Occupational Health and Safety Management: Key Elements
VerifiedAdded on 2019/09/30

Q.1. Depending on the workplace or environment where the operation is carried out, there are a
number of health and safety risks take place. Some of the common risks are-
Risk with electricity- skin burn, shocks, disability
Asbestos- Lungs failure on inhaling, mesothelioma (a type of cancer)
Fire- skin burn, disability of person
Gas- Suffocation, air borne diseases, eye irritation etc.
Noise- Permanent hearing loss, neurological disorder etc.
Hazardous substances- Cancer, dermatitis and asthma
Bullying- Depression, anxiety, loneliness etc.
Working in confined space- breathe out, sensory damage, skin diseases etc.
Q.2. Occupational Health and Safety Management is essentially put into practice in organizations
which will lead the organization to be a safe and healthy workplace. Workplace Health and
Safety (WHS) Act.2011 acts as a regulatory framework for this management system. Here are
some key areas-
Incident notification
Consultation with workers.
Issue resolutions
Inspector powers and functions
Offences and Penalties
This Act covers workers or employees in a wider spectrum which includes- employees,
contractors, subcontractors, outworkers, apprentices and trainees, work experience students,
volunteers and employers who perform work. Now a days, this Act is covering protection for
general public. A person conducting business must get certificate of OHS under this act.
Q.3. Obligations for Health and Safety requirements at workplace-
If I am an employer then-
Examine workplace conditions to make sure as per OSHA standard.
Paraphrase This Document

hazardous things.
Employees and workers are given safety training program.
Provision is made for medical examination and emergency situation.
Inspection and recording of injuries and accidents are reported.
If I am an employee/worker-
Take care of own health and safety.
Take reasonable care for health and safety of others who may be affected by their acts or
negligence.
Cooperate with anything that come under OHS requirement with employer.
Don’t misuse or interfere provided under OHS.
Q.4. Advisory standards requirements-
Asbestos advisory standard-
Create asbestos register to record asbestos presence at workplace.
Provide access to asbestos register to those who engaged to remove asbestos.
Inform contractor before entering workplace.
Control the risk.
Concrete Pumping Supplement-
Reasonable practice has applied at workplace to follow OHS under its duty to exercise due
diligence.
Consultation with workers
Consulting, coordinating and cooperating activities with other duty holders.
Training and supervision at work.
Risk management
Falling object advisory standard-
Adequate protection is provided to minimise risk of falling.
Use of isolation \at workplace.
Training and subversion of workers.

Q.5. Key elements in best practices of OHS Planning-
Establishment of protocols and distributed up-to date documents for health and safety
information across organization.
Safety inspection check-list
Risk assessment is done periodically.
Emergency response services
Training program for Health and Safety measures to all workers.
Internal safety audit
Compliance with OHS guidelines
Measurable performance matrix for health and safety
Regular meeting and communication strategy where various risks and hazardous situation is
addressed.
Q.6. Key elements within OHS Management System-
Safety plan- It is a strategic action plan where management analyses current and future risk
and hazards in relation to health and safety that can be managed and controlled over next
calendar period.
Policies, procedures and processes- It is the code of conduct for OHS in organization. It
includes, safety behaviour, expectations, incident reporting and record keeping.
Training and induction- Everyone goes through this process whether he/she is exposed to
low or high risk. Intensity of training differs according to level of risk.
Monitoring, supervision and reporting- overviewing the OHS program effectiveness,
watching personnel whether they are following OHS guidelines or not and finally reporting
is done to make necessary changes in behaviour or people or in OHS program.
Q.7. Roles and responsibility of Health and Safety Officer-
Inspection of site to ensure workers are working in a hazard free environment.
Enhancement of safety behaviour by representing project safety council.
Verify accidents and injuries log report and submit to government agencies.
Verify all tools and equipment are safe to use.
⊘ This is a preview!⊘
Do you want full access?
Subscribe today to unlock all pages.

Trusted by 1+ million students worldwide

Trains and carries drill in case of emergency situation like fire breakout.
Conduct job hazard analysis.
Q.8. Legislative requirements for OHS audit
Auditor’s requirement- He is required to have WHS management system training,
qualification and relevant work experience.
Audit program- This program is normally prepared with a 3 year cycle outlines according
to WHS verification audit schedule.
Audit methodology- It should involve the date and scope of audit, meeting with
management and key personnel, audit conducted interviews and records, closer meeting
and detailing drafting of report.
Reporting of results- The report will go to WHS committee who will give confirmation of
OHS standard.
Corrective action plan- If any deficiency is there in audit, here it will be rectified.
Review and evaluation- Every period, the OHS guidelines would be complied with
organizational guidelines.
Q.9. Types of documentation required in determining potential risk-
Observation by H&S Officer
Material Safety Data Sheet.
Hazard and risk survey report
Record of accidents and injuries
Legislative requirements under OHS standard
System failure reporting
Health report of workers.
Training report on OHS.
Policies, procedures and guidelines for OHS.
Q.10. It is the Occupational Health and Safety Officer and Medical representative in the
organization who will help in OHS inspection and risk analysis. At first, the Health and Safety
committee will do health and safety hazard identification analysis where they will find the type
Paraphrase This Document

i.e. what type of hazard will be conducted by OHS officer. The intensity of hazard is measured
by the OHS committee after preliminary report submission by OHS Officer. Finally, the risk
analysis and further actions will be done by the committee itself with OHS Officer and
sometimes help from government or medical representatives are taken.
Q.11. Key consideration while conducting workplace safety inspection-
At first listen to the concerns of workers and their representatives.
Analyse the workplace hazards and incident reporting
Identifying the potential hazards and the causes that are responsible for such hazards.
Reviewing effectiveness of previously implemented hazard control.
Inspection schedule will be prepared prior to inspection conduct.
The inspector will check the frequency of inspection to adjust schedule.
Before inspection starts, an inspection team will be formed where alongside the inspector
a local manager or supervisor or worker representative will be there.
Inspection checklist will be prepared.
Whenever the inspection is done, the inspector will tick the point in checklist to ensure
all stages are gone through.
Q.12. Contents of inspection report-
Details about the contractor and his roles and responsibility for OHS.
Project details
Confidentiality and distribution details alongside internal health auditor details.
Administrative requirements in OHS.
Training, risk management and other general requirements
Safe work method statement
Work environment safety
Falling objects and public protection
Falls
Ladders and platform supported by ladders
Scaffolding
Demolition

Electrical
Hazardous substances and dangerous goods
Asbestos management
General traffic management
Manual task
Noise and other hazardous risks.
Q13. Consultation regarding OHS compliance issues and statutory requirements-
This type of action takes place when the existing OHS policies and procedures don’t fulfil the
requirements. In this case, consultation is done with workers and other duty holders at the
workplace. The WHS Act.2011 requires that where more than one person has a duty of same
matter, each person has the responsibility for their duty and they must discharge their duty to that
extent which he/she can control or influence. The Act. Also says that each duty holder will share
information in a timely manner to meet health and safety obligation. Overall, any health and
safety issue is addressed at worker level first, then it goes to the H&S Officer who further reports
to OHS committee. They do evaluation and revision in OHS guidelines take place. In any
statutory case, reference is taken from representatives of OHS at government level.
Q.14. Control measures goes in this way-
After risk assessment is done, OHS committee decide what are the hazards, the level of
hazards, how likely to happen, frequency of happening, who will face, skill, experience
and knowledge of people about hazard facing and working condition.- Identification
Implementation- 1. Design or reorganize materials, machines or work system to eliminate
hazards 2. Removal of hazard substances if possible 3. Isolate the hazard 4. Minimise
through engineering control 5. Minimise risk through administrative control 6. PPE
implementation.
Review- Risk assessment checklist is carried and then the checklist is evaluated by the
OHS Committee to bring further changes.
Q15. Examples of OHS Communication Strategy-
⊘ This is a preview!⊘
Do you want full access?
Subscribe today to unlock all pages.

Trusted by 1+ million students worldwide
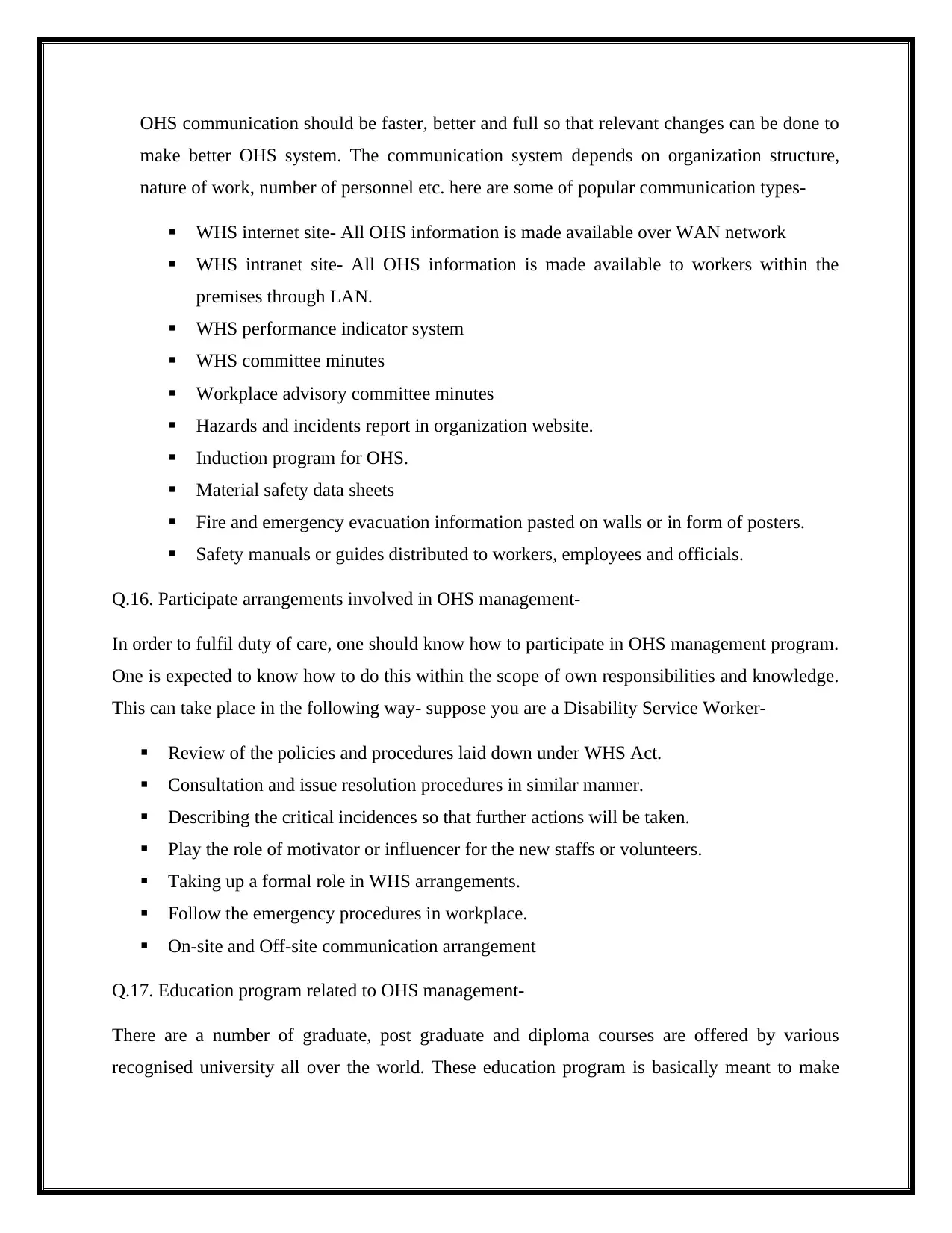
make better OHS system. The communication system depends on organization structure,
nature of work, number of personnel etc. here are some of popular communication types-
WHS internet site- All OHS information is made available over WAN network
WHS intranet site- All OHS information is made available to workers within the
premises through LAN.
WHS performance indicator system
WHS committee minutes
Workplace advisory committee minutes
Hazards and incidents report in organization website.
Induction program for OHS.
Material safety data sheets
Fire and emergency evacuation information pasted on walls or in form of posters.
Safety manuals or guides distributed to workers, employees and officials.
Q.16. Participate arrangements involved in OHS management-
In order to fulfil duty of care, one should know how to participate in OHS management program.
One is expected to know how to do this within the scope of own responsibilities and knowledge.
This can take place in the following way- suppose you are a Disability Service Worker-
Review of the policies and procedures laid down under WHS Act.
Consultation and issue resolution procedures in similar manner.
Describing the critical incidences so that further actions will be taken.
Play the role of motivator or influencer for the new staffs or volunteers.
Taking up a formal role in WHS arrangements.
Follow the emergency procedures in workplace.
On-site and Off-site communication arrangement
Q.17. Education program related to OHS management-
There are a number of graduate, post graduate and diploma courses are offered by various
recognised university all over the world. These education program is basically meant to make
Paraphrase This Document

manner is the main motive of the course. Such programs teach us-
1. Basic theory of Occupational Health and Safety
2. Rules, regulation, procedures and compliances relating to WHS.
3. Quality improvement
4. Fire prevention
5. Environmental Toxicology
6. Waste management
7. Industry Hygiene
8. Health and Safety Communication strategy
9. Safety engineering
Q.18. 6 places on building sites where edge protection is required-
Roof area working- Most of the worker falls due to lack of safety protection from this
area.
Casting, erecting and striking level of workers while working on storeys.
On ladders- Any casualty on this part can lead to death of worker if the ladder is of 15-
20ft high.
Cranes- When worker is there to colour whole building or use cement on walls, they sit
on these cranes to do so in case where ladder can’t reach. Such cranes must be provided
edge protection so that they won’t fall down.
Excavation- When some digging work is going on, worker may fall in hole if no edge
protection has given.
Timber framed building- To support the structure, sometimes this timber framed is given
and workers tend to climb such timber to do finishing work. There too edge protection is
needed.
Q.19. Duty of care-
Each person has duty to ensure their action or failure to take action doesn’t harm any other
person. This becomes a part of OHS responsibilities for both employer and workforce. It is the

workforce to follow OHS standard guidelines while in work.
This “Duty of Care” can be understood with a simple example. Suppose, You are an employer,
so your duty of care towards employee will be-
Any risk to their health and safety
The procedures that are in place ensuring no harm and injuries to workers.
Instructions and PPE provided to workers.
Q.20. A code of practice can’t be used as evidence in prosecutions under this act is correct.
Part-2 – Conduct an onsite OHS inspection
Section-1- Management Responsibility
Sub-section YES/NO Comment
1.1 Yes
1.2 Yes
1.3 Yes
1.4 Yes Except drilling area
1.5 Yes
1.6 Yes
1.7 Yes
1.8 No At administrative office
1.9 Yes
1.10 Yes
1.11 Yes Except on floor site
1.12 Yes
Section-2- Amenities
⊘ This is a preview!⊘
Do you want full access?
Subscribe today to unlock all pages.

Trusted by 1+ million students worldwide

2.1 Yes
2.2 Yes
2.3 Yes
2.4 Yes
2.5 Yes
2.6 No Need water facility
2.7 Yes Repairing needed
Section-3- Emergency response/First aid
Sub section Yes/No Comment
3.1 Yes
3.2 No Ointment for burning needed
3.3 Yes
3.4 Yes
3.5 Yes 15th Jan, 2018
3.6 Yes
Section-4- Traffic Management
Sub section Yes/No Comment
4.1 Yes
4.2 Yes
4.3 Yes
4.4 Yes Painting on few areas needed
Section-5- Training and Consultation
Paraphrase This Document

5.1 Yes
5.2 No At admin office
5.3 Yes
5.4 Yes
5.5 Yes
5.6 Yes
5.7 Yes
5.8 Yes
5.9 Yes
5.10 Yes
5.11 Yes
5.12 Yes
5.13 Yes
5.14 Yes
5.15 Yes
Section-6- Electrical
Sub section Yes/No Comment
6.1 Yes
6.2 Yes
6.3 Yes
6.4 Yes
6.5 Yes
6.6 Yes
6.7 No Drilling machine needs to be
replaced
Section-7- Scaffolding

7.1 Yes
7.2 Yes
7.3 Yes
7.4 Yes
7.5 No
7.6 Yes
7.7 Yes
7.8 No Generator room access is
limited
7.9 Yes
7.10 Yes
7.11 Yes
7.12 Yes
7.13 Yes
7.14 Yes
7.15 Yes
Section-8- Hazardous Materials
Sub section Yes/No Comment
8.1 Yes
8.2 Yes
8.3 Yes
8.4 Yes
8.5 Yes
8.6 Yes
8.7 No Shortage for 15 workers
Section-9- Cranes and rigging
⊘ This is a preview!⊘
Do you want full access?
Subscribe today to unlock all pages.

Trusted by 1+ million students worldwide
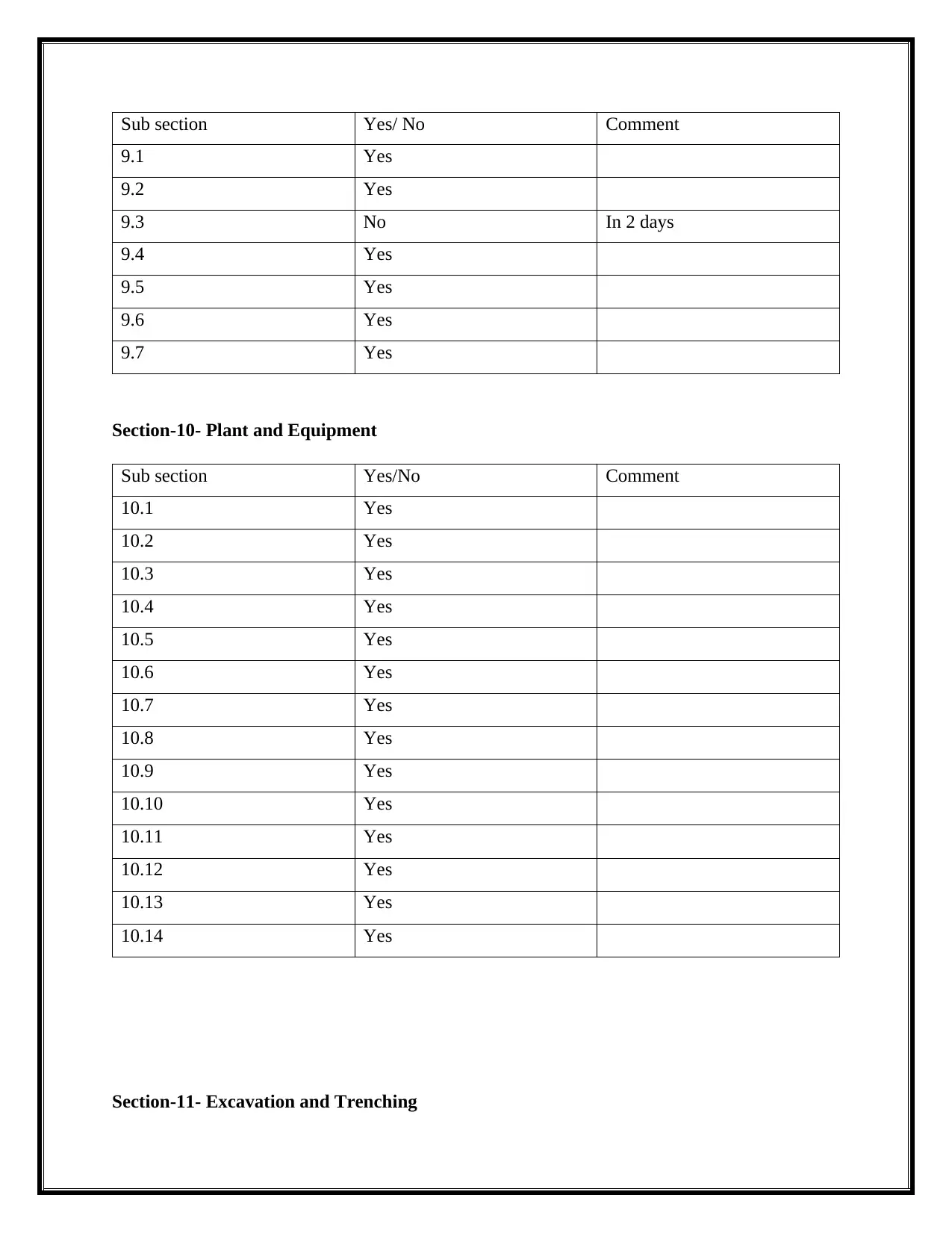
9.1 Yes
9.2 Yes
9.3 No In 2 days
9.4 Yes
9.5 Yes
9.6 Yes
9.7 Yes
Section-10- Plant and Equipment
Sub section Yes/No Comment
10.1 Yes
10.2 Yes
10.3 Yes
10.4 Yes
10.5 Yes
10.6 Yes
10.7 Yes
10.8 Yes
10.9 Yes
10.10 Yes
10.11 Yes
10.12 Yes
10.13 Yes
10.14 Yes
Section-11- Excavation and Trenching
Paraphrase This Document

11.1
11.2
11.3
11.4
11.5
11.6
11.7
11.8
11.9
11.10
11.11
Section-12- OXY-Acetylene cutting and welding
Sub section Yes/No Comment
12.1 Yes
12.2 Yes
12.3 Yes
12.4 Yes
12.5 Yes
12.6 Yes
12.7 Yes
12.8 Yes
12.9 Yes
12.10 Yes
12.11 No
Section-13- Confined Space
Sub section Yes/No Comment

13.2 Yes
13.3 Yes
13.4 Yes
Section-14- Work at Height
Sub section Yes/No Comment
14.1 Yes
14.2 Yes
14.3 Yes
14.4 Yes
14.5 Yes
14.6 Yes
14.7 Yes
Section-15- Environment
Sub section Yes/No Comment
15.1 Yes
15.2 Yes
15.3 Yes
15.4 Yes
15.5 Yes
15.6 Yes
15.7 Yes
Section-16- Personal Protective Equipment
Sub section Yes/No Comment
⊘ This is a preview!⊘
Do you want full access?
Subscribe today to unlock all pages.

Trusted by 1+ million students worldwide
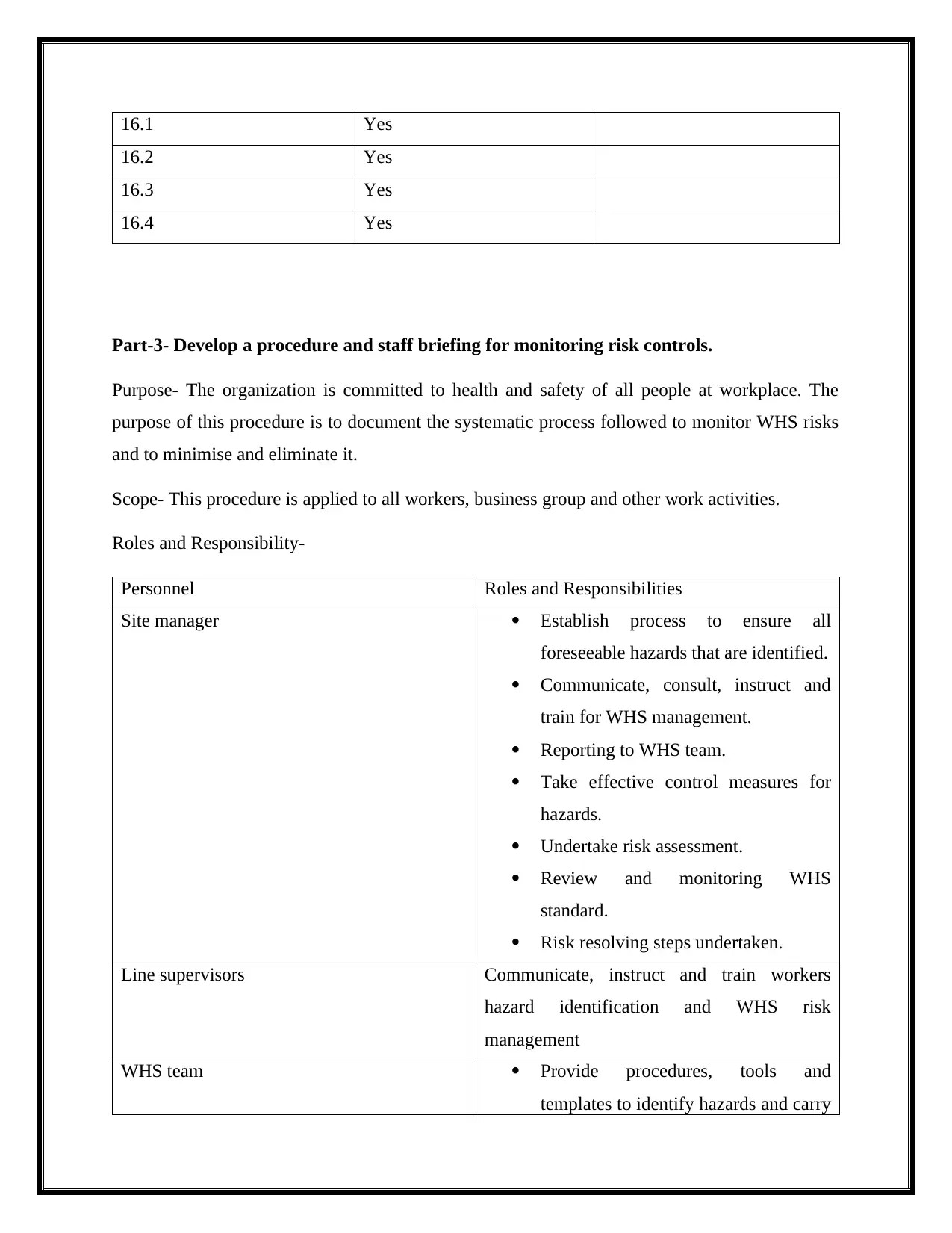
16.2 Yes
16.3 Yes
16.4 Yes
Part-3- Develop a procedure and staff briefing for monitoring risk controls.
Purpose- The organization is committed to health and safety of all people at workplace. The
purpose of this procedure is to document the systematic process followed to monitor WHS risks
and to minimise and eliminate it.
Scope- This procedure is applied to all workers, business group and other work activities.
Roles and Responsibility-
Personnel Roles and Responsibilities
Site manager Establish process to ensure all
foreseeable hazards that are identified.
Communicate, consult, instruct and
train for WHS management.
Reporting to WHS team.
Take effective control measures for
hazards.
Undertake risk assessment.
Review and monitoring WHS
standard.
Risk resolving steps undertaken.
Line supervisors Communicate, instruct and train workers
hazard identification and WHS risk
management
WHS team Provide procedures, tools and
templates to identify hazards and carry
Paraphrase This Document

Advice to hazard identification, risk
management and effective control
Report of hazards and risk assessment
to stakeholders.
Monitoring workplace risk assessment
Provide support for implication of
procedures
Workers Proactively identify and report
hazards.
Undertake risk assessments and
implement procedures
Stop or refuse to work in risky
environment.
Procedures followed-
Step-1- Hazard Identification
At first, immediate action is taken by the worker before any planning and controlling measures.
A worker will-
Notify others in worksite
Will take actions to eliminate hazards immediately so far it is practicable and safe to do
Not possible to eliminate then, preventive measures will be taken.
Reporting is done to immediate supervisor.
Further reporting is done to WHS centre in the worksite through emergency phone call.
Line supervisor will inspect the area and will take necessary information and feedback which he
will report to the WHS team for further action. Then WHS team will inspect the worksite. The
whole actions will be recorded in data sheet and it is uploaded in computer database.
Step-2- Risk Assessment

prescribed by the organization and WHS guide. The following actions will be taken-
Identify the consequences of hazards
Identify the likelihood of hazard
Rate of inherent risk.
Step-3- Control risk
The following order is followed to control risk-
Eliminate risk completely
If not possible to eliminate, then minimise the risk with something that gives lesser risk.
Isolate the hazard from the person who is exposed to.
Implementing engineering control.
How to ensure effective risk control-
Each control is assigned with responsibility within timeframe and agreed on it
implementation.
For necessary implementation of control, utilize existing capital works and maintenance
process.
Safe work procedures and instruction reviewed.
Communication, consultation, training and supervision for WHS. Control.
Monitoring of activity.
Set-4- Risk Assessment with control measure
In this case, risk rating is done and how the risk will be addressed are placed in WHS risk matrix.
For ex- Suppose there is an extreme risk situation, the control measure approval in this case will
be given by CEO or Board. What actions are to be done?- 1. No worker should take any action
before reporting is done to CEO or Board. 2. The person will notify WHS team either through
emergency helpline or meeting personally.
Step-5- Monitor and Review Control Measures
⊘ This is a preview!⊘
Do you want full access?
Subscribe today to unlock all pages.

Trusted by 1+ million students worldwide

situation-
Control measure is insufficient
Notifiable incident occur
New hazard identified
If Health and Safety Representative requests review.
Documents for procedure- Workplace and operation site specific activities list, project risks
register, contractor templates and data sheet, training report, monitoring and audit reports.
Recording- All documents are retained, archived and disposed in accordance OHSA standard.
Overall, records are kept both in manual and electronic forms. Manual reports are kept in locker
and digital reports and datasheets are stored in a secured cloud network.
Part-4- 3 Risk Control Adjustments
From our analysis, we come to know that there is a shortage of 15-20 anti-dust and paint
respirator masks and glass goggles for the workers at site. At present, there are 56 workers who
are engaged in painting and smoothening the wall of a building site. The contractor provided 33
masks and goggles to worker and rest are wearing disposable masks and normal black goggles to
carry out the work.
The factors this suggested action may be not so effective-
The place where the construction is going on has faced virus attack to locals which
caused fever, cold, measles etc. This current disposable mask is not enough to protect
dust.
Existence of toluene, xylene and methylene chloride are causing breathing problem to 5-
6 workers in recent past despite wearing the disposable masks.
Excessive dust is causing irritation to eyes causing redness and itching despite wearing
normal sun glasses.
There is no compromise or neglecting for health and safety matter. So until, workers are
provided adequate PPE, it won’t help to overcome the issues. For the time being, they were
instructed to wear black goggles and disposable masks to minimise risk of biological attack and
Paraphrase This Document

adequate PPE are facing health issues. This is an alarming situation and can be categorised as
medium category risk.
What are the steps now needed to be taken?
Preliminary step- At first, the workers who are not given the right PPE will be kept out of the
work until risk assessment is done. Instructions will be given to workers to wear anti-dust and
paint respirator mask.
Risk Assessment- At first, Contractor will collect the information about how many workers have
been going through health issues? He will keep it recorded in hazard identification register. This
will be informed to WHS team for further evaluation.
Risk Matrix- The WHS team will put the symptoms and problems of the workers into the risk
matrix so that intensity of risk will be identified. This will be reported to the concerned party
who will give approval to take action.
Bring Adequate PPE- All workers who are doing this task will be provided anti-dust and paint
respiratory mask so that complete elimination of gas or virus risk at work site can be done.
Review- At every 5 days interval, health inspection will be done for workers so that whether
improvement has made or not can be identified.
Part-1- Develop Safe Working Method Statement
To measure the Health and Safety case in working method, I have selected electrical work as
the case under study.
Safe Working Method Statement or SWMS is a statement that enables supervisors, workers and
any other persons at workplace. It makes them understand the requirements that have been
established to carry out high risk electrical work in a safe and healthy manner. It sets out the
work activities in a logical sequence and identify hazards relating to it and how control measures
can be taken to minimize or eliminate hazard.
For the purpose explaining the statement, here I am going to take 3 high risk tasks in electrical
works.

2. Fit-off electrical equipment
3. Testing and Commissioning of system
Task steps Involvement, Hazard and control measures – Electrical testing
One of the important rule or truth that human being is needed to understand that our body is an
electric conductor and if current passes above a certain voltage, then it can harm human being.
Thus, while conducting electrical task, the risk of injury or harm is extremely high. Here are the
list of tasks under electrical works that can lead to these hazardous situation-
Tasks steps under Electric
works
Hazard situation Control measures
Conduct/Confirm workplace
risk assessment HRA and
secured area
Electric shocks Test before you touch
Identify the suitability of
work process, inspection of
are and potential hazard
identification, identification
of characteristics of task
and person appointed for
that
Plan and ensure coordination Unscheduled disruption Notify power disruption,
consult the person with
management, worker and
other trade areas.
Requirement of safety
observer
Electric shocks Required if it is a serious
level of risk exposure like
high voltage shocks.
Select tools, test equipment
and PPE
Cuts, Abrasions and Shocks Well maintained, suitably
rated, checked and tested
⊘ This is a preview!⊘
Do you want full access?
Subscribe today to unlock all pages.

Trusted by 1+ million students worldwide

property.
Fit off Electrical Equipment
Tasks Hazards Control measures
While fit off of an article Consultation with employees
Drilling of materials for fit
off
Electric shock, cutting of
arm, legs, broken ribs, hands
and legs, disability and
extreme case death
Fit off of equipment only
after permission and planning
process.
Working at height to fit off Wearing of PPE while fit off
work is going on
Manual handling of objects Use of standard and tested fit
off equipment which are
passed by safety supervisors
Absence of PPE while fit off Ergonomics to handle and
carry fit off equipment
While monitoring fit off work Carrying risk matrix and
descriptors
Live electrical working-
Tasks Hazards Control measure
While working with live
electrical equipment
Electric shocks, burns,
disability
Need of control and
supervision of authorised
person.
The equipment on which live
testing is to be done is safe to
work on.
Adequate safeguard has
taken.
Working with voltage issues Electric shocks Supervisory arrangements are
Related Documents

Your All-in-One AI-Powered Toolkit for Academic Success.
+13062052269
info@desklib.com
Available 24*7 on WhatsApp / Email
© 2024 | Zucol Services PVT LTD | All rights reserved.