Pipeline Design for CO2 Transport
VerifiedAdded on 2023/01/17
|11
|3991
|90
AI Summary
This article discusses the design considerations for carbon dioxide (CO2) transport pipelines, including route selection, flow rates, velocity, and wall thickness. It also explores the management of impurities in CO2 streams and the health and safety concerns associated with pipeline transportation. The article provides valuable insights for understanding the design and operation of CO2 transport pipelines for carbon capture and storage (CCS) purposes.
Contribute Materials
Your contribution can guide someone’s learning journey. Share your
documents today.
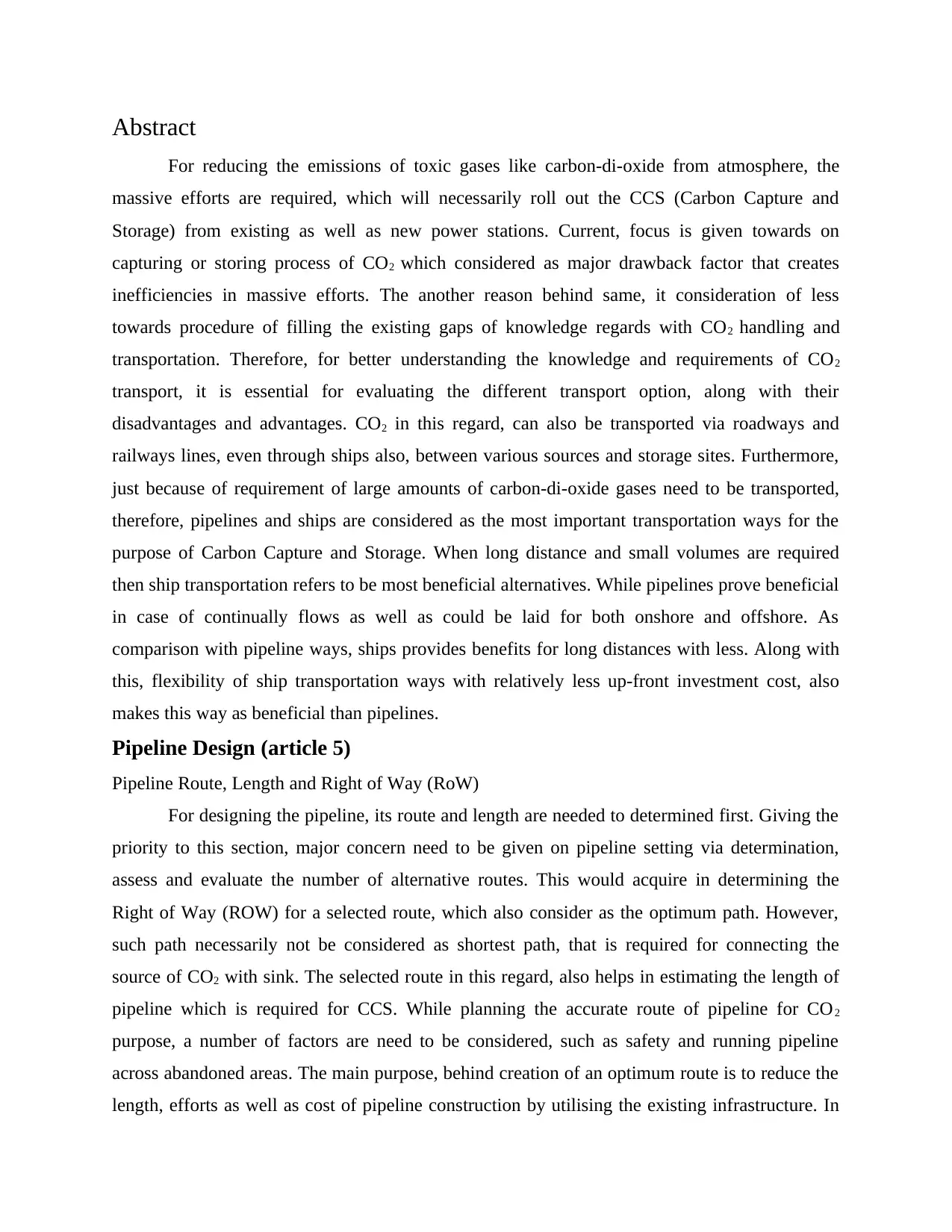
Abstract
For reducing the emissions of toxic gases like carbon-di-oxide from atmosphere, the
massive efforts are required, which will necessarily roll out the CCS (Carbon Capture and
Storage) from existing as well as new power stations. Current, focus is given towards on
capturing or storing process of CO2 which considered as major drawback factor that creates
inefficiencies in massive efforts. The another reason behind same, it consideration of less
towards procedure of filling the existing gaps of knowledge regards with CO2 handling and
transportation. Therefore, for better understanding the knowledge and requirements of CO2
transport, it is essential for evaluating the different transport option, along with their
disadvantages and advantages. CO2 in this regard, can also be transported via roadways and
railways lines, even through ships also, between various sources and storage sites. Furthermore,
just because of requirement of large amounts of carbon-di-oxide gases need to be transported,
therefore, pipelines and ships are considered as the most important transportation ways for the
purpose of Carbon Capture and Storage. When long distance and small volumes are required
then ship transportation refers to be most beneficial alternatives. While pipelines prove beneficial
in case of continually flows as well as could be laid for both onshore and offshore. As
comparison with pipeline ways, ships provides benefits for long distances with less. Along with
this, flexibility of ship transportation ways with relatively less up-front investment cost, also
makes this way as beneficial than pipelines.
Pipeline Design (article 5)
Pipeline Route, Length and Right of Way (RoW)
For designing the pipeline, its route and length are needed to determined first. Giving the
priority to this section, major concern need to be given on pipeline setting via determination,
assess and evaluate the number of alternative routes. This would acquire in determining the
Right of Way (ROW) for a selected route, which also consider as the optimum path. However,
such path necessarily not be considered as shortest path, that is required for connecting the
source of CO2 with sink. The selected route in this regard, also helps in estimating the length of
pipeline which is required for CCS. While planning the accurate route of pipeline for CO2
purpose, a number of factors are need to be considered, such as safety and running pipeline
across abandoned areas. The main purpose, behind creation of an optimum route is to reduce the
length, efforts as well as cost of pipeline construction by utilising the existing infrastructure. In
For reducing the emissions of toxic gases like carbon-di-oxide from atmosphere, the
massive efforts are required, which will necessarily roll out the CCS (Carbon Capture and
Storage) from existing as well as new power stations. Current, focus is given towards on
capturing or storing process of CO2 which considered as major drawback factor that creates
inefficiencies in massive efforts. The another reason behind same, it consideration of less
towards procedure of filling the existing gaps of knowledge regards with CO2 handling and
transportation. Therefore, for better understanding the knowledge and requirements of CO2
transport, it is essential for evaluating the different transport option, along with their
disadvantages and advantages. CO2 in this regard, can also be transported via roadways and
railways lines, even through ships also, between various sources and storage sites. Furthermore,
just because of requirement of large amounts of carbon-di-oxide gases need to be transported,
therefore, pipelines and ships are considered as the most important transportation ways for the
purpose of Carbon Capture and Storage. When long distance and small volumes are required
then ship transportation refers to be most beneficial alternatives. While pipelines prove beneficial
in case of continually flows as well as could be laid for both onshore and offshore. As
comparison with pipeline ways, ships provides benefits for long distances with less. Along with
this, flexibility of ship transportation ways with relatively less up-front investment cost, also
makes this way as beneficial than pipelines.
Pipeline Design (article 5)
Pipeline Route, Length and Right of Way (RoW)
For designing the pipeline, its route and length are needed to determined first. Giving the
priority to this section, major concern need to be given on pipeline setting via determination,
assess and evaluate the number of alternative routes. This would acquire in determining the
Right of Way (ROW) for a selected route, which also consider as the optimum path. However,
such path necessarily not be considered as shortest path, that is required for connecting the
source of CO2 with sink. The selected route in this regard, also helps in estimating the length of
pipeline which is required for CCS. While planning the accurate route of pipeline for CO2
purpose, a number of factors are need to be considered, such as safety and running pipeline
across abandoned areas. The main purpose, behind creation of an optimum route is to reduce the
length, efforts as well as cost of pipeline construction by utilising the existing infrastructure. In
Secure Best Marks with AI Grader
Need help grading? Try our AI Grader for instant feedback on your assignments.
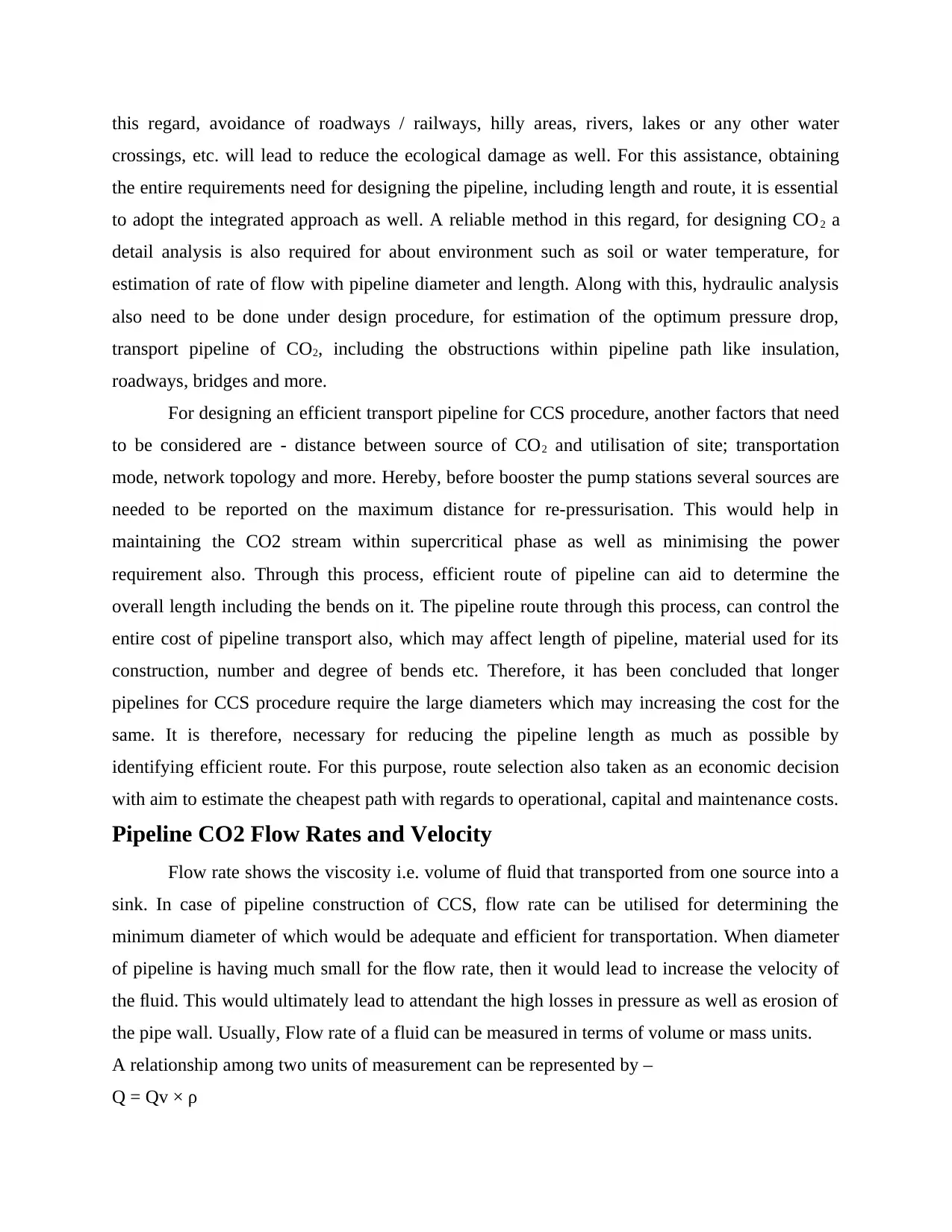
this regard, avoidance of roadways / railways, hilly areas, rivers, lakes or any other water
crossings, etc. will lead to reduce the ecological damage as well. For this assistance, obtaining
the entire requirements need for designing the pipeline, including length and route, it is essential
to adopt the integrated approach as well. A reliable method in this regard, for designing CO2 a
detail analysis is also required for about environment such as soil or water temperature, for
estimation of rate of flow with pipeline diameter and length. Along with this, hydraulic analysis
also need to be done under design procedure, for estimation of the optimum pressure drop,
transport pipeline of CO2, including the obstructions within pipeline path like insulation,
roadways, bridges and more.
For designing an efficient transport pipeline for CCS procedure, another factors that need
to be considered are - distance between source of CO2 and utilisation of site; transportation
mode, network topology and more. Hereby, before booster the pump stations several sources are
needed to be reported on the maximum distance for re-pressurisation. This would help in
maintaining the CO2 stream within supercritical phase as well as minimising the power
requirement also. Through this process, efficient route of pipeline can aid to determine the
overall length including the bends on it. The pipeline route through this process, can control the
entire cost of pipeline transport also, which may affect length of pipeline, material used for its
construction, number and degree of bends etc. Therefore, it has been concluded that longer
pipelines for CCS procedure require the large diameters which may increasing the cost for the
same. It is therefore, necessary for reducing the pipeline length as much as possible by
identifying efficient route. For this purpose, route selection also taken as an economic decision
with aim to estimate the cheapest path with regards to operational, capital and maintenance costs.
Pipeline CO2 Flow Rates and Velocity
Flow rate shows the viscosity i.e. volume of fluid that transported from one source into a
sink. In case of pipeline construction of CCS, flow rate can be utilised for determining the
minimum diameter of which would be adequate and efficient for transportation. When diameter
of pipeline is having much small for the flow rate, then it would lead to increase the velocity of
the fluid. This would ultimately lead to attendant the high losses in pressure as well as erosion of
the pipe wall. Usually, Flow rate of a fluid can be measured in terms of volume or mass units.
A relationship among two units of measurement can be represented by –
Q = Qv × ρ
crossings, etc. will lead to reduce the ecological damage as well. For this assistance, obtaining
the entire requirements need for designing the pipeline, including length and route, it is essential
to adopt the integrated approach as well. A reliable method in this regard, for designing CO2 a
detail analysis is also required for about environment such as soil or water temperature, for
estimation of rate of flow with pipeline diameter and length. Along with this, hydraulic analysis
also need to be done under design procedure, for estimation of the optimum pressure drop,
transport pipeline of CO2, including the obstructions within pipeline path like insulation,
roadways, bridges and more.
For designing an efficient transport pipeline for CCS procedure, another factors that need
to be considered are - distance between source of CO2 and utilisation of site; transportation
mode, network topology and more. Hereby, before booster the pump stations several sources are
needed to be reported on the maximum distance for re-pressurisation. This would help in
maintaining the CO2 stream within supercritical phase as well as minimising the power
requirement also. Through this process, efficient route of pipeline can aid to determine the
overall length including the bends on it. The pipeline route through this process, can control the
entire cost of pipeline transport also, which may affect length of pipeline, material used for its
construction, number and degree of bends etc. Therefore, it has been concluded that longer
pipelines for CCS procedure require the large diameters which may increasing the cost for the
same. It is therefore, necessary for reducing the pipeline length as much as possible by
identifying efficient route. For this purpose, route selection also taken as an economic decision
with aim to estimate the cheapest path with regards to operational, capital and maintenance costs.
Pipeline CO2 Flow Rates and Velocity
Flow rate shows the viscosity i.e. volume of fluid that transported from one source into a
sink. In case of pipeline construction of CCS, flow rate can be utilised for determining the
minimum diameter of which would be adequate and efficient for transportation. When diameter
of pipeline is having much small for the flow rate, then it would lead to increase the velocity of
the fluid. This would ultimately lead to attendant the high losses in pressure as well as erosion of
the pipe wall. Usually, Flow rate of a fluid can be measured in terms of volume or mass units.
A relationship among two units of measurement can be represented by –
Q = Qv × ρ
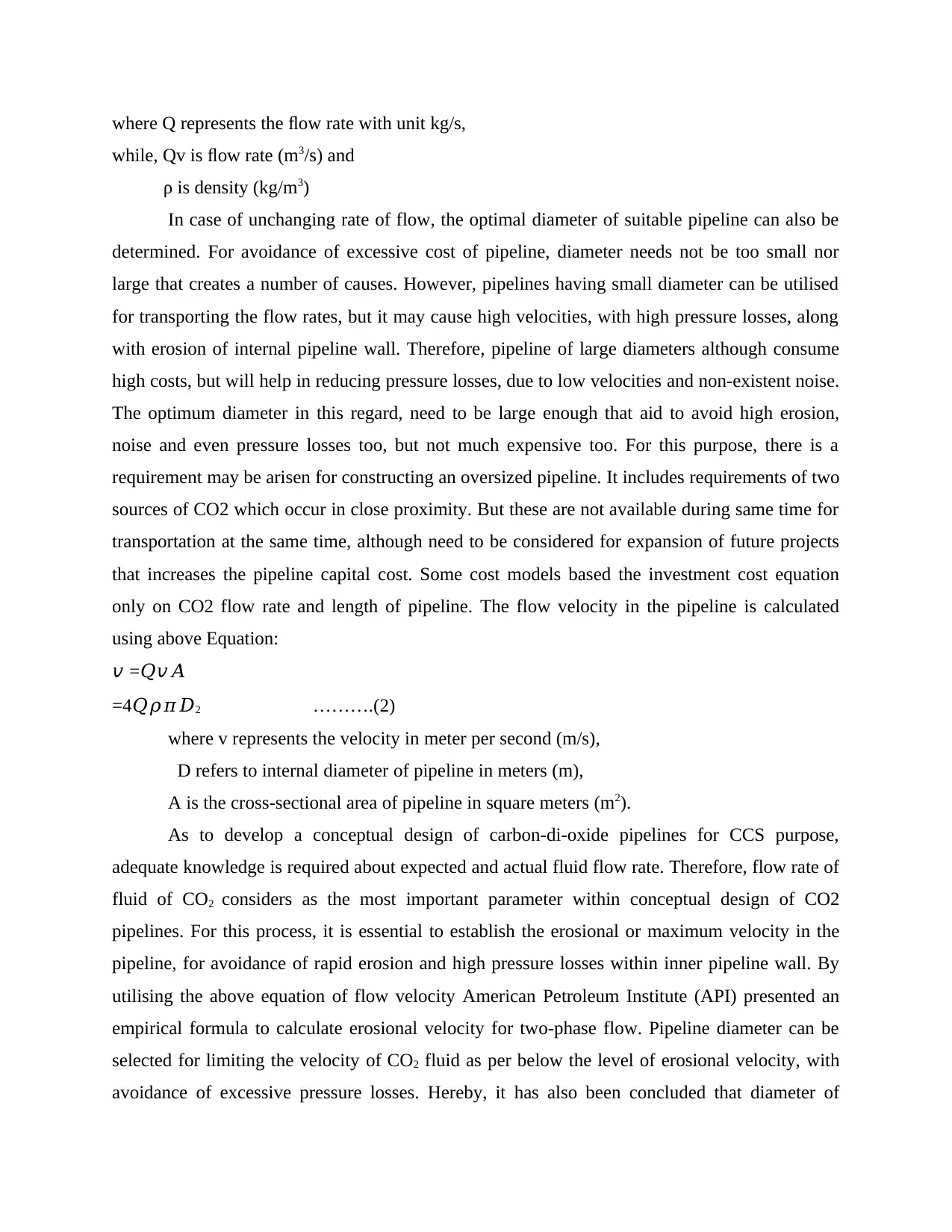
where Q represents the flow rate with unit kg/s,
while, Qv is flow rate (m3/s) and
ρ is density (kg/m3)
In case of unchanging rate of flow, the optimal diameter of suitable pipeline can also be
determined. For avoidance of excessive cost of pipeline, diameter needs not be too small nor
large that creates a number of causes. However, pipelines having small diameter can be utilised
for transporting the flow rates, but it may cause high velocities, with high pressure losses, along
with erosion of internal pipeline wall. Therefore, pipeline of large diameters although consume
high costs, but will help in reducing pressure losses, due to low velocities and non-existent noise.
The optimum diameter in this regard, need to be large enough that aid to avoid high erosion,
noise and even pressure losses too, but not much expensive too. For this purpose, there is a
requirement may be arisen for constructing an oversized pipeline. It includes requirements of two
sources of CO2 which occur in close proximity. But these are not available during same time for
transportation at the same time, although need to be considered for expansion of future projects
that increases the pipeline capital cost. Some cost models based the investment cost equation
only on CO2 flow rate and length of pipeline. The flow velocity in the pipeline is calculated
using above Equation:
𝑣 =𝑄𝑣𝐴
=4𝑄𝜌𝜋𝐷2 ……….(2)
where v represents the velocity in meter per second (m/s),
D refers to internal diameter of pipeline in meters (m),
A is the cross-sectional area of pipeline in square meters (m2).
As to develop a conceptual design of carbon-di-oxide pipelines for CCS purpose,
adequate knowledge is required about expected and actual fluid flow rate. Therefore, flow rate of
fluid of CO2 considers as the most important parameter within conceptual design of CO2
pipelines. For this process, it is essential to establish the erosional or maximum velocity in the
pipeline, for avoidance of rapid erosion and high pressure losses within inner pipeline wall. By
utilising the above equation of flow velocity American Petroleum Institute (API) presented an
empirical formula to calculate erosional velocity for two-phase flow. Pipeline diameter can be
selected for limiting the velocity of CO2 fluid as per below the level of erosional velocity, with
avoidance of excessive pressure losses. Hereby, it has also been concluded that diameter of
while, Qv is flow rate (m3/s) and
ρ is density (kg/m3)
In case of unchanging rate of flow, the optimal diameter of suitable pipeline can also be
determined. For avoidance of excessive cost of pipeline, diameter needs not be too small nor
large that creates a number of causes. However, pipelines having small diameter can be utilised
for transporting the flow rates, but it may cause high velocities, with high pressure losses, along
with erosion of internal pipeline wall. Therefore, pipeline of large diameters although consume
high costs, but will help in reducing pressure losses, due to low velocities and non-existent noise.
The optimum diameter in this regard, need to be large enough that aid to avoid high erosion,
noise and even pressure losses too, but not much expensive too. For this purpose, there is a
requirement may be arisen for constructing an oversized pipeline. It includes requirements of two
sources of CO2 which occur in close proximity. But these are not available during same time for
transportation at the same time, although need to be considered for expansion of future projects
that increases the pipeline capital cost. Some cost models based the investment cost equation
only on CO2 flow rate and length of pipeline. The flow velocity in the pipeline is calculated
using above Equation:
𝑣 =𝑄𝑣𝐴
=4𝑄𝜌𝜋𝐷2 ……….(2)
where v represents the velocity in meter per second (m/s),
D refers to internal diameter of pipeline in meters (m),
A is the cross-sectional area of pipeline in square meters (m2).
As to develop a conceptual design of carbon-di-oxide pipelines for CCS purpose,
adequate knowledge is required about expected and actual fluid flow rate. Therefore, flow rate of
fluid of CO2 considers as the most important parameter within conceptual design of CO2
pipelines. For this process, it is essential to establish the erosional or maximum velocity in the
pipeline, for avoidance of rapid erosion and high pressure losses within inner pipeline wall. By
utilising the above equation of flow velocity American Petroleum Institute (API) presented an
empirical formula to calculate erosional velocity for two-phase flow. Pipeline diameter can be
selected for limiting the velocity of CO2 fluid as per below the level of erosional velocity, with
avoidance of excessive pressure losses. Hereby, it has also been concluded that diameter of
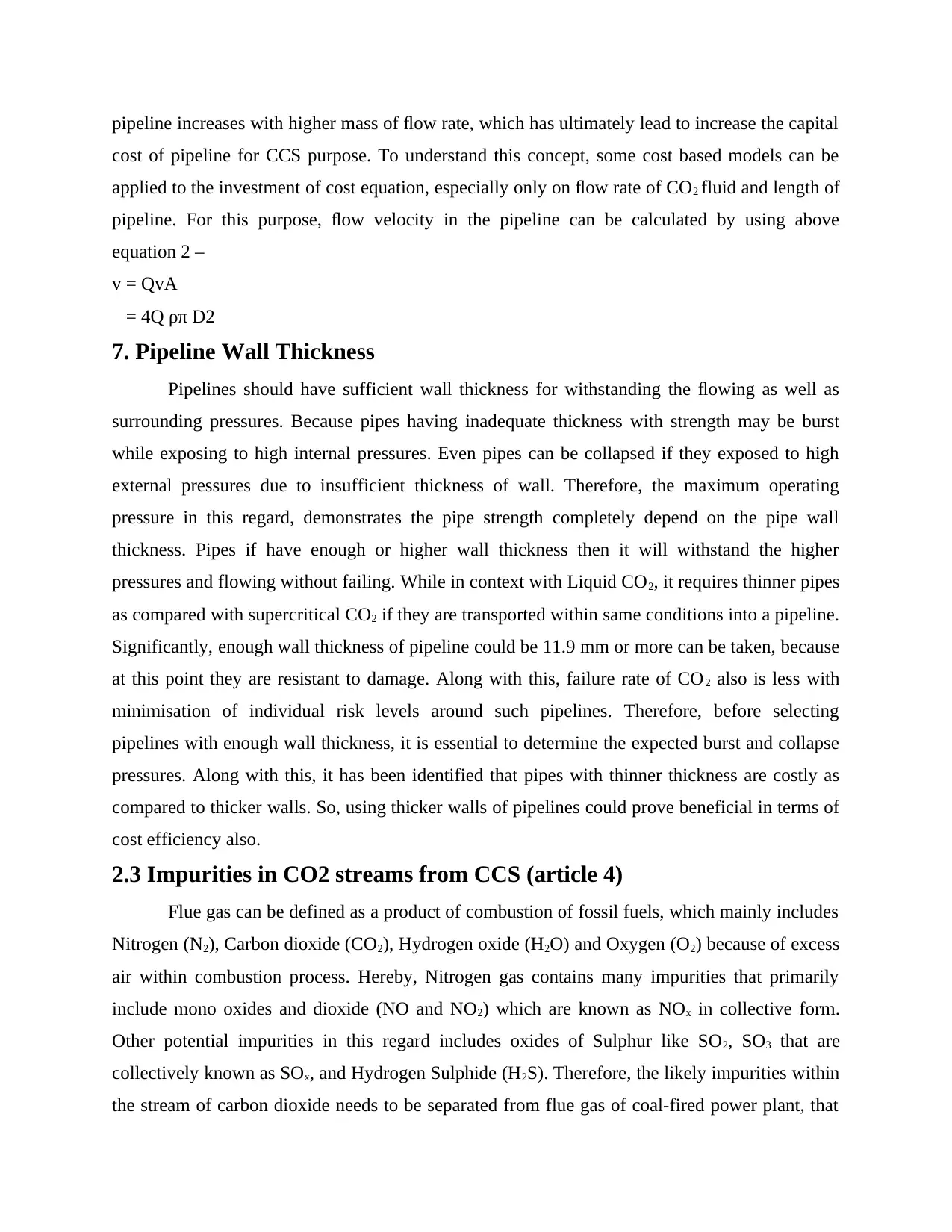
pipeline increases with higher mass of flow rate, which has ultimately lead to increase the capital
cost of pipeline for CCS purpose. To understand this concept, some cost based models can be
applied to the investment of cost equation, especially only on flow rate of CO2 fluid and length of
pipeline. For this purpose, flow velocity in the pipeline can be calculated by using above
equation 2 –
v = QvA
= 4Q ρπ D2
7. Pipeline Wall Thickness
Pipelines should have sufficient wall thickness for withstanding the flowing as well as
surrounding pressures. Because pipes having inadequate thickness with strength may be burst
while exposing to high internal pressures. Even pipes can be collapsed if they exposed to high
external pressures due to insufficient thickness of wall. Therefore, the maximum operating
pressure in this regard, demonstrates the pipe strength completely depend on the pipe wall
thickness. Pipes if have enough or higher wall thickness then it will withstand the higher
pressures and flowing without failing. While in context with Liquid CO2, it requires thinner pipes
as compared with supercritical CO2 if they are transported within same conditions into a pipeline.
Significantly, enough wall thickness of pipeline could be 11.9 mm or more can be taken, because
at this point they are resistant to damage. Along with this, failure rate of CO2 also is less with
minimisation of individual risk levels around such pipelines. Therefore, before selecting
pipelines with enough wall thickness, it is essential to determine the expected burst and collapse
pressures. Along with this, it has been identified that pipes with thinner thickness are costly as
compared to thicker walls. So, using thicker walls of pipelines could prove beneficial in terms of
cost efficiency also.
2.3 Impurities in CO2 streams from CCS (article 4)
Flue gas can be defined as a product of combustion of fossil fuels, which mainly includes
Nitrogen (N2), Carbon dioxide (CO2), Hydrogen oxide (H2O) and Oxygen (O2) because of excess
air within combustion process. Hereby, Nitrogen gas contains many impurities that primarily
include mono oxides and dioxide (NO and NO2) which are known as NOx in collective form.
Other potential impurities in this regard includes oxides of Sulphur like SO2, SO3 that are
collectively known as SOx, and Hydrogen Sulphide (H2S). Therefore, the likely impurities within
the stream of carbon dioxide needs to be separated from flue gas of coal-fired power plant, that
cost of pipeline for CCS purpose. To understand this concept, some cost based models can be
applied to the investment of cost equation, especially only on flow rate of CO2 fluid and length of
pipeline. For this purpose, flow velocity in the pipeline can be calculated by using above
equation 2 –
v = QvA
= 4Q ρπ D2
7. Pipeline Wall Thickness
Pipelines should have sufficient wall thickness for withstanding the flowing as well as
surrounding pressures. Because pipes having inadequate thickness with strength may be burst
while exposing to high internal pressures. Even pipes can be collapsed if they exposed to high
external pressures due to insufficient thickness of wall. Therefore, the maximum operating
pressure in this regard, demonstrates the pipe strength completely depend on the pipe wall
thickness. Pipes if have enough or higher wall thickness then it will withstand the higher
pressures and flowing without failing. While in context with Liquid CO2, it requires thinner pipes
as compared with supercritical CO2 if they are transported within same conditions into a pipeline.
Significantly, enough wall thickness of pipeline could be 11.9 mm or more can be taken, because
at this point they are resistant to damage. Along with this, failure rate of CO2 also is less with
minimisation of individual risk levels around such pipelines. Therefore, before selecting
pipelines with enough wall thickness, it is essential to determine the expected burst and collapse
pressures. Along with this, it has been identified that pipes with thinner thickness are costly as
compared to thicker walls. So, using thicker walls of pipelines could prove beneficial in terms of
cost efficiency also.
2.3 Impurities in CO2 streams from CCS (article 4)
Flue gas can be defined as a product of combustion of fossil fuels, which mainly includes
Nitrogen (N2), Carbon dioxide (CO2), Hydrogen oxide (H2O) and Oxygen (O2) because of excess
air within combustion process. Hereby, Nitrogen gas contains many impurities that primarily
include mono oxides and dioxide (NO and NO2) which are known as NOx in collective form.
Other potential impurities in this regard includes oxides of Sulphur like SO2, SO3 that are
collectively known as SOx, and Hydrogen Sulphide (H2S). Therefore, the likely impurities within
the stream of carbon dioxide needs to be separated from flue gas of coal-fired power plant, that
Secure Best Marks with AI Grader
Need help grading? Try our AI Grader for instant feedback on your assignments.
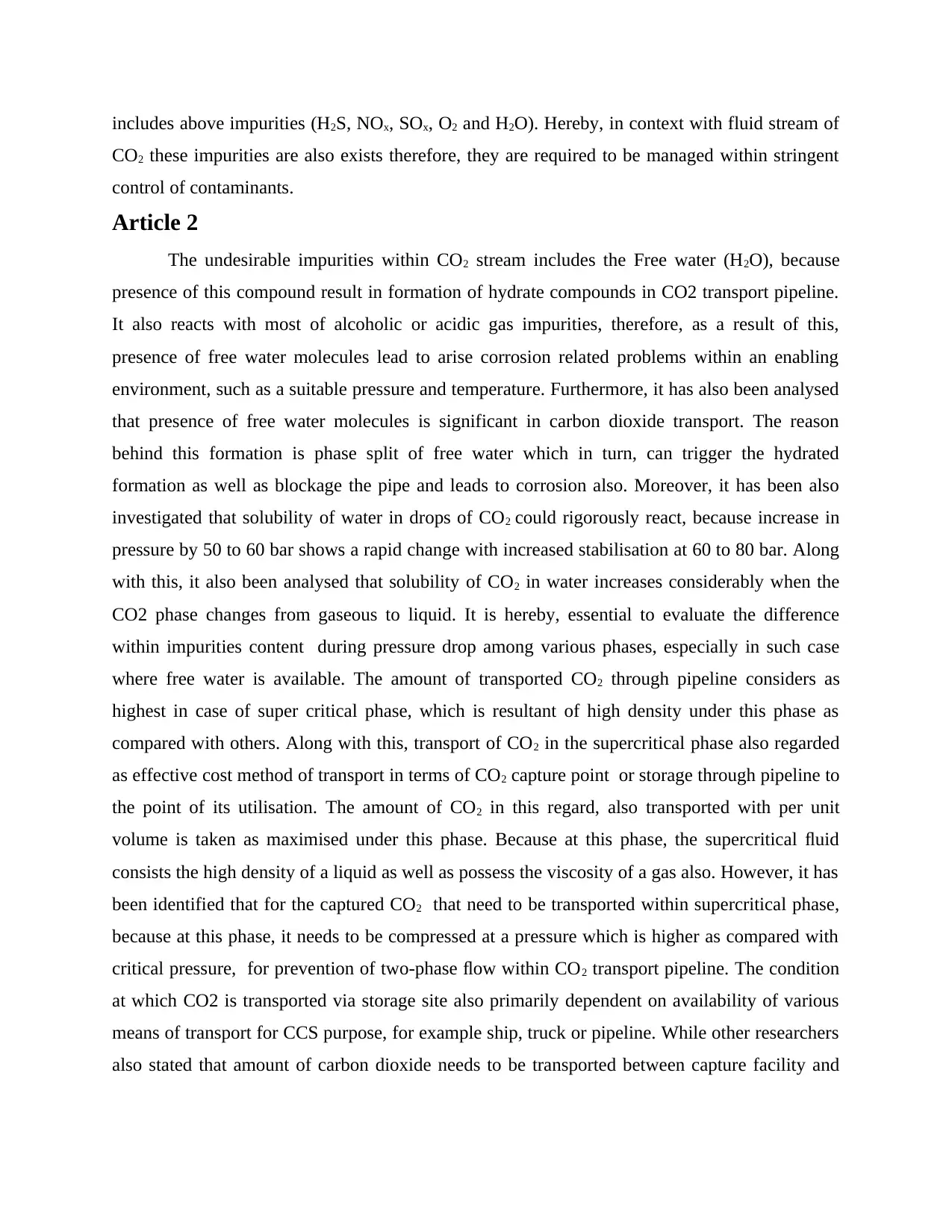
includes above impurities (H2S, NOx, SOx, O2 and H2O). Hereby, in context with fluid stream of
CO2 these impurities are also exists therefore, they are required to be managed within stringent
control of contaminants.
Article 2
The undesirable impurities within CO2 stream includes the Free water (H2O), because
presence of this compound result in formation of hydrate compounds in CO2 transport pipeline.
It also reacts with most of alcoholic or acidic gas impurities, therefore, as a result of this,
presence of free water molecules lead to arise corrosion related problems within an enabling
environment, such as a suitable pressure and temperature. Furthermore, it has also been analysed
that presence of free water molecules is significant in carbon dioxide transport. The reason
behind this formation is phase split of free water which in turn, can trigger the hydrated
formation as well as blockage the pipe and leads to corrosion also. Moreover, it has been also
investigated that solubility of water in drops of CO2 could rigorously react, because increase in
pressure by 50 to 60 bar shows a rapid change with increased stabilisation at 60 to 80 bar. Along
with this, it also been analysed that solubility of CO2 in water increases considerably when the
CO2 phase changes from gaseous to liquid. It is hereby, essential to evaluate the difference
within impurities content during pressure drop among various phases, especially in such case
where free water is available. The amount of transported CO2 through pipeline considers as
highest in case of super critical phase, which is resultant of high density under this phase as
compared with others. Along with this, transport of CO2 in the supercritical phase also regarded
as effective cost method of transport in terms of CO2 capture point or storage through pipeline to
the point of its utilisation. The amount of CO2 in this regard, also transported with per unit
volume is taken as maximised under this phase. Because at this phase, the supercritical fluid
consists the high density of a liquid as well as possess the viscosity of a gas also. However, it has
been identified that for the captured CO2 that need to be transported within supercritical phase,
because at this phase, it needs to be compressed at a pressure which is higher as compared with
critical pressure, for prevention of two-phase flow within CO2 transport pipeline. The condition
at which CO2 is transported via storage site also primarily dependent on availability of various
means of transport for CCS purpose, for example ship, truck or pipeline. While other researchers
also stated that amount of carbon dioxide needs to be transported between capture facility and
CO2 these impurities are also exists therefore, they are required to be managed within stringent
control of contaminants.
Article 2
The undesirable impurities within CO2 stream includes the Free water (H2O), because
presence of this compound result in formation of hydrate compounds in CO2 transport pipeline.
It also reacts with most of alcoholic or acidic gas impurities, therefore, as a result of this,
presence of free water molecules lead to arise corrosion related problems within an enabling
environment, such as a suitable pressure and temperature. Furthermore, it has also been analysed
that presence of free water molecules is significant in carbon dioxide transport. The reason
behind this formation is phase split of free water which in turn, can trigger the hydrated
formation as well as blockage the pipe and leads to corrosion also. Moreover, it has been also
investigated that solubility of water in drops of CO2 could rigorously react, because increase in
pressure by 50 to 60 bar shows a rapid change with increased stabilisation at 60 to 80 bar. Along
with this, it also been analysed that solubility of CO2 in water increases considerably when the
CO2 phase changes from gaseous to liquid. It is hereby, essential to evaluate the difference
within impurities content during pressure drop among various phases, especially in such case
where free water is available. The amount of transported CO2 through pipeline considers as
highest in case of super critical phase, which is resultant of high density under this phase as
compared with others. Along with this, transport of CO2 in the supercritical phase also regarded
as effective cost method of transport in terms of CO2 capture point or storage through pipeline to
the point of its utilisation. The amount of CO2 in this regard, also transported with per unit
volume is taken as maximised under this phase. Because at this phase, the supercritical fluid
consists the high density of a liquid as well as possess the viscosity of a gas also. However, it has
been identified that for the captured CO2 that need to be transported within supercritical phase,
because at this phase, it needs to be compressed at a pressure which is higher as compared with
critical pressure, for prevention of two-phase flow within CO2 transport pipeline. The condition
at which CO2 is transported via storage site also primarily dependent on availability of various
means of transport for CCS purpose, for example ship, truck or pipeline. While other researchers
also stated that amount of carbon dioxide needs to be transported between capture facility and
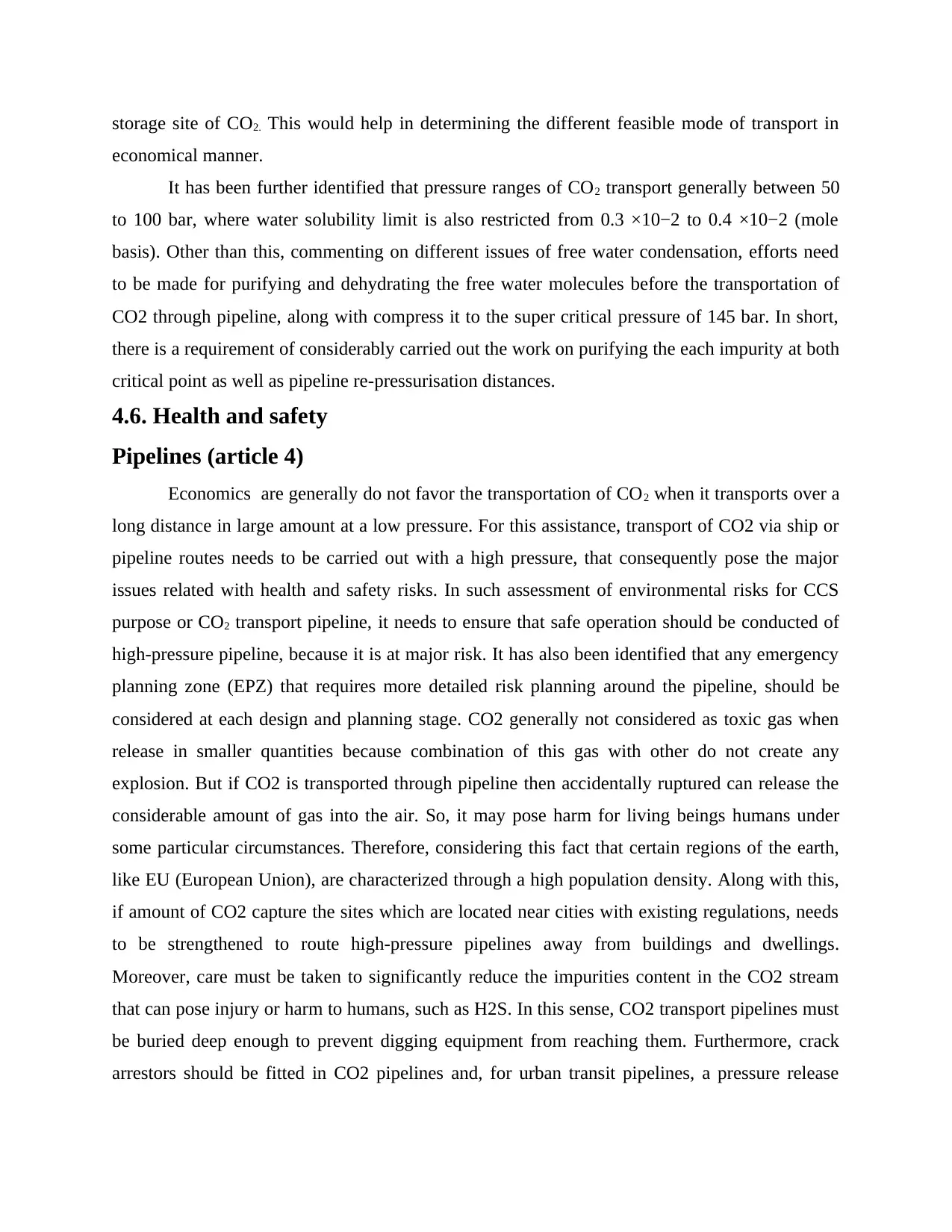
storage site of CO2. This would help in determining the different feasible mode of transport in
economical manner.
It has been further identified that pressure ranges of CO2 transport generally between 50
to 100 bar, where water solubility limit is also restricted from 0.3 ×10−2 to 0.4 ×10−2 (mole
basis). Other than this, commenting on different issues of free water condensation, efforts need
to be made for purifying and dehydrating the free water molecules before the transportation of
CO2 through pipeline, along with compress it to the super critical pressure of 145 bar. In short,
there is a requirement of considerably carried out the work on purifying the each impurity at both
critical point as well as pipeline re-pressurisation distances.
4.6. Health and safety
Pipelines (article 4)
Economics are generally do not favor the transportation of CO2 when it transports over a
long distance in large amount at a low pressure. For this assistance, transport of CO2 via ship or
pipeline routes needs to be carried out with a high pressure, that consequently pose the major
issues related with health and safety risks. In such assessment of environmental risks for CCS
purpose or CO2 transport pipeline, it needs to ensure that safe operation should be conducted of
high-pressure pipeline, because it is at major risk. It has also been identified that any emergency
planning zone (EPZ) that requires more detailed risk planning around the pipeline, should be
considered at each design and planning stage. CO2 generally not considered as toxic gas when
release in smaller quantities because combination of this gas with other do not create any
explosion. But if CO2 is transported through pipeline then accidentally ruptured can release the
considerable amount of gas into the air. So, it may pose harm for living beings humans under
some particular circumstances. Therefore, considering this fact that certain regions of the earth,
like EU (European Union), are characterized through a high population density. Along with this,
if amount of CO2 capture the sites which are located near cities with existing regulations, needs
to be strengthened to route high-pressure pipelines away from buildings and dwellings.
Moreover, care must be taken to significantly reduce the impurities content in the CO2 stream
that can pose injury or harm to humans, such as H2S. In this sense, CO2 transport pipelines must
be buried deep enough to prevent digging equipment from reaching them. Furthermore, crack
arrestors should be fitted in CO2 pipelines and, for urban transit pipelines, a pressure release
economical manner.
It has been further identified that pressure ranges of CO2 transport generally between 50
to 100 bar, where water solubility limit is also restricted from 0.3 ×10−2 to 0.4 ×10−2 (mole
basis). Other than this, commenting on different issues of free water condensation, efforts need
to be made for purifying and dehydrating the free water molecules before the transportation of
CO2 through pipeline, along with compress it to the super critical pressure of 145 bar. In short,
there is a requirement of considerably carried out the work on purifying the each impurity at both
critical point as well as pipeline re-pressurisation distances.
4.6. Health and safety
Pipelines (article 4)
Economics are generally do not favor the transportation of CO2 when it transports over a
long distance in large amount at a low pressure. For this assistance, transport of CO2 via ship or
pipeline routes needs to be carried out with a high pressure, that consequently pose the major
issues related with health and safety risks. In such assessment of environmental risks for CCS
purpose or CO2 transport pipeline, it needs to ensure that safe operation should be conducted of
high-pressure pipeline, because it is at major risk. It has also been identified that any emergency
planning zone (EPZ) that requires more detailed risk planning around the pipeline, should be
considered at each design and planning stage. CO2 generally not considered as toxic gas when
release in smaller quantities because combination of this gas with other do not create any
explosion. But if CO2 is transported through pipeline then accidentally ruptured can release the
considerable amount of gas into the air. So, it may pose harm for living beings humans under
some particular circumstances. Therefore, considering this fact that certain regions of the earth,
like EU (European Union), are characterized through a high population density. Along with this,
if amount of CO2 capture the sites which are located near cities with existing regulations, needs
to be strengthened to route high-pressure pipelines away from buildings and dwellings.
Moreover, care must be taken to significantly reduce the impurities content in the CO2 stream
that can pose injury or harm to humans, such as H2S. In this sense, CO2 transport pipelines must
be buried deep enough to prevent digging equipment from reaching them. Furthermore, crack
arrestors should be fitted in CO2 pipelines and, for urban transit pipelines, a pressure release
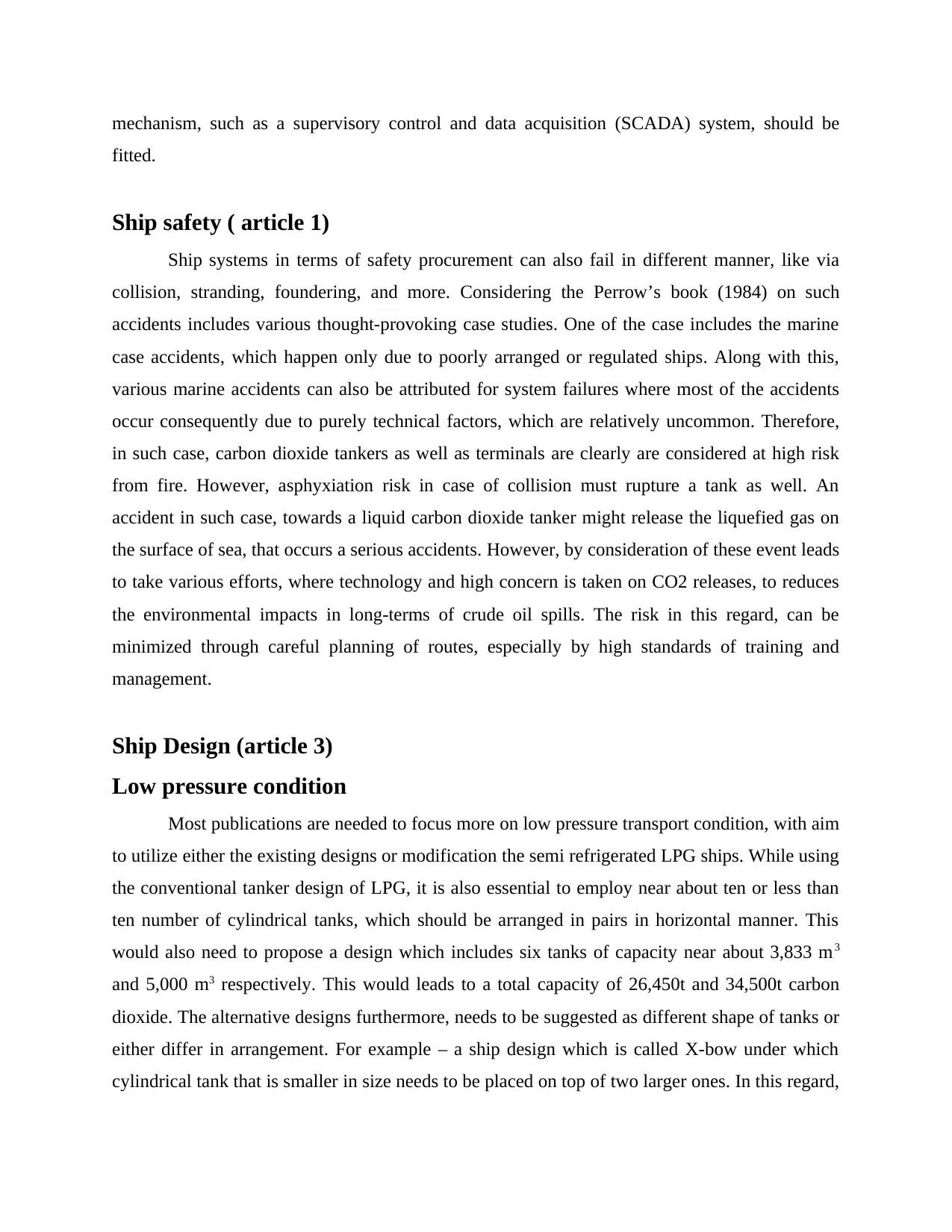
mechanism, such as a supervisory control and data acquisition (SCADA) system, should be
fitted.
Ship safety ( article 1)
Ship systems in terms of safety procurement can also fail in different manner, like via
collision, stranding, foundering, and more. Considering the Perrow’s book (1984) on such
accidents includes various thought-provoking case studies. One of the case includes the marine
case accidents, which happen only due to poorly arranged or regulated ships. Along with this,
various marine accidents can also be attributed for system failures where most of the accidents
occur consequently due to purely technical factors, which are relatively uncommon. Therefore,
in such case, carbon dioxide tankers as well as terminals are clearly are considered at high risk
from fire. However, asphyxiation risk in case of collision must rupture a tank as well. An
accident in such case, towards a liquid carbon dioxide tanker might release the liquefied gas on
the surface of sea, that occurs a serious accidents. However, by consideration of these event leads
to take various efforts, where technology and high concern is taken on CO2 releases, to reduces
the environmental impacts in long-terms of crude oil spills. The risk in this regard, can be
minimized through careful planning of routes, especially by high standards of training and
management.
Ship Design (article 3)
Low pressure condition
Most publications are needed to focus more on low pressure transport condition, with aim
to utilize either the existing designs or modification the semi refrigerated LPG ships. While using
the conventional tanker design of LPG, it is also essential to employ near about ten or less than
ten number of cylindrical tanks, which should be arranged in pairs in horizontal manner. This
would also need to propose a design which includes six tanks of capacity near about 3,833 m3
and 5,000 m3 respectively. This would leads to a total capacity of 26,450t and 34,500t carbon
dioxide. The alternative designs furthermore, needs to be suggested as different shape of tanks or
either differ in arrangement. For example – a ship design which is called X-bow under which
cylindrical tank that is smaller in size needs to be placed on top of two larger ones. In this regard,
fitted.
Ship safety ( article 1)
Ship systems in terms of safety procurement can also fail in different manner, like via
collision, stranding, foundering, and more. Considering the Perrow’s book (1984) on such
accidents includes various thought-provoking case studies. One of the case includes the marine
case accidents, which happen only due to poorly arranged or regulated ships. Along with this,
various marine accidents can also be attributed for system failures where most of the accidents
occur consequently due to purely technical factors, which are relatively uncommon. Therefore,
in such case, carbon dioxide tankers as well as terminals are clearly are considered at high risk
from fire. However, asphyxiation risk in case of collision must rupture a tank as well. An
accident in such case, towards a liquid carbon dioxide tanker might release the liquefied gas on
the surface of sea, that occurs a serious accidents. However, by consideration of these event leads
to take various efforts, where technology and high concern is taken on CO2 releases, to reduces
the environmental impacts in long-terms of crude oil spills. The risk in this regard, can be
minimized through careful planning of routes, especially by high standards of training and
management.
Ship Design (article 3)
Low pressure condition
Most publications are needed to focus more on low pressure transport condition, with aim
to utilize either the existing designs or modification the semi refrigerated LPG ships. While using
the conventional tanker design of LPG, it is also essential to employ near about ten or less than
ten number of cylindrical tanks, which should be arranged in pairs in horizontal manner. This
would also need to propose a design which includes six tanks of capacity near about 3,833 m3
and 5,000 m3 respectively. This would leads to a total capacity of 26,450t and 34,500t carbon
dioxide. The alternative designs furthermore, needs to be suggested as different shape of tanks or
either differ in arrangement. For example – a ship design which is called X-bow under which
cylindrical tank that is smaller in size needs to be placed on top of two larger ones. In this regard,
Paraphrase This Document
Need a fresh take? Get an instant paraphrase of this document with our AI Paraphraser
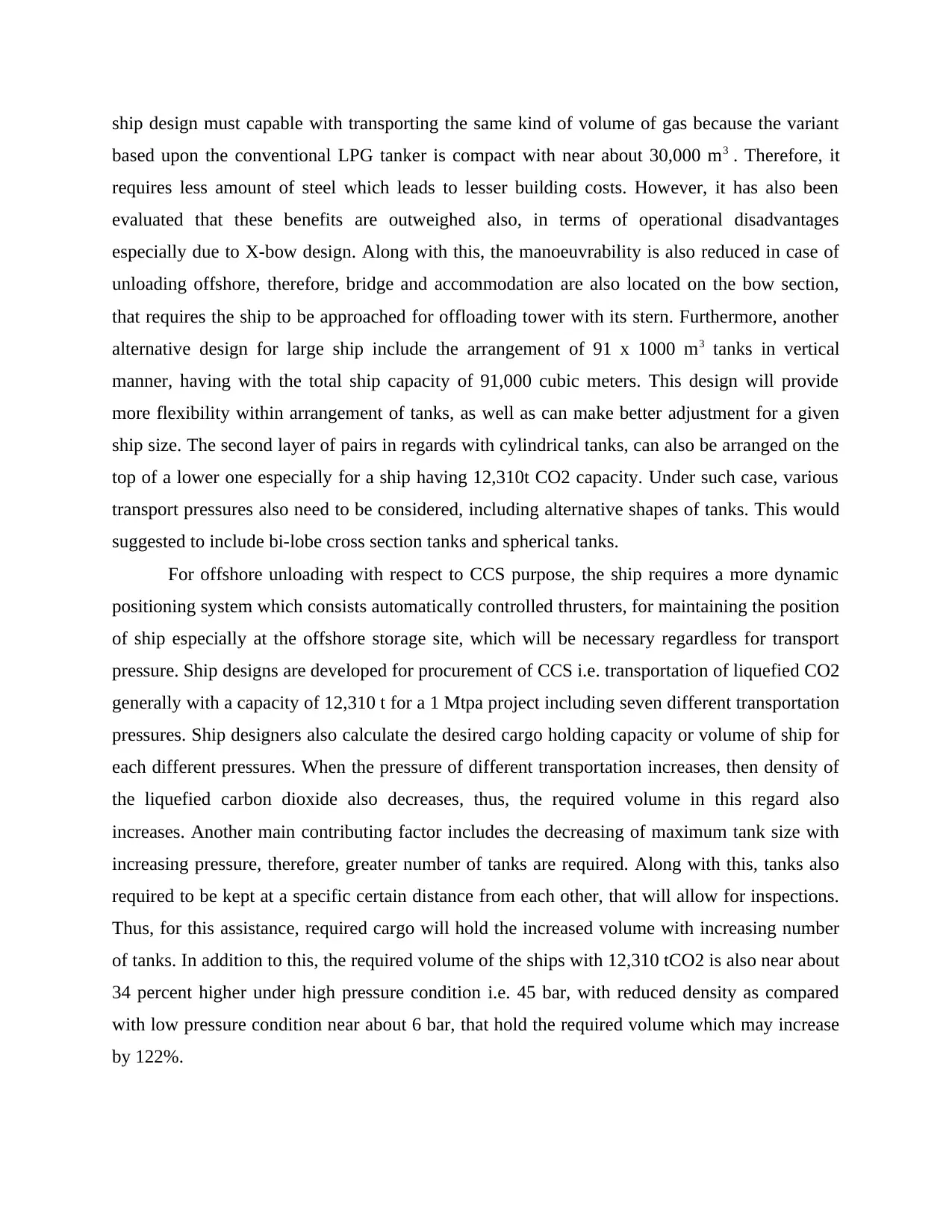
ship design must capable with transporting the same kind of volume of gas because the variant
based upon the conventional LPG tanker is compact with near about 30,000 m3 . Therefore, it
requires less amount of steel which leads to lesser building costs. However, it has also been
evaluated that these benefits are outweighed also, in terms of operational disadvantages
especially due to X-bow design. Along with this, the manoeuvrability is also reduced in case of
unloading offshore, therefore, bridge and accommodation are also located on the bow section,
that requires the ship to be approached for offloading tower with its stern. Furthermore, another
alternative design for large ship include the arrangement of 91 x 1000 m3 tanks in vertical
manner, having with the total ship capacity of 91,000 cubic meters. This design will provide
more flexibility within arrangement of tanks, as well as can make better adjustment for a given
ship size. The second layer of pairs in regards with cylindrical tanks, can also be arranged on the
top of a lower one especially for a ship having 12,310t CO2 capacity. Under such case, various
transport pressures also need to be considered, including alternative shapes of tanks. This would
suggested to include bi-lobe cross section tanks and spherical tanks.
For offshore unloading with respect to CCS purpose, the ship requires a more dynamic
positioning system which consists automatically controlled thrusters, for maintaining the position
of ship especially at the offshore storage site, which will be necessary regardless for transport
pressure. Ship designs are developed for procurement of CCS i.e. transportation of liquefied CO2
generally with a capacity of 12,310 t for a 1 Mtpa project including seven different transportation
pressures. Ship designers also calculate the desired cargo holding capacity or volume of ship for
each different pressures. When the pressure of different transportation increases, then density of
the liquefied carbon dioxide also decreases, thus, the required volume in this regard also
increases. Another main contributing factor includes the decreasing of maximum tank size with
increasing pressure, therefore, greater number of tanks are required. Along with this, tanks also
required to be kept at a specific certain distance from each other, that will allow for inspections.
Thus, for this assistance, required cargo will hold the increased volume with increasing number
of tanks. In addition to this, the required volume of the ships with 12,310 tCO2 is also near about
34 percent higher under high pressure condition i.e. 45 bar, with reduced density as compared
with low pressure condition near about 6 bar, that hold the required volume which may increase
by 122%.
based upon the conventional LPG tanker is compact with near about 30,000 m3 . Therefore, it
requires less amount of steel which leads to lesser building costs. However, it has also been
evaluated that these benefits are outweighed also, in terms of operational disadvantages
especially due to X-bow design. Along with this, the manoeuvrability is also reduced in case of
unloading offshore, therefore, bridge and accommodation are also located on the bow section,
that requires the ship to be approached for offloading tower with its stern. Furthermore, another
alternative design for large ship include the arrangement of 91 x 1000 m3 tanks in vertical
manner, having with the total ship capacity of 91,000 cubic meters. This design will provide
more flexibility within arrangement of tanks, as well as can make better adjustment for a given
ship size. The second layer of pairs in regards with cylindrical tanks, can also be arranged on the
top of a lower one especially for a ship having 12,310t CO2 capacity. Under such case, various
transport pressures also need to be considered, including alternative shapes of tanks. This would
suggested to include bi-lobe cross section tanks and spherical tanks.
For offshore unloading with respect to CCS purpose, the ship requires a more dynamic
positioning system which consists automatically controlled thrusters, for maintaining the position
of ship especially at the offshore storage site, which will be necessary regardless for transport
pressure. Ship designs are developed for procurement of CCS i.e. transportation of liquefied CO2
generally with a capacity of 12,310 t for a 1 Mtpa project including seven different transportation
pressures. Ship designers also calculate the desired cargo holding capacity or volume of ship for
each different pressures. When the pressure of different transportation increases, then density of
the liquefied carbon dioxide also decreases, thus, the required volume in this regard also
increases. Another main contributing factor includes the decreasing of maximum tank size with
increasing pressure, therefore, greater number of tanks are required. Along with this, tanks also
required to be kept at a specific certain distance from each other, that will allow for inspections.
Thus, for this assistance, required cargo will hold the increased volume with increasing number
of tanks. In addition to this, the required volume of the ships with 12,310 tCO2 is also near about
34 percent higher under high pressure condition i.e. 45 bar, with reduced density as compared
with low pressure condition near about 6 bar, that hold the required volume which may increase
by 122%.
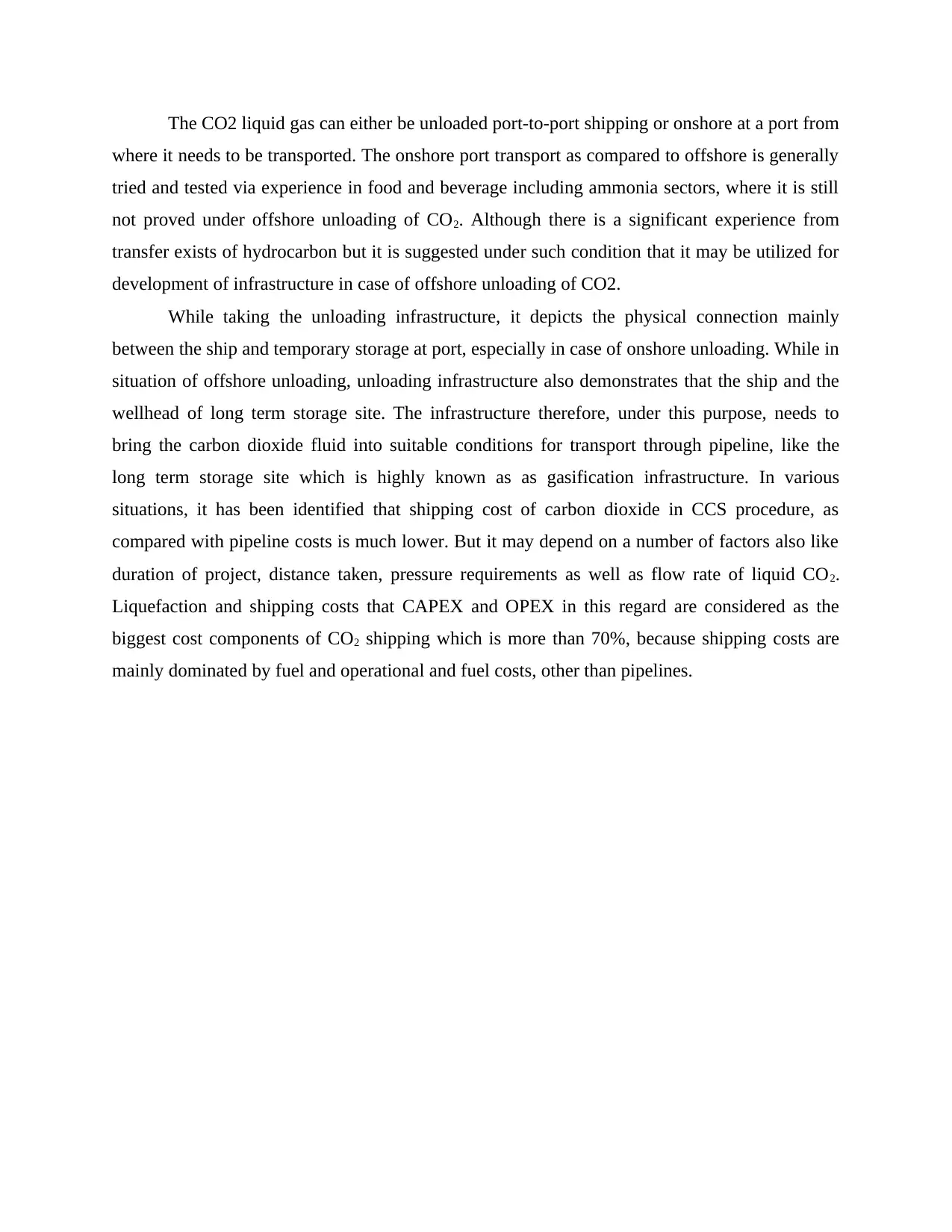
The CO2 liquid gas can either be unloaded port-to-port shipping or onshore at a port from
where it needs to be transported. The onshore port transport as compared to offshore is generally
tried and tested via experience in food and beverage including ammonia sectors, where it is still
not proved under offshore unloading of CO2. Although there is a significant experience from
transfer exists of hydrocarbon but it is suggested under such condition that it may be utilized for
development of infrastructure in case of offshore unloading of CO2.
While taking the unloading infrastructure, it depicts the physical connection mainly
between the ship and temporary storage at port, especially in case of onshore unloading. While in
situation of offshore unloading, unloading infrastructure also demonstrates that the ship and the
wellhead of long term storage site. The infrastructure therefore, under this purpose, needs to
bring the carbon dioxide fluid into suitable conditions for transport through pipeline, like the
long term storage site which is highly known as as gasification infrastructure. In various
situations, it has been identified that shipping cost of carbon dioxide in CCS procedure, as
compared with pipeline costs is much lower. But it may depend on a number of factors also like
duration of project, distance taken, pressure requirements as well as flow rate of liquid CO2.
Liquefaction and shipping costs that CAPEX and OPEX in this regard are considered as the
biggest cost components of CO2 shipping which is more than 70%, because shipping costs are
mainly dominated by fuel and operational and fuel costs, other than pipelines.
where it needs to be transported. The onshore port transport as compared to offshore is generally
tried and tested via experience in food and beverage including ammonia sectors, where it is still
not proved under offshore unloading of CO2. Although there is a significant experience from
transfer exists of hydrocarbon but it is suggested under such condition that it may be utilized for
development of infrastructure in case of offshore unloading of CO2.
While taking the unloading infrastructure, it depicts the physical connection mainly
between the ship and temporary storage at port, especially in case of onshore unloading. While in
situation of offshore unloading, unloading infrastructure also demonstrates that the ship and the
wellhead of long term storage site. The infrastructure therefore, under this purpose, needs to
bring the carbon dioxide fluid into suitable conditions for transport through pipeline, like the
long term storage site which is highly known as as gasification infrastructure. In various
situations, it has been identified that shipping cost of carbon dioxide in CCS procedure, as
compared with pipeline costs is much lower. But it may depend on a number of factors also like
duration of project, distance taken, pressure requirements as well as flow rate of liquid CO2.
Liquefaction and shipping costs that CAPEX and OPEX in this regard are considered as the
biggest cost components of CO2 shipping which is more than 70%, because shipping costs are
mainly dominated by fuel and operational and fuel costs, other than pipelines.
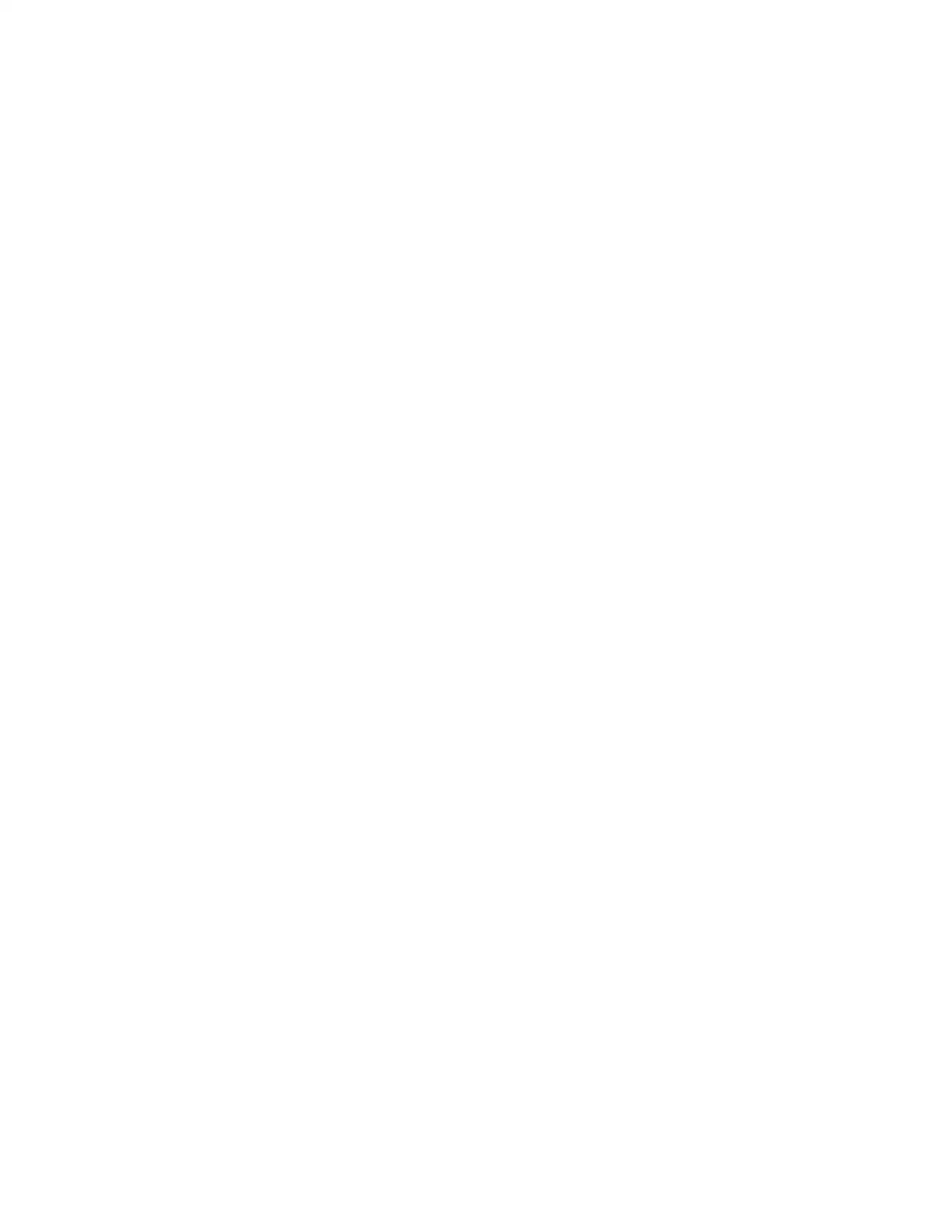
Secure Best Marks with AI Grader
Need help grading? Try our AI Grader for instant feedback on your assignments.
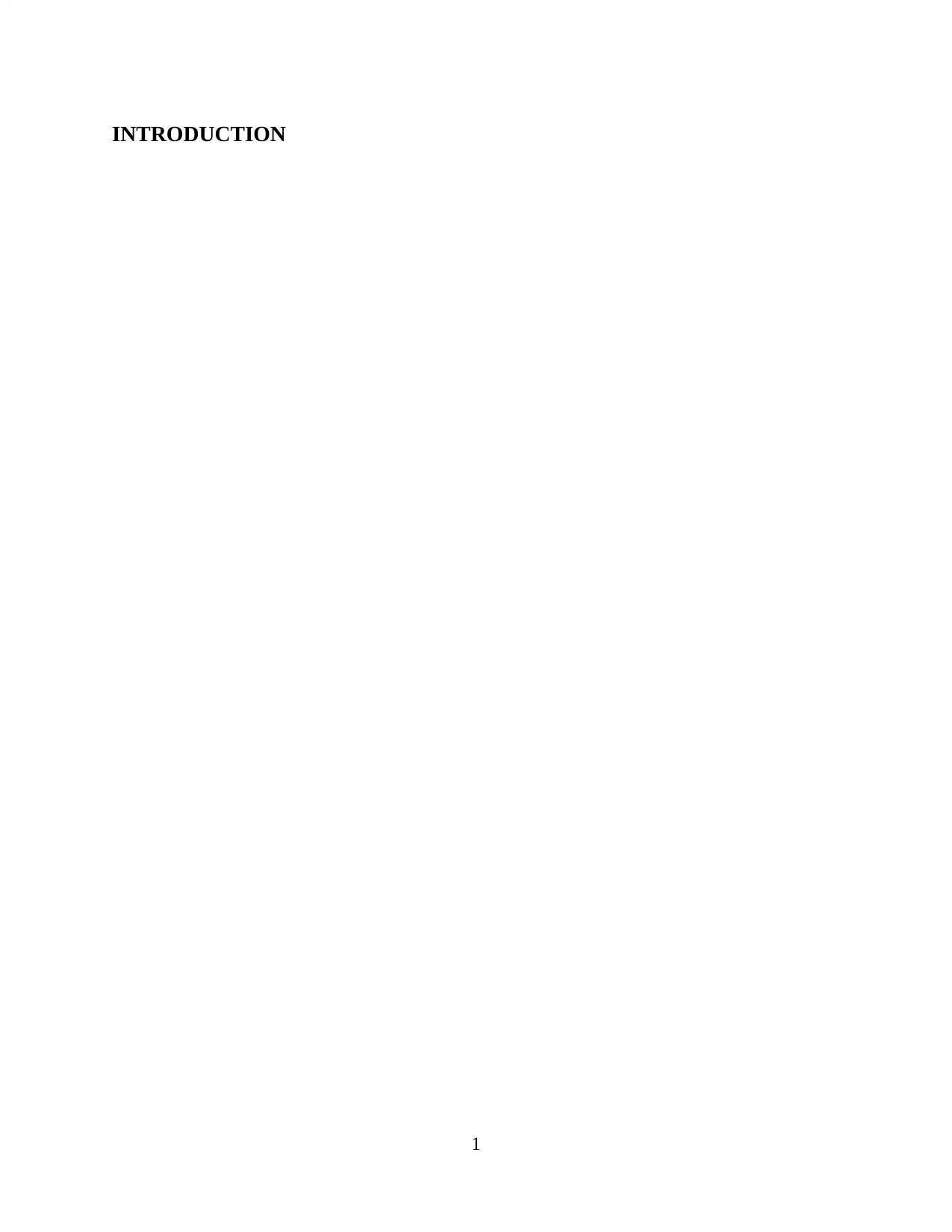
INTRODUCTION
1
1
1 out of 11
![[object Object]](/_next/image/?url=%2F_next%2Fstatic%2Fmedia%2Flogo.6d15ce61.png&w=640&q=75)
Your All-in-One AI-Powered Toolkit for Academic Success.
+13062052269
info@desklib.com
Available 24*7 on WhatsApp / Email
Unlock your academic potential
© 2024 | Zucol Services PVT LTD | All rights reserved.