OPTIMISATION OF SHELL AND TUBE HEAT EXCHANGER 24.
Added on 2022-11-11
45 Pages9969 Words2 Views
OPTIMISATION OF SHELL AND TUBE HEAT EXCHANGER i
M o u n t H e l e n C a m p u s
S c h o o l o f S c i e n c e , E n g i n e e r i n g a n d
I n f o r m a t i o n T e c h n o l o g y
Master of Eng in eerin g
Techn olog y Deg ree
Research Project Thesis
2019
Optimization of Shell and
Tube Heat Exchanger
S u b m i t t e d b y :
S t u d e n t I D :
S t r e a m :
S u p e r v i s o r :
D a t e :
M o u n t H e l e n C a m p u s
S c h o o l o f S c i e n c e , E n g i n e e r i n g a n d
I n f o r m a t i o n T e c h n o l o g y
Master of Eng in eerin g
Techn olog y Deg ree
Research Project Thesis
2019
Optimization of Shell and
Tube Heat Exchanger
S u b m i t t e d b y :
S t u d e n t I D :
S t r e a m :
S u p e r v i s o r :
D a t e :

OPTIMISATION OF SHELL AND TUBE HEAT EXCHANGER ii
Acknowledgement:
Before starting with the research proposal, it’s with great pleasure to thank Dr.Ibrahim Sultan my
supervisor and advisor for his overwhelmingly help in the selection of topic and the fruitful
discussion which we had on the topic “Optimization of shell and tube heat exchanger”. Secondly I
share my gratitude to all friends who had all been part and parcel in helping me out in the successful
completion of my project proposal. It takes my immense privilege in proclaiming that without all
these people my project which includes the analysis of working of the Heat exchanger would all
have been in vain.
Acknowledgement:
Before starting with the research proposal, it’s with great pleasure to thank Dr.Ibrahim Sultan my
supervisor and advisor for his overwhelmingly help in the selection of topic and the fruitful
discussion which we had on the topic “Optimization of shell and tube heat exchanger”. Secondly I
share my gratitude to all friends who had all been part and parcel in helping me out in the successful
completion of my project proposal. It takes my immense privilege in proclaiming that without all
these people my project which includes the analysis of working of the Heat exchanger would all
have been in vain.
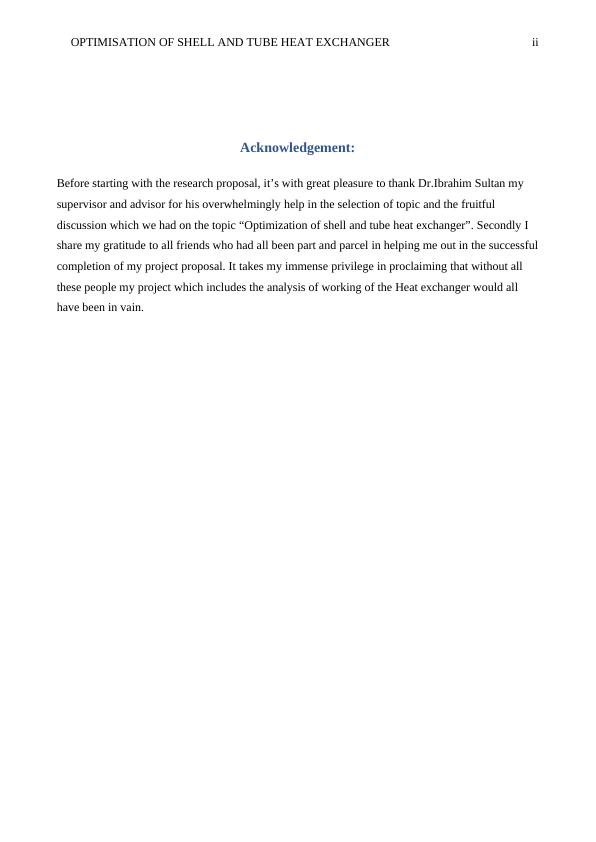
OPTIMISATION OF SHELL AND TUBE HEAT EXCHANGER iii
ABSTRACT.
Most if not all industrial processes in one way or another are associated with heat transfer in the
form of thermal energy differences in working fluids having thermal disparity. The device that
facilitates this thermal energy transfer is referred as heat exchanger. Heat exchangers are essential
in many industrial processes. Thus the productivity of any process is affected by the working
condition, status and overall efficiency of this device. Because of their importance, they widely
applied in chemical plants, mechanical manufacturing, air conditioning, and even refrigeration.
Shell and tube heat exchangers STHEs are most efficient exchanger of all types of heat exchangers,
and this has seen its application widen in different industrial applications such as chemical process,
power production industries, and refining plants. Most general solicitation of thermal transfer is in
designing of heat transfer apparatus for thermal exchange from fluid to another. Heat exchangers
are normally categorized concerning transfer process taking place in them
The objective of this project is to analyze performance efficiency of optimum shell and tube heat
exchangers through experimentation and software analysis (Naphon, 207). Design parameters are
formulated and computed in the form of optimization problems which are solved through Particle
Swarm Optimization (PSO). This optimization intends to reduce cost and expenses such as pumping
and area cost of these devices. All calculations and specification of the design parameters in this
paper are arrived at in consideration to Tubular Exchanger Manufacturers Association with pressure
drops and fouling limits. Values obtained in chapter four of this paper are considered most
appropriate in designing an optimized shell and tube heat exchanger. Verification results are also
listed providing proof of validation on the design calculations.
This report begins with bits of theory, providing general knowledge on heat exchanger with a
summarised introduction to heat exchangers. Overview of literature together with some recent
developments achieved towards optimization of heat exchangers. Matlab simulations and design
diagrams are also featured.
ABSTRACT.
Most if not all industrial processes in one way or another are associated with heat transfer in the
form of thermal energy differences in working fluids having thermal disparity. The device that
facilitates this thermal energy transfer is referred as heat exchanger. Heat exchangers are essential
in many industrial processes. Thus the productivity of any process is affected by the working
condition, status and overall efficiency of this device. Because of their importance, they widely
applied in chemical plants, mechanical manufacturing, air conditioning, and even refrigeration.
Shell and tube heat exchangers STHEs are most efficient exchanger of all types of heat exchangers,
and this has seen its application widen in different industrial applications such as chemical process,
power production industries, and refining plants. Most general solicitation of thermal transfer is in
designing of heat transfer apparatus for thermal exchange from fluid to another. Heat exchangers
are normally categorized concerning transfer process taking place in them
The objective of this project is to analyze performance efficiency of optimum shell and tube heat
exchangers through experimentation and software analysis (Naphon, 207). Design parameters are
formulated and computed in the form of optimization problems which are solved through Particle
Swarm Optimization (PSO). This optimization intends to reduce cost and expenses such as pumping
and area cost of these devices. All calculations and specification of the design parameters in this
paper are arrived at in consideration to Tubular Exchanger Manufacturers Association with pressure
drops and fouling limits. Values obtained in chapter four of this paper are considered most
appropriate in designing an optimized shell and tube heat exchanger. Verification results are also
listed providing proof of validation on the design calculations.
This report begins with bits of theory, providing general knowledge on heat exchanger with a
summarised introduction to heat exchangers. Overview of literature together with some recent
developments achieved towards optimization of heat exchangers. Matlab simulations and design
diagrams are also featured.
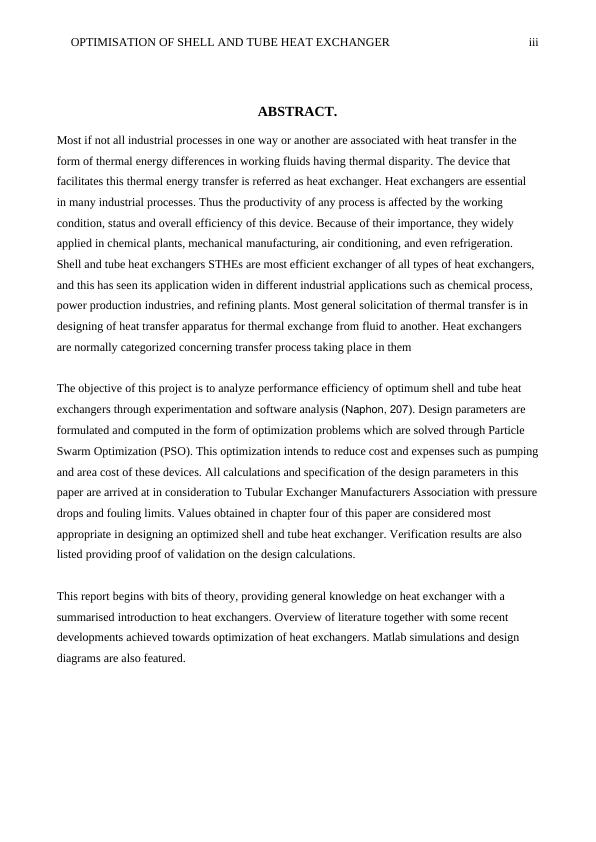
OPTIMISATION OF SHELL AND TUBE HEAT EXCHANGER iv
Table of Content
DECLARATION..................................................................................................................................i
ACKNOWLEDGEMENT:..................................................................................................................II
ABSTRACT........................................................................................................................................iii
List of figures.....................................................................................................
List of tables.......................................................................................................
Nomenclature....................................................................................................
CHAPTER 1.........................................................................................................................................6
INTRODUCTION................................................................................................................................6
1.1 Background information.............................................................................................................6
1.2 Problem Statement.....................................................................................................................7
1.2.1 Selection of shell and tube heat exchanger:........................................................................8
1.2.2 Fixed tube heat exchanger.............................................................................................9
1.2.3 Removable type heat exchanger:.........................................................................................9
1.3 Classification of Heat Exchangers:....................................................................................10
1.3.1 Heat Exchanger Nomenclature:.........................................................................................11
1.3.2 Part names.........................................................................................................................11
CHAPTER TWO................................................................................................................................14
OVERVIEW OF OPTIMIZING SHELL AND TUBE HEAT EXCHANGER................................14
2.1 Overview of Heat Exchangers..................................................................................................14
2.1.1 The gravity film heat exchanger........................................................................................15
2.1.2 Plate Heat Exchangers.......................................................................................................15
2.1.3 Tube and Coil Drain Heat Recovery.................................................................................16
2.3 Existing heat exchangers..........................................................................................................16
2.3.1 Fixed tube sheet.................................................................................................................16
2.3.2 U-Tube...............................................................................................................................17
2.3.3Floating tubesheet...............................................................................................................17
2.4 Thermal Design Consideration:................................................................................................17
2.4.1 Shell design consideration:................................................................................................17
2.4.2 Tube design consideration:................................................................................................18
2.4.3 Tube pitch and tube layout:...............................................................................................18
2.4.4 Tube sheet design:.............................................................................................................18
2.4.5 Baffle Design:....................................................................................................................18
2.4.6 Valves.....................................................................................................
2.5 Two types of passes..................................................................................................................20
Table of Content
DECLARATION..................................................................................................................................i
ACKNOWLEDGEMENT:..................................................................................................................II
ABSTRACT........................................................................................................................................iii
List of figures.....................................................................................................
List of tables.......................................................................................................
Nomenclature....................................................................................................
CHAPTER 1.........................................................................................................................................6
INTRODUCTION................................................................................................................................6
1.1 Background information.............................................................................................................6
1.2 Problem Statement.....................................................................................................................7
1.2.1 Selection of shell and tube heat exchanger:........................................................................8
1.2.2 Fixed tube heat exchanger.............................................................................................9
1.2.3 Removable type heat exchanger:.........................................................................................9
1.3 Classification of Heat Exchangers:....................................................................................10
1.3.1 Heat Exchanger Nomenclature:.........................................................................................11
1.3.2 Part names.........................................................................................................................11
CHAPTER TWO................................................................................................................................14
OVERVIEW OF OPTIMIZING SHELL AND TUBE HEAT EXCHANGER................................14
2.1 Overview of Heat Exchangers..................................................................................................14
2.1.1 The gravity film heat exchanger........................................................................................15
2.1.2 Plate Heat Exchangers.......................................................................................................15
2.1.3 Tube and Coil Drain Heat Recovery.................................................................................16
2.3 Existing heat exchangers..........................................................................................................16
2.3.1 Fixed tube sheet.................................................................................................................16
2.3.2 U-Tube...............................................................................................................................17
2.3.3Floating tubesheet...............................................................................................................17
2.4 Thermal Design Consideration:................................................................................................17
2.4.1 Shell design consideration:................................................................................................17
2.4.2 Tube design consideration:................................................................................................18
2.4.3 Tube pitch and tube layout:...............................................................................................18
2.4.4 Tube sheet design:.............................................................................................................18
2.4.5 Baffle Design:....................................................................................................................18
2.4.6 Valves.....................................................................................................
2.5 Two types of passes..................................................................................................................20
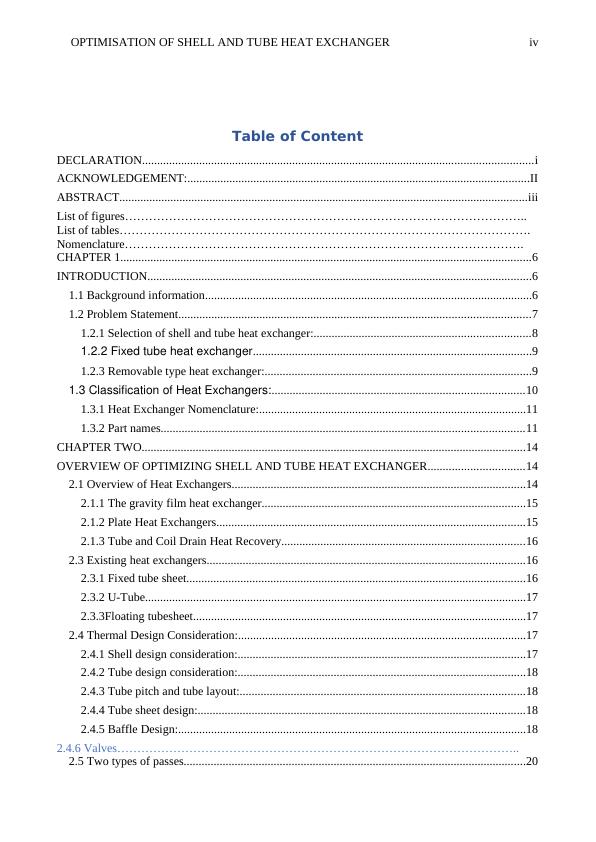
OPTIMISATION OF SHELL AND TUBE HEAT EXCHANGER v
2.5.1 Single pass unit..................................................................................................................20
2.5.2 Multipass unit....................................................................................................................20
CHAPTER THREE............................................................................................................................21
RESEARCH METHODOLOGY AND DESIGN PROCESS...........................................................21
3.1 Design process..........................................................................................................................21
3.2 Maintenance.............................................................................................................................21
3.3 Cost...........................................................................................................................................21
3.4 Safety........................................................................................................................................21
3.5 Design procedure......................................................................................................................22
3.5.2 Convective heat transfer coefficient (h)............................................................................23
3.5.3 Baffle cut and spacing.......................................................................................................24
3.6 Correction factor.......................................................................................................................25
3.7 Experimental calculation:.........................................................................................................28
Chapter 4............................................................................................................................................29
Optimization of the design process....................................................................................................29
4.1 Tube design calculations..........................................................................................................29
Chapter 5...........................................................................................................................................32
Design of shell and tube heat exchanger:-..........................................................................................32
5.1 Design of 3DModel of shell and tube heat exchanger by using Autodesk Inventor................33
5.2 Efficiency:................................................................................................................................33
5.3 Effectiveness:........................................................................................................................33
5.3.1 Tube pass...........................................................................................................................34
5.3.2 Tube pitch..........................................................................................................................34
Chapter - 6..........................................................................................................................................35
Results for CFD analysis: -................................................................................................................35
Chapter - 7..........................................................................................................................................38
Conclusion: -......................................................................................................................................38
Chapter - 8..........................................................................................................................................39
Recommendations of future work: -...................................................................................................39
Chapter - 9..........................................................................................................................................40
Reference:...........................................................................................................................................40
2.5.1 Single pass unit..................................................................................................................20
2.5.2 Multipass unit....................................................................................................................20
CHAPTER THREE............................................................................................................................21
RESEARCH METHODOLOGY AND DESIGN PROCESS...........................................................21
3.1 Design process..........................................................................................................................21
3.2 Maintenance.............................................................................................................................21
3.3 Cost...........................................................................................................................................21
3.4 Safety........................................................................................................................................21
3.5 Design procedure......................................................................................................................22
3.5.2 Convective heat transfer coefficient (h)............................................................................23
3.5.3 Baffle cut and spacing.......................................................................................................24
3.6 Correction factor.......................................................................................................................25
3.7 Experimental calculation:.........................................................................................................28
Chapter 4............................................................................................................................................29
Optimization of the design process....................................................................................................29
4.1 Tube design calculations..........................................................................................................29
Chapter 5...........................................................................................................................................32
Design of shell and tube heat exchanger:-..........................................................................................32
5.1 Design of 3DModel of shell and tube heat exchanger by using Autodesk Inventor................33
5.2 Efficiency:................................................................................................................................33
5.3 Effectiveness:........................................................................................................................33
5.3.1 Tube pass...........................................................................................................................34
5.3.2 Tube pitch..........................................................................................................................34
Chapter - 6..........................................................................................................................................35
Results for CFD analysis: -................................................................................................................35
Chapter - 7..........................................................................................................................................38
Conclusion: -......................................................................................................................................38
Chapter - 8..........................................................................................................................................39
Recommendations of future work: -...................................................................................................39
Chapter - 9..........................................................................................................................................40
Reference:...........................................................................................................................................40
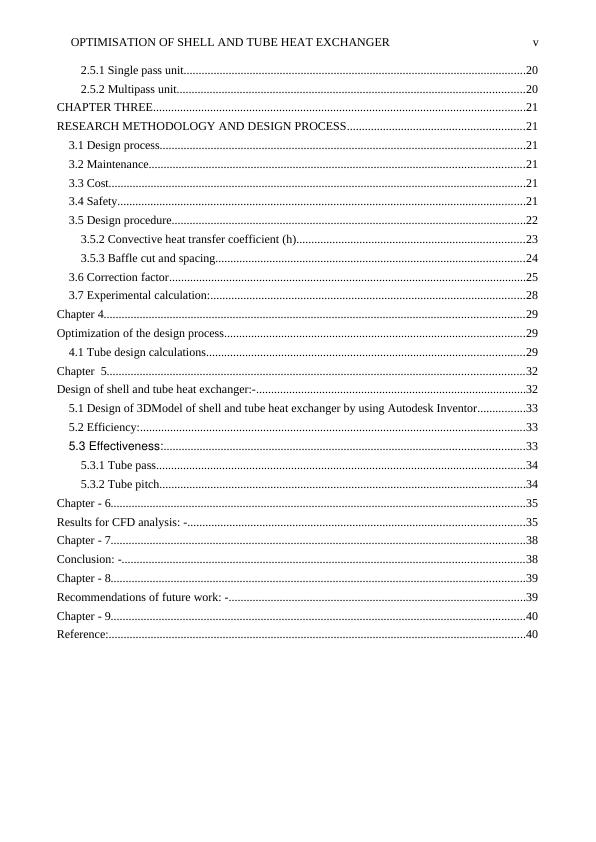
OPTIMISATION OF SHELL AND TUBE HEAT EXCHANGER vi
List of Figures
Figure 1.1 simple shell and tube heat exchanger
Figure 1.2 components of shell and tube heat exchanger (Wilfried & Deiying, 2007)
Figure 1.3 Heat exchangers based on application
Figure 1.4 shell and tube heat exchanger
Figure 1.5 parts shell and tube heat exchanger
Figure 1.6 TEMA standards configuration of STHE (Wen et al., 2016)
Figure 2.1 Tube Layout types (Wen et al., 2016)
Figure 3.1 Triangular Pitch and Clearance
5.1 Design of 3DModel of shell and tube heat exchanger by using Autodesk Inventor
5.2 Design of 3DModel of shell and tube heat exchanger by using Autodesk Inventor
Figure 6.1 Velocity Profile
Figure 6.2 Velocity Vector
List of Tables
Table 4.1 shows the design dimensions
Table 6.1 Velocity Magnitude
Table 6.2 Temperature Magnitude
Table 6.3 Pressure Magnitude
Nomenclature
List of Figures
Figure 1.1 simple shell and tube heat exchanger
Figure 1.2 components of shell and tube heat exchanger (Wilfried & Deiying, 2007)
Figure 1.3 Heat exchangers based on application
Figure 1.4 shell and tube heat exchanger
Figure 1.5 parts shell and tube heat exchanger
Figure 1.6 TEMA standards configuration of STHE (Wen et al., 2016)
Figure 2.1 Tube Layout types (Wen et al., 2016)
Figure 3.1 Triangular Pitch and Clearance
5.1 Design of 3DModel of shell and tube heat exchanger by using Autodesk Inventor
5.2 Design of 3DModel of shell and tube heat exchanger by using Autodesk Inventor
Figure 6.1 Velocity Profile
Figure 6.2 Velocity Vector
List of Tables
Table 4.1 shows the design dimensions
Table 6.1 Velocity Magnitude
Table 6.2 Temperature Magnitude
Table 6.3 Pressure Magnitude
Nomenclature
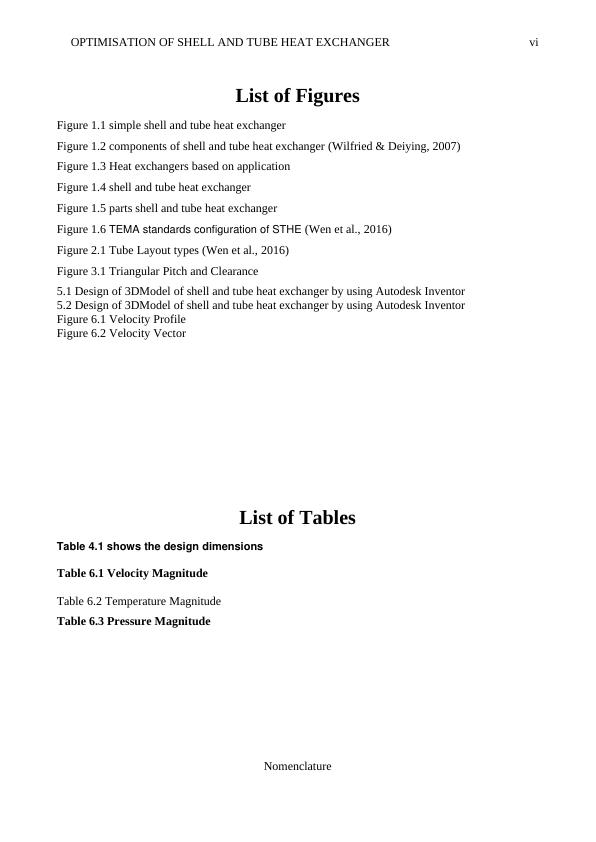
OPTIMISATION OF SHELL AND TUBE HEAT EXCHANGER vii
TEMA
STHE
Q = total rate of heat transfer
U = Is the overall average heat transfer coefficient.
ΔTm = Log Mean Temperature Difference
F = factor of correction
h = heat transfer coefficient
ho=¿overall coefficient of heat transfer
P = high temperature effectiveness
R = rate of heat capacity ratio
hc=¿overall heat transfer coefficient for clean surface
hf =¿overall heat transfer coefficient for fouled surface
Rf, total = the total fouling resistance
at = the tube flow area
PT = pitch of tube
Ds= diameter of the shell
V s =¿Velocity of the flow in shell side
η = efficiency
q = actual rate of heat transfer
qopt=optimumRate of heat transfer
C = a quantity called the shell clearance
Re=¿Reynolds number
Pr❑ = the Prandtl number
Nu❑=¿ the nusselt number -
TEMA
STHE
Q = total rate of heat transfer
U = Is the overall average heat transfer coefficient.
ΔTm = Log Mean Temperature Difference
F = factor of correction
h = heat transfer coefficient
ho=¿overall coefficient of heat transfer
P = high temperature effectiveness
R = rate of heat capacity ratio
hc=¿overall heat transfer coefficient for clean surface
hf =¿overall heat transfer coefficient for fouled surface
Rf, total = the total fouling resistance
at = the tube flow area
PT = pitch of tube
Ds= diameter of the shell
V s =¿Velocity of the flow in shell side
η = efficiency
q = actual rate of heat transfer
qopt=optimumRate of heat transfer
C = a quantity called the shell clearance
Re=¿Reynolds number
Pr❑ = the Prandtl number
Nu❑=¿ the nusselt number -
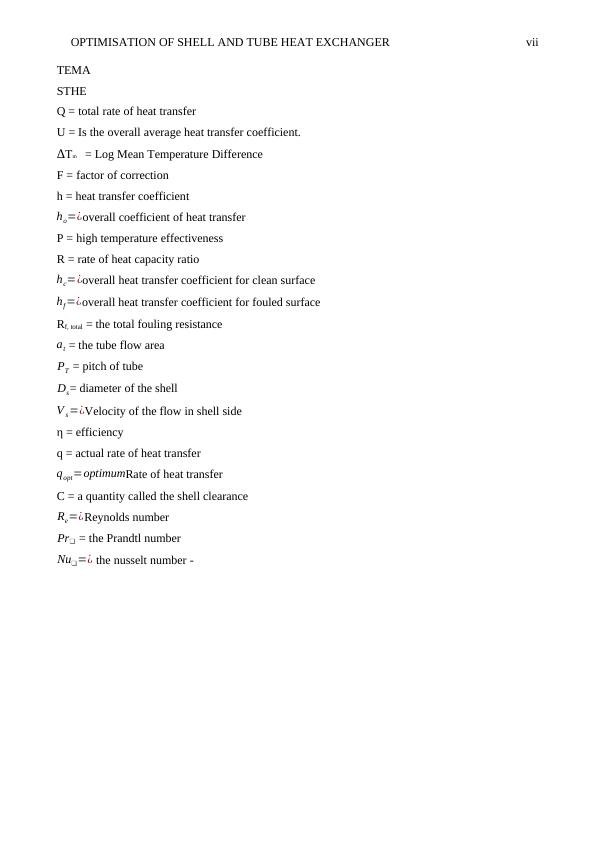
OPTIMISATION OF SHELL AND TUBE HEAT EXCHANGER viii
CHAPTER 1
INTRODUCTION
1.1 Background information
Objective: -
Best design and material selection should be considered to achieve the best efficiency of a heat
exchanger. The design parameters have to look at different conditions of exchanger use and feel
their needs. The best design can be achieved for heat exchanger (Mirzaei el al., 2017) influence the
efficiency of the diameter of the pipelines. It seeks shell and tube heat exchanger is the best among
several types and has high in demand (Gay et al., 2012) A shell and tube heat exchanger is a class of
heat exchanger designs. It is the most common type of heat exchanger in oil refineries and other
extensive chemical processes and is suited for higher -pressure applications (Coulson &
Richardson, 2005).
This type of heat exchanger consists of a shell which is a high-pressure vessel with a bundle of
tubes inside it. One fluid runs through the tubes, and another fluid flows over the tubes, which
means through the shell to transfer heat between the two fluids (Martinez el al., 2018). The set of
tubes is called a tube bundle and may be composed of several types of tubes such as dull,
longitudinally finned. In most industrial applications of nowadays involve application of heat
exchangers. Their popularity is widely contributed by cost minimisation thus making their use more
economical both for the designers and industrial users (Rao et al., 2017). Designers have been
working all time around the clock to improve in the working efficiency by incorporating more
complex processes that into details include selection operating parameters together with geometric
parameters. Latest models of these shell and tube heat exchangers have more advantages over the
conventional ones since they assure optimal solutions and takes less time thus doesn’t waste time as
compared to the traditional design approach.
On this account the study tends to explore and expound on the use of modern optimisation
techniques such as particle swarm optimisation (PSO) in shell and tube heat exchangers
optimisation design (Mohanty, 2016). Through this economic efficiency of the design is achieved.
One of the objectives in the design of these shell and tube heat exchangers is minimising the yearly
operation cost. This can only be achieved by considering three different design variables such as
baffle spacing for optimization, internal shell diameter and tube outer diameter in both two layouts,
that is square and triangle layouts.( Bevevino et al., 2014)
CHAPTER 1
INTRODUCTION
1.1 Background information
Objective: -
Best design and material selection should be considered to achieve the best efficiency of a heat
exchanger. The design parameters have to look at different conditions of exchanger use and feel
their needs. The best design can be achieved for heat exchanger (Mirzaei el al., 2017) influence the
efficiency of the diameter of the pipelines. It seeks shell and tube heat exchanger is the best among
several types and has high in demand (Gay et al., 2012) A shell and tube heat exchanger is a class of
heat exchanger designs. It is the most common type of heat exchanger in oil refineries and other
extensive chemical processes and is suited for higher -pressure applications (Coulson &
Richardson, 2005).
This type of heat exchanger consists of a shell which is a high-pressure vessel with a bundle of
tubes inside it. One fluid runs through the tubes, and another fluid flows over the tubes, which
means through the shell to transfer heat between the two fluids (Martinez el al., 2018). The set of
tubes is called a tube bundle and may be composed of several types of tubes such as dull,
longitudinally finned. In most industrial applications of nowadays involve application of heat
exchangers. Their popularity is widely contributed by cost minimisation thus making their use more
economical both for the designers and industrial users (Rao et al., 2017). Designers have been
working all time around the clock to improve in the working efficiency by incorporating more
complex processes that into details include selection operating parameters together with geometric
parameters. Latest models of these shell and tube heat exchangers have more advantages over the
conventional ones since they assure optimal solutions and takes less time thus doesn’t waste time as
compared to the traditional design approach.
On this account the study tends to explore and expound on the use of modern optimisation
techniques such as particle swarm optimisation (PSO) in shell and tube heat exchangers
optimisation design (Mohanty, 2016). Through this economic efficiency of the design is achieved.
One of the objectives in the design of these shell and tube heat exchangers is minimising the yearly
operation cost. This can only be achieved by considering three different design variables such as
baffle spacing for optimization, internal shell diameter and tube outer diameter in both two layouts,
that is square and triangle layouts.( Bevevino et al., 2014)
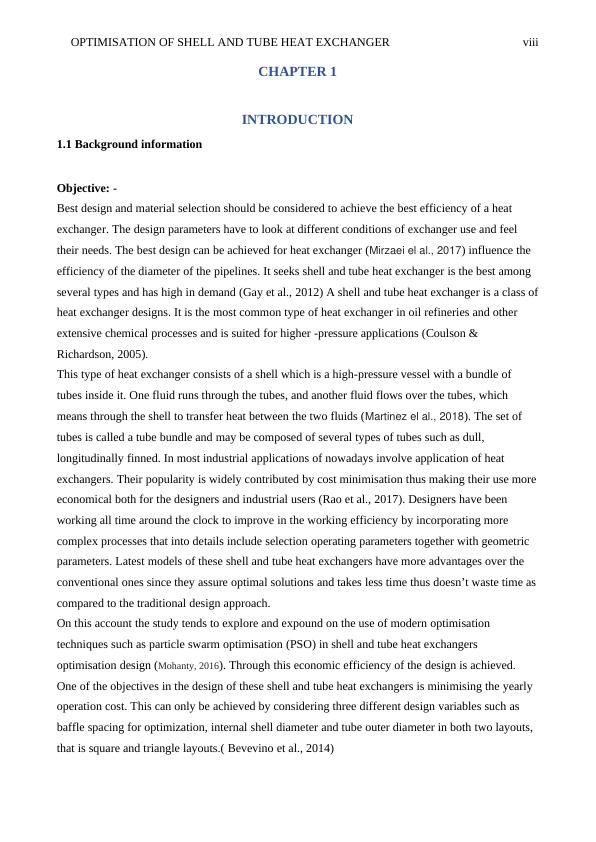
End of preview
Want to access all the pages? Upload your documents or become a member.
Related Documents
A Fresh New Look at Heat Exchanger Designlg...
|56
|12160
|215
Effect of Tube Arrangement on Performance of Shell and Tube Heat Exchangerlg...
|20
|5770
|39
Chemistry Assignment: Heat Exchange Analysislg...
|8
|1521
|176
Shell and Tube Exchanger Construction Assignmentlg...
|12
|1792
|118
Shell and Tube Heat Exchanger | Thermal Design and Analysis | Reportlg...
|22
|3493
|17
Design Considerations for Shell and Tube Heat Exchangerlg...
|12
|1633
|36