Operations and Project Management: A Case Study of Unilever UK
VerifiedAdded on 2023/06/10
|16
|4751
|238
Report
AI Summary
This report provides a detailed analysis of operations and project management within Unilever UK, a leading consumer goods company. It explores key concepts such as operation management, its principles within Unilever's context, and an evaluation of how well the company's operations meet its organizational requirements. The report further discusses continuous improvement as a philosophy, detailing Lean principles and proposing a continuous improvement plan based on a critique of Unilever's operational management. Methodologies like Six Sigma and Kaizen are examined, along with their potential benefits and drawbacks for Unilever. The analysis includes a discussion of value stream mapping, waste reduction, and the importance of customer focus, ultimately aiming to enhance Unilever's operational efficiency and competitive advantage through strategic improvements and alignment with consumer values. Desklib offers similar solved assignments and study resources for students.
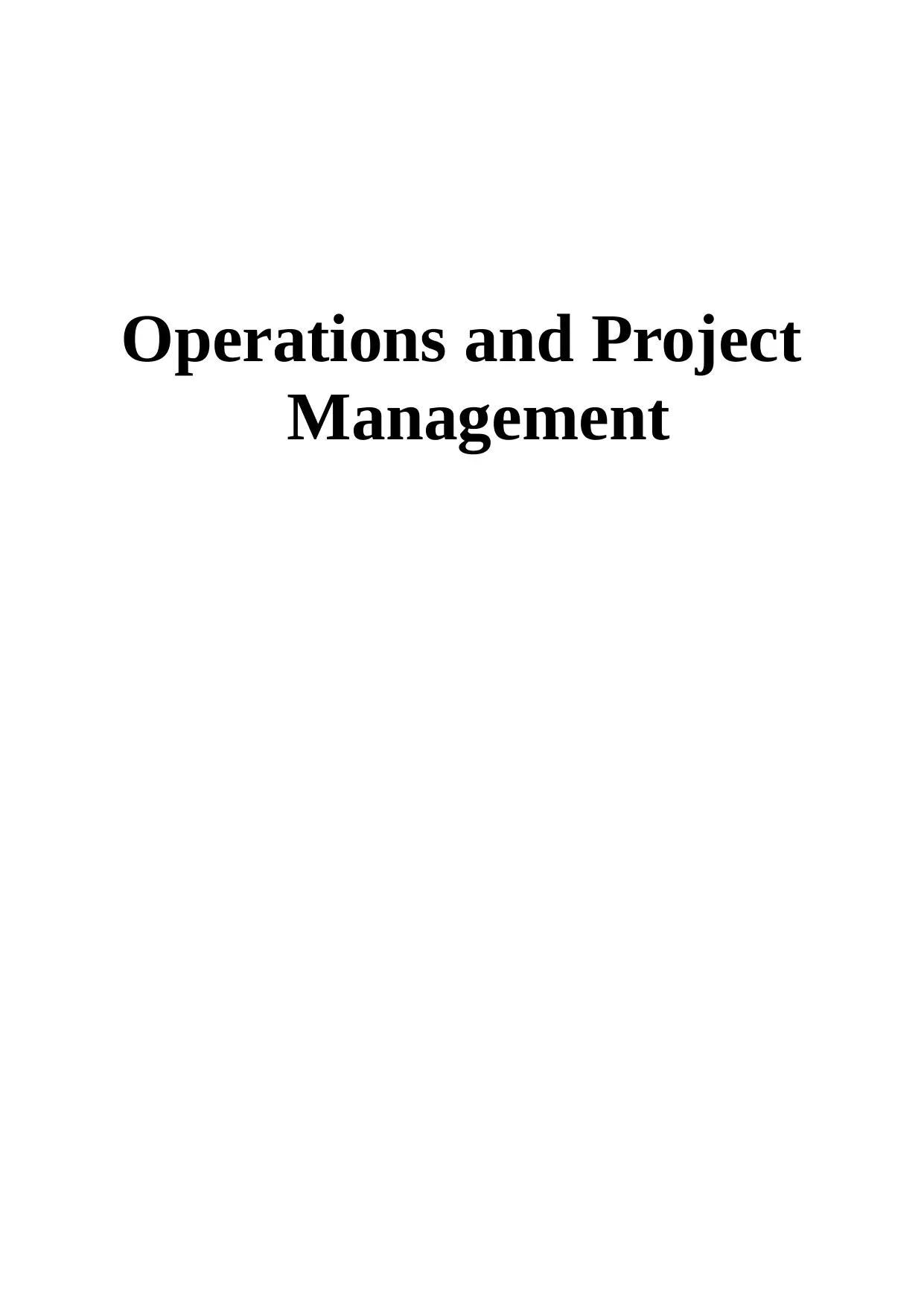
Operations and Project
Management
Management
Paraphrase This Document
Need a fresh take? Get an instant paraphrase of this document with our AI Paraphraser
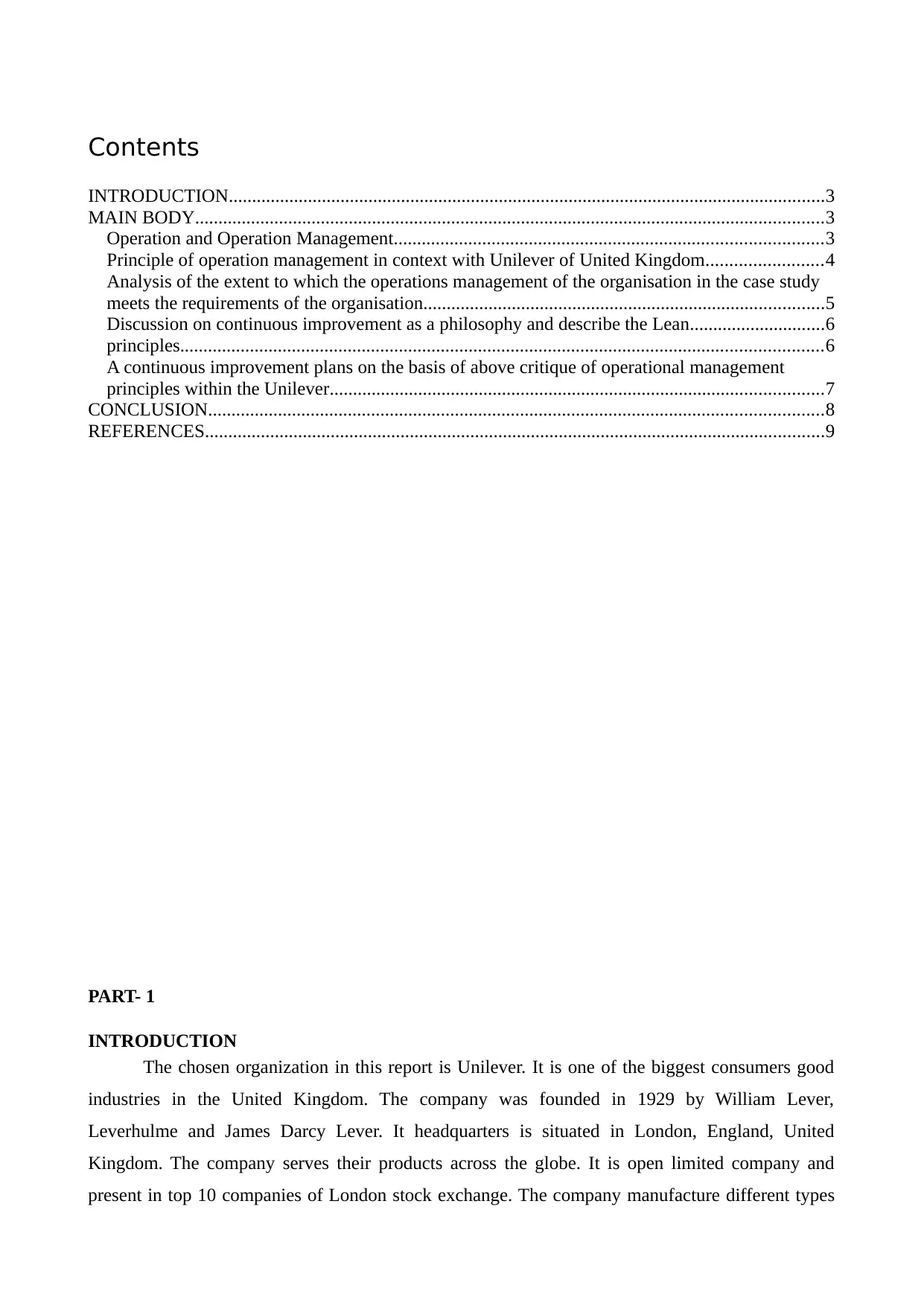
Contents
INTRODUCTION................................................................................................................................3
MAIN BODY.......................................................................................................................................3
Operation and Operation Management............................................................................................3
Principle of operation management in context with Unilever of United Kingdom.........................4
Analysis of the extent to which the operations management of the organisation in the case study
meets the requirements of the organisation......................................................................................5
Discussion on continuous improvement as a philosophy and describe the Lean.............................6
principles..........................................................................................................................................6
A continuous improvement plans on the basis of above critique of operational management
principles within the Unilever..........................................................................................................7
CONCLUSION....................................................................................................................................8
REFERENCES.....................................................................................................................................9
PART- 1
INTRODUCTION
The chosen organization in this report is Unilever. It is one of the biggest consumers good
industries in the United Kingdom. The company was founded in 1929 by William Lever,
Leverhulme and James Darcy Lever. It headquarters is situated in London, England, United
Kingdom. The company serves their products across the globe. It is open limited company and
present in top 10 companies of London stock exchange. The company manufacture different types
INTRODUCTION................................................................................................................................3
MAIN BODY.......................................................................................................................................3
Operation and Operation Management............................................................................................3
Principle of operation management in context with Unilever of United Kingdom.........................4
Analysis of the extent to which the operations management of the organisation in the case study
meets the requirements of the organisation......................................................................................5
Discussion on continuous improvement as a philosophy and describe the Lean.............................6
principles..........................................................................................................................................6
A continuous improvement plans on the basis of above critique of operational management
principles within the Unilever..........................................................................................................7
CONCLUSION....................................................................................................................................8
REFERENCES.....................................................................................................................................9
PART- 1
INTRODUCTION
The chosen organization in this report is Unilever. It is one of the biggest consumers good
industries in the United Kingdom. The company was founded in 1929 by William Lever,
Leverhulme and James Darcy Lever. It headquarters is situated in London, England, United
Kingdom. The company serves their products across the globe. It is open limited company and
present in top 10 companies of London stock exchange. The company manufacture different types
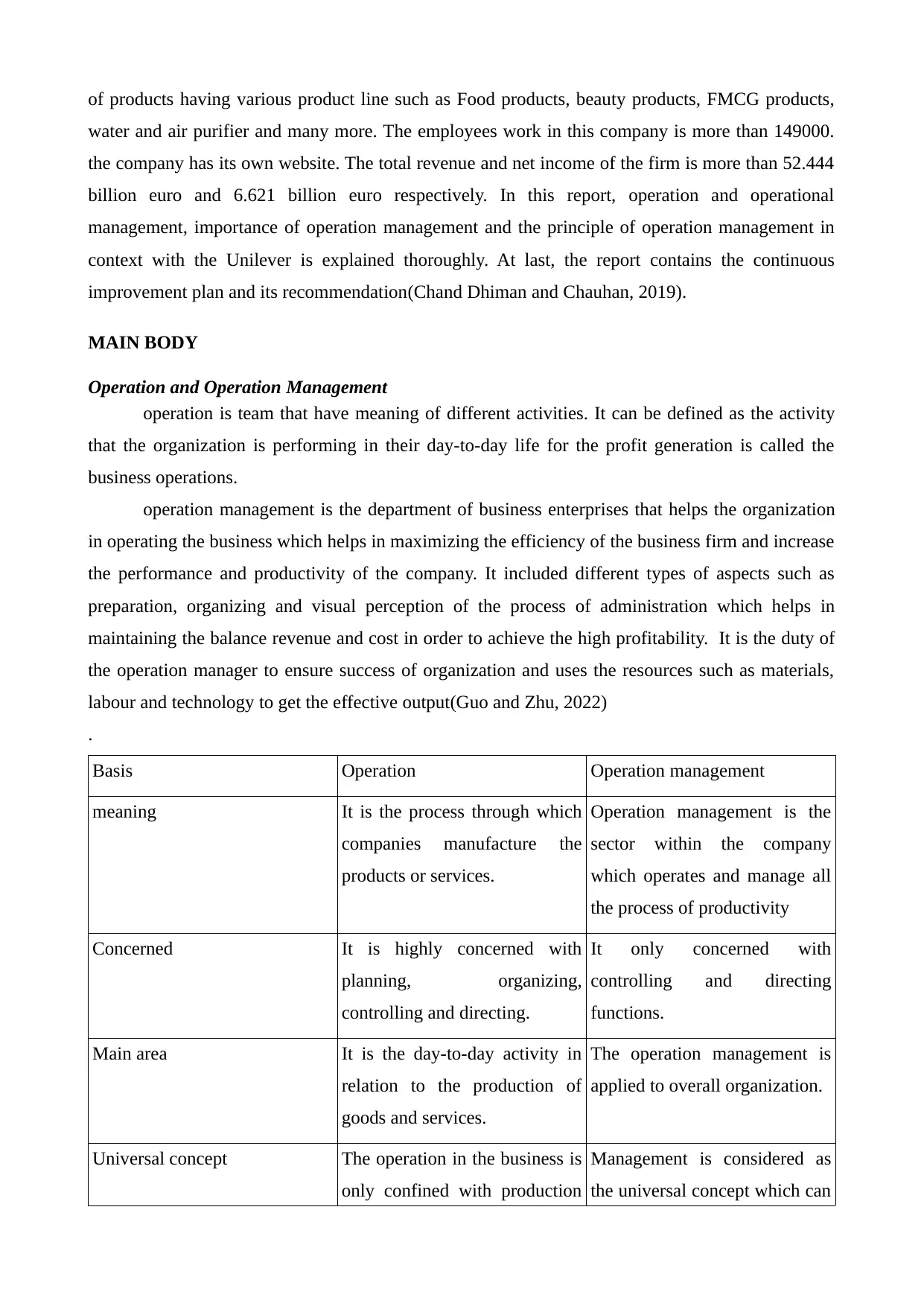
of products having various product line such as Food products, beauty products, FMCG products,
water and air purifier and many more. The employees work in this company is more than 149000.
the company has its own website. The total revenue and net income of the firm is more than 52.444
billion euro and 6.621 billion euro respectively. In this report, operation and operational
management, importance of operation management and the principle of operation management in
context with the Unilever is explained thoroughly. At last, the report contains the continuous
improvement plan and its recommendation(Chand Dhiman and Chauhan, 2019).
MAIN BODY
Operation and Operation Management
operation is team that have meaning of different activities. It can be defined as the activity
that the organization is performing in their day-to-day life for the profit generation is called the
business operations.
operation management is the department of business enterprises that helps the organization
in operating the business which helps in maximizing the efficiency of the business firm and increase
the performance and productivity of the company. It included different types of aspects such as
preparation, organizing and visual perception of the process of administration which helps in
maintaining the balance revenue and cost in order to achieve the high profitability. It is the duty of
the operation manager to ensure success of organization and uses the resources such as materials,
labour and technology to get the effective output(Guo and Zhu, 2022)
.
Basis Operation Operation management
meaning It is the process through which
companies manufacture the
products or services.
Operation management is the
sector within the company
which operates and manage all
the process of productivity
Concerned It is highly concerned with
planning, organizing,
controlling and directing.
It only concerned with
controlling and directing
functions.
Main area It is the day-to-day activity in
relation to the production of
goods and services.
The operation management is
applied to overall organization.
Universal concept The operation in the business is
only confined with production
Management is considered as
the universal concept which can
water and air purifier and many more. The employees work in this company is more than 149000.
the company has its own website. The total revenue and net income of the firm is more than 52.444
billion euro and 6.621 billion euro respectively. In this report, operation and operational
management, importance of operation management and the principle of operation management in
context with the Unilever is explained thoroughly. At last, the report contains the continuous
improvement plan and its recommendation(Chand Dhiman and Chauhan, 2019).
MAIN BODY
Operation and Operation Management
operation is team that have meaning of different activities. It can be defined as the activity
that the organization is performing in their day-to-day life for the profit generation is called the
business operations.
operation management is the department of business enterprises that helps the organization
in operating the business which helps in maximizing the efficiency of the business firm and increase
the performance and productivity of the company. It included different types of aspects such as
preparation, organizing and visual perception of the process of administration which helps in
maintaining the balance revenue and cost in order to achieve the high profitability. It is the duty of
the operation manager to ensure success of organization and uses the resources such as materials,
labour and technology to get the effective output(Guo and Zhu, 2022)
.
Basis Operation Operation management
meaning It is the process through which
companies manufacture the
products or services.
Operation management is the
sector within the company
which operates and manage all
the process of productivity
Concerned It is highly concerned with
planning, organizing,
controlling and directing.
It only concerned with
controlling and directing
functions.
Main area It is the day-to-day activity in
relation to the production of
goods and services.
The operation management is
applied to overall organization.
Universal concept The operation in the business is
only confined with production
Management is considered as
the universal concept which can
You're viewing a preview
Unlock full access by subscribing today!
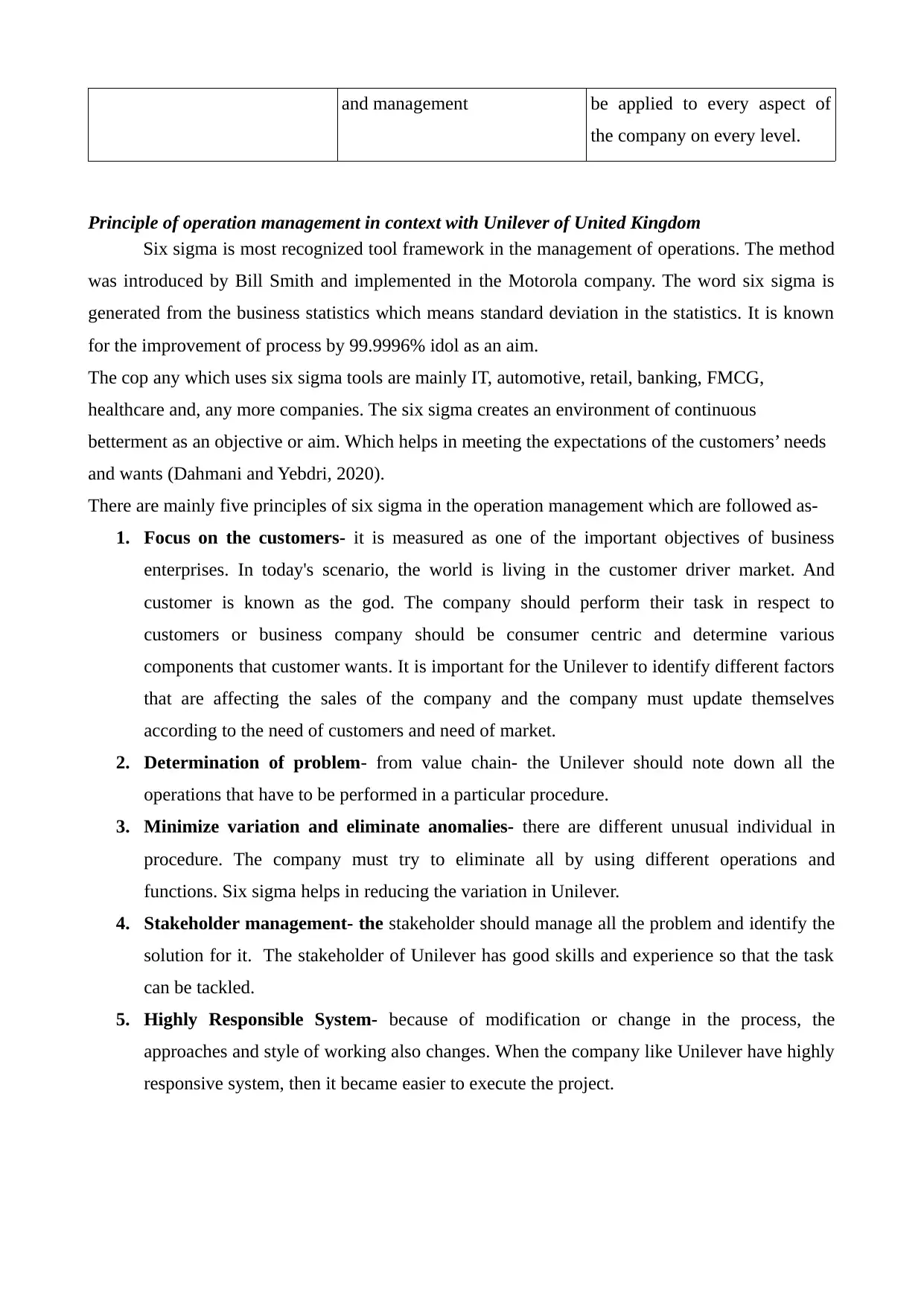
and management be applied to every aspect of
the company on every level.
Principle of operation management in context with Unilever of United Kingdom
Six sigma is most recognized tool framework in the management of operations. The method
was introduced by Bill Smith and implemented in the Motorola company. The word six sigma is
generated from the business statistics which means standard deviation in the statistics. It is known
for the improvement of process by 99.9996% idol as an aim.
The cop any which uses six sigma tools are mainly IT, automotive, retail, banking, FMCG,
healthcare and, any more companies. The six sigma creates an environment of continuous
betterment as an objective or aim. Which helps in meeting the expectations of the customers’ needs
and wants (Dahmani and Yebdri, 2020).
There are mainly five principles of six sigma in the operation management which are followed as-
1. Focus on the customers- it is measured as one of the important objectives of business
enterprises. In today's scenario, the world is living in the customer driver market. And
customer is known as the god. The company should perform their task in respect to
customers or business company should be consumer centric and determine various
components that customer wants. It is important for the Unilever to identify different factors
that are affecting the sales of the company and the company must update themselves
according to the need of customers and need of market.
2. Determination of problem- from value chain- the Unilever should note down all the
operations that have to be performed in a particular procedure.
3. Minimize variation and eliminate anomalies- there are different unusual individual in
procedure. The company must try to eliminate all by using different operations and
functions. Six sigma helps in reducing the variation in Unilever.
4. Stakeholder management- the stakeholder should manage all the problem and identify the
solution for it. The stakeholder of Unilever has good skills and experience so that the task
can be tackled.
5. Highly Responsible System- because of modification or change in the process, the
approaches and style of working also changes. When the company like Unilever have highly
responsive system, then it became easier to execute the project.
the company on every level.
Principle of operation management in context with Unilever of United Kingdom
Six sigma is most recognized tool framework in the management of operations. The method
was introduced by Bill Smith and implemented in the Motorola company. The word six sigma is
generated from the business statistics which means standard deviation in the statistics. It is known
for the improvement of process by 99.9996% idol as an aim.
The cop any which uses six sigma tools are mainly IT, automotive, retail, banking, FMCG,
healthcare and, any more companies. The six sigma creates an environment of continuous
betterment as an objective or aim. Which helps in meeting the expectations of the customers’ needs
and wants (Dahmani and Yebdri, 2020).
There are mainly five principles of six sigma in the operation management which are followed as-
1. Focus on the customers- it is measured as one of the important objectives of business
enterprises. In today's scenario, the world is living in the customer driver market. And
customer is known as the god. The company should perform their task in respect to
customers or business company should be consumer centric and determine various
components that customer wants. It is important for the Unilever to identify different factors
that are affecting the sales of the company and the company must update themselves
according to the need of customers and need of market.
2. Determination of problem- from value chain- the Unilever should note down all the
operations that have to be performed in a particular procedure.
3. Minimize variation and eliminate anomalies- there are different unusual individual in
procedure. The company must try to eliminate all by using different operations and
functions. Six sigma helps in reducing the variation in Unilever.
4. Stakeholder management- the stakeholder should manage all the problem and identify the
solution for it. The stakeholder of Unilever has good skills and experience so that the task
can be tackled.
5. Highly Responsible System- because of modification or change in the process, the
approaches and style of working also changes. When the company like Unilever have highly
responsive system, then it became easier to execute the project.
Paraphrase This Document
Need a fresh take? Get an instant paraphrase of this document with our AI Paraphraser
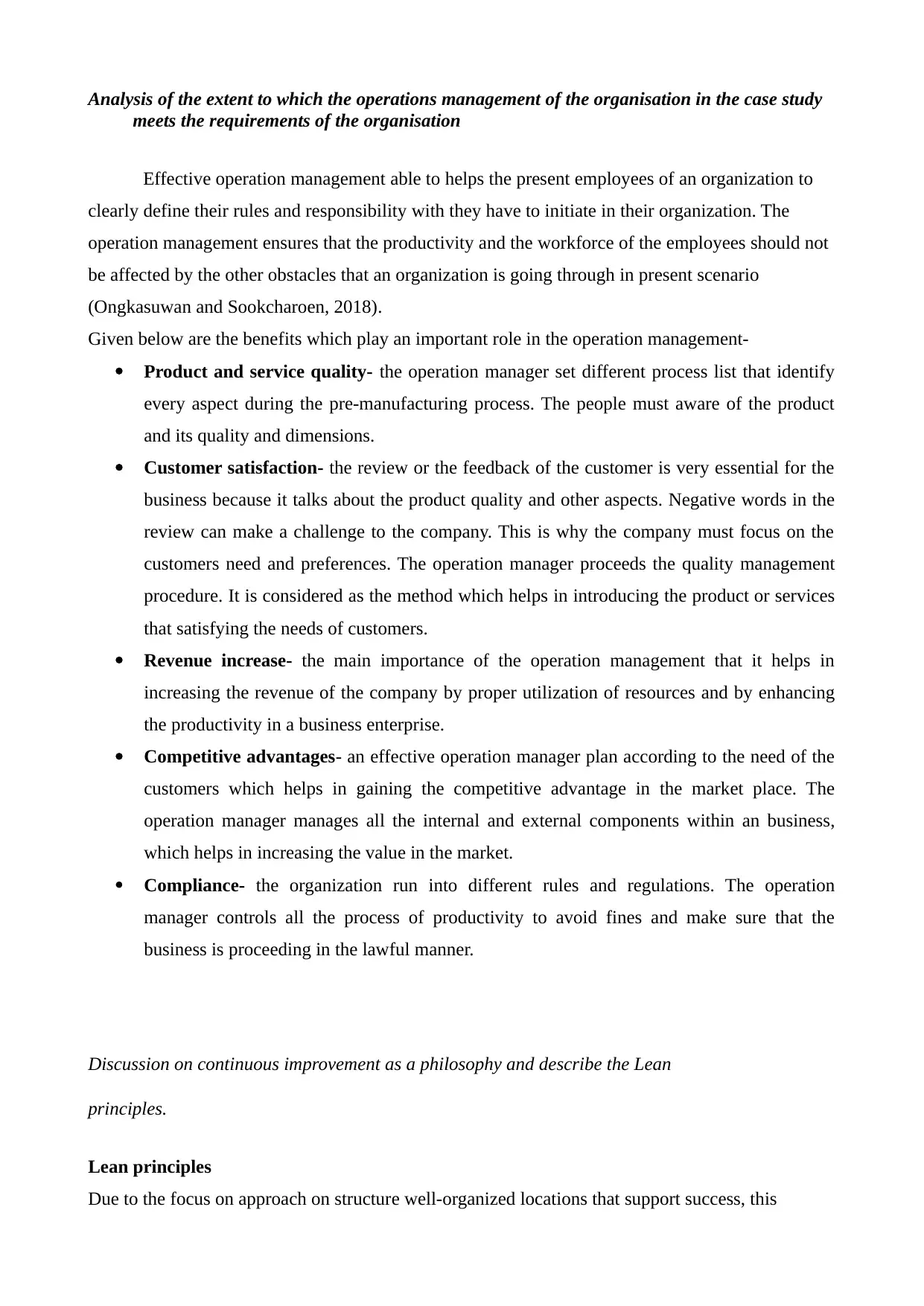
Analysis of the extent to which the operations management of the organisation in the case study
meets the requirements of the organisation
Effective operation management able to helps the present employees of an organization to
clearly define their rules and responsibility with they have to initiate in their organization. The
operation management ensures that the productivity and the workforce of the employees should not
be affected by the other obstacles that an organization is going through in present scenario
(Ongkasuwan and Sookcharoen, 2018).
Given below are the benefits which play an important role in the operation management-
Product and service quality- the operation manager set different process list that identify
every aspect during the pre-manufacturing process. The people must aware of the product
and its quality and dimensions.
Customer satisfaction- the review or the feedback of the customer is very essential for the
business because it talks about the product quality and other aspects. Negative words in the
review can make a challenge to the company. This is why the company must focus on the
customers need and preferences. The operation manager proceeds the quality management
procedure. It is considered as the method which helps in introducing the product or services
that satisfying the needs of customers.
Revenue increase- the main importance of the operation management that it helps in
increasing the revenue of the company by proper utilization of resources and by enhancing
the productivity in a business enterprise.
Competitive advantages- an effective operation manager plan according to the need of the
customers which helps in gaining the competitive advantage in the market place. The
operation manager manages all the internal and external components within an business,
which helps in increasing the value in the market.
Compliance- the organization run into different rules and regulations. The operation
manager controls all the process of productivity to avoid fines and make sure that the
business is proceeding in the lawful manner.
Discussion on continuous improvement as a philosophy and describe the Lean
principles.
Lean principles
Due to the focus on approach on structure well-organized locations that support success, this
meets the requirements of the organisation
Effective operation management able to helps the present employees of an organization to
clearly define their rules and responsibility with they have to initiate in their organization. The
operation management ensures that the productivity and the workforce of the employees should not
be affected by the other obstacles that an organization is going through in present scenario
(Ongkasuwan and Sookcharoen, 2018).
Given below are the benefits which play an important role in the operation management-
Product and service quality- the operation manager set different process list that identify
every aspect during the pre-manufacturing process. The people must aware of the product
and its quality and dimensions.
Customer satisfaction- the review or the feedback of the customer is very essential for the
business because it talks about the product quality and other aspects. Negative words in the
review can make a challenge to the company. This is why the company must focus on the
customers need and preferences. The operation manager proceeds the quality management
procedure. It is considered as the method which helps in introducing the product or services
that satisfying the needs of customers.
Revenue increase- the main importance of the operation management that it helps in
increasing the revenue of the company by proper utilization of resources and by enhancing
the productivity in a business enterprise.
Competitive advantages- an effective operation manager plan according to the need of the
customers which helps in gaining the competitive advantage in the market place. The
operation manager manages all the internal and external components within an business,
which helps in increasing the value in the market.
Compliance- the organization run into different rules and regulations. The operation
manager controls all the process of productivity to avoid fines and make sure that the
business is proceeding in the lawful manner.
Discussion on continuous improvement as a philosophy and describe the Lean
principles.
Lean principles
Due to the focus on approach on structure well-organized locations that support success, this
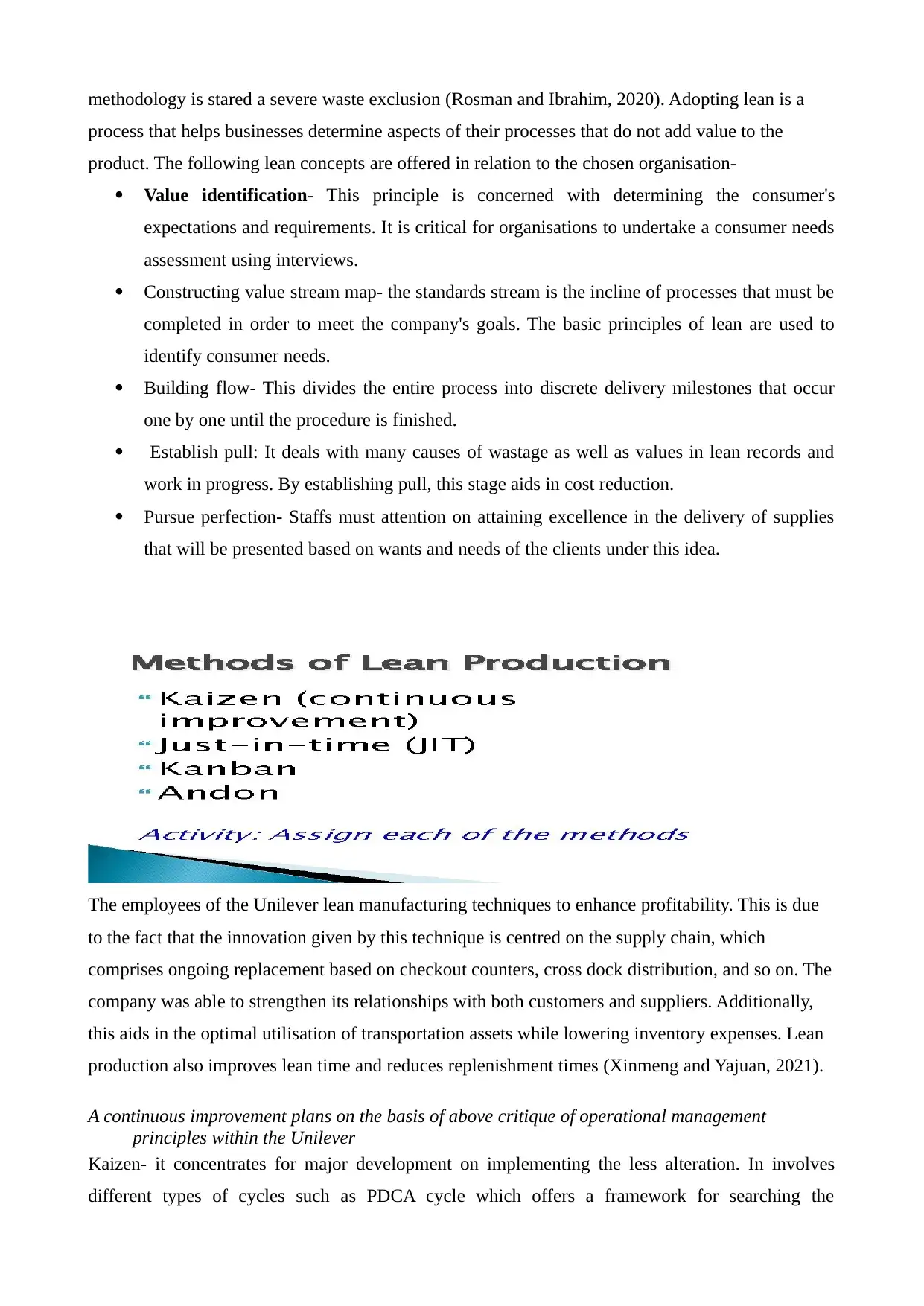
methodology is stared a severe waste exclusion (Rosman and Ibrahim, 2020). Adopting lean is a
process that helps businesses determine aspects of their processes that do not add value to the
product. The following lean concepts are offered in relation to the chosen organisation-
Value identification- This principle is concerned with determining the consumer's
expectations and requirements. It is critical for organisations to undertake a consumer needs
assessment using interviews.
Constructing value stream map- the standards stream is the incline of processes that must be
completed in order to meet the company's goals. The basic principles of lean are used to
identify consumer needs.
Building flow- This divides the entire process into discrete delivery milestones that occur
one by one until the procedure is finished.
Establish pull: It deals with many causes of wastage as well as values in lean records and
work in progress. By establishing pull, this stage aids in cost reduction.
Pursue perfection- Staffs must attention on attaining excellence in the delivery of supplies
that will be presented based on wants and needs of the clients under this idea.
The employees of the Unilever lean manufacturing techniques to enhance profitability. This is due
to the fact that the innovation given by this technique is centred on the supply chain, which
comprises ongoing replacement based on checkout counters, cross dock distribution, and so on. The
company was able to strengthen its relationships with both customers and suppliers. Additionally,
this aids in the optimal utilisation of transportation assets while lowering inventory expenses. Lean
production also improves lean time and reduces replenishment times (Xinmeng and Yajuan, 2021).
A continuous improvement plans on the basis of above critique of operational management
principles within the Unilever
Kaizen- it concentrates for major development on implementing the less alteration. In involves
different types of cycles such as PDCA cycle which offers a framework for searching the
process that helps businesses determine aspects of their processes that do not add value to the
product. The following lean concepts are offered in relation to the chosen organisation-
Value identification- This principle is concerned with determining the consumer's
expectations and requirements. It is critical for organisations to undertake a consumer needs
assessment using interviews.
Constructing value stream map- the standards stream is the incline of processes that must be
completed in order to meet the company's goals. The basic principles of lean are used to
identify consumer needs.
Building flow- This divides the entire process into discrete delivery milestones that occur
one by one until the procedure is finished.
Establish pull: It deals with many causes of wastage as well as values in lean records and
work in progress. By establishing pull, this stage aids in cost reduction.
Pursue perfection- Staffs must attention on attaining excellence in the delivery of supplies
that will be presented based on wants and needs of the clients under this idea.
The employees of the Unilever lean manufacturing techniques to enhance profitability. This is due
to the fact that the innovation given by this technique is centred on the supply chain, which
comprises ongoing replacement based on checkout counters, cross dock distribution, and so on. The
company was able to strengthen its relationships with both customers and suppliers. Additionally,
this aids in the optimal utilisation of transportation assets while lowering inventory expenses. Lean
production also improves lean time and reduces replenishment times (Xinmeng and Yajuan, 2021).
A continuous improvement plans on the basis of above critique of operational management
principles within the Unilever
Kaizen- it concentrates for major development on implementing the less alteration. In involves
different types of cycles such as PDCA cycle which offers a framework for searching the
You're viewing a preview
Unlock full access by subscribing today!
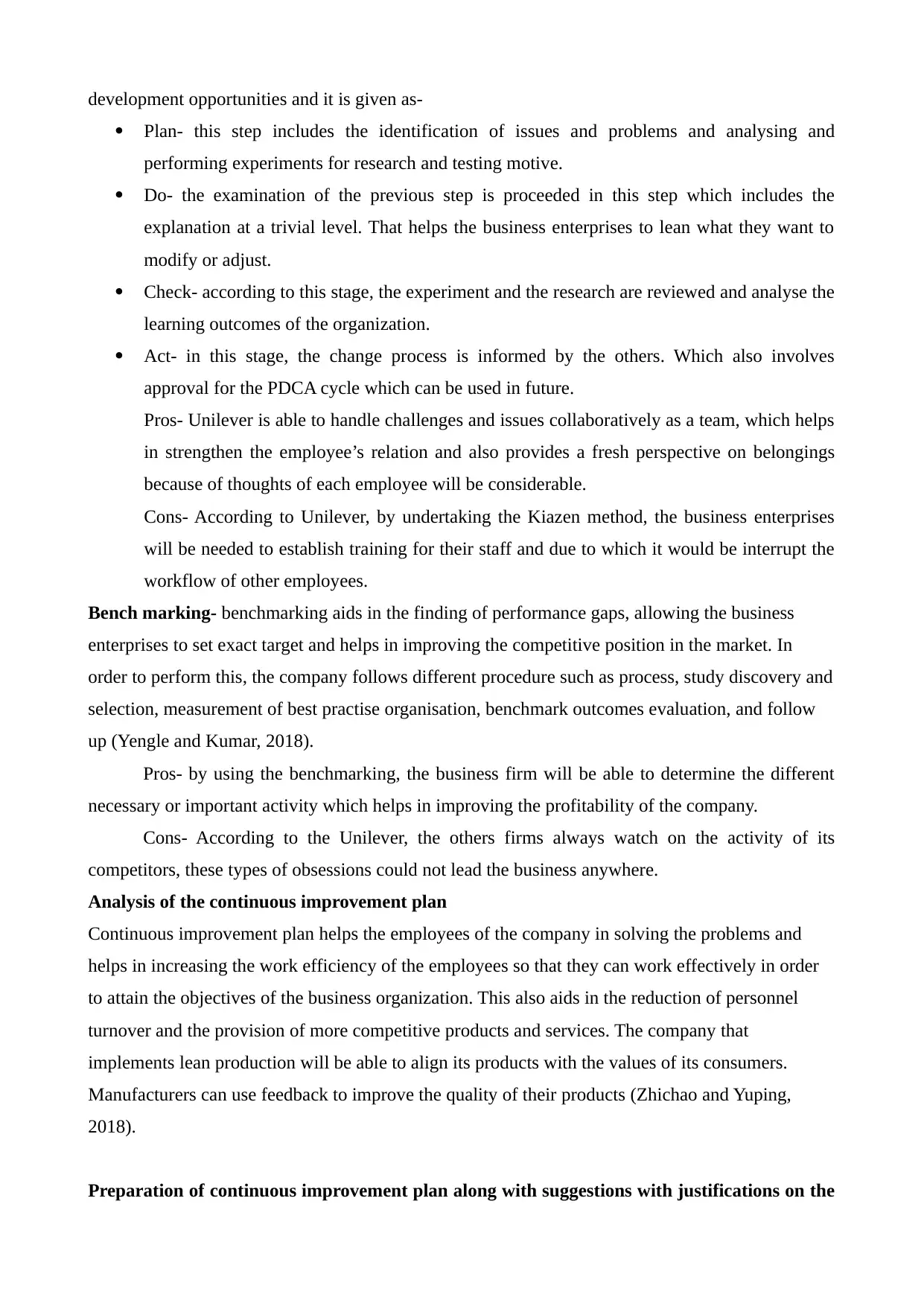
development opportunities and it is given as-
Plan- this step includes the identification of issues and problems and analysing and
performing experiments for research and testing motive.
Do- the examination of the previous step is proceeded in this step which includes the
explanation at a trivial level. That helps the business enterprises to lean what they want to
modify or adjust.
Check- according to this stage, the experiment and the research are reviewed and analyse the
learning outcomes of the organization.
Act- in this stage, the change process is informed by the others. Which also involves
approval for the PDCA cycle which can be used in future.
Pros- Unilever is able to handle challenges and issues collaboratively as a team, which helps
in strengthen the employee’s relation and also provides a fresh perspective on belongings
because of thoughts of each employee will be considerable.
Cons- According to Unilever, by undertaking the Kiazen method, the business enterprises
will be needed to establish training for their staff and due to which it would be interrupt the
workflow of other employees.
Bench marking- benchmarking aids in the finding of performance gaps, allowing the business
enterprises to set exact target and helps in improving the competitive position in the market. In
order to perform this, the company follows different procedure such as process, study discovery and
selection, measurement of best practise organisation, benchmark outcomes evaluation, and follow
up (Yengle and Kumar, 2018).
Pros- by using the benchmarking, the business firm will be able to determine the different
necessary or important activity which helps in improving the profitability of the company.
Cons- According to the Unilever, the others firms always watch on the activity of its
competitors, these types of obsessions could not lead the business anywhere.
Analysis of the continuous improvement plan
Continuous improvement plan helps the employees of the company in solving the problems and
helps in increasing the work efficiency of the employees so that they can work effectively in order
to attain the objectives of the business organization. This also aids in the reduction of personnel
turnover and the provision of more competitive products and services. The company that
implements lean production will be able to align its products with the values of its consumers.
Manufacturers can use feedback to improve the quality of their products (Zhichao and Yuping,
2018).
Preparation of continuous improvement plan along with suggestions with justifications on the
Plan- this step includes the identification of issues and problems and analysing and
performing experiments for research and testing motive.
Do- the examination of the previous step is proceeded in this step which includes the
explanation at a trivial level. That helps the business enterprises to lean what they want to
modify or adjust.
Check- according to this stage, the experiment and the research are reviewed and analyse the
learning outcomes of the organization.
Act- in this stage, the change process is informed by the others. Which also involves
approval for the PDCA cycle which can be used in future.
Pros- Unilever is able to handle challenges and issues collaboratively as a team, which helps
in strengthen the employee’s relation and also provides a fresh perspective on belongings
because of thoughts of each employee will be considerable.
Cons- According to Unilever, by undertaking the Kiazen method, the business enterprises
will be needed to establish training for their staff and due to which it would be interrupt the
workflow of other employees.
Bench marking- benchmarking aids in the finding of performance gaps, allowing the business
enterprises to set exact target and helps in improving the competitive position in the market. In
order to perform this, the company follows different procedure such as process, study discovery and
selection, measurement of best practise organisation, benchmark outcomes evaluation, and follow
up (Yengle and Kumar, 2018).
Pros- by using the benchmarking, the business firm will be able to determine the different
necessary or important activity which helps in improving the profitability of the company.
Cons- According to the Unilever, the others firms always watch on the activity of its
competitors, these types of obsessions could not lead the business anywhere.
Analysis of the continuous improvement plan
Continuous improvement plan helps the employees of the company in solving the problems and
helps in increasing the work efficiency of the employees so that they can work effectively in order
to attain the objectives of the business organization. This also aids in the reduction of personnel
turnover and the provision of more competitive products and services. The company that
implements lean production will be able to align its products with the values of its consumers.
Manufacturers can use feedback to improve the quality of their products (Zhichao and Yuping,
2018).
Preparation of continuous improvement plan along with suggestions with justifications on the
Paraphrase This Document
Need a fresh take? Get an instant paraphrase of this document with our AI Paraphraser
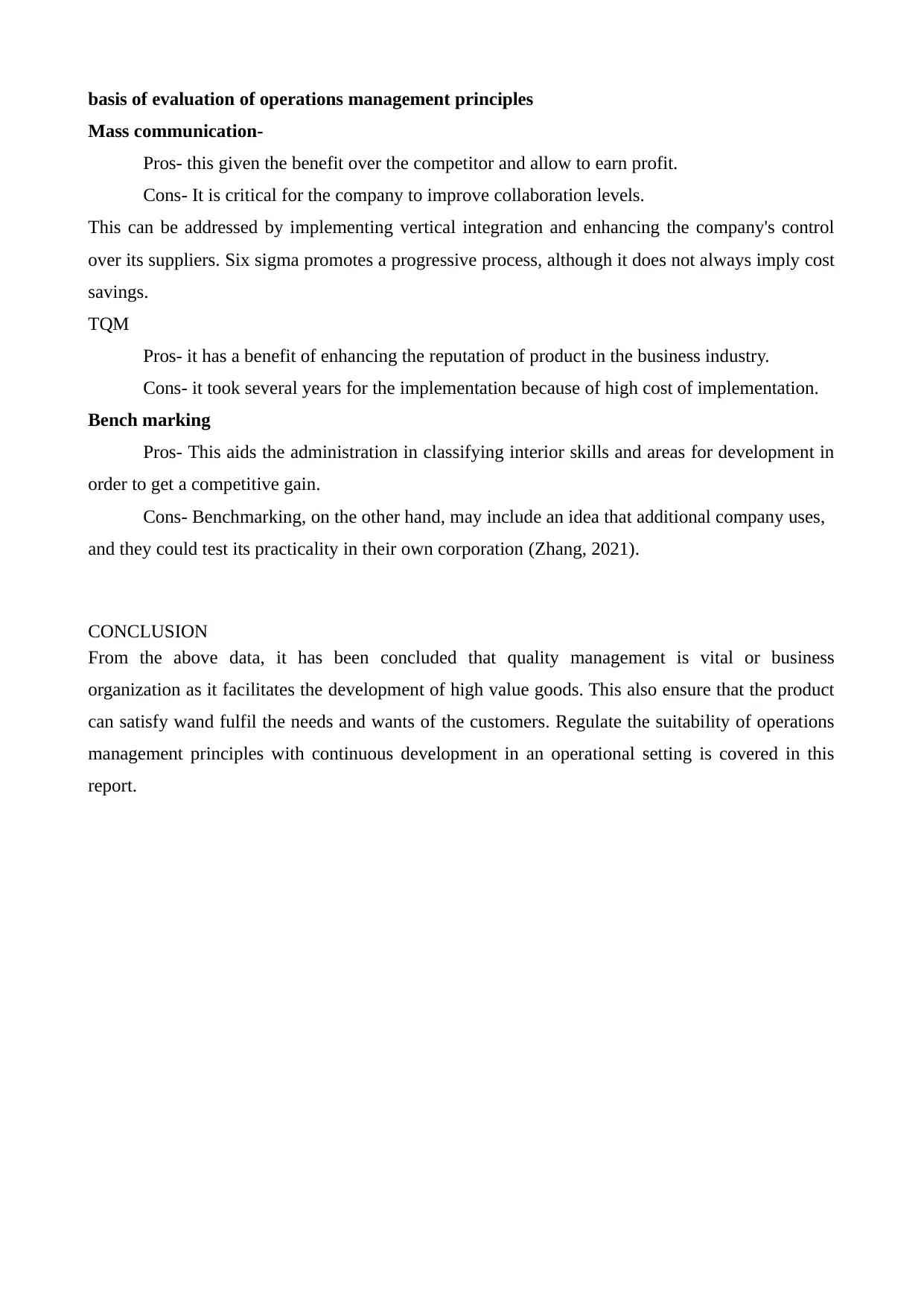
basis of evaluation of operations management principles
Mass communication-
Pros- this given the benefit over the competitor and allow to earn profit.
Cons- It is critical for the company to improve collaboration levels.
This can be addressed by implementing vertical integration and enhancing the company's control
over its suppliers. Six sigma promotes a progressive process, although it does not always imply cost
savings.
TQM
Pros- it has a benefit of enhancing the reputation of product in the business industry.
Cons- it took several years for the implementation because of high cost of implementation.
Bench marking
Pros- This aids the administration in classifying interior skills and areas for development in
order to get a competitive gain.
Cons- Benchmarking, on the other hand, may include an idea that additional company uses,
and they could test its practicality in their own corporation (Zhang, 2021).
CONCLUSION
From the above data, it has been concluded that quality management is vital or business
organization as it facilitates the development of high value goods. This also ensure that the product
can satisfy wand fulfil the needs and wants of the customers. Regulate the suitability of operations
management principles with continuous development in an operational setting is covered in this
report.
Mass communication-
Pros- this given the benefit over the competitor and allow to earn profit.
Cons- It is critical for the company to improve collaboration levels.
This can be addressed by implementing vertical integration and enhancing the company's control
over its suppliers. Six sigma promotes a progressive process, although it does not always imply cost
savings.
TQM
Pros- it has a benefit of enhancing the reputation of product in the business industry.
Cons- it took several years for the implementation because of high cost of implementation.
Bench marking
Pros- This aids the administration in classifying interior skills and areas for development in
order to get a competitive gain.
Cons- Benchmarking, on the other hand, may include an idea that additional company uses,
and they could test its practicality in their own corporation (Zhang, 2021).
CONCLUSION
From the above data, it has been concluded that quality management is vital or business
organization as it facilitates the development of high value goods. This also ensure that the product
can satisfy wand fulfil the needs and wants of the customers. Regulate the suitability of operations
management principles with continuous development in an operational setting is covered in this
report.
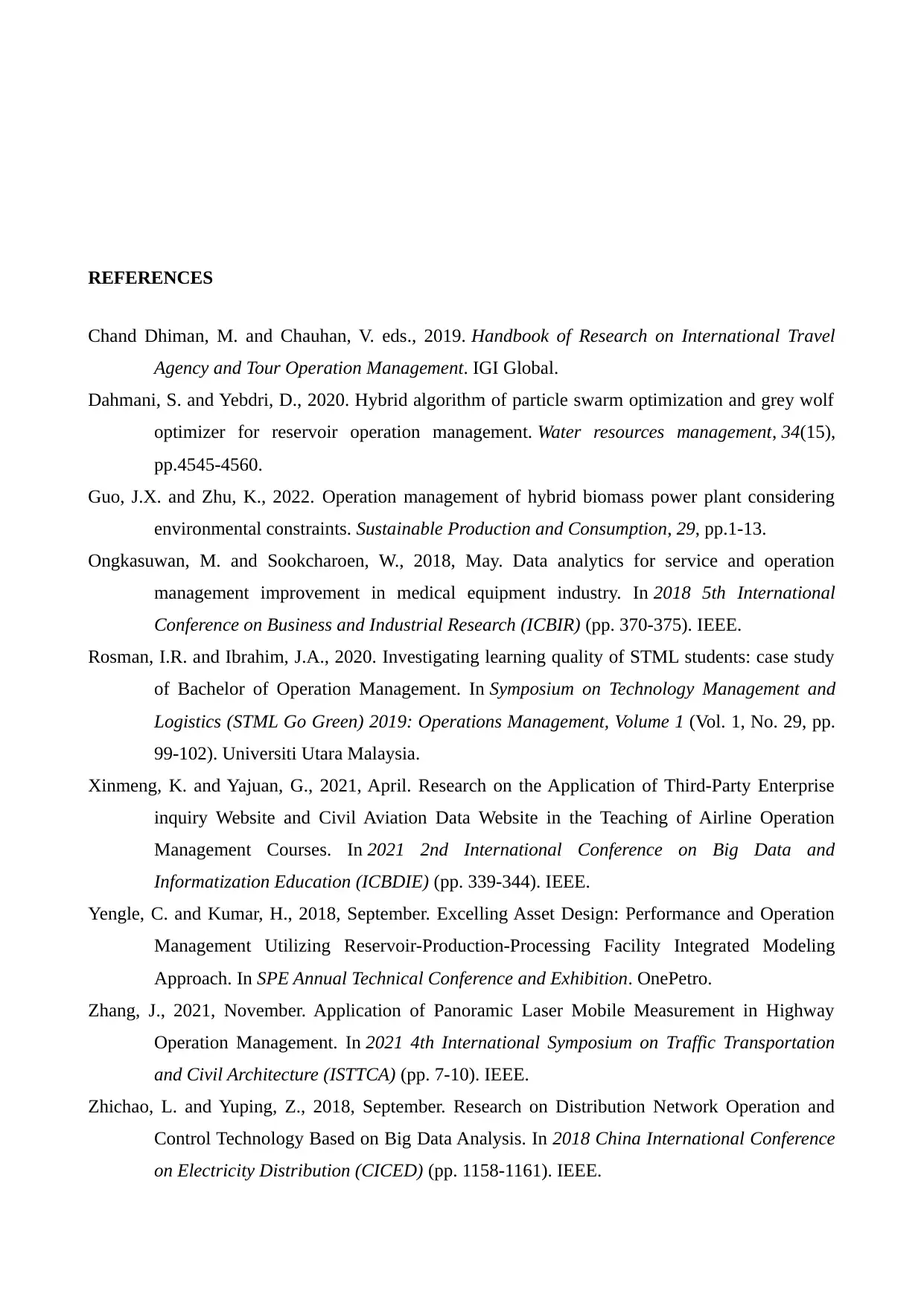
REFERENCES
Chand Dhiman, M. and Chauhan, V. eds., 2019. Handbook of Research on International Travel
Agency and Tour Operation Management. IGI Global.
Dahmani, S. and Yebdri, D., 2020. Hybrid algorithm of particle swarm optimization and grey wolf
optimizer for reservoir operation management. Water resources management, 34(15),
pp.4545-4560.
Guo, J.X. and Zhu, K., 2022. Operation management of hybrid biomass power plant considering
environmental constraints. Sustainable Production and Consumption, 29, pp.1-13.
Ongkasuwan, M. and Sookcharoen, W., 2018, May. Data analytics for service and operation
management improvement in medical equipment industry. In 2018 5th International
Conference on Business and Industrial Research (ICBIR) (pp. 370-375). IEEE.
Rosman, I.R. and Ibrahim, J.A., 2020. Investigating learning quality of STML students: case study
of Bachelor of Operation Management. In Symposium on Technology Management and
Logistics (STML Go Green) 2019: Operations Management, Volume 1 (Vol. 1, No. 29, pp.
99-102). Universiti Utara Malaysia.
Xinmeng, K. and Yajuan, G., 2021, April. Research on the Application of Third-Party Enterprise
inquiry Website and Civil Aviation Data Website in the Teaching of Airline Operation
Management Courses. In 2021 2nd International Conference on Big Data and
Informatization Education (ICBDIE) (pp. 339-344). IEEE.
Yengle, C. and Kumar, H., 2018, September. Excelling Asset Design: Performance and Operation
Management Utilizing Reservoir-Production-Processing Facility Integrated Modeling
Approach. In SPE Annual Technical Conference and Exhibition. OnePetro.
Zhang, J., 2021, November. Application of Panoramic Laser Mobile Measurement in Highway
Operation Management. In 2021 4th International Symposium on Traffic Transportation
and Civil Architecture (ISTTCA) (pp. 7-10). IEEE.
Zhichao, L. and Yuping, Z., 2018, September. Research on Distribution Network Operation and
Control Technology Based on Big Data Analysis. In 2018 China International Conference
on Electricity Distribution (CICED) (pp. 1158-1161). IEEE.
Chand Dhiman, M. and Chauhan, V. eds., 2019. Handbook of Research on International Travel
Agency and Tour Operation Management. IGI Global.
Dahmani, S. and Yebdri, D., 2020. Hybrid algorithm of particle swarm optimization and grey wolf
optimizer for reservoir operation management. Water resources management, 34(15),
pp.4545-4560.
Guo, J.X. and Zhu, K., 2022. Operation management of hybrid biomass power plant considering
environmental constraints. Sustainable Production and Consumption, 29, pp.1-13.
Ongkasuwan, M. and Sookcharoen, W., 2018, May. Data analytics for service and operation
management improvement in medical equipment industry. In 2018 5th International
Conference on Business and Industrial Research (ICBIR) (pp. 370-375). IEEE.
Rosman, I.R. and Ibrahim, J.A., 2020. Investigating learning quality of STML students: case study
of Bachelor of Operation Management. In Symposium on Technology Management and
Logistics (STML Go Green) 2019: Operations Management, Volume 1 (Vol. 1, No. 29, pp.
99-102). Universiti Utara Malaysia.
Xinmeng, K. and Yajuan, G., 2021, April. Research on the Application of Third-Party Enterprise
inquiry Website and Civil Aviation Data Website in the Teaching of Airline Operation
Management Courses. In 2021 2nd International Conference on Big Data and
Informatization Education (ICBDIE) (pp. 339-344). IEEE.
Yengle, C. and Kumar, H., 2018, September. Excelling Asset Design: Performance and Operation
Management Utilizing Reservoir-Production-Processing Facility Integrated Modeling
Approach. In SPE Annual Technical Conference and Exhibition. OnePetro.
Zhang, J., 2021, November. Application of Panoramic Laser Mobile Measurement in Highway
Operation Management. In 2021 4th International Symposium on Traffic Transportation
and Civil Architecture (ISTTCA) (pp. 7-10). IEEE.
Zhichao, L. and Yuping, Z., 2018, September. Research on Distribution Network Operation and
Control Technology Based on Big Data Analysis. In 2018 China International Conference
on Electricity Distribution (CICED) (pp. 1158-1161). IEEE.
You're viewing a preview
Unlock full access by subscribing today!
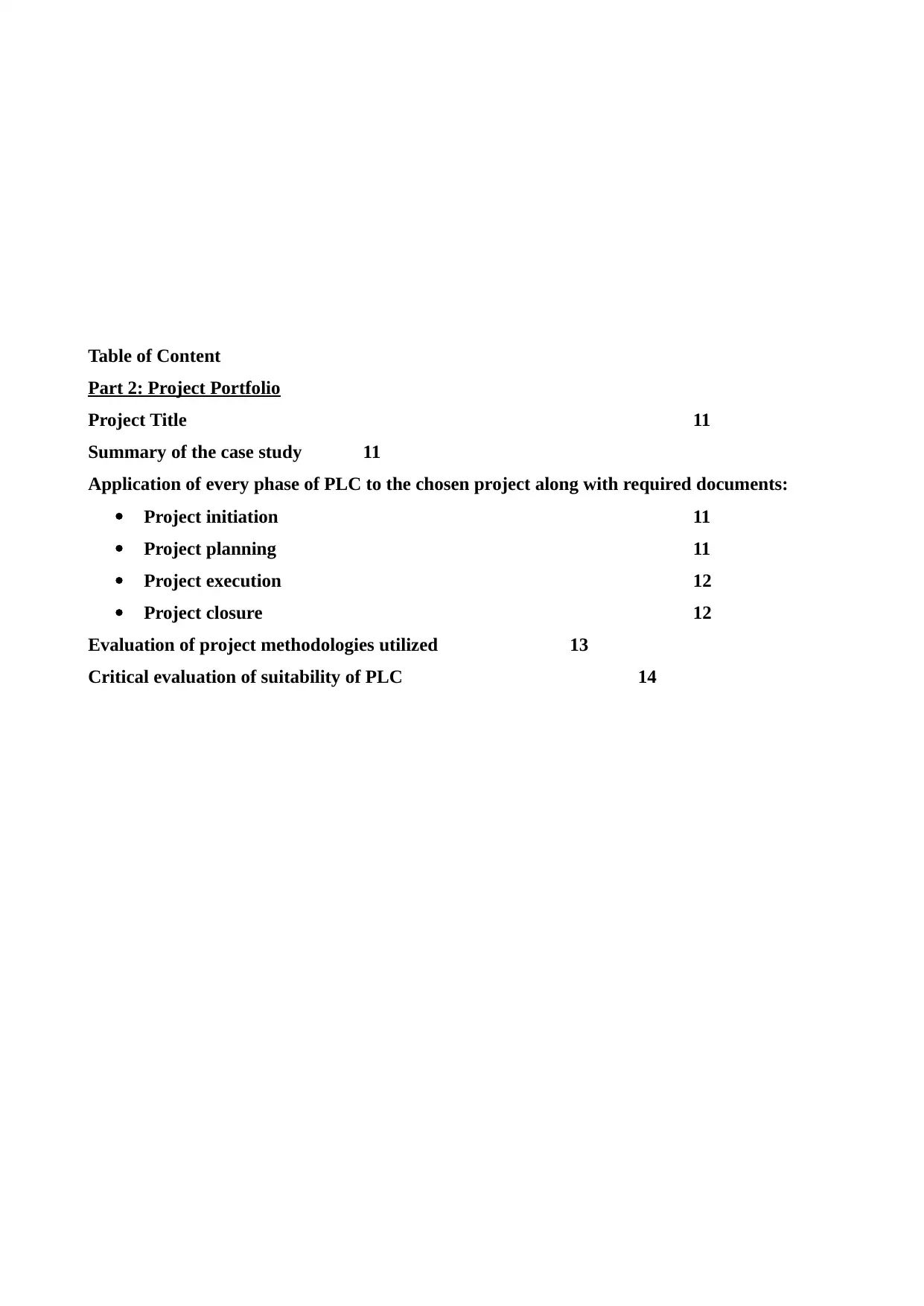
Table of Content
Part 2: Project Portfolio
Project Title 11
Summary of the case study 11
Application of every phase of PLC to the chosen project along with required documents:
Project initiation 11
Project planning 11
Project execution 12
Project closure 12
Evaluation of project methodologies utilized 13
Critical evaluation of suitability of PLC 14
Part 2: Project Portfolio
Project Title 11
Summary of the case study 11
Application of every phase of PLC to the chosen project along with required documents:
Project initiation 11
Project planning 11
Project execution 12
Project closure 12
Evaluation of project methodologies utilized 13
Critical evaluation of suitability of PLC 14
Paraphrase This Document
Need a fresh take? Get an instant paraphrase of this document with our AI Paraphraser
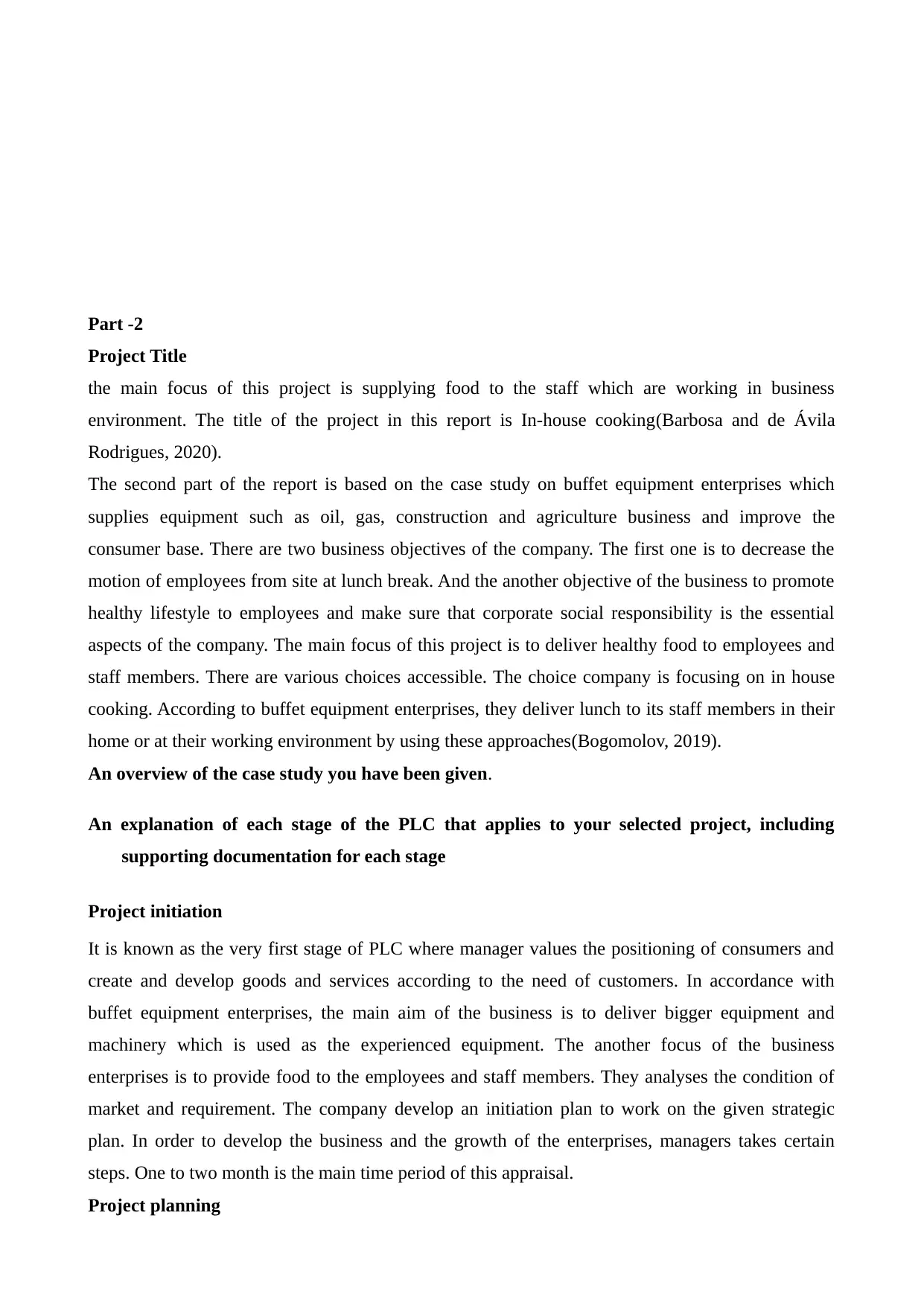
Part -2
Project Title
the main focus of this project is supplying food to the staff which are working in business
environment. The title of the project in this report is In-house cooking(Barbosa and de Ávila
Rodrigues, 2020).
The second part of the report is based on the case study on buffet equipment enterprises which
supplies equipment such as oil, gas, construction and agriculture business and improve the
consumer base. There are two business objectives of the company. The first one is to decrease the
motion of employees from site at lunch break. And the another objective of the business to promote
healthy lifestyle to employees and make sure that corporate social responsibility is the essential
aspects of the company. The main focus of this project is to deliver healthy food to employees and
staff members. There are various choices accessible. The choice company is focusing on in house
cooking. According to buffet equipment enterprises, they deliver lunch to its staff members in their
home or at their working environment by using these approaches(Bogomolov, 2019).
An overview of the case study you have been given.
An explanation of each stage of the PLC that applies to your selected project, including
supporting documentation for each stage
Project initiation
It is known as the very first stage of PLC where manager values the positioning of consumers and
create and develop goods and services according to the need of customers. In accordance with
buffet equipment enterprises, the main aim of the business is to deliver bigger equipment and
machinery which is used as the experienced equipment. The another focus of the business
enterprises is to provide food to the employees and staff members. They analyses the condition of
market and requirement. The company develop an initiation plan to work on the given strategic
plan. In order to develop the business and the growth of the enterprises, managers takes certain
steps. One to two month is the main time period of this appraisal.
Project planning
Project Title
the main focus of this project is supplying food to the staff which are working in business
environment. The title of the project in this report is In-house cooking(Barbosa and de Ávila
Rodrigues, 2020).
The second part of the report is based on the case study on buffet equipment enterprises which
supplies equipment such as oil, gas, construction and agriculture business and improve the
consumer base. There are two business objectives of the company. The first one is to decrease the
motion of employees from site at lunch break. And the another objective of the business to promote
healthy lifestyle to employees and make sure that corporate social responsibility is the essential
aspects of the company. The main focus of this project is to deliver healthy food to employees and
staff members. There are various choices accessible. The choice company is focusing on in house
cooking. According to buffet equipment enterprises, they deliver lunch to its staff members in their
home or at their working environment by using these approaches(Bogomolov, 2019).
An overview of the case study you have been given.
An explanation of each stage of the PLC that applies to your selected project, including
supporting documentation for each stage
Project initiation
It is known as the very first stage of PLC where manager values the positioning of consumers and
create and develop goods and services according to the need of customers. In accordance with
buffet equipment enterprises, the main aim of the business is to deliver bigger equipment and
machinery which is used as the experienced equipment. The another focus of the business
enterprises is to provide food to the employees and staff members. They analyses the condition of
market and requirement. The company develop an initiation plan to work on the given strategic
plan. In order to develop the business and the growth of the enterprises, managers takes certain
steps. One to two month is the main time period of this appraisal.
Project planning
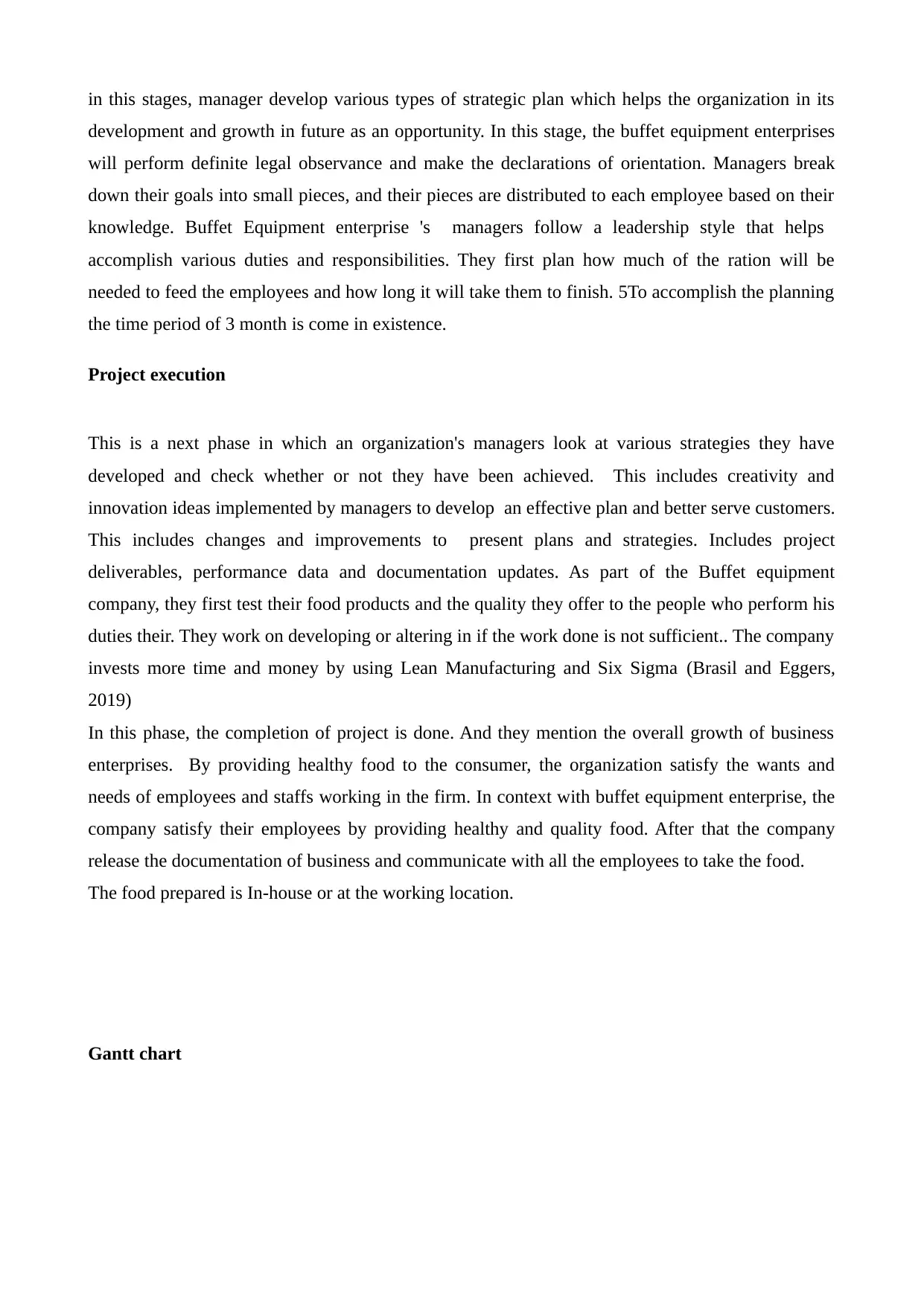
in this stages, manager develop various types of strategic plan which helps the organization in its
development and growth in future as an opportunity. In this stage, the buffet equipment enterprises
will perform definite legal observance and make the declarations of orientation. Managers break
down their goals into small pieces, and their pieces are distributed to each employee based on their
knowledge. Buffet Equipment enterprise 's managers follow a leadership style that helps
accomplish various duties and responsibilities. They first plan how much of the ration will be
needed to feed the employees and how long it will take them to finish. 5To accomplish the planning
the time period of 3 month is come in existence.
Project execution
This is a next phase in which an organization's managers look at various strategies they have
developed and check whether or not they have been achieved. This includes creativity and
innovation ideas implemented by managers to develop an effective plan and better serve customers.
This includes changes and improvements to present plans and strategies. Includes project
deliverables, performance data and documentation updates. As part of the Buffet equipment
company, they first test their food products and the quality they offer to the people who perform his
duties their. They work on developing or altering in if the work done is not sufficient.. The company
invests more time and money by using Lean Manufacturing and Six Sigma (Brasil and Eggers,
2019)
In this phase, the completion of project is done. And they mention the overall growth of business
enterprises. By providing healthy food to the consumer, the organization satisfy the wants and
needs of employees and staffs working in the firm. In context with buffet equipment enterprise, the
company satisfy their employees by providing healthy and quality food. After that the company
release the documentation of business and communicate with all the employees to take the food.
The food prepared is In-house or at the working location.
Gantt chart
development and growth in future as an opportunity. In this stage, the buffet equipment enterprises
will perform definite legal observance and make the declarations of orientation. Managers break
down their goals into small pieces, and their pieces are distributed to each employee based on their
knowledge. Buffet Equipment enterprise 's managers follow a leadership style that helps
accomplish various duties and responsibilities. They first plan how much of the ration will be
needed to feed the employees and how long it will take them to finish. 5To accomplish the planning
the time period of 3 month is come in existence.
Project execution
This is a next phase in which an organization's managers look at various strategies they have
developed and check whether or not they have been achieved. This includes creativity and
innovation ideas implemented by managers to develop an effective plan and better serve customers.
This includes changes and improvements to present plans and strategies. Includes project
deliverables, performance data and documentation updates. As part of the Buffet equipment
company, they first test their food products and the quality they offer to the people who perform his
duties their. They work on developing or altering in if the work done is not sufficient.. The company
invests more time and money by using Lean Manufacturing and Six Sigma (Brasil and Eggers,
2019)
In this phase, the completion of project is done. And they mention the overall growth of business
enterprises. By providing healthy food to the consumer, the organization satisfy the wants and
needs of employees and staffs working in the firm. In context with buffet equipment enterprise, the
company satisfy their employees by providing healthy and quality food. After that the company
release the documentation of business and communicate with all the employees to take the food.
The food prepared is In-house or at the working location.
Gantt chart
You're viewing a preview
Unlock full access by subscribing today!
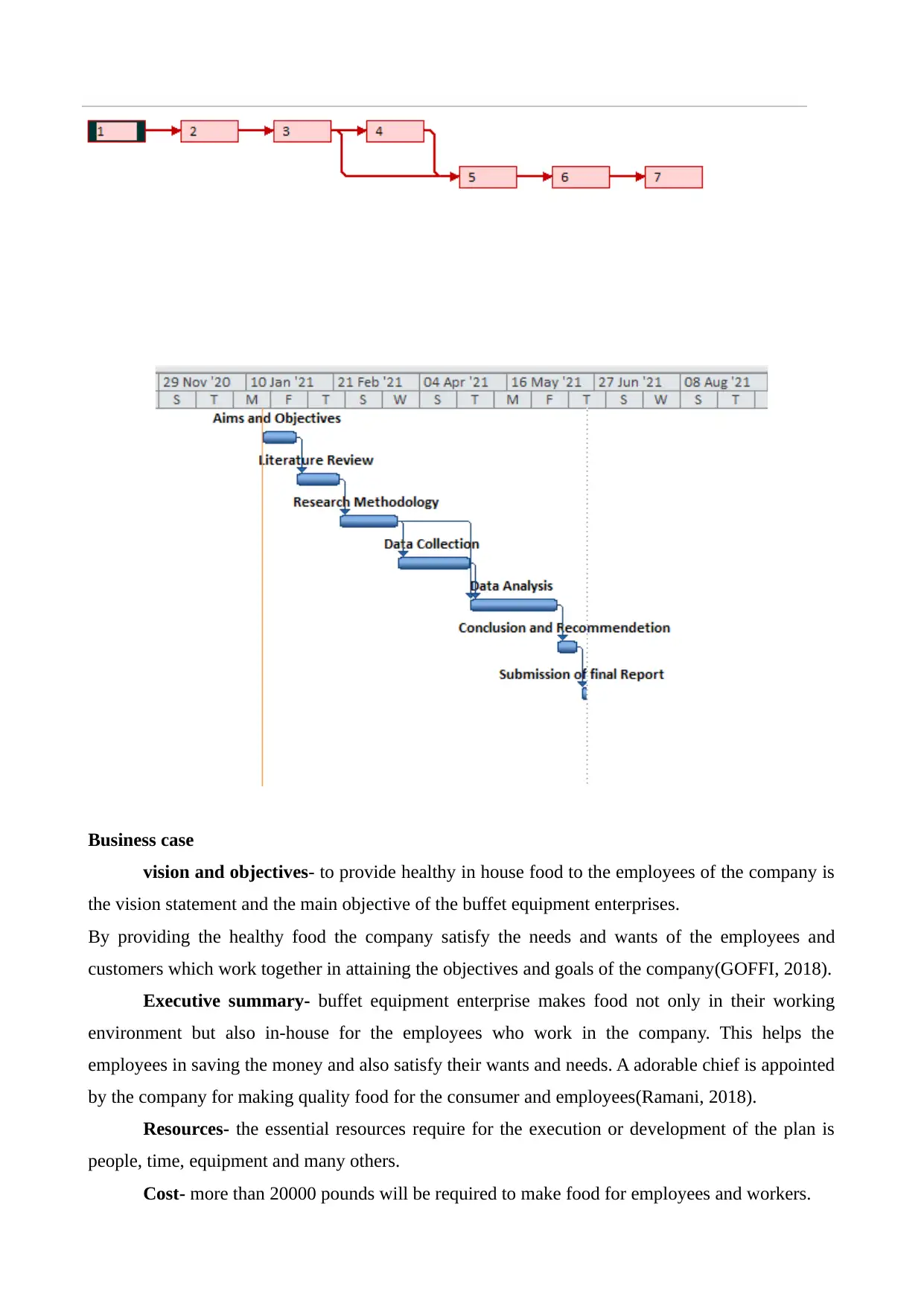
Business case
vision and objectives- to provide healthy in house food to the employees of the company is
the vision statement and the main objective of the buffet equipment enterprises.
By providing the healthy food the company satisfy the needs and wants of the employees and
customers which work together in attaining the objectives and goals of the company(GOFFI, 2018).
Executive summary- buffet equipment enterprise makes food not only in their working
environment but also in-house for the employees who work in the company. This helps the
employees in saving the money and also satisfy their wants and needs. A adorable chief is appointed
by the company for making quality food for the consumer and employees(Ramani, 2018).
Resources- the essential resources require for the execution or development of the plan is
people, time, equipment and many others.
Cost- more than 20000 pounds will be required to make food for employees and workers.
vision and objectives- to provide healthy in house food to the employees of the company is
the vision statement and the main objective of the buffet equipment enterprises.
By providing the healthy food the company satisfy the needs and wants of the employees and
customers which work together in attaining the objectives and goals of the company(GOFFI, 2018).
Executive summary- buffet equipment enterprise makes food not only in their working
environment but also in-house for the employees who work in the company. This helps the
employees in saving the money and also satisfy their wants and needs. A adorable chief is appointed
by the company for making quality food for the consumer and employees(Ramani, 2018).
Resources- the essential resources require for the execution or development of the plan is
people, time, equipment and many others.
Cost- more than 20000 pounds will be required to make food for employees and workers.
Paraphrase This Document
Need a fresh take? Get an instant paraphrase of this document with our AI Paraphraser
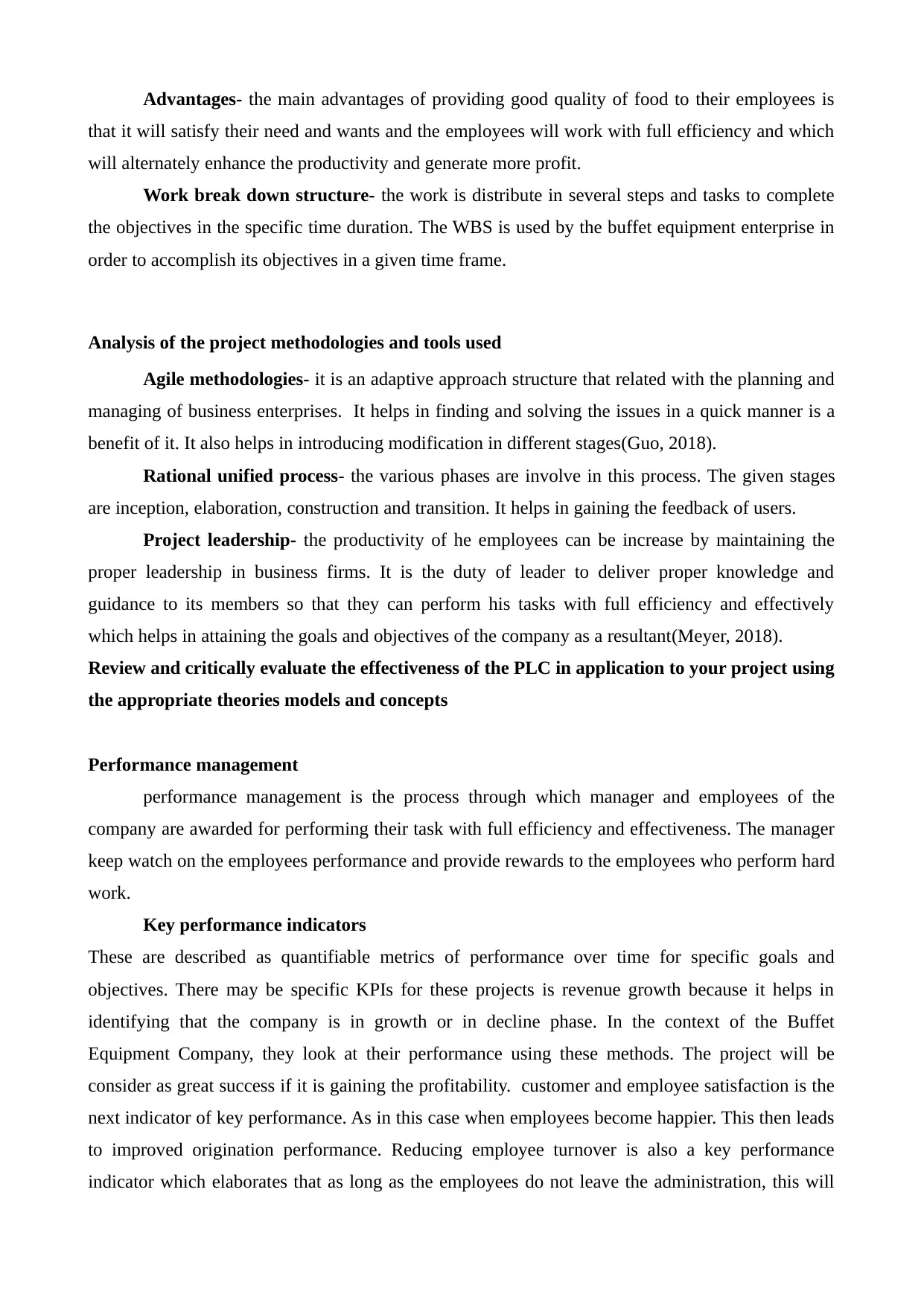
Advantages- the main advantages of providing good quality of food to their employees is
that it will satisfy their need and wants and the employees will work with full efficiency and which
will alternately enhance the productivity and generate more profit.
Work break down structure- the work is distribute in several steps and tasks to complete
the objectives in the specific time duration. The WBS is used by the buffet equipment enterprise in
order to accomplish its objectives in a given time frame.
Analysis of the project methodologies and tools used
Agile methodologies- it is an adaptive approach structure that related with the planning and
managing of business enterprises. It helps in finding and solving the issues in a quick manner is a
benefit of it. It also helps in introducing modification in different stages(Guo, 2018).
Rational unified process- the various phases are involve in this process. The given stages
are inception, elaboration, construction and transition. It helps in gaining the feedback of users.
Project leadership- the productivity of he employees can be increase by maintaining the
proper leadership in business firms. It is the duty of leader to deliver proper knowledge and
guidance to its members so that they can perform his tasks with full efficiency and effectively
which helps in attaining the goals and objectives of the company as a resultant(Meyer, 2018).
Review and critically evaluate the effectiveness of the PLC in application to your project using
the appropriate theories models and concepts
Performance management
performance management is the process through which manager and employees of the
company are awarded for performing their task with full efficiency and effectiveness. The manager
keep watch on the employees performance and provide rewards to the employees who perform hard
work.
Key performance indicators
These are described as quantifiable metrics of performance over time for specific goals and
objectives. There may be specific KPIs for these projects is revenue growth because it helps in
identifying that the company is in growth or in decline phase. In the context of the Buffet
Equipment Company, they look at their performance using these methods. The project will be
consider as great success if it is gaining the profitability. customer and employee satisfaction is the
next indicator of key performance. As in this case when employees become happier. This then leads
to improved origination performance. Reducing employee turnover is also a key performance
indicator which elaborates that as long as the employees do not leave the administration, this will
that it will satisfy their need and wants and the employees will work with full efficiency and which
will alternately enhance the productivity and generate more profit.
Work break down structure- the work is distribute in several steps and tasks to complete
the objectives in the specific time duration. The WBS is used by the buffet equipment enterprise in
order to accomplish its objectives in a given time frame.
Analysis of the project methodologies and tools used
Agile methodologies- it is an adaptive approach structure that related with the planning and
managing of business enterprises. It helps in finding and solving the issues in a quick manner is a
benefit of it. It also helps in introducing modification in different stages(Guo, 2018).
Rational unified process- the various phases are involve in this process. The given stages
are inception, elaboration, construction and transition. It helps in gaining the feedback of users.
Project leadership- the productivity of he employees can be increase by maintaining the
proper leadership in business firms. It is the duty of leader to deliver proper knowledge and
guidance to its members so that they can perform his tasks with full efficiency and effectively
which helps in attaining the goals and objectives of the company as a resultant(Meyer, 2018).
Review and critically evaluate the effectiveness of the PLC in application to your project using
the appropriate theories models and concepts
Performance management
performance management is the process through which manager and employees of the
company are awarded for performing their task with full efficiency and effectiveness. The manager
keep watch on the employees performance and provide rewards to the employees who perform hard
work.
Key performance indicators
These are described as quantifiable metrics of performance over time for specific goals and
objectives. There may be specific KPIs for these projects is revenue growth because it helps in
identifying that the company is in growth or in decline phase. In the context of the Buffet
Equipment Company, they look at their performance using these methods. The project will be
consider as great success if it is gaining the profitability. customer and employee satisfaction is the
next indicator of key performance. As in this case when employees become happier. This then leads
to improved origination performance. Reducing employee turnover is also a key performance
indicator which elaborates that as long as the employees do not leave the administration, this will
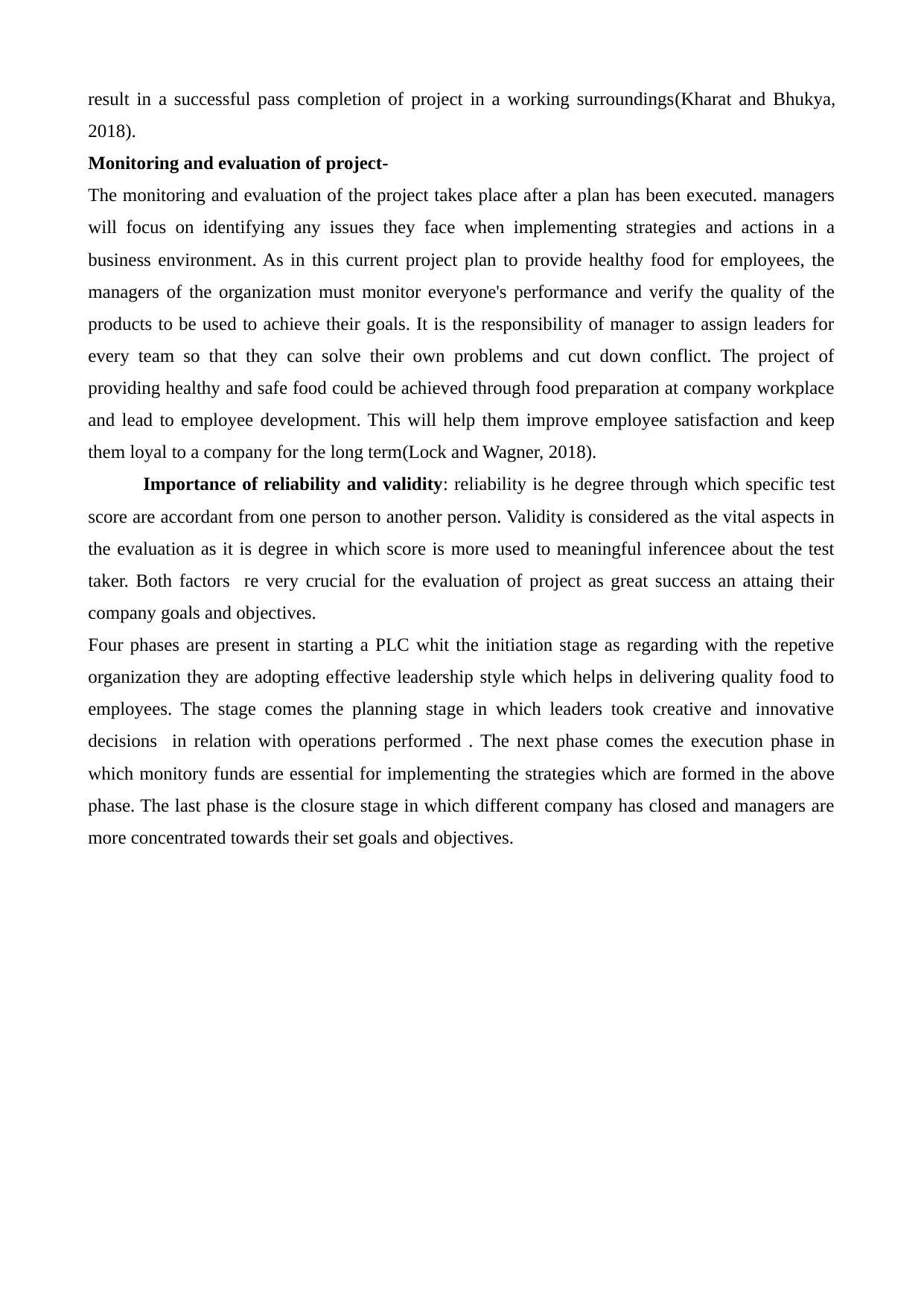
result in a successful pass completion of project in a working surroundings(Kharat and Bhukya,
2018).
Monitoring and evaluation of project-
The monitoring and evaluation of the project takes place after a plan has been executed. managers
will focus on identifying any issues they face when implementing strategies and actions in a
business environment. As in this current project plan to provide healthy food for employees, the
managers of the organization must monitor everyone's performance and verify the quality of the
products to be used to achieve their goals. It is the responsibility of manager to assign leaders for
every team so that they can solve their own problems and cut down conflict. The project of
providing healthy and safe food could be achieved through food preparation at company workplace
and lead to employee development. This will help them improve employee satisfaction and keep
them loyal to a company for the long term(Lock and Wagner, 2018).
Importance of reliability and validity: reliability is he degree through which specific test
score are accordant from one person to another person. Validity is considered as the vital aspects in
the evaluation as it is degree in which score is more used to meaningful inferencee about the test
taker. Both factors re very crucial for the evaluation of project as great success an attaing their
company goals and objectives.
Four phases are present in starting a PLC whit the initiation stage as regarding with the repetive
organization they are adopting effective leadership style which helps in delivering quality food to
employees. The stage comes the planning stage in which leaders took creative and innovative
decisions in relation with operations performed . The next phase comes the execution phase in
which monitory funds are essential for implementing the strategies which are formed in the above
phase. The last phase is the closure stage in which different company has closed and managers are
more concentrated towards their set goals and objectives.
2018).
Monitoring and evaluation of project-
The monitoring and evaluation of the project takes place after a plan has been executed. managers
will focus on identifying any issues they face when implementing strategies and actions in a
business environment. As in this current project plan to provide healthy food for employees, the
managers of the organization must monitor everyone's performance and verify the quality of the
products to be used to achieve their goals. It is the responsibility of manager to assign leaders for
every team so that they can solve their own problems and cut down conflict. The project of
providing healthy and safe food could be achieved through food preparation at company workplace
and lead to employee development. This will help them improve employee satisfaction and keep
them loyal to a company for the long term(Lock and Wagner, 2018).
Importance of reliability and validity: reliability is he degree through which specific test
score are accordant from one person to another person. Validity is considered as the vital aspects in
the evaluation as it is degree in which score is more used to meaningful inferencee about the test
taker. Both factors re very crucial for the evaluation of project as great success an attaing their
company goals and objectives.
Four phases are present in starting a PLC whit the initiation stage as regarding with the repetive
organization they are adopting effective leadership style which helps in delivering quality food to
employees. The stage comes the planning stage in which leaders took creative and innovative
decisions in relation with operations performed . The next phase comes the execution phase in
which monitory funds are essential for implementing the strategies which are formed in the above
phase. The last phase is the closure stage in which different company has closed and managers are
more concentrated towards their set goals and objectives.
You're viewing a preview
Unlock full access by subscribing today!
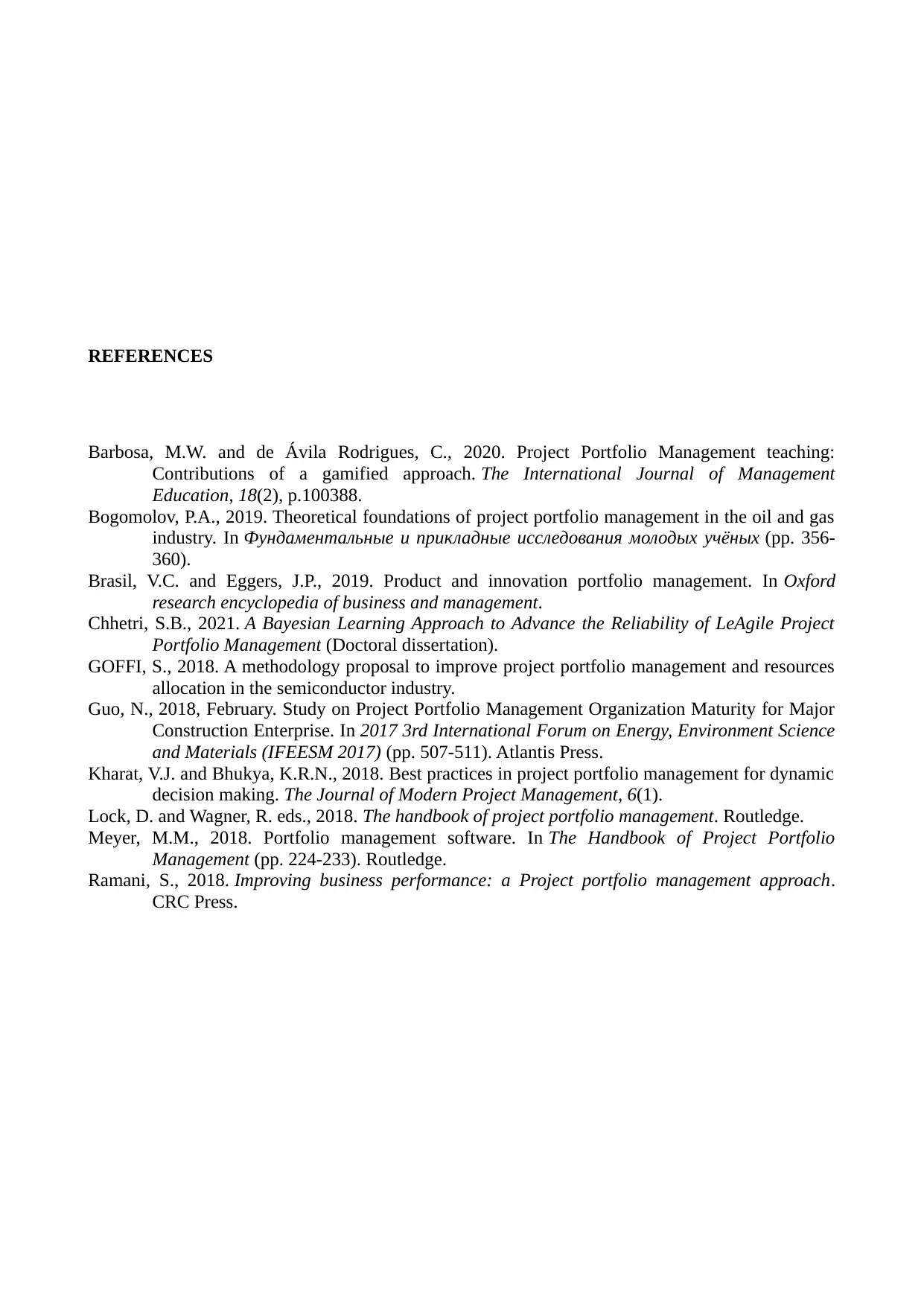
REFERENCES
Barbosa, M.W. and de Ávila Rodrigues, C., 2020. Project Portfolio Management teaching:
Contributions of a gamified approach. The International Journal of Management
Education, 18(2), p.100388.
Bogomolov, P.A., 2019. Theoretical foundations of project portfolio management in the oil and gas
industry. In Фундаментальные и прикладные исследования молодых учёных (pp. 356-
360).
Brasil, V.C. and Eggers, J.P., 2019. Product and innovation portfolio management. In Oxford
research encyclopedia of business and management.
Chhetri, S.B., 2021. A Bayesian Learning Approach to Advance the Reliability of LeAgile Project
Portfolio Management (Doctoral dissertation).
GOFFI, S., 2018. A methodology proposal to improve project portfolio management and resources
allocation in the semiconductor industry.
Guo, N., 2018, February. Study on Project Portfolio Management Organization Maturity for Major
Construction Enterprise. In 2017 3rd International Forum on Energy, Environment Science
and Materials (IFEESM 2017) (pp. 507-511). Atlantis Press.
Kharat, V.J. and Bhukya, K.R.N., 2018. Best practices in project portfolio management for dynamic
decision making. The Journal of Modern Project Management, 6(1).
Lock, D. and Wagner, R. eds., 2018. The handbook of project portfolio management. Routledge.
Meyer, M.M., 2018. Portfolio management software. In The Handbook of Project Portfolio
Management (pp. 224-233). Routledge.
Ramani, S., 2018. Improving business performance: a Project portfolio management approach.
CRC Press.
Barbosa, M.W. and de Ávila Rodrigues, C., 2020. Project Portfolio Management teaching:
Contributions of a gamified approach. The International Journal of Management
Education, 18(2), p.100388.
Bogomolov, P.A., 2019. Theoretical foundations of project portfolio management in the oil and gas
industry. In Фундаментальные и прикладные исследования молодых учёных (pp. 356-
360).
Brasil, V.C. and Eggers, J.P., 2019. Product and innovation portfolio management. In Oxford
research encyclopedia of business and management.
Chhetri, S.B., 2021. A Bayesian Learning Approach to Advance the Reliability of LeAgile Project
Portfolio Management (Doctoral dissertation).
GOFFI, S., 2018. A methodology proposal to improve project portfolio management and resources
allocation in the semiconductor industry.
Guo, N., 2018, February. Study on Project Portfolio Management Organization Maturity for Major
Construction Enterprise. In 2017 3rd International Forum on Energy, Environment Science
and Materials (IFEESM 2017) (pp. 507-511). Atlantis Press.
Kharat, V.J. and Bhukya, K.R.N., 2018. Best practices in project portfolio management for dynamic
decision making. The Journal of Modern Project Management, 6(1).
Lock, D. and Wagner, R. eds., 2018. The handbook of project portfolio management. Routledge.
Meyer, M.M., 2018. Portfolio management software. In The Handbook of Project Portfolio
Management (pp. 224-233). Routledge.
Ramani, S., 2018. Improving business performance: a Project portfolio management approach.
CRC Press.
1 out of 16
Related Documents

Your All-in-One AI-Powered Toolkit for Academic Success.
+13062052269
info@desklib.com
Available 24*7 on WhatsApp / Email
Unlock your academic potential
© 2024 | Zucol Services PVT LTD | All rights reserved.