Toyota Production System
VerifiedAdded on 2022/08/15
|17
|4689
|120
AI Summary
Running Head: OPERATIONS & INFORMATIONS MANAGEMENT 10 Running Head: OPERATIONS & INFORMATIONS MANAGEMENT 0 OPERATIONS & INFORMATIONS MANAGEMENT Introduction 2 Inventory management 3 Key operations 4 Failure of the organization delivery system 6 Lean approach 6 Key findings 8 Conclusion 9 Bibliography 10 Introduction The production system of Toyota has been developed by Toyota after World War II (Toyota Production System, 2019). An organization like GM and Ford uses mass production, big equipment, and economies of scale to produce the many parts at
Contribute Materials
Your contribution can guide someone’s learning journey. Share your
documents today.
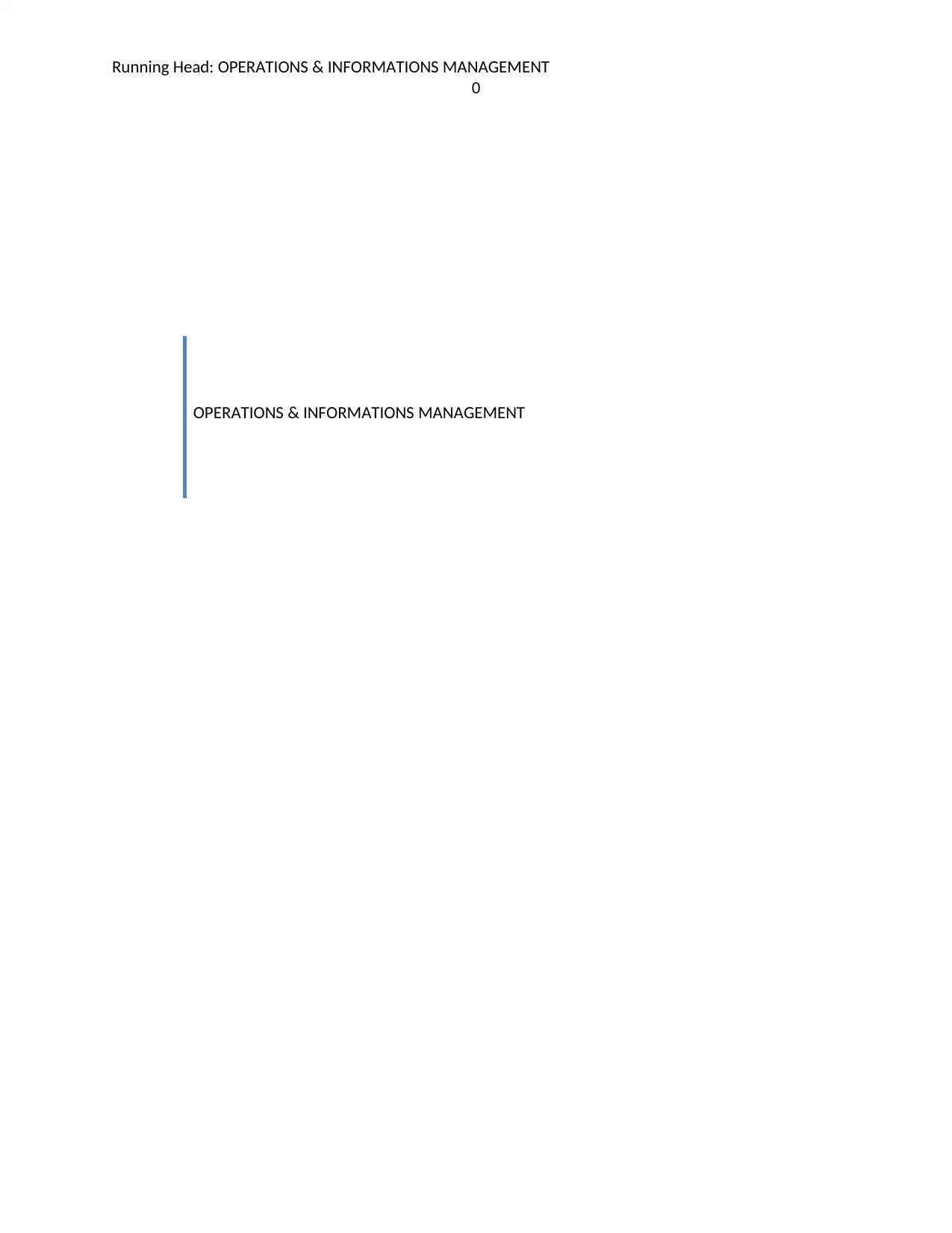
Running Head: OPERATIONS & INFORMATIONS MANAGEMENT
0
OPERATIONS & INFORMATIONS MANAGEMENT
0
OPERATIONS & INFORMATIONS MANAGEMENT
Secure Best Marks with AI Grader
Need help grading? Try our AI Grader for instant feedback on your assignments.
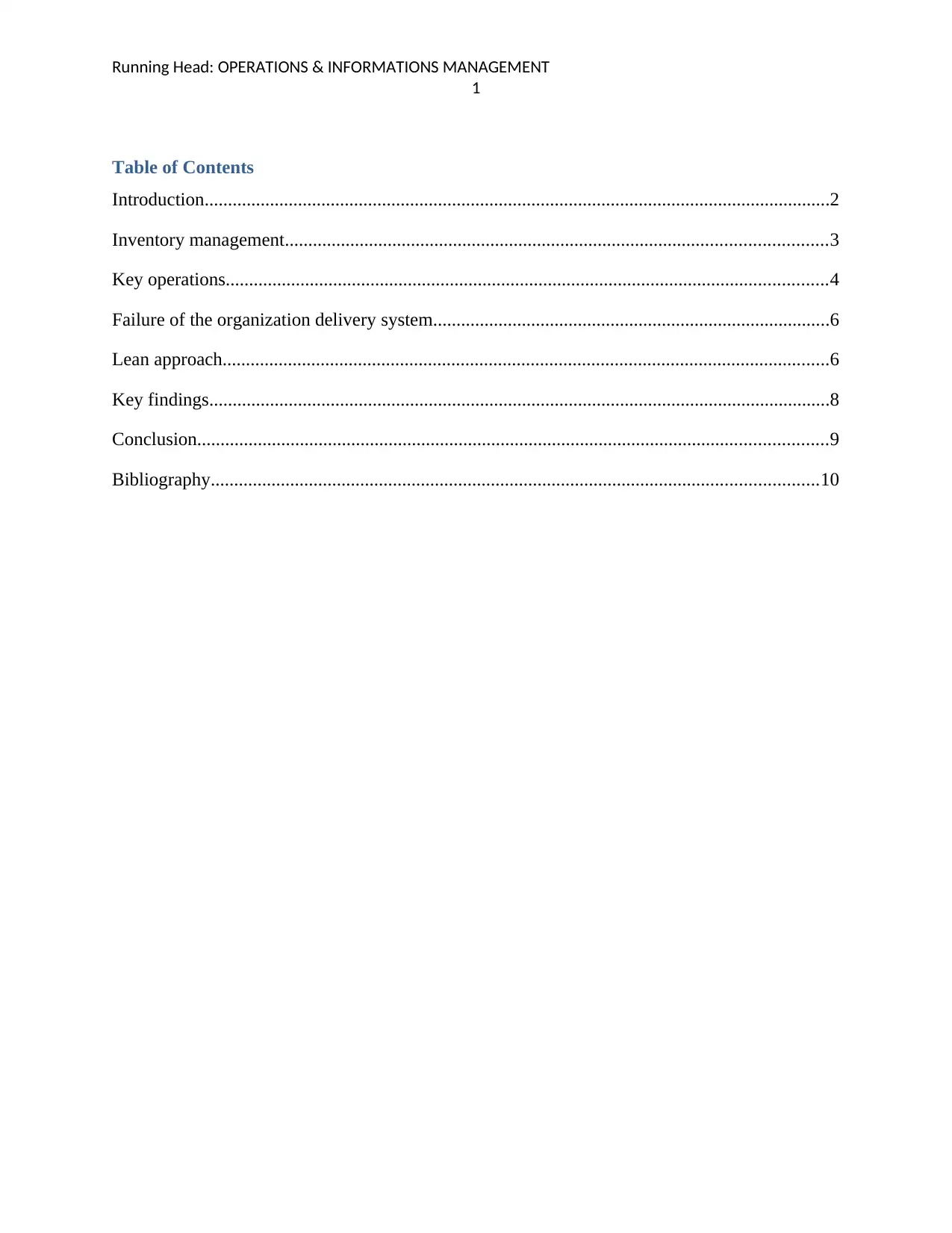
Running Head: OPERATIONS & INFORMATIONS MANAGEMENT
1
Table of Contents
Introduction......................................................................................................................................2
Inventory management....................................................................................................................3
Key operations.................................................................................................................................4
Failure of the organization delivery system.....................................................................................6
Lean approach..................................................................................................................................6
Key findings.....................................................................................................................................8
Conclusion.......................................................................................................................................9
Bibliography..................................................................................................................................10
1
Table of Contents
Introduction......................................................................................................................................2
Inventory management....................................................................................................................3
Key operations.................................................................................................................................4
Failure of the organization delivery system.....................................................................................6
Lean approach..................................................................................................................................6
Key findings.....................................................................................................................................8
Conclusion.......................................................................................................................................9
Bibliography..................................................................................................................................10
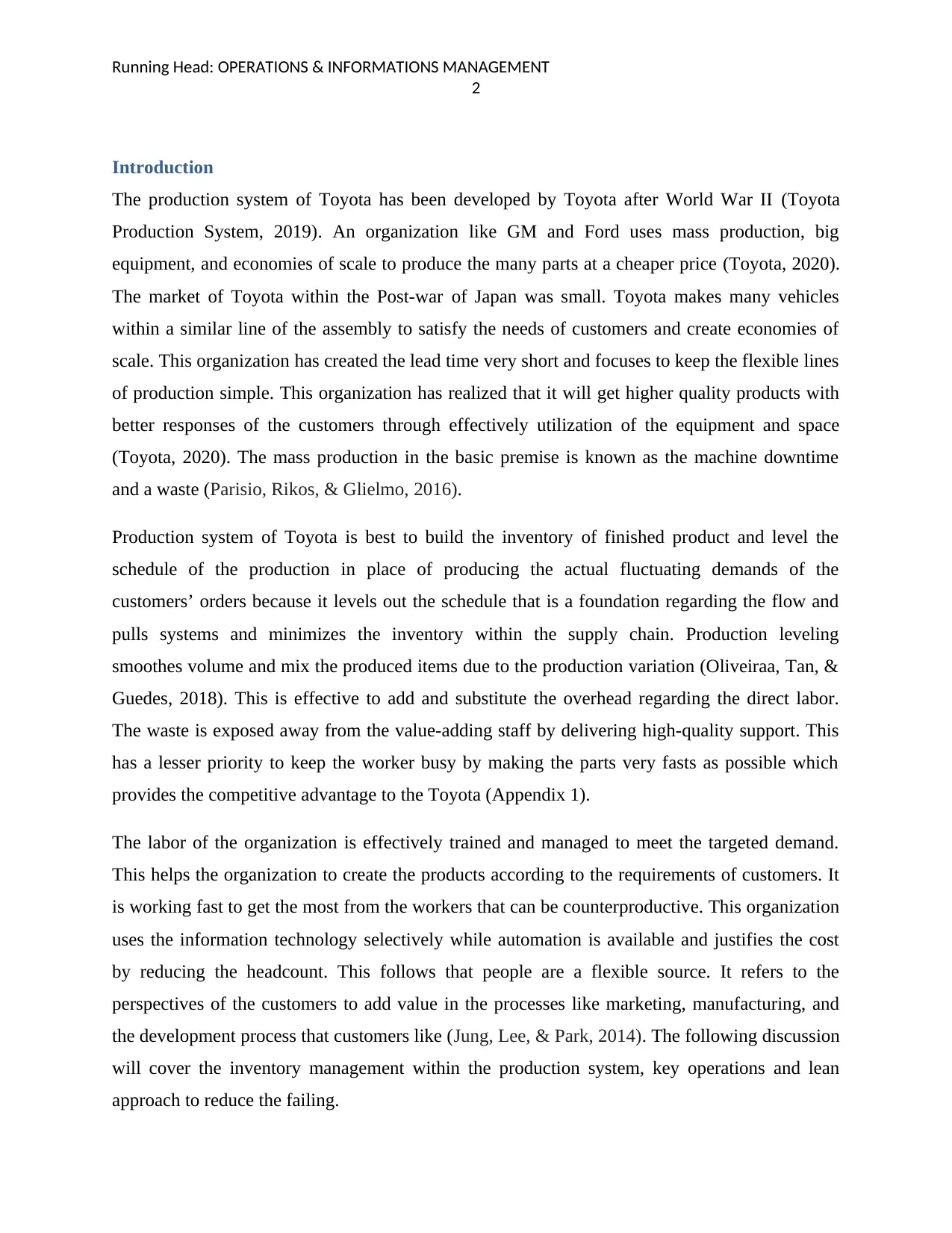
Running Head: OPERATIONS & INFORMATIONS MANAGEMENT
2
Introduction
The production system of Toyota has been developed by Toyota after World War II (Toyota
Production System, 2019). An organization like GM and Ford uses mass production, big
equipment, and economies of scale to produce the many parts at a cheaper price (Toyota, 2020).
The market of Toyota within the Post-war of Japan was small. Toyota makes many vehicles
within a similar line of the assembly to satisfy the needs of customers and create economies of
scale. This organization has created the lead time very short and focuses to keep the flexible lines
of production simple. This organization has realized that it will get higher quality products with
better responses of the customers through effectively utilization of the equipment and space
(Toyota, 2020). The mass production in the basic premise is known as the machine downtime
and a waste (Parisio, Rikos, & Glielmo, 2016).
Production system of Toyota is best to build the inventory of finished product and level the
schedule of the production in place of producing the actual fluctuating demands of the
customers’ orders because it levels out the schedule that is a foundation regarding the flow and
pulls systems and minimizes the inventory within the supply chain. Production leveling
smoothes volume and mix the produced items due to the production variation (Oliveiraa, Tan, &
Guedes, 2018). This is effective to add and substitute the overhead regarding the direct labor.
The waste is exposed away from the value-adding staff by delivering high-quality support. This
has a lesser priority to keep the worker busy by making the parts very fasts as possible which
provides the competitive advantage to the Toyota (Appendix 1).
The labor of the organization is effectively trained and managed to meet the targeted demand.
This helps the organization to create the products according to the requirements of customers. It
is working fast to get the most from the workers that can be counterproductive. This organization
uses the information technology selectively while automation is available and justifies the cost
by reducing the headcount. This follows that people are a flexible source. It refers to the
perspectives of the customers to add value in the processes like marketing, manufacturing, and
the development process that customers like (Jung, Lee, & Park, 2014). The following discussion
will cover the inventory management within the production system, key operations and lean
approach to reduce the failing.
2
Introduction
The production system of Toyota has been developed by Toyota after World War II (Toyota
Production System, 2019). An organization like GM and Ford uses mass production, big
equipment, and economies of scale to produce the many parts at a cheaper price (Toyota, 2020).
The market of Toyota within the Post-war of Japan was small. Toyota makes many vehicles
within a similar line of the assembly to satisfy the needs of customers and create economies of
scale. This organization has created the lead time very short and focuses to keep the flexible lines
of production simple. This organization has realized that it will get higher quality products with
better responses of the customers through effectively utilization of the equipment and space
(Toyota, 2020). The mass production in the basic premise is known as the machine downtime
and a waste (Parisio, Rikos, & Glielmo, 2016).
Production system of Toyota is best to build the inventory of finished product and level the
schedule of the production in place of producing the actual fluctuating demands of the
customers’ orders because it levels out the schedule that is a foundation regarding the flow and
pulls systems and minimizes the inventory within the supply chain. Production leveling
smoothes volume and mix the produced items due to the production variation (Oliveiraa, Tan, &
Guedes, 2018). This is effective to add and substitute the overhead regarding the direct labor.
The waste is exposed away from the value-adding staff by delivering high-quality support. This
has a lesser priority to keep the worker busy by making the parts very fasts as possible which
provides the competitive advantage to the Toyota (Appendix 1).
The labor of the organization is effectively trained and managed to meet the targeted demand.
This helps the organization to create the products according to the requirements of customers. It
is working fast to get the most from the workers that can be counterproductive. This organization
uses the information technology selectively while automation is available and justifies the cost
by reducing the headcount. This follows that people are a flexible source. It refers to the
perspectives of the customers to add value in the processes like marketing, manufacturing, and
the development process that customers like (Jung, Lee, & Park, 2014). The following discussion
will cover the inventory management within the production system, key operations and lean
approach to reduce the failing.
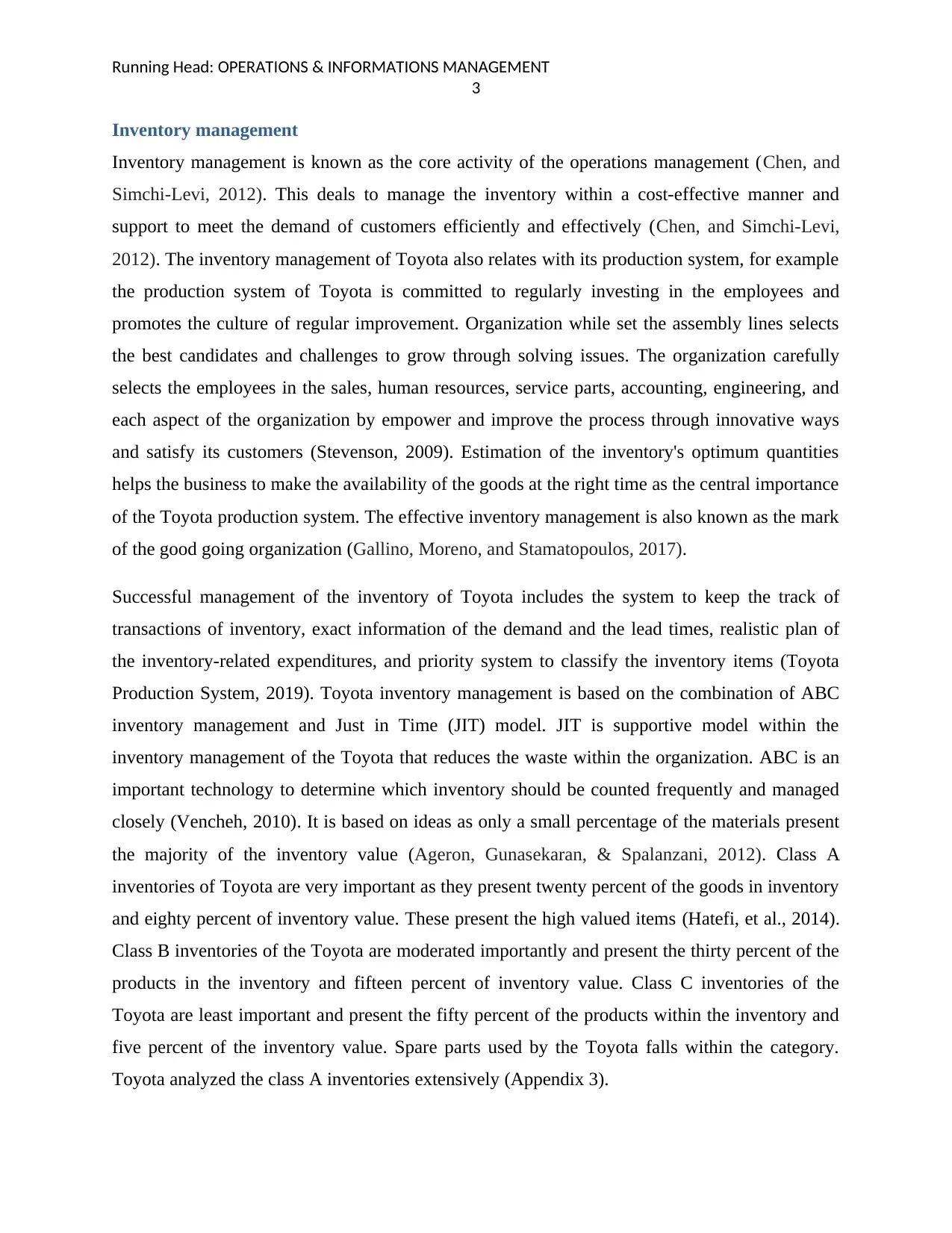
Running Head: OPERATIONS & INFORMATIONS MANAGEMENT
3
Inventory management
Inventory management is known as the core activity of the operations management (Chen, and
Simchi-Levi, 2012). This deals to manage the inventory within a cost-effective manner and
support to meet the demand of customers efficiently and effectively (Chen, and Simchi-Levi,
2012). The inventory management of Toyota also relates with its production system, for example
the production system of Toyota is committed to regularly investing in the employees and
promotes the culture of regular improvement. Organization while set the assembly lines selects
the best candidates and challenges to grow through solving issues. The organization carefully
selects the employees in the sales, human resources, service parts, accounting, engineering, and
each aspect of the organization by empower and improve the process through innovative ways
and satisfy its customers (Stevenson, 2009). Estimation of the inventory's optimum quantities
helps the business to make the availability of the goods at the right time as the central importance
of the Toyota production system. The effective inventory management is also known as the mark
of the good going organization (Gallino, Moreno, and Stamatopoulos, 2017).
Successful management of the inventory of Toyota includes the system to keep the track of
transactions of inventory, exact information of the demand and the lead times, realistic plan of
the inventory-related expenditures, and priority system to classify the inventory items (Toyota
Production System, 2019). Toyota inventory management is based on the combination of ABC
inventory management and Just in Time (JIT) model. JIT is supportive model within the
inventory management of the Toyota that reduces the waste within the organization. ABC is an
important technology to determine which inventory should be counted frequently and managed
closely (Vencheh, 2010). It is based on ideas as only a small percentage of the materials present
the majority of the inventory value (Ageron, Gunasekaran, & Spalanzani, 2012). Class A
inventories of Toyota are very important as they present twenty percent of the goods in inventory
and eighty percent of inventory value. These present the high valued items (Hatefi, et al., 2014).
Class B inventories of the Toyota are moderated importantly and present the thirty percent of the
products in the inventory and fifteen percent of inventory value. Class C inventories of the
Toyota are least important and present the fifty percent of the products within the inventory and
five percent of the inventory value. Spare parts used by the Toyota falls within the category.
Toyota analyzed the class A inventories extensively (Appendix 3).
3
Inventory management
Inventory management is known as the core activity of the operations management (Chen, and
Simchi-Levi, 2012). This deals to manage the inventory within a cost-effective manner and
support to meet the demand of customers efficiently and effectively (Chen, and Simchi-Levi,
2012). The inventory management of Toyota also relates with its production system, for example
the production system of Toyota is committed to regularly investing in the employees and
promotes the culture of regular improvement. Organization while set the assembly lines selects
the best candidates and challenges to grow through solving issues. The organization carefully
selects the employees in the sales, human resources, service parts, accounting, engineering, and
each aspect of the organization by empower and improve the process through innovative ways
and satisfy its customers (Stevenson, 2009). Estimation of the inventory's optimum quantities
helps the business to make the availability of the goods at the right time as the central importance
of the Toyota production system. The effective inventory management is also known as the mark
of the good going organization (Gallino, Moreno, and Stamatopoulos, 2017).
Successful management of the inventory of Toyota includes the system to keep the track of
transactions of inventory, exact information of the demand and the lead times, realistic plan of
the inventory-related expenditures, and priority system to classify the inventory items (Toyota
Production System, 2019). Toyota inventory management is based on the combination of ABC
inventory management and Just in Time (JIT) model. JIT is supportive model within the
inventory management of the Toyota that reduces the waste within the organization. ABC is an
important technology to determine which inventory should be counted frequently and managed
closely (Vencheh, 2010). It is based on ideas as only a small percentage of the materials present
the majority of the inventory value (Ageron, Gunasekaran, & Spalanzani, 2012). Class A
inventories of Toyota are very important as they present twenty percent of the goods in inventory
and eighty percent of inventory value. These present the high valued items (Hatefi, et al., 2014).
Class B inventories of the Toyota are moderated importantly and present the thirty percent of the
products in the inventory and fifteen percent of inventory value. Class C inventories of the
Toyota are least important and present the fifty percent of the products within the inventory and
five percent of the inventory value. Spare parts used by the Toyota falls within the category.
Toyota analyzed the class A inventories extensively (Appendix 3).
Secure Best Marks with AI Grader
Need help grading? Try our AI Grader for instant feedback on your assignments.
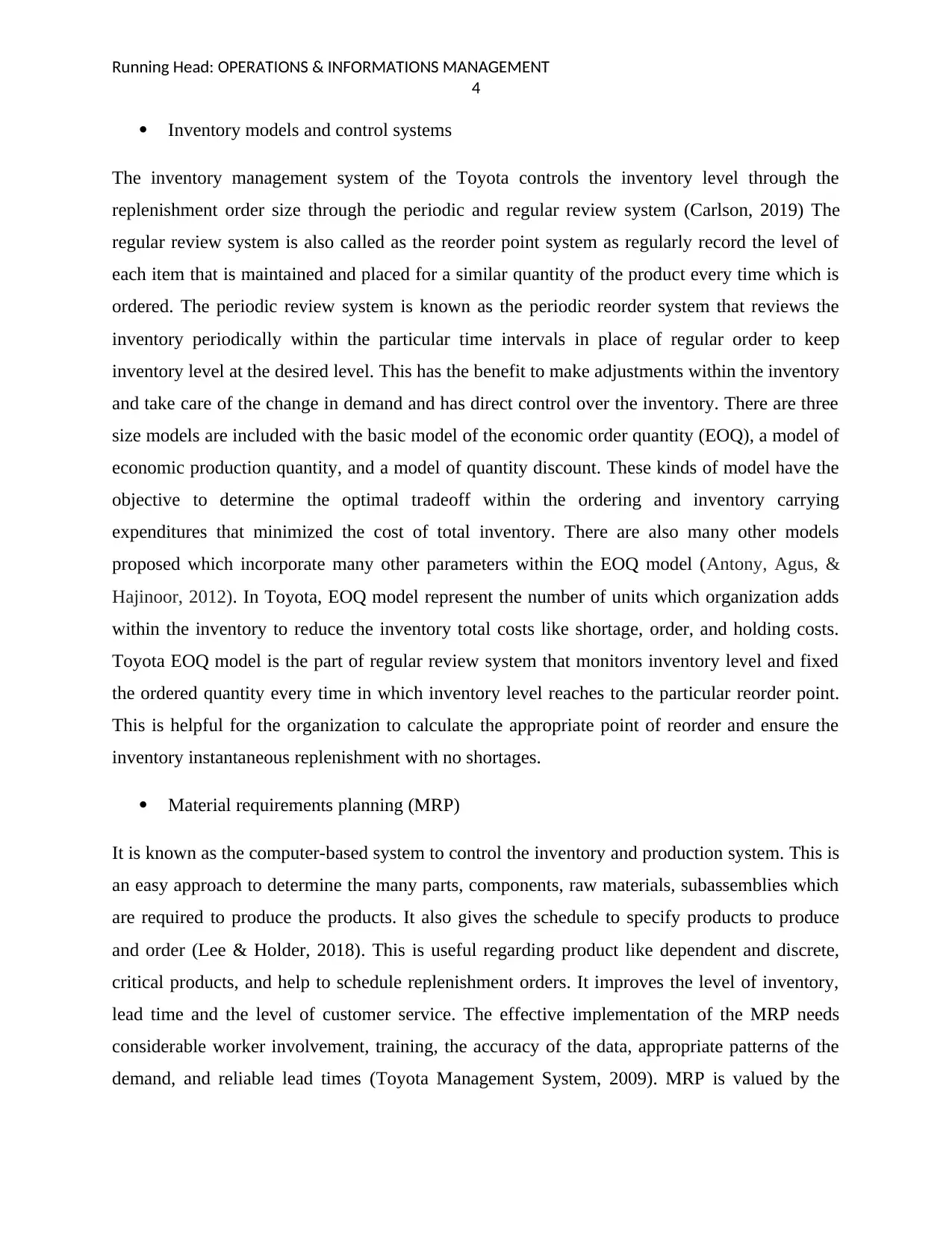
Running Head: OPERATIONS & INFORMATIONS MANAGEMENT
4
Inventory models and control systems
The inventory management system of the Toyota controls the inventory level through the
replenishment order size through the periodic and regular review system (Carlson, 2019) The
regular review system is also called as the reorder point system as regularly record the level of
each item that is maintained and placed for a similar quantity of the product every time which is
ordered. The periodic review system is known as the periodic reorder system that reviews the
inventory periodically within the particular time intervals in place of regular order to keep
inventory level at the desired level. This has the benefit to make adjustments within the inventory
and take care of the change in demand and has direct control over the inventory. There are three
size models are included with the basic model of the economic order quantity (EOQ), a model of
economic production quantity, and a model of quantity discount. These kinds of model have the
objective to determine the optimal tradeoff within the ordering and inventory carrying
expenditures that minimized the cost of total inventory. There are also many other models
proposed which incorporate many other parameters within the EOQ model (Antony, Agus, &
Hajinoor, 2012). In Toyota, EOQ model represent the number of units which organization adds
within the inventory to reduce the inventory total costs like shortage, order, and holding costs.
Toyota EOQ model is the part of regular review system that monitors inventory level and fixed
the ordered quantity every time in which inventory level reaches to the particular reorder point.
This is helpful for the organization to calculate the appropriate point of reorder and ensure the
inventory instantaneous replenishment with no shortages.
Material requirements planning (MRP)
It is known as the computer-based system to control the inventory and production system. This is
an easy approach to determine the many parts, components, raw materials, subassemblies which
are required to produce the products. It also gives the schedule to specify products to produce
and order (Lee & Holder, 2018). This is useful regarding product like dependent and discrete,
critical products, and help to schedule replenishment orders. It improves the level of inventory,
lead time and the level of customer service. The effective implementation of the MRP needs
considerable worker involvement, training, the accuracy of the data, appropriate patterns of the
demand, and reliable lead times (Toyota Management System, 2009). MRP is valued by the
4
Inventory models and control systems
The inventory management system of the Toyota controls the inventory level through the
replenishment order size through the periodic and regular review system (Carlson, 2019) The
regular review system is also called as the reorder point system as regularly record the level of
each item that is maintained and placed for a similar quantity of the product every time which is
ordered. The periodic review system is known as the periodic reorder system that reviews the
inventory periodically within the particular time intervals in place of regular order to keep
inventory level at the desired level. This has the benefit to make adjustments within the inventory
and take care of the change in demand and has direct control over the inventory. There are three
size models are included with the basic model of the economic order quantity (EOQ), a model of
economic production quantity, and a model of quantity discount. These kinds of model have the
objective to determine the optimal tradeoff within the ordering and inventory carrying
expenditures that minimized the cost of total inventory. There are also many other models
proposed which incorporate many other parameters within the EOQ model (Antony, Agus, &
Hajinoor, 2012). In Toyota, EOQ model represent the number of units which organization adds
within the inventory to reduce the inventory total costs like shortage, order, and holding costs.
Toyota EOQ model is the part of regular review system that monitors inventory level and fixed
the ordered quantity every time in which inventory level reaches to the particular reorder point.
This is helpful for the organization to calculate the appropriate point of reorder and ensure the
inventory instantaneous replenishment with no shortages.
Material requirements planning (MRP)
It is known as the computer-based system to control the inventory and production system. This is
an easy approach to determine the many parts, components, raw materials, subassemblies which
are required to produce the products. It also gives the schedule to specify products to produce
and order (Lee & Holder, 2018). This is useful regarding product like dependent and discrete,
critical products, and help to schedule replenishment orders. It improves the level of inventory,
lead time and the level of customer service. The effective implementation of the MRP needs
considerable worker involvement, training, the accuracy of the data, appropriate patterns of the
demand, and reliable lead times (Toyota Management System, 2009). MRP is valued by the
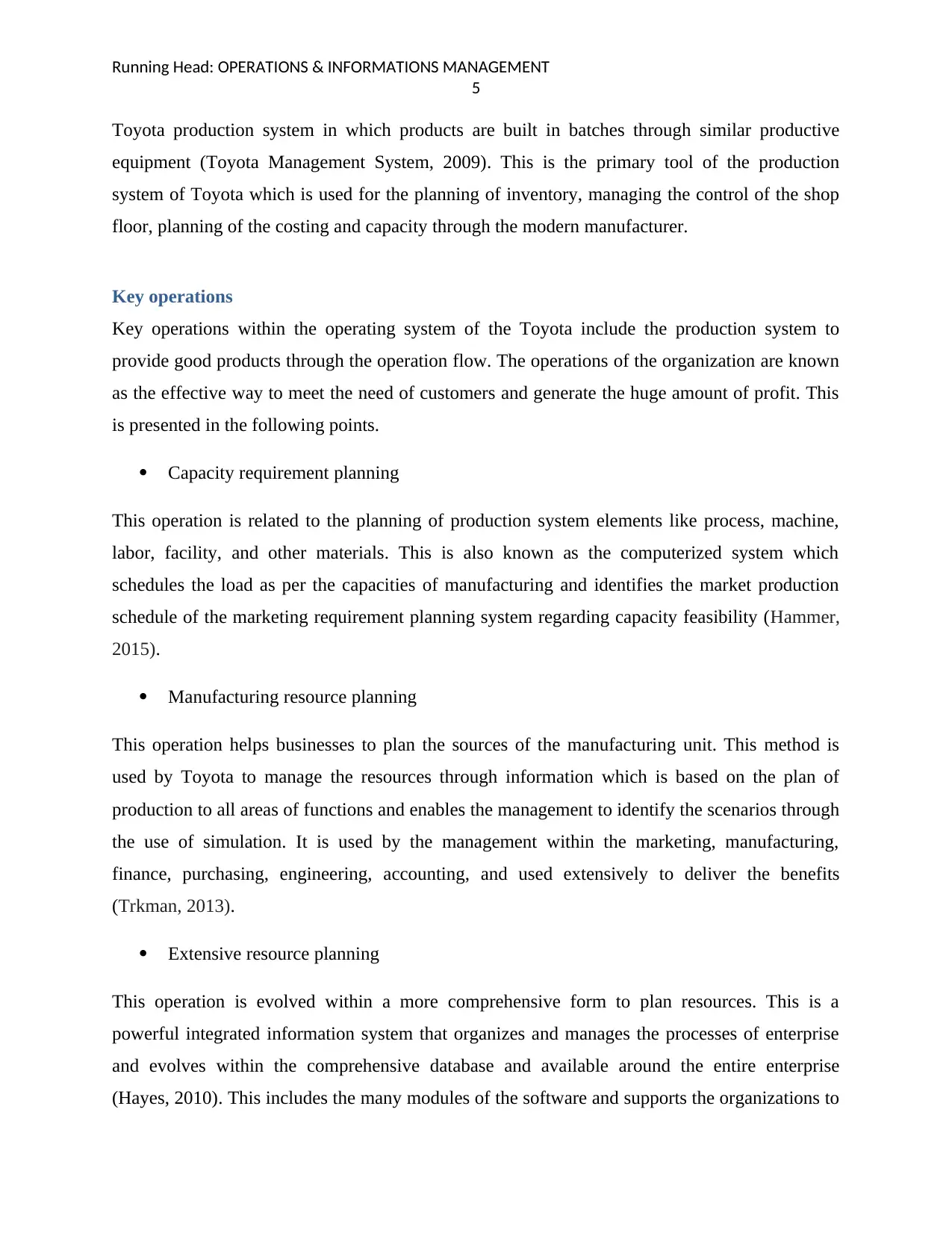
Running Head: OPERATIONS & INFORMATIONS MANAGEMENT
5
Toyota production system in which products are built in batches through similar productive
equipment (Toyota Management System, 2009). This is the primary tool of the production
system of Toyota which is used for the planning of inventory, managing the control of the shop
floor, planning of the costing and capacity through the modern manufacturer.
Key operations
Key operations within the operating system of the Toyota include the production system to
provide good products through the operation flow. The operations of the organization are known
as the effective way to meet the need of customers and generate the huge amount of profit. This
is presented in the following points.
Capacity requirement planning
This operation is related to the planning of production system elements like process, machine,
labor, facility, and other materials. This is also known as the computerized system which
schedules the load as per the capacities of manufacturing and identifies the market production
schedule of the marketing requirement planning system regarding capacity feasibility (Hammer,
2015).
Manufacturing resource planning
This operation helps businesses to plan the sources of the manufacturing unit. This method is
used by Toyota to manage the resources through information which is based on the plan of
production to all areas of functions and enables the management to identify the scenarios through
the use of simulation. It is used by the management within the marketing, manufacturing,
finance, purchasing, engineering, accounting, and used extensively to deliver the benefits
(Trkman, 2013).
Extensive resource planning
This operation is evolved within a more comprehensive form to plan resources. This is a
powerful integrated information system that organizes and manages the processes of enterprise
and evolves within the comprehensive database and available around the entire enterprise
(Hayes, 2010). This includes the many modules of the software and supports the organizations to
5
Toyota production system in which products are built in batches through similar productive
equipment (Toyota Management System, 2009). This is the primary tool of the production
system of Toyota which is used for the planning of inventory, managing the control of the shop
floor, planning of the costing and capacity through the modern manufacturer.
Key operations
Key operations within the operating system of the Toyota include the production system to
provide good products through the operation flow. The operations of the organization are known
as the effective way to meet the need of customers and generate the huge amount of profit. This
is presented in the following points.
Capacity requirement planning
This operation is related to the planning of production system elements like process, machine,
labor, facility, and other materials. This is also known as the computerized system which
schedules the load as per the capacities of manufacturing and identifies the market production
schedule of the marketing requirement planning system regarding capacity feasibility (Hammer,
2015).
Manufacturing resource planning
This operation helps businesses to plan the sources of the manufacturing unit. This method is
used by Toyota to manage the resources through information which is based on the plan of
production to all areas of functions and enables the management to identify the scenarios through
the use of simulation. It is used by the management within the marketing, manufacturing,
finance, purchasing, engineering, accounting, and used extensively to deliver the benefits
(Trkman, 2013).
Extensive resource planning
This operation is evolved within a more comprehensive form to plan resources. This is a
powerful integrated information system that organizes and manages the processes of enterprise
and evolves within the comprehensive database and available around the entire enterprise
(Hayes, 2010). This includes the many modules of the software and supports the organizations to
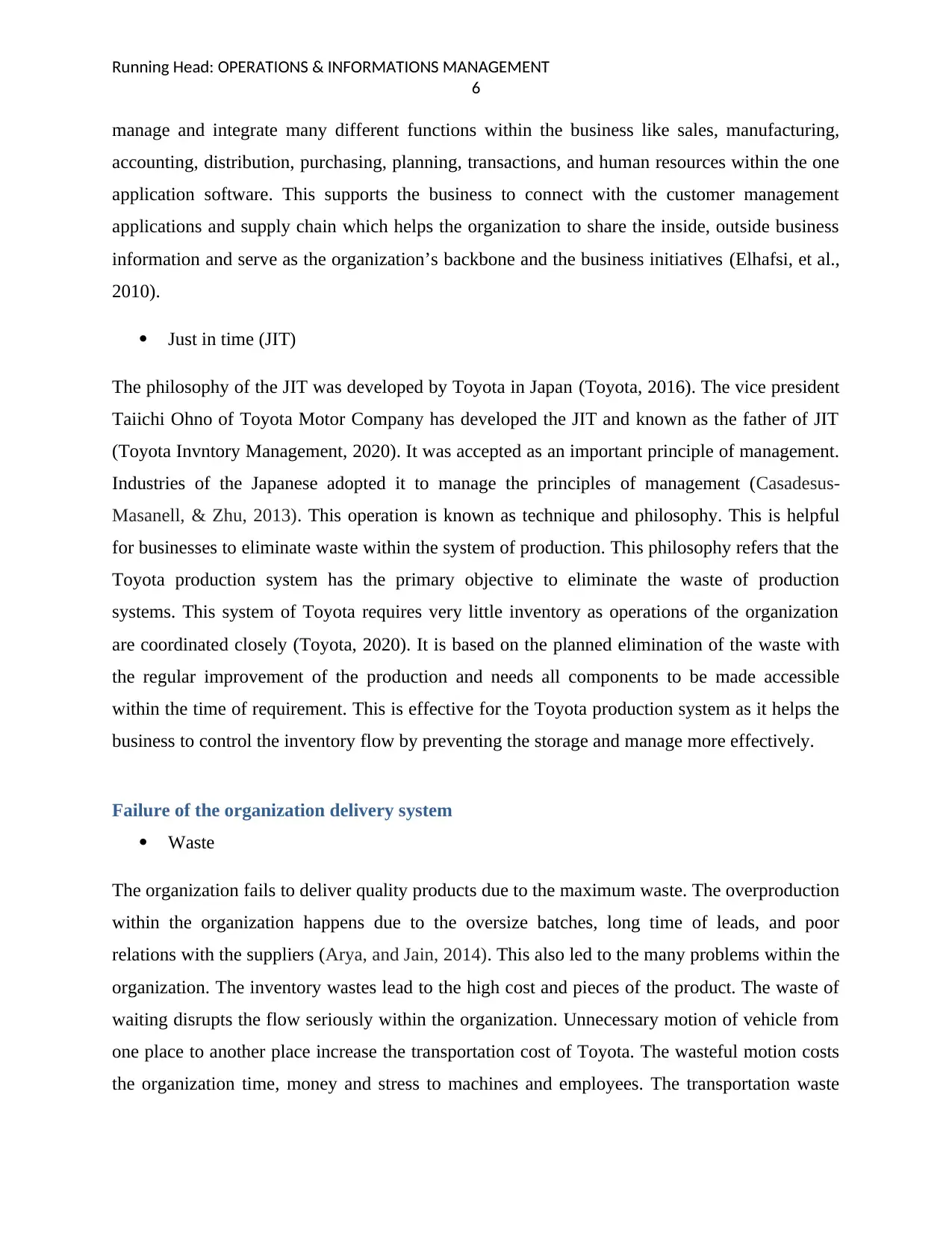
Running Head: OPERATIONS & INFORMATIONS MANAGEMENT
6
manage and integrate many different functions within the business like sales, manufacturing,
accounting, distribution, purchasing, planning, transactions, and human resources within the one
application software. This supports the business to connect with the customer management
applications and supply chain which helps the organization to share the inside, outside business
information and serve as the organization’s backbone and the business initiatives (Elhafsi, et al.,
2010).
Just in time (JIT)
The philosophy of the JIT was developed by Toyota in Japan (Toyota, 2016). The vice president
Taiichi Ohno of Toyota Motor Company has developed the JIT and known as the father of JIT
(Toyota Invntory Management, 2020). It was accepted as an important principle of management.
Industries of the Japanese adopted it to manage the principles of management (Casadesus‐
Masanell, & Zhu, 2013). This operation is known as technique and philosophy. This is helpful
for businesses to eliminate waste within the system of production. This philosophy refers that the
Toyota production system has the primary objective to eliminate the waste of production
systems. This system of Toyota requires very little inventory as operations of the organization
are coordinated closely (Toyota, 2020). It is based on the planned elimination of the waste with
the regular improvement of the production and needs all components to be made accessible
within the time of requirement. This is effective for the Toyota production system as it helps the
business to control the inventory flow by preventing the storage and manage more effectively.
Failure of the organization delivery system
Waste
The organization fails to deliver quality products due to the maximum waste. The overproduction
within the organization happens due to the oversize batches, long time of leads, and poor
relations with the suppliers (Arya, and Jain, 2014). This also led to the many problems within the
organization. The inventory wastes lead to the high cost and pieces of the product. The waste of
waiting disrupts the flow seriously within the organization. Unnecessary motion of vehicle from
one place to another place increase the transportation cost of Toyota. The wasteful motion costs
the organization time, money and stress to machines and employees. The transportation waste
6
manage and integrate many different functions within the business like sales, manufacturing,
accounting, distribution, purchasing, planning, transactions, and human resources within the one
application software. This supports the business to connect with the customer management
applications and supply chain which helps the organization to share the inside, outside business
information and serve as the organization’s backbone and the business initiatives (Elhafsi, et al.,
2010).
Just in time (JIT)
The philosophy of the JIT was developed by Toyota in Japan (Toyota, 2016). The vice president
Taiichi Ohno of Toyota Motor Company has developed the JIT and known as the father of JIT
(Toyota Invntory Management, 2020). It was accepted as an important principle of management.
Industries of the Japanese adopted it to manage the principles of management (Casadesus‐
Masanell, & Zhu, 2013). This operation is known as technique and philosophy. This is helpful
for businesses to eliminate waste within the system of production. This philosophy refers that the
Toyota production system has the primary objective to eliminate the waste of production
systems. This system of Toyota requires very little inventory as operations of the organization
are coordinated closely (Toyota, 2020). It is based on the planned elimination of the waste with
the regular improvement of the production and needs all components to be made accessible
within the time of requirement. This is effective for the Toyota production system as it helps the
business to control the inventory flow by preventing the storage and manage more effectively.
Failure of the organization delivery system
Waste
The organization fails to deliver quality products due to the maximum waste. The overproduction
within the organization happens due to the oversize batches, long time of leads, and poor
relations with the suppliers (Arya, and Jain, 2014). This also led to the many problems within the
organization. The inventory wastes lead to the high cost and pieces of the product. The waste of
waiting disrupts the flow seriously within the organization. Unnecessary motion of vehicle from
one place to another place increase the transportation cost of Toyota. The wasteful motion costs
the organization time, money and stress to machines and employees. The transportation waste
Paraphrase This Document
Need a fresh take? Get an instant paraphrase of this document with our AI Paraphraser
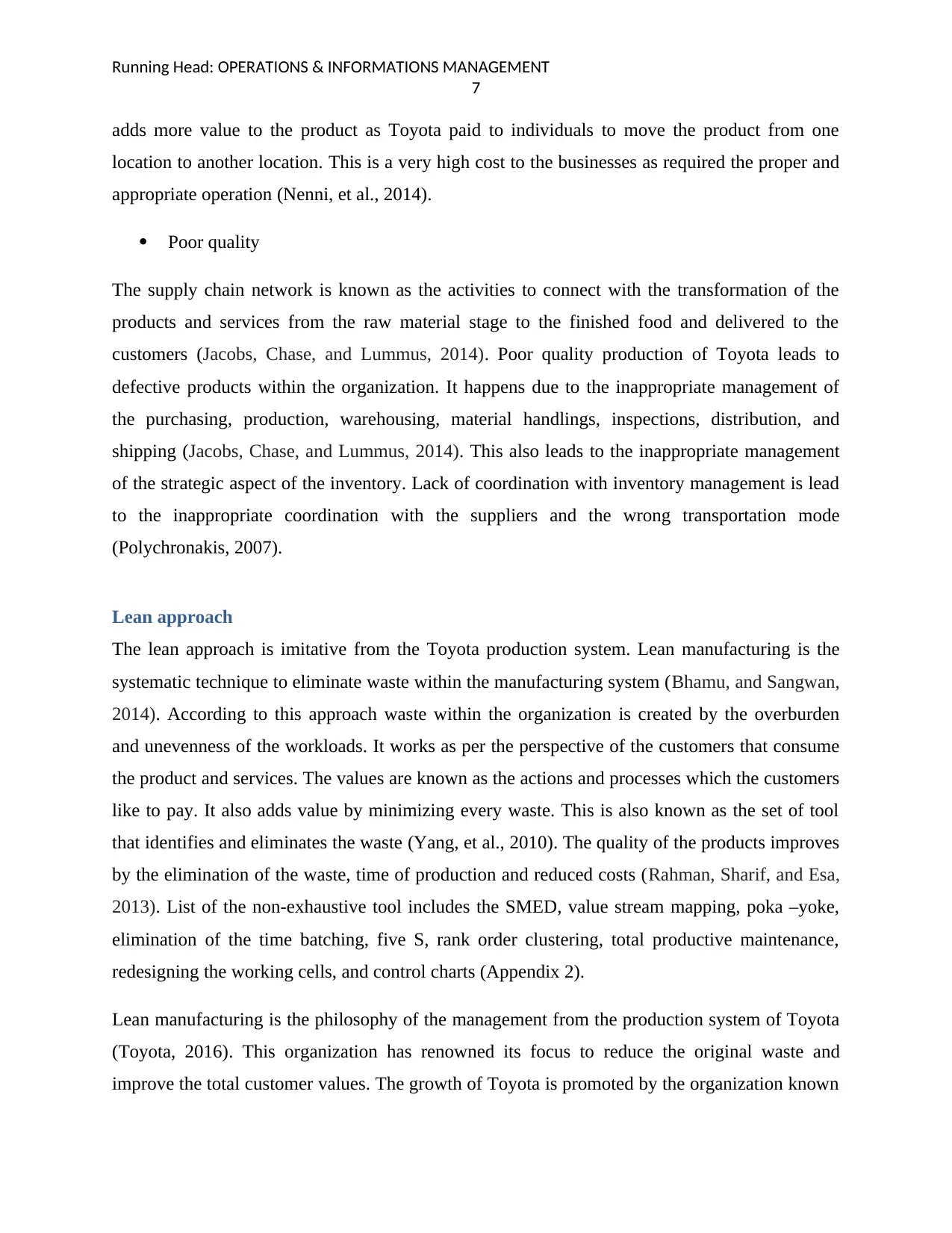
Running Head: OPERATIONS & INFORMATIONS MANAGEMENT
7
adds more value to the product as Toyota paid to individuals to move the product from one
location to another location. This is a very high cost to the businesses as required the proper and
appropriate operation (Nenni, et al., 2014).
Poor quality
The supply chain network is known as the activities to connect with the transformation of the
products and services from the raw material stage to the finished food and delivered to the
customers (Jacobs, Chase, and Lummus, 2014). Poor quality production of Toyota leads to
defective products within the organization. It happens due to the inappropriate management of
the purchasing, production, warehousing, material handlings, inspections, distribution, and
shipping (Jacobs, Chase, and Lummus, 2014). This also leads to the inappropriate management
of the strategic aspect of the inventory. Lack of coordination with inventory management is lead
to the inappropriate coordination with the suppliers and the wrong transportation mode
(Polychronakis, 2007).
Lean approach
The lean approach is imitative from the Toyota production system. Lean manufacturing is the
systematic technique to eliminate waste within the manufacturing system (Bhamu, and Sangwan,
2014). According to this approach waste within the organization is created by the overburden
and unevenness of the workloads. It works as per the perspective of the customers that consume
the product and services. The values are known as the actions and processes which the customers
like to pay. It also adds value by minimizing every waste. This is also known as the set of tool
that identifies and eliminates the waste (Yang, et al., 2010). The quality of the products improves
by the elimination of the waste, time of production and reduced costs (Rahman, Sharif, and Esa,
2013). List of the non-exhaustive tool includes the SMED, value stream mapping, poka –yoke,
elimination of the time batching, five S, rank order clustering, total productive maintenance,
redesigning the working cells, and control charts (Appendix 2).
Lean manufacturing is the philosophy of the management from the production system of Toyota
(Toyota, 2016). This organization has renowned its focus to reduce the original waste and
improve the total customer values. The growth of Toyota is promoted by the organization known
7
adds more value to the product as Toyota paid to individuals to move the product from one
location to another location. This is a very high cost to the businesses as required the proper and
appropriate operation (Nenni, et al., 2014).
Poor quality
The supply chain network is known as the activities to connect with the transformation of the
products and services from the raw material stage to the finished food and delivered to the
customers (Jacobs, Chase, and Lummus, 2014). Poor quality production of Toyota leads to
defective products within the organization. It happens due to the inappropriate management of
the purchasing, production, warehousing, material handlings, inspections, distribution, and
shipping (Jacobs, Chase, and Lummus, 2014). This also leads to the inappropriate management
of the strategic aspect of the inventory. Lack of coordination with inventory management is lead
to the inappropriate coordination with the suppliers and the wrong transportation mode
(Polychronakis, 2007).
Lean approach
The lean approach is imitative from the Toyota production system. Lean manufacturing is the
systematic technique to eliminate waste within the manufacturing system (Bhamu, and Sangwan,
2014). According to this approach waste within the organization is created by the overburden
and unevenness of the workloads. It works as per the perspective of the customers that consume
the product and services. The values are known as the actions and processes which the customers
like to pay. It also adds value by minimizing every waste. This is also known as the set of tool
that identifies and eliminates the waste (Yang, et al., 2010). The quality of the products improves
by the elimination of the waste, time of production and reduced costs (Rahman, Sharif, and Esa,
2013). List of the non-exhaustive tool includes the SMED, value stream mapping, poka –yoke,
elimination of the time batching, five S, rank order clustering, total productive maintenance,
redesigning the working cells, and control charts (Appendix 2).
Lean manufacturing is the philosophy of the management from the production system of Toyota
(Toyota, 2016). This organization has renowned its focus to reduce the original waste and
improve the total customer values. The growth of Toyota is promoted by the organization known
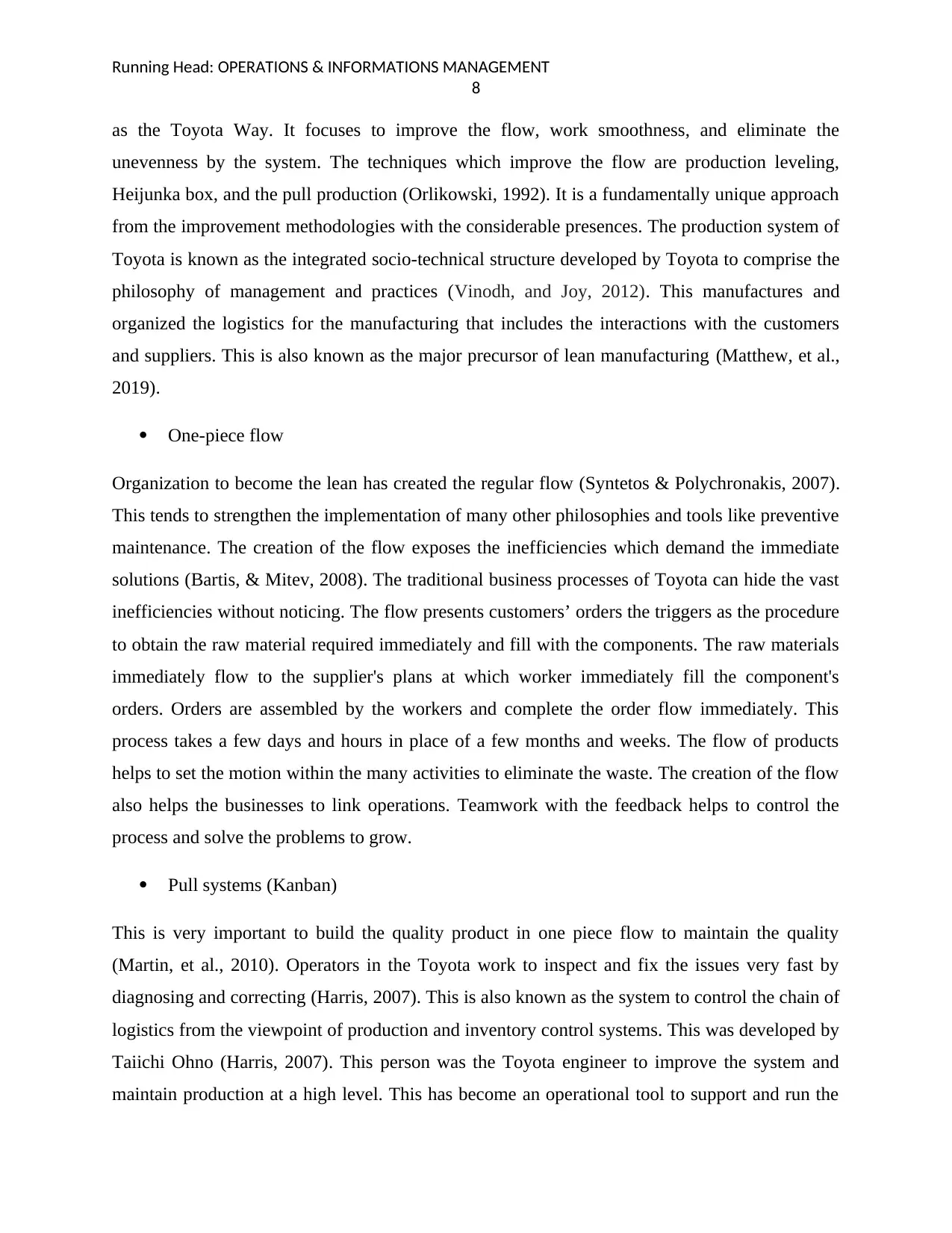
Running Head: OPERATIONS & INFORMATIONS MANAGEMENT
8
as the Toyota Way. It focuses to improve the flow, work smoothness, and eliminate the
unevenness by the system. The techniques which improve the flow are production leveling,
Heijunka box, and the pull production (Orlikowski, 1992). It is a fundamentally unique approach
from the improvement methodologies with the considerable presences. The production system of
Toyota is known as the integrated socio-technical structure developed by Toyota to comprise the
philosophy of management and practices (Vinodh, and Joy, 2012). This manufactures and
organized the logistics for the manufacturing that includes the interactions with the customers
and suppliers. This is also known as the major precursor of lean manufacturing (Matthew, et al.,
2019).
One-piece flow
Organization to become the lean has created the regular flow (Syntetos & Polychronakis, 2007).
This tends to strengthen the implementation of many other philosophies and tools like preventive
maintenance. The creation of the flow exposes the inefficiencies which demand the immediate
solutions (Bartis, & Mitev, 2008). The traditional business processes of Toyota can hide the vast
inefficiencies without noticing. The flow presents customers’ orders the triggers as the procedure
to obtain the raw material required immediately and fill with the components. The raw materials
immediately flow to the supplier's plans at which worker immediately fill the component's
orders. Orders are assembled by the workers and complete the order flow immediately. This
process takes a few days and hours in place of a few months and weeks. The flow of products
helps to set the motion within the many activities to eliminate the waste. The creation of the flow
also helps the businesses to link operations. Teamwork with the feedback helps to control the
process and solve the problems to grow.
Pull systems (Kanban)
This is very important to build the quality product in one piece flow to maintain the quality
(Martin, et al., 2010). Operators in the Toyota work to inspect and fix the issues very fast by
diagnosing and correcting (Harris, 2007). This is also known as the system to control the chain of
logistics from the viewpoint of production and inventory control systems. This was developed by
Taiichi Ohno (Harris, 2007). This person was the Toyota engineer to improve the system and
maintain production at a high level. This has become an operational tool to support and run the
8
as the Toyota Way. It focuses to improve the flow, work smoothness, and eliminate the
unevenness by the system. The techniques which improve the flow are production leveling,
Heijunka box, and the pull production (Orlikowski, 1992). It is a fundamentally unique approach
from the improvement methodologies with the considerable presences. The production system of
Toyota is known as the integrated socio-technical structure developed by Toyota to comprise the
philosophy of management and practices (Vinodh, and Joy, 2012). This manufactures and
organized the logistics for the manufacturing that includes the interactions with the customers
and suppliers. This is also known as the major precursor of lean manufacturing (Matthew, et al.,
2019).
One-piece flow
Organization to become the lean has created the regular flow (Syntetos & Polychronakis, 2007).
This tends to strengthen the implementation of many other philosophies and tools like preventive
maintenance. The creation of the flow exposes the inefficiencies which demand the immediate
solutions (Bartis, & Mitev, 2008). The traditional business processes of Toyota can hide the vast
inefficiencies without noticing. The flow presents customers’ orders the triggers as the procedure
to obtain the raw material required immediately and fill with the components. The raw materials
immediately flow to the supplier's plans at which worker immediately fill the component's
orders. Orders are assembled by the workers and complete the order flow immediately. This
process takes a few days and hours in place of a few months and weeks. The flow of products
helps to set the motion within the many activities to eliminate the waste. The creation of the flow
also helps the businesses to link operations. Teamwork with the feedback helps to control the
process and solve the problems to grow.
Pull systems (Kanban)
This is very important to build the quality product in one piece flow to maintain the quality
(Martin, et al., 2010). Operators in the Toyota work to inspect and fix the issues very fast by
diagnosing and correcting (Harris, 2007). This is also known as the system to control the chain of
logistics from the viewpoint of production and inventory control systems. This was developed by
Taiichi Ohno (Harris, 2007). This person was the Toyota engineer to improve the system and
maintain production at a high level. This has become an operational tool to support and run the
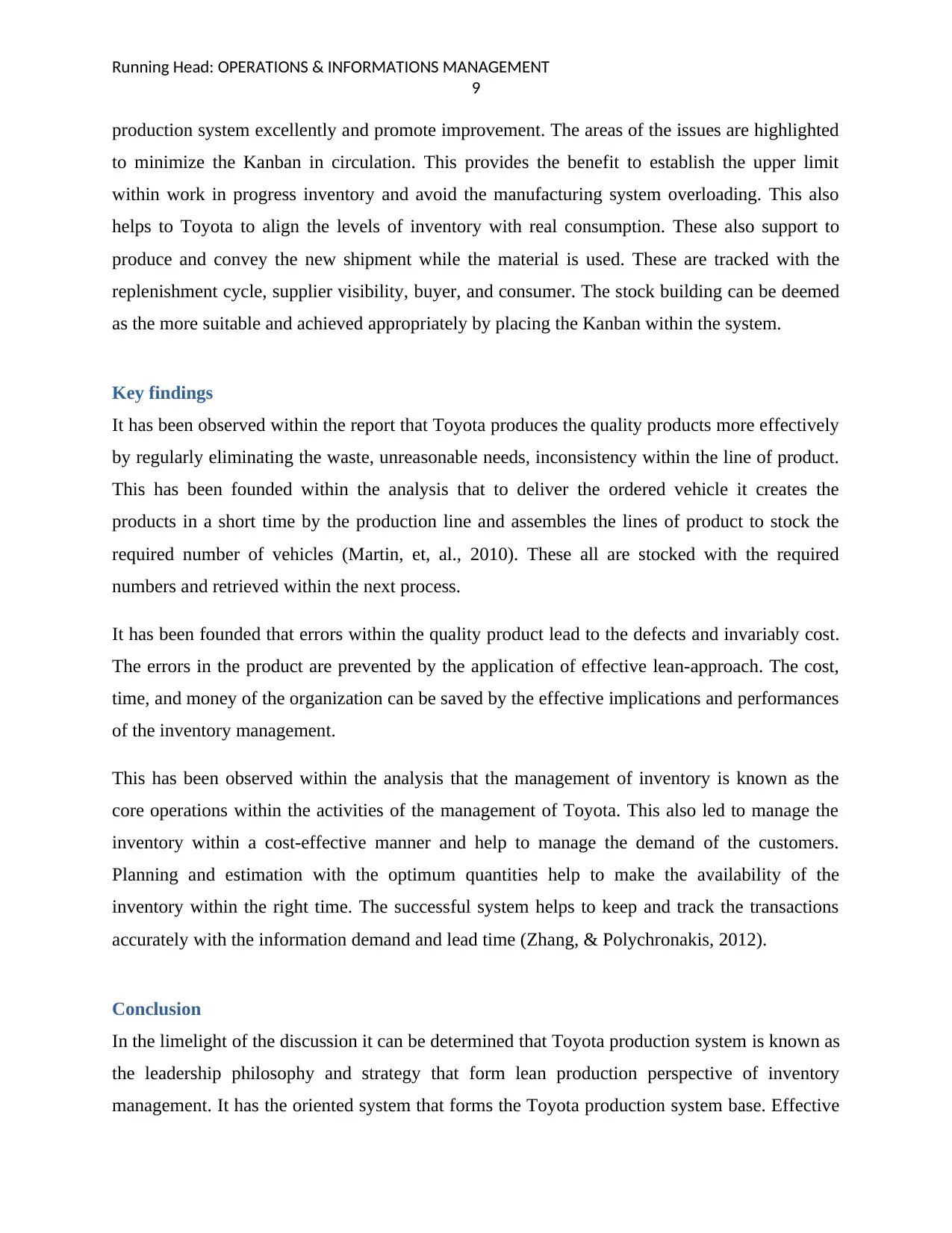
Running Head: OPERATIONS & INFORMATIONS MANAGEMENT
9
production system excellently and promote improvement. The areas of the issues are highlighted
to minimize the Kanban in circulation. This provides the benefit to establish the upper limit
within work in progress inventory and avoid the manufacturing system overloading. This also
helps to Toyota to align the levels of inventory with real consumption. These also support to
produce and convey the new shipment while the material is used. These are tracked with the
replenishment cycle, supplier visibility, buyer, and consumer. The stock building can be deemed
as the more suitable and achieved appropriately by placing the Kanban within the system.
Key findings
It has been observed within the report that Toyota produces the quality products more effectively
by regularly eliminating the waste, unreasonable needs, inconsistency within the line of product.
This has been founded within the analysis that to deliver the ordered vehicle it creates the
products in a short time by the production line and assembles the lines of product to stock the
required number of vehicles (Martin, et, al., 2010). These all are stocked with the required
numbers and retrieved within the next process.
It has been founded that errors within the quality product lead to the defects and invariably cost.
The errors in the product are prevented by the application of effective lean-approach. The cost,
time, and money of the organization can be saved by the effective implications and performances
of the inventory management.
This has been observed within the analysis that the management of inventory is known as the
core operations within the activities of the management of Toyota. This also led to manage the
inventory within a cost-effective manner and help to manage the demand of the customers.
Planning and estimation with the optimum quantities help to make the availability of the
inventory within the right time. The successful system helps to keep and track the transactions
accurately with the information demand and lead time (Zhang, & Polychronakis, 2012).
Conclusion
In the limelight of the discussion it can be determined that Toyota production system is known as
the leadership philosophy and strategy that form lean production perspective of inventory
management. It has the oriented system that forms the Toyota production system base. Effective
9
production system excellently and promote improvement. The areas of the issues are highlighted
to minimize the Kanban in circulation. This provides the benefit to establish the upper limit
within work in progress inventory and avoid the manufacturing system overloading. This also
helps to Toyota to align the levels of inventory with real consumption. These also support to
produce and convey the new shipment while the material is used. These are tracked with the
replenishment cycle, supplier visibility, buyer, and consumer. The stock building can be deemed
as the more suitable and achieved appropriately by placing the Kanban within the system.
Key findings
It has been observed within the report that Toyota produces the quality products more effectively
by regularly eliminating the waste, unreasonable needs, inconsistency within the line of product.
This has been founded within the analysis that to deliver the ordered vehicle it creates the
products in a short time by the production line and assembles the lines of product to stock the
required number of vehicles (Martin, et, al., 2010). These all are stocked with the required
numbers and retrieved within the next process.
It has been founded that errors within the quality product lead to the defects and invariably cost.
The errors in the product are prevented by the application of effective lean-approach. The cost,
time, and money of the organization can be saved by the effective implications and performances
of the inventory management.
This has been observed within the analysis that the management of inventory is known as the
core operations within the activities of the management of Toyota. This also led to manage the
inventory within a cost-effective manner and help to manage the demand of the customers.
Planning and estimation with the optimum quantities help to make the availability of the
inventory within the right time. The successful system helps to keep and track the transactions
accurately with the information demand and lead time (Zhang, & Polychronakis, 2012).
Conclusion
In the limelight of the discussion it can be determined that Toyota production system is known as
the leadership philosophy and strategy that form lean production perspective of inventory
management. It has the oriented system that forms the Toyota production system base. Effective
Secure Best Marks with AI Grader
Need help grading? Try our AI Grader for instant feedback on your assignments.
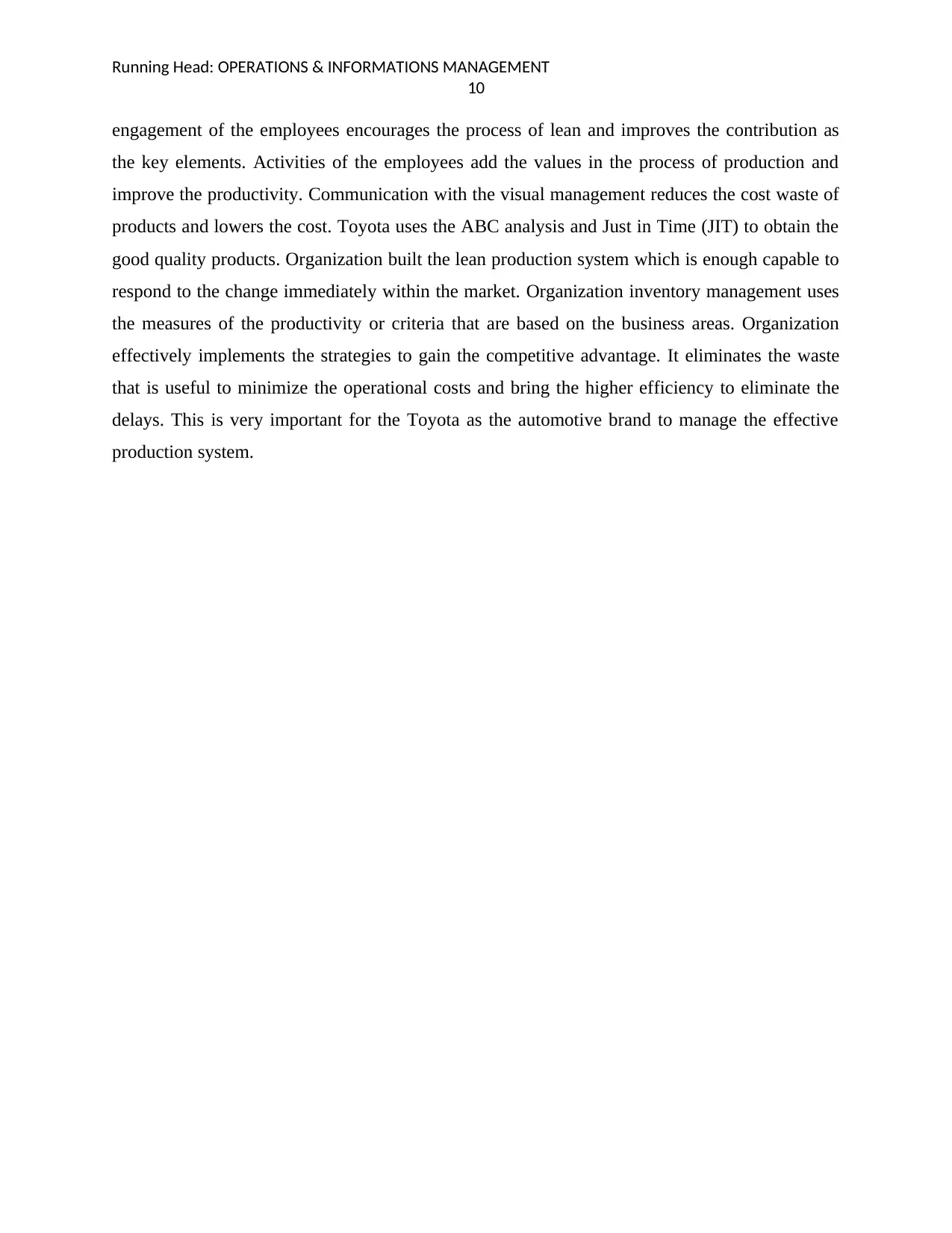
Running Head: OPERATIONS & INFORMATIONS MANAGEMENT
10
engagement of the employees encourages the process of lean and improves the contribution as
the key elements. Activities of the employees add the values in the process of production and
improve the productivity. Communication with the visual management reduces the cost waste of
products and lowers the cost. Toyota uses the ABC analysis and Just in Time (JIT) to obtain the
good quality products. Organization built the lean production system which is enough capable to
respond to the change immediately within the market. Organization inventory management uses
the measures of the productivity or criteria that are based on the business areas. Organization
effectively implements the strategies to gain the competitive advantage. It eliminates the waste
that is useful to minimize the operational costs and bring the higher efficiency to eliminate the
delays. This is very important for the Toyota as the automotive brand to manage the effective
production system.
10
engagement of the employees encourages the process of lean and improves the contribution as
the key elements. Activities of the employees add the values in the process of production and
improve the productivity. Communication with the visual management reduces the cost waste of
products and lowers the cost. Toyota uses the ABC analysis and Just in Time (JIT) to obtain the
good quality products. Organization built the lean production system which is enough capable to
respond to the change immediately within the market. Organization inventory management uses
the measures of the productivity or criteria that are based on the business areas. Organization
effectively implements the strategies to gain the competitive advantage. It eliminates the waste
that is useful to minimize the operational costs and bring the higher efficiency to eliminate the
delays. This is very important for the Toyota as the automotive brand to manage the effective
production system.
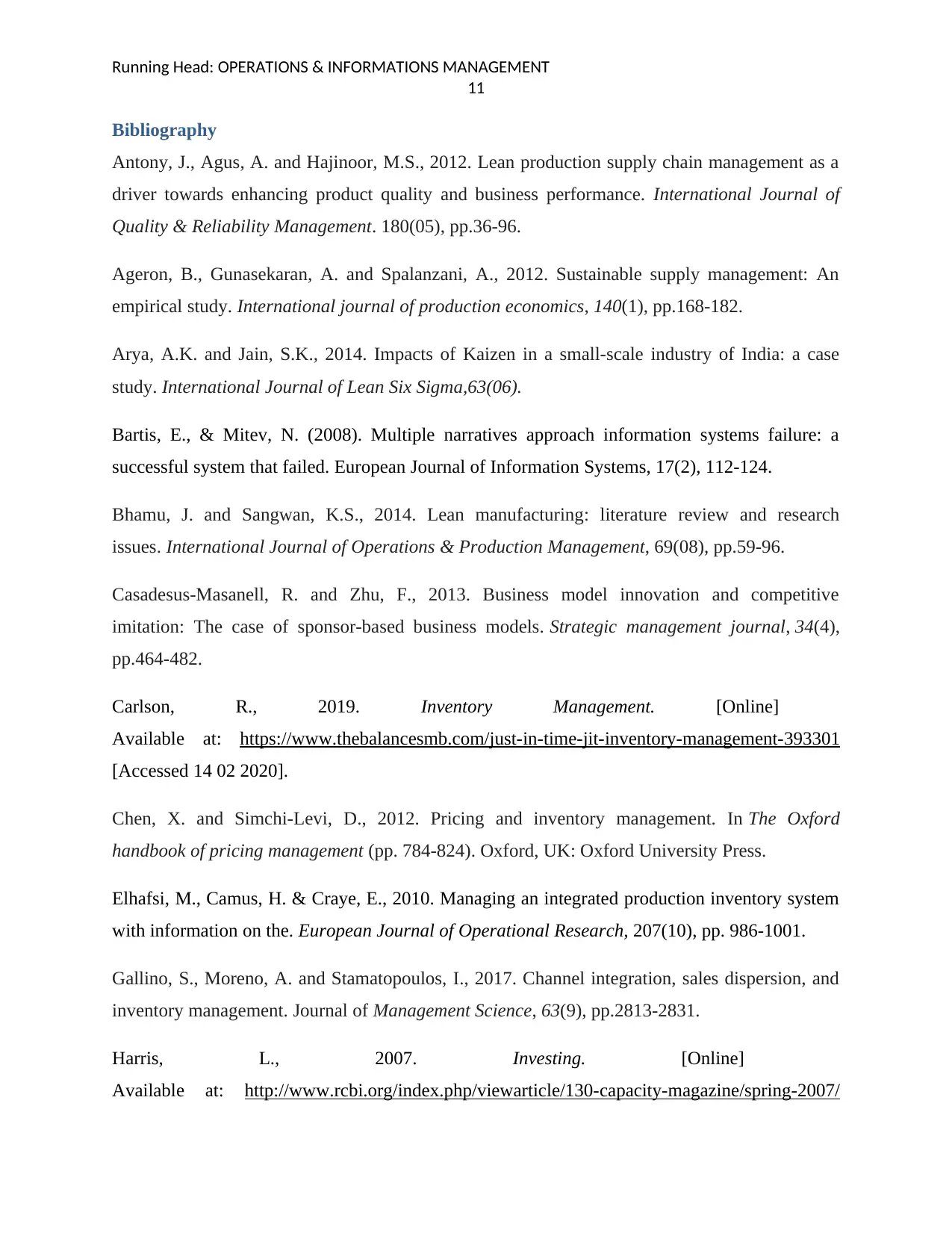
Running Head: OPERATIONS & INFORMATIONS MANAGEMENT
11
Bibliography
Antony, J., Agus, A. and Hajinoor, M.S., 2012. Lean production supply chain management as a
driver towards enhancing product quality and business performance. International Journal of
Quality & Reliability Management. 180(05), pp.36-96.
Ageron, B., Gunasekaran, A. and Spalanzani, A., 2012. Sustainable supply management: An
empirical study. International journal of production economics, 140(1), pp.168-182.
Arya, A.K. and Jain, S.K., 2014. Impacts of Kaizen in a small-scale industry of India: a case
study. International Journal of Lean Six Sigma,63(06).
Bartis, E., & Mitev, N. (2008). Multiple narratives approach information systems failure: a
successful system that failed. European Journal of Information Systems, 17(2), 112-124.
Bhamu, J. and Sangwan, K.S., 2014. Lean manufacturing: literature review and research
issues. International Journal of Operations & Production Management, 69(08), pp.59-96.
Casadesus‐Masanell, R. and Zhu, F., 2013. Business model innovation and competitive
imitation: The case of sponsor‐based business models. Strategic management journal, 34(4),
pp.464-482.
Carlson, R., 2019. Inventory Management. [Online]
Available at: https://www.thebalancesmb.com/just-in-time-jit-inventory-management-393301
[Accessed 14 02 2020].
Chen, X. and Simchi-Levi, D., 2012. Pricing and inventory management. In The Oxford
handbook of pricing management (pp. 784-824). Oxford, UK: Oxford University Press.
Elhafsi, M., Camus, H. & Craye, E., 2010. Managing an integrated production inventory system
with information on the. European Journal of Operational Research, 207(10), pp. 986-1001.
Gallino, S., Moreno, A. and Stamatopoulos, I., 2017. Channel integration, sales dispersion, and
inventory management. Journal of Management Science, 63(9), pp.2813-2831.
Harris, L., 2007. Investing. [Online]
Available at: http://www.rcbi.org/index.php/viewarticle/130-capacity-magazine/spring-2007/
11
Bibliography
Antony, J., Agus, A. and Hajinoor, M.S., 2012. Lean production supply chain management as a
driver towards enhancing product quality and business performance. International Journal of
Quality & Reliability Management. 180(05), pp.36-96.
Ageron, B., Gunasekaran, A. and Spalanzani, A., 2012. Sustainable supply management: An
empirical study. International journal of production economics, 140(1), pp.168-182.
Arya, A.K. and Jain, S.K., 2014. Impacts of Kaizen in a small-scale industry of India: a case
study. International Journal of Lean Six Sigma,63(06).
Bartis, E., & Mitev, N. (2008). Multiple narratives approach information systems failure: a
successful system that failed. European Journal of Information Systems, 17(2), 112-124.
Bhamu, J. and Sangwan, K.S., 2014. Lean manufacturing: literature review and research
issues. International Journal of Operations & Production Management, 69(08), pp.59-96.
Casadesus‐Masanell, R. and Zhu, F., 2013. Business model innovation and competitive
imitation: The case of sponsor‐based business models. Strategic management journal, 34(4),
pp.464-482.
Carlson, R., 2019. Inventory Management. [Online]
Available at: https://www.thebalancesmb.com/just-in-time-jit-inventory-management-393301
[Accessed 14 02 2020].
Chen, X. and Simchi-Levi, D., 2012. Pricing and inventory management. In The Oxford
handbook of pricing management (pp. 784-824). Oxford, UK: Oxford University Press.
Elhafsi, M., Camus, H. & Craye, E., 2010. Managing an integrated production inventory system
with information on the. European Journal of Operational Research, 207(10), pp. 986-1001.
Gallino, S., Moreno, A. and Stamatopoulos, I., 2017. Channel integration, sales dispersion, and
inventory management. Journal of Management Science, 63(9), pp.2813-2831.
Harris, L., 2007. Investing. [Online]
Available at: http://www.rcbi.org/index.php/viewarticle/130-capacity-magazine/spring-2007/
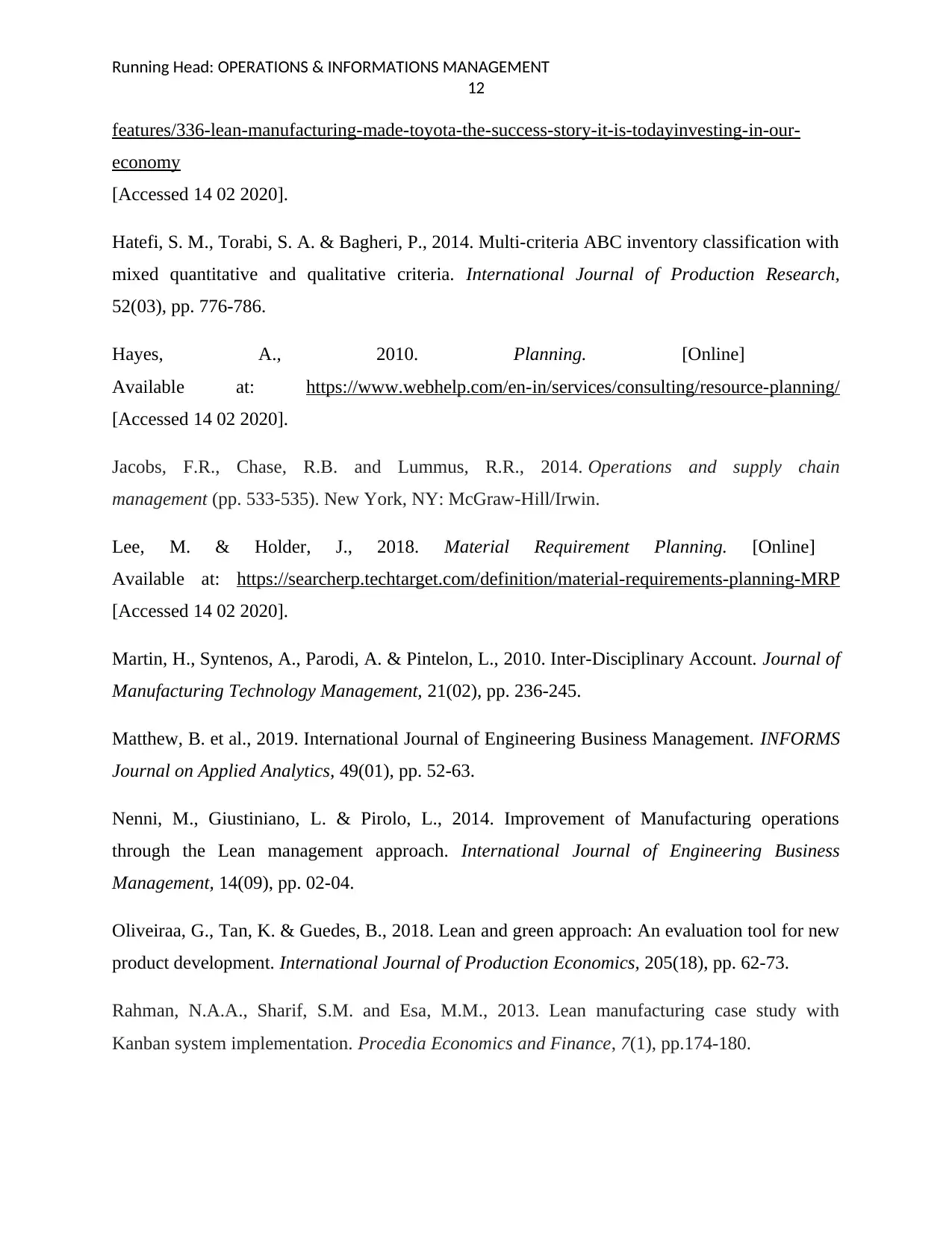
Running Head: OPERATIONS & INFORMATIONS MANAGEMENT
12
features/336-lean-manufacturing-made-toyota-the-success-story-it-is-todayinvesting-in-our-
economy
[Accessed 14 02 2020].
Hatefi, S. M., Torabi, S. A. & Bagheri, P., 2014. Multi-criteria ABC inventory classification with
mixed quantitative and qualitative criteria. International Journal of Production Research,
52(03), pp. 776-786.
Hayes, A., 2010. Planning. [Online]
Available at: https://www.webhelp.com/en-in/services/consulting/resource-planning/
[Accessed 14 02 2020].
Jacobs, F.R., Chase, R.B. and Lummus, R.R., 2014. Operations and supply chain
management (pp. 533-535). New York, NY: McGraw-Hill/Irwin.
Lee, M. & Holder, J., 2018. Material Requirement Planning. [Online]
Available at: https://searcherp.techtarget.com/definition/material-requirements-planning-MRP
[Accessed 14 02 2020].
Martin, H., Syntenos, A., Parodi, A. & Pintelon, L., 2010. Inter-Disciplinary Account. Journal of
Manufacturing Technology Management, 21(02), pp. 236-245.
Matthew, B. et al., 2019. International Journal of Engineering Business Management. INFORMS
Journal on Applied Analytics, 49(01), pp. 52-63.
Nenni, M., Giustiniano, L. & Pirolo, L., 2014. Improvement of Manufacturing operations
through the Lean management approach. International Journal of Engineering Business
Management, 14(09), pp. 02-04.
Oliveiraa, G., Tan, K. & Guedes, B., 2018. Lean and green approach: An evaluation tool for new
product development. International Journal of Production Economics, 205(18), pp. 62-73.
Rahman, N.A.A., Sharif, S.M. and Esa, M.M., 2013. Lean manufacturing case study with
Kanban system implementation. Procedia Economics and Finance, 7(1), pp.174-180.
12
features/336-lean-manufacturing-made-toyota-the-success-story-it-is-todayinvesting-in-our-
economy
[Accessed 14 02 2020].
Hatefi, S. M., Torabi, S. A. & Bagheri, P., 2014. Multi-criteria ABC inventory classification with
mixed quantitative and qualitative criteria. International Journal of Production Research,
52(03), pp. 776-786.
Hayes, A., 2010. Planning. [Online]
Available at: https://www.webhelp.com/en-in/services/consulting/resource-planning/
[Accessed 14 02 2020].
Jacobs, F.R., Chase, R.B. and Lummus, R.R., 2014. Operations and supply chain
management (pp. 533-535). New York, NY: McGraw-Hill/Irwin.
Lee, M. & Holder, J., 2018. Material Requirement Planning. [Online]
Available at: https://searcherp.techtarget.com/definition/material-requirements-planning-MRP
[Accessed 14 02 2020].
Martin, H., Syntenos, A., Parodi, A. & Pintelon, L., 2010. Inter-Disciplinary Account. Journal of
Manufacturing Technology Management, 21(02), pp. 236-245.
Matthew, B. et al., 2019. International Journal of Engineering Business Management. INFORMS
Journal on Applied Analytics, 49(01), pp. 52-63.
Nenni, M., Giustiniano, L. & Pirolo, L., 2014. Improvement of Manufacturing operations
through the Lean management approach. International Journal of Engineering Business
Management, 14(09), pp. 02-04.
Oliveiraa, G., Tan, K. & Guedes, B., 2018. Lean and green approach: An evaluation tool for new
product development. International Journal of Production Economics, 205(18), pp. 62-73.
Rahman, N.A.A., Sharif, S.M. and Esa, M.M., 2013. Lean manufacturing case study with
Kanban system implementation. Procedia Economics and Finance, 7(1), pp.174-180.
Paraphrase This Document
Need a fresh take? Get an instant paraphrase of this document with our AI Paraphraser
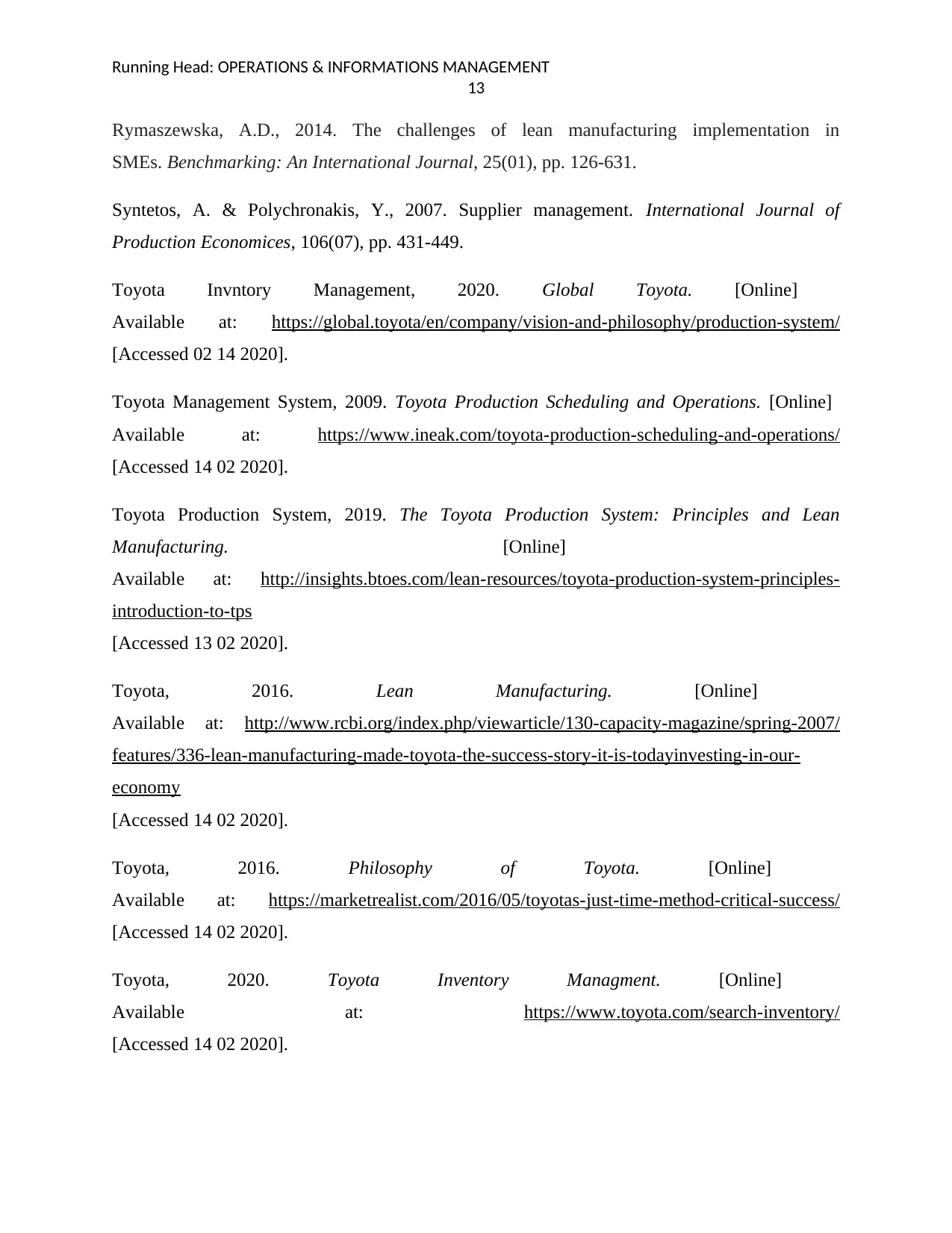
Running Head: OPERATIONS & INFORMATIONS MANAGEMENT
13
Rymaszewska, A.D., 2014. The challenges of lean manufacturing implementation in
SMEs. Benchmarking: An International Journal, 25(01), pp. 126-631.
Syntetos, A. & Polychronakis, Y., 2007. Supplier management. International Journal of
Production Economices, 106(07), pp. 431-449.
Toyota Invntory Management, 2020. Global Toyota. [Online]
Available at: https://global.toyota/en/company/vision-and-philosophy/production-system/
[Accessed 02 14 2020].
Toyota Management System, 2009. Toyota Production Scheduling and Operations. [Online]
Available at: https://www.ineak.com/toyota-production-scheduling-and-operations/
[Accessed 14 02 2020].
Toyota Production System, 2019. The Toyota Production System: Principles and Lean
Manufacturing. [Online]
Available at: http://insights.btoes.com/lean-resources/toyota-production-system-principles-
introduction-to-tps
[Accessed 13 02 2020].
Toyota, 2016. Lean Manufacturing. [Online]
Available at: http://www.rcbi.org/index.php/viewarticle/130-capacity-magazine/spring-2007/
features/336-lean-manufacturing-made-toyota-the-success-story-it-is-todayinvesting-in-our-
economy
[Accessed 14 02 2020].
Toyota, 2016. Philosophy of Toyota. [Online]
Available at: https://marketrealist.com/2016/05/toyotas-just-time-method-critical-success/
[Accessed 14 02 2020].
Toyota, 2020. Toyota Inventory Managment. [Online]
Available at: https://www.toyota.com/search-inventory/
[Accessed 14 02 2020].
13
Rymaszewska, A.D., 2014. The challenges of lean manufacturing implementation in
SMEs. Benchmarking: An International Journal, 25(01), pp. 126-631.
Syntetos, A. & Polychronakis, Y., 2007. Supplier management. International Journal of
Production Economices, 106(07), pp. 431-449.
Toyota Invntory Management, 2020. Global Toyota. [Online]
Available at: https://global.toyota/en/company/vision-and-philosophy/production-system/
[Accessed 02 14 2020].
Toyota Management System, 2009. Toyota Production Scheduling and Operations. [Online]
Available at: https://www.ineak.com/toyota-production-scheduling-and-operations/
[Accessed 14 02 2020].
Toyota Production System, 2019. The Toyota Production System: Principles and Lean
Manufacturing. [Online]
Available at: http://insights.btoes.com/lean-resources/toyota-production-system-principles-
introduction-to-tps
[Accessed 13 02 2020].
Toyota, 2016. Lean Manufacturing. [Online]
Available at: http://www.rcbi.org/index.php/viewarticle/130-capacity-magazine/spring-2007/
features/336-lean-manufacturing-made-toyota-the-success-story-it-is-todayinvesting-in-our-
economy
[Accessed 14 02 2020].
Toyota, 2016. Philosophy of Toyota. [Online]
Available at: https://marketrealist.com/2016/05/toyotas-just-time-method-critical-success/
[Accessed 14 02 2020].
Toyota, 2020. Toyota Inventory Managment. [Online]
Available at: https://www.toyota.com/search-inventory/
[Accessed 14 02 2020].
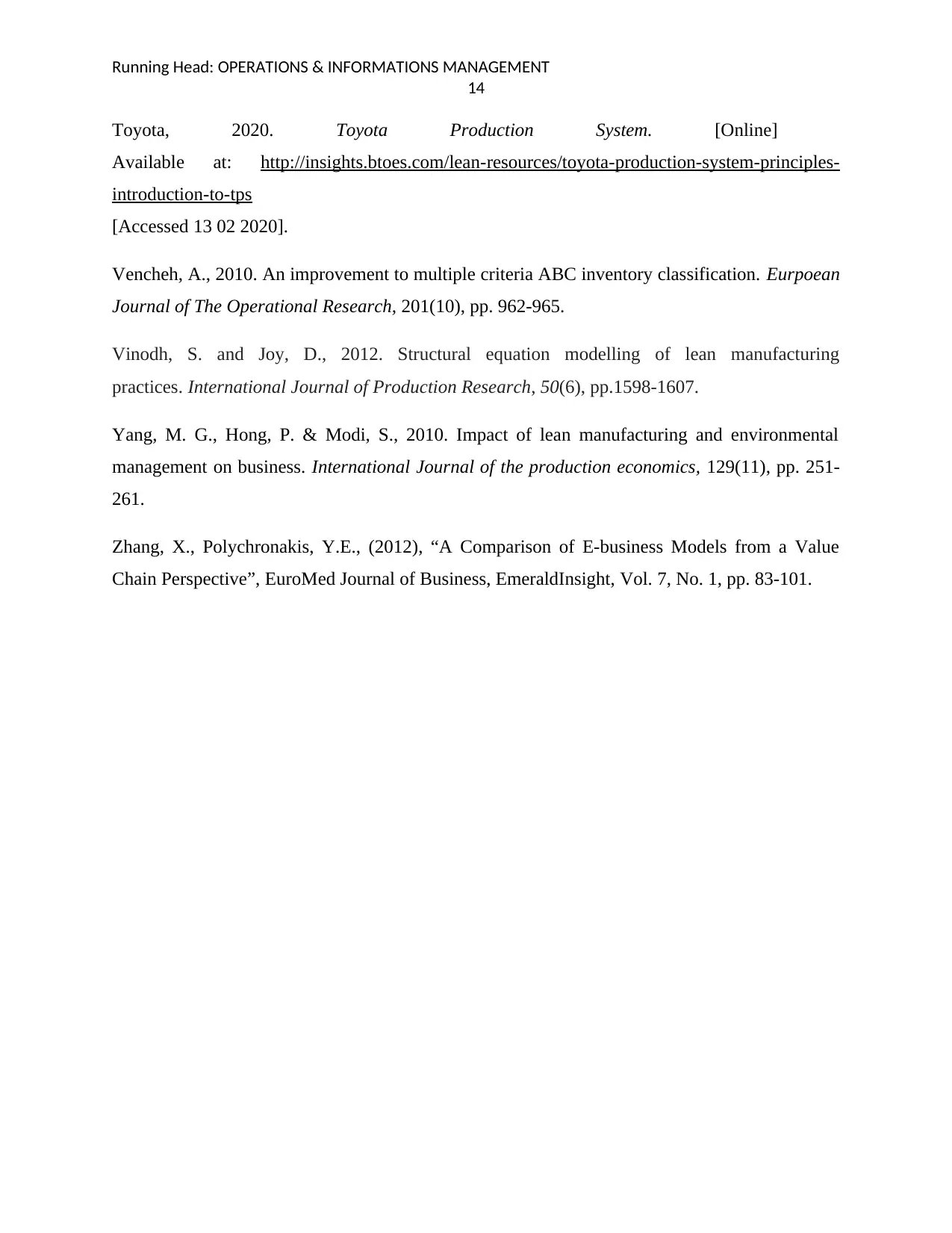
Running Head: OPERATIONS & INFORMATIONS MANAGEMENT
14
Toyota, 2020. Toyota Production System. [Online]
Available at: http://insights.btoes.com/lean-resources/toyota-production-system-principles-
introduction-to-tps
[Accessed 13 02 2020].
Vencheh, A., 2010. An improvement to multiple criteria ABC inventory classification. Eurpoean
Journal of The Operational Research, 201(10), pp. 962-965.
Vinodh, S. and Joy, D., 2012. Structural equation modelling of lean manufacturing
practices. International Journal of Production Research, 50(6), pp.1598-1607.
Yang, M. G., Hong, P. & Modi, S., 2010. Impact of lean manufacturing and environmental
management on business. International Journal of the production economics, 129(11), pp. 251-
261.
Zhang, X., Polychronakis, Y.E., (2012), “A Comparison of E-business Models from a Value
Chain Perspective”, EuroMed Journal of Business, EmeraldInsight, Vol. 7, No. 1, pp. 83-101.
14
Toyota, 2020. Toyota Production System. [Online]
Available at: http://insights.btoes.com/lean-resources/toyota-production-system-principles-
introduction-to-tps
[Accessed 13 02 2020].
Vencheh, A., 2010. An improvement to multiple criteria ABC inventory classification. Eurpoean
Journal of The Operational Research, 201(10), pp. 962-965.
Vinodh, S. and Joy, D., 2012. Structural equation modelling of lean manufacturing
practices. International Journal of Production Research, 50(6), pp.1598-1607.
Yang, M. G., Hong, P. & Modi, S., 2010. Impact of lean manufacturing and environmental
management on business. International Journal of the production economics, 129(11), pp. 251-
261.
Zhang, X., Polychronakis, Y.E., (2012), “A Comparison of E-business Models from a Value
Chain Perspective”, EuroMed Journal of Business, EmeraldInsight, Vol. 7, No. 1, pp. 83-101.
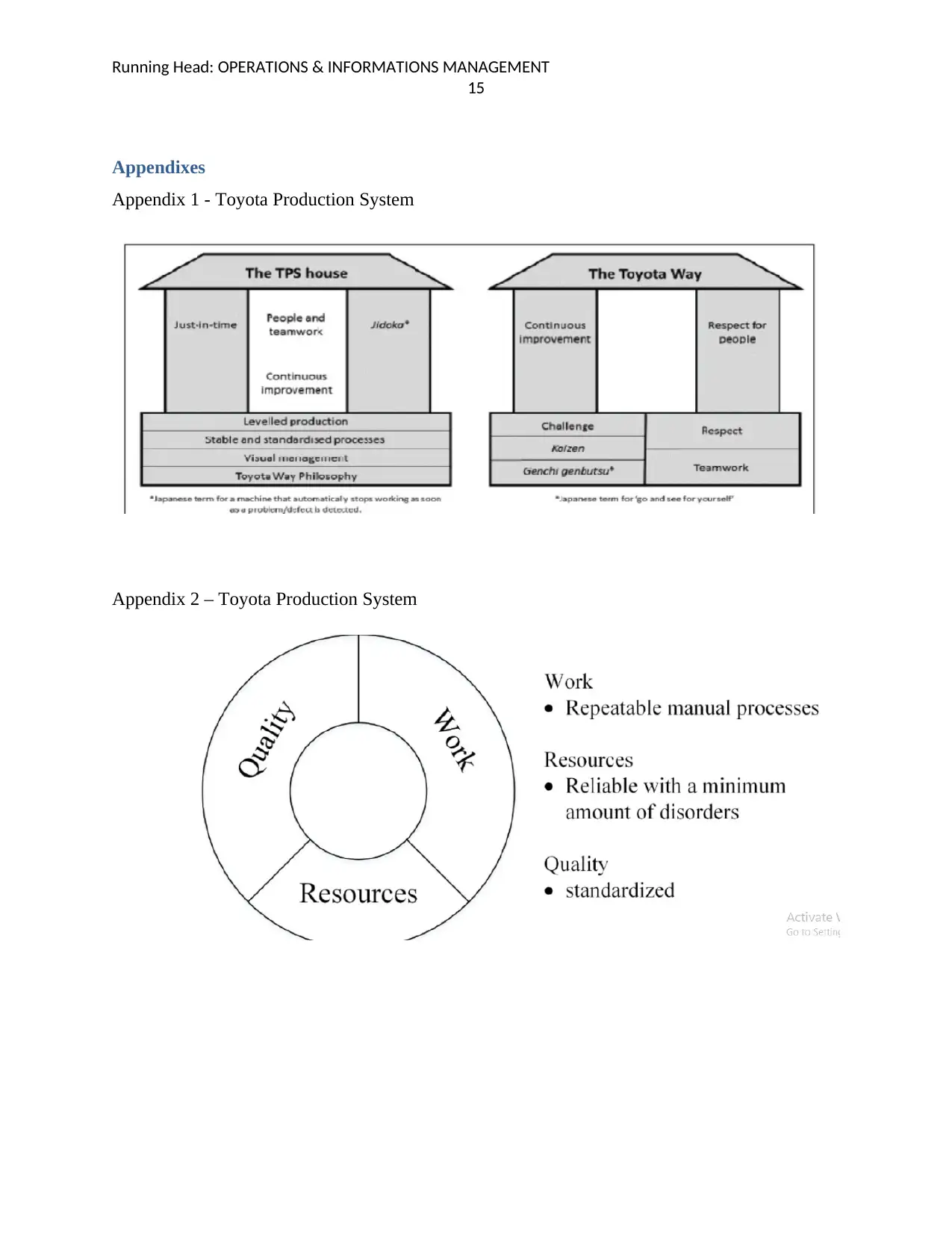
Running Head: OPERATIONS & INFORMATIONS MANAGEMENT
15
Appendixes
Appendix 1 - Toyota Production System
Appendix 2 – Toyota Production System
15
Appendixes
Appendix 1 - Toyota Production System
Appendix 2 – Toyota Production System
Secure Best Marks with AI Grader
Need help grading? Try our AI Grader for instant feedback on your assignments.
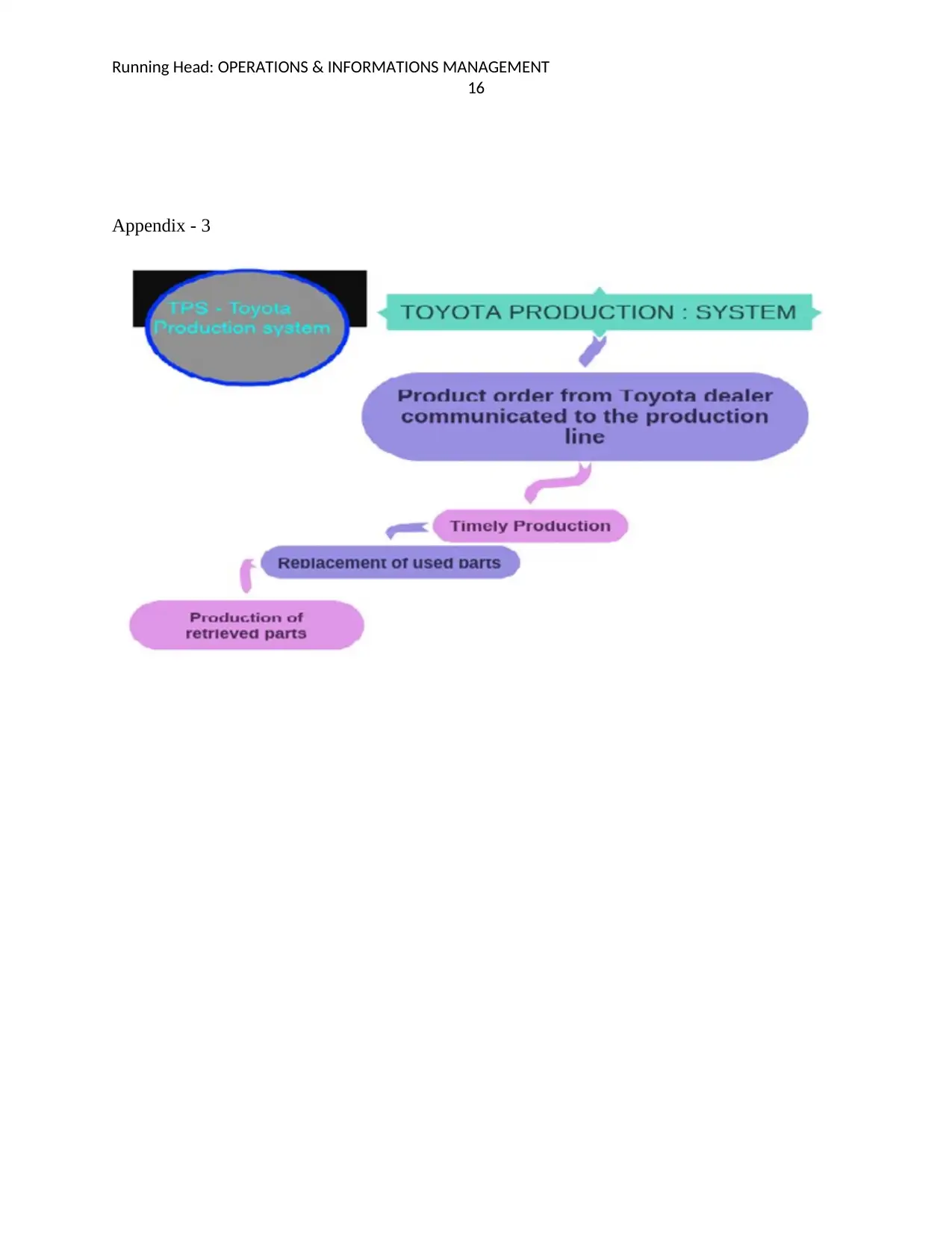
Running Head: OPERATIONS & INFORMATIONS MANAGEMENT
16
Appendix - 3
16
Appendix - 3
1 out of 17
Related Documents
![[object Object]](/_next/image/?url=%2F_next%2Fstatic%2Fmedia%2Flogo.6d15ce61.png&w=640&q=75)
Your All-in-One AI-Powered Toolkit for Academic Success.
+13062052269
info@desklib.com
Available 24*7 on WhatsApp / Email
Unlock your academic potential
© 2024 | Zucol Services PVT LTD | All rights reserved.