Parametric Optimization Of Automobile Structural Member
Added on 2020-05-03
38 Pages6581 Words107 Views
Parametric Optimization Of Automobile Structural Member 1PARAMETRIC OPTIMIZATION OF AUTOMOBILE STRUCTURAL MEMBERBy NameCourseInstructorInstitutionLocationDate
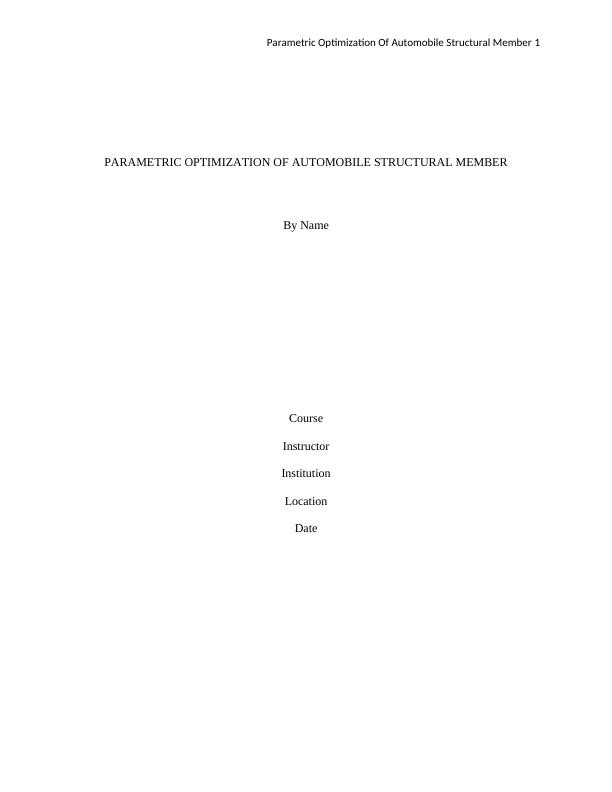
Parametric Optimization Of Automobile Structural Member 2Executive summary The chassis plays a significant role in providing the support of the different componentsof the automobiles. The chassis should be rigid enough such that it will be able to endure thevarious loads and forces such as twists, stress, vibrations, and shock. This implies that thestrength should not only be a great factor when considering the material to use in the design ofthe chassis but also the bending stiffness. The chief aim of this research is to come up with aminimum weight of the Eicher chassis frame. The design of this frame comprises of two majorparts which are connected together with a variety of cross members .hence, the design variablesincludes the lotion of the cross member, their number, and the size of both the cross and sidemembers. This reduction is attained by varying the parameters by the aid of an orthogonal arrayand then a finite element analysis done on the models to obtain a precise solution. This techniquehelps in saving both time and the cost of production[ CITATION Dir15 \l 1033 ].
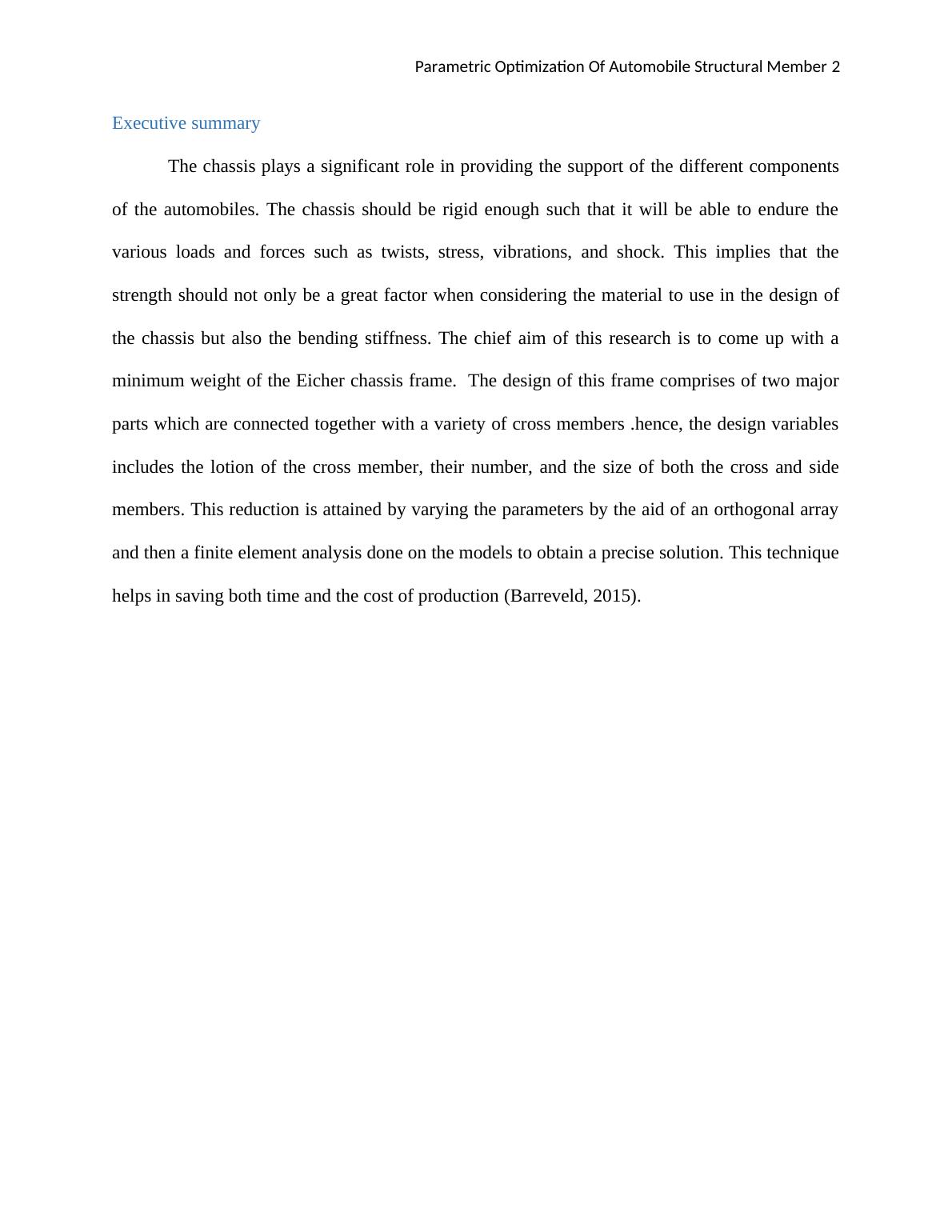
Parametric Optimization Of Automobile Structural Member 3ContentsExecutive summary.....................................................................................................................................2Introduction.................................................................................................................................................3Research question and objectives...........................................................................................................5Literature review.........................................................................................................................................6Methodology.........................................................................................................................................10Experimental set-up..............................................................................................................................20DESIGN OF CHASIS.......................................................................................................................20ANALYSIS, DISCUSSIONS AND PERFORMANCE............................................................................27Performance of finite element analysis of the frame............................................................................27Conclusion.................................................................................................................................................31References.................................................................................................................................................32
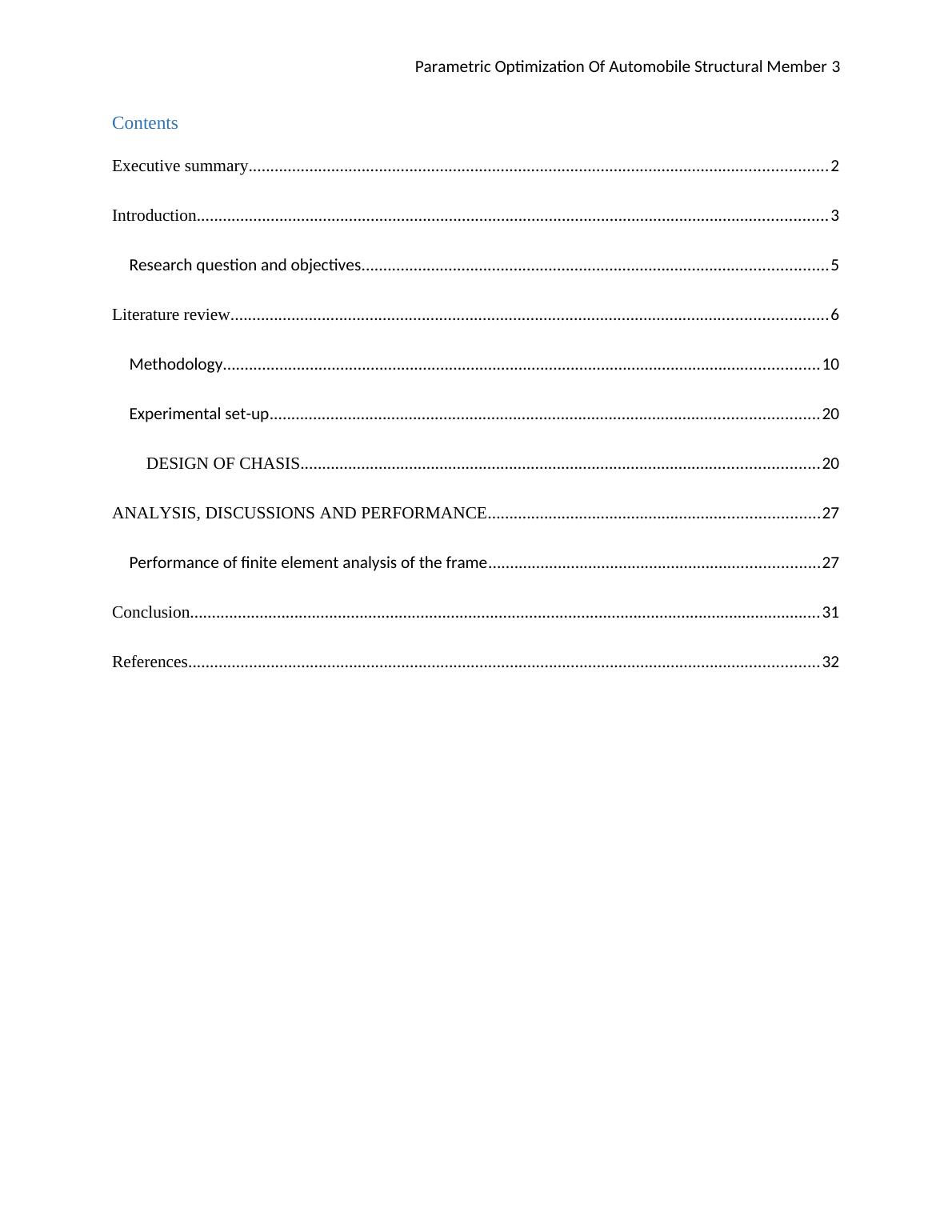
Parametric Optimization Of Automobile Structural Member 4Introduction The chassis is mostly concerned on the lower part of the body of the automobile such asthe frame, suspension, tires, driveline and the engine .among the mentioned parts, the frames istaken as the core part of the chassis of the automobile. The frame basically offers the support tothe components which are mounted on the vehicle. Besides the duty of supporting the load , thesuspension and the frame transfers the stresses and the loads to the structure of the vehicle,which includes the brake torque forces and the drive forces which make the vehicle to move.inorder to offer support to the load and forces , the frame is required to be rigid enough . Besides, itmust also be flexible enough to be able to sustain the twist and shock loads which areencountered in the road under different conditions[ CITATION Fed09 \l 1033 ]. The frame of the chassis should be strong enough to withstand the shocks and thevibrations. It consists of the side member which are connected to the side members which areattached to the side cross members .besides the strength of the chassis frame, the design of thechassis should significantly consider the stiffness of the chassis or in other terms the bending andthe torsion characteristics. Sufficient torsional stiffness is important when one wants to achievethe handling characteristics. The chassis is normally designed such that they take intoconsideration the strength and the stiffness. Conventionally, the design is more concerned withthe strength first and thereafter emphasize on the increasing the stiffness while paying lessattention to the weight of the chassis. Such design procedure comprises the addition of structuralloads across the members to the ones which exists in the chassis with the aim of increasing thetorsional stiffness. This results in an increase in the weight of the frame which overall minimizesthe efficiency of the fuel and increases the production cost due to the additional material.
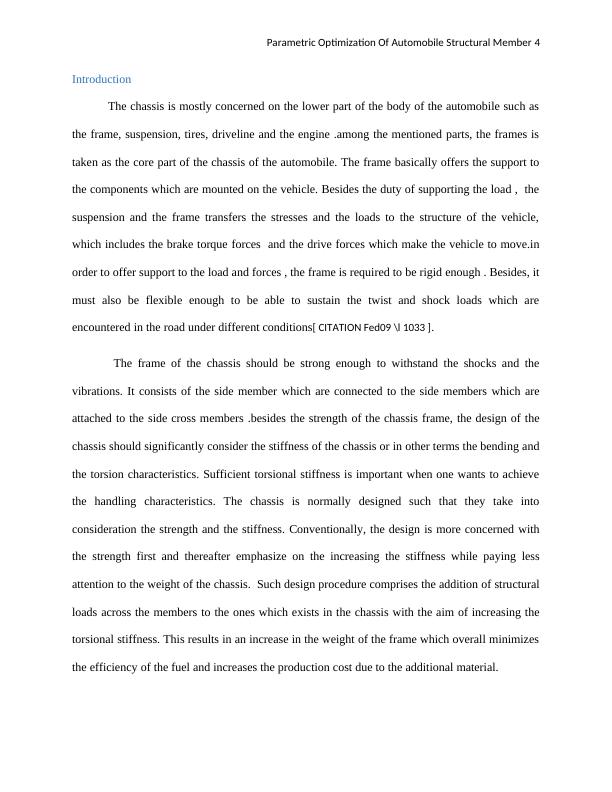
Parametric Optimization Of Automobile Structural Member 5 Hence, the motivation of this research project is to offer all the three aspects whichinclude, the strength, stiffness and reduced weight. Besides, the aim of the research is to obtainthe reduced weight of the component and satisfy the requirements for the loads and stresses. Thisprocess of attaining the desired structural performance is also referred to as structuraloptimization. The analysis of stress and loads of the structural systems are easily enabled by thehelp of a finite element analysis tools. The constraints for the optimization includes thelimitations which arise from the strength stiffness and weight[ CITATION Jam02 \l 1033 ]. Research question and objectives Does the minimization of chassis weight is significant in the consumption of fuel Is the method of finite element simulation a better method for the weight and designoptimization?In the perspective of the practitioner, enumerate the effective techniques for theoptimization of weight, do these techniques offer better performance The main aim of this research project is to minimize the weight of the chassis .the constraints ofthe optimized design come from the maximum strength and the requirements for the stiffness.The frame of the chassis consists of two side member which are connected using cross members.The design variable includes the locations of the members, the number of the members, the sizeof the side and the numbers of the cross, member’s .over the past years, finite element analysistool has been widely used by many types of research more so in the subject of structuraloptimization. While performing an analysis on the weight of the frame of the chassis, a model which isoptimized is being developed varying the parameters of both the crossbar and the sidebar helps
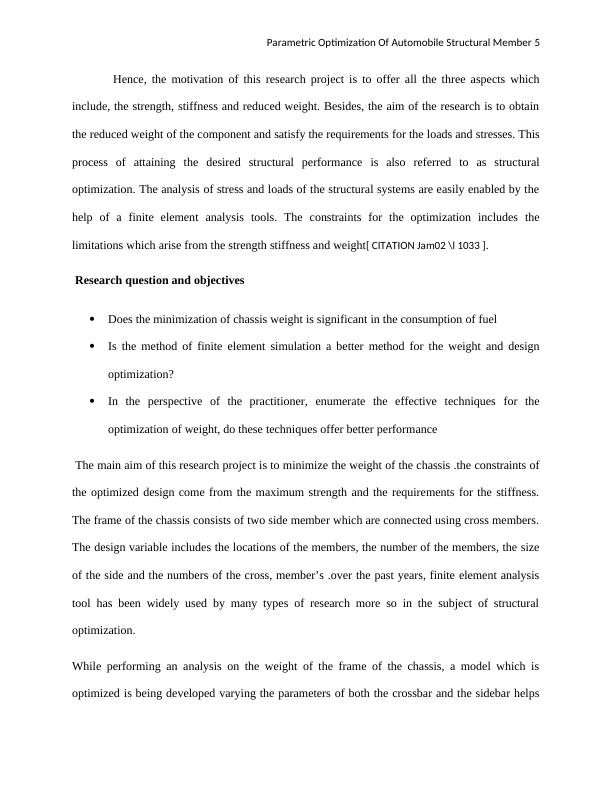
Parametric Optimization Of Automobile Structural Member 6in reducing the weight.in the application of the finite element analysis tool, the input variablesare used in determining the output variable. In some cases, the number of the models producedare more than one. On the other hand, while performing all these, there may be an increase in thecost of production and also in the prior determination of the results to be obtained. hence, thisstudy attempts to come with a suitable approach that combines the finite element analysismethod with modelling techniques such that it will be easy to predict the shear and other stressexperienced in the chassis frame .besides, the response surface method used employed in the metmodeling since it is easier to estimate and it requires slower amount of input data as co pared toother techniques of met modeling[ CITATION Sea06 \l 1033 ].Literature review The chassis serves as the backbone whereby all the components of the vehicle get attached.For the chassis in the modern automotive, the automotive is anticipated to offer the mountingsfor the suspensions system, the steering wheel system, the fuel tank, the seats, the final drive andthe engine drive system. Besides, the chassis should also be in a position to provide a distinctrigidity for the accurate handling of the chassis and also be able to offer protection to thepassengers from any external impacts when the vehicle is in motion. In order to satisfy all theserequirements, the chassis is supposed to possess a smaller weight such that it is able to minimizethe inertia and tentative provision of effective performance. it should also pose the features ofrigidity for the purposes of counteracting the fatigues emanating from the loads that will becarried by the automotive .taking a close look at the frame of the chassis, we realize that Itcomprises of a variety of components which are located differently and usually the componentsare made of heat treated alloy steel or at times made of cold rolled steel.
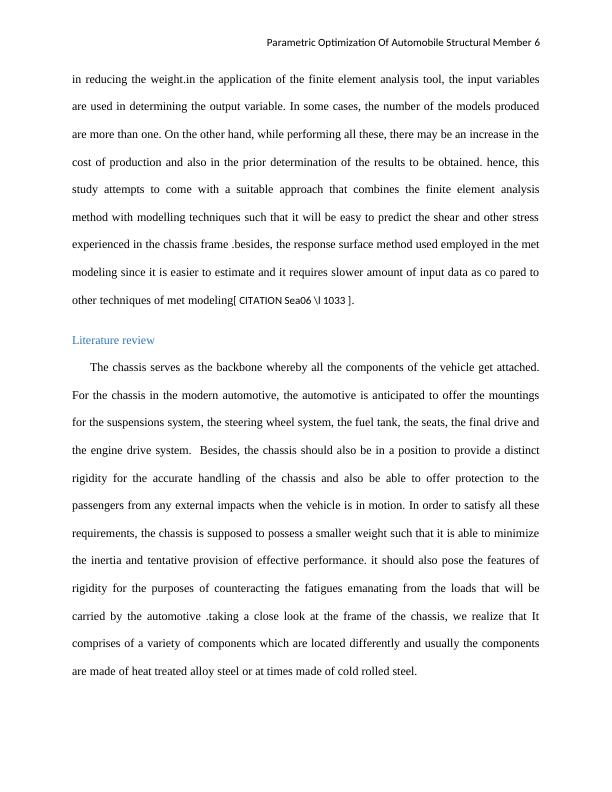
Parametric Optimization Of Automobile Structural Member 7The steel is the material which provides the chassis with the particular characteristicsmentioned above. I.e. rigidity, lightweight, and toughness. Below is the diagram[ CITATION Geo07\l 1033 ].It comprises of the •Diagonal components•Rear, Front, an intermediate component, • Longitudinal side component, Requirements for a good chassis frame The ram must be able to provide sufficient support to the chassis The frame must be able to be light in weight but sufficiently strong The frame must be rigid enough Material for Chassis Frame
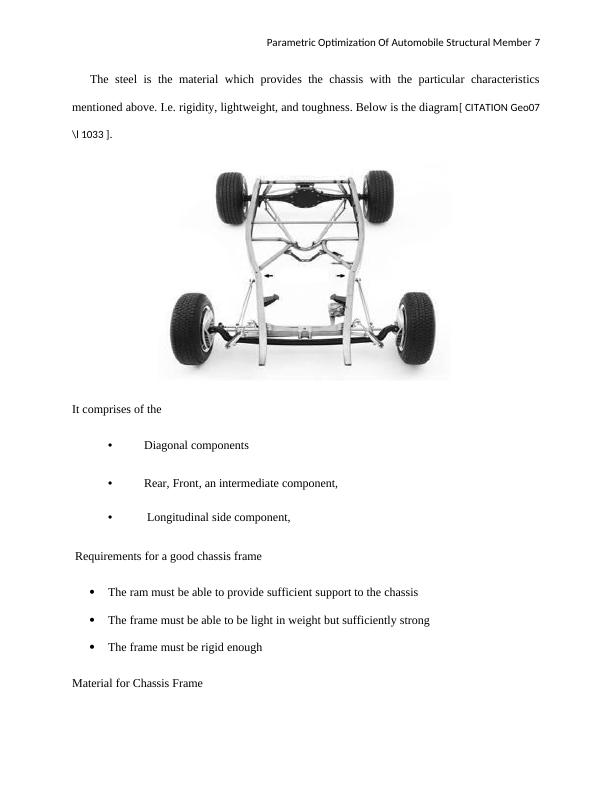
Parametric Optimization Of Automobile Structural Member 8The most conventionally used material for the making of the frame of the chassis is steel. Thesteel can be either cold rolled steel or at times heat treated steel. This is because of thelightweight nature of steel and also its strength.Loads experience by the frame The frame experiences various loads which includes Flexural loads – these are loads which are produced by the vertical plane of thecomponents and comprises of the engine torques, the weight of the passengers, the brakingtorques and the dead weight of the vehicle .also, the lateral components experience the roadcamber, side wind, and the cornering force [ CITATION And11 \l 1033 ]The torsional load – this is caused as a result of the vehicle coming across bumps. Dynamic load – this comes about as a result of the obstacles and the wheel impacts .thisloads results into longitudinal and lateral loads. K. Moto Yama et al. (2014) came up with a welding process design tool that would assist inobtaining the optimal arc by the use of response surface method and the finite element methodtogether with genetic algorithms. This integrated system was aimed at minimizing the induced
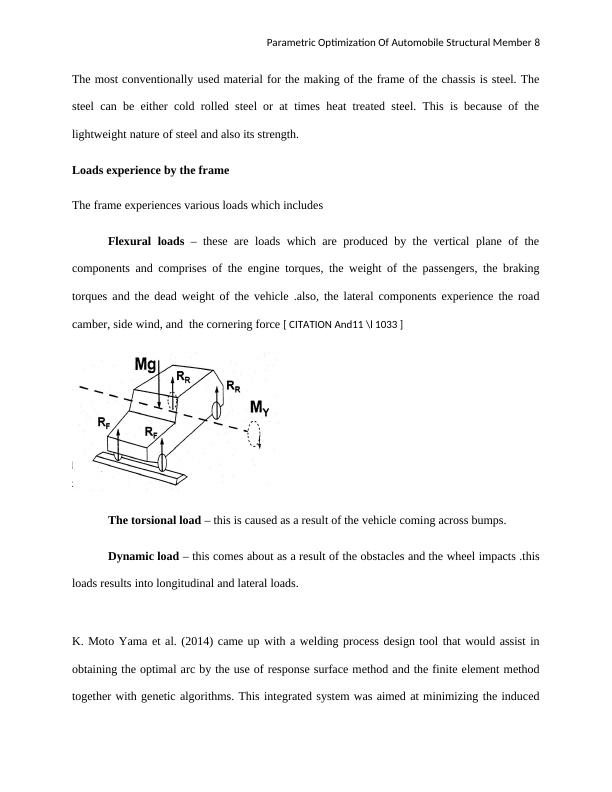
End of preview
Want to access all the pages? Upload your documents or become a member.