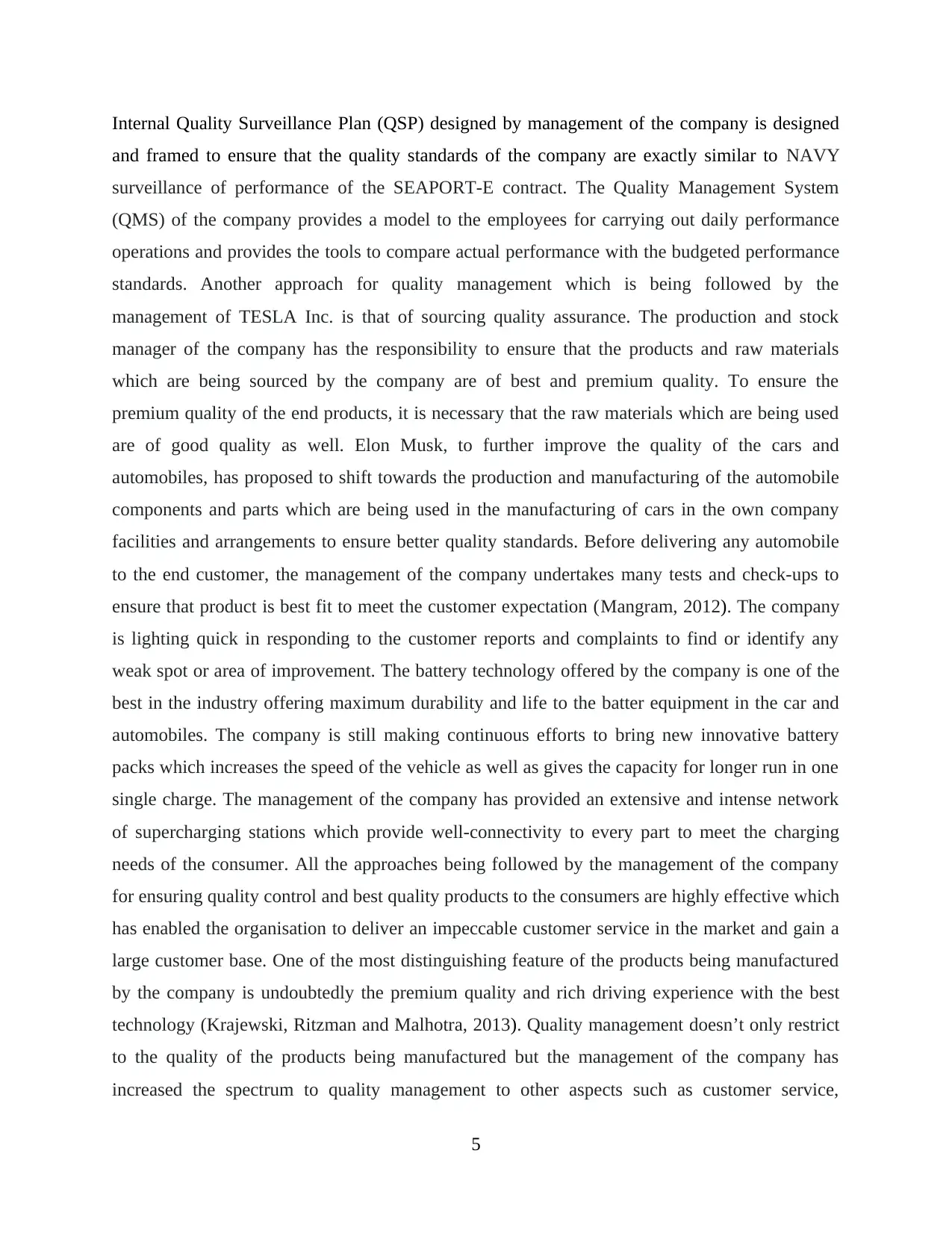
Internal Quality Surveillance Plan (QSP) designed by management of the company is designed
and framed to ensure that the quality standards of the company are exactly similar to NAVY
surveillance of performance of the SEAPORT-E contract. The Quality Management System
(QMS) of the company provides a model to the employees for carrying out daily performance
operations and provides the tools to compare actual performance with the budgeted performance
standards. Another approach for quality management which is being followed by the
management of TESLA Inc. is that of sourcing quality assurance. The production and stock
manager of the company has the responsibility to ensure that the products and raw materials
which are being sourced by the company are of best and premium quality. To ensure the
premium quality of the end products, it is necessary that the raw materials which are being used
are of good quality as well. Elon Musk, to further improve the quality of the cars and
automobiles, has proposed to shift towards the production and manufacturing of the automobile
components and parts which are being used in the manufacturing of cars in the own company
facilities and arrangements to ensure better quality standards. Before delivering any automobile
to the end customer, the management of the company undertakes many tests and check-ups to
ensure that product is best fit to meet the customer expectation (Mangram, 2012). The company
is lighting quick in responding to the customer reports and complaints to find or identify any
weak spot or area of improvement. The battery technology offered by the company is one of the
best in the industry offering maximum durability and life to the batter equipment in the car and
automobiles. The company is still making continuous efforts to bring new innovative battery
packs which increases the speed of the vehicle as well as gives the capacity for longer run in one
single charge. The management of the company has provided an extensive and intense network
of supercharging stations which provide well-connectivity to every part to meet the charging
needs of the consumer. All the approaches being followed by the management of the company
for ensuring quality control and best quality products to the consumers are highly effective which
has enabled the organisation to deliver an impeccable customer service in the market and gain a
large customer base. One of the most distinguishing feature of the products being manufactured
by the company is undoubtedly the premium quality and rich driving experience with the best
technology (Krajewski, Ritzman and Malhotra, 2013). Quality management doesn’t only restrict
to the quality of the products being manufactured but the management of the company has
increased the spectrum to quality management to other aspects such as customer service,
5
and framed to ensure that the quality standards of the company are exactly similar to NAVY
surveillance of performance of the SEAPORT-E contract. The Quality Management System
(QMS) of the company provides a model to the employees for carrying out daily performance
operations and provides the tools to compare actual performance with the budgeted performance
standards. Another approach for quality management which is being followed by the
management of TESLA Inc. is that of sourcing quality assurance. The production and stock
manager of the company has the responsibility to ensure that the products and raw materials
which are being sourced by the company are of best and premium quality. To ensure the
premium quality of the end products, it is necessary that the raw materials which are being used
are of good quality as well. Elon Musk, to further improve the quality of the cars and
automobiles, has proposed to shift towards the production and manufacturing of the automobile
components and parts which are being used in the manufacturing of cars in the own company
facilities and arrangements to ensure better quality standards. Before delivering any automobile
to the end customer, the management of the company undertakes many tests and check-ups to
ensure that product is best fit to meet the customer expectation (Mangram, 2012). The company
is lighting quick in responding to the customer reports and complaints to find or identify any
weak spot or area of improvement. The battery technology offered by the company is one of the
best in the industry offering maximum durability and life to the batter equipment in the car and
automobiles. The company is still making continuous efforts to bring new innovative battery
packs which increases the speed of the vehicle as well as gives the capacity for longer run in one
single charge. The management of the company has provided an extensive and intense network
of supercharging stations which provide well-connectivity to every part to meet the charging
needs of the consumer. All the approaches being followed by the management of the company
for ensuring quality control and best quality products to the consumers are highly effective which
has enabled the organisation to deliver an impeccable customer service in the market and gain a
large customer base. One of the most distinguishing feature of the products being manufactured
by the company is undoubtedly the premium quality and rich driving experience with the best
technology (Krajewski, Ritzman and Malhotra, 2013). Quality management doesn’t only restrict
to the quality of the products being manufactured but the management of the company has
increased the spectrum to quality management to other aspects such as customer service,
5
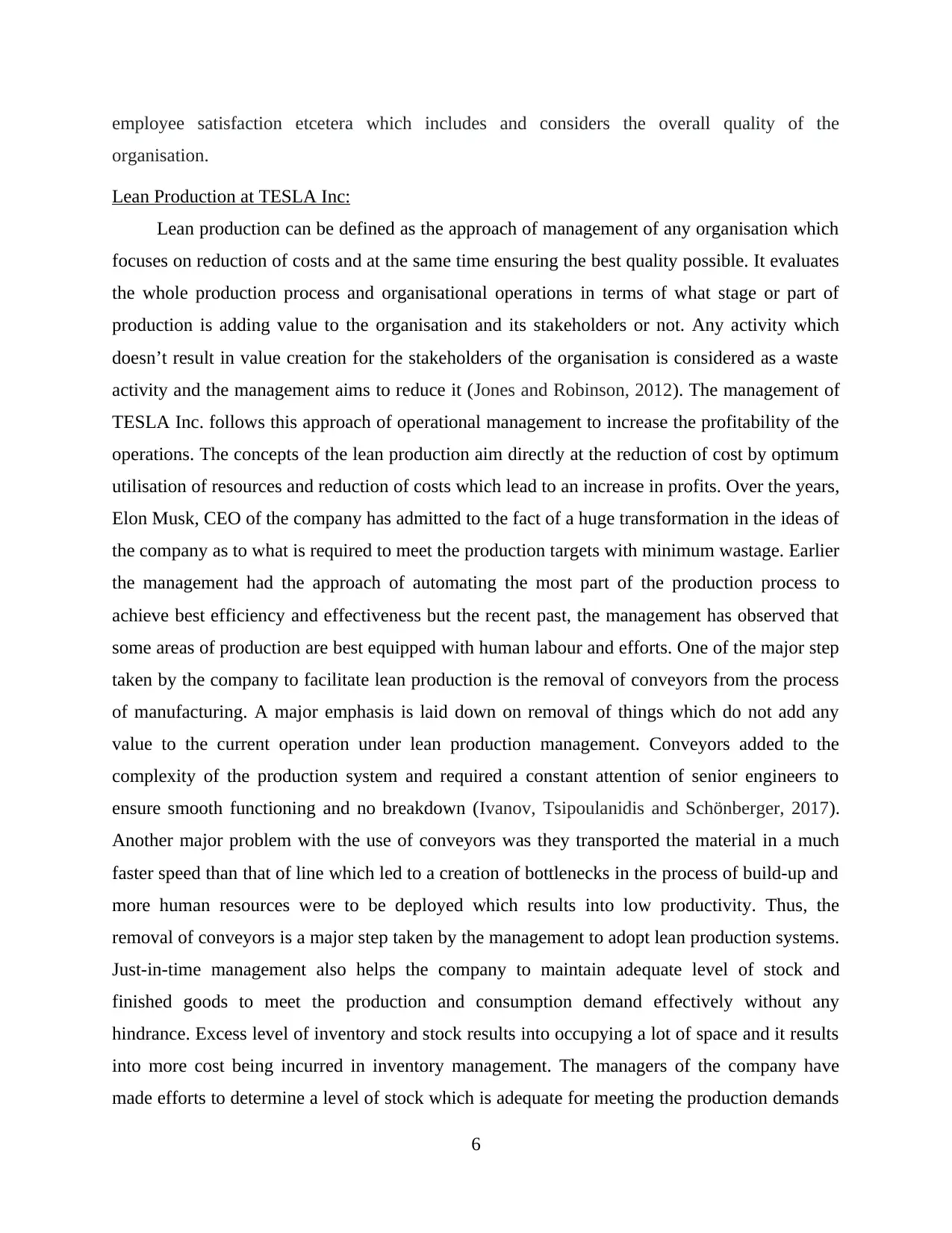
employee satisfaction etcetera which includes and considers the overall quality of the
organisation.
Lean Production at TESLA Inc:
Lean production can be defined as the approach of management of any organisation which
focuses on reduction of costs and at the same time ensuring the best quality possible. It evaluates
the whole production process and organisational operations in terms of what stage or part of
production is adding value to the organisation and its stakeholders or not. Any activity which
doesn’t result in value creation for the stakeholders of the organisation is considered as a waste
activity and the management aims to reduce it (Jones and Robinson, 2012). The management of
TESLA Inc. follows this approach of operational management to increase the profitability of the
operations. The concepts of the lean production aim directly at the reduction of cost by optimum
utilisation of resources and reduction of costs which lead to an increase in profits. Over the years,
Elon Musk, CEO of the company has admitted to the fact of a huge transformation in the ideas of
the company as to what is required to meet the production targets with minimum wastage. Earlier
the management had the approach of automating the most part of the production process to
achieve best efficiency and effectiveness but the recent past, the management has observed that
some areas of production are best equipped with human labour and efforts. One of the major step
taken by the company to facilitate lean production is the removal of conveyors from the process
of manufacturing. A major emphasis is laid down on removal of things which do not add any
value to the current operation under lean production management. Conveyors added to the
complexity of the production system and required a constant attention of senior engineers to
ensure smooth functioning and no breakdown (Ivanov, Tsipoulanidis and Schönberger, 2017).
Another major problem with the use of conveyors was they transported the material in a much
faster speed than that of line which led to a creation of bottlenecks in the process of build-up and
more human resources were to be deployed which results into low productivity. Thus, the
removal of conveyors is a major step taken by the management to adopt lean production systems.
Just-in-time management also helps the company to maintain adequate level of stock and
finished goods to meet the production and consumption demand effectively without any
hindrance. Excess level of inventory and stock results into occupying a lot of space and it results
into more cost being incurred in inventory management. The managers of the company have
made efforts to determine a level of stock which is adequate for meeting the production demands
6
organisation.
Lean Production at TESLA Inc:
Lean production can be defined as the approach of management of any organisation which
focuses on reduction of costs and at the same time ensuring the best quality possible. It evaluates
the whole production process and organisational operations in terms of what stage or part of
production is adding value to the organisation and its stakeholders or not. Any activity which
doesn’t result in value creation for the stakeholders of the organisation is considered as a waste
activity and the management aims to reduce it (Jones and Robinson, 2012). The management of
TESLA Inc. follows this approach of operational management to increase the profitability of the
operations. The concepts of the lean production aim directly at the reduction of cost by optimum
utilisation of resources and reduction of costs which lead to an increase in profits. Over the years,
Elon Musk, CEO of the company has admitted to the fact of a huge transformation in the ideas of
the company as to what is required to meet the production targets with minimum wastage. Earlier
the management had the approach of automating the most part of the production process to
achieve best efficiency and effectiveness but the recent past, the management has observed that
some areas of production are best equipped with human labour and efforts. One of the major step
taken by the company to facilitate lean production is the removal of conveyors from the process
of manufacturing. A major emphasis is laid down on removal of things which do not add any
value to the current operation under lean production management. Conveyors added to the
complexity of the production system and required a constant attention of senior engineers to
ensure smooth functioning and no breakdown (Ivanov, Tsipoulanidis and Schönberger, 2017).
Another major problem with the use of conveyors was they transported the material in a much
faster speed than that of line which led to a creation of bottlenecks in the process of build-up and
more human resources were to be deployed which results into low productivity. Thus, the
removal of conveyors is a major step taken by the management to adopt lean production systems.
Just-in-time management also helps the company to maintain adequate level of stock and
finished goods to meet the production and consumption demand effectively without any
hindrance. Excess level of inventory and stock results into occupying a lot of space and it results
into more cost being incurred in inventory management. The managers of the company have
made efforts to determine a level of stock which is adequate for meeting the production demands
6
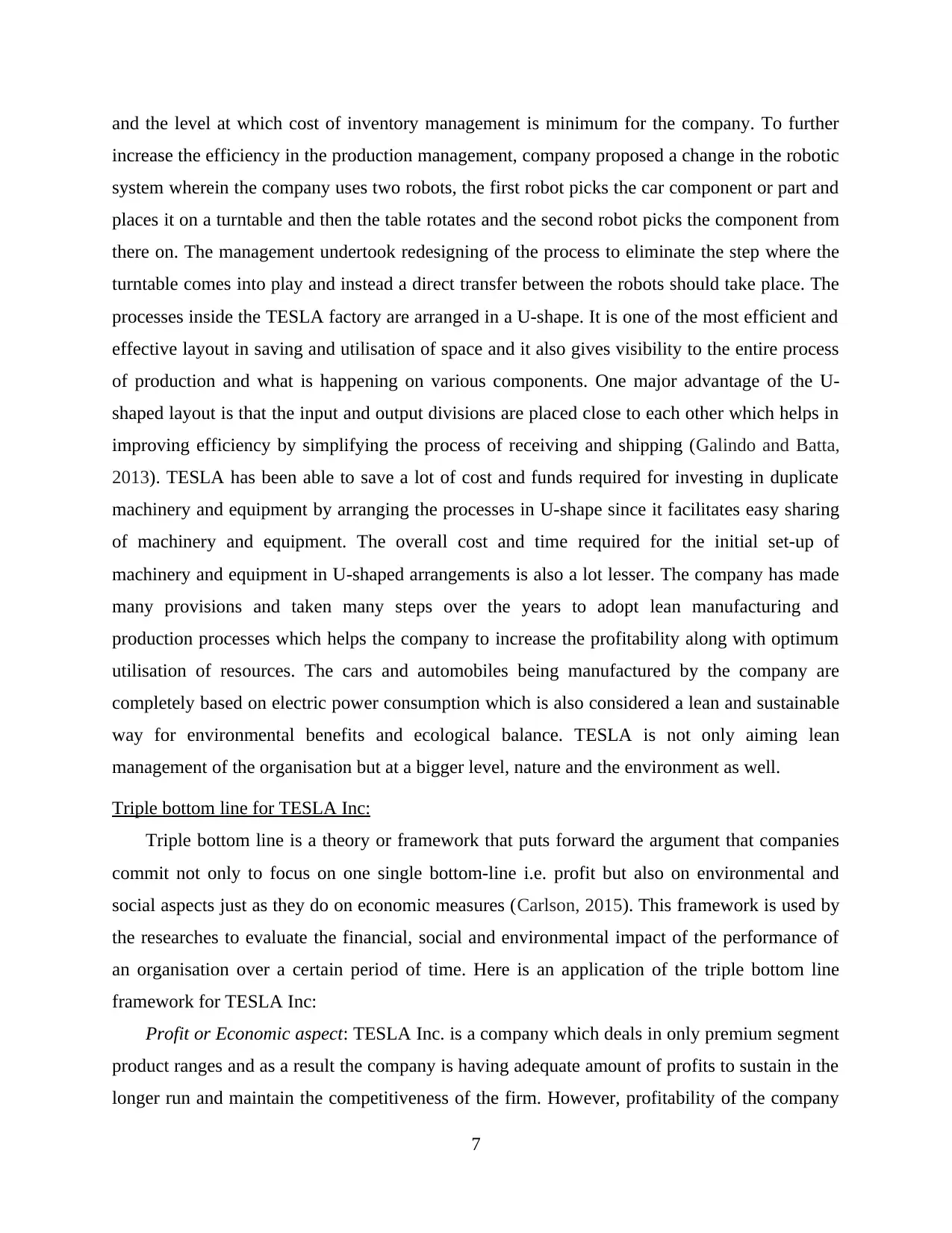
and the level at which cost of inventory management is minimum for the company. To further
increase the efficiency in the production management, company proposed a change in the robotic
system wherein the company uses two robots, the first robot picks the car component or part and
places it on a turntable and then the table rotates and the second robot picks the component from
there on. The management undertook redesigning of the process to eliminate the step where the
turntable comes into play and instead a direct transfer between the robots should take place. The
processes inside the TESLA factory are arranged in a U-shape. It is one of the most efficient and
effective layout in saving and utilisation of space and it also gives visibility to the entire process
of production and what is happening on various components. One major advantage of the U-
shaped layout is that the input and output divisions are placed close to each other which helps in
improving efficiency by simplifying the process of receiving and shipping (Galindo and Batta,
2013). TESLA has been able to save a lot of cost and funds required for investing in duplicate
machinery and equipment by arranging the processes in U-shape since it facilitates easy sharing
of machinery and equipment. The overall cost and time required for the initial set-up of
machinery and equipment in U-shaped arrangements is also a lot lesser. The company has made
many provisions and taken many steps over the years to adopt lean manufacturing and
production processes which helps the company to increase the profitability along with optimum
utilisation of resources. The cars and automobiles being manufactured by the company are
completely based on electric power consumption which is also considered a lean and sustainable
way for environmental benefits and ecological balance. TESLA is not only aiming lean
management of the organisation but at a bigger level, nature and the environment as well.
Triple bottom line for TESLA Inc:
Triple bottom line is a theory or framework that puts forward the argument that companies
commit not only to focus on one single bottom-line i.e. profit but also on environmental and
social aspects just as they do on economic measures (Carlson, 2015). This framework is used by
the researches to evaluate the financial, social and environmental impact of the performance of
an organisation over a certain period of time. Here is an application of the triple bottom line
framework for TESLA Inc:
Profit or Economic aspect: TESLA Inc. is a company which deals in only premium segment
product ranges and as a result the company is having adequate amount of profits to sustain in the
longer run and maintain the competitiveness of the firm. However, profitability of the company
7
increase the efficiency in the production management, company proposed a change in the robotic
system wherein the company uses two robots, the first robot picks the car component or part and
places it on a turntable and then the table rotates and the second robot picks the component from
there on. The management undertook redesigning of the process to eliminate the step where the
turntable comes into play and instead a direct transfer between the robots should take place. The
processes inside the TESLA factory are arranged in a U-shape. It is one of the most efficient and
effective layout in saving and utilisation of space and it also gives visibility to the entire process
of production and what is happening on various components. One major advantage of the U-
shaped layout is that the input and output divisions are placed close to each other which helps in
improving efficiency by simplifying the process of receiving and shipping (Galindo and Batta,
2013). TESLA has been able to save a lot of cost and funds required for investing in duplicate
machinery and equipment by arranging the processes in U-shape since it facilitates easy sharing
of machinery and equipment. The overall cost and time required for the initial set-up of
machinery and equipment in U-shaped arrangements is also a lot lesser. The company has made
many provisions and taken many steps over the years to adopt lean manufacturing and
production processes which helps the company to increase the profitability along with optimum
utilisation of resources. The cars and automobiles being manufactured by the company are
completely based on electric power consumption which is also considered a lean and sustainable
way for environmental benefits and ecological balance. TESLA is not only aiming lean
management of the organisation but at a bigger level, nature and the environment as well.
Triple bottom line for TESLA Inc:
Triple bottom line is a theory or framework that puts forward the argument that companies
commit not only to focus on one single bottom-line i.e. profit but also on environmental and
social aspects just as they do on economic measures (Carlson, 2015). This framework is used by
the researches to evaluate the financial, social and environmental impact of the performance of
an organisation over a certain period of time. Here is an application of the triple bottom line
framework for TESLA Inc:
Profit or Economic aspect: TESLA Inc. is a company which deals in only premium segment
product ranges and as a result the company is having adequate amount of profits to sustain in the
longer run and maintain the competitiveness of the firm. However, profitability of the company
7
Paraphrase This Document
Need a fresh take? Get an instant paraphrase of this document with our AI Paraphraser
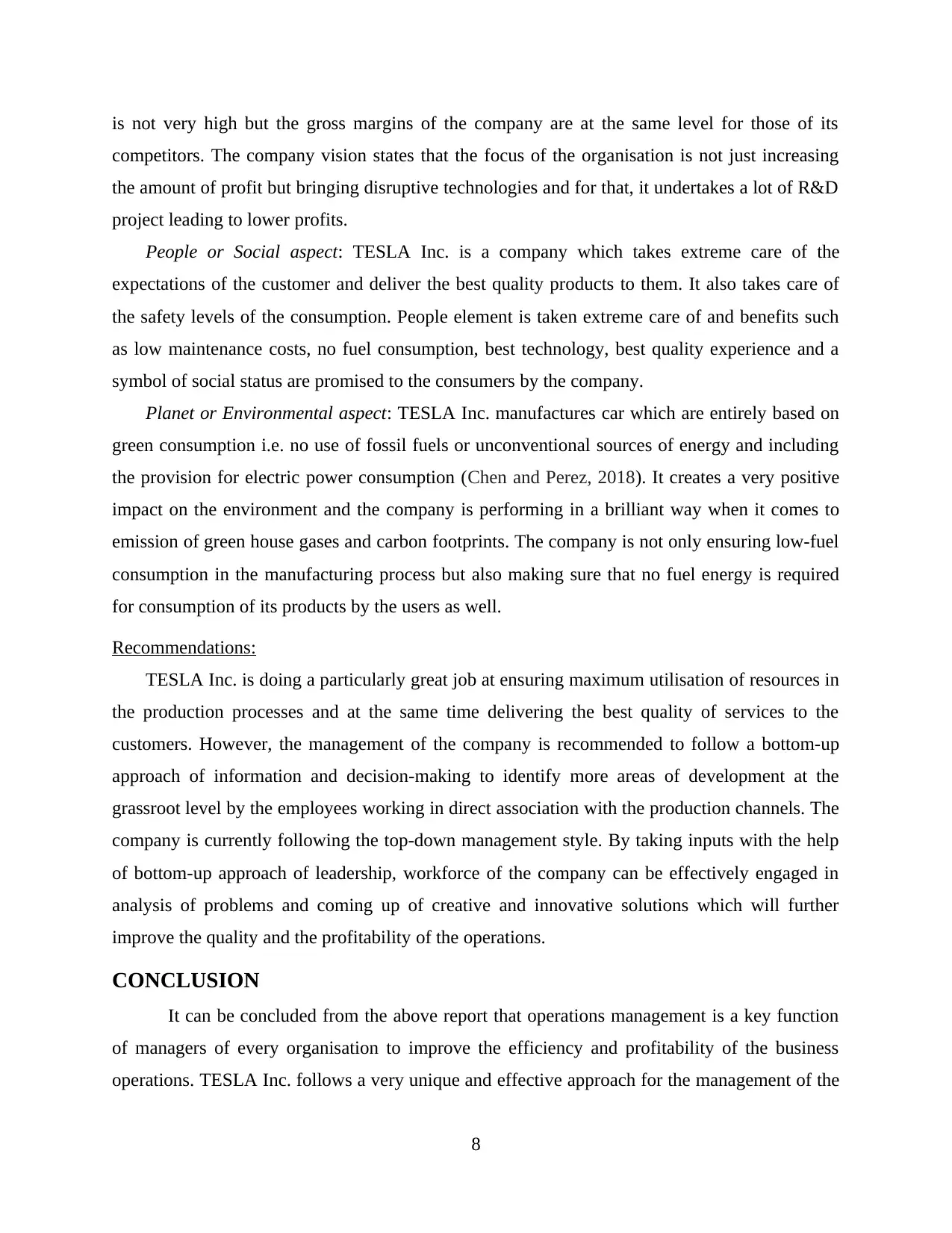
is not very high but the gross margins of the company are at the same level for those of its
competitors. The company vision states that the focus of the organisation is not just increasing
the amount of profit but bringing disruptive technologies and for that, it undertakes a lot of R&D
project leading to lower profits.
People or Social aspect: TESLA Inc. is a company which takes extreme care of the
expectations of the customer and deliver the best quality products to them. It also takes care of
the safety levels of the consumption. People element is taken extreme care of and benefits such
as low maintenance costs, no fuel consumption, best technology, best quality experience and a
symbol of social status are promised to the consumers by the company.
Planet or Environmental aspect: TESLA Inc. manufactures car which are entirely based on
green consumption i.e. no use of fossil fuels or unconventional sources of energy and including
the provision for electric power consumption (Chen and Perez, 2018). It creates a very positive
impact on the environment and the company is performing in a brilliant way when it comes to
emission of green house gases and carbon footprints. The company is not only ensuring low-fuel
consumption in the manufacturing process but also making sure that no fuel energy is required
for consumption of its products by the users as well.
Recommendations:
TESLA Inc. is doing a particularly great job at ensuring maximum utilisation of resources in
the production processes and at the same time delivering the best quality of services to the
customers. However, the management of the company is recommended to follow a bottom-up
approach of information and decision-making to identify more areas of development at the
grassroot level by the employees working in direct association with the production channels. The
company is currently following the top-down management style. By taking inputs with the help
of bottom-up approach of leadership, workforce of the company can be effectively engaged in
analysis of problems and coming up of creative and innovative solutions which will further
improve the quality and the profitability of the operations.
CONCLUSION
It can be concluded from the above report that operations management is a key function
of managers of every organisation to improve the efficiency and profitability of the business
operations. TESLA Inc. follows a very unique and effective approach for the management of the
8
competitors. The company vision states that the focus of the organisation is not just increasing
the amount of profit but bringing disruptive technologies and for that, it undertakes a lot of R&D
project leading to lower profits.
People or Social aspect: TESLA Inc. is a company which takes extreme care of the
expectations of the customer and deliver the best quality products to them. It also takes care of
the safety levels of the consumption. People element is taken extreme care of and benefits such
as low maintenance costs, no fuel consumption, best technology, best quality experience and a
symbol of social status are promised to the consumers by the company.
Planet or Environmental aspect: TESLA Inc. manufactures car which are entirely based on
green consumption i.e. no use of fossil fuels or unconventional sources of energy and including
the provision for electric power consumption (Chen and Perez, 2018). It creates a very positive
impact on the environment and the company is performing in a brilliant way when it comes to
emission of green house gases and carbon footprints. The company is not only ensuring low-fuel
consumption in the manufacturing process but also making sure that no fuel energy is required
for consumption of its products by the users as well.
Recommendations:
TESLA Inc. is doing a particularly great job at ensuring maximum utilisation of resources in
the production processes and at the same time delivering the best quality of services to the
customers. However, the management of the company is recommended to follow a bottom-up
approach of information and decision-making to identify more areas of development at the
grassroot level by the employees working in direct association with the production channels. The
company is currently following the top-down management style. By taking inputs with the help
of bottom-up approach of leadership, workforce of the company can be effectively engaged in
analysis of problems and coming up of creative and innovative solutions which will further
improve the quality and the profitability of the operations.
CONCLUSION
It can be concluded from the above report that operations management is a key function
of managers of every organisation to improve the efficiency and profitability of the business
operations. TESLA Inc. follows a very unique and effective approach for the management of the
8
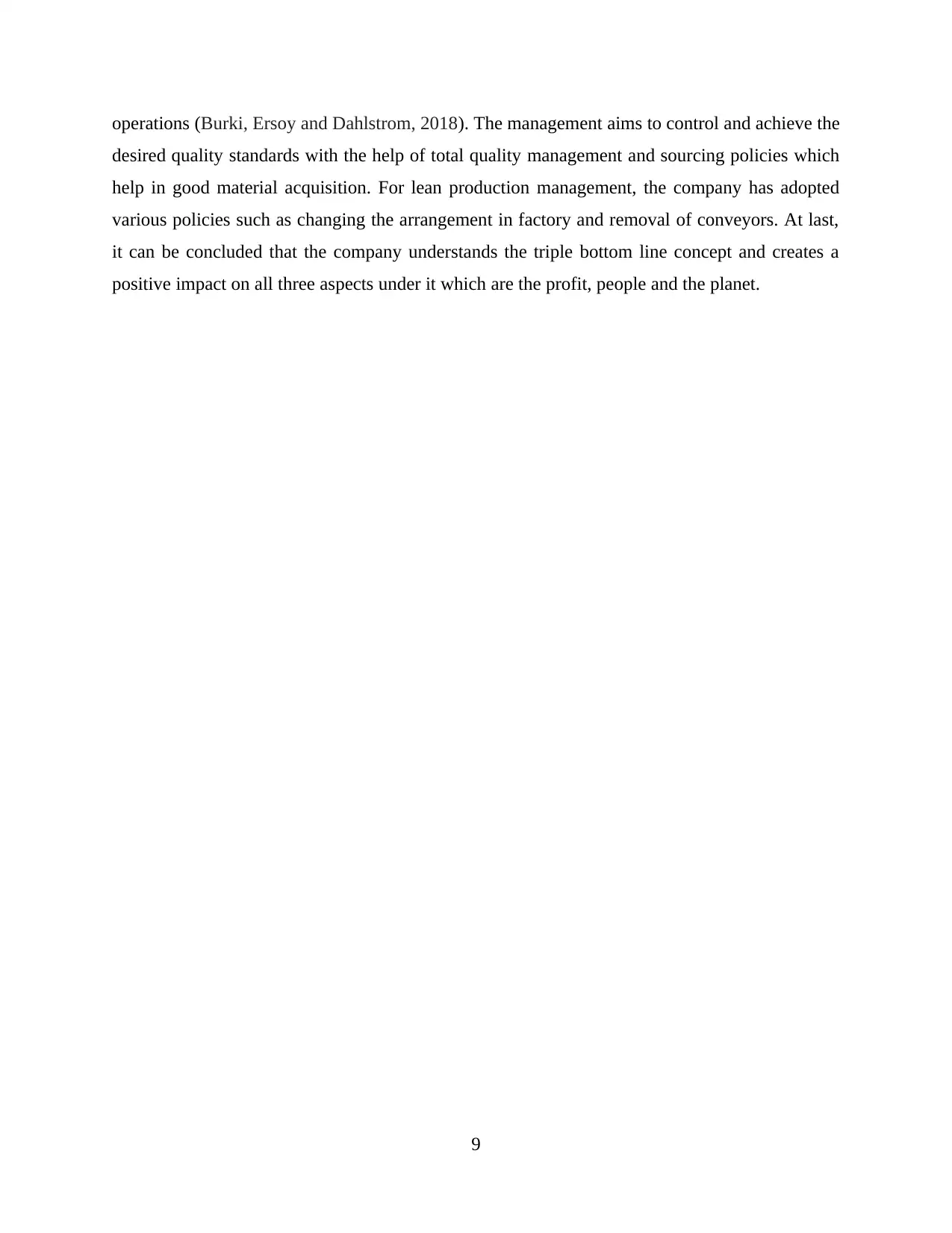
operations (Burki, Ersoy and Dahlstrom, 2018). The management aims to control and achieve the
desired quality standards with the help of total quality management and sourcing policies which
help in good material acquisition. For lean production management, the company has adopted
various policies such as changing the arrangement in factory and removal of conveyors. At last,
it can be concluded that the company understands the triple bottom line concept and creates a
positive impact on all three aspects under it which are the profit, people and the planet.
9
desired quality standards with the help of total quality management and sourcing policies which
help in good material acquisition. For lean production management, the company has adopted
various policies such as changing the arrangement in factory and removal of conveyors. At last,
it can be concluded that the company understands the triple bottom line concept and creates a
positive impact on all three aspects under it which are the profit, people and the planet.
9
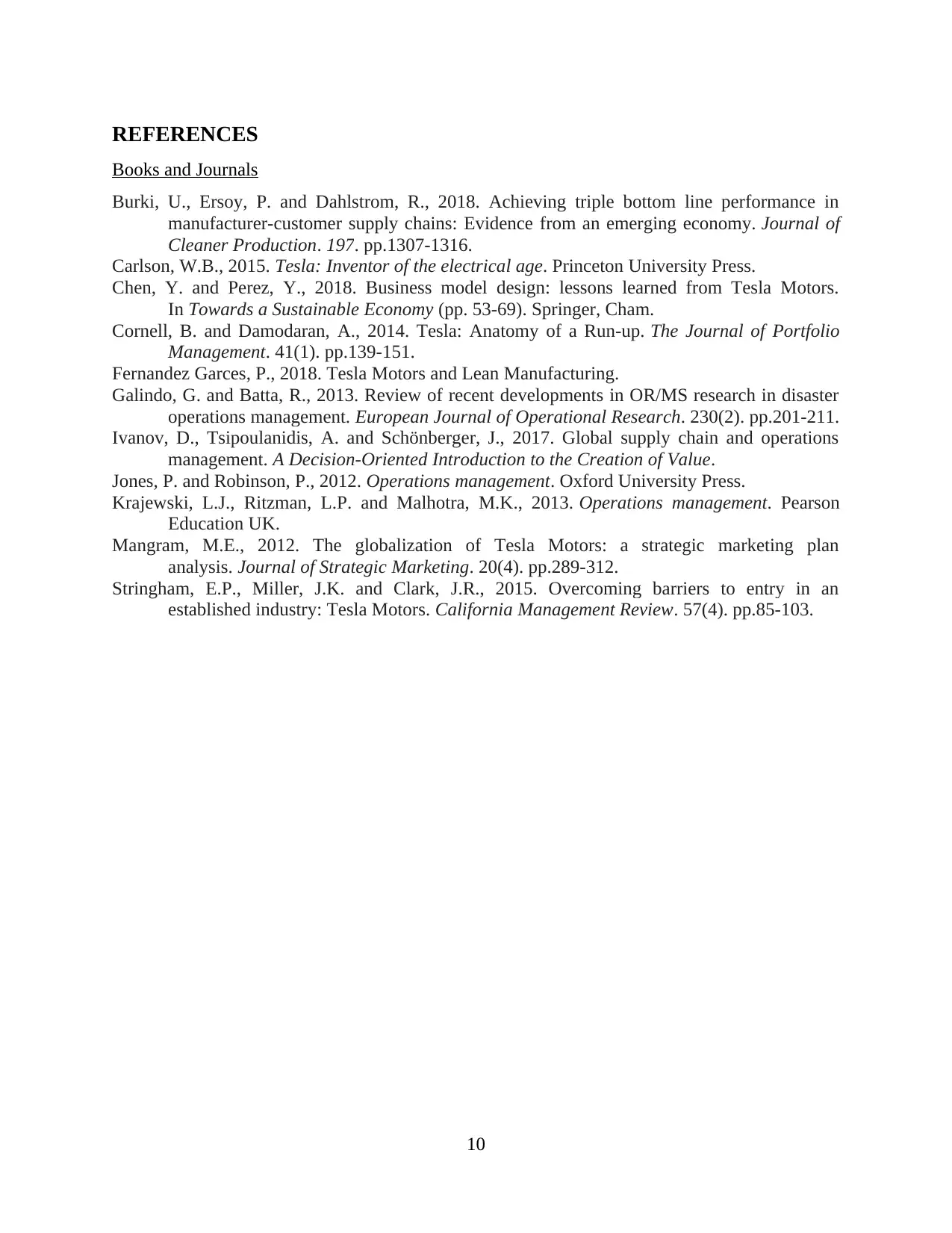
REFERENCES
Books and Journals
Burki, U., Ersoy, P. and Dahlstrom, R., 2018. Achieving triple bottom line performance in
manufacturer-customer supply chains: Evidence from an emerging economy. Journal of
Cleaner Production. 197. pp.1307-1316.
Carlson, W.B., 2015. Tesla: Inventor of the electrical age. Princeton University Press.
Chen, Y. and Perez, Y., 2018. Business model design: lessons learned from Tesla Motors.
In Towards a Sustainable Economy (pp. 53-69). Springer, Cham.
Cornell, B. and Damodaran, A., 2014. Tesla: Anatomy of a Run-up. The Journal of Portfolio
Management. 41(1). pp.139-151.
Fernandez Garces, P., 2018. Tesla Motors and Lean Manufacturing.
Galindo, G. and Batta, R., 2013. Review of recent developments in OR/MS research in disaster
operations management. European Journal of Operational Research. 230(2). pp.201-211.
Ivanov, D., Tsipoulanidis, A. and Schönberger, J., 2017. Global supply chain and operations
management. A Decision-Oriented Introduction to the Creation of Value.
Jones, P. and Robinson, P., 2012. Operations management. Oxford University Press.
Krajewski, L.J., Ritzman, L.P. and Malhotra, M.K., 2013. Operations management. Pearson
Education UK.
Mangram, M.E., 2012. The globalization of Tesla Motors: a strategic marketing plan
analysis. Journal of Strategic Marketing. 20(4). pp.289-312.
Stringham, E.P., Miller, J.K. and Clark, J.R., 2015. Overcoming barriers to entry in an
established industry: Tesla Motors. California Management Review. 57(4). pp.85-103.
10
Books and Journals
Burki, U., Ersoy, P. and Dahlstrom, R., 2018. Achieving triple bottom line performance in
manufacturer-customer supply chains: Evidence from an emerging economy. Journal of
Cleaner Production. 197. pp.1307-1316.
Carlson, W.B., 2015. Tesla: Inventor of the electrical age. Princeton University Press.
Chen, Y. and Perez, Y., 2018. Business model design: lessons learned from Tesla Motors.
In Towards a Sustainable Economy (pp. 53-69). Springer, Cham.
Cornell, B. and Damodaran, A., 2014. Tesla: Anatomy of a Run-up. The Journal of Portfolio
Management. 41(1). pp.139-151.
Fernandez Garces, P., 2018. Tesla Motors and Lean Manufacturing.
Galindo, G. and Batta, R., 2013. Review of recent developments in OR/MS research in disaster
operations management. European Journal of Operational Research. 230(2). pp.201-211.
Ivanov, D., Tsipoulanidis, A. and Schönberger, J., 2017. Global supply chain and operations
management. A Decision-Oriented Introduction to the Creation of Value.
Jones, P. and Robinson, P., 2012. Operations management. Oxford University Press.
Krajewski, L.J., Ritzman, L.P. and Malhotra, M.K., 2013. Operations management. Pearson
Education UK.
Mangram, M.E., 2012. The globalization of Tesla Motors: a strategic marketing plan
analysis. Journal of Strategic Marketing. 20(4). pp.289-312.
Stringham, E.P., Miller, J.K. and Clark, J.R., 2015. Overcoming barriers to entry in an
established industry: Tesla Motors. California Management Review. 57(4). pp.85-103.
10
1 out of 10
Related Documents
![[object Object]](/_next/image/?url=%2F_next%2Fstatic%2Fmedia%2Flogo.6d15ce61.png&w=640&q=75)
Your All-in-One AI-Powered Toolkit for Academic Success.
 +13062052269
info@desklib.com
Available 24*7 on WhatsApp / Email
Unlock your academic potential
© 2024  |  Zucol Services PVT LTD  |  All rights reserved.