Metal Foam: Literature, Applications, Modelling and Experimentation Study
VerifiedAdded on 2023/06/03
|18
|1585
|196
AI Summary
This presentation discusses the properties, manufacturing, characterization, modelling, and applications of metal foam. It covers topics such as thermal and electrical properties, mechanical properties, mathematical models, material selection, cost analysis, and more.
Contribute Materials
Your contribution can guide someone’s learning journey. Share your
documents today.

Advanced Engineering
Materials: Metal foam
Student Name:
Student R. N.:
Materials: Metal foam
Student Name:
Student R. N.:
Secure Best Marks with AI Grader
Need help grading? Try our AI Grader for instant feedback on your assignments.
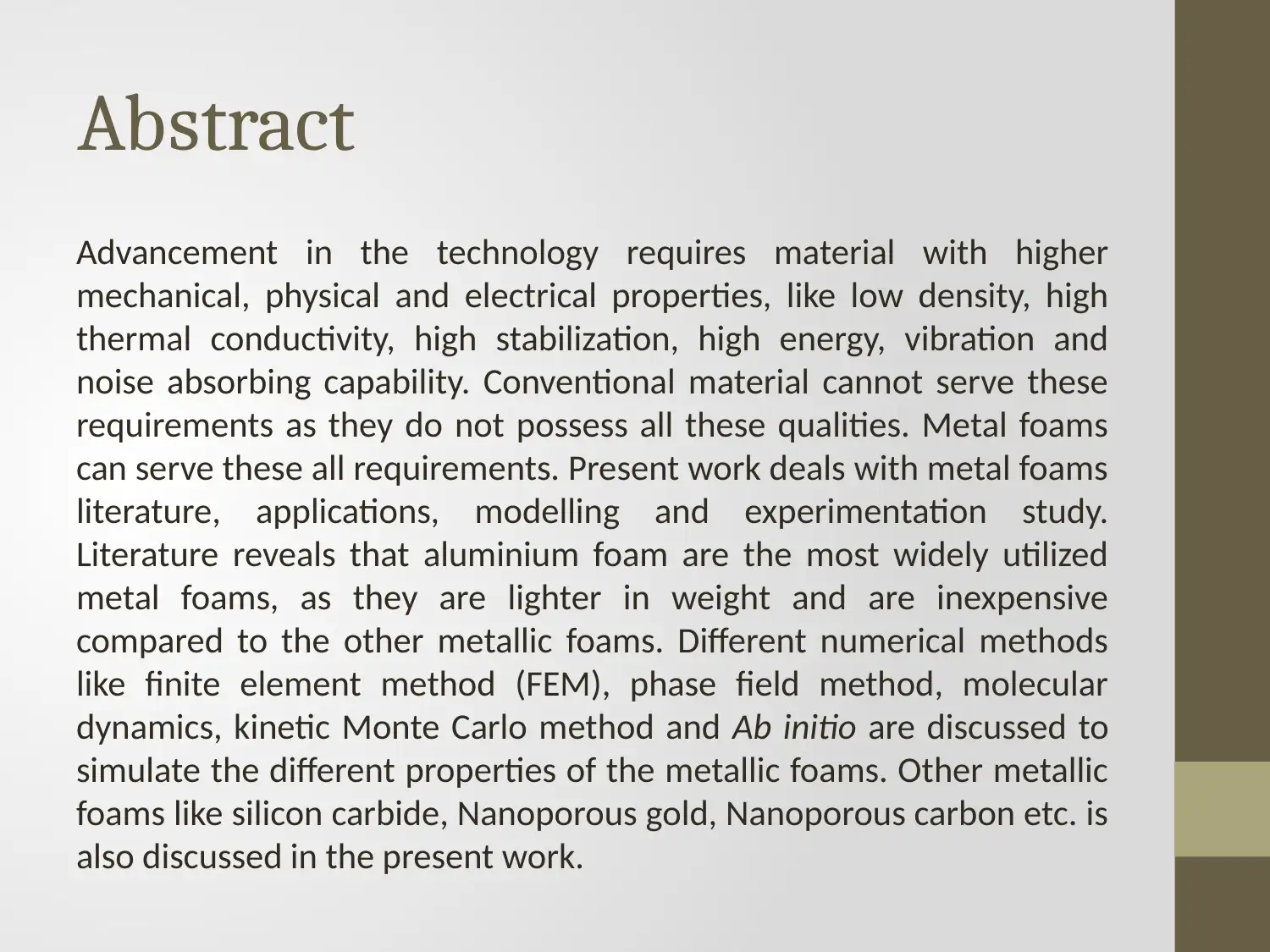
Abstract
Advancement in the technology requires material with higher
mechanical, physical and electrical properties, like low density, high
thermal conductivity, high stabilization, high energy, vibration and
noise absorbing capability. Conventional material cannot serve these
requirements as they do not possess all these qualities. Metal foams
can serve these all requirements. Present work deals with metal foams
literature, applications, modelling and experimentation study.
Literature reveals that aluminium foam are the most widely utilized
metal foams, as they are lighter in weight and are inexpensive
compared to the other metallic foams. Different numerical methods
like finite element method (FEM), phase field method, molecular
dynamics, kinetic Monte Carlo method and Ab initio are discussed to
simulate the different properties of the metallic foams. Other metallic
foams like silicon carbide, Nanoporous gold, Nanoporous carbon etc. is
also discussed in the present work.
Advancement in the technology requires material with higher
mechanical, physical and electrical properties, like low density, high
thermal conductivity, high stabilization, high energy, vibration and
noise absorbing capability. Conventional material cannot serve these
requirements as they do not possess all these qualities. Metal foams
can serve these all requirements. Present work deals with metal foams
literature, applications, modelling and experimentation study.
Literature reveals that aluminium foam are the most widely utilized
metal foams, as they are lighter in weight and are inexpensive
compared to the other metallic foams. Different numerical methods
like finite element method (FEM), phase field method, molecular
dynamics, kinetic Monte Carlo method and Ab initio are discussed to
simulate the different properties of the metallic foams. Other metallic
foams like silicon carbide, Nanoporous gold, Nanoporous carbon etc. is
also discussed in the present work.
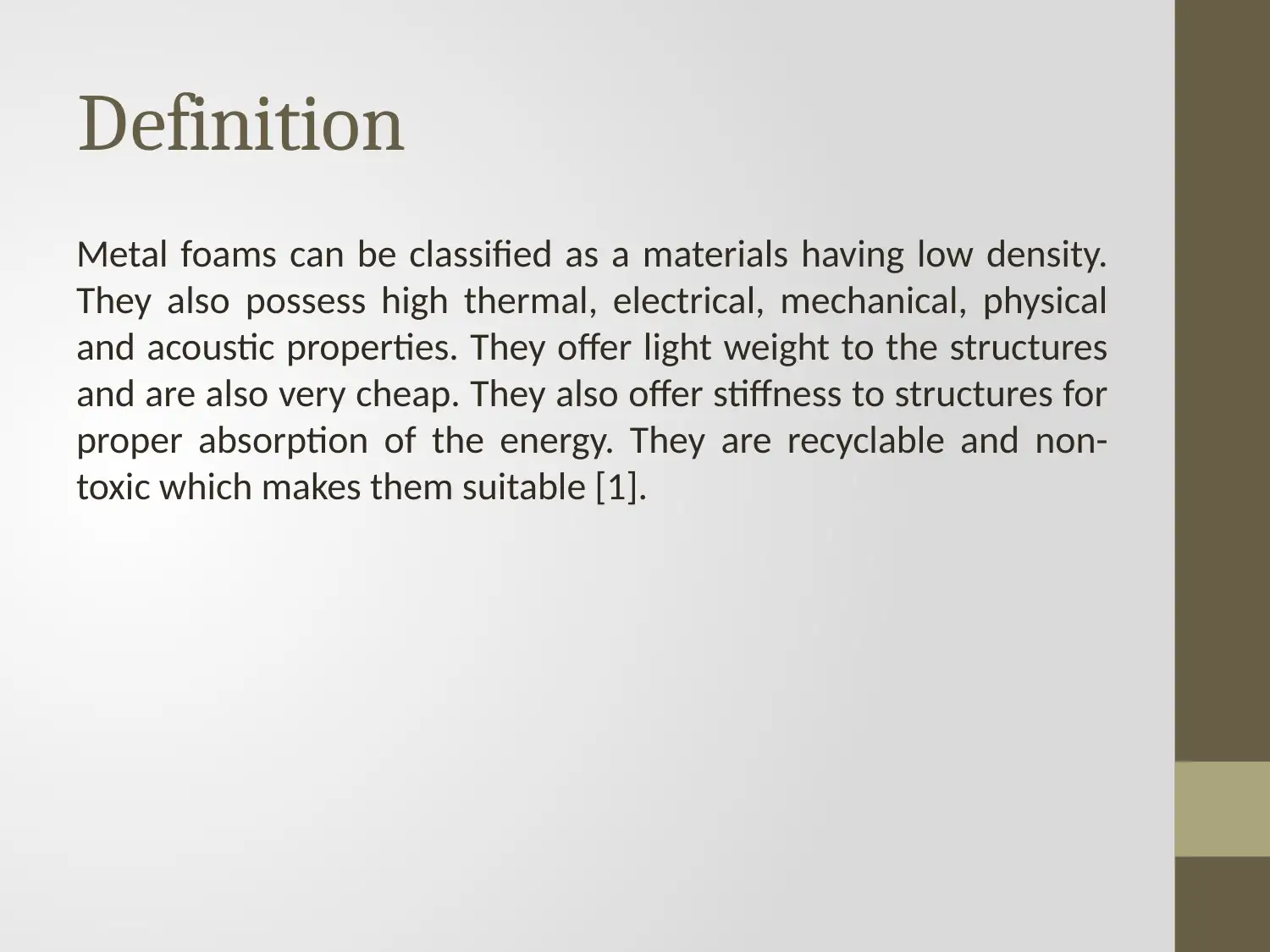
Definition
Metal foams can be classified as a materials having low density.
They also possess high thermal, electrical, mechanical, physical
and acoustic properties. They offer light weight to the structures
and are also very cheap. They also offer stiffness to structures for
proper absorption of the energy. They are recyclable and non-
toxic which makes them suitable [1].
Metal foams can be classified as a materials having low density.
They also possess high thermal, electrical, mechanical, physical
and acoustic properties. They offer light weight to the structures
and are also very cheap. They also offer stiffness to structures for
proper absorption of the energy. They are recyclable and non-
toxic which makes them suitable [1].
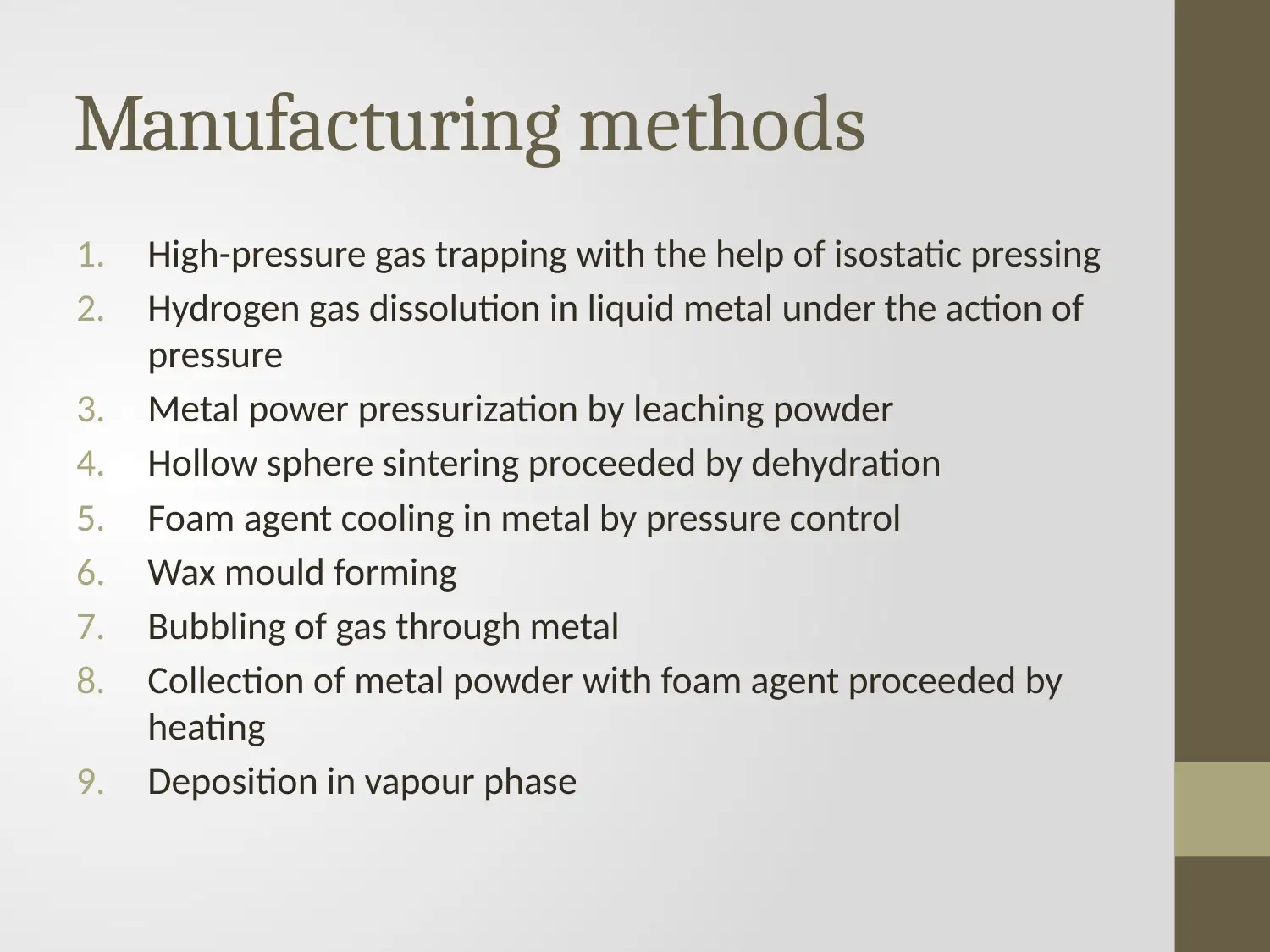
Manufacturing methods
1. High-pressure gas trapping with the help of isostatic pressing
2. Hydrogen gas dissolution in liquid metal under the action of
pressure
3. Metal power pressurization by leaching powder
4. Hollow sphere sintering proceeded by dehydration
5. Foam agent cooling in metal by pressure control
6. Wax mould forming
7. Bubbling of gas through metal
8. Collection of metal powder with foam agent proceeded by
heating
9. Deposition in vapour phase
1. High-pressure gas trapping with the help of isostatic pressing
2. Hydrogen gas dissolution in liquid metal under the action of
pressure
3. Metal power pressurization by leaching powder
4. Hollow sphere sintering proceeded by dehydration
5. Foam agent cooling in metal by pressure control
6. Wax mould forming
7. Bubbling of gas through metal
8. Collection of metal powder with foam agent proceeded by
heating
9. Deposition in vapour phase
Secure Best Marks with AI Grader
Need help grading? Try our AI Grader for instant feedback on your assignments.
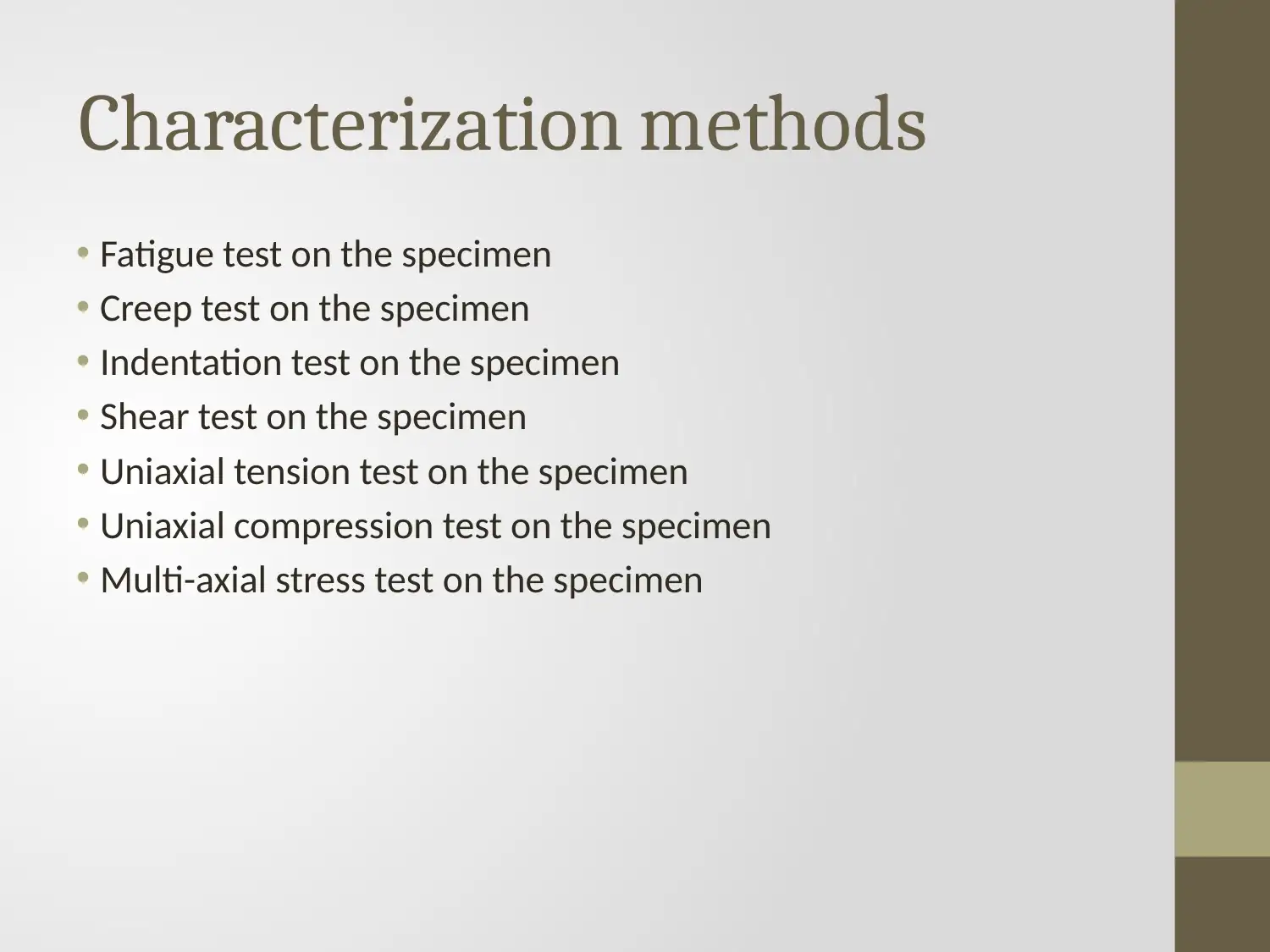
Characterization methods
• Fatigue test on the specimen
• Creep test on the specimen
• Indentation test on the specimen
• Shear test on the specimen
• Uniaxial tension test on the specimen
• Uniaxial compression test on the specimen
• Multi-axial stress test on the specimen
• Fatigue test on the specimen
• Creep test on the specimen
• Indentation test on the specimen
• Shear test on the specimen
• Uniaxial tension test on the specimen
• Uniaxial compression test on the specimen
• Multi-axial stress test on the specimen
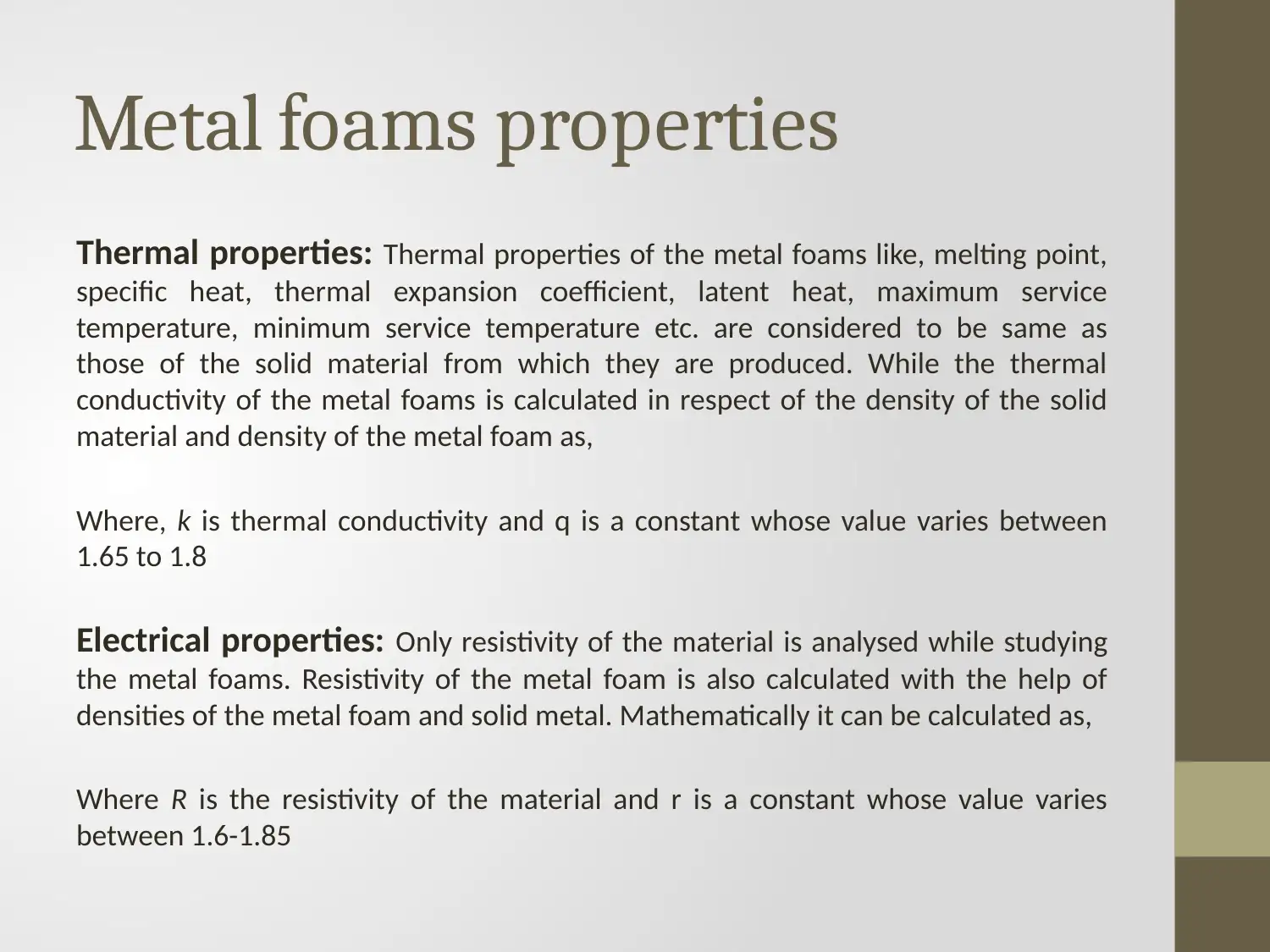
Metal foams properties
Thermal properties: Thermal properties of the metal foams like, melting point,
specific heat, thermal expansion coefficient, latent heat, maximum service
temperature, minimum service temperature etc. are considered to be same as
those of the solid material from which they are produced. While the thermal
conductivity of the metal foams is calculated in respect of the density of the solid
material and density of the metal foam as,
Where, k is thermal conductivity and q is a constant whose value varies between
1.65 to 1.8
Electrical properties: Only resistivity of the material is analysed while studying
the metal foams. Resistivity of the metal foam is also calculated with the help of
densities of the metal foam and solid metal. Mathematically it can be calculated as,
Where R is the resistivity of the material and r is a constant whose value varies
between 1.6-1.85
Thermal properties: Thermal properties of the metal foams like, melting point,
specific heat, thermal expansion coefficient, latent heat, maximum service
temperature, minimum service temperature etc. are considered to be same as
those of the solid material from which they are produced. While the thermal
conductivity of the metal foams is calculated in respect of the density of the solid
material and density of the metal foam as,
Where, k is thermal conductivity and q is a constant whose value varies between
1.65 to 1.8
Electrical properties: Only resistivity of the material is analysed while studying
the metal foams. Resistivity of the metal foam is also calculated with the help of
densities of the metal foam and solid metal. Mathematically it can be calculated as,
Where R is the resistivity of the material and r is a constant whose value varies
between 1.6-1.85
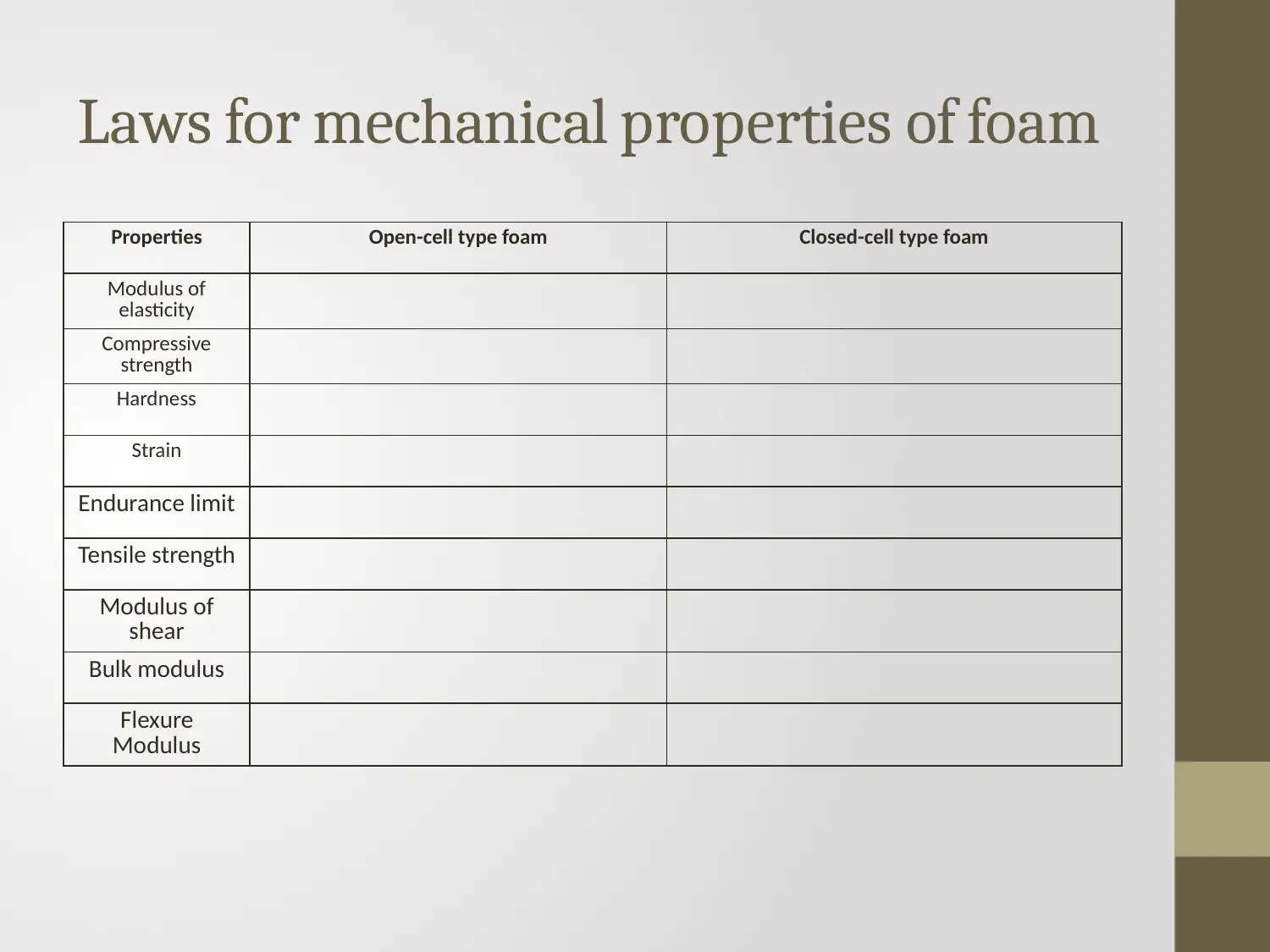
Laws for mechanical properties of foam
Properties Open-cell type foam Closed-cell type foam
Modulus of
elasticity
Compressive
strength
Hardness
Strain
Endurance limit
Tensile strength
Modulus of
shear
Bulk modulus
Flexure
Modulus
Properties Open-cell type foam Closed-cell type foam
Modulus of
elasticity
Compressive
strength
Hardness
Strain
Endurance limit
Tensile strength
Modulus of
shear
Bulk modulus
Flexure
Modulus
Paraphrase This Document
Need a fresh take? Get an instant paraphrase of this document with our AI Paraphraser
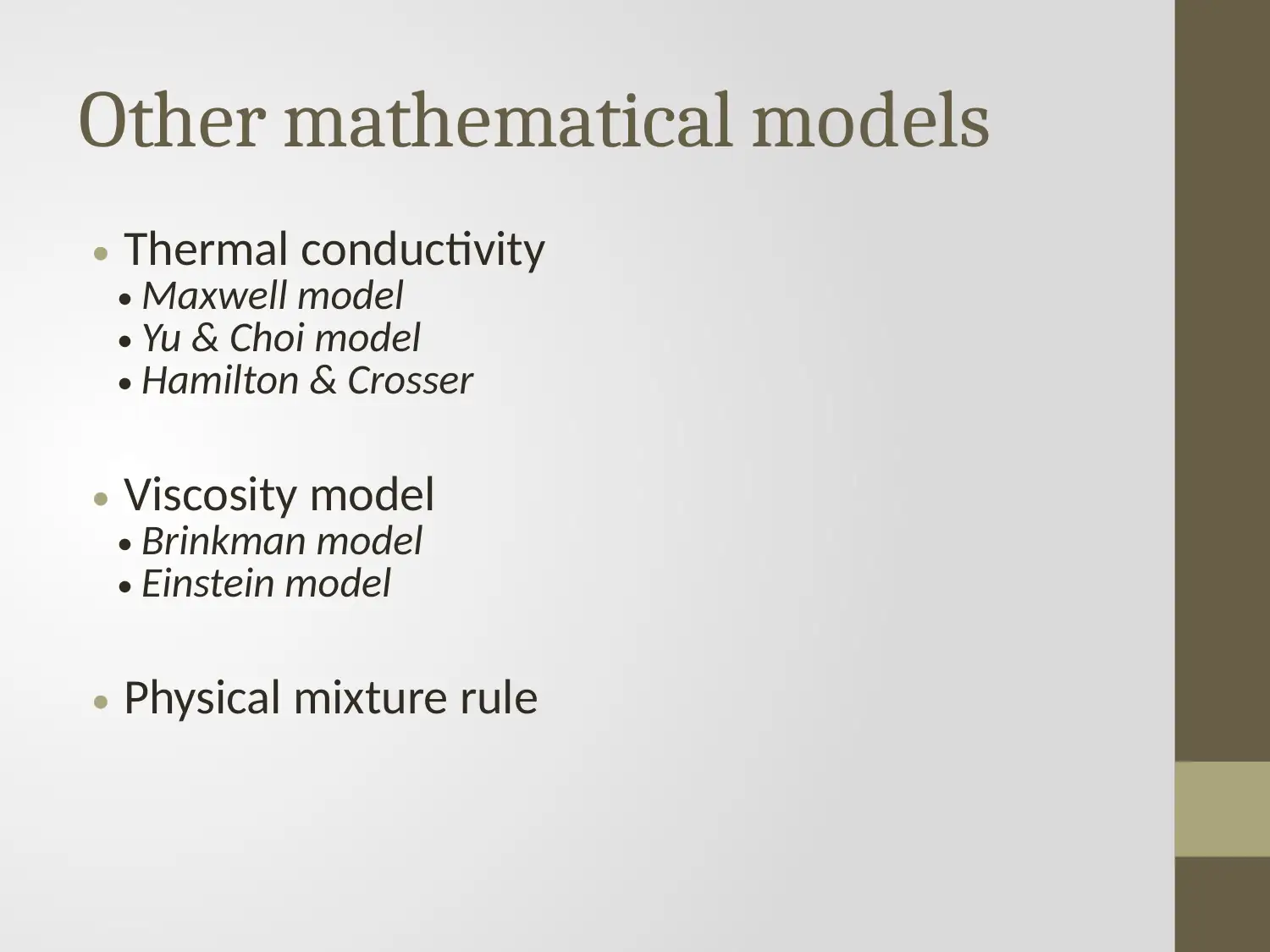
Other mathematical models
• Thermal conductivity
• Maxwell model
• Yu & Choi model
• Hamilton & Crosser
• Viscosity model
• Brinkman model
• Einstein model
• Physical mixture rule
• Thermal conductivity
• Maxwell model
• Yu & Choi model
• Hamilton & Crosser
• Viscosity model
• Brinkman model
• Einstein model
• Physical mixture rule
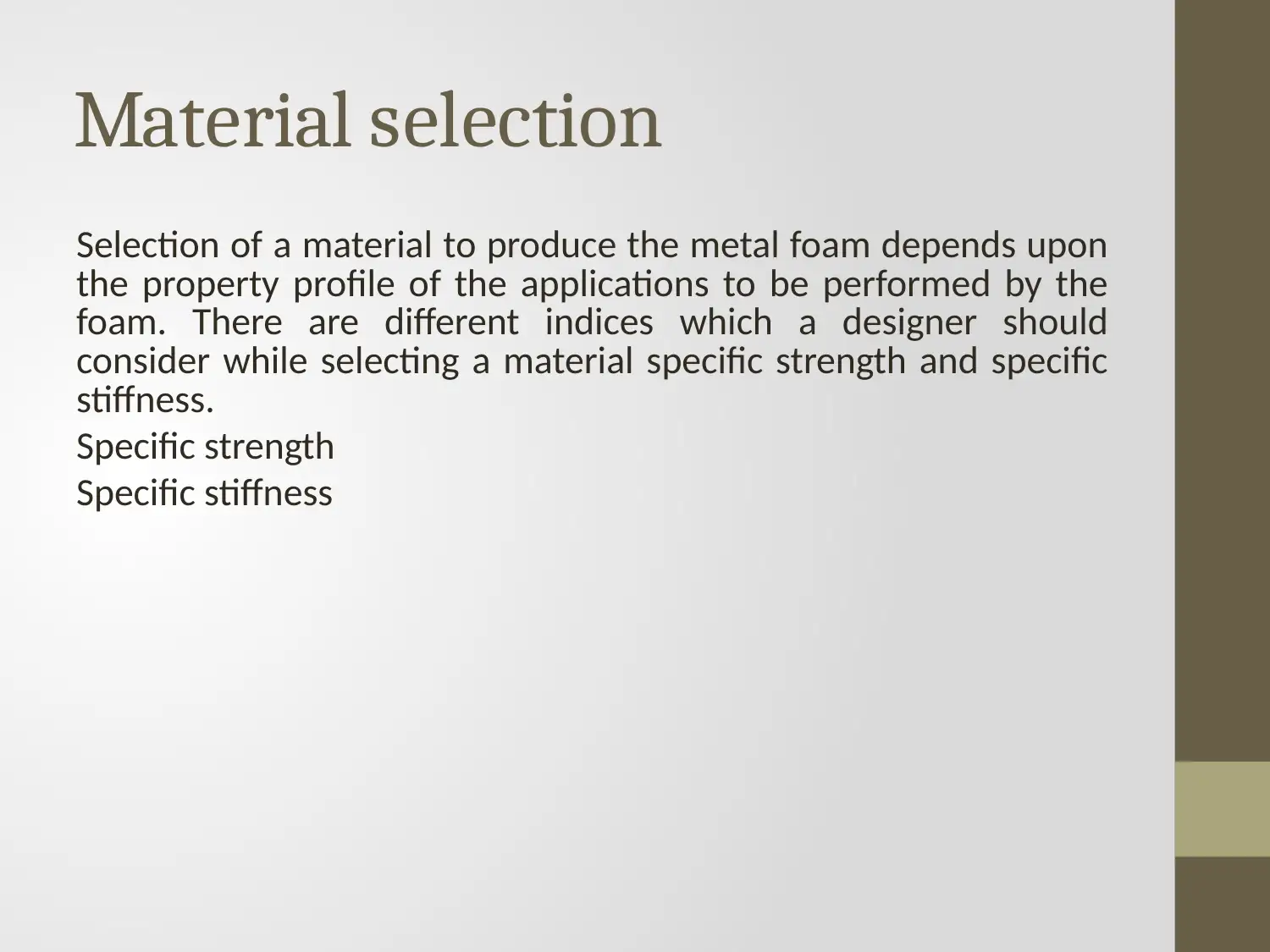
Material selection
Selection of a material to produce the metal foam depends upon
the property profile of the applications to be performed by the
foam. There are different indices which a designer should
consider while selecting a material specific strength and specific
stiffness.
Specific strength
Specific stiffness
Selection of a material to produce the metal foam depends upon
the property profile of the applications to be performed by the
foam. There are different indices which a designer should
consider while selecting a material specific strength and specific
stiffness.
Specific strength
Specific stiffness
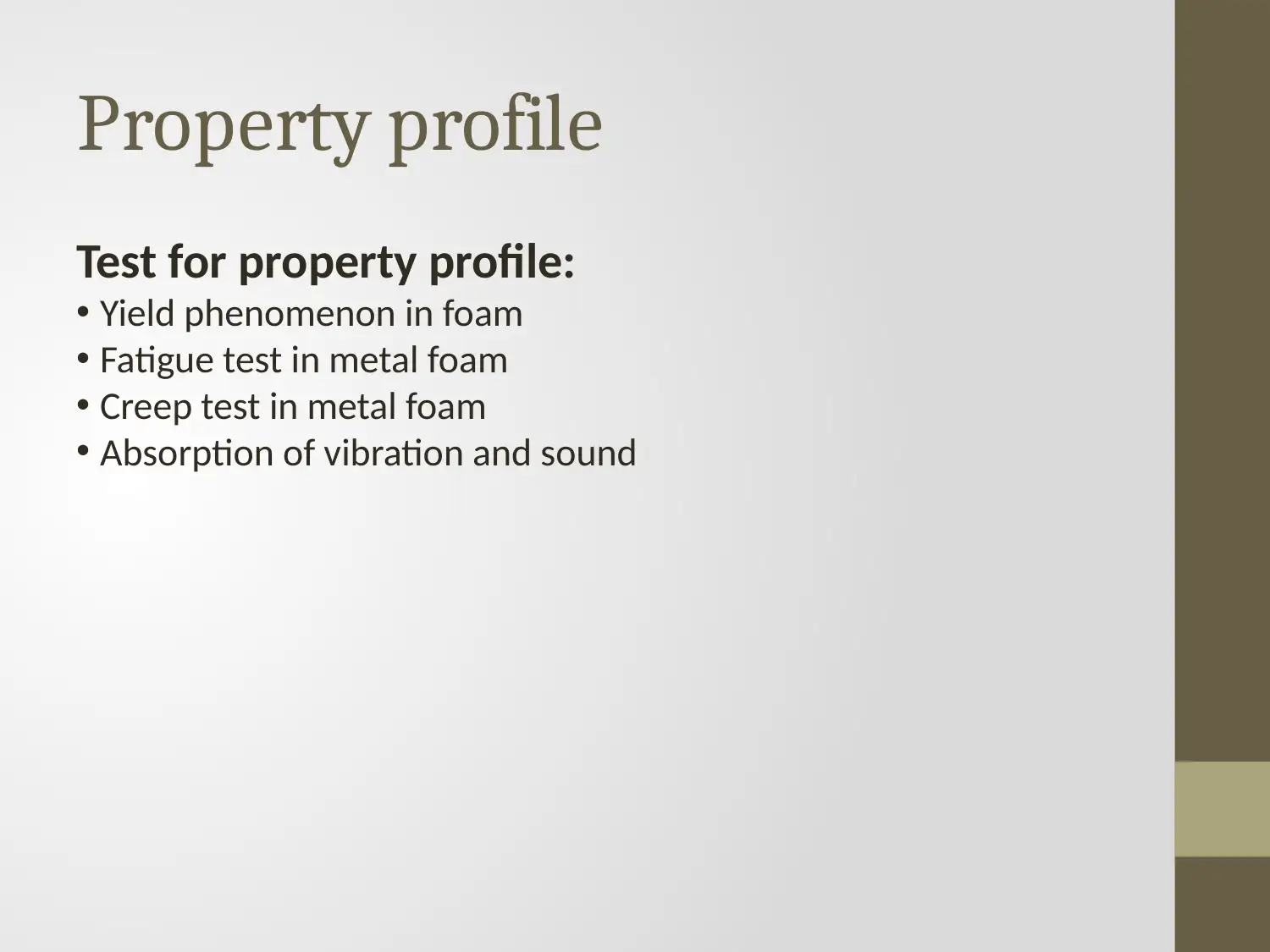
Property profile
Test for property profile:
• Yield phenomenon in foam
• Fatigue test in metal foam
• Creep test in metal foam
• Absorption of vibration and sound
Test for property profile:
• Yield phenomenon in foam
• Fatigue test in metal foam
• Creep test in metal foam
• Absorption of vibration and sound
Secure Best Marks with AI Grader
Need help grading? Try our AI Grader for instant feedback on your assignments.
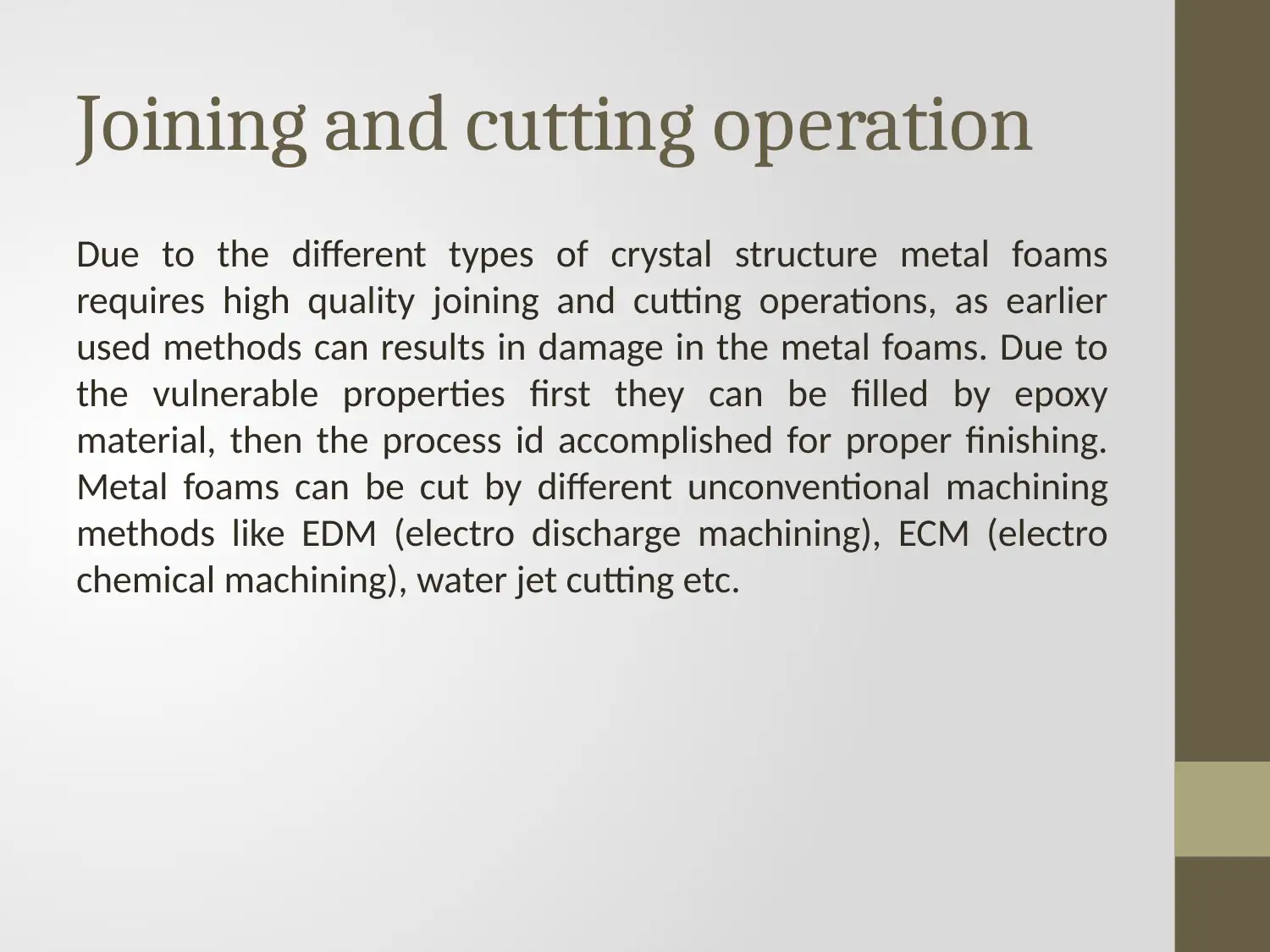
Joining and cutting operation
Due to the different types of crystal structure metal foams
requires high quality joining and cutting operations, as earlier
used methods can results in damage in the metal foams. Due to
the vulnerable properties first they can be filled by epoxy
material, then the process id accomplished for proper finishing.
Metal foams can be cut by different unconventional machining
methods like EDM (electro discharge machining), ECM (electro
chemical machining), water jet cutting etc.
Due to the different types of crystal structure metal foams
requires high quality joining and cutting operations, as earlier
used methods can results in damage in the metal foams. Due to
the vulnerable properties first they can be filled by epoxy
material, then the process id accomplished for proper finishing.
Metal foams can be cut by different unconventional machining
methods like EDM (electro discharge machining), ECM (electro
chemical machining), water jet cutting etc.
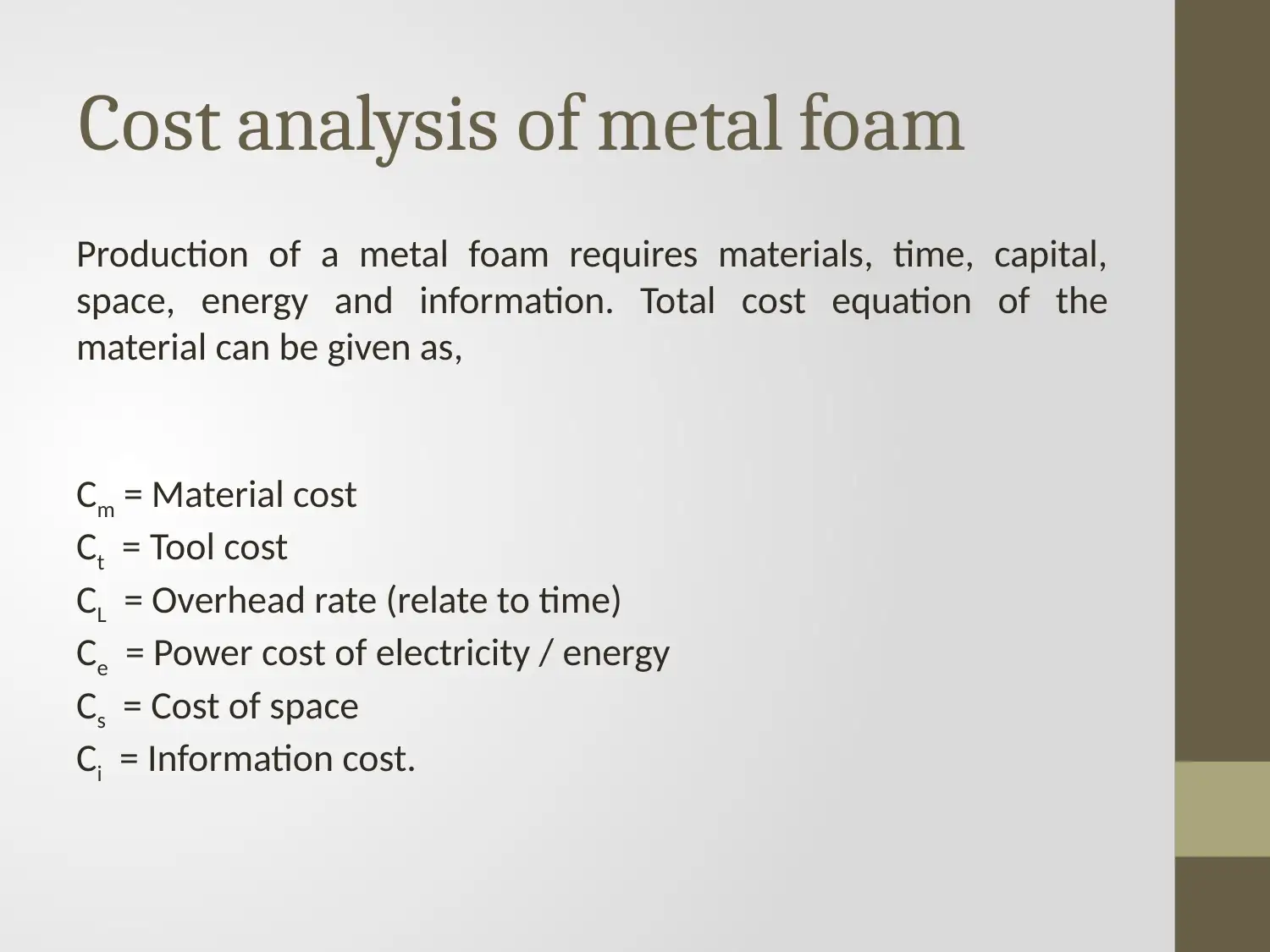
Cost analysis of metal foam
Production of a metal foam requires materials, time, capital,
space, energy and information. Total cost equation of the
material can be given as,
Cm = Material cost
Ct = Tool cost
CL = Overhead rate (relate to time)
Ce = Power cost of electricity / energy
Cs = Cost of space
Ci = Information cost.
Production of a metal foam requires materials, time, capital,
space, energy and information. Total cost equation of the
material can be given as,
Cm = Material cost
Ct = Tool cost
CL = Overhead rate (relate to time)
Ce = Power cost of electricity / energy
Cs = Cost of space
Ci = Information cost.
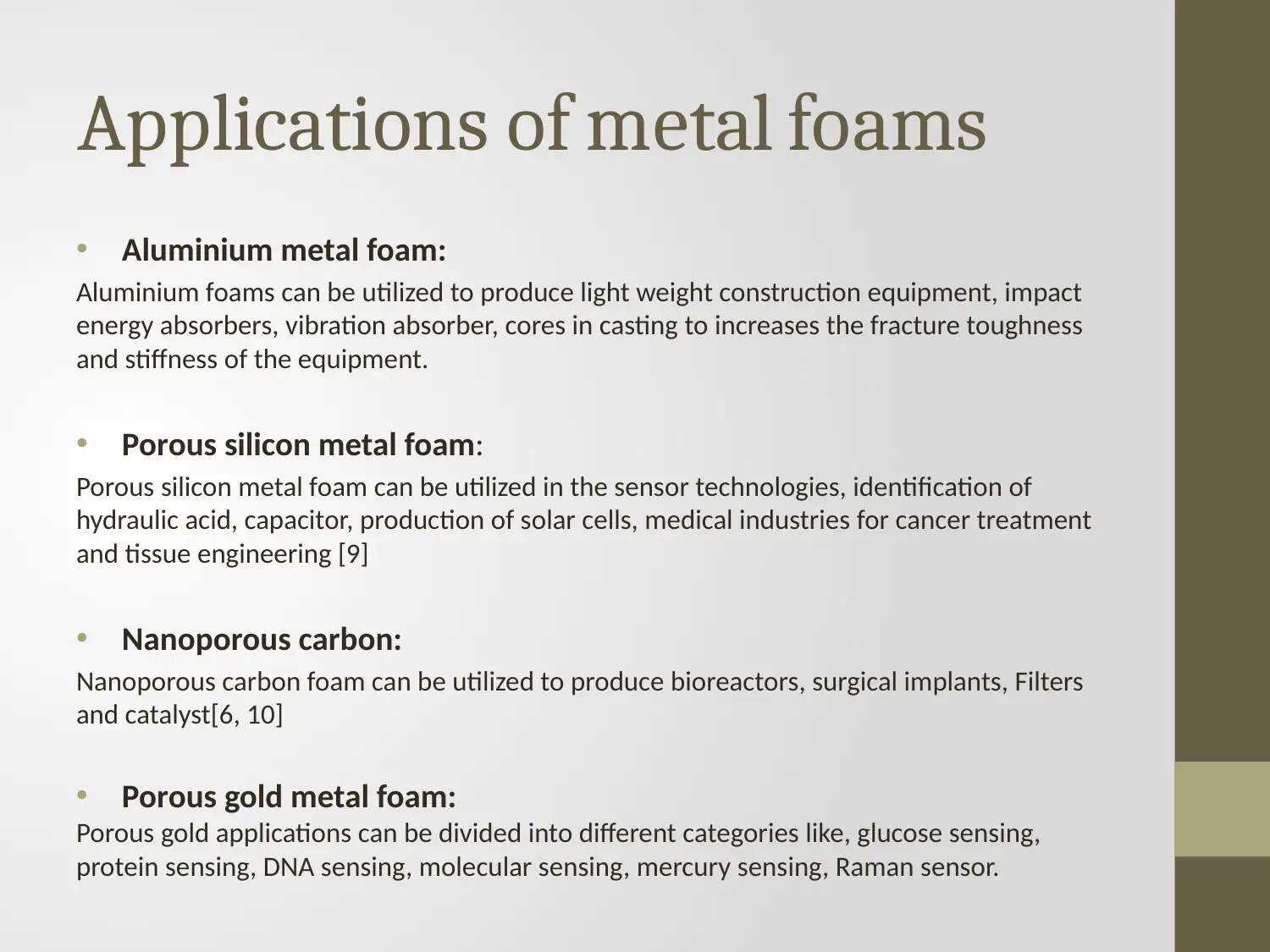
Applications of metal foams
• Aluminium metal foam:
Aluminium foams can be utilized to produce light weight construction equipment, impact
energy absorbers, vibration absorber, cores in casting to increases the fracture toughness
and stiffness of the equipment.
• Porous silicon metal foam:
Porous silicon metal foam can be utilized in the sensor technologies, identification of
hydraulic acid, capacitor, production of solar cells, medical industries for cancer treatment
and tissue engineering [9]
• Nanoporous carbon:
Nanoporous carbon foam can be utilized to produce bioreactors, surgical implants, Filters
and catalyst[6, 10]
• Porous gold metal foam:
Porous gold applications can be divided into different categories like, glucose sensing,
protein sensing, DNA sensing, molecular sensing, mercury sensing, Raman sensor.
• Aluminium metal foam:
Aluminium foams can be utilized to produce light weight construction equipment, impact
energy absorbers, vibration absorber, cores in casting to increases the fracture toughness
and stiffness of the equipment.
• Porous silicon metal foam:
Porous silicon metal foam can be utilized in the sensor technologies, identification of
hydraulic acid, capacitor, production of solar cells, medical industries for cancer treatment
and tissue engineering [9]
• Nanoporous carbon:
Nanoporous carbon foam can be utilized to produce bioreactors, surgical implants, Filters
and catalyst[6, 10]
• Porous gold metal foam:
Porous gold applications can be divided into different categories like, glucose sensing,
protein sensing, DNA sensing, molecular sensing, mercury sensing, Raman sensor.
Paraphrase This Document
Need a fresh take? Get an instant paraphrase of this document with our AI Paraphraser
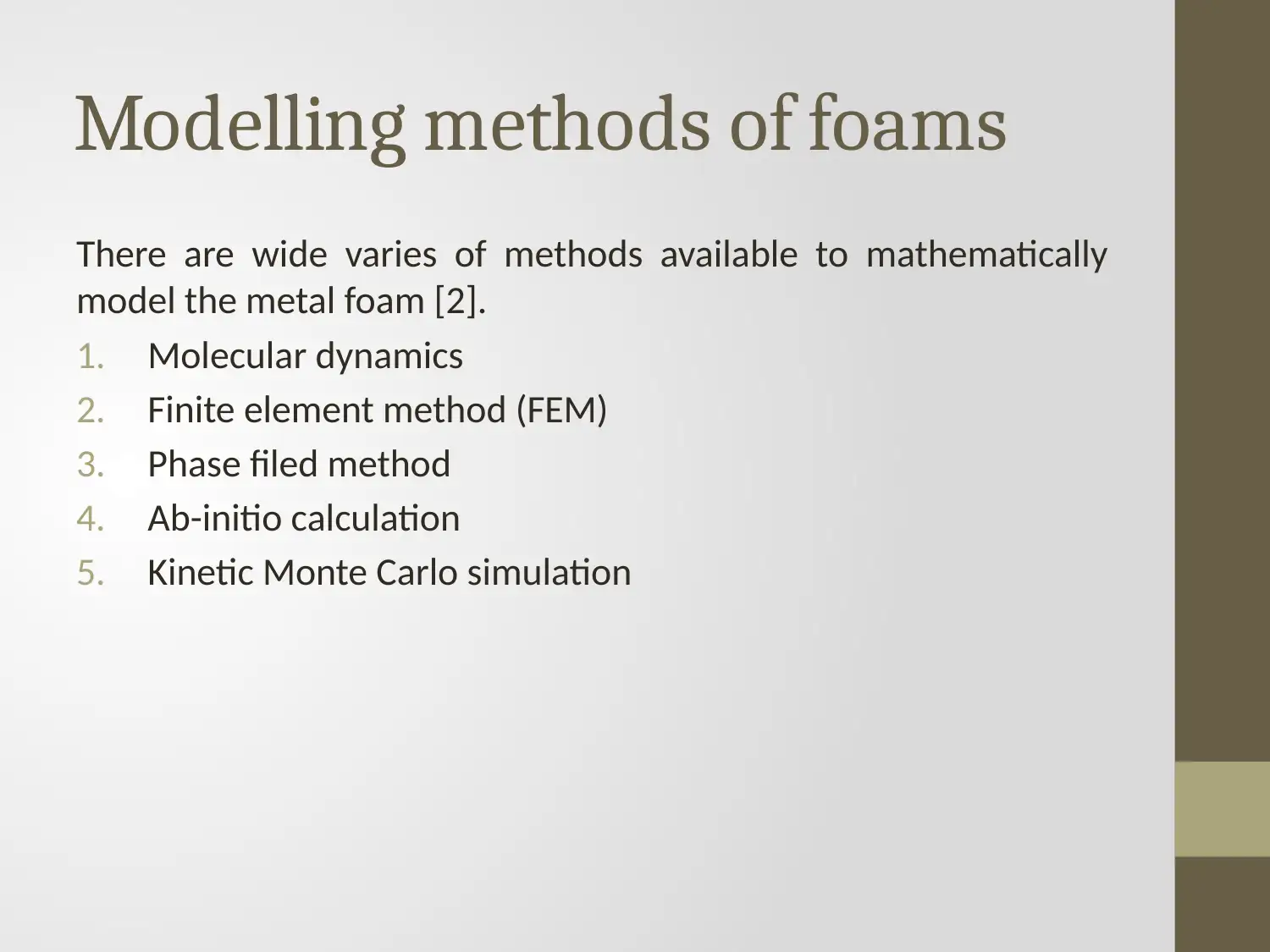
Modelling methods of foams
There are wide varies of methods available to mathematically
model the metal foam [2].
1. Molecular dynamics
2. Finite element method (FEM)
3. Phase filed method
4. Ab-initio calculation
5. Kinetic Monte Carlo simulation
There are wide varies of methods available to mathematically
model the metal foam [2].
1. Molecular dynamics
2. Finite element method (FEM)
3. Phase filed method
4. Ab-initio calculation
5. Kinetic Monte Carlo simulation
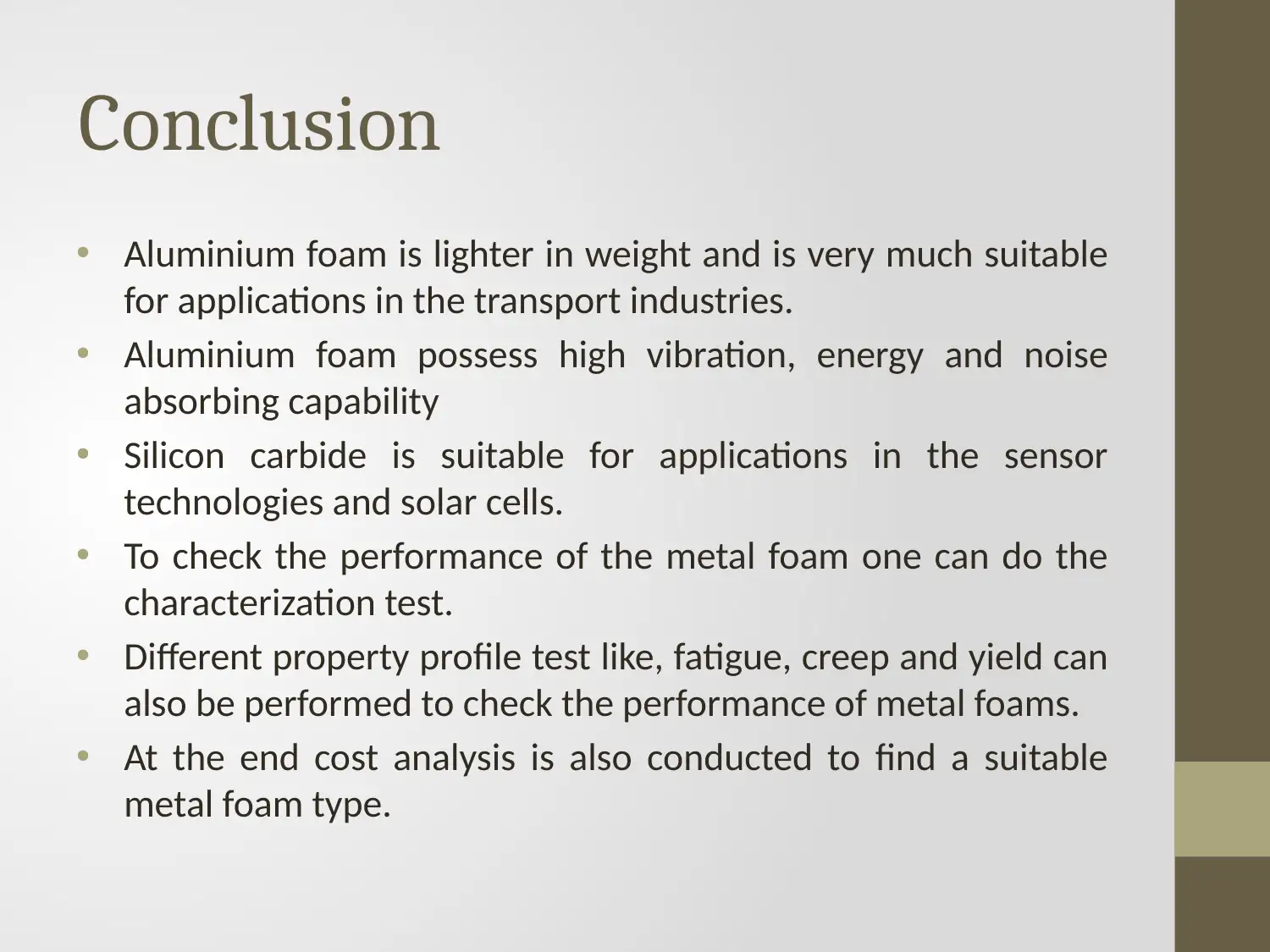
Conclusion
• Aluminium foam is lighter in weight and is very much suitable
for applications in the transport industries.
• Aluminium foam possess high vibration, energy and noise
absorbing capability
• Silicon carbide is suitable for applications in the sensor
technologies and solar cells.
• To check the performance of the metal foam one can do the
characterization test.
• Different property profile test like, fatigue, creep and yield can
also be performed to check the performance of metal foams.
• At the end cost analysis is also conducted to find a suitable
metal foam type.
• Aluminium foam is lighter in weight and is very much suitable
for applications in the transport industries.
• Aluminium foam possess high vibration, energy and noise
absorbing capability
• Silicon carbide is suitable for applications in the sensor
technologies and solar cells.
• To check the performance of the metal foam one can do the
characterization test.
• Different property profile test like, fatigue, creep and yield can
also be performed to check the performance of metal foams.
• At the end cost analysis is also conducted to find a suitable
metal foam type.
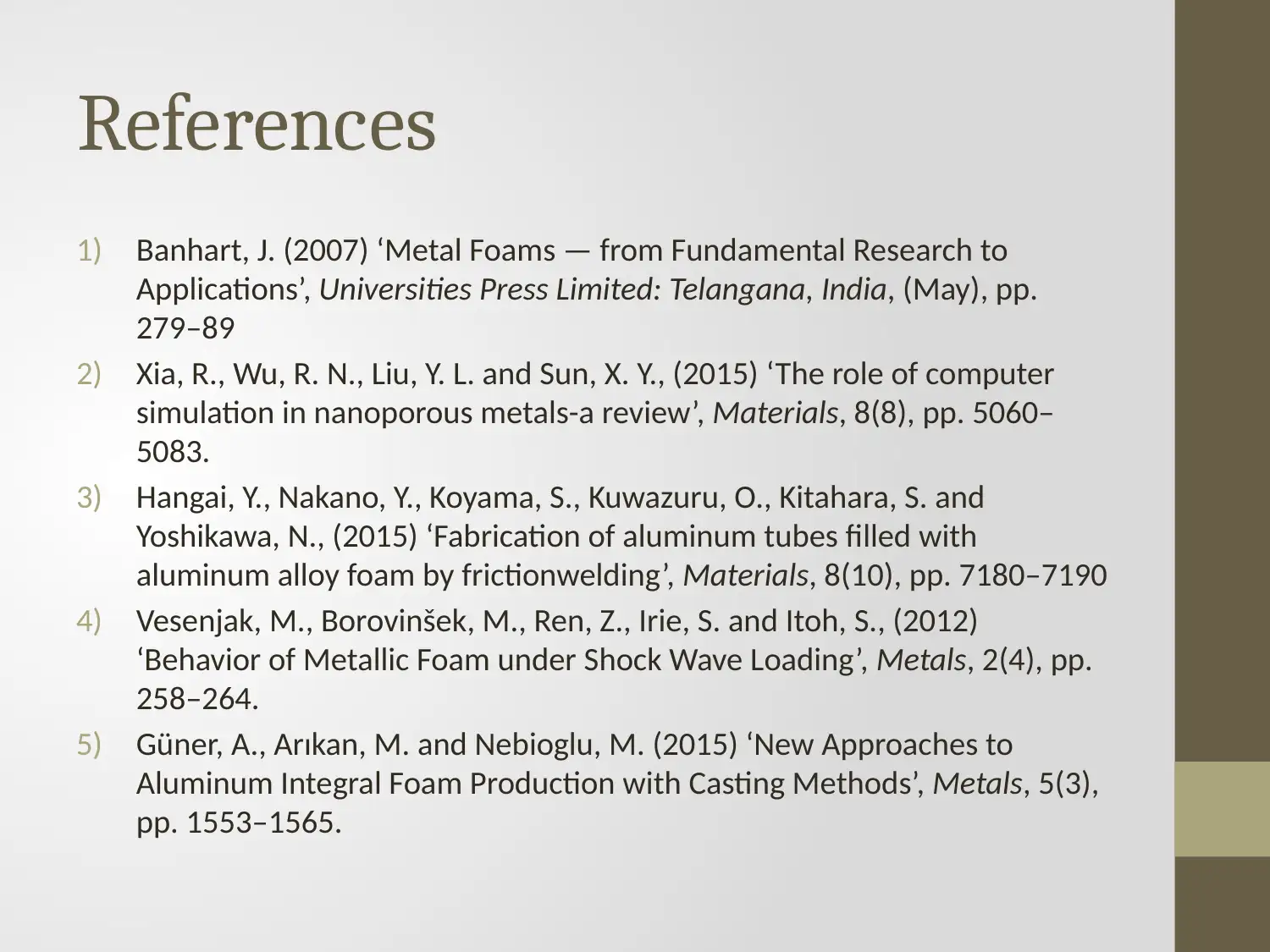
References
1) Banhart, J. (2007) ‘Metal Foams — from Fundamental Research to
Applications’, Universities Press Limited: Telangana, India, (May), pp.
279–89
2) Xia, R., Wu, R. N., Liu, Y. L. and Sun, X. Y., (2015) ‘The role of computer
simulation in nanoporous metals-a review’, Materials, 8(8), pp. 5060–
5083.
3) Hangai, Y., Nakano, Y., Koyama, S., Kuwazuru, O., Kitahara, S. and
Yoshikawa, N., (2015) ‘Fabrication of aluminum tubes filled with
aluminum alloy foam by frictionwelding’, Materials, 8(10), pp. 7180–7190
4) Vesenjak, M., Borovinšek, M., Ren, Z., Irie, S. and Itoh, S., (2012)
‘Behavior of Metallic Foam under Shock Wave Loading’, Metals, 2(4), pp.
258–264.
5) Güner, A., Arıkan, M. and Nebioglu, M. (2015) ‘New Approaches to
Aluminum Integral Foam Production with Casting Methods’, Metals, 5(3),
pp. 1553–1565.
1) Banhart, J. (2007) ‘Metal Foams — from Fundamental Research to
Applications’, Universities Press Limited: Telangana, India, (May), pp.
279–89
2) Xia, R., Wu, R. N., Liu, Y. L. and Sun, X. Y., (2015) ‘The role of computer
simulation in nanoporous metals-a review’, Materials, 8(8), pp. 5060–
5083.
3) Hangai, Y., Nakano, Y., Koyama, S., Kuwazuru, O., Kitahara, S. and
Yoshikawa, N., (2015) ‘Fabrication of aluminum tubes filled with
aluminum alloy foam by frictionwelding’, Materials, 8(10), pp. 7180–7190
4) Vesenjak, M., Borovinšek, M., Ren, Z., Irie, S. and Itoh, S., (2012)
‘Behavior of Metallic Foam under Shock Wave Loading’, Metals, 2(4), pp.
258–264.
5) Güner, A., Arıkan, M. and Nebioglu, M. (2015) ‘New Approaches to
Aluminum Integral Foam Production with Casting Methods’, Metals, 5(3),
pp. 1553–1565.
Secure Best Marks with AI Grader
Need help grading? Try our AI Grader for instant feedback on your assignments.
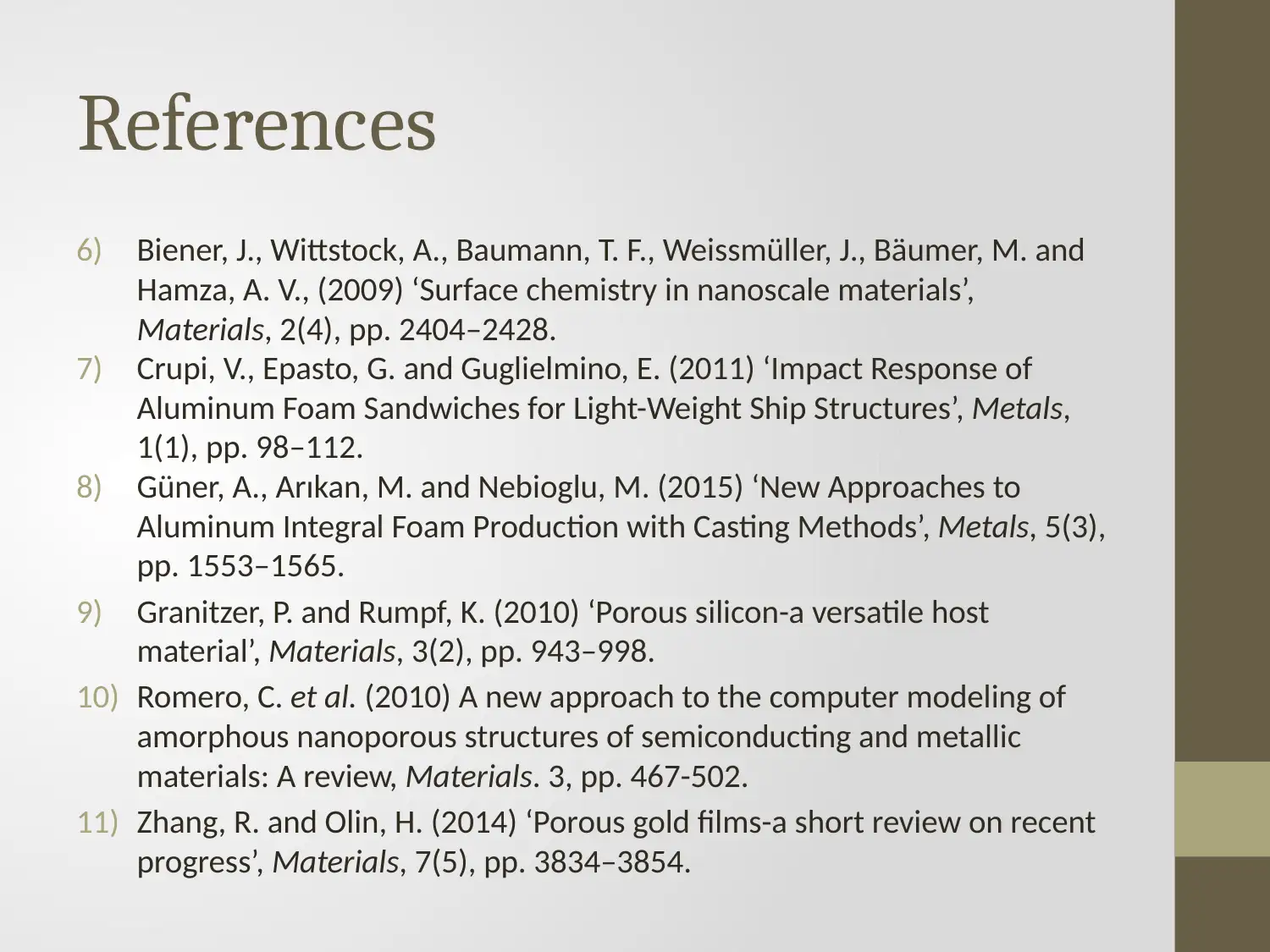
References
6) Biener, J., Wittstock, A., Baumann, T. F., Weissmüller, J., Bäumer, M. and
Hamza, A. V., (2009) ‘Surface chemistry in nanoscale materials’,
Materials, 2(4), pp. 2404–2428.
7) Crupi, V., Epasto, G. and Guglielmino, E. (2011) ‘Impact Response of
Aluminum Foam Sandwiches for Light-Weight Ship Structures’, Metals,
1(1), pp. 98–112.
8) Güner, A., Arıkan, M. and Nebioglu, M. (2015) ‘New Approaches to
Aluminum Integral Foam Production with Casting Methods’, Metals, 5(3),
pp. 1553–1565.
9) Granitzer, P. and Rumpf, K. (2010) ‘Porous silicon-a versatile host
material’, Materials, 3(2), pp. 943–998.
10) Romero, C. et al. (2010) A new approach to the computer modeling of
amorphous nanoporous structures of semiconducting and metallic
materials: A review, Materials. 3, pp. 467-502.
11) Zhang, R. and Olin, H. (2014) ‘Porous gold films-a short review on recent
progress’, Materials, 7(5), pp. 3834–3854.
6) Biener, J., Wittstock, A., Baumann, T. F., Weissmüller, J., Bäumer, M. and
Hamza, A. V., (2009) ‘Surface chemistry in nanoscale materials’,
Materials, 2(4), pp. 2404–2428.
7) Crupi, V., Epasto, G. and Guglielmino, E. (2011) ‘Impact Response of
Aluminum Foam Sandwiches for Light-Weight Ship Structures’, Metals,
1(1), pp. 98–112.
8) Güner, A., Arıkan, M. and Nebioglu, M. (2015) ‘New Approaches to
Aluminum Integral Foam Production with Casting Methods’, Metals, 5(3),
pp. 1553–1565.
9) Granitzer, P. and Rumpf, K. (2010) ‘Porous silicon-a versatile host
material’, Materials, 3(2), pp. 943–998.
10) Romero, C. et al. (2010) A new approach to the computer modeling of
amorphous nanoporous structures of semiconducting and metallic
materials: A review, Materials. 3, pp. 467-502.
11) Zhang, R. and Olin, H. (2014) ‘Porous gold films-a short review on recent
progress’, Materials, 7(5), pp. 3834–3854.
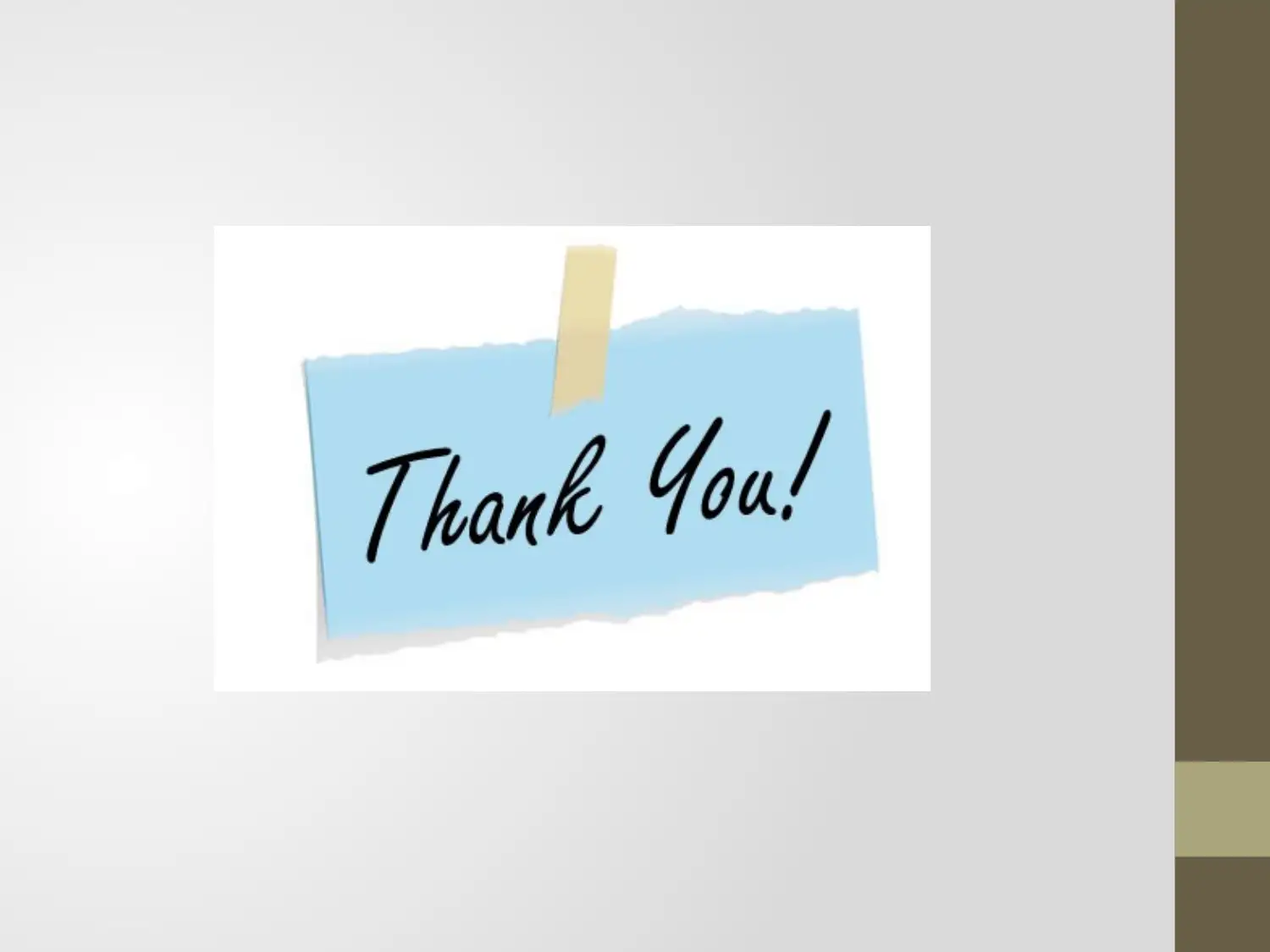
1 out of 18
Related Documents
![[object Object]](/_next/image/?url=%2F_next%2Fstatic%2Fmedia%2Flogo.6d15ce61.png&w=640&q=75)
Your All-in-One AI-Powered Toolkit for Academic Success.
+13062052269
info@desklib.com
Available 24*7 on WhatsApp / Email
Unlock your academic potential
© 2024 | Zucol Services PVT LTD | All rights reserved.