Comprehensive Report on Manufacturing Systems and Performance
VerifiedAdded on 2023/04/21
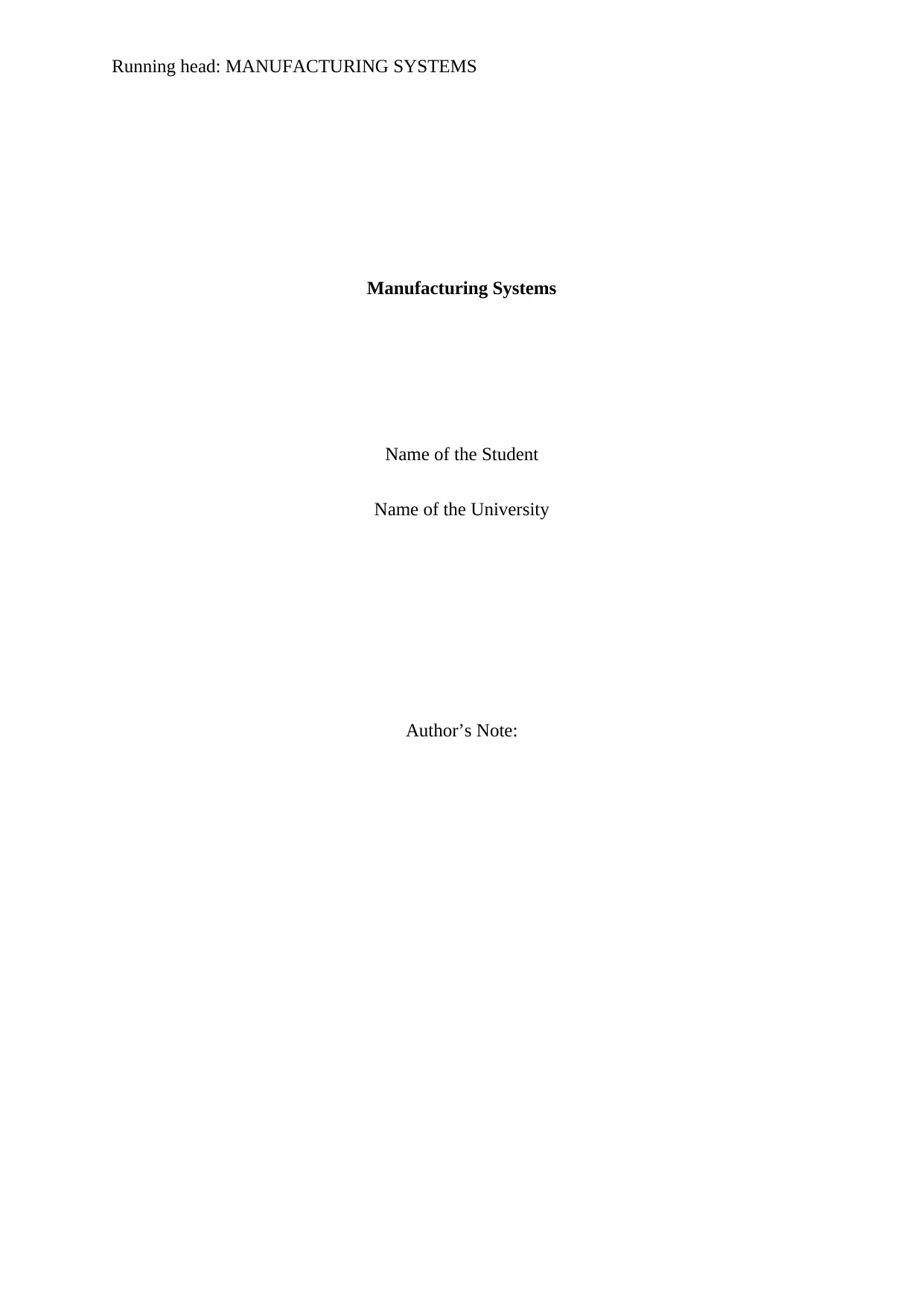
Manufacturing Systems
Name of the Student
Name of the University
Author’s Note:
Paraphrase This Document
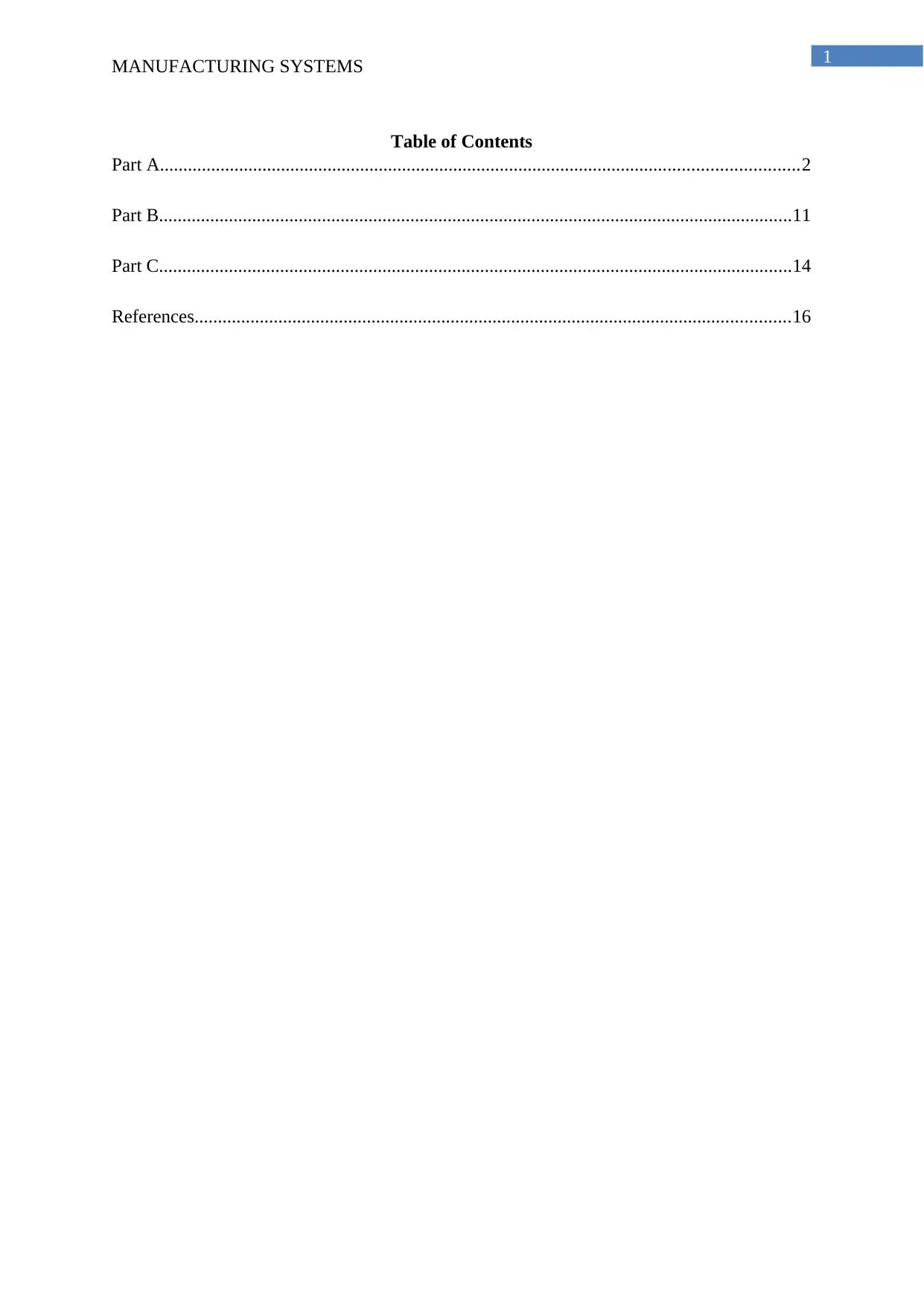
MANUFACTURING SYSTEMS
Table of Contents
Part A.........................................................................................................................................2
Part B........................................................................................................................................11
Part C........................................................................................................................................14
References................................................................................................................................16
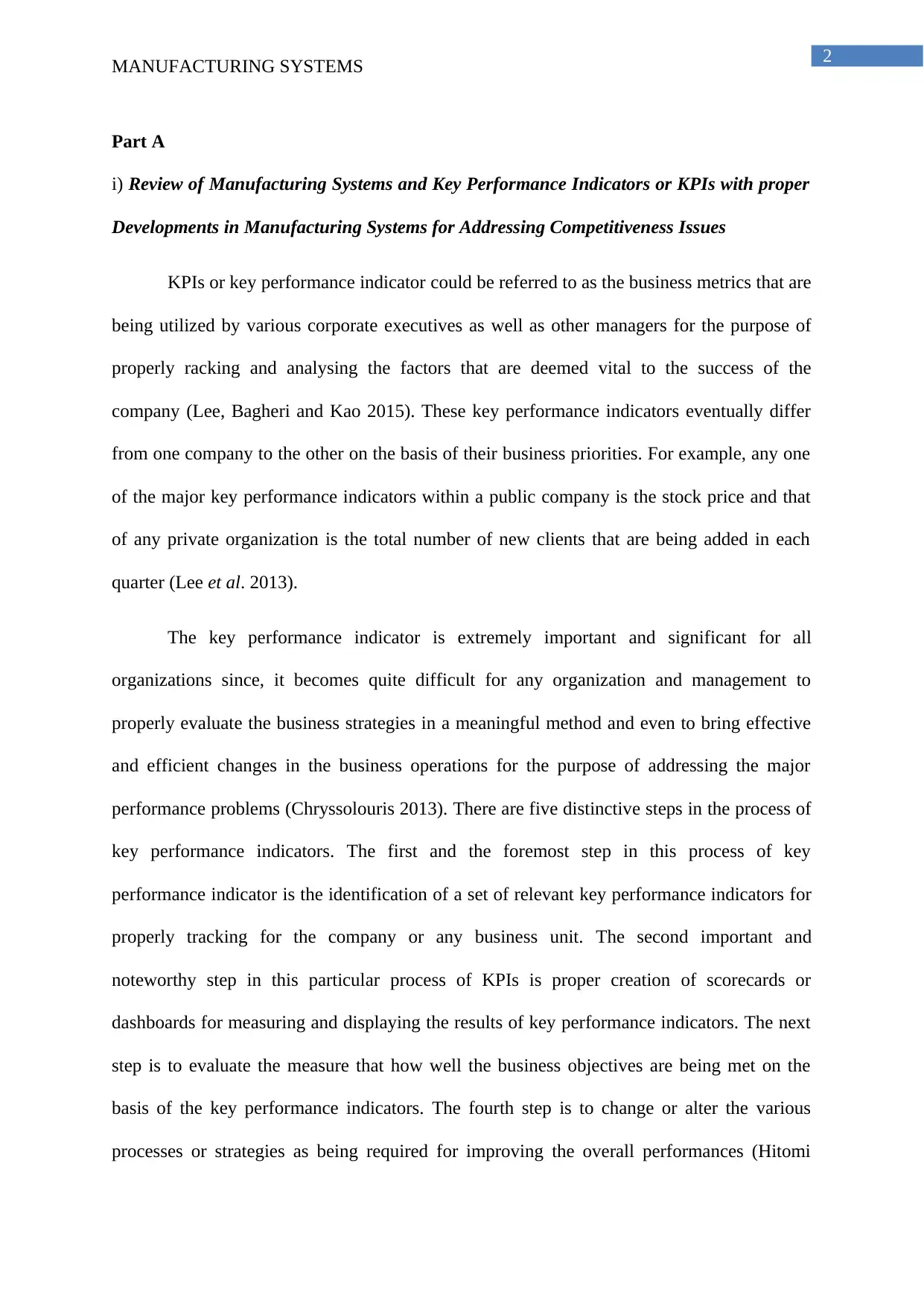
MANUFACTURING SYSTEMS
Part A
i) Review of Manufacturing Systems and Key Performance Indicators or KPIs with proper
Developments in Manufacturing Systems for Addressing Competitiveness Issues
KPIs or key performance indicator could be referred to as the business metrics that are
being utilized by various corporate executives as well as other managers for the purpose of
properly racking and analysing the factors that are deemed vital to the success of the
company (Lee, Bagheri and Kao 2015). These key performance indicators eventually differ
from one company to the other on the basis of their business priorities. For example, any one
of the major key performance indicators within a public company is the stock price and that
of any private organization is the total number of new clients that are being added in each
quarter (Lee et al. 2013).
The key performance indicator is extremely important and significant for all
organizations since, it becomes quite difficult for any organization and management to
properly evaluate the business strategies in a meaningful method and even to bring effective
and efficient changes in the business operations for the purpose of addressing the major
performance problems (Chryssolouris 2013). There are five distinctive steps in the process of
key performance indicators. The first and the foremost step in this process of key
performance indicator is the identification of a set of relevant key performance indicators for
properly tracking for the company or any business unit. The second important and
noteworthy step in this particular process of KPIs is proper creation of scorecards or
dashboards for measuring and displaying the results of key performance indicators. The next
step is to evaluate the measure that how well the business objectives are being met on the
basis of the key performance indicators. The fourth step is to change or alter the various
processes or strategies as being required for improving the overall performances (Hitomi
⊘ This is a preview!⊘
Do you want full access?
Subscribe today to unlock all pages.

Trusted by 1+ million students worldwide
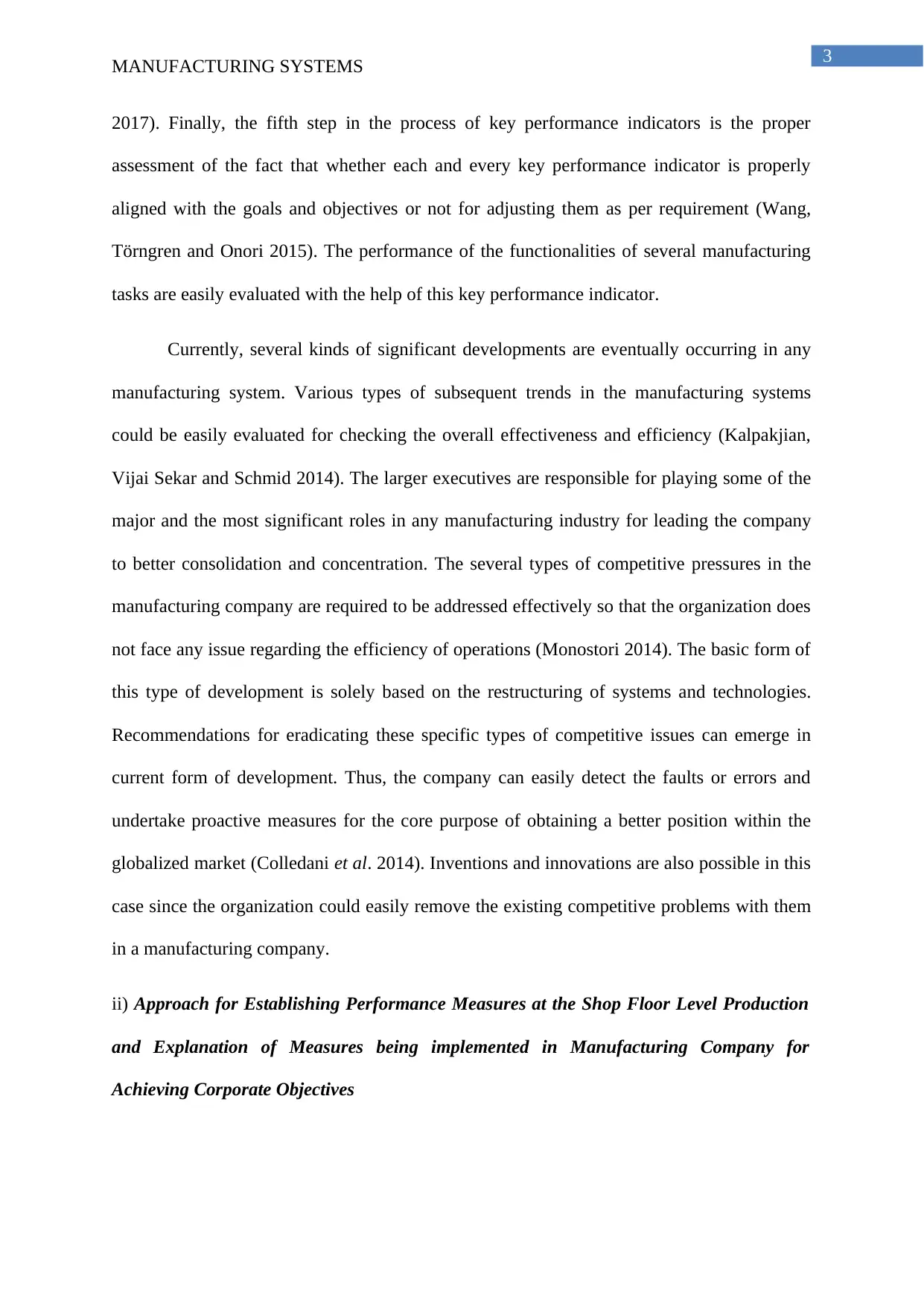
MANUFACTURING SYSTEMS
2017). Finally, the fifth step in the process of key performance indicators is the proper
assessment of the fact that whether each and every key performance indicator is properly
aligned with the goals and objectives or not for adjusting them as per requirement (Wang,
Törngren and Onori 2015). The performance of the functionalities of several manufacturing
tasks are easily evaluated with the help of this key performance indicator.
Currently, several kinds of significant developments are eventually occurring in any
manufacturing system. Various types of subsequent trends in the manufacturing systems
could be easily evaluated for checking the overall effectiveness and efficiency (Kalpakjian,
Vijai Sekar and Schmid 2014). The larger executives are responsible for playing some of the
major and the most significant roles in any manufacturing industry for leading the company
to better consolidation and concentration. The several types of competitive pressures in the
manufacturing company are required to be addressed effectively so that the organization does
not face any issue regarding the efficiency of operations (Monostori 2014). The basic form of
this type of development is solely based on the restructuring of systems and technologies.
Recommendations for eradicating these specific types of competitive issues can emerge in
current form of development. Thus, the company can easily detect the faults or errors and
undertake proactive measures for the core purpose of obtaining a better position within the
globalized market (Colledani et al. 2014). Inventions and innovations are also possible in this
case since the organization could easily remove the existing competitive problems with them
in a manufacturing company.
ii) Approach for Establishing Performance Measures at the Shop Floor Level Production
and Explanation of Measures being implemented in Manufacturing Company for
Achieving Corporate Objectives
Paraphrase This Document

MANUFACTURING SYSTEMS
Within any manufacturing company, the respective and accurate measurement of
performance is one of the major and the most important requirement (Chen, Li and Zhou
2014). This specific technique of performance measurement can be easily applied in the
organization on the basis of measurement at the core level of performance that is being made
by the company. The major indirect methodologies of measures on the basis of performance
are also evaluated effectively and efficiently. Moreover, this measurement of performance is
also subsequently applicable to the costing of operation in any organization. Important and
noteworthy types of methodologies or planning techniques on the basis of scheduling are also
developed for the proper utilization within manufacturing industries (Wu et al. 2013). The
major types of approaches on the basis of modelling are also highly needed in such systems
and there are some of the basic approaches that are being utilized by production plant
management for the core purpose of prioritizing the product quality eventually.
The approach of simple heuristic is termed as the one of the most basic and important
approach within the level of shop floor and it is quite helpful for providing definition to the
sequencing of several optimal products on the basis of the due data within one single machine
of manufacturing (Jeschke et al. 2017). In simple heuristic, each and every model that is
based on the linear programming are being developed and it is majorly applied to solve
several types of problems. Simple heuristic approaches are also applicable to the larger scale
constraint satisfaction as well as scheduling issues. Most of the popular or famous
manufacturing organizations have applied this particular approach in their business and it has
been helpful to the several scheduling operations on the basis of exploiting the critical path in
network.
The next important and significant approach that is quite popular and is being utilized
in the manufacturing companies is termed as the model of linear programming (Putnik et al.
2013). This particular model is absolutely dependent on the synchronized and systematic
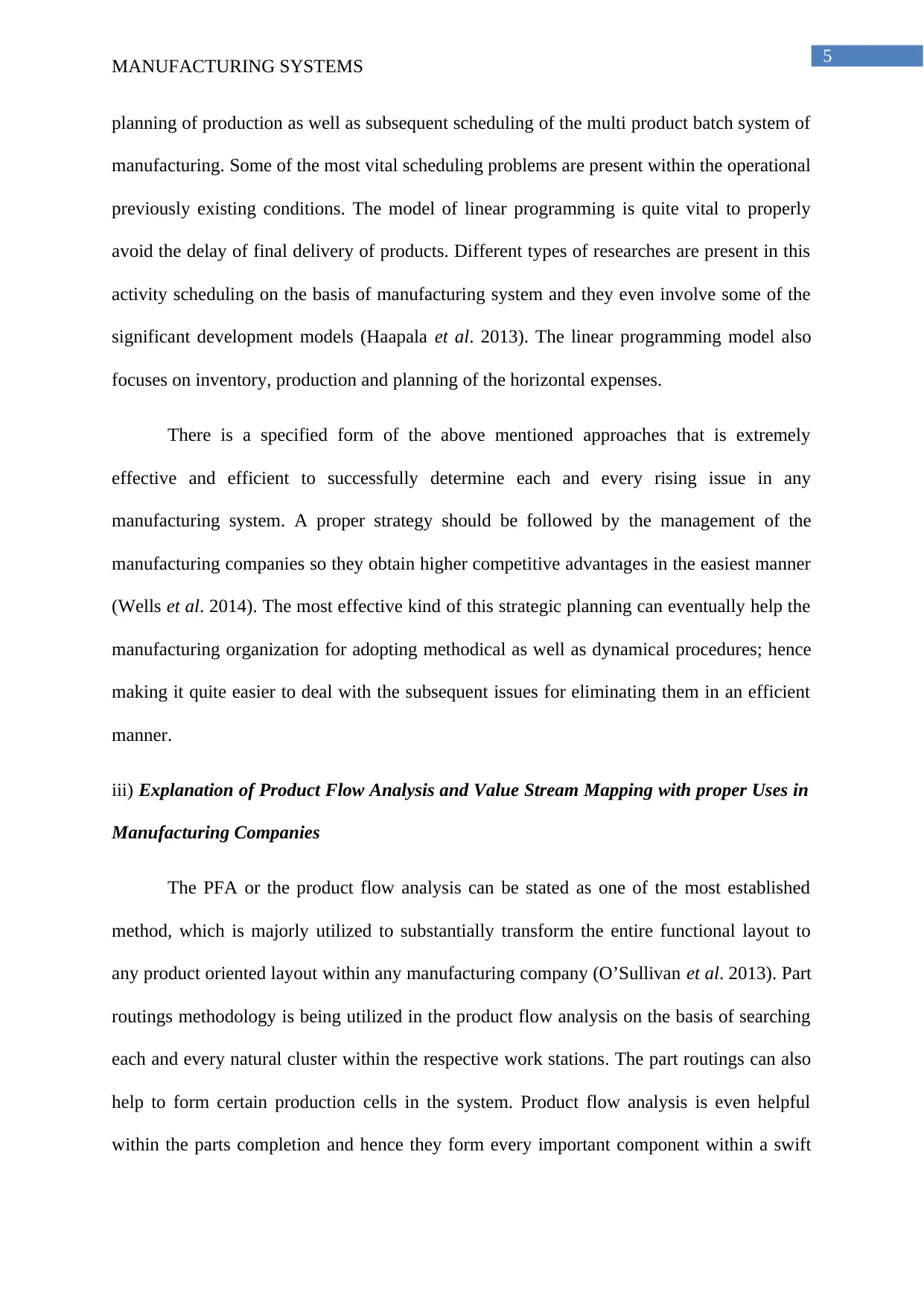
MANUFACTURING SYSTEMS
planning of production as well as subsequent scheduling of the multi product batch system of
manufacturing. Some of the most vital scheduling problems are present within the operational
previously existing conditions. The model of linear programming is quite vital to properly
avoid the delay of final delivery of products. Different types of researches are present in this
activity scheduling on the basis of manufacturing system and they even involve some of the
significant development models (Haapala et al. 2013). The linear programming model also
focuses on inventory, production and planning of the horizontal expenses.
There is a specified form of the above mentioned approaches that is extremely
effective and efficient to successfully determine each and every rising issue in any
manufacturing system. A proper strategy should be followed by the management of the
manufacturing companies so they obtain higher competitive advantages in the easiest manner
(Wells et al. 2014). The most effective kind of this strategic planning can eventually help the
manufacturing organization for adopting methodical as well as dynamical procedures; hence
making it quite easier to deal with the subsequent issues for eliminating them in an efficient
manner.
iii) Explanation of Product Flow Analysis and Value Stream Mapping with proper Uses in
Manufacturing Companies
The PFA or the product flow analysis can be stated as one of the most established
method, which is majorly utilized to substantially transform the entire functional layout to
any product oriented layout within any manufacturing company (O’Sullivan et al. 2013). Part
routings methodology is being utilized in the product flow analysis on the basis of searching
each and every natural cluster within the respective work stations. The part routings can also
help to form certain production cells in the system. Product flow analysis is even helpful
within the parts completion and hence they form every important component within a swift
⊘ This is a preview!⊘
Do you want full access?
Subscribe today to unlock all pages.

Trusted by 1+ million students worldwide
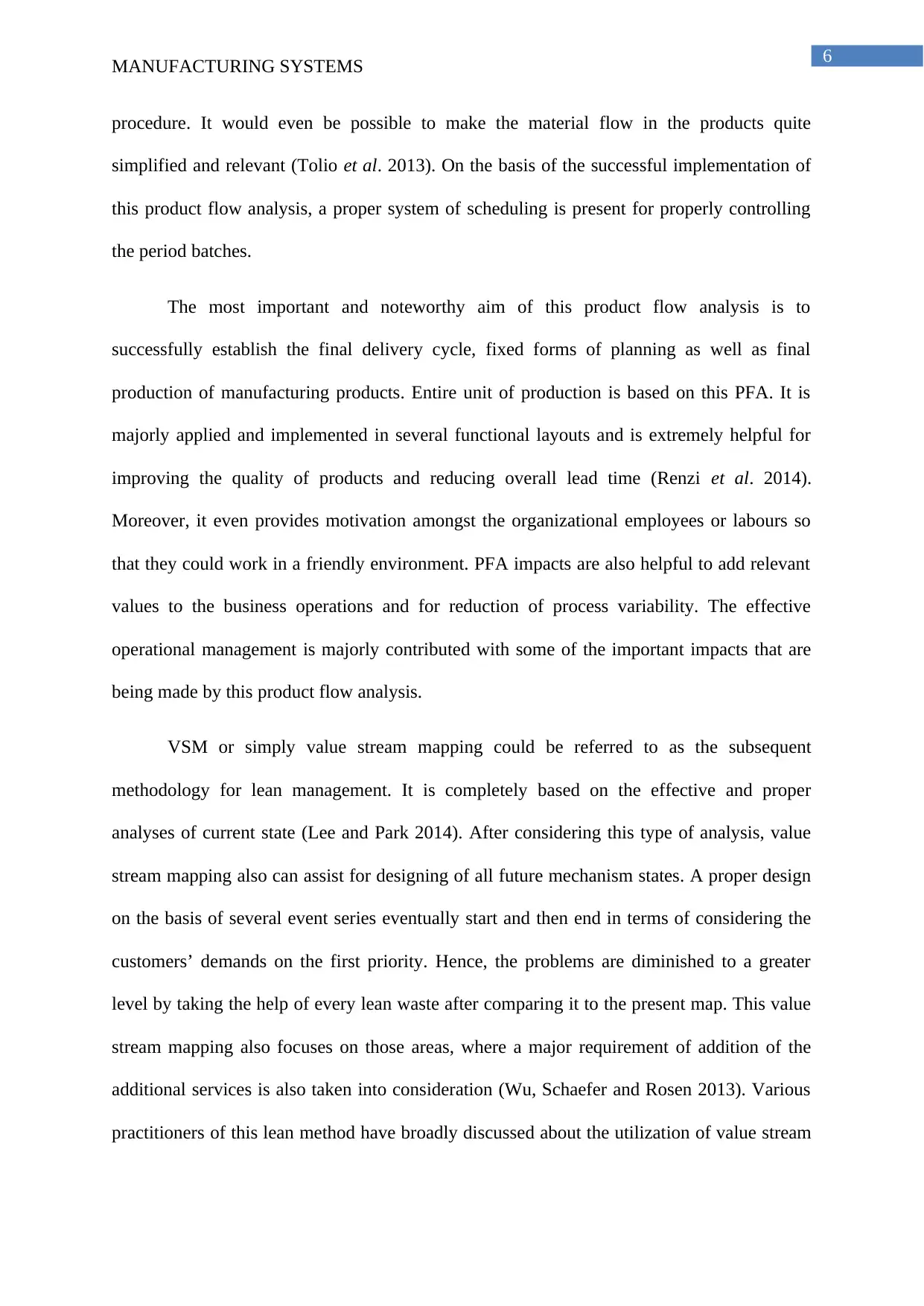
MANUFACTURING SYSTEMS
procedure. It would even be possible to make the material flow in the products quite
simplified and relevant (Tolio et al. 2013). On the basis of the successful implementation of
this product flow analysis, a proper system of scheduling is present for properly controlling
the period batches.
The most important and noteworthy aim of this product flow analysis is to
successfully establish the final delivery cycle, fixed forms of planning as well as final
production of manufacturing products. Entire unit of production is based on this PFA. It is
majorly applied and implemented in several functional layouts and is extremely helpful for
improving the quality of products and reducing overall lead time (Renzi et al. 2014).
Moreover, it even provides motivation amongst the organizational employees or labours so
that they could work in a friendly environment. PFA impacts are also helpful to add relevant
values to the business operations and for reduction of process variability. The effective
operational management is majorly contributed with some of the important impacts that are
being made by this product flow analysis.
VSM or simply value stream mapping could be referred to as the subsequent
methodology for lean management. It is completely based on the effective and proper
analyses of current state (Lee and Park 2014). After considering this type of analysis, value
stream mapping also can assist for designing of all future mechanism states. A proper design
on the basis of several event series eventually start and then end in terms of considering the
customers’ demands on the first priority. Hence, the problems are diminished to a greater
level by taking the help of every lean waste after comparing it to the present map. This value
stream mapping also focuses on those areas, where a major requirement of addition of the
additional services is also taken into consideration (Wu, Schaefer and Rosen 2013). Various
practitioners of this lean method have broadly discussed about the utilization of value stream
Paraphrase This Document
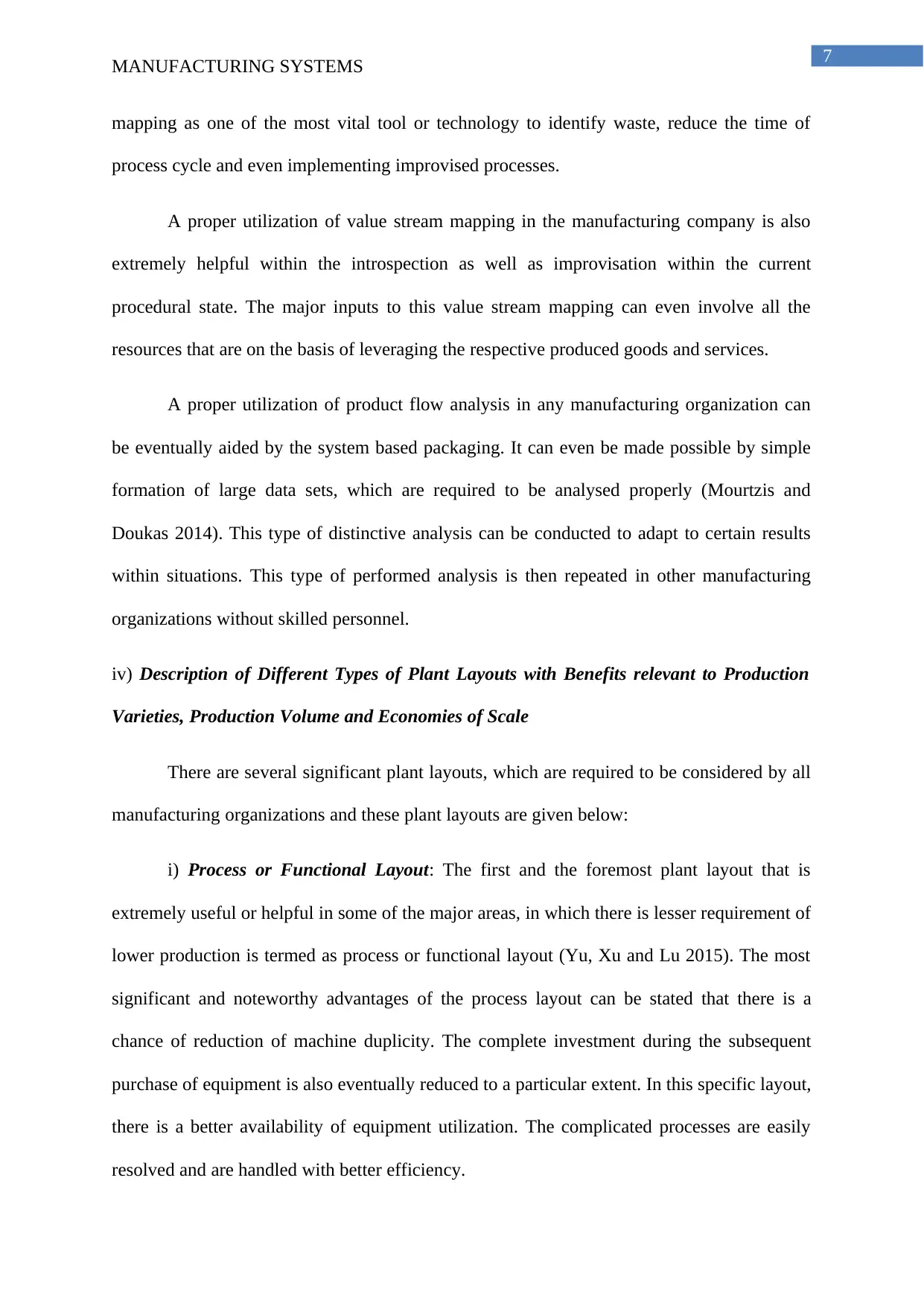
MANUFACTURING SYSTEMS
mapping as one of the most vital tool or technology to identify waste, reduce the time of
process cycle and even implementing improvised processes.
A proper utilization of value stream mapping in the manufacturing company is also
extremely helpful within the introspection as well as improvisation within the current
procedural state. The major inputs to this value stream mapping can even involve all the
resources that are on the basis of leveraging the respective produced goods and services.
A proper utilization of product flow analysis in any manufacturing organization can
be eventually aided by the system based packaging. It can even be made possible by simple
formation of large data sets, which are required to be analysed properly (Mourtzis and
Doukas 2014). This type of distinctive analysis can be conducted to adapt to certain results
within situations. This type of performed analysis is then repeated in other manufacturing
organizations without skilled personnel.
iv) Description of Different Types of Plant Layouts with Benefits relevant to Production
Varieties, Production Volume and Economies of Scale
There are several significant plant layouts, which are required to be considered by all
manufacturing organizations and these plant layouts are given below:
i) Process or Functional Layout: The first and the foremost plant layout that is
extremely useful or helpful in some of the major areas, in which there is lesser requirement of
lower production is termed as process or functional layout (Yu, Xu and Lu 2015). The most
significant and noteworthy advantages of the process layout can be stated that there is a
chance of reduction of machine duplicity. The complete investment during the subsequent
purchase of equipment is also eventually reduced to a particular extent. In this specific layout,
there is a better availability of equipment utilization. The complicated processes are easily
resolved and are handled with better efficiency.
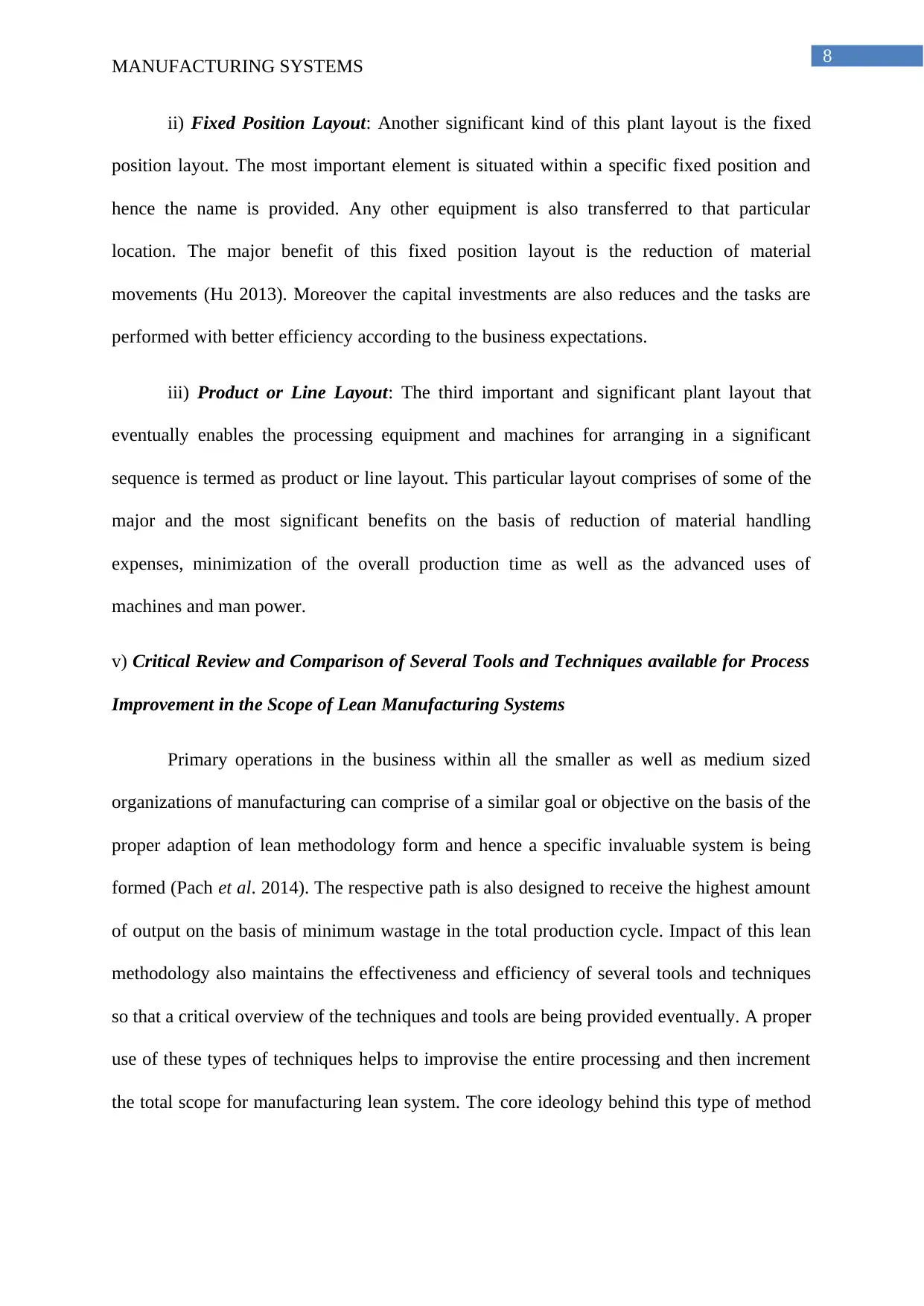
MANUFACTURING SYSTEMS
ii) Fixed Position Layout: Another significant kind of this plant layout is the fixed
position layout. The most important element is situated within a specific fixed position and
hence the name is provided. Any other equipment is also transferred to that particular
location. The major benefit of this fixed position layout is the reduction of material
movements (Hu 2013). Moreover the capital investments are also reduces and the tasks are
performed with better efficiency according to the business expectations.
iii) Product or Line Layout: The third important and significant plant layout that
eventually enables the processing equipment and machines for arranging in a significant
sequence is termed as product or line layout. This particular layout comprises of some of the
major and the most significant benefits on the basis of reduction of material handling
expenses, minimization of the overall production time as well as the advanced uses of
machines and man power.
v) Critical Review and Comparison of Several Tools and Techniques available for Process
Improvement in the Scope of Lean Manufacturing Systems
Primary operations in the business within all the smaller as well as medium sized
organizations of manufacturing can comprise of a similar goal or objective on the basis of the
proper adaption of lean methodology form and hence a specific invaluable system is being
formed (Pach et al. 2014). The respective path is also designed to receive the highest amount
of output on the basis of minimum wastage in the total production cycle. Impact of this lean
methodology also maintains the effectiveness and efficiency of several tools and techniques
so that a critical overview of the techniques and tools are being provided eventually. A proper
use of these types of techniques helps to improvise the entire processing and then increment
the total scope for manufacturing lean system. The core ideology behind this type of method
⊘ This is a preview!⊘
Do you want full access?
Subscribe today to unlock all pages.

Trusted by 1+ million students worldwide
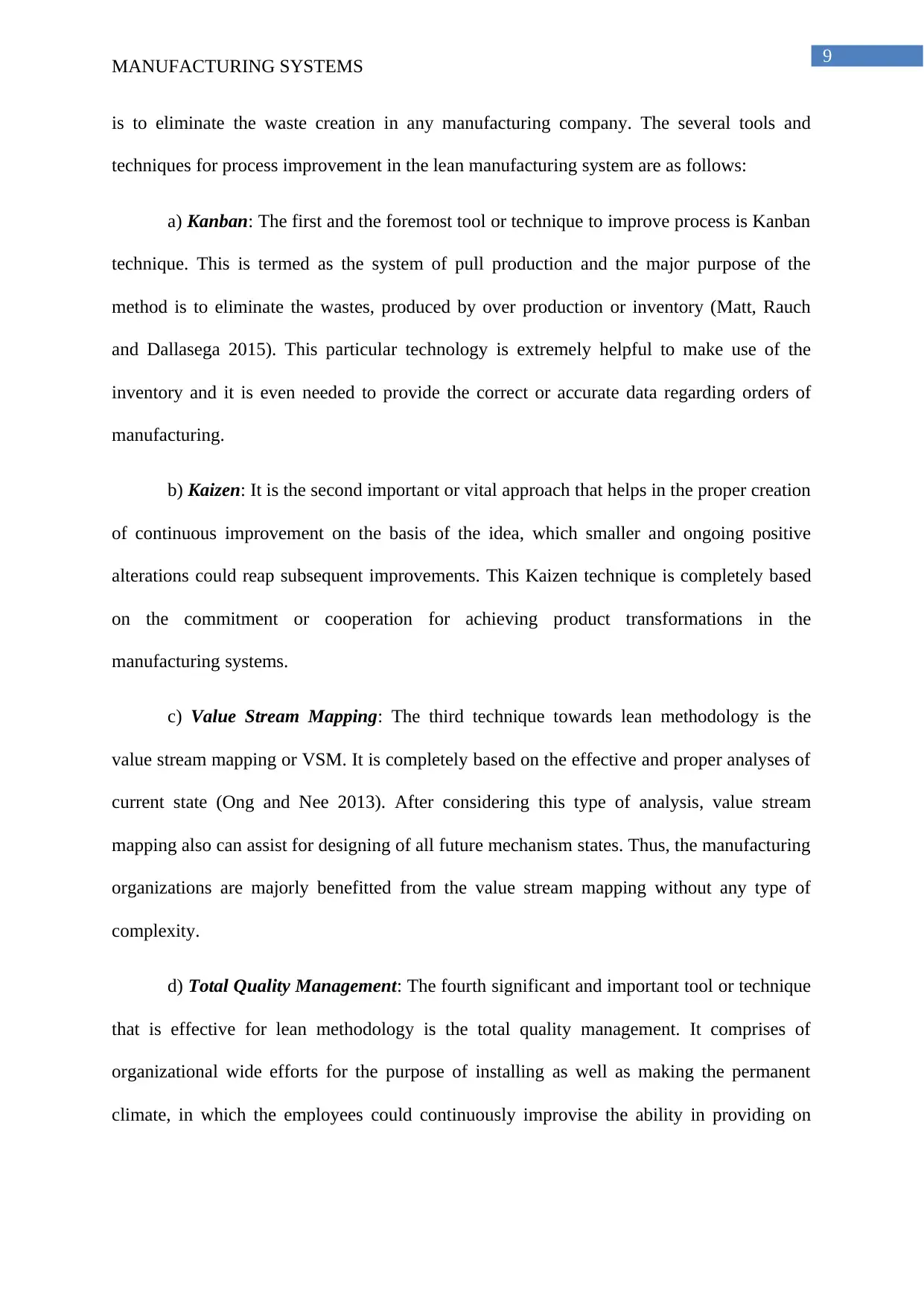
MANUFACTURING SYSTEMS
is to eliminate the waste creation in any manufacturing company. The several tools and
techniques for process improvement in the lean manufacturing system are as follows:
a) Kanban: The first and the foremost tool or technique to improve process is Kanban
technique. This is termed as the system of pull production and the major purpose of the
method is to eliminate the wastes, produced by over production or inventory (Matt, Rauch
and Dallasega 2015). This particular technology is extremely helpful to make use of the
inventory and it is even needed to provide the correct or accurate data regarding orders of
manufacturing.
b) Kaizen: It is the second important or vital approach that helps in the proper creation
of continuous improvement on the basis of the idea, which smaller and ongoing positive
alterations could reap subsequent improvements. This Kaizen technique is completely based
on the commitment or cooperation for achieving product transformations in the
manufacturing systems.
c) Value Stream Mapping: The third technique towards lean methodology is the
value stream mapping or VSM. It is completely based on the effective and proper analyses of
current state (Ong and Nee 2013). After considering this type of analysis, value stream
mapping also can assist for designing of all future mechanism states. Thus, the manufacturing
organizations are majorly benefitted from the value stream mapping without any type of
complexity.
d) Total Quality Management: The fourth significant and important tool or technique
that is effective for lean methodology is the total quality management. It comprises of
organizational wide efforts for the purpose of installing as well as making the permanent
climate, in which the employees could continuously improvise the ability in providing on
Paraphrase This Document
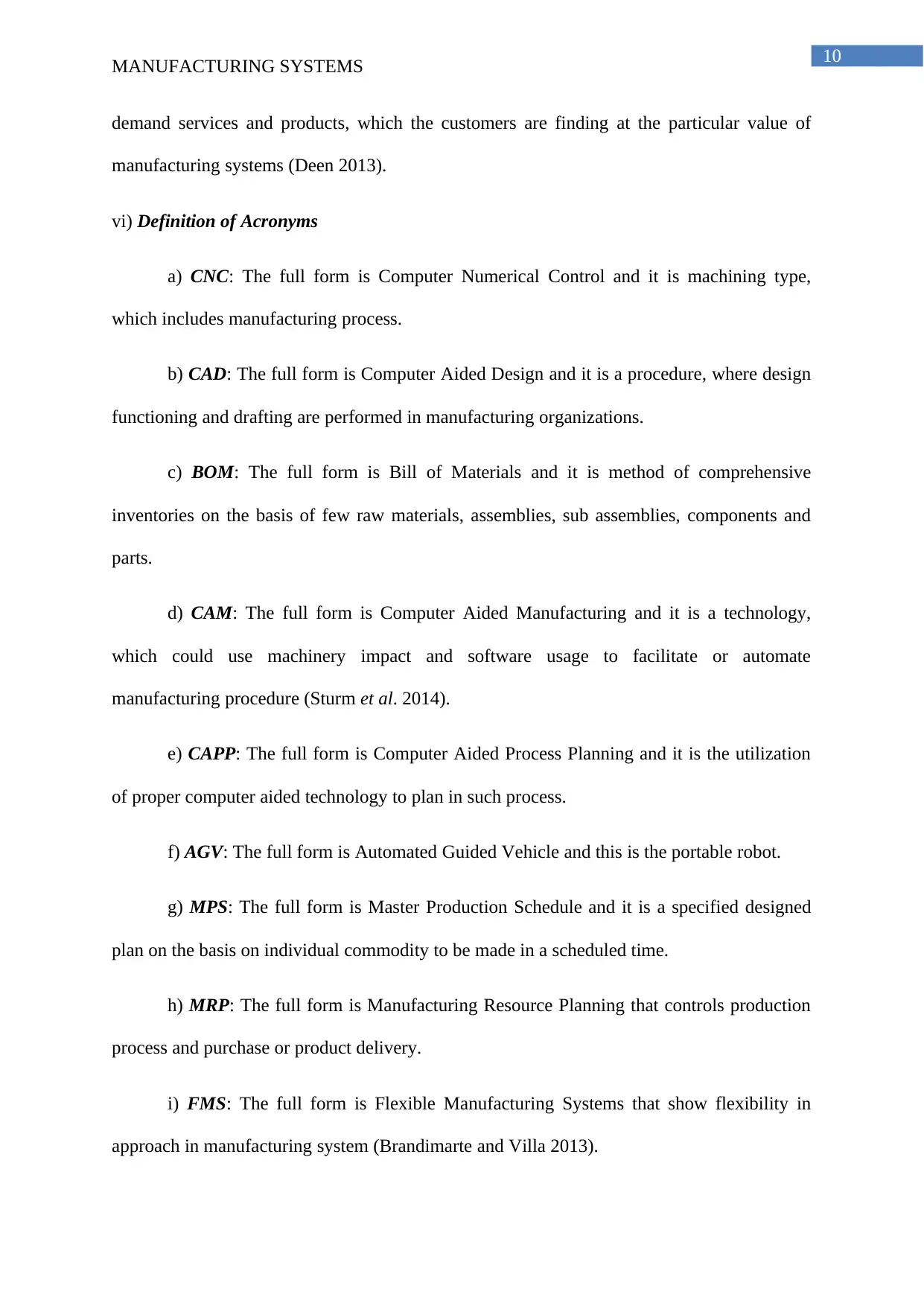
MANUFACTURING SYSTEMS
demand services and products, which the customers are finding at the particular value of
manufacturing systems (Deen 2013).
vi) Definition of Acronyms
a) CNC: The full form is Computer Numerical Control and it is machining type,
which includes manufacturing process.
b) CAD: The full form is Computer Aided Design and it is a procedure, where design
functioning and drafting are performed in manufacturing organizations.
c) BOM: The full form is Bill of Materials and it is method of comprehensive
inventories on the basis of few raw materials, assemblies, sub assemblies, components and
parts.
d) CAM: The full form is Computer Aided Manufacturing and it is a technology,
which could use machinery impact and software usage to facilitate or automate
manufacturing procedure (Sturm et al. 2014).
e) CAPP: The full form is Computer Aided Process Planning and it is the utilization
of proper computer aided technology to plan in such process.
f) AGV: The full form is Automated Guided Vehicle and this is the portable robot.
g) MPS: The full form is Master Production Schedule and it is a specified designed
plan on the basis on individual commodity to be made in a scheduled time.
h) MRP: The full form is Manufacturing Resource Planning that controls production
process and purchase or product delivery.
i) FMS: The full form is Flexible Manufacturing Systems that show flexibility in
approach in manufacturing system (Brandimarte and Villa 2013).
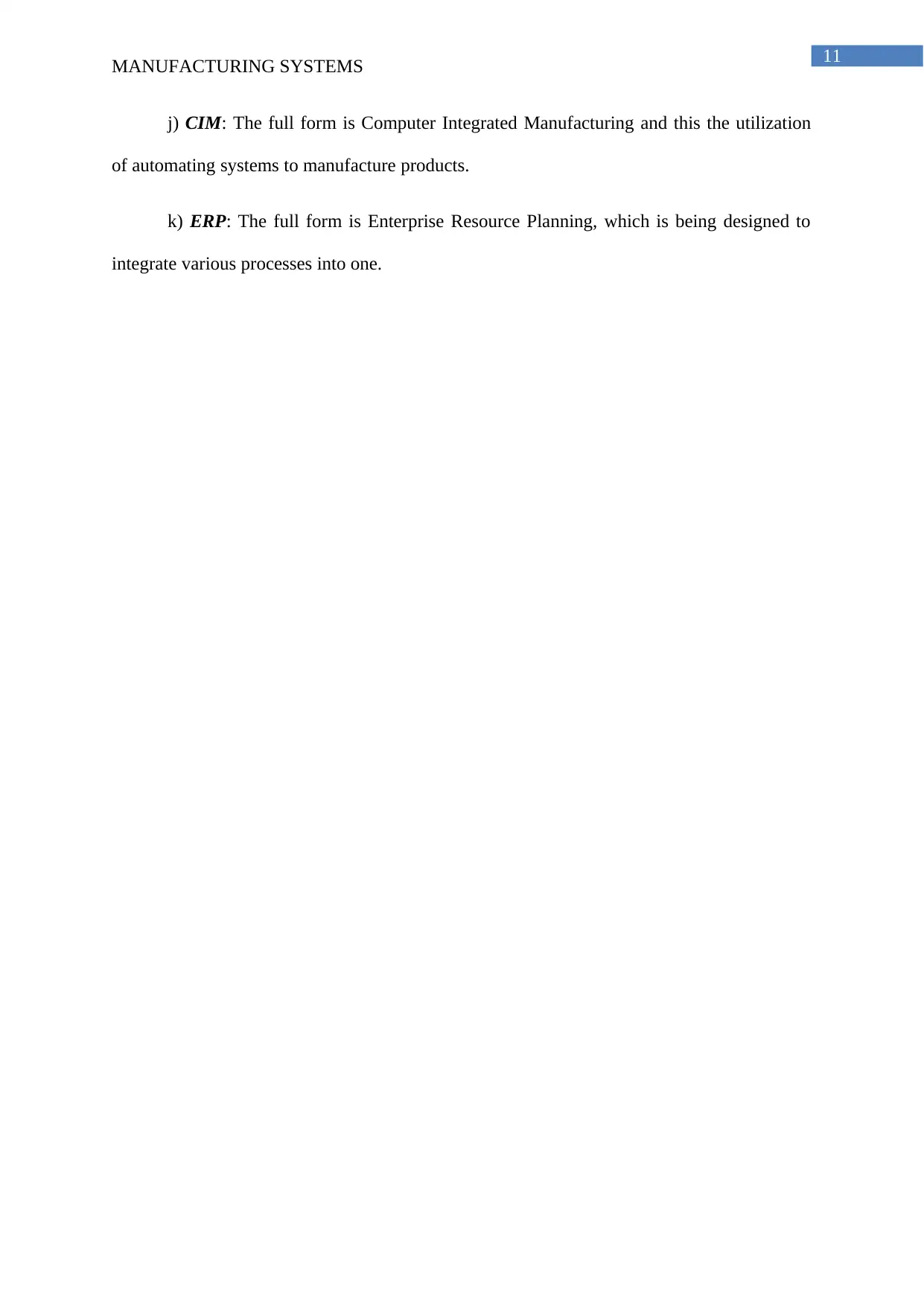
MANUFACTURING SYSTEMS
j) CIM: The full form is Computer Integrated Manufacturing and this the utilization
of automating systems to manufacture products.
k) ERP: The full form is Enterprise Resource Planning, which is being designed to
integrate various processes into one.
⊘ This is a preview!⊘
Do you want full access?
Subscribe today to unlock all pages.

Trusted by 1+ million students worldwide
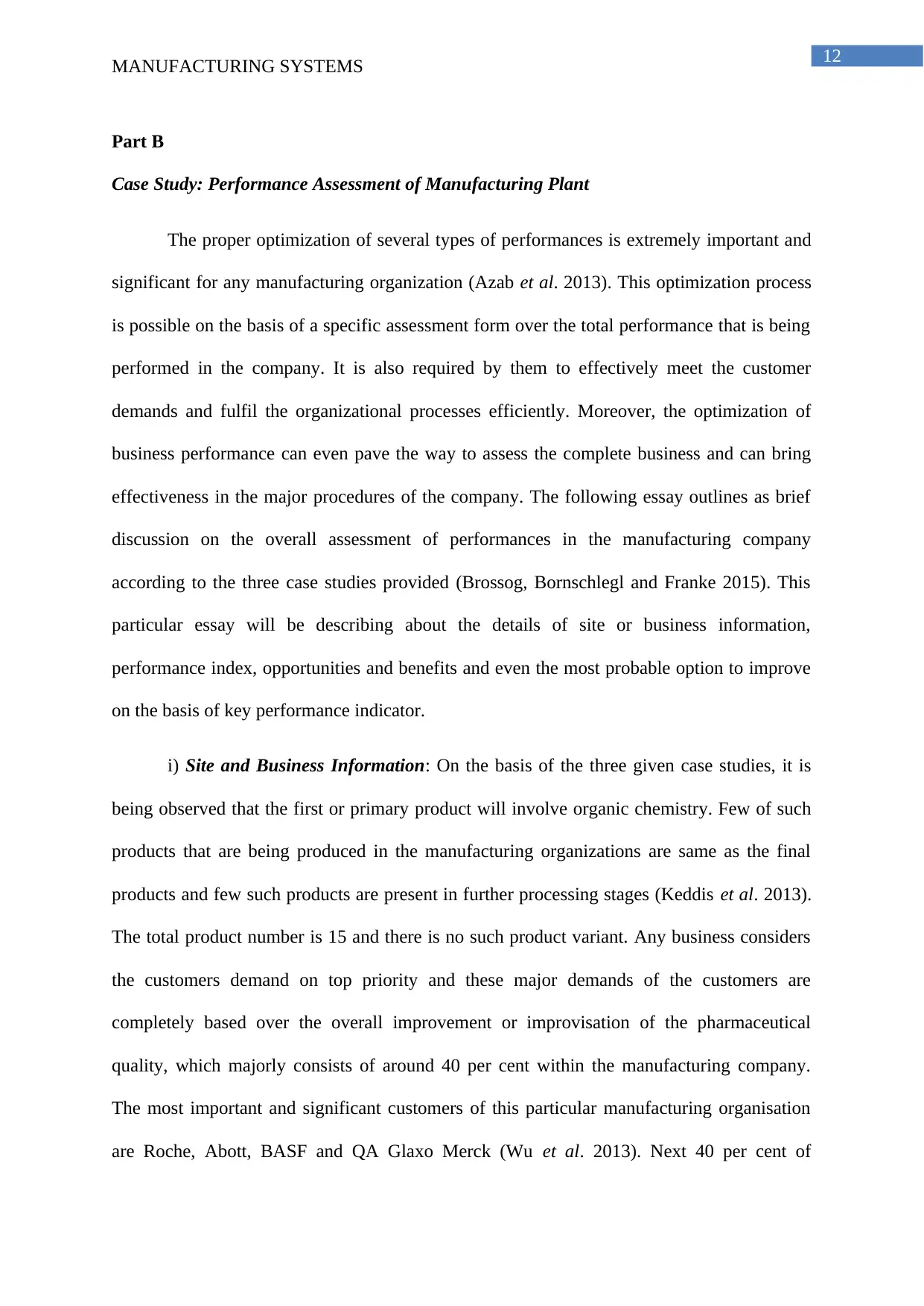
MANUFACTURING SYSTEMS
Part B
Case Study: Performance Assessment of Manufacturing Plant
The proper optimization of several types of performances is extremely important and
significant for any manufacturing organization (Azab et al. 2013). This optimization process
is possible on the basis of a specific assessment form over the total performance that is being
performed in the company. It is also required by them to effectively meet the customer
demands and fulfil the organizational processes efficiently. Moreover, the optimization of
business performance can even pave the way to assess the complete business and can bring
effectiveness in the major procedures of the company. The following essay outlines as brief
discussion on the overall assessment of performances in the manufacturing company
according to the three case studies provided (Brossog, Bornschlegl and Franke 2015). This
particular essay will be describing about the details of site or business information,
performance index, opportunities and benefits and even the most probable option to improve
on the basis of key performance indicator.
i) Site and Business Information: On the basis of the three given case studies, it is
being observed that the first or primary product will involve organic chemistry. Few of such
products that are being produced in the manufacturing organizations are same as the final
products and few such products are present in further processing stages (Keddis et al. 2013).
The total product number is 15 and there is no such product variant. Any business considers
the customers demand on top priority and these major demands of the customers are
completely based over the overall improvement or improvisation of the pharmaceutical
quality, which majorly consists of around 40 per cent within the manufacturing company.
The most important and significant customers of this particular manufacturing organisation
are Roche, Abott, BASF and QA Glaxo Merck (Wu et al. 2013). Next 40 per cent of
Paraphrase This Document
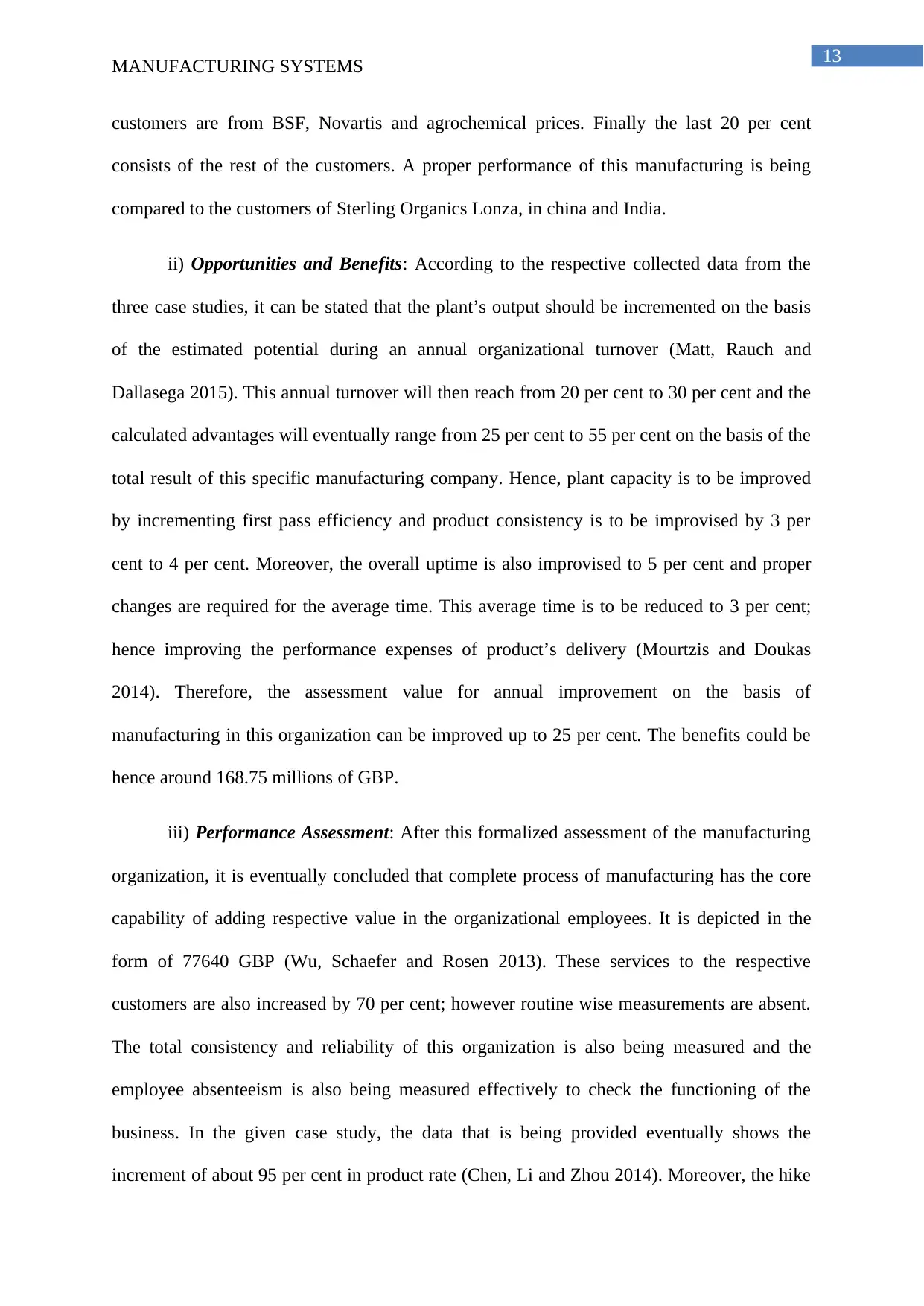
MANUFACTURING SYSTEMS
customers are from BSF, Novartis and agrochemical prices. Finally the last 20 per cent
consists of the rest of the customers. A proper performance of this manufacturing is being
compared to the customers of Sterling Organics Lonza, in china and India.
ii) Opportunities and Benefits: According to the respective collected data from the
three case studies, it can be stated that the plant’s output should be incremented on the basis
of the estimated potential during an annual organizational turnover (Matt, Rauch and
Dallasega 2015). This annual turnover will then reach from 20 per cent to 30 per cent and the
calculated advantages will eventually range from 25 per cent to 55 per cent on the basis of the
total result of this specific manufacturing company. Hence, plant capacity is to be improved
by incrementing first pass efficiency and product consistency is to be improvised by 3 per
cent to 4 per cent. Moreover, the overall uptime is also improvised to 5 per cent and proper
changes are required for the average time. This average time is to be reduced to 3 per cent;
hence improving the performance expenses of product’s delivery (Mourtzis and Doukas
2014). Therefore, the assessment value for annual improvement on the basis of
manufacturing in this organization can be improved up to 25 per cent. The benefits could be
hence around 168.75 millions of GBP.
iii) Performance Assessment: After this formalized assessment of the manufacturing
organization, it is eventually concluded that complete process of manufacturing has the core
capability of adding respective value in the organizational employees. It is depicted in the
form of 77640 GBP (Wu, Schaefer and Rosen 2013). These services to the respective
customers are also increased by 70 per cent; however routine wise measurements are absent.
The total consistency and reliability of this organization is also being measured and the
employee absenteeism is also being measured effectively to check the functioning of the
business. In the given case study, the data that is being provided eventually shows the
increment of about 95 per cent in product rate (Chen, Li and Zhou 2014). Moreover, the hike
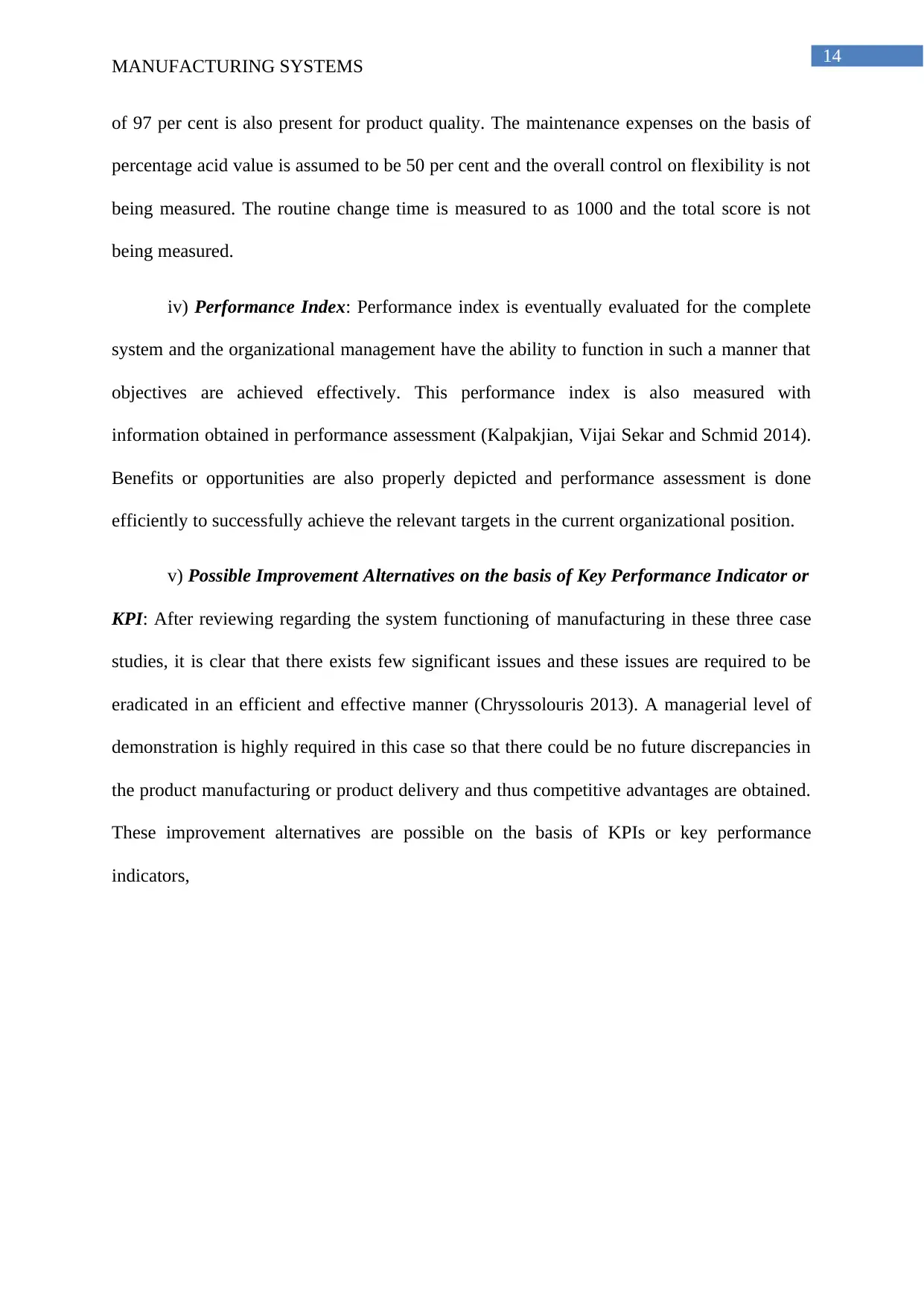
MANUFACTURING SYSTEMS
of 97 per cent is also present for product quality. The maintenance expenses on the basis of
percentage acid value is assumed to be 50 per cent and the overall control on flexibility is not
being measured. The routine change time is measured to as 1000 and the total score is not
being measured.
iv) Performance Index: Performance index is eventually evaluated for the complete
system and the organizational management have the ability to function in such a manner that
objectives are achieved effectively. This performance index is also measured with
information obtained in performance assessment (Kalpakjian, Vijai Sekar and Schmid 2014).
Benefits or opportunities are also properly depicted and performance assessment is done
efficiently to successfully achieve the relevant targets in the current organizational position.
v) Possible Improvement Alternatives on the basis of Key Performance Indicator or
KPI: After reviewing regarding the system functioning of manufacturing in these three case
studies, it is clear that there exists few significant issues and these issues are required to be
eradicated in an efficient and effective manner (Chryssolouris 2013). A managerial level of
demonstration is highly required in this case so that there could be no future discrepancies in
the product manufacturing or product delivery and thus competitive advantages are obtained.
These improvement alternatives are possible on the basis of KPIs or key performance
indicators,
⊘ This is a preview!⊘
Do you want full access?
Subscribe today to unlock all pages.

Trusted by 1+ million students worldwide
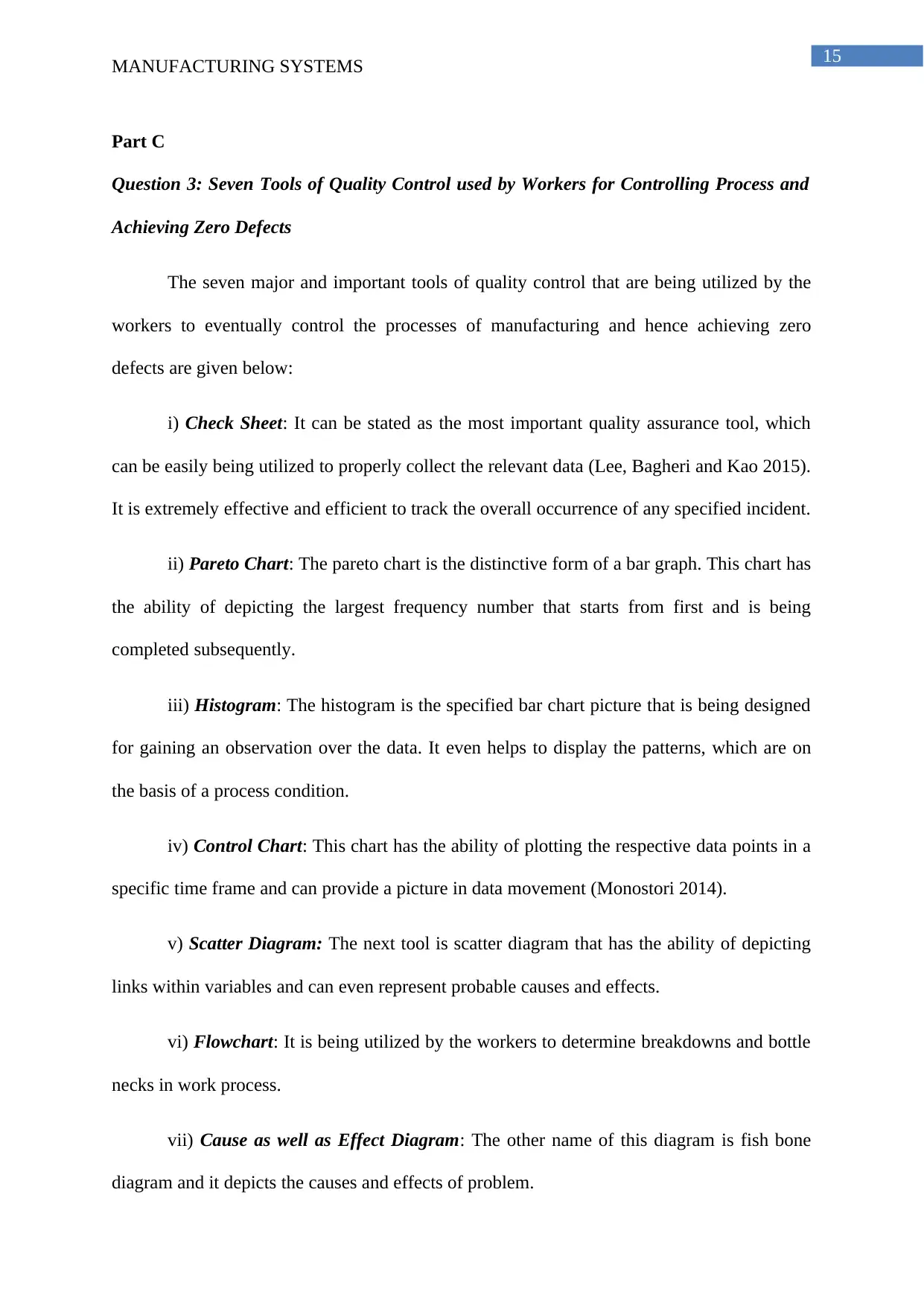
MANUFACTURING SYSTEMS
Part C
Question 3: Seven Tools of Quality Control used by Workers for Controlling Process and
Achieving Zero Defects
The seven major and important tools of quality control that are being utilized by the
workers to eventually control the processes of manufacturing and hence achieving zero
defects are given below:
i) Check Sheet: It can be stated as the most important quality assurance tool, which
can be easily being utilized to properly collect the relevant data (Lee, Bagheri and Kao 2015).
It is extremely effective and efficient to track the overall occurrence of any specified incident.
ii) Pareto Chart: The pareto chart is the distinctive form of a bar graph. This chart has
the ability of depicting the largest frequency number that starts from first and is being
completed subsequently.
iii) Histogram: The histogram is the specified bar chart picture that is being designed
for gaining an observation over the data. It even helps to display the patterns, which are on
the basis of a process condition.
iv) Control Chart: This chart has the ability of plotting the respective data points in a
specific time frame and can provide a picture in data movement (Monostori 2014).
v) Scatter Diagram: The next tool is scatter diagram that has the ability of depicting
links within variables and can even represent probable causes and effects.
vi) Flowchart: It is being utilized by the workers to determine breakdowns and bottle
necks in work process.
vii) Cause as well as Effect Diagram: The other name of this diagram is fish bone
diagram and it depicts the causes and effects of problem.
Paraphrase This Document
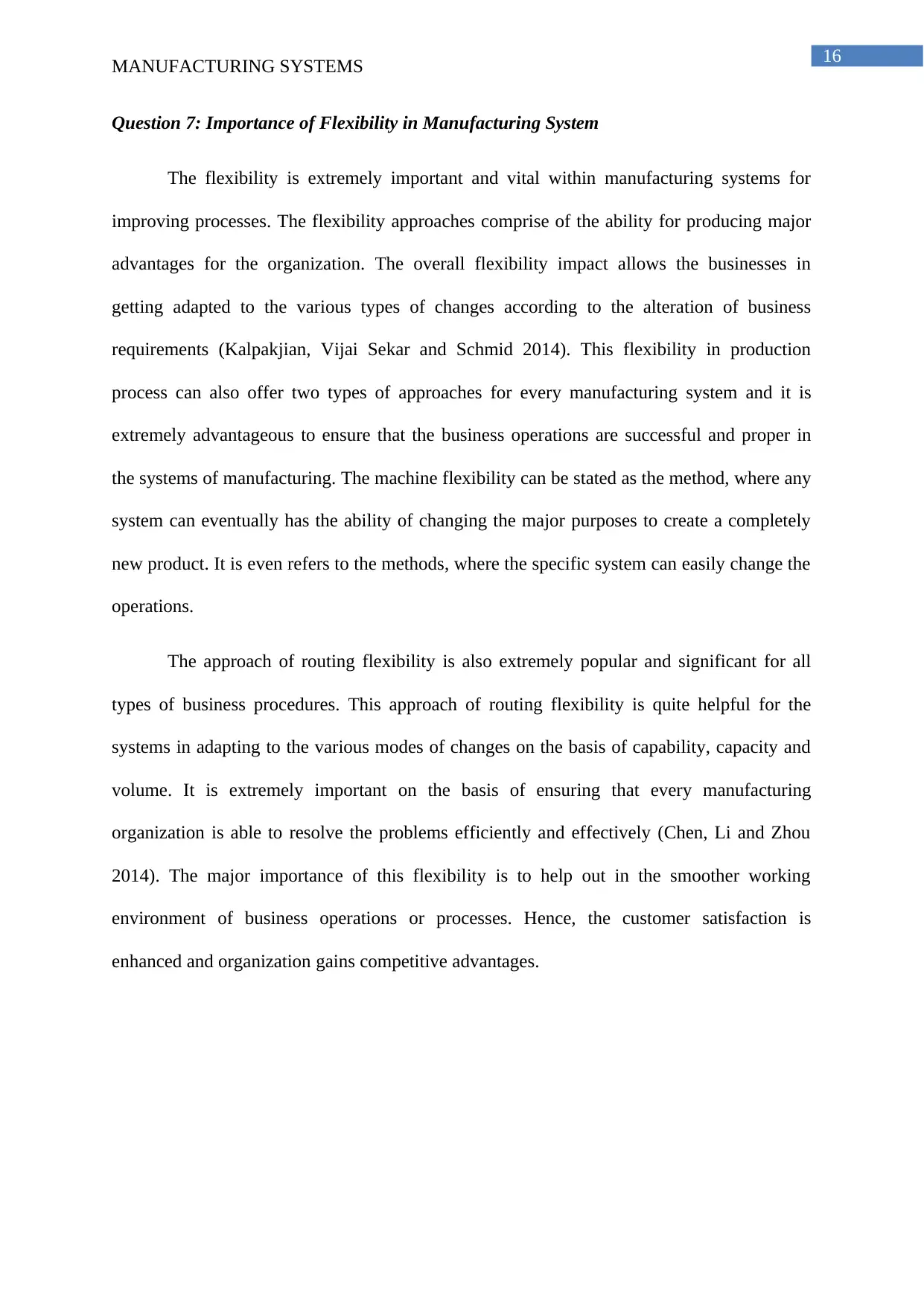
MANUFACTURING SYSTEMS
Question 7: Importance of Flexibility in Manufacturing System
The flexibility is extremely important and vital within manufacturing systems for
improving processes. The flexibility approaches comprise of the ability for producing major
advantages for the organization. The overall flexibility impact allows the businesses in
getting adapted to the various types of changes according to the alteration of business
requirements (Kalpakjian, Vijai Sekar and Schmid 2014). This flexibility in production
process can also offer two types of approaches for every manufacturing system and it is
extremely advantageous to ensure that the business operations are successful and proper in
the systems of manufacturing. The machine flexibility can be stated as the method, where any
system can eventually has the ability of changing the major purposes to create a completely
new product. It is even refers to the methods, where the specific system can easily change the
operations.
The approach of routing flexibility is also extremely popular and significant for all
types of business procedures. This approach of routing flexibility is quite helpful for the
systems in adapting to the various modes of changes on the basis of capability, capacity and
volume. It is extremely important on the basis of ensuring that every manufacturing
organization is able to resolve the problems efficiently and effectively (Chen, Li and Zhou
2014). The major importance of this flexibility is to help out in the smoother working
environment of business operations or processes. Hence, the customer satisfaction is
enhanced and organization gains competitive advantages.
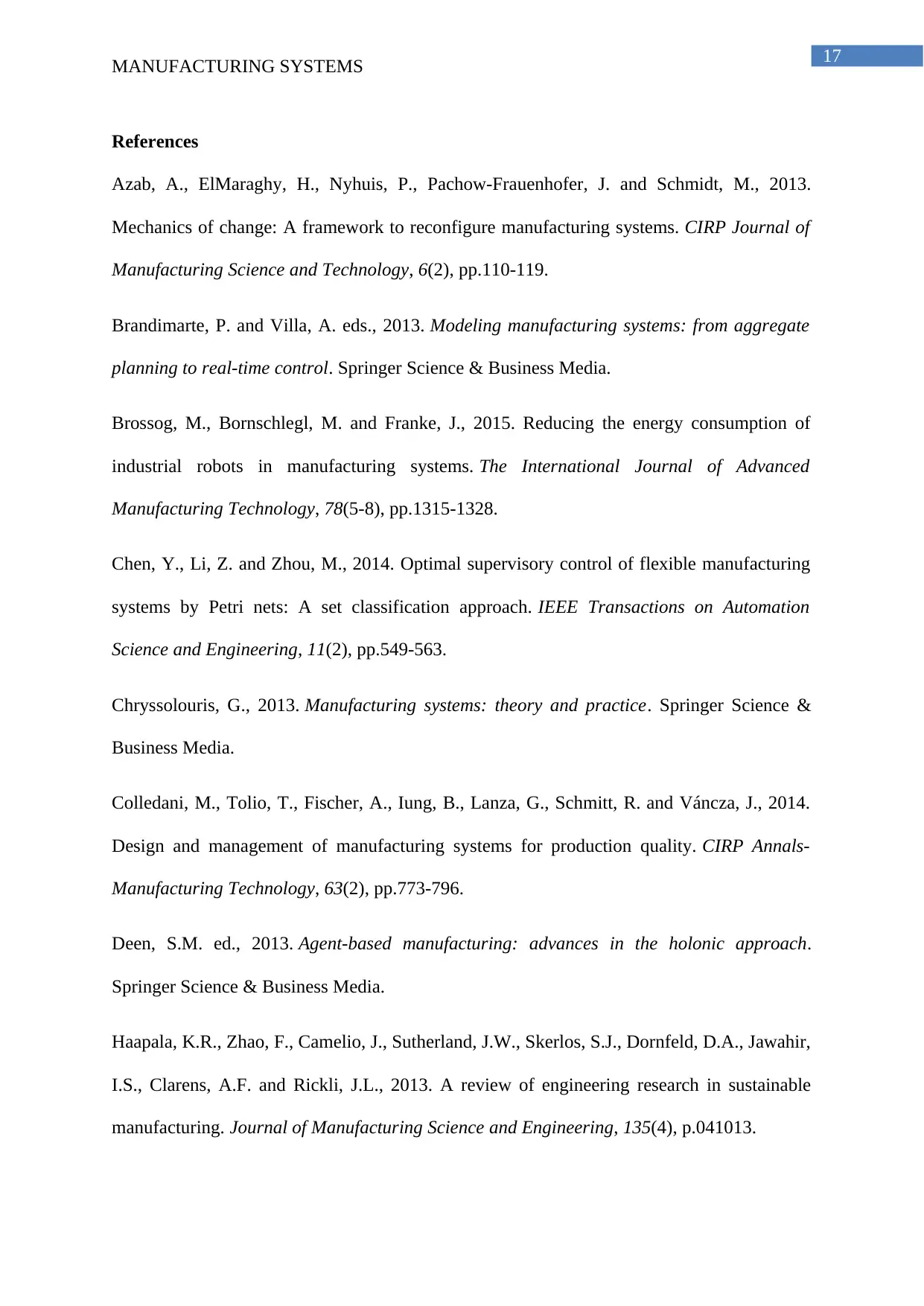
MANUFACTURING SYSTEMS
References
Azab, A., ElMaraghy, H., Nyhuis, P., Pachow-Frauenhofer, J. and Schmidt, M., 2013.
Mechanics of change: A framework to reconfigure manufacturing systems. CIRP Journal of
Manufacturing Science and Technology, 6(2), pp.110-119.
Brandimarte, P. and Villa, A. eds., 2013. Modeling manufacturing systems: from aggregate
planning to real-time control. Springer Science & Business Media.
Brossog, M., Bornschlegl, M. and Franke, J., 2015. Reducing the energy consumption of
industrial robots in manufacturing systems. The International Journal of Advanced
Manufacturing Technology, 78(5-8), pp.1315-1328.
Chen, Y., Li, Z. and Zhou, M., 2014. Optimal supervisory control of flexible manufacturing
systems by Petri nets: A set classification approach. IEEE Transactions on Automation
Science and Engineering, 11(2), pp.549-563.
Chryssolouris, G., 2013. Manufacturing systems: theory and practice. Springer Science &
Business Media.
Colledani, M., Tolio, T., Fischer, A., Iung, B., Lanza, G., Schmitt, R. and Váncza, J., 2014.
Design and management of manufacturing systems for production quality. CIRP Annals-
Manufacturing Technology, 63(2), pp.773-796.
Deen, S.M. ed., 2013. Agent-based manufacturing: advances in the holonic approach.
Springer Science & Business Media.
Haapala, K.R., Zhao, F., Camelio, J., Sutherland, J.W., Skerlos, S.J., Dornfeld, D.A., Jawahir,
I.S., Clarens, A.F. and Rickli, J.L., 2013. A review of engineering research in sustainable
manufacturing. Journal of Manufacturing Science and Engineering, 135(4), p.041013.
⊘ This is a preview!⊘
Do you want full access?
Subscribe today to unlock all pages.

Trusted by 1+ million students worldwide
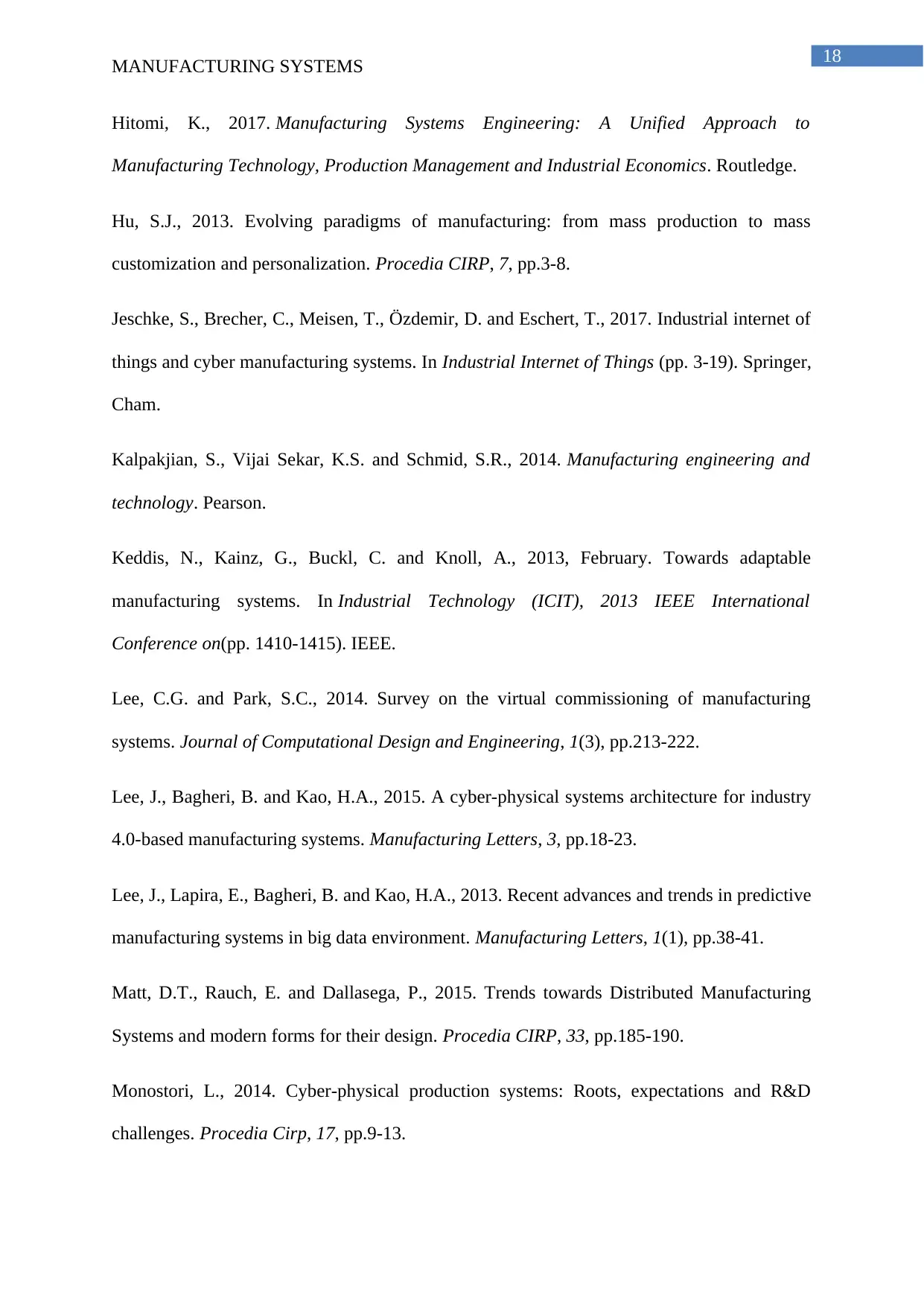
MANUFACTURING SYSTEMS
Hitomi, K., 2017. Manufacturing Systems Engineering: A Unified Approach to
Manufacturing Technology, Production Management and Industrial Economics. Routledge.
Hu, S.J., 2013. Evolving paradigms of manufacturing: from mass production to mass
customization and personalization. Procedia CIRP, 7, pp.3-8.
Jeschke, S., Brecher, C., Meisen, T., Özdemir, D. and Eschert, T., 2017. Industrial internet of
things and cyber manufacturing systems. In Industrial Internet of Things (pp. 3-19). Springer,
Cham.
Kalpakjian, S., Vijai Sekar, K.S. and Schmid, S.R., 2014. Manufacturing engineering and
technology. Pearson.
Keddis, N., Kainz, G., Buckl, C. and Knoll, A., 2013, February. Towards adaptable
manufacturing systems. In Industrial Technology (ICIT), 2013 IEEE International
Conference on(pp. 1410-1415). IEEE.
Lee, C.G. and Park, S.C., 2014. Survey on the virtual commissioning of manufacturing
systems. Journal of Computational Design and Engineering, 1(3), pp.213-222.
Lee, J., Bagheri, B. and Kao, H.A., 2015. A cyber-physical systems architecture for industry
4.0-based manufacturing systems. Manufacturing Letters, 3, pp.18-23.
Lee, J., Lapira, E., Bagheri, B. and Kao, H.A., 2013. Recent advances and trends in predictive
manufacturing systems in big data environment. Manufacturing Letters, 1(1), pp.38-41.
Matt, D.T., Rauch, E. and Dallasega, P., 2015. Trends towards Distributed Manufacturing
Systems and modern forms for their design. Procedia CIRP, 33, pp.185-190.
Monostori, L., 2014. Cyber-physical production systems: Roots, expectations and R&D
challenges. Procedia Cirp, 17, pp.9-13.
Paraphrase This Document
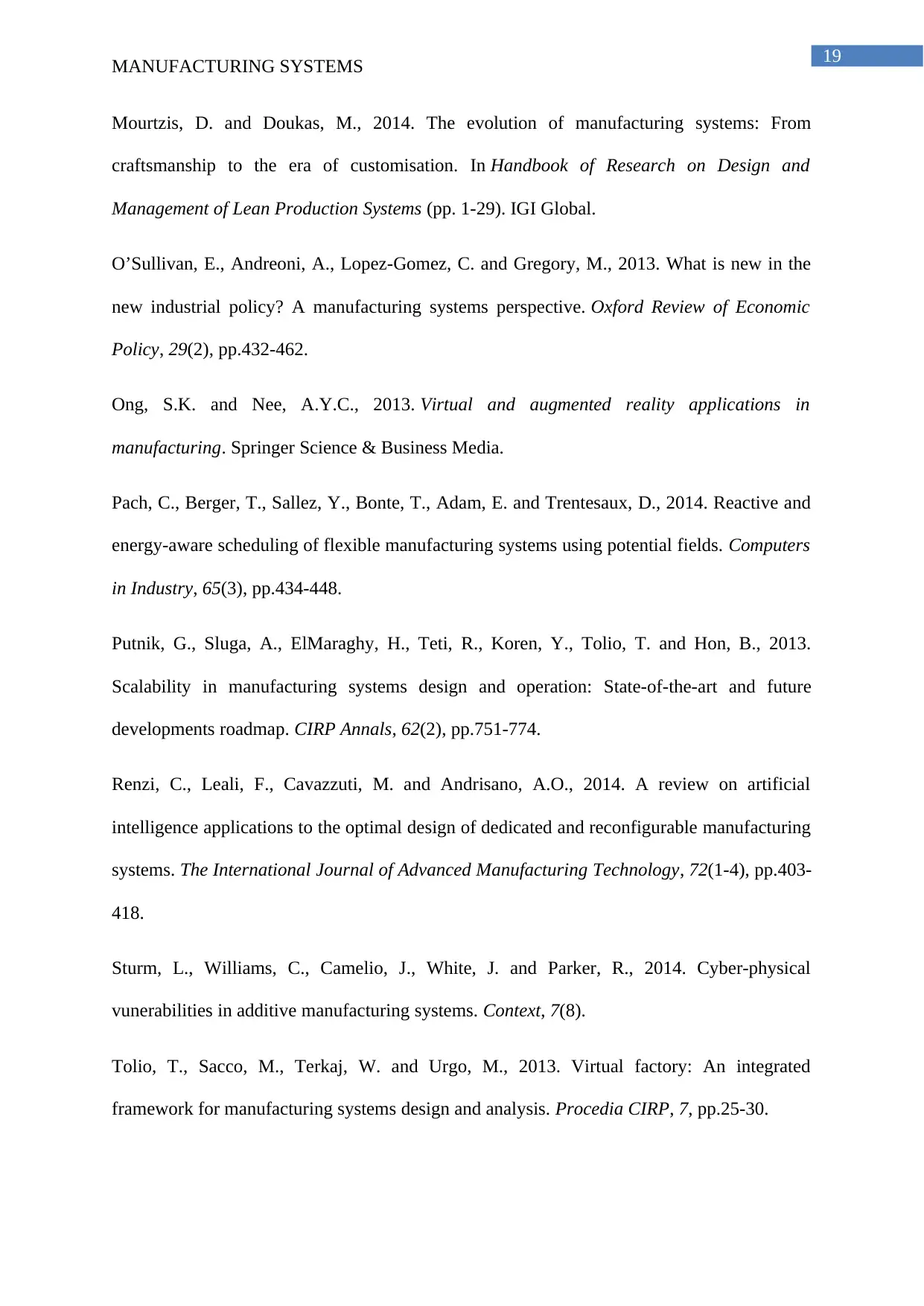
MANUFACTURING SYSTEMS
Mourtzis, D. and Doukas, M., 2014. The evolution of manufacturing systems: From
craftsmanship to the era of customisation. In Handbook of Research on Design and
Management of Lean Production Systems (pp. 1-29). IGI Global.
O’Sullivan, E., Andreoni, A., Lopez-Gomez, C. and Gregory, M., 2013. What is new in the
new industrial policy? A manufacturing systems perspective. Oxford Review of Economic
Policy, 29(2), pp.432-462.
Ong, S.K. and Nee, A.Y.C., 2013. Virtual and augmented reality applications in
manufacturing. Springer Science & Business Media.
Pach, C., Berger, T., Sallez, Y., Bonte, T., Adam, E. and Trentesaux, D., 2014. Reactive and
energy-aware scheduling of flexible manufacturing systems using potential fields. Computers
in Industry, 65(3), pp.434-448.
Putnik, G., Sluga, A., ElMaraghy, H., Teti, R., Koren, Y., Tolio, T. and Hon, B., 2013.
Scalability in manufacturing systems design and operation: State-of-the-art and future
developments roadmap. CIRP Annals, 62(2), pp.751-774.
Renzi, C., Leali, F., Cavazzuti, M. and Andrisano, A.O., 2014. A review on artificial
intelligence applications to the optimal design of dedicated and reconfigurable manufacturing
systems. The International Journal of Advanced Manufacturing Technology, 72(1-4), pp.403-
418.
Sturm, L., Williams, C., Camelio, J., White, J. and Parker, R., 2014. Cyber-physical
vunerabilities in additive manufacturing systems. Context, 7(8).
Tolio, T., Sacco, M., Terkaj, W. and Urgo, M., 2013. Virtual factory: An integrated
framework for manufacturing systems design and analysis. Procedia CIRP, 7, pp.25-30.
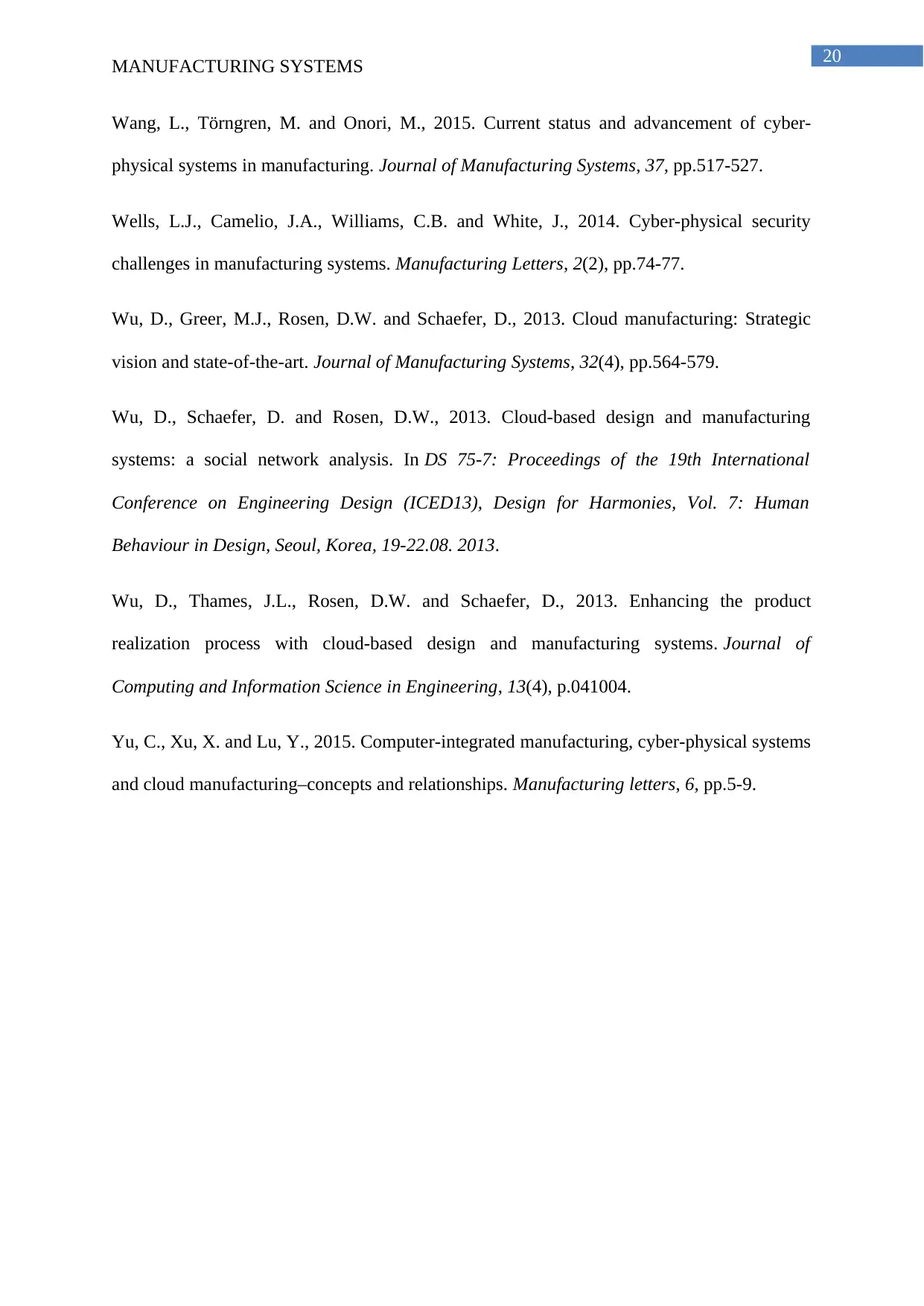
MANUFACTURING SYSTEMS
Wang, L., Törngren, M. and Onori, M., 2015. Current status and advancement of cyber-
physical systems in manufacturing. Journal of Manufacturing Systems, 37, pp.517-527.
Wells, L.J., Camelio, J.A., Williams, C.B. and White, J., 2014. Cyber-physical security
challenges in manufacturing systems. Manufacturing Letters, 2(2), pp.74-77.
Wu, D., Greer, M.J., Rosen, D.W. and Schaefer, D., 2013. Cloud manufacturing: Strategic
vision and state-of-the-art. Journal of Manufacturing Systems, 32(4), pp.564-579.
Wu, D., Schaefer, D. and Rosen, D.W., 2013. Cloud-based design and manufacturing
systems: a social network analysis. In DS 75-7: Proceedings of the 19th International
Conference on Engineering Design (ICED13), Design for Harmonies, Vol. 7: Human
Behaviour in Design, Seoul, Korea, 19-22.08. 2013.
Wu, D., Thames, J.L., Rosen, D.W. and Schaefer, D., 2013. Enhancing the product
realization process with cloud-based design and manufacturing systems. Journal of
Computing and Information Science in Engineering, 13(4), p.041004.
Yu, C., Xu, X. and Lu, Y., 2015. Computer-integrated manufacturing, cyber-physical systems
and cloud manufacturing–concepts and relationships. Manufacturing letters, 6, pp.5-9.
⊘ This is a preview!⊘
Do you want full access?
Subscribe today to unlock all pages.

Trusted by 1+ million students worldwide
Related Documents

Your All-in-One AI-Powered Toolkit for Academic Success.
+13062052269
info@desklib.com
Available 24*7 on WhatsApp / Email
© 2024 | Zucol Services PVT LTD | All rights reserved.