Operations and Project Management
Added on 2023-01-06
34 Pages5281 Words87 Views
Unit Number & Unit Title Unit 16 – Operations and Project Management
Project Title Operations managment in Toyota
Project Title Operations managment in Toyota
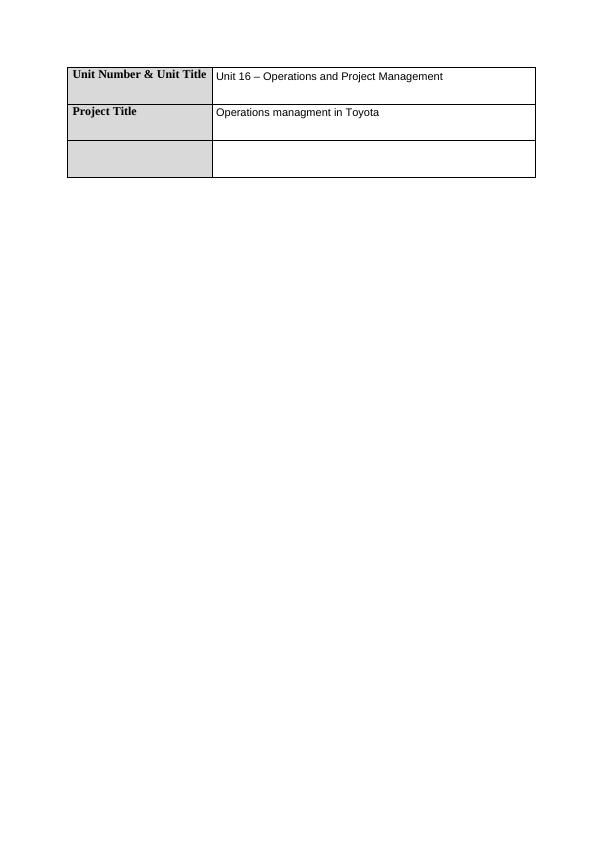
Page 1 of 19
Operations management in Toyota
Operations management in Toyota
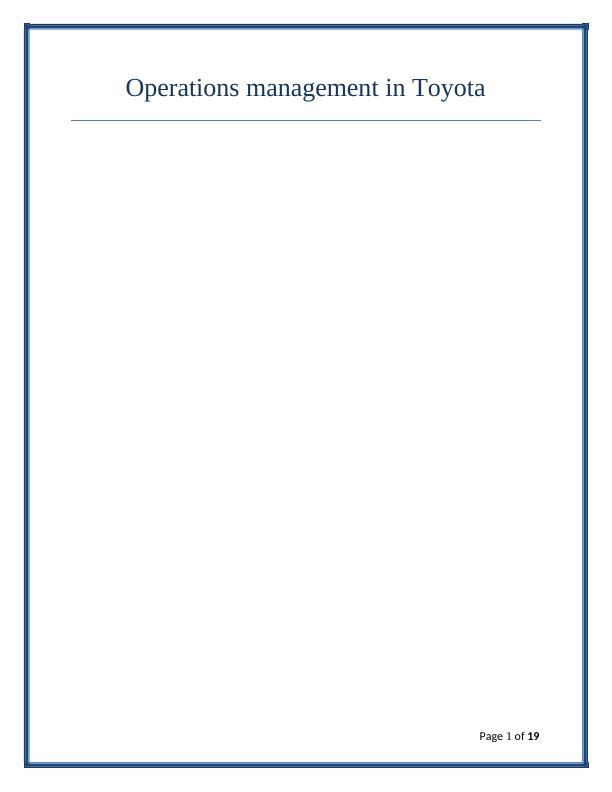
Page 2 of 19
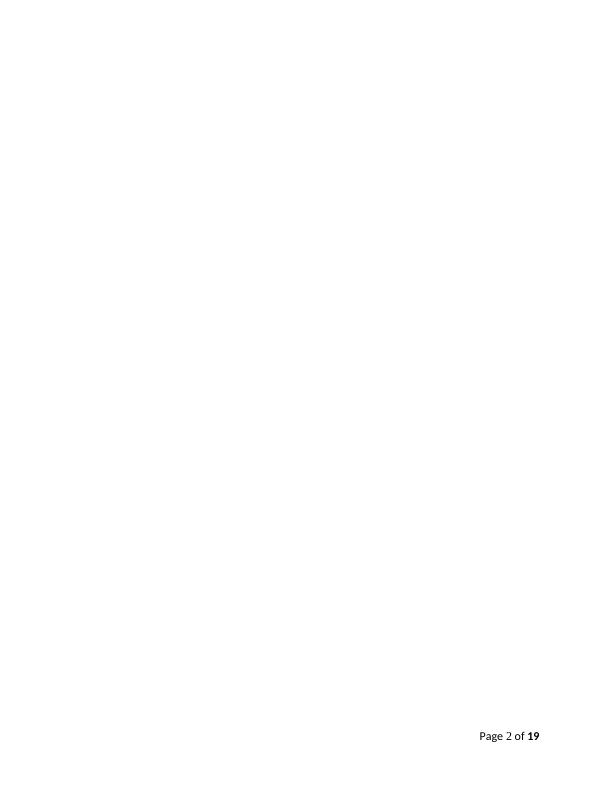
Page 3 of 19
Table of Contents
Activity 1...........................................................................................................................................4
Introduction......................................................................................................................................4
Implementation of principles of operations management in Toyota...............................................4
Design of products and services....................................................................................................5
Quality assurance...........................................................................................................................5
Process and capacity design.........................................................................................................5
Location principle........................................................................................................................5
Job design and human resources..................................................................................................5
Supply chain management...........................................................................................................6
Invertor management...................................................................................................................6
Scheduling....................................................................................................................................6
Operations management and six sigma methodology.......................................................................6
Long term philosophy..................................................................................................................6
Continuous flow.............................................................................................................................7
Avoid over production...................................................................................................................7
Consistency....................................................................................................................................7
Building right culture.....................................................................................................................7
Standardize tasks............................................................................................................................8
Visual control.................................................................................................................................8
Tested technology..........................................................................................................................8
Leadership skill..............................................................................................................................8
Team building................................................................................................................................8
Observations and reflection...........................................................................................................8
Slow decision and fast implementation.........................................................................................9
Reflection is the continuous process..............................................................................................9
Table of Contents
Activity 1...........................................................................................................................................4
Introduction......................................................................................................................................4
Implementation of principles of operations management in Toyota...............................................4
Design of products and services....................................................................................................5
Quality assurance...........................................................................................................................5
Process and capacity design.........................................................................................................5
Location principle........................................................................................................................5
Job design and human resources..................................................................................................5
Supply chain management...........................................................................................................6
Invertor management...................................................................................................................6
Scheduling....................................................................................................................................6
Operations management and six sigma methodology.......................................................................6
Long term philosophy..................................................................................................................6
Continuous flow.............................................................................................................................7
Avoid over production...................................................................................................................7
Consistency....................................................................................................................................7
Building right culture.....................................................................................................................7
Standardize tasks............................................................................................................................8
Visual control.................................................................................................................................8
Tested technology..........................................................................................................................8
Leadership skill..............................................................................................................................8
Team building................................................................................................................................8
Observations and reflection...........................................................................................................8
Slow decision and fast implementation.........................................................................................9
Reflection is the continuous process..............................................................................................9
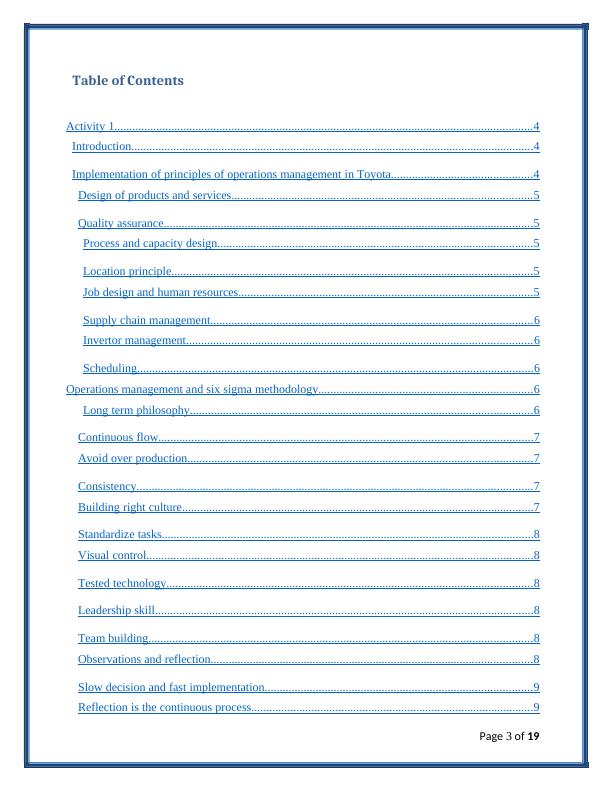
Page 4 of 19
Lean principle in context of Toyota..................................................................................................9
Conclusion.........................................................................................................................................9
Activity 2.........................................................................................................................................11
Introduction......................................................................................................................................11
Continuous improvement plan.........................................................................................................12
Kaizen..........................................................................................................................................12
PDCA cycle.................................................................................................................................13
Plan..........................................................................................................................................13
Do............................................................................................................................................13
Check.......................................................................................................................................14
Act............................................................................................................................................14
Effectiveness of the plan based on theories...................................................................................14
Increased productivity and profits...............................................................................................14
Employee’s morale and accountability........................................................................................14
Agility..........................................................................................................................................15
Lower cost...................................................................................................................................15
Decreased delivery times.............................................................................................................15
Improved quality..........................................................................................................................15
Strategies for continuous improvement based on theories..............................................................15
Flow management........................................................................................................................16
Lean manufacturing system.........................................................................................................16
Six Sigma...................................................................................................................................16
Conclusion.......................................................................................................................................16
References........................................................................................................................................18
Lean principle in context of Toyota..................................................................................................9
Conclusion.........................................................................................................................................9
Activity 2.........................................................................................................................................11
Introduction......................................................................................................................................11
Continuous improvement plan.........................................................................................................12
Kaizen..........................................................................................................................................12
PDCA cycle.................................................................................................................................13
Plan..........................................................................................................................................13
Do............................................................................................................................................13
Check.......................................................................................................................................14
Act............................................................................................................................................14
Effectiveness of the plan based on theories...................................................................................14
Increased productivity and profits...............................................................................................14
Employee’s morale and accountability........................................................................................14
Agility..........................................................................................................................................15
Lower cost...................................................................................................................................15
Decreased delivery times.............................................................................................................15
Improved quality..........................................................................................................................15
Strategies for continuous improvement based on theories..............................................................15
Flow management........................................................................................................................16
Lean manufacturing system.........................................................................................................16
Six Sigma...................................................................................................................................16
Conclusion.......................................................................................................................................16
References........................................................................................................................................18
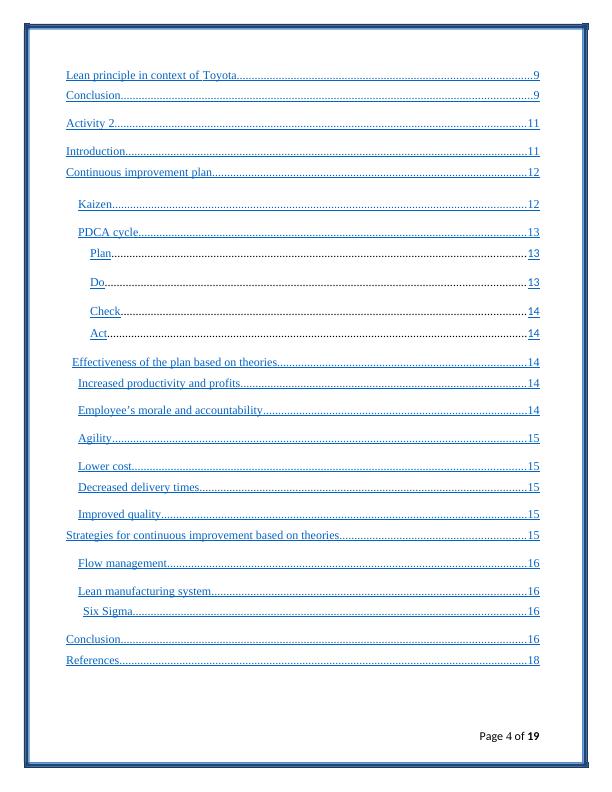
Activity 1
Introduction
The business operations are the variety of processes that a Toyota company carried out to
produce goods and services. Every process has its unique features and sensitivity, advantages
and disadvantages as well as implications. Smooth business operations help an organization to
grow continuously and achieve company objectives and targets in sales. Business operations
include production, arrangement of supply chain, inventory matters, delivery of goods and
services, administration and many other activities that comes under operations management. To
assure business operations accuracy and timely delivery of all tasks as per company standards
there is a department within an organization named operations management.
Operations management department helps to monitor business operations and removes flaws and
supports continuous improvement in business processes. Operations management is an area of
Toyota Company which is responsible for production processes and keeps them efficient in the
form of cost effectiveness, time management, streamlining business activities, and minimum
waste of material; keep all resources productive and efficient. Operations management helps the
compliance of standard operating procedures outlined by company management. Human
resource management, asset management, cost management, and administration comes under
operations management.
Operation means that perform actions and decision made by owner of Toyota enterprise
and member of business that affect service, management, distribution and production.
Operation management is based on the administration of enterprise practices to create the
highest level of efficiency. It can possible when converting the raw materials into better
good and services. Afterwards, it will be increasing the maximum profitability as well as
productivity in marketplace.
Introduction
The business operations are the variety of processes that a Toyota company carried out to
produce goods and services. Every process has its unique features and sensitivity, advantages
and disadvantages as well as implications. Smooth business operations help an organization to
grow continuously and achieve company objectives and targets in sales. Business operations
include production, arrangement of supply chain, inventory matters, delivery of goods and
services, administration and many other activities that comes under operations management. To
assure business operations accuracy and timely delivery of all tasks as per company standards
there is a department within an organization named operations management.
Operations management department helps to monitor business operations and removes flaws and
supports continuous improvement in business processes. Operations management is an area of
Toyota Company which is responsible for production processes and keeps them efficient in the
form of cost effectiveness, time management, streamlining business activities, and minimum
waste of material; keep all resources productive and efficient. Operations management helps the
compliance of standard operating procedures outlined by company management. Human
resource management, asset management, cost management, and administration comes under
operations management.
Operation means that perform actions and decision made by owner of Toyota enterprise
and member of business that affect service, management, distribution and production.
Operation management is based on the administration of enterprise practices to create the
highest level of efficiency. It can possible when converting the raw materials into better
good and services. Afterwards, it will be increasing the maximum profitability as well as
productivity in marketplace.
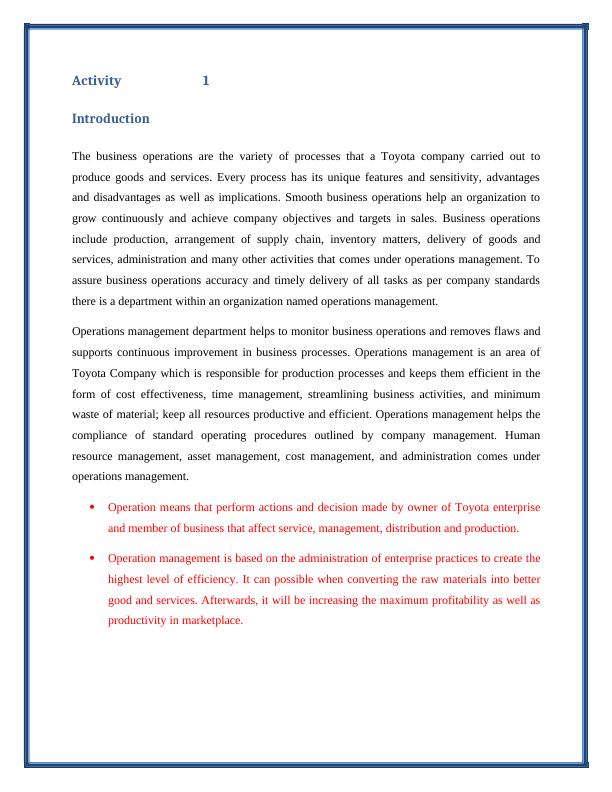
Implementation of principles of operations management in Toyota
The Toyota motor company practices variety of operations management principles to keep
business operations effective and efficient. The Toyota Company uses well defined practices and
theories combine to avoid any ambiguity in business processes. This is the reason of company’s
unique operations management which is being admired not only by the consumers but corporate
sector as well around the globe. The company has is practicing following operations management
principals to keep business efficient (Cousins et al., 2008).
Design of products and services
To have cutting edge design of products and service the company uses technology and innovative
tools and highly talented experts. The R&D investment style of company helps to assure excellent
features of products and services. Toyota uses integration system for dealership sand after sales
services to assure maximum customer satisfaction (Cousins et al., 2008).
Quality assurance
For quality assurance purpose the company uses Toyota production system which is built within
the organization. Quality maintenance is the key factor to have competitive edge over competitors.
Toyota uses operations management principles for continuous improvement to assure quality in
every aspect of the business.
Process and capacity design
For business process and the capacity design of company uses lean manufacturing principal. The
company is focused on minimum waste and increased efficiency of processes. Cost effectiveness
in business process and capacity design is the company’s focus (Cousins et al., 2008).
Location principle
The Toyota Company has choses locations of business as per country’s circumstances. Around the
world in some countries the company has manufacturing plants and in some countries the
company has assembling plants but in some countries the company has only dealerships but
company sends products from nearby locations or countries.
The Toyota motor company practices variety of operations management principles to keep
business operations effective and efficient. The Toyota Company uses well defined practices and
theories combine to avoid any ambiguity in business processes. This is the reason of company’s
unique operations management which is being admired not only by the consumers but corporate
sector as well around the globe. The company has is practicing following operations management
principals to keep business efficient (Cousins et al., 2008).
Design of products and services
To have cutting edge design of products and service the company uses technology and innovative
tools and highly talented experts. The R&D investment style of company helps to assure excellent
features of products and services. Toyota uses integration system for dealership sand after sales
services to assure maximum customer satisfaction (Cousins et al., 2008).
Quality assurance
For quality assurance purpose the company uses Toyota production system which is built within
the organization. Quality maintenance is the key factor to have competitive edge over competitors.
Toyota uses operations management principles for continuous improvement to assure quality in
every aspect of the business.
Process and capacity design
For business process and the capacity design of company uses lean manufacturing principal. The
company is focused on minimum waste and increased efficiency of processes. Cost effectiveness
in business process and capacity design is the company’s focus (Cousins et al., 2008).
Location principle
The Toyota Company has choses locations of business as per country’s circumstances. Around the
world in some countries the company has manufacturing plants and in some countries the
company has assembling plants but in some countries the company has only dealerships but
company sends products from nearby locations or countries.
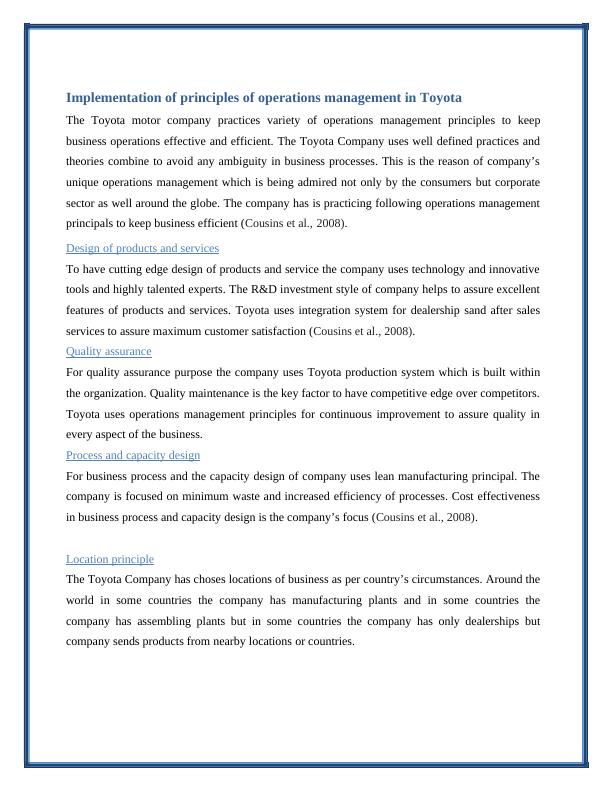
Job design and human resources
Toyota practices its production system for employees and supply chain. The Toyota way culture is
the company’s instinct to provide environment for employees and services providers. Company
respects a lot of its employees and contractors or dealers (Chhajed & Lowe, 2008).
Supply chain management
Company uses lean manufacturing principal in supply chain management. There are automated
systems installed within the organization which monitors real-time adjustments in supply chain
process
Invertor management
For inventory management the company uses Toyota production system which assures minimum
levels of inventory by producing timely required unites and making sure of timely delivery.
Scheduling
In scheduling the company uses lean manufacturing principal. With the help of scheduling the
company minimizes operational cost.
Toyota has been implementing the different parameters in term of business progress or
improvement. It includes quality of goods, proper scheduling, HR management, process and
capacity of entire business activities. By considerations of all essential elements that always
support for creating an effective design pattern of each product so that they can easily targeting
the potential consumers in global marketplace. In order to increase production and sales in global
marketplace.
Operations management and six sigma methodology
The Six Sigma methodology is the framework to increase the efficiency of the operations
management. This methodology helps to point out flaws in operations management and suggest
some recommendations to fix errors timely. It also helps to reduce operational cost and helps in
time saving. The Six Sigma is an expansive technique to implement in an organization but its
proper implementation helps an organization to become industry leader. The Toyota Company
with the help of Six Sigma methodology is continuously improving its operations management,
which is the secret of company’s long term sustained success in automobile industry. The
company is enjoying consumer’s trust this is why company’s enjoys outstanding sales around the
globe through advance booking of car unites. Following are the main elements of six sigma
framework which I have discussed below (Chhajed & Lowe, 2008).
Toyota practices its production system for employees and supply chain. The Toyota way culture is
the company’s instinct to provide environment for employees and services providers. Company
respects a lot of its employees and contractors or dealers (Chhajed & Lowe, 2008).
Supply chain management
Company uses lean manufacturing principal in supply chain management. There are automated
systems installed within the organization which monitors real-time adjustments in supply chain
process
Invertor management
For inventory management the company uses Toyota production system which assures minimum
levels of inventory by producing timely required unites and making sure of timely delivery.
Scheduling
In scheduling the company uses lean manufacturing principal. With the help of scheduling the
company minimizes operational cost.
Toyota has been implementing the different parameters in term of business progress or
improvement. It includes quality of goods, proper scheduling, HR management, process and
capacity of entire business activities. By considerations of all essential elements that always
support for creating an effective design pattern of each product so that they can easily targeting
the potential consumers in global marketplace. In order to increase production and sales in global
marketplace.
Operations management and six sigma methodology
The Six Sigma methodology is the framework to increase the efficiency of the operations
management. This methodology helps to point out flaws in operations management and suggest
some recommendations to fix errors timely. It also helps to reduce operational cost and helps in
time saving. The Six Sigma is an expansive technique to implement in an organization but its
proper implementation helps an organization to become industry leader. The Toyota Company
with the help of Six Sigma methodology is continuously improving its operations management,
which is the secret of company’s long term sustained success in automobile industry. The
company is enjoying consumer’s trust this is why company’s enjoys outstanding sales around the
globe through advance booking of car unites. Following are the main elements of six sigma
framework which I have discussed below (Chhajed & Lowe, 2008).
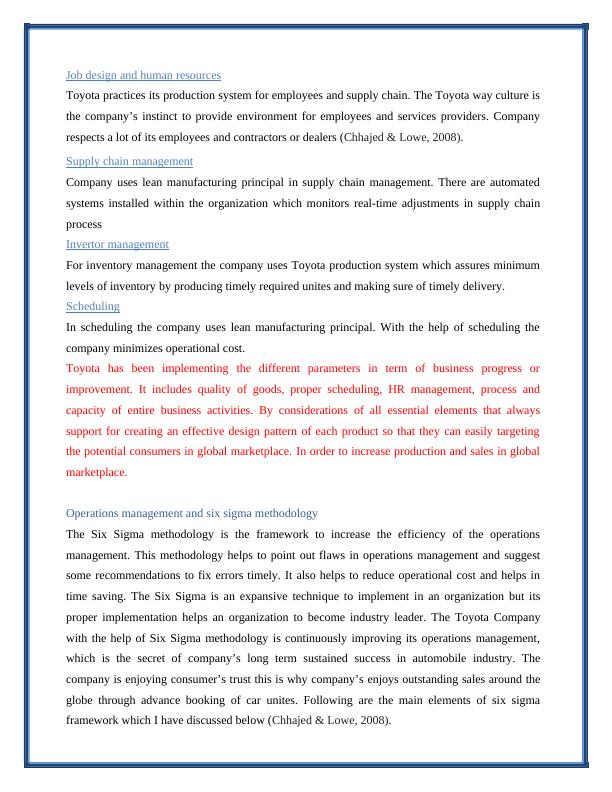
End of preview
Want to access all the pages? Upload your documents or become a member.
Related Documents
Assignment on Lean Six Sigma Framework.lg...
|23
|5026
|24
Project and Operational Management Assignmentlg...
|25
|8767
|65
Lean Six Sigma in Industrieslg...
|18
|6773
|460
Quality Management Principles and Strategies for A-1 Express Delivery Servicelg...
|17
|2754
|140
Operational and Project Management in Product Life Cyclelg...
|16
|4285
|393
Quality Management in A-1 Express Delivery Servicelg...
|15
|2284
|413