Operations and Project Management Report: XYZ Company Analysis
VerifiedAdded on 2020/11/12
|13
|4006
|225
Report
AI Summary
This report provides a comprehensive analysis of operations and project management principles, focusing on their application within XYZ Company. It begins with an introduction to operation management and project management, highlighting their importance in enhancing organizational effici...
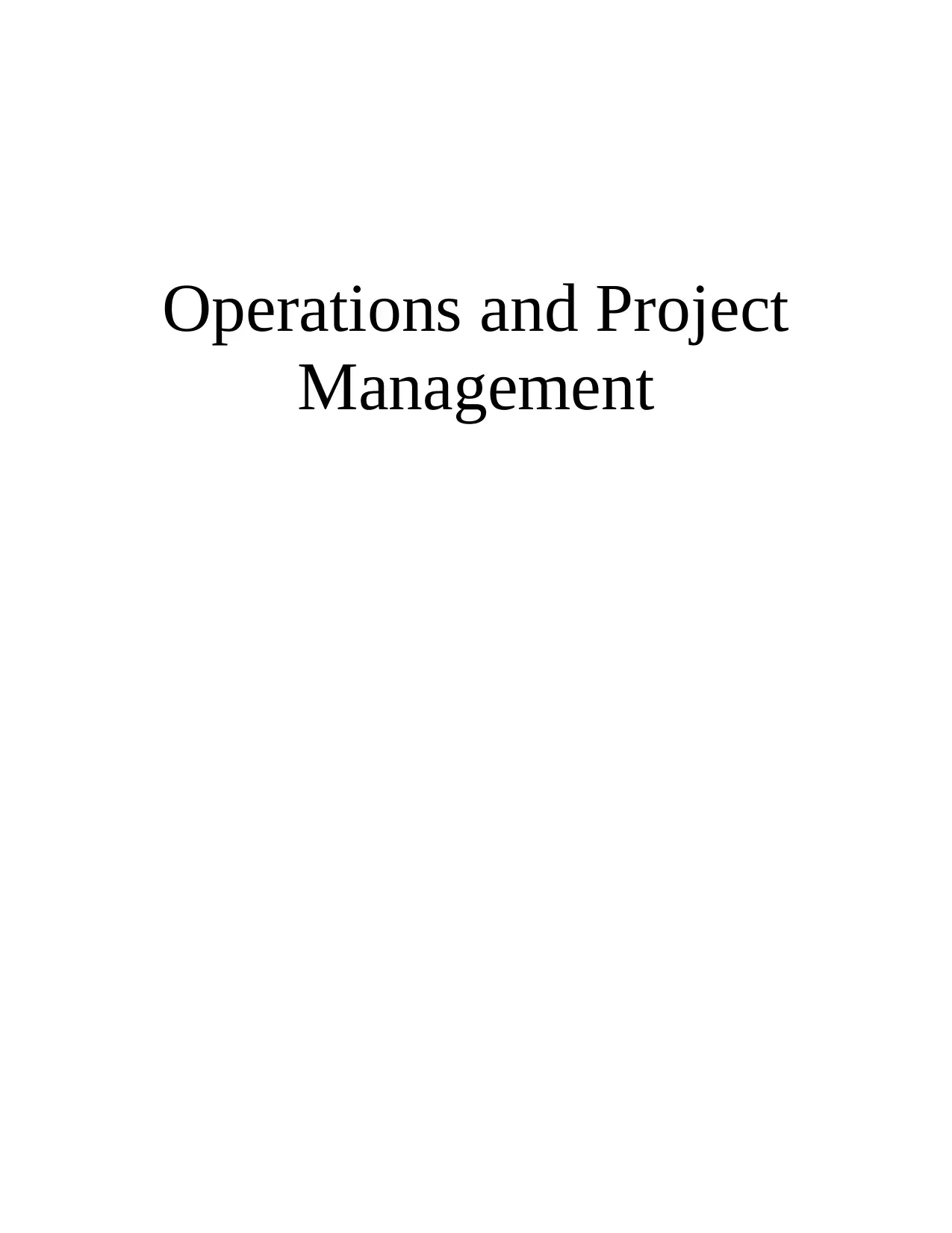
Operations and Project
Management
Management
Paraphrase This Document
Need a fresh take? Get an instant paraphrase of this document with our AI Paraphraser
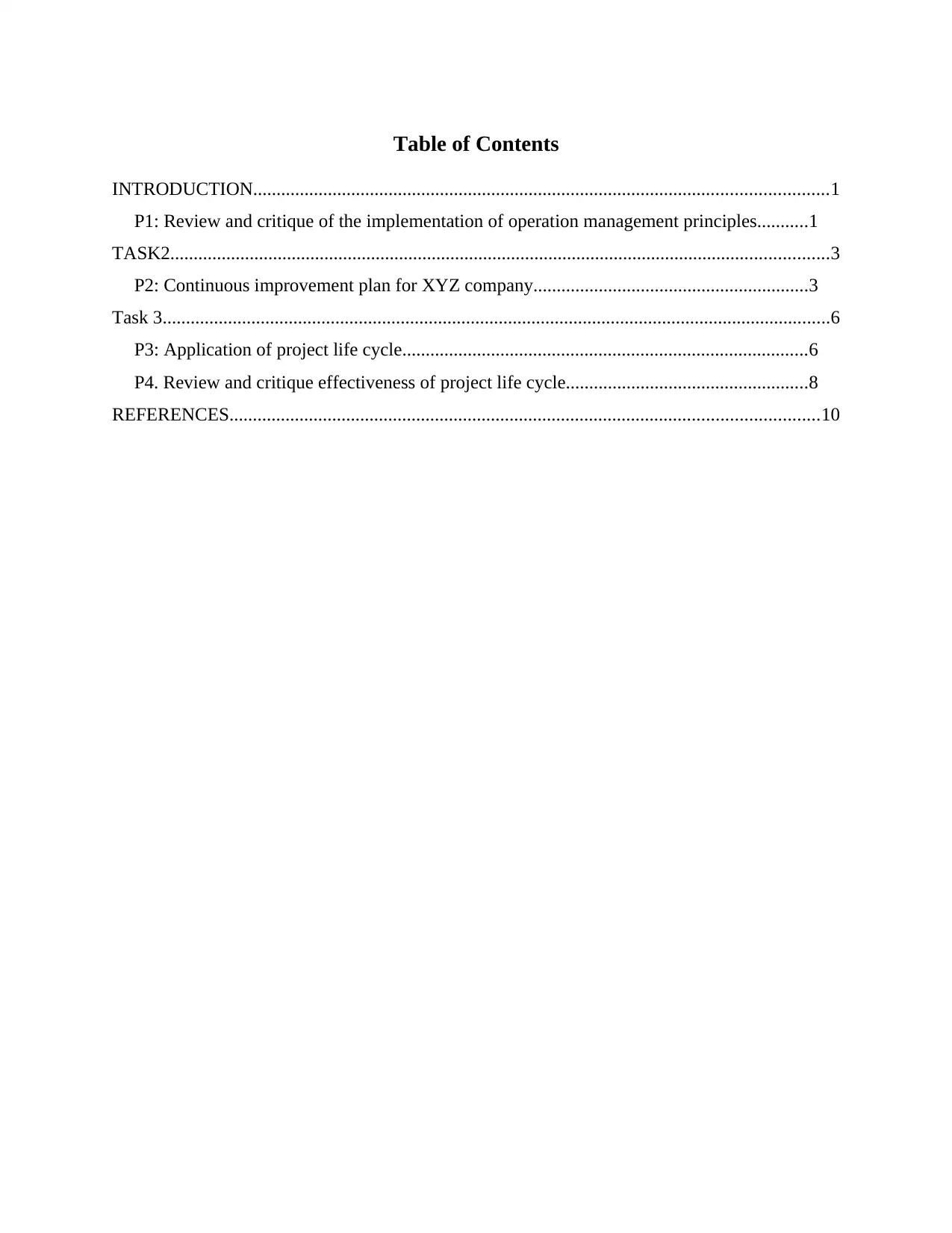
Table of Contents
INTRODUCTION...........................................................................................................................1
P1: Review and critique of the implementation of operation management principles...........1
TASK2.............................................................................................................................................3
P2: Continuous improvement plan for XYZ company...........................................................3
Task 3...............................................................................................................................................6
P3: Application of project life cycle.......................................................................................6
P4. Review and critique effectiveness of project life cycle....................................................8
REFERENCES..............................................................................................................................10
INTRODUCTION...........................................................................................................................1
P1: Review and critique of the implementation of operation management principles...........1
TASK2.............................................................................................................................................3
P2: Continuous improvement plan for XYZ company...........................................................3
Task 3...............................................................................................................................................6
P3: Application of project life cycle.......................................................................................6
P4. Review and critique effectiveness of project life cycle....................................................8
REFERENCES..............................................................................................................................10
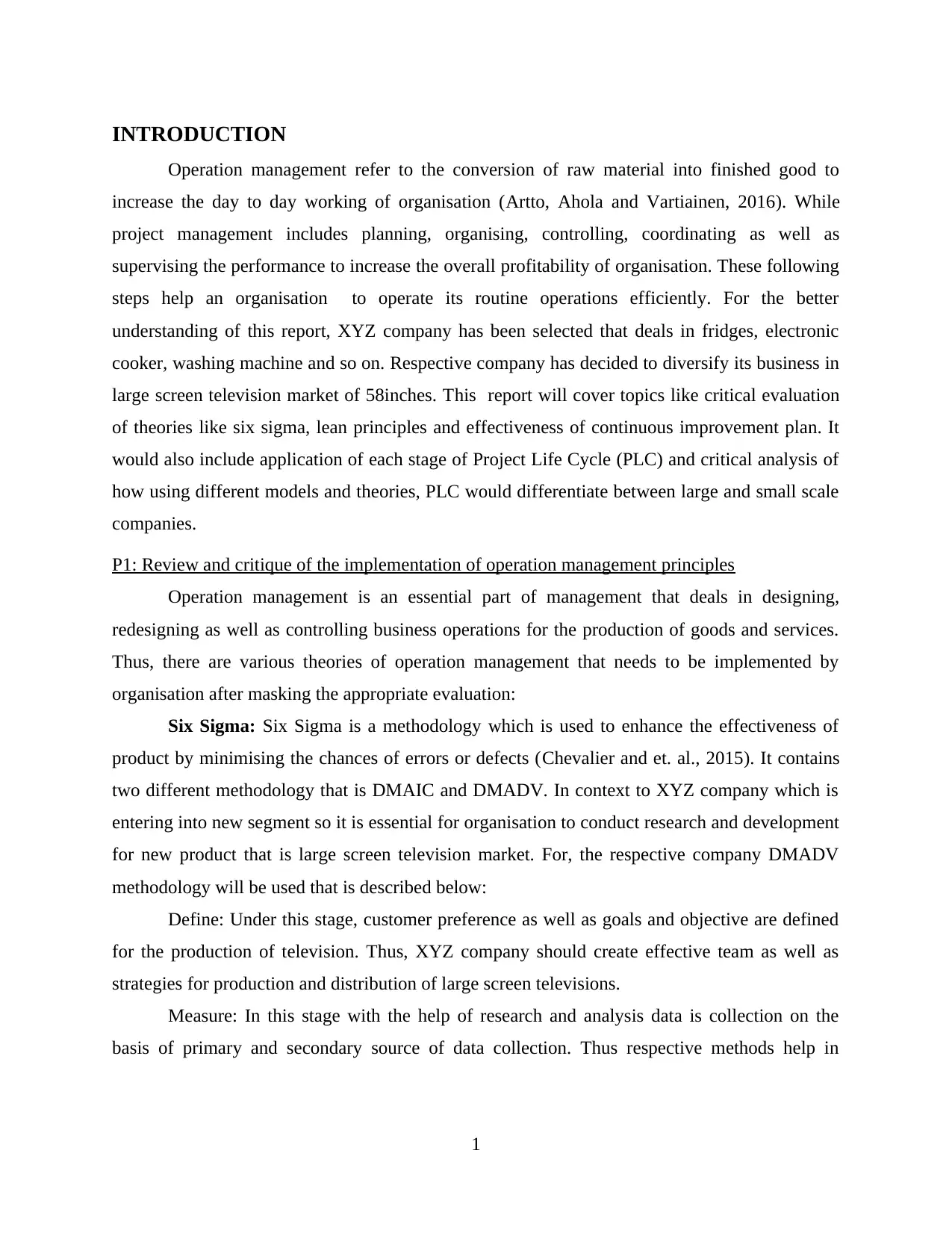
INTRODUCTION
Operation management refer to the conversion of raw material into finished good to
increase the day to day working of organisation (Artto, Ahola and Vartiainen, 2016). While
project management includes planning, organising, controlling, coordinating as well as
supervising the performance to increase the overall profitability of organisation. These following
steps help an organisation to operate its routine operations efficiently. For the better
understanding of this report, XYZ company has been selected that deals in fridges, electronic
cooker, washing machine and so on. Respective company has decided to diversify its business in
large screen television market of 58inches. This report will cover topics like critical evaluation
of theories like six sigma, lean principles and effectiveness of continuous improvement plan. It
would also include application of each stage of Project Life Cycle (PLC) and critical analysis of
how using different models and theories, PLC would differentiate between large and small scale
companies.
P1: Review and critique of the implementation of operation management principles
Operation management is an essential part of management that deals in designing,
redesigning as well as controlling business operations for the production of goods and services.
Thus, there are various theories of operation management that needs to be implemented by
organisation after masking the appropriate evaluation:
Six Sigma: Six Sigma is a methodology which is used to enhance the effectiveness of
product by minimising the chances of errors or defects (Chevalier and et. al., 2015). It contains
two different methodology that is DMAIC and DMADV. In context to XYZ company which is
entering into new segment so it is essential for organisation to conduct research and development
for new product that is large screen television market. For, the respective company DMADV
methodology will be used that is described below:
Define: Under this stage, customer preference as well as goals and objective are defined
for the production of television. Thus, XYZ company should create effective team as well as
strategies for production and distribution of large screen televisions.
Measure: In this stage with the help of research and analysis data is collection on the
basis of primary and secondary source of data collection. Thus respective methods help in
1
Operation management refer to the conversion of raw material into finished good to
increase the day to day working of organisation (Artto, Ahola and Vartiainen, 2016). While
project management includes planning, organising, controlling, coordinating as well as
supervising the performance to increase the overall profitability of organisation. These following
steps help an organisation to operate its routine operations efficiently. For the better
understanding of this report, XYZ company has been selected that deals in fridges, electronic
cooker, washing machine and so on. Respective company has decided to diversify its business in
large screen television market of 58inches. This report will cover topics like critical evaluation
of theories like six sigma, lean principles and effectiveness of continuous improvement plan. It
would also include application of each stage of Project Life Cycle (PLC) and critical analysis of
how using different models and theories, PLC would differentiate between large and small scale
companies.
P1: Review and critique of the implementation of operation management principles
Operation management is an essential part of management that deals in designing,
redesigning as well as controlling business operations for the production of goods and services.
Thus, there are various theories of operation management that needs to be implemented by
organisation after masking the appropriate evaluation:
Six Sigma: Six Sigma is a methodology which is used to enhance the effectiveness of
product by minimising the chances of errors or defects (Chevalier and et. al., 2015). It contains
two different methodology that is DMAIC and DMADV. In context to XYZ company which is
entering into new segment so it is essential for organisation to conduct research and development
for new product that is large screen television market. For, the respective company DMADV
methodology will be used that is described below:
Define: Under this stage, customer preference as well as goals and objective are defined
for the production of television. Thus, XYZ company should create effective team as well as
strategies for production and distribution of large screen televisions.
Measure: In this stage with the help of research and analysis data is collection on the
basis of primary and secondary source of data collection. Thus respective methods help in
1
You're viewing a preview
Unlock full access by subscribing today!
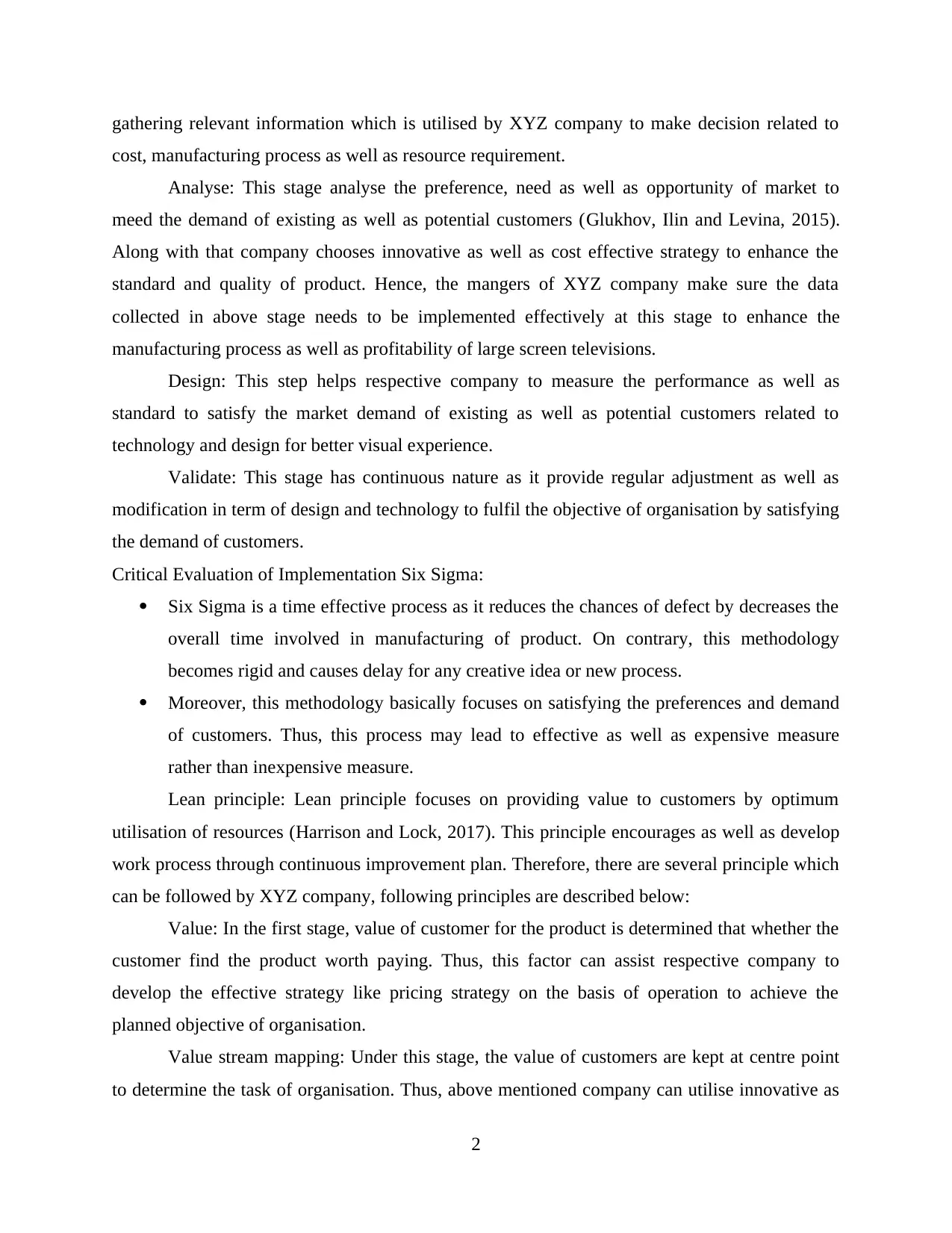
gathering relevant information which is utilised by XYZ company to make decision related to
cost, manufacturing process as well as resource requirement.
Analyse: This stage analyse the preference, need as well as opportunity of market to
meed the demand of existing as well as potential customers (Glukhov, Ilin and Levina, 2015).
Along with that company chooses innovative as well as cost effective strategy to enhance the
standard and quality of product. Hence, the mangers of XYZ company make sure the data
collected in above stage needs to be implemented effectively at this stage to enhance the
manufacturing process as well as profitability of large screen televisions.
Design: This step helps respective company to measure the performance as well as
standard to satisfy the market demand of existing as well as potential customers related to
technology and design for better visual experience.
Validate: This stage has continuous nature as it provide regular adjustment as well as
modification in term of design and technology to fulfil the objective of organisation by satisfying
the demand of customers.
Critical Evaluation of Implementation Six Sigma:
ï‚· Six Sigma is a time effective process as it reduces the chances of defect by decreases the
overall time involved in manufacturing of product. On contrary, this methodology
becomes rigid and causes delay for any creative idea or new process.
ï‚· Moreover, this methodology basically focuses on satisfying the preferences and demand
of customers. Thus, this process may lead to effective as well as expensive measure
rather than inexpensive measure.
Lean principle: Lean principle focuses on providing value to customers by optimum
utilisation of resources (Harrison and Lock, 2017). This principle encourages as well as develop
work process through continuous improvement plan. Therefore, there are several principle which
can be followed by XYZ company, following principles are described below:
Value: In the first stage, value of customer for the product is determined that whether the
customer find the product worth paying. Thus, this factor can assist respective company to
develop the effective strategy like pricing strategy on the basis of operation to achieve the
planned objective of organisation.
Value stream mapping: Under this stage, the value of customers are kept at centre point
to determine the task of organisation. Thus, above mentioned company can utilise innovative as
2
cost, manufacturing process as well as resource requirement.
Analyse: This stage analyse the preference, need as well as opportunity of market to
meed the demand of existing as well as potential customers (Glukhov, Ilin and Levina, 2015).
Along with that company chooses innovative as well as cost effective strategy to enhance the
standard and quality of product. Hence, the mangers of XYZ company make sure the data
collected in above stage needs to be implemented effectively at this stage to enhance the
manufacturing process as well as profitability of large screen televisions.
Design: This step helps respective company to measure the performance as well as
standard to satisfy the market demand of existing as well as potential customers related to
technology and design for better visual experience.
Validate: This stage has continuous nature as it provide regular adjustment as well as
modification in term of design and technology to fulfil the objective of organisation by satisfying
the demand of customers.
Critical Evaluation of Implementation Six Sigma:
ï‚· Six Sigma is a time effective process as it reduces the chances of defect by decreases the
overall time involved in manufacturing of product. On contrary, this methodology
becomes rigid and causes delay for any creative idea or new process.
ï‚· Moreover, this methodology basically focuses on satisfying the preferences and demand
of customers. Thus, this process may lead to effective as well as expensive measure
rather than inexpensive measure.
Lean principle: Lean principle focuses on providing value to customers by optimum
utilisation of resources (Harrison and Lock, 2017). This principle encourages as well as develop
work process through continuous improvement plan. Therefore, there are several principle which
can be followed by XYZ company, following principles are described below:
Value: In the first stage, value of customer for the product is determined that whether the
customer find the product worth paying. Thus, this factor can assist respective company to
develop the effective strategy like pricing strategy on the basis of operation to achieve the
planned objective of organisation.
Value stream mapping: Under this stage, the value of customers are kept at centre point
to determine the task of organisation. Thus, above mentioned company can utilise innovative as
2
Paraphrase This Document
Need a fresh take? Get an instant paraphrase of this document with our AI Paraphraser
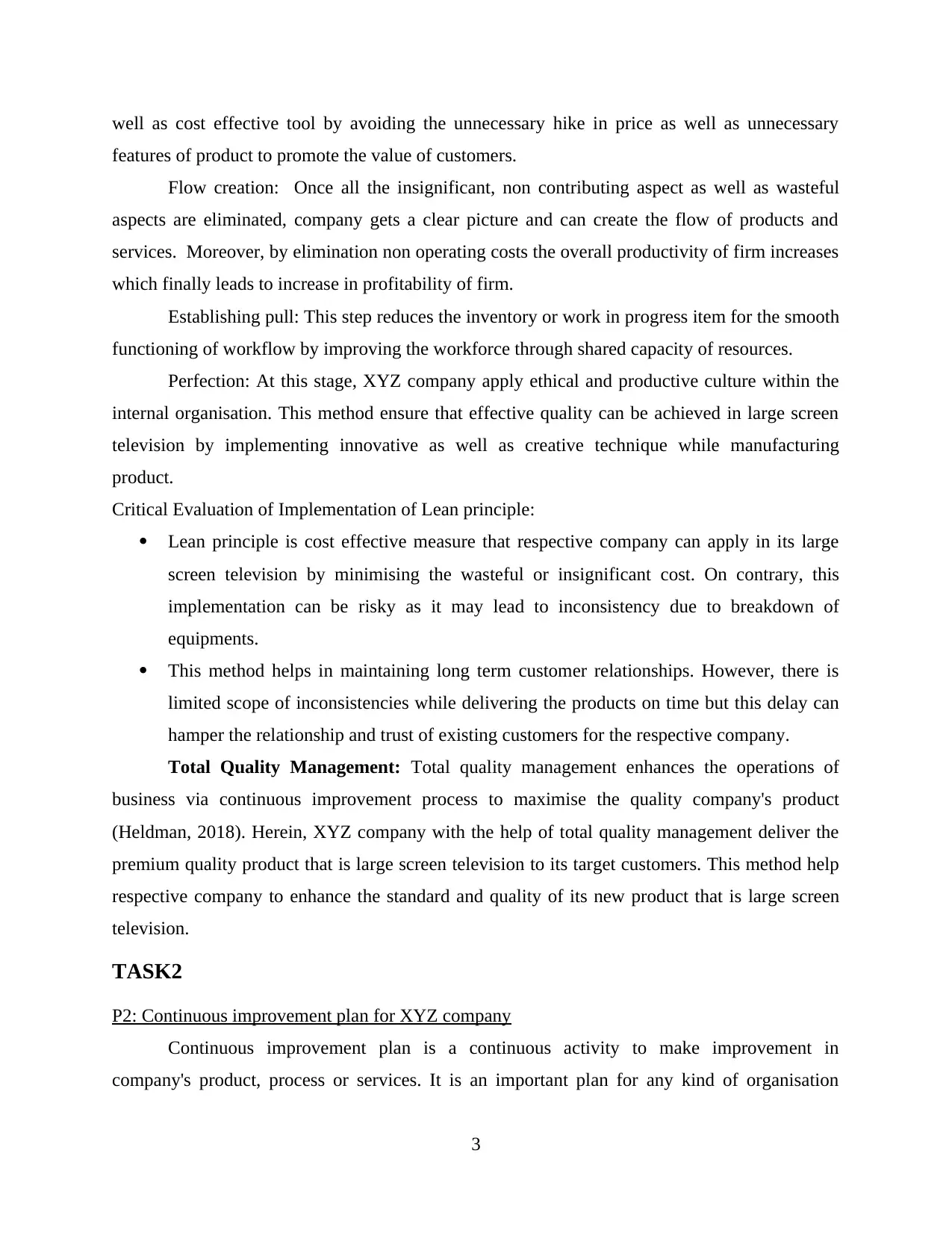
well as cost effective tool by avoiding the unnecessary hike in price as well as unnecessary
features of product to promote the value of customers.
Flow creation: Once all the insignificant, non contributing aspect as well as wasteful
aspects are eliminated, company gets a clear picture and can create the flow of products and
services. Moreover, by elimination non operating costs the overall productivity of firm increases
which finally leads to increase in profitability of firm.
Establishing pull: This step reduces the inventory or work in progress item for the smooth
functioning of workflow by improving the workforce through shared capacity of resources.
Perfection: At this stage, XYZ company apply ethical and productive culture within the
internal organisation. This method ensure that effective quality can be achieved in large screen
television by implementing innovative as well as creative technique while manufacturing
product.
Critical Evaluation of Implementation of Lean principle:
ï‚· Lean principle is cost effective measure that respective company can apply in its large
screen television by minimising the wasteful or insignificant cost. On contrary, this
implementation can be risky as it may lead to inconsistency due to breakdown of
equipments.
ï‚· This method helps in maintaining long term customer relationships. However, there is
limited scope of inconsistencies while delivering the products on time but this delay can
hamper the relationship and trust of existing customers for the respective company.
Total Quality Management: Total quality management enhances the operations of
business via continuous improvement process to maximise the quality company's product
(Heldman, 2018). Herein, XYZ company with the help of total quality management deliver the
premium quality product that is large screen television to its target customers. This method help
respective company to enhance the standard and quality of its new product that is large screen
television.
TASK2
P2: Continuous improvement plan for XYZ company
Continuous improvement plan is a continuous activity to make improvement in
company's product, process or services. It is an important plan for any kind of organisation
3
features of product to promote the value of customers.
Flow creation: Once all the insignificant, non contributing aspect as well as wasteful
aspects are eliminated, company gets a clear picture and can create the flow of products and
services. Moreover, by elimination non operating costs the overall productivity of firm increases
which finally leads to increase in profitability of firm.
Establishing pull: This step reduces the inventory or work in progress item for the smooth
functioning of workflow by improving the workforce through shared capacity of resources.
Perfection: At this stage, XYZ company apply ethical and productive culture within the
internal organisation. This method ensure that effective quality can be achieved in large screen
television by implementing innovative as well as creative technique while manufacturing
product.
Critical Evaluation of Implementation of Lean principle:
ï‚· Lean principle is cost effective measure that respective company can apply in its large
screen television by minimising the wasteful or insignificant cost. On contrary, this
implementation can be risky as it may lead to inconsistency due to breakdown of
equipments.
ï‚· This method helps in maintaining long term customer relationships. However, there is
limited scope of inconsistencies while delivering the products on time but this delay can
hamper the relationship and trust of existing customers for the respective company.
Total Quality Management: Total quality management enhances the operations of
business via continuous improvement process to maximise the quality company's product
(Heldman, 2018). Herein, XYZ company with the help of total quality management deliver the
premium quality product that is large screen television to its target customers. This method help
respective company to enhance the standard and quality of its new product that is large screen
television.
TASK2
P2: Continuous improvement plan for XYZ company
Continuous improvement plan is a continuous activity to make improvement in
company's product, process or services. It is an important plan for any kind of organisation
3
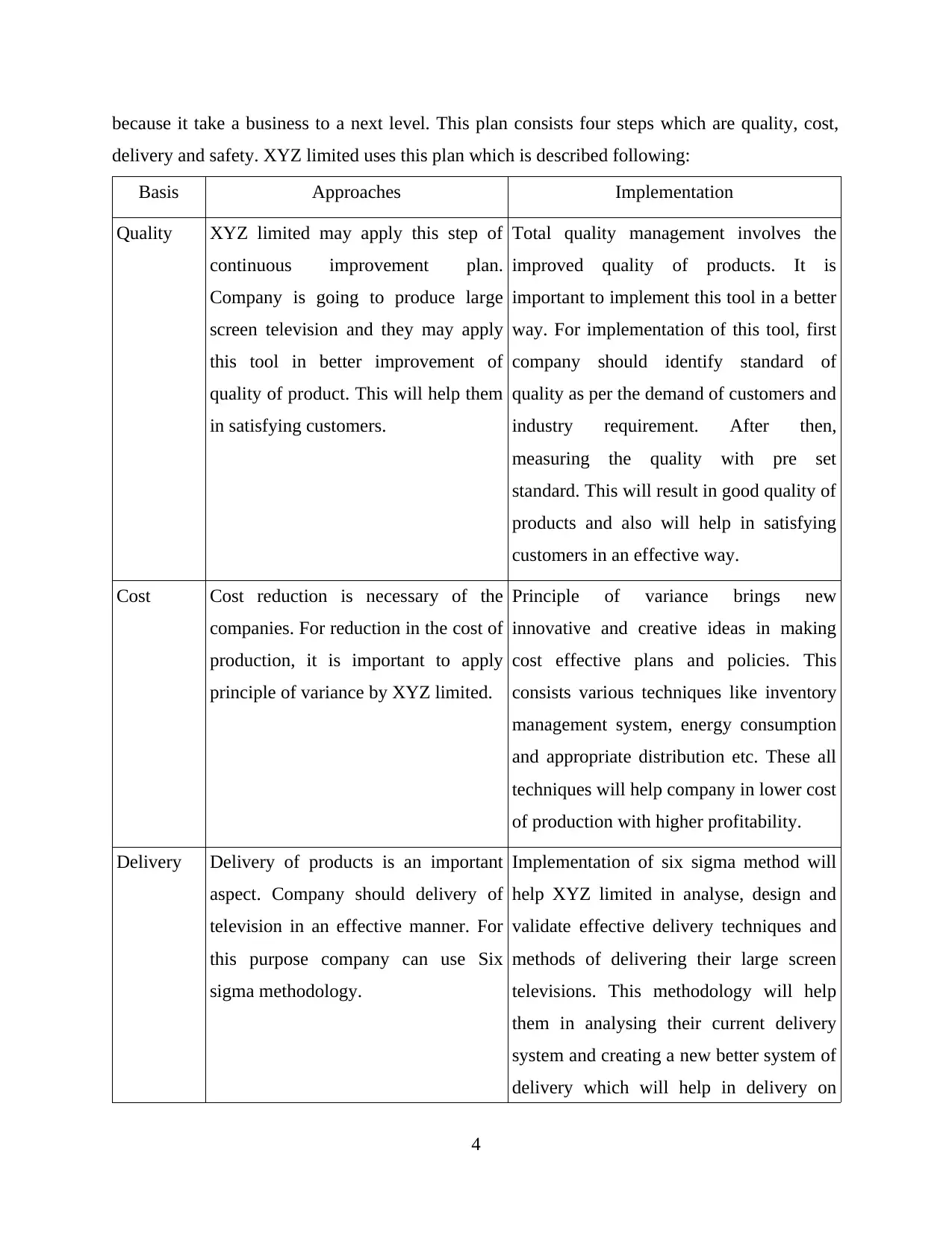
because it take a business to a next level. This plan consists four steps which are quality, cost,
delivery and safety. XYZ limited uses this plan which is described following:
Basis Approaches Implementation
Quality XYZ limited may apply this step of
continuous improvement plan.
Company is going to produce large
screen television and they may apply
this tool in better improvement of
quality of product. This will help them
in satisfying customers.
Total quality management involves the
improved quality of products. It is
important to implement this tool in a better
way. For implementation of this tool, first
company should identify standard of
quality as per the demand of customers and
industry requirement. After then,
measuring the quality with pre set
standard. This will result in good quality of
products and also will help in satisfying
customers in an effective way.
Cost Cost reduction is necessary of the
companies. For reduction in the cost of
production, it is important to apply
principle of variance by XYZ limited.
Principle of variance brings new
innovative and creative ideas in making
cost effective plans and policies. This
consists various techniques like inventory
management system, energy consumption
and appropriate distribution etc. These all
techniques will help company in lower cost
of production with higher profitability.
Delivery Delivery of products is an important
aspect. Company should delivery of
television in an effective manner. For
this purpose company can use Six
sigma methodology.
Implementation of six sigma method will
help XYZ limited in analyse, design and
validate effective delivery techniques and
methods of delivering their large screen
televisions. This methodology will help
them in analysing their current delivery
system and creating a new better system of
delivery which will help in delivery on
4
delivery and safety. XYZ limited uses this plan which is described following:
Basis Approaches Implementation
Quality XYZ limited may apply this step of
continuous improvement plan.
Company is going to produce large
screen television and they may apply
this tool in better improvement of
quality of product. This will help them
in satisfying customers.
Total quality management involves the
improved quality of products. It is
important to implement this tool in a better
way. For implementation of this tool, first
company should identify standard of
quality as per the demand of customers and
industry requirement. After then,
measuring the quality with pre set
standard. This will result in good quality of
products and also will help in satisfying
customers in an effective way.
Cost Cost reduction is necessary of the
companies. For reduction in the cost of
production, it is important to apply
principle of variance by XYZ limited.
Principle of variance brings new
innovative and creative ideas in making
cost effective plans and policies. This
consists various techniques like inventory
management system, energy consumption
and appropriate distribution etc. These all
techniques will help company in lower cost
of production with higher profitability.
Delivery Delivery of products is an important
aspect. Company should delivery of
television in an effective manner. For
this purpose company can use Six
sigma methodology.
Implementation of six sigma method will
help XYZ limited in analyse, design and
validate effective delivery techniques and
methods of delivering their large screen
televisions. This methodology will help
them in analysing their current delivery
system and creating a new better system of
delivery which will help in delivery on
4
You're viewing a preview
Unlock full access by subscribing today!
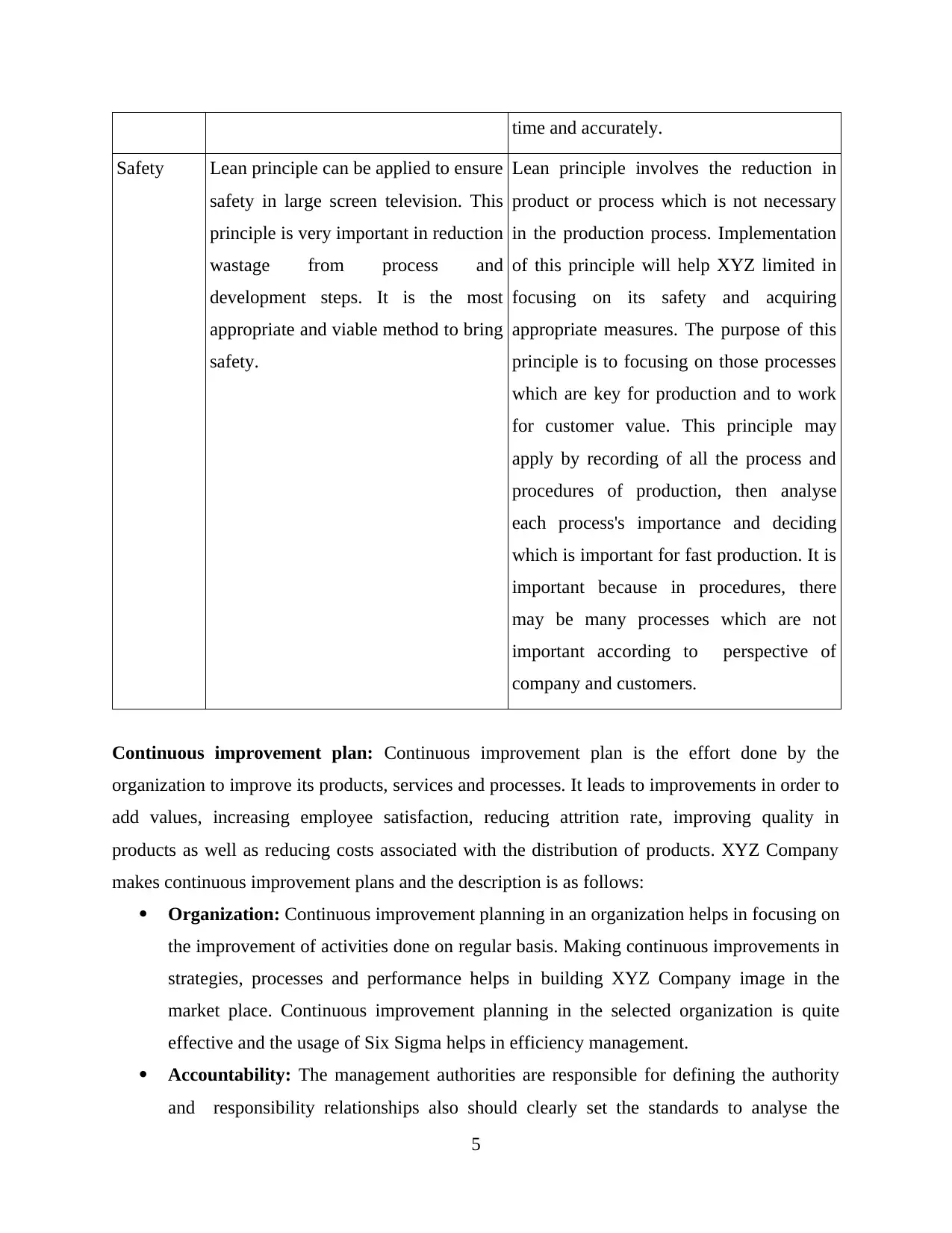
time and accurately.
Safety Lean principle can be applied to ensure
safety in large screen television. This
principle is very important in reduction
wastage from process and
development steps. It is the most
appropriate and viable method to bring
safety.
Lean principle involves the reduction in
product or process which is not necessary
in the production process. Implementation
of this principle will help XYZ limited in
focusing on its safety and acquiring
appropriate measures. The purpose of this
principle is to focusing on those processes
which are key for production and to work
for customer value. This principle may
apply by recording of all the process and
procedures of production, then analyse
each process's importance and deciding
which is important for fast production. It is
important because in procedures, there
may be many processes which are not
important according to perspective of
company and customers.
Continuous improvement plan: Continuous improvement plan is the effort done by the
organization to improve its products, services and processes. It leads to improvements in order to
add values, increasing employee satisfaction, reducing attrition rate, improving quality in
products as well as reducing costs associated with the distribution of products. XYZ Company
makes continuous improvement plans and the description is as follows:
ï‚· Organization: Continuous improvement planning in an organization helps in focusing on
the improvement of activities done on regular basis. Making continuous improvements in
strategies, processes and performance helps in building XYZ Company image in the
market place. Continuous improvement planning in the selected organization is quite
effective and the usage of Six Sigma helps in efficiency management.
ï‚· Accountability: The management authorities are responsible for defining the authority
and responsibility relationships also should clearly set the standards to analyse the
5
Safety Lean principle can be applied to ensure
safety in large screen television. This
principle is very important in reduction
wastage from process and
development steps. It is the most
appropriate and viable method to bring
safety.
Lean principle involves the reduction in
product or process which is not necessary
in the production process. Implementation
of this principle will help XYZ limited in
focusing on its safety and acquiring
appropriate measures. The purpose of this
principle is to focusing on those processes
which are key for production and to work
for customer value. This principle may
apply by recording of all the process and
procedures of production, then analyse
each process's importance and deciding
which is important for fast production. It is
important because in procedures, there
may be many processes which are not
important according to perspective of
company and customers.
Continuous improvement plan: Continuous improvement plan is the effort done by the
organization to improve its products, services and processes. It leads to improvements in order to
add values, increasing employee satisfaction, reducing attrition rate, improving quality in
products as well as reducing costs associated with the distribution of products. XYZ Company
makes continuous improvement plans and the description is as follows:
ï‚· Organization: Continuous improvement planning in an organization helps in focusing on
the improvement of activities done on regular basis. Making continuous improvements in
strategies, processes and performance helps in building XYZ Company image in the
market place. Continuous improvement planning in the selected organization is quite
effective and the usage of Six Sigma helps in efficiency management.
ï‚· Accountability: The management authorities are responsible for defining the authority
and responsibility relationships also should clearly set the standards to analyse the
5
Paraphrase This Document
Need a fresh take? Get an instant paraphrase of this document with our AI Paraphraser
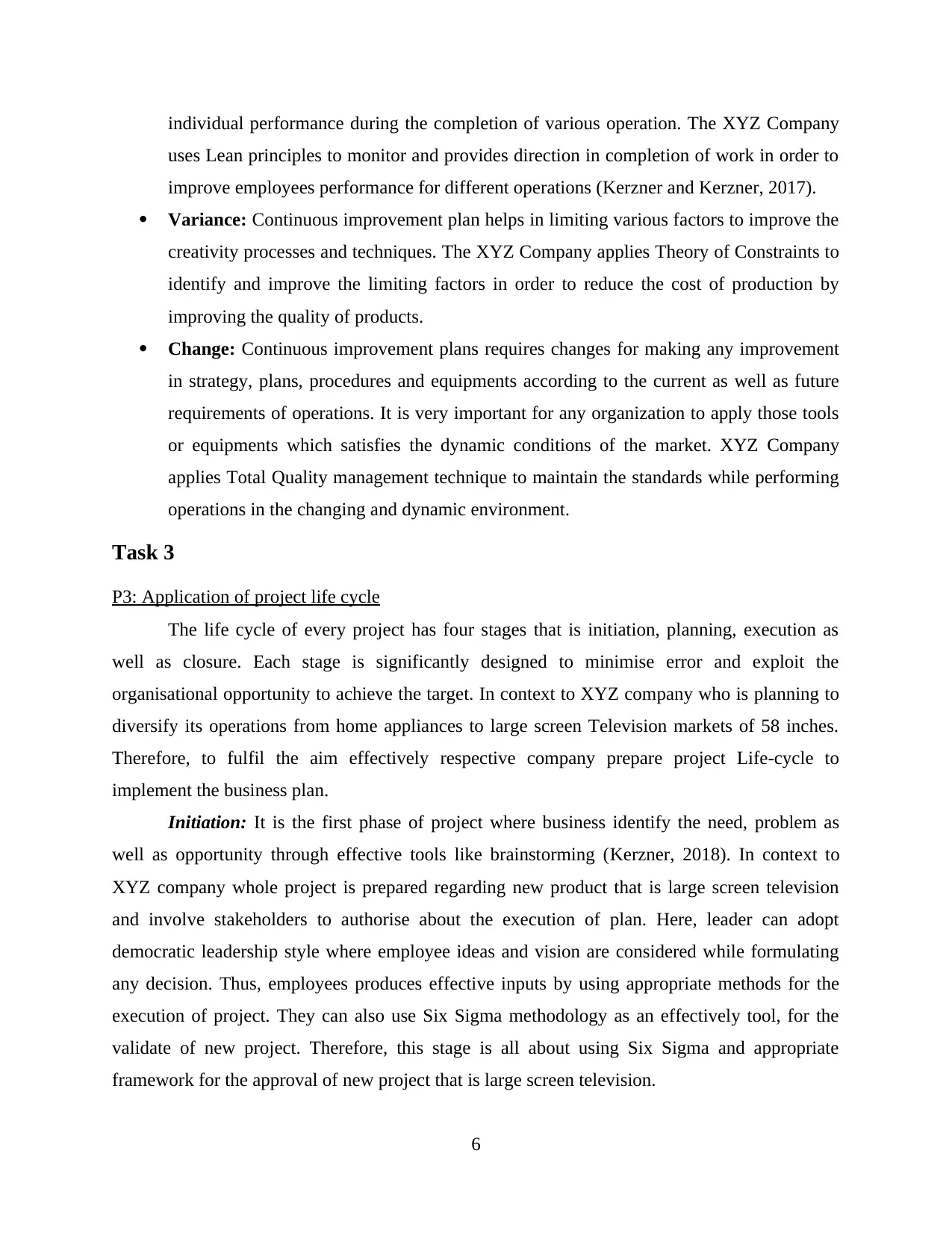
individual performance during the completion of various operation. The XYZ Company
uses Lean principles to monitor and provides direction in completion of work in order to
improve employees performance for different operations (Kerzner and Kerzner, 2017).
ï‚· Variance: Continuous improvement plan helps in limiting various factors to improve the
creativity processes and techniques. The XYZ Company applies Theory of Constraints to
identify and improve the limiting factors in order to reduce the cost of production by
improving the quality of products.
ï‚· Change: Continuous improvement plans requires changes for making any improvement
in strategy, plans, procedures and equipments according to the current as well as future
requirements of operations. It is very important for any organization to apply those tools
or equipments which satisfies the dynamic conditions of the market. XYZ Company
applies Total Quality management technique to maintain the standards while performing
operations in the changing and dynamic environment.
Task 3
P3: Application of project life cycle
The life cycle of every project has four stages that is initiation, planning, execution as
well as closure. Each stage is significantly designed to minimise error and exploit the
organisational opportunity to achieve the target. In context to XYZ company who is planning to
diversify its operations from home appliances to large screen Television markets of 58 inches.
Therefore, to fulfil the aim effectively respective company prepare project Life-cycle to
implement the business plan.
Initiation: It is the first phase of project where business identify the need, problem as
well as opportunity through effective tools like brainstorming (Kerzner, 2018). In context to
XYZ company whole project is prepared regarding new product that is large screen television
and involve stakeholders to authorise about the execution of plan. Here, leader can adopt
democratic leadership style where employee ideas and vision are considered while formulating
any decision. Thus, employees produces effective inputs by using appropriate methods for the
execution of project. They can also use Six Sigma methodology as an effectively tool, for the
validate of new project. Therefore, this stage is all about using Six Sigma and appropriate
framework for the approval of new project that is large screen television.
6
uses Lean principles to monitor and provides direction in completion of work in order to
improve employees performance for different operations (Kerzner and Kerzner, 2017).
ï‚· Variance: Continuous improvement plan helps in limiting various factors to improve the
creativity processes and techniques. The XYZ Company applies Theory of Constraints to
identify and improve the limiting factors in order to reduce the cost of production by
improving the quality of products.
ï‚· Change: Continuous improvement plans requires changes for making any improvement
in strategy, plans, procedures and equipments according to the current as well as future
requirements of operations. It is very important for any organization to apply those tools
or equipments which satisfies the dynamic conditions of the market. XYZ Company
applies Total Quality management technique to maintain the standards while performing
operations in the changing and dynamic environment.
Task 3
P3: Application of project life cycle
The life cycle of every project has four stages that is initiation, planning, execution as
well as closure. Each stage is significantly designed to minimise error and exploit the
organisational opportunity to achieve the target. In context to XYZ company who is planning to
diversify its operations from home appliances to large screen Television markets of 58 inches.
Therefore, to fulfil the aim effectively respective company prepare project Life-cycle to
implement the business plan.
Initiation: It is the first phase of project where business identify the need, problem as
well as opportunity through effective tools like brainstorming (Kerzner, 2018). In context to
XYZ company whole project is prepared regarding new product that is large screen television
and involve stakeholders to authorise about the execution of plan. Here, leader can adopt
democratic leadership style where employee ideas and vision are considered while formulating
any decision. Thus, employees produces effective inputs by using appropriate methods for the
execution of project. They can also use Six Sigma methodology as an effectively tool, for the
validate of new project. Therefore, this stage is all about using Six Sigma and appropriate
framework for the approval of new project that is large screen television.
6
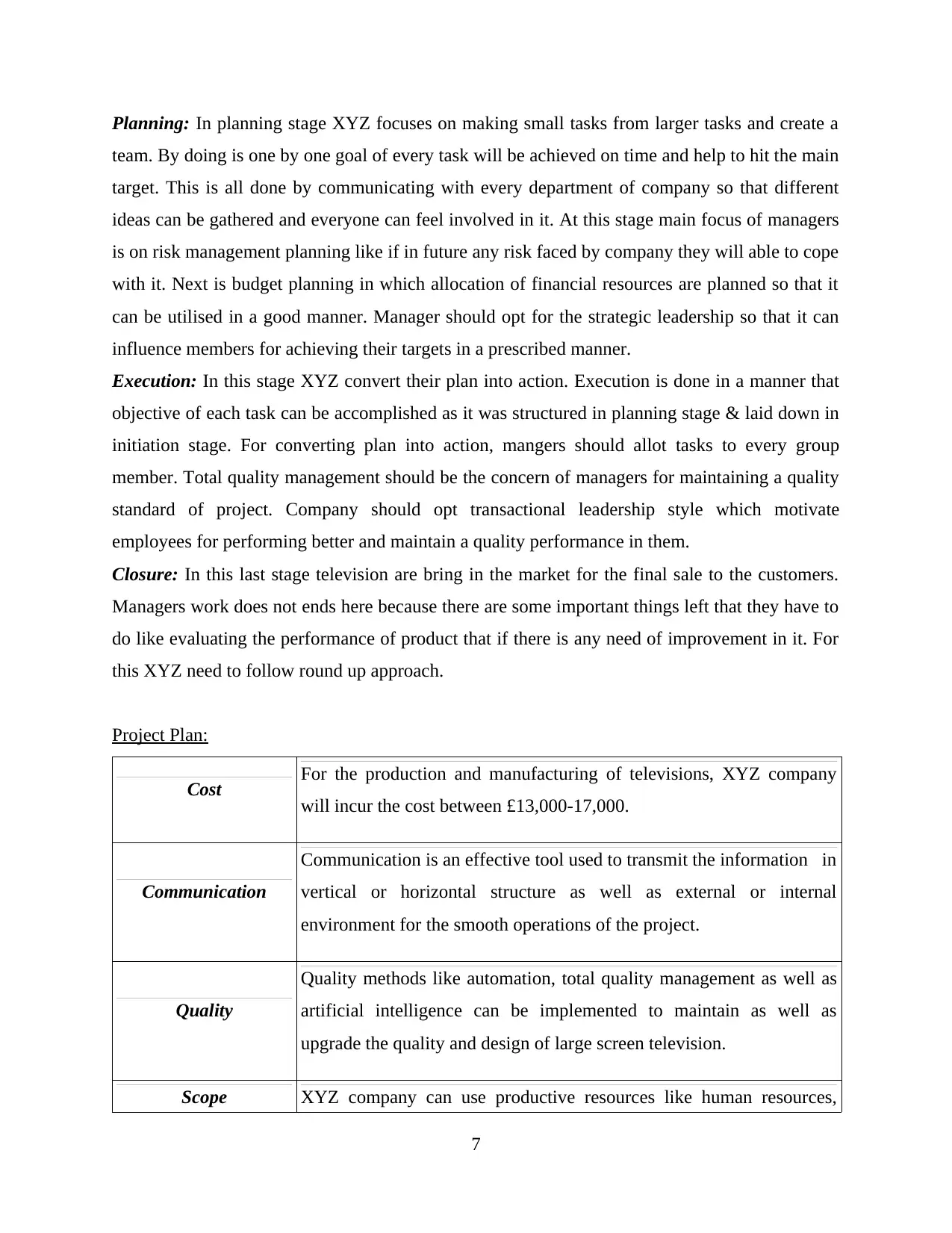
Planning: In planning stage XYZ focuses on making small tasks from larger tasks and create a
team. By doing is one by one goal of every task will be achieved on time and help to hit the main
target. This is all done by communicating with every department of company so that different
ideas can be gathered and everyone can feel involved in it. At this stage main focus of managers
is on risk management planning like if in future any risk faced by company they will able to cope
with it. Next is budget planning in which allocation of financial resources are planned so that it
can be utilised in a good manner. Manager should opt for the strategic leadership so that it can
influence members for achieving their targets in a prescribed manner.
Execution: In this stage XYZ convert their plan into action. Execution is done in a manner that
objective of each task can be accomplished as it was structured in planning stage & laid down in
initiation stage. For converting plan into action, mangers should allot tasks to every group
member. Total quality management should be the concern of managers for maintaining a quality
standard of project. Company should opt transactional leadership style which motivate
employees for performing better and maintain a quality performance in them.
Closure: In this last stage television are bring in the market for the final sale to the customers.
Managers work does not ends here because there are some important things left that they have to
do like evaluating the performance of product that if there is any need of improvement in it. For
this XYZ need to follow round up approach.
Project Plan:
Cost For the production and manufacturing of televisions, XYZ company
will incur the cost between £13,000-17,000.
Communication
Communication is an effective tool used to transmit the information in
vertical or horizontal structure as well as external or internal
environment for the smooth operations of the project.
Quality
Quality methods like automation, total quality management as well as
artificial intelligence can be implemented to maintain as well as
upgrade the quality and design of large screen television.
Scope XYZ company can use productive resources like human resources,
7
team. By doing is one by one goal of every task will be achieved on time and help to hit the main
target. This is all done by communicating with every department of company so that different
ideas can be gathered and everyone can feel involved in it. At this stage main focus of managers
is on risk management planning like if in future any risk faced by company they will able to cope
with it. Next is budget planning in which allocation of financial resources are planned so that it
can be utilised in a good manner. Manager should opt for the strategic leadership so that it can
influence members for achieving their targets in a prescribed manner.
Execution: In this stage XYZ convert their plan into action. Execution is done in a manner that
objective of each task can be accomplished as it was structured in planning stage & laid down in
initiation stage. For converting plan into action, mangers should allot tasks to every group
member. Total quality management should be the concern of managers for maintaining a quality
standard of project. Company should opt transactional leadership style which motivate
employees for performing better and maintain a quality performance in them.
Closure: In this last stage television are bring in the market for the final sale to the customers.
Managers work does not ends here because there are some important things left that they have to
do like evaluating the performance of product that if there is any need of improvement in it. For
this XYZ need to follow round up approach.
Project Plan:
Cost For the production and manufacturing of televisions, XYZ company
will incur the cost between £13,000-17,000.
Communication
Communication is an effective tool used to transmit the information in
vertical or horizontal structure as well as external or internal
environment for the smooth operations of the project.
Quality
Quality methods like automation, total quality management as well as
artificial intelligence can be implemented to maintain as well as
upgrade the quality and design of large screen television.
Scope XYZ company can use productive resources like human resources,
7
You're viewing a preview
Unlock full access by subscribing today!
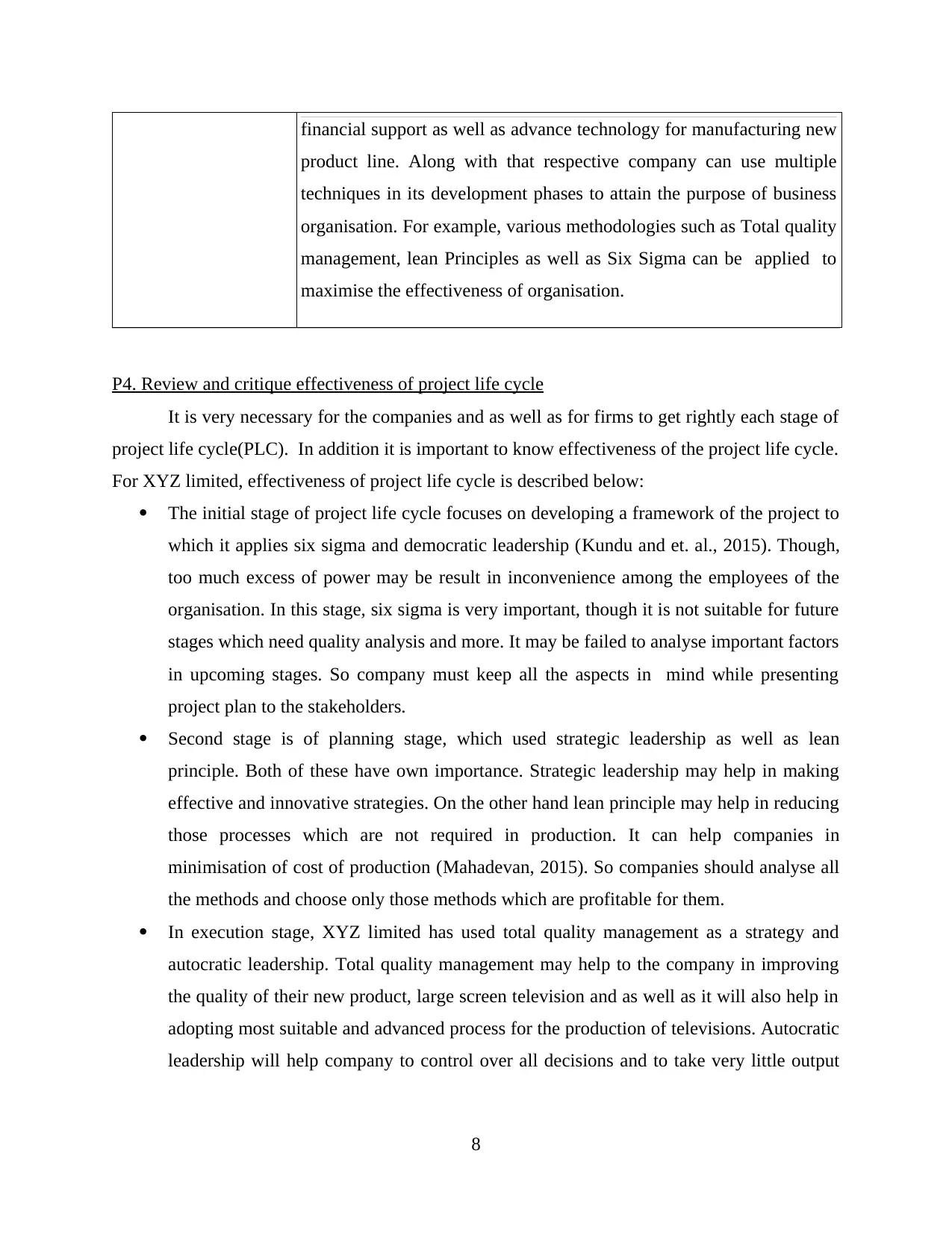
financial support as well as advance technology for manufacturing new
product line. Along with that respective company can use multiple
techniques in its development phases to attain the purpose of business
organisation. For example, various methodologies such as Total quality
management, lean Principles as well as Six Sigma can be applied to
maximise the effectiveness of organisation.
P4. Review and critique effectiveness of project life cycle
It is very necessary for the companies and as well as for firms to get rightly each stage of
project life cycle(PLC). In addition it is important to know effectiveness of the project life cycle.
For XYZ limited, effectiveness of project life cycle is described below:
ï‚· The initial stage of project life cycle focuses on developing a framework of the project to
which it applies six sigma and democratic leadership (Kundu and et. al., 2015). Though,
too much excess of power may be result in inconvenience among the employees of the
organisation. In this stage, six sigma is very important, though it is not suitable for future
stages which need quality analysis and more. It may be failed to analyse important factors
in upcoming stages. So company must keep all the aspects in mind while presenting
project plan to the stakeholders.
ï‚· Second stage is of planning stage, which used strategic leadership as well as lean
principle. Both of these have own importance. Strategic leadership may help in making
effective and innovative strategies. On the other hand lean principle may help in reducing
those processes which are not required in production. It can help companies in
minimisation of cost of production (Mahadevan, 2015). So companies should analyse all
the methods and choose only those methods which are profitable for them.
ï‚· In execution stage, XYZ limited has used total quality management as a strategy and
autocratic leadership. Total quality management may help to the company in improving
the quality of their new product, large screen television and as well as it will also help in
adopting most suitable and advanced process for the production of televisions. Autocratic
leadership will help company to control over all decisions and to take very little output
8
product line. Along with that respective company can use multiple
techniques in its development phases to attain the purpose of business
organisation. For example, various methodologies such as Total quality
management, lean Principles as well as Six Sigma can be applied to
maximise the effectiveness of organisation.
P4. Review and critique effectiveness of project life cycle
It is very necessary for the companies and as well as for firms to get rightly each stage of
project life cycle(PLC). In addition it is important to know effectiveness of the project life cycle.
For XYZ limited, effectiveness of project life cycle is described below:
ï‚· The initial stage of project life cycle focuses on developing a framework of the project to
which it applies six sigma and democratic leadership (Kundu and et. al., 2015). Though,
too much excess of power may be result in inconvenience among the employees of the
organisation. In this stage, six sigma is very important, though it is not suitable for future
stages which need quality analysis and more. It may be failed to analyse important factors
in upcoming stages. So company must keep all the aspects in mind while presenting
project plan to the stakeholders.
ï‚· Second stage is of planning stage, which used strategic leadership as well as lean
principle. Both of these have own importance. Strategic leadership may help in making
effective and innovative strategies. On the other hand lean principle may help in reducing
those processes which are not required in production. It can help companies in
minimisation of cost of production (Mahadevan, 2015). So companies should analyse all
the methods and choose only those methods which are profitable for them.
ï‚· In execution stage, XYZ limited has used total quality management as a strategy and
autocratic leadership. Total quality management may help to the company in improving
the quality of their new product, large screen television and as well as it will also help in
adopting most suitable and advanced process for the production of televisions. Autocratic
leadership will help company to control over all decisions and to take very little output
8
Paraphrase This Document
Need a fresh take? Get an instant paraphrase of this document with our AI Paraphraser
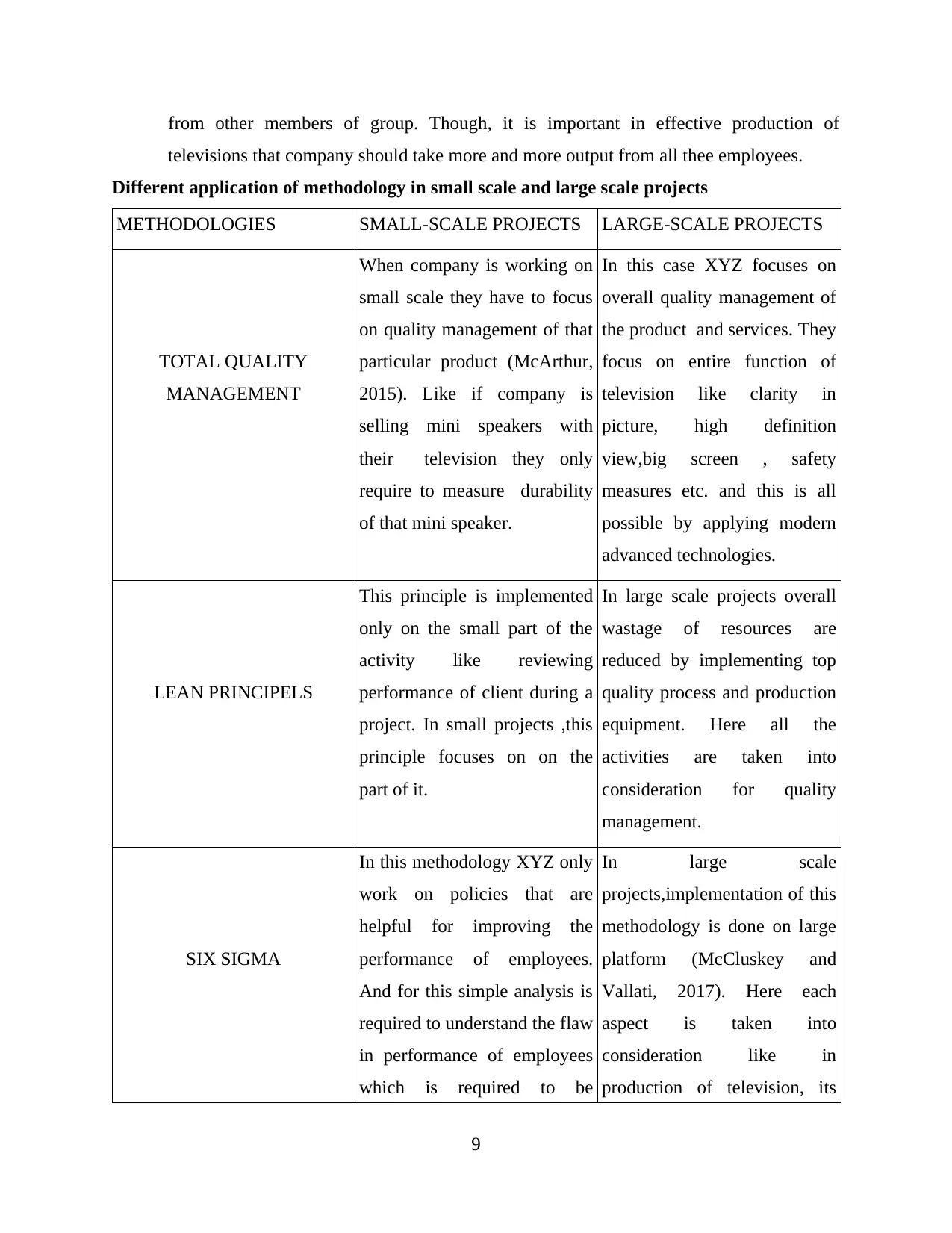
from other members of group. Though, it is important in effective production of
televisions that company should take more and more output from all thee employees.
Different application of methodology in small scale and large scale projects
METHODOLOGIES SMALL-SCALE PROJECTS LARGE-SCALE PROJECTS
TOTAL QUALITY
MANAGEMENT
When company is working on
small scale they have to focus
on quality management of that
particular product (McArthur,
2015). Like if company is
selling mini speakers with
their television they only
require to measure durability
of that mini speaker.
In this case XYZ focuses on
overall quality management of
the product and services. They
focus on entire function of
television like clarity in
picture, high definition
view,big screen , safety
measures etc. and this is all
possible by applying modern
advanced technologies.
LEAN PRINCIPELS
This principle is implemented
only on the small part of the
activity like reviewing
performance of client during a
project. In small projects ,this
principle focuses on on the
part of it.
In large scale projects overall
wastage of resources are
reduced by implementing top
quality process and production
equipment. Here all the
activities are taken into
consideration for quality
management.
SIX SIGMA
In this methodology XYZ only
work on policies that are
helpful for improving the
performance of employees.
And for this simple analysis is
required to understand the flaw
in performance of employees
which is required to be
In large scale
projects,implementation of this
methodology is done on large
platform (McCluskey and
Vallati, 2017). Here each
aspect is taken into
consideration like in
production of television, its
9
televisions that company should take more and more output from all thee employees.
Different application of methodology in small scale and large scale projects
METHODOLOGIES SMALL-SCALE PROJECTS LARGE-SCALE PROJECTS
TOTAL QUALITY
MANAGEMENT
When company is working on
small scale they have to focus
on quality management of that
particular product (McArthur,
2015). Like if company is
selling mini speakers with
their television they only
require to measure durability
of that mini speaker.
In this case XYZ focuses on
overall quality management of
the product and services. They
focus on entire function of
television like clarity in
picture, high definition
view,big screen , safety
measures etc. and this is all
possible by applying modern
advanced technologies.
LEAN PRINCIPELS
This principle is implemented
only on the small part of the
activity like reviewing
performance of client during a
project. In small projects ,this
principle focuses on on the
part of it.
In large scale projects overall
wastage of resources are
reduced by implementing top
quality process and production
equipment. Here all the
activities are taken into
consideration for quality
management.
SIX SIGMA
In this methodology XYZ only
work on policies that are
helpful for improving the
performance of employees.
And for this simple analysis is
required to understand the flaw
in performance of employees
which is required to be
In large scale
projects,implementation of this
methodology is done on large
platform (McCluskey and
Vallati, 2017). Here each
aspect is taken into
consideration like in
production of television, its
9
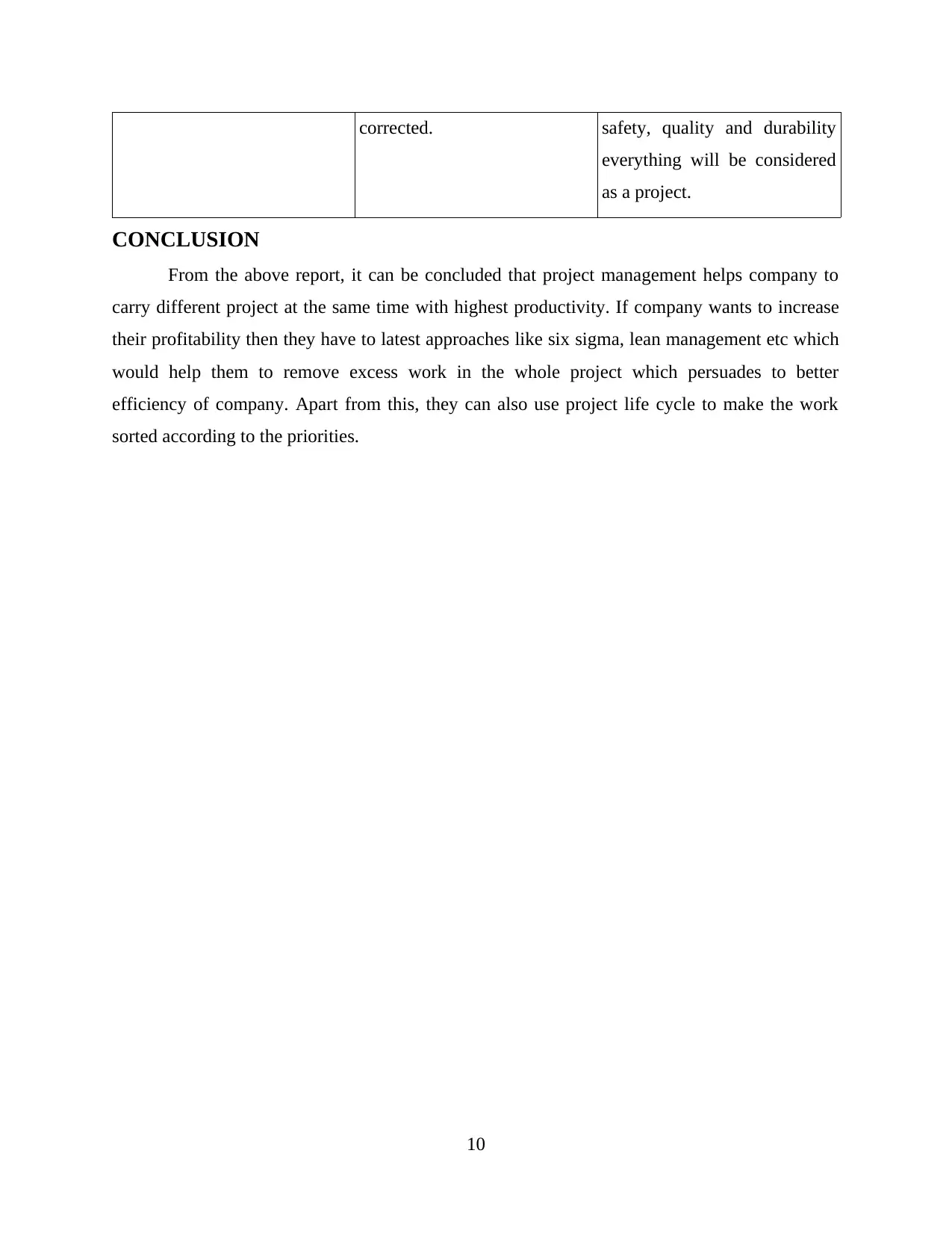
corrected. safety, quality and durability
everything will be considered
as a project.
CONCLUSION
From the above report, it can be concluded that project management helps company to
carry different project at the same time with highest productivity. If company wants to increase
their profitability then they have to latest approaches like six sigma, lean management etc which
would help them to remove excess work in the whole project which persuades to better
efficiency of company. Apart from this, they can also use project life cycle to make the work
sorted according to the priorities.
10
everything will be considered
as a project.
CONCLUSION
From the above report, it can be concluded that project management helps company to
carry different project at the same time with highest productivity. If company wants to increase
their profitability then they have to latest approaches like six sigma, lean management etc which
would help them to remove excess work in the whole project which persuades to better
efficiency of company. Apart from this, they can also use project life cycle to make the work
sorted according to the priorities.
10
You're viewing a preview
Unlock full access by subscribing today!
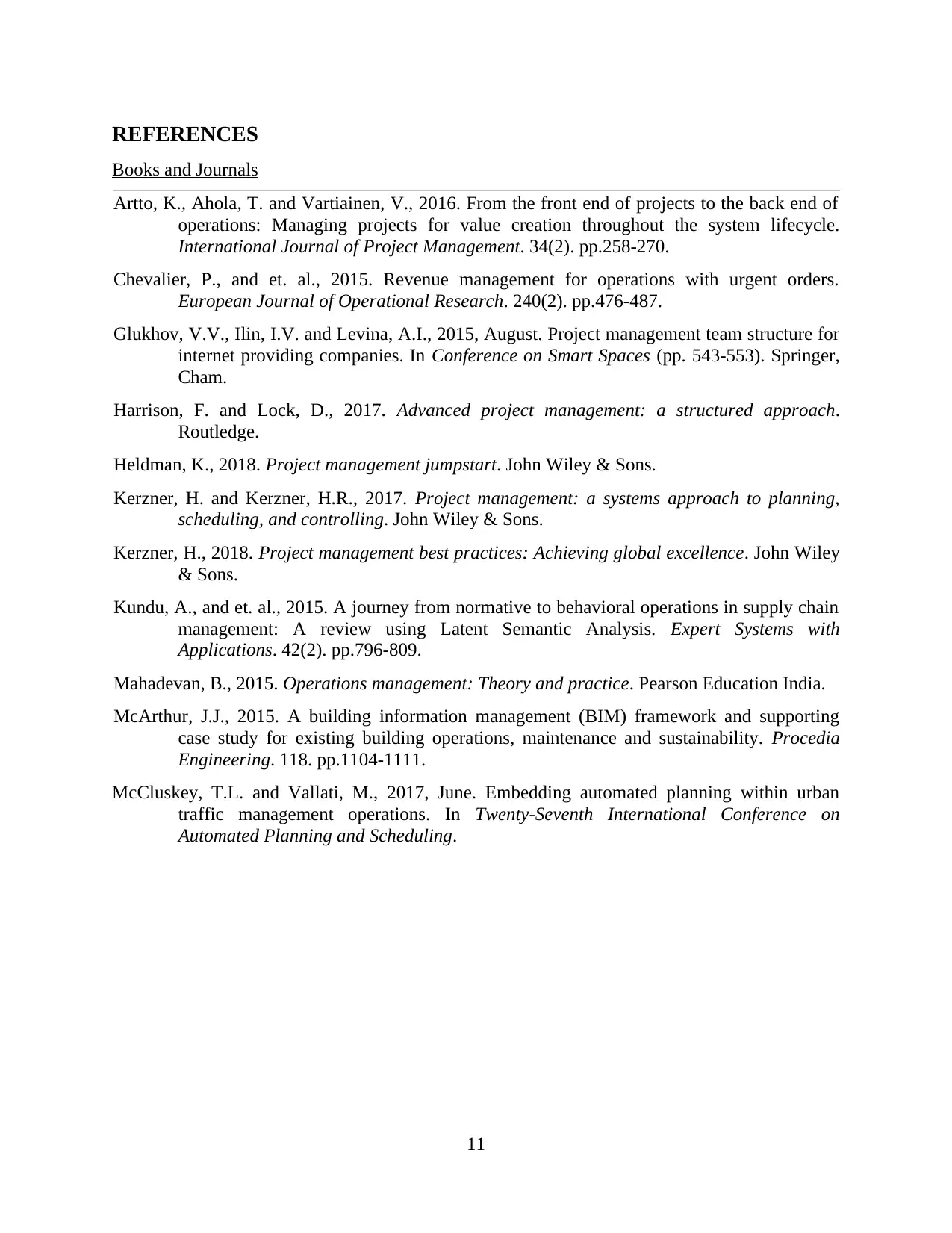
REFERENCES
Books and Journals
Artto, K., Ahola, T. and Vartiainen, V., 2016. From the front end of projects to the back end of
operations: Managing projects for value creation throughout the system lifecycle.
International Journal of Project Management. 34(2). pp.258-270.
Chevalier, P., and et. al., 2015. Revenue management for operations with urgent orders.
European Journal of Operational Research. 240(2). pp.476-487.
Glukhov, V.V., Ilin, I.V. and Levina, A.I., 2015, August. Project management team structure for
internet providing companies. In Conference on Smart Spaces (pp. 543-553). Springer,
Cham.
Harrison, F. and Lock, D., 2017. Advanced project management: a structured approach.
Routledge.
Heldman, K., 2018. Project management jumpstart. John Wiley & Sons.
Kerzner, H. and Kerzner, H.R., 2017. Project management: a systems approach to planning,
scheduling, and controlling. John Wiley & Sons.
Kerzner, H., 2018. Project management best practices: Achieving global excellence. John Wiley
& Sons.
Kundu, A., and et. al., 2015. A journey from normative to behavioral operations in supply chain
management: A review using Latent Semantic Analysis. Expert Systems with
Applications. 42(2). pp.796-809.
Mahadevan, B., 2015. Operations management: Theory and practice. Pearson Education India.
McArthur, J.J., 2015. A building information management (BIM) framework and supporting
case study for existing building operations, maintenance and sustainability. Procedia
Engineering. 118. pp.1104-1111.
McCluskey, T.L. and Vallati, M., 2017, June. Embedding automated planning within urban
traffic management operations. In Twenty-Seventh International Conference on
Automated Planning and Scheduling.
11
Books and Journals
Artto, K., Ahola, T. and Vartiainen, V., 2016. From the front end of projects to the back end of
operations: Managing projects for value creation throughout the system lifecycle.
International Journal of Project Management. 34(2). pp.258-270.
Chevalier, P., and et. al., 2015. Revenue management for operations with urgent orders.
European Journal of Operational Research. 240(2). pp.476-487.
Glukhov, V.V., Ilin, I.V. and Levina, A.I., 2015, August. Project management team structure for
internet providing companies. In Conference on Smart Spaces (pp. 543-553). Springer,
Cham.
Harrison, F. and Lock, D., 2017. Advanced project management: a structured approach.
Routledge.
Heldman, K., 2018. Project management jumpstart. John Wiley & Sons.
Kerzner, H. and Kerzner, H.R., 2017. Project management: a systems approach to planning,
scheduling, and controlling. John Wiley & Sons.
Kerzner, H., 2018. Project management best practices: Achieving global excellence. John Wiley
& Sons.
Kundu, A., and et. al., 2015. A journey from normative to behavioral operations in supply chain
management: A review using Latent Semantic Analysis. Expert Systems with
Applications. 42(2). pp.796-809.
Mahadevan, B., 2015. Operations management: Theory and practice. Pearson Education India.
McArthur, J.J., 2015. A building information management (BIM) framework and supporting
case study for existing building operations, maintenance and sustainability. Procedia
Engineering. 118. pp.1104-1111.
McCluskey, T.L. and Vallati, M., 2017, June. Embedding automated planning within urban
traffic management operations. In Twenty-Seventh International Conference on
Automated Planning and Scheduling.
11
1 out of 13
Related Documents

Your All-in-One AI-Powered Toolkit for Academic Success.
+13062052269
info@desklib.com
Available 24*7 on WhatsApp / Email
Unlock your academic potential
© 2024 | Zucol Services PVT LTD | All rights reserved.