Occupational Health and Safety
VerifiedAdded on 2023/03/30
|16
|2515
|94
AI Summary
This report discusses occupational health and safety, specifically ergonomic hazards at the workplace. It explains the impact of these hazards and provides strategies to mitigate risks. The report also includes a management plan and emergency response for a safer workplace.
Contribute Materials
Your contribution can guide someone’s learning journey. Share your
documents today.
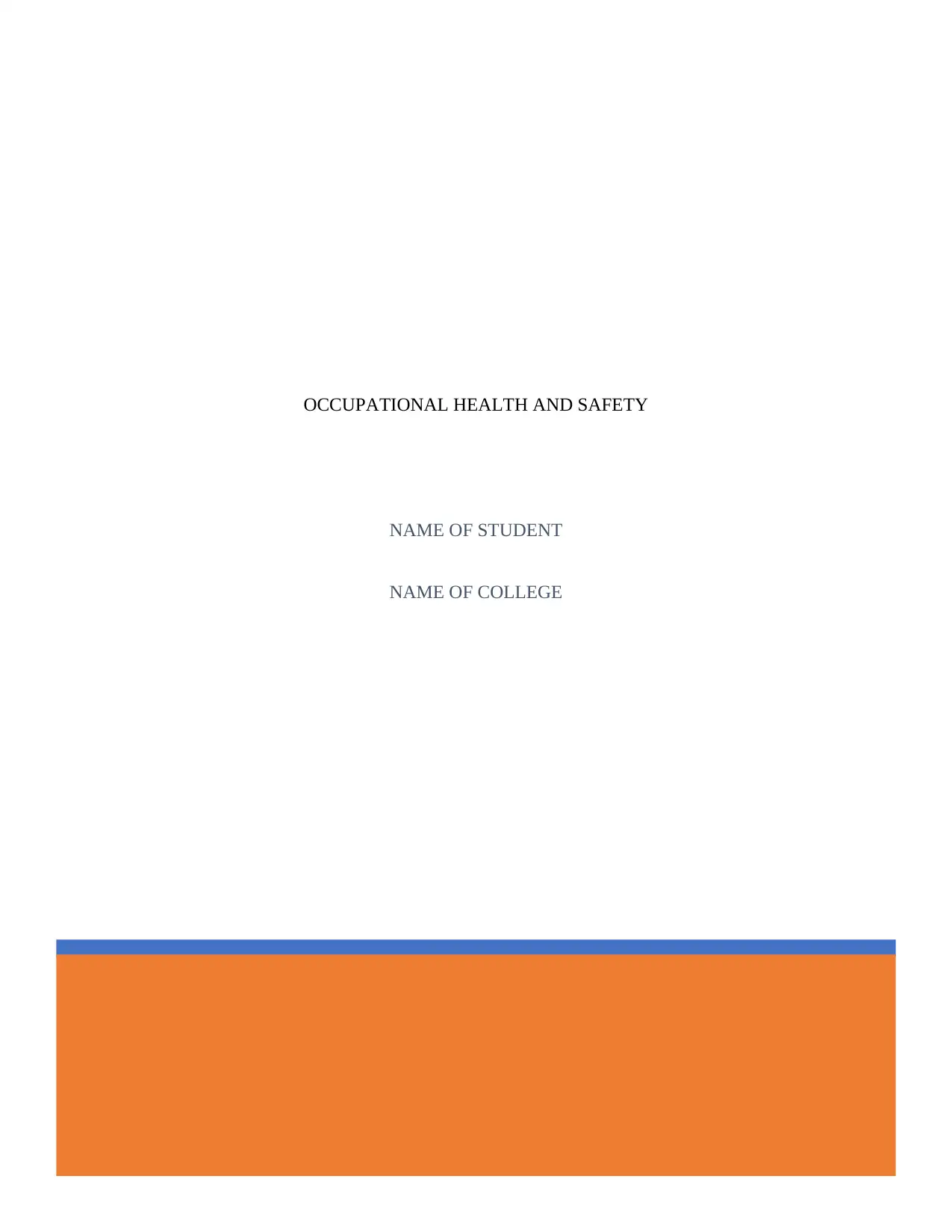
OCCUPATIONAL HEALTH AND SAFETY
NAME OF STUDENT
NAME OF COLLEGE
NAME OF STUDENT
NAME OF COLLEGE
Secure Best Marks with AI Grader
Need help grading? Try our AI Grader for instant feedback on your assignments.
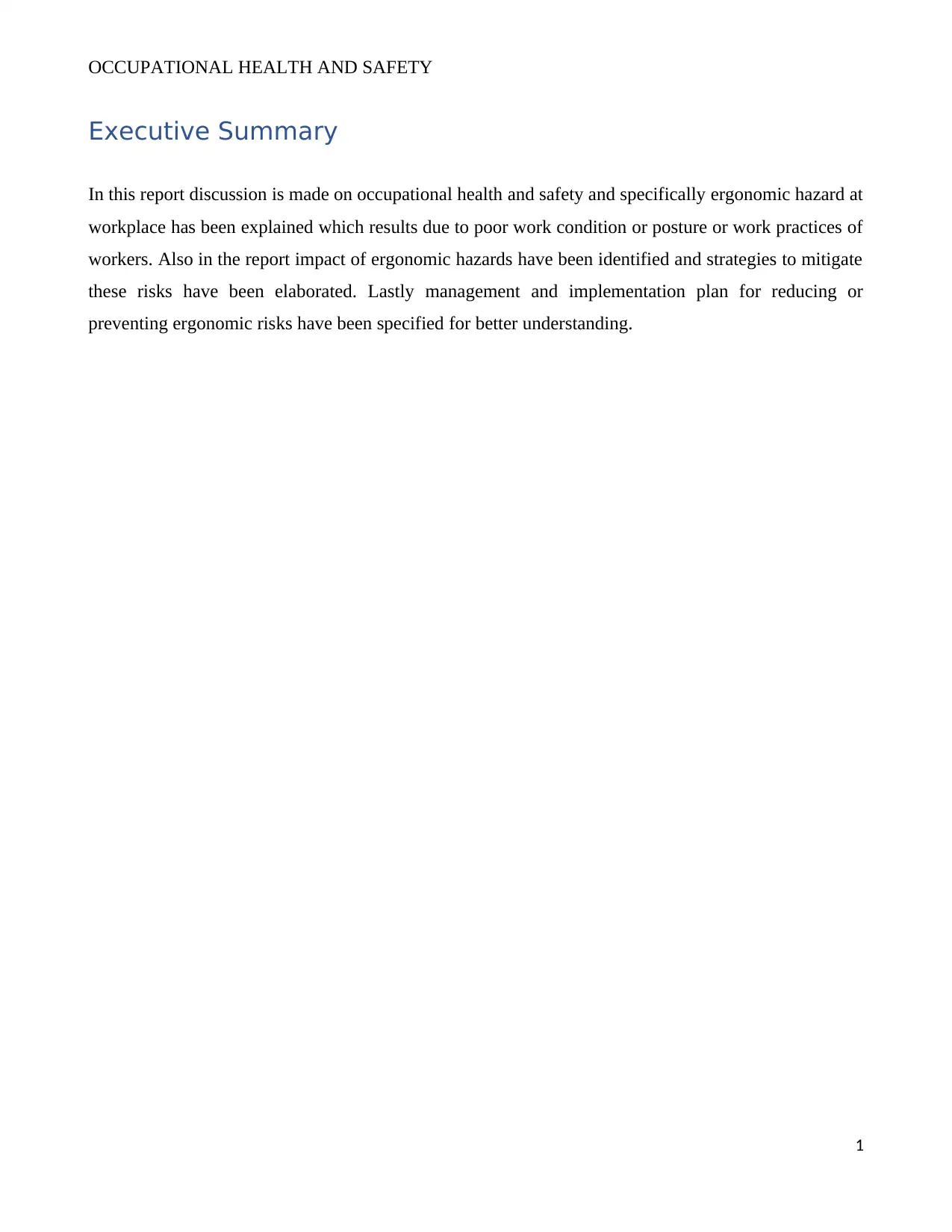
OCCUPATIONAL HEALTH AND SAFETY
Executive Summary
In this report discussion is made on occupational health and safety and specifically ergonomic hazard at
workplace has been explained which results due to poor work condition or posture or work practices of
workers. Also in the report impact of ergonomic hazards have been identified and strategies to mitigate
these risks have been elaborated. Lastly management and implementation plan for reducing or
preventing ergonomic risks have been specified for better understanding.
1
Executive Summary
In this report discussion is made on occupational health and safety and specifically ergonomic hazard at
workplace has been explained which results due to poor work condition or posture or work practices of
workers. Also in the report impact of ergonomic hazards have been identified and strategies to mitigate
these risks have been elaborated. Lastly management and implementation plan for reducing or
preventing ergonomic risks have been specified for better understanding.
1
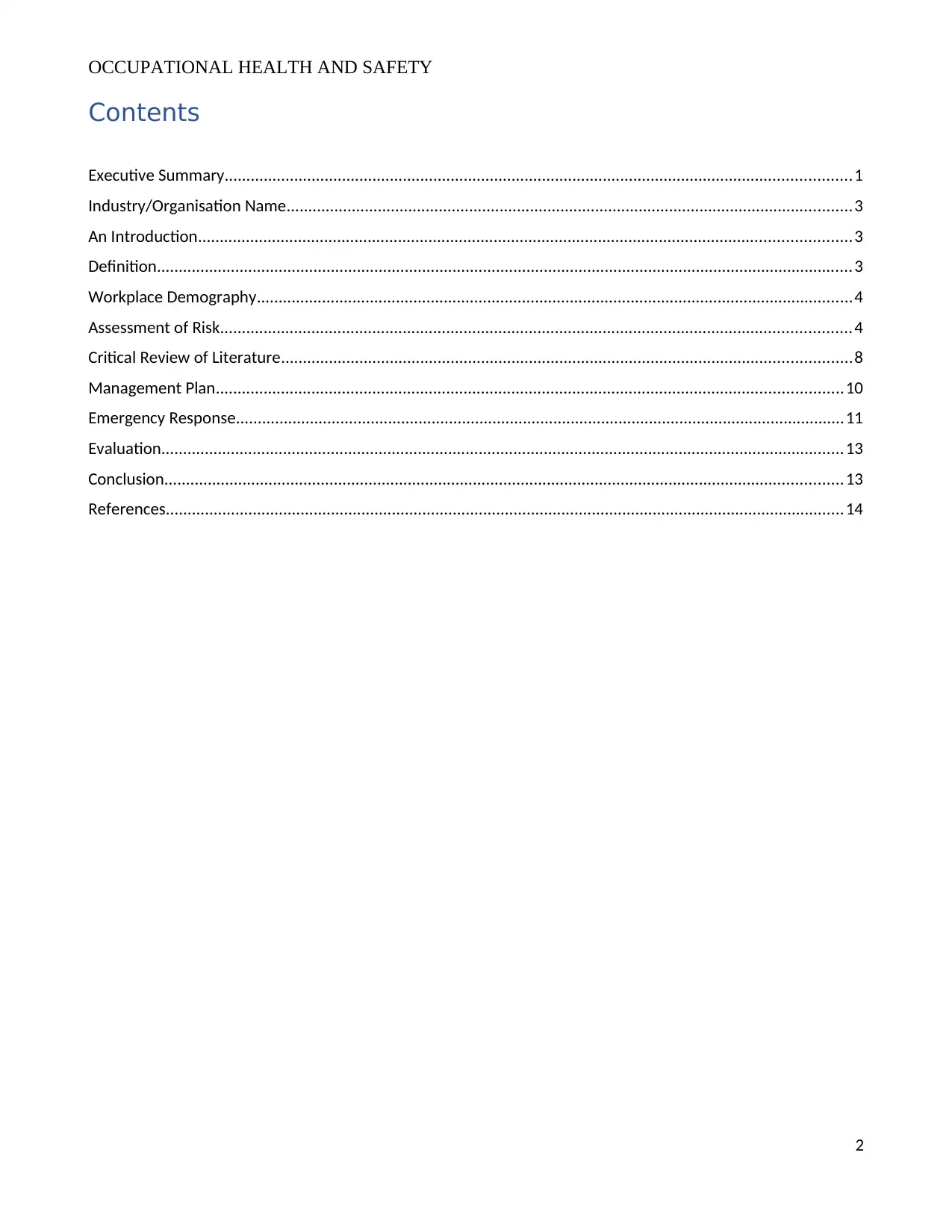
OCCUPATIONAL HEALTH AND SAFETY
Contents
Executive Summary................................................................................................................................................1
Industry/Organisation Name..................................................................................................................................3
An Introduction......................................................................................................................................................3
Definition................................................................................................................................................................3
Workplace Demography.........................................................................................................................................4
Assessment of Risk.................................................................................................................................................4
Critical Review of Literature...................................................................................................................................8
Management Plan................................................................................................................................................10
Emergency Response............................................................................................................................................11
Evaluation.............................................................................................................................................................13
Conclusion............................................................................................................................................................13
References............................................................................................................................................................14
2
Contents
Executive Summary................................................................................................................................................1
Industry/Organisation Name..................................................................................................................................3
An Introduction......................................................................................................................................................3
Definition................................................................................................................................................................3
Workplace Demography.........................................................................................................................................4
Assessment of Risk.................................................................................................................................................4
Critical Review of Literature...................................................................................................................................8
Management Plan................................................................................................................................................10
Emergency Response............................................................................................................................................11
Evaluation.............................................................................................................................................................13
Conclusion............................................................................................................................................................13
References............................................................................................................................................................14
2
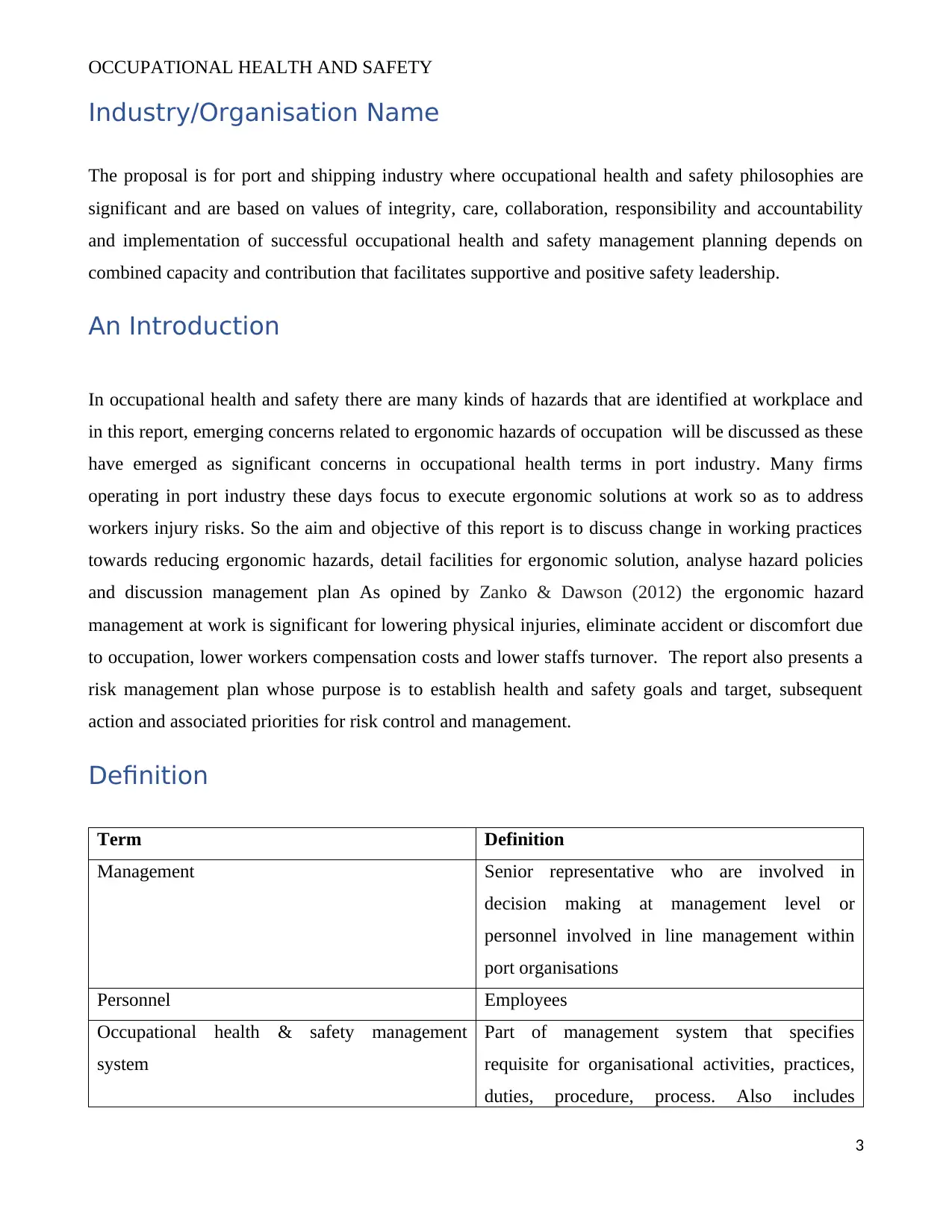
OCCUPATIONAL HEALTH AND SAFETY
Industry/Organisation Name
The proposal is for port and shipping industry where occupational health and safety philosophies are
significant and are based on values of integrity, care, collaboration, responsibility and accountability
and implementation of successful occupational health and safety management planning depends on
combined capacity and contribution that facilitates supportive and positive safety leadership.
An Introduction
In occupational health and safety there are many kinds of hazards that are identified at workplace and
in this report, emerging concerns related to ergonomic hazards of occupation will be discussed as these
have emerged as significant concerns in occupational health terms in port industry. Many firms
operating in port industry these days focus to execute ergonomic solutions at work so as to address
workers injury risks. So the aim and objective of this report is to discuss change in working practices
towards reducing ergonomic hazards, detail facilities for ergonomic solution, analyse hazard policies
and discussion management plan As opined by Zanko & Dawson (2012) the ergonomic hazard
management at work is significant for lowering physical injuries, eliminate accident or discomfort due
to occupation, lower workers compensation costs and lower staffs turnover. The report also presents a
risk management plan whose purpose is to establish health and safety goals and target, subsequent
action and associated priorities for risk control and management.
Definition
Term Definition
Management Senior representative who are involved in
decision making at management level or
personnel involved in line management within
port organisations
Personnel Employees
Occupational health & safety management
system
Part of management system that specifies
requisite for organisational activities, practices,
duties, procedure, process. Also includes
3
Industry/Organisation Name
The proposal is for port and shipping industry where occupational health and safety philosophies are
significant and are based on values of integrity, care, collaboration, responsibility and accountability
and implementation of successful occupational health and safety management planning depends on
combined capacity and contribution that facilitates supportive and positive safety leadership.
An Introduction
In occupational health and safety there are many kinds of hazards that are identified at workplace and
in this report, emerging concerns related to ergonomic hazards of occupation will be discussed as these
have emerged as significant concerns in occupational health terms in port industry. Many firms
operating in port industry these days focus to execute ergonomic solutions at work so as to address
workers injury risks. So the aim and objective of this report is to discuss change in working practices
towards reducing ergonomic hazards, detail facilities for ergonomic solution, analyse hazard policies
and discussion management plan As opined by Zanko & Dawson (2012) the ergonomic hazard
management at work is significant for lowering physical injuries, eliminate accident or discomfort due
to occupation, lower workers compensation costs and lower staffs turnover. The report also presents a
risk management plan whose purpose is to establish health and safety goals and target, subsequent
action and associated priorities for risk control and management.
Definition
Term Definition
Management Senior representative who are involved in
decision making at management level or
personnel involved in line management within
port organisations
Personnel Employees
Occupational health & safety management
system
Part of management system that specifies
requisite for organisational activities, practices,
duties, procedure, process. Also includes
3
Secure Best Marks with AI Grader
Need help grading? Try our AI Grader for instant feedback on your assignments.
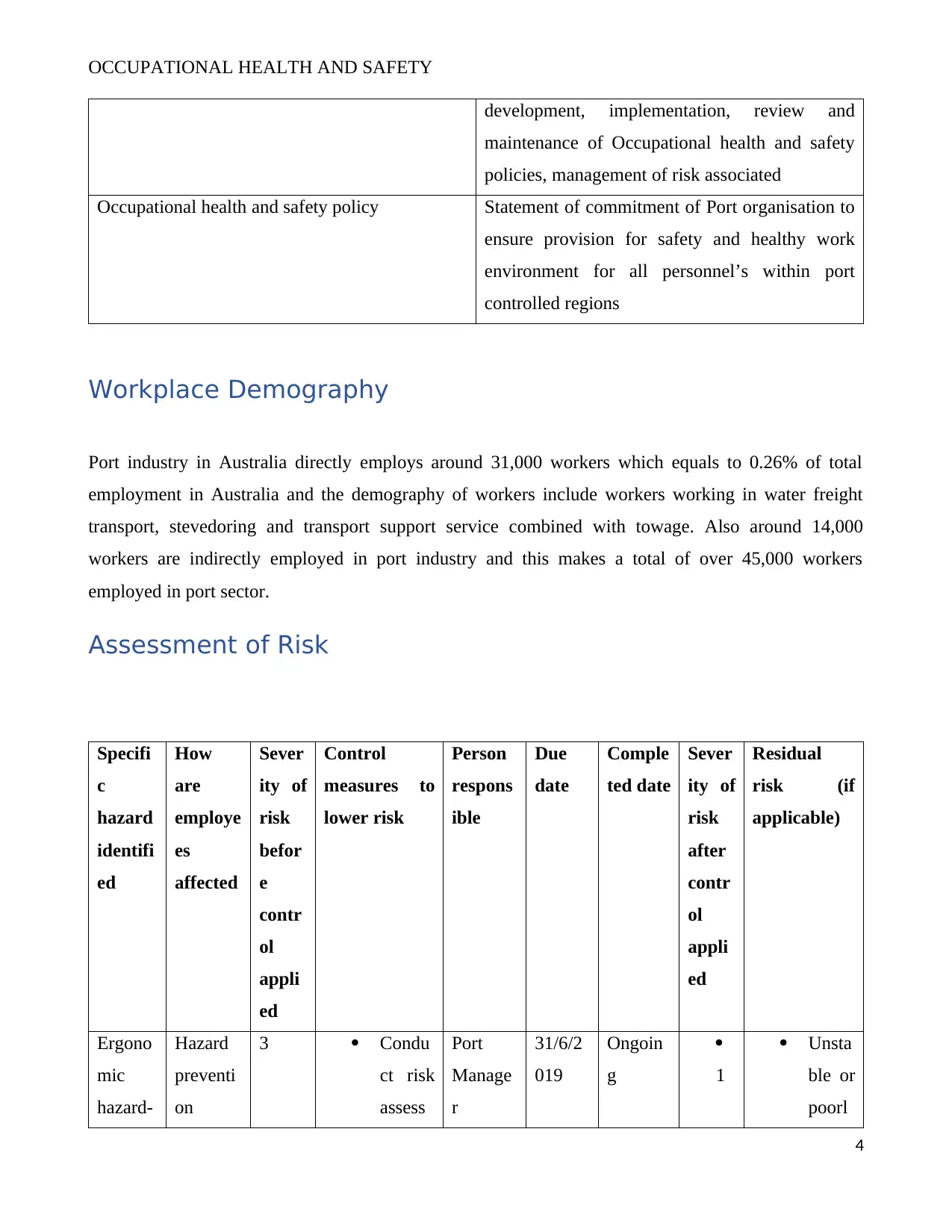
OCCUPATIONAL HEALTH AND SAFETY
development, implementation, review and
maintenance of Occupational health and safety
policies, management of risk associated
Occupational health and safety policy Statement of commitment of Port organisation to
ensure provision for safety and healthy work
environment for all personnel’s within port
controlled regions
Workplace Demography
Port industry in Australia directly employs around 31,000 workers which equals to 0.26% of total
employment in Australia and the demography of workers include workers working in water freight
transport, stevedoring and transport support service combined with towage. Also around 14,000
workers are indirectly employed in port industry and this makes a total of over 45,000 workers
employed in port sector.
Assessment of Risk
Specifi
c
hazard
identifi
ed
How
are
employe
es
affected
Sever
ity of
risk
befor
e
contr
ol
appli
ed
Control
measures to
lower risk
Person
respons
ible
Due
date
Comple
ted date
Sever
ity of
risk
after
contr
ol
appli
ed
Residual
risk (if
applicable)
Ergono
mic
hazard-
Hazard
preventi
on
3 Condu
ct risk
assess
Port
Manage
r
31/6/2
019
Ongoin
g
1
Unsta
ble or
poorl
4
development, implementation, review and
maintenance of Occupational health and safety
policies, management of risk associated
Occupational health and safety policy Statement of commitment of Port organisation to
ensure provision for safety and healthy work
environment for all personnel’s within port
controlled regions
Workplace Demography
Port industry in Australia directly employs around 31,000 workers which equals to 0.26% of total
employment in Australia and the demography of workers include workers working in water freight
transport, stevedoring and transport support service combined with towage. Also around 14,000
workers are indirectly employed in port industry and this makes a total of over 45,000 workers
employed in port sector.
Assessment of Risk
Specifi
c
hazard
identifi
ed
How
are
employe
es
affected
Sever
ity of
risk
befor
e
contr
ol
appli
ed
Control
measures to
lower risk
Person
respons
ible
Due
date
Comple
ted date
Sever
ity of
risk
after
contr
ol
appli
ed
Residual
risk (if
applicable)
Ergono
mic
hazard-
Hazard
preventi
on
3 Condu
ct risk
assess
Port
Manage
r
31/6/2
019
Ongoin
g
1
Unsta
ble or
poorl
4
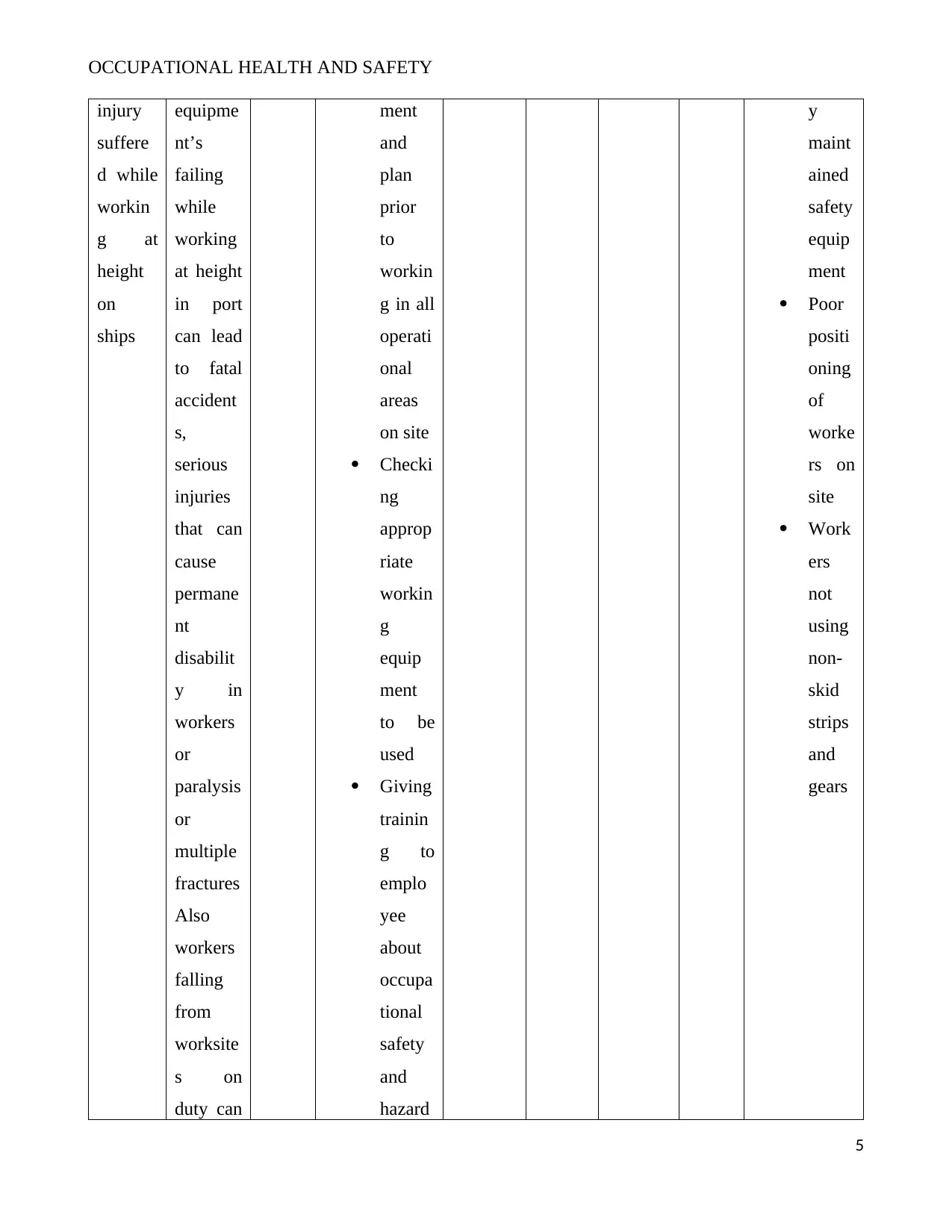
OCCUPATIONAL HEALTH AND SAFETY
injury
suffere
d while
workin
g at
height
on
ships
equipme
nt’s
failing
while
working
at height
in port
can lead
to fatal
accident
s,
serious
injuries
that can
cause
permane
nt
disabilit
y in
workers
or
paralysis
or
multiple
fractures
Also
workers
falling
from
worksite
s on
duty can
ment
and
plan
prior
to
workin
g in all
operati
onal
areas
on site
Checki
ng
approp
riate
workin
g
equip
ment
to be
used
Giving
trainin
g to
emplo
yee
about
occupa
tional
safety
and
hazard
y
maint
ained
safety
equip
ment
Poor
positi
oning
of
worke
rs on
site
Work
ers
not
using
non-
skid
strips
and
gears
5
injury
suffere
d while
workin
g at
height
on
ships
equipme
nt’s
failing
while
working
at height
in port
can lead
to fatal
accident
s,
serious
injuries
that can
cause
permane
nt
disabilit
y in
workers
or
paralysis
or
multiple
fractures
Also
workers
falling
from
worksite
s on
duty can
ment
and
plan
prior
to
workin
g in all
operati
onal
areas
on site
Checki
ng
approp
riate
workin
g
equip
ment
to be
used
Giving
trainin
g to
emplo
yee
about
occupa
tional
safety
and
hazard
y
maint
ained
safety
equip
ment
Poor
positi
oning
of
worke
rs on
site
Work
ers
not
using
non-
skid
strips
and
gears
5
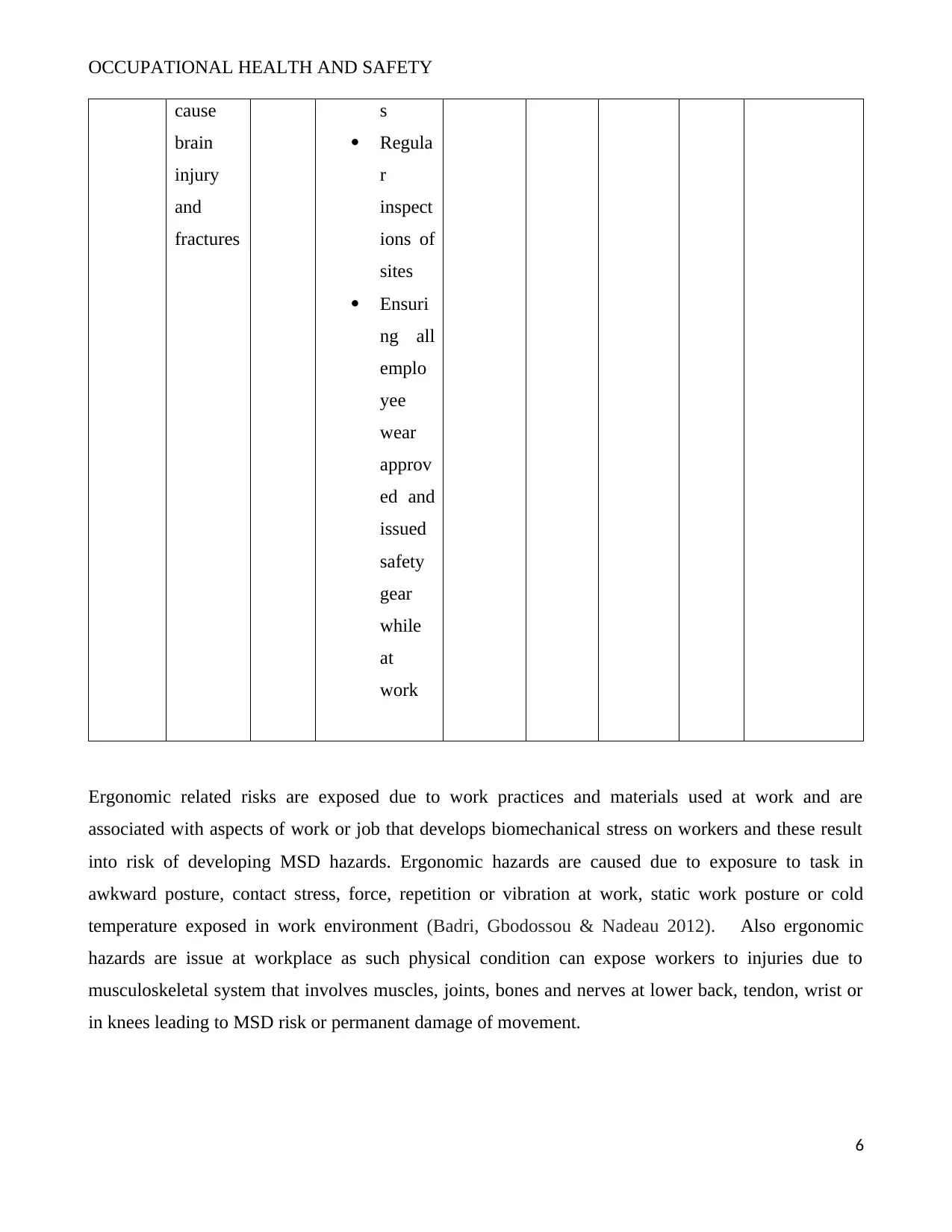
OCCUPATIONAL HEALTH AND SAFETY
cause
brain
injury
and
fractures
s
Regula
r
inspect
ions of
sites
Ensuri
ng all
emplo
yee
wear
approv
ed and
issued
safety
gear
while
at
work
Ergonomic related risks are exposed due to work practices and materials used at work and are
associated with aspects of work or job that develops biomechanical stress on workers and these result
into risk of developing MSD hazards. Ergonomic hazards are caused due to exposure to task in
awkward posture, contact stress, force, repetition or vibration at work, static work posture or cold
temperature exposed in work environment (Badri, Gbodossou & Nadeau 2012). Also ergonomic
hazards are issue at workplace as such physical condition can expose workers to injuries due to
musculoskeletal system that involves muscles, joints, bones and nerves at lower back, tendon, wrist or
in knees leading to MSD risk or permanent damage of movement.
6
cause
brain
injury
and
fractures
s
Regula
r
inspect
ions of
sites
Ensuri
ng all
emplo
yee
wear
approv
ed and
issued
safety
gear
while
at
work
Ergonomic related risks are exposed due to work practices and materials used at work and are
associated with aspects of work or job that develops biomechanical stress on workers and these result
into risk of developing MSD hazards. Ergonomic hazards are caused due to exposure to task in
awkward posture, contact stress, force, repetition or vibration at work, static work posture or cold
temperature exposed in work environment (Badri, Gbodossou & Nadeau 2012). Also ergonomic
hazards are issue at workplace as such physical condition can expose workers to injuries due to
musculoskeletal system that involves muscles, joints, bones and nerves at lower back, tendon, wrist or
in knees leading to MSD risk or permanent damage of movement.
6
Paraphrase This Document
Need a fresh take? Get an instant paraphrase of this document with our AI Paraphraser
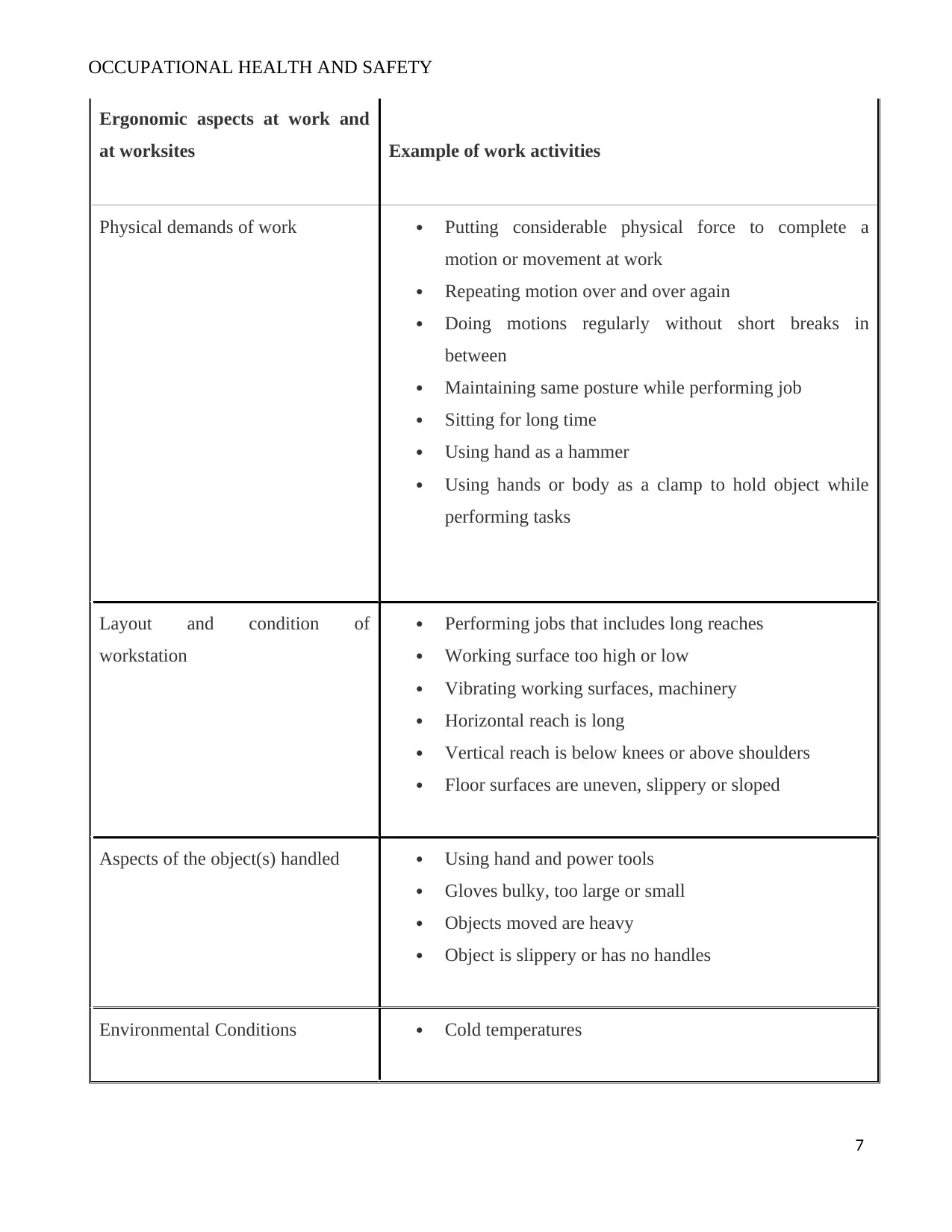
OCCUPATIONAL HEALTH AND SAFETY
Ergonomic aspects at work and
at worksites Example of work activities
Physical demands of work Putting considerable physical force to complete a
motion or movement at work
Repeating motion over and over again
Doing motions regularly without short breaks in
between
Maintaining same posture while performing job
Sitting for long time
Using hand as a hammer
Using hands or body as a clamp to hold object while
performing tasks
Layout and condition of
workstation
Performing jobs that includes long reaches
Working surface too high or low
Vibrating working surfaces, machinery
Horizontal reach is long
Vertical reach is below knees or above shoulders
Floor surfaces are uneven, slippery or sloped
Aspects of the object(s) handled Using hand and power tools
Gloves bulky, too large or small
Objects moved are heavy
Object is slippery or has no handles
Environmental Conditions Cold temperatures
7
Ergonomic aspects at work and
at worksites Example of work activities
Physical demands of work Putting considerable physical force to complete a
motion or movement at work
Repeating motion over and over again
Doing motions regularly without short breaks in
between
Maintaining same posture while performing job
Sitting for long time
Using hand as a hammer
Using hands or body as a clamp to hold object while
performing tasks
Layout and condition of
workstation
Performing jobs that includes long reaches
Working surface too high or low
Vibrating working surfaces, machinery
Horizontal reach is long
Vertical reach is below knees or above shoulders
Floor surfaces are uneven, slippery or sloped
Aspects of the object(s) handled Using hand and power tools
Gloves bulky, too large or small
Objects moved are heavy
Object is slippery or has no handles
Environmental Conditions Cold temperatures
7
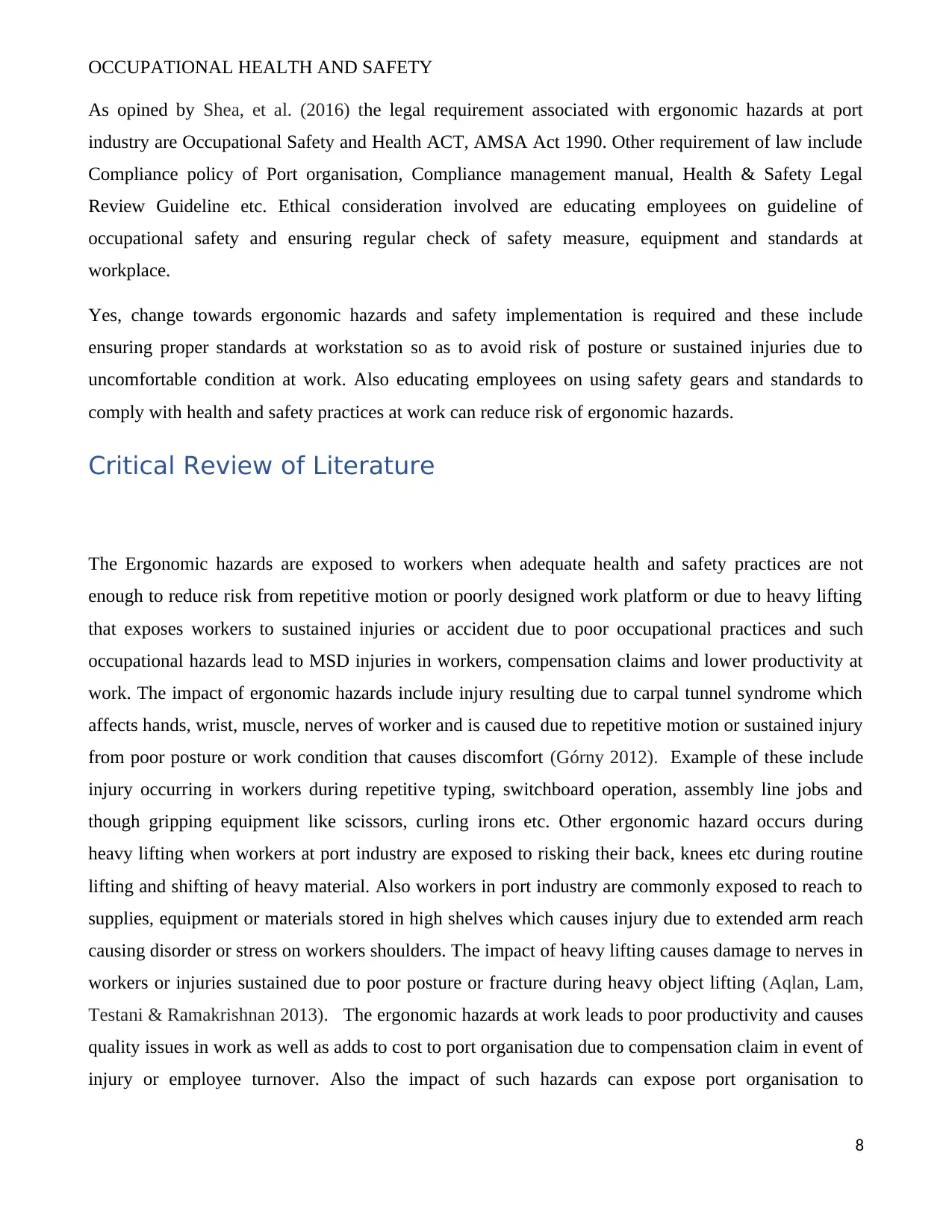
OCCUPATIONAL HEALTH AND SAFETY
As opined by Shea, et al. (2016) the legal requirement associated with ergonomic hazards at port
industry are Occupational Safety and Health ACT, AMSA Act 1990. Other requirement of law include
Compliance policy of Port organisation, Compliance management manual, Health & Safety Legal
Review Guideline etc. Ethical consideration involved are educating employees on guideline of
occupational safety and ensuring regular check of safety measure, equipment and standards at
workplace.
Yes, change towards ergonomic hazards and safety implementation is required and these include
ensuring proper standards at workstation so as to avoid risk of posture or sustained injuries due to
uncomfortable condition at work. Also educating employees on using safety gears and standards to
comply with health and safety practices at work can reduce risk of ergonomic hazards.
Critical Review of Literature
The Ergonomic hazards are exposed to workers when adequate health and safety practices are not
enough to reduce risk from repetitive motion or poorly designed work platform or due to heavy lifting
that exposes workers to sustained injuries or accident due to poor occupational practices and such
occupational hazards lead to MSD injuries in workers, compensation claims and lower productivity at
work. The impact of ergonomic hazards include injury resulting due to carpal tunnel syndrome which
affects hands, wrist, muscle, nerves of worker and is caused due to repetitive motion or sustained injury
from poor posture or work condition that causes discomfort (Górny 2012). Example of these include
injury occurring in workers during repetitive typing, switchboard operation, assembly line jobs and
though gripping equipment like scissors, curling irons etc. Other ergonomic hazard occurs during
heavy lifting when workers at port industry are exposed to risking their back, knees etc during routine
lifting and shifting of heavy material. Also workers in port industry are commonly exposed to reach to
supplies, equipment or materials stored in high shelves which causes injury due to extended arm reach
causing disorder or stress on workers shoulders. The impact of heavy lifting causes damage to nerves in
workers or injuries sustained due to poor posture or fracture during heavy object lifting (Aqlan, Lam,
Testani & Ramakrishnan 2013). The ergonomic hazards at work leads to poor productivity and causes
quality issues in work as well as adds to cost to port organisation due to compensation claim in event of
injury or employee turnover. Also the impact of such hazards can expose port organisation to
8
As opined by Shea, et al. (2016) the legal requirement associated with ergonomic hazards at port
industry are Occupational Safety and Health ACT, AMSA Act 1990. Other requirement of law include
Compliance policy of Port organisation, Compliance management manual, Health & Safety Legal
Review Guideline etc. Ethical consideration involved are educating employees on guideline of
occupational safety and ensuring regular check of safety measure, equipment and standards at
workplace.
Yes, change towards ergonomic hazards and safety implementation is required and these include
ensuring proper standards at workstation so as to avoid risk of posture or sustained injuries due to
uncomfortable condition at work. Also educating employees on using safety gears and standards to
comply with health and safety practices at work can reduce risk of ergonomic hazards.
Critical Review of Literature
The Ergonomic hazards are exposed to workers when adequate health and safety practices are not
enough to reduce risk from repetitive motion or poorly designed work platform or due to heavy lifting
that exposes workers to sustained injuries or accident due to poor occupational practices and such
occupational hazards lead to MSD injuries in workers, compensation claims and lower productivity at
work. The impact of ergonomic hazards include injury resulting due to carpal tunnel syndrome which
affects hands, wrist, muscle, nerves of worker and is caused due to repetitive motion or sustained injury
from poor posture or work condition that causes discomfort (Górny 2012). Example of these include
injury occurring in workers during repetitive typing, switchboard operation, assembly line jobs and
though gripping equipment like scissors, curling irons etc. Other ergonomic hazard occurs during
heavy lifting when workers at port industry are exposed to risking their back, knees etc during routine
lifting and shifting of heavy material. Also workers in port industry are commonly exposed to reach to
supplies, equipment or materials stored in high shelves which causes injury due to extended arm reach
causing disorder or stress on workers shoulders. The impact of heavy lifting causes damage to nerves in
workers or injuries sustained due to poor posture or fracture during heavy object lifting (Aqlan, Lam,
Testani & Ramakrishnan 2013). The ergonomic hazards at work leads to poor productivity and causes
quality issues in work as well as adds to cost to port organisation due to compensation claim in event of
injury or employee turnover. Also the impact of such hazards can expose port organisation to
8
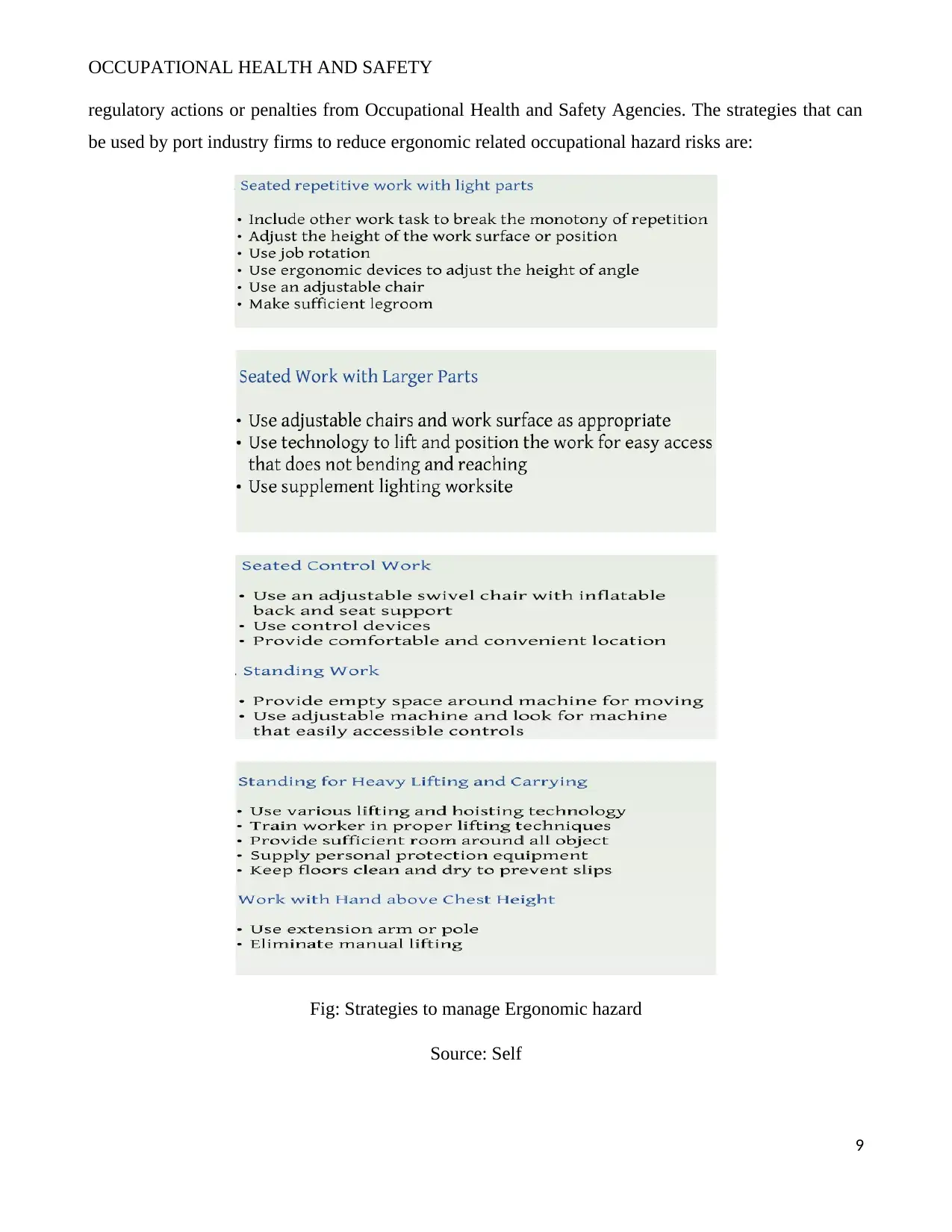
OCCUPATIONAL HEALTH AND SAFETY
regulatory actions or penalties from Occupational Health and Safety Agencies. The strategies that can
be used by port industry firms to reduce ergonomic related occupational hazard risks are:
Fig: Strategies to manage Ergonomic hazard
Source: Self
9
regulatory actions or penalties from Occupational Health and Safety Agencies. The strategies that can
be used by port industry firms to reduce ergonomic related occupational hazard risks are:
Fig: Strategies to manage Ergonomic hazard
Source: Self
9
Secure Best Marks with AI Grader
Need help grading? Try our AI Grader for instant feedback on your assignments.
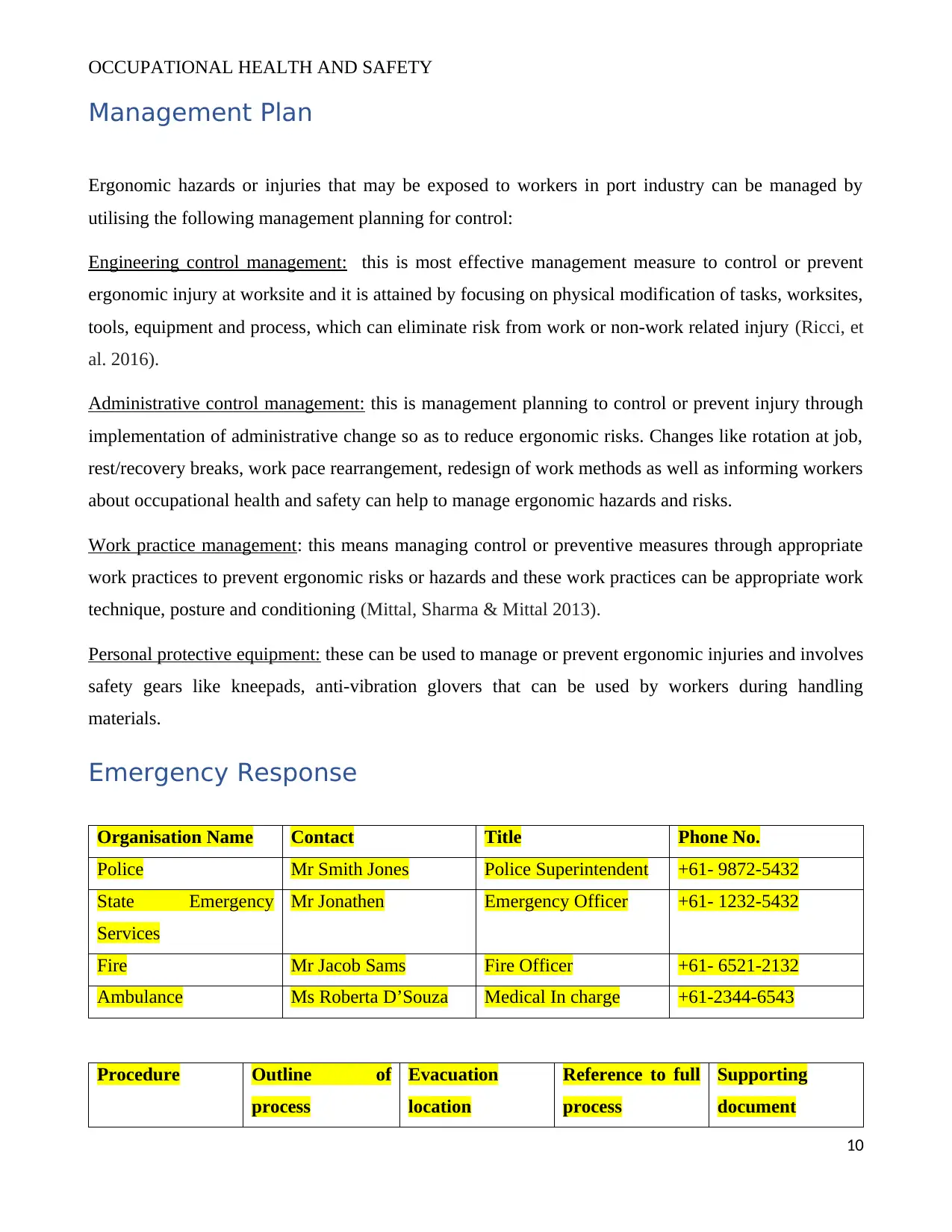
OCCUPATIONAL HEALTH AND SAFETY
Management Plan
Ergonomic hazards or injuries that may be exposed to workers in port industry can be managed by
utilising the following management planning for control:
Engineering control management: this is most effective management measure to control or prevent
ergonomic injury at worksite and it is attained by focusing on physical modification of tasks, worksites,
tools, equipment and process, which can eliminate risk from work or non-work related injury (Ricci, et
al. 2016).
Administrative control management: this is management planning to control or prevent injury through
implementation of administrative change so as to reduce ergonomic risks. Changes like rotation at job,
rest/recovery breaks, work pace rearrangement, redesign of work methods as well as informing workers
about occupational health and safety can help to manage ergonomic hazards and risks.
Work practice management: this means managing control or preventive measures through appropriate
work practices to prevent ergonomic risks or hazards and these work practices can be appropriate work
technique, posture and conditioning (Mittal, Sharma & Mittal 2013).
Personal protective equipment: these can be used to manage or prevent ergonomic injuries and involves
safety gears like kneepads, anti-vibration glovers that can be used by workers during handling
materials.
Emergency Response
Organisation Name Contact Title Phone No.
Police Mr Smith Jones Police Superintendent +61- 9872-5432
State Emergency
Services
Mr Jonathen Emergency Officer +61- 1232-5432
Fire Mr Jacob Sams Fire Officer +61- 6521-2132
Ambulance Ms Roberta D’Souza Medical In charge +61-2344-6543
Procedure Outline of
process
Evacuation
location
Reference to full
process
Supporting
document
10
Management Plan
Ergonomic hazards or injuries that may be exposed to workers in port industry can be managed by
utilising the following management planning for control:
Engineering control management: this is most effective management measure to control or prevent
ergonomic injury at worksite and it is attained by focusing on physical modification of tasks, worksites,
tools, equipment and process, which can eliminate risk from work or non-work related injury (Ricci, et
al. 2016).
Administrative control management: this is management planning to control or prevent injury through
implementation of administrative change so as to reduce ergonomic risks. Changes like rotation at job,
rest/recovery breaks, work pace rearrangement, redesign of work methods as well as informing workers
about occupational health and safety can help to manage ergonomic hazards and risks.
Work practice management: this means managing control or preventive measures through appropriate
work practices to prevent ergonomic risks or hazards and these work practices can be appropriate work
technique, posture and conditioning (Mittal, Sharma & Mittal 2013).
Personal protective equipment: these can be used to manage or prevent ergonomic injuries and involves
safety gears like kneepads, anti-vibration glovers that can be used by workers during handling
materials.
Emergency Response
Organisation Name Contact Title Phone No.
Police Mr Smith Jones Police Superintendent +61- 9872-5432
State Emergency
Services
Mr Jonathen Emergency Officer +61- 1232-5432
Fire Mr Jacob Sams Fire Officer +61- 6521-2132
Ambulance Ms Roberta D’Souza Medical In charge +61-2344-6543
Procedure Outline of
process
Evacuation
location
Reference to full
process
Supporting
document
10
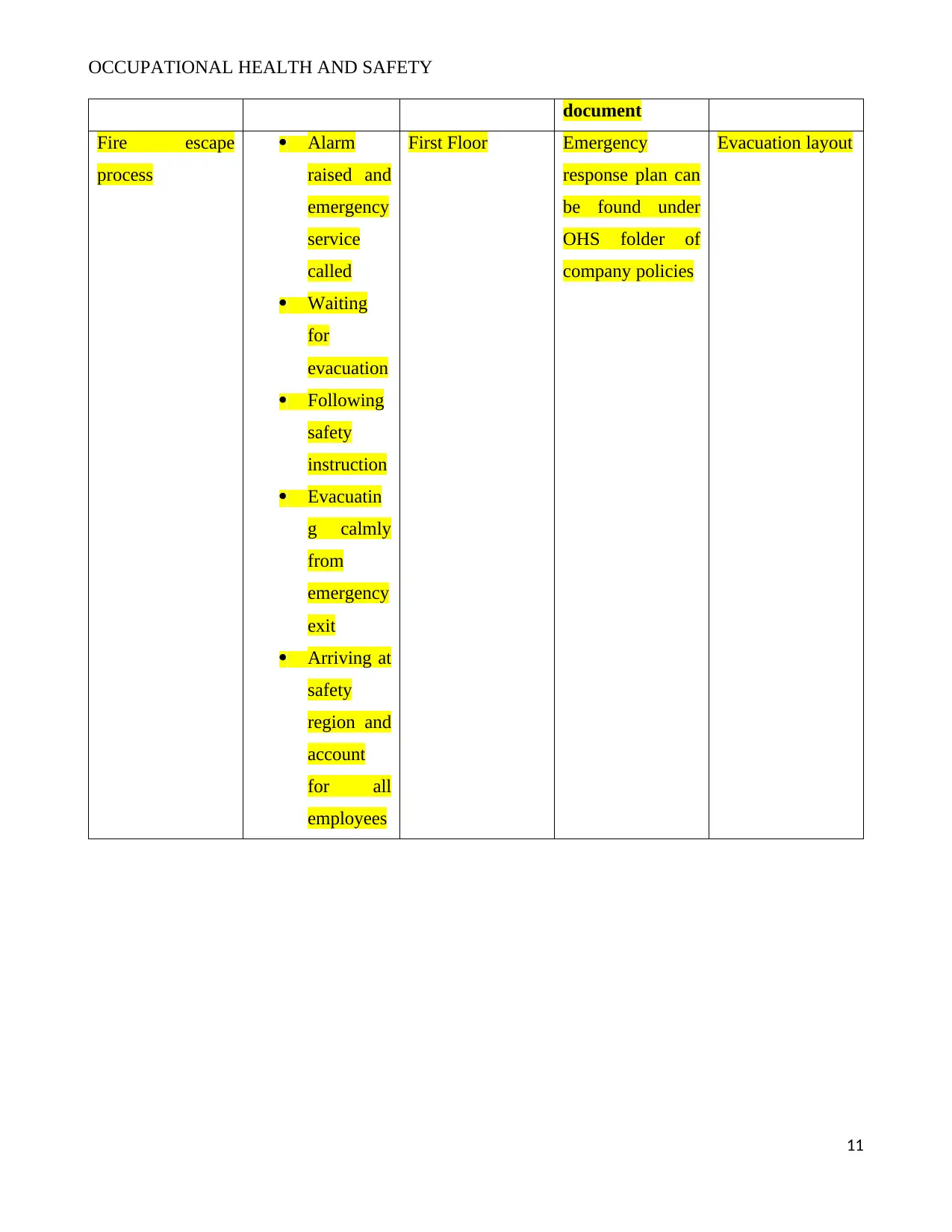
OCCUPATIONAL HEALTH AND SAFETY
document
Fire escape
process
Alarm
raised and
emergency
service
called
Waiting
for
evacuation
Following
safety
instruction
Evacuatin
g calmly
from
emergency
exit
Arriving at
safety
region and
account
for all
employees
First Floor Emergency
response plan can
be found under
OHS folder of
company policies
Evacuation layout
11
document
Fire escape
process
Alarm
raised and
emergency
service
called
Waiting
for
evacuation
Following
safety
instruction
Evacuatin
g calmly
from
emergency
exit
Arriving at
safety
region and
account
for all
employees
First Floor Emergency
response plan can
be found under
OHS folder of
company policies
Evacuation layout
11
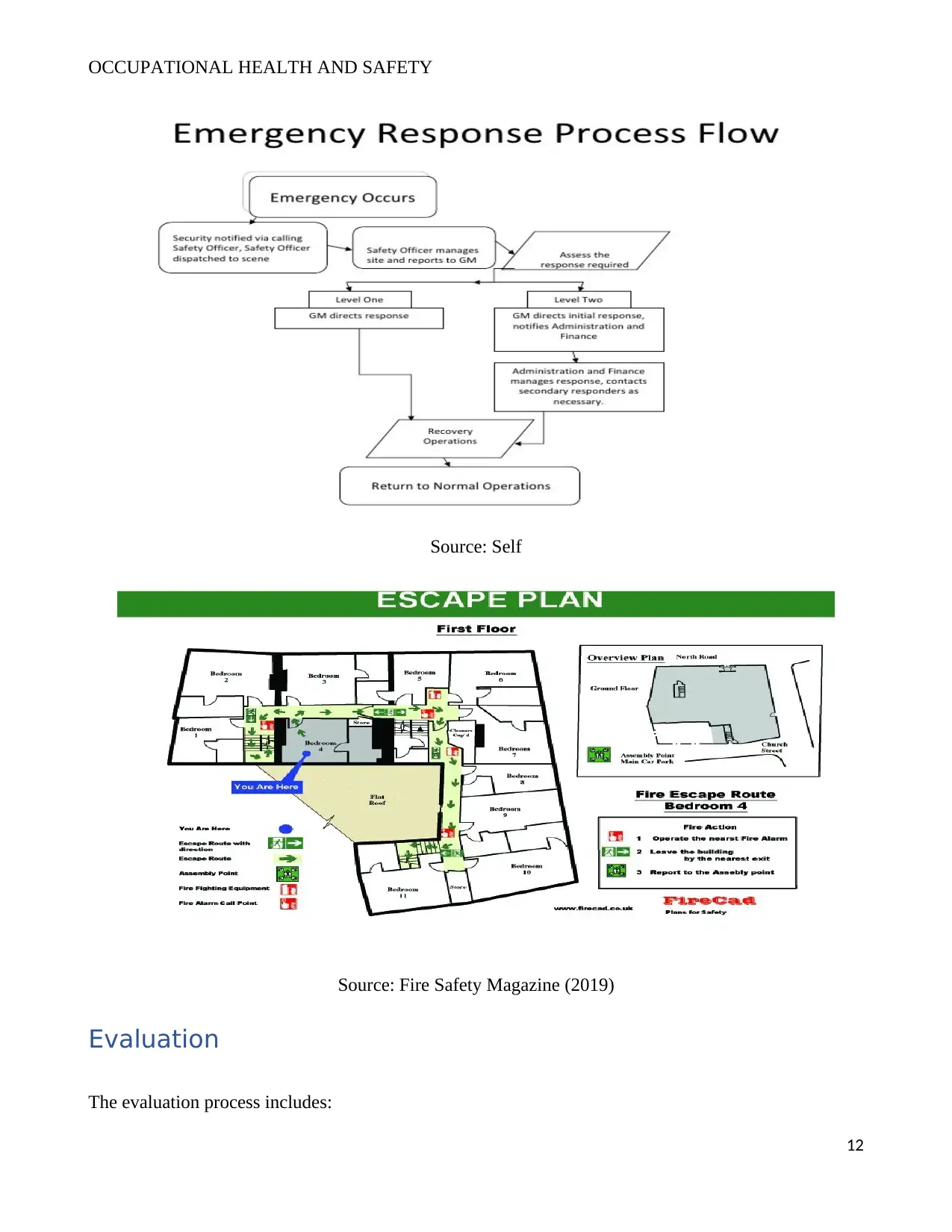
OCCUPATIONAL HEALTH AND SAFETY
Source: Self
Source: Fire Safety Magazine (2019)
Evaluation
The evaluation process includes:
12
Source: Self
Source: Fire Safety Magazine (2019)
Evaluation
The evaluation process includes:
12
Paraphrase This Document
Need a fresh take? Get an instant paraphrase of this document with our AI Paraphraser
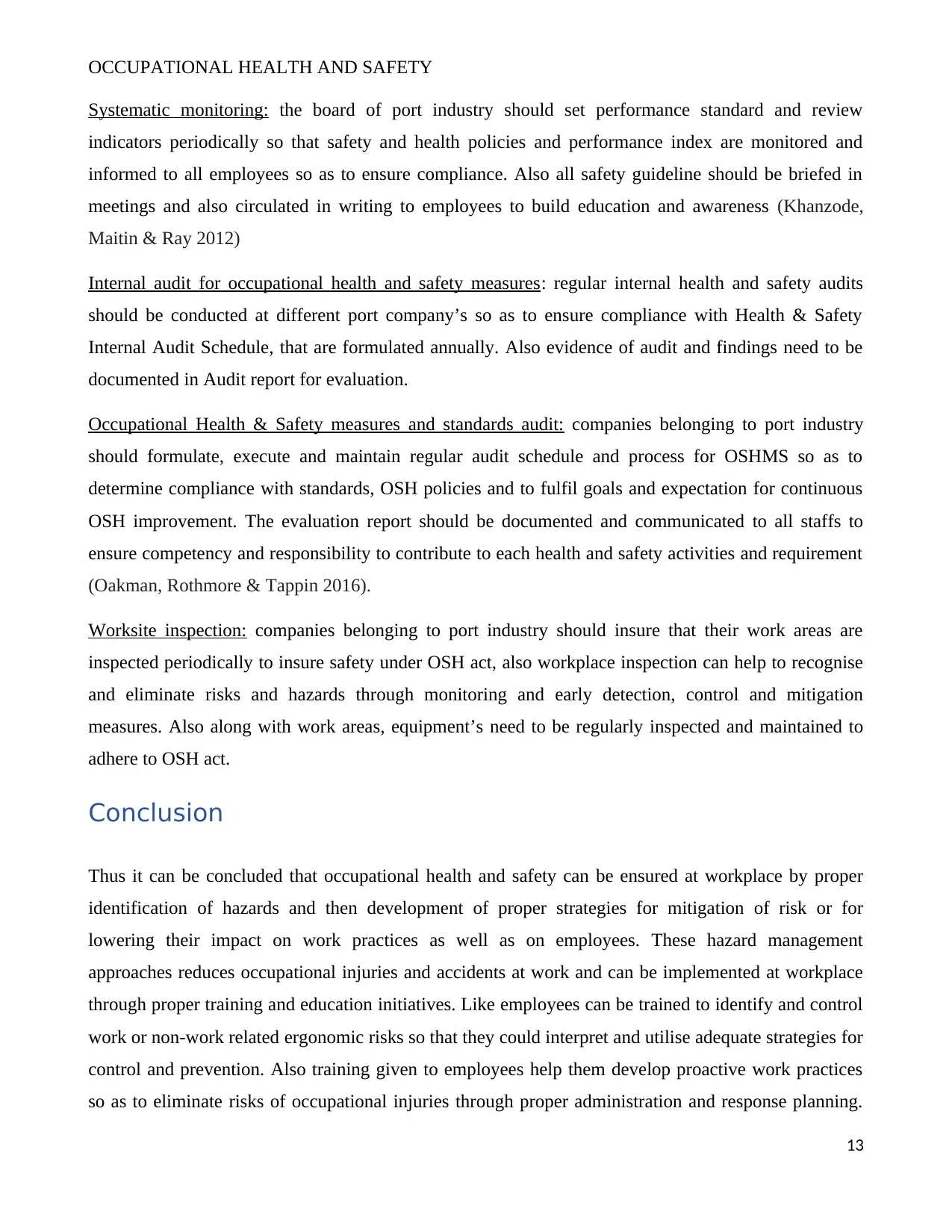
OCCUPATIONAL HEALTH AND SAFETY
Systematic monitoring: the board of port industry should set performance standard and review
indicators periodically so that safety and health policies and performance index are monitored and
informed to all employees so as to ensure compliance. Also all safety guideline should be briefed in
meetings and also circulated in writing to employees to build education and awareness (Khanzode,
Maitin & Ray 2012)
Internal audit for occupational health and safety measures: regular internal health and safety audits
should be conducted at different port company’s so as to ensure compliance with Health & Safety
Internal Audit Schedule, that are formulated annually. Also evidence of audit and findings need to be
documented in Audit report for evaluation.
Occupational Health & Safety measures and standards audit: companies belonging to port industry
should formulate, execute and maintain regular audit schedule and process for OSHMS so as to
determine compliance with standards, OSH policies and to fulfil goals and expectation for continuous
OSH improvement. The evaluation report should be documented and communicated to all staffs to
ensure competency and responsibility to contribute to each health and safety activities and requirement
(Oakman, Rothmore & Tappin 2016).
Worksite inspection: companies belonging to port industry should insure that their work areas are
inspected periodically to insure safety under OSH act, also workplace inspection can help to recognise
and eliminate risks and hazards through monitoring and early detection, control and mitigation
measures. Also along with work areas, equipment’s need to be regularly inspected and maintained to
adhere to OSH act.
Conclusion
Thus it can be concluded that occupational health and safety can be ensured at workplace by proper
identification of hazards and then development of proper strategies for mitigation of risk or for
lowering their impact on work practices as well as on employees. These hazard management
approaches reduces occupational injuries and accidents at work and can be implemented at workplace
through proper training and education initiatives. Like employees can be trained to identify and control
work or non-work related ergonomic risks so that they could interpret and utilise adequate strategies for
control and prevention. Also training given to employees help them develop proactive work practices
so as to eliminate risks of occupational injuries through proper administration and response planning.
13
Systematic monitoring: the board of port industry should set performance standard and review
indicators periodically so that safety and health policies and performance index are monitored and
informed to all employees so as to ensure compliance. Also all safety guideline should be briefed in
meetings and also circulated in writing to employees to build education and awareness (Khanzode,
Maitin & Ray 2012)
Internal audit for occupational health and safety measures: regular internal health and safety audits
should be conducted at different port company’s so as to ensure compliance with Health & Safety
Internal Audit Schedule, that are formulated annually. Also evidence of audit and findings need to be
documented in Audit report for evaluation.
Occupational Health & Safety measures and standards audit: companies belonging to port industry
should formulate, execute and maintain regular audit schedule and process for OSHMS so as to
determine compliance with standards, OSH policies and to fulfil goals and expectation for continuous
OSH improvement. The evaluation report should be documented and communicated to all staffs to
ensure competency and responsibility to contribute to each health and safety activities and requirement
(Oakman, Rothmore & Tappin 2016).
Worksite inspection: companies belonging to port industry should insure that their work areas are
inspected periodically to insure safety under OSH act, also workplace inspection can help to recognise
and eliminate risks and hazards through monitoring and early detection, control and mitigation
measures. Also along with work areas, equipment’s need to be regularly inspected and maintained to
adhere to OSH act.
Conclusion
Thus it can be concluded that occupational health and safety can be ensured at workplace by proper
identification of hazards and then development of proper strategies for mitigation of risk or for
lowering their impact on work practices as well as on employees. These hazard management
approaches reduces occupational injuries and accidents at work and can be implemented at workplace
through proper training and education initiatives. Like employees can be trained to identify and control
work or non-work related ergonomic risks so that they could interpret and utilise adequate strategies for
control and prevention. Also training given to employees help them develop proactive work practices
so as to eliminate risks of occupational injuries through proper administration and response planning.
13
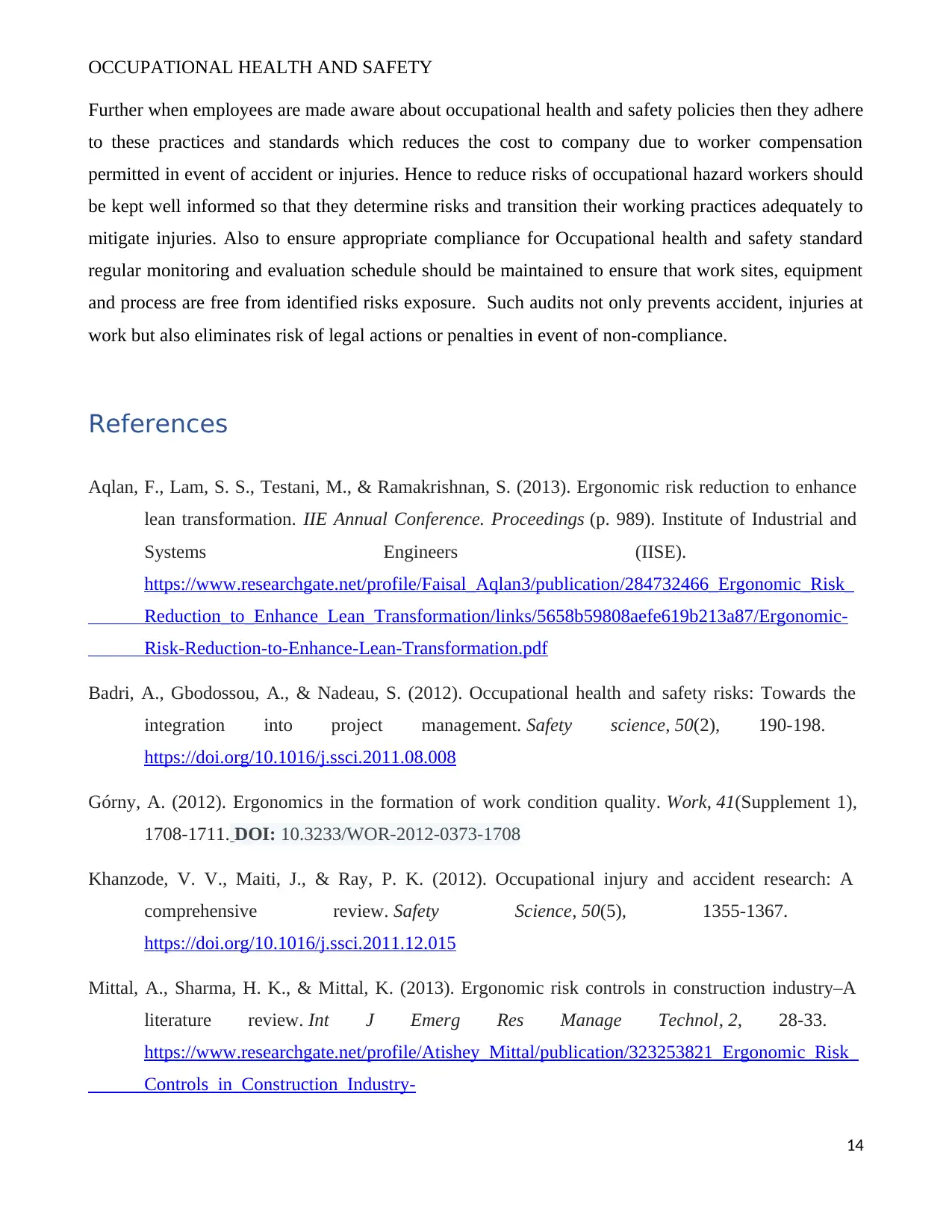
OCCUPATIONAL HEALTH AND SAFETY
Further when employees are made aware about occupational health and safety policies then they adhere
to these practices and standards which reduces the cost to company due to worker compensation
permitted in event of accident or injuries. Hence to reduce risks of occupational hazard workers should
be kept well informed so that they determine risks and transition their working practices adequately to
mitigate injuries. Also to ensure appropriate compliance for Occupational health and safety standard
regular monitoring and evaluation schedule should be maintained to ensure that work sites, equipment
and process are free from identified risks exposure. Such audits not only prevents accident, injuries at
work but also eliminates risk of legal actions or penalties in event of non-compliance.
References
Aqlan, F., Lam, S. S., Testani, M., & Ramakrishnan, S. (2013). Ergonomic risk reduction to enhance
lean transformation. IIE Annual Conference. Proceedings (p. 989). Institute of Industrial and
Systems Engineers (IISE).
https://www.researchgate.net/profile/Faisal_Aqlan3/publication/284732466_Ergonomic_Risk_
Reduction_to_Enhance_Lean_Transformation/links/5658b59808aefe619b213a87/Ergonomic-
Risk-Reduction-to-Enhance-Lean-Transformation.pdf
Badri, A., Gbodossou, A., & Nadeau, S. (2012). Occupational health and safety risks: Towards the
integration into project management. Safety science, 50(2), 190-198.
https://doi.org/10.1016/j.ssci.2011.08.008
Górny, A. (2012). Ergonomics in the formation of work condition quality. Work, 41(Supplement 1),
1708-1711. DOI: 10.3233/WOR-2012-0373-1708
Khanzode, V. V., Maiti, J., & Ray, P. K. (2012). Occupational injury and accident research: A
comprehensive review. Safety Science, 50(5), 1355-1367.
https://doi.org/10.1016/j.ssci.2011.12.015
Mittal, A., Sharma, H. K., & Mittal, K. (2013). Ergonomic risk controls in construction industry–A
literature review. Int J Emerg Res Manage Technol, 2, 28-33.
https://www.researchgate.net/profile/Atishey_Mittal/publication/323253821_Ergonomic_Risk_
Controls_in_Construction_Industry-
14
Further when employees are made aware about occupational health and safety policies then they adhere
to these practices and standards which reduces the cost to company due to worker compensation
permitted in event of accident or injuries. Hence to reduce risks of occupational hazard workers should
be kept well informed so that they determine risks and transition their working practices adequately to
mitigate injuries. Also to ensure appropriate compliance for Occupational health and safety standard
regular monitoring and evaluation schedule should be maintained to ensure that work sites, equipment
and process are free from identified risks exposure. Such audits not only prevents accident, injuries at
work but also eliminates risk of legal actions or penalties in event of non-compliance.
References
Aqlan, F., Lam, S. S., Testani, M., & Ramakrishnan, S. (2013). Ergonomic risk reduction to enhance
lean transformation. IIE Annual Conference. Proceedings (p. 989). Institute of Industrial and
Systems Engineers (IISE).
https://www.researchgate.net/profile/Faisal_Aqlan3/publication/284732466_Ergonomic_Risk_
Reduction_to_Enhance_Lean_Transformation/links/5658b59808aefe619b213a87/Ergonomic-
Risk-Reduction-to-Enhance-Lean-Transformation.pdf
Badri, A., Gbodossou, A., & Nadeau, S. (2012). Occupational health and safety risks: Towards the
integration into project management. Safety science, 50(2), 190-198.
https://doi.org/10.1016/j.ssci.2011.08.008
Górny, A. (2012). Ergonomics in the formation of work condition quality. Work, 41(Supplement 1),
1708-1711. DOI: 10.3233/WOR-2012-0373-1708
Khanzode, V. V., Maiti, J., & Ray, P. K. (2012). Occupational injury and accident research: A
comprehensive review. Safety Science, 50(5), 1355-1367.
https://doi.org/10.1016/j.ssci.2011.12.015
Mittal, A., Sharma, H. K., & Mittal, K. (2013). Ergonomic risk controls in construction industry–A
literature review. Int J Emerg Res Manage Technol, 2, 28-33.
https://www.researchgate.net/profile/Atishey_Mittal/publication/323253821_Ergonomic_Risk_
Controls_in_Construction_Industry-
14
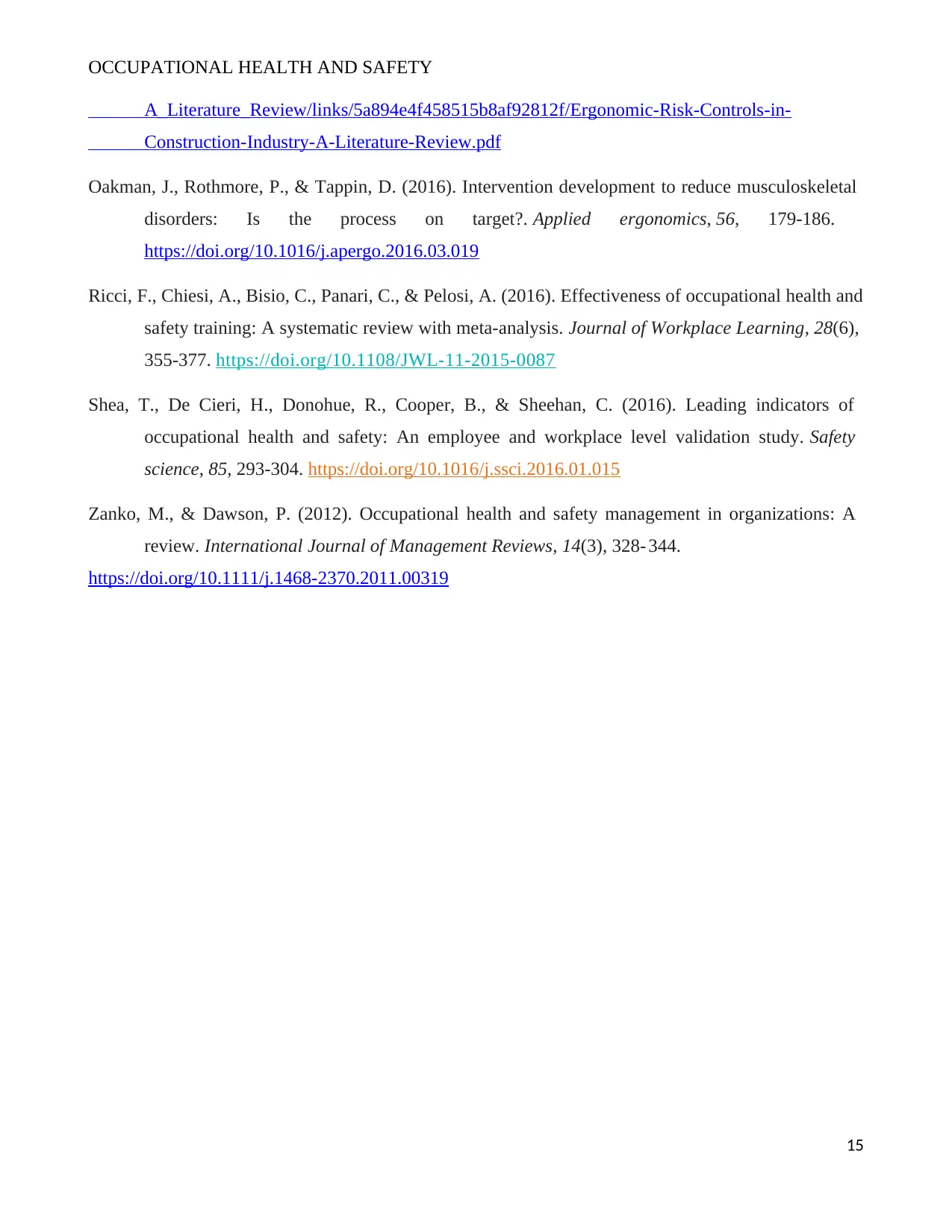
OCCUPATIONAL HEALTH AND SAFETY
A_Literature_Review/links/5a894e4f458515b8af92812f/Ergonomic-Risk-Controls-in-
Construction-Industry-A-Literature-Review.pdf
Oakman, J., Rothmore, P., & Tappin, D. (2016). Intervention development to reduce musculoskeletal
disorders: Is the process on target?. Applied ergonomics, 56, 179-186.
https://doi.org/10.1016/j.apergo.2016.03.019
Ricci, F., Chiesi, A., Bisio, C., Panari, C., & Pelosi, A. (2016). Effectiveness of occupational health and
safety training: A systematic review with meta-analysis. Journal of Workplace Learning, 28(6),
355-377. https://doi.org/10.1108/JWL-11-2015-0087
Shea, T., De Cieri, H., Donohue, R., Cooper, B., & Sheehan, C. (2016). Leading indicators of
occupational health and safety: An employee and workplace level validation study. Safety
science, 85, 293-304. https://doi.org/10.1016/j.ssci.2016.01.015
Zanko, M., & Dawson, P. (2012). Occupational health and safety management in organizations: A
review. International Journal of Management Reviews, 14(3), 328- 344.
https://doi.org/10.1111/j.1468-2370.2011.00319
15
A_Literature_Review/links/5a894e4f458515b8af92812f/Ergonomic-Risk-Controls-in-
Construction-Industry-A-Literature-Review.pdf
Oakman, J., Rothmore, P., & Tappin, D. (2016). Intervention development to reduce musculoskeletal
disorders: Is the process on target?. Applied ergonomics, 56, 179-186.
https://doi.org/10.1016/j.apergo.2016.03.019
Ricci, F., Chiesi, A., Bisio, C., Panari, C., & Pelosi, A. (2016). Effectiveness of occupational health and
safety training: A systematic review with meta-analysis. Journal of Workplace Learning, 28(6),
355-377. https://doi.org/10.1108/JWL-11-2015-0087
Shea, T., De Cieri, H., Donohue, R., Cooper, B., & Sheehan, C. (2016). Leading indicators of
occupational health and safety: An employee and workplace level validation study. Safety
science, 85, 293-304. https://doi.org/10.1016/j.ssci.2016.01.015
Zanko, M., & Dawson, P. (2012). Occupational health and safety management in organizations: A
review. International Journal of Management Reviews, 14(3), 328- 344.
https://doi.org/10.1111/j.1468-2370.2011.00319
15
1 out of 16
Related Documents
![[object Object]](/_next/image/?url=%2F_next%2Fstatic%2Fmedia%2Flogo.6d15ce61.png&w=640&q=75)
Your All-in-One AI-Powered Toolkit for Academic Success.
+13062052269
info@desklib.com
Available 24*7 on WhatsApp / Email
Unlock your academic potential
© 2024 | Zucol Services PVT LTD | All rights reserved.