Mechatronic Design Question Answer 2022
VerifiedAdded on 2022/09/18
|16
|1326
|47
AI Summary
Contribute Materials
Your contribution can guide someone’s learning journey. Share your
documents today.
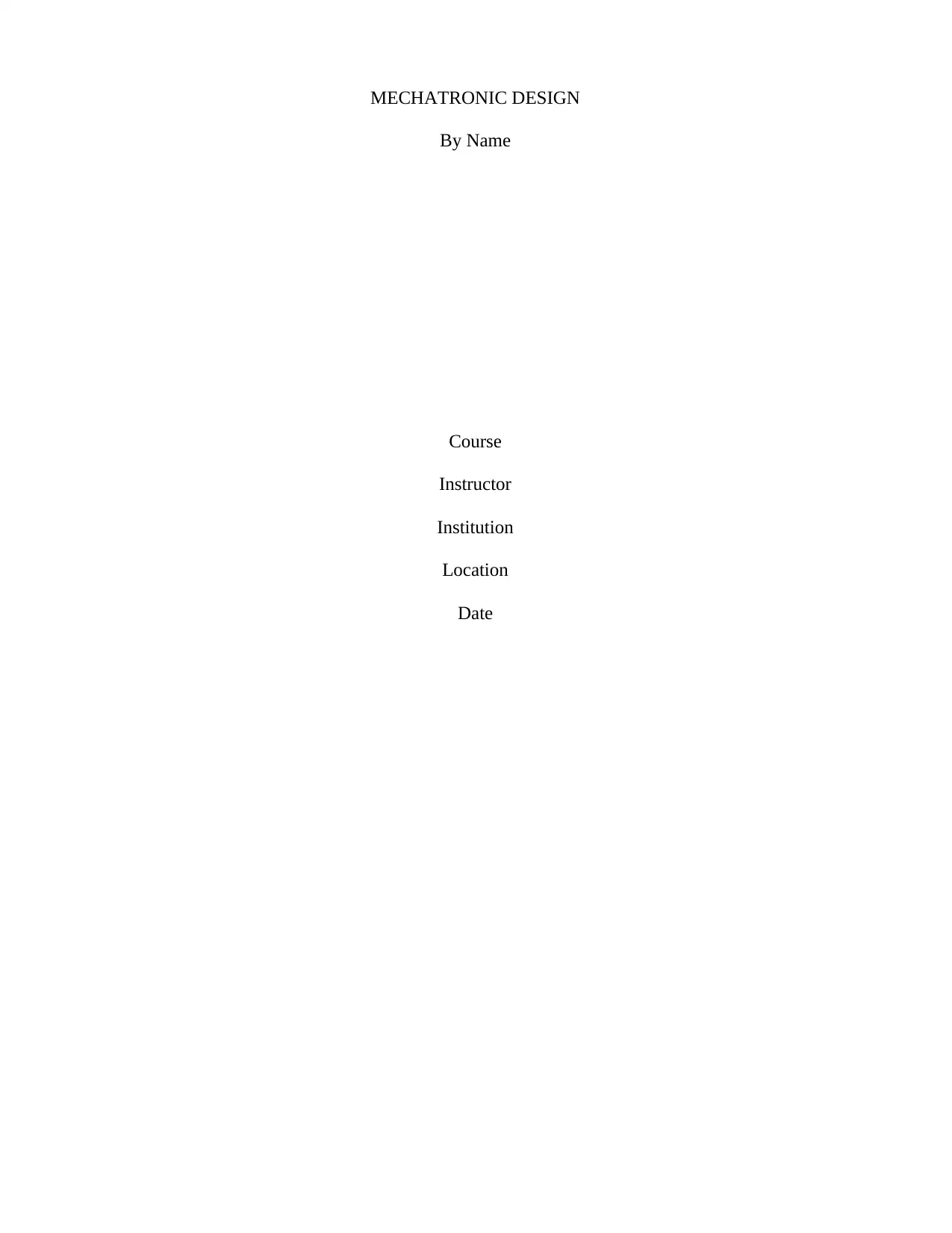
MECHATRONIC DESIGN
By Name
Course
Instructor
Institution
Location
Date
By Name
Course
Instructor
Institution
Location
Date
Secure Best Marks with AI Grader
Need help grading? Try our AI Grader for instant feedback on your assignments.
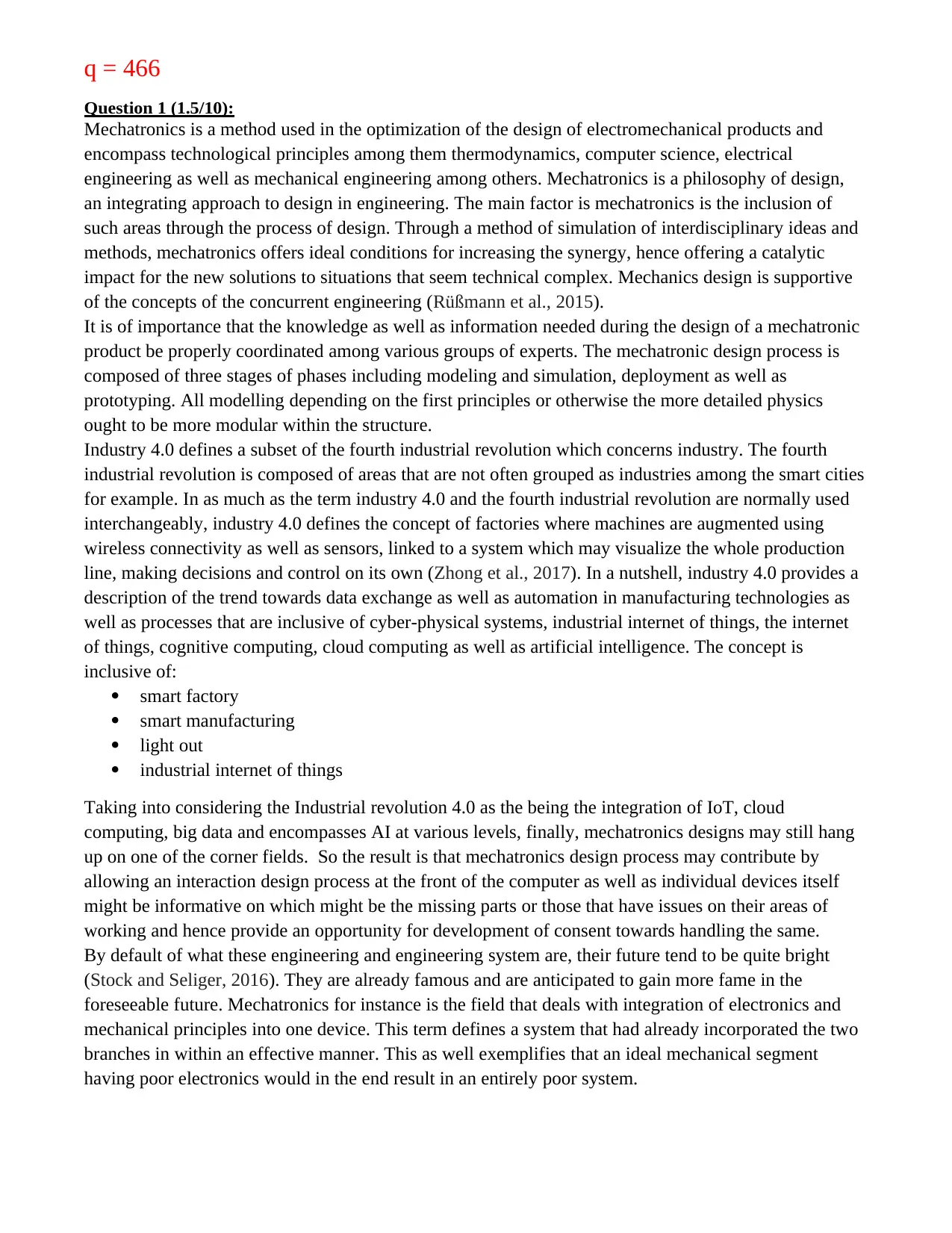
q = 466
Question 1 (1.5/10):
Mechatronics is a method used in the optimization of the design of electromechanical products and
encompass technological principles among them thermodynamics, computer science, electrical
engineering as well as mechanical engineering among others. Mechatronics is a philosophy of design,
an integrating approach to design in engineering. The main factor is mechatronics is the inclusion of
such areas through the process of design. Through a method of simulation of interdisciplinary ideas and
methods, mechatronics offers ideal conditions for increasing the synergy, hence offering a catalytic
impact for the new solutions to situations that seem technical complex. Mechanics design is supportive
of the concepts of the concurrent engineering (Rüßmann et al., 2015).
It is of importance that the knowledge as well as information needed during the design of a mechatronic
product be properly coordinated among various groups of experts. The mechatronic design process is
composed of three stages of phases including modeling and simulation, deployment as well as
prototyping. All modelling depending on the first principles or otherwise the more detailed physics
ought to be more modular within the structure.
Industry 4.0 defines a subset of the fourth industrial revolution which concerns industry. The fourth
industrial revolution is composed of areas that are not often grouped as industries among the smart cities
for example. In as much as the term industry 4.0 and the fourth industrial revolution are normally used
interchangeably, industry 4.0 defines the concept of factories where machines are augmented using
wireless connectivity as well as sensors, linked to a system which may visualize the whole production
line, making decisions and control on its own (Zhong et al., 2017). In a nutshell, industry 4.0 provides a
description of the trend towards data exchange as well as automation in manufacturing technologies as
well as processes that are inclusive of cyber-physical systems, industrial internet of things, the internet
of things, cognitive computing, cloud computing as well as artificial intelligence. The concept is
inclusive of:
smart factory
smart manufacturing
light out
industrial internet of things
Taking into considering the Industrial revolution 4.0 as the being the integration of IoT, cloud
computing, big data and encompasses AI at various levels, finally, mechatronics designs may still hang
up on one of the corner fields. So the result is that mechatronics design process may contribute by
allowing an interaction design process at the front of the computer as well as individual devices itself
might be informative on which might be the missing parts or those that have issues on their areas of
working and hence provide an opportunity for development of consent towards handling the same.
By default of what these engineering and engineering system are, their future tend to be quite bright
(Stock and Seliger, 2016). They are already famous and are anticipated to gain more fame in the
foreseeable future. Mechatronics for instance is the field that deals with integration of electronics and
mechanical principles into one device. This term defines a system that had already incorporated the two
branches in within an effective manner. This as well exemplifies that an ideal mechanical segment
having poor electronics would in the end result in an entirely poor system.
Question 1 (1.5/10):
Mechatronics is a method used in the optimization of the design of electromechanical products and
encompass technological principles among them thermodynamics, computer science, electrical
engineering as well as mechanical engineering among others. Mechatronics is a philosophy of design,
an integrating approach to design in engineering. The main factor is mechatronics is the inclusion of
such areas through the process of design. Through a method of simulation of interdisciplinary ideas and
methods, mechatronics offers ideal conditions for increasing the synergy, hence offering a catalytic
impact for the new solutions to situations that seem technical complex. Mechanics design is supportive
of the concepts of the concurrent engineering (Rüßmann et al., 2015).
It is of importance that the knowledge as well as information needed during the design of a mechatronic
product be properly coordinated among various groups of experts. The mechatronic design process is
composed of three stages of phases including modeling and simulation, deployment as well as
prototyping. All modelling depending on the first principles or otherwise the more detailed physics
ought to be more modular within the structure.
Industry 4.0 defines a subset of the fourth industrial revolution which concerns industry. The fourth
industrial revolution is composed of areas that are not often grouped as industries among the smart cities
for example. In as much as the term industry 4.0 and the fourth industrial revolution are normally used
interchangeably, industry 4.0 defines the concept of factories where machines are augmented using
wireless connectivity as well as sensors, linked to a system which may visualize the whole production
line, making decisions and control on its own (Zhong et al., 2017). In a nutshell, industry 4.0 provides a
description of the trend towards data exchange as well as automation in manufacturing technologies as
well as processes that are inclusive of cyber-physical systems, industrial internet of things, the internet
of things, cognitive computing, cloud computing as well as artificial intelligence. The concept is
inclusive of:
smart factory
smart manufacturing
light out
industrial internet of things
Taking into considering the Industrial revolution 4.0 as the being the integration of IoT, cloud
computing, big data and encompasses AI at various levels, finally, mechatronics designs may still hang
up on one of the corner fields. So the result is that mechatronics design process may contribute by
allowing an interaction design process at the front of the computer as well as individual devices itself
might be informative on which might be the missing parts or those that have issues on their areas of
working and hence provide an opportunity for development of consent towards handling the same.
By default of what these engineering and engineering system are, their future tend to be quite bright
(Stock and Seliger, 2016). They are already famous and are anticipated to gain more fame in the
foreseeable future. Mechatronics for instance is the field that deals with integration of electronics and
mechanical principles into one device. This term defines a system that had already incorporated the two
branches in within an effective manner. This as well exemplifies that an ideal mechanical segment
having poor electronics would in the end result in an entirely poor system.
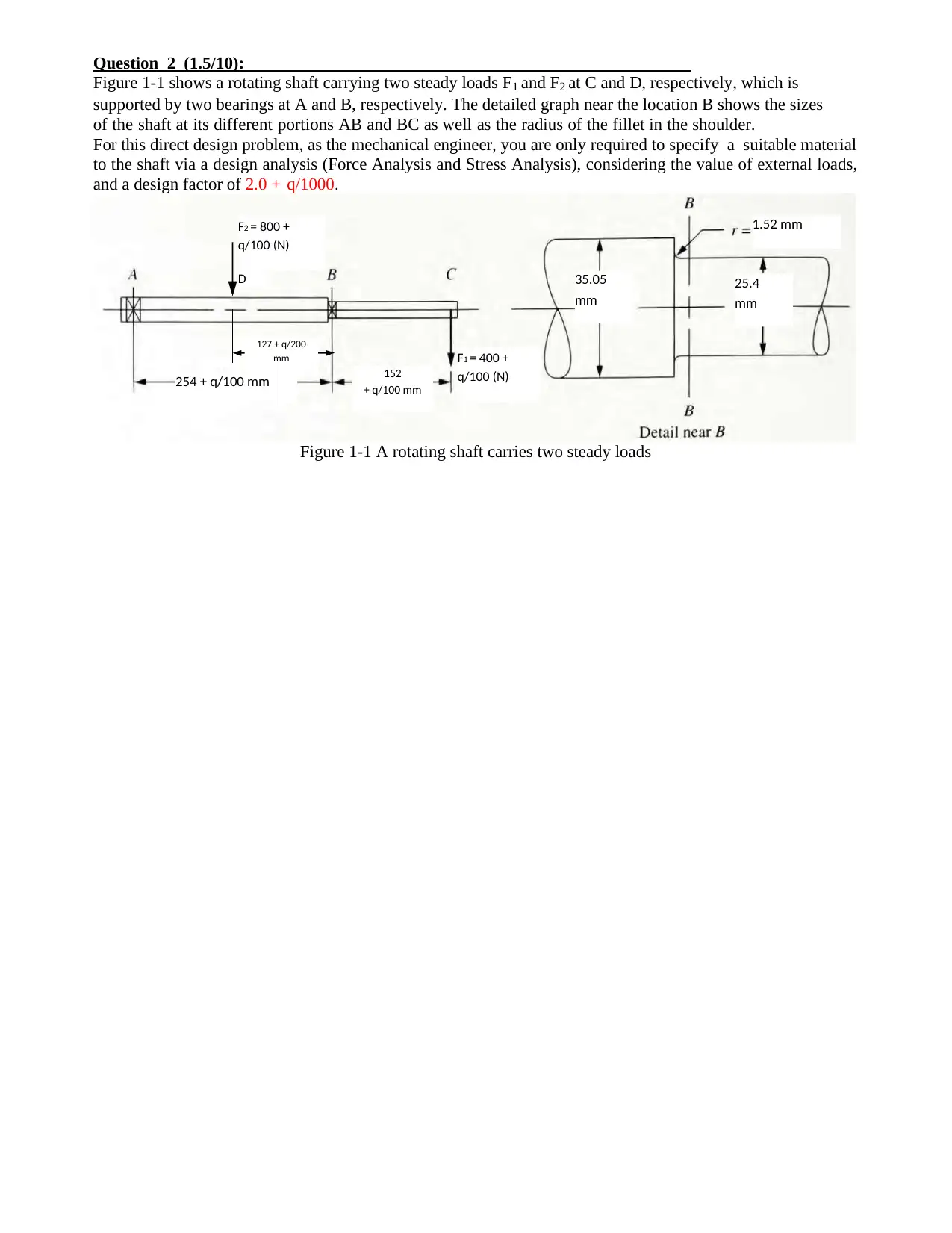
Question 2 (1.5/10):
Figure 1-1 shows a rotating shaft carrying two steady loads F1 and F2 at C and D, respectively, which is
supported by two bearings at A and B, respectively. The detailed graph near the location B shows the sizes
of the shaft at its different portions AB and BC as well as the radius of the fillet in the shoulder.
For this direct design problem, as the mechanical engineer, you are only required to specify a suitable material
to the shaft via a design analysis (Force Analysis and Stress Analysis), considering the value of external loads,
and a design factor of 2.0 + q/1000.
Figure 1-1 A rotating shaft carries two steady loads
254 + q/100 mm
127 + q/200
mm
D
F2 = 800 +
q/100 (N)
152
+ q/100 mm
F1 = 400 +
q/100 (N)
25.4
mm
35.05
mm
1.52 mm
Figure 1-1 shows a rotating shaft carrying two steady loads F1 and F2 at C and D, respectively, which is
supported by two bearings at A and B, respectively. The detailed graph near the location B shows the sizes
of the shaft at its different portions AB and BC as well as the radius of the fillet in the shoulder.
For this direct design problem, as the mechanical engineer, you are only required to specify a suitable material
to the shaft via a design analysis (Force Analysis and Stress Analysis), considering the value of external loads,
and a design factor of 2.0 + q/1000.
Figure 1-1 A rotating shaft carries two steady loads
254 + q/100 mm
127 + q/200
mm
D
F2 = 800 +
q/100 (N)
152
+ q/100 mm
F1 = 400 +
q/100 (N)
25.4
mm
35.05
mm
1.52 mm
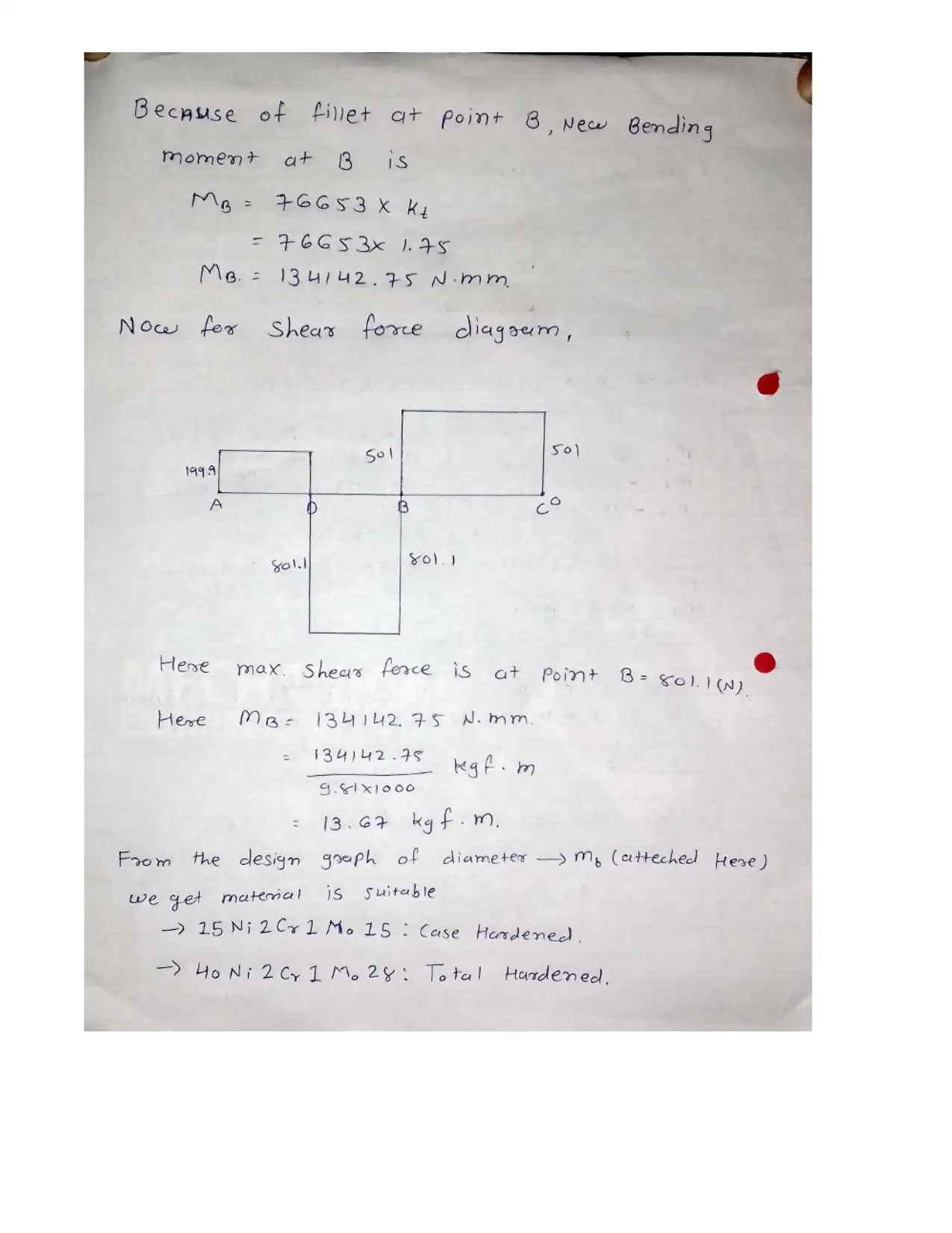
Secure Best Marks with AI Grader
Need help grading? Try our AI Grader for instant feedback on your assignments.
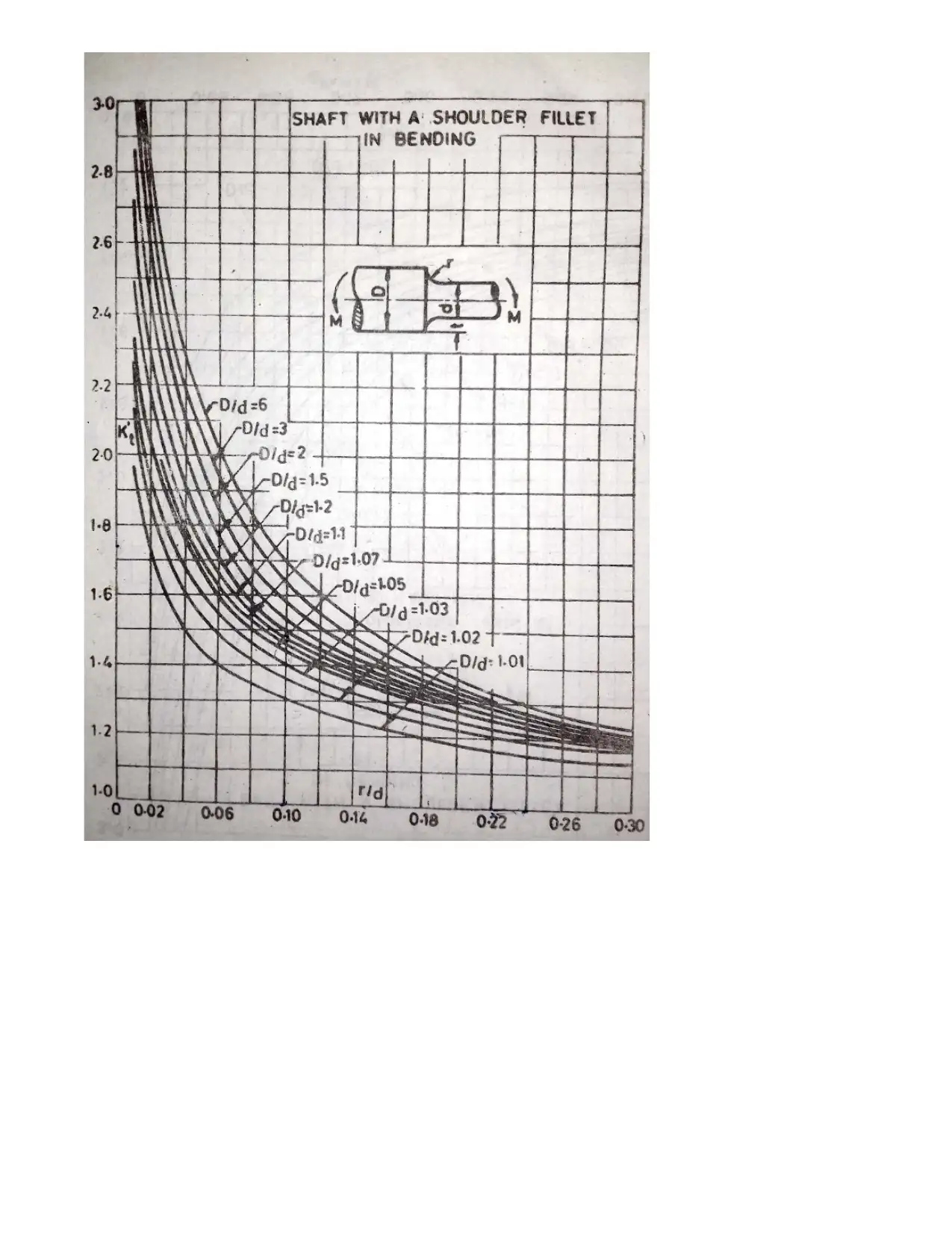
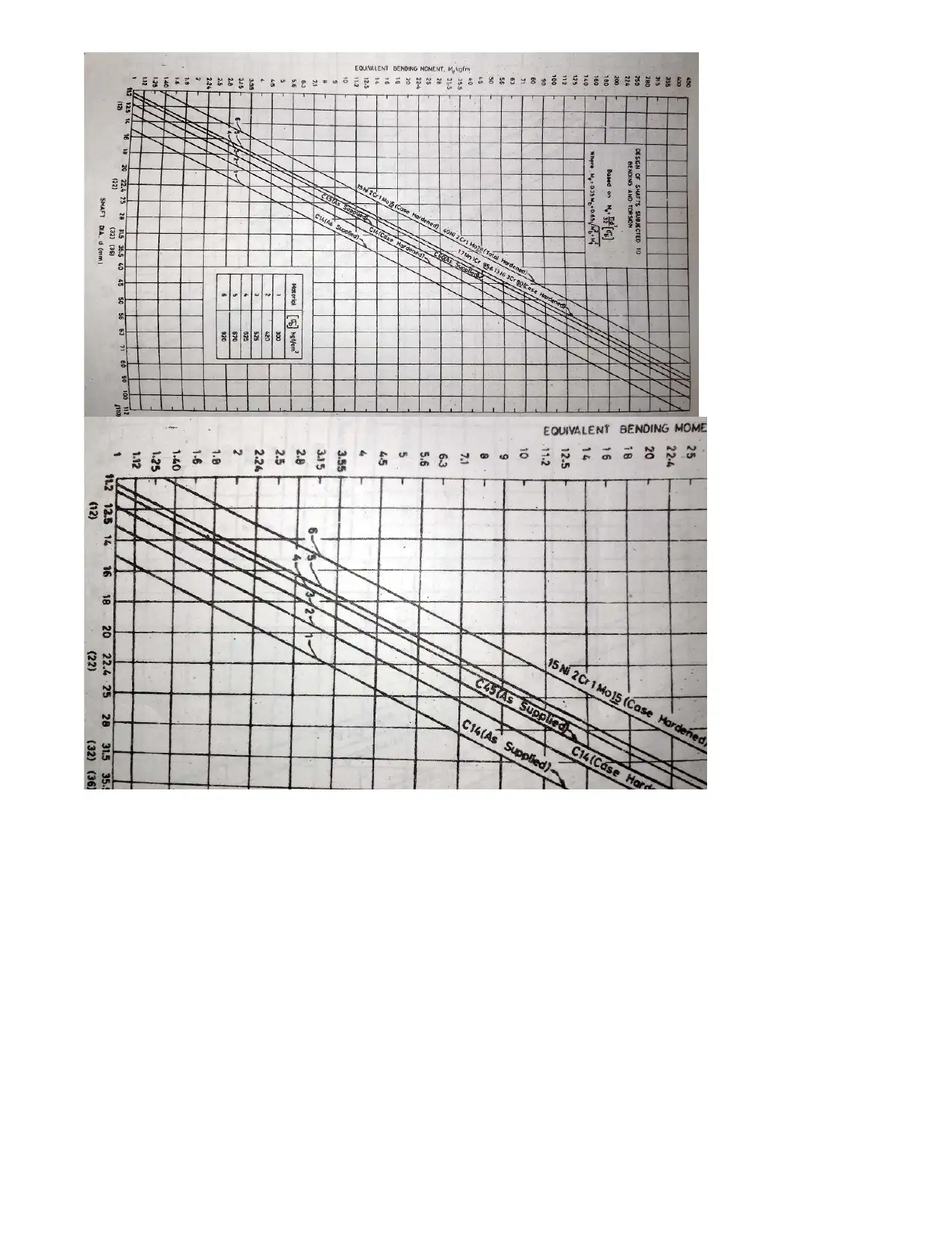
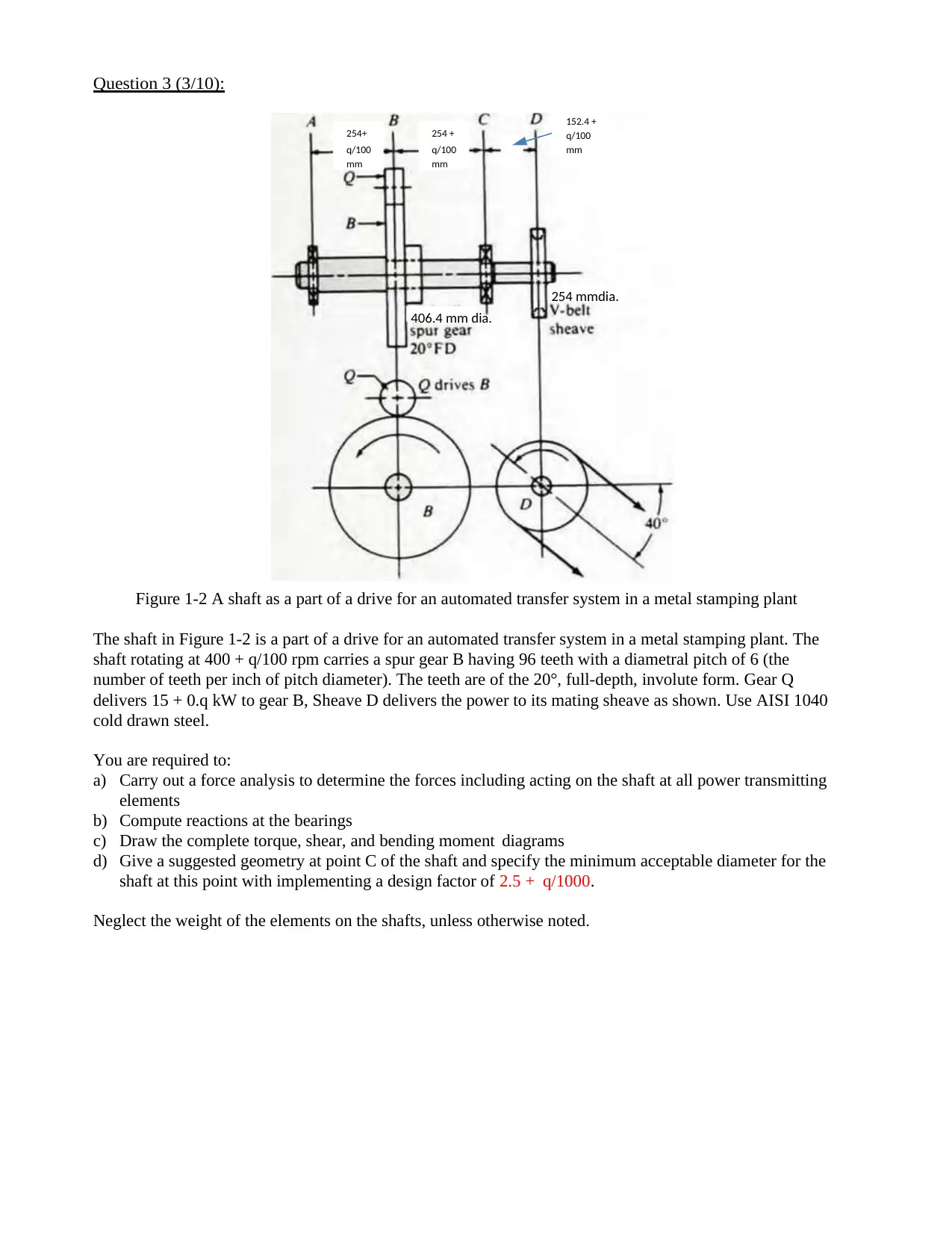
254+
q/100
mm
254 +
q/100
mm
152.4 +
q/100
mm
254 mmdia.
406.4 mm dia.
Question 3 (3/10):
Figure 1-2 A shaft as a part of a drive for an automated transfer system in a metal stamping plant
The shaft in Figure 1-2 is a part of a drive for an automated transfer system in a metal stamping plant. The
shaft rotating at 400 + q/100 rpm carries a spur gear B having 96 teeth with a diametral pitch of 6 (the
number of teeth per inch of pitch diameter). The teeth are of the 20°, full-depth, involute form. Gear Q
delivers 15 + 0.q kW to gear B, Sheave D delivers the power to its mating sheave as shown. Use AISI 1040
cold drawn steel.
You are required to:
a) Carry out a force analysis to determine the forces including acting on the shaft at all power transmitting
elements
b) Compute reactions at the bearings
c) Draw the complete torque, shear, and bending moment diagrams
d) Give a suggested geometry at point C of the shaft and specify the minimum acceptable diameter for the
shaft at this point with implementing a design factor of 2.5 + q/1000.
Neglect the weight of the elements on the shafts, unless otherwise noted.
q/100
mm
254 +
q/100
mm
152.4 +
q/100
mm
254 mmdia.
406.4 mm dia.
Question 3 (3/10):
Figure 1-2 A shaft as a part of a drive for an automated transfer system in a metal stamping plant
The shaft in Figure 1-2 is a part of a drive for an automated transfer system in a metal stamping plant. The
shaft rotating at 400 + q/100 rpm carries a spur gear B having 96 teeth with a diametral pitch of 6 (the
number of teeth per inch of pitch diameter). The teeth are of the 20°, full-depth, involute form. Gear Q
delivers 15 + 0.q kW to gear B, Sheave D delivers the power to its mating sheave as shown. Use AISI 1040
cold drawn steel.
You are required to:
a) Carry out a force analysis to determine the forces including acting on the shaft at all power transmitting
elements
b) Compute reactions at the bearings
c) Draw the complete torque, shear, and bending moment diagrams
d) Give a suggested geometry at point C of the shaft and specify the minimum acceptable diameter for the
shaft at this point with implementing a design factor of 2.5 + q/1000.
Neglect the weight of the elements on the shafts, unless otherwise noted.
Paraphrase This Document
Need a fresh take? Get an instant paraphrase of this document with our AI Paraphraser
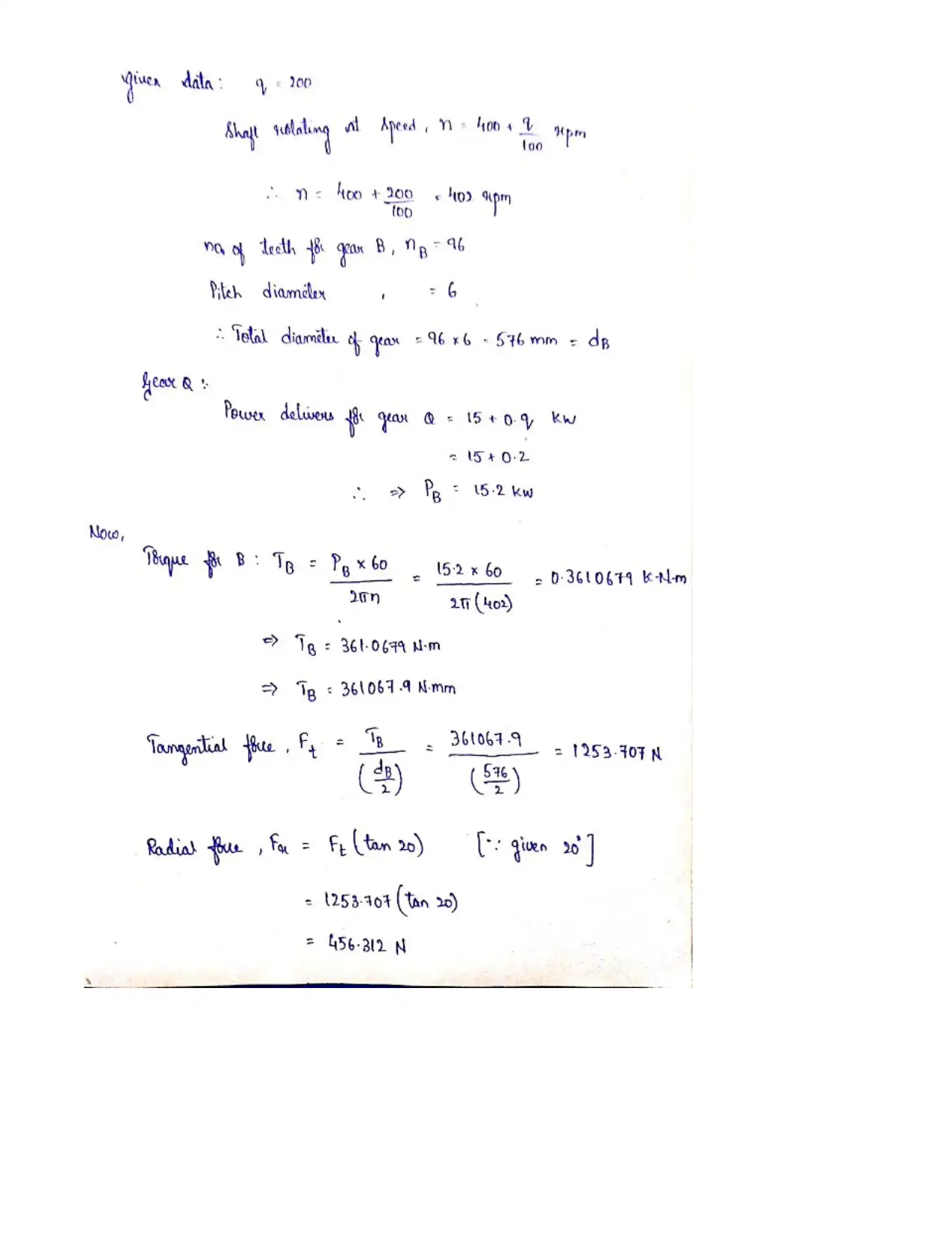
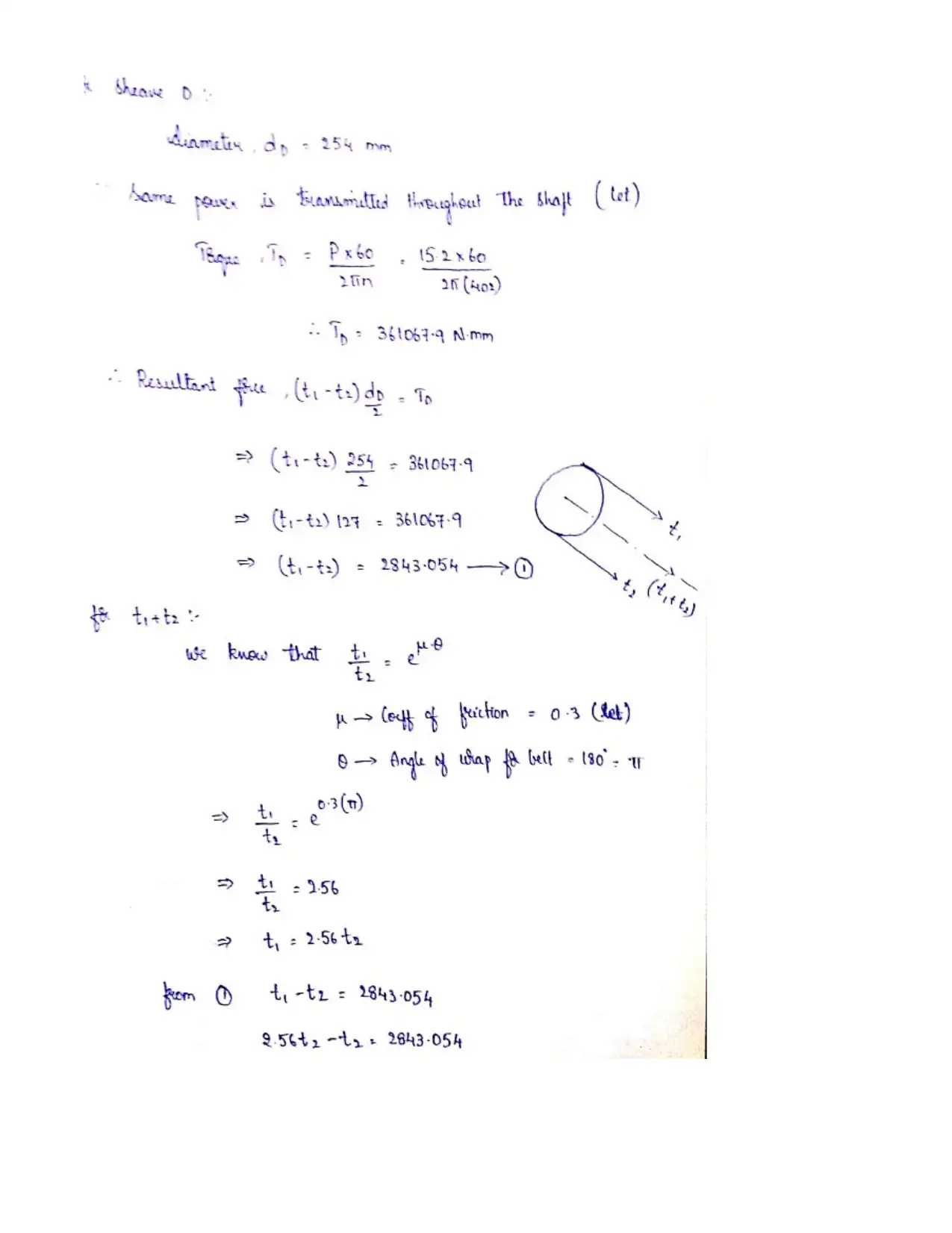
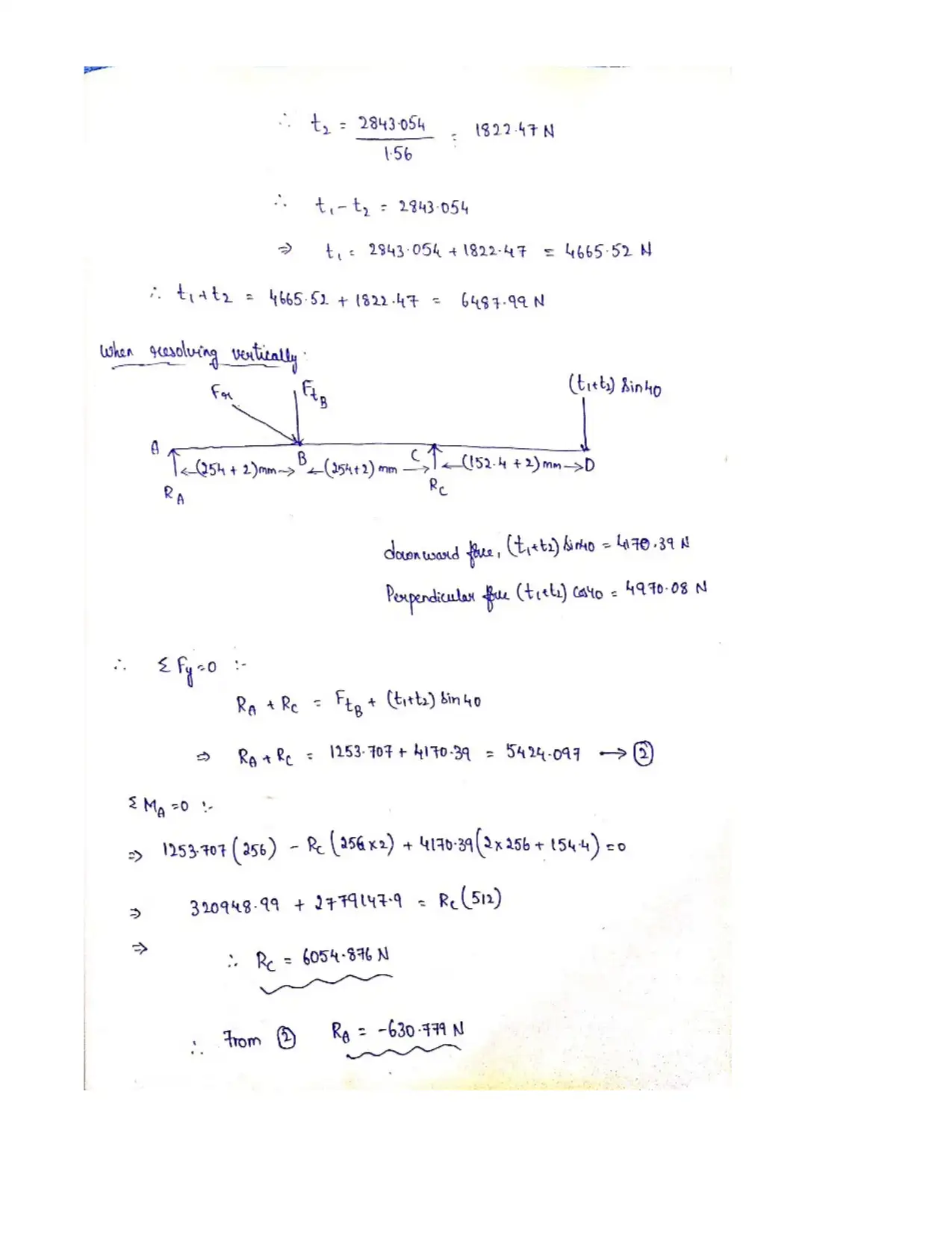
Secure Best Marks with AI Grader
Need help grading? Try our AI Grader for instant feedback on your assignments.
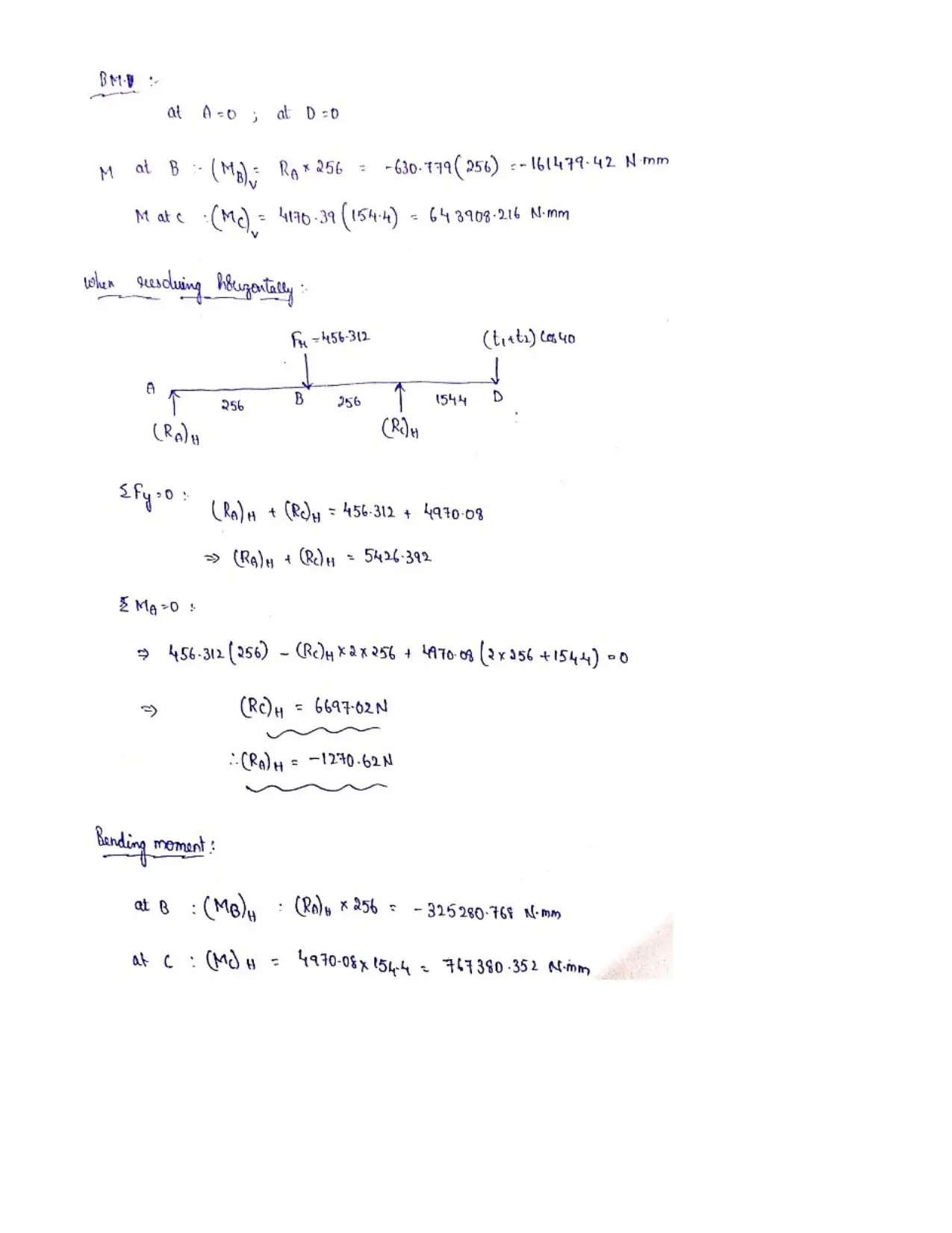
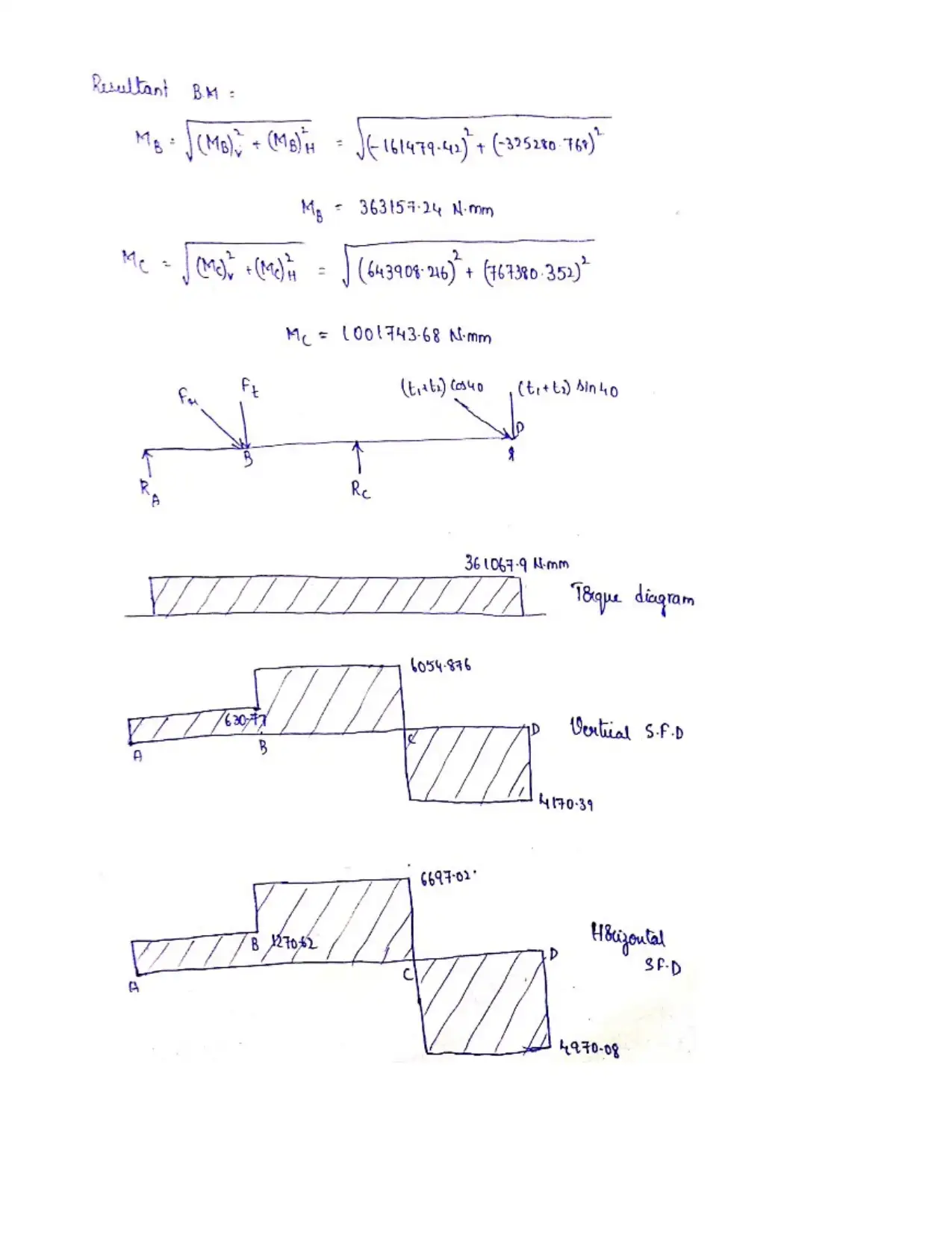
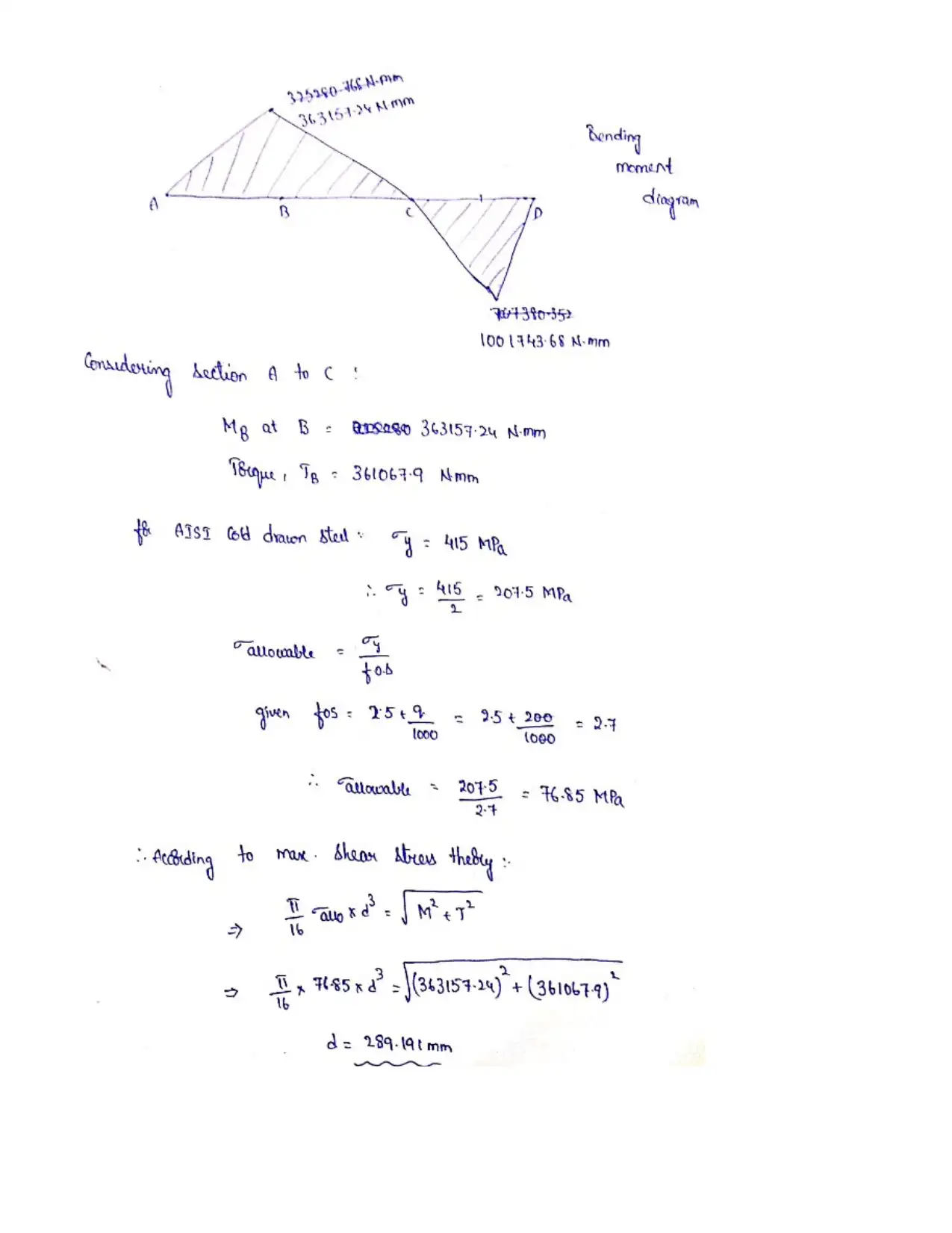
Paraphrase This Document
Need a fresh take? Get an instant paraphrase of this document with our AI Paraphraser
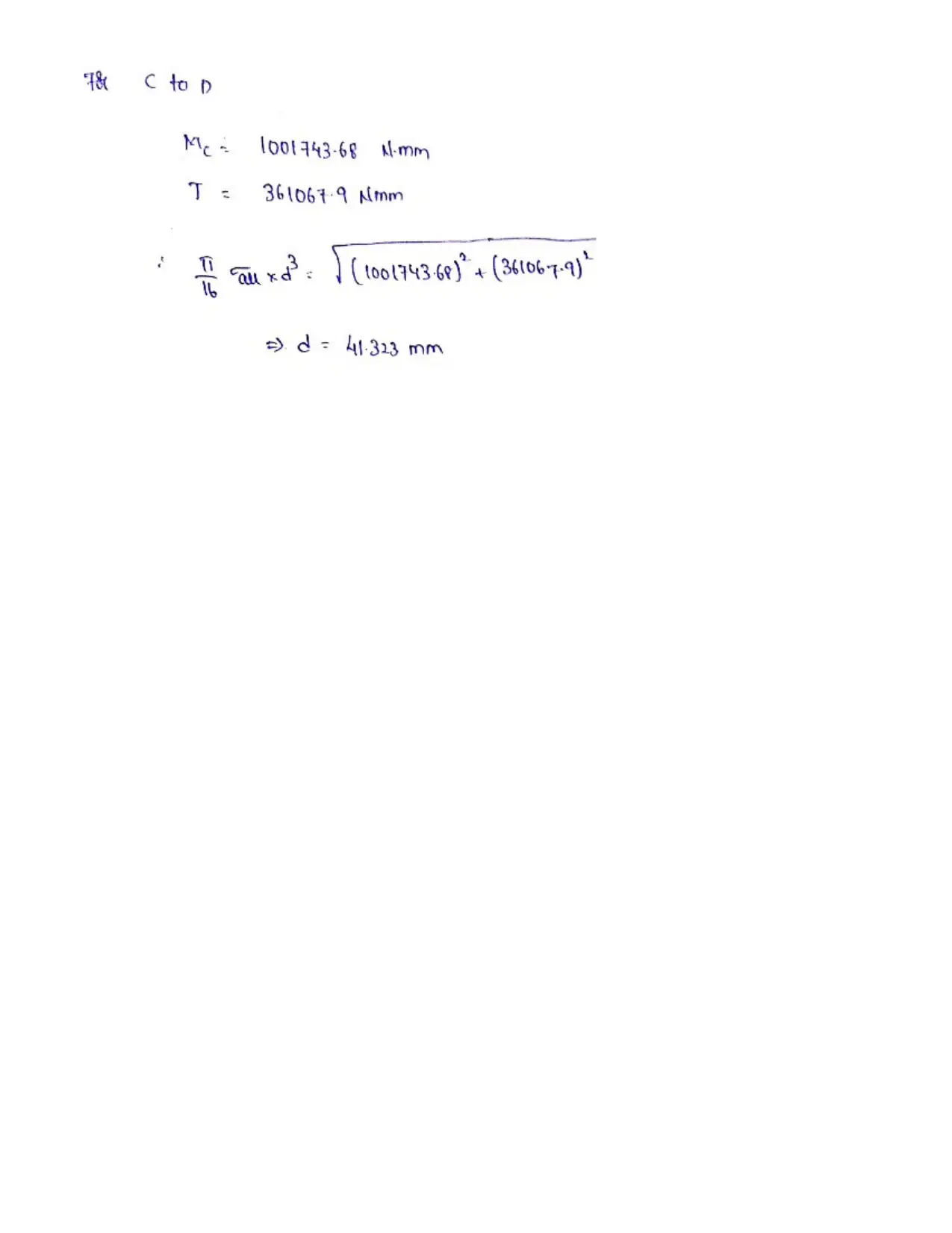
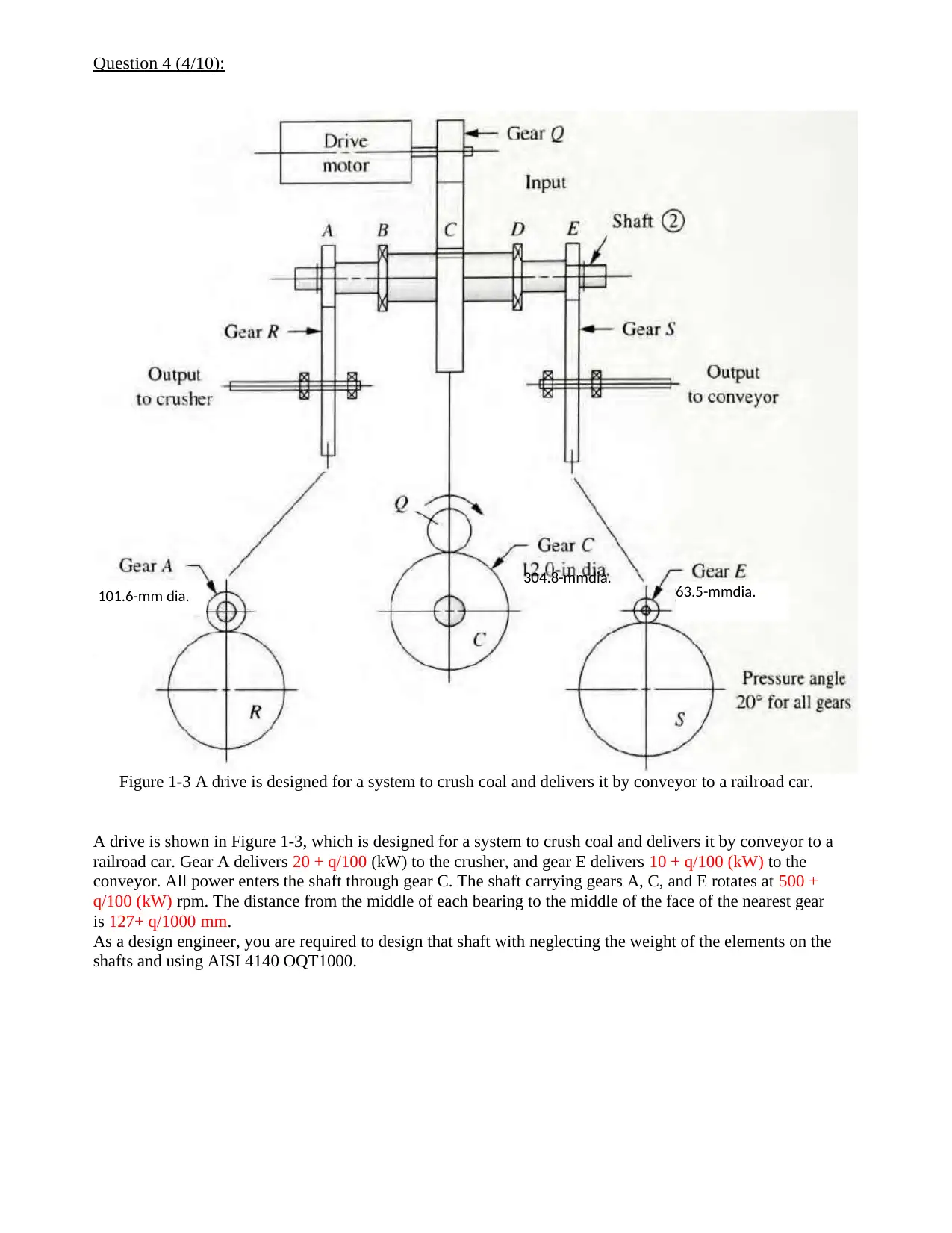
304.8-mmdia.
101.6-mm dia. 63.5-mmdia.
Question 4 (4/10):
Figure 1-3 A drive is designed for a system to crush coal and delivers it by conveyor to a railroad car.
A drive is shown in Figure 1-3, which is designed for a system to crush coal and delivers it by conveyor to a
railroad car. Gear A delivers 20 + q/100 (kW) to the crusher, and gear E delivers 10 + q/100 (kW) to the
conveyor. All power enters the shaft through gear C. The shaft carrying gears A, C, and E rotates at 500 +
q/100 (kW) rpm. The distance from the middle of each bearing to the middle of the face of the nearest gear
is 127+ q/1000 mm.
As a design engineer, you are required to design that shaft with neglecting the weight of the elements on the
shafts and using AISI 4140 OQT1000.
101.6-mm dia. 63.5-mmdia.
Question 4 (4/10):
Figure 1-3 A drive is designed for a system to crush coal and delivers it by conveyor to a railroad car.
A drive is shown in Figure 1-3, which is designed for a system to crush coal and delivers it by conveyor to a
railroad car. Gear A delivers 20 + q/100 (kW) to the crusher, and gear E delivers 10 + q/100 (kW) to the
conveyor. All power enters the shaft through gear C. The shaft carrying gears A, C, and E rotates at 500 +
q/100 (kW) rpm. The distance from the middle of each bearing to the middle of the face of the nearest gear
is 127+ q/1000 mm.
As a design engineer, you are required to design that shaft with neglecting the weight of the elements on the
shafts and using AISI 4140 OQT1000.
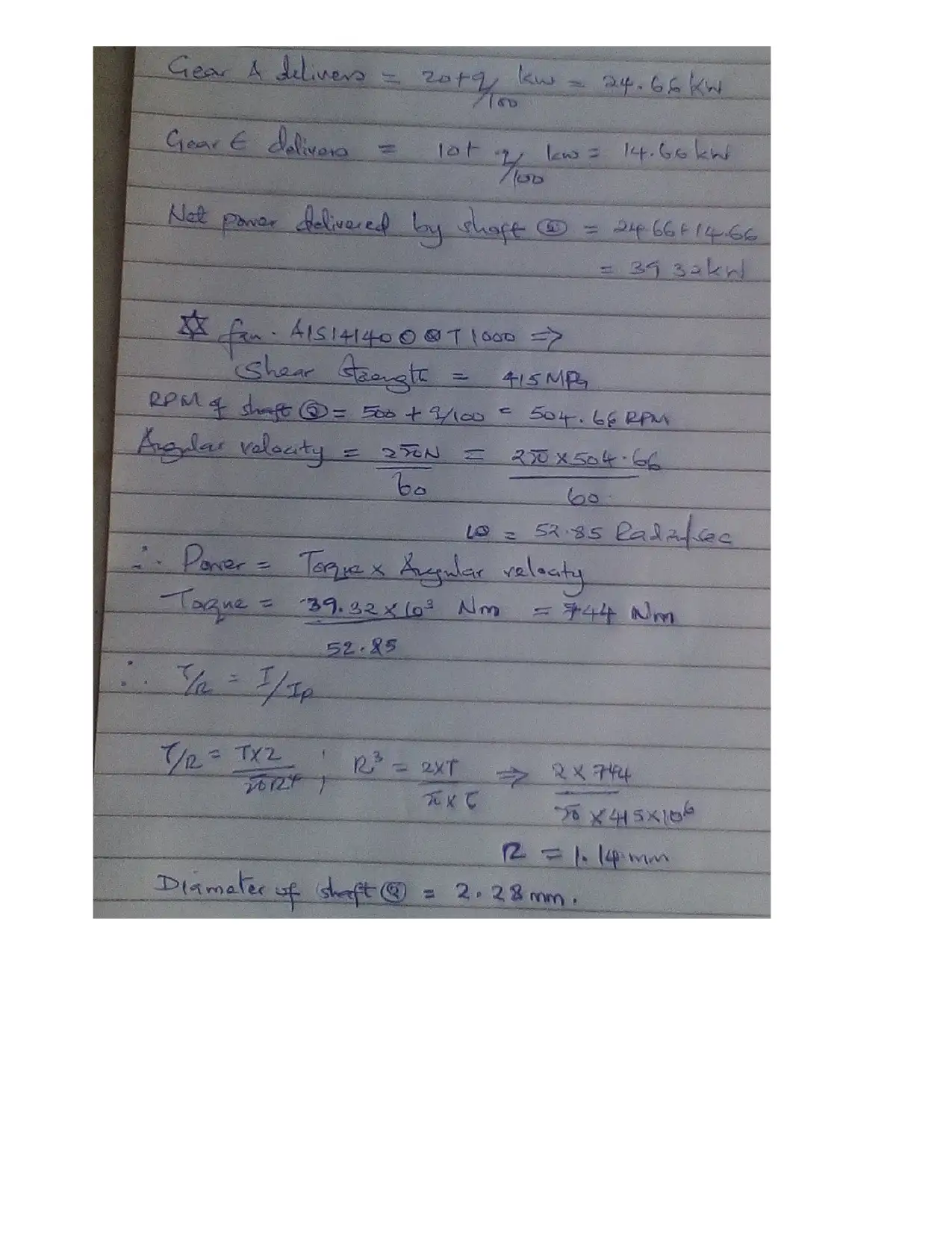
1 out of 16
Related Documents
![[object Object]](/_next/image/?url=%2F_next%2Fstatic%2Fmedia%2Flogo.6d15ce61.png&w=640&q=75)
Your All-in-One AI-Powered Toolkit for Academic Success.
+13062052269
info@desklib.com
Available 24*7 on WhatsApp / Email
Unlock your academic potential
© 2024 | Zucol Services PVT LTD | All rights reserved.