Performance Analysis of a Combustion Engine (4 Stroke)
Added on 2022-12-02
26 Pages10560 Words268 Views
Performance analysis of a combustion engine (4 stroke)
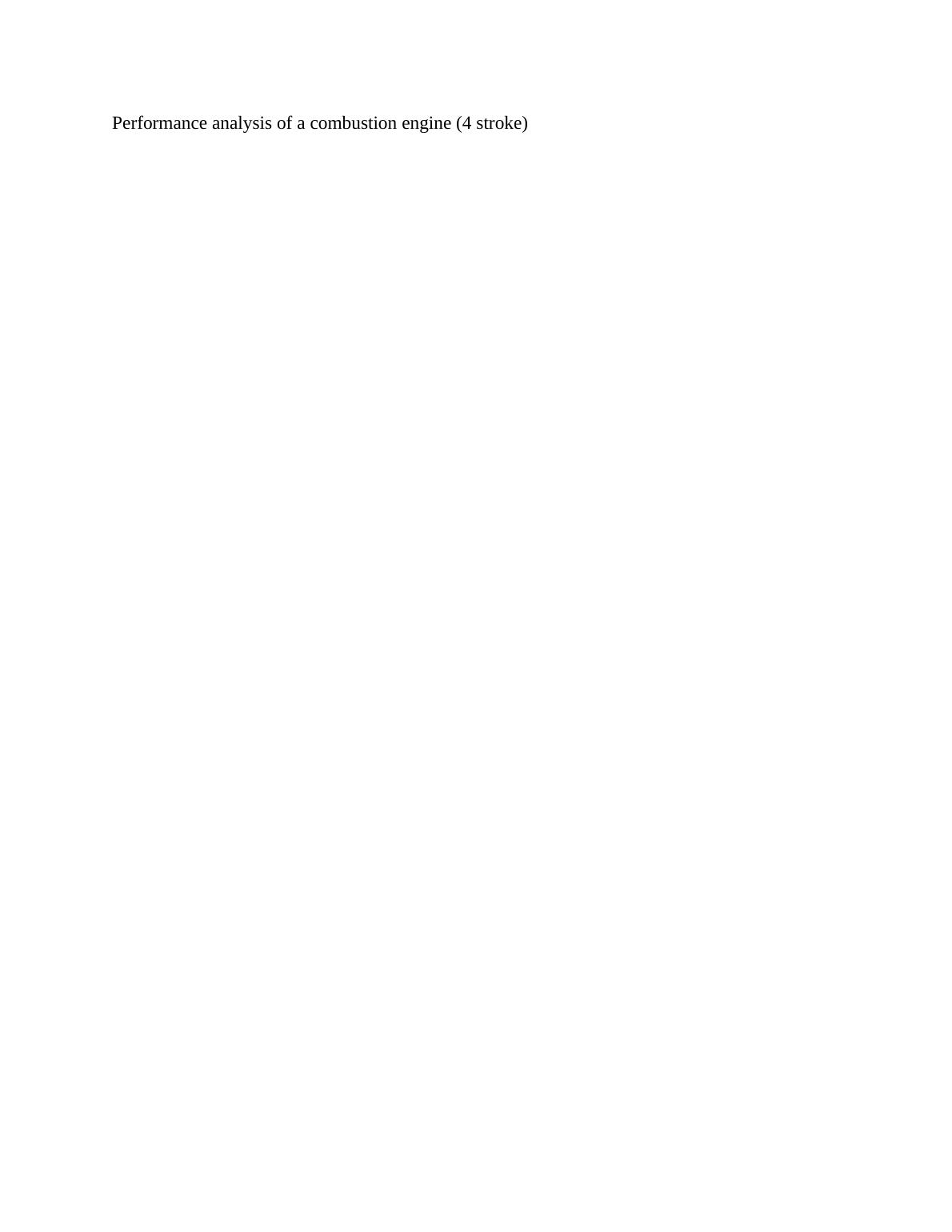
Contents
Abstract.......................................................................................................................................................3
Acknowledgements.....................................................................................................................................3
1.0 Introduction...........................................................................................................................................3
1.1 Technical background........................................................................................................................4
1.1 Literature review..........................................................................................................................4
1.2 Aims and objectives.....................................................................................................................8
2.0 performance analysis.............................................................................................................................8
2. 1 Comparison of air fuel ratio............................................................................................................12
2.2 Experiment setup.............................................................................................................................16
3. results and discussion............................................................................................................................19
4.0 conclusion............................................................................................................................................20
4.1 Future work.....................................................................................................................................21
References.............................................................................................................................................23
Figure 1 inside a 4 stroke Engine - image credits to (Dumitrache, 2019)....................................................7
Figure 2 bottom view of the Engine block. The cylinders, oil spray nozzle and half of the main bearings
can easily be identified................................................................................................................................8
Figure 3 a graph of speed verses load showing pressure iterations of an Engine.......................................10
Figure 4 comparing torque performances..................................................................................................11
Figure 5 a graph showing the effiect of compresion ratio in an Engine.....................................................12
Figure 6 a diagram showing the power engine variance at different compression ratios...........................12
Table 1fuel charachterictics.......................................................................................................................19
Table 2 experiment model.........................................................................................................................19
Abstract
The popularity of internal combustion engines such as petrol and diesel engines stem from the
combined elevated take level and low energy consumption of their appealing conducting
capacity. The crucial function of these features has resulted to the growth of charger technology,
which has resulted in significant power density and a significant rise in efficient stress.
Consequently, the purpose is to characterize and parameterize the output of internal combustion
Abstract.......................................................................................................................................................3
Acknowledgements.....................................................................................................................................3
1.0 Introduction...........................................................................................................................................3
1.1 Technical background........................................................................................................................4
1.1 Literature review..........................................................................................................................4
1.2 Aims and objectives.....................................................................................................................8
2.0 performance analysis.............................................................................................................................8
2. 1 Comparison of air fuel ratio............................................................................................................12
2.2 Experiment setup.............................................................................................................................16
3. results and discussion............................................................................................................................19
4.0 conclusion............................................................................................................................................20
4.1 Future work.....................................................................................................................................21
References.............................................................................................................................................23
Figure 1 inside a 4 stroke Engine - image credits to (Dumitrache, 2019)....................................................7
Figure 2 bottom view of the Engine block. The cylinders, oil spray nozzle and half of the main bearings
can easily be identified................................................................................................................................8
Figure 3 a graph of speed verses load showing pressure iterations of an Engine.......................................10
Figure 4 comparing torque performances..................................................................................................11
Figure 5 a graph showing the effiect of compresion ratio in an Engine.....................................................12
Figure 6 a diagram showing the power engine variance at different compression ratios...........................12
Table 1fuel charachterictics.......................................................................................................................19
Table 2 experiment model.........................................................................................................................19
Abstract
The popularity of internal combustion engines such as petrol and diesel engines stem from the
combined elevated take level and low energy consumption of their appealing conducting
capacity. The crucial function of these features has resulted to the growth of charger technology,
which has resulted in significant power density and a significant rise in efficient stress.
Consequently, the purpose is to characterize and parameterize the output of internal combustion
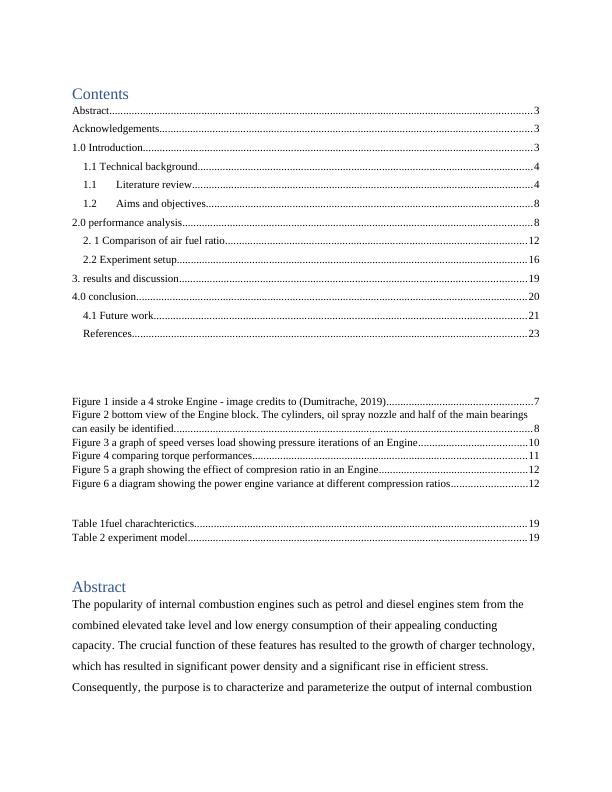
enginery in order to study the reasons and impacts that determine the functionality of the IC
engine.
Acknowledgements
1.0 Introduction
The internal combustion engine (ICE) is a thermal motor in which a petrol combustion takes
place in the combustion chamber with an oxidizer (typically air) that is component and parcel of
the operating stream loop. The extension of high temperature and high-pressure gases generated
by combustion in an internal combustion engine adds immediate power to a certain engine
element. Typically, the force is introduced to pistons, blades, rotors or a piston. This force
transforms the element into helpful mechanical energy through the range.
Energy is the fundamental requirement for any country's economic development. A number of
indispensable tasks are to be stopped when the energy supply ends. As a result, the real extent of
the role played by electricity in the construction of the advanced countries can be virtually
difficult to evaluate, resulting in longer operating hours, increased agriculture and industrial
manufacturing, healthier and more balanced lives.
Indeed, the energy used per individual is closely related to his living standards. The higher a
country's precipitate energy consumption, the higher its people live standards. The elevated
demographic growth level and rapidly evolving way of life have changed significantly and
gradually in the industry and transport industry. As a result, the consumption of oil derivatives
has risen to a high degree, which is much greater than appreciated.
The piston's highest dead centre (TDC) is the place closest to the pumps; the lowest dead zone
(BDC) is on the reverse end. The motion, in conjunction with the related method, of a piston
from a TDC to a BDC is a stroke. The crank shaft rotates at an almost steady velocity while an
engine is in service. Each piston gets two kicks, in the following order, in a 4-stroke ICE.
1.1 Technical background
An internal combustion engine is a four-stroke cycle motor which uses four separate piston strokes for a
single working cycle (take-in, compression, energy and exhaust). The piston completes a single operating
cycle in two full cylinder passes. Two revolutions (720 °) of the crankshaft are required for an operational
cycle. The four-cycle engine is the smaller engine's most prevalent form. In addition to input,
engine.
Acknowledgements
1.0 Introduction
The internal combustion engine (ICE) is a thermal motor in which a petrol combustion takes
place in the combustion chamber with an oxidizer (typically air) that is component and parcel of
the operating stream loop. The extension of high temperature and high-pressure gases generated
by combustion in an internal combustion engine adds immediate power to a certain engine
element. Typically, the force is introduced to pistons, blades, rotors or a piston. This force
transforms the element into helpful mechanical energy through the range.
Energy is the fundamental requirement for any country's economic development. A number of
indispensable tasks are to be stopped when the energy supply ends. As a result, the real extent of
the role played by electricity in the construction of the advanced countries can be virtually
difficult to evaluate, resulting in longer operating hours, increased agriculture and industrial
manufacturing, healthier and more balanced lives.
Indeed, the energy used per individual is closely related to his living standards. The higher a
country's precipitate energy consumption, the higher its people live standards. The elevated
demographic growth level and rapidly evolving way of life have changed significantly and
gradually in the industry and transport industry. As a result, the consumption of oil derivatives
has risen to a high degree, which is much greater than appreciated.
The piston's highest dead centre (TDC) is the place closest to the pumps; the lowest dead zone
(BDC) is on the reverse end. The motion, in conjunction with the related method, of a piston
from a TDC to a BDC is a stroke. The crank shaft rotates at an almost steady velocity while an
engine is in service. Each piston gets two kicks, in the following order, in a 4-stroke ICE.
1.1 Technical background
An internal combustion engine is a four-stroke cycle motor which uses four separate piston strokes for a
single working cycle (take-in, compression, energy and exhaust). The piston completes a single operating
cycle in two full cylinder passes. Two revolutions (720 °) of the crankshaft are required for an operational
cycle. The four-cycle engine is the smaller engine's most prevalent form. In addition to input,
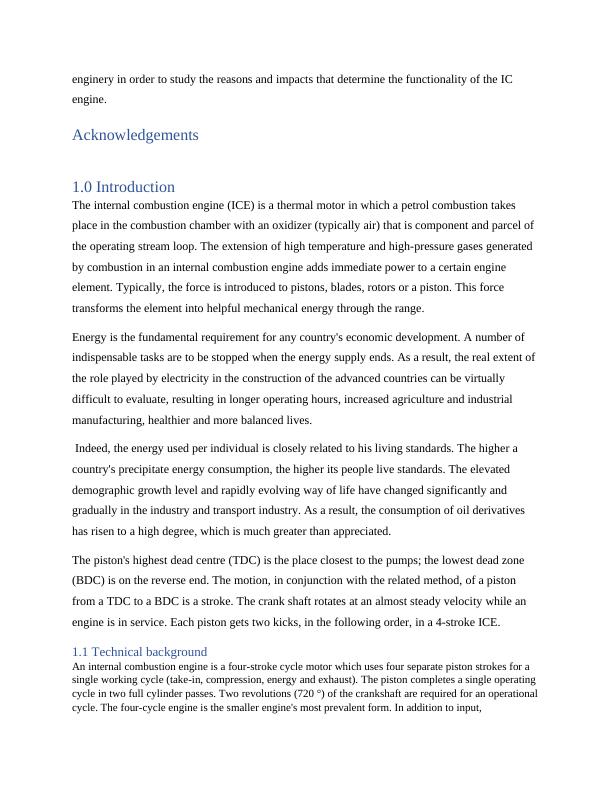
compression, ignition, energy and exhaust strokes, the four-stroke cycle motor completes five strokes in a
single working cycle.
The intake incident occurs when the combustion chamber is filled with an air-fuel blend. When the piston
passes from TDC to BDC, the intake activity takes place, and the intake valve is open. The piston motion
to BDC causes a small cylinder pressure. Atmospheric stress forces the air / fuel combination to fill the
low-pressure region generated by piston motion through the open intake valve into the engine. As the air-
fuel-mix continues to run through its own inertia while the piston started to alter direction, the cylinders
still fill slightly past BDC. The intake valve is still open a few degrees after BDC. The layout depends on
the motor.
A few degrees of crankshaft rotation after BDC remain open for the intake Valve. Depending on the
layout of the motor. The valve of intake is then shut and the combination of air and fuel inside the
cylinder is closed.
A compression stroke happens when the air-fuel blend is pulled into the cylinder. The room is screened
for load forming. The charge is the quantity of the blend of air and fuel that is trapped inside the
incinerator chamber. The compression of the air-to-fuel mixture allows more energy to be released when
charges are fired. For compression sealing of cylinders, the intake and exhaust valves must be closed.
Compression is the method by which the charge is reduced or reduced in the combustion chamber from a
big volume to a lower volume. The flywheel keeps the momentum needed to reduce the load.
The present prominence of inward ignition motors, for example, gas and diesel motors, begins
from the mix of their appealing driving exhibition because of high toque levels and low fuel
utilization. The unequivocal job of these attributes has prompted the advancement of charger
innovation, bringing about a surprising increment in power thickness and mean viable weight.
Turbo charging innovation has been broadly utilized in motors for various applications, going
from little vehicles to enormous marine vessels, on account of its specialized points of interest,
for example, no interest for driving force from the motor and magnificent charging impacts
during sac task at mid to high motor rates. Be that as it may, there is a reaction time delay,
particularly for traveller vehicle turbochargers, which can be tricky since witticism driving is
done under downtown conditions at mid to low motor velocities bringing about a "turbo slack"
when there is abrupt acceleration[6].In late years, the engine vehicle industry goes for the little
estimated and high power thickness motor, while cutting back (little size and weight sparing) and
estimating the improvement in fuel utilization, and canalization.
When the engine piston compresses the load, increased compressive force from the job of the
piston generates heat. The compression and heating of air-fuel vapor in the load increases the
load temperature and the vaporisation of the oil. The load temperature increases consistently in
single working cycle.
The intake incident occurs when the combustion chamber is filled with an air-fuel blend. When the piston
passes from TDC to BDC, the intake activity takes place, and the intake valve is open. The piston motion
to BDC causes a small cylinder pressure. Atmospheric stress forces the air / fuel combination to fill the
low-pressure region generated by piston motion through the open intake valve into the engine. As the air-
fuel-mix continues to run through its own inertia while the piston started to alter direction, the cylinders
still fill slightly past BDC. The intake valve is still open a few degrees after BDC. The layout depends on
the motor.
A few degrees of crankshaft rotation after BDC remain open for the intake Valve. Depending on the
layout of the motor. The valve of intake is then shut and the combination of air and fuel inside the
cylinder is closed.
A compression stroke happens when the air-fuel blend is pulled into the cylinder. The room is screened
for load forming. The charge is the quantity of the blend of air and fuel that is trapped inside the
incinerator chamber. The compression of the air-to-fuel mixture allows more energy to be released when
charges are fired. For compression sealing of cylinders, the intake and exhaust valves must be closed.
Compression is the method by which the charge is reduced or reduced in the combustion chamber from a
big volume to a lower volume. The flywheel keeps the momentum needed to reduce the load.
The present prominence of inward ignition motors, for example, gas and diesel motors, begins
from the mix of their appealing driving exhibition because of high toque levels and low fuel
utilization. The unequivocal job of these attributes has prompted the advancement of charger
innovation, bringing about a surprising increment in power thickness and mean viable weight.
Turbo charging innovation has been broadly utilized in motors for various applications, going
from little vehicles to enormous marine vessels, on account of its specialized points of interest,
for example, no interest for driving force from the motor and magnificent charging impacts
during sac task at mid to high motor rates. Be that as it may, there is a reaction time delay,
particularly for traveller vehicle turbochargers, which can be tricky since witticism driving is
done under downtown conditions at mid to low motor velocities bringing about a "turbo slack"
when there is abrupt acceleration[6].In late years, the engine vehicle industry goes for the little
estimated and high power thickness motor, while cutting back (little size and weight sparing) and
estimating the improvement in fuel utilization, and canalization.
When the engine piston compresses the load, increased compressive force from the job of the
piston generates heat. The compression and heating of air-fuel vapor in the load increases the
load temperature and the vaporisation of the oil. The load temperature increases consistently in
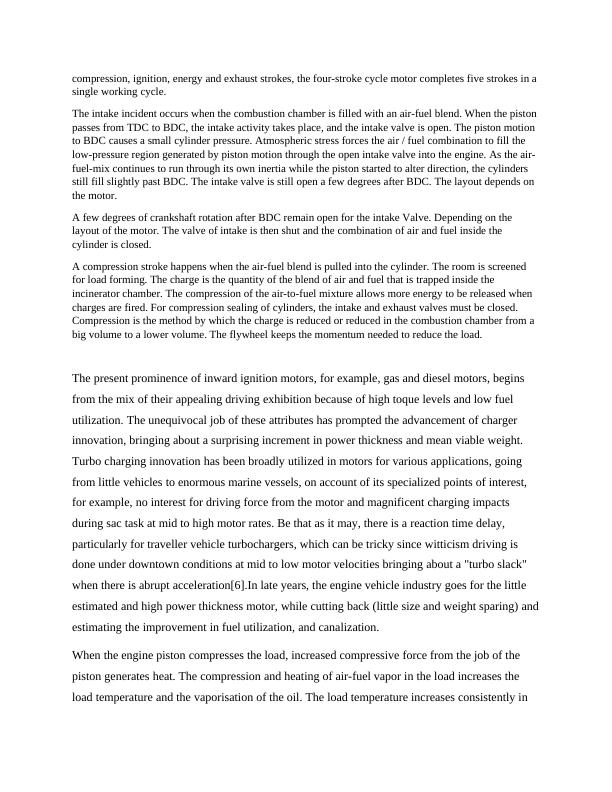
the entire combustion chamber to result in quicker (fuel oxidation) combustion after ignition.
The rise in fuel vaporization happens when tiny fuel droplets are more fully vaporized from heat.
The more atoms are placed in loading vapours, the more vitality the ignition process gained.
During the burning procedure, the vitality expected to pack the charge is not exactly the power
supplied. For example, the vitality required to pack up the cargo in a normal small motor is only
one-fourth the vitality measure generated during ignition.
The pressure ratio of an engine is a check of burning chamber quantity with the cylinder at BDC
to the inflammatory chamber quantity of the cylinder at TDC. The pressure ratio is determined in
this land, together with the burning chamber design and style. Gas engines usually have a
pressure ratio of 6:1 to 10:1. The greater the pressure, the greener the engine. In order to improve
the pressure ratio, burning weight or energy in the cylinders is usually important. Whatever the
case, greater pressure levels increase the manager's work to switch over the engine. Some small
engines include a weight-enhancing frame during the pressure stroke to reduce the manager's
effort needed to turn over the engine. When charging is removed and rapidly oxidized by
synthesis the beginning (burning) occurring occasion. response to discharge heat vitality.
Ignition is the fast, oxidizing concoction response in which a fuel artificially joins with oxygen in
the environment and discharges vitality as warmth.
Legitimate ignition encompasses a brief yet restricted time for a fire throughout the combustion
chamber. The flash starts to ignite with a crankshaft turn before TDC (BTDC) at around 20 °. A
progressing front of fire consumes the barometric oxygen and oil vapour. A burning front is the
boundary separator that isolates the charge from the outcomes of burning. The front of the fire
passes through the ignition chamber until the entire charge is consumed.
The power supply is an engine job Stroke where the cylinders are powered by warm gases far
away from the chamber head. The cylindrical force and subsequent motion are shifted to the
crankshaft through the associated bar to apply the torque. The linked torque begins to turn
crankshaft. The measurement of the supplied torque is governed by the weight of the cylinder,
the cylinder size and the engine toss. The two valves are closed during the power strike.
The rise in fuel vaporization happens when tiny fuel droplets are more fully vaporized from heat.
The more atoms are placed in loading vapours, the more vitality the ignition process gained.
During the burning procedure, the vitality expected to pack the charge is not exactly the power
supplied. For example, the vitality required to pack up the cargo in a normal small motor is only
one-fourth the vitality measure generated during ignition.
The pressure ratio of an engine is a check of burning chamber quantity with the cylinder at BDC
to the inflammatory chamber quantity of the cylinder at TDC. The pressure ratio is determined in
this land, together with the burning chamber design and style. Gas engines usually have a
pressure ratio of 6:1 to 10:1. The greater the pressure, the greener the engine. In order to improve
the pressure ratio, burning weight or energy in the cylinders is usually important. Whatever the
case, greater pressure levels increase the manager's work to switch over the engine. Some small
engines include a weight-enhancing frame during the pressure stroke to reduce the manager's
effort needed to turn over the engine. When charging is removed and rapidly oxidized by
synthesis the beginning (burning) occurring occasion. response to discharge heat vitality.
Ignition is the fast, oxidizing concoction response in which a fuel artificially joins with oxygen in
the environment and discharges vitality as warmth.
Legitimate ignition encompasses a brief yet restricted time for a fire throughout the combustion
chamber. The flash starts to ignite with a crankshaft turn before TDC (BTDC) at around 20 °. A
progressing front of fire consumes the barometric oxygen and oil vapour. A burning front is the
boundary separator that isolates the charge from the outcomes of burning. The front of the fire
passes through the ignition chamber until the entire charge is consumed.
The power supply is an engine job Stroke where the cylinders are powered by warm gases far
away from the chamber head. The cylindrical force and subsequent motion are shifted to the
crankshaft through the associated bar to apply the torque. The linked torque begins to turn
crankshaft. The measurement of the supplied torque is governed by the weight of the cylinder,
the cylinder size and the engine toss. The two valves are closed during the power strike.
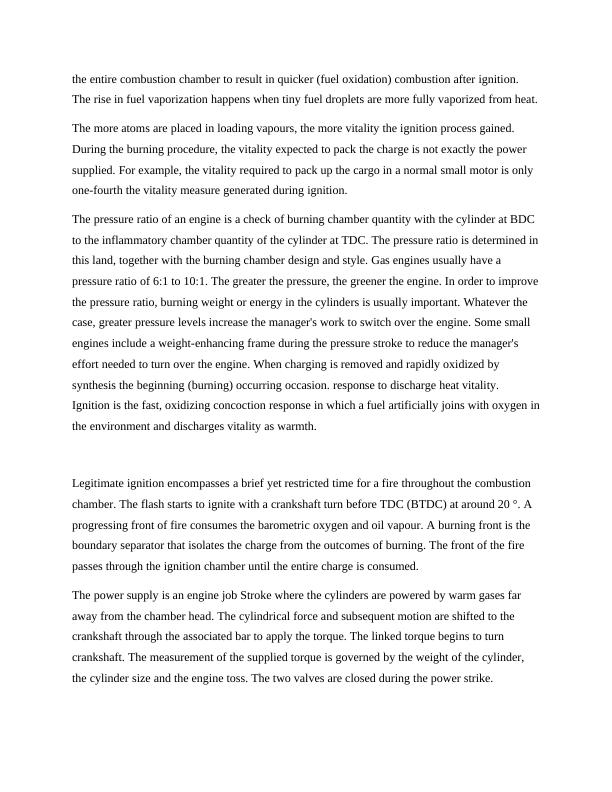
The stroke occurs when particulates are thrown away and discharged into the environment from
the ignition chamber. The stroke of fumes is the final stroke and occurs when the fume valve is
opened and the input valve is shut off. The growth of cylinder clears the atmosphere from fumes.
The cylinders arrive at BDC and the chamber is charged with smoke gas when the energy Stroke
ignition is completed. The smoke valve will be opened, and the flywheel and other moving parts
will push the cylinder back to TDC, limiting the gaseous fumes through the open fumes valve.
The cylinder is at TDC, and a working cycle is completed towards the completion of the stroke.
1.1 Literature review
For a diesel motor, fuel infusion weight (FIP) and infusion timings are significant parameters,
which impact the motor execution, discharges, and burning. Other infusion parameters
influencing motor execution are rate of infusion, infusion design, number of infusions and so on.
A solitary chamber inquire about motor was utilized to tentatively decide the impacts of fuel
infusion methodologies and infusion timings on motor burning, execution and outflow attributes.
The tests were led at steady speed (2500 rpm) with two FIPs (500 and 1000 bars individually)
and diverse beginning of infusion (SOI) timings. Chamber weight and rate of warmth discharge
(ROHR) were observed to be higher for lower FIPs anyway propelled infusion timings gave
higher ROHR in early ignition stages. Brake warm productivity (BTE) expanded with expanded
infusion weights while fumes gas temperature and brake mean successful weight (BMEP)
expanded up to 500 bars. These parameters decreased somewhat with increment in FIP.
Different researchers and specialists added to the advancement of inside burning motors. In
1791, John Barber built up the gas turbine. In 1794 Thomas Mead protected a gas motor.
Additionally, in 1794, Robert Street protected an inside burning motor, which was likewise the
first to utilize fluid fuel, and manufactured a motor around that time. In 1798, John Stevens
assembled the main American inside ignition motor. In 1807, French architects Nicephorus
Niepce (who proceeded to imagine photography) and Claude Niepce ran a model inner ignition
motor, utilizing controlled residue blasts, the Pyréolophore. This motor fuelled a pontoon on the
Saône waterway, France. That year, the Swiss designer François Isaac de Rivaz assembled an
inside burning motor touched off by an electric sparkle. In 1823, Samuel Brown protected the
primary interior burning motor to be connected mechanically.
In 1854 in the UK, the Italian innovators Eugenio Barsanti and Felice Matteucci acquired an
affirmation "Getting thought process control by the blast of gases". In 1857 the Great Seal Patent
Office surrendered them patent No.1655 for the innovation of an Improved Apparatus for
Obtaining Motive Power from Gases. In 1860, Belgium's Jean Joseph Etienne Lenoir supplied a
the ignition chamber. The stroke of fumes is the final stroke and occurs when the fume valve is
opened and the input valve is shut off. The growth of cylinder clears the atmosphere from fumes.
The cylinders arrive at BDC and the chamber is charged with smoke gas when the energy Stroke
ignition is completed. The smoke valve will be opened, and the flywheel and other moving parts
will push the cylinder back to TDC, limiting the gaseous fumes through the open fumes valve.
The cylinder is at TDC, and a working cycle is completed towards the completion of the stroke.
1.1 Literature review
For a diesel motor, fuel infusion weight (FIP) and infusion timings are significant parameters,
which impact the motor execution, discharges, and burning. Other infusion parameters
influencing motor execution are rate of infusion, infusion design, number of infusions and so on.
A solitary chamber inquire about motor was utilized to tentatively decide the impacts of fuel
infusion methodologies and infusion timings on motor burning, execution and outflow attributes.
The tests were led at steady speed (2500 rpm) with two FIPs (500 and 1000 bars individually)
and diverse beginning of infusion (SOI) timings. Chamber weight and rate of warmth discharge
(ROHR) were observed to be higher for lower FIPs anyway propelled infusion timings gave
higher ROHR in early ignition stages. Brake warm productivity (BTE) expanded with expanded
infusion weights while fumes gas temperature and brake mean successful weight (BMEP)
expanded up to 500 bars. These parameters decreased somewhat with increment in FIP.
Different researchers and specialists added to the advancement of inside burning motors. In
1791, John Barber built up the gas turbine. In 1794 Thomas Mead protected a gas motor.
Additionally, in 1794, Robert Street protected an inside burning motor, which was likewise the
first to utilize fluid fuel, and manufactured a motor around that time. In 1798, John Stevens
assembled the main American inside ignition motor. In 1807, French architects Nicephorus
Niepce (who proceeded to imagine photography) and Claude Niepce ran a model inner ignition
motor, utilizing controlled residue blasts, the Pyréolophore. This motor fuelled a pontoon on the
Saône waterway, France. That year, the Swiss designer François Isaac de Rivaz assembled an
inside burning motor touched off by an electric sparkle. In 1823, Samuel Brown protected the
primary interior burning motor to be connected mechanically.
In 1854 in the UK, the Italian innovators Eugenio Barsanti and Felice Matteucci acquired an
affirmation "Getting thought process control by the blast of gases". In 1857 the Great Seal Patent
Office surrendered them patent No.1655 for the innovation of an Improved Apparatus for
Obtaining Motive Power from Gases. In 1860, Belgium's Jean Joseph Etienne Lenoir supplied a
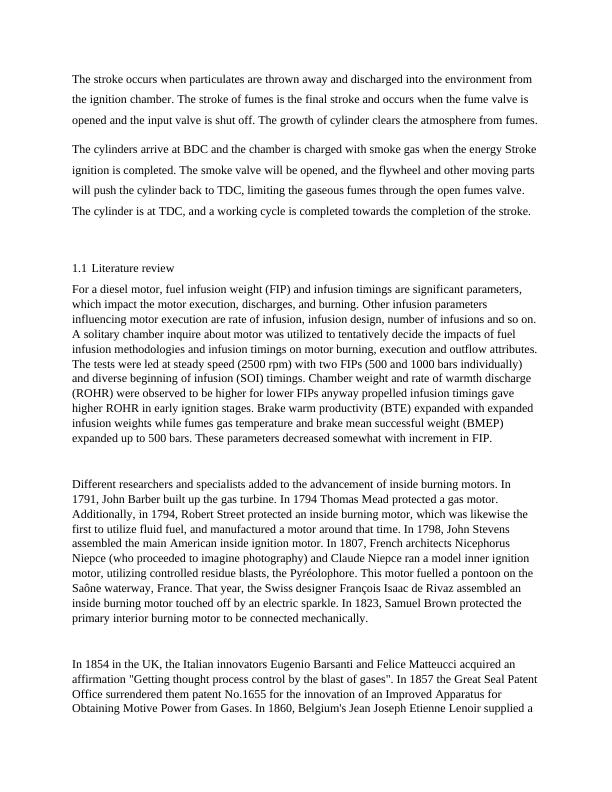
End of preview
Want to access all the pages? Upload your documents or become a member.
Related Documents
Thermodynamics: Four-Stroke and Two-Stroke Engineslg...
|12
|2732
|459
CFD Simulation of Air Movement Inside the Cylinder of an Internal Combustionlg...
|19
|4844
|295
Types of TEG Efficient Materialslg...
|69
|8656
|27