Non-Linear Programming for Design Optimization of Step-Cone Pulley
VerifiedAdded on 2023/06/12
|8
|1855
|101
Project
AI Summary
This project focuses on the design optimization of a step-cone pulley for transmitting a power of at least 0.75 hp, with an input shaft speed of 350 rpm and output speed requirements of 750, 450, 250, and 150 rpm. The problem is formulated to minimize the weight of the pulley by determining optim...
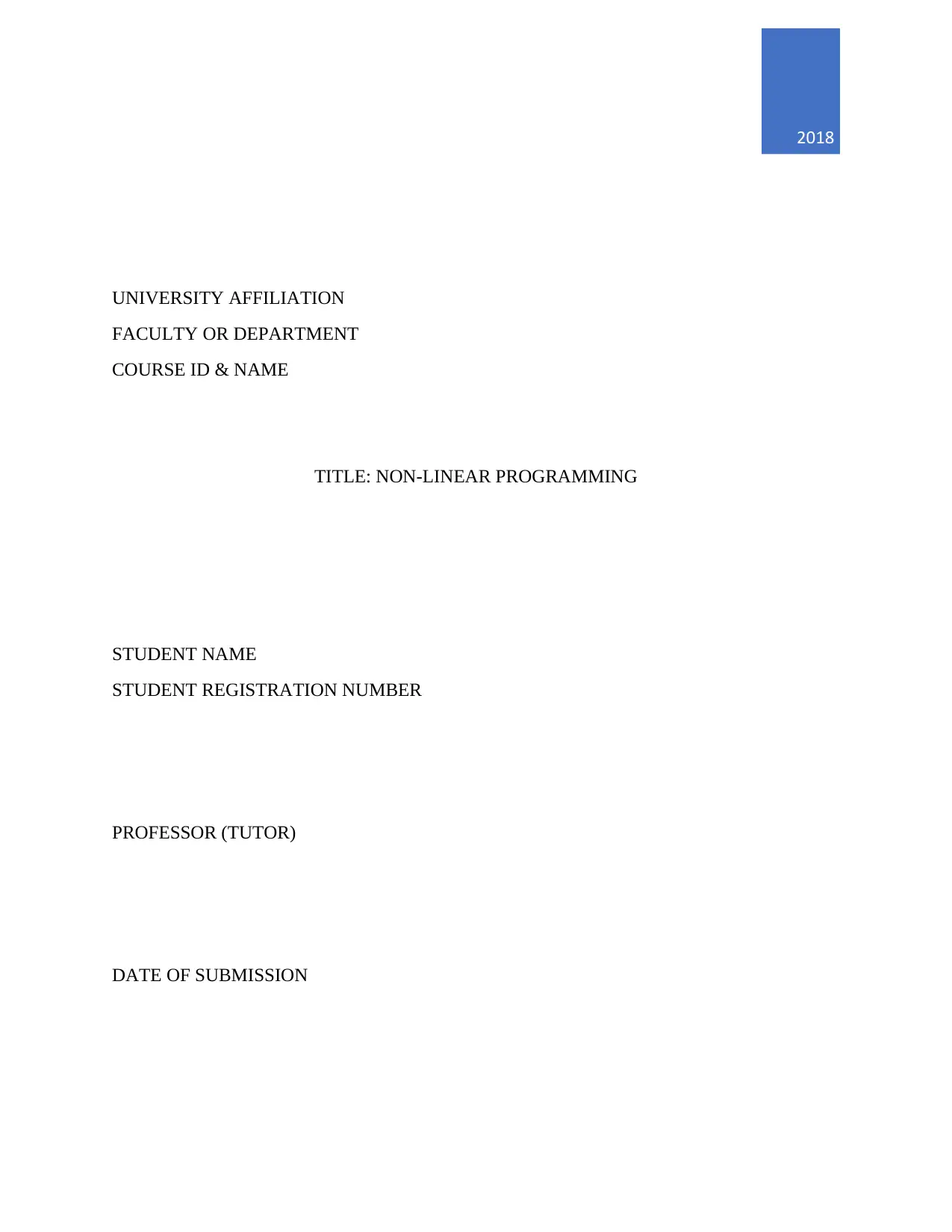
UNIVERSITY AFFILIATION
FACULTY OR DEPARTMENT
COURSE ID & NAME
TITLE: NON-LINEAR PROGRAMMING
STUDENT NAME
STUDENT REGISTRATION NUMBER
PROFESSOR (TUTOR)
DATE OF SUBMISSION
2018
FACULTY OR DEPARTMENT
COURSE ID & NAME
TITLE: NON-LINEAR PROGRAMMING
STUDENT NAME
STUDENT REGISTRATION NUMBER
PROFESSOR (TUTOR)
DATE OF SUBMISSION
2018
Paraphrase This Document
Need a fresh take? Get an instant paraphrase of this document with our AI Paraphraser

PROBLEM 2
Transmitted power: at least 0.75hp
Speed of the input shaft 350 rpm
Output speed requirements 750, 450, 250, 150 rpm
T= thickness of the belt
μ= the coefficient of friction between the belt and the pulley
SCOPE STATEMENT AND ASSUMPTIONS
Some design assumptions are made considering that not all the parameters have been stated in
this equation.
(i) The belt thickness is assumed to be t=10 mm
(ii) The density of the cast iron that makes up the pulley, ρ=7.3 x 10−6 kg
m m3
(iii) The design stress for the leather belt is assumed to be σ =2 MPa
(iv) The material that makes up the pulley belt is fiber material
(v) The material that makes up the pulley is the cast iron; cast iron is used in machine
parts such as those of the pulley as the parts are totally inexpensive, tend to resist the
rust
and its effects. The cast iron is easy to mold and it may be strong incredibly strong or
very weak depending on the mixture or alloy made from it.
(vi) The friction coefficient read between the belt and the pulley is given as, μ=0.30
Transmitted power: at least 0.75hp
Speed of the input shaft 350 rpm
Output speed requirements 750, 450, 250, 150 rpm
T= thickness of the belt
μ= the coefficient of friction between the belt and the pulley
SCOPE STATEMENT AND ASSUMPTIONS
Some design assumptions are made considering that not all the parameters have been stated in
this equation.
(i) The belt thickness is assumed to be t=10 mm
(ii) The density of the cast iron that makes up the pulley, ρ=7.3 x 10−6 kg
m m3
(iii) The design stress for the leather belt is assumed to be σ =2 MPa
(iv) The material that makes up the pulley belt is fiber material
(v) The material that makes up the pulley is the cast iron; cast iron is used in machine
parts such as those of the pulley as the parts are totally inexpensive, tend to resist the
rust
and its effects. The cast iron is easy to mold and it may be strong incredibly strong or
very weak depending on the mixture or alloy made from it.
(vi) The friction coefficient read between the belt and the pulley is given as, μ=0.30
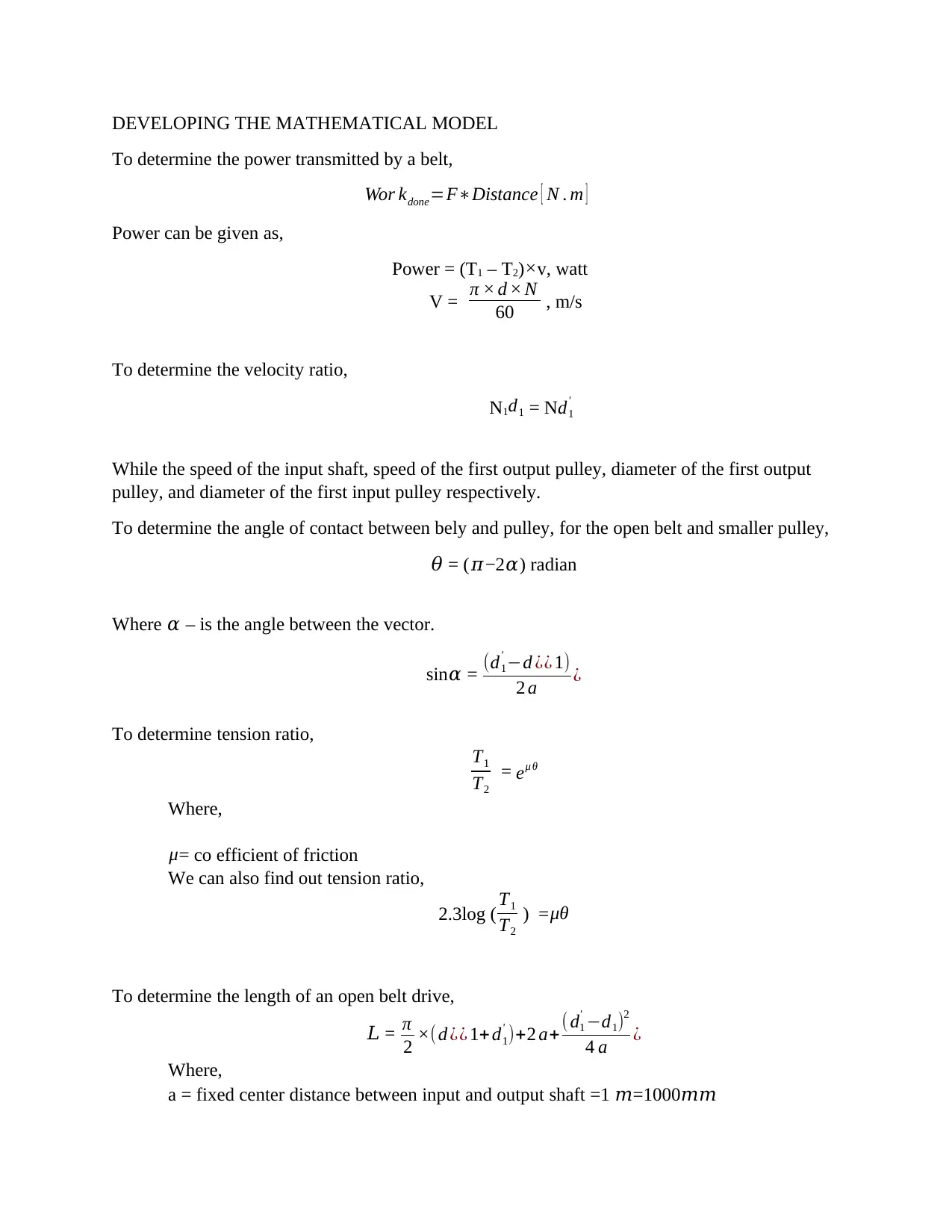
DEVELOPING THE MATHEMATICAL MODEL
To determine the power transmitted by a belt,
Wor kdone=F∗Distance [ N . m ]
Power can be given as,
Power = (T1 – T2)×v, watt
V = π × d × N
60 , m/s
To determine the velocity ratio,
N1d1 = N d1
'
While the speed of the input shaft, speed of the first output pulley, diameter of the first output
pulley, and diameter of the first input pulley respectively.
To determine the angle of contact between bely and pulley, for the open belt and smaller pulley,
𝜃 = (𝜋−2𝛼) radian
Where 𝛼 – is the angle between the vector.
sin𝛼 = (d1
' −d ¿¿ 1)
2 a ¿
To determine tension ratio,
T1
T2
= eμ θ
Where,
μ= co efficient of friction
We can also find out tension ratio,
2.3log ( T1
T2
) =μθ
To determine the length of an open belt drive,
𝐿 = π
2 ×(d ¿¿ 1+d1
' )+2 a+( d1
' −d1)2
4 a ¿
Where,
a = fixed center distance between input and output shaft =1 𝑚=1000𝑚𝑚
To determine the power transmitted by a belt,
Wor kdone=F∗Distance [ N . m ]
Power can be given as,
Power = (T1 – T2)×v, watt
V = π × d × N
60 , m/s
To determine the velocity ratio,
N1d1 = N d1
'
While the speed of the input shaft, speed of the first output pulley, diameter of the first output
pulley, and diameter of the first input pulley respectively.
To determine the angle of contact between bely and pulley, for the open belt and smaller pulley,
𝜃 = (𝜋−2𝛼) radian
Where 𝛼 – is the angle between the vector.
sin𝛼 = (d1
' −d ¿¿ 1)
2 a ¿
To determine tension ratio,
T1
T2
= eμ θ
Where,
μ= co efficient of friction
We can also find out tension ratio,
2.3log ( T1
T2
) =μθ
To determine the length of an open belt drive,
𝐿 = π
2 ×(d ¿¿ 1+d1
' )+2 a+( d1
' −d1)2
4 a ¿
Where,
a = fixed center distance between input and output shaft =1 𝑚=1000𝑚𝑚
⊘ This is a preview!⊘
Do you want full access?
Subscribe today to unlock all pages.

Trusted by 1+ million students worldwide

To determine the maximum tension
T1 = σ × t×w
Where,
σ = Maximum allowable stress
t = Thickness of the belt
w = Width of step = Width of belt
OPTIMIZATION TECHNIQUES
It is required that the length of the belt that passes over the driver and that which passes over the
follower does so in a single minute. The velocity ratio is given as,
N1 d1=N d1
'
750 x d1=350 d1
'
d1
' = 750
350∗d1
The other diameters are equally tested against the inequality constraints as given below,
d2
' = 450
350 ∗d2
d3
' = 250
350∗d3
d4
' = 150
350∗d4
The above equations are simplified to smaller finite values. In the problem set figure, the pulley
diameters are illustrated. The relation between the tight side and slack side tensions, with regards
to coefficient of friction and the angle of contact.
T1
T2
=eμθ
Given that the eμθ ≥ 2,
Such that, eμθ- 2 ≥ 0
T1 = σ × t×w
Where,
σ = Maximum allowable stress
t = Thickness of the belt
w = Width of step = Width of belt
OPTIMIZATION TECHNIQUES
It is required that the length of the belt that passes over the driver and that which passes over the
follower does so in a single minute. The velocity ratio is given as,
N1 d1=N d1
'
750 x d1=350 d1
'
d1
' = 750
350∗d1
The other diameters are equally tested against the inequality constraints as given below,
d2
' = 450
350 ∗d2
d3
' = 250
350∗d3
d4
' = 150
350∗d4
The above equations are simplified to smaller finite values. In the problem set figure, the pulley
diameters are illustrated. The relation between the tight side and slack side tensions, with regards
to coefficient of friction and the angle of contact.
T1
T2
=eμθ
Given that the eμθ ≥ 2,
Such that, eμθ- 2 ≥ 0
Paraphrase This Document
Need a fresh take? Get an instant paraphrase of this document with our AI Paraphraser
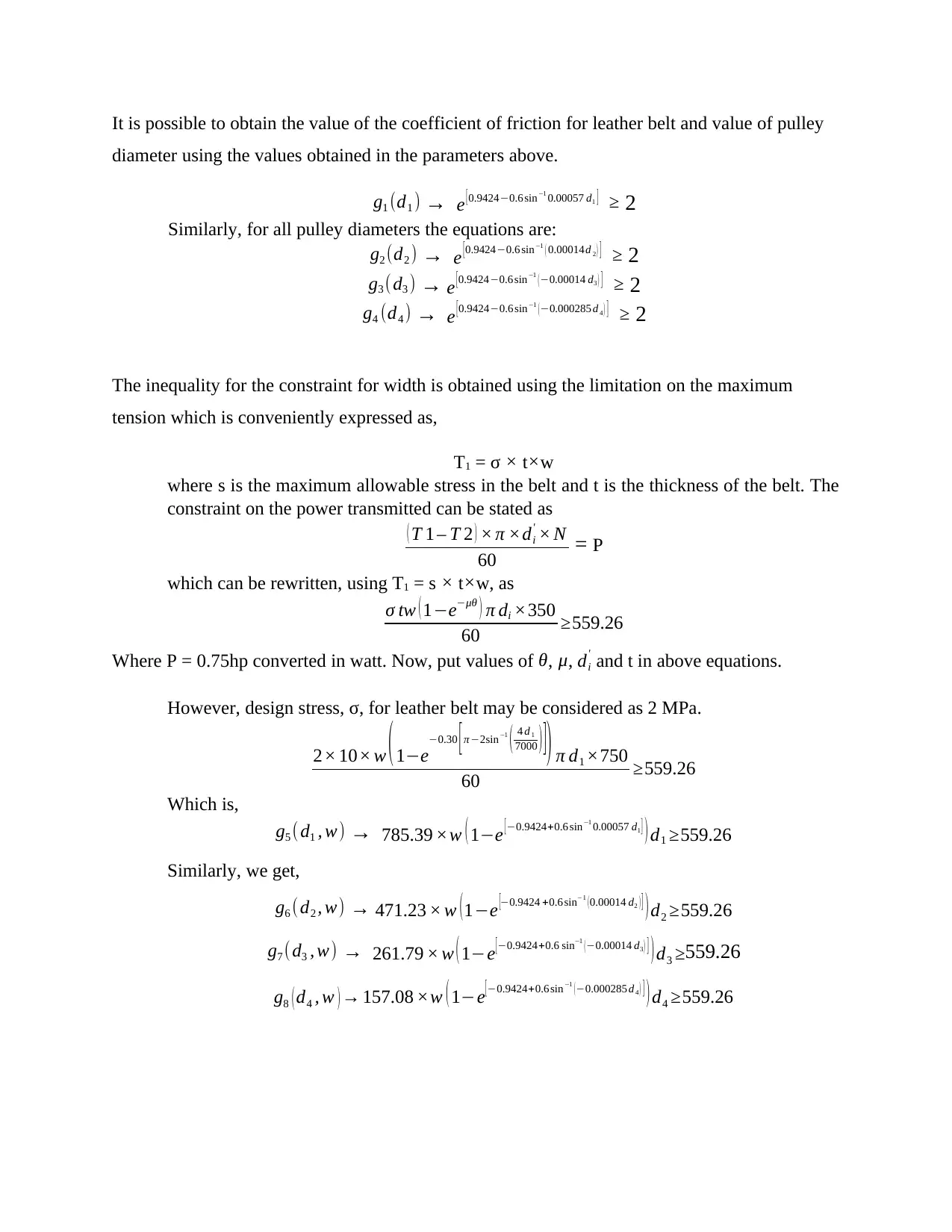
It is possible to obtain the value of the coefficient of friction for leather belt and value of pulley
diameter using the values obtained in the parameters above.
g1 (d1 ) → e [0.9424−0.6sin−1 0.00057 d1 ] ≥ 2
Similarly, for all pulley diameters the equations are:
g2 (d2 ) → e [ 0.9424−0.6 sin−1
( 0.00014d 2 ) ] ≥ 2
g3 (d3 ) → e [0.9424−0.6sin−1
(−0.00014 d3 ) ] ≥ 2
g4 (d4 ) → e [0.9424−0.6sin−1
(−0.000285 d 4 ) ] ≥ 2
The inequality for the constraint for width is obtained using the limitation on the maximum
tension which is conveniently expressed as,
T1 = σ × t×w
where s is the maximum allowable stress in the belt and t is the thickness of the belt. The
constraint on the power transmitted can be stated as
( T 1 – T 2 ) × π ×di
' × N
60 = P
which can be rewritten, using T1 = s × t×w, as
σ tw ( 1−e−μθ ) π di ×350
60 ≥559.26
Where P = 0.75hp converted in watt. Now, put values of θ, μ, di
' and t in above equations.
However, design stress, σ, for leather belt may be considered as 2 MPa.
2× 10× w (1−e
−0.30 [π −2sin−1
( 4 d 1
7000 ) ]) π d1 ×750
60 ≥559.26
Which is,
g5 (d1 , w) → 785.39 ×w ( 1−e [ −0.9424+0.6 sin−1 0.00057 d1 ] ) d1 ≥559.26
Similarly, we get,
g6 (d2 , w) → 471.23 × w ( 1−e [−0.9424 +0.6sin−1
( 0.00014 d2 ) ] ) d2 ≥559.26
g7 (d3 , w) → 261.79 × w ( 1−e
[−0.9424+0.6 sin−1
(−0.00014 d3 ) ] ) d3 ≥559.26
g8 ( d4 , w ) → 157.08 ×w ( 1−e
[ −0.9424+0.6sin−1
( −0.000285 d 4 ) ] ) d4 ≥559.26
diameter using the values obtained in the parameters above.
g1 (d1 ) → e [0.9424−0.6sin−1 0.00057 d1 ] ≥ 2
Similarly, for all pulley diameters the equations are:
g2 (d2 ) → e [ 0.9424−0.6 sin−1
( 0.00014d 2 ) ] ≥ 2
g3 (d3 ) → e [0.9424−0.6sin−1
(−0.00014 d3 ) ] ≥ 2
g4 (d4 ) → e [0.9424−0.6sin−1
(−0.000285 d 4 ) ] ≥ 2
The inequality for the constraint for width is obtained using the limitation on the maximum
tension which is conveniently expressed as,
T1 = σ × t×w
where s is the maximum allowable stress in the belt and t is the thickness of the belt. The
constraint on the power transmitted can be stated as
( T 1 – T 2 ) × π ×di
' × N
60 = P
which can be rewritten, using T1 = s × t×w, as
σ tw ( 1−e−μθ ) π di ×350
60 ≥559.26
Where P = 0.75hp converted in watt. Now, put values of θ, μ, di
' and t in above equations.
However, design stress, σ, for leather belt may be considered as 2 MPa.
2× 10× w (1−e
−0.30 [π −2sin−1
( 4 d 1
7000 ) ]) π d1 ×750
60 ≥559.26
Which is,
g5 (d1 , w) → 785.39 ×w ( 1−e [ −0.9424+0.6 sin−1 0.00057 d1 ] ) d1 ≥559.26
Similarly, we get,
g6 (d2 , w) → 471.23 × w ( 1−e [−0.9424 +0.6sin−1
( 0.00014 d2 ) ] ) d2 ≥559.26
g7 (d3 , w) → 261.79 × w ( 1−e
[−0.9424+0.6 sin−1
(−0.00014 d3 ) ] ) d3 ≥559.26
g8 ( d4 , w ) → 157.08 ×w ( 1−e
[ −0.9424+0.6sin−1
( −0.000285 d 4 ) ] ) d4 ≥559.26
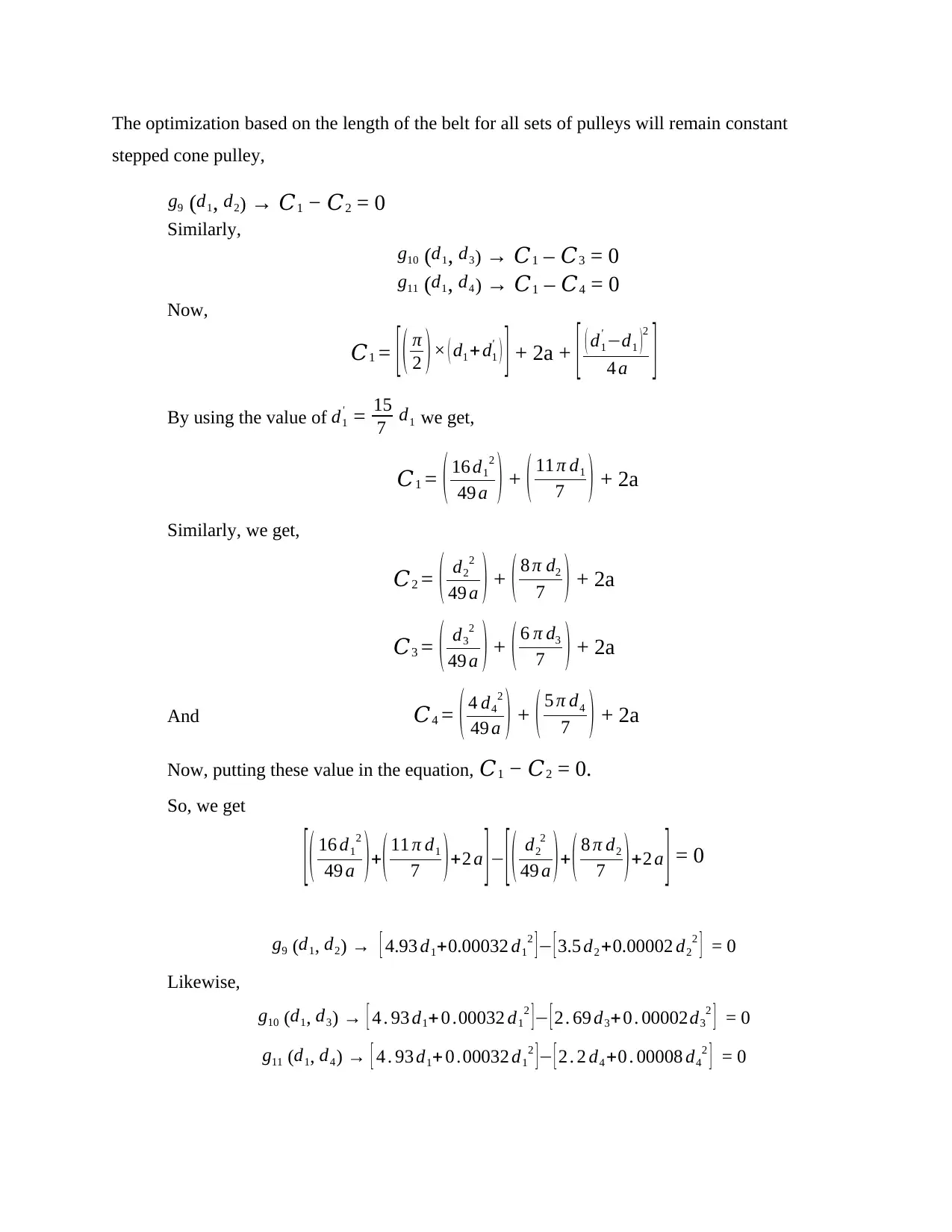
The optimization based on the length of the belt for all sets of pulleys will remain constant
stepped cone pulley,
g9 (d1, d2) → 𝐶1 − 𝐶2 = 0
Similarly,
g10 (d1, d3) → 𝐶1 – 𝐶3 = 0
g11 (d1, d4) → 𝐶1 – 𝐶4 = 0
Now,
𝐶1 = [ ( π
2 )× ( d1 + d1
'
) ] + 2a + [ ( d1
' −d1 )
2
4 a ]
By using the value of d1
' = 15
7 d1 we get,
𝐶1 = ( 16 d1
2
49 a ) + ( 11 π d1
7 ) + 2a
Similarly, we get,
𝐶2 = ( d2
2
49 a ) + ( 8 π d2
7 ) + 2a
𝐶3 = ( d3
2
49 a ) + ( 6 π d3
7 ) + 2a
And 𝐶4 = ( 4 d4
2
49 a ) + ( 5 π d4
7 ) + 2a
Now, putting these value in the equation, 𝐶1 − 𝐶2 = 0.
So, we get
[ ( 16 d1
2
49 a )+( 11 π d1
7 )+2 a ]− [ ( d2
2
49 a )+ ( 8 π d2
7 )+2 a ] = 0
g9 (d1, d2) → [ 4.93 d1+0.00032 d1
2 ] − [ 3.5 d2 +0.00002 d2
2 ] = 0
Likewise,
g10 (d1, d3) → [ 4 . 93 d1+ 0 .00032 d1
2 ]− [ 2 . 69 d3+ 0 . 00002d3
2 ] = 0
g11 (d1, d4) → [ 4 . 93 d1+ 0 .00032 d1
2 ] − [ 2 . 2 d4 +0 . 00008 d4
2 ] = 0
stepped cone pulley,
g9 (d1, d2) → 𝐶1 − 𝐶2 = 0
Similarly,
g10 (d1, d3) → 𝐶1 – 𝐶3 = 0
g11 (d1, d4) → 𝐶1 – 𝐶4 = 0
Now,
𝐶1 = [ ( π
2 )× ( d1 + d1
'
) ] + 2a + [ ( d1
' −d1 )
2
4 a ]
By using the value of d1
' = 15
7 d1 we get,
𝐶1 = ( 16 d1
2
49 a ) + ( 11 π d1
7 ) + 2a
Similarly, we get,
𝐶2 = ( d2
2
49 a ) + ( 8 π d2
7 ) + 2a
𝐶3 = ( d3
2
49 a ) + ( 6 π d3
7 ) + 2a
And 𝐶4 = ( 4 d4
2
49 a ) + ( 5 π d4
7 ) + 2a
Now, putting these value in the equation, 𝐶1 − 𝐶2 = 0.
So, we get
[ ( 16 d1
2
49 a )+( 11 π d1
7 )+2 a ]− [ ( d2
2
49 a )+ ( 8 π d2
7 )+2 a ] = 0
g9 (d1, d2) → [ 4.93 d1+0.00032 d1
2 ] − [ 3.5 d2 +0.00002 d2
2 ] = 0
Likewise,
g10 (d1, d3) → [ 4 . 93 d1+ 0 .00032 d1
2 ]− [ 2 . 69 d3+ 0 . 00002d3
2 ] = 0
g11 (d1, d4) → [ 4 . 93 d1+ 0 .00032 d1
2 ] − [ 2 . 2 d4 +0 . 00008 d4
2 ] = 0
⊘ This is a preview!⊘
Do you want full access?
Subscribe today to unlock all pages.

Trusted by 1+ million students worldwide
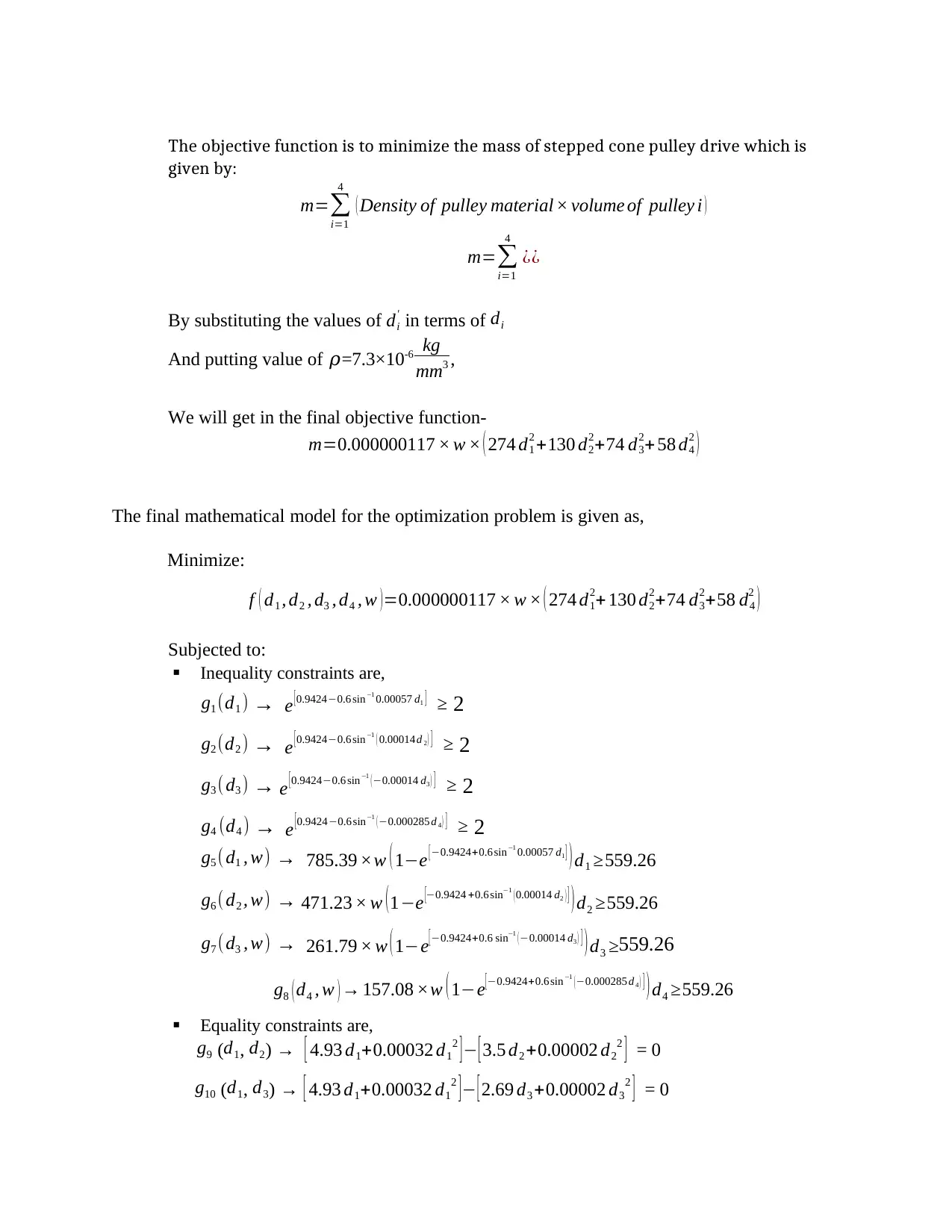
The objective function is to minimize the mass of stepped cone pulley drive which is
given by:
m=∑
i=1
4
( Density of pulley material × volume of pulley i )
m=∑
i=1
4
¿¿
By substituting the values of di
' in terms of di
And putting value of 𝜌=7.3×10-6 kg
mm3 ,
We will get in the final objective function-
m=0.000000117 × w × ( 274 d1
2 +130 d2
2+74 d3
2+ 58 d4
2 )
The final mathematical model for the optimization problem is given as,
Minimize:
f ( d1 , d2 , d3 , d4 , w ) =0.000000117 × w × ( 274 d1
2+ 130 d2
2+74 d3
2+58 d4
2 )
Subjected to:
Inequality constraints are,
g1 (d1 ) → e [ 0.9424−0.6 sin−1 0.00057 d1 ] ≥ 2
g2 (d2 ) → e [0.9424−0.6sin−1
( 0.00014d 2 ) ] ≥ 2
g3 ( d3 ) → e [0.9424−0.6 sin−1
(−0.00014 d3 ) ] ≥ 2
g4 (d4 ) → e [0.9424−0.6sin−1
(−0.000285 d 4 ) ] ≥ 2
g5 ( d1 , w) → 785.39 ×w ( 1−e [−0.9424+0.6 sin−1 0.00057 d1 ] ) d1 ≥559.26
g6 ( d2 , w) → 471.23 × w (1−e [−0.9424 +0.6 sin−1
(0.00014 d2 ) ] ) d2 ≥559.26
g7 (d3 , w) → 261.79 × w ( 1−e
[−0.9424+0.6 sin−1
(−0.00014 d3 ) ] ) d3 ≥559.26
g8 ( d4 , w ) → 157.08 ×w ( 1−e[ −0.9424+0.6sin−1
( −0.000285 d 4 ) ] ) d4 ≥559.26
Equality constraints are,
g9 (d1, d2) → [ 4.93 d1+0.00032 d1
2 ]− [ 3.5 d2 +0.00002 d2
2 ] = 0
g10 (d1, d3) → [ 4.93 d1+0.00032 d1
2 ] − [ 2.69 d3 +0.00002 d3
2 ] = 0
given by:
m=∑
i=1
4
( Density of pulley material × volume of pulley i )
m=∑
i=1
4
¿¿
By substituting the values of di
' in terms of di
And putting value of 𝜌=7.3×10-6 kg
mm3 ,
We will get in the final objective function-
m=0.000000117 × w × ( 274 d1
2 +130 d2
2+74 d3
2+ 58 d4
2 )
The final mathematical model for the optimization problem is given as,
Minimize:
f ( d1 , d2 , d3 , d4 , w ) =0.000000117 × w × ( 274 d1
2+ 130 d2
2+74 d3
2+58 d4
2 )
Subjected to:
Inequality constraints are,
g1 (d1 ) → e [ 0.9424−0.6 sin−1 0.00057 d1 ] ≥ 2
g2 (d2 ) → e [0.9424−0.6sin−1
( 0.00014d 2 ) ] ≥ 2
g3 ( d3 ) → e [0.9424−0.6 sin−1
(−0.00014 d3 ) ] ≥ 2
g4 (d4 ) → e [0.9424−0.6sin−1
(−0.000285 d 4 ) ] ≥ 2
g5 ( d1 , w) → 785.39 ×w ( 1−e [−0.9424+0.6 sin−1 0.00057 d1 ] ) d1 ≥559.26
g6 ( d2 , w) → 471.23 × w (1−e [−0.9424 +0.6 sin−1
(0.00014 d2 ) ] ) d2 ≥559.26
g7 (d3 , w) → 261.79 × w ( 1−e
[−0.9424+0.6 sin−1
(−0.00014 d3 ) ] ) d3 ≥559.26
g8 ( d4 , w ) → 157.08 ×w ( 1−e[ −0.9424+0.6sin−1
( −0.000285 d 4 ) ] ) d4 ≥559.26
Equality constraints are,
g9 (d1, d2) → [ 4.93 d1+0.00032 d1
2 ]− [ 3.5 d2 +0.00002 d2
2 ] = 0
g10 (d1, d3) → [ 4.93 d1+0.00032 d1
2 ] − [ 2.69 d3 +0.00002 d3
2 ] = 0
Paraphrase This Document
Need a fresh take? Get an instant paraphrase of this document with our AI Paraphraser
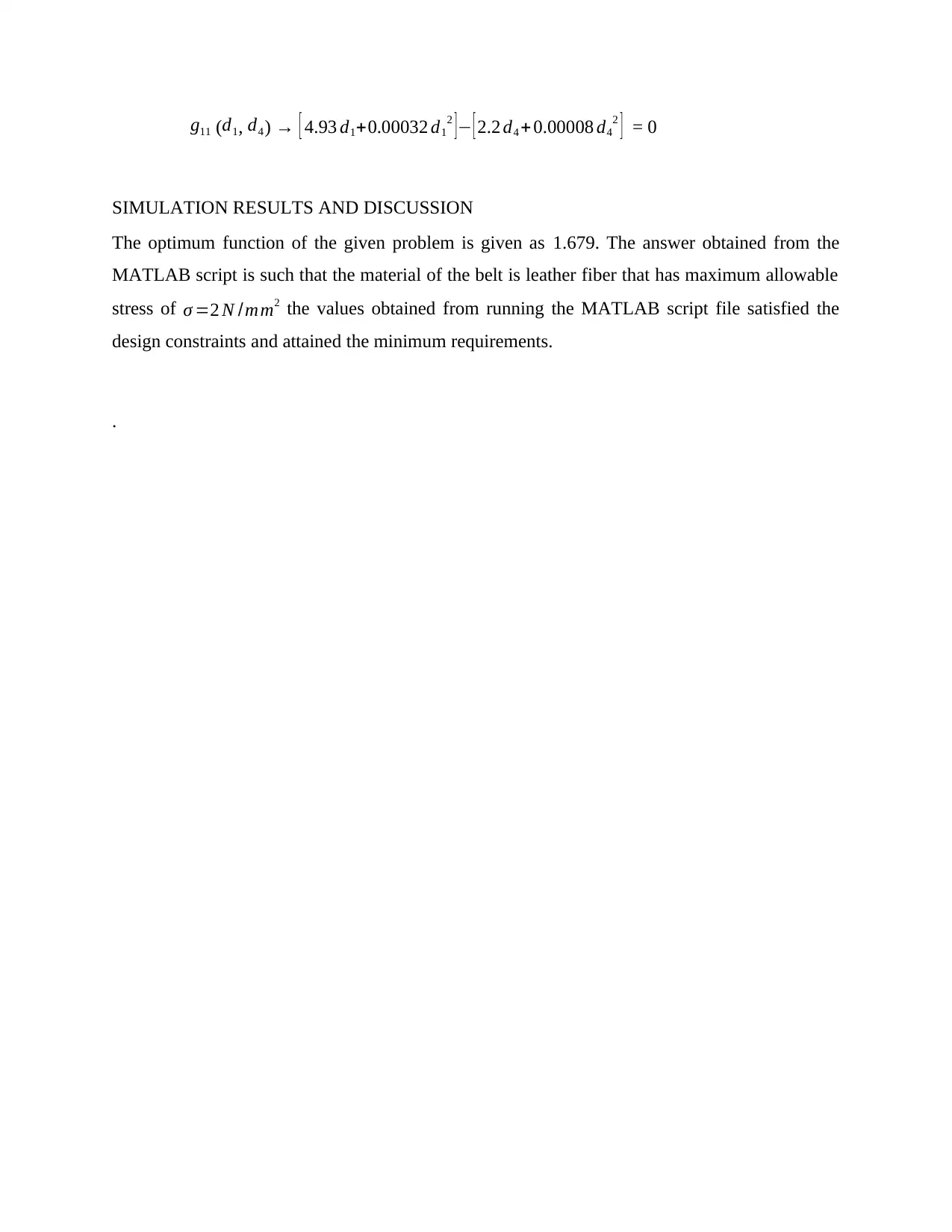
g11 (d1, d4) → [ 4.93 d1+0.00032 d1
2 ] − [ 2.2 d4 + 0.00008 d4
2 ] = 0
SIMULATION RESULTS AND DISCUSSION
The optimum function of the given problem is given as 1.679. The answer obtained from the
MATLAB script is such that the material of the belt is leather fiber that has maximum allowable
stress of σ =2 N /mm2 the values obtained from running the MATLAB script file satisfied the
design constraints and attained the minimum requirements.
.
2 ] − [ 2.2 d4 + 0.00008 d4
2 ] = 0
SIMULATION RESULTS AND DISCUSSION
The optimum function of the given problem is given as 1.679. The answer obtained from the
MATLAB script is such that the material of the belt is leather fiber that has maximum allowable
stress of σ =2 N /mm2 the values obtained from running the MATLAB script file satisfied the
design constraints and attained the minimum requirements.
.
1 out of 8

Your All-in-One AI-Powered Toolkit for Academic Success.
+13062052269
info@desklib.com
Available 24*7 on WhatsApp / Email
Unlock your academic potential
© 2024 | Zucol Services PVT LTD | All rights reserved.