Operations Management Plan Assignment
VerifiedAdded on 2022/08/08
|19
|4068
|47
AI Summary
Contribute Materials
Your contribution can guide someone’s learning journey. Share your
documents today.
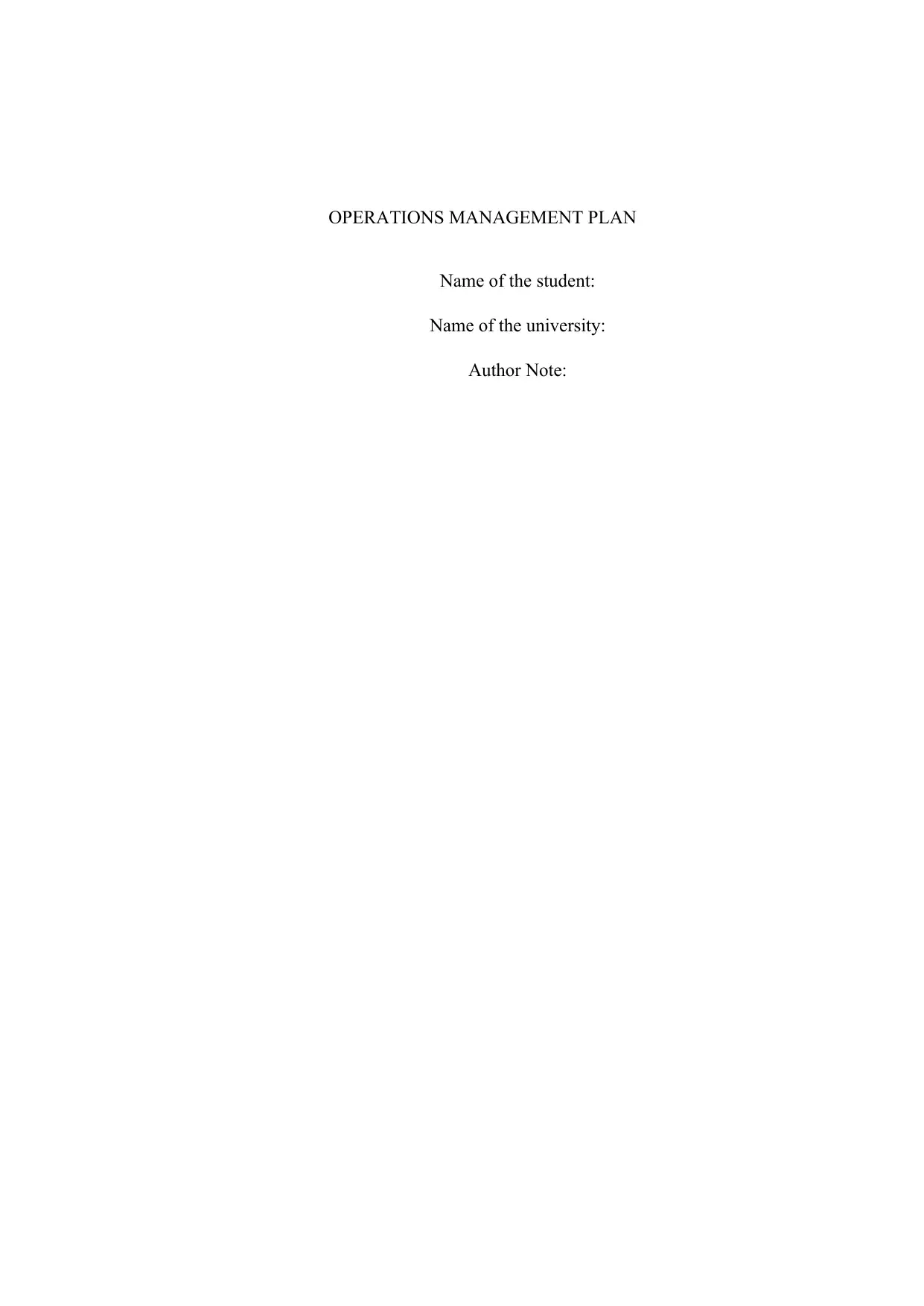
OPERATIONS MANAGEMENT PLAN
Name of the student:
Name of the university:
Author Note:
Name of the student:
Name of the university:
Author Note:
Secure Best Marks with AI Grader
Need help grading? Try our AI Grader for instant feedback on your assignments.
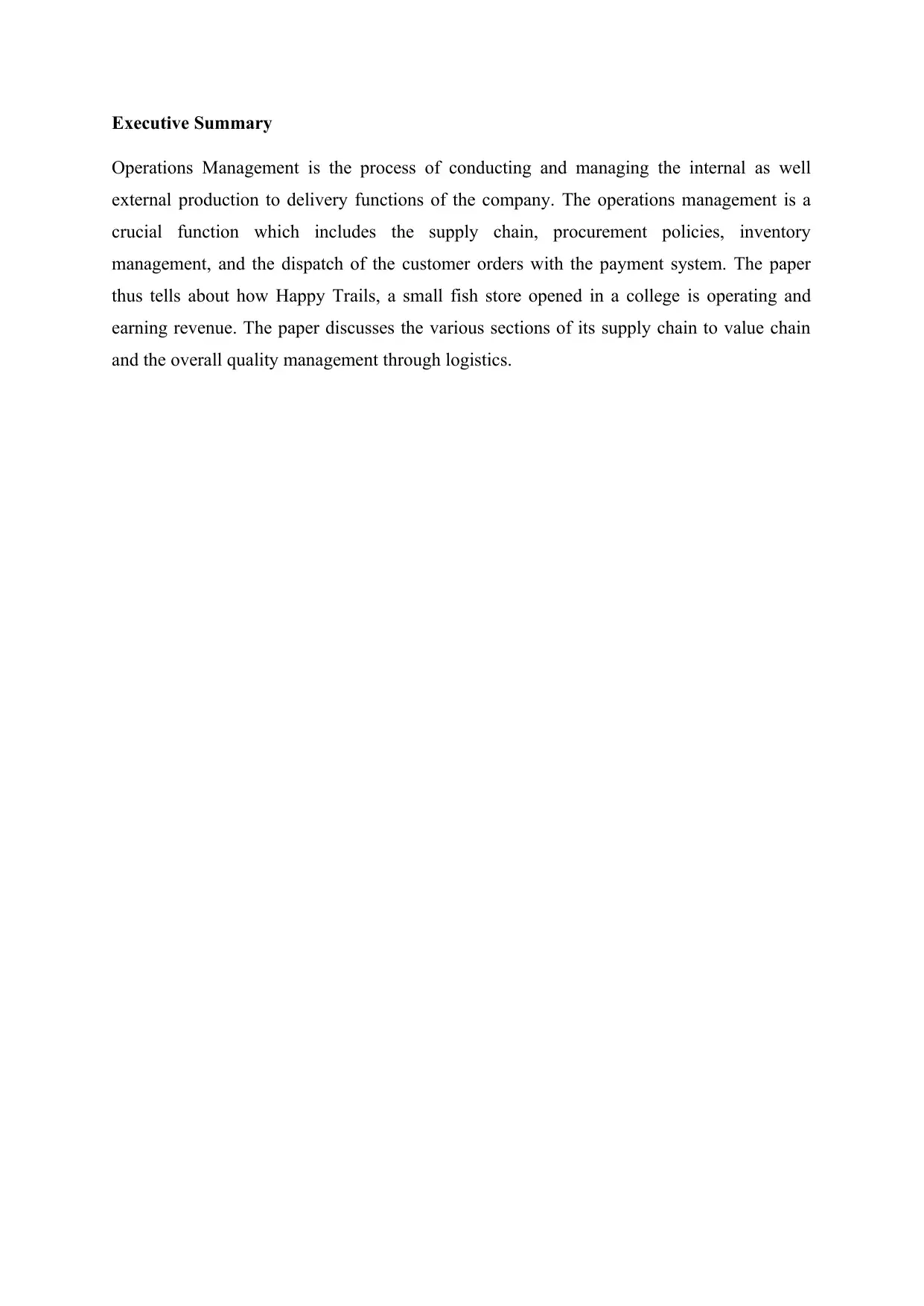
Executive Summary
Operations Management is the process of conducting and managing the internal as well
external production to delivery functions of the company. The operations management is a
crucial function which includes the supply chain, procurement policies, inventory
management, and the dispatch of the customer orders with the payment system. The paper
thus tells about how Happy Trails, a small fish store opened in a college is operating and
earning revenue. The paper discusses the various sections of its supply chain to value chain
and the overall quality management through logistics.
Operations Management is the process of conducting and managing the internal as well
external production to delivery functions of the company. The operations management is a
crucial function which includes the supply chain, procurement policies, inventory
management, and the dispatch of the customer orders with the payment system. The paper
thus tells about how Happy Trails, a small fish store opened in a college is operating and
earning revenue. The paper discusses the various sections of its supply chain to value chain
and the overall quality management through logistics.
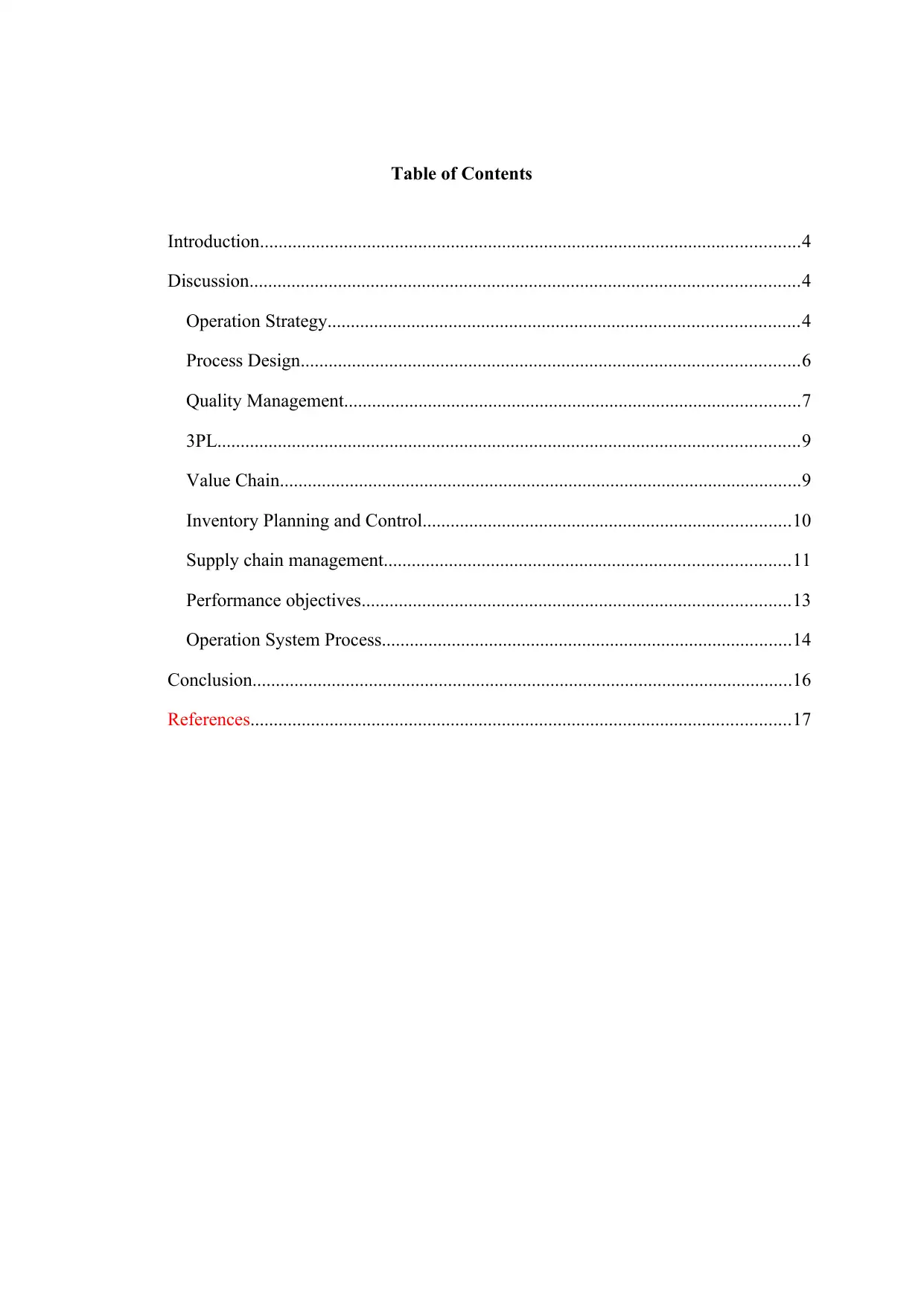
Table of Contents
Introduction....................................................................................................................4
Discussion......................................................................................................................4
Operation Strategy.....................................................................................................4
Process Design...........................................................................................................6
Quality Management..................................................................................................7
3PL.............................................................................................................................9
Value Chain................................................................................................................9
Inventory Planning and Control...............................................................................10
Supply chain management.......................................................................................11
Performance objectives............................................................................................13
Operation System Process........................................................................................14
Conclusion....................................................................................................................16
References....................................................................................................................17
Introduction....................................................................................................................4
Discussion......................................................................................................................4
Operation Strategy.....................................................................................................4
Process Design...........................................................................................................6
Quality Management..................................................................................................7
3PL.............................................................................................................................9
Value Chain................................................................................................................9
Inventory Planning and Control...............................................................................10
Supply chain management.......................................................................................11
Performance objectives............................................................................................13
Operation System Process........................................................................................14
Conclusion....................................................................................................................16
References....................................................................................................................17

Introduction
Happy Trails is a small-sized fish shop outlet located in the canteen of Imperial
College, London. The company has its branches in the north-east of London and has opened
its outlet in this college for one year. It has gained massive popularity among the college
students who are non-vegetarian and earn quite a lot of revenue from the canteen store beside
the other shop outlets scattered in the region. The consumers of the fish shop are mainly the
students, teachers and the working staff. The company is operating in the market for four
years with origins in the Buntingford, a small market town in East Hertfordshire. The targeted
customer segment is the fish lovers who are mainly into seafood. The fish market is quite
popular in London, and the company is growing through it’s positioning in top colleges of
London.
Discussion
Operation Strategy
Figure 1: Operational strategy design
Source: Manufacturing strategy formulation process| ResearchGate
The role of the operations strategy is to oversee the proper allocation of resources in the
organisation and support the long-term strategy of the company in the competitive market
(Bozarth and Handfield, 2019). There are limited resources in nature, so a sustainable
operational strategy with marketing goals, finance strategies and the overall supply chain is
needed (Olsen and Tomlin 2020). The corporate strategy is the main crux of the organisation
where the operational strategy is the sub-part involving the corporate goals, objectives,
strategies and the contexts under which the planning, implementation and evaluation of the
Happy Trails is a small-sized fish shop outlet located in the canteen of Imperial
College, London. The company has its branches in the north-east of London and has opened
its outlet in this college for one year. It has gained massive popularity among the college
students who are non-vegetarian and earn quite a lot of revenue from the canteen store beside
the other shop outlets scattered in the region. The consumers of the fish shop are mainly the
students, teachers and the working staff. The company is operating in the market for four
years with origins in the Buntingford, a small market town in East Hertfordshire. The targeted
customer segment is the fish lovers who are mainly into seafood. The fish market is quite
popular in London, and the company is growing through it’s positioning in top colleges of
London.
Discussion
Operation Strategy
Figure 1: Operational strategy design
Source: Manufacturing strategy formulation process| ResearchGate
The role of the operations strategy is to oversee the proper allocation of resources in the
organisation and support the long-term strategy of the company in the competitive market
(Bozarth and Handfield, 2019). There are limited resources in nature, so a sustainable
operational strategy with marketing goals, finance strategies and the overall supply chain is
needed (Olsen and Tomlin 2020). The corporate strategy is the main crux of the organisation
where the operational strategy is the sub-part involving the corporate goals, objectives,
strategies and the contexts under which the planning, implementation and evaluation of the
Secure Best Marks with AI Grader
Need help grading? Try our AI Grader for instant feedback on your assignments.
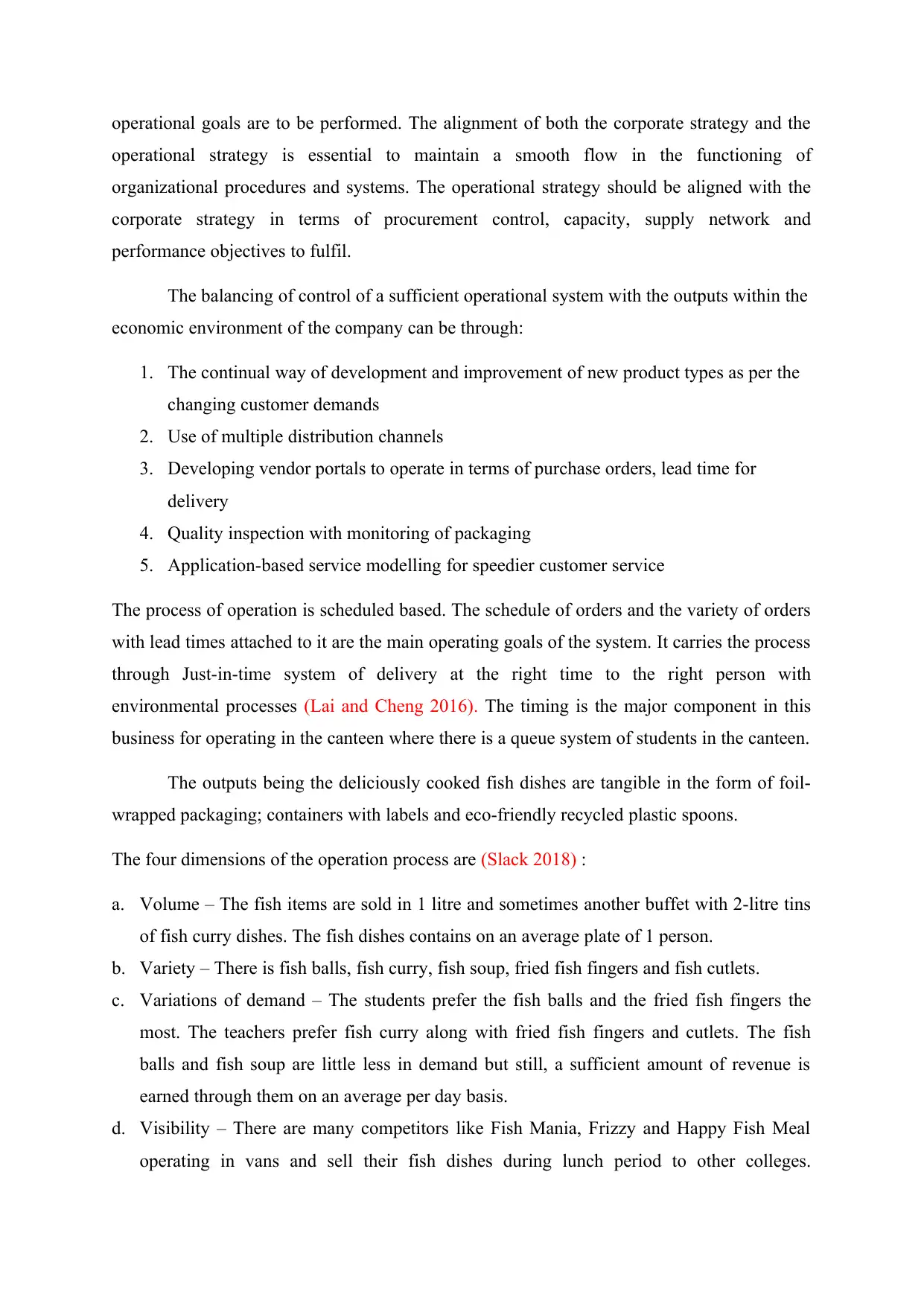
operational goals are to be performed. The alignment of both the corporate strategy and the
operational strategy is essential to maintain a smooth flow in the functioning of
organizational procedures and systems. The operational strategy should be aligned with the
corporate strategy in terms of procurement control, capacity, supply network and
performance objectives to fulfil.
The balancing of control of a sufficient operational system with the outputs within the
economic environment of the company can be through:
1. The continual way of development and improvement of new product types as per the
changing customer demands
2. Use of multiple distribution channels
3. Developing vendor portals to operate in terms of purchase orders, lead time for
delivery
4. Quality inspection with monitoring of packaging
5. Application-based service modelling for speedier customer service
The process of operation is scheduled based. The schedule of orders and the variety of orders
with lead times attached to it are the main operating goals of the system. It carries the process
through Just-in-time system of delivery at the right time to the right person with
environmental processes (Lai and Cheng 2016). The timing is the major component in this
business for operating in the canteen where there is a queue system of students in the canteen.
The outputs being the deliciously cooked fish dishes are tangible in the form of foil-
wrapped packaging; containers with labels and eco-friendly recycled plastic spoons.
The four dimensions of the operation process are (Slack 2018) :
a. Volume – The fish items are sold in 1 litre and sometimes another buffet with 2-litre tins
of fish curry dishes. The fish dishes contains on an average plate of 1 person.
b. Variety – There is fish balls, fish curry, fish soup, fried fish fingers and fish cutlets.
c. Variations of demand – The students prefer the fish balls and the fried fish fingers the
most. The teachers prefer fish curry along with fried fish fingers and cutlets. The fish
balls and fish soup are little less in demand but still, a sufficient amount of revenue is
earned through them on an average per day basis.
d. Visibility – There are many competitors like Fish Mania, Frizzy and Happy Fish Meal
operating in vans and sell their fish dishes during lunch period to other colleges.
operational strategy is essential to maintain a smooth flow in the functioning of
organizational procedures and systems. The operational strategy should be aligned with the
corporate strategy in terms of procurement control, capacity, supply network and
performance objectives to fulfil.
The balancing of control of a sufficient operational system with the outputs within the
economic environment of the company can be through:
1. The continual way of development and improvement of new product types as per the
changing customer demands
2. Use of multiple distribution channels
3. Developing vendor portals to operate in terms of purchase orders, lead time for
delivery
4. Quality inspection with monitoring of packaging
5. Application-based service modelling for speedier customer service
The process of operation is scheduled based. The schedule of orders and the variety of orders
with lead times attached to it are the main operating goals of the system. It carries the process
through Just-in-time system of delivery at the right time to the right person with
environmental processes (Lai and Cheng 2016). The timing is the major component in this
business for operating in the canteen where there is a queue system of students in the canteen.
The outputs being the deliciously cooked fish dishes are tangible in the form of foil-
wrapped packaging; containers with labels and eco-friendly recycled plastic spoons.
The four dimensions of the operation process are (Slack 2018) :
a. Volume – The fish items are sold in 1 litre and sometimes another buffet with 2-litre tins
of fish curry dishes. The fish dishes contains on an average plate of 1 person.
b. Variety – There is fish balls, fish curry, fish soup, fried fish fingers and fish cutlets.
c. Variations of demand – The students prefer the fish balls and the fried fish fingers the
most. The teachers prefer fish curry along with fried fish fingers and cutlets. The fish
balls and fish soup are little less in demand but still, a sufficient amount of revenue is
earned through them on an average per day basis.
d. Visibility – There are many competitors like Fish Mania, Frizzy and Happy Fish Meal
operating in vans and sell their fish dishes during lunch period to other colleges.
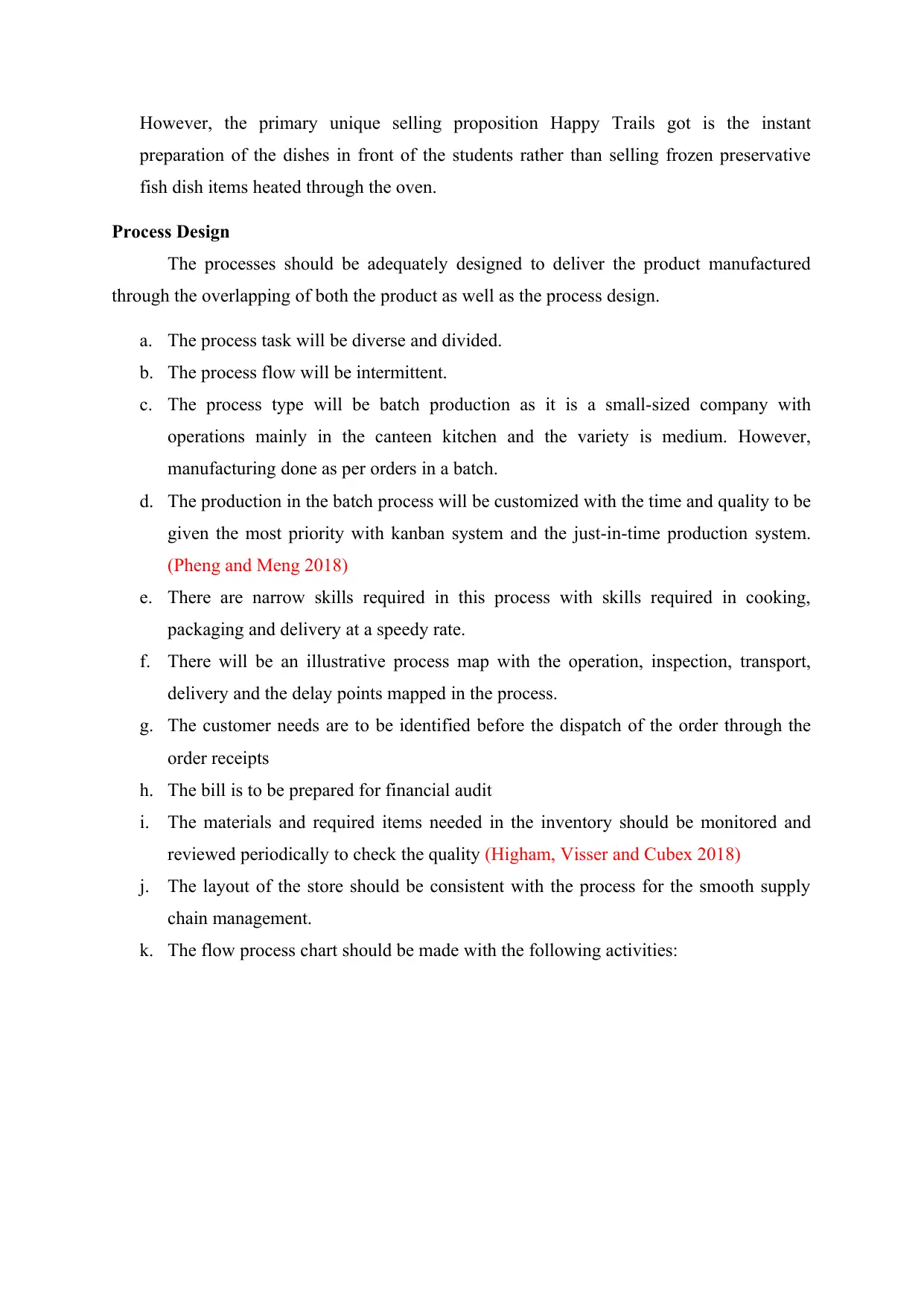
However, the primary unique selling proposition Happy Trails got is the instant
preparation of the dishes in front of the students rather than selling frozen preservative
fish dish items heated through the oven.
Process Design
The processes should be adequately designed to deliver the product manufactured
through the overlapping of both the product as well as the process design.
a. The process task will be diverse and divided.
b. The process flow will be intermittent.
c. The process type will be batch production as it is a small-sized company with
operations mainly in the canteen kitchen and the variety is medium. However,
manufacturing done as per orders in a batch.
d. The production in the batch process will be customized with the time and quality to be
given the most priority with kanban system and the just-in-time production system.
(Pheng and Meng 2018)
e. There are narrow skills required in this process with skills required in cooking,
packaging and delivery at a speedy rate.
f. There will be an illustrative process map with the operation, inspection, transport,
delivery and the delay points mapped in the process.
g. The customer needs are to be identified before the dispatch of the order through the
order receipts
h. The bill is to be prepared for financial audit
i. The materials and required items needed in the inventory should be monitored and
reviewed periodically to check the quality (Higham, Visser and Cubex 2018)
j. The layout of the store should be consistent with the process for the smooth supply
chain management.
k. The flow process chart should be made with the following activities:
preparation of the dishes in front of the students rather than selling frozen preservative
fish dish items heated through the oven.
Process Design
The processes should be adequately designed to deliver the product manufactured
through the overlapping of both the product as well as the process design.
a. The process task will be diverse and divided.
b. The process flow will be intermittent.
c. The process type will be batch production as it is a small-sized company with
operations mainly in the canteen kitchen and the variety is medium. However,
manufacturing done as per orders in a batch.
d. The production in the batch process will be customized with the time and quality to be
given the most priority with kanban system and the just-in-time production system.
(Pheng and Meng 2018)
e. There are narrow skills required in this process with skills required in cooking,
packaging and delivery at a speedy rate.
f. There will be an illustrative process map with the operation, inspection, transport,
delivery and the delay points mapped in the process.
g. The customer needs are to be identified before the dispatch of the order through the
order receipts
h. The bill is to be prepared for financial audit
i. The materials and required items needed in the inventory should be monitored and
reviewed periodically to check the quality (Higham, Visser and Cubex 2018)
j. The layout of the store should be consistent with the process for the smooth supply
chain management.
k. The flow process chart should be made with the following activities:
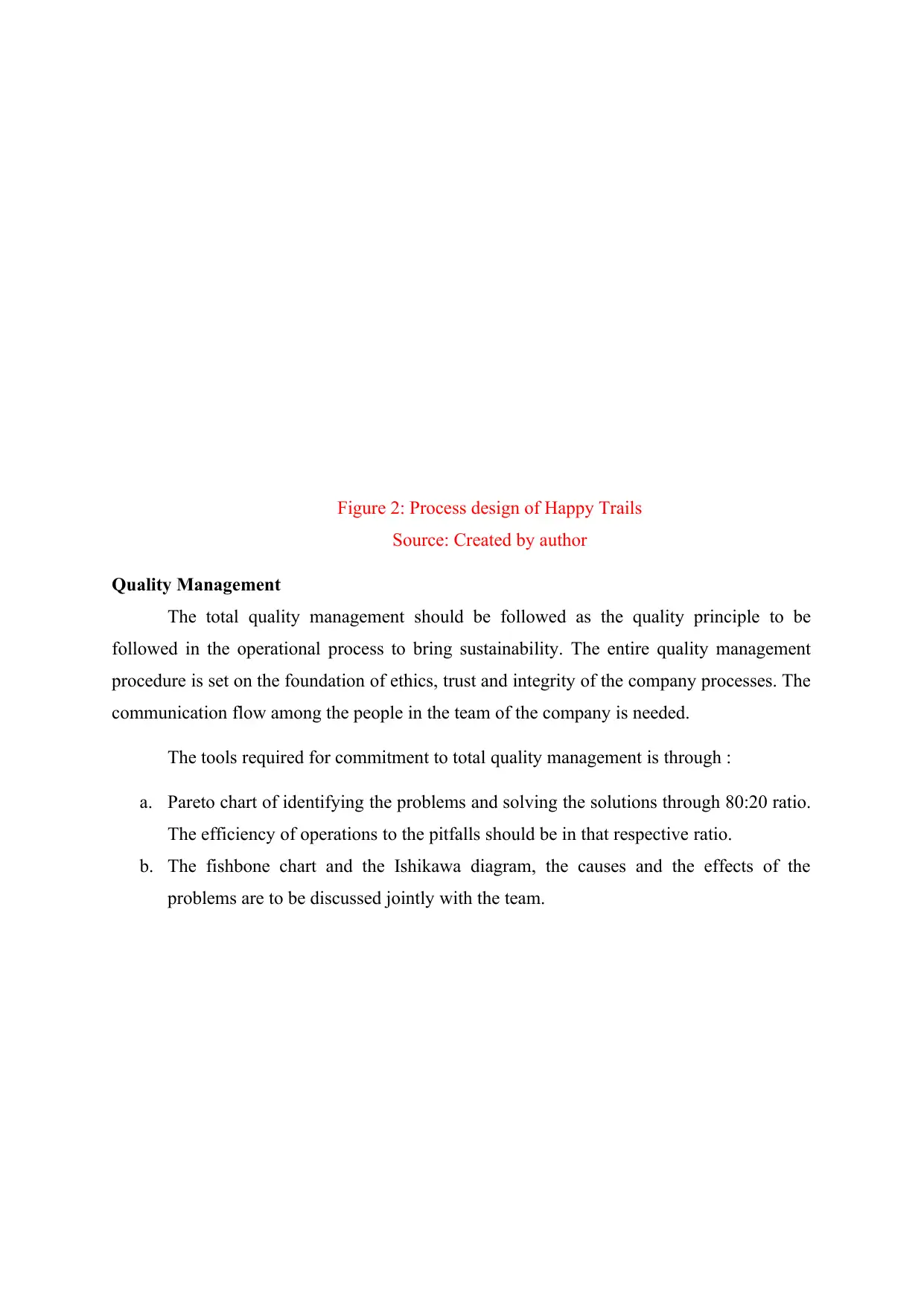
Figure 2: Process design of Happy Trails
Source: Created by author
Quality Management
The total quality management should be followed as the quality principle to be
followed in the operational process to bring sustainability. The entire quality management
procedure is set on the foundation of ethics, trust and integrity of the company processes. The
communication flow among the people in the team of the company is needed.
The tools required for commitment to total quality management is through :
a. Pareto chart of identifying the problems and solving the solutions through 80:20 ratio.
The efficiency of operations to the pitfalls should be in that respective ratio.
b. The fishbone chart and the Ishikawa diagram, the causes and the effects of the
problems are to be discussed jointly with the team.
Getcustomerrequest
Source: Created by author
Quality Management
The total quality management should be followed as the quality principle to be
followed in the operational process to bring sustainability. The entire quality management
procedure is set on the foundation of ethics, trust and integrity of the company processes. The
communication flow among the people in the team of the company is needed.
The tools required for commitment to total quality management is through :
a. Pareto chart of identifying the problems and solving the solutions through 80:20 ratio.
The efficiency of operations to the pitfalls should be in that respective ratio.
b. The fishbone chart and the Ishikawa diagram, the causes and the effects of the
problems are to be discussed jointly with the team.
Getcustomerrequest
Paraphrase This Document
Need a fresh take? Get an instant paraphrase of this document with our AI Paraphraser

Figure 3: Ishikawa diagram for the total quality production system
Source: Ishikawa Diagram by Adam Hayes | Investopedia
c. The scatter diagram can also be performed to construct a relationship between the
variables of problems to find solutions.
The four types of operational quality initiatives are:
1. The conformance to ISO quality standards in terms of environmental standards like
ISO 14001 for maintaining the environmental sustainability report and monitoring of
the system is to be performed. The ISO 9000 standards are also implemented.
2. The certification in terms of food and hygiene concerning government regulations and
the consumer safety law should be there.
3. The green labeling standards on the products are needed for the marine seafood and
fish used in the manufacturing process with non-vegetarian food labels.
4. The energy-saving certificates in terms of polluter pay principle and the reduction of
carbon emissions to be taken care of due to cooking and use of non-renewable energy
sources to cook and fry the fish dishes.
Source: Ishikawa Diagram by Adam Hayes | Investopedia
c. The scatter diagram can also be performed to construct a relationship between the
variables of problems to find solutions.
The four types of operational quality initiatives are:
1. The conformance to ISO quality standards in terms of environmental standards like
ISO 14001 for maintaining the environmental sustainability report and monitoring of
the system is to be performed. The ISO 9000 standards are also implemented.
2. The certification in terms of food and hygiene concerning government regulations and
the consumer safety law should be there.
3. The green labeling standards on the products are needed for the marine seafood and
fish used in the manufacturing process with non-vegetarian food labels.
4. The energy-saving certificates in terms of polluter pay principle and the reduction of
carbon emissions to be taken care of due to cooking and use of non-renewable energy
sources to cook and fry the fish dishes.
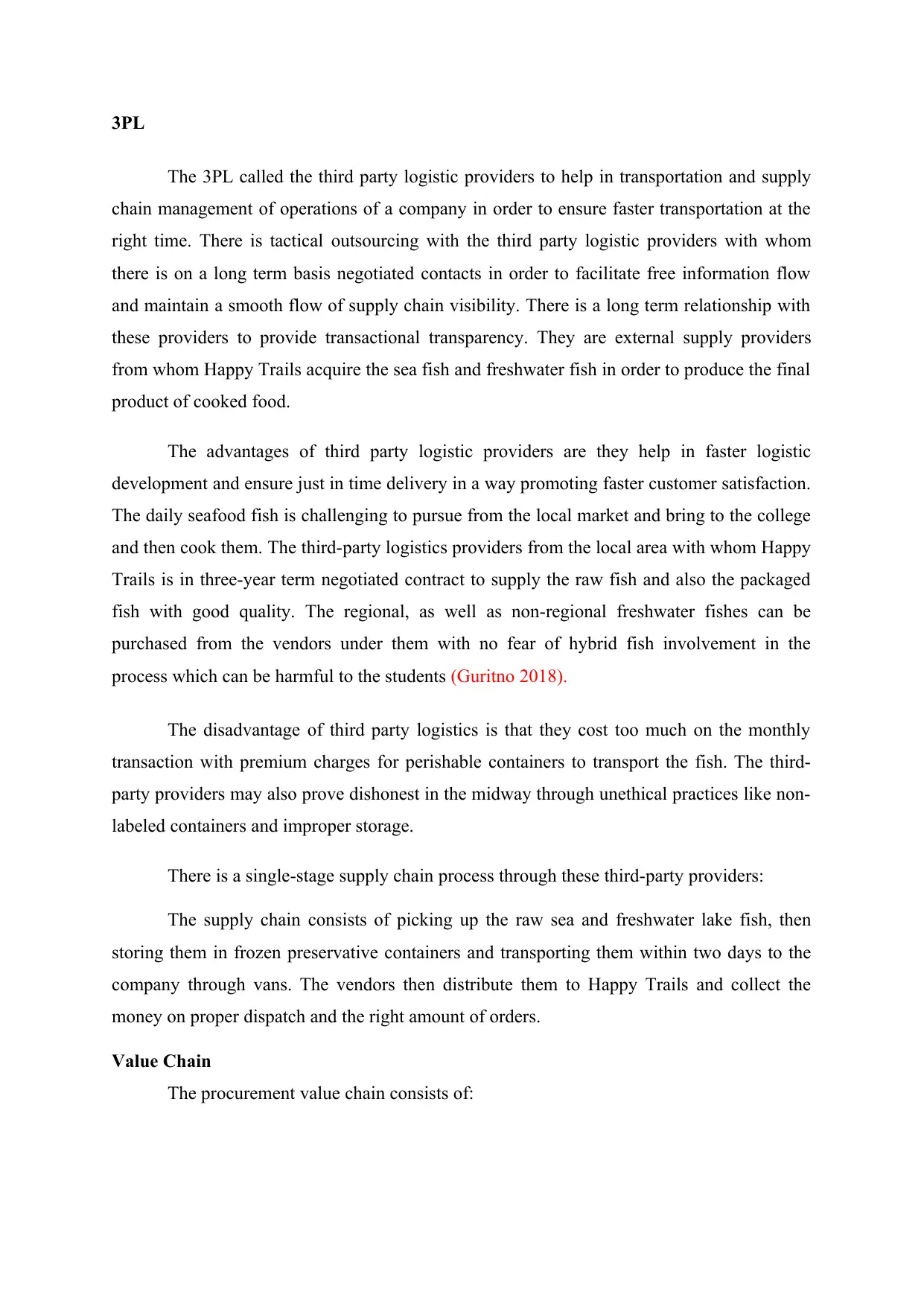
3PL
The 3PL called the third party logistic providers to help in transportation and supply
chain management of operations of a company in order to ensure faster transportation at the
right time. There is tactical outsourcing with the third party logistic providers with whom
there is on a long term basis negotiated contacts in order to facilitate free information flow
and maintain a smooth flow of supply chain visibility. There is a long term relationship with
these providers to provide transactional transparency. They are external supply providers
from whom Happy Trails acquire the sea fish and freshwater fish in order to produce the final
product of cooked food.
The advantages of third party logistic providers are they help in faster logistic
development and ensure just in time delivery in a way promoting faster customer satisfaction.
The daily seafood fish is challenging to pursue from the local market and bring to the college
and then cook them. The third-party logistics providers from the local area with whom Happy
Trails is in three-year term negotiated contract to supply the raw fish and also the packaged
fish with good quality. The regional, as well as non-regional freshwater fishes can be
purchased from the vendors under them with no fear of hybrid fish involvement in the
process which can be harmful to the students (Guritno 2018).
The disadvantage of third party logistics is that they cost too much on the monthly
transaction with premium charges for perishable containers to transport the fish. The third-
party providers may also prove dishonest in the midway through unethical practices like non-
labeled containers and improper storage.
There is a single-stage supply chain process through these third-party providers:
The supply chain consists of picking up the raw sea and freshwater lake fish, then
storing them in frozen preservative containers and transporting them within two days to the
company through vans. The vendors then distribute them to Happy Trails and collect the
money on proper dispatch and the right amount of orders.
Value Chain
The procurement value chain consists of:
The 3PL called the third party logistic providers to help in transportation and supply
chain management of operations of a company in order to ensure faster transportation at the
right time. There is tactical outsourcing with the third party logistic providers with whom
there is on a long term basis negotiated contacts in order to facilitate free information flow
and maintain a smooth flow of supply chain visibility. There is a long term relationship with
these providers to provide transactional transparency. They are external supply providers
from whom Happy Trails acquire the sea fish and freshwater fish in order to produce the final
product of cooked food.
The advantages of third party logistic providers are they help in faster logistic
development and ensure just in time delivery in a way promoting faster customer satisfaction.
The daily seafood fish is challenging to pursue from the local market and bring to the college
and then cook them. The third-party logistics providers from the local area with whom Happy
Trails is in three-year term negotiated contract to supply the raw fish and also the packaged
fish with good quality. The regional, as well as non-regional freshwater fishes can be
purchased from the vendors under them with no fear of hybrid fish involvement in the
process which can be harmful to the students (Guritno 2018).
The disadvantage of third party logistics is that they cost too much on the monthly
transaction with premium charges for perishable containers to transport the fish. The third-
party providers may also prove dishonest in the midway through unethical practices like non-
labeled containers and improper storage.
There is a single-stage supply chain process through these third-party providers:
The supply chain consists of picking up the raw sea and freshwater lake fish, then
storing them in frozen preservative containers and transporting them within two days to the
company through vans. The vendors then distribute them to Happy Trails and collect the
money on proper dispatch and the right amount of orders.
Value Chain
The procurement value chain consists of:
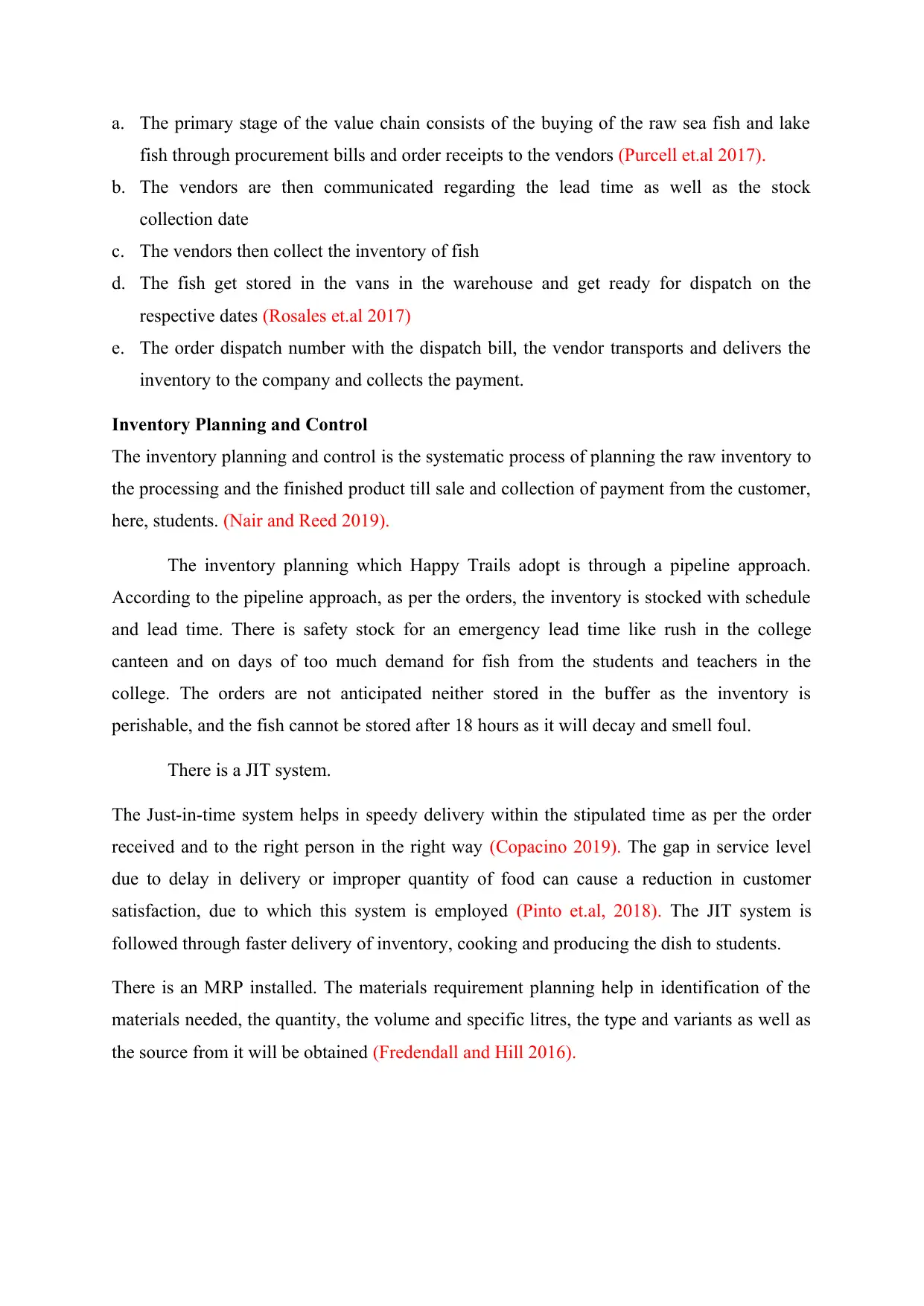
a. The primary stage of the value chain consists of the buying of the raw sea fish and lake
fish through procurement bills and order receipts to the vendors (Purcell et.al 2017).
b. The vendors are then communicated regarding the lead time as well as the stock
collection date
c. The vendors then collect the inventory of fish
d. The fish get stored in the vans in the warehouse and get ready for dispatch on the
respective dates (Rosales et.al 2017)
e. The order dispatch number with the dispatch bill, the vendor transports and delivers the
inventory to the company and collects the payment.
Inventory Planning and Control
The inventory planning and control is the systematic process of planning the raw inventory to
the processing and the finished product till sale and collection of payment from the customer,
here, students. (Nair and Reed 2019).
The inventory planning which Happy Trails adopt is through a pipeline approach.
According to the pipeline approach, as per the orders, the inventory is stocked with schedule
and lead time. There is safety stock for an emergency lead time like rush in the college
canteen and on days of too much demand for fish from the students and teachers in the
college. The orders are not anticipated neither stored in the buffer as the inventory is
perishable, and the fish cannot be stored after 18 hours as it will decay and smell foul.
There is a JIT system.
The Just-in-time system helps in speedy delivery within the stipulated time as per the order
received and to the right person in the right way (Copacino 2019). The gap in service level
due to delay in delivery or improper quantity of food can cause a reduction in customer
satisfaction, due to which this system is employed (Pinto et.al, 2018). The JIT system is
followed through faster delivery of inventory, cooking and producing the dish to students.
There is an MRP installed. The materials requirement planning help in identification of the
materials needed, the quantity, the volume and specific litres, the type and variants as well as
the source from it will be obtained (Fredendall and Hill 2016).
fish through procurement bills and order receipts to the vendors (Purcell et.al 2017).
b. The vendors are then communicated regarding the lead time as well as the stock
collection date
c. The vendors then collect the inventory of fish
d. The fish get stored in the vans in the warehouse and get ready for dispatch on the
respective dates (Rosales et.al 2017)
e. The order dispatch number with the dispatch bill, the vendor transports and delivers the
inventory to the company and collects the payment.
Inventory Planning and Control
The inventory planning and control is the systematic process of planning the raw inventory to
the processing and the finished product till sale and collection of payment from the customer,
here, students. (Nair and Reed 2019).
The inventory planning which Happy Trails adopt is through a pipeline approach.
According to the pipeline approach, as per the orders, the inventory is stocked with schedule
and lead time. There is safety stock for an emergency lead time like rush in the college
canteen and on days of too much demand for fish from the students and teachers in the
college. The orders are not anticipated neither stored in the buffer as the inventory is
perishable, and the fish cannot be stored after 18 hours as it will decay and smell foul.
There is a JIT system.
The Just-in-time system helps in speedy delivery within the stipulated time as per the order
received and to the right person in the right way (Copacino 2019). The gap in service level
due to delay in delivery or improper quantity of food can cause a reduction in customer
satisfaction, due to which this system is employed (Pinto et.al, 2018). The JIT system is
followed through faster delivery of inventory, cooking and producing the dish to students.
There is an MRP installed. The materials requirement planning help in identification of the
materials needed, the quantity, the volume and specific litres, the type and variants as well as
the source from it will be obtained (Fredendall and Hill 2016).
Secure Best Marks with AI Grader
Need help grading? Try our AI Grader for instant feedback on your assignments.
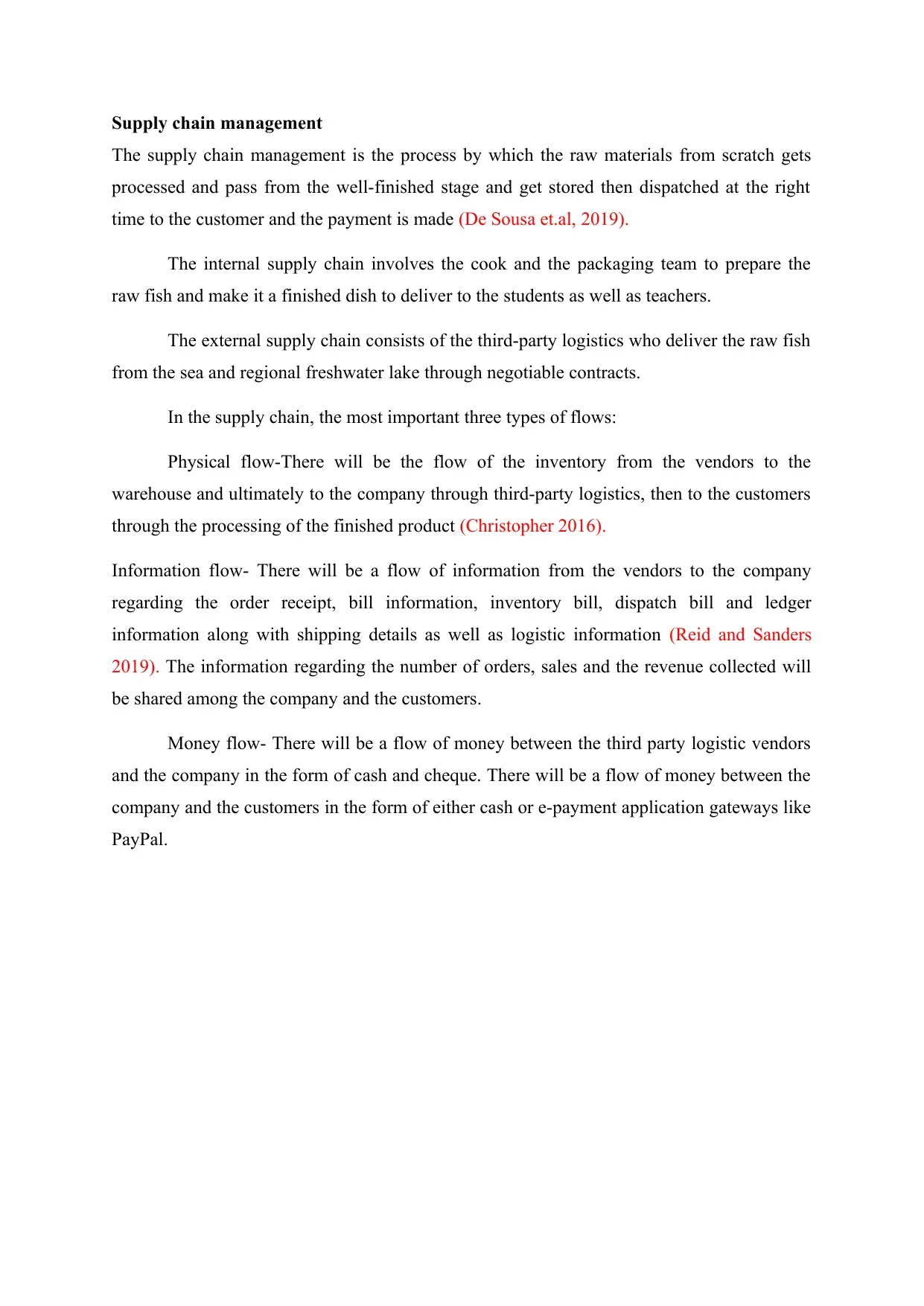
Supply chain management
The supply chain management is the process by which the raw materials from scratch gets
processed and pass from the well-finished stage and get stored then dispatched at the right
time to the customer and the payment is made (De Sousa et.al, 2019).
The internal supply chain involves the cook and the packaging team to prepare the
raw fish and make it a finished dish to deliver to the students as well as teachers.
The external supply chain consists of the third-party logistics who deliver the raw fish
from the sea and regional freshwater lake through negotiable contracts.
In the supply chain, the most important three types of flows:
Physical flow-There will be the flow of the inventory from the vendors to the
warehouse and ultimately to the company through third-party logistics, then to the customers
through the processing of the finished product (Christopher 2016).
Information flow- There will be a flow of information from the vendors to the company
regarding the order receipt, bill information, inventory bill, dispatch bill and ledger
information along with shipping details as well as logistic information (Reid and Sanders
2019). The information regarding the number of orders, sales and the revenue collected will
be shared among the company and the customers.
Money flow- There will be a flow of money between the third party logistic vendors
and the company in the form of cash and cheque. There will be a flow of money between the
company and the customers in the form of either cash or e-payment application gateways like
PayPal.
The supply chain management is the process by which the raw materials from scratch gets
processed and pass from the well-finished stage and get stored then dispatched at the right
time to the customer and the payment is made (De Sousa et.al, 2019).
The internal supply chain involves the cook and the packaging team to prepare the
raw fish and make it a finished dish to deliver to the students as well as teachers.
The external supply chain consists of the third-party logistics who deliver the raw fish
from the sea and regional freshwater lake through negotiable contracts.
In the supply chain, the most important three types of flows:
Physical flow-There will be the flow of the inventory from the vendors to the
warehouse and ultimately to the company through third-party logistics, then to the customers
through the processing of the finished product (Christopher 2016).
Information flow- There will be a flow of information from the vendors to the company
regarding the order receipt, bill information, inventory bill, dispatch bill and ledger
information along with shipping details as well as logistic information (Reid and Sanders
2019). The information regarding the number of orders, sales and the revenue collected will
be shared among the company and the customers.
Money flow- There will be a flow of money between the third party logistic vendors
and the company in the form of cash and cheque. There will be a flow of money between the
company and the customers in the form of either cash or e-payment application gateways like
PayPal.
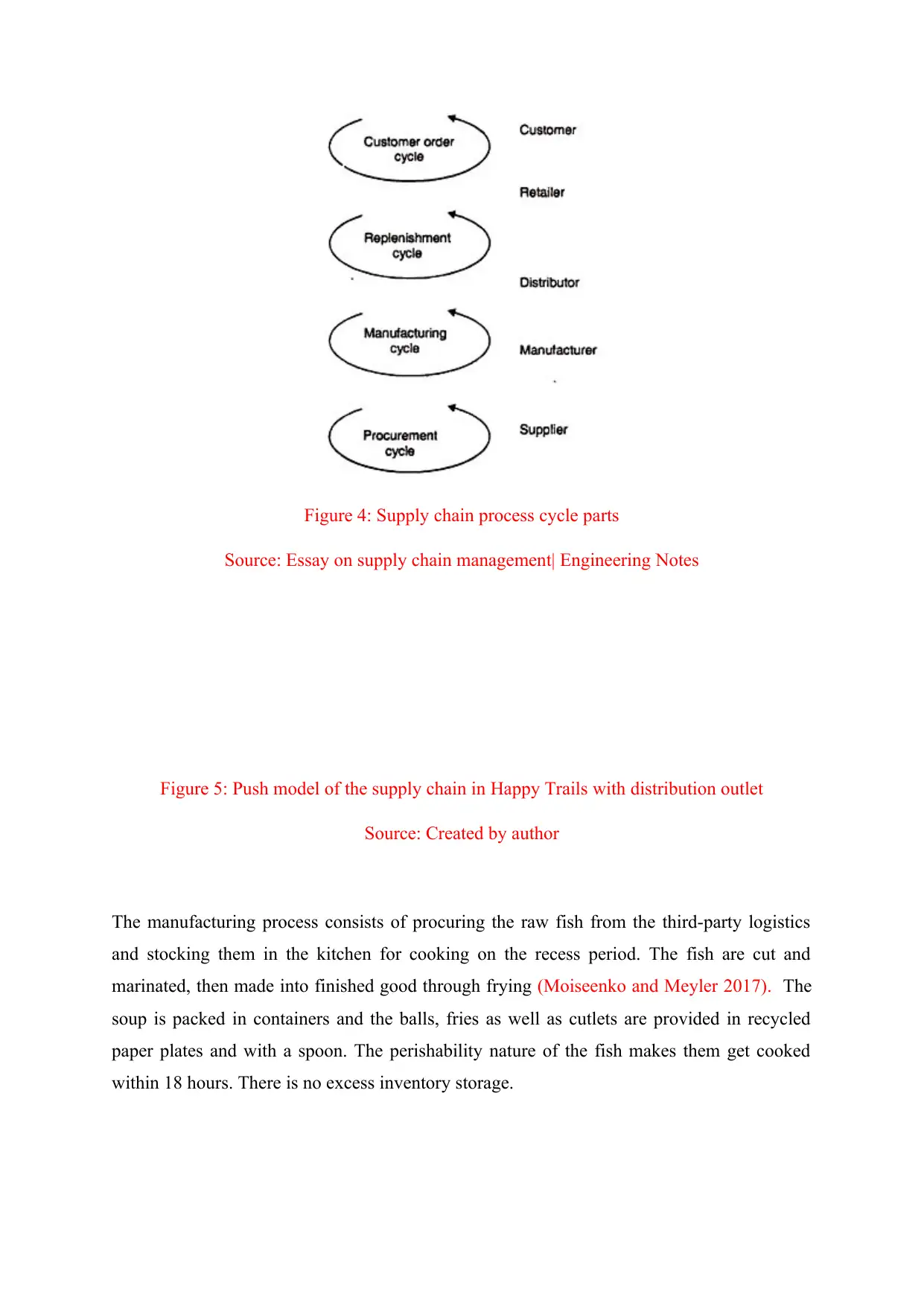
Figure 4: Supply chain process cycle parts
Source: Essay on supply chain management| Engineering Notes
Figure 5: Push model of the supply chain in Happy Trails with distribution outlet
Source: Created by author
The manufacturing process consists of procuring the raw fish from the third-party logistics
and stocking them in the kitchen for cooking on the recess period. The fish are cut and
marinated, then made into finished good through frying (Moiseenko and Meyler 2017). The
soup is packed in containers and the balls, fries as well as cutlets are provided in recycled
paper plates and with a spoon. The perishability nature of the fish makes them get cooked
within 18 hours. There is no excess inventory storage.
Source: Essay on supply chain management| Engineering Notes
Figure 5: Push model of the supply chain in Happy Trails with distribution outlet
Source: Created by author
The manufacturing process consists of procuring the raw fish from the third-party logistics
and stocking them in the kitchen for cooking on the recess period. The fish are cut and
marinated, then made into finished good through frying (Moiseenko and Meyler 2017). The
soup is packed in containers and the balls, fries as well as cutlets are provided in recycled
paper plates and with a spoon. The perishability nature of the fish makes them get cooked
within 18 hours. There is no excess inventory storage.
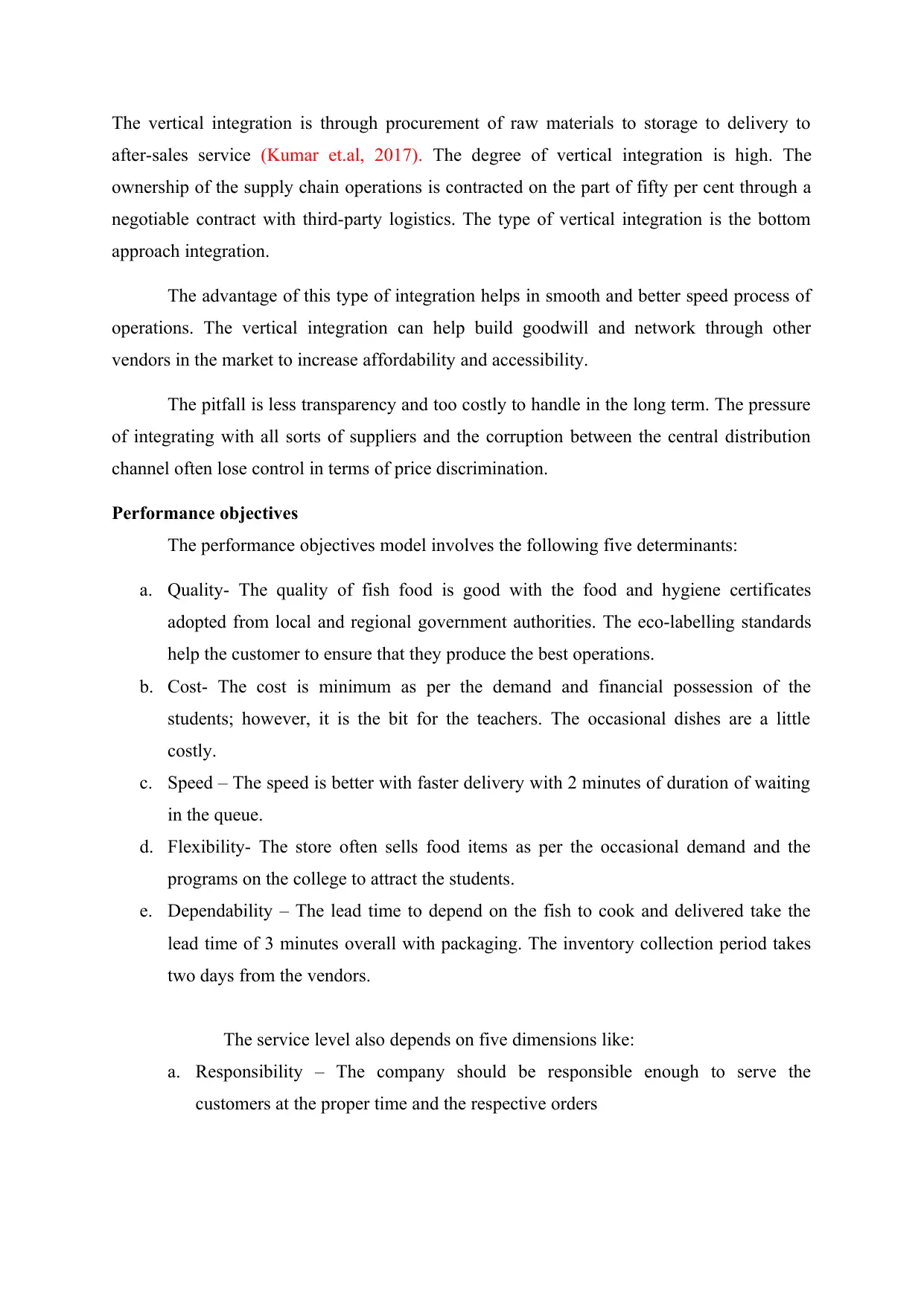
The vertical integration is through procurement of raw materials to storage to delivery to
after-sales service (Kumar et.al, 2017). The degree of vertical integration is high. The
ownership of the supply chain operations is contracted on the part of fifty per cent through a
negotiable contract with third-party logistics. The type of vertical integration is the bottom
approach integration.
The advantage of this type of integration helps in smooth and better speed process of
operations. The vertical integration can help build goodwill and network through other
vendors in the market to increase affordability and accessibility.
The pitfall is less transparency and too costly to handle in the long term. The pressure
of integrating with all sorts of suppliers and the corruption between the central distribution
channel often lose control in terms of price discrimination.
Performance objectives
The performance objectives model involves the following five determinants:
a. Quality- The quality of fish food is good with the food and hygiene certificates
adopted from local and regional government authorities. The eco-labelling standards
help the customer to ensure that they produce the best operations.
b. Cost- The cost is minimum as per the demand and financial possession of the
students; however, it is the bit for the teachers. The occasional dishes are a little
costly.
c. Speed – The speed is better with faster delivery with 2 minutes of duration of waiting
in the queue.
d. Flexibility- The store often sells food items as per the occasional demand and the
programs on the college to attract the students.
e. Dependability – The lead time to depend on the fish to cook and delivered take the
lead time of 3 minutes overall with packaging. The inventory collection period takes
two days from the vendors.
The service level also depends on five dimensions like:
a. Responsibility – The company should be responsible enough to serve the
customers at the proper time and the respective orders
after-sales service (Kumar et.al, 2017). The degree of vertical integration is high. The
ownership of the supply chain operations is contracted on the part of fifty per cent through a
negotiable contract with third-party logistics. The type of vertical integration is the bottom
approach integration.
The advantage of this type of integration helps in smooth and better speed process of
operations. The vertical integration can help build goodwill and network through other
vendors in the market to increase affordability and accessibility.
The pitfall is less transparency and too costly to handle in the long term. The pressure
of integrating with all sorts of suppliers and the corruption between the central distribution
channel often lose control in terms of price discrimination.
Performance objectives
The performance objectives model involves the following five determinants:
a. Quality- The quality of fish food is good with the food and hygiene certificates
adopted from local and regional government authorities. The eco-labelling standards
help the customer to ensure that they produce the best operations.
b. Cost- The cost is minimum as per the demand and financial possession of the
students; however, it is the bit for the teachers. The occasional dishes are a little
costly.
c. Speed – The speed is better with faster delivery with 2 minutes of duration of waiting
in the queue.
d. Flexibility- The store often sells food items as per the occasional demand and the
programs on the college to attract the students.
e. Dependability – The lead time to depend on the fish to cook and delivered take the
lead time of 3 minutes overall with packaging. The inventory collection period takes
two days from the vendors.
The service level also depends on five dimensions like:
a. Responsibility – The company should be responsible enough to serve the
customers at the proper time and the respective orders
Paraphrase This Document
Need a fresh take? Get an instant paraphrase of this document with our AI Paraphraser
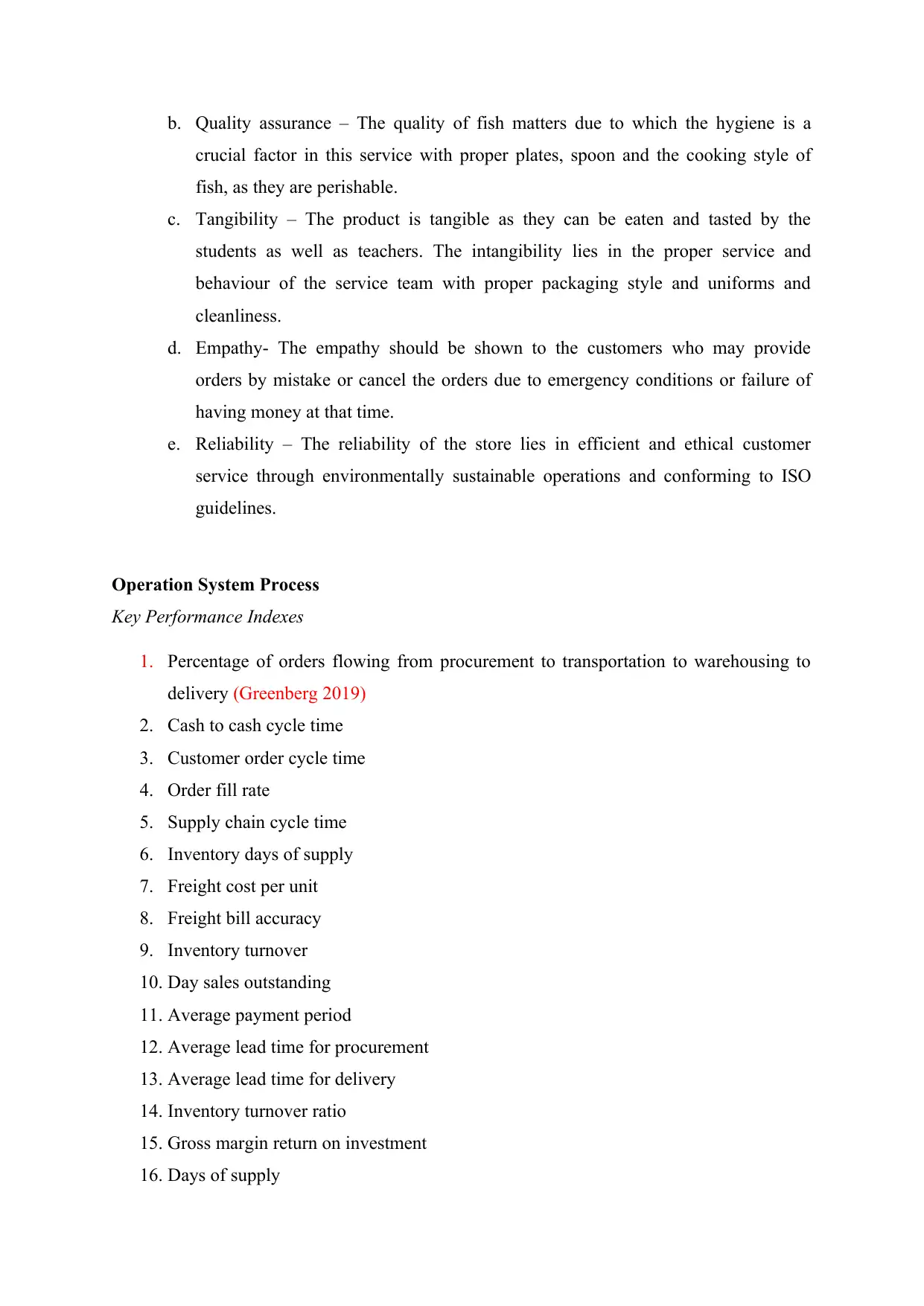
b. Quality assurance – The quality of fish matters due to which the hygiene is a
crucial factor in this service with proper plates, spoon and the cooking style of
fish, as they are perishable.
c. Tangibility – The product is tangible as they can be eaten and tasted by the
students as well as teachers. The intangibility lies in the proper service and
behaviour of the service team with proper packaging style and uniforms and
cleanliness.
d. Empathy- The empathy should be shown to the customers who may provide
orders by mistake or cancel the orders due to emergency conditions or failure of
having money at that time.
e. Reliability – The reliability of the store lies in efficient and ethical customer
service through environmentally sustainable operations and conforming to ISO
guidelines.
Operation System Process
Key Performance Indexes
1. Percentage of orders flowing from procurement to transportation to warehousing to
delivery (Greenberg 2019)
2. Cash to cash cycle time
3. Customer order cycle time
4. Order fill rate
5. Supply chain cycle time
6. Inventory days of supply
7. Freight cost per unit
8. Freight bill accuracy
9. Inventory turnover
10. Day sales outstanding
11. Average payment period
12. Average lead time for procurement
13. Average lead time for delivery
14. Inventory turnover ratio
15. Gross margin return on investment
16. Days of supply
crucial factor in this service with proper plates, spoon and the cooking style of
fish, as they are perishable.
c. Tangibility – The product is tangible as they can be eaten and tasted by the
students as well as teachers. The intangibility lies in the proper service and
behaviour of the service team with proper packaging style and uniforms and
cleanliness.
d. Empathy- The empathy should be shown to the customers who may provide
orders by mistake or cancel the orders due to emergency conditions or failure of
having money at that time.
e. Reliability – The reliability of the store lies in efficient and ethical customer
service through environmentally sustainable operations and conforming to ISO
guidelines.
Operation System Process
Key Performance Indexes
1. Percentage of orders flowing from procurement to transportation to warehousing to
delivery (Greenberg 2019)
2. Cash to cash cycle time
3. Customer order cycle time
4. Order fill rate
5. Supply chain cycle time
6. Inventory days of supply
7. Freight cost per unit
8. Freight bill accuracy
9. Inventory turnover
10. Day sales outstanding
11. Average payment period
12. Average lead time for procurement
13. Average lead time for delivery
14. Inventory turnover ratio
15. Gross margin return on investment
16. Days of supply
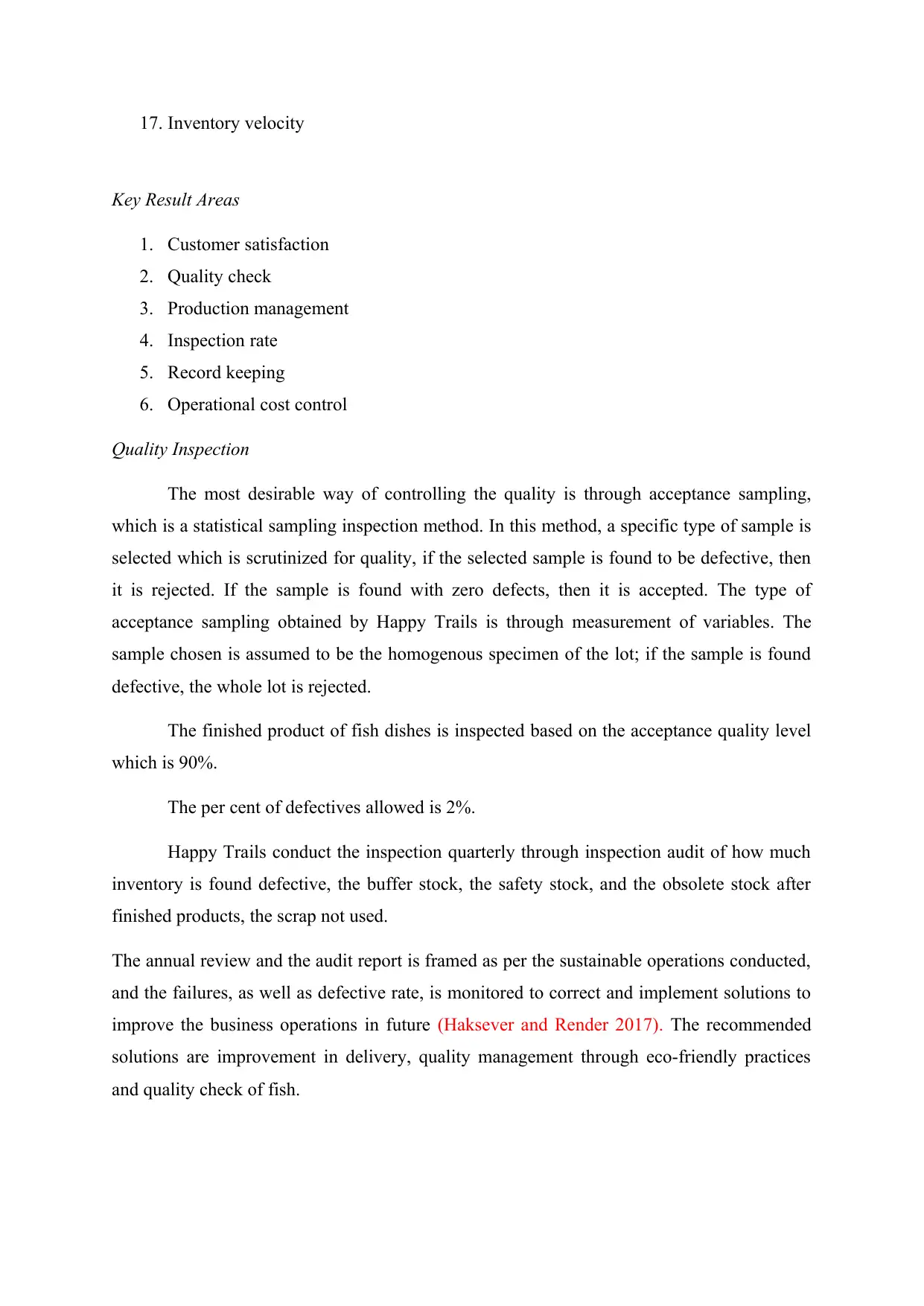
17. Inventory velocity
Key Result Areas
1. Customer satisfaction
2. Quality check
3. Production management
4. Inspection rate
5. Record keeping
6. Operational cost control
Quality Inspection
The most desirable way of controlling the quality is through acceptance sampling,
which is a statistical sampling inspection method. In this method, a specific type of sample is
selected which is scrutinized for quality, if the selected sample is found to be defective, then
it is rejected. If the sample is found with zero defects, then it is accepted. The type of
acceptance sampling obtained by Happy Trails is through measurement of variables. The
sample chosen is assumed to be the homogenous specimen of the lot; if the sample is found
defective, the whole lot is rejected.
The finished product of fish dishes is inspected based on the acceptance quality level
which is 90%.
The per cent of defectives allowed is 2%.
Happy Trails conduct the inspection quarterly through inspection audit of how much
inventory is found defective, the buffer stock, the safety stock, and the obsolete stock after
finished products, the scrap not used.
The annual review and the audit report is framed as per the sustainable operations conducted,
and the failures, as well as defective rate, is monitored to correct and implement solutions to
improve the business operations in future (Haksever and Render 2017). The recommended
solutions are improvement in delivery, quality management through eco-friendly practices
and quality check of fish.
Key Result Areas
1. Customer satisfaction
2. Quality check
3. Production management
4. Inspection rate
5. Record keeping
6. Operational cost control
Quality Inspection
The most desirable way of controlling the quality is through acceptance sampling,
which is a statistical sampling inspection method. In this method, a specific type of sample is
selected which is scrutinized for quality, if the selected sample is found to be defective, then
it is rejected. If the sample is found with zero defects, then it is accepted. The type of
acceptance sampling obtained by Happy Trails is through measurement of variables. The
sample chosen is assumed to be the homogenous specimen of the lot; if the sample is found
defective, the whole lot is rejected.
The finished product of fish dishes is inspected based on the acceptance quality level
which is 90%.
The per cent of defectives allowed is 2%.
Happy Trails conduct the inspection quarterly through inspection audit of how much
inventory is found defective, the buffer stock, the safety stock, and the obsolete stock after
finished products, the scrap not used.
The annual review and the audit report is framed as per the sustainable operations conducted,
and the failures, as well as defective rate, is monitored to correct and implement solutions to
improve the business operations in future (Haksever and Render 2017). The recommended
solutions are improvement in delivery, quality management through eco-friendly practices
and quality check of fish.
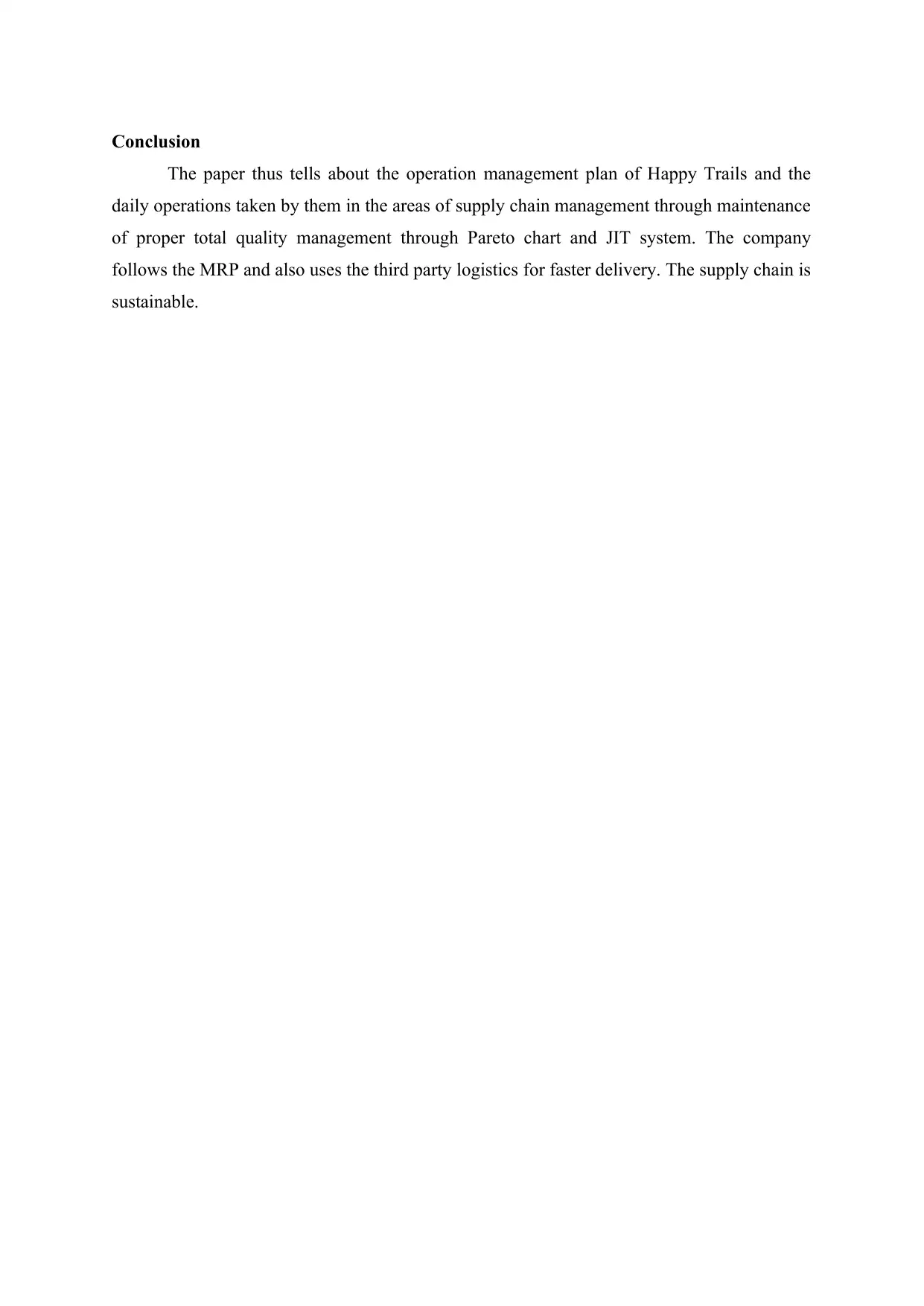
Conclusion
The paper thus tells about the operation management plan of Happy Trails and the
daily operations taken by them in the areas of supply chain management through maintenance
of proper total quality management through Pareto chart and JIT system. The company
follows the MRP and also uses the third party logistics for faster delivery. The supply chain is
sustainable.
The paper thus tells about the operation management plan of Happy Trails and the
daily operations taken by them in the areas of supply chain management through maintenance
of proper total quality management through Pareto chart and JIT system. The company
follows the MRP and also uses the third party logistics for faster delivery. The supply chain is
sustainable.
Secure Best Marks with AI Grader
Need help grading? Try our AI Grader for instant feedback on your assignments.
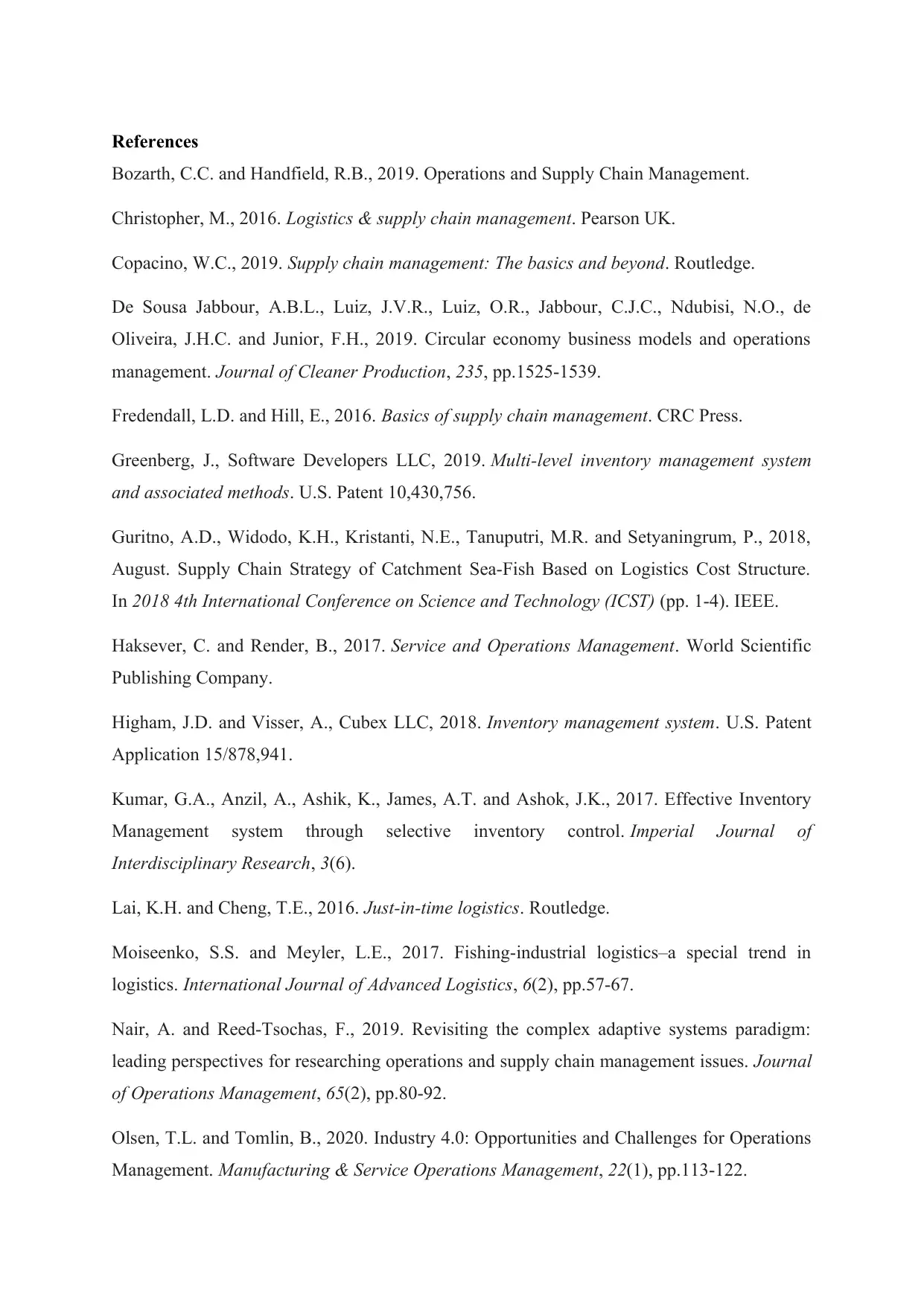
References
Bozarth, C.C. and Handfield, R.B., 2019. Operations and Supply Chain Management.
Christopher, M., 2016. Logistics & supply chain management. Pearson UK.
Copacino, W.C., 2019. Supply chain management: The basics and beyond. Routledge.
De Sousa Jabbour, A.B.L., Luiz, J.V.R., Luiz, O.R., Jabbour, C.J.C., Ndubisi, N.O., de
Oliveira, J.H.C. and Junior, F.H., 2019. Circular economy business models and operations
management. Journal of Cleaner Production, 235, pp.1525-1539.
Fredendall, L.D. and Hill, E., 2016. Basics of supply chain management. CRC Press.
Greenberg, J., Software Developers LLC, 2019. Multi-level inventory management system
and associated methods. U.S. Patent 10,430,756.
Guritno, A.D., Widodo, K.H., Kristanti, N.E., Tanuputri, M.R. and Setyaningrum, P., 2018,
August. Supply Chain Strategy of Catchment Sea-Fish Based on Logistics Cost Structure.
In 2018 4th International Conference on Science and Technology (ICST) (pp. 1-4). IEEE.
Haksever, C. and Render, B., 2017. Service and Operations Management. World Scientific
Publishing Company.
Higham, J.D. and Visser, A., Cubex LLC, 2018. Inventory management system. U.S. Patent
Application 15/878,941.
Kumar, G.A., Anzil, A., Ashik, K., James, A.T. and Ashok, J.K., 2017. Effective Inventory
Management system through selective inventory control. Imperial Journal of
Interdisciplinary Research, 3(6).
Lai, K.H. and Cheng, T.E., 2016. Just-in-time logistics. Routledge.
Moiseenko, S.S. and Meyler, L.E., 2017. Fishing-industrial logistics–a special trend in
logistics. International Journal of Advanced Logistics, 6(2), pp.57-67.
Nair, A. and Reed‐Tsochas, F., 2019. Revisiting the complex adaptive systems paradigm:
leading perspectives for researching operations and supply chain management issues. Journal
of Operations Management, 65(2), pp.80-92.
Olsen, T.L. and Tomlin, B., 2020. Industry 4.0: Opportunities and Challenges for Operations
Management. Manufacturing & Service Operations Management, 22(1), pp.113-122.
Bozarth, C.C. and Handfield, R.B., 2019. Operations and Supply Chain Management.
Christopher, M., 2016. Logistics & supply chain management. Pearson UK.
Copacino, W.C., 2019. Supply chain management: The basics and beyond. Routledge.
De Sousa Jabbour, A.B.L., Luiz, J.V.R., Luiz, O.R., Jabbour, C.J.C., Ndubisi, N.O., de
Oliveira, J.H.C. and Junior, F.H., 2019. Circular economy business models and operations
management. Journal of Cleaner Production, 235, pp.1525-1539.
Fredendall, L.D. and Hill, E., 2016. Basics of supply chain management. CRC Press.
Greenberg, J., Software Developers LLC, 2019. Multi-level inventory management system
and associated methods. U.S. Patent 10,430,756.
Guritno, A.D., Widodo, K.H., Kristanti, N.E., Tanuputri, M.R. and Setyaningrum, P., 2018,
August. Supply Chain Strategy of Catchment Sea-Fish Based on Logistics Cost Structure.
In 2018 4th International Conference on Science and Technology (ICST) (pp. 1-4). IEEE.
Haksever, C. and Render, B., 2017. Service and Operations Management. World Scientific
Publishing Company.
Higham, J.D. and Visser, A., Cubex LLC, 2018. Inventory management system. U.S. Patent
Application 15/878,941.
Kumar, G.A., Anzil, A., Ashik, K., James, A.T. and Ashok, J.K., 2017. Effective Inventory
Management system through selective inventory control. Imperial Journal of
Interdisciplinary Research, 3(6).
Lai, K.H. and Cheng, T.E., 2016. Just-in-time logistics. Routledge.
Moiseenko, S.S. and Meyler, L.E., 2017. Fishing-industrial logistics–a special trend in
logistics. International Journal of Advanced Logistics, 6(2), pp.57-67.
Nair, A. and Reed‐Tsochas, F., 2019. Revisiting the complex adaptive systems paradigm:
leading perspectives for researching operations and supply chain management issues. Journal
of Operations Management, 65(2), pp.80-92.
Olsen, T.L. and Tomlin, B., 2020. Industry 4.0: Opportunities and Challenges for Operations
Management. Manufacturing & Service Operations Management, 22(1), pp.113-122.
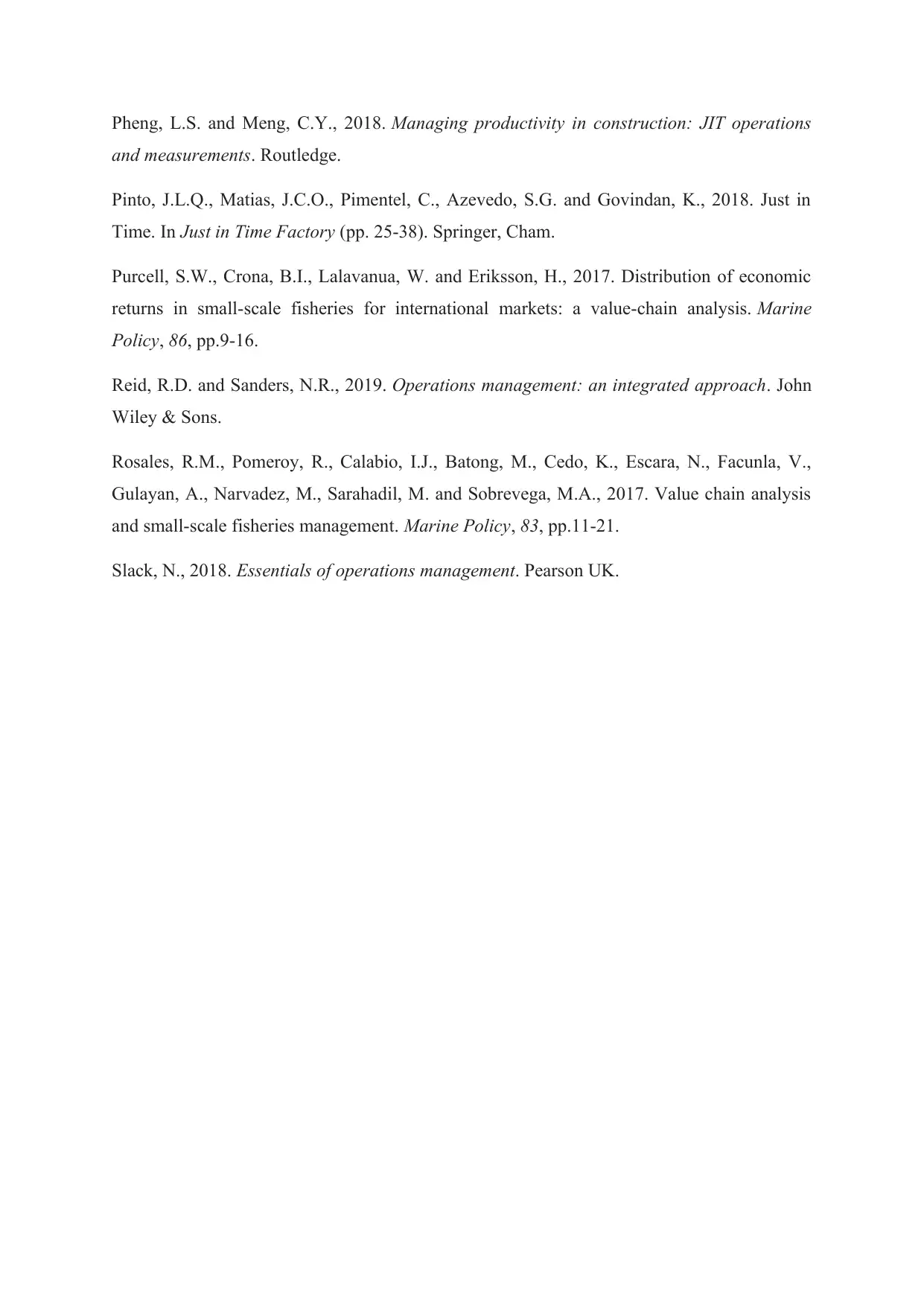
Pheng, L.S. and Meng, C.Y., 2018. Managing productivity in construction: JIT operations
and measurements. Routledge.
Pinto, J.L.Q., Matias, J.C.O., Pimentel, C., Azevedo, S.G. and Govindan, K., 2018. Just in
Time. In Just in Time Factory (pp. 25-38). Springer, Cham.
Purcell, S.W., Crona, B.I., Lalavanua, W. and Eriksson, H., 2017. Distribution of economic
returns in small-scale fisheries for international markets: a value-chain analysis. Marine
Policy, 86, pp.9-16.
Reid, R.D. and Sanders, N.R., 2019. Operations management: an integrated approach. John
Wiley & Sons.
Rosales, R.M., Pomeroy, R., Calabio, I.J., Batong, M., Cedo, K., Escara, N., Facunla, V.,
Gulayan, A., Narvadez, M., Sarahadil, M. and Sobrevega, M.A., 2017. Value chain analysis
and small-scale fisheries management. Marine Policy, 83, pp.11-21.
Slack, N., 2018. Essentials of operations management. Pearson UK.
and measurements. Routledge.
Pinto, J.L.Q., Matias, J.C.O., Pimentel, C., Azevedo, S.G. and Govindan, K., 2018. Just in
Time. In Just in Time Factory (pp. 25-38). Springer, Cham.
Purcell, S.W., Crona, B.I., Lalavanua, W. and Eriksson, H., 2017. Distribution of economic
returns in small-scale fisheries for international markets: a value-chain analysis. Marine
Policy, 86, pp.9-16.
Reid, R.D. and Sanders, N.R., 2019. Operations management: an integrated approach. John
Wiley & Sons.
Rosales, R.M., Pomeroy, R., Calabio, I.J., Batong, M., Cedo, K., Escara, N., Facunla, V.,
Gulayan, A., Narvadez, M., Sarahadil, M. and Sobrevega, M.A., 2017. Value chain analysis
and small-scale fisheries management. Marine Policy, 83, pp.11-21.
Slack, N., 2018. Essentials of operations management. Pearson UK.
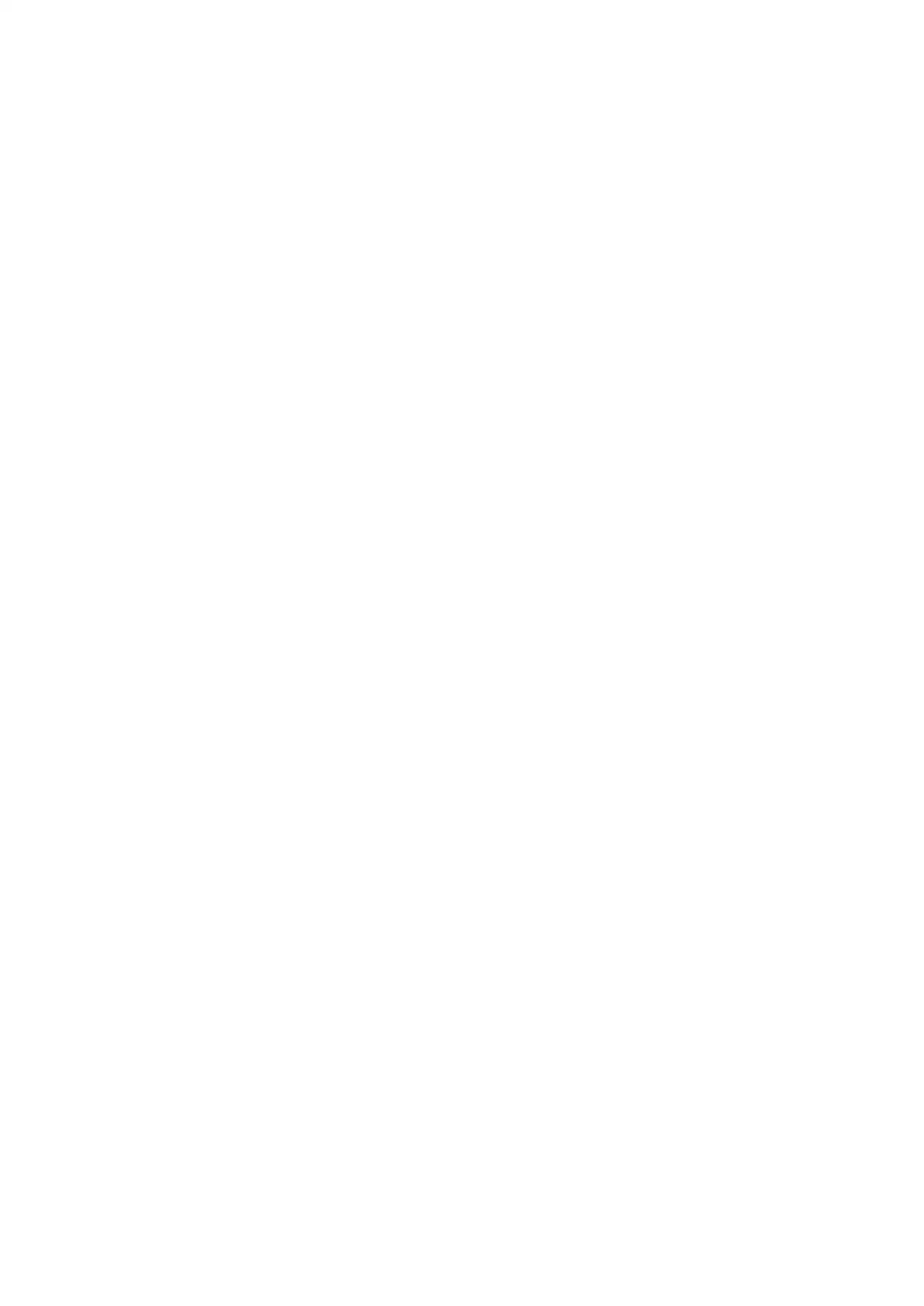
1 out of 19
Related Documents
![[object Object]](/_next/image/?url=%2F_next%2Fstatic%2Fmedia%2Flogo.6d15ce61.png&w=640&q=75)
Your All-in-One AI-Powered Toolkit for Academic Success.
+13062052269
info@desklib.com
Available 24*7 on WhatsApp / Email
Unlock your academic potential
© 2024 | Zucol Services PVT LTD | All rights reserved.