Operations and Project Management Report: Evaluating PLC Stages
VerifiedAdded on 2020/10/05
|17
|4793
|204
Report
AI Summary
This report examines operations and project management within the context of XYZ Company's entry into the large-screen television market. It begins by defining operations and production management, then delves into the implementation of operations management principles, including Six Sigma and Lean methodologies, to enhance business efficiency and reduce waste. The report then analyzes the preparation and effectiveness of a continuous improvement plan, outlining areas of focus, issues faced by the company, and proposed improvements using models like PDCA and Lean. Furthermore, it evaluates the stages of the Project Life Cycle (PLC), and differentiates between large and small-scale projects by applying relevant theories, models, and concepts. The report concludes by summarizing the key findings and providing recommendations for XYZ Company's success in the new market.
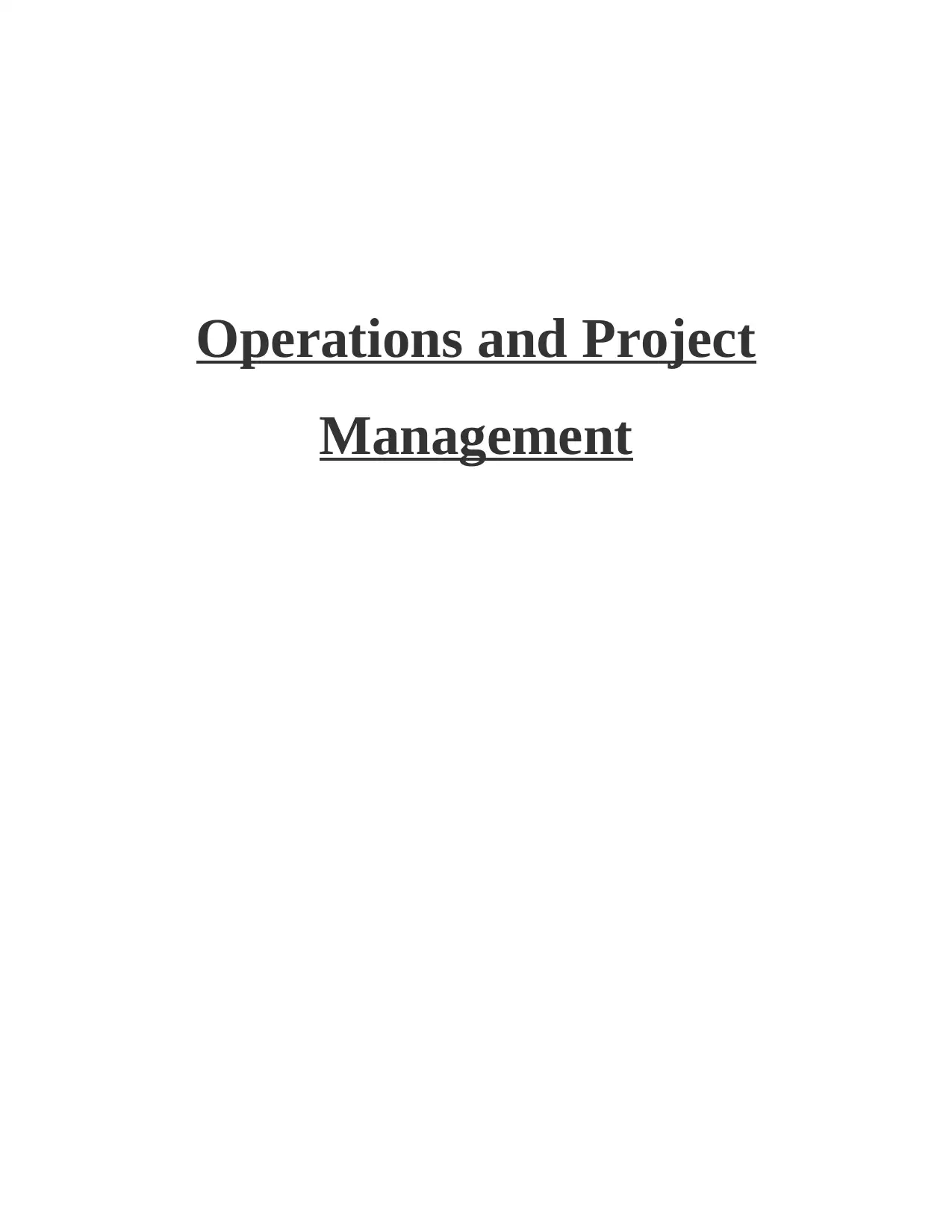
Operations and Project
Management
Management
Paraphrase This Document
Need a fresh take? Get an instant paraphrase of this document with our AI Paraphraser
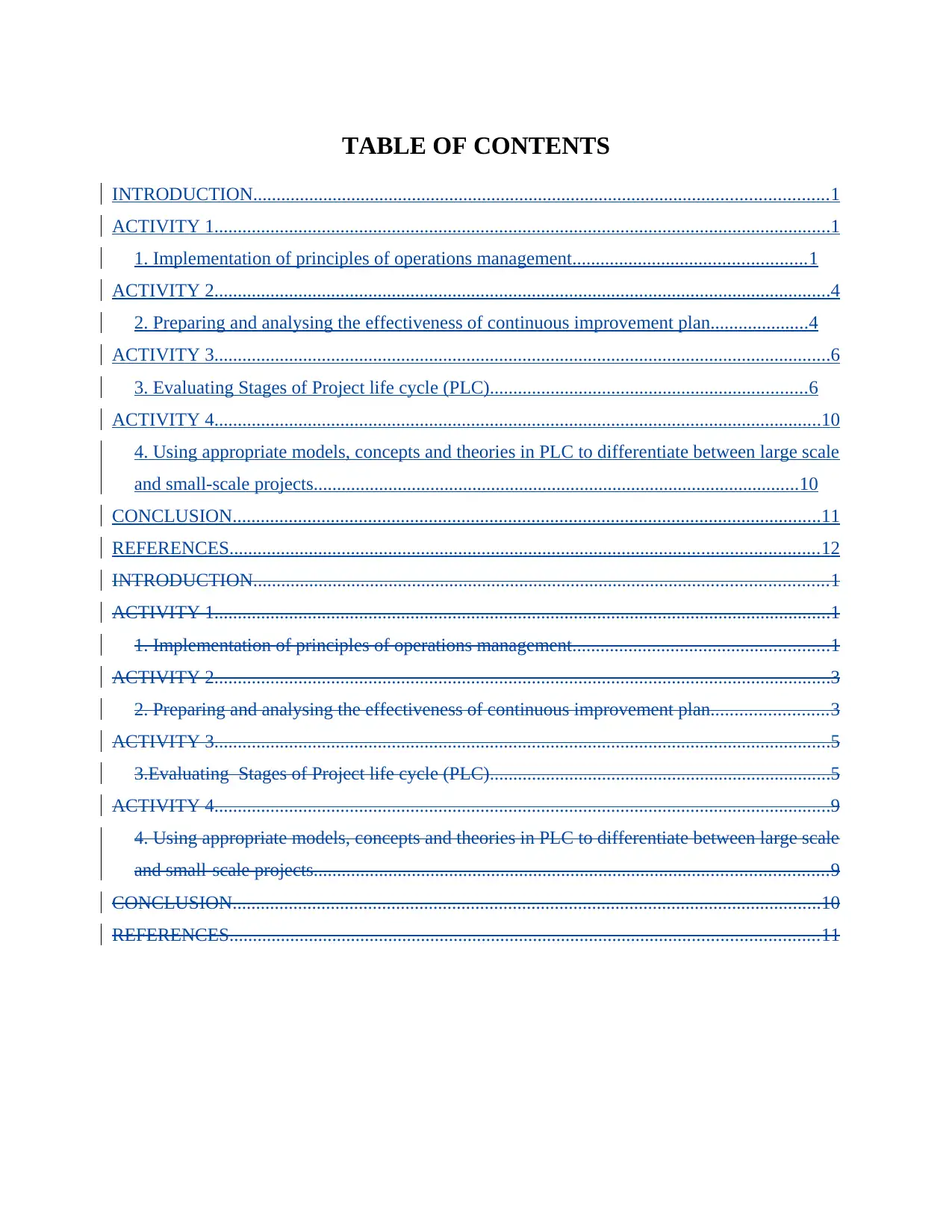
TABLE OF CONTENTS
INTRODUCTION...........................................................................................................................1
ACTIVITY 1....................................................................................................................................1
1. Implementation of principles of operations management..................................................1
ACTIVITY 2....................................................................................................................................4
2. Preparing and analysing the effectiveness of continuous improvement plan.....................4
ACTIVITY 3....................................................................................................................................6
3. Evaluating Stages of Project life cycle (PLC)....................................................................6
ACTIVITY 4..................................................................................................................................10
4. Using appropriate models, concepts and theories in PLC to differentiate between large scale
and small-scale projects........................................................................................................10
CONCLUSION..............................................................................................................................11
REFERENCES..............................................................................................................................12
INTRODUCTION...........................................................................................................................1
ACTIVITY 1....................................................................................................................................1
1. Implementation of principles of operations management.......................................................1
ACTIVITY 2....................................................................................................................................3
2. Preparing and analysing the effectiveness of continuous improvement plan.........................3
ACTIVITY 3....................................................................................................................................5
3.Evaluating Stages of Project life cycle (PLC).........................................................................5
ACTIVITY 4....................................................................................................................................9
4. Using appropriate models, concepts and theories in PLC to differentiate between large scale
and small-scale projects..............................................................................................................9
CONCLUSION..............................................................................................................................10
REFERENCES..............................................................................................................................11
INTRODUCTION...........................................................................................................................1
ACTIVITY 1....................................................................................................................................1
1. Implementation of principles of operations management..................................................1
ACTIVITY 2....................................................................................................................................4
2. Preparing and analysing the effectiveness of continuous improvement plan.....................4
ACTIVITY 3....................................................................................................................................6
3. Evaluating Stages of Project life cycle (PLC)....................................................................6
ACTIVITY 4..................................................................................................................................10
4. Using appropriate models, concepts and theories in PLC to differentiate between large scale
and small-scale projects........................................................................................................10
CONCLUSION..............................................................................................................................11
REFERENCES..............................................................................................................................12
INTRODUCTION...........................................................................................................................1
ACTIVITY 1....................................................................................................................................1
1. Implementation of principles of operations management.......................................................1
ACTIVITY 2....................................................................................................................................3
2. Preparing and analysing the effectiveness of continuous improvement plan.........................3
ACTIVITY 3....................................................................................................................................5
3.Evaluating Stages of Project life cycle (PLC).........................................................................5
ACTIVITY 4....................................................................................................................................9
4. Using appropriate models, concepts and theories in PLC to differentiate between large scale
and small-scale projects..............................................................................................................9
CONCLUSION..............................................................................................................................10
REFERENCES..............................................................................................................................11
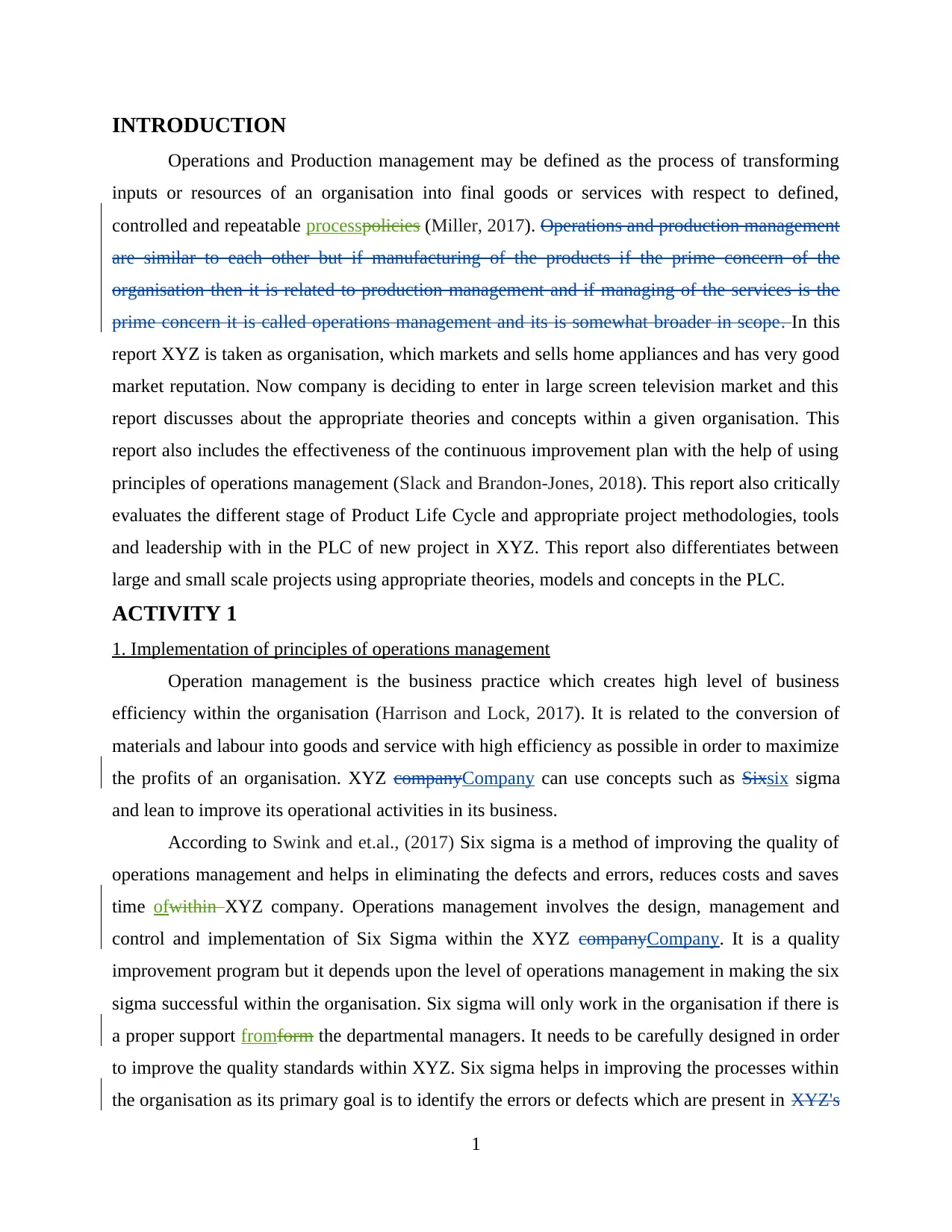
INTRODUCTION
Operations and Production management may be defined as the process of transforming
inputs or resources of an organisation into final goods or services with respect to defined,
controlled and repeatable processpolicies (Miller, 2017). Operations and production management
are similar to each other but if manufacturing of the products if the prime concern of the
organisation then it is related to production management and if managing of the services is the
prime concern it is called operations management and its is somewhat broader in scope. In this
report XYZ is taken as organisation, which markets and sells home appliances and has very good
market reputation. Now company is deciding to enter in large screen television market and this
report discusses about the appropriate theories and concepts within a given organisation. This
report also includes the effectiveness of the continuous improvement plan with the help of using
principles of operations management (Slack and Brandon-Jones, 2018). This report also critically
evaluates the different stage of Product Life Cycle and appropriate project methodologies, tools
and leadership with in the PLC of new project in XYZ. This report also differentiates between
large and small scale projects using appropriate theories, models and concepts in the PLC.
ACTIVITY 1
1. Implementation of principles of operations management
Operation management is the business practice which creates high level of business
efficiency within the organisation (Harrison and Lock, 2017). It is related to the conversion of
materials and labour into goods and service with high efficiency as possible in order to maximize
the profits of an organisation. XYZ companyCompany can use concepts such as Sixsix sigma
and lean to improve its operational activities in its business.
According to Swink and et.al., (2017) Six sigma is a method of improving the quality of
operations management and helps in eliminating the defects and errors, reduces costs and saves
time ofwithin XYZ company. Operations management involves the design, management and
control and implementation of Six Sigma within the XYZ companyCompany. It is a quality
improvement program but it depends upon the level of operations management in making the six
sigma successful within the organisation. Six sigma will only work in the organisation if there is
a proper support fromform the departmental managers. It needs to be carefully designed in order
to improve the quality standards within XYZ. Six sigma helps in improving the processes within
the organisation as its primary goal is to identify the errors or defects which are present in XYZ's
1
Operations and Production management may be defined as the process of transforming
inputs or resources of an organisation into final goods or services with respect to defined,
controlled and repeatable processpolicies (Miller, 2017). Operations and production management
are similar to each other but if manufacturing of the products if the prime concern of the
organisation then it is related to production management and if managing of the services is the
prime concern it is called operations management and its is somewhat broader in scope. In this
report XYZ is taken as organisation, which markets and sells home appliances and has very good
market reputation. Now company is deciding to enter in large screen television market and this
report discusses about the appropriate theories and concepts within a given organisation. This
report also includes the effectiveness of the continuous improvement plan with the help of using
principles of operations management (Slack and Brandon-Jones, 2018). This report also critically
evaluates the different stage of Product Life Cycle and appropriate project methodologies, tools
and leadership with in the PLC of new project in XYZ. This report also differentiates between
large and small scale projects using appropriate theories, models and concepts in the PLC.
ACTIVITY 1
1. Implementation of principles of operations management
Operation management is the business practice which creates high level of business
efficiency within the organisation (Harrison and Lock, 2017). It is related to the conversion of
materials and labour into goods and service with high efficiency as possible in order to maximize
the profits of an organisation. XYZ companyCompany can use concepts such as Sixsix sigma
and lean to improve its operational activities in its business.
According to Swink and et.al., (2017) Six sigma is a method of improving the quality of
operations management and helps in eliminating the defects and errors, reduces costs and saves
time ofwithin XYZ company. Operations management involves the design, management and
control and implementation of Six Sigma within the XYZ companyCompany. It is a quality
improvement program but it depends upon the level of operations management in making the six
sigma successful within the organisation. Six sigma will only work in the organisation if there is
a proper support fromform the departmental managers. It needs to be carefully designed in order
to improve the quality standards within XYZ. Six sigma helps in improving the processes within
the organisation as its primary goal is to identify the errors or defects which are present in XYZ's
1
⊘ This is a preview!⊘
Do you want full access?
Subscribe today to unlock all pages.

Trusted by 1+ million students worldwide
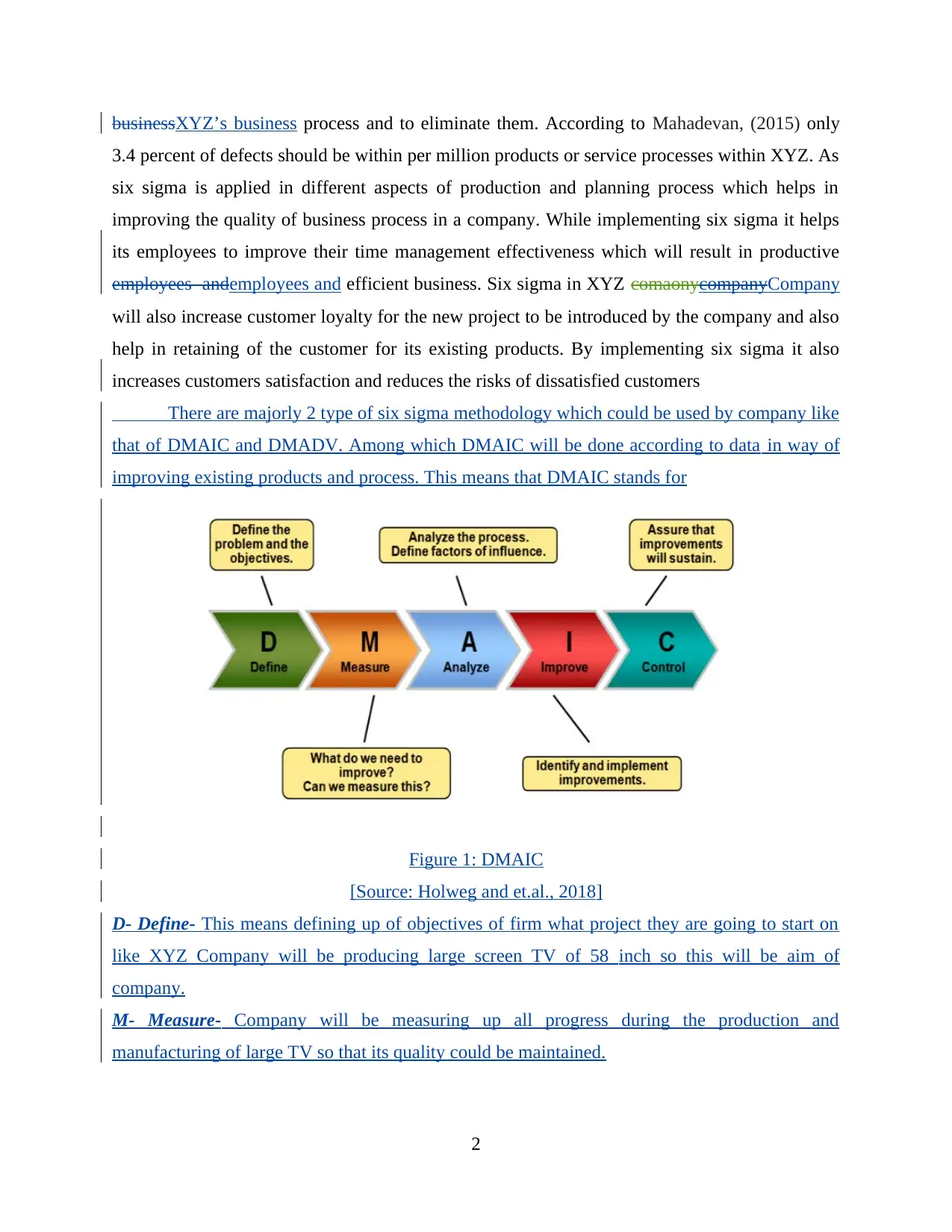
businessXYZ’s business process and to eliminate them. According to Mahadevan, (2015) only
3.4 percent of defects should be within per million products or service processes within XYZ. As
six sigma is applied in different aspects of production and planning process which helps in
improving the quality of business process in a company. While implementing six sigma it helps
its employees to improve their time management effectiveness which will result in productive
employees andemployees and efficient business. Six sigma in XYZ comaonycompanyCompany
will also increase customer loyalty for the new project to be introduced by the company and also
help in retaining of the customer for its existing products. By implementing six sigma it also
increases customers satisfaction and reduces the risks of dissatisfied customers
There are majorly 2 type of six sigma methodology which could be used by company like
that of DMAIC and DMADV. Among which DMAIC will be done according to data in way of
improving existing products and process. This means that DMAIC stands for
Figure 1: DMAIC
[Source: Holweg and et.al., 2018]
D- Define- This means defining up of objectives of firm what project they are going to start on
like XYZ Company will be producing large screen TV of 58 inch so this will be aim of
company.
M- Measure- Company will be measuring up all progress during the production and
manufacturing of large TV so that its quality could be maintained.
2
3.4 percent of defects should be within per million products or service processes within XYZ. As
six sigma is applied in different aspects of production and planning process which helps in
improving the quality of business process in a company. While implementing six sigma it helps
its employees to improve their time management effectiveness which will result in productive
employees andemployees and efficient business. Six sigma in XYZ comaonycompanyCompany
will also increase customer loyalty for the new project to be introduced by the company and also
help in retaining of the customer for its existing products. By implementing six sigma it also
increases customers satisfaction and reduces the risks of dissatisfied customers
There are majorly 2 type of six sigma methodology which could be used by company like
that of DMAIC and DMADV. Among which DMAIC will be done according to data in way of
improving existing products and process. This means that DMAIC stands for
Figure 1: DMAIC
[Source: Holweg and et.al., 2018]
D- Define- This means defining up of objectives of firm what project they are going to start on
like XYZ Company will be producing large screen TV of 58 inch so this will be aim of
company.
M- Measure- Company will be measuring up all progress during the production and
manufacturing of large TV so that its quality could be maintained.
2
Paraphrase This Document
Need a fresh take? Get an instant paraphrase of this document with our AI Paraphraser
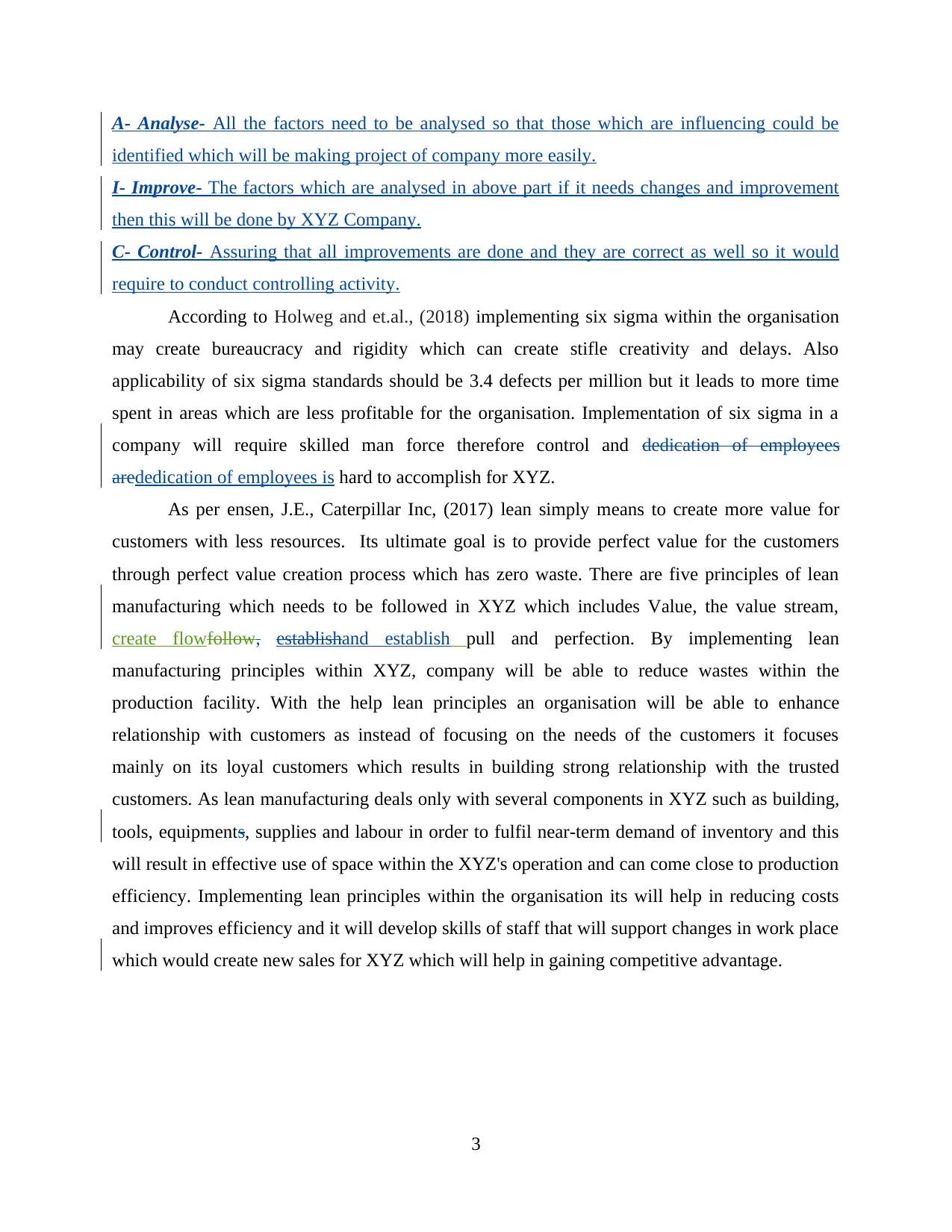
A- Analyse- All the factors need to be analysed so that those which are influencing could be
identified which will be making project of company more easily.
I- Improve- The factors which are analysed in above part if it needs changes and improvement
then this will be done by XYZ Company.
C- Control- Assuring that all improvements are done and they are correct as well so it would
require to conduct controlling activity.
According to Holweg and et.al., (2018) implementing six sigma within the organisation
may create bureaucracy and rigidity which can create stifle creativity and delays. Also
applicability of six sigma standards should be 3.4 defects per million but it leads to more time
spent in areas which are less profitable for the organisation. Implementation of six sigma in a
company will require skilled man force therefore control and dedication of employees
arededication of employees is hard to accomplish for XYZ.
As per ensen, J.E., Caterpillar Inc, (2017) lean simply means to create more value for
customers with less resources. Its ultimate goal is to provide perfect value for the customers
through perfect value creation process which has zero waste. There are five principles of lean
manufacturing which needs to be followed in XYZ which includes Value, the value stream,
create flowfollow, establishand establish pull and perfection. By implementing lean
manufacturing principles within XYZ, company will be able to reduce wastes within the
production facility. With the help lean principles an organisation will be able to enhance
relationship with customers as instead of focusing on the needs of the customers it focuses
mainly on its loyal customers which results in building strong relationship with the trusted
customers. As lean manufacturing deals only with several components in XYZ such as building,
tools, equipments, supplies and labour in order to fulfil near-term demand of inventory and this
will result in effective use of space within the XYZ's operation and can come close to production
efficiency. Implementing lean principles within the organisation its will help in reducing costs
and improves efficiency and it will develop skills of staff that will support changes in work place
which would create new sales for XYZ which will help in gaining competitive advantage.
3
identified which will be making project of company more easily.
I- Improve- The factors which are analysed in above part if it needs changes and improvement
then this will be done by XYZ Company.
C- Control- Assuring that all improvements are done and they are correct as well so it would
require to conduct controlling activity.
According to Holweg and et.al., (2018) implementing six sigma within the organisation
may create bureaucracy and rigidity which can create stifle creativity and delays. Also
applicability of six sigma standards should be 3.4 defects per million but it leads to more time
spent in areas which are less profitable for the organisation. Implementation of six sigma in a
company will require skilled man force therefore control and dedication of employees
arededication of employees is hard to accomplish for XYZ.
As per ensen, J.E., Caterpillar Inc, (2017) lean simply means to create more value for
customers with less resources. Its ultimate goal is to provide perfect value for the customers
through perfect value creation process which has zero waste. There are five principles of lean
manufacturing which needs to be followed in XYZ which includes Value, the value stream,
create flowfollow, establishand establish pull and perfection. By implementing lean
manufacturing principles within XYZ, company will be able to reduce wastes within the
production facility. With the help lean principles an organisation will be able to enhance
relationship with customers as instead of focusing on the needs of the customers it focuses
mainly on its loyal customers which results in building strong relationship with the trusted
customers. As lean manufacturing deals only with several components in XYZ such as building,
tools, equipments, supplies and labour in order to fulfil near-term demand of inventory and this
will result in effective use of space within the XYZ's operation and can come close to production
efficiency. Implementing lean principles within the organisation its will help in reducing costs
and improves efficiency and it will develop skills of staff that will support changes in work place
which would create new sales for XYZ which will help in gaining competitive advantage.
3
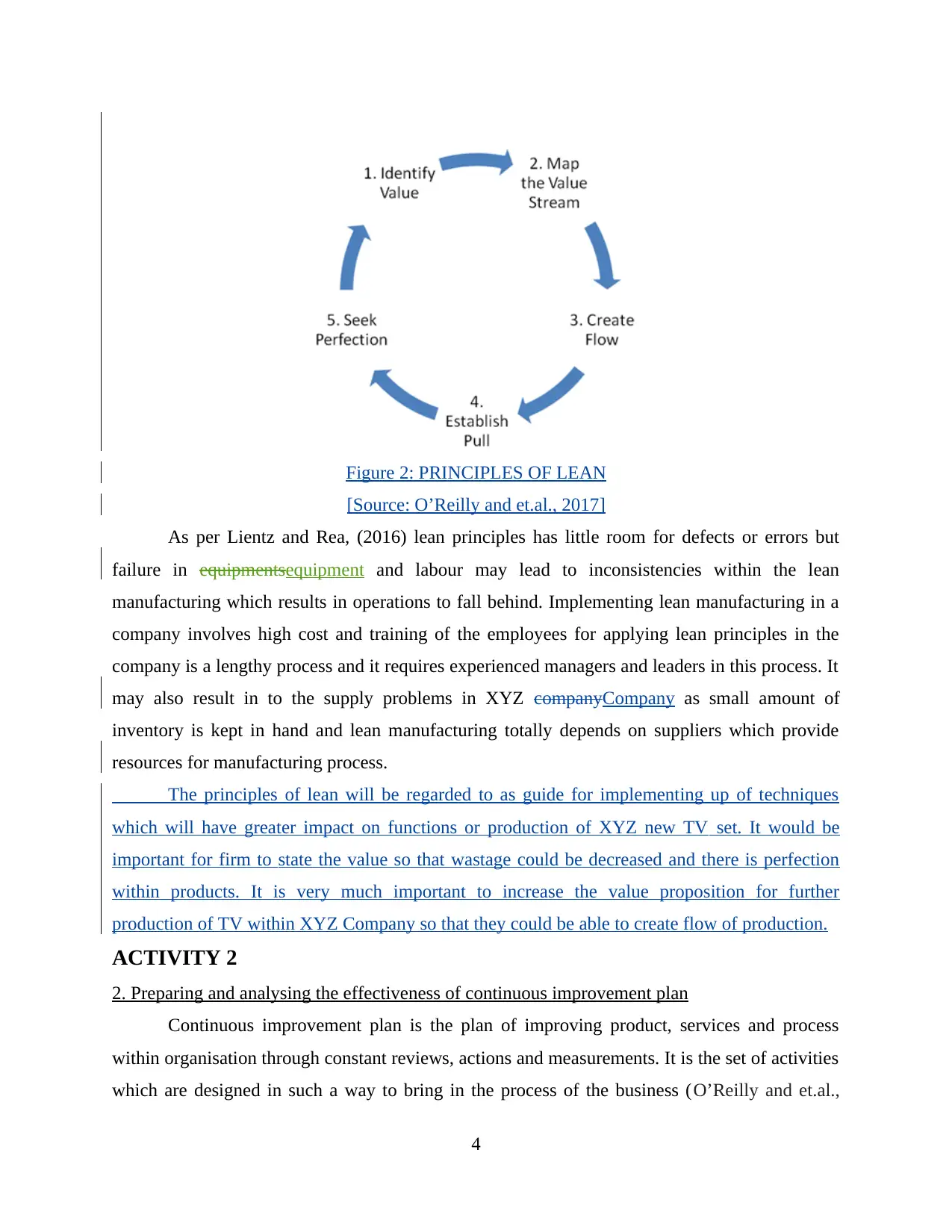
Figure 2: PRINCIPLES OF LEAN
[Source: O’Reilly and et.al., 2017]
As per Lientz and Rea, (2016) lean principles has little room for defects or errors but
failure in equipmentsequipment and labour may lead to inconsistencies within the lean
manufacturing which results in operations to fall behind. Implementing lean manufacturing in a
company involves high cost and training of the employees for applying lean principles in the
company is a lengthy process and it requires experienced managers and leaders in this process. It
may also result in to the supply problems in XYZ companyCompany as small amount of
inventory is kept in hand and lean manufacturing totally depends on suppliers which provide
resources for manufacturing process.
The principles of lean will be regarded to as guide for implementing up of techniques
which will have greater impact on functions or production of XYZ new TV set. It would be
important for firm to state the value so that wastage could be decreased and there is perfection
within products. It is very much important to increase the value proposition for further
production of TV within XYZ Company so that they could be able to create flow of production.
ACTIVITY 2
2. Preparing and analysing the effectiveness of continuous improvement plan
Continuous improvement plan is the plan of improving product, services and process
within organisation through constant reviews, actions and measurements. It is the set of activities
which are designed in such a way to bring in the process of the business (O’Reilly and et.al.,
4
[Source: O’Reilly and et.al., 2017]
As per Lientz and Rea, (2016) lean principles has little room for defects or errors but
failure in equipmentsequipment and labour may lead to inconsistencies within the lean
manufacturing which results in operations to fall behind. Implementing lean manufacturing in a
company involves high cost and training of the employees for applying lean principles in the
company is a lengthy process and it requires experienced managers and leaders in this process. It
may also result in to the supply problems in XYZ companyCompany as small amount of
inventory is kept in hand and lean manufacturing totally depends on suppliers which provide
resources for manufacturing process.
The principles of lean will be regarded to as guide for implementing up of techniques
which will have greater impact on functions or production of XYZ new TV set. It would be
important for firm to state the value so that wastage could be decreased and there is perfection
within products. It is very much important to increase the value proposition for further
production of TV within XYZ Company so that they could be able to create flow of production.
ACTIVITY 2
2. Preparing and analysing the effectiveness of continuous improvement plan
Continuous improvement plan is the plan of improving product, services and process
within organisation through constant reviews, actions and measurements. It is the set of activities
which are designed in such a way to bring in the process of the business (O’Reilly and et.al.,
4
⊘ This is a preview!⊘
Do you want full access?
Subscribe today to unlock all pages.

Trusted by 1+ million students worldwide
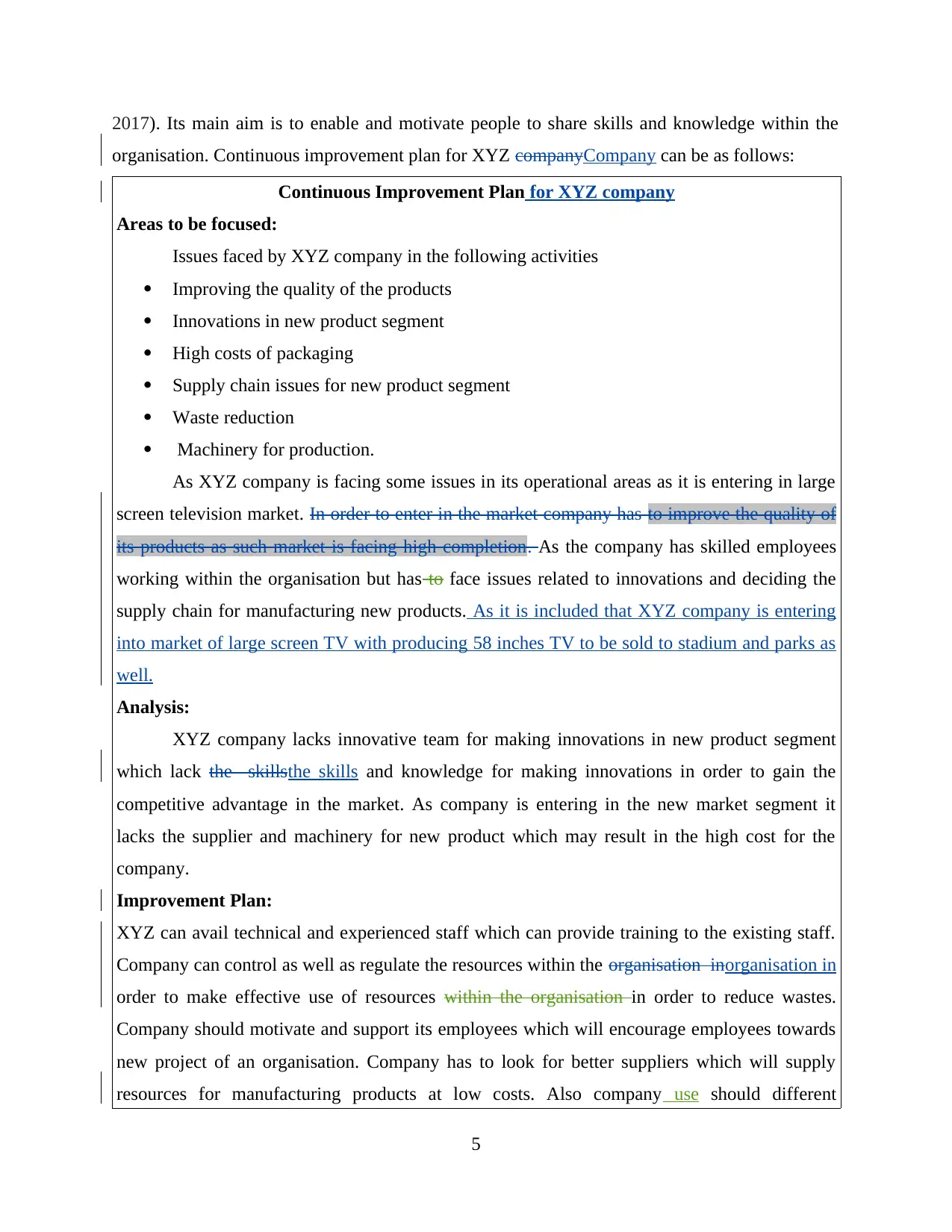
2017). Its main aim is to enable and motivate people to share skills and knowledge within the
organisation. Continuous improvement plan for XYZ companyCompany can be as follows:
Continuous Improvement Plan for XYZ company
Areas to be focused:
Issues faced by XYZ company in the following activities
Improving the quality of the products
Innovations in new product segment
High costs of packaging
Supply chain issues for new product segment
Waste reduction
Machinery for production.
As XYZ company is facing some issues in its operational areas as it is entering in large
screen television market. In order to enter in the market company has to improve the quality of
its products as such market is facing high completion. As the company has skilled employees
working within the organisation but has to face issues related to innovations and deciding the
supply chain for manufacturing new products. As it is included that XYZ company is entering
into market of large screen TV with producing 58 inches TV to be sold to stadium and parks as
well.
Analysis:
XYZ company lacks innovative team for making innovations in new product segment
which lack the skillsthe skills and knowledge for making innovations in order to gain the
competitive advantage in the market. As company is entering in the new market segment it
lacks the supplier and machinery for new product which may result in the high cost for the
company.
Improvement Plan:
XYZ can avail technical and experienced staff which can provide training to the existing staff.
Company can control as well as regulate the resources within the organisation inorganisation in
order to make effective use of resources within the organisation in order to reduce wastes.
Company should motivate and support its employees which will encourage employees towards
new project of an organisation. Company has to look for better suppliers which will supply
resources for manufacturing products at low costs. Also company use should different
5
organisation. Continuous improvement plan for XYZ companyCompany can be as follows:
Continuous Improvement Plan for XYZ company
Areas to be focused:
Issues faced by XYZ company in the following activities
Improving the quality of the products
Innovations in new product segment
High costs of packaging
Supply chain issues for new product segment
Waste reduction
Machinery for production.
As XYZ company is facing some issues in its operational areas as it is entering in large
screen television market. In order to enter in the market company has to improve the quality of
its products as such market is facing high completion. As the company has skilled employees
working within the organisation but has to face issues related to innovations and deciding the
supply chain for manufacturing new products. As it is included that XYZ company is entering
into market of large screen TV with producing 58 inches TV to be sold to stadium and parks as
well.
Analysis:
XYZ company lacks innovative team for making innovations in new product segment
which lack the skillsthe skills and knowledge for making innovations in order to gain the
competitive advantage in the market. As company is entering in the new market segment it
lacks the supplier and machinery for new product which may result in the high cost for the
company.
Improvement Plan:
XYZ can avail technical and experienced staff which can provide training to the existing staff.
Company can control as well as regulate the resources within the organisation inorganisation in
order to make effective use of resources within the organisation in order to reduce wastes.
Company should motivate and support its employees which will encourage employees towards
new project of an organisation. Company has to look for better suppliers which will supply
resources for manufacturing products at low costs. Also company use should different
5
Paraphrase This Document
Need a fresh take? Get an instant paraphrase of this document with our AI Paraphraser
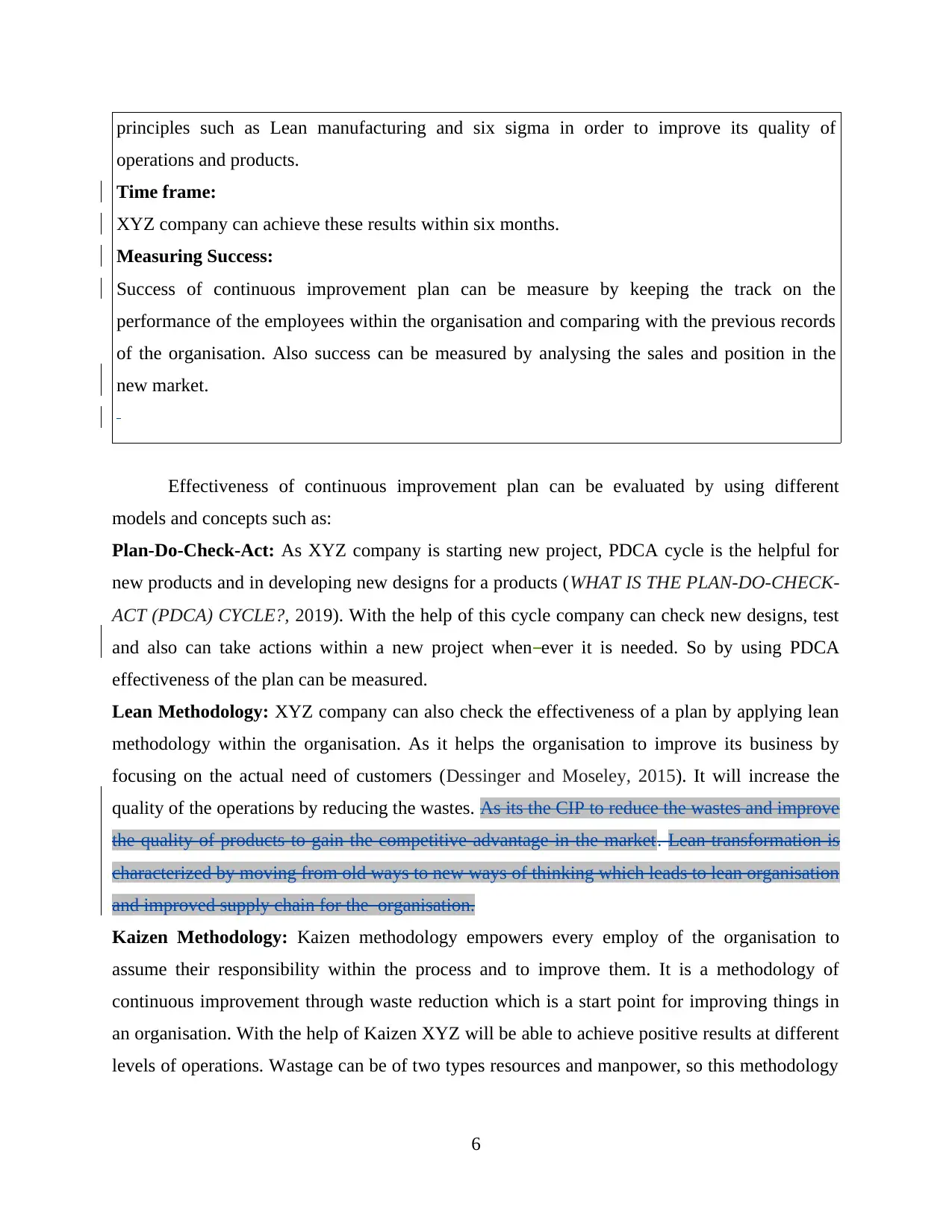
principles such as Lean manufacturing and six sigma in order to improve its quality of
operations and products.
Time frame:
XYZ company can achieve these results within six months.
Measuring Success:
Success of continuous improvement plan can be measure by keeping the track on the
performance of the employees within the organisation and comparing with the previous records
of the organisation. Also success can be measured by analysing the sales and position in the
new market.
Effectiveness of continuous improvement plan can be evaluated by using different
models and concepts such as:
Plan-Do-Check-Act: As XYZ company is starting new project, PDCA cycle is the helpful for
new products and in developing new designs for a products (WHAT IS THE PLAN-DO-CHECK-
ACT (PDCA) CYCLE?, 2019). With the help of this cycle company can check new designs, test
and also can take actions within a new project when ever it is needed. So by using PDCA
effectiveness of the plan can be measured.
Lean Methodology: XYZ company can also check the effectiveness of a plan by applying lean
methodology within the organisation. As it helps the organisation to improve its business by
focusing on the actual need of customers (Dessinger and Moseley, 2015). It will increase the
quality of the operations by reducing the wastes. As its the CIP to reduce the wastes and improve
the quality of products to gain the competitive advantage in the market. Lean transformation is
characterized by moving from old ways to new ways of thinking which leads to lean organisation
and improved supply chain for the organisation.
Kaizen Methodology: Kaizen methodology empowers every employ of the organisation to
assume their responsibility within the process and to improve them. It is a methodology of
continuous improvement through waste reduction which is a start point for improving things in
an organisation. With the help of Kaizen XYZ will be able to achieve positive results at different
levels of operations. Wastage can be of two types resources and manpower, so this methodology
6
operations and products.
Time frame:
XYZ company can achieve these results within six months.
Measuring Success:
Success of continuous improvement plan can be measure by keeping the track on the
performance of the employees within the organisation and comparing with the previous records
of the organisation. Also success can be measured by analysing the sales and position in the
new market.
Effectiveness of continuous improvement plan can be evaluated by using different
models and concepts such as:
Plan-Do-Check-Act: As XYZ company is starting new project, PDCA cycle is the helpful for
new products and in developing new designs for a products (WHAT IS THE PLAN-DO-CHECK-
ACT (PDCA) CYCLE?, 2019). With the help of this cycle company can check new designs, test
and also can take actions within a new project when ever it is needed. So by using PDCA
effectiveness of the plan can be measured.
Lean Methodology: XYZ company can also check the effectiveness of a plan by applying lean
methodology within the organisation. As it helps the organisation to improve its business by
focusing on the actual need of customers (Dessinger and Moseley, 2015). It will increase the
quality of the operations by reducing the wastes. As its the CIP to reduce the wastes and improve
the quality of products to gain the competitive advantage in the market. Lean transformation is
characterized by moving from old ways to new ways of thinking which leads to lean organisation
and improved supply chain for the organisation.
Kaizen Methodology: Kaizen methodology empowers every employ of the organisation to
assume their responsibility within the process and to improve them. It is a methodology of
continuous improvement through waste reduction which is a start point for improving things in
an organisation. With the help of Kaizen XYZ will be able to achieve positive results at different
levels of operations. Wastage can be of two types resources and manpower, so this methodology
6
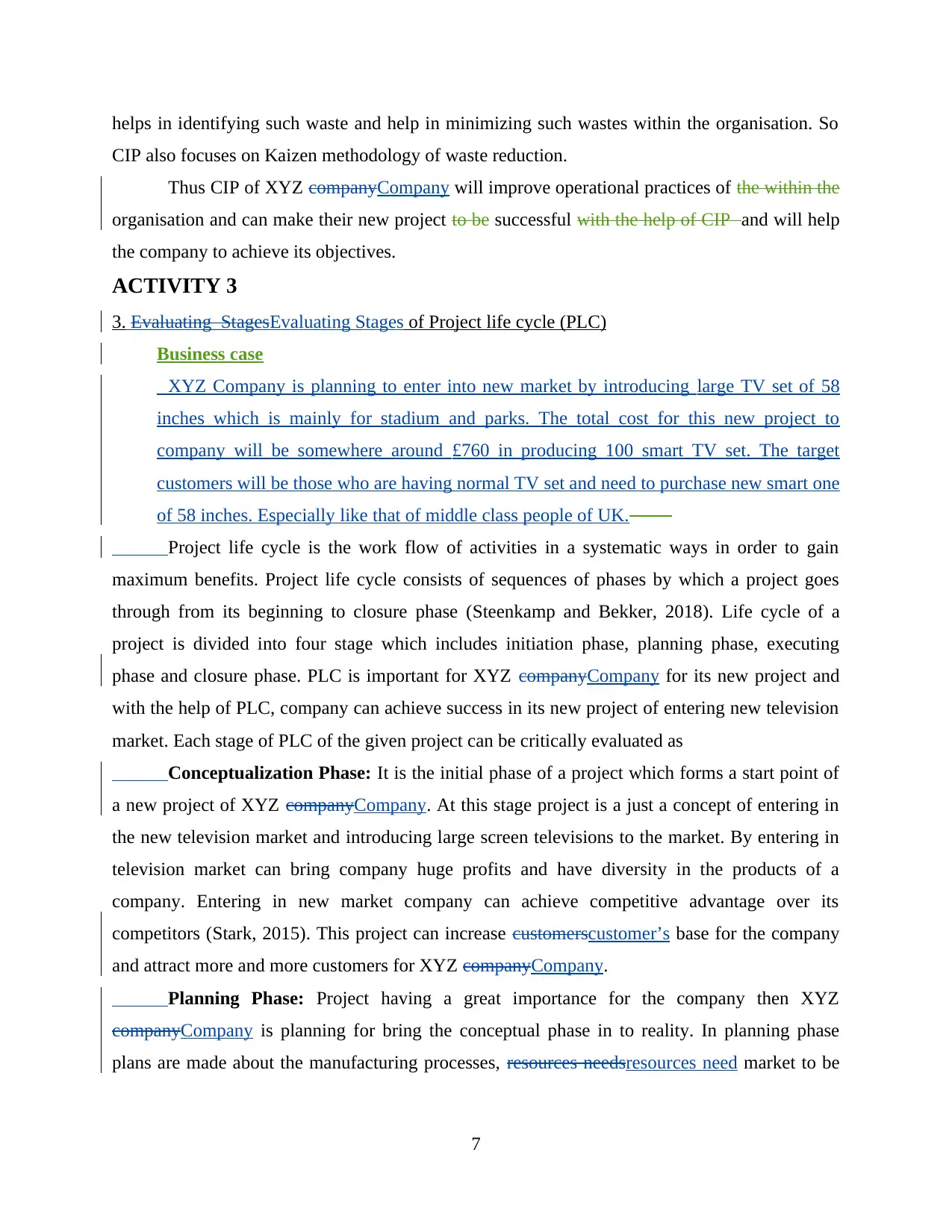
helps in identifying such waste and help in minimizing such wastes within the organisation. So
CIP also focuses on Kaizen methodology of waste reduction.
Thus CIP of XYZ companyCompany will improve operational practices of the within the
organisation and can make their new project to be successful with the help of CIP and will help
the company to achieve its objectives.
ACTIVITY 3
3. Evaluating StagesEvaluating Stages of Project life cycle (PLC)
Business case
XYZ Company is planning to enter into new market by introducing large TV set of 58
inches which is mainly for stadium and parks. The total cost for this new project to
company will be somewhere around £760 in producing 100 smart TV set. The target
customers will be those who are having normal TV set and need to purchase new smart one
of 58 inches. Especially like that of middle class people of UK.
Project life cycle is the work flow of activities in a systematic ways in order to gain
maximum benefits. Project life cycle consists of sequences of phases by which a project goes
through from its beginning to closure phase (Steenkamp and Bekker, 2018). Life cycle of a
project is divided into four stage which includes initiation phase, planning phase, executing
phase and closure phase. PLC is important for XYZ companyCompany for its new project and
with the help of PLC, company can achieve success in its new project of entering new television
market. Each stage of PLC of the given project can be critically evaluated as
Conceptualization Phase: It is the initial phase of a project which forms a start point of
a new project of XYZ companyCompany. At this stage project is a just a concept of entering in
the new television market and introducing large screen televisions to the market. By entering in
television market can bring company huge profits and have diversity in the products of a
company. Entering in new market company can achieve competitive advantage over its
competitors (Stark, 2015). This project can increase customerscustomer’s base for the company
and attract more and more customers for XYZ companyCompany.
Planning Phase: Project having a great importance for the company then XYZ
companyCompany is planning for bring the conceptual phase in to reality. In planning phase
plans are made about the manufacturing processes, resources needsresources need market to be
7
CIP also focuses on Kaizen methodology of waste reduction.
Thus CIP of XYZ companyCompany will improve operational practices of the within the
organisation and can make their new project to be successful with the help of CIP and will help
the company to achieve its objectives.
ACTIVITY 3
3. Evaluating StagesEvaluating Stages of Project life cycle (PLC)
Business case
XYZ Company is planning to enter into new market by introducing large TV set of 58
inches which is mainly for stadium and parks. The total cost for this new project to
company will be somewhere around £760 in producing 100 smart TV set. The target
customers will be those who are having normal TV set and need to purchase new smart one
of 58 inches. Especially like that of middle class people of UK.
Project life cycle is the work flow of activities in a systematic ways in order to gain
maximum benefits. Project life cycle consists of sequences of phases by which a project goes
through from its beginning to closure phase (Steenkamp and Bekker, 2018). Life cycle of a
project is divided into four stage which includes initiation phase, planning phase, executing
phase and closure phase. PLC is important for XYZ companyCompany for its new project and
with the help of PLC, company can achieve success in its new project of entering new television
market. Each stage of PLC of the given project can be critically evaluated as
Conceptualization Phase: It is the initial phase of a project which forms a start point of
a new project of XYZ companyCompany. At this stage project is a just a concept of entering in
the new television market and introducing large screen televisions to the market. By entering in
television market can bring company huge profits and have diversity in the products of a
company. Entering in new market company can achieve competitive advantage over its
competitors (Stark, 2015). This project can increase customerscustomer’s base for the company
and attract more and more customers for XYZ companyCompany.
Planning Phase: Project having a great importance for the company then XYZ
companyCompany is planning for bring the conceptual phase in to reality. In planning phase
plans are made about the manufacturing processes, resources needsresources need market to be
7
⊘ This is a preview!⊘
Do you want full access?
Subscribe today to unlock all pages.

Trusted by 1+ million students worldwide
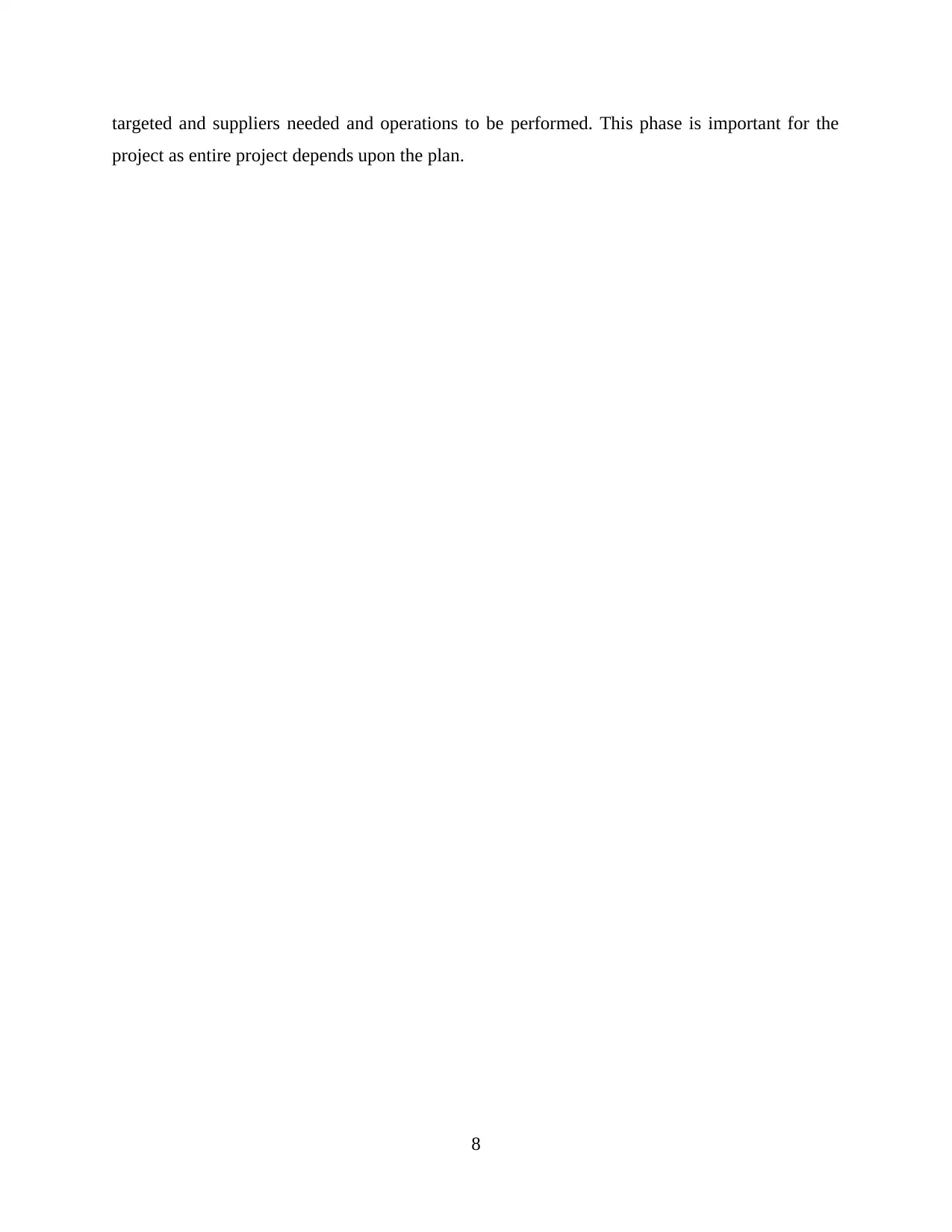
targeted and suppliers needed and operations to be performed. This phase is important for the
project as entire project depends upon the plan.
8
project as entire project depends upon the plan.
8
Paraphrase This Document
Need a fresh take? Get an instant paraphrase of this document with our AI Paraphraser
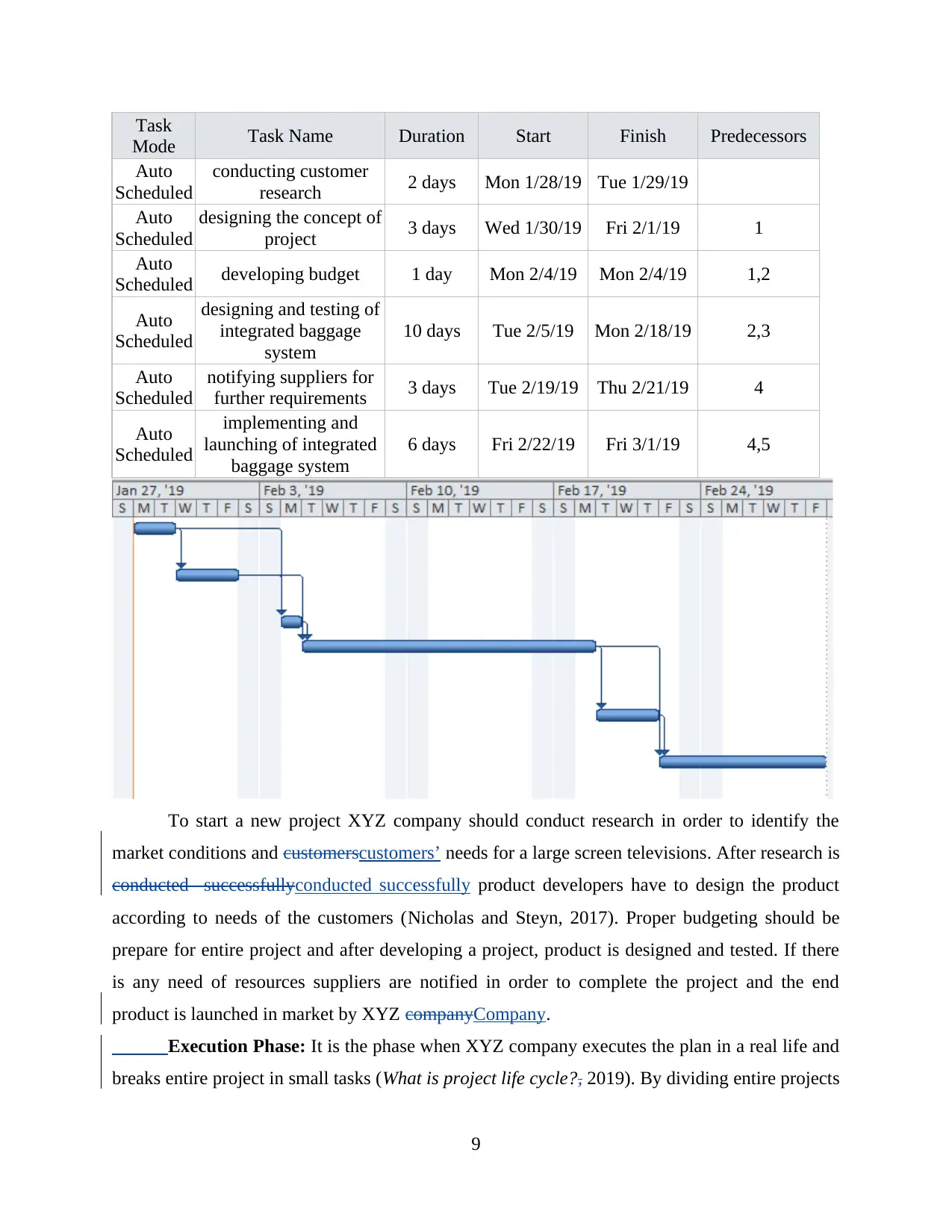
Task
Mode Task Name Duration Start Finish Predecessors
Auto
Scheduled
conducting customer
research 2 days Mon 1/28/19 Tue 1/29/19
Auto
Scheduled
designing the concept of
project 3 days Wed 1/30/19 Fri 2/1/19 1
Auto
Scheduled developing budget 1 day Mon 2/4/19 Mon 2/4/19 1,2
Auto
Scheduled
designing and testing of
integrated baggage
system
10 days Tue 2/5/19 Mon 2/18/19 2,3
Auto
Scheduled
notifying suppliers for
further requirements 3 days Tue 2/19/19 Thu 2/21/19 4
Auto
Scheduled
implementing and
launching of integrated
baggage system
6 days Fri 2/22/19 Fri 3/1/19 4,5
To start a new project XYZ company should conduct research in order to identify the
market conditions and customerscustomers’ needs for a large screen televisions. After research is
conducted successfullyconducted successfully product developers have to design the product
according to needs of the customers (Nicholas and Steyn, 2017). Proper budgeting should be
prepare for entire project and after developing a project, product is designed and tested. If there
is any need of resources suppliers are notified in order to complete the project and the end
product is launched in market by XYZ companyCompany.
Execution Phase: It is the phase when XYZ company executes the plan in a real life and
breaks entire project in small tasks (What is project life cycle?, 2019). By dividing entire projects
9
Mode Task Name Duration Start Finish Predecessors
Auto
Scheduled
conducting customer
research 2 days Mon 1/28/19 Tue 1/29/19
Auto
Scheduled
designing the concept of
project 3 days Wed 1/30/19 Fri 2/1/19 1
Auto
Scheduled developing budget 1 day Mon 2/4/19 Mon 2/4/19 1,2
Auto
Scheduled
designing and testing of
integrated baggage
system
10 days Tue 2/5/19 Mon 2/18/19 2,3
Auto
Scheduled
notifying suppliers for
further requirements 3 days Tue 2/19/19 Thu 2/21/19 4
Auto
Scheduled
implementing and
launching of integrated
baggage system
6 days Fri 2/22/19 Fri 3/1/19 4,5
To start a new project XYZ company should conduct research in order to identify the
market conditions and customerscustomers’ needs for a large screen televisions. After research is
conducted successfullyconducted successfully product developers have to design the product
according to needs of the customers (Nicholas and Steyn, 2017). Proper budgeting should be
prepare for entire project and after developing a project, product is designed and tested. If there
is any need of resources suppliers are notified in order to complete the project and the end
product is launched in market by XYZ companyCompany.
Execution Phase: It is the phase when XYZ company executes the plan in a real life and
breaks entire project in small tasks (What is project life cycle?, 2019). By dividing entire projects
9
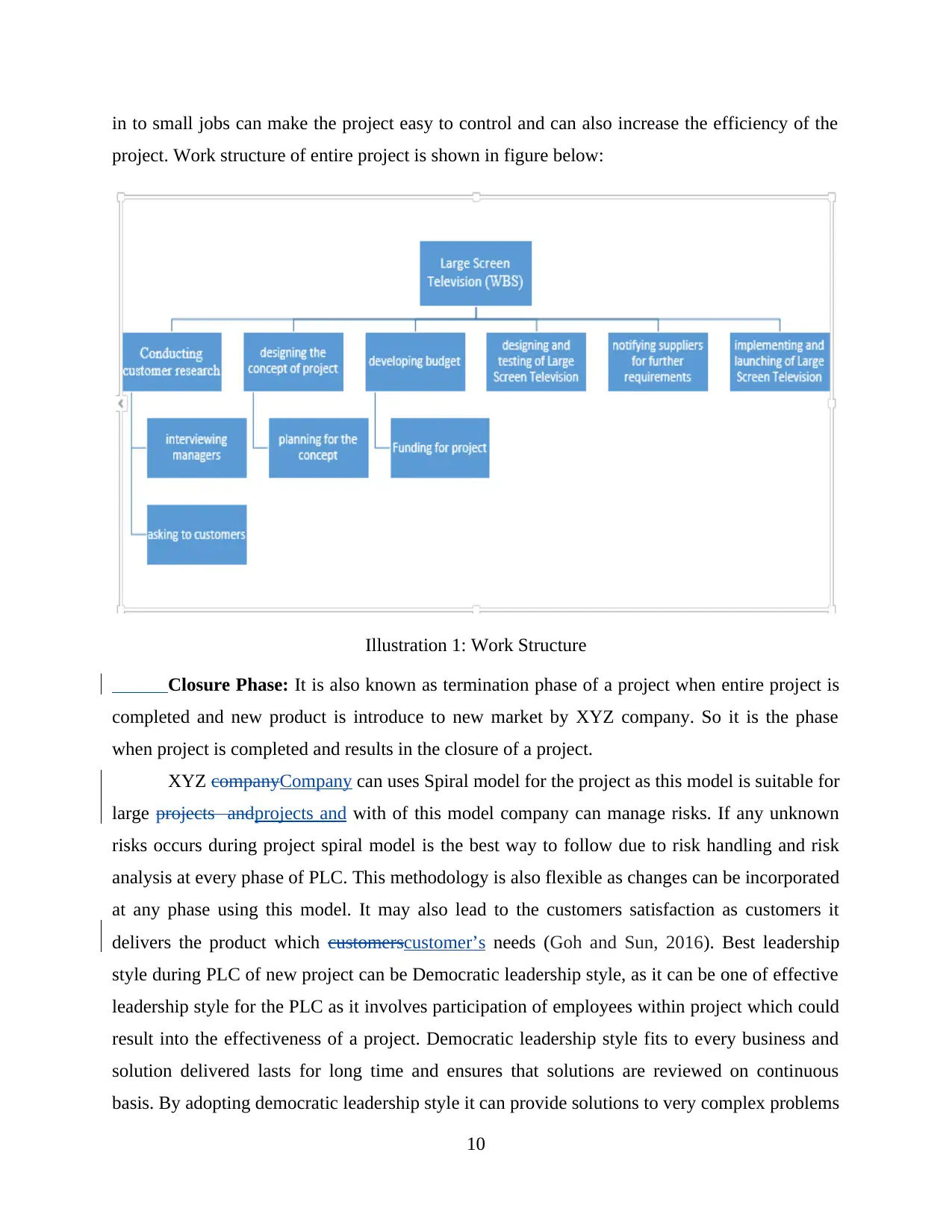
in to small jobs can make the project easy to control and can also increase the efficiency of the
project. Work structure of entire project is shown in figure below:
Illustration 1: Work Structure
Closure Phase: It is also known as termination phase of a project when entire project is
completed and new product is introduce to new market by XYZ company. So it is the phase
when project is completed and results in the closure of a project.
XYZ companyCompany can uses Spiral model for the project as this model is suitable for
large projects andprojects and with of this model company can manage risks. If any unknown
risks occurs during project spiral model is the best way to follow due to risk handling and risk
analysis at every phase of PLC. This methodology is also flexible as changes can be incorporated
at any phase using this model. It may also lead to the customers satisfaction as customers it
delivers the product which customerscustomer’s needs (Goh and Sun, 2016). Best leadership
style during PLC of new project can be Democratic leadership style, as it can be one of effective
leadership style for the PLC as it involves participation of employees within project which could
result into the effectiveness of a project. Democratic leadership style fits to every business and
solution delivered lasts for long time and ensures that solutions are reviewed on continuous
basis. By adopting democratic leadership style it can provide solutions to very complex problems
10
project. Work structure of entire project is shown in figure below:
Illustration 1: Work Structure
Closure Phase: It is also known as termination phase of a project when entire project is
completed and new product is introduce to new market by XYZ company. So it is the phase
when project is completed and results in the closure of a project.
XYZ companyCompany can uses Spiral model for the project as this model is suitable for
large projects andprojects and with of this model company can manage risks. If any unknown
risks occurs during project spiral model is the best way to follow due to risk handling and risk
analysis at every phase of PLC. This methodology is also flexible as changes can be incorporated
at any phase using this model. It may also lead to the customers satisfaction as customers it
delivers the product which customerscustomer’s needs (Goh and Sun, 2016). Best leadership
style during PLC of new project can be Democratic leadership style, as it can be one of effective
leadership style for the PLC as it involves participation of employees within project which could
result into the effectiveness of a project. Democratic leadership style fits to every business and
solution delivered lasts for long time and ensures that solutions are reviewed on continuous
basis. By adopting democratic leadership style it can provide solutions to very complex problems
10
⊘ This is a preview!⊘
Do you want full access?
Subscribe today to unlock all pages.

Trusted by 1+ million students worldwide
1 out of 17