Occupational Health and Safety Procedures for Plants, Equipment, and Hazardous Chemicals
21 Pages4271 Words397 Views
Added on 2023-06-05
About This Document
This guide covers the occupational health and safety procedures for plants, equipment, and hazardous chemicals. It includes legal requirements, risk identification, risk assessment, risk control, and more. The guide also covers the importance of consultation, planning, and purchasing, as well as the development of standard operating procedures. Additionally, it provides information on licensing and certification, training and instruction, and record-keeping.
Occupational Health and Safety Procedures for Plants, Equipment, and Hazardous Chemicals
Added on 2023-06-05
ShareRelated Documents
Occupational health and safety procedures 1
OCCUPATIONAL HEALTH AND SAFETY PROCEDURES
By (Name)
Course
Tutor
University
City
Date
OCCUPATIONAL HEALTH AND SAFETY PROCEDURES
By (Name)
Course
Tutor
University
City
Date
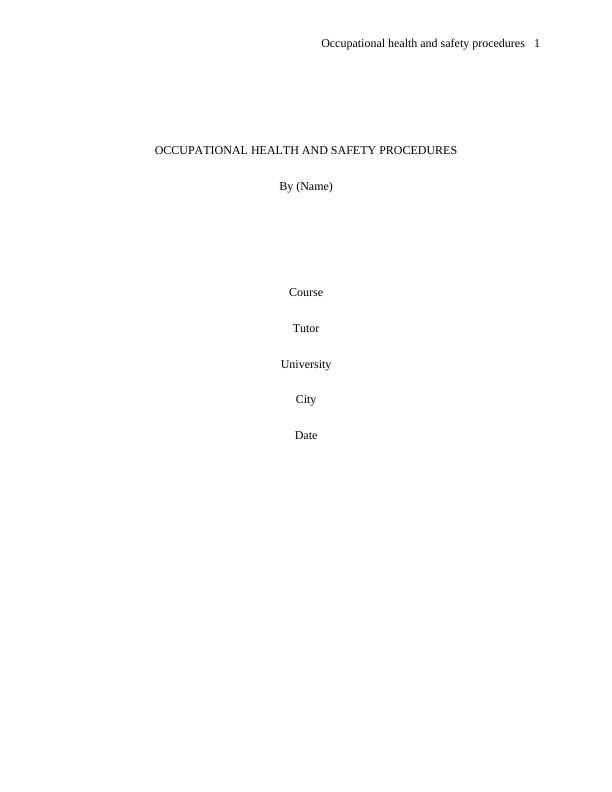
Occupational health and safety procedures 2
1. HEALTH AND SAFETY PROCEDURES FOR PLANTS AND EQUIPMENT
1.1 Definitions
A plant is any machinery used for processing materials by means of mechanical action which
could either be through; drilling, punching, mixing, cutting, assembling and molding
(Richardson, 2013).
Hazard refers to the possibility of an illness or injury arising out of the effects of a plant.
Potential harms include; crushing by tipping over of plant or moving objects, burns out of
friction, and injury by fluids of high pressure, being electrocuted, explosions and cuts by
flying/sharp objects (Collins, et al., 2014).
1.2 legal requirements
In Australia, any organization or institution seeking to install operation plants must comply to all
guidelines outlined by Part 4, Division 3 of the Occupational Safety and Health Regulations
(1996), later amended in 1999 December, the Occupational Safety and Health Act of 1984 later
amended in 1999 March, related Australian standards, codes of guidance and Practice and all
appropriate laws pertinent to plant operation.
1.3 Consultation
A health and safety representative of the designated work group should be consulted by the
organization seeking to install a plant (Jeynes, 2007). It is also the duty of purchasers to maintain
consistent contact with sellers to pave way for discussions on health and safety issues related to
plant before plans to introduce a modified or new plant and subsequently allow for any changes
possible.
1. HEALTH AND SAFETY PROCEDURES FOR PLANTS AND EQUIPMENT
1.1 Definitions
A plant is any machinery used for processing materials by means of mechanical action which
could either be through; drilling, punching, mixing, cutting, assembling and molding
(Richardson, 2013).
Hazard refers to the possibility of an illness or injury arising out of the effects of a plant.
Potential harms include; crushing by tipping over of plant or moving objects, burns out of
friction, and injury by fluids of high pressure, being electrocuted, explosions and cuts by
flying/sharp objects (Collins, et al., 2014).
1.2 legal requirements
In Australia, any organization or institution seeking to install operation plants must comply to all
guidelines outlined by Part 4, Division 3 of the Occupational Safety and Health Regulations
(1996), later amended in 1999 December, the Occupational Safety and Health Act of 1984 later
amended in 1999 March, related Australian standards, codes of guidance and Practice and all
appropriate laws pertinent to plant operation.
1.3 Consultation
A health and safety representative of the designated work group should be consulted by the
organization seeking to install a plant (Jeynes, 2007). It is also the duty of purchasers to maintain
consistent contact with sellers to pave way for discussions on health and safety issues related to
plant before plans to introduce a modified or new plant and subsequently allow for any changes
possible.
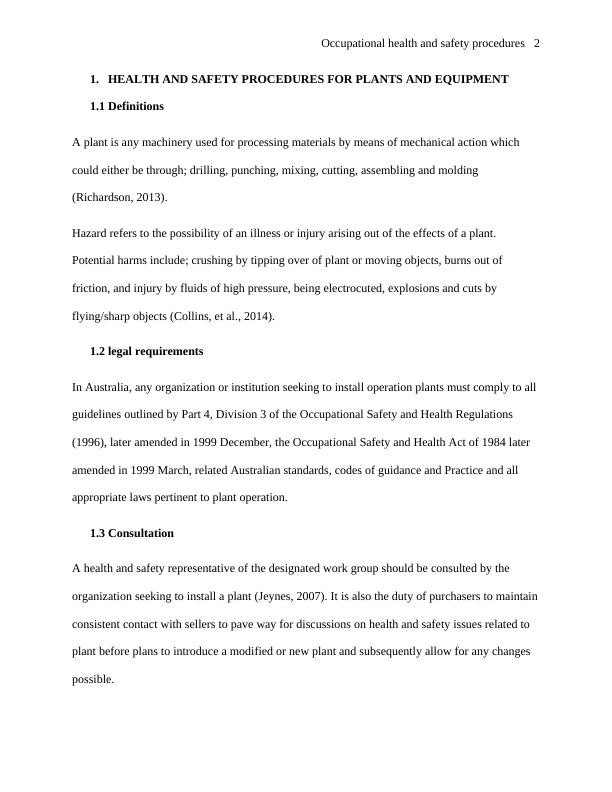
Occupational health and safety procedures 3
1.4 planning and purchasing
It is the duty of suppliers to provide relevant information related to the use of the plant and
equipment (Hughes & Ferrett, 2009). During the designing, purchasing and planning stages,
controls for substitution, engineering and Elimination can be effectively applied. Whenever any
organization or institution is intending to buy any plant and equipment, all the risks that could
emanate from the risk of the specific plant and equipment must be put into consideration.
1.5 Risk identification
All hazards that could emanate from erection, commissioning, use of plant and systems of work
(SoWs), and installation of plant must be identified by sections, schools, departments and/or
offices of facilities’ management that are aiming to purchase and install a plant and equipment
(Appendix 1,2) (Scheule & Rösch, 2010). Considerations must be given to the following when
identifying hazards of plants:
Crushing by plant tipping over or by moving or falling objects
Entanglement leading to injury
Burns due to friction
Crushing when people are thrown under or off the plant
Piercing or cutting by flying or sharp objects
Suffocation
High-pressure fluids injuries
Explosion injuries
Radiation, vibration, dust, noise
Falls and slips trips
1.4 planning and purchasing
It is the duty of suppliers to provide relevant information related to the use of the plant and
equipment (Hughes & Ferrett, 2009). During the designing, purchasing and planning stages,
controls for substitution, engineering and Elimination can be effectively applied. Whenever any
organization or institution is intending to buy any plant and equipment, all the risks that could
emanate from the risk of the specific plant and equipment must be put into consideration.
1.5 Risk identification
All hazards that could emanate from erection, commissioning, use of plant and systems of work
(SoWs), and installation of plant must be identified by sections, schools, departments and/or
offices of facilities’ management that are aiming to purchase and install a plant and equipment
(Appendix 1,2) (Scheule & Rösch, 2010). Considerations must be given to the following when
identifying hazards of plants:
Crushing by plant tipping over or by moving or falling objects
Entanglement leading to injury
Burns due to friction
Crushing when people are thrown under or off the plant
Piercing or cutting by flying or sharp objects
Suffocation
High-pressure fluids injuries
Explosion injuries
Radiation, vibration, dust, noise
Falls and slips trips
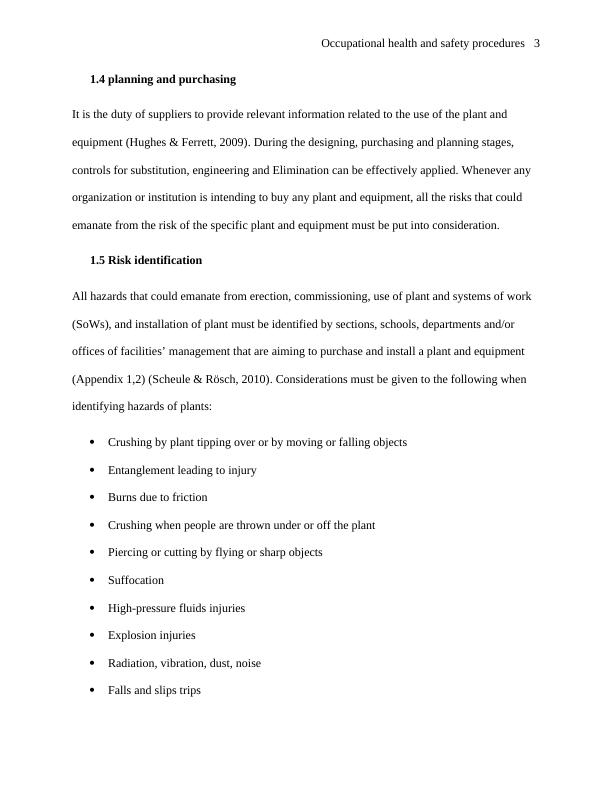
Occupational health and safety procedures 4
High temperatures
suffocation
1.6 risk assessment
Upon identification of risks associable with a plant, a Plant Hazard identification checklist
(Appendix 2) could be used hand in hand with the specific organization/institution’s procedures
of safety risk management (Rausand, 2013). Identified hazards play a crucial role in categorizing
the risks into either low, medium or high priority.
1.7 Risk Control
As mentioned in the regulations of any organization/ institution, in relation to control of risks, it
is the primary role of departments, sections, schools and supervisors to identify and eliminate or
help in eliminating any risk whenever practicable, associable with systems of work and
associable with a plant. For all the risks identified, implementation of controls must be too as far
as possible. The hierarchy of controls must be followed at all times. It involves; elimination,
substitution, engineering, administrative, and PPE (Personal Protective Equipment) (Holloway,
et al., 2012).
1.8 (SOPs) Standard Operating Procedures
Development of a standard operating procedure will follow the assessment of risk identification
and control measures. The SOPs are to be displayed near or on the plant and should be followed
to alert students, staff and operators of all the hazards associated with the plant (Sutton, 2017).
1.9 installation, Erection, and commissioning of the plant
High temperatures
suffocation
1.6 risk assessment
Upon identification of risks associable with a plant, a Plant Hazard identification checklist
(Appendix 2) could be used hand in hand with the specific organization/institution’s procedures
of safety risk management (Rausand, 2013). Identified hazards play a crucial role in categorizing
the risks into either low, medium or high priority.
1.7 Risk Control
As mentioned in the regulations of any organization/ institution, in relation to control of risks, it
is the primary role of departments, sections, schools and supervisors to identify and eliminate or
help in eliminating any risk whenever practicable, associable with systems of work and
associable with a plant. For all the risks identified, implementation of controls must be too as far
as possible. The hierarchy of controls must be followed at all times. It involves; elimination,
substitution, engineering, administrative, and PPE (Personal Protective Equipment) (Holloway,
et al., 2012).
1.8 (SOPs) Standard Operating Procedures
Development of a standard operating procedure will follow the assessment of risk identification
and control measures. The SOPs are to be displayed near or on the plant and should be followed
to alert students, staff and operators of all the hazards associated with the plant (Sutton, 2017).
1.9 installation, Erection, and commissioning of the plant
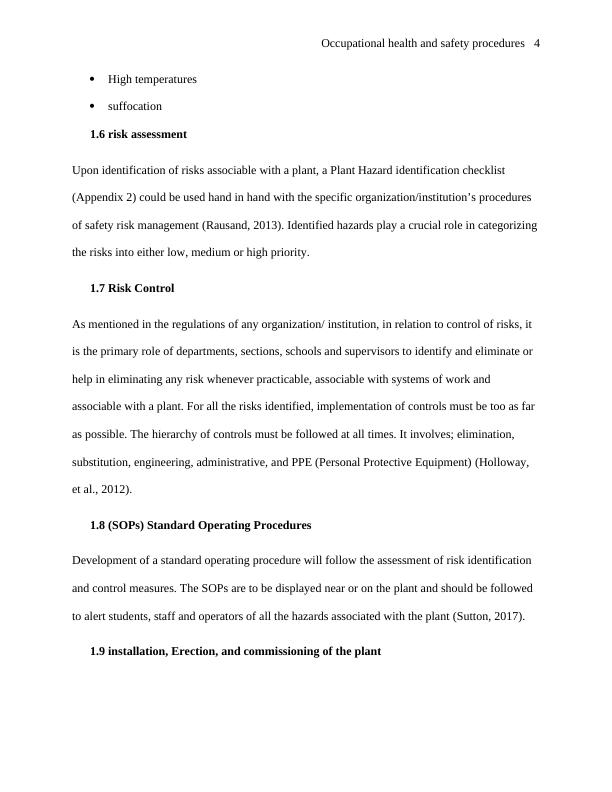
Occupational health and safety procedures 5
Sections, departments, schools, supervisors, and facility/institution management offices and/or
other coordinators of plant installation and management must complete Appendix 2 so as to;
Ensure that egress and access from and to the workplace are not affected by the plant's
layout.
Ensure that a clear working area has been provided around the plant.
Incorporate inspections to ensure that monitoring of risks associable to the operation of
the plant is conducted.
Ensure that the operation of a plant has not commenced until the establishment of the
commissioning process is done (Helmus, 2008).
1.10 Inspection and Maintenance for Plant in Use
Recommendations of the supplier, designer, and manufacturer should be followed in the
maintenance, cleaning, and inspection of the plant. All warning devices and safety features
should be regularly tested (Richardson, 2013). Before the onset of repairs, maintenance or
cleaning, stopping of the plant should be recommended by the systems of work (SOP). Devices
for lockout or isolation should also be used.
1.11 Registration of Plant
Unless registered with Work safe WA, there are certain plant items not usable in the workplace
as ruled by the Occupational Safety and Health Regulation of 1996. They are;
Tower cranes
Maintenance units for building
Gas cylinders
Boilers of hazard categories A, B, C.
Sections, departments, schools, supervisors, and facility/institution management offices and/or
other coordinators of plant installation and management must complete Appendix 2 so as to;
Ensure that egress and access from and to the workplace are not affected by the plant's
layout.
Ensure that a clear working area has been provided around the plant.
Incorporate inspections to ensure that monitoring of risks associable to the operation of
the plant is conducted.
Ensure that the operation of a plant has not commenced until the establishment of the
commissioning process is done (Helmus, 2008).
1.10 Inspection and Maintenance for Plant in Use
Recommendations of the supplier, designer, and manufacturer should be followed in the
maintenance, cleaning, and inspection of the plant. All warning devices and safety features
should be regularly tested (Richardson, 2013). Before the onset of repairs, maintenance or
cleaning, stopping of the plant should be recommended by the systems of work (SOP). Devices
for lockout or isolation should also be used.
1.11 Registration of Plant
Unless registered with Work safe WA, there are certain plant items not usable in the workplace
as ruled by the Occupational Safety and Health Regulation of 1996. They are;
Tower cranes
Maintenance units for building
Gas cylinders
Boilers of hazard categories A, B, C.
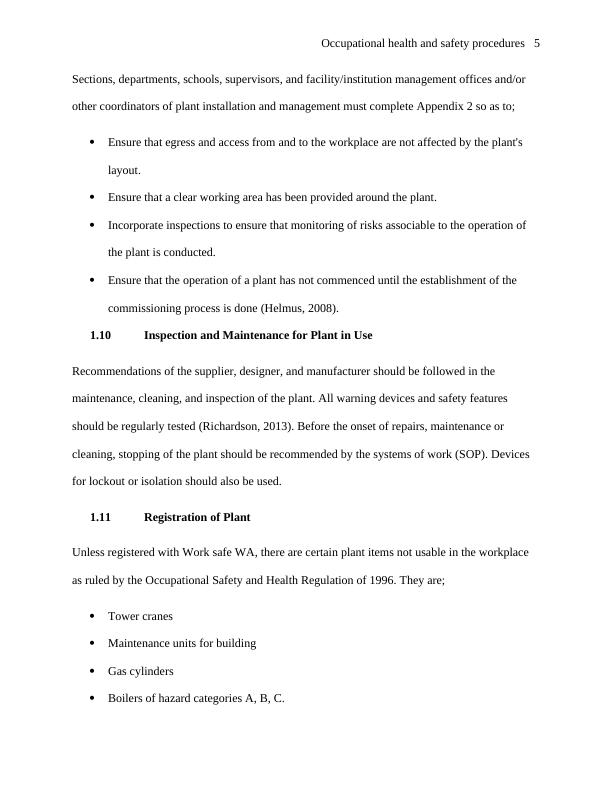
Occupational health and safety procedures 6
Pressure vessels of hazard levels A, B, C other than pressure pipes, LPG fuel vessels, and
gas cylinders.
Elevating work platforms of boom type.
Bridge cranes with a working load of more than 10 tons.
1.12 Licensing and Certificate of Competency
A competency certificate is compulsory for anyone using or operating high-risk plant items.
Departments, schools, supervisors or section personnel must see to it that their staff are in
possession of competency certificates for the plant that they operate. Working under the close
supervision of a professional with the relevant certificate of competency is an alternative way for
individuals to gain the necessary training.
1.13 Information, Training, and Instruction
Under the Occupational Health and Safety Act, it is a requirement that organizations or
institutions in possession of plant and equipment to avail instruction, training and information to
employees to ensure that they are in a capacity to perform work free from health risks and in a
safe manner. upon identification of hazards related to a plant and its systems of work and
subsequent assessment warranting it to be a risk, it is upon the employer to ensure that such
employees with the highest likelihood of exposure to the risk and any supervisor of such
employees must be trained and given relevant instructions and information (Smedley, et al.,
2013).
2. HEALTH AND SAFETY PROCEDURES FOR HAZARDOUS CHEMICALS
2.1 Establishment/ reviewing of Chemical Register
Pressure vessels of hazard levels A, B, C other than pressure pipes, LPG fuel vessels, and
gas cylinders.
Elevating work platforms of boom type.
Bridge cranes with a working load of more than 10 tons.
1.12 Licensing and Certificate of Competency
A competency certificate is compulsory for anyone using or operating high-risk plant items.
Departments, schools, supervisors or section personnel must see to it that their staff are in
possession of competency certificates for the plant that they operate. Working under the close
supervision of a professional with the relevant certificate of competency is an alternative way for
individuals to gain the necessary training.
1.13 Information, Training, and Instruction
Under the Occupational Health and Safety Act, it is a requirement that organizations or
institutions in possession of plant and equipment to avail instruction, training and information to
employees to ensure that they are in a capacity to perform work free from health risks and in a
safe manner. upon identification of hazards related to a plant and its systems of work and
subsequent assessment warranting it to be a risk, it is upon the employer to ensure that such
employees with the highest likelihood of exposure to the risk and any supervisor of such
employees must be trained and given relevant instructions and information (Smedley, et al.,
2013).
2. HEALTH AND SAFETY PROCEDURES FOR HAZARDOUS CHEMICALS
2.1 Establishment/ reviewing of Chemical Register
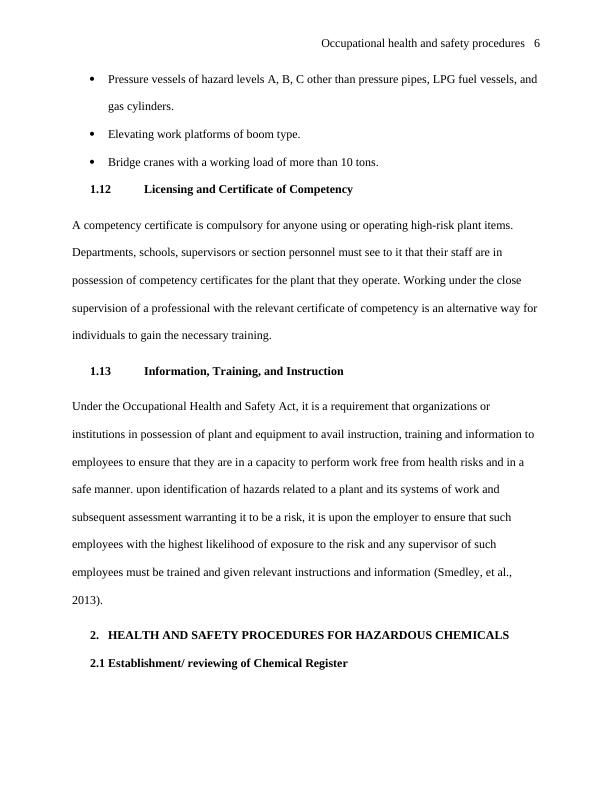
End of preview
Want to access all the pages? Upload your documents or become a member.
Related Documents
Occupational Health Hazards in Chemical Industrieslg...
|8
|2148
|69
Workplace Health and Safety Assignmentslg...
|10
|2354
|323
Safety Risks and Reliability PDFlg...
|12
|3612
|28
Ensure a Safe Workplace: Hazardous Occupations, Stress Management Techniques, Natural Disasters, and Workplace Hazardslg...
|7
|2014
|439
Hotel Hazard Analysis Report: Tips for Maintaining a Safe Work Environmentlg...
|8
|1691
|312