Operations and Project Management: A Case Study of Morrisons and MG Motor UK Ltd
VerifiedAdded on 2023/06/18
|16
|4530
|210
AI Summary
This report discusses the implementation of operations management principles and project life cycle in Morrisons and MG Motor UK Ltd. It covers continuous improvement and lean principles, recommendations for improving operations functions, and critical evaluation of project life cycle.
Contribute Materials
Your contribution can guide someone’s learning journey. Share your
documents today.
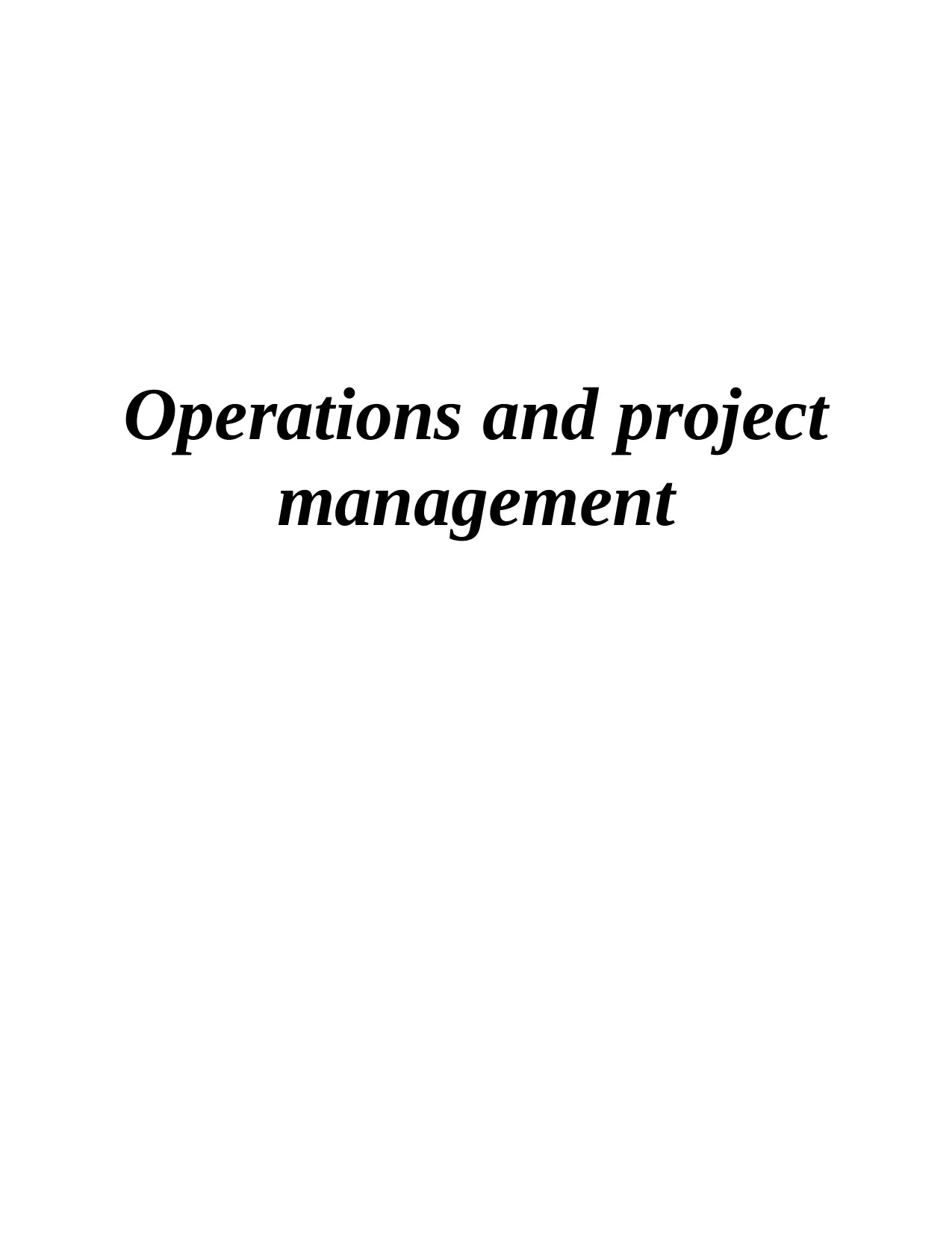
Operations and project
management
management
Secure Best Marks with AI Grader
Need help grading? Try our AI Grader for instant feedback on your assignments.
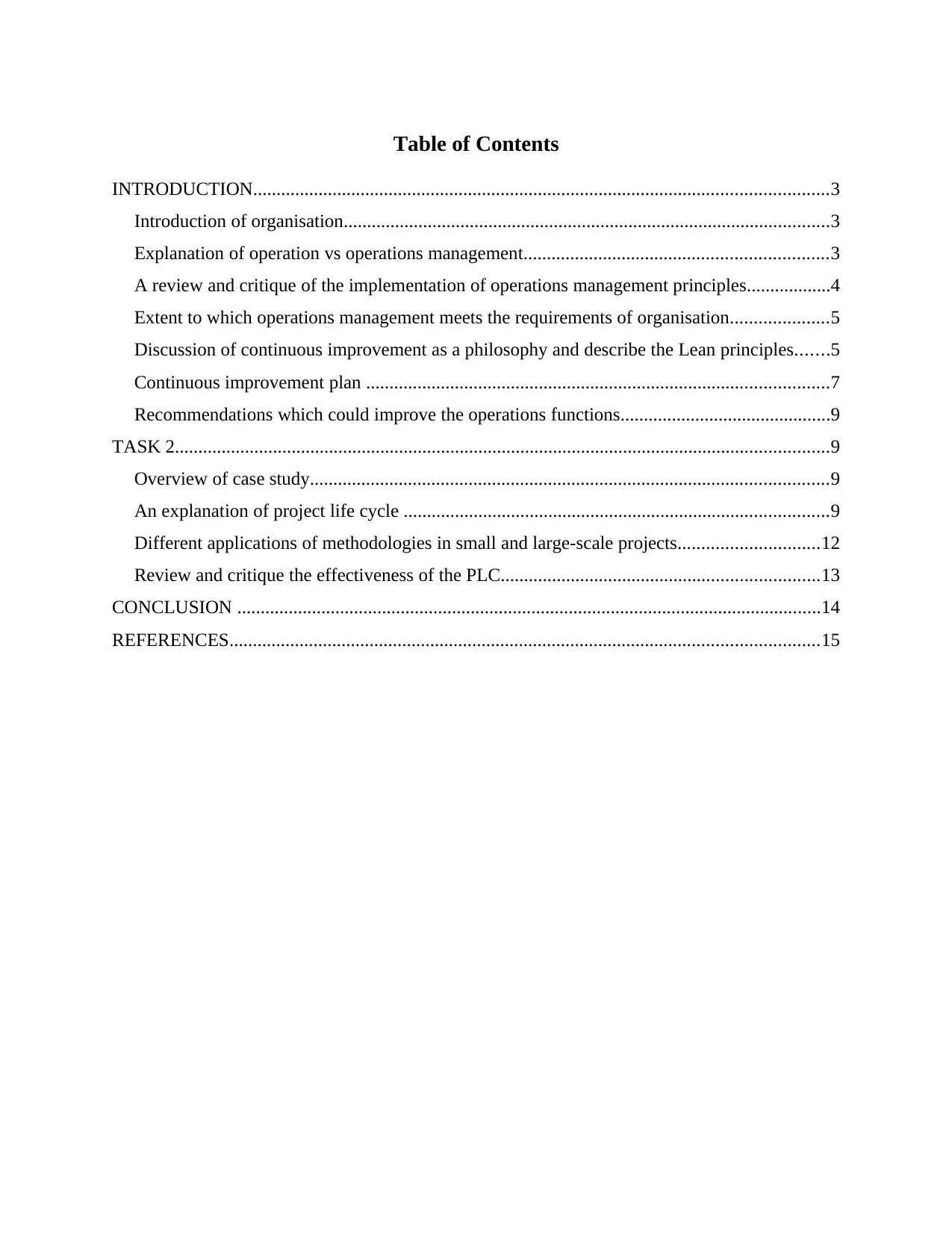
Table of Contents
INTRODUCTION...........................................................................................................................3
Introduction of organisation........................................................................................................3
Explanation of operation vs operations management.................................................................3
A review and critique of the implementation of operations management principles..................4
Extent to which operations management meets the requirements of organisation.....................5
Discussion of continuous improvement as a philosophy and describe the Lean principles.......5
Continuous improvement plan ...................................................................................................7
Recommendations which could improve the operations functions.............................................9
TASK 2............................................................................................................................................9
Overview of case study...............................................................................................................9
An explanation of project life cycle ...........................................................................................9
Different applications of methodologies in small and large-scale projects..............................12
Review and critique the effectiveness of the PLC....................................................................13
CONCLUSION .............................................................................................................................14
REFERENCES..............................................................................................................................15
INTRODUCTION...........................................................................................................................3
Introduction of organisation........................................................................................................3
Explanation of operation vs operations management.................................................................3
A review and critique of the implementation of operations management principles..................4
Extent to which operations management meets the requirements of organisation.....................5
Discussion of continuous improvement as a philosophy and describe the Lean principles.......5
Continuous improvement plan ...................................................................................................7
Recommendations which could improve the operations functions.............................................9
TASK 2............................................................................................................................................9
Overview of case study...............................................................................................................9
An explanation of project life cycle ...........................................................................................9
Different applications of methodologies in small and large-scale projects..............................12
Review and critique the effectiveness of the PLC....................................................................13
CONCLUSION .............................................................................................................................14
REFERENCES..............................................................................................................................15
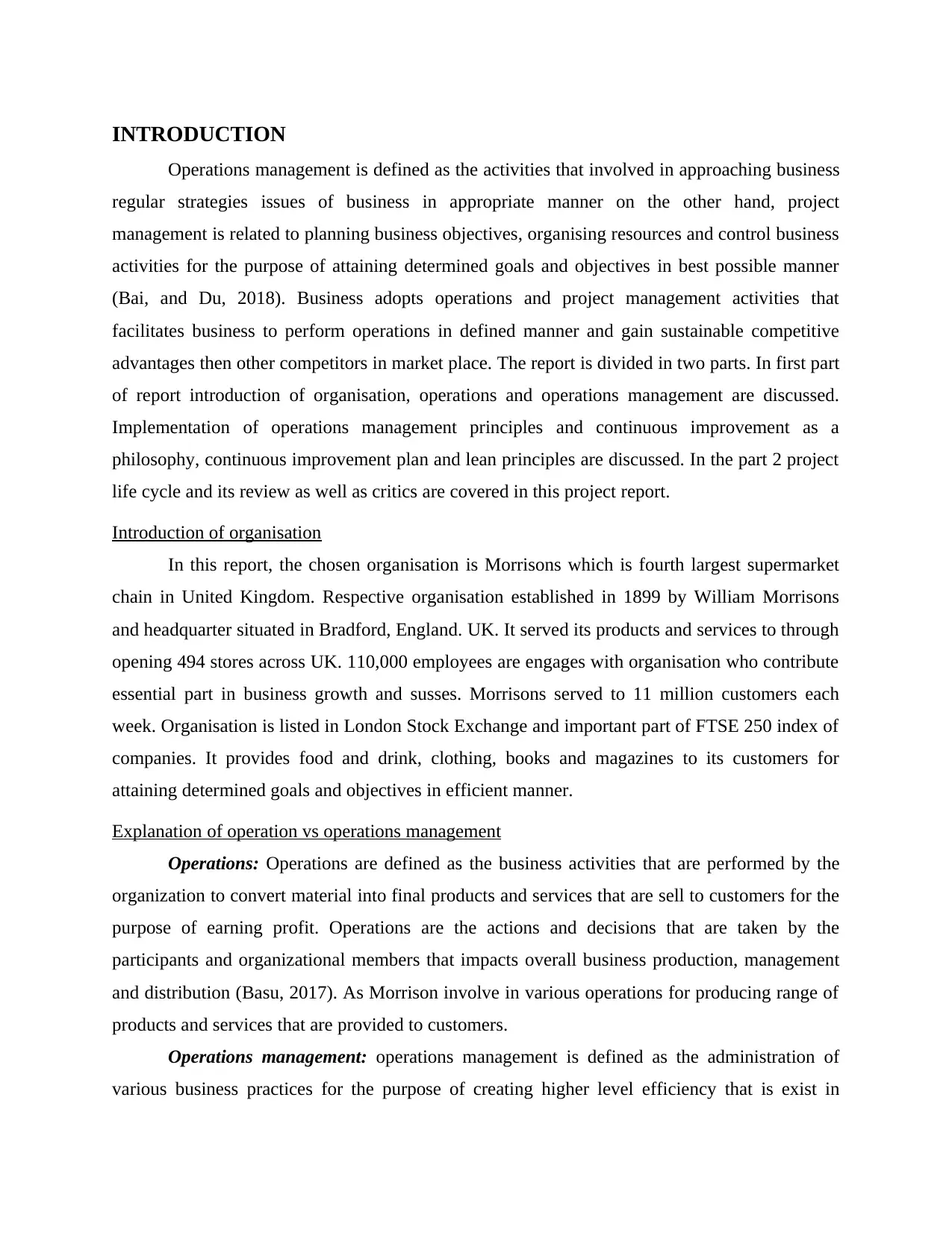
INTRODUCTION
Operations management is defined as the activities that involved in approaching business
regular strategies issues of business in appropriate manner on the other hand, project
management is related to planning business objectives, organising resources and control business
activities for the purpose of attaining determined goals and objectives in best possible manner
(Bai, and Du, 2018). Business adopts operations and project management activities that
facilitates business to perform operations in defined manner and gain sustainable competitive
advantages then other competitors in market place. The report is divided in two parts. In first part
of report introduction of organisation, operations and operations management are discussed.
Implementation of operations management principles and continuous improvement as a
philosophy, continuous improvement plan and lean principles are discussed. In the part 2 project
life cycle and its review as well as critics are covered in this project report.
Introduction of organisation
In this report, the chosen organisation is Morrisons which is fourth largest supermarket
chain in United Kingdom. Respective organisation established in 1899 by William Morrisons
and headquarter situated in Bradford, England. UK. It served its products and services to through
opening 494 stores across UK. 110,000 employees are engages with organisation who contribute
essential part in business growth and susses. Morrisons served to 11 million customers each
week. Organisation is listed in London Stock Exchange and important part of FTSE 250 index of
companies. It provides food and drink, clothing, books and magazines to its customers for
attaining determined goals and objectives in efficient manner.
Explanation of operation vs operations management
Operations: Operations are defined as the business activities that are performed by the
organization to convert material into final products and services that are sell to customers for the
purpose of earning profit. Operations are the actions and decisions that are taken by the
participants and organizational members that impacts overall business production, management
and distribution (Basu, 2017). As Morrison involve in various operations for producing range of
products and services that are provided to customers.
Operations management: operations management is defined as the administration of
various business practices for the purpose of creating higher level efficiency that is exist in
Operations management is defined as the activities that involved in approaching business
regular strategies issues of business in appropriate manner on the other hand, project
management is related to planning business objectives, organising resources and control business
activities for the purpose of attaining determined goals and objectives in best possible manner
(Bai, and Du, 2018). Business adopts operations and project management activities that
facilitates business to perform operations in defined manner and gain sustainable competitive
advantages then other competitors in market place. The report is divided in two parts. In first part
of report introduction of organisation, operations and operations management are discussed.
Implementation of operations management principles and continuous improvement as a
philosophy, continuous improvement plan and lean principles are discussed. In the part 2 project
life cycle and its review as well as critics are covered in this project report.
Introduction of organisation
In this report, the chosen organisation is Morrisons which is fourth largest supermarket
chain in United Kingdom. Respective organisation established in 1899 by William Morrisons
and headquarter situated in Bradford, England. UK. It served its products and services to through
opening 494 stores across UK. 110,000 employees are engages with organisation who contribute
essential part in business growth and susses. Morrisons served to 11 million customers each
week. Organisation is listed in London Stock Exchange and important part of FTSE 250 index of
companies. It provides food and drink, clothing, books and magazines to its customers for
attaining determined goals and objectives in efficient manner.
Explanation of operation vs operations management
Operations: Operations are defined as the business activities that are performed by the
organization to convert material into final products and services that are sell to customers for the
purpose of earning profit. Operations are the actions and decisions that are taken by the
participants and organizational members that impacts overall business production, management
and distribution (Basu, 2017). As Morrison involve in various operations for producing range of
products and services that are provided to customers.
Operations management: operations management is defined as the administration of
various business practices for the purpose of creating higher level efficiency that is exist in

business organization. The concept of operations management is related to converting raw
material as well as labor in productive products and services to maximize organizational
profitability. It concentrates on balancing cost and revenue in order to attain higher operating
profit and determined objectives in best possible manner. Morrison implements proper
operations management techniques that facilitates organization to perform operations in efficient
manner and attain defined goals and objectives.
A review and critique of the implementation of operations management principles
There are various principles of operations management are used in organization for
maintaining business operations in proper manner. Morrison uses various principles that
facilitates organization to perform various operations in defined manner for the purpose of
attaining business goals and objectives properly (Berbegal, Gil and Alegre, 2017). Some
operations management principles are mentioned below:
Organization: As whole process of producing and manufacturing products are
interconnected with each other. All business elements are consistent and predictable, proper
organization of resources helps organization to attain business objectives in appropriate manner.
Morrison organizes all resources and allot employees on right job positioning so, they can
perform their determined operations in best possible manner.
Change: There are continuous changes are occurred in the market that that need to be
adopt for business to sustain in competitive business environment. Morrison conduct proper
market research for the purpose of understand customers requirements, current market trends and
target customers. Respective organization adopts latest technologies and other changes to run
business operations properly.
Variance: In business operations various variance are founded by the organizational
managers that are encourages by them because these variances can be the source of creativity
and innovation (Carydias and Gregory, 2019). Morrison continuously examine organizations
performance and find out variances and implement appropriate policies to mitigate variances to
attain higher performance objectives.
Causality: There are various problems are raised in business that impacts overall business
performance and functionality. Morrison creates efforts to find out source and root of problems
as compared to avoiding it or solving efforts. Through identifying root problem, organization can
mitigate these issues forever.
material as well as labor in productive products and services to maximize organizational
profitability. It concentrates on balancing cost and revenue in order to attain higher operating
profit and determined objectives in best possible manner. Morrison implements proper
operations management techniques that facilitates organization to perform operations in efficient
manner and attain defined goals and objectives.
A review and critique of the implementation of operations management principles
There are various principles of operations management are used in organization for
maintaining business operations in proper manner. Morrison uses various principles that
facilitates organization to perform various operations in defined manner for the purpose of
attaining business goals and objectives properly (Berbegal, Gil and Alegre, 2017). Some
operations management principles are mentioned below:
Organization: As whole process of producing and manufacturing products are
interconnected with each other. All business elements are consistent and predictable, proper
organization of resources helps organization to attain business objectives in appropriate manner.
Morrison organizes all resources and allot employees on right job positioning so, they can
perform their determined operations in best possible manner.
Change: There are continuous changes are occurred in the market that that need to be
adopt for business to sustain in competitive business environment. Morrison conduct proper
market research for the purpose of understand customers requirements, current market trends and
target customers. Respective organization adopts latest technologies and other changes to run
business operations properly.
Variance: In business operations various variance are founded by the organizational
managers that are encourages by them because these variances can be the source of creativity
and innovation (Carydias and Gregory, 2019). Morrison continuously examine organizations
performance and find out variances and implement appropriate policies to mitigate variances to
attain higher performance objectives.
Causality: There are various problems are raised in business that impacts overall business
performance and functionality. Morrison creates efforts to find out source and root of problems
as compared to avoiding it or solving efforts. Through identifying root problem, organization can
mitigate these issues forever.
Secure Best Marks with AI Grader
Need help grading? Try our AI Grader for instant feedback on your assignments.
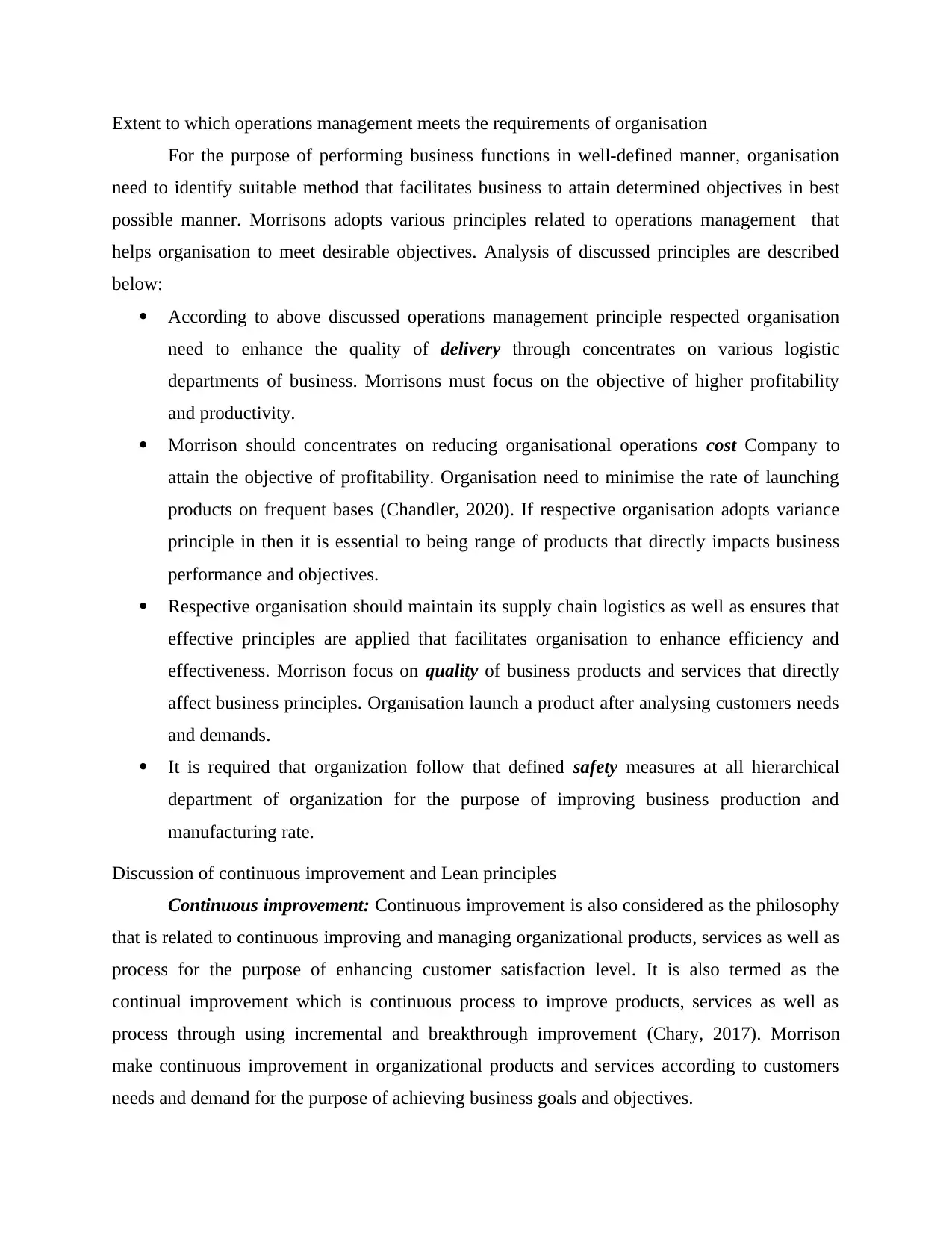
Extent to which operations management meets the requirements of organisation
For the purpose of performing business functions in well-defined manner, organisation
need to identify suitable method that facilitates business to attain determined objectives in best
possible manner. Morrisons adopts various principles related to operations management that
helps organisation to meet desirable objectives. Analysis of discussed principles are described
below:
According to above discussed operations management principle respected organisation
need to enhance the quality of delivery through concentrates on various logistic
departments of business. Morrisons must focus on the objective of higher profitability
and productivity.
Morrison should concentrates on reducing organisational operations cost Company to
attain the objective of profitability. Organisation need to minimise the rate of launching
products on frequent bases (Chandler, 2020). If respective organisation adopts variance
principle in then it is essential to being range of products that directly impacts business
performance and objectives.
Respective organisation should maintain its supply chain logistics as well as ensures that
effective principles are applied that facilitates organisation to enhance efficiency and
effectiveness. Morrison focus on quality of business products and services that directly
affect business principles. Organisation launch a product after analysing customers needs
and demands.
It is required that organization follow that defined safety measures at all hierarchical
department of organization for the purpose of improving business production and
manufacturing rate.
Discussion of continuous improvement and Lean principles
Continuous improvement: Continuous improvement is also considered as the philosophy
that is related to continuous improving and managing organizational products, services as well as
process for the purpose of enhancing customer satisfaction level. It is also termed as the
continual improvement which is continuous process to improve products, services as well as
process through using incremental and breakthrough improvement (Chary, 2017). Morrison
make continuous improvement in organizational products and services according to customers
needs and demand for the purpose of achieving business goals and objectives.
For the purpose of performing business functions in well-defined manner, organisation
need to identify suitable method that facilitates business to attain determined objectives in best
possible manner. Morrisons adopts various principles related to operations management that
helps organisation to meet desirable objectives. Analysis of discussed principles are described
below:
According to above discussed operations management principle respected organisation
need to enhance the quality of delivery through concentrates on various logistic
departments of business. Morrisons must focus on the objective of higher profitability
and productivity.
Morrison should concentrates on reducing organisational operations cost Company to
attain the objective of profitability. Organisation need to minimise the rate of launching
products on frequent bases (Chandler, 2020). If respective organisation adopts variance
principle in then it is essential to being range of products that directly impacts business
performance and objectives.
Respective organisation should maintain its supply chain logistics as well as ensures that
effective principles are applied that facilitates organisation to enhance efficiency and
effectiveness. Morrison focus on quality of business products and services that directly
affect business principles. Organisation launch a product after analysing customers needs
and demands.
It is required that organization follow that defined safety measures at all hierarchical
department of organization for the purpose of improving business production and
manufacturing rate.
Discussion of continuous improvement and Lean principles
Continuous improvement: Continuous improvement is also considered as the philosophy
that is related to continuous improving and managing organizational products, services as well as
process for the purpose of enhancing customer satisfaction level. It is also termed as the
continual improvement which is continuous process to improve products, services as well as
process through using incremental and breakthrough improvement (Chary, 2017). Morrison
make continuous improvement in organizational products and services according to customers
needs and demand for the purpose of achieving business goals and objectives.
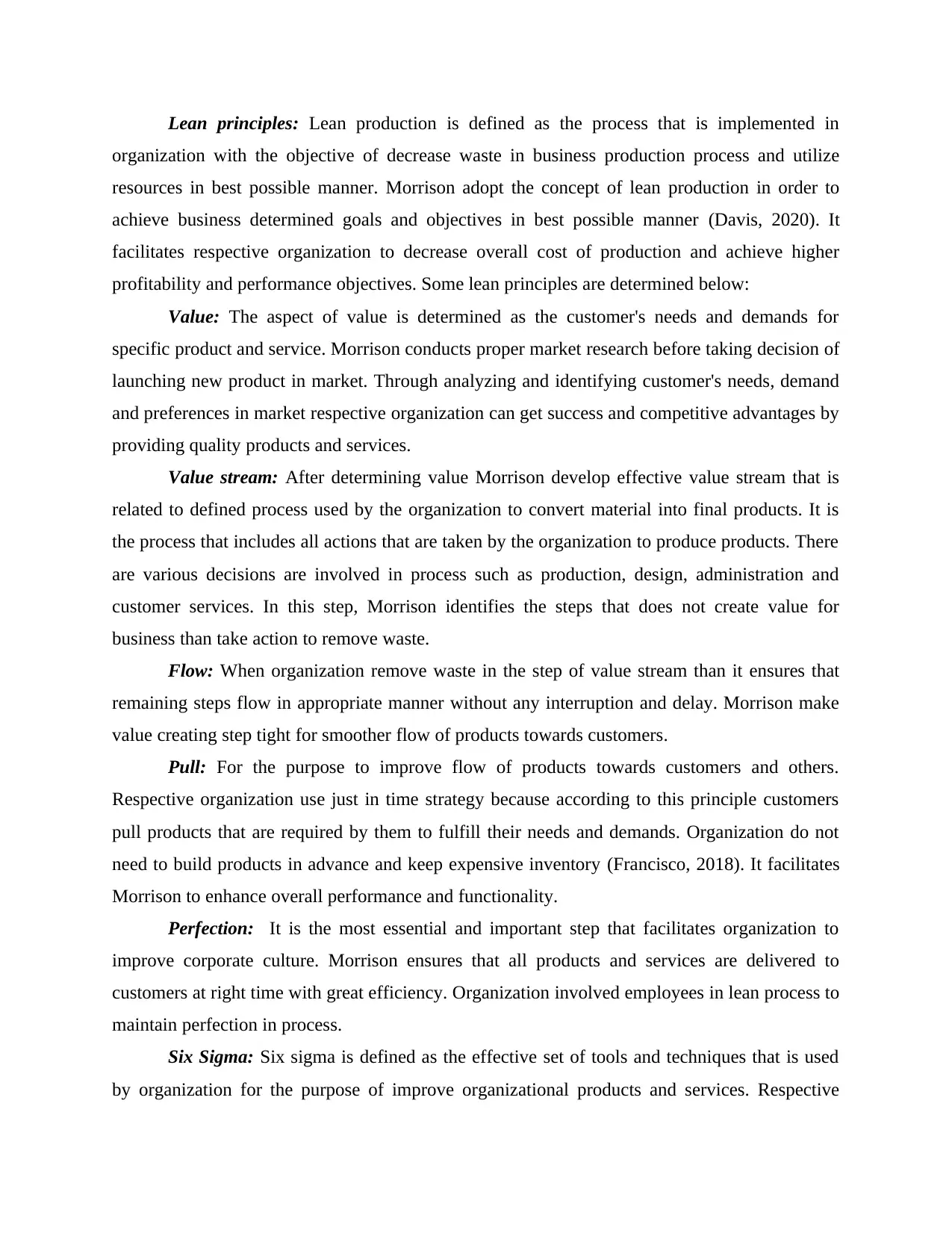
Lean principles: Lean production is defined as the process that is implemented in
organization with the objective of decrease waste in business production process and utilize
resources in best possible manner. Morrison adopt the concept of lean production in order to
achieve business determined goals and objectives in best possible manner (Davis, 2020). It
facilitates respective organization to decrease overall cost of production and achieve higher
profitability and performance objectives. Some lean principles are determined below:
Value: The aspect of value is determined as the customer's needs and demands for
specific product and service. Morrison conducts proper market research before taking decision of
launching new product in market. Through analyzing and identifying customer's needs, demand
and preferences in market respective organization can get success and competitive advantages by
providing quality products and services.
Value stream: After determining value Morrison develop effective value stream that is
related to defined process used by the organization to convert material into final products. It is
the process that includes all actions that are taken by the organization to produce products. There
are various decisions are involved in process such as production, design, administration and
customer services. In this step, Morrison identifies the steps that does not create value for
business than take action to remove waste.
Flow: When organization remove waste in the step of value stream than it ensures that
remaining steps flow in appropriate manner without any interruption and delay. Morrison make
value creating step tight for smoother flow of products towards customers.
Pull: For the purpose to improve flow of products towards customers and others.
Respective organization use just in time strategy because according to this principle customers
pull products that are required by them to fulfill their needs and demands. Organization do not
need to build products in advance and keep expensive inventory (Francisco, 2018). It facilitates
Morrison to enhance overall performance and functionality.
Perfection: It is the most essential and important step that facilitates organization to
improve corporate culture. Morrison ensures that all products and services are delivered to
customers at right time with great efficiency. Organization involved employees in lean process to
maintain perfection in process.
Six Sigma: Six sigma is defined as the effective set of tools and techniques that is used
by organization for the purpose of improve organizational products and services. Respective
organization with the objective of decrease waste in business production process and utilize
resources in best possible manner. Morrison adopt the concept of lean production in order to
achieve business determined goals and objectives in best possible manner (Davis, 2020). It
facilitates respective organization to decrease overall cost of production and achieve higher
profitability and performance objectives. Some lean principles are determined below:
Value: The aspect of value is determined as the customer's needs and demands for
specific product and service. Morrison conducts proper market research before taking decision of
launching new product in market. Through analyzing and identifying customer's needs, demand
and preferences in market respective organization can get success and competitive advantages by
providing quality products and services.
Value stream: After determining value Morrison develop effective value stream that is
related to defined process used by the organization to convert material into final products. It is
the process that includes all actions that are taken by the organization to produce products. There
are various decisions are involved in process such as production, design, administration and
customer services. In this step, Morrison identifies the steps that does not create value for
business than take action to remove waste.
Flow: When organization remove waste in the step of value stream than it ensures that
remaining steps flow in appropriate manner without any interruption and delay. Morrison make
value creating step tight for smoother flow of products towards customers.
Pull: For the purpose to improve flow of products towards customers and others.
Respective organization use just in time strategy because according to this principle customers
pull products that are required by them to fulfill their needs and demands. Organization do not
need to build products in advance and keep expensive inventory (Francisco, 2018). It facilitates
Morrison to enhance overall performance and functionality.
Perfection: It is the most essential and important step that facilitates organization to
improve corporate culture. Morrison ensures that all products and services are delivered to
customers at right time with great efficiency. Organization involved employees in lean process to
maintain perfection in process.
Six Sigma: Six sigma is defined as the effective set of tools and techniques that is used
by organization for the purpose of improve organizational products and services. Respective
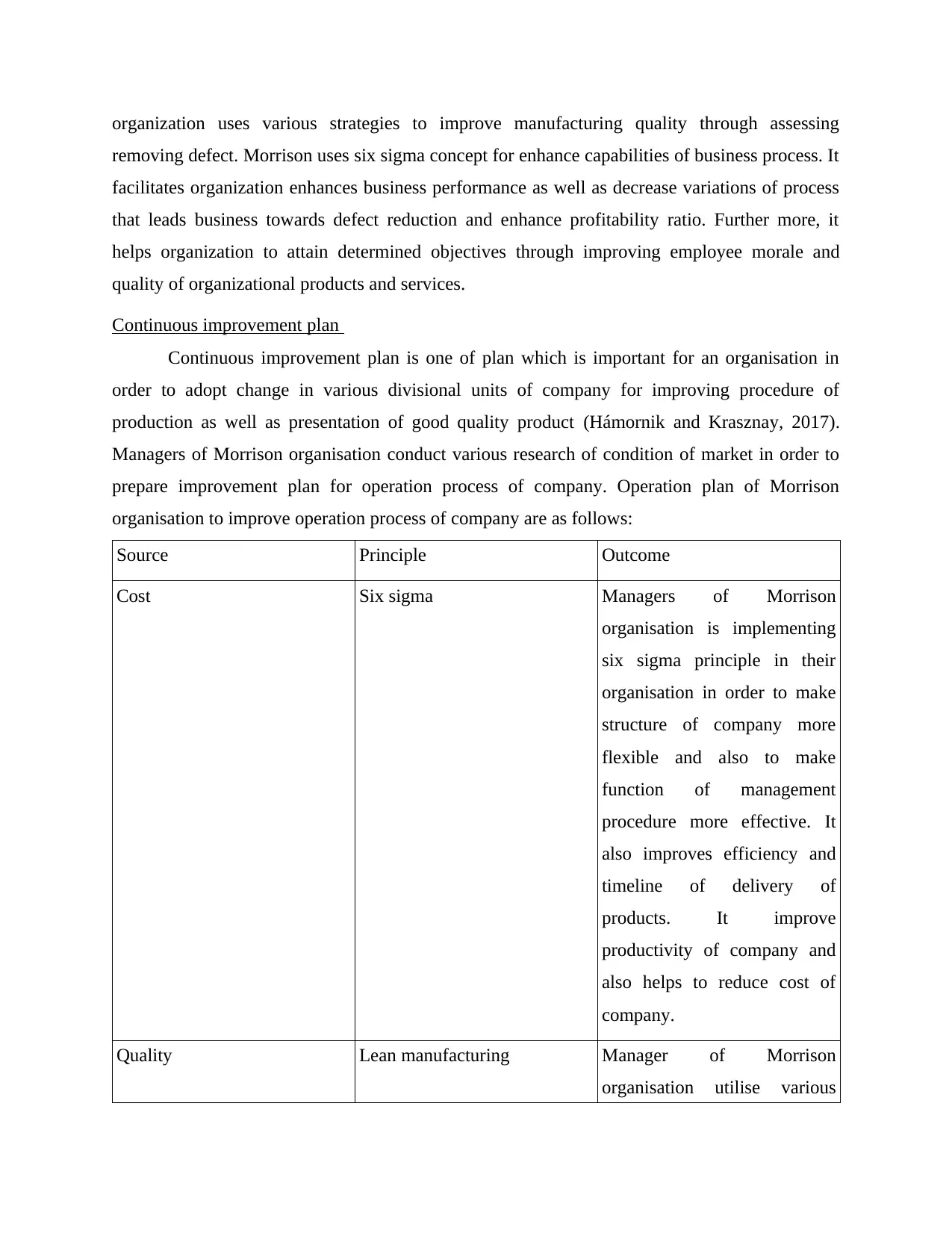
organization uses various strategies to improve manufacturing quality through assessing
removing defect. Morrison uses six sigma concept for enhance capabilities of business process. It
facilitates organization enhances business performance as well as decrease variations of process
that leads business towards defect reduction and enhance profitability ratio. Further more, it
helps organization to attain determined objectives through improving employee morale and
quality of organizational products and services.
Continuous improvement plan
Continuous improvement plan is one of plan which is important for an organisation in
order to adopt change in various divisional units of company for improving procedure of
production as well as presentation of good quality product (Hámornik and Krasznay, 2017).
Managers of Morrison organisation conduct various research of condition of market in order to
prepare improvement plan for operation process of company. Operation plan of Morrison
organisation to improve operation process of company are as follows:
Source Principle Outcome
Cost Six sigma Managers of Morrison
organisation is implementing
six sigma principle in their
organisation in order to make
structure of company more
flexible and also to make
function of management
procedure more effective. It
also improves efficiency and
timeline of delivery of
products. It improve
productivity of company and
also helps to reduce cost of
company.
Quality Lean manufacturing Manager of Morrison
organisation utilise various
removing defect. Morrison uses six sigma concept for enhance capabilities of business process. It
facilitates organization enhances business performance as well as decrease variations of process
that leads business towards defect reduction and enhance profitability ratio. Further more, it
helps organization to attain determined objectives through improving employee morale and
quality of organizational products and services.
Continuous improvement plan
Continuous improvement plan is one of plan which is important for an organisation in
order to adopt change in various divisional units of company for improving procedure of
production as well as presentation of good quality product (Hámornik and Krasznay, 2017).
Managers of Morrison organisation conduct various research of condition of market in order to
prepare improvement plan for operation process of company. Operation plan of Morrison
organisation to improve operation process of company are as follows:
Source Principle Outcome
Cost Six sigma Managers of Morrison
organisation is implementing
six sigma principle in their
organisation in order to make
structure of company more
flexible and also to make
function of management
procedure more effective. It
also improves efficiency and
timeline of delivery of
products. It improve
productivity of company and
also helps to reduce cost of
company.
Quality Lean manufacturing Manager of Morrison
organisation utilise various
Paraphrase This Document
Need a fresh take? Get an instant paraphrase of this document with our AI Paraphraser
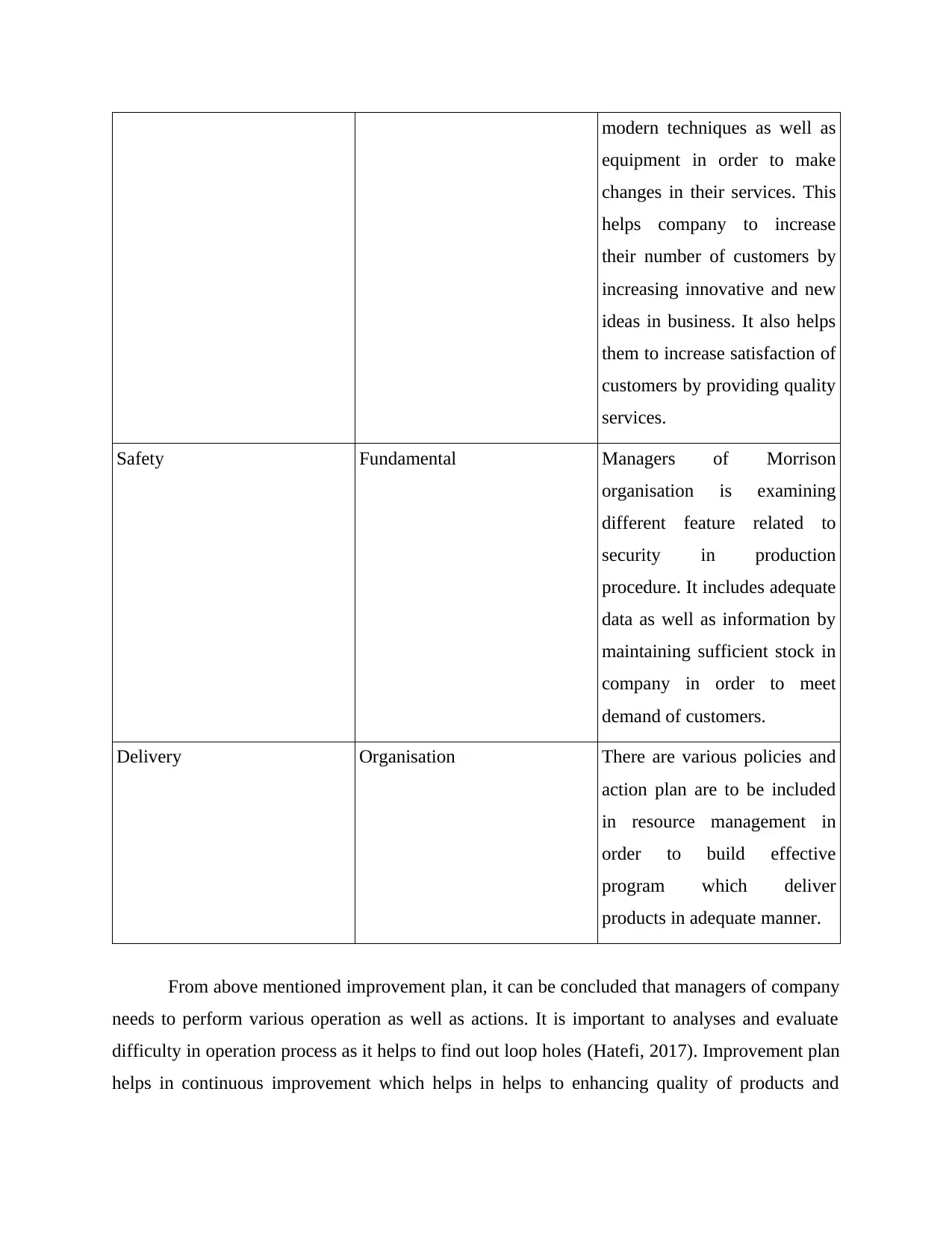
modern techniques as well as
equipment in order to make
changes in their services. This
helps company to increase
their number of customers by
increasing innovative and new
ideas in business. It also helps
them to increase satisfaction of
customers by providing quality
services.
Safety Fundamental Managers of Morrison
organisation is examining
different feature related to
security in production
procedure. It includes adequate
data as well as information by
maintaining sufficient stock in
company in order to meet
demand of customers.
Delivery Organisation There are various policies and
action plan are to be included
in resource management in
order to build effective
program which deliver
products in adequate manner.
From above mentioned improvement plan, it can be concluded that managers of company
needs to perform various operation as well as actions. It is important to analyses and evaluate
difficulty in operation process as it helps to find out loop holes (Hatefi, 2017). Improvement plan
helps in continuous improvement which helps in helps to enhancing quality of products and
equipment in order to make
changes in their services. This
helps company to increase
their number of customers by
increasing innovative and new
ideas in business. It also helps
them to increase satisfaction of
customers by providing quality
services.
Safety Fundamental Managers of Morrison
organisation is examining
different feature related to
security in production
procedure. It includes adequate
data as well as information by
maintaining sufficient stock in
company in order to meet
demand of customers.
Delivery Organisation There are various policies and
action plan are to be included
in resource management in
order to build effective
program which deliver
products in adequate manner.
From above mentioned improvement plan, it can be concluded that managers of company
needs to perform various operation as well as actions. It is important to analyses and evaluate
difficulty in operation process as it helps to find out loop holes (Hatefi, 2017). Improvement plan
helps in continuous improvement which helps in helps to enhancing quality of products and
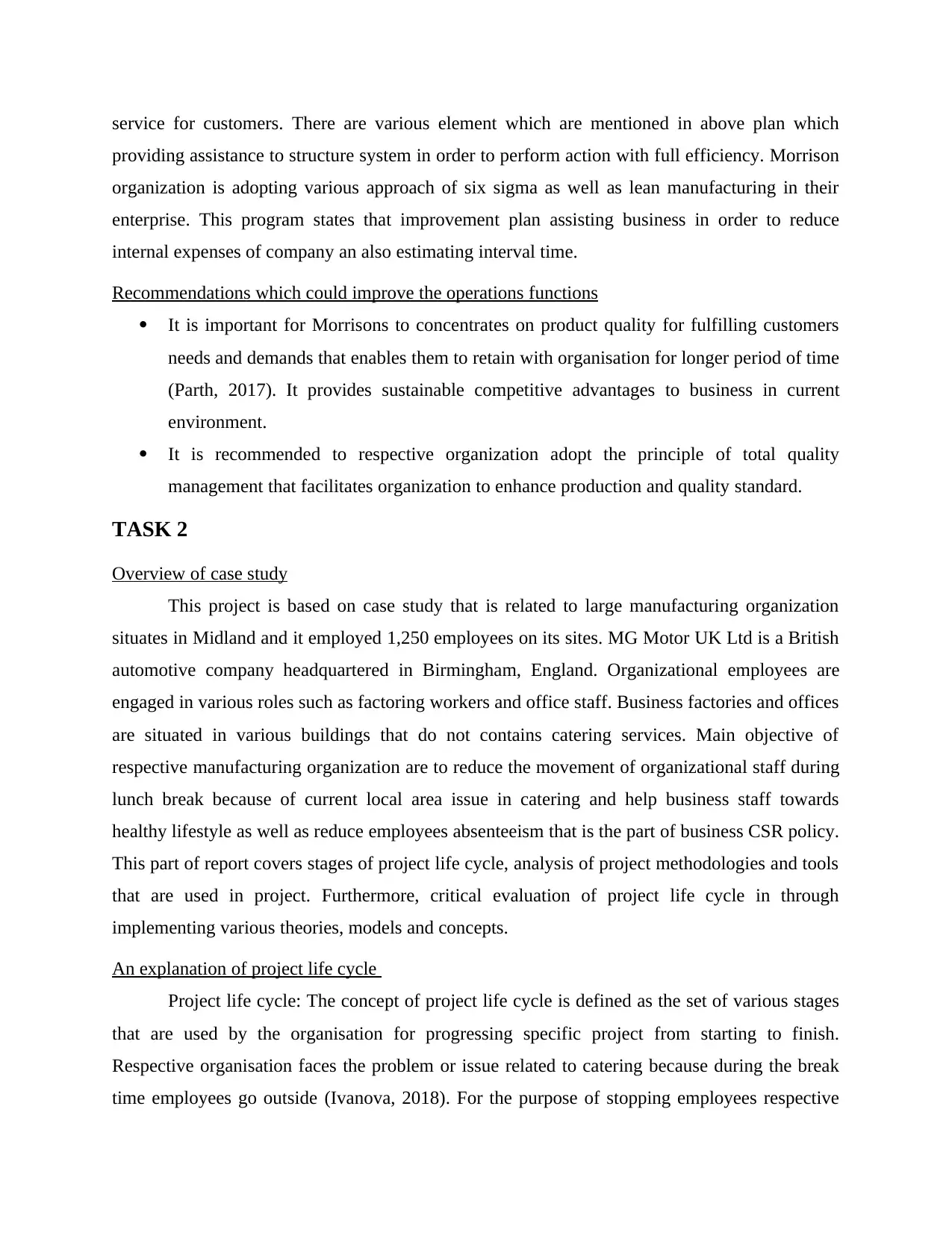
service for customers. There are various element which are mentioned in above plan which
providing assistance to structure system in order to perform action with full efficiency. Morrison
organization is adopting various approach of six sigma as well as lean manufacturing in their
enterprise. This program states that improvement plan assisting business in order to reduce
internal expenses of company an also estimating interval time.
Recommendations which could improve the operations functions
It is important for Morrisons to concentrates on product quality for fulfilling customers
needs and demands that enables them to retain with organisation for longer period of time
(Parth, 2017). It provides sustainable competitive advantages to business in current
environment.
It is recommended to respective organization adopt the principle of total quality
management that facilitates organization to enhance production and quality standard.
TASK 2
Overview of case study
This project is based on case study that is related to large manufacturing organization
situates in Midland and it employed 1,250 employees on its sites. MG Motor UK Ltd is a British
automotive company headquartered in Birmingham, England. Organizational employees are
engaged in various roles such as factoring workers and office staff. Business factories and offices
are situated in various buildings that do not contains catering services. Main objective of
respective manufacturing organization are to reduce the movement of organizational staff during
lunch break because of current local area issue in catering and help business staff towards
healthy lifestyle as well as reduce employees absenteeism that is the part of business CSR policy.
This part of report covers stages of project life cycle, analysis of project methodologies and tools
that are used in project. Furthermore, critical evaluation of project life cycle in through
implementing various theories, models and concepts.
An explanation of project life cycle
Project life cycle: The concept of project life cycle is defined as the set of various stages
that are used by the organisation for progressing specific project from starting to finish.
Respective organisation faces the problem or issue related to catering because during the break
time employees go outside (Ivanova, 2018). For the purpose of stopping employees respective
providing assistance to structure system in order to perform action with full efficiency. Morrison
organization is adopting various approach of six sigma as well as lean manufacturing in their
enterprise. This program states that improvement plan assisting business in order to reduce
internal expenses of company an also estimating interval time.
Recommendations which could improve the operations functions
It is important for Morrisons to concentrates on product quality for fulfilling customers
needs and demands that enables them to retain with organisation for longer period of time
(Parth, 2017). It provides sustainable competitive advantages to business in current
environment.
It is recommended to respective organization adopt the principle of total quality
management that facilitates organization to enhance production and quality standard.
TASK 2
Overview of case study
This project is based on case study that is related to large manufacturing organization
situates in Midland and it employed 1,250 employees on its sites. MG Motor UK Ltd is a British
automotive company headquartered in Birmingham, England. Organizational employees are
engaged in various roles such as factoring workers and office staff. Business factories and offices
are situated in various buildings that do not contains catering services. Main objective of
respective manufacturing organization are to reduce the movement of organizational staff during
lunch break because of current local area issue in catering and help business staff towards
healthy lifestyle as well as reduce employees absenteeism that is the part of business CSR policy.
This part of report covers stages of project life cycle, analysis of project methodologies and tools
that are used in project. Furthermore, critical evaluation of project life cycle in through
implementing various theories, models and concepts.
An explanation of project life cycle
Project life cycle: The concept of project life cycle is defined as the set of various stages
that are used by the organisation for progressing specific project from starting to finish.
Respective organisation faces the problem or issue related to catering because during the break
time employees go outside (Ivanova, 2018). For the purpose of stopping employees respective
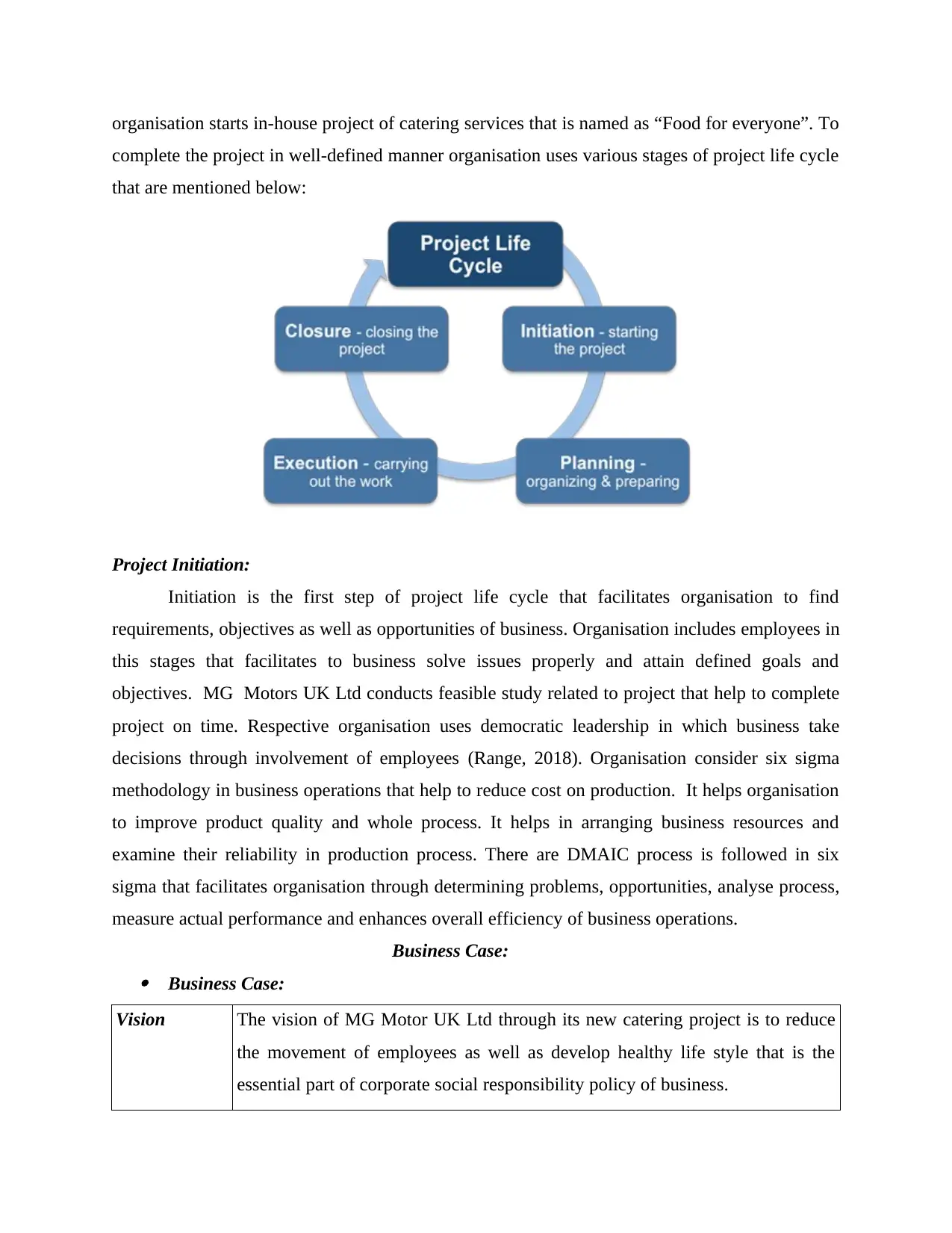
organisation starts in-house project of catering services that is named as “Food for everyone”. To
complete the project in well-defined manner organisation uses various stages of project life cycle
that are mentioned below:
Project Initiation:
Initiation is the first step of project life cycle that facilitates organisation to find
requirements, objectives as well as opportunities of business. Organisation includes employees in
this stages that facilitates to business solve issues properly and attain defined goals and
objectives. MG Motors UK Ltd conducts feasible study related to project that help to complete
project on time. Respective organisation uses democratic leadership in which business take
decisions through involvement of employees (Range, 2018). Organisation consider six sigma
methodology in business operations that help to reduce cost on production. It helps organisation
to improve product quality and whole process. It helps in arranging business resources and
examine their reliability in production process. There are DMAIC process is followed in six
sigma that facilitates organisation through determining problems, opportunities, analyse process,
measure actual performance and enhances overall efficiency of business operations.
Business Case: Business Case:
Vision The vision of MG Motor UK Ltd through its new catering project is to reduce
the movement of employees as well as develop healthy life style that is the
essential part of corporate social responsibility policy of business.
complete the project in well-defined manner organisation uses various stages of project life cycle
that are mentioned below:
Project Initiation:
Initiation is the first step of project life cycle that facilitates organisation to find
requirements, objectives as well as opportunities of business. Organisation includes employees in
this stages that facilitates to business solve issues properly and attain defined goals and
objectives. MG Motors UK Ltd conducts feasible study related to project that help to complete
project on time. Respective organisation uses democratic leadership in which business take
decisions through involvement of employees (Range, 2018). Organisation consider six sigma
methodology in business operations that help to reduce cost on production. It helps organisation
to improve product quality and whole process. It helps in arranging business resources and
examine their reliability in production process. There are DMAIC process is followed in six
sigma that facilitates organisation through determining problems, opportunities, analyse process,
measure actual performance and enhances overall efficiency of business operations.
Business Case: Business Case:
Vision The vision of MG Motor UK Ltd through its new catering project is to reduce
the movement of employees as well as develop healthy life style that is the
essential part of corporate social responsibility policy of business.
Secure Best Marks with AI Grader
Need help grading? Try our AI Grader for instant feedback on your assignments.
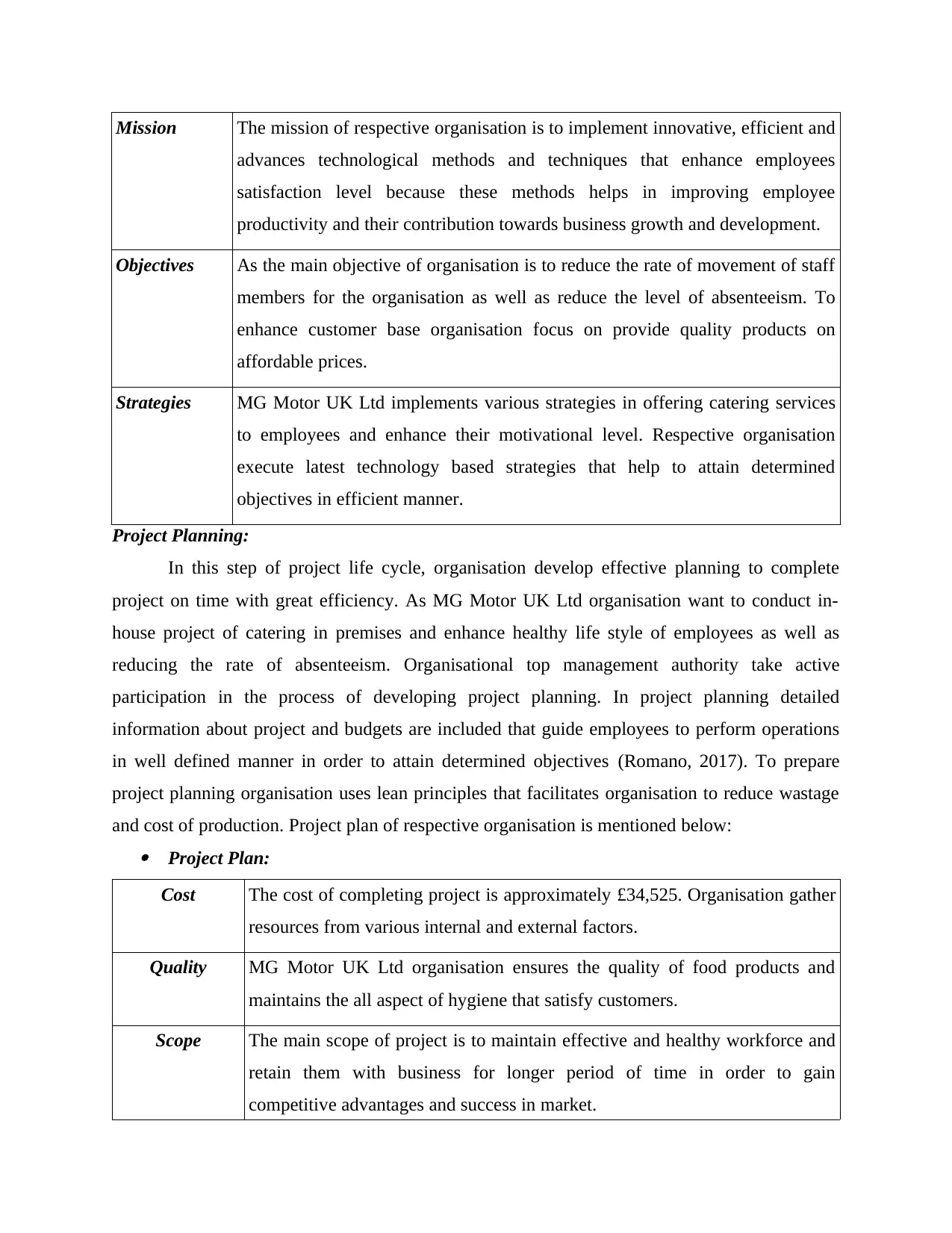
Mission The mission of respective organisation is to implement innovative, efficient and
advances technological methods and techniques that enhance employees
satisfaction level because these methods helps in improving employee
productivity and their contribution towards business growth and development.
Objectives As the main objective of organisation is to reduce the rate of movement of staff
members for the organisation as well as reduce the level of absenteeism. To
enhance customer base organisation focus on provide quality products on
affordable prices.
Strategies MG Motor UK Ltd implements various strategies in offering catering services
to employees and enhance their motivational level. Respective organisation
execute latest technology based strategies that help to attain determined
objectives in efficient manner.
Project Planning:
In this step of project life cycle, organisation develop effective planning to complete
project on time with great efficiency. As MG Motor UK Ltd organisation want to conduct in-
house project of catering in premises and enhance healthy life style of employees as well as
reducing the rate of absenteeism. Organisational top management authority take active
participation in the process of developing project planning. In project planning detailed
information about project and budgets are included that guide employees to perform operations
in well defined manner in order to attain determined objectives (Romano, 2017). To prepare
project planning organisation uses lean principles that facilitates organisation to reduce wastage
and cost of production. Project plan of respective organisation is mentioned below: Project Plan:
Cost The cost of completing project is approximately £34,525. Organisation gather
resources from various internal and external factors.
Quality MG Motor UK Ltd organisation ensures the quality of food products and
maintains the all aspect of hygiene that satisfy customers.
Scope The main scope of project is to maintain effective and healthy workforce and
retain them with business for longer period of time in order to gain
competitive advantages and success in market.
advances technological methods and techniques that enhance employees
satisfaction level because these methods helps in improving employee
productivity and their contribution towards business growth and development.
Objectives As the main objective of organisation is to reduce the rate of movement of staff
members for the organisation as well as reduce the level of absenteeism. To
enhance customer base organisation focus on provide quality products on
affordable prices.
Strategies MG Motor UK Ltd implements various strategies in offering catering services
to employees and enhance their motivational level. Respective organisation
execute latest technology based strategies that help to attain determined
objectives in efficient manner.
Project Planning:
In this step of project life cycle, organisation develop effective planning to complete
project on time with great efficiency. As MG Motor UK Ltd organisation want to conduct in-
house project of catering in premises and enhance healthy life style of employees as well as
reducing the rate of absenteeism. Organisational top management authority take active
participation in the process of developing project planning. In project planning detailed
information about project and budgets are included that guide employees to perform operations
in well defined manner in order to attain determined objectives (Romano, 2017). To prepare
project planning organisation uses lean principles that facilitates organisation to reduce wastage
and cost of production. Project plan of respective organisation is mentioned below: Project Plan:
Cost The cost of completing project is approximately £34,525. Organisation gather
resources from various internal and external factors.
Quality MG Motor UK Ltd organisation ensures the quality of food products and
maintains the all aspect of hygiene that satisfy customers.
Scope The main scope of project is to maintain effective and healthy workforce and
retain them with business for longer period of time in order to gain
competitive advantages and success in market.
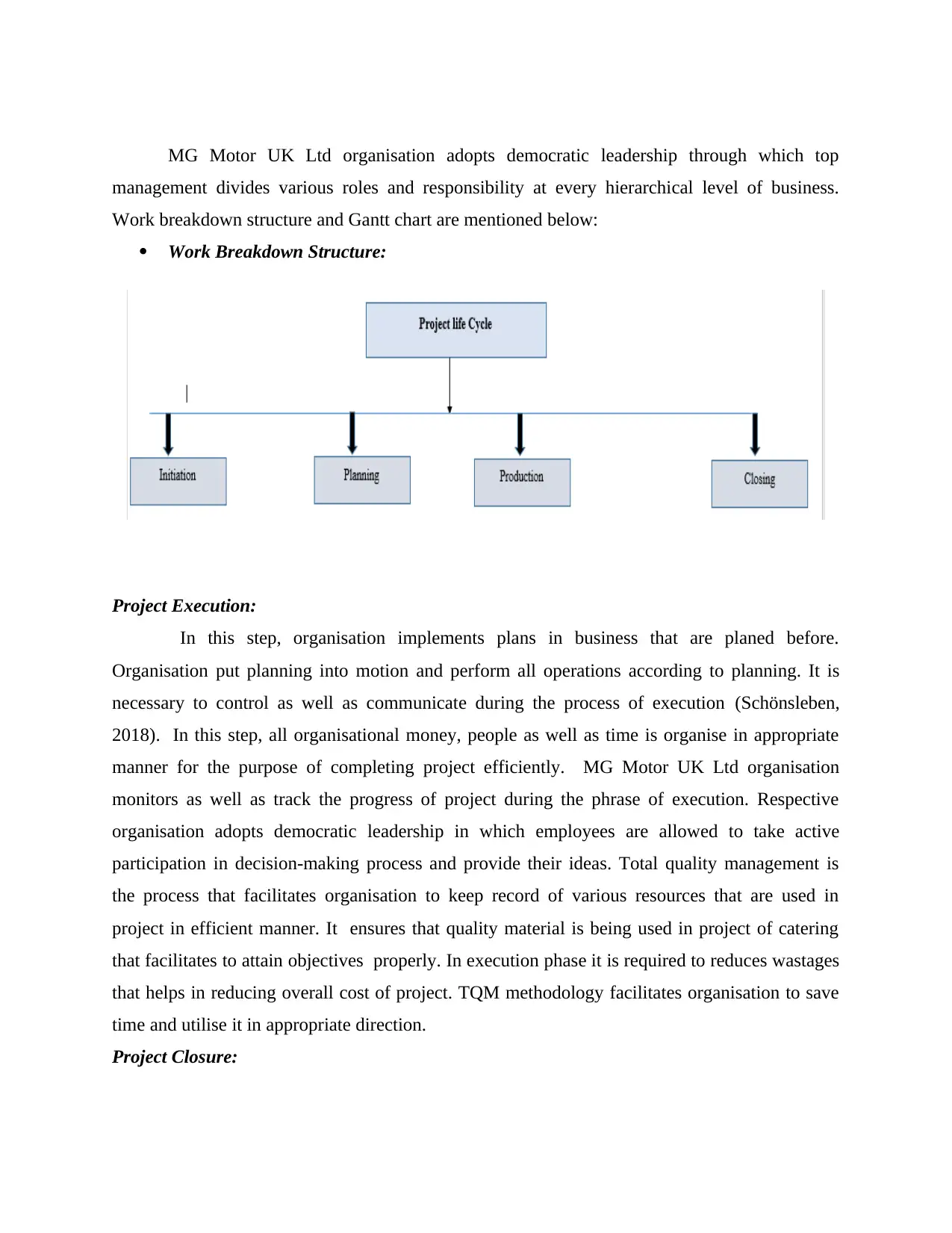
MG Motor UK Ltd organisation adopts democratic leadership through which top
management divides various roles and responsibility at every hierarchical level of business.
Work breakdown structure and Gantt chart are mentioned below:
Work Breakdown Structure:
Project Execution:
In this step, organisation implements plans in business that are planed before.
Organisation put planning into motion and perform all operations according to planning. It is
necessary to control as well as communicate during the process of execution (Schönsleben,
2018). In this step, all organisational money, people as well as time is organise in appropriate
manner for the purpose of completing project efficiently. MG Motor UK Ltd organisation
monitors as well as track the progress of project during the phrase of execution. Respective
organisation adopts democratic leadership in which employees are allowed to take active
participation in decision-making process and provide their ideas. Total quality management is
the process that facilitates organisation to keep record of various resources that are used in
project in efficient manner. It ensures that quality material is being used in project of catering
that facilitates to attain objectives properly. In execution phase it is required to reduces wastages
that helps in reducing overall cost of project. TQM methodology facilitates organisation to save
time and utilise it in appropriate direction.
Project Closure:
management divides various roles and responsibility at every hierarchical level of business.
Work breakdown structure and Gantt chart are mentioned below:
Work Breakdown Structure:
Project Execution:
In this step, organisation implements plans in business that are planed before.
Organisation put planning into motion and perform all operations according to planning. It is
necessary to control as well as communicate during the process of execution (Schönsleben,
2018). In this step, all organisational money, people as well as time is organise in appropriate
manner for the purpose of completing project efficiently. MG Motor UK Ltd organisation
monitors as well as track the progress of project during the phrase of execution. Respective
organisation adopts democratic leadership in which employees are allowed to take active
participation in decision-making process and provide their ideas. Total quality management is
the process that facilitates organisation to keep record of various resources that are used in
project in efficient manner. It ensures that quality material is being used in project of catering
that facilitates to attain objectives properly. In execution phase it is required to reduces wastages
that helps in reducing overall cost of project. TQM methodology facilitates organisation to save
time and utilise it in appropriate direction.
Project Closure:
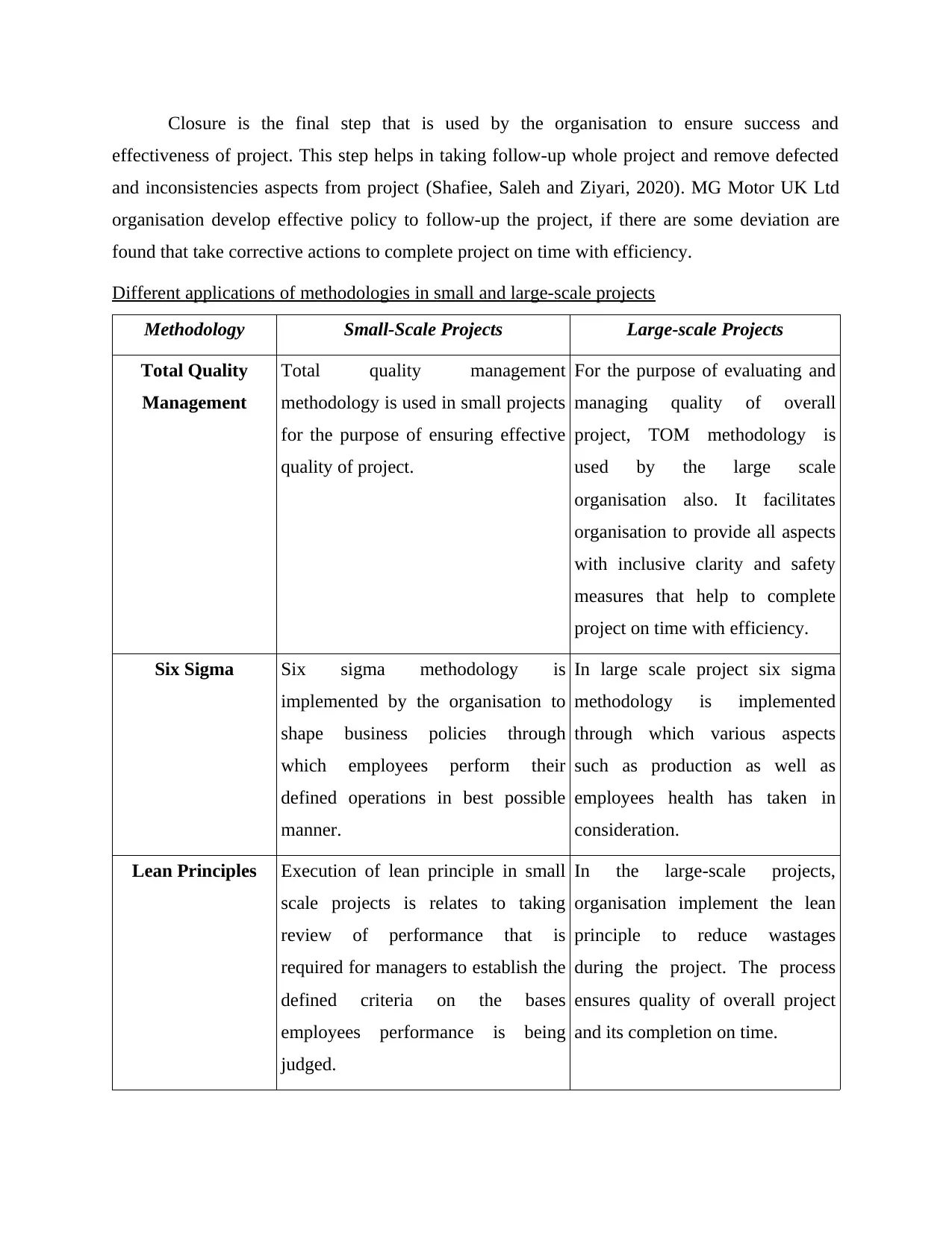
Closure is the final step that is used by the organisation to ensure success and
effectiveness of project. This step helps in taking follow-up whole project and remove defected
and inconsistencies aspects from project (Shafiee, Saleh and Ziyari, 2020). MG Motor UK Ltd
organisation develop effective policy to follow-up the project, if there are some deviation are
found that take corrective actions to complete project on time with efficiency.
Different applications of methodologies in small and large-scale projects
Methodology Small-Scale Projects Large-scale Projects
Total Quality
Management
Total quality management
methodology is used in small projects
for the purpose of ensuring effective
quality of project.
For the purpose of evaluating and
managing quality of overall
project, TOM methodology is
used by the large scale
organisation also. It facilitates
organisation to provide all aspects
with inclusive clarity and safety
measures that help to complete
project on time with efficiency.
Six Sigma Six sigma methodology is
implemented by the organisation to
shape business policies through
which employees perform their
defined operations in best possible
manner.
In large scale project six sigma
methodology is implemented
through which various aspects
such as production as well as
employees health has taken in
consideration.
Lean Principles Execution of lean principle in small
scale projects is relates to taking
review of performance that is
required for managers to establish the
defined criteria on the bases
employees performance is being
judged.
In the large-scale projects,
organisation implement the lean
principle to reduce wastages
during the project. The process
ensures quality of overall project
and its completion on time.
effectiveness of project. This step helps in taking follow-up whole project and remove defected
and inconsistencies aspects from project (Shafiee, Saleh and Ziyari, 2020). MG Motor UK Ltd
organisation develop effective policy to follow-up the project, if there are some deviation are
found that take corrective actions to complete project on time with efficiency.
Different applications of methodologies in small and large-scale projects
Methodology Small-Scale Projects Large-scale Projects
Total Quality
Management
Total quality management
methodology is used in small projects
for the purpose of ensuring effective
quality of project.
For the purpose of evaluating and
managing quality of overall
project, TOM methodology is
used by the large scale
organisation also. It facilitates
organisation to provide all aspects
with inclusive clarity and safety
measures that help to complete
project on time with efficiency.
Six Sigma Six sigma methodology is
implemented by the organisation to
shape business policies through
which employees perform their
defined operations in best possible
manner.
In large scale project six sigma
methodology is implemented
through which various aspects
such as production as well as
employees health has taken in
consideration.
Lean Principles Execution of lean principle in small
scale projects is relates to taking
review of performance that is
required for managers to establish the
defined criteria on the bases
employees performance is being
judged.
In the large-scale projects,
organisation implement the lean
principle to reduce wastages
during the project. The process
ensures quality of overall project
and its completion on time.
Paraphrase This Document
Need a fresh take? Get an instant paraphrase of this document with our AI Paraphraser
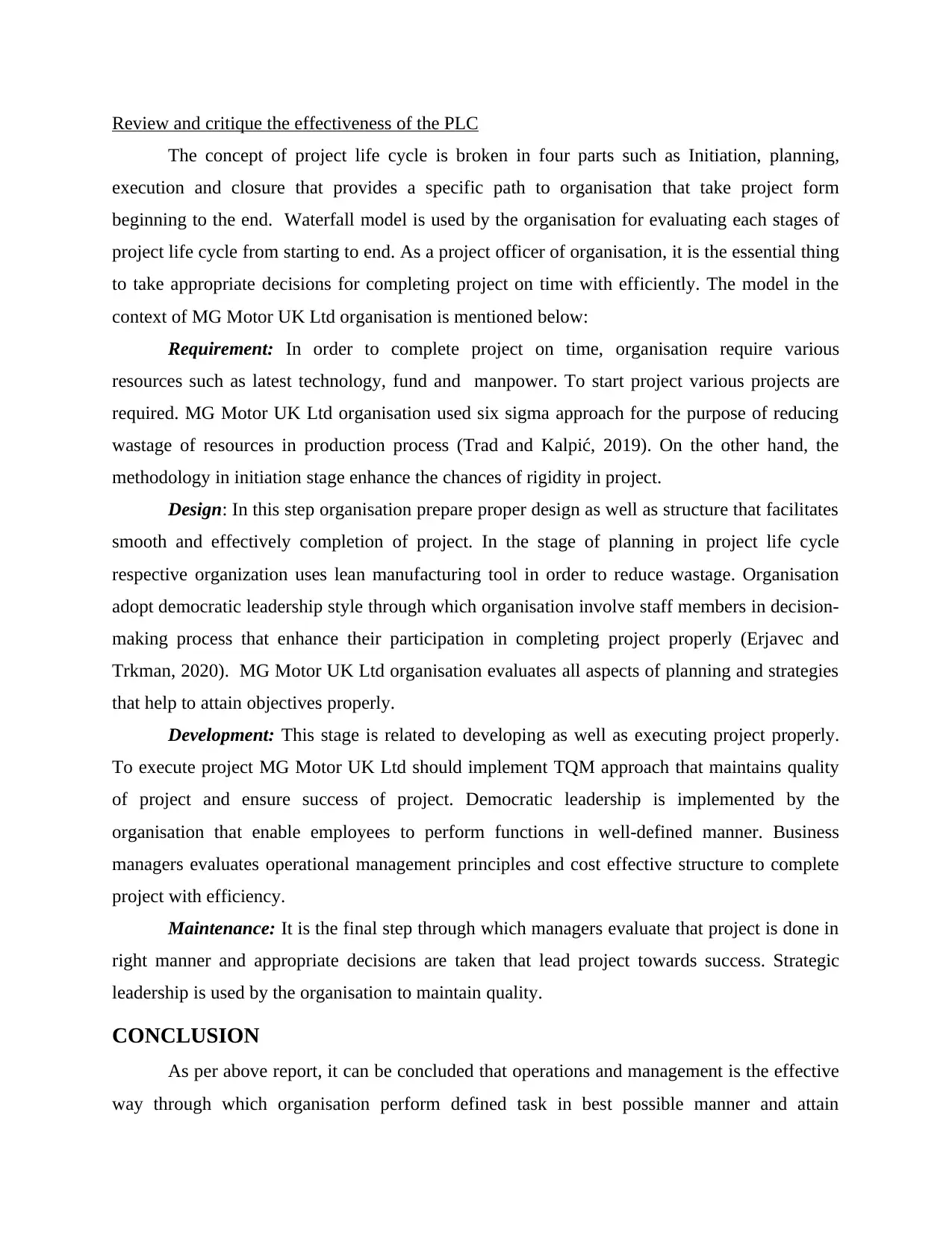
Review and critique the effectiveness of the PLC
The concept of project life cycle is broken in four parts such as Initiation, planning,
execution and closure that provides a specific path to organisation that take project form
beginning to the end. Waterfall model is used by the organisation for evaluating each stages of
project life cycle from starting to end. As a project officer of organisation, it is the essential thing
to take appropriate decisions for completing project on time with efficiently. The model in the
context of MG Motor UK Ltd organisation is mentioned below:
Requirement: In order to complete project on time, organisation require various
resources such as latest technology, fund and manpower. To start project various projects are
required. MG Motor UK Ltd organisation used six sigma approach for the purpose of reducing
wastage of resources in production process (Trad and Kalpić, 2019). On the other hand, the
methodology in initiation stage enhance the chances of rigidity in project.
Design: In this step organisation prepare proper design as well as structure that facilitates
smooth and effectively completion of project. In the stage of planning in project life cycle
respective organization uses lean manufacturing tool in order to reduce wastage. Organisation
adopt democratic leadership style through which organisation involve staff members in decision-
making process that enhance their participation in completing project properly (Erjavec and
Trkman, 2020). MG Motor UK Ltd organisation evaluates all aspects of planning and strategies
that help to attain objectives properly.
Development: This stage is related to developing as well as executing project properly.
To execute project MG Motor UK Ltd should implement TQM approach that maintains quality
of project and ensure success of project. Democratic leadership is implemented by the
organisation that enable employees to perform functions in well-defined manner. Business
managers evaluates operational management principles and cost effective structure to complete
project with efficiency.
Maintenance: It is the final step through which managers evaluate that project is done in
right manner and appropriate decisions are taken that lead project towards success. Strategic
leadership is used by the organisation to maintain quality.
CONCLUSION
As per above report, it can be concluded that operations and management is the effective
way through which organisation perform defined task in best possible manner and attain
The concept of project life cycle is broken in four parts such as Initiation, planning,
execution and closure that provides a specific path to organisation that take project form
beginning to the end. Waterfall model is used by the organisation for evaluating each stages of
project life cycle from starting to end. As a project officer of organisation, it is the essential thing
to take appropriate decisions for completing project on time with efficiently. The model in the
context of MG Motor UK Ltd organisation is mentioned below:
Requirement: In order to complete project on time, organisation require various
resources such as latest technology, fund and manpower. To start project various projects are
required. MG Motor UK Ltd organisation used six sigma approach for the purpose of reducing
wastage of resources in production process (Trad and Kalpić, 2019). On the other hand, the
methodology in initiation stage enhance the chances of rigidity in project.
Design: In this step organisation prepare proper design as well as structure that facilitates
smooth and effectively completion of project. In the stage of planning in project life cycle
respective organization uses lean manufacturing tool in order to reduce wastage. Organisation
adopt democratic leadership style through which organisation involve staff members in decision-
making process that enhance their participation in completing project properly (Erjavec and
Trkman, 2020). MG Motor UK Ltd organisation evaluates all aspects of planning and strategies
that help to attain objectives properly.
Development: This stage is related to developing as well as executing project properly.
To execute project MG Motor UK Ltd should implement TQM approach that maintains quality
of project and ensure success of project. Democratic leadership is implemented by the
organisation that enable employees to perform functions in well-defined manner. Business
managers evaluates operational management principles and cost effective structure to complete
project with efficiency.
Maintenance: It is the final step through which managers evaluate that project is done in
right manner and appropriate decisions are taken that lead project towards success. Strategic
leadership is used by the organisation to maintain quality.
CONCLUSION
As per above report, it can be concluded that operations and management is the effective
way through which organisation perform defined task in best possible manner and attain
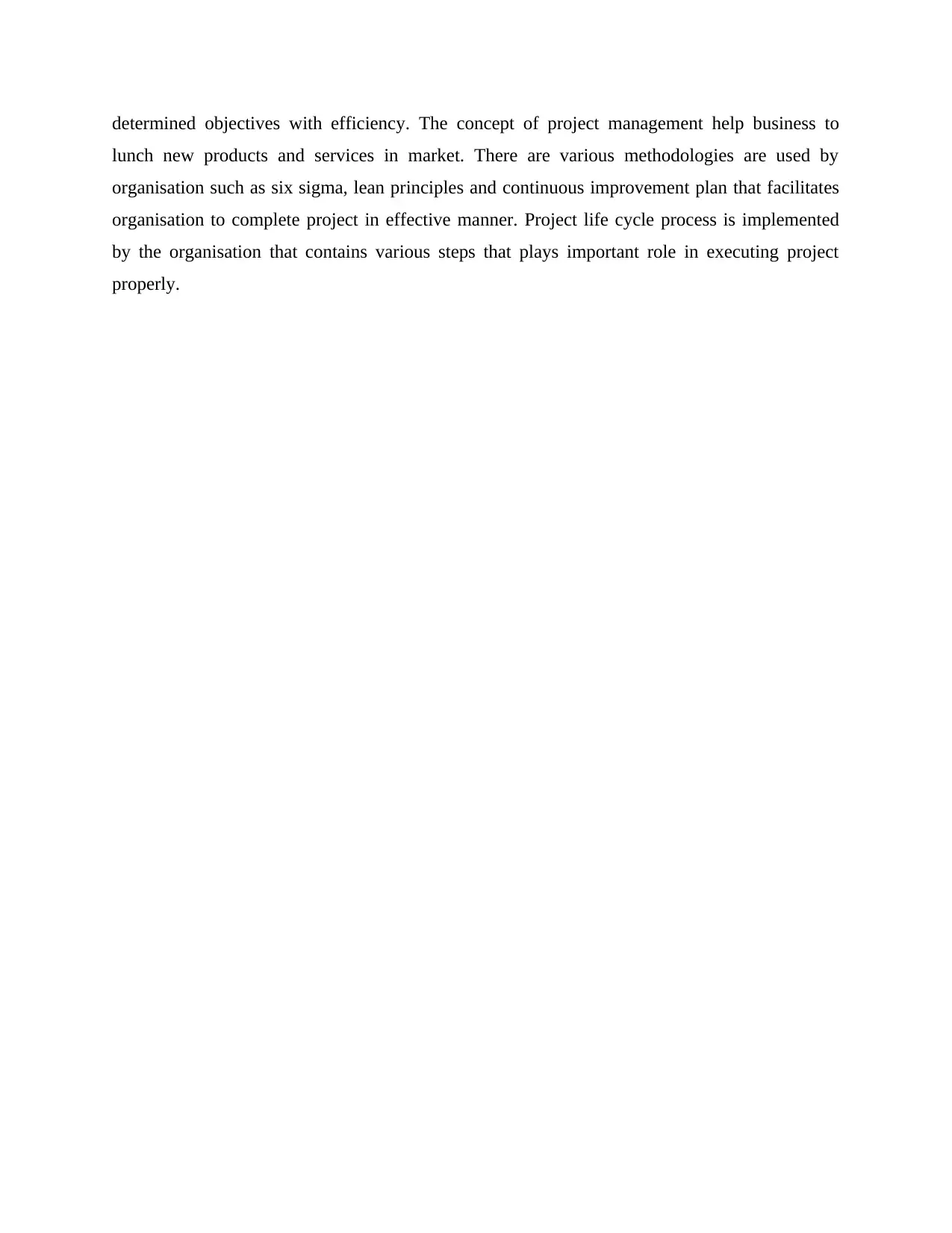
determined objectives with efficiency. The concept of project management help business to
lunch new products and services in market. There are various methodologies are used by
organisation such as six sigma, lean principles and continuous improvement plan that facilitates
organisation to complete project in effective manner. Project life cycle process is implemented
by the organisation that contains various steps that plays important role in executing project
properly.
lunch new products and services in market. There are various methodologies are used by
organisation such as six sigma, lean principles and continuous improvement plan that facilitates
organisation to complete project in effective manner. Project life cycle process is implemented
by the organisation that contains various steps that plays important role in executing project
properly.
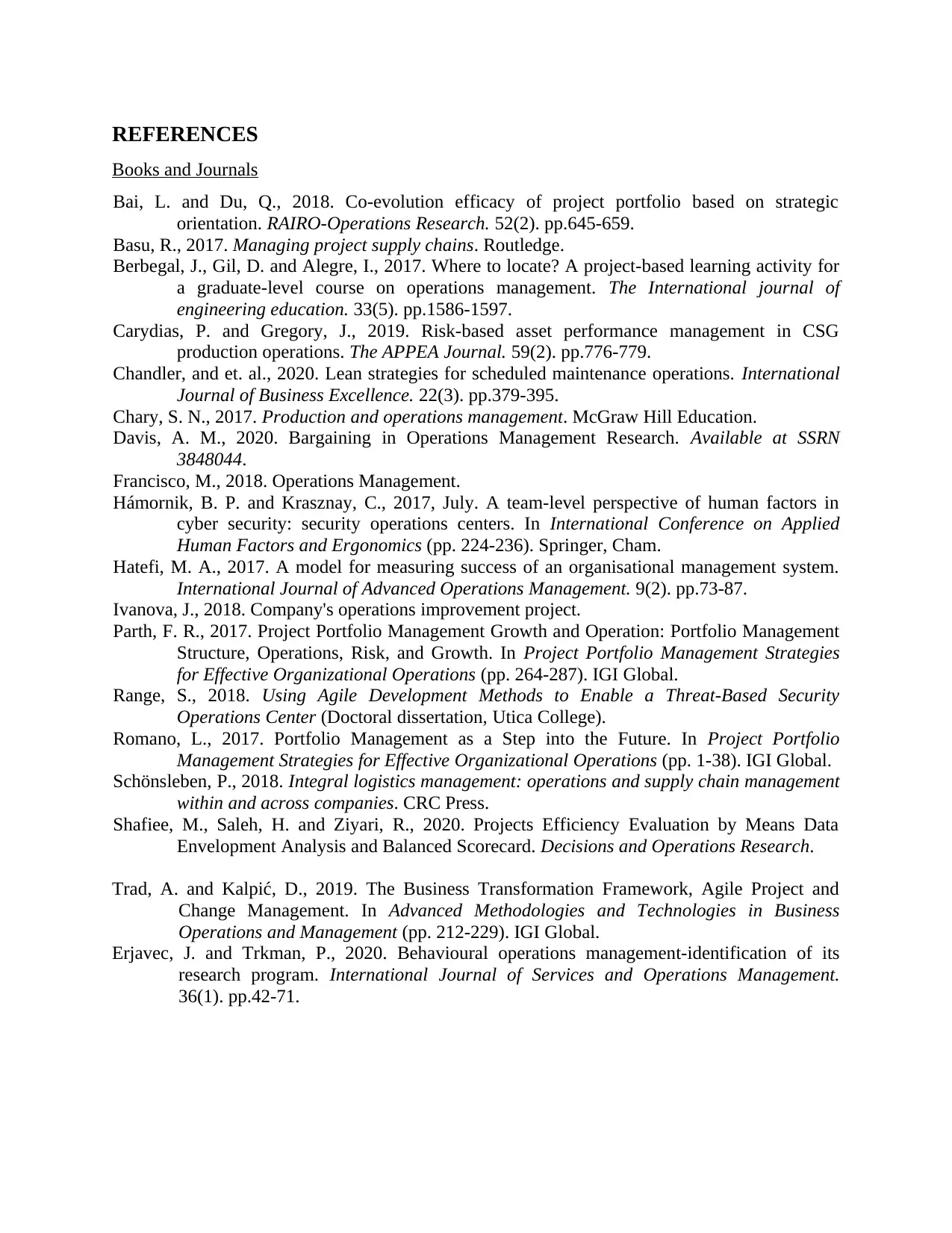
REFERENCES
Books and Journals
Bai, L. and Du, Q., 2018. Co-evolution efficacy of project portfolio based on strategic
orientation. RAIRO-Operations Research. 52(2). pp.645-659.
Basu, R., 2017. Managing project supply chains. Routledge.
Berbegal, J., Gil, D. and Alegre, I., 2017. Where to locate? A project-based learning activity for
a graduate-level course on operations management. The International journal of
engineering education. 33(5). pp.1586-1597.
Carydias, P. and Gregory, J., 2019. Risk-based asset performance management in CSG
production operations. The APPEA Journal. 59(2). pp.776-779.
Chandler, and et. al., 2020. Lean strategies for scheduled maintenance operations. International
Journal of Business Excellence. 22(3). pp.379-395.
Chary, S. N., 2017. Production and operations management. McGraw Hill Education.
Davis, A. M., 2020. Bargaining in Operations Management Research. Available at SSRN
3848044.
Francisco, M., 2018. Operations Management.
Hámornik, B. P. and Krasznay, C., 2017, July. A team-level perspective of human factors in
cyber security: security operations centers. In International Conference on Applied
Human Factors and Ergonomics (pp. 224-236). Springer, Cham.
Hatefi, M. A., 2017. A model for measuring success of an organisational management system.
International Journal of Advanced Operations Management. 9(2). pp.73-87.
Ivanova, J., 2018. Company's operations improvement project.
Parth, F. R., 2017. Project Portfolio Management Growth and Operation: Portfolio Management
Structure, Operations, Risk, and Growth. In Project Portfolio Management Strategies
for Effective Organizational Operations (pp. 264-287). IGI Global.
Range, S., 2018. Using Agile Development Methods to Enable a Threat-Based Security
Operations Center (Doctoral dissertation, Utica College).
Romano, L., 2017. Portfolio Management as a Step into the Future. In Project Portfolio
Management Strategies for Effective Organizational Operations (pp. 1-38). IGI Global.
Schönsleben, P., 2018. Integral logistics management: operations and supply chain management
within and across companies. CRC Press.
Shafiee, M., Saleh, H. and Ziyari, R., 2020. Projects Efficiency Evaluation by Means Data
Envelopment Analysis and Balanced Scorecard. Decisions and Operations Research.
Trad, A. and Kalpić, D., 2019. The Business Transformation Framework, Agile Project and
Change Management. In Advanced Methodologies and Technologies in Business
Operations and Management (pp. 212-229). IGI Global.
Erjavec, J. and Trkman, P., 2020. Behavioural operations management-identification of its
research program. International Journal of Services and Operations Management.
36(1). pp.42-71.
Books and Journals
Bai, L. and Du, Q., 2018. Co-evolution efficacy of project portfolio based on strategic
orientation. RAIRO-Operations Research. 52(2). pp.645-659.
Basu, R., 2017. Managing project supply chains. Routledge.
Berbegal, J., Gil, D. and Alegre, I., 2017. Where to locate? A project-based learning activity for
a graduate-level course on operations management. The International journal of
engineering education. 33(5). pp.1586-1597.
Carydias, P. and Gregory, J., 2019. Risk-based asset performance management in CSG
production operations. The APPEA Journal. 59(2). pp.776-779.
Chandler, and et. al., 2020. Lean strategies for scheduled maintenance operations. International
Journal of Business Excellence. 22(3). pp.379-395.
Chary, S. N., 2017. Production and operations management. McGraw Hill Education.
Davis, A. M., 2020. Bargaining in Operations Management Research. Available at SSRN
3848044.
Francisco, M., 2018. Operations Management.
Hámornik, B. P. and Krasznay, C., 2017, July. A team-level perspective of human factors in
cyber security: security operations centers. In International Conference on Applied
Human Factors and Ergonomics (pp. 224-236). Springer, Cham.
Hatefi, M. A., 2017. A model for measuring success of an organisational management system.
International Journal of Advanced Operations Management. 9(2). pp.73-87.
Ivanova, J., 2018. Company's operations improvement project.
Parth, F. R., 2017. Project Portfolio Management Growth and Operation: Portfolio Management
Structure, Operations, Risk, and Growth. In Project Portfolio Management Strategies
for Effective Organizational Operations (pp. 264-287). IGI Global.
Range, S., 2018. Using Agile Development Methods to Enable a Threat-Based Security
Operations Center (Doctoral dissertation, Utica College).
Romano, L., 2017. Portfolio Management as a Step into the Future. In Project Portfolio
Management Strategies for Effective Organizational Operations (pp. 1-38). IGI Global.
Schönsleben, P., 2018. Integral logistics management: operations and supply chain management
within and across companies. CRC Press.
Shafiee, M., Saleh, H. and Ziyari, R., 2020. Projects Efficiency Evaluation by Means Data
Envelopment Analysis and Balanced Scorecard. Decisions and Operations Research.
Trad, A. and Kalpić, D., 2019. The Business Transformation Framework, Agile Project and
Change Management. In Advanced Methodologies and Technologies in Business
Operations and Management (pp. 212-229). IGI Global.
Erjavec, J. and Trkman, P., 2020. Behavioural operations management-identification of its
research program. International Journal of Services and Operations Management.
36(1). pp.42-71.
1 out of 16
Related Documents

Your All-in-One AI-Powered Toolkit for Academic Success.
+13062052269
info@desklib.com
Available 24*7 on WhatsApp / Email
Unlock your academic potential
© 2024 | Zucol Services PVT LTD | All rights reserved.