Operations & Project Management
VerifiedAdded on  2023/01/19
|19
|5282
|26
AI Summary
This assignment discusses the effectiveness of operations management principles and the concept of continuous improvement in an operational context. It also defines the project life cycle and critiques the application of PLC. The case study of Unilever is used as an example throughout the assignment.
Contribute Materials
Your contribution can guide someone’s learning journey. Share your
documents today.
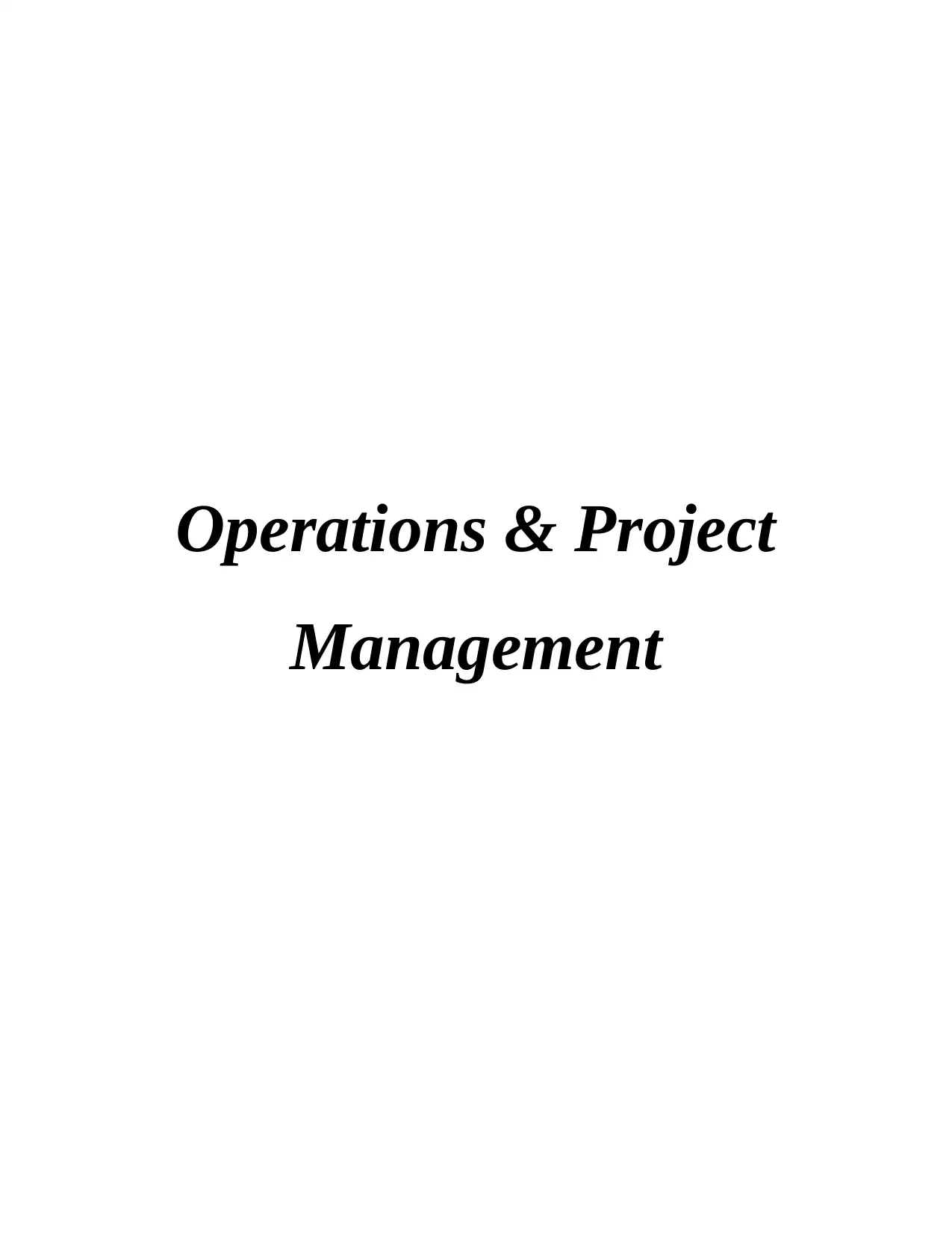
Operations & Project
Management
Management
Secure Best Marks with AI Grader
Need help grading? Try our AI Grader for instant feedback on your assignments.
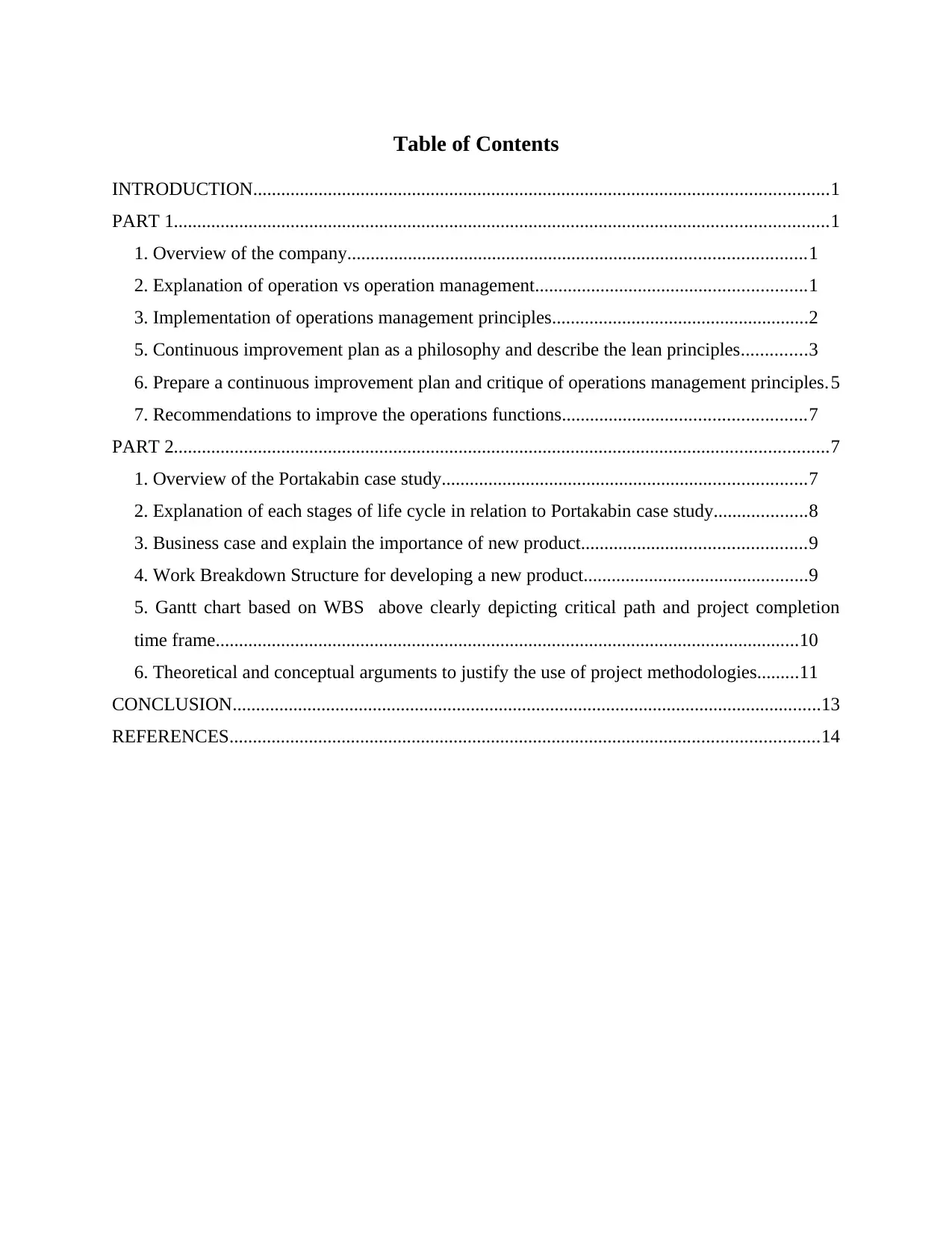
Table of Contents
INTRODUCTION...........................................................................................................................1
PART 1............................................................................................................................................1
1. Overview of the company..................................................................................................1
2. Explanation of operation vs operation management..........................................................1
3. Implementation of operations management principles.......................................................2
5. Continuous improvement plan as a philosophy and describe the lean principles..............3
6. Prepare a continuous improvement plan and critique of operations management principles.5
7. Recommendations to improve the operations functions....................................................7
PART 2............................................................................................................................................7
1. Overview of the Portakabin case study..............................................................................7
2. Explanation of each stages of life cycle in relation to Portakabin case study....................8
3. Business case and explain the importance of new product................................................9
4. Work Breakdown Structure for developing a new product................................................9
5. Gantt chart based on WBS above clearly depicting critical path and project completion
time frame.............................................................................................................................10
6. Theoretical and conceptual arguments to justify the use of project methodologies.........11
CONCLUSION..............................................................................................................................13
REFERENCES..............................................................................................................................14
INTRODUCTION...........................................................................................................................1
PART 1............................................................................................................................................1
1. Overview of the company..................................................................................................1
2. Explanation of operation vs operation management..........................................................1
3. Implementation of operations management principles.......................................................2
5. Continuous improvement plan as a philosophy and describe the lean principles..............3
6. Prepare a continuous improvement plan and critique of operations management principles.5
7. Recommendations to improve the operations functions....................................................7
PART 2............................................................................................................................................7
1. Overview of the Portakabin case study..............................................................................7
2. Explanation of each stages of life cycle in relation to Portakabin case study....................8
3. Business case and explain the importance of new product................................................9
4. Work Breakdown Structure for developing a new product................................................9
5. Gantt chart based on WBS above clearly depicting critical path and project completion
time frame.............................................................................................................................10
6. Theoretical and conceptual arguments to justify the use of project methodologies.........11
CONCLUSION..............................................................................................................................13
REFERENCES..............................................................................................................................14
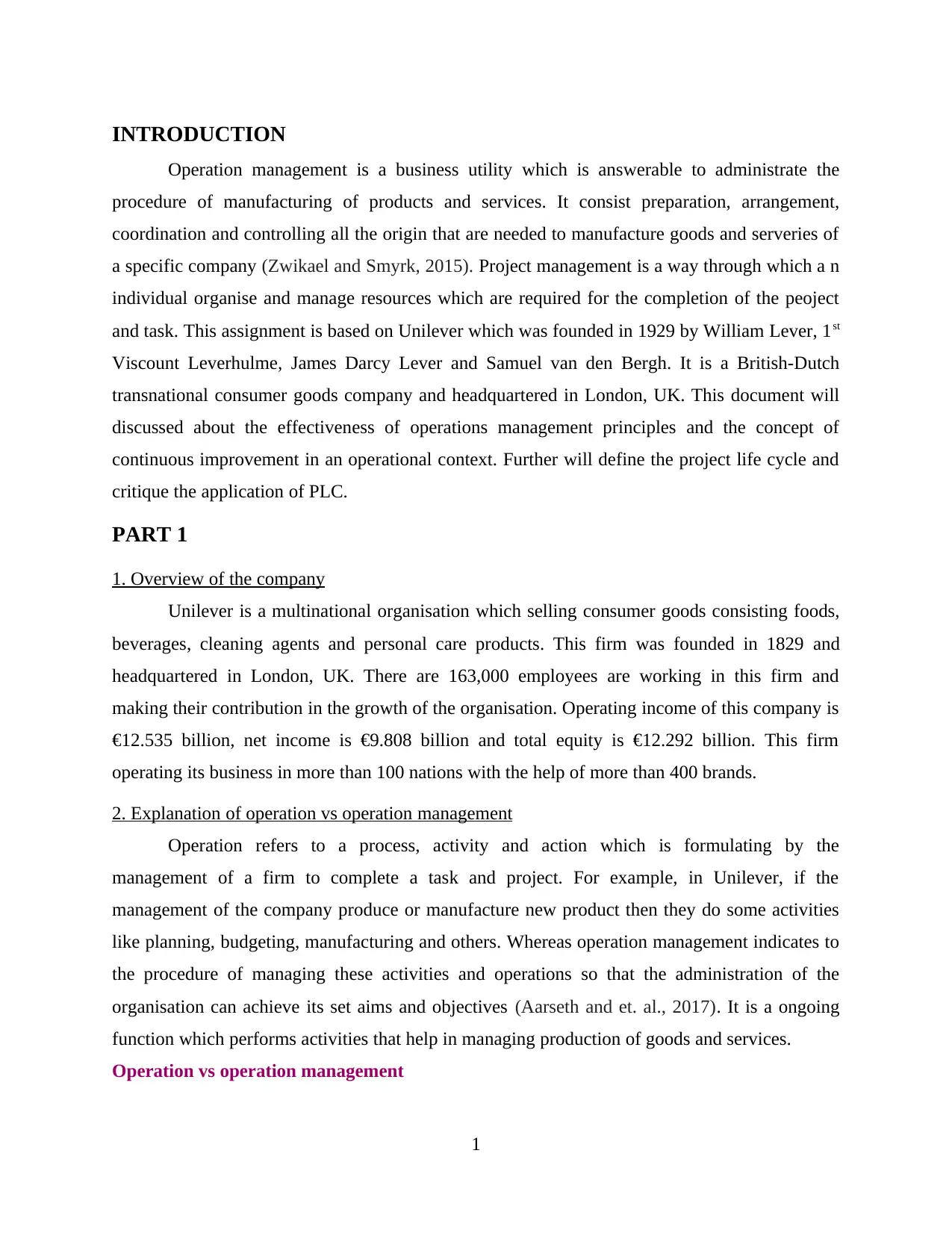
INTRODUCTION
Operation management is a business utility which is answerable to administrate the
procedure of manufacturing of products and services. It consist preparation, arrangement,
coordination and controlling all the origin that are needed to manufacture goods and serveries of
a specific company (Zwikael and Smyrk, 2015). Project management is a way through which a n
individual organise and manage resources which are required for the completion of the peoject
and task. This assignment is based on Unilever which was founded in 1929 by William Lever, 1st
Viscount Leverhulme, James Darcy Lever and Samuel van den Bergh. It is a British-Dutch
transnational consumer goods company and headquartered in London, UK. This document will
discussed about the effectiveness of operations management principles and the concept of
continuous improvement in an operational context. Further will define the project life cycle and
critique the application of PLC.
PART 1
1. Overview of the company
Unilever is a multinational organisation which selling consumer goods consisting foods,
beverages, cleaning agents and personal care products. This firm was founded in 1829 and
headquartered in London, UK. There are 163,000 employees are working in this firm and
making their contribution in the growth of the organisation. Operating income of this company is
€12.535 billion, net income is €9.808 billion and total equity is €12.292 billion. This firm
operating its business in more than 100 nations with the help of more than 400 brands.
2. Explanation of operation vs operation management
Operation refers to a process, activity and action which is formulating by the
management of a firm to complete a task and project. For example, in Unilever, if the
management of the company produce or manufacture new product then they do some activities
like planning, budgeting, manufacturing and others. Whereas operation management indicates to
the procedure of managing these activities and operations so that the administration of the
organisation can achieve its set aims and objectives (Aarseth and et. al., 2017). It is a ongoing
function which performs activities that help in managing production of goods and services.
Operation vs operation management
1
Operation management is a business utility which is answerable to administrate the
procedure of manufacturing of products and services. It consist preparation, arrangement,
coordination and controlling all the origin that are needed to manufacture goods and serveries of
a specific company (Zwikael and Smyrk, 2015). Project management is a way through which a n
individual organise and manage resources which are required for the completion of the peoject
and task. This assignment is based on Unilever which was founded in 1929 by William Lever, 1st
Viscount Leverhulme, James Darcy Lever and Samuel van den Bergh. It is a British-Dutch
transnational consumer goods company and headquartered in London, UK. This document will
discussed about the effectiveness of operations management principles and the concept of
continuous improvement in an operational context. Further will define the project life cycle and
critique the application of PLC.
PART 1
1. Overview of the company
Unilever is a multinational organisation which selling consumer goods consisting foods,
beverages, cleaning agents and personal care products. This firm was founded in 1829 and
headquartered in London, UK. There are 163,000 employees are working in this firm and
making their contribution in the growth of the organisation. Operating income of this company is
€12.535 billion, net income is €9.808 billion and total equity is €12.292 billion. This firm
operating its business in more than 100 nations with the help of more than 400 brands.
2. Explanation of operation vs operation management
Operation refers to a process, activity and action which is formulating by the
management of a firm to complete a task and project. For example, in Unilever, if the
management of the company produce or manufacture new product then they do some activities
like planning, budgeting, manufacturing and others. Whereas operation management indicates to
the procedure of managing these activities and operations so that the administration of the
organisation can achieve its set aims and objectives (Aarseth and et. al., 2017). It is a ongoing
function which performs activities that help in managing production of goods and services.
Operation vs operation management
1
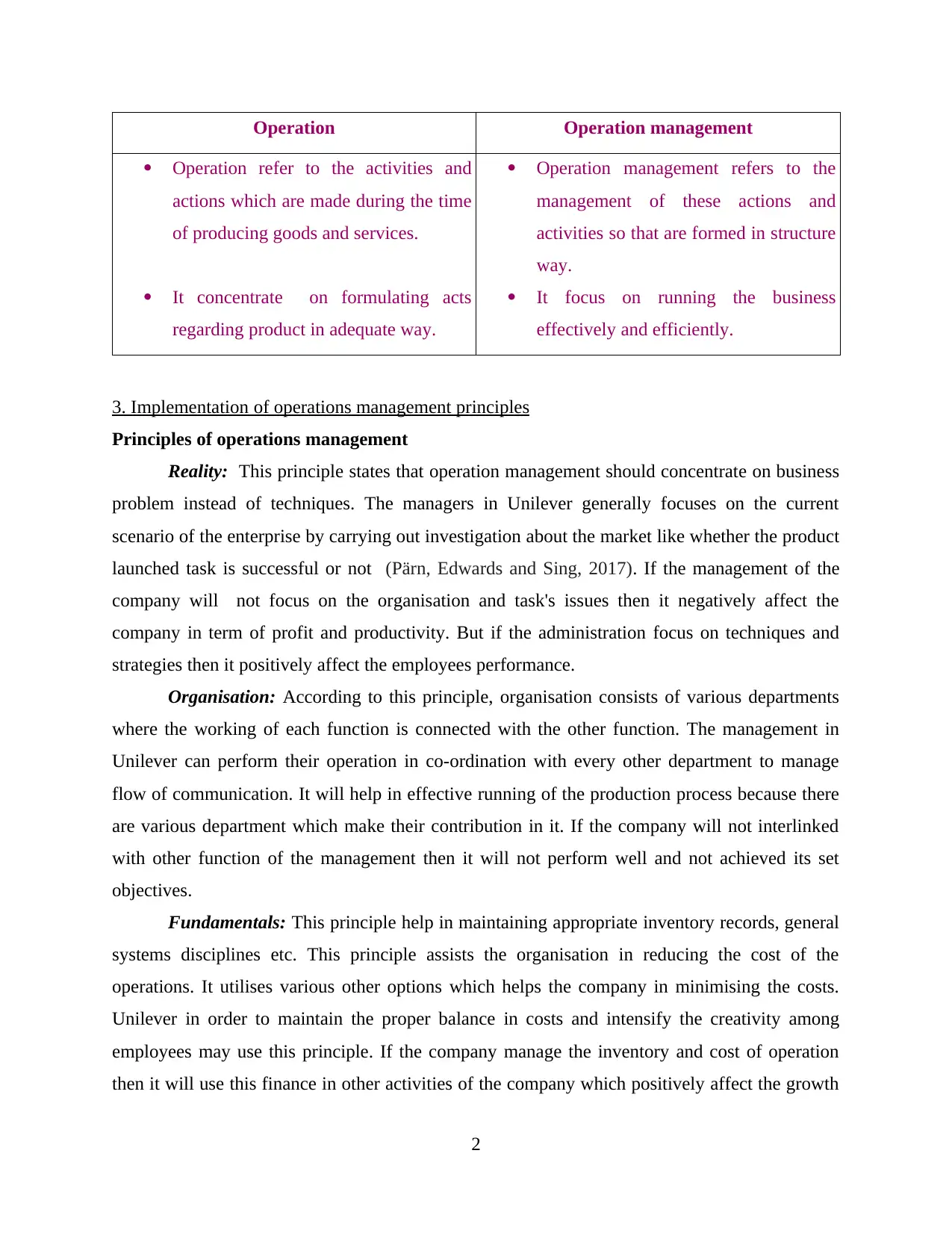
Operation Operation management
ď‚· Operation refer to the activities and
actions which are made during the time
of producing goods and services.
ď‚· It concentrate on formulating acts
regarding product in adequate way.
ď‚· Operation management refers to the
management of these actions and
activities so that are formed in structure
way.
ď‚· It focus on running the business
effectively and efficiently.
3. Implementation of operations management principles
Principles of operations management
Reality: This principle states that operation management should concentrate on business
problem instead of techniques. The managers in Unilever generally focuses on the current
scenario of the enterprise by carrying out investigation about the market like whether the product
launched task is successful or not (Pärn, Edwards and Sing, 2017). If the management of the
company will not focus on the organisation and task's issues then it negatively affect the
company in term of profit and productivity. But if the administration focus on techniques and
strategies then it positively affect the employees performance.
Organisation: According to this principle, organisation consists of various departments
where the working of each function is connected with the other function. The management in
Unilever can perform their operation in co-ordination with every other department to manage
flow of communication. It will help in effective running of the production process because there
are various department which make their contribution in it. If the company will not interlinked
with other function of the management then it will not perform well and not achieved its set
objectives.
Fundamentals: This principle help in maintaining appropriate inventory records, general
systems disciplines etc. This principle assists the organisation in reducing the cost of the
operations. It utilises various other options which helps the company in minimising the costs.
Unilever in order to maintain the proper balance in costs and intensify the creativity among
employees may use this principle. If the company manage the inventory and cost of operation
then it will use this finance in other activities of the company which positively affect the growth
2
ď‚· Operation refer to the activities and
actions which are made during the time
of producing goods and services.
ď‚· It concentrate on formulating acts
regarding product in adequate way.
ď‚· Operation management refers to the
management of these actions and
activities so that are formed in structure
way.
ď‚· It focus on running the business
effectively and efficiently.
3. Implementation of operations management principles
Principles of operations management
Reality: This principle states that operation management should concentrate on business
problem instead of techniques. The managers in Unilever generally focuses on the current
scenario of the enterprise by carrying out investigation about the market like whether the product
launched task is successful or not (Pärn, Edwards and Sing, 2017). If the management of the
company will not focus on the organisation and task's issues then it negatively affect the
company in term of profit and productivity. But if the administration focus on techniques and
strategies then it positively affect the employees performance.
Organisation: According to this principle, organisation consists of various departments
where the working of each function is connected with the other function. The management in
Unilever can perform their operation in co-ordination with every other department to manage
flow of communication. It will help in effective running of the production process because there
are various department which make their contribution in it. If the company will not interlinked
with other function of the management then it will not perform well and not achieved its set
objectives.
Fundamentals: This principle help in maintaining appropriate inventory records, general
systems disciplines etc. This principle assists the organisation in reducing the cost of the
operations. It utilises various other options which helps the company in minimising the costs.
Unilever in order to maintain the proper balance in costs and intensify the creativity among
employees may use this principle. If the company manage the inventory and cost of operation
then it will use this finance in other activities of the company which positively affect the growth
2
Secure Best Marks with AI Grader
Need help grading? Try our AI Grader for instant feedback on your assignments.
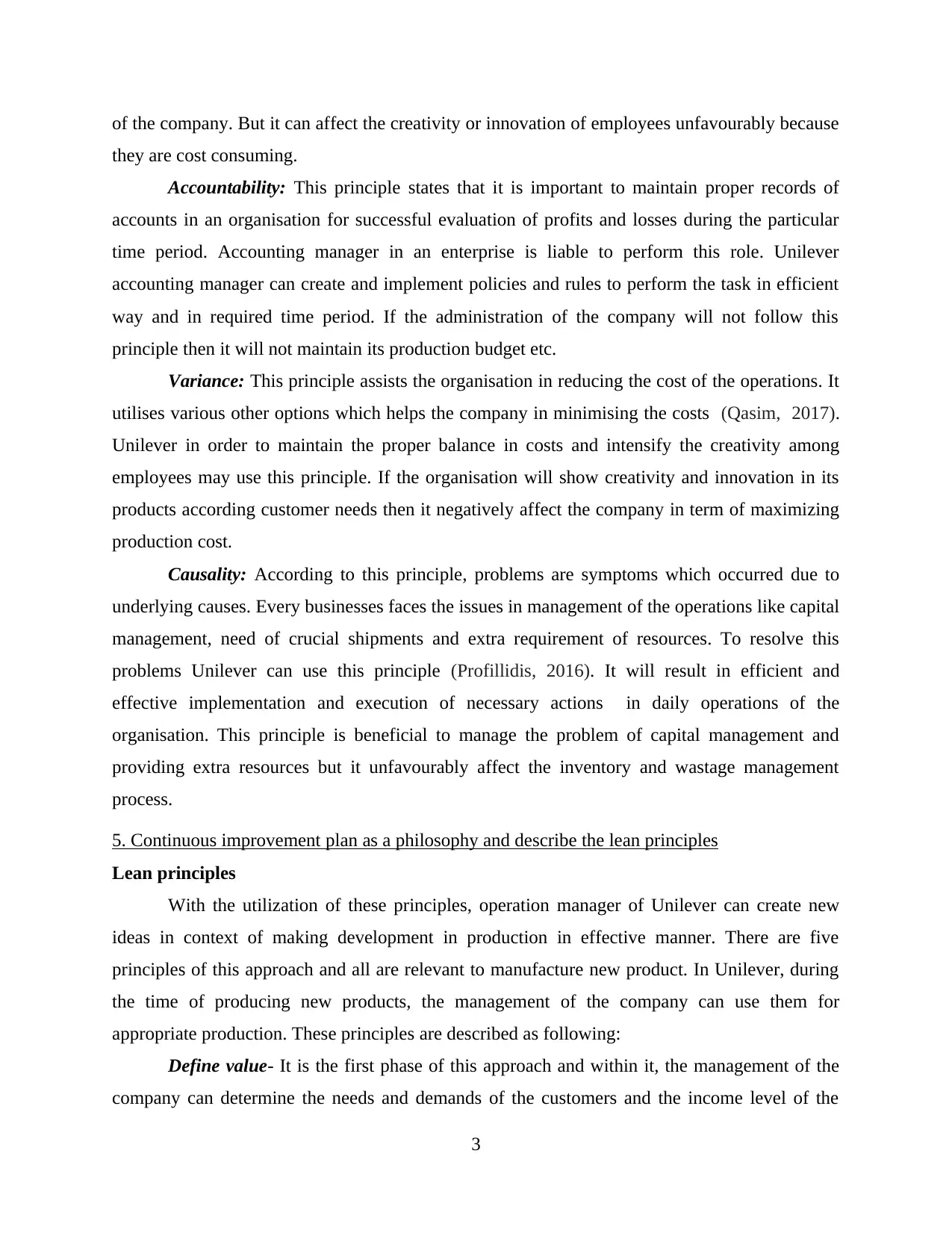
of the company. But it can affect the creativity or innovation of employees unfavourably because
they are cost consuming.
Accountability: This principle states that it is important to maintain proper records of
accounts in an organisation for successful evaluation of profits and losses during the particular
time period. Accounting manager in an enterprise is liable to perform this role. Unilever
accounting manager can create and implement policies and rules to perform the task in efficient
way and in required time period. If the administration of the company will not follow this
principle then it will not maintain its production budget etc.
Variance: This principle assists the organisation in reducing the cost of the operations. It
utilises various other options which helps the company in minimising the costs (Qasim, 2017).
Unilever in order to maintain the proper balance in costs and intensify the creativity among
employees may use this principle. If the organisation will show creativity and innovation in its
products according customer needs then it negatively affect the company in term of maximizing
production cost.
Causality: According to this principle, problems are symptoms which occurred due to
underlying causes. Every businesses faces the issues in management of the operations like capital
management, need of crucial shipments and extra requirement of resources. To resolve this
problems Unilever can use this principle (Profillidis, 2016). It will result in efficient and
effective implementation and execution of necessary actions in daily operations of the
organisation. This principle is beneficial to manage the problem of capital management and
providing extra resources but it unfavourably affect the inventory and wastage management
process.
5. Continuous improvement plan as a philosophy and describe the lean principles
Lean principles
With the utilization of these principles, operation manager of Unilever can create new
ideas in context of making development in production in effective manner. There are five
principles of this approach and all are relevant to manufacture new product. In Unilever, during
the time of producing new products, the management of the company can use them for
appropriate production. These principles are described as following:
Define value- It is the first phase of this approach and within it, the management of the
company can determine the needs and demands of the customers and the income level of the
3
they are cost consuming.
Accountability: This principle states that it is important to maintain proper records of
accounts in an organisation for successful evaluation of profits and losses during the particular
time period. Accounting manager in an enterprise is liable to perform this role. Unilever
accounting manager can create and implement policies and rules to perform the task in efficient
way and in required time period. If the administration of the company will not follow this
principle then it will not maintain its production budget etc.
Variance: This principle assists the organisation in reducing the cost of the operations. It
utilises various other options which helps the company in minimising the costs (Qasim, 2017).
Unilever in order to maintain the proper balance in costs and intensify the creativity among
employees may use this principle. If the organisation will show creativity and innovation in its
products according customer needs then it negatively affect the company in term of maximizing
production cost.
Causality: According to this principle, problems are symptoms which occurred due to
underlying causes. Every businesses faces the issues in management of the operations like capital
management, need of crucial shipments and extra requirement of resources. To resolve this
problems Unilever can use this principle (Profillidis, 2016). It will result in efficient and
effective implementation and execution of necessary actions in daily operations of the
organisation. This principle is beneficial to manage the problem of capital management and
providing extra resources but it unfavourably affect the inventory and wastage management
process.
5. Continuous improvement plan as a philosophy and describe the lean principles
Lean principles
With the utilization of these principles, operation manager of Unilever can create new
ideas in context of making development in production in effective manner. There are five
principles of this approach and all are relevant to manufacture new product. In Unilever, during
the time of producing new products, the management of the company can use them for
appropriate production. These principles are described as following:
Define value- It is the first phase of this approach and within it, the management of the
company can determine the needs and demands of the customers and the income level of the
3
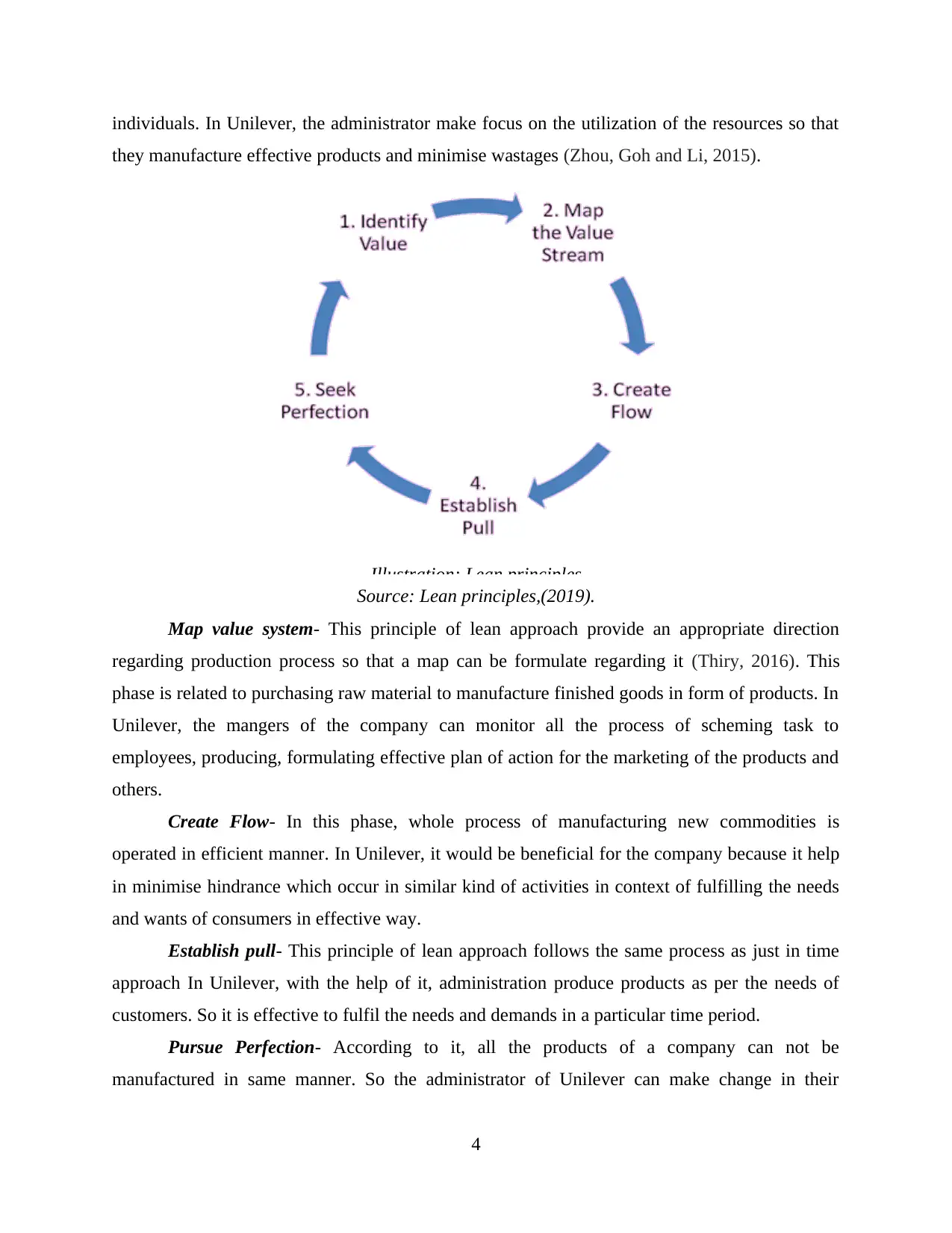
individuals. In Unilever, the administrator make focus on the utilization of the resources so that
they manufacture effective products and minimise wastages (Zhou, Goh and Li, 2015).
Source: Lean principles,(2019).
Map value system- This principle of lean approach provide an appropriate direction
regarding production process so that a map can be formulate regarding it (Thiry, 2016). This
phase is related to purchasing raw material to manufacture finished goods in form of products. In
Unilever, the mangers of the company can monitor all the process of scheming task to
employees, producing, formulating effective plan of action for the marketing of the products and
others.
Create Flow- In this phase, whole process of manufacturing new commodities is
operated in efficient manner. In Unilever, it would be beneficial for the company because it help
in minimise hindrance which occur in similar kind of activities in context of fulfilling the needs
and wants of consumers in effective way.
Establish pull- This principle of lean approach follows the same process as just in time
approach In Unilever, with the help of it, administration produce products as per the needs of
customers. So it is effective to fulfil the needs and demands in a particular time period.
Pursue Perfection- According to it, all the products of a company can not be
manufactured in same manner. So the administrator of Unilever can make change in their
4
Illustration: Lean principles
they manufacture effective products and minimise wastages (Zhou, Goh and Li, 2015).
Source: Lean principles,(2019).
Map value system- This principle of lean approach provide an appropriate direction
regarding production process so that a map can be formulate regarding it (Thiry, 2016). This
phase is related to purchasing raw material to manufacture finished goods in form of products. In
Unilever, the mangers of the company can monitor all the process of scheming task to
employees, producing, formulating effective plan of action for the marketing of the products and
others.
Create Flow- In this phase, whole process of manufacturing new commodities is
operated in efficient manner. In Unilever, it would be beneficial for the company because it help
in minimise hindrance which occur in similar kind of activities in context of fulfilling the needs
and wants of consumers in effective way.
Establish pull- This principle of lean approach follows the same process as just in time
approach In Unilever, with the help of it, administration produce products as per the needs of
customers. So it is effective to fulfil the needs and demands in a particular time period.
Pursue Perfection- According to it, all the products of a company can not be
manufactured in same manner. So the administrator of Unilever can make change in their
4
Illustration: Lean principles
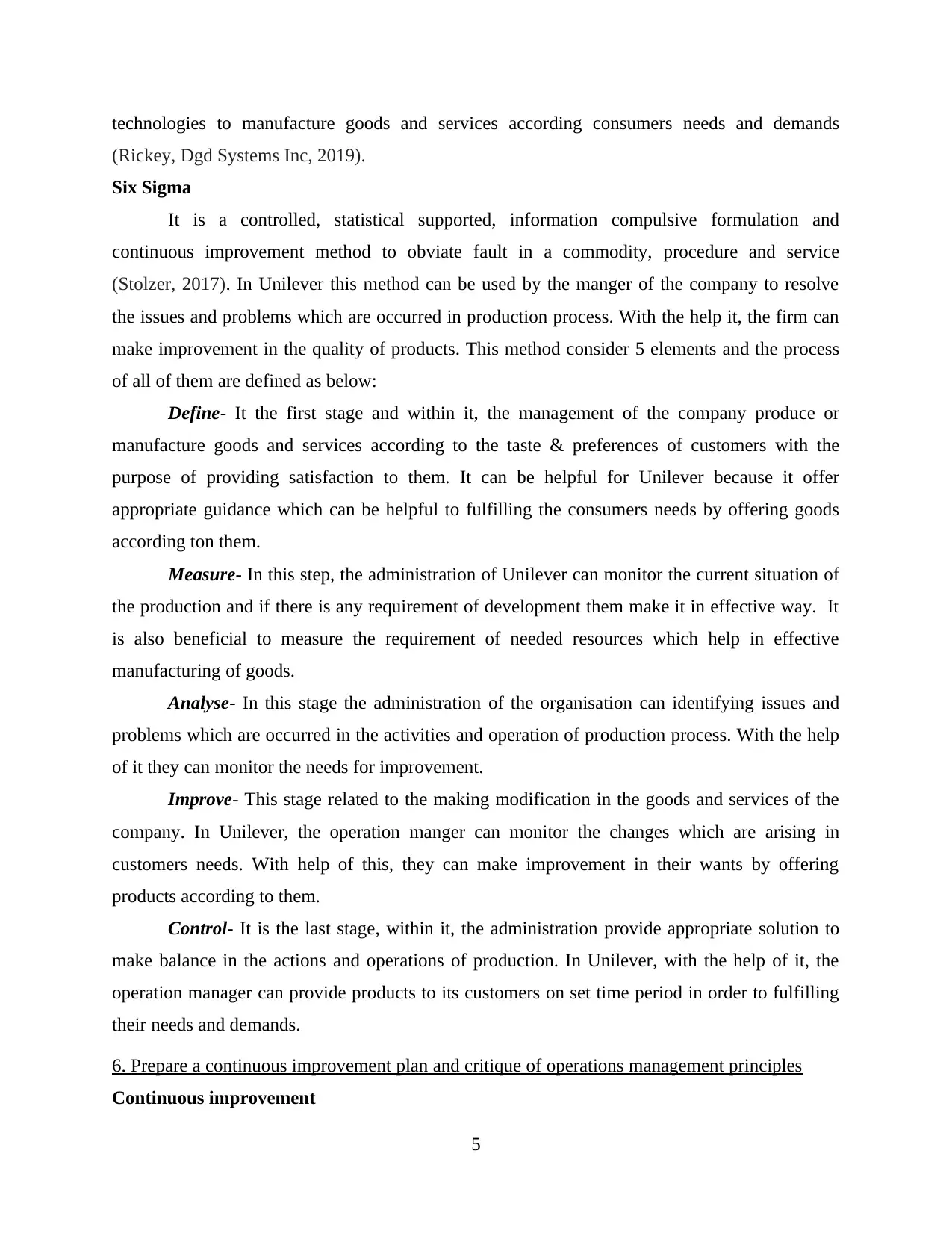
technologies to manufacture goods and services according consumers needs and demands
(Rickey, Dgd Systems Inc, 2019).
Six Sigma
It is a controlled, statistical supported, information compulsive formulation and
continuous improvement method to obviate fault in a commodity, procedure and service
(Stolzer, 2017). In Unilever this method can be used by the manger of the company to resolve
the issues and problems which are occurred in production process. With the help it, the firm can
make improvement in the quality of products. This method consider 5 elements and the process
of all of them are defined as below:
Define- It the first stage and within it, the management of the company produce or
manufacture goods and services according to the taste & preferences of customers with the
purpose of providing satisfaction to them. It can be helpful for Unilever because it offer
appropriate guidance which can be helpful to fulfilling the consumers needs by offering goods
according ton them.
Measure- In this step, the administration of Unilever can monitor the current situation of
the production and if there is any requirement of development them make it in effective way. It
is also beneficial to measure the requirement of needed resources which help in effective
manufacturing of goods.
Analyse- In this stage the administration of the organisation can identifying issues and
problems which are occurred in the activities and operation of production process. With the help
of it they can monitor the needs for improvement.
Improve- This stage related to the making modification in the goods and services of the
company. In Unilever, the operation manger can monitor the changes which are arising in
customers needs. With help of this, they can make improvement in their wants by offering
products according to them.
Control- It is the last stage, within it, the administration provide appropriate solution to
make balance in the actions and operations of production. In Unilever, with the help of it, the
operation manager can provide products to its customers on set time period in order to fulfilling
their needs and demands.
6. Prepare a continuous improvement plan and critique of operations management principles
Continuous improvement
5
(Rickey, Dgd Systems Inc, 2019).
Six Sigma
It is a controlled, statistical supported, information compulsive formulation and
continuous improvement method to obviate fault in a commodity, procedure and service
(Stolzer, 2017). In Unilever this method can be used by the manger of the company to resolve
the issues and problems which are occurred in production process. With the help it, the firm can
make improvement in the quality of products. This method consider 5 elements and the process
of all of them are defined as below:
Define- It the first stage and within it, the management of the company produce or
manufacture goods and services according to the taste & preferences of customers with the
purpose of providing satisfaction to them. It can be helpful for Unilever because it offer
appropriate guidance which can be helpful to fulfilling the consumers needs by offering goods
according ton them.
Measure- In this step, the administration of Unilever can monitor the current situation of
the production and if there is any requirement of development them make it in effective way. It
is also beneficial to measure the requirement of needed resources which help in effective
manufacturing of goods.
Analyse- In this stage the administration of the organisation can identifying issues and
problems which are occurred in the activities and operation of production process. With the help
of it they can monitor the needs for improvement.
Improve- This stage related to the making modification in the goods and services of the
company. In Unilever, the operation manger can monitor the changes which are arising in
customers needs. With help of this, they can make improvement in their wants by offering
products according to them.
Control- It is the last stage, within it, the administration provide appropriate solution to
make balance in the actions and operations of production. In Unilever, with the help of it, the
operation manager can provide products to its customers on set time period in order to fulfilling
their needs and demands.
6. Prepare a continuous improvement plan and critique of operations management principles
Continuous improvement
5
Paraphrase This Document
Need a fresh take? Get an instant paraphrase of this document with our AI Paraphraser
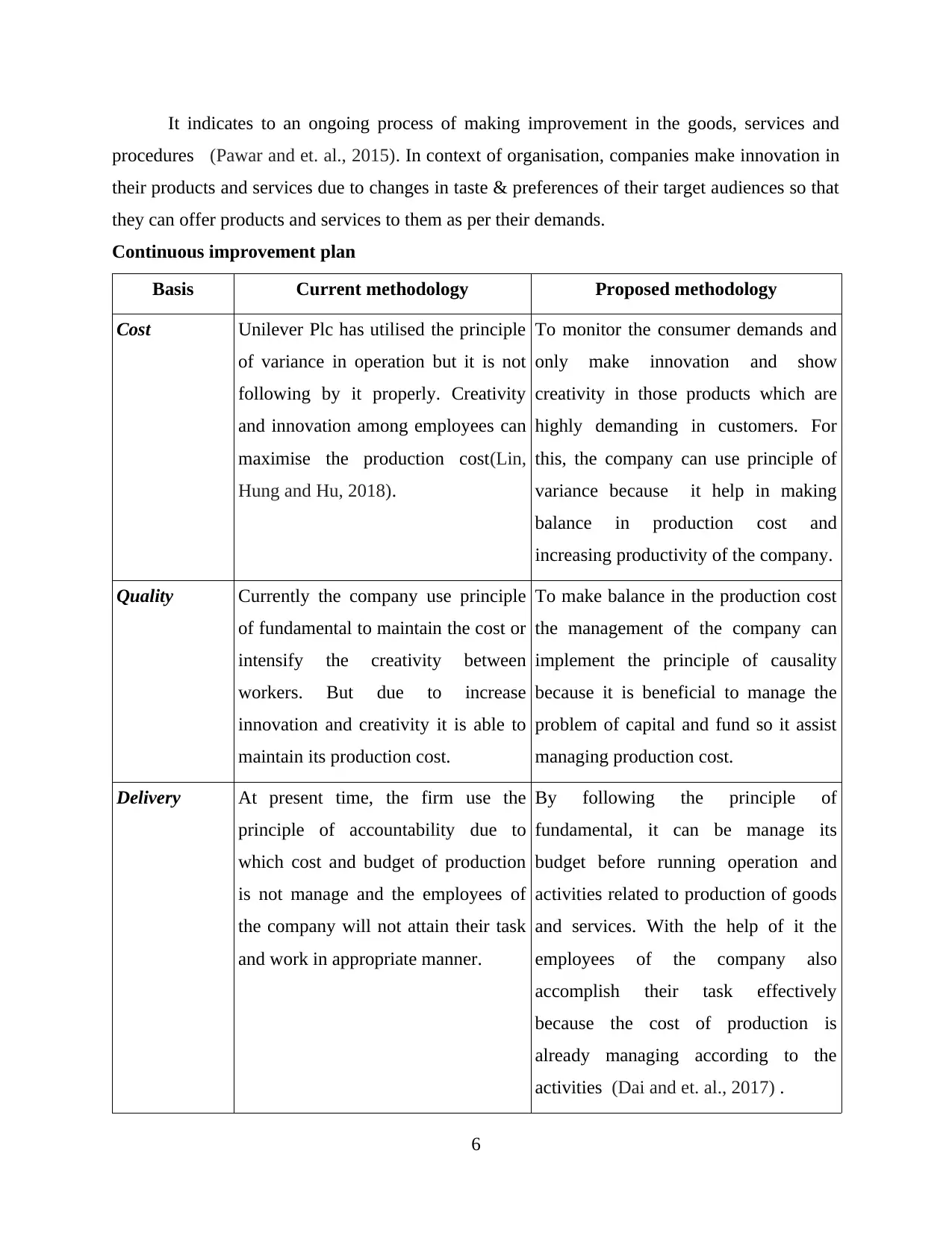
It indicates to an ongoing process of making improvement in the goods, services and
procedures (Pawar and et. al., 2015). In context of organisation, companies make innovation in
their products and services due to changes in taste & preferences of their target audiences so that
they can offer products and services to them as per their demands.
Continuous improvement plan
Basis Current methodology Proposed methodology
Cost Unilever Plc has utilised the principle
of variance in operation but it is not
following by it properly. Creativity
and innovation among employees can
maximise the production cost(Lin,
Hung and Hu, 2018).
To monitor the consumer demands and
only make innovation and show
creativity in those products which are
highly demanding in customers. For
this, the company can use principle of
variance because it help in making
balance in production cost and
increasing productivity of the company.
Quality Currently the company use principle
of fundamental to maintain the cost or
intensify the creativity between
workers. But due to increase
innovation and creativity it is able to
maintain its production cost.
To make balance in the production cost
the management of the company can
implement the principle of causality
because it is beneficial to manage the
problem of capital and fund so it assist
managing production cost.
Delivery At present time, the firm use the
principle of accountability due to
which cost and budget of production
is not manage and the employees of
the company will not attain their task
and work in appropriate manner.
By following the principle of
fundamental, it can be manage its
budget before running operation and
activities related to production of goods
and services. With the help of it the
employees of the company also
accomplish their task effectively
because the cost of production is
already managing according to the
activities (Dai and et. al., 2017) .
6
procedures (Pawar and et. al., 2015). In context of organisation, companies make innovation in
their products and services due to changes in taste & preferences of their target audiences so that
they can offer products and services to them as per their demands.
Continuous improvement plan
Basis Current methodology Proposed methodology
Cost Unilever Plc has utilised the principle
of variance in operation but it is not
following by it properly. Creativity
and innovation among employees can
maximise the production cost(Lin,
Hung and Hu, 2018).
To monitor the consumer demands and
only make innovation and show
creativity in those products which are
highly demanding in customers. For
this, the company can use principle of
variance because it help in making
balance in production cost and
increasing productivity of the company.
Quality Currently the company use principle
of fundamental to maintain the cost or
intensify the creativity between
workers. But due to increase
innovation and creativity it is able to
maintain its production cost.
To make balance in the production cost
the management of the company can
implement the principle of causality
because it is beneficial to manage the
problem of capital and fund so it assist
managing production cost.
Delivery At present time, the firm use the
principle of accountability due to
which cost and budget of production
is not manage and the employees of
the company will not attain their task
and work in appropriate manner.
By following the principle of
fundamental, it can be manage its
budget before running operation and
activities related to production of goods
and services. With the help of it the
employees of the company also
accomplish their task effectively
because the cost of production is
already managing according to the
activities (Dai and et. al., 2017) .
6
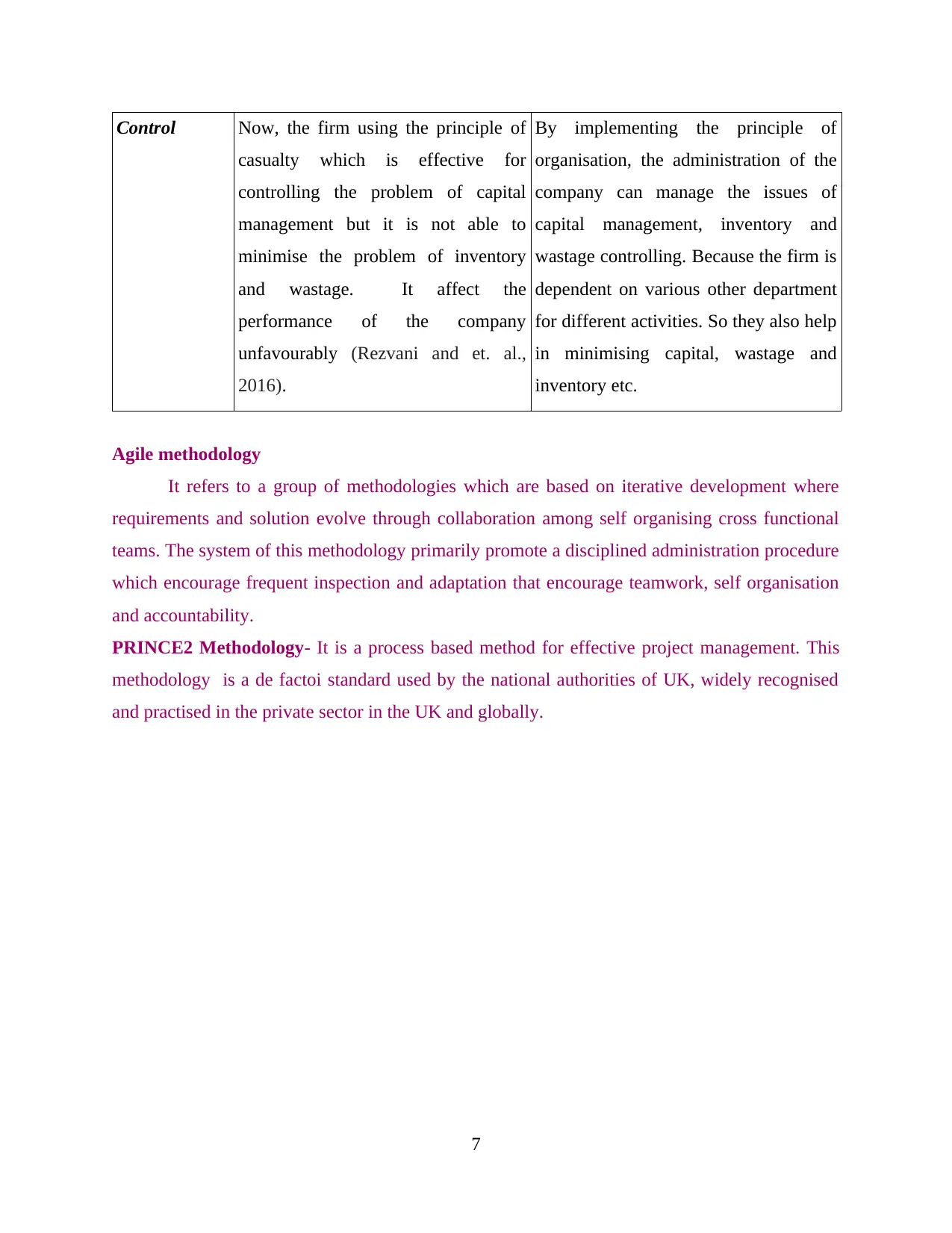
Control Now, the firm using the principle of
casualty which is effective for
controlling the problem of capital
management but it is not able to
minimise the problem of inventory
and wastage. It affect the
performance of the company
unfavourably (Rezvani and et. al.,
2016).
By implementing the principle of
organisation, the administration of the
company can manage the issues of
capital management, inventory and
wastage controlling. Because the firm is
dependent on various other department
for different activities. So they also help
in minimising capital, wastage and
inventory etc.
Agile methodology
It refers to a group of methodologies which are based on iterative development where
requirements and solution evolve through collaboration among self organising cross functional
teams. The system of this methodology primarily promote a disciplined administration procedure
which encourage frequent inspection and adaptation that encourage teamwork, self organisation
and accountability.
PRINCE2 Methodology- It is a process based method for effective project management. This
methodology is a de factoi standard used by the national authorities of UK, widely recognised
and practised in the private sector in the UK and globally.
7
casualty which is effective for
controlling the problem of capital
management but it is not able to
minimise the problem of inventory
and wastage. It affect the
performance of the company
unfavourably (Rezvani and et. al.,
2016).
By implementing the principle of
organisation, the administration of the
company can manage the issues of
capital management, inventory and
wastage controlling. Because the firm is
dependent on various other department
for different activities. So they also help
in minimising capital, wastage and
inventory etc.
Agile methodology
It refers to a group of methodologies which are based on iterative development where
requirements and solution evolve through collaboration among self organising cross functional
teams. The system of this methodology primarily promote a disciplined administration procedure
which encourage frequent inspection and adaptation that encourage teamwork, self organisation
and accountability.
PRINCE2 Methodology- It is a process based method for effective project management. This
methodology is a de factoi standard used by the national authorities of UK, widely recognised
and practised in the private sector in the UK and globally.
7
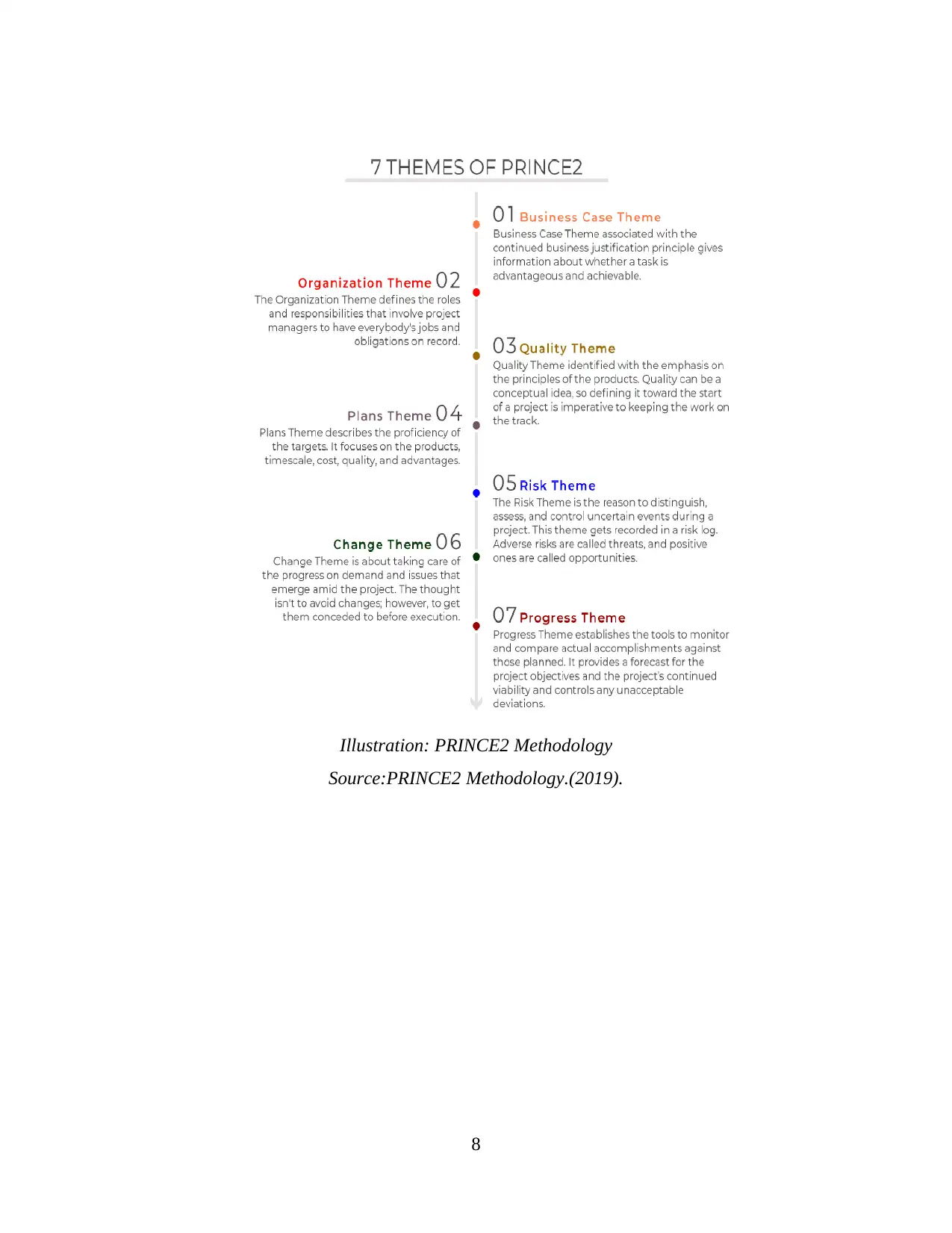
Source:PRINCE2 Methodology.(2019).
8
Illustration: PRINCE2 Methodology
8
Illustration: PRINCE2 Methodology
Secure Best Marks with AI Grader
Need help grading? Try our AI Grader for instant feedback on your assignments.

7. Recommendations to improve the operations functions
As per the preceding defined improvement plan, it can be monitored that the organisation
faced several issues during the time of producing goods and services. The operation
administrator of the company should use the principle of organisation because to run the business
operations, he firm interlinked with other functions of management. If the company will not
make control on capital management and production cost then finance department will prepare
budget and cash flow for its production process. Marketing department will help in monitoring
the needs and demands of the customers so that the firm can produce goods and services
according consumers demand and minimise the wastages and extra production. It can also
recommanded to Unilever that if it is following principle of fundamental, the management of the
company can develop budget before running activities and operations of production then
employees can perform their job roles and assigned work in appropriate manner because it will
be already structure according to the budget.
PART 2
1. Overview of the Portakabin case study
Overview of case study
Portakabin Ltd is an organisation which deal in designs and manufactures modular,
portable and temporary building for several customers. This firm was founded in 1961 and
headquartered in Huntington York, UK. It is operating its business in 6 nation of the world and
there are 1300 employees who are working their and making their participation in the success of
the company (Haydo, 2018). It is a business to business firm and currently this organisation
launched its latest product the “Yorkon Building System”. It is advance technology which help
in constructing multi sectional building.
2. Explanation of each stages of life cycle in relation to Portakabin case study
Project life cycle
It refers to the sequences and series of steps through which a specific project undergoes
form starting to closing. It is a series of actions which are essential for accomplishing project
objectives or targets. Projects may have different dimensions and difficulty extent but whatever
the size such as large or small may be all project could be mapped to the lifestyle structure. This
9
As per the preceding defined improvement plan, it can be monitored that the organisation
faced several issues during the time of producing goods and services. The operation
administrator of the company should use the principle of organisation because to run the business
operations, he firm interlinked with other functions of management. If the company will not
make control on capital management and production cost then finance department will prepare
budget and cash flow for its production process. Marketing department will help in monitoring
the needs and demands of the customers so that the firm can produce goods and services
according consumers demand and minimise the wastages and extra production. It can also
recommanded to Unilever that if it is following principle of fundamental, the management of the
company can develop budget before running activities and operations of production then
employees can perform their job roles and assigned work in appropriate manner because it will
be already structure according to the budget.
PART 2
1. Overview of the Portakabin case study
Overview of case study
Portakabin Ltd is an organisation which deal in designs and manufactures modular,
portable and temporary building for several customers. This firm was founded in 1961 and
headquartered in Huntington York, UK. It is operating its business in 6 nation of the world and
there are 1300 employees who are working their and making their participation in the success of
the company (Haydo, 2018). It is a business to business firm and currently this organisation
launched its latest product the “Yorkon Building System”. It is advance technology which help
in constructing multi sectional building.
2. Explanation of each stages of life cycle in relation to Portakabin case study
Project life cycle
It refers to the sequences and series of steps through which a specific project undergoes
form starting to closing. It is a series of actions which are essential for accomplishing project
objectives or targets. Projects may have different dimensions and difficulty extent but whatever
the size such as large or small may be all project could be mapped to the lifestyle structure. This
9
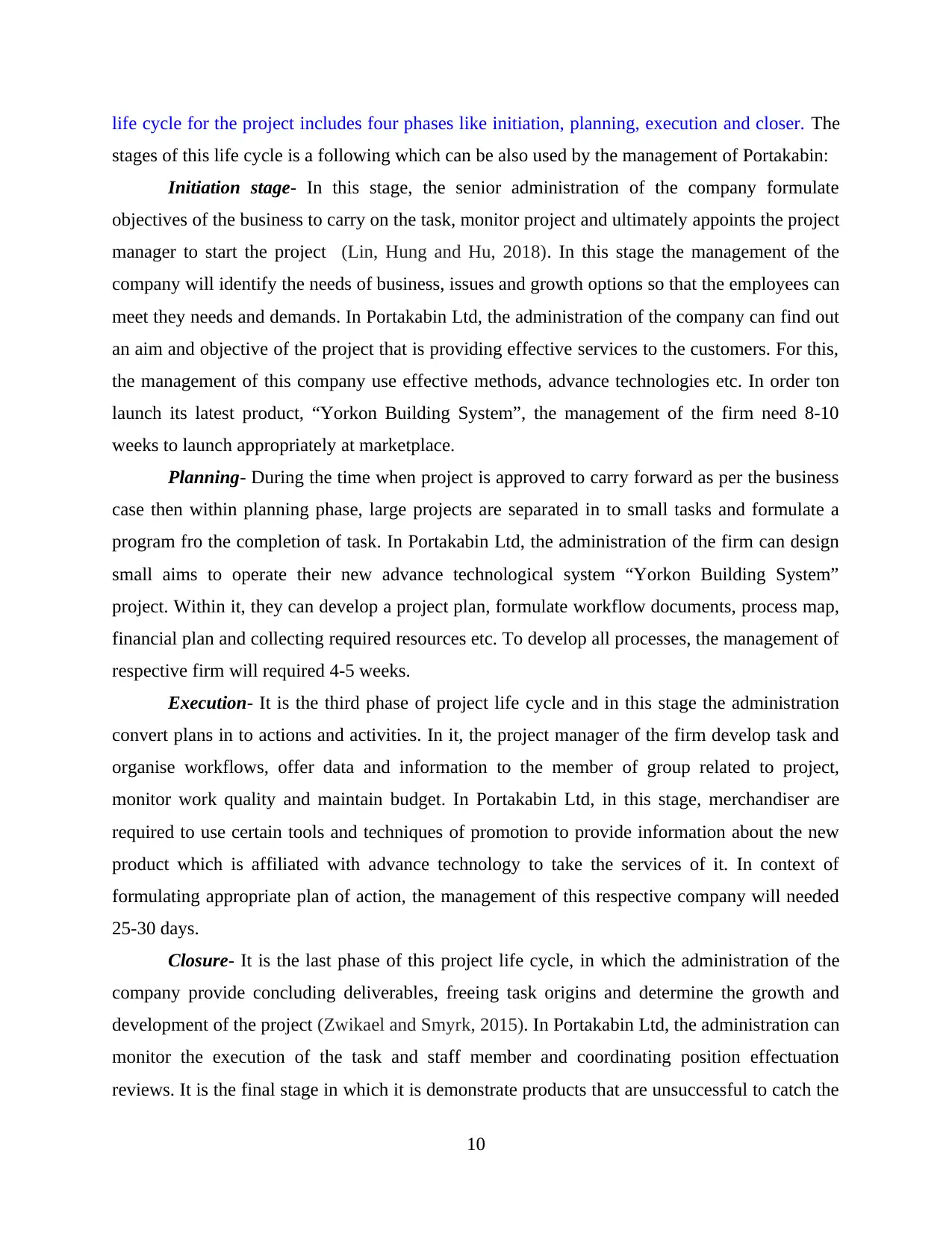
life cycle for the project includes four phases like initiation, planning, execution and closer. The
stages of this life cycle is a following which can be also used by the management of Portakabin:
Initiation stage- In this stage, the senior administration of the company formulate
objectives of the business to carry on the task, monitor project and ultimately appoints the project
manager to start the project (Lin, Hung and Hu, 2018). In this stage the management of the
company will identify the needs of business, issues and growth options so that the employees can
meet they needs and demands. In Portakabin Ltd, the administration of the company can find out
an aim and objective of the project that is providing effective services to the customers. For this,
the management of this company use effective methods, advance technologies etc. In order ton
launch its latest product, “Yorkon Building System”, the management of the firm need 8-10
weeks to launch appropriately at marketplace.
Planning- During the time when project is approved to carry forward as per the business
case then within planning phase, large projects are separated in to small tasks and formulate a
program fro the completion of task. In Portakabin Ltd, the administration of the firm can design
small aims to operate their new advance technological system “Yorkon Building System”
project. Within it, they can develop a project plan, formulate workflow documents, process map,
financial plan and collecting required resources etc. To develop all processes, the management of
respective firm will required 4-5 weeks.
Execution- It is the third phase of project life cycle and in this stage the administration
convert plans in to actions and activities. In it, the project manager of the firm develop task and
organise workflows, offer data and information to the member of group related to project,
monitor work quality and maintain budget. In Portakabin Ltd, in this stage, merchandiser are
required to use certain tools and techniques of promotion to provide information about the new
product which is affiliated with advance technology to take the services of it. In context of
formulating appropriate plan of action, the management of this respective company will needed
25-30 days.
Closure- It is the last phase of this project life cycle, in which the administration of the
company provide concluding deliverables, freeing task origins and determine the growth and
development of the project (Zwikael and Smyrk, 2015). In Portakabin Ltd, the administration can
monitor the execution of the task and staff member and coordinating position effectuation
reviews. It is the final stage in which it is demonstrate products that are unsuccessful to catch the
10
stages of this life cycle is a following which can be also used by the management of Portakabin:
Initiation stage- In this stage, the senior administration of the company formulate
objectives of the business to carry on the task, monitor project and ultimately appoints the project
manager to start the project (Lin, Hung and Hu, 2018). In this stage the management of the
company will identify the needs of business, issues and growth options so that the employees can
meet they needs and demands. In Portakabin Ltd, the administration of the company can find out
an aim and objective of the project that is providing effective services to the customers. For this,
the management of this company use effective methods, advance technologies etc. In order ton
launch its latest product, “Yorkon Building System”, the management of the firm need 8-10
weeks to launch appropriately at marketplace.
Planning- During the time when project is approved to carry forward as per the business
case then within planning phase, large projects are separated in to small tasks and formulate a
program fro the completion of task. In Portakabin Ltd, the administration of the firm can design
small aims to operate their new advance technological system “Yorkon Building System”
project. Within it, they can develop a project plan, formulate workflow documents, process map,
financial plan and collecting required resources etc. To develop all processes, the management of
respective firm will required 4-5 weeks.
Execution- It is the third phase of project life cycle and in this stage the administration
convert plans in to actions and activities. In it, the project manager of the firm develop task and
organise workflows, offer data and information to the member of group related to project,
monitor work quality and maintain budget. In Portakabin Ltd, in this stage, merchandiser are
required to use certain tools and techniques of promotion to provide information about the new
product which is affiliated with advance technology to take the services of it. In context of
formulating appropriate plan of action, the management of this respective company will needed
25-30 days.
Closure- It is the last phase of this project life cycle, in which the administration of the
company provide concluding deliverables, freeing task origins and determine the growth and
development of the project (Zwikael and Smyrk, 2015). In Portakabin Ltd, the administration can
monitor the execution of the task and staff member and coordinating position effectuation
reviews. It is the final stage in which it is demonstrate products that are unsuccessful to catch the
10
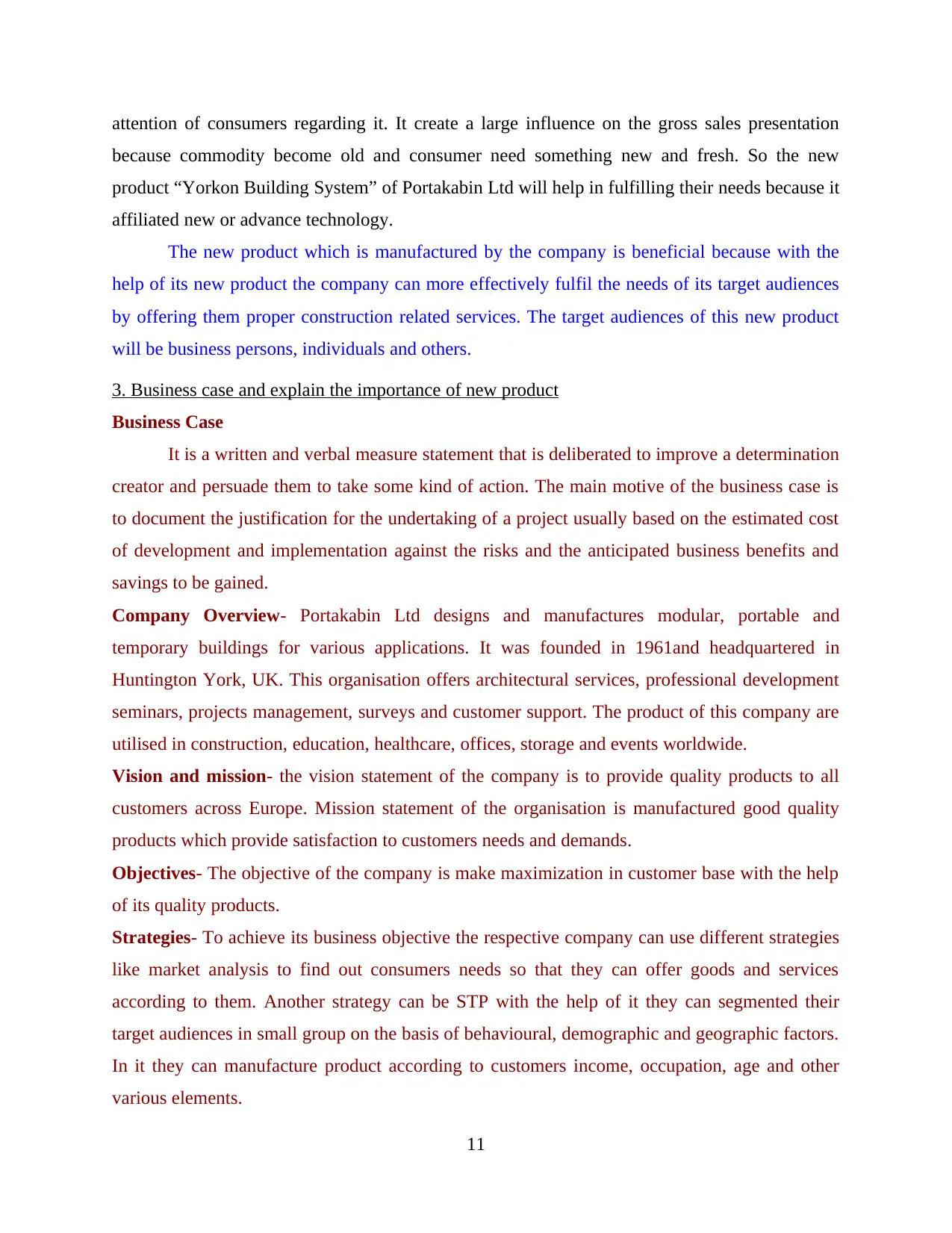
attention of consumers regarding it. It create a large influence on the gross sales presentation
because commodity become old and consumer need something new and fresh. So the new
product “Yorkon Building System” of Portakabin Ltd will help in fulfilling their needs because it
affiliated new or advance technology.
The new product which is manufactured by the company is beneficial because with the
help of its new product the company can more effectively fulfil the needs of its target audiences
by offering them proper construction related services. The target audiences of this new product
will be business persons, individuals and others.
3. Business case and explain the importance of new product
Business Case
It is a written and verbal measure statement that is deliberated to improve a determination
creator and persuade them to take some kind of action. The main motive of the business case is
to document the justification for the undertaking of a project usually based on the estimated cost
of development and implementation against the risks and the anticipated business benefits and
savings to be gained.
Company Overview- Portakabin Ltd designs and manufactures modular, portable and
temporary buildings for various applications. It was founded in 1961and headquartered in
Huntington York, UK. This organisation offers architectural services, professional development
seminars, projects management, surveys and customer support. The product of this company are
utilised in construction, education, healthcare, offices, storage and events worldwide.
Vision and mission- the vision statement of the company is to provide quality products to all
customers across Europe. Mission statement of the organisation is manufactured good quality
products which provide satisfaction to customers needs and demands.
Objectives- The objective of the company is make maximization in customer base with the help
of its quality products.
Strategies- To achieve its business objective the respective company can use different strategies
like market analysis to find out consumers needs so that they can offer goods and services
according to them. Another strategy can be STP with the help of it they can segmented their
target audiences in small group on the basis of behavioural, demographic and geographic factors.
In it they can manufacture product according to customers income, occupation, age and other
various elements.
11
because commodity become old and consumer need something new and fresh. So the new
product “Yorkon Building System” of Portakabin Ltd will help in fulfilling their needs because it
affiliated new or advance technology.
The new product which is manufactured by the company is beneficial because with the
help of its new product the company can more effectively fulfil the needs of its target audiences
by offering them proper construction related services. The target audiences of this new product
will be business persons, individuals and others.
3. Business case and explain the importance of new product
Business Case
It is a written and verbal measure statement that is deliberated to improve a determination
creator and persuade them to take some kind of action. The main motive of the business case is
to document the justification for the undertaking of a project usually based on the estimated cost
of development and implementation against the risks and the anticipated business benefits and
savings to be gained.
Company Overview- Portakabin Ltd designs and manufactures modular, portable and
temporary buildings for various applications. It was founded in 1961and headquartered in
Huntington York, UK. This organisation offers architectural services, professional development
seminars, projects management, surveys and customer support. The product of this company are
utilised in construction, education, healthcare, offices, storage and events worldwide.
Vision and mission- the vision statement of the company is to provide quality products to all
customers across Europe. Mission statement of the organisation is manufactured good quality
products which provide satisfaction to customers needs and demands.
Objectives- The objective of the company is make maximization in customer base with the help
of its quality products.
Strategies- To achieve its business objective the respective company can use different strategies
like market analysis to find out consumers needs so that they can offer goods and services
according to them. Another strategy can be STP with the help of it they can segmented their
target audiences in small group on the basis of behavioural, demographic and geographic factors.
In it they can manufacture product according to customers income, occupation, age and other
various elements.
11
Paraphrase This Document
Need a fresh take? Get an instant paraphrase of this document with our AI Paraphraser
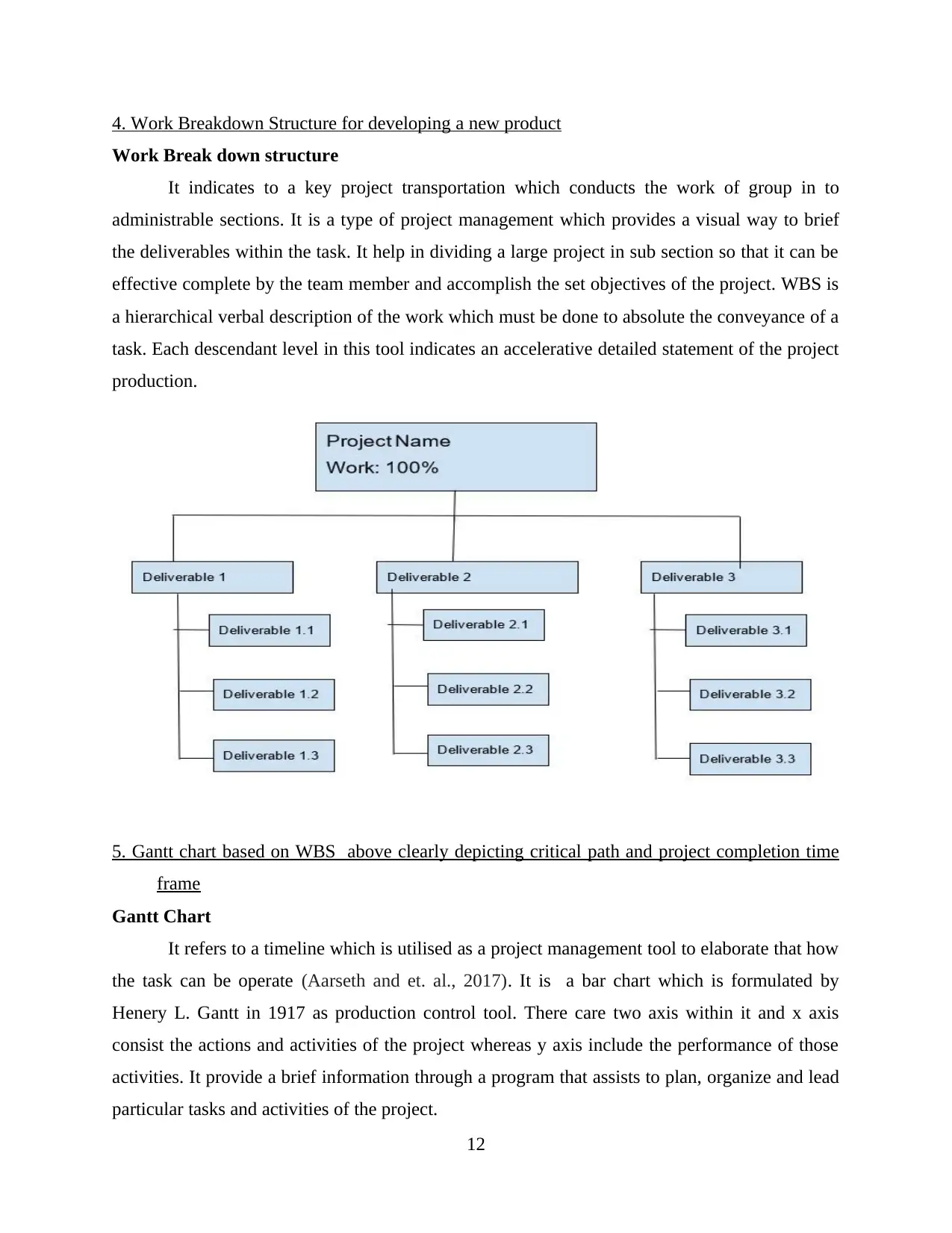
4. Work Breakdown Structure for developing a new product
Work Break down structure
It indicates to a key project transportation which conducts the work of group in to
administrable sections. It is a type of project management which provides a visual way to brief
the deliverables within the task. It help in dividing a large project in sub section so that it can be
effective complete by the team member and accomplish the set objectives of the project. WBS is
a hierarchical verbal description of the work which must be done to absolute the conveyance of a
task. Each descendant level in this tool indicates an accelerative detailed statement of the project
production.
5. Gantt chart based on WBS above clearly depicting critical path and project completion time
frame
Gantt Chart
It refers to a timeline which is utilised as a project management tool to elaborate that how
the task can be operate (Aarseth and et. al., 2017). It is a bar chart which is formulated by
Henery L. Gantt in 1917 as production control tool. There care two axis within it and x axis
consist the actions and activities of the project whereas y axis include the performance of those
activities. It provide a brief information through a program that assists to plan, organize and lead
particular tasks and activities of the project.
12
Work Break down structure
It indicates to a key project transportation which conducts the work of group in to
administrable sections. It is a type of project management which provides a visual way to brief
the deliverables within the task. It help in dividing a large project in sub section so that it can be
effective complete by the team member and accomplish the set objectives of the project. WBS is
a hierarchical verbal description of the work which must be done to absolute the conveyance of a
task. Each descendant level in this tool indicates an accelerative detailed statement of the project
production.
5. Gantt chart based on WBS above clearly depicting critical path and project completion time
frame
Gantt Chart
It refers to a timeline which is utilised as a project management tool to elaborate that how
the task can be operate (Aarseth and et. al., 2017). It is a bar chart which is formulated by
Henery L. Gantt in 1917 as production control tool. There care two axis within it and x axis
consist the actions and activities of the project whereas y axis include the performance of those
activities. It provide a brief information through a program that assists to plan, organize and lead
particular tasks and activities of the project.
12
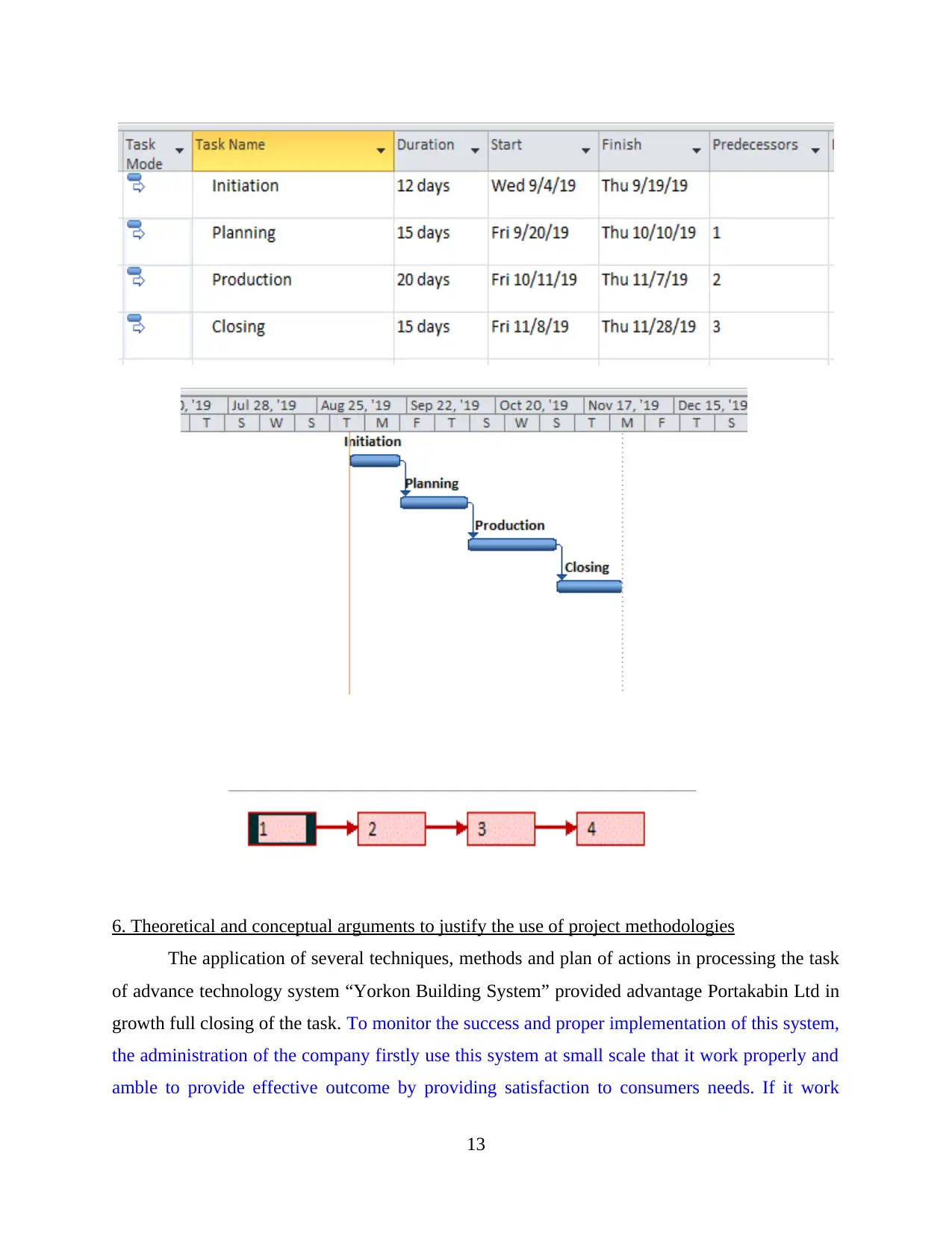
6. Theoretical and conceptual arguments to justify the use of project methodologies
The application of several techniques, methods and plan of actions in processing the task
of advance technology system “Yorkon Building System” provided advantage Portakabin Ltd in
growth full closing of the task. To monitor the success and proper implementation of this system,
the administration of the company firstly use this system at small scale that it work properly and
amble to provide effective outcome by providing satisfaction to consumers needs. If it work
13
The application of several techniques, methods and plan of actions in processing the task
of advance technology system “Yorkon Building System” provided advantage Portakabin Ltd in
growth full closing of the task. To monitor the success and proper implementation of this system,
the administration of the company firstly use this system at small scale that it work properly and
amble to provide effective outcome by providing satisfaction to consumers needs. If it work
13
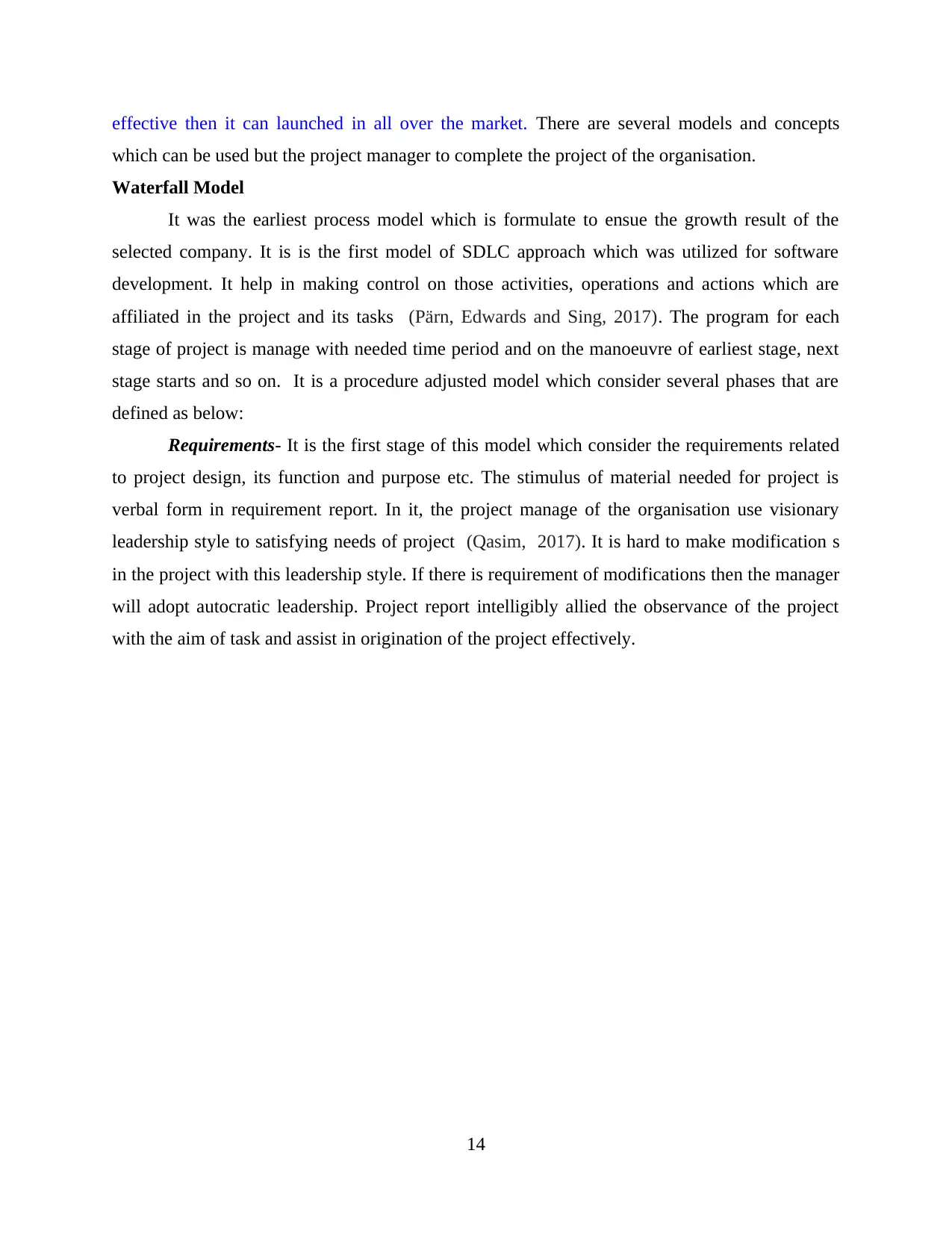
effective then it can launched in all over the market. There are several models and concepts
which can be used but the project manager to complete the project of the organisation.
Waterfall Model
It was the earliest process model which is formulate to ensue the growth result of the
selected company. It is is the first model of SDLC approach which was utilized for software
development. It help in making control on those activities, operations and actions which are
affiliated in the project and its tasks (Pärn, Edwards and Sing, 2017). The program for each
stage of project is manage with needed time period and on the manoeuvre of earliest stage, next
stage starts and so on. It is a procedure adjusted model which consider several phases that are
defined as below:
Requirements- It is the first stage of this model which consider the requirements related
to project design, its function and purpose etc. The stimulus of material needed for project is
verbal form in requirement report. In it, the project manage of the organisation use visionary
leadership style to satisfying needs of project (Qasim, 2017). It is hard to make modification s
in the project with this leadership style. If there is requirement of modifications then the manager
will adopt autocratic leadership. Project report intelligibly allied the observance of the project
with the aim of task and assist in origination of the project effectively.
14
which can be used but the project manager to complete the project of the organisation.
Waterfall Model
It was the earliest process model which is formulate to ensue the growth result of the
selected company. It is is the first model of SDLC approach which was utilized for software
development. It help in making control on those activities, operations and actions which are
affiliated in the project and its tasks (Pärn, Edwards and Sing, 2017). The program for each
stage of project is manage with needed time period and on the manoeuvre of earliest stage, next
stage starts and so on. It is a procedure adjusted model which consider several phases that are
defined as below:
Requirements- It is the first stage of this model which consider the requirements related
to project design, its function and purpose etc. The stimulus of material needed for project is
verbal form in requirement report. In it, the project manage of the organisation use visionary
leadership style to satisfying needs of project (Qasim, 2017). It is hard to make modification s
in the project with this leadership style. If there is requirement of modifications then the manager
will adopt autocratic leadership. Project report intelligibly allied the observance of the project
with the aim of task and assist in origination of the project effectively.
14
Secure Best Marks with AI Grader
Need help grading? Try our AI Grader for instant feedback on your assignments.
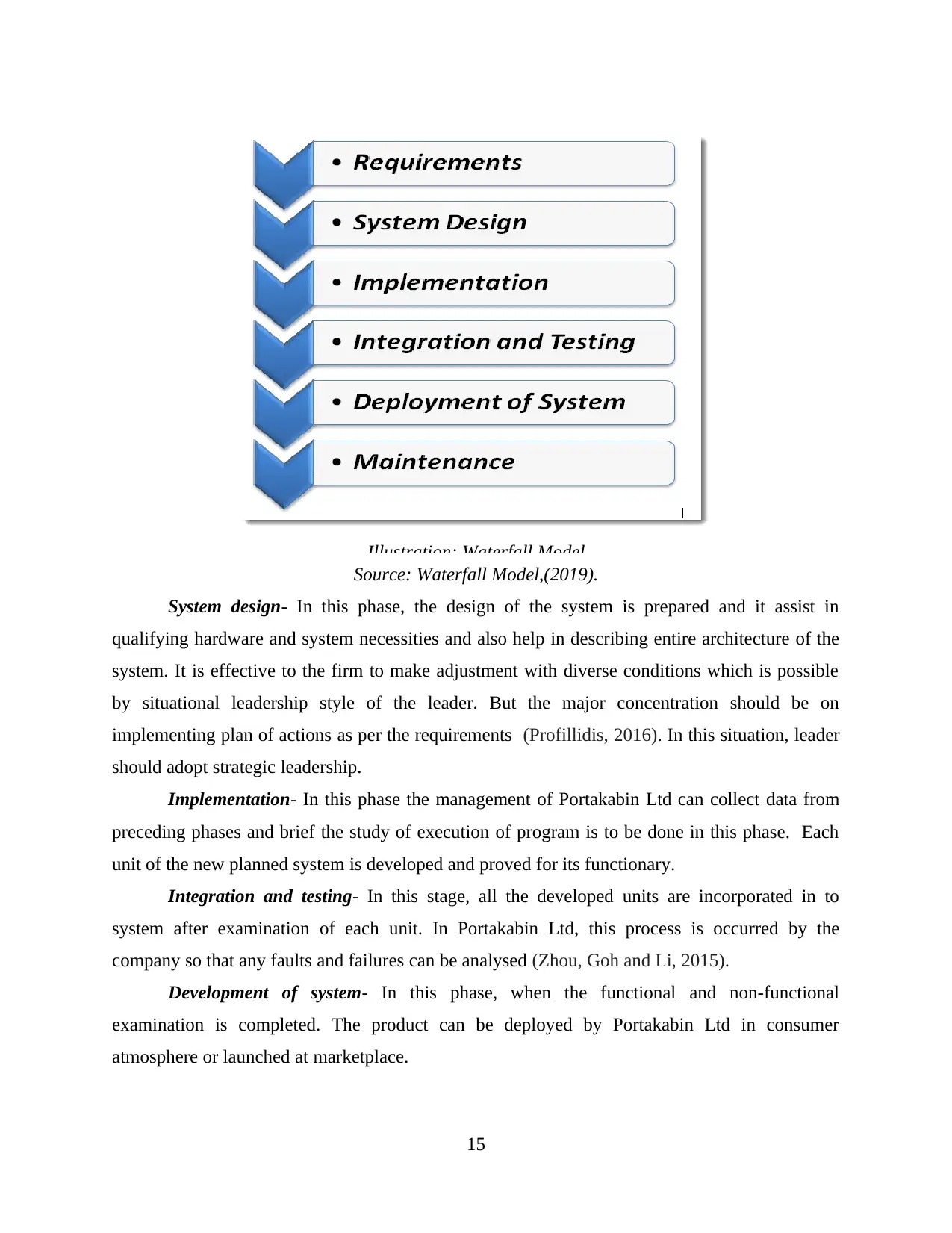
Source: Waterfall Model,(2019).
System design- In this phase, the design of the system is prepared and it assist in
qualifying hardware and system necessities and also help in describing entire architecture of the
system. It is effective to the firm to make adjustment with diverse conditions which is possible
by situational leadership style of the leader. But the major concentration should be on
implementing plan of actions as per the requirements (Profillidis, 2016). In this situation, leader
should adopt strategic leadership.
Implementation- In this phase the management of Portakabin Ltd can collect data from
preceding phases and brief the study of execution of program is to be done in this phase. Each
unit of the new planned system is developed and proved for its functionary.
Integration and testing- In this stage, all the developed units are incorporated in to
system after examination of each unit. In Portakabin Ltd, this process is occurred by the
company so that any faults and failures can be analysed (Zhou, Goh and Li, 2015).
Development of system- In this phase, when the functional and non-functional
examination is completed. The product can be deployed by Portakabin Ltd in consumer
atmosphere or launched at marketplace.
15
Illustration: Waterfall Model
System design- In this phase, the design of the system is prepared and it assist in
qualifying hardware and system necessities and also help in describing entire architecture of the
system. It is effective to the firm to make adjustment with diverse conditions which is possible
by situational leadership style of the leader. But the major concentration should be on
implementing plan of actions as per the requirements (Profillidis, 2016). In this situation, leader
should adopt strategic leadership.
Implementation- In this phase the management of Portakabin Ltd can collect data from
preceding phases and brief the study of execution of program is to be done in this phase. Each
unit of the new planned system is developed and proved for its functionary.
Integration and testing- In this stage, all the developed units are incorporated in to
system after examination of each unit. In Portakabin Ltd, this process is occurred by the
company so that any faults and failures can be analysed (Zhou, Goh and Li, 2015).
Development of system- In this phase, when the functional and non-functional
examination is completed. The product can be deployed by Portakabin Ltd in consumer
atmosphere or launched at marketplace.
15
Illustration: Waterfall Model
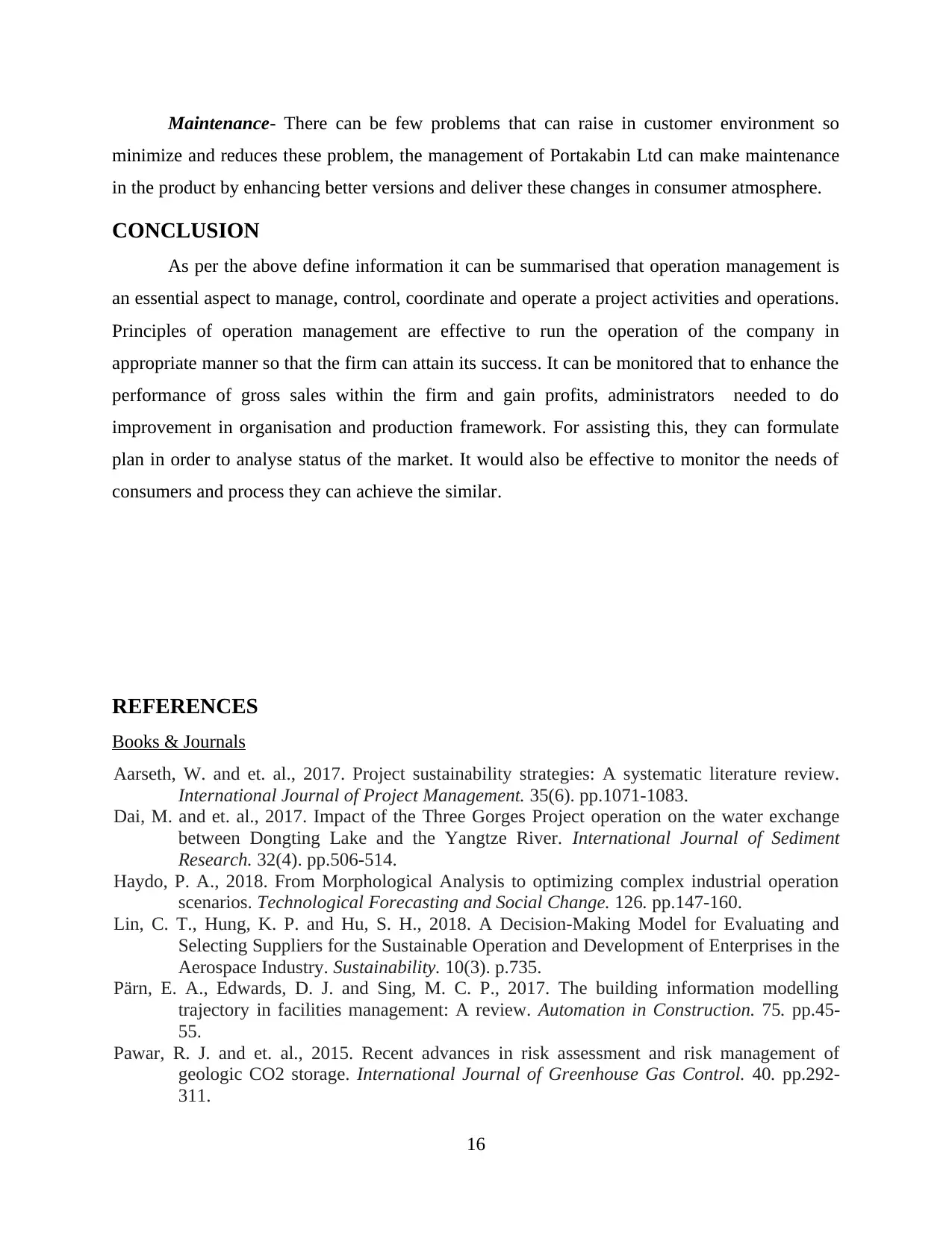
Maintenance- There can be few problems that can raise in customer environment so
minimize and reduces these problem, the management of Portakabin Ltd can make maintenance
in the product by enhancing better versions and deliver these changes in consumer atmosphere.
CONCLUSION
As per the above define information it can be summarised that operation management is
an essential aspect to manage, control, coordinate and operate a project activities and operations.
Principles of operation management are effective to run the operation of the company in
appropriate manner so that the firm can attain its success. It can be monitored that to enhance the
performance of gross sales within the firm and gain profits, administrators needed to do
improvement in organisation and production framework. For assisting this, they can formulate
plan in order to analyse status of the market. It would also be effective to monitor the needs of
consumers and process they can achieve the similar.
REFERENCES
Books & Journals
Aarseth, W. and et. al., 2017. Project sustainability strategies: A systematic literature review.
International Journal of Project Management. 35(6). pp.1071-1083.
Dai, M. and et. al., 2017. Impact of the Three Gorges Project operation on the water exchange
between Dongting Lake and the Yangtze River. International Journal of Sediment
Research. 32(4). pp.506-514.
Haydo, P. A., 2018. From Morphological Analysis to optimizing complex industrial operation
scenarios. Technological Forecasting and Social Change. 126. pp.147-160.
Lin, C. T., Hung, K. P. and Hu, S. H., 2018. A Decision-Making Model for Evaluating and
Selecting Suppliers for the Sustainable Operation and Development of Enterprises in the
Aerospace Industry. Sustainability. 10(3). p.735.
Pärn, E. A., Edwards, D. J. and Sing, M. C. P., 2017. The building information modelling
trajectory in facilities management: A review. Automation in Construction. 75. pp.45-
55.
Pawar, R. J. and et. al., 2015. Recent advances in risk assessment and risk management of
geologic CO2 storage. International Journal of Greenhouse Gas Control. 40. pp.292-
311.
16
minimize and reduces these problem, the management of Portakabin Ltd can make maintenance
in the product by enhancing better versions and deliver these changes in consumer atmosphere.
CONCLUSION
As per the above define information it can be summarised that operation management is
an essential aspect to manage, control, coordinate and operate a project activities and operations.
Principles of operation management are effective to run the operation of the company in
appropriate manner so that the firm can attain its success. It can be monitored that to enhance the
performance of gross sales within the firm and gain profits, administrators needed to do
improvement in organisation and production framework. For assisting this, they can formulate
plan in order to analyse status of the market. It would also be effective to monitor the needs of
consumers and process they can achieve the similar.
REFERENCES
Books & Journals
Aarseth, W. and et. al., 2017. Project sustainability strategies: A systematic literature review.
International Journal of Project Management. 35(6). pp.1071-1083.
Dai, M. and et. al., 2017. Impact of the Three Gorges Project operation on the water exchange
between Dongting Lake and the Yangtze River. International Journal of Sediment
Research. 32(4). pp.506-514.
Haydo, P. A., 2018. From Morphological Analysis to optimizing complex industrial operation
scenarios. Technological Forecasting and Social Change. 126. pp.147-160.
Lin, C. T., Hung, K. P. and Hu, S. H., 2018. A Decision-Making Model for Evaluating and
Selecting Suppliers for the Sustainable Operation and Development of Enterprises in the
Aerospace Industry. Sustainability. 10(3). p.735.
Pärn, E. A., Edwards, D. J. and Sing, M. C. P., 2017. The building information modelling
trajectory in facilities management: A review. Automation in Construction. 75. pp.45-
55.
Pawar, R. J. and et. al., 2015. Recent advances in risk assessment and risk management of
geologic CO2 storage. International Journal of Greenhouse Gas Control. 40. pp.292-
311.
16
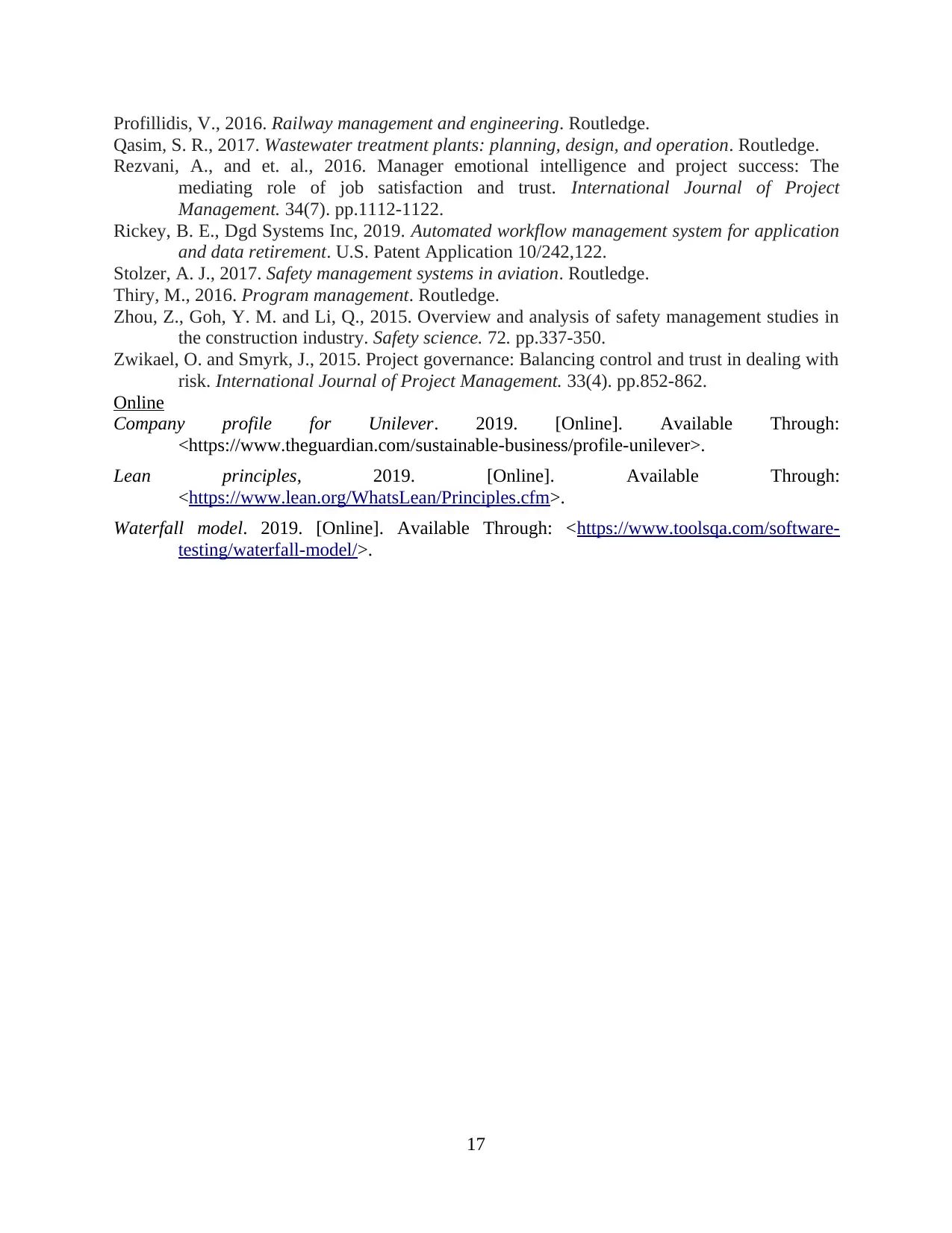
Profillidis, V., 2016. Railway management and engineering. Routledge.
Qasim, S. R., 2017. Wastewater treatment plants: planning, design, and operation. Routledge.
Rezvani, A., and et. al., 2016. Manager emotional intelligence and project success: The
mediating role of job satisfaction and trust. International Journal of Project
Management. 34(7). pp.1112-1122.
Rickey, B. E., Dgd Systems Inc, 2019. Automated workflow management system for application
and data retirement. U.S. Patent Application 10/242,122.
Stolzer, A. J., 2017. Safety management systems in aviation. Routledge.
Thiry, M., 2016. Program management. Routledge.
Zhou, Z., Goh, Y. M. and Li, Q., 2015. Overview and analysis of safety management studies in
the construction industry. Safety science. 72. pp.337-350.
Zwikael, O. and Smyrk, J., 2015. Project governance: Balancing control and trust in dealing with
risk. International Journal of Project Management. 33(4). pp.852-862.
Online
Company profile for Unilever. 2019. [Online]. Available Through:
<https://www.theguardian.com/sustainable-business/profile-unilever>.
Lean principles, 2019. [Online]. Available Through:
<https://www.lean.org/WhatsLean/Principles.cfm>.
Waterfall model. 2019. [Online]. Available Through: <https://www.toolsqa.com/software-
testing/waterfall-model/>.
17
Qasim, S. R., 2017. Wastewater treatment plants: planning, design, and operation. Routledge.
Rezvani, A., and et. al., 2016. Manager emotional intelligence and project success: The
mediating role of job satisfaction and trust. International Journal of Project
Management. 34(7). pp.1112-1122.
Rickey, B. E., Dgd Systems Inc, 2019. Automated workflow management system for application
and data retirement. U.S. Patent Application 10/242,122.
Stolzer, A. J., 2017. Safety management systems in aviation. Routledge.
Thiry, M., 2016. Program management. Routledge.
Zhou, Z., Goh, Y. M. and Li, Q., 2015. Overview and analysis of safety management studies in
the construction industry. Safety science. 72. pp.337-350.
Zwikael, O. and Smyrk, J., 2015. Project governance: Balancing control and trust in dealing with
risk. International Journal of Project Management. 33(4). pp.852-862.
Online
Company profile for Unilever. 2019. [Online]. Available Through:
<https://www.theguardian.com/sustainable-business/profile-unilever>.
Lean principles, 2019. [Online]. Available Through:
<https://www.lean.org/WhatsLean/Principles.cfm>.
Waterfall model. 2019. [Online]. Available Through: <https://www.toolsqa.com/software-
testing/waterfall-model/>.
17
1 out of 19
Related Documents
![[object Object]](/_next/image/?url=%2F_next%2Fstatic%2Fmedia%2Flogo.6d15ce61.png&w=640&q=75)
Your All-in-One AI-Powered Toolkit for Academic Success.
 +13062052269
info@desklib.com
Available 24*7 on WhatsApp / Email
Unlock your academic potential
© 2024  |  Zucol Services PVT LTD  |  All rights reserved.