MP4706 - Electronics Sensors, Instrumentation and Control
VerifiedAdded on 2022/08/18
|9
|2443
|10
AI Summary
Contribute Materials
Your contribution can guide someone’s learning journey. Share your
documents today.
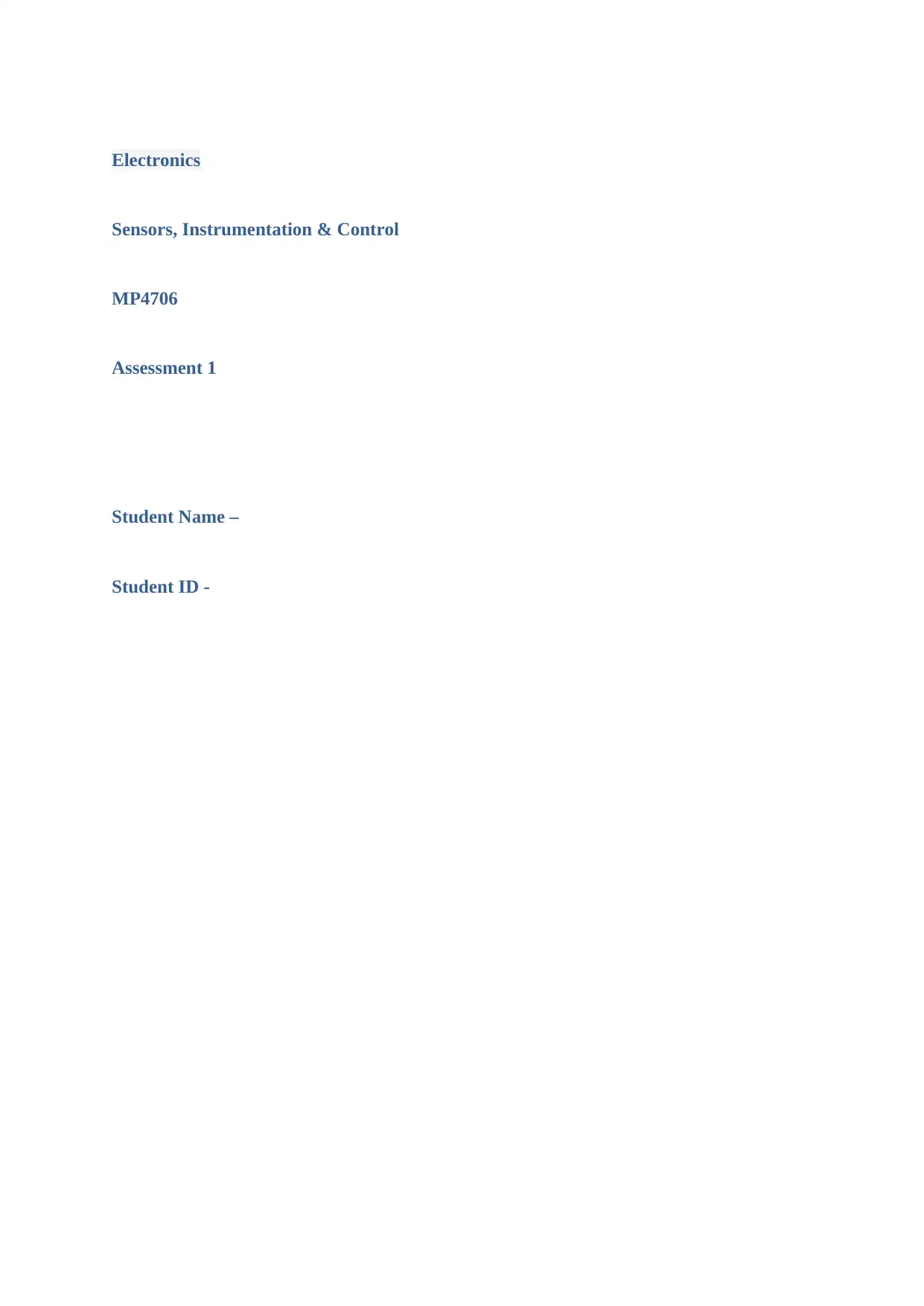
Electronics
Sensors, Instrumentation & Control
MP4706
Assessment 1
Student Name –
Student ID -
Sensors, Instrumentation & Control
MP4706
Assessment 1
Student Name –
Student ID -
Secure Best Marks with AI Grader
Need help grading? Try our AI Grader for instant feedback on your assignments.
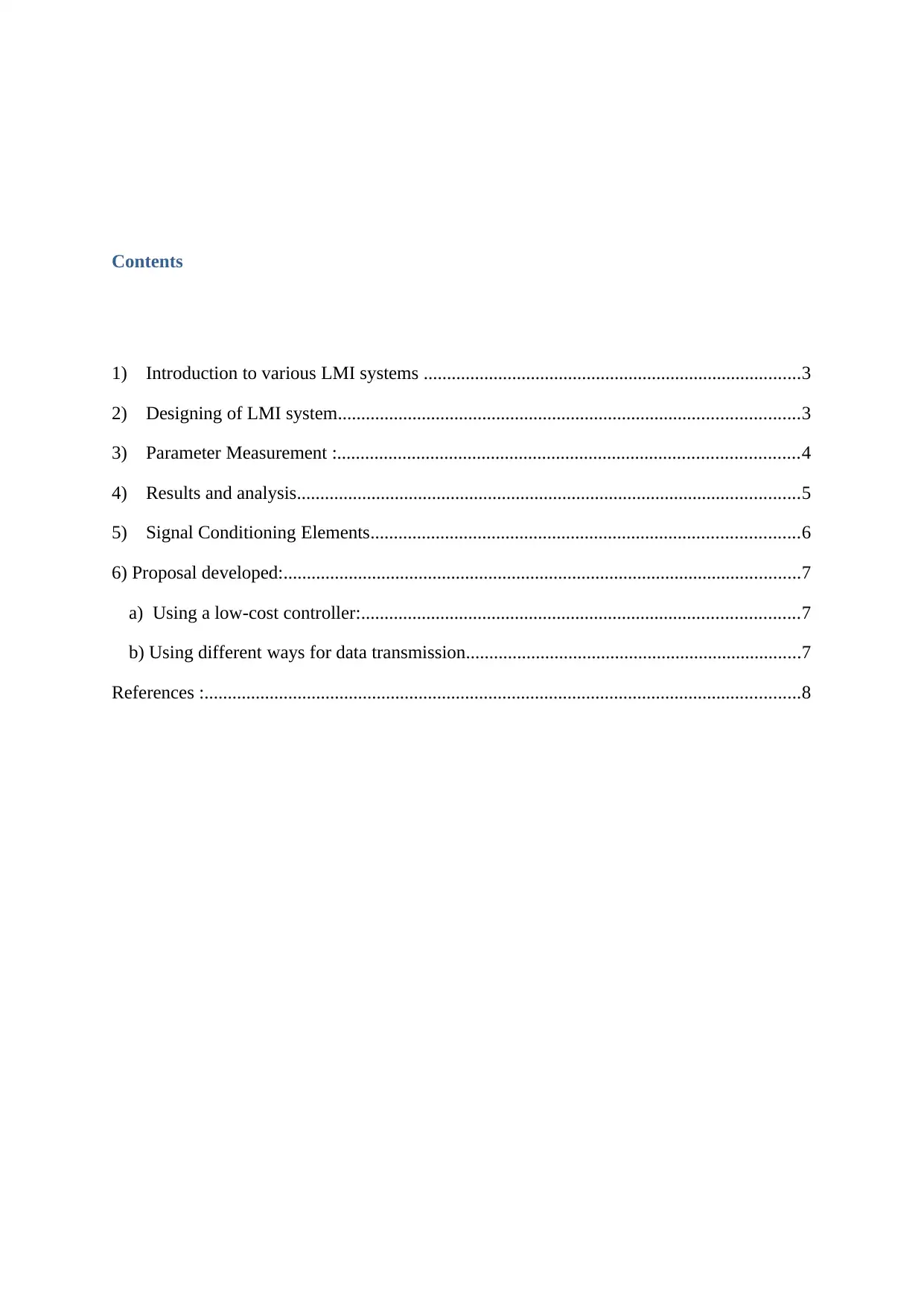
Contents
1) Introduction to various LMI systems .................................................................................3
2) Designing of LMI system...................................................................................................3
3) Parameter Measurement :...................................................................................................4
4) Results and analysis............................................................................................................5
5) Signal Conditioning Elements............................................................................................6
6) Proposal developed:...............................................................................................................7
a) Using a low-cost controller:..............................................................................................7
b) Using different ways for data transmission........................................................................7
References :................................................................................................................................8
1) Introduction to various LMI systems .................................................................................3
2) Designing of LMI system...................................................................................................3
3) Parameter Measurement :...................................................................................................4
4) Results and analysis............................................................................................................5
5) Signal Conditioning Elements............................................................................................6
6) Proposal developed:...............................................................................................................7
a) Using a low-cost controller:..............................................................................................7
b) Using different ways for data transmission........................................................................7
References :................................................................................................................................8
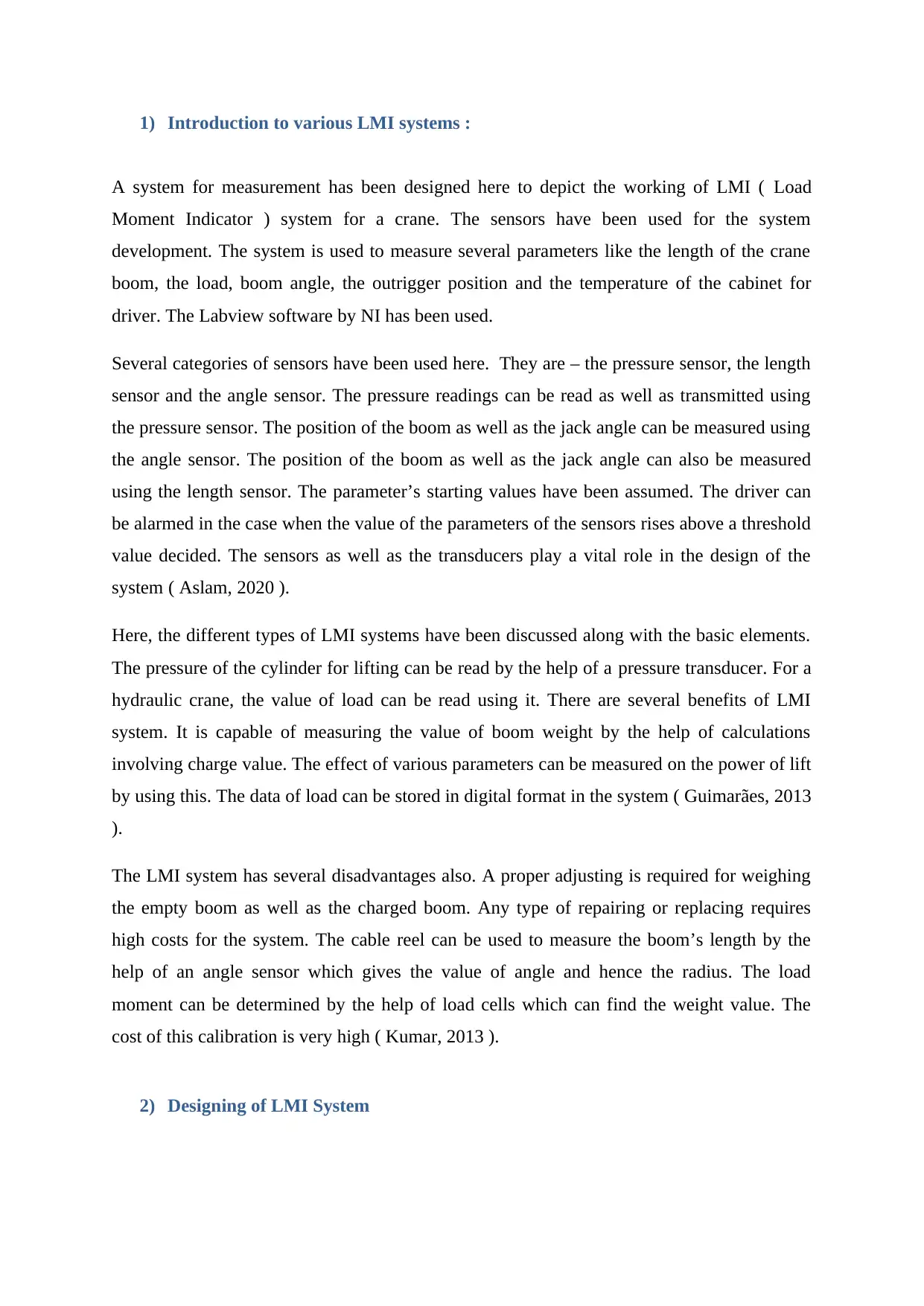
1) Introduction to various LMI systems :
A system for measurement has been designed here to depict the working of LMI ( Load
Moment Indicator ) system for a crane. The sensors have been used for the system
development. The system is used to measure several parameters like the length of the crane
boom, the load, boom angle, the outrigger position and the temperature of the cabinet for
driver. The Labview software by NI has been used.
Several categories of sensors have been used here. They are – the pressure sensor, the length
sensor and the angle sensor. The pressure readings can be read as well as transmitted using
the pressure sensor. The position of the boom as well as the jack angle can be measured using
the angle sensor. The position of the boom as well as the jack angle can also be measured
using the length sensor. The parameter’s starting values have been assumed. The driver can
be alarmed in the case when the value of the parameters of the sensors rises above a threshold
value decided. The sensors as well as the transducers play a vital role in the design of the
system ( Aslam, 2020 ).
Here, the different types of LMI systems have been discussed along with the basic elements.
The pressure of the cylinder for lifting can be read by the help of a pressure transducer. For a
hydraulic crane, the value of load can be read using it. There are several benefits of LMI
system. It is capable of measuring the value of boom weight by the help of calculations
involving charge value. The effect of various parameters can be measured on the power of lift
by using this. The data of load can be stored in digital format in the system ( Guimarães, 2013
).
The LMI system has several disadvantages also. A proper adjusting is required for weighing
the empty boom as well as the charged boom. Any type of repairing or replacing requires
high costs for the system. The cable reel can be used to measure the boom’s length by the
help of an angle sensor which gives the value of angle and hence the radius. The load
moment can be determined by the help of load cells which can find the weight value. The
cost of this calibration is very high ( Kumar, 2013 ).
2) Designing of LMI System
A system for measurement has been designed here to depict the working of LMI ( Load
Moment Indicator ) system for a crane. The sensors have been used for the system
development. The system is used to measure several parameters like the length of the crane
boom, the load, boom angle, the outrigger position and the temperature of the cabinet for
driver. The Labview software by NI has been used.
Several categories of sensors have been used here. They are – the pressure sensor, the length
sensor and the angle sensor. The pressure readings can be read as well as transmitted using
the pressure sensor. The position of the boom as well as the jack angle can be measured using
the angle sensor. The position of the boom as well as the jack angle can also be measured
using the length sensor. The parameter’s starting values have been assumed. The driver can
be alarmed in the case when the value of the parameters of the sensors rises above a threshold
value decided. The sensors as well as the transducers play a vital role in the design of the
system ( Aslam, 2020 ).
Here, the different types of LMI systems have been discussed along with the basic elements.
The pressure of the cylinder for lifting can be read by the help of a pressure transducer. For a
hydraulic crane, the value of load can be read using it. There are several benefits of LMI
system. It is capable of measuring the value of boom weight by the help of calculations
involving charge value. The effect of various parameters can be measured on the power of lift
by using this. The data of load can be stored in digital format in the system ( Guimarães, 2013
).
The LMI system has several disadvantages also. A proper adjusting is required for weighing
the empty boom as well as the charged boom. Any type of repairing or replacing requires
high costs for the system. The cable reel can be used to measure the boom’s length by the
help of an angle sensor which gives the value of angle and hence the radius. The load
moment can be determined by the help of load cells which can find the weight value. The
cost of this calibration is very high ( Kumar, 2013 ).
2) Designing of LMI System
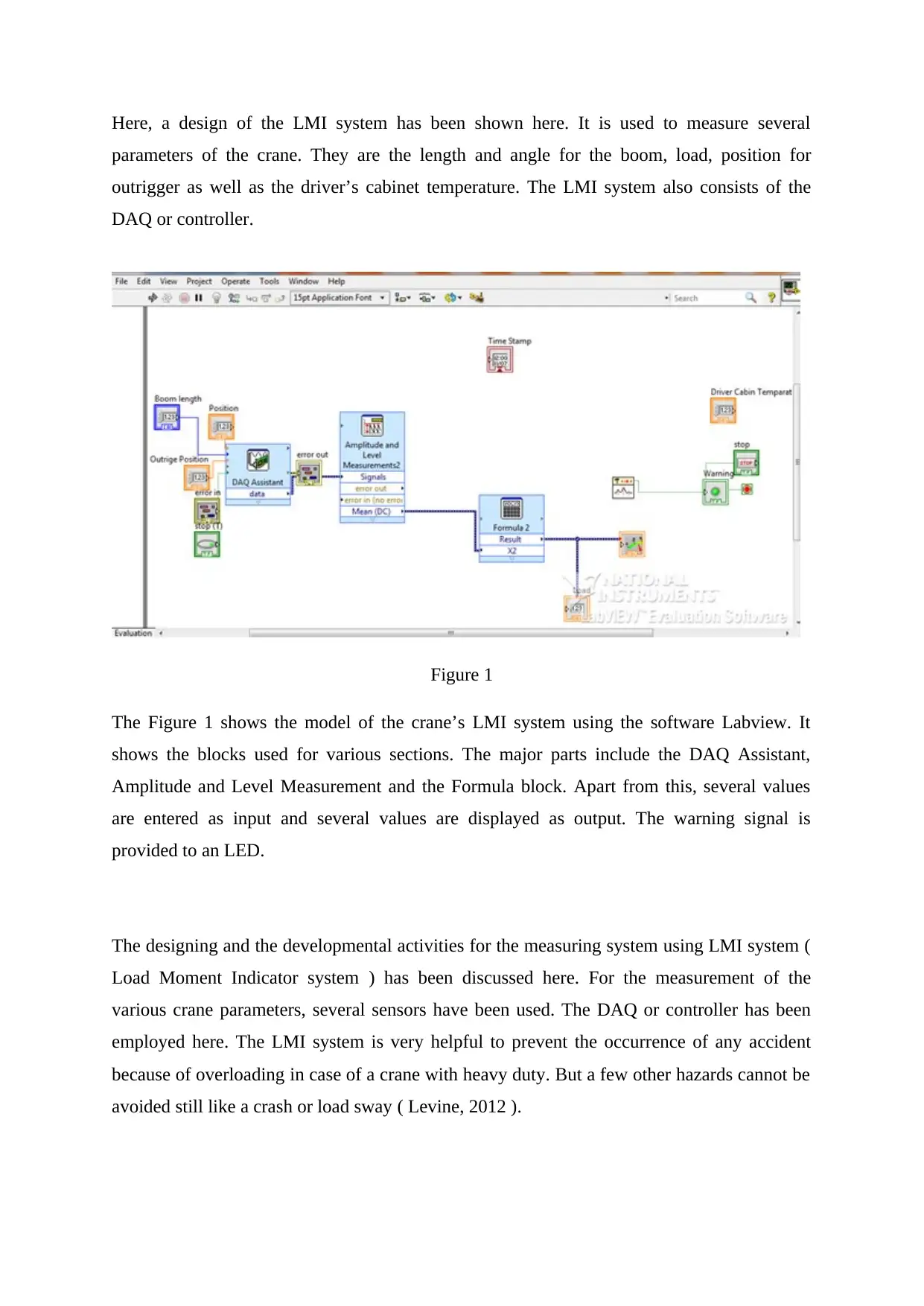
Here, a design of the LMI system has been shown here. It is used to measure several
parameters of the crane. They are the length and angle for the boom, load, position for
outrigger as well as the driver’s cabinet temperature. The LMI system also consists of the
DAQ or controller.
Figure 1
The Figure 1 shows the model of the crane’s LMI system using the software Labview. It
shows the blocks used for various sections. The major parts include the DAQ Assistant,
Amplitude and Level Measurement and the Formula block. Apart from this, several values
are entered as input and several values are displayed as output. The warning signal is
provided to an LED.
The designing and the developmental activities for the measuring system using LMI system (
Load Moment Indicator system ) has been discussed here. For the measurement of the
various crane parameters, several sensors have been used. The DAQ or controller has been
employed here. The LMI system is very helpful to prevent the occurrence of any accident
because of overloading in case of a crane with heavy duty. But a few other hazards cannot be
avoided still like a crash or load sway ( Levine, 2012 ).
parameters of the crane. They are the length and angle for the boom, load, position for
outrigger as well as the driver’s cabinet temperature. The LMI system also consists of the
DAQ or controller.
Figure 1
The Figure 1 shows the model of the crane’s LMI system using the software Labview. It
shows the blocks used for various sections. The major parts include the DAQ Assistant,
Amplitude and Level Measurement and the Formula block. Apart from this, several values
are entered as input and several values are displayed as output. The warning signal is
provided to an LED.
The designing and the developmental activities for the measuring system using LMI system (
Load Moment Indicator system ) has been discussed here. For the measurement of the
various crane parameters, several sensors have been used. The DAQ or controller has been
employed here. The LMI system is very helpful to prevent the occurrence of any accident
because of overloading in case of a crane with heavy duty. But a few other hazards cannot be
avoided still like a crash or load sway ( Levine, 2012 ).
Secure Best Marks with AI Grader
Need help grading? Try our AI Grader for instant feedback on your assignments.
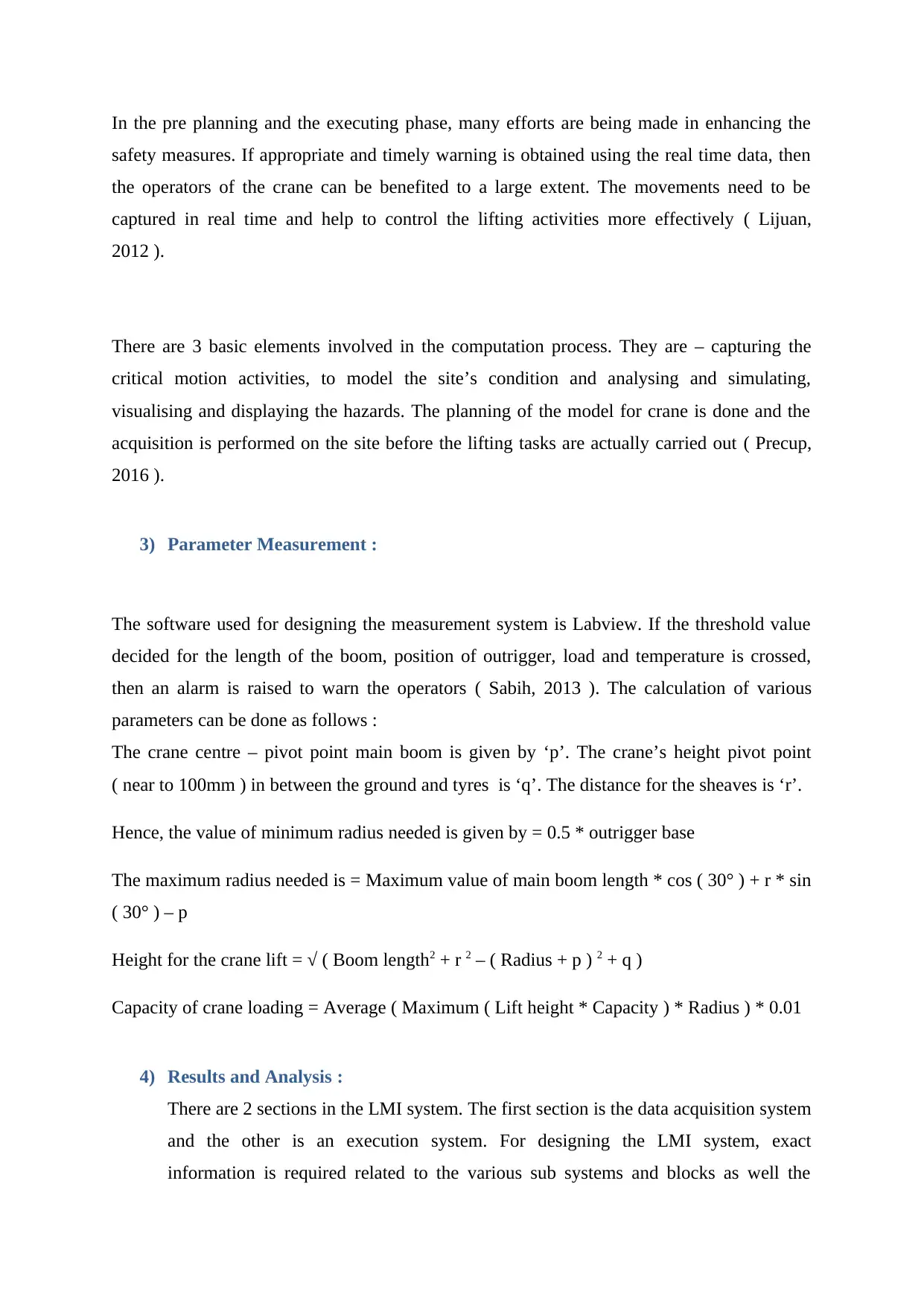
In the pre planning and the executing phase, many efforts are being made in enhancing the
safety measures. If appropriate and timely warning is obtained using the real time data, then
the operators of the crane can be benefited to a large extent. The movements need to be
captured in real time and help to control the lifting activities more effectively ( Lijuan,
2012 ).
There are 3 basic elements involved in the computation process. They are – capturing the
critical motion activities, to model the site’s condition and analysing and simulating,
visualising and displaying the hazards. The planning of the model for crane is done and the
acquisition is performed on the site before the lifting tasks are actually carried out ( Precup,
2016 ).
3) Parameter Measurement :
The software used for designing the measurement system is Labview. If the threshold value
decided for the length of the boom, position of outrigger, load and temperature is crossed,
then an alarm is raised to warn the operators ( Sabih, 2013 ). The calculation of various
parameters can be done as follows :
The crane centre – pivot point main boom is given by ‘p’. The crane’s height pivot point
( near to 100mm ) in between the ground and tyres is ‘q’. The distance for the sheaves is ‘r’.
Hence, the value of minimum radius needed is given by = 0.5 * outrigger base
The maximum radius needed is = Maximum value of main boom length * cos ( 30° ) + r * sin
( 30° ) – p
Height for the crane lift = √ ( Boom length2 + r 2 – ( Radius + p ) 2 + q )
Capacity of crane loading = Average ( Maximum ( Lift height * Capacity ) * Radius ) * 0.01
4) Results and Analysis :
There are 2 sections in the LMI system. The first section is the data acquisition system
and the other is an execution system. For designing the LMI system, exact
information is required related to the various sub systems and blocks as well the
safety measures. If appropriate and timely warning is obtained using the real time data, then
the operators of the crane can be benefited to a large extent. The movements need to be
captured in real time and help to control the lifting activities more effectively ( Lijuan,
2012 ).
There are 3 basic elements involved in the computation process. They are – capturing the
critical motion activities, to model the site’s condition and analysing and simulating,
visualising and displaying the hazards. The planning of the model for crane is done and the
acquisition is performed on the site before the lifting tasks are actually carried out ( Precup,
2016 ).
3) Parameter Measurement :
The software used for designing the measurement system is Labview. If the threshold value
decided for the length of the boom, position of outrigger, load and temperature is crossed,
then an alarm is raised to warn the operators ( Sabih, 2013 ). The calculation of various
parameters can be done as follows :
The crane centre – pivot point main boom is given by ‘p’. The crane’s height pivot point
( near to 100mm ) in between the ground and tyres is ‘q’. The distance for the sheaves is ‘r’.
Hence, the value of minimum radius needed is given by = 0.5 * outrigger base
The maximum radius needed is = Maximum value of main boom length * cos ( 30° ) + r * sin
( 30° ) – p
Height for the crane lift = √ ( Boom length2 + r 2 – ( Radius + p ) 2 + q )
Capacity of crane loading = Average ( Maximum ( Lift height * Capacity ) * Radius ) * 0.01
4) Results and Analysis :
There are 2 sections in the LMI system. The first section is the data acquisition system
and the other is an execution system. For designing the LMI system, exact
information is required related to the various sub systems and blocks as well the
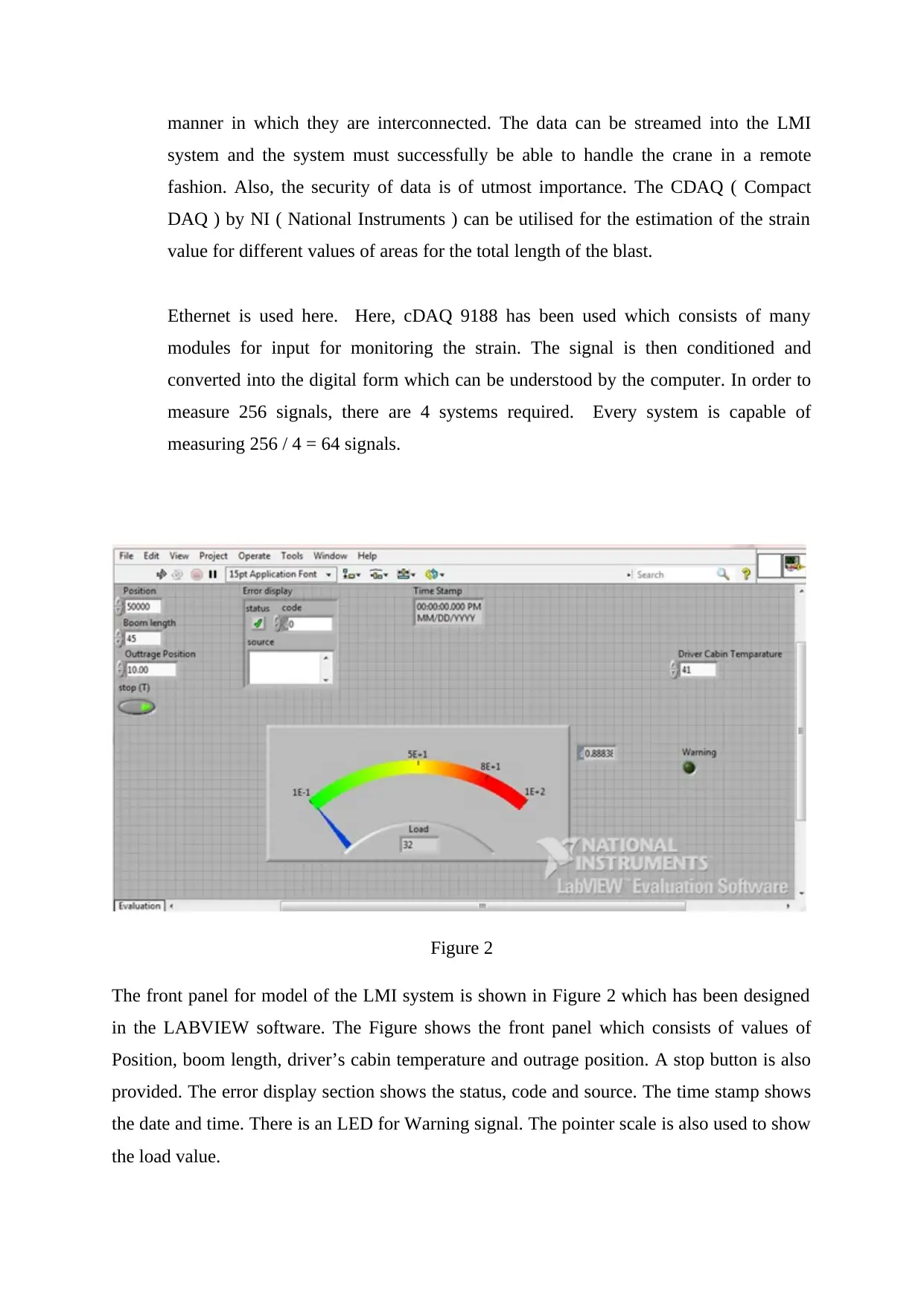
manner in which they are interconnected. The data can be streamed into the LMI
system and the system must successfully be able to handle the crane in a remote
fashion. Also, the security of data is of utmost importance. The CDAQ ( Compact
DAQ ) by NI ( National Instruments ) can be utilised for the estimation of the strain
value for different values of areas for the total length of the blast.
Ethernet is used here. Here, cDAQ 9188 has been used which consists of many
modules for input for monitoring the strain. The signal is then conditioned and
converted into the digital form which can be understood by the computer. In order to
measure 256 signals, there are 4 systems required. Every system is capable of
measuring 256 / 4 = 64 signals.
Figure 2
The front panel for model of the LMI system is shown in Figure 2 which has been designed
in the LABVIEW software. The Figure shows the front panel which consists of values of
Position, boom length, driver’s cabin temperature and outrage position. A stop button is also
provided. The error display section shows the status, code and source. The time stamp shows
the date and time. There is an LED for Warning signal. The pointer scale is also used to show
the load value.
system and the system must successfully be able to handle the crane in a remote
fashion. Also, the security of data is of utmost importance. The CDAQ ( Compact
DAQ ) by NI ( National Instruments ) can be utilised for the estimation of the strain
value for different values of areas for the total length of the blast.
Ethernet is used here. Here, cDAQ 9188 has been used which consists of many
modules for input for monitoring the strain. The signal is then conditioned and
converted into the digital form which can be understood by the computer. In order to
measure 256 signals, there are 4 systems required. Every system is capable of
measuring 256 / 4 = 64 signals.
Figure 2
The front panel for model of the LMI system is shown in Figure 2 which has been designed
in the LABVIEW software. The Figure shows the front panel which consists of values of
Position, boom length, driver’s cabin temperature and outrage position. A stop button is also
provided. The error display section shows the status, code and source. The time stamp shows
the date and time. There is an LED for Warning signal. The pointer scale is also used to show
the load value.
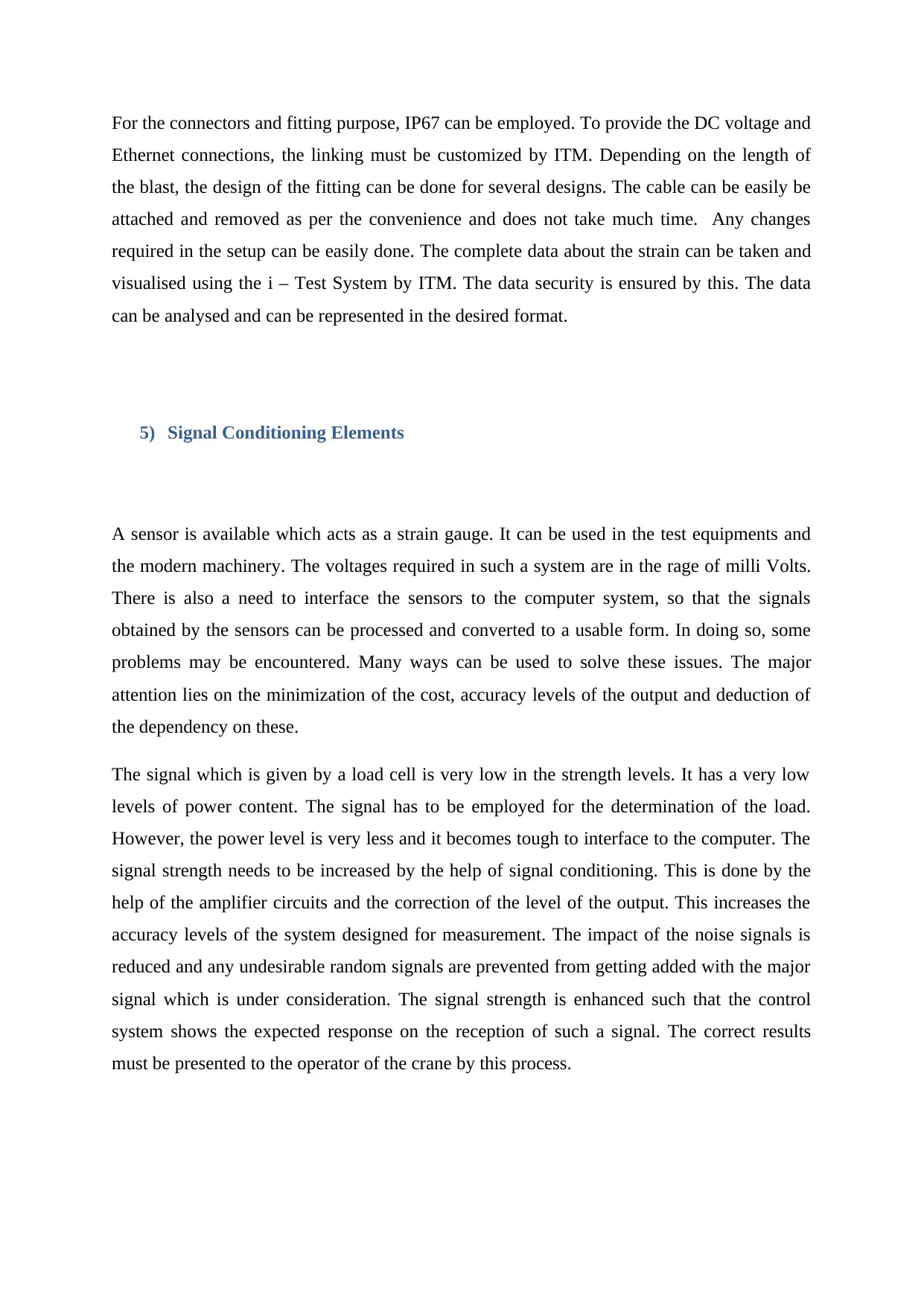
For the connectors and fitting purpose, IP67 can be employed. To provide the DC voltage and
Ethernet connections, the linking must be customized by ITM. Depending on the length of
the blast, the design of the fitting can be done for several designs. The cable can be easily be
attached and removed as per the convenience and does not take much time. Any changes
required in the setup can be easily done. The complete data about the strain can be taken and
visualised using the i – Test System by ITM. The data security is ensured by this. The data
can be analysed and can be represented in the desired format.
5) Signal Conditioning Elements
A sensor is available which acts as a strain gauge. It can be used in the test equipments and
the modern machinery. The voltages required in such a system are in the rage of milli Volts.
There is also a need to interface the sensors to the computer system, so that the signals
obtained by the sensors can be processed and converted to a usable form. In doing so, some
problems may be encountered. Many ways can be used to solve these issues. The major
attention lies on the minimization of the cost, accuracy levels of the output and deduction of
the dependency on these.
The signal which is given by a load cell is very low in the strength levels. It has a very low
levels of power content. The signal has to be employed for the determination of the load.
However, the power level is very less and it becomes tough to interface to the computer. The
signal strength needs to be increased by the help of signal conditioning. This is done by the
help of the amplifier circuits and the correction of the level of the output. This increases the
accuracy levels of the system designed for measurement. The impact of the noise signals is
reduced and any undesirable random signals are prevented from getting added with the major
signal which is under consideration. The signal strength is enhanced such that the control
system shows the expected response on the reception of such a signal. The correct results
must be presented to the operator of the crane by this process.
Ethernet connections, the linking must be customized by ITM. Depending on the length of
the blast, the design of the fitting can be done for several designs. The cable can be easily be
attached and removed as per the convenience and does not take much time. Any changes
required in the setup can be easily done. The complete data about the strain can be taken and
visualised using the i – Test System by ITM. The data security is ensured by this. The data
can be analysed and can be represented in the desired format.
5) Signal Conditioning Elements
A sensor is available which acts as a strain gauge. It can be used in the test equipments and
the modern machinery. The voltages required in such a system are in the rage of milli Volts.
There is also a need to interface the sensors to the computer system, so that the signals
obtained by the sensors can be processed and converted to a usable form. In doing so, some
problems may be encountered. Many ways can be used to solve these issues. The major
attention lies on the minimization of the cost, accuracy levels of the output and deduction of
the dependency on these.
The signal which is given by a load cell is very low in the strength levels. It has a very low
levels of power content. The signal has to be employed for the determination of the load.
However, the power level is very less and it becomes tough to interface to the computer. The
signal strength needs to be increased by the help of signal conditioning. This is done by the
help of the amplifier circuits and the correction of the level of the output. This increases the
accuracy levels of the system designed for measurement. The impact of the noise signals is
reduced and any undesirable random signals are prevented from getting added with the major
signal which is under consideration. The signal strength is enhanced such that the control
system shows the expected response on the reception of such a signal. The correct results
must be presented to the operator of the crane by this process.
Paraphrase This Document
Need a fresh take? Get an instant paraphrase of this document with our AI Paraphraser
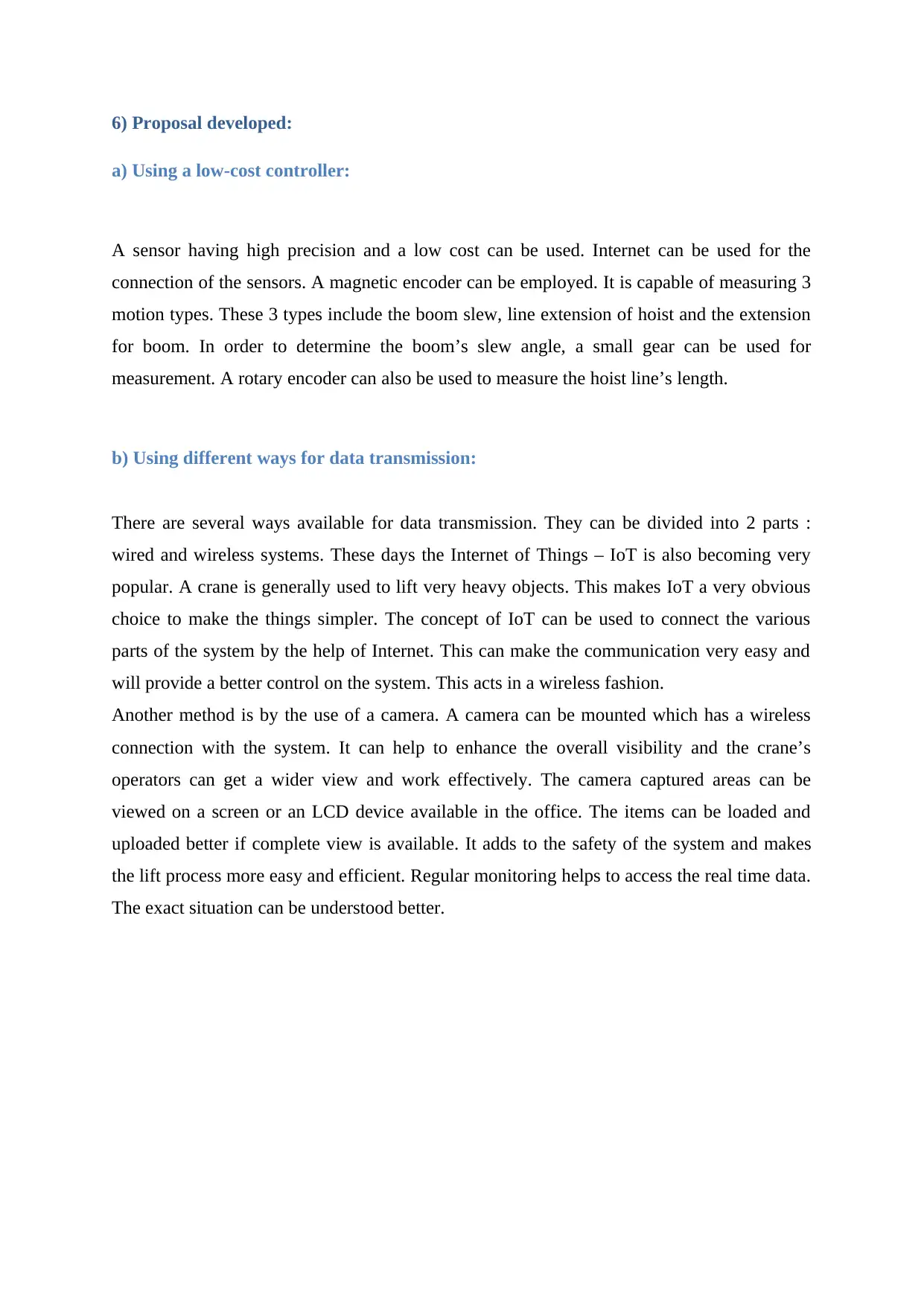
6) Proposal developed:
a) Using a low-cost controller:
A sensor having high precision and a low cost can be used. Internet can be used for the
connection of the sensors. A magnetic encoder can be employed. It is capable of measuring 3
motion types. These 3 types include the boom slew, line extension of hoist and the extension
for boom. In order to determine the boom’s slew angle, a small gear can be used for
measurement. A rotary encoder can also be used to measure the hoist line’s length.
b) Using different ways for data transmission:
There are several ways available for data transmission. They can be divided into 2 parts :
wired and wireless systems. These days the Internet of Things – IoT is also becoming very
popular. A crane is generally used to lift very heavy objects. This makes IoT a very obvious
choice to make the things simpler. The concept of IoT can be used to connect the various
parts of the system by the help of Internet. This can make the communication very easy and
will provide a better control on the system. This acts in a wireless fashion.
Another method is by the use of a camera. A camera can be mounted which has a wireless
connection with the system. It can help to enhance the overall visibility and the crane’s
operators can get a wider view and work effectively. The camera captured areas can be
viewed on a screen or an LCD device available in the office. The items can be loaded and
uploaded better if complete view is available. It adds to the safety of the system and makes
the lift process more easy and efficient. Regular monitoring helps to access the real time data.
The exact situation can be understood better.
a) Using a low-cost controller:
A sensor having high precision and a low cost can be used. Internet can be used for the
connection of the sensors. A magnetic encoder can be employed. It is capable of measuring 3
motion types. These 3 types include the boom slew, line extension of hoist and the extension
for boom. In order to determine the boom’s slew angle, a small gear can be used for
measurement. A rotary encoder can also be used to measure the hoist line’s length.
b) Using different ways for data transmission:
There are several ways available for data transmission. They can be divided into 2 parts :
wired and wireless systems. These days the Internet of Things – IoT is also becoming very
popular. A crane is generally used to lift very heavy objects. This makes IoT a very obvious
choice to make the things simpler. The concept of IoT can be used to connect the various
parts of the system by the help of Internet. This can make the communication very easy and
will provide a better control on the system. This acts in a wireless fashion.
Another method is by the use of a camera. A camera can be mounted which has a wireless
connection with the system. It can help to enhance the overall visibility and the crane’s
operators can get a wider view and work effectively. The camera captured areas can be
viewed on a screen or an LCD device available in the office. The items can be loaded and
uploaded better if complete view is available. It adds to the safety of the system and makes
the lift process more easy and efficient. Regular monitoring helps to access the real time data.
The exact situation can be understood better.
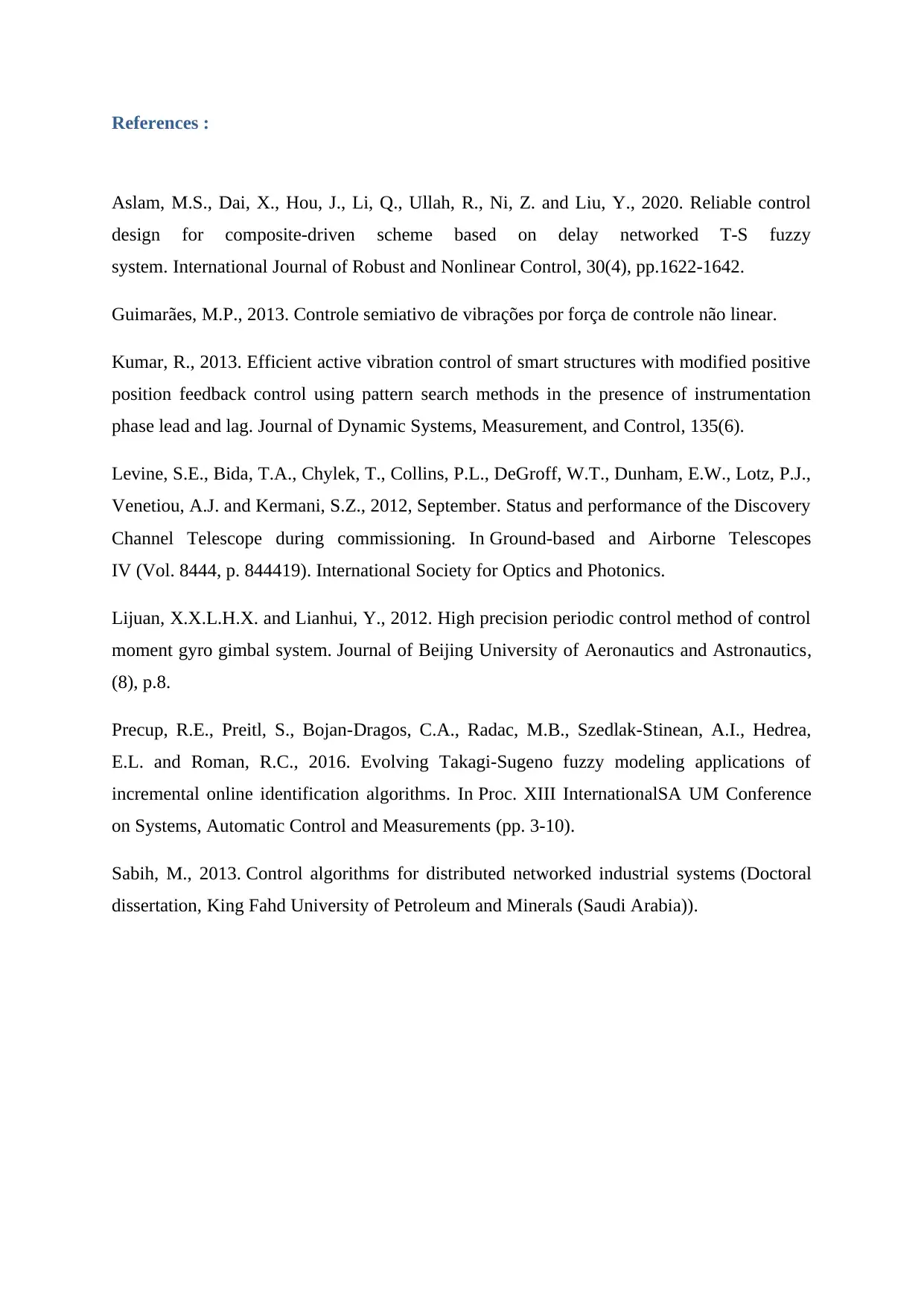
References :
Aslam, M.S., Dai, X., Hou, J., Li, Q., Ullah, R., Ni, Z. and Liu, Y., 2020. Reliable control
design for composite‐driven scheme based on delay networked T‐S fuzzy
system. International Journal of Robust and Nonlinear Control, 30(4), pp.1622-1642.
Guimarães, M.P., 2013. Controle semiativo de vibrações por força de controle não linear.
Kumar, R., 2013. Efficient active vibration control of smart structures with modified positive
position feedback control using pattern search methods in the presence of instrumentation
phase lead and lag. Journal of Dynamic Systems, Measurement, and Control, 135(6).
Levine, S.E., Bida, T.A., Chylek, T., Collins, P.L., DeGroff, W.T., Dunham, E.W., Lotz, P.J.,
Venetiou, A.J. and Kermani, S.Z., 2012, September. Status and performance of the Discovery
Channel Telescope during commissioning. In Ground-based and Airborne Telescopes
IV (Vol. 8444, p. 844419). International Society for Optics and Photonics.
Lijuan, X.X.L.H.X. and Lianhui, Y., 2012. High precision periodic control method of control
moment gyro gimbal system. Journal of Beijing University of Aeronautics and Astronautics,
(8), p.8.
Precup, R.E., Preitl, S., Bojan-Dragos, C.A., Radac, M.B., Szedlak-Stinean, A.I., Hedrea,
E.L. and Roman, R.C., 2016. Evolving Takagi-Sugeno fuzzy modeling applications of
incremental online identification algorithms. In Proc. XIII InternationalSA UM Conference
on Systems, Automatic Control and Measurements (pp. 3-10).
Sabih, M., 2013. Control algorithms for distributed networked industrial systems (Doctoral
dissertation, King Fahd University of Petroleum and Minerals (Saudi Arabia)).
Aslam, M.S., Dai, X., Hou, J., Li, Q., Ullah, R., Ni, Z. and Liu, Y., 2020. Reliable control
design for composite‐driven scheme based on delay networked T‐S fuzzy
system. International Journal of Robust and Nonlinear Control, 30(4), pp.1622-1642.
Guimarães, M.P., 2013. Controle semiativo de vibrações por força de controle não linear.
Kumar, R., 2013. Efficient active vibration control of smart structures with modified positive
position feedback control using pattern search methods in the presence of instrumentation
phase lead and lag. Journal of Dynamic Systems, Measurement, and Control, 135(6).
Levine, S.E., Bida, T.A., Chylek, T., Collins, P.L., DeGroff, W.T., Dunham, E.W., Lotz, P.J.,
Venetiou, A.J. and Kermani, S.Z., 2012, September. Status and performance of the Discovery
Channel Telescope during commissioning. In Ground-based and Airborne Telescopes
IV (Vol. 8444, p. 844419). International Society for Optics and Photonics.
Lijuan, X.X.L.H.X. and Lianhui, Y., 2012. High precision periodic control method of control
moment gyro gimbal system. Journal of Beijing University of Aeronautics and Astronautics,
(8), p.8.
Precup, R.E., Preitl, S., Bojan-Dragos, C.A., Radac, M.B., Szedlak-Stinean, A.I., Hedrea,
E.L. and Roman, R.C., 2016. Evolving Takagi-Sugeno fuzzy modeling applications of
incremental online identification algorithms. In Proc. XIII InternationalSA UM Conference
on Systems, Automatic Control and Measurements (pp. 3-10).
Sabih, M., 2013. Control algorithms for distributed networked industrial systems (Doctoral
dissertation, King Fahd University of Petroleum and Minerals (Saudi Arabia)).
1 out of 9
Related Documents
![[object Object]](/_next/image/?url=%2F_next%2Fstatic%2Fmedia%2Flogo.6d15ce61.png&w=640&q=75)
Your All-in-One AI-Powered Toolkit for Academic Success.
+13062052269
info@desklib.com
Available 24*7 on WhatsApp / Email
Unlock your academic potential
© 2024 | Zucol Services PVT LTD | All rights reserved.