Mechanical Engineering Heat Transfer Assignment
VerifiedAdded on 2022/09/12
|17
|734
|47
AI Summary
Contribute Materials
Your contribution can guide someone’s learning journey. Share your
documents today.
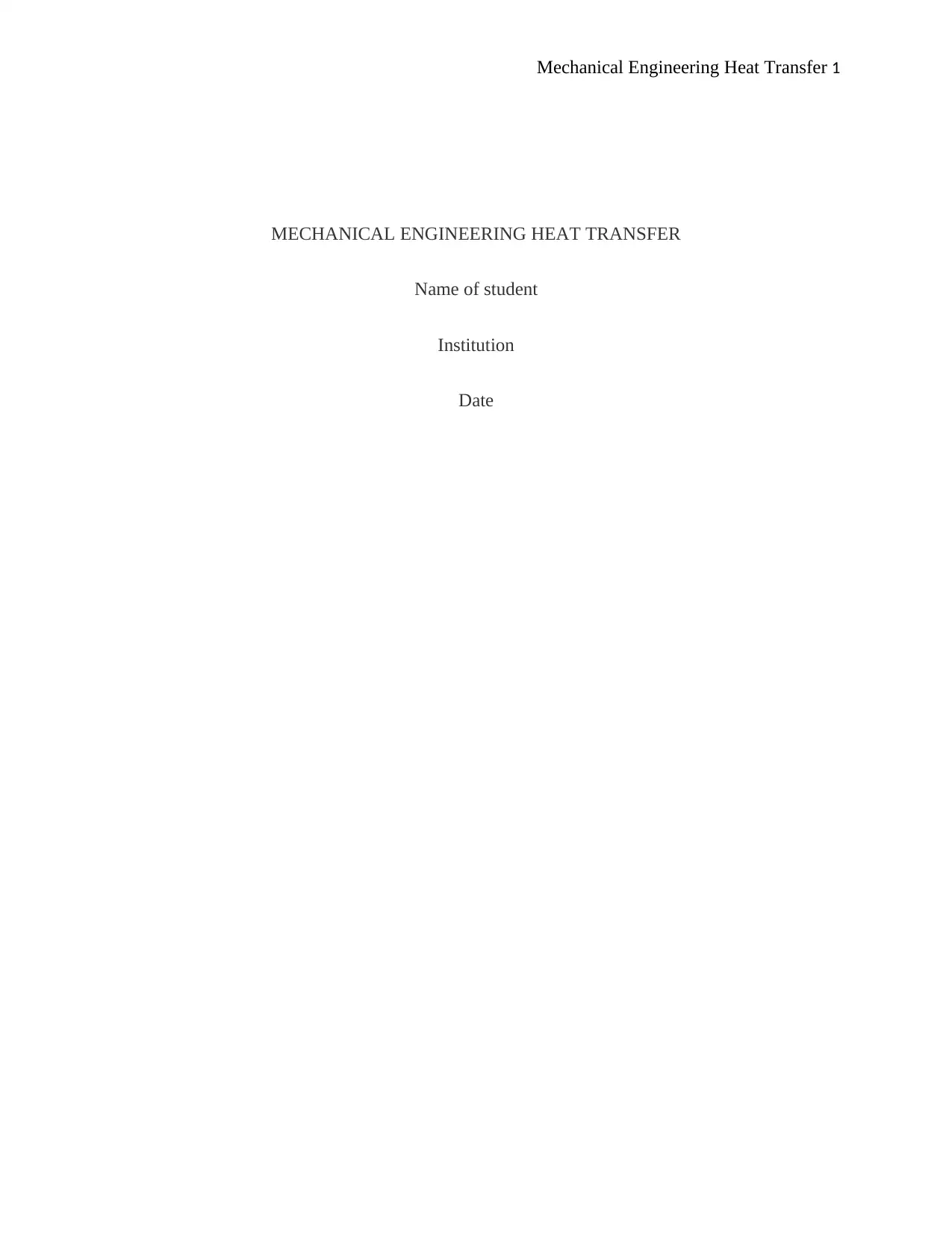
Mechanical Engineering Heat Transfer 1
MECHANICAL ENGINEERING HEAT TRANSFER
Name of student
Institution
Date
MECHANICAL ENGINEERING HEAT TRANSFER
Name of student
Institution
Date
Secure Best Marks with AI Grader
Need help grading? Try our AI Grader for instant feedback on your assignments.
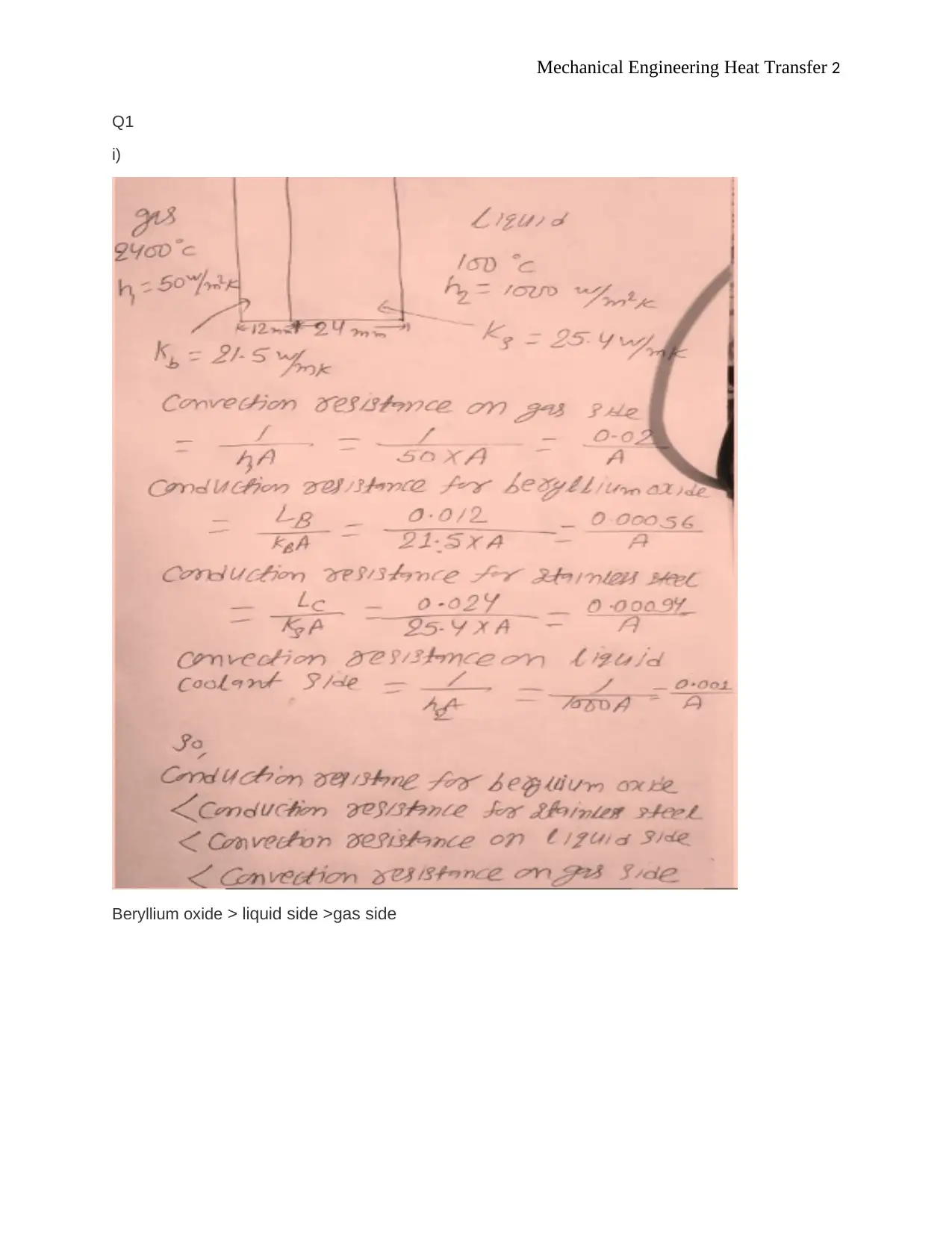
Mechanical Engineering Heat Transfer 2
Q1
i)
Beryllium oxide > liquid side >gas side
Q1
i)
Beryllium oxide > liquid side >gas side
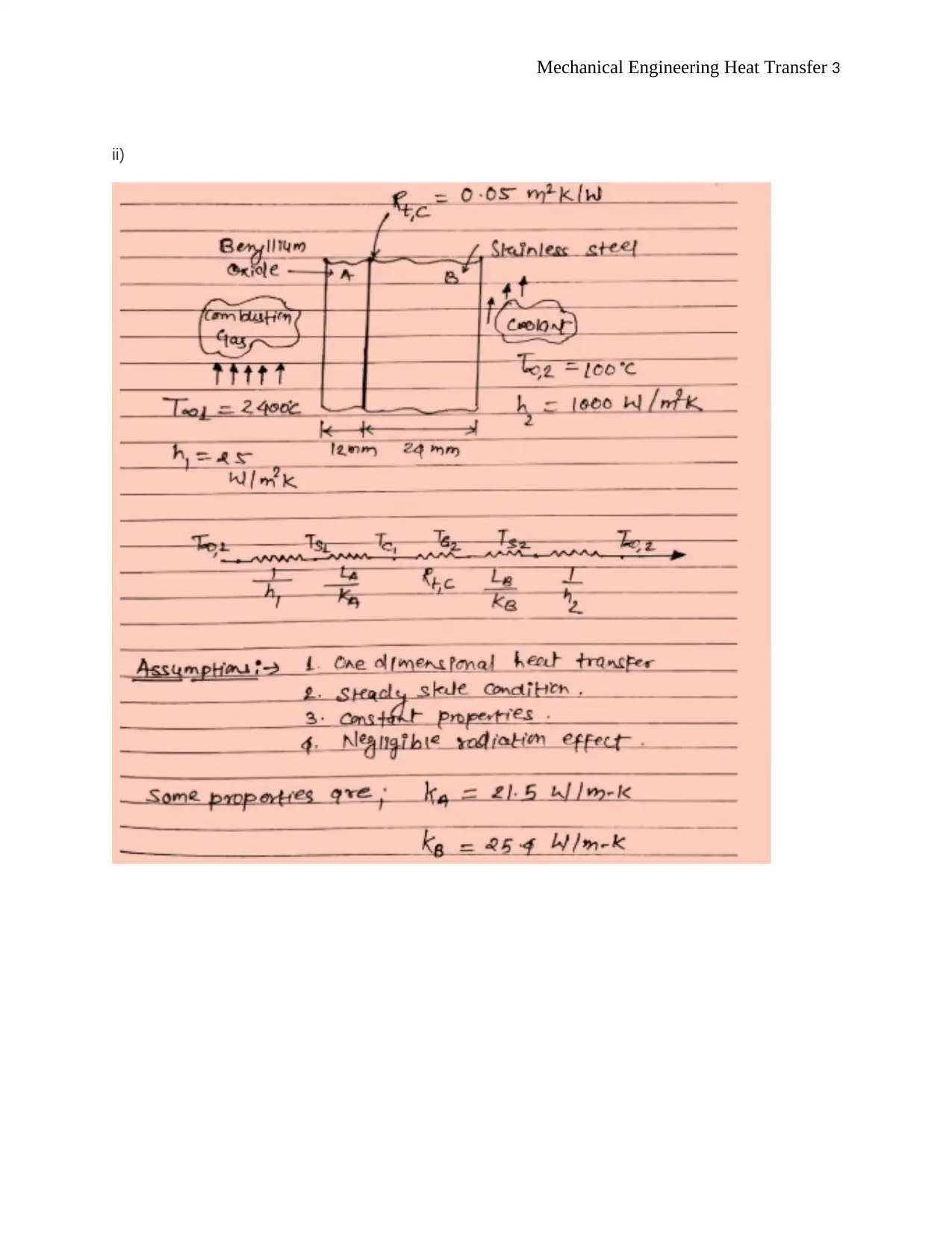
Mechanical Engineering Heat Transfer 3
ii)
ii)
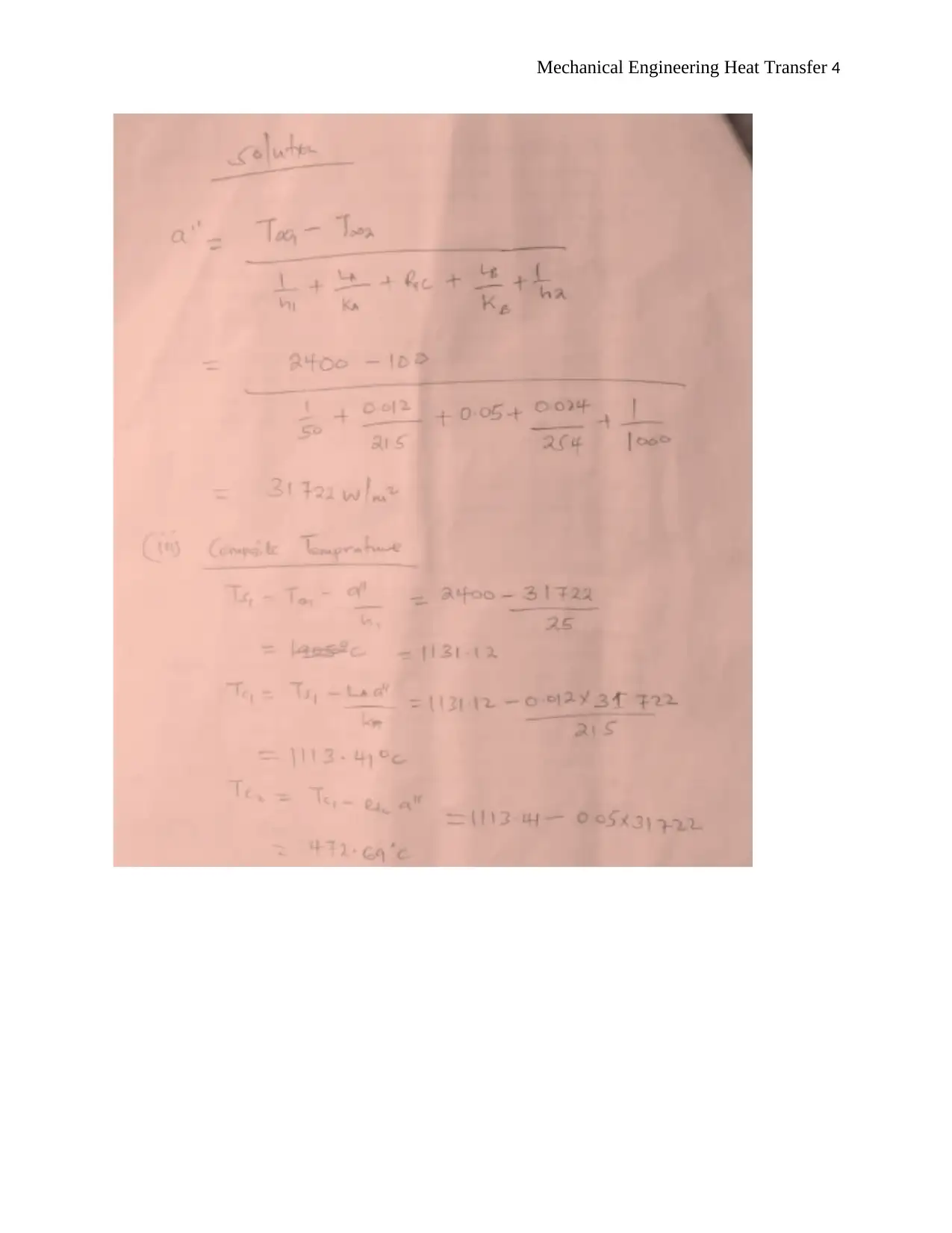
Mechanical Engineering Heat Transfer 4
Secure Best Marks with AI Grader
Need help grading? Try our AI Grader for instant feedback on your assignments.
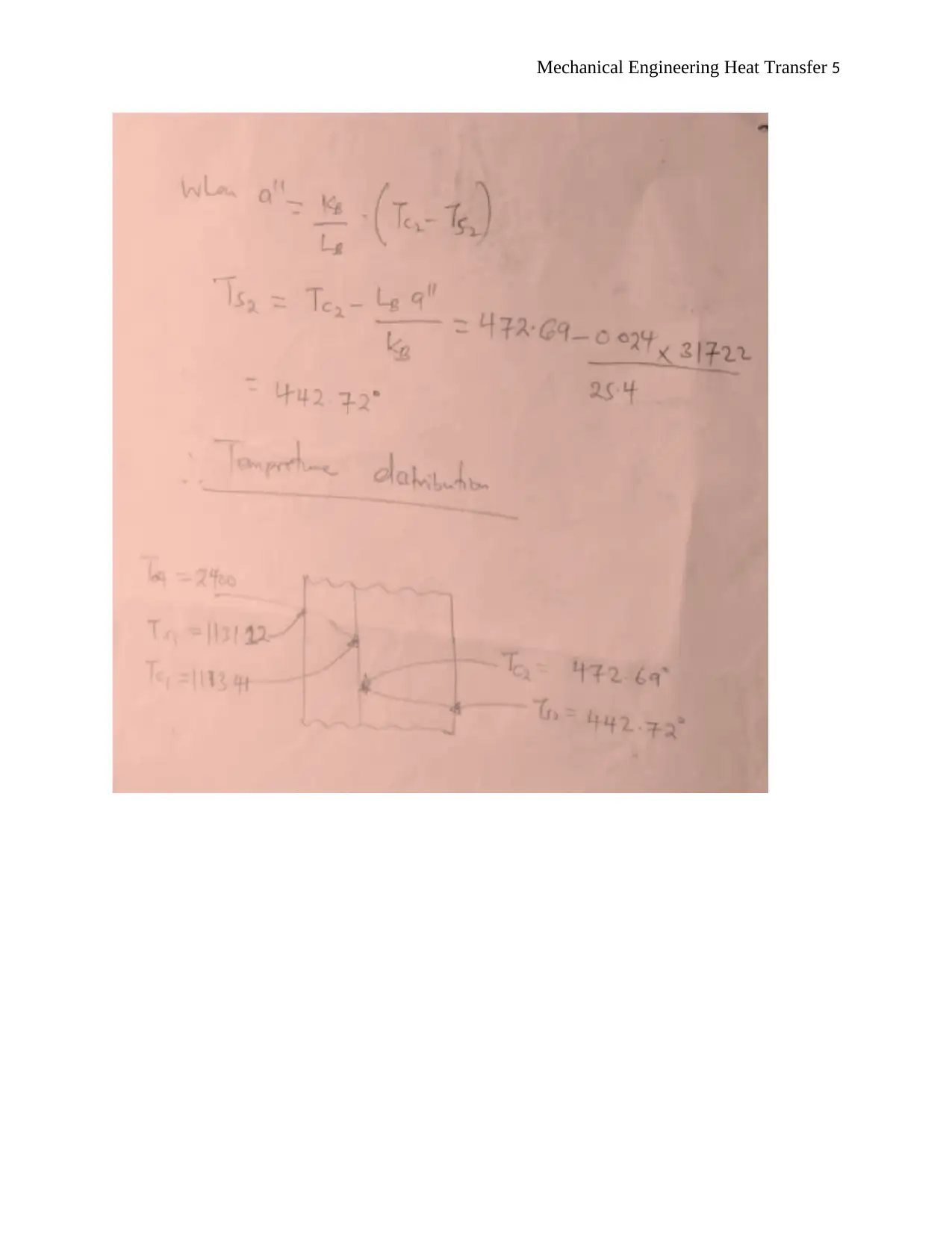
Mechanical Engineering Heat Transfer 5
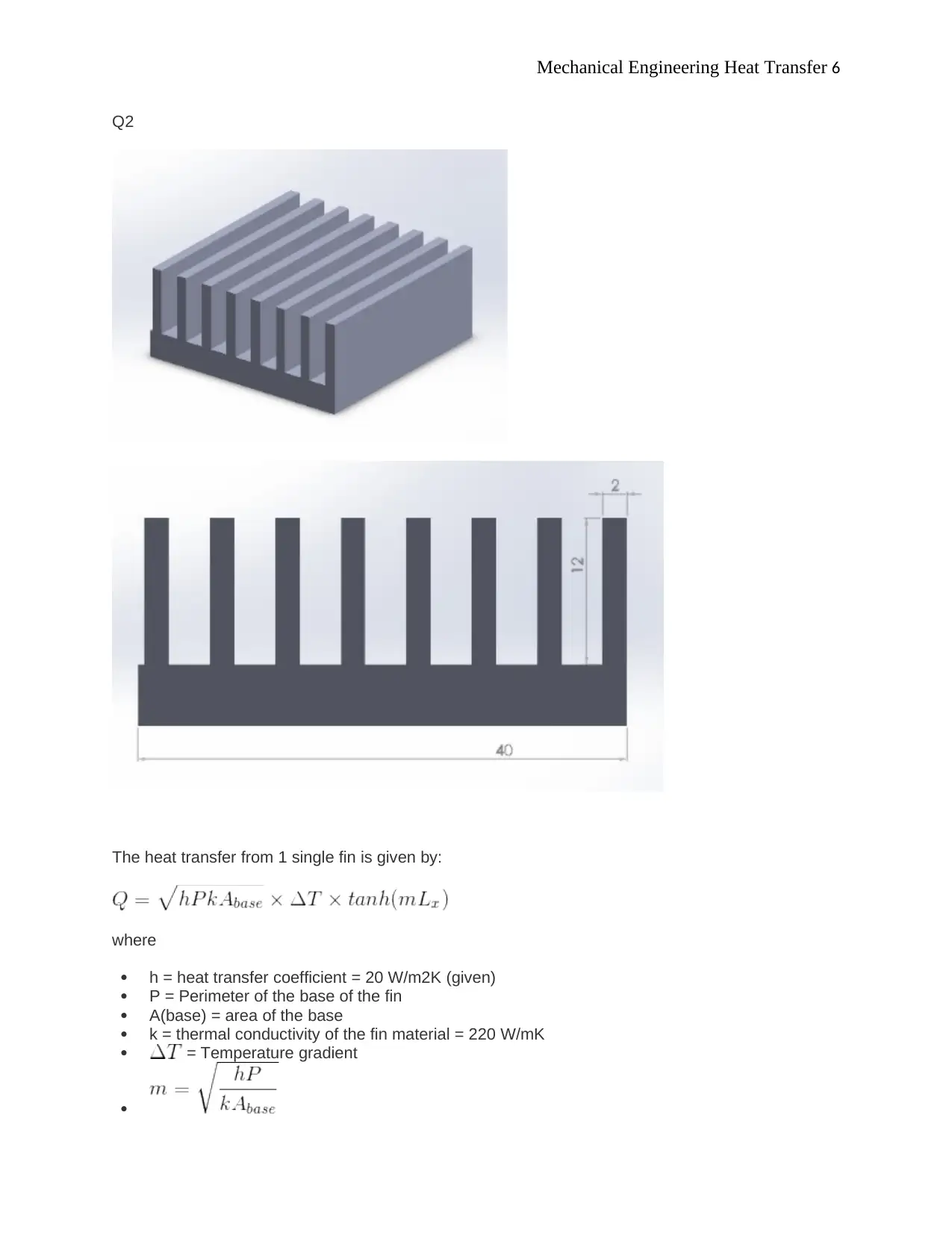
Mechanical Engineering Heat Transfer 6
Q2
The heat transfer from 1 single fin is given by:
where
h = heat transfer coefficient = 20 W/m2K (given)
P = Perimeter of the base of the fin
A(base) = area of the base
k = thermal conductivity of the fin material = 220 W/mK
= Temperature gradient
Q2
The heat transfer from 1 single fin is given by:
where
h = heat transfer coefficient = 20 W/m2K (given)
P = Perimeter of the base of the fin
A(base) = area of the base
k = thermal conductivity of the fin material = 220 W/mK
= Temperature gradient
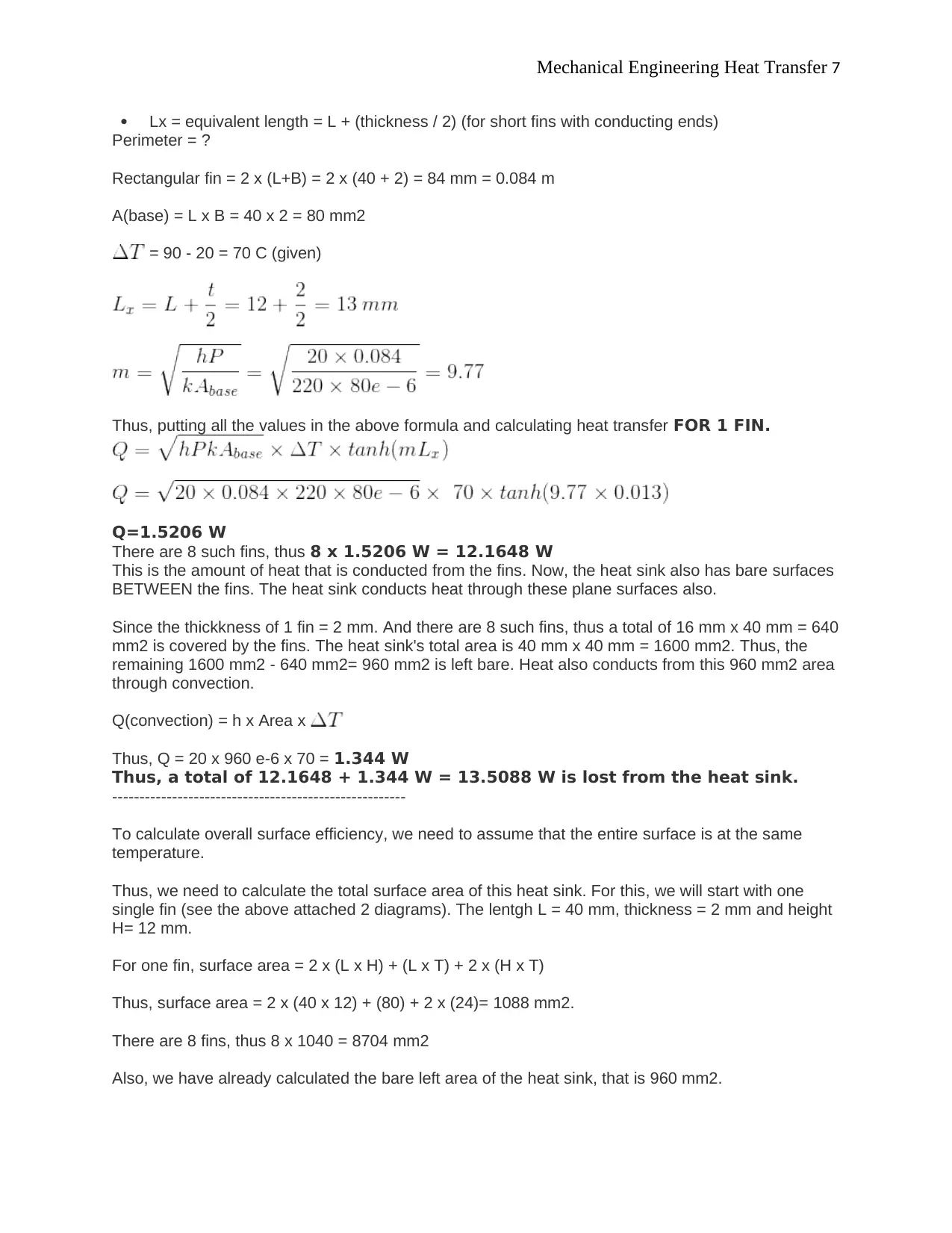
Mechanical Engineering Heat Transfer 7
Lx = equivalent length = L + (thickness / 2) (for short fins with conducting ends)
Perimeter = ?
Rectangular fin = 2 x (L+B) = 2 x (40 + 2) = 84 mm = 0.084 m
A(base) = L x B = 40 x 2 = 80 mm2
= 90 - 20 = 70 C (given)
Thus, putting all the values in the above formula and calculating heat transfer FOR 1 FIN.
Q=1.5206 W
There are 8 such fins, thus 8 x 1.5206 W = 12.1648 W
This is the amount of heat that is conducted from the fins. Now, the heat sink also has bare surfaces
BETWEEN the fins. The heat sink conducts heat through these plane surfaces also.
Since the thickkness of 1 fin = 2 mm. And there are 8 such fins, thus a total of 16 mm x 40 mm = 640
mm2 is covered by the fins. The heat sink's total area is 40 mm x 40 mm = 1600 mm2. Thus, the
remaining 1600 mm2 - 640 mm2= 960 mm2 is left bare. Heat also conducts from this 960 mm2 area
through convection.
Q(convection) = h x Area x
Thus, Q = 20 x 960 e-6 x 70 = 1.344 W
Thus, a total of 12.1648 + 1.344 W = 13.5088 W is lost from the heat sink.
------------------------------------------------------
To calculate overall surface efficiency, we need to assume that the entire surface is at the same
temperature.
Thus, we need to calculate the total surface area of this heat sink. For this, we will start with one
single fin (see the above attached 2 diagrams). The lentgh L = 40 mm, thickness = 2 mm and height
H= 12 mm.
For one fin, surface area = 2 x (L x H) + (L x T) + 2 x (H x T)
Thus, surface area = 2 x (40 x 12) + (80) + 2 x (24)= 1088 mm2.
There are 8 fins, thus 8 x 1040 = 8704 mm2
Also, we have already calculated the bare left area of the heat sink, that is 960 mm2.
Lx = equivalent length = L + (thickness / 2) (for short fins with conducting ends)
Perimeter = ?
Rectangular fin = 2 x (L+B) = 2 x (40 + 2) = 84 mm = 0.084 m
A(base) = L x B = 40 x 2 = 80 mm2
= 90 - 20 = 70 C (given)
Thus, putting all the values in the above formula and calculating heat transfer FOR 1 FIN.
Q=1.5206 W
There are 8 such fins, thus 8 x 1.5206 W = 12.1648 W
This is the amount of heat that is conducted from the fins. Now, the heat sink also has bare surfaces
BETWEEN the fins. The heat sink conducts heat through these plane surfaces also.
Since the thickkness of 1 fin = 2 mm. And there are 8 such fins, thus a total of 16 mm x 40 mm = 640
mm2 is covered by the fins. The heat sink's total area is 40 mm x 40 mm = 1600 mm2. Thus, the
remaining 1600 mm2 - 640 mm2= 960 mm2 is left bare. Heat also conducts from this 960 mm2 area
through convection.
Q(convection) = h x Area x
Thus, Q = 20 x 960 e-6 x 70 = 1.344 W
Thus, a total of 12.1648 + 1.344 W = 13.5088 W is lost from the heat sink.
------------------------------------------------------
To calculate overall surface efficiency, we need to assume that the entire surface is at the same
temperature.
Thus, we need to calculate the total surface area of this heat sink. For this, we will start with one
single fin (see the above attached 2 diagrams). The lentgh L = 40 mm, thickness = 2 mm and height
H= 12 mm.
For one fin, surface area = 2 x (L x H) + (L x T) + 2 x (H x T)
Thus, surface area = 2 x (40 x 12) + (80) + 2 x (24)= 1088 mm2.
There are 8 fins, thus 8 x 1040 = 8704 mm2
Also, we have already calculated the bare left area of the heat sink, that is 960 mm2.
Paraphrase This Document
Need a fresh take? Get an instant paraphrase of this document with our AI Paraphraser
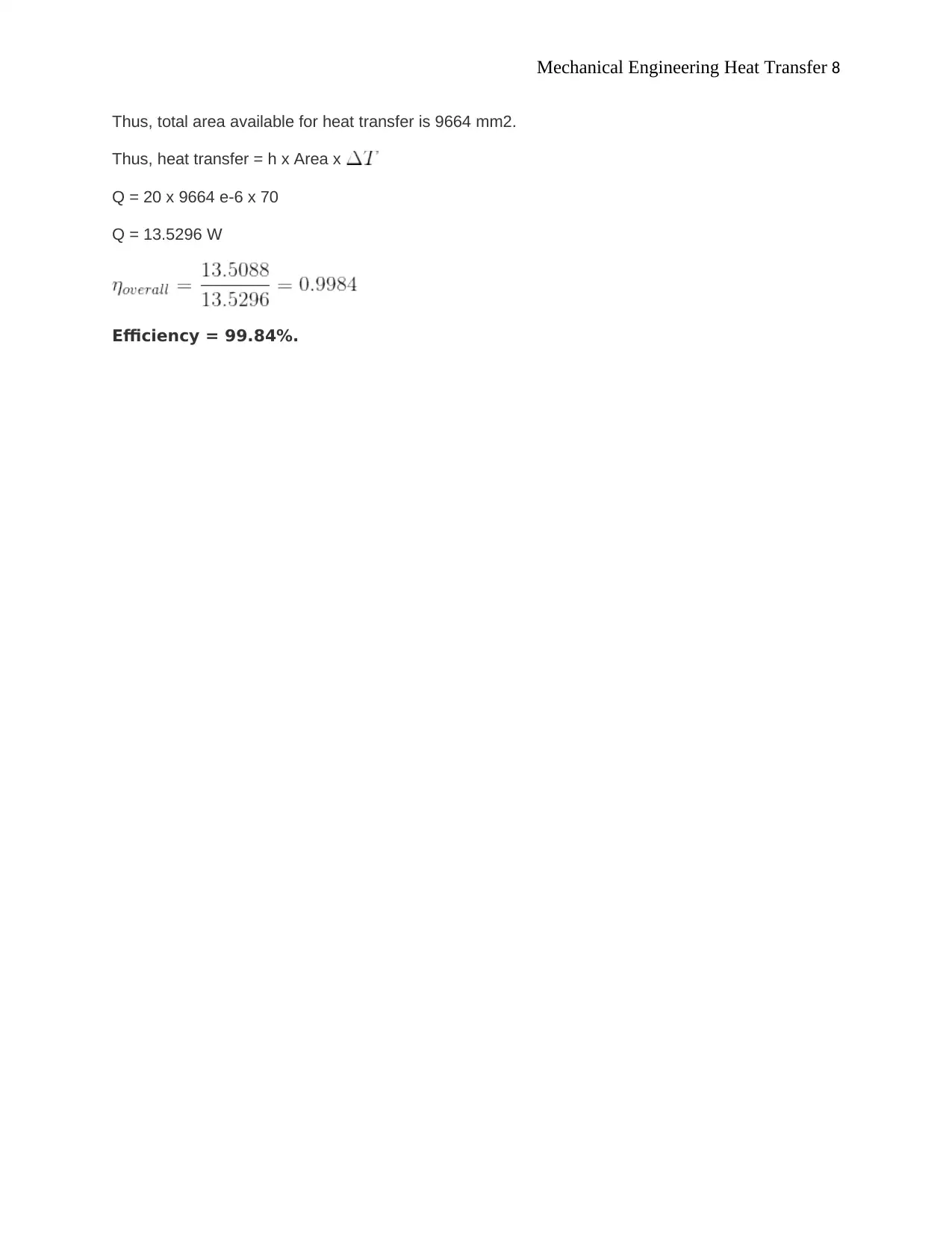
Mechanical Engineering Heat Transfer 8
Thus, total area available for heat transfer is 9664 mm2.
Thus, heat transfer = h x Area x
Q = 20 x 9664 e-6 x 70
Q = 13.5296 W
Efficiency = 99.84%.
Thus, total area available for heat transfer is 9664 mm2.
Thus, heat transfer = h x Area x
Q = 20 x 9664 e-6 x 70
Q = 13.5296 W
Efficiency = 99.84%.
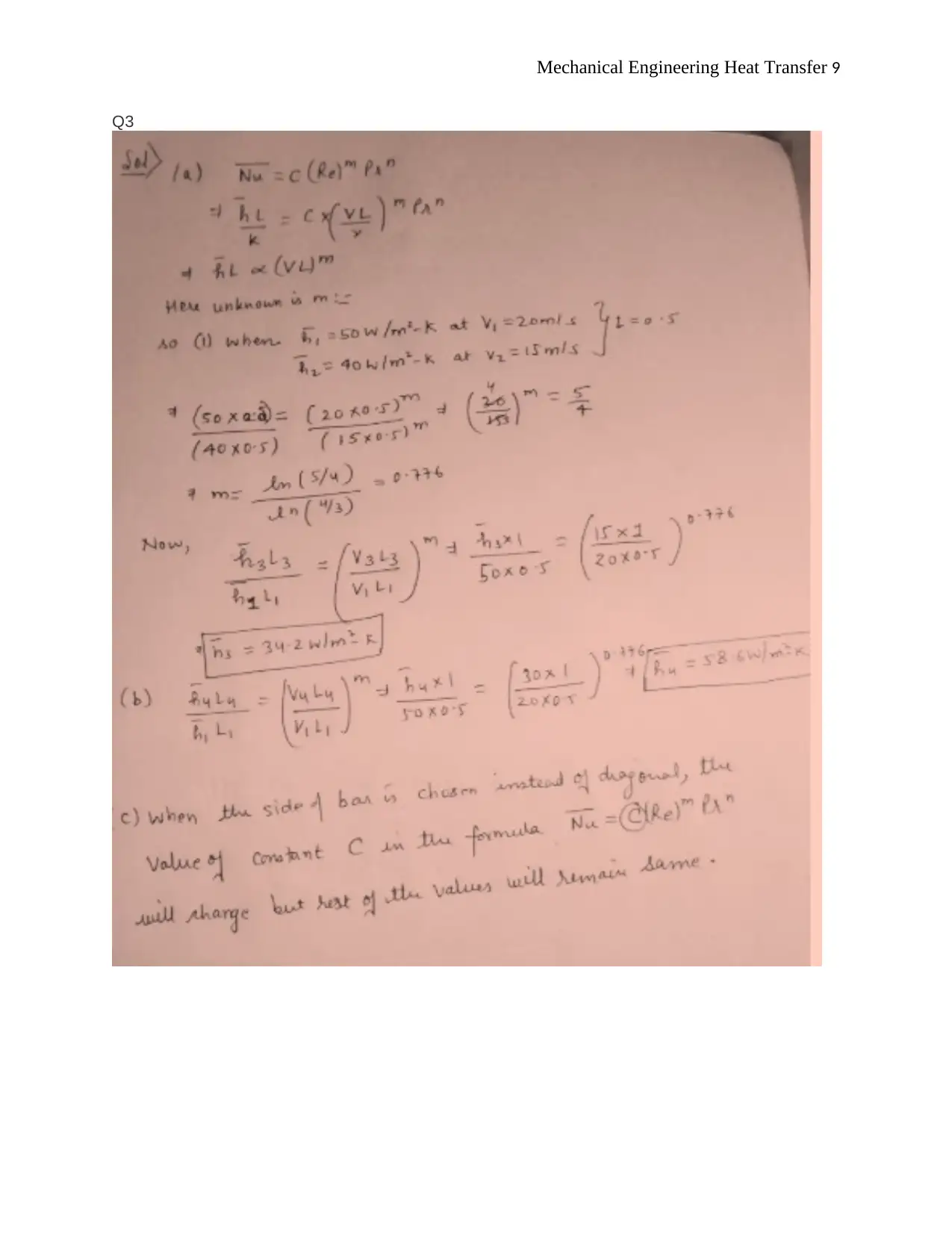
Mechanical Engineering Heat Transfer 9
Q3
Q3
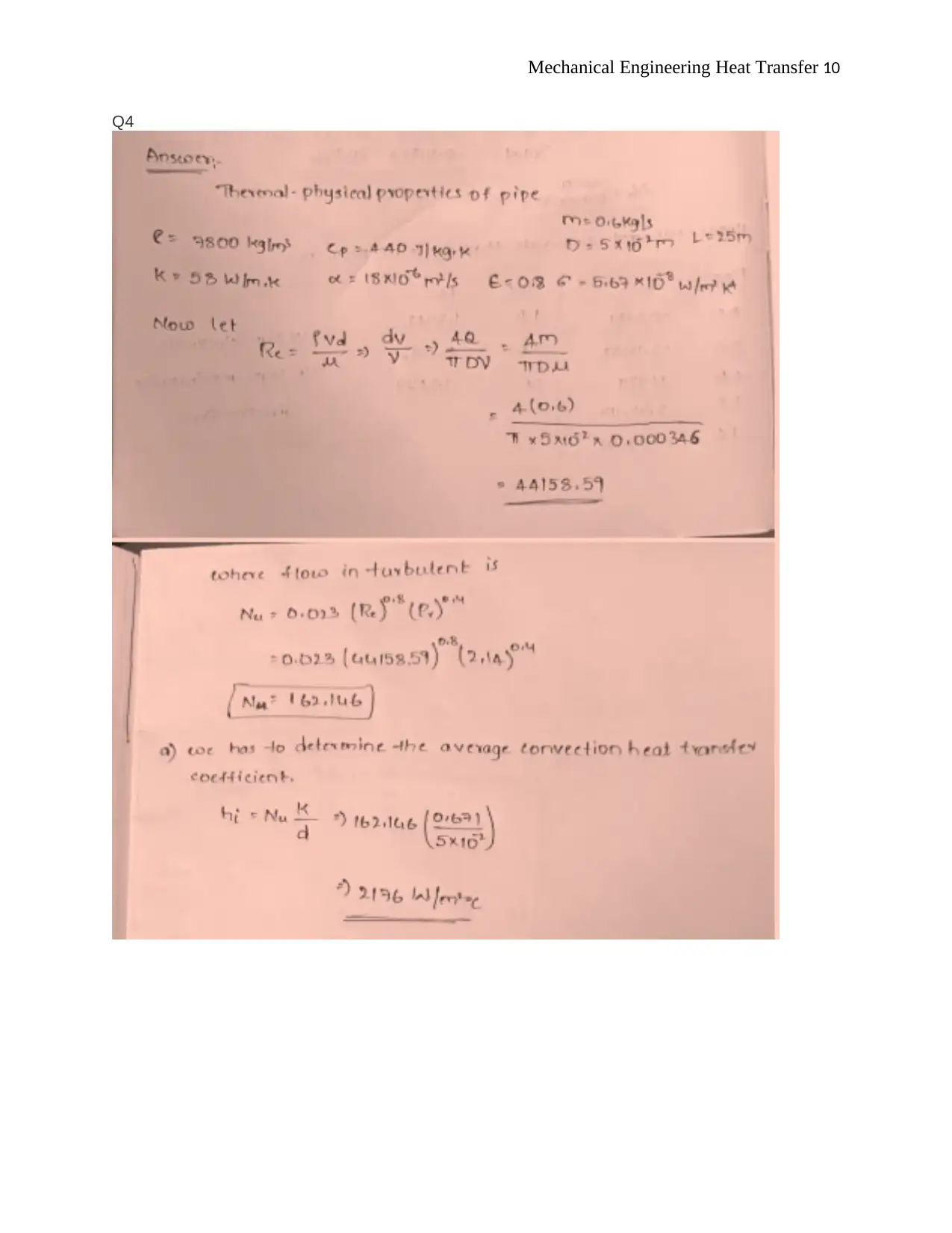
Mechanical Engineering Heat Transfer 10
Q4
Q4
Secure Best Marks with AI Grader
Need help grading? Try our AI Grader for instant feedback on your assignments.
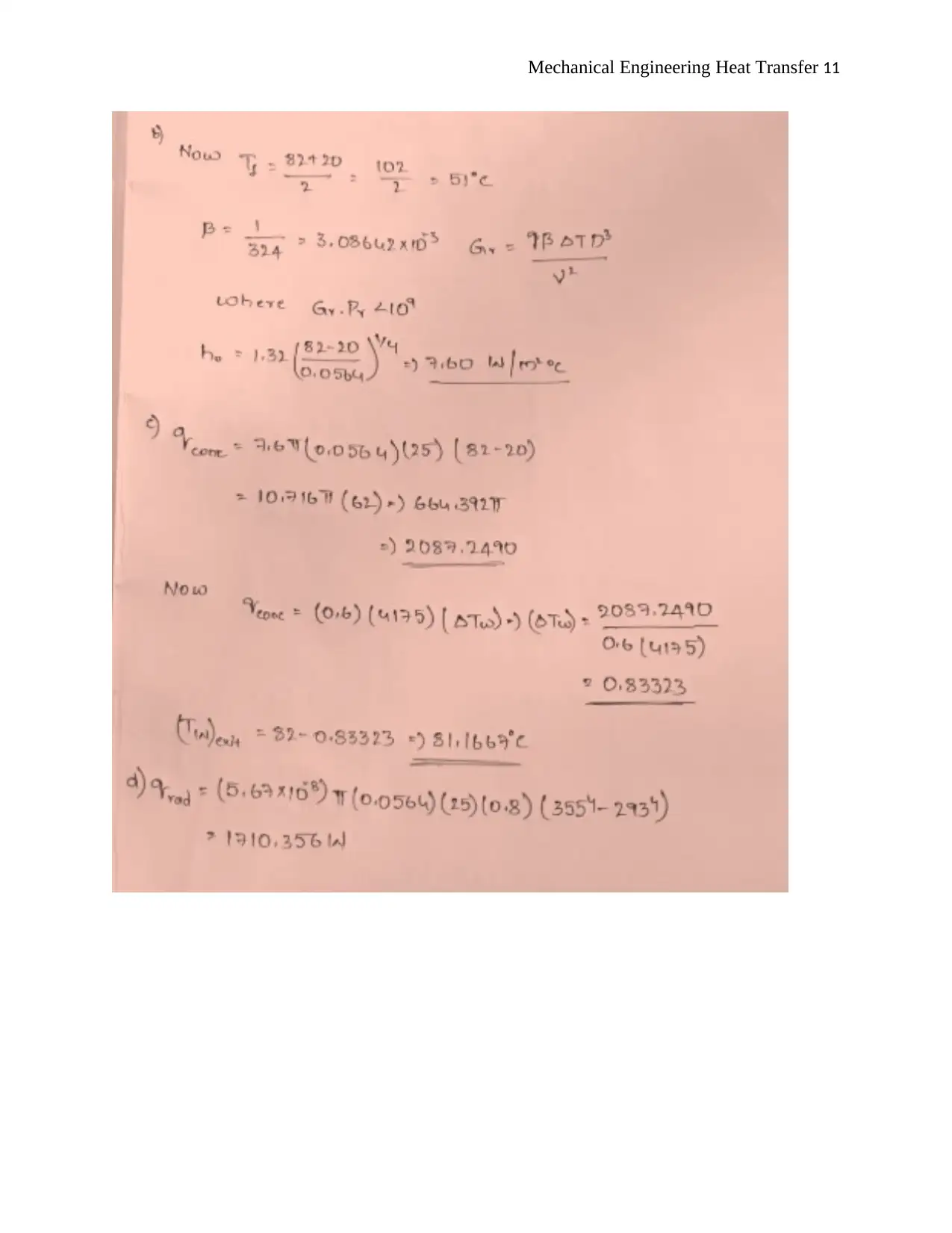
Mechanical Engineering Heat Transfer 11
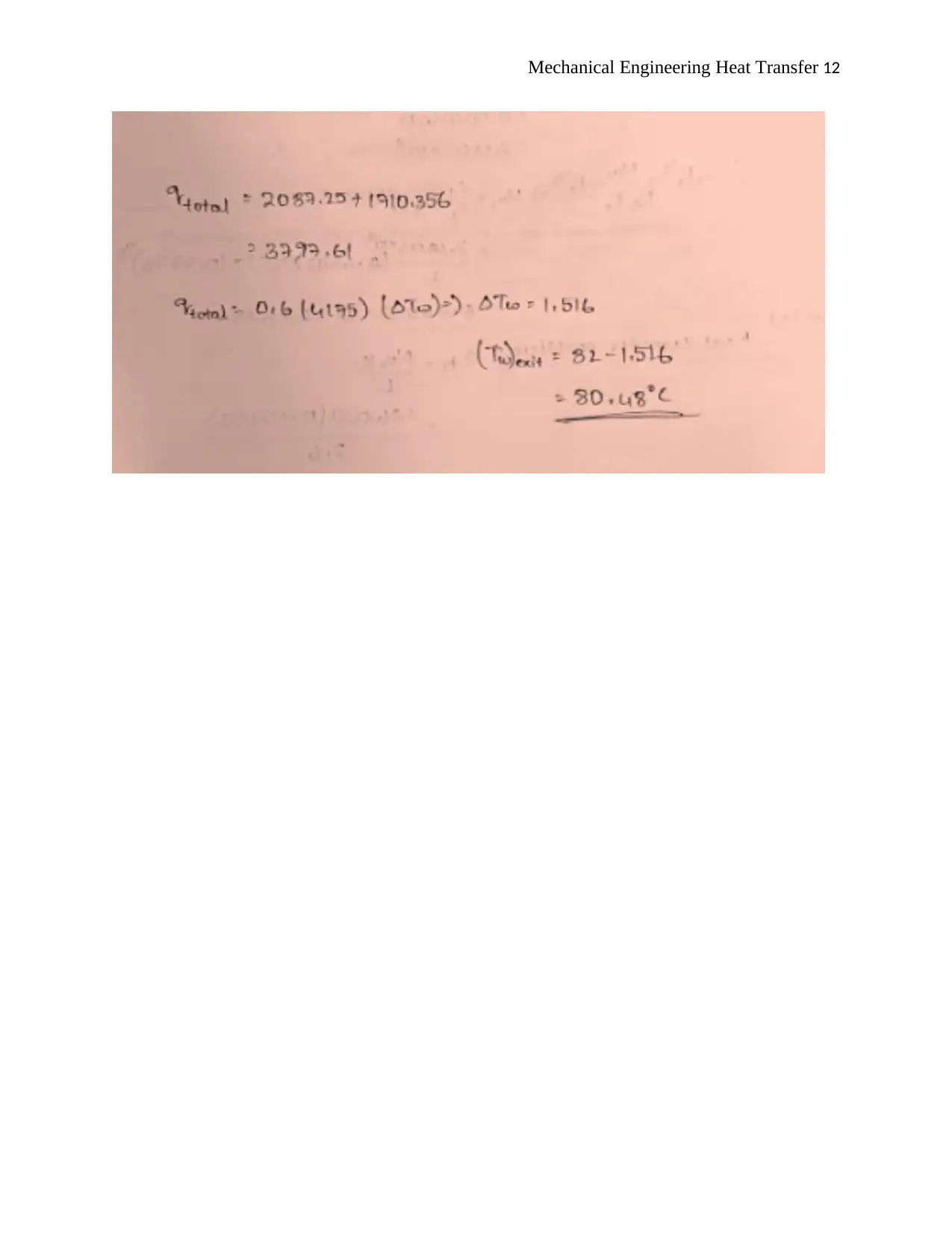
Mechanical Engineering Heat Transfer 12
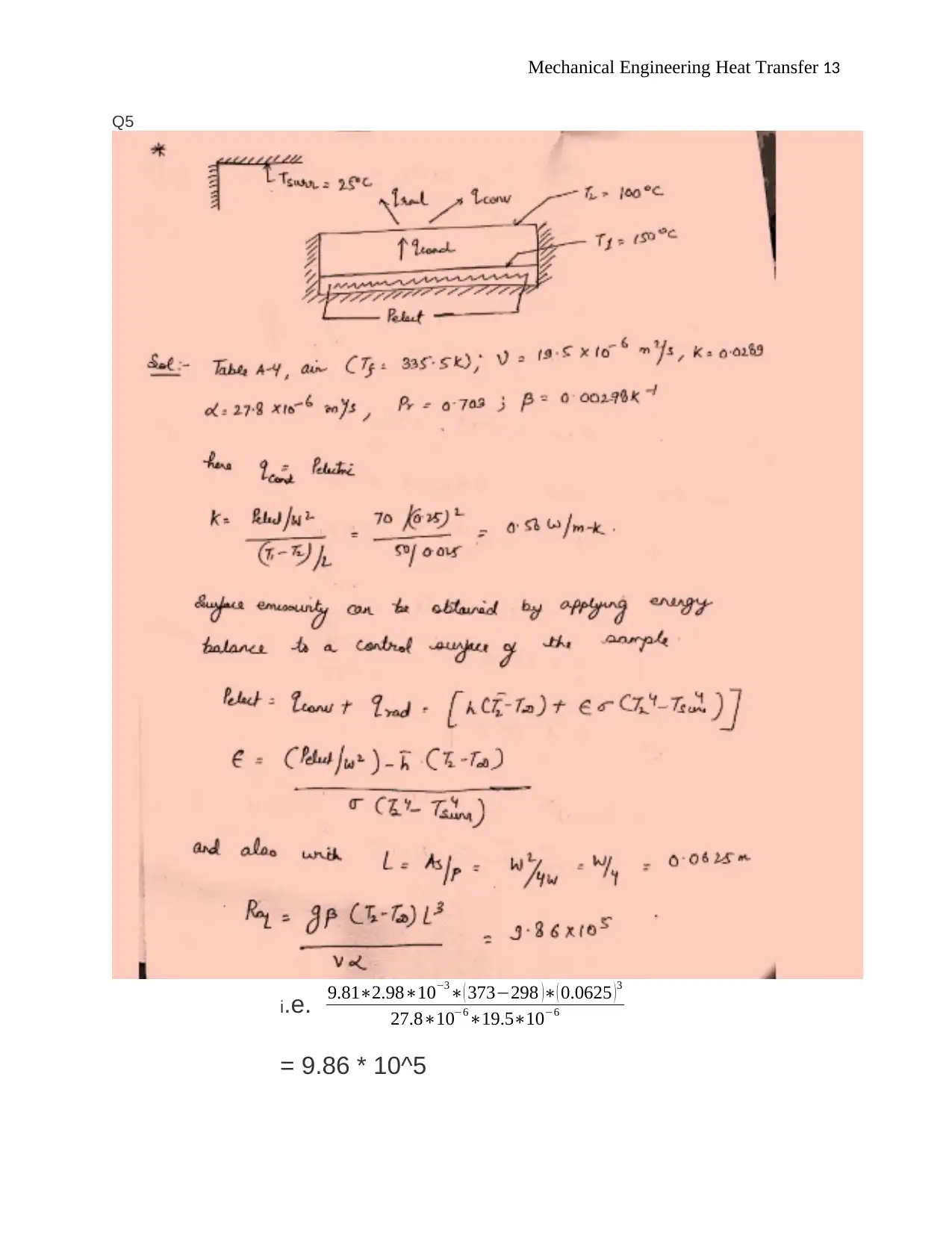
Mechanical Engineering Heat Transfer 13
Q5
i.e. 9.81∗2.98∗10−3∗( 373−298 )∗( 0.0625 ) 3
27.8∗10−6∗19.5∗10−6
= 9.86 * 10^5
Q5
i.e. 9.81∗2.98∗10−3∗( 373−298 )∗( 0.0625 ) 3
27.8∗10−6∗19.5∗10−6
= 9.86 * 10^5
Paraphrase This Document
Need a fresh take? Get an instant paraphrase of this document with our AI Paraphraser
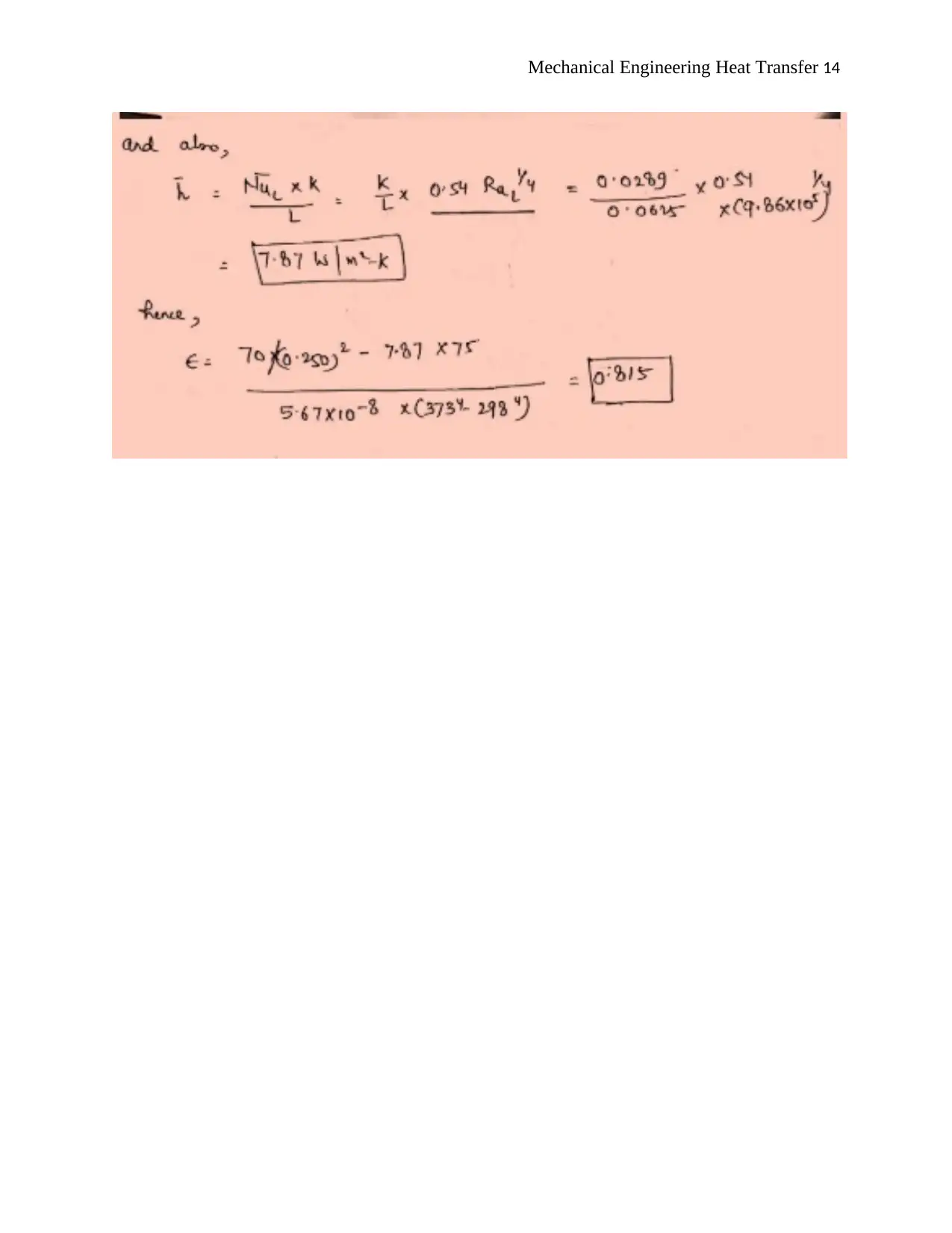
Mechanical Engineering Heat Transfer 14
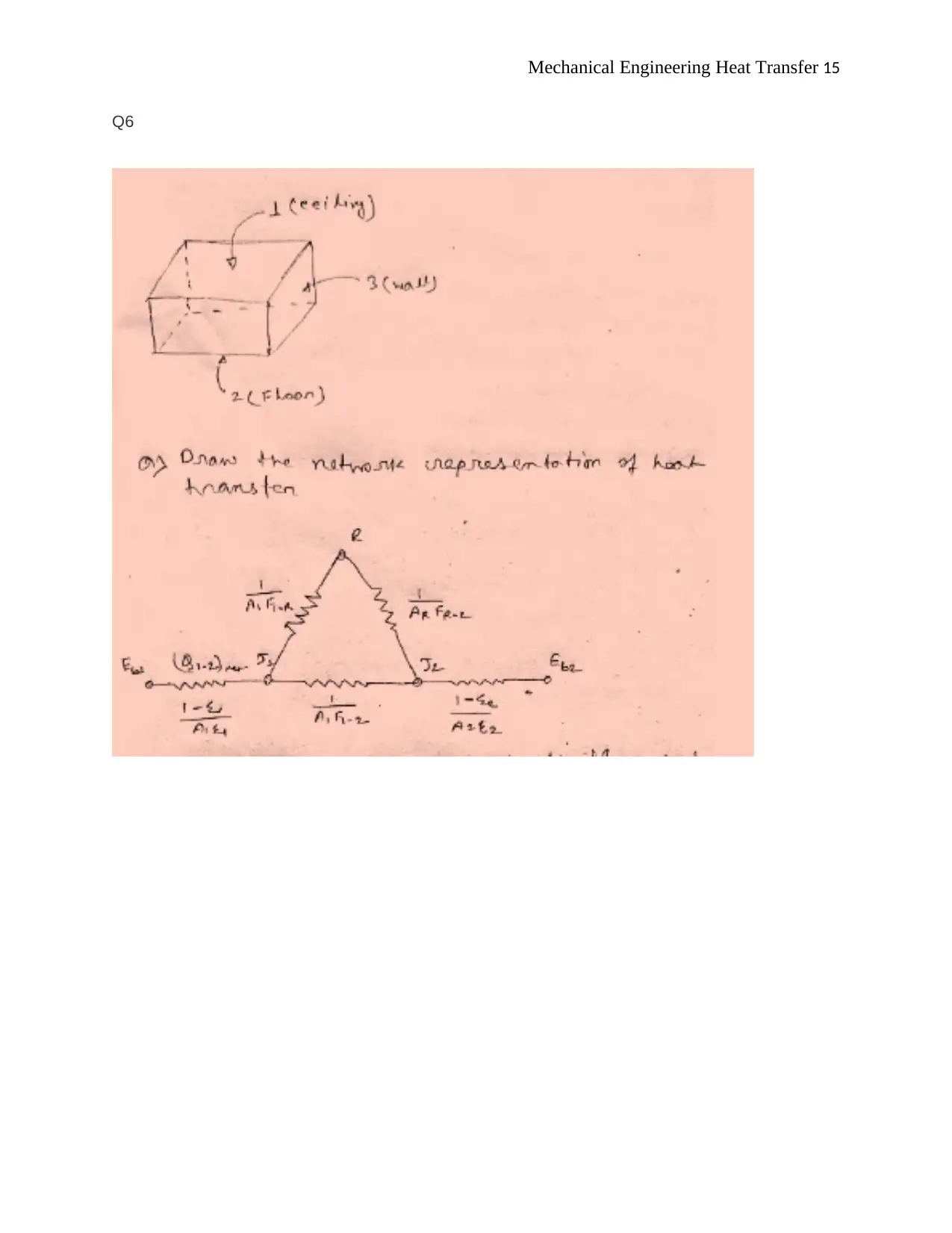
Mechanical Engineering Heat Transfer 15
Q6
Q6
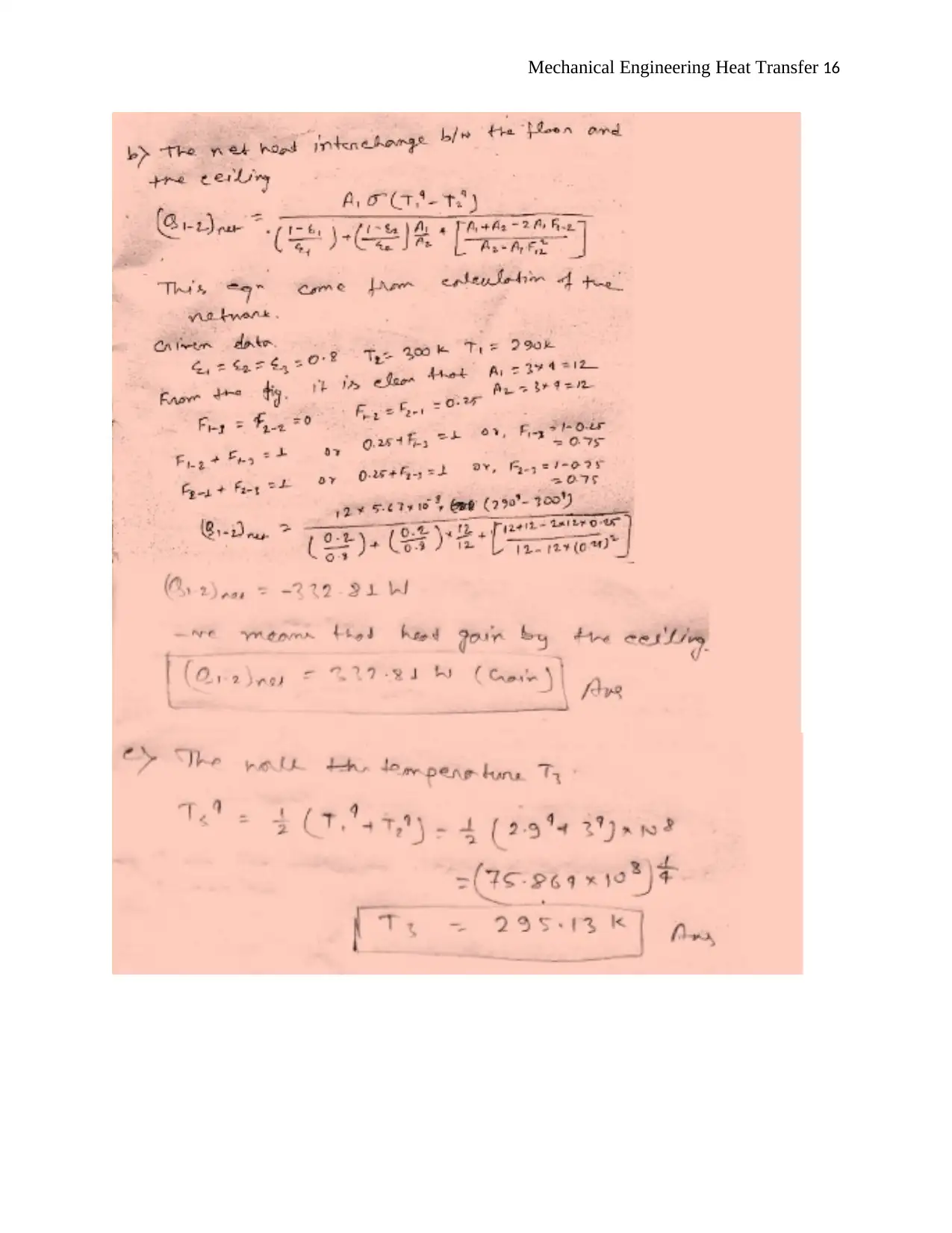
Mechanical Engineering Heat Transfer 16
Secure Best Marks with AI Grader
Need help grading? Try our AI Grader for instant feedback on your assignments.
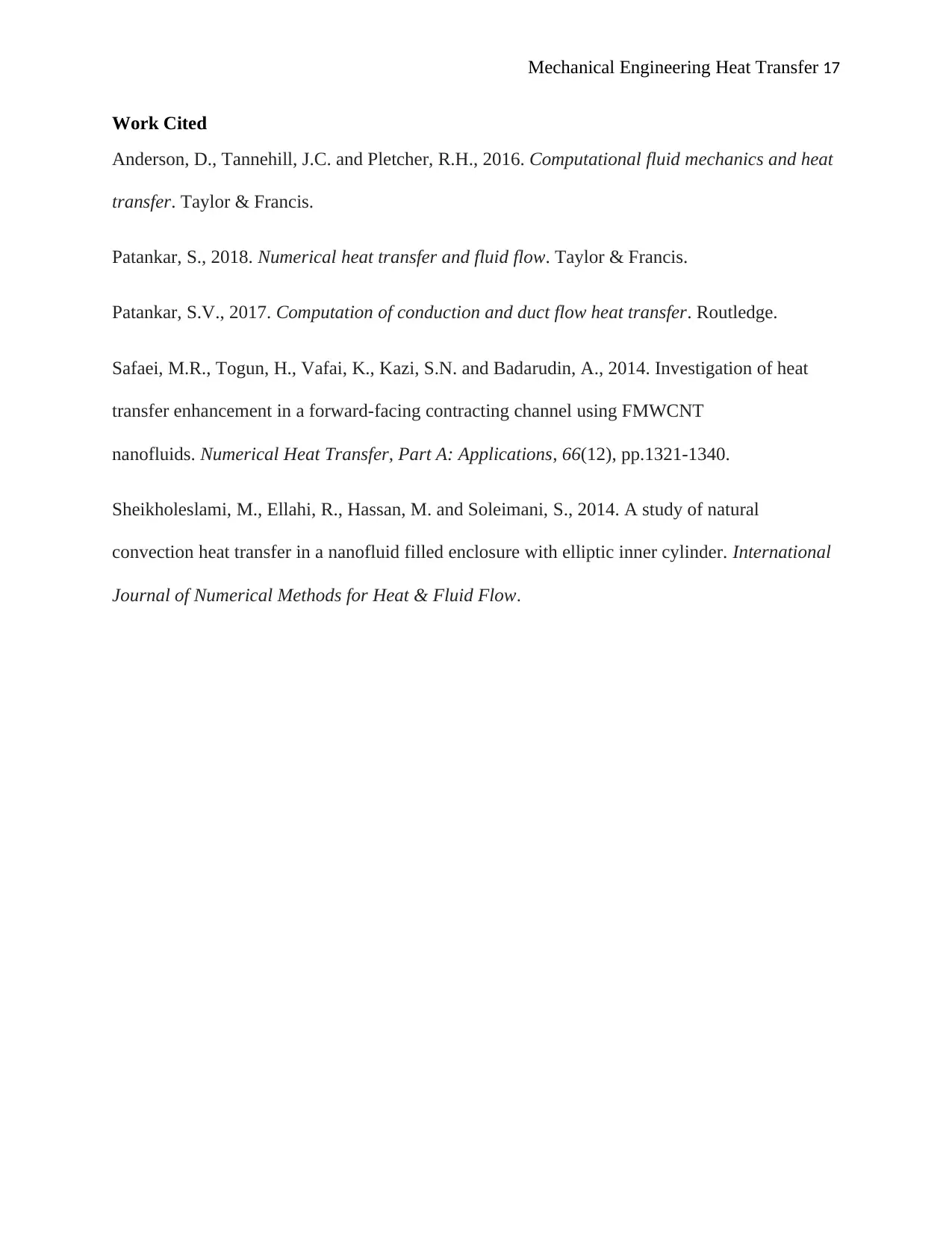
Mechanical Engineering Heat Transfer 17
Work Cited
Anderson, D., Tannehill, J.C. and Pletcher, R.H., 2016. Computational fluid mechanics and heat
transfer. Taylor & Francis.
Patankar, S., 2018. Numerical heat transfer and fluid flow. Taylor & Francis.
Patankar, S.V., 2017. Computation of conduction and duct flow heat transfer. Routledge.
Safaei, M.R., Togun, H., Vafai, K., Kazi, S.N. and Badarudin, A., 2014. Investigation of heat
transfer enhancement in a forward-facing contracting channel using FMWCNT
nanofluids. Numerical Heat Transfer, Part A: Applications, 66(12), pp.1321-1340.
Sheikholeslami, M., Ellahi, R., Hassan, M. and Soleimani, S., 2014. A study of natural
convection heat transfer in a nanofluid filled enclosure with elliptic inner cylinder. International
Journal of Numerical Methods for Heat & Fluid Flow.
Work Cited
Anderson, D., Tannehill, J.C. and Pletcher, R.H., 2016. Computational fluid mechanics and heat
transfer. Taylor & Francis.
Patankar, S., 2018. Numerical heat transfer and fluid flow. Taylor & Francis.
Patankar, S.V., 2017. Computation of conduction and duct flow heat transfer. Routledge.
Safaei, M.R., Togun, H., Vafai, K., Kazi, S.N. and Badarudin, A., 2014. Investigation of heat
transfer enhancement in a forward-facing contracting channel using FMWCNT
nanofluids. Numerical Heat Transfer, Part A: Applications, 66(12), pp.1321-1340.
Sheikholeslami, M., Ellahi, R., Hassan, M. and Soleimani, S., 2014. A study of natural
convection heat transfer in a nanofluid filled enclosure with elliptic inner cylinder. International
Journal of Numerical Methods for Heat & Fluid Flow.
1 out of 17
![[object Object]](/_next/image/?url=%2F_next%2Fstatic%2Fmedia%2Flogo.6d15ce61.png&w=640&q=75)
Your All-in-One AI-Powered Toolkit for Academic Success.
+13062052269
info@desklib.com
Available 24*7 on WhatsApp / Email
Unlock your academic potential
© 2024 | Zucol Services PVT LTD | All rights reserved.