Analysis of Sami Design Ltd. Job Costing and Overhead Allocation
VerifiedAdded on 2023/01/11
|11
|2518
|65
Homework Assignment
AI Summary
This assignment addresses job costing for Sami Design Ltd., a manufacturer of musical instruments. It begins by calculating the predetermined overhead rate and then completes a job cost sheet for a specific job. The solution includes preparing journal entries to record March's events, setting up le...
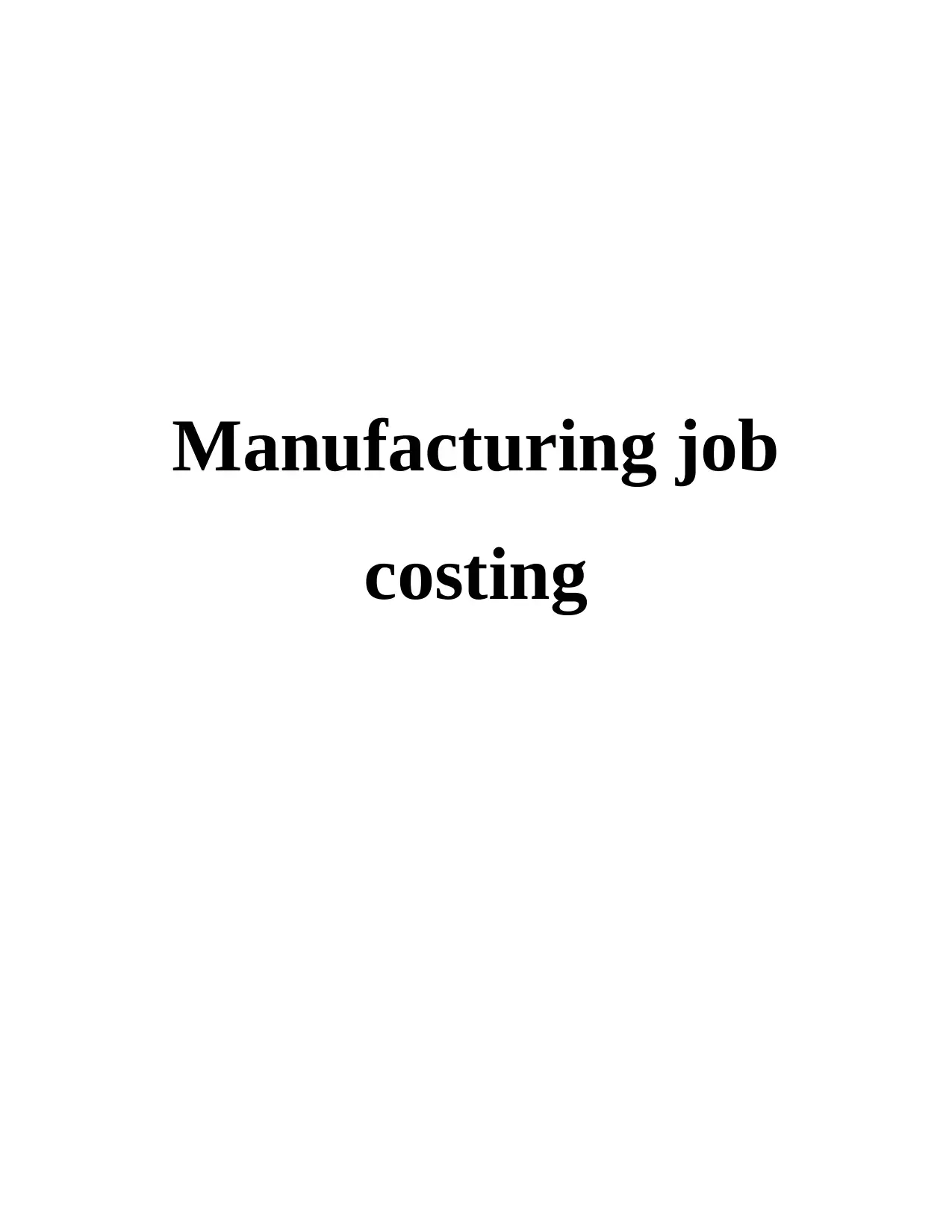
Manufacturing job
costing
costing
Paraphrase This Document
Need a fresh take? Get an instant paraphrase of this document with our AI Paraphraser
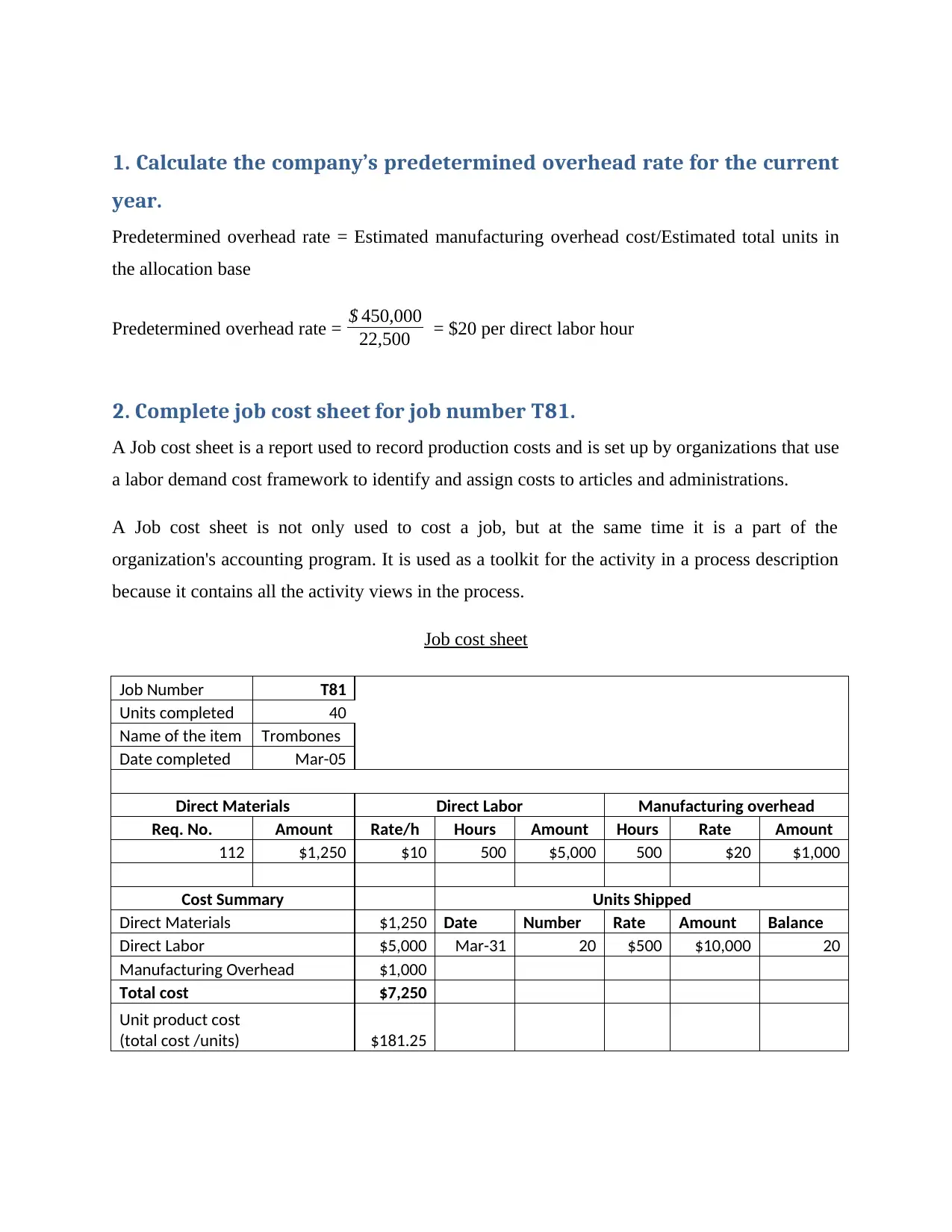
1. Calculate the company’s predetermined overhead rate for the current
year.
Predetermined overhead rate = Estimated manufacturing overhead cost/Estimated total units in
the allocation base
Predetermined overhead rate = $ 450,000
22,500 = $20 per direct labor hour
2. Complete job cost sheet for job number T81.
A Job cost sheet is a report used to record production costs and is set up by organizations that use
a labor demand cost framework to identify and assign costs to articles and administrations.
A Job cost sheet is not only used to cost a job, but at the same time it is a part of the
organization's accounting program. It is used as a toolkit for the activity in a process description
because it contains all the activity views in the process.
Job cost sheet
Job Number T81
Units completed 40
Name of the item Trombones
Date completed Mar-05
Direct Materials Direct Labor Manufacturing overhead
Req. No. Amount Rate/h Hours Amount Hours Rate Amount
112 $1,250 $10 500 $5,000 500 $20 $1,000
Cost Summary Units Shipped
Direct Materials $1,250 Date Number Rate Amount Balance
Direct Labor $5,000 Mar-31 20 $500 $10,000 20
Manufacturing Overhead $1,000
Total cost $7,250
Unit product cost
(total cost /units) $181.25
year.
Predetermined overhead rate = Estimated manufacturing overhead cost/Estimated total units in
the allocation base
Predetermined overhead rate = $ 450,000
22,500 = $20 per direct labor hour
2. Complete job cost sheet for job number T81.
A Job cost sheet is a report used to record production costs and is set up by organizations that use
a labor demand cost framework to identify and assign costs to articles and administrations.
A Job cost sheet is not only used to cost a job, but at the same time it is a part of the
organization's accounting program. It is used as a toolkit for the activity in a process description
because it contains all the activity views in the process.
Job cost sheet
Job Number T81
Units completed 40
Name of the item Trombones
Date completed Mar-05
Direct Materials Direct Labor Manufacturing overhead
Req. No. Amount Rate/h Hours Amount Hours Rate Amount
112 $1,250 $10 500 $5,000 500 $20 $1,000
Cost Summary Units Shipped
Direct Materials $1,250 Date Number Rate Amount Balance
Direct Labor $5,000 Mar-31 20 $500 $10,000 20
Manufacturing Overhead $1,000
Total cost $7,250
Unit product cost
(total cost /units) $181.25
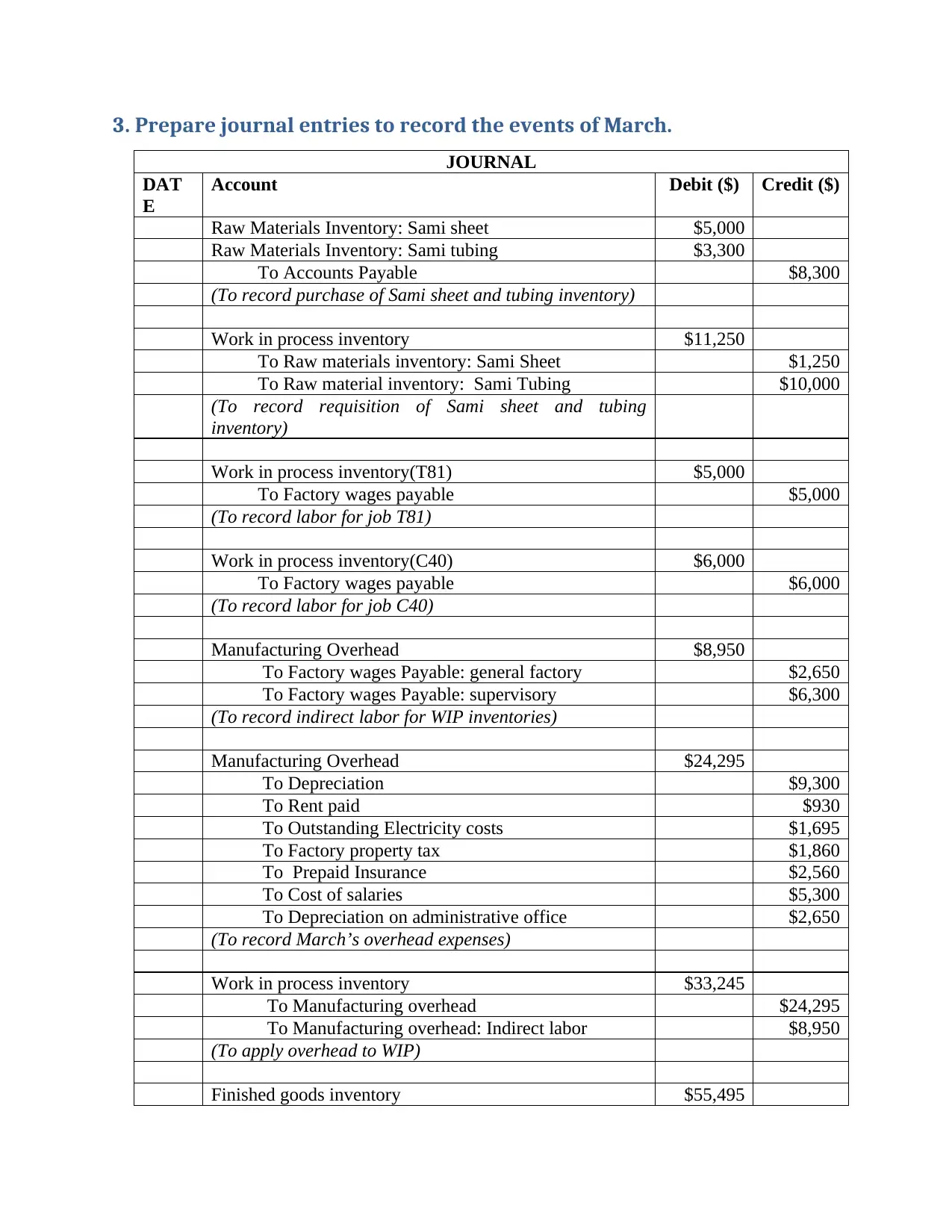
3. Prepare journal entries to record the events of March.
JOURNAL
DAT
E
Account Debit ($) Credit ($)
Raw Materials Inventory: Sami sheet $5,000
Raw Materials Inventory: Sami tubing $3,300
To Accounts Payable $8,300
(To record purchase of Sami sheet and tubing inventory)
Work in process inventory $11,250
To Raw materials inventory: Sami Sheet $1,250
To Raw material inventory: Sami Tubing $10,000
(To record requisition of Sami sheet and tubing
inventory)
Work in process inventory(T81) $5,000
To Factory wages payable $5,000
(To record labor for job T81)
Work in process inventory(C40) $6,000
To Factory wages payable $6,000
(To record labor for job C40)
Manufacturing Overhead $8,950
To Factory wages Payable: general factory $2,650
To Factory wages Payable: supervisory $6,300
(To record indirect labor for WIP inventories)
Manufacturing Overhead $24,295
To Depreciation $9,300
To Rent paid $930
To Outstanding Electricity costs $1,695
To Factory property tax $1,860
To Prepaid Insurance $2,560
To Cost of salaries $5,300
To Depreciation on administrative office $2,650
(To record March’s overhead expenses)
Work in process inventory $33,245
To Manufacturing overhead $24,295
To Manufacturing overhead: Indirect labor $8,950
(To apply overhead to WIP)
Finished goods inventory $55,495
JOURNAL
DAT
E
Account Debit ($) Credit ($)
Raw Materials Inventory: Sami sheet $5,000
Raw Materials Inventory: Sami tubing $3,300
To Accounts Payable $8,300
(To record purchase of Sami sheet and tubing inventory)
Work in process inventory $11,250
To Raw materials inventory: Sami Sheet $1,250
To Raw material inventory: Sami Tubing $10,000
(To record requisition of Sami sheet and tubing
inventory)
Work in process inventory(T81) $5,000
To Factory wages payable $5,000
(To record labor for job T81)
Work in process inventory(C40) $6,000
To Factory wages payable $6,000
(To record labor for job C40)
Manufacturing Overhead $8,950
To Factory wages Payable: general factory $2,650
To Factory wages Payable: supervisory $6,300
(To record indirect labor for WIP inventories)
Manufacturing Overhead $24,295
To Depreciation $9,300
To Rent paid $930
To Outstanding Electricity costs $1,695
To Factory property tax $1,860
To Prepaid Insurance $2,560
To Cost of salaries $5,300
To Depreciation on administrative office $2,650
(To record March’s overhead expenses)
Work in process inventory $33,245
To Manufacturing overhead $24,295
To Manufacturing overhead: Indirect labor $8,950
(To apply overhead to WIP)
Finished goods inventory $55,495
⊘ This is a preview!⊘
Do you want full access?
Subscribe today to unlock all pages.

Trusted by 1+ million students worldwide
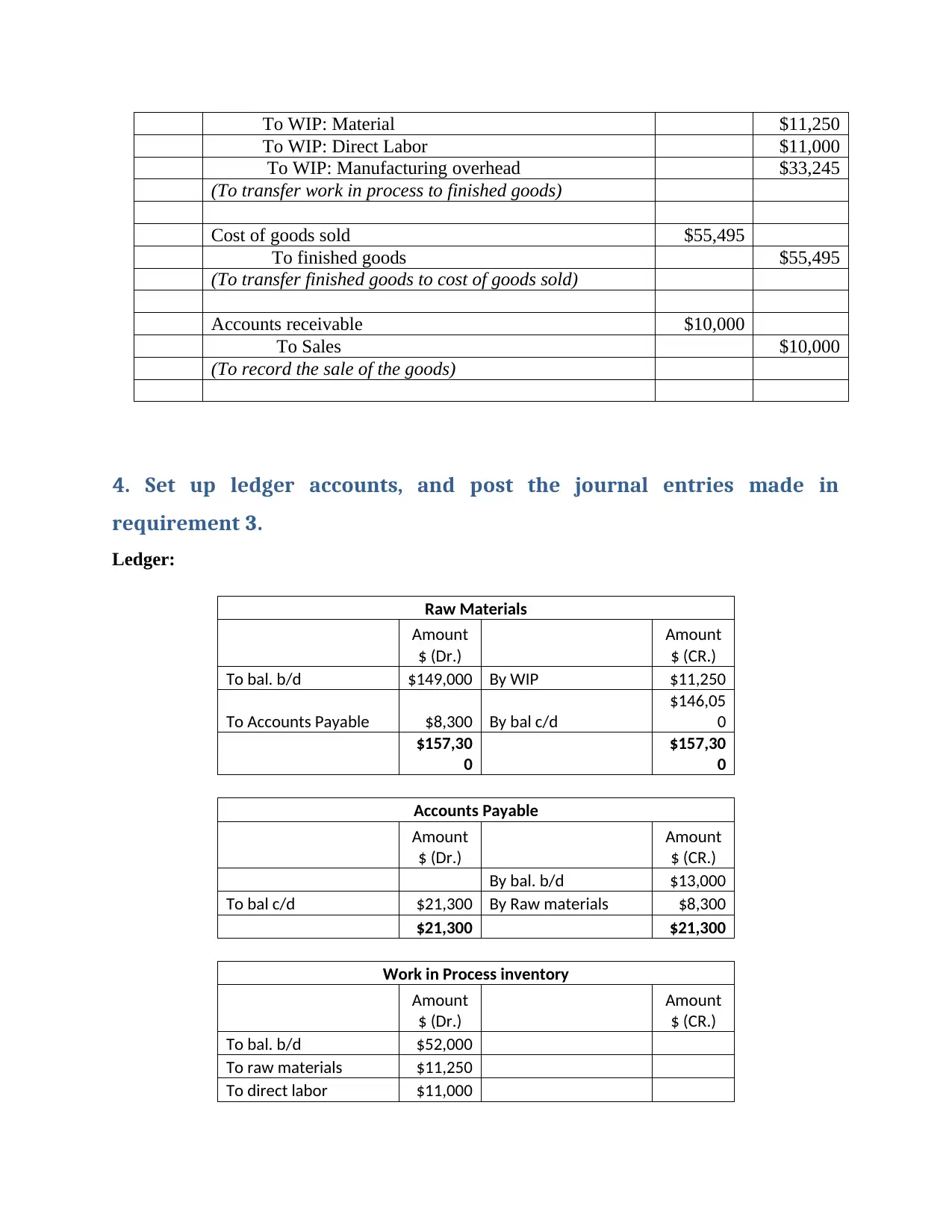
To WIP: Material $11,250
To WIP: Direct Labor $11,000
To WIP: Manufacturing overhead $33,245
(To transfer work in process to finished goods)
Cost of goods sold $55,495
To finished goods $55,495
(To transfer finished goods to cost of goods sold)
Accounts receivable $10,000
To Sales $10,000
(To record the sale of the goods)
4. Set up ledger accounts, and post the journal entries made in
requirement 3.
Ledger:
Raw Materials
Amount
$ (Dr.)
Amount
$ (CR.)
To bal. b/d $149,000 By WIP $11,250
To Accounts Payable $8,300 By bal c/d
$146,05
0
$157,30
0
$157,30
0
Accounts Payable
Amount
$ (Dr.)
Amount
$ (CR.)
By bal. b/d $13,000
To bal c/d $21,300 By Raw materials $8,300
$21,300 $21,300
Work in Process inventory
Amount
$ (Dr.)
Amount
$ (CR.)
To bal. b/d $52,000
To raw materials $11,250
To direct labor $11,000
To WIP: Direct Labor $11,000
To WIP: Manufacturing overhead $33,245
(To transfer work in process to finished goods)
Cost of goods sold $55,495
To finished goods $55,495
(To transfer finished goods to cost of goods sold)
Accounts receivable $10,000
To Sales $10,000
(To record the sale of the goods)
4. Set up ledger accounts, and post the journal entries made in
requirement 3.
Ledger:
Raw Materials
Amount
$ (Dr.)
Amount
$ (CR.)
To bal. b/d $149,000 By WIP $11,250
To Accounts Payable $8,300 By bal c/d
$146,05
0
$157,30
0
$157,30
0
Accounts Payable
Amount
$ (Dr.)
Amount
$ (CR.)
By bal. b/d $13,000
To bal c/d $21,300 By Raw materials $8,300
$21,300 $21,300
Work in Process inventory
Amount
$ (Dr.)
Amount
$ (CR.)
To bal. b/d $52,000
To raw materials $11,250
To direct labor $11,000
Paraphrase This Document
Need a fresh take? Get an instant paraphrase of this document with our AI Paraphraser
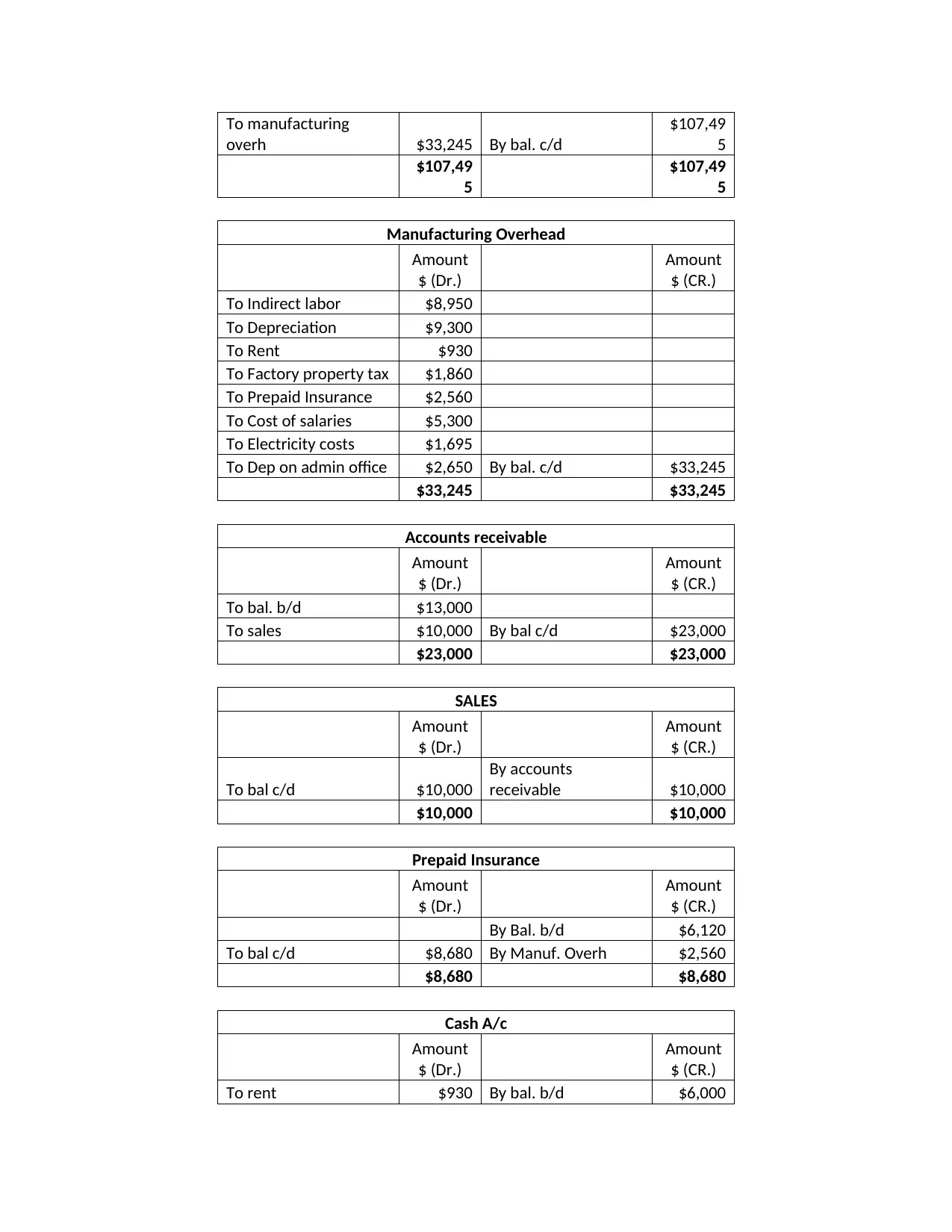
To manufacturing
overh $33,245 By bal. c/d
$107,49
5
$107,49
5
$107,49
5
Manufacturing Overhead
Amount
$ (Dr.)
Amount
$ (CR.)
To Indirect labor $8,950
To Depreciation $9,300
To Rent $930
To Factory property tax $1,860
To Prepaid Insurance $2,560
To Cost of salaries $5,300
To Electricity costs $1,695
To Dep on admin office $2,650 By bal. c/d $33,245
$33,245 $33,245
Accounts receivable
Amount
$ (Dr.)
Amount
$ (CR.)
To bal. b/d $13,000
To sales $10,000 By bal c/d $23,000
$23,000 $23,000
SALES
Amount
$ (Dr.)
Amount
$ (CR.)
To bal c/d $10,000
By accounts
receivable $10,000
$10,000 $10,000
Prepaid Insurance
Amount
$ (Dr.)
Amount
$ (CR.)
By Bal. b/d $6,120
To bal c/d $8,680 By Manuf. Overh $2,560
$8,680 $8,680
Cash A/c
Amount
$ (Dr.)
Amount
$ (CR.)
To rent $930 By bal. b/d $6,000
overh $33,245 By bal. c/d
$107,49
5
$107,49
5
$107,49
5
Manufacturing Overhead
Amount
$ (Dr.)
Amount
$ (CR.)
To Indirect labor $8,950
To Depreciation $9,300
To Rent $930
To Factory property tax $1,860
To Prepaid Insurance $2,560
To Cost of salaries $5,300
To Electricity costs $1,695
To Dep on admin office $2,650 By bal. c/d $33,245
$33,245 $33,245
Accounts receivable
Amount
$ (Dr.)
Amount
$ (CR.)
To bal. b/d $13,000
To sales $10,000 By bal c/d $23,000
$23,000 $23,000
SALES
Amount
$ (Dr.)
Amount
$ (CR.)
To bal c/d $10,000
By accounts
receivable $10,000
$10,000 $10,000
Prepaid Insurance
Amount
$ (Dr.)
Amount
$ (CR.)
By Bal. b/d $6,120
To bal c/d $8,680 By Manuf. Overh $2,560
$8,680 $8,680
Cash A/c
Amount
$ (Dr.)
Amount
$ (CR.)
To rent $930 By bal. b/d $6,000
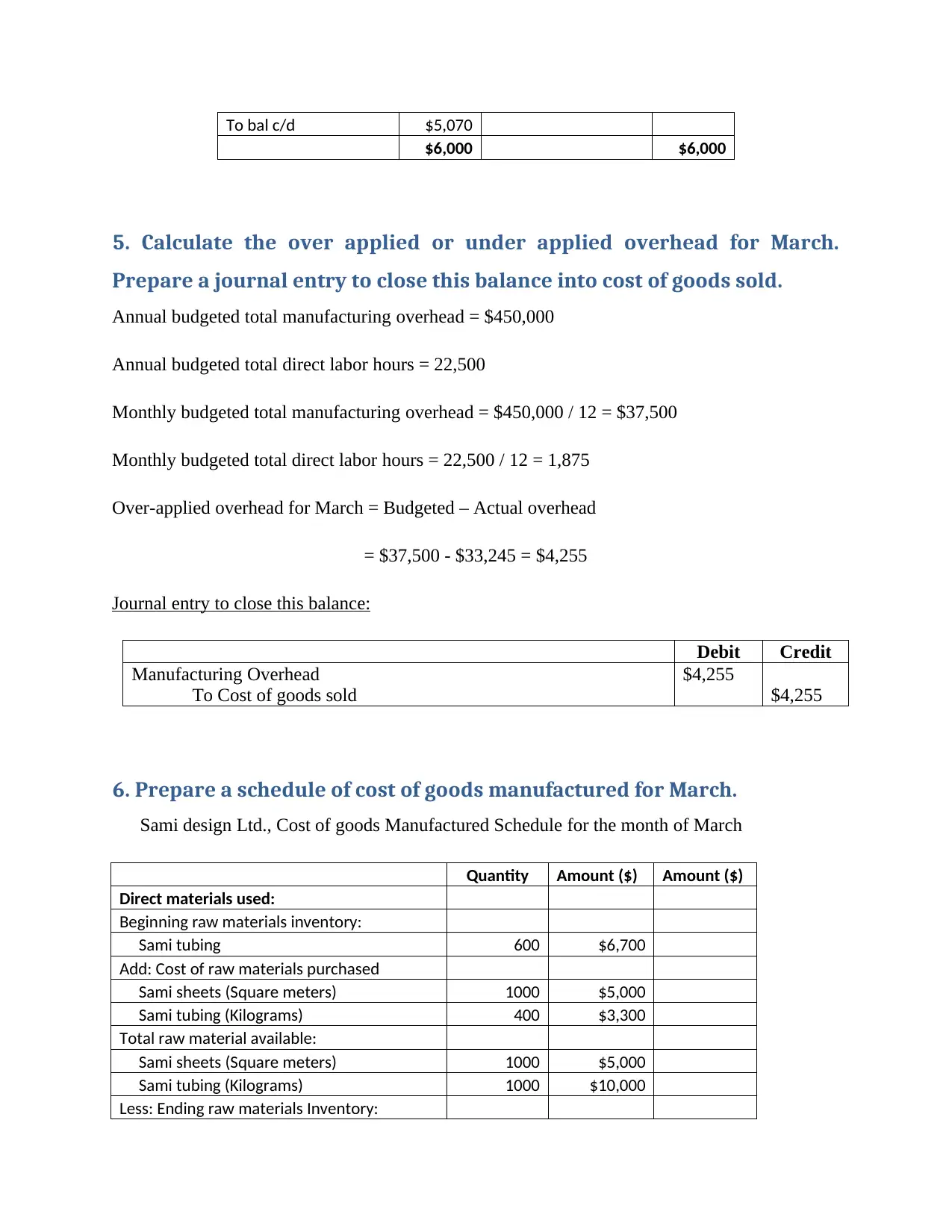
To bal c/d $5,070
$6,000 $6,000
5. Calculate the over applied or under applied overhead for March.
Prepare a journal entry to close this balance into cost of goods sold.
Annual budgeted total manufacturing overhead = $450,000
Annual budgeted total direct labor hours = 22,500
Monthly budgeted total manufacturing overhead = $450,000 / 12 = $37,500
Monthly budgeted total direct labor hours = 22,500 / 12 = 1,875
Over-applied overhead for March = Budgeted – Actual overhead
= $37,500 - $33,245 = $4,255
Journal entry to close this balance:
Debit Credit
Manufacturing Overhead
To Cost of goods sold
$4,255
$4,255
6. Prepare a schedule of cost of goods manufactured for March.
Sami design Ltd., Cost of goods Manufactured Schedule for the month of March
Quantity Amount ($) Amount ($)
Direct materials used:
Beginning raw materials inventory:
Sami tubing 600 $6,700
Add: Cost of raw materials purchased
Sami sheets (Square meters) 1000 $5,000
Sami tubing (Kilograms) 400 $3,300
Total raw material available:
Sami sheets (Square meters) 1000 $5,000
Sami tubing (Kilograms) 1000 $10,000
Less: Ending raw materials Inventory:
$6,000 $6,000
5. Calculate the over applied or under applied overhead for March.
Prepare a journal entry to close this balance into cost of goods sold.
Annual budgeted total manufacturing overhead = $450,000
Annual budgeted total direct labor hours = 22,500
Monthly budgeted total manufacturing overhead = $450,000 / 12 = $37,500
Monthly budgeted total direct labor hours = 22,500 / 12 = 1,875
Over-applied overhead for March = Budgeted – Actual overhead
= $37,500 - $33,245 = $4,255
Journal entry to close this balance:
Debit Credit
Manufacturing Overhead
To Cost of goods sold
$4,255
$4,255
6. Prepare a schedule of cost of goods manufactured for March.
Sami design Ltd., Cost of goods Manufactured Schedule for the month of March
Quantity Amount ($) Amount ($)
Direct materials used:
Beginning raw materials inventory:
Sami tubing 600 $6,700
Add: Cost of raw materials purchased
Sami sheets (Square meters) 1000 $5,000
Sami tubing (Kilograms) 400 $3,300
Total raw material available:
Sami sheets (Square meters) 1000 $5,000
Sami tubing (Kilograms) 1000 $10,000
Less: Ending raw materials Inventory:
⊘ This is a preview!⊘
Do you want full access?
Subscribe today to unlock all pages.

Trusted by 1+ million students worldwide
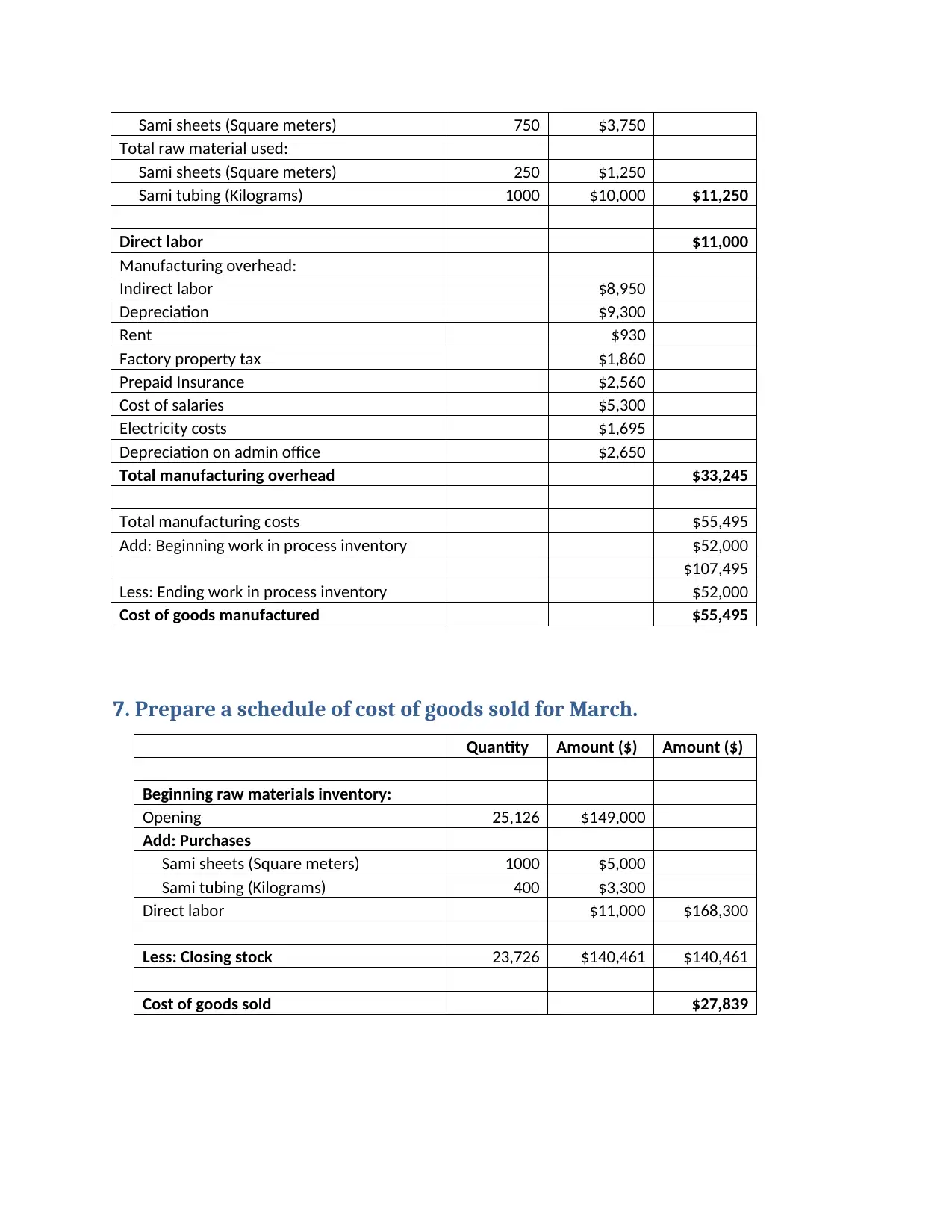
Sami sheets (Square meters) 750 $3,750
Total raw material used:
Sami sheets (Square meters) 250 $1,250
Sami tubing (Kilograms) 1000 $10,000 $11,250
Direct labor $11,000
Manufacturing overhead:
Indirect labor $8,950
Depreciation $9,300
Rent $930
Factory property tax $1,860
Prepaid Insurance $2,560
Cost of salaries $5,300
Electricity costs $1,695
Depreciation on admin office $2,650
Total manufacturing overhead $33,245
Total manufacturing costs $55,495
Add: Beginning work in process inventory $52,000
$107,495
Less: Ending work in process inventory $52,000
Cost of goods manufactured $55,495
7. Prepare a schedule of cost of goods sold for March.
Quantity Amount ($) Amount ($)
Beginning raw materials inventory:
Opening 25,126 $149,000
Add: Purchases
Sami sheets (Square meters) 1000 $5,000
Sami tubing (Kilograms) 400 $3,300
Direct labor $11,000 $168,300
Less: Closing stock 23,726 $140,461 $140,461
Cost of goods sold $27,839
Total raw material used:
Sami sheets (Square meters) 250 $1,250
Sami tubing (Kilograms) 1000 $10,000 $11,250
Direct labor $11,000
Manufacturing overhead:
Indirect labor $8,950
Depreciation $9,300
Rent $930
Factory property tax $1,860
Prepaid Insurance $2,560
Cost of salaries $5,300
Electricity costs $1,695
Depreciation on admin office $2,650
Total manufacturing overhead $33,245
Total manufacturing costs $55,495
Add: Beginning work in process inventory $52,000
$107,495
Less: Ending work in process inventory $52,000
Cost of goods manufactured $55,495
7. Prepare a schedule of cost of goods sold for March.
Quantity Amount ($) Amount ($)
Beginning raw materials inventory:
Opening 25,126 $149,000
Add: Purchases
Sami sheets (Square meters) 1000 $5,000
Sami tubing (Kilograms) 400 $3,300
Direct labor $11,000 $168,300
Less: Closing stock 23,726 $140,461 $140,461
Cost of goods sold $27,839
Paraphrase This Document
Need a fresh take? Get an instant paraphrase of this document with our AI Paraphraser
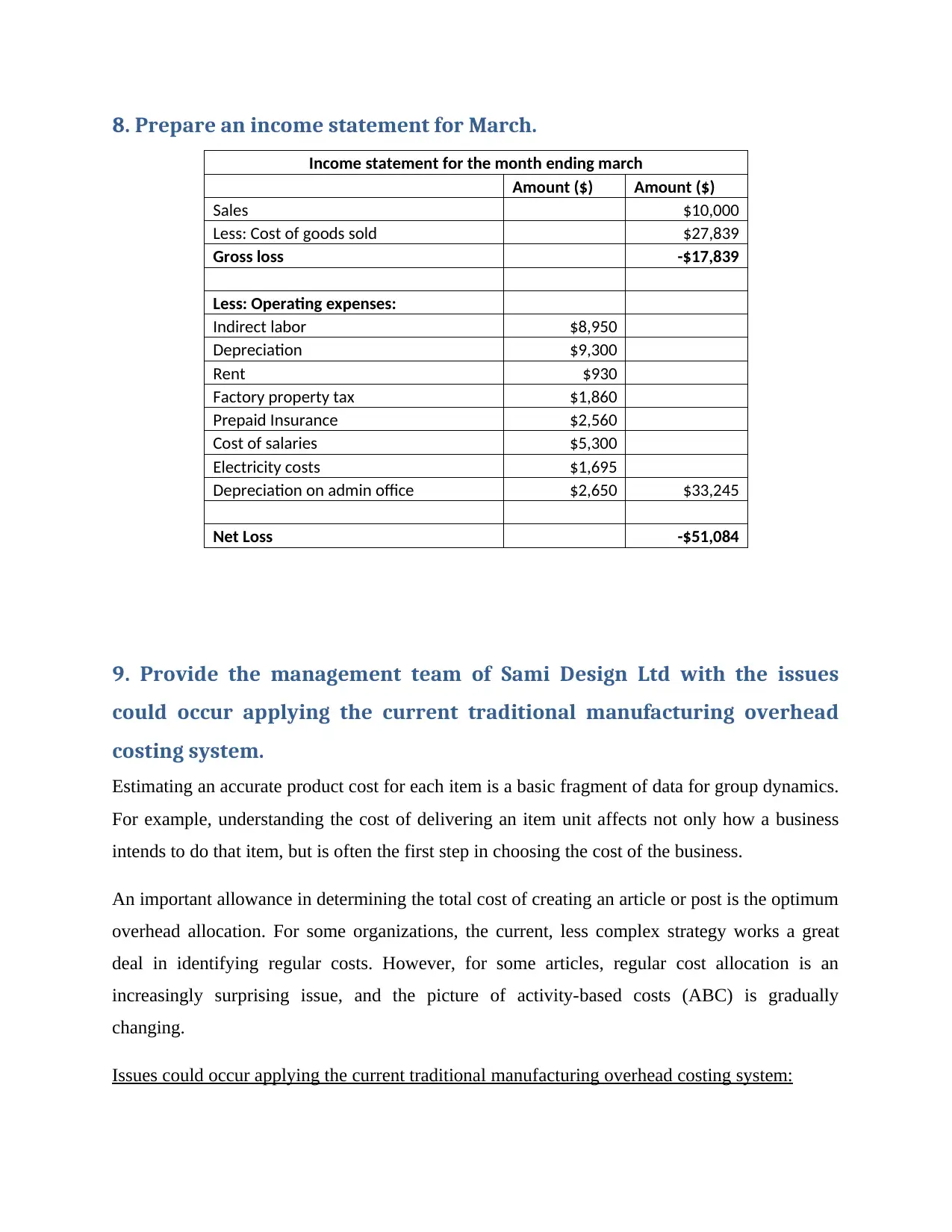
8. Prepare an income statement for March.
Income statement for the month ending march
Amount ($) Amount ($)
Sales $10,000
Less: Cost of goods sold $27,839
Gross loss -$17,839
Less: Operating expenses:
Indirect labor $8,950
Depreciation $9,300
Rent $930
Factory property tax $1,860
Prepaid Insurance $2,560
Cost of salaries $5,300
Electricity costs $1,695
Depreciation on admin office $2,650 $33,245
Net Loss -$51,084
9. Provide the management team of Sami Design Ltd with the issues
could occur applying the current traditional manufacturing overhead
costing system.
Estimating an accurate product cost for each item is a basic fragment of data for group dynamics.
For example, understanding the cost of delivering an item unit affects not only how a business
intends to do that item, but is often the first step in choosing the cost of the business.
An important allowance in determining the total cost of creating an article or post is the optimum
overhead allocation. For some organizations, the current, less complex strategy works a great
deal in identifying regular costs. However, for some articles, regular cost allocation is an
increasingly surprising issue, and the picture of activity-based costs (ABC) is gradually
changing.
Issues could occur applying the current traditional manufacturing overhead costing system:
Income statement for the month ending march
Amount ($) Amount ($)
Sales $10,000
Less: Cost of goods sold $27,839
Gross loss -$17,839
Less: Operating expenses:
Indirect labor $8,950
Depreciation $9,300
Rent $930
Factory property tax $1,860
Prepaid Insurance $2,560
Cost of salaries $5,300
Electricity costs $1,695
Depreciation on admin office $2,650 $33,245
Net Loss -$51,084
9. Provide the management team of Sami Design Ltd with the issues
could occur applying the current traditional manufacturing overhead
costing system.
Estimating an accurate product cost for each item is a basic fragment of data for group dynamics.
For example, understanding the cost of delivering an item unit affects not only how a business
intends to do that item, but is often the first step in choosing the cost of the business.
An important allowance in determining the total cost of creating an article or post is the optimum
overhead allocation. For some organizations, the current, less complex strategy works a great
deal in identifying regular costs. However, for some articles, regular cost allocation is an
increasingly surprising issue, and the picture of activity-based costs (ABC) is gradually
changing.
Issues could occur applying the current traditional manufacturing overhead costing system:
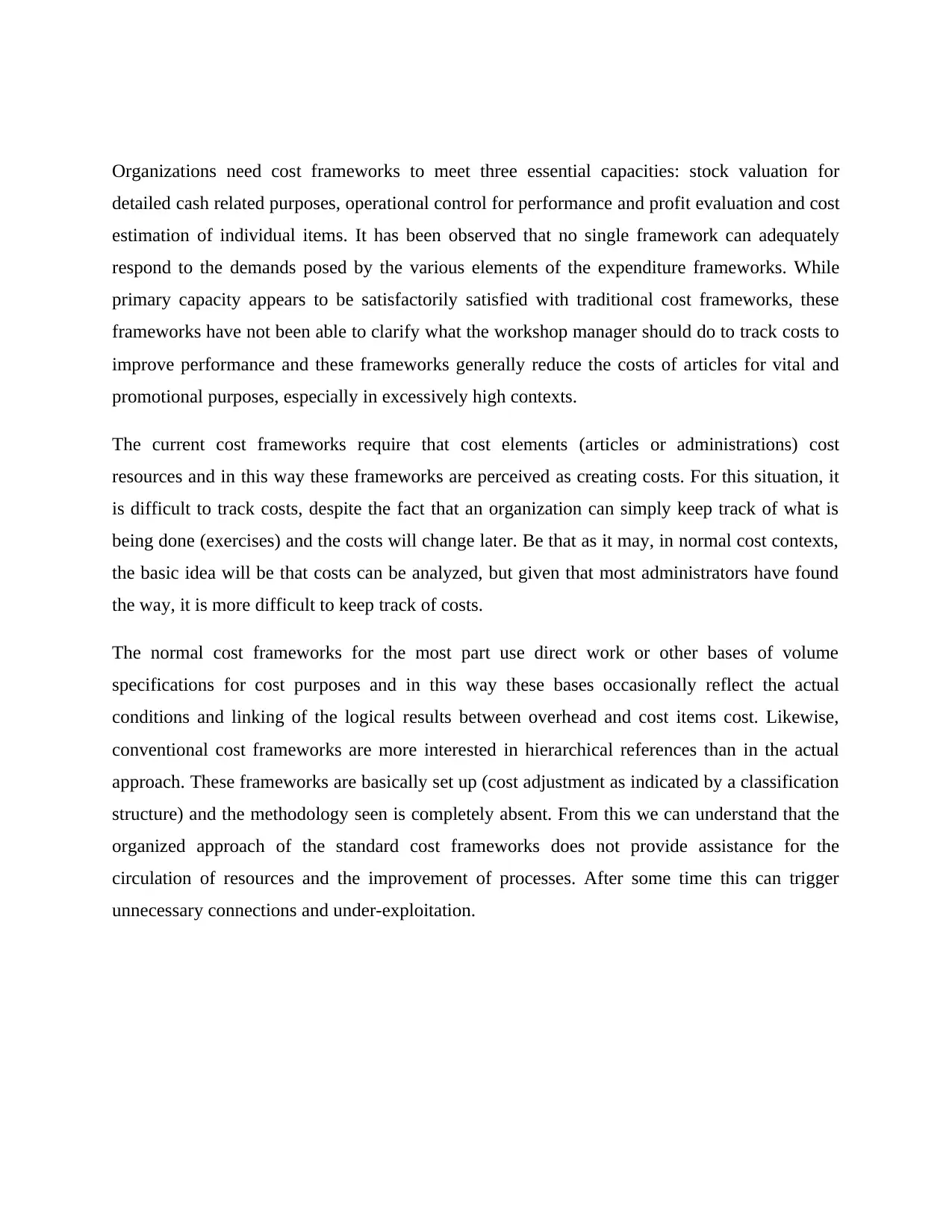
Organizations need cost frameworks to meet three essential capacities: stock valuation for
detailed cash related purposes, operational control for performance and profit evaluation and cost
estimation of individual items. It has been observed that no single framework can adequately
respond to the demands posed by the various elements of the expenditure frameworks. While
primary capacity appears to be satisfactorily satisfied with traditional cost frameworks, these
frameworks have not been able to clarify what the workshop manager should do to track costs to
improve performance and these frameworks generally reduce the costs of articles for vital and
promotional purposes, especially in excessively high contexts.
The current cost frameworks require that cost elements (articles or administrations) cost
resources and in this way these frameworks are perceived as creating costs. For this situation, it
is difficult to track costs, despite the fact that an organization can simply keep track of what is
being done (exercises) and the costs will change later. Be that as it may, in normal cost contexts,
the basic idea will be that costs can be analyzed, but given that most administrators have found
the way, it is more difficult to keep track of costs.
The normal cost frameworks for the most part use direct work or other bases of volume
specifications for cost purposes and in this way these bases occasionally reflect the actual
conditions and linking of the logical results between overhead and cost items cost. Likewise,
conventional cost frameworks are more interested in hierarchical references than in the actual
approach. These frameworks are basically set up (cost adjustment as indicated by a classification
structure) and the methodology seen is completely absent. From this we can understand that the
organized approach of the standard cost frameworks does not provide assistance for the
circulation of resources and the improvement of processes. After some time this can trigger
unnecessary connections and under-exploitation.
detailed cash related purposes, operational control for performance and profit evaluation and cost
estimation of individual items. It has been observed that no single framework can adequately
respond to the demands posed by the various elements of the expenditure frameworks. While
primary capacity appears to be satisfactorily satisfied with traditional cost frameworks, these
frameworks have not been able to clarify what the workshop manager should do to track costs to
improve performance and these frameworks generally reduce the costs of articles for vital and
promotional purposes, especially in excessively high contexts.
The current cost frameworks require that cost elements (articles or administrations) cost
resources and in this way these frameworks are perceived as creating costs. For this situation, it
is difficult to track costs, despite the fact that an organization can simply keep track of what is
being done (exercises) and the costs will change later. Be that as it may, in normal cost contexts,
the basic idea will be that costs can be analyzed, but given that most administrators have found
the way, it is more difficult to keep track of costs.
The normal cost frameworks for the most part use direct work or other bases of volume
specifications for cost purposes and in this way these bases occasionally reflect the actual
conditions and linking of the logical results between overhead and cost items cost. Likewise,
conventional cost frameworks are more interested in hierarchical references than in the actual
approach. These frameworks are basically set up (cost adjustment as indicated by a classification
structure) and the methodology seen is completely absent. From this we can understand that the
organized approach of the standard cost frameworks does not provide assistance for the
circulation of resources and the improvement of processes. After some time this can trigger
unnecessary connections and under-exploitation.
⊘ This is a preview!⊘
Do you want full access?
Subscribe today to unlock all pages.

Trusted by 1+ million students worldwide
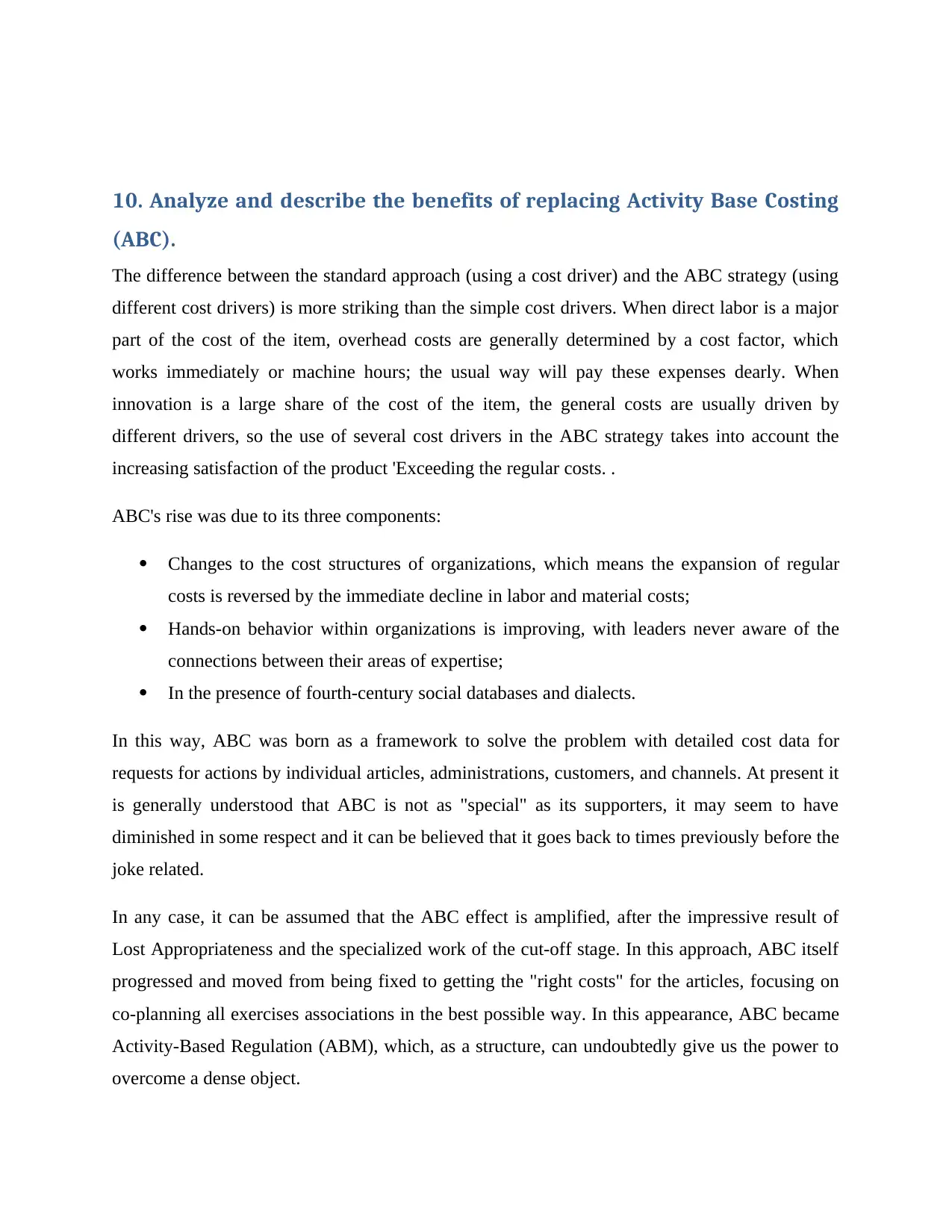
10. Analyze and describe the benefits of replacing Activity Base Costing
(ABC).
The difference between the standard approach (using a cost driver) and the ABC strategy (using
different cost drivers) is more striking than the simple cost drivers. When direct labor is a major
part of the cost of the item, overhead costs are generally determined by a cost factor, which
works immediately or machine hours; the usual way will pay these expenses dearly. When
innovation is a large share of the cost of the item, the general costs are usually driven by
different drivers, so the use of several cost drivers in the ABC strategy takes into account the
increasing satisfaction of the product 'Exceeding the regular costs. .
ABC's rise was due to its three components:
Changes to the cost structures of organizations, which means the expansion of regular
costs is reversed by the immediate decline in labor and material costs;
Hands-on behavior within organizations is improving, with leaders never aware of the
connections between their areas of expertise;
In the presence of fourth-century social databases and dialects.
In this way, ABC was born as a framework to solve the problem with detailed cost data for
requests for actions by individual articles, administrations, customers, and channels. At present it
is generally understood that ABC is not as "special" as its supporters, it may seem to have
diminished in some respect and it can be believed that it goes back to times previously before the
joke related.
In any case, it can be assumed that the ABC effect is amplified, after the impressive result of
Lost Appropriateness and the specialized work of the cut-off stage. In this approach, ABC itself
progressed and moved from being fixed to getting the "right costs" for the articles, focusing on
co-planning all exercises associations in the best possible way. In this appearance, ABC became
Activity-Based Regulation (ABM), which, as a structure, can undoubtedly give us the power to
overcome a dense object.
(ABC).
The difference between the standard approach (using a cost driver) and the ABC strategy (using
different cost drivers) is more striking than the simple cost drivers. When direct labor is a major
part of the cost of the item, overhead costs are generally determined by a cost factor, which
works immediately or machine hours; the usual way will pay these expenses dearly. When
innovation is a large share of the cost of the item, the general costs are usually driven by
different drivers, so the use of several cost drivers in the ABC strategy takes into account the
increasing satisfaction of the product 'Exceeding the regular costs. .
ABC's rise was due to its three components:
Changes to the cost structures of organizations, which means the expansion of regular
costs is reversed by the immediate decline in labor and material costs;
Hands-on behavior within organizations is improving, with leaders never aware of the
connections between their areas of expertise;
In the presence of fourth-century social databases and dialects.
In this way, ABC was born as a framework to solve the problem with detailed cost data for
requests for actions by individual articles, administrations, customers, and channels. At present it
is generally understood that ABC is not as "special" as its supporters, it may seem to have
diminished in some respect and it can be believed that it goes back to times previously before the
joke related.
In any case, it can be assumed that the ABC effect is amplified, after the impressive result of
Lost Appropriateness and the specialized work of the cut-off stage. In this approach, ABC itself
progressed and moved from being fixed to getting the "right costs" for the articles, focusing on
co-planning all exercises associations in the best possible way. In this appearance, ABC became
Activity-Based Regulation (ABM), which, as a structure, can undoubtedly give us the power to
overcome a dense object.
Paraphrase This Document
Need a fresh take? Get an instant paraphrase of this document with our AI Paraphraser
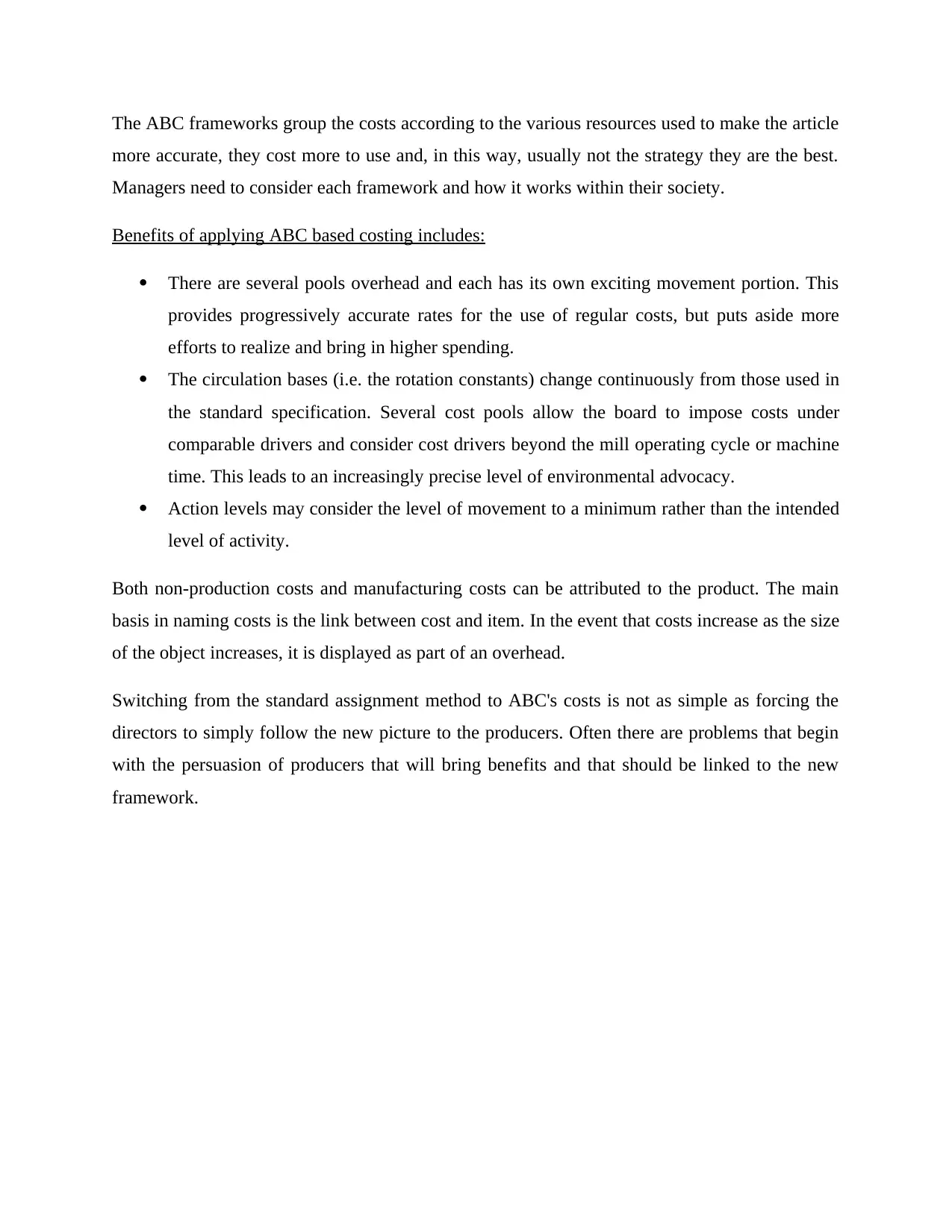
The ABC frameworks group the costs according to the various resources used to make the article
more accurate, they cost more to use and, in this way, usually not the strategy they are the best.
Managers need to consider each framework and how it works within their society.
Benefits of applying ABC based costing includes:
There are several pools overhead and each has its own exciting movement portion. This
provides progressively accurate rates for the use of regular costs, but puts aside more
efforts to realize and bring in higher spending.
The circulation bases (i.e. the rotation constants) change continuously from those used in
the standard specification. Several cost pools allow the board to impose costs under
comparable drivers and consider cost drivers beyond the mill operating cycle or machine
time. This leads to an increasingly precise level of environmental advocacy.
Action levels may consider the level of movement to a minimum rather than the intended
level of activity.
Both non-production costs and manufacturing costs can be attributed to the product. The main
basis in naming costs is the link between cost and item. In the event that costs increase as the size
of the object increases, it is displayed as part of an overhead.
Switching from the standard assignment method to ABC's costs is not as simple as forcing the
directors to simply follow the new picture to the producers. Often there are problems that begin
with the persuasion of producers that will bring benefits and that should be linked to the new
framework.
more accurate, they cost more to use and, in this way, usually not the strategy they are the best.
Managers need to consider each framework and how it works within their society.
Benefits of applying ABC based costing includes:
There are several pools overhead and each has its own exciting movement portion. This
provides progressively accurate rates for the use of regular costs, but puts aside more
efforts to realize and bring in higher spending.
The circulation bases (i.e. the rotation constants) change continuously from those used in
the standard specification. Several cost pools allow the board to impose costs under
comparable drivers and consider cost drivers beyond the mill operating cycle or machine
time. This leads to an increasingly precise level of environmental advocacy.
Action levels may consider the level of movement to a minimum rather than the intended
level of activity.
Both non-production costs and manufacturing costs can be attributed to the product. The main
basis in naming costs is the link between cost and item. In the event that costs increase as the size
of the object increases, it is displayed as part of an overhead.
Switching from the standard assignment method to ABC's costs is not as simple as forcing the
directors to simply follow the new picture to the producers. Often there are problems that begin
with the persuasion of producers that will bring benefits and that should be linked to the new
framework.
1 out of 11
Related Documents

Your All-in-One AI-Powered Toolkit for Academic Success.
+13062052269
info@desklib.com
Available 24*7 on WhatsApp / Email
Unlock your academic potential
© 2024 | Zucol Services PVT LTD | All rights reserved.