Operations, Logistics and Supply Chain Management
VerifiedAdded on  2020/12/09
|10
|3418
|124
Report
AI Summary
This report examines the operations, logistics, and supply chain management practices of Toyota, a leading automotive manufacturer. It analyzes key areas such as logistics mix, location and layout, and explores the application of lean manufacturing and Just-In-Time principles. The report also identifies potential areas for improvement in Toyota's operations. Desklib provides past papers and solved assignments for students.
Contribute Materials
Your contribution can guide someone’s learning journey. Share your
documents today.
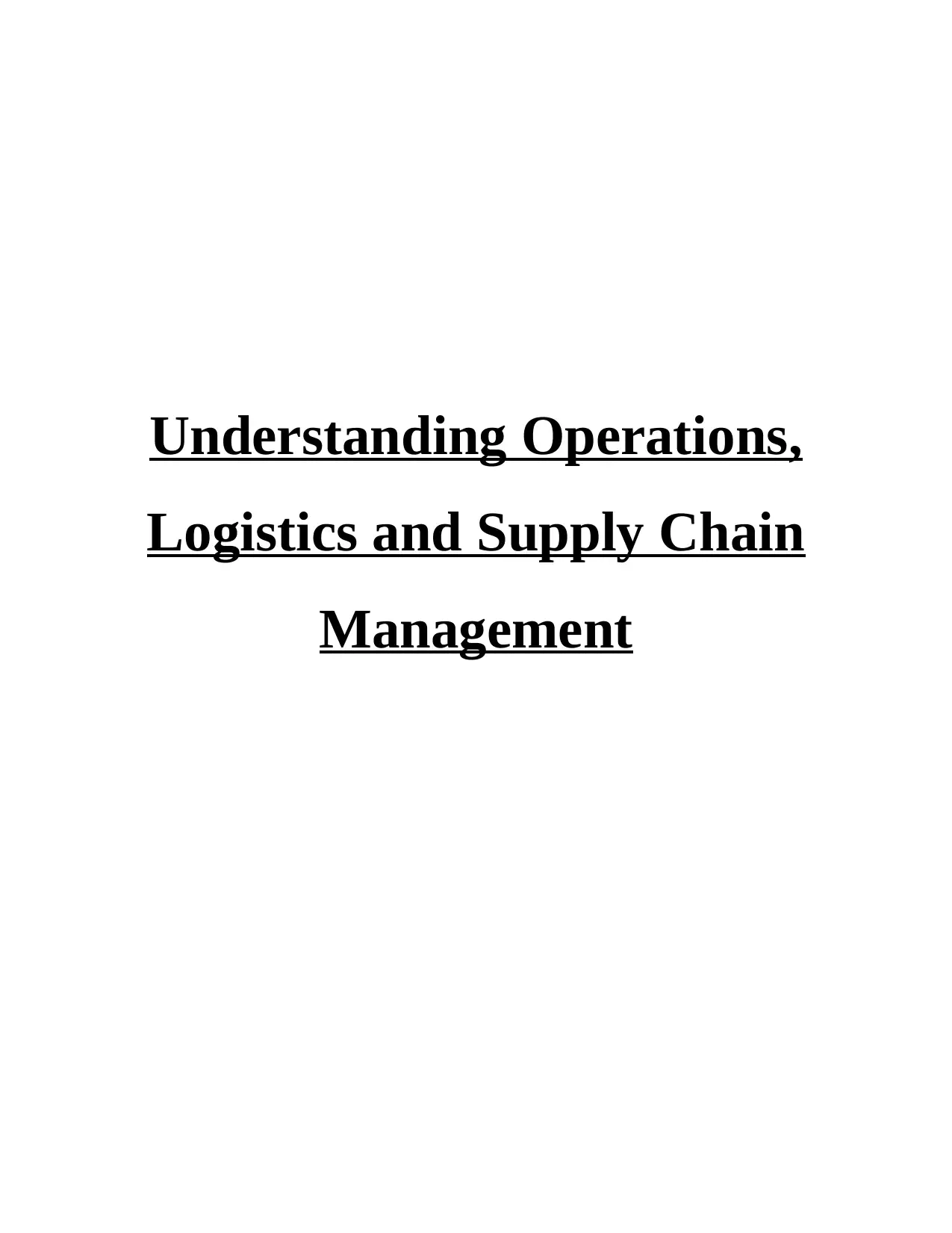
Understanding Operations,
Logistics and Supply Chain
Management
Logistics and Supply Chain
Management
Secure Best Marks with AI Grader
Need help grading? Try our AI Grader for instant feedback on your assignments.
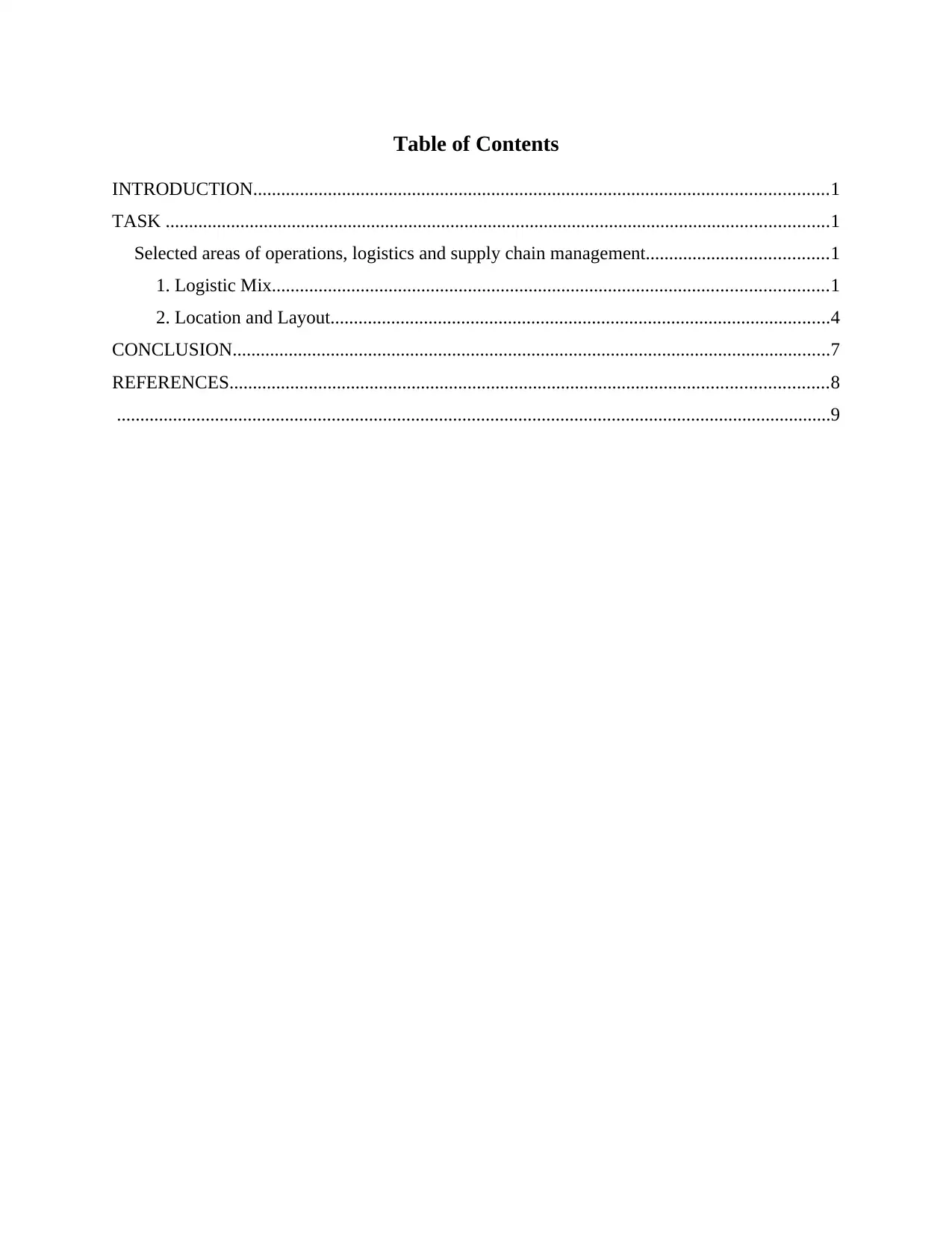
Table of Contents
INTRODUCTION...........................................................................................................................1
TASK ..............................................................................................................................................1
Selected areas of operations, logistics and supply chain management.......................................1
1. Logistic Mix.......................................................................................................................1
2. Location and Layout...........................................................................................................4
CONCLUSION................................................................................................................................7
REFERENCES................................................................................................................................8
.........................................................................................................................................................9
INTRODUCTION...........................................................................................................................1
TASK ..............................................................................................................................................1
Selected areas of operations, logistics and supply chain management.......................................1
1. Logistic Mix.......................................................................................................................1
2. Location and Layout...........................................................................................................4
CONCLUSION................................................................................................................................7
REFERENCES................................................................................................................................8
.........................................................................................................................................................9
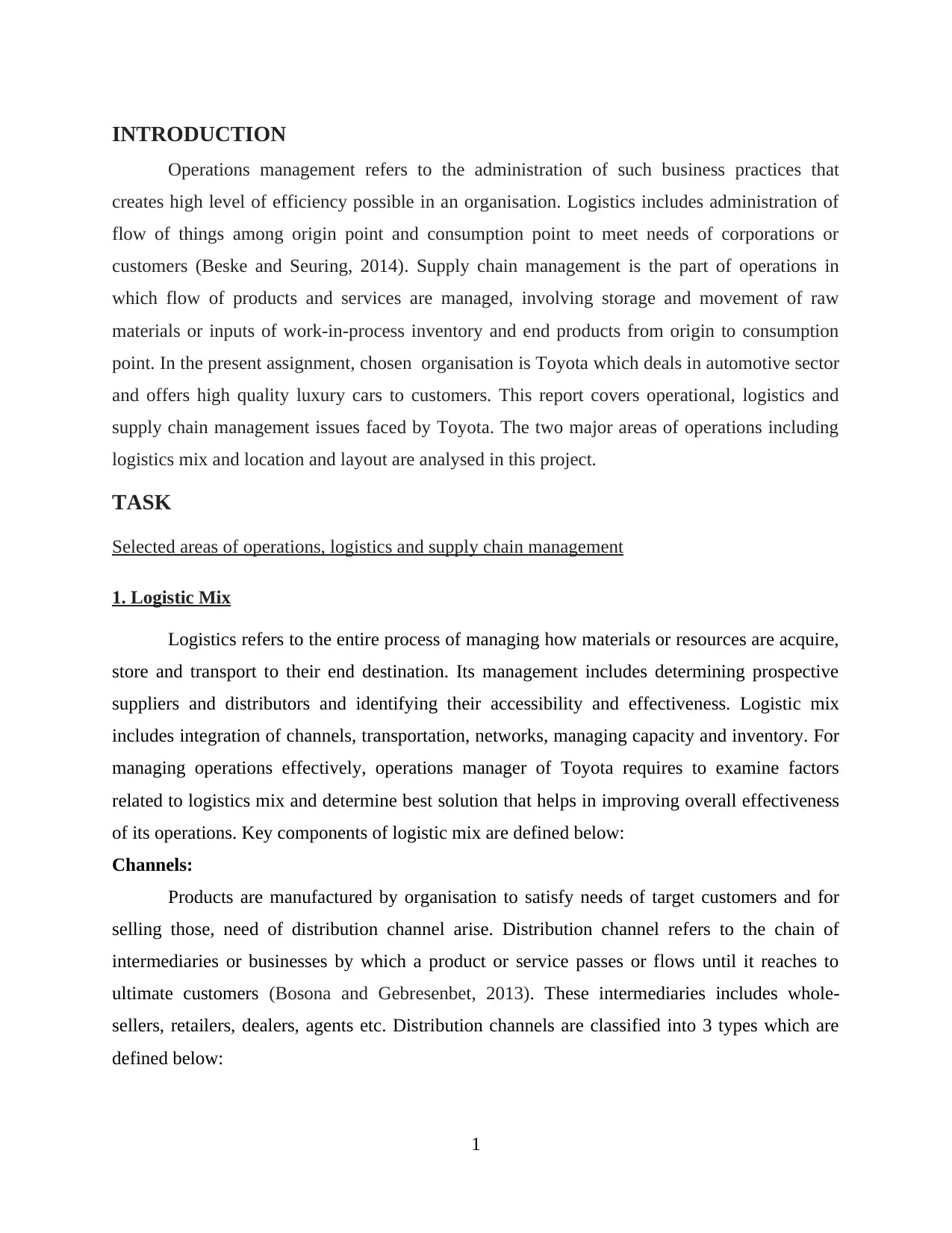
INTRODUCTION
Operations management refers to the administration of such business practices that
creates high level of efficiency possible in an organisation. Logistics includes administration of
flow of things among origin point and consumption point to meet needs of corporations or
customers (Beske and Seuring, 2014). Supply chain management is the part of operations in
which flow of products and services are managed, involving storage and movement of raw
materials or inputs of work-in-process inventory and end products from origin to consumption
point. In the present assignment, chosen organisation is Toyota which deals in automotive sector
and offers high quality luxury cars to customers. This report covers operational, logistics and
supply chain management issues faced by Toyota. The two major areas of operations including
logistics mix and location and layout are analysed in this project.
TASK
Selected areas of operations, logistics and supply chain management
1. Logistic Mix
Logistics refers to the entire process of managing how materials or resources are acquire,
store and transport to their end destination. Its management includes determining prospective
suppliers and distributors and identifying their accessibility and effectiveness. Logistic mix
includes integration of channels, transportation, networks, managing capacity and inventory. For
managing operations effectively, operations manager of Toyota requires to examine factors
related to logistics mix and determine best solution that helps in improving overall effectiveness
of its operations. Key components of logistic mix are defined below:
Channels:
Products are manufactured by organisation to satisfy needs of target customers and for
selling those, need of distribution channel arise. Distribution channel refers to the chain of
intermediaries or businesses by which a product or service passes or flows until it reaches to
ultimate customers (Bosona and Gebresenbet, 2013). These intermediaries includes whole-
sellers, retailers, dealers, agents etc. Distribution channels are classified into 3 types which are
defined below:
1
Operations management refers to the administration of such business practices that
creates high level of efficiency possible in an organisation. Logistics includes administration of
flow of things among origin point and consumption point to meet needs of corporations or
customers (Beske and Seuring, 2014). Supply chain management is the part of operations in
which flow of products and services are managed, involving storage and movement of raw
materials or inputs of work-in-process inventory and end products from origin to consumption
point. In the present assignment, chosen organisation is Toyota which deals in automotive sector
and offers high quality luxury cars to customers. This report covers operational, logistics and
supply chain management issues faced by Toyota. The two major areas of operations including
logistics mix and location and layout are analysed in this project.
TASK
Selected areas of operations, logistics and supply chain management
1. Logistic Mix
Logistics refers to the entire process of managing how materials or resources are acquire,
store and transport to their end destination. Its management includes determining prospective
suppliers and distributors and identifying their accessibility and effectiveness. Logistic mix
includes integration of channels, transportation, networks, managing capacity and inventory. For
managing operations effectively, operations manager of Toyota requires to examine factors
related to logistics mix and determine best solution that helps in improving overall effectiveness
of its operations. Key components of logistic mix are defined below:
Channels:
Products are manufactured by organisation to satisfy needs of target customers and for
selling those, need of distribution channel arise. Distribution channel refers to the chain of
intermediaries or businesses by which a product or service passes or flows until it reaches to
ultimate customers (Bosona and Gebresenbet, 2013). These intermediaries includes whole-
sellers, retailers, dealers, agents etc. Distribution channels are classified into 3 types which are
defined below:
1
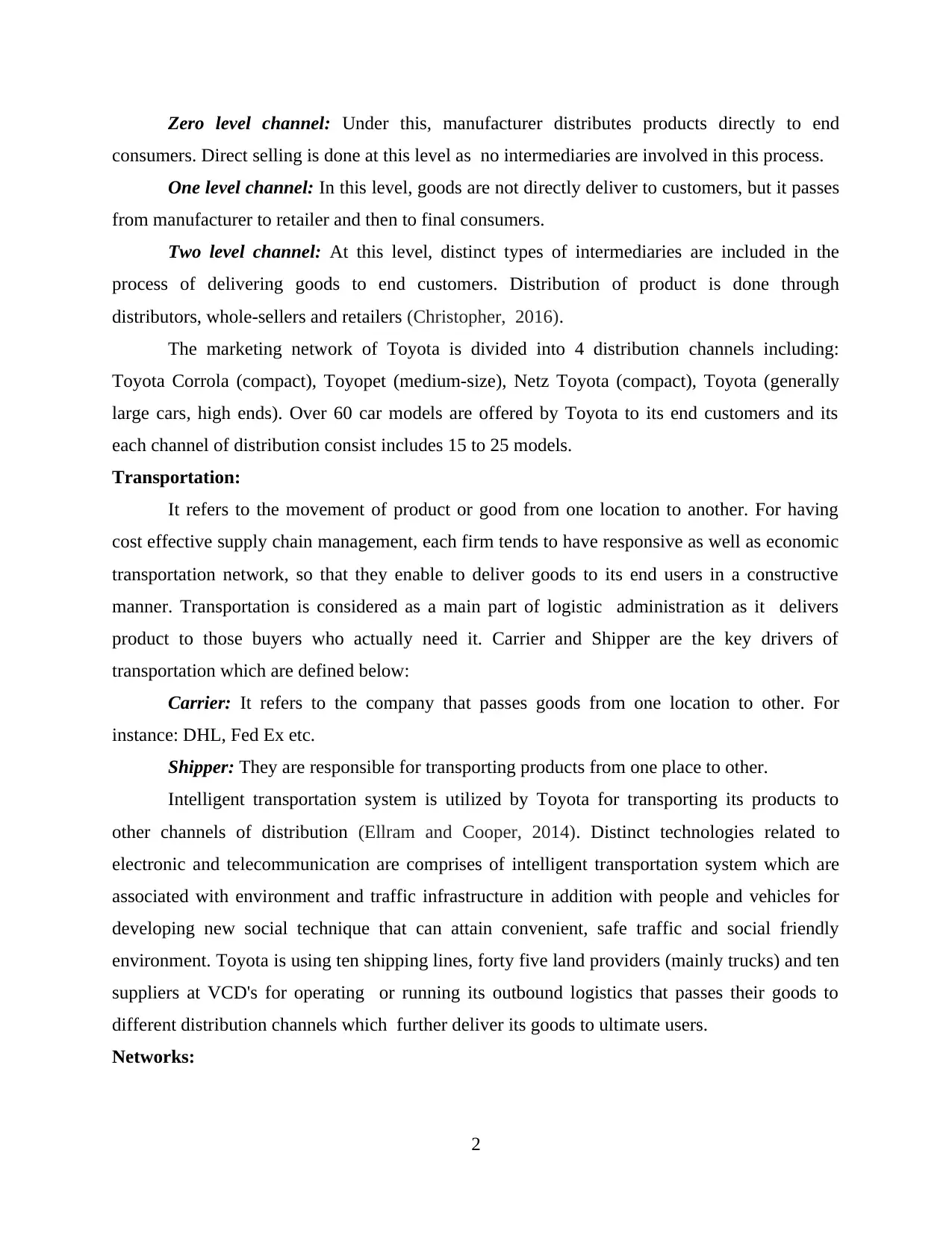
Zero level channel: Under this, manufacturer distributes products directly to end
consumers. Direct selling is done at this level as no intermediaries are involved in this process.
One level channel: In this level, goods are not directly deliver to customers, but it passes
from manufacturer to retailer and then to final consumers.
Two level channel: At this level, distinct types of intermediaries are included in the
process of delivering goods to end customers. Distribution of product is done through
distributors, whole-sellers and retailers (Christopher, 2016).
The marketing network of Toyota is divided into 4 distribution channels including:
Toyota Corrola (compact), Toyopet (medium-size), Netz Toyota (compact), Toyota (generally
large cars, high ends). Over 60 car models are offered by Toyota to its end customers and its
each channel of distribution consist includes 15 to 25 models.
Transportation:
It refers to the movement of product or good from one location to another. For having
cost effective supply chain management, each firm tends to have responsive as well as economic
transportation network, so that they enable to deliver goods to its end users in a constructive
manner. Transportation is considered as a main part of logistic administration as it delivers
product to those buyers who actually need it. Carrier and Shipper are the key drivers of
transportation which are defined below:
Carrier: It refers to the company that passes goods from one location to other. For
instance: DHL, Fed Ex etc.
Shipper: They are responsible for transporting products from one place to other.
Intelligent transportation system is utilized by Toyota for transporting its products to
other channels of distribution (Ellram and Cooper, 2014). Distinct technologies related to
electronic and telecommunication are comprises of intelligent transportation system which are
associated with environment and traffic infrastructure in addition with people and vehicles for
developing new social technique that can attain convenient, safe traffic and social friendly
environment. Toyota is using ten shipping lines, forty five land providers (mainly trucks) and ten
suppliers at VCD's for operating or running its outbound logistics that passes their goods to
different distribution channels which further deliver its goods to ultimate users.
Networks:
2
consumers. Direct selling is done at this level as no intermediaries are involved in this process.
One level channel: In this level, goods are not directly deliver to customers, but it passes
from manufacturer to retailer and then to final consumers.
Two level channel: At this level, distinct types of intermediaries are included in the
process of delivering goods to end customers. Distribution of product is done through
distributors, whole-sellers and retailers (Christopher, 2016).
The marketing network of Toyota is divided into 4 distribution channels including:
Toyota Corrola (compact), Toyopet (medium-size), Netz Toyota (compact), Toyota (generally
large cars, high ends). Over 60 car models are offered by Toyota to its end customers and its
each channel of distribution consist includes 15 to 25 models.
Transportation:
It refers to the movement of product or good from one location to another. For having
cost effective supply chain management, each firm tends to have responsive as well as economic
transportation network, so that they enable to deliver goods to its end users in a constructive
manner. Transportation is considered as a main part of logistic administration as it delivers
product to those buyers who actually need it. Carrier and Shipper are the key drivers of
transportation which are defined below:
Carrier: It refers to the company that passes goods from one location to other. For
instance: DHL, Fed Ex etc.
Shipper: They are responsible for transporting products from one place to other.
Intelligent transportation system is utilized by Toyota for transporting its products to
other channels of distribution (Ellram and Cooper, 2014). Distinct technologies related to
electronic and telecommunication are comprises of intelligent transportation system which are
associated with environment and traffic infrastructure in addition with people and vehicles for
developing new social technique that can attain convenient, safe traffic and social friendly
environment. Toyota is using ten shipping lines, forty five land providers (mainly trucks) and ten
suppliers at VCD's for operating or running its outbound logistics that passes their goods to
different distribution channels which further deliver its goods to ultimate users.
Networks:
2
Secure Best Marks with AI Grader
Need help grading? Try our AI Grader for instant feedback on your assignments.
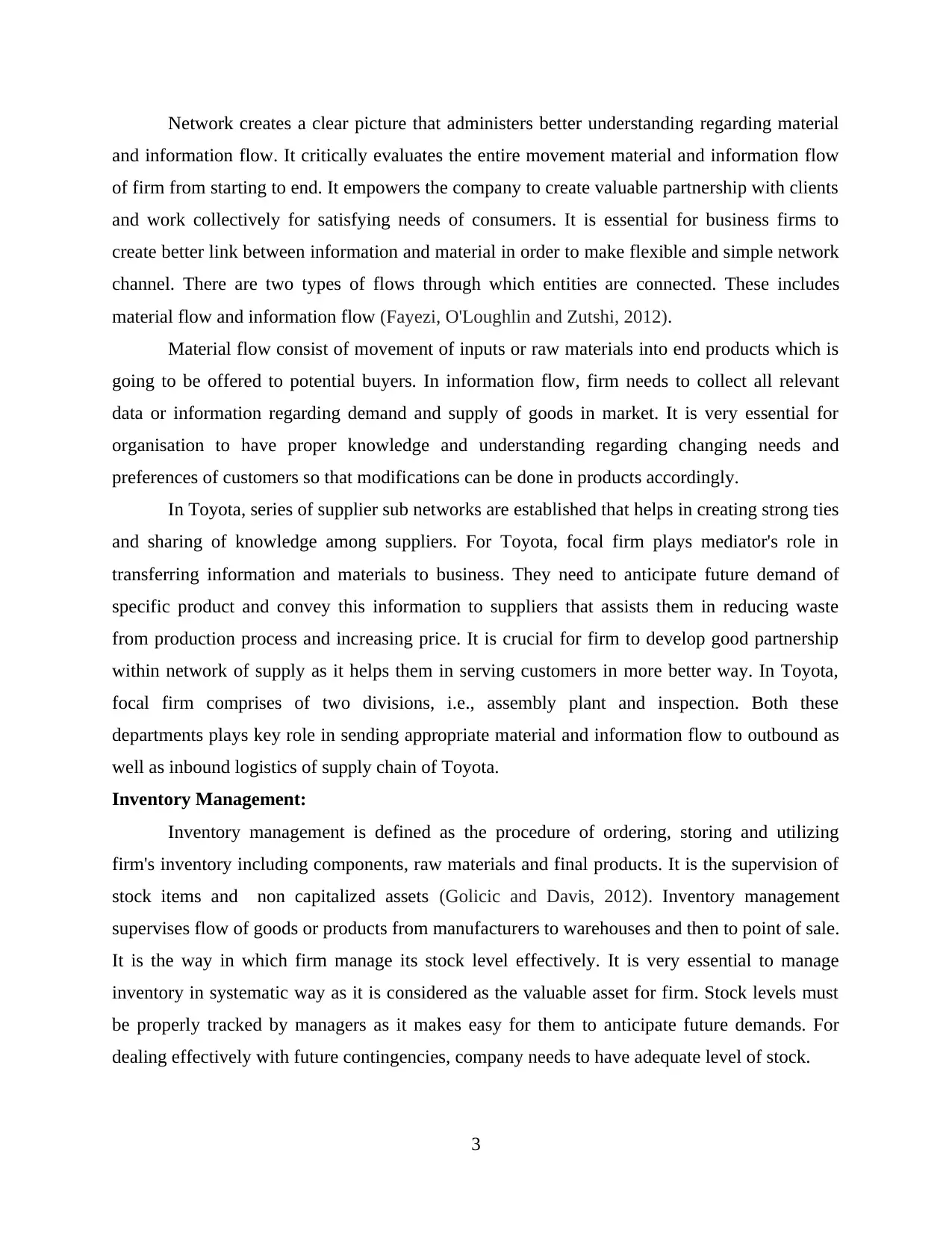
Network creates a clear picture that administers better understanding regarding material
and information flow. It critically evaluates the entire movement material and information flow
of firm from starting to end. It empowers the company to create valuable partnership with clients
and work collectively for satisfying needs of consumers. It is essential for business firms to
create better link between information and material in order to make flexible and simple network
channel. There are two types of flows through which entities are connected. These includes
material flow and information flow (Fayezi, O'Loughlin and Zutshi, 2012).
Material flow consist of movement of inputs or raw materials into end products which is
going to be offered to potential buyers. In information flow, firm needs to collect all relevant
data or information regarding demand and supply of goods in market. It is very essential for
organisation to have proper knowledge and understanding regarding changing needs and
preferences of customers so that modifications can be done in products accordingly.
In Toyota, series of supplier sub networks are established that helps in creating strong ties
and sharing of knowledge among suppliers. For Toyota, focal firm plays mediator's role in
transferring information and materials to business. They need to anticipate future demand of
specific product and convey this information to suppliers that assists them in reducing waste
from production process and increasing price. It is crucial for firm to develop good partnership
within network of supply as it helps them in serving customers in more better way. In Toyota,
focal firm comprises of two divisions, i.e., assembly plant and inspection. Both these
departments plays key role in sending appropriate material and information flow to outbound as
well as inbound logistics of supply chain of Toyota.
Inventory Management:
Inventory management is defined as the procedure of ordering, storing and utilizing
firm's inventory including components, raw materials and final products. It is the supervision of
stock items and non capitalized assets (Golicic and Davis, 2012). Inventory management
supervises flow of goods or products from manufacturers to warehouses and then to point of sale.
It is the way in which firm manage its stock level effectively. It is very essential to manage
inventory in systematic way as it is considered as the valuable asset for firm. Stock levels must
be properly tracked by managers as it makes easy for them to anticipate future demands. For
dealing effectively with future contingencies, company needs to have adequate level of stock.
3
and information flow. It critically evaluates the entire movement material and information flow
of firm from starting to end. It empowers the company to create valuable partnership with clients
and work collectively for satisfying needs of consumers. It is essential for business firms to
create better link between information and material in order to make flexible and simple network
channel. There are two types of flows through which entities are connected. These includes
material flow and information flow (Fayezi, O'Loughlin and Zutshi, 2012).
Material flow consist of movement of inputs or raw materials into end products which is
going to be offered to potential buyers. In information flow, firm needs to collect all relevant
data or information regarding demand and supply of goods in market. It is very essential for
organisation to have proper knowledge and understanding regarding changing needs and
preferences of customers so that modifications can be done in products accordingly.
In Toyota, series of supplier sub networks are established that helps in creating strong ties
and sharing of knowledge among suppliers. For Toyota, focal firm plays mediator's role in
transferring information and materials to business. They need to anticipate future demand of
specific product and convey this information to suppliers that assists them in reducing waste
from production process and increasing price. It is crucial for firm to develop good partnership
within network of supply as it helps them in serving customers in more better way. In Toyota,
focal firm comprises of two divisions, i.e., assembly plant and inspection. Both these
departments plays key role in sending appropriate material and information flow to outbound as
well as inbound logistics of supply chain of Toyota.
Inventory Management:
Inventory management is defined as the procedure of ordering, storing and utilizing
firm's inventory including components, raw materials and final products. It is the supervision of
stock items and non capitalized assets (Golicic and Davis, 2012). Inventory management
supervises flow of goods or products from manufacturers to warehouses and then to point of sale.
It is the way in which firm manage its stock level effectively. It is very essential to manage
inventory in systematic way as it is considered as the valuable asset for firm. Stock levels must
be properly tracked by managers as it makes easy for them to anticipate future demands. For
dealing effectively with future contingencies, company needs to have adequate level of stock.
3
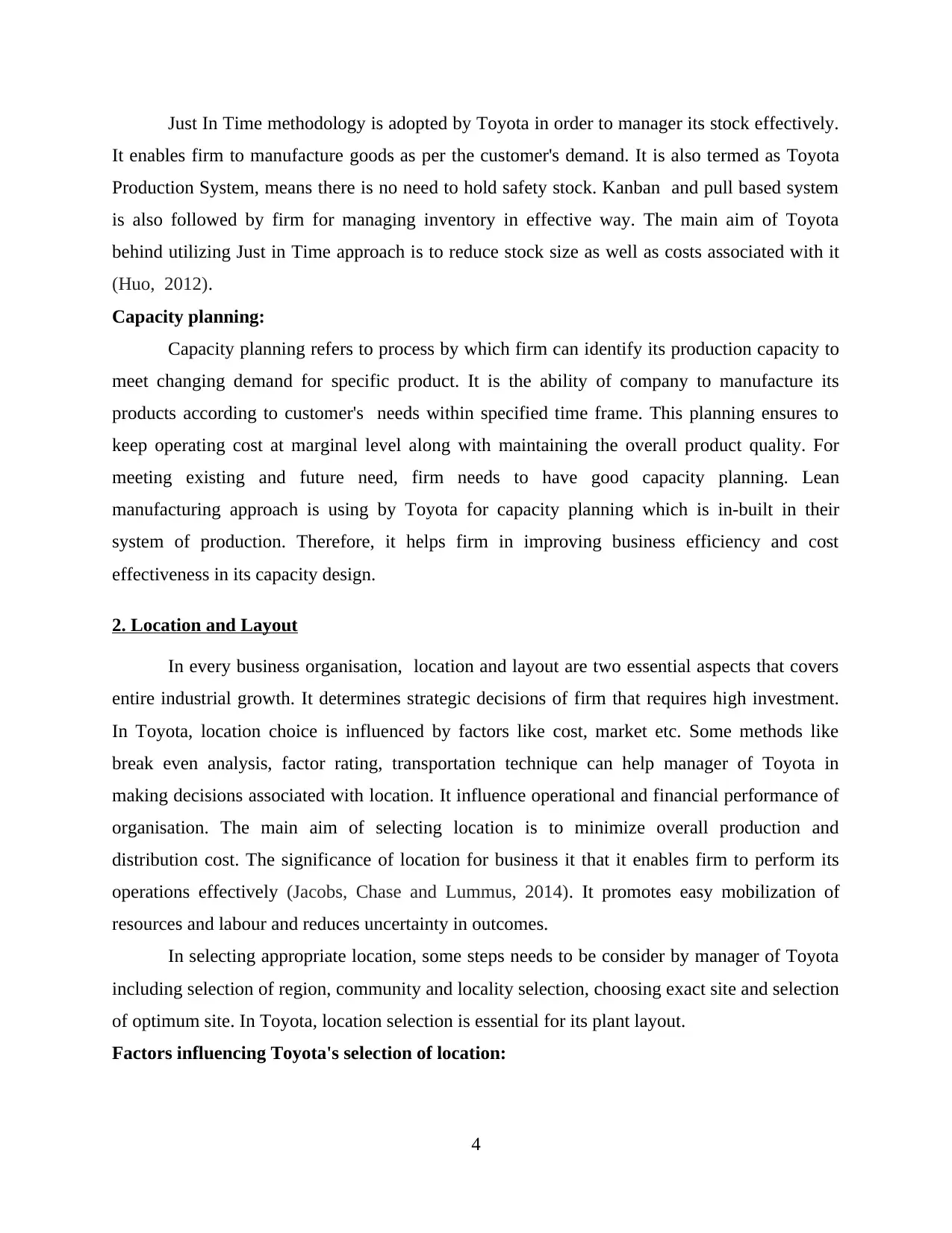
Just In Time methodology is adopted by Toyota in order to manager its stock effectively.
It enables firm to manufacture goods as per the customer's demand. It is also termed as Toyota
Production System, means there is no need to hold safety stock. Kanban and pull based system
is also followed by firm for managing inventory in effective way. The main aim of Toyota
behind utilizing Just in Time approach is to reduce stock size as well as costs associated with it
(Huo, 2012).
Capacity planning:
Capacity planning refers to process by which firm can identify its production capacity to
meet changing demand for specific product. It is the ability of company to manufacture its
products according to customer's needs within specified time frame. This planning ensures to
keep operating cost at marginal level along with maintaining the overall product quality. For
meeting existing and future need, firm needs to have good capacity planning. Lean
manufacturing approach is using by Toyota for capacity planning which is in-built in their
system of production. Therefore, it helps firm in improving business efficiency and cost
effectiveness in its capacity design.
2. Location and Layout
In every business organisation, location and layout are two essential aspects that covers
entire industrial growth. It determines strategic decisions of firm that requires high investment.
In Toyota, location choice is influenced by factors like cost, market etc. Some methods like
break even analysis, factor rating, transportation technique can help manager of Toyota in
making decisions associated with location. It influence operational and financial performance of
organisation. The main aim of selecting location is to minimize overall production and
distribution cost. The significance of location for business it that it enables firm to perform its
operations effectively (Jacobs, Chase and Lummus, 2014). It promotes easy mobilization of
resources and labour and reduces uncertainty in outcomes.
In selecting appropriate location, some steps needs to be consider by manager of Toyota
including selection of region, community and locality selection, choosing exact site and selection
of optimum site. In Toyota, location selection is essential for its plant layout.
Factors influencing Toyota's selection of location:
4
It enables firm to manufacture goods as per the customer's demand. It is also termed as Toyota
Production System, means there is no need to hold safety stock. Kanban and pull based system
is also followed by firm for managing inventory in effective way. The main aim of Toyota
behind utilizing Just in Time approach is to reduce stock size as well as costs associated with it
(Huo, 2012).
Capacity planning:
Capacity planning refers to process by which firm can identify its production capacity to
meet changing demand for specific product. It is the ability of company to manufacture its
products according to customer's needs within specified time frame. This planning ensures to
keep operating cost at marginal level along with maintaining the overall product quality. For
meeting existing and future need, firm needs to have good capacity planning. Lean
manufacturing approach is using by Toyota for capacity planning which is in-built in their
system of production. Therefore, it helps firm in improving business efficiency and cost
effectiveness in its capacity design.
2. Location and Layout
In every business organisation, location and layout are two essential aspects that covers
entire industrial growth. It determines strategic decisions of firm that requires high investment.
In Toyota, location choice is influenced by factors like cost, market etc. Some methods like
break even analysis, factor rating, transportation technique can help manager of Toyota in
making decisions associated with location. It influence operational and financial performance of
organisation. The main aim of selecting location is to minimize overall production and
distribution cost. The significance of location for business it that it enables firm to perform its
operations effectively (Jacobs, Chase and Lummus, 2014). It promotes easy mobilization of
resources and labour and reduces uncertainty in outcomes.
In selecting appropriate location, some steps needs to be consider by manager of Toyota
including selection of region, community and locality selection, choosing exact site and selection
of optimum site. In Toyota, location selection is essential for its plant layout.
Factors influencing Toyota's selection of location:
4
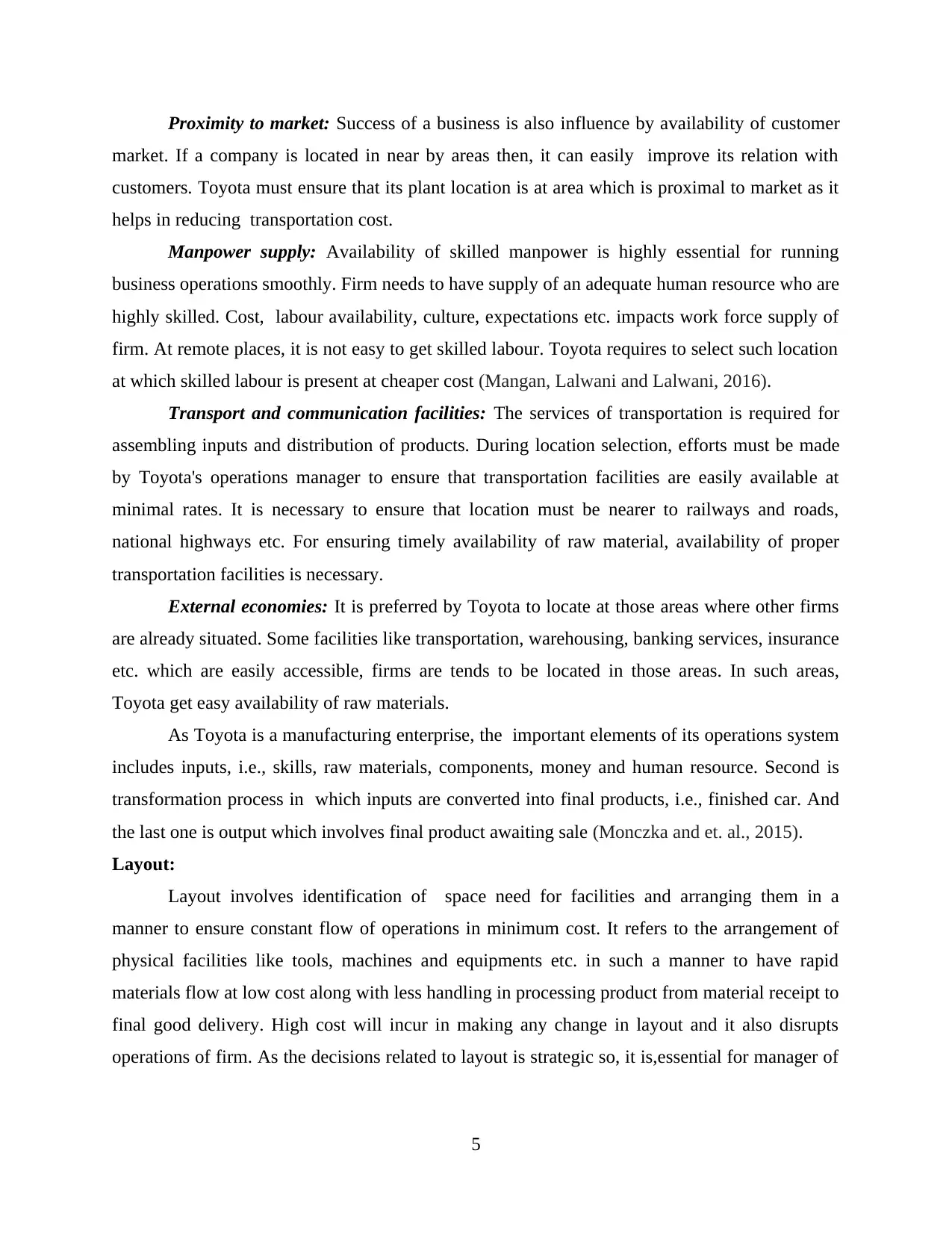
Proximity to market: Success of a business is also influence by availability of customer
market. If a company is located in near by areas then, it can easily improve its relation with
customers. Toyota must ensure that its plant location is at area which is proximal to market as it
helps in reducing transportation cost.
Manpower supply: Availability of skilled manpower is highly essential for running
business operations smoothly. Firm needs to have supply of an adequate human resource who are
highly skilled. Cost, labour availability, culture, expectations etc. impacts work force supply of
firm. At remote places, it is not easy to get skilled labour. Toyota requires to select such location
at which skilled labour is present at cheaper cost (Mangan, Lalwani and Lalwani, 2016).
Transport and communication facilities: The services of transportation is required for
assembling inputs and distribution of products. During location selection, efforts must be made
by Toyota's operations manager to ensure that transportation facilities are easily available at
minimal rates. It is necessary to ensure that location must be nearer to railways and roads,
national highways etc. For ensuring timely availability of raw material, availability of proper
transportation facilities is necessary.
External economies: It is preferred by Toyota to locate at those areas where other firms
are already situated. Some facilities like transportation, warehousing, banking services, insurance
etc. which are easily accessible, firms are tends to be located in those areas. In such areas,
Toyota get easy availability of raw materials.
As Toyota is a manufacturing enterprise, the important elements of its operations system
includes inputs, i.e., skills, raw materials, components, money and human resource. Second is
transformation process in which inputs are converted into final products, i.e., finished car. And
the last one is output which involves final product awaiting sale (Monczka and et. al., 2015).
Layout:
Layout involves identification of space need for facilities and arranging them in a
manner to ensure constant flow of operations in minimum cost. It refers to the arrangement of
physical facilities like tools, machines and equipments etc. in such a manner to have rapid
materials flow at low cost along with less handling in processing product from material receipt to
final good delivery. High cost will incur in making any change in layout and it also disrupts
operations of firm. As the decisions related to layout is strategic so, it is,essential for manager of
5
market. If a company is located in near by areas then, it can easily improve its relation with
customers. Toyota must ensure that its plant location is at area which is proximal to market as it
helps in reducing transportation cost.
Manpower supply: Availability of skilled manpower is highly essential for running
business operations smoothly. Firm needs to have supply of an adequate human resource who are
highly skilled. Cost, labour availability, culture, expectations etc. impacts work force supply of
firm. At remote places, it is not easy to get skilled labour. Toyota requires to select such location
at which skilled labour is present at cheaper cost (Mangan, Lalwani and Lalwani, 2016).
Transport and communication facilities: The services of transportation is required for
assembling inputs and distribution of products. During location selection, efforts must be made
by Toyota's operations manager to ensure that transportation facilities are easily available at
minimal rates. It is necessary to ensure that location must be nearer to railways and roads,
national highways etc. For ensuring timely availability of raw material, availability of proper
transportation facilities is necessary.
External economies: It is preferred by Toyota to locate at those areas where other firms
are already situated. Some facilities like transportation, warehousing, banking services, insurance
etc. which are easily accessible, firms are tends to be located in those areas. In such areas,
Toyota get easy availability of raw materials.
As Toyota is a manufacturing enterprise, the important elements of its operations system
includes inputs, i.e., skills, raw materials, components, money and human resource. Second is
transformation process in which inputs are converted into final products, i.e., finished car. And
the last one is output which involves final product awaiting sale (Monczka and et. al., 2015).
Layout:
Layout involves identification of space need for facilities and arranging them in a
manner to ensure constant flow of operations in minimum cost. It refers to the arrangement of
physical facilities like tools, machines and equipments etc. in such a manner to have rapid
materials flow at low cost along with less handling in processing product from material receipt to
final good delivery. High cost will incur in making any change in layout and it also disrupts
operations of firm. As the decisions related to layout is strategic so, it is,essential for manager of
5
Paraphrase This Document
Need a fresh take? Get an instant paraphrase of this document with our AI Paraphraser
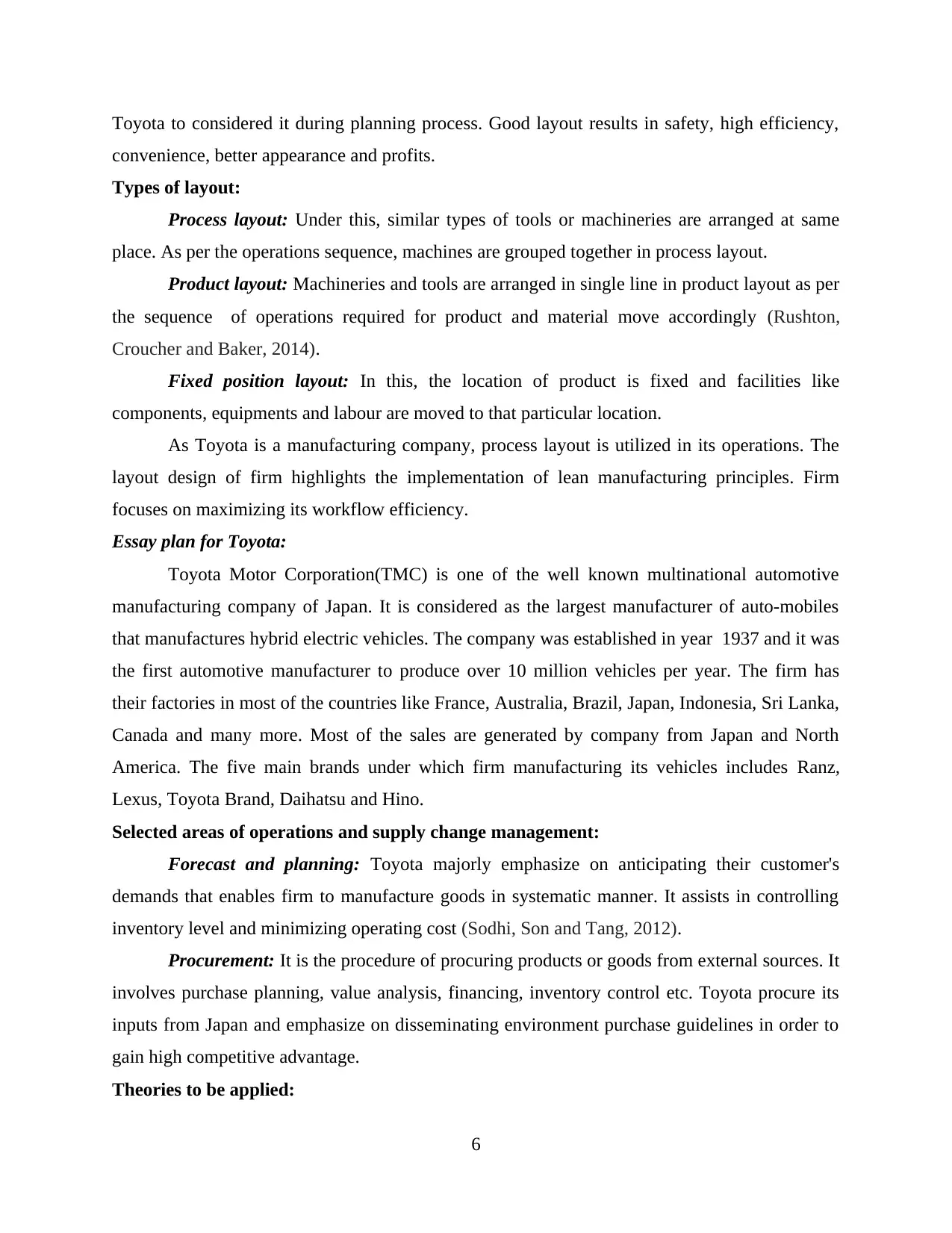
Toyota to considered it during planning process. Good layout results in safety, high efficiency,
convenience, better appearance and profits.
Types of layout:
Process layout: Under this, similar types of tools or machineries are arranged at same
place. As per the operations sequence, machines are grouped together in process layout.
Product layout: Machineries and tools are arranged in single line in product layout as per
the sequence of operations required for product and material move accordingly (Rushton,
Croucher and Baker, 2014).
Fixed position layout: In this, the location of product is fixed and facilities like
components, equipments and labour are moved to that particular location.
As Toyota is a manufacturing company, process layout is utilized in its operations. The
layout design of firm highlights the implementation of lean manufacturing principles. Firm
focuses on maximizing its workflow efficiency.
Essay plan for Toyota:
Toyota Motor Corporation(TMC) is one of the well known multinational automotive
manufacturing company of Japan. It is considered as the largest manufacturer of auto-mobiles
that manufactures hybrid electric vehicles. The company was established in year 1937 and it was
the first automotive manufacturer to produce over 10 million vehicles per year. The firm has
their factories in most of the countries like France, Australia, Brazil, Japan, Indonesia, Sri Lanka,
Canada and many more. Most of the sales are generated by company from Japan and North
America. The five main brands under which firm manufacturing its vehicles includes Ranz,
Lexus, Toyota Brand, Daihatsu and Hino.
Selected areas of operations and supply change management:
Forecast and planning: Toyota majorly emphasize on anticipating their customer's
demands that enables firm to manufacture goods in systematic manner. It assists in controlling
inventory level and minimizing operating cost (Sodhi, Son and Tang, 2012).
Procurement: It is the procedure of procuring products or goods from external sources. It
involves purchase planning, value analysis, financing, inventory control etc. Toyota procure its
inputs from Japan and emphasize on disseminating environment purchase guidelines in order to
gain high competitive advantage.
Theories to be applied:
6
convenience, better appearance and profits.
Types of layout:
Process layout: Under this, similar types of tools or machineries are arranged at same
place. As per the operations sequence, machines are grouped together in process layout.
Product layout: Machineries and tools are arranged in single line in product layout as per
the sequence of operations required for product and material move accordingly (Rushton,
Croucher and Baker, 2014).
Fixed position layout: In this, the location of product is fixed and facilities like
components, equipments and labour are moved to that particular location.
As Toyota is a manufacturing company, process layout is utilized in its operations. The
layout design of firm highlights the implementation of lean manufacturing principles. Firm
focuses on maximizing its workflow efficiency.
Essay plan for Toyota:
Toyota Motor Corporation(TMC) is one of the well known multinational automotive
manufacturing company of Japan. It is considered as the largest manufacturer of auto-mobiles
that manufactures hybrid electric vehicles. The company was established in year 1937 and it was
the first automotive manufacturer to produce over 10 million vehicles per year. The firm has
their factories in most of the countries like France, Australia, Brazil, Japan, Indonesia, Sri Lanka,
Canada and many more. Most of the sales are generated by company from Japan and North
America. The five main brands under which firm manufacturing its vehicles includes Ranz,
Lexus, Toyota Brand, Daihatsu and Hino.
Selected areas of operations and supply change management:
Forecast and planning: Toyota majorly emphasize on anticipating their customer's
demands that enables firm to manufacture goods in systematic manner. It assists in controlling
inventory level and minimizing operating cost (Sodhi, Son and Tang, 2012).
Procurement: It is the procedure of procuring products or goods from external sources. It
involves purchase planning, value analysis, financing, inventory control etc. Toyota procure its
inputs from Japan and emphasize on disseminating environment purchase guidelines in order to
gain high competitive advantage.
Theories to be applied:
6
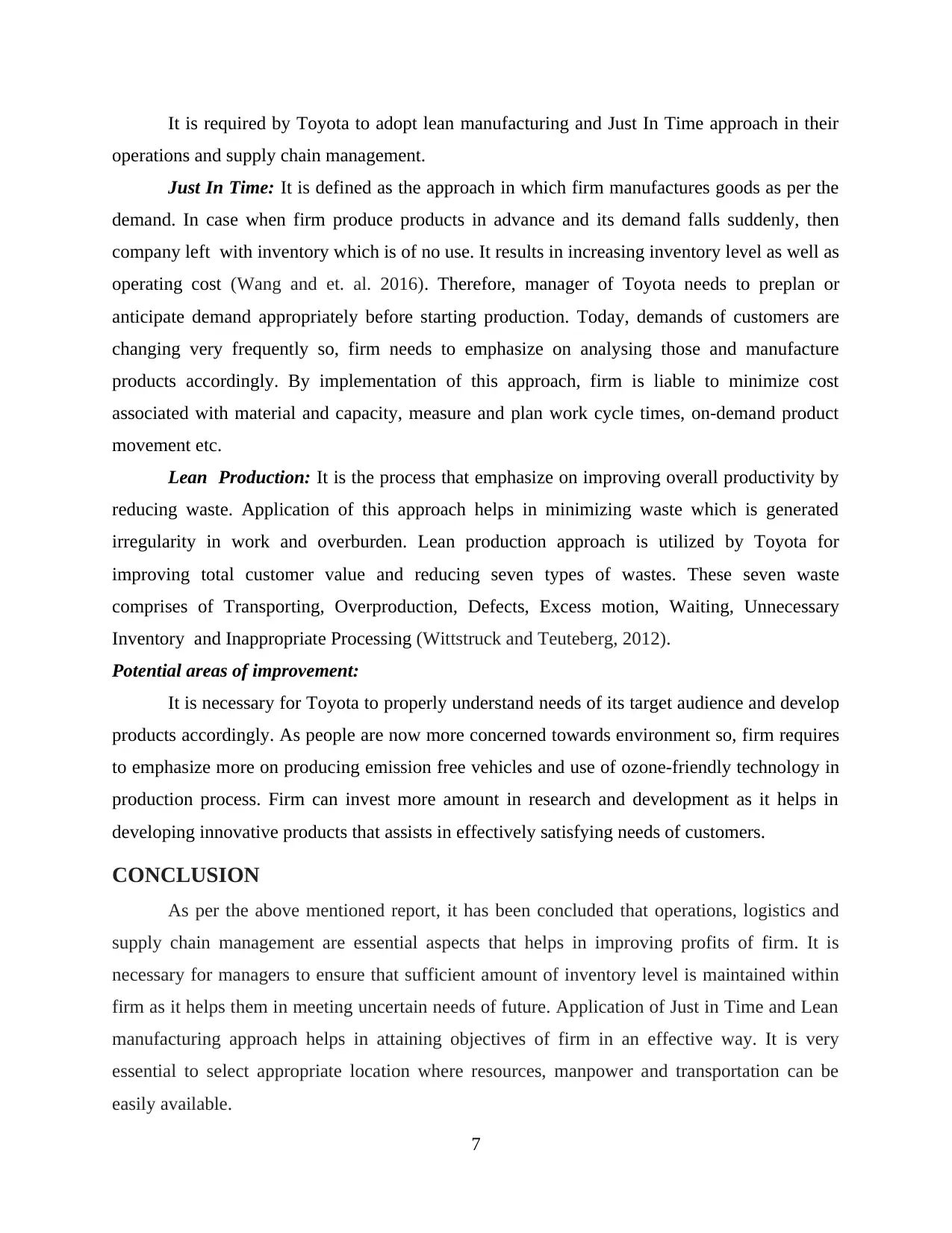
It is required by Toyota to adopt lean manufacturing and Just In Time approach in their
operations and supply chain management.
Just In Time: It is defined as the approach in which firm manufactures goods as per the
demand. In case when firm produce products in advance and its demand falls suddenly, then
company left with inventory which is of no use. It results in increasing inventory level as well as
operating cost (Wang and et. al. 2016). Therefore, manager of Toyota needs to preplan or
anticipate demand appropriately before starting production. Today, demands of customers are
changing very frequently so, firm needs to emphasize on analysing those and manufacture
products accordingly. By implementation of this approach, firm is liable to minimize cost
associated with material and capacity, measure and plan work cycle times, on-demand product
movement etc.
Lean Production: It is the process that emphasize on improving overall productivity by
reducing waste. Application of this approach helps in minimizing waste which is generated
irregularity in work and overburden. Lean production approach is utilized by Toyota for
improving total customer value and reducing seven types of wastes. These seven waste
comprises of Transporting, Overproduction, Defects, Excess motion, Waiting, Unnecessary
Inventory and Inappropriate Processing (Wittstruck and Teuteberg, 2012).
Potential areas of improvement:
It is necessary for Toyota to properly understand needs of its target audience and develop
products accordingly. As people are now more concerned towards environment so, firm requires
to emphasize more on producing emission free vehicles and use of ozone-friendly technology in
production process. Firm can invest more amount in research and development as it helps in
developing innovative products that assists in effectively satisfying needs of customers.
CONCLUSION
As per the above mentioned report, it has been concluded that operations, logistics and
supply chain management are essential aspects that helps in improving profits of firm. It is
necessary for managers to ensure that sufficient amount of inventory level is maintained within
firm as it helps them in meeting uncertain needs of future. Application of Just in Time and Lean
manufacturing approach helps in attaining objectives of firm in an effective way. It is very
essential to select appropriate location where resources, manpower and transportation can be
easily available.
7
operations and supply chain management.
Just In Time: It is defined as the approach in which firm manufactures goods as per the
demand. In case when firm produce products in advance and its demand falls suddenly, then
company left with inventory which is of no use. It results in increasing inventory level as well as
operating cost (Wang and et. al. 2016). Therefore, manager of Toyota needs to preplan or
anticipate demand appropriately before starting production. Today, demands of customers are
changing very frequently so, firm needs to emphasize on analysing those and manufacture
products accordingly. By implementation of this approach, firm is liable to minimize cost
associated with material and capacity, measure and plan work cycle times, on-demand product
movement etc.
Lean Production: It is the process that emphasize on improving overall productivity by
reducing waste. Application of this approach helps in minimizing waste which is generated
irregularity in work and overburden. Lean production approach is utilized by Toyota for
improving total customer value and reducing seven types of wastes. These seven waste
comprises of Transporting, Overproduction, Defects, Excess motion, Waiting, Unnecessary
Inventory and Inappropriate Processing (Wittstruck and Teuteberg, 2012).
Potential areas of improvement:
It is necessary for Toyota to properly understand needs of its target audience and develop
products accordingly. As people are now more concerned towards environment so, firm requires
to emphasize more on producing emission free vehicles and use of ozone-friendly technology in
production process. Firm can invest more amount in research and development as it helps in
developing innovative products that assists in effectively satisfying needs of customers.
CONCLUSION
As per the above mentioned report, it has been concluded that operations, logistics and
supply chain management are essential aspects that helps in improving profits of firm. It is
necessary for managers to ensure that sufficient amount of inventory level is maintained within
firm as it helps them in meeting uncertain needs of future. Application of Just in Time and Lean
manufacturing approach helps in attaining objectives of firm in an effective way. It is very
essential to select appropriate location where resources, manpower and transportation can be
easily available.
7
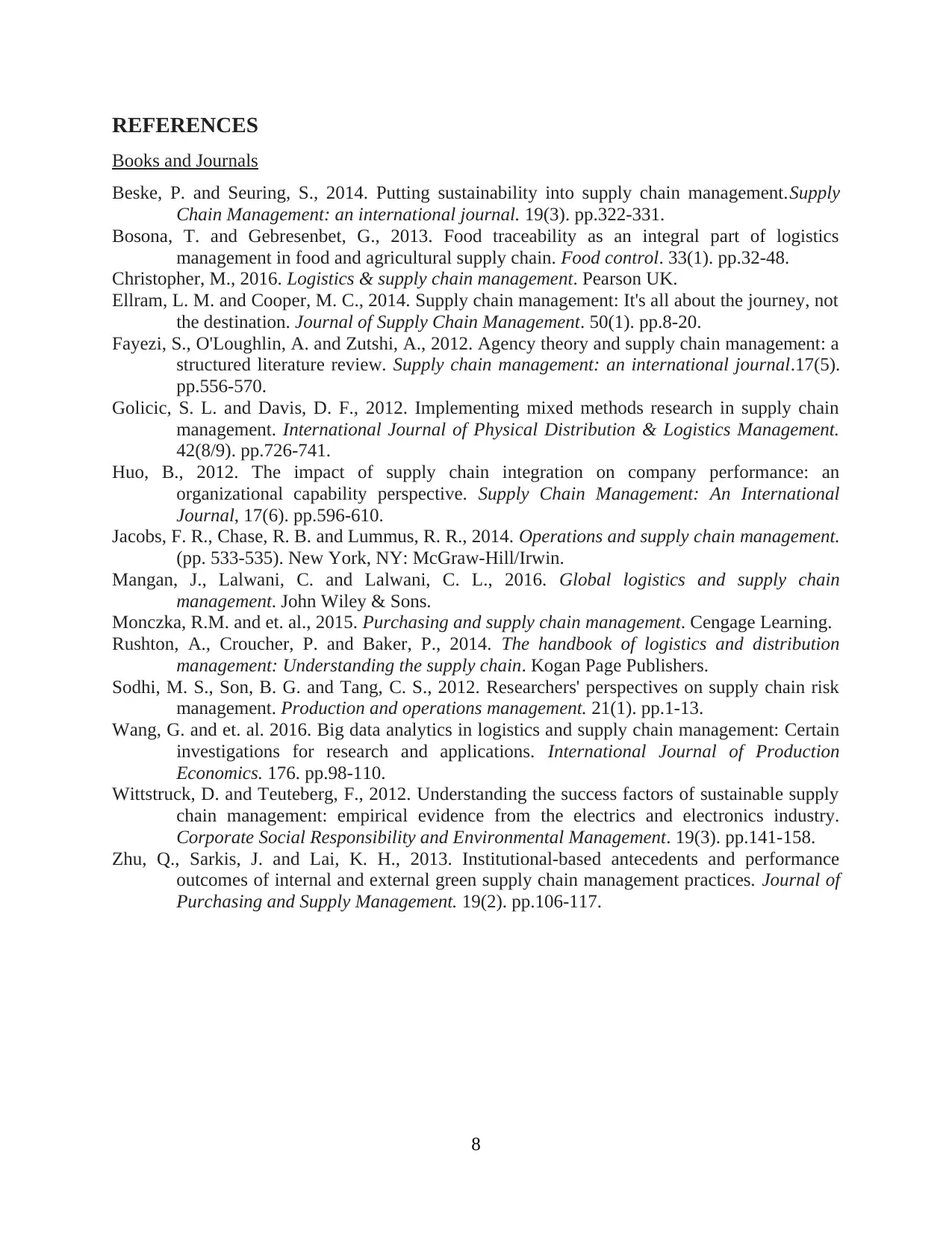
REFERENCES
Books and Journals
Beske, P. and Seuring, S., 2014. Putting sustainability into supply chain management.Supply
Chain Management: an international journal. 19(3). pp.322-331.
Bosona, T. and Gebresenbet, G., 2013. Food traceability as an integral part of logistics
management in food and agricultural supply chain. Food control. 33(1). pp.32-48.
Christopher, M., 2016. Logistics & supply chain management. Pearson UK.
Ellram, L. M. and Cooper, M. C., 2014. Supply chain management: It's all about the journey, not
the destination. Journal of Supply Chain Management. 50(1). pp.8-20.
Fayezi, S., O'Loughlin, A. and Zutshi, A., 2012. Agency theory and supply chain management: a
structured literature review. Supply chain management: an international journal.17(5).
pp.556-570.
Golicic, S. L. and Davis, D. F., 2012. Implementing mixed methods research in supply chain
management. International Journal of Physical Distribution & Logistics Management.
42(8/9). pp.726-741.
Huo, B., 2012. The impact of supply chain integration on company performance: an
organizational capability perspective. Supply Chain Management: An International
Journal, 17(6). pp.596-610.
Jacobs, F. R., Chase, R. B. and Lummus, R. R., 2014. Operations and supply chain management.
(pp. 533-535). New York, NY: McGraw-Hill/Irwin.
Mangan, J., Lalwani, C. and Lalwani, C. L., 2016. Global logistics and supply chain
management. John Wiley & Sons.
Monczka, R.M. and et. al., 2015. Purchasing and supply chain management. Cengage Learning.
Rushton, A., Croucher, P. and Baker, P., 2014. The handbook of logistics and distribution
management: Understanding the supply chain. Kogan Page Publishers.
Sodhi, M. S., Son, B. G. and Tang, C. S., 2012. Researchers' perspectives on supply chain risk
management. Production and operations management. 21(1). pp.1-13.
Wang, G. and et. al. 2016. Big data analytics in logistics and supply chain management: Certain
investigations for research and applications. International Journal of Production
Economics. 176. pp.98-110.
Wittstruck, D. and Teuteberg, F., 2012. Understanding the success factors of sustainable supply
chain management: empirical evidence from the electrics and electronics industry.
Corporate Social Responsibility and Environmental Management. 19(3). pp.141-158.
Zhu, Q., Sarkis, J. and Lai, K. H., 2013. Institutional-based antecedents and performance
outcomes of internal and external green supply chain management practices. Journal of
Purchasing and Supply Management. 19(2). pp.106-117.
8
Books and Journals
Beske, P. and Seuring, S., 2014. Putting sustainability into supply chain management.Supply
Chain Management: an international journal. 19(3). pp.322-331.
Bosona, T. and Gebresenbet, G., 2013. Food traceability as an integral part of logistics
management in food and agricultural supply chain. Food control. 33(1). pp.32-48.
Christopher, M., 2016. Logistics & supply chain management. Pearson UK.
Ellram, L. M. and Cooper, M. C., 2014. Supply chain management: It's all about the journey, not
the destination. Journal of Supply Chain Management. 50(1). pp.8-20.
Fayezi, S., O'Loughlin, A. and Zutshi, A., 2012. Agency theory and supply chain management: a
structured literature review. Supply chain management: an international journal.17(5).
pp.556-570.
Golicic, S. L. and Davis, D. F., 2012. Implementing mixed methods research in supply chain
management. International Journal of Physical Distribution & Logistics Management.
42(8/9). pp.726-741.
Huo, B., 2012. The impact of supply chain integration on company performance: an
organizational capability perspective. Supply Chain Management: An International
Journal, 17(6). pp.596-610.
Jacobs, F. R., Chase, R. B. and Lummus, R. R., 2014. Operations and supply chain management.
(pp. 533-535). New York, NY: McGraw-Hill/Irwin.
Mangan, J., Lalwani, C. and Lalwani, C. L., 2016. Global logistics and supply chain
management. John Wiley & Sons.
Monczka, R.M. and et. al., 2015. Purchasing and supply chain management. Cengage Learning.
Rushton, A., Croucher, P. and Baker, P., 2014. The handbook of logistics and distribution
management: Understanding the supply chain. Kogan Page Publishers.
Sodhi, M. S., Son, B. G. and Tang, C. S., 2012. Researchers' perspectives on supply chain risk
management. Production and operations management. 21(1). pp.1-13.
Wang, G. and et. al. 2016. Big data analytics in logistics and supply chain management: Certain
investigations for research and applications. International Journal of Production
Economics. 176. pp.98-110.
Wittstruck, D. and Teuteberg, F., 2012. Understanding the success factors of sustainable supply
chain management: empirical evidence from the electrics and electronics industry.
Corporate Social Responsibility and Environmental Management. 19(3). pp.141-158.
Zhu, Q., Sarkis, J. and Lai, K. H., 2013. Institutional-based antecedents and performance
outcomes of internal and external green supply chain management practices. Journal of
Purchasing and Supply Management. 19(2). pp.106-117.
8
1 out of 10
Related Documents
![[object Object]](/_next/image/?url=%2F_next%2Fstatic%2Fmedia%2Flogo.6d15ce61.png&w=640&q=75)
Your All-in-One AI-Powered Toolkit for Academic Success.
 +13062052269
info@desklib.com
Available 24*7 on WhatsApp / Email
Unlock your academic potential
© 2024  |  Zucol Services PVT LTD  |  All rights reserved.