Mechanical Vibrations: Analysis and Solutions for Centrifugal Fans
VerifiedAdded on 2023/06/15
|10
|1662
|151
Report
AI Summary
This report addresses the issue of excessive vibration in a centrifugal fan system used for forcing heated air over drying malt. It identifies likely causes of vibration, including misalignment of the shaft, resonance, loose mechanical connections, cracked rotors and shafts, and unbalanced rotor mass. ...
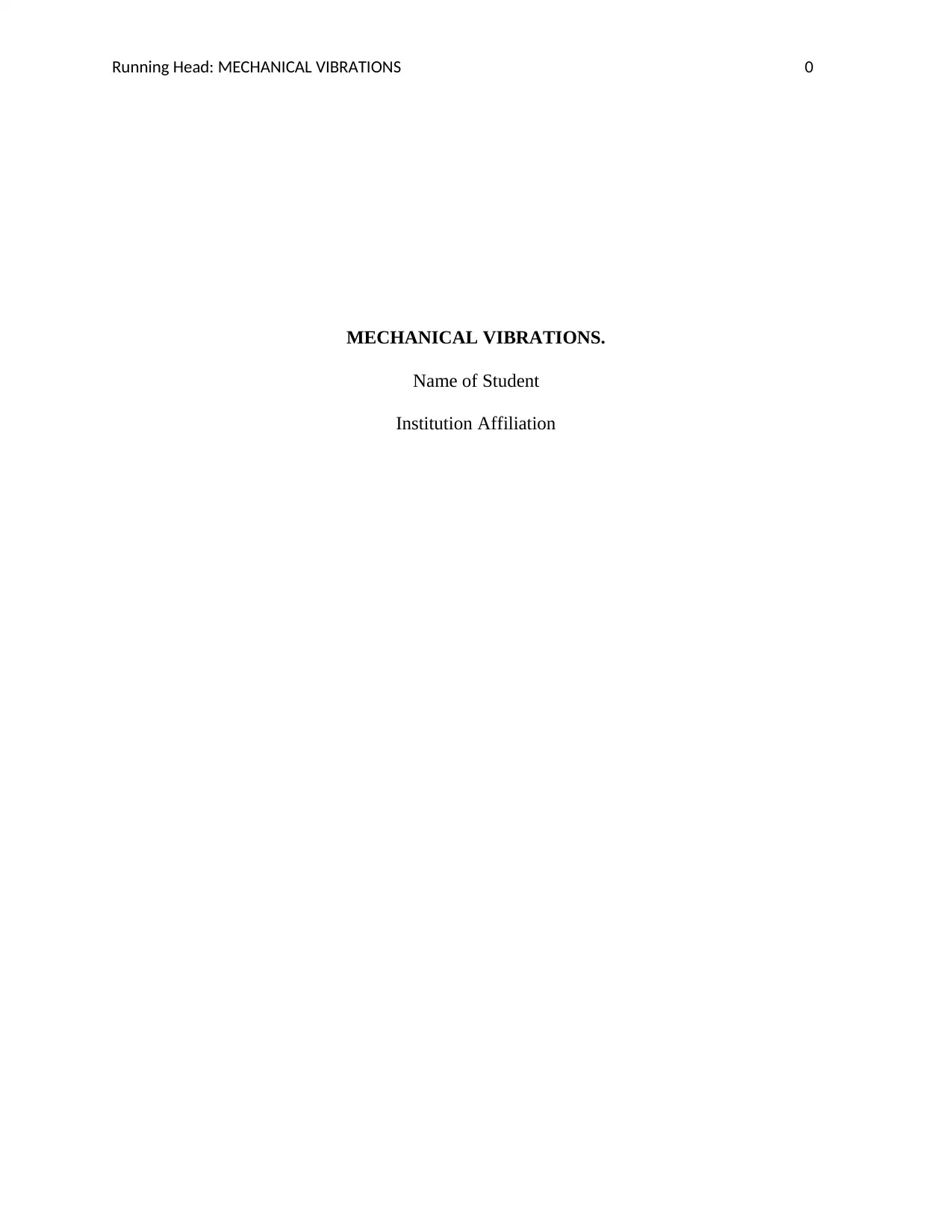
Running Head: MECHANICAL VIBRATIONS 0
MECHANICAL VIBRATIONS.
Name of Student
Institution Affiliation
MECHANICAL VIBRATIONS.
Name of Student
Institution Affiliation
Paraphrase This Document
Need a fresh take? Get an instant paraphrase of this document with our AI Paraphraser
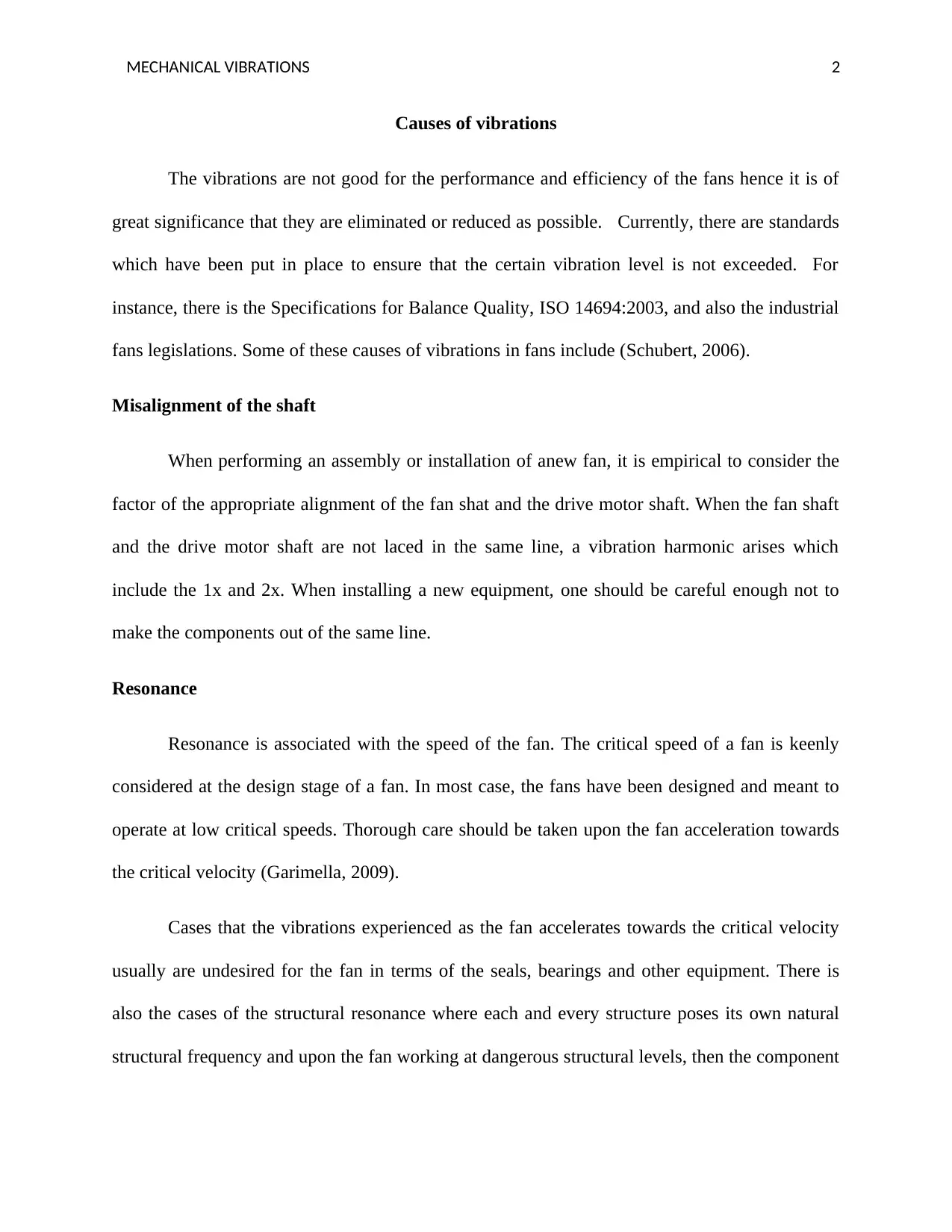
MECHANICAL VIBRATIONS 2
Causes of vibrations
The vibrations are not good for the performance and efficiency of the fans hence it is of
great significance that they are eliminated or reduced as possible. Currently, there are standards
which have been put in place to ensure that the certain vibration level is not exceeded. For
instance, there is the Specifications for Balance Quality, ISO 14694:2003, and also the industrial
fans legislations. Some of these causes of vibrations in fans include (Schubert, 2006).
Misalignment of the shaft
When performing an assembly or installation of anew fan, it is empirical to consider the
factor of the appropriate alignment of the fan shat and the drive motor shaft. When the fan shaft
and the drive motor shaft are not laced in the same line, a vibration harmonic arises which
include the 1x and 2x. When installing a new equipment, one should be careful enough not to
make the components out of the same line.
Resonance
Resonance is associated with the speed of the fan. The critical speed of a fan is keenly
considered at the design stage of a fan. In most case, the fans have been designed and meant to
operate at low critical speeds. Thorough care should be taken upon the fan acceleration towards
the critical velocity (Garimella, 2009).
Cases that the vibrations experienced as the fan accelerates towards the critical velocity
usually are undesired for the fan in terms of the seals, bearings and other equipment. There is
also the cases of the structural resonance where each and every structure poses its own natural
structural frequency and upon the fan working at dangerous structural levels, then the component
Causes of vibrations
The vibrations are not good for the performance and efficiency of the fans hence it is of
great significance that they are eliminated or reduced as possible. Currently, there are standards
which have been put in place to ensure that the certain vibration level is not exceeded. For
instance, there is the Specifications for Balance Quality, ISO 14694:2003, and also the industrial
fans legislations. Some of these causes of vibrations in fans include (Schubert, 2006).
Misalignment of the shaft
When performing an assembly or installation of anew fan, it is empirical to consider the
factor of the appropriate alignment of the fan shat and the drive motor shaft. When the fan shaft
and the drive motor shaft are not laced in the same line, a vibration harmonic arises which
include the 1x and 2x. When installing a new equipment, one should be careful enough not to
make the components out of the same line.
Resonance
Resonance is associated with the speed of the fan. The critical speed of a fan is keenly
considered at the design stage of a fan. In most case, the fans have been designed and meant to
operate at low critical speeds. Thorough care should be taken upon the fan acceleration towards
the critical velocity (Garimella, 2009).
Cases that the vibrations experienced as the fan accelerates towards the critical velocity
usually are undesired for the fan in terms of the seals, bearings and other equipment. There is
also the cases of the structural resonance where each and every structure poses its own natural
structural frequency and upon the fan working at dangerous structural levels, then the component
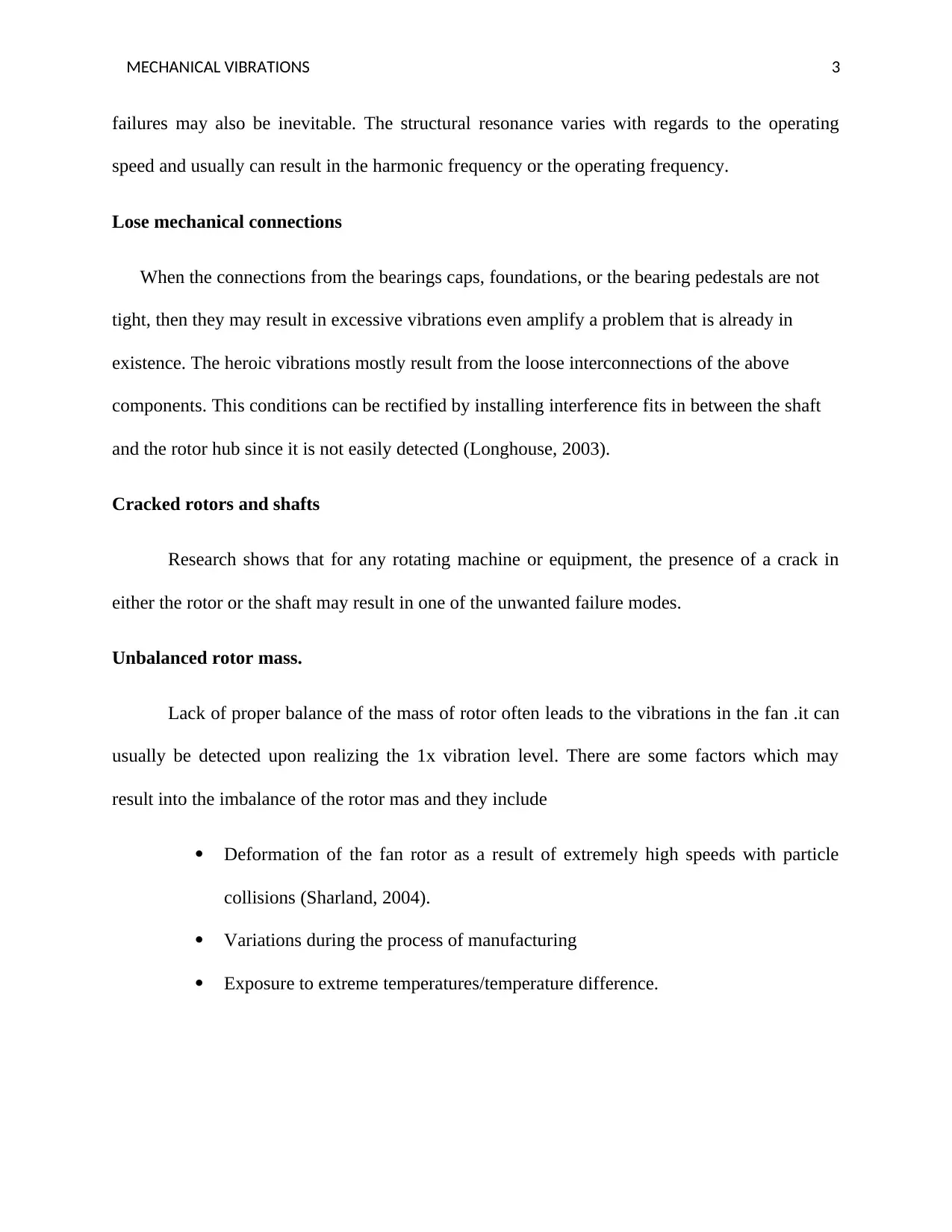
MECHANICAL VIBRATIONS 3
failures may also be inevitable. The structural resonance varies with regards to the operating
speed and usually can result in the harmonic frequency or the operating frequency.
Lose mechanical connections
When the connections from the bearings caps, foundations, or the bearing pedestals are not
tight, then they may result in excessive vibrations even amplify a problem that is already in
existence. The heroic vibrations mostly result from the loose interconnections of the above
components. This conditions can be rectified by installing interference fits in between the shaft
and the rotor hub since it is not easily detected (Longhouse, 2003).
Cracked rotors and shafts
Research shows that for any rotating machine or equipment, the presence of a crack in
either the rotor or the shaft may result in one of the unwanted failure modes.
Unbalanced rotor mass.
Lack of proper balance of the mass of rotor often leads to the vibrations in the fan .it can
usually be detected upon realizing the 1x vibration level. There are some factors which may
result into the imbalance of the rotor mas and they include
Deformation of the fan rotor as a result of extremely high speeds with particle
collisions (Sharland, 2004).
Variations during the process of manufacturing
Exposure to extreme temperatures/temperature difference.
failures may also be inevitable. The structural resonance varies with regards to the operating
speed and usually can result in the harmonic frequency or the operating frequency.
Lose mechanical connections
When the connections from the bearings caps, foundations, or the bearing pedestals are not
tight, then they may result in excessive vibrations even amplify a problem that is already in
existence. The heroic vibrations mostly result from the loose interconnections of the above
components. This conditions can be rectified by installing interference fits in between the shaft
and the rotor hub since it is not easily detected (Longhouse, 2003).
Cracked rotors and shafts
Research shows that for any rotating machine or equipment, the presence of a crack in
either the rotor or the shaft may result in one of the unwanted failure modes.
Unbalanced rotor mass.
Lack of proper balance of the mass of rotor often leads to the vibrations in the fan .it can
usually be detected upon realizing the 1x vibration level. There are some factors which may
result into the imbalance of the rotor mas and they include
Deformation of the fan rotor as a result of extremely high speeds with particle
collisions (Sharland, 2004).
Variations during the process of manufacturing
Exposure to extreme temperatures/temperature difference.
⊘ This is a preview!⊘
Do you want full access?
Subscribe today to unlock all pages.

Trusted by 1+ million students worldwide
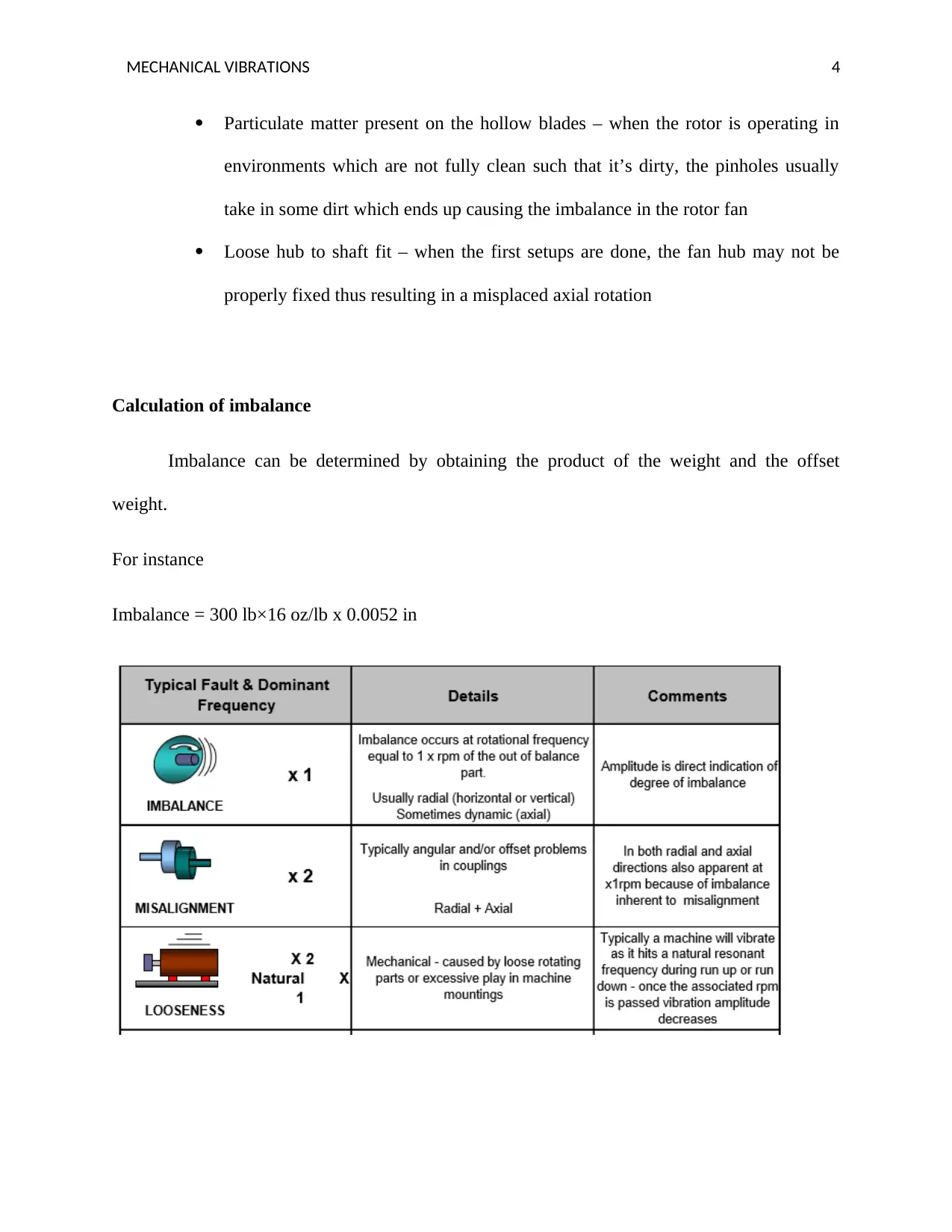
MECHANICAL VIBRATIONS 4
Particulate matter present on the hollow blades – when the rotor is operating in
environments which are not fully clean such that it’s dirty, the pinholes usually
take in some dirt which ends up causing the imbalance in the rotor fan
Loose hub to shaft fit – when the first setups are done, the fan hub may not be
properly fixed thus resulting in a misplaced axial rotation
Calculation of imbalance
Imbalance can be determined by obtaining the product of the weight and the offset
weight.
For instance
Imbalance = 300 lb×16 oz/lb x 0.0052 in
Particulate matter present on the hollow blades – when the rotor is operating in
environments which are not fully clean such that it’s dirty, the pinholes usually
take in some dirt which ends up causing the imbalance in the rotor fan
Loose hub to shaft fit – when the first setups are done, the fan hub may not be
properly fixed thus resulting in a misplaced axial rotation
Calculation of imbalance
Imbalance can be determined by obtaining the product of the weight and the offset
weight.
For instance
Imbalance = 300 lb×16 oz/lb x 0.0052 in
Paraphrase This Document
Need a fresh take? Get an instant paraphrase of this document with our AI Paraphraser
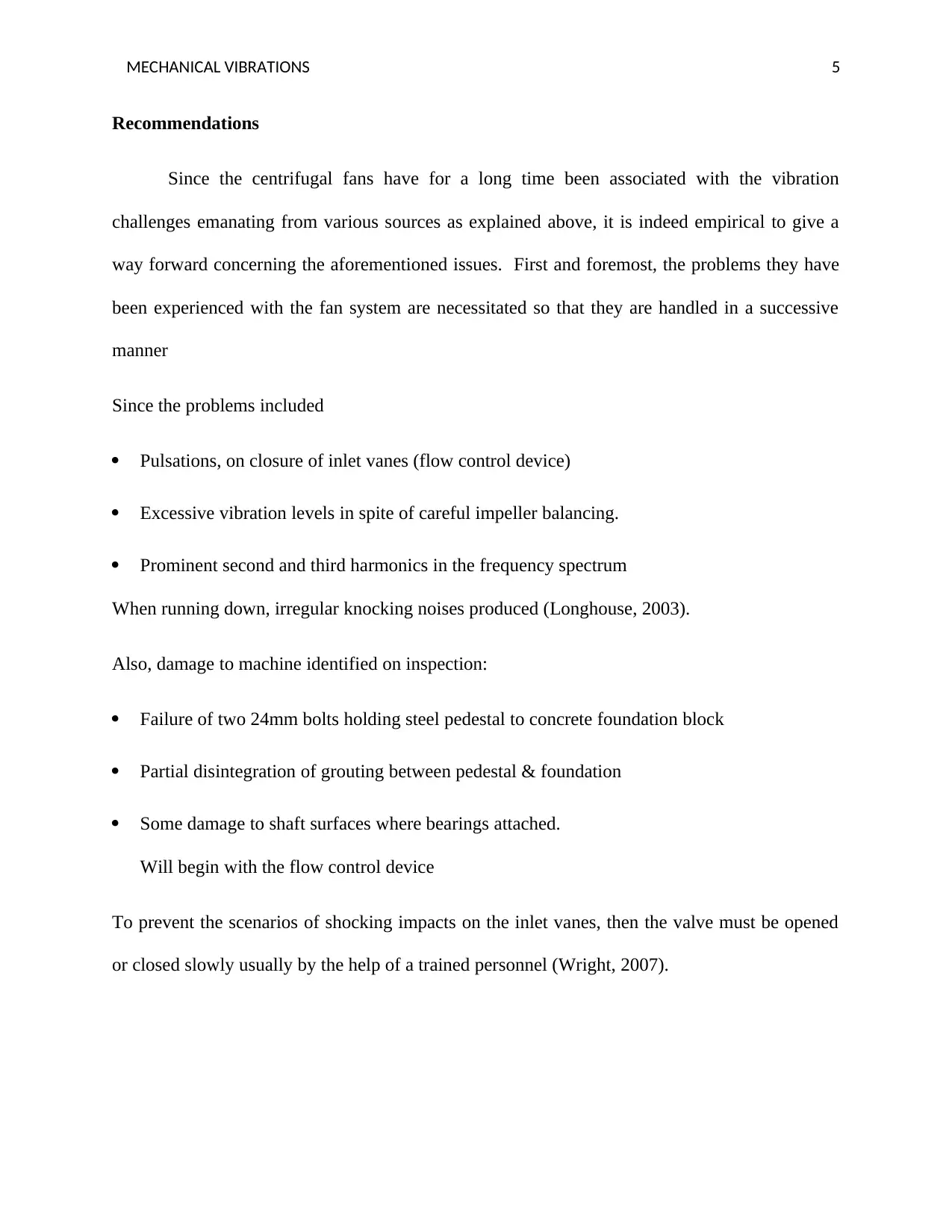
MECHANICAL VIBRATIONS 5
Recommendations
Since the centrifugal fans have for a long time been associated with the vibration
challenges emanating from various sources as explained above, it is indeed empirical to give a
way forward concerning the aforementioned issues. First and foremost, the problems they have
been experienced with the fan system are necessitated so that they are handled in a successive
manner
Since the problems included
Pulsations, on closure of inlet vanes (flow control device)
Excessive vibration levels in spite of careful impeller balancing.
Prominent second and third harmonics in the frequency spectrum
When running down, irregular knocking noises produced (Longhouse, 2003).
Also, damage to machine identified on inspection:
Failure of two 24mm bolts holding steel pedestal to concrete foundation block
Partial disintegration of grouting between pedestal & foundation
Some damage to shaft surfaces where bearings attached.
Will begin with the flow control device
To prevent the scenarios of shocking impacts on the inlet vanes, then the valve must be opened
or closed slowly usually by the help of a trained personnel (Wright, 2007).
Recommendations
Since the centrifugal fans have for a long time been associated with the vibration
challenges emanating from various sources as explained above, it is indeed empirical to give a
way forward concerning the aforementioned issues. First and foremost, the problems they have
been experienced with the fan system are necessitated so that they are handled in a successive
manner
Since the problems included
Pulsations, on closure of inlet vanes (flow control device)
Excessive vibration levels in spite of careful impeller balancing.
Prominent second and third harmonics in the frequency spectrum
When running down, irregular knocking noises produced (Longhouse, 2003).
Also, damage to machine identified on inspection:
Failure of two 24mm bolts holding steel pedestal to concrete foundation block
Partial disintegration of grouting between pedestal & foundation
Some damage to shaft surfaces where bearings attached.
Will begin with the flow control device
To prevent the scenarios of shocking impacts on the inlet vanes, then the valve must be opened
or closed slowly usually by the help of a trained personnel (Wright, 2007).
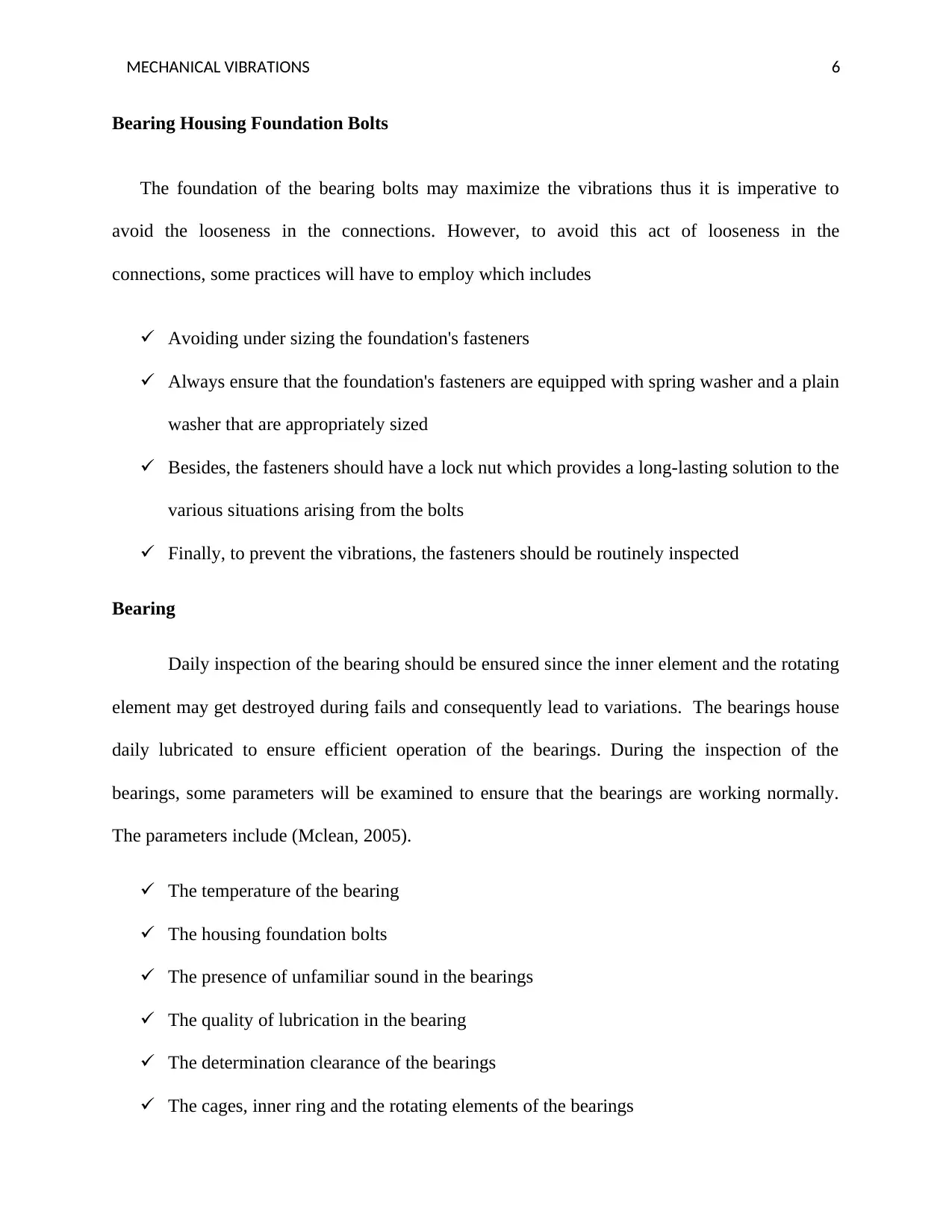
MECHANICAL VIBRATIONS 6
Bearing Housing Foundation Bolts
The foundation of the bearing bolts may maximize the vibrations thus it is imperative to
avoid the looseness in the connections. However, to avoid this act of looseness in the
connections, some practices will have to employ which includes
Avoiding under sizing the foundation's fasteners
Always ensure that the foundation's fasteners are equipped with spring washer and a plain
washer that are appropriately sized
Besides, the fasteners should have a lock nut which provides a long-lasting solution to the
various situations arising from the bolts
Finally, to prevent the vibrations, the fasteners should be routinely inspected
Bearing
Daily inspection of the bearing should be ensured since the inner element and the rotating
element may get destroyed during fails and consequently lead to variations. The bearings house
daily lubricated to ensure efficient operation of the bearings. During the inspection of the
bearings, some parameters will be examined to ensure that the bearings are working normally.
The parameters include (Mclean, 2005).
The temperature of the bearing
The housing foundation bolts
The presence of unfamiliar sound in the bearings
The quality of lubrication in the bearing
The determination clearance of the bearings
The cages, inner ring and the rotating elements of the bearings
Bearing Housing Foundation Bolts
The foundation of the bearing bolts may maximize the vibrations thus it is imperative to
avoid the looseness in the connections. However, to avoid this act of looseness in the
connections, some practices will have to employ which includes
Avoiding under sizing the foundation's fasteners
Always ensure that the foundation's fasteners are equipped with spring washer and a plain
washer that are appropriately sized
Besides, the fasteners should have a lock nut which provides a long-lasting solution to the
various situations arising from the bolts
Finally, to prevent the vibrations, the fasteners should be routinely inspected
Bearing
Daily inspection of the bearing should be ensured since the inner element and the rotating
element may get destroyed during fails and consequently lead to variations. The bearings house
daily lubricated to ensure efficient operation of the bearings. During the inspection of the
bearings, some parameters will be examined to ensure that the bearings are working normally.
The parameters include (Mclean, 2005).
The temperature of the bearing
The housing foundation bolts
The presence of unfamiliar sound in the bearings
The quality of lubrication in the bearing
The determination clearance of the bearings
The cages, inner ring and the rotating elements of the bearings
⊘ This is a preview!⊘
Do you want full access?
Subscribe today to unlock all pages.

Trusted by 1+ million students worldwide
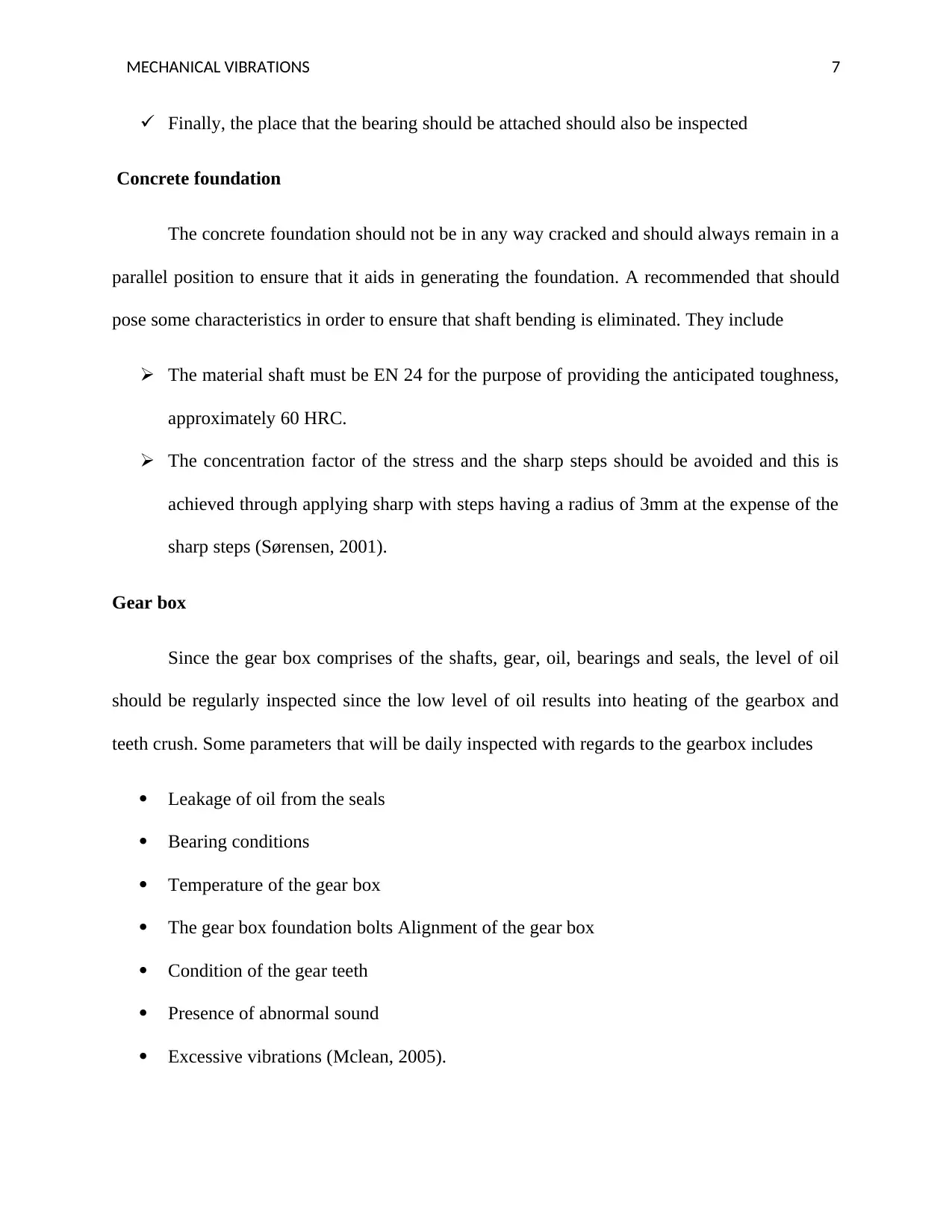
MECHANICAL VIBRATIONS 7
Finally, the place that the bearing should be attached should also be inspected
Concrete foundation
The concrete foundation should not be in any way cracked and should always remain in a
parallel position to ensure that it aids in generating the foundation. A recommended that should
pose some characteristics in order to ensure that shaft bending is eliminated. They include
The material shaft must be EN 24 for the purpose of providing the anticipated toughness,
approximately 60 HRC.
The concentration factor of the stress and the sharp steps should be avoided and this is
achieved through applying sharp with steps having a radius of 3mm at the expense of the
sharp steps (Sørensen, 2001).
Gear box
Since the gear box comprises of the shafts, gear, oil, bearings and seals, the level of oil
should be regularly inspected since the low level of oil results into heating of the gearbox and
teeth crush. Some parameters that will be daily inspected with regards to the gearbox includes
Leakage of oil from the seals
Bearing conditions
Temperature of the gear box
The gear box foundation bolts Alignment of the gear box
Condition of the gear teeth
Presence of abnormal sound
Excessive vibrations (Mclean, 2005).
Finally, the place that the bearing should be attached should also be inspected
Concrete foundation
The concrete foundation should not be in any way cracked and should always remain in a
parallel position to ensure that it aids in generating the foundation. A recommended that should
pose some characteristics in order to ensure that shaft bending is eliminated. They include
The material shaft must be EN 24 for the purpose of providing the anticipated toughness,
approximately 60 HRC.
The concentration factor of the stress and the sharp steps should be avoided and this is
achieved through applying sharp with steps having a radius of 3mm at the expense of the
sharp steps (Sørensen, 2001).
Gear box
Since the gear box comprises of the shafts, gear, oil, bearings and seals, the level of oil
should be regularly inspected since the low level of oil results into heating of the gearbox and
teeth crush. Some parameters that will be daily inspected with regards to the gearbox includes
Leakage of oil from the seals
Bearing conditions
Temperature of the gear box
The gear box foundation bolts Alignment of the gear box
Condition of the gear teeth
Presence of abnormal sound
Excessive vibrations (Mclean, 2005).
Paraphrase This Document
Need a fresh take? Get an instant paraphrase of this document with our AI Paraphraser
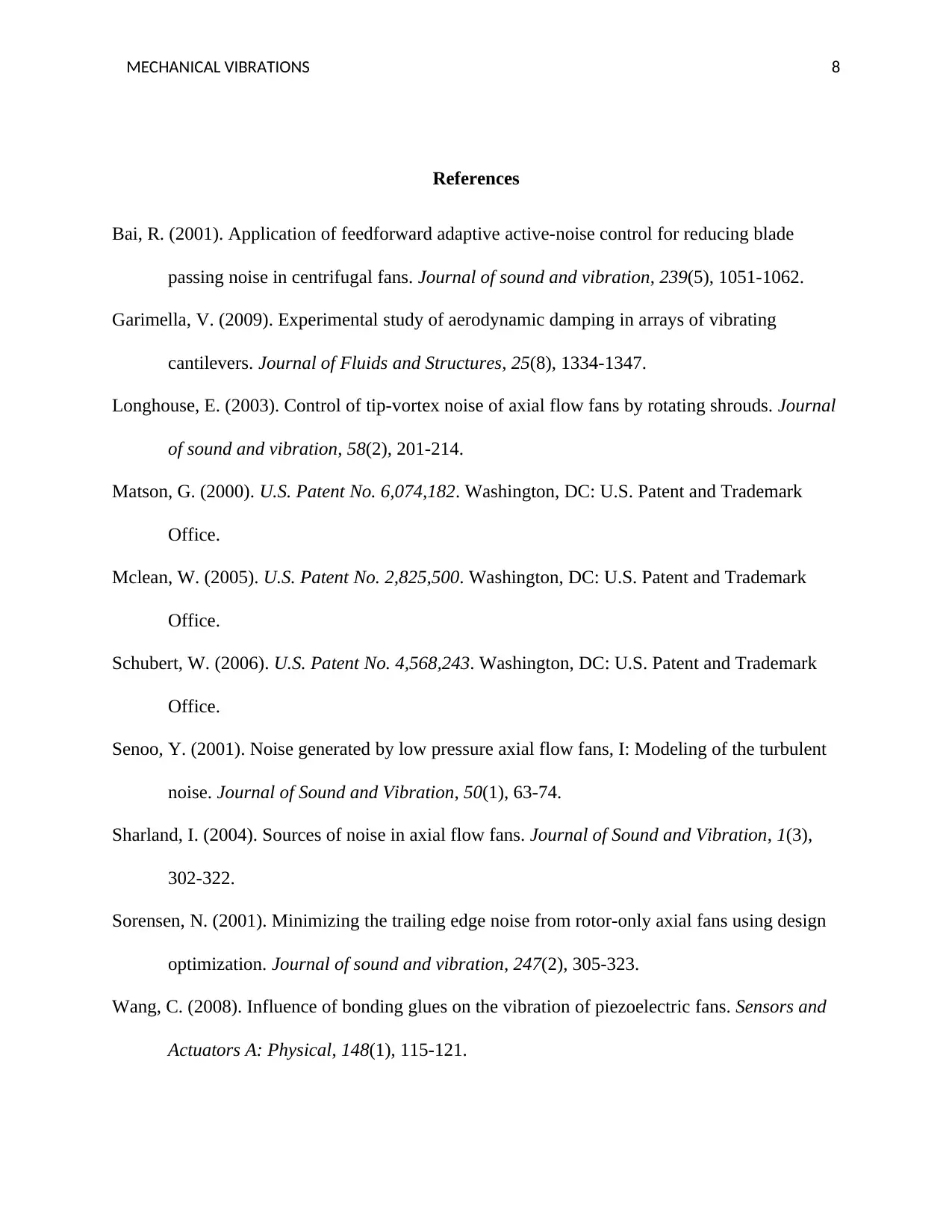
MECHANICAL VIBRATIONS 8
References
Bai, R. (2001). Application of feedforward adaptive active-noise control for reducing blade
passing noise in centrifugal fans. Journal of sound and vibration, 239(5), 1051-1062.
Garimella, V. (2009). Experimental study of aerodynamic damping in arrays of vibrating
cantilevers. Journal of Fluids and Structures, 25(8), 1334-1347.
Longhouse, E. (2003). Control of tip-vortex noise of axial flow fans by rotating shrouds. Journal
of sound and vibration, 58(2), 201-214.
Matson, G. (2000). U.S. Patent No. 6,074,182. Washington, DC: U.S. Patent and Trademark
Office.
Mclean, W. (2005). U.S. Patent No. 2,825,500. Washington, DC: U.S. Patent and Trademark
Office.
Schubert, W. (2006). U.S. Patent No. 4,568,243. Washington, DC: U.S. Patent and Trademark
Office.
Senoo, Y. (2001). Noise generated by low pressure axial flow fans, I: Modeling of the turbulent
noise. Journal of Sound and Vibration, 50(1), 63-74.
Sharland, I. (2004). Sources of noise in axial flow fans. Journal of Sound and Vibration, 1(3),
302-322.
Sorensen, N. (2001). Minimizing the trailing edge noise from rotor-only axial fans using design
optimization. Journal of sound and vibration, 247(2), 305-323.
Wang, C. (2008). Influence of bonding glues on the vibration of piezoelectric fans. Sensors and
Actuators A: Physical, 148(1), 115-121.
References
Bai, R. (2001). Application of feedforward adaptive active-noise control for reducing blade
passing noise in centrifugal fans. Journal of sound and vibration, 239(5), 1051-1062.
Garimella, V. (2009). Experimental study of aerodynamic damping in arrays of vibrating
cantilevers. Journal of Fluids and Structures, 25(8), 1334-1347.
Longhouse, E. (2003). Control of tip-vortex noise of axial flow fans by rotating shrouds. Journal
of sound and vibration, 58(2), 201-214.
Matson, G. (2000). U.S. Patent No. 6,074,182. Washington, DC: U.S. Patent and Trademark
Office.
Mclean, W. (2005). U.S. Patent No. 2,825,500. Washington, DC: U.S. Patent and Trademark
Office.
Schubert, W. (2006). U.S. Patent No. 4,568,243. Washington, DC: U.S. Patent and Trademark
Office.
Senoo, Y. (2001). Noise generated by low pressure axial flow fans, I: Modeling of the turbulent
noise. Journal of Sound and Vibration, 50(1), 63-74.
Sharland, I. (2004). Sources of noise in axial flow fans. Journal of Sound and Vibration, 1(3),
302-322.
Sorensen, N. (2001). Minimizing the trailing edge noise from rotor-only axial fans using design
optimization. Journal of sound and vibration, 247(2), 305-323.
Wang, C. (2008). Influence of bonding glues on the vibration of piezoelectric fans. Sensors and
Actuators A: Physical, 148(1), 115-121.
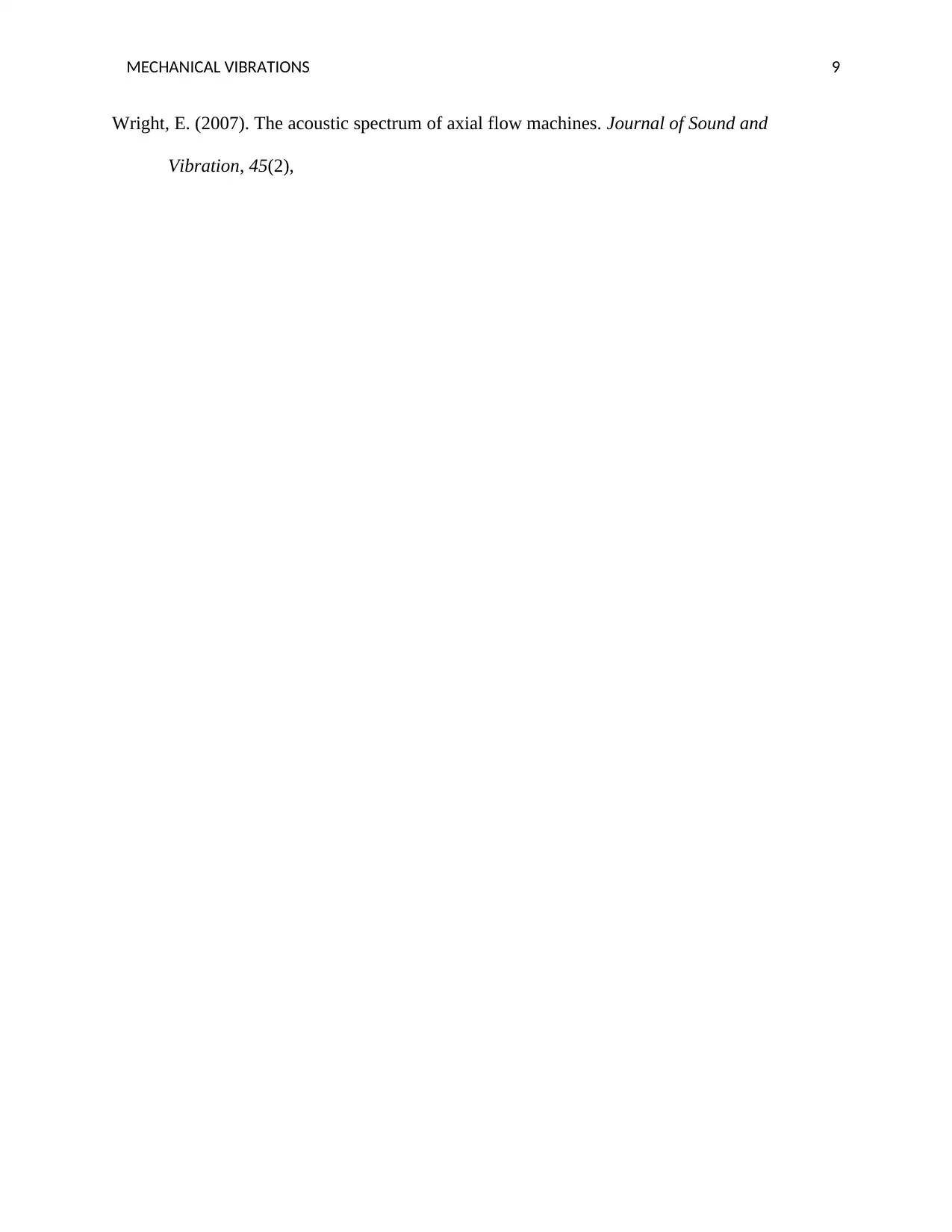
MECHANICAL VIBRATIONS 9
Wright, E. (2007). The acoustic spectrum of axial flow machines. Journal of Sound and
Vibration, 45(2),
Wright, E. (2007). The acoustic spectrum of axial flow machines. Journal of Sound and
Vibration, 45(2),
⊘ This is a preview!⊘
Do you want full access?
Subscribe today to unlock all pages.

Trusted by 1+ million students worldwide
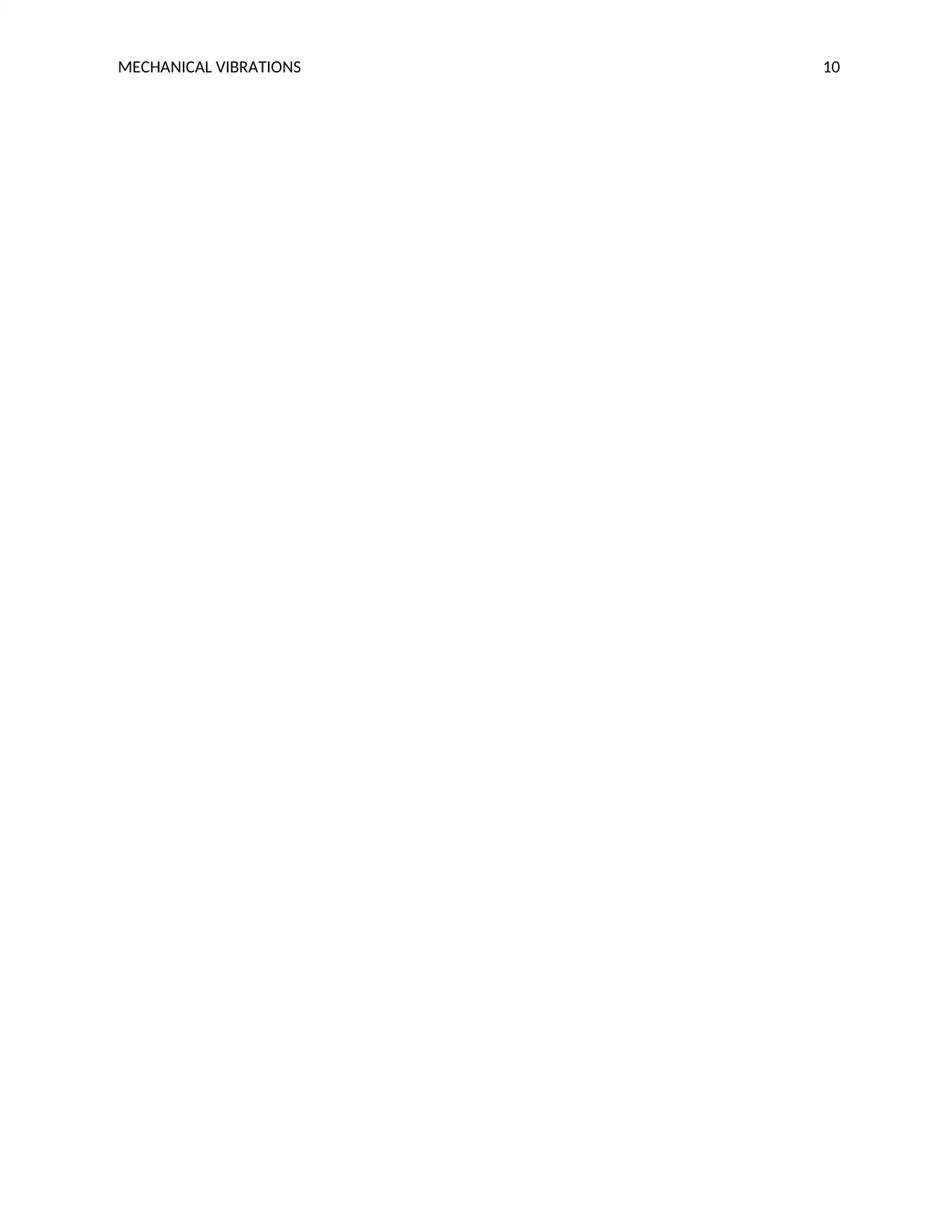
MECHANICAL VIBRATIONS 10
1 out of 10

Your All-in-One AI-Powered Toolkit for Academic Success.
+13062052269
info@desklib.com
Available 24*7 on WhatsApp / Email
Unlock your academic potential
© 2024 | Zucol Services PVT LTD | All rights reserved.