Review and Critique of Operations Management and Project Life Cycle
VerifiedAdded on 2023/06/07
|14
|4649
|52
AI Summary
This report discusses the concepts of operations and operations management, reviews and critiques the implementation of operations management principles within Hammond manufacturing, analyzes the extent to which the operations management of the organization meets its requirements, and presents a continuous improvement plan with recommendations for improvement. It also describes the Lean principles and their application in the manufacturing industry.
Contribute Materials
Your contribution can guide someone’s learning journey. Share your
documents today.
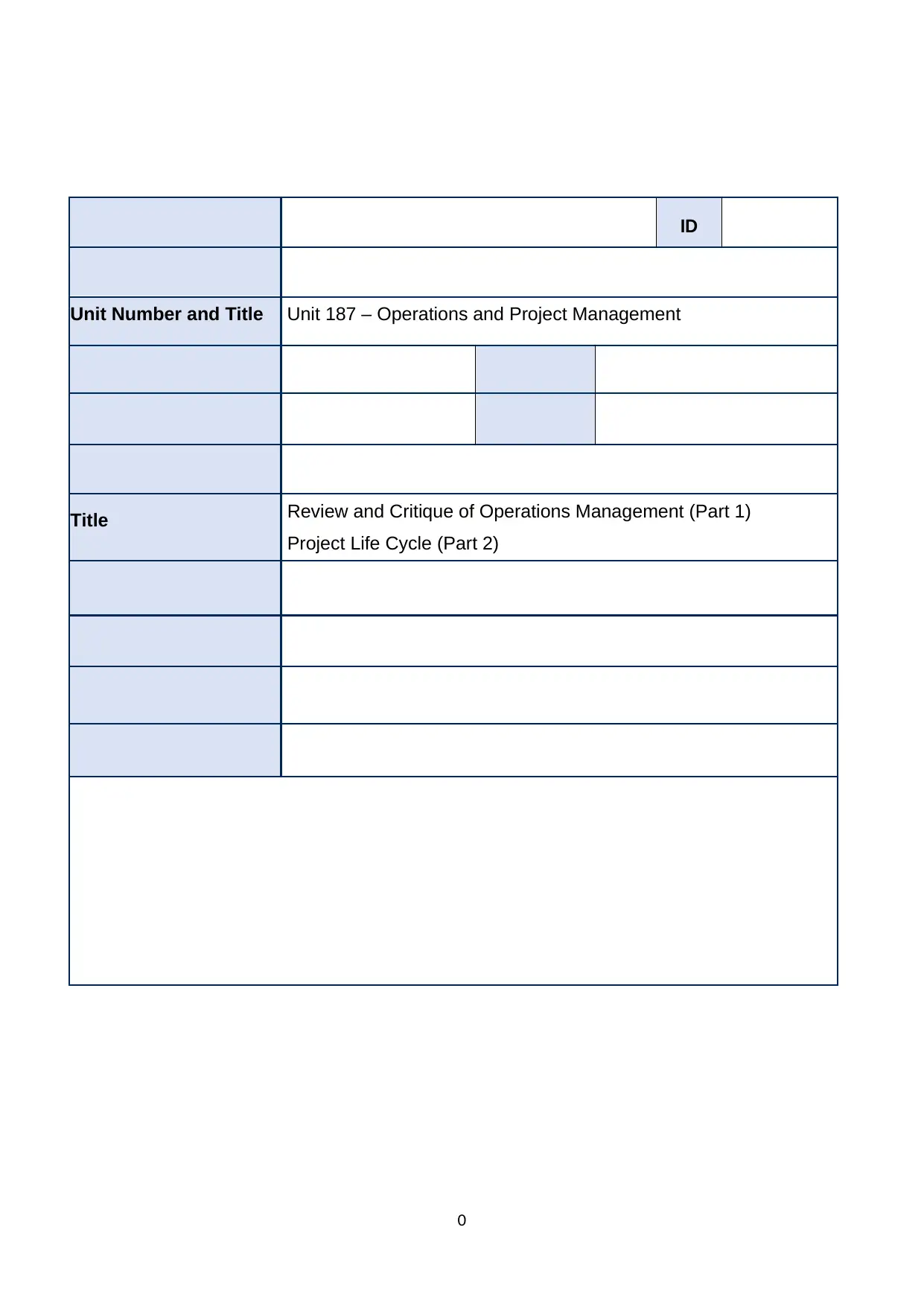
ID
Unit Number and Title Unit 187 – Operations and Project Management
Title Review and Critique of Operations Management (Part 1)
Project Life Cycle (Part 2)
0
Unit Number and Title Unit 187 – Operations and Project Management
Title Review and Critique of Operations Management (Part 1)
Project Life Cycle (Part 2)
0
Secure Best Marks with AI Grader
Need help grading? Try our AI Grader for instant feedback on your assignments.
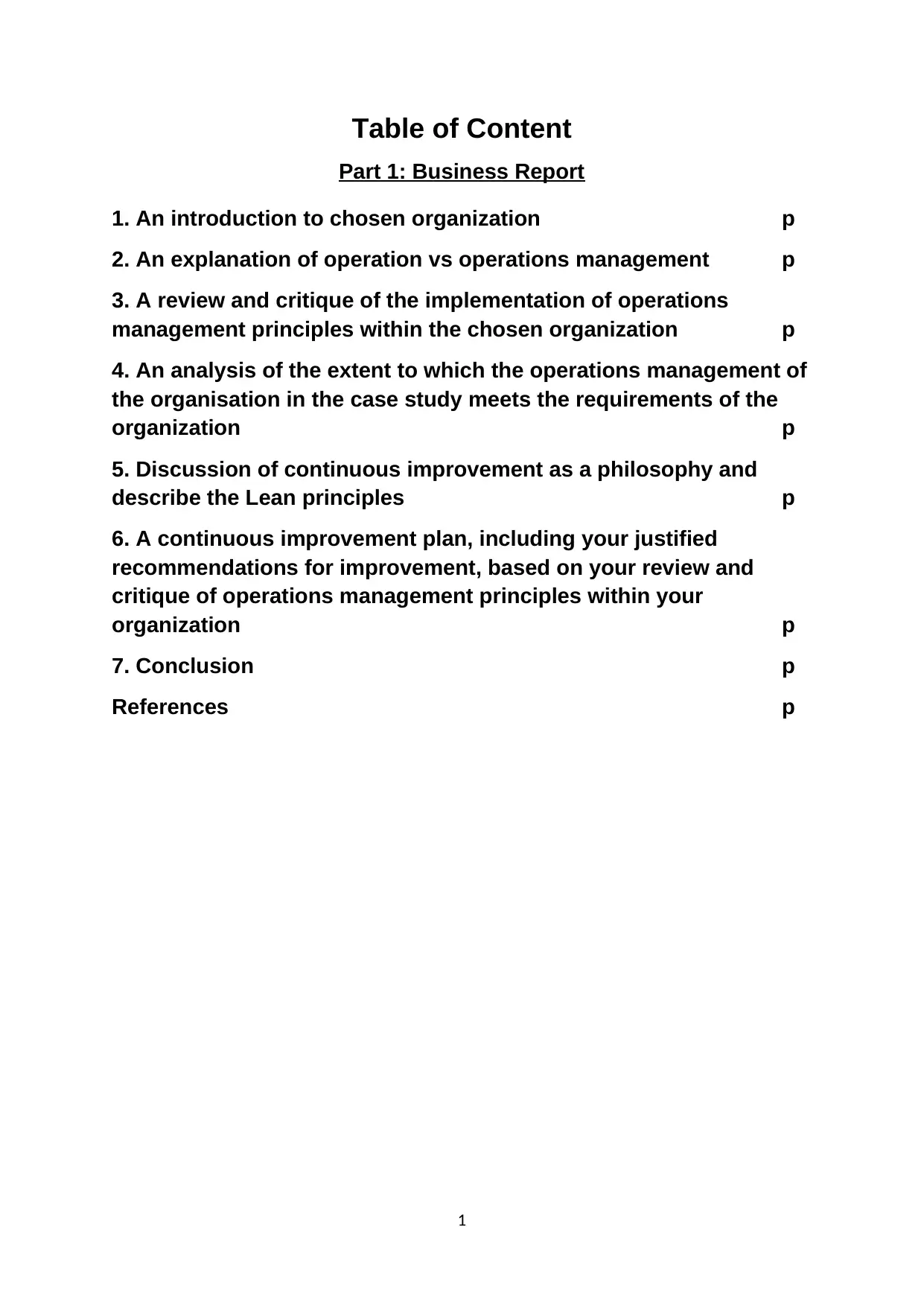
Table of Content
Part 1: Business Report
1. An introduction to chosen organization p
2. An explanation of operation vs operations management p
3. A review and critique of the implementation of operations
management principles within the chosen organization p
4. An analysis of the extent to which the operations management of
the organisation in the case study meets the requirements of the
organization p
5. Discussion of continuous improvement as a philosophy and
describe the Lean principles p
6. A continuous improvement plan, including your justified
recommendations for improvement, based on your review and
critique of operations management principles within your
organization p
7. Conclusion p
References p
1
Part 1: Business Report
1. An introduction to chosen organization p
2. An explanation of operation vs operations management p
3. A review and critique of the implementation of operations
management principles within the chosen organization p
4. An analysis of the extent to which the operations management of
the organisation in the case study meets the requirements of the
organization p
5. Discussion of continuous improvement as a philosophy and
describe the Lean principles p
6. A continuous improvement plan, including your justified
recommendations for improvement, based on your review and
critique of operations management principles within your
organization p
7. Conclusion p
References p
1
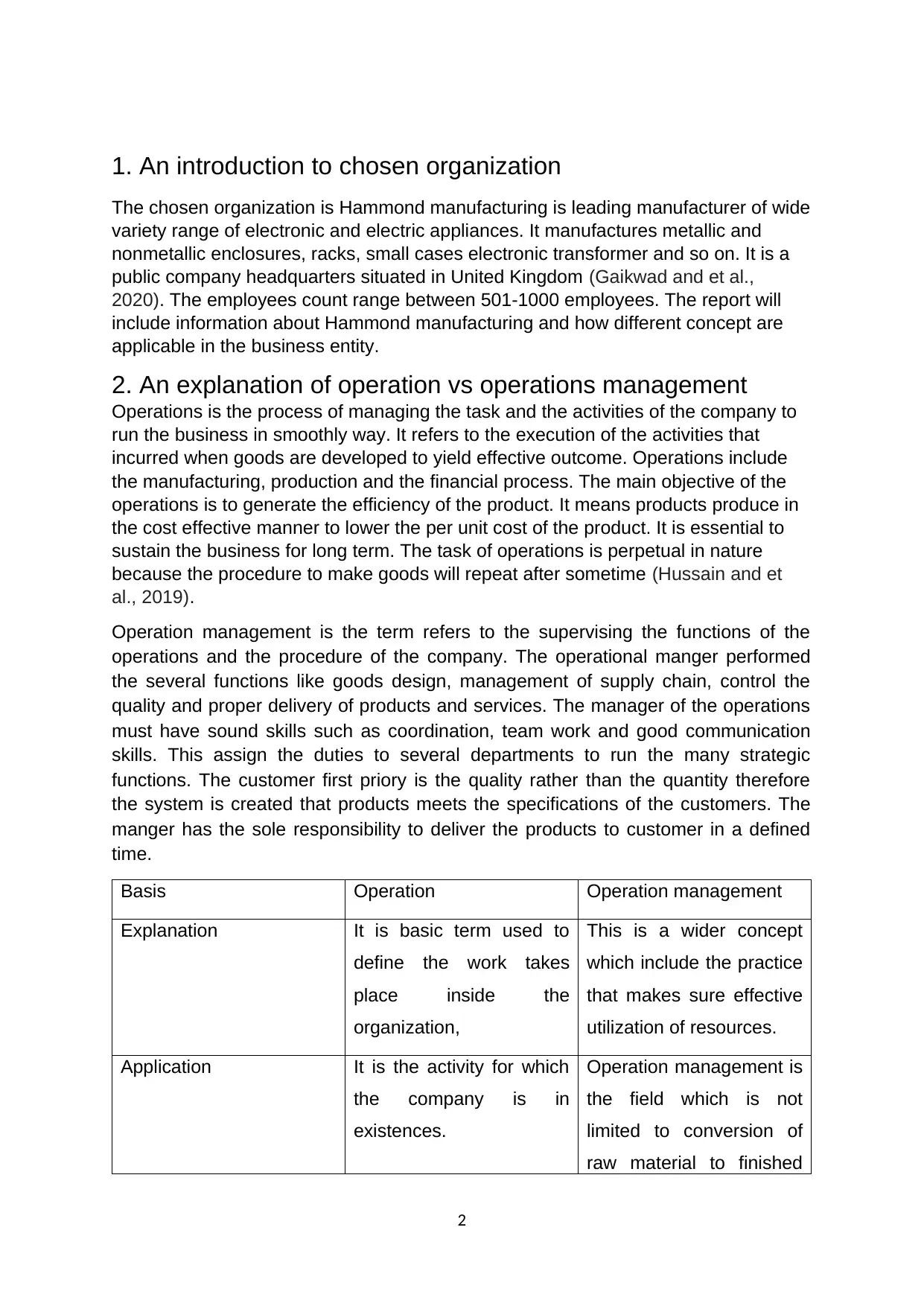
1. An introduction to chosen organization
The chosen organization is Hammond manufacturing is leading manufacturer of wide
variety range of electronic and electric appliances. It manufactures metallic and
nonmetallic enclosures, racks, small cases electronic transformer and so on. It is a
public company headquarters situated in United Kingdom (Gaikwad and et al.,
2020). The employees count range between 501-1000 employees. The report will
include information about Hammond manufacturing and how different concept are
applicable in the business entity.
2. An explanation of operation vs operations management
Operations is the process of managing the task and the activities of the company to
run the business in smoothly way. It refers to the execution of the activities that
incurred when goods are developed to yield effective outcome. Operations include
the manufacturing, production and the financial process. The main objective of the
operations is to generate the efficiency of the product. It means products produce in
the cost effective manner to lower the per unit cost of the product. It is essential to
sustain the business for long term. The task of operations is perpetual in nature
because the procedure to make goods will repeat after sometime (Hussain and et
al., 2019).
Operation management is the term refers to the supervising the functions of the
operations and the procedure of the company. The operational manger performed
the several functions like goods design, management of supply chain, control the
quality and proper delivery of products and services. The manager of the operations
must have sound skills such as coordination, team work and good communication
skills. This assign the duties to several departments to run the many strategic
functions. The customer first priory is the quality rather than the quantity therefore
the system is created that products meets the specifications of the customers. The
manger has the sole responsibility to deliver the products to customer in a defined
time.
Basis Operation Operation management
Explanation It is basic term used to
define the work takes
place inside the
organization,
This is a wider concept
which include the practice
that makes sure effective
utilization of resources.
Application It is the activity for which
the company is in
existences.
Operation management is
the field which is not
limited to conversion of
raw material to finished
2
The chosen organization is Hammond manufacturing is leading manufacturer of wide
variety range of electronic and electric appliances. It manufactures metallic and
nonmetallic enclosures, racks, small cases electronic transformer and so on. It is a
public company headquarters situated in United Kingdom (Gaikwad and et al.,
2020). The employees count range between 501-1000 employees. The report will
include information about Hammond manufacturing and how different concept are
applicable in the business entity.
2. An explanation of operation vs operations management
Operations is the process of managing the task and the activities of the company to
run the business in smoothly way. It refers to the execution of the activities that
incurred when goods are developed to yield effective outcome. Operations include
the manufacturing, production and the financial process. The main objective of the
operations is to generate the efficiency of the product. It means products produce in
the cost effective manner to lower the per unit cost of the product. It is essential to
sustain the business for long term. The task of operations is perpetual in nature
because the procedure to make goods will repeat after sometime (Hussain and et
al., 2019).
Operation management is the term refers to the supervising the functions of the
operations and the procedure of the company. The operational manger performed
the several functions like goods design, management of supply chain, control the
quality and proper delivery of products and services. The manager of the operations
must have sound skills such as coordination, team work and good communication
skills. This assign the duties to several departments to run the many strategic
functions. The customer first priory is the quality rather than the quantity therefore
the system is created that products meets the specifications of the customers. The
manger has the sole responsibility to deliver the products to customer in a defined
time.
Basis Operation Operation management
Explanation It is basic term used to
define the work takes
place inside the
organization,
This is a wider concept
which include the practice
that makes sure effective
utilization of resources.
Application It is the activity for which
the company is in
existences.
Operation management is
the field which is not
limited to conversion of
raw material to finished
2
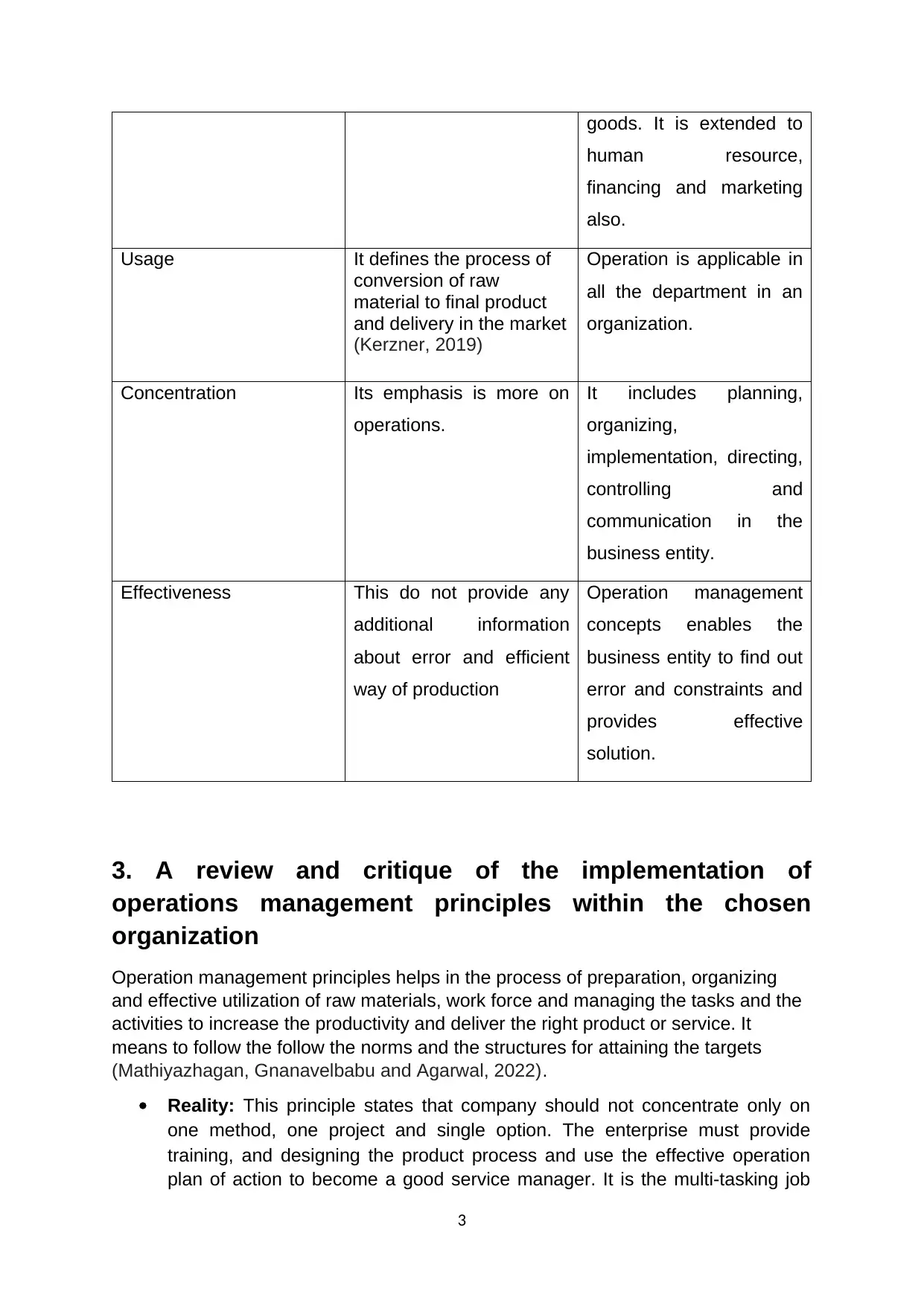
goods. It is extended to
human resource,
financing and marketing
also.
Usage It defines the process of
conversion of raw
material to final product
and delivery in the market
(Kerzner, 2019)
Operation is applicable in
all the department in an
organization.
Concentration Its emphasis is more on
operations.
It includes planning,
organizing,
implementation, directing,
controlling and
communication in the
business entity.
Effectiveness This do not provide any
additional information
about error and efficient
way of production
Operation management
concepts enables the
business entity to find out
error and constraints and
provides effective
solution.
3. A review and critique of the implementation of
operations management principles within the chosen
organization
Operation management principles helps in the process of preparation, organizing
and effective utilization of raw materials, work force and managing the tasks and the
activities to increase the productivity and deliver the right product or service. It
means to follow the follow the norms and the structures for attaining the targets
(Mathiyazhagan, Gnanavelbabu and Agarwal, 2022).
Reality: This principle states that company should not concentrate only on
one method, one project and single option. The enterprise must provide
training, and designing the product process and use the effective operation
plan of action to become a good service manager. It is the multi-tasking job
3
human resource,
financing and marketing
also.
Usage It defines the process of
conversion of raw
material to final product
and delivery in the market
(Kerzner, 2019)
Operation is applicable in
all the department in an
organization.
Concentration Its emphasis is more on
operations.
It includes planning,
organizing,
implementation, directing,
controlling and
communication in the
business entity.
Effectiveness This do not provide any
additional information
about error and efficient
way of production
Operation management
concepts enables the
business entity to find out
error and constraints and
provides effective
solution.
3. A review and critique of the implementation of
operations management principles within the chosen
organization
Operation management principles helps in the process of preparation, organizing
and effective utilization of raw materials, work force and managing the tasks and the
activities to increase the productivity and deliver the right product or service. It
means to follow the follow the norms and the structures for attaining the targets
(Mathiyazhagan, Gnanavelbabu and Agarwal, 2022).
Reality: This principle states that company should not concentrate only on
one method, one project and single option. The enterprise must provide
training, and designing the product process and use the effective operation
plan of action to become a good service manager. It is the multi-tasking job
3
Secure Best Marks with AI Grader
Need help grading? Try our AI Grader for instant feedback on your assignments.
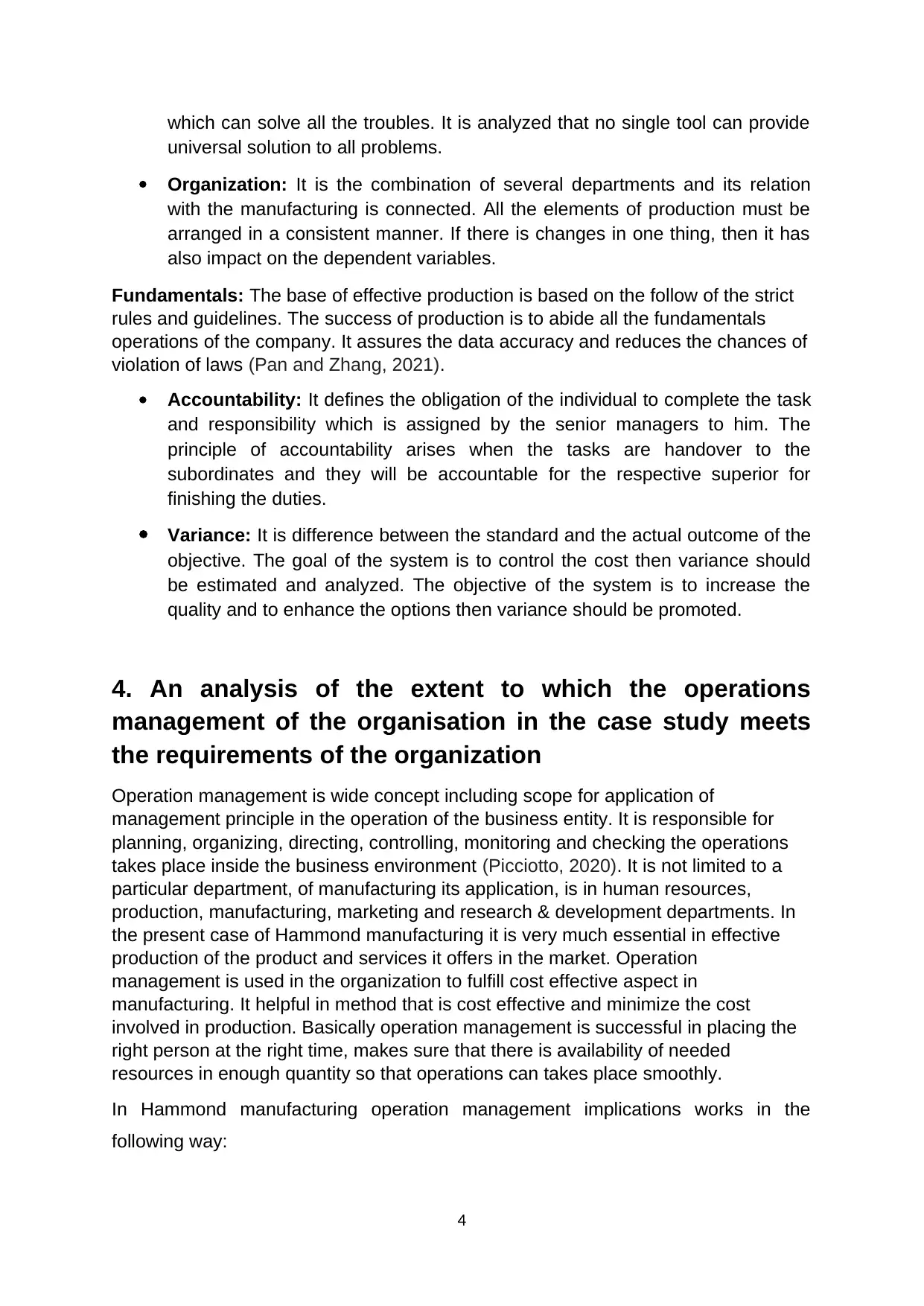
which can solve all the troubles. It is analyzed that no single tool can provide
universal solution to all problems.
Organization: It is the combination of several departments and its relation
with the manufacturing is connected. All the elements of production must be
arranged in a consistent manner. If there is changes in one thing, then it has
also impact on the dependent variables.
Fundamentals: The base of effective production is based on the follow of the strict
rules and guidelines. The success of production is to abide all the fundamentals
operations of the company. It assures the data accuracy and reduces the chances of
violation of laws (Pan and Zhang, 2021).
Accountability: It defines the obligation of the individual to complete the task
and responsibility which is assigned by the senior managers to him. The
principle of accountability arises when the tasks are handover to the
subordinates and they will be accountable for the respective superior for
finishing the duties.
Variance: It is difference between the standard and the actual outcome of the
objective. The goal of the system is to control the cost then variance should
be estimated and analyzed. The objective of the system is to increase the
quality and to enhance the options then variance should be promoted.
4. An analysis of the extent to which the operations
management of the organisation in the case study meets
the requirements of the organization
Operation management is wide concept including scope for application of
management principle in the operation of the business entity. It is responsible for
planning, organizing, directing, controlling, monitoring and checking the operations
takes place inside the business environment (Picciotto, 2020). It is not limited to a
particular department, of manufacturing its application, is in human resources,
production, manufacturing, marketing and research & development departments. In
the present case of Hammond manufacturing it is very much essential in effective
production of the product and services it offers in the market. Operation
management is used in the organization to fulfill cost effective aspect in
manufacturing. It helpful in method that is cost effective and minimize the cost
involved in production. Basically operation management is successful in placing the
right person at the right time, makes sure that there is availability of needed
resources in enough quantity so that operations can takes place smoothly.
In Hammond manufacturing operation management implications works in the
following way:
4
universal solution to all problems.
Organization: It is the combination of several departments and its relation
with the manufacturing is connected. All the elements of production must be
arranged in a consistent manner. If there is changes in one thing, then it has
also impact on the dependent variables.
Fundamentals: The base of effective production is based on the follow of the strict
rules and guidelines. The success of production is to abide all the fundamentals
operations of the company. It assures the data accuracy and reduces the chances of
violation of laws (Pan and Zhang, 2021).
Accountability: It defines the obligation of the individual to complete the task
and responsibility which is assigned by the senior managers to him. The
principle of accountability arises when the tasks are handover to the
subordinates and they will be accountable for the respective superior for
finishing the duties.
Variance: It is difference between the standard and the actual outcome of the
objective. The goal of the system is to control the cost then variance should
be estimated and analyzed. The objective of the system is to increase the
quality and to enhance the options then variance should be promoted.
4. An analysis of the extent to which the operations
management of the organisation in the case study meets
the requirements of the organization
Operation management is wide concept including scope for application of
management principle in the operation of the business entity. It is responsible for
planning, organizing, directing, controlling, monitoring and checking the operations
takes place inside the business environment (Picciotto, 2020). It is not limited to a
particular department, of manufacturing its application, is in human resources,
production, manufacturing, marketing and research & development departments. In
the present case of Hammond manufacturing it is very much essential in effective
production of the product and services it offers in the market. Operation
management is used in the organization to fulfill cost effective aspect in
manufacturing. It helpful in method that is cost effective and minimize the cost
involved in production. Basically operation management is successful in placing the
right person at the right time, makes sure that there is availability of needed
resources in enough quantity so that operations can takes place smoothly.
In Hammond manufacturing operation management implications works in the
following way:
4
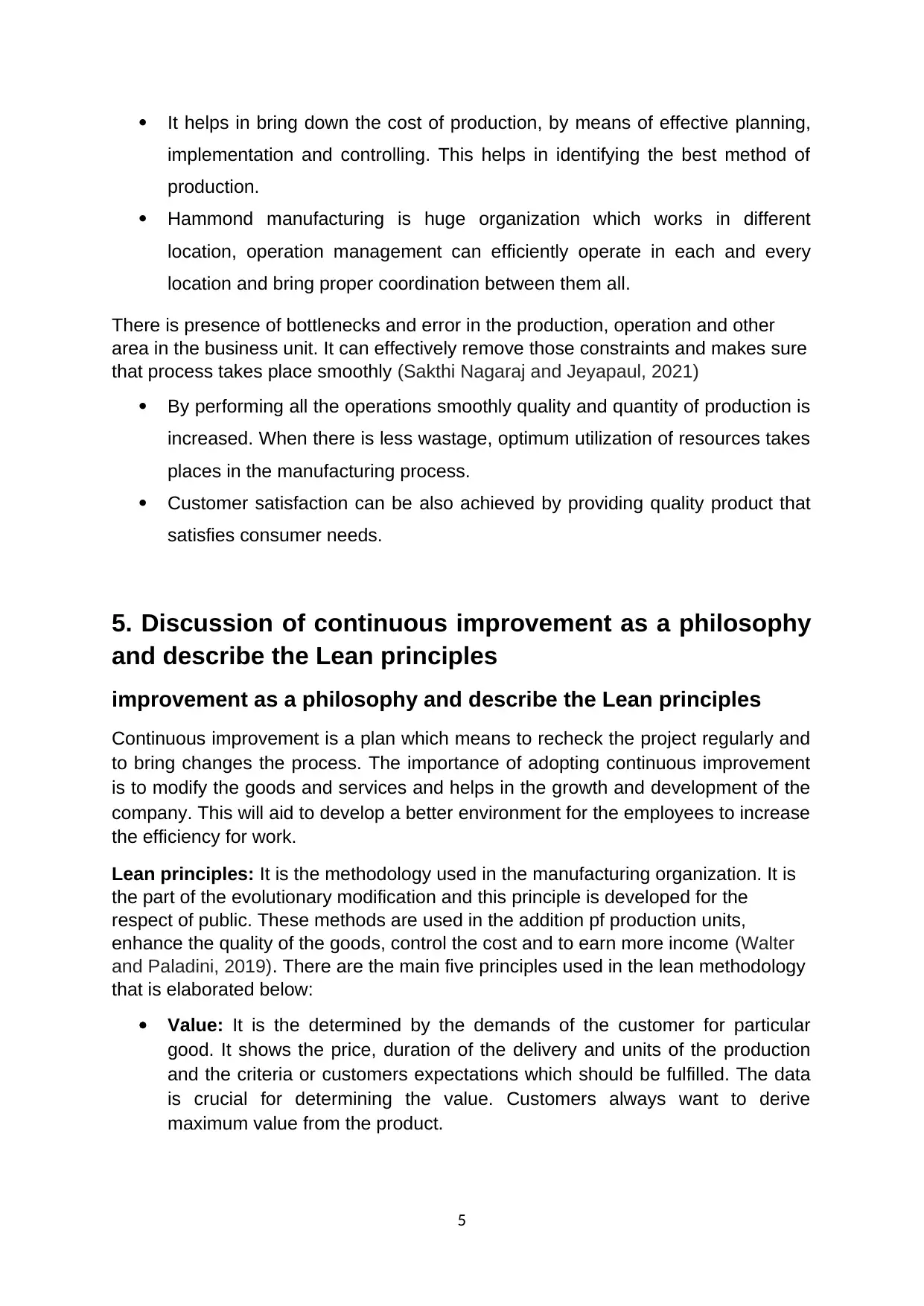
It helps in bring down the cost of production, by means of effective planning,
implementation and controlling. This helps in identifying the best method of
production.
Hammond manufacturing is huge organization which works in different
location, operation management can efficiently operate in each and every
location and bring proper coordination between them all.
There is presence of bottlenecks and error in the production, operation and other
area in the business unit. It can effectively remove those constraints and makes sure
that process takes place smoothly (Sakthi Nagaraj and Jeyapaul, 2021)
By performing all the operations smoothly quality and quantity of production is
increased. When there is less wastage, optimum utilization of resources takes
places in the manufacturing process.
Customer satisfaction can be also achieved by providing quality product that
satisfies consumer needs.
5. Discussion of continuous improvement as a philosophy
and describe the Lean principles
improvement as a philosophy and describe the Lean principles
Continuous improvement is a plan which means to recheck the project regularly and
to bring changes the process. The importance of adopting continuous improvement
is to modify the goods and services and helps in the growth and development of the
company. This will aid to develop a better environment for the employees to increase
the efficiency for work.
Lean principles: It is the methodology used in the manufacturing organization. It is
the part of the evolutionary modification and this principle is developed for the
respect of public. These methods are used in the addition pf production units,
enhance the quality of the goods, control the cost and to earn more income (Walter
and Paladini, 2019). There are the main five principles used in the lean methodology
that is elaborated below:
Value: It is the determined by the demands of the customer for particular
good. It shows the price, duration of the delivery and units of the production
and the criteria or customers expectations which should be fulfilled. The data
is crucial for determining the value. Customers always want to derive
maximum value from the product.
5
implementation and controlling. This helps in identifying the best method of
production.
Hammond manufacturing is huge organization which works in different
location, operation management can efficiently operate in each and every
location and bring proper coordination between them all.
There is presence of bottlenecks and error in the production, operation and other
area in the business unit. It can effectively remove those constraints and makes sure
that process takes place smoothly (Sakthi Nagaraj and Jeyapaul, 2021)
By performing all the operations smoothly quality and quantity of production is
increased. When there is less wastage, optimum utilization of resources takes
places in the manufacturing process.
Customer satisfaction can be also achieved by providing quality product that
satisfies consumer needs.
5. Discussion of continuous improvement as a philosophy
and describe the Lean principles
improvement as a philosophy and describe the Lean principles
Continuous improvement is a plan which means to recheck the project regularly and
to bring changes the process. The importance of adopting continuous improvement
is to modify the goods and services and helps in the growth and development of the
company. This will aid to develop a better environment for the employees to increase
the efficiency for work.
Lean principles: It is the methodology used in the manufacturing organization. It is
the part of the evolutionary modification and this principle is developed for the
respect of public. These methods are used in the addition pf production units,
enhance the quality of the goods, control the cost and to earn more income (Walter
and Paladini, 2019). There are the main five principles used in the lean methodology
that is elaborated below:
Value: It is the determined by the demands of the customer for particular
good. It shows the price, duration of the delivery and units of the production
and the criteria or customers expectations which should be fulfilled. The data
is crucial for determining the value. Customers always want to derive
maximum value from the product.
5
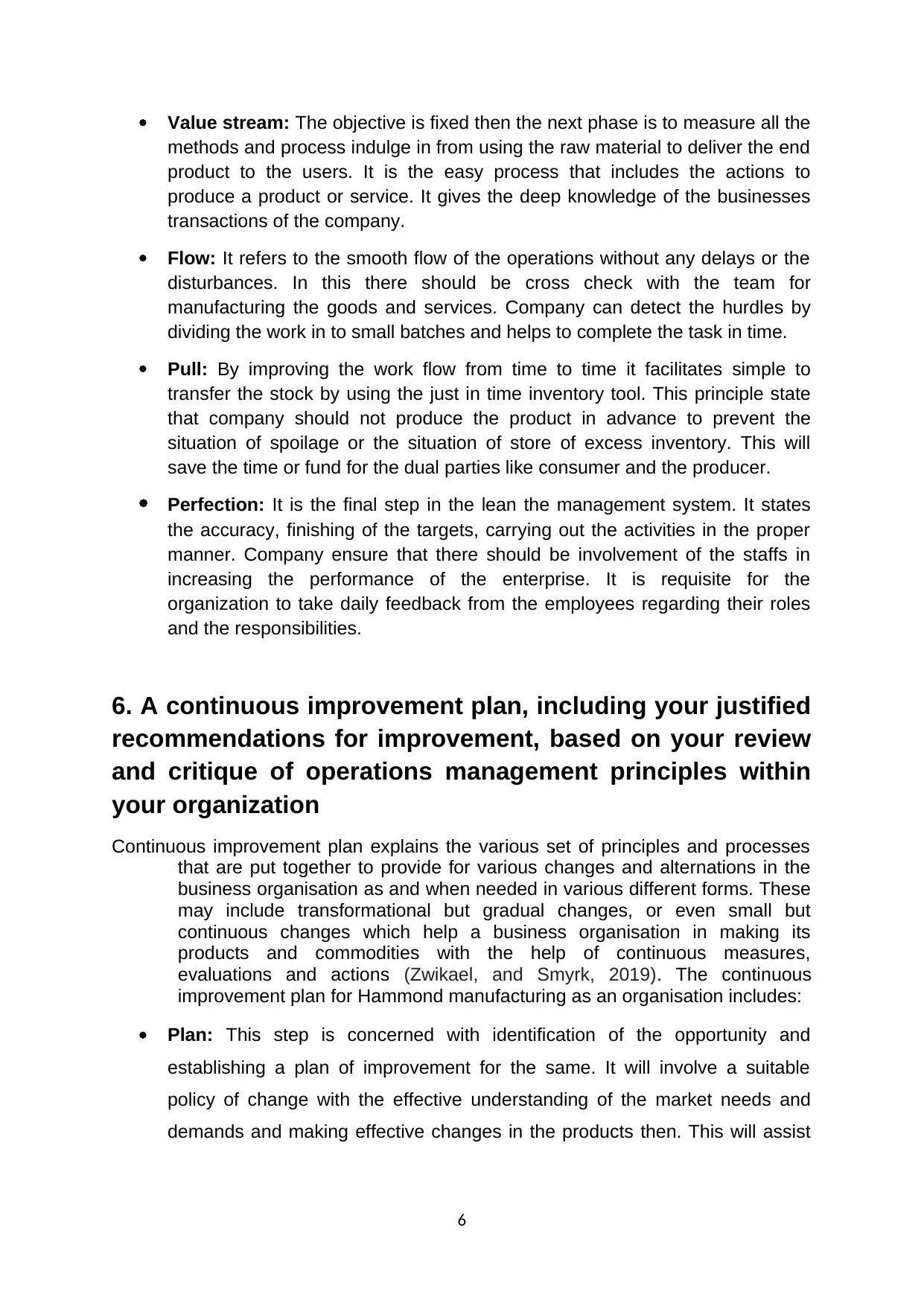
Value stream: The objective is fixed then the next phase is to measure all the
methods and process indulge in from using the raw material to deliver the end
product to the users. It is the easy process that includes the actions to
produce a product or service. It gives the deep knowledge of the businesses
transactions of the company.
Flow: It refers to the smooth flow of the operations without any delays or the
disturbances. In this there should be cross check with the team for
manufacturing the goods and services. Company can detect the hurdles by
dividing the work in to small batches and helps to complete the task in time.
Pull: By improving the work flow from time to time it facilitates simple to
transfer the stock by using the just in time inventory tool. This principle state
that company should not produce the product in advance to prevent the
situation of spoilage or the situation of store of excess inventory. This will
save the time or fund for the dual parties like consumer and the producer.
Perfection: It is the final step in the lean the management system. It states
the accuracy, finishing of the targets, carrying out the activities in the proper
manner. Company ensure that there should be involvement of the staffs in
increasing the performance of the enterprise. It is requisite for the
organization to take daily feedback from the employees regarding their roles
and the responsibilities.
6. A continuous improvement plan, including your justified
recommendations for improvement, based on your review
and critique of operations management principles within
your organization
Continuous improvement plan explains the various set of principles and processes
that are put together to provide for various changes and alternations in the
business organisation as and when needed in various different forms. These
may include transformational but gradual changes, or even small but
continuous changes which help a business organisation in making its
products and commodities with the help of continuous measures,
evaluations and actions (Zwikael, and Smyrk, 2019). The continuous
improvement plan for Hammond manufacturing as an organisation includes:
Plan: This step is concerned with identification of the opportunity and
establishing a plan of improvement for the same. It will involve a suitable
policy of change with the effective understanding of the market needs and
demands and making effective changes in the products then. This will assist
6
methods and process indulge in from using the raw material to deliver the end
product to the users. It is the easy process that includes the actions to
produce a product or service. It gives the deep knowledge of the businesses
transactions of the company.
Flow: It refers to the smooth flow of the operations without any delays or the
disturbances. In this there should be cross check with the team for
manufacturing the goods and services. Company can detect the hurdles by
dividing the work in to small batches and helps to complete the task in time.
Pull: By improving the work flow from time to time it facilitates simple to
transfer the stock by using the just in time inventory tool. This principle state
that company should not produce the product in advance to prevent the
situation of spoilage or the situation of store of excess inventory. This will
save the time or fund for the dual parties like consumer and the producer.
Perfection: It is the final step in the lean the management system. It states
the accuracy, finishing of the targets, carrying out the activities in the proper
manner. Company ensure that there should be involvement of the staffs in
increasing the performance of the enterprise. It is requisite for the
organization to take daily feedback from the employees regarding their roles
and the responsibilities.
6. A continuous improvement plan, including your justified
recommendations for improvement, based on your review
and critique of operations management principles within
your organization
Continuous improvement plan explains the various set of principles and processes
that are put together to provide for various changes and alternations in the
business organisation as and when needed in various different forms. These
may include transformational but gradual changes, or even small but
continuous changes which help a business organisation in making its
products and commodities with the help of continuous measures,
evaluations and actions (Zwikael, and Smyrk, 2019). The continuous
improvement plan for Hammond manufacturing as an organisation includes:
Plan: This step is concerned with identification of the opportunity and
establishing a plan of improvement for the same. It will involve a suitable
policy of change with the effective understanding of the market needs and
demands and making effective changes in the products then. This will assist
6
Paraphrase This Document
Need a fresh take? Get an instant paraphrase of this document with our AI Paraphraser
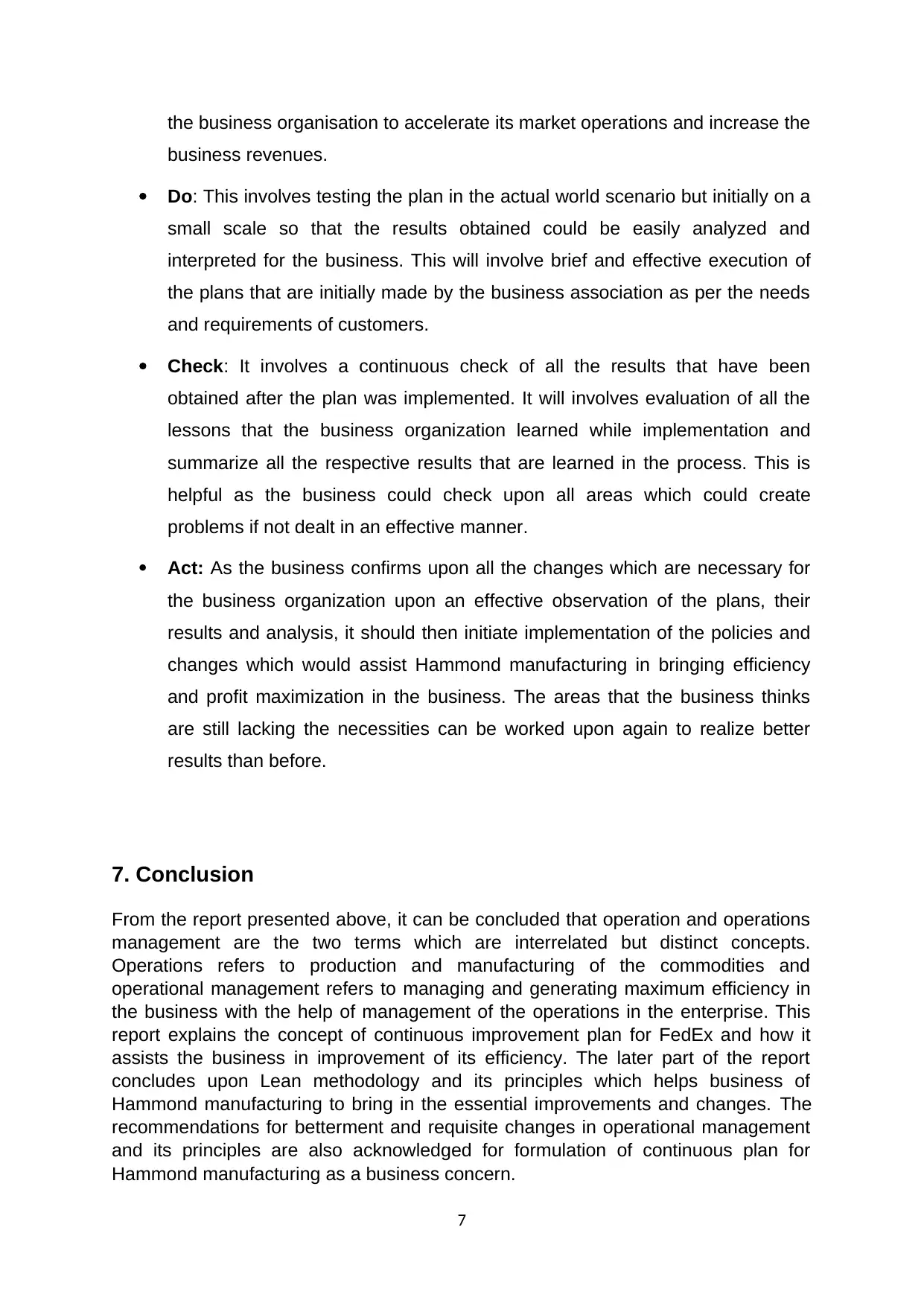
the business organisation to accelerate its market operations and increase the
business revenues.
Do: This involves testing the plan in the actual world scenario but initially on a
small scale so that the results obtained could be easily analyzed and
interpreted for the business. This will involve brief and effective execution of
the plans that are initially made by the business association as per the needs
and requirements of customers.
Check: It involves a continuous check of all the results that have been
obtained after the plan was implemented. It will involves evaluation of all the
lessons that the business organization learned while implementation and
summarize all the respective results that are learned in the process. This is
helpful as the business could check upon all areas which could create
problems if not dealt in an effective manner.
Act: As the business confirms upon all the changes which are necessary for
the business organization upon an effective observation of the plans, their
results and analysis, it should then initiate implementation of the policies and
changes which would assist Hammond manufacturing in bringing efficiency
and profit maximization in the business. The areas that the business thinks
are still lacking the necessities can be worked upon again to realize better
results than before.
7. Conclusion
From the report presented above, it can be concluded that operation and operations
management are the two terms which are interrelated but distinct concepts.
Operations refers to production and manufacturing of the commodities and
operational management refers to managing and generating maximum efficiency in
the business with the help of management of the operations in the enterprise. This
report explains the concept of continuous improvement plan for FedEx and how it
assists the business in improvement of its efficiency. The later part of the report
concludes upon Lean methodology and its principles which helps business of
Hammond manufacturing to bring in the essential improvements and changes. The
recommendations for betterment and requisite changes in operational management
and its principles are also acknowledged for formulation of continuous plan for
Hammond manufacturing as a business concern.
7
business revenues.
Do: This involves testing the plan in the actual world scenario but initially on a
small scale so that the results obtained could be easily analyzed and
interpreted for the business. This will involve brief and effective execution of
the plans that are initially made by the business association as per the needs
and requirements of customers.
Check: It involves a continuous check of all the results that have been
obtained after the plan was implemented. It will involves evaluation of all the
lessons that the business organization learned while implementation and
summarize all the respective results that are learned in the process. This is
helpful as the business could check upon all areas which could create
problems if not dealt in an effective manner.
Act: As the business confirms upon all the changes which are necessary for
the business organization upon an effective observation of the plans, their
results and analysis, it should then initiate implementation of the policies and
changes which would assist Hammond manufacturing in bringing efficiency
and profit maximization in the business. The areas that the business thinks
are still lacking the necessities can be worked upon again to realize better
results than before.
7. Conclusion
From the report presented above, it can be concluded that operation and operations
management are the two terms which are interrelated but distinct concepts.
Operations refers to production and manufacturing of the commodities and
operational management refers to managing and generating maximum efficiency in
the business with the help of management of the operations in the enterprise. This
report explains the concept of continuous improvement plan for FedEx and how it
assists the business in improvement of its efficiency. The later part of the report
concludes upon Lean methodology and its principles which helps business of
Hammond manufacturing to bring in the essential improvements and changes. The
recommendations for betterment and requisite changes in operational management
and its principles are also acknowledged for formulation of continuous plan for
Hammond manufacturing as a business concern.
7
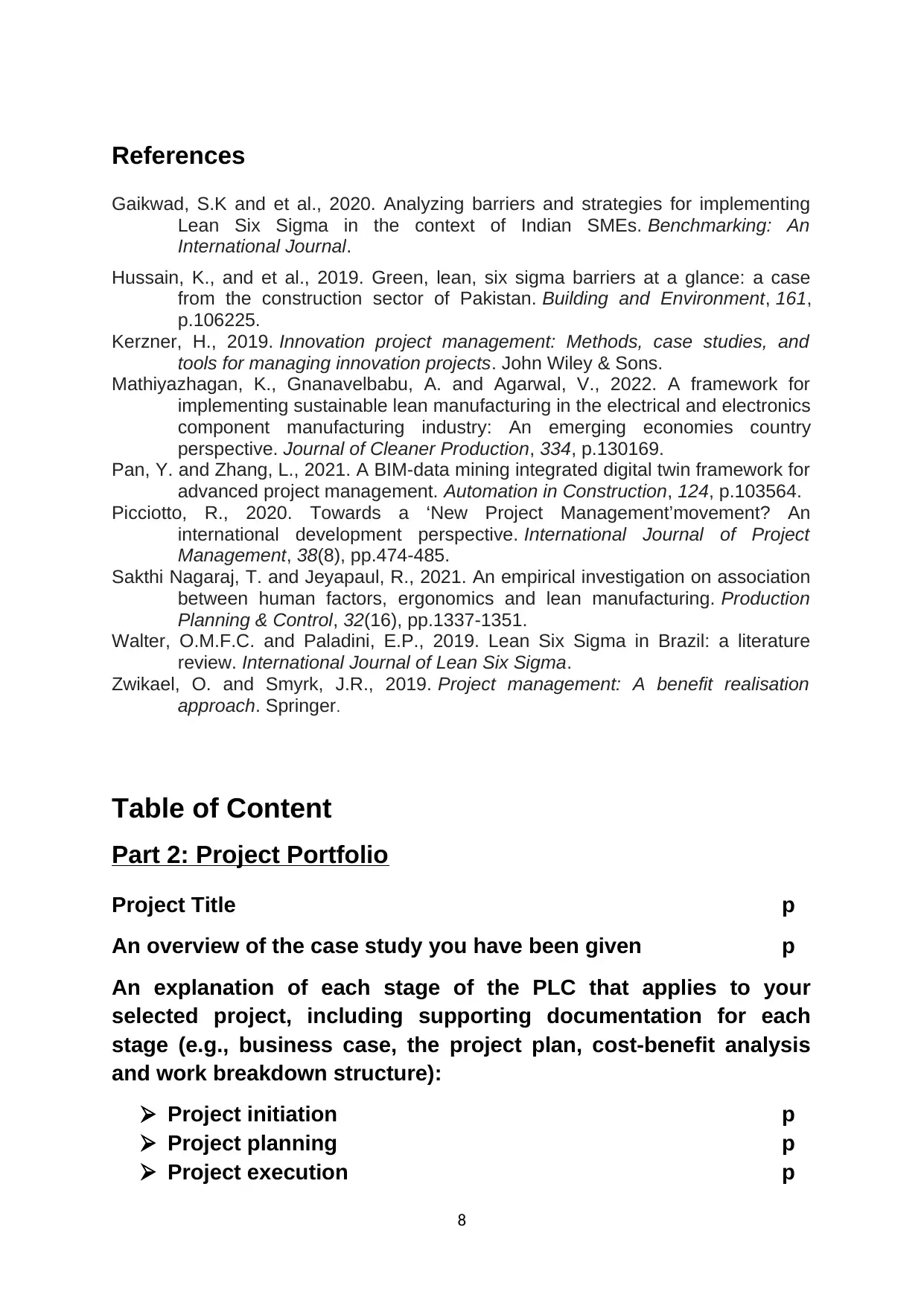
References
Gaikwad, S.K and et al., 2020. Analyzing barriers and strategies for implementing
Lean Six Sigma in the context of Indian SMEs. Benchmarking: An
International Journal.
Hussain, K., and et al., 2019. Green, lean, six sigma barriers at a glance: a case
from the construction sector of Pakistan. Building and Environment, 161,
p.106225.
Kerzner, H., 2019. Innovation project management: Methods, case studies, and
tools for managing innovation projects. John Wiley & Sons.
Mathiyazhagan, K., Gnanavelbabu, A. and Agarwal, V., 2022. A framework for
implementing sustainable lean manufacturing in the electrical and electronics
component manufacturing industry: An emerging economies country
perspective. Journal of Cleaner Production, 334, p.130169.
Pan, Y. and Zhang, L., 2021. A BIM-data mining integrated digital twin framework for
advanced project management. Automation in Construction, 124, p.103564.
Picciotto, R., 2020. Towards a ‘New Project Management’movement? An
international development perspective. International Journal of Project
Management, 38(8), pp.474-485.
Sakthi Nagaraj, T. and Jeyapaul, R., 2021. An empirical investigation on association
between human factors, ergonomics and lean manufacturing. Production
Planning & Control, 32(16), pp.1337-1351.
Walter, O.M.F.C. and Paladini, E.P., 2019. Lean Six Sigma in Brazil: a literature
review. International Journal of Lean Six Sigma.
Zwikael, O. and Smyrk, J.R., 2019. Project management: A benefit realisation
approach. Springer.
Table of Content
Part 2: Project Portfolio
Project Title p
An overview of the case study you have been given p
An explanation of each stage of the PLC that applies to your
selected project, including supporting documentation for each
stage (e.g., business case, the project plan, cost-benefit analysis
and work breakdown structure):
Project initiation p
Project planning p
Project execution p
8
Gaikwad, S.K and et al., 2020. Analyzing barriers and strategies for implementing
Lean Six Sigma in the context of Indian SMEs. Benchmarking: An
International Journal.
Hussain, K., and et al., 2019. Green, lean, six sigma barriers at a glance: a case
from the construction sector of Pakistan. Building and Environment, 161,
p.106225.
Kerzner, H., 2019. Innovation project management: Methods, case studies, and
tools for managing innovation projects. John Wiley & Sons.
Mathiyazhagan, K., Gnanavelbabu, A. and Agarwal, V., 2022. A framework for
implementing sustainable lean manufacturing in the electrical and electronics
component manufacturing industry: An emerging economies country
perspective. Journal of Cleaner Production, 334, p.130169.
Pan, Y. and Zhang, L., 2021. A BIM-data mining integrated digital twin framework for
advanced project management. Automation in Construction, 124, p.103564.
Picciotto, R., 2020. Towards a ‘New Project Management’movement? An
international development perspective. International Journal of Project
Management, 38(8), pp.474-485.
Sakthi Nagaraj, T. and Jeyapaul, R., 2021. An empirical investigation on association
between human factors, ergonomics and lean manufacturing. Production
Planning & Control, 32(16), pp.1337-1351.
Walter, O.M.F.C. and Paladini, E.P., 2019. Lean Six Sigma in Brazil: a literature
review. International Journal of Lean Six Sigma.
Zwikael, O. and Smyrk, J.R., 2019. Project management: A benefit realisation
approach. Springer.
Table of Content
Part 2: Project Portfolio
Project Title p
An overview of the case study you have been given p
An explanation of each stage of the PLC that applies to your
selected project, including supporting documentation for each
stage (e.g., business case, the project plan, cost-benefit analysis
and work breakdown structure):
Project initiation p
Project planning p
Project execution p
8
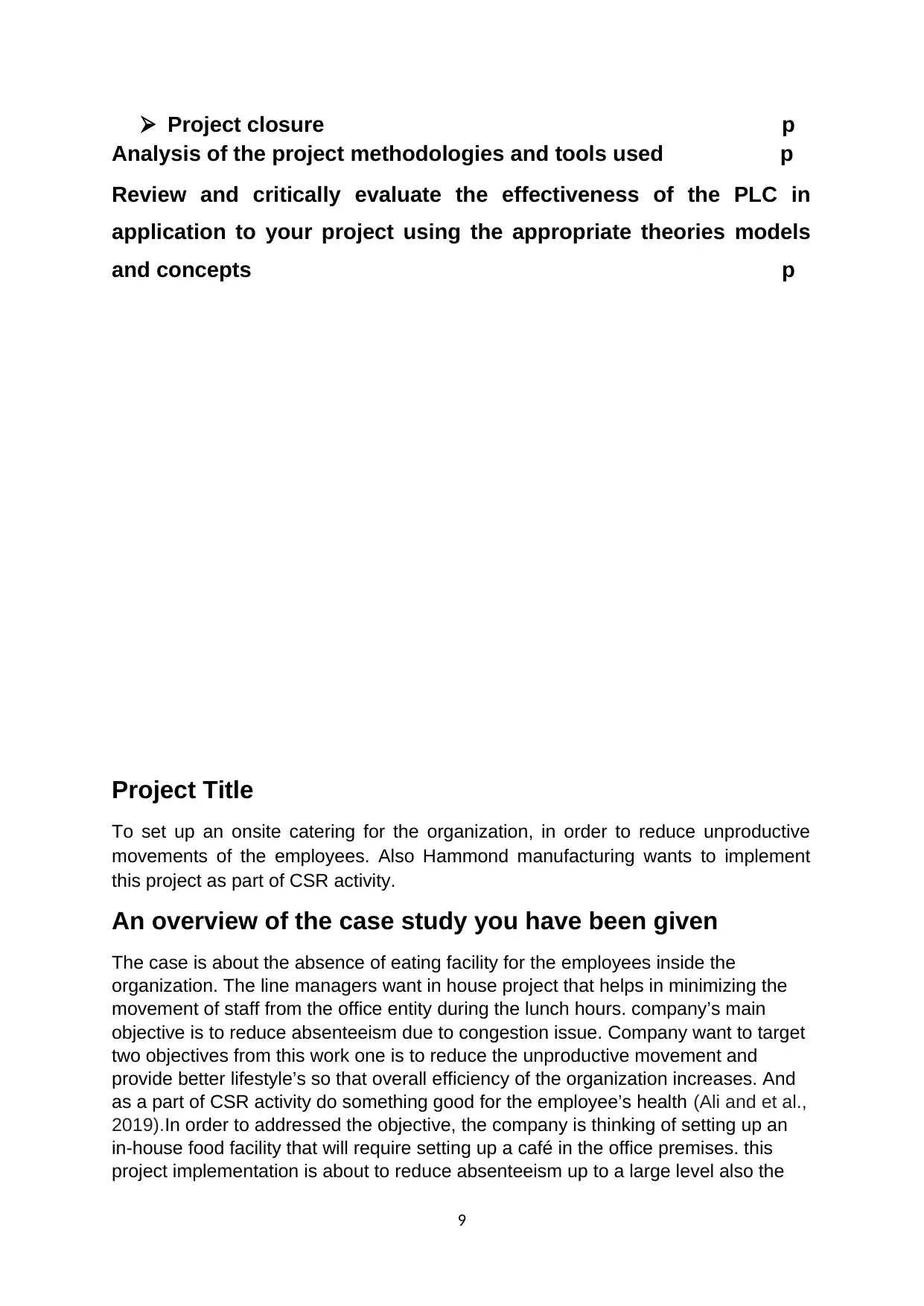
Project closure p
Analysis of the project methodologies and tools used p
Review and critically evaluate the effectiveness of the PLC in
application to your project using the appropriate theories models
and concepts p
Project Title
To set up an onsite catering for the organization, in order to reduce unproductive
movements of the employees. Also Hammond manufacturing wants to implement
this project as part of CSR activity.
An overview of the case study you have been given
The case is about the absence of eating facility for the employees inside the
organization. The line managers want in house project that helps in minimizing the
movement of staff from the office entity during the lunch hours. company’s main
objective is to reduce absenteeism due to congestion issue. Company want to target
two objectives from this work one is to reduce the unproductive movement and
provide better lifestyle’s so that overall efficiency of the organization increases. And
as a part of CSR activity do something good for the employee’s health (Ali and et al.,
2019).In order to addressed the objective, the company is thinking of setting up an
in-house food facility that will require setting up a café in the office premises. this
project implementation is about to reduce absenteeism up to a large level also the
9
Analysis of the project methodologies and tools used p
Review and critically evaluate the effectiveness of the PLC in
application to your project using the appropriate theories models
and concepts p
Project Title
To set up an onsite catering for the organization, in order to reduce unproductive
movements of the employees. Also Hammond manufacturing wants to implement
this project as part of CSR activity.
An overview of the case study you have been given
The case is about the absence of eating facility for the employees inside the
organization. The line managers want in house project that helps in minimizing the
movement of staff from the office entity during the lunch hours. company’s main
objective is to reduce absenteeism due to congestion issue. Company want to target
two objectives from this work one is to reduce the unproductive movement and
provide better lifestyle’s so that overall efficiency of the organization increases. And
as a part of CSR activity do something good for the employee’s health (Ali and et al.,
2019).In order to addressed the objective, the company is thinking of setting up an
in-house food facility that will require setting up a café in the office premises. this
project implementation is about to reduce absenteeism up to a large level also the
9
Secure Best Marks with AI Grader
Need help grading? Try our AI Grader for instant feedback on your assignments.
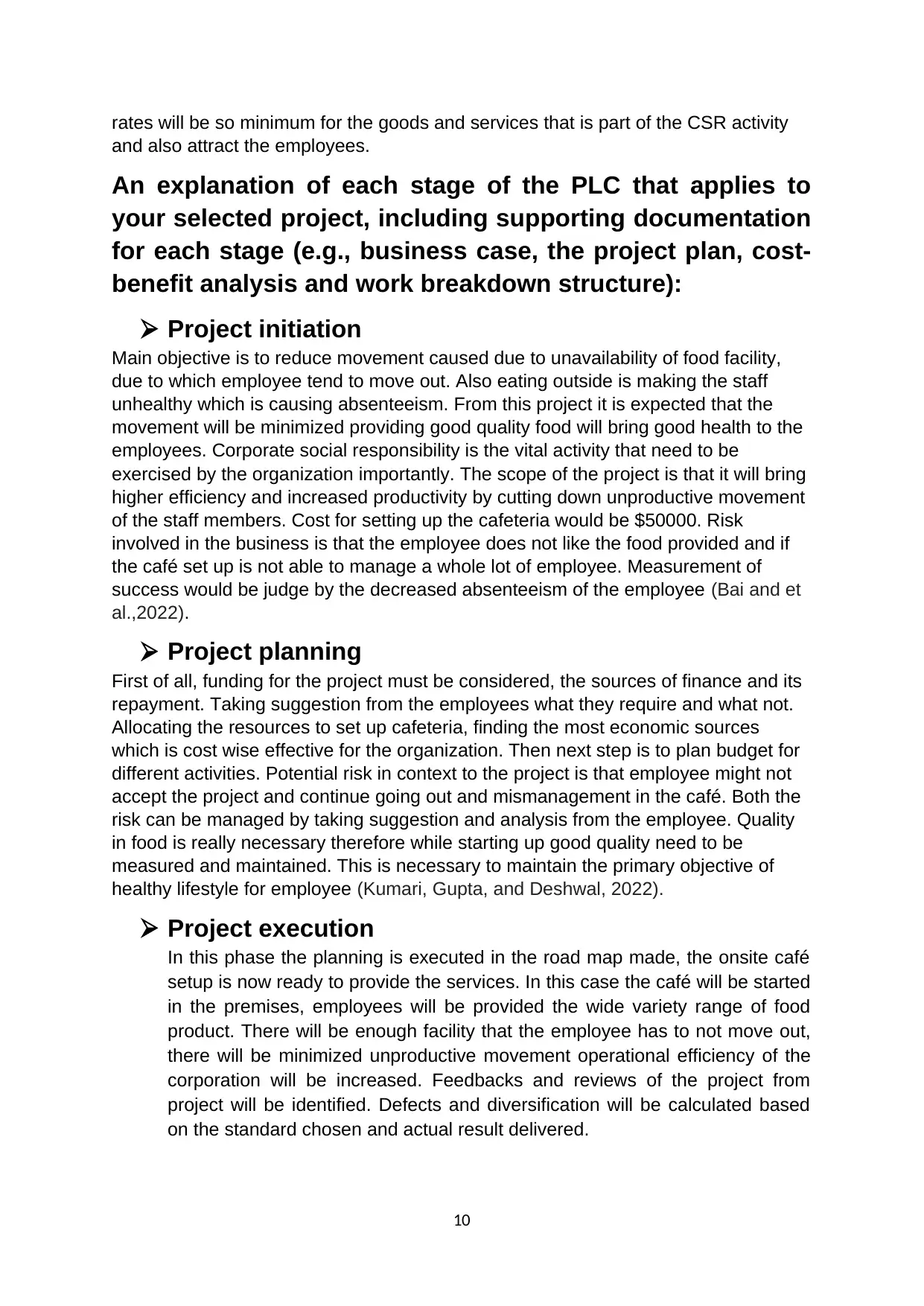
rates will be so minimum for the goods and services that is part of the CSR activity
and also attract the employees.
An explanation of each stage of the PLC that applies to
your selected project, including supporting documentation
for each stage (e.g., business case, the project plan, cost-
benefit analysis and work breakdown structure):
Project initiation
Main objective is to reduce movement caused due to unavailability of food facility,
due to which employee tend to move out. Also eating outside is making the staff
unhealthy which is causing absenteeism. From this project it is expected that the
movement will be minimized providing good quality food will bring good health to the
employees. Corporate social responsibility is the vital activity that need to be
exercised by the organization importantly. The scope of the project is that it will bring
higher efficiency and increased productivity by cutting down unproductive movement
of the staff members. Cost for setting up the cafeteria would be $50000. Risk
involved in the business is that the employee does not like the food provided and if
the café set up is not able to manage a whole lot of employee. Measurement of
success would be judge by the decreased absenteeism of the employee (Bai and et
al.,2022).
Project planning
First of all, funding for the project must be considered, the sources of finance and its
repayment. Taking suggestion from the employees what they require and what not.
Allocating the resources to set up cafeteria, finding the most economic sources
which is cost wise effective for the organization. Then next step is to plan budget for
different activities. Potential risk in context to the project is that employee might not
accept the project and continue going out and mismanagement in the café. Both the
risk can be managed by taking suggestion and analysis from the employee. Quality
in food is really necessary therefore while starting up good quality need to be
measured and maintained. This is necessary to maintain the primary objective of
healthy lifestyle for employee (Kumari, Gupta, and Deshwal, 2022).
Project execution
In this phase the planning is executed in the road map made, the onsite café
setup is now ready to provide the services. In this case the café will be started
in the premises, employees will be provided the wide variety range of food
product. There will be enough facility that the employee has to not move out,
there will be minimized unproductive movement operational efficiency of the
corporation will be increased. Feedbacks and reviews of the project from
project will be identified. Defects and diversification will be calculated based
on the standard chosen and actual result delivered.
10
and also attract the employees.
An explanation of each stage of the PLC that applies to
your selected project, including supporting documentation
for each stage (e.g., business case, the project plan, cost-
benefit analysis and work breakdown structure):
Project initiation
Main objective is to reduce movement caused due to unavailability of food facility,
due to which employee tend to move out. Also eating outside is making the staff
unhealthy which is causing absenteeism. From this project it is expected that the
movement will be minimized providing good quality food will bring good health to the
employees. Corporate social responsibility is the vital activity that need to be
exercised by the organization importantly. The scope of the project is that it will bring
higher efficiency and increased productivity by cutting down unproductive movement
of the staff members. Cost for setting up the cafeteria would be $50000. Risk
involved in the business is that the employee does not like the food provided and if
the café set up is not able to manage a whole lot of employee. Measurement of
success would be judge by the decreased absenteeism of the employee (Bai and et
al.,2022).
Project planning
First of all, funding for the project must be considered, the sources of finance and its
repayment. Taking suggestion from the employees what they require and what not.
Allocating the resources to set up cafeteria, finding the most economic sources
which is cost wise effective for the organization. Then next step is to plan budget for
different activities. Potential risk in context to the project is that employee might not
accept the project and continue going out and mismanagement in the café. Both the
risk can be managed by taking suggestion and analysis from the employee. Quality
in food is really necessary therefore while starting up good quality need to be
measured and maintained. This is necessary to maintain the primary objective of
healthy lifestyle for employee (Kumari, Gupta, and Deshwal, 2022).
Project execution
In this phase the planning is executed in the road map made, the onsite café
setup is now ready to provide the services. In this case the café will be started
in the premises, employees will be provided the wide variety range of food
product. There will be enough facility that the employee has to not move out,
there will be minimized unproductive movement operational efficiency of the
corporation will be increased. Feedbacks and reviews of the project from
project will be identified. Defects and diversification will be calculated based
on the standard chosen and actual result delivered.
10
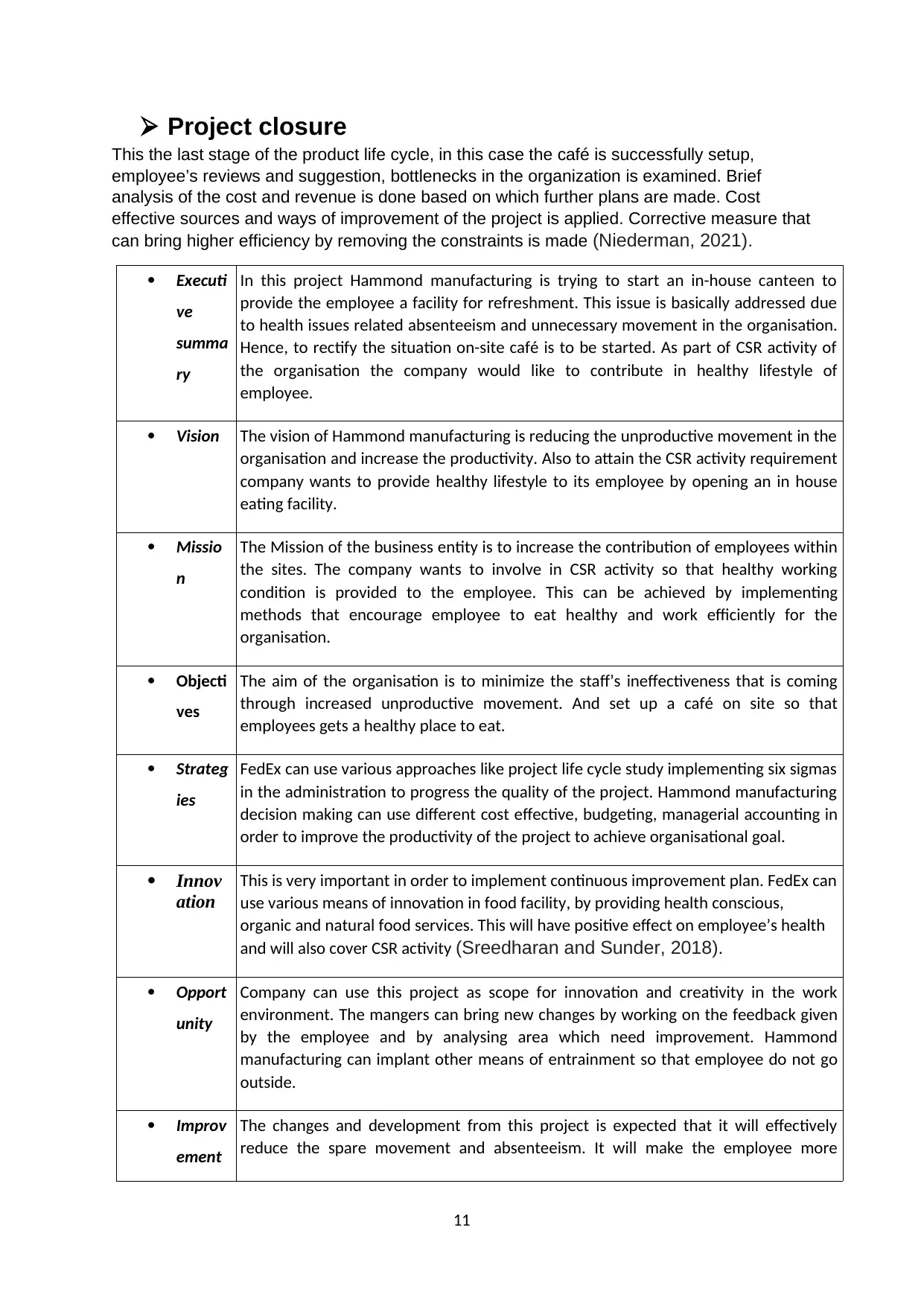
Project closure
This the last stage of the product life cycle, in this case the café is successfully setup,
employee’s reviews and suggestion, bottlenecks in the organization is examined. Brief
analysis of the cost and revenue is done based on which further plans are made. Cost
effective sources and ways of improvement of the project is applied. Corrective measure that
can bring higher efficiency by removing the constraints is made (Niederman, 2021).
Executi
ve
summa
ry
In this project Hammond manufacturing is trying to start an in-house canteen to
provide the employee a facility for refreshment. This issue is basically addressed due
to health issues related absenteeism and unnecessary movement in the organisation.
Hence, to rectify the situation on-site café is to be started. As part of CSR activity of
the organisation the company would like to contribute in healthy lifestyle of
employee.
Vision The vision of Hammond manufacturing is reducing the unproductive movement in the
organisation and increase the productivity. Also to attain the CSR activity requirement
company wants to provide healthy lifestyle to its employee by opening an in house
eating facility.
Missio
n
The Mission of the business entity is to increase the contribution of employees within
the sites. The company wants to involve in CSR activity so that healthy working
condition is provided to the employee. This can be achieved by implementing
methods that encourage employee to eat healthy and work efficiently for the
organisation.
Objecti
ves
The aim of the organisation is to minimize the staff’s ineffectiveness that is coming
through increased unproductive movement. And set up a café on site so that
employees gets a healthy place to eat.
Strateg
ies
FedEx can use various approaches like project life cycle study implementing six sigmas
in the administration to progress the quality of the project. Hammond manufacturing
decision making can use different cost effective, budgeting, managerial accounting in
order to improve the productivity of the project to achieve organisational goal.
Innov
ation
This is very important in order to implement continuous improvement plan. FedEx can
use various means of innovation in food facility, by providing health conscious,
organic and natural food services. This will have positive effect on employee’s health
and will also cover CSR activity (Sreedharan and Sunder, 2018).
Opport
unity
Company can use this project as scope for innovation and creativity in the work
environment. The mangers can bring new changes by working on the feedback given
by the employee and by analysing area which need improvement. Hammond
manufacturing can implant other means of entrainment so that employee do not go
outside.
Improv
ement
The changes and development from this project is expected that it will effectively
reduce the spare movement and absenteeism. It will make the employee more
11
This the last stage of the product life cycle, in this case the café is successfully setup,
employee’s reviews and suggestion, bottlenecks in the organization is examined. Brief
analysis of the cost and revenue is done based on which further plans are made. Cost
effective sources and ways of improvement of the project is applied. Corrective measure that
can bring higher efficiency by removing the constraints is made (Niederman, 2021).
Executi
ve
summa
ry
In this project Hammond manufacturing is trying to start an in-house canteen to
provide the employee a facility for refreshment. This issue is basically addressed due
to health issues related absenteeism and unnecessary movement in the organisation.
Hence, to rectify the situation on-site café is to be started. As part of CSR activity of
the organisation the company would like to contribute in healthy lifestyle of
employee.
Vision The vision of Hammond manufacturing is reducing the unproductive movement in the
organisation and increase the productivity. Also to attain the CSR activity requirement
company wants to provide healthy lifestyle to its employee by opening an in house
eating facility.
Missio
n
The Mission of the business entity is to increase the contribution of employees within
the sites. The company wants to involve in CSR activity so that healthy working
condition is provided to the employee. This can be achieved by implementing
methods that encourage employee to eat healthy and work efficiently for the
organisation.
Objecti
ves
The aim of the organisation is to minimize the staff’s ineffectiveness that is coming
through increased unproductive movement. And set up a café on site so that
employees gets a healthy place to eat.
Strateg
ies
FedEx can use various approaches like project life cycle study implementing six sigmas
in the administration to progress the quality of the project. Hammond manufacturing
decision making can use different cost effective, budgeting, managerial accounting in
order to improve the productivity of the project to achieve organisational goal.
Innov
ation
This is very important in order to implement continuous improvement plan. FedEx can
use various means of innovation in food facility, by providing health conscious,
organic and natural food services. This will have positive effect on employee’s health
and will also cover CSR activity (Sreedharan and Sunder, 2018).
Opport
unity
Company can use this project as scope for innovation and creativity in the work
environment. The mangers can bring new changes by working on the feedback given
by the employee and by analysing area which need improvement. Hammond
manufacturing can implant other means of entrainment so that employee do not go
outside.
Improv
ement
The changes and development from this project is expected that it will effectively
reduce the spare movement and absenteeism. It will make the employee more
11
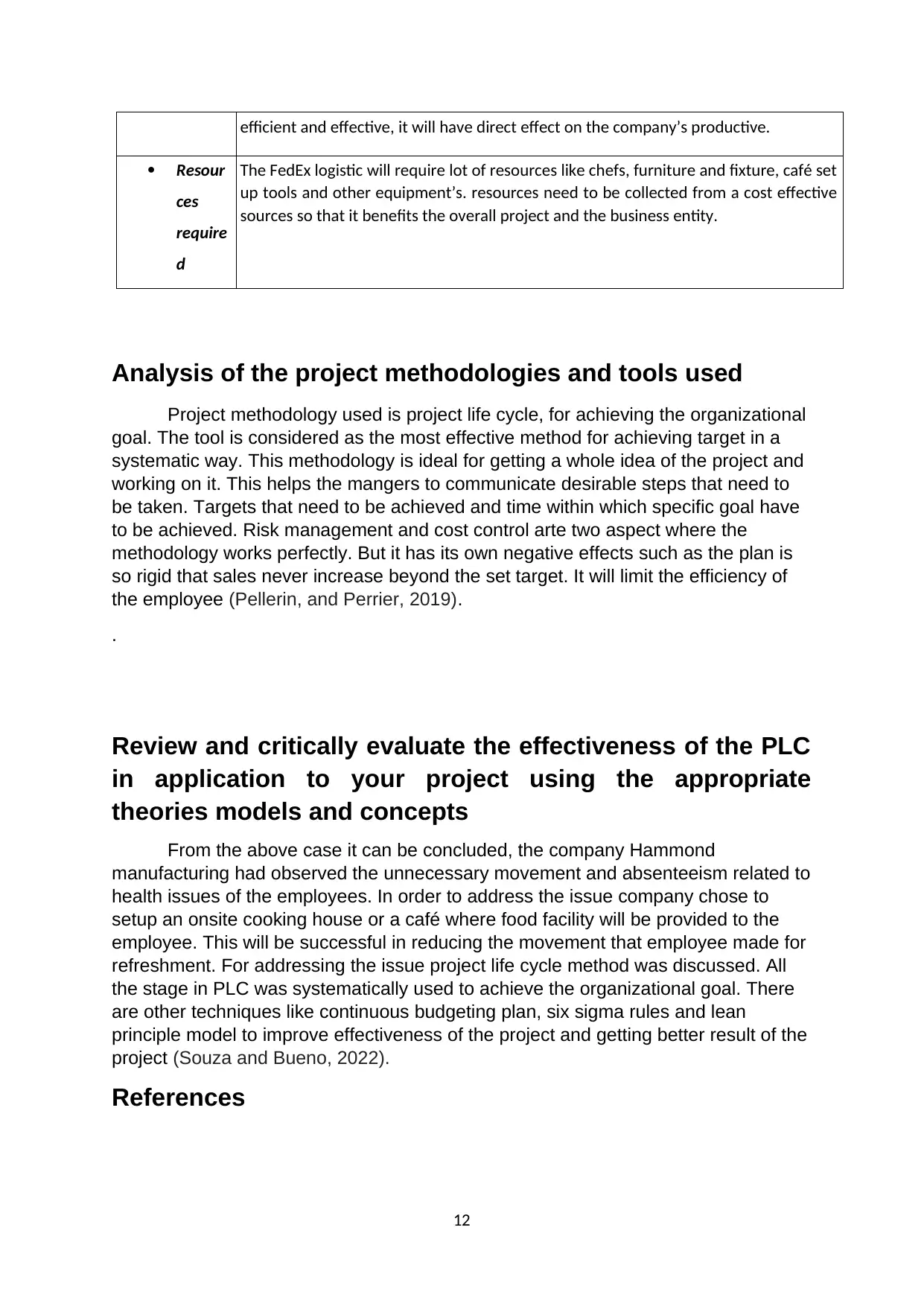
efficient and effective, it will have direct effect on the company’s productive.
Resour
ces
require
d
The FedEx logistic will require lot of resources like chefs, furniture and fixture, café set
up tools and other equipment’s. resources need to be collected from a cost effective
sources so that it benefits the overall project and the business entity.
Analysis of the project methodologies and tools used
Project methodology used is project life cycle, for achieving the organizational
goal. The tool is considered as the most effective method for achieving target in a
systematic way. This methodology is ideal for getting a whole idea of the project and
working on it. This helps the mangers to communicate desirable steps that need to
be taken. Targets that need to be achieved and time within which specific goal have
to be achieved. Risk management and cost control arte two aspect where the
methodology works perfectly. But it has its own negative effects such as the plan is
so rigid that sales never increase beyond the set target. It will limit the efficiency of
the employee (Pellerin, and Perrier, 2019).
.
Review and critically evaluate the effectiveness of the PLC
in application to your project using the appropriate
theories models and concepts
From the above case it can be concluded, the company Hammond
manufacturing had observed the unnecessary movement and absenteeism related to
health issues of the employees. In order to address the issue company chose to
setup an onsite cooking house or a café where food facility will be provided to the
employee. This will be successful in reducing the movement that employee made for
refreshment. For addressing the issue project life cycle method was discussed. All
the stage in PLC was systematically used to achieve the organizational goal. There
are other techniques like continuous budgeting plan, six sigma rules and lean
principle model to improve effectiveness of the project and getting better result of the
project (Souza and Bueno, 2022).
References
12
Resour
ces
require
d
The FedEx logistic will require lot of resources like chefs, furniture and fixture, café set
up tools and other equipment’s. resources need to be collected from a cost effective
sources so that it benefits the overall project and the business entity.
Analysis of the project methodologies and tools used
Project methodology used is project life cycle, for achieving the organizational
goal. The tool is considered as the most effective method for achieving target in a
systematic way. This methodology is ideal for getting a whole idea of the project and
working on it. This helps the mangers to communicate desirable steps that need to
be taken. Targets that need to be achieved and time within which specific goal have
to be achieved. Risk management and cost control arte two aspect where the
methodology works perfectly. But it has its own negative effects such as the plan is
so rigid that sales never increase beyond the set target. It will limit the efficiency of
the employee (Pellerin, and Perrier, 2019).
.
Review and critically evaluate the effectiveness of the PLC
in application to your project using the appropriate
theories models and concepts
From the above case it can be concluded, the company Hammond
manufacturing had observed the unnecessary movement and absenteeism related to
health issues of the employees. In order to address the issue company chose to
setup an onsite cooking house or a café where food facility will be provided to the
employee. This will be successful in reducing the movement that employee made for
refreshment. For addressing the issue project life cycle method was discussed. All
the stage in PLC was systematically used to achieve the organizational goal. There
are other techniques like continuous budgeting plan, six sigma rules and lean
principle model to improve effectiveness of the project and getting better result of the
project (Souza and Bueno, 2022).
References
12
Paraphrase This Document
Need a fresh take? Get an instant paraphrase of this document with our AI Paraphraser
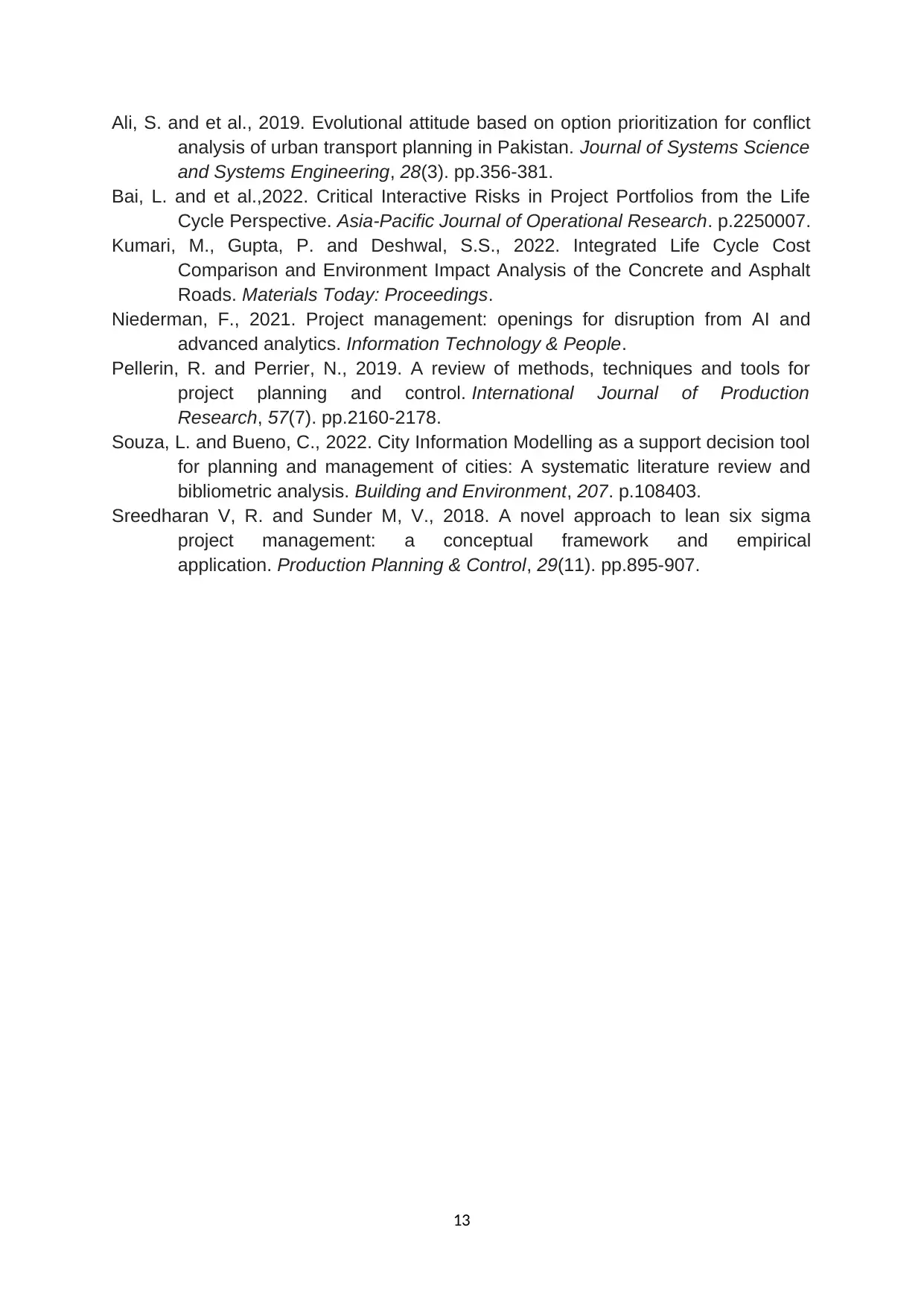
Ali, S. and et al., 2019. Evolutional attitude based on option prioritization for conflict
analysis of urban transport planning in Pakistan. Journal of Systems Science
and Systems Engineering, 28(3). pp.356-381.
Bai, L. and et al.,2022. Critical Interactive Risks in Project Portfolios from the Life
Cycle Perspective. Asia-Pacific Journal of Operational Research. p.2250007.
Kumari, M., Gupta, P. and Deshwal, S.S., 2022. Integrated Life Cycle Cost
Comparison and Environment Impact Analysis of the Concrete and Asphalt
Roads. Materials Today: Proceedings.
Niederman, F., 2021. Project management: openings for disruption from AI and
advanced analytics. Information Technology & People.
Pellerin, R. and Perrier, N., 2019. A review of methods, techniques and tools for
project planning and control. International Journal of Production
Research, 57(7). pp.2160-2178.
Souza, L. and Bueno, C., 2022. City Information Modelling as a support decision tool
for planning and management of cities: A systematic literature review and
bibliometric analysis. Building and Environment, 207. p.108403.
Sreedharan V, R. and Sunder M, V., 2018. A novel approach to lean six sigma
project management: a conceptual framework and empirical
application. Production Planning & Control, 29(11). pp.895-907.
13
analysis of urban transport planning in Pakistan. Journal of Systems Science
and Systems Engineering, 28(3). pp.356-381.
Bai, L. and et al.,2022. Critical Interactive Risks in Project Portfolios from the Life
Cycle Perspective. Asia-Pacific Journal of Operational Research. p.2250007.
Kumari, M., Gupta, P. and Deshwal, S.S., 2022. Integrated Life Cycle Cost
Comparison and Environment Impact Analysis of the Concrete and Asphalt
Roads. Materials Today: Proceedings.
Niederman, F., 2021. Project management: openings for disruption from AI and
advanced analytics. Information Technology & People.
Pellerin, R. and Perrier, N., 2019. A review of methods, techniques and tools for
project planning and control. International Journal of Production
Research, 57(7). pp.2160-2178.
Souza, L. and Bueno, C., 2022. City Information Modelling as a support decision tool
for planning and management of cities: A systematic literature review and
bibliometric analysis. Building and Environment, 207. p.108403.
Sreedharan V, R. and Sunder M, V., 2018. A novel approach to lean six sigma
project management: a conceptual framework and empirical
application. Production Planning & Control, 29(11). pp.895-907.
13
1 out of 14
Related Documents

Your All-in-One AI-Powered Toolkit for Academic Success.
+13062052269
info@desklib.com
Available 24*7 on WhatsApp / Email
Unlock your academic potential
© 2024 | Zucol Services PVT LTD | All rights reserved.