Operations Management: Inventory and Key Operations at Toyota
VerifiedAdded on 2023/04/05
|15
|3978
|489
Report
AI Summary
This report provides a comprehensive analysis of Toyota's production system, focusing on inventory management through the Kanban system and key operational elements such as Just-In-Time (JIT), Kaizen, and Jidoka. It evaluates the effectiveness of Toyota's inventory management, highlighting the benefits of Kanban in controlling inventory flows and minimizing waste. The report also addresses potential challenges, including suspension in sourcing and issues in managing distribution, and suggests leveraging lean approaches, particularly waste management and quality improvement strategies, to mitigate these risks. Furthermore, it emphasizes the importance of integrating suppliers into a flexible production process and utilizing technology to enhance quality and reduce burdens on individual machines, ultimately aiming for continuous improvement and customer satisfaction.
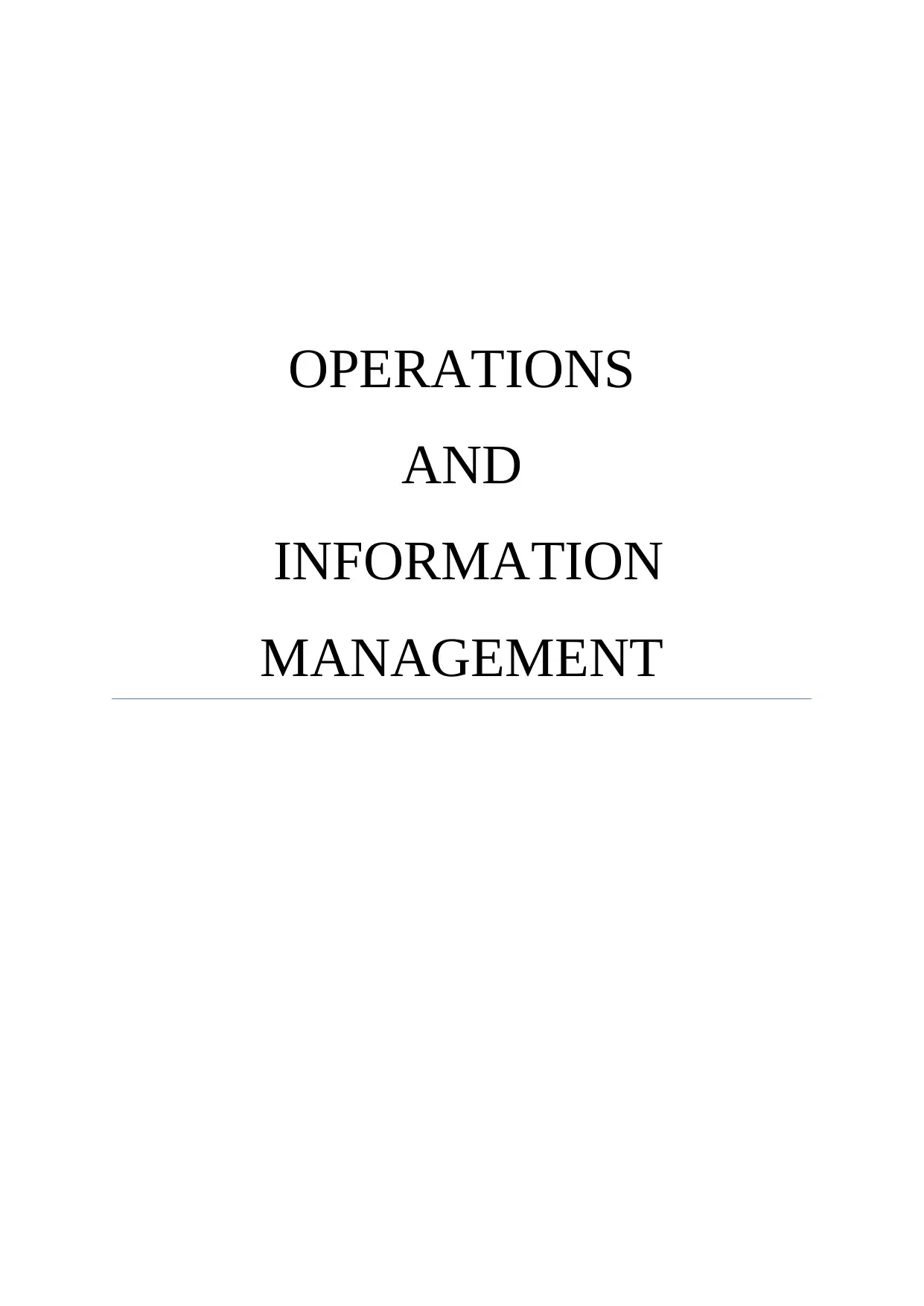
OPERATIONS
AND
INFORMATION
MANAGEMENT
AND
INFORMATION
MANAGEMENT
Paraphrase This Document
Need a fresh take? Get an instant paraphrase of this document with our AI Paraphraser
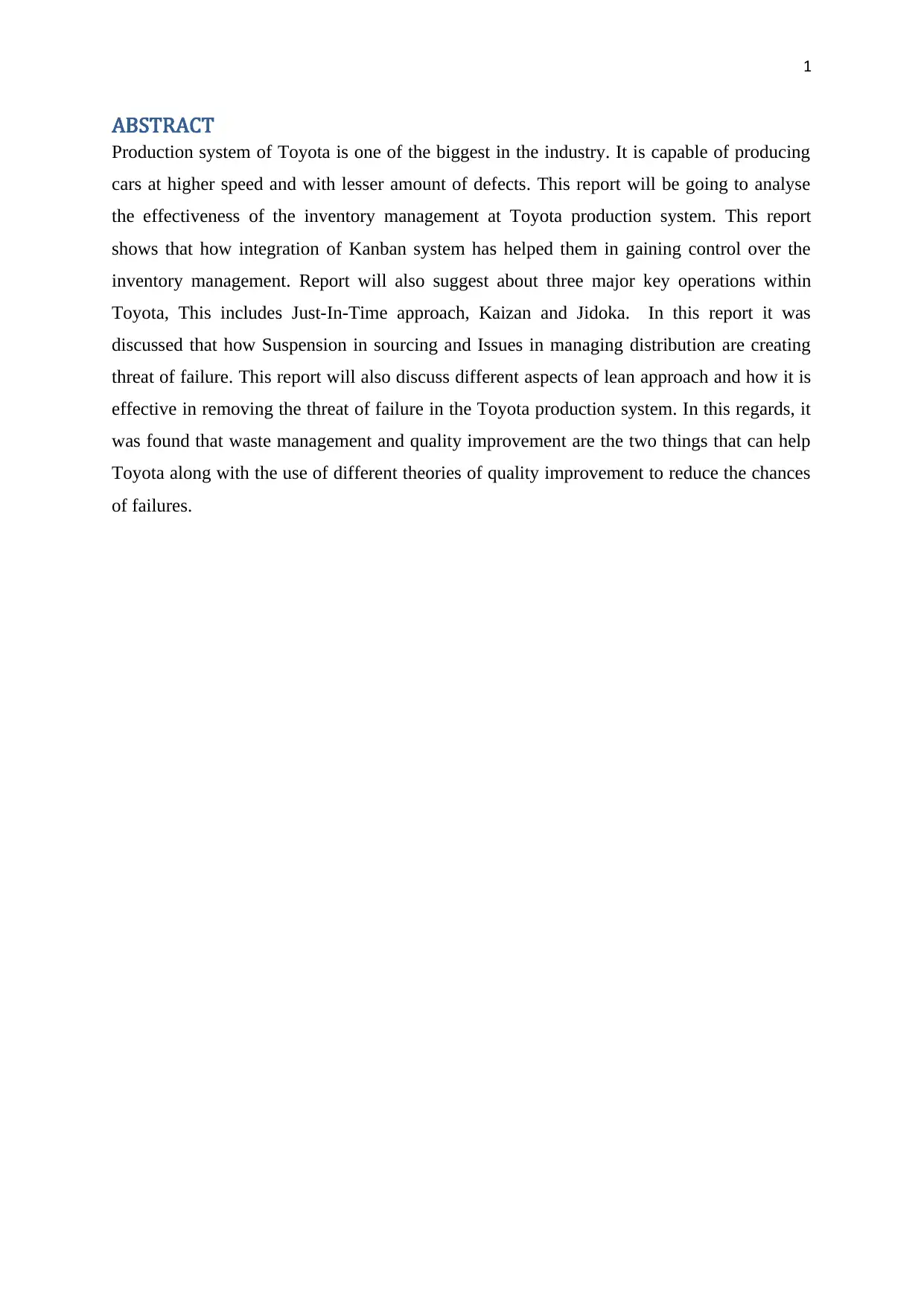
1
ABSTRACT
Production system of Toyota is one of the biggest in the industry. It is capable of producing
cars at higher speed and with lesser amount of defects. This report will be going to analyse
the effectiveness of the inventory management at Toyota production system. This report
shows that how integration of Kanban system has helped them in gaining control over the
inventory management. Report will also suggest about three major key operations within
Toyota, This includes Just-In-Time approach, Kaizan and Jidoka. In this report it was
discussed that how Suspension in sourcing and Issues in managing distribution are creating
threat of failure. This report will also discuss different aspects of lean approach and how it is
effective in removing the threat of failure in the Toyota production system. In this regards, it
was found that waste management and quality improvement are the two things that can help
Toyota along with the use of different theories of quality improvement to reduce the chances
of failures.
ABSTRACT
Production system of Toyota is one of the biggest in the industry. It is capable of producing
cars at higher speed and with lesser amount of defects. This report will be going to analyse
the effectiveness of the inventory management at Toyota production system. This report
shows that how integration of Kanban system has helped them in gaining control over the
inventory management. Report will also suggest about three major key operations within
Toyota, This includes Just-In-Time approach, Kaizan and Jidoka. In this report it was
discussed that how Suspension in sourcing and Issues in managing distribution are creating
threat of failure. This report will also discuss different aspects of lean approach and how it is
effective in removing the threat of failure in the Toyota production system. In this regards, it
was found that waste management and quality improvement are the two things that can help
Toyota along with the use of different theories of quality improvement to reduce the chances
of failures.
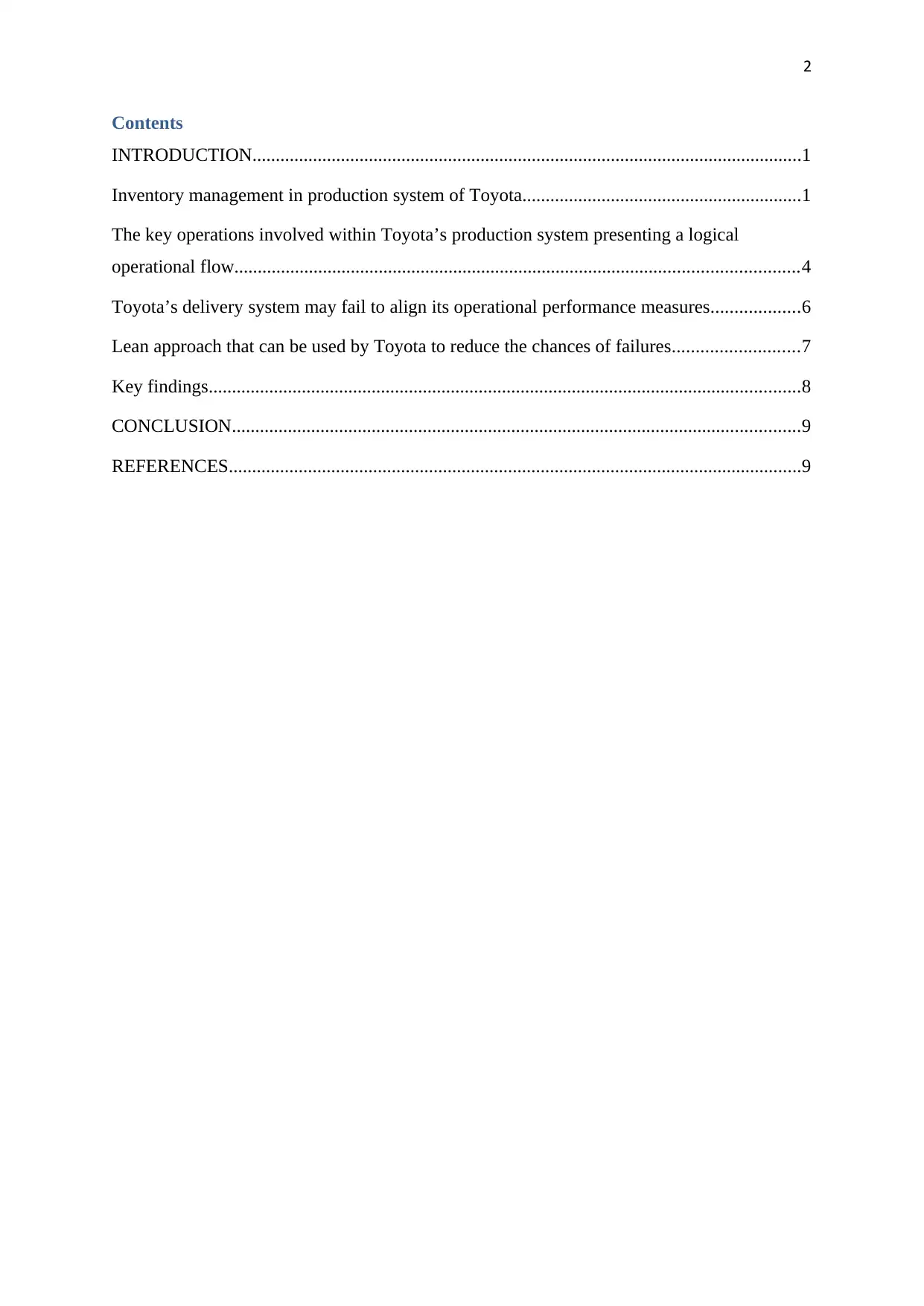
2
Contents
INTRODUCTION......................................................................................................................1
Inventory management in production system of Toyota............................................................1
The key operations involved within Toyota’s production system presenting a logical
operational flow.........................................................................................................................4
Toyota’s delivery system may fail to align its operational performance measures...................6
Lean approach that can be used by Toyota to reduce the chances of failures...........................7
Key findings...............................................................................................................................8
CONCLUSION..........................................................................................................................9
REFERENCES...........................................................................................................................9
Contents
INTRODUCTION......................................................................................................................1
Inventory management in production system of Toyota............................................................1
The key operations involved within Toyota’s production system presenting a logical
operational flow.........................................................................................................................4
Toyota’s delivery system may fail to align its operational performance measures...................6
Lean approach that can be used by Toyota to reduce the chances of failures...........................7
Key findings...............................................................................................................................8
CONCLUSION..........................................................................................................................9
REFERENCES...........................................................................................................................9
⊘ This is a preview!⊘
Do you want full access?
Subscribe today to unlock all pages.

Trusted by 1+ million students worldwide
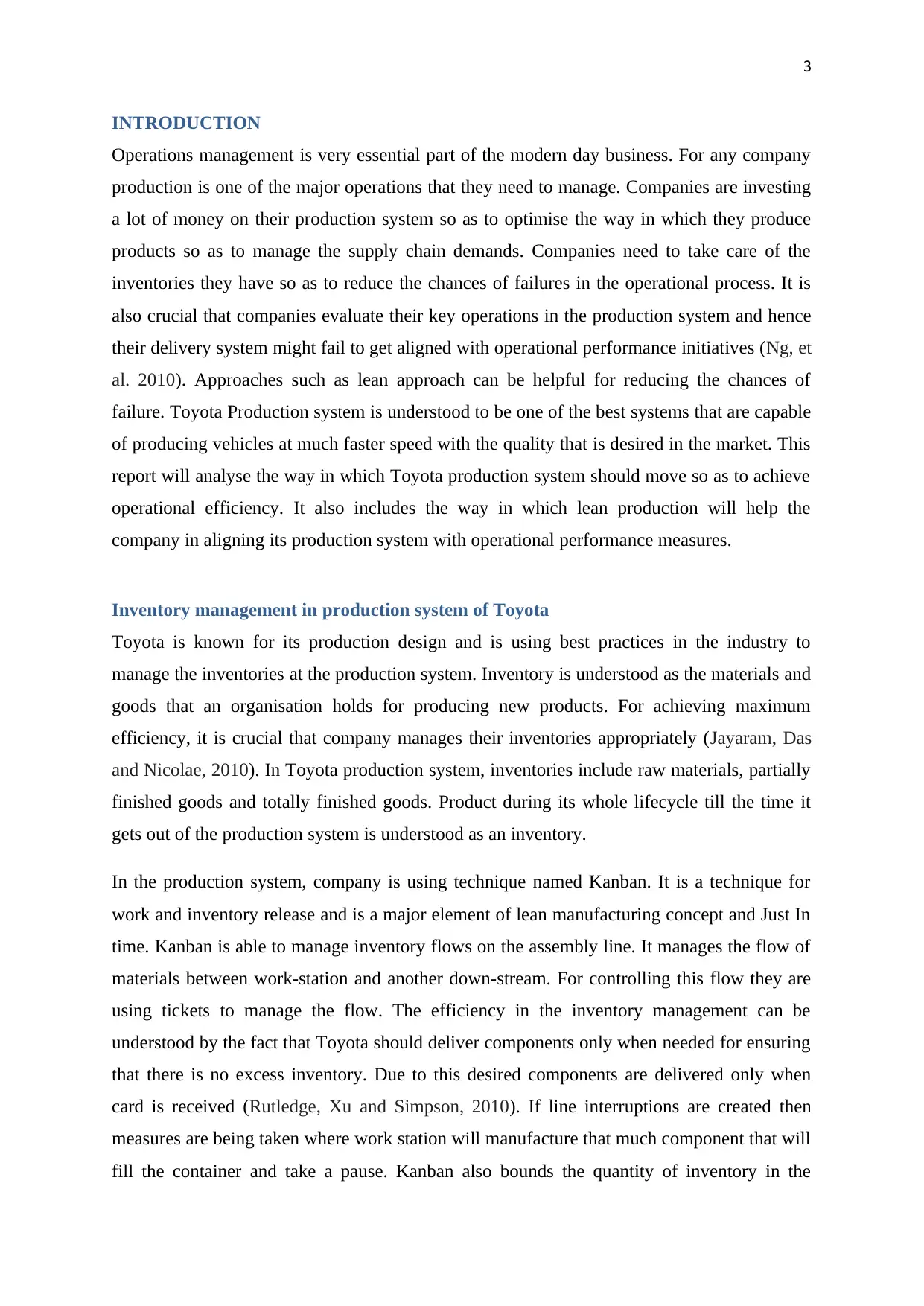
3
INTRODUCTION
Operations management is very essential part of the modern day business. For any company
production is one of the major operations that they need to manage. Companies are investing
a lot of money on their production system so as to optimise the way in which they produce
products so as to manage the supply chain demands. Companies need to take care of the
inventories they have so as to reduce the chances of failures in the operational process. It is
also crucial that companies evaluate their key operations in the production system and hence
their delivery system might fail to get aligned with operational performance initiatives (Ng, et
al. 2010). Approaches such as lean approach can be helpful for reducing the chances of
failure. Toyota Production system is understood to be one of the best systems that are capable
of producing vehicles at much faster speed with the quality that is desired in the market. This
report will analyse the way in which Toyota production system should move so as to achieve
operational efficiency. It also includes the way in which lean production will help the
company in aligning its production system with operational performance measures.
Inventory management in production system of Toyota
Toyota is known for its production design and is using best practices in the industry to
manage the inventories at the production system. Inventory is understood as the materials and
goods that an organisation holds for producing new products. For achieving maximum
efficiency, it is crucial that company manages their inventories appropriately (Jayaram, Das
and Nicolae, 2010). In Toyota production system, inventories include raw materials, partially
finished goods and totally finished goods. Product during its whole lifecycle till the time it
gets out of the production system is understood as an inventory.
In the production system, company is using technique named Kanban. It is a technique for
work and inventory release and is a major element of lean manufacturing concept and Just In
time. Kanban is able to manage inventory flows on the assembly line. It manages the flow of
materials between work-station and another down-stream. For controlling this flow they are
using tickets to manage the flow. The efficiency in the inventory management can be
understood by the fact that Toyota should deliver components only when needed for ensuring
that there is no excess inventory. Due to this desired components are delivered only when
card is received (Rutledge, Xu and Simpson, 2010). If line interruptions are created then
measures are being taken where work station will manufacture that much component that will
fill the container and take a pause. Kanban also bounds the quantity of inventory in the
INTRODUCTION
Operations management is very essential part of the modern day business. For any company
production is one of the major operations that they need to manage. Companies are investing
a lot of money on their production system so as to optimise the way in which they produce
products so as to manage the supply chain demands. Companies need to take care of the
inventories they have so as to reduce the chances of failures in the operational process. It is
also crucial that companies evaluate their key operations in the production system and hence
their delivery system might fail to get aligned with operational performance initiatives (Ng, et
al. 2010). Approaches such as lean approach can be helpful for reducing the chances of
failure. Toyota Production system is understood to be one of the best systems that are capable
of producing vehicles at much faster speed with the quality that is desired in the market. This
report will analyse the way in which Toyota production system should move so as to achieve
operational efficiency. It also includes the way in which lean production will help the
company in aligning its production system with operational performance measures.
Inventory management in production system of Toyota
Toyota is known for its production design and is using best practices in the industry to
manage the inventories at the production system. Inventory is understood as the materials and
goods that an organisation holds for producing new products. For achieving maximum
efficiency, it is crucial that company manages their inventories appropriately (Jayaram, Das
and Nicolae, 2010). In Toyota production system, inventories include raw materials, partially
finished goods and totally finished goods. Product during its whole lifecycle till the time it
gets out of the production system is understood as an inventory.
In the production system, company is using technique named Kanban. It is a technique for
work and inventory release and is a major element of lean manufacturing concept and Just In
time. Kanban is able to manage inventory flows on the assembly line. It manages the flow of
materials between work-station and another down-stream. For controlling this flow they are
using tickets to manage the flow. The efficiency in the inventory management can be
understood by the fact that Toyota should deliver components only when needed for ensuring
that there is no excess inventory. Due to this desired components are delivered only when
card is received (Rutledge, Xu and Simpson, 2010). If line interruptions are created then
measures are being taken where work station will manufacture that much component that will
fill the container and take a pause. Kanban also bounds the quantity of inventory in the
Paraphrase This Document
Need a fresh take? Get an instant paraphrase of this document with our AI Paraphraser
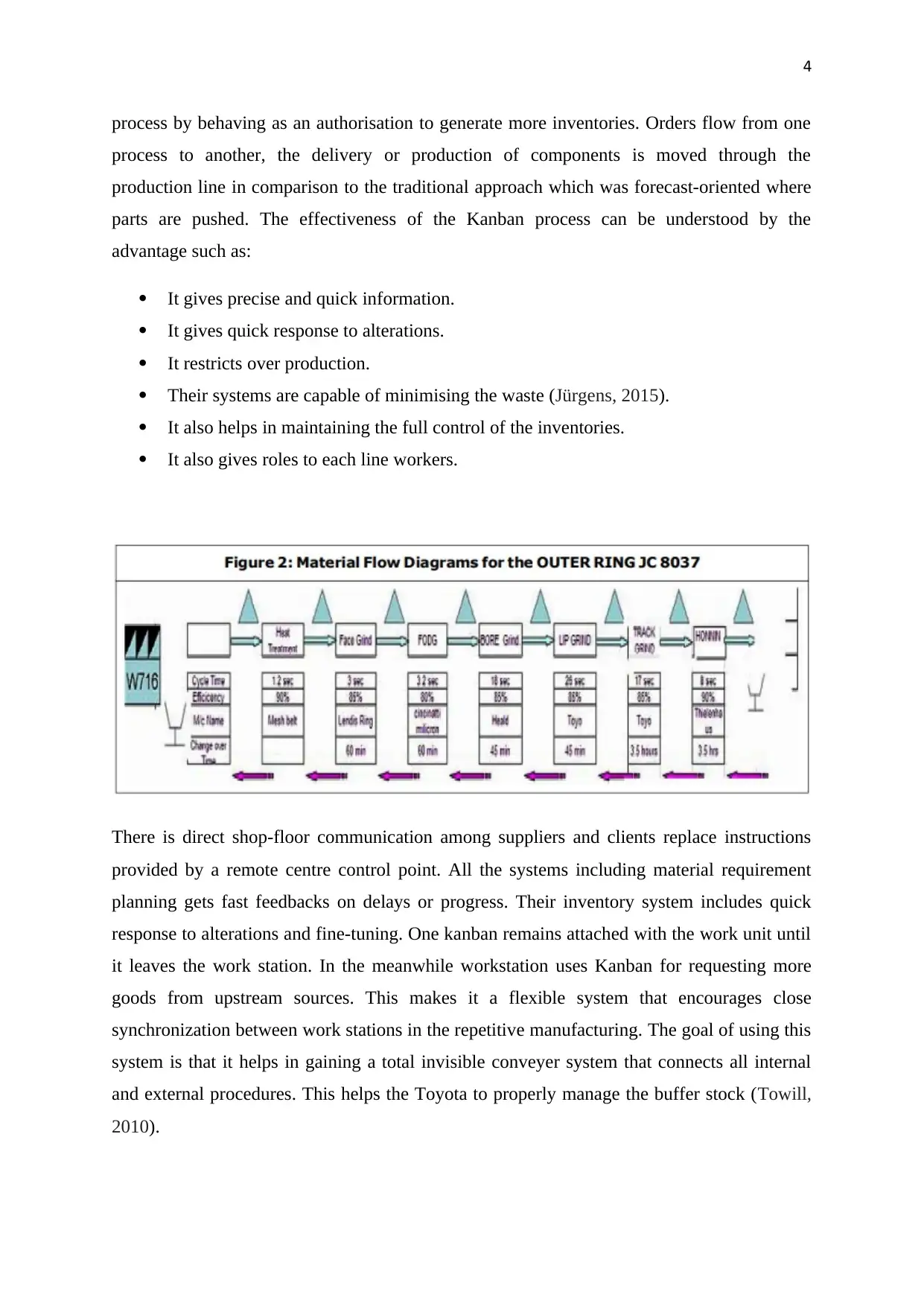
4
process by behaving as an authorisation to generate more inventories. Orders flow from one
process to another, the delivery or production of components is moved through the
production line in comparison to the traditional approach which was forecast-oriented where
parts are pushed. The effectiveness of the Kanban process can be understood by the
advantage such as:
It gives precise and quick information.
It gives quick response to alterations.
It restricts over production.
Their systems are capable of minimising the waste (Jürgens, 2015).
It also helps in maintaining the full control of the inventories.
It also gives roles to each line workers.
There is direct shop-floor communication among suppliers and clients replace instructions
provided by a remote centre control point. All the systems including material requirement
planning gets fast feedbacks on delays or progress. Their inventory system includes quick
response to alterations and fine-tuning. One kanban remains attached with the work unit until
it leaves the work station. In the meanwhile workstation uses Kanban for requesting more
goods from upstream sources. This makes it a flexible system that encourages close
synchronization between work stations in the repetitive manufacturing. The goal of using this
system is that it helps in gaining a total invisible conveyer system that connects all internal
and external procedures. This helps the Toyota to properly manage the buffer stock (Towill,
2010).
process by behaving as an authorisation to generate more inventories. Orders flow from one
process to another, the delivery or production of components is moved through the
production line in comparison to the traditional approach which was forecast-oriented where
parts are pushed. The effectiveness of the Kanban process can be understood by the
advantage such as:
It gives precise and quick information.
It gives quick response to alterations.
It restricts over production.
Their systems are capable of minimising the waste (Jürgens, 2015).
It also helps in maintaining the full control of the inventories.
It also gives roles to each line workers.
There is direct shop-floor communication among suppliers and clients replace instructions
provided by a remote centre control point. All the systems including material requirement
planning gets fast feedbacks on delays or progress. Their inventory system includes quick
response to alterations and fine-tuning. One kanban remains attached with the work unit until
it leaves the work station. In the meanwhile workstation uses Kanban for requesting more
goods from upstream sources. This makes it a flexible system that encourages close
synchronization between work stations in the repetitive manufacturing. The goal of using this
system is that it helps in gaining a total invisible conveyer system that connects all internal
and external procedures. This helps the Toyota to properly manage the buffer stock (Towill,
2010).
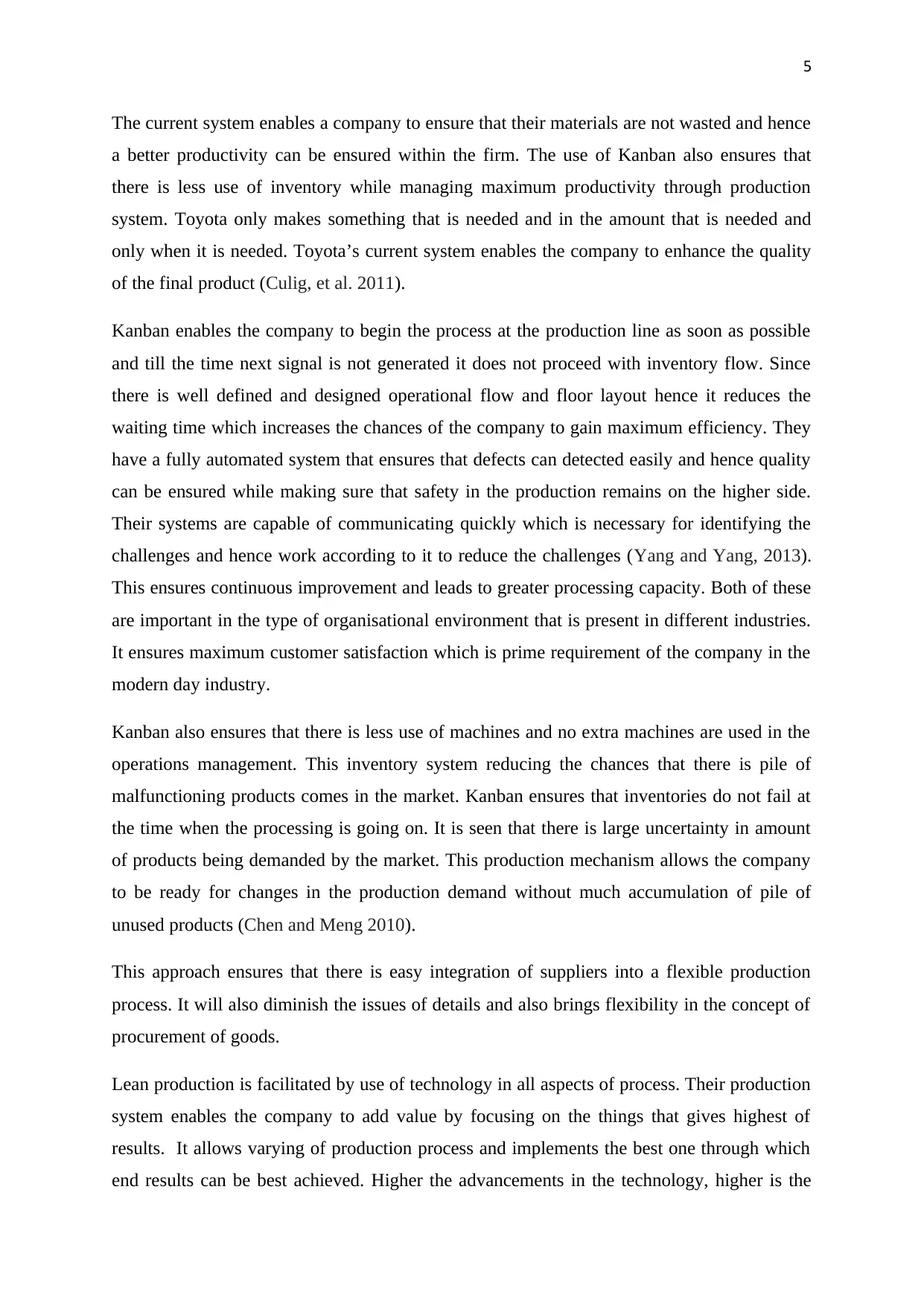
5
The current system enables a company to ensure that their materials are not wasted and hence
a better productivity can be ensured within the firm. The use of Kanban also ensures that
there is less use of inventory while managing maximum productivity through production
system. Toyota only makes something that is needed and in the amount that is needed and
only when it is needed. Toyota’s current system enables the company to enhance the quality
of the final product (Culig, et al. 2011).
Kanban enables the company to begin the process at the production line as soon as possible
and till the time next signal is not generated it does not proceed with inventory flow. Since
there is well defined and designed operational flow and floor layout hence it reduces the
waiting time which increases the chances of the company to gain maximum efficiency. They
have a fully automated system that ensures that defects can detected easily and hence quality
can be ensured while making sure that safety in the production remains on the higher side.
Their systems are capable of communicating quickly which is necessary for identifying the
challenges and hence work according to it to reduce the challenges (Yang and Yang, 2013).
This ensures continuous improvement and leads to greater processing capacity. Both of these
are important in the type of organisational environment that is present in different industries.
It ensures maximum customer satisfaction which is prime requirement of the company in the
modern day industry.
Kanban also ensures that there is less use of machines and no extra machines are used in the
operations management. This inventory system reducing the chances that there is pile of
malfunctioning products comes in the market. Kanban ensures that inventories do not fail at
the time when the processing is going on. It is seen that there is large uncertainty in amount
of products being demanded by the market. This production mechanism allows the company
to be ready for changes in the production demand without much accumulation of pile of
unused products (Chen and Meng 2010).
This approach ensures that there is easy integration of suppliers into a flexible production
process. It will also diminish the issues of details and also brings flexibility in the concept of
procurement of goods.
Lean production is facilitated by use of technology in all aspects of process. Their production
system enables the company to add value by focusing on the things that gives highest of
results. It allows varying of production process and implements the best one through which
end results can be best achieved. Higher the advancements in the technology, higher is the
The current system enables a company to ensure that their materials are not wasted and hence
a better productivity can be ensured within the firm. The use of Kanban also ensures that
there is less use of inventory while managing maximum productivity through production
system. Toyota only makes something that is needed and in the amount that is needed and
only when it is needed. Toyota’s current system enables the company to enhance the quality
of the final product (Culig, et al. 2011).
Kanban enables the company to begin the process at the production line as soon as possible
and till the time next signal is not generated it does not proceed with inventory flow. Since
there is well defined and designed operational flow and floor layout hence it reduces the
waiting time which increases the chances of the company to gain maximum efficiency. They
have a fully automated system that ensures that defects can detected easily and hence quality
can be ensured while making sure that safety in the production remains on the higher side.
Their systems are capable of communicating quickly which is necessary for identifying the
challenges and hence work according to it to reduce the challenges (Yang and Yang, 2013).
This ensures continuous improvement and leads to greater processing capacity. Both of these
are important in the type of organisational environment that is present in different industries.
It ensures maximum customer satisfaction which is prime requirement of the company in the
modern day industry.
Kanban also ensures that there is less use of machines and no extra machines are used in the
operations management. This inventory system reducing the chances that there is pile of
malfunctioning products comes in the market. Kanban ensures that inventories do not fail at
the time when the processing is going on. It is seen that there is large uncertainty in amount
of products being demanded by the market. This production mechanism allows the company
to be ready for changes in the production demand without much accumulation of pile of
unused products (Chen and Meng 2010).
This approach ensures that there is easy integration of suppliers into a flexible production
process. It will also diminish the issues of details and also brings flexibility in the concept of
procurement of goods.
Lean production is facilitated by use of technology in all aspects of process. Their production
system enables the company to add value by focusing on the things that gives highest of
results. It allows varying of production process and implements the best one through which
end results can be best achieved. Higher the advancements in the technology, higher is the
⊘ This is a preview!⊘
Do you want full access?
Subscribe today to unlock all pages.

Trusted by 1+ million students worldwide
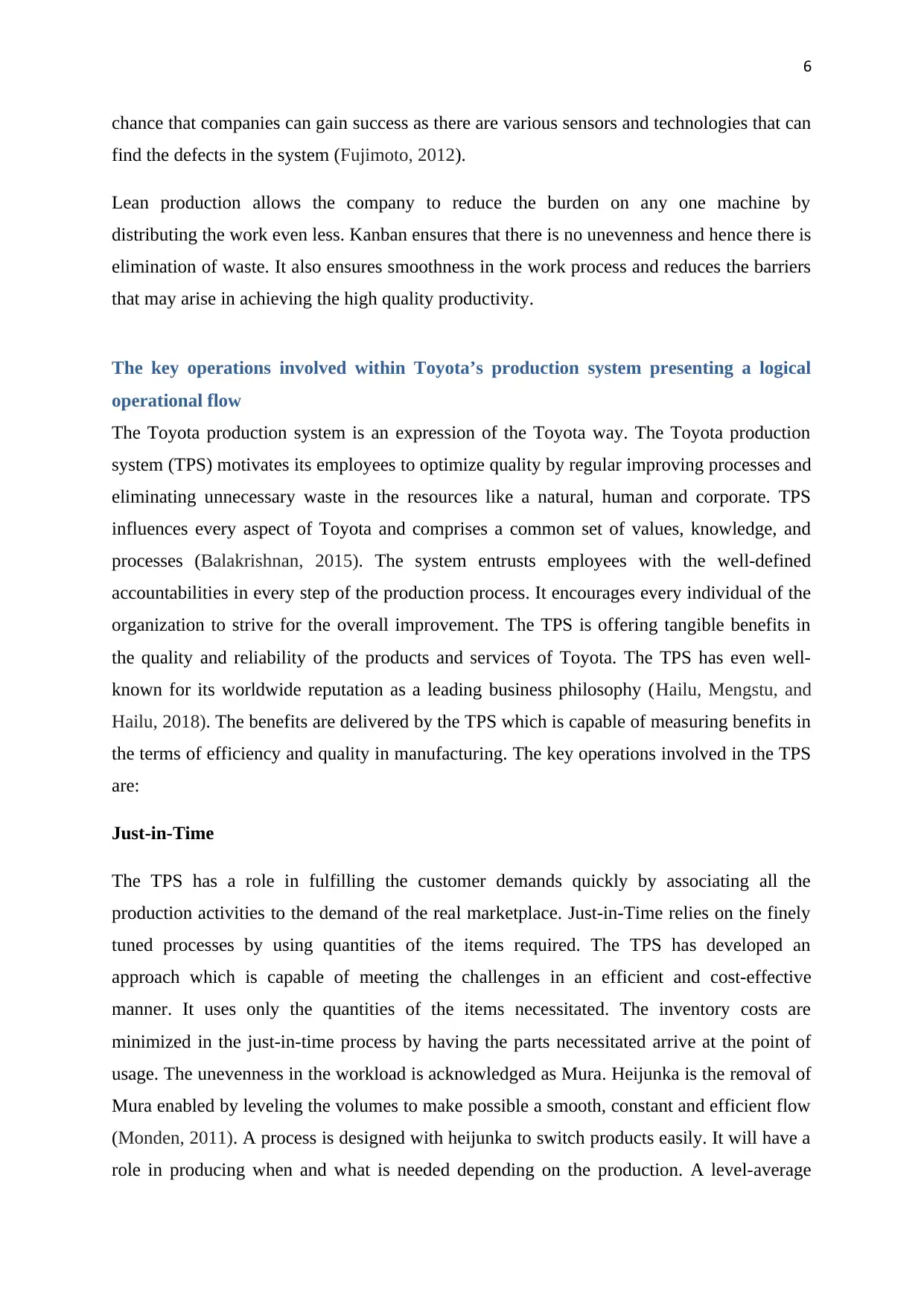
6
chance that companies can gain success as there are various sensors and technologies that can
find the defects in the system (Fujimoto, 2012).
Lean production allows the company to reduce the burden on any one machine by
distributing the work even less. Kanban ensures that there is no unevenness and hence there is
elimination of waste. It also ensures smoothness in the work process and reduces the barriers
that may arise in achieving the high quality productivity.
The key operations involved within Toyota’s production system presenting a logical
operational flow
The Toyota production system is an expression of the Toyota way. The Toyota production
system (TPS) motivates its employees to optimize quality by regular improving processes and
eliminating unnecessary waste in the resources like a natural, human and corporate. TPS
influences every aspect of Toyota and comprises a common set of values, knowledge, and
processes (Balakrishnan, 2015). The system entrusts employees with the well-defined
accountabilities in every step of the production process. It encourages every individual of the
organization to strive for the overall improvement. The TPS is offering tangible benefits in
the quality and reliability of the products and services of Toyota. The TPS has even well-
known for its worldwide reputation as a leading business philosophy (Hailu, Mengstu, and
Hailu, 2018). The benefits are delivered by the TPS which is capable of measuring benefits in
the terms of efficiency and quality in manufacturing. The key operations involved in the TPS
are:
Just-in-Time
The TPS has a role in fulfilling the customer demands quickly by associating all the
production activities to the demand of the real marketplace. Just-in-Time relies on the finely
tuned processes by using quantities of the items required. The TPS has developed an
approach which is capable of meeting the challenges in an efficient and cost-effective
manner. It uses only the quantities of the items necessitated. The inventory costs are
minimized in the just-in-time process by having the parts necessitated arrive at the point of
usage. The unevenness in the workload is acknowledged as Mura. Heijunka is the removal of
Mura enabled by leveling the volumes to make possible a smooth, constant and efficient flow
(Monden, 2011). A process is designed with heijunka to switch products easily. It will have a
role in producing when and what is needed depending on the production. A level-average
chance that companies can gain success as there are various sensors and technologies that can
find the defects in the system (Fujimoto, 2012).
Lean production allows the company to reduce the burden on any one machine by
distributing the work even less. Kanban ensures that there is no unevenness and hence there is
elimination of waste. It also ensures smoothness in the work process and reduces the barriers
that may arise in achieving the high quality productivity.
The key operations involved within Toyota’s production system presenting a logical
operational flow
The Toyota production system is an expression of the Toyota way. The Toyota production
system (TPS) motivates its employees to optimize quality by regular improving processes and
eliminating unnecessary waste in the resources like a natural, human and corporate. TPS
influences every aspect of Toyota and comprises a common set of values, knowledge, and
processes (Balakrishnan, 2015). The system entrusts employees with the well-defined
accountabilities in every step of the production process. It encourages every individual of the
organization to strive for the overall improvement. The TPS is offering tangible benefits in
the quality and reliability of the products and services of Toyota. The TPS has even well-
known for its worldwide reputation as a leading business philosophy (Hailu, Mengstu, and
Hailu, 2018). The benefits are delivered by the TPS which is capable of measuring benefits in
the terms of efficiency and quality in manufacturing. The key operations involved in the TPS
are:
Just-in-Time
The TPS has a role in fulfilling the customer demands quickly by associating all the
production activities to the demand of the real marketplace. Just-in-Time relies on the finely
tuned processes by using quantities of the items required. The TPS has developed an
approach which is capable of meeting the challenges in an efficient and cost-effective
manner. It uses only the quantities of the items necessitated. The inventory costs are
minimized in the just-in-time process by having the parts necessitated arrive at the point of
usage. The unevenness in the workload is acknowledged as Mura. Heijunka is the removal of
Mura enabled by leveling the volumes to make possible a smooth, constant and efficient flow
(Monden, 2011). A process is designed with heijunka to switch products easily. It will have a
role in producing when and what is needed depending on the production. A level-average
Paraphrase This Document
Need a fresh take? Get an instant paraphrase of this document with our AI Paraphraser
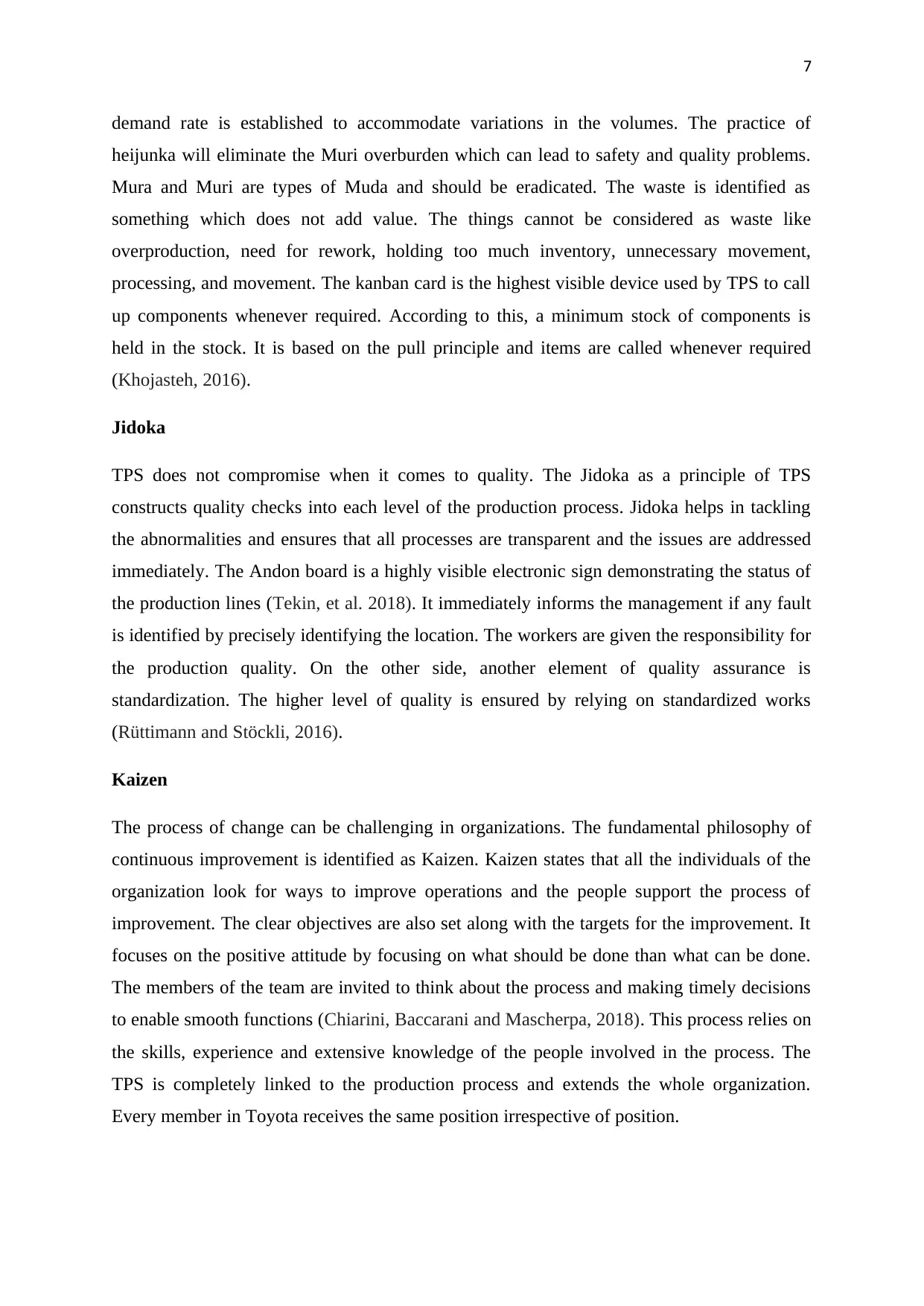
7
demand rate is established to accommodate variations in the volumes. The practice of
heijunka will eliminate the Muri overburden which can lead to safety and quality problems.
Mura and Muri are types of Muda and should be eradicated. The waste is identified as
something which does not add value. The things cannot be considered as waste like
overproduction, need for rework, holding too much inventory, unnecessary movement,
processing, and movement. The kanban card is the highest visible device used by TPS to call
up components whenever required. According to this, a minimum stock of components is
held in the stock. It is based on the pull principle and items are called whenever required
(Khojasteh, 2016).
Jidoka
TPS does not compromise when it comes to quality. The Jidoka as a principle of TPS
constructs quality checks into each level of the production process. Jidoka helps in tackling
the abnormalities and ensures that all processes are transparent and the issues are addressed
immediately. The Andon board is a highly visible electronic sign demonstrating the status of
the production lines (Tekin, et al. 2018). It immediately informs the management if any fault
is identified by precisely identifying the location. The workers are given the responsibility for
the production quality. On the other side, another element of quality assurance is
standardization. The higher level of quality is ensured by relying on standardized works
(Rüttimann and Stöckli, 2016).
Kaizen
The process of change can be challenging in organizations. The fundamental philosophy of
continuous improvement is identified as Kaizen. Kaizen states that all the individuals of the
organization look for ways to improve operations and the people support the process of
improvement. The clear objectives are also set along with the targets for the improvement. It
focuses on the positive attitude by focusing on what should be done than what can be done.
The members of the team are invited to think about the process and making timely decisions
to enable smooth functions (Chiarini, Baccarani and Mascherpa, 2018). This process relies on
the skills, experience and extensive knowledge of the people involved in the process. The
TPS is completely linked to the production process and extends the whole organization.
Every member in Toyota receives the same position irrespective of position.
demand rate is established to accommodate variations in the volumes. The practice of
heijunka will eliminate the Muri overburden which can lead to safety and quality problems.
Mura and Muri are types of Muda and should be eradicated. The waste is identified as
something which does not add value. The things cannot be considered as waste like
overproduction, need for rework, holding too much inventory, unnecessary movement,
processing, and movement. The kanban card is the highest visible device used by TPS to call
up components whenever required. According to this, a minimum stock of components is
held in the stock. It is based on the pull principle and items are called whenever required
(Khojasteh, 2016).
Jidoka
TPS does not compromise when it comes to quality. The Jidoka as a principle of TPS
constructs quality checks into each level of the production process. Jidoka helps in tackling
the abnormalities and ensures that all processes are transparent and the issues are addressed
immediately. The Andon board is a highly visible electronic sign demonstrating the status of
the production lines (Tekin, et al. 2018). It immediately informs the management if any fault
is identified by precisely identifying the location. The workers are given the responsibility for
the production quality. On the other side, another element of quality assurance is
standardization. The higher level of quality is ensured by relying on standardized works
(Rüttimann and Stöckli, 2016).
Kaizen
The process of change can be challenging in organizations. The fundamental philosophy of
continuous improvement is identified as Kaizen. Kaizen states that all the individuals of the
organization look for ways to improve operations and the people support the process of
improvement. The clear objectives are also set along with the targets for the improvement. It
focuses on the positive attitude by focusing on what should be done than what can be done.
The members of the team are invited to think about the process and making timely decisions
to enable smooth functions (Chiarini, Baccarani and Mascherpa, 2018). This process relies on
the skills, experience and extensive knowledge of the people involved in the process. The
TPS is completely linked to the production process and extends the whole organization.
Every member in Toyota receives the same position irrespective of position.
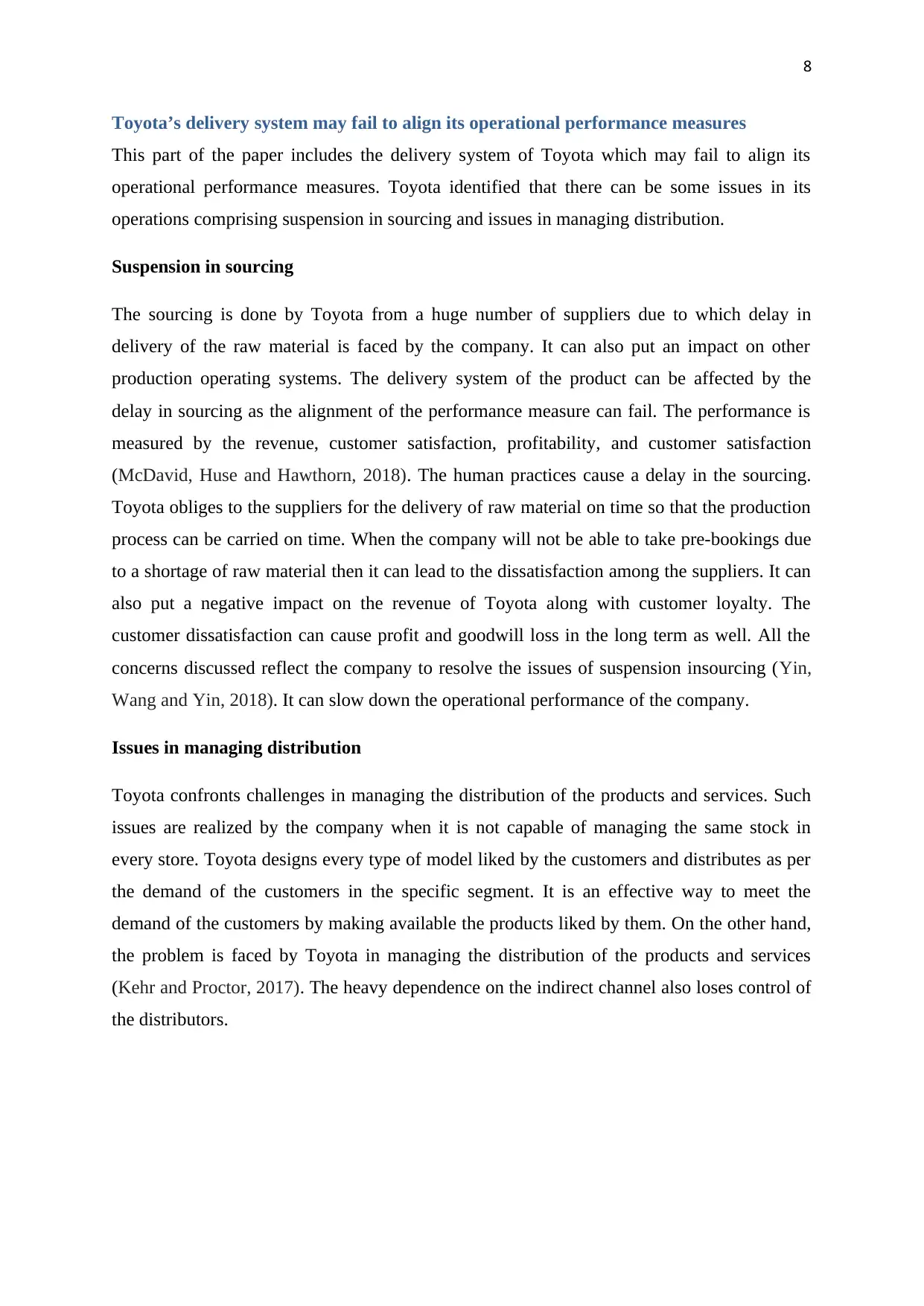
8
Toyota’s delivery system may fail to align its operational performance measures
This part of the paper includes the delivery system of Toyota which may fail to align its
operational performance measures. Toyota identified that there can be some issues in its
operations comprising suspension in sourcing and issues in managing distribution.
Suspension in sourcing
The sourcing is done by Toyota from a huge number of suppliers due to which delay in
delivery of the raw material is faced by the company. It can also put an impact on other
production operating systems. The delivery system of the product can be affected by the
delay in sourcing as the alignment of the performance measure can fail. The performance is
measured by the revenue, customer satisfaction, profitability, and customer satisfaction
(McDavid, Huse and Hawthorn, 2018). The human practices cause a delay in the sourcing.
Toyota obliges to the suppliers for the delivery of raw material on time so that the production
process can be carried on time. When the company will not be able to take pre-bookings due
to a shortage of raw material then it can lead to the dissatisfaction among the suppliers. It can
also put a negative impact on the revenue of Toyota along with customer loyalty. The
customer dissatisfaction can cause profit and goodwill loss in the long term as well. All the
concerns discussed reflect the company to resolve the issues of suspension insourcing (Yin,
Wang and Yin, 2018). It can slow down the operational performance of the company.
Issues in managing distribution
Toyota confronts challenges in managing the distribution of the products and services. Such
issues are realized by the company when it is not capable of managing the same stock in
every store. Toyota designs every type of model liked by the customers and distributes as per
the demand of the customers in the specific segment. It is an effective way to meet the
demand of the customers by making available the products liked by them. On the other hand,
the problem is faced by Toyota in managing the distribution of the products and services
(Kehr and Proctor, 2017). The heavy dependence on the indirect channel also loses control of
the distributors.
Toyota’s delivery system may fail to align its operational performance measures
This part of the paper includes the delivery system of Toyota which may fail to align its
operational performance measures. Toyota identified that there can be some issues in its
operations comprising suspension in sourcing and issues in managing distribution.
Suspension in sourcing
The sourcing is done by Toyota from a huge number of suppliers due to which delay in
delivery of the raw material is faced by the company. It can also put an impact on other
production operating systems. The delivery system of the product can be affected by the
delay in sourcing as the alignment of the performance measure can fail. The performance is
measured by the revenue, customer satisfaction, profitability, and customer satisfaction
(McDavid, Huse and Hawthorn, 2018). The human practices cause a delay in the sourcing.
Toyota obliges to the suppliers for the delivery of raw material on time so that the production
process can be carried on time. When the company will not be able to take pre-bookings due
to a shortage of raw material then it can lead to the dissatisfaction among the suppliers. It can
also put a negative impact on the revenue of Toyota along with customer loyalty. The
customer dissatisfaction can cause profit and goodwill loss in the long term as well. All the
concerns discussed reflect the company to resolve the issues of suspension insourcing (Yin,
Wang and Yin, 2018). It can slow down the operational performance of the company.
Issues in managing distribution
Toyota confronts challenges in managing the distribution of the products and services. Such
issues are realized by the company when it is not capable of managing the same stock in
every store. Toyota designs every type of model liked by the customers and distributes as per
the demand of the customers in the specific segment. It is an effective way to meet the
demand of the customers by making available the products liked by them. On the other hand,
the problem is faced by Toyota in managing the distribution of the products and services
(Kehr and Proctor, 2017). The heavy dependence on the indirect channel also loses control of
the distributors.
⊘ This is a preview!⊘
Do you want full access?
Subscribe today to unlock all pages.

Trusted by 1+ million students worldwide
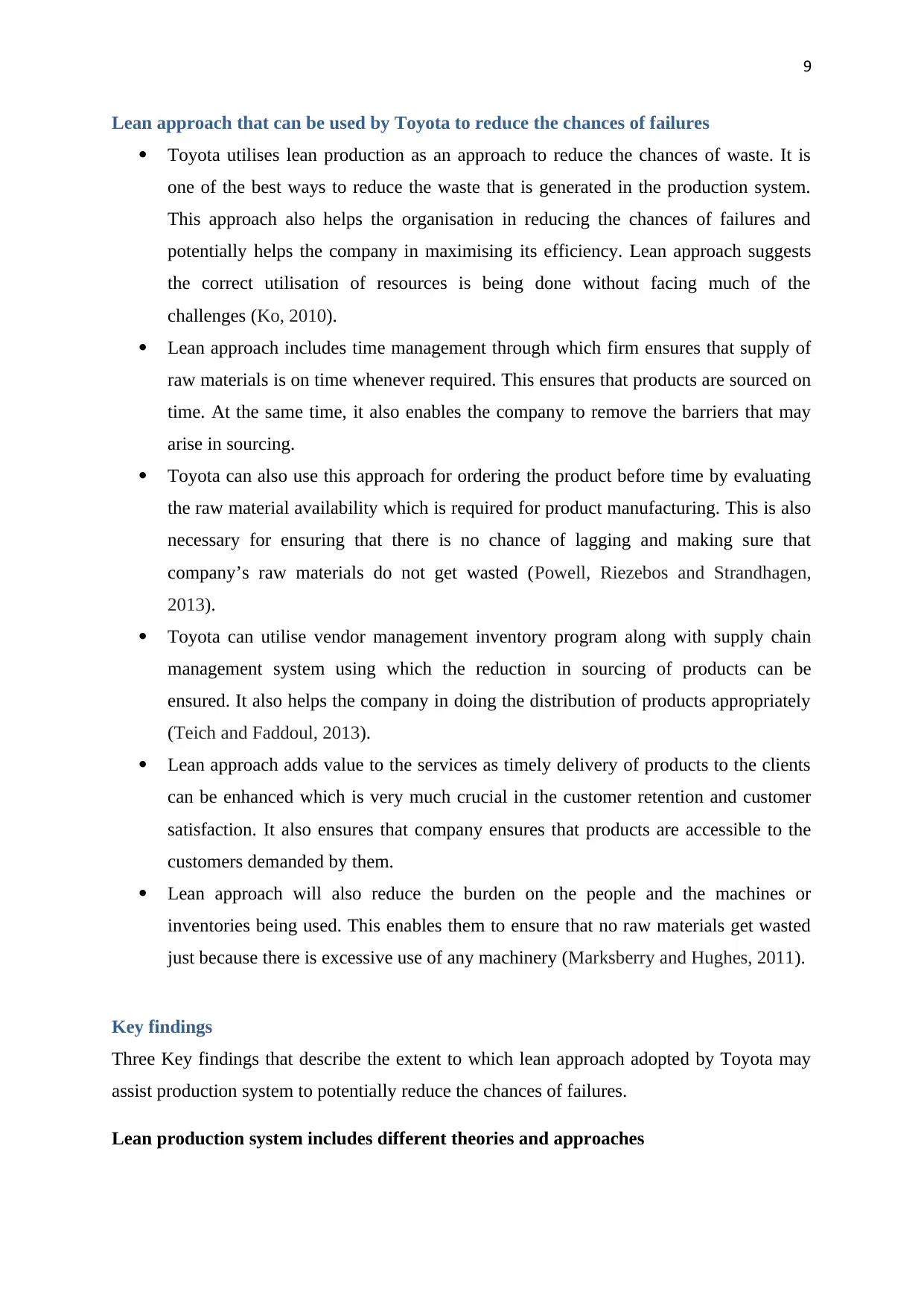
9
Lean approach that can be used by Toyota to reduce the chances of failures
Toyota utilises lean production as an approach to reduce the chances of waste. It is
one of the best ways to reduce the waste that is generated in the production system.
This approach also helps the organisation in reducing the chances of failures and
potentially helps the company in maximising its efficiency. Lean approach suggests
the correct utilisation of resources is being done without facing much of the
challenges (Ko, 2010).
Lean approach includes time management through which firm ensures that supply of
raw materials is on time whenever required. This ensures that products are sourced on
time. At the same time, it also enables the company to remove the barriers that may
arise in sourcing.
Toyota can also use this approach for ordering the product before time by evaluating
the raw material availability which is required for product manufacturing. This is also
necessary for ensuring that there is no chance of lagging and making sure that
company’s raw materials do not get wasted (Powell, Riezebos and Strandhagen,
2013).
Toyota can utilise vendor management inventory program along with supply chain
management system using which the reduction in sourcing of products can be
ensured. It also helps the company in doing the distribution of products appropriately
(Teich and Faddoul, 2013).
Lean approach adds value to the services as timely delivery of products to the clients
can be enhanced which is very much crucial in the customer retention and customer
satisfaction. It also ensures that company ensures that products are accessible to the
customers demanded by them.
Lean approach will also reduce the burden on the people and the machines or
inventories being used. This enables them to ensure that no raw materials get wasted
just because there is excessive use of any machinery (Marksberry and Hughes, 2011).
Key findings
Three Key findings that describe the extent to which lean approach adopted by Toyota may
assist production system to potentially reduce the chances of failures.
Lean production system includes different theories and approaches
Lean approach that can be used by Toyota to reduce the chances of failures
Toyota utilises lean production as an approach to reduce the chances of waste. It is
one of the best ways to reduce the waste that is generated in the production system.
This approach also helps the organisation in reducing the chances of failures and
potentially helps the company in maximising its efficiency. Lean approach suggests
the correct utilisation of resources is being done without facing much of the
challenges (Ko, 2010).
Lean approach includes time management through which firm ensures that supply of
raw materials is on time whenever required. This ensures that products are sourced on
time. At the same time, it also enables the company to remove the barriers that may
arise in sourcing.
Toyota can also use this approach for ordering the product before time by evaluating
the raw material availability which is required for product manufacturing. This is also
necessary for ensuring that there is no chance of lagging and making sure that
company’s raw materials do not get wasted (Powell, Riezebos and Strandhagen,
2013).
Toyota can utilise vendor management inventory program along with supply chain
management system using which the reduction in sourcing of products can be
ensured. It also helps the company in doing the distribution of products appropriately
(Teich and Faddoul, 2013).
Lean approach adds value to the services as timely delivery of products to the clients
can be enhanced which is very much crucial in the customer retention and customer
satisfaction. It also ensures that company ensures that products are accessible to the
customers demanded by them.
Lean approach will also reduce the burden on the people and the machines or
inventories being used. This enables them to ensure that no raw materials get wasted
just because there is excessive use of any machinery (Marksberry and Hughes, 2011).
Key findings
Three Key findings that describe the extent to which lean approach adopted by Toyota may
assist production system to potentially reduce the chances of failures.
Lean production system includes different theories and approaches
Paraphrase This Document
Need a fresh take? Get an instant paraphrase of this document with our AI Paraphraser
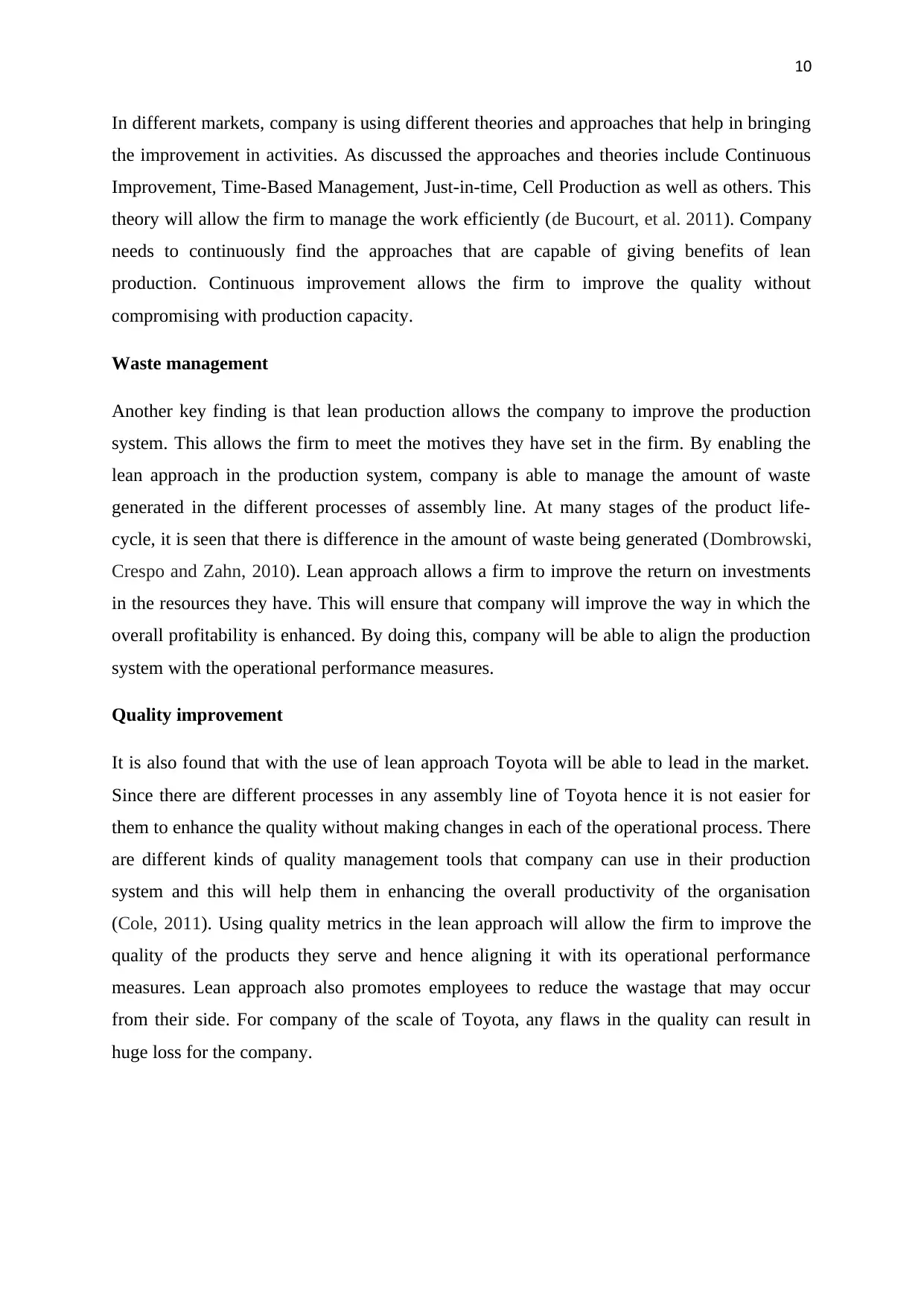
10
In different markets, company is using different theories and approaches that help in bringing
the improvement in activities. As discussed the approaches and theories include Continuous
Improvement, Time-Based Management, Just-in-time, Cell Production as well as others. This
theory will allow the firm to manage the work efficiently (de Bucourt, et al. 2011). Company
needs to continuously find the approaches that are capable of giving benefits of lean
production. Continuous improvement allows the firm to improve the quality without
compromising with production capacity.
Waste management
Another key finding is that lean production allows the company to improve the production
system. This allows the firm to meet the motives they have set in the firm. By enabling the
lean approach in the production system, company is able to manage the amount of waste
generated in the different processes of assembly line. At many stages of the product life-
cycle, it is seen that there is difference in the amount of waste being generated (Dombrowski,
Crespo and Zahn, 2010). Lean approach allows a firm to improve the return on investments
in the resources they have. This will ensure that company will improve the way in which the
overall profitability is enhanced. By doing this, company will be able to align the production
system with the operational performance measures.
Quality improvement
It is also found that with the use of lean approach Toyota will be able to lead in the market.
Since there are different processes in any assembly line of Toyota hence it is not easier for
them to enhance the quality without making changes in each of the operational process. There
are different kinds of quality management tools that company can use in their production
system and this will help them in enhancing the overall productivity of the organisation
(Cole, 2011). Using quality metrics in the lean approach will allow the firm to improve the
quality of the products they serve and hence aligning it with its operational performance
measures. Lean approach also promotes employees to reduce the wastage that may occur
from their side. For company of the scale of Toyota, any flaws in the quality can result in
huge loss for the company.
In different markets, company is using different theories and approaches that help in bringing
the improvement in activities. As discussed the approaches and theories include Continuous
Improvement, Time-Based Management, Just-in-time, Cell Production as well as others. This
theory will allow the firm to manage the work efficiently (de Bucourt, et al. 2011). Company
needs to continuously find the approaches that are capable of giving benefits of lean
production. Continuous improvement allows the firm to improve the quality without
compromising with production capacity.
Waste management
Another key finding is that lean production allows the company to improve the production
system. This allows the firm to meet the motives they have set in the firm. By enabling the
lean approach in the production system, company is able to manage the amount of waste
generated in the different processes of assembly line. At many stages of the product life-
cycle, it is seen that there is difference in the amount of waste being generated (Dombrowski,
Crespo and Zahn, 2010). Lean approach allows a firm to improve the return on investments
in the resources they have. This will ensure that company will improve the way in which the
overall profitability is enhanced. By doing this, company will be able to align the production
system with the operational performance measures.
Quality improvement
It is also found that with the use of lean approach Toyota will be able to lead in the market.
Since there are different processes in any assembly line of Toyota hence it is not easier for
them to enhance the quality without making changes in each of the operational process. There
are different kinds of quality management tools that company can use in their production
system and this will help them in enhancing the overall productivity of the organisation
(Cole, 2011). Using quality metrics in the lean approach will allow the firm to improve the
quality of the products they serve and hence aligning it with its operational performance
measures. Lean approach also promotes employees to reduce the wastage that may occur
from their side. For company of the scale of Toyota, any flaws in the quality can result in
huge loss for the company.
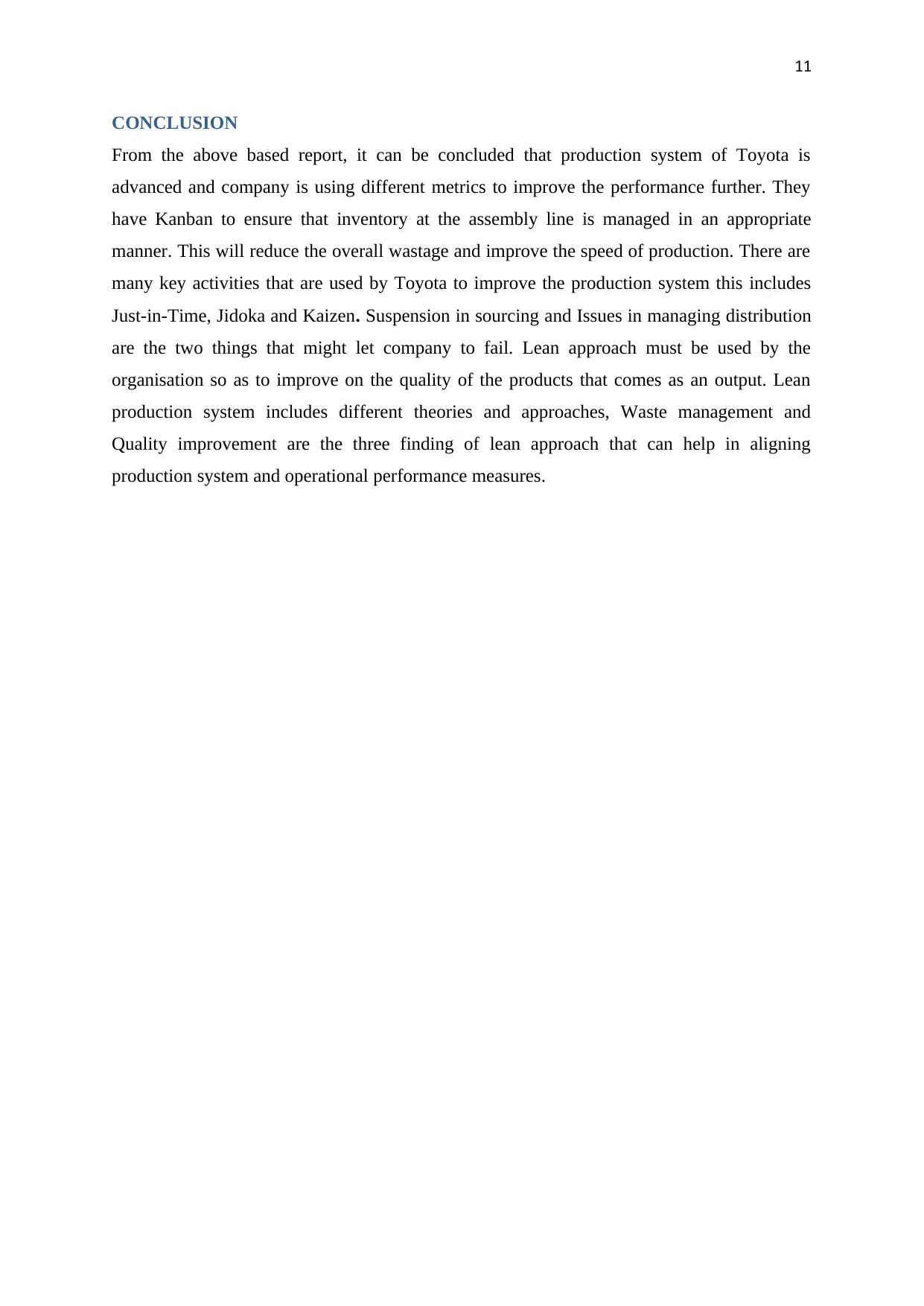
11
CONCLUSION
From the above based report, it can be concluded that production system of Toyota is
advanced and company is using different metrics to improve the performance further. They
have Kanban to ensure that inventory at the assembly line is managed in an appropriate
manner. This will reduce the overall wastage and improve the speed of production. There are
many key activities that are used by Toyota to improve the production system this includes
Just-in-Time, Jidoka and Kaizen. Suspension in sourcing and Issues in managing distribution
are the two things that might let company to fail. Lean approach must be used by the
organisation so as to improve on the quality of the products that comes as an output. Lean
production system includes different theories and approaches, Waste management and
Quality improvement are the three finding of lean approach that can help in aligning
production system and operational performance measures.
CONCLUSION
From the above based report, it can be concluded that production system of Toyota is
advanced and company is using different metrics to improve the performance further. They
have Kanban to ensure that inventory at the assembly line is managed in an appropriate
manner. This will reduce the overall wastage and improve the speed of production. There are
many key activities that are used by Toyota to improve the production system this includes
Just-in-Time, Jidoka and Kaizen. Suspension in sourcing and Issues in managing distribution
are the two things that might let company to fail. Lean approach must be used by the
organisation so as to improve on the quality of the products that comes as an output. Lean
production system includes different theories and approaches, Waste management and
Quality improvement are the three finding of lean approach that can help in aligning
production system and operational performance measures.
⊘ This is a preview!⊘
Do you want full access?
Subscribe today to unlock all pages.

Trusted by 1+ million students worldwide
1 out of 15