Optimization of the Delivery Process of the Machinery Leasing Logistics
VerifiedAdded on 2023/01/04
|51
|20652
|50
AI Summary
This research focuses on the optimization of the delivery process of machinery leasing logistics, specifically in the case of Johnson Arabia Company in the United Arab Emirates. The research aims to identify and address the potential obstacles causing delays in the shipment process. The main research questions revolve around the current shipment process, goals of the company, internal and external factors contributing to delays, performance of the delivery, and possible solutions to minimize disruption risks. By conducting interviews with employees from different positions within the company, this research aims to provide recommendations for optimizing the delivery time of shipments.
Contribute Materials
Your contribution can guide someone’s learning journey. Share your
documents today.
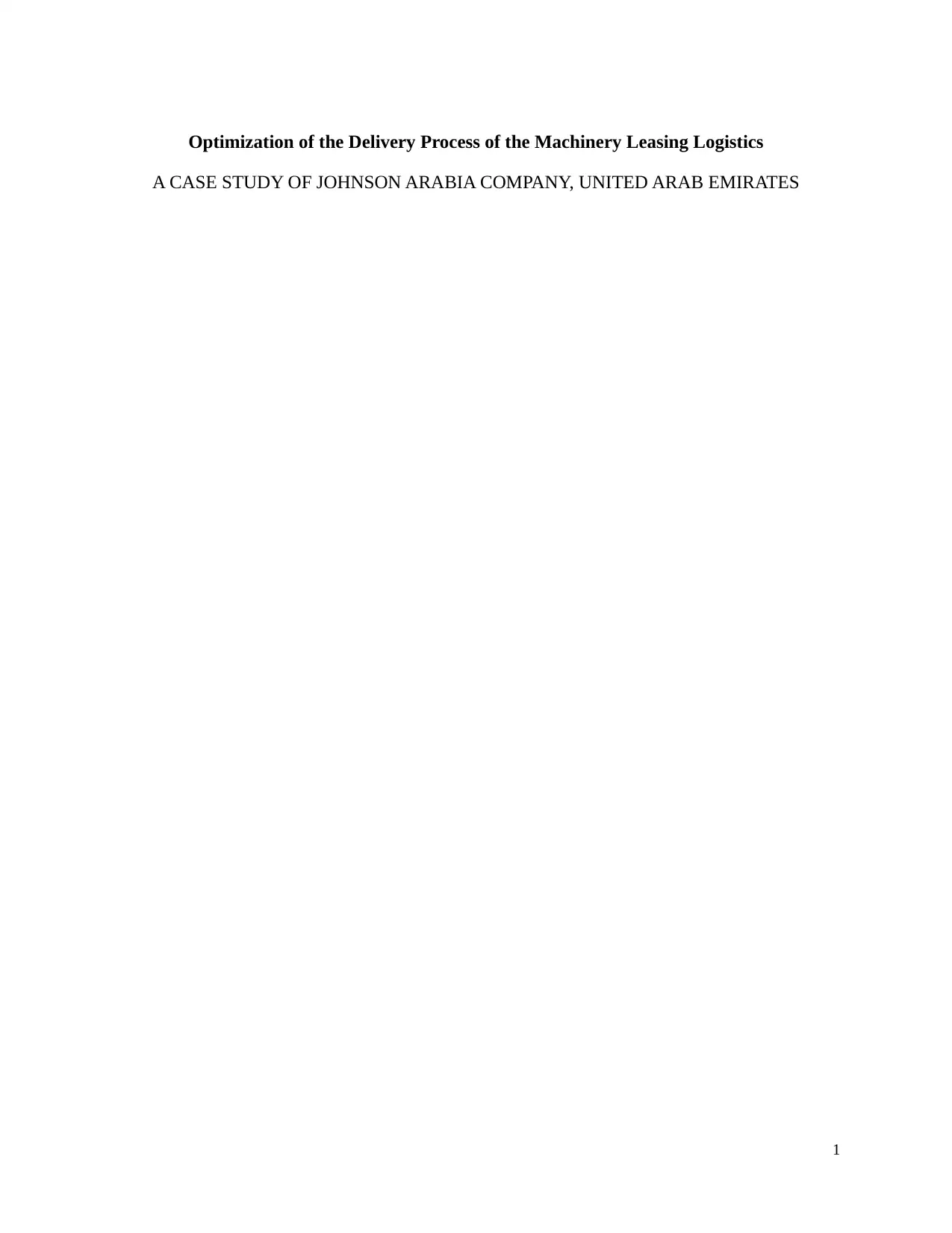
Optimization of the Delivery Process of the Machinery Leasing Logistics
A CASE STUDY OF JOHNSON ARABIA COMPANY, UNITED ARAB EMIRATES
1
A CASE STUDY OF JOHNSON ARABIA COMPANY, UNITED ARAB EMIRATES
1
Secure Best Marks with AI Grader
Need help grading? Try our AI Grader for instant feedback on your assignments.
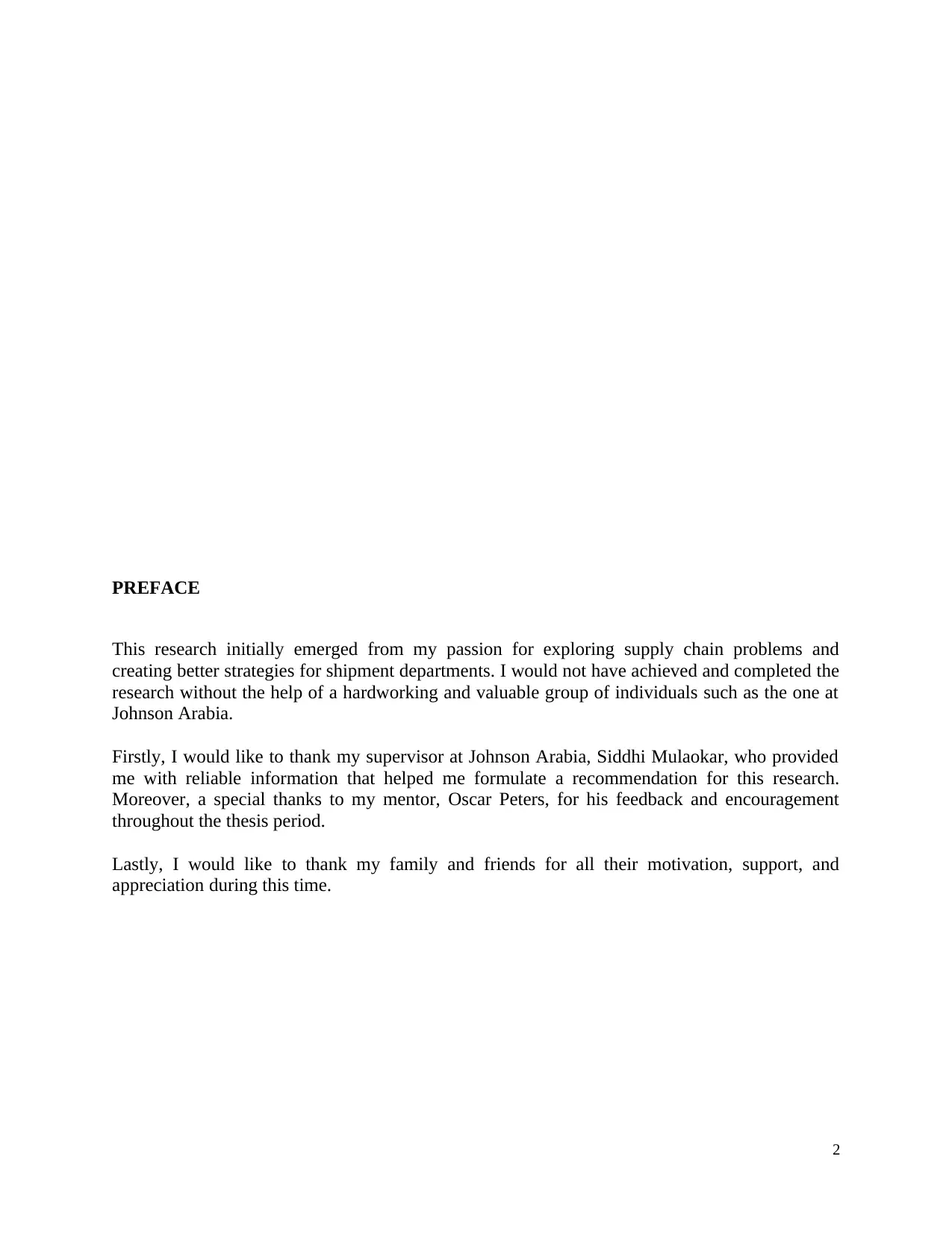
PREFACE
This research initially emerged from my passion for exploring supply chain problems and
creating better strategies for shipment departments. I would not have achieved and completed the
research without the help of a hardworking and valuable group of individuals such as the one at
Johnson Arabia.
Firstly, I would like to thank my supervisor at Johnson Arabia, Siddhi Mulaokar, who provided
me with reliable information that helped me formulate a recommendation for this research.
Moreover, a special thanks to my mentor, Oscar Peters, for his feedback and encouragement
throughout the thesis period.
Lastly, I would like to thank my family and friends for all their motivation, support, and
appreciation during this time.
2
This research initially emerged from my passion for exploring supply chain problems and
creating better strategies for shipment departments. I would not have achieved and completed the
research without the help of a hardworking and valuable group of individuals such as the one at
Johnson Arabia.
Firstly, I would like to thank my supervisor at Johnson Arabia, Siddhi Mulaokar, who provided
me with reliable information that helped me formulate a recommendation for this research.
Moreover, a special thanks to my mentor, Oscar Peters, for his feedback and encouragement
throughout the thesis period.
Lastly, I would like to thank my family and friends for all their motivation, support, and
appreciation during this time.
2
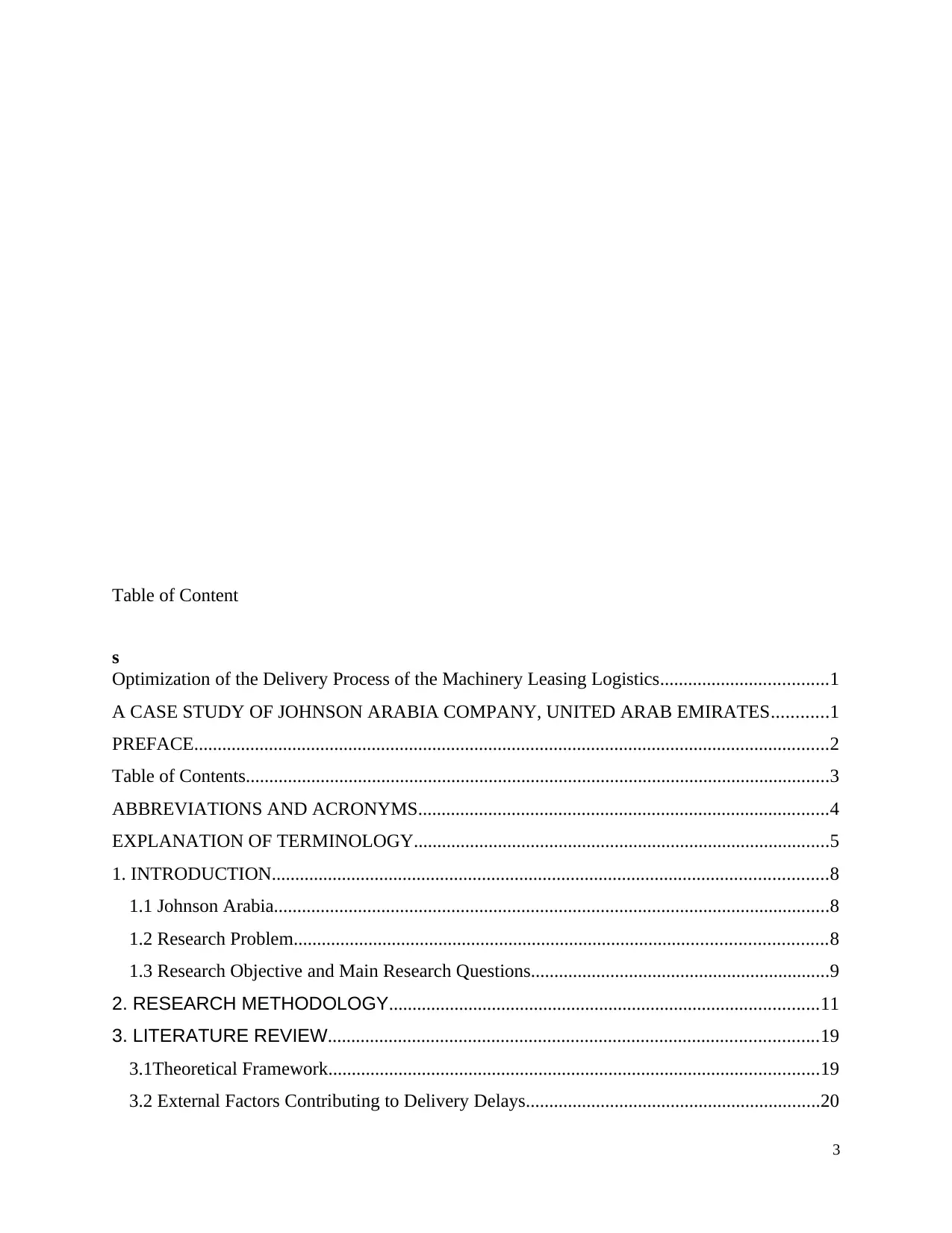
Table of Content
s
Optimization of the Delivery Process of the Machinery Leasing Logistics....................................1
A CASE STUDY OF JOHNSON ARABIA COMPANY, UNITED ARAB EMIRATES............1
PREFACE........................................................................................................................................2
Table of Contents.............................................................................................................................3
ABBREVIATIONS AND ACRONYMS........................................................................................4
EXPLANATION OF TERMINOLOGY.........................................................................................5
1. INTRODUCTION.......................................................................................................................8
1.1 Johnson Arabia.......................................................................................................................8
1.2 Research Problem..................................................................................................................8
1.3 Research Objective and Main Research Questions................................................................9
2. RESEARCH METHODOLOGY............................................................................................11
3. LITERATURE REVIEW.........................................................................................................19
3.1Theoretical Framework.........................................................................................................19
3.2 External Factors Contributing to Delivery Delays...............................................................20
3
s
Optimization of the Delivery Process of the Machinery Leasing Logistics....................................1
A CASE STUDY OF JOHNSON ARABIA COMPANY, UNITED ARAB EMIRATES............1
PREFACE........................................................................................................................................2
Table of Contents.............................................................................................................................3
ABBREVIATIONS AND ACRONYMS........................................................................................4
EXPLANATION OF TERMINOLOGY.........................................................................................5
1. INTRODUCTION.......................................................................................................................8
1.1 Johnson Arabia.......................................................................................................................8
1.2 Research Problem..................................................................................................................8
1.3 Research Objective and Main Research Questions................................................................9
2. RESEARCH METHODOLOGY............................................................................................11
3. LITERATURE REVIEW.........................................................................................................19
3.1Theoretical Framework.........................................................................................................19
3.2 External Factors Contributing to Delivery Delays...............................................................20
3
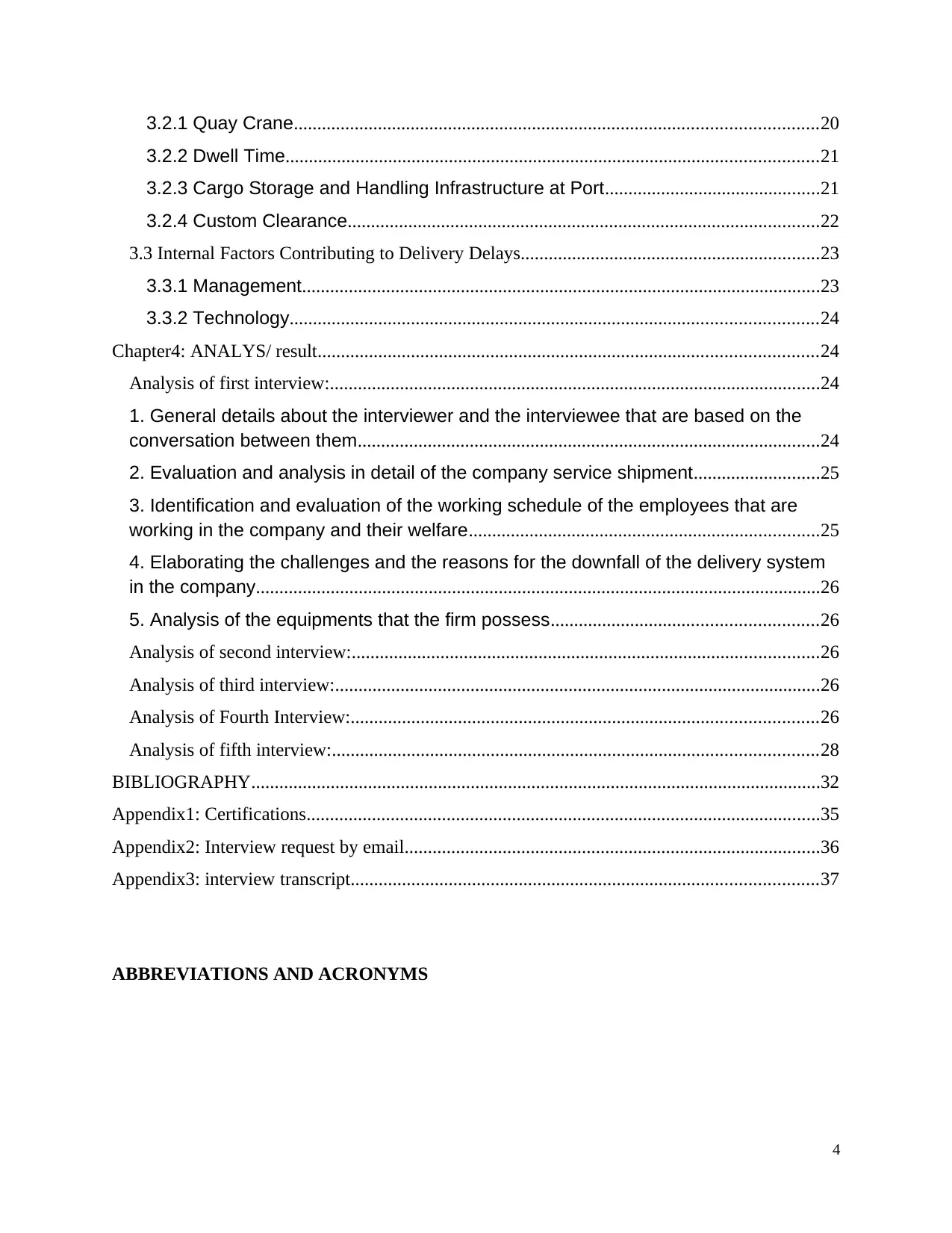
3.2.1 Quay Crane................................................................................................................20
3.2.2 Dwell Time..................................................................................................................21
3.2.3 Cargo Storage and Handling Infrastructure at Port..............................................21
3.2.4 Custom Clearance.....................................................................................................22
3.3 Internal Factors Contributing to Delivery Delays................................................................23
3.3.1 Management...............................................................................................................23
3.3.2 Technology.................................................................................................................24
Chapter4: ANALYS/ result...........................................................................................................24
Analysis of first interview:.........................................................................................................24
1. General details about the interviewer and the interviewee that are based on the
conversation between them...................................................................................................24
2. Evaluation and analysis in detail of the company service shipment...........................25
3. Identification and evaluation of the working schedule of the employees that are
working in the company and their welfare...........................................................................25
4. Elaborating the challenges and the reasons for the downfall of the delivery system
in the company.........................................................................................................................26
5. Analysis of the equipments that the firm possess.........................................................26
Analysis of second interview:....................................................................................................26
Analysis of third interview:........................................................................................................26
Analysis of Fourth Interview:....................................................................................................26
Analysis of fifth interview:........................................................................................................28
BIBLIOGRAPHY..........................................................................................................................32
Appendix1: Certifications..............................................................................................................35
Appendix2: Interview request by email.........................................................................................36
Appendix3: interview transcript....................................................................................................37
ABBREVIATIONS AND ACRONYMS
4
3.2.2 Dwell Time..................................................................................................................21
3.2.3 Cargo Storage and Handling Infrastructure at Port..............................................21
3.2.4 Custom Clearance.....................................................................................................22
3.3 Internal Factors Contributing to Delivery Delays................................................................23
3.3.1 Management...............................................................................................................23
3.3.2 Technology.................................................................................................................24
Chapter4: ANALYS/ result...........................................................................................................24
Analysis of first interview:.........................................................................................................24
1. General details about the interviewer and the interviewee that are based on the
conversation between them...................................................................................................24
2. Evaluation and analysis in detail of the company service shipment...........................25
3. Identification and evaluation of the working schedule of the employees that are
working in the company and their welfare...........................................................................25
4. Elaborating the challenges and the reasons for the downfall of the delivery system
in the company.........................................................................................................................26
5. Analysis of the equipments that the firm possess.........................................................26
Analysis of second interview:....................................................................................................26
Analysis of third interview:........................................................................................................26
Analysis of Fourth Interview:....................................................................................................26
Analysis of fifth interview:........................................................................................................28
BIBLIOGRAPHY..........................................................................................................................32
Appendix1: Certifications..............................................................................................................35
Appendix2: Interview request by email.........................................................................................36
Appendix3: interview transcript....................................................................................................37
ABBREVIATIONS AND ACRONYMS
4
Secure Best Marks with AI Grader
Need help grading? Try our AI Grader for instant feedback on your assignments.
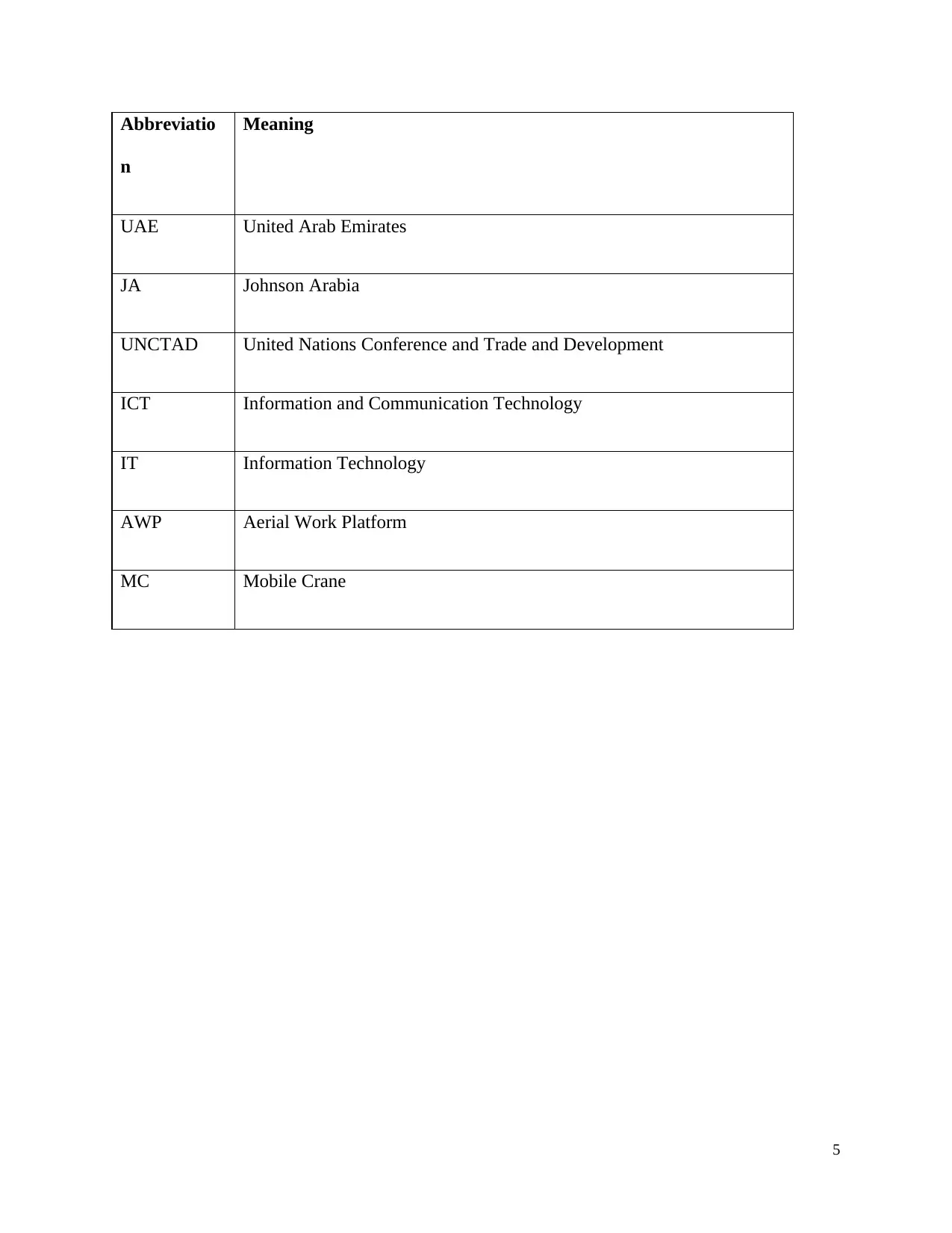
Abbreviatio
n
Meaning
UAE United Arab Emirates
JA Johnson Arabia
UNCTAD United Nations Conference and Trade and Development
ICT Information and Communication Technology
IT Information Technology
AWP Aerial Work Platform
MC Mobile Crane
5
n
Meaning
UAE United Arab Emirates
JA Johnson Arabia
UNCTAD United Nations Conference and Trade and Development
ICT Information and Communication Technology
IT Information Technology
AWP Aerial Work Platform
MC Mobile Crane
5
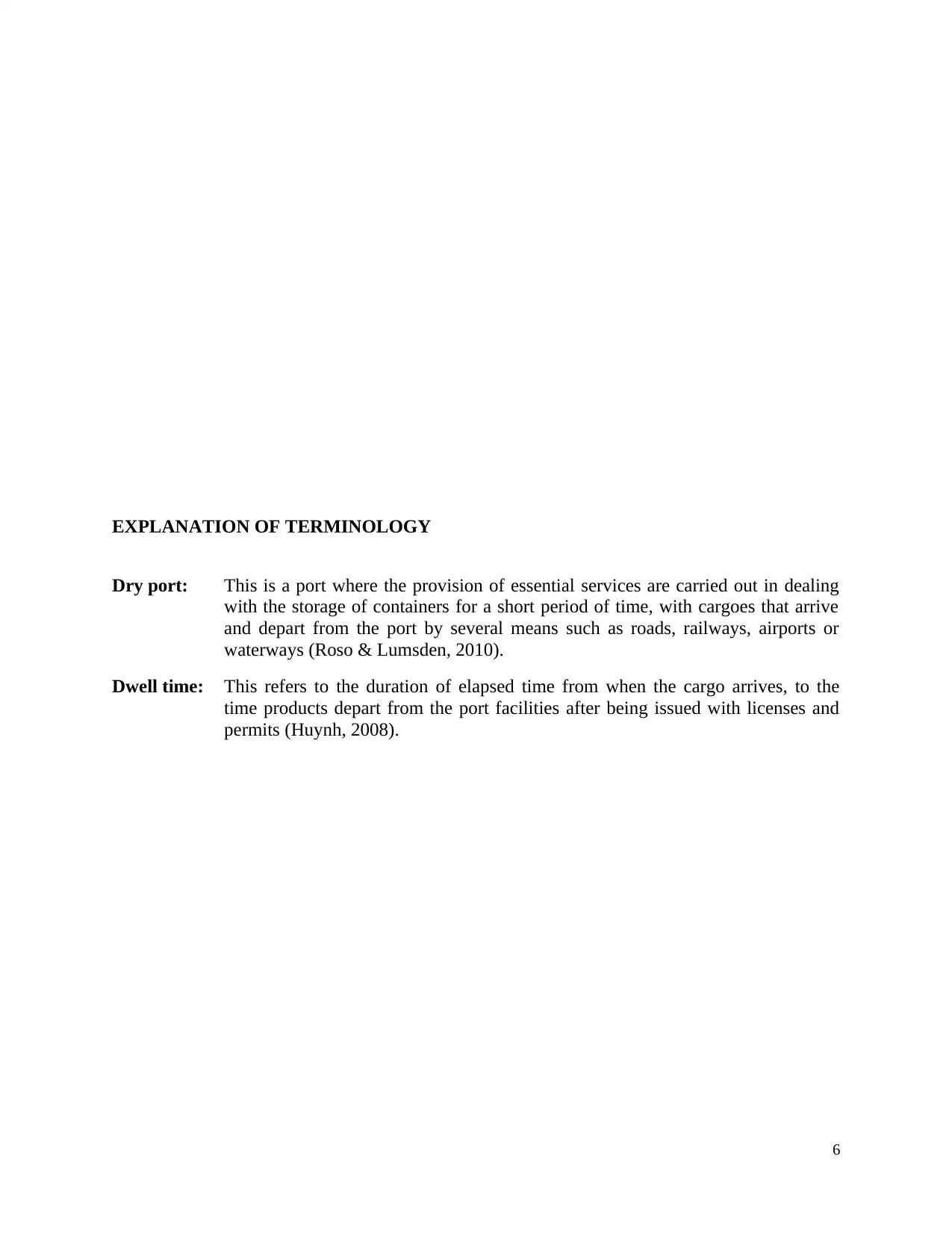
EXPLANATION OF TERMINOLOGY
Dry port: This is a port where the provision of essential services are carried out in dealing
with the storage of containers for a short period of time, with cargoes that arrive
and depart from the port by several means such as roads, railways, airports or
waterways (Roso & Lumsden, 2010).
Dwell time: This refers to the duration of elapsed time from when the cargo arrives, to the
time products depart from the port facilities after being issued with licenses and
permits (Huynh, 2008).
6
Dry port: This is a port where the provision of essential services are carried out in dealing
with the storage of containers for a short period of time, with cargoes that arrive
and depart from the port by several means such as roads, railways, airports or
waterways (Roso & Lumsden, 2010).
Dwell time: This refers to the duration of elapsed time from when the cargo arrives, to the
time products depart from the port facilities after being issued with licenses and
permits (Huynh, 2008).
6
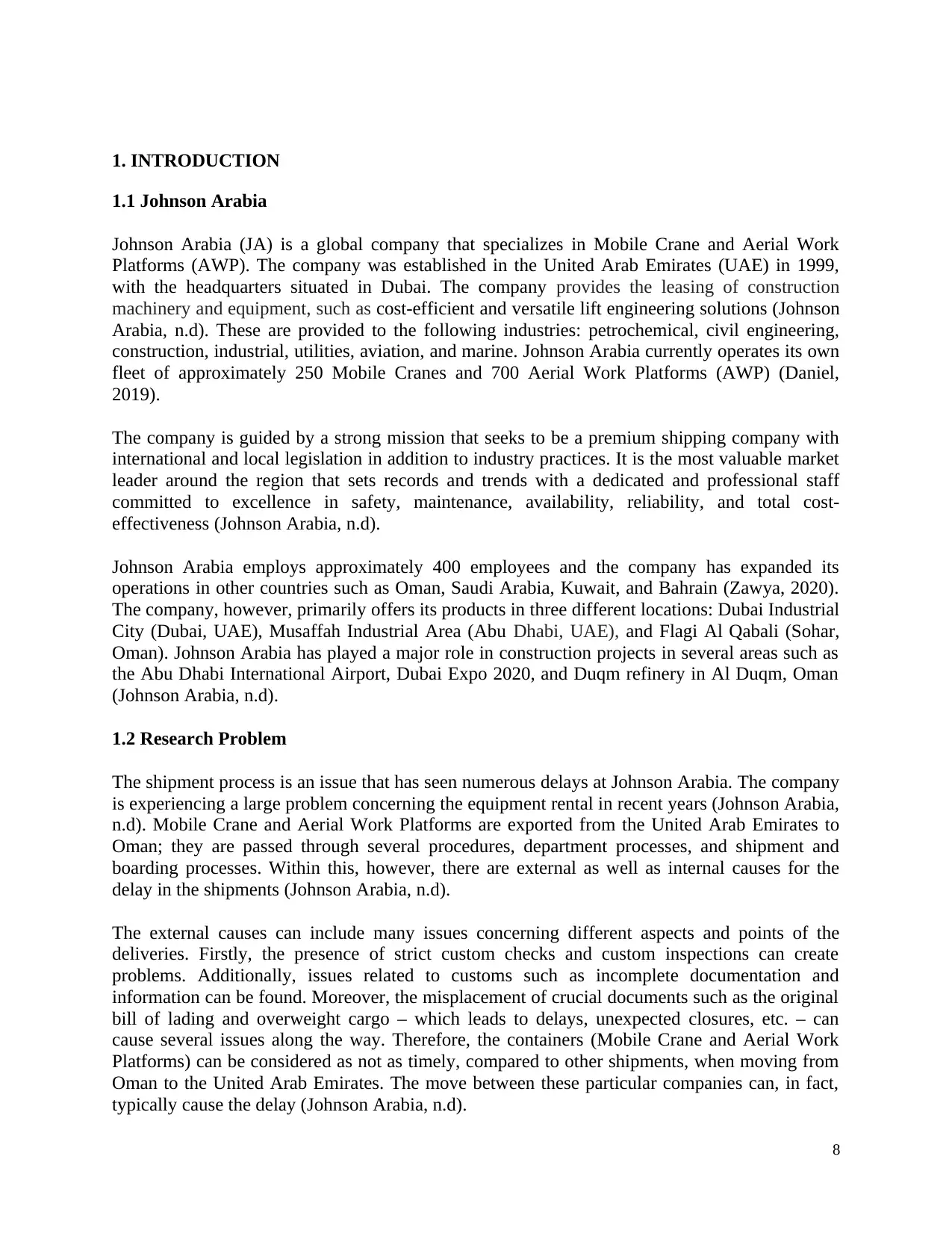
1. INTRODUCTION
1.1 Johnson Arabia
Johnson Arabia (JA) is a global company that specializes in Mobile Crane and Aerial Work
Platforms (AWP). The company was established in the United Arab Emirates (UAE) in 1999,
with the headquarters situated in Dubai. The company provides the leasing of construction
machinery and equipment, such as cost-efficient and versatile lift engineering solutions (Johnson
Arabia, n.d). These are provided to the following industries: petrochemical, civil engineering,
construction, industrial, utilities, aviation, and marine. Johnson Arabia currently operates its own
fleet of approximately 250 Mobile Cranes and 700 Aerial Work Platforms (AWP) (Daniel,
2019).
The company is guided by a strong mission that seeks to be a premium shipping company with
international and local legislation in addition to industry practices. It is the most valuable market
leader around the region that sets records and trends with a dedicated and professional staff
committed to excellence in safety, maintenance, availability, reliability, and total cost-
effectiveness (Johnson Arabia, n.d).
Johnson Arabia employs approximately 400 employees and the company has expanded its
operations in other countries such as Oman, Saudi Arabia, Kuwait, and Bahrain (Zawya, 2020).
The company, however, primarily offers its products in three different locations: Dubai Industrial
City (Dubai, UAE), Musaffah Industrial Area (Abu Dhabi, UAE), and Flagi Al Qabali (Sohar,
Oman). Johnson Arabia has played a major role in construction projects in several areas such as
the Abu Dhabi International Airport, Dubai Expo 2020, and Duqm refinery in Al Duqm, Oman
(Johnson Arabia, n.d).
1.2 Research Problem
The shipment process is an issue that has seen numerous delays at Johnson Arabia. The company
is experiencing a large problem concerning the equipment rental in recent years (Johnson Arabia,
n.d). Mobile Crane and Aerial Work Platforms are exported from the United Arab Emirates to
Oman; they are passed through several procedures, department processes, and shipment and
boarding processes. Within this, however, there are external as well as internal causes for the
delay in the shipments (Johnson Arabia, n.d).
The external causes can include many issues concerning different aspects and points of the
deliveries. Firstly, the presence of strict custom checks and custom inspections can create
problems. Additionally, issues related to customs such as incomplete documentation and
information can be found. Moreover, the misplacement of crucial documents such as the original
bill of lading and overweight cargo – which leads to delays, unexpected closures, etc. – can
cause several issues along the way. Therefore, the containers (Mobile Crane and Aerial Work
Platforms) can be considered as not as timely, compared to other shipments, when moving from
Oman to the United Arab Emirates. The move between these particular companies can, in fact,
typically cause the delay (Johnson Arabia, n.d).
8
1.1 Johnson Arabia
Johnson Arabia (JA) is a global company that specializes in Mobile Crane and Aerial Work
Platforms (AWP). The company was established in the United Arab Emirates (UAE) in 1999,
with the headquarters situated in Dubai. The company provides the leasing of construction
machinery and equipment, such as cost-efficient and versatile lift engineering solutions (Johnson
Arabia, n.d). These are provided to the following industries: petrochemical, civil engineering,
construction, industrial, utilities, aviation, and marine. Johnson Arabia currently operates its own
fleet of approximately 250 Mobile Cranes and 700 Aerial Work Platforms (AWP) (Daniel,
2019).
The company is guided by a strong mission that seeks to be a premium shipping company with
international and local legislation in addition to industry practices. It is the most valuable market
leader around the region that sets records and trends with a dedicated and professional staff
committed to excellence in safety, maintenance, availability, reliability, and total cost-
effectiveness (Johnson Arabia, n.d).
Johnson Arabia employs approximately 400 employees and the company has expanded its
operations in other countries such as Oman, Saudi Arabia, Kuwait, and Bahrain (Zawya, 2020).
The company, however, primarily offers its products in three different locations: Dubai Industrial
City (Dubai, UAE), Musaffah Industrial Area (Abu Dhabi, UAE), and Flagi Al Qabali (Sohar,
Oman). Johnson Arabia has played a major role in construction projects in several areas such as
the Abu Dhabi International Airport, Dubai Expo 2020, and Duqm refinery in Al Duqm, Oman
(Johnson Arabia, n.d).
1.2 Research Problem
The shipment process is an issue that has seen numerous delays at Johnson Arabia. The company
is experiencing a large problem concerning the equipment rental in recent years (Johnson Arabia,
n.d). Mobile Crane and Aerial Work Platforms are exported from the United Arab Emirates to
Oman; they are passed through several procedures, department processes, and shipment and
boarding processes. Within this, however, there are external as well as internal causes for the
delay in the shipments (Johnson Arabia, n.d).
The external causes can include many issues concerning different aspects and points of the
deliveries. Firstly, the presence of strict custom checks and custom inspections can create
problems. Additionally, issues related to customs such as incomplete documentation and
information can be found. Moreover, the misplacement of crucial documents such as the original
bill of lading and overweight cargo – which leads to delays, unexpected closures, etc. – can
cause several issues along the way. Therefore, the containers (Mobile Crane and Aerial Work
Platforms) can be considered as not as timely, compared to other shipments, when moving from
Oman to the United Arab Emirates. The move between these particular companies can, in fact,
typically cause the delay (Johnson Arabia, n.d).
8
Paraphrase This Document
Need a fresh take? Get an instant paraphrase of this document with our AI Paraphraser
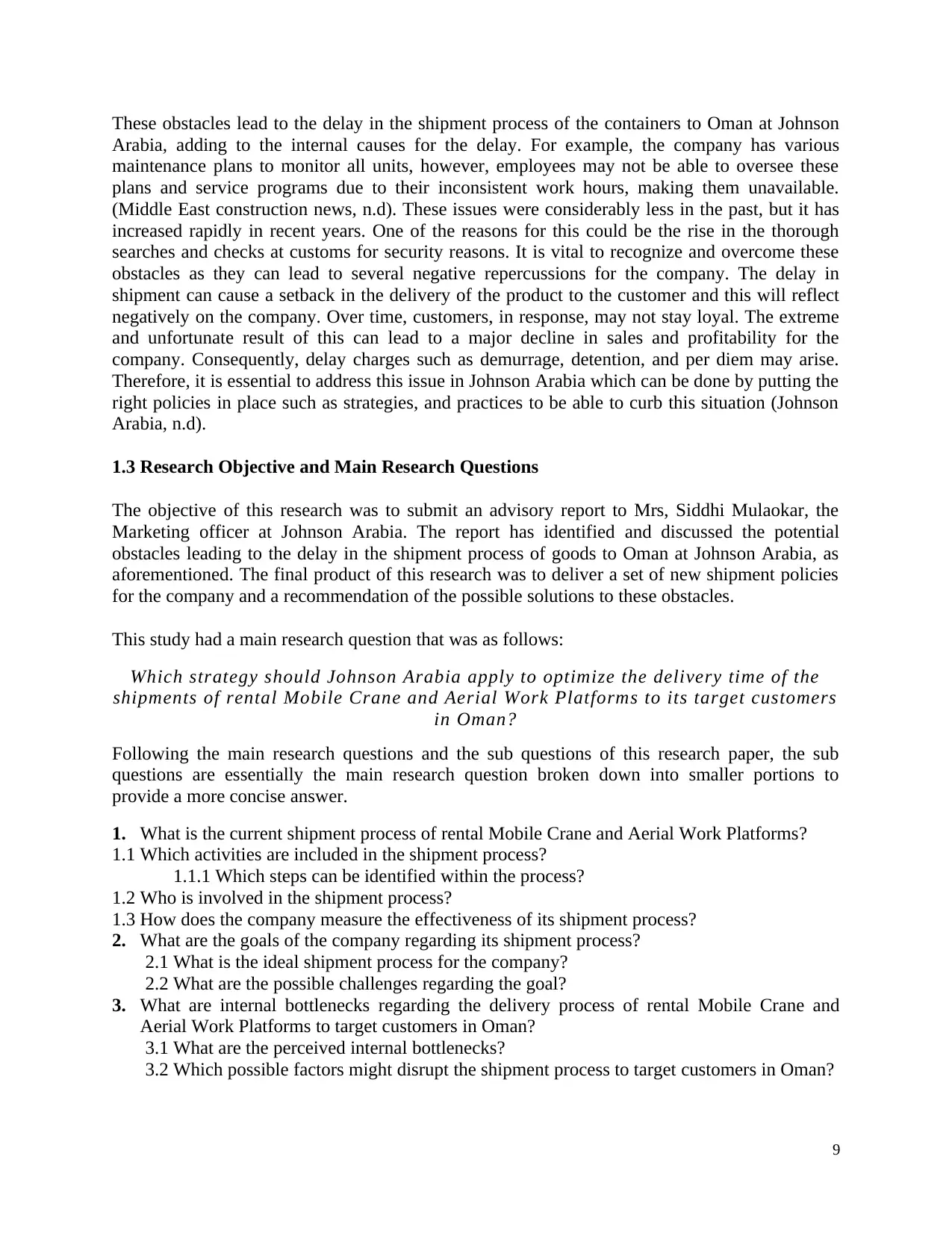
These obstacles lead to the delay in the shipment process of the containers to Oman at Johnson
Arabia, adding to the internal causes for the delay. For example, the company has various
maintenance plans to monitor all units, however, employees may not be able to oversee these
plans and service programs due to their inconsistent work hours, making them unavailable.
(Middle East construction news, n.d). These issues were considerably less in the past, but it has
increased rapidly in recent years. One of the reasons for this could be the rise in the thorough
searches and checks at customs for security reasons. It is vital to recognize and overcome these
obstacles as they can lead to several negative repercussions for the company. The delay in
shipment can cause a setback in the delivery of the product to the customer and this will reflect
negatively on the company. Over time, customers, in response, may not stay loyal. The extreme
and unfortunate result of this can lead to a major decline in sales and profitability for the
company. Consequently, delay charges such as demurrage, detention, and per diem may arise.
Therefore, it is essential to address this issue in Johnson Arabia which can be done by putting the
right policies in place such as strategies, and practices to be able to curb this situation (Johnson
Arabia, n.d).
1.3 Research Objective and Main Research Questions
The objective of this research was to submit an advisory report to Mrs, Siddhi Mulaokar, the
Marketing officer at Johnson Arabia. The report has identified and discussed the potential
obstacles leading to the delay in the shipment process of goods to Oman at Johnson Arabia, as
aforementioned. The final product of this research was to deliver a set of new shipment policies
for the company and a recommendation of the possible solutions to these obstacles.
This study had a main research question that was as follows:
Which strategy should Johnson Arabia apply to optimize the delivery time of the
shipments of rental Mobile Crane and Aerial Work Platforms to its target customers
in Oman?
Following the main research questions and the sub questions of this research paper, the sub
questions are essentially the main research question broken down into smaller portions to
provide a more concise answer.
1. What is the current shipment process of rental Mobile Crane and Aerial Work Platforms?
1.1 Which activities are included in the shipment process?
1.1.1 Which steps can be identified within the process?
1.2 Who is involved in the shipment process?
1.3 How does the company measure the effectiveness of its shipment process?
2. What are the goals of the company regarding its shipment process?
2.1 What is the ideal shipment process for the company?
2.2 What are the possible challenges regarding the goal?
3. What are internal bottlenecks regarding the delivery process of rental Mobile Crane and
Aerial Work Platforms to target customers in Oman?
3.1 What are the perceived internal bottlenecks?
3.2 Which possible factors might disrupt the shipment process to target customers in Oman?
9
Arabia, adding to the internal causes for the delay. For example, the company has various
maintenance plans to monitor all units, however, employees may not be able to oversee these
plans and service programs due to their inconsistent work hours, making them unavailable.
(Middle East construction news, n.d). These issues were considerably less in the past, but it has
increased rapidly in recent years. One of the reasons for this could be the rise in the thorough
searches and checks at customs for security reasons. It is vital to recognize and overcome these
obstacles as they can lead to several negative repercussions for the company. The delay in
shipment can cause a setback in the delivery of the product to the customer and this will reflect
negatively on the company. Over time, customers, in response, may not stay loyal. The extreme
and unfortunate result of this can lead to a major decline in sales and profitability for the
company. Consequently, delay charges such as demurrage, detention, and per diem may arise.
Therefore, it is essential to address this issue in Johnson Arabia which can be done by putting the
right policies in place such as strategies, and practices to be able to curb this situation (Johnson
Arabia, n.d).
1.3 Research Objective and Main Research Questions
The objective of this research was to submit an advisory report to Mrs, Siddhi Mulaokar, the
Marketing officer at Johnson Arabia. The report has identified and discussed the potential
obstacles leading to the delay in the shipment process of goods to Oman at Johnson Arabia, as
aforementioned. The final product of this research was to deliver a set of new shipment policies
for the company and a recommendation of the possible solutions to these obstacles.
This study had a main research question that was as follows:
Which strategy should Johnson Arabia apply to optimize the delivery time of the
shipments of rental Mobile Crane and Aerial Work Platforms to its target customers
in Oman?
Following the main research questions and the sub questions of this research paper, the sub
questions are essentially the main research question broken down into smaller portions to
provide a more concise answer.
1. What is the current shipment process of rental Mobile Crane and Aerial Work Platforms?
1.1 Which activities are included in the shipment process?
1.1.1 Which steps can be identified within the process?
1.2 Who is involved in the shipment process?
1.3 How does the company measure the effectiveness of its shipment process?
2. What are the goals of the company regarding its shipment process?
2.1 What is the ideal shipment process for the company?
2.2 What are the possible challenges regarding the goal?
3. What are internal bottlenecks regarding the delivery process of rental Mobile Crane and
Aerial Work Platforms to target customers in Oman?
3.1 What are the perceived internal bottlenecks?
3.2 Which possible factors might disrupt the shipment process to target customers in Oman?
9
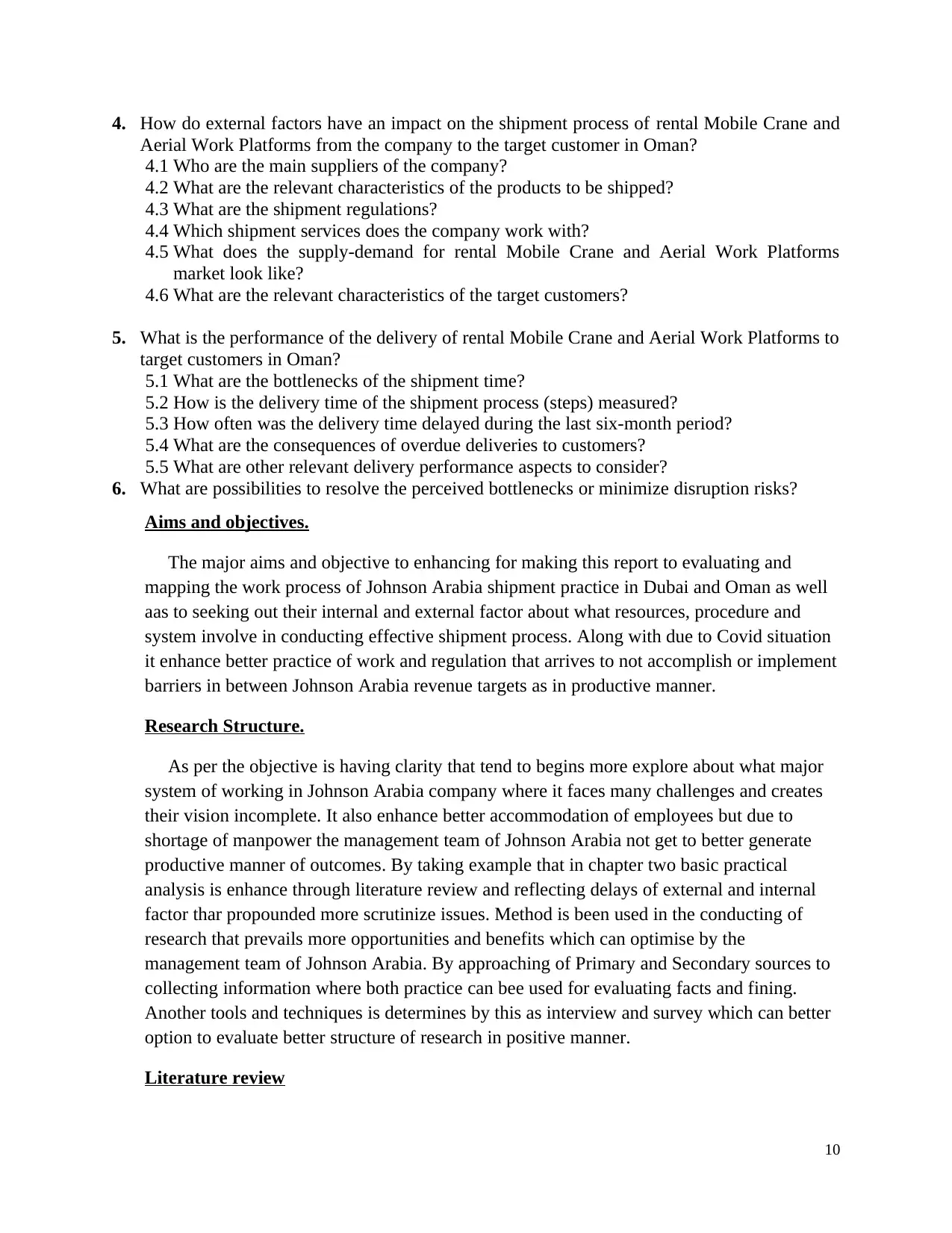
4. How do external factors have an impact on the shipment process of rental Mobile Crane and
Aerial Work Platforms from the company to the target customer in Oman?
4.1 Who are the main suppliers of the company?
4.2 What are the relevant characteristics of the products to be shipped?
4.3 What are the shipment regulations?
4.4 Which shipment services does the company work with?
4.5 What does the supply-demand for rental Mobile Crane and Aerial Work Platforms
market look like?
4.6 What are the relevant characteristics of the target customers?
5. What is the performance of the delivery of rental Mobile Crane and Aerial Work Platforms to
target customers in Oman?
5.1 What are the bottlenecks of the shipment time?
5.2 How is the delivery time of the shipment process (steps) measured?
5.3 How often was the delivery time delayed during the last six-month period?
5.4 What are the consequences of overdue deliveries to customers?
5.5 What are other relevant delivery performance aspects to consider?
6. What are possibilities to resolve the perceived bottlenecks or minimize disruption risks?
Aims and objectives.
The major aims and objective to enhancing for making this report to evaluating and
mapping the work process of Johnson Arabia shipment practice in Dubai and Oman as well
aas to seeking out their internal and external factor about what resources, procedure and
system involve in conducting effective shipment process. Along with due to Covid situation
it enhance better practice of work and regulation that arrives to not accomplish or implement
barriers in between Johnson Arabia revenue targets as in productive manner.
Research Structure.
As per the objective is having clarity that tend to begins more explore about what major
system of working in Johnson Arabia company where it faces many challenges and creates
their vision incomplete. It also enhance better accommodation of employees but due to
shortage of manpower the management team of Johnson Arabia not get to better generate
productive manner of outcomes. By taking example that in chapter two basic practical
analysis is enhance through literature review and reflecting delays of external and internal
factor thar propounded more scrutinize issues. Method is been used in the conducting of
research that prevails more opportunities and benefits which can optimise by the
management team of Johnson Arabia. By approaching of Primary and Secondary sources to
collecting information where both practice can bee used for evaluating facts and fining.
Another tools and techniques is determines by this as interview and survey which can better
option to evaluate better structure of research in positive manner.
Literature review
10
Aerial Work Platforms from the company to the target customer in Oman?
4.1 Who are the main suppliers of the company?
4.2 What are the relevant characteristics of the products to be shipped?
4.3 What are the shipment regulations?
4.4 Which shipment services does the company work with?
4.5 What does the supply-demand for rental Mobile Crane and Aerial Work Platforms
market look like?
4.6 What are the relevant characteristics of the target customers?
5. What is the performance of the delivery of rental Mobile Crane and Aerial Work Platforms to
target customers in Oman?
5.1 What are the bottlenecks of the shipment time?
5.2 How is the delivery time of the shipment process (steps) measured?
5.3 How often was the delivery time delayed during the last six-month period?
5.4 What are the consequences of overdue deliveries to customers?
5.5 What are other relevant delivery performance aspects to consider?
6. What are possibilities to resolve the perceived bottlenecks or minimize disruption risks?
Aims and objectives.
The major aims and objective to enhancing for making this report to evaluating and
mapping the work process of Johnson Arabia shipment practice in Dubai and Oman as well
aas to seeking out their internal and external factor about what resources, procedure and
system involve in conducting effective shipment process. Along with due to Covid situation
it enhance better practice of work and regulation that arrives to not accomplish or implement
barriers in between Johnson Arabia revenue targets as in productive manner.
Research Structure.
As per the objective is having clarity that tend to begins more explore about what major
system of working in Johnson Arabia company where it faces many challenges and creates
their vision incomplete. It also enhance better accommodation of employees but due to
shortage of manpower the management team of Johnson Arabia not get to better generate
productive manner of outcomes. By taking example that in chapter two basic practical
analysis is enhance through literature review and reflecting delays of external and internal
factor thar propounded more scrutinize issues. Method is been used in the conducting of
research that prevails more opportunities and benefits which can optimise by the
management team of Johnson Arabia. By approaching of Primary and Secondary sources to
collecting information where both practice can bee used for evaluating facts and fining.
Another tools and techniques is determines by this as interview and survey which can better
option to evaluate better structure of research in positive manner.
Literature review
10
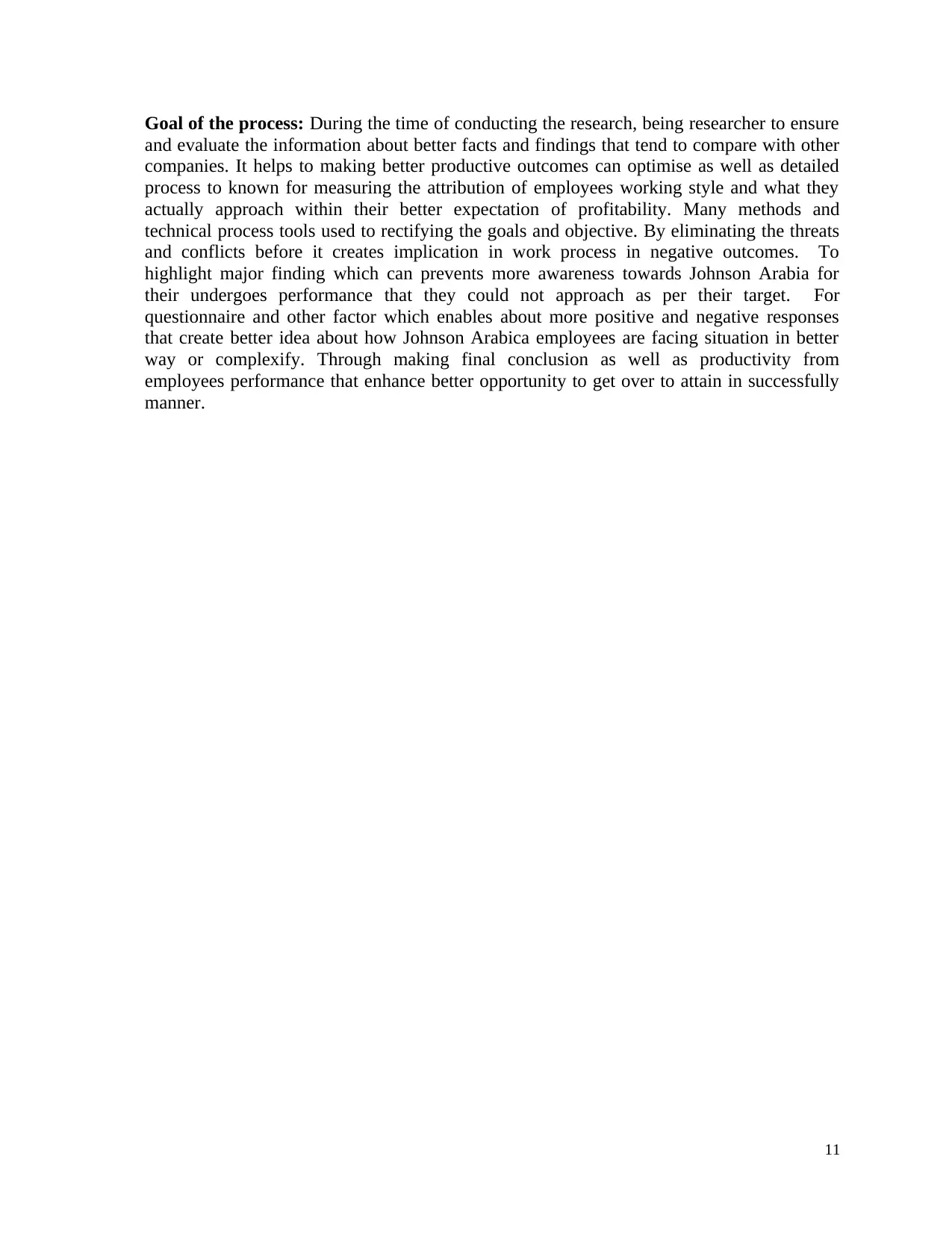
Goal of the process: During the time of conducting the research, being researcher to ensure
and evaluate the information about better facts and findings that tend to compare with other
companies. It helps to making better productive outcomes can optimise as well as detailed
process to known for measuring the attribution of employees working style and what they
actually approach within their better expectation of profitability. Many methods and
technical process tools used to rectifying the goals and objective. By eliminating the threats
and conflicts before it creates implication in work process in negative outcomes. To
highlight major finding which can prevents more awareness towards Johnson Arabia for
their undergoes performance that they could not approach as per their target. For
questionnaire and other factor which enables about more positive and negative responses
that create better idea about how Johnson Arabica employees are facing situation in better
way or complexify. Through making final conclusion as well as productivity from
employees performance that enhance better opportunity to get over to attain in successfully
manner.
11
and evaluate the information about better facts and findings that tend to compare with other
companies. It helps to making better productive outcomes can optimise as well as detailed
process to known for measuring the attribution of employees working style and what they
actually approach within their better expectation of profitability. Many methods and
technical process tools used to rectifying the goals and objective. By eliminating the threats
and conflicts before it creates implication in work process in negative outcomes. To
highlight major finding which can prevents more awareness towards Johnson Arabia for
their undergoes performance that they could not approach as per their target. For
questionnaire and other factor which enables about more positive and negative responses
that create better idea about how Johnson Arabica employees are facing situation in better
way or complexify. Through making final conclusion as well as productivity from
employees performance that enhance better opportunity to get over to attain in successfully
manner.
11
Secure Best Marks with AI Grader
Need help grading? Try our AI Grader for instant feedback on your assignments.
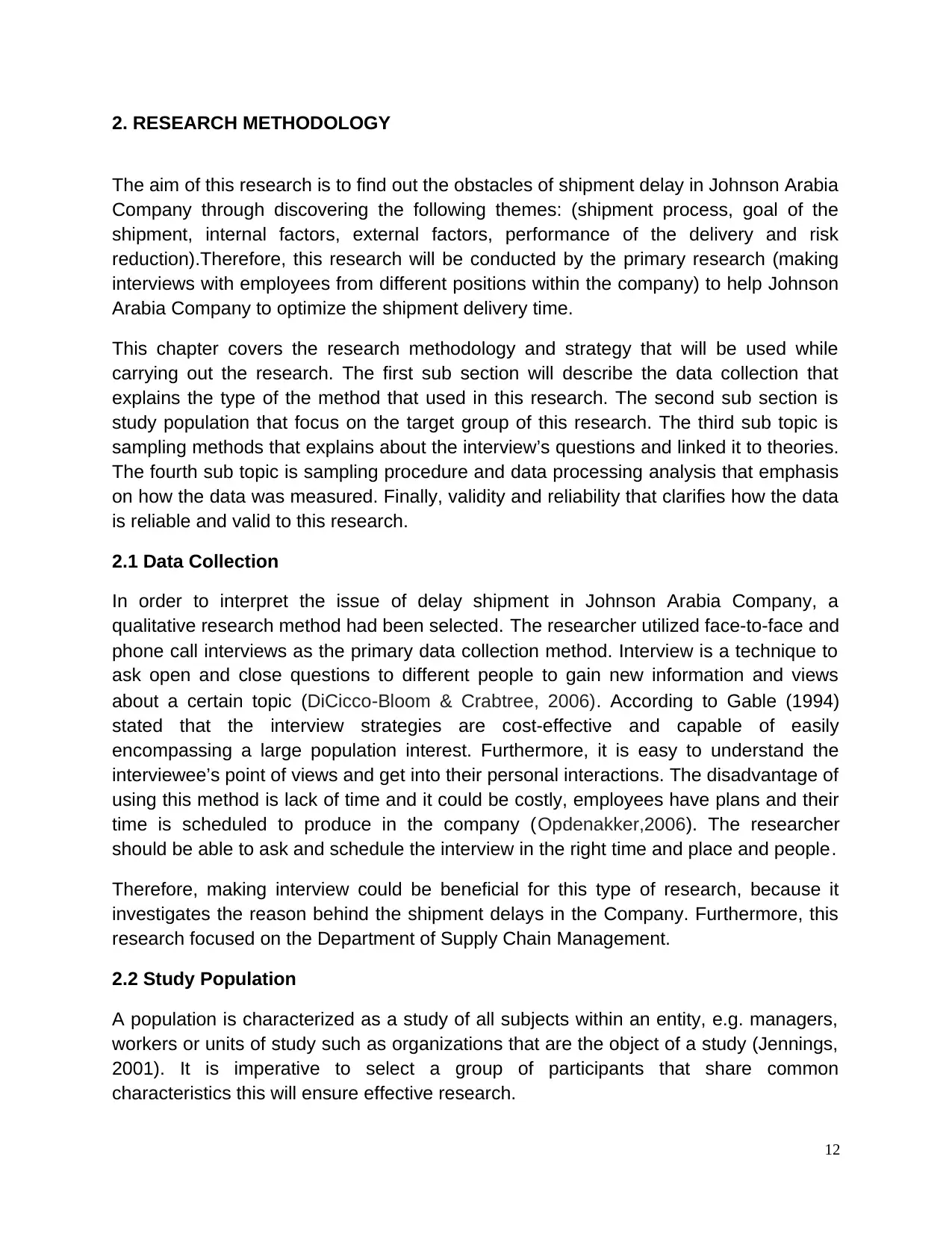
2. RESEARCH METHODOLOGY
The aim of this research is to find out the obstacles of shipment delay in Johnson Arabia
Company through discovering the following themes: (shipment process, goal of the
shipment, internal factors, external factors, performance of the delivery and risk
reduction).Therefore, this research will be conducted by the primary research (making
interviews with employees from different positions within the company) to help Johnson
Arabia Company to optimize the shipment delivery time.
This chapter covers the research methodology and strategy that will be used while
carrying out the research. The first sub section will describe the data collection that
explains the type of the method that used in this research. The second sub section is
study population that focus on the target group of this research. The third sub topic is
sampling methods that explains about the interview’s questions and linked it to theories.
The fourth sub topic is sampling procedure and data processing analysis that emphasis
on how the data was measured. Finally, validity and reliability that clarifies how the data
is reliable and valid to this research.
2.1 Data Collection
In order to interpret the issue of delay shipment in Johnson Arabia Company, a
qualitative research method had been selected. The researcher utilized face-to-face and
phone call interviews as the primary data collection method. Interview is a technique to
ask open and close questions to different people to gain new information and views
about a certain topic (DiCicco‐Bloom & Crabtree, 2006). According to Gable (1994)
stated that the interview strategies are cost-effective and capable of easily
encompassing a large population interest. Furthermore, it is easy to understand the
interviewee’s point of views and get into their personal interactions. The disadvantage of
using this method is lack of time and it could be costly, employees have plans and their
time is scheduled to produce in the company (Opdenakker,2006). The researcher
should be able to ask and schedule the interview in the right time and place and people.
Therefore, making interview could be beneficial for this type of research, because it
investigates the reason behind the shipment delays in the Company. Furthermore, this
research focused on the Department of Supply Chain Management.
2.2 Study Population
A population is characterized as a study of all subjects within an entity, e.g. managers,
workers or units of study such as organizations that are the object of a study (Jennings,
2001). It is imperative to select a group of participants that share common
characteristics this will ensure effective research.
12
The aim of this research is to find out the obstacles of shipment delay in Johnson Arabia
Company through discovering the following themes: (shipment process, goal of the
shipment, internal factors, external factors, performance of the delivery and risk
reduction).Therefore, this research will be conducted by the primary research (making
interviews with employees from different positions within the company) to help Johnson
Arabia Company to optimize the shipment delivery time.
This chapter covers the research methodology and strategy that will be used while
carrying out the research. The first sub section will describe the data collection that
explains the type of the method that used in this research. The second sub section is
study population that focus on the target group of this research. The third sub topic is
sampling methods that explains about the interview’s questions and linked it to theories.
The fourth sub topic is sampling procedure and data processing analysis that emphasis
on how the data was measured. Finally, validity and reliability that clarifies how the data
is reliable and valid to this research.
2.1 Data Collection
In order to interpret the issue of delay shipment in Johnson Arabia Company, a
qualitative research method had been selected. The researcher utilized face-to-face and
phone call interviews as the primary data collection method. Interview is a technique to
ask open and close questions to different people to gain new information and views
about a certain topic (DiCicco‐Bloom & Crabtree, 2006). According to Gable (1994)
stated that the interview strategies are cost-effective and capable of easily
encompassing a large population interest. Furthermore, it is easy to understand the
interviewee’s point of views and get into their personal interactions. The disadvantage of
using this method is lack of time and it could be costly, employees have plans and their
time is scheduled to produce in the company (Opdenakker,2006). The researcher
should be able to ask and schedule the interview in the right time and place and people.
Therefore, making interview could be beneficial for this type of research, because it
investigates the reason behind the shipment delays in the Company. Furthermore, this
research focused on the Department of Supply Chain Management.
2.2 Study Population
A population is characterized as a study of all subjects within an entity, e.g. managers,
workers or units of study such as organizations that are the object of a study (Jennings,
2001). It is imperative to select a group of participants that share common
characteristics this will ensure effective research.
12
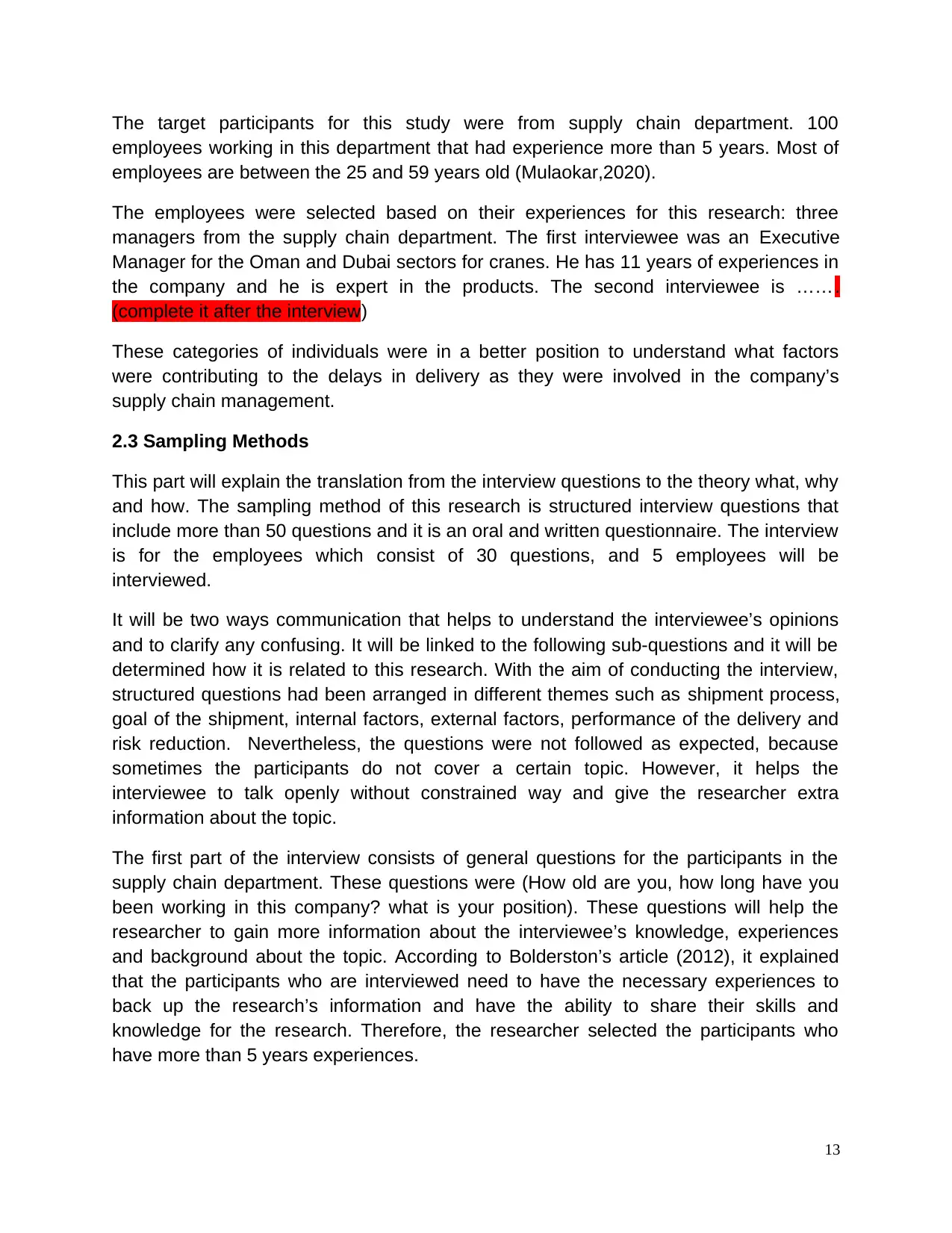
The target participants for this study were from supply chain department. 100
employees working in this department that had experience more than 5 years. Most of
employees are between the 25 and 59 years old (Mulaokar,2020).
The employees were selected based on their experiences for this research: three
managers from the supply chain department. The first interviewee was an Executive
Manager for the Oman and Dubai sectors for cranes. He has 11 years of experiences in
the company and he is expert in the products. The second interviewee is …….
(complete it after the interview)
These categories of individuals were in a better position to understand what factors
were contributing to the delays in delivery as they were involved in the company’s
supply chain management.
2.3 Sampling Methods
This part will explain the translation from the interview questions to the theory what, why
and how. The sampling method of this research is structured interview questions that
include more than 50 questions and it is an oral and written questionnaire. The interview
is for the employees which consist of 30 questions, and 5 employees will be
interviewed.
It will be two ways communication that helps to understand the interviewee’s opinions
and to clarify any confusing. It will be linked to the following sub-questions and it will be
determined how it is related to this research. With the aim of conducting the interview,
structured questions had been arranged in different themes such as shipment process,
goal of the shipment, internal factors, external factors, performance of the delivery and
risk reduction. Nevertheless, the questions were not followed as expected, because
sometimes the participants do not cover a certain topic. However, it helps the
interviewee to talk openly without constrained way and give the researcher extra
information about the topic.
The first part of the interview consists of general questions for the participants in the
supply chain department. These questions were (How old are you, how long have you
been working in this company? what is your position). These questions will help the
researcher to gain more information about the interviewee’s knowledge, experiences
and background about the topic. According to Bolderston’s article (2012), it explained
that the participants who are interviewed need to have the necessary experiences to
back up the research’s information and have the ability to share their skills and
knowledge for the research. Therefore, the researcher selected the participants who
have more than 5 years experiences.
13
employees working in this department that had experience more than 5 years. Most of
employees are between the 25 and 59 years old (Mulaokar,2020).
The employees were selected based on their experiences for this research: three
managers from the supply chain department. The first interviewee was an Executive
Manager for the Oman and Dubai sectors for cranes. He has 11 years of experiences in
the company and he is expert in the products. The second interviewee is …….
(complete it after the interview)
These categories of individuals were in a better position to understand what factors
were contributing to the delays in delivery as they were involved in the company’s
supply chain management.
2.3 Sampling Methods
This part will explain the translation from the interview questions to the theory what, why
and how. The sampling method of this research is structured interview questions that
include more than 50 questions and it is an oral and written questionnaire. The interview
is for the employees which consist of 30 questions, and 5 employees will be
interviewed.
It will be two ways communication that helps to understand the interviewee’s opinions
and to clarify any confusing. It will be linked to the following sub-questions and it will be
determined how it is related to this research. With the aim of conducting the interview,
structured questions had been arranged in different themes such as shipment process,
goal of the shipment, internal factors, external factors, performance of the delivery and
risk reduction. Nevertheless, the questions were not followed as expected, because
sometimes the participants do not cover a certain topic. However, it helps the
interviewee to talk openly without constrained way and give the researcher extra
information about the topic.
The first part of the interview consists of general questions for the participants in the
supply chain department. These questions were (How old are you, how long have you
been working in this company? what is your position). These questions will help the
researcher to gain more information about the interviewee’s knowledge, experiences
and background about the topic. According to Bolderston’s article (2012), it explained
that the participants who are interviewed need to have the necessary experiences to
back up the research’s information and have the ability to share their skills and
knowledge for the research. Therefore, the researcher selected the participants who
have more than 5 years experiences.
13
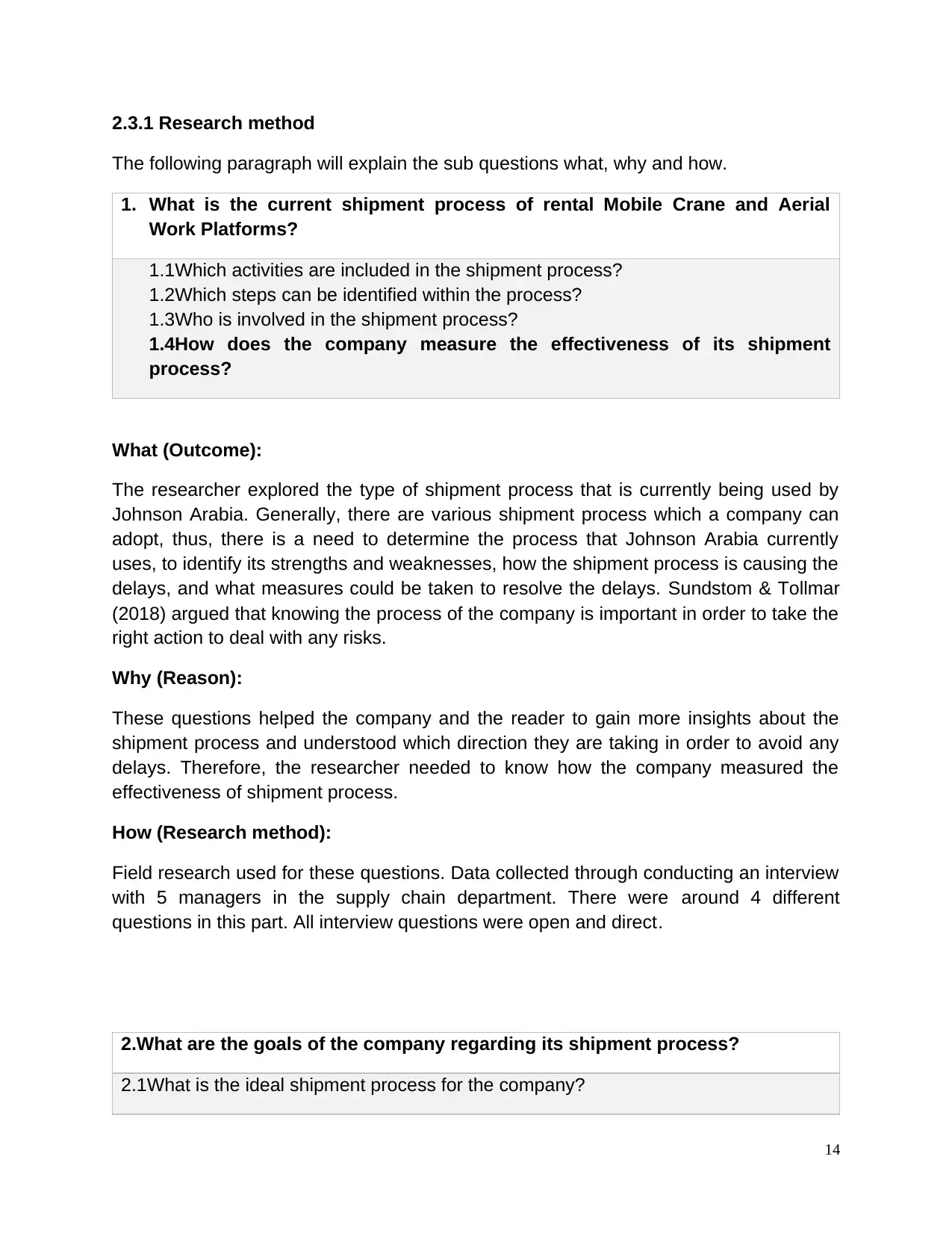
2.3.1 Research method
The following paragraph will explain the sub questions what, why and how.
1. What is the current shipment process of rental Mobile Crane and Aerial
Work Platforms?
1.1Which activities are included in the shipment process?
1.2Which steps can be identified within the process?
1.3Who is involved in the shipment process?
1.4How does the company measure the effectiveness of its shipment
process?
What (Outcome):
The researcher explored the type of shipment process that is currently being used by
Johnson Arabia. Generally, there are various shipment process which a company can
adopt, thus, there is a need to determine the process that Johnson Arabia currently
uses, to identify its strengths and weaknesses, how the shipment process is causing the
delays, and what measures could be taken to resolve the delays. Sundstom & Tollmar
(2018) argued that knowing the process of the company is important in order to take the
right action to deal with any risks.
Why (Reason):
These questions helped the company and the reader to gain more insights about the
shipment process and understood which direction they are taking in order to avoid any
delays. Therefore, the researcher needed to know how the company measured the
effectiveness of shipment process.
How (Research method):
Field research used for these questions. Data collected through conducting an interview
with 5 managers in the supply chain department. There were around 4 different
questions in this part. All interview questions were open and direct.
2.What are the goals of the company regarding its shipment process?
2.1What is the ideal shipment process for the company?
14
The following paragraph will explain the sub questions what, why and how.
1. What is the current shipment process of rental Mobile Crane and Aerial
Work Platforms?
1.1Which activities are included in the shipment process?
1.2Which steps can be identified within the process?
1.3Who is involved in the shipment process?
1.4How does the company measure the effectiveness of its shipment
process?
What (Outcome):
The researcher explored the type of shipment process that is currently being used by
Johnson Arabia. Generally, there are various shipment process which a company can
adopt, thus, there is a need to determine the process that Johnson Arabia currently
uses, to identify its strengths and weaknesses, how the shipment process is causing the
delays, and what measures could be taken to resolve the delays. Sundstom & Tollmar
(2018) argued that knowing the process of the company is important in order to take the
right action to deal with any risks.
Why (Reason):
These questions helped the company and the reader to gain more insights about the
shipment process and understood which direction they are taking in order to avoid any
delays. Therefore, the researcher needed to know how the company measured the
effectiveness of shipment process.
How (Research method):
Field research used for these questions. Data collected through conducting an interview
with 5 managers in the supply chain department. There were around 4 different
questions in this part. All interview questions were open and direct.
2.What are the goals of the company regarding its shipment process?
2.1What is the ideal shipment process for the company?
14
Paraphrase This Document
Need a fresh take? Get an instant paraphrase of this document with our AI Paraphraser
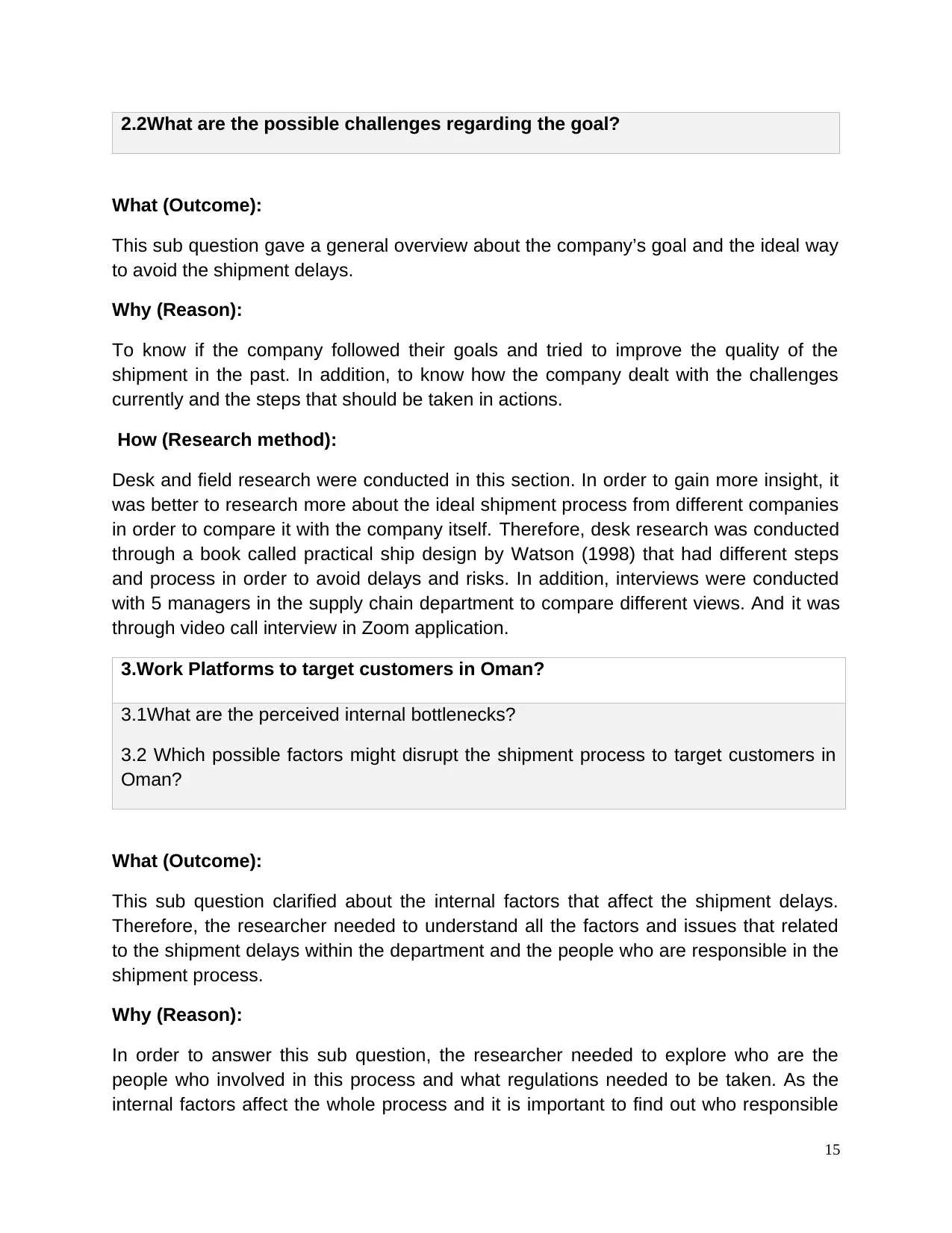
2.2What are the possible challenges regarding the goal?
What (Outcome):
This sub question gave a general overview about the company’s goal and the ideal way
to avoid the shipment delays.
Why (Reason):
To know if the company followed their goals and tried to improve the quality of the
shipment in the past. In addition, to know how the company dealt with the challenges
currently and the steps that should be taken in actions.
How (Research method):
Desk and field research were conducted in this section. In order to gain more insight, it
was better to research more about the ideal shipment process from different companies
in order to compare it with the company itself. Therefore, desk research was conducted
through a book called practical ship design by Watson (1998) that had different steps
and process in order to avoid delays and risks. In addition, interviews were conducted
with 5 managers in the supply chain department to compare different views. And it was
through video call interview in Zoom application.
3.Work Platforms to target customers in Oman?
3.1What are the perceived internal bottlenecks?
3.2 Which possible factors might disrupt the shipment process to target customers in
Oman?
What (Outcome):
This sub question clarified about the internal factors that affect the shipment delays.
Therefore, the researcher needed to understand all the factors and issues that related
to the shipment delays within the department and the people who are responsible in the
shipment process.
Why (Reason):
In order to answer this sub question, the researcher needed to explore who are the
people who involved in this process and what regulations needed to be taken. As the
internal factors affect the whole process and it is important to find out who responsible
15
What (Outcome):
This sub question gave a general overview about the company’s goal and the ideal way
to avoid the shipment delays.
Why (Reason):
To know if the company followed their goals and tried to improve the quality of the
shipment in the past. In addition, to know how the company dealt with the challenges
currently and the steps that should be taken in actions.
How (Research method):
Desk and field research were conducted in this section. In order to gain more insight, it
was better to research more about the ideal shipment process from different companies
in order to compare it with the company itself. Therefore, desk research was conducted
through a book called practical ship design by Watson (1998) that had different steps
and process in order to avoid delays and risks. In addition, interviews were conducted
with 5 managers in the supply chain department to compare different views. And it was
through video call interview in Zoom application.
3.Work Platforms to target customers in Oman?
3.1What are the perceived internal bottlenecks?
3.2 Which possible factors might disrupt the shipment process to target customers in
Oman?
What (Outcome):
This sub question clarified about the internal factors that affect the shipment delays.
Therefore, the researcher needed to understand all the factors and issues that related
to the shipment delays within the department and the people who are responsible in the
shipment process.
Why (Reason):
In order to answer this sub question, the researcher needed to explore who are the
people who involved in this process and what regulations needed to be taken. As the
internal factors affect the whole process and it is important to find out who responsible
15
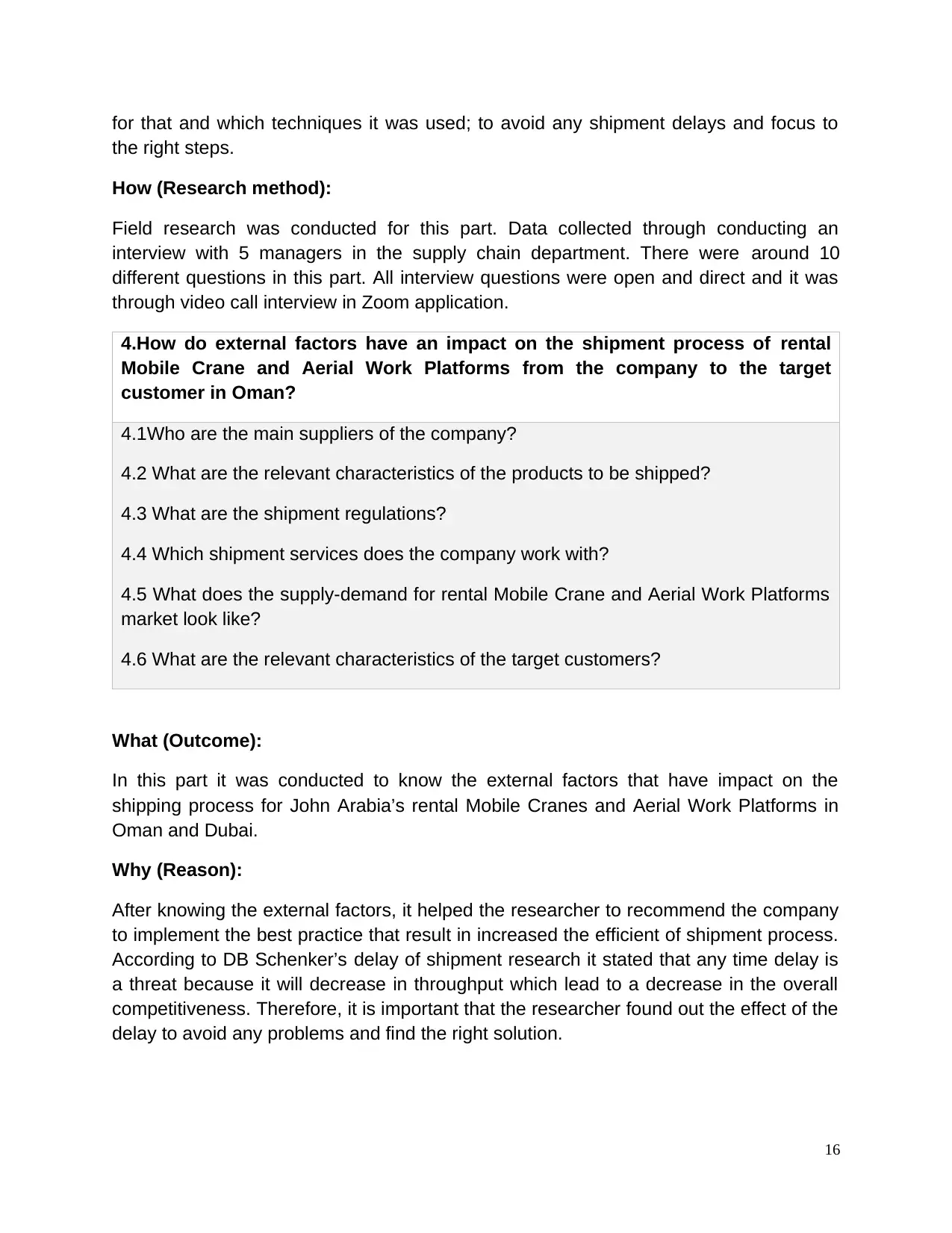
for that and which techniques it was used; to avoid any shipment delays and focus to
the right steps.
How (Research method):
Field research was conducted for this part. Data collected through conducting an
interview with 5 managers in the supply chain department. There were around 10
different questions in this part. All interview questions were open and direct and it was
through video call interview in Zoom application.
4.How do external factors have an impact on the shipment process of rental
Mobile Crane and Aerial Work Platforms from the company to the target
customer in Oman?
4.1Who are the main suppliers of the company?
4.2 What are the relevant characteristics of the products to be shipped?
4.3 What are the shipment regulations?
4.4 Which shipment services does the company work with?
4.5 What does the supply-demand for rental Mobile Crane and Aerial Work Platforms
market look like?
4.6 What are the relevant characteristics of the target customers?
What (Outcome):
In this part it was conducted to know the external factors that have impact on the
shipping process for John Arabia’s rental Mobile Cranes and Aerial Work Platforms in
Oman and Dubai.
Why (Reason):
After knowing the external factors, it helped the researcher to recommend the company
to implement the best practice that result in increased the efficient of shipment process.
According to DB Schenker’s delay of shipment research it stated that any time delay is
a threat because it will decrease in throughput which lead to a decrease in the overall
competitiveness. Therefore, it is important that the researcher found out the effect of the
delay to avoid any problems and find the right solution.
16
the right steps.
How (Research method):
Field research was conducted for this part. Data collected through conducting an
interview with 5 managers in the supply chain department. There were around 10
different questions in this part. All interview questions were open and direct and it was
through video call interview in Zoom application.
4.How do external factors have an impact on the shipment process of rental
Mobile Crane and Aerial Work Platforms from the company to the target
customer in Oman?
4.1Who are the main suppliers of the company?
4.2 What are the relevant characteristics of the products to be shipped?
4.3 What are the shipment regulations?
4.4 Which shipment services does the company work with?
4.5 What does the supply-demand for rental Mobile Crane and Aerial Work Platforms
market look like?
4.6 What are the relevant characteristics of the target customers?
What (Outcome):
In this part it was conducted to know the external factors that have impact on the
shipping process for John Arabia’s rental Mobile Cranes and Aerial Work Platforms in
Oman and Dubai.
Why (Reason):
After knowing the external factors, it helped the researcher to recommend the company
to implement the best practice that result in increased the efficient of shipment process.
According to DB Schenker’s delay of shipment research it stated that any time delay is
a threat because it will decrease in throughput which lead to a decrease in the overall
competitiveness. Therefore, it is important that the researcher found out the effect of the
delay to avoid any problems and find the right solution.
16
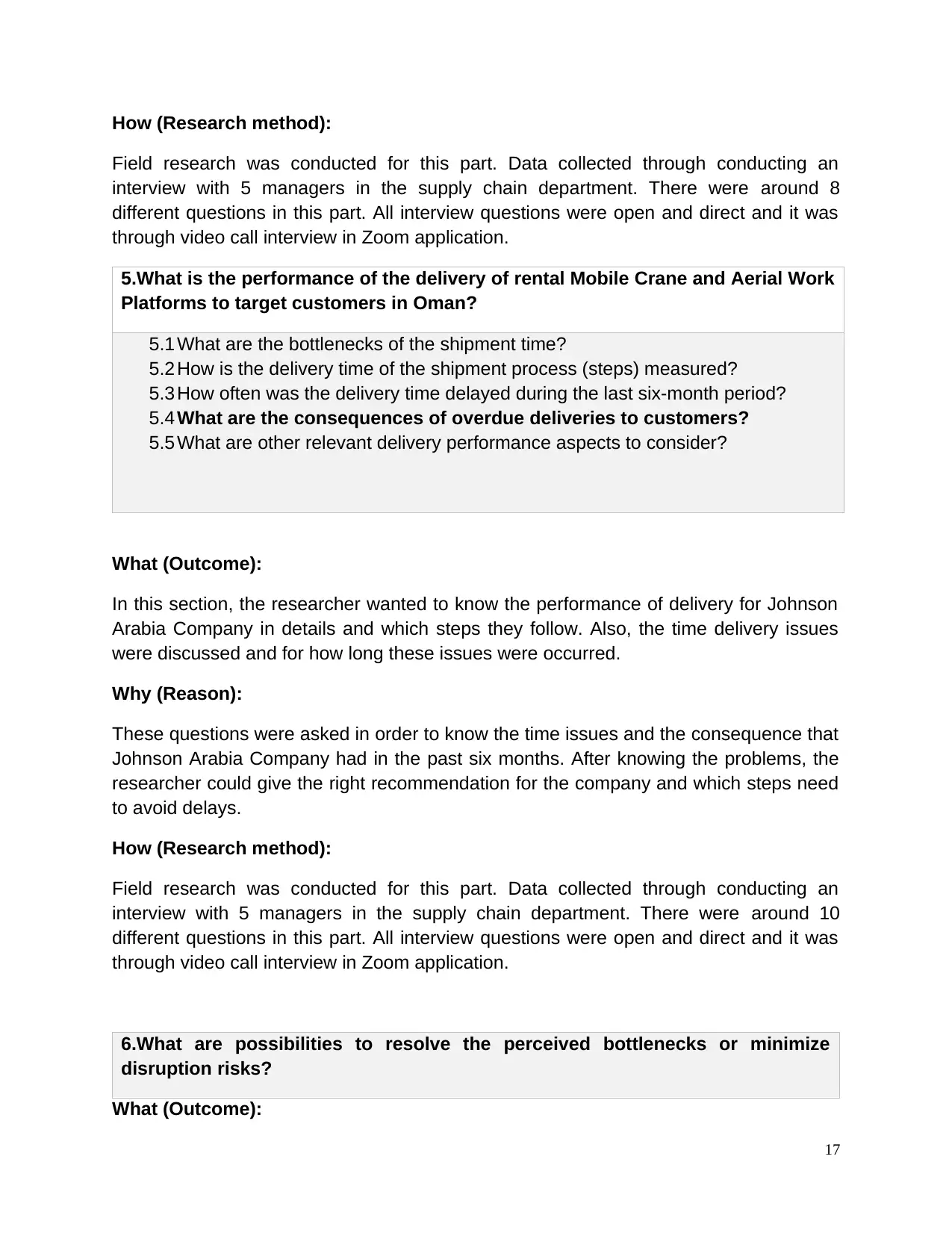
How (Research method):
Field research was conducted for this part. Data collected through conducting an
interview with 5 managers in the supply chain department. There were around 8
different questions in this part. All interview questions were open and direct and it was
through video call interview in Zoom application.
5.What is the performance of the delivery of rental Mobile Crane and Aerial Work
Platforms to target customers in Oman?
5.1 What are the bottlenecks of the shipment time?
5.2 How is the delivery time of the shipment process (steps) measured?
5.3 How often was the delivery time delayed during the last six-month period?
5.4 What are the consequences of overdue deliveries to customers?
5.5 What are other relevant delivery performance aspects to consider?
What (Outcome):
In this section, the researcher wanted to know the performance of delivery for Johnson
Arabia Company in details and which steps they follow. Also, the time delivery issues
were discussed and for how long these issues were occurred.
Why (Reason):
These questions were asked in order to know the time issues and the consequence that
Johnson Arabia Company had in the past six months. After knowing the problems, the
researcher could give the right recommendation for the company and which steps need
to avoid delays.
How (Research method):
Field research was conducted for this part. Data collected through conducting an
interview with 5 managers in the supply chain department. There were around 10
different questions in this part. All interview questions were open and direct and it was
through video call interview in Zoom application.
6.What are possibilities to resolve the perceived bottlenecks or minimize
disruption risks?
What (Outcome):
17
Field research was conducted for this part. Data collected through conducting an
interview with 5 managers in the supply chain department. There were around 8
different questions in this part. All interview questions were open and direct and it was
through video call interview in Zoom application.
5.What is the performance of the delivery of rental Mobile Crane and Aerial Work
Platforms to target customers in Oman?
5.1 What are the bottlenecks of the shipment time?
5.2 How is the delivery time of the shipment process (steps) measured?
5.3 How often was the delivery time delayed during the last six-month period?
5.4 What are the consequences of overdue deliveries to customers?
5.5 What are other relevant delivery performance aspects to consider?
What (Outcome):
In this section, the researcher wanted to know the performance of delivery for Johnson
Arabia Company in details and which steps they follow. Also, the time delivery issues
were discussed and for how long these issues were occurred.
Why (Reason):
These questions were asked in order to know the time issues and the consequence that
Johnson Arabia Company had in the past six months. After knowing the problems, the
researcher could give the right recommendation for the company and which steps need
to avoid delays.
How (Research method):
Field research was conducted for this part. Data collected through conducting an
interview with 5 managers in the supply chain department. There were around 10
different questions in this part. All interview questions were open and direct and it was
through video call interview in Zoom application.
6.What are possibilities to resolve the perceived bottlenecks or minimize
disruption risks?
What (Outcome):
17
Secure Best Marks with AI Grader
Need help grading? Try our AI Grader for instant feedback on your assignments.
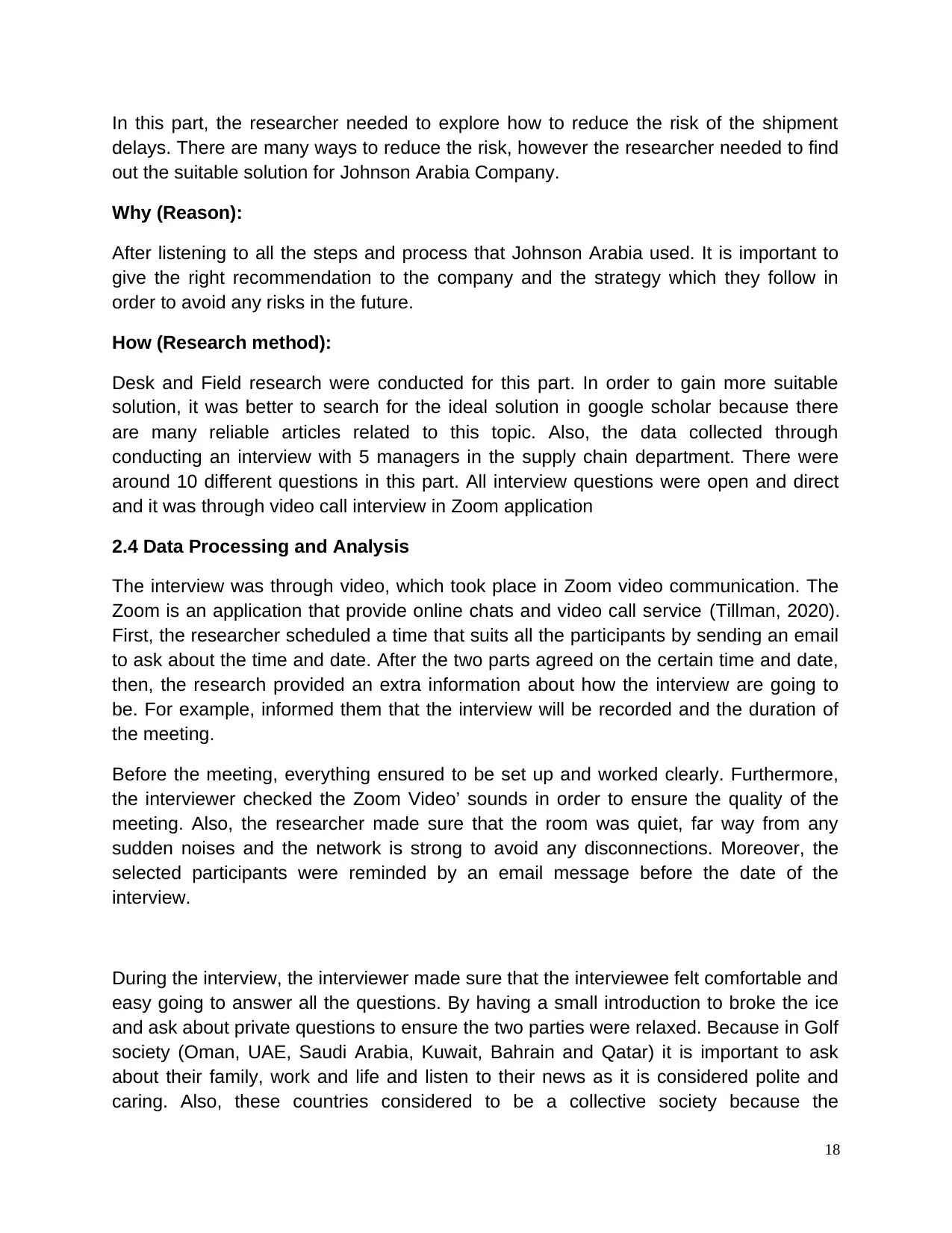
In this part, the researcher needed to explore how to reduce the risk of the shipment
delays. There are many ways to reduce the risk, however the researcher needed to find
out the suitable solution for Johnson Arabia Company.
Why (Reason):
After listening to all the steps and process that Johnson Arabia used. It is important to
give the right recommendation to the company and the strategy which they follow in
order to avoid any risks in the future.
How (Research method):
Desk and Field research were conducted for this part. In order to gain more suitable
solution, it was better to search for the ideal solution in google scholar because there
are many reliable articles related to this topic. Also, the data collected through
conducting an interview with 5 managers in the supply chain department. There were
around 10 different questions in this part. All interview questions were open and direct
and it was through video call interview in Zoom application
2.4 Data Processing and Analysis
The interview was through video, which took place in Zoom video communication. The
Zoom is an application that provide online chats and video call service (Tillman, 2020).
First, the researcher scheduled a time that suits all the participants by sending an email
to ask about the time and date. After the two parts agreed on the certain time and date,
then, the research provided an extra information about how the interview are going to
be. For example, informed them that the interview will be recorded and the duration of
the meeting.
Before the meeting, everything ensured to be set up and worked clearly. Furthermore,
the interviewer checked the Zoom Video’ sounds in order to ensure the quality of the
meeting. Also, the researcher made sure that the room was quiet, far way from any
sudden noises and the network is strong to avoid any disconnections. Moreover, the
selected participants were reminded by an email message before the date of the
interview.
During the interview, the interviewer made sure that the interviewee felt comfortable and
easy going to answer all the questions. By having a small introduction to broke the ice
and ask about private questions to ensure the two parties were relaxed. Because in Golf
society (Oman, UAE, Saudi Arabia, Kuwait, Bahrain and Qatar) it is important to ask
about their family, work and life and listen to their news as it is considered polite and
caring. Also, these countries considered to be a collective society because the
18
delays. There are many ways to reduce the risk, however the researcher needed to find
out the suitable solution for Johnson Arabia Company.
Why (Reason):
After listening to all the steps and process that Johnson Arabia used. It is important to
give the right recommendation to the company and the strategy which they follow in
order to avoid any risks in the future.
How (Research method):
Desk and Field research were conducted for this part. In order to gain more suitable
solution, it was better to search for the ideal solution in google scholar because there
are many reliable articles related to this topic. Also, the data collected through
conducting an interview with 5 managers in the supply chain department. There were
around 10 different questions in this part. All interview questions were open and direct
and it was through video call interview in Zoom application
2.4 Data Processing and Analysis
The interview was through video, which took place in Zoom video communication. The
Zoom is an application that provide online chats and video call service (Tillman, 2020).
First, the researcher scheduled a time that suits all the participants by sending an email
to ask about the time and date. After the two parts agreed on the certain time and date,
then, the research provided an extra information about how the interview are going to
be. For example, informed them that the interview will be recorded and the duration of
the meeting.
Before the meeting, everything ensured to be set up and worked clearly. Furthermore,
the interviewer checked the Zoom Video’ sounds in order to ensure the quality of the
meeting. Also, the researcher made sure that the room was quiet, far way from any
sudden noises and the network is strong to avoid any disconnections. Moreover, the
selected participants were reminded by an email message before the date of the
interview.
During the interview, the interviewer made sure that the interviewee felt comfortable and
easy going to answer all the questions. By having a small introduction to broke the ice
and ask about private questions to ensure the two parties were relaxed. Because in Golf
society (Oman, UAE, Saudi Arabia, Kuwait, Bahrain and Qatar) it is important to ask
about their family, work and life and listen to their news as it is considered polite and
caring. Also, these countries considered to be a collective society because the
18
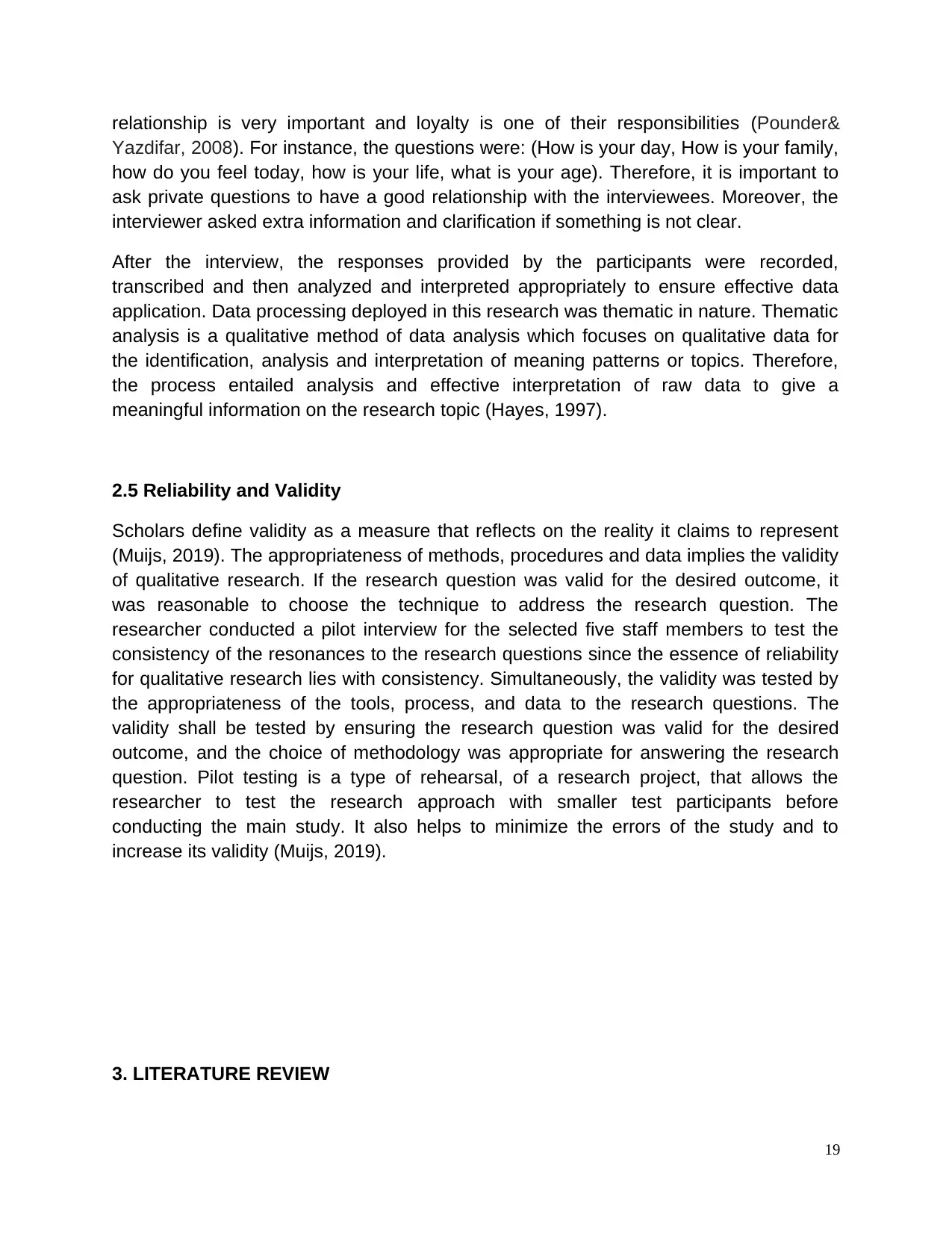
relationship is very important and loyalty is one of their responsibilities (Pounder&
Yazdifar, 2008). For instance, the questions were: (How is your day, How is your family,
how do you feel today, how is your life, what is your age). Therefore, it is important to
ask private questions to have a good relationship with the interviewees. Moreover, the
interviewer asked extra information and clarification if something is not clear.
After the interview, the responses provided by the participants were recorded,
transcribed and then analyzed and interpreted appropriately to ensure effective data
application. Data processing deployed in this research was thematic in nature. Thematic
analysis is a qualitative method of data analysis which focuses on qualitative data for
the identification, analysis and interpretation of meaning patterns or topics. Therefore,
the process entailed analysis and effective interpretation of raw data to give a
meaningful information on the research topic (Hayes, 1997).
2.5 Reliability and Validity
Scholars define validity as a measure that reflects on the reality it claims to represent
(Muijs, 2019). The appropriateness of methods, procedures and data implies the validity
of qualitative research. If the research question was valid for the desired outcome, it
was reasonable to choose the technique to address the research question. The
researcher conducted a pilot interview for the selected five staff members to test the
consistency of the resonances to the research questions since the essence of reliability
for qualitative research lies with consistency. Simultaneously, the validity was tested by
the appropriateness of the tools, process, and data to the research questions. The
validity shall be tested by ensuring the research question was valid for the desired
outcome, and the choice of methodology was appropriate for answering the research
question. Pilot testing is a type of rehearsal, of a research project, that allows the
researcher to test the research approach with smaller test participants before
conducting the main study. It also helps to minimize the errors of the study and to
increase its validity (Muijs, 2019).
3. LITERATURE REVIEW
19
Yazdifar, 2008). For instance, the questions were: (How is your day, How is your family,
how do you feel today, how is your life, what is your age). Therefore, it is important to
ask private questions to have a good relationship with the interviewees. Moreover, the
interviewer asked extra information and clarification if something is not clear.
After the interview, the responses provided by the participants were recorded,
transcribed and then analyzed and interpreted appropriately to ensure effective data
application. Data processing deployed in this research was thematic in nature. Thematic
analysis is a qualitative method of data analysis which focuses on qualitative data for
the identification, analysis and interpretation of meaning patterns or topics. Therefore,
the process entailed analysis and effective interpretation of raw data to give a
meaningful information on the research topic (Hayes, 1997).
2.5 Reliability and Validity
Scholars define validity as a measure that reflects on the reality it claims to represent
(Muijs, 2019). The appropriateness of methods, procedures and data implies the validity
of qualitative research. If the research question was valid for the desired outcome, it
was reasonable to choose the technique to address the research question. The
researcher conducted a pilot interview for the selected five staff members to test the
consistency of the resonances to the research questions since the essence of reliability
for qualitative research lies with consistency. Simultaneously, the validity was tested by
the appropriateness of the tools, process, and data to the research questions. The
validity shall be tested by ensuring the research question was valid for the desired
outcome, and the choice of methodology was appropriate for answering the research
question. Pilot testing is a type of rehearsal, of a research project, that allows the
researcher to test the research approach with smaller test participants before
conducting the main study. It also helps to minimize the errors of the study and to
increase its validity (Muijs, 2019).
3. LITERATURE REVIEW
19
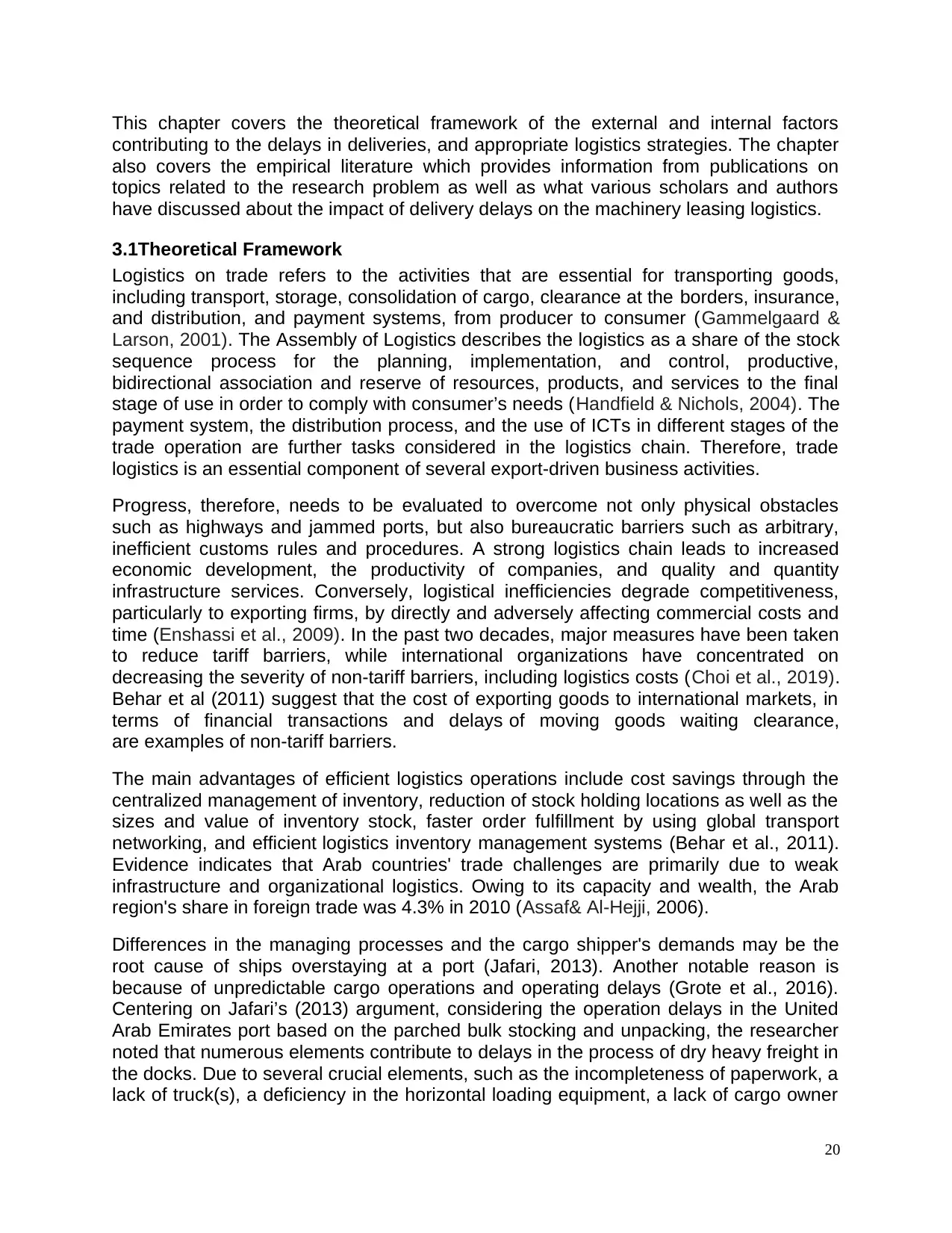
This chapter covers the theoretical framework of the external and internal factors
contributing to the delays in deliveries, and appropriate logistics strategies. The chapter
also covers the empirical literature which provides information from publications on
topics related to the research problem as well as what various scholars and authors
have discussed about the impact of delivery delays on the machinery leasing logistics.
3.1Theoretical Framework
Logistics on trade refers to the activities that are essential for transporting goods,
including transport, storage, consolidation of cargo, clearance at the borders, insurance,
and distribution, and payment systems, from producer to consumer (Gammelgaard &
Larson, 2001). The Assembly of Logistics describes the logistics as a share of the stock
sequence process for the planning, implementation, and control, productive,
bidirectional association and reserve of resources, products, and services to the final
stage of use in order to comply with consumer’s needs (Handfield & Nichols, 2004). The
payment system, the distribution process, and the use of ICTs in different stages of the
trade operation are further tasks considered in the logistics chain. Therefore, trade
logistics is an essential component of several export-driven business activities.
Progress, therefore, needs to be evaluated to overcome not only physical obstacles
such as highways and jammed ports, but also bureaucratic barriers such as arbitrary,
inefficient customs rules and procedures. A strong logistics chain leads to increased
economic development, the productivity of companies, and quality and quantity
infrastructure services. Conversely, logistical inefficiencies degrade competitiveness,
particularly to exporting firms, by directly and adversely affecting commercial costs and
time (Enshassi et al., 2009). In the past two decades, major measures have been taken
to reduce tariff barriers, while international organizations have concentrated on
decreasing the severity of non-tariff barriers, including logistics costs (Choi et al., 2019).
Behar et al (2011) suggest that the cost of exporting goods to international markets, in
terms of financial transactions and delays of moving goods waiting clearance,
are examples of non-tariff barriers.
The main advantages of efficient logistics operations include cost savings through the
centralized management of inventory, reduction of stock holding locations as well as the
sizes and value of inventory stock, faster order fulfillment by using global transport
networking, and efficient logistics inventory management systems (Behar et al., 2011).
Evidence indicates that Arab countries' trade challenges are primarily due to weak
infrastructure and organizational logistics. Owing to its capacity and wealth, the Arab
region's share in foreign trade was 4.3% in 2010 (Assaf& Al-Hejji, 2006).
Differences in the managing processes and the cargo shipper's demands may be the
root cause of ships overstaying at a port (Jafari, 2013). Another notable reason is
because of unpredictable cargo operations and operating delays (Grote et al., 2016).
Centering on Jafari’s (2013) argument, considering the operation delays in the United
Arab Emirates port based on the parched bulk stocking and unpacking, the researcher
noted that numerous elements contribute to delays in the process of dry heavy freight in
the docks. Due to several crucial elements, such as the incompleteness of paperwork, a
lack of truck(s), a deficiency in the horizontal loading equipment, a lack of cargo owner
20
contributing to the delays in deliveries, and appropriate logistics strategies. The chapter
also covers the empirical literature which provides information from publications on
topics related to the research problem as well as what various scholars and authors
have discussed about the impact of delivery delays on the machinery leasing logistics.
3.1Theoretical Framework
Logistics on trade refers to the activities that are essential for transporting goods,
including transport, storage, consolidation of cargo, clearance at the borders, insurance,
and distribution, and payment systems, from producer to consumer (Gammelgaard &
Larson, 2001). The Assembly of Logistics describes the logistics as a share of the stock
sequence process for the planning, implementation, and control, productive,
bidirectional association and reserve of resources, products, and services to the final
stage of use in order to comply with consumer’s needs (Handfield & Nichols, 2004). The
payment system, the distribution process, and the use of ICTs in different stages of the
trade operation are further tasks considered in the logistics chain. Therefore, trade
logistics is an essential component of several export-driven business activities.
Progress, therefore, needs to be evaluated to overcome not only physical obstacles
such as highways and jammed ports, but also bureaucratic barriers such as arbitrary,
inefficient customs rules and procedures. A strong logistics chain leads to increased
economic development, the productivity of companies, and quality and quantity
infrastructure services. Conversely, logistical inefficiencies degrade competitiveness,
particularly to exporting firms, by directly and adversely affecting commercial costs and
time (Enshassi et al., 2009). In the past two decades, major measures have been taken
to reduce tariff barriers, while international organizations have concentrated on
decreasing the severity of non-tariff barriers, including logistics costs (Choi et al., 2019).
Behar et al (2011) suggest that the cost of exporting goods to international markets, in
terms of financial transactions and delays of moving goods waiting clearance,
are examples of non-tariff barriers.
The main advantages of efficient logistics operations include cost savings through the
centralized management of inventory, reduction of stock holding locations as well as the
sizes and value of inventory stock, faster order fulfillment by using global transport
networking, and efficient logistics inventory management systems (Behar et al., 2011).
Evidence indicates that Arab countries' trade challenges are primarily due to weak
infrastructure and organizational logistics. Owing to its capacity and wealth, the Arab
region's share in foreign trade was 4.3% in 2010 (Assaf& Al-Hejji, 2006).
Differences in the managing processes and the cargo shipper's demands may be the
root cause of ships overstaying at a port (Jafari, 2013). Another notable reason is
because of unpredictable cargo operations and operating delays (Grote et al., 2016).
Centering on Jafari’s (2013) argument, considering the operation delays in the United
Arab Emirates port based on the parched bulk stocking and unpacking, the researcher
noted that numerous elements contribute to delays in the process of dry heavy freight in
the docks. Due to several crucial elements, such as the incompleteness of paperwork, a
lack of truck(s), a deficiency in the horizontal loading equipment, a lack of cargo owner
20
Paraphrase This Document
Need a fresh take? Get an instant paraphrase of this document with our AI Paraphraser
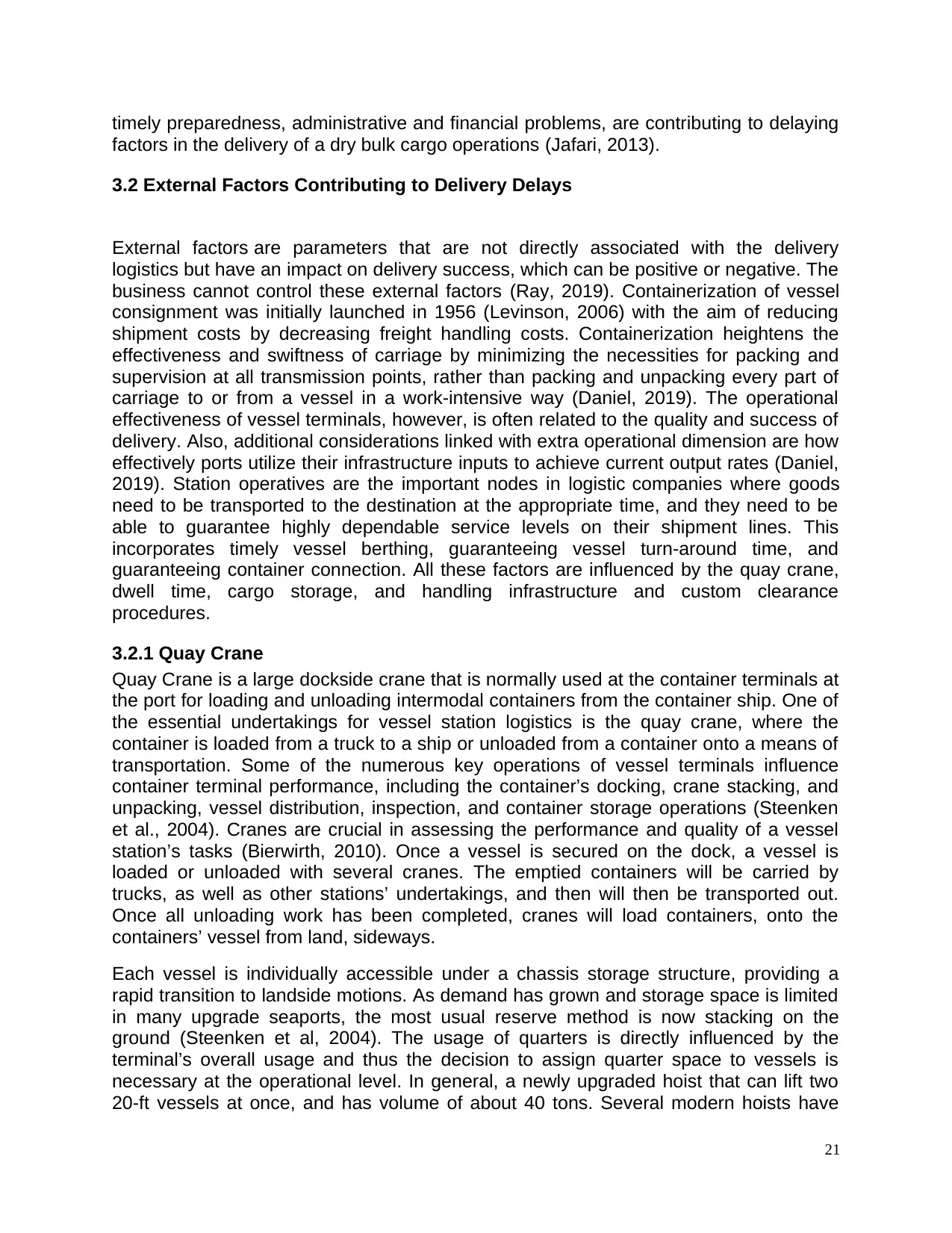
timely preparedness, administrative and financial problems, are contributing to delaying
factors in the delivery of a dry bulk cargo operations (Jafari, 2013).
3.2 External Factors Contributing to Delivery Delays
External factors are parameters that are not directly associated with the delivery
logistics but have an impact on delivery success, which can be positive or negative. The
business cannot control these external factors (Ray, 2019). Containerization of vessel
consignment was initially launched in 1956 (Levinson, 2006) with the aim of reducing
shipment costs by decreasing freight handling costs. Containerization heightens the
effectiveness and swiftness of carriage by minimizing the necessities for packing and
supervision at all transmission points, rather than packing and unpacking every part of
carriage to or from a vessel in a work-intensive way (Daniel, 2019). The operational
effectiveness of vessel terminals, however, is often related to the quality and success of
delivery. Also, additional considerations linked with extra operational dimension are how
effectively ports utilize their infrastructure inputs to achieve current output rates (Daniel,
2019). Station operatives are the important nodes in logistic companies where goods
need to be transported to the destination at the appropriate time, and they need to be
able to guarantee highly dependable service levels on their shipment lines. This
incorporates timely vessel berthing, guaranteeing vessel turn-around time, and
guaranteeing container connection. All these factors are influenced by the quay crane,
dwell time, cargo storage, and handling infrastructure and custom clearance
procedures.
3.2.1 Quay Crane
Quay Crane is a large dockside crane that is normally used at the container terminals at
the port for loading and unloading intermodal containers from the container ship. One of
the essential undertakings for vessel station logistics is the quay crane, where the
container is loaded from a truck to a ship or unloaded from a container onto a means of
transportation. Some of the numerous key operations of vessel terminals influence
container terminal performance, including the container’s docking, crane stacking, and
unpacking, vessel distribution, inspection, and container storage operations (Steenken
et al., 2004). Cranes are crucial in assessing the performance and quality of a vessel
station’s tasks (Bierwirth, 2010). Once a vessel is secured on the dock, a vessel is
loaded or unloaded with several cranes. The emptied containers will be carried by
trucks, as well as other stations’ undertakings, and then will then be transported out.
Once all unloading work has been completed, cranes will load containers, onto the
containers’ vessel from land, sideways.
Each vessel is individually accessible under a chassis storage structure, providing a
rapid transition to landside motions. As demand has grown and storage space is limited
in many upgrade seaports, the most usual reserve method is now stacking on the
ground (Steenken et al, 2004). The usage of quarters is directly influenced by the
terminal’s overall usage and thus the decision to assign quarter space to vessels is
necessary at the operational level. In general, a newly upgraded hoist that can lift two
20-ft vessels at once, and has volume of about 40 tons. Several modern hoists have
21
factors in the delivery of a dry bulk cargo operations (Jafari, 2013).
3.2 External Factors Contributing to Delivery Delays
External factors are parameters that are not directly associated with the delivery
logistics but have an impact on delivery success, which can be positive or negative. The
business cannot control these external factors (Ray, 2019). Containerization of vessel
consignment was initially launched in 1956 (Levinson, 2006) with the aim of reducing
shipment costs by decreasing freight handling costs. Containerization heightens the
effectiveness and swiftness of carriage by minimizing the necessities for packing and
supervision at all transmission points, rather than packing and unpacking every part of
carriage to or from a vessel in a work-intensive way (Daniel, 2019). The operational
effectiveness of vessel terminals, however, is often related to the quality and success of
delivery. Also, additional considerations linked with extra operational dimension are how
effectively ports utilize their infrastructure inputs to achieve current output rates (Daniel,
2019). Station operatives are the important nodes in logistic companies where goods
need to be transported to the destination at the appropriate time, and they need to be
able to guarantee highly dependable service levels on their shipment lines. This
incorporates timely vessel berthing, guaranteeing vessel turn-around time, and
guaranteeing container connection. All these factors are influenced by the quay crane,
dwell time, cargo storage, and handling infrastructure and custom clearance
procedures.
3.2.1 Quay Crane
Quay Crane is a large dockside crane that is normally used at the container terminals at
the port for loading and unloading intermodal containers from the container ship. One of
the essential undertakings for vessel station logistics is the quay crane, where the
container is loaded from a truck to a ship or unloaded from a container onto a means of
transportation. Some of the numerous key operations of vessel terminals influence
container terminal performance, including the container’s docking, crane stacking, and
unpacking, vessel distribution, inspection, and container storage operations (Steenken
et al., 2004). Cranes are crucial in assessing the performance and quality of a vessel
station’s tasks (Bierwirth, 2010). Once a vessel is secured on the dock, a vessel is
loaded or unloaded with several cranes. The emptied containers will be carried by
trucks, as well as other stations’ undertakings, and then will then be transported out.
Once all unloading work has been completed, cranes will load containers, onto the
containers’ vessel from land, sideways.
Each vessel is individually accessible under a chassis storage structure, providing a
rapid transition to landside motions. As demand has grown and storage space is limited
in many upgrade seaports, the most usual reserve method is now stacking on the
ground (Steenken et al, 2004). The usage of quarters is directly influenced by the
terminal’s overall usage and thus the decision to assign quarter space to vessels is
necessary at the operational level. In general, a newly upgraded hoist that can lift two
20-ft vessels at once, and has volume of about 40 tons. Several modern hoists have
21
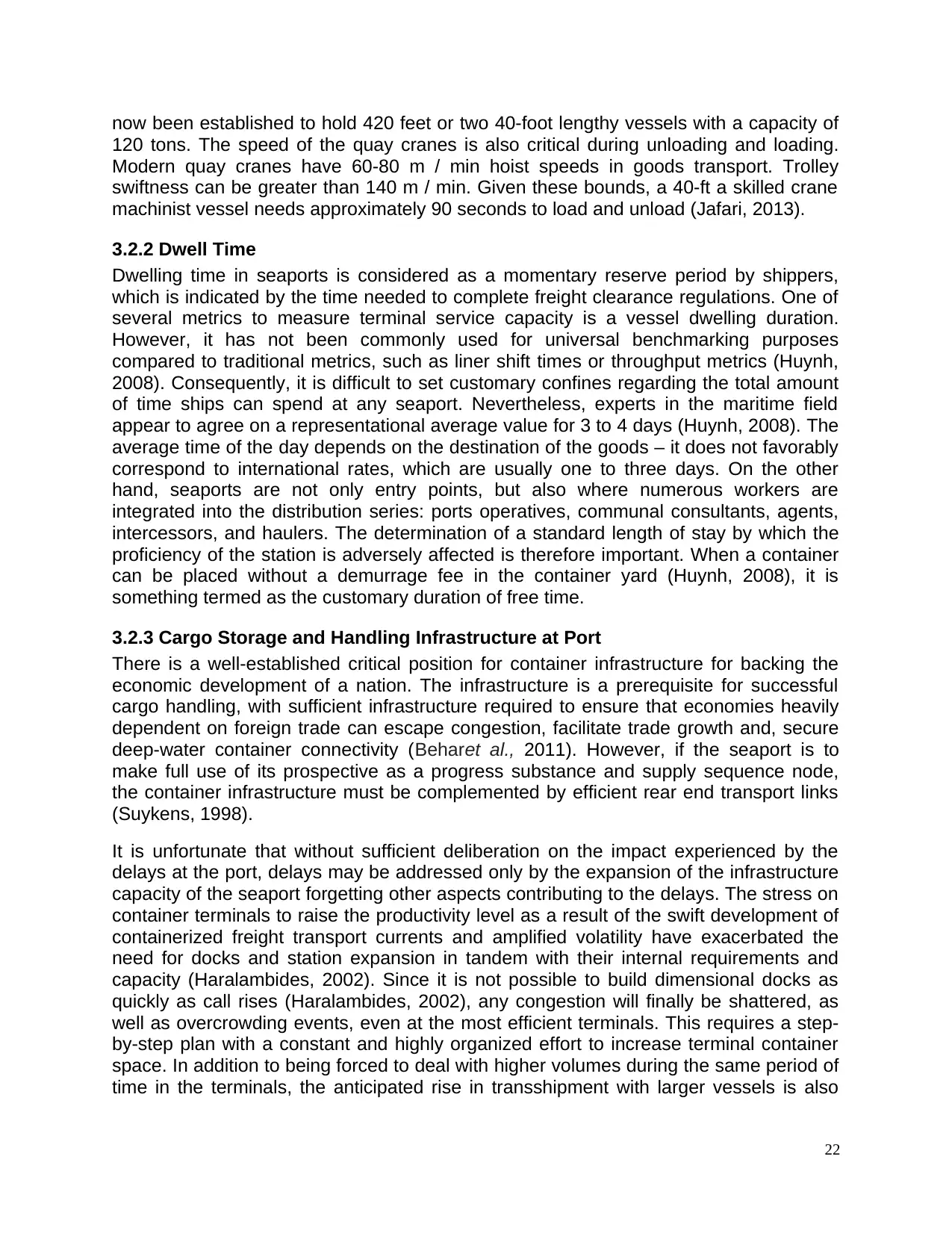
now been established to hold 420 feet or two 40-foot lengthy vessels with a capacity of
120 tons. The speed of the quay cranes is also critical during unloading and loading.
Modern quay cranes have 60-80 m / min hoist speeds in goods transport. Trolley
swiftness can be greater than 140 m / min. Given these bounds, a 40-ft a skilled crane
machinist vessel needs approximately 90 seconds to load and unload (Jafari, 2013).
3.2.2 Dwell Time
Dwelling time in seaports is considered as a momentary reserve period by shippers,
which is indicated by the time needed to complete freight clearance regulations. One of
several metrics to measure terminal service capacity is a vessel dwelling duration.
However, it has not been commonly used for universal benchmarking purposes
compared to traditional metrics, such as liner shift times or throughput metrics (Huynh,
2008). Consequently, it is difficult to set customary confines regarding the total amount
of time ships can spend at any seaport. Nevertheless, experts in the maritime field
appear to agree on a representational average value for 3 to 4 days (Huynh, 2008). The
average time of the day depends on the destination of the goods – it does not favorably
correspond to international rates, which are usually one to three days. On the other
hand, seaports are not only entry points, but also where numerous workers are
integrated into the distribution series: ports operatives, communal consultants, agents,
intercessors, and haulers. The determination of a standard length of stay by which the
proficiency of the station is adversely affected is therefore important. When a container
can be placed without a demurrage fee in the container yard (Huynh, 2008), it is
something termed as the customary duration of free time.
3.2.3 Cargo Storage and Handling Infrastructure at Port
There is a well-established critical position for container infrastructure for backing the
economic development of a nation. The infrastructure is a prerequisite for successful
cargo handling, with sufficient infrastructure required to ensure that economies heavily
dependent on foreign trade can escape congestion, facilitate trade growth and, secure
deep-water container connectivity (Beharet al., 2011). However, if the seaport is to
make full use of its prospective as a progress substance and supply sequence node,
the container infrastructure must be complemented by efficient rear end transport links
(Suykens, 1998).
It is unfortunate that without sufficient deliberation on the impact experienced by the
delays at the port, delays may be addressed only by the expansion of the infrastructure
capacity of the seaport forgetting other aspects contributing to the delays. The stress on
container terminals to raise the productivity level as a result of the swift development of
containerized freight transport currents and amplified volatility have exacerbated the
need for docks and station expansion in tandem with their internal requirements and
capacity (Haralambides, 2002). Since it is not possible to build dimensional docks as
quickly as call rises (Haralambides, 2002), any congestion will finally be shattered, as
well as overcrowding events, even at the most efficient terminals. This requires a step-
by-step plan with a constant and highly organized effort to increase terminal container
space. In addition to being forced to deal with higher volumes during the same period of
time in the terminals, the anticipated rise in transshipment with larger vessels is also
22
120 tons. The speed of the quay cranes is also critical during unloading and loading.
Modern quay cranes have 60-80 m / min hoist speeds in goods transport. Trolley
swiftness can be greater than 140 m / min. Given these bounds, a 40-ft a skilled crane
machinist vessel needs approximately 90 seconds to load and unload (Jafari, 2013).
3.2.2 Dwell Time
Dwelling time in seaports is considered as a momentary reserve period by shippers,
which is indicated by the time needed to complete freight clearance regulations. One of
several metrics to measure terminal service capacity is a vessel dwelling duration.
However, it has not been commonly used for universal benchmarking purposes
compared to traditional metrics, such as liner shift times or throughput metrics (Huynh,
2008). Consequently, it is difficult to set customary confines regarding the total amount
of time ships can spend at any seaport. Nevertheless, experts in the maritime field
appear to agree on a representational average value for 3 to 4 days (Huynh, 2008). The
average time of the day depends on the destination of the goods – it does not favorably
correspond to international rates, which are usually one to three days. On the other
hand, seaports are not only entry points, but also where numerous workers are
integrated into the distribution series: ports operatives, communal consultants, agents,
intercessors, and haulers. The determination of a standard length of stay by which the
proficiency of the station is adversely affected is therefore important. When a container
can be placed without a demurrage fee in the container yard (Huynh, 2008), it is
something termed as the customary duration of free time.
3.2.3 Cargo Storage and Handling Infrastructure at Port
There is a well-established critical position for container infrastructure for backing the
economic development of a nation. The infrastructure is a prerequisite for successful
cargo handling, with sufficient infrastructure required to ensure that economies heavily
dependent on foreign trade can escape congestion, facilitate trade growth and, secure
deep-water container connectivity (Beharet al., 2011). However, if the seaport is to
make full use of its prospective as a progress substance and supply sequence node,
the container infrastructure must be complemented by efficient rear end transport links
(Suykens, 1998).
It is unfortunate that without sufficient deliberation on the impact experienced by the
delays at the port, delays may be addressed only by the expansion of the infrastructure
capacity of the seaport forgetting other aspects contributing to the delays. The stress on
container terminals to raise the productivity level as a result of the swift development of
containerized freight transport currents and amplified volatility have exacerbated the
need for docks and station expansion in tandem with their internal requirements and
capacity (Haralambides, 2002). Since it is not possible to build dimensional docks as
quickly as call rises (Haralambides, 2002), any congestion will finally be shattered, as
well as overcrowding events, even at the most efficient terminals. This requires a step-
by-step plan with a constant and highly organized effort to increase terminal container
space. In addition to being forced to deal with higher volumes during the same period of
time in the terminals, the anticipated rise in transshipment with larger vessels is also
22
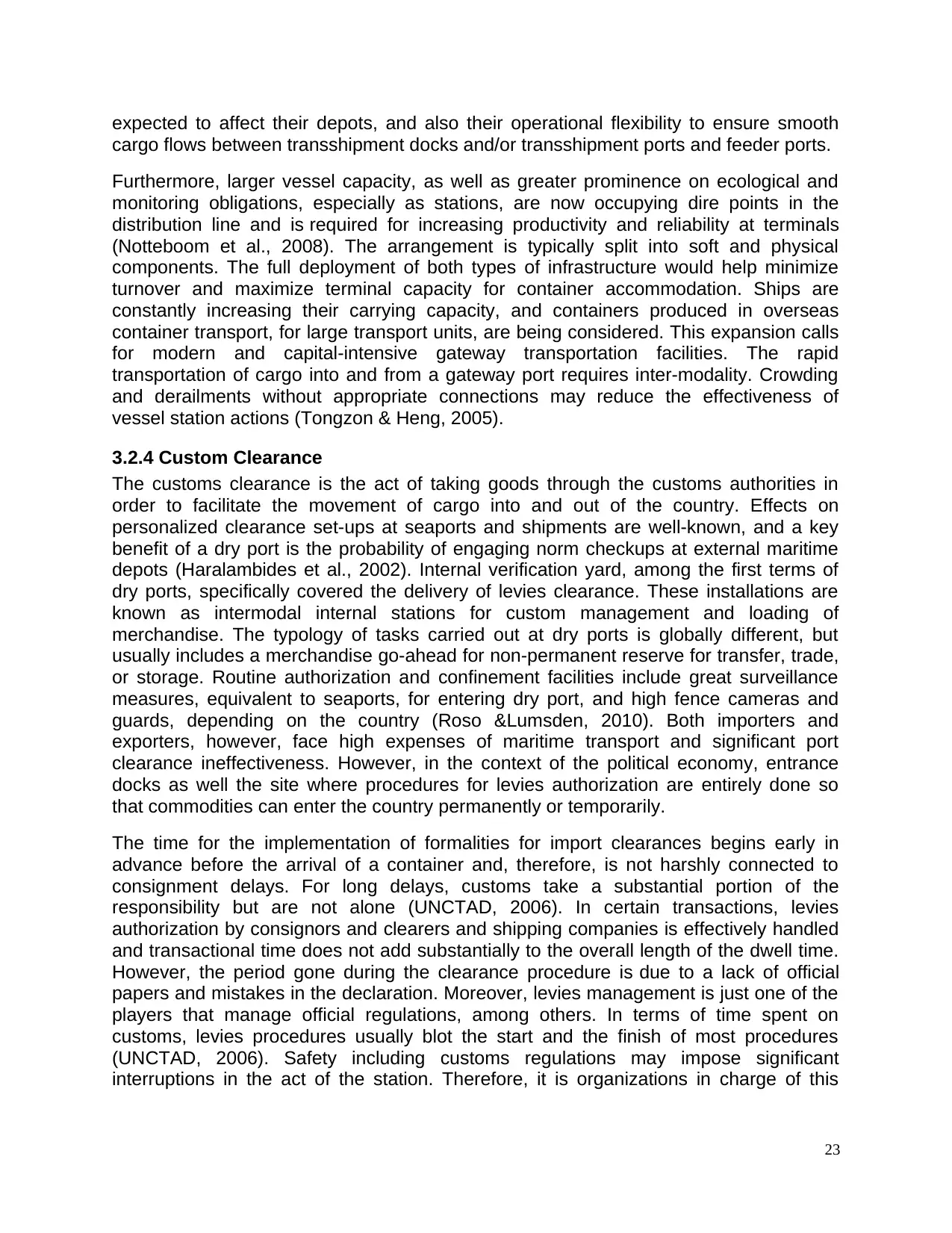
expected to affect their depots, and also their operational flexibility to ensure smooth
cargo flows between transshipment docks and/or transshipment ports and feeder ports.
Furthermore, larger vessel capacity, as well as greater prominence on ecological and
monitoring obligations, especially as stations, are now occupying dire points in the
distribution line and is required for increasing productivity and reliability at terminals
(Notteboom et al., 2008). The arrangement is typically split into soft and physical
components. The full deployment of both types of infrastructure would help minimize
turnover and maximize terminal capacity for container accommodation. Ships are
constantly increasing their carrying capacity, and containers produced in overseas
container transport, for large transport units, are being considered. This expansion calls
for modern and capital-intensive gateway transportation facilities. The rapid
transportation of cargo into and from a gateway port requires inter-modality. Crowding
and derailments without appropriate connections may reduce the effectiveness of
vessel station actions (Tongzon & Heng, 2005).
3.2.4 Custom Clearance
The customs clearance is the act of taking goods through the customs authorities in
order to facilitate the movement of cargo into and out of the country. Effects on
personalized clearance set-ups at seaports and shipments are well-known, and a key
benefit of a dry port is the probability of engaging norm checkups at external maritime
depots (Haralambides et al., 2002). Internal verification yard, among the first terms of
dry ports, specifically covered the delivery of levies clearance. These installations are
known as intermodal internal stations for custom management and loading of
merchandise. The typology of tasks carried out at dry ports is globally different, but
usually includes a merchandise go-ahead for non-permanent reserve for transfer, trade,
or storage. Routine authorization and confinement facilities include great surveillance
measures, equivalent to seaports, for entering dry port, and high fence cameras and
guards, depending on the country (Roso &Lumsden, 2010). Both importers and
exporters, however, face high expenses of maritime transport and significant port
clearance ineffectiveness. However, in the context of the political economy, entrance
docks as well the site where procedures for levies authorization are entirely done so
that commodities can enter the country permanently or temporarily.
The time for the implementation of formalities for import clearances begins early in
advance before the arrival of a container and, therefore, is not harshly connected to
consignment delays. For long delays, customs take a substantial portion of the
responsibility but are not alone (UNCTAD, 2006). In certain transactions, levies
authorization by consignors and clearers and shipping companies is effectively handled
and transactional time does not add substantially to the overall length of the dwell time.
However, the period gone during the clearance procedure is due to a lack of official
papers and mistakes in the declaration. Moreover, levies management is just one of the
players that manage official regulations, among others. In terms of time spent on
customs, levies procedures usually blot the start and the finish of most procedures
(UNCTAD, 2006). Safety including customs regulations may impose significant
interruptions in the act of the station. Therefore, it is organizations in charge of this
23
cargo flows between transshipment docks and/or transshipment ports and feeder ports.
Furthermore, larger vessel capacity, as well as greater prominence on ecological and
monitoring obligations, especially as stations, are now occupying dire points in the
distribution line and is required for increasing productivity and reliability at terminals
(Notteboom et al., 2008). The arrangement is typically split into soft and physical
components. The full deployment of both types of infrastructure would help minimize
turnover and maximize terminal capacity for container accommodation. Ships are
constantly increasing their carrying capacity, and containers produced in overseas
container transport, for large transport units, are being considered. This expansion calls
for modern and capital-intensive gateway transportation facilities. The rapid
transportation of cargo into and from a gateway port requires inter-modality. Crowding
and derailments without appropriate connections may reduce the effectiveness of
vessel station actions (Tongzon & Heng, 2005).
3.2.4 Custom Clearance
The customs clearance is the act of taking goods through the customs authorities in
order to facilitate the movement of cargo into and out of the country. Effects on
personalized clearance set-ups at seaports and shipments are well-known, and a key
benefit of a dry port is the probability of engaging norm checkups at external maritime
depots (Haralambides et al., 2002). Internal verification yard, among the first terms of
dry ports, specifically covered the delivery of levies clearance. These installations are
known as intermodal internal stations for custom management and loading of
merchandise. The typology of tasks carried out at dry ports is globally different, but
usually includes a merchandise go-ahead for non-permanent reserve for transfer, trade,
or storage. Routine authorization and confinement facilities include great surveillance
measures, equivalent to seaports, for entering dry port, and high fence cameras and
guards, depending on the country (Roso &Lumsden, 2010). Both importers and
exporters, however, face high expenses of maritime transport and significant port
clearance ineffectiveness. However, in the context of the political economy, entrance
docks as well the site where procedures for levies authorization are entirely done so
that commodities can enter the country permanently or temporarily.
The time for the implementation of formalities for import clearances begins early in
advance before the arrival of a container and, therefore, is not harshly connected to
consignment delays. For long delays, customs take a substantial portion of the
responsibility but are not alone (UNCTAD, 2006). In certain transactions, levies
authorization by consignors and clearers and shipping companies is effectively handled
and transactional time does not add substantially to the overall length of the dwell time.
However, the period gone during the clearance procedure is due to a lack of official
papers and mistakes in the declaration. Moreover, levies management is just one of the
players that manage official regulations, among others. In terms of time spent on
customs, levies procedures usually blot the start and the finish of most procedures
(UNCTAD, 2006). Safety including customs regulations may impose significant
interruptions in the act of the station. Therefore, it is organizations in charge of this
23
Secure Best Marks with AI Grader
Need help grading? Try our AI Grader for instant feedback on your assignments.
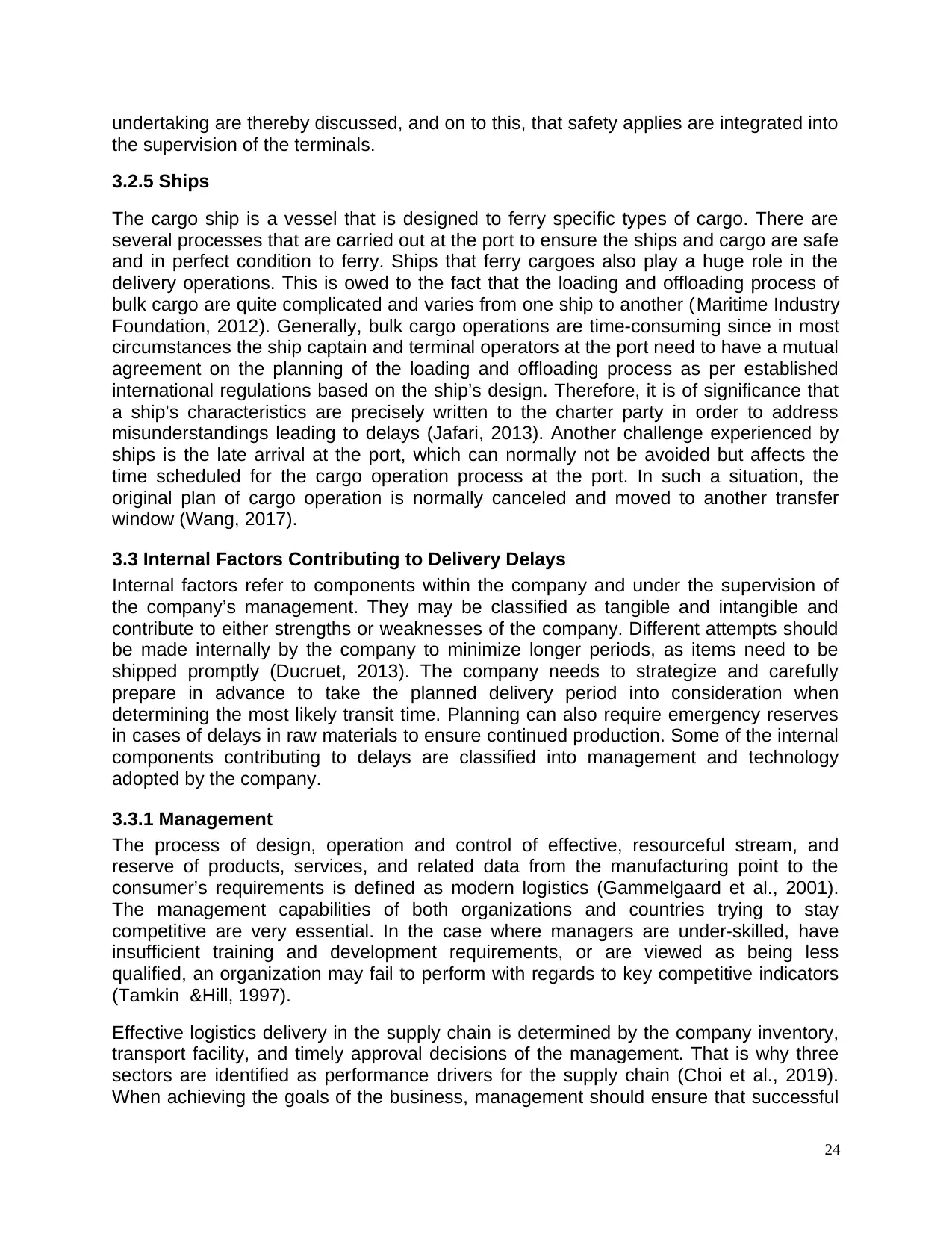
undertaking are thereby discussed, and on to this, that safety applies are integrated into
the supervision of the terminals.
3.2.5 Ships
The cargo ship is a vessel that is designed to ferry specific types of cargo. There are
several processes that are carried out at the port to ensure the ships and cargo are safe
and in perfect condition to ferry. Ships that ferry cargoes also play a huge role in the
delivery operations. This is owed to the fact that the loading and offloading process of
bulk cargo are quite complicated and varies from one ship to another (Maritime Industry
Foundation, 2012). Generally, bulk cargo operations are time-consuming since in most
circumstances the ship captain and terminal operators at the port need to have a mutual
agreement on the planning of the loading and offloading process as per established
international regulations based on the ship’s design. Therefore, it is of significance that
a ship’s characteristics are precisely written to the charter party in order to address
misunderstandings leading to delays (Jafari, 2013). Another challenge experienced by
ships is the late arrival at the port, which can normally not be avoided but affects the
time scheduled for the cargo operation process at the port. In such a situation, the
original plan of cargo operation is normally canceled and moved to another transfer
window (Wang, 2017).
3.3 Internal Factors Contributing to Delivery Delays
Internal factors refer to components within the company and under the supervision of
the company’s management. They may be classified as tangible and intangible and
contribute to either strengths or weaknesses of the company. Different attempts should
be made internally by the company to minimize longer periods, as items need to be
shipped promptly (Ducruet, 2013). The company needs to strategize and carefully
prepare in advance to take the planned delivery period into consideration when
determining the most likely transit time. Planning can also require emergency reserves
in cases of delays in raw materials to ensure continued production. Some of the internal
components contributing to delays are classified into management and technology
adopted by the company.
3.3.1 Management
The process of design, operation and control of effective, resourceful stream, and
reserve of products, services, and related data from the manufacturing point to the
consumer’s requirements is defined as modern logistics (Gammelgaard et al., 2001).
The management capabilities of both organizations and countries trying to stay
competitive are very essential. In the case where managers are under-skilled, have
insufficient training and development requirements, or are viewed as being less
qualified, an organization may fail to perform with regards to key competitive indicators
(Tamkin &Hill, 1997).
Effective logistics delivery in the supply chain is determined by the company inventory,
transport facility, and timely approval decisions of the management. That is why three
sectors are identified as performance drivers for the supply chain (Choi et al., 2019).
When achieving the goals of the business, management should ensure that successful
24
the supervision of the terminals.
3.2.5 Ships
The cargo ship is a vessel that is designed to ferry specific types of cargo. There are
several processes that are carried out at the port to ensure the ships and cargo are safe
and in perfect condition to ferry. Ships that ferry cargoes also play a huge role in the
delivery operations. This is owed to the fact that the loading and offloading process of
bulk cargo are quite complicated and varies from one ship to another (Maritime Industry
Foundation, 2012). Generally, bulk cargo operations are time-consuming since in most
circumstances the ship captain and terminal operators at the port need to have a mutual
agreement on the planning of the loading and offloading process as per established
international regulations based on the ship’s design. Therefore, it is of significance that
a ship’s characteristics are precisely written to the charter party in order to address
misunderstandings leading to delays (Jafari, 2013). Another challenge experienced by
ships is the late arrival at the port, which can normally not be avoided but affects the
time scheduled for the cargo operation process at the port. In such a situation, the
original plan of cargo operation is normally canceled and moved to another transfer
window (Wang, 2017).
3.3 Internal Factors Contributing to Delivery Delays
Internal factors refer to components within the company and under the supervision of
the company’s management. They may be classified as tangible and intangible and
contribute to either strengths or weaknesses of the company. Different attempts should
be made internally by the company to minimize longer periods, as items need to be
shipped promptly (Ducruet, 2013). The company needs to strategize and carefully
prepare in advance to take the planned delivery period into consideration when
determining the most likely transit time. Planning can also require emergency reserves
in cases of delays in raw materials to ensure continued production. Some of the internal
components contributing to delays are classified into management and technology
adopted by the company.
3.3.1 Management
The process of design, operation and control of effective, resourceful stream, and
reserve of products, services, and related data from the manufacturing point to the
consumer’s requirements is defined as modern logistics (Gammelgaard et al., 2001).
The management capabilities of both organizations and countries trying to stay
competitive are very essential. In the case where managers are under-skilled, have
insufficient training and development requirements, or are viewed as being less
qualified, an organization may fail to perform with regards to key competitive indicators
(Tamkin &Hill, 1997).
Effective logistics delivery in the supply chain is determined by the company inventory,
transport facility, and timely approval decisions of the management. That is why three
sectors are identified as performance drivers for the supply chain (Choi et al., 2019).
When achieving the goals of the business, management should ensure that successful
24
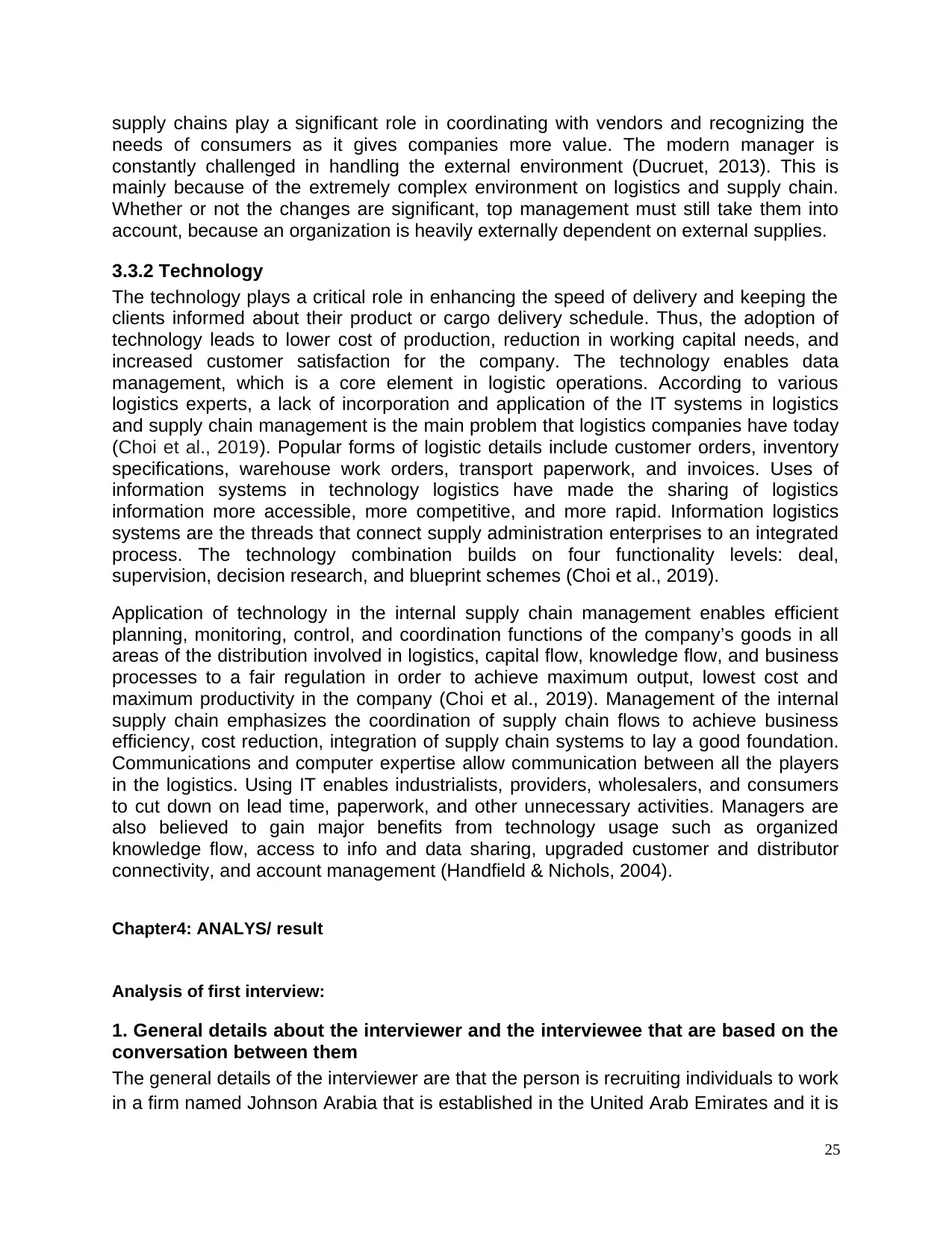
supply chains play a significant role in coordinating with vendors and recognizing the
needs of consumers as it gives companies more value. The modern manager is
constantly challenged in handling the external environment (Ducruet, 2013). This is
mainly because of the extremely complex environment on logistics and supply chain.
Whether or not the changes are significant, top management must still take them into
account, because an organization is heavily externally dependent on external supplies.
3.3.2 Technology
The technology plays a critical role in enhancing the speed of delivery and keeping the
clients informed about their product or cargo delivery schedule. Thus, the adoption of
technology leads to lower cost of production, reduction in working capital needs, and
increased customer satisfaction for the company. The technology enables data
management, which is a core element in logistic operations. According to various
logistics experts, a lack of incorporation and application of the IT systems in logistics
and supply chain management is the main problem that logistics companies have today
(Choi et al., 2019). Popular forms of logistic details include customer orders, inventory
specifications, warehouse work orders, transport paperwork, and invoices. Uses of
information systems in technology logistics have made the sharing of logistics
information more accessible, more competitive, and more rapid. Information logistics
systems are the threads that connect supply administration enterprises to an integrated
process. The technology combination builds on four functionality levels: deal,
supervision, decision research, and blueprint schemes (Choi et al., 2019).
Application of technology in the internal supply chain management enables efficient
planning, monitoring, control, and coordination functions of the company’s goods in all
areas of the distribution involved in logistics, capital flow, knowledge flow, and business
processes to a fair regulation in order to achieve maximum output, lowest cost and
maximum productivity in the company (Choi et al., 2019). Management of the internal
supply chain emphasizes the coordination of supply chain flows to achieve business
efficiency, cost reduction, integration of supply chain systems to lay a good foundation.
Communications and computer expertise allow communication between all the players
in the logistics. Using IT enables industrialists, providers, wholesalers, and consumers
to cut down on lead time, paperwork, and other unnecessary activities. Managers are
also believed to gain major benefits from technology usage such as organized
knowledge flow, access to info and data sharing, upgraded customer and distributor
connectivity, and account management (Handfield & Nichols, 2004).
Chapter4: ANALYS/ result
Analysis of first interview:
1. General details about the interviewer and the interviewee that are based on the
conversation between them
The general details of the interviewer are that the person is recruiting individuals to work
in a firm named Johnson Arabia that is established in the United Arab Emirates and it is
25
needs of consumers as it gives companies more value. The modern manager is
constantly challenged in handling the external environment (Ducruet, 2013). This is
mainly because of the extremely complex environment on logistics and supply chain.
Whether or not the changes are significant, top management must still take them into
account, because an organization is heavily externally dependent on external supplies.
3.3.2 Technology
The technology plays a critical role in enhancing the speed of delivery and keeping the
clients informed about their product or cargo delivery schedule. Thus, the adoption of
technology leads to lower cost of production, reduction in working capital needs, and
increased customer satisfaction for the company. The technology enables data
management, which is a core element in logistic operations. According to various
logistics experts, a lack of incorporation and application of the IT systems in logistics
and supply chain management is the main problem that logistics companies have today
(Choi et al., 2019). Popular forms of logistic details include customer orders, inventory
specifications, warehouse work orders, transport paperwork, and invoices. Uses of
information systems in technology logistics have made the sharing of logistics
information more accessible, more competitive, and more rapid. Information logistics
systems are the threads that connect supply administration enterprises to an integrated
process. The technology combination builds on four functionality levels: deal,
supervision, decision research, and blueprint schemes (Choi et al., 2019).
Application of technology in the internal supply chain management enables efficient
planning, monitoring, control, and coordination functions of the company’s goods in all
areas of the distribution involved in logistics, capital flow, knowledge flow, and business
processes to a fair regulation in order to achieve maximum output, lowest cost and
maximum productivity in the company (Choi et al., 2019). Management of the internal
supply chain emphasizes the coordination of supply chain flows to achieve business
efficiency, cost reduction, integration of supply chain systems to lay a good foundation.
Communications and computer expertise allow communication between all the players
in the logistics. Using IT enables industrialists, providers, wholesalers, and consumers
to cut down on lead time, paperwork, and other unnecessary activities. Managers are
also believed to gain major benefits from technology usage such as organized
knowledge flow, access to info and data sharing, upgraded customer and distributor
connectivity, and account management (Handfield & Nichols, 2004).
Chapter4: ANALYS/ result
Analysis of first interview:
1. General details about the interviewer and the interviewee that are based on the
conversation between them
The general details of the interviewer are that the person is recruiting individuals to work
in a firm named Johnson Arabia that is established in the United Arab Emirates and it is
25
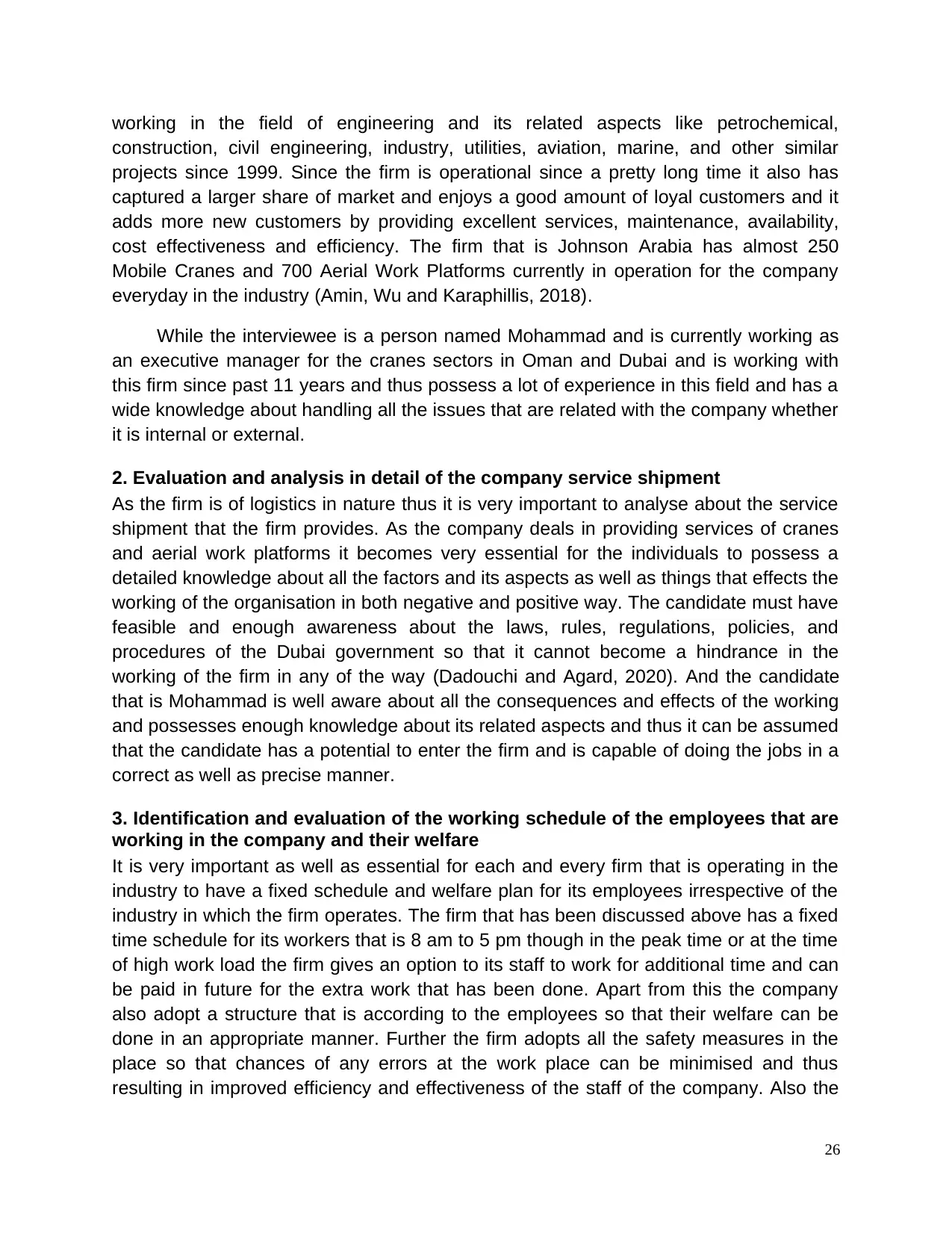
working in the field of engineering and its related aspects like petrochemical,
construction, civil engineering, industry, utilities, aviation, marine, and other similar
projects since 1999. Since the firm is operational since a pretty long time it also has
captured a larger share of market and enjoys a good amount of loyal customers and it
adds more new customers by providing excellent services, maintenance, availability,
cost effectiveness and efficiency. The firm that is Johnson Arabia has almost 250
Mobile Cranes and 700 Aerial Work Platforms currently in operation for the company
everyday in the industry (Amin, Wu and Karaphillis, 2018).
While the interviewee is a person named Mohammad and is currently working as
an executive manager for the cranes sectors in Oman and Dubai and is working with
this firm since past 11 years and thus possess a lot of experience in this field and has a
wide knowledge about handling all the issues that are related with the company whether
it is internal or external.
2. Evaluation and analysis in detail of the company service shipment
As the firm is of logistics in nature thus it is very important to analyse about the service
shipment that the firm provides. As the company deals in providing services of cranes
and aerial work platforms it becomes very essential for the individuals to possess a
detailed knowledge about all the factors and its aspects as well as things that effects the
working of the organisation in both negative and positive way. The candidate must have
feasible and enough awareness about the laws, rules, regulations, policies, and
procedures of the Dubai government so that it cannot become a hindrance in the
working of the firm in any of the way (Dadouchi and Agard, 2020). And the candidate
that is Mohammad is well aware about all the consequences and effects of the working
and possesses enough knowledge about its related aspects and thus it can be assumed
that the candidate has a potential to enter the firm and is capable of doing the jobs in a
correct as well as precise manner.
3. Identification and evaluation of the working schedule of the employees that are
working in the company and their welfare
It is very important as well as essential for each and every firm that is operating in the
industry to have a fixed schedule and welfare plan for its employees irrespective of the
industry in which the firm operates. The firm that has been discussed above has a fixed
time schedule for its workers that is 8 am to 5 pm though in the peak time or at the time
of high work load the firm gives an option to its staff to work for additional time and can
be paid in future for the extra work that has been done. Apart from this the company
also adopt a structure that is according to the employees so that their welfare can be
done in an appropriate manner. Further the firm adopts all the safety measures in the
place so that chances of any errors at the work place can be minimised and thus
resulting in improved efficiency and effectiveness of the staff of the company. Also the
26
construction, civil engineering, industry, utilities, aviation, marine, and other similar
projects since 1999. Since the firm is operational since a pretty long time it also has
captured a larger share of market and enjoys a good amount of loyal customers and it
adds more new customers by providing excellent services, maintenance, availability,
cost effectiveness and efficiency. The firm that is Johnson Arabia has almost 250
Mobile Cranes and 700 Aerial Work Platforms currently in operation for the company
everyday in the industry (Amin, Wu and Karaphillis, 2018).
While the interviewee is a person named Mohammad and is currently working as
an executive manager for the cranes sectors in Oman and Dubai and is working with
this firm since past 11 years and thus possess a lot of experience in this field and has a
wide knowledge about handling all the issues that are related with the company whether
it is internal or external.
2. Evaluation and analysis in detail of the company service shipment
As the firm is of logistics in nature thus it is very important to analyse about the service
shipment that the firm provides. As the company deals in providing services of cranes
and aerial work platforms it becomes very essential for the individuals to possess a
detailed knowledge about all the factors and its aspects as well as things that effects the
working of the organisation in both negative and positive way. The candidate must have
feasible and enough awareness about the laws, rules, regulations, policies, and
procedures of the Dubai government so that it cannot become a hindrance in the
working of the firm in any of the way (Dadouchi and Agard, 2020). And the candidate
that is Mohammad is well aware about all the consequences and effects of the working
and possesses enough knowledge about its related aspects and thus it can be assumed
that the candidate has a potential to enter the firm and is capable of doing the jobs in a
correct as well as precise manner.
3. Identification and evaluation of the working schedule of the employees that are
working in the company and their welfare
It is very important as well as essential for each and every firm that is operating in the
industry to have a fixed schedule and welfare plan for its employees irrespective of the
industry in which the firm operates. The firm that has been discussed above has a fixed
time schedule for its workers that is 8 am to 5 pm though in the peak time or at the time
of high work load the firm gives an option to its staff to work for additional time and can
be paid in future for the extra work that has been done. Apart from this the company
also adopt a structure that is according to the employees so that their welfare can be
done in an appropriate manner. Further the firm adopts all the safety measures in the
place so that chances of any errors at the work place can be minimised and thus
resulting in improved efficiency and effectiveness of the staff of the company. Also the
26
Paraphrase This Document
Need a fresh take? Get an instant paraphrase of this document with our AI Paraphraser
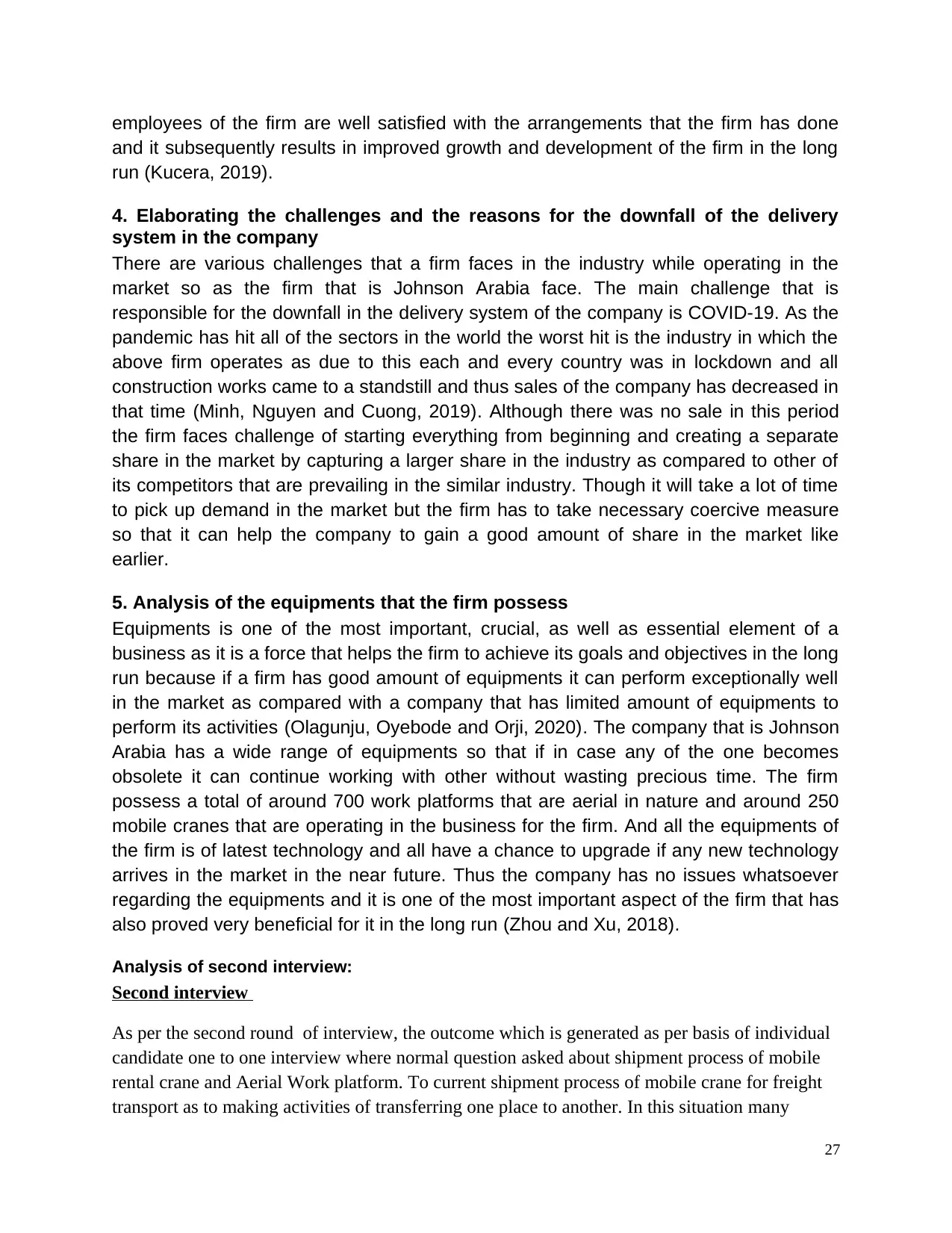
employees of the firm are well satisfied with the arrangements that the firm has done
and it subsequently results in improved growth and development of the firm in the long
run (Kucera, 2019).
4. Elaborating the challenges and the reasons for the downfall of the delivery
system in the company
There are various challenges that a firm faces in the industry while operating in the
market so as the firm that is Johnson Arabia face. The main challenge that is
responsible for the downfall in the delivery system of the company is COVID-19. As the
pandemic has hit all of the sectors in the world the worst hit is the industry in which the
above firm operates as due to this each and every country was in lockdown and all
construction works came to a standstill and thus sales of the company has decreased in
that time (Minh, Nguyen and Cuong, 2019). Although there was no sale in this period
the firm faces challenge of starting everything from beginning and creating a separate
share in the market by capturing a larger share in the industry as compared to other of
its competitors that are prevailing in the similar industry. Though it will take a lot of time
to pick up demand in the market but the firm has to take necessary coercive measure
so that it can help the company to gain a good amount of share in the market like
earlier.
5. Analysis of the equipments that the firm possess
Equipments is one of the most important, crucial, as well as essential element of a
business as it is a force that helps the firm to achieve its goals and objectives in the long
run because if a firm has good amount of equipments it can perform exceptionally well
in the market as compared with a company that has limited amount of equipments to
perform its activities (Olagunju, Oyebode and Orji, 2020). The company that is Johnson
Arabia has a wide range of equipments so that if in case any of the one becomes
obsolete it can continue working with other without wasting precious time. The firm
possess a total of around 700 work platforms that are aerial in nature and around 250
mobile cranes that are operating in the business for the firm. And all the equipments of
the firm is of latest technology and all have a chance to upgrade if any new technology
arrives in the market in the near future. Thus the company has no issues whatsoever
regarding the equipments and it is one of the most important aspect of the firm that has
also proved very beneficial for it in the long run (Zhou and Xu, 2018).
Analysis of second interview:
Second interview
As per the second round of interview, the outcome which is generated as per basis of individual
candidate one to one interview where normal question asked about shipment process of mobile
rental crane and Aerial Work platform. To current shipment process of mobile crane for freight
transport as to making activities of transferring one place to another. In this situation many
27
and it subsequently results in improved growth and development of the firm in the long
run (Kucera, 2019).
4. Elaborating the challenges and the reasons for the downfall of the delivery
system in the company
There are various challenges that a firm faces in the industry while operating in the
market so as the firm that is Johnson Arabia face. The main challenge that is
responsible for the downfall in the delivery system of the company is COVID-19. As the
pandemic has hit all of the sectors in the world the worst hit is the industry in which the
above firm operates as due to this each and every country was in lockdown and all
construction works came to a standstill and thus sales of the company has decreased in
that time (Minh, Nguyen and Cuong, 2019). Although there was no sale in this period
the firm faces challenge of starting everything from beginning and creating a separate
share in the market by capturing a larger share in the industry as compared to other of
its competitors that are prevailing in the similar industry. Though it will take a lot of time
to pick up demand in the market but the firm has to take necessary coercive measure
so that it can help the company to gain a good amount of share in the market like
earlier.
5. Analysis of the equipments that the firm possess
Equipments is one of the most important, crucial, as well as essential element of a
business as it is a force that helps the firm to achieve its goals and objectives in the long
run because if a firm has good amount of equipments it can perform exceptionally well
in the market as compared with a company that has limited amount of equipments to
perform its activities (Olagunju, Oyebode and Orji, 2020). The company that is Johnson
Arabia has a wide range of equipments so that if in case any of the one becomes
obsolete it can continue working with other without wasting precious time. The firm
possess a total of around 700 work platforms that are aerial in nature and around 250
mobile cranes that are operating in the business for the firm. And all the equipments of
the firm is of latest technology and all have a chance to upgrade if any new technology
arrives in the market in the near future. Thus the company has no issues whatsoever
regarding the equipments and it is one of the most important aspect of the firm that has
also proved very beneficial for it in the long run (Zhou and Xu, 2018).
Analysis of second interview:
Second interview
As per the second round of interview, the outcome which is generated as per basis of individual
candidate one to one interview where normal question asked about shipment process of mobile
rental crane and Aerial Work platform. To current shipment process of mobile crane for freight
transport as to making activities of transferring one place to another. In this situation many
27

doubts were there in which candidates were more into Johnson Arabia company. The employees
are very energetic where they tend t know about their company culture in better manner. Some of
the interview result were well structure and allow for asking relatable question on the basis of
COVID situation where huge loss has to be face by Johnson Arabica venture is tend to be raised
in better and economic related factor. By highlighting the steps of results is effectively structured
that assorting where it conceptual model applies like recruitment cycle and various selection
process to approach different or random employees to asking about their view point on shipment
process. By assessing from employees about what kind of operation and management which they
,mainly procure in betterment towards enhancing better shipment activities in an effectiveness.
The maor highlight point is noted in form of tabular form:
Sample Size of employees in Johnson Arabia is 100.
Key Performance Indicator Johnson Arabia Employees
response
Agree Disagree
Perfect Shipping Time 80 20
Order Accuracy 90 10
Workplace Incident 15 85
Proper Delivery of product
and service
95 5
Optimum Resource provided 95 5
Client Feedback 50 50
Through these above evaluation makes a point clear that few employees of Johnson Arabia
company is not well ware about structure and policies of working regulation that follows by
managerial department. But in other and after assessing some questions from production and
operating department employees they are satisfy with their working system as well as they
flexible procure and fulfil their clients expectation in efficient manner. On the basis of
assumption advanced resources are provide to labour in which they assort to better way for
accomplish their task in productive way. As many other new labour are not well versed about
shipment process, for them Human resource department provides valuable effective traits of
training and development to improvise their skills and knowledge for making them eficent
enough to optimising better outcomes.
Goal of the Shipment process:
28
are very energetic where they tend t know about their company culture in better manner. Some of
the interview result were well structure and allow for asking relatable question on the basis of
COVID situation where huge loss has to be face by Johnson Arabica venture is tend to be raised
in better and economic related factor. By highlighting the steps of results is effectively structured
that assorting where it conceptual model applies like recruitment cycle and various selection
process to approach different or random employees to asking about their view point on shipment
process. By assessing from employees about what kind of operation and management which they
,mainly procure in betterment towards enhancing better shipment activities in an effectiveness.
The maor highlight point is noted in form of tabular form:
Sample Size of employees in Johnson Arabia is 100.
Key Performance Indicator Johnson Arabia Employees
response
Agree Disagree
Perfect Shipping Time 80 20
Order Accuracy 90 10
Workplace Incident 15 85
Proper Delivery of product
and service
95 5
Optimum Resource provided 95 5
Client Feedback 50 50
Through these above evaluation makes a point clear that few employees of Johnson Arabia
company is not well ware about structure and policies of working regulation that follows by
managerial department. But in other and after assessing some questions from production and
operating department employees they are satisfy with their working system as well as they
flexible procure and fulfil their clients expectation in efficient manner. On the basis of
assumption advanced resources are provide to labour in which they assort to better way for
accomplish their task in productive way. As many other new labour are not well versed about
shipment process, for them Human resource department provides valuable effective traits of
training and development to improvise their skills and knowledge for making them eficent
enough to optimising better outcomes.
Goal of the Shipment process:
28
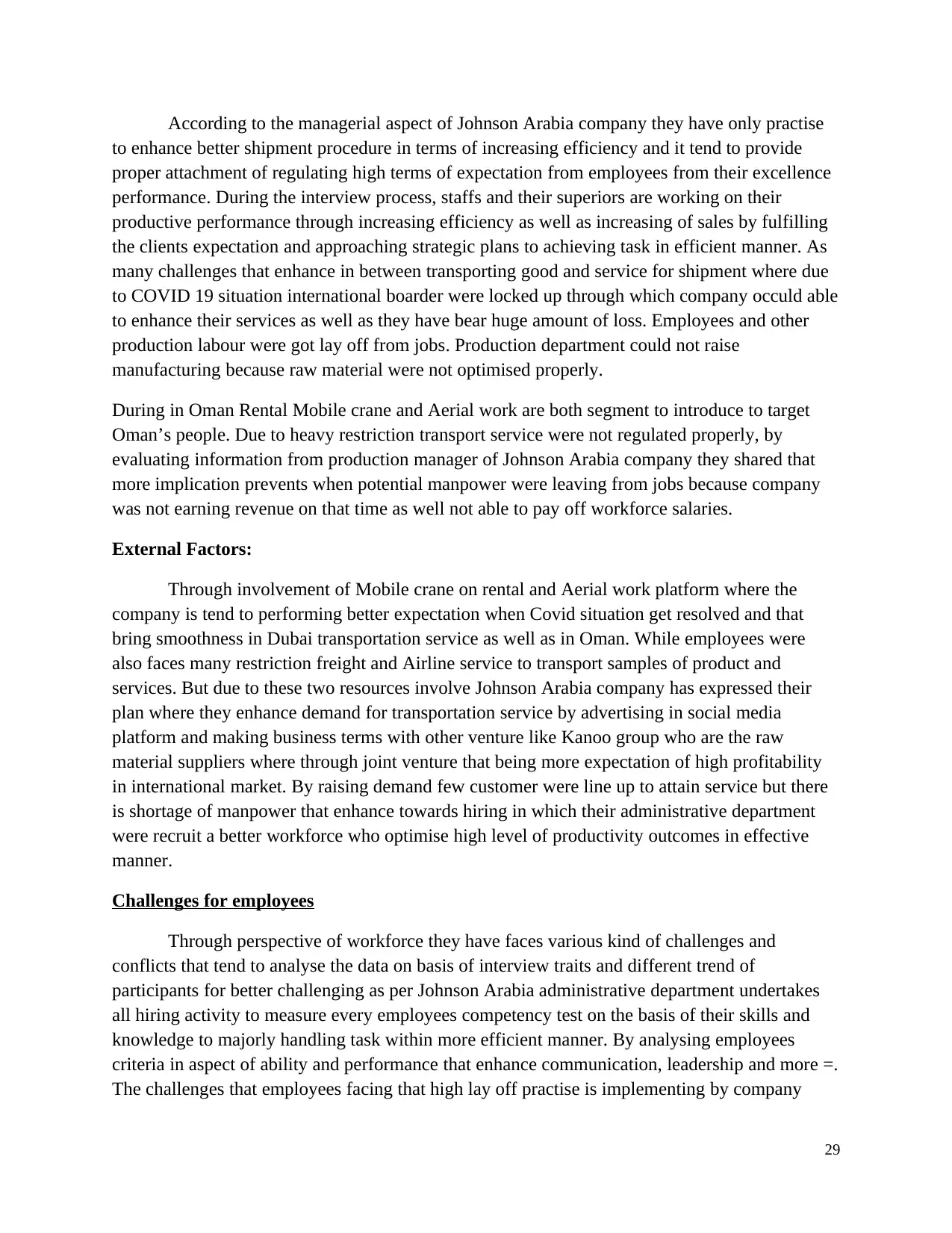
According to the managerial aspect of Johnson Arabia company they have only practise
to enhance better shipment procedure in terms of increasing efficiency and it tend to provide
proper attachment of regulating high terms of expectation from employees from their excellence
performance. During the interview process, staffs and their superiors are working on their
productive performance through increasing efficiency as well as increasing of sales by fulfilling
the clients expectation and approaching strategic plans to achieving task in efficient manner. As
many challenges that enhance in between transporting good and service for shipment where due
to COVID 19 situation international boarder were locked up through which company occuld able
to enhance their services as well as they have bear huge amount of loss. Employees and other
production labour were got lay off from jobs. Production department could not raise
manufacturing because raw material were not optimised properly.
During in Oman Rental Mobile crane and Aerial work are both segment to introduce to target
Oman’s people. Due to heavy restriction transport service were not regulated properly, by
evaluating information from production manager of Johnson Arabia company they shared that
more implication prevents when potential manpower were leaving from jobs because company
was not earning revenue on that time as well not able to pay off workforce salaries.
External Factors:
Through involvement of Mobile crane on rental and Aerial work platform where the
company is tend to performing better expectation when Covid situation get resolved and that
bring smoothness in Dubai transportation service as well as in Oman. While employees were
also faces many restriction freight and Airline service to transport samples of product and
services. But due to these two resources involve Johnson Arabia company has expressed their
plan where they enhance demand for transportation service by advertising in social media
platform and making business terms with other venture like Kanoo group who are the raw
material suppliers where through joint venture that being more expectation of high profitability
in international market. By raising demand few customer were line up to attain service but there
is shortage of manpower that enhance towards hiring in which their administrative department
were recruit a better workforce who optimise high level of productivity outcomes in effective
manner.
Challenges for employees
Through perspective of workforce they have faces various kind of challenges and
conflicts that tend to analyse the data on basis of interview traits and different trend of
participants for better challenging as per Johnson Arabia administrative department undertakes
all hiring activity to measure every employees competency test on the basis of their skills and
knowledge to majorly handling task within more efficient manner. By analysing employees
criteria in aspect of ability and performance that enhance communication, leadership and more =.
The challenges that employees facing that high lay off practise is implementing by company
29
to enhance better shipment procedure in terms of increasing efficiency and it tend to provide
proper attachment of regulating high terms of expectation from employees from their excellence
performance. During the interview process, staffs and their superiors are working on their
productive performance through increasing efficiency as well as increasing of sales by fulfilling
the clients expectation and approaching strategic plans to achieving task in efficient manner. As
many challenges that enhance in between transporting good and service for shipment where due
to COVID 19 situation international boarder were locked up through which company occuld able
to enhance their services as well as they have bear huge amount of loss. Employees and other
production labour were got lay off from jobs. Production department could not raise
manufacturing because raw material were not optimised properly.
During in Oman Rental Mobile crane and Aerial work are both segment to introduce to target
Oman’s people. Due to heavy restriction transport service were not regulated properly, by
evaluating information from production manager of Johnson Arabia company they shared that
more implication prevents when potential manpower were leaving from jobs because company
was not earning revenue on that time as well not able to pay off workforce salaries.
External Factors:
Through involvement of Mobile crane on rental and Aerial work platform where the
company is tend to performing better expectation when Covid situation get resolved and that
bring smoothness in Dubai transportation service as well as in Oman. While employees were
also faces many restriction freight and Airline service to transport samples of product and
services. But due to these two resources involve Johnson Arabia company has expressed their
plan where they enhance demand for transportation service by advertising in social media
platform and making business terms with other venture like Kanoo group who are the raw
material suppliers where through joint venture that being more expectation of high profitability
in international market. By raising demand few customer were line up to attain service but there
is shortage of manpower that enhance towards hiring in which their administrative department
were recruit a better workforce who optimise high level of productivity outcomes in effective
manner.
Challenges for employees
Through perspective of workforce they have faces various kind of challenges and
conflicts that tend to analyse the data on basis of interview traits and different trend of
participants for better challenging as per Johnson Arabia administrative department undertakes
all hiring activity to measure every employees competency test on the basis of their skills and
knowledge to majorly handling task within more efficient manner. By analysing employees
criteria in aspect of ability and performance that enhance communication, leadership and more =.
The challenges that employees facing that high lay off practise is implementing by company
29
Secure Best Marks with AI Grader
Need help grading? Try our AI Grader for instant feedback on your assignments.
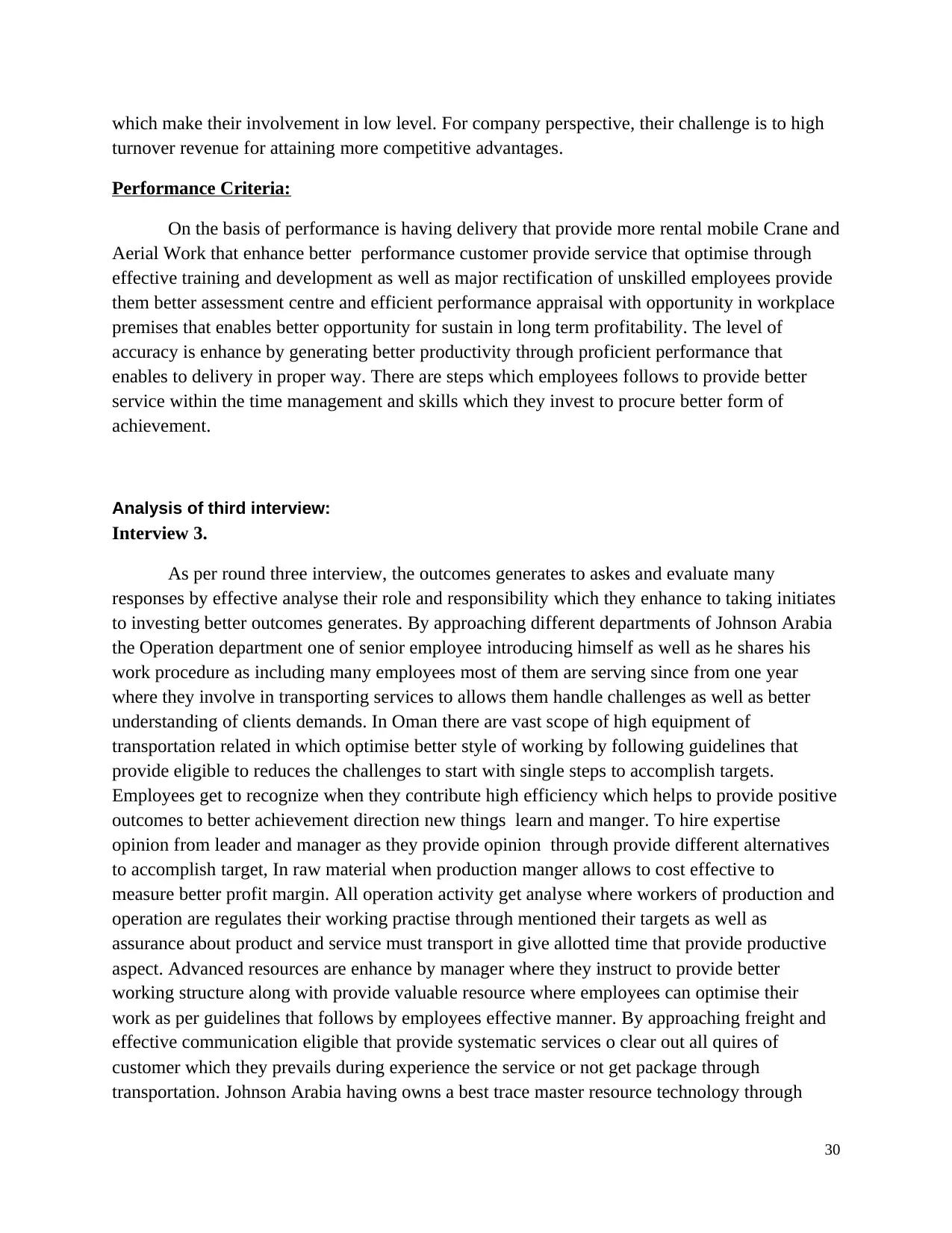
which make their involvement in low level. For company perspective, their challenge is to high
turnover revenue for attaining more competitive advantages.
Performance Criteria:
On the basis of performance is having delivery that provide more rental mobile Crane and
Aerial Work that enhance better performance customer provide service that optimise through
effective training and development as well as major rectification of unskilled employees provide
them better assessment centre and efficient performance appraisal with opportunity in workplace
premises that enables better opportunity for sustain in long term profitability. The level of
accuracy is enhance by generating better productivity through proficient performance that
enables to delivery in proper way. There are steps which employees follows to provide better
service within the time management and skills which they invest to procure better form of
achievement.
Analysis of third interview:
Interview 3.
As per round three interview, the outcomes generates to askes and evaluate many
responses by effective analyse their role and responsibility which they enhance to taking initiates
to investing better outcomes generates. By approaching different departments of Johnson Arabia
the Operation department one of senior employee introducing himself as well as he shares his
work procedure as including many employees most of them are serving since from one year
where they involve in transporting services to allows them handle challenges as well as better
understanding of clients demands. In Oman there are vast scope of high equipment of
transportation related in which optimise better style of working by following guidelines that
provide eligible to reduces the challenges to start with single steps to accomplish targets.
Employees get to recognize when they contribute high efficiency which helps to provide positive
outcomes to better achievement direction new things learn and manger. To hire expertise
opinion from leader and manager as they provide opinion through provide different alternatives
to accomplish target, In raw material when production manger allows to cost effective to
measure better profit margin. All operation activity get analyse where workers of production and
operation are regulates their working practise through mentioned their targets as well as
assurance about product and service must transport in give allotted time that provide productive
aspect. Advanced resources are enhance by manager where they instruct to provide better
working structure along with provide valuable resource where employees can optimise their
work as per guidelines that follows by employees effective manner. By approaching freight and
effective communication eligible that provide systematic services o clear out all quires of
customer which they prevails during experience the service or not get package through
transportation. Johnson Arabia having owns a best trace master resource technology through
30
turnover revenue for attaining more competitive advantages.
Performance Criteria:
On the basis of performance is having delivery that provide more rental mobile Crane and
Aerial Work that enhance better performance customer provide service that optimise through
effective training and development as well as major rectification of unskilled employees provide
them better assessment centre and efficient performance appraisal with opportunity in workplace
premises that enables better opportunity for sustain in long term profitability. The level of
accuracy is enhance by generating better productivity through proficient performance that
enables to delivery in proper way. There are steps which employees follows to provide better
service within the time management and skills which they invest to procure better form of
achievement.
Analysis of third interview:
Interview 3.
As per round three interview, the outcomes generates to askes and evaluate many
responses by effective analyse their role and responsibility which they enhance to taking initiates
to investing better outcomes generates. By approaching different departments of Johnson Arabia
the Operation department one of senior employee introducing himself as well as he shares his
work procedure as including many employees most of them are serving since from one year
where they involve in transporting services to allows them handle challenges as well as better
understanding of clients demands. In Oman there are vast scope of high equipment of
transportation related in which optimise better style of working by following guidelines that
provide eligible to reduces the challenges to start with single steps to accomplish targets.
Employees get to recognize when they contribute high efficiency which helps to provide positive
outcomes to better achievement direction new things learn and manger. To hire expertise
opinion from leader and manager as they provide opinion through provide different alternatives
to accomplish target, In raw material when production manger allows to cost effective to
measure better profit margin. All operation activity get analyse where workers of production and
operation are regulates their working practise through mentioned their targets as well as
assurance about product and service must transport in give allotted time that provide productive
aspect. Advanced resources are enhance by manager where they instruct to provide better
working structure along with provide valuable resource where employees can optimise their
work as per guidelines that follows by employees effective manner. By approaching freight and
effective communication eligible that provide systematic services o clear out all quires of
customer which they prevails during experience the service or not get package through
transportation. Johnson Arabia having owns a best trace master resource technology through
30
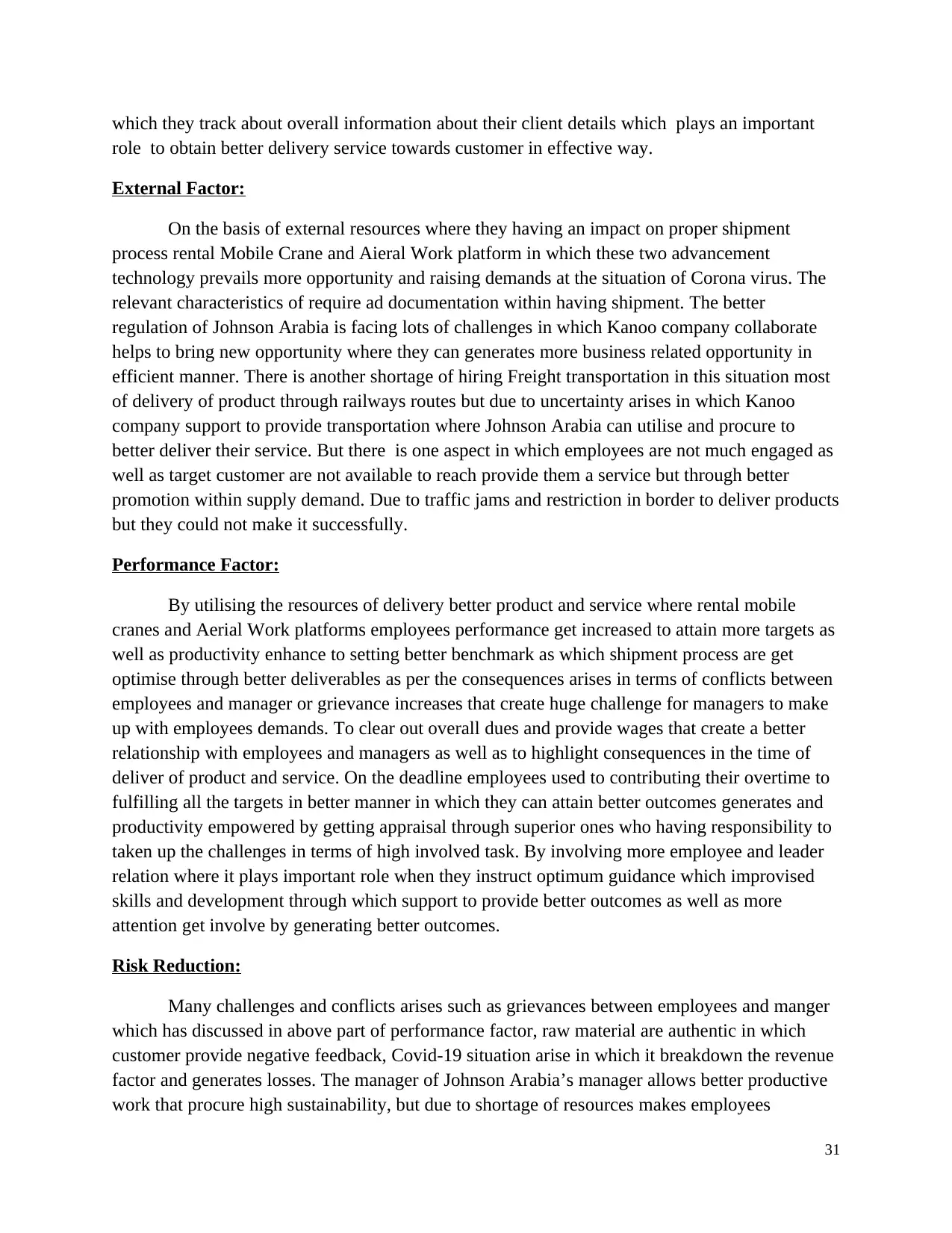
which they track about overall information about their client details which plays an important
role to obtain better delivery service towards customer in effective way.
External Factor:
On the basis of external resources where they having an impact on proper shipment
process rental Mobile Crane and Aieral Work platform in which these two advancement
technology prevails more opportunity and raising demands at the situation of Corona virus. The
relevant characteristics of require ad documentation within having shipment. The better
regulation of Johnson Arabia is facing lots of challenges in which Kanoo company collaborate
helps to bring new opportunity where they can generates more business related opportunity in
efficient manner. There is another shortage of hiring Freight transportation in this situation most
of delivery of product through railways routes but due to uncertainty arises in which Kanoo
company support to provide transportation where Johnson Arabia can utilise and procure to
better deliver their service. But there is one aspect in which employees are not much engaged as
well as target customer are not available to reach provide them a service but through better
promotion within supply demand. Due to traffic jams and restriction in border to deliver products
but they could not make it successfully.
Performance Factor:
By utilising the resources of delivery better product and service where rental mobile
cranes and Aerial Work platforms employees performance get increased to attain more targets as
well as productivity enhance to setting better benchmark as which shipment process are get
optimise through better deliverables as per the consequences arises in terms of conflicts between
employees and manager or grievance increases that create huge challenge for managers to make
up with employees demands. To clear out overall dues and provide wages that create a better
relationship with employees and managers as well as to highlight consequences in the time of
deliver of product and service. On the deadline employees used to contributing their overtime to
fulfilling all the targets in better manner in which they can attain better outcomes generates and
productivity empowered by getting appraisal through superior ones who having responsibility to
taken up the challenges in terms of high involved task. By involving more employee and leader
relation where it plays important role when they instruct optimum guidance which improvised
skills and development through which support to provide better outcomes as well as more
attention get involve by generating better outcomes.
Risk Reduction:
Many challenges and conflicts arises such as grievances between employees and manger
which has discussed in above part of performance factor, raw material are authentic in which
customer provide negative feedback, Covid-19 situation arise in which it breakdown the revenue
factor and generates losses. The manager of Johnson Arabia’s manager allows better productive
work that procure high sustainability, but due to shortage of resources makes employees
31
role to obtain better delivery service towards customer in effective way.
External Factor:
On the basis of external resources where they having an impact on proper shipment
process rental Mobile Crane and Aieral Work platform in which these two advancement
technology prevails more opportunity and raising demands at the situation of Corona virus. The
relevant characteristics of require ad documentation within having shipment. The better
regulation of Johnson Arabia is facing lots of challenges in which Kanoo company collaborate
helps to bring new opportunity where they can generates more business related opportunity in
efficient manner. There is another shortage of hiring Freight transportation in this situation most
of delivery of product through railways routes but due to uncertainty arises in which Kanoo
company support to provide transportation where Johnson Arabia can utilise and procure to
better deliver their service. But there is one aspect in which employees are not much engaged as
well as target customer are not available to reach provide them a service but through better
promotion within supply demand. Due to traffic jams and restriction in border to deliver products
but they could not make it successfully.
Performance Factor:
By utilising the resources of delivery better product and service where rental mobile
cranes and Aerial Work platforms employees performance get increased to attain more targets as
well as productivity enhance to setting better benchmark as which shipment process are get
optimise through better deliverables as per the consequences arises in terms of conflicts between
employees and manager or grievance increases that create huge challenge for managers to make
up with employees demands. To clear out overall dues and provide wages that create a better
relationship with employees and managers as well as to highlight consequences in the time of
deliver of product and service. On the deadline employees used to contributing their overtime to
fulfilling all the targets in better manner in which they can attain better outcomes generates and
productivity empowered by getting appraisal through superior ones who having responsibility to
taken up the challenges in terms of high involved task. By involving more employee and leader
relation where it plays important role when they instruct optimum guidance which improvised
skills and development through which support to provide better outcomes as well as more
attention get involve by generating better outcomes.
Risk Reduction:
Many challenges and conflicts arises such as grievances between employees and manger
which has discussed in above part of performance factor, raw material are authentic in which
customer provide negative feedback, Covid-19 situation arise in which it breakdown the revenue
factor and generates losses. The manager of Johnson Arabia’s manager allows better productive
work that procure high sustainability, but due to shortage of resources makes employees
31
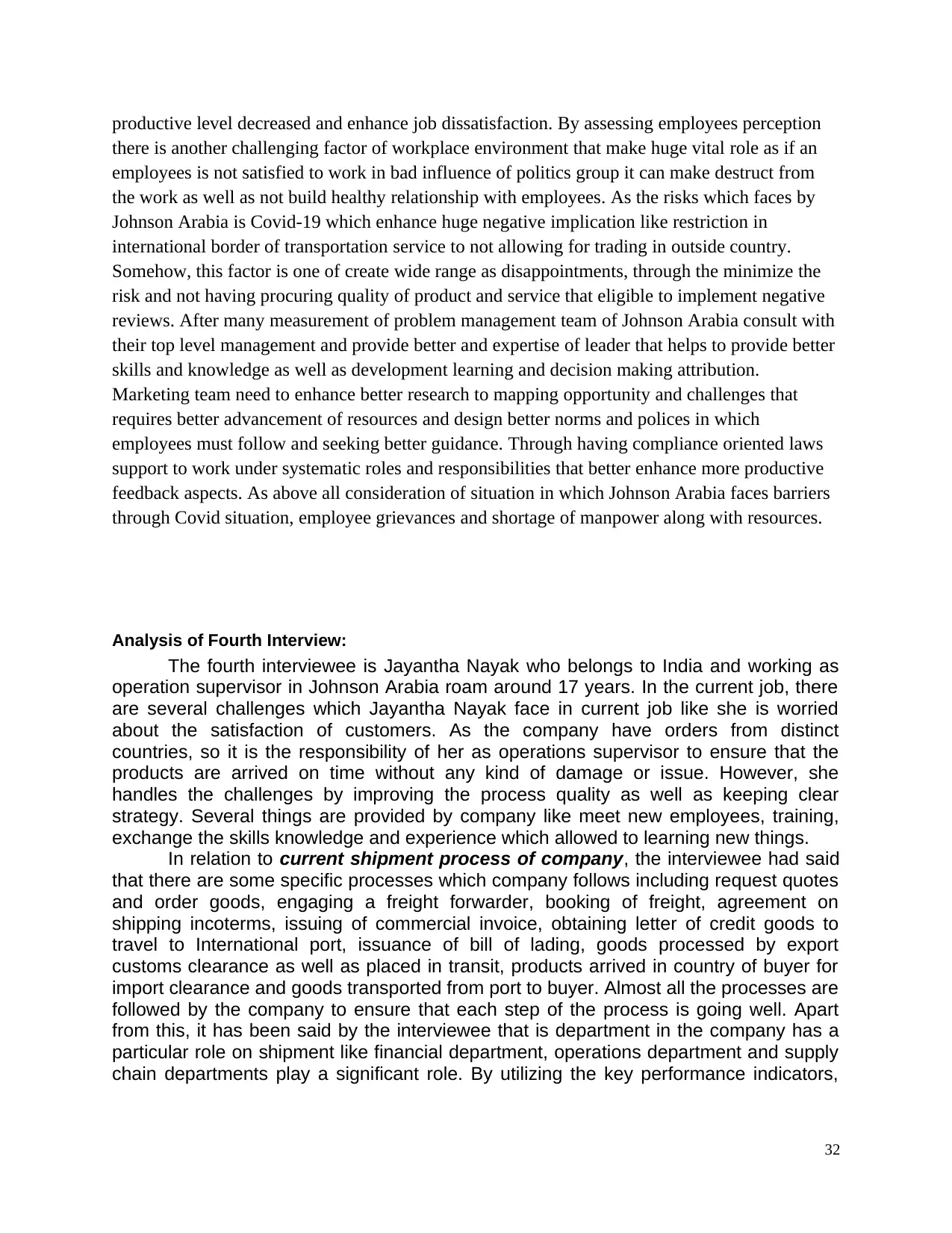
productive level decreased and enhance job dissatisfaction. By assessing employees perception
there is another challenging factor of workplace environment that make huge vital role as if an
employees is not satisfied to work in bad influence of politics group it can make destruct from
the work as well as not build healthy relationship with employees. As the risks which faces by
Johnson Arabia is Covid-19 which enhance huge negative implication like restriction in
international border of transportation service to not allowing for trading in outside country.
Somehow, this factor is one of create wide range as disappointments, through the minimize the
risk and not having procuring quality of product and service that eligible to implement negative
reviews. After many measurement of problem management team of Johnson Arabia consult with
their top level management and provide better and expertise of leader that helps to provide better
skills and knowledge as well as development learning and decision making attribution.
Marketing team need to enhance better research to mapping opportunity and challenges that
requires better advancement of resources and design better norms and polices in which
employees must follow and seeking better guidance. Through having compliance oriented laws
support to work under systematic roles and responsibilities that better enhance more productive
feedback aspects. As above all consideration of situation in which Johnson Arabia faces barriers
through Covid situation, employee grievances and shortage of manpower along with resources.
Analysis of Fourth Interview:
The fourth interviewee is Jayantha Nayak who belongs to India and working as
operation supervisor in Johnson Arabia roam around 17 years. In the current job, there
are several challenges which Jayantha Nayak face in current job like she is worried
about the satisfaction of customers. As the company have orders from distinct
countries, so it is the responsibility of her as operations supervisor to ensure that the
products are arrived on time without any kind of damage or issue. However, she
handles the challenges by improving the process quality as well as keeping clear
strategy. Several things are provided by company like meet new employees, training,
exchange the skills knowledge and experience which allowed to learning new things.
In relation to current shipment process of company, the interviewee had said
that there are some specific processes which company follows including request quotes
and order goods, engaging a freight forwarder, booking of freight, agreement on
shipping incoterms, issuing of commercial invoice, obtaining letter of credit goods to
travel to International port, issuance of bill of lading, goods processed by export
customs clearance as well as placed in transit, products arrived in country of buyer for
import clearance and goods transported from port to buyer. Almost all the processes are
followed by the company to ensure that each step of the process is going well. Apart
from this, it has been said by the interviewee that is department in the company has a
particular role on shipment like financial department, operations department and supply
chain departments play a significant role. By utilizing the key performance indicators,
32
there is another challenging factor of workplace environment that make huge vital role as if an
employees is not satisfied to work in bad influence of politics group it can make destruct from
the work as well as not build healthy relationship with employees. As the risks which faces by
Johnson Arabia is Covid-19 which enhance huge negative implication like restriction in
international border of transportation service to not allowing for trading in outside country.
Somehow, this factor is one of create wide range as disappointments, through the minimize the
risk and not having procuring quality of product and service that eligible to implement negative
reviews. After many measurement of problem management team of Johnson Arabia consult with
their top level management and provide better and expertise of leader that helps to provide better
skills and knowledge as well as development learning and decision making attribution.
Marketing team need to enhance better research to mapping opportunity and challenges that
requires better advancement of resources and design better norms and polices in which
employees must follow and seeking better guidance. Through having compliance oriented laws
support to work under systematic roles and responsibilities that better enhance more productive
feedback aspects. As above all consideration of situation in which Johnson Arabia faces barriers
through Covid situation, employee grievances and shortage of manpower along with resources.
Analysis of Fourth Interview:
The fourth interviewee is Jayantha Nayak who belongs to India and working as
operation supervisor in Johnson Arabia roam around 17 years. In the current job, there
are several challenges which Jayantha Nayak face in current job like she is worried
about the satisfaction of customers. As the company have orders from distinct
countries, so it is the responsibility of her as operations supervisor to ensure that the
products are arrived on time without any kind of damage or issue. However, she
handles the challenges by improving the process quality as well as keeping clear
strategy. Several things are provided by company like meet new employees, training,
exchange the skills knowledge and experience which allowed to learning new things.
In relation to current shipment process of company, the interviewee had said
that there are some specific processes which company follows including request quotes
and order goods, engaging a freight forwarder, booking of freight, agreement on
shipping incoterms, issuing of commercial invoice, obtaining letter of credit goods to
travel to International port, issuance of bill of lading, goods processed by export
customs clearance as well as placed in transit, products arrived in country of buyer for
import clearance and goods transported from port to buyer. Almost all the processes are
followed by the company to ensure that each step of the process is going well. Apart
from this, it has been said by the interviewee that is department in the company has a
particular role on shipment like financial department, operations department and supply
chain departments play a significant role. By utilizing the key performance indicators,
32
Paraphrase This Document
Need a fresh take? Get an instant paraphrase of this document with our AI Paraphraser
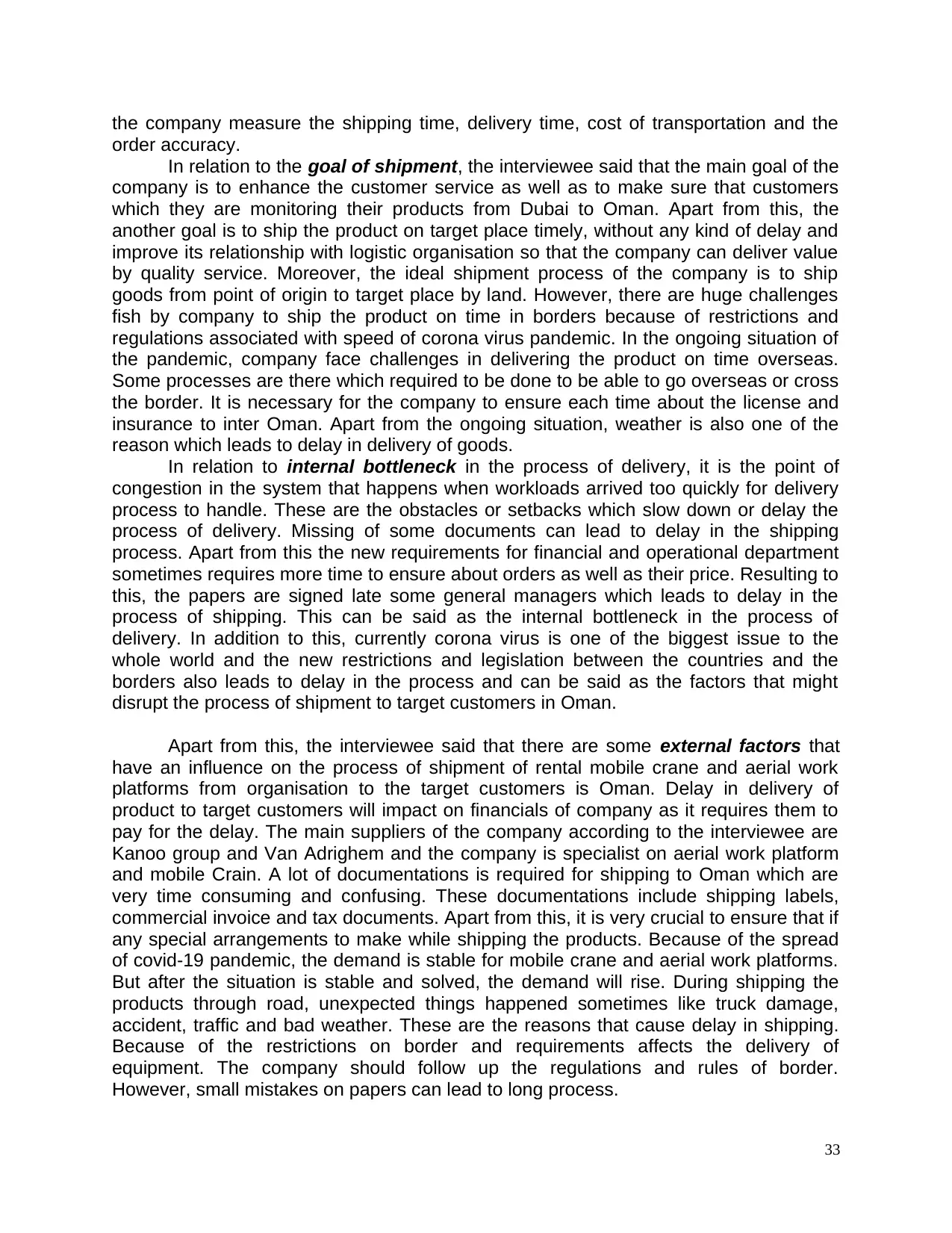
the company measure the shipping time, delivery time, cost of transportation and the
order accuracy.
In relation to the goal of shipment, the interviewee said that the main goal of the
company is to enhance the customer service as well as to make sure that customers
which they are monitoring their products from Dubai to Oman. Apart from this, the
another goal is to ship the product on target place timely, without any kind of delay and
improve its relationship with logistic organisation so that the company can deliver value
by quality service. Moreover, the ideal shipment process of the company is to ship
goods from point of origin to target place by land. However, there are huge challenges
fish by company to ship the product on time in borders because of restrictions and
regulations associated with speed of corona virus pandemic. In the ongoing situation of
the pandemic, company face challenges in delivering the product on time overseas.
Some processes are there which required to be done to be able to go overseas or cross
the border. It is necessary for the company to ensure each time about the license and
insurance to inter Oman. Apart from the ongoing situation, weather is also one of the
reason which leads to delay in delivery of goods.
In relation to internal bottleneck in the process of delivery, it is the point of
congestion in the system that happens when workloads arrived too quickly for delivery
process to handle. These are the obstacles or setbacks which slow down or delay the
process of delivery. Missing of some documents can lead to delay in the shipping
process. Apart from this the new requirements for financial and operational department
sometimes requires more time to ensure about orders as well as their price. Resulting to
this, the papers are signed late some general managers which leads to delay in the
process of shipping. This can be said as the internal bottleneck in the process of
delivery. In addition to this, currently corona virus is one of the biggest issue to the
whole world and the new restrictions and legislation between the countries and the
borders also leads to delay in the process and can be said as the factors that might
disrupt the process of shipment to target customers in Oman.
Apart from this, the interviewee said that there are some external factors that
have an influence on the process of shipment of rental mobile crane and aerial work
platforms from organisation to the target customers is Oman. Delay in delivery of
product to target customers will impact on financials of company as it requires them to
pay for the delay. The main suppliers of the company according to the interviewee are
Kanoo group and Van Adrighem and the company is specialist on aerial work platform
and mobile Crain. A lot of documentations is required for shipping to Oman which are
very time consuming and confusing. These documentations include shipping labels,
commercial invoice and tax documents. Apart from this, it is very crucial to ensure that if
any special arrangements to make while shipping the products. Because of the spread
of covid-19 pandemic, the demand is stable for mobile crane and aerial work platforms.
But after the situation is stable and solved, the demand will rise. During shipping the
products through road, unexpected things happened sometimes like truck damage,
accident, traffic and bad weather. These are the reasons that cause delay in shipping.
Because of the restrictions on border and requirements affects the delivery of
equipment. The company should follow up the regulations and rules of border.
However, small mistakes on papers can lead to long process.
33
order accuracy.
In relation to the goal of shipment, the interviewee said that the main goal of the
company is to enhance the customer service as well as to make sure that customers
which they are monitoring their products from Dubai to Oman. Apart from this, the
another goal is to ship the product on target place timely, without any kind of delay and
improve its relationship with logistic organisation so that the company can deliver value
by quality service. Moreover, the ideal shipment process of the company is to ship
goods from point of origin to target place by land. However, there are huge challenges
fish by company to ship the product on time in borders because of restrictions and
regulations associated with speed of corona virus pandemic. In the ongoing situation of
the pandemic, company face challenges in delivering the product on time overseas.
Some processes are there which required to be done to be able to go overseas or cross
the border. It is necessary for the company to ensure each time about the license and
insurance to inter Oman. Apart from the ongoing situation, weather is also one of the
reason which leads to delay in delivery of goods.
In relation to internal bottleneck in the process of delivery, it is the point of
congestion in the system that happens when workloads arrived too quickly for delivery
process to handle. These are the obstacles or setbacks which slow down or delay the
process of delivery. Missing of some documents can lead to delay in the shipping
process. Apart from this the new requirements for financial and operational department
sometimes requires more time to ensure about orders as well as their price. Resulting to
this, the papers are signed late some general managers which leads to delay in the
process of shipping. This can be said as the internal bottleneck in the process of
delivery. In addition to this, currently corona virus is one of the biggest issue to the
whole world and the new restrictions and legislation between the countries and the
borders also leads to delay in the process and can be said as the factors that might
disrupt the process of shipment to target customers in Oman.
Apart from this, the interviewee said that there are some external factors that
have an influence on the process of shipment of rental mobile crane and aerial work
platforms from organisation to the target customers is Oman. Delay in delivery of
product to target customers will impact on financials of company as it requires them to
pay for the delay. The main suppliers of the company according to the interviewee are
Kanoo group and Van Adrighem and the company is specialist on aerial work platform
and mobile Crain. A lot of documentations is required for shipping to Oman which are
very time consuming and confusing. These documentations include shipping labels,
commercial invoice and tax documents. Apart from this, it is very crucial to ensure that if
any special arrangements to make while shipping the products. Because of the spread
of covid-19 pandemic, the demand is stable for mobile crane and aerial work platforms.
But after the situation is stable and solved, the demand will rise. During shipping the
products through road, unexpected things happened sometimes like truck damage,
accident, traffic and bad weather. These are the reasons that cause delay in shipping.
Because of the restrictions on border and requirements affects the delivery of
equipment. The company should follow up the regulations and rules of border.
However, small mistakes on papers can lead to long process.
33
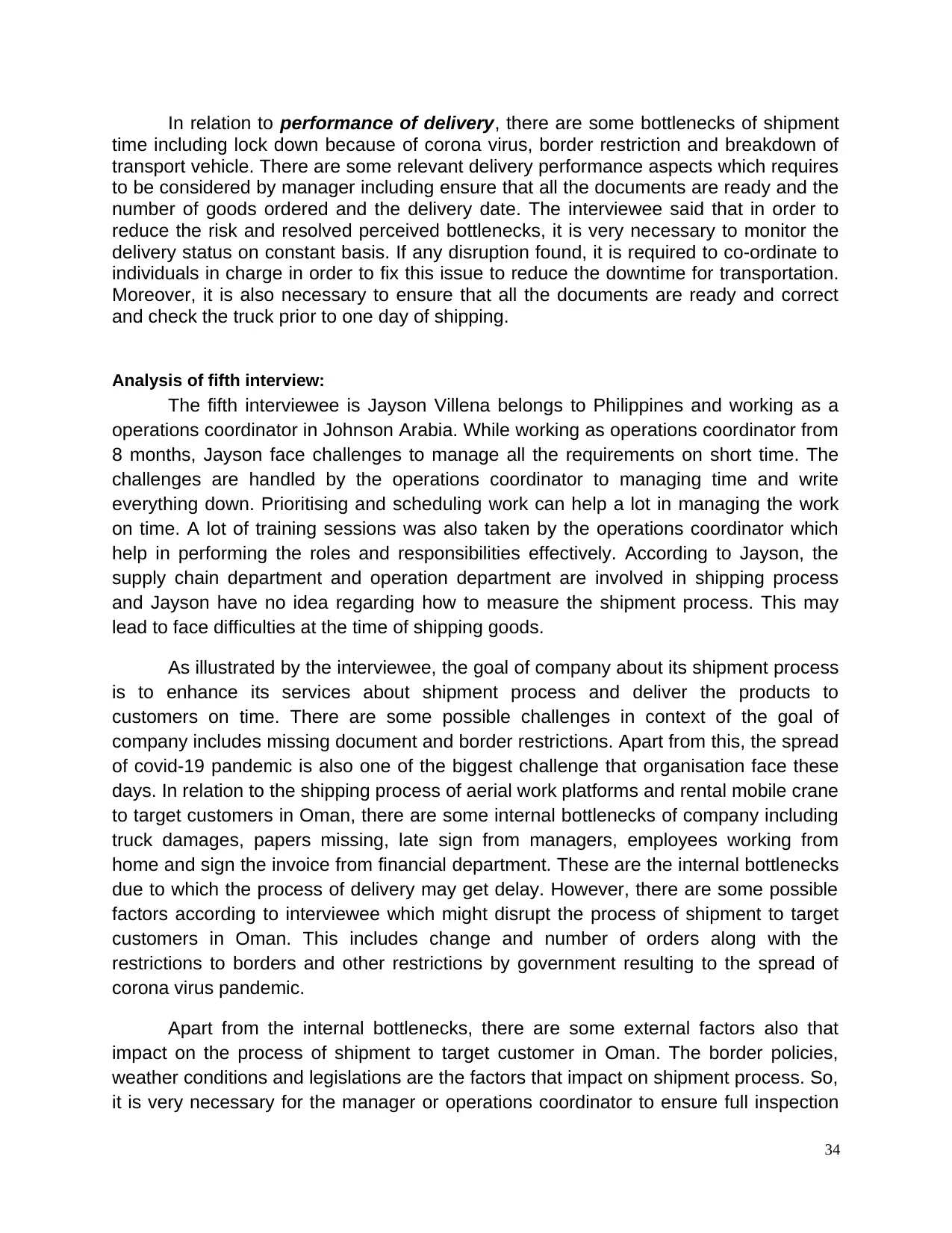
In relation to performance of delivery, there are some bottlenecks of shipment
time including lock down because of corona virus, border restriction and breakdown of
transport vehicle. There are some relevant delivery performance aspects which requires
to be considered by manager including ensure that all the documents are ready and the
number of goods ordered and the delivery date. The interviewee said that in order to
reduce the risk and resolved perceived bottlenecks, it is very necessary to monitor the
delivery status on constant basis. If any disruption found, it is required to co-ordinate to
individuals in charge in order to fix this issue to reduce the downtime for transportation.
Moreover, it is also necessary to ensure that all the documents are ready and correct
and check the truck prior to one day of shipping.
Analysis of fifth interview:
The fifth interviewee is Jayson Villena belongs to Philippines and working as a
operations coordinator in Johnson Arabia. While working as operations coordinator from
8 months, Jayson face challenges to manage all the requirements on short time. The
challenges are handled by the operations coordinator to managing time and write
everything down. Prioritising and scheduling work can help a lot in managing the work
on time. A lot of training sessions was also taken by the operations coordinator which
help in performing the roles and responsibilities effectively. According to Jayson, the
supply chain department and operation department are involved in shipping process
and Jayson have no idea regarding how to measure the shipment process. This may
lead to face difficulties at the time of shipping goods.
As illustrated by the interviewee, the goal of company about its shipment process
is to enhance its services about shipment process and deliver the products to
customers on time. There are some possible challenges in context of the goal of
company includes missing document and border restrictions. Apart from this, the spread
of covid-19 pandemic is also one of the biggest challenge that organisation face these
days. In relation to the shipping process of aerial work platforms and rental mobile crane
to target customers in Oman, there are some internal bottlenecks of company including
truck damages, papers missing, late sign from managers, employees working from
home and sign the invoice from financial department. These are the internal bottlenecks
due to which the process of delivery may get delay. However, there are some possible
factors according to interviewee which might disrupt the process of shipment to target
customers in Oman. This includes change and number of orders along with the
restrictions to borders and other restrictions by government resulting to the spread of
corona virus pandemic.
Apart from the internal bottlenecks, there are some external factors also that
impact on the process of shipment to target customer in Oman. The border policies,
weather conditions and legislations are the factors that impact on shipment process. So,
it is very necessary for the manager or operations coordinator to ensure full inspection
34
time including lock down because of corona virus, border restriction and breakdown of
transport vehicle. There are some relevant delivery performance aspects which requires
to be considered by manager including ensure that all the documents are ready and the
number of goods ordered and the delivery date. The interviewee said that in order to
reduce the risk and resolved perceived bottlenecks, it is very necessary to monitor the
delivery status on constant basis. If any disruption found, it is required to co-ordinate to
individuals in charge in order to fix this issue to reduce the downtime for transportation.
Moreover, it is also necessary to ensure that all the documents are ready and correct
and check the truck prior to one day of shipping.
Analysis of fifth interview:
The fifth interviewee is Jayson Villena belongs to Philippines and working as a
operations coordinator in Johnson Arabia. While working as operations coordinator from
8 months, Jayson face challenges to manage all the requirements on short time. The
challenges are handled by the operations coordinator to managing time and write
everything down. Prioritising and scheduling work can help a lot in managing the work
on time. A lot of training sessions was also taken by the operations coordinator which
help in performing the roles and responsibilities effectively. According to Jayson, the
supply chain department and operation department are involved in shipping process
and Jayson have no idea regarding how to measure the shipment process. This may
lead to face difficulties at the time of shipping goods.
As illustrated by the interviewee, the goal of company about its shipment process
is to enhance its services about shipment process and deliver the products to
customers on time. There are some possible challenges in context of the goal of
company includes missing document and border restrictions. Apart from this, the spread
of covid-19 pandemic is also one of the biggest challenge that organisation face these
days. In relation to the shipping process of aerial work platforms and rental mobile crane
to target customers in Oman, there are some internal bottlenecks of company including
truck damages, papers missing, late sign from managers, employees working from
home and sign the invoice from financial department. These are the internal bottlenecks
due to which the process of delivery may get delay. However, there are some possible
factors according to interviewee which might disrupt the process of shipment to target
customers in Oman. This includes change and number of orders along with the
restrictions to borders and other restrictions by government resulting to the spread of
corona virus pandemic.
Apart from the internal bottlenecks, there are some external factors also that
impact on the process of shipment to target customer in Oman. The border policies,
weather conditions and legislations are the factors that impact on shipment process. So,
it is very necessary for the manager or operations coordinator to ensure full inspection
34
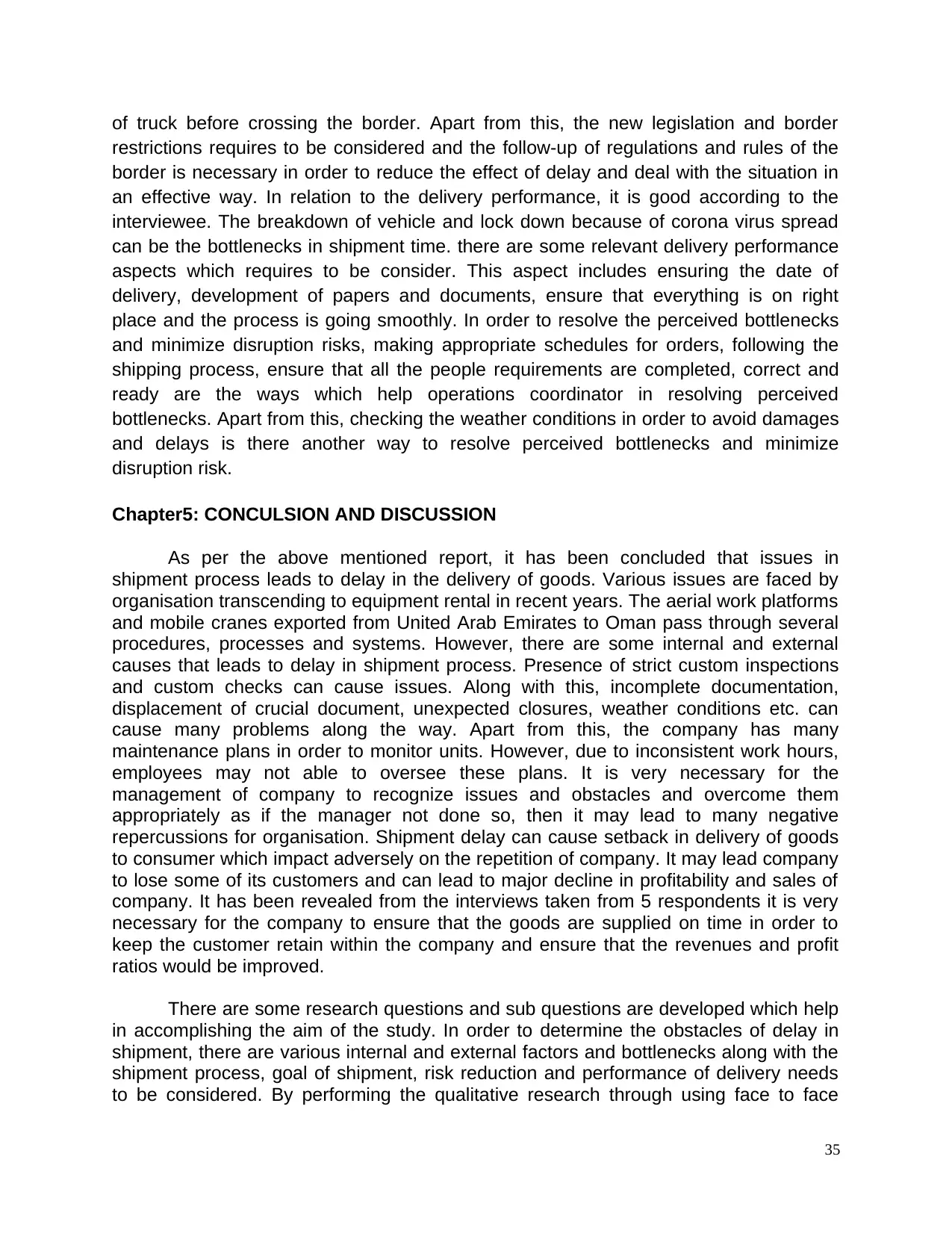
of truck before crossing the border. Apart from this, the new legislation and border
restrictions requires to be considered and the follow-up of regulations and rules of the
border is necessary in order to reduce the effect of delay and deal with the situation in
an effective way. In relation to the delivery performance, it is good according to the
interviewee. The breakdown of vehicle and lock down because of corona virus spread
can be the bottlenecks in shipment time. there are some relevant delivery performance
aspects which requires to be consider. This aspect includes ensuring the date of
delivery, development of papers and documents, ensure that everything is on right
place and the process is going smoothly. In order to resolve the perceived bottlenecks
and minimize disruption risks, making appropriate schedules for orders, following the
shipping process, ensure that all the people requirements are completed, correct and
ready are the ways which help operations coordinator in resolving perceived
bottlenecks. Apart from this, checking the weather conditions in order to avoid damages
and delays is there another way to resolve perceived bottlenecks and minimize
disruption risk.
Chapter5: CONCULSION AND DISCUSSION
As per the above mentioned report, it has been concluded that issues in
shipment process leads to delay in the delivery of goods. Various issues are faced by
organisation transcending to equipment rental in recent years. The aerial work platforms
and mobile cranes exported from United Arab Emirates to Oman pass through several
procedures, processes and systems. However, there are some internal and external
causes that leads to delay in shipment process. Presence of strict custom inspections
and custom checks can cause issues. Along with this, incomplete documentation,
displacement of crucial document, unexpected closures, weather conditions etc. can
cause many problems along the way. Apart from this, the company has many
maintenance plans in order to monitor units. However, due to inconsistent work hours,
employees may not able to oversee these plans. It is very necessary for the
management of company to recognize issues and obstacles and overcome them
appropriately as if the manager not done so, then it may lead to many negative
repercussions for organisation. Shipment delay can cause setback in delivery of goods
to consumer which impact adversely on the repetition of company. It may lead company
to lose some of its customers and can lead to major decline in profitability and sales of
company. It has been revealed from the interviews taken from 5 respondents it is very
necessary for the company to ensure that the goods are supplied on time in order to
keep the customer retain within the company and ensure that the revenues and profit
ratios would be improved.
There are some research questions and sub questions are developed which help
in accomplishing the aim of the study. In order to determine the obstacles of delay in
shipment, there are various internal and external factors and bottlenecks along with the
shipment process, goal of shipment, risk reduction and performance of delivery needs
to be considered. By performing the qualitative research through using face to face
35
restrictions requires to be considered and the follow-up of regulations and rules of the
border is necessary in order to reduce the effect of delay and deal with the situation in
an effective way. In relation to the delivery performance, it is good according to the
interviewee. The breakdown of vehicle and lock down because of corona virus spread
can be the bottlenecks in shipment time. there are some relevant delivery performance
aspects which requires to be consider. This aspect includes ensuring the date of
delivery, development of papers and documents, ensure that everything is on right
place and the process is going smoothly. In order to resolve the perceived bottlenecks
and minimize disruption risks, making appropriate schedules for orders, following the
shipping process, ensure that all the people requirements are completed, correct and
ready are the ways which help operations coordinator in resolving perceived
bottlenecks. Apart from this, checking the weather conditions in order to avoid damages
and delays is there another way to resolve perceived bottlenecks and minimize
disruption risk.
Chapter5: CONCULSION AND DISCUSSION
As per the above mentioned report, it has been concluded that issues in
shipment process leads to delay in the delivery of goods. Various issues are faced by
organisation transcending to equipment rental in recent years. The aerial work platforms
and mobile cranes exported from United Arab Emirates to Oman pass through several
procedures, processes and systems. However, there are some internal and external
causes that leads to delay in shipment process. Presence of strict custom inspections
and custom checks can cause issues. Along with this, incomplete documentation,
displacement of crucial document, unexpected closures, weather conditions etc. can
cause many problems along the way. Apart from this, the company has many
maintenance plans in order to monitor units. However, due to inconsistent work hours,
employees may not able to oversee these plans. It is very necessary for the
management of company to recognize issues and obstacles and overcome them
appropriately as if the manager not done so, then it may lead to many negative
repercussions for organisation. Shipment delay can cause setback in delivery of goods
to consumer which impact adversely on the repetition of company. It may lead company
to lose some of its customers and can lead to major decline in profitability and sales of
company. It has been revealed from the interviews taken from 5 respondents it is very
necessary for the company to ensure that the goods are supplied on time in order to
keep the customer retain within the company and ensure that the revenues and profit
ratios would be improved.
There are some research questions and sub questions are developed which help
in accomplishing the aim of the study. In order to determine the obstacles of delay in
shipment, there are various internal and external factors and bottlenecks along with the
shipment process, goal of shipment, risk reduction and performance of delivery needs
to be considered. By performing the qualitative research through using face to face
35
Secure Best Marks with AI Grader
Need help grading? Try our AI Grader for instant feedback on your assignments.
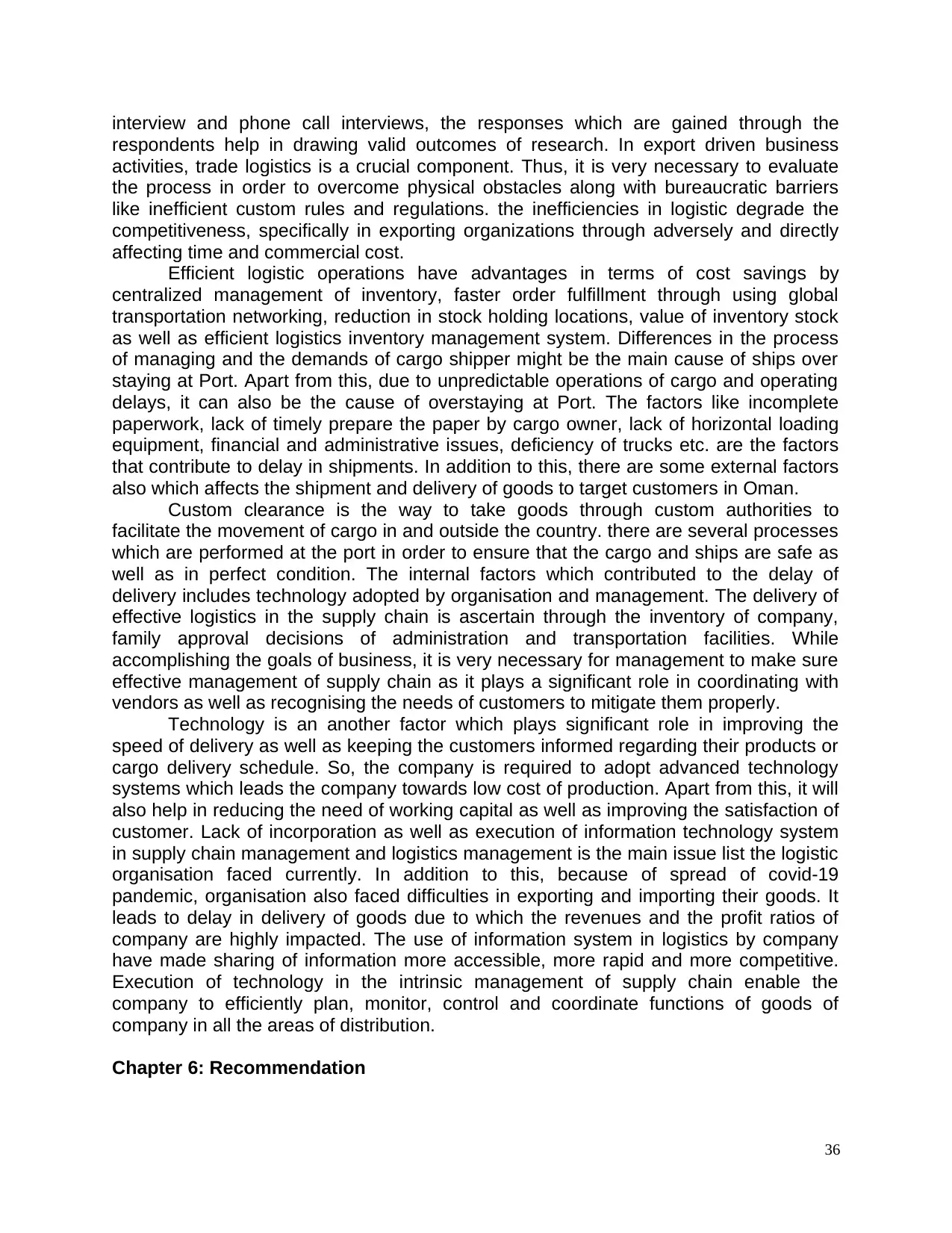
interview and phone call interviews, the responses which are gained through the
respondents help in drawing valid outcomes of research. In export driven business
activities, trade logistics is a crucial component. Thus, it is very necessary to evaluate
the process in order to overcome physical obstacles along with bureaucratic barriers
like inefficient custom rules and regulations. the inefficiencies in logistic degrade the
competitiveness, specifically in exporting organizations through adversely and directly
affecting time and commercial cost.
Efficient logistic operations have advantages in terms of cost savings by
centralized management of inventory, faster order fulfillment through using global
transportation networking, reduction in stock holding locations, value of inventory stock
as well as efficient logistics inventory management system. Differences in the process
of managing and the demands of cargo shipper might be the main cause of ships over
staying at Port. Apart from this, due to unpredictable operations of cargo and operating
delays, it can also be the cause of overstaying at Port. The factors like incomplete
paperwork, lack of timely prepare the paper by cargo owner, lack of horizontal loading
equipment, financial and administrative issues, deficiency of trucks etc. are the factors
that contribute to delay in shipments. In addition to this, there are some external factors
also which affects the shipment and delivery of goods to target customers in Oman.
Custom clearance is the way to take goods through custom authorities to
facilitate the movement of cargo in and outside the country. there are several processes
which are performed at the port in order to ensure that the cargo and ships are safe as
well as in perfect condition. The internal factors which contributed to the delay of
delivery includes technology adopted by organisation and management. The delivery of
effective logistics in the supply chain is ascertain through the inventory of company,
family approval decisions of administration and transportation facilities. While
accomplishing the goals of business, it is very necessary for management to make sure
effective management of supply chain as it plays a significant role in coordinating with
vendors as well as recognising the needs of customers to mitigate them properly.
Technology is an another factor which plays significant role in improving the
speed of delivery as well as keeping the customers informed regarding their products or
cargo delivery schedule. So, the company is required to adopt advanced technology
systems which leads the company towards low cost of production. Apart from this, it will
also help in reducing the need of working capital as well as improving the satisfaction of
customer. Lack of incorporation as well as execution of information technology system
in supply chain management and logistics management is the main issue list the logistic
organisation faced currently. In addition to this, because of spread of covid-19
pandemic, organisation also faced difficulties in exporting and importing their goods. It
leads to delay in delivery of goods due to which the revenues and the profit ratios of
company are highly impacted. The use of information system in logistics by company
have made sharing of information more accessible, more rapid and more competitive.
Execution of technology in the intrinsic management of supply chain enable the
company to efficiently plan, monitor, control and coordinate functions of goods of
company in all the areas of distribution.
Chapter 6: Recommendation
36
respondents help in drawing valid outcomes of research. In export driven business
activities, trade logistics is a crucial component. Thus, it is very necessary to evaluate
the process in order to overcome physical obstacles along with bureaucratic barriers
like inefficient custom rules and regulations. the inefficiencies in logistic degrade the
competitiveness, specifically in exporting organizations through adversely and directly
affecting time and commercial cost.
Efficient logistic operations have advantages in terms of cost savings by
centralized management of inventory, faster order fulfillment through using global
transportation networking, reduction in stock holding locations, value of inventory stock
as well as efficient logistics inventory management system. Differences in the process
of managing and the demands of cargo shipper might be the main cause of ships over
staying at Port. Apart from this, due to unpredictable operations of cargo and operating
delays, it can also be the cause of overstaying at Port. The factors like incomplete
paperwork, lack of timely prepare the paper by cargo owner, lack of horizontal loading
equipment, financial and administrative issues, deficiency of trucks etc. are the factors
that contribute to delay in shipments. In addition to this, there are some external factors
also which affects the shipment and delivery of goods to target customers in Oman.
Custom clearance is the way to take goods through custom authorities to
facilitate the movement of cargo in and outside the country. there are several processes
which are performed at the port in order to ensure that the cargo and ships are safe as
well as in perfect condition. The internal factors which contributed to the delay of
delivery includes technology adopted by organisation and management. The delivery of
effective logistics in the supply chain is ascertain through the inventory of company,
family approval decisions of administration and transportation facilities. While
accomplishing the goals of business, it is very necessary for management to make sure
effective management of supply chain as it plays a significant role in coordinating with
vendors as well as recognising the needs of customers to mitigate them properly.
Technology is an another factor which plays significant role in improving the
speed of delivery as well as keeping the customers informed regarding their products or
cargo delivery schedule. So, the company is required to adopt advanced technology
systems which leads the company towards low cost of production. Apart from this, it will
also help in reducing the need of working capital as well as improving the satisfaction of
customer. Lack of incorporation as well as execution of information technology system
in supply chain management and logistics management is the main issue list the logistic
organisation faced currently. In addition to this, because of spread of covid-19
pandemic, organisation also faced difficulties in exporting and importing their goods. It
leads to delay in delivery of goods due to which the revenues and the profit ratios of
company are highly impacted. The use of information system in logistics by company
have made sharing of information more accessible, more rapid and more competitive.
Execution of technology in the intrinsic management of supply chain enable the
company to efficiently plan, monitor, control and coordinate functions of goods of
company in all the areas of distribution.
Chapter 6: Recommendation
36
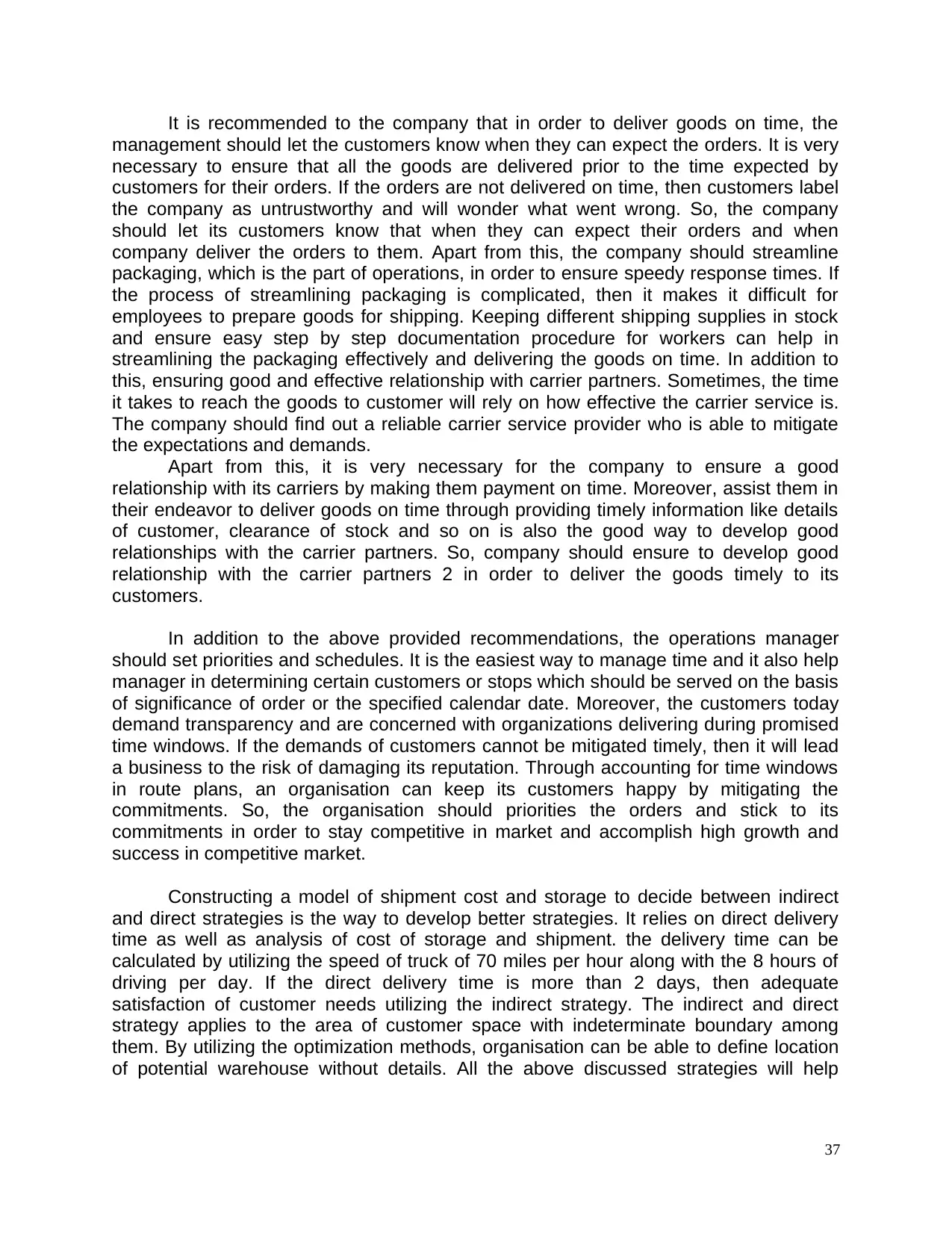
It is recommended to the company that in order to deliver goods on time, the
management should let the customers know when they can expect the orders. It is very
necessary to ensure that all the goods are delivered prior to the time expected by
customers for their orders. If the orders are not delivered on time, then customers label
the company as untrustworthy and will wonder what went wrong. So, the company
should let its customers know that when they can expect their orders and when
company deliver the orders to them. Apart from this, the company should streamline
packaging, which is the part of operations, in order to ensure speedy response times. If
the process of streamlining packaging is complicated, then it makes it difficult for
employees to prepare goods for shipping. Keeping different shipping supplies in stock
and ensure easy step by step documentation procedure for workers can help in
streamlining the packaging effectively and delivering the goods on time. In addition to
this, ensuring good and effective relationship with carrier partners. Sometimes, the time
it takes to reach the goods to customer will rely on how effective the carrier service is.
The company should find out a reliable carrier service provider who is able to mitigate
the expectations and demands.
Apart from this, it is very necessary for the company to ensure a good
relationship with its carriers by making them payment on time. Moreover, assist them in
their endeavor to deliver goods on time through providing timely information like details
of customer, clearance of stock and so on is also the good way to develop good
relationships with the carrier partners. So, company should ensure to develop good
relationship with the carrier partners 2 in order to deliver the goods timely to its
customers.
In addition to the above provided recommendations, the operations manager
should set priorities and schedules. It is the easiest way to manage time and it also help
manager in determining certain customers or stops which should be served on the basis
of significance of order or the specified calendar date. Moreover, the customers today
demand transparency and are concerned with organizations delivering during promised
time windows. If the demands of customers cannot be mitigated timely, then it will lead
a business to the risk of damaging its reputation. Through accounting for time windows
in route plans, an organisation can keep its customers happy by mitigating the
commitments. So, the organisation should priorities the orders and stick to its
commitments in order to stay competitive in market and accomplish high growth and
success in competitive market.
Constructing a model of shipment cost and storage to decide between indirect
and direct strategies is the way to develop better strategies. It relies on direct delivery
time as well as analysis of cost of storage and shipment. the delivery time can be
calculated by utilizing the speed of truck of 70 miles per hour along with the 8 hours of
driving per day. If the direct delivery time is more than 2 days, then adequate
satisfaction of customer needs utilizing the indirect strategy. The indirect and direct
strategy applies to the area of customer space with indeterminate boundary among
them. By utilizing the optimization methods, organisation can be able to define location
of potential warehouse without details. All the above discussed strategies will help
37
management should let the customers know when they can expect the orders. It is very
necessary to ensure that all the goods are delivered prior to the time expected by
customers for their orders. If the orders are not delivered on time, then customers label
the company as untrustworthy and will wonder what went wrong. So, the company
should let its customers know that when they can expect their orders and when
company deliver the orders to them. Apart from this, the company should streamline
packaging, which is the part of operations, in order to ensure speedy response times. If
the process of streamlining packaging is complicated, then it makes it difficult for
employees to prepare goods for shipping. Keeping different shipping supplies in stock
and ensure easy step by step documentation procedure for workers can help in
streamlining the packaging effectively and delivering the goods on time. In addition to
this, ensuring good and effective relationship with carrier partners. Sometimes, the time
it takes to reach the goods to customer will rely on how effective the carrier service is.
The company should find out a reliable carrier service provider who is able to mitigate
the expectations and demands.
Apart from this, it is very necessary for the company to ensure a good
relationship with its carriers by making them payment on time. Moreover, assist them in
their endeavor to deliver goods on time through providing timely information like details
of customer, clearance of stock and so on is also the good way to develop good
relationships with the carrier partners. So, company should ensure to develop good
relationship with the carrier partners 2 in order to deliver the goods timely to its
customers.
In addition to the above provided recommendations, the operations manager
should set priorities and schedules. It is the easiest way to manage time and it also help
manager in determining certain customers or stops which should be served on the basis
of significance of order or the specified calendar date. Moreover, the customers today
demand transparency and are concerned with organizations delivering during promised
time windows. If the demands of customers cannot be mitigated timely, then it will lead
a business to the risk of damaging its reputation. Through accounting for time windows
in route plans, an organisation can keep its customers happy by mitigating the
commitments. So, the organisation should priorities the orders and stick to its
commitments in order to stay competitive in market and accomplish high growth and
success in competitive market.
Constructing a model of shipment cost and storage to decide between indirect
and direct strategies is the way to develop better strategies. It relies on direct delivery
time as well as analysis of cost of storage and shipment. the delivery time can be
calculated by utilizing the speed of truck of 70 miles per hour along with the 8 hours of
driving per day. If the direct delivery time is more than 2 days, then adequate
satisfaction of customer needs utilizing the indirect strategy. The indirect and direct
strategy applies to the area of customer space with indeterminate boundary among
them. By utilizing the optimization methods, organisation can be able to define location
of potential warehouse without details. All the above discussed strategies will help
37
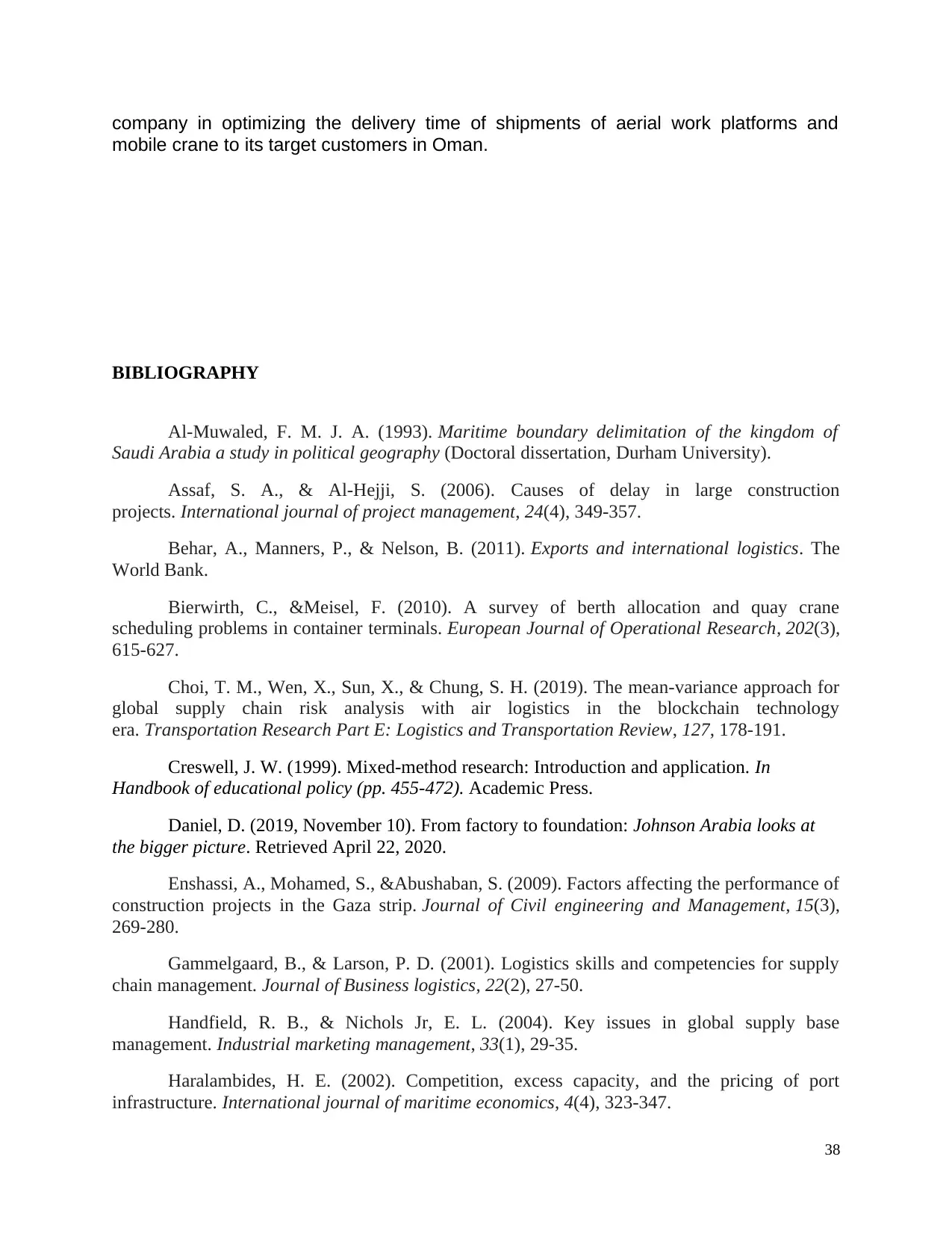
company in optimizing the delivery time of shipments of aerial work platforms and
mobile crane to its target customers in Oman.
BIBLIOGRAPHY
Al-Muwaled, F. M. J. A. (1993). Maritime boundary delimitation of the kingdom of
Saudi Arabia a study in political geography (Doctoral dissertation, Durham University).
Assaf, S. A., & Al-Hejji, S. (2006). Causes of delay in large construction
projects. International journal of project management, 24(4), 349-357.
Behar, A., Manners, P., & Nelson, B. (2011). Exports and international logistics. The
World Bank.
Bierwirth, C., &Meisel, F. (2010). A survey of berth allocation and quay crane
scheduling problems in container terminals. European Journal of Operational Research, 202(3),
615-627.
Choi, T. M., Wen, X., Sun, X., & Chung, S. H. (2019). The mean-variance approach for
global supply chain risk analysis with air logistics in the blockchain technology
era. Transportation Research Part E: Logistics and Transportation Review, 127, 178-191.
Creswell, J. W. (1999). Mixed-method research: Introduction and application. In
Handbook of educational policy (pp. 455-472). Academic Press.
Daniel, D. (2019, November 10). From factory to foundation: Johnson Arabia looks at
the bigger picture. Retrieved April 22, 2020.
Enshassi, A., Mohamed, S., &Abushaban, S. (2009). Factors affecting the performance of
construction projects in the Gaza strip. Journal of Civil engineering and Management, 15(3),
269-280.
Gammelgaard, B., & Larson, P. D. (2001). Logistics skills and competencies for supply
chain management. Journal of Business logistics, 22(2), 27-50.
Handfield, R. B., & Nichols Jr, E. L. (2004). Key issues in global supply base
management. Industrial marketing management, 33(1), 29-35.
Haralambides, H. E. (2002). Competition, excess capacity, and the pricing of port
infrastructure. International journal of maritime economics, 4(4), 323-347.
38
mobile crane to its target customers in Oman.
BIBLIOGRAPHY
Al-Muwaled, F. M. J. A. (1993). Maritime boundary delimitation of the kingdom of
Saudi Arabia a study in political geography (Doctoral dissertation, Durham University).
Assaf, S. A., & Al-Hejji, S. (2006). Causes of delay in large construction
projects. International journal of project management, 24(4), 349-357.
Behar, A., Manners, P., & Nelson, B. (2011). Exports and international logistics. The
World Bank.
Bierwirth, C., &Meisel, F. (2010). A survey of berth allocation and quay crane
scheduling problems in container terminals. European Journal of Operational Research, 202(3),
615-627.
Choi, T. M., Wen, X., Sun, X., & Chung, S. H. (2019). The mean-variance approach for
global supply chain risk analysis with air logistics in the blockchain technology
era. Transportation Research Part E: Logistics and Transportation Review, 127, 178-191.
Creswell, J. W. (1999). Mixed-method research: Introduction and application. In
Handbook of educational policy (pp. 455-472). Academic Press.
Daniel, D. (2019, November 10). From factory to foundation: Johnson Arabia looks at
the bigger picture. Retrieved April 22, 2020.
Enshassi, A., Mohamed, S., &Abushaban, S. (2009). Factors affecting the performance of
construction projects in the Gaza strip. Journal of Civil engineering and Management, 15(3),
269-280.
Gammelgaard, B., & Larson, P. D. (2001). Logistics skills and competencies for supply
chain management. Journal of Business logistics, 22(2), 27-50.
Handfield, R. B., & Nichols Jr, E. L. (2004). Key issues in global supply base
management. Industrial marketing management, 33(1), 29-35.
Haralambides, H. E. (2002). Competition, excess capacity, and the pricing of port
infrastructure. International journal of maritime economics, 4(4), 323-347.
38
Paraphrase This Document
Need a fresh take? Get an instant paraphrase of this document with our AI Paraphraser
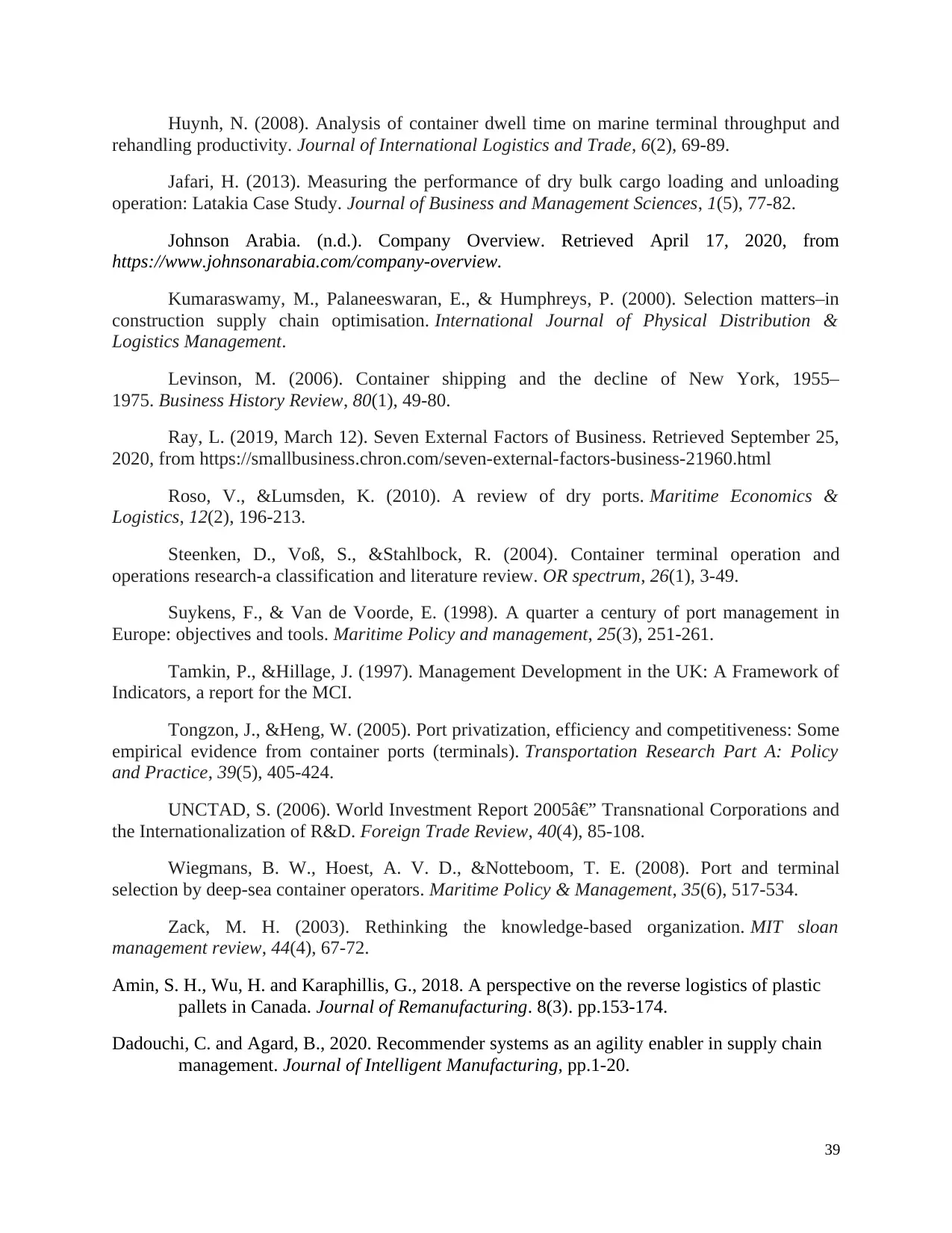
Huynh, N. (2008). Analysis of container dwell time on marine terminal throughput and
rehandling productivity. Journal of International Logistics and Trade, 6(2), 69-89.
Jafari, H. (2013). Measuring the performance of dry bulk cargo loading and unloading
operation: Latakia Case Study. Journal of Business and Management Sciences, 1(5), 77-82.
Johnson Arabia. (n.d.). Company Overview. Retrieved April 17, 2020, from
https://www.johnsonarabia.com/company-overview.
Kumaraswamy, M., Palaneeswaran, E., & Humphreys, P. (2000). Selection matters–in
construction supply chain optimisation. International Journal of Physical Distribution &
Logistics Management.
Levinson, M. (2006). Container shipping and the decline of New York, 1955–
1975. Business History Review, 80(1), 49-80.
Ray, L. (2019, March 12). Seven External Factors of Business. Retrieved September 25,
2020, from https://smallbusiness.chron.com/seven-external-factors-business-21960.html
Roso, V., &Lumsden, K. (2010). A review of dry ports. Maritime Economics &
Logistics, 12(2), 196-213.
Steenken, D., Voß, S., &Stahlbock, R. (2004). Container terminal operation and
operations research-a classification and literature review. OR spectrum, 26(1), 3-49.
Suykens, F., & Van de Voorde, E. (1998). A quarter a century of port management in
Europe: objectives and tools. Maritime Policy and management, 25(3), 251-261.
Tamkin, P., &Hillage, J. (1997). Management Development in the UK: A Framework of
Indicators, a report for the MCI.
Tongzon, J., &Heng, W. (2005). Port privatization, efficiency and competitiveness: Some
empirical evidence from container ports (terminals). Transportation Research Part A: Policy
and Practice, 39(5), 405-424.
UNCTAD, S. (2006). World Investment Report 2005— Transnational Corporations and
the Internationalization of R&D. Foreign Trade Review, 40(4), 85-108.
Wiegmans, B. W., Hoest, A. V. D., &Notteboom, T. E. (2008). Port and terminal
selection by deep-sea container operators. Maritime Policy & Management, 35(6), 517-534.
Zack, M. H. (2003). Rethinking the knowledge-based organization. MIT sloan
management review, 44(4), 67-72.
Amin, S. H., Wu, H. and Karaphillis, G., 2018. A perspective on the reverse logistics of plastic
pallets in Canada. Journal of Remanufacturing. 8(3). pp.153-174.
Dadouchi, C. and Agard, B., 2020. Recommender systems as an agility enabler in supply chain
management. Journal of Intelligent Manufacturing, pp.1-20.
39
rehandling productivity. Journal of International Logistics and Trade, 6(2), 69-89.
Jafari, H. (2013). Measuring the performance of dry bulk cargo loading and unloading
operation: Latakia Case Study. Journal of Business and Management Sciences, 1(5), 77-82.
Johnson Arabia. (n.d.). Company Overview. Retrieved April 17, 2020, from
https://www.johnsonarabia.com/company-overview.
Kumaraswamy, M., Palaneeswaran, E., & Humphreys, P. (2000). Selection matters–in
construction supply chain optimisation. International Journal of Physical Distribution &
Logistics Management.
Levinson, M. (2006). Container shipping and the decline of New York, 1955–
1975. Business History Review, 80(1), 49-80.
Ray, L. (2019, March 12). Seven External Factors of Business. Retrieved September 25,
2020, from https://smallbusiness.chron.com/seven-external-factors-business-21960.html
Roso, V., &Lumsden, K. (2010). A review of dry ports. Maritime Economics &
Logistics, 12(2), 196-213.
Steenken, D., Voß, S., &Stahlbock, R. (2004). Container terminal operation and
operations research-a classification and literature review. OR spectrum, 26(1), 3-49.
Suykens, F., & Van de Voorde, E. (1998). A quarter a century of port management in
Europe: objectives and tools. Maritime Policy and management, 25(3), 251-261.
Tamkin, P., &Hillage, J. (1997). Management Development in the UK: A Framework of
Indicators, a report for the MCI.
Tongzon, J., &Heng, W. (2005). Port privatization, efficiency and competitiveness: Some
empirical evidence from container ports (terminals). Transportation Research Part A: Policy
and Practice, 39(5), 405-424.
UNCTAD, S. (2006). World Investment Report 2005— Transnational Corporations and
the Internationalization of R&D. Foreign Trade Review, 40(4), 85-108.
Wiegmans, B. W., Hoest, A. V. D., &Notteboom, T. E. (2008). Port and terminal
selection by deep-sea container operators. Maritime Policy & Management, 35(6), 517-534.
Zack, M. H. (2003). Rethinking the knowledge-based organization. MIT sloan
management review, 44(4), 67-72.
Amin, S. H., Wu, H. and Karaphillis, G., 2018. A perspective on the reverse logistics of plastic
pallets in Canada. Journal of Remanufacturing. 8(3). pp.153-174.
Dadouchi, C. and Agard, B., 2020. Recommender systems as an agility enabler in supply chain
management. Journal of Intelligent Manufacturing, pp.1-20.
39
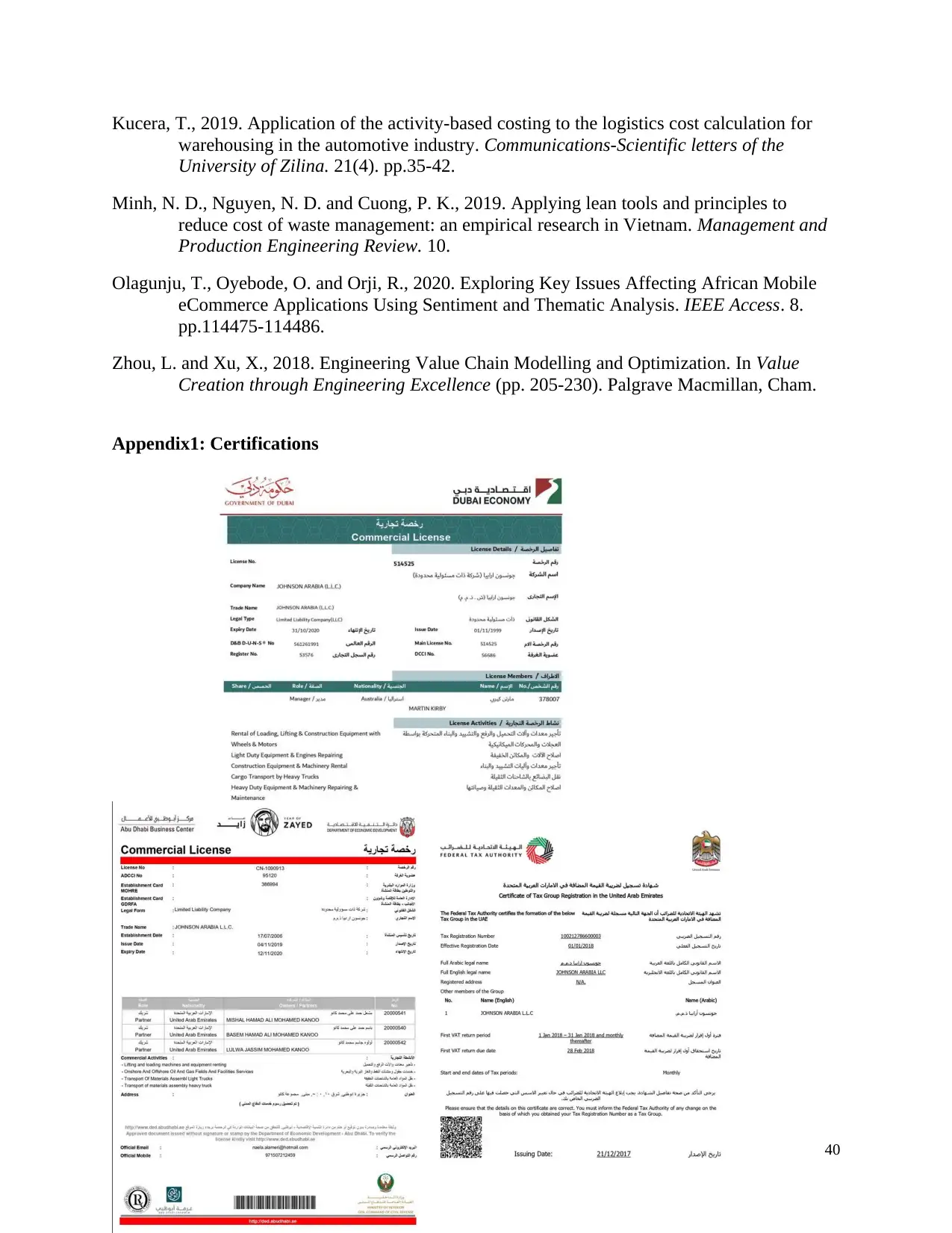
Kucera, T., 2019. Application of the activity-based costing to the logistics cost calculation for
warehousing in the automotive industry. Communications-Scientific letters of the
University of Zilina. 21(4). pp.35-42.
Minh, N. D., Nguyen, N. D. and Cuong, P. K., 2019. Applying lean tools and principles to
reduce cost of waste management: an empirical research in Vietnam. Management and
Production Engineering Review. 10.
Olagunju, T., Oyebode, O. and Orji, R., 2020. Exploring Key Issues Affecting African Mobile
eCommerce Applications Using Sentiment and Thematic Analysis. IEEE Access. 8.
pp.114475-114486.
Zhou, L. and Xu, X., 2018. Engineering Value Chain Modelling and Optimization. In Value
Creation through Engineering Excellence (pp. 205-230). Palgrave Macmillan, Cham.
Appendix1: Certifications
40
warehousing in the automotive industry. Communications-Scientific letters of the
University of Zilina. 21(4). pp.35-42.
Minh, N. D., Nguyen, N. D. and Cuong, P. K., 2019. Applying lean tools and principles to
reduce cost of waste management: an empirical research in Vietnam. Management and
Production Engineering Review. 10.
Olagunju, T., Oyebode, O. and Orji, R., 2020. Exploring Key Issues Affecting African Mobile
eCommerce Applications Using Sentiment and Thematic Analysis. IEEE Access. 8.
pp.114475-114486.
Zhou, L. and Xu, X., 2018. Engineering Value Chain Modelling and Optimization. In Value
Creation through Engineering Excellence (pp. 205-230). Palgrave Macmillan, Cham.
Appendix1: Certifications
40
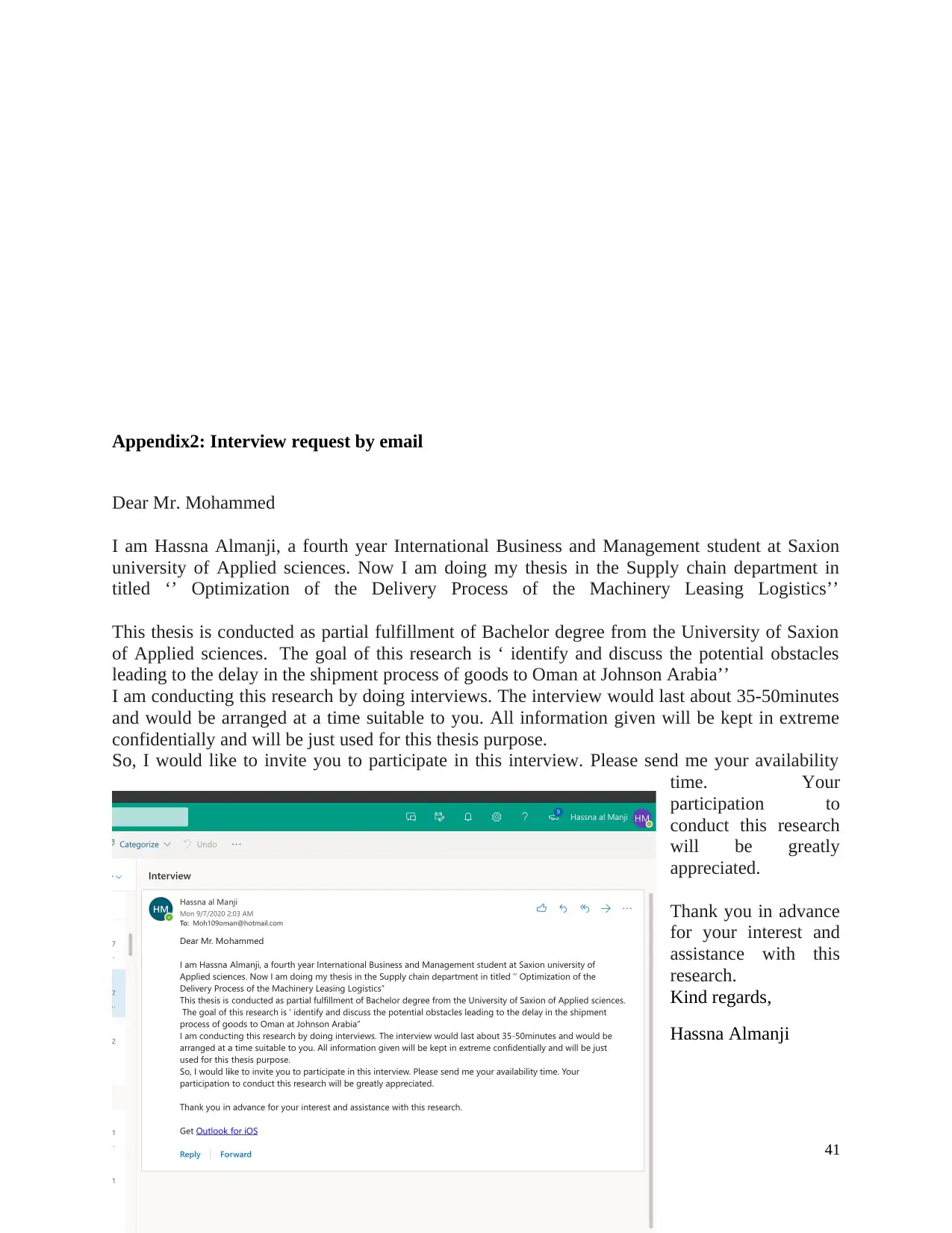
Appendix2: Interview request by email
Dear Mr. Mohammed
I am Hassna Almanji, a fourth year International Business and Management student at Saxion
university of Applied sciences. Now I am doing my thesis in the Supply chain department in
titled ‘’ Optimization of the Delivery Process of the Machinery Leasing Logistics’’
This thesis is conducted as partial fulfillment of Bachelor degree from the University of Saxion
of Applied sciences. The goal of this research is ‘ identify and discuss the potential obstacles
leading to the delay in the shipment process of goods to Oman at Johnson Arabia’’
I am conducting this research by doing interviews. The interview would last about 35-50minutes
and would be arranged at a time suitable to you. All information given will be kept in extreme
confidentially and will be just used for this thesis purpose.
So, I would like to invite you to participate in this interview. Please send me your availability
time. Your
participation to
conduct this research
will be greatly
appreciated.
Thank you in advance
for your interest and
assistance with this
research.
Kind regards,
Hassna Almanji
41
Dear Mr. Mohammed
I am Hassna Almanji, a fourth year International Business and Management student at Saxion
university of Applied sciences. Now I am doing my thesis in the Supply chain department in
titled ‘’ Optimization of the Delivery Process of the Machinery Leasing Logistics’’
This thesis is conducted as partial fulfillment of Bachelor degree from the University of Saxion
of Applied sciences. The goal of this research is ‘ identify and discuss the potential obstacles
leading to the delay in the shipment process of goods to Oman at Johnson Arabia’’
I am conducting this research by doing interviews. The interview would last about 35-50minutes
and would be arranged at a time suitable to you. All information given will be kept in extreme
confidentially and will be just used for this thesis purpose.
So, I would like to invite you to participate in this interview. Please send me your availability
time. Your
participation to
conduct this research
will be greatly
appreciated.
Thank you in advance
for your interest and
assistance with this
research.
Kind regards,
Hassna Almanji
41
Secure Best Marks with AI Grader
Need help grading? Try our AI Grader for instant feedback on your assignments.
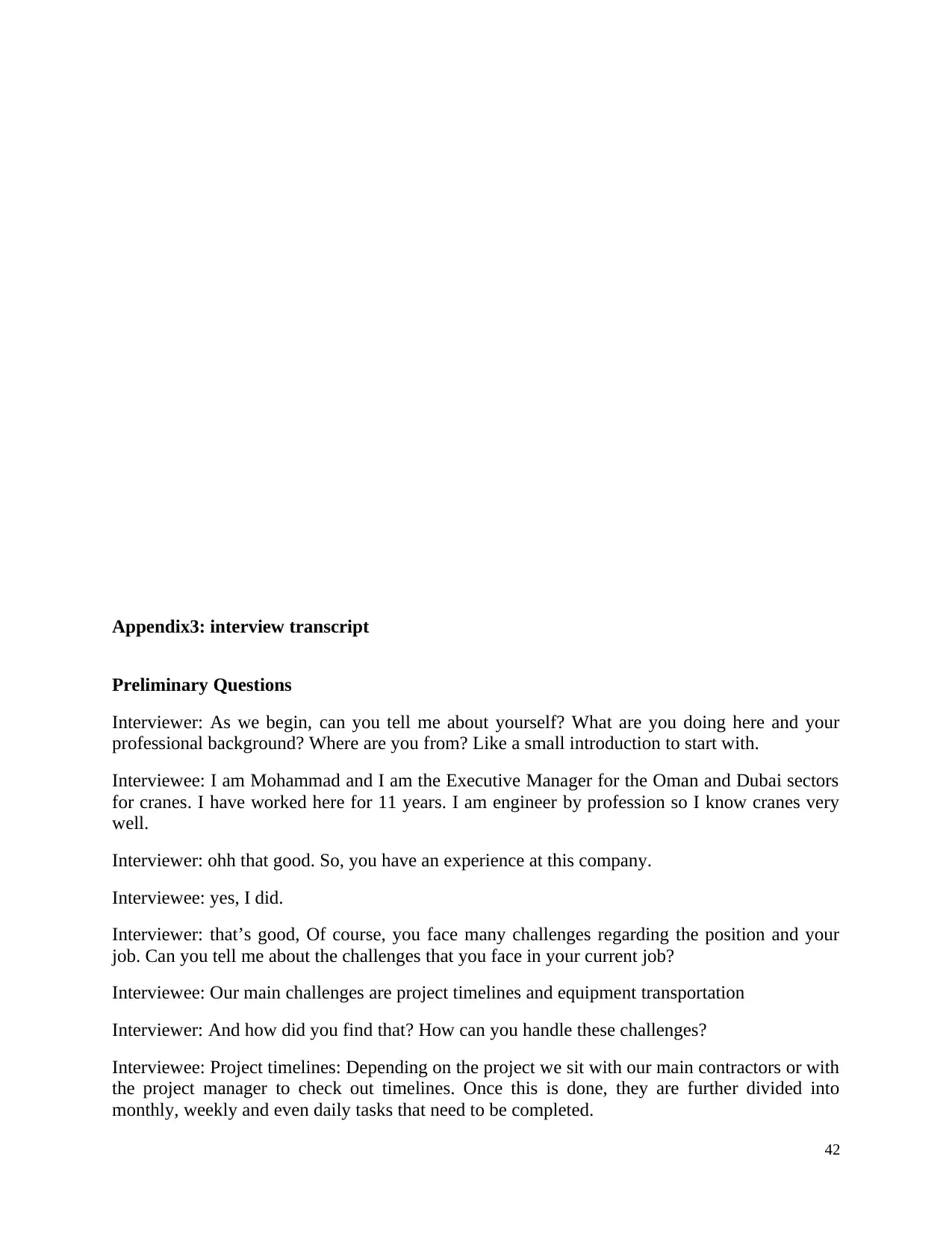
Appendix3: interview transcript
Preliminary Questions
Interviewer: As we begin, can you tell me about yourself? What are you doing here and your
professional background? Where are you from? Like a small introduction to start with.
Interviewee: I am Mohammad and I am the Executive Manager for the Oman and Dubai sectors
for cranes. I have worked here for 11 years. I am engineer by profession so I know cranes very
well.
Interviewer: ohh that good. So, you have an experience at this company.
Interviewee: yes, I did.
Interviewer: that’s good, Of course, you face many challenges regarding the position and your
job. Can you tell me about the challenges that you face in your current job?
Interviewee: Our main challenges are project timelines and equipment transportation
Interviewer: And how did you find that? How can you handle these challenges?
Interviewee: Project timelines: Depending on the project we sit with our main contractors or with
the project manager to check out timelines. Once this is done, they are further divided into
monthly, weekly and even daily tasks that need to be completed.
42
Preliminary Questions
Interviewer: As we begin, can you tell me about yourself? What are you doing here and your
professional background? Where are you from? Like a small introduction to start with.
Interviewee: I am Mohammad and I am the Executive Manager for the Oman and Dubai sectors
for cranes. I have worked here for 11 years. I am engineer by profession so I know cranes very
well.
Interviewer: ohh that good. So, you have an experience at this company.
Interviewee: yes, I did.
Interviewer: that’s good, Of course, you face many challenges regarding the position and your
job. Can you tell me about the challenges that you face in your current job?
Interviewee: Our main challenges are project timelines and equipment transportation
Interviewer: And how did you find that? How can you handle these challenges?
Interviewee: Project timelines: Depending on the project we sit with our main contractors or with
the project manager to check out timelines. Once this is done, they are further divided into
monthly, weekly and even daily tasks that need to be completed.
42
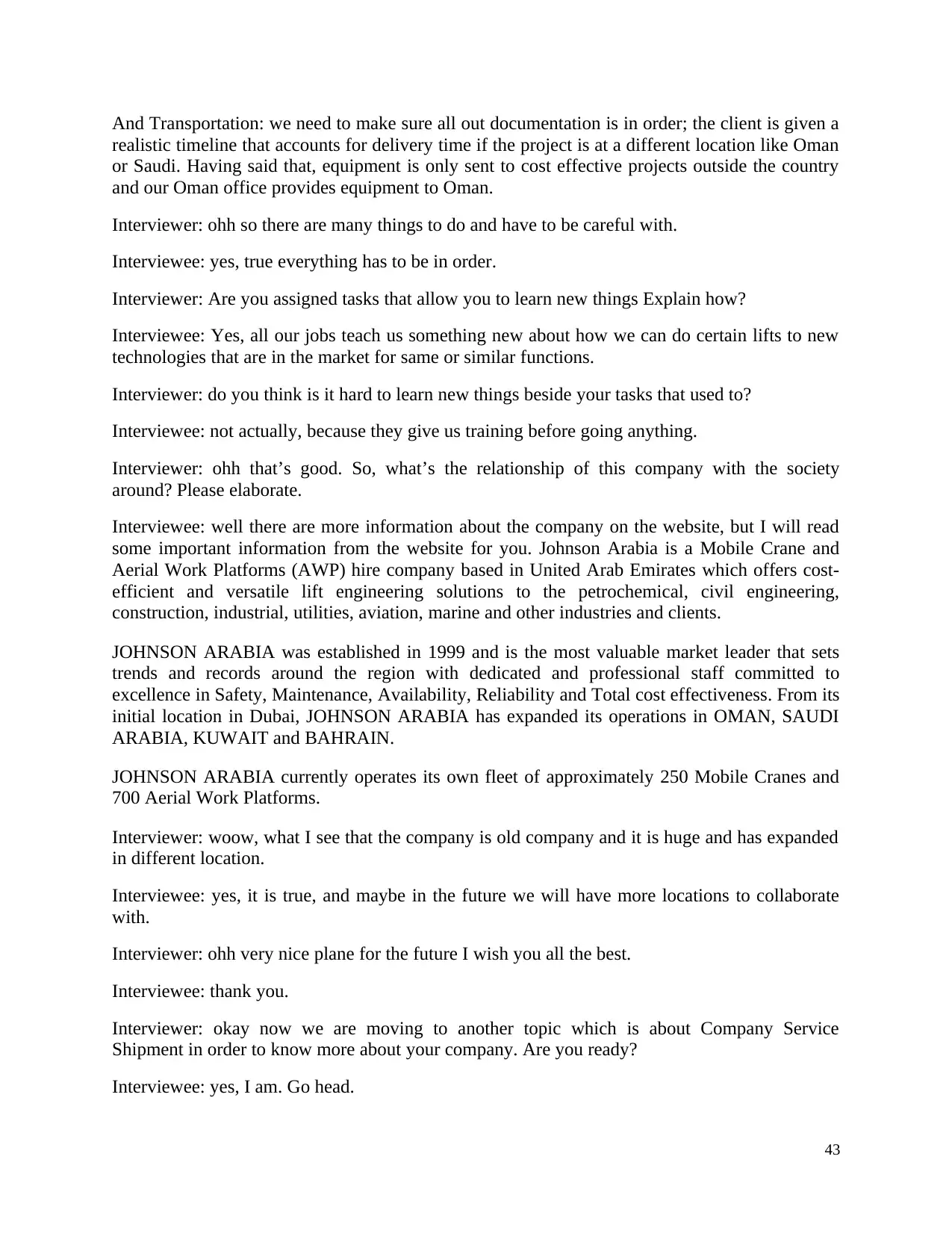
And Transportation: we need to make sure all out documentation is in order; the client is given a
realistic timeline that accounts for delivery time if the project is at a different location like Oman
or Saudi. Having said that, equipment is only sent to cost effective projects outside the country
and our Oman office provides equipment to Oman.
Interviewer: ohh so there are many things to do and have to be careful with.
Interviewee: yes, true everything has to be in order.
Interviewer: Are you assigned tasks that allow you to learn new things Explain how?
Interviewee: Yes, all our jobs teach us something new about how we can do certain lifts to new
technologies that are in the market for same or similar functions.
Interviewer: do you think is it hard to learn new things beside your tasks that used to?
Interviewee: not actually, because they give us training before going anything.
Interviewer: ohh that’s good. So, what’s the relationship of this company with the society
around? Please elaborate.
Interviewee: well there are more information about the company on the website, but I will read
some important information from the website for you. Johnson Arabia is a Mobile Crane and
Aerial Work Platforms (AWP) hire company based in United Arab Emirates which offers cost-
efficient and versatile lift engineering solutions to the petrochemical, civil engineering,
construction, industrial, utilities, aviation, marine and other industries and clients.
JOHNSON ARABIA was established in 1999 and is the most valuable market leader that sets
trends and records around the region with dedicated and professional staff committed to
excellence in Safety, Maintenance, Availability, Reliability and Total cost effectiveness. From its
initial location in Dubai, JOHNSON ARABIA has expanded its operations in OMAN, SAUDI
ARABIA, KUWAIT and BAHRAIN.
JOHNSON ARABIA currently operates its own fleet of approximately 250 Mobile Cranes and
700 Aerial Work Platforms.
Interviewer: woow, what I see that the company is old company and it is huge and has expanded
in different location.
Interviewee: yes, it is true, and maybe in the future we will have more locations to collaborate
with.
Interviewer: ohh very nice plane for the future I wish you all the best.
Interviewee: thank you.
Interviewer: okay now we are moving to another topic which is about Company Service
Shipment in order to know more about your company. Are you ready?
Interviewee: yes, I am. Go head.
43
realistic timeline that accounts for delivery time if the project is at a different location like Oman
or Saudi. Having said that, equipment is only sent to cost effective projects outside the country
and our Oman office provides equipment to Oman.
Interviewer: ohh so there are many things to do and have to be careful with.
Interviewee: yes, true everything has to be in order.
Interviewer: Are you assigned tasks that allow you to learn new things Explain how?
Interviewee: Yes, all our jobs teach us something new about how we can do certain lifts to new
technologies that are in the market for same or similar functions.
Interviewer: do you think is it hard to learn new things beside your tasks that used to?
Interviewee: not actually, because they give us training before going anything.
Interviewer: ohh that’s good. So, what’s the relationship of this company with the society
around? Please elaborate.
Interviewee: well there are more information about the company on the website, but I will read
some important information from the website for you. Johnson Arabia is a Mobile Crane and
Aerial Work Platforms (AWP) hire company based in United Arab Emirates which offers cost-
efficient and versatile lift engineering solutions to the petrochemical, civil engineering,
construction, industrial, utilities, aviation, marine and other industries and clients.
JOHNSON ARABIA was established in 1999 and is the most valuable market leader that sets
trends and records around the region with dedicated and professional staff committed to
excellence in Safety, Maintenance, Availability, Reliability and Total cost effectiveness. From its
initial location in Dubai, JOHNSON ARABIA has expanded its operations in OMAN, SAUDI
ARABIA, KUWAIT and BAHRAIN.
JOHNSON ARABIA currently operates its own fleet of approximately 250 Mobile Cranes and
700 Aerial Work Platforms.
Interviewer: woow, what I see that the company is old company and it is huge and has expanded
in different location.
Interviewee: yes, it is true, and maybe in the future we will have more locations to collaborate
with.
Interviewer: ohh very nice plane for the future I wish you all the best.
Interviewee: thank you.
Interviewer: okay now we are moving to another topic which is about Company Service
Shipment in order to know more about your company. Are you ready?
Interviewee: yes, I am. Go head.
43
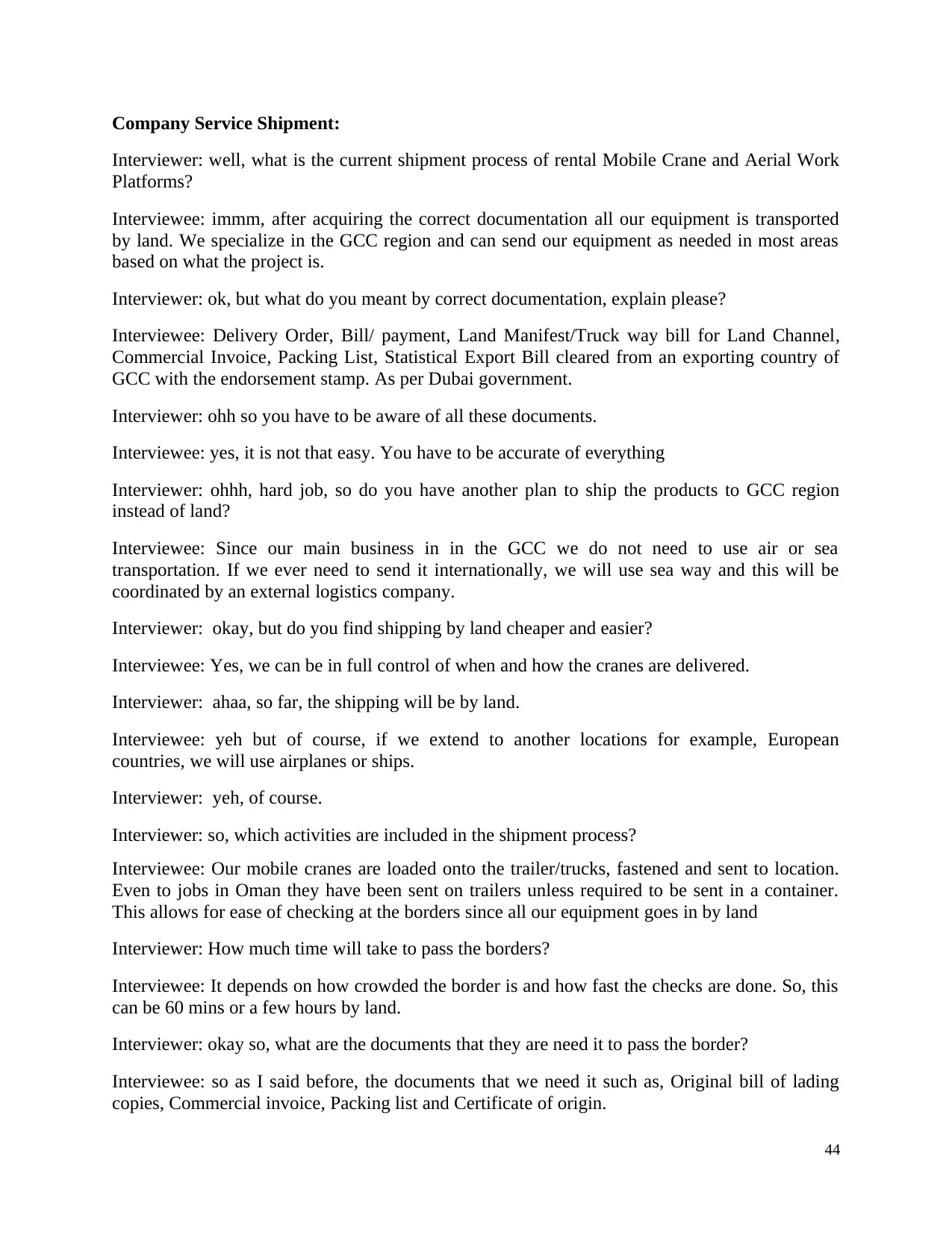
Company Service Shipment:
Interviewer: well, what is the current shipment process of rental Mobile Crane and Aerial Work
Platforms?
Interviewee: immm, after acquiring the correct documentation all our equipment is transported
by land. We specialize in the GCC region and can send our equipment as needed in most areas
based on what the project is.
Interviewer: ok, but what do you meant by correct documentation, explain please?
Interviewee: Delivery Order, Bill/ payment, Land Manifest/Truck way bill for Land Channel,
Commercial Invoice, Packing List, Statistical Export Bill cleared from an exporting country of
GCC with the endorsement stamp. As per Dubai government.
Interviewer: ohh so you have to be aware of all these documents.
Interviewee: yes, it is not that easy. You have to be accurate of everything
Interviewer: ohhh, hard job, so do you have another plan to ship the products to GCC region
instead of land?
Interviewee: Since our main business in in the GCC we do not need to use air or sea
transportation. If we ever need to send it internationally, we will use sea way and this will be
coordinated by an external logistics company.
Interviewer: okay, but do you find shipping by land cheaper and easier?
Interviewee: Yes, we can be in full control of when and how the cranes are delivered.
Interviewer: ahaa, so far, the shipping will be by land.
Interviewee: yeh but of course, if we extend to another locations for example, European
countries, we will use airplanes or ships.
Interviewer: yeh, of course.
Interviewer: so, which activities are included in the shipment process?
Interviewee: Our mobile cranes are loaded onto the trailer/trucks, fastened and sent to location.
Even to jobs in Oman they have been sent on trailers unless required to be sent in a container.
This allows for ease of checking at the borders since all our equipment goes in by land
Interviewer: How much time will take to pass the borders?
Interviewee: It depends on how crowded the border is and how fast the checks are done. So, this
can be 60 mins or a few hours by land.
Interviewer: okay so, what are the documents that they are need it to pass the border?
Interviewee: so as I said before, the documents that we need it such as, Original bill of lading
copies, Commercial invoice, Packing list and Certificate of origin.
44
Interviewer: well, what is the current shipment process of rental Mobile Crane and Aerial Work
Platforms?
Interviewee: immm, after acquiring the correct documentation all our equipment is transported
by land. We specialize in the GCC region and can send our equipment as needed in most areas
based on what the project is.
Interviewer: ok, but what do you meant by correct documentation, explain please?
Interviewee: Delivery Order, Bill/ payment, Land Manifest/Truck way bill for Land Channel,
Commercial Invoice, Packing List, Statistical Export Bill cleared from an exporting country of
GCC with the endorsement stamp. As per Dubai government.
Interviewer: ohh so you have to be aware of all these documents.
Interviewee: yes, it is not that easy. You have to be accurate of everything
Interviewer: ohhh, hard job, so do you have another plan to ship the products to GCC region
instead of land?
Interviewee: Since our main business in in the GCC we do not need to use air or sea
transportation. If we ever need to send it internationally, we will use sea way and this will be
coordinated by an external logistics company.
Interviewer: okay, but do you find shipping by land cheaper and easier?
Interviewee: Yes, we can be in full control of when and how the cranes are delivered.
Interviewer: ahaa, so far, the shipping will be by land.
Interviewee: yeh but of course, if we extend to another locations for example, European
countries, we will use airplanes or ships.
Interviewer: yeh, of course.
Interviewer: so, which activities are included in the shipment process?
Interviewee: Our mobile cranes are loaded onto the trailer/trucks, fastened and sent to location.
Even to jobs in Oman they have been sent on trailers unless required to be sent in a container.
This allows for ease of checking at the borders since all our equipment goes in by land
Interviewer: How much time will take to pass the borders?
Interviewee: It depends on how crowded the border is and how fast the checks are done. So, this
can be 60 mins or a few hours by land.
Interviewer: okay so, what are the documents that they are need it to pass the border?
Interviewee: so as I said before, the documents that we need it such as, Original bill of lading
copies, Commercial invoice, Packing list and Certificate of origin.
44
Paraphrase This Document
Need a fresh take? Get an instant paraphrase of this document with our AI Paraphraser
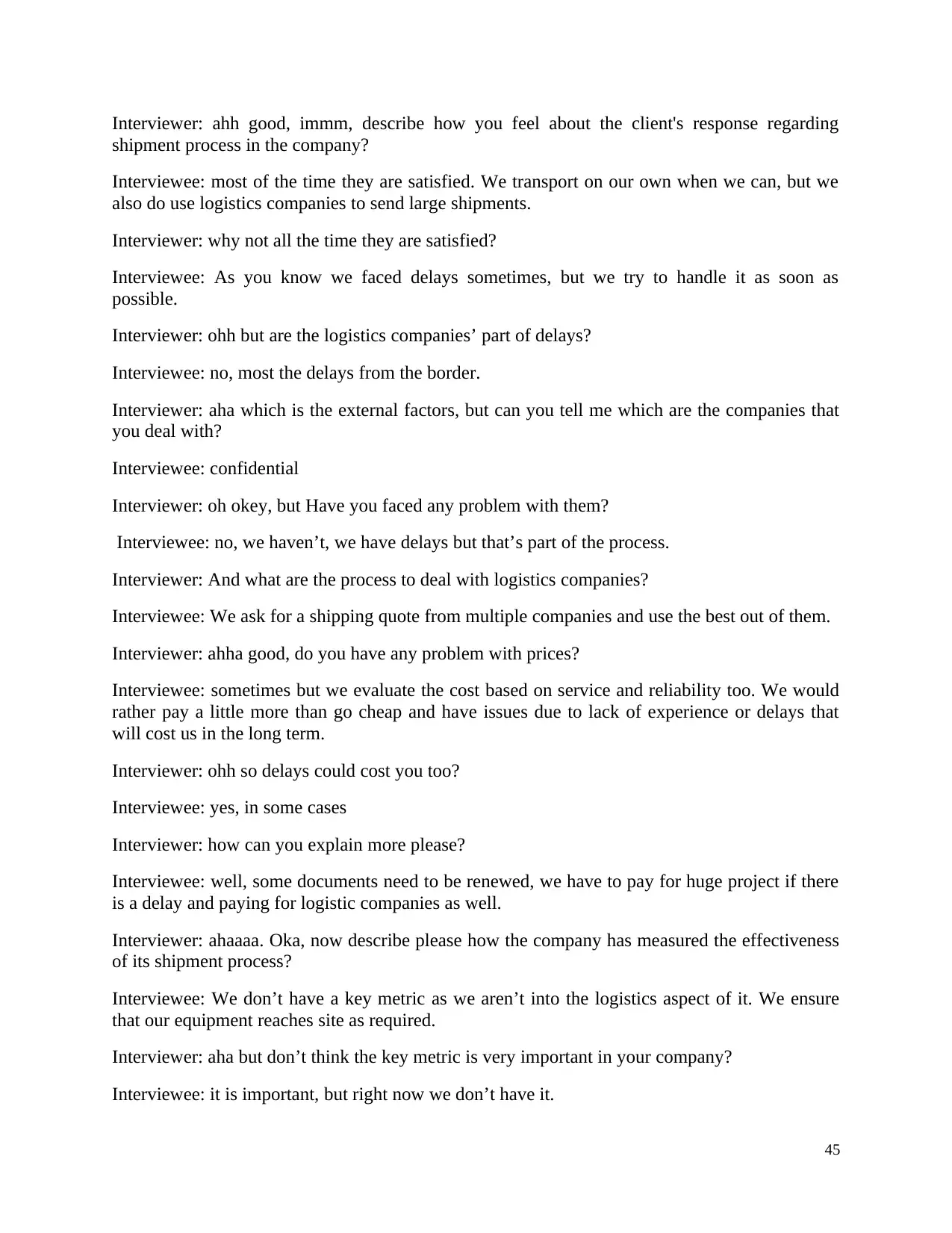
Interviewer: ahh good, immm, describe how you feel about the client's response regarding
shipment process in the company?
Interviewee: most of the time they are satisfied. We transport on our own when we can, but we
also do use logistics companies to send large shipments.
Interviewer: why not all the time they are satisfied?
Interviewee: As you know we faced delays sometimes, but we try to handle it as soon as
possible.
Interviewer: ohh but are the logistics companies’ part of delays?
Interviewee: no, most the delays from the border.
Interviewer: aha which is the external factors, but can you tell me which are the companies that
you deal with?
Interviewee: confidential
Interviewer: oh okey, but Have you faced any problem with them?
Interviewee: no, we haven’t, we have delays but that’s part of the process.
Interviewer: And what are the process to deal with logistics companies?
Interviewee: We ask for a shipping quote from multiple companies and use the best out of them.
Interviewer: ahha good, do you have any problem with prices?
Interviewee: sometimes but we evaluate the cost based on service and reliability too. We would
rather pay a little more than go cheap and have issues due to lack of experience or delays that
will cost us in the long term.
Interviewer: ohh so delays could cost you too?
Interviewee: yes, in some cases
Interviewer: how can you explain more please?
Interviewee: well, some documents need to be renewed, we have to pay for huge project if there
is a delay and paying for logistic companies as well.
Interviewer: ahaaaa. Oka, now describe please how the company has measured the effectiveness
of its shipment process?
Interviewee: We don’t have a key metric as we aren’t into the logistics aspect of it. We ensure
that our equipment reaches site as required.
Interviewer: aha but don’t think the key metric is very important in your company?
Interviewee: it is important, but right now we don’t have it.
45
shipment process in the company?
Interviewee: most of the time they are satisfied. We transport on our own when we can, but we
also do use logistics companies to send large shipments.
Interviewer: why not all the time they are satisfied?
Interviewee: As you know we faced delays sometimes, but we try to handle it as soon as
possible.
Interviewer: ohh but are the logistics companies’ part of delays?
Interviewee: no, most the delays from the border.
Interviewer: aha which is the external factors, but can you tell me which are the companies that
you deal with?
Interviewee: confidential
Interviewer: oh okey, but Have you faced any problem with them?
Interviewee: no, we haven’t, we have delays but that’s part of the process.
Interviewer: And what are the process to deal with logistics companies?
Interviewee: We ask for a shipping quote from multiple companies and use the best out of them.
Interviewer: ahha good, do you have any problem with prices?
Interviewee: sometimes but we evaluate the cost based on service and reliability too. We would
rather pay a little more than go cheap and have issues due to lack of experience or delays that
will cost us in the long term.
Interviewer: ohh so delays could cost you too?
Interviewee: yes, in some cases
Interviewer: how can you explain more please?
Interviewee: well, some documents need to be renewed, we have to pay for huge project if there
is a delay and paying for logistic companies as well.
Interviewer: ahaaaa. Oka, now describe please how the company has measured the effectiveness
of its shipment process?
Interviewee: We don’t have a key metric as we aren’t into the logistics aspect of it. We ensure
that our equipment reaches site as required.
Interviewer: aha but don’t think the key metric is very important in your company?
Interviewee: it is important, but right now we don’t have it.
45
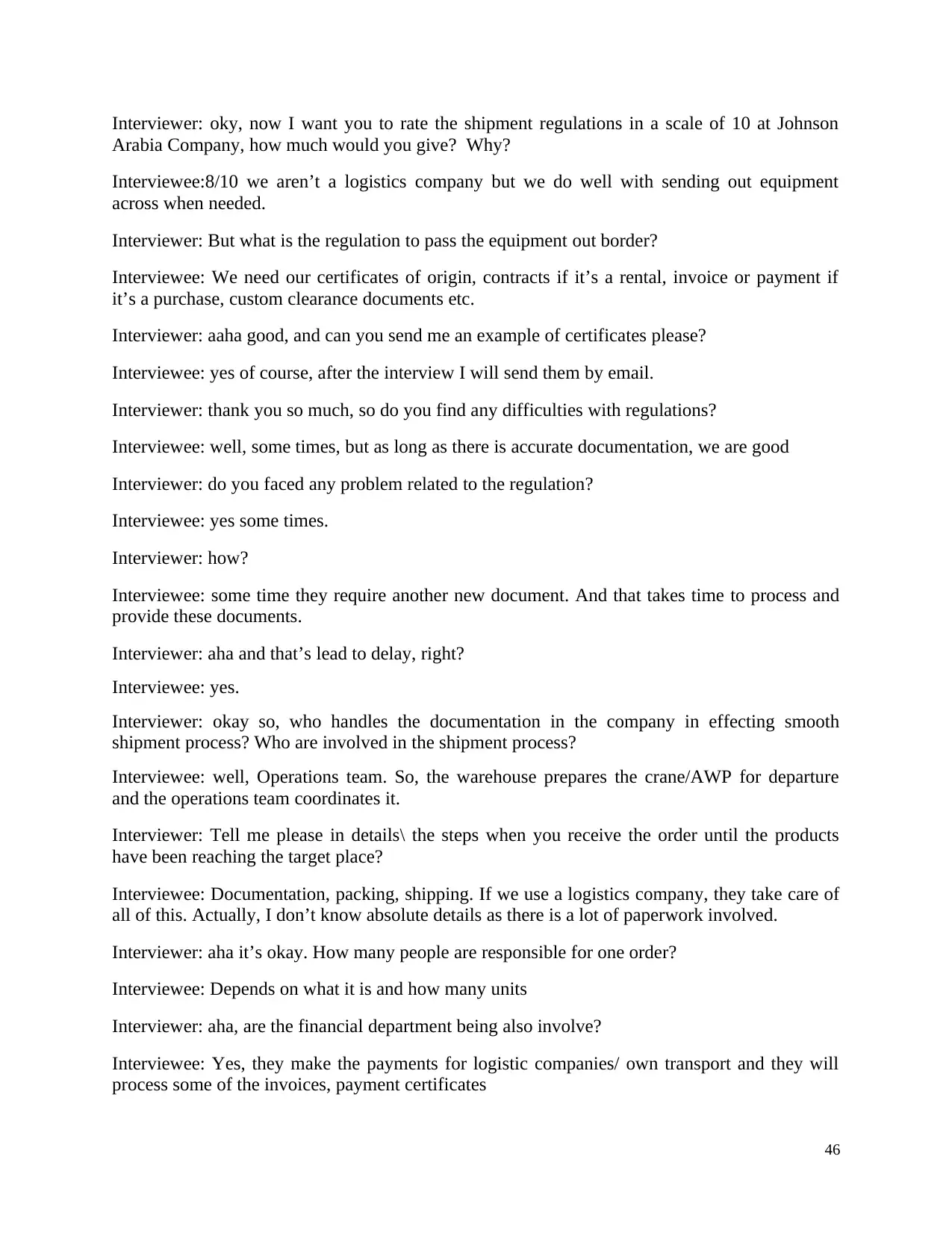
Interviewer: oky, now I want you to rate the shipment regulations in a scale of 10 at Johnson
Arabia Company, how much would you give? Why?
Interviewee:8/10 we aren’t a logistics company but we do well with sending out equipment
across when needed.
Interviewer: But what is the regulation to pass the equipment out border?
Interviewee: We need our certificates of origin, contracts if it’s a rental, invoice or payment if
it’s a purchase, custom clearance documents etc.
Interviewer: aaha good, and can you send me an example of certificates please?
Interviewee: yes of course, after the interview I will send them by email.
Interviewer: thank you so much, so do you find any difficulties with regulations?
Interviewee: well, some times, but as long as there is accurate documentation, we are good
Interviewer: do you faced any problem related to the regulation?
Interviewee: yes some times.
Interviewer: how?
Interviewee: some time they require another new document. And that takes time to process and
provide these documents.
Interviewer: aha and that’s lead to delay, right?
Interviewee: yes.
Interviewer: okay so, who handles the documentation in the company in effecting smooth
shipment process? Who are involved in the shipment process?
Interviewee: well, Operations team. So, the warehouse prepares the crane/AWP for departure
and the operations team coordinates it.
Interviewer: Tell me please in details\ the steps when you receive the order until the products
have been reaching the target place?
Interviewee: Documentation, packing, shipping. If we use a logistics company, they take care of
all of this. Actually, I don’t know absolute details as there is a lot of paperwork involved.
Interviewer: aha it’s okay. How many people are responsible for one order?
Interviewee: Depends on what it is and how many units
Interviewer: aha, are the financial department being also involve?
Interviewee: Yes, they make the payments for logistic companies/ own transport and they will
process some of the invoices, payment certificates
46
Arabia Company, how much would you give? Why?
Interviewee:8/10 we aren’t a logistics company but we do well with sending out equipment
across when needed.
Interviewer: But what is the regulation to pass the equipment out border?
Interviewee: We need our certificates of origin, contracts if it’s a rental, invoice or payment if
it’s a purchase, custom clearance documents etc.
Interviewer: aaha good, and can you send me an example of certificates please?
Interviewee: yes of course, after the interview I will send them by email.
Interviewer: thank you so much, so do you find any difficulties with regulations?
Interviewee: well, some times, but as long as there is accurate documentation, we are good
Interviewer: do you faced any problem related to the regulation?
Interviewee: yes some times.
Interviewer: how?
Interviewee: some time they require another new document. And that takes time to process and
provide these documents.
Interviewer: aha and that’s lead to delay, right?
Interviewee: yes.
Interviewer: okay so, who handles the documentation in the company in effecting smooth
shipment process? Who are involved in the shipment process?
Interviewee: well, Operations team. So, the warehouse prepares the crane/AWP for departure
and the operations team coordinates it.
Interviewer: Tell me please in details\ the steps when you receive the order until the products
have been reaching the target place?
Interviewee: Documentation, packing, shipping. If we use a logistics company, they take care of
all of this. Actually, I don’t know absolute details as there is a lot of paperwork involved.
Interviewer: aha it’s okay. How many people are responsible for one order?
Interviewee: Depends on what it is and how many units
Interviewer: aha, are the financial department being also involve?
Interviewee: Yes, they make the payments for logistic companies/ own transport and they will
process some of the invoices, payment certificates
46
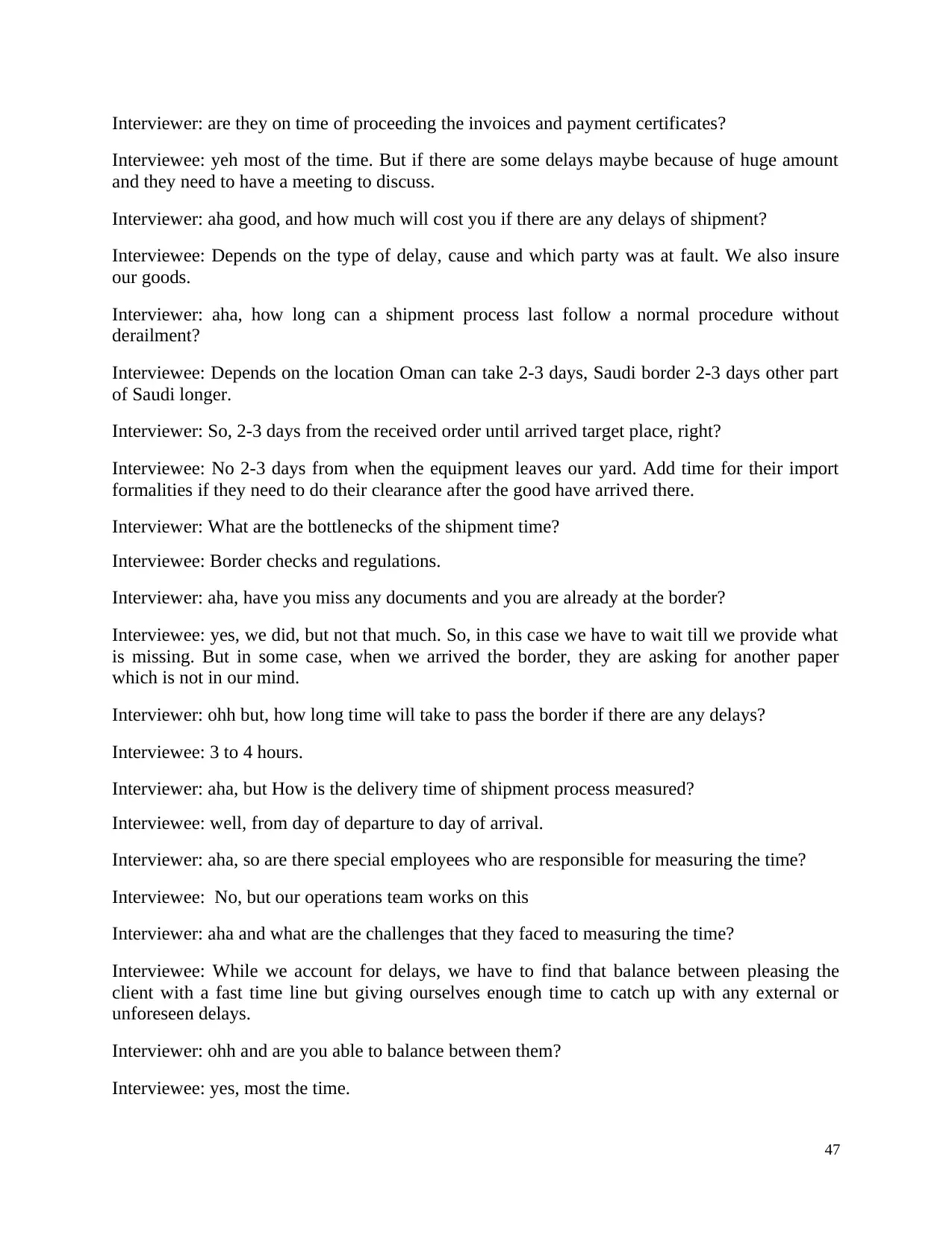
Interviewer: are they on time of proceeding the invoices and payment certificates?
Interviewee: yeh most of the time. But if there are some delays maybe because of huge amount
and they need to have a meeting to discuss.
Interviewer: aha good, and how much will cost you if there are any delays of shipment?
Interviewee: Depends on the type of delay, cause and which party was at fault. We also insure
our goods.
Interviewer: aha, how long can a shipment process last follow a normal procedure without
derailment?
Interviewee: Depends on the location Oman can take 2-3 days, Saudi border 2-3 days other part
of Saudi longer.
Interviewer: So, 2-3 days from the received order until arrived target place, right?
Interviewee: No 2-3 days from when the equipment leaves our yard. Add time for their import
formalities if they need to do their clearance after the good have arrived there.
Interviewer: What are the bottlenecks of the shipment time?
Interviewee: Border checks and regulations.
Interviewer: aha, have you miss any documents and you are already at the border?
Interviewee: yes, we did, but not that much. So, in this case we have to wait till we provide what
is missing. But in some case, when we arrived the border, they are asking for another paper
which is not in our mind.
Interviewer: ohh but, how long time will take to pass the border if there are any delays?
Interviewee: 3 to 4 hours.
Interviewer: aha, but How is the delivery time of shipment process measured?
Interviewee: well, from day of departure to day of arrival.
Interviewer: aha, so are there special employees who are responsible for measuring the time?
Interviewee: No, but our operations team works on this
Interviewer: aha and what are the challenges that they faced to measuring the time?
Interviewee: While we account for delays, we have to find that balance between pleasing the
client with a fast time line but giving ourselves enough time to catch up with any external or
unforeseen delays.
Interviewer: ohh and are you able to balance between them?
Interviewee: yes, most the time.
47
Interviewee: yeh most of the time. But if there are some delays maybe because of huge amount
and they need to have a meeting to discuss.
Interviewer: aha good, and how much will cost you if there are any delays of shipment?
Interviewee: Depends on the type of delay, cause and which party was at fault. We also insure
our goods.
Interviewer: aha, how long can a shipment process last follow a normal procedure without
derailment?
Interviewee: Depends on the location Oman can take 2-3 days, Saudi border 2-3 days other part
of Saudi longer.
Interviewer: So, 2-3 days from the received order until arrived target place, right?
Interviewee: No 2-3 days from when the equipment leaves our yard. Add time for their import
formalities if they need to do their clearance after the good have arrived there.
Interviewer: What are the bottlenecks of the shipment time?
Interviewee: Border checks and regulations.
Interviewer: aha, have you miss any documents and you are already at the border?
Interviewee: yes, we did, but not that much. So, in this case we have to wait till we provide what
is missing. But in some case, when we arrived the border, they are asking for another paper
which is not in our mind.
Interviewer: ohh but, how long time will take to pass the border if there are any delays?
Interviewee: 3 to 4 hours.
Interviewer: aha, but How is the delivery time of shipment process measured?
Interviewee: well, from day of departure to day of arrival.
Interviewer: aha, so are there special employees who are responsible for measuring the time?
Interviewee: No, but our operations team works on this
Interviewer: aha and what are the challenges that they faced to measuring the time?
Interviewee: While we account for delays, we have to find that balance between pleasing the
client with a fast time line but giving ourselves enough time to catch up with any external or
unforeseen delays.
Interviewer: ohh and are you able to balance between them?
Interviewee: yes, most the time.
47
Secure Best Marks with AI Grader
Need help grading? Try our AI Grader for instant feedback on your assignments.
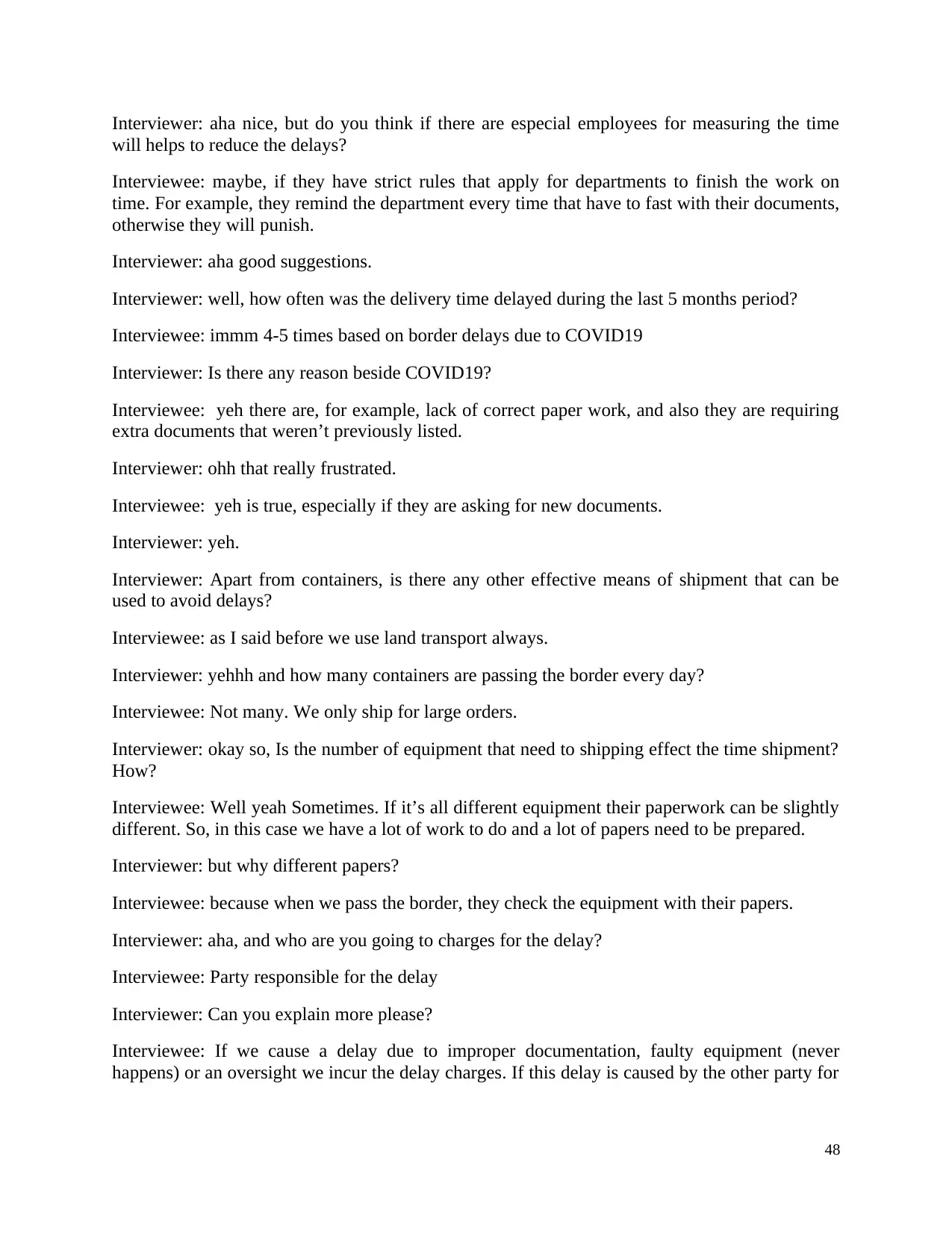
Interviewer: aha nice, but do you think if there are especial employees for measuring the time
will helps to reduce the delays?
Interviewee: maybe, if they have strict rules that apply for departments to finish the work on
time. For example, they remind the department every time that have to fast with their documents,
otherwise they will punish.
Interviewer: aha good suggestions.
Interviewer: well, how often was the delivery time delayed during the last 5 months period?
Interviewee: immm 4-5 times based on border delays due to COVID19
Interviewer: Is there any reason beside COVID19?
Interviewee: yeh there are, for example, lack of correct paper work, and also they are requiring
extra documents that weren’t previously listed.
Interviewer: ohh that really frustrated.
Interviewee: yeh is true, especially if they are asking for new documents.
Interviewer: yeh.
Interviewer: Apart from containers, is there any other effective means of shipment that can be
used to avoid delays?
Interviewee: as I said before we use land transport always.
Interviewer: yehhh and how many containers are passing the border every day?
Interviewee: Not many. We only ship for large orders.
Interviewer: okay so, Is the number of equipment that need to shipping effect the time shipment?
How?
Interviewee: Well yeah Sometimes. If it’s all different equipment their paperwork can be slightly
different. So, in this case we have a lot of work to do and a lot of papers need to be prepared.
Interviewer: but why different papers?
Interviewee: because when we pass the border, they check the equipment with their papers.
Interviewer: aha, and who are you going to charges for the delay?
Interviewee: Party responsible for the delay
Interviewer: Can you explain more please?
Interviewee: If we cause a delay due to improper documentation, faulty equipment (never
happens) or an oversight we incur the delay charges. If this delay is caused by the other party for
48
will helps to reduce the delays?
Interviewee: maybe, if they have strict rules that apply for departments to finish the work on
time. For example, they remind the department every time that have to fast with their documents,
otherwise they will punish.
Interviewer: aha good suggestions.
Interviewer: well, how often was the delivery time delayed during the last 5 months period?
Interviewee: immm 4-5 times based on border delays due to COVID19
Interviewer: Is there any reason beside COVID19?
Interviewee: yeh there are, for example, lack of correct paper work, and also they are requiring
extra documents that weren’t previously listed.
Interviewer: ohh that really frustrated.
Interviewee: yeh is true, especially if they are asking for new documents.
Interviewer: yeh.
Interviewer: Apart from containers, is there any other effective means of shipment that can be
used to avoid delays?
Interviewee: as I said before we use land transport always.
Interviewer: yehhh and how many containers are passing the border every day?
Interviewee: Not many. We only ship for large orders.
Interviewer: okay so, Is the number of equipment that need to shipping effect the time shipment?
How?
Interviewee: Well yeah Sometimes. If it’s all different equipment their paperwork can be slightly
different. So, in this case we have a lot of work to do and a lot of papers need to be prepared.
Interviewer: but why different papers?
Interviewee: because when we pass the border, they check the equipment with their papers.
Interviewer: aha, and who are you going to charges for the delay?
Interviewee: Party responsible for the delay
Interviewer: Can you explain more please?
Interviewee: If we cause a delay due to improper documentation, faulty equipment (never
happens) or an oversight we incur the delay charges. If this delay is caused by the other party for
48
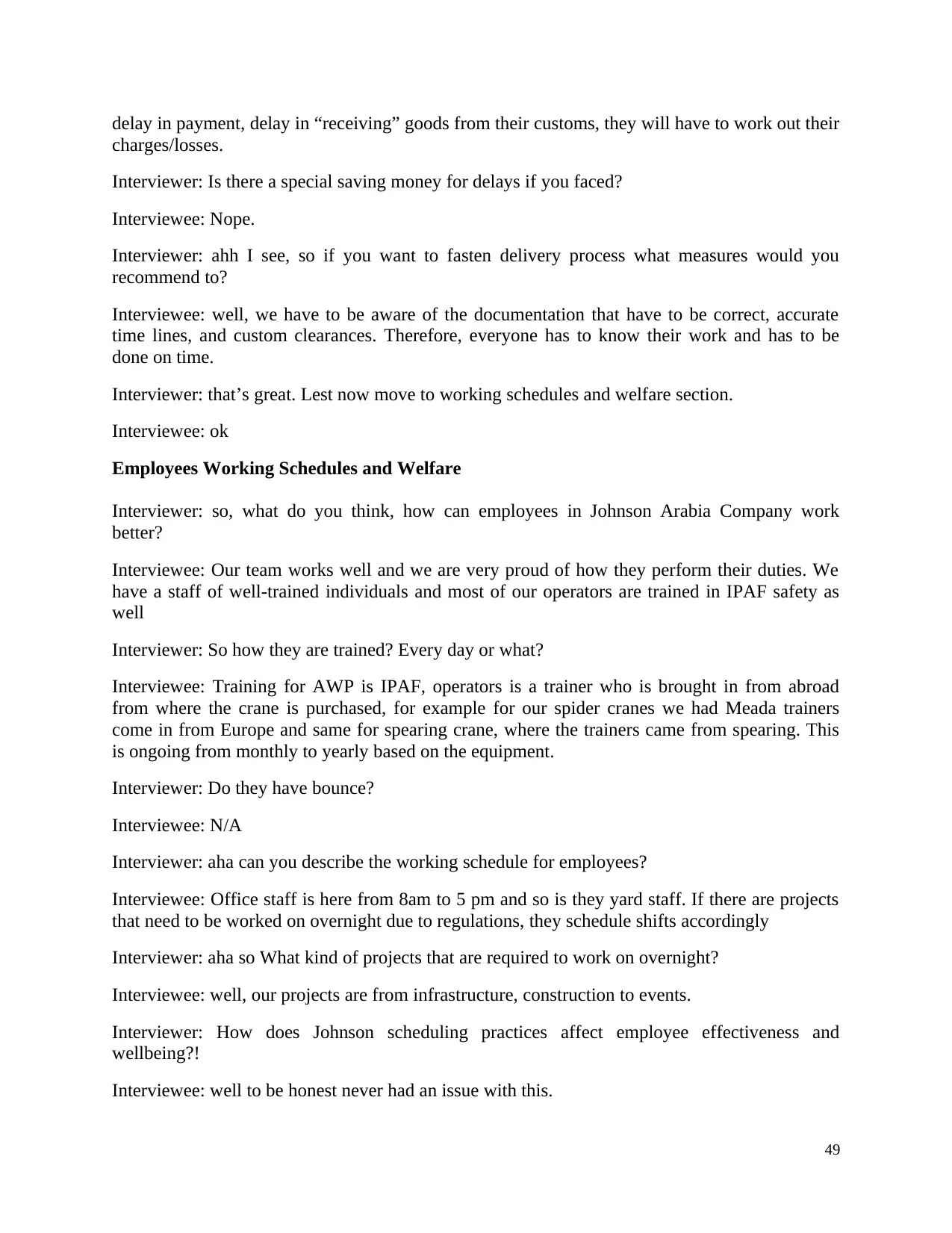
delay in payment, delay in “receiving” goods from their customs, they will have to work out their
charges/losses.
Interviewer: Is there a special saving money for delays if you faced?
Interviewee: Nope.
Interviewer: ahh I see, so if you want to fasten delivery process what measures would you
recommend to?
Interviewee: well, we have to be aware of the documentation that have to be correct, accurate
time lines, and custom clearances. Therefore, everyone has to know their work and has to be
done on time.
Interviewer: that’s great. Lest now move to working schedules and welfare section.
Interviewee: ok
Employees Working Schedules and Welfare
Interviewer: so, what do you think, how can employees in Johnson Arabia Company work
better?
Interviewee: Our team works well and we are very proud of how they perform their duties. We
have a staff of well-trained individuals and most of our operators are trained in IPAF safety as
well
Interviewer: So how they are trained? Every day or what?
Interviewee: Training for AWP is IPAF, operators is a trainer who is brought in from abroad
from where the crane is purchased, for example for our spider cranes we had Meada trainers
come in from Europe and same for spearing crane, where the trainers came from spearing. This
is ongoing from monthly to yearly based on the equipment.
Interviewer: Do they have bounce?
Interviewee: N/A
Interviewer: aha can you describe the working schedule for employees?
Interviewee: Office staff is here from 8am to 5 pm and so is they yard staff. If there are projects
that need to be worked on overnight due to regulations, they schedule shifts accordingly
Interviewer: aha so What kind of projects that are required to work on overnight?
Interviewee: well, our projects are from infrastructure, construction to events.
Interviewer: How does Johnson scheduling practices affect employee effectiveness and
wellbeing?!
Interviewee: well to be honest never had an issue with this.
49
charges/losses.
Interviewer: Is there a special saving money for delays if you faced?
Interviewee: Nope.
Interviewer: ahh I see, so if you want to fasten delivery process what measures would you
recommend to?
Interviewee: well, we have to be aware of the documentation that have to be correct, accurate
time lines, and custom clearances. Therefore, everyone has to know their work and has to be
done on time.
Interviewer: that’s great. Lest now move to working schedules and welfare section.
Interviewee: ok
Employees Working Schedules and Welfare
Interviewer: so, what do you think, how can employees in Johnson Arabia Company work
better?
Interviewee: Our team works well and we are very proud of how they perform their duties. We
have a staff of well-trained individuals and most of our operators are trained in IPAF safety as
well
Interviewer: So how they are trained? Every day or what?
Interviewee: Training for AWP is IPAF, operators is a trainer who is brought in from abroad
from where the crane is purchased, for example for our spider cranes we had Meada trainers
come in from Europe and same for spearing crane, where the trainers came from spearing. This
is ongoing from monthly to yearly based on the equipment.
Interviewer: Do they have bounce?
Interviewee: N/A
Interviewer: aha can you describe the working schedule for employees?
Interviewee: Office staff is here from 8am to 5 pm and so is they yard staff. If there are projects
that need to be worked on overnight due to regulations, they schedule shifts accordingly
Interviewer: aha so What kind of projects that are required to work on overnight?
Interviewee: well, our projects are from infrastructure, construction to events.
Interviewer: How does Johnson scheduling practices affect employee effectiveness and
wellbeing?!
Interviewee: well to be honest never had an issue with this.
49
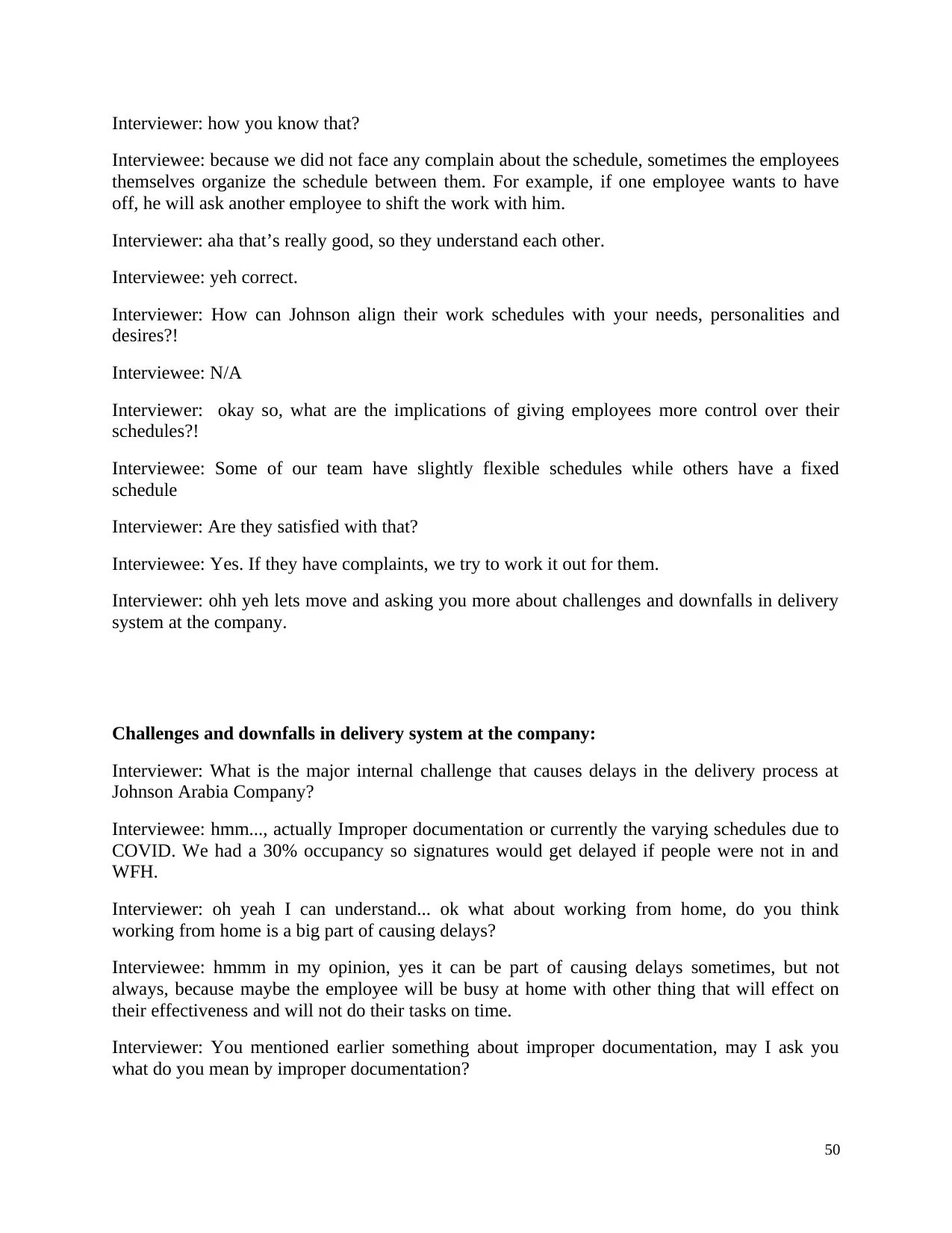
Interviewer: how you know that?
Interviewee: because we did not face any complain about the schedule, sometimes the employees
themselves organize the schedule between them. For example, if one employee wants to have
off, he will ask another employee to shift the work with him.
Interviewer: aha that’s really good, so they understand each other.
Interviewee: yeh correct.
Interviewer: How can Johnson align their work schedules with your needs, personalities and
desires?!
Interviewee: N/A
Interviewer: okay so, what are the implications of giving employees more control over their
schedules?!
Interviewee: Some of our team have slightly flexible schedules while others have a fixed
schedule
Interviewer: Are they satisfied with that?
Interviewee: Yes. If they have complaints, we try to work it out for them.
Interviewer: ohh yeh lets move and asking you more about challenges and downfalls in delivery
system at the company.
Challenges and downfalls in delivery system at the company:
Interviewer: What is the major internal challenge that causes delays in the delivery process at
Johnson Arabia Company?
Interviewee: hmm..., actually Improper documentation or currently the varying schedules due to
COVID. We had a 30% occupancy so signatures would get delayed if people were not in and
WFH.
Interviewer: oh yeah I can understand... ok what about working from home, do you think
working from home is a big part of causing delays?
Interviewee: hmmm in my opinion, yes it can be part of causing delays sometimes, but not
always, because maybe the employee will be busy at home with other thing that will effect on
their effectiveness and will not do their tasks on time.
Interviewer: You mentioned earlier something about improper documentation, may I ask you
what do you mean by improper documentation?
50
Interviewee: because we did not face any complain about the schedule, sometimes the employees
themselves organize the schedule between them. For example, if one employee wants to have
off, he will ask another employee to shift the work with him.
Interviewer: aha that’s really good, so they understand each other.
Interviewee: yeh correct.
Interviewer: How can Johnson align their work schedules with your needs, personalities and
desires?!
Interviewee: N/A
Interviewer: okay so, what are the implications of giving employees more control over their
schedules?!
Interviewee: Some of our team have slightly flexible schedules while others have a fixed
schedule
Interviewer: Are they satisfied with that?
Interviewee: Yes. If they have complaints, we try to work it out for them.
Interviewer: ohh yeh lets move and asking you more about challenges and downfalls in delivery
system at the company.
Challenges and downfalls in delivery system at the company:
Interviewer: What is the major internal challenge that causes delays in the delivery process at
Johnson Arabia Company?
Interviewee: hmm..., actually Improper documentation or currently the varying schedules due to
COVID. We had a 30% occupancy so signatures would get delayed if people were not in and
WFH.
Interviewer: oh yeah I can understand... ok what about working from home, do you think
working from home is a big part of causing delays?
Interviewee: hmmm in my opinion, yes it can be part of causing delays sometimes, but not
always, because maybe the employee will be busy at home with other thing that will effect on
their effectiveness and will not do their tasks on time.
Interviewer: You mentioned earlier something about improper documentation, may I ask you
what do you mean by improper documentation?
50
Paraphrase This Document
Need a fresh take? Get an instant paraphrase of this document with our AI Paraphraser
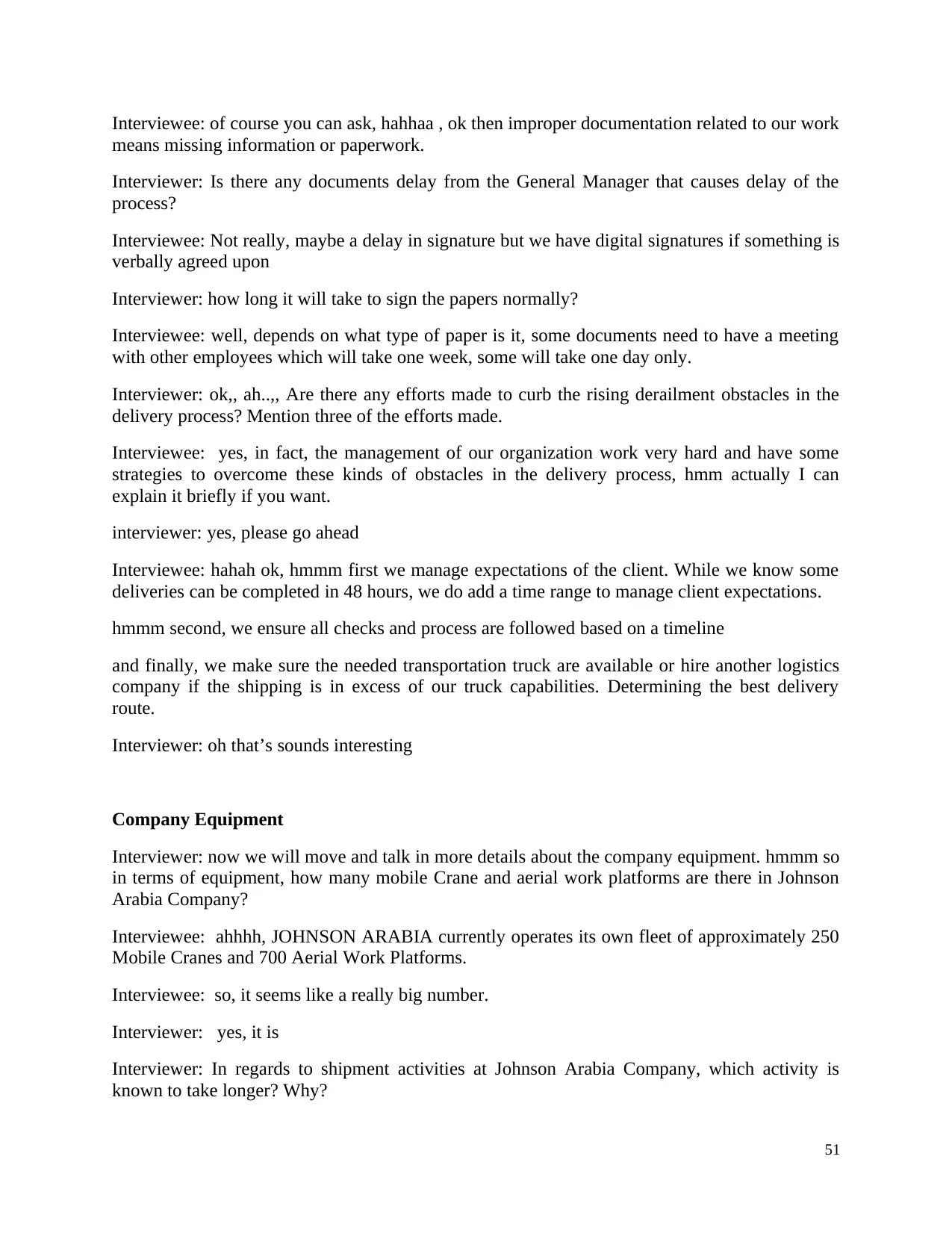
Interviewee: of course you can ask, hahhaa , ok then improper documentation related to our work
means missing information or paperwork.
Interviewer: Is there any documents delay from the General Manager that causes delay of the
process?
Interviewee: Not really, maybe a delay in signature but we have digital signatures if something is
verbally agreed upon
Interviewer: how long it will take to sign the papers normally?
Interviewee: well, depends on what type of paper is it, some documents need to have a meeting
with other employees which will take one week, some will take one day only.
Interviewer: ok,, ah..,, Are there any efforts made to curb the rising derailment obstacles in the
delivery process? Mention three of the efforts made.
Interviewee: yes, in fact, the management of our organization work very hard and have some
strategies to overcome these kinds of obstacles in the delivery process, hmm actually I can
explain it briefly if you want.
interviewer: yes, please go ahead
Interviewee: hahah ok, hmmm first we manage expectations of the client. While we know some
deliveries can be completed in 48 hours, we do add a time range to manage client expectations.
hmmm second, we ensure all checks and process are followed based on a timeline
and finally, we make sure the needed transportation truck are available or hire another logistics
company if the shipping is in excess of our truck capabilities. Determining the best delivery
route.
Interviewer: oh that’s sounds interesting
Company Equipment
Interviewer: now we will move and talk in more details about the company equipment. hmmm so
in terms of equipment, how many mobile Crane and aerial work platforms are there in Johnson
Arabia Company?
Interviewee: ahhhh, JOHNSON ARABIA currently operates its own fleet of approximately 250
Mobile Cranes and 700 Aerial Work Platforms.
Interviewee: so, it seems like a really big number.
Interviewer: yes, it is
Interviewer: In regards to shipment activities at Johnson Arabia Company, which activity is
known to take longer? Why?
51
means missing information or paperwork.
Interviewer: Is there any documents delay from the General Manager that causes delay of the
process?
Interviewee: Not really, maybe a delay in signature but we have digital signatures if something is
verbally agreed upon
Interviewer: how long it will take to sign the papers normally?
Interviewee: well, depends on what type of paper is it, some documents need to have a meeting
with other employees which will take one week, some will take one day only.
Interviewer: ok,, ah..,, Are there any efforts made to curb the rising derailment obstacles in the
delivery process? Mention three of the efforts made.
Interviewee: yes, in fact, the management of our organization work very hard and have some
strategies to overcome these kinds of obstacles in the delivery process, hmm actually I can
explain it briefly if you want.
interviewer: yes, please go ahead
Interviewee: hahah ok, hmmm first we manage expectations of the client. While we know some
deliveries can be completed in 48 hours, we do add a time range to manage client expectations.
hmmm second, we ensure all checks and process are followed based on a timeline
and finally, we make sure the needed transportation truck are available or hire another logistics
company if the shipping is in excess of our truck capabilities. Determining the best delivery
route.
Interviewer: oh that’s sounds interesting
Company Equipment
Interviewer: now we will move and talk in more details about the company equipment. hmmm so
in terms of equipment, how many mobile Crane and aerial work platforms are there in Johnson
Arabia Company?
Interviewee: ahhhh, JOHNSON ARABIA currently operates its own fleet of approximately 250
Mobile Cranes and 700 Aerial Work Platforms.
Interviewee: so, it seems like a really big number.
Interviewer: yes, it is
Interviewer: In regards to shipment activities at Johnson Arabia Company, which activity is
known to take longer? Why?
51
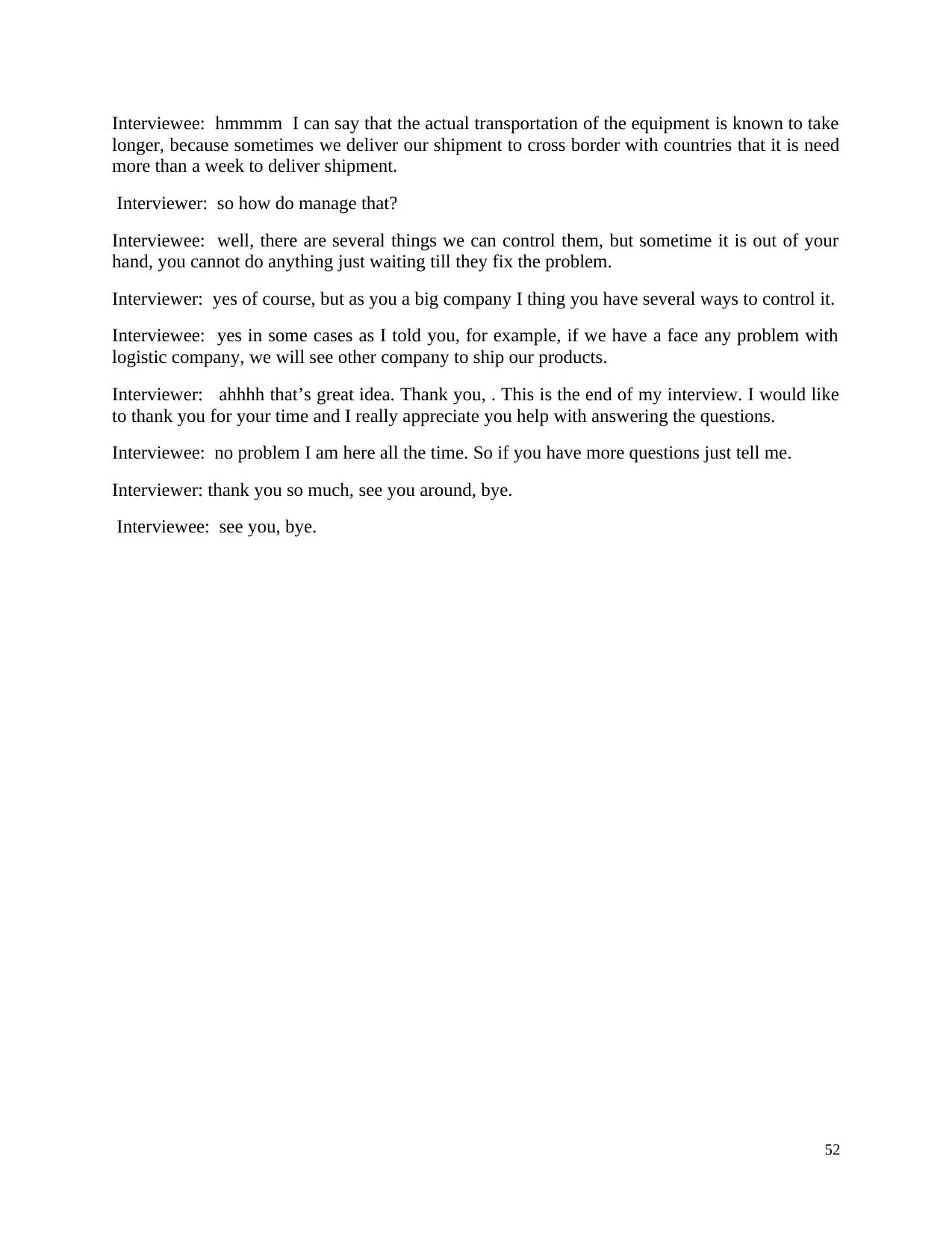
Interviewee: hmmmm I can say that the actual transportation of the equipment is known to take
longer, because sometimes we deliver our shipment to cross border with countries that it is need
more than a week to deliver shipment.
Interviewer: so how do manage that?
Interviewee: well, there are several things we can control them, but sometime it is out of your
hand, you cannot do anything just waiting till they fix the problem.
Interviewer: yes of course, but as you a big company I thing you have several ways to control it.
Interviewee: yes in some cases as I told you, for example, if we have a face any problem with
logistic company, we will see other company to ship our products.
Interviewer: ahhhh that’s great idea. Thank you, . This is the end of my interview. I would like
to thank you for your time and I really appreciate you help with answering the questions.
Interviewee: no problem I am here all the time. So if you have more questions just tell me.
Interviewer: thank you so much, see you around, bye.
Interviewee: see you, bye.
52
longer, because sometimes we deliver our shipment to cross border with countries that it is need
more than a week to deliver shipment.
Interviewer: so how do manage that?
Interviewee: well, there are several things we can control them, but sometime it is out of your
hand, you cannot do anything just waiting till they fix the problem.
Interviewer: yes of course, but as you a big company I thing you have several ways to control it.
Interviewee: yes in some cases as I told you, for example, if we have a face any problem with
logistic company, we will see other company to ship our products.
Interviewer: ahhhh that’s great idea. Thank you, . This is the end of my interview. I would like
to thank you for your time and I really appreciate you help with answering the questions.
Interviewee: no problem I am here all the time. So if you have more questions just tell me.
Interviewer: thank you so much, see you around, bye.
Interviewee: see you, bye.
52
1 out of 51
![[object Object]](/_next/image/?url=%2F_next%2Fstatic%2Fmedia%2Flogo.6d15ce61.png&w=640&q=75)
Your All-in-One AI-Powered Toolkit for Academic Success.
+13062052269
info@desklib.com
Available 24*7 on WhatsApp / Email
Unlock your academic potential
© 2024 | Zucol Services PVT LTD | All rights reserved.