Operations and Services Management
VerifiedAdded on 2023/06/10
|11
|2556
|459
AI Summary
This report discusses the importance of operations and services management in a business organization, with a focus on Unilever. It covers various theories, concepts, and principles related to operations and service management, as well as alternative techniques like capacity, quality, and supply chain management. The report also explores the importance of evaluating functions interactions with operations and aid their success.
Contribute Materials
Your contribution can guide someone’s learning journey. Share your
documents today.
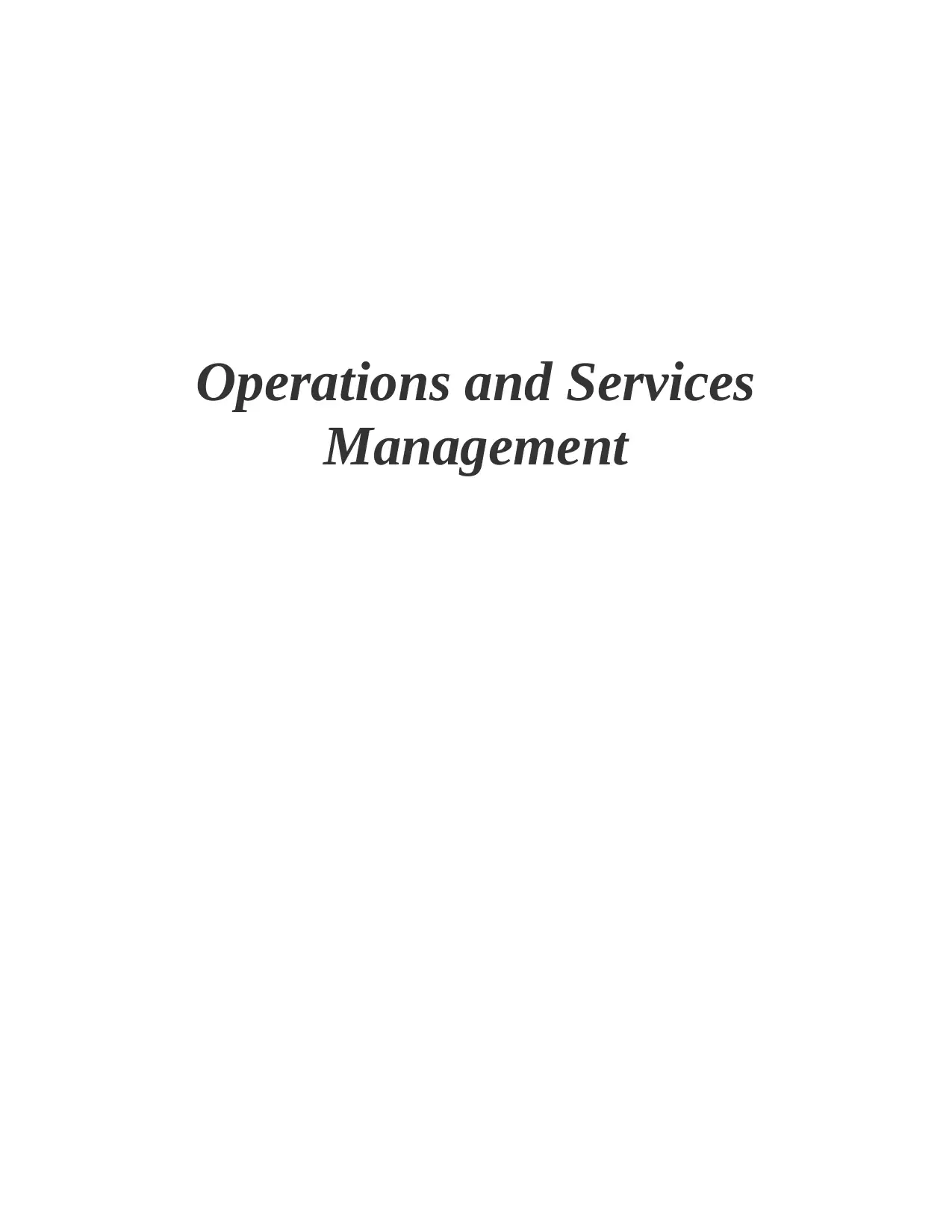
Operations and Services
Management
Management
Secure Best Marks with AI Grader
Need help grading? Try our AI Grader for instant feedback on your assignments.
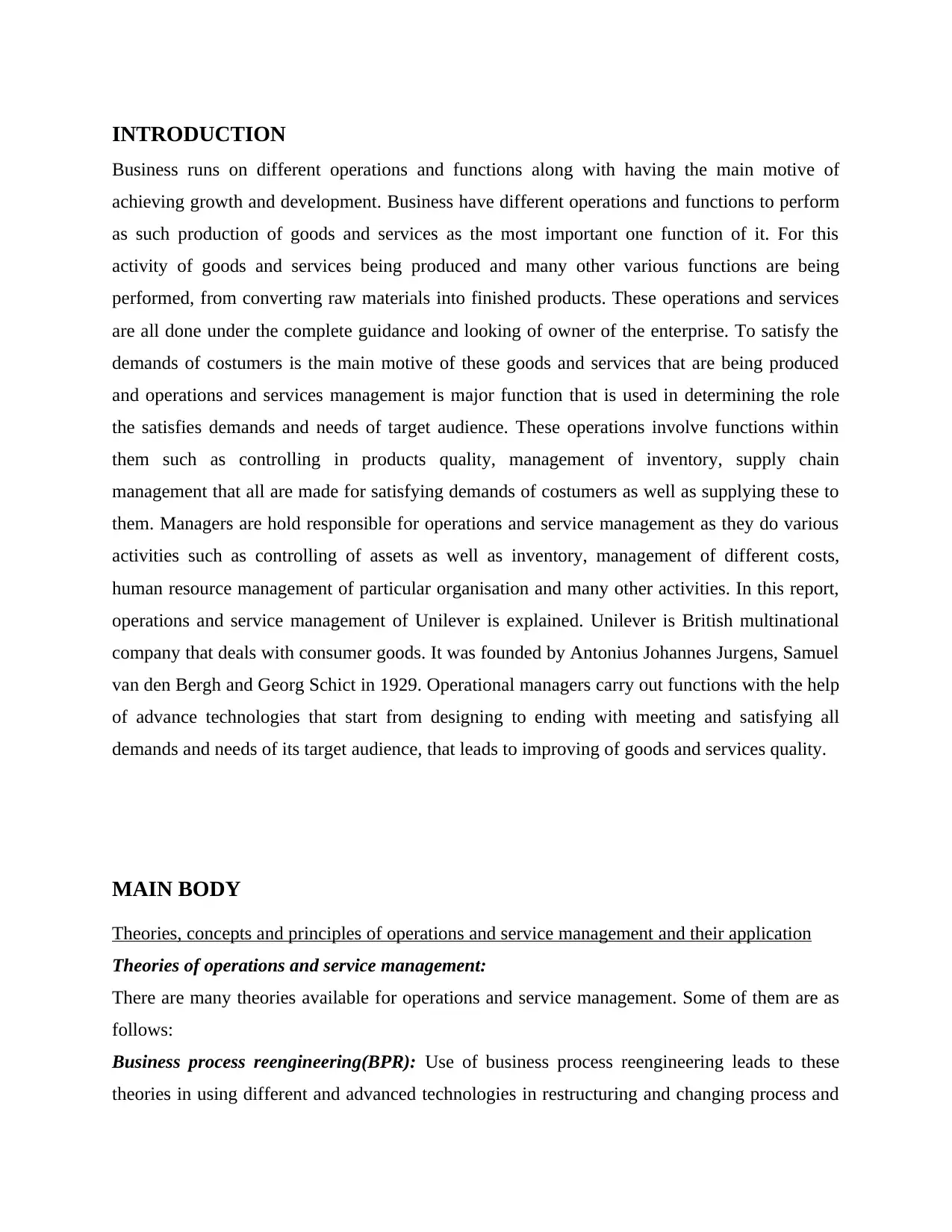
INTRODUCTION
Business runs on different operations and functions along with having the main motive of
achieving growth and development. Business have different operations and functions to perform
as such production of goods and services as the most important one function of it. For this
activity of goods and services being produced and many other various functions are being
performed, from converting raw materials into finished products. These operations and services
are all done under the complete guidance and looking of owner of the enterprise. To satisfy the
demands of costumers is the main motive of these goods and services that are being produced
and operations and services management is major function that is used in determining the role
the satisfies demands and needs of target audience. These operations involve functions within
them such as controlling in products quality, management of inventory, supply chain
management that all are made for satisfying demands of costumers as well as supplying these to
them. Managers are hold responsible for operations and service management as they do various
activities such as controlling of assets as well as inventory, management of different costs,
human resource management of particular organisation and many other activities. In this report,
operations and service management of Unilever is explained. Unilever is British multinational
company that deals with consumer goods. It was founded by Antonius Johannes Jurgens, Samuel
van den Bergh and Georg Schict in 1929. Operational managers carry out functions with the help
of advance technologies that start from designing to ending with meeting and satisfying all
demands and needs of its target audience, that leads to improving of goods and services quality.
MAIN BODY
Theories, concepts and principles of operations and service management and their application
Theories of operations and service management:
There are many theories available for operations and service management. Some of them are as
follows:
Business process reengineering(BPR): Use of business process reengineering leads to these
theories in using different and advanced technologies in restructuring and changing process and
Business runs on different operations and functions along with having the main motive of
achieving growth and development. Business have different operations and functions to perform
as such production of goods and services as the most important one function of it. For this
activity of goods and services being produced and many other various functions are being
performed, from converting raw materials into finished products. These operations and services
are all done under the complete guidance and looking of owner of the enterprise. To satisfy the
demands of costumers is the main motive of these goods and services that are being produced
and operations and services management is major function that is used in determining the role
the satisfies demands and needs of target audience. These operations involve functions within
them such as controlling in products quality, management of inventory, supply chain
management that all are made for satisfying demands of costumers as well as supplying these to
them. Managers are hold responsible for operations and service management as they do various
activities such as controlling of assets as well as inventory, management of different costs,
human resource management of particular organisation and many other activities. In this report,
operations and service management of Unilever is explained. Unilever is British multinational
company that deals with consumer goods. It was founded by Antonius Johannes Jurgens, Samuel
van den Bergh and Georg Schict in 1929. Operational managers carry out functions with the help
of advance technologies that start from designing to ending with meeting and satisfying all
demands and needs of its target audience, that leads to improving of goods and services quality.
MAIN BODY
Theories, concepts and principles of operations and service management and their application
Theories of operations and service management:
There are many theories available for operations and service management. Some of them are as
follows:
Business process reengineering(BPR): Use of business process reengineering leads to these
theories in using different and advanced technologies in restructuring and changing process and
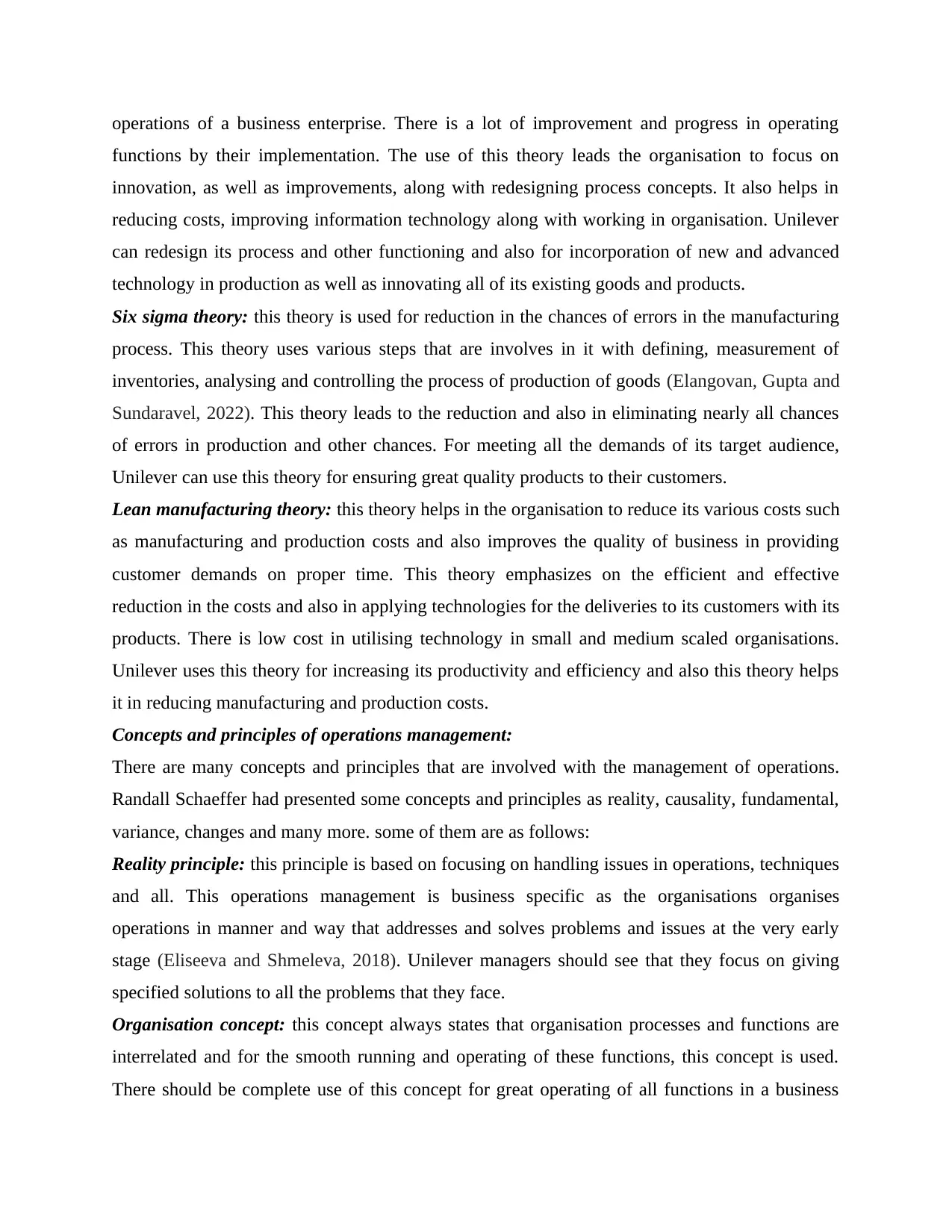
operations of a business enterprise. There is a lot of improvement and progress in operating
functions by their implementation. The use of this theory leads the organisation to focus on
innovation, as well as improvements, along with redesigning process concepts. It also helps in
reducing costs, improving information technology along with working in organisation. Unilever
can redesign its process and other functioning and also for incorporation of new and advanced
technology in production as well as innovating all of its existing goods and products.
Six sigma theory: this theory is used for reduction in the chances of errors in the manufacturing
process. This theory uses various steps that are involves in it with defining, measurement of
inventories, analysing and controlling the process of production of goods (Elangovan, Gupta and
Sundaravel, 2022). This theory leads to the reduction and also in eliminating nearly all chances
of errors in production and other chances. For meeting all the demands of its target audience,
Unilever can use this theory for ensuring great quality products to their customers.
Lean manufacturing theory: this theory helps in the organisation to reduce its various costs such
as manufacturing and production costs and also improves the quality of business in providing
customer demands on proper time. This theory emphasizes on the efficient and effective
reduction in the costs and also in applying technologies for the deliveries to its customers with its
products. There is low cost in utilising technology in small and medium scaled organisations.
Unilever uses this theory for increasing its productivity and efficiency and also this theory helps
it in reducing manufacturing and production costs.
Concepts and principles of operations management:
There are many concepts and principles that are involved with the management of operations.
Randall Schaeffer had presented some concepts and principles as reality, causality, fundamental,
variance, changes and many more. some of them are as follows:
Reality principle: this principle is based on focusing on handling issues in operations, techniques
and all. This operations management is business specific as the organisations organises
operations in manner and way that addresses and solves problems and issues at the very early
stage (Eliseeva and Shmeleva, 2018). Unilever managers should see that they focus on giving
specified solutions to all the problems that they face.
Organisation concept: this concept always states that organisation processes and functions are
interrelated and for the smooth running and operating of these functions, this concept is used.
There should be complete use of this concept for great operating of all functions in a business
functions by their implementation. The use of this theory leads the organisation to focus on
innovation, as well as improvements, along with redesigning process concepts. It also helps in
reducing costs, improving information technology along with working in organisation. Unilever
can redesign its process and other functioning and also for incorporation of new and advanced
technology in production as well as innovating all of its existing goods and products.
Six sigma theory: this theory is used for reduction in the chances of errors in the manufacturing
process. This theory uses various steps that are involves in it with defining, measurement of
inventories, analysing and controlling the process of production of goods (Elangovan, Gupta and
Sundaravel, 2022). This theory leads to the reduction and also in eliminating nearly all chances
of errors in production and other chances. For meeting all the demands of its target audience,
Unilever can use this theory for ensuring great quality products to their customers.
Lean manufacturing theory: this theory helps in the organisation to reduce its various costs such
as manufacturing and production costs and also improves the quality of business in providing
customer demands on proper time. This theory emphasizes on the efficient and effective
reduction in the costs and also in applying technologies for the deliveries to its customers with its
products. There is low cost in utilising technology in small and medium scaled organisations.
Unilever uses this theory for increasing its productivity and efficiency and also this theory helps
it in reducing manufacturing and production costs.
Concepts and principles of operations management:
There are many concepts and principles that are involved with the management of operations.
Randall Schaeffer had presented some concepts and principles as reality, causality, fundamental,
variance, changes and many more. some of them are as follows:
Reality principle: this principle is based on focusing on handling issues in operations, techniques
and all. This operations management is business specific as the organisations organises
operations in manner and way that addresses and solves problems and issues at the very early
stage (Eliseeva and Shmeleva, 2018). Unilever managers should see that they focus on giving
specified solutions to all the problems that they face.
Organisation concept: this concept always states that organisation processes and functions are
interrelated and for the smooth running and operating of these functions, this concept is used.
There should be complete use of this concept for great operating of all functions in a business
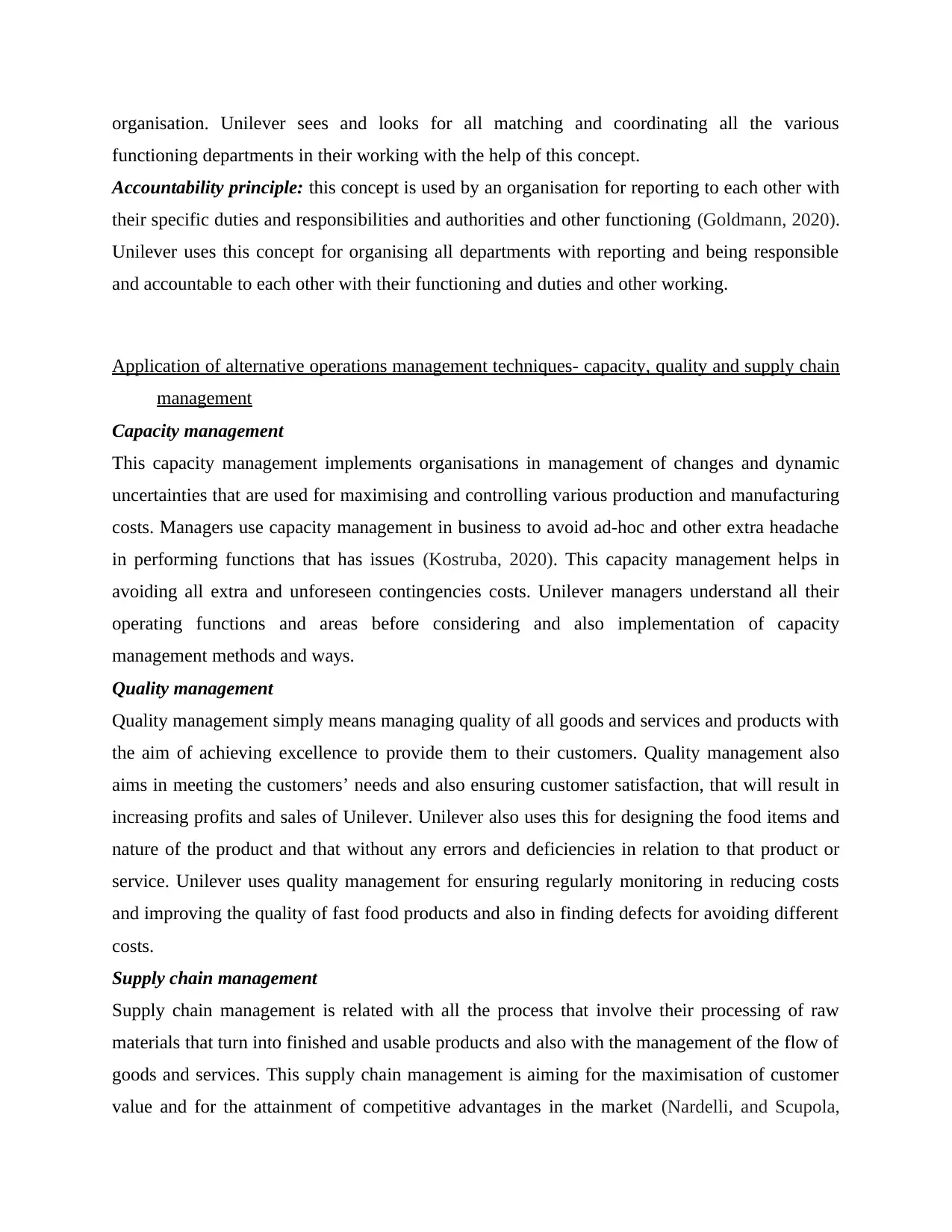
organisation. Unilever sees and looks for all matching and coordinating all the various
functioning departments in their working with the help of this concept.
Accountability principle: this concept is used by an organisation for reporting to each other with
their specific duties and responsibilities and authorities and other functioning (Goldmann, 2020).
Unilever uses this concept for organising all departments with reporting and being responsible
and accountable to each other with their functioning and duties and other working.
Application of alternative operations management techniques- capacity, quality and supply chain
management
Capacity management
This capacity management implements organisations in management of changes and dynamic
uncertainties that are used for maximising and controlling various production and manufacturing
costs. Managers use capacity management in business to avoid ad-hoc and other extra headache
in performing functions that has issues (Kostruba, 2020). This capacity management helps in
avoiding all extra and unforeseen contingencies costs. Unilever managers understand all their
operating functions and areas before considering and also implementation of capacity
management methods and ways.
Quality management
Quality management simply means managing quality of all goods and services and products with
the aim of achieving excellence to provide them to their customers. Quality management also
aims in meeting the customers’ needs and also ensuring customer satisfaction, that will result in
increasing profits and sales of Unilever. Unilever also uses this for designing the food items and
nature of the product and that without any errors and deficiencies in relation to that product or
service. Unilever uses quality management for ensuring regularly monitoring in reducing costs
and improving the quality of fast food products and also in finding defects for avoiding different
costs.
Supply chain management
Supply chain management is related with all the process that involve their processing of raw
materials that turn into finished and usable products and also with the management of the flow of
goods and services. This supply chain management is aiming for the maximisation of customer
value and for the attainment of competitive advantages in the market (Nardelli, and Scupola,
functioning departments in their working with the help of this concept.
Accountability principle: this concept is used by an organisation for reporting to each other with
their specific duties and responsibilities and authorities and other functioning (Goldmann, 2020).
Unilever uses this concept for organising all departments with reporting and being responsible
and accountable to each other with their functioning and duties and other working.
Application of alternative operations management techniques- capacity, quality and supply chain
management
Capacity management
This capacity management implements organisations in management of changes and dynamic
uncertainties that are used for maximising and controlling various production and manufacturing
costs. Managers use capacity management in business to avoid ad-hoc and other extra headache
in performing functions that has issues (Kostruba, 2020). This capacity management helps in
avoiding all extra and unforeseen contingencies costs. Unilever managers understand all their
operating functions and areas before considering and also implementation of capacity
management methods and ways.
Quality management
Quality management simply means managing quality of all goods and services and products with
the aim of achieving excellence to provide them to their customers. Quality management also
aims in meeting the customers’ needs and also ensuring customer satisfaction, that will result in
increasing profits and sales of Unilever. Unilever also uses this for designing the food items and
nature of the product and that without any errors and deficiencies in relation to that product or
service. Unilever uses quality management for ensuring regularly monitoring in reducing costs
and improving the quality of fast food products and also in finding defects for avoiding different
costs.
Supply chain management
Supply chain management is related with all the process that involve their processing of raw
materials that turn into finished and usable products and also with the management of the flow of
goods and services. This supply chain management is aiming for the maximisation of customer
value and for the attainment of competitive advantages in the market (Nardelli, and Scupola,
Secure Best Marks with AI Grader
Need help grading? Try our AI Grader for instant feedback on your assignments.
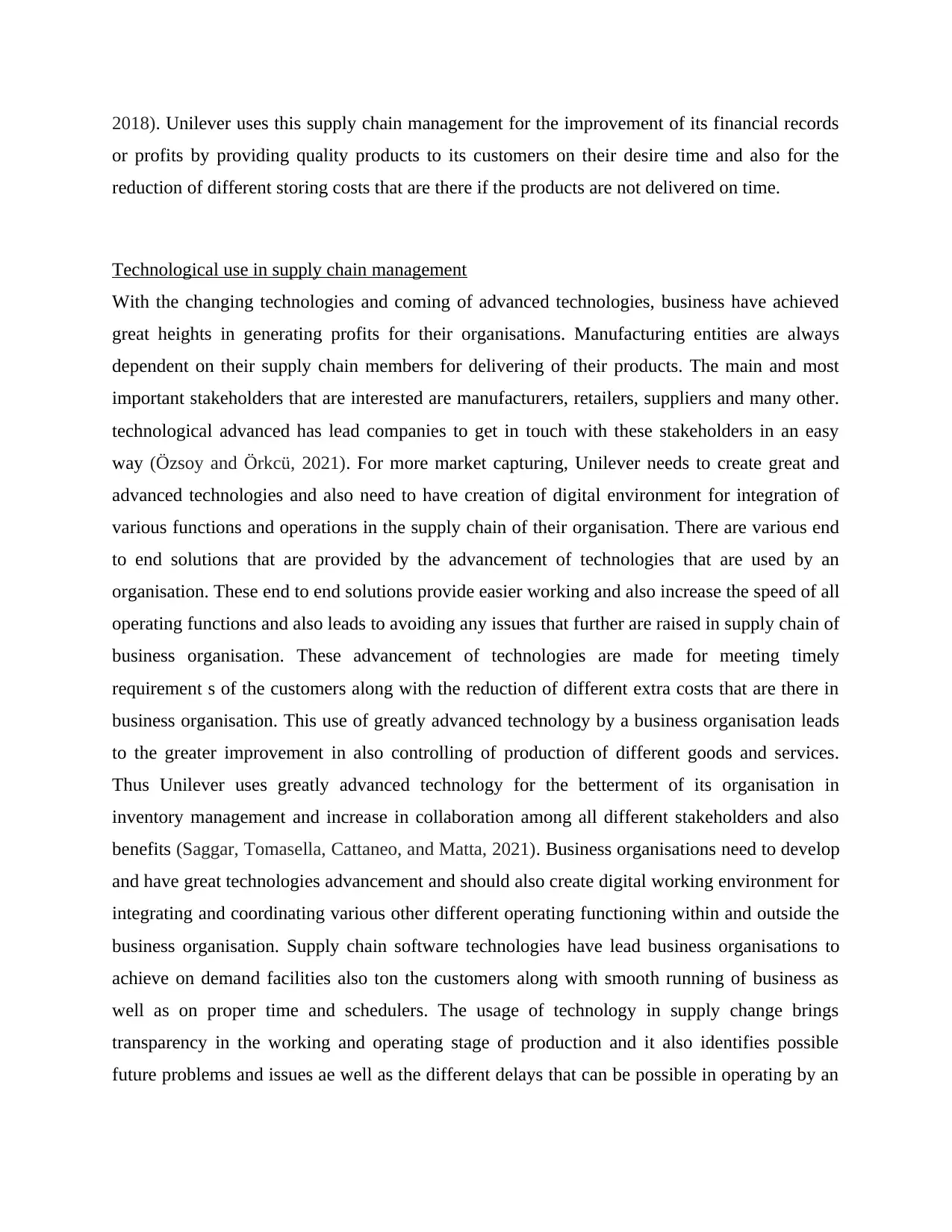
2018). Unilever uses this supply chain management for the improvement of its financial records
or profits by providing quality products to its customers on their desire time and also for the
reduction of different storing costs that are there if the products are not delivered on time.
Technological use in supply chain management
With the changing technologies and coming of advanced technologies, business have achieved
great heights in generating profits for their organisations. Manufacturing entities are always
dependent on their supply chain members for delivering of their products. The main and most
important stakeholders that are interested are manufacturers, retailers, suppliers and many other.
technological advanced has lead companies to get in touch with these stakeholders in an easy
way (Özsoy and Örkcü, 2021). For more market capturing, Unilever needs to create great and
advanced technologies and also need to have creation of digital environment for integration of
various functions and operations in the supply chain of their organisation. There are various end
to end solutions that are provided by the advancement of technologies that are used by an
organisation. These end to end solutions provide easier working and also increase the speed of all
operating functions and also leads to avoiding any issues that further are raised in supply chain of
business organisation. These advancement of technologies are made for meeting timely
requirement s of the customers along with the reduction of different extra costs that are there in
business organisation. This use of greatly advanced technology by a business organisation leads
to the greater improvement in also controlling of production of different goods and services.
Thus Unilever uses greatly advanced technology for the betterment of its organisation in
inventory management and increase in collaboration among all different stakeholders and also
benefits (Saggar, Tomasella, Cattaneo, and Matta, 2021). Business organisations need to develop
and have great technologies advancement and should also create digital working environment for
integrating and coordinating various other different operating functioning within and outside the
business organisation. Supply chain software technologies have lead business organisations to
achieve on demand facilities also ton the customers along with smooth running of business as
well as on proper time and schedulers. The usage of technology in supply change brings
transparency in the working and operating stage of production and it also identifies possible
future problems and issues ae well as the different delays that can be possible in operating by an
or profits by providing quality products to its customers on their desire time and also for the
reduction of different storing costs that are there if the products are not delivered on time.
Technological use in supply chain management
With the changing technologies and coming of advanced technologies, business have achieved
great heights in generating profits for their organisations. Manufacturing entities are always
dependent on their supply chain members for delivering of their products. The main and most
important stakeholders that are interested are manufacturers, retailers, suppliers and many other.
technological advanced has lead companies to get in touch with these stakeholders in an easy
way (Özsoy and Örkcü, 2021). For more market capturing, Unilever needs to create great and
advanced technologies and also need to have creation of digital environment for integration of
various functions and operations in the supply chain of their organisation. There are various end
to end solutions that are provided by the advancement of technologies that are used by an
organisation. These end to end solutions provide easier working and also increase the speed of all
operating functions and also leads to avoiding any issues that further are raised in supply chain of
business organisation. These advancement of technologies are made for meeting timely
requirement s of the customers along with the reduction of different extra costs that are there in
business organisation. This use of greatly advanced technology by a business organisation leads
to the greater improvement in also controlling of production of different goods and services.
Thus Unilever uses greatly advanced technology for the betterment of its organisation in
inventory management and increase in collaboration among all different stakeholders and also
benefits (Saggar, Tomasella, Cattaneo, and Matta, 2021). Business organisations need to develop
and have great technologies advancement and should also create digital working environment for
integrating and coordinating various other different operating functioning within and outside the
business organisation. Supply chain software technologies have lead business organisations to
achieve on demand facilities also ton the customers along with smooth running of business as
well as on proper time and schedulers. The usage of technology in supply change brings
transparency in the working and operating stage of production and it also identifies possible
future problems and issues ae well as the different delays that can be possible in operating by an
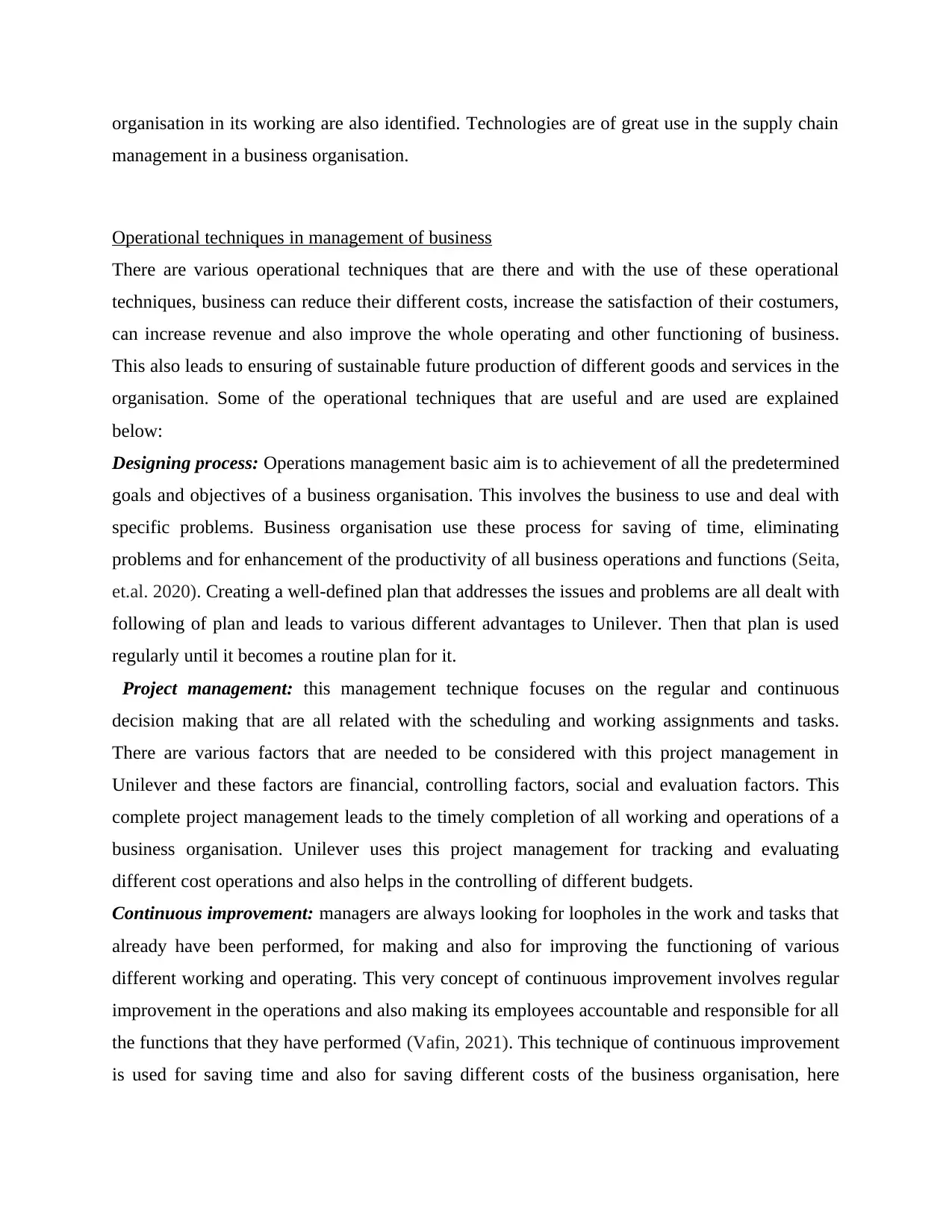
organisation in its working are also identified. Technologies are of great use in the supply chain
management in a business organisation.
Operational techniques in management of business
There are various operational techniques that are there and with the use of these operational
techniques, business can reduce their different costs, increase the satisfaction of their costumers,
can increase revenue and also improve the whole operating and other functioning of business.
This also leads to ensuring of sustainable future production of different goods and services in the
organisation. Some of the operational techniques that are useful and are used are explained
below:
Designing process: Operations management basic aim is to achievement of all the predetermined
goals and objectives of a business organisation. This involves the business to use and deal with
specific problems. Business organisation use these process for saving of time, eliminating
problems and for enhancement of the productivity of all business operations and functions (Seita,
et.al. 2020). Creating a well-defined plan that addresses the issues and problems are all dealt with
following of plan and leads to various different advantages to Unilever. Then that plan is used
regularly until it becomes a routine plan for it.
Project management: this management technique focuses on the regular and continuous
decision making that are all related with the scheduling and working assignments and tasks.
There are various factors that are needed to be considered with this project management in
Unilever and these factors are financial, controlling factors, social and evaluation factors. This
complete project management leads to the timely completion of all working and operations of a
business organisation. Unilever uses this project management for tracking and evaluating
different cost operations and also helps in the controlling of different budgets.
Continuous improvement: managers are always looking for loopholes in the work and tasks that
already have been performed, for making and also for improving the functioning of various
different working and operating. This very concept of continuous improvement involves regular
improvement in the operations and also making its employees accountable and responsible for all
the functions that they have performed (Vafin, 2021). This technique of continuous improvement
is used for saving time and also for saving different costs of the business organisation, here
management in a business organisation.
Operational techniques in management of business
There are various operational techniques that are there and with the use of these operational
techniques, business can reduce their different costs, increase the satisfaction of their costumers,
can increase revenue and also improve the whole operating and other functioning of business.
This also leads to ensuring of sustainable future production of different goods and services in the
organisation. Some of the operational techniques that are useful and are used are explained
below:
Designing process: Operations management basic aim is to achievement of all the predetermined
goals and objectives of a business organisation. This involves the business to use and deal with
specific problems. Business organisation use these process for saving of time, eliminating
problems and for enhancement of the productivity of all business operations and functions (Seita,
et.al. 2020). Creating a well-defined plan that addresses the issues and problems are all dealt with
following of plan and leads to various different advantages to Unilever. Then that plan is used
regularly until it becomes a routine plan for it.
Project management: this management technique focuses on the regular and continuous
decision making that are all related with the scheduling and working assignments and tasks.
There are various factors that are needed to be considered with this project management in
Unilever and these factors are financial, controlling factors, social and evaluation factors. This
complete project management leads to the timely completion of all working and operations of a
business organisation. Unilever uses this project management for tracking and evaluating
different cost operations and also helps in the controlling of different budgets.
Continuous improvement: managers are always looking for loopholes in the work and tasks that
already have been performed, for making and also for improving the functioning of various
different working and operating. This very concept of continuous improvement involves regular
improvement in the operations and also making its employees accountable and responsible for all
the functions that they have performed (Vafin, 2021). This technique of continuous improvement
is used for saving time and also for saving different costs of the business organisation, here
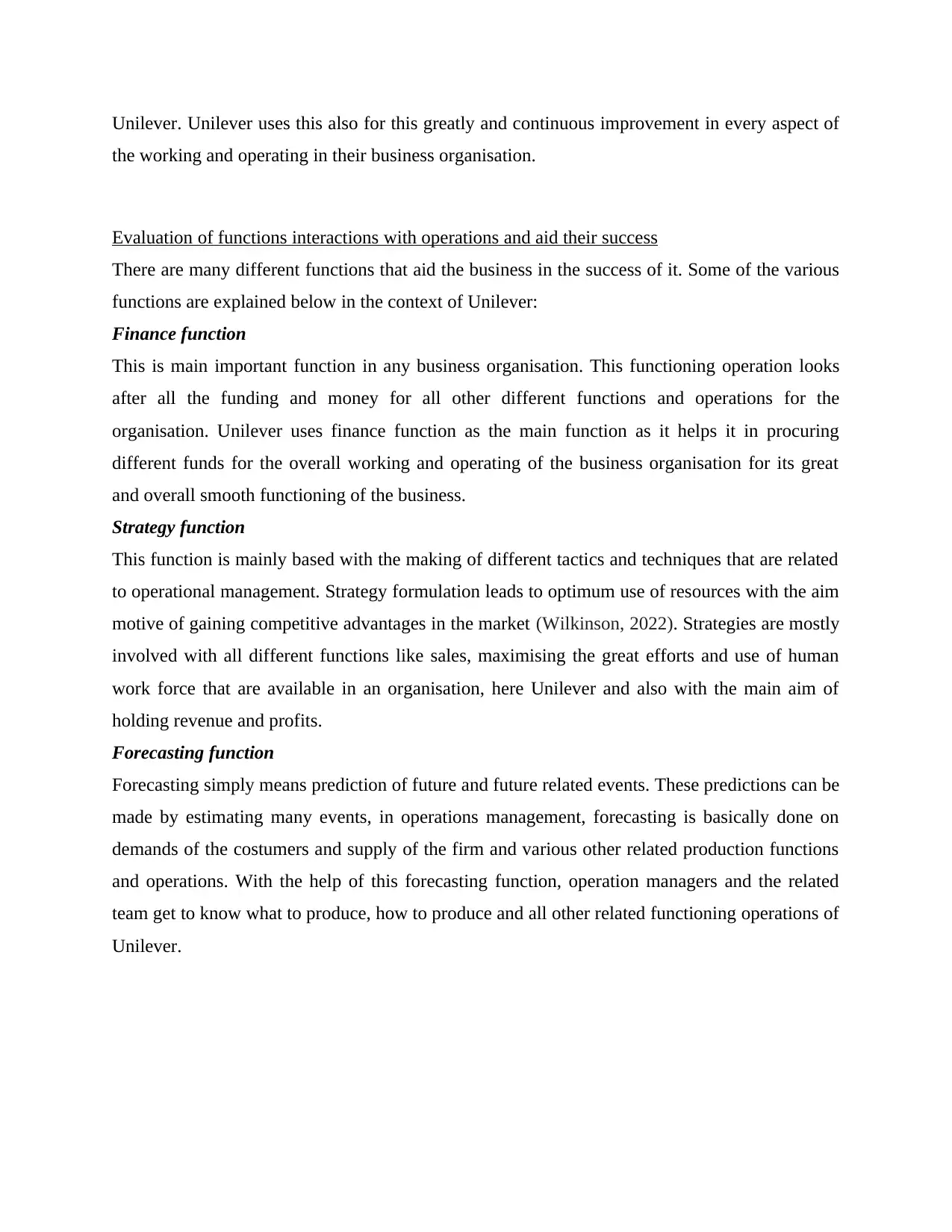
Unilever. Unilever uses this also for this greatly and continuous improvement in every aspect of
the working and operating in their business organisation.
Evaluation of functions interactions with operations and aid their success
There are many different functions that aid the business in the success of it. Some of the various
functions are explained below in the context of Unilever:
Finance function
This is main important function in any business organisation. This functioning operation looks
after all the funding and money for all other different functions and operations for the
organisation. Unilever uses finance function as the main function as it helps it in procuring
different funds for the overall working and operating of the business organisation for its great
and overall smooth functioning of the business.
Strategy function
This function is mainly based with the making of different tactics and techniques that are related
to operational management. Strategy formulation leads to optimum use of resources with the aim
motive of gaining competitive advantages in the market (Wilkinson, 2022). Strategies are mostly
involved with all different functions like sales, maximising the great efforts and use of human
work force that are available in an organisation, here Unilever and also with the main aim of
holding revenue and profits.
Forecasting function
Forecasting simply means prediction of future and future related events. These predictions can be
made by estimating many events, in operations management, forecasting is basically done on
demands of the costumers and supply of the firm and various other related production functions
and operations. With the help of this forecasting function, operation managers and the related
team get to know what to produce, how to produce and all other related functioning operations of
Unilever.
the working and operating in their business organisation.
Evaluation of functions interactions with operations and aid their success
There are many different functions that aid the business in the success of it. Some of the various
functions are explained below in the context of Unilever:
Finance function
This is main important function in any business organisation. This functioning operation looks
after all the funding and money for all other different functions and operations for the
organisation. Unilever uses finance function as the main function as it helps it in procuring
different funds for the overall working and operating of the business organisation for its great
and overall smooth functioning of the business.
Strategy function
This function is mainly based with the making of different tactics and techniques that are related
to operational management. Strategy formulation leads to optimum use of resources with the aim
motive of gaining competitive advantages in the market (Wilkinson, 2022). Strategies are mostly
involved with all different functions like sales, maximising the great efforts and use of human
work force that are available in an organisation, here Unilever and also with the main aim of
holding revenue and profits.
Forecasting function
Forecasting simply means prediction of future and future related events. These predictions can be
made by estimating many events, in operations management, forecasting is basically done on
demands of the costumers and supply of the firm and various other related production functions
and operations. With the help of this forecasting function, operation managers and the related
team get to know what to produce, how to produce and all other related functioning operations of
Unilever.
Paraphrase This Document
Need a fresh take? Get an instant paraphrase of this document with our AI Paraphraser
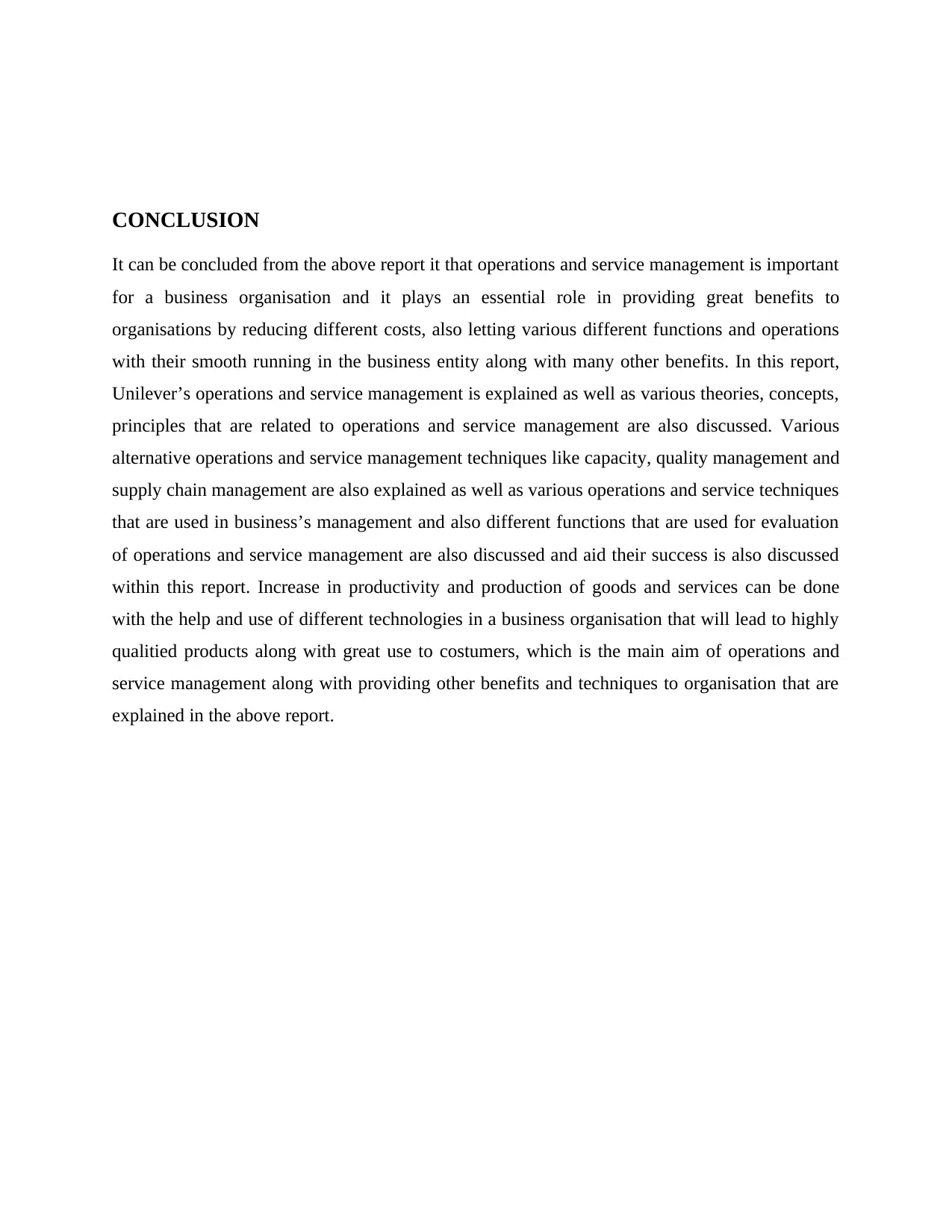
CONCLUSION
It can be concluded from the above report it that operations and service management is important
for a business organisation and it plays an essential role in providing great benefits to
organisations by reducing different costs, also letting various different functions and operations
with their smooth running in the business entity along with many other benefits. In this report,
Unilever’s operations and service management is explained as well as various theories, concepts,
principles that are related to operations and service management are also discussed. Various
alternative operations and service management techniques like capacity, quality management and
supply chain management are also explained as well as various operations and service techniques
that are used in business’s management and also different functions that are used for evaluation
of operations and service management are also discussed and aid their success is also discussed
within this report. Increase in productivity and production of goods and services can be done
with the help and use of different technologies in a business organisation that will lead to highly
qualitied products along with great use to costumers, which is the main aim of operations and
service management along with providing other benefits and techniques to organisation that are
explained in the above report.
It can be concluded from the above report it that operations and service management is important
for a business organisation and it plays an essential role in providing great benefits to
organisations by reducing different costs, also letting various different functions and operations
with their smooth running in the business entity along with many other benefits. In this report,
Unilever’s operations and service management is explained as well as various theories, concepts,
principles that are related to operations and service management are also discussed. Various
alternative operations and service management techniques like capacity, quality management and
supply chain management are also explained as well as various operations and service techniques
that are used in business’s management and also different functions that are used for evaluation
of operations and service management are also discussed and aid their success is also discussed
within this report. Increase in productivity and production of goods and services can be done
with the help and use of different technologies in a business organisation that will lead to highly
qualitied products along with great use to costumers, which is the main aim of operations and
service management along with providing other benefits and techniques to organisation that are
explained in the above report.
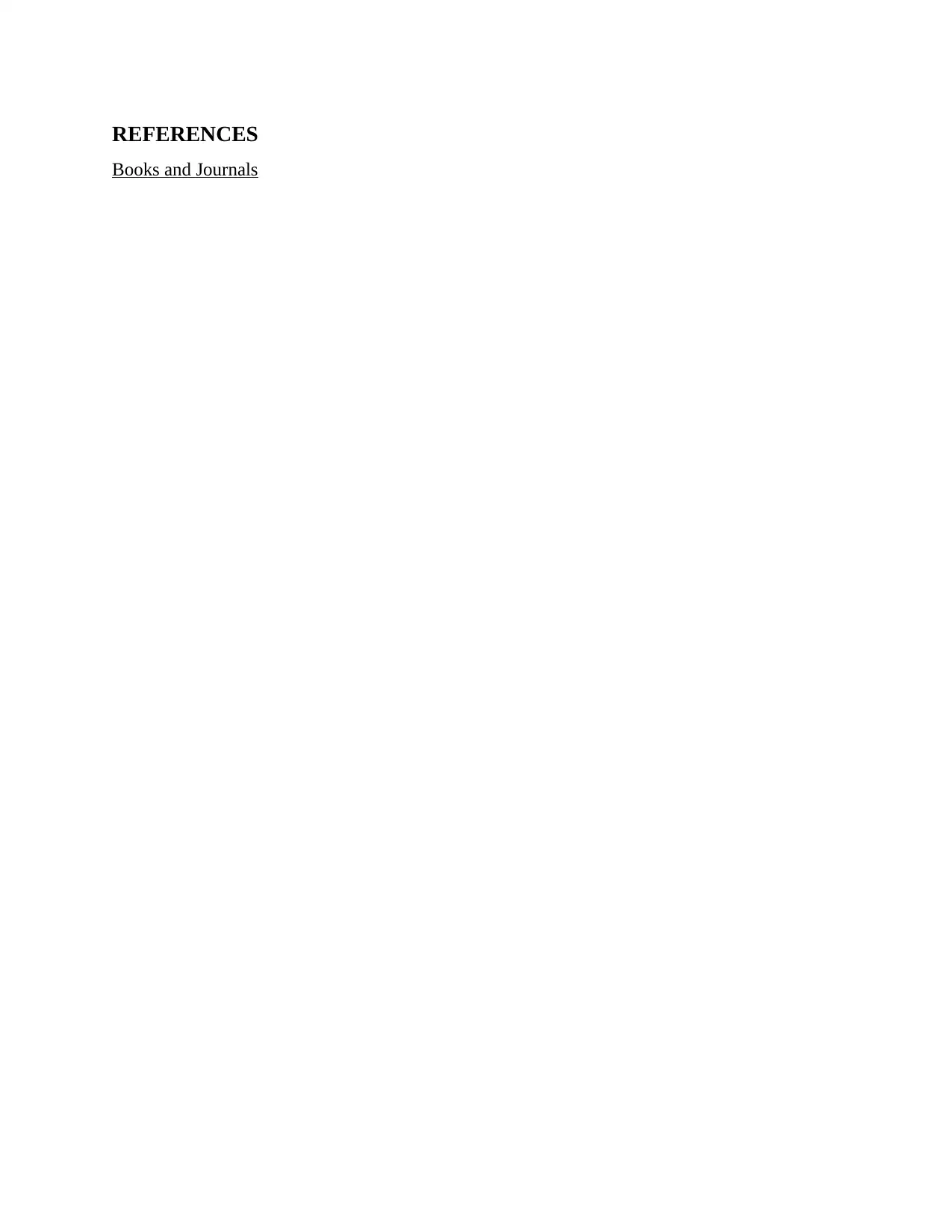
REFERENCES
Books and Journals
Books and Journals
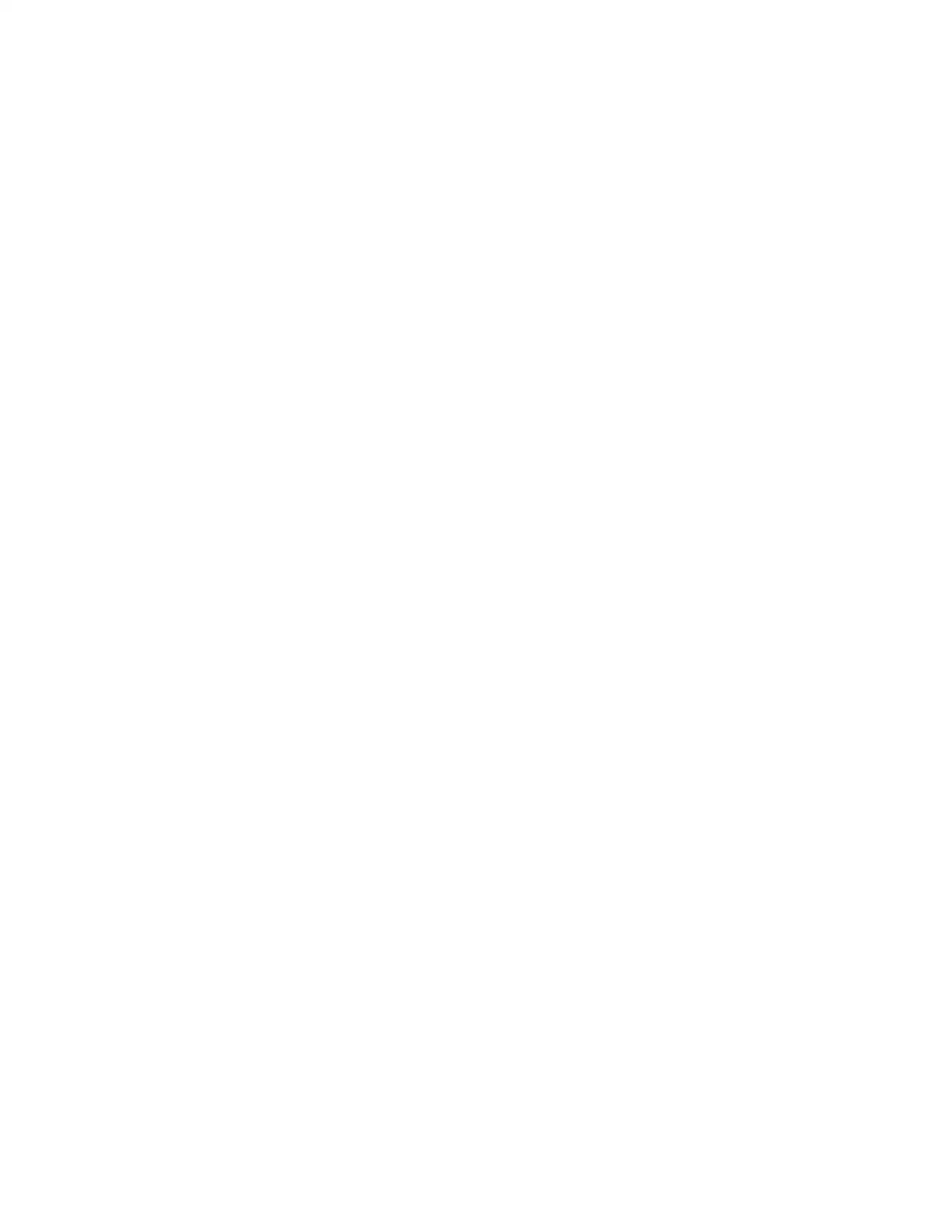
Secure Best Marks with AI Grader
Need help grading? Try our AI Grader for instant feedback on your assignments.

1 out of 11
Related Documents
![[object Object]](/_next/image/?url=%2F_next%2Fstatic%2Fmedia%2Flogo.6d15ce61.png&w=640&q=75)
Your All-in-One AI-Powered Toolkit for Academic Success.
+13062052269
info@desklib.com
Available 24*7 on WhatsApp / Email
Unlock your academic potential
© 2024 | Zucol Services PVT LTD | All rights reserved.