Operations Management: Quality and Supply Chain Activities at Active Electrical Suppliers Ltd.
VerifiedAdded on 2023/06/11
|13
|3273
|300
AI Summary
This report discusses the management of quality and supply chain activities at Active Electrical Suppliers Ltd. in New Zealand, specifically focusing on the production of solar LED lights. It covers topics such as ISO certification, total quality management, and inventory management techniques like EOQ, stock turnover ratio, JIT, and Kanban.
Contribute Materials
Your contribution can guide someone’s learning journey. Share your
documents today.
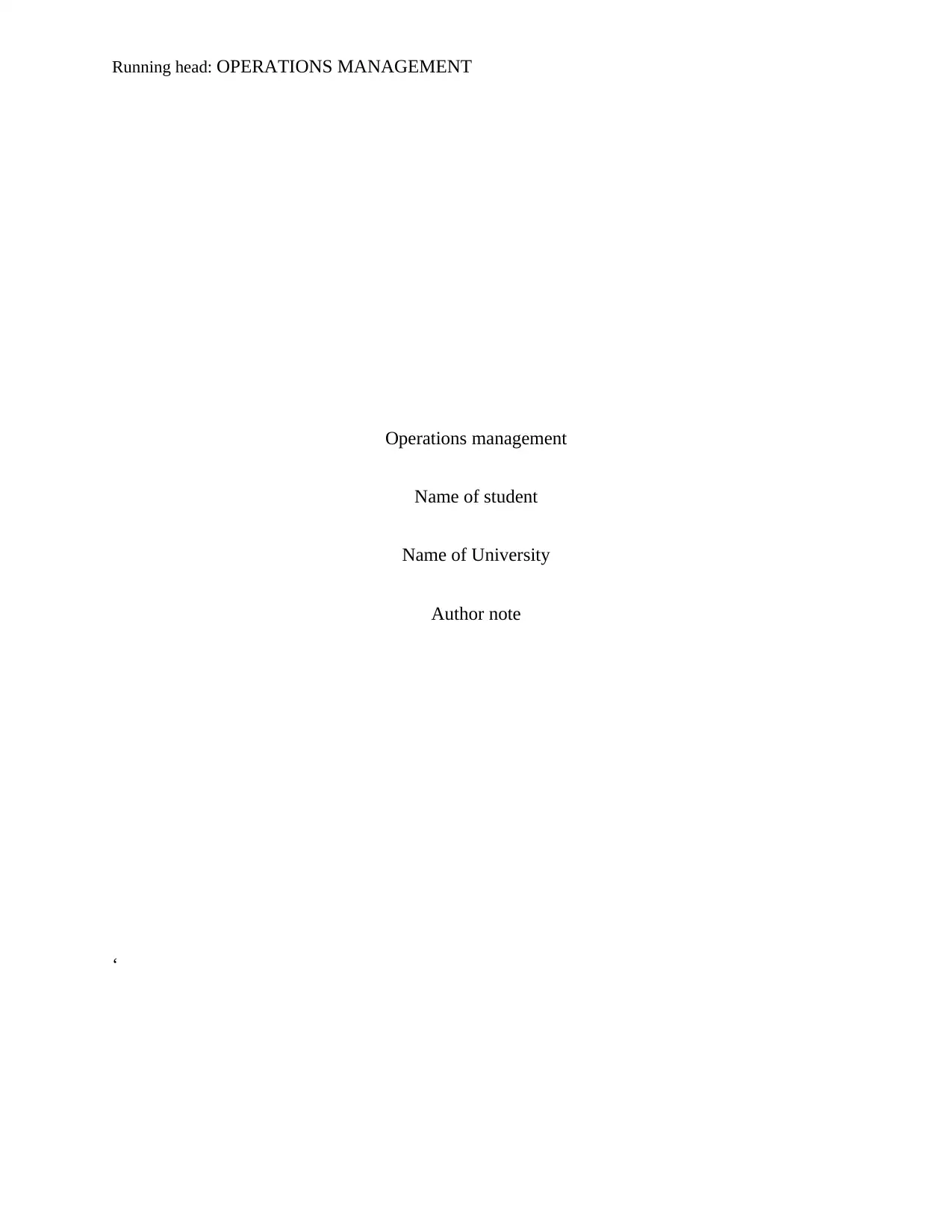
Running head: OPERATIONS MANAGEMENT
Operations management
Name of student
Name of University
Author note
‘
Operations management
Name of student
Name of University
Author note
‘
Secure Best Marks with AI Grader
Need help grading? Try our AI Grader for instant feedback on your assignments.
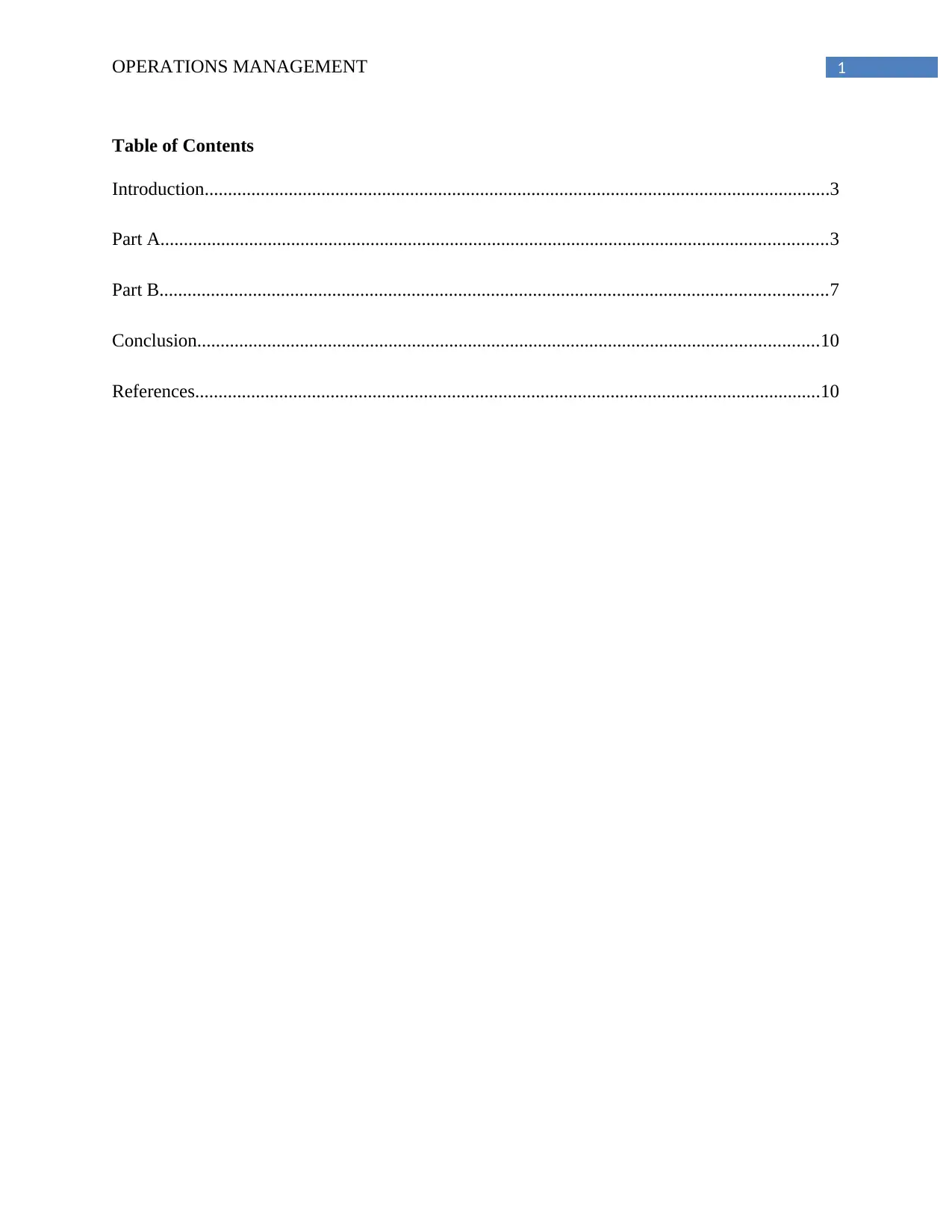
1OPERATIONS MANAGEMENT
Table of Contents
Introduction......................................................................................................................................3
Part A...............................................................................................................................................3
Part B...............................................................................................................................................7
Conclusion.....................................................................................................................................10
References......................................................................................................................................10
Table of Contents
Introduction......................................................................................................................................3
Part A...............................................................................................................................................3
Part B...............................................................................................................................................7
Conclusion.....................................................................................................................................10
References......................................................................................................................................10
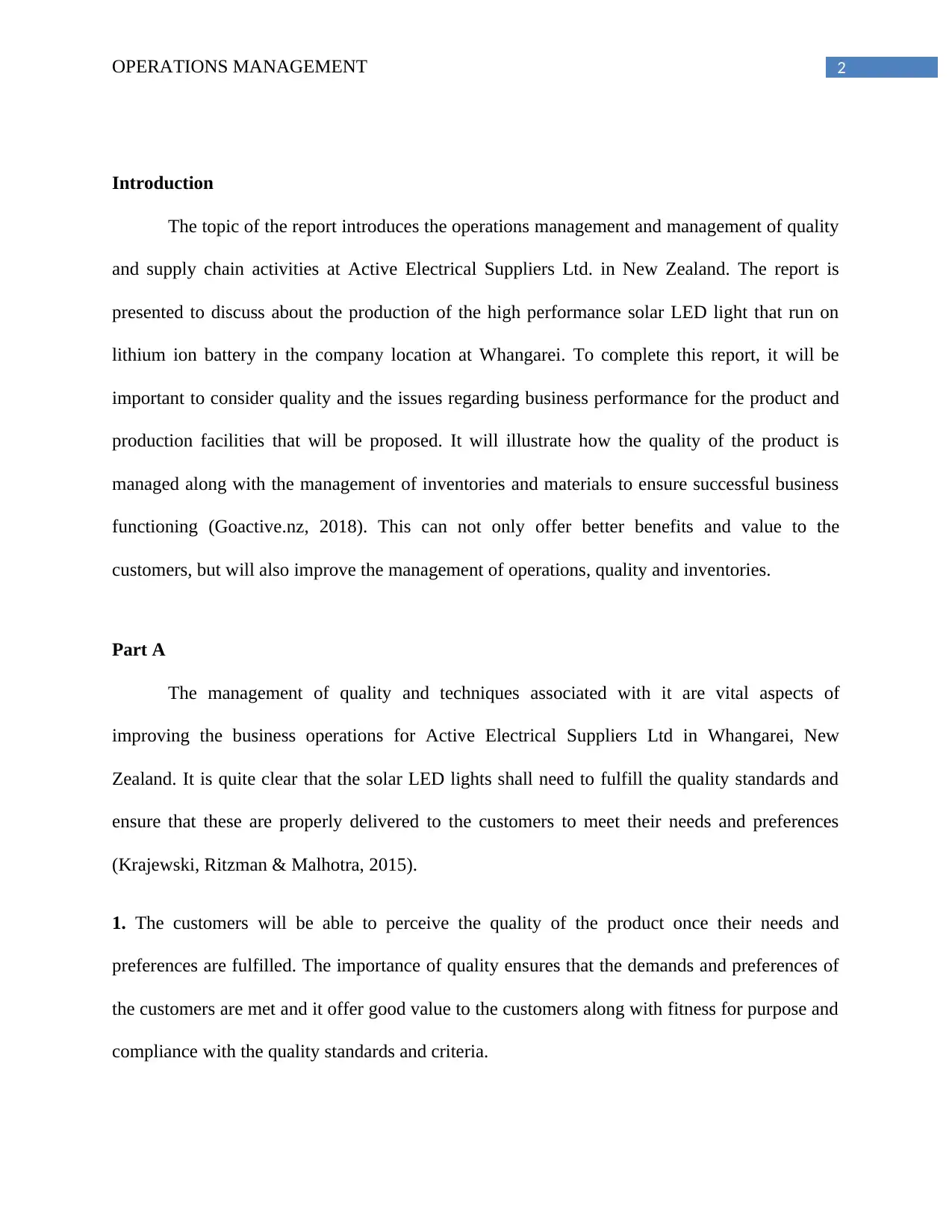
2OPERATIONS MANAGEMENT
Introduction
The topic of the report introduces the operations management and management of quality
and supply chain activities at Active Electrical Suppliers Ltd. in New Zealand. The report is
presented to discuss about the production of the high performance solar LED light that run on
lithium ion battery in the company location at Whangarei. To complete this report, it will be
important to consider quality and the issues regarding business performance for the product and
production facilities that will be proposed. It will illustrate how the quality of the product is
managed along with the management of inventories and materials to ensure successful business
functioning (Goactive.nz, 2018). This can not only offer better benefits and value to the
customers, but will also improve the management of operations, quality and inventories.
Part A
The management of quality and techniques associated with it are vital aspects of
improving the business operations for Active Electrical Suppliers Ltd in Whangarei, New
Zealand. It is quite clear that the solar LED lights shall need to fulfill the quality standards and
ensure that these are properly delivered to the customers to meet their needs and preferences
(Krajewski, Ritzman & Malhotra, 2015).
1. The customers will be able to perceive the quality of the product once their needs and
preferences are fulfilled. The importance of quality ensures that the demands and preferences of
the customers are met and it offer good value to the customers along with fitness for purpose and
compliance with the quality standards and criteria.
Introduction
The topic of the report introduces the operations management and management of quality
and supply chain activities at Active Electrical Suppliers Ltd. in New Zealand. The report is
presented to discuss about the production of the high performance solar LED light that run on
lithium ion battery in the company location at Whangarei. To complete this report, it will be
important to consider quality and the issues regarding business performance for the product and
production facilities that will be proposed. It will illustrate how the quality of the product is
managed along with the management of inventories and materials to ensure successful business
functioning (Goactive.nz, 2018). This can not only offer better benefits and value to the
customers, but will also improve the management of operations, quality and inventories.
Part A
The management of quality and techniques associated with it are vital aspects of
improving the business operations for Active Electrical Suppliers Ltd in Whangarei, New
Zealand. It is quite clear that the solar LED lights shall need to fulfill the quality standards and
ensure that these are properly delivered to the customers to meet their needs and preferences
(Krajewski, Ritzman & Malhotra, 2015).
1. The customers will be able to perceive the quality of the product once their needs and
preferences are fulfilled. The importance of quality ensures that the demands and preferences of
the customers are met and it offer good value to the customers along with fitness for purpose and
compliance with the quality standards and criteria.
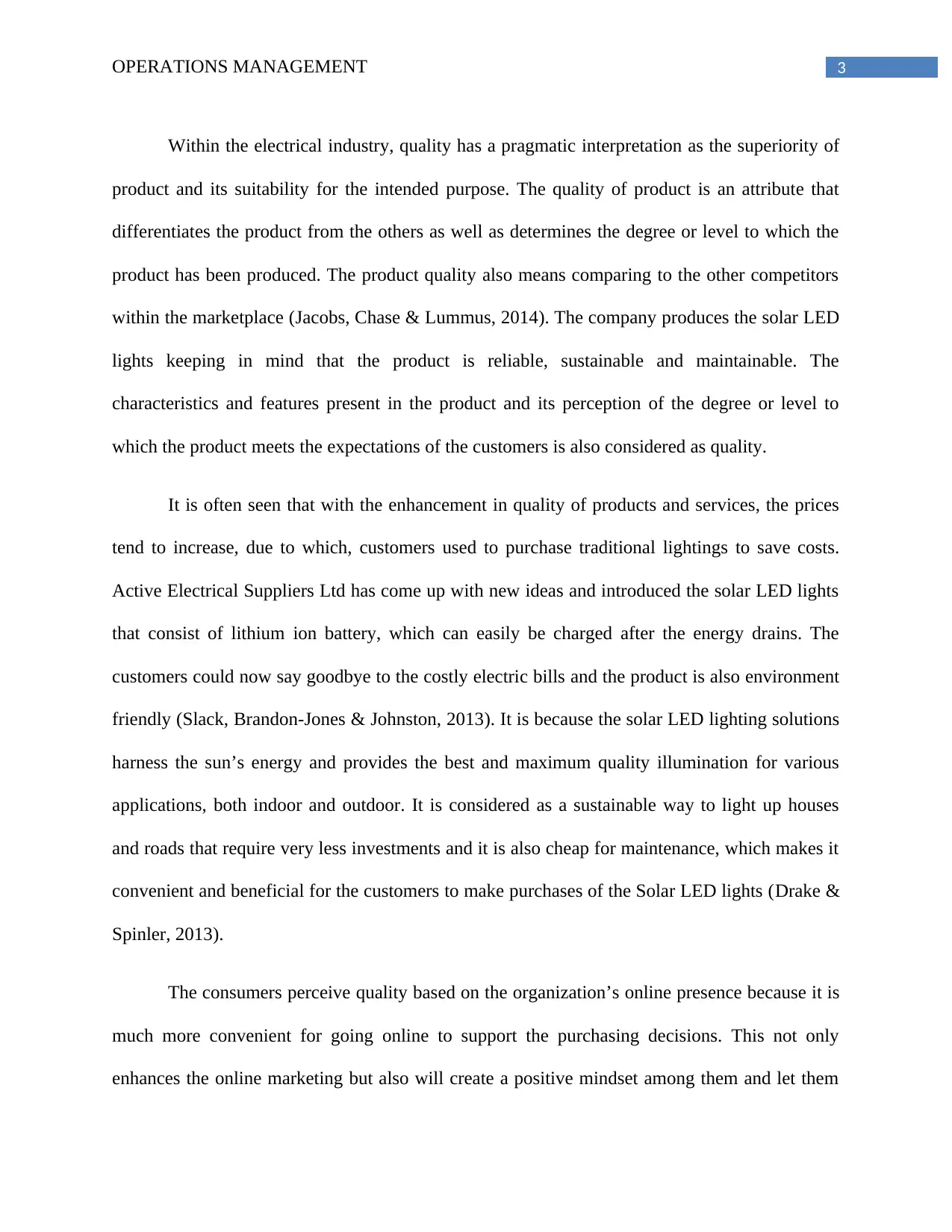
3OPERATIONS MANAGEMENT
Within the electrical industry, quality has a pragmatic interpretation as the superiority of
product and its suitability for the intended purpose. The quality of product is an attribute that
differentiates the product from the others as well as determines the degree or level to which the
product has been produced. The product quality also means comparing to the other competitors
within the marketplace (Jacobs, Chase & Lummus, 2014). The company produces the solar LED
lights keeping in mind that the product is reliable, sustainable and maintainable. The
characteristics and features present in the product and its perception of the degree or level to
which the product meets the expectations of the customers is also considered as quality.
It is often seen that with the enhancement in quality of products and services, the prices
tend to increase, due to which, customers used to purchase traditional lightings to save costs.
Active Electrical Suppliers Ltd has come up with new ideas and introduced the solar LED lights
that consist of lithium ion battery, which can easily be charged after the energy drains. The
customers could now say goodbye to the costly electric bills and the product is also environment
friendly (Slack, Brandon-Jones & Johnston, 2013). It is because the solar LED lighting solutions
harness the sun’s energy and provides the best and maximum quality illumination for various
applications, both indoor and outdoor. It is considered as a sustainable way to light up houses
and roads that require very less investments and it is also cheap for maintenance, which makes it
convenient and beneficial for the customers to make purchases of the Solar LED lights (Drake &
Spinler, 2013).
The consumers perceive quality based on the organization’s online presence because it is
much more convenient for going online to support the purchasing decisions. This not only
enhances the online marketing but also will create a positive mindset among them and let them
Within the electrical industry, quality has a pragmatic interpretation as the superiority of
product and its suitability for the intended purpose. The quality of product is an attribute that
differentiates the product from the others as well as determines the degree or level to which the
product has been produced. The product quality also means comparing to the other competitors
within the marketplace (Jacobs, Chase & Lummus, 2014). The company produces the solar LED
lights keeping in mind that the product is reliable, sustainable and maintainable. The
characteristics and features present in the product and its perception of the degree or level to
which the product meets the expectations of the customers is also considered as quality.
It is often seen that with the enhancement in quality of products and services, the prices
tend to increase, due to which, customers used to purchase traditional lightings to save costs.
Active Electrical Suppliers Ltd has come up with new ideas and introduced the solar LED lights
that consist of lithium ion battery, which can easily be charged after the energy drains. The
customers could now say goodbye to the costly electric bills and the product is also environment
friendly (Slack, Brandon-Jones & Johnston, 2013). It is because the solar LED lighting solutions
harness the sun’s energy and provides the best and maximum quality illumination for various
applications, both indoor and outdoor. It is considered as a sustainable way to light up houses
and roads that require very less investments and it is also cheap for maintenance, which makes it
convenient and beneficial for the customers to make purchases of the Solar LED lights (Drake &
Spinler, 2013).
The consumers perceive quality based on the organization’s online presence because it is
much more convenient for going online to support the purchasing decisions. This not only
enhances the online marketing but also will create a positive mindset among them and let them
Secure Best Marks with AI Grader
Need help grading? Try our AI Grader for instant feedback on your assignments.
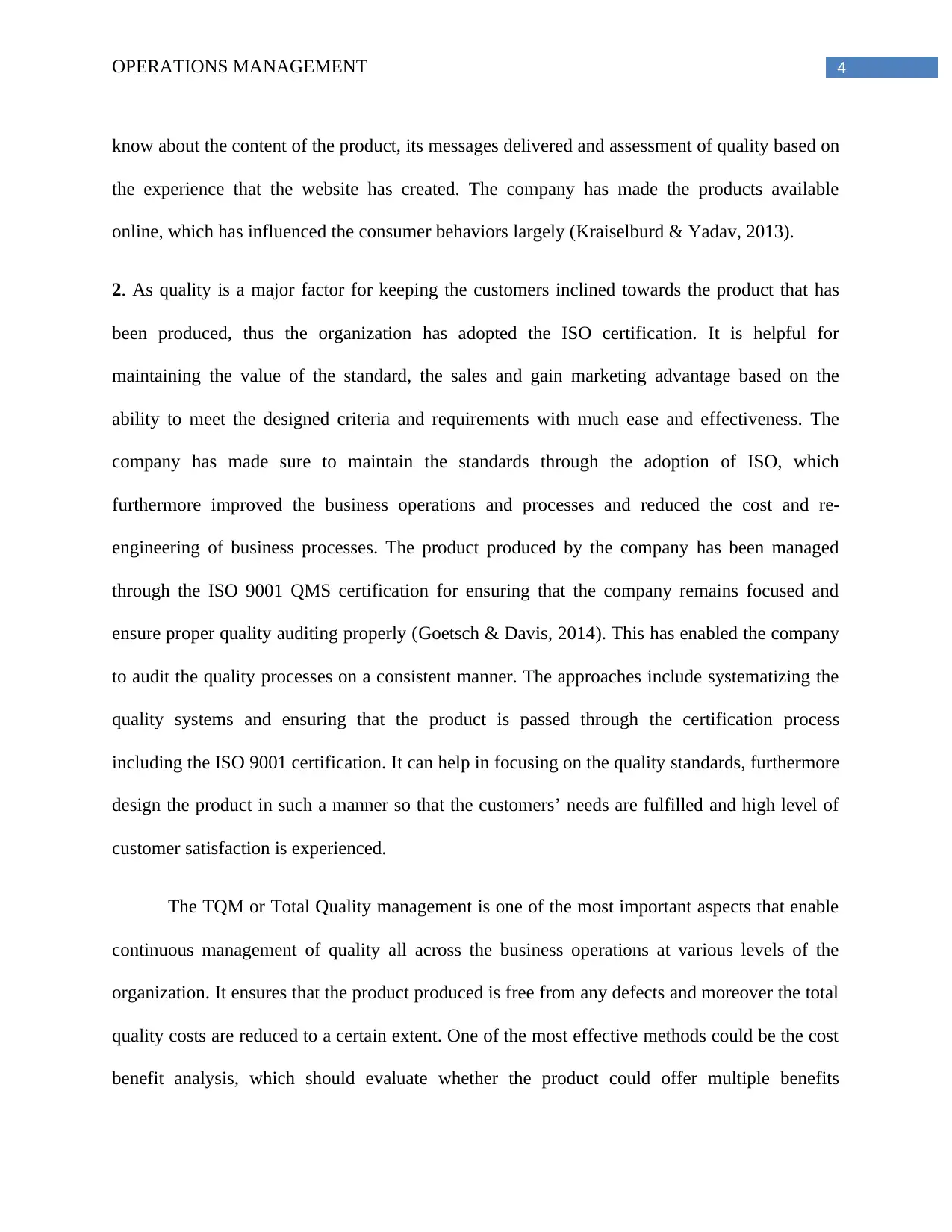
4OPERATIONS MANAGEMENT
know about the content of the product, its messages delivered and assessment of quality based on
the experience that the website has created. The company has made the products available
online, which has influenced the consumer behaviors largely (Kraiselburd & Yadav, 2013).
2. As quality is a major factor for keeping the customers inclined towards the product that has
been produced, thus the organization has adopted the ISO certification. It is helpful for
maintaining the value of the standard, the sales and gain marketing advantage based on the
ability to meet the designed criteria and requirements with much ease and effectiveness. The
company has made sure to maintain the standards through the adoption of ISO, which
furthermore improved the business operations and processes and reduced the cost and re-
engineering of business processes. The product produced by the company has been managed
through the ISO 9001 QMS certification for ensuring that the company remains focused and
ensure proper quality auditing properly (Goetsch & Davis, 2014). This has enabled the company
to audit the quality processes on a consistent manner. The approaches include systematizing the
quality systems and ensuring that the product is passed through the certification process
including the ISO 9001 certification. It can help in focusing on the quality standards, furthermore
design the product in such a manner so that the customers’ needs are fulfilled and high level of
customer satisfaction is experienced.
The TQM or Total Quality management is one of the most important aspects that enable
continuous management of quality all across the business operations at various levels of the
organization. It ensures that the product produced is free from any defects and moreover the total
quality costs are reduced to a certain extent. One of the most effective methods could be the cost
benefit analysis, which should evaluate whether the product could offer multiple benefits
know about the content of the product, its messages delivered and assessment of quality based on
the experience that the website has created. The company has made the products available
online, which has influenced the consumer behaviors largely (Kraiselburd & Yadav, 2013).
2. As quality is a major factor for keeping the customers inclined towards the product that has
been produced, thus the organization has adopted the ISO certification. It is helpful for
maintaining the value of the standard, the sales and gain marketing advantage based on the
ability to meet the designed criteria and requirements with much ease and effectiveness. The
company has made sure to maintain the standards through the adoption of ISO, which
furthermore improved the business operations and processes and reduced the cost and re-
engineering of business processes. The product produced by the company has been managed
through the ISO 9001 QMS certification for ensuring that the company remains focused and
ensure proper quality auditing properly (Goetsch & Davis, 2014). This has enabled the company
to audit the quality processes on a consistent manner. The approaches include systematizing the
quality systems and ensuring that the product is passed through the certification process
including the ISO 9001 certification. It can help in focusing on the quality standards, furthermore
design the product in such a manner so that the customers’ needs are fulfilled and high level of
customer satisfaction is experienced.
The TQM or Total Quality management is one of the most important aspects that enable
continuous management of quality all across the business operations at various levels of the
organization. It ensures that the product produced is free from any defects and moreover the total
quality costs are reduced to a certain extent. One of the most effective methods could be the cost
benefit analysis, which should evaluate whether the product could offer multiple benefits
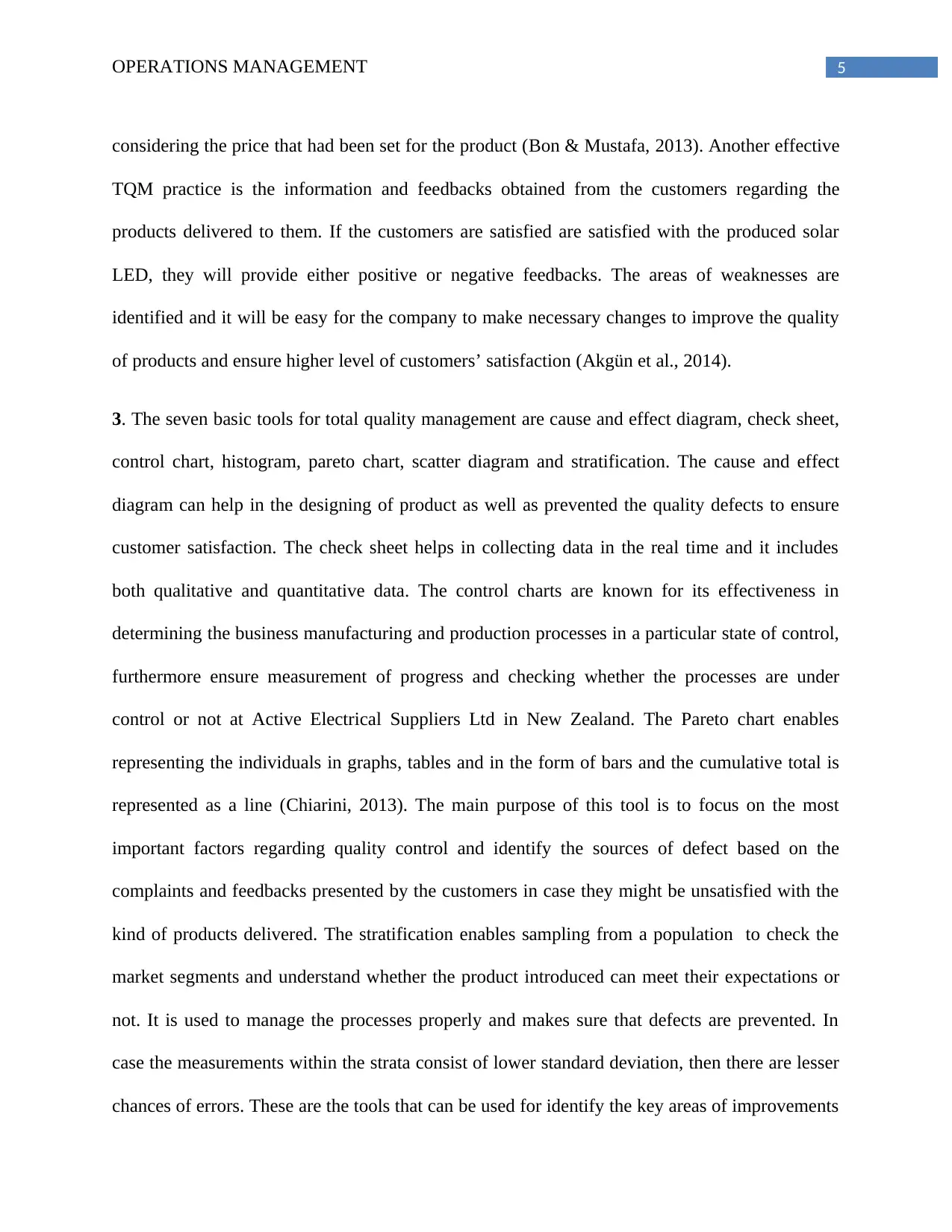
5OPERATIONS MANAGEMENT
considering the price that had been set for the product (Bon & Mustafa, 2013). Another effective
TQM practice is the information and feedbacks obtained from the customers regarding the
products delivered to them. If the customers are satisfied are satisfied with the produced solar
LED, they will provide either positive or negative feedbacks. The areas of weaknesses are
identified and it will be easy for the company to make necessary changes to improve the quality
of products and ensure higher level of customers’ satisfaction (Akgün et al., 2014).
3. The seven basic tools for total quality management are cause and effect diagram, check sheet,
control chart, histogram, pareto chart, scatter diagram and stratification. The cause and effect
diagram can help in the designing of product as well as prevented the quality defects to ensure
customer satisfaction. The check sheet helps in collecting data in the real time and it includes
both qualitative and quantitative data. The control charts are known for its effectiveness in
determining the business manufacturing and production processes in a particular state of control,
furthermore ensure measurement of progress and checking whether the processes are under
control or not at Active Electrical Suppliers Ltd in New Zealand. The Pareto chart enables
representing the individuals in graphs, tables and in the form of bars and the cumulative total is
represented as a line (Chiarini, 2013). The main purpose of this tool is to focus on the most
important factors regarding quality control and identify the sources of defect based on the
complaints and feedbacks presented by the customers in case they might be unsatisfied with the
kind of products delivered. The stratification enables sampling from a population to check the
market segments and understand whether the product introduced can meet their expectations or
not. It is used to manage the processes properly and makes sure that defects are prevented. In
case the measurements within the strata consist of lower standard deviation, then there are lesser
chances of errors. These are the tools that can be used for identify the key areas of improvements
considering the price that had been set for the product (Bon & Mustafa, 2013). Another effective
TQM practice is the information and feedbacks obtained from the customers regarding the
products delivered to them. If the customers are satisfied are satisfied with the produced solar
LED, they will provide either positive or negative feedbacks. The areas of weaknesses are
identified and it will be easy for the company to make necessary changes to improve the quality
of products and ensure higher level of customers’ satisfaction (Akgün et al., 2014).
3. The seven basic tools for total quality management are cause and effect diagram, check sheet,
control chart, histogram, pareto chart, scatter diagram and stratification. The cause and effect
diagram can help in the designing of product as well as prevented the quality defects to ensure
customer satisfaction. The check sheet helps in collecting data in the real time and it includes
both qualitative and quantitative data. The control charts are known for its effectiveness in
determining the business manufacturing and production processes in a particular state of control,
furthermore ensure measurement of progress and checking whether the processes are under
control or not at Active Electrical Suppliers Ltd in New Zealand. The Pareto chart enables
representing the individuals in graphs, tables and in the form of bars and the cumulative total is
represented as a line (Chiarini, 2013). The main purpose of this tool is to focus on the most
important factors regarding quality control and identify the sources of defect based on the
complaints and feedbacks presented by the customers in case they might be unsatisfied with the
kind of products delivered. The stratification enables sampling from a population to check the
market segments and understand whether the product introduced can meet their expectations or
not. It is used to manage the processes properly and makes sure that defects are prevented. In
case the measurements within the strata consist of lower standard deviation, then there are lesser
chances of errors. These are the tools that can be used for identify the key areas of improvements
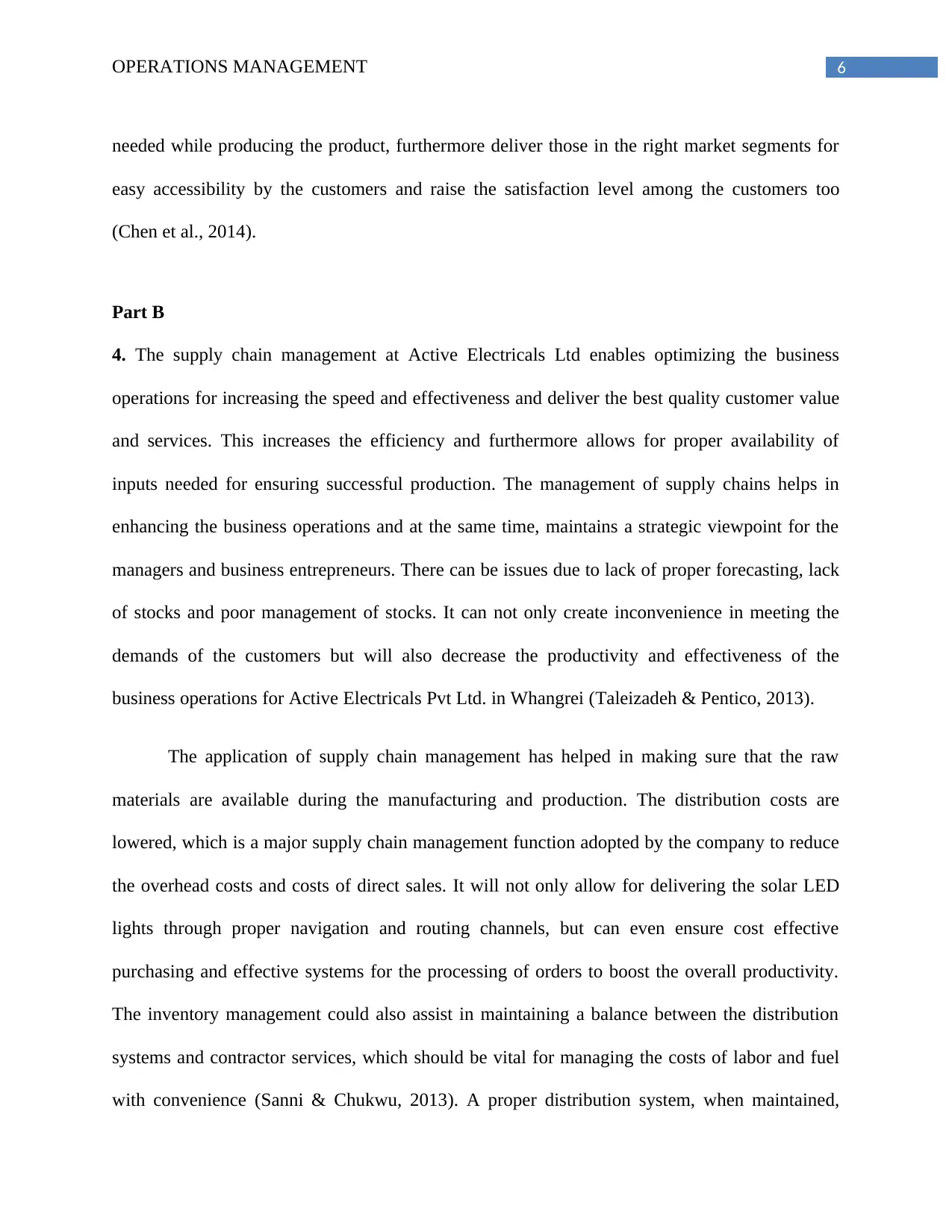
6OPERATIONS MANAGEMENT
needed while producing the product, furthermore deliver those in the right market segments for
easy accessibility by the customers and raise the satisfaction level among the customers too
(Chen et al., 2014).
Part B
4. The supply chain management at Active Electricals Ltd enables optimizing the business
operations for increasing the speed and effectiveness and deliver the best quality customer value
and services. This increases the efficiency and furthermore allows for proper availability of
inputs needed for ensuring successful production. The management of supply chains helps in
enhancing the business operations and at the same time, maintains a strategic viewpoint for the
managers and business entrepreneurs. There can be issues due to lack of proper forecasting, lack
of stocks and poor management of stocks. It can not only create inconvenience in meeting the
demands of the customers but will also decrease the productivity and effectiveness of the
business operations for Active Electricals Pvt Ltd. in Whangrei (Taleizadeh & Pentico, 2013).
The application of supply chain management has helped in making sure that the raw
materials are available during the manufacturing and production. The distribution costs are
lowered, which is a major supply chain management function adopted by the company to reduce
the overhead costs and costs of direct sales. It will not only allow for delivering the solar LED
lights through proper navigation and routing channels, but can even ensure cost effective
purchasing and effective systems for the processing of orders to boost the overall productivity.
The inventory management could also assist in maintaining a balance between the distribution
systems and contractor services, which should be vital for managing the costs of labor and fuel
with convenience (Sanni & Chukwu, 2013). A proper distribution system, when maintained,
needed while producing the product, furthermore deliver those in the right market segments for
easy accessibility by the customers and raise the satisfaction level among the customers too
(Chen et al., 2014).
Part B
4. The supply chain management at Active Electricals Ltd enables optimizing the business
operations for increasing the speed and effectiveness and deliver the best quality customer value
and services. This increases the efficiency and furthermore allows for proper availability of
inputs needed for ensuring successful production. The management of supply chains helps in
enhancing the business operations and at the same time, maintains a strategic viewpoint for the
managers and business entrepreneurs. There can be issues due to lack of proper forecasting, lack
of stocks and poor management of stocks. It can not only create inconvenience in meeting the
demands of the customers but will also decrease the productivity and effectiveness of the
business operations for Active Electricals Pvt Ltd. in Whangrei (Taleizadeh & Pentico, 2013).
The application of supply chain management has helped in making sure that the raw
materials are available during the manufacturing and production. The distribution costs are
lowered, which is a major supply chain management function adopted by the company to reduce
the overhead costs and costs of direct sales. It will not only allow for delivering the solar LED
lights through proper navigation and routing channels, but can even ensure cost effective
purchasing and effective systems for the processing of orders to boost the overall productivity.
The inventory management could also assist in maintaining a balance between the distribution
systems and contractor services, which should be vital for managing the costs of labor and fuel
with convenience (Sanni & Chukwu, 2013). A proper distribution system, when maintained,
Paraphrase This Document
Need a fresh take? Get an instant paraphrase of this document with our AI Paraphraser
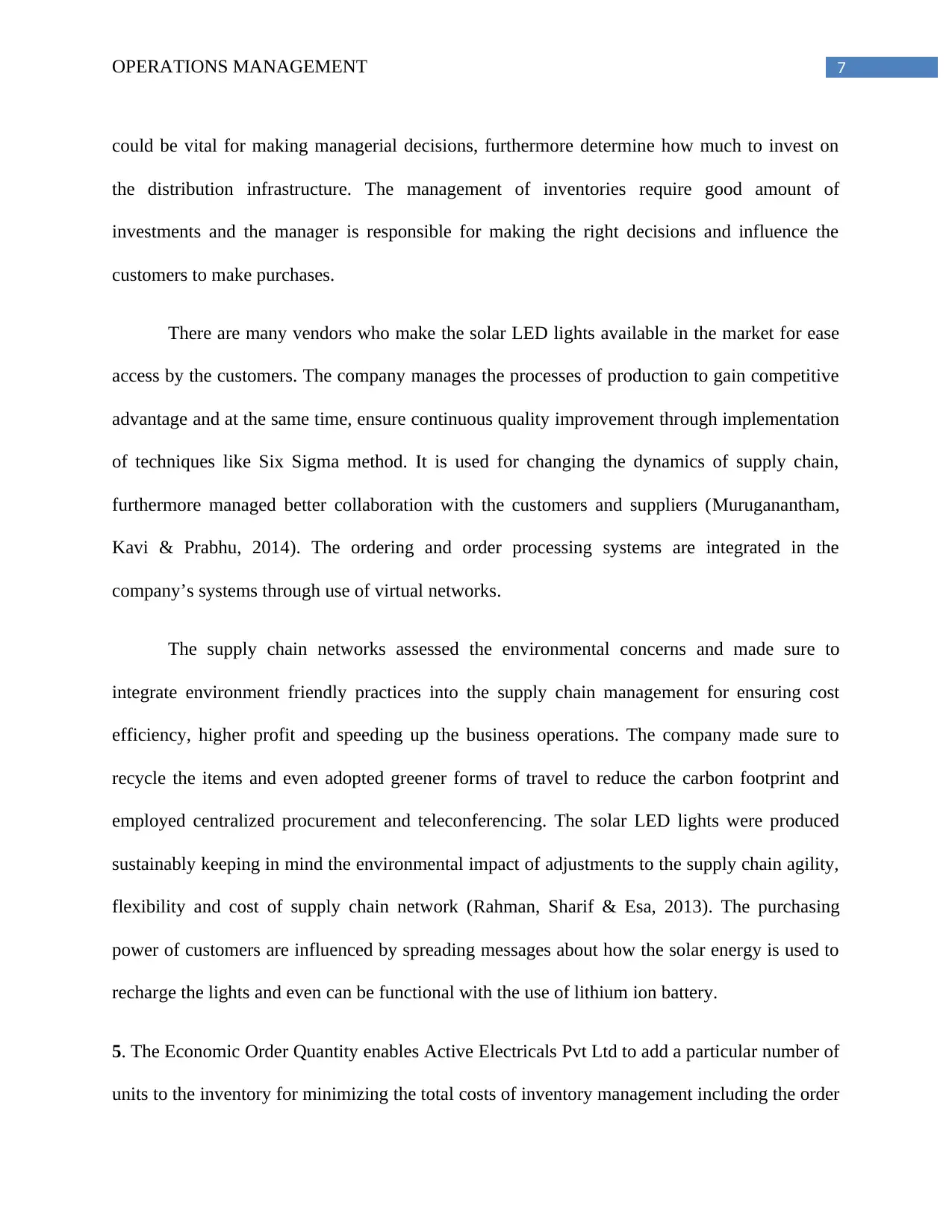
7OPERATIONS MANAGEMENT
could be vital for making managerial decisions, furthermore determine how much to invest on
the distribution infrastructure. The management of inventories require good amount of
investments and the manager is responsible for making the right decisions and influence the
customers to make purchases.
There are many vendors who make the solar LED lights available in the market for ease
access by the customers. The company manages the processes of production to gain competitive
advantage and at the same time, ensure continuous quality improvement through implementation
of techniques like Six Sigma method. It is used for changing the dynamics of supply chain,
furthermore managed better collaboration with the customers and suppliers (Muruganantham,
Kavi & Prabhu, 2014). The ordering and order processing systems are integrated in the
company’s systems through use of virtual networks.
The supply chain networks assessed the environmental concerns and made sure to
integrate environment friendly practices into the supply chain management for ensuring cost
efficiency, higher profit and speeding up the business operations. The company made sure to
recycle the items and even adopted greener forms of travel to reduce the carbon footprint and
employed centralized procurement and teleconferencing. The solar LED lights were produced
sustainably keeping in mind the environmental impact of adjustments to the supply chain agility,
flexibility and cost of supply chain network (Rahman, Sharif & Esa, 2013). The purchasing
power of customers are influenced by spreading messages about how the solar energy is used to
recharge the lights and even can be functional with the use of lithium ion battery.
5. The Economic Order Quantity enables Active Electricals Pvt Ltd to add a particular number of
units to the inventory for minimizing the total costs of inventory management including the order
could be vital for making managerial decisions, furthermore determine how much to invest on
the distribution infrastructure. The management of inventories require good amount of
investments and the manager is responsible for making the right decisions and influence the
customers to make purchases.
There are many vendors who make the solar LED lights available in the market for ease
access by the customers. The company manages the processes of production to gain competitive
advantage and at the same time, ensure continuous quality improvement through implementation
of techniques like Six Sigma method. It is used for changing the dynamics of supply chain,
furthermore managed better collaboration with the customers and suppliers (Muruganantham,
Kavi & Prabhu, 2014). The ordering and order processing systems are integrated in the
company’s systems through use of virtual networks.
The supply chain networks assessed the environmental concerns and made sure to
integrate environment friendly practices into the supply chain management for ensuring cost
efficiency, higher profit and speeding up the business operations. The company made sure to
recycle the items and even adopted greener forms of travel to reduce the carbon footprint and
employed centralized procurement and teleconferencing. The solar LED lights were produced
sustainably keeping in mind the environmental impact of adjustments to the supply chain agility,
flexibility and cost of supply chain network (Rahman, Sharif & Esa, 2013). The purchasing
power of customers are influenced by spreading messages about how the solar energy is used to
recharge the lights and even can be functional with the use of lithium ion battery.
5. The Economic Order Quantity enables Active Electricals Pvt Ltd to add a particular number of
units to the inventory for minimizing the total costs of inventory management including the order
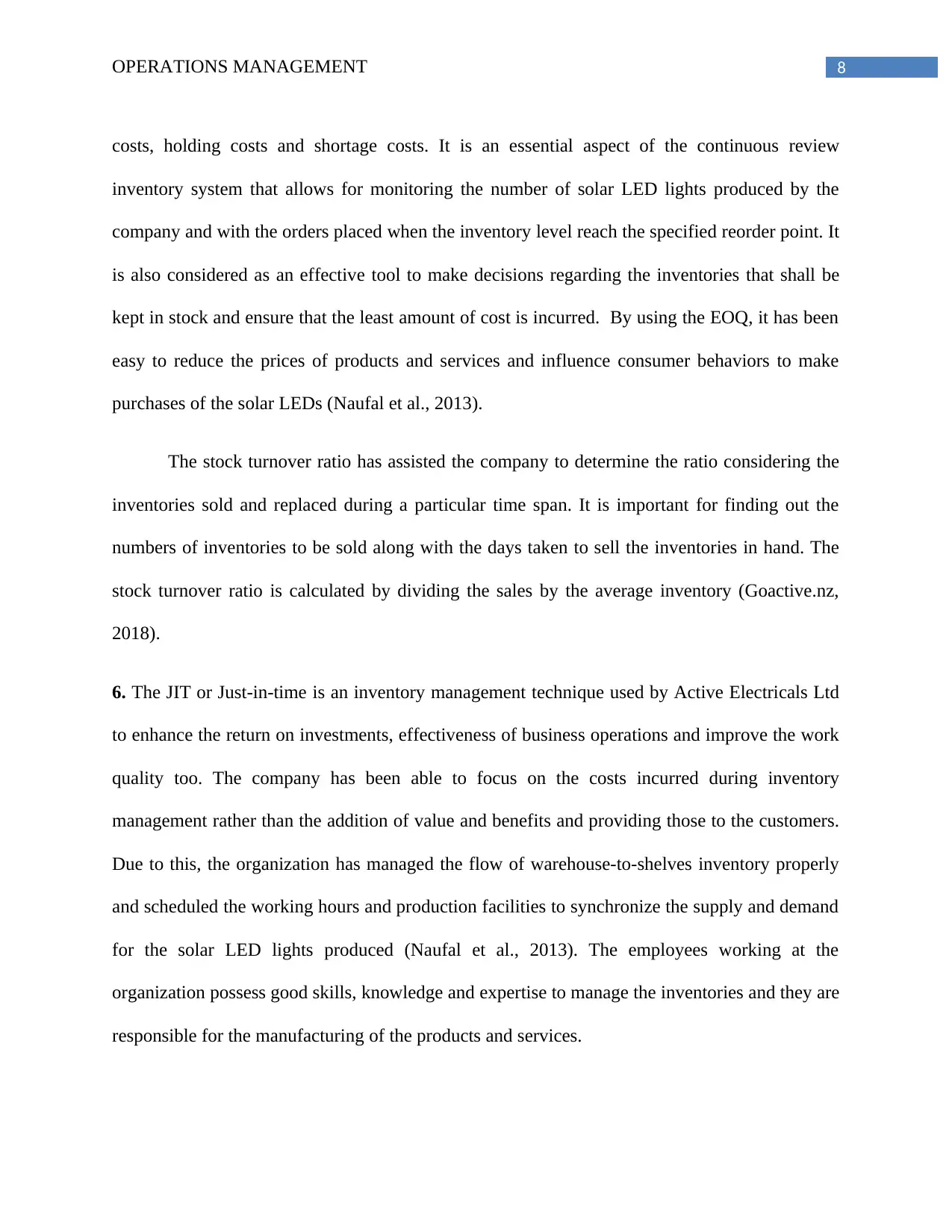
8OPERATIONS MANAGEMENT
costs, holding costs and shortage costs. It is an essential aspect of the continuous review
inventory system that allows for monitoring the number of solar LED lights produced by the
company and with the orders placed when the inventory level reach the specified reorder point. It
is also considered as an effective tool to make decisions regarding the inventories that shall be
kept in stock and ensure that the least amount of cost is incurred. By using the EOQ, it has been
easy to reduce the prices of products and services and influence consumer behaviors to make
purchases of the solar LEDs (Naufal et al., 2013).
The stock turnover ratio has assisted the company to determine the ratio considering the
inventories sold and replaced during a particular time span. It is important for finding out the
numbers of inventories to be sold along with the days taken to sell the inventories in hand. The
stock turnover ratio is calculated by dividing the sales by the average inventory (Goactive.nz,
2018).
6. The JIT or Just-in-time is an inventory management technique used by Active Electricals Ltd
to enhance the return on investments, effectiveness of business operations and improve the work
quality too. The company has been able to focus on the costs incurred during inventory
management rather than the addition of value and benefits and providing those to the customers.
Due to this, the organization has managed the flow of warehouse-to-shelves inventory properly
and scheduled the working hours and production facilities to synchronize the supply and demand
for the solar LED lights produced (Naufal et al., 2013). The employees working at the
organization possess good skills, knowledge and expertise to manage the inventories and they are
responsible for the manufacturing of the products and services.
costs, holding costs and shortage costs. It is an essential aspect of the continuous review
inventory system that allows for monitoring the number of solar LED lights produced by the
company and with the orders placed when the inventory level reach the specified reorder point. It
is also considered as an effective tool to make decisions regarding the inventories that shall be
kept in stock and ensure that the least amount of cost is incurred. By using the EOQ, it has been
easy to reduce the prices of products and services and influence consumer behaviors to make
purchases of the solar LEDs (Naufal et al., 2013).
The stock turnover ratio has assisted the company to determine the ratio considering the
inventories sold and replaced during a particular time span. It is important for finding out the
numbers of inventories to be sold along with the days taken to sell the inventories in hand. The
stock turnover ratio is calculated by dividing the sales by the average inventory (Goactive.nz,
2018).
6. The JIT or Just-in-time is an inventory management technique used by Active Electricals Ltd
to enhance the return on investments, effectiveness of business operations and improve the work
quality too. The company has been able to focus on the costs incurred during inventory
management rather than the addition of value and benefits and providing those to the customers.
Due to this, the organization has managed the flow of warehouse-to-shelves inventory properly
and scheduled the working hours and production facilities to synchronize the supply and demand
for the solar LED lights produced (Naufal et al., 2013). The employees working at the
organization possess good skills, knowledge and expertise to manage the inventories and they are
responsible for the manufacturing of the products and services.
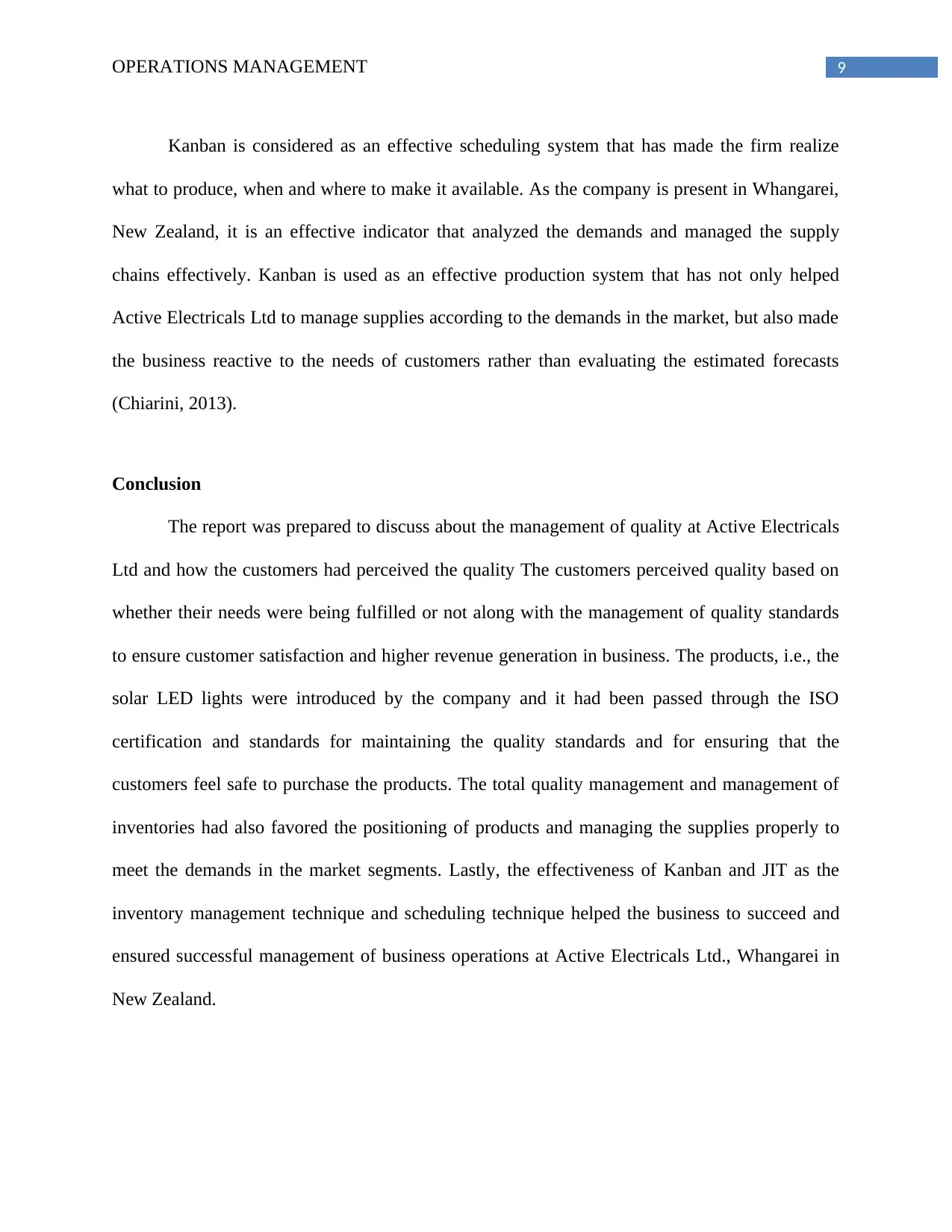
9OPERATIONS MANAGEMENT
Kanban is considered as an effective scheduling system that has made the firm realize
what to produce, when and where to make it available. As the company is present in Whangarei,
New Zealand, it is an effective indicator that analyzed the demands and managed the supply
chains effectively. Kanban is used as an effective production system that has not only helped
Active Electricals Ltd to manage supplies according to the demands in the market, but also made
the business reactive to the needs of customers rather than evaluating the estimated forecasts
(Chiarini, 2013).
Conclusion
The report was prepared to discuss about the management of quality at Active Electricals
Ltd and how the customers had perceived the quality The customers perceived quality based on
whether their needs were being fulfilled or not along with the management of quality standards
to ensure customer satisfaction and higher revenue generation in business. The products, i.e., the
solar LED lights were introduced by the company and it had been passed through the ISO
certification and standards for maintaining the quality standards and for ensuring that the
customers feel safe to purchase the products. The total quality management and management of
inventories had also favored the positioning of products and managing the supplies properly to
meet the demands in the market segments. Lastly, the effectiveness of Kanban and JIT as the
inventory management technique and scheduling technique helped the business to succeed and
ensured successful management of business operations at Active Electricals Ltd., Whangarei in
New Zealand.
Kanban is considered as an effective scheduling system that has made the firm realize
what to produce, when and where to make it available. As the company is present in Whangarei,
New Zealand, it is an effective indicator that analyzed the demands and managed the supply
chains effectively. Kanban is used as an effective production system that has not only helped
Active Electricals Ltd to manage supplies according to the demands in the market, but also made
the business reactive to the needs of customers rather than evaluating the estimated forecasts
(Chiarini, 2013).
Conclusion
The report was prepared to discuss about the management of quality at Active Electricals
Ltd and how the customers had perceived the quality The customers perceived quality based on
whether their needs were being fulfilled or not along with the management of quality standards
to ensure customer satisfaction and higher revenue generation in business. The products, i.e., the
solar LED lights were introduced by the company and it had been passed through the ISO
certification and standards for maintaining the quality standards and for ensuring that the
customers feel safe to purchase the products. The total quality management and management of
inventories had also favored the positioning of products and managing the supplies properly to
meet the demands in the market segments. Lastly, the effectiveness of Kanban and JIT as the
inventory management technique and scheduling technique helped the business to succeed and
ensured successful management of business operations at Active Electricals Ltd., Whangarei in
New Zealand.
Secure Best Marks with AI Grader
Need help grading? Try our AI Grader for instant feedback on your assignments.
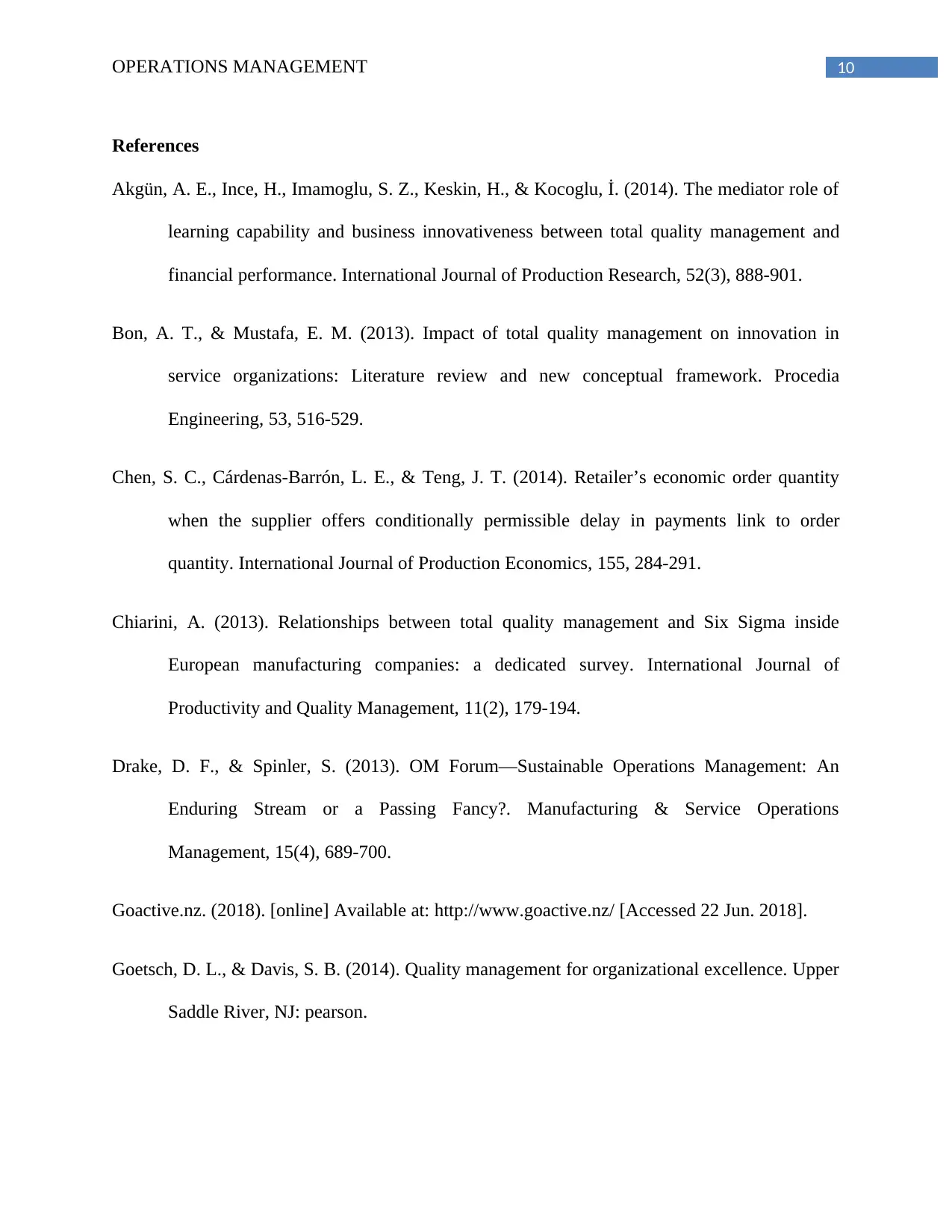
10OPERATIONS MANAGEMENT
References
Akgün, A. E., Ince, H., Imamoglu, S. Z., Keskin, H., & Kocoglu, İ. (2014). The mediator role of
learning capability and business innovativeness between total quality management and
financial performance. International Journal of Production Research, 52(3), 888-901.
Bon, A. T., & Mustafa, E. M. (2013). Impact of total quality management on innovation in
service organizations: Literature review and new conceptual framework. Procedia
Engineering, 53, 516-529.
Chen, S. C., Cárdenas-Barrón, L. E., & Teng, J. T. (2014). Retailer’s economic order quantity
when the supplier offers conditionally permissible delay in payments link to order
quantity. International Journal of Production Economics, 155, 284-291.
Chiarini, A. (2013). Relationships between total quality management and Six Sigma inside
European manufacturing companies: a dedicated survey. International Journal of
Productivity and Quality Management, 11(2), 179-194.
Drake, D. F., & Spinler, S. (2013). OM Forum—Sustainable Operations Management: An
Enduring Stream or a Passing Fancy?. Manufacturing & Service Operations
Management, 15(4), 689-700.
Goactive.nz. (2018). [online] Available at: http://www.goactive.nz/ [Accessed 22 Jun. 2018].
Goetsch, D. L., & Davis, S. B. (2014). Quality management for organizational excellence. Upper
Saddle River, NJ: pearson.
References
Akgün, A. E., Ince, H., Imamoglu, S. Z., Keskin, H., & Kocoglu, İ. (2014). The mediator role of
learning capability and business innovativeness between total quality management and
financial performance. International Journal of Production Research, 52(3), 888-901.
Bon, A. T., & Mustafa, E. M. (2013). Impact of total quality management on innovation in
service organizations: Literature review and new conceptual framework. Procedia
Engineering, 53, 516-529.
Chen, S. C., Cárdenas-Barrón, L. E., & Teng, J. T. (2014). Retailer’s economic order quantity
when the supplier offers conditionally permissible delay in payments link to order
quantity. International Journal of Production Economics, 155, 284-291.
Chiarini, A. (2013). Relationships between total quality management and Six Sigma inside
European manufacturing companies: a dedicated survey. International Journal of
Productivity and Quality Management, 11(2), 179-194.
Drake, D. F., & Spinler, S. (2013). OM Forum—Sustainable Operations Management: An
Enduring Stream or a Passing Fancy?. Manufacturing & Service Operations
Management, 15(4), 689-700.
Goactive.nz. (2018). [online] Available at: http://www.goactive.nz/ [Accessed 22 Jun. 2018].
Goetsch, D. L., & Davis, S. B. (2014). Quality management for organizational excellence. Upper
Saddle River, NJ: pearson.
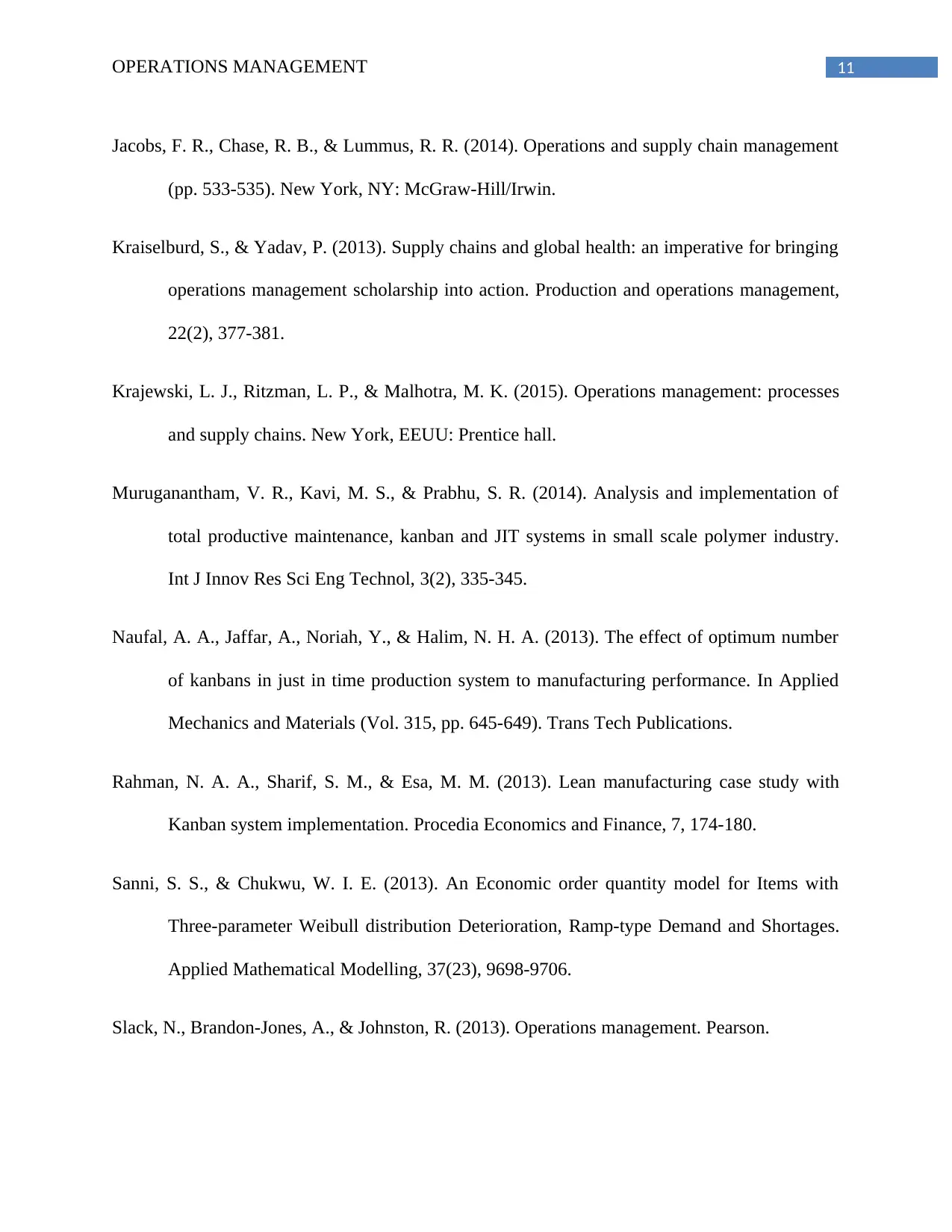
11OPERATIONS MANAGEMENT
Jacobs, F. R., Chase, R. B., & Lummus, R. R. (2014). Operations and supply chain management
(pp. 533-535). New York, NY: McGraw-Hill/Irwin.
Kraiselburd, S., & Yadav, P. (2013). Supply chains and global health: an imperative for bringing
operations management scholarship into action. Production and operations management,
22(2), 377-381.
Krajewski, L. J., Ritzman, L. P., & Malhotra, M. K. (2015). Operations management: processes
and supply chains. New York, EEUU: Prentice hall.
Muruganantham, V. R., Kavi, M. S., & Prabhu, S. R. (2014). Analysis and implementation of
total productive maintenance, kanban and JIT systems in small scale polymer industry.
Int J Innov Res Sci Eng Technol, 3(2), 335-345.
Naufal, A. A., Jaffar, A., Noriah, Y., & Halim, N. H. A. (2013). The effect of optimum number
of kanbans in just in time production system to manufacturing performance. In Applied
Mechanics and Materials (Vol. 315, pp. 645-649). Trans Tech Publications.
Rahman, N. A. A., Sharif, S. M., & Esa, M. M. (2013). Lean manufacturing case study with
Kanban system implementation. Procedia Economics and Finance, 7, 174-180.
Sanni, S. S., & Chukwu, W. I. E. (2013). An Economic order quantity model for Items with
Three-parameter Weibull distribution Deterioration, Ramp-type Demand and Shortages.
Applied Mathematical Modelling, 37(23), 9698-9706.
Slack, N., Brandon-Jones, A., & Johnston, R. (2013). Operations management. Pearson.
Jacobs, F. R., Chase, R. B., & Lummus, R. R. (2014). Operations and supply chain management
(pp. 533-535). New York, NY: McGraw-Hill/Irwin.
Kraiselburd, S., & Yadav, P. (2013). Supply chains and global health: an imperative for bringing
operations management scholarship into action. Production and operations management,
22(2), 377-381.
Krajewski, L. J., Ritzman, L. P., & Malhotra, M. K. (2015). Operations management: processes
and supply chains. New York, EEUU: Prentice hall.
Muruganantham, V. R., Kavi, M. S., & Prabhu, S. R. (2014). Analysis and implementation of
total productive maintenance, kanban and JIT systems in small scale polymer industry.
Int J Innov Res Sci Eng Technol, 3(2), 335-345.
Naufal, A. A., Jaffar, A., Noriah, Y., & Halim, N. H. A. (2013). The effect of optimum number
of kanbans in just in time production system to manufacturing performance. In Applied
Mechanics and Materials (Vol. 315, pp. 645-649). Trans Tech Publications.
Rahman, N. A. A., Sharif, S. M., & Esa, M. M. (2013). Lean manufacturing case study with
Kanban system implementation. Procedia Economics and Finance, 7, 174-180.
Sanni, S. S., & Chukwu, W. I. E. (2013). An Economic order quantity model for Items with
Three-parameter Weibull distribution Deterioration, Ramp-type Demand and Shortages.
Applied Mathematical Modelling, 37(23), 9698-9706.
Slack, N., Brandon-Jones, A., & Johnston, R. (2013). Operations management. Pearson.
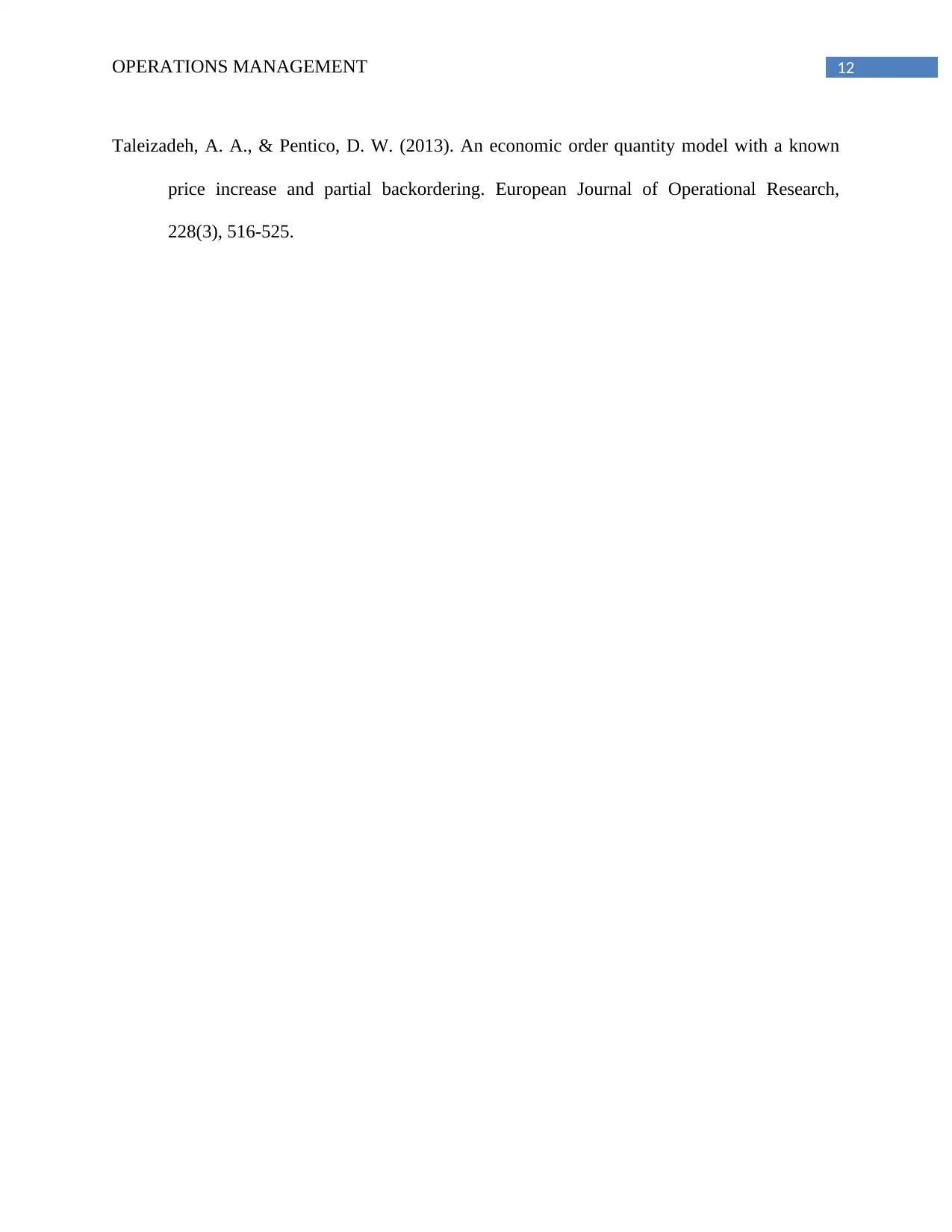
12OPERATIONS MANAGEMENT
Taleizadeh, A. A., & Pentico, D. W. (2013). An economic order quantity model with a known
price increase and partial backordering. European Journal of Operational Research,
228(3), 516-525.
Taleizadeh, A. A., & Pentico, D. W. (2013). An economic order quantity model with a known
price increase and partial backordering. European Journal of Operational Research,
228(3), 516-525.
1 out of 13
![[object Object]](/_next/image/?url=%2F_next%2Fstatic%2Fmedia%2Flogo.6d15ce61.png&w=640&q=75)
Your All-in-One AI-Powered Toolkit for Academic Success.
+13062052269
info@desklib.com
Available 24*7 on WhatsApp / Email
Unlock your academic potential
© 2024 | Zucol Services PVT LTD | All rights reserved.