Burberry Operations and Project Management: A Detailed Report
VerifiedAdded on 2023/06/07
|14
|4733
|118
Report
AI Summary
This report provides a detailed analysis of operations and project management principles within Burberry Group plc. It reviews the implementation of operations management, focusing on Six Sigma methodology and Lean principles, and prepares a continuous improvement plan based on these reviews. The report also applies each stage of the Project Lifecycle (PLC) to a given project, producing necessary supporting documentation and analyzing the rationale for project methodologies and leadership. Furthermore, it critiques the effectiveness of the PLC, differentiating between large and small-scale projects and evaluating the PLC's effectiveness through practical and theoretical exploration, ultimately offering conclusions and recommendations for improvement. The analysis covers aspects such as monetary productivity, resource management, and the importance of continuous improvement in achieving organizational goals within Burberry Group plc.
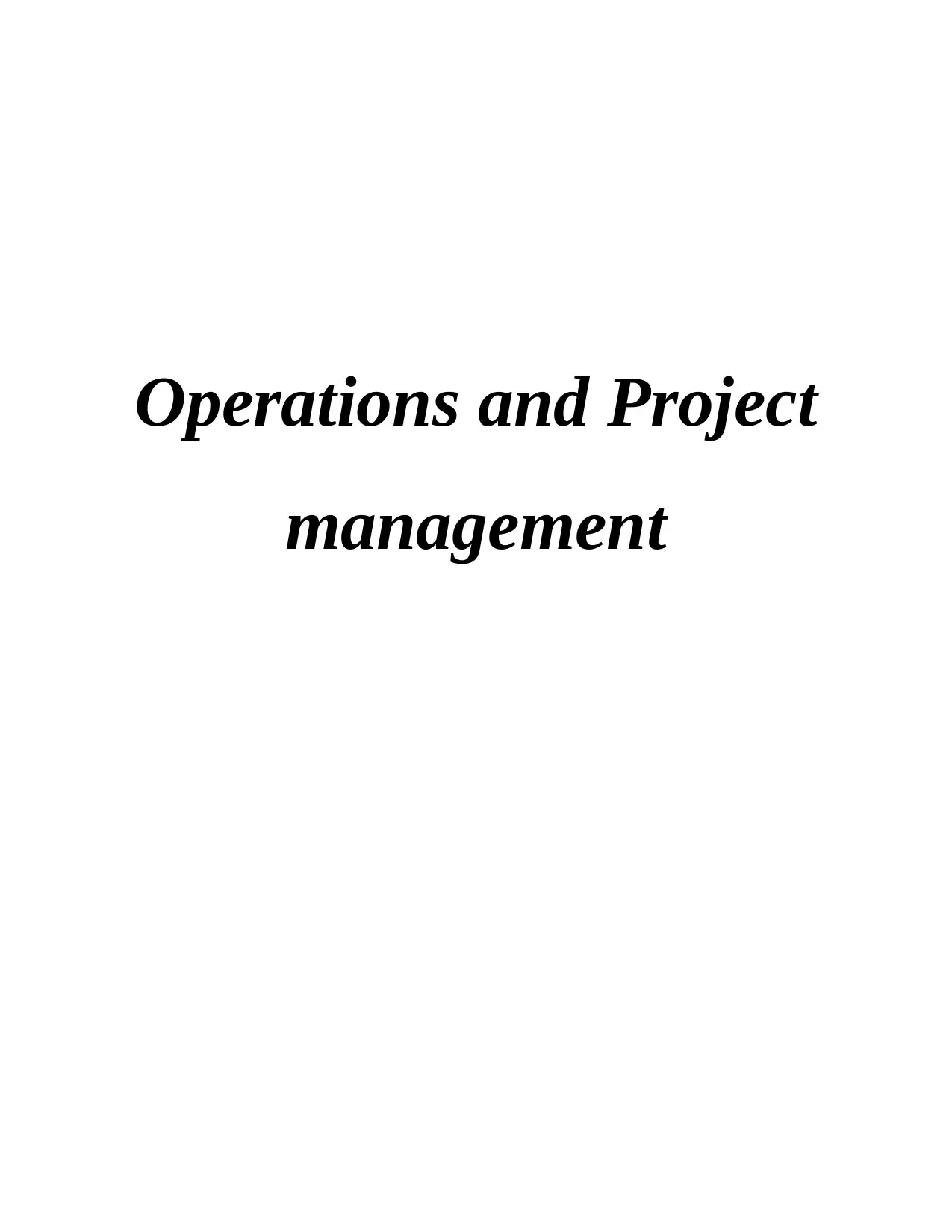
Operations and Project
management
management
Paraphrase This Document
Need a fresh take? Get an instant paraphrase of this document with our AI Paraphraser
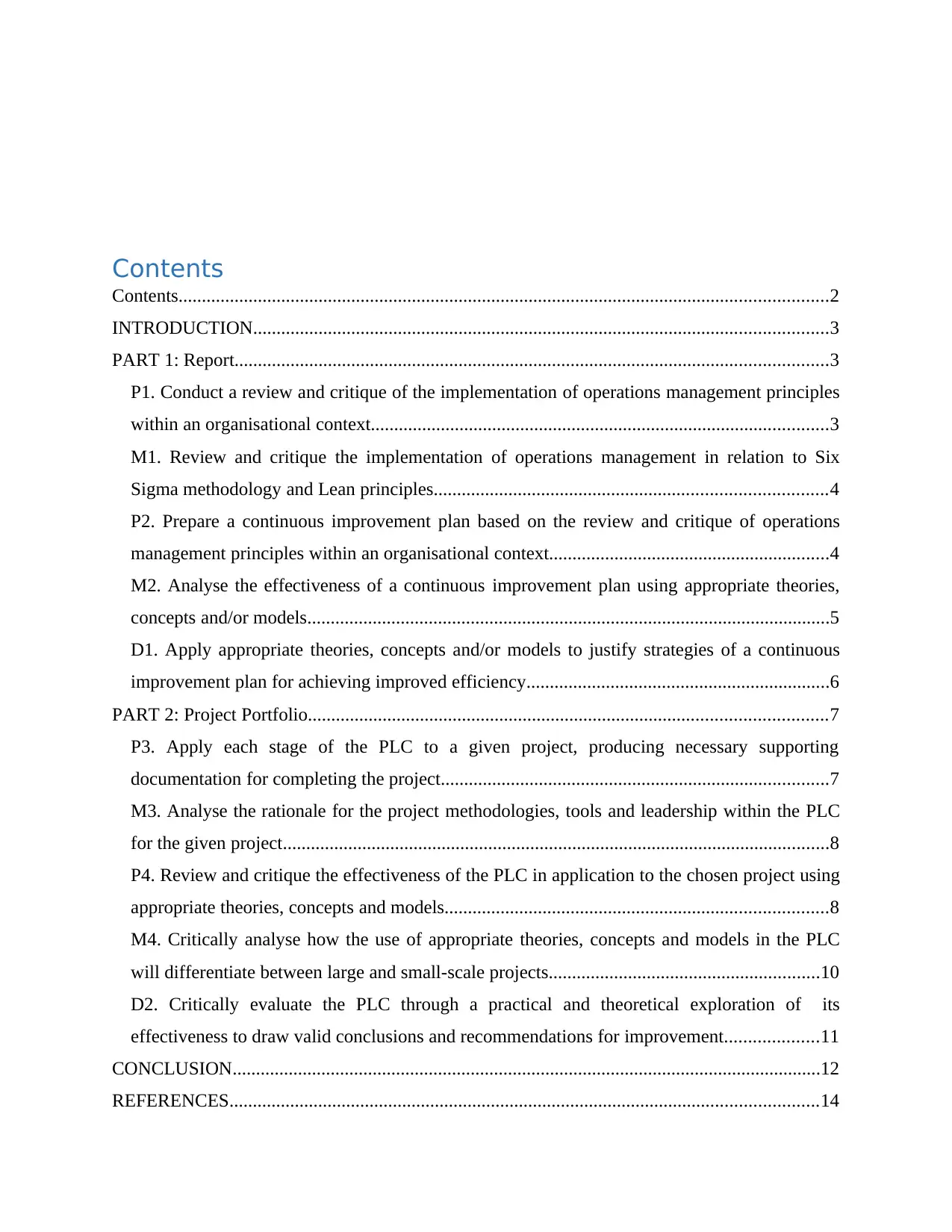
Contents
Contents...........................................................................................................................................2
INTRODUCTION...........................................................................................................................3
PART 1: Report...............................................................................................................................3
P1. Conduct a review and critique of the implementation of operations management principles
within an organisational context..................................................................................................3
M1. Review and critique the implementation of operations management in relation to Six
Sigma methodology and Lean principles....................................................................................4
P2. Prepare a continuous improvement plan based on the review and critique of operations
management principles within an organisational context............................................................4
M2. Analyse the effectiveness of a continuous improvement plan using appropriate theories,
concepts and/or models................................................................................................................5
D1. Apply appropriate theories, concepts and/or models to justify strategies of a continuous
improvement plan for achieving improved efficiency.................................................................6
PART 2: Project Portfolio...............................................................................................................7
P3. Apply each stage of the PLC to a given project, producing necessary supporting
documentation for completing the project...................................................................................7
M3. Analyse the rationale for the project methodologies, tools and leadership within the PLC
for the given project.....................................................................................................................8
P4. Review and critique the effectiveness of the PLC in application to the chosen project using
appropriate theories, concepts and models..................................................................................8
M4. Critically analyse how the use of appropriate theories, concepts and models in the PLC
will differentiate between large and small-scale projects..........................................................10
D2. Critically evaluate the PLC through a practical and theoretical exploration of its
effectiveness to draw valid conclusions and recommendations for improvement....................11
CONCLUSION..............................................................................................................................12
REFERENCES..............................................................................................................................14
Contents...........................................................................................................................................2
INTRODUCTION...........................................................................................................................3
PART 1: Report...............................................................................................................................3
P1. Conduct a review and critique of the implementation of operations management principles
within an organisational context..................................................................................................3
M1. Review and critique the implementation of operations management in relation to Six
Sigma methodology and Lean principles....................................................................................4
P2. Prepare a continuous improvement plan based on the review and critique of operations
management principles within an organisational context............................................................4
M2. Analyse the effectiveness of a continuous improvement plan using appropriate theories,
concepts and/or models................................................................................................................5
D1. Apply appropriate theories, concepts and/or models to justify strategies of a continuous
improvement plan for achieving improved efficiency.................................................................6
PART 2: Project Portfolio...............................................................................................................7
P3. Apply each stage of the PLC to a given project, producing necessary supporting
documentation for completing the project...................................................................................7
M3. Analyse the rationale for the project methodologies, tools and leadership within the PLC
for the given project.....................................................................................................................8
P4. Review and critique the effectiveness of the PLC in application to the chosen project using
appropriate theories, concepts and models..................................................................................8
M4. Critically analyse how the use of appropriate theories, concepts and models in the PLC
will differentiate between large and small-scale projects..........................................................10
D2. Critically evaluate the PLC through a practical and theoretical exploration of its
effectiveness to draw valid conclusions and recommendations for improvement....................11
CONCLUSION..............................................................................................................................12
REFERENCES..............................................................................................................................14
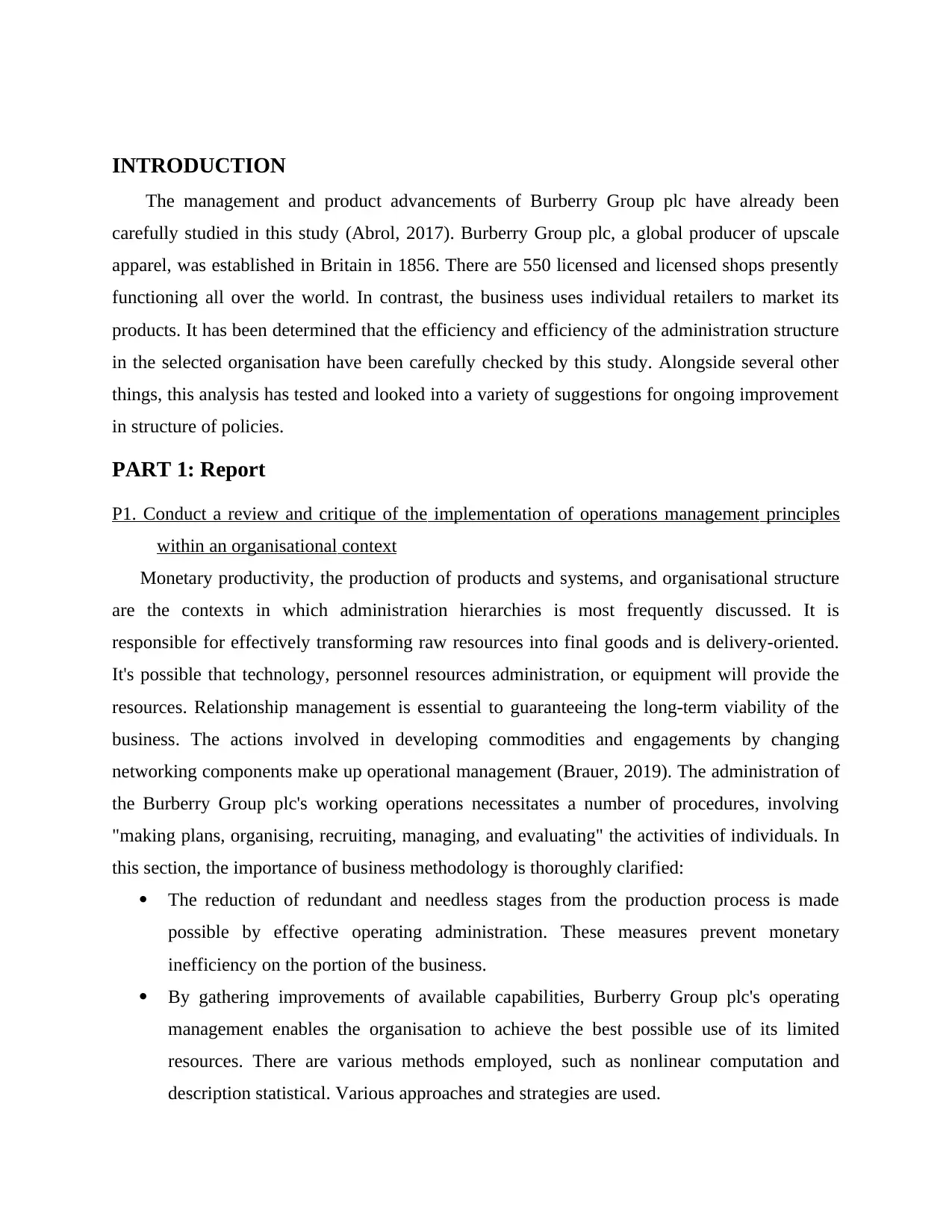
INTRODUCTION
The management and product advancements of Burberry Group plc have already been
carefully studied in this study (Abrol, 2017). Burberry Group plc, a global producer of upscale
apparel, was established in Britain in 1856. There are 550 licensed and licensed shops presently
functioning all over the world. In contrast, the business uses individual retailers to market its
products. It has been determined that the efficiency and efficiency of the administration structure
in the selected organisation have been carefully checked by this study. Alongside several other
things, this analysis has tested and looked into a variety of suggestions for ongoing improvement
in structure of policies.
PART 1: Report
P1. Conduct a review and critique of the implementation of operations management principles
within an organisational context
Monetary productivity, the production of products and systems, and organisational structure
are the contexts in which administration hierarchies is most frequently discussed. It is
responsible for effectively transforming raw resources into final goods and is delivery-oriented.
It's possible that technology, personnel resources administration, or equipment will provide the
resources. Relationship management is essential to guaranteeing the long-term viability of the
business. The actions involved in developing commodities and engagements by changing
networking components make up operational management (Brauer, 2019). The administration of
the Burberry Group plc's working operations necessitates a number of procedures, involving
"making plans, organising, recruiting, managing, and evaluating" the activities of individuals. In
this section, the importance of business methodology is thoroughly clarified:
The reduction of redundant and needless stages from the production process is made
possible by effective operating administration. These measures prevent monetary
inefficiency on the portion of the business.
By gathering improvements of available capabilities, Burberry Group plc's operating
management enables the organisation to achieve the best possible use of its limited
resources. There are various methods employed, such as nonlinear computation and
description statistical. Various approaches and strategies are used.
The management and product advancements of Burberry Group plc have already been
carefully studied in this study (Abrol, 2017). Burberry Group plc, a global producer of upscale
apparel, was established in Britain in 1856. There are 550 licensed and licensed shops presently
functioning all over the world. In contrast, the business uses individual retailers to market its
products. It has been determined that the efficiency and efficiency of the administration structure
in the selected organisation have been carefully checked by this study. Alongside several other
things, this analysis has tested and looked into a variety of suggestions for ongoing improvement
in structure of policies.
PART 1: Report
P1. Conduct a review and critique of the implementation of operations management principles
within an organisational context
Monetary productivity, the production of products and systems, and organisational structure
are the contexts in which administration hierarchies is most frequently discussed. It is
responsible for effectively transforming raw resources into final goods and is delivery-oriented.
It's possible that technology, personnel resources administration, or equipment will provide the
resources. Relationship management is essential to guaranteeing the long-term viability of the
business. The actions involved in developing commodities and engagements by changing
networking components make up operational management (Brauer, 2019). The administration of
the Burberry Group plc's working operations necessitates a number of procedures, involving
"making plans, organising, recruiting, managing, and evaluating" the activities of individuals. In
this section, the importance of business methodology is thoroughly clarified:
The reduction of redundant and needless stages from the production process is made
possible by effective operating administration. These measures prevent monetary
inefficiency on the portion of the business.
By gathering improvements of available capabilities, Burberry Group plc's operating
management enables the organisation to achieve the best possible use of its limited
resources. There are various methods employed, such as nonlinear computation and
description statistical. Various approaches and strategies are used.
You're viewing a preview
Unlock full access by subscribing today!
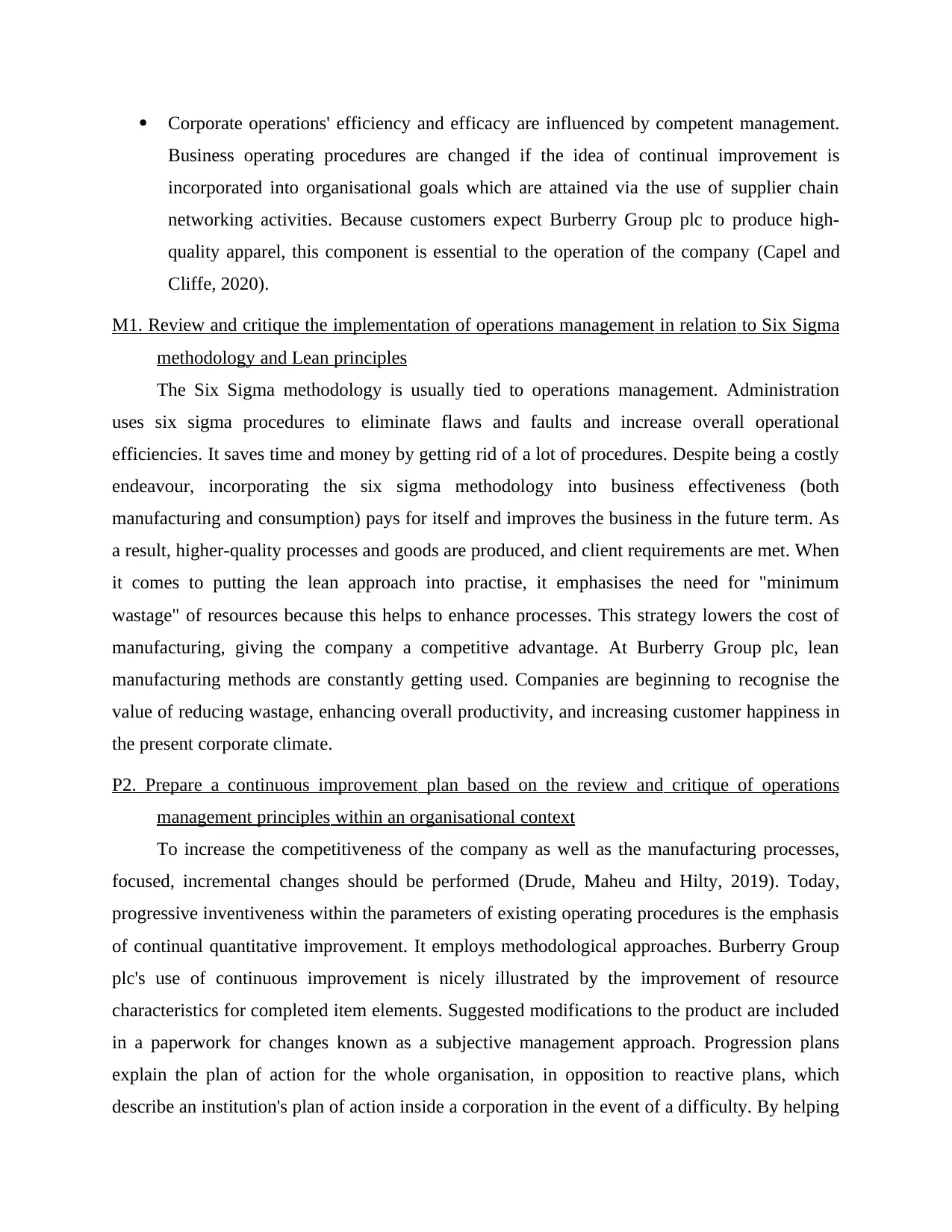
Corporate operations' efficiency and efficacy are influenced by competent management.
Business operating procedures are changed if the idea of continual improvement is
incorporated into organisational goals which are attained via the use of supplier chain
networking activities. Because customers expect Burberry Group plc to produce high-
quality apparel, this component is essential to the operation of the company (Capel and
Cliffe, 2020).
M1. Review and critique the implementation of operations management in relation to Six Sigma
methodology and Lean principles
The Six Sigma methodology is usually tied to operations management. Administration
uses six sigma procedures to eliminate flaws and faults and increase overall operational
efficiencies. It saves time and money by getting rid of a lot of procedures. Despite being a costly
endeavour, incorporating the six sigma methodology into business effectiveness (both
manufacturing and consumption) pays for itself and improves the business in the future term. As
a result, higher-quality processes and goods are produced, and client requirements are met. When
it comes to putting the lean approach into practise, it emphasises the need for "minimum
wastage" of resources because this helps to enhance processes. This strategy lowers the cost of
manufacturing, giving the company a competitive advantage. At Burberry Group plc, lean
manufacturing methods are constantly getting used. Companies are beginning to recognise the
value of reducing wastage, enhancing overall productivity, and increasing customer happiness in
the present corporate climate.
P2. Prepare a continuous improvement plan based on the review and critique of operations
management principles within an organisational context
To increase the competitiveness of the company as well as the manufacturing processes,
focused, incremental changes should be performed (Drude, Maheu and Hilty, 2019). Today,
progressive inventiveness within the parameters of existing operating procedures is the emphasis
of continual quantitative improvement. It employs methodological approaches. Burberry Group
plc's use of continuous improvement is nicely illustrated by the improvement of resource
characteristics for completed item elements. Suggested modifications to the product are included
in a paperwork for changes known as a subjective management approach. Progression plans
explain the plan of action for the whole organisation, in opposition to reactive plans, which
describe an institution's plan of action inside a corporation in the event of a difficulty. By helping
Business operating procedures are changed if the idea of continual improvement is
incorporated into organisational goals which are attained via the use of supplier chain
networking activities. Because customers expect Burberry Group plc to produce high-
quality apparel, this component is essential to the operation of the company (Capel and
Cliffe, 2020).
M1. Review and critique the implementation of operations management in relation to Six Sigma
methodology and Lean principles
The Six Sigma methodology is usually tied to operations management. Administration
uses six sigma procedures to eliminate flaws and faults and increase overall operational
efficiencies. It saves time and money by getting rid of a lot of procedures. Despite being a costly
endeavour, incorporating the six sigma methodology into business effectiveness (both
manufacturing and consumption) pays for itself and improves the business in the future term. As
a result, higher-quality processes and goods are produced, and client requirements are met. When
it comes to putting the lean approach into practise, it emphasises the need for "minimum
wastage" of resources because this helps to enhance processes. This strategy lowers the cost of
manufacturing, giving the company a competitive advantage. At Burberry Group plc, lean
manufacturing methods are constantly getting used. Companies are beginning to recognise the
value of reducing wastage, enhancing overall productivity, and increasing customer happiness in
the present corporate climate.
P2. Prepare a continuous improvement plan based on the review and critique of operations
management principles within an organisational context
To increase the competitiveness of the company as well as the manufacturing processes,
focused, incremental changes should be performed (Drude, Maheu and Hilty, 2019). Today,
progressive inventiveness within the parameters of existing operating procedures is the emphasis
of continual quantitative improvement. It employs methodological approaches. Burberry Group
plc's use of continuous improvement is nicely illustrated by the improvement of resource
characteristics for completed item elements. Suggested modifications to the product are included
in a paperwork for changes known as a subjective management approach. Progression plans
explain the plan of action for the whole organisation, in opposition to reactive plans, which
describe an institution's plan of action inside a corporation in the event of a difficulty. By helping
Paraphrase This Document
Need a fresh take? Get an instant paraphrase of this document with our AI Paraphraser
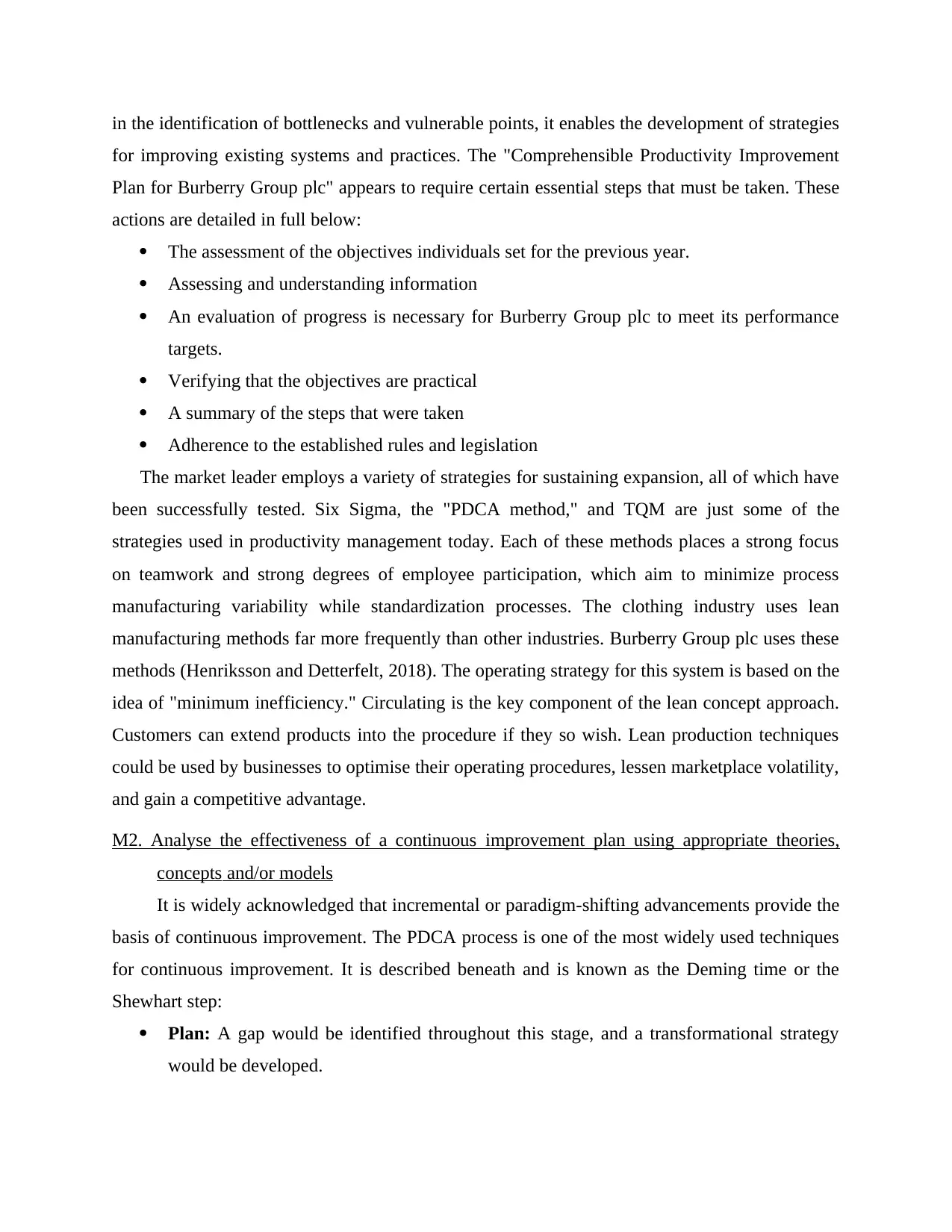
in the identification of bottlenecks and vulnerable points, it enables the development of strategies
for improving existing systems and practices. The "Comprehensible Productivity Improvement
Plan for Burberry Group plc" appears to require certain essential steps that must be taken. These
actions are detailed in full below:
The assessment of the objectives individuals set for the previous year.
Assessing and understanding information
An evaluation of progress is necessary for Burberry Group plc to meet its performance
targets.
Verifying that the objectives are practical
A summary of the steps that were taken
Adherence to the established rules and legislation
The market leader employs a variety of strategies for sustaining expansion, all of which have
been successfully tested. Six Sigma, the "PDCA method," and TQM are just some of the
strategies used in productivity management today. Each of these methods places a strong focus
on teamwork and strong degrees of employee participation, which aim to minimize process
manufacturing variability while standardization processes. The clothing industry uses lean
manufacturing methods far more frequently than other industries. Burberry Group plc uses these
methods (Henriksson and Detterfelt, 2018). The operating strategy for this system is based on the
idea of "minimum inefficiency." Circulating is the key component of the lean concept approach.
Customers can extend products into the procedure if they so wish. Lean production techniques
could be used by businesses to optimise their operating procedures, lessen marketplace volatility,
and gain a competitive advantage.
M2. Analyse the effectiveness of a continuous improvement plan using appropriate theories,
concepts and/or models
It is widely acknowledged that incremental or paradigm-shifting advancements provide the
basis of continuous improvement. The PDCA process is one of the most widely used techniques
for continuous improvement. It is described beneath and is known as the Deming time or the
Shewhart step:
Plan: A gap would be identified throughout this stage, and a transformational strategy
would be developed.
for improving existing systems and practices. The "Comprehensible Productivity Improvement
Plan for Burberry Group plc" appears to require certain essential steps that must be taken. These
actions are detailed in full below:
The assessment of the objectives individuals set for the previous year.
Assessing and understanding information
An evaluation of progress is necessary for Burberry Group plc to meet its performance
targets.
Verifying that the objectives are practical
A summary of the steps that were taken
Adherence to the established rules and legislation
The market leader employs a variety of strategies for sustaining expansion, all of which have
been successfully tested. Six Sigma, the "PDCA method," and TQM are just some of the
strategies used in productivity management today. Each of these methods places a strong focus
on teamwork and strong degrees of employee participation, which aim to minimize process
manufacturing variability while standardization processes. The clothing industry uses lean
manufacturing methods far more frequently than other industries. Burberry Group plc uses these
methods (Henriksson and Detterfelt, 2018). The operating strategy for this system is based on the
idea of "minimum inefficiency." Circulating is the key component of the lean concept approach.
Customers can extend products into the procedure if they so wish. Lean production techniques
could be used by businesses to optimise their operating procedures, lessen marketplace volatility,
and gain a competitive advantage.
M2. Analyse the effectiveness of a continuous improvement plan using appropriate theories,
concepts and/or models
It is widely acknowledged that incremental or paradigm-shifting advancements provide the
basis of continuous improvement. The PDCA process is one of the most widely used techniques
for continuous improvement. It is described beneath and is known as the Deming time or the
Shewhart step:
Plan: A gap would be identified throughout this stage, and a transformational strategy
would be developed.
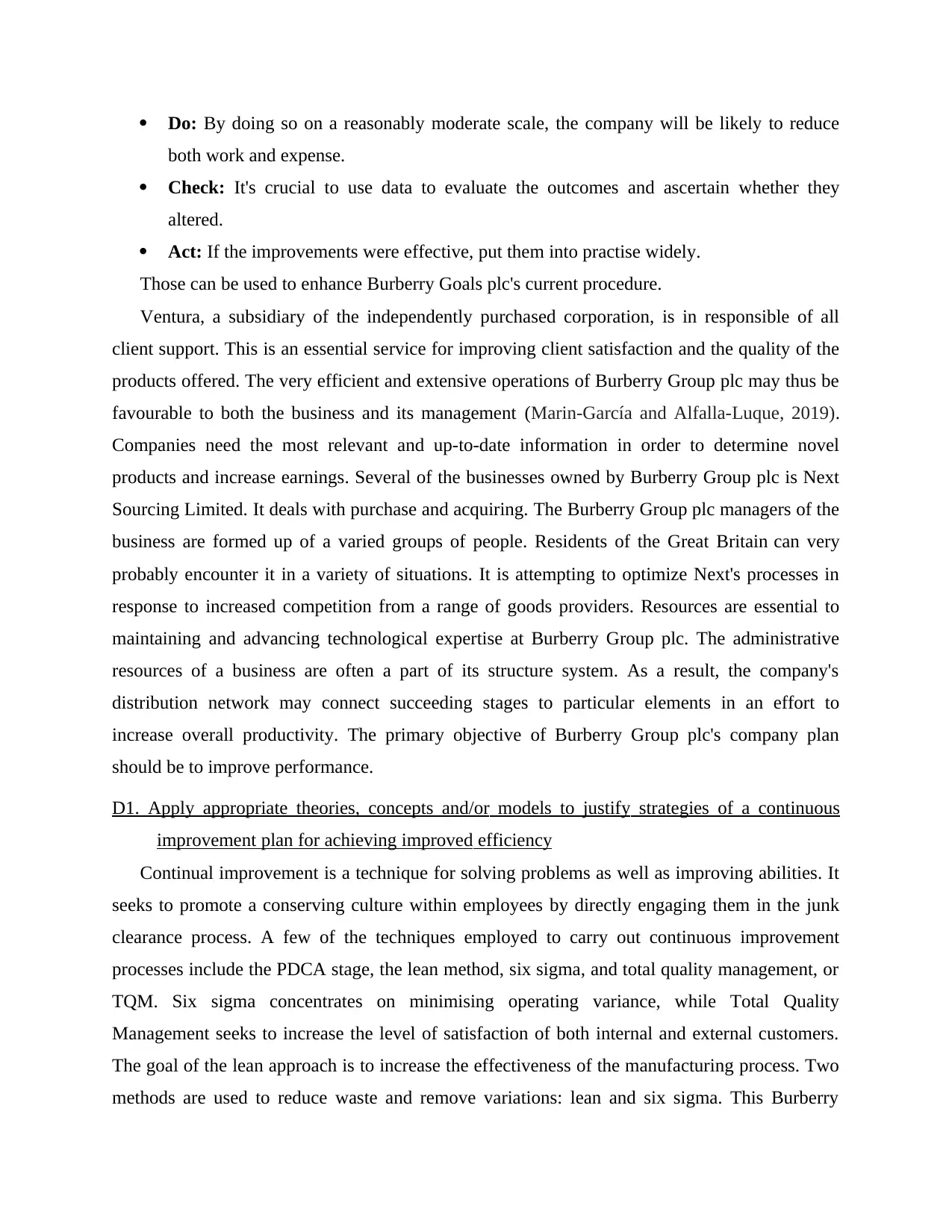
Do: By doing so on a reasonably moderate scale, the company will be likely to reduce
both work and expense.
Check: It's crucial to use data to evaluate the outcomes and ascertain whether they
altered.
Act: If the improvements were effective, put them into practise widely.
Those can be used to enhance Burberry Goals plc's current procedure.
Ventura, a subsidiary of the independently purchased corporation, is in responsible of all
client support. This is an essential service for improving client satisfaction and the quality of the
products offered. The very efficient and extensive operations of Burberry Group plc may thus be
favourable to both the business and its management (Marin-García and Alfalla-Luque, 2019).
Companies need the most relevant and up-to-date information in order to determine novel
products and increase earnings. Several of the businesses owned by Burberry Group plc is Next
Sourcing Limited. It deals with purchase and acquiring. The Burberry Group plc managers of the
business are formed up of a varied groups of people. Residents of the Great Britain can very
probably encounter it in a variety of situations. It is attempting to optimize Next's processes in
response to increased competition from a range of goods providers. Resources are essential to
maintaining and advancing technological expertise at Burberry Group plc. The administrative
resources of a business are often a part of its structure system. As a result, the company's
distribution network may connect succeeding stages to particular elements in an effort to
increase overall productivity. The primary objective of Burberry Group plc's company plan
should be to improve performance.
D1. Apply appropriate theories, concepts and/or models to justify strategies of a continuous
improvement plan for achieving improved efficiency
Continual improvement is a technique for solving problems as well as improving abilities. It
seeks to promote a conserving culture within employees by directly engaging them in the junk
clearance process. A few of the techniques employed to carry out continuous improvement
processes include the PDCA stage, the lean method, six sigma, and total quality management, or
TQM. Six sigma concentrates on minimising operating variance, while Total Quality
Management seeks to increase the level of satisfaction of both internal and external customers.
The goal of the lean approach is to increase the effectiveness of the manufacturing process. Two
methods are used to reduce waste and remove variations: lean and six sigma. This Burberry
both work and expense.
Check: It's crucial to use data to evaluate the outcomes and ascertain whether they
altered.
Act: If the improvements were effective, put them into practise widely.
Those can be used to enhance Burberry Goals plc's current procedure.
Ventura, a subsidiary of the independently purchased corporation, is in responsible of all
client support. This is an essential service for improving client satisfaction and the quality of the
products offered. The very efficient and extensive operations of Burberry Group plc may thus be
favourable to both the business and its management (Marin-García and Alfalla-Luque, 2019).
Companies need the most relevant and up-to-date information in order to determine novel
products and increase earnings. Several of the businesses owned by Burberry Group plc is Next
Sourcing Limited. It deals with purchase and acquiring. The Burberry Group plc managers of the
business are formed up of a varied groups of people. Residents of the Great Britain can very
probably encounter it in a variety of situations. It is attempting to optimize Next's processes in
response to increased competition from a range of goods providers. Resources are essential to
maintaining and advancing technological expertise at Burberry Group plc. The administrative
resources of a business are often a part of its structure system. As a result, the company's
distribution network may connect succeeding stages to particular elements in an effort to
increase overall productivity. The primary objective of Burberry Group plc's company plan
should be to improve performance.
D1. Apply appropriate theories, concepts and/or models to justify strategies of a continuous
improvement plan for achieving improved efficiency
Continual improvement is a technique for solving problems as well as improving abilities. It
seeks to promote a conserving culture within employees by directly engaging them in the junk
clearance process. A few of the techniques employed to carry out continuous improvement
processes include the PDCA stage, the lean method, six sigma, and total quality management, or
TQM. Six sigma concentrates on minimising operating variance, while Total Quality
Management seeks to increase the level of satisfaction of both internal and external customers.
The goal of the lean approach is to increase the effectiveness of the manufacturing process. Two
methods are used to reduce waste and remove variations: lean and six sigma. This Burberry
You're viewing a preview
Unlock full access by subscribing today!
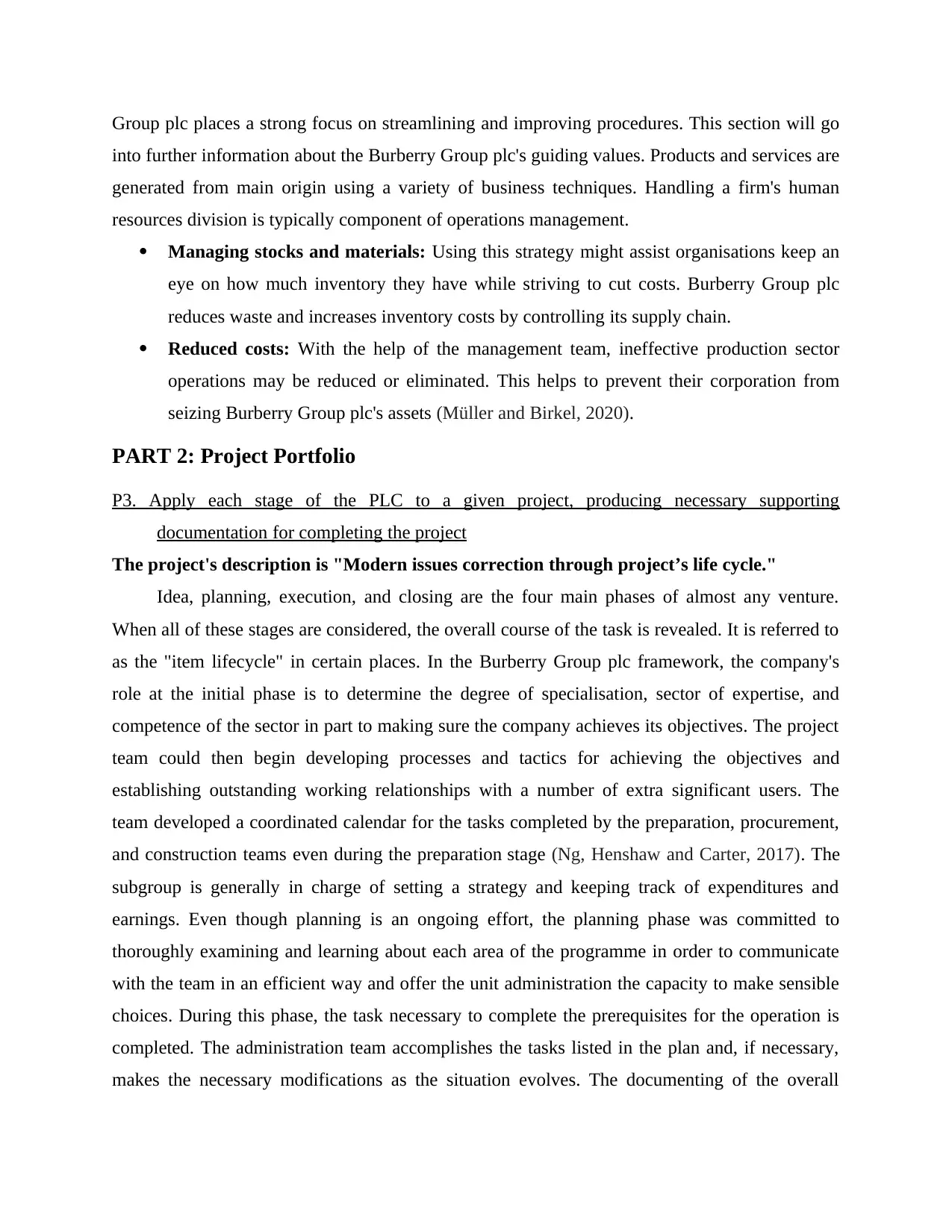
Group plc places a strong focus on streamlining and improving procedures. This section will go
into further information about the Burberry Group plc's guiding values. Products and services are
generated from main origin using a variety of business techniques. Handling a firm's human
resources division is typically component of operations management.
Managing stocks and materials: Using this strategy might assist organisations keep an
eye on how much inventory they have while striving to cut costs. Burberry Group plc
reduces waste and increases inventory costs by controlling its supply chain.
Reduced costs: With the help of the management team, ineffective production sector
operations may be reduced or eliminated. This helps to prevent their corporation from
seizing Burberry Group plc's assets (Müller and Birkel, 2020).
PART 2: Project Portfolio
P3. Apply each stage of the PLC to a given project, producing necessary supporting
documentation for completing the project
The project's description is "Modern issues correction through project’s life cycle."
Idea, planning, execution, and closing are the four main phases of almost any venture.
When all of these stages are considered, the overall course of the task is revealed. It is referred to
as the "item lifecycle" in certain places. In the Burberry Group plc framework, the company's
role at the initial phase is to determine the degree of specialisation, sector of expertise, and
competence of the sector in part to making sure the company achieves its objectives. The project
team could then begin developing processes and tactics for achieving the objectives and
establishing outstanding working relationships with a number of extra significant users. The
team developed a coordinated calendar for the tasks completed by the preparation, procurement,
and construction teams even during the preparation stage (Ng, Henshaw and Carter, 2017). The
subgroup is generally in charge of setting a strategy and keeping track of expenditures and
earnings. Even though planning is an ongoing effort, the planning phase was committed to
thoroughly examining and learning about each area of the programme in order to communicate
with the team in an efficient way and offer the unit administration the capacity to make sensible
choices. During this phase, the task necessary to complete the prerequisites for the operation is
completed. The administration team accomplishes the tasks listed in the plan and, if necessary,
makes the necessary modifications as the situation evolves. The documenting of the overall
into further information about the Burberry Group plc's guiding values. Products and services are
generated from main origin using a variety of business techniques. Handling a firm's human
resources division is typically component of operations management.
Managing stocks and materials: Using this strategy might assist organisations keep an
eye on how much inventory they have while striving to cut costs. Burberry Group plc
reduces waste and increases inventory costs by controlling its supply chain.
Reduced costs: With the help of the management team, ineffective production sector
operations may be reduced or eliminated. This helps to prevent their corporation from
seizing Burberry Group plc's assets (Müller and Birkel, 2020).
PART 2: Project Portfolio
P3. Apply each stage of the PLC to a given project, producing necessary supporting
documentation for completing the project
The project's description is "Modern issues correction through project’s life cycle."
Idea, planning, execution, and closing are the four main phases of almost any venture.
When all of these stages are considered, the overall course of the task is revealed. It is referred to
as the "item lifecycle" in certain places. In the Burberry Group plc framework, the company's
role at the initial phase is to determine the degree of specialisation, sector of expertise, and
competence of the sector in part to making sure the company achieves its objectives. The project
team could then begin developing processes and tactics for achieving the objectives and
establishing outstanding working relationships with a number of extra significant users. The
team developed a coordinated calendar for the tasks completed by the preparation, procurement,
and construction teams even during the preparation stage (Ng, Henshaw and Carter, 2017). The
subgroup is generally in charge of setting a strategy and keeping track of expenditures and
earnings. Even though planning is an ongoing effort, the planning phase was committed to
thoroughly examining and learning about each area of the programme in order to communicate
with the team in an efficient way and offer the unit administration the capacity to make sensible
choices. During this phase, the task necessary to complete the prerequisites for the operation is
completed. The administration team accomplishes the tasks listed in the plan and, if necessary,
makes the necessary modifications as the situation evolves. The documenting of the overall
Paraphrase This Document
Need a fresh take? Get an instant paraphrase of this document with our AI Paraphraser
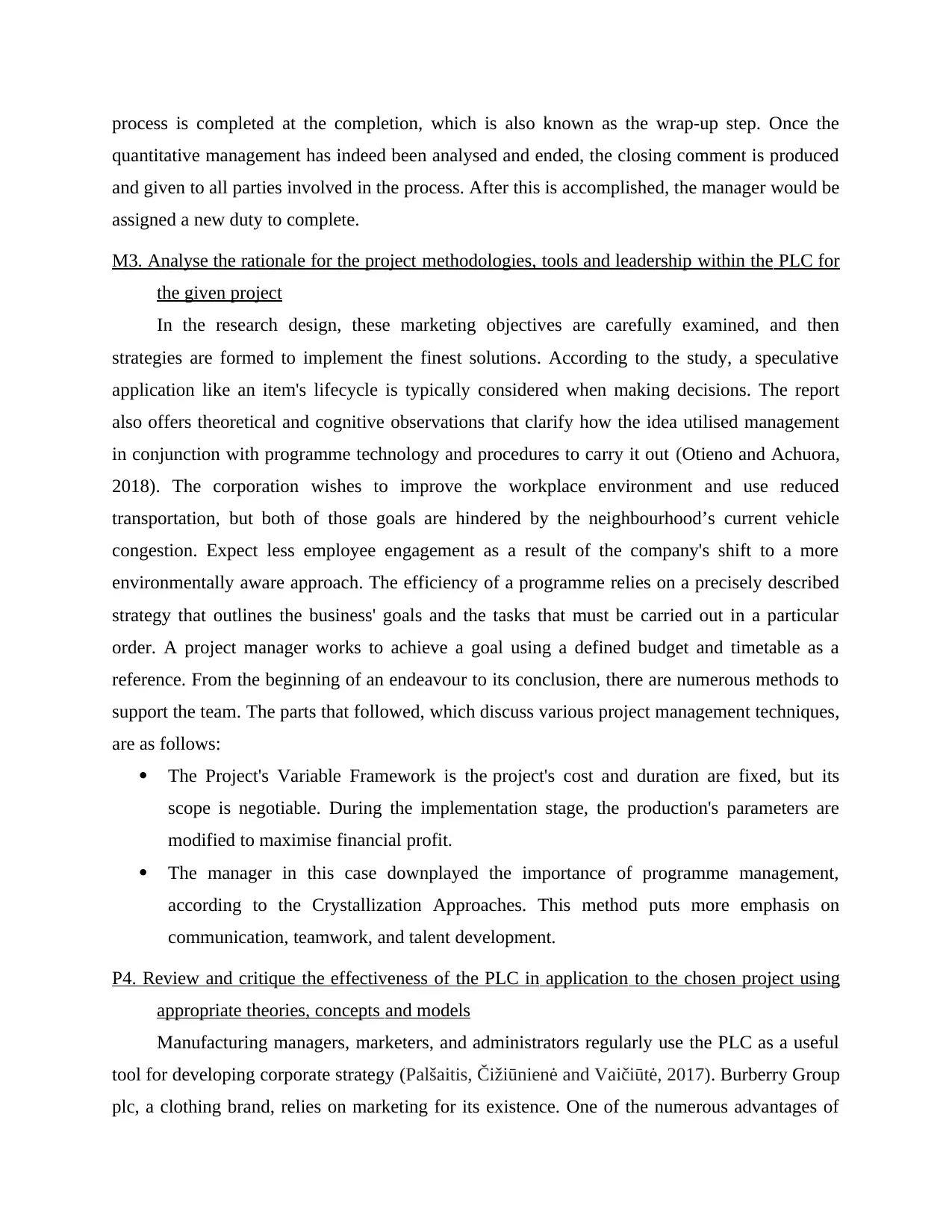
process is completed at the completion, which is also known as the wrap-up step. Once the
quantitative management has indeed been analysed and ended, the closing comment is produced
and given to all parties involved in the process. After this is accomplished, the manager would be
assigned a new duty to complete.
M3. Analyse the rationale for the project methodologies, tools and leadership within the PLC for
the given project
In the research design, these marketing objectives are carefully examined, and then
strategies are formed to implement the finest solutions. According to the study, a speculative
application like an item's lifecycle is typically considered when making decisions. The report
also offers theoretical and cognitive observations that clarify how the idea utilised management
in conjunction with programme technology and procedures to carry it out (Otieno and Achuora,
2018). The corporation wishes to improve the workplace environment and use reduced
transportation, but both of those goals are hindered by the neighbourhood’s current vehicle
congestion. Expect less employee engagement as a result of the company's shift to a more
environmentally aware approach. The efficiency of a programme relies on a precisely described
strategy that outlines the business' goals and the tasks that must be carried out in a particular
order. A project manager works to achieve a goal using a defined budget and timetable as a
reference. From the beginning of an endeavour to its conclusion, there are numerous methods to
support the team. The parts that followed, which discuss various project management techniques,
are as follows:
The Project's Variable Framework is the project's cost and duration are fixed, but its
scope is negotiable. During the implementation stage, the production's parameters are
modified to maximise financial profit.
The manager in this case downplayed the importance of programme management,
according to the Crystallization Approaches. This method puts more emphasis on
communication, teamwork, and talent development.
P4. Review and critique the effectiveness of the PLC in application to the chosen project using
appropriate theories, concepts and models
Manufacturing managers, marketers, and administrators regularly use the PLC as a useful
tool for developing corporate strategy (Palšaitis, Čižiūnienė and Vaičiūtė, 2017). Burberry Group
plc, a clothing brand, relies on marketing for its existence. One of the numerous advantages of
quantitative management has indeed been analysed and ended, the closing comment is produced
and given to all parties involved in the process. After this is accomplished, the manager would be
assigned a new duty to complete.
M3. Analyse the rationale for the project methodologies, tools and leadership within the PLC for
the given project
In the research design, these marketing objectives are carefully examined, and then
strategies are formed to implement the finest solutions. According to the study, a speculative
application like an item's lifecycle is typically considered when making decisions. The report
also offers theoretical and cognitive observations that clarify how the idea utilised management
in conjunction with programme technology and procedures to carry it out (Otieno and Achuora,
2018). The corporation wishes to improve the workplace environment and use reduced
transportation, but both of those goals are hindered by the neighbourhood’s current vehicle
congestion. Expect less employee engagement as a result of the company's shift to a more
environmentally aware approach. The efficiency of a programme relies on a precisely described
strategy that outlines the business' goals and the tasks that must be carried out in a particular
order. A project manager works to achieve a goal using a defined budget and timetable as a
reference. From the beginning of an endeavour to its conclusion, there are numerous methods to
support the team. The parts that followed, which discuss various project management techniques,
are as follows:
The Project's Variable Framework is the project's cost and duration are fixed, but its
scope is negotiable. During the implementation stage, the production's parameters are
modified to maximise financial profit.
The manager in this case downplayed the importance of programme management,
according to the Crystallization Approaches. This method puts more emphasis on
communication, teamwork, and talent development.
P4. Review and critique the effectiveness of the PLC in application to the chosen project using
appropriate theories, concepts and models
Manufacturing managers, marketers, and administrators regularly use the PLC as a useful
tool for developing corporate strategy (Palšaitis, Čižiūnienė and Vaičiūtė, 2017). Burberry Group
plc, a clothing brand, relies on marketing for its existence. One of the numerous advantages of
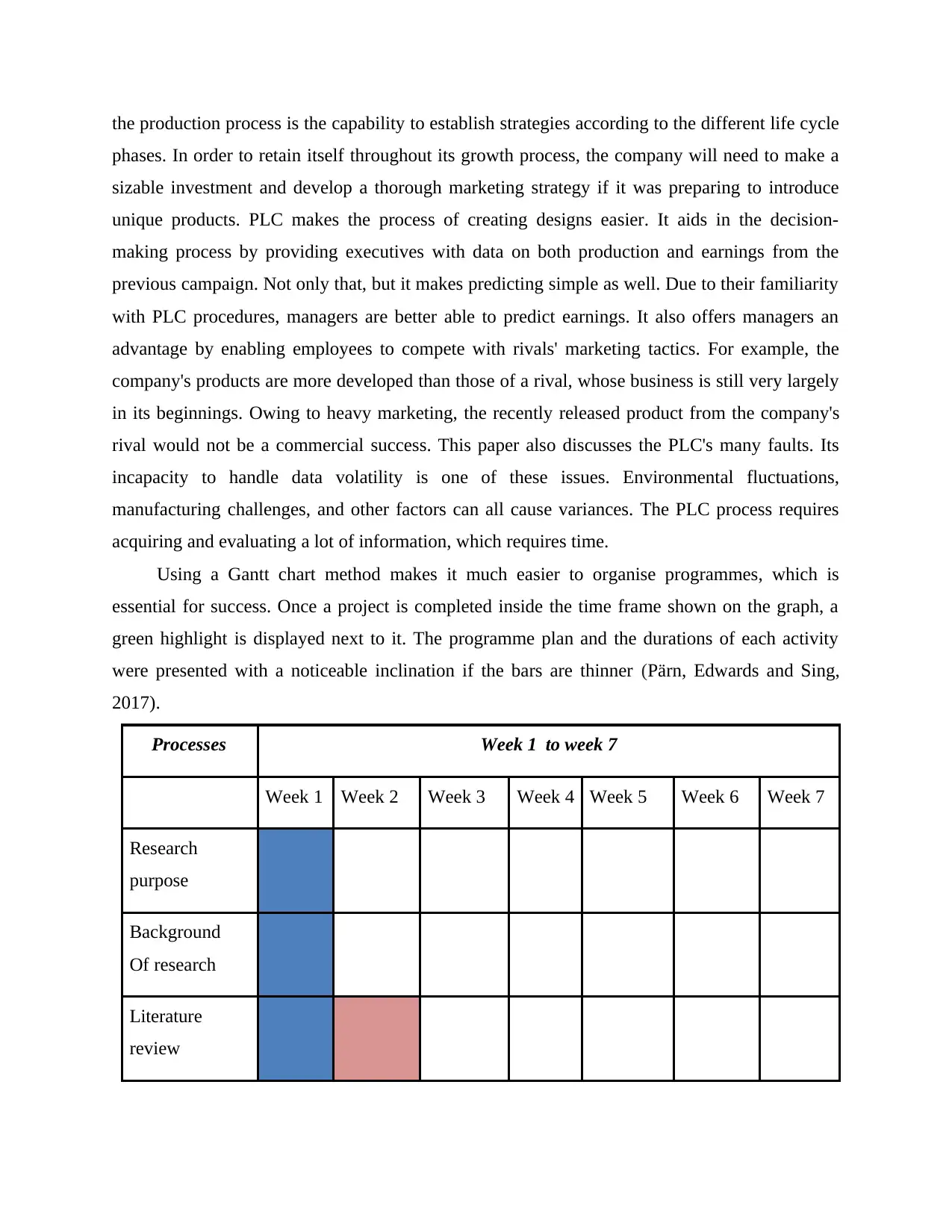
the production process is the capability to establish strategies according to the different life cycle
phases. In order to retain itself throughout its growth process, the company will need to make a
sizable investment and develop a thorough marketing strategy if it was preparing to introduce
unique products. PLC makes the process of creating designs easier. It aids in the decision-
making process by providing executives with data on both production and earnings from the
previous campaign. Not only that, but it makes predicting simple as well. Due to their familiarity
with PLC procedures, managers are better able to predict earnings. It also offers managers an
advantage by enabling employees to compete with rivals' marketing tactics. For example, the
company's products are more developed than those of a rival, whose business is still very largely
in its beginnings. Owing to heavy marketing, the recently released product from the company's
rival would not be a commercial success. This paper also discusses the PLC's many faults. Its
incapacity to handle data volatility is one of these issues. Environmental fluctuations,
manufacturing challenges, and other factors can all cause variances. The PLC process requires
acquiring and evaluating a lot of information, which requires time.
Using a Gantt chart method makes it much easier to organise programmes, which is
essential for success. Once a project is completed inside the time frame shown on the graph, a
green highlight is displayed next to it. The programme plan and the durations of each activity
were presented with a noticeable inclination if the bars are thinner (Pärn, Edwards and Sing,
2017).
Processes Week 1 to week 7
Week 1 Week 2 Week 3 Week 4 Week 5 Week 6 Week 7
Research
purpose
Background
Of research
Literature
review
phases. In order to retain itself throughout its growth process, the company will need to make a
sizable investment and develop a thorough marketing strategy if it was preparing to introduce
unique products. PLC makes the process of creating designs easier. It aids in the decision-
making process by providing executives with data on both production and earnings from the
previous campaign. Not only that, but it makes predicting simple as well. Due to their familiarity
with PLC procedures, managers are better able to predict earnings. It also offers managers an
advantage by enabling employees to compete with rivals' marketing tactics. For example, the
company's products are more developed than those of a rival, whose business is still very largely
in its beginnings. Owing to heavy marketing, the recently released product from the company's
rival would not be a commercial success. This paper also discusses the PLC's many faults. Its
incapacity to handle data volatility is one of these issues. Environmental fluctuations,
manufacturing challenges, and other factors can all cause variances. The PLC process requires
acquiring and evaluating a lot of information, which requires time.
Using a Gantt chart method makes it much easier to organise programmes, which is
essential for success. Once a project is completed inside the time frame shown on the graph, a
green highlight is displayed next to it. The programme plan and the durations of each activity
were presented with a noticeable inclination if the bars are thinner (Pärn, Edwards and Sing,
2017).
Processes Week 1 to week 7
Week 1 Week 2 Week 3 Week 4 Week 5 Week 6 Week 7
Research
purpose
Background
Of research
Literature
review
You're viewing a preview
Unlock full access by subscribing today!
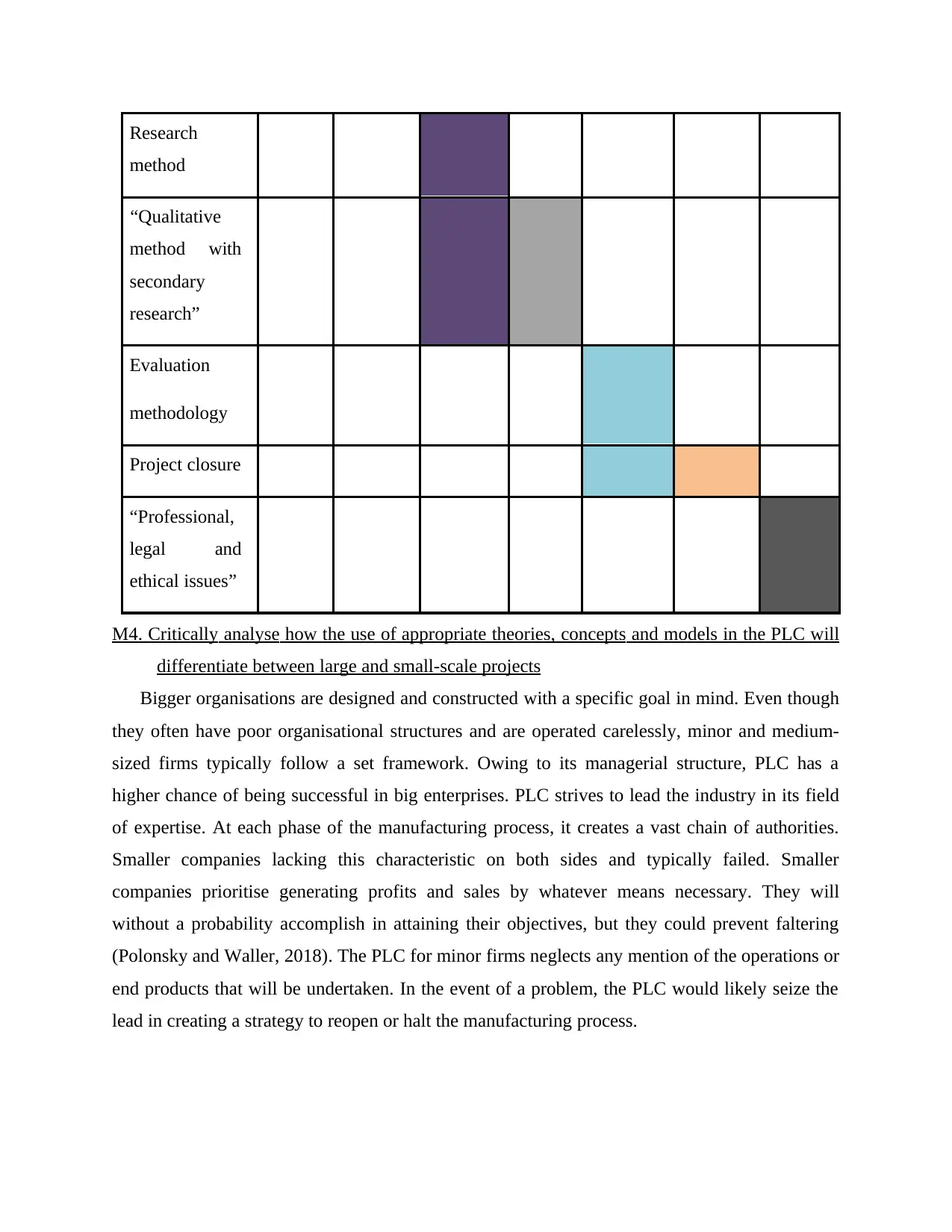
Research
method
“Qualitative
method with
secondary
research”
Evaluation
methodology
Project closure
“Professional,
legal and
ethical issues”
M4. Critically analyse how the use of appropriate theories, concepts and models in the PLC will
differentiate between large and small-scale projects
Bigger organisations are designed and constructed with a specific goal in mind. Even though
they often have poor organisational structures and are operated carelessly, minor and medium-
sized firms typically follow a set framework. Owing to its managerial structure, PLC has a
higher chance of being successful in big enterprises. PLC strives to lead the industry in its field
of expertise. At each phase of the manufacturing process, it creates a vast chain of authorities.
Smaller companies lacking this characteristic on both sides and typically failed. Smaller
companies prioritise generating profits and sales by whatever means necessary. They will
without a probability accomplish in attaining their objectives, but they could prevent faltering
(Polonsky and Waller, 2018). The PLC for minor firms neglects any mention of the operations or
end products that will be undertaken. In the event of a problem, the PLC would likely seize the
lead in creating a strategy to reopen or halt the manufacturing process.
method
“Qualitative
method with
secondary
research”
Evaluation
methodology
Project closure
“Professional,
legal and
ethical issues”
M4. Critically analyse how the use of appropriate theories, concepts and models in the PLC will
differentiate between large and small-scale projects
Bigger organisations are designed and constructed with a specific goal in mind. Even though
they often have poor organisational structures and are operated carelessly, minor and medium-
sized firms typically follow a set framework. Owing to its managerial structure, PLC has a
higher chance of being successful in big enterprises. PLC strives to lead the industry in its field
of expertise. At each phase of the manufacturing process, it creates a vast chain of authorities.
Smaller companies lacking this characteristic on both sides and typically failed. Smaller
companies prioritise generating profits and sales by whatever means necessary. They will
without a probability accomplish in attaining their objectives, but they could prevent faltering
(Polonsky and Waller, 2018). The PLC for minor firms neglects any mention of the operations or
end products that will be undertaken. In the event of a problem, the PLC would likely seize the
lead in creating a strategy to reopen or halt the manufacturing process.
Paraphrase This Document
Need a fresh take? Get an instant paraphrase of this document with our AI Paraphraser
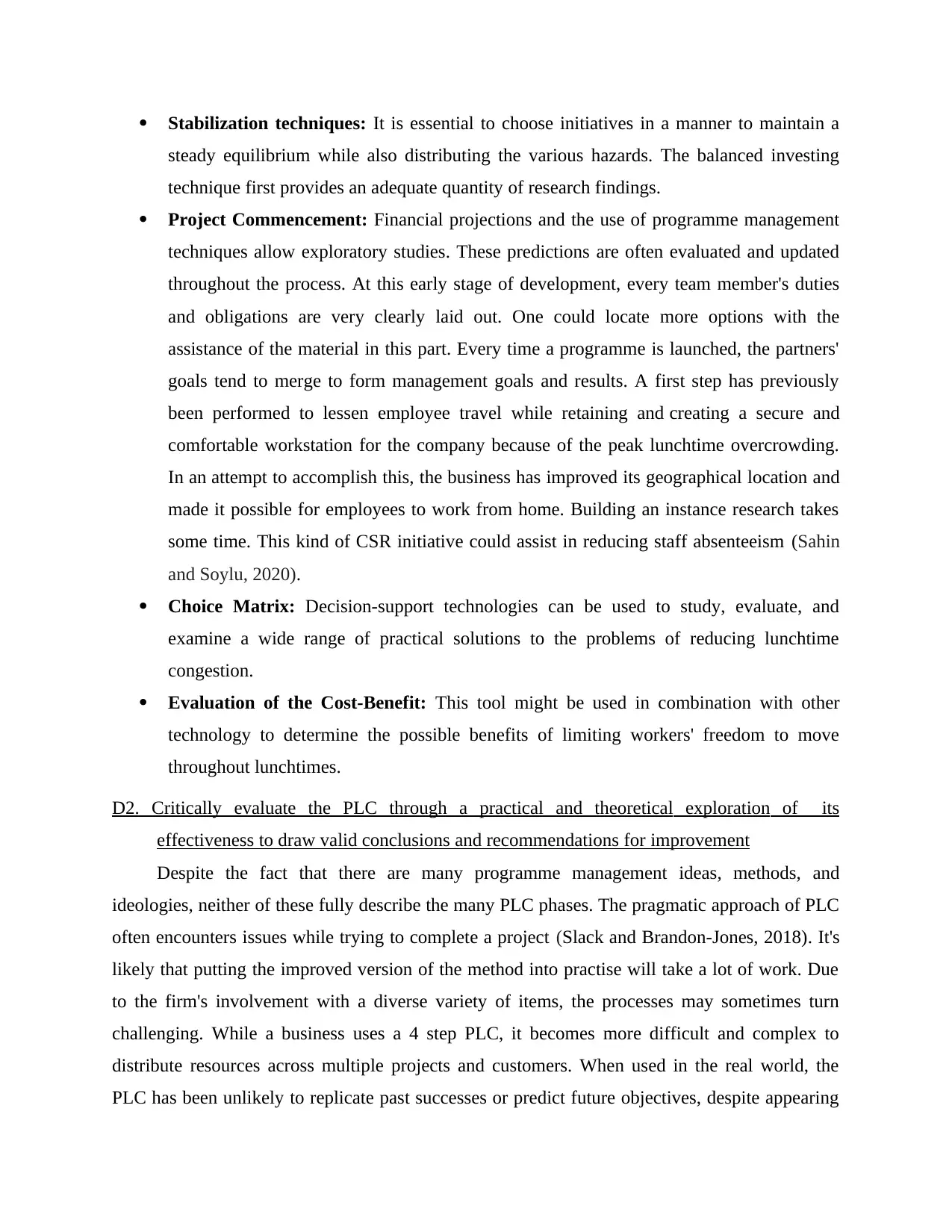
Stabilization techniques: It is essential to choose initiatives in a manner to maintain a
steady equilibrium while also distributing the various hazards. The balanced investing
technique first provides an adequate quantity of research findings.
Project Commencement: Financial projections and the use of programme management
techniques allow exploratory studies. These predictions are often evaluated and updated
throughout the process. At this early stage of development, every team member's duties
and obligations are very clearly laid out. One could locate more options with the
assistance of the material in this part. Every time a programme is launched, the partners'
goals tend to merge to form management goals and results. A first step has previously
been performed to lessen employee travel while retaining and creating a secure and
comfortable workstation for the company because of the peak lunchtime overcrowding.
In an attempt to accomplish this, the business has improved its geographical location and
made it possible for employees to work from home. Building an instance research takes
some time. This kind of CSR initiative could assist in reducing staff absenteeism (Sahin
and Soylu, 2020).
Choice Matrix: Decision-support technologies can be used to study, evaluate, and
examine a wide range of practical solutions to the problems of reducing lunchtime
congestion.
Evaluation of the Cost-Benefit: This tool might be used in combination with other
technology to determine the possible benefits of limiting workers' freedom to move
throughout lunchtimes.
D2. Critically evaluate the PLC through a practical and theoretical exploration of its
effectiveness to draw valid conclusions and recommendations for improvement
Despite the fact that there are many programme management ideas, methods, and
ideologies, neither of these fully describe the many PLC phases. The pragmatic approach of PLC
often encounters issues while trying to complete a project (Slack and Brandon-Jones, 2018). It's
likely that putting the improved version of the method into practise will take a lot of work. Due
to the firm's involvement with a diverse variety of items, the processes may sometimes turn
challenging. While a business uses a 4 step PLC, it becomes more difficult and complex to
distribute resources across multiple projects and customers. When used in the real world, the
PLC has been unlikely to replicate past successes or predict future objectives, despite appearing
steady equilibrium while also distributing the various hazards. The balanced investing
technique first provides an adequate quantity of research findings.
Project Commencement: Financial projections and the use of programme management
techniques allow exploratory studies. These predictions are often evaluated and updated
throughout the process. At this early stage of development, every team member's duties
and obligations are very clearly laid out. One could locate more options with the
assistance of the material in this part. Every time a programme is launched, the partners'
goals tend to merge to form management goals and results. A first step has previously
been performed to lessen employee travel while retaining and creating a secure and
comfortable workstation for the company because of the peak lunchtime overcrowding.
In an attempt to accomplish this, the business has improved its geographical location and
made it possible for employees to work from home. Building an instance research takes
some time. This kind of CSR initiative could assist in reducing staff absenteeism (Sahin
and Soylu, 2020).
Choice Matrix: Decision-support technologies can be used to study, evaluate, and
examine a wide range of practical solutions to the problems of reducing lunchtime
congestion.
Evaluation of the Cost-Benefit: This tool might be used in combination with other
technology to determine the possible benefits of limiting workers' freedom to move
throughout lunchtimes.
D2. Critically evaluate the PLC through a practical and theoretical exploration of its
effectiveness to draw valid conclusions and recommendations for improvement
Despite the fact that there are many programme management ideas, methods, and
ideologies, neither of these fully describe the many PLC phases. The pragmatic approach of PLC
often encounters issues while trying to complete a project (Slack and Brandon-Jones, 2018). It's
likely that putting the improved version of the method into practise will take a lot of work. Due
to the firm's involvement with a diverse variety of items, the processes may sometimes turn
challenging. While a business uses a 4 step PLC, it becomes more difficult and complex to
distribute resources across multiple projects and customers. When used in the real world, the
PLC has been unlikely to replicate past successes or predict future objectives, despite appearing
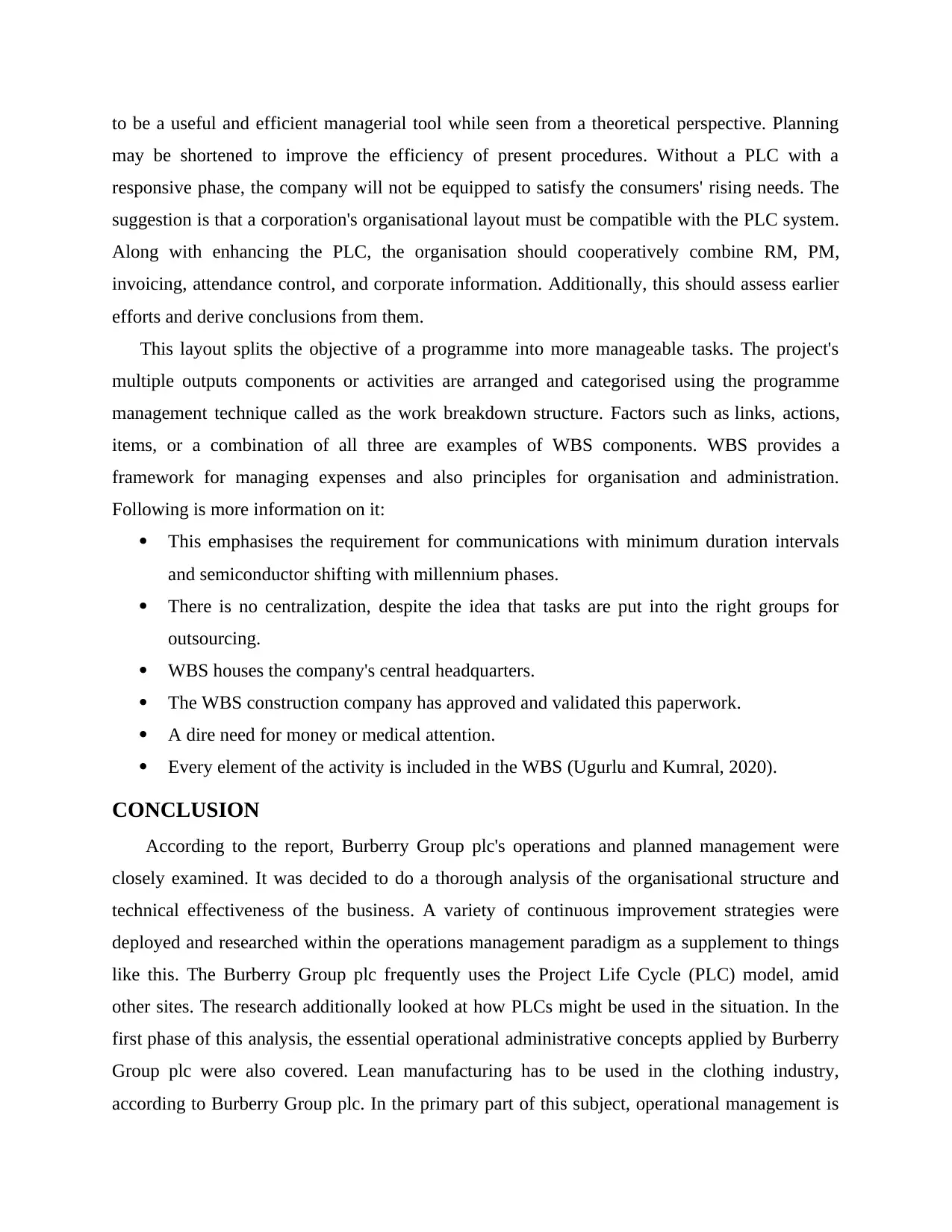
to be a useful and efficient managerial tool while seen from a theoretical perspective. Planning
may be shortened to improve the efficiency of present procedures. Without a PLC with a
responsive phase, the company will not be equipped to satisfy the consumers' rising needs. The
suggestion is that a corporation's organisational layout must be compatible with the PLC system.
Along with enhancing the PLC, the organisation should cooperatively combine RM, PM,
invoicing, attendance control, and corporate information. Additionally, this should assess earlier
efforts and derive conclusions from them.
This layout splits the objective of a programme into more manageable tasks. The project's
multiple outputs components or activities are arranged and categorised using the programme
management technique called as the work breakdown structure. Factors such as links, actions,
items, or a combination of all three are examples of WBS components. WBS provides a
framework for managing expenses and also principles for organisation and administration.
Following is more information on it:
This emphasises the requirement for communications with minimum duration intervals
and semiconductor shifting with millennium phases.
There is no centralization, despite the idea that tasks are put into the right groups for
outsourcing.
WBS houses the company's central headquarters.
The WBS construction company has approved and validated this paperwork.
A dire need for money or medical attention.
Every element of the activity is included in the WBS (Ugurlu and Kumral, 2020).
CONCLUSION
According to the report, Burberry Group plc's operations and planned management were
closely examined. It was decided to do a thorough analysis of the organisational structure and
technical effectiveness of the business. A variety of continuous improvement strategies were
deployed and researched within the operations management paradigm as a supplement to things
like this. The Burberry Group plc frequently uses the Project Life Cycle (PLC) model, amid
other sites. The research additionally looked at how PLCs might be used in the situation. In the
first phase of this analysis, the essential operational administrative concepts applied by Burberry
Group plc were also covered. Lean manufacturing has to be used in the clothing industry,
according to Burberry Group plc. In the primary part of this subject, operational management is
may be shortened to improve the efficiency of present procedures. Without a PLC with a
responsive phase, the company will not be equipped to satisfy the consumers' rising needs. The
suggestion is that a corporation's organisational layout must be compatible with the PLC system.
Along with enhancing the PLC, the organisation should cooperatively combine RM, PM,
invoicing, attendance control, and corporate information. Additionally, this should assess earlier
efforts and derive conclusions from them.
This layout splits the objective of a programme into more manageable tasks. The project's
multiple outputs components or activities are arranged and categorised using the programme
management technique called as the work breakdown structure. Factors such as links, actions,
items, or a combination of all three are examples of WBS components. WBS provides a
framework for managing expenses and also principles for organisation and administration.
Following is more information on it:
This emphasises the requirement for communications with minimum duration intervals
and semiconductor shifting with millennium phases.
There is no centralization, despite the idea that tasks are put into the right groups for
outsourcing.
WBS houses the company's central headquarters.
The WBS construction company has approved and validated this paperwork.
A dire need for money or medical attention.
Every element of the activity is included in the WBS (Ugurlu and Kumral, 2020).
CONCLUSION
According to the report, Burberry Group plc's operations and planned management were
closely examined. It was decided to do a thorough analysis of the organisational structure and
technical effectiveness of the business. A variety of continuous improvement strategies were
deployed and researched within the operations management paradigm as a supplement to things
like this. The Burberry Group plc frequently uses the Project Life Cycle (PLC) model, amid
other sites. The research additionally looked at how PLCs might be used in the situation. In the
first phase of this analysis, the essential operational administrative concepts applied by Burberry
Group plc were also covered. Lean manufacturing has to be used in the clothing industry,
according to Burberry Group plc. In the primary part of this subject, operational management is
You're viewing a preview
Unlock full access by subscribing today!
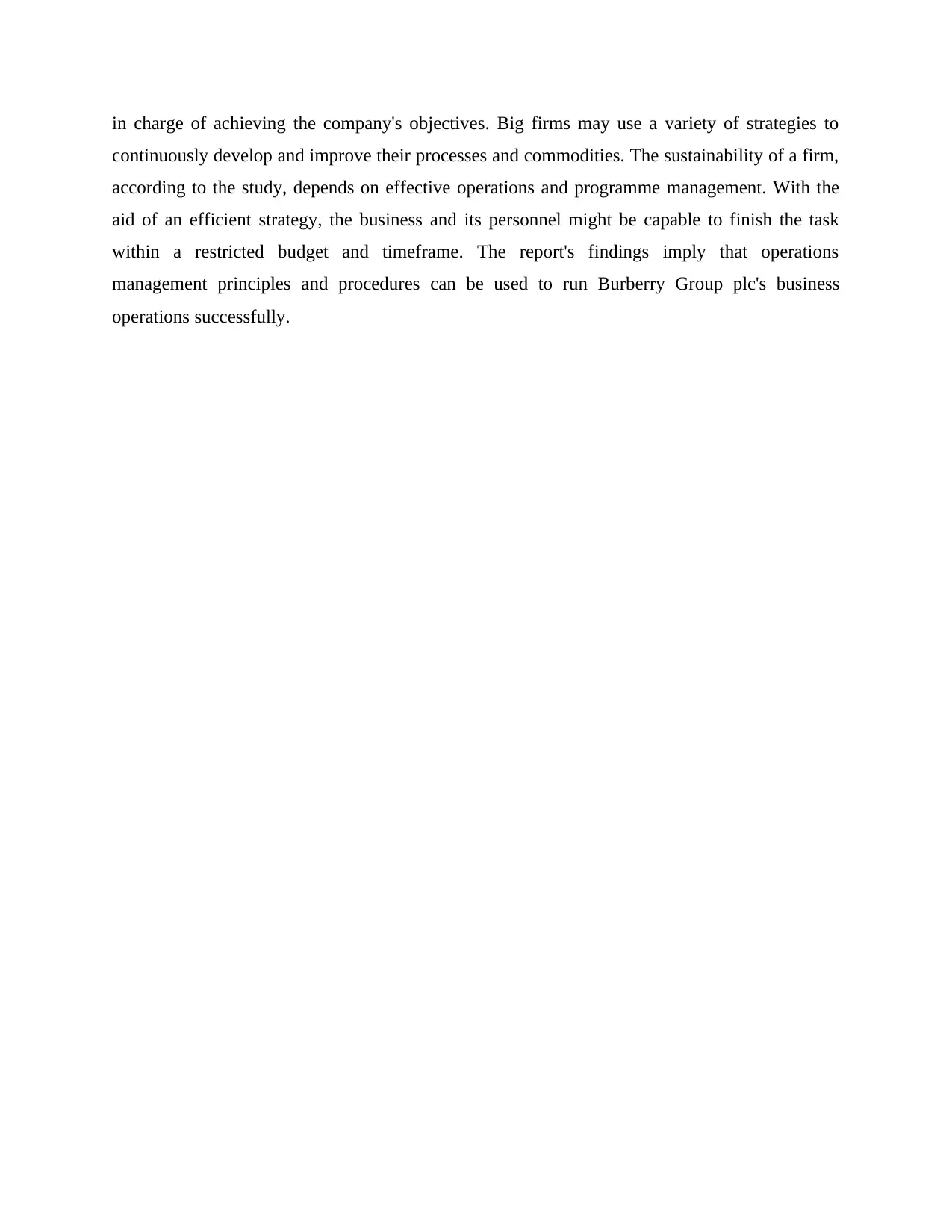
in charge of achieving the company's objectives. Big firms may use a variety of strategies to
continuously develop and improve their processes and commodities. The sustainability of a firm,
according to the study, depends on effective operations and programme management. With the
aid of an efficient strategy, the business and its personnel might be capable to finish the task
within a restricted budget and timeframe. The report's findings imply that operations
management principles and procedures can be used to run Burberry Group plc's business
operations successfully.
continuously develop and improve their processes and commodities. The sustainability of a firm,
according to the study, depends on effective operations and programme management. With the
aid of an efficient strategy, the business and its personnel might be capable to finish the task
within a restricted budget and timeframe. The report's findings imply that operations
management principles and procedures can be used to run Burberry Group plc's business
operations successfully.
Paraphrase This Document
Need a fresh take? Get an instant paraphrase of this document with our AI Paraphraser
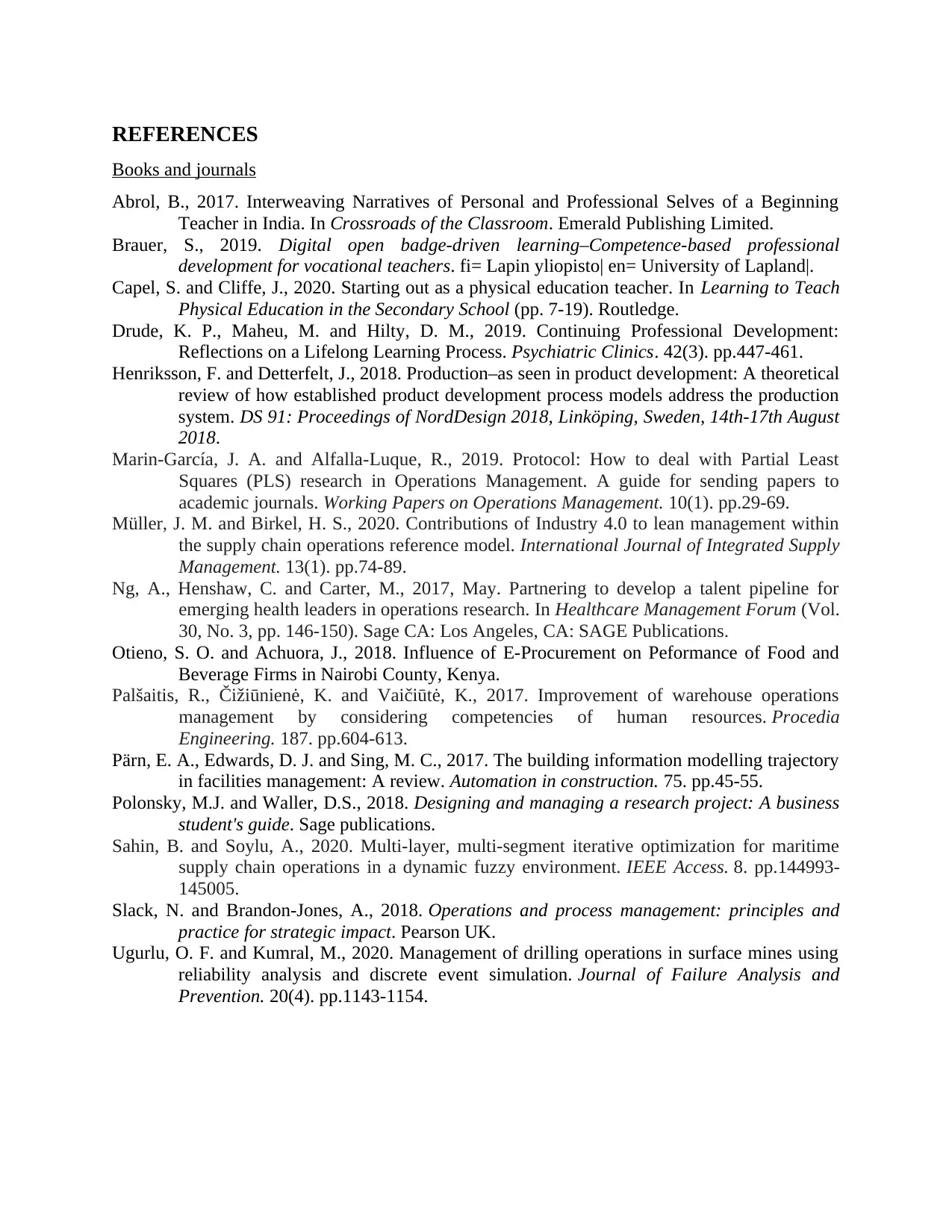
REFERENCES
Books and journals
Abrol, B., 2017. Interweaving Narratives of Personal and Professional Selves of a Beginning
Teacher in India. In Crossroads of the Classroom. Emerald Publishing Limited.
Brauer, S., 2019. Digital open badge-driven learning–Competence-based professional
development for vocational teachers. fi= Lapin yliopisto| en= University of Lapland|.
Capel, S. and Cliffe, J., 2020. Starting out as a physical education teacher. In Learning to Teach
Physical Education in the Secondary School (pp. 7-19). Routledge.
Drude, K. P., Maheu, M. and Hilty, D. M., 2019. Continuing Professional Development:
Reflections on a Lifelong Learning Process. Psychiatric Clinics. 42(3). pp.447-461.
Henriksson, F. and Detterfelt, J., 2018. Production–as seen in product development: A theoretical
review of how established product development process models address the production
system. DS 91: Proceedings of NordDesign 2018, Linköping, Sweden, 14th-17th August
2018.
Marin-García, J. A. and Alfalla-Luque, R., 2019. Protocol: How to deal with Partial Least
Squares (PLS) research in Operations Management. A guide for sending papers to
academic journals. Working Papers on Operations Management. 10(1). pp.29-69.
Müller, J. M. and Birkel, H. S., 2020. Contributions of Industry 4.0 to lean management within
the supply chain operations reference model. International Journal of Integrated Supply
Management. 13(1). pp.74-89.
Ng, A., Henshaw, C. and Carter, M., 2017, May. Partnering to develop a talent pipeline for
emerging health leaders in operations research. In Healthcare Management Forum (Vol.
30, No. 3, pp. 146-150). Sage CA: Los Angeles, CA: SAGE Publications.
Otieno, S. O. and Achuora, J., 2018. Influence of E-Procurement on Peformance of Food and
Beverage Firms in Nairobi County, Kenya.
Palšaitis, R., Čižiūnienė, K. and Vaičiūtė, K., 2017. Improvement of warehouse operations
management by considering competencies of human resources. Procedia
Engineering. 187. pp.604-613.
Pärn, E. A., Edwards, D. J. and Sing, M. C., 2017. The building information modelling trajectory
in facilities management: A review. Automation in construction. 75. pp.45-55.
Polonsky, M.J. and Waller, D.S., 2018. Designing and managing a research project: A business
student's guide. Sage publications.
Sahin, B. and Soylu, A., 2020. Multi-layer, multi-segment iterative optimization for maritime
supply chain operations in a dynamic fuzzy environment. IEEE Access. 8. pp.144993-
145005.
Slack, N. and Brandon-Jones, A., 2018. Operations and process management: principles and
practice for strategic impact. Pearson UK.
Ugurlu, O. F. and Kumral, M., 2020. Management of drilling operations in surface mines using
reliability analysis and discrete event simulation. Journal of Failure Analysis and
Prevention. 20(4). pp.1143-1154.
Books and journals
Abrol, B., 2017. Interweaving Narratives of Personal and Professional Selves of a Beginning
Teacher in India. In Crossroads of the Classroom. Emerald Publishing Limited.
Brauer, S., 2019. Digital open badge-driven learning–Competence-based professional
development for vocational teachers. fi= Lapin yliopisto| en= University of Lapland|.
Capel, S. and Cliffe, J., 2020. Starting out as a physical education teacher. In Learning to Teach
Physical Education in the Secondary School (pp. 7-19). Routledge.
Drude, K. P., Maheu, M. and Hilty, D. M., 2019. Continuing Professional Development:
Reflections on a Lifelong Learning Process. Psychiatric Clinics. 42(3). pp.447-461.
Henriksson, F. and Detterfelt, J., 2018. Production–as seen in product development: A theoretical
review of how established product development process models address the production
system. DS 91: Proceedings of NordDesign 2018, Linköping, Sweden, 14th-17th August
2018.
Marin-García, J. A. and Alfalla-Luque, R., 2019. Protocol: How to deal with Partial Least
Squares (PLS) research in Operations Management. A guide for sending papers to
academic journals. Working Papers on Operations Management. 10(1). pp.29-69.
Müller, J. M. and Birkel, H. S., 2020. Contributions of Industry 4.0 to lean management within
the supply chain operations reference model. International Journal of Integrated Supply
Management. 13(1). pp.74-89.
Ng, A., Henshaw, C. and Carter, M., 2017, May. Partnering to develop a talent pipeline for
emerging health leaders in operations research. In Healthcare Management Forum (Vol.
30, No. 3, pp. 146-150). Sage CA: Los Angeles, CA: SAGE Publications.
Otieno, S. O. and Achuora, J., 2018. Influence of E-Procurement on Peformance of Food and
Beverage Firms in Nairobi County, Kenya.
Palšaitis, R., Čižiūnienė, K. and Vaičiūtė, K., 2017. Improvement of warehouse operations
management by considering competencies of human resources. Procedia
Engineering. 187. pp.604-613.
Pärn, E. A., Edwards, D. J. and Sing, M. C., 2017. The building information modelling trajectory
in facilities management: A review. Automation in construction. 75. pp.45-55.
Polonsky, M.J. and Waller, D.S., 2018. Designing and managing a research project: A business
student's guide. Sage publications.
Sahin, B. and Soylu, A., 2020. Multi-layer, multi-segment iterative optimization for maritime
supply chain operations in a dynamic fuzzy environment. IEEE Access. 8. pp.144993-
145005.
Slack, N. and Brandon-Jones, A., 2018. Operations and process management: principles and
practice for strategic impact. Pearson UK.
Ugurlu, O. F. and Kumral, M., 2020. Management of drilling operations in surface mines using
reliability analysis and discrete event simulation. Journal of Failure Analysis and
Prevention. 20(4). pp.1143-1154.
1 out of 14
Related Documents

Your All-in-One AI-Powered Toolkit for Academic Success.
+13062052269
info@desklib.com
Available 24*7 on WhatsApp / Email
Unlock your academic potential
© 2024 | Zucol Services PVT LTD | All rights reserved.