Performance Management: Costing, Variance Analysis, and Budgeting
VerifiedAdded on 2023/01/10
|12
|3217
|66
Homework Assignment
AI Summary
This document presents a comprehensive solution to a performance management assignment. The solution begins with an analysis of costing methods, including overhead absorption using labor hours and activity-based costing, along with an evaluation of the results. It then delves into variance a...
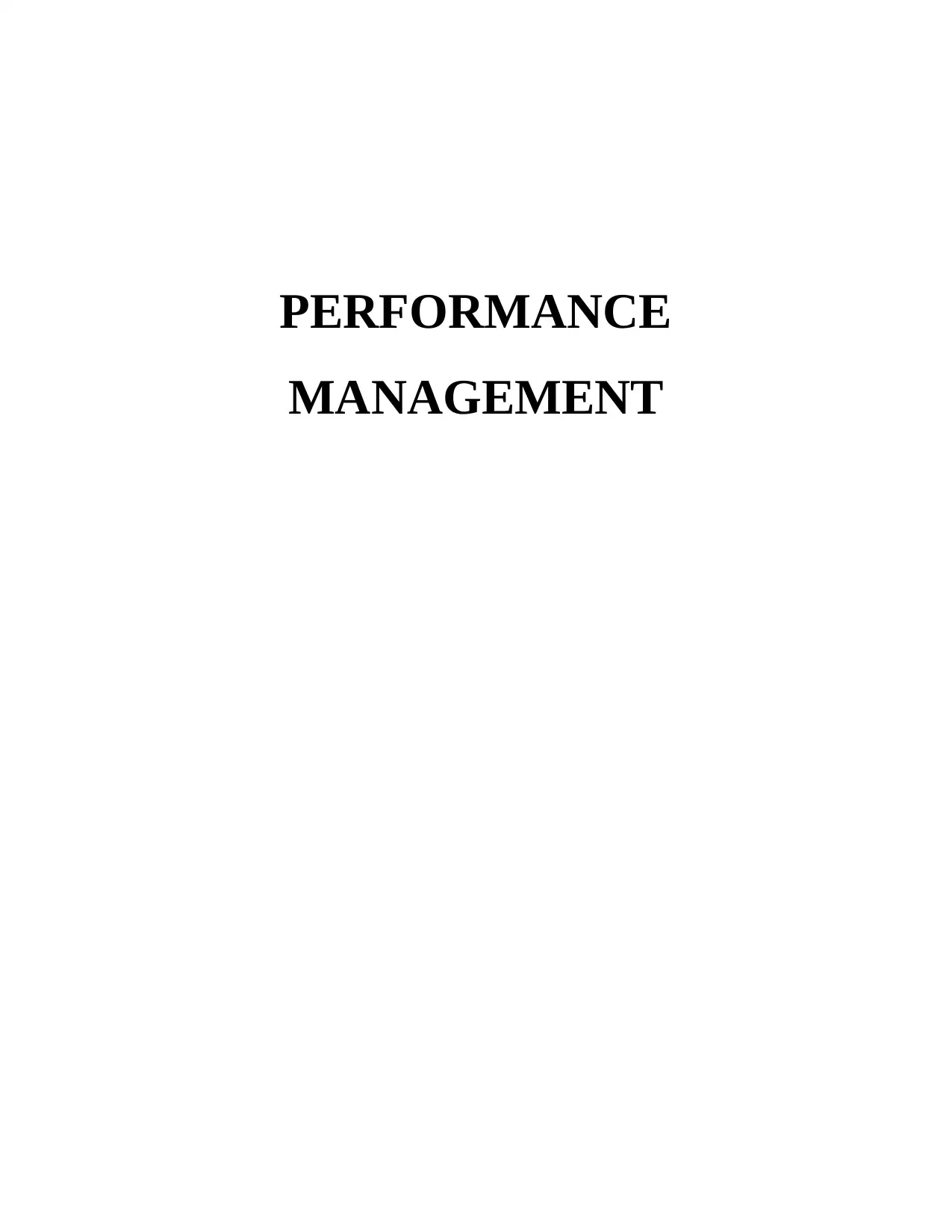
PERFORMANCE
MANAGEMENT
MANAGEMENT
Paraphrase This Document
Need a fresh take? Get an instant paraphrase of this document with our AI Paraphraser
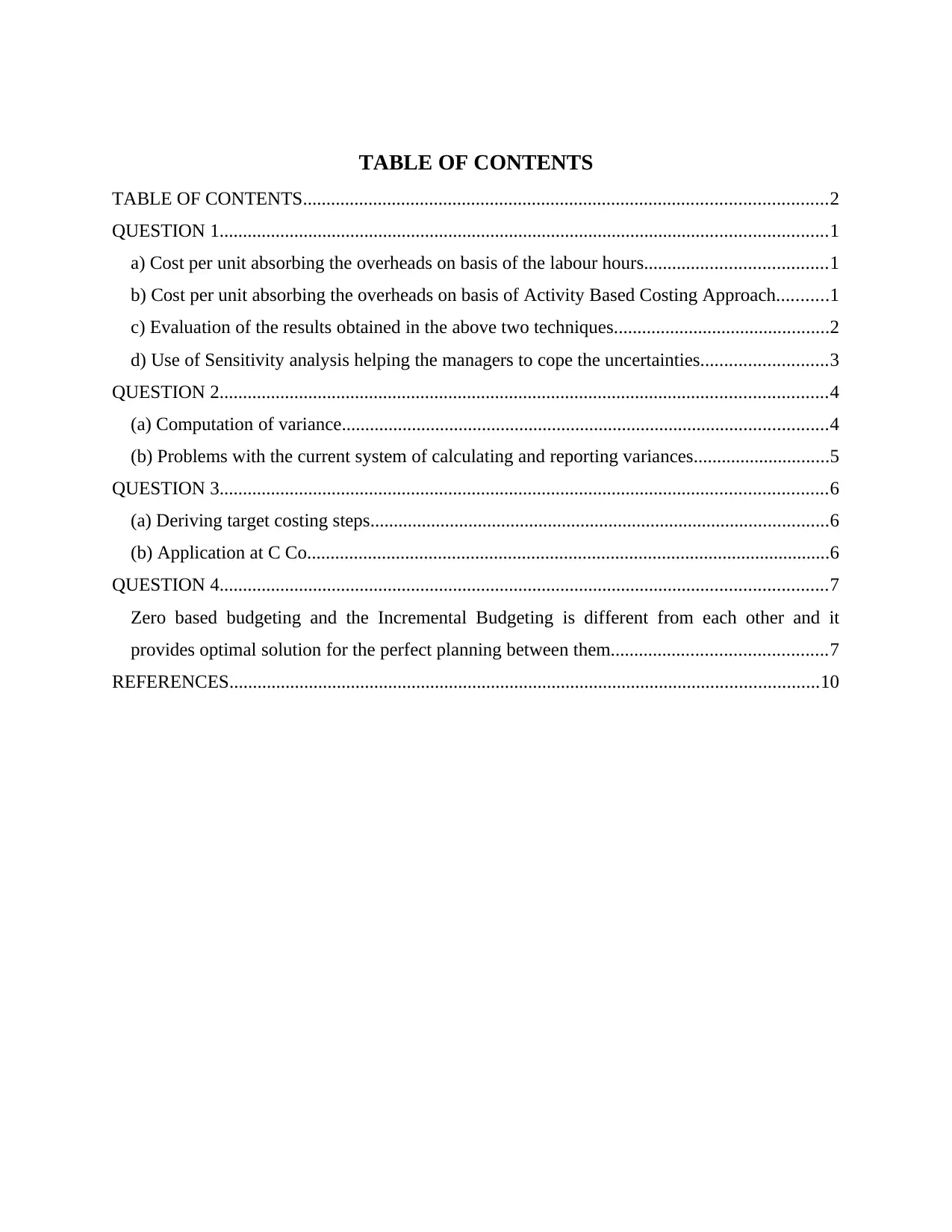
TABLE OF CONTENTS
TABLE OF CONTENTS................................................................................................................2
QUESTION 1..................................................................................................................................1
a) Cost per unit absorbing the overheads on basis of the labour hours.......................................1
b) Cost per unit absorbing the overheads on basis of Activity Based Costing Approach...........1
c) Evaluation of the results obtained in the above two techniques..............................................2
d) Use of Sensitivity analysis helping the managers to cope the uncertainties...........................3
QUESTION 2..................................................................................................................................4
(a) Computation of variance........................................................................................................4
(b) Problems with the current system of calculating and reporting variances.............................5
QUESTION 3..................................................................................................................................6
(a) Deriving target costing steps..................................................................................................6
(b) Application at C Co................................................................................................................6
QUESTION 4..................................................................................................................................7
Zero based budgeting and the Incremental Budgeting is different from each other and it
provides optimal solution for the perfect planning between them..............................................7
REFERENCES..............................................................................................................................10
TABLE OF CONTENTS................................................................................................................2
QUESTION 1..................................................................................................................................1
a) Cost per unit absorbing the overheads on basis of the labour hours.......................................1
b) Cost per unit absorbing the overheads on basis of Activity Based Costing Approach...........1
c) Evaluation of the results obtained in the above two techniques..............................................2
d) Use of Sensitivity analysis helping the managers to cope the uncertainties...........................3
QUESTION 2..................................................................................................................................4
(a) Computation of variance........................................................................................................4
(b) Problems with the current system of calculating and reporting variances.............................5
QUESTION 3..................................................................................................................................6
(a) Deriving target costing steps..................................................................................................6
(b) Application at C Co................................................................................................................6
QUESTION 4..................................................................................................................................7
Zero based budgeting and the Incremental Budgeting is different from each other and it
provides optimal solution for the perfect planning between them..............................................7
REFERENCES..............................................................................................................................10
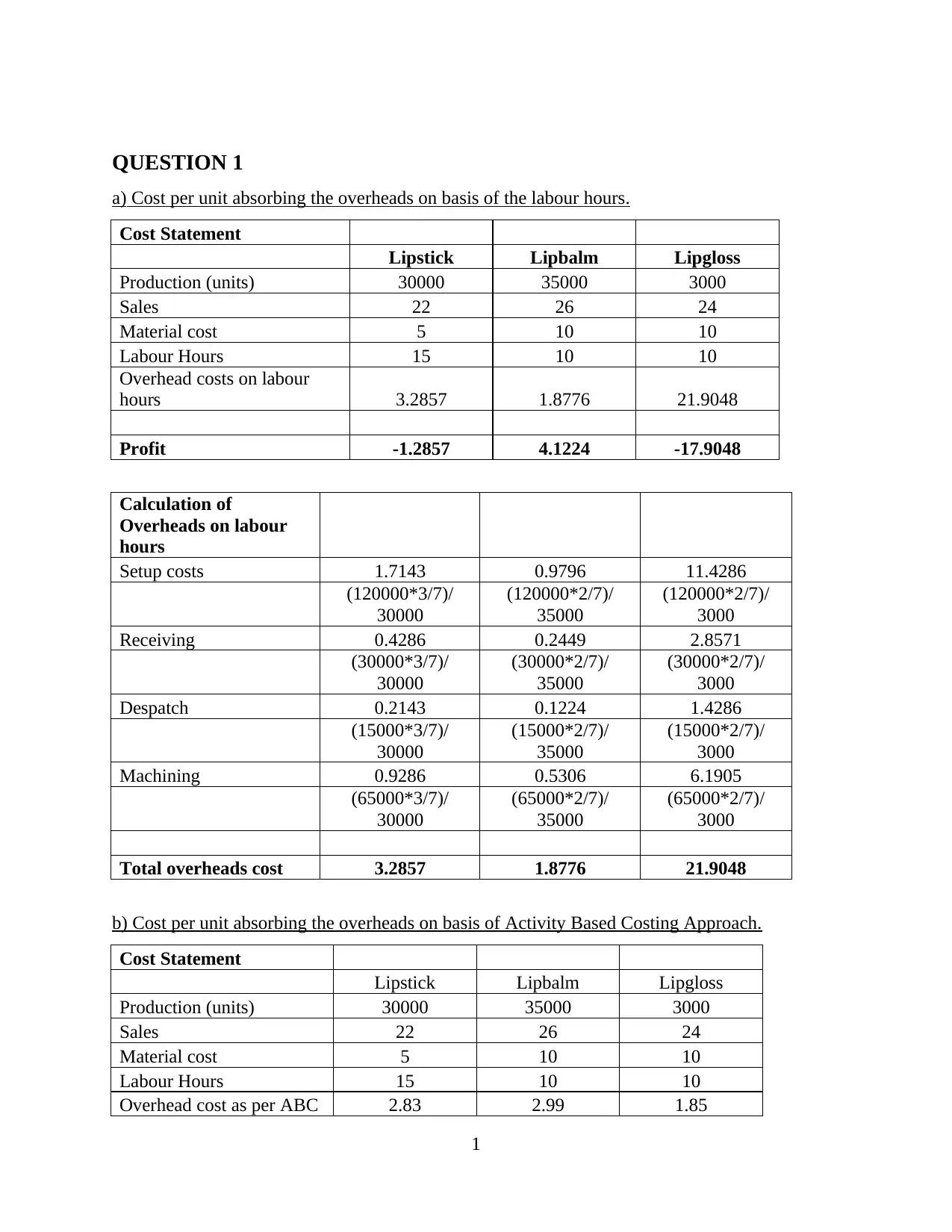
QUESTION 1
a) Cost per unit absorbing the overheads on basis of the labour hours.
Cost Statement
Lipstick Lipbalm Lipgloss
Production (units) 30000 35000 3000
Sales 22 26 24
Material cost 5 10 10
Labour Hours 15 10 10
Overhead costs on labour
hours 3.2857 1.8776 21.9048
Profit -1.2857 4.1224 -17.9048
Calculation of
Overheads on labour
hours
Setup costs 1.7143 0.9796 11.4286
(120000*3/7)/
30000
(120000*2/7)/
35000
(120000*2/7)/
3000
Receiving 0.4286 0.2449 2.8571
(30000*3/7)/
30000
(30000*2/7)/
35000
(30000*2/7)/
3000
Despatch 0.2143 0.1224 1.4286
(15000*3/7)/
30000
(15000*2/7)/
35000
(15000*2/7)/
3000
Machining 0.9286 0.5306 6.1905
(65000*3/7)/
30000
(65000*2/7)/
35000
(65000*2/7)/
3000
Total overheads cost 3.2857 1.8776 21.9048
b) Cost per unit absorbing the overheads on basis of Activity Based Costing Approach.
Cost Statement
Lipstick Lipbalm Lipgloss
Production (units) 30000 35000 3000
Sales 22 26 24
Material cost 5 10 10
Labour Hours 15 10 10
Overhead cost as per ABC 2.83 2.99 1.85
1
a) Cost per unit absorbing the overheads on basis of the labour hours.
Cost Statement
Lipstick Lipbalm Lipgloss
Production (units) 30000 35000 3000
Sales 22 26 24
Material cost 5 10 10
Labour Hours 15 10 10
Overhead costs on labour
hours 3.2857 1.8776 21.9048
Profit -1.2857 4.1224 -17.9048
Calculation of
Overheads on labour
hours
Setup costs 1.7143 0.9796 11.4286
(120000*3/7)/
30000
(120000*2/7)/
35000
(120000*2/7)/
3000
Receiving 0.4286 0.2449 2.8571
(30000*3/7)/
30000
(30000*2/7)/
35000
(30000*2/7)/
3000
Despatch 0.2143 0.1224 1.4286
(15000*3/7)/
30000
(15000*2/7)/
35000
(15000*2/7)/
3000
Machining 0.9286 0.5306 6.1905
(65000*3/7)/
30000
(65000*2/7)/
35000
(65000*2/7)/
3000
Total overheads cost 3.2857 1.8776 21.9048
b) Cost per unit absorbing the overheads on basis of Activity Based Costing Approach.
Cost Statement
Lipstick Lipbalm Lipgloss
Production (units) 30000 35000 3000
Sales 22 26 24
Material cost 5 10 10
Labour Hours 15 10 10
Overhead cost as per ABC 2.83 2.99 1.85
1
You're viewing a preview
Unlock full access by subscribing today!
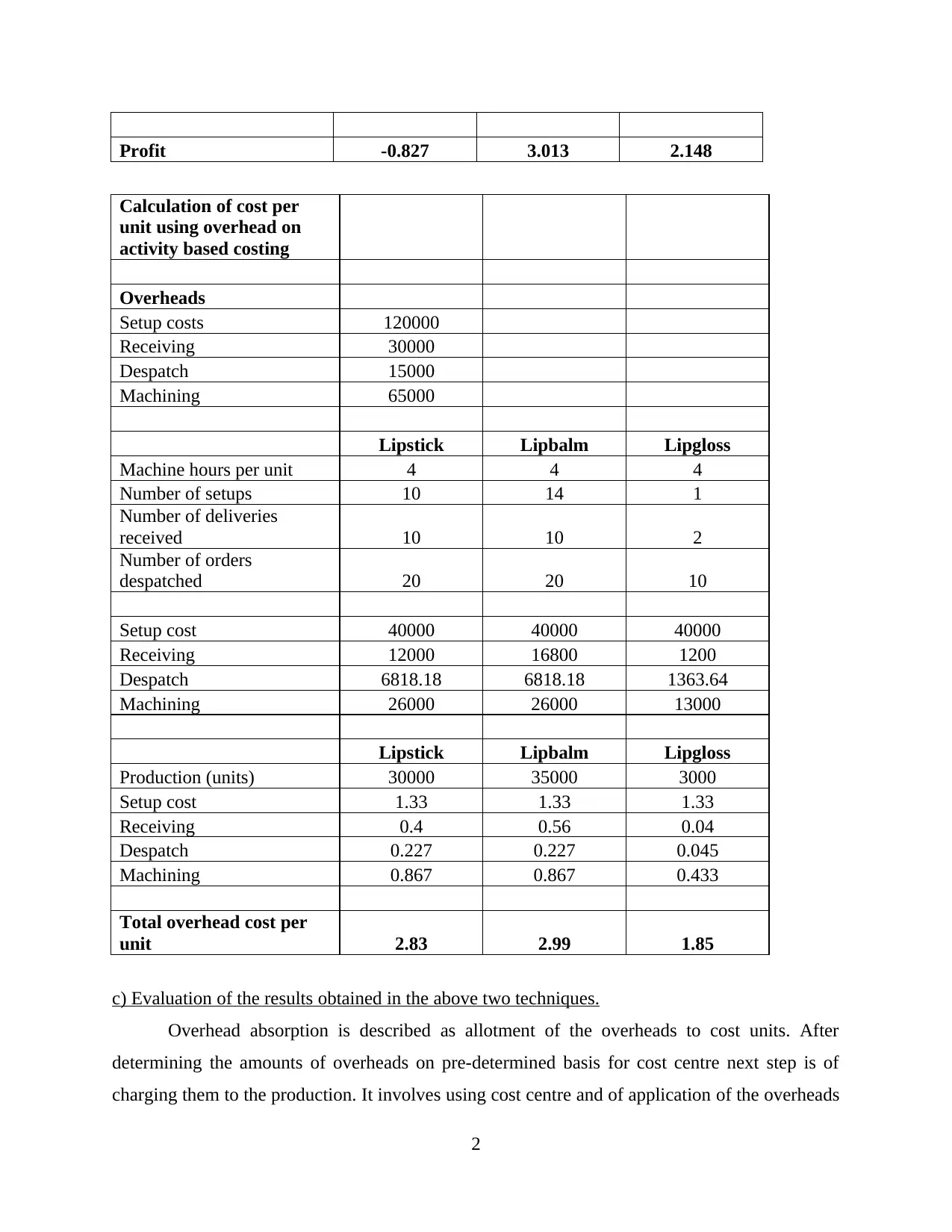
Profit -0.827 3.013 2.148
Calculation of cost per
unit using overhead on
activity based costing
Overheads
Setup costs 120000
Receiving 30000
Despatch 15000
Machining 65000
Lipstick Lipbalm Lipgloss
Machine hours per unit 4 4 4
Number of setups 10 14 1
Number of deliveries
received 10 10 2
Number of orders
despatched 20 20 10
Setup cost 40000 40000 40000
Receiving 12000 16800 1200
Despatch 6818.18 6818.18 1363.64
Machining 26000 26000 13000
Lipstick Lipbalm Lipgloss
Production (units) 30000 35000 3000
Setup cost 1.33 1.33 1.33
Receiving 0.4 0.56 0.04
Despatch 0.227 0.227 0.045
Machining 0.867 0.867 0.433
Total overhead cost per
unit 2.83 2.99 1.85
c) Evaluation of the results obtained in the above two techniques.
Overhead absorption is described as allotment of the overheads to cost units. After
determining the amounts of overheads on pre-determined basis for cost centre next step is of
charging them to the production. It involves using cost centre and of application of the overheads
2
Calculation of cost per
unit using overhead on
activity based costing
Overheads
Setup costs 120000
Receiving 30000
Despatch 15000
Machining 65000
Lipstick Lipbalm Lipgloss
Machine hours per unit 4 4 4
Number of setups 10 14 1
Number of deliveries
received 10 10 2
Number of orders
despatched 20 20 10
Setup cost 40000 40000 40000
Receiving 12000 16800 1200
Despatch 6818.18 6818.18 1363.64
Machining 26000 26000 13000
Lipstick Lipbalm Lipgloss
Production (units) 30000 35000 3000
Setup cost 1.33 1.33 1.33
Receiving 0.4 0.56 0.04
Despatch 0.227 0.227 0.045
Machining 0.867 0.867 0.433
Total overhead cost per
unit 2.83 2.99 1.85
c) Evaluation of the results obtained in the above two techniques.
Overhead absorption is described as allotment of the overheads to cost units. After
determining the amounts of overheads on pre-determined basis for cost centre next step is of
charging them to the production. It involves using cost centre and of application of the overheads
2
Paraphrase This Document
Need a fresh take? Get an instant paraphrase of this document with our AI Paraphraser
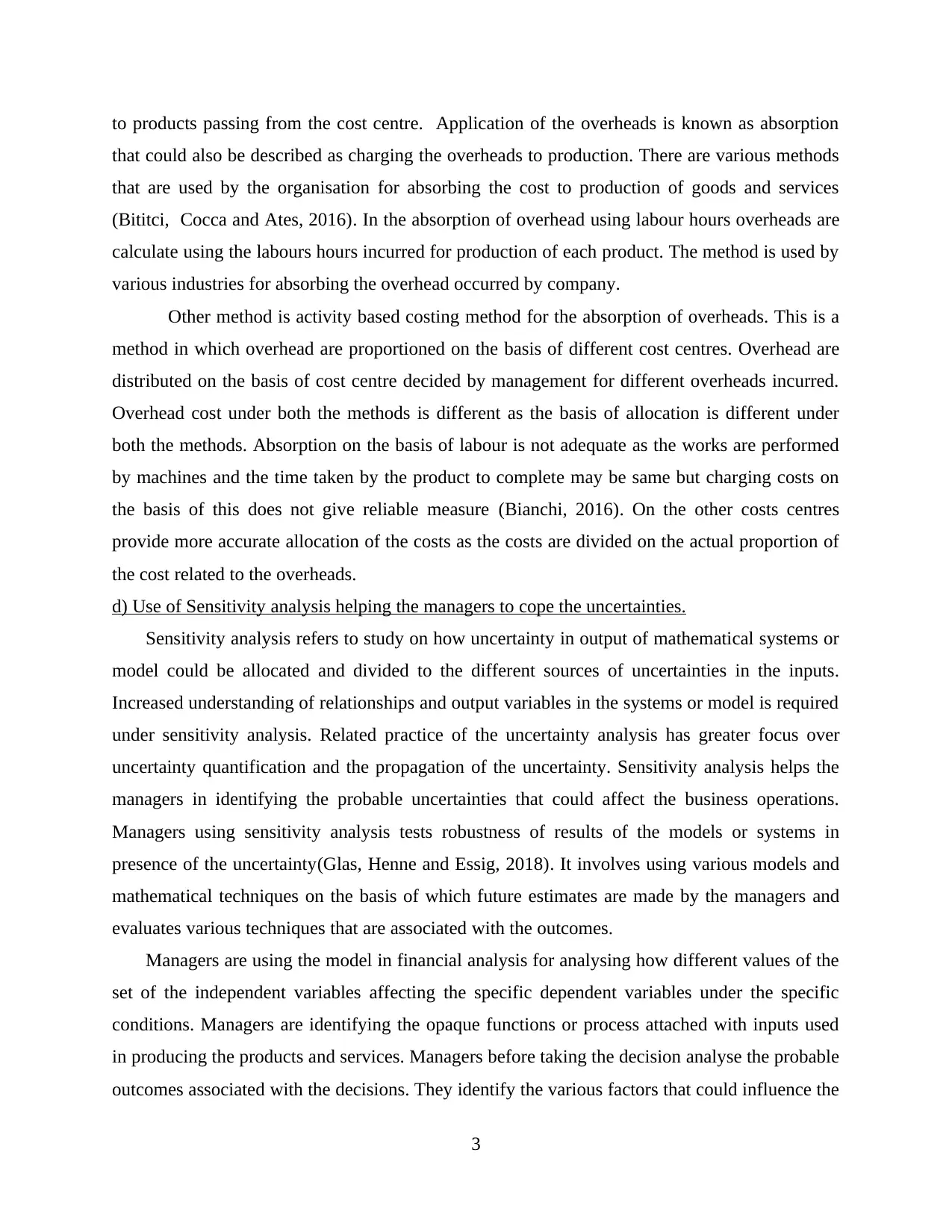
to products passing from the cost centre. Application of the overheads is known as absorption
that could also be described as charging the overheads to production. There are various methods
that are used by the organisation for absorbing the cost to production of goods and services
(Bititci, Cocca and Ates, 2016). In the absorption of overhead using labour hours overheads are
calculate using the labours hours incurred for production of each product. The method is used by
various industries for absorbing the overhead occurred by company.
Other method is activity based costing method for the absorption of overheads. This is a
method in which overhead are proportioned on the basis of different cost centres. Overhead are
distributed on the basis of cost centre decided by management for different overheads incurred.
Overhead cost under both the methods is different as the basis of allocation is different under
both the methods. Absorption on the basis of labour is not adequate as the works are performed
by machines and the time taken by the product to complete may be same but charging costs on
the basis of this does not give reliable measure (Bianchi, 2016). On the other costs centres
provide more accurate allocation of the costs as the costs are divided on the actual proportion of
the cost related to the overheads.
d) Use of Sensitivity analysis helping the managers to cope the uncertainties.
Sensitivity analysis refers to study on how uncertainty in output of mathematical systems or
model could be allocated and divided to the different sources of uncertainties in the inputs.
Increased understanding of relationships and output variables in the systems or model is required
under sensitivity analysis. Related practice of the uncertainty analysis has greater focus over
uncertainty quantification and the propagation of the uncertainty. Sensitivity analysis helps the
managers in identifying the probable uncertainties that could affect the business operations.
Managers using sensitivity analysis tests robustness of results of the models or systems in
presence of the uncertainty(Glas, Henne and Essig, 2018). It involves using various models and
mathematical techniques on the basis of which future estimates are made by the managers and
evaluates various techniques that are associated with the outcomes.
Managers are using the model in financial analysis for analysing how different values of the
set of the independent variables affecting the specific dependent variables under the specific
conditions. Managers are identifying the opaque functions or process attached with inputs used
in producing the products and services. Managers before taking the decision analyse the probable
outcomes associated with the decisions. They identify the various factors that could influence the
3
that could also be described as charging the overheads to production. There are various methods
that are used by the organisation for absorbing the cost to production of goods and services
(Bititci, Cocca and Ates, 2016). In the absorption of overhead using labour hours overheads are
calculate using the labours hours incurred for production of each product. The method is used by
various industries for absorbing the overhead occurred by company.
Other method is activity based costing method for the absorption of overheads. This is a
method in which overhead are proportioned on the basis of different cost centres. Overhead are
distributed on the basis of cost centre decided by management for different overheads incurred.
Overhead cost under both the methods is different as the basis of allocation is different under
both the methods. Absorption on the basis of labour is not adequate as the works are performed
by machines and the time taken by the product to complete may be same but charging costs on
the basis of this does not give reliable measure (Bianchi, 2016). On the other costs centres
provide more accurate allocation of the costs as the costs are divided on the actual proportion of
the cost related to the overheads.
d) Use of Sensitivity analysis helping the managers to cope the uncertainties.
Sensitivity analysis refers to study on how uncertainty in output of mathematical systems or
model could be allocated and divided to the different sources of uncertainties in the inputs.
Increased understanding of relationships and output variables in the systems or model is required
under sensitivity analysis. Related practice of the uncertainty analysis has greater focus over
uncertainty quantification and the propagation of the uncertainty. Sensitivity analysis helps the
managers in identifying the probable uncertainties that could affect the business operations.
Managers using sensitivity analysis tests robustness of results of the models or systems in
presence of the uncertainty(Glas, Henne and Essig, 2018). It involves using various models and
mathematical techniques on the basis of which future estimates are made by the managers and
evaluates various techniques that are associated with the outcomes.
Managers are using the model in financial analysis for analysing how different values of the
set of the independent variables affecting the specific dependent variables under the specific
conditions. Managers are identifying the opaque functions or process attached with inputs used
in producing the products and services. Managers before taking the decision analyse the probable
outcomes associated with the decisions. They identify the various factors that could influence the
3
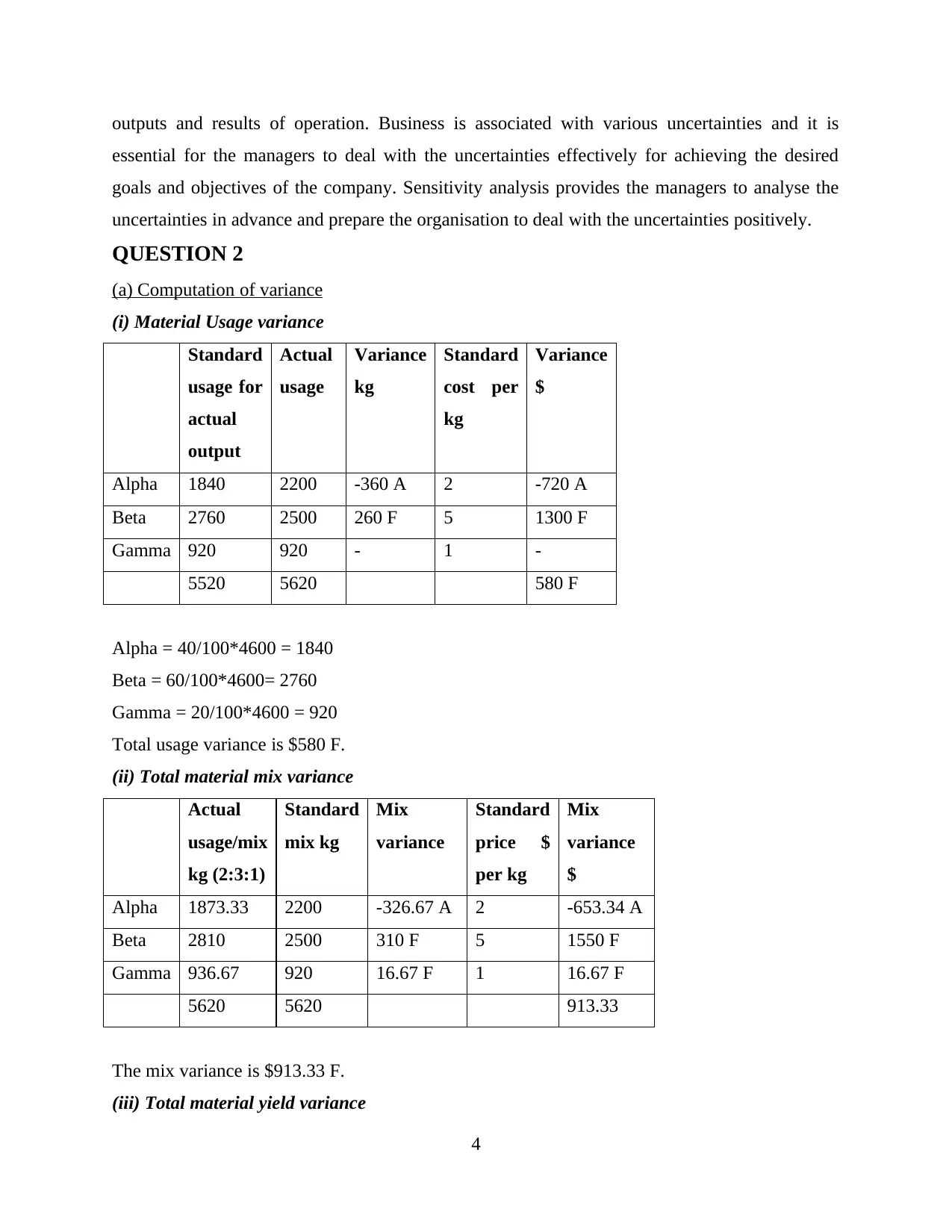
outputs and results of operation. Business is associated with various uncertainties and it is
essential for the managers to deal with the uncertainties effectively for achieving the desired
goals and objectives of the company. Sensitivity analysis provides the managers to analyse the
uncertainties in advance and prepare the organisation to deal with the uncertainties positively.
QUESTION 2
(a) Computation of variance
(i) Material Usage variance
Standard
usage for
actual
output
Actual
usage
Variance
kg
Standard
cost per
kg
Variance
$
Alpha 1840 2200 -360 A 2 -720 A
Beta 2760 2500 260 F 5 1300 F
Gamma 920 920 - 1 -
5520 5620 580 F
Alpha = 40/100*4600 = 1840
Beta = 60/100*4600= 2760
Gamma = 20/100*4600 = 920
Total usage variance is $580 F.
(ii) Total material mix variance
Actual
usage/mix
kg (2:3:1)
Standard
mix kg
Mix
variance
Standard
price $
per kg
Mix
variance
$
Alpha 1873.33 2200 -326.67 A 2 -653.34 A
Beta 2810 2500 310 F 5 1550 F
Gamma 936.67 920 16.67 F 1 16.67 F
5620 5620 913.33
The mix variance is $913.33 F.
(iii) Total material yield variance
4
essential for the managers to deal with the uncertainties effectively for achieving the desired
goals and objectives of the company. Sensitivity analysis provides the managers to analyse the
uncertainties in advance and prepare the organisation to deal with the uncertainties positively.
QUESTION 2
(a) Computation of variance
(i) Material Usage variance
Standard
usage for
actual
output
Actual
usage
Variance
kg
Standard
cost per
kg
Variance
$
Alpha 1840 2200 -360 A 2 -720 A
Beta 2760 2500 260 F 5 1300 F
Gamma 920 920 - 1 -
5520 5620 580 F
Alpha = 40/100*4600 = 1840
Beta = 60/100*4600= 2760
Gamma = 20/100*4600 = 920
Total usage variance is $580 F.
(ii) Total material mix variance
Actual
usage/mix
kg (2:3:1)
Standard
mix kg
Mix
variance
Standard
price $
per kg
Mix
variance
$
Alpha 1873.33 2200 -326.67 A 2 -653.34 A
Beta 2810 2500 310 F 5 1550 F
Gamma 936.67 920 16.67 F 1 16.67 F
5620 5620 913.33
The mix variance is $913.33 F.
(iii) Total material yield variance
4
You're viewing a preview
Unlock full access by subscribing today!
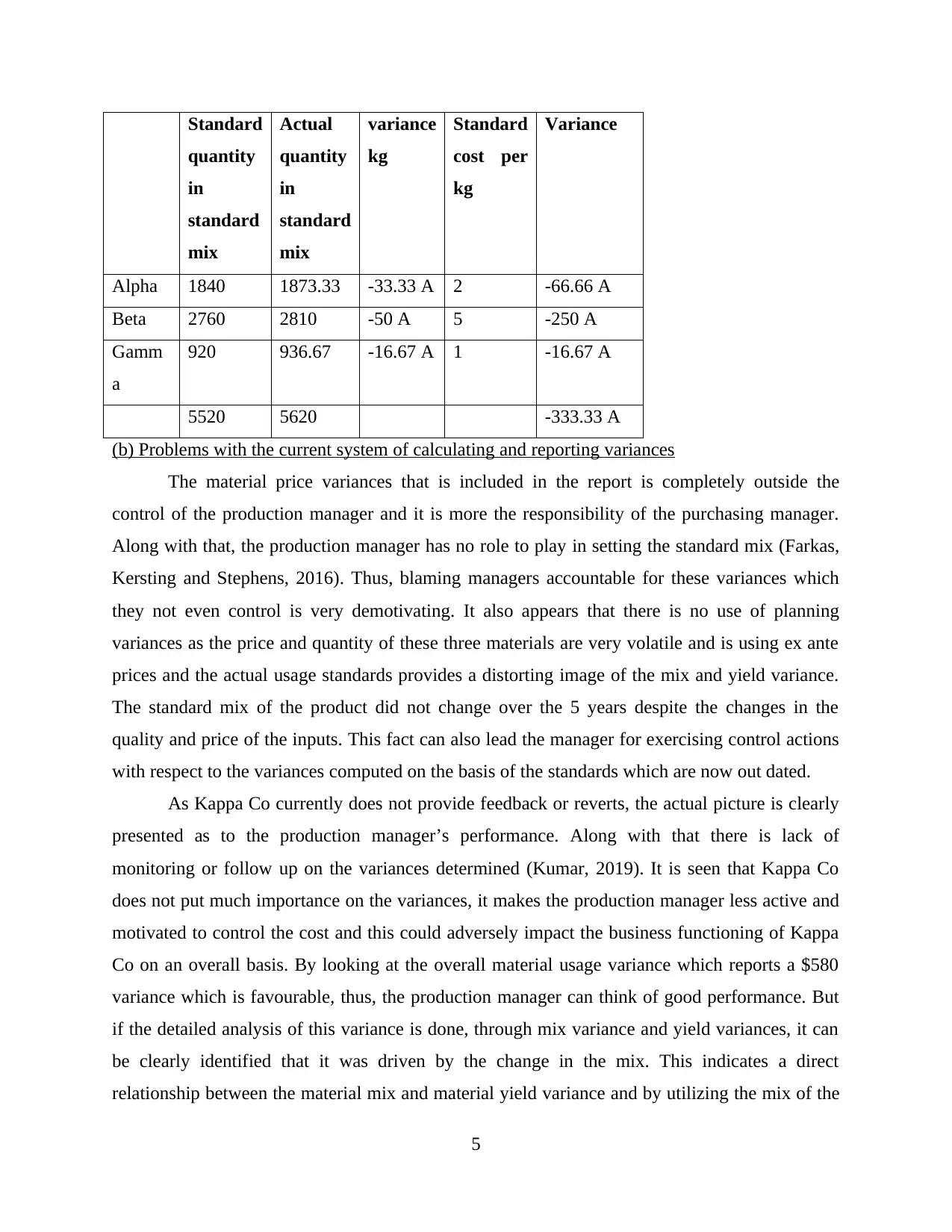
Standard
quantity
in
standard
mix
Actual
quantity
in
standard
mix
variance
kg
Standard
cost per
kg
Variance
Alpha 1840 1873.33 -33.33 A 2 -66.66 A
Beta 2760 2810 -50 A 5 -250 A
Gamm
a
920 936.67 -16.67 A 1 -16.67 A
5520 5620 -333.33 A
(b) Problems with the current system of calculating and reporting variances
The material price variances that is included in the report is completely outside the
control of the production manager and it is more the responsibility of the purchasing manager.
Along with that, the production manager has no role to play in setting the standard mix (Farkas,
Kersting and Stephens, 2016). Thus, blaming managers accountable for these variances which
they not even control is very demotivating. It also appears that there is no use of planning
variances as the price and quantity of these three materials are very volatile and is using ex ante
prices and the actual usage standards provides a distorting image of the mix and yield variance.
The standard mix of the product did not change over the 5 years despite the changes in the
quality and price of the inputs. This fact can also lead the manager for exercising control actions
with respect to the variances computed on the basis of the standards which are now out dated.
As Kappa Co currently does not provide feedback or reverts, the actual picture is clearly
presented as to the production manager’s performance. Along with that there is lack of
monitoring or follow up on the variances determined (Kumar, 2019). It is seen that Kappa Co
does not put much importance on the variances, it makes the production manager less active and
motivated to control the cost and this could adversely impact the business functioning of Kappa
Co on an overall basis. By looking at the overall material usage variance which reports a $580
variance which is favourable, thus, the production manager can think of good performance. But
if the detailed analysis of this variance is done, through mix variance and yield variances, it can
be clearly identified that it was driven by the change in the mix. This indicates a direct
relationship between the material mix and material yield variance and by utilizing the mix of the
5
quantity
in
standard
mix
Actual
quantity
in
standard
mix
variance
kg
Standard
cost per
kg
Variance
Alpha 1840 1873.33 -33.33 A 2 -66.66 A
Beta 2760 2810 -50 A 5 -250 A
Gamm
a
920 936.67 -16.67 A 1 -16.67 A
5520 5620 -333.33 A
(b) Problems with the current system of calculating and reporting variances
The material price variances that is included in the report is completely outside the
control of the production manager and it is more the responsibility of the purchasing manager.
Along with that, the production manager has no role to play in setting the standard mix (Farkas,
Kersting and Stephens, 2016). Thus, blaming managers accountable for these variances which
they not even control is very demotivating. It also appears that there is no use of planning
variances as the price and quantity of these three materials are very volatile and is using ex ante
prices and the actual usage standards provides a distorting image of the mix and yield variance.
The standard mix of the product did not change over the 5 years despite the changes in the
quality and price of the inputs. This fact can also lead the manager for exercising control actions
with respect to the variances computed on the basis of the standards which are now out dated.
As Kappa Co currently does not provide feedback or reverts, the actual picture is clearly
presented as to the production manager’s performance. Along with that there is lack of
monitoring or follow up on the variances determined (Kumar, 2019). It is seen that Kappa Co
does not put much importance on the variances, it makes the production manager less active and
motivated to control the cost and this could adversely impact the business functioning of Kappa
Co on an overall basis. By looking at the overall material usage variance which reports a $580
variance which is favourable, thus, the production manager can think of good performance. But
if the detailed analysis of this variance is done, through mix variance and yield variances, it can
be clearly identified that it was driven by the change in the mix. This indicates a direct
relationship between the material mix and material yield variance and by utilizing the mix of the
5
Paraphrase This Document
Need a fresh take? Get an instant paraphrase of this document with our AI Paraphraser
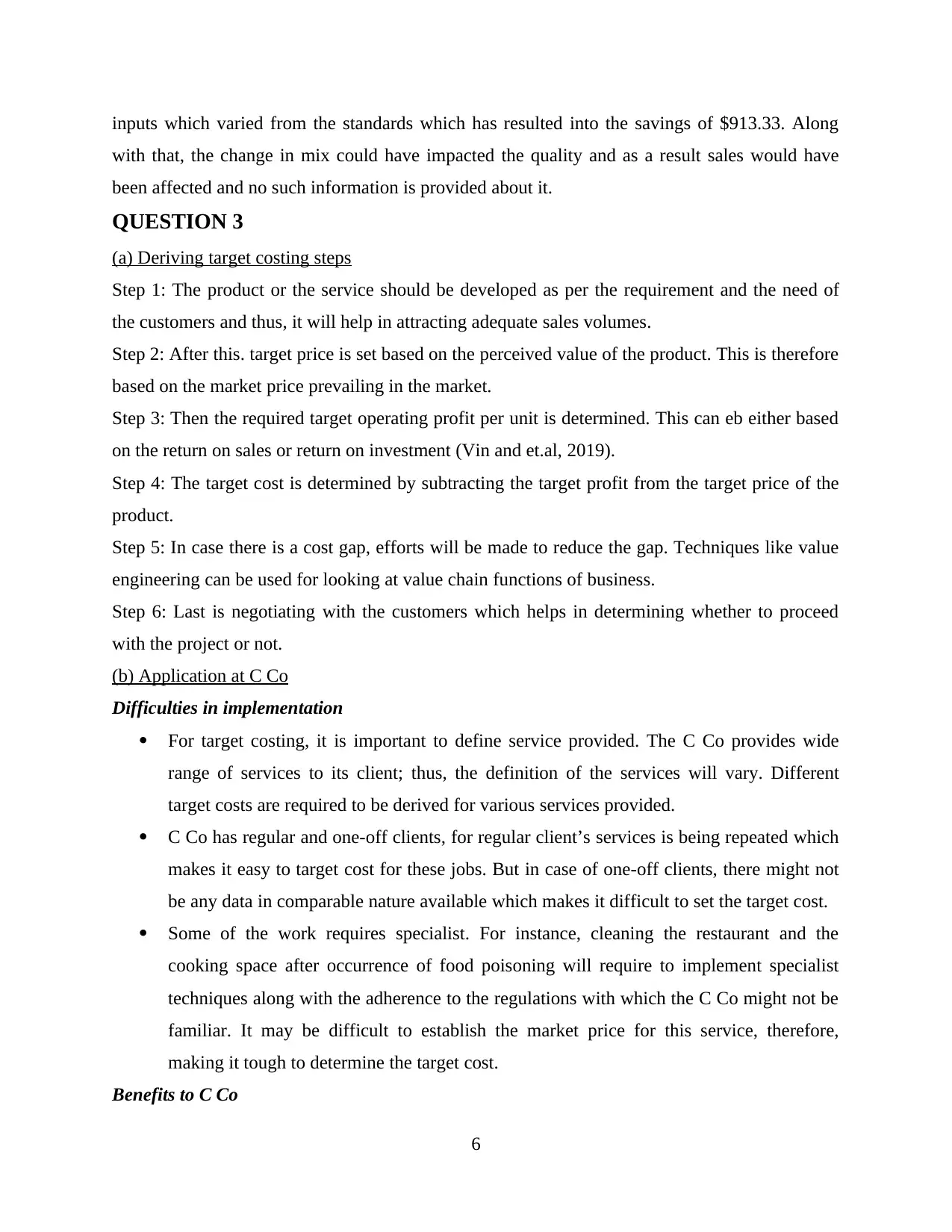
inputs which varied from the standards which has resulted into the savings of $913.33. Along
with that, the change in mix could have impacted the quality and as a result sales would have
been affected and no such information is provided about it.
QUESTION 3
(a) Deriving target costing steps
Step 1: The product or the service should be developed as per the requirement and the need of
the customers and thus, it will help in attracting adequate sales volumes.
Step 2: After this. target price is set based on the perceived value of the product. This is therefore
based on the market price prevailing in the market.
Step 3: Then the required target operating profit per unit is determined. This can eb either based
on the return on sales or return on investment (Vin and et.al, 2019).
Step 4: The target cost is determined by subtracting the target profit from the target price of the
product.
Step 5: In case there is a cost gap, efforts will be made to reduce the gap. Techniques like value
engineering can be used for looking at value chain functions of business.
Step 6: Last is negotiating with the customers which helps in determining whether to proceed
with the project or not.
(b) Application at C Co
Difficulties in implementation
For target costing, it is important to define service provided. The C Co provides wide
range of services to its client; thus, the definition of the services will vary. Different
target costs are required to be derived for various services provided.
C Co has regular and one-off clients, for regular client’s services is being repeated which
makes it easy to target cost for these jobs. But in case of one-off clients, there might not
be any data in comparable nature available which makes it difficult to set the target cost.
Some of the work requires specialist. For instance, cleaning the restaurant and the
cooking space after occurrence of food poisoning will require to implement specialist
techniques along with the adherence to the regulations with which the C Co might not be
familiar. It may be difficult to establish the market price for this service, therefore,
making it tough to determine the target cost.
Benefits to C Co
6
with that, the change in mix could have impacted the quality and as a result sales would have
been affected and no such information is provided about it.
QUESTION 3
(a) Deriving target costing steps
Step 1: The product or the service should be developed as per the requirement and the need of
the customers and thus, it will help in attracting adequate sales volumes.
Step 2: After this. target price is set based on the perceived value of the product. This is therefore
based on the market price prevailing in the market.
Step 3: Then the required target operating profit per unit is determined. This can eb either based
on the return on sales or return on investment (Vin and et.al, 2019).
Step 4: The target cost is determined by subtracting the target profit from the target price of the
product.
Step 5: In case there is a cost gap, efforts will be made to reduce the gap. Techniques like value
engineering can be used for looking at value chain functions of business.
Step 6: Last is negotiating with the customers which helps in determining whether to proceed
with the project or not.
(b) Application at C Co
Difficulties in implementation
For target costing, it is important to define service provided. The C Co provides wide
range of services to its client; thus, the definition of the services will vary. Different
target costs are required to be derived for various services provided.
C Co has regular and one-off clients, for regular client’s services is being repeated which
makes it easy to target cost for these jobs. But in case of one-off clients, there might not
be any data in comparable nature available which makes it difficult to set the target cost.
Some of the work requires specialist. For instance, cleaning the restaurant and the
cooking space after occurrence of food poisoning will require to implement specialist
techniques along with the adherence to the regulations with which the C Co might not be
familiar. It may be difficult to establish the market price for this service, therefore,
making it tough to determine the target cost.
Benefits to C Co
6
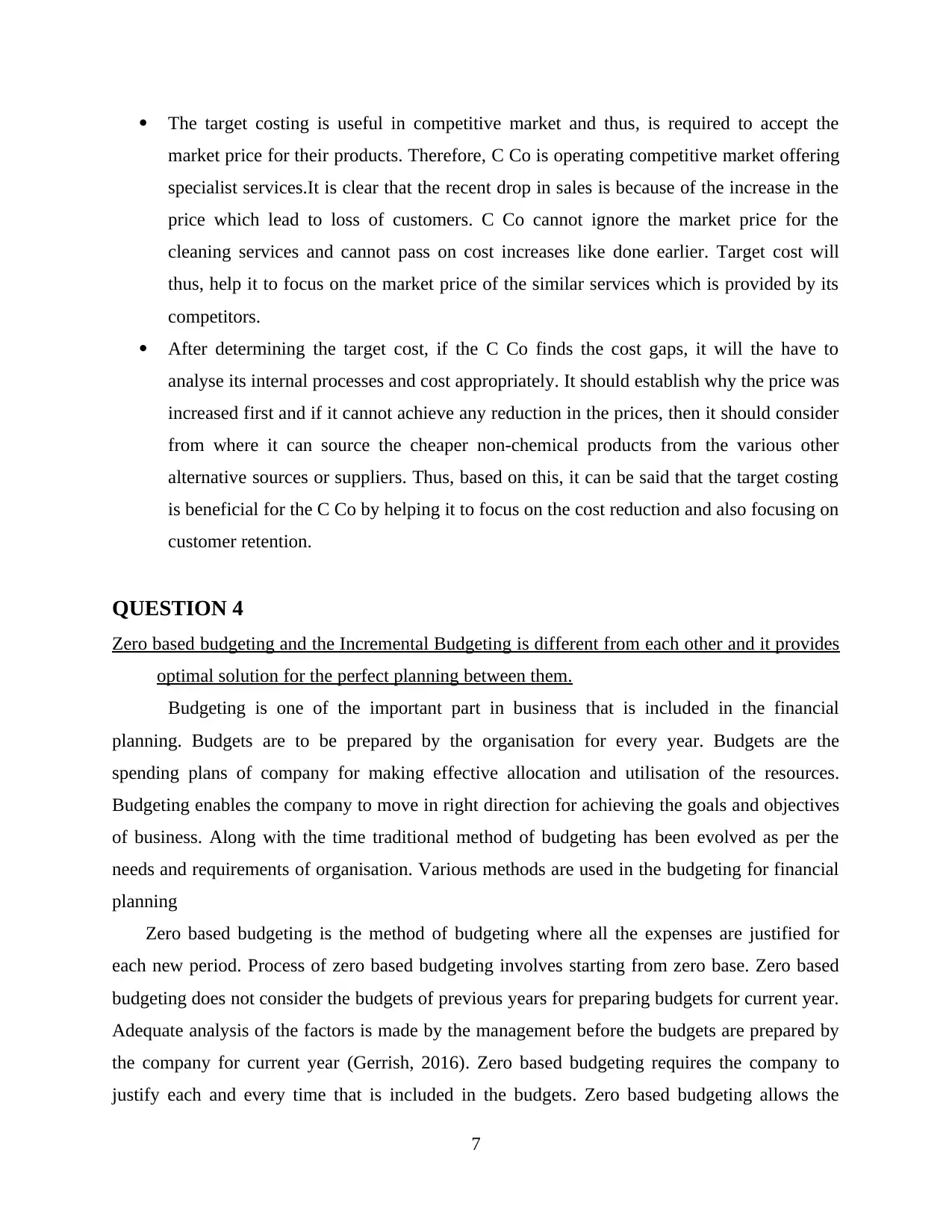
The target costing is useful in competitive market and thus, is required to accept the
market price for their products. Therefore, C Co is operating competitive market offering
specialist services.It is clear that the recent drop in sales is because of the increase in the
price which lead to loss of customers. C Co cannot ignore the market price for the
cleaning services and cannot pass on cost increases like done earlier. Target cost will
thus, help it to focus on the market price of the similar services which is provided by its
competitors.
After determining the target cost, if the C Co finds the cost gaps, it will the have to
analyse its internal processes and cost appropriately. It should establish why the price was
increased first and if it cannot achieve any reduction in the prices, then it should consider
from where it can source the cheaper non-chemical products from the various other
alternative sources or suppliers. Thus, based on this, it can be said that the target costing
is beneficial for the C Co by helping it to focus on the cost reduction and also focusing on
customer retention.
QUESTION 4
Zero based budgeting and the Incremental Budgeting is different from each other and it provides
optimal solution for the perfect planning between them.
Budgeting is one of the important part in business that is included in the financial
planning. Budgets are to be prepared by the organisation for every year. Budgets are the
spending plans of company for making effective allocation and utilisation of the resources.
Budgeting enables the company to move in right direction for achieving the goals and objectives
of business. Along with the time traditional method of budgeting has been evolved as per the
needs and requirements of organisation. Various methods are used in the budgeting for financial
planning
Zero based budgeting is the method of budgeting where all the expenses are justified for
each new period. Process of zero based budgeting involves starting from zero base. Zero based
budgeting does not consider the budgets of previous years for preparing budgets for current year.
Adequate analysis of the factors is made by the management before the budgets are prepared by
the company for current year (Gerrish, 2016). Zero based budgeting requires the company to
justify each and every time that is included in the budgets. Zero based budgeting allows the
7
market price for their products. Therefore, C Co is operating competitive market offering
specialist services.It is clear that the recent drop in sales is because of the increase in the
price which lead to loss of customers. C Co cannot ignore the market price for the
cleaning services and cannot pass on cost increases like done earlier. Target cost will
thus, help it to focus on the market price of the similar services which is provided by its
competitors.
After determining the target cost, if the C Co finds the cost gaps, it will the have to
analyse its internal processes and cost appropriately. It should establish why the price was
increased first and if it cannot achieve any reduction in the prices, then it should consider
from where it can source the cheaper non-chemical products from the various other
alternative sources or suppliers. Thus, based on this, it can be said that the target costing
is beneficial for the C Co by helping it to focus on the cost reduction and also focusing on
customer retention.
QUESTION 4
Zero based budgeting and the Incremental Budgeting is different from each other and it provides
optimal solution for the perfect planning between them.
Budgeting is one of the important part in business that is included in the financial
planning. Budgets are to be prepared by the organisation for every year. Budgets are the
spending plans of company for making effective allocation and utilisation of the resources.
Budgeting enables the company to move in right direction for achieving the goals and objectives
of business. Along with the time traditional method of budgeting has been evolved as per the
needs and requirements of organisation. Various methods are used in the budgeting for financial
planning
Zero based budgeting is the method of budgeting where all the expenses are justified for
each new period. Process of zero based budgeting involves starting from zero base. Zero based
budgeting does not consider the budgets of previous years for preparing budgets for current year.
Adequate analysis of the factors is made by the management before the budgets are prepared by
the company for current year (Gerrish, 2016). Zero based budgeting requires the company to
justify each and every time that is included in the budgets. Zero based budgeting allows the
7
You're viewing a preview
Unlock full access by subscribing today!
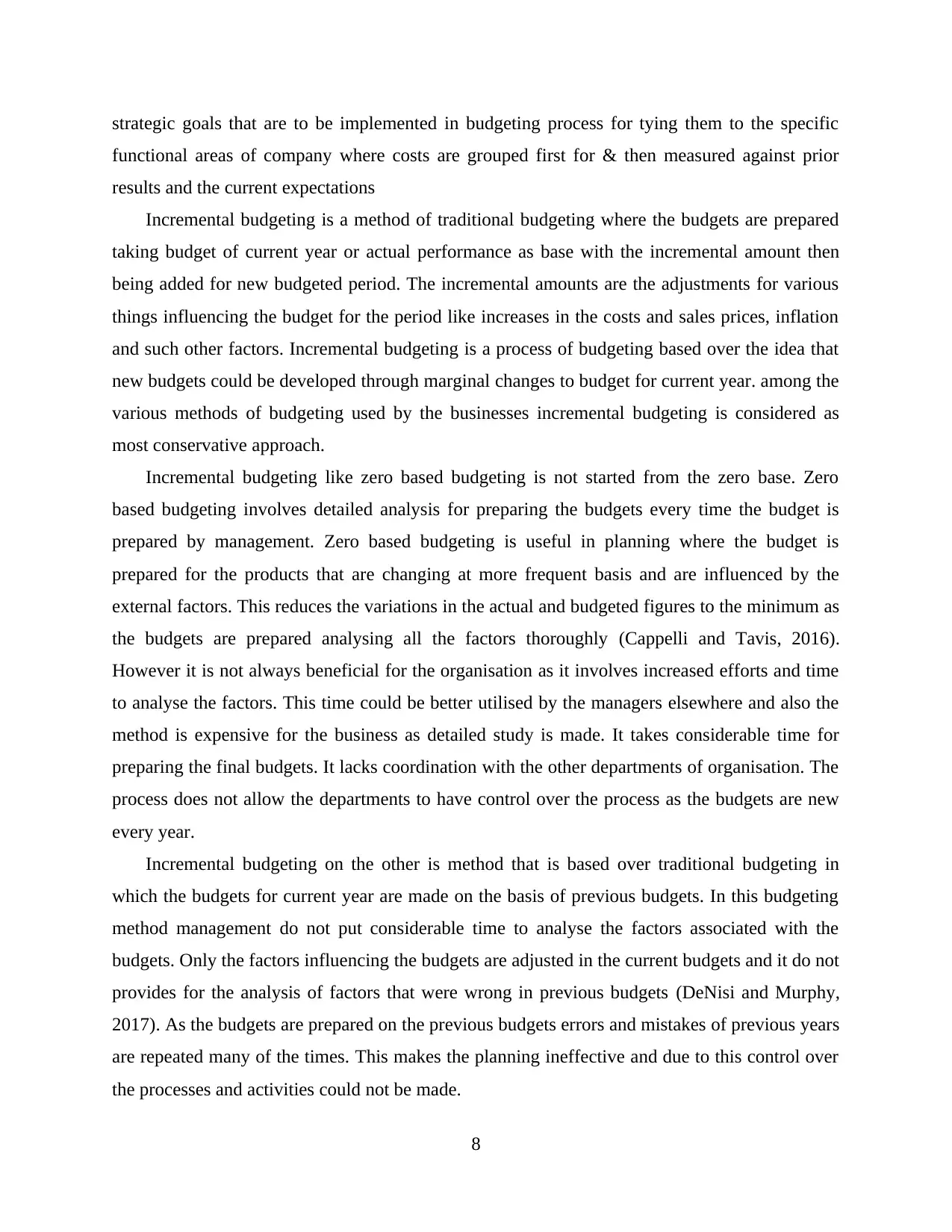
strategic goals that are to be implemented in budgeting process for tying them to the specific
functional areas of company where costs are grouped first for & then measured against prior
results and the current expectations
Incremental budgeting is a method of traditional budgeting where the budgets are prepared
taking budget of current year or actual performance as base with the incremental amount then
being added for new budgeted period. The incremental amounts are the adjustments for various
things influencing the budget for the period like increases in the costs and sales prices, inflation
and such other factors. Incremental budgeting is a process of budgeting based over the idea that
new budgets could be developed through marginal changes to budget for current year. among the
various methods of budgeting used by the businesses incremental budgeting is considered as
most conservative approach.
Incremental budgeting like zero based budgeting is not started from the zero base. Zero
based budgeting involves detailed analysis for preparing the budgets every time the budget is
prepared by management. Zero based budgeting is useful in planning where the budget is
prepared for the products that are changing at more frequent basis and are influenced by the
external factors. This reduces the variations in the actual and budgeted figures to the minimum as
the budgets are prepared analysing all the factors thoroughly (Cappelli and Tavis, 2016).
However it is not always beneficial for the organisation as it involves increased efforts and time
to analyse the factors. This time could be better utilised by the managers elsewhere and also the
method is expensive for the business as detailed study is made. It takes considerable time for
preparing the final budgets. It lacks coordination with the other departments of organisation. The
process does not allow the departments to have control over the process as the budgets are new
every year.
Incremental budgeting on the other is method that is based over traditional budgeting in
which the budgets for current year are made on the basis of previous budgets. In this budgeting
method management do not put considerable time to analyse the factors associated with the
budgets. Only the factors influencing the budgets are adjusted in the current budgets and it do not
provides for the analysis of factors that were wrong in previous budgets (DeNisi and Murphy,
2017). As the budgets are prepared on the previous budgets errors and mistakes of previous years
are repeated many of the times. This makes the planning ineffective and due to this control over
the processes and activities could not be made.
8
functional areas of company where costs are grouped first for & then measured against prior
results and the current expectations
Incremental budgeting is a method of traditional budgeting where the budgets are prepared
taking budget of current year or actual performance as base with the incremental amount then
being added for new budgeted period. The incremental amounts are the adjustments for various
things influencing the budget for the period like increases in the costs and sales prices, inflation
and such other factors. Incremental budgeting is a process of budgeting based over the idea that
new budgets could be developed through marginal changes to budget for current year. among the
various methods of budgeting used by the businesses incremental budgeting is considered as
most conservative approach.
Incremental budgeting like zero based budgeting is not started from the zero base. Zero
based budgeting involves detailed analysis for preparing the budgets every time the budget is
prepared by management. Zero based budgeting is useful in planning where the budget is
prepared for the products that are changing at more frequent basis and are influenced by the
external factors. This reduces the variations in the actual and budgeted figures to the minimum as
the budgets are prepared analysing all the factors thoroughly (Cappelli and Tavis, 2016).
However it is not always beneficial for the organisation as it involves increased efforts and time
to analyse the factors. This time could be better utilised by the managers elsewhere and also the
method is expensive for the business as detailed study is made. It takes considerable time for
preparing the final budgets. It lacks coordination with the other departments of organisation. The
process does not allow the departments to have control over the process as the budgets are new
every year.
Incremental budgeting on the other is method that is based over traditional budgeting in
which the budgets for current year are made on the basis of previous budgets. In this budgeting
method management do not put considerable time to analyse the factors associated with the
budgets. Only the factors influencing the budgets are adjusted in the current budgets and it do not
provides for the analysis of factors that were wrong in previous budgets (DeNisi and Murphy,
2017). As the budgets are prepared on the previous budgets errors and mistakes of previous years
are repeated many of the times. This makes the planning ineffective and due to this control over
the processes and activities could not be made.
8
Paraphrase This Document
Need a fresh take? Get an instant paraphrase of this document with our AI Paraphraser
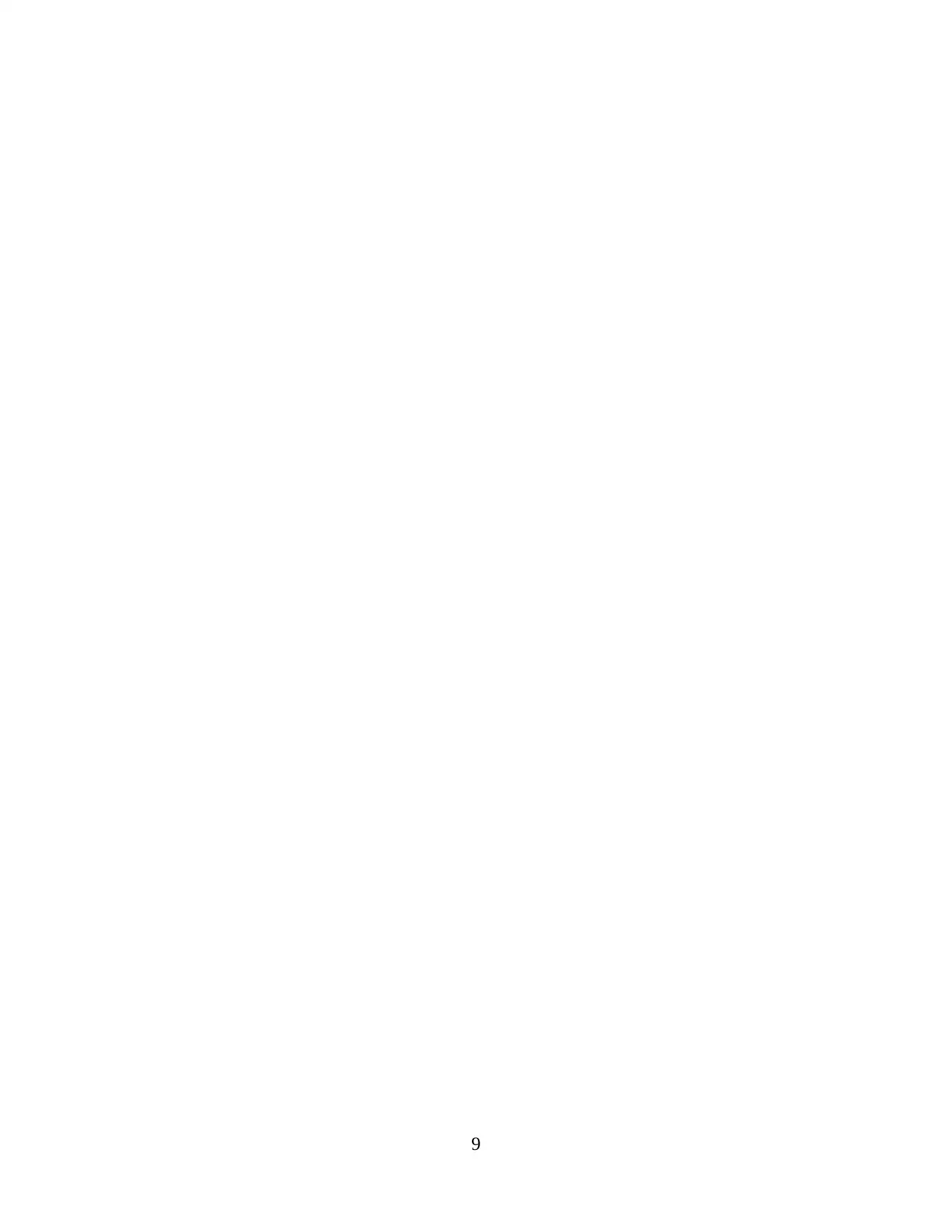
9
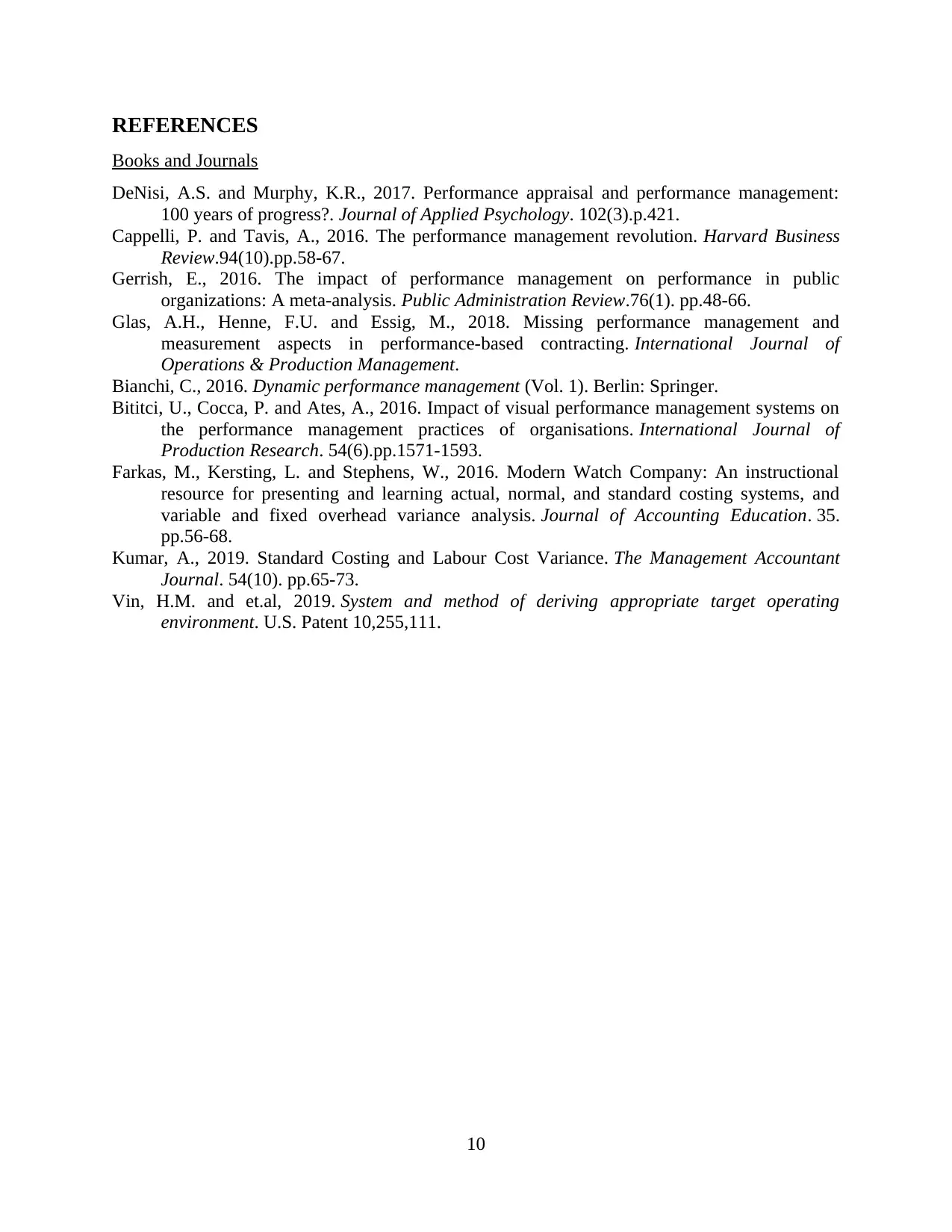
REFERENCES
Books and Journals
DeNisi, A.S. and Murphy, K.R., 2017. Performance appraisal and performance management:
100 years of progress?. Journal of Applied Psychology. 102(3).p.421.
Cappelli, P. and Tavis, A., 2016. The performance management revolution. Harvard Business
Review.94(10).pp.58-67.
Gerrish, E., 2016. The impact of performance management on performance in public
organizations: A meta‐analysis. Public Administration Review.76(1). pp.48-66.
Glas, A.H., Henne, F.U. and Essig, M., 2018. Missing performance management and
measurement aspects in performance-based contracting. International Journal of
Operations & Production Management.
Bianchi, C., 2016. Dynamic performance management (Vol. 1). Berlin: Springer.
Bititci, U., Cocca, P. and Ates, A., 2016. Impact of visual performance management systems on
the performance management practices of organisations. International Journal of
Production Research. 54(6).pp.1571-1593.
Farkas, M., Kersting, L. and Stephens, W., 2016. Modern Watch Company: An instructional
resource for presenting and learning actual, normal, and standard costing systems, and
variable and fixed overhead variance analysis. Journal of Accounting Education. 35.
pp.56-68.
Kumar, A., 2019. Standard Costing and Labour Cost Variance. The Management Accountant
Journal. 54(10). pp.65-73.
Vin, H.M. and et.al, 2019. System and method of deriving appropriate target operating
environment. U.S. Patent 10,255,111.
10
Books and Journals
DeNisi, A.S. and Murphy, K.R., 2017. Performance appraisal and performance management:
100 years of progress?. Journal of Applied Psychology. 102(3).p.421.
Cappelli, P. and Tavis, A., 2016. The performance management revolution. Harvard Business
Review.94(10).pp.58-67.
Gerrish, E., 2016. The impact of performance management on performance in public
organizations: A meta‐analysis. Public Administration Review.76(1). pp.48-66.
Glas, A.H., Henne, F.U. and Essig, M., 2018. Missing performance management and
measurement aspects in performance-based contracting. International Journal of
Operations & Production Management.
Bianchi, C., 2016. Dynamic performance management (Vol. 1). Berlin: Springer.
Bititci, U., Cocca, P. and Ates, A., 2016. Impact of visual performance management systems on
the performance management practices of organisations. International Journal of
Production Research. 54(6).pp.1571-1593.
Farkas, M., Kersting, L. and Stephens, W., 2016. Modern Watch Company: An instructional
resource for presenting and learning actual, normal, and standard costing systems, and
variable and fixed overhead variance analysis. Journal of Accounting Education. 35.
pp.56-68.
Kumar, A., 2019. Standard Costing and Labour Cost Variance. The Management Accountant
Journal. 54(10). pp.65-73.
Vin, H.M. and et.al, 2019. System and method of deriving appropriate target operating
environment. U.S. Patent 10,255,111.
10
You're viewing a preview
Unlock full access by subscribing today!
1 out of 12
Related Documents

Your All-in-One AI-Powered Toolkit for Academic Success.
+13062052269
info@desklib.com
Available 24*7 on WhatsApp / Email
Unlock your academic potential
© 2024 | Zucol Services PVT LTD | All rights reserved.