Operations and Project Management: Review and Critique of Operations Management Principles in Marks & Spencer
VerifiedAdded on 2023/06/07
|15
|4642
|385
AI Summary
This report provides an introduction to Marks & Spencer, explains the difference between operations and operations management, reviews and critiques the implementation of operations management principles within the organization, analyzes the extent to which the operations management of the organization meets the requirements of the organization, discusses continuous improvement as a philosophy and describes the Lean principles, and provides a continuous improvement plan with justified recommendations for improvement.
Contribute Materials
Your contribution can guide someone’s learning journey. Share your
documents today.
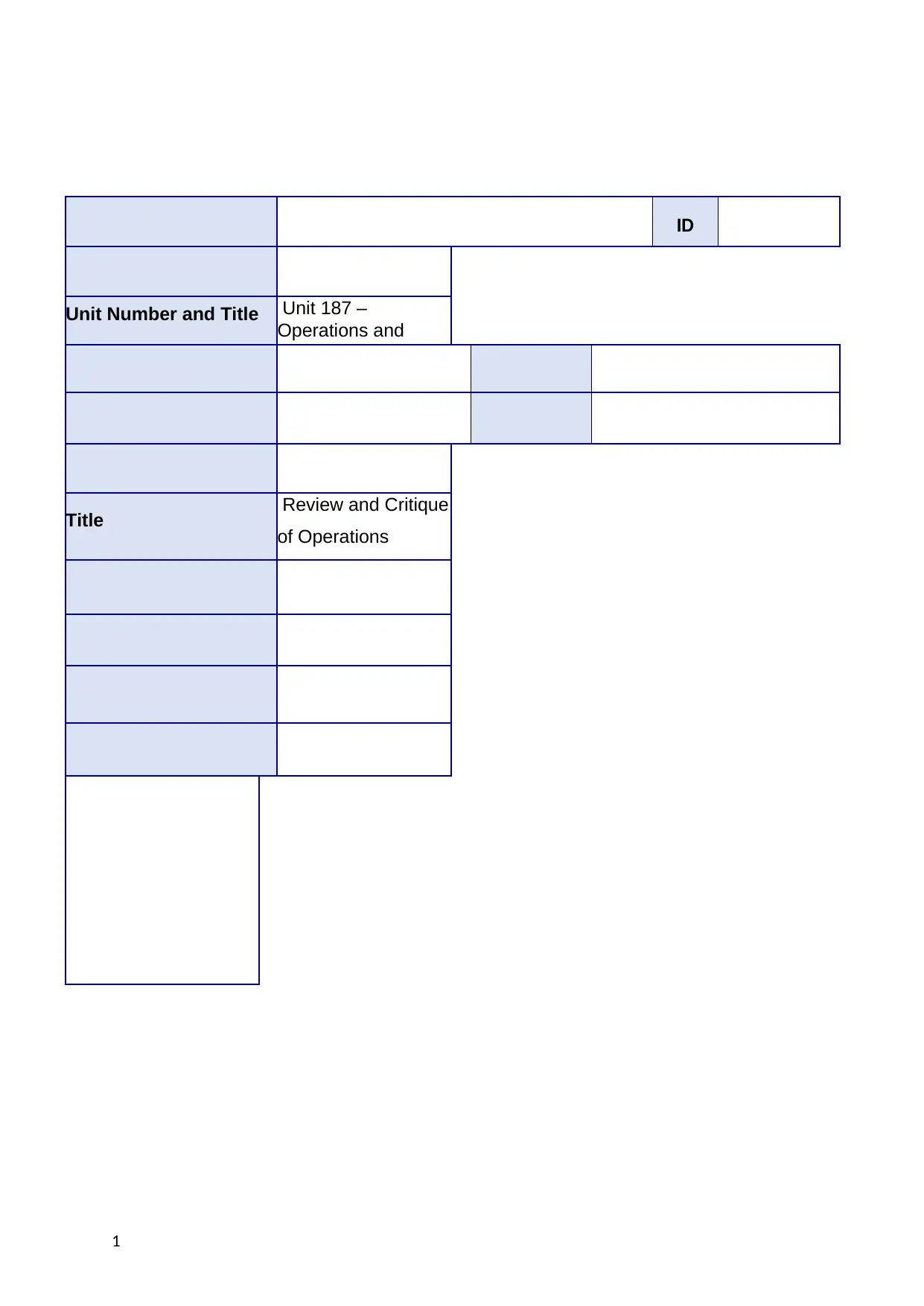
ID
Unit Number and Title Unit 187 –
Operations and
Project Management
Title Review and Critique
of Operations
Management (Part
1
Unit Number and Title Unit 187 –
Operations and
Project Management
Title Review and Critique
of Operations
Management (Part
1
Secure Best Marks with AI Grader
Need help grading? Try our AI Grader for instant feedback on your assignments.
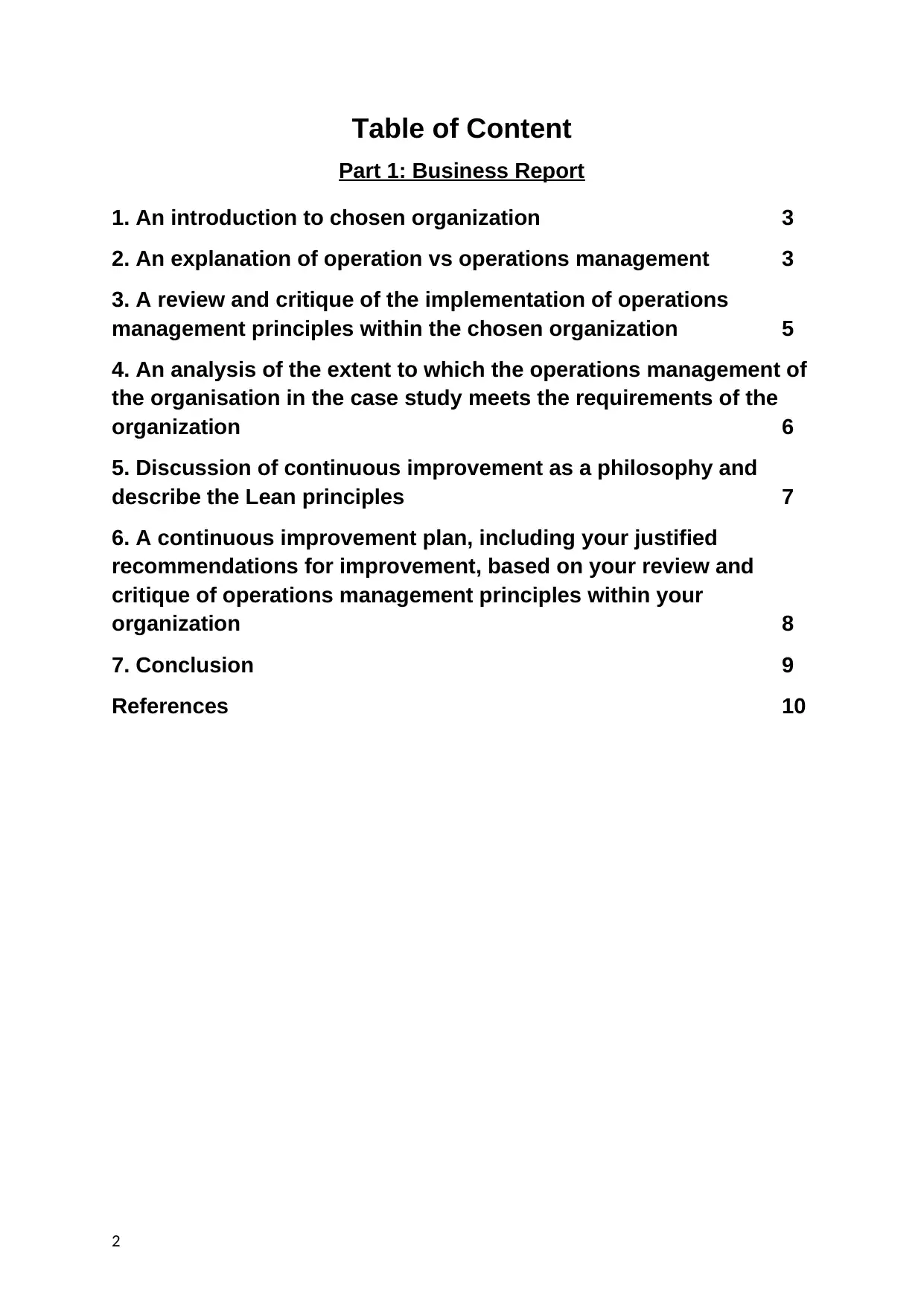
Table of Content
Part 1: Business Report
1. An introduction to chosen organization 3
2. An explanation of operation vs operations management 3
3. A review and critique of the implementation of operations
management principles within the chosen organization 5
4. An analysis of the extent to which the operations management of
the organisation in the case study meets the requirements of the
organization 6
5. Discussion of continuous improvement as a philosophy and
describe the Lean principles 7
6. A continuous improvement plan, including your justified
recommendations for improvement, based on your review and
critique of operations management principles within your
organization 8
7. Conclusion 9
References 10
2
Part 1: Business Report
1. An introduction to chosen organization 3
2. An explanation of operation vs operations management 3
3. A review and critique of the implementation of operations
management principles within the chosen organization 5
4. An analysis of the extent to which the operations management of
the organisation in the case study meets the requirements of the
organization 6
5. Discussion of continuous improvement as a philosophy and
describe the Lean principles 7
6. A continuous improvement plan, including your justified
recommendations for improvement, based on your review and
critique of operations management principles within your
organization 8
7. Conclusion 9
References 10
2
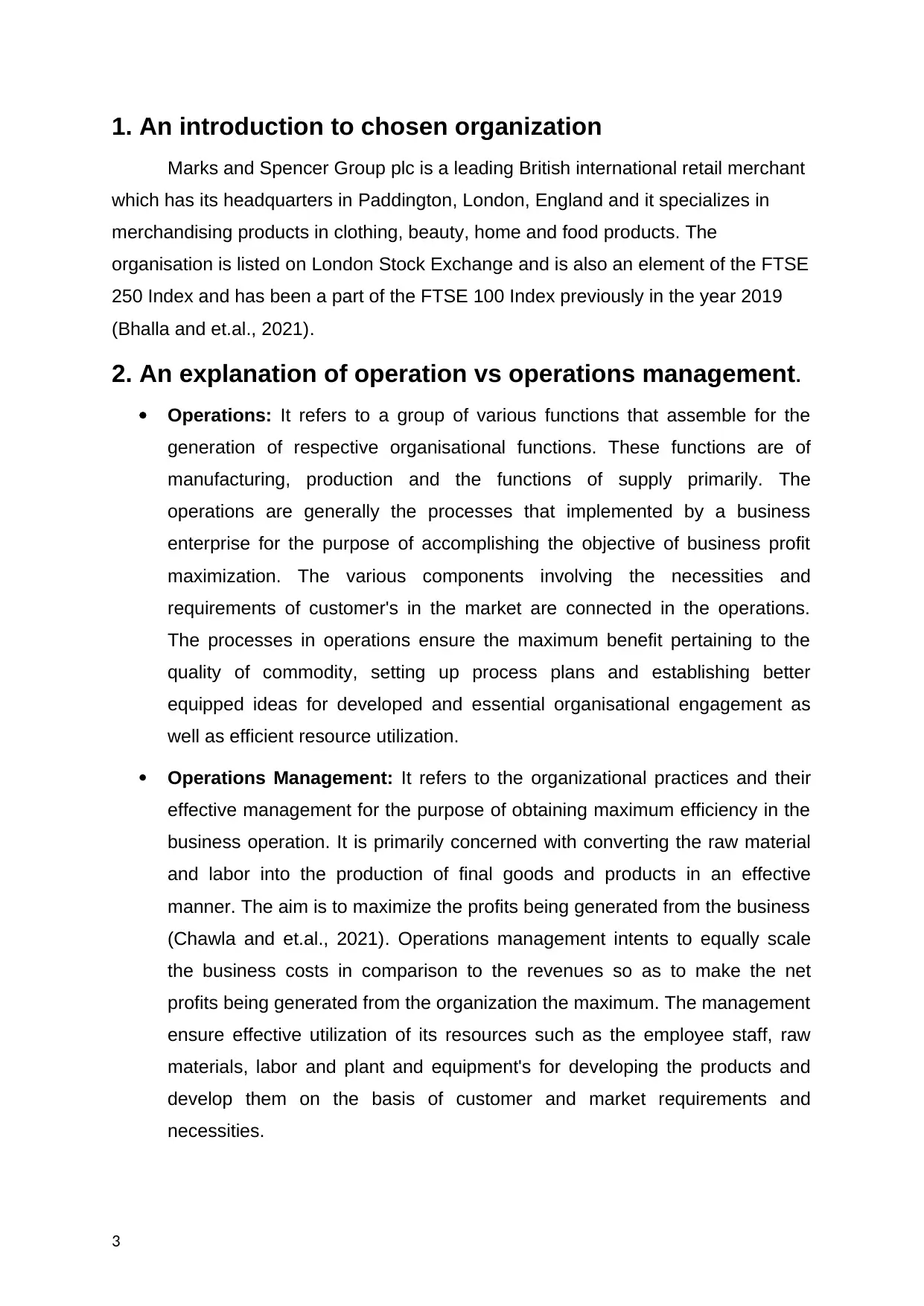
1. An introduction to chosen organization
Marks and Spencer Group plc is a leading British international retail merchant
which has its headquarters in Paddington, London, England and it specializes in
merchandising products in clothing, beauty, home and food products. The
organisation is listed on London Stock Exchange and is also an element of the FTSE
250 Index and has been a part of the FTSE 100 Index previously in the year 2019
(Bhalla and et.al., 2021).
2. An explanation of operation vs operations management.
Operations: It refers to a group of various functions that assemble for the
generation of respective organisational functions. These functions are of
manufacturing, production and the functions of supply primarily. The
operations are generally the processes that implemented by a business
enterprise for the purpose of accomplishing the objective of business profit
maximization. The various components involving the necessities and
requirements of customer's in the market are connected in the operations.
The processes in operations ensure the maximum benefit pertaining to the
quality of commodity, setting up process plans and establishing better
equipped ideas for developed and essential organisational engagement as
well as efficient resource utilization.
Operations Management: It refers to the organizational practices and their
effective management for the purpose of obtaining maximum efficiency in the
business operation. It is primarily concerned with converting the raw material
and labor into the production of final goods and products in an effective
manner. The aim is to maximize the profits being generated from the business
(Chawla and et.al., 2021). Operations management intents to equally scale
the business costs in comparison to the revenues so as to make the net
profits being generated from the organization the maximum. The management
ensure effective utilization of its resources such as the employee staff, raw
materials, labor and plant and equipment's for developing the products and
develop them on the basis of customer and market requirements and
necessities.
3
Marks and Spencer Group plc is a leading British international retail merchant
which has its headquarters in Paddington, London, England and it specializes in
merchandising products in clothing, beauty, home and food products. The
organisation is listed on London Stock Exchange and is also an element of the FTSE
250 Index and has been a part of the FTSE 100 Index previously in the year 2019
(Bhalla and et.al., 2021).
2. An explanation of operation vs operations management.
Operations: It refers to a group of various functions that assemble for the
generation of respective organisational functions. These functions are of
manufacturing, production and the functions of supply primarily. The
operations are generally the processes that implemented by a business
enterprise for the purpose of accomplishing the objective of business profit
maximization. The various components involving the necessities and
requirements of customer's in the market are connected in the operations.
The processes in operations ensure the maximum benefit pertaining to the
quality of commodity, setting up process plans and establishing better
equipped ideas for developed and essential organisational engagement as
well as efficient resource utilization.
Operations Management: It refers to the organizational practices and their
effective management for the purpose of obtaining maximum efficiency in the
business operation. It is primarily concerned with converting the raw material
and labor into the production of final goods and products in an effective
manner. The aim is to maximize the profits being generated from the business
(Chawla and et.al., 2021). Operations management intents to equally scale
the business costs in comparison to the revenues so as to make the net
profits being generated from the organization the maximum. The management
ensure effective utilization of its resources such as the employee staff, raw
materials, labor and plant and equipment's for developing the products and
develop them on the basis of customer and market requirements and
necessities.
3
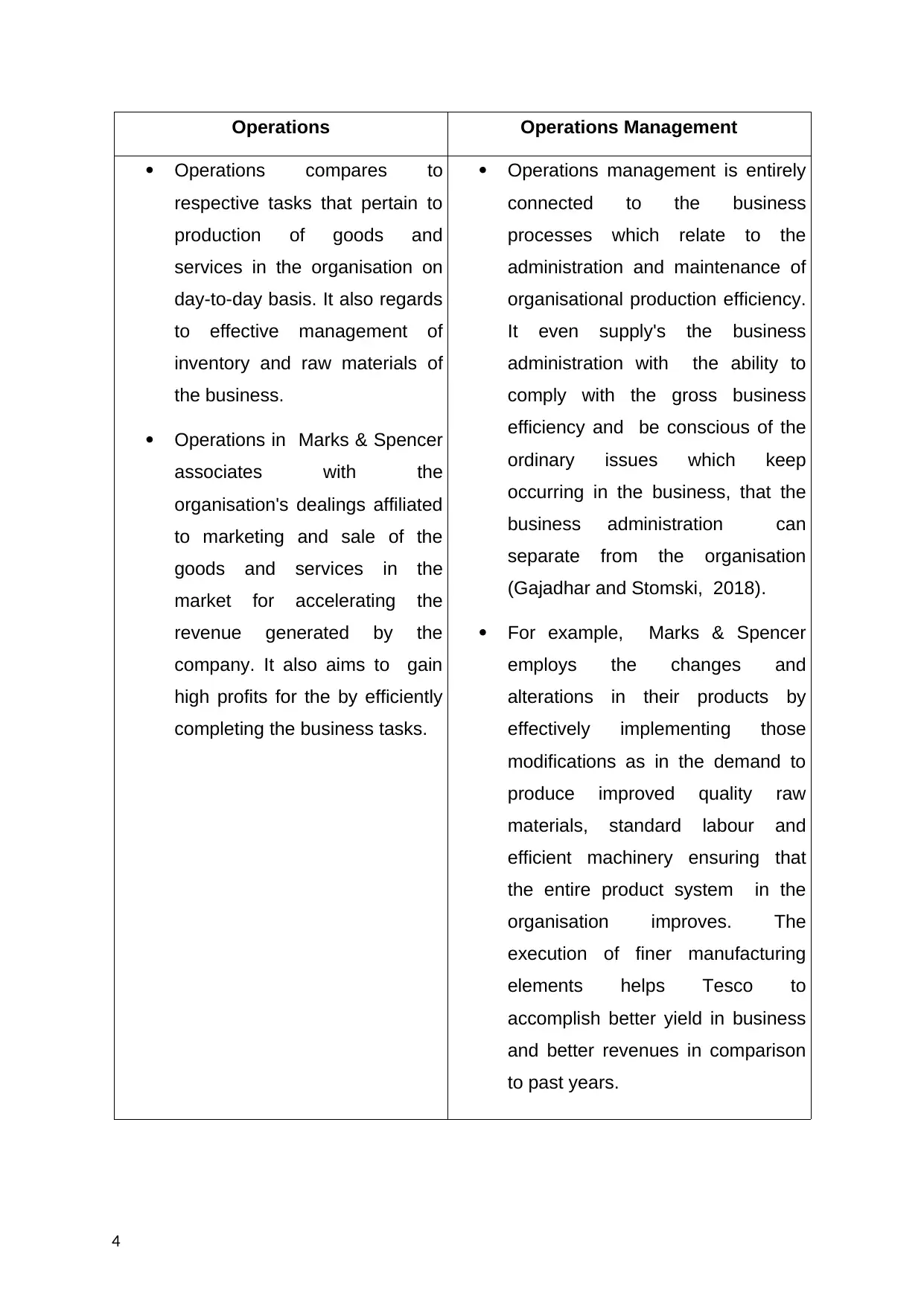
Operations Operations Management
Operations compares to
respective tasks that pertain to
production of goods and
services in the organisation on
day-to-day basis. It also regards
to effective management of
inventory and raw materials of
the business.
Operations in Marks & Spencer
associates with the
organisation's dealings affiliated
to marketing and sale of the
goods and services in the
market for accelerating the
revenue generated by the
company. It also aims to gain
high profits for the by efficiently
completing the business tasks.
Operations management is entirely
connected to the business
processes which relate to the
administration and maintenance of
organisational production efficiency.
It even supply's the business
administration with the ability to
comply with the gross business
efficiency and be conscious of the
ordinary issues which keep
occurring in the business, that the
business administration can
separate from the organisation
(Gajadhar and Stomski, 2018).
For example, Marks & Spencer
employs the changes and
alterations in their products by
effectively implementing those
modifications as in the demand to
produce improved quality raw
materials, standard labour and
efficient machinery ensuring that
the entire product system in the
organisation improves. The
execution of finer manufacturing
elements helps Tesco to
accomplish better yield in business
and better revenues in comparison
to past years.
4
Operations compares to
respective tasks that pertain to
production of goods and
services in the organisation on
day-to-day basis. It also regards
to effective management of
inventory and raw materials of
the business.
Operations in Marks & Spencer
associates with the
organisation's dealings affiliated
to marketing and sale of the
goods and services in the
market for accelerating the
revenue generated by the
company. It also aims to gain
high profits for the by efficiently
completing the business tasks.
Operations management is entirely
connected to the business
processes which relate to the
administration and maintenance of
organisational production efficiency.
It even supply's the business
administration with the ability to
comply with the gross business
efficiency and be conscious of the
ordinary issues which keep
occurring in the business, that the
business administration can
separate from the organisation
(Gajadhar and Stomski, 2018).
For example, Marks & Spencer
employs the changes and
alterations in their products by
effectively implementing those
modifications as in the demand to
produce improved quality raw
materials, standard labour and
efficient machinery ensuring that
the entire product system in the
organisation improves. The
execution of finer manufacturing
elements helps Tesco to
accomplish better yield in business
and better revenues in comparison
to past years.
4
Secure Best Marks with AI Grader
Need help grading? Try our AI Grader for instant feedback on your assignments.

3. A review and critique of the implementation of
operations management principles within the chosen
organization.
The principles of operations management are a mix of various principles in
the form of quality controls, proper plannings which help the business concern and
are of an effective use when enforced while directing the administration of the
business for achievement of desirable outcomes.
Reality: This principle says that the operations and the management should
put high focus on bigger problem against the smaller techniques that are a
component of the entire problem (Khan, 2019). This explains that only utilizing
the tools and techniques would never solve the organizational problems until
the administration doesn't tries to understand the actual issue. Implementation
of this principle would assist Marks & Spencer to understand the generally
occurring organizational issues better and solve them effectively.
Humility: The management and the business managers must realize and
respect the fact that there are always some limitations and hence should be
avoiding unnecessary trial and errors in each situation. Implementation of this
principle saves a lot of time and finances of the organization and imparts a
positive effect. Adopting this principle effectively in Marks & Spencer would
help them in effectively reducing any unwanted cost which would otherwise
take place.
Accountability: This principle of operations management says that every
individual who is responsible to manage the business operations must be
accountable for their actions and management. The managers should always
maintain for the checks and balances to ensure effectiveness and
accountability (Kuznetsov, Tsyrkov and Tsyrkov, 2020). Taking accountability
for their actions would help the managers of Marks & Spencer to handle the
business management better as they are aware of their work properly and be
quick and efficient with their tasks.
Organization: As the production process of the organization is internally
connected throughout therefore all the elements involves should be
predictable and consistent. The operational management will fail to be
5
operations management principles within the chosen
organization.
The principles of operations management are a mix of various principles in
the form of quality controls, proper plannings which help the business concern and
are of an effective use when enforced while directing the administration of the
business for achievement of desirable outcomes.
Reality: This principle says that the operations and the management should
put high focus on bigger problem against the smaller techniques that are a
component of the entire problem (Khan, 2019). This explains that only utilizing
the tools and techniques would never solve the organizational problems until
the administration doesn't tries to understand the actual issue. Implementation
of this principle would assist Marks & Spencer to understand the generally
occurring organizational issues better and solve them effectively.
Humility: The management and the business managers must realize and
respect the fact that there are always some limitations and hence should be
avoiding unnecessary trial and errors in each situation. Implementation of this
principle saves a lot of time and finances of the organization and imparts a
positive effect. Adopting this principle effectively in Marks & Spencer would
help them in effectively reducing any unwanted cost which would otherwise
take place.
Accountability: This principle of operations management says that every
individual who is responsible to manage the business operations must be
accountable for their actions and management. The managers should always
maintain for the checks and balances to ensure effectiveness and
accountability (Kuznetsov, Tsyrkov and Tsyrkov, 2020). Taking accountability
for their actions would help the managers of Marks & Spencer to handle the
business management better as they are aware of their work properly and be
quick and efficient with their tasks.
Organization: As the production process of the organization is internally
connected throughout therefore all the elements involves should be
predictable and consistent. The operational management will fail to be
5
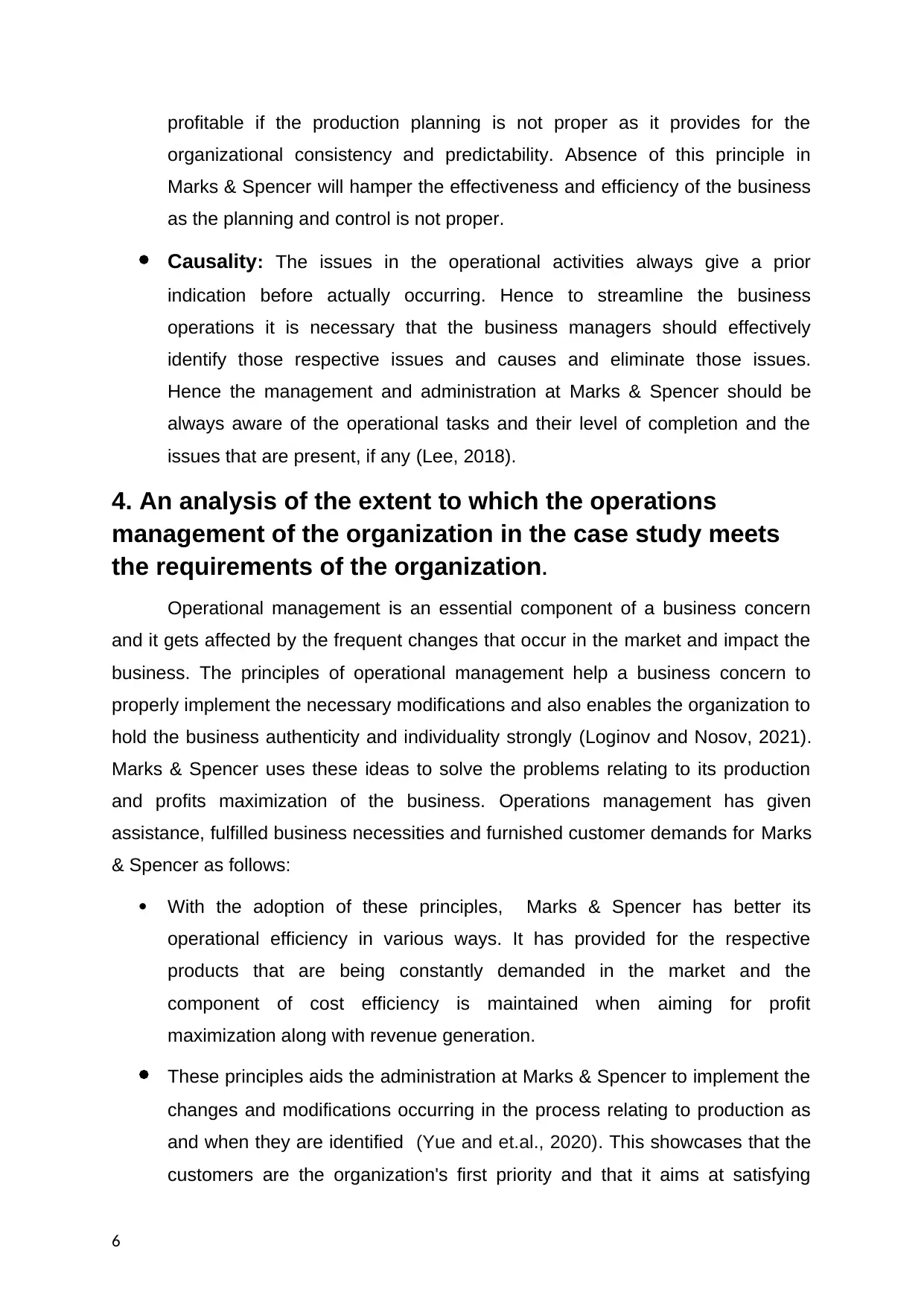
profitable if the production planning is not proper as it provides for the
organizational consistency and predictability. Absence of this principle in
Marks & Spencer will hamper the effectiveness and efficiency of the business
as the planning and control is not proper.
Causality: The issues in the operational activities always give a prior
indication before actually occurring. Hence to streamline the business
operations it is necessary that the business managers should effectively
identify those respective issues and causes and eliminate those issues.
Hence the management and administration at Marks & Spencer should be
always aware of the operational tasks and their level of completion and the
issues that are present, if any (Lee, 2018).
4. An analysis of the extent to which the operations
management of the organization in the case study meets
the requirements of the organization.
Operational management is an essential component of a business concern
and it gets affected by the frequent changes that occur in the market and impact the
business. The principles of operational management help a business concern to
properly implement the necessary modifications and also enables the organization to
hold the business authenticity and individuality strongly (Loginov and Nosov, 2021).
Marks & Spencer uses these ideas to solve the problems relating to its production
and profits maximization of the business. Operations management has given
assistance, fulfilled business necessities and furnished customer demands for Marks
& Spencer as follows:
With the adoption of these principles, Marks & Spencer has better its
operational efficiency in various ways. It has provided for the respective
products that are being constantly demanded in the market and the
component of cost efficiency is maintained when aiming for profit
maximization along with revenue generation.
These principles aids the administration at Marks & Spencer to implement the
changes and modifications occurring in the process relating to production as
and when they are identified (Yue and et.al., 2020). This showcases that the
customers are the organization's first priority and that it aims at satisfying
6
organizational consistency and predictability. Absence of this principle in
Marks & Spencer will hamper the effectiveness and efficiency of the business
as the planning and control is not proper.
Causality: The issues in the operational activities always give a prior
indication before actually occurring. Hence to streamline the business
operations it is necessary that the business managers should effectively
identify those respective issues and causes and eliminate those issues.
Hence the management and administration at Marks & Spencer should be
always aware of the operational tasks and their level of completion and the
issues that are present, if any (Lee, 2018).
4. An analysis of the extent to which the operations
management of the organization in the case study meets
the requirements of the organization.
Operational management is an essential component of a business concern
and it gets affected by the frequent changes that occur in the market and impact the
business. The principles of operational management help a business concern to
properly implement the necessary modifications and also enables the organization to
hold the business authenticity and individuality strongly (Loginov and Nosov, 2021).
Marks & Spencer uses these ideas to solve the problems relating to its production
and profits maximization of the business. Operations management has given
assistance, fulfilled business necessities and furnished customer demands for Marks
& Spencer as follows:
With the adoption of these principles, Marks & Spencer has better its
operational efficiency in various ways. It has provided for the respective
products that are being constantly demanded in the market and the
component of cost efficiency is maintained when aiming for profit
maximization along with revenue generation.
These principles aids the administration at Marks & Spencer to implement the
changes and modifications occurring in the process relating to production as
and when they are identified (Yue and et.al., 2020). This showcases that the
customers are the organization's first priority and that it aims at satisfying
6
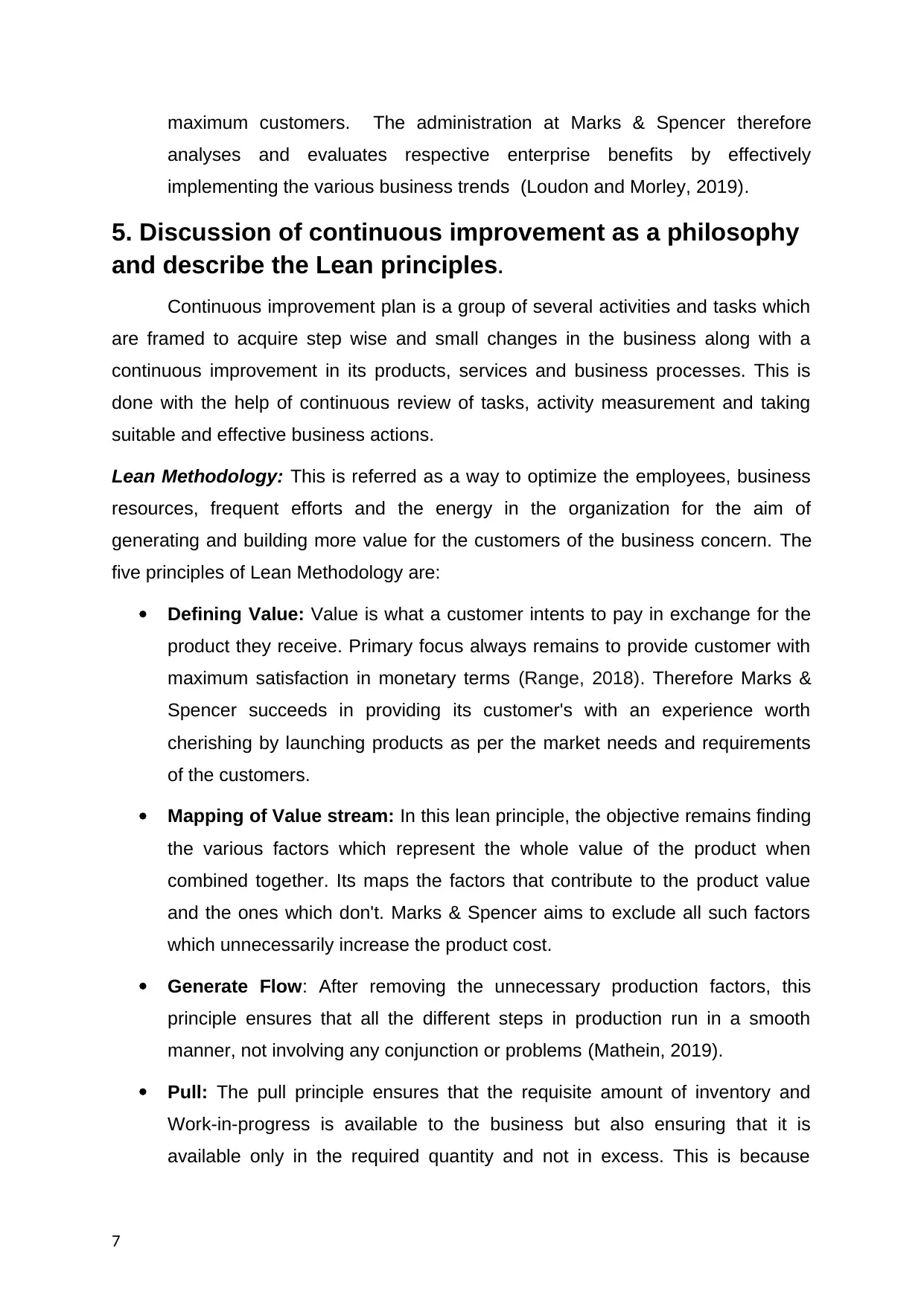
maximum customers. The administration at Marks & Spencer therefore
analyses and evaluates respective enterprise benefits by effectively
implementing the various business trends (Loudon and Morley, 2019).
5. Discussion of continuous improvement as a philosophy
and describe the Lean principles.
Continuous improvement plan is a group of several activities and tasks which
are framed to acquire step wise and small changes in the business along with a
continuous improvement in its products, services and business processes. This is
done with the help of continuous review of tasks, activity measurement and taking
suitable and effective business actions.
Lean Methodology: This is referred as a way to optimize the employees, business
resources, frequent efforts and the energy in the organization for the aim of
generating and building more value for the customers of the business concern. The
five principles of Lean Methodology are:
Defining Value: Value is what a customer intents to pay in exchange for the
product they receive. Primary focus always remains to provide customer with
maximum satisfaction in monetary terms (Range, 2018). Therefore Marks &
Spencer succeeds in providing its customer's with an experience worth
cherishing by launching products as per the market needs and requirements
of the customers.
Mapping of Value stream: In this lean principle, the objective remains finding
the various factors which represent the whole value of the product when
combined together. Its maps the factors that contribute to the product value
and the ones which don't. Marks & Spencer aims to exclude all such factors
which unnecessarily increase the product cost.
Generate Flow: After removing the unnecessary production factors, this
principle ensures that all the different steps in production run in a smooth
manner, not involving any conjunction or problems (Mathein, 2019).
Pull: The pull principle ensures that the requisite amount of inventory and
Work-in-progress is available to the business but also ensuring that it is
available only in the required quantity and not in excess. This is because
7
analyses and evaluates respective enterprise benefits by effectively
implementing the various business trends (Loudon and Morley, 2019).
5. Discussion of continuous improvement as a philosophy
and describe the Lean principles.
Continuous improvement plan is a group of several activities and tasks which
are framed to acquire step wise and small changes in the business along with a
continuous improvement in its products, services and business processes. This is
done with the help of continuous review of tasks, activity measurement and taking
suitable and effective business actions.
Lean Methodology: This is referred as a way to optimize the employees, business
resources, frequent efforts and the energy in the organization for the aim of
generating and building more value for the customers of the business concern. The
five principles of Lean Methodology are:
Defining Value: Value is what a customer intents to pay in exchange for the
product they receive. Primary focus always remains to provide customer with
maximum satisfaction in monetary terms (Range, 2018). Therefore Marks &
Spencer succeeds in providing its customer's with an experience worth
cherishing by launching products as per the market needs and requirements
of the customers.
Mapping of Value stream: In this lean principle, the objective remains finding
the various factors which represent the whole value of the product when
combined together. Its maps the factors that contribute to the product value
and the ones which don't. Marks & Spencer aims to exclude all such factors
which unnecessarily increase the product cost.
Generate Flow: After removing the unnecessary production factors, this
principle ensures that all the different steps in production run in a smooth
manner, not involving any conjunction or problems (Mathein, 2019).
Pull: The pull principle ensures that the requisite amount of inventory and
Work-in-progress is available to the business but also ensuring that it is
available only in the required quantity and not in excess. This is because
7
Paraphrase This Document
Need a fresh take? Get an instant paraphrase of this document with our AI Paraphraser
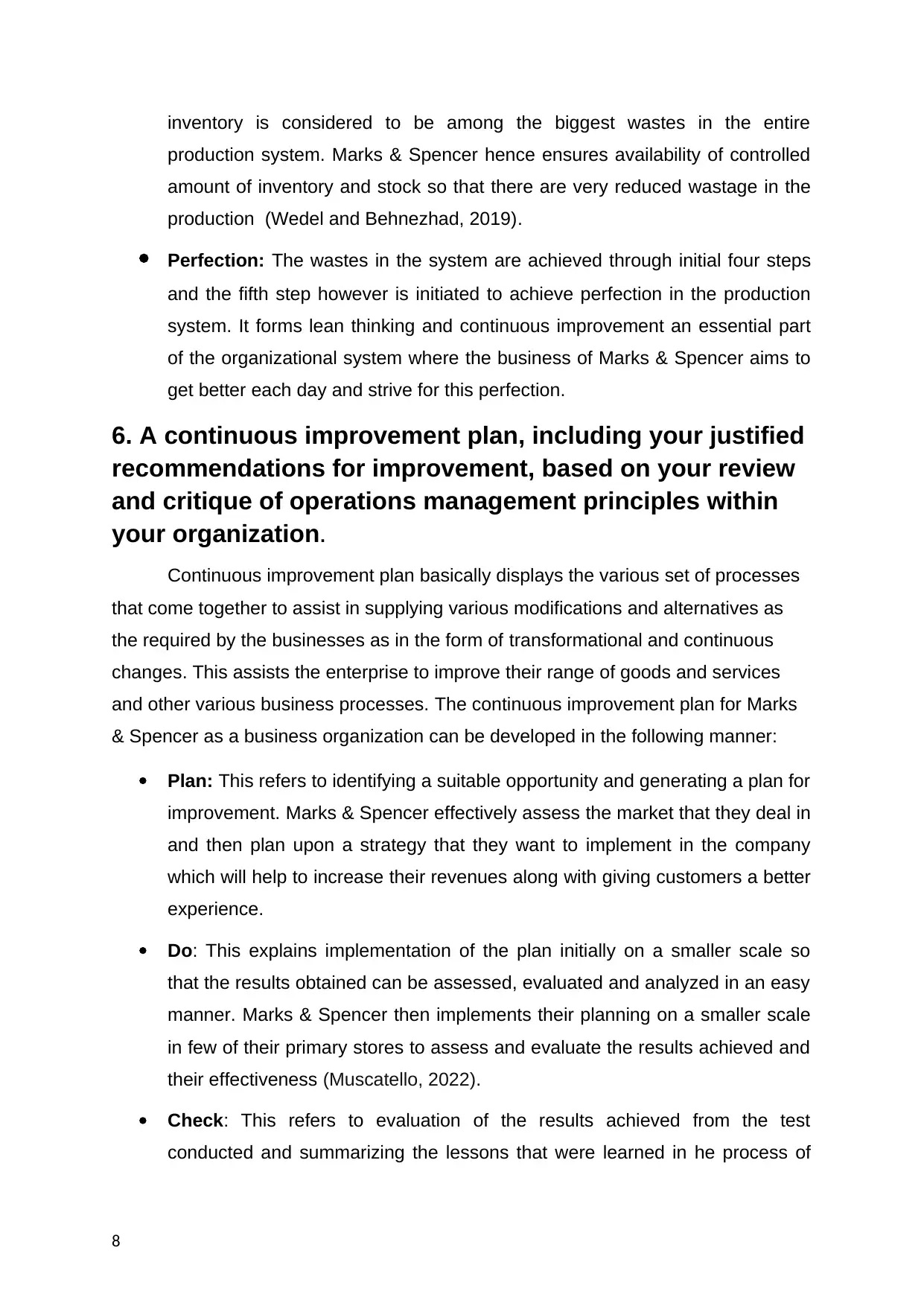
inventory is considered to be among the biggest wastes in the entire
production system. Marks & Spencer hence ensures availability of controlled
amount of inventory and stock so that there are very reduced wastage in the
production (Wedel and Behnezhad, 2019).
Perfection: The wastes in the system are achieved through initial four steps
and the fifth step however is initiated to achieve perfection in the production
system. It forms lean thinking and continuous improvement an essential part
of the organizational system where the business of Marks & Spencer aims to
get better each day and strive for this perfection.
6. A continuous improvement plan, including your justified
recommendations for improvement, based on your review
and critique of operations management principles within
your organization.
Continuous improvement plan basically displays the various set of processes
that come together to assist in supplying various modifications and alternatives as
the required by the businesses as in the form of transformational and continuous
changes. This assists the enterprise to improve their range of goods and services
and other various business processes. The continuous improvement plan for Marks
& Spencer as a business organization can be developed in the following manner:
Plan: This refers to identifying a suitable opportunity and generating a plan for
improvement. Marks & Spencer effectively assess the market that they deal in
and then plan upon a strategy that they want to implement in the company
which will help to increase their revenues along with giving customers a better
experience.
Do: This explains implementation of the plan initially on a smaller scale so
that the results obtained can be assessed, evaluated and analyzed in an easy
manner. Marks & Spencer then implements their planning on a smaller scale
in few of their primary stores to assess and evaluate the results achieved and
their effectiveness (Muscatello, 2022).
Check: This refers to evaluation of the results achieved from the test
conducted and summarizing the lessons that were learned in he process of
8
production system. Marks & Spencer hence ensures availability of controlled
amount of inventory and stock so that there are very reduced wastage in the
production (Wedel and Behnezhad, 2019).
Perfection: The wastes in the system are achieved through initial four steps
and the fifth step however is initiated to achieve perfection in the production
system. It forms lean thinking and continuous improvement an essential part
of the organizational system where the business of Marks & Spencer aims to
get better each day and strive for this perfection.
6. A continuous improvement plan, including your justified
recommendations for improvement, based on your review
and critique of operations management principles within
your organization.
Continuous improvement plan basically displays the various set of processes
that come together to assist in supplying various modifications and alternatives as
the required by the businesses as in the form of transformational and continuous
changes. This assists the enterprise to improve their range of goods and services
and other various business processes. The continuous improvement plan for Marks
& Spencer as a business organization can be developed in the following manner:
Plan: This refers to identifying a suitable opportunity and generating a plan for
improvement. Marks & Spencer effectively assess the market that they deal in
and then plan upon a strategy that they want to implement in the company
which will help to increase their revenues along with giving customers a better
experience.
Do: This explains implementation of the plan initially on a smaller scale so
that the results obtained can be assessed, evaluated and analyzed in an easy
manner. Marks & Spencer then implements their planning on a smaller scale
in few of their primary stores to assess and evaluate the results achieved and
their effectiveness (Muscatello, 2022).
Check: This refers to evaluation of the results achieved from the test
conducted and summarizing the lessons that were learned in he process of
8
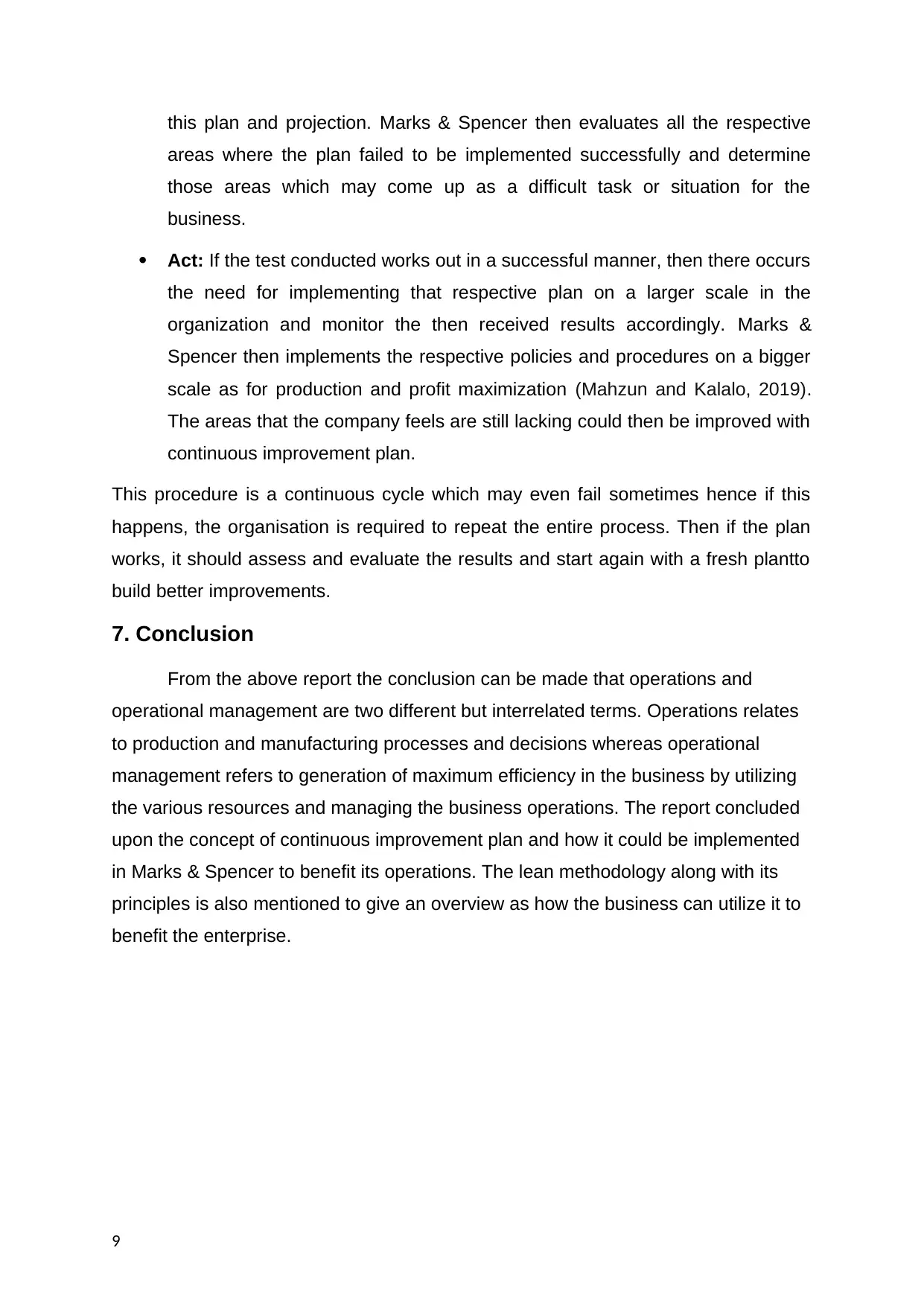
this plan and projection. Marks & Spencer then evaluates all the respective
areas where the plan failed to be implemented successfully and determine
those areas which may come up as a difficult task or situation for the
business.
Act: If the test conducted works out in a successful manner, then there occurs
the need for implementing that respective plan on a larger scale in the
organization and monitor the then received results accordingly. Marks &
Spencer then implements the respective policies and procedures on a bigger
scale as for production and profit maximization (Mahzun and Kalalo, 2019).
The areas that the company feels are still lacking could then be improved with
continuous improvement plan.
This procedure is a continuous cycle which may even fail sometimes hence if this
happens, the organisation is required to repeat the entire process. Then if the plan
works, it should assess and evaluate the results and start again with a fresh plantto
build better improvements.
7. Conclusion
From the above report the conclusion can be made that operations and
operational management are two different but interrelated terms. Operations relates
to production and manufacturing processes and decisions whereas operational
management refers to generation of maximum efficiency in the business by utilizing
the various resources and managing the business operations. The report concluded
upon the concept of continuous improvement plan and how it could be implemented
in Marks & Spencer to benefit its operations. The lean methodology along with its
principles is also mentioned to give an overview as how the business can utilize it to
benefit the enterprise.
9
areas where the plan failed to be implemented successfully and determine
those areas which may come up as a difficult task or situation for the
business.
Act: If the test conducted works out in a successful manner, then there occurs
the need for implementing that respective plan on a larger scale in the
organization and monitor the then received results accordingly. Marks &
Spencer then implements the respective policies and procedures on a bigger
scale as for production and profit maximization (Mahzun and Kalalo, 2019).
The areas that the company feels are still lacking could then be improved with
continuous improvement plan.
This procedure is a continuous cycle which may even fail sometimes hence if this
happens, the organisation is required to repeat the entire process. Then if the plan
works, it should assess and evaluate the results and start again with a fresh plantto
build better improvements.
7. Conclusion
From the above report the conclusion can be made that operations and
operational management are two different but interrelated terms. Operations relates
to production and manufacturing processes and decisions whereas operational
management refers to generation of maximum efficiency in the business by utilizing
the various resources and managing the business operations. The report concluded
upon the concept of continuous improvement plan and how it could be implemented
in Marks & Spencer to benefit its operations. The lean methodology along with its
principles is also mentioned to give an overview as how the business can utilize it to
benefit the enterprise.
9
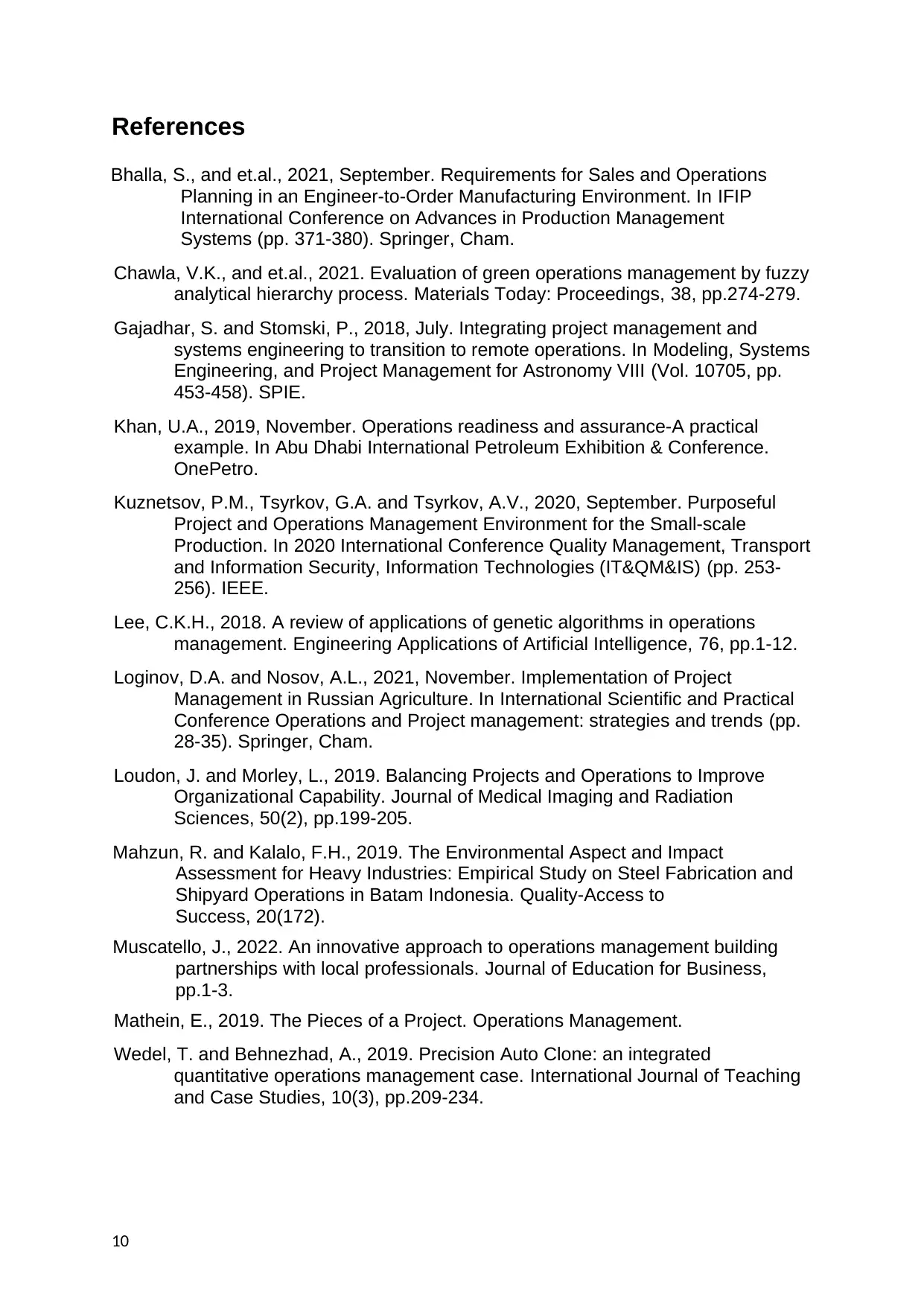
References
Bhalla, S., and et.al., 2021, September. Requirements for Sales and Operations
Planning in an Engineer-to-Order Manufacturing Environment. In IFIP
International Conference on Advances in Production Management
Systems (pp. 371-380). Springer, Cham.
Chawla, V.K., and et.al., 2021. Evaluation of green operations management by fuzzy
analytical hierarchy process. Materials Today: Proceedings, 38, pp.274-279.
Gajadhar, S. and Stomski, P., 2018, July. Integrating project management and
systems engineering to transition to remote operations. In Modeling, Systems
Engineering, and Project Management for Astronomy VIII (Vol. 10705, pp.
453-458). SPIE.
Khan, U.A., 2019, November. Operations readiness and assurance-A practical
example. In Abu Dhabi International Petroleum Exhibition & Conference.
OnePetro.
Kuznetsov, P.M., Tsyrkov, G.A. and Tsyrkov, A.V., 2020, September. Purposeful
Project and Operations Management Environment for the Small-scale
Production. In 2020 International Conference Quality Management, Transport
and Information Security, Information Technologies (IT&QM&IS) (pp. 253-
256). IEEE.
Lee, C.K.H., 2018. A review of applications of genetic algorithms in operations
management. Engineering Applications of Artificial Intelligence, 76, pp.1-12.
Loginov, D.A. and Nosov, A.L., 2021, November. Implementation of Project
Management in Russian Agriculture. In International Scientific and Practical
Conference Operations and Project management: strategies and trends (pp.
28-35). Springer, Cham.
Loudon, J. and Morley, L., 2019. Balancing Projects and Operations to Improve
Organizational Capability. Journal of Medical Imaging and Radiation
Sciences, 50(2), pp.199-205.
Mahzun, R. and Kalalo, F.H., 2019. The Environmental Aspect and Impact
Assessment for Heavy Industries: Empirical Study on Steel Fabrication and
Shipyard Operations in Batam Indonesia. Quality-Access to
Success, 20(172).
Muscatello, J., 2022. An innovative approach to operations management building
partnerships with local professionals. Journal of Education for Business,
pp.1-3.
Mathein, E., 2019. The Pieces of a Project. Operations Management.
Wedel, T. and Behnezhad, A., 2019. Precision Auto Clone: an integrated
quantitative operations management case. International Journal of Teaching
and Case Studies, 10(3), pp.209-234.
10
Bhalla, S., and et.al., 2021, September. Requirements for Sales and Operations
Planning in an Engineer-to-Order Manufacturing Environment. In IFIP
International Conference on Advances in Production Management
Systems (pp. 371-380). Springer, Cham.
Chawla, V.K., and et.al., 2021. Evaluation of green operations management by fuzzy
analytical hierarchy process. Materials Today: Proceedings, 38, pp.274-279.
Gajadhar, S. and Stomski, P., 2018, July. Integrating project management and
systems engineering to transition to remote operations. In Modeling, Systems
Engineering, and Project Management for Astronomy VIII (Vol. 10705, pp.
453-458). SPIE.
Khan, U.A., 2019, November. Operations readiness and assurance-A practical
example. In Abu Dhabi International Petroleum Exhibition & Conference.
OnePetro.
Kuznetsov, P.M., Tsyrkov, G.A. and Tsyrkov, A.V., 2020, September. Purposeful
Project and Operations Management Environment for the Small-scale
Production. In 2020 International Conference Quality Management, Transport
and Information Security, Information Technologies (IT&QM&IS) (pp. 253-
256). IEEE.
Lee, C.K.H., 2018. A review of applications of genetic algorithms in operations
management. Engineering Applications of Artificial Intelligence, 76, pp.1-12.
Loginov, D.A. and Nosov, A.L., 2021, November. Implementation of Project
Management in Russian Agriculture. In International Scientific and Practical
Conference Operations and Project management: strategies and trends (pp.
28-35). Springer, Cham.
Loudon, J. and Morley, L., 2019. Balancing Projects and Operations to Improve
Organizational Capability. Journal of Medical Imaging and Radiation
Sciences, 50(2), pp.199-205.
Mahzun, R. and Kalalo, F.H., 2019. The Environmental Aspect and Impact
Assessment for Heavy Industries: Empirical Study on Steel Fabrication and
Shipyard Operations in Batam Indonesia. Quality-Access to
Success, 20(172).
Muscatello, J., 2022. An innovative approach to operations management building
partnerships with local professionals. Journal of Education for Business,
pp.1-3.
Mathein, E., 2019. The Pieces of a Project. Operations Management.
Wedel, T. and Behnezhad, A., 2019. Precision Auto Clone: an integrated
quantitative operations management case. International Journal of Teaching
and Case Studies, 10(3), pp.209-234.
10
Secure Best Marks with AI Grader
Need help grading? Try our AI Grader for instant feedback on your assignments.
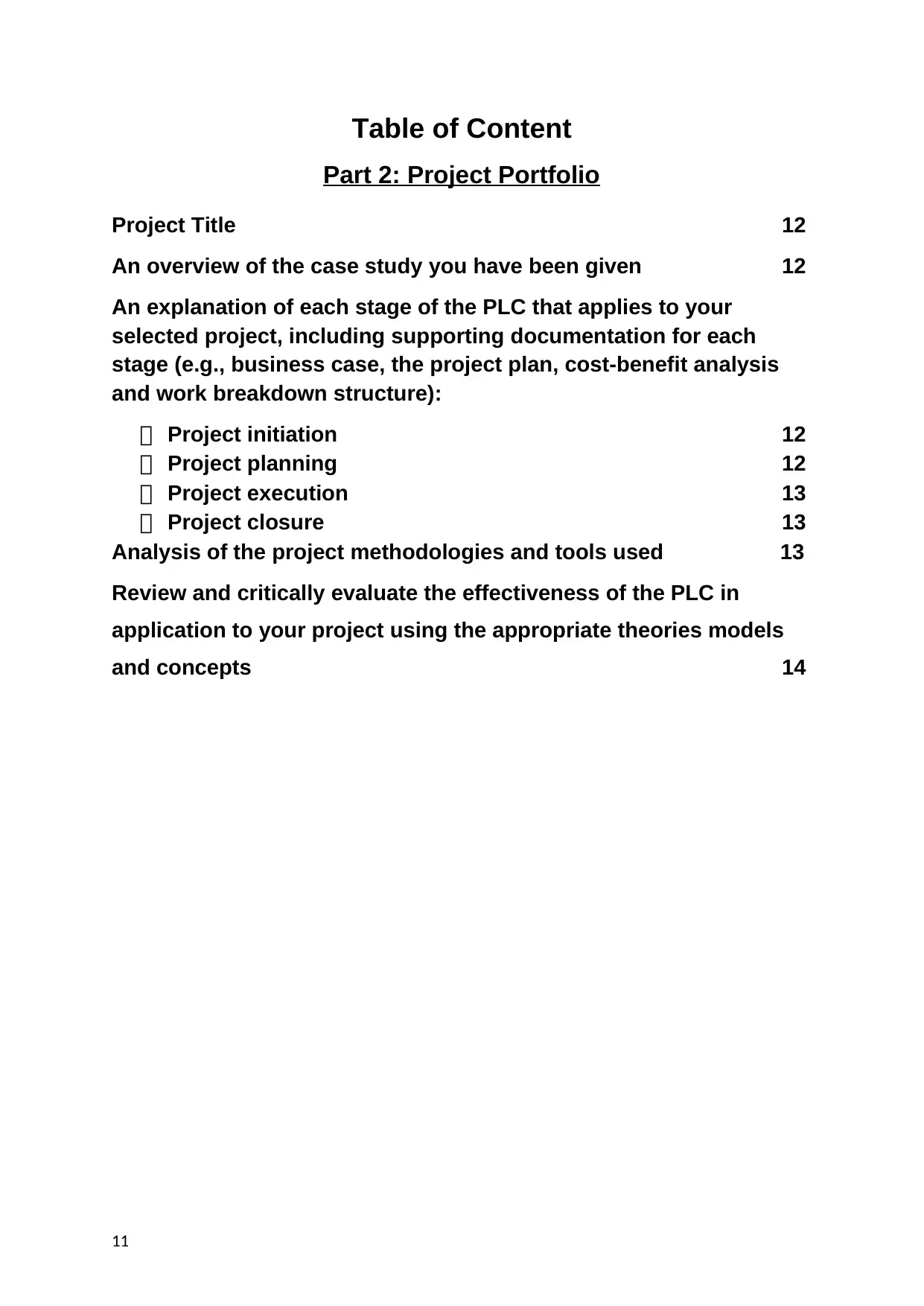
Table of Content
Part 2: Project Portfolio
Project Title 12
An overview of the case study you have been given 12
An explanation of each stage of the PLC that applies to your
selected project, including supporting documentation for each
stage (e.g., business case, the project plan, cost-benefit analysis
and work breakdown structure):
Project initiation 12
Project planning 12
Project execution 13
Project closure 13
Analysis of the project methodologies and tools used 13
Review and critically evaluate the effectiveness of the PLC in
application to your project using the appropriate theories models
and concepts 14
11
Part 2: Project Portfolio
Project Title 12
An overview of the case study you have been given 12
An explanation of each stage of the PLC that applies to your
selected project, including supporting documentation for each
stage (e.g., business case, the project plan, cost-benefit analysis
and work breakdown structure):
Project initiation 12
Project planning 12
Project execution 13
Project closure 13
Analysis of the project methodologies and tools used 13
Review and critically evaluate the effectiveness of the PLC in
application to your project using the appropriate theories models
and concepts 14
11
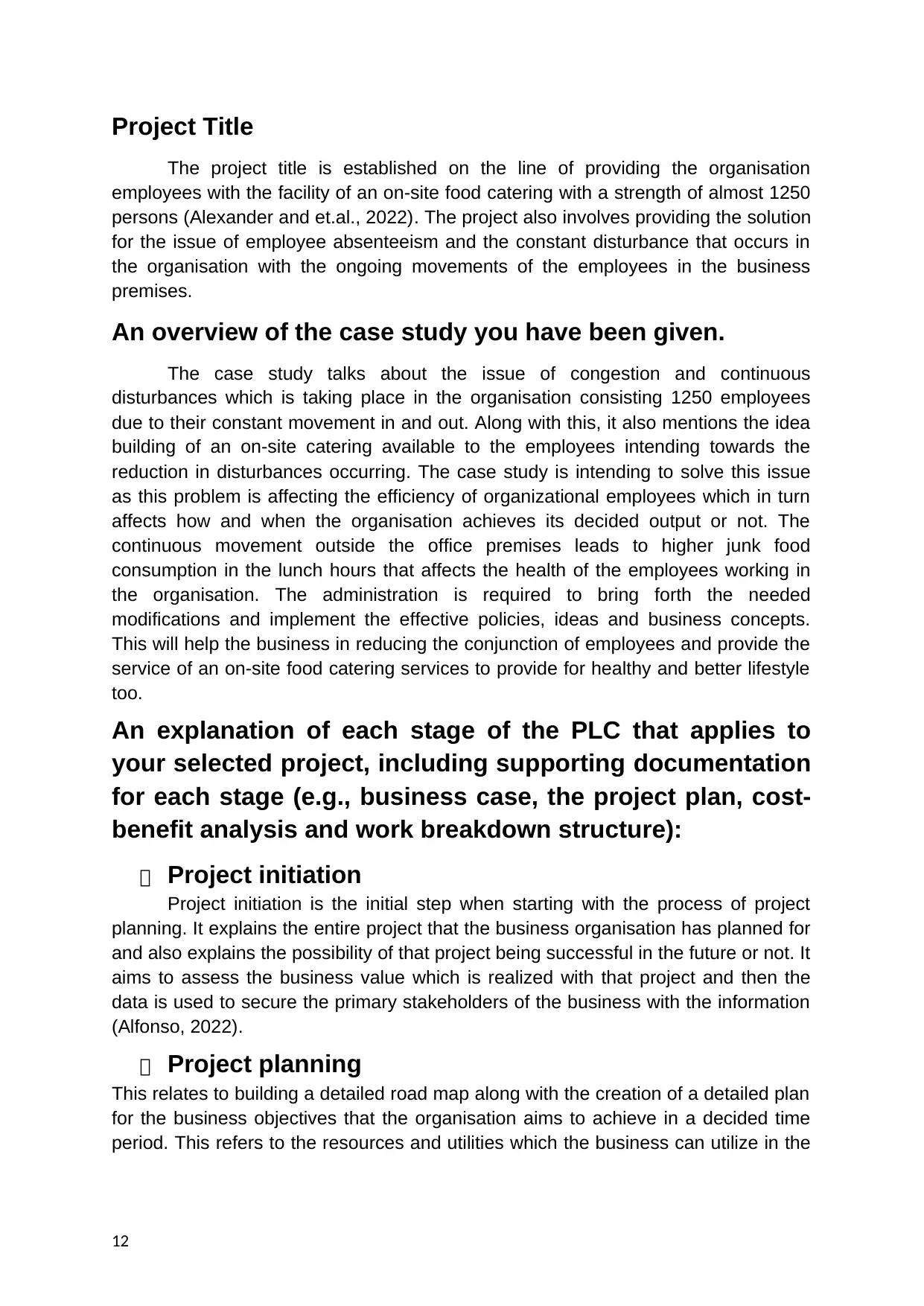
Project Title
The project title is established on the line of providing the organisation
employees with the facility of an on-site food catering with a strength of almost 1250
persons (Alexander and et.al., 2022). The project also involves providing the solution
for the issue of employee absenteeism and the constant disturbance that occurs in
the organisation with the ongoing movements of the employees in the business
premises.
An overview of the case study you have been given.
The case study talks about the issue of congestion and continuous
disturbances which is taking place in the organisation consisting 1250 employees
due to their constant movement in and out. Along with this, it also mentions the idea
building of an on-site catering available to the employees intending towards the
reduction in disturbances occurring. The case study is intending to solve this issue
as this problem is affecting the efficiency of organizational employees which in turn
affects how and when the organisation achieves its decided output or not. The
continuous movement outside the office premises leads to higher junk food
consumption in the lunch hours that affects the health of the employees working in
the organisation. The administration is required to bring forth the needed
modifications and implement the effective policies, ideas and business concepts.
This will help the business in reducing the conjunction of employees and provide the
service of an on-site food catering services to provide for healthy and better lifestyle
too.
An explanation of each stage of the PLC that applies to
your selected project, including supporting documentation
for each stage (e.g., business case, the project plan, cost-
benefit analysis and work breakdown structure):
Project initiation
Project initiation is the initial step when starting with the process of project
planning. It explains the entire project that the business organisation has planned for
and also explains the possibility of that project being successful in the future or not. It
aims to assess the business value which is realized with that project and then the
data is used to secure the primary stakeholders of the business with the information
(Alfonso, 2022).
Project planning
This relates to building a detailed road map along with the creation of a detailed plan
for the business objectives that the organisation aims to achieve in a decided time
period. This refers to the resources and utilities which the business can utilize in the
12
The project title is established on the line of providing the organisation
employees with the facility of an on-site food catering with a strength of almost 1250
persons (Alexander and et.al., 2022). The project also involves providing the solution
for the issue of employee absenteeism and the constant disturbance that occurs in
the organisation with the ongoing movements of the employees in the business
premises.
An overview of the case study you have been given.
The case study talks about the issue of congestion and continuous
disturbances which is taking place in the organisation consisting 1250 employees
due to their constant movement in and out. Along with this, it also mentions the idea
building of an on-site catering available to the employees intending towards the
reduction in disturbances occurring. The case study is intending to solve this issue
as this problem is affecting the efficiency of organizational employees which in turn
affects how and when the organisation achieves its decided output or not. The
continuous movement outside the office premises leads to higher junk food
consumption in the lunch hours that affects the health of the employees working in
the organisation. The administration is required to bring forth the needed
modifications and implement the effective policies, ideas and business concepts.
This will help the business in reducing the conjunction of employees and provide the
service of an on-site food catering services to provide for healthy and better lifestyle
too.
An explanation of each stage of the PLC that applies to
your selected project, including supporting documentation
for each stage (e.g., business case, the project plan, cost-
benefit analysis and work breakdown structure):
Project initiation
Project initiation is the initial step when starting with the process of project
planning. It explains the entire project that the business organisation has planned for
and also explains the possibility of that project being successful in the future or not. It
aims to assess the business value which is realized with that project and then the
data is used to secure the primary stakeholders of the business with the information
(Alfonso, 2022).
Project planning
This relates to building a detailed road map along with the creation of a detailed plan
for the business objectives that the organisation aims to achieve in a decided time
period. This refers to the resources and utilities which the business can utilize in the
12
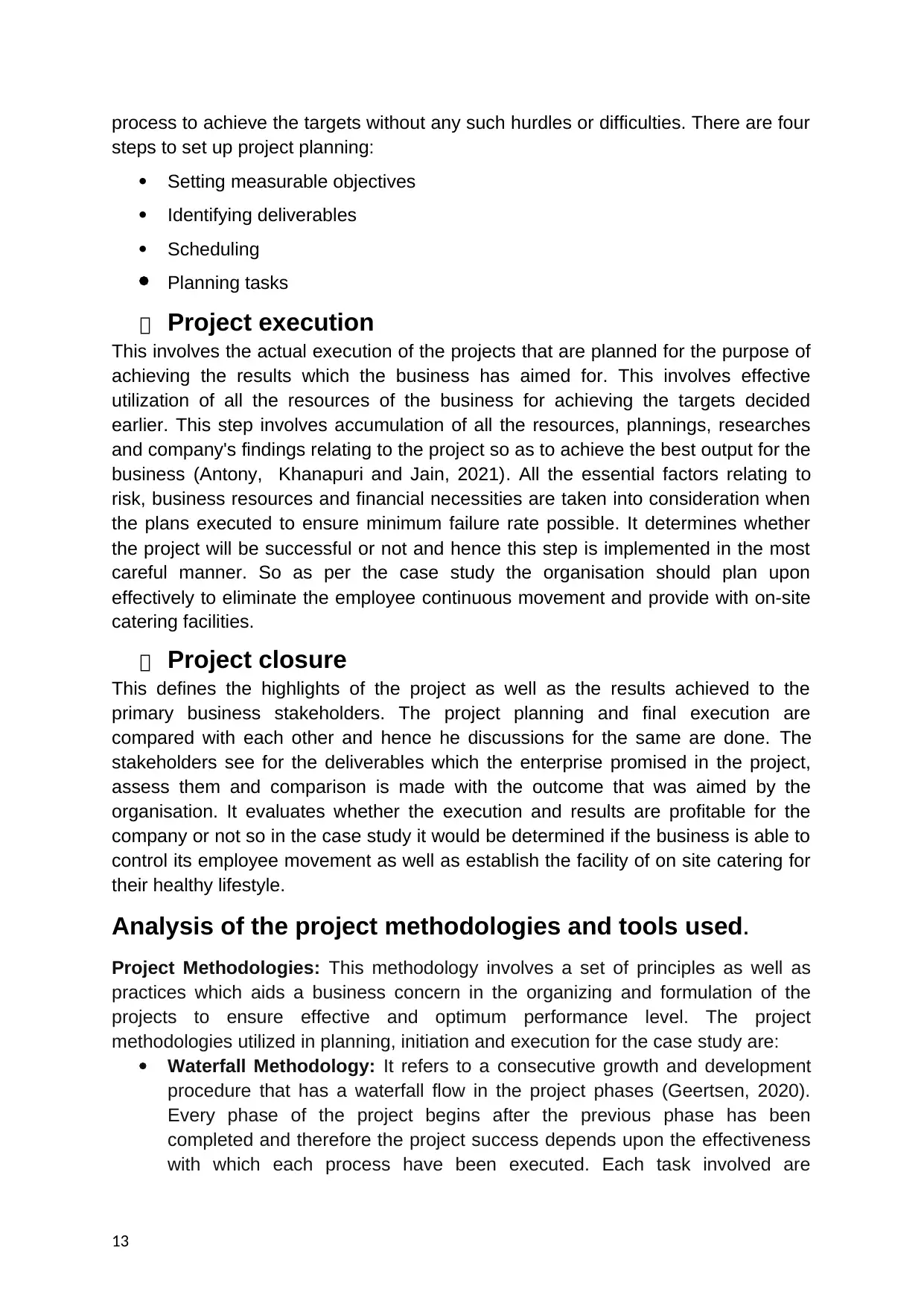
process to achieve the targets without any such hurdles or difficulties. There are four
steps to set up project planning:
Setting measurable objectives
Identifying deliverables
Scheduling
Planning tasks
Project execution
This involves the actual execution of the projects that are planned for the purpose of
achieving the results which the business has aimed for. This involves effective
utilization of all the resources of the business for achieving the targets decided
earlier. This step involves accumulation of all the resources, plannings, researches
and company's findings relating to the project so as to achieve the best output for the
business (Antony, Khanapuri and Jain, 2021). All the essential factors relating to
risk, business resources and financial necessities are taken into consideration when
the plans executed to ensure minimum failure rate possible. It determines whether
the project will be successful or not and hence this step is implemented in the most
careful manner. So as per the case study the organisation should plan upon
effectively to eliminate the employee continuous movement and provide with on-site
catering facilities.
Project closure
This defines the highlights of the project as well as the results achieved to the
primary business stakeholders. The project planning and final execution are
compared with each other and hence he discussions for the same are done. The
stakeholders see for the deliverables which the enterprise promised in the project,
assess them and comparison is made with the outcome that was aimed by the
organisation. It evaluates whether the execution and results are profitable for the
company or not so in the case study it would be determined if the business is able to
control its employee movement as well as establish the facility of on site catering for
their healthy lifestyle.
Analysis of the project methodologies and tools used.
Project Methodologies: This methodology involves a set of principles as well as
practices which aids a business concern in the organizing and formulation of the
projects to ensure effective and optimum performance level. The project
methodologies utilized in planning, initiation and execution for the case study are:
Waterfall Methodology: It refers to a consecutive growth and development
procedure that has a waterfall flow in the project phases (Geertsen, 2020).
Every phase of the project begins after the previous phase has been
completed and therefore the project success depends upon the effectiveness
with which each process have been executed. Each task involved are
13
steps to set up project planning:
Setting measurable objectives
Identifying deliverables
Scheduling
Planning tasks
Project execution
This involves the actual execution of the projects that are planned for the purpose of
achieving the results which the business has aimed for. This involves effective
utilization of all the resources of the business for achieving the targets decided
earlier. This step involves accumulation of all the resources, plannings, researches
and company's findings relating to the project so as to achieve the best output for the
business (Antony, Khanapuri and Jain, 2021). All the essential factors relating to
risk, business resources and financial necessities are taken into consideration when
the plans executed to ensure minimum failure rate possible. It determines whether
the project will be successful or not and hence this step is implemented in the most
careful manner. So as per the case study the organisation should plan upon
effectively to eliminate the employee continuous movement and provide with on-site
catering facilities.
Project closure
This defines the highlights of the project as well as the results achieved to the
primary business stakeholders. The project planning and final execution are
compared with each other and hence he discussions for the same are done. The
stakeholders see for the deliverables which the enterprise promised in the project,
assess them and comparison is made with the outcome that was aimed by the
organisation. It evaluates whether the execution and results are profitable for the
company or not so in the case study it would be determined if the business is able to
control its employee movement as well as establish the facility of on site catering for
their healthy lifestyle.
Analysis of the project methodologies and tools used.
Project Methodologies: This methodology involves a set of principles as well as
practices which aids a business concern in the organizing and formulation of the
projects to ensure effective and optimum performance level. The project
methodologies utilized in planning, initiation and execution for the case study are:
Waterfall Methodology: It refers to a consecutive growth and development
procedure that has a waterfall flow in the project phases (Geertsen, 2020).
Every phase of the project begins after the previous phase has been
completed and therefore the project success depends upon the effectiveness
with which each process have been executed. Each task involved are
13
Paraphrase This Document
Need a fresh take? Get an instant paraphrase of this document with our AI Paraphraser
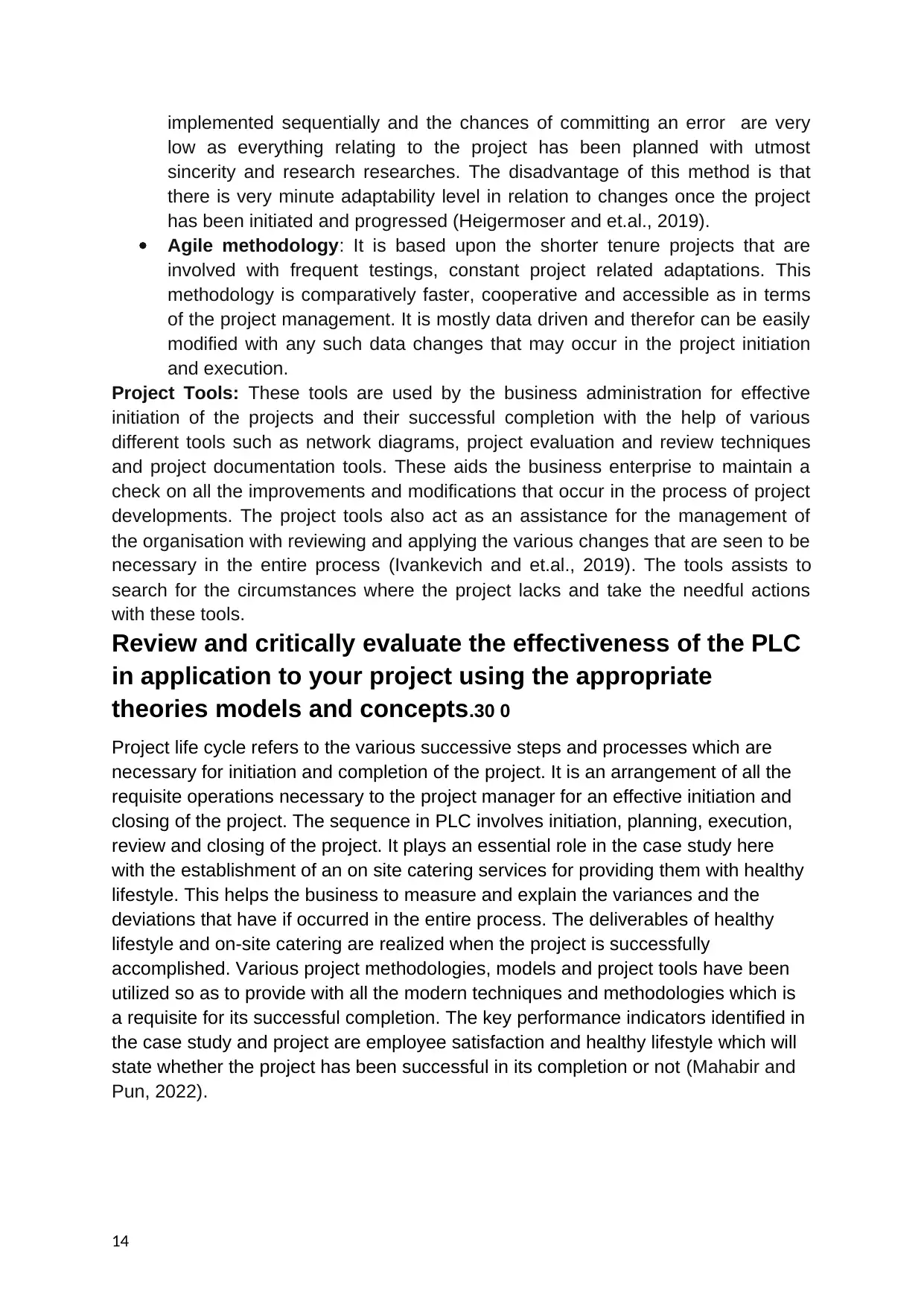
implemented sequentially and the chances of committing an error are very
low as everything relating to the project has been planned with utmost
sincerity and research researches. The disadvantage of this method is that
there is very minute adaptability level in relation to changes once the project
has been initiated and progressed (Heigermoser and et.al., 2019).
Agile methodology: It is based upon the shorter tenure projects that are
involved with frequent testings, constant project related adaptations. This
methodology is comparatively faster, cooperative and accessible as in terms
of the project management. It is mostly data driven and therefor can be easily
modified with any such data changes that may occur in the project initiation
and execution.
Project Tools: These tools are used by the business administration for effective
initiation of the projects and their successful completion with the help of various
different tools such as network diagrams, project evaluation and review techniques
and project documentation tools. These aids the business enterprise to maintain a
check on all the improvements and modifications that occur in the process of project
developments. The project tools also act as an assistance for the management of
the organisation with reviewing and applying the various changes that are seen to be
necessary in the entire process (Ivankevich and et.al., 2019). The tools assists to
search for the circumstances where the project lacks and take the needful actions
with these tools.
Review and critically evaluate the effectiveness of the PLC
in application to your project using the appropriate
theories models and concepts.30 0
Project life cycle refers to the various successive steps and processes which are
necessary for initiation and completion of the project. It is an arrangement of all the
requisite operations necessary to the project manager for an effective initiation and
closing of the project. The sequence in PLC involves initiation, planning, execution,
review and closing of the project. It plays an essential role in the case study here
with the establishment of an on site catering services for providing them with healthy
lifestyle. This helps the business to measure and explain the variances and the
deviations that have if occurred in the entire process. The deliverables of healthy
lifestyle and on-site catering are realized when the project is successfully
accomplished. Various project methodologies, models and project tools have been
utilized so as to provide with all the modern techniques and methodologies which is
a requisite for its successful completion. The key performance indicators identified in
the case study and project are employee satisfaction and healthy lifestyle which will
state whether the project has been successful in its completion or not (Mahabir and
Pun, 2022).
14
low as everything relating to the project has been planned with utmost
sincerity and research researches. The disadvantage of this method is that
there is very minute adaptability level in relation to changes once the project
has been initiated and progressed (Heigermoser and et.al., 2019).
Agile methodology: It is based upon the shorter tenure projects that are
involved with frequent testings, constant project related adaptations. This
methodology is comparatively faster, cooperative and accessible as in terms
of the project management. It is mostly data driven and therefor can be easily
modified with any such data changes that may occur in the project initiation
and execution.
Project Tools: These tools are used by the business administration for effective
initiation of the projects and their successful completion with the help of various
different tools such as network diagrams, project evaluation and review techniques
and project documentation tools. These aids the business enterprise to maintain a
check on all the improvements and modifications that occur in the process of project
developments. The project tools also act as an assistance for the management of
the organisation with reviewing and applying the various changes that are seen to be
necessary in the entire process (Ivankevich and et.al., 2019). The tools assists to
search for the circumstances where the project lacks and take the needful actions
with these tools.
Review and critically evaluate the effectiveness of the PLC
in application to your project using the appropriate
theories models and concepts.30 0
Project life cycle refers to the various successive steps and processes which are
necessary for initiation and completion of the project. It is an arrangement of all the
requisite operations necessary to the project manager for an effective initiation and
closing of the project. The sequence in PLC involves initiation, planning, execution,
review and closing of the project. It plays an essential role in the case study here
with the establishment of an on site catering services for providing them with healthy
lifestyle. This helps the business to measure and explain the variances and the
deviations that have if occurred in the entire process. The deliverables of healthy
lifestyle and on-site catering are realized when the project is successfully
accomplished. Various project methodologies, models and project tools have been
utilized so as to provide with all the modern techniques and methodologies which is
a requisite for its successful completion. The key performance indicators identified in
the case study and project are employee satisfaction and healthy lifestyle which will
state whether the project has been successful in its completion or not (Mahabir and
Pun, 2022).
14
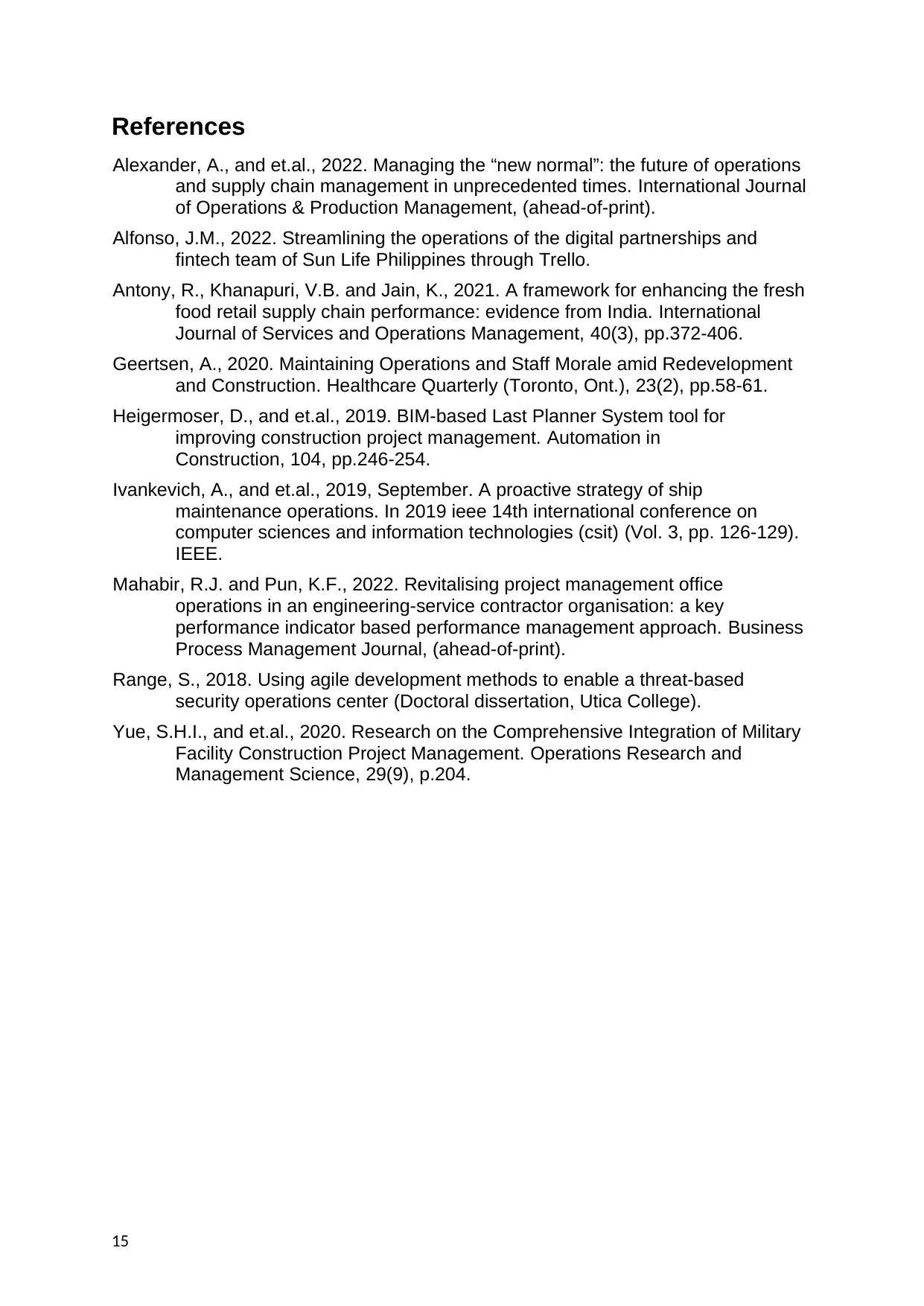
References
Alexander, A., and et.al., 2022. Managing the “new normal”: the future of operations
and supply chain management in unprecedented times. International Journal
of Operations & Production Management, (ahead-of-print).
Alfonso, J.M., 2022. Streamlining the operations of the digital partnerships and
fintech team of Sun Life Philippines through Trello.
Antony, R., Khanapuri, V.B. and Jain, K., 2021. A framework for enhancing the fresh
food retail supply chain performance: evidence from India. International
Journal of Services and Operations Management, 40(3), pp.372-406.
Geertsen, A., 2020. Maintaining Operations and Staff Morale amid Redevelopment
and Construction. Healthcare Quarterly (Toronto, Ont.), 23(2), pp.58-61.
Heigermoser, D., and et.al., 2019. BIM-based Last Planner System tool for
improving construction project management. Automation in
Construction, 104, pp.246-254.
Ivankevich, A., and et.al., 2019, September. A proactive strategy of ship
maintenance operations. In 2019 ieee 14th international conference on
computer sciences and information technologies (csit) (Vol. 3, pp. 126-129).
IEEE.
Mahabir, R.J. and Pun, K.F., 2022. Revitalising project management office
operations in an engineering-service contractor organisation: a key
performance indicator based performance management approach. Business
Process Management Journal, (ahead-of-print).
Range, S., 2018. Using agile development methods to enable a threat-based
security operations center (Doctoral dissertation, Utica College).
Yue, S.H.I., and et.al., 2020. Research on the Comprehensive Integration of Military
Facility Construction Project Management. Operations Research and
Management Science, 29(9), p.204.
15
Alexander, A., and et.al., 2022. Managing the “new normal”: the future of operations
and supply chain management in unprecedented times. International Journal
of Operations & Production Management, (ahead-of-print).
Alfonso, J.M., 2022. Streamlining the operations of the digital partnerships and
fintech team of Sun Life Philippines through Trello.
Antony, R., Khanapuri, V.B. and Jain, K., 2021. A framework for enhancing the fresh
food retail supply chain performance: evidence from India. International
Journal of Services and Operations Management, 40(3), pp.372-406.
Geertsen, A., 2020. Maintaining Operations and Staff Morale amid Redevelopment
and Construction. Healthcare Quarterly (Toronto, Ont.), 23(2), pp.58-61.
Heigermoser, D., and et.al., 2019. BIM-based Last Planner System tool for
improving construction project management. Automation in
Construction, 104, pp.246-254.
Ivankevich, A., and et.al., 2019, September. A proactive strategy of ship
maintenance operations. In 2019 ieee 14th international conference on
computer sciences and information technologies (csit) (Vol. 3, pp. 126-129).
IEEE.
Mahabir, R.J. and Pun, K.F., 2022. Revitalising project management office
operations in an engineering-service contractor organisation: a key
performance indicator based performance management approach. Business
Process Management Journal, (ahead-of-print).
Range, S., 2018. Using agile development methods to enable a threat-based
security operations center (Doctoral dissertation, Utica College).
Yue, S.H.I., and et.al., 2020. Research on the Comprehensive Integration of Military
Facility Construction Project Management. Operations Research and
Management Science, 29(9), p.204.
15
1 out of 15
Related Documents

Your All-in-One AI-Powered Toolkit for Academic Success.
+13062052269
info@desklib.com
Available 24*7 on WhatsApp / Email
Unlock your academic potential
© 2024 | Zucol Services PVT LTD | All rights reserved.