Friction Welding in Production
The assignment is about the process of friction welding, its applications in joining dissimilar materials, and the parameters involved in the welding process.
32 Pages6570 Words493 Views
Added on 2023-01-17
About This Document
This document provides an overview of friction welding in production. It discusses the working principle, advantages, disadvantages, and industrial applications of friction welding. The document also includes a feasibility study and types of friction welding. The content is relevant to the course ENC0R 4010 - Research Project 1 at the Master of Engineering Technology program.
Friction Welding in Production
The assignment is about the process of friction welding, its applications in joining dissimilar materials, and the parameters involved in the welding process.
Added on 2023-01-17
ShareRelated Documents
Master of Engineering technology
Student ID 30340364 Student Name Karan Saggu
Assignment Title Friction Welding in Production
Feedback / Assessment:
LECTURER’S SIGNATURE: DATE:
RESEARCH PROPOSAL
Course Code ENCOR 4010 Course Name Research Project 1
Date Submitted Lecturer’s Name Dr Ibrahim A Sultan
Tutor’s Name
Student ID 30340364 Student Name Karan Saggu
Assignment Title Friction Welding in Production
Feedback / Assessment:
LECTURER’S SIGNATURE: DATE:
RESEARCH PROPOSAL
Course Code ENCOR 4010 Course Name Research Project 1
Date Submitted Lecturer’s Name Dr Ibrahim A Sultan
Tutor’s Name
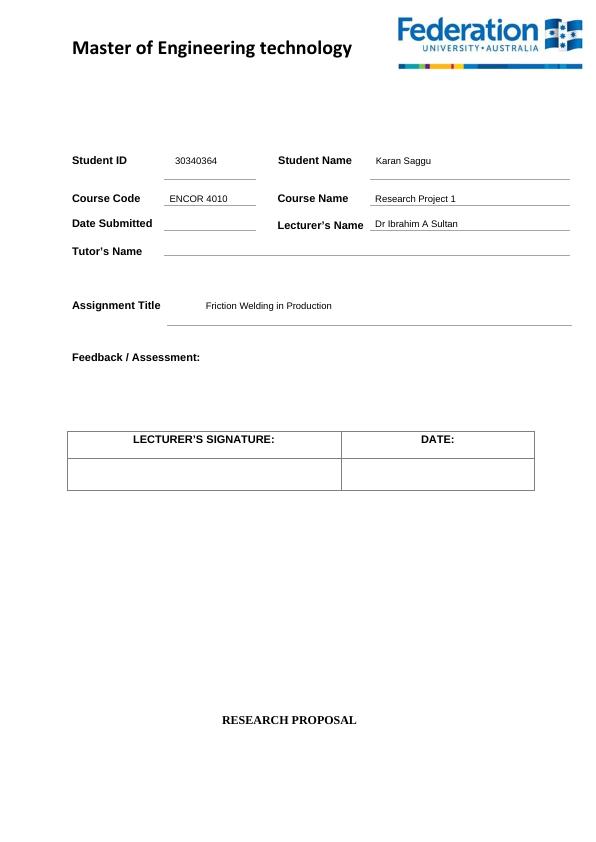
FRICTION WELDING 2
1 Table of Contents
2. Background...................................................................................................................................4
3. working Principle..........................................................................................................................4
5. Advantages and disadvantages of friction welding......................................................................5
5.1. Advantages of friction welding..................................................................................................5
5.2. Disadvantages of friction welding..............................................................................................6
6. Industrial applications of friction welding....................................................................................7
6.1. Marine and shipbuilding industries..........................................................................................7
6.2. Aerospace industry...................................................................................................................8
6.3. Railway industry........................................................................................................................8
6.4. Other industries include............................................................................................................8
7. Types of friction welding..............................................................................................................9
7.1. Inertial friction welding..............................................................................................................9
7.2. Continuous induction method................................................................................................10
7.3. Linear friction welding.............................................................................................................10
7.3.1. Process parameters.............................................................................................................13
7.3.2. Numerical simulation of inertia friction welding process of gh4169 alloy.........................14
7.4. Friction surfacing.....................................................................................................................18
9. Timeline.......................................................................................................................................22
10. Proposal metrics......................................................................................................................23
10.1. Scientific and Technical Merit..............................................................................................23
11. Conclusion...............................................................................................................................28
12. References...............................................................................................................................29
Table of Figures
Figure 1 .............................................................................................................................................................................................11
Figure 2 .............................................................................................................................................................................................12
Figure 3 .............................................................................................................................................................................................13
Figure 4 ..............................................................................................................................................................................................14
Table 1 ............................................................................................................................................................22
Table 2............................................................................................................................................................23
Table 3 ............................................................................................................................................................26
Table 4 ............................................................................................................................................................27
1 Table of Contents
2. Background...................................................................................................................................4
3. working Principle..........................................................................................................................4
5. Advantages and disadvantages of friction welding......................................................................5
5.1. Advantages of friction welding..................................................................................................5
5.2. Disadvantages of friction welding..............................................................................................6
6. Industrial applications of friction welding....................................................................................7
6.1. Marine and shipbuilding industries..........................................................................................7
6.2. Aerospace industry...................................................................................................................8
6.3. Railway industry........................................................................................................................8
6.4. Other industries include............................................................................................................8
7. Types of friction welding..............................................................................................................9
7.1. Inertial friction welding..............................................................................................................9
7.2. Continuous induction method................................................................................................10
7.3. Linear friction welding.............................................................................................................10
7.3.1. Process parameters.............................................................................................................13
7.3.2. Numerical simulation of inertia friction welding process of gh4169 alloy.........................14
7.4. Friction surfacing.....................................................................................................................18
9. Timeline.......................................................................................................................................22
10. Proposal metrics......................................................................................................................23
10.1. Scientific and Technical Merit..............................................................................................23
11. Conclusion...............................................................................................................................28
12. References...............................................................................................................................29
Table of Figures
Figure 1 .............................................................................................................................................................................................11
Figure 2 .............................................................................................................................................................................................12
Figure 3 .............................................................................................................................................................................................13
Figure 4 ..............................................................................................................................................................................................14
Table 1 ............................................................................................................................................................22
Table 2............................................................................................................................................................23
Table 3 ............................................................................................................................................................26
Table 4 ............................................................................................................................................................27
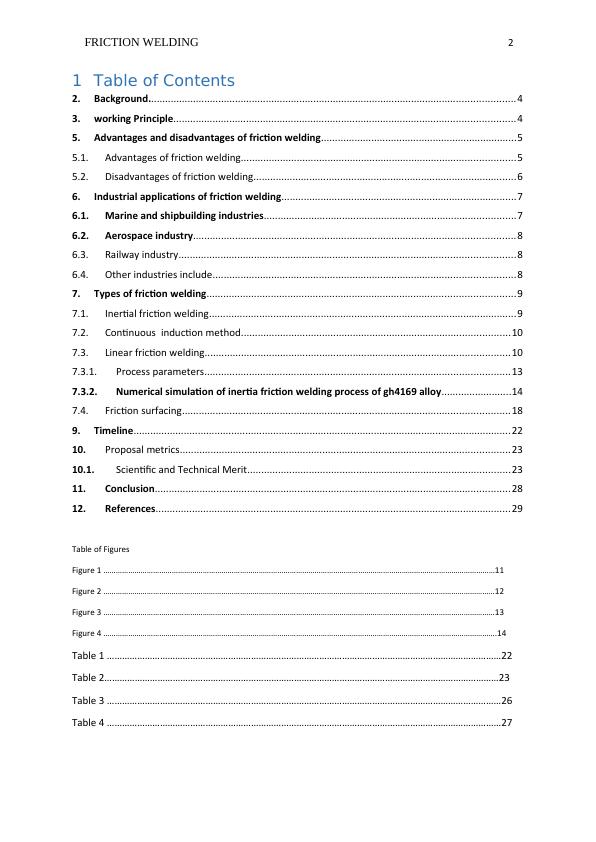
FRICTION WELDING 3
Problem statement
The process of friction welding is augmenting rapidly in the amalgamation of dissimilar
materials within a less time and joints free of defection (Sahin, 2009). For instance,
nowadays, joining of dissimilar materials such as ferritic stainless steel and copper id
commonly applied for numerous industrial processes such as nuclear, automotive, electrical,
and chemical industries. While in a solid state, materials are continuously rubbed together
using friction welding and in the process, a lot of heat is generated between their interfaces.
When enough energy is produced, the rotation ceases and a comprehensive or an upset force
is provided in order to amalgamate the joint and produce a bond in solid state (Reddy & Rao,
2009). Some friction welding parameters such as the speed of rotation, comprehensive
pressure, friction pressure, and burn-off length apparently affect the strength of the resultant
joint. Thus, it is prudent to investigate on this impact to ascertain duration of the material
formed as well the safety of the users.
Problem statement
The process of friction welding is augmenting rapidly in the amalgamation of dissimilar
materials within a less time and joints free of defection (Sahin, 2009). For instance,
nowadays, joining of dissimilar materials such as ferritic stainless steel and copper id
commonly applied for numerous industrial processes such as nuclear, automotive, electrical,
and chemical industries. While in a solid state, materials are continuously rubbed together
using friction welding and in the process, a lot of heat is generated between their interfaces.
When enough energy is produced, the rotation ceases and a comprehensive or an upset force
is provided in order to amalgamate the joint and produce a bond in solid state (Reddy & Rao,
2009). Some friction welding parameters such as the speed of rotation, comprehensive
pressure, friction pressure, and burn-off length apparently affect the strength of the resultant
joint. Thus, it is prudent to investigate on this impact to ascertain duration of the material
formed as well the safety of the users.
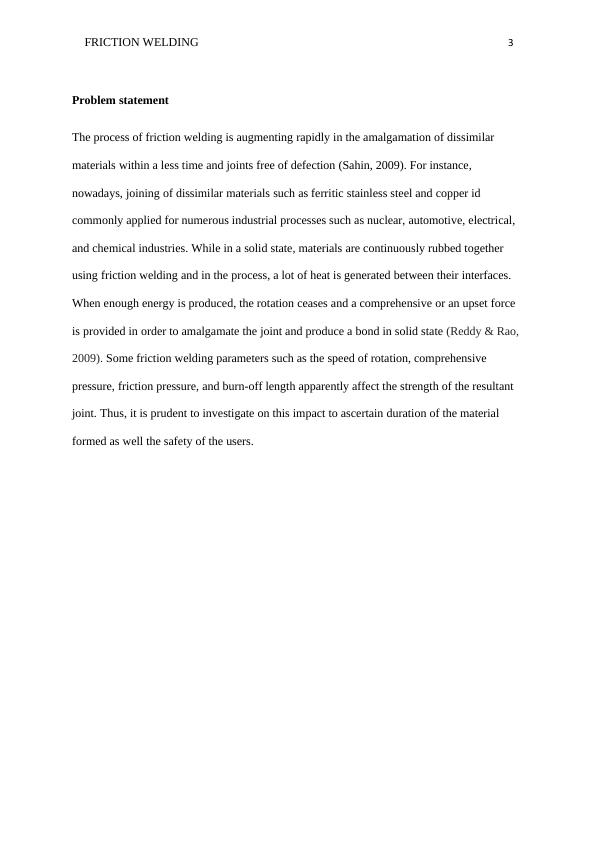
FRICTION WELDING 4
Abstract
Friction welding is a solid state welding technique with high automation and good quality.it
has been broadly applied in various industries especially in aerospace and automobile
industries. Because of high level of automation and less process parameters, the inertial
friction is common in many fields. There are many merits which are associated with the use
of friction welding in production such as, it is fast method of welding as compared to other
welding techniques. Even though there are many benefits which are associated with it, there
are also some drawbacks such as, is mainly used in round bars which have the same cross
section.
Abstract
Friction welding is a solid state welding technique with high automation and good quality.it
has been broadly applied in various industries especially in aerospace and automobile
industries. Because of high level of automation and less process parameters, the inertial
friction is common in many fields. There are many merits which are associated with the use
of friction welding in production such as, it is fast method of welding as compared to other
welding techniques. Even though there are many benefits which are associated with it, there
are also some drawbacks such as, is mainly used in round bars which have the same cross
section.
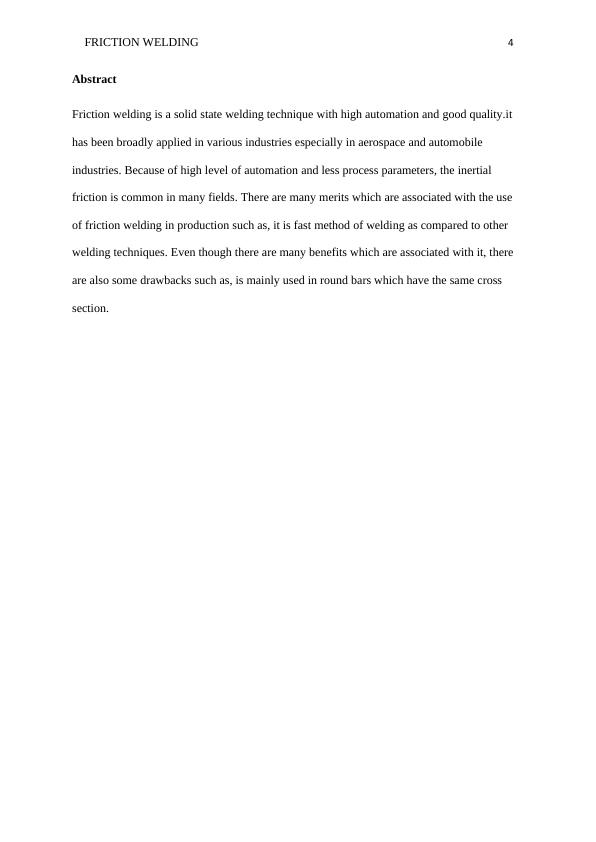
FRICTION WELDING 5
1. Introduction
Friction welding is defined as Solid state or a simply forge whereby the welding process
occurs between two mating surfaces of metals through the application of friction between
them. The welding technique has been adopted by well-known international companies in in
America and Europe such as American Manufacturing Foundry and Rockwell international to
manufacture their machines.
Friction welding is considered to be very essential in the production industry, by adopting
this welding method the high overhead costs which the companies will undergo to have this
technique in place will be balanced with the high production rates and lower labour
requirements.
The friction welding technique has many dimensional and hardware which are easily
adjustable making it to be very significant in the production of very small parts and
components. There are many industrial applications where friction welding can be applied
such as the machine and spare part production.
2. Background.
The process of friction welding was first discovered in the late 1920s, however during
that time there was very little data which was recorded about its use. A detailed discussion
about friction welding was recorded in the USSR in the early 1960s, but that time it was
described as ‘very doubtful, as a production technique due to the challenges in generating
reciprocating linear motion. The fist well-structured industrial research into friction welding
took place in the 1980s at TWI, UK, while the first ever research academic to be to be
recorded took place at Ohio State University, and the University of Bristol, UK.
1. Introduction
Friction welding is defined as Solid state or a simply forge whereby the welding process
occurs between two mating surfaces of metals through the application of friction between
them. The welding technique has been adopted by well-known international companies in in
America and Europe such as American Manufacturing Foundry and Rockwell international to
manufacture their machines.
Friction welding is considered to be very essential in the production industry, by adopting
this welding method the high overhead costs which the companies will undergo to have this
technique in place will be balanced with the high production rates and lower labour
requirements.
The friction welding technique has many dimensional and hardware which are easily
adjustable making it to be very significant in the production of very small parts and
components. There are many industrial applications where friction welding can be applied
such as the machine and spare part production.
2. Background.
The process of friction welding was first discovered in the late 1920s, however during
that time there was very little data which was recorded about its use. A detailed discussion
about friction welding was recorded in the USSR in the early 1960s, but that time it was
described as ‘very doubtful, as a production technique due to the challenges in generating
reciprocating linear motion. The fist well-structured industrial research into friction welding
took place in the 1980s at TWI, UK, while the first ever research academic to be to be
recorded took place at Ohio State University, and the University of Bristol, UK.
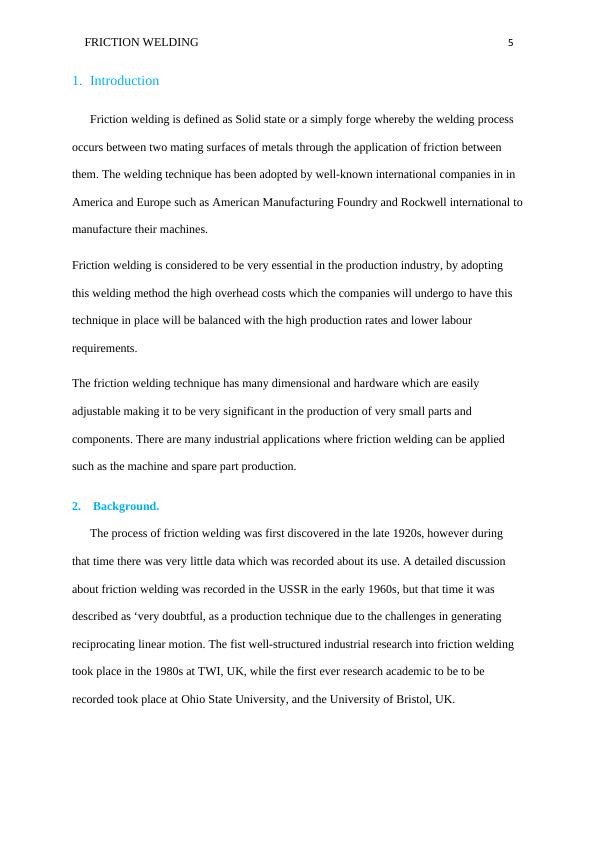
FRICTION WELDING 6
3. Working Principle
The friction welding technique works on the basic principle of friction. In the process of
welding, friction is used to create heat at the interfaces surfaces (Anderson, 2016). The heat is
used to join the two work pieces through the application of the external pressure at the work
pieces surfaces. In friction welding, the friction is applied until the plastic forming
temperature is reached which is usually900-1300oc for steel. After the heating process,
pressure which is uniformly increasing is applied to both of the metal work pieces until they
make a permanent joint.
4. Feasibility Study
This study evaluates the feasibility of friction welding for production at the
Federation University of Australia. As the project is new, it consumes much
resource, therefore it is prudent to do feasibility check. This illustrates that the
research is workable as well giving benefits to this research. The research will
be conducted in the Laboratory and Friction Welding Australia which is a
specialist in this type of technology since 2012. Thus, the research is technically
feasible.
A compressive study has been done for financial feasibility to ascertain it.
(Overfield, 2010) The total cost was analysed. The financial merits outweighed
the financial demerits. The benefits were analysed to gage the study whether is
viable and significant in terms of financial aspects. It was proved that, financial
feasibility of the research is important within the reach.
3. Working Principle
The friction welding technique works on the basic principle of friction. In the process of
welding, friction is used to create heat at the interfaces surfaces (Anderson, 2016). The heat is
used to join the two work pieces through the application of the external pressure at the work
pieces surfaces. In friction welding, the friction is applied until the plastic forming
temperature is reached which is usually900-1300oc for steel. After the heating process,
pressure which is uniformly increasing is applied to both of the metal work pieces until they
make a permanent joint.
4. Feasibility Study
This study evaluates the feasibility of friction welding for production at the
Federation University of Australia. As the project is new, it consumes much
resource, therefore it is prudent to do feasibility check. This illustrates that the
research is workable as well giving benefits to this research. The research will
be conducted in the Laboratory and Friction Welding Australia which is a
specialist in this type of technology since 2012. Thus, the research is technically
feasible.
A compressive study has been done for financial feasibility to ascertain it.
(Overfield, 2010) The total cost was analysed. The financial merits outweighed
the financial demerits. The benefits were analysed to gage the study whether is
viable and significant in terms of financial aspects. It was proved that, financial
feasibility of the research is important within the reach.
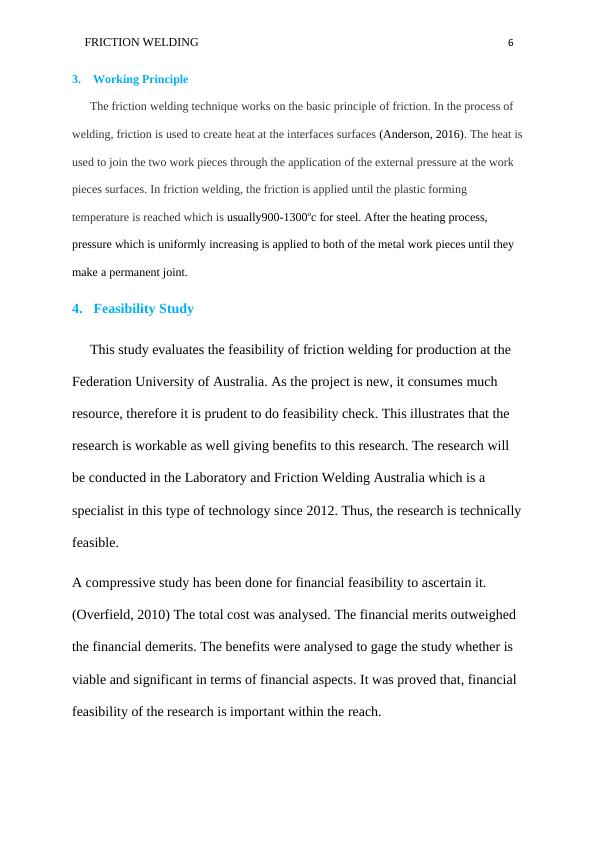
FRICTION WELDING 7
5. Advantages and disadvantages of friction welding
5.1. Advantages of friction welding
There are many merits which are associated with the use of friction we in production.
(Mahadzir, 2016)Some of the merits include:
It’s easier and convenient to join metals which are not similar and some of which are
considered to be unweldable or incompatible.
Friction welding is very fast method of welding as compared to other welding
techniques (Granjon, 2014).
Due to their versatility the friction welders are able to join a wide range of materials,
shapes and sizes without any challenge.
In this friction welding joint preparation is not of great importance since, saw cut,
machine and even the sheared surfaces are weldable.
The resulting joints are of forged quality, with up to 100% butt joint weld through the
contact area.
Human errors are eliminated by machine controlled process, and the quality of the
weld is independent of the operator skill.
It is environmental friendly as there is no objectionable fumes, gases or smoke that
are generated which needs to be exhausted.
In friction welding there are no consumable that are required, no filler material, flux
or shielding gases.
The power requirements for friction welding as low as 20% of that which is required
for conventional welding processes.
Since there is no melting which occurs there is no solidification defects such as gas
porosity, slag or segregation inclusions.
5. Advantages and disadvantages of friction welding
5.1. Advantages of friction welding
There are many merits which are associated with the use of friction we in production.
(Mahadzir, 2016)Some of the merits include:
It’s easier and convenient to join metals which are not similar and some of which are
considered to be unweldable or incompatible.
Friction welding is very fast method of welding as compared to other welding
techniques (Granjon, 2014).
Due to their versatility the friction welders are able to join a wide range of materials,
shapes and sizes without any challenge.
In this friction welding joint preparation is not of great importance since, saw cut,
machine and even the sheared surfaces are weldable.
The resulting joints are of forged quality, with up to 100% butt joint weld through the
contact area.
Human errors are eliminated by machine controlled process, and the quality of the
weld is independent of the operator skill.
It is environmental friendly as there is no objectionable fumes, gases or smoke that
are generated which needs to be exhausted.
In friction welding there are no consumable that are required, no filler material, flux
or shielding gases.
The power requirements for friction welding as low as 20% of that which is required
for conventional welding processes.
Since there is no melting which occurs there is no solidification defects such as gas
porosity, slag or segregation inclusions.
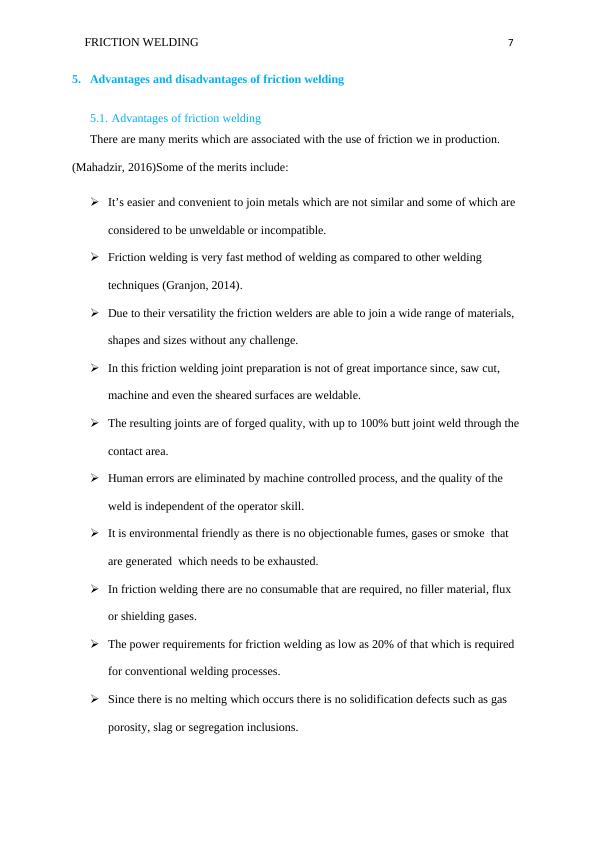
FRICTION WELDING 8
5.2. Disadvantages of friction welding
Even though there are many benefits which are associated with friction welding it has
also some drawbacks such as: (Benini, 2011)
This technique of welding is mainly used in round bars which have the same cross
section. Due to that the bars which are not of the same cross section cannot be welded. In
some industries welding of metals which are not round in shape is very common the
application pf friction welding for such cases is limited (Sahin, 2016).
There are exist holes left when the tools are withdrawn. Most of the metal bars which are
to be joined together are held by strong tools which drills holes through them.
Friction welding requires extensive clamping
Needs special backing support
The cost of setting up a friction welding facility are very high. The equipment and
machines which are used for friction welding are very expensive to acquire. This makes a
lot of people to move to the convention welding which is much easier and cheaper.
The design of the joints is very limited.
It involves critical preparations of work pieces (Welding InstituteElsevier Science &
Technology, 2010).
6. Industrial applications of friction welding
Many production industries all over the world are experiencing the high costs of energy
due to the amount of energy which is consumed during the production process’s adoption of
friction welding can greatly assist in solving this challenges (Yilbas, 2016). The friction
welding has been applied in various industrial applications as discussed below:
5.2. Disadvantages of friction welding
Even though there are many benefits which are associated with friction welding it has
also some drawbacks such as: (Benini, 2011)
This technique of welding is mainly used in round bars which have the same cross
section. Due to that the bars which are not of the same cross section cannot be welded. In
some industries welding of metals which are not round in shape is very common the
application pf friction welding for such cases is limited (Sahin, 2016).
There are exist holes left when the tools are withdrawn. Most of the metal bars which are
to be joined together are held by strong tools which drills holes through them.
Friction welding requires extensive clamping
Needs special backing support
The cost of setting up a friction welding facility are very high. The equipment and
machines which are used for friction welding are very expensive to acquire. This makes a
lot of people to move to the convention welding which is much easier and cheaper.
The design of the joints is very limited.
It involves critical preparations of work pieces (Welding InstituteElsevier Science &
Technology, 2010).
6. Industrial applications of friction welding
Many production industries all over the world are experiencing the high costs of energy
due to the amount of energy which is consumed during the production process’s adoption of
friction welding can greatly assist in solving this challenges (Yilbas, 2016). The friction
welding has been applied in various industrial applications as discussed below:
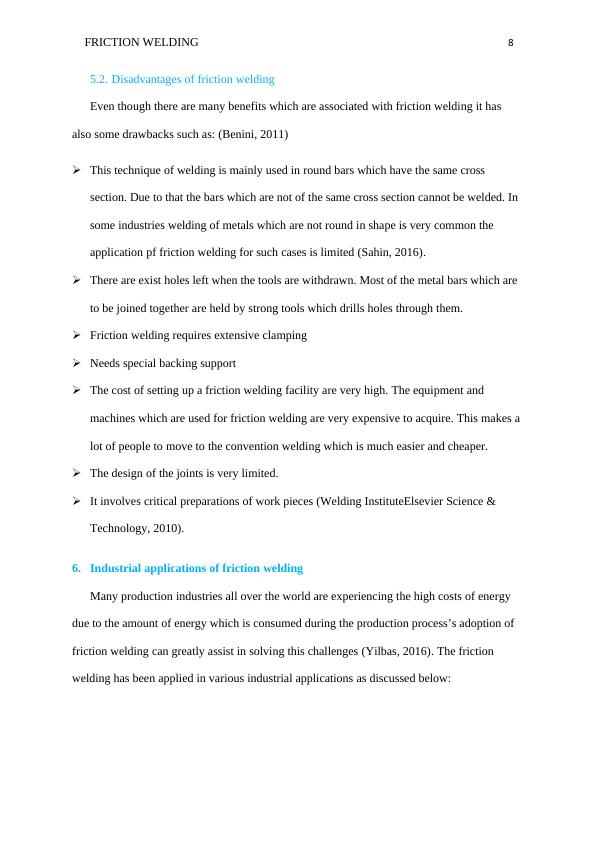
End of preview
Want to access all the pages? Upload your documents or become a member.
Related Documents
Friction Welding: Working Principle, Advantages, Disadvantages, and Industrial Applicationslg...
|20
|3709
|159
Thermal Analysis of Friction Welding using Abaqus CAE Softwarelg...
|58
|12052
|352