Mechanical Design and Development
VerifiedAdded on 2023/04/21
|29
|4365
|177
AI Summary
This article discusses the research on burst pressure and mechanical behavior of filament wound pressure vessels. It explores the manufacturing process, types of pressure vessels, and finite element analysis. The study aims to increase the strength of pressure vessels by using composite materials. It also discusses the importance of proper preservation of gas and petroleum fuels.
Contribute Materials
Your contribution can guide someone’s learning journey. Share your
documents today.
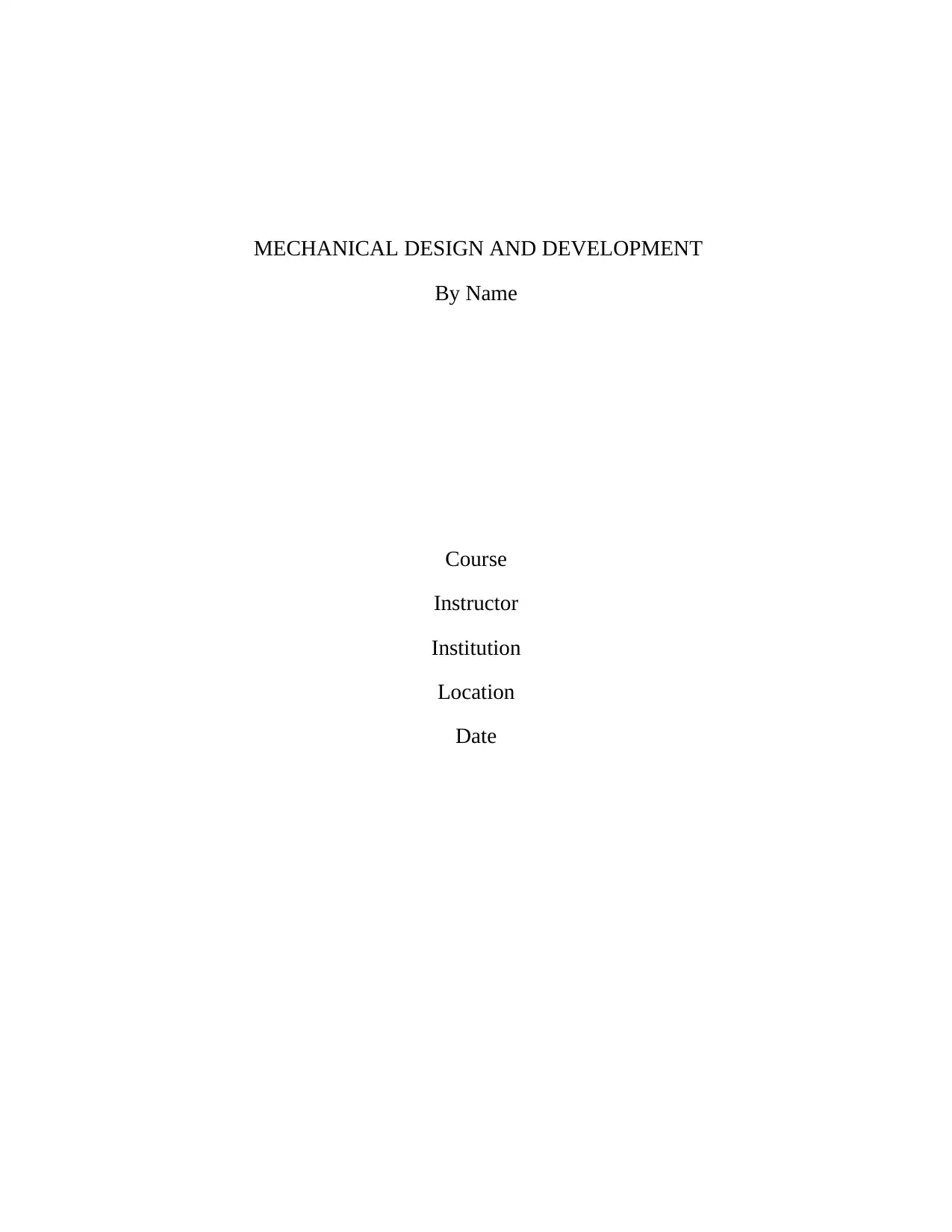
MECHANICAL DESIGN AND DEVELOPMENT
By Name
Course
Instructor
Institution
Location
Date
By Name
Course
Instructor
Institution
Location
Date
Secure Best Marks with AI Grader
Need help grading? Try our AI Grader for instant feedback on your assignments.
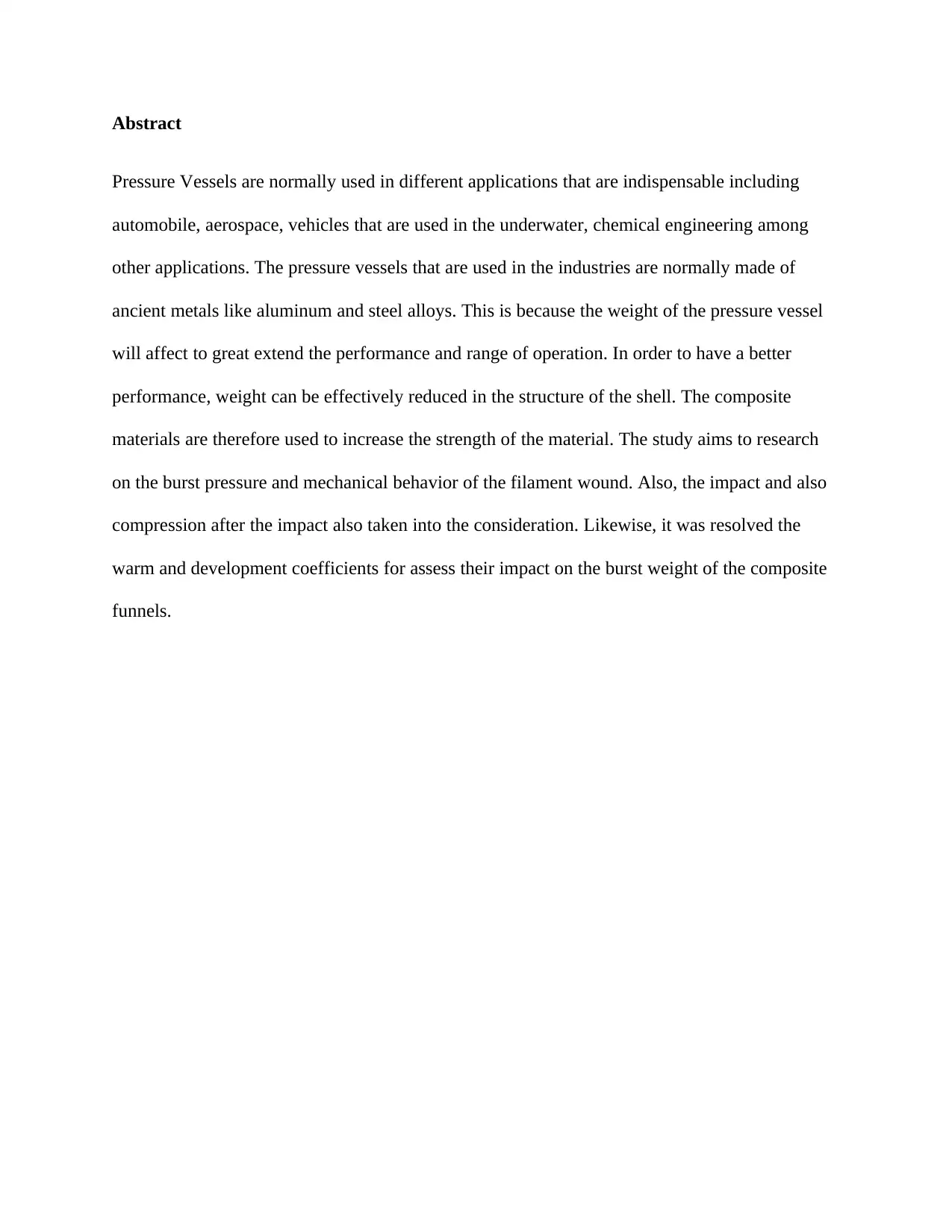
Abstract
Pressure Vessels are normally used in different applications that are indispensable including
automobile, aerospace, vehicles that are used in the underwater, chemical engineering among
other applications. The pressure vessels that are used in the industries are normally made of
ancient metals like aluminum and steel alloys. This is because the weight of the pressure vessel
will affect to great extend the performance and range of operation. In order to have a better
performance, weight can be effectively reduced in the structure of the shell. The composite
materials are therefore used to increase the strength of the material. The study aims to research
on the burst pressure and mechanical behavior of the filament wound. Also, the impact and also
compression after the impact also taken into the consideration. Likewise, it was resolved the
warm and development coefficients for assess their impact on the burst weight of the composite
funnels.
Pressure Vessels are normally used in different applications that are indispensable including
automobile, aerospace, vehicles that are used in the underwater, chemical engineering among
other applications. The pressure vessels that are used in the industries are normally made of
ancient metals like aluminum and steel alloys. This is because the weight of the pressure vessel
will affect to great extend the performance and range of operation. In order to have a better
performance, weight can be effectively reduced in the structure of the shell. The composite
materials are therefore used to increase the strength of the material. The study aims to research
on the burst pressure and mechanical behavior of the filament wound. Also, the impact and also
compression after the impact also taken into the consideration. Likewise, it was resolved the
warm and development coefficients for assess their impact on the burst weight of the composite
funnels.
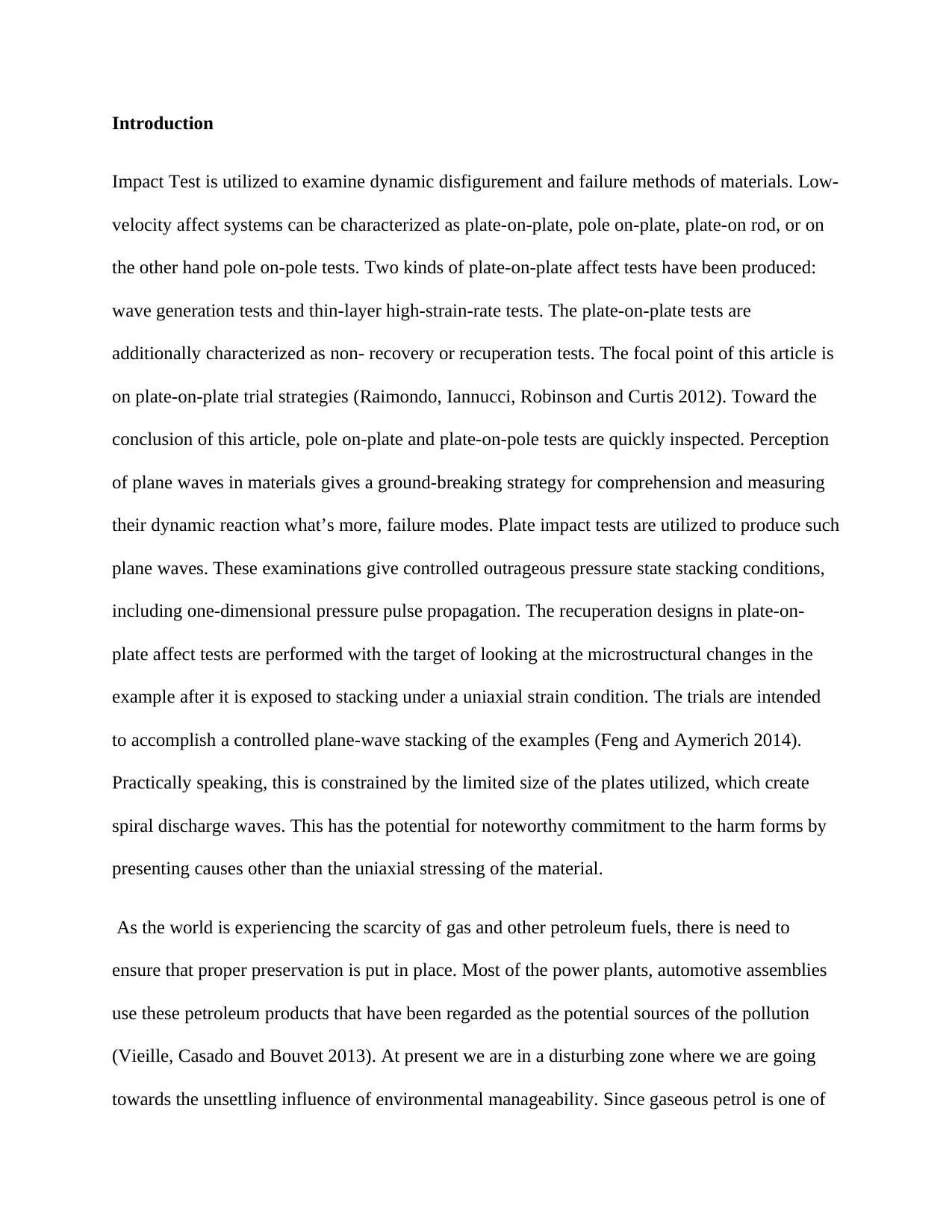
Introduction
Impact Test is utilized to examine dynamic disfigurement and failure methods of materials. Low-
velocity affect systems can be characterized as plate-on-plate, pole on-plate, plate-on rod, or on
the other hand pole on-pole tests. Two kinds of plate-on-plate affect tests have been produced:
wave generation tests and thin-layer high-strain-rate tests. The plate-on-plate tests are
additionally characterized as non- recovery or recuperation tests. The focal point of this article is
on plate-on-plate trial strategies (Raimondo, Iannucci, Robinson and Curtis 2012). Toward the
conclusion of this article, pole on-plate and plate-on-pole tests are quickly inspected. Perception
of plane waves in materials gives a ground-breaking strategy for comprehension and measuring
their dynamic reaction what’s more, failure modes. Plate impact tests are utilized to produce such
plane waves. These examinations give controlled outrageous pressure state stacking conditions,
including one-dimensional pressure pulse propagation. The recuperation designs in plate-on-
plate affect tests are performed with the target of looking at the microstructural changes in the
example after it is exposed to stacking under a uniaxial strain condition. The trials are intended
to accomplish a controlled plane-wave stacking of the examples (Feng and Aymerich 2014).
Practically speaking, this is constrained by the limited size of the plates utilized, which create
spiral discharge waves. This has the potential for noteworthy commitment to the harm forms by
presenting causes other than the uniaxial stressing of the material.
As the world is experiencing the scarcity of gas and other petroleum fuels, there is need to
ensure that proper preservation is put in place. Most of the power plants, automotive assemblies
use these petroleum products that have been regarded as the potential sources of the pollution
(Vieille, Casado and Bouvet 2013). At present we are in a disturbing zone where we are going
towards the unsettling influence of environmental manageability. Since gaseous petrol is one of
Impact Test is utilized to examine dynamic disfigurement and failure methods of materials. Low-
velocity affect systems can be characterized as plate-on-plate, pole on-plate, plate-on rod, or on
the other hand pole on-pole tests. Two kinds of plate-on-plate affect tests have been produced:
wave generation tests and thin-layer high-strain-rate tests. The plate-on-plate tests are
additionally characterized as non- recovery or recuperation tests. The focal point of this article is
on plate-on-plate trial strategies (Raimondo, Iannucci, Robinson and Curtis 2012). Toward the
conclusion of this article, pole on-plate and plate-on-pole tests are quickly inspected. Perception
of plane waves in materials gives a ground-breaking strategy for comprehension and measuring
their dynamic reaction what’s more, failure modes. Plate impact tests are utilized to produce such
plane waves. These examinations give controlled outrageous pressure state stacking conditions,
including one-dimensional pressure pulse propagation. The recuperation designs in plate-on-
plate affect tests are performed with the target of looking at the microstructural changes in the
example after it is exposed to stacking under a uniaxial strain condition. The trials are intended
to accomplish a controlled plane-wave stacking of the examples (Feng and Aymerich 2014).
Practically speaking, this is constrained by the limited size of the plates utilized, which create
spiral discharge waves. This has the potential for noteworthy commitment to the harm forms by
presenting causes other than the uniaxial stressing of the material.
As the world is experiencing the scarcity of gas and other petroleum fuels, there is need to
ensure that proper preservation is put in place. Most of the power plants, automotive assemblies
use these petroleum products that have been regarded as the potential sources of the pollution
(Vieille, Casado and Bouvet 2013). At present we are in a disturbing zone where we are going
towards the unsettling influence of environmental manageability. Since gaseous petrol is one of
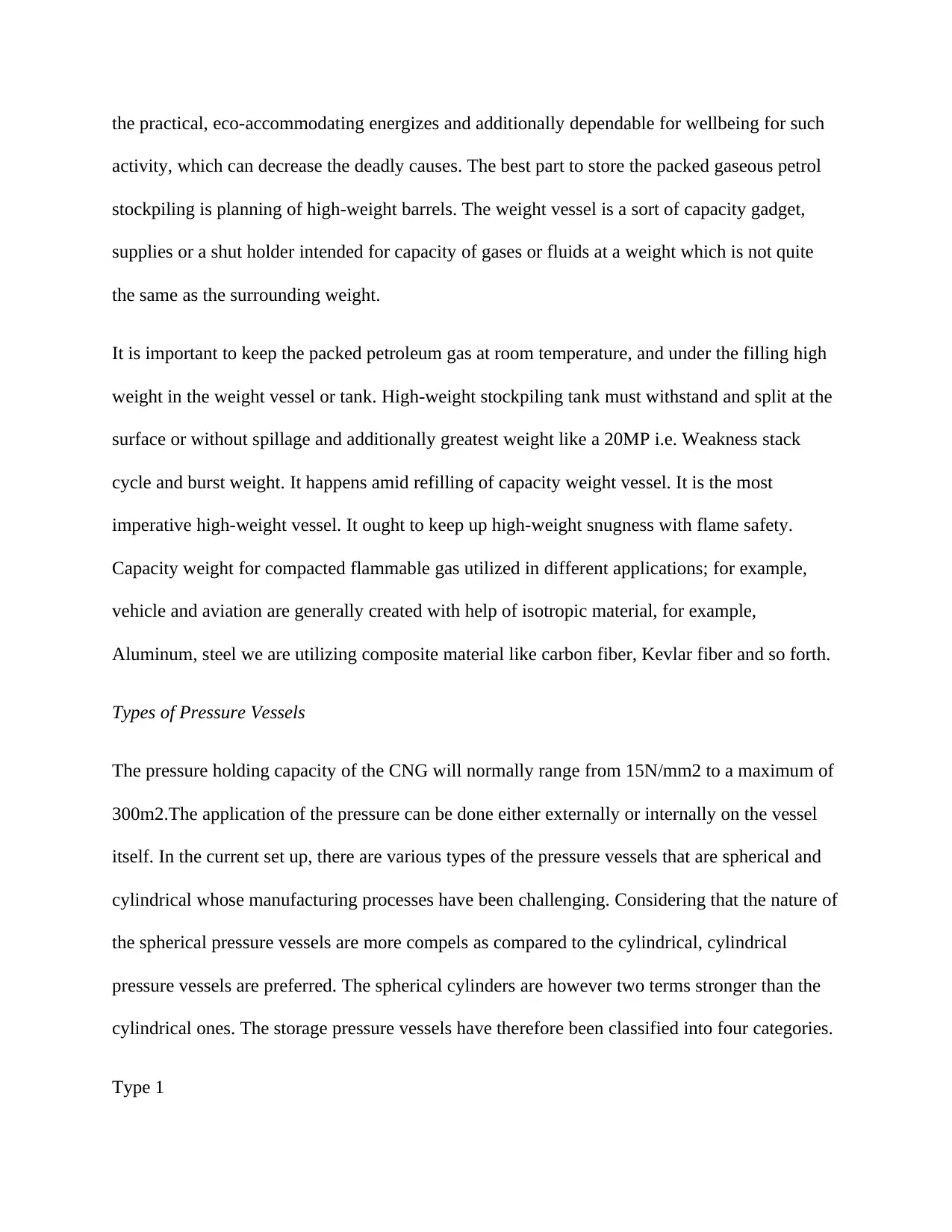
the practical, eco-accommodating energizes and additionally dependable for wellbeing for such
activity, which can decrease the deadly causes. The best part to store the packed gaseous petrol
stockpiling is planning of high-weight barrels. The weight vessel is a sort of capacity gadget,
supplies or a shut holder intended for capacity of gases or fluids at a weight which is not quite
the same as the surrounding weight.
It is important to keep the packed petroleum gas at room temperature, and under the filling high
weight in the weight vessel or tank. High-weight stockpiling tank must withstand and split at the
surface or without spillage and additionally greatest weight like a 20MP i.e. Weakness stack
cycle and burst weight. It happens amid refilling of capacity weight vessel. It is the most
imperative high-weight vessel. It ought to keep up high-weight snugness with flame safety.
Capacity weight for compacted flammable gas utilized in different applications; for example,
vehicle and aviation are generally created with help of isotropic material, for example,
Aluminum, steel we are utilizing composite material like carbon fiber, Kevlar fiber and so forth.
Types of Pressure Vessels
The pressure holding capacity of the CNG will normally range from 15N/mm2 to a maximum of
300m2.The application of the pressure can be done either externally or internally on the vessel
itself. In the current set up, there are various types of the pressure vessels that are spherical and
cylindrical whose manufacturing processes have been challenging. Considering that the nature of
the spherical pressure vessels are more compels as compared to the cylindrical, cylindrical
pressure vessels are preferred. The spherical cylinders are however two terms stronger than the
cylindrical ones. The storage pressure vessels have therefore been classified into four categories.
Type 1
activity, which can decrease the deadly causes. The best part to store the packed gaseous petrol
stockpiling is planning of high-weight barrels. The weight vessel is a sort of capacity gadget,
supplies or a shut holder intended for capacity of gases or fluids at a weight which is not quite
the same as the surrounding weight.
It is important to keep the packed petroleum gas at room temperature, and under the filling high
weight in the weight vessel or tank. High-weight stockpiling tank must withstand and split at the
surface or without spillage and additionally greatest weight like a 20MP i.e. Weakness stack
cycle and burst weight. It happens amid refilling of capacity weight vessel. It is the most
imperative high-weight vessel. It ought to keep up high-weight snugness with flame safety.
Capacity weight for compacted flammable gas utilized in different applications; for example,
vehicle and aviation are generally created with help of isotropic material, for example,
Aluminum, steel we are utilizing composite material like carbon fiber, Kevlar fiber and so forth.
Types of Pressure Vessels
The pressure holding capacity of the CNG will normally range from 15N/mm2 to a maximum of
300m2.The application of the pressure can be done either externally or internally on the vessel
itself. In the current set up, there are various types of the pressure vessels that are spherical and
cylindrical whose manufacturing processes have been challenging. Considering that the nature of
the spherical pressure vessels are more compels as compared to the cylindrical, cylindrical
pressure vessels are preferred. The spherical cylinders are however two terms stronger than the
cylindrical ones. The storage pressure vessels have therefore been classified into four categories.
Type 1
Secure Best Marks with AI Grader
Need help grading? Try our AI Grader for instant feedback on your assignments.
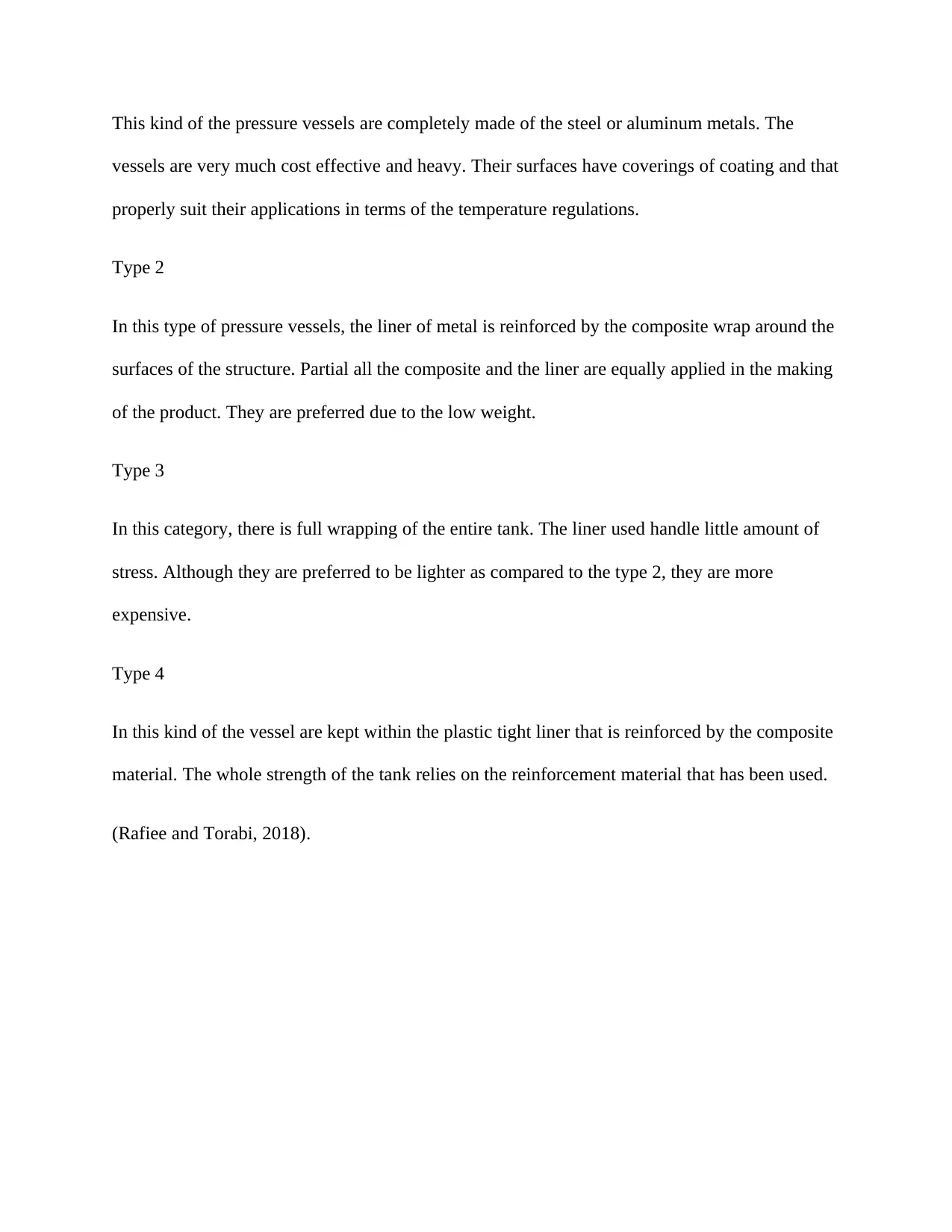
This kind of the pressure vessels are completely made of the steel or aluminum metals. The
vessels are very much cost effective and heavy. Their surfaces have coverings of coating and that
properly suit their applications in terms of the temperature regulations.
Type 2
In this type of pressure vessels, the liner of metal is reinforced by the composite wrap around the
surfaces of the structure. Partial all the composite and the liner are equally applied in the making
of the product. They are preferred due to the low weight.
Type 3
In this category, there is full wrapping of the entire tank. The liner used handle little amount of
stress. Although they are preferred to be lighter as compared to the type 2, they are more
expensive.
Type 4
In this kind of the vessel are kept within the plastic tight liner that is reinforced by the composite
material. The whole strength of the tank relies on the reinforcement material that has been used.
(Rafiee and Torabi, 2018).
vessels are very much cost effective and heavy. Their surfaces have coverings of coating and that
properly suit their applications in terms of the temperature regulations.
Type 2
In this type of pressure vessels, the liner of metal is reinforced by the composite wrap around the
surfaces of the structure. Partial all the composite and the liner are equally applied in the making
of the product. They are preferred due to the low weight.
Type 3
In this category, there is full wrapping of the entire tank. The liner used handle little amount of
stress. Although they are preferred to be lighter as compared to the type 2, they are more
expensive.
Type 4
In this kind of the vessel are kept within the plastic tight liner that is reinforced by the composite
material. The whole strength of the tank relies on the reinforcement material that has been used.
(Rafiee and Torabi, 2018).
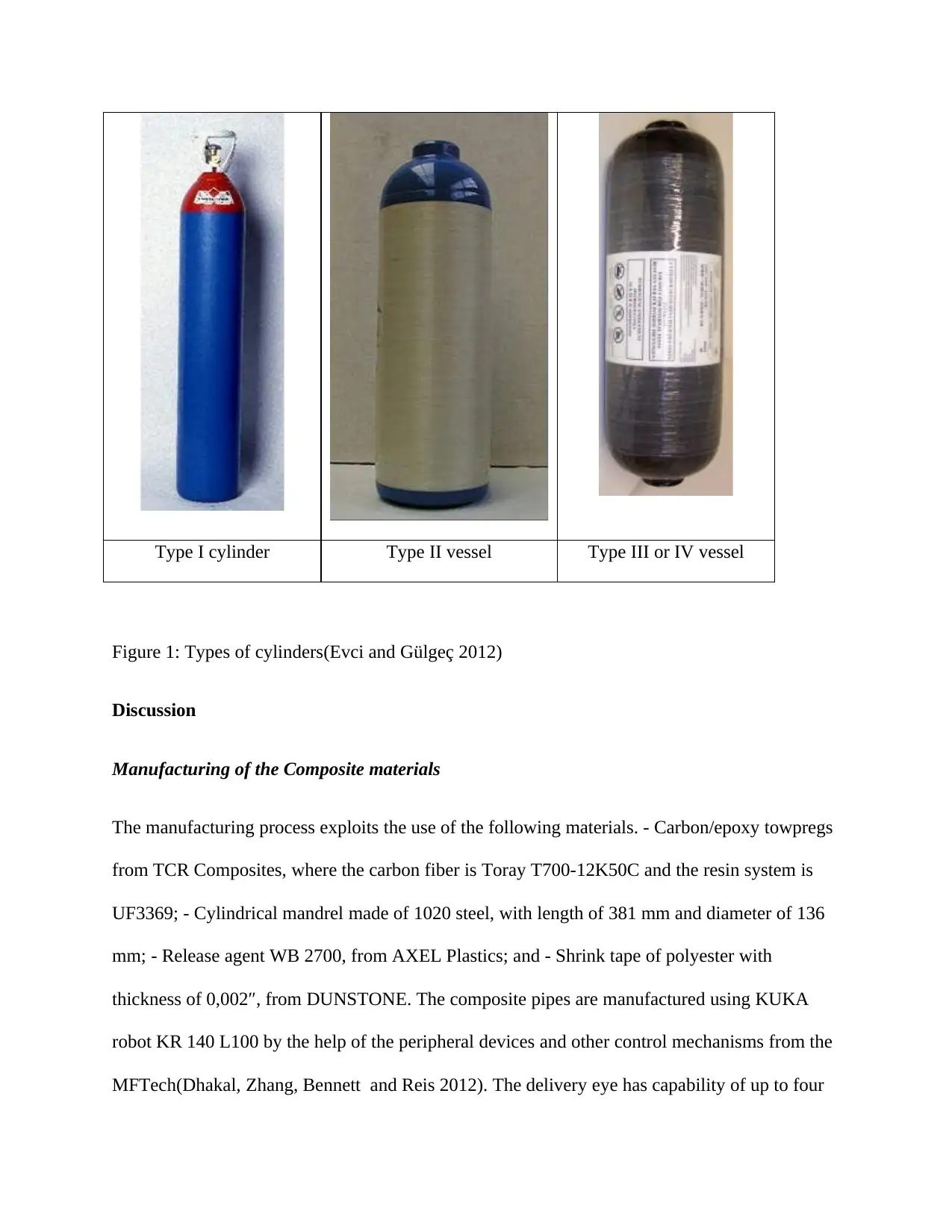
Type I cylinder Type II vessel Type III or IV vessel
Figure 1: Types of cylinders(Evci and Gülgeç 2012)
Discussion
Manufacturing of the Composite materials
The manufacturing process exploits the use of the following materials. - Carbon/epoxy towpregs
from TCR Composites, where the carbon fiber is Toray T700-12K50C and the resin system is
UF3369; - Cylindrical mandrel made of 1020 steel, with length of 381 mm and diameter of 136
mm; - Release agent WB 2700, from AXEL Plastics; and - Shrink tape of polyester with
thickness of 0,002″, from DUNSTONE. The composite pipes are manufactured using KUKA
robot KR 140 L100 by the help of the peripheral devices and other control mechanisms from the
MFTech(Dhakal, Zhang, Bennett and Reis 2012). The delivery eye has capability of up to four
Figure 1: Types of cylinders(Evci and Gülgeç 2012)
Discussion
Manufacturing of the Composite materials
The manufacturing process exploits the use of the following materials. - Carbon/epoxy towpregs
from TCR Composites, where the carbon fiber is Toray T700-12K50C and the resin system is
UF3369; - Cylindrical mandrel made of 1020 steel, with length of 381 mm and diameter of 136
mm; - Release agent WB 2700, from AXEL Plastics; and - Shrink tape of polyester with
thickness of 0,002″, from DUNSTONE. The composite pipes are manufactured using KUKA
robot KR 140 L100 by the help of the peripheral devices and other control mechanisms from the
MFTech(Dhakal, Zhang, Bennett and Reis 2012). The delivery eye has capability of up to four
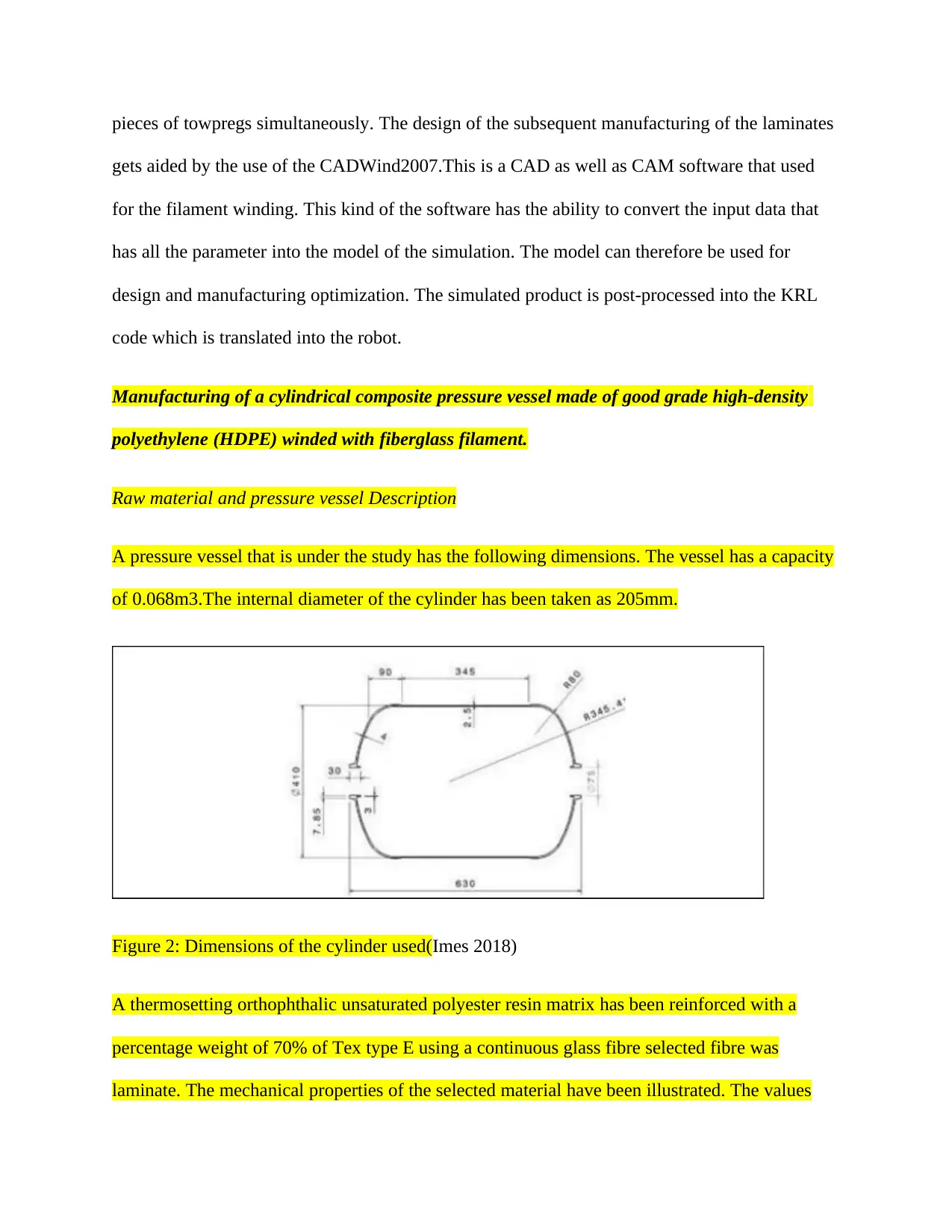
pieces of towpregs simultaneously. The design of the subsequent manufacturing of the laminates
gets aided by the use of the CADWind2007.This is a CAD as well as CAM software that used
for the filament winding. This kind of the software has the ability to convert the input data that
has all the parameter into the model of the simulation. The model can therefore be used for
design and manufacturing optimization. The simulated product is post-processed into the KRL
code which is translated into the robot.
Manufacturing of a cylindrical composite pressure vessel made of good grade high-density
polyethylene (HDPE) winded with fiberglass filament.
Raw material and pressure vessel Description
A pressure vessel that is under the study has the following dimensions. The vessel has a capacity
of 0.068m3.The internal diameter of the cylinder has been taken as 205mm.
Figure 2: Dimensions of the cylinder used(Imes 2018)
A thermosetting orthophthalic unsaturated polyester resin matrix has been reinforced with a
percentage weight of 70% of Tex type E using a continuous glass fibre selected fibre was
laminate. The mechanical properties of the selected material have been illustrated. The values
gets aided by the use of the CADWind2007.This is a CAD as well as CAM software that used
for the filament winding. This kind of the software has the ability to convert the input data that
has all the parameter into the model of the simulation. The model can therefore be used for
design and manufacturing optimization. The simulated product is post-processed into the KRL
code which is translated into the robot.
Manufacturing of a cylindrical composite pressure vessel made of good grade high-density
polyethylene (HDPE) winded with fiberglass filament.
Raw material and pressure vessel Description
A pressure vessel that is under the study has the following dimensions. The vessel has a capacity
of 0.068m3.The internal diameter of the cylinder has been taken as 205mm.
Figure 2: Dimensions of the cylinder used(Imes 2018)
A thermosetting orthophthalic unsaturated polyester resin matrix has been reinforced with a
percentage weight of 70% of Tex type E using a continuous glass fibre selected fibre was
laminate. The mechanical properties of the selected material have been illustrated. The values
Paraphrase This Document
Need a fresh take? Get an instant paraphrase of this document with our AI Paraphraser
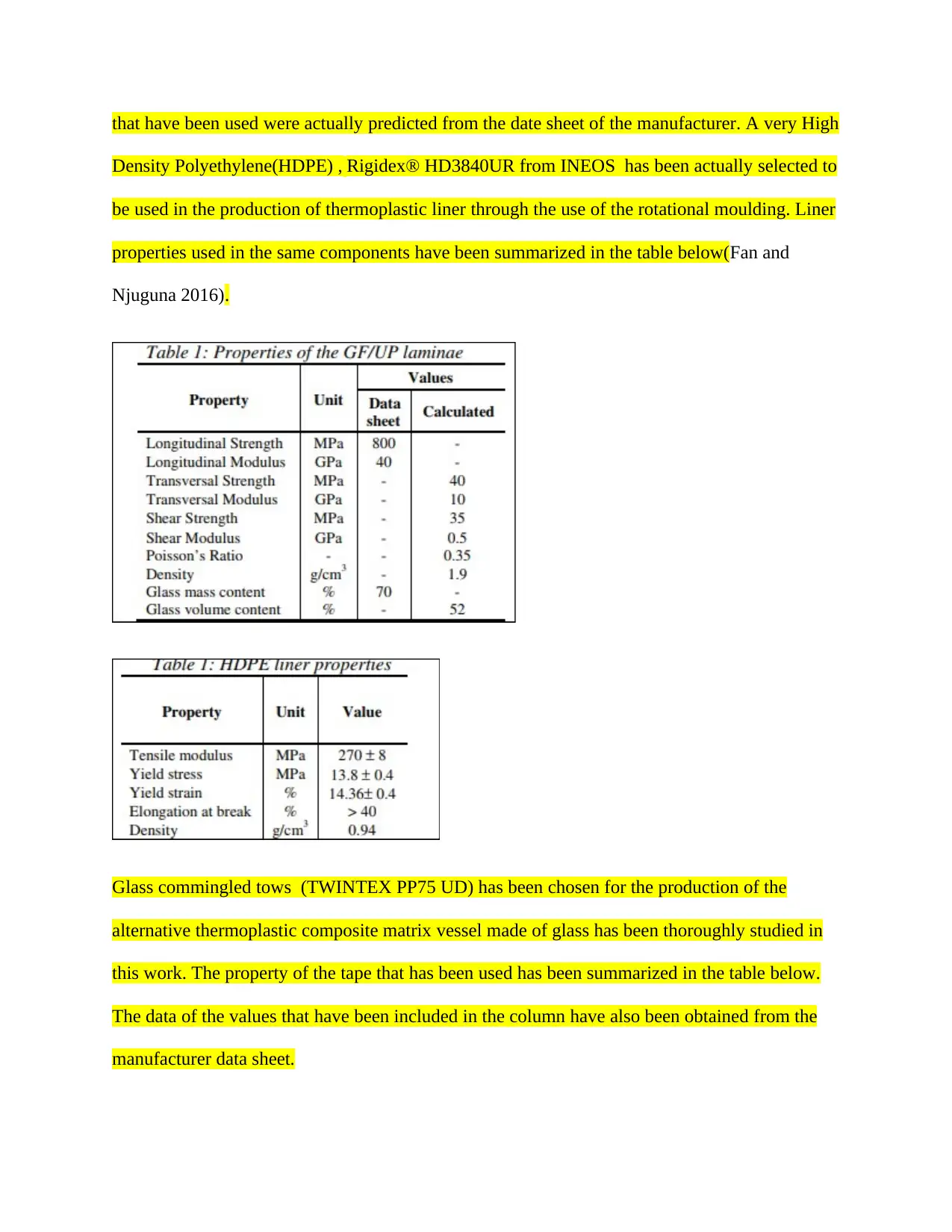
that have been used were actually predicted from the date sheet of the manufacturer. A very High
Density Polyethylene(HDPE) , Rigidex® HD3840UR from INEOS has been actually selected to
be used in the production of thermoplastic liner through the use of the rotational moulding. Liner
properties used in the same components have been summarized in the table below(Fan and
Njuguna 2016).
Glass commingled tows (TWINTEX PP75 UD) has been chosen for the production of the
alternative thermoplastic composite matrix vessel made of glass has been thoroughly studied in
this work. The property of the tape that has been used has been summarized in the table below.
The data of the values that have been included in the column have also been obtained from the
manufacturer data sheet.
Density Polyethylene(HDPE) , Rigidex® HD3840UR from INEOS has been actually selected to
be used in the production of thermoplastic liner through the use of the rotational moulding. Liner
properties used in the same components have been summarized in the table below(Fan and
Njuguna 2016).
Glass commingled tows (TWINTEX PP75 UD) has been chosen for the production of the
alternative thermoplastic composite matrix vessel made of glass has been thoroughly studied in
this work. The property of the tape that has been used has been summarized in the table below.
The data of the values that have been included in the column have also been obtained from the
manufacturer data sheet.
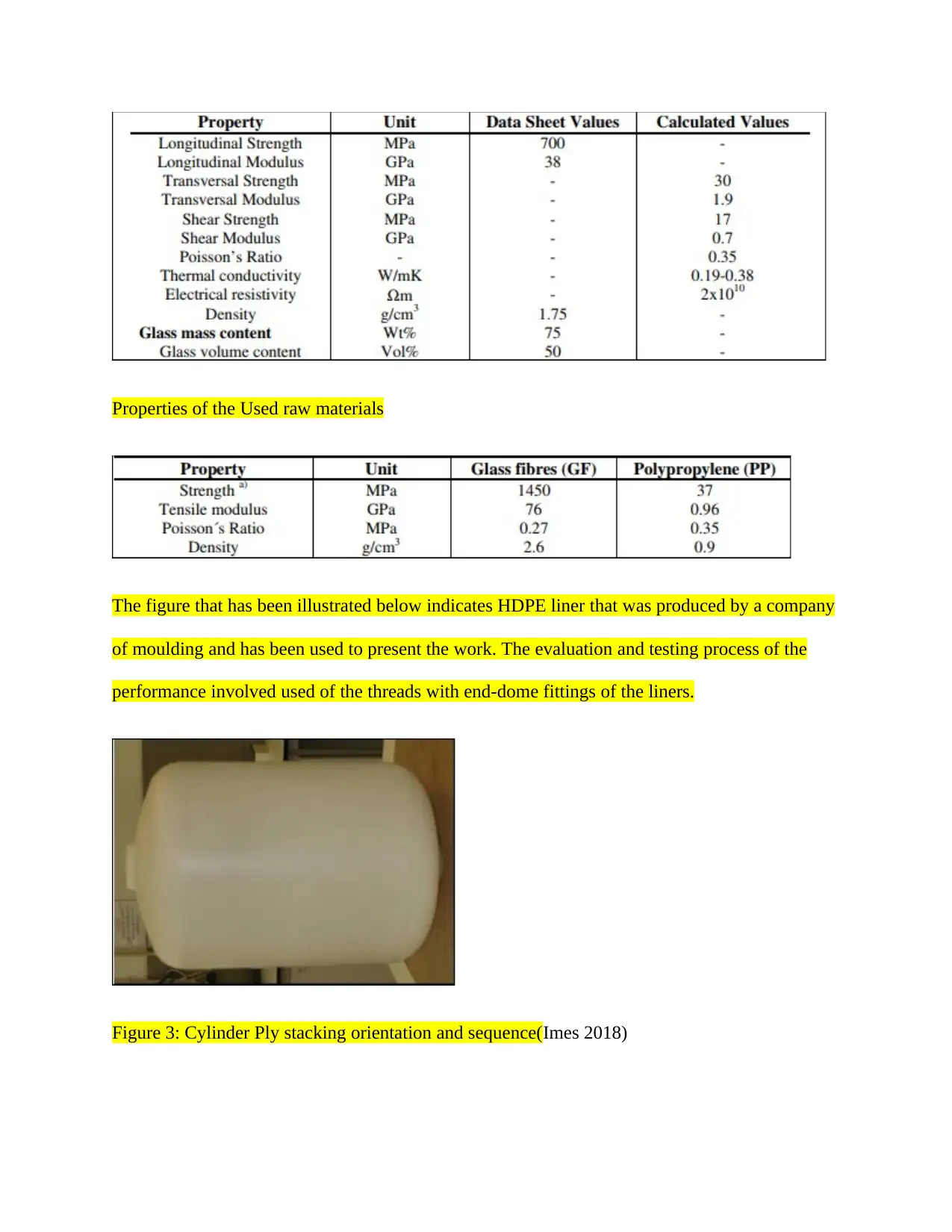
Properties of the Used raw materials
The figure that has been illustrated below indicates HDPE liner that was produced by a company
of moulding and has been used to present the work. The evaluation and testing process of the
performance involved used of the threads with end-dome fittings of the liners.
Figure 3: Cylinder Ply stacking orientation and sequence(Imes 2018)
The figure that has been illustrated below indicates HDPE liner that was produced by a company
of moulding and has been used to present the work. The evaluation and testing process of the
performance involved used of the threads with end-dome fittings of the liners.
Figure 3: Cylinder Ply stacking orientation and sequence(Imes 2018)
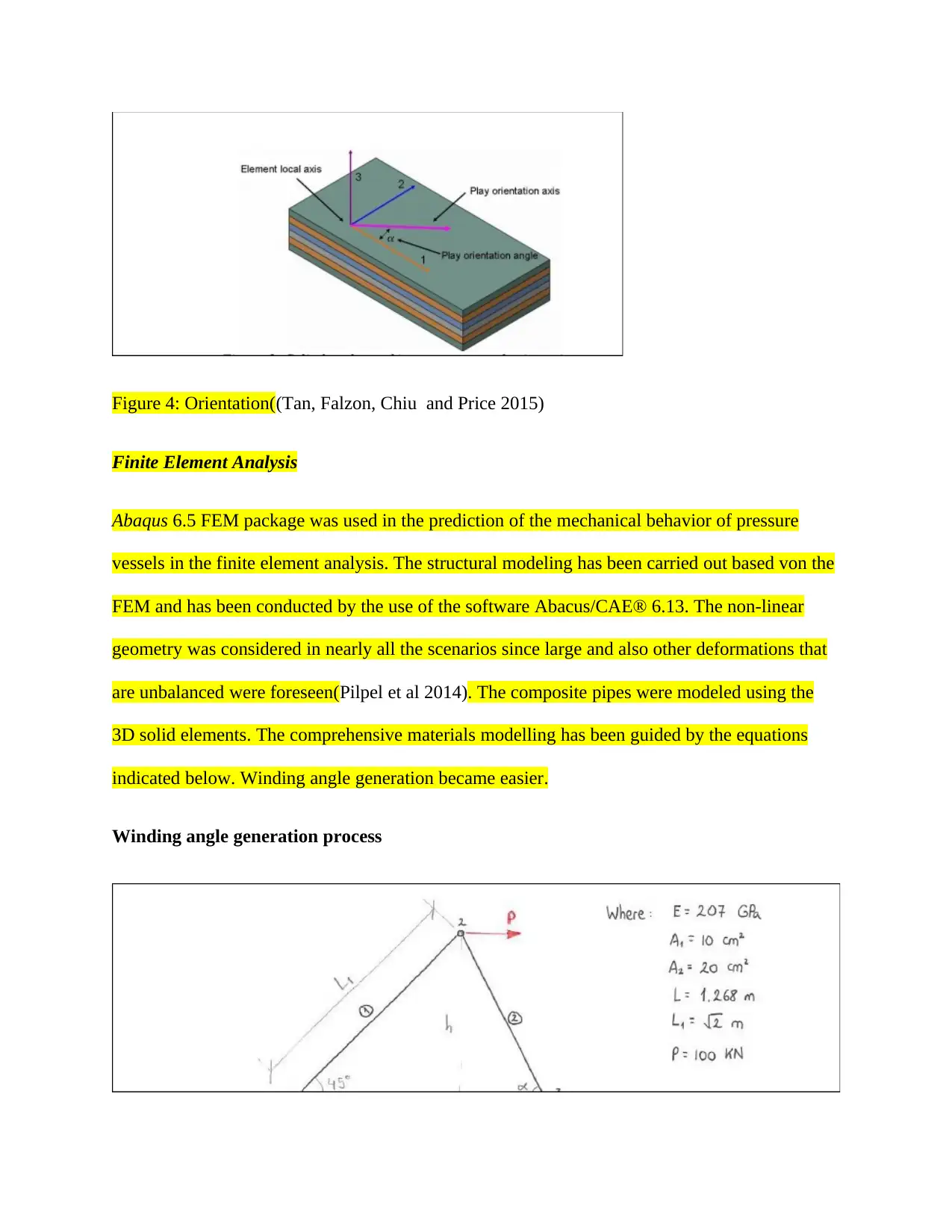
Figure 4: Orientation((Tan, Falzon, Chiu and Price 2015)
Finite Element Analysis
Abaqus 6.5 FEM package was used in the prediction of the mechanical behavior of pressure
vessels in the finite element analysis. The structural modeling has been carried out based von the
FEM and has been conducted by the use of the software Abacus/CAE® 6.13. The non-linear
geometry was considered in nearly all the scenarios since large and also other deformations that
are unbalanced were foreseen(Pilpel et al 2014). The composite pipes were modeled using the
3D solid elements. The comprehensive materials modelling has been guided by the equations
indicated below. Winding angle generation became easier.
Winding angle generation process
Finite Element Analysis
Abaqus 6.5 FEM package was used in the prediction of the mechanical behavior of pressure
vessels in the finite element analysis. The structural modeling has been carried out based von the
FEM and has been conducted by the use of the software Abacus/CAE® 6.13. The non-linear
geometry was considered in nearly all the scenarios since large and also other deformations that
are unbalanced were foreseen(Pilpel et al 2014). The composite pipes were modeled using the
3D solid elements. The comprehensive materials modelling has been guided by the equations
indicated below. Winding angle generation became easier.
Winding angle generation process
Secure Best Marks with AI Grader
Need help grading? Try our AI Grader for instant feedback on your assignments.
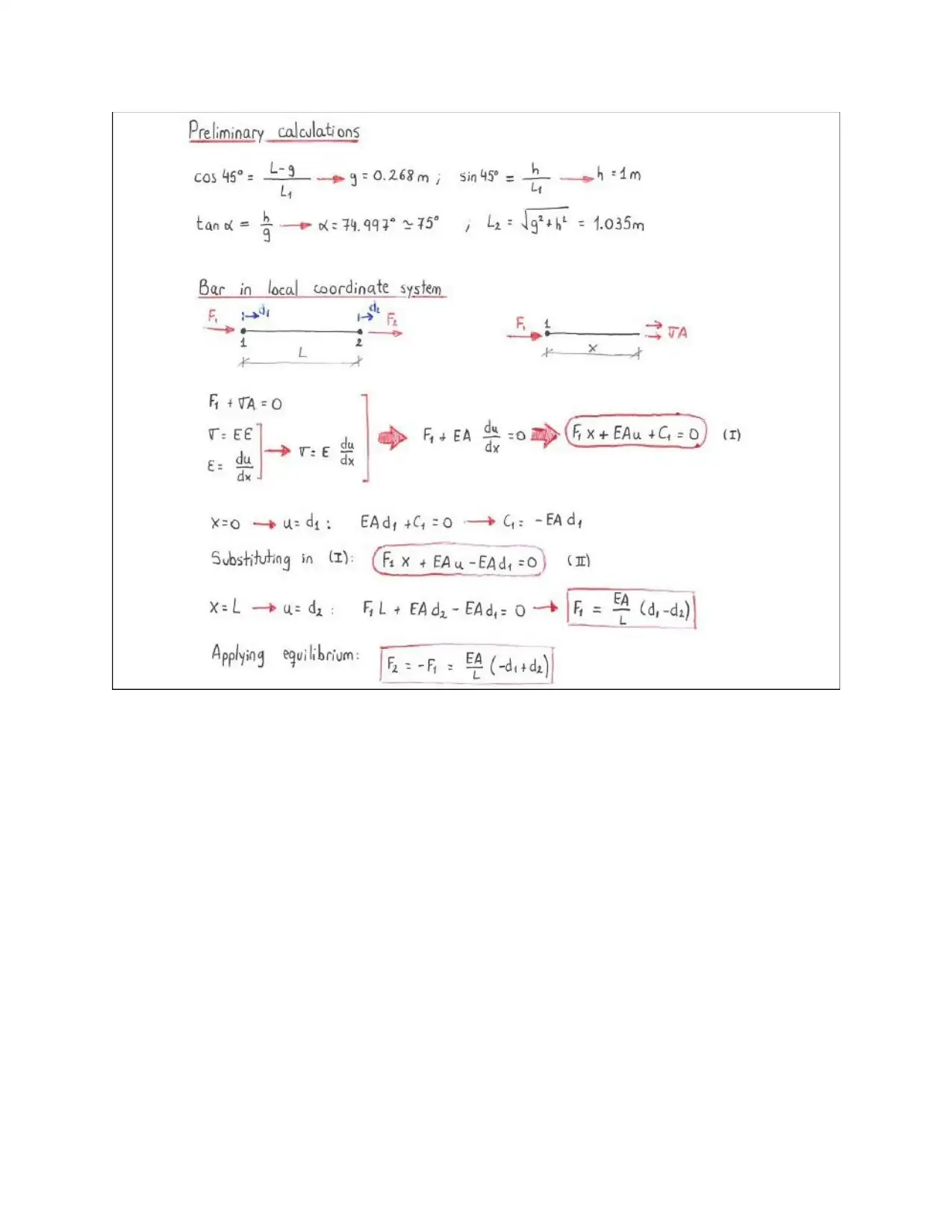
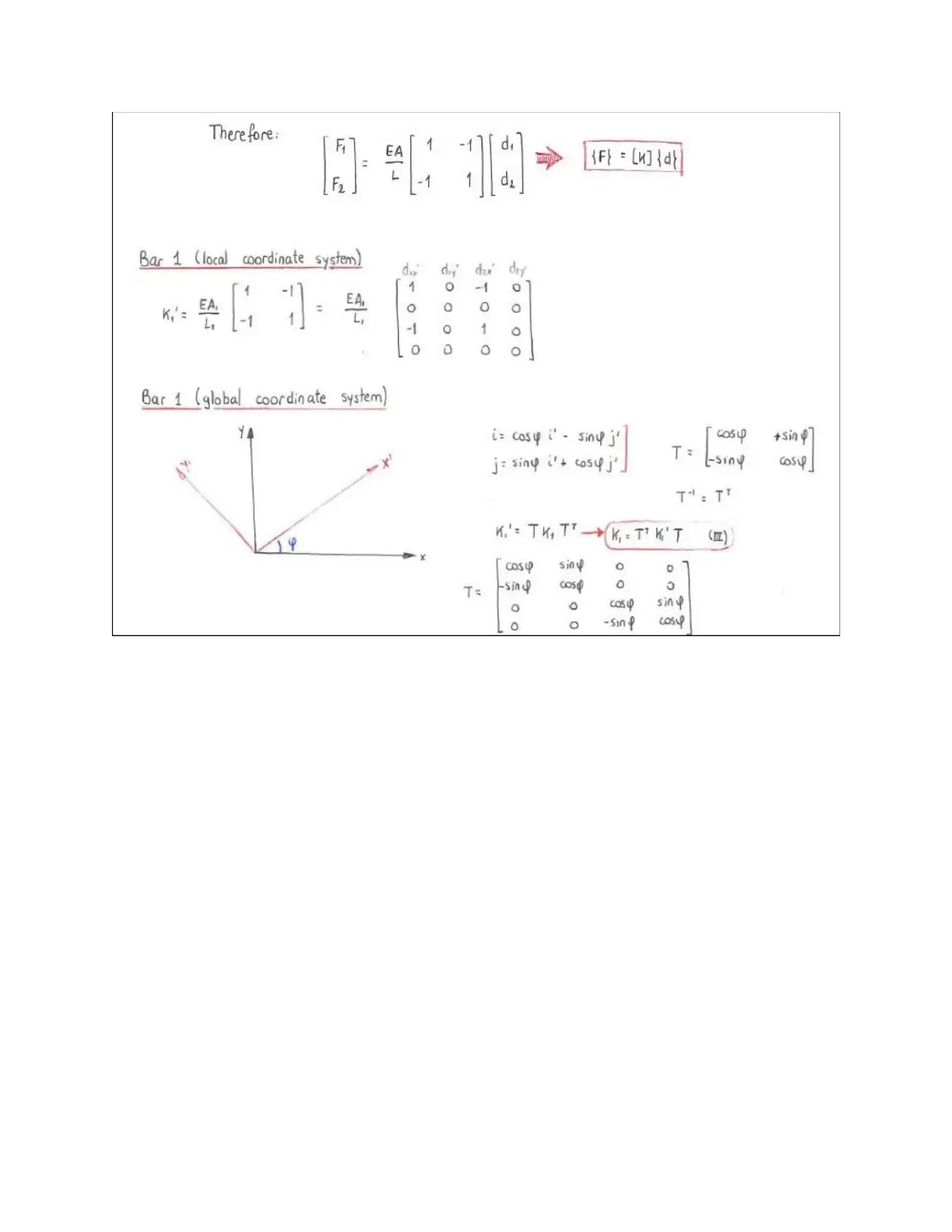
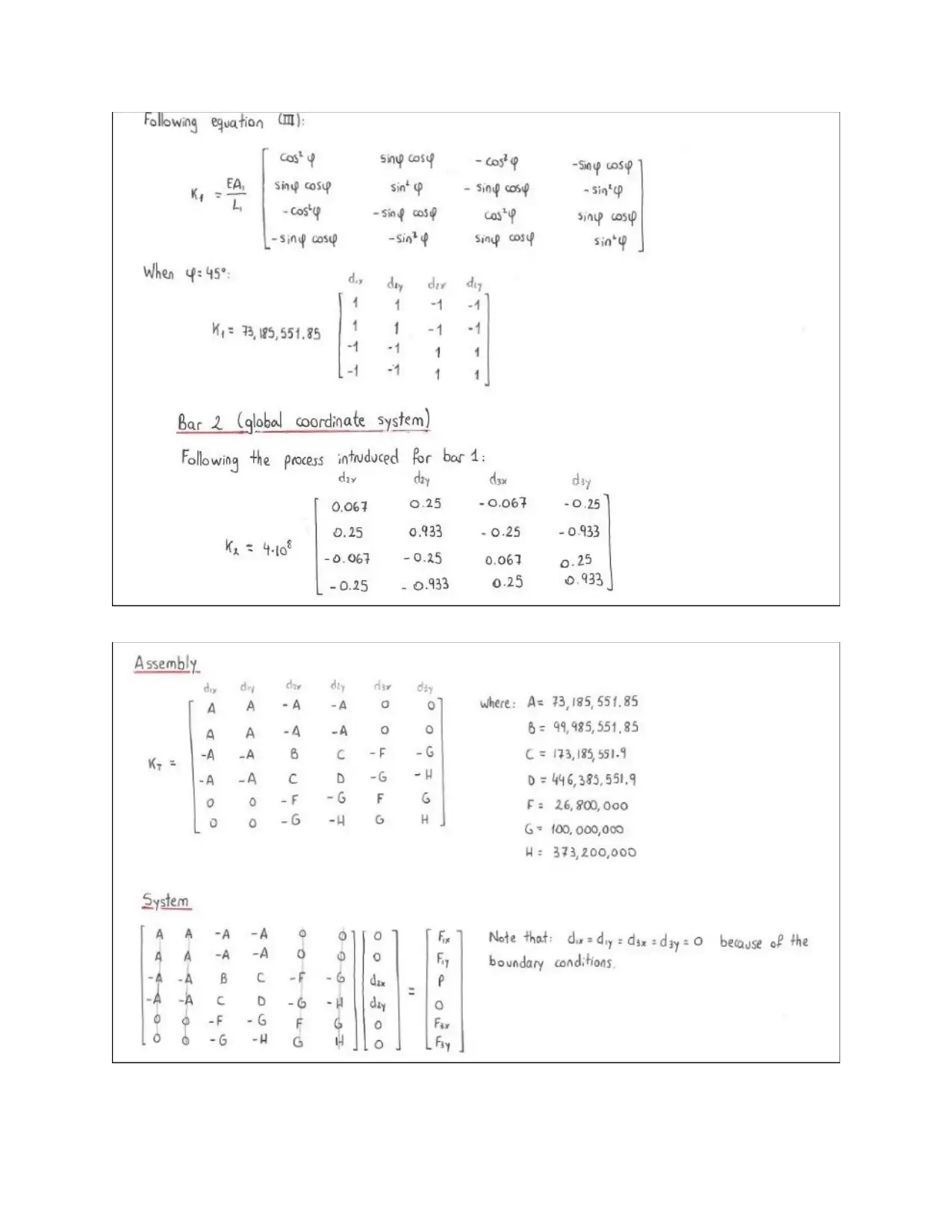
Paraphrase This Document
Need a fresh take? Get an instant paraphrase of this document with our AI Paraphraser
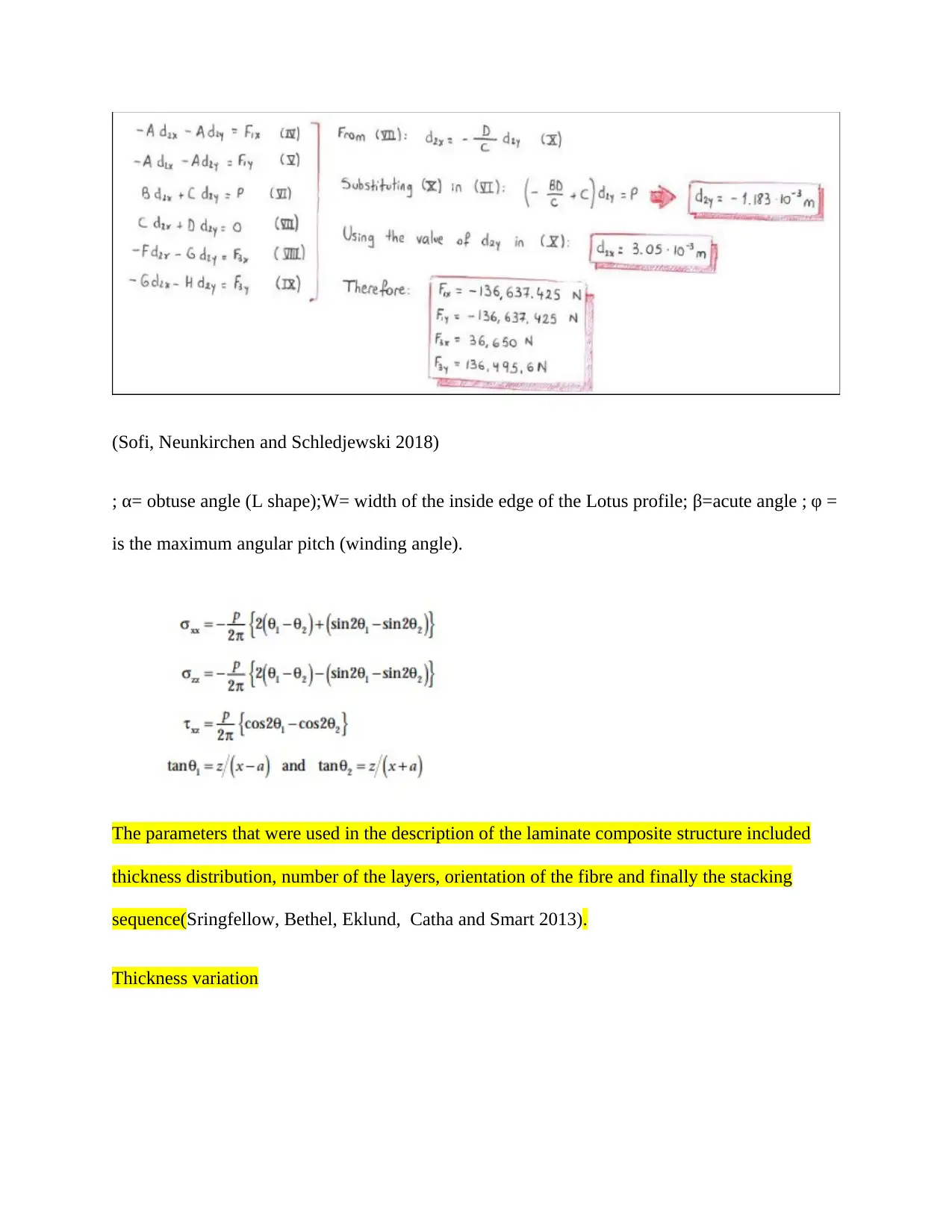
(Sofi, Neunkirchen and Schledjewski 2018)
; α= obtuse angle (L shape);W= width of the inside edge of the Lotus profile; β=acute angle ; φ =
is the maximum angular pitch (winding angle).
The parameters that were used in the description of the laminate composite structure included
thickness distribution, number of the layers, orientation of the fibre and finally the stacking
sequence(Sringfellow, Bethel, Eklund, Catha and Smart 2013).
Thickness variation
; α= obtuse angle (L shape);W= width of the inside edge of the Lotus profile; β=acute angle ; φ =
is the maximum angular pitch (winding angle).
The parameters that were used in the description of the laminate composite structure included
thickness distribution, number of the layers, orientation of the fibre and finally the stacking
sequence(Sringfellow, Bethel, Eklund, Catha and Smart 2013).
Thickness variation
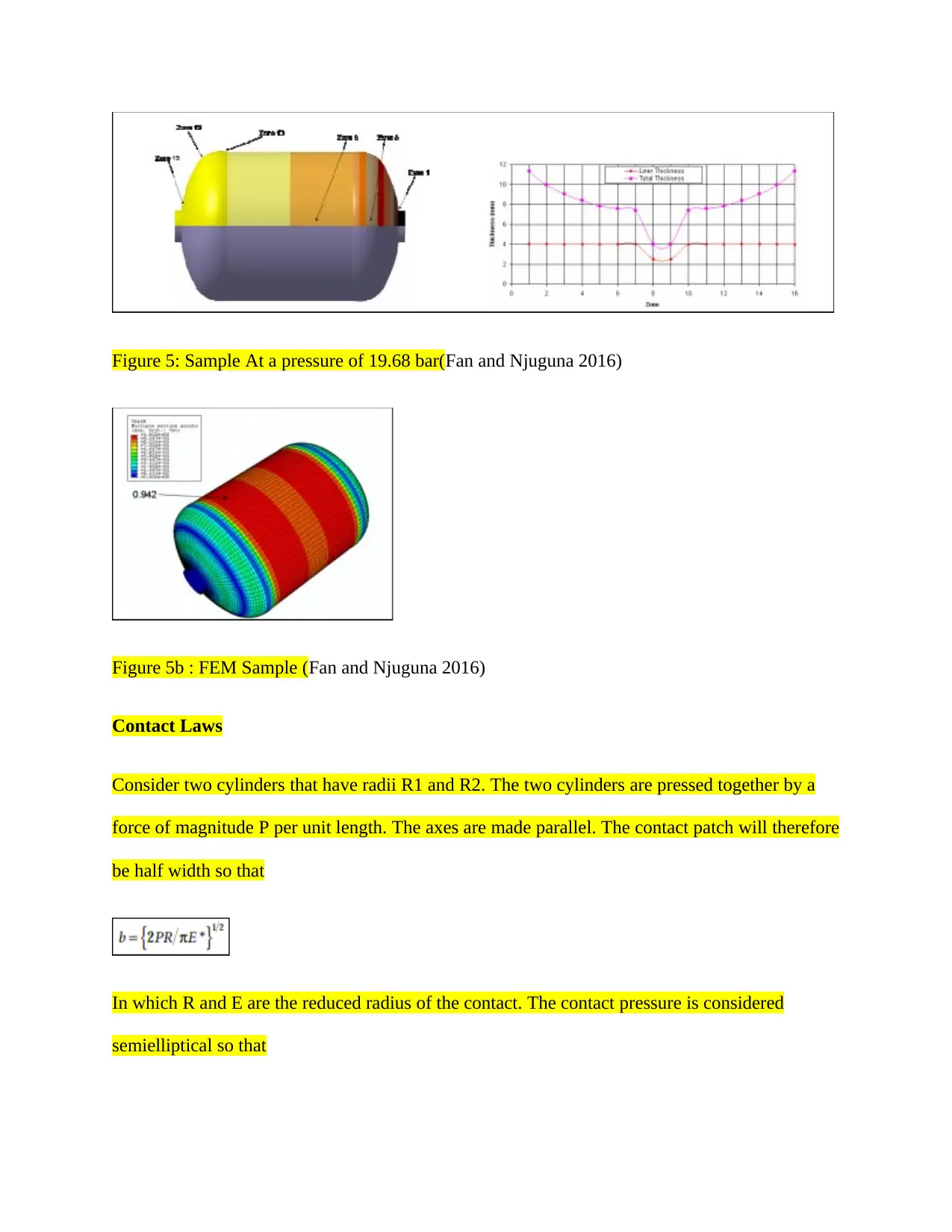
Figure 5: Sample At a pressure of 19.68 bar(Fan and Njuguna 2016)
Figure 5b : FEM Sample (Fan and Njuguna 2016)
Contact Laws
Consider two cylinders that have radii R1 and R2. The two cylinders are pressed together by a
force of magnitude P per unit length. The axes are made parallel. The contact patch will therefore
be half width so that
In which R and E are the reduced radius of the contact. The contact pressure is considered
semielliptical so that
Figure 5b : FEM Sample (Fan and Njuguna 2016)
Contact Laws
Consider two cylinders that have radii R1 and R2. The two cylinders are pressed together by a
force of magnitude P per unit length. The axes are made parallel. The contact patch will therefore
be half width so that
In which R and E are the reduced radius of the contact. The contact pressure is considered
semielliptical so that
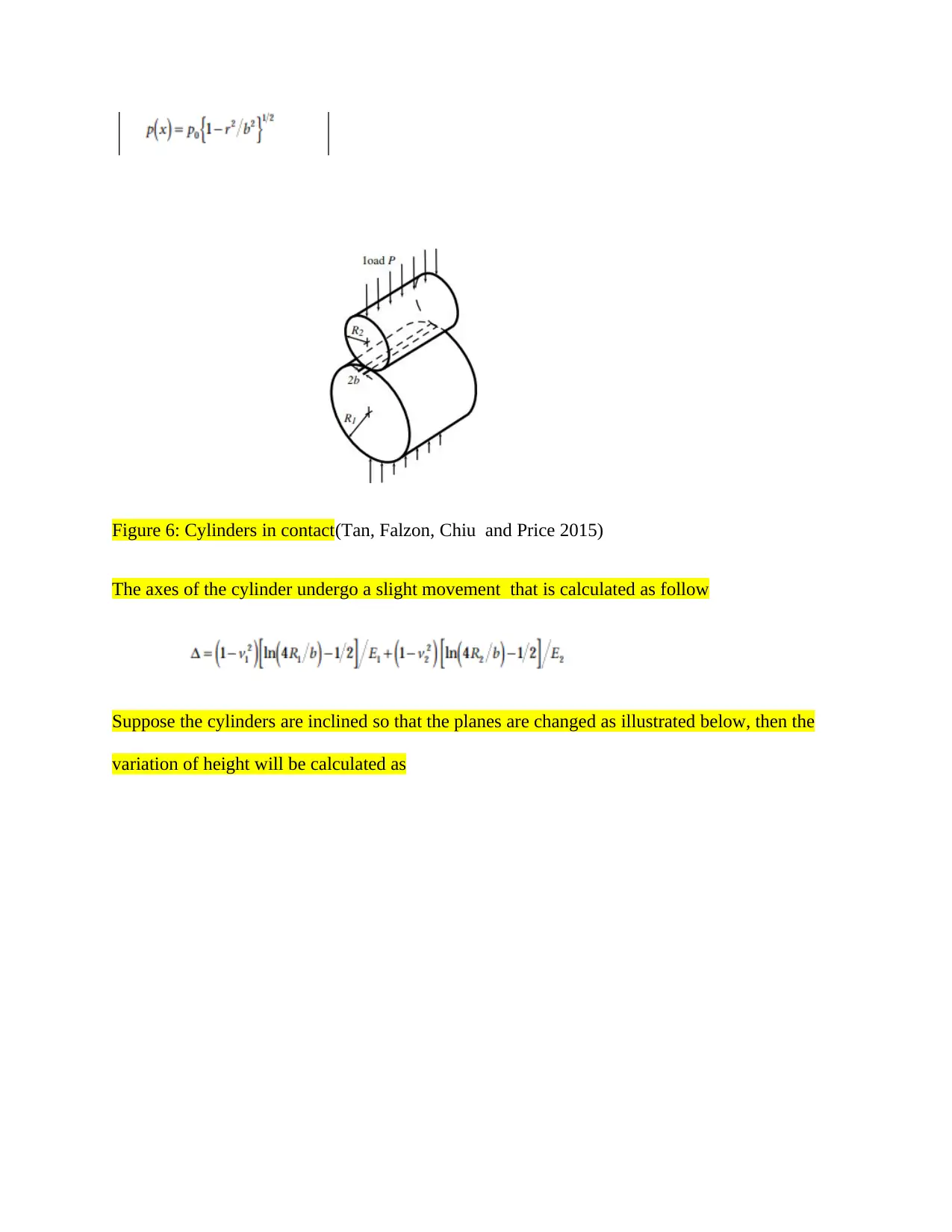
Figure 6: Cylinders in contact(Tan, Falzon, Chiu and Price 2015)
The axes of the cylinder undergo a slight movement that is calculated as follow
Suppose the cylinders are inclined so that the planes are changed as illustrated below, then the
variation of height will be calculated as
The axes of the cylinder undergo a slight movement that is calculated as follow
Suppose the cylinders are inclined so that the planes are changed as illustrated below, then the
variation of height will be calculated as
Secure Best Marks with AI Grader
Need help grading? Try our AI Grader for instant feedback on your assignments.
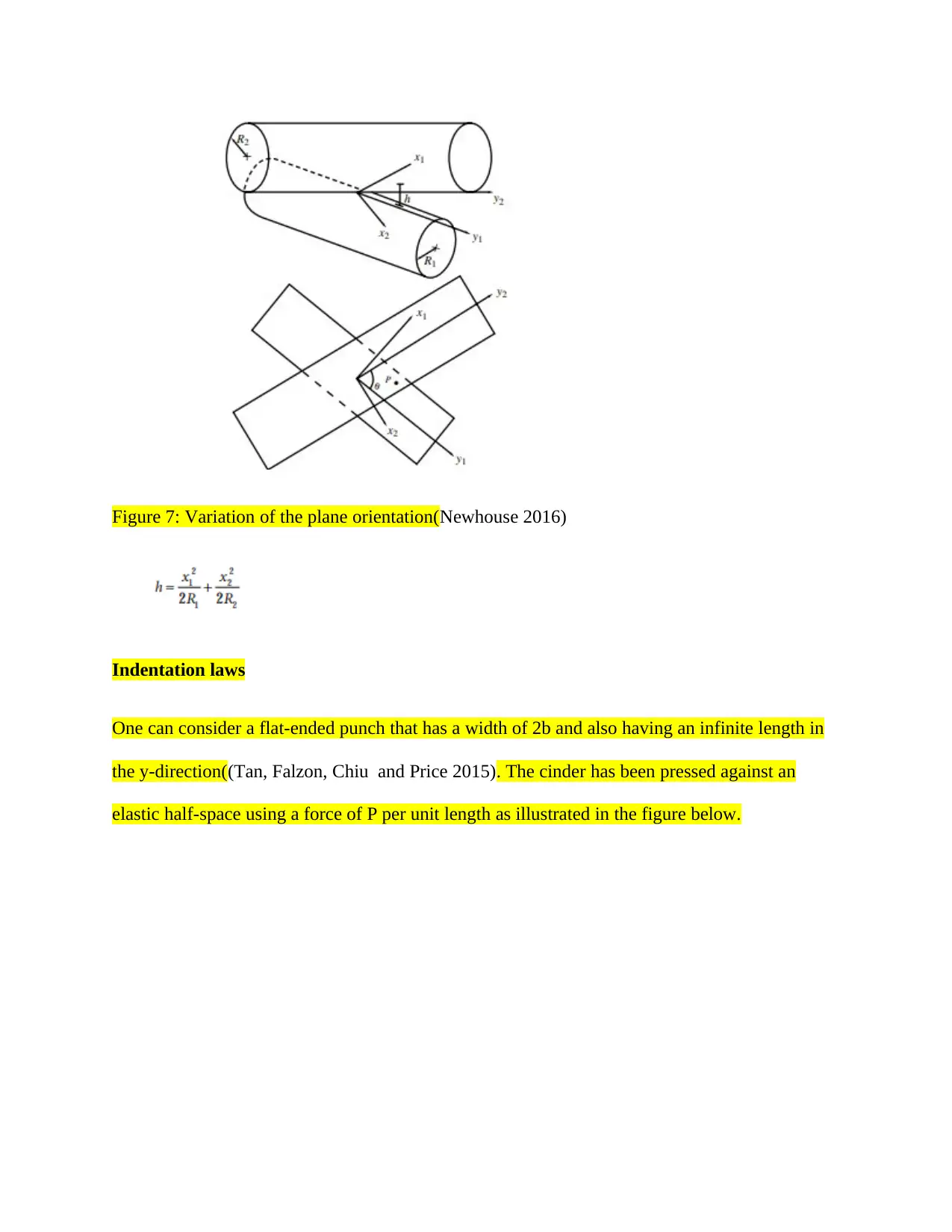
Figure 7: Variation of the plane orientation(Newhouse 2016)
Indentation laws
One can consider a flat-ended punch that has a width of 2b and also having an infinite length in
the y-direction((Tan, Falzon, Chiu and Price 2015). The cinder has been pressed against an
elastic half-space using a force of P per unit length as illustrated in the figure below.
Indentation laws
One can consider a flat-ended punch that has a width of 2b and also having an infinite length in
the y-direction((Tan, Falzon, Chiu and Price 2015). The cinder has been pressed against an
elastic half-space using a force of P per unit length as illustrated in the figure below.
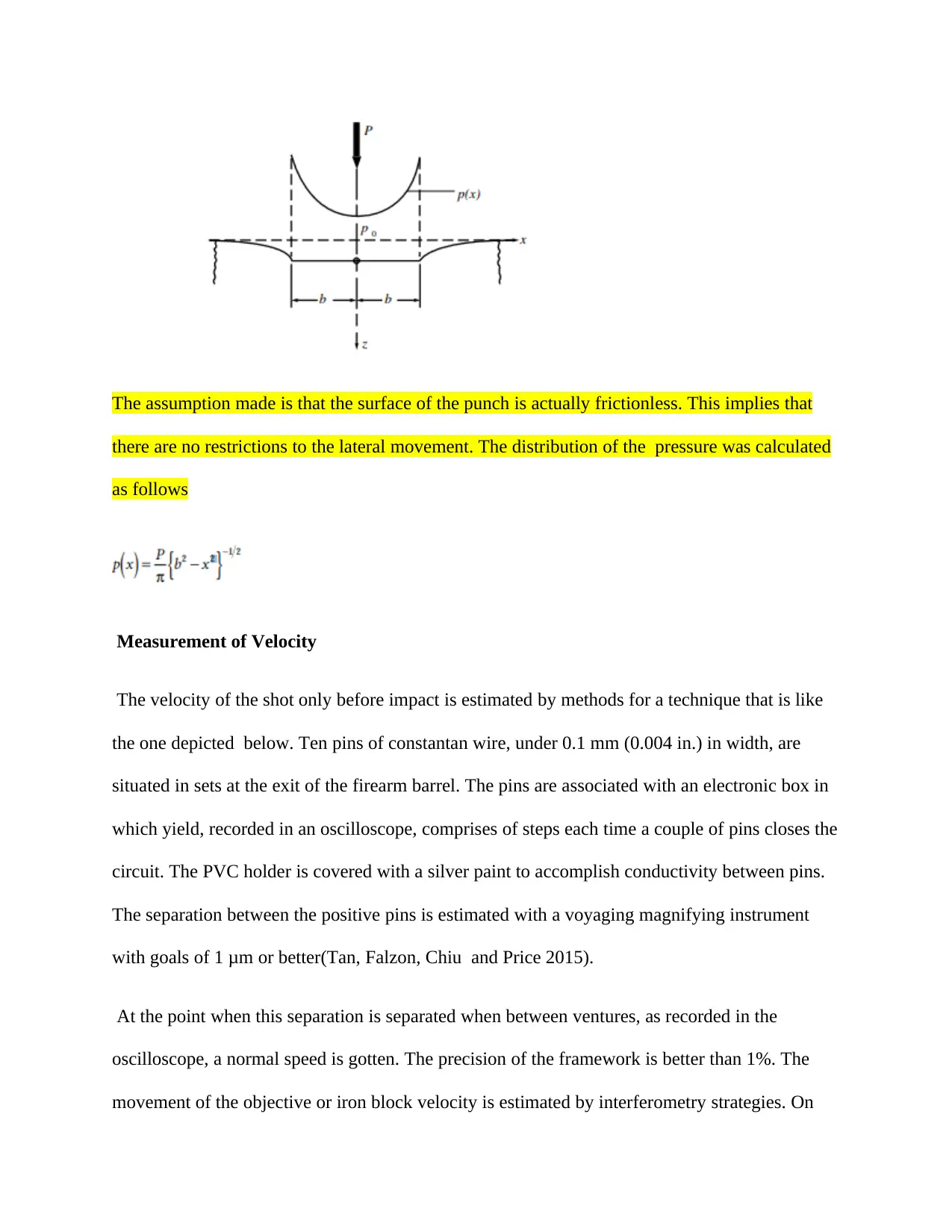
The assumption made is that the surface of the punch is actually frictionless. This implies that
there are no restrictions to the lateral movement. The distribution of the pressure was calculated
as follows
Measurement of Velocity
The velocity of the shot only before impact is estimated by methods for a technique that is like
the one depicted below. Ten pins of constantan wire, under 0.1 mm (0.004 in.) in width, are
situated in sets at the exit of the firearm barrel. The pins are associated with an electronic box in
which yield, recorded in an oscilloscope, comprises of steps each time a couple of pins closes the
circuit. The PVC holder is covered with a silver paint to accomplish conductivity between pins.
The separation between the positive pins is estimated with a voyaging magnifying instrument
with goals of 1 μm or better(Tan, Falzon, Chiu and Price 2015).
At the point when this separation is separated when between ventures, as recorded in the
oscilloscope, a normal speed is gotten. The precision of the framework is better than 1%. The
movement of the objective or iron block velocity is estimated by interferometry strategies. On
there are no restrictions to the lateral movement. The distribution of the pressure was calculated
as follows
Measurement of Velocity
The velocity of the shot only before impact is estimated by methods for a technique that is like
the one depicted below. Ten pins of constantan wire, under 0.1 mm (0.004 in.) in width, are
situated in sets at the exit of the firearm barrel. The pins are associated with an electronic box in
which yield, recorded in an oscilloscope, comprises of steps each time a couple of pins closes the
circuit. The PVC holder is covered with a silver paint to accomplish conductivity between pins.
The separation between the positive pins is estimated with a voyaging magnifying instrument
with goals of 1 μm or better(Tan, Falzon, Chiu and Price 2015).
At the point when this separation is separated when between ventures, as recorded in the
oscilloscope, a normal speed is gotten. The precision of the framework is better than 1%. The
movement of the objective or iron block velocity is estimated by interferometry strategies. On
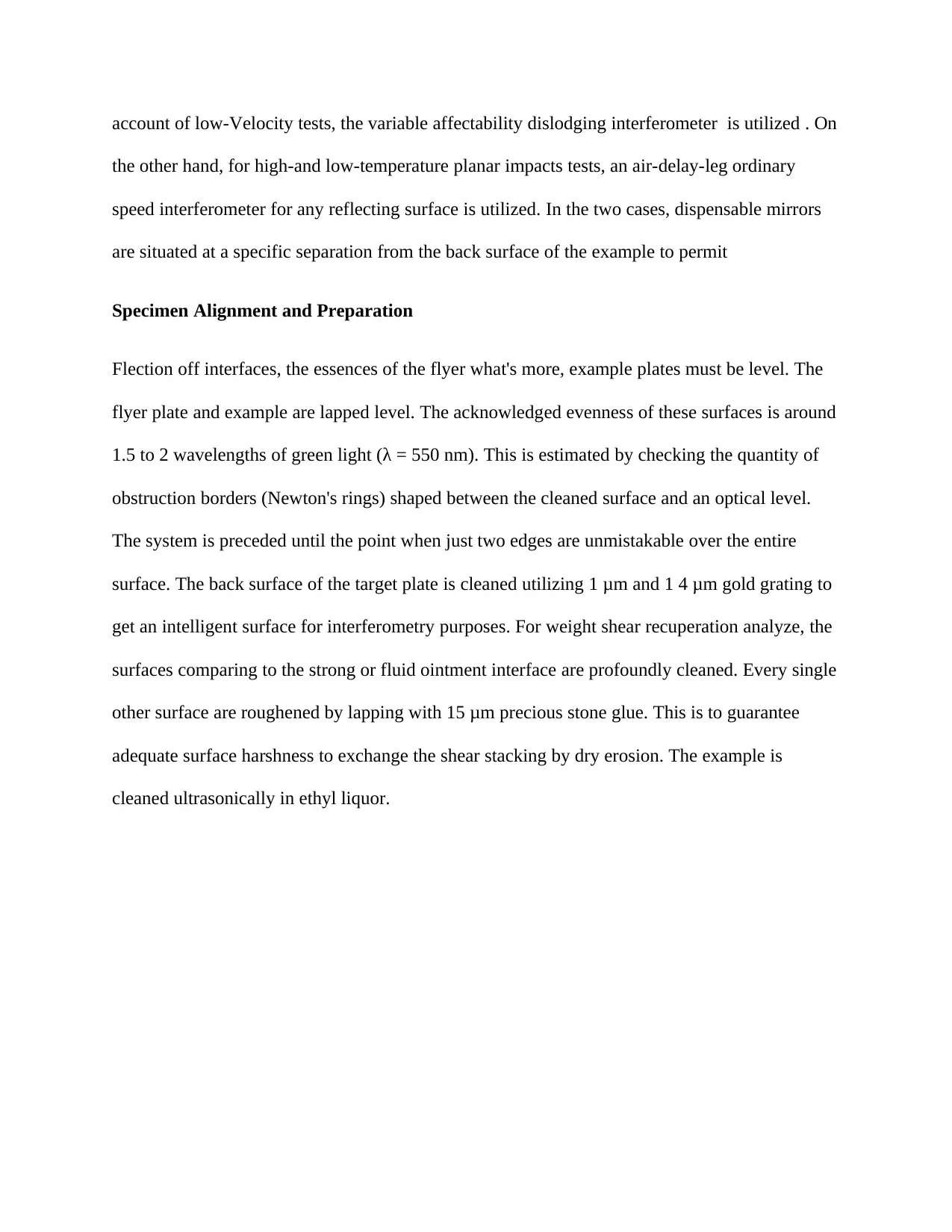
account of low-Velocity tests, the variable affectability dislodging interferometer is utilized . On
the other hand, for high-and low-temperature planar impacts tests, an air-delay-leg ordinary
speed interferometer for any reflecting surface is utilized. In the two cases, dispensable mirrors
are situated at a specific separation from the back surface of the example to permit
Specimen Alignment and Preparation
Flection off interfaces, the essences of the flyer what's more, example plates must be level. The
flyer plate and example are lapped level. The acknowledged evenness of these surfaces is around
1.5 to 2 wavelengths of green light (λ = 550 nm). This is estimated by checking the quantity of
obstruction borders (Newton's rings) shaped between the cleaned surface and an optical level.
The system is preceded until the point when just two edges are unmistakable over the entire
surface. The back surface of the target plate is cleaned utilizing 1 μm and 1 4 μm gold grating to
get an intelligent surface for interferometry purposes. For weight shear recuperation analyze, the
surfaces comparing to the strong or fluid ointment interface are profoundly cleaned. Every single
other surface are roughened by lapping with 15 μm precious stone glue. This is to guarantee
adequate surface harshness to exchange the shear stacking by dry erosion. The example is
cleaned ultrasonically in ethyl liquor.
the other hand, for high-and low-temperature planar impacts tests, an air-delay-leg ordinary
speed interferometer for any reflecting surface is utilized. In the two cases, dispensable mirrors
are situated at a specific separation from the back surface of the example to permit
Specimen Alignment and Preparation
Flection off interfaces, the essences of the flyer what's more, example plates must be level. The
flyer plate and example are lapped level. The acknowledged evenness of these surfaces is around
1.5 to 2 wavelengths of green light (λ = 550 nm). This is estimated by checking the quantity of
obstruction borders (Newton's rings) shaped between the cleaned surface and an optical level.
The system is preceded until the point when just two edges are unmistakable over the entire
surface. The back surface of the target plate is cleaned utilizing 1 μm and 1 4 μm gold grating to
get an intelligent surface for interferometry purposes. For weight shear recuperation analyze, the
surfaces comparing to the strong or fluid ointment interface are profoundly cleaned. Every single
other surface are roughened by lapping with 15 μm precious stone glue. This is to guarantee
adequate surface harshness to exchange the shear stacking by dry erosion. The example is
cleaned ultrasonically in ethyl liquor.
Paraphrase This Document
Need a fresh take? Get an instant paraphrase of this document with our AI Paraphraser

Figure 8: Component set up(Vieille, Casado and Bouvet 2013)
Plate Impact Soft-Recovery Experiment
Ordinary and weight shear plate impact delicate recuperation tests offer alluring potential
outcomes for distinguishing the foremost systems of inelasticity under unique strain and
pressure, with and without an going with shearing. The examples are recouped, permitting their
examination by methods for minuscule portrayal. This element, together with the continuous
pressure narratives, may be utilized to survey the legitimacy of constitutive models. This sort of
investigates weak materials gives data on the beginning of versatile forerunner rot, spall quality,
and material softening due to micro cracking. A plate affect try includes the effect of a moving
level plate, called a flyer, with another stationary plate, called the objective, which might be the
Plate Impact Soft-Recovery Experiment
Ordinary and weight shear plate impact delicate recuperation tests offer alluring potential
outcomes for distinguishing the foremost systems of inelasticity under unique strain and
pressure, with and without an going with shearing. The examples are recouped, permitting their
examination by methods for minuscule portrayal. This element, together with the continuous
pressure narratives, may be utilized to survey the legitimacy of constitutive models. This sort of
investigates weak materials gives data on the beginning of versatile forerunner rot, spall quality,
and material softening due to micro cracking. A plate affect try includes the effect of a moving
level plate, called a flyer, with another stationary plate, called the objective, which might be the
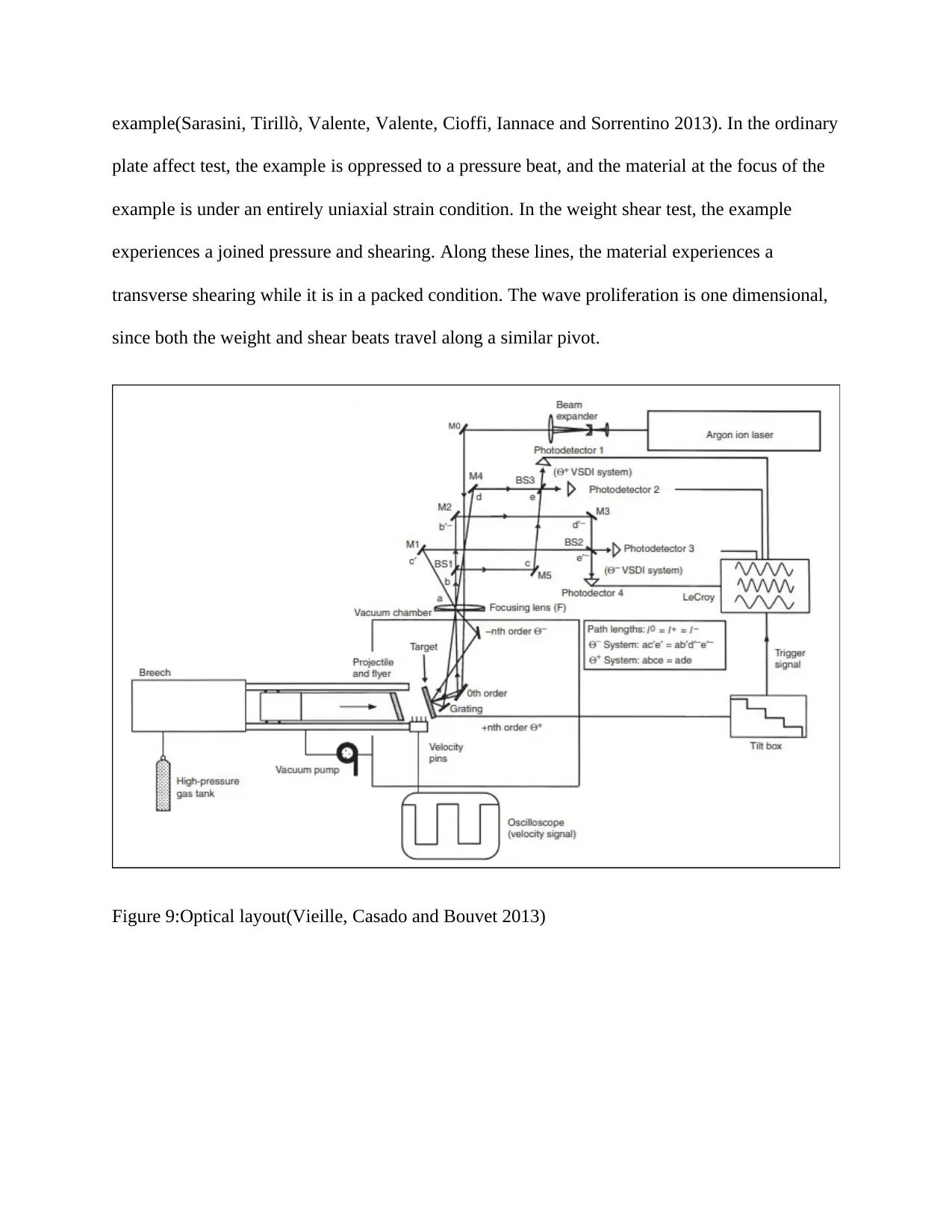
example(Sarasini, Tirillò, Valente, Valente, Cioffi, Iannace and Sorrentino 2013). In the ordinary
plate affect test, the example is oppressed to a pressure beat, and the material at the focus of the
example is under an entirely uniaxial strain condition. In the weight shear test, the example
experiences a joined pressure and shearing. Along these lines, the material experiences a
transverse shearing while it is in a packed condition. The wave proliferation is one dimensional,
since both the weight and shear beats travel along a similar pivot.
Figure 9:Optical layout(Vieille, Casado and Bouvet 2013)
plate affect test, the example is oppressed to a pressure beat, and the material at the focus of the
example is under an entirely uniaxial strain condition. In the weight shear test, the example
experiences a joined pressure and shearing. Along these lines, the material experiences a
transverse shearing while it is in a packed condition. The wave proliferation is one dimensional,
since both the weight and shear beats travel along a similar pivot.
Figure 9:Optical layout(Vieille, Casado and Bouvet 2013)
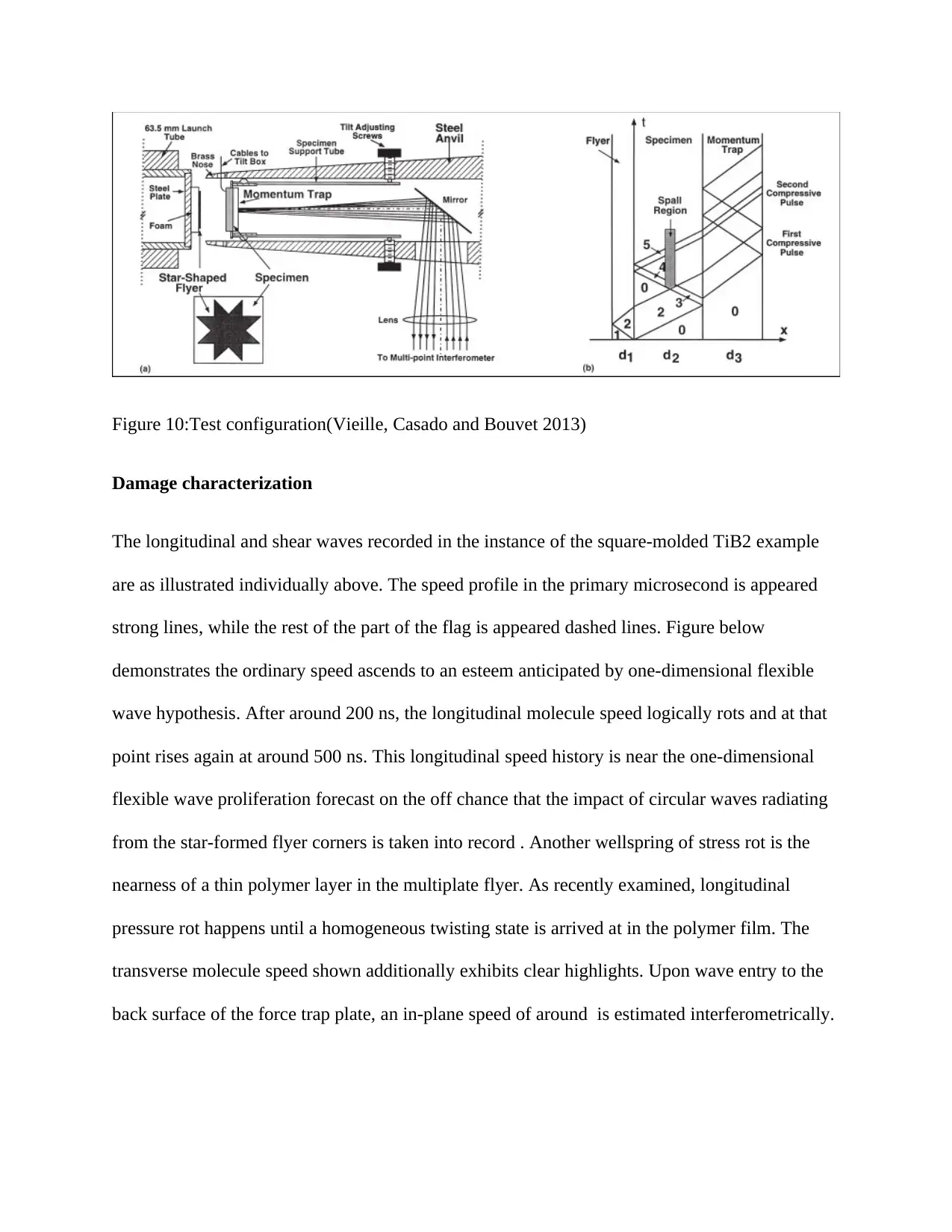
Figure 10:Test configuration(Vieille, Casado and Bouvet 2013)
Damage characterization
The longitudinal and shear waves recorded in the instance of the square-molded TiB2 example
are as illustrated individually above. The speed profile in the primary microsecond is appeared
strong lines, while the rest of the part of the flag is appeared dashed lines. Figure below
demonstrates the ordinary speed ascends to an esteem anticipated by one-dimensional flexible
wave hypothesis. After around 200 ns, the longitudinal molecule speed logically rots and at that
point rises again at around 500 ns. This longitudinal speed history is near the one-dimensional
flexible wave proliferation forecast on the off chance that the impact of circular waves radiating
from the star-formed flyer corners is taken into record . Another wellspring of stress rot is the
nearness of a thin polymer layer in the multiplate flyer. As recently examined, longitudinal
pressure rot happens until a homogeneous twisting state is arrived at in the polymer film. The
transverse molecule speed shown additionally exhibits clear highlights. Upon wave entry to the
back surface of the force trap plate, an in-plane speed of around is estimated interferometrically.
Damage characterization
The longitudinal and shear waves recorded in the instance of the square-molded TiB2 example
are as illustrated individually above. The speed profile in the primary microsecond is appeared
strong lines, while the rest of the part of the flag is appeared dashed lines. Figure below
demonstrates the ordinary speed ascends to an esteem anticipated by one-dimensional flexible
wave hypothesis. After around 200 ns, the longitudinal molecule speed logically rots and at that
point rises again at around 500 ns. This longitudinal speed history is near the one-dimensional
flexible wave proliferation forecast on the off chance that the impact of circular waves radiating
from the star-formed flyer corners is taken into record . Another wellspring of stress rot is the
nearness of a thin polymer layer in the multiplate flyer. As recently examined, longitudinal
pressure rot happens until a homogeneous twisting state is arrived at in the polymer film. The
transverse molecule speed shown additionally exhibits clear highlights. Upon wave entry to the
back surface of the force trap plate, an in-plane speed of around is estimated interferometrically.
Secure Best Marks with AI Grader
Need help grading? Try our AI Grader for instant feedback on your assignments.
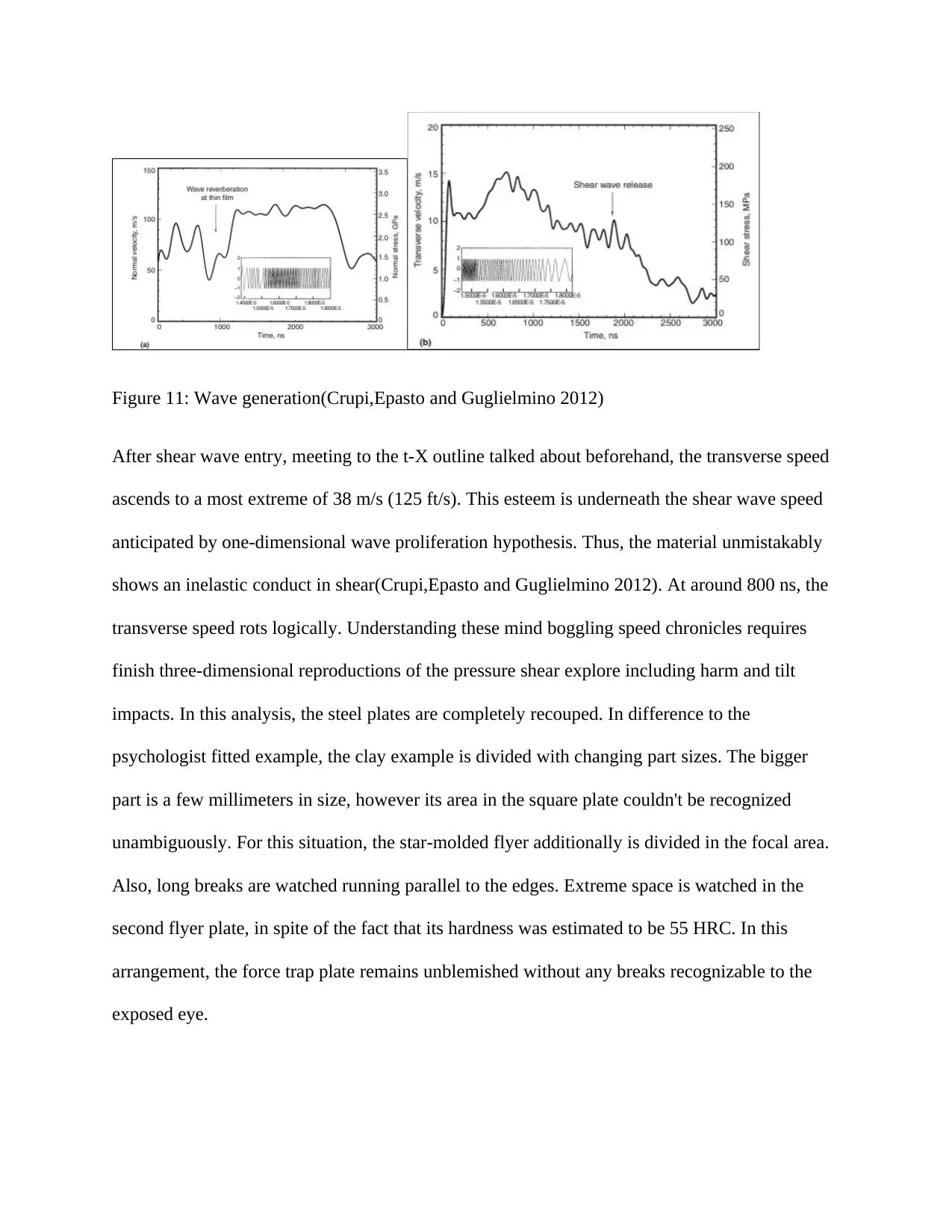
Figure 11: Wave generation(Crupi,Epasto and Guglielmino 2012)
After shear wave entry, meeting to the t-X outline talked about beforehand, the transverse speed
ascends to a most extreme of 38 m/s (125 ft/s). This esteem is underneath the shear wave speed
anticipated by one-dimensional wave proliferation hypothesis. Thus, the material unmistakably
shows an inelastic conduct in shear(Crupi,Epasto and Guglielmino 2012). At around 800 ns, the
transverse speed rots logically. Understanding these mind boggling speed chronicles requires
finish three-dimensional reproductions of the pressure shear explore including harm and tilt
impacts. In this analysis, the steel plates are completely recouped. In difference to the
psychologist fitted example, the clay example is divided with changing part sizes. The bigger
part is a few millimeters in size, however its area in the square plate couldn't be recognized
unambiguously. For this situation, the star-molded flyer additionally is divided in the focal area.
Also, long breaks are watched running parallel to the edges. Extreme space is watched in the
second flyer plate, in spite of the fact that its hardness was estimated to be 55 HRC. In this
arrangement, the force trap plate remains unblemished without any breaks recognizable to the
exposed eye.
After shear wave entry, meeting to the t-X outline talked about beforehand, the transverse speed
ascends to a most extreme of 38 m/s (125 ft/s). This esteem is underneath the shear wave speed
anticipated by one-dimensional wave proliferation hypothesis. Thus, the material unmistakably
shows an inelastic conduct in shear(Crupi,Epasto and Guglielmino 2012). At around 800 ns, the
transverse speed rots logically. Understanding these mind boggling speed chronicles requires
finish three-dimensional reproductions of the pressure shear explore including harm and tilt
impacts. In this analysis, the steel plates are completely recouped. In difference to the
psychologist fitted example, the clay example is divided with changing part sizes. The bigger
part is a few millimeters in size, however its area in the square plate couldn't be recognized
unambiguously. For this situation, the star-molded flyer additionally is divided in the focal area.
Also, long breaks are watched running parallel to the edges. Extreme space is watched in the
second flyer plate, in spite of the fact that its hardness was estimated to be 55 HRC. In this
arrangement, the force trap plate remains unblemished without any breaks recognizable to the
exposed eye.
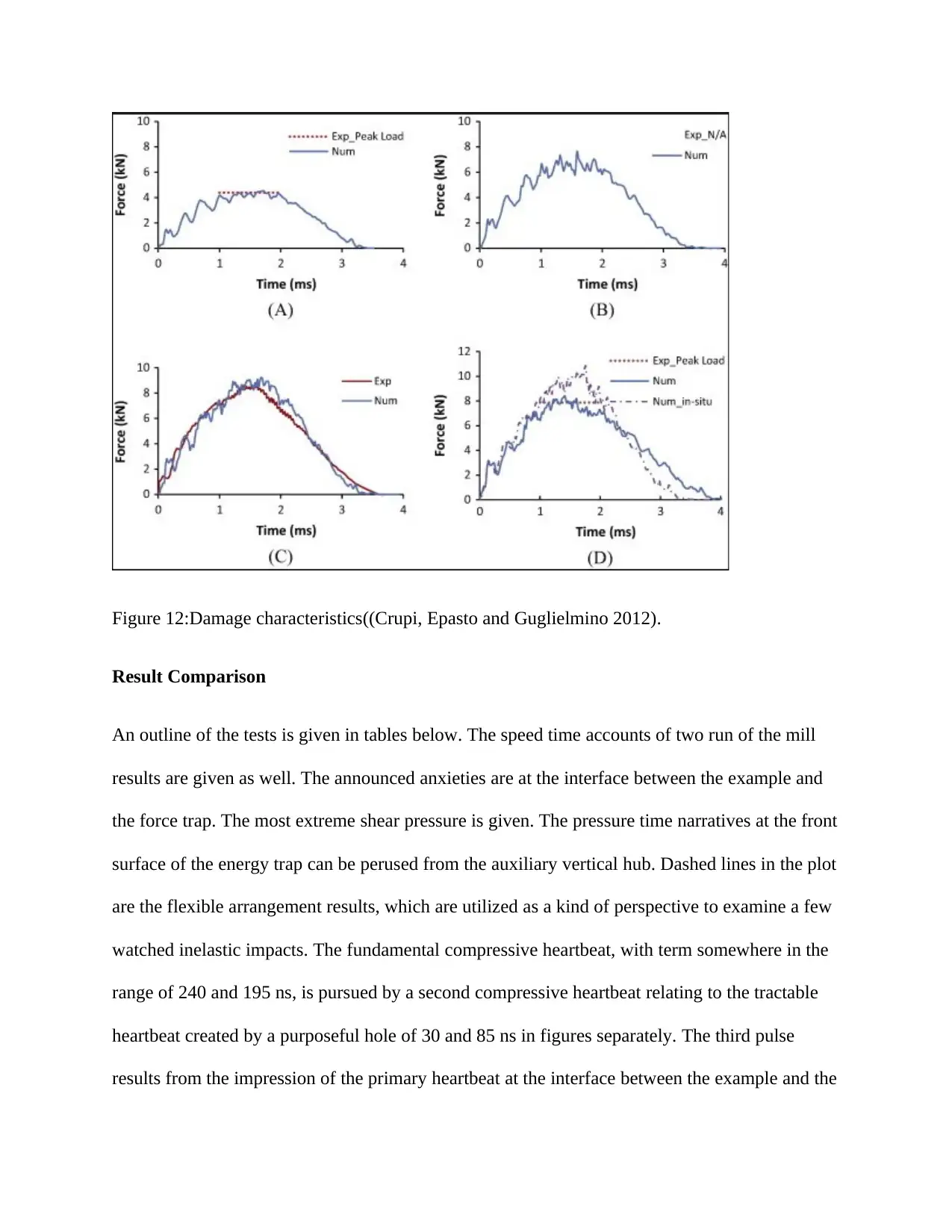
Figure 12:Damage characteristics((Crupi, Epasto and Guglielmino 2012).
Result Comparison
An outline of the tests is given in tables below. The speed time accounts of two run of the mill
results are given as well. The announced anxieties are at the interface between the example and
the force trap. The most extreme shear pressure is given. The pressure time narratives at the front
surface of the energy trap can be perused from the auxiliary vertical hub. Dashed lines in the plot
are the flexible arrangement results, which are utilized as a kind of perspective to examine a few
watched inelastic impacts. The fundamental compressive heartbeat, with term somewhere in the
range of 240 and 195 ns, is pursued by a second compressive heartbeat relating to the tractable
heartbeat created by a purposeful hole of 30 and 85 ns in figures separately. The third pulse
results from the impression of the primary heartbeat at the interface between the example and the
Result Comparison
An outline of the tests is given in tables below. The speed time accounts of two run of the mill
results are given as well. The announced anxieties are at the interface between the example and
the force trap. The most extreme shear pressure is given. The pressure time narratives at the front
surface of the energy trap can be perused from the auxiliary vertical hub. Dashed lines in the plot
are the flexible arrangement results, which are utilized as a kind of perspective to examine a few
watched inelastic impacts. The fundamental compressive heartbeat, with term somewhere in the
range of 240 and 195 ns, is pursued by a second compressive heartbeat relating to the tractable
heartbeat created by a purposeful hole of 30 and 85 ns in figures separately. The third pulse
results from the impression of the primary heartbeat at the interface between the example and the
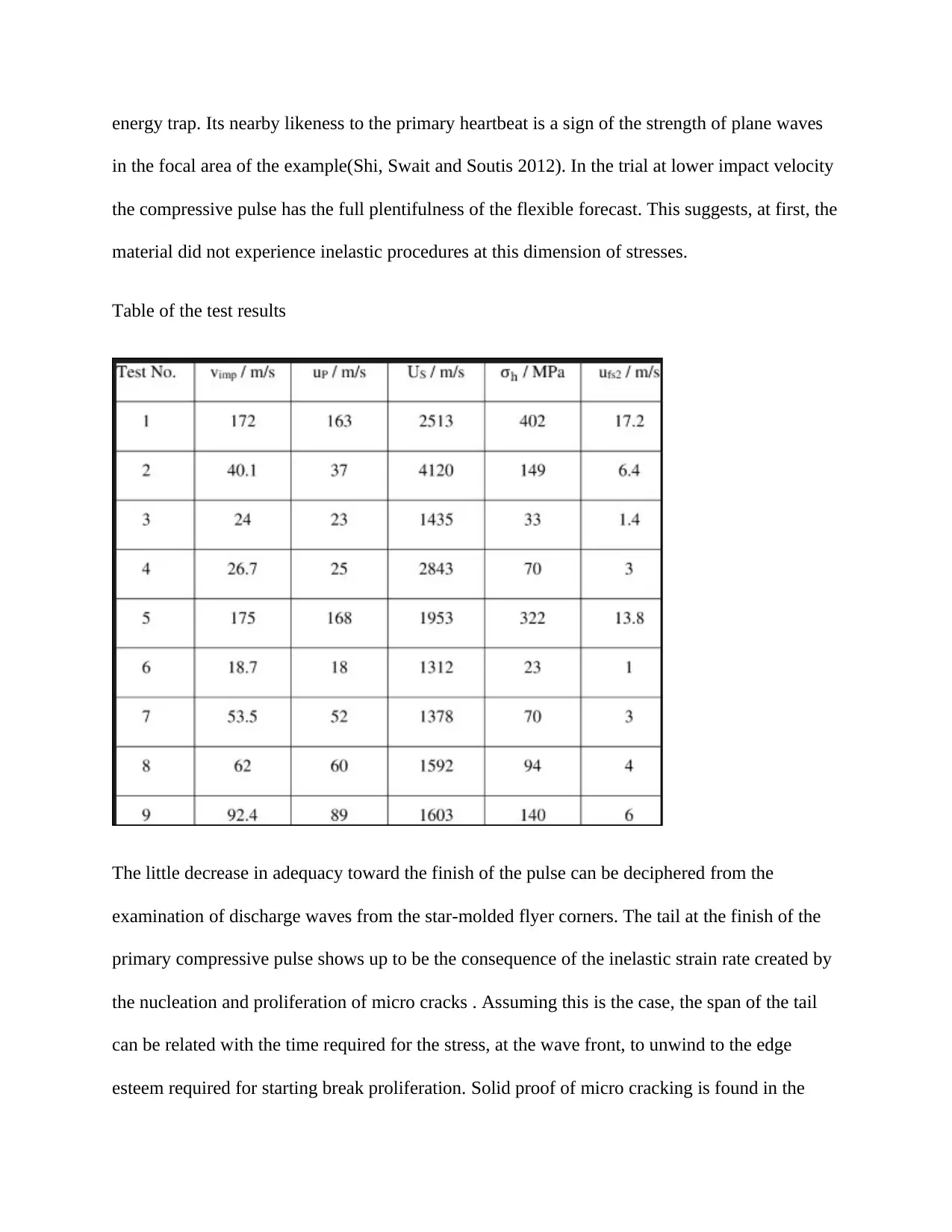
energy trap. Its nearby likeness to the primary heartbeat is a sign of the strength of plane waves
in the focal area of the example(Shi, Swait and Soutis 2012). In the trial at lower impact velocity
the compressive pulse has the full plentifulness of the flexible forecast. This suggests, at first, the
material did not experience inelastic procedures at this dimension of stresses.
Table of the test results
The little decrease in adequacy toward the finish of the pulse can be deciphered from the
examination of discharge waves from the star-molded flyer corners. The tail at the finish of the
primary compressive pulse shows up to be the consequence of the inelastic strain rate created by
the nucleation and proliferation of micro cracks . Assuming this is the case, the span of the tail
can be related with the time required for the stress, at the wave front, to unwind to the edge
esteem required for starting break proliferation. Solid proof of micro cracking is found in the
in the focal area of the example(Shi, Swait and Soutis 2012). In the trial at lower impact velocity
the compressive pulse has the full plentifulness of the flexible forecast. This suggests, at first, the
material did not experience inelastic procedures at this dimension of stresses.
Table of the test results
The little decrease in adequacy toward the finish of the pulse can be deciphered from the
examination of discharge waves from the star-molded flyer corners. The tail at the finish of the
primary compressive pulse shows up to be the consequence of the inelastic strain rate created by
the nucleation and proliferation of micro cracks . Assuming this is the case, the span of the tail
can be related with the time required for the stress, at the wave front, to unwind to the edge
esteem required for starting break proliferation. Solid proof of micro cracking is found in the
Paraphrase This Document
Need a fresh take? Get an instant paraphrase of this document with our AI Paraphraser
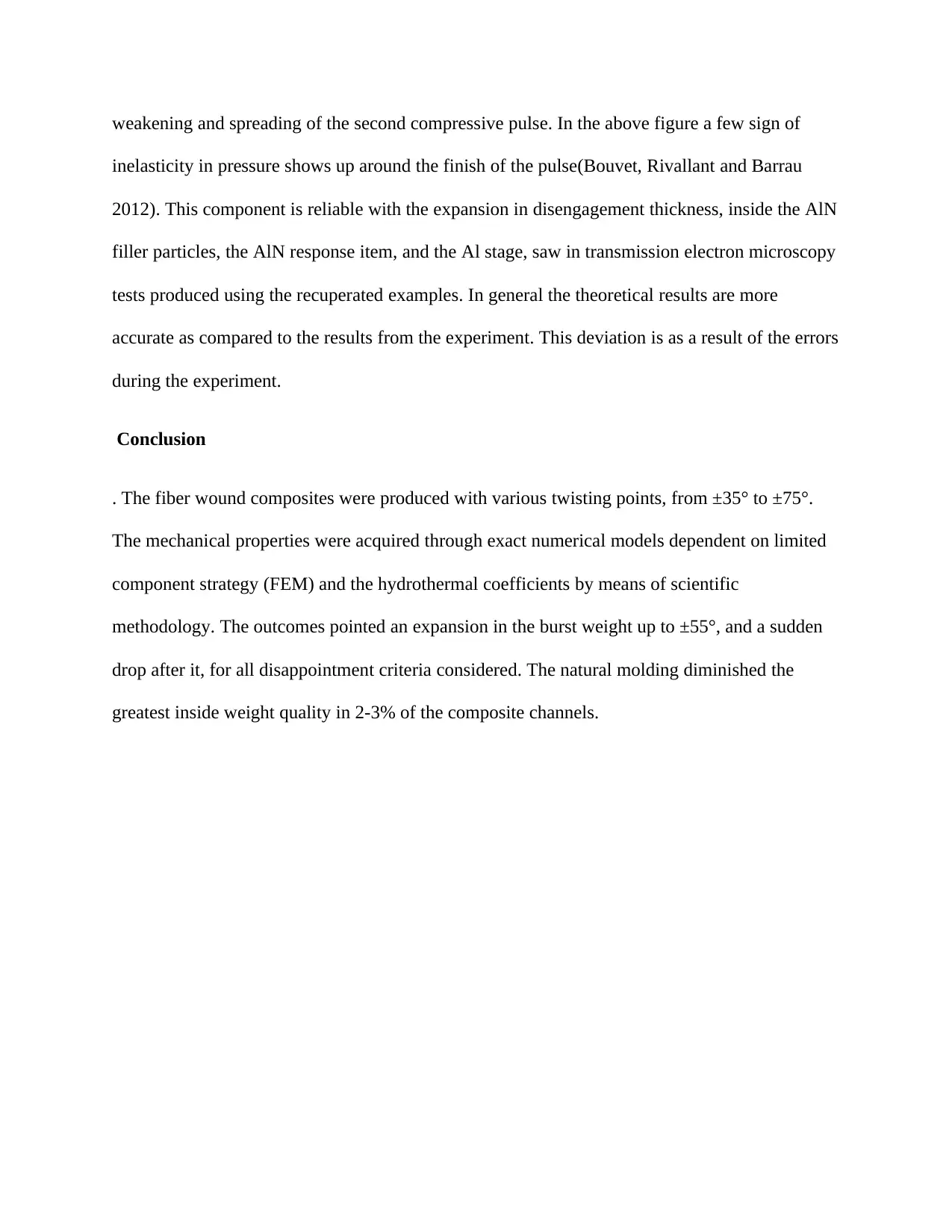
weakening and spreading of the second compressive pulse. In the above figure a few sign of
inelasticity in pressure shows up around the finish of the pulse(Bouvet, Rivallant and Barrau
2012). This component is reliable with the expansion in disengagement thickness, inside the AlN
filler particles, the AlN response item, and the Al stage, saw in transmission electron microscopy
tests produced using the recuperated examples. In general the theoretical results are more
accurate as compared to the results from the experiment. This deviation is as a result of the errors
during the experiment.
Conclusion
. The fiber wound composites were produced with various twisting points, from ±35° to ±75°.
The mechanical properties were acquired through exact numerical models dependent on limited
component strategy (FEM) and the hydrothermal coefficients by means of scientific
methodology. The outcomes pointed an expansion in the burst weight up to ±55°, and a sudden
drop after it, for all disappointment criteria considered. The natural molding diminished the
greatest inside weight quality in 2-3% of the composite channels.
inelasticity in pressure shows up around the finish of the pulse(Bouvet, Rivallant and Barrau
2012). This component is reliable with the expansion in disengagement thickness, inside the AlN
filler particles, the AlN response item, and the Al stage, saw in transmission electron microscopy
tests produced using the recuperated examples. In general the theoretical results are more
accurate as compared to the results from the experiment. This deviation is as a result of the errors
during the experiment.
Conclusion
. The fiber wound composites were produced with various twisting points, from ±35° to ±75°.
The mechanical properties were acquired through exact numerical models dependent on limited
component strategy (FEM) and the hydrothermal coefficients by means of scientific
methodology. The outcomes pointed an expansion in the burst weight up to ±55°, and a sudden
drop after it, for all disappointment criteria considered. The natural molding diminished the
greatest inside weight quality in 2-3% of the composite channels.
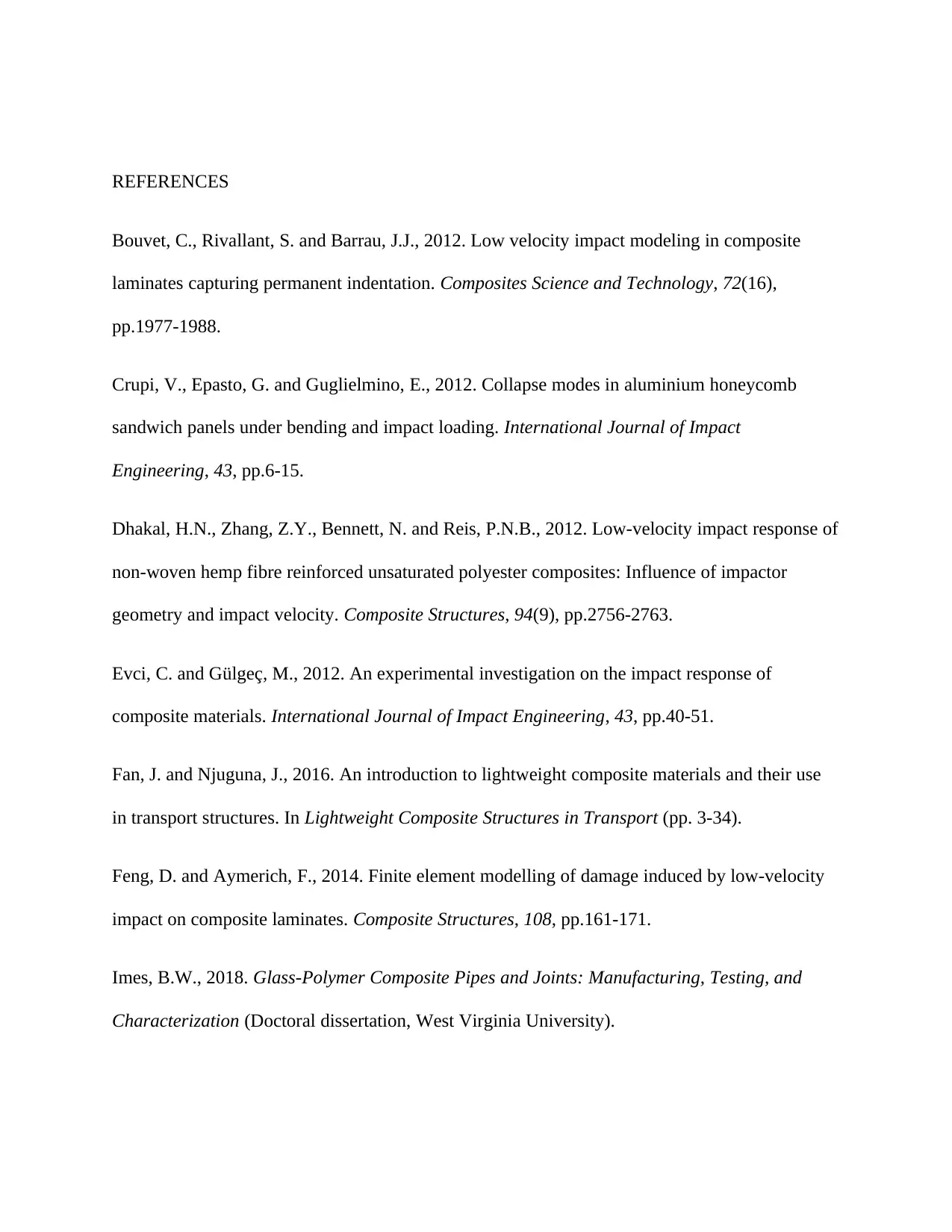
REFERENCES
Bouvet, C., Rivallant, S. and Barrau, J.J., 2012. Low velocity impact modeling in composite
laminates capturing permanent indentation. Composites Science and Technology, 72(16),
pp.1977-1988.
Crupi, V., Epasto, G. and Guglielmino, E., 2012. Collapse modes in aluminium honeycomb
sandwich panels under bending and impact loading. International Journal of Impact
Engineering, 43, pp.6-15.
Dhakal, H.N., Zhang, Z.Y., Bennett, N. and Reis, P.N.B., 2012. Low-velocity impact response of
non-woven hemp fibre reinforced unsaturated polyester composites: Influence of impactor
geometry and impact velocity. Composite Structures, 94(9), pp.2756-2763.
Evci, C. and Gülgeç, M., 2012. An experimental investigation on the impact response of
composite materials. International Journal of Impact Engineering, 43, pp.40-51.
Fan, J. and Njuguna, J., 2016. An introduction to lightweight composite materials and their use
in transport structures. In Lightweight Composite Structures in Transport (pp. 3-34).
Feng, D. and Aymerich, F., 2014. Finite element modelling of damage induced by low-velocity
impact on composite laminates. Composite Structures, 108, pp.161-171.
Imes, B.W., 2018. Glass-Polymer Composite Pipes and Joints: Manufacturing, Testing, and
Characterization (Doctoral dissertation, West Virginia University).
Bouvet, C., Rivallant, S. and Barrau, J.J., 2012. Low velocity impact modeling in composite
laminates capturing permanent indentation. Composites Science and Technology, 72(16),
pp.1977-1988.
Crupi, V., Epasto, G. and Guglielmino, E., 2012. Collapse modes in aluminium honeycomb
sandwich panels under bending and impact loading. International Journal of Impact
Engineering, 43, pp.6-15.
Dhakal, H.N., Zhang, Z.Y., Bennett, N. and Reis, P.N.B., 2012. Low-velocity impact response of
non-woven hemp fibre reinforced unsaturated polyester composites: Influence of impactor
geometry and impact velocity. Composite Structures, 94(9), pp.2756-2763.
Evci, C. and Gülgeç, M., 2012. An experimental investigation on the impact response of
composite materials. International Journal of Impact Engineering, 43, pp.40-51.
Fan, J. and Njuguna, J., 2016. An introduction to lightweight composite materials and their use
in transport structures. In Lightweight Composite Structures in Transport (pp. 3-34).
Feng, D. and Aymerich, F., 2014. Finite element modelling of damage induced by low-velocity
impact on composite laminates. Composite Structures, 108, pp.161-171.
Imes, B.W., 2018. Glass-Polymer Composite Pipes and Joints: Manufacturing, Testing, and
Characterization (Doctoral dissertation, West Virginia University).
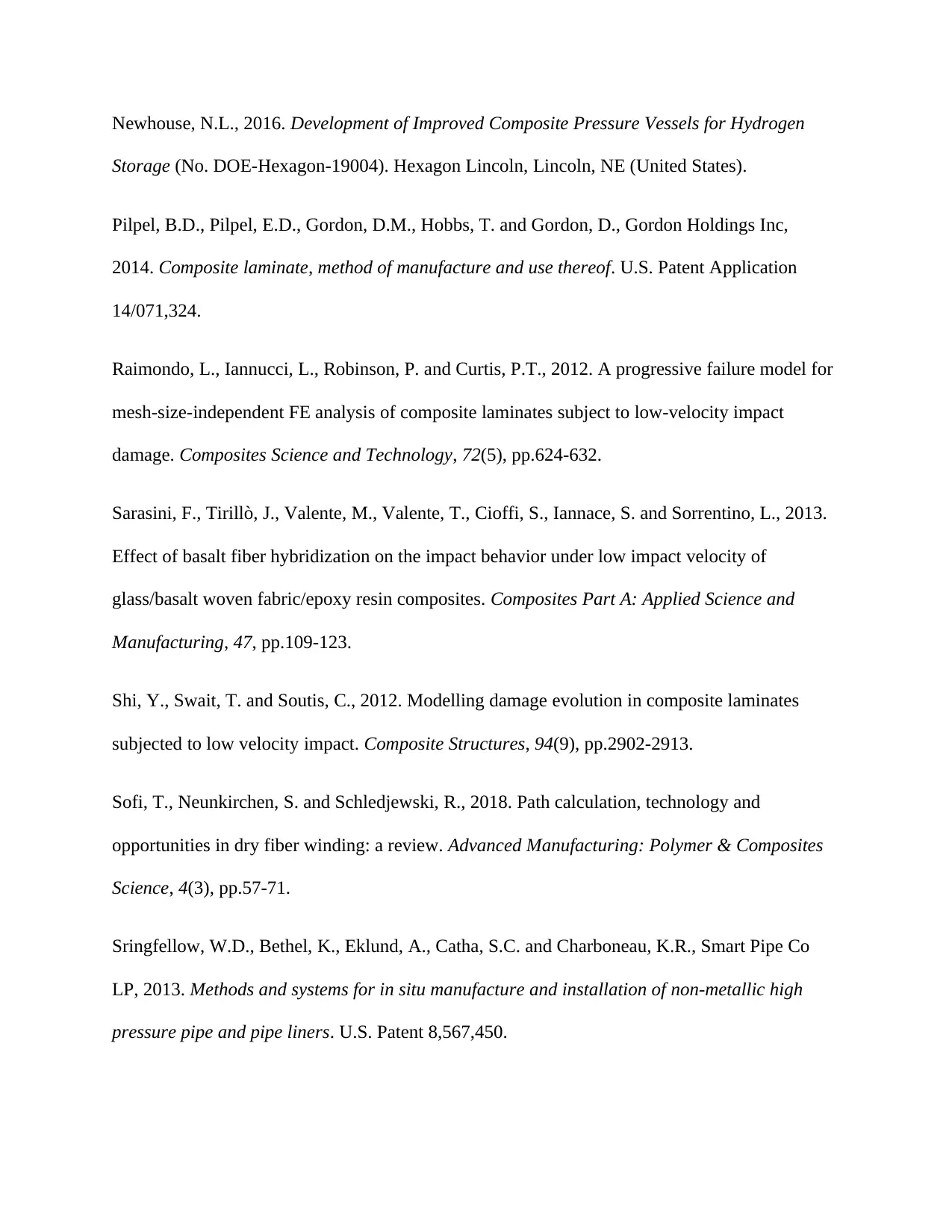
Newhouse, N.L., 2016. Development of Improved Composite Pressure Vessels for Hydrogen
Storage (No. DOE-Hexagon-19004). Hexagon Lincoln, Lincoln, NE (United States).
Pilpel, B.D., Pilpel, E.D., Gordon, D.M., Hobbs, T. and Gordon, D., Gordon Holdings Inc,
2014. Composite laminate, method of manufacture and use thereof. U.S. Patent Application
14/071,324.
Raimondo, L., Iannucci, L., Robinson, P. and Curtis, P.T., 2012. A progressive failure model for
mesh-size-independent FE analysis of composite laminates subject to low-velocity impact
damage. Composites Science and Technology, 72(5), pp.624-632.
Sarasini, F., Tirillò, J., Valente, M., Valente, T., Cioffi, S., Iannace, S. and Sorrentino, L., 2013.
Effect of basalt fiber hybridization on the impact behavior under low impact velocity of
glass/basalt woven fabric/epoxy resin composites. Composites Part A: Applied Science and
Manufacturing, 47, pp.109-123.
Shi, Y., Swait, T. and Soutis, C., 2012. Modelling damage evolution in composite laminates
subjected to low velocity impact. Composite Structures, 94(9), pp.2902-2913.
Sofi, T., Neunkirchen, S. and Schledjewski, R., 2018. Path calculation, technology and
opportunities in dry fiber winding: a review. Advanced Manufacturing: Polymer & Composites
Science, 4(3), pp.57-71.
Sringfellow, W.D., Bethel, K., Eklund, A., Catha, S.C. and Charboneau, K.R., Smart Pipe Co
LP, 2013. Methods and systems for in situ manufacture and installation of non-metallic high
pressure pipe and pipe liners. U.S. Patent 8,567,450.
Storage (No. DOE-Hexagon-19004). Hexagon Lincoln, Lincoln, NE (United States).
Pilpel, B.D., Pilpel, E.D., Gordon, D.M., Hobbs, T. and Gordon, D., Gordon Holdings Inc,
2014. Composite laminate, method of manufacture and use thereof. U.S. Patent Application
14/071,324.
Raimondo, L., Iannucci, L., Robinson, P. and Curtis, P.T., 2012. A progressive failure model for
mesh-size-independent FE analysis of composite laminates subject to low-velocity impact
damage. Composites Science and Technology, 72(5), pp.624-632.
Sarasini, F., Tirillò, J., Valente, M., Valente, T., Cioffi, S., Iannace, S. and Sorrentino, L., 2013.
Effect of basalt fiber hybridization on the impact behavior under low impact velocity of
glass/basalt woven fabric/epoxy resin composites. Composites Part A: Applied Science and
Manufacturing, 47, pp.109-123.
Shi, Y., Swait, T. and Soutis, C., 2012. Modelling damage evolution in composite laminates
subjected to low velocity impact. Composite Structures, 94(9), pp.2902-2913.
Sofi, T., Neunkirchen, S. and Schledjewski, R., 2018. Path calculation, technology and
opportunities in dry fiber winding: a review. Advanced Manufacturing: Polymer & Composites
Science, 4(3), pp.57-71.
Sringfellow, W.D., Bethel, K., Eklund, A., Catha, S.C. and Charboneau, K.R., Smart Pipe Co
LP, 2013. Methods and systems for in situ manufacture and installation of non-metallic high
pressure pipe and pipe liners. U.S. Patent 8,567,450.
Secure Best Marks with AI Grader
Need help grading? Try our AI Grader for instant feedback on your assignments.
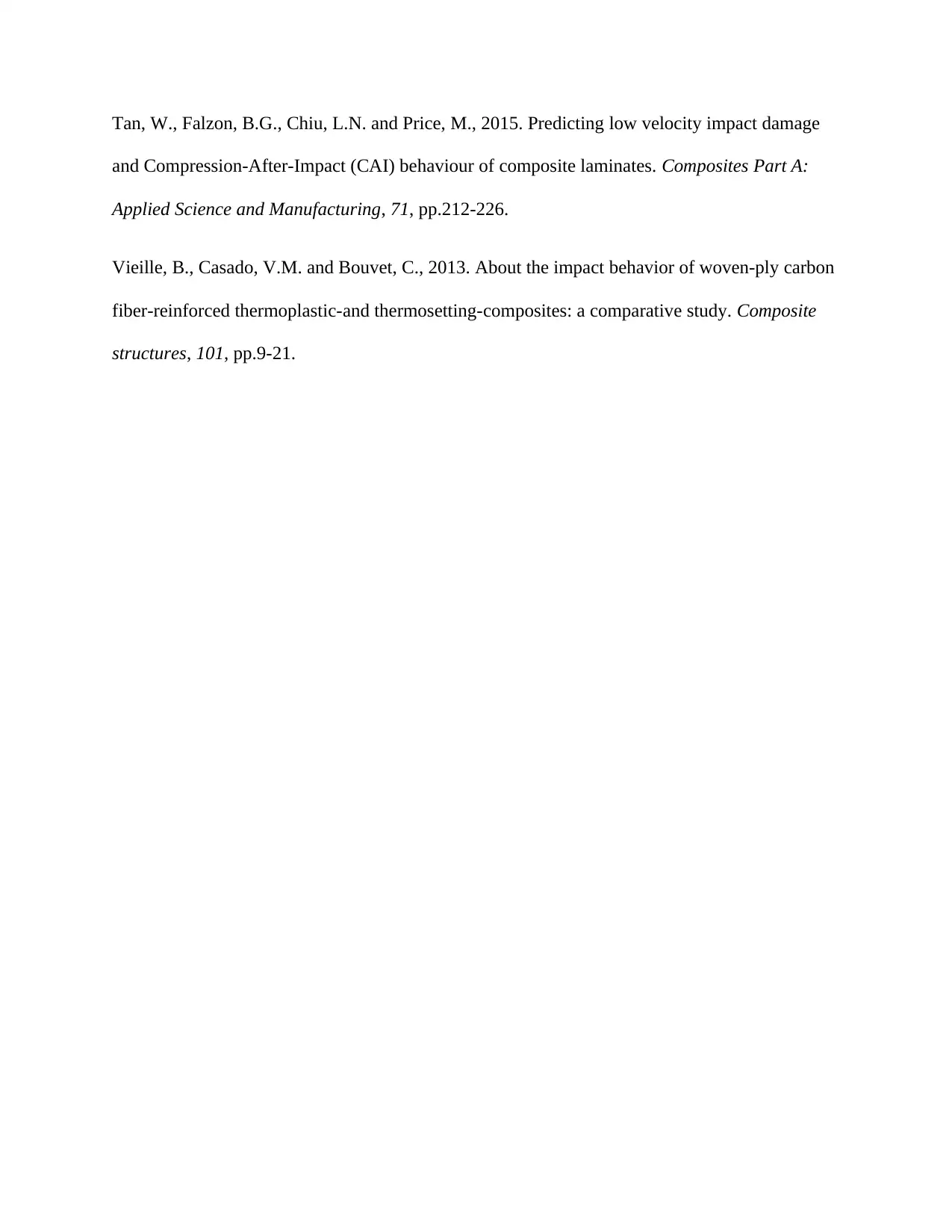
Tan, W., Falzon, B.G., Chiu, L.N. and Price, M., 2015. Predicting low velocity impact damage
and Compression-After-Impact (CAI) behaviour of composite laminates. Composites Part A:
Applied Science and Manufacturing, 71, pp.212-226.
Vieille, B., Casado, V.M. and Bouvet, C., 2013. About the impact behavior of woven-ply carbon
fiber-reinforced thermoplastic-and thermosetting-composites: a comparative study. Composite
structures, 101, pp.9-21.
and Compression-After-Impact (CAI) behaviour of composite laminates. Composites Part A:
Applied Science and Manufacturing, 71, pp.212-226.
Vieille, B., Casado, V.M. and Bouvet, C., 2013. About the impact behavior of woven-ply carbon
fiber-reinforced thermoplastic-and thermosetting-composites: a comparative study. Composite
structures, 101, pp.9-21.
1 out of 29
![[object Object]](/_next/image/?url=%2F_next%2Fstatic%2Fmedia%2Flogo.6d15ce61.png&w=640&q=75)
Your All-in-One AI-Powered Toolkit for Academic Success.
+13062052269
info@desklib.com
Available 24*7 on WhatsApp / Email
Unlock your academic potential
© 2024 | Zucol Services PVT LTD | All rights reserved.