Operation and Project Management
VerifiedAdded on 2023/06/07
|21
|5123
|201
AI Summary
This report discusses the execution of operation management standards within a firm, including Six Sigma approaches and Lean principles. It also covers the study of the application of each stage of the project life cycle to create supported documents that will assist in completing the project. The report includes recommendations for operation managers of Marks & Spencer.
Contribute Materials
Your contribution can guide someone’s learning journey. Share your
documents today.
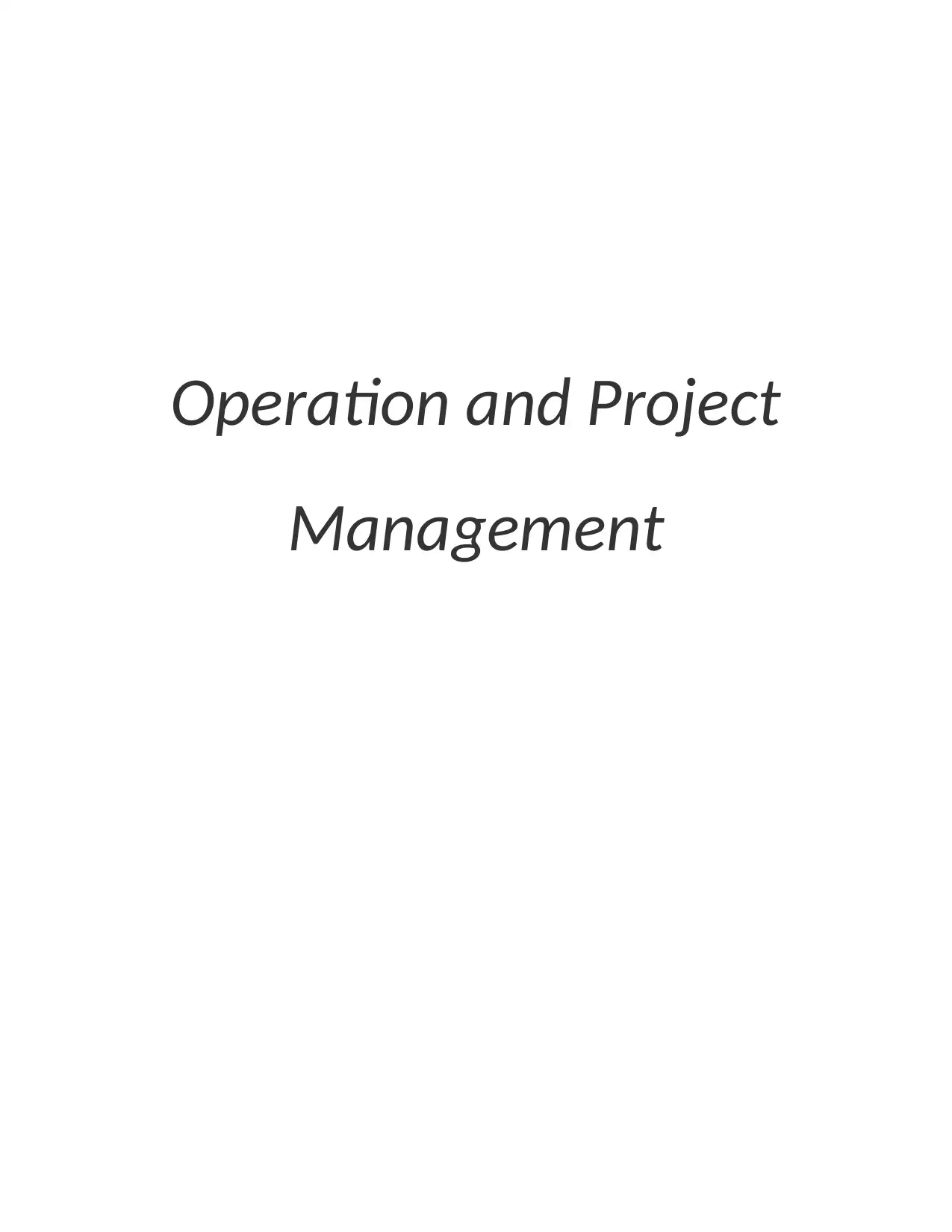
Operation and Project
Management
Management
Secure Best Marks with AI Grader
Need help grading? Try our AI Grader for instant feedback on your assignments.
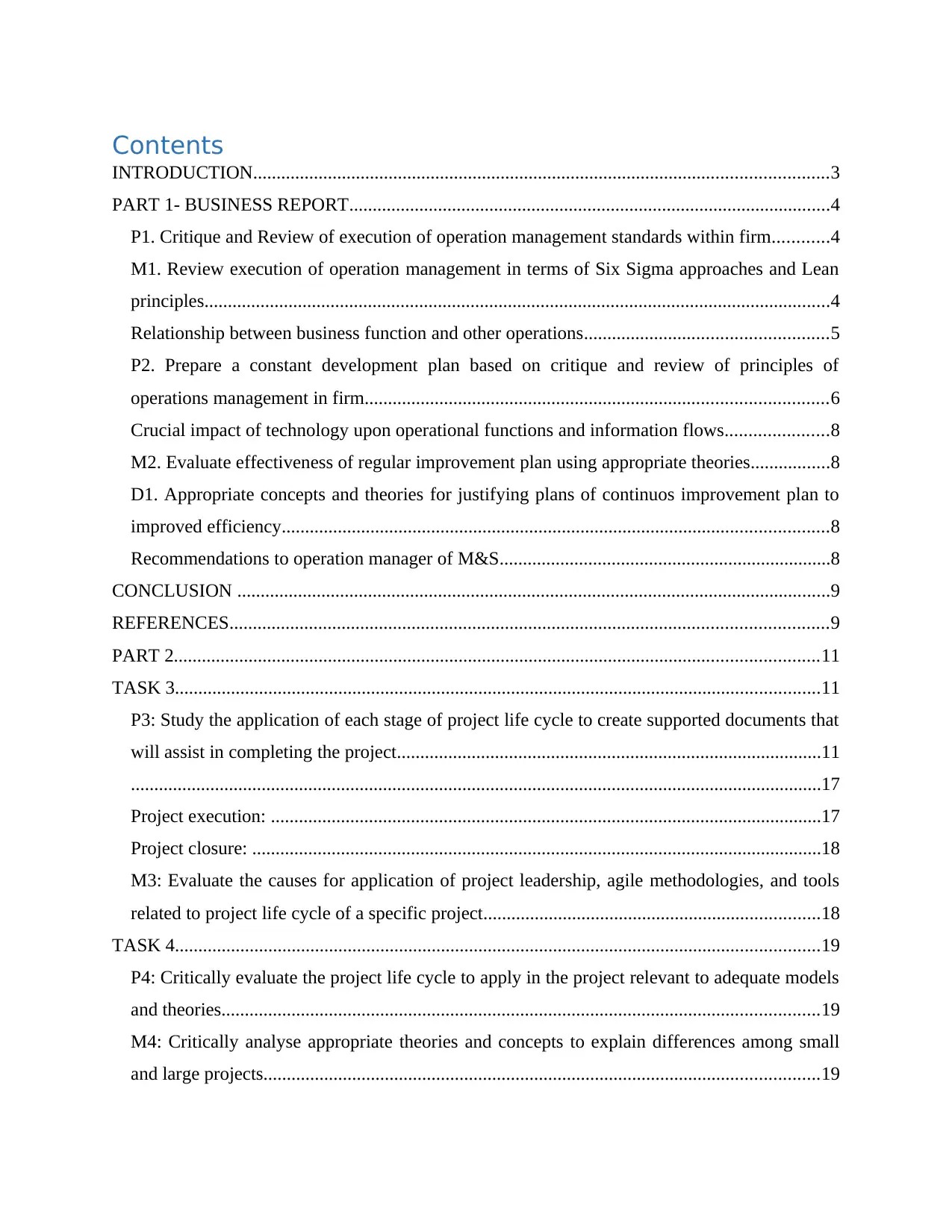
Contents
INTRODUCTION...........................................................................................................................3
PART 1- BUSINESS REPORT.......................................................................................................4
P1. Critique and Review of execution of operation management standards within firm............4
M1. Review execution of operation management in terms of Six Sigma approaches and Lean
principles......................................................................................................................................4
Relationship between business function and other operations....................................................5
P2. Prepare a constant development plan based on critique and review of principles of
operations management in firm...................................................................................................6
Crucial impact of technology upon operational functions and information flows......................8
M2. Evaluate effectiveness of regular improvement plan using appropriate theories.................8
D1. Appropriate concepts and theories for justifying plans of continuos improvement plan to
improved efficiency.....................................................................................................................8
Recommendations to operation manager of M&S.......................................................................8
CONCLUSION ...............................................................................................................................9
REFERENCES................................................................................................................................9
PART 2..........................................................................................................................................11
TASK 3..........................................................................................................................................11
P3: Study the application of each stage of project life cycle to create supported documents that
will assist in completing the project...........................................................................................11
....................................................................................................................................................17
Project execution: ......................................................................................................................17
Project closure: ..........................................................................................................................18
M3: Evaluate the causes for application of project leadership, agile methodologies, and tools
related to project life cycle of a specific project........................................................................18
TASK 4..........................................................................................................................................19
P4: Critically evaluate the project life cycle to apply in the project relevant to adequate models
and theories................................................................................................................................19
M4: Critically analyse appropriate theories and concepts to explain differences among small
and large projects.......................................................................................................................19
INTRODUCTION...........................................................................................................................3
PART 1- BUSINESS REPORT.......................................................................................................4
P1. Critique and Review of execution of operation management standards within firm............4
M1. Review execution of operation management in terms of Six Sigma approaches and Lean
principles......................................................................................................................................4
Relationship between business function and other operations....................................................5
P2. Prepare a constant development plan based on critique and review of principles of
operations management in firm...................................................................................................6
Crucial impact of technology upon operational functions and information flows......................8
M2. Evaluate effectiveness of regular improvement plan using appropriate theories.................8
D1. Appropriate concepts and theories for justifying plans of continuos improvement plan to
improved efficiency.....................................................................................................................8
Recommendations to operation manager of M&S.......................................................................8
CONCLUSION ...............................................................................................................................9
REFERENCES................................................................................................................................9
PART 2..........................................................................................................................................11
TASK 3..........................................................................................................................................11
P3: Study the application of each stage of project life cycle to create supported documents that
will assist in completing the project...........................................................................................11
....................................................................................................................................................17
Project execution: ......................................................................................................................17
Project closure: ..........................................................................................................................18
M3: Evaluate the causes for application of project leadership, agile methodologies, and tools
related to project life cycle of a specific project........................................................................18
TASK 4..........................................................................................................................................19
P4: Critically evaluate the project life cycle to apply in the project relevant to adequate models
and theories................................................................................................................................19
M4: Critically analyse appropriate theories and concepts to explain differences among small
and large projects.......................................................................................................................19
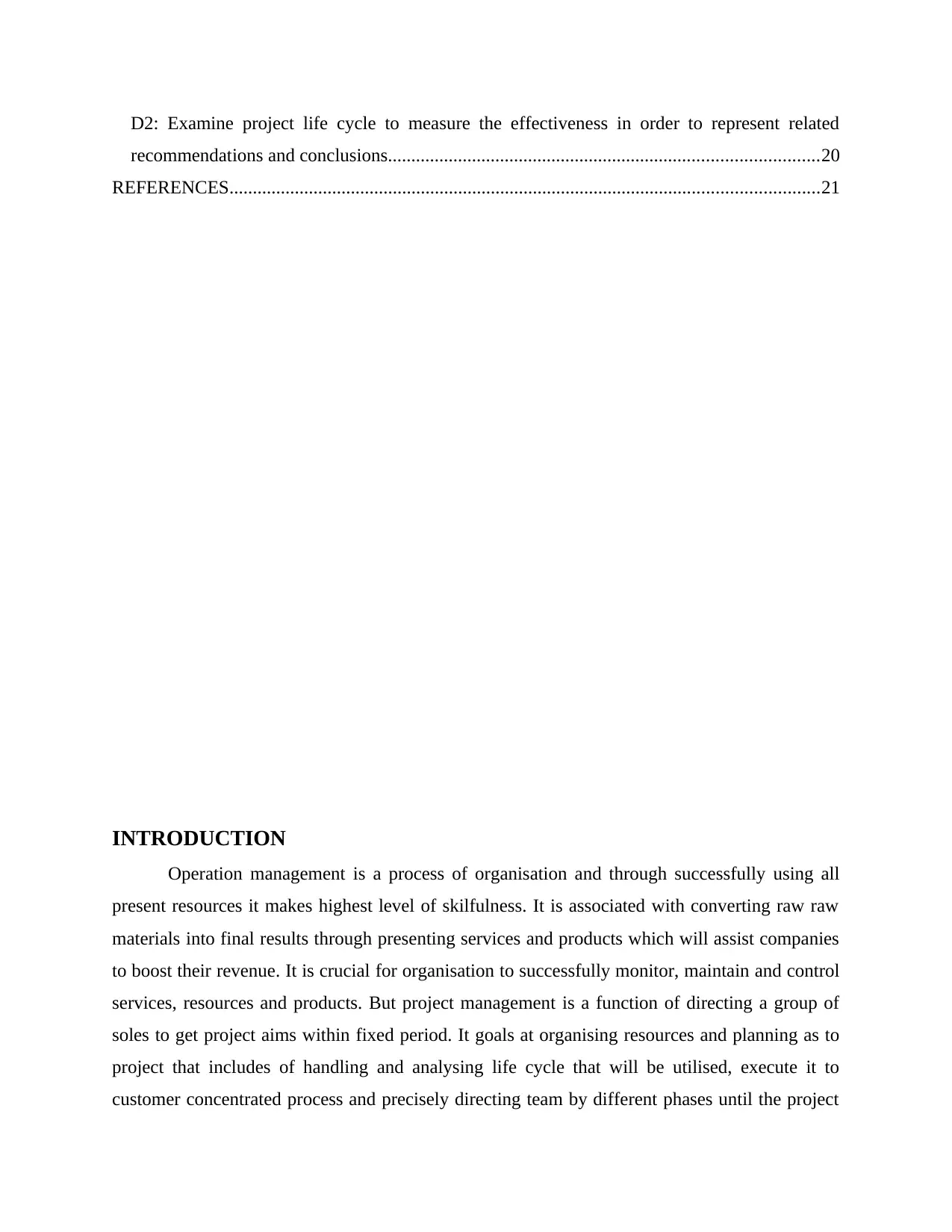
D2: Examine project life cycle to measure the effectiveness in order to represent related
recommendations and conclusions............................................................................................20
REFERENCES..............................................................................................................................21
INTRODUCTION
Operation management is a process of organisation and through successfully using all
present resources it makes highest level of skilfulness. It is associated with converting raw raw
materials into final results through presenting services and products which will assist companies
to boost their revenue. It is crucial for organisation to successfully monitor, maintain and control
services, resources and products. But project management is a function of directing a group of
soles to get project aims within fixed period. It goals at organising resources and planning as to
project that includes of handling and analysing life cycle that will be utilised, execute it to
customer concentrated process and precisely directing team by different phases until the project
recommendations and conclusions............................................................................................20
REFERENCES..............................................................................................................................21
INTRODUCTION
Operation management is a process of organisation and through successfully using all
present resources it makes highest level of skilfulness. It is associated with converting raw raw
materials into final results through presenting services and products which will assist companies
to boost their revenue. It is crucial for organisation to successfully monitor, maintain and control
services, resources and products. But project management is a function of directing a group of
soles to get project aims within fixed period. It goals at organising resources and planning as to
project that includes of handling and analysing life cycle that will be utilised, execute it to
customer concentrated process and precisely directing team by different phases until the project
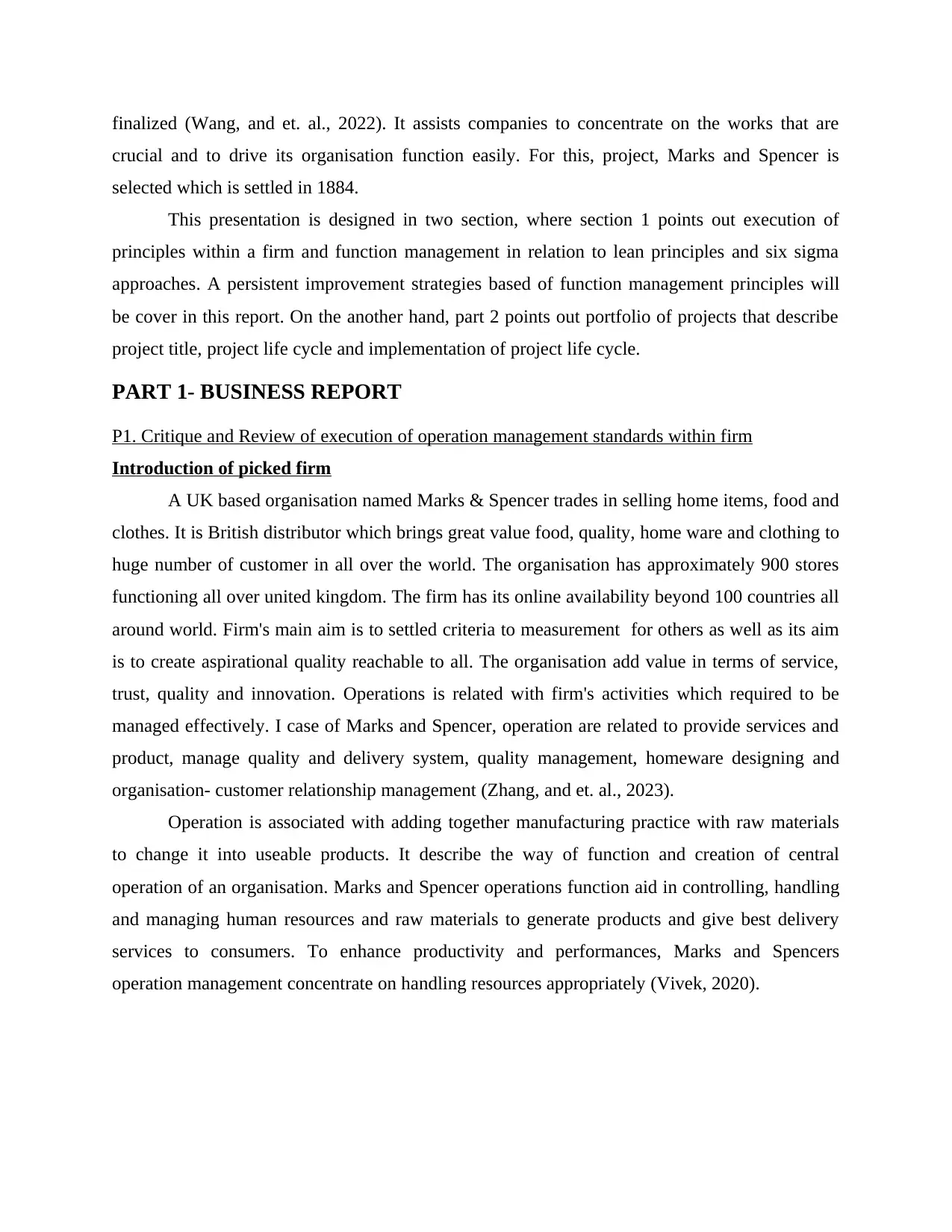
finalized (Wang, and et. al., 2022). It assists companies to concentrate on the works that are
crucial and to drive its organisation function easily. For this, project, Marks and Spencer is
selected which is settled in 1884.
This presentation is designed in two section, where section 1 points out execution of
principles within a firm and function management in relation to lean principles and six sigma
approaches. A persistent improvement strategies based of function management principles will
be cover in this report. On the another hand, part 2 points out portfolio of projects that describe
project title, project life cycle and implementation of project life cycle.
PART 1- BUSINESS REPORT
P1. Critique and Review of execution of operation management standards within firm
Introduction of picked firm
A UK based organisation named Marks & Spencer trades in selling home items, food and
clothes. It is British distributor which brings great value food, quality, home ware and clothing to
huge number of customer in all over the world. The organisation has approximately 900 stores
functioning all over united kingdom. The firm has its online availability beyond 100 countries all
around world. Firm's main aim is to settled criteria to measurement for others as well as its aim
is to create aspirational quality reachable to all. The organisation add value in terms of service,
trust, quality and innovation. Operations is related with firm's activities which required to be
managed effectively. I case of Marks and Spencer, operation are related to provide services and
product, manage quality and delivery system, quality management, homeware designing and
organisation- customer relationship management (Zhang, and et. al., 2023).
Operation is associated with adding together manufacturing practice with raw materials
to change it into useable products. It describe the way of function and creation of central
operation of an organisation. Marks and Spencer operations function aid in controlling, handling
and managing human resources and raw materials to generate products and give best delivery
services to consumers. To enhance productivity and performances, Marks and Spencers
operation management concentrate on handling resources appropriately (Vivek, 2020).
crucial and to drive its organisation function easily. For this, project, Marks and Spencer is
selected which is settled in 1884.
This presentation is designed in two section, where section 1 points out execution of
principles within a firm and function management in relation to lean principles and six sigma
approaches. A persistent improvement strategies based of function management principles will
be cover in this report. On the another hand, part 2 points out portfolio of projects that describe
project title, project life cycle and implementation of project life cycle.
PART 1- BUSINESS REPORT
P1. Critique and Review of execution of operation management standards within firm
Introduction of picked firm
A UK based organisation named Marks & Spencer trades in selling home items, food and
clothes. It is British distributor which brings great value food, quality, home ware and clothing to
huge number of customer in all over the world. The organisation has approximately 900 stores
functioning all over united kingdom. The firm has its online availability beyond 100 countries all
around world. Firm's main aim is to settled criteria to measurement for others as well as its aim
is to create aspirational quality reachable to all. The organisation add value in terms of service,
trust, quality and innovation. Operations is related with firm's activities which required to be
managed effectively. I case of Marks and Spencer, operation are related to provide services and
product, manage quality and delivery system, quality management, homeware designing and
organisation- customer relationship management (Zhang, and et. al., 2023).
Operation is associated with adding together manufacturing practice with raw materials
to change it into useable products. It describe the way of function and creation of central
operation of an organisation. Marks and Spencer operations function aid in controlling, handling
and managing human resources and raw materials to generate products and give best delivery
services to consumers. To enhance productivity and performances, Marks and Spencers
operation management concentrate on handling resources appropriately (Vivek, 2020).
Secure Best Marks with AI Grader
Need help grading? Try our AI Grader for instant feedback on your assignments.
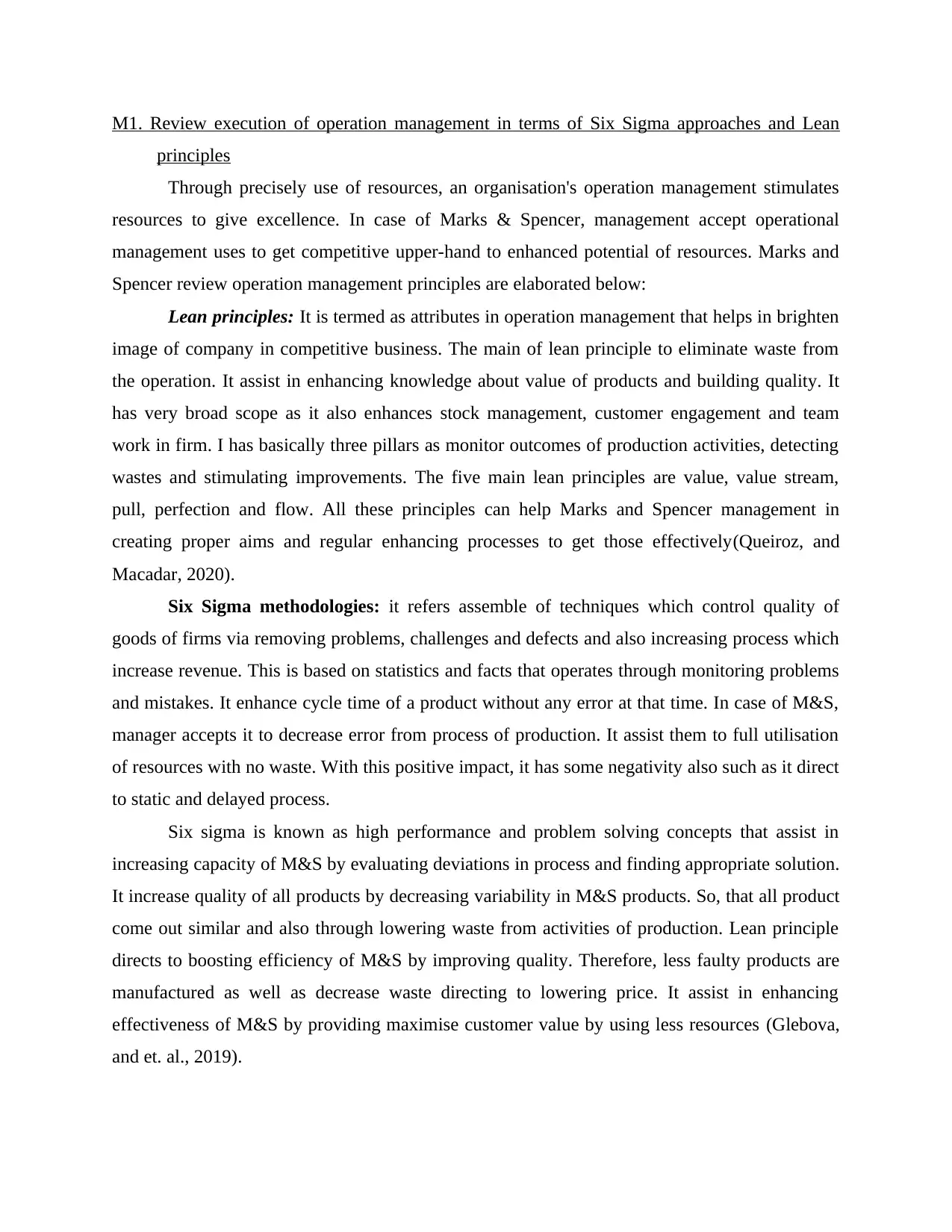
M1. Review execution of operation management in terms of Six Sigma approaches and Lean
principles
Through precisely use of resources, an organisation's operation management stimulates
resources to give excellence. In case of Marks & Spencer, management accept operational
management uses to get competitive upper-hand to enhanced potential of resources. Marks and
Spencer review operation management principles are elaborated below:
Lean principles: It is termed as attributes in operation management that helps in brighten
image of company in competitive business. The main of lean principle to eliminate waste from
the operation. It assist in enhancing knowledge about value of products and building quality. It
has very broad scope as it also enhances stock management, customer engagement and team
work in firm. I has basically three pillars as monitor outcomes of production activities, detecting
wastes and stimulating improvements. The five main lean principles are value, value stream,
pull, perfection and flow. All these principles can help Marks and Spencer management in
creating proper aims and regular enhancing processes to get those effectively(Queiroz, and
Macadar, 2020).
Six Sigma methodologies: it refers assemble of techniques which control quality of
goods of firms via removing problems, challenges and defects and also increasing process which
increase revenue. This is based on statistics and facts that operates through monitoring problems
and mistakes. It enhance cycle time of a product without any error at that time. In case of M&S,
manager accepts it to decrease error from process of production. It assist them to full utilisation
of resources with no waste. With this positive impact, it has some negativity also such as it direct
to static and delayed process.
Six sigma is known as high performance and problem solving concepts that assist in
increasing capacity of M&S by evaluating deviations in process and finding appropriate solution.
It increase quality of all products by decreasing variability in M&S products. So, that all product
come out similar and also through lowering waste from activities of production. Lean principle
directs to boosting efficiency of M&S by improving quality. Therefore, less faulty products are
manufactured as well as decrease waste directing to lowering price. It assist in enhancing
effectiveness of M&S by providing maximise customer value by using less resources (Glebova,
and et. al., 2019).
principles
Through precisely use of resources, an organisation's operation management stimulates
resources to give excellence. In case of Marks & Spencer, management accept operational
management uses to get competitive upper-hand to enhanced potential of resources. Marks and
Spencer review operation management principles are elaborated below:
Lean principles: It is termed as attributes in operation management that helps in brighten
image of company in competitive business. The main of lean principle to eliminate waste from
the operation. It assist in enhancing knowledge about value of products and building quality. It
has very broad scope as it also enhances stock management, customer engagement and team
work in firm. I has basically three pillars as monitor outcomes of production activities, detecting
wastes and stimulating improvements. The five main lean principles are value, value stream,
pull, perfection and flow. All these principles can help Marks and Spencer management in
creating proper aims and regular enhancing processes to get those effectively(Queiroz, and
Macadar, 2020).
Six Sigma methodologies: it refers assemble of techniques which control quality of
goods of firms via removing problems, challenges and defects and also increasing process which
increase revenue. This is based on statistics and facts that operates through monitoring problems
and mistakes. It enhance cycle time of a product without any error at that time. In case of M&S,
manager accepts it to decrease error from process of production. It assist them to full utilisation
of resources with no waste. With this positive impact, it has some negativity also such as it direct
to static and delayed process.
Six sigma is known as high performance and problem solving concepts that assist in
increasing capacity of M&S by evaluating deviations in process and finding appropriate solution.
It increase quality of all products by decreasing variability in M&S products. So, that all product
come out similar and also through lowering waste from activities of production. Lean principle
directs to boosting efficiency of M&S by improving quality. Therefore, less faulty products are
manufactured as well as decrease waste directing to lowering price. It assist in enhancing
effectiveness of M&S by providing maximise customer value by using less resources (Glebova,
and et. al., 2019).
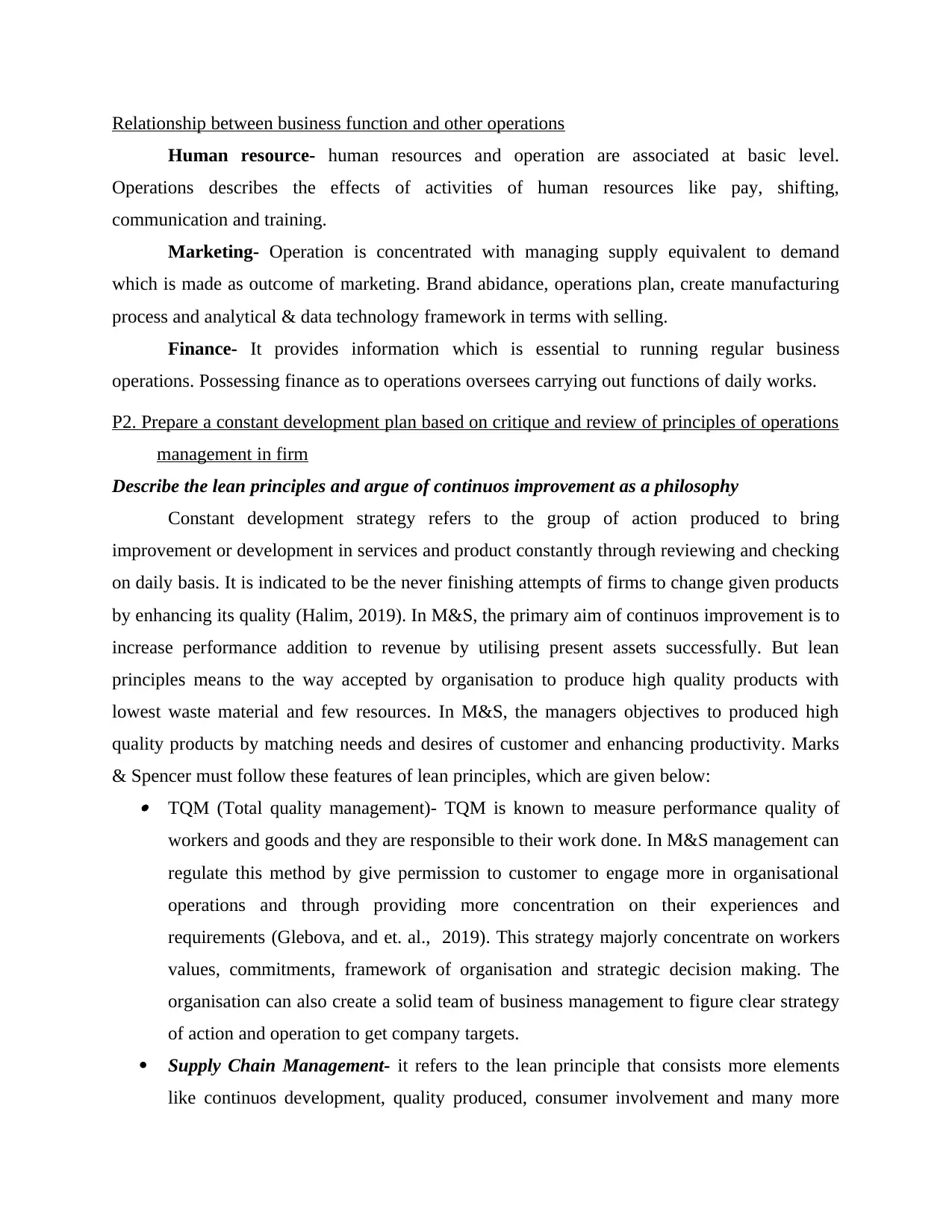
Relationship between business function and other operations
Human resource- human resources and operation are associated at basic level.
Operations describes the effects of activities of human resources like pay, shifting,
communication and training.
Marketing- Operation is concentrated with managing supply equivalent to demand
which is made as outcome of marketing. Brand abidance, operations plan, create manufacturing
process and analytical & data technology framework in terms with selling.
Finance- It provides information which is essential to running regular business
operations. Possessing finance as to operations oversees carrying out functions of daily works.
P2. Prepare a constant development plan based on critique and review of principles of operations
management in firm
Describe the lean principles and argue of continuos improvement as a philosophy
Constant development strategy refers to the group of action produced to bring
improvement or development in services and product constantly through reviewing and checking
on daily basis. It is indicated to be the never finishing attempts of firms to change given products
by enhancing its quality (Halim, 2019). In M&S, the primary aim of continuos improvement is to
increase performance addition to revenue by utilising present assets successfully. But lean
principles means to the way accepted by organisation to produce high quality products with
lowest waste material and few resources. In M&S, the managers objectives to produced high
quality products by matching needs and desires of customer and enhancing productivity. Marks
& Spencer must follow these features of lean principles, which are given below: TQM (Total quality management)- TQM is known to measure performance quality of
workers and goods and they are responsible to their work done. In M&S management can
regulate this method by give permission to customer to engage more in organisational
operations and through providing more concentration on their experiences and
requirements (Glebova, and et. al., 2019). This strategy majorly concentrate on workers
values, commitments, framework of organisation and strategic decision making. The
organisation can also create a solid team of business management to figure clear strategy
of action and operation to get company targets.
Supply Chain Management- it refers to the lean principle that consists more elements
like continuos development, quality produced, consumer involvement and many more
Human resource- human resources and operation are associated at basic level.
Operations describes the effects of activities of human resources like pay, shifting,
communication and training.
Marketing- Operation is concentrated with managing supply equivalent to demand
which is made as outcome of marketing. Brand abidance, operations plan, create manufacturing
process and analytical & data technology framework in terms with selling.
Finance- It provides information which is essential to running regular business
operations. Possessing finance as to operations oversees carrying out functions of daily works.
P2. Prepare a constant development plan based on critique and review of principles of operations
management in firm
Describe the lean principles and argue of continuos improvement as a philosophy
Constant development strategy refers to the group of action produced to bring
improvement or development in services and product constantly through reviewing and checking
on daily basis. It is indicated to be the never finishing attempts of firms to change given products
by enhancing its quality (Halim, 2019). In M&S, the primary aim of continuos improvement is to
increase performance addition to revenue by utilising present assets successfully. But lean
principles means to the way accepted by organisation to produce high quality products with
lowest waste material and few resources. In M&S, the managers objectives to produced high
quality products by matching needs and desires of customer and enhancing productivity. Marks
& Spencer must follow these features of lean principles, which are given below: TQM (Total quality management)- TQM is known to measure performance quality of
workers and goods and they are responsible to their work done. In M&S management can
regulate this method by give permission to customer to engage more in organisational
operations and through providing more concentration on their experiences and
requirements (Glebova, and et. al., 2019). This strategy majorly concentrate on workers
values, commitments, framework of organisation and strategic decision making. The
organisation can also create a solid team of business management to figure clear strategy
of action and operation to get company targets.
Supply Chain Management- it refers to the lean principle that consists more elements
like continuos development, quality produced, consumer involvement and many more
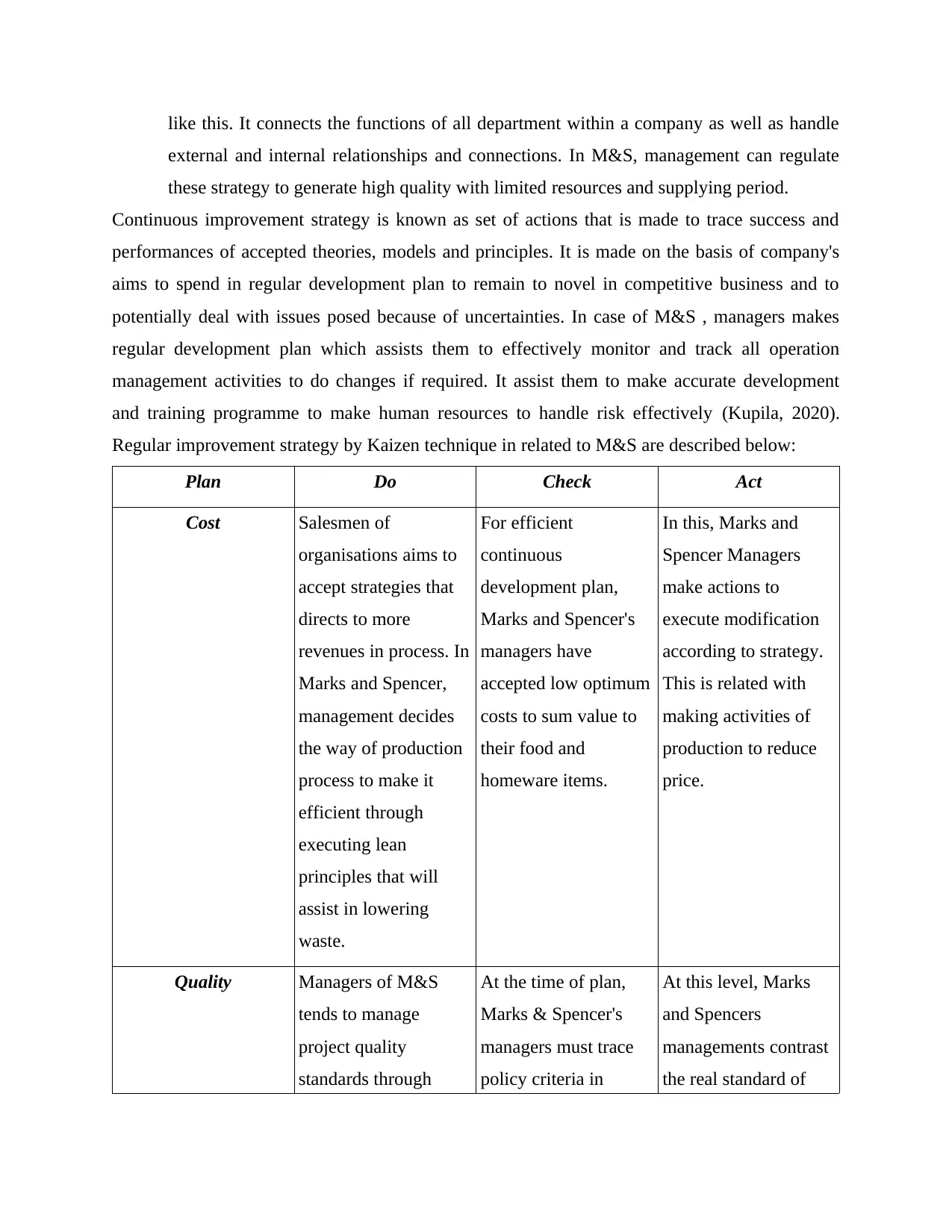
like this. It connects the functions of all department within a company as well as handle
external and internal relationships and connections. In M&S, management can regulate
these strategy to generate high quality with limited resources and supplying period.
Continuous improvement strategy is known as set of actions that is made to trace success and
performances of accepted theories, models and principles. It is made on the basis of company's
aims to spend in regular development plan to remain to novel in competitive business and to
potentially deal with issues posed because of uncertainties. In case of M&S , managers makes
regular development plan which assists them to effectively monitor and track all operation
management activities to do changes if required. It assist them to make accurate development
and training programme to make human resources to handle risk effectively (Kupila, 2020).
Regular improvement strategy by Kaizen technique in related to M&S are described below:
Plan Do Check Act
Cost Salesmen of
organisations aims to
accept strategies that
directs to more
revenues in process. In
Marks and Spencer,
management decides
the way of production
process to make it
efficient through
executing lean
principles that will
assist in lowering
waste.
For efficient
continuous
development plan,
Marks and Spencer's
managers have
accepted low optimum
costs to sum value to
their food and
homeware items.
In this, Marks and
Spencer Managers
make actions to
execute modification
according to strategy.
This is related with
making activities of
production to reduce
price.
Quality Managers of M&S
tends to manage
project quality
standards through
At the time of plan,
Marks & Spencer's
managers must trace
policy criteria in
At this level, Marks
and Spencers
managements contrast
the real standard of
external and internal relationships and connections. In M&S, management can regulate
these strategy to generate high quality with limited resources and supplying period.
Continuous improvement strategy is known as set of actions that is made to trace success and
performances of accepted theories, models and principles. It is made on the basis of company's
aims to spend in regular development plan to remain to novel in competitive business and to
potentially deal with issues posed because of uncertainties. In case of M&S , managers makes
regular development plan which assists them to effectively monitor and track all operation
management activities to do changes if required. It assist them to make accurate development
and training programme to make human resources to handle risk effectively (Kupila, 2020).
Regular improvement strategy by Kaizen technique in related to M&S are described below:
Plan Do Check Act
Cost Salesmen of
organisations aims to
accept strategies that
directs to more
revenues in process. In
Marks and Spencer,
management decides
the way of production
process to make it
efficient through
executing lean
principles that will
assist in lowering
waste.
For efficient
continuous
development plan,
Marks and Spencer's
managers have
accepted low optimum
costs to sum value to
their food and
homeware items.
In this, Marks and
Spencer Managers
make actions to
execute modification
according to strategy.
This is related with
making activities of
production to reduce
price.
Quality Managers of M&S
tends to manage
project quality
standards through
At the time of plan,
Marks & Spencer's
managers must trace
policy criteria in
At this level, Marks
and Spencers
managements contrast
the real standard of
Paraphrase This Document
Need a fresh take? Get an instant paraphrase of this document with our AI Paraphraser
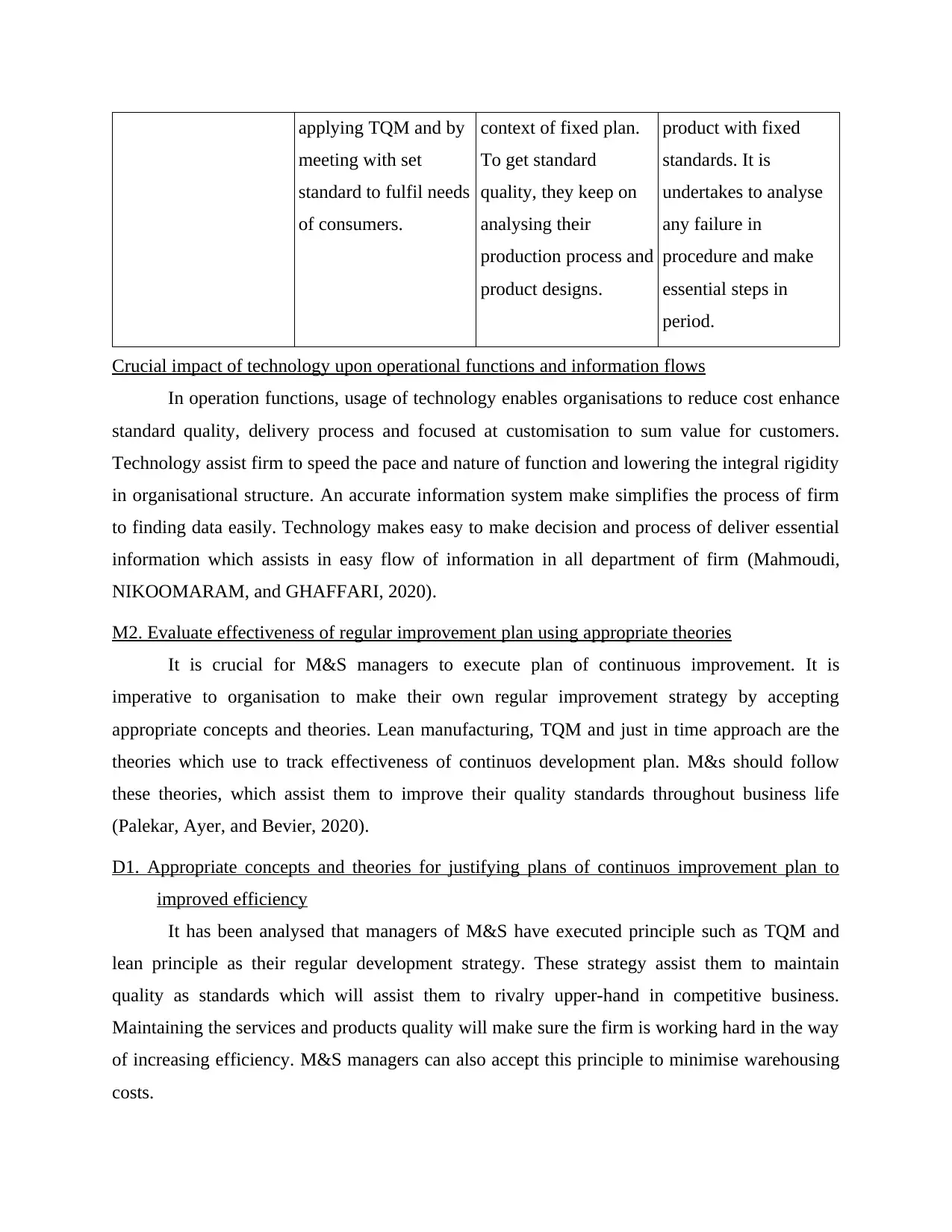
applying TQM and by
meeting with set
standard to fulfil needs
of consumers.
context of fixed plan.
To get standard
quality, they keep on
analysing their
production process and
product designs.
product with fixed
standards. It is
undertakes to analyse
any failure in
procedure and make
essential steps in
period.
Crucial impact of technology upon operational functions and information flows
In operation functions, usage of technology enables organisations to reduce cost enhance
standard quality, delivery process and focused at customisation to sum value for customers.
Technology assist firm to speed the pace and nature of function and lowering the integral rigidity
in organisational structure. An accurate information system make simplifies the process of firm
to finding data easily. Technology makes easy to make decision and process of deliver essential
information which assists in easy flow of information in all department of firm (Mahmoudi,
NIKOOMARAM, and GHAFFARI, 2020).
M2. Evaluate effectiveness of regular improvement plan using appropriate theories
It is crucial for M&S managers to execute plan of continuous improvement. It is
imperative to organisation to make their own regular improvement strategy by accepting
appropriate concepts and theories. Lean manufacturing, TQM and just in time approach are the
theories which use to track effectiveness of continuos development plan. M&s should follow
these theories, which assist them to improve their quality standards throughout business life
(Palekar, Ayer, and Bevier, 2020).
D1. Appropriate concepts and theories for justifying plans of continuos improvement plan to
improved efficiency
It has been analysed that managers of M&S have executed principle such as TQM and
lean principle as their regular development strategy. These strategy assist them to maintain
quality as standards which will assist them to rivalry upper-hand in competitive business.
Maintaining the services and products quality will make sure the firm is working hard in the way
of increasing efficiency. M&S managers can also accept this principle to minimise warehousing
costs.
meeting with set
standard to fulfil needs
of consumers.
context of fixed plan.
To get standard
quality, they keep on
analysing their
production process and
product designs.
product with fixed
standards. It is
undertakes to analyse
any failure in
procedure and make
essential steps in
period.
Crucial impact of technology upon operational functions and information flows
In operation functions, usage of technology enables organisations to reduce cost enhance
standard quality, delivery process and focused at customisation to sum value for customers.
Technology assist firm to speed the pace and nature of function and lowering the integral rigidity
in organisational structure. An accurate information system make simplifies the process of firm
to finding data easily. Technology makes easy to make decision and process of deliver essential
information which assists in easy flow of information in all department of firm (Mahmoudi,
NIKOOMARAM, and GHAFFARI, 2020).
M2. Evaluate effectiveness of regular improvement plan using appropriate theories
It is crucial for M&S managers to execute plan of continuous improvement. It is
imperative to organisation to make their own regular improvement strategy by accepting
appropriate concepts and theories. Lean manufacturing, TQM and just in time approach are the
theories which use to track effectiveness of continuos development plan. M&s should follow
these theories, which assist them to improve their quality standards throughout business life
(Palekar, Ayer, and Bevier, 2020).
D1. Appropriate concepts and theories for justifying plans of continuos improvement plan to
improved efficiency
It has been analysed that managers of M&S have executed principle such as TQM and
lean principle as their regular development strategy. These strategy assist them to maintain
quality as standards which will assist them to rivalry upper-hand in competitive business.
Maintaining the services and products quality will make sure the firm is working hard in the way
of increasing efficiency. M&S managers can also accept this principle to minimise warehousing
costs.
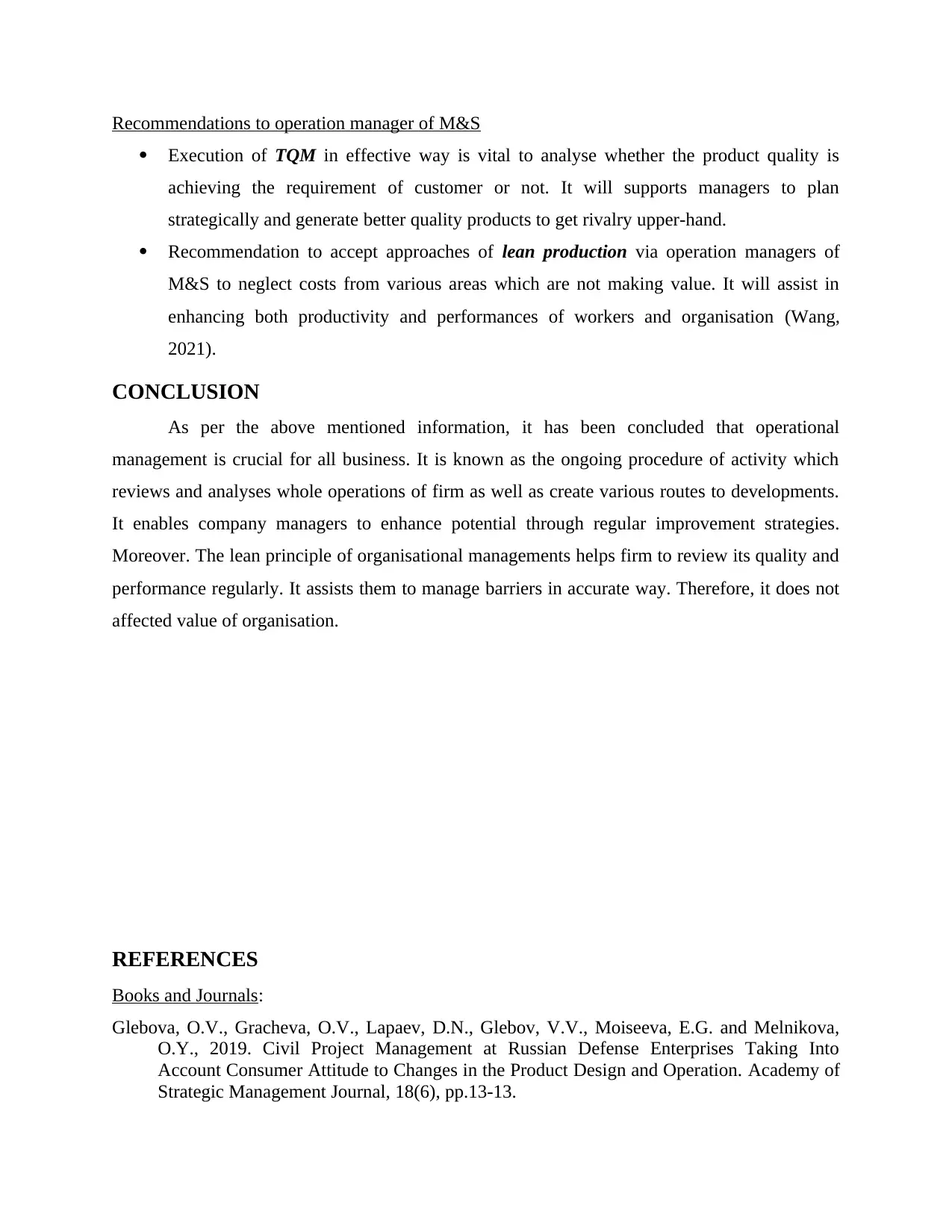
Recommendations to operation manager of M&S
Execution of TQM in effective way is vital to analyse whether the product quality is
achieving the requirement of customer or not. It will supports managers to plan
strategically and generate better quality products to get rivalry upper-hand.
Recommendation to accept approaches of lean production via operation managers of
M&S to neglect costs from various areas which are not making value. It will assist in
enhancing both productivity and performances of workers and organisation (Wang,
2021).
CONCLUSION
As per the above mentioned information, it has been concluded that operational
management is crucial for all business. It is known as the ongoing procedure of activity which
reviews and analyses whole operations of firm as well as create various routes to developments.
It enables company managers to enhance potential through regular improvement strategies.
Moreover. The lean principle of organisational managements helps firm to review its quality and
performance regularly. It assists them to manage barriers in accurate way. Therefore, it does not
affected value of organisation.
REFERENCES
Books and Journals:
Glebova, O.V., Gracheva, O.V., Lapaev, D.N., Glebov, V.V., Moiseeva, E.G. and Melnikova,
O.Y., 2019. Civil Project Management at Russian Defense Enterprises Taking Into
Account Consumer Attitude to Changes in the Product Design and Operation. Academy of
Strategic Management Journal, 18(6), pp.13-13.
Execution of TQM in effective way is vital to analyse whether the product quality is
achieving the requirement of customer or not. It will supports managers to plan
strategically and generate better quality products to get rivalry upper-hand.
Recommendation to accept approaches of lean production via operation managers of
M&S to neglect costs from various areas which are not making value. It will assist in
enhancing both productivity and performances of workers and organisation (Wang,
2021).
CONCLUSION
As per the above mentioned information, it has been concluded that operational
management is crucial for all business. It is known as the ongoing procedure of activity which
reviews and analyses whole operations of firm as well as create various routes to developments.
It enables company managers to enhance potential through regular improvement strategies.
Moreover. The lean principle of organisational managements helps firm to review its quality and
performance regularly. It assists them to manage barriers in accurate way. Therefore, it does not
affected value of organisation.
REFERENCES
Books and Journals:
Glebova, O.V., Gracheva, O.V., Lapaev, D.N., Glebov, V.V., Moiseeva, E.G. and Melnikova,
O.Y., 2019. Civil Project Management at Russian Defense Enterprises Taking Into
Account Consumer Attitude to Changes in the Product Design and Operation. Academy of
Strategic Management Journal, 18(6), pp.13-13.
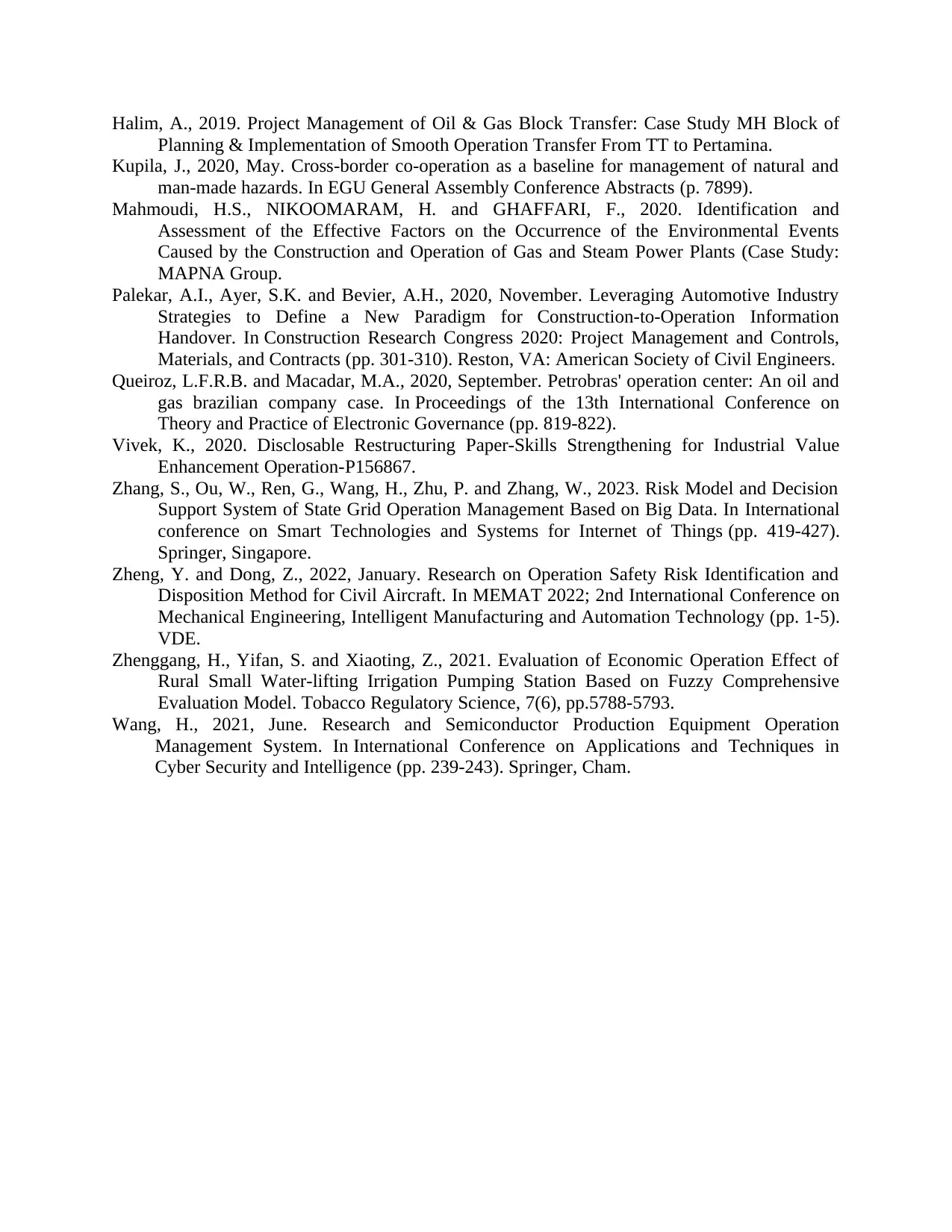
Halim, A., 2019. Project Management of Oil & Gas Block Transfer: Case Study MH Block of
Planning & Implementation of Smooth Operation Transfer From TT to Pertamina.
Kupila, J., 2020, May. Cross-border co-operation as a baseline for management of natural and
man-made hazards. In EGU General Assembly Conference Abstracts (p. 7899).
Mahmoudi, H.S., NIKOOMARAM, H. and GHAFFARI, F., 2020. Identification and
Assessment of the Effective Factors on the Occurrence of the Environmental Events
Caused by the Construction and Operation of Gas and Steam Power Plants (Case Study:
MAPNA Group.
Palekar, A.I., Ayer, S.K. and Bevier, A.H., 2020, November. Leveraging Automotive Industry
Strategies to Define a New Paradigm for Construction-to-Operation Information
Handover. In Construction Research Congress 2020: Project Management and Controls,
Materials, and Contracts (pp. 301-310). Reston, VA: American Society of Civil Engineers.
Queiroz, L.F.R.B. and Macadar, M.A., 2020, September. Petrobras' operation center: An oil and
gas brazilian company case. In Proceedings of the 13th International Conference on
Theory and Practice of Electronic Governance (pp. 819-822).
Vivek, K., 2020. Disclosable Restructuring Paper-Skills Strengthening for Industrial Value
Enhancement Operation-P156867.
Zhang, S., Ou, W., Ren, G., Wang, H., Zhu, P. and Zhang, W., 2023. Risk Model and Decision
Support System of State Grid Operation Management Based on Big Data. In International
conference on Smart Technologies and Systems for Internet of Things (pp. 419-427).
Springer, Singapore.
Zheng, Y. and Dong, Z., 2022, January. Research on Operation Safety Risk Identification and
Disposition Method for Civil Aircraft. In MEMAT 2022; 2nd International Conference on
Mechanical Engineering, Intelligent Manufacturing and Automation Technology (pp. 1-5).
VDE.
Zhenggang, H., Yifan, S. and Xiaoting, Z., 2021. Evaluation of Economic Operation Effect of
Rural Small Water-lifting Irrigation Pumping Station Based on Fuzzy Comprehensive
Evaluation Model. Tobacco Regulatory Science, 7(6), pp.5788-5793.
Wang, H., 2021, June. Research and Semiconductor Production Equipment Operation
Management System. In International Conference on Applications and Techniques in
Cyber Security and Intelligence (pp. 239-243). Springer, Cham.
Planning & Implementation of Smooth Operation Transfer From TT to Pertamina.
Kupila, J., 2020, May. Cross-border co-operation as a baseline for management of natural and
man-made hazards. In EGU General Assembly Conference Abstracts (p. 7899).
Mahmoudi, H.S., NIKOOMARAM, H. and GHAFFARI, F., 2020. Identification and
Assessment of the Effective Factors on the Occurrence of the Environmental Events
Caused by the Construction and Operation of Gas and Steam Power Plants (Case Study:
MAPNA Group.
Palekar, A.I., Ayer, S.K. and Bevier, A.H., 2020, November. Leveraging Automotive Industry
Strategies to Define a New Paradigm for Construction-to-Operation Information
Handover. In Construction Research Congress 2020: Project Management and Controls,
Materials, and Contracts (pp. 301-310). Reston, VA: American Society of Civil Engineers.
Queiroz, L.F.R.B. and Macadar, M.A., 2020, September. Petrobras' operation center: An oil and
gas brazilian company case. In Proceedings of the 13th International Conference on
Theory and Practice of Electronic Governance (pp. 819-822).
Vivek, K., 2020. Disclosable Restructuring Paper-Skills Strengthening for Industrial Value
Enhancement Operation-P156867.
Zhang, S., Ou, W., Ren, G., Wang, H., Zhu, P. and Zhang, W., 2023. Risk Model and Decision
Support System of State Grid Operation Management Based on Big Data. In International
conference on Smart Technologies and Systems for Internet of Things (pp. 419-427).
Springer, Singapore.
Zheng, Y. and Dong, Z., 2022, January. Research on Operation Safety Risk Identification and
Disposition Method for Civil Aircraft. In MEMAT 2022; 2nd International Conference on
Mechanical Engineering, Intelligent Manufacturing and Automation Technology (pp. 1-5).
VDE.
Zhenggang, H., Yifan, S. and Xiaoting, Z., 2021. Evaluation of Economic Operation Effect of
Rural Small Water-lifting Irrigation Pumping Station Based on Fuzzy Comprehensive
Evaluation Model. Tobacco Regulatory Science, 7(6), pp.5788-5793.
Wang, H., 2021, June. Research and Semiconductor Production Equipment Operation
Management System. In International Conference on Applications and Techniques in
Cyber Security and Intelligence (pp. 239-243). Springer, Cham.
Secure Best Marks with AI Grader
Need help grading? Try our AI Grader for instant feedback on your assignments.
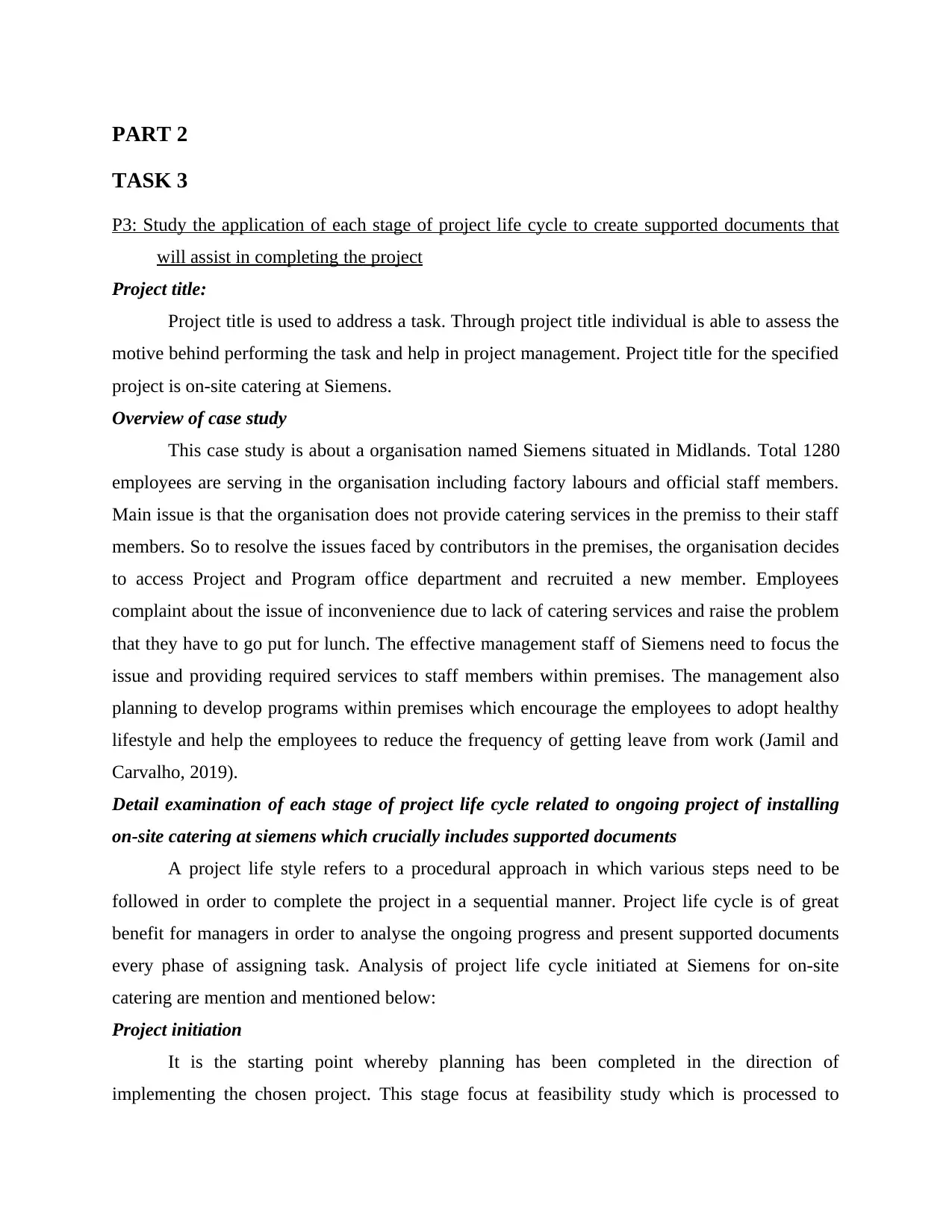
PART 2
TASK 3
P3: Study the application of each stage of project life cycle to create supported documents that
will assist in completing the project
Project title:
Project title is used to address a task. Through project title individual is able to assess the
motive behind performing the task and help in project management. Project title for the specified
project is on-site catering at Siemens.
Overview of case study
This case study is about a organisation named Siemens situated in Midlands. Total 1280
employees are serving in the organisation including factory labours and official staff members.
Main issue is that the organisation does not provide catering services in the premiss to their staff
members. So to resolve the issues faced by contributors in the premises, the organisation decides
to access Project and Program office department and recruited a new member. Employees
complaint about the issue of inconvenience due to lack of catering services and raise the problem
that they have to go put for lunch. The effective management staff of Siemens need to focus the
issue and providing required services to staff members within premises. The management also
planning to develop programs within premises which encourage the employees to adopt healthy
lifestyle and help the employees to reduce the frequency of getting leave from work (Jamil and
Carvalho, 2019).
Detail examination of each stage of project life cycle related to ongoing project of installing
on-site catering at siemens which crucially includes supported documents
A project life style refers to a procedural approach in which various steps need to be
followed in order to complete the project in a sequential manner. Project life cycle is of great
benefit for managers in order to analyse the ongoing progress and present supported documents
every phase of assigning task. Analysis of project life cycle initiated at Siemens for on-site
catering are mention and mentioned below:
Project initiation
It is the starting point whereby planning has been completed in the direction of
implementing the chosen project. This stage focus at feasibility study which is processed to
TASK 3
P3: Study the application of each stage of project life cycle to create supported documents that
will assist in completing the project
Project title:
Project title is used to address a task. Through project title individual is able to assess the
motive behind performing the task and help in project management. Project title for the specified
project is on-site catering at Siemens.
Overview of case study
This case study is about a organisation named Siemens situated in Midlands. Total 1280
employees are serving in the organisation including factory labours and official staff members.
Main issue is that the organisation does not provide catering services in the premiss to their staff
members. So to resolve the issues faced by contributors in the premises, the organisation decides
to access Project and Program office department and recruited a new member. Employees
complaint about the issue of inconvenience due to lack of catering services and raise the problem
that they have to go put for lunch. The effective management staff of Siemens need to focus the
issue and providing required services to staff members within premises. The management also
planning to develop programs within premises which encourage the employees to adopt healthy
lifestyle and help the employees to reduce the frequency of getting leave from work (Jamil and
Carvalho, 2019).
Detail examination of each stage of project life cycle related to ongoing project of installing
on-site catering at siemens which crucially includes supported documents
A project life style refers to a procedural approach in which various steps need to be
followed in order to complete the project in a sequential manner. Project life cycle is of great
benefit for managers in order to analyse the ongoing progress and present supported documents
every phase of assigning task. Analysis of project life cycle initiated at Siemens for on-site
catering are mention and mentioned below:
Project initiation
It is the starting point whereby planning has been completed in the direction of
implementing the chosen project. This stage focus at feasibility study which is processed to
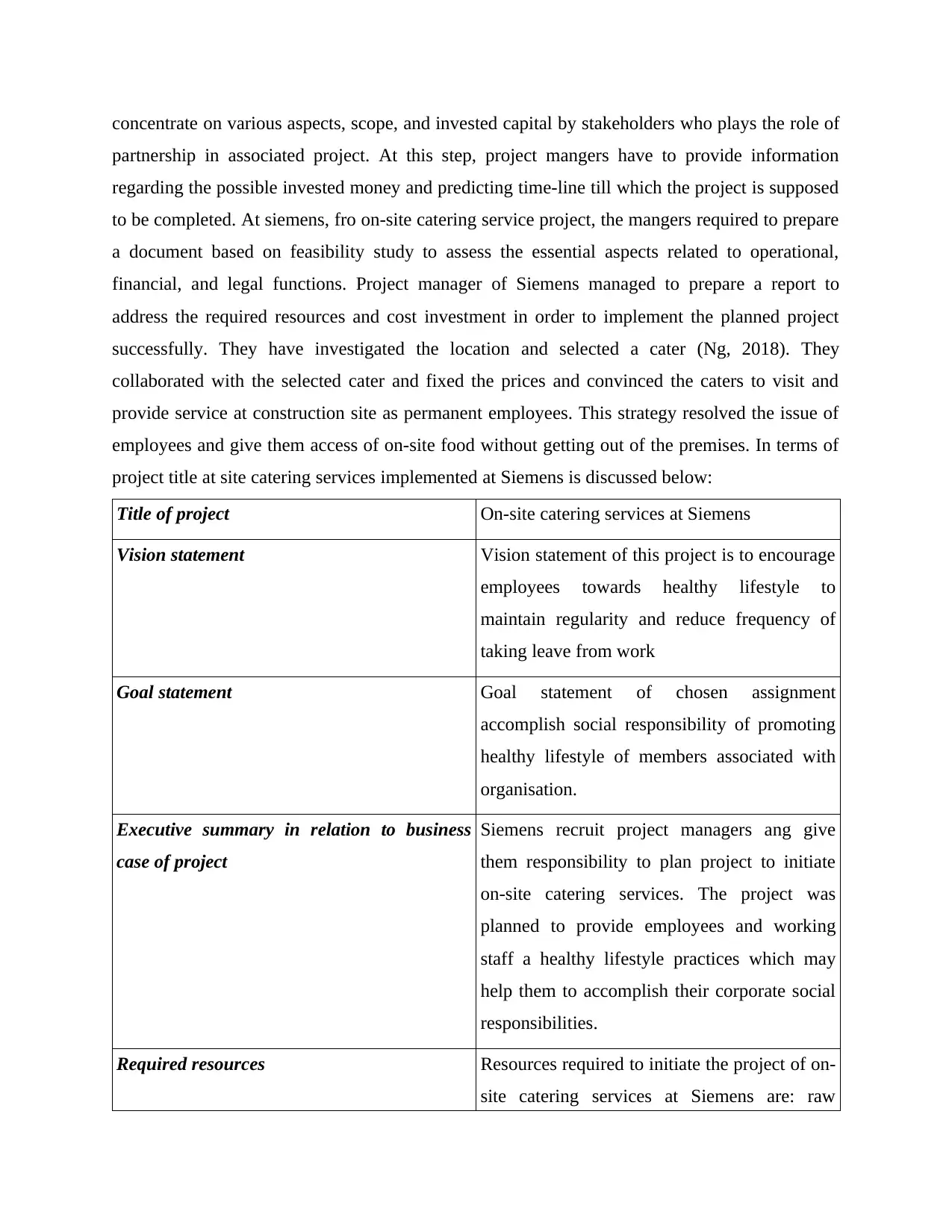
concentrate on various aspects, scope, and invested capital by stakeholders who plays the role of
partnership in associated project. At this step, project mangers have to provide information
regarding the possible invested money and predicting time-line till which the project is supposed
to be completed. At siemens, fro on-site catering service project, the mangers required to prepare
a document based on feasibility study to assess the essential aspects related to operational,
financial, and legal functions. Project manager of Siemens managed to prepare a report to
address the required resources and cost investment in order to implement the planned project
successfully. They have investigated the location and selected a cater (Ng, 2018). They
collaborated with the selected cater and fixed the prices and convinced the caters to visit and
provide service at construction site as permanent employees. This strategy resolved the issue of
employees and give them access of on-site food without getting out of the premises. In terms of
project title at site catering services implemented at Siemens is discussed below:
Title of project On-site catering services at Siemens
Vision statement Vision statement of this project is to encourage
employees towards healthy lifestyle to
maintain regularity and reduce frequency of
taking leave from work
Goal statement Goal statement of chosen assignment
accomplish social responsibility of promoting
healthy lifestyle of members associated with
organisation.
Executive summary in relation to business
case of project
Siemens recruit project managers ang give
them responsibility to plan project to initiate
on-site catering services. The project was
planned to provide employees and working
staff a healthy lifestyle practices which may
help them to accomplish their corporate social
responsibilities.
Required resources Resources required to initiate the project of on-
site catering services at Siemens are: raw
partnership in associated project. At this step, project mangers have to provide information
regarding the possible invested money and predicting time-line till which the project is supposed
to be completed. At siemens, fro on-site catering service project, the mangers required to prepare
a document based on feasibility study to assess the essential aspects related to operational,
financial, and legal functions. Project manager of Siemens managed to prepare a report to
address the required resources and cost investment in order to implement the planned project
successfully. They have investigated the location and selected a cater (Ng, 2018). They
collaborated with the selected cater and fixed the prices and convinced the caters to visit and
provide service at construction site as permanent employees. This strategy resolved the issue of
employees and give them access of on-site food without getting out of the premises. In terms of
project title at site catering services implemented at Siemens is discussed below:
Title of project On-site catering services at Siemens
Vision statement Vision statement of this project is to encourage
employees towards healthy lifestyle to
maintain regularity and reduce frequency of
taking leave from work
Goal statement Goal statement of chosen assignment
accomplish social responsibility of promoting
healthy lifestyle of members associated with
organisation.
Executive summary in relation to business
case of project
Siemens recruit project managers ang give
them responsibility to plan project to initiate
on-site catering services. The project was
planned to provide employees and working
staff a healthy lifestyle practices which may
help them to accomplish their corporate social
responsibilities.
Required resources Resources required to initiate the project of on-
site catering services at Siemens are: raw
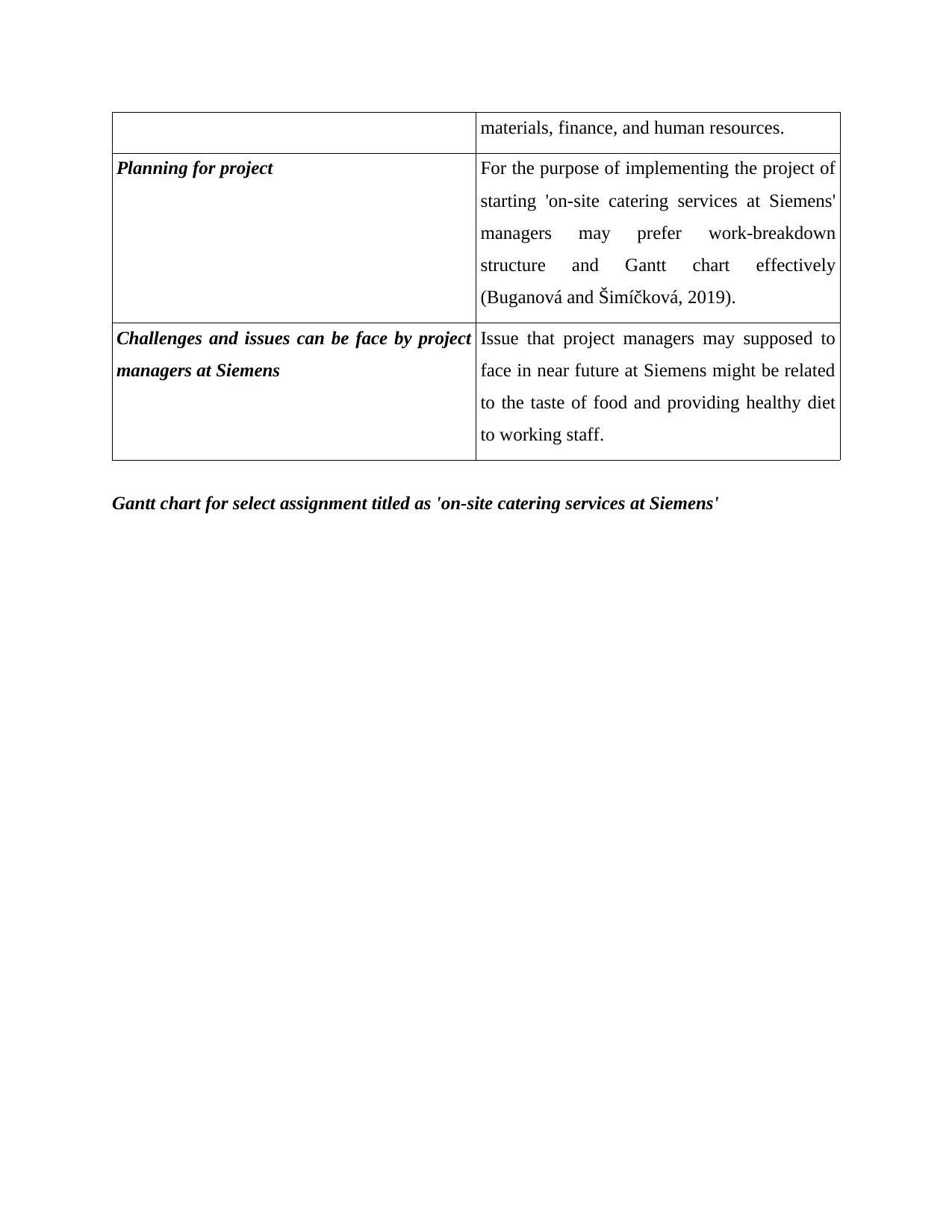
materials, finance, and human resources.
Planning for project For the purpose of implementing the project of
starting 'on-site catering services at Siemens'
managers may prefer work-breakdown
structure and Gantt chart effectively
(Buganová and Šimíčková, 2019).
Challenges and issues can be face by project
managers at Siemens
Issue that project managers may supposed to
face in near future at Siemens might be related
to the taste of food and providing healthy diet
to working staff.
Gantt chart for select assignment titled as 'on-site catering services at Siemens'
Planning for project For the purpose of implementing the project of
starting 'on-site catering services at Siemens'
managers may prefer work-breakdown
structure and Gantt chart effectively
(Buganová and Šimíčková, 2019).
Challenges and issues can be face by project
managers at Siemens
Issue that project managers may supposed to
face in near future at Siemens might be related
to the taste of food and providing healthy diet
to working staff.
Gantt chart for select assignment titled as 'on-site catering services at Siemens'
Paraphrase This Document
Need a fresh take? Get an instant paraphrase of this document with our AI Paraphraser
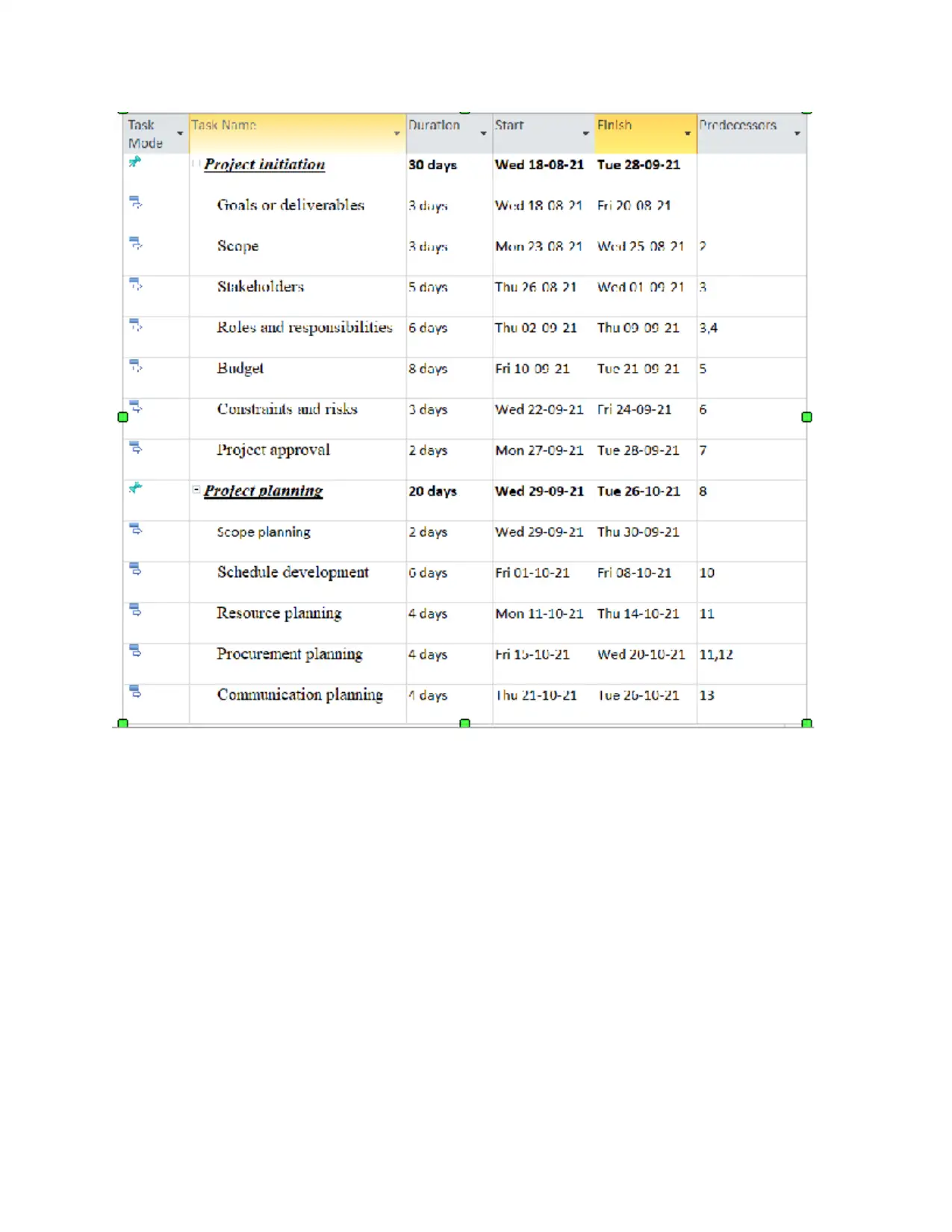
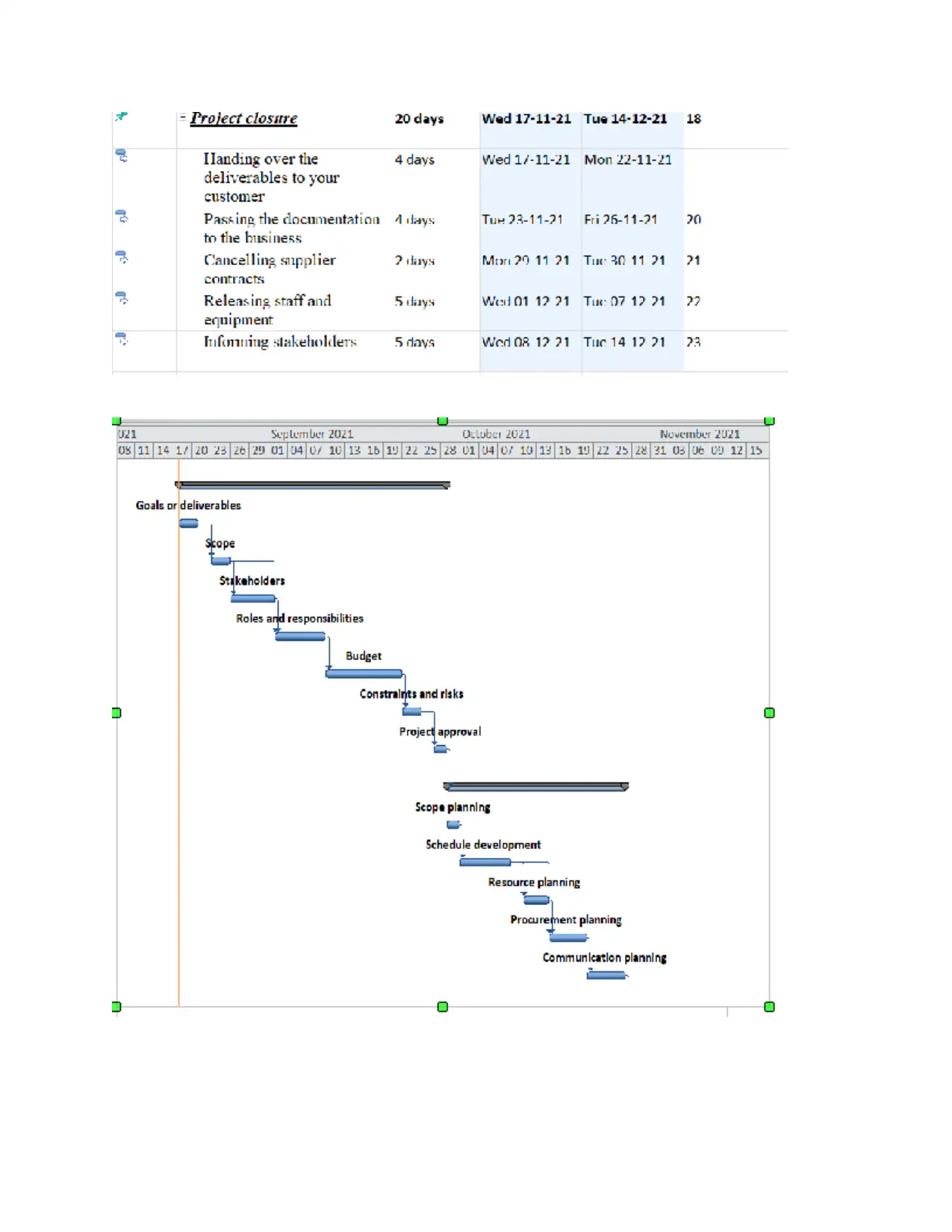
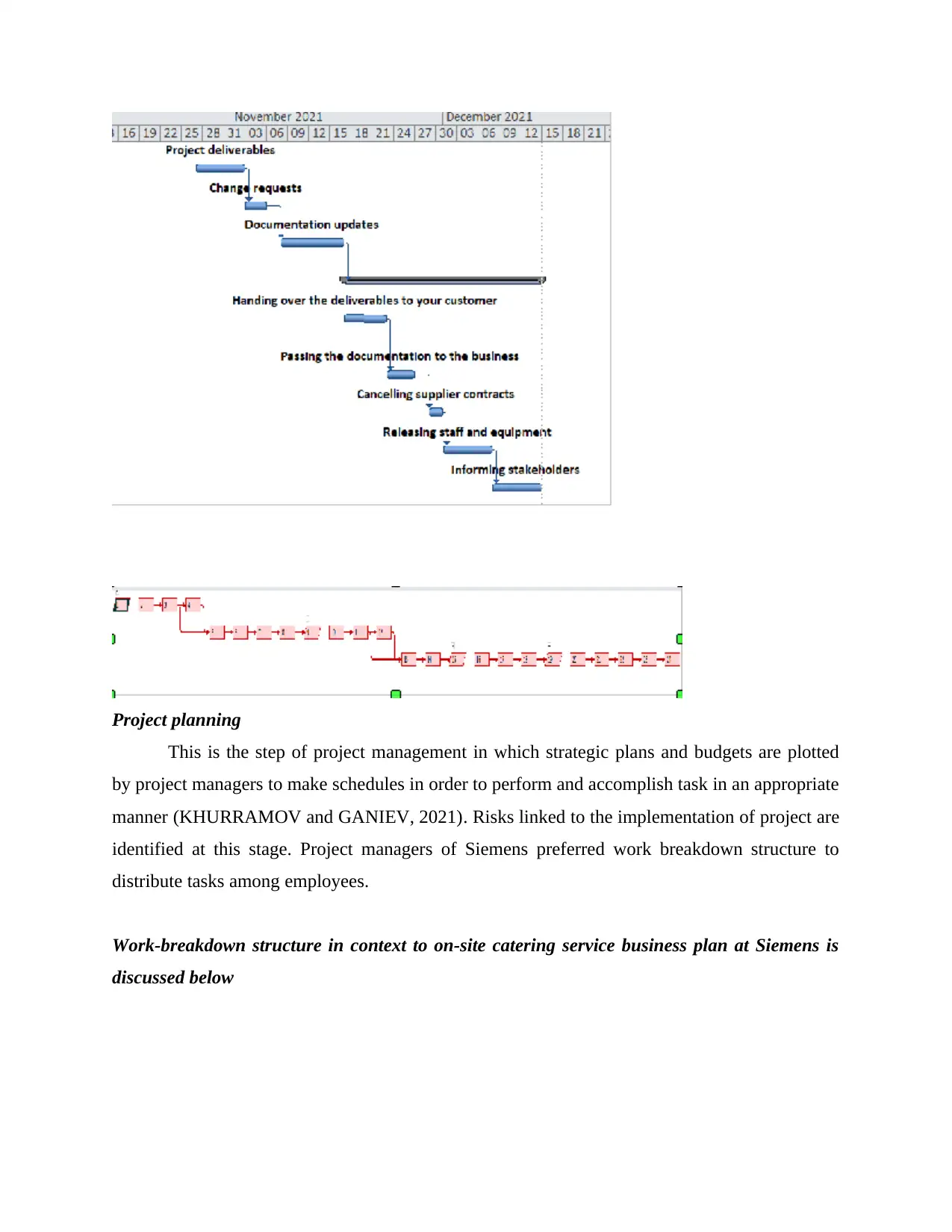
Project planning
This is the step of project management in which strategic plans and budgets are plotted
by project managers to make schedules in order to perform and accomplish task in an appropriate
manner (KHURRAMOV and GANIEV, 2021). Risks linked to the implementation of project are
identified at this stage. Project managers of Siemens preferred work breakdown structure to
distribute tasks among employees.
Work-breakdown structure in context to on-site catering service business plan at Siemens is
discussed below
This is the step of project management in which strategic plans and budgets are plotted
by project managers to make schedules in order to perform and accomplish task in an appropriate
manner (KHURRAMOV and GANIEV, 2021). Risks linked to the implementation of project are
identified at this stage. Project managers of Siemens preferred work breakdown structure to
distribute tasks among employees.
Work-breakdown structure in context to on-site catering service business plan at Siemens is
discussed below
Secure Best Marks with AI Grader
Need help grading? Try our AI Grader for instant feedback on your assignments.
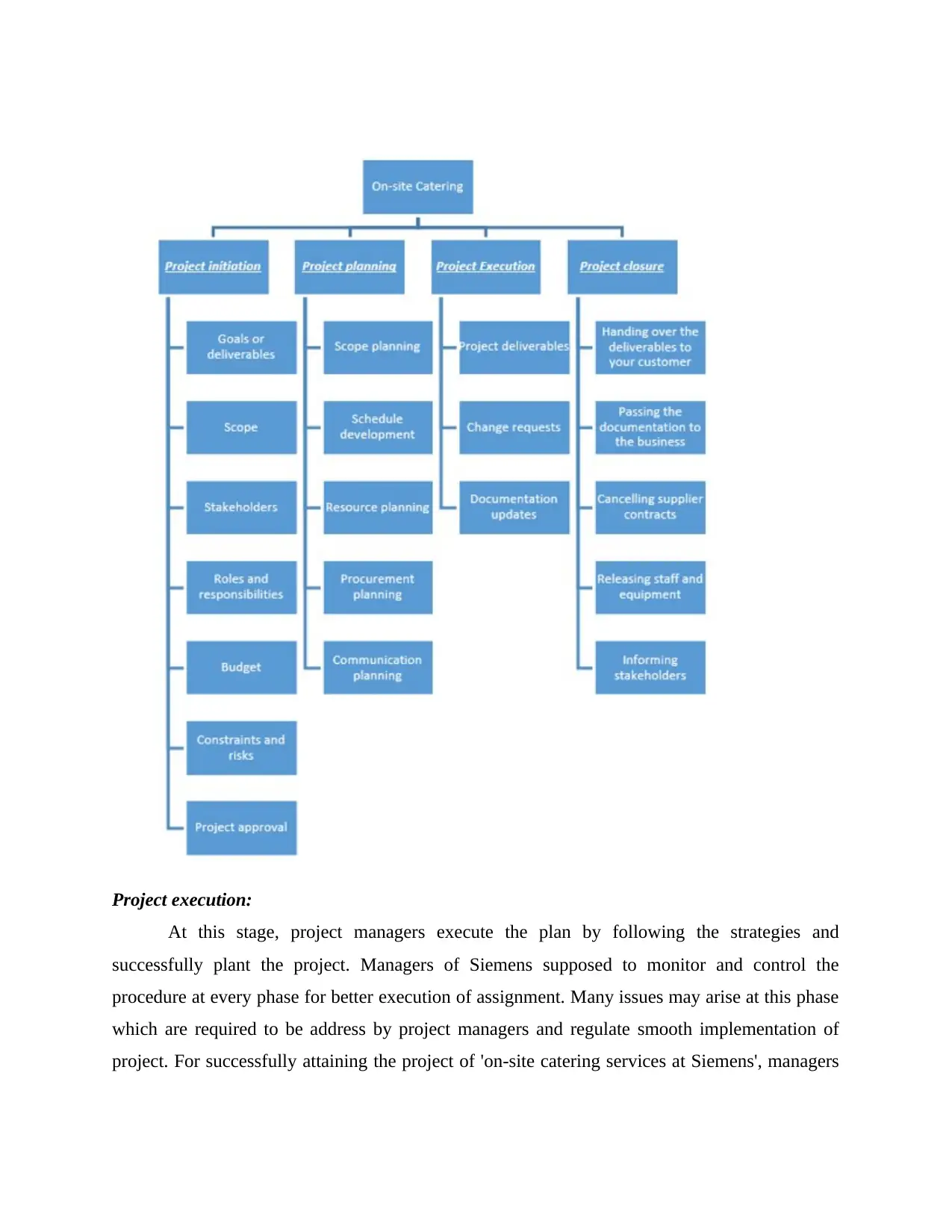
Project execution:
At this stage, project managers execute the plan by following the strategies and
successfully plant the project. Managers of Siemens supposed to monitor and control the
procedure at every phase for better execution of assignment. Many issues may arise at this phase
which are required to be address by project managers and regulate smooth implementation of
project. For successfully attaining the project of 'on-site catering services at Siemens', managers
At this stage, project managers execute the plan by following the strategies and
successfully plant the project. Managers of Siemens supposed to monitor and control the
procedure at every phase for better execution of assignment. Many issues may arise at this phase
which are required to be address by project managers and regulate smooth implementation of
project. For successfully attaining the project of 'on-site catering services at Siemens', managers
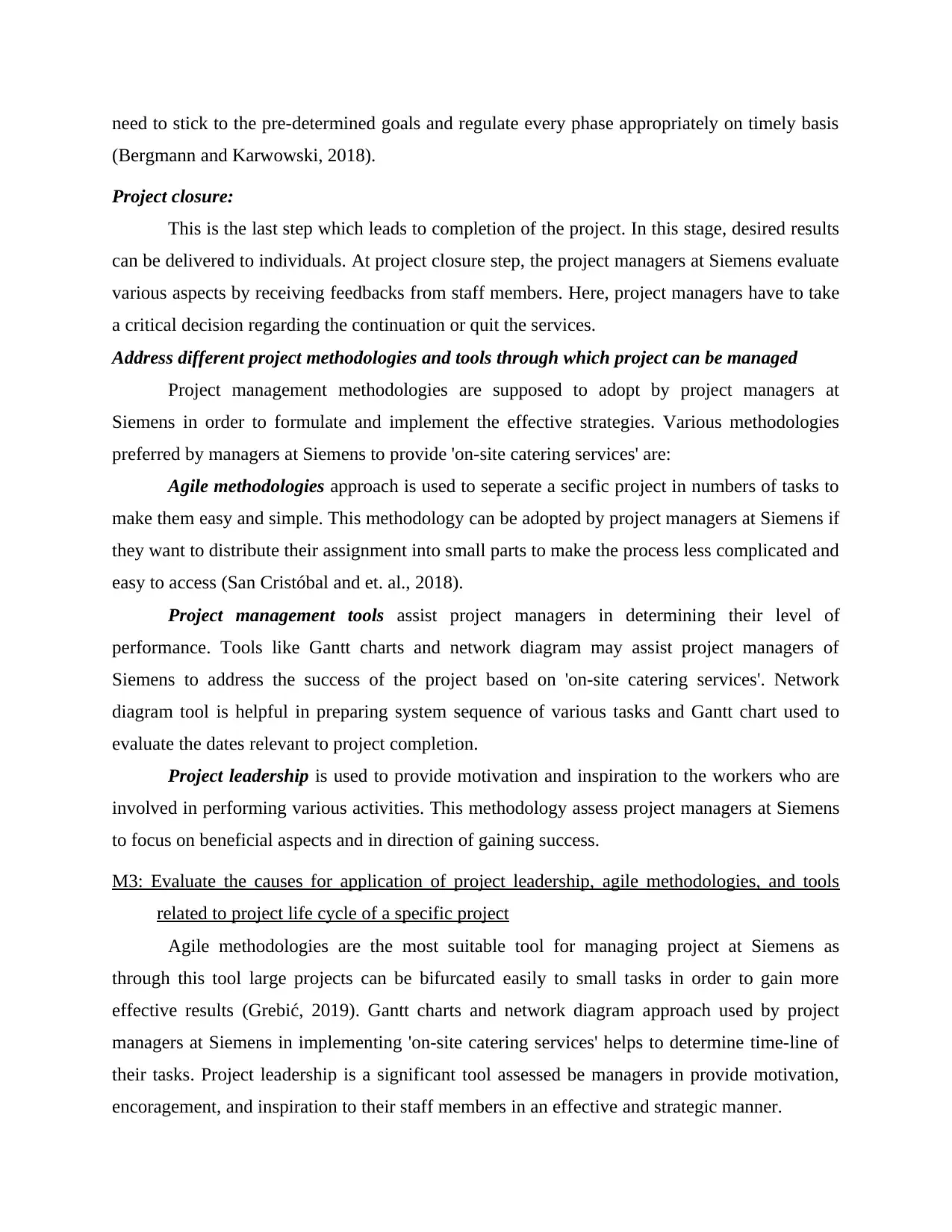
need to stick to the pre-determined goals and regulate every phase appropriately on timely basis
(Bergmann and Karwowski, 2018).
Project closure:
This is the last step which leads to completion of the project. In this stage, desired results
can be delivered to individuals. At project closure step, the project managers at Siemens evaluate
various aspects by receiving feedbacks from staff members. Here, project managers have to take
a critical decision regarding the continuation or quit the services.
Address different project methodologies and tools through which project can be managed
Project management methodologies are supposed to adopt by project managers at
Siemens in order to formulate and implement the effective strategies. Various methodologies
preferred by managers at Siemens to provide 'on-site catering services' are:
Agile methodologies approach is used to seperate a secific project in numbers of tasks to
make them easy and simple. This methodology can be adopted by project managers at Siemens if
they want to distribute their assignment into small parts to make the process less complicated and
easy to access (San Cristóbal and et. al., 2018).
Project management tools assist project managers in determining their level of
performance. Tools like Gantt charts and network diagram may assist project managers of
Siemens to address the success of the project based on 'on-site catering services'. Network
diagram tool is helpful in preparing system sequence of various tasks and Gantt chart used to
evaluate the dates relevant to project completion.
Project leadership is used to provide motivation and inspiration to the workers who are
involved in performing various activities. This methodology assess project managers at Siemens
to focus on beneficial aspects and in direction of gaining success.
M3: Evaluate the causes for application of project leadership, agile methodologies, and tools
related to project life cycle of a specific project
Agile methodologies are the most suitable tool for managing project at Siemens as
through this tool large projects can be bifurcated easily to small tasks in order to gain more
effective results (Grebić, 2019). Gantt charts and network diagram approach used by project
managers at Siemens in implementing 'on-site catering services' helps to determine time-line of
their tasks. Project leadership is a significant tool assessed be managers in provide motivation,
encoragement, and inspiration to their staff members in an effective and strategic manner.
(Bergmann and Karwowski, 2018).
Project closure:
This is the last step which leads to completion of the project. In this stage, desired results
can be delivered to individuals. At project closure step, the project managers at Siemens evaluate
various aspects by receiving feedbacks from staff members. Here, project managers have to take
a critical decision regarding the continuation or quit the services.
Address different project methodologies and tools through which project can be managed
Project management methodologies are supposed to adopt by project managers at
Siemens in order to formulate and implement the effective strategies. Various methodologies
preferred by managers at Siemens to provide 'on-site catering services' are:
Agile methodologies approach is used to seperate a secific project in numbers of tasks to
make them easy and simple. This methodology can be adopted by project managers at Siemens if
they want to distribute their assignment into small parts to make the process less complicated and
easy to access (San Cristóbal and et. al., 2018).
Project management tools assist project managers in determining their level of
performance. Tools like Gantt charts and network diagram may assist project managers of
Siemens to address the success of the project based on 'on-site catering services'. Network
diagram tool is helpful in preparing system sequence of various tasks and Gantt chart used to
evaluate the dates relevant to project completion.
Project leadership is used to provide motivation and inspiration to the workers who are
involved in performing various activities. This methodology assess project managers at Siemens
to focus on beneficial aspects and in direction of gaining success.
M3: Evaluate the causes for application of project leadership, agile methodologies, and tools
related to project life cycle of a specific project
Agile methodologies are the most suitable tool for managing project at Siemens as
through this tool large projects can be bifurcated easily to small tasks in order to gain more
effective results (Grebić, 2019). Gantt charts and network diagram approach used by project
managers at Siemens in implementing 'on-site catering services' helps to determine time-line of
their tasks. Project leadership is a significant tool assessed be managers in provide motivation,
encoragement, and inspiration to their staff members in an effective and strategic manner.
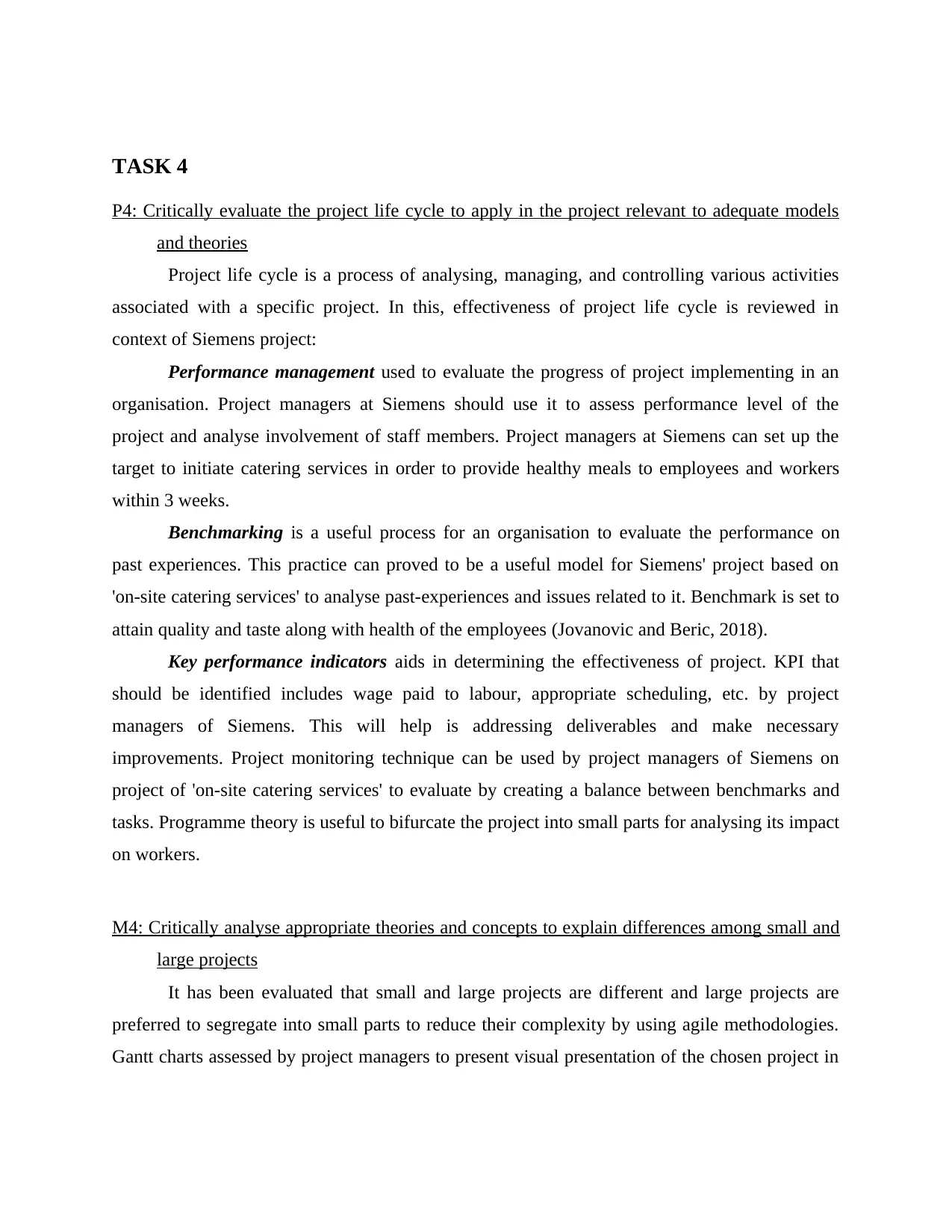
TASK 4
P4: Critically evaluate the project life cycle to apply in the project relevant to adequate models
and theories
Project life cycle is a process of analysing, managing, and controlling various activities
associated with a specific project. In this, effectiveness of project life cycle is reviewed in
context of Siemens project:
Performance management used to evaluate the progress of project implementing in an
organisation. Project managers at Siemens should use it to assess performance level of the
project and analyse involvement of staff members. Project managers at Siemens can set up the
target to initiate catering services in order to provide healthy meals to employees and workers
within 3 weeks.
Benchmarking is a useful process for an organisation to evaluate the performance on
past experiences. This practice can proved to be a useful model for Siemens' project based on
'on-site catering services' to analyse past-experiences and issues related to it. Benchmark is set to
attain quality and taste along with health of the employees (Jovanovic and Beric, 2018).
Key performance indicators aids in determining the effectiveness of project. KPI that
should be identified includes wage paid to labour, appropriate scheduling, etc. by project
managers of Siemens. This will help is addressing deliverables and make necessary
improvements. Project monitoring technique can be used by project managers of Siemens on
project of 'on-site catering services' to evaluate by creating a balance between benchmarks and
tasks. Programme theory is useful to bifurcate the project into small parts for analysing its impact
on workers.
M4: Critically analyse appropriate theories and concepts to explain differences among small and
large projects
It has been evaluated that small and large projects are different and large projects are
preferred to segregate into small parts to reduce their complexity by using agile methodologies.
Gantt charts assessed by project managers to present visual presentation of the chosen project in
P4: Critically evaluate the project life cycle to apply in the project relevant to adequate models
and theories
Project life cycle is a process of analysing, managing, and controlling various activities
associated with a specific project. In this, effectiveness of project life cycle is reviewed in
context of Siemens project:
Performance management used to evaluate the progress of project implementing in an
organisation. Project managers at Siemens should use it to assess performance level of the
project and analyse involvement of staff members. Project managers at Siemens can set up the
target to initiate catering services in order to provide healthy meals to employees and workers
within 3 weeks.
Benchmarking is a useful process for an organisation to evaluate the performance on
past experiences. This practice can proved to be a useful model for Siemens' project based on
'on-site catering services' to analyse past-experiences and issues related to it. Benchmark is set to
attain quality and taste along with health of the employees (Jovanovic and Beric, 2018).
Key performance indicators aids in determining the effectiveness of project. KPI that
should be identified includes wage paid to labour, appropriate scheduling, etc. by project
managers of Siemens. This will help is addressing deliverables and make necessary
improvements. Project monitoring technique can be used by project managers of Siemens on
project of 'on-site catering services' to evaluate by creating a balance between benchmarks and
tasks. Programme theory is useful to bifurcate the project into small parts for analysing its impact
on workers.
M4: Critically analyse appropriate theories and concepts to explain differences among small and
large projects
It has been evaluated that small and large projects are different and large projects are
preferred to segregate into small parts to reduce their complexity by using agile methodologies.
Gantt charts assessed by project managers to present visual presentation of the chosen project in
Paraphrase This Document
Need a fresh take? Get an instant paraphrase of this document with our AI Paraphraser
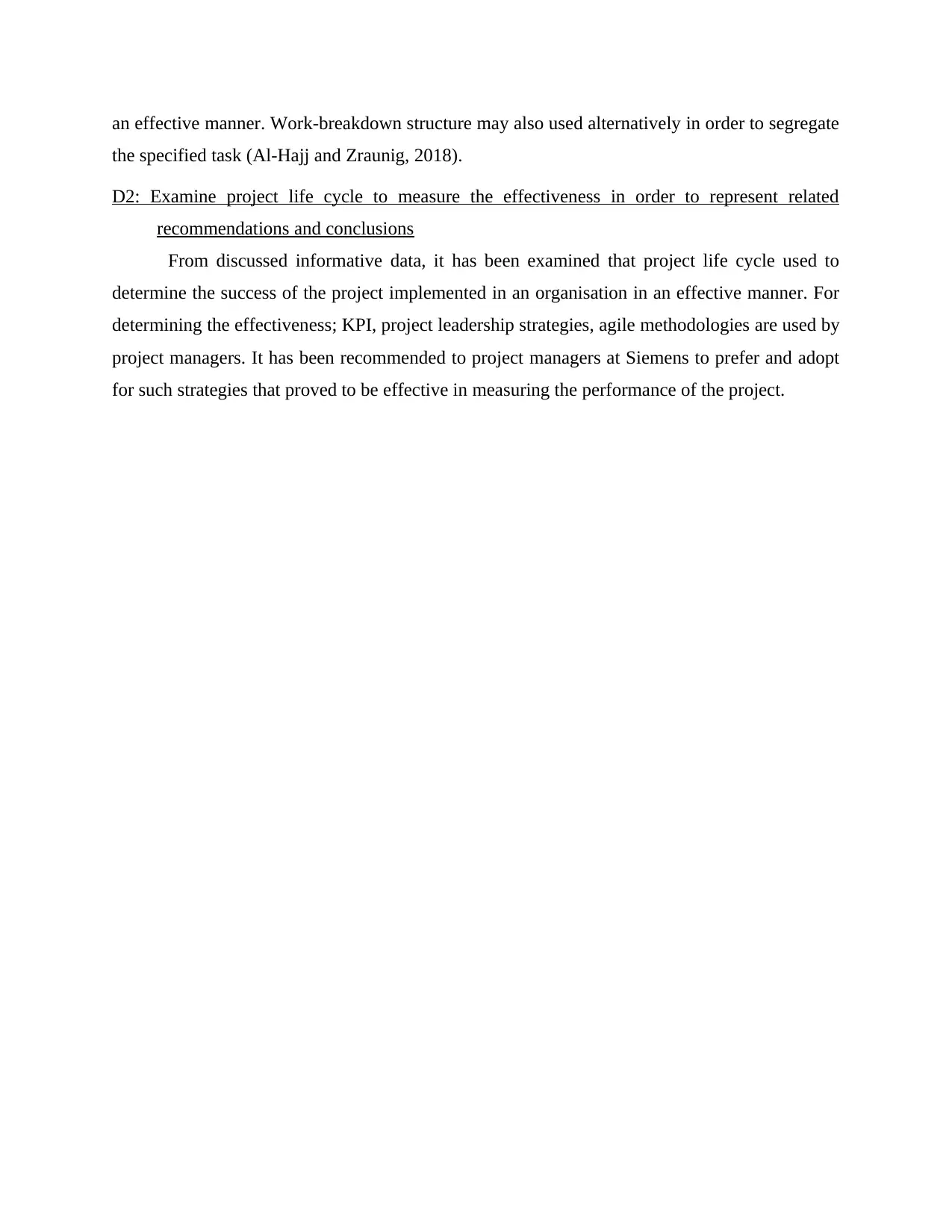
an effective manner. Work-breakdown structure may also used alternatively in order to segregate
the specified task (Al-Hajj and Zraunig, 2018).
D2: Examine project life cycle to measure the effectiveness in order to represent related
recommendations and conclusions
From discussed informative data, it has been examined that project life cycle used to
determine the success of the project implemented in an organisation in an effective manner. For
determining the effectiveness; KPI, project leadership strategies, agile methodologies are used by
project managers. It has been recommended to project managers at Siemens to prefer and adopt
for such strategies that proved to be effective in measuring the performance of the project.
the specified task (Al-Hajj and Zraunig, 2018).
D2: Examine project life cycle to measure the effectiveness in order to represent related
recommendations and conclusions
From discussed informative data, it has been examined that project life cycle used to
determine the success of the project implemented in an organisation in an effective manner. For
determining the effectiveness; KPI, project leadership strategies, agile methodologies are used by
project managers. It has been recommended to project managers at Siemens to prefer and adopt
for such strategies that proved to be effective in measuring the performance of the project.
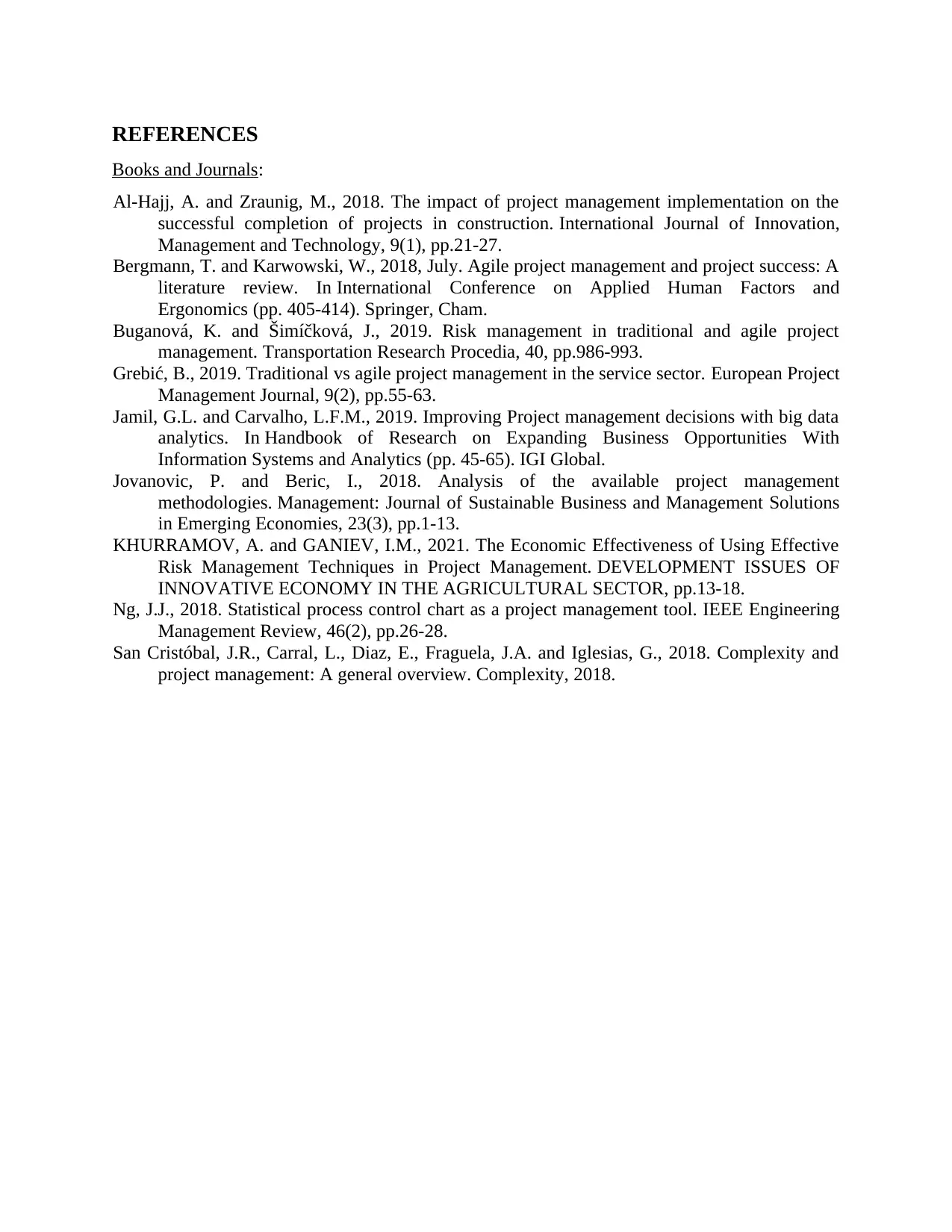
REFERENCES
Books and Journals:
Al-Hajj, A. and Zraunig, M., 2018. The impact of project management implementation on the
successful completion of projects in construction. International Journal of Innovation,
Management and Technology, 9(1), pp.21-27.
Bergmann, T. and Karwowski, W., 2018, July. Agile project management and project success: A
literature review. In International Conference on Applied Human Factors and
Ergonomics (pp. 405-414). Springer, Cham.
Buganová, K. and Šimíčková, J., 2019. Risk management in traditional and agile project
management. Transportation Research Procedia, 40, pp.986-993.
Grebić, B., 2019. Traditional vs agile project management in the service sector. European Project
Management Journal, 9(2), pp.55-63.
Jamil, G.L. and Carvalho, L.F.M., 2019. Improving Project management decisions with big data
analytics. In Handbook of Research on Expanding Business Opportunities With
Information Systems and Analytics (pp. 45-65). IGI Global.
Jovanovic, P. and Beric, I., 2018. Analysis of the available project management
methodologies. Management: Journal of Sustainable Business and Management Solutions
in Emerging Economies, 23(3), pp.1-13.
KHURRAMOV, A. and GANIEV, I.M., 2021. The Economic Effectiveness of Using Effective
Risk Management Techniques in Project Management. DEVELOPMENT ISSUES OF
INNOVATIVE ECONOMY IN THE AGRICULTURAL SECTOR, pp.13-18.
Ng, J.J., 2018. Statistical process control chart as a project management tool. IEEE Engineering
Management Review, 46(2), pp.26-28.
San Cristóbal, J.R., Carral, L., Diaz, E., Fraguela, J.A. and Iglesias, G., 2018. Complexity and
project management: A general overview. Complexity, 2018.
Books and Journals:
Al-Hajj, A. and Zraunig, M., 2018. The impact of project management implementation on the
successful completion of projects in construction. International Journal of Innovation,
Management and Technology, 9(1), pp.21-27.
Bergmann, T. and Karwowski, W., 2018, July. Agile project management and project success: A
literature review. In International Conference on Applied Human Factors and
Ergonomics (pp. 405-414). Springer, Cham.
Buganová, K. and Šimíčková, J., 2019. Risk management in traditional and agile project
management. Transportation Research Procedia, 40, pp.986-993.
Grebić, B., 2019. Traditional vs agile project management in the service sector. European Project
Management Journal, 9(2), pp.55-63.
Jamil, G.L. and Carvalho, L.F.M., 2019. Improving Project management decisions with big data
analytics. In Handbook of Research on Expanding Business Opportunities With
Information Systems and Analytics (pp. 45-65). IGI Global.
Jovanovic, P. and Beric, I., 2018. Analysis of the available project management
methodologies. Management: Journal of Sustainable Business and Management Solutions
in Emerging Economies, 23(3), pp.1-13.
KHURRAMOV, A. and GANIEV, I.M., 2021. The Economic Effectiveness of Using Effective
Risk Management Techniques in Project Management. DEVELOPMENT ISSUES OF
INNOVATIVE ECONOMY IN THE AGRICULTURAL SECTOR, pp.13-18.
Ng, J.J., 2018. Statistical process control chart as a project management tool. IEEE Engineering
Management Review, 46(2), pp.26-28.
San Cristóbal, J.R., Carral, L., Diaz, E., Fraguela, J.A. and Iglesias, G., 2018. Complexity and
project management: A general overview. Complexity, 2018.
1 out of 21
Related Documents
![[object Object]](/_next/image/?url=%2F_next%2Fstatic%2Fmedia%2Flogo.6d15ce61.png&w=640&q=75)
Your All-in-One AI-Powered Toolkit for Academic Success.
+13062052269
info@desklib.com
Available 24*7 on WhatsApp / Email
Unlock your academic potential
© 2024 | Zucol Services PVT LTD | All rights reserved.