School of Engineering: University of Ulster Ceramics Report (MEC103)
VerifiedAdded on 2022/03/19
|10
|3411
|27
Report
AI Summary
This report provides a detailed overview of ceramic materials, encompassing their structure, mechanical properties, and various manufacturing processes. It begins with an introduction to ceramics, differentiating them from other materials and highlighting their common applications like clay product...
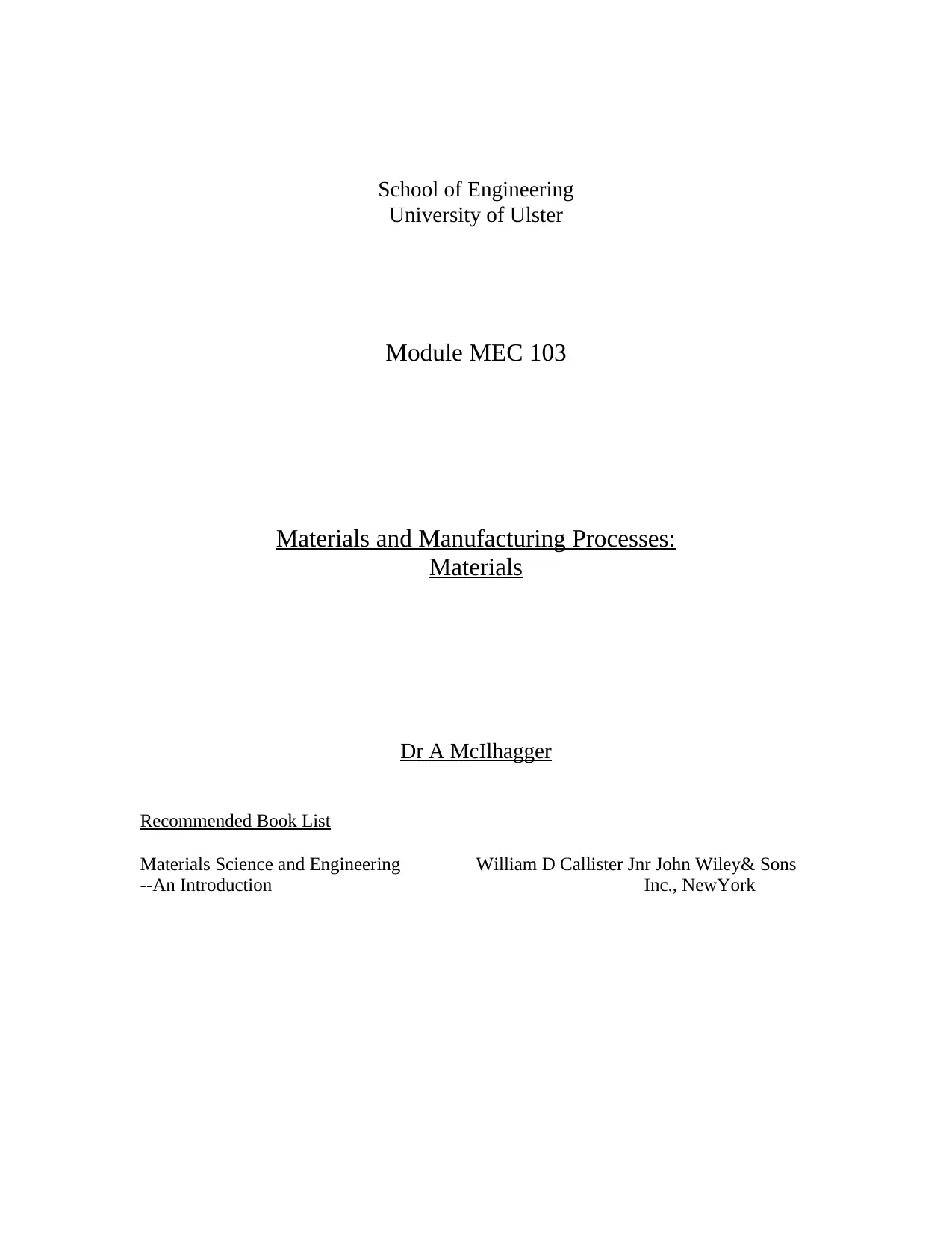
School of Engineering
University of Ulster
Module MEC 103
Materials and Manufacturing Processes:
Materials
Dr A McIlhagger
Recommended Book List
Materials Science and Engineering William D Callister Jnr John Wiley& Sons
--An Introduction Inc., NewYork
University of Ulster
Module MEC 103
Materials and Manufacturing Processes:
Materials
Dr A McIlhagger
Recommended Book List
Materials Science and Engineering William D Callister Jnr John Wiley& Sons
--An Introduction Inc., NewYork
Paraphrase This Document
Need a fresh take? Get an instant paraphrase of this document with our AI Paraphraser
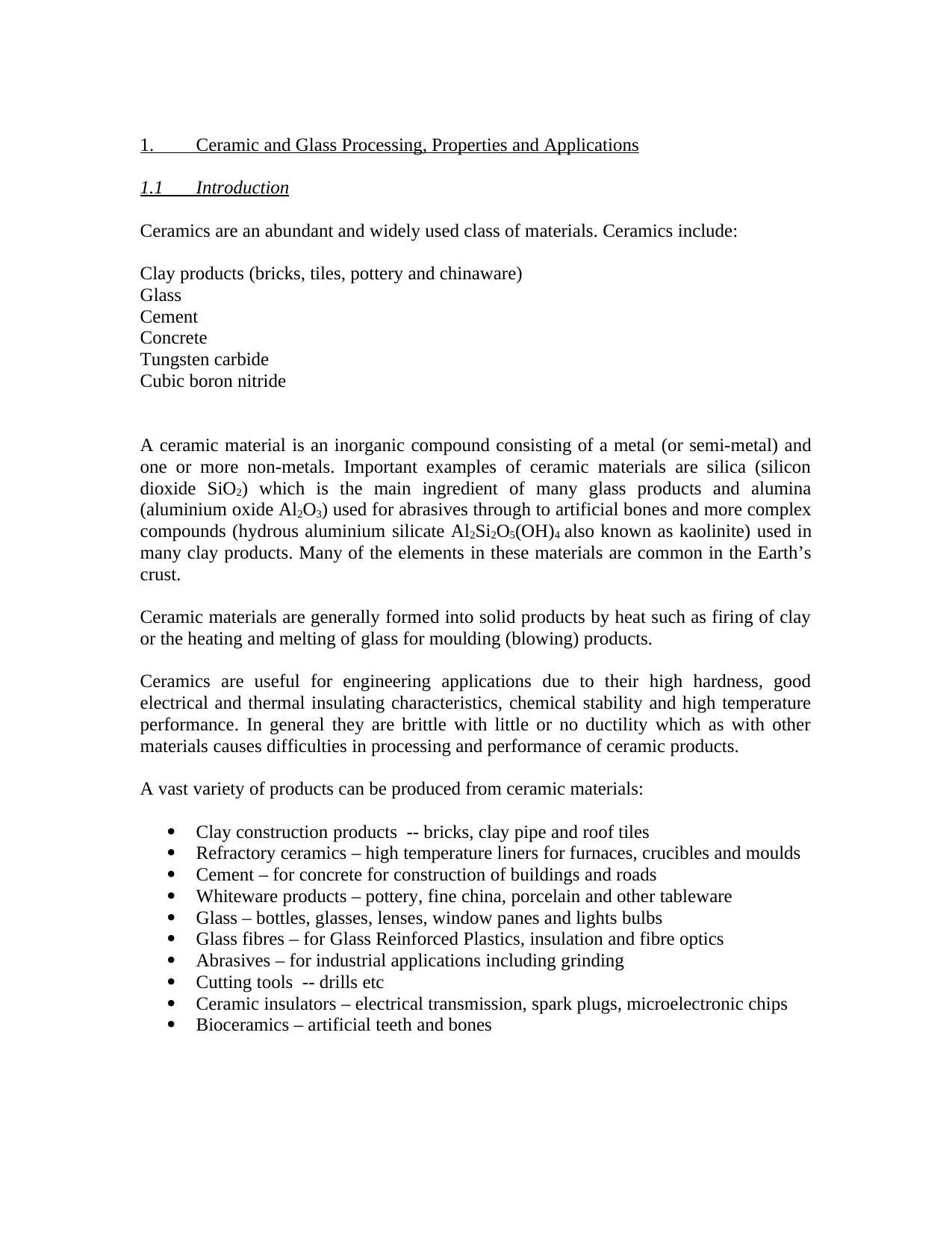
1. Ceramic and Glass Processing, Properties and Applications
1.1 Introduction
Ceramics are an abundant and widely used class of materials. Ceramics include:
Clay products (bricks, tiles, pottery and chinaware)
Glass
Cement
Concrete
Tungsten carbide
Cubic boron nitride
A ceramic material is an inorganic compound consisting of a metal (or semi-metal) and
one or more non-metals. Important examples of ceramic materials are silica (silicon
dioxide SiO2) which is the main ingredient of many glass products and alumina
(aluminium oxide Al2O3) used for abrasives through to artificial bones and more complex
compounds (hydrous aluminium silicate Al2Si2O5(OH)4 also known as kaolinite) used in
many clay products. Many of the elements in these materials are common in the Earth’s
crust.
Ceramic materials are generally formed into solid products by heat such as firing of clay
or the heating and melting of glass for moulding (blowing) products.
Ceramics are useful for engineering applications due to their high hardness, good
electrical and thermal insulating characteristics, chemical stability and high temperature
performance. In general they are brittle with little or no ductility which as with other
materials causes difficulties in processing and performance of ceramic products.
A vast variety of products can be produced from ceramic materials:
Clay construction products -- bricks, clay pipe and roof tiles
Refractory ceramics – high temperature liners for furnaces, crucibles and moulds
Cement – for concrete for construction of buildings and roads
Whiteware products – pottery, fine china, porcelain and other tableware
Glass – bottles, glasses, lenses, window panes and lights bulbs
Glass fibres – for Glass Reinforced Plastics, insulation and fibre optics
Abrasives – for industrial applications including grinding
Cutting tools -- drills etc
Ceramic insulators – electrical transmission, spark plugs, microelectronic chips
Bioceramics – artificial teeth and bones
1.1 Introduction
Ceramics are an abundant and widely used class of materials. Ceramics include:
Clay products (bricks, tiles, pottery and chinaware)
Glass
Cement
Concrete
Tungsten carbide
Cubic boron nitride
A ceramic material is an inorganic compound consisting of a metal (or semi-metal) and
one or more non-metals. Important examples of ceramic materials are silica (silicon
dioxide SiO2) which is the main ingredient of many glass products and alumina
(aluminium oxide Al2O3) used for abrasives through to artificial bones and more complex
compounds (hydrous aluminium silicate Al2Si2O5(OH)4 also known as kaolinite) used in
many clay products. Many of the elements in these materials are common in the Earth’s
crust.
Ceramic materials are generally formed into solid products by heat such as firing of clay
or the heating and melting of glass for moulding (blowing) products.
Ceramics are useful for engineering applications due to their high hardness, good
electrical and thermal insulating characteristics, chemical stability and high temperature
performance. In general they are brittle with little or no ductility which as with other
materials causes difficulties in processing and performance of ceramic products.
A vast variety of products can be produced from ceramic materials:
Clay construction products -- bricks, clay pipe and roof tiles
Refractory ceramics – high temperature liners for furnaces, crucibles and moulds
Cement – for concrete for construction of buildings and roads
Whiteware products – pottery, fine china, porcelain and other tableware
Glass – bottles, glasses, lenses, window panes and lights bulbs
Glass fibres – for Glass Reinforced Plastics, insulation and fibre optics
Abrasives – for industrial applications including grinding
Cutting tools -- drills etc
Ceramic insulators – electrical transmission, spark plugs, microelectronic chips
Bioceramics – artificial teeth and bones
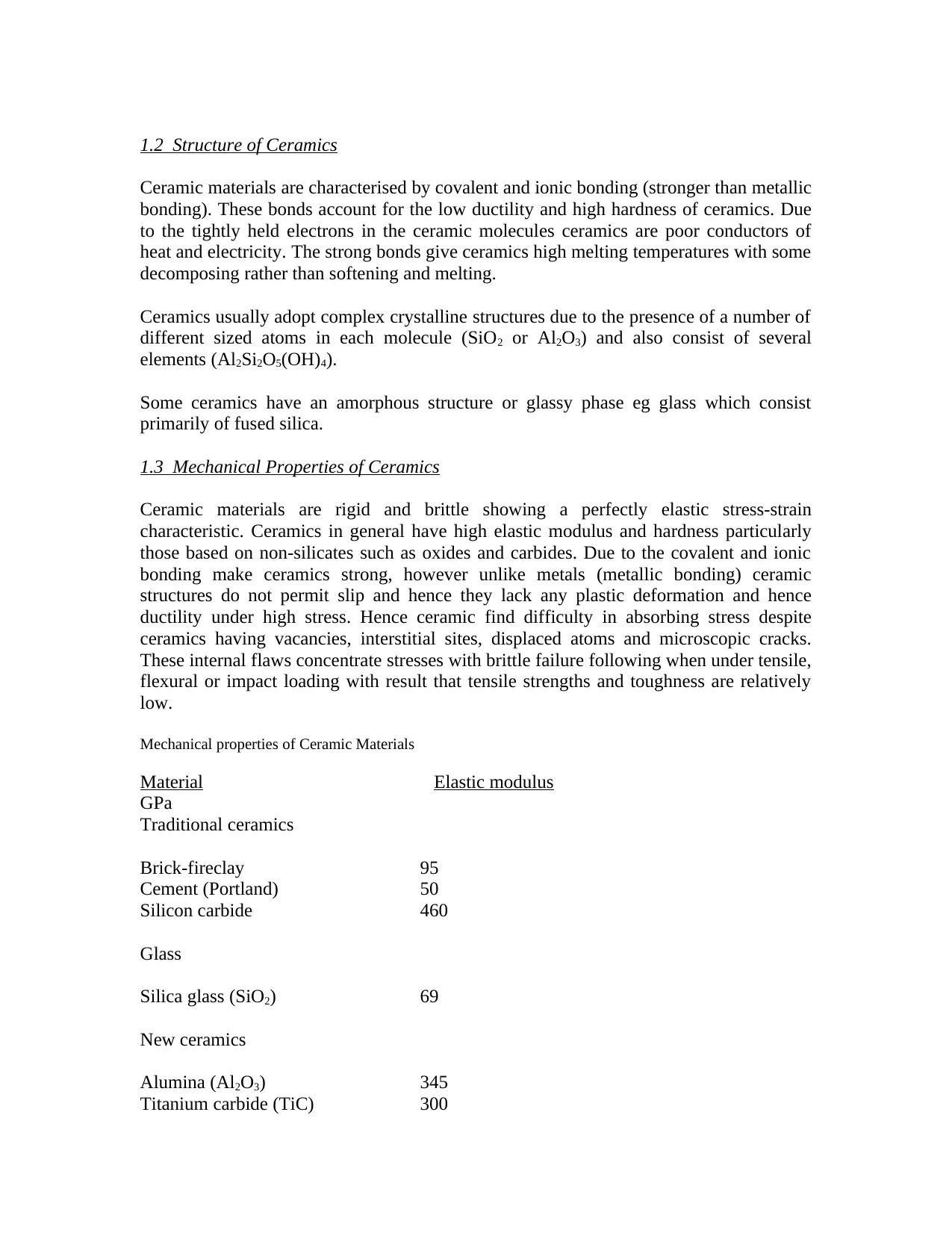
1.2 Structure of Ceramics
Ceramic materials are characterised by covalent and ionic bonding (stronger than metallic
bonding). These bonds account for the low ductility and high hardness of ceramics. Due
to the tightly held electrons in the ceramic molecules ceramics are poor conductors of
heat and electricity. The strong bonds give ceramics high melting temperatures with some
decomposing rather than softening and melting.
Ceramics usually adopt complex crystalline structures due to the presence of a number of
different sized atoms in each molecule (SiO2 or Al2O3) and also consist of several
elements (Al2Si2O5(OH)4).
Some ceramics have an amorphous structure or glassy phase eg glass which consist
primarily of fused silica.
1.3 Mechanical Properties of Ceramics
Ceramic materials are rigid and brittle showing a perfectly elastic stress-strain
characteristic. Ceramics in general have high elastic modulus and hardness particularly
those based on non-silicates such as oxides and carbides. Due to the covalent and ionic
bonding make ceramics strong, however unlike metals (metallic bonding) ceramic
structures do not permit slip and hence they lack any plastic deformation and hence
ductility under high stress. Hence ceramic find difficulty in absorbing stress despite
ceramics having vacancies, interstitial sites, displaced atoms and microscopic cracks.
These internal flaws concentrate stresses with brittle failure following when under tensile,
flexural or impact loading with result that tensile strengths and toughness are relatively
low.
Mechanical properties of Ceramic Materials
Material Elastic modulus
GPa
Traditional ceramics
Brick-fireclay 95
Cement (Portland) 50
Silicon carbide 460
Glass
Silica glass (SiO2) 69
New ceramics
Alumina (Al2O3) 345
Titanium carbide (TiC) 300
Ceramic materials are characterised by covalent and ionic bonding (stronger than metallic
bonding). These bonds account for the low ductility and high hardness of ceramics. Due
to the tightly held electrons in the ceramic molecules ceramics are poor conductors of
heat and electricity. The strong bonds give ceramics high melting temperatures with some
decomposing rather than softening and melting.
Ceramics usually adopt complex crystalline structures due to the presence of a number of
different sized atoms in each molecule (SiO2 or Al2O3) and also consist of several
elements (Al2Si2O5(OH)4).
Some ceramics have an amorphous structure or glassy phase eg glass which consist
primarily of fused silica.
1.3 Mechanical Properties of Ceramics
Ceramic materials are rigid and brittle showing a perfectly elastic stress-strain
characteristic. Ceramics in general have high elastic modulus and hardness particularly
those based on non-silicates such as oxides and carbides. Due to the covalent and ionic
bonding make ceramics strong, however unlike metals (metallic bonding) ceramic
structures do not permit slip and hence they lack any plastic deformation and hence
ductility under high stress. Hence ceramic find difficulty in absorbing stress despite
ceramics having vacancies, interstitial sites, displaced atoms and microscopic cracks.
These internal flaws concentrate stresses with brittle failure following when under tensile,
flexural or impact loading with result that tensile strengths and toughness are relatively
low.
Mechanical properties of Ceramic Materials
Material Elastic modulus
GPa
Traditional ceramics
Brick-fireclay 95
Cement (Portland) 50
Silicon carbide 460
Glass
Silica glass (SiO2) 69
New ceramics
Alumina (Al2O3) 345
Titanium carbide (TiC) 300
⊘ This is a preview!⊘
Do you want full access?
Subscribe today to unlock all pages.

Trusted by 1+ million students worldwide
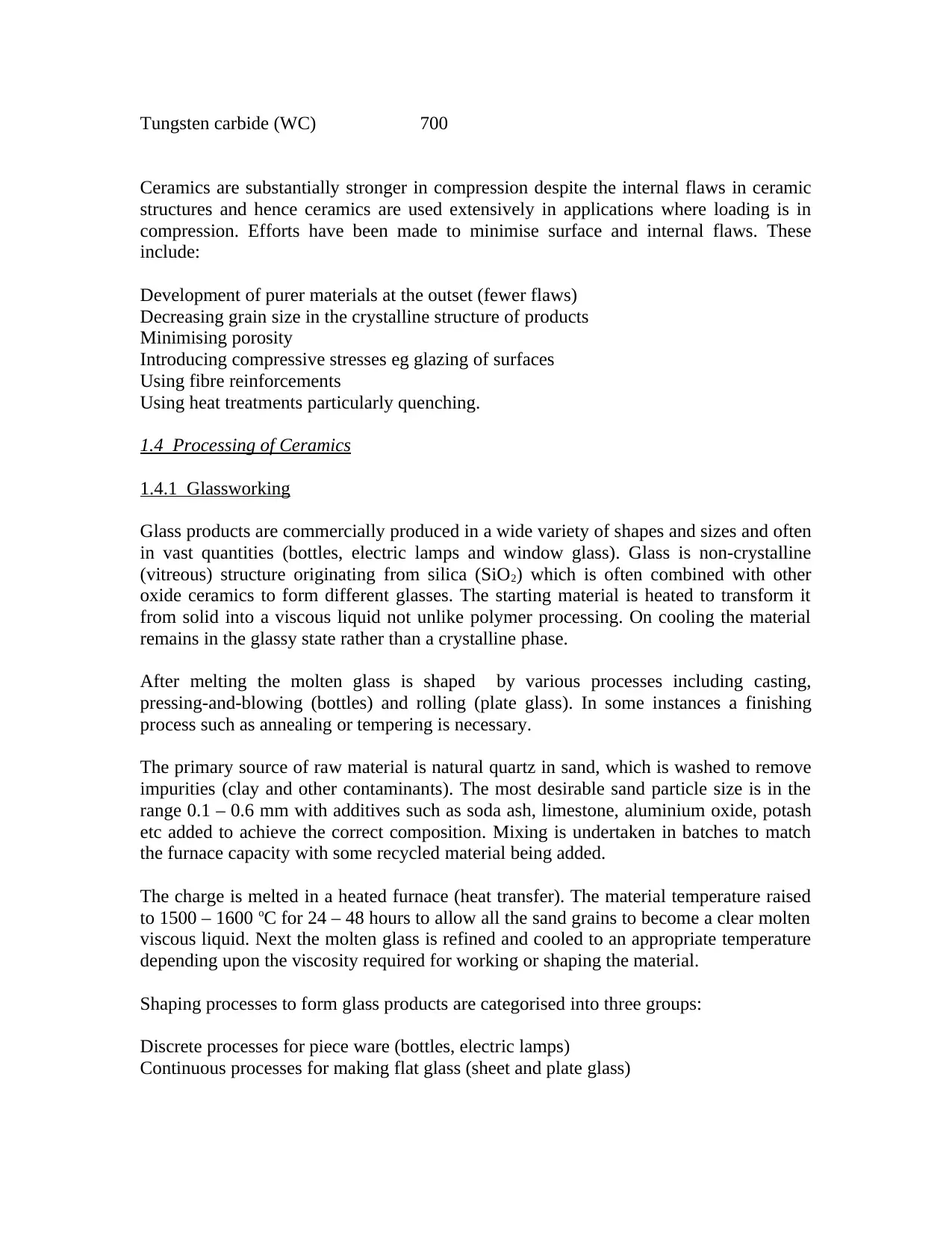
Tungsten carbide (WC) 700
Ceramics are substantially stronger in compression despite the internal flaws in ceramic
structures and hence ceramics are used extensively in applications where loading is in
compression. Efforts have been made to minimise surface and internal flaws. These
include:
Development of purer materials at the outset (fewer flaws)
Decreasing grain size in the crystalline structure of products
Minimising porosity
Introducing compressive stresses eg glazing of surfaces
Using fibre reinforcements
Using heat treatments particularly quenching.
1.4 Processing of Ceramics
1.4.1 Glassworking
Glass products are commercially produced in a wide variety of shapes and sizes and often
in vast quantities (bottles, electric lamps and window glass). Glass is non-crystalline
(vitreous) structure originating from silica (SiO2) which is often combined with other
oxide ceramics to form different glasses. The starting material is heated to transform it
from solid into a viscous liquid not unlike polymer processing. On cooling the material
remains in the glassy state rather than a crystalline phase.
After melting the molten glass is shaped by various processes including casting,
pressing-and-blowing (bottles) and rolling (plate glass). In some instances a finishing
process such as annealing or tempering is necessary.
The primary source of raw material is natural quartz in sand, which is washed to remove
impurities (clay and other contaminants). The most desirable sand particle size is in the
range 0.1 – 0.6 mm with additives such as soda ash, limestone, aluminium oxide, potash
etc added to achieve the correct composition. Mixing is undertaken in batches to match
the furnace capacity with some recycled material being added.
The charge is melted in a heated furnace (heat transfer). The material temperature raised
to 1500 – 1600 oC for 24 – 48 hours to allow all the sand grains to become a clear molten
viscous liquid. Next the molten glass is refined and cooled to an appropriate temperature
depending upon the viscosity required for working or shaping the material.
Shaping processes to form glass products are categorised into three groups:
Discrete processes for piece ware (bottles, electric lamps)
Continuous processes for making flat glass (sheet and plate glass)
Ceramics are substantially stronger in compression despite the internal flaws in ceramic
structures and hence ceramics are used extensively in applications where loading is in
compression. Efforts have been made to minimise surface and internal flaws. These
include:
Development of purer materials at the outset (fewer flaws)
Decreasing grain size in the crystalline structure of products
Minimising porosity
Introducing compressive stresses eg glazing of surfaces
Using fibre reinforcements
Using heat treatments particularly quenching.
1.4 Processing of Ceramics
1.4.1 Glassworking
Glass products are commercially produced in a wide variety of shapes and sizes and often
in vast quantities (bottles, electric lamps and window glass). Glass is non-crystalline
(vitreous) structure originating from silica (SiO2) which is often combined with other
oxide ceramics to form different glasses. The starting material is heated to transform it
from solid into a viscous liquid not unlike polymer processing. On cooling the material
remains in the glassy state rather than a crystalline phase.
After melting the molten glass is shaped by various processes including casting,
pressing-and-blowing (bottles) and rolling (plate glass). In some instances a finishing
process such as annealing or tempering is necessary.
The primary source of raw material is natural quartz in sand, which is washed to remove
impurities (clay and other contaminants). The most desirable sand particle size is in the
range 0.1 – 0.6 mm with additives such as soda ash, limestone, aluminium oxide, potash
etc added to achieve the correct composition. Mixing is undertaken in batches to match
the furnace capacity with some recycled material being added.
The charge is melted in a heated furnace (heat transfer). The material temperature raised
to 1500 – 1600 oC for 24 – 48 hours to allow all the sand grains to become a clear molten
viscous liquid. Next the molten glass is refined and cooled to an appropriate temperature
depending upon the viscosity required for working or shaping the material.
Shaping processes to form glass products are categorised into three groups:
Discrete processes for piece ware (bottles, electric lamps)
Continuous processes for making flat glass (sheet and plate glass)
Paraphrase This Document
Need a fresh take? Get an instant paraphrase of this document with our AI Paraphraser
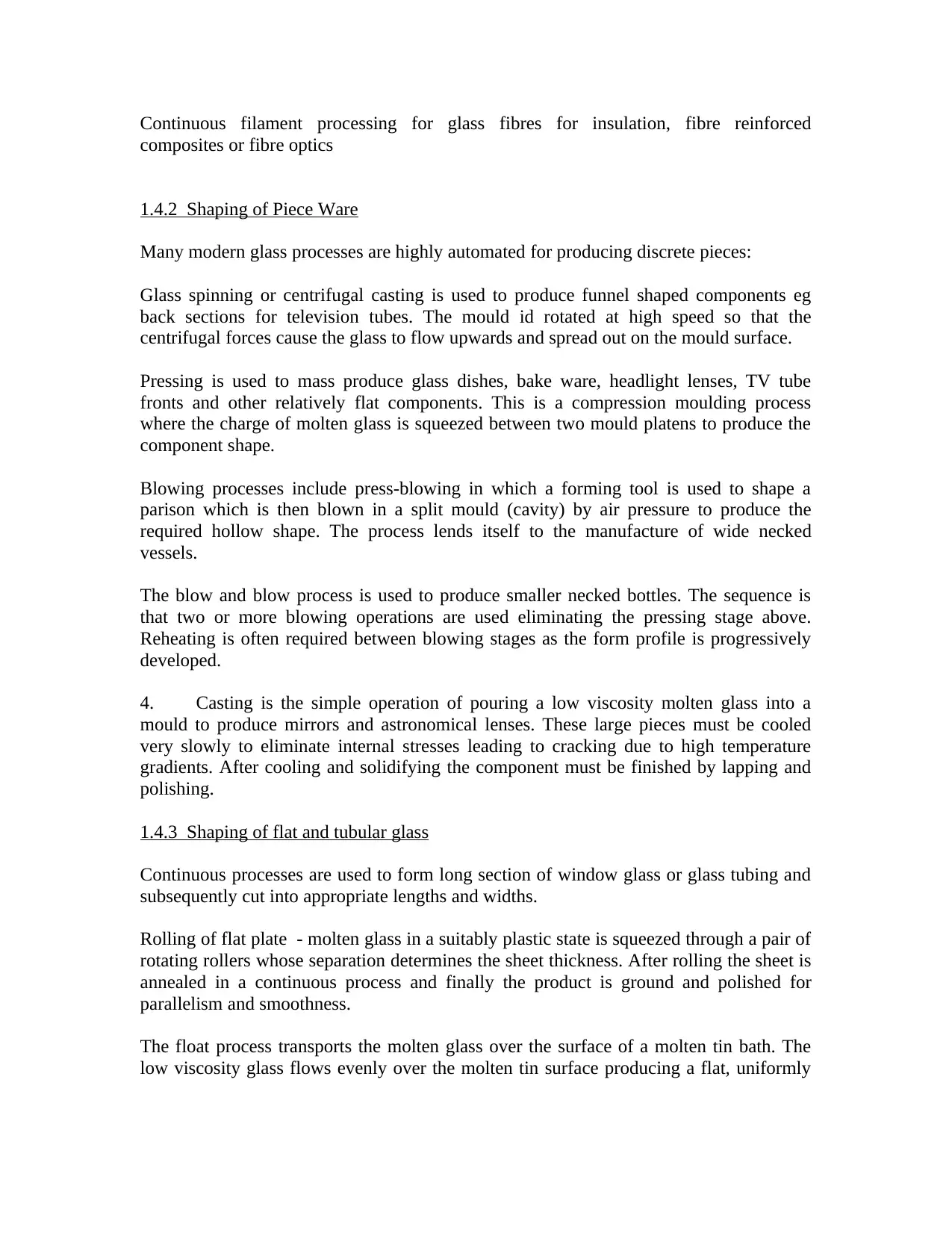
Continuous filament processing for glass fibres for insulation, fibre reinforced
composites or fibre optics
1.4.2 Shaping of Piece Ware
Many modern glass processes are highly automated for producing discrete pieces:
Glass spinning or centrifugal casting is used to produce funnel shaped components eg
back sections for television tubes. The mould id rotated at high speed so that the
centrifugal forces cause the glass to flow upwards and spread out on the mould surface.
Pressing is used to mass produce glass dishes, bake ware, headlight lenses, TV tube
fronts and other relatively flat components. This is a compression moulding process
where the charge of molten glass is squeezed between two mould platens to produce the
component shape.
Blowing processes include press-blowing in which a forming tool is used to shape a
parison which is then blown in a split mould (cavity) by air pressure to produce the
required hollow shape. The process lends itself to the manufacture of wide necked
vessels.
The blow and blow process is used to produce smaller necked bottles. The sequence is
that two or more blowing operations are used eliminating the pressing stage above.
Reheating is often required between blowing stages as the form profile is progressively
developed.
4. Casting is the simple operation of pouring a low viscosity molten glass into a
mould to produce mirrors and astronomical lenses. These large pieces must be cooled
very slowly to eliminate internal stresses leading to cracking due to high temperature
gradients. After cooling and solidifying the component must be finished by lapping and
polishing.
1.4.3 Shaping of flat and tubular glass
Continuous processes are used to form long section of window glass or glass tubing and
subsequently cut into appropriate lengths and widths.
Rolling of flat plate - molten glass in a suitably plastic state is squeezed through a pair of
rotating rollers whose separation determines the sheet thickness. After rolling the sheet is
annealed in a continuous process and finally the product is ground and polished for
parallelism and smoothness.
The float process transports the molten glass over the surface of a molten tin bath. The
low viscosity glass flows evenly over the molten tin surface producing a flat, uniformly
composites or fibre optics
1.4.2 Shaping of Piece Ware
Many modern glass processes are highly automated for producing discrete pieces:
Glass spinning or centrifugal casting is used to produce funnel shaped components eg
back sections for television tubes. The mould id rotated at high speed so that the
centrifugal forces cause the glass to flow upwards and spread out on the mould surface.
Pressing is used to mass produce glass dishes, bake ware, headlight lenses, TV tube
fronts and other relatively flat components. This is a compression moulding process
where the charge of molten glass is squeezed between two mould platens to produce the
component shape.
Blowing processes include press-blowing in which a forming tool is used to shape a
parison which is then blown in a split mould (cavity) by air pressure to produce the
required hollow shape. The process lends itself to the manufacture of wide necked
vessels.
The blow and blow process is used to produce smaller necked bottles. The sequence is
that two or more blowing operations are used eliminating the pressing stage above.
Reheating is often required between blowing stages as the form profile is progressively
developed.
4. Casting is the simple operation of pouring a low viscosity molten glass into a
mould to produce mirrors and astronomical lenses. These large pieces must be cooled
very slowly to eliminate internal stresses leading to cracking due to high temperature
gradients. After cooling and solidifying the component must be finished by lapping and
polishing.
1.4.3 Shaping of flat and tubular glass
Continuous processes are used to form long section of window glass or glass tubing and
subsequently cut into appropriate lengths and widths.
Rolling of flat plate - molten glass in a suitably plastic state is squeezed through a pair of
rotating rollers whose separation determines the sheet thickness. After rolling the sheet is
annealed in a continuous process and finally the product is ground and polished for
parallelism and smoothness.
The float process transports the molten glass over the surface of a molten tin bath. The
low viscosity glass flows evenly over the molten tin surface producing a flat, uniformly
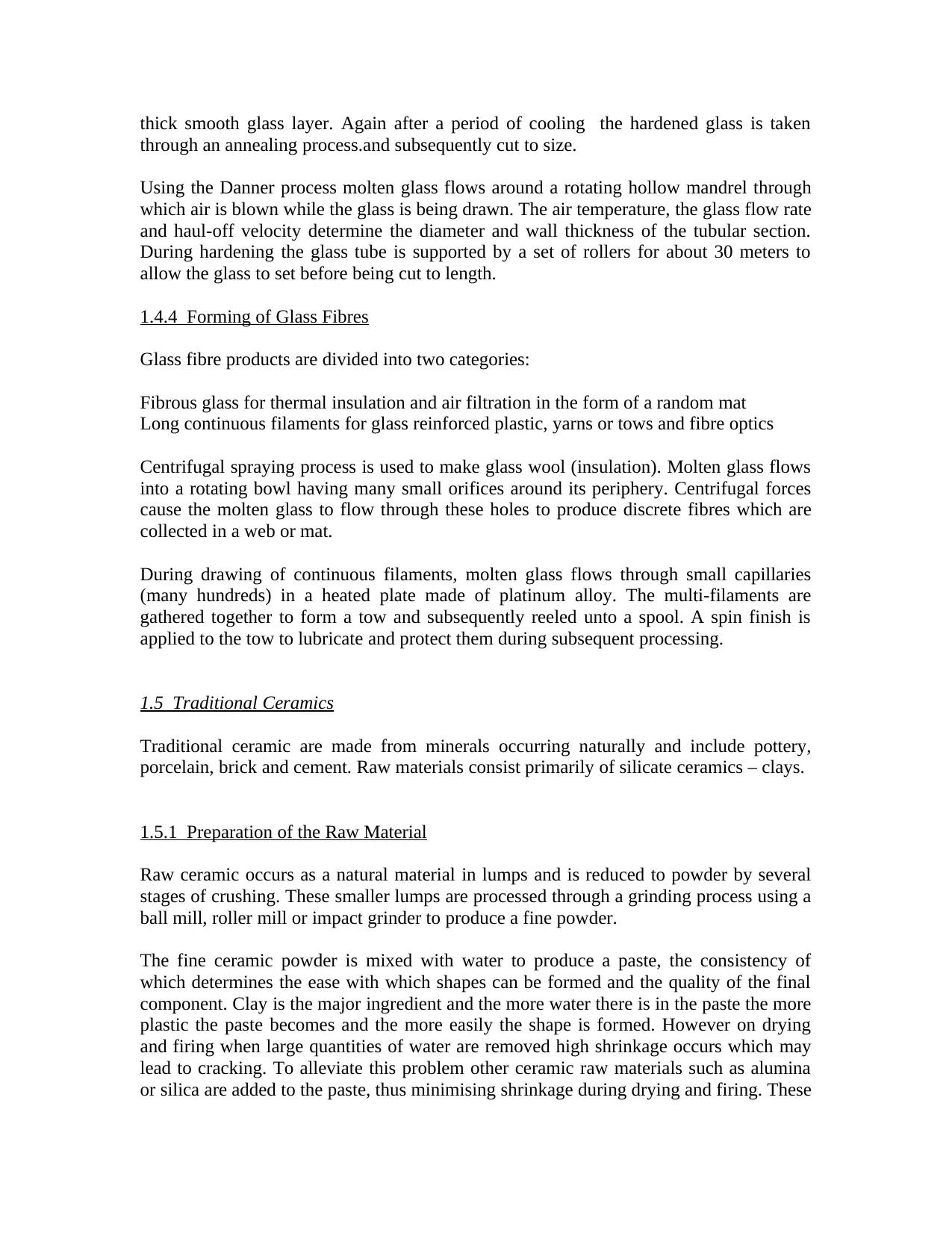
thick smooth glass layer. Again after a period of cooling the hardened glass is taken
through an annealing process.and subsequently cut to size.
Using the Danner process molten glass flows around a rotating hollow mandrel through
which air is blown while the glass is being drawn. The air temperature, the glass flow rate
and haul-off velocity determine the diameter and wall thickness of the tubular section.
During hardening the glass tube is supported by a set of rollers for about 30 meters to
allow the glass to set before being cut to length.
1.4.4 Forming of Glass Fibres
Glass fibre products are divided into two categories:
Fibrous glass for thermal insulation and air filtration in the form of a random mat
Long continuous filaments for glass reinforced plastic, yarns or tows and fibre optics
Centrifugal spraying process is used to make glass wool (insulation). Molten glass flows
into a rotating bowl having many small orifices around its periphery. Centrifugal forces
cause the molten glass to flow through these holes to produce discrete fibres which are
collected in a web or mat.
During drawing of continuous filaments, molten glass flows through small capillaries
(many hundreds) in a heated plate made of platinum alloy. The multi-filaments are
gathered together to form a tow and subsequently reeled unto a spool. A spin finish is
applied to the tow to lubricate and protect them during subsequent processing.
1.5 Traditional Ceramics
Traditional ceramic are made from minerals occurring naturally and include pottery,
porcelain, brick and cement. Raw materials consist primarily of silicate ceramics – clays.
1.5.1 Preparation of the Raw Material
Raw ceramic occurs as a natural material in lumps and is reduced to powder by several
stages of crushing. These smaller lumps are processed through a grinding process using a
ball mill, roller mill or impact grinder to produce a fine powder.
The fine ceramic powder is mixed with water to produce a paste, the consistency of
which determines the ease with which shapes can be formed and the quality of the final
component. Clay is the major ingredient and the more water there is in the paste the more
plastic the paste becomes and the more easily the shape is formed. However on drying
and firing when large quantities of water are removed high shrinkage occurs which may
lead to cracking. To alleviate this problem other ceramic raw materials such as alumina
or silica are added to the paste, thus minimising shrinkage during drying and firing. These
through an annealing process.and subsequently cut to size.
Using the Danner process molten glass flows around a rotating hollow mandrel through
which air is blown while the glass is being drawn. The air temperature, the glass flow rate
and haul-off velocity determine the diameter and wall thickness of the tubular section.
During hardening the glass tube is supported by a set of rollers for about 30 meters to
allow the glass to set before being cut to length.
1.4.4 Forming of Glass Fibres
Glass fibre products are divided into two categories:
Fibrous glass for thermal insulation and air filtration in the form of a random mat
Long continuous filaments for glass reinforced plastic, yarns or tows and fibre optics
Centrifugal spraying process is used to make glass wool (insulation). Molten glass flows
into a rotating bowl having many small orifices around its periphery. Centrifugal forces
cause the molten glass to flow through these holes to produce discrete fibres which are
collected in a web or mat.
During drawing of continuous filaments, molten glass flows through small capillaries
(many hundreds) in a heated plate made of platinum alloy. The multi-filaments are
gathered together to form a tow and subsequently reeled unto a spool. A spin finish is
applied to the tow to lubricate and protect them during subsequent processing.
1.5 Traditional Ceramics
Traditional ceramic are made from minerals occurring naturally and include pottery,
porcelain, brick and cement. Raw materials consist primarily of silicate ceramics – clays.
1.5.1 Preparation of the Raw Material
Raw ceramic occurs as a natural material in lumps and is reduced to powder by several
stages of crushing. These smaller lumps are processed through a grinding process using a
ball mill, roller mill or impact grinder to produce a fine powder.
The fine ceramic powder is mixed with water to produce a paste, the consistency of
which determines the ease with which shapes can be formed and the quality of the final
component. Clay is the major ingredient and the more water there is in the paste the more
plastic the paste becomes and the more easily the shape is formed. However on drying
and firing when large quantities of water are removed high shrinkage occurs which may
lead to cracking. To alleviate this problem other ceramic raw materials such as alumina
or silica are added to the paste, thus minimising shrinkage during drying and firing. These
⊘ This is a preview!⊘
Do you want full access?
Subscribe today to unlock all pages.

Trusted by 1+ million students worldwide
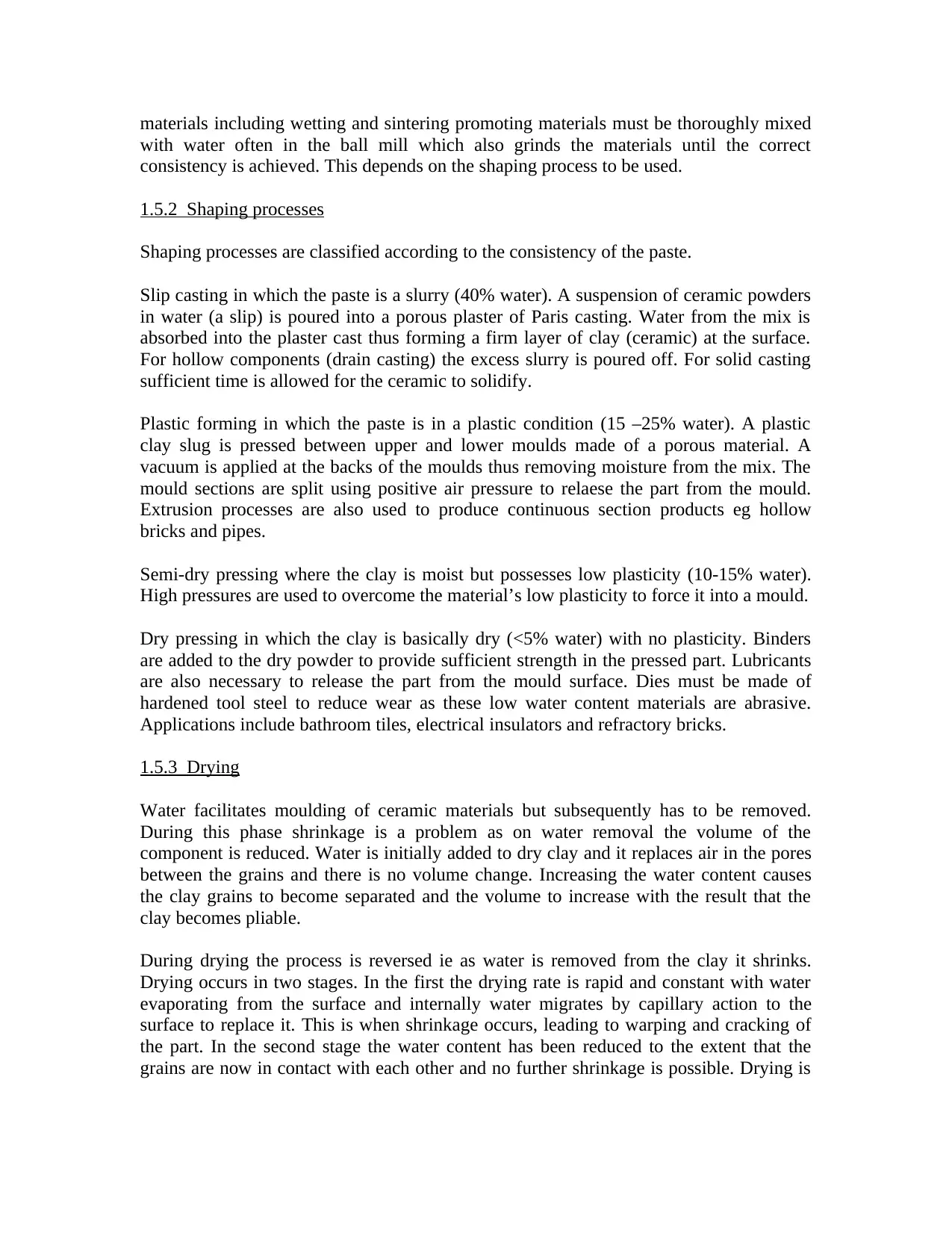
materials including wetting and sintering promoting materials must be thoroughly mixed
with water often in the ball mill which also grinds the materials until the correct
consistency is achieved. This depends on the shaping process to be used.
1.5.2 Shaping processes
Shaping processes are classified according to the consistency of the paste.
Slip casting in which the paste is a slurry (40% water). A suspension of ceramic powders
in water (a slip) is poured into a porous plaster of Paris casting. Water from the mix is
absorbed into the plaster cast thus forming a firm layer of clay (ceramic) at the surface.
For hollow components (drain casting) the excess slurry is poured off. For solid casting
sufficient time is allowed for the ceramic to solidify.
Plastic forming in which the paste is in a plastic condition (15 –25% water). A plastic
clay slug is pressed between upper and lower moulds made of a porous material. A
vacuum is applied at the backs of the moulds thus removing moisture from the mix. The
mould sections are split using positive air pressure to relaese the part from the mould.
Extrusion processes are also used to produce continuous section products eg hollow
bricks and pipes.
Semi-dry pressing where the clay is moist but possesses low plasticity (10-15% water).
High pressures are used to overcome the material’s low plasticity to force it into a mould.
Dry pressing in which the clay is basically dry (<5% water) with no plasticity. Binders
are added to the dry powder to provide sufficient strength in the pressed part. Lubricants
are also necessary to release the part from the mould surface. Dies must be made of
hardened tool steel to reduce wear as these low water content materials are abrasive.
Applications include bathroom tiles, electrical insulators and refractory bricks.
1.5.3 Drying
Water facilitates moulding of ceramic materials but subsequently has to be removed.
During this phase shrinkage is a problem as on water removal the volume of the
component is reduced. Water is initially added to dry clay and it replaces air in the pores
between the grains and there is no volume change. Increasing the water content causes
the clay grains to become separated and the volume to increase with the result that the
clay becomes pliable.
During drying the process is reversed ie as water is removed from the clay it shrinks.
Drying occurs in two stages. In the first the drying rate is rapid and constant with water
evaporating from the surface and internally water migrates by capillary action to the
surface to replace it. This is when shrinkage occurs, leading to warping and cracking of
the part. In the second stage the water content has been reduced to the extent that the
grains are now in contact with each other and no further shrinkage is possible. Drying is
with water often in the ball mill which also grinds the materials until the correct
consistency is achieved. This depends on the shaping process to be used.
1.5.2 Shaping processes
Shaping processes are classified according to the consistency of the paste.
Slip casting in which the paste is a slurry (40% water). A suspension of ceramic powders
in water (a slip) is poured into a porous plaster of Paris casting. Water from the mix is
absorbed into the plaster cast thus forming a firm layer of clay (ceramic) at the surface.
For hollow components (drain casting) the excess slurry is poured off. For solid casting
sufficient time is allowed for the ceramic to solidify.
Plastic forming in which the paste is in a plastic condition (15 –25% water). A plastic
clay slug is pressed between upper and lower moulds made of a porous material. A
vacuum is applied at the backs of the moulds thus removing moisture from the mix. The
mould sections are split using positive air pressure to relaese the part from the mould.
Extrusion processes are also used to produce continuous section products eg hollow
bricks and pipes.
Semi-dry pressing where the clay is moist but possesses low plasticity (10-15% water).
High pressures are used to overcome the material’s low plasticity to force it into a mould.
Dry pressing in which the clay is basically dry (<5% water) with no plasticity. Binders
are added to the dry powder to provide sufficient strength in the pressed part. Lubricants
are also necessary to release the part from the mould surface. Dies must be made of
hardened tool steel to reduce wear as these low water content materials are abrasive.
Applications include bathroom tiles, electrical insulators and refractory bricks.
1.5.3 Drying
Water facilitates moulding of ceramic materials but subsequently has to be removed.
During this phase shrinkage is a problem as on water removal the volume of the
component is reduced. Water is initially added to dry clay and it replaces air in the pores
between the grains and there is no volume change. Increasing the water content causes
the clay grains to become separated and the volume to increase with the result that the
clay becomes pliable.
During drying the process is reversed ie as water is removed from the clay it shrinks.
Drying occurs in two stages. In the first the drying rate is rapid and constant with water
evaporating from the surface and internally water migrates by capillary action to the
surface to replace it. This is when shrinkage occurs, leading to warping and cracking of
the part. In the second stage the water content has been reduced to the extent that the
grains are now in contact with each other and no further shrinkage is possible. Drying is
Paraphrase This Document
Need a fresh take? Get an instant paraphrase of this document with our AI Paraphraser
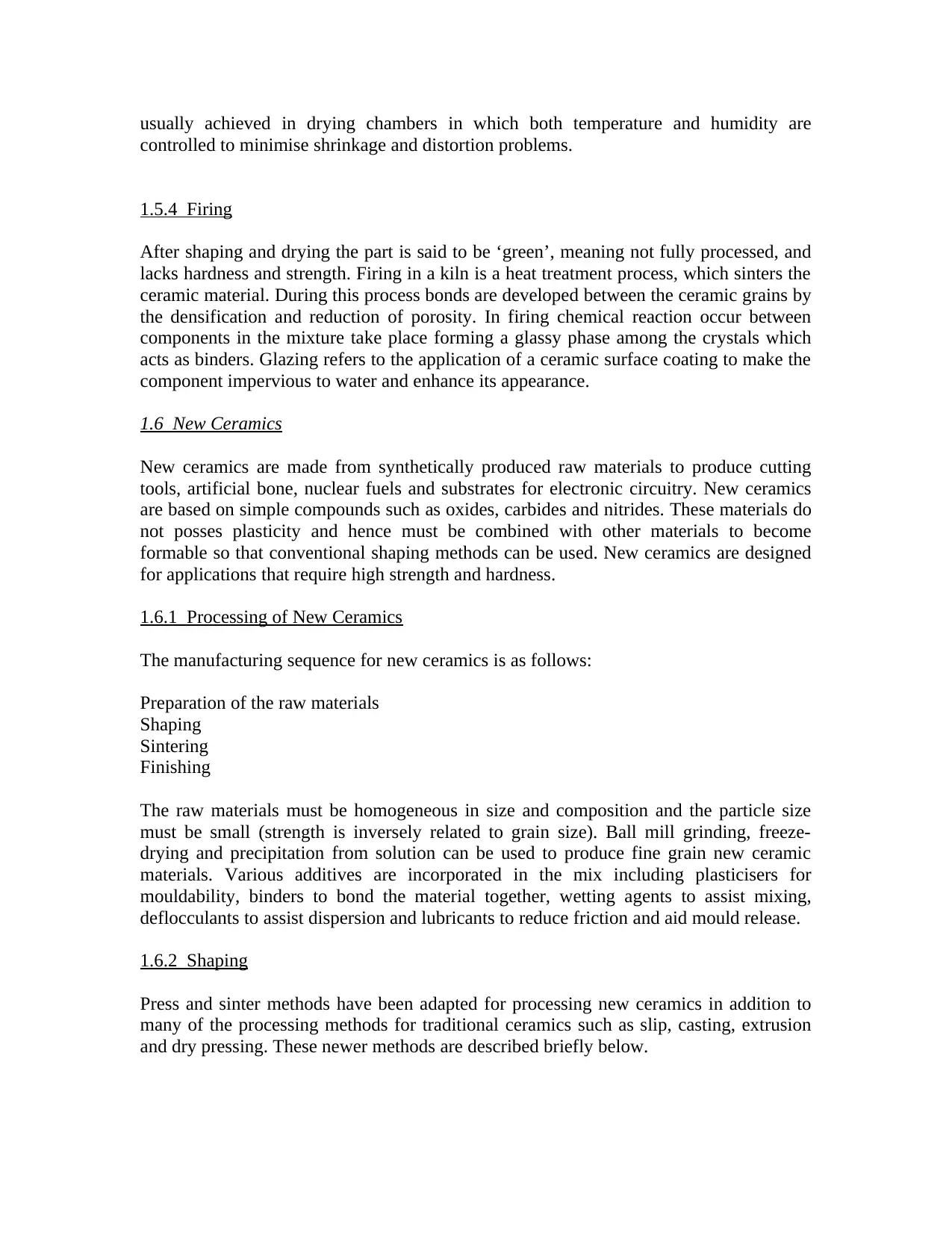
usually achieved in drying chambers in which both temperature and humidity are
controlled to minimise shrinkage and distortion problems.
1.5.4 Firing
After shaping and drying the part is said to be ‘green’, meaning not fully processed, and
lacks hardness and strength. Firing in a kiln is a heat treatment process, which sinters the
ceramic material. During this process bonds are developed between the ceramic grains by
the densification and reduction of porosity. In firing chemical reaction occur between
components in the mixture take place forming a glassy phase among the crystals which
acts as binders. Glazing refers to the application of a ceramic surface coating to make the
component impervious to water and enhance its appearance.
1.6 New Ceramics
New ceramics are made from synthetically produced raw materials to produce cutting
tools, artificial bone, nuclear fuels and substrates for electronic circuitry. New ceramics
are based on simple compounds such as oxides, carbides and nitrides. These materials do
not posses plasticity and hence must be combined with other materials to become
formable so that conventional shaping methods can be used. New ceramics are designed
for applications that require high strength and hardness.
1.6.1 Processing of New Ceramics
The manufacturing sequence for new ceramics is as follows:
Preparation of the raw materials
Shaping
Sintering
Finishing
The raw materials must be homogeneous in size and composition and the particle size
must be small (strength is inversely related to grain size). Ball mill grinding, freeze-
drying and precipitation from solution can be used to produce fine grain new ceramic
materials. Various additives are incorporated in the mix including plasticisers for
mouldability, binders to bond the material together, wetting agents to assist mixing,
deflocculants to assist dispersion and lubricants to reduce friction and aid mould release.
1.6.2 Shaping
Press and sinter methods have been adapted for processing new ceramics in addition to
many of the processing methods for traditional ceramics such as slip, casting, extrusion
and dry pressing. These newer methods are described briefly below.
controlled to minimise shrinkage and distortion problems.
1.5.4 Firing
After shaping and drying the part is said to be ‘green’, meaning not fully processed, and
lacks hardness and strength. Firing in a kiln is a heat treatment process, which sinters the
ceramic material. During this process bonds are developed between the ceramic grains by
the densification and reduction of porosity. In firing chemical reaction occur between
components in the mixture take place forming a glassy phase among the crystals which
acts as binders. Glazing refers to the application of a ceramic surface coating to make the
component impervious to water and enhance its appearance.
1.6 New Ceramics
New ceramics are made from synthetically produced raw materials to produce cutting
tools, artificial bone, nuclear fuels and substrates for electronic circuitry. New ceramics
are based on simple compounds such as oxides, carbides and nitrides. These materials do
not posses plasticity and hence must be combined with other materials to become
formable so that conventional shaping methods can be used. New ceramics are designed
for applications that require high strength and hardness.
1.6.1 Processing of New Ceramics
The manufacturing sequence for new ceramics is as follows:
Preparation of the raw materials
Shaping
Sintering
Finishing
The raw materials must be homogeneous in size and composition and the particle size
must be small (strength is inversely related to grain size). Ball mill grinding, freeze-
drying and precipitation from solution can be used to produce fine grain new ceramic
materials. Various additives are incorporated in the mix including plasticisers for
mouldability, binders to bond the material together, wetting agents to assist mixing,
deflocculants to assist dispersion and lubricants to reduce friction and aid mould release.
1.6.2 Shaping
Press and sinter methods have been adapted for processing new ceramics in addition to
many of the processing methods for traditional ceramics such as slip, casting, extrusion
and dry pressing. These newer methods are described briefly below.
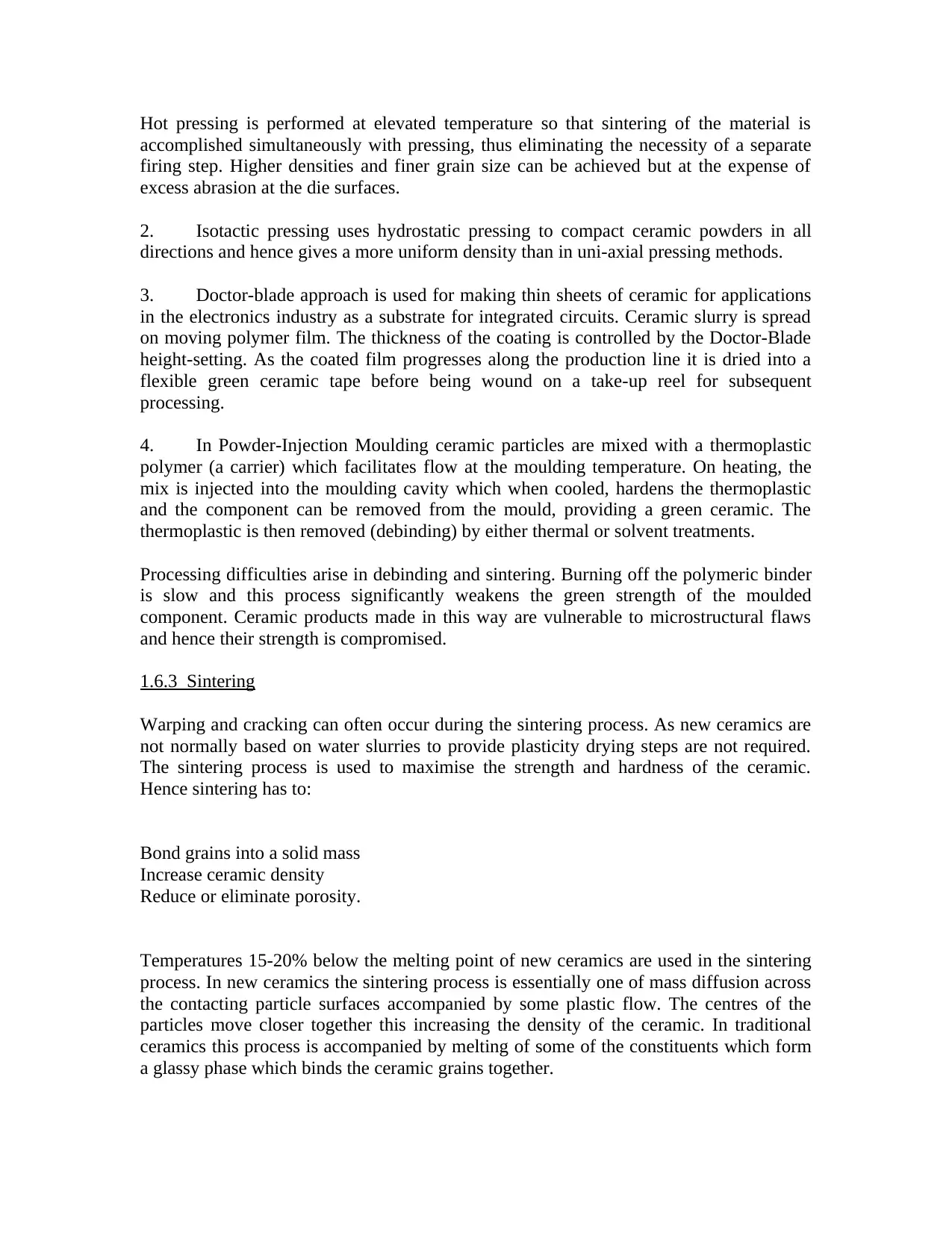
Hot pressing is performed at elevated temperature so that sintering of the material is
accomplished simultaneously with pressing, thus eliminating the necessity of a separate
firing step. Higher densities and finer grain size can be achieved but at the expense of
excess abrasion at the die surfaces.
2. Isotactic pressing uses hydrostatic pressing to compact ceramic powders in all
directions and hence gives a more uniform density than in uni-axial pressing methods.
3. Doctor-blade approach is used for making thin sheets of ceramic for applications
in the electronics industry as a substrate for integrated circuits. Ceramic slurry is spread
on moving polymer film. The thickness of the coating is controlled by the Doctor-Blade
height-setting. As the coated film progresses along the production line it is dried into a
flexible green ceramic tape before being wound on a take-up reel for subsequent
processing.
4. In Powder-Injection Moulding ceramic particles are mixed with a thermoplastic
polymer (a carrier) which facilitates flow at the moulding temperature. On heating, the
mix is injected into the moulding cavity which when cooled, hardens the thermoplastic
and the component can be removed from the mould, providing a green ceramic. The
thermoplastic is then removed (debinding) by either thermal or solvent treatments.
Processing difficulties arise in debinding and sintering. Burning off the polymeric binder
is slow and this process significantly weakens the green strength of the moulded
component. Ceramic products made in this way are vulnerable to microstructural flaws
and hence their strength is compromised.
1.6.3 Sintering
Warping and cracking can often occur during the sintering process. As new ceramics are
not normally based on water slurries to provide plasticity drying steps are not required.
The sintering process is used to maximise the strength and hardness of the ceramic.
Hence sintering has to:
Bond grains into a solid mass
Increase ceramic density
Reduce or eliminate porosity.
Temperatures 15-20% below the melting point of new ceramics are used in the sintering
process. In new ceramics the sintering process is essentially one of mass diffusion across
the contacting particle surfaces accompanied by some plastic flow. The centres of the
particles move closer together this increasing the density of the ceramic. In traditional
ceramics this process is accompanied by melting of some of the constituents which form
a glassy phase which binds the ceramic grains together.
accomplished simultaneously with pressing, thus eliminating the necessity of a separate
firing step. Higher densities and finer grain size can be achieved but at the expense of
excess abrasion at the die surfaces.
2. Isotactic pressing uses hydrostatic pressing to compact ceramic powders in all
directions and hence gives a more uniform density than in uni-axial pressing methods.
3. Doctor-blade approach is used for making thin sheets of ceramic for applications
in the electronics industry as a substrate for integrated circuits. Ceramic slurry is spread
on moving polymer film. The thickness of the coating is controlled by the Doctor-Blade
height-setting. As the coated film progresses along the production line it is dried into a
flexible green ceramic tape before being wound on a take-up reel for subsequent
processing.
4. In Powder-Injection Moulding ceramic particles are mixed with a thermoplastic
polymer (a carrier) which facilitates flow at the moulding temperature. On heating, the
mix is injected into the moulding cavity which when cooled, hardens the thermoplastic
and the component can be removed from the mould, providing a green ceramic. The
thermoplastic is then removed (debinding) by either thermal or solvent treatments.
Processing difficulties arise in debinding and sintering. Burning off the polymeric binder
is slow and this process significantly weakens the green strength of the moulded
component. Ceramic products made in this way are vulnerable to microstructural flaws
and hence their strength is compromised.
1.6.3 Sintering
Warping and cracking can often occur during the sintering process. As new ceramics are
not normally based on water slurries to provide plasticity drying steps are not required.
The sintering process is used to maximise the strength and hardness of the ceramic.
Hence sintering has to:
Bond grains into a solid mass
Increase ceramic density
Reduce or eliminate porosity.
Temperatures 15-20% below the melting point of new ceramics are used in the sintering
process. In new ceramics the sintering process is essentially one of mass diffusion across
the contacting particle surfaces accompanied by some plastic flow. The centres of the
particles move closer together this increasing the density of the ceramic. In traditional
ceramics this process is accompanied by melting of some of the constituents which form
a glassy phase which binds the ceramic grains together.
⊘ This is a preview!⊘
Do you want full access?
Subscribe today to unlock all pages.

Trusted by 1+ million students worldwide
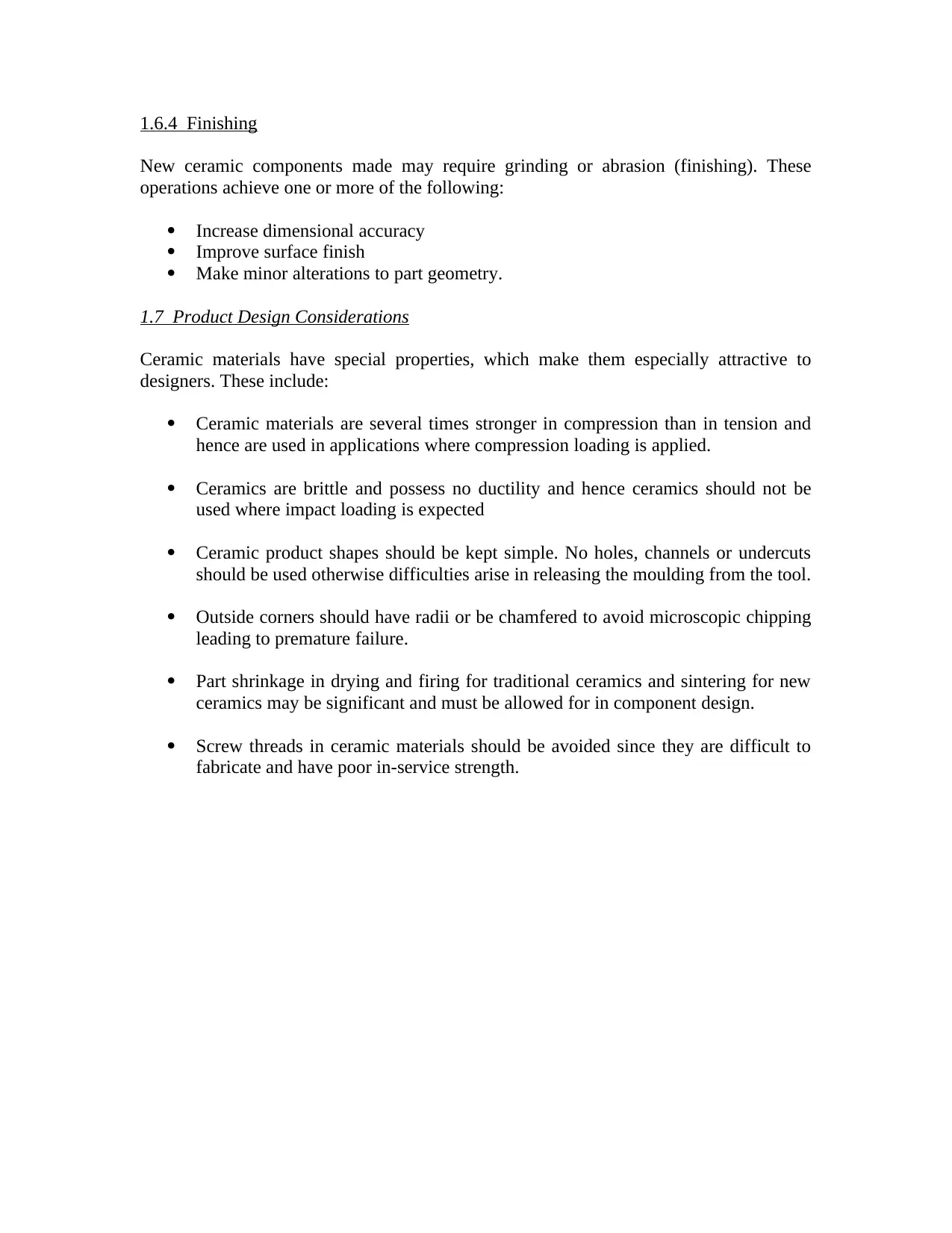
1.6.4 Finishing
New ceramic components made may require grinding or abrasion (finishing). These
operations achieve one or more of the following:
Increase dimensional accuracy
Improve surface finish
Make minor alterations to part geometry.
1.7 Product Design Considerations
Ceramic materials have special properties, which make them especially attractive to
designers. These include:
Ceramic materials are several times stronger in compression than in tension and
hence are used in applications where compression loading is applied.
Ceramics are brittle and possess no ductility and hence ceramics should not be
used where impact loading is expected
Ceramic product shapes should be kept simple. No holes, channels or undercuts
should be used otherwise difficulties arise in releasing the moulding from the tool.
Outside corners should have radii or be chamfered to avoid microscopic chipping
leading to premature failure.
Part shrinkage in drying and firing for traditional ceramics and sintering for new
ceramics may be significant and must be allowed for in component design.
Screw threads in ceramic materials should be avoided since they are difficult to
fabricate and have poor in-service strength.
New ceramic components made may require grinding or abrasion (finishing). These
operations achieve one or more of the following:
Increase dimensional accuracy
Improve surface finish
Make minor alterations to part geometry.
1.7 Product Design Considerations
Ceramic materials have special properties, which make them especially attractive to
designers. These include:
Ceramic materials are several times stronger in compression than in tension and
hence are used in applications where compression loading is applied.
Ceramics are brittle and possess no ductility and hence ceramics should not be
used where impact loading is expected
Ceramic product shapes should be kept simple. No holes, channels or undercuts
should be used otherwise difficulties arise in releasing the moulding from the tool.
Outside corners should have radii or be chamfered to avoid microscopic chipping
leading to premature failure.
Part shrinkage in drying and firing for traditional ceramics and sintering for new
ceramics may be significant and must be allowed for in component design.
Screw threads in ceramic materials should be avoided since they are difficult to
fabricate and have poor in-service strength.
1 out of 10

Your All-in-One AI-Powered Toolkit for Academic Success.
+13062052269
info@desklib.com
Available 24*7 on WhatsApp / Email
Unlock your academic potential
© 2024 | Zucol Services PVT LTD | All rights reserved.