Personal Commitment : Eoc
VerifiedAdded on 2020/10/22
|33
|14302
|200
AI Summary
Contribute Materials
Your contribution can guide someone’s learning journey. Share your
documents today.
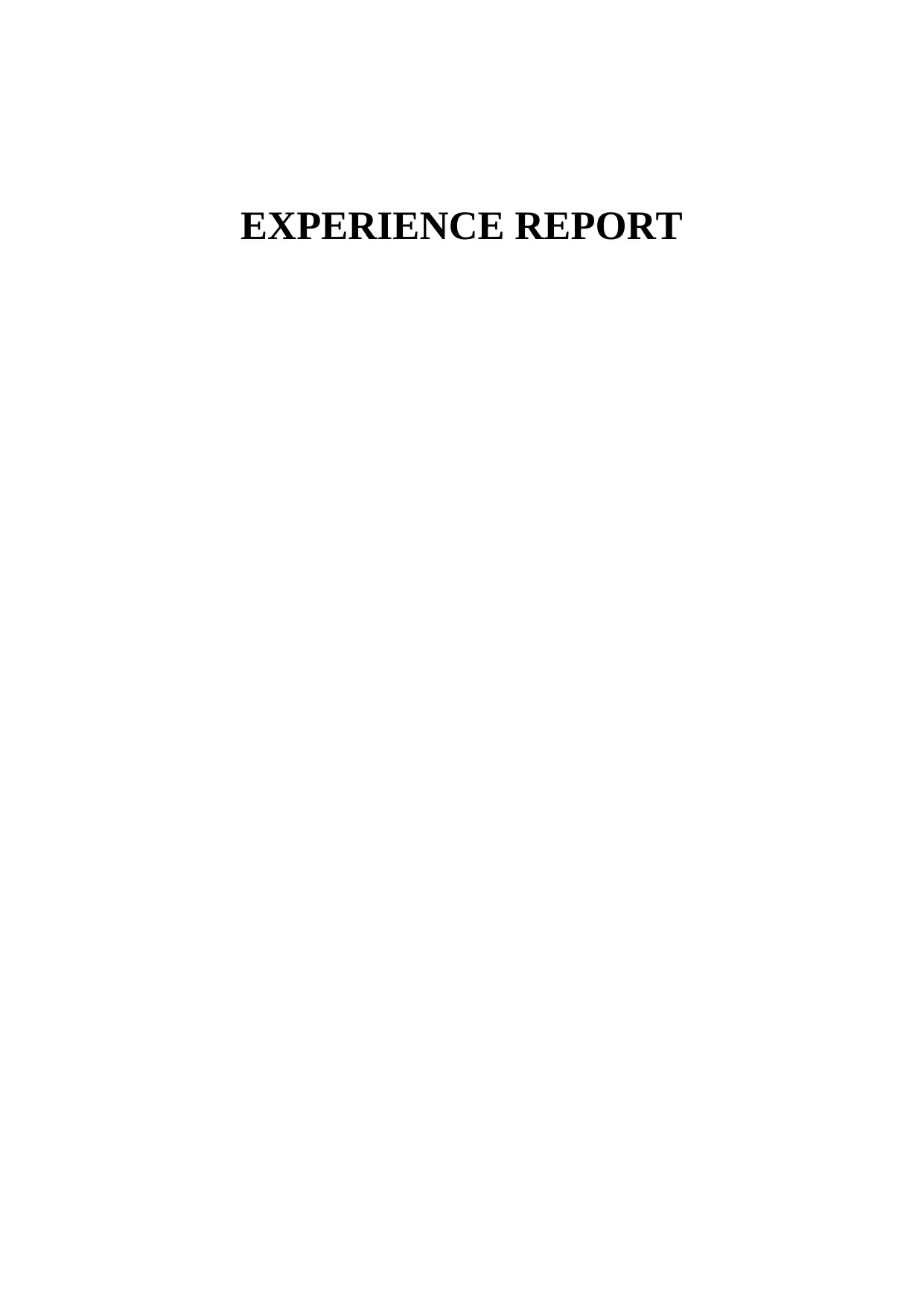
EXPERIENCE REPORT
Secure Best Marks with AI Grader
Need help grading? Try our AI Grader for instant feedback on your assignments.
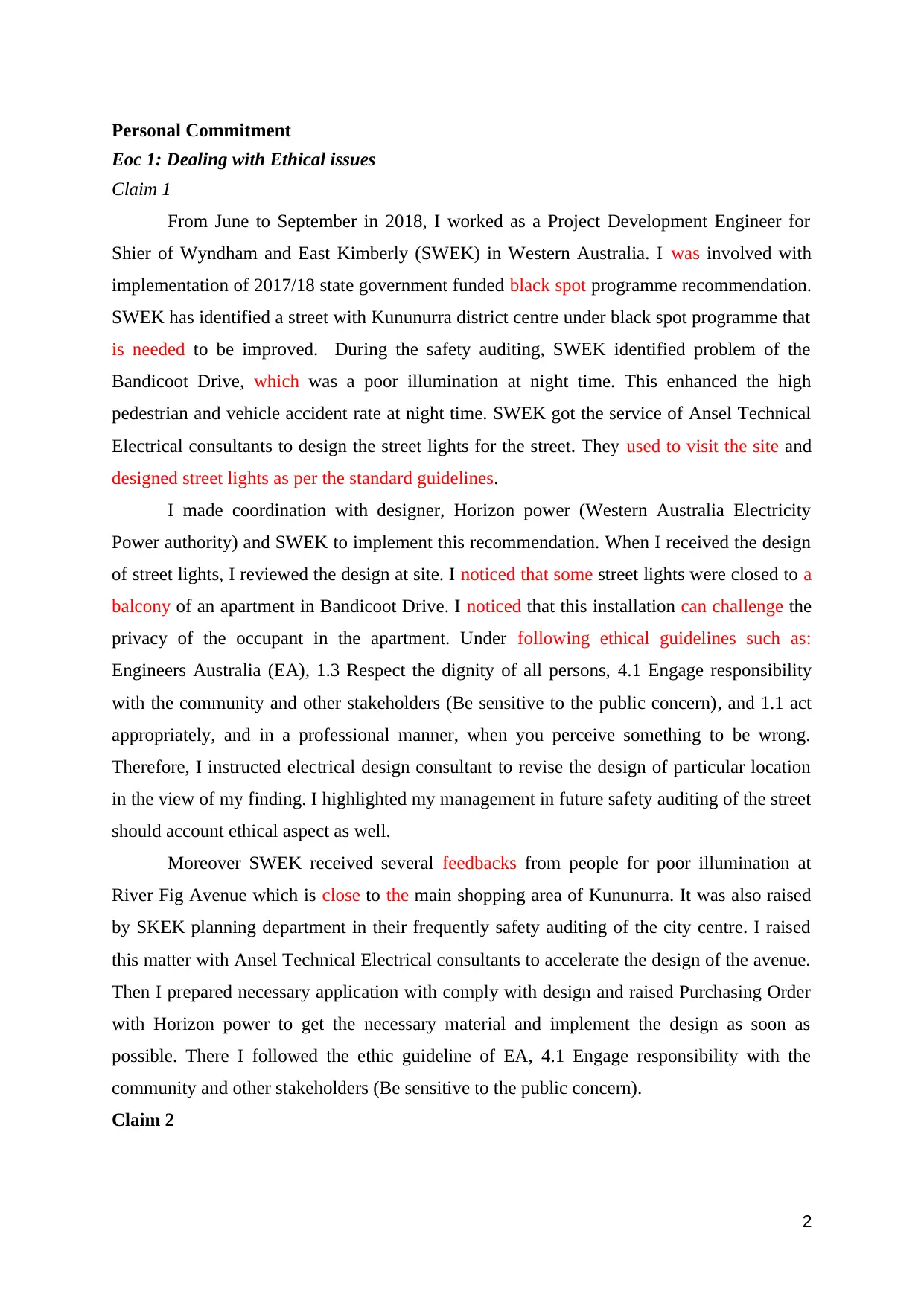
Personal Commitment
Eoc 1: Dealing with Ethical issues
Claim 1
From June to September in 2018, I worked as a Project Development Engineer for
Shier of Wyndham and East Kimberly (SWEK) in Western Australia. I was involved with
implementation of 2017/18 state government funded black spot programme recommendation.
SWEK has identified a street with Kununurra district centre under black spot programme that
is needed to be improved. During the safety auditing, SWEK identified problem of the
Bandicoot Drive, which was a poor illumination at night time. This enhanced the high
pedestrian and vehicle accident rate at night time. SWEK got the service of Ansel Technical
Electrical consultants to design the street lights for the street. They used to visit the site and
designed street lights as per the standard guidelines.
I made coordination with designer, Horizon power (Western Australia Electricity
Power authority) and SWEK to implement this recommendation. When I received the design
of street lights, I reviewed the design at site. I noticed that some street lights were closed to a
balcony of an apartment in Bandicoot Drive. I noticed that this installation can challenge the
privacy of the occupant in the apartment. Under following ethical guidelines such as:
Engineers Australia (EA), 1.3 Respect the dignity of all persons, 4.1 Engage responsibility
with the community and other stakeholders (Be sensitive to the public concern), and 1.1 act
appropriately, and in a professional manner, when you perceive something to be wrong.
Therefore, I instructed electrical design consultant to revise the design of particular location
in the view of my finding. I highlighted my management in future safety auditing of the street
should account ethical aspect as well.
Moreover SWEK received several feedbacks from people for poor illumination at
River Fig Avenue which is close to the main shopping area of Kununurra. It was also raised
by SKEK planning department in their frequently safety auditing of the city centre. I raised
this matter with Ansel Technical Electrical consultants to accelerate the design of the avenue.
Then I prepared necessary application with comply with design and raised Purchasing Order
with Horizon power to get the necessary material and implement the design as soon as
possible. There I followed the ethic guideline of EA, 4.1 Engage responsibility with the
community and other stakeholders (Be sensitive to the public concern).
Claim 2
2
Eoc 1: Dealing with Ethical issues
Claim 1
From June to September in 2018, I worked as a Project Development Engineer for
Shier of Wyndham and East Kimberly (SWEK) in Western Australia. I was involved with
implementation of 2017/18 state government funded black spot programme recommendation.
SWEK has identified a street with Kununurra district centre under black spot programme that
is needed to be improved. During the safety auditing, SWEK identified problem of the
Bandicoot Drive, which was a poor illumination at night time. This enhanced the high
pedestrian and vehicle accident rate at night time. SWEK got the service of Ansel Technical
Electrical consultants to design the street lights for the street. They used to visit the site and
designed street lights as per the standard guidelines.
I made coordination with designer, Horizon power (Western Australia Electricity
Power authority) and SWEK to implement this recommendation. When I received the design
of street lights, I reviewed the design at site. I noticed that some street lights were closed to a
balcony of an apartment in Bandicoot Drive. I noticed that this installation can challenge the
privacy of the occupant in the apartment. Under following ethical guidelines such as:
Engineers Australia (EA), 1.3 Respect the dignity of all persons, 4.1 Engage responsibility
with the community and other stakeholders (Be sensitive to the public concern), and 1.1 act
appropriately, and in a professional manner, when you perceive something to be wrong.
Therefore, I instructed electrical design consultant to revise the design of particular location
in the view of my finding. I highlighted my management in future safety auditing of the street
should account ethical aspect as well.
Moreover SWEK received several feedbacks from people for poor illumination at
River Fig Avenue which is close to the main shopping area of Kununurra. It was also raised
by SKEK planning department in their frequently safety auditing of the city centre. I raised
this matter with Ansel Technical Electrical consultants to accelerate the design of the avenue.
Then I prepared necessary application with comply with design and raised Purchasing Order
with Horizon power to get the necessary material and implement the design as soon as
possible. There I followed the ethic guideline of EA, 4.1 Engage responsibility with the
community and other stakeholders (Be sensitive to the public concern).
Claim 2
2
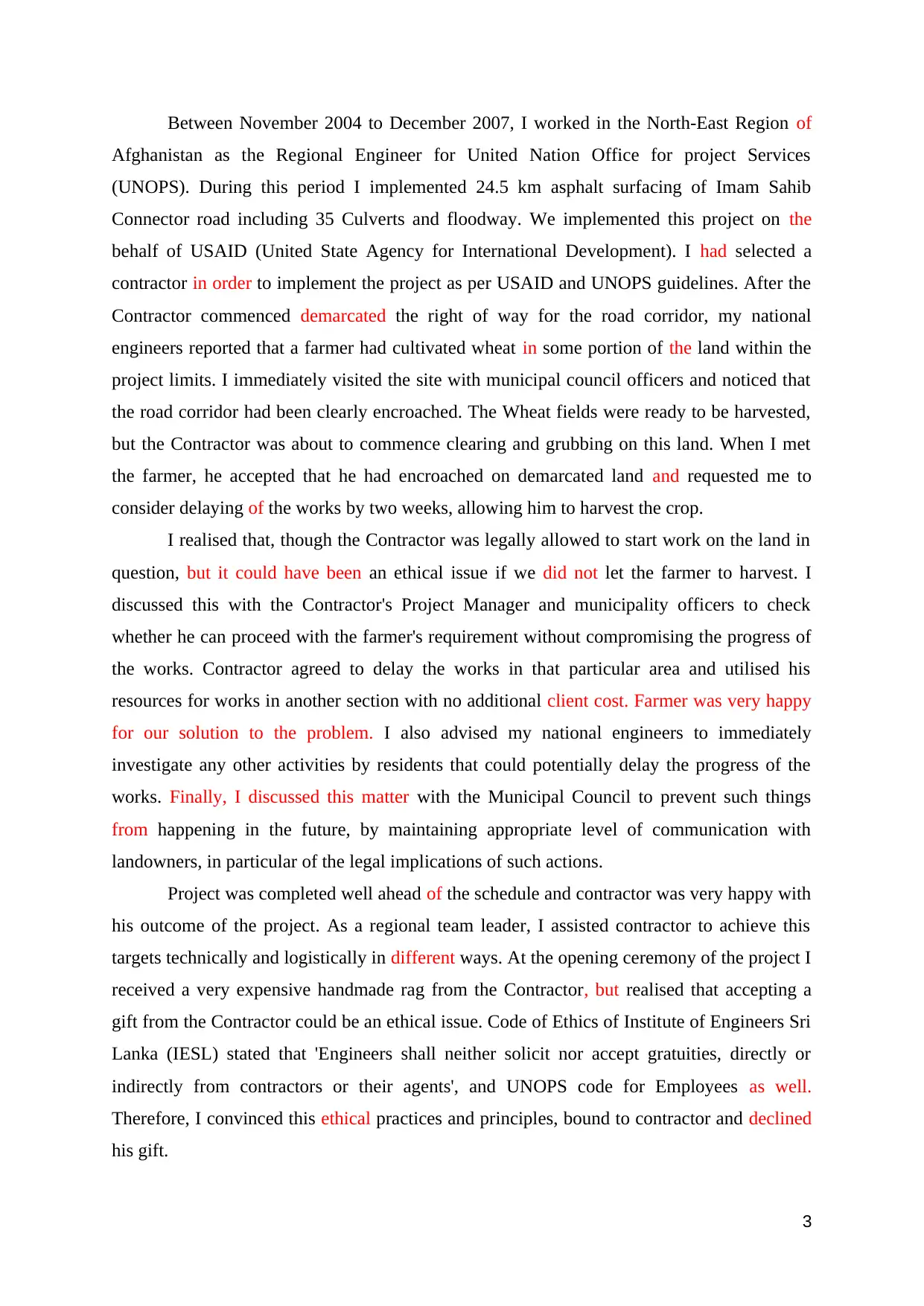
Between November 2004 to December 2007, I worked in the North-East Region of
Afghanistan as the Regional Engineer for United Nation Office for project Services
(UNOPS). During this period I implemented 24.5 km asphalt surfacing of Imam Sahib
Connector road including 35 Culverts and floodway. We implemented this project on the
behalf of USAID (United State Agency for International Development). I had selected a
contractor in order to implement the project as per USAID and UNOPS guidelines. After the
Contractor commenced demarcated the right of way for the road corridor, my national
engineers reported that a farmer had cultivated wheat in some portion of the land within the
project limits. I immediately visited the site with municipal council officers and noticed that
the road corridor had been clearly encroached. The Wheat fields were ready to be harvested,
but the Contractor was about to commence clearing and grubbing on this land. When I met
the farmer, he accepted that he had encroached on demarcated land and requested me to
consider delaying of the works by two weeks, allowing him to harvest the crop.
I realised that, though the Contractor was legally allowed to start work on the land in
question, but it could have been an ethical issue if we did not let the farmer to harvest. I
discussed this with the Contractor's Project Manager and municipality officers to check
whether he can proceed with the farmer's requirement without compromising the progress of
the works. Contractor agreed to delay the works in that particular area and utilised his
resources for works in another section with no additional client cost. Farmer was very happy
for our solution to the problem. I also advised my national engineers to immediately
investigate any other activities by residents that could potentially delay the progress of the
works. Finally, I discussed this matter with the Municipal Council to prevent such things
from happening in the future, by maintaining appropriate level of communication with
landowners, in particular of the legal implications of such actions.
Project was completed well ahead of the schedule and contractor was very happy with
his outcome of the project. As a regional team leader, I assisted contractor to achieve this
targets technically and logistically in different ways. At the opening ceremony of the project I
received a very expensive handmade rag from the Contractor, but realised that accepting a
gift from the Contractor could be an ethical issue. Code of Ethics of Institute of Engineers Sri
Lanka (IESL) stated that 'Engineers shall neither solicit nor accept gratuities, directly or
indirectly from contractors or their agents', and UNOPS code for Employees as well.
Therefore, I convinced this ethical practices and principles, bound to contractor and declined
his gift.
3
Afghanistan as the Regional Engineer for United Nation Office for project Services
(UNOPS). During this period I implemented 24.5 km asphalt surfacing of Imam Sahib
Connector road including 35 Culverts and floodway. We implemented this project on the
behalf of USAID (United State Agency for International Development). I had selected a
contractor in order to implement the project as per USAID and UNOPS guidelines. After the
Contractor commenced demarcated the right of way for the road corridor, my national
engineers reported that a farmer had cultivated wheat in some portion of the land within the
project limits. I immediately visited the site with municipal council officers and noticed that
the road corridor had been clearly encroached. The Wheat fields were ready to be harvested,
but the Contractor was about to commence clearing and grubbing on this land. When I met
the farmer, he accepted that he had encroached on demarcated land and requested me to
consider delaying of the works by two weeks, allowing him to harvest the crop.
I realised that, though the Contractor was legally allowed to start work on the land in
question, but it could have been an ethical issue if we did not let the farmer to harvest. I
discussed this with the Contractor's Project Manager and municipality officers to check
whether he can proceed with the farmer's requirement without compromising the progress of
the works. Contractor agreed to delay the works in that particular area and utilised his
resources for works in another section with no additional client cost. Farmer was very happy
for our solution to the problem. I also advised my national engineers to immediately
investigate any other activities by residents that could potentially delay the progress of the
works. Finally, I discussed this matter with the Municipal Council to prevent such things
from happening in the future, by maintaining appropriate level of communication with
landowners, in particular of the legal implications of such actions.
Project was completed well ahead of the schedule and contractor was very happy with
his outcome of the project. As a regional team leader, I assisted contractor to achieve this
targets technically and logistically in different ways. At the opening ceremony of the project I
received a very expensive handmade rag from the Contractor, but realised that accepting a
gift from the Contractor could be an ethical issue. Code of Ethics of Institute of Engineers Sri
Lanka (IESL) stated that 'Engineers shall neither solicit nor accept gratuities, directly or
indirectly from contractors or their agents', and UNOPS code for Employees as well.
Therefore, I convinced this ethical practices and principles, bound to contractor and declined
his gift.
3
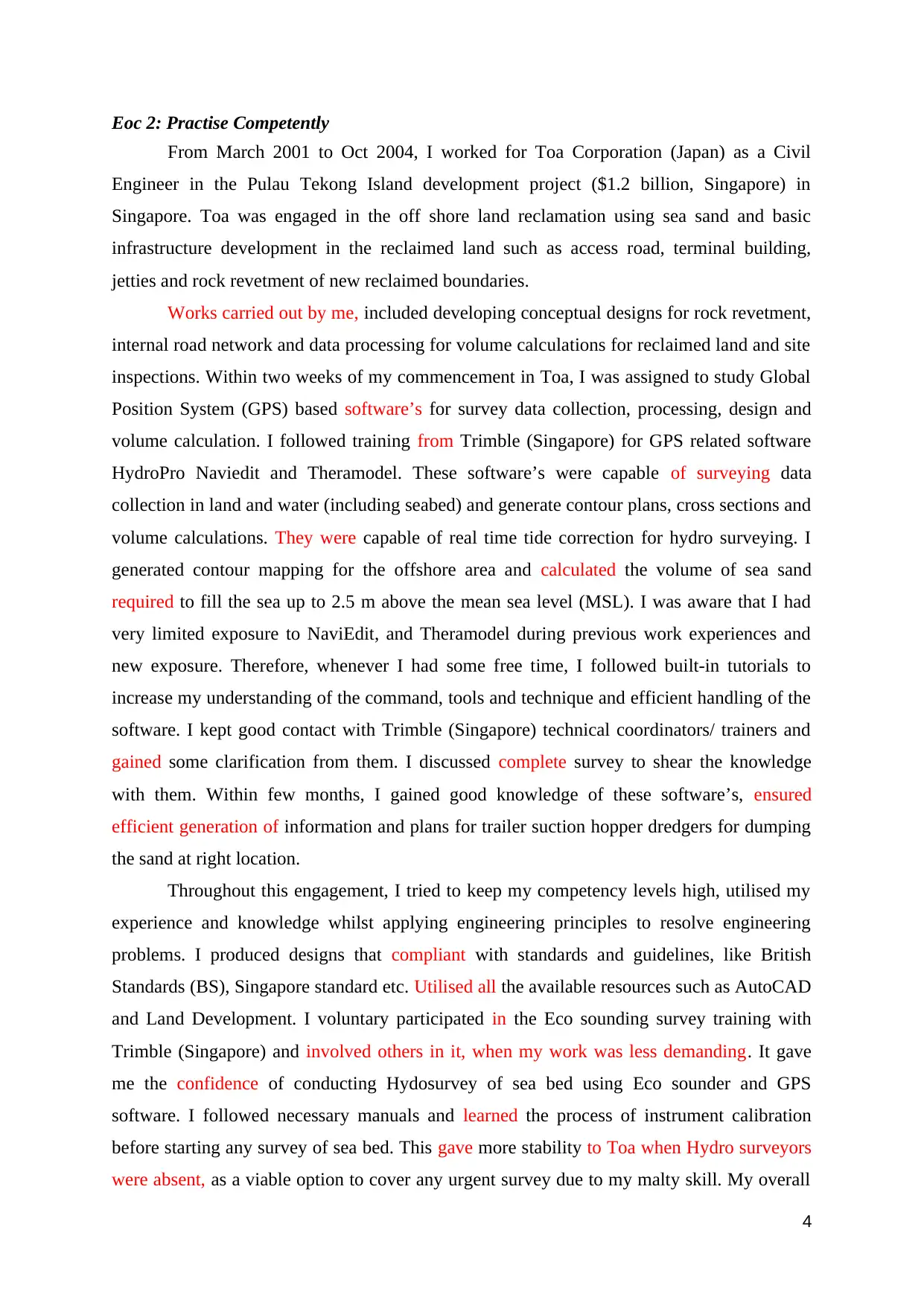
Eoc 2: Practise Competently
From March 2001 to Oct 2004, I worked for Toa Corporation (Japan) as a Civil
Engineer in the Pulau Tekong Island development project ($1.2 billion, Singapore) in
Singapore. Toa was engaged in the off shore land reclamation using sea sand and basic
infrastructure development in the reclaimed land such as access road, terminal building,
jetties and rock revetment of new reclaimed boundaries.
Works carried out by me, included developing conceptual designs for rock revetment,
internal road network and data processing for volume calculations for reclaimed land and site
inspections. Within two weeks of my commencement in Toa, I was assigned to study Global
Position System (GPS) based software’s for survey data collection, processing, design and
volume calculation. I followed training from Trimble (Singapore) for GPS related software
HydroPro Naviedit and Theramodel. These software’s were capable of surveying data
collection in land and water (including seabed) and generate contour plans, cross sections and
volume calculations. They were capable of real time tide correction for hydro surveying. I
generated contour mapping for the offshore area and calculated the volume of sea sand
required to fill the sea up to 2.5 m above the mean sea level (MSL). I was aware that I had
very limited exposure to NaviEdit, and Theramodel during previous work experiences and
new exposure. Therefore, whenever I had some free time, I followed built-in tutorials to
increase my understanding of the command, tools and technique and efficient handling of the
software. I kept good contact with Trimble (Singapore) technical coordinators/ trainers and
gained some clarification from them. I discussed complete survey to shear the knowledge
with them. Within few months, I gained good knowledge of these software’s, ensured
efficient generation of information and plans for trailer suction hopper dredgers for dumping
the sand at right location.
Throughout this engagement, I tried to keep my competency levels high, utilised my
experience and knowledge whilst applying engineering principles to resolve engineering
problems. I produced designs that compliant with standards and guidelines, like British
Standards (BS), Singapore standard etc. Utilised all the available resources such as AutoCAD
and Land Development. I voluntary participated in the Eco sounding survey training with
Trimble (Singapore) and involved others in it, when my work was less demanding. It gave
me the confidence of conducting Hydosurvey of sea bed using Eco sounder and GPS
software. I followed necessary manuals and learned the process of instrument calibration
before starting any survey of sea bed. This gave more stability to Toa when Hydro surveyors
were absent, as a viable option to cover any urgent survey due to my malty skill. My overall
4
From March 2001 to Oct 2004, I worked for Toa Corporation (Japan) as a Civil
Engineer in the Pulau Tekong Island development project ($1.2 billion, Singapore) in
Singapore. Toa was engaged in the off shore land reclamation using sea sand and basic
infrastructure development in the reclaimed land such as access road, terminal building,
jetties and rock revetment of new reclaimed boundaries.
Works carried out by me, included developing conceptual designs for rock revetment,
internal road network and data processing for volume calculations for reclaimed land and site
inspections. Within two weeks of my commencement in Toa, I was assigned to study Global
Position System (GPS) based software’s for survey data collection, processing, design and
volume calculation. I followed training from Trimble (Singapore) for GPS related software
HydroPro Naviedit and Theramodel. These software’s were capable of surveying data
collection in land and water (including seabed) and generate contour plans, cross sections and
volume calculations. They were capable of real time tide correction for hydro surveying. I
generated contour mapping for the offshore area and calculated the volume of sea sand
required to fill the sea up to 2.5 m above the mean sea level (MSL). I was aware that I had
very limited exposure to NaviEdit, and Theramodel during previous work experiences and
new exposure. Therefore, whenever I had some free time, I followed built-in tutorials to
increase my understanding of the command, tools and technique and efficient handling of the
software. I kept good contact with Trimble (Singapore) technical coordinators/ trainers and
gained some clarification from them. I discussed complete survey to shear the knowledge
with them. Within few months, I gained good knowledge of these software’s, ensured
efficient generation of information and plans for trailer suction hopper dredgers for dumping
the sand at right location.
Throughout this engagement, I tried to keep my competency levels high, utilised my
experience and knowledge whilst applying engineering principles to resolve engineering
problems. I produced designs that compliant with standards and guidelines, like British
Standards (BS), Singapore standard etc. Utilised all the available resources such as AutoCAD
and Land Development. I voluntary participated in the Eco sounding survey training with
Trimble (Singapore) and involved others in it, when my work was less demanding. It gave
me the confidence of conducting Hydosurvey of sea bed using Eco sounder and GPS
software. I followed necessary manuals and learned the process of instrument calibration
before starting any survey of sea bed. This gave more stability to Toa when Hydro surveyors
were absent, as a viable option to cover any urgent survey due to my malty skill. My overall
4
Secure Best Marks with AI Grader
Need help grading? Try our AI Grader for instant feedback on your assignments.
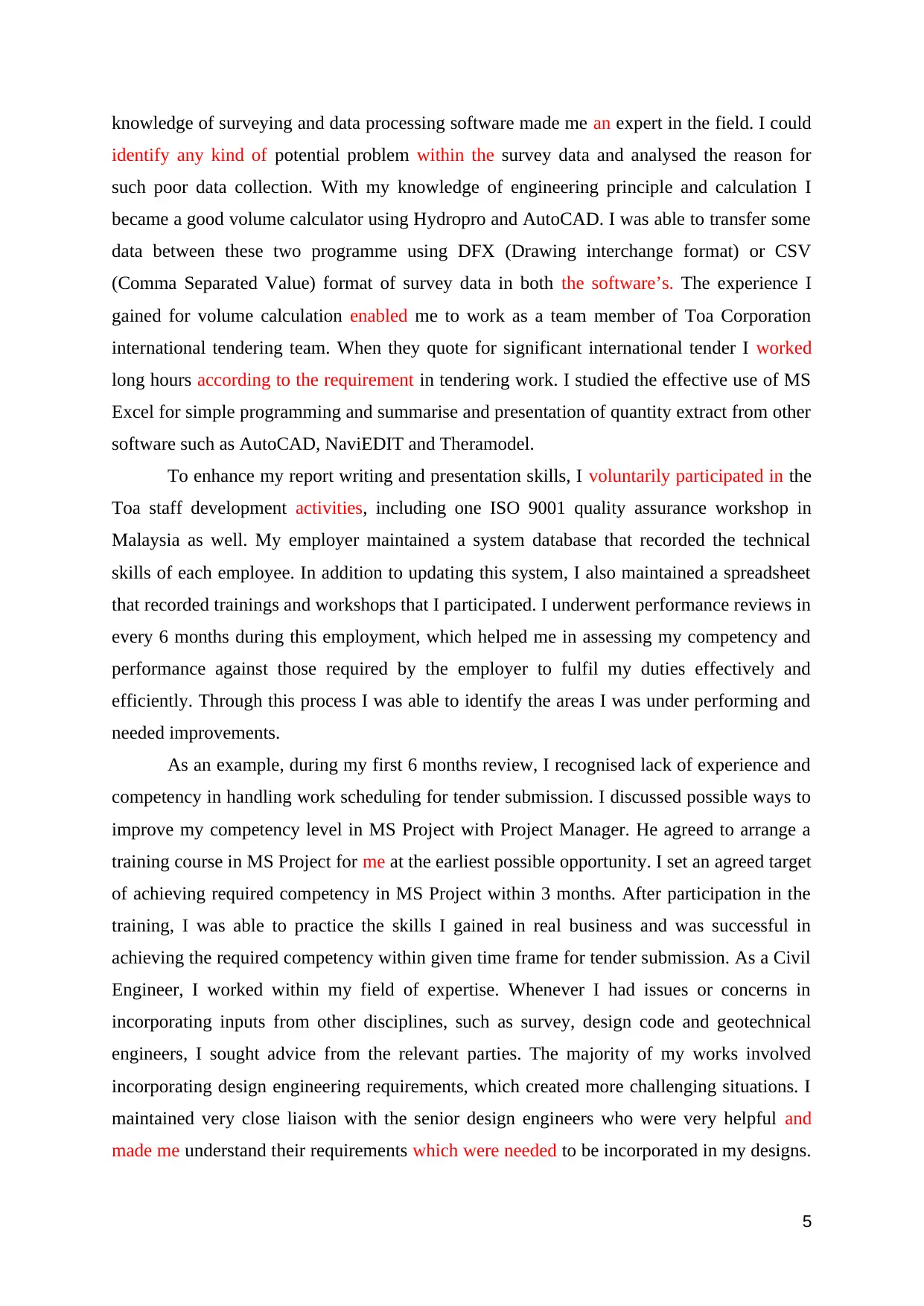
knowledge of surveying and data processing software made me an expert in the field. I could
identify any kind of potential problem within the survey data and analysed the reason for
such poor data collection. With my knowledge of engineering principle and calculation I
became a good volume calculator using Hydropro and AutoCAD. I was able to transfer some
data between these two programme using DFX (Drawing interchange format) or CSV
(Comma Separated Value) format of survey data in both the software’s. The experience I
gained for volume calculation enabled me to work as a team member of Toa Corporation
international tendering team. When they quote for significant international tender I worked
long hours according to the requirement in tendering work. I studied the effective use of MS
Excel for simple programming and summarise and presentation of quantity extract from other
software such as AutoCAD, NaviEDIT and Theramodel.
To enhance my report writing and presentation skills, I voluntarily participated in the
Toa staff development activities, including one ISO 9001 quality assurance workshop in
Malaysia as well. My employer maintained a system database that recorded the technical
skills of each employee. In addition to updating this system, I also maintained a spreadsheet
that recorded trainings and workshops that I participated. I underwent performance reviews in
every 6 months during this employment, which helped me in assessing my competency and
performance against those required by the employer to fulfil my duties effectively and
efficiently. Through this process I was able to identify the areas I was under performing and
needed improvements.
As an example, during my first 6 months review, I recognised lack of experience and
competency in handling work scheduling for tender submission. I discussed possible ways to
improve my competency level in MS Project with Project Manager. He agreed to arrange a
training course in MS Project for me at the earliest possible opportunity. I set an agreed target
of achieving required competency in MS Project within 3 months. After participation in the
training, I was able to practice the skills I gained in real business and was successful in
achieving the required competency within given time frame for tender submission. As a Civil
Engineer, I worked within my field of expertise. Whenever I had issues or concerns in
incorporating inputs from other disciplines, such as survey, design code and geotechnical
engineers, I sought advice from the relevant parties. The majority of my works involved
incorporating design engineering requirements, which created more challenging situations. I
maintained very close liaison with the senior design engineers who were very helpful and
made me understand their requirements which were needed to be incorporated in my designs.
5
identify any kind of potential problem within the survey data and analysed the reason for
such poor data collection. With my knowledge of engineering principle and calculation I
became a good volume calculator using Hydropro and AutoCAD. I was able to transfer some
data between these two programme using DFX (Drawing interchange format) or CSV
(Comma Separated Value) format of survey data in both the software’s. The experience I
gained for volume calculation enabled me to work as a team member of Toa Corporation
international tendering team. When they quote for significant international tender I worked
long hours according to the requirement in tendering work. I studied the effective use of MS
Excel for simple programming and summarise and presentation of quantity extract from other
software such as AutoCAD, NaviEDIT and Theramodel.
To enhance my report writing and presentation skills, I voluntarily participated in the
Toa staff development activities, including one ISO 9001 quality assurance workshop in
Malaysia as well. My employer maintained a system database that recorded the technical
skills of each employee. In addition to updating this system, I also maintained a spreadsheet
that recorded trainings and workshops that I participated. I underwent performance reviews in
every 6 months during this employment, which helped me in assessing my competency and
performance against those required by the employer to fulfil my duties effectively and
efficiently. Through this process I was able to identify the areas I was under performing and
needed improvements.
As an example, during my first 6 months review, I recognised lack of experience and
competency in handling work scheduling for tender submission. I discussed possible ways to
improve my competency level in MS Project with Project Manager. He agreed to arrange a
training course in MS Project for me at the earliest possible opportunity. I set an agreed target
of achieving required competency in MS Project within 3 months. After participation in the
training, I was able to practice the skills I gained in real business and was successful in
achieving the required competency within given time frame for tender submission. As a Civil
Engineer, I worked within my field of expertise. Whenever I had issues or concerns in
incorporating inputs from other disciplines, such as survey, design code and geotechnical
engineers, I sought advice from the relevant parties. The majority of my works involved
incorporating design engineering requirements, which created more challenging situations. I
maintained very close liaison with the senior design engineers who were very helpful and
made me understand their requirements which were needed to be incorporated in my designs.
5
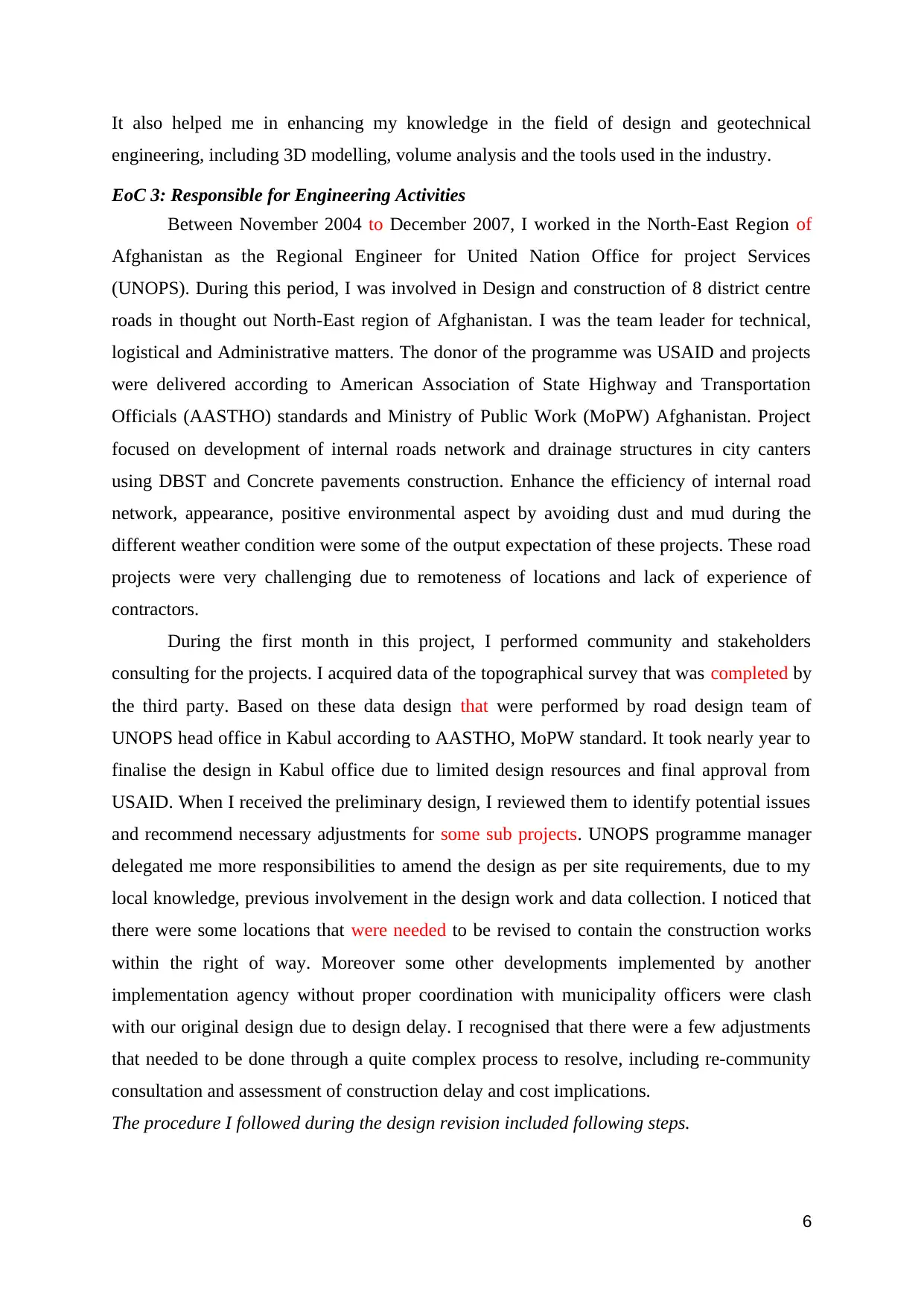
It also helped me in enhancing my knowledge in the field of design and geotechnical
engineering, including 3D modelling, volume analysis and the tools used in the industry.
EoC 3: Responsible for Engineering Activities
Between November 2004 to December 2007, I worked in the North-East Region of
Afghanistan as the Regional Engineer for United Nation Office for project Services
(UNOPS). During this period, I was involved in Design and construction of 8 district centre
roads in thought out North-East region of Afghanistan. I was the team leader for technical,
logistical and Administrative matters. The donor of the programme was USAID and projects
were delivered according to American Association of State Highway and Transportation
Officials (AASTHO) standards and Ministry of Public Work (MoPW) Afghanistan. Project
focused on development of internal roads network and drainage structures in city canters
using DBST and Concrete pavements construction. Enhance the efficiency of internal road
network, appearance, positive environmental aspect by avoiding dust and mud during the
different weather condition were some of the output expectation of these projects. These road
projects were very challenging due to remoteness of locations and lack of experience of
contractors.
During the first month in this project, I performed community and stakeholders
consulting for the projects. I acquired data of the topographical survey that was completed by
the third party. Based on these data design that were performed by road design team of
UNOPS head office in Kabul according to AASTHO, MoPW standard. It took nearly year to
finalise the design in Kabul office due to limited design resources and final approval from
USAID. When I received the preliminary design, I reviewed them to identify potential issues
and recommend necessary adjustments for some sub projects. UNOPS programme manager
delegated me more responsibilities to amend the design as per site requirements, due to my
local knowledge, previous involvement in the design work and data collection. I noticed that
there were some locations that were needed to be revised to contain the construction works
within the right of way. Moreover some other developments implemented by another
implementation agency without proper coordination with municipality officers were clash
with our original design due to design delay. I recognised that there were a few adjustments
that needed to be done through a quite complex process to resolve, including re-community
consultation and assessment of construction delay and cost implications.
The procedure I followed during the design revision included following steps.
6
engineering, including 3D modelling, volume analysis and the tools used in the industry.
EoC 3: Responsible for Engineering Activities
Between November 2004 to December 2007, I worked in the North-East Region of
Afghanistan as the Regional Engineer for United Nation Office for project Services
(UNOPS). During this period, I was involved in Design and construction of 8 district centre
roads in thought out North-East region of Afghanistan. I was the team leader for technical,
logistical and Administrative matters. The donor of the programme was USAID and projects
were delivered according to American Association of State Highway and Transportation
Officials (AASTHO) standards and Ministry of Public Work (MoPW) Afghanistan. Project
focused on development of internal roads network and drainage structures in city canters
using DBST and Concrete pavements construction. Enhance the efficiency of internal road
network, appearance, positive environmental aspect by avoiding dust and mud during the
different weather condition were some of the output expectation of these projects. These road
projects were very challenging due to remoteness of locations and lack of experience of
contractors.
During the first month in this project, I performed community and stakeholders
consulting for the projects. I acquired data of the topographical survey that was completed by
the third party. Based on these data design that were performed by road design team of
UNOPS head office in Kabul according to AASTHO, MoPW standard. It took nearly year to
finalise the design in Kabul office due to limited design resources and final approval from
USAID. When I received the preliminary design, I reviewed them to identify potential issues
and recommend necessary adjustments for some sub projects. UNOPS programme manager
delegated me more responsibilities to amend the design as per site requirements, due to my
local knowledge, previous involvement in the design work and data collection. I noticed that
there were some locations that were needed to be revised to contain the construction works
within the right of way. Moreover some other developments implemented by another
implementation agency without proper coordination with municipality officers were clash
with our original design due to design delay. I recognised that there were a few adjustments
that needed to be done through a quite complex process to resolve, including re-community
consultation and assessment of construction delay and cost implications.
The procedure I followed during the design revision included following steps.
6
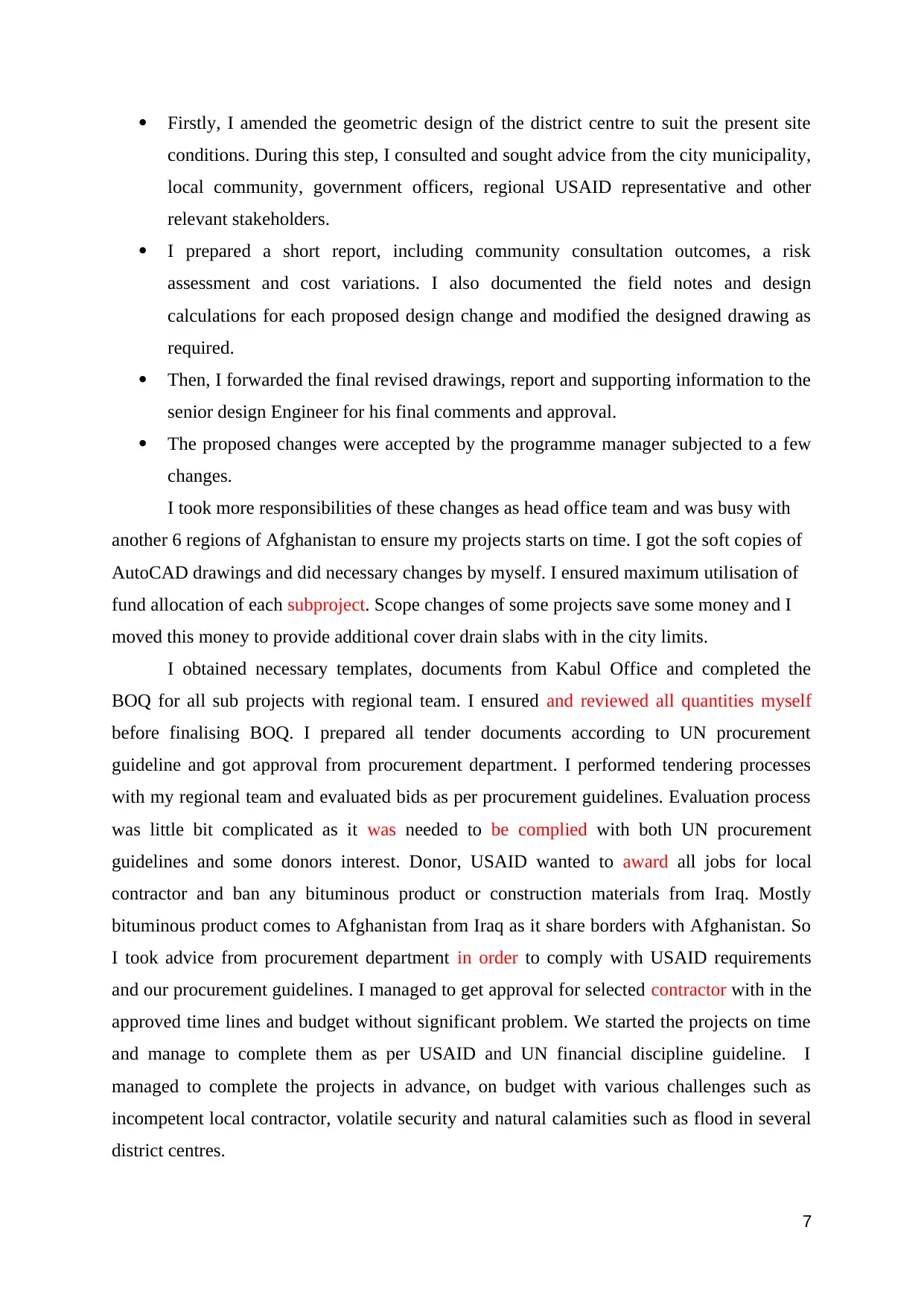
Firstly, I amended the geometric design of the district centre to suit the present site
conditions. During this step, I consulted and sought advice from the city municipality,
local community, government officers, regional USAID representative and other
relevant stakeholders.
I prepared a short report, including community consultation outcomes, a risk
assessment and cost variations. I also documented the field notes and design
calculations for each proposed design change and modified the designed drawing as
required.
Then, I forwarded the final revised drawings, report and supporting information to the
senior design Engineer for his final comments and approval.
The proposed changes were accepted by the programme manager subjected to a few
changes.
I took more responsibilities of these changes as head office team and was busy with
another 6 regions of Afghanistan to ensure my projects starts on time. I got the soft copies of
AutoCAD drawings and did necessary changes by myself. I ensured maximum utilisation of
fund allocation of each subproject. Scope changes of some projects save some money and I
moved this money to provide additional cover drain slabs with in the city limits.
I obtained necessary templates, documents from Kabul Office and completed the
BOQ for all sub projects with regional team. I ensured and reviewed all quantities myself
before finalising BOQ. I prepared all tender documents according to UN procurement
guideline and got approval from procurement department. I performed tendering processes
with my regional team and evaluated bids as per procurement guidelines. Evaluation process
was little bit complicated as it was needed to be complied with both UN procurement
guidelines and some donors interest. Donor, USAID wanted to award all jobs for local
contractor and ban any bituminous product or construction materials from Iraq. Mostly
bituminous product comes to Afghanistan from Iraq as it share borders with Afghanistan. So
I took advice from procurement department in order to comply with USAID requirements
and our procurement guidelines. I managed to get approval for selected contractor with in the
approved time lines and budget without significant problem. We started the projects on time
and manage to complete them as per USAID and UN financial discipline guideline. I
managed to complete the projects in advance, on budget with various challenges such as
incompetent local contractor, volatile security and natural calamities such as flood in several
district centres.
7
conditions. During this step, I consulted and sought advice from the city municipality,
local community, government officers, regional USAID representative and other
relevant stakeholders.
I prepared a short report, including community consultation outcomes, a risk
assessment and cost variations. I also documented the field notes and design
calculations for each proposed design change and modified the designed drawing as
required.
Then, I forwarded the final revised drawings, report and supporting information to the
senior design Engineer for his final comments and approval.
The proposed changes were accepted by the programme manager subjected to a few
changes.
I took more responsibilities of these changes as head office team and was busy with
another 6 regions of Afghanistan to ensure my projects starts on time. I got the soft copies of
AutoCAD drawings and did necessary changes by myself. I ensured maximum utilisation of
fund allocation of each subproject. Scope changes of some projects save some money and I
moved this money to provide additional cover drain slabs with in the city limits.
I obtained necessary templates, documents from Kabul Office and completed the
BOQ for all sub projects with regional team. I ensured and reviewed all quantities myself
before finalising BOQ. I prepared all tender documents according to UN procurement
guideline and got approval from procurement department. I performed tendering processes
with my regional team and evaluated bids as per procurement guidelines. Evaluation process
was little bit complicated as it was needed to be complied with both UN procurement
guidelines and some donors interest. Donor, USAID wanted to award all jobs for local
contractor and ban any bituminous product or construction materials from Iraq. Mostly
bituminous product comes to Afghanistan from Iraq as it share borders with Afghanistan. So
I took advice from procurement department in order to comply with USAID requirements
and our procurement guidelines. I managed to get approval for selected contractor with in the
approved time lines and budget without significant problem. We started the projects on time
and manage to complete them as per USAID and UN financial discipline guideline. I
managed to complete the projects in advance, on budget with various challenges such as
incompetent local contractor, volatile security and natural calamities such as flood in several
district centres.
7
Paraphrase This Document
Need a fresh take? Get an instant paraphrase of this document with our AI Paraphraser
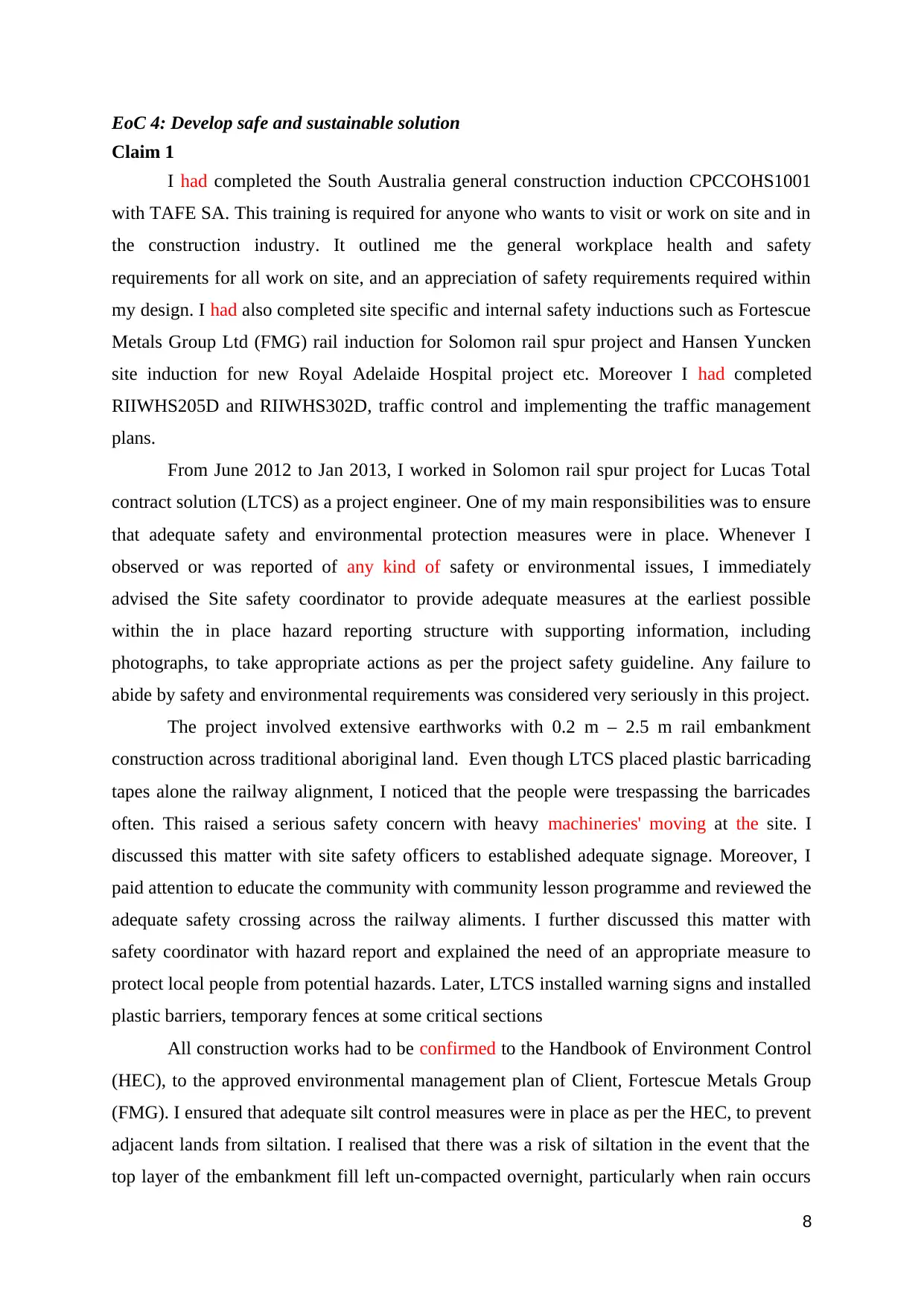
EoC 4: Develop safe and sustainable solution
Claim 1
I had completed the South Australia general construction induction CPCCOHS1001
with TAFE SA. This training is required for anyone who wants to visit or work on site and in
the construction industry. It outlined me the general workplace health and safety
requirements for all work on site, and an appreciation of safety requirements required within
my design. I had also completed site specific and internal safety inductions such as Fortescue
Metals Group Ltd (FMG) rail induction for Solomon rail spur project and Hansen Yuncken
site induction for new Royal Adelaide Hospital project etc. Moreover I had completed
RIIWHS205D and RIIWHS302D, traffic control and implementing the traffic management
plans.
From June 2012 to Jan 2013, I worked in Solomon rail spur project for Lucas Total
contract solution (LTCS) as a project engineer. One of my main responsibilities was to ensure
that adequate safety and environmental protection measures were in place. Whenever I
observed or was reported of any kind of safety or environmental issues, I immediately
advised the Site safety coordinator to provide adequate measures at the earliest possible
within the in place hazard reporting structure with supporting information, including
photographs, to take appropriate actions as per the project safety guideline. Any failure to
abide by safety and environmental requirements was considered very seriously in this project.
The project involved extensive earthworks with 0.2 m – 2.5 m rail embankment
construction across traditional aboriginal land. Even though LTCS placed plastic barricading
tapes alone the railway alignment, I noticed that the people were trespassing the barricades
often. This raised a serious safety concern with heavy machineries' moving at the site. I
discussed this matter with site safety officers to established adequate signage. Moreover, I
paid attention to educate the community with community lesson programme and reviewed the
adequate safety crossing across the railway aliments. I further discussed this matter with
safety coordinator with hazard report and explained the need of an appropriate measure to
protect local people from potential hazards. Later, LTCS installed warning signs and installed
plastic barriers, temporary fences at some critical sections
All construction works had to be confirmed to the Handbook of Environment Control
(HEC), to the approved environmental management plan of Client, Fortescue Metals Group
(FMG). I ensured that adequate silt control measures were in place as per the HEC, to prevent
adjacent lands from siltation. I realised that there was a risk of siltation in the event that the
top layer of the embankment fill left un-compacted overnight, particularly when rain occurs
8
Claim 1
I had completed the South Australia general construction induction CPCCOHS1001
with TAFE SA. This training is required for anyone who wants to visit or work on site and in
the construction industry. It outlined me the general workplace health and safety
requirements for all work on site, and an appreciation of safety requirements required within
my design. I had also completed site specific and internal safety inductions such as Fortescue
Metals Group Ltd (FMG) rail induction for Solomon rail spur project and Hansen Yuncken
site induction for new Royal Adelaide Hospital project etc. Moreover I had completed
RIIWHS205D and RIIWHS302D, traffic control and implementing the traffic management
plans.
From June 2012 to Jan 2013, I worked in Solomon rail spur project for Lucas Total
contract solution (LTCS) as a project engineer. One of my main responsibilities was to ensure
that adequate safety and environmental protection measures were in place. Whenever I
observed or was reported of any kind of safety or environmental issues, I immediately
advised the Site safety coordinator to provide adequate measures at the earliest possible
within the in place hazard reporting structure with supporting information, including
photographs, to take appropriate actions as per the project safety guideline. Any failure to
abide by safety and environmental requirements was considered very seriously in this project.
The project involved extensive earthworks with 0.2 m – 2.5 m rail embankment
construction across traditional aboriginal land. Even though LTCS placed plastic barricading
tapes alone the railway alignment, I noticed that the people were trespassing the barricades
often. This raised a serious safety concern with heavy machineries' moving at the site. I
discussed this matter with site safety officers to established adequate signage. Moreover, I
paid attention to educate the community with community lesson programme and reviewed the
adequate safety crossing across the railway aliments. I further discussed this matter with
safety coordinator with hazard report and explained the need of an appropriate measure to
protect local people from potential hazards. Later, LTCS installed warning signs and installed
plastic barriers, temporary fences at some critical sections
All construction works had to be confirmed to the Handbook of Environment Control
(HEC), to the approved environmental management plan of Client, Fortescue Metals Group
(FMG). I ensured that adequate silt control measures were in place as per the HEC, to prevent
adjacent lands from siltation. I realised that there was a risk of siltation in the event that the
top layer of the embankment fill left un-compacted overnight, particularly when rain occurs
8
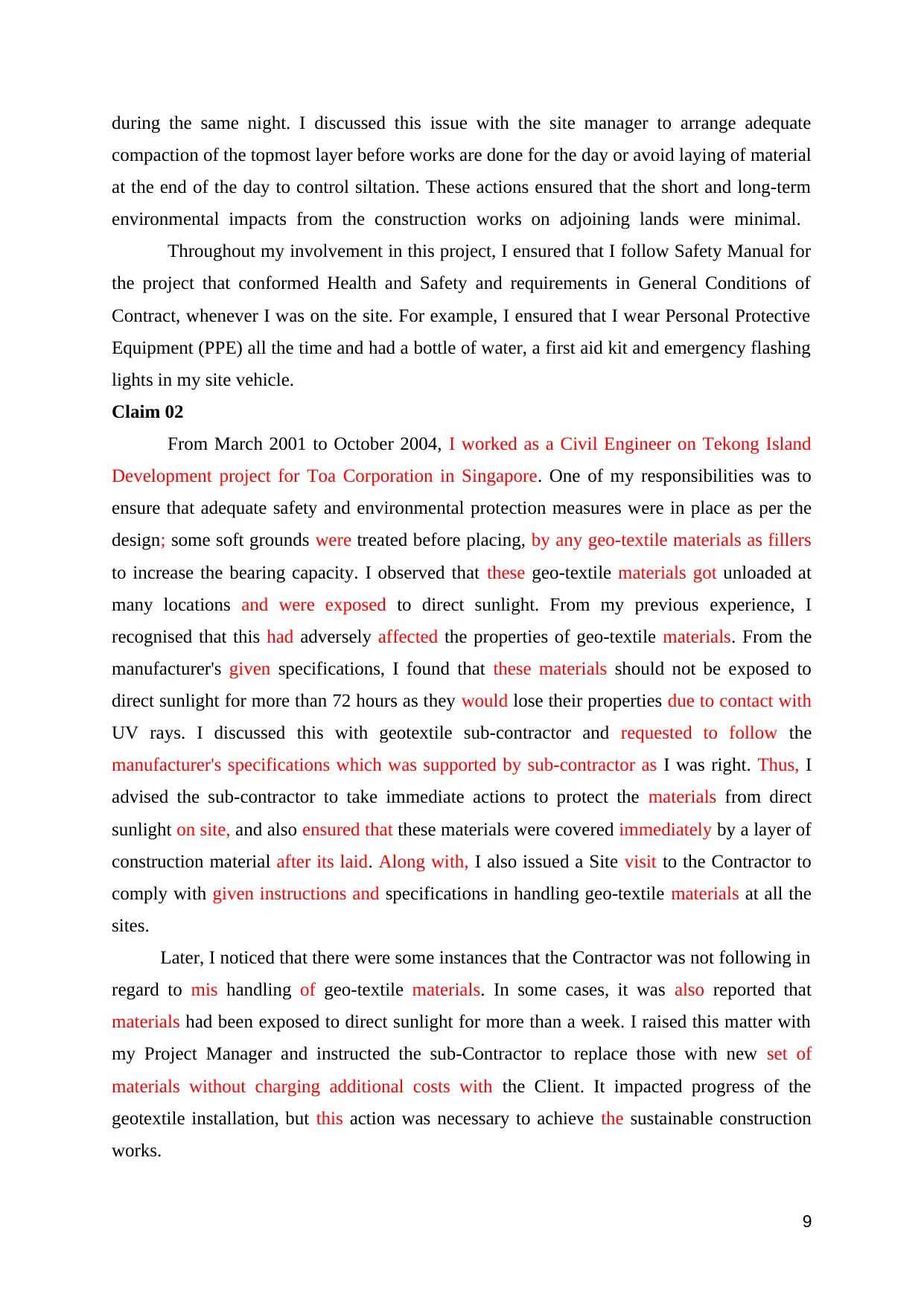
during the same night. I discussed this issue with the site manager to arrange adequate
compaction of the topmost layer before works are done for the day or avoid laying of material
at the end of the day to control siltation. These actions ensured that the short and long-term
environmental impacts from the construction works on adjoining lands were minimal.
Throughout my involvement in this project, I ensured that I follow Safety Manual for
the project that conformed Health and Safety and requirements in General Conditions of
Contract, whenever I was on the site. For example, I ensured that I wear Personal Protective
Equipment (PPE) all the time and had a bottle of water, a first aid kit and emergency flashing
lights in my site vehicle.
Claim 02
From March 2001 to October 2004, I worked as a Civil Engineer on Tekong Island
Development project for Toa Corporation in Singapore. One of my responsibilities was to
ensure that adequate safety and environmental protection measures were in place as per the
design; some soft grounds were treated before placing, by any geo-textile materials as fillers
to increase the bearing capacity. I observed that these geo-textile materials got unloaded at
many locations and were exposed to direct sunlight. From my previous experience, I
recognised that this had adversely affected the properties of geo-textile materials. From the
manufacturer's given specifications, I found that these materials should not be exposed to
direct sunlight for more than 72 hours as they would lose their properties due to contact with
UV rays. I discussed this with geotextile sub-contractor and requested to follow the
manufacturer's specifications which was supported by sub-contractor as I was right. Thus, I
advised the sub-contractor to take immediate actions to protect the materials from direct
sunlight on site, and also ensured that these materials were covered immediately by a layer of
construction material after its laid. Along with, I also issued a Site visit to the Contractor to
comply with given instructions and specifications in handling geo-textile materials at all the
sites.
Later, I noticed that there were some instances that the Contractor was not following in
regard to mis handling of geo-textile materials. In some cases, it was also reported that
materials had been exposed to direct sunlight for more than a week. I raised this matter with
my Project Manager and instructed the sub-Contractor to replace those with new set of
materials without charging additional costs with the Client. It impacted progress of the
geotextile installation, but this action was necessary to achieve the sustainable construction
works.
9
compaction of the topmost layer before works are done for the day or avoid laying of material
at the end of the day to control siltation. These actions ensured that the short and long-term
environmental impacts from the construction works on adjoining lands were minimal.
Throughout my involvement in this project, I ensured that I follow Safety Manual for
the project that conformed Health and Safety and requirements in General Conditions of
Contract, whenever I was on the site. For example, I ensured that I wear Personal Protective
Equipment (PPE) all the time and had a bottle of water, a first aid kit and emergency flashing
lights in my site vehicle.
Claim 02
From March 2001 to October 2004, I worked as a Civil Engineer on Tekong Island
Development project for Toa Corporation in Singapore. One of my responsibilities was to
ensure that adequate safety and environmental protection measures were in place as per the
design; some soft grounds were treated before placing, by any geo-textile materials as fillers
to increase the bearing capacity. I observed that these geo-textile materials got unloaded at
many locations and were exposed to direct sunlight. From my previous experience, I
recognised that this had adversely affected the properties of geo-textile materials. From the
manufacturer's given specifications, I found that these materials should not be exposed to
direct sunlight for more than 72 hours as they would lose their properties due to contact with
UV rays. I discussed this with geotextile sub-contractor and requested to follow the
manufacturer's specifications which was supported by sub-contractor as I was right. Thus, I
advised the sub-contractor to take immediate actions to protect the materials from direct
sunlight on site, and also ensured that these materials were covered immediately by a layer of
construction material after its laid. Along with, I also issued a Site visit to the Contractor to
comply with given instructions and specifications in handling geo-textile materials at all the
sites.
Later, I noticed that there were some instances that the Contractor was not following in
regard to mis handling of geo-textile materials. In some cases, it was also reported that
materials had been exposed to direct sunlight for more than a week. I raised this matter with
my Project Manager and instructed the sub-Contractor to replace those with new set of
materials without charging additional costs with the Client. It impacted progress of the
geotextile installation, but this action was necessary to achieve the sustainable construction
works.
9
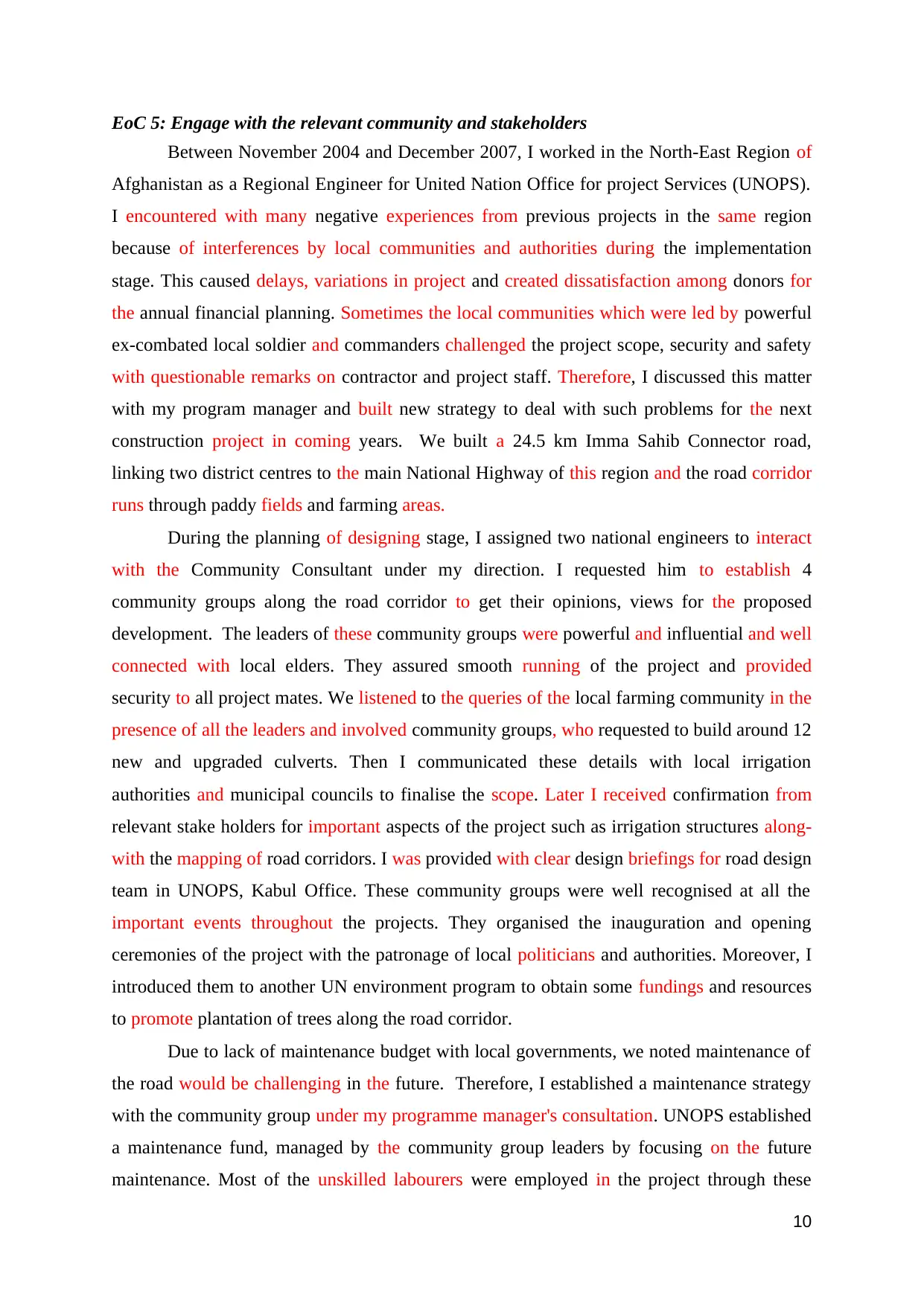
EoC 5: Engage with the relevant community and stakeholders
Between November 2004 and December 2007, I worked in the North-East Region of
Afghanistan as a Regional Engineer for United Nation Office for project Services (UNOPS).
I encountered with many negative experiences from previous projects in the same region
because of interferences by local communities and authorities during the implementation
stage. This caused delays, variations in project and created dissatisfaction among donors for
the annual financial planning. Sometimes the local communities which were led by powerful
ex-combated local soldier and commanders challenged the project scope, security and safety
with questionable remarks on contractor and project staff. Therefore, I discussed this matter
with my program manager and built new strategy to deal with such problems for the next
construction project in coming years. We built a 24.5 km Imma Sahib Connector road,
linking two district centres to the main National Highway of this region and the road corridor
runs through paddy fields and farming areas.
During the planning of designing stage, I assigned two national engineers to interact
with the Community Consultant under my direction. I requested him to establish 4
community groups along the road corridor to get their opinions, views for the proposed
development. The leaders of these community groups were powerful and influential and well
connected with local elders. They assured smooth running of the project and provided
security to all project mates. We listened to the queries of the local farming community in the
presence of all the leaders and involved community groups, who requested to build around 12
new and upgraded culverts. Then I communicated these details with local irrigation
authorities and municipal councils to finalise the scope. Later I received confirmation from
relevant stake holders for important aspects of the project such as irrigation structures along-
with the mapping of road corridors. I was provided with clear design briefings for road design
team in UNOPS, Kabul Office. These community groups were well recognised at all the
important events throughout the projects. They organised the inauguration and opening
ceremonies of the project with the patronage of local politicians and authorities. Moreover, I
introduced them to another UN environment program to obtain some fundings and resources
to promote plantation of trees along the road corridor.
Due to lack of maintenance budget with local governments, we noted maintenance of
the road would be challenging in the future. Therefore, I established a maintenance strategy
with the community group under my programme manager's consultation. UNOPS established
a maintenance fund, managed by the community group leaders by focusing on the future
maintenance. Most of the unskilled labourers were employed in the project through these
10
Between November 2004 and December 2007, I worked in the North-East Region of
Afghanistan as a Regional Engineer for United Nation Office for project Services (UNOPS).
I encountered with many negative experiences from previous projects in the same region
because of interferences by local communities and authorities during the implementation
stage. This caused delays, variations in project and created dissatisfaction among donors for
the annual financial planning. Sometimes the local communities which were led by powerful
ex-combated local soldier and commanders challenged the project scope, security and safety
with questionable remarks on contractor and project staff. Therefore, I discussed this matter
with my program manager and built new strategy to deal with such problems for the next
construction project in coming years. We built a 24.5 km Imma Sahib Connector road,
linking two district centres to the main National Highway of this region and the road corridor
runs through paddy fields and farming areas.
During the planning of designing stage, I assigned two national engineers to interact
with the Community Consultant under my direction. I requested him to establish 4
community groups along the road corridor to get their opinions, views for the proposed
development. The leaders of these community groups were powerful and influential and well
connected with local elders. They assured smooth running of the project and provided
security to all project mates. We listened to the queries of the local farming community in the
presence of all the leaders and involved community groups, who requested to build around 12
new and upgraded culverts. Then I communicated these details with local irrigation
authorities and municipal councils to finalise the scope. Later I received confirmation from
relevant stake holders for important aspects of the project such as irrigation structures along-
with the mapping of road corridors. I was provided with clear design briefings for road design
team in UNOPS, Kabul Office. These community groups were well recognised at all the
important events throughout the projects. They organised the inauguration and opening
ceremonies of the project with the patronage of local politicians and authorities. Moreover, I
introduced them to another UN environment program to obtain some fundings and resources
to promote plantation of trees along the road corridor.
Due to lack of maintenance budget with local governments, we noted maintenance of
the road would be challenging in the future. Therefore, I established a maintenance strategy
with the community group under my programme manager's consultation. UNOPS established
a maintenance fund, managed by the community group leaders by focusing on the future
maintenance. Most of the unskilled labourers were employed in the project through these
10
Secure Best Marks with AI Grader
Need help grading? Try our AI Grader for instant feedback on your assignments.
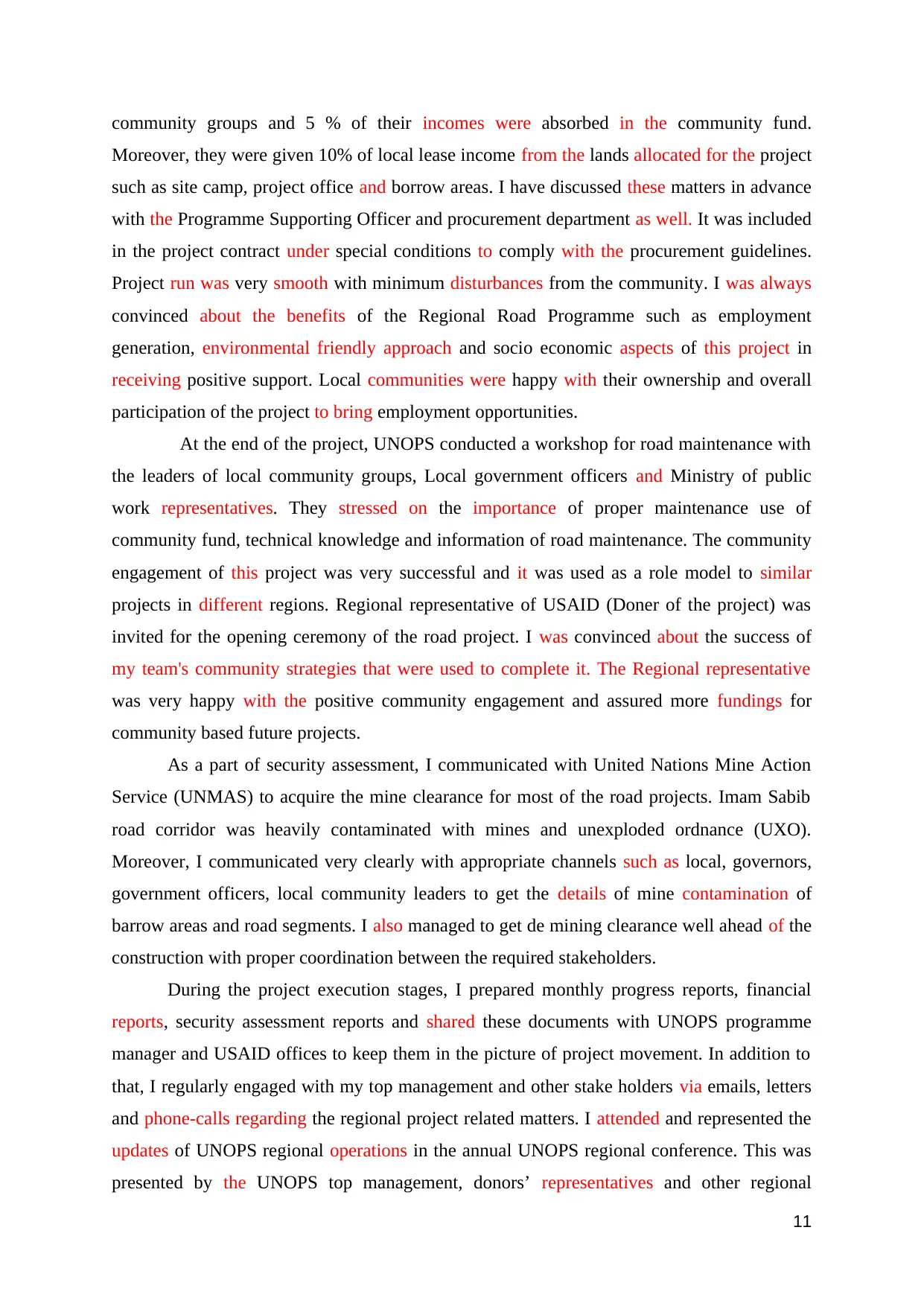
community groups and 5 % of their incomes were absorbed in the community fund.
Moreover, they were given 10% of local lease income from the lands allocated for the project
such as site camp, project office and borrow areas. I have discussed these matters in advance
with the Programme Supporting Officer and procurement department as well. It was included
in the project contract under special conditions to comply with the procurement guidelines.
Project run was very smooth with minimum disturbances from the community. I was always
convinced about the benefits of the Regional Road Programme such as employment
generation, environmental friendly approach and socio economic aspects of this project in
receiving positive support. Local communities were happy with their ownership and overall
participation of the project to bring employment opportunities.
At the end of the project, UNOPS conducted a workshop for road maintenance with
the leaders of local community groups, Local government officers and Ministry of public
work representatives. They stressed on the importance of proper maintenance use of
community fund, technical knowledge and information of road maintenance. The community
engagement of this project was very successful and it was used as a role model to similar
projects in different regions. Regional representative of USAID (Doner of the project) was
invited for the opening ceremony of the road project. I was convinced about the success of
my team's community strategies that were used to complete it. The Regional representative
was very happy with the positive community engagement and assured more fundings for
community based future projects.
As a part of security assessment, I communicated with United Nations Mine Action
Service (UNMAS) to acquire the mine clearance for most of the road projects. Imam Sabib
road corridor was heavily contaminated with mines and unexploded ordnance (UXO).
Moreover, I communicated very clearly with appropriate channels such as local, governors,
government officers, local community leaders to get the details of mine contamination of
barrow areas and road segments. I also managed to get de mining clearance well ahead of the
construction with proper coordination between the required stakeholders.
During the project execution stages, I prepared monthly progress reports, financial
reports, security assessment reports and shared these documents with UNOPS programme
manager and USAID offices to keep them in the picture of project movement. In addition to
that, I regularly engaged with my top management and other stake holders via emails, letters
and phone-calls regarding the regional project related matters. I attended and represented the
updates of UNOPS regional operations in the annual UNOPS regional conference. This was
presented by the UNOPS top management, donors’ representatives and other regional
11
Moreover, they were given 10% of local lease income from the lands allocated for the project
such as site camp, project office and borrow areas. I have discussed these matters in advance
with the Programme Supporting Officer and procurement department as well. It was included
in the project contract under special conditions to comply with the procurement guidelines.
Project run was very smooth with minimum disturbances from the community. I was always
convinced about the benefits of the Regional Road Programme such as employment
generation, environmental friendly approach and socio economic aspects of this project in
receiving positive support. Local communities were happy with their ownership and overall
participation of the project to bring employment opportunities.
At the end of the project, UNOPS conducted a workshop for road maintenance with
the leaders of local community groups, Local government officers and Ministry of public
work representatives. They stressed on the importance of proper maintenance use of
community fund, technical knowledge and information of road maintenance. The community
engagement of this project was very successful and it was used as a role model to similar
projects in different regions. Regional representative of USAID (Doner of the project) was
invited for the opening ceremony of the road project. I was convinced about the success of
my team's community strategies that were used to complete it. The Regional representative
was very happy with the positive community engagement and assured more fundings for
community based future projects.
As a part of security assessment, I communicated with United Nations Mine Action
Service (UNMAS) to acquire the mine clearance for most of the road projects. Imam Sabib
road corridor was heavily contaminated with mines and unexploded ordnance (UXO).
Moreover, I communicated very clearly with appropriate channels such as local, governors,
government officers, local community leaders to get the details of mine contamination of
barrow areas and road segments. I also managed to get de mining clearance well ahead of the
construction with proper coordination between the required stakeholders.
During the project execution stages, I prepared monthly progress reports, financial
reports, security assessment reports and shared these documents with UNOPS programme
manager and USAID offices to keep them in the picture of project movement. In addition to
that, I regularly engaged with my top management and other stake holders via emails, letters
and phone-calls regarding the regional project related matters. I attended and represented the
updates of UNOPS regional operations in the annual UNOPS regional conference. This was
presented by the UNOPS top management, donors’ representatives and other regional
11
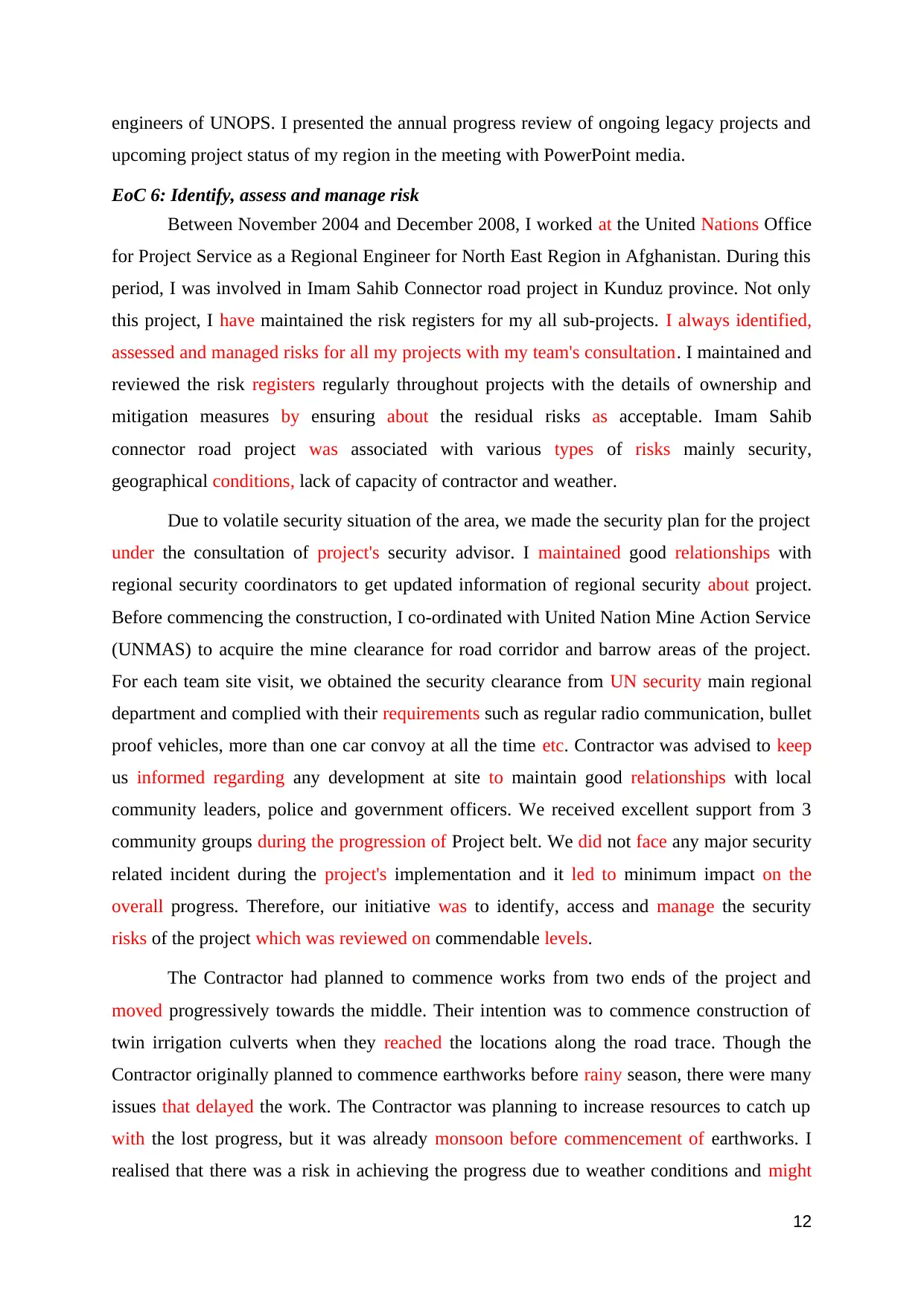
engineers of UNOPS. I presented the annual progress review of ongoing legacy projects and
upcoming project status of my region in the meeting with PowerPoint media.
EoC 6: Identify, assess and manage risk
Between November 2004 and December 2008, I worked at the United Nations Office
for Project Service as a Regional Engineer for North East Region in Afghanistan. During this
period, I was involved in Imam Sahib Connector road project in Kunduz province. Not only
this project, I have maintained the risk registers for my all sub-projects. I always identified,
assessed and managed risks for all my projects with my team's consultation. I maintained and
reviewed the risk registers regularly throughout projects with the details of ownership and
mitigation measures by ensuring about the residual risks as acceptable. Imam Sahib
connector road project was associated with various types of risks mainly security,
geographical conditions, lack of capacity of contractor and weather.
Due to volatile security situation of the area, we made the security plan for the project
under the consultation of project's security advisor. I maintained good relationships with
regional security coordinators to get updated information of regional security about project.
Before commencing the construction, I co-ordinated with United Nation Mine Action Service
(UNMAS) to acquire the mine clearance for road corridor and barrow areas of the project.
For each team site visit, we obtained the security clearance from UN security main regional
department and complied with their requirements such as regular radio communication, bullet
proof vehicles, more than one car convoy at all the time etc. Contractor was advised to keep
us informed regarding any development at site to maintain good relationships with local
community leaders, police and government officers. We received excellent support from 3
community groups during the progression of Project belt. We did not face any major security
related incident during the project's implementation and it led to minimum impact on the
overall progress. Therefore, our initiative was to identify, access and manage the security
risks of the project which was reviewed on commendable levels.
The Contractor had planned to commence works from two ends of the project and
moved progressively towards the middle. Their intention was to commence construction of
twin irrigation culverts when they reached the locations along the road trace. Though the
Contractor originally planned to commence earthworks before rainy season, there were many
issues that delayed the work. The Contractor was planning to increase resources to catch up
with the lost progress, but it was already monsoon before commencement of earthworks. I
realised that there was a risk in achieving the progress due to weather conditions and might
12
upcoming project status of my region in the meeting with PowerPoint media.
EoC 6: Identify, assess and manage risk
Between November 2004 and December 2008, I worked at the United Nations Office
for Project Service as a Regional Engineer for North East Region in Afghanistan. During this
period, I was involved in Imam Sahib Connector road project in Kunduz province. Not only
this project, I have maintained the risk registers for my all sub-projects. I always identified,
assessed and managed risks for all my projects with my team's consultation. I maintained and
reviewed the risk registers regularly throughout projects with the details of ownership and
mitigation measures by ensuring about the residual risks as acceptable. Imam Sahib
connector road project was associated with various types of risks mainly security,
geographical conditions, lack of capacity of contractor and weather.
Due to volatile security situation of the area, we made the security plan for the project
under the consultation of project's security advisor. I maintained good relationships with
regional security coordinators to get updated information of regional security about project.
Before commencing the construction, I co-ordinated with United Nation Mine Action Service
(UNMAS) to acquire the mine clearance for road corridor and barrow areas of the project.
For each team site visit, we obtained the security clearance from UN security main regional
department and complied with their requirements such as regular radio communication, bullet
proof vehicles, more than one car convoy at all the time etc. Contractor was advised to keep
us informed regarding any development at site to maintain good relationships with local
community leaders, police and government officers. We received excellent support from 3
community groups during the progression of Project belt. We did not face any major security
related incident during the project's implementation and it led to minimum impact on the
overall progress. Therefore, our initiative was to identify, access and manage the security
risks of the project which was reviewed on commendable levels.
The Contractor had planned to commence works from two ends of the project and
moved progressively towards the middle. Their intention was to commence construction of
twin irrigation culverts when they reached the locations along the road trace. Though the
Contractor originally planned to commence earthworks before rainy season, there were many
issues that delayed the work. The Contractor was planning to increase resources to catch up
with the lost progress, but it was already monsoon before commencement of earthworks. I
realised that there was a risk in achieving the progress due to weather conditions and might
12
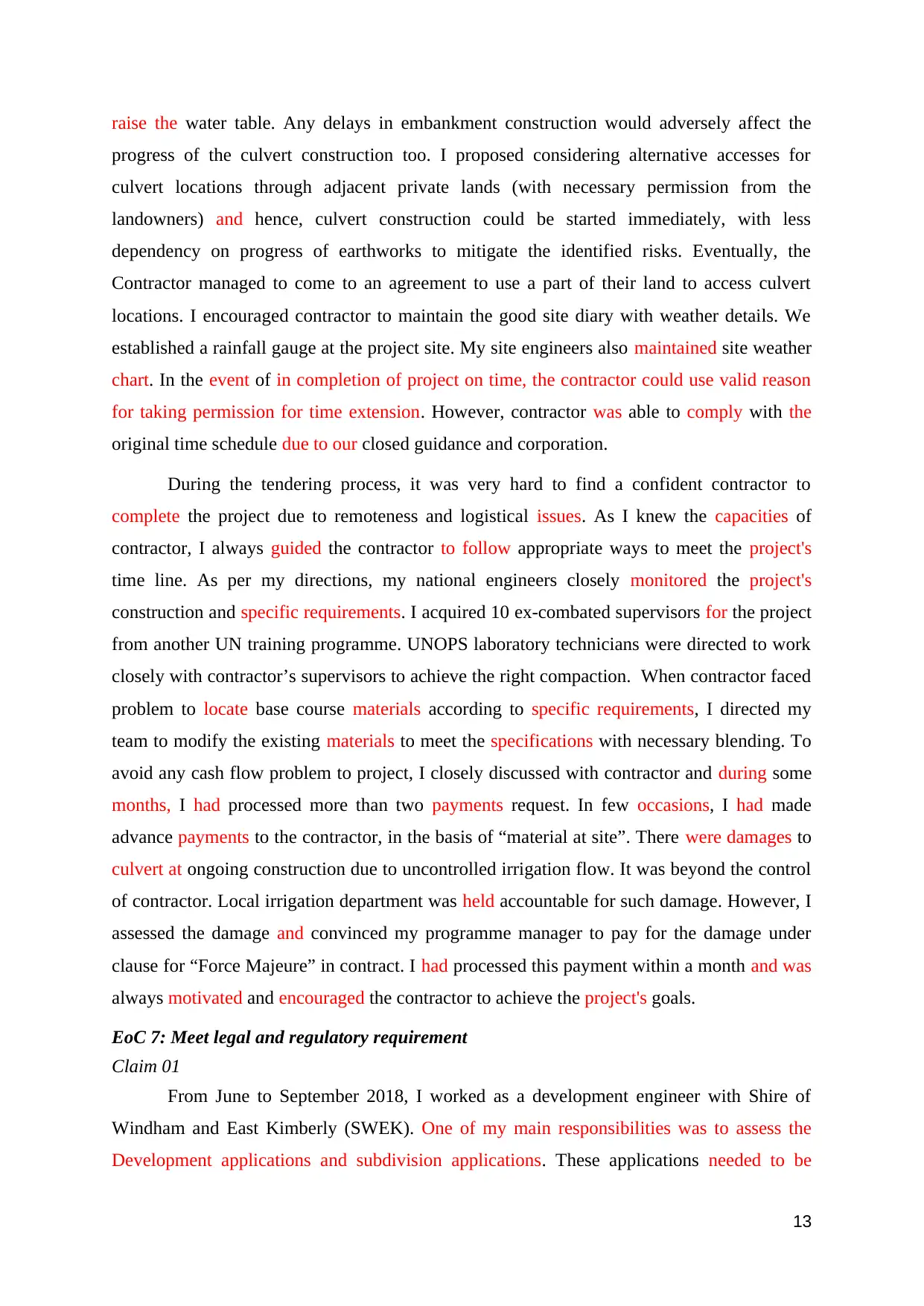
raise the water table. Any delays in embankment construction would adversely affect the
progress of the culvert construction too. I proposed considering alternative accesses for
culvert locations through adjacent private lands (with necessary permission from the
landowners) and hence, culvert construction could be started immediately, with less
dependency on progress of earthworks to mitigate the identified risks. Eventually, the
Contractor managed to come to an agreement to use a part of their land to access culvert
locations. I encouraged contractor to maintain the good site diary with weather details. We
established a rainfall gauge at the project site. My site engineers also maintained site weather
chart. In the event of in completion of project on time, the contractor could use valid reason
for taking permission for time extension. However, contractor was able to comply with the
original time schedule due to our closed guidance and corporation.
During the tendering process, it was very hard to find a confident contractor to
complete the project due to remoteness and logistical issues. As I knew the capacities of
contractor, I always guided the contractor to follow appropriate ways to meet the project's
time line. As per my directions, my national engineers closely monitored the project's
construction and specific requirements. I acquired 10 ex-combated supervisors for the project
from another UN training programme. UNOPS laboratory technicians were directed to work
closely with contractor’s supervisors to achieve the right compaction. When contractor faced
problem to locate base course materials according to specific requirements, I directed my
team to modify the existing materials to meet the specifications with necessary blending. To
avoid any cash flow problem to project, I closely discussed with contractor and during some
months, I had processed more than two payments request. In few occasions, I had made
advance payments to the contractor, in the basis of “material at site”. There were damages to
culvert at ongoing construction due to uncontrolled irrigation flow. It was beyond the control
of contractor. Local irrigation department was held accountable for such damage. However, I
assessed the damage and convinced my programme manager to pay for the damage under
clause for “Force Majeure” in contract. I had processed this payment within a month and was
always motivated and encouraged the contractor to achieve the project's goals.
EoC 7: Meet legal and regulatory requirement
Claim 01
From June to September 2018, I worked as a development engineer with Shire of
Windham and East Kimberly (SWEK). One of my main responsibilities was to assess the
Development applications and subdivision applications. These applications needed to be
13
progress of the culvert construction too. I proposed considering alternative accesses for
culvert locations through adjacent private lands (with necessary permission from the
landowners) and hence, culvert construction could be started immediately, with less
dependency on progress of earthworks to mitigate the identified risks. Eventually, the
Contractor managed to come to an agreement to use a part of their land to access culvert
locations. I encouraged contractor to maintain the good site diary with weather details. We
established a rainfall gauge at the project site. My site engineers also maintained site weather
chart. In the event of in completion of project on time, the contractor could use valid reason
for taking permission for time extension. However, contractor was able to comply with the
original time schedule due to our closed guidance and corporation.
During the tendering process, it was very hard to find a confident contractor to
complete the project due to remoteness and logistical issues. As I knew the capacities of
contractor, I always guided the contractor to follow appropriate ways to meet the project's
time line. As per my directions, my national engineers closely monitored the project's
construction and specific requirements. I acquired 10 ex-combated supervisors for the project
from another UN training programme. UNOPS laboratory technicians were directed to work
closely with contractor’s supervisors to achieve the right compaction. When contractor faced
problem to locate base course materials according to specific requirements, I directed my
team to modify the existing materials to meet the specifications with necessary blending. To
avoid any cash flow problem to project, I closely discussed with contractor and during some
months, I had processed more than two payments request. In few occasions, I had made
advance payments to the contractor, in the basis of “material at site”. There were damages to
culvert at ongoing construction due to uncontrolled irrigation flow. It was beyond the control
of contractor. Local irrigation department was held accountable for such damage. However, I
assessed the damage and convinced my programme manager to pay for the damage under
clause for “Force Majeure” in contract. I had processed this payment within a month and was
always motivated and encouraged the contractor to achieve the project's goals.
EoC 7: Meet legal and regulatory requirement
Claim 01
From June to September 2018, I worked as a development engineer with Shire of
Windham and East Kimberly (SWEK). One of my main responsibilities was to assess the
Development applications and subdivision applications. These applications needed to be
13
Paraphrase This Document
Need a fresh take? Get an instant paraphrase of this document with our AI Paraphraser
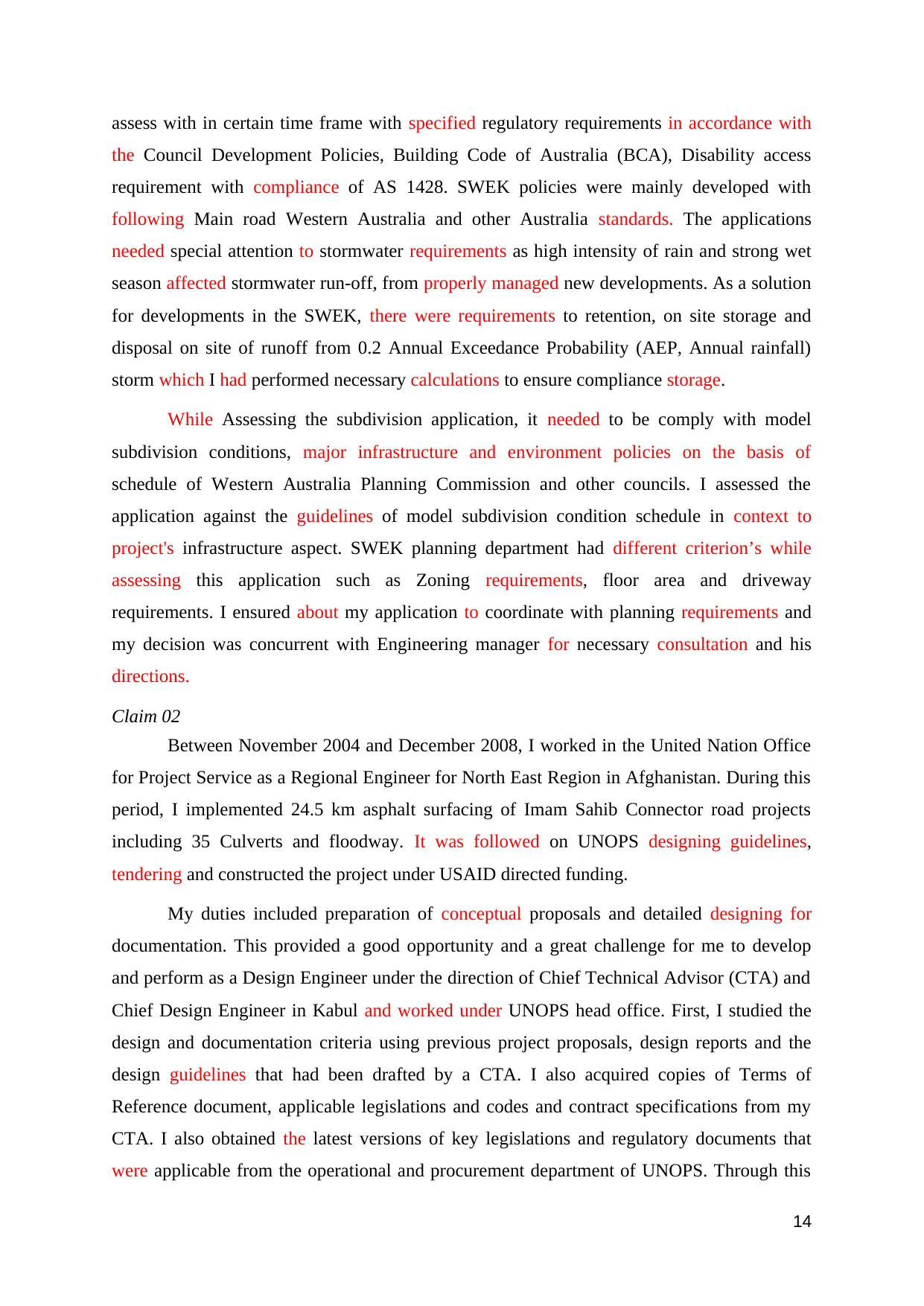
assess with in certain time frame with specified regulatory requirements in accordance with
the Council Development Policies, Building Code of Australia (BCA), Disability access
requirement with compliance of AS 1428. SWEK policies were mainly developed with
following Main road Western Australia and other Australia standards. The applications
needed special attention to stormwater requirements as high intensity of rain and strong wet
season affected stormwater run-off, from properly managed new developments. As a solution
for developments in the SWEK, there were requirements to retention, on site storage and
disposal on site of runoff from 0.2 Annual Exceedance Probability (AEP, Annual rainfall)
storm which I had performed necessary calculations to ensure compliance storage.
While Assessing the subdivision application, it needed to be comply with model
subdivision conditions, major infrastructure and environment policies on the basis of
schedule of Western Australia Planning Commission and other councils. I assessed the
application against the guidelines of model subdivision condition schedule in context to
project's infrastructure aspect. SWEK planning department had different criterion’s while
assessing this application such as Zoning requirements, floor area and driveway
requirements. I ensured about my application to coordinate with planning requirements and
my decision was concurrent with Engineering manager for necessary consultation and his
directions.
Claim 02
Between November 2004 and December 2008, I worked in the United Nation Office
for Project Service as a Regional Engineer for North East Region in Afghanistan. During this
period, I implemented 24.5 km asphalt surfacing of Imam Sahib Connector road projects
including 35 Culverts and floodway. It was followed on UNOPS designing guidelines,
tendering and constructed the project under USAID directed funding.
My duties included preparation of conceptual proposals and detailed designing for
documentation. This provided a good opportunity and a great challenge for me to develop
and perform as a Design Engineer under the direction of Chief Technical Advisor (CTA) and
Chief Design Engineer in Kabul and worked under UNOPS head office. First, I studied the
design and documentation criteria using previous project proposals, design reports and the
design guidelines that had been drafted by a CTA. I also acquired copies of Terms of
Reference document, applicable legislations and codes and contract specifications from my
CTA. I also obtained the latest versions of key legislations and regulatory documents that
were applicable from the operational and procurement department of UNOPS. Through this
14
the Council Development Policies, Building Code of Australia (BCA), Disability access
requirement with compliance of AS 1428. SWEK policies were mainly developed with
following Main road Western Australia and other Australia standards. The applications
needed special attention to stormwater requirements as high intensity of rain and strong wet
season affected stormwater run-off, from properly managed new developments. As a solution
for developments in the SWEK, there were requirements to retention, on site storage and
disposal on site of runoff from 0.2 Annual Exceedance Probability (AEP, Annual rainfall)
storm which I had performed necessary calculations to ensure compliance storage.
While Assessing the subdivision application, it needed to be comply with model
subdivision conditions, major infrastructure and environment policies on the basis of
schedule of Western Australia Planning Commission and other councils. I assessed the
application against the guidelines of model subdivision condition schedule in context to
project's infrastructure aspect. SWEK planning department had different criterion’s while
assessing this application such as Zoning requirements, floor area and driveway
requirements. I ensured about my application to coordinate with planning requirements and
my decision was concurrent with Engineering manager for necessary consultation and his
directions.
Claim 02
Between November 2004 and December 2008, I worked in the United Nation Office
for Project Service as a Regional Engineer for North East Region in Afghanistan. During this
period, I implemented 24.5 km asphalt surfacing of Imam Sahib Connector road projects
including 35 Culverts and floodway. It was followed on UNOPS designing guidelines,
tendering and constructed the project under USAID directed funding.
My duties included preparation of conceptual proposals and detailed designing for
documentation. This provided a good opportunity and a great challenge for me to develop
and perform as a Design Engineer under the direction of Chief Technical Advisor (CTA) and
Chief Design Engineer in Kabul and worked under UNOPS head office. First, I studied the
design and documentation criteria using previous project proposals, design reports and the
design guidelines that had been drafted by a CTA. I also acquired copies of Terms of
Reference document, applicable legislations and codes and contract specifications from my
CTA. I also obtained the latest versions of key legislations and regulatory documents that
were applicable from the operational and procurement department of UNOPS. Through this
14
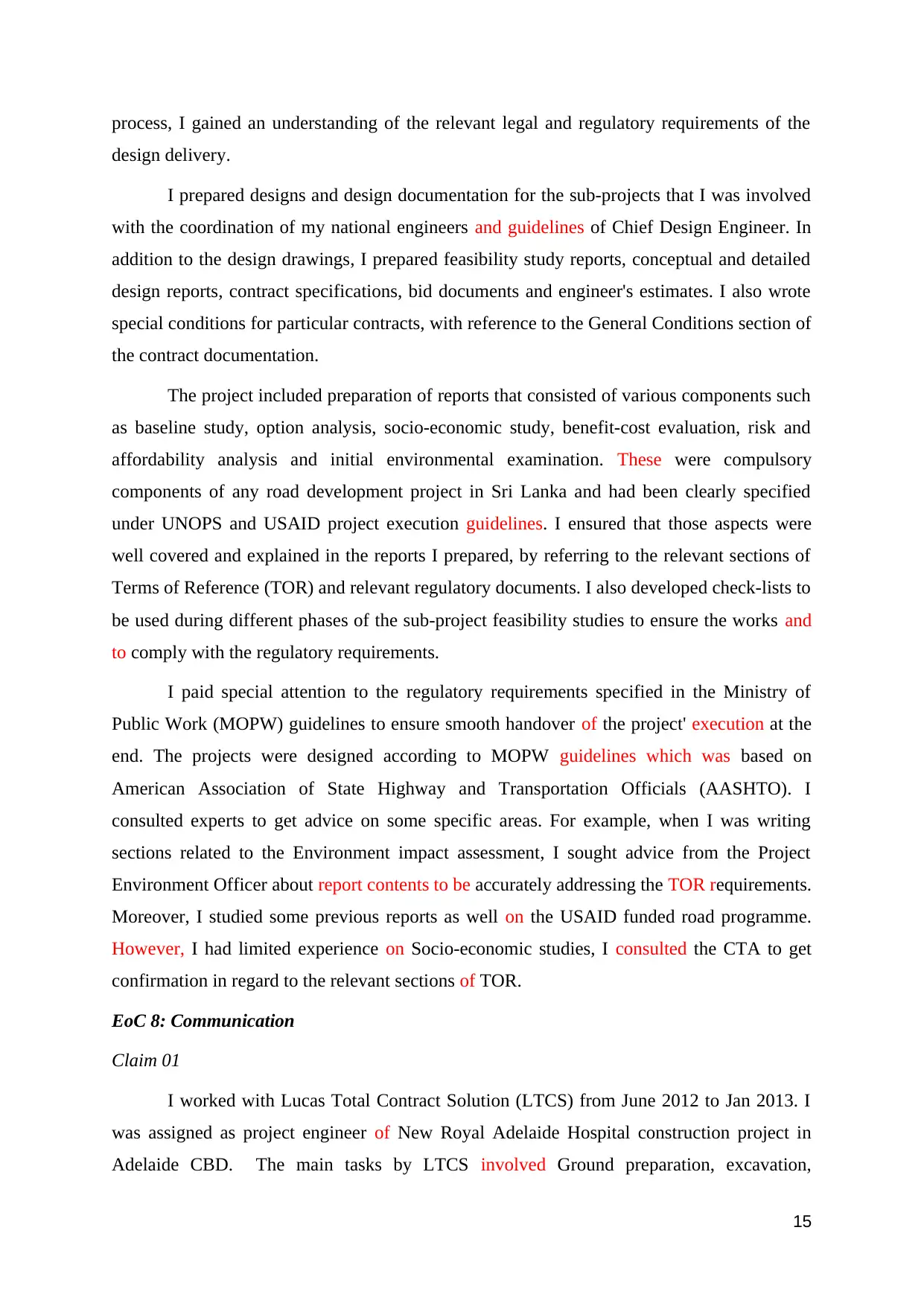
process, I gained an understanding of the relevant legal and regulatory requirements of the
design delivery.
I prepared designs and design documentation for the sub-projects that I was involved
with the coordination of my national engineers and guidelines of Chief Design Engineer. In
addition to the design drawings, I prepared feasibility study reports, conceptual and detailed
design reports, contract specifications, bid documents and engineer's estimates. I also wrote
special conditions for particular contracts, with reference to the General Conditions section of
the contract documentation.
The project included preparation of reports that consisted of various components such
as baseline study, option analysis, socio-economic study, benefit-cost evaluation, risk and
affordability analysis and initial environmental examination. These were compulsory
components of any road development project in Sri Lanka and had been clearly specified
under UNOPS and USAID project execution guidelines. I ensured that those aspects were
well covered and explained in the reports I prepared, by referring to the relevant sections of
Terms of Reference (TOR) and relevant regulatory documents. I also developed check-lists to
be used during different phases of the sub-project feasibility studies to ensure the works and
to comply with the regulatory requirements.
I paid special attention to the regulatory requirements specified in the Ministry of
Public Work (MOPW) guidelines to ensure smooth handover of the project' execution at the
end. The projects were designed according to MOPW guidelines which was based on
American Association of State Highway and Transportation Officials (AASHTO). I
consulted experts to get advice on some specific areas. For example, when I was writing
sections related to the Environment impact assessment, I sought advice from the Project
Environment Officer about report contents to be accurately addressing the TOR requirements.
Moreover, I studied some previous reports as well on the USAID funded road programme.
However, I had limited experience on Socio-economic studies, I consulted the CTA to get
confirmation in regard to the relevant sections of TOR.
EoC 8: Communication
Claim 01
I worked with Lucas Total Contract Solution (LTCS) from June 2012 to Jan 2013. I
was assigned as project engineer of New Royal Adelaide Hospital construction project in
Adelaide CBD. The main tasks by LTCS involved Ground preparation, excavation,
15
design delivery.
I prepared designs and design documentation for the sub-projects that I was involved
with the coordination of my national engineers and guidelines of Chief Design Engineer. In
addition to the design drawings, I prepared feasibility study reports, conceptual and detailed
design reports, contract specifications, bid documents and engineer's estimates. I also wrote
special conditions for particular contracts, with reference to the General Conditions section of
the contract documentation.
The project included preparation of reports that consisted of various components such
as baseline study, option analysis, socio-economic study, benefit-cost evaluation, risk and
affordability analysis and initial environmental examination. These were compulsory
components of any road development project in Sri Lanka and had been clearly specified
under UNOPS and USAID project execution guidelines. I ensured that those aspects were
well covered and explained in the reports I prepared, by referring to the relevant sections of
Terms of Reference (TOR) and relevant regulatory documents. I also developed check-lists to
be used during different phases of the sub-project feasibility studies to ensure the works and
to comply with the regulatory requirements.
I paid special attention to the regulatory requirements specified in the Ministry of
Public Work (MOPW) guidelines to ensure smooth handover of the project' execution at the
end. The projects were designed according to MOPW guidelines which was based on
American Association of State Highway and Transportation Officials (AASHTO). I
consulted experts to get advice on some specific areas. For example, when I was writing
sections related to the Environment impact assessment, I sought advice from the Project
Environment Officer about report contents to be accurately addressing the TOR requirements.
Moreover, I studied some previous reports as well on the USAID funded road programme.
However, I had limited experience on Socio-economic studies, I consulted the CTA to get
confirmation in regard to the relevant sections of TOR.
EoC 8: Communication
Claim 01
I worked with Lucas Total Contract Solution (LTCS) from June 2012 to Jan 2013. I
was assigned as project engineer of New Royal Adelaide Hospital construction project in
Adelaide CBD. The main tasks by LTCS involved Ground preparation, excavation,
15
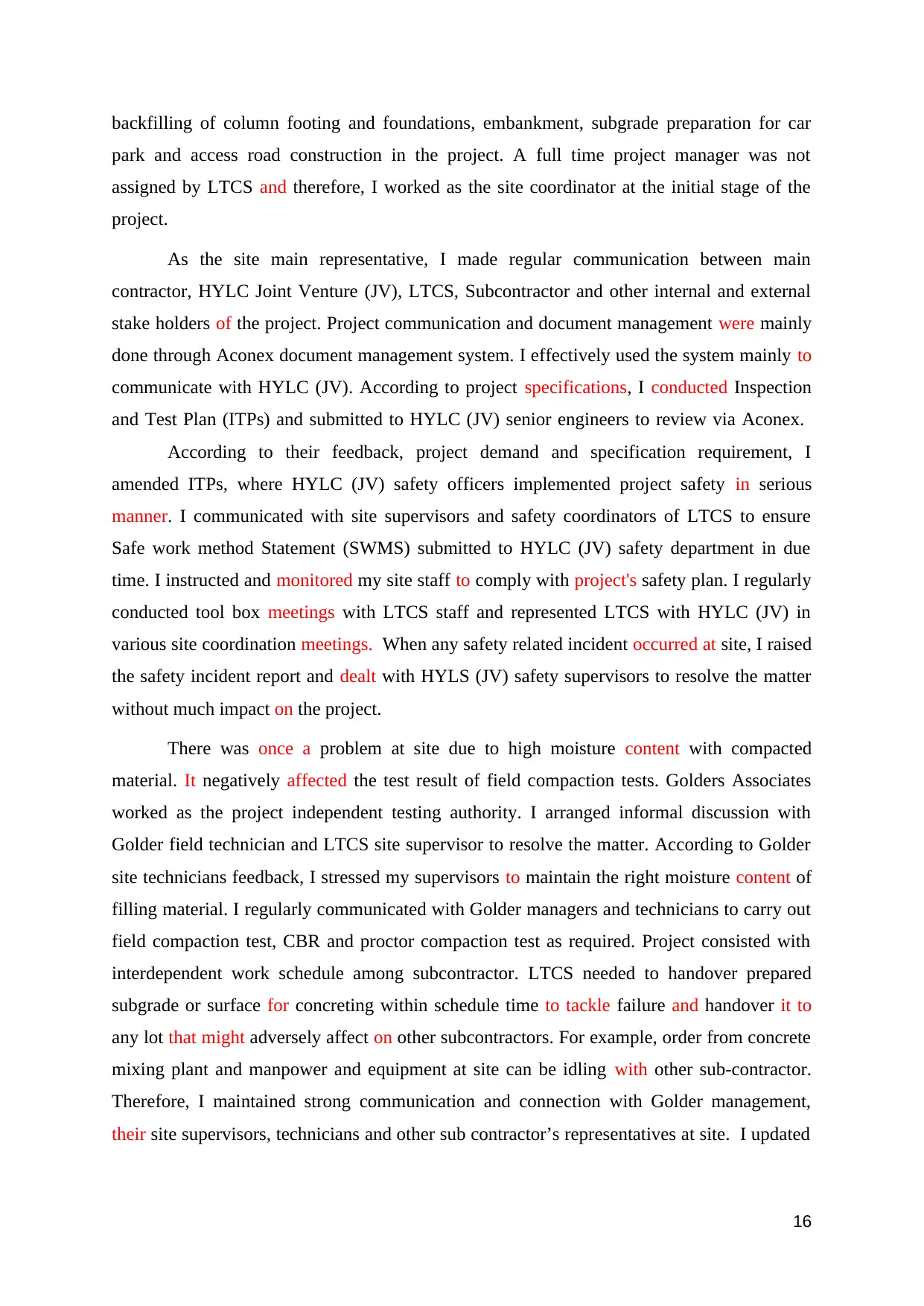
backfilling of column footing and foundations, embankment, subgrade preparation for car
park and access road construction in the project. A full time project manager was not
assigned by LTCS and therefore, I worked as the site coordinator at the initial stage of the
project.
As the site main representative, I made regular communication between main
contractor, HYLC Joint Venture (JV), LTCS, Subcontractor and other internal and external
stake holders of the project. Project communication and document management were mainly
done through Aconex document management system. I effectively used the system mainly to
communicate with HYLC (JV). According to project specifications, I conducted Inspection
and Test Plan (ITPs) and submitted to HYLC (JV) senior engineers to review via Aconex.
According to their feedback, project demand and specification requirement, I
amended ITPs, where HYLC (JV) safety officers implemented project safety in serious
manner. I communicated with site supervisors and safety coordinators of LTCS to ensure
Safe work method Statement (SWMS) submitted to HYLC (JV) safety department in due
time. I instructed and monitored my site staff to comply with project's safety plan. I regularly
conducted tool box meetings with LTCS staff and represented LTCS with HYLC (JV) in
various site coordination meetings. When any safety related incident occurred at site, I raised
the safety incident report and dealt with HYLS (JV) safety supervisors to resolve the matter
without much impact on the project.
There was once a problem at site due to high moisture content with compacted
material. It negatively affected the test result of field compaction tests. Golders Associates
worked as the project independent testing authority. I arranged informal discussion with
Golder field technician and LTCS site supervisor to resolve the matter. According to Golder
site technicians feedback, I stressed my supervisors to maintain the right moisture content of
filling material. I regularly communicated with Golder managers and technicians to carry out
field compaction test, CBR and proctor compaction test as required. Project consisted with
interdependent work schedule among subcontractor. LTCS needed to handover prepared
subgrade or surface for concreting within schedule time to tackle failure and handover it to
any lot that might adversely affect on other subcontractors. For example, order from concrete
mixing plant and manpower and equipment at site can be idling with other sub-contractor.
Therefore, I maintained strong communication and connection with Golder management,
their site supervisors, technicians and other sub contractor’s representatives at site. I updated
16
park and access road construction in the project. A full time project manager was not
assigned by LTCS and therefore, I worked as the site coordinator at the initial stage of the
project.
As the site main representative, I made regular communication between main
contractor, HYLC Joint Venture (JV), LTCS, Subcontractor and other internal and external
stake holders of the project. Project communication and document management were mainly
done through Aconex document management system. I effectively used the system mainly to
communicate with HYLC (JV). According to project specifications, I conducted Inspection
and Test Plan (ITPs) and submitted to HYLC (JV) senior engineers to review via Aconex.
According to their feedback, project demand and specification requirement, I
amended ITPs, where HYLC (JV) safety officers implemented project safety in serious
manner. I communicated with site supervisors and safety coordinators of LTCS to ensure
Safe work method Statement (SWMS) submitted to HYLC (JV) safety department in due
time. I instructed and monitored my site staff to comply with project's safety plan. I regularly
conducted tool box meetings with LTCS staff and represented LTCS with HYLC (JV) in
various site coordination meetings. When any safety related incident occurred at site, I raised
the safety incident report and dealt with HYLS (JV) safety supervisors to resolve the matter
without much impact on the project.
There was once a problem at site due to high moisture content with compacted
material. It negatively affected the test result of field compaction tests. Golders Associates
worked as the project independent testing authority. I arranged informal discussion with
Golder field technician and LTCS site supervisor to resolve the matter. According to Golder
site technicians feedback, I stressed my supervisors to maintain the right moisture content of
filling material. I regularly communicated with Golder managers and technicians to carry out
field compaction test, CBR and proctor compaction test as required. Project consisted with
interdependent work schedule among subcontractor. LTCS needed to handover prepared
subgrade or surface for concreting within schedule time to tackle failure and handover it to
any lot that might adversely affect on other subcontractors. For example, order from concrete
mixing plant and manpower and equipment at site can be idling with other sub-contractor.
Therefore, I maintained strong communication and connection with Golder management,
their site supervisors, technicians and other sub contractor’s representatives at site. I updated
16
Secure Best Marks with AI Grader
Need help grading? Try our AI Grader for instant feedback on your assignments.
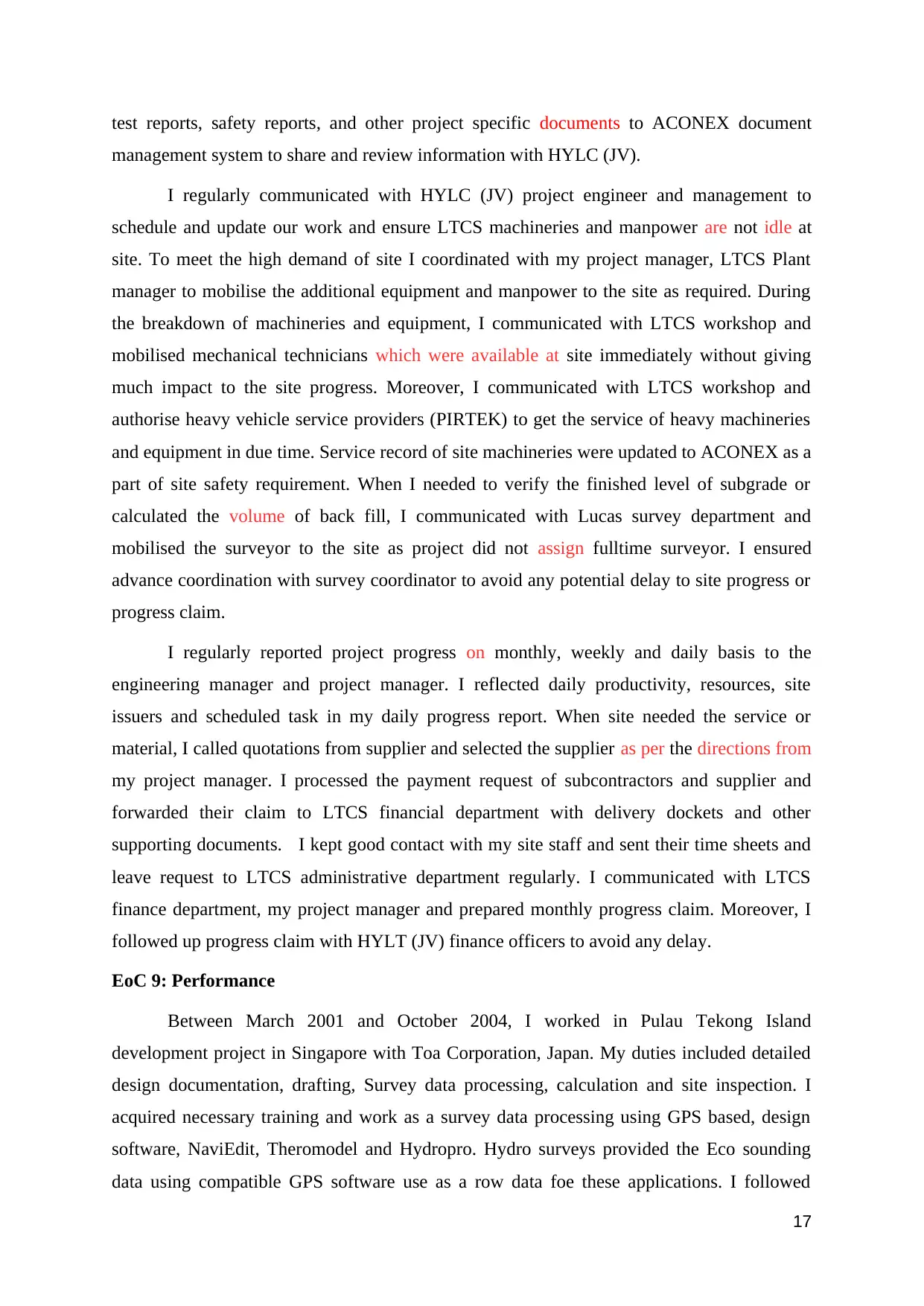
test reports, safety reports, and other project specific documents to ACONEX document
management system to share and review information with HYLC (JV).
I regularly communicated with HYLC (JV) project engineer and management to
schedule and update our work and ensure LTCS machineries and manpower are not idle at
site. To meet the high demand of site I coordinated with my project manager, LTCS Plant
manager to mobilise the additional equipment and manpower to the site as required. During
the breakdown of machineries and equipment, I communicated with LTCS workshop and
mobilised mechanical technicians which were available at site immediately without giving
much impact to the site progress. Moreover, I communicated with LTCS workshop and
authorise heavy vehicle service providers (PIRTEK) to get the service of heavy machineries
and equipment in due time. Service record of site machineries were updated to ACONEX as a
part of site safety requirement. When I needed to verify the finished level of subgrade or
calculated the volume of back fill, I communicated with Lucas survey department and
mobilised the surveyor to the site as project did not assign fulltime surveyor. I ensured
advance coordination with survey coordinator to avoid any potential delay to site progress or
progress claim.
I regularly reported project progress on monthly, weekly and daily basis to the
engineering manager and project manager. I reflected daily productivity, resources, site
issuers and scheduled task in my daily progress report. When site needed the service or
material, I called quotations from supplier and selected the supplier as per the directions from
my project manager. I processed the payment request of subcontractors and supplier and
forwarded their claim to LTCS financial department with delivery dockets and other
supporting documents. I kept good contact with my site staff and sent their time sheets and
leave request to LTCS administrative department regularly. I communicated with LTCS
finance department, my project manager and prepared monthly progress claim. Moreover, I
followed up progress claim with HYLT (JV) finance officers to avoid any delay.
EoC 9: Performance
Between March 2001 and October 2004, I worked in Pulau Tekong Island
development project in Singapore with Toa Corporation, Japan. My duties included detailed
design documentation, drafting, Survey data processing, calculation and site inspection. I
acquired necessary training and work as a survey data processing using GPS based, design
software, NaviEdit, Theromodel and Hydropro. Hydro surveys provided the Eco sounding
data using compatible GPS software use as a row data foe these applications. I followed
17
management system to share and review information with HYLC (JV).
I regularly communicated with HYLC (JV) project engineer and management to
schedule and update our work and ensure LTCS machineries and manpower are not idle at
site. To meet the high demand of site I coordinated with my project manager, LTCS Plant
manager to mobilise the additional equipment and manpower to the site as required. During
the breakdown of machineries and equipment, I communicated with LTCS workshop and
mobilised mechanical technicians which were available at site immediately without giving
much impact to the site progress. Moreover, I communicated with LTCS workshop and
authorise heavy vehicle service providers (PIRTEK) to get the service of heavy machineries
and equipment in due time. Service record of site machineries were updated to ACONEX as a
part of site safety requirement. When I needed to verify the finished level of subgrade or
calculated the volume of back fill, I communicated with Lucas survey department and
mobilised the surveyor to the site as project did not assign fulltime surveyor. I ensured
advance coordination with survey coordinator to avoid any potential delay to site progress or
progress claim.
I regularly reported project progress on monthly, weekly and daily basis to the
engineering manager and project manager. I reflected daily productivity, resources, site
issuers and scheduled task in my daily progress report. When site needed the service or
material, I called quotations from supplier and selected the supplier as per the directions from
my project manager. I processed the payment request of subcontractors and supplier and
forwarded their claim to LTCS financial department with delivery dockets and other
supporting documents. I kept good contact with my site staff and sent their time sheets and
leave request to LTCS administrative department regularly. I communicated with LTCS
finance department, my project manager and prepared monthly progress claim. Moreover, I
followed up progress claim with HYLT (JV) finance officers to avoid any delay.
EoC 9: Performance
Between March 2001 and October 2004, I worked in Pulau Tekong Island
development project in Singapore with Toa Corporation, Japan. My duties included detailed
design documentation, drafting, Survey data processing, calculation and site inspection. I
acquired necessary training and work as a survey data processing using GPS based, design
software, NaviEdit, Theromodel and Hydropro. Hydro surveys provided the Eco sounding
data using compatible GPS software use as a row data foe these applications. I followed
17
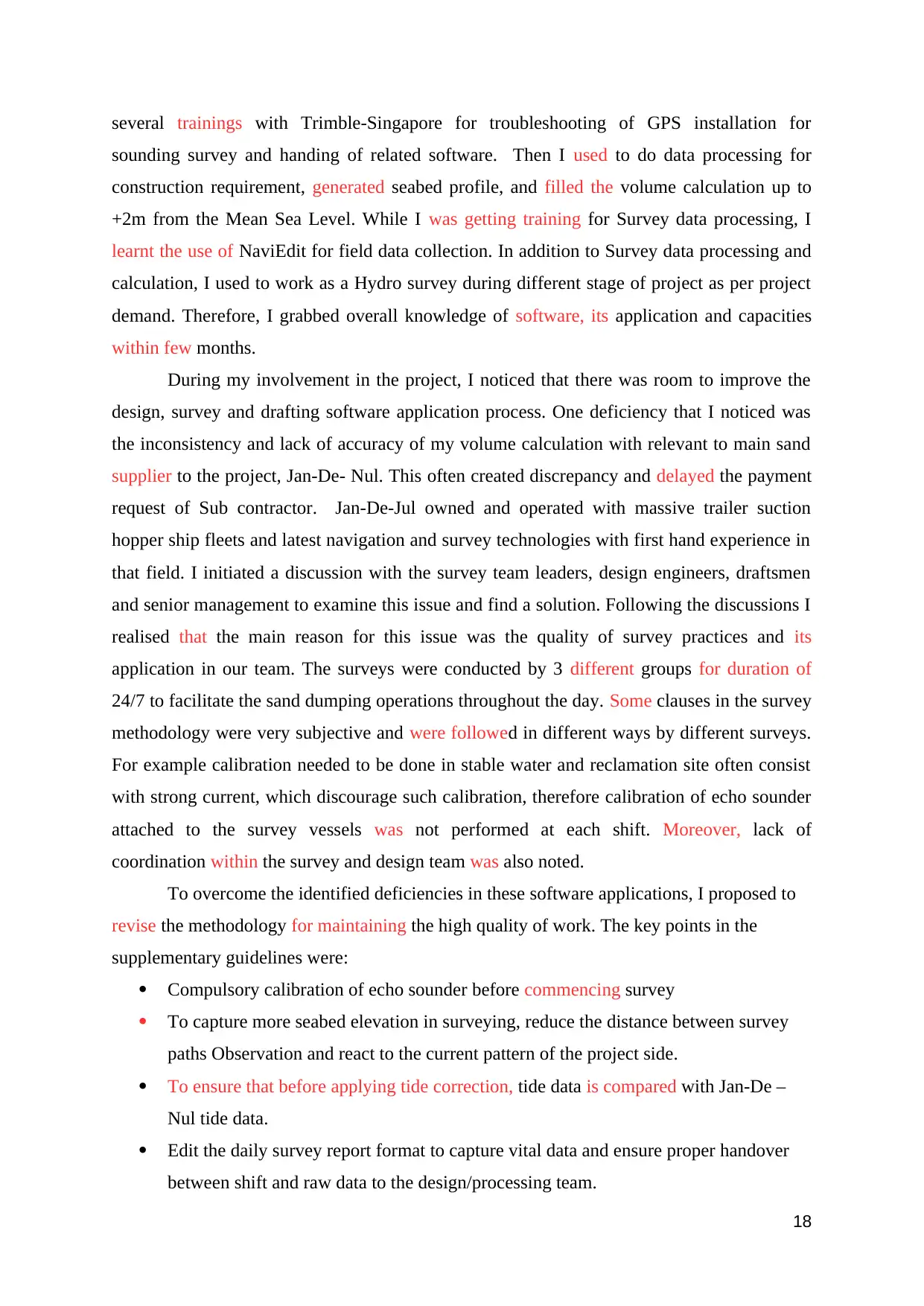
several trainings with Trimble-Singapore for troubleshooting of GPS installation for
sounding survey and handing of related software. Then I used to do data processing for
construction requirement, generated seabed profile, and filled the volume calculation up to
+2m from the Mean Sea Level. While I was getting training for Survey data processing, I
learnt the use of NaviEdit for field data collection. In addition to Survey data processing and
calculation, I used to work as a Hydro survey during different stage of project as per project
demand. Therefore, I grabbed overall knowledge of software, its application and capacities
within few months.
During my involvement in the project, I noticed that there was room to improve the
design, survey and drafting software application process. One deficiency that I noticed was
the inconsistency and lack of accuracy of my volume calculation with relevant to main sand
supplier to the project, Jan-De- Nul. This often created discrepancy and delayed the payment
request of Sub contractor. Jan-De-Jul owned and operated with massive trailer suction
hopper ship fleets and latest navigation and survey technologies with first hand experience in
that field. I initiated a discussion with the survey team leaders, design engineers, draftsmen
and senior management to examine this issue and find a solution. Following the discussions I
realised that the main reason for this issue was the quality of survey practices and its
application in our team. The surveys were conducted by 3 different groups for duration of
24/7 to facilitate the sand dumping operations throughout the day. Some clauses in the survey
methodology were very subjective and were followed in different ways by different surveys.
For example calibration needed to be done in stable water and reclamation site often consist
with strong current, which discourage such calibration, therefore calibration of echo sounder
attached to the survey vessels was not performed at each shift. Moreover, lack of
coordination within the survey and design team was also noted.
To overcome the identified deficiencies in these software applications, I proposed to
revise the methodology for maintaining the high quality of work. The key points in the
supplementary guidelines were:
Compulsory calibration of echo sounder before commencing survey
To capture more seabed elevation in surveying, reduce the distance between survey
paths Observation and react to the current pattern of the project side.
To ensure that before applying tide correction, tide data is compared with Jan-De –
Nul tide data.
Edit the daily survey report format to capture vital data and ensure proper handover
between shift and raw data to the design/processing team.
18
sounding survey and handing of related software. Then I used to do data processing for
construction requirement, generated seabed profile, and filled the volume calculation up to
+2m from the Mean Sea Level. While I was getting training for Survey data processing, I
learnt the use of NaviEdit for field data collection. In addition to Survey data processing and
calculation, I used to work as a Hydro survey during different stage of project as per project
demand. Therefore, I grabbed overall knowledge of software, its application and capacities
within few months.
During my involvement in the project, I noticed that there was room to improve the
design, survey and drafting software application process. One deficiency that I noticed was
the inconsistency and lack of accuracy of my volume calculation with relevant to main sand
supplier to the project, Jan-De- Nul. This often created discrepancy and delayed the payment
request of Sub contractor. Jan-De-Jul owned and operated with massive trailer suction
hopper ship fleets and latest navigation and survey technologies with first hand experience in
that field. I initiated a discussion with the survey team leaders, design engineers, draftsmen
and senior management to examine this issue and find a solution. Following the discussions I
realised that the main reason for this issue was the quality of survey practices and its
application in our team. The surveys were conducted by 3 different groups for duration of
24/7 to facilitate the sand dumping operations throughout the day. Some clauses in the survey
methodology were very subjective and were followed in different ways by different surveys.
For example calibration needed to be done in stable water and reclamation site often consist
with strong current, which discourage such calibration, therefore calibration of echo sounder
attached to the survey vessels was not performed at each shift. Moreover, lack of
coordination within the survey and design team was also noted.
To overcome the identified deficiencies in these software applications, I proposed to
revise the methodology for maintaining the high quality of work. The key points in the
supplementary guidelines were:
Compulsory calibration of echo sounder before commencing survey
To capture more seabed elevation in surveying, reduce the distance between survey
paths Observation and react to the current pattern of the project side.
To ensure that before applying tide correction, tide data is compared with Jan-De –
Nul tide data.
Edit the daily survey report format to capture vital data and ensure proper handover
between shift and raw data to the design/processing team.
18
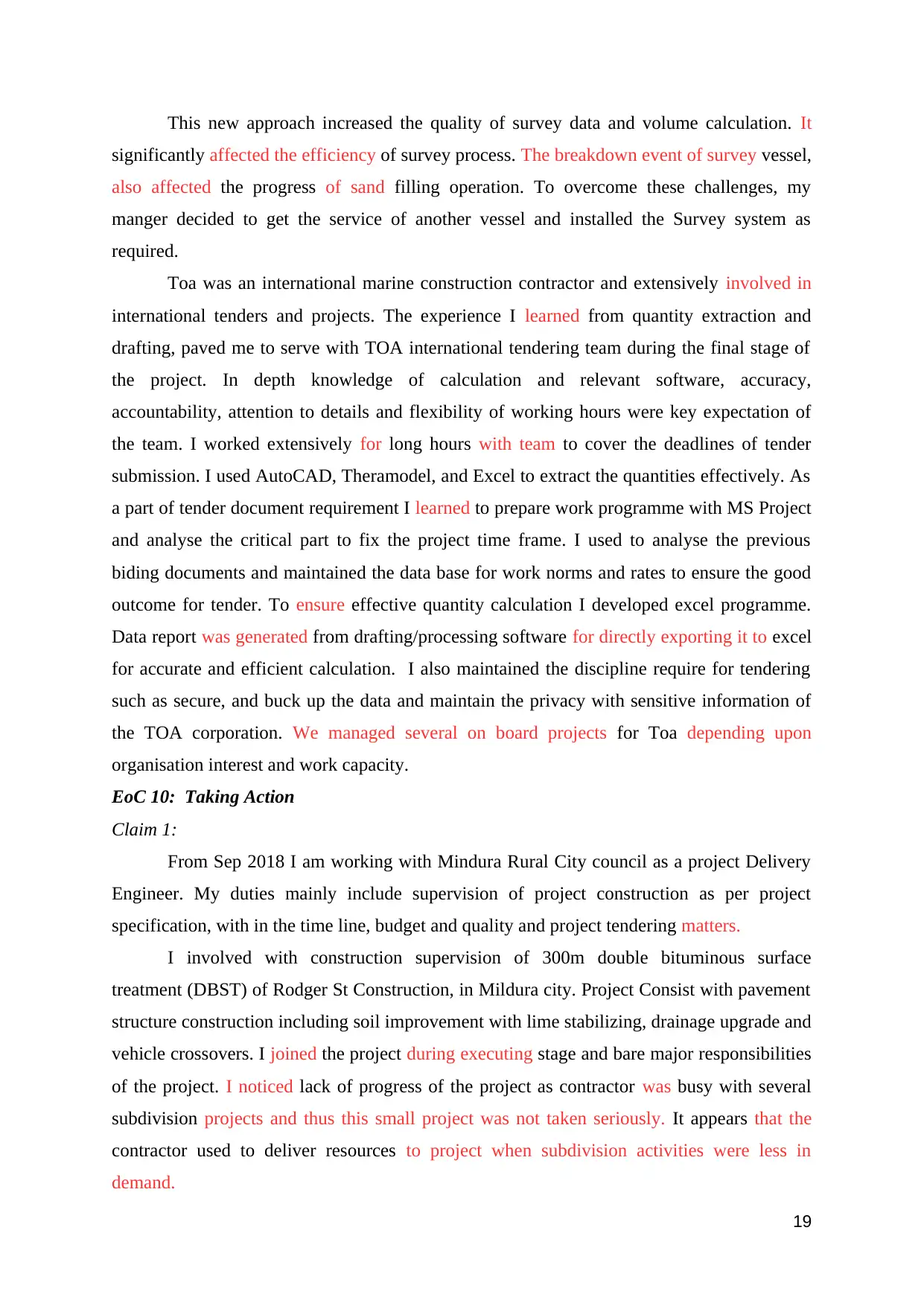
This new approach increased the quality of survey data and volume calculation. It
significantly affected the efficiency of survey process. The breakdown event of survey vessel,
also affected the progress of sand filling operation. To overcome these challenges, my
manger decided to get the service of another vessel and installed the Survey system as
required.
Toa was an international marine construction contractor and extensively involved in
international tenders and projects. The experience I learned from quantity extraction and
drafting, paved me to serve with TOA international tendering team during the final stage of
the project. In depth knowledge of calculation and relevant software, accuracy,
accountability, attention to details and flexibility of working hours were key expectation of
the team. I worked extensively for long hours with team to cover the deadlines of tender
submission. I used AutoCAD, Theramodel, and Excel to extract the quantities effectively. As
a part of tender document requirement I learned to prepare work programme with MS Project
and analyse the critical part to fix the project time frame. I used to analyse the previous
biding documents and maintained the data base for work norms and rates to ensure the good
outcome for tender. To ensure effective quantity calculation I developed excel programme.
Data report was generated from drafting/processing software for directly exporting it to excel
for accurate and efficient calculation. I also maintained the discipline require for tendering
such as secure, and buck up the data and maintain the privacy with sensitive information of
the TOA corporation. We managed several on board projects for Toa depending upon
organisation interest and work capacity.
EoC 10: Taking Action
Claim 1:
From Sep 2018 I am working with Mindura Rural City council as a project Delivery
Engineer. My duties mainly include supervision of project construction as per project
specification, with in the time line, budget and quality and project tendering matters.
I involved with construction supervision of 300m double bituminous surface
treatment (DBST) of Rodger St Construction, in Mildura city. Project Consist with pavement
structure construction including soil improvement with lime stabilizing, drainage upgrade and
vehicle crossovers. I joined the project during executing stage and bare major responsibilities
of the project. I noticed lack of progress of the project as contractor was busy with several
subdivision projects and thus this small project was not taken seriously. It appears that the
contractor used to deliver resources to project when subdivision activities were less in
demand.
19
significantly affected the efficiency of survey process. The breakdown event of survey vessel,
also affected the progress of sand filling operation. To overcome these challenges, my
manger decided to get the service of another vessel and installed the Survey system as
required.
Toa was an international marine construction contractor and extensively involved in
international tenders and projects. The experience I learned from quantity extraction and
drafting, paved me to serve with TOA international tendering team during the final stage of
the project. In depth knowledge of calculation and relevant software, accuracy,
accountability, attention to details and flexibility of working hours were key expectation of
the team. I worked extensively for long hours with team to cover the deadlines of tender
submission. I used AutoCAD, Theramodel, and Excel to extract the quantities effectively. As
a part of tender document requirement I learned to prepare work programme with MS Project
and analyse the critical part to fix the project time frame. I used to analyse the previous
biding documents and maintained the data base for work norms and rates to ensure the good
outcome for tender. To ensure effective quantity calculation I developed excel programme.
Data report was generated from drafting/processing software for directly exporting it to excel
for accurate and efficient calculation. I also maintained the discipline require for tendering
such as secure, and buck up the data and maintain the privacy with sensitive information of
the TOA corporation. We managed several on board projects for Toa depending upon
organisation interest and work capacity.
EoC 10: Taking Action
Claim 1:
From Sep 2018 I am working with Mindura Rural City council as a project Delivery
Engineer. My duties mainly include supervision of project construction as per project
specification, with in the time line, budget and quality and project tendering matters.
I involved with construction supervision of 300m double bituminous surface
treatment (DBST) of Rodger St Construction, in Mildura city. Project Consist with pavement
structure construction including soil improvement with lime stabilizing, drainage upgrade and
vehicle crossovers. I joined the project during executing stage and bare major responsibilities
of the project. I noticed lack of progress of the project as contractor was busy with several
subdivision projects and thus this small project was not taken seriously. It appears that the
contractor used to deliver resources to project when subdivision activities were less in
demand.
19
Paraphrase This Document
Need a fresh take? Get an instant paraphrase of this document with our AI Paraphraser
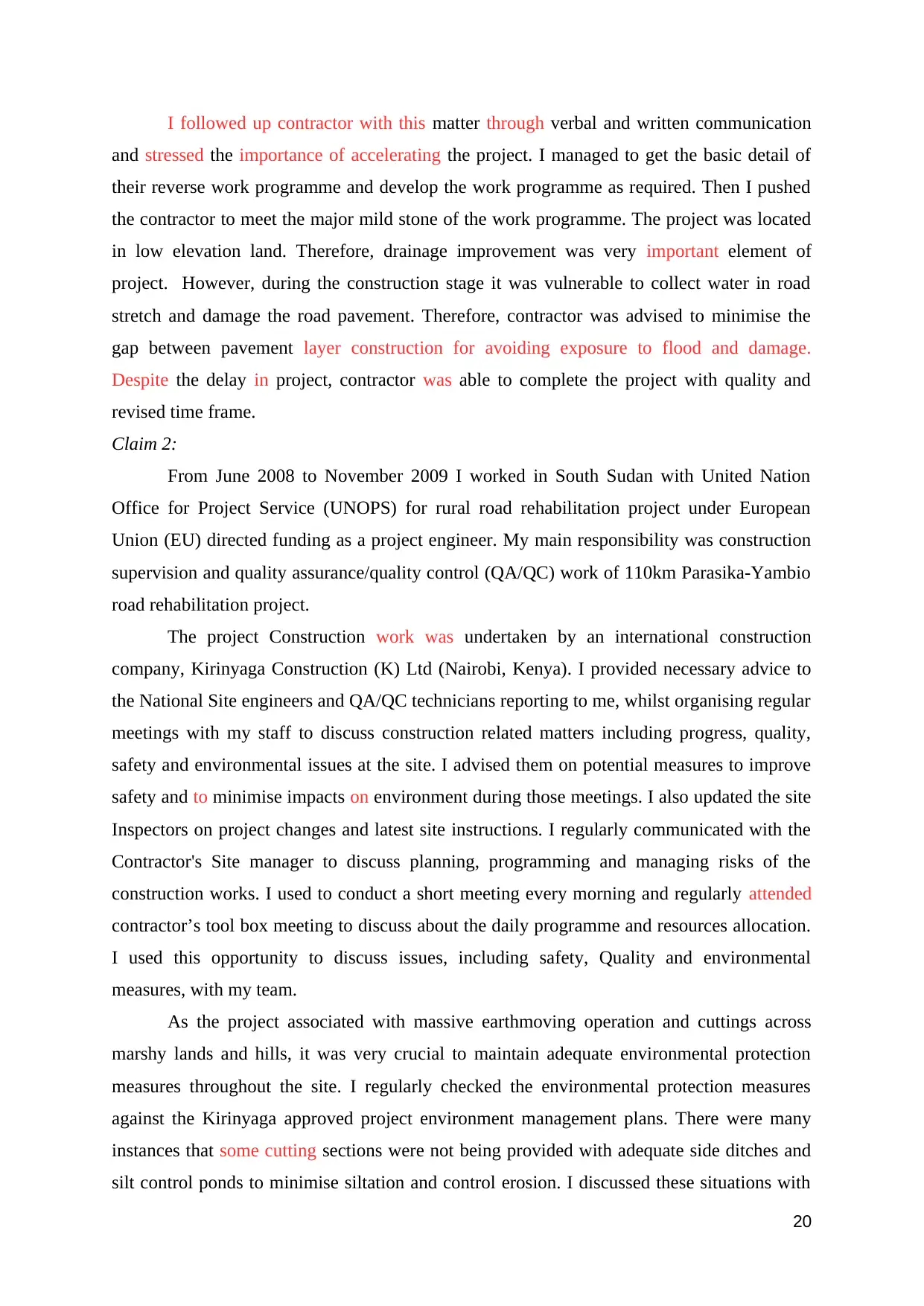
I followed up contractor with this matter through verbal and written communication
and stressed the importance of accelerating the project. I managed to get the basic detail of
their reverse work programme and develop the work programme as required. Then I pushed
the contractor to meet the major mild stone of the work programme. The project was located
in low elevation land. Therefore, drainage improvement was very important element of
project. However, during the construction stage it was vulnerable to collect water in road
stretch and damage the road pavement. Therefore, contractor was advised to minimise the
gap between pavement layer construction for avoiding exposure to flood and damage.
Despite the delay in project, contractor was able to complete the project with quality and
revised time frame.
Claim 2:
From June 2008 to November 2009 I worked in South Sudan with United Nation
Office for Project Service (UNOPS) for rural road rehabilitation project under European
Union (EU) directed funding as a project engineer. My main responsibility was construction
supervision and quality assurance/quality control (QA/QC) work of 110km Parasika-Yambio
road rehabilitation project.
The project Construction work was undertaken by an international construction
company, Kirinyaga Construction (K) Ltd (Nairobi, Kenya). I provided necessary advice to
the National Site engineers and QA/QC technicians reporting to me, whilst organising regular
meetings with my staff to discuss construction related matters including progress, quality,
safety and environmental issues at the site. I advised them on potential measures to improve
safety and to minimise impacts on environment during those meetings. I also updated the site
Inspectors on project changes and latest site instructions. I regularly communicated with the
Contractor's Site manager to discuss planning, programming and managing risks of the
construction works. I used to conduct a short meeting every morning and regularly attended
contractor’s tool box meeting to discuss about the daily programme and resources allocation.
I used this opportunity to discuss issues, including safety, Quality and environmental
measures, with my team.
As the project associated with massive earthmoving operation and cuttings across
marshy lands and hills, it was very crucial to maintain adequate environmental protection
measures throughout the site. I regularly checked the environmental protection measures
against the Kirinyaga approved project environment management plans. There were many
instances that some cutting sections were not being provided with adequate side ditches and
silt control ponds to minimise siltation and control erosion. I discussed these situations with
20
and stressed the importance of accelerating the project. I managed to get the basic detail of
their reverse work programme and develop the work programme as required. Then I pushed
the contractor to meet the major mild stone of the work programme. The project was located
in low elevation land. Therefore, drainage improvement was very important element of
project. However, during the construction stage it was vulnerable to collect water in road
stretch and damage the road pavement. Therefore, contractor was advised to minimise the
gap between pavement layer construction for avoiding exposure to flood and damage.
Despite the delay in project, contractor was able to complete the project with quality and
revised time frame.
Claim 2:
From June 2008 to November 2009 I worked in South Sudan with United Nation
Office for Project Service (UNOPS) for rural road rehabilitation project under European
Union (EU) directed funding as a project engineer. My main responsibility was construction
supervision and quality assurance/quality control (QA/QC) work of 110km Parasika-Yambio
road rehabilitation project.
The project Construction work was undertaken by an international construction
company, Kirinyaga Construction (K) Ltd (Nairobi, Kenya). I provided necessary advice to
the National Site engineers and QA/QC technicians reporting to me, whilst organising regular
meetings with my staff to discuss construction related matters including progress, quality,
safety and environmental issues at the site. I advised them on potential measures to improve
safety and to minimise impacts on environment during those meetings. I also updated the site
Inspectors on project changes and latest site instructions. I regularly communicated with the
Contractor's Site manager to discuss planning, programming and managing risks of the
construction works. I used to conduct a short meeting every morning and regularly attended
contractor’s tool box meeting to discuss about the daily programme and resources allocation.
I used this opportunity to discuss issues, including safety, Quality and environmental
measures, with my team.
As the project associated with massive earthmoving operation and cuttings across
marshy lands and hills, it was very crucial to maintain adequate environmental protection
measures throughout the site. I regularly checked the environmental protection measures
against the Kirinyaga approved project environment management plans. There were many
instances that some cutting sections were not being provided with adequate side ditches and
silt control ponds to minimise siltation and control erosion. I discussed these situations with
20
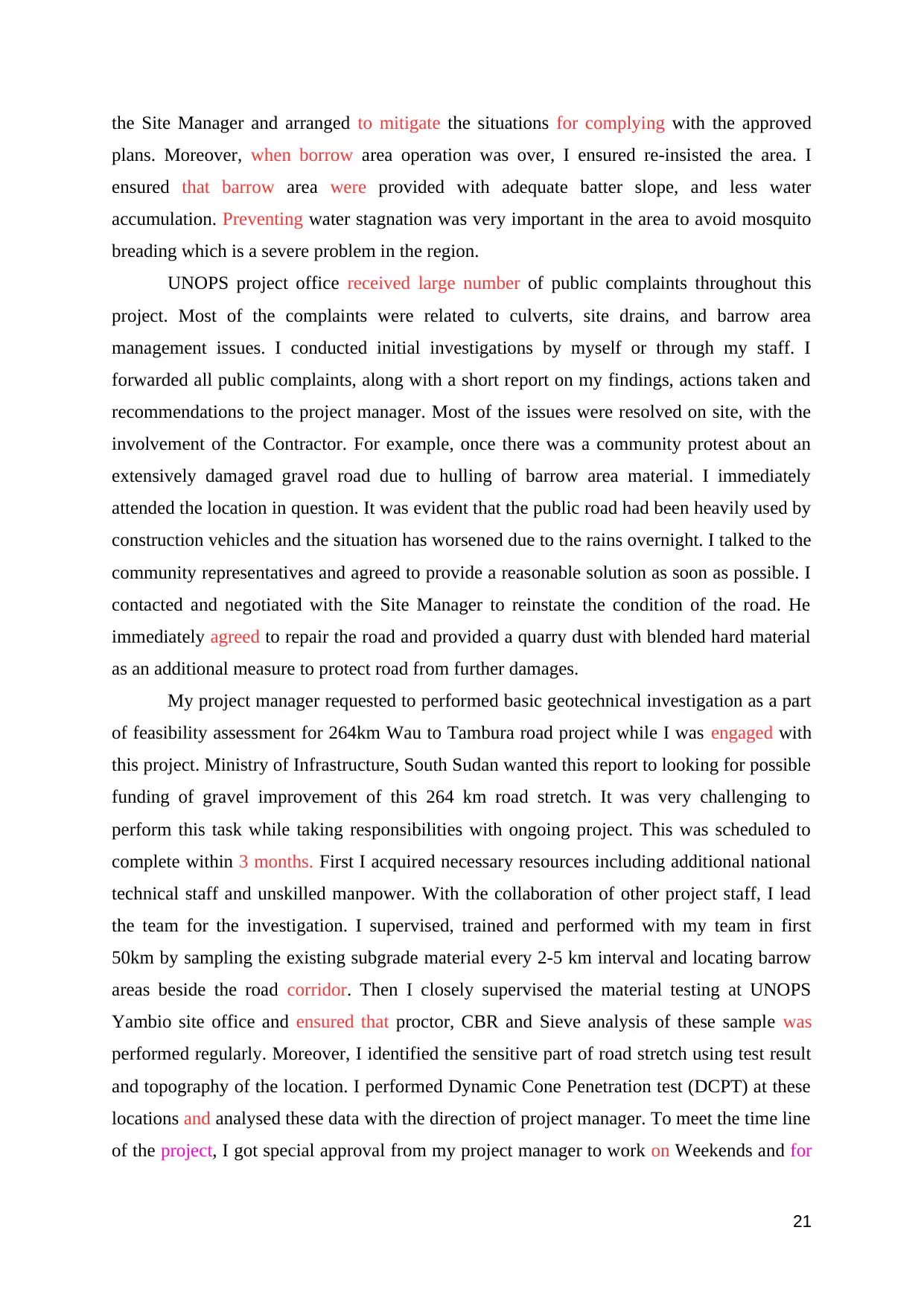
the Site Manager and arranged to mitigate the situations for complying with the approved
plans. Moreover, when borrow area operation was over, I ensured re-insisted the area. I
ensured that barrow area were provided with adequate batter slope, and less water
accumulation. Preventing water stagnation was very important in the area to avoid mosquito
breading which is a severe problem in the region.
UNOPS project office received large number of public complaints throughout this
project. Most of the complaints were related to culverts, site drains, and barrow area
management issues. I conducted initial investigations by myself or through my staff. I
forwarded all public complaints, along with a short report on my findings, actions taken and
recommendations to the project manager. Most of the issues were resolved on site, with the
involvement of the Contractor. For example, once there was a community protest about an
extensively damaged gravel road due to hulling of barrow area material. I immediately
attended the location in question. It was evident that the public road had been heavily used by
construction vehicles and the situation has worsened due to the rains overnight. I talked to the
community representatives and agreed to provide a reasonable solution as soon as possible. I
contacted and negotiated with the Site Manager to reinstate the condition of the road. He
immediately agreed to repair the road and provided a quarry dust with blended hard material
as an additional measure to protect road from further damages.
My project manager requested to performed basic geotechnical investigation as a part
of feasibility assessment for 264km Wau to Tambura road project while I was engaged with
this project. Ministry of Infrastructure, South Sudan wanted this report to looking for possible
funding of gravel improvement of this 264 km road stretch. It was very challenging to
perform this task while taking responsibilities with ongoing project. This was scheduled to
complete within 3 months. First I acquired necessary resources including additional national
technical staff and unskilled manpower. With the collaboration of other project staff, I lead
the team for the investigation. I supervised, trained and performed with my team in first
50km by sampling the existing subgrade material every 2-5 km interval and locating barrow
areas beside the road corridor. Then I closely supervised the material testing at UNOPS
Yambio site office and ensured that proctor, CBR and Sieve analysis of these sample was
performed regularly. Moreover, I identified the sensitive part of road stretch using test result
and topography of the location. I performed Dynamic Cone Penetration test (DCPT) at these
locations and analysed these data with the direction of project manager. To meet the time line
of the project, I got special approval from my project manager to work on Weekends and for
21
plans. Moreover, when borrow area operation was over, I ensured re-insisted the area. I
ensured that barrow area were provided with adequate batter slope, and less water
accumulation. Preventing water stagnation was very important in the area to avoid mosquito
breading which is a severe problem in the region.
UNOPS project office received large number of public complaints throughout this
project. Most of the complaints were related to culverts, site drains, and barrow area
management issues. I conducted initial investigations by myself or through my staff. I
forwarded all public complaints, along with a short report on my findings, actions taken and
recommendations to the project manager. Most of the issues were resolved on site, with the
involvement of the Contractor. For example, once there was a community protest about an
extensively damaged gravel road due to hulling of barrow area material. I immediately
attended the location in question. It was evident that the public road had been heavily used by
construction vehicles and the situation has worsened due to the rains overnight. I talked to the
community representatives and agreed to provide a reasonable solution as soon as possible. I
contacted and negotiated with the Site Manager to reinstate the condition of the road. He
immediately agreed to repair the road and provided a quarry dust with blended hard material
as an additional measure to protect road from further damages.
My project manager requested to performed basic geotechnical investigation as a part
of feasibility assessment for 264km Wau to Tambura road project while I was engaged with
this project. Ministry of Infrastructure, South Sudan wanted this report to looking for possible
funding of gravel improvement of this 264 km road stretch. It was very challenging to
perform this task while taking responsibilities with ongoing project. This was scheduled to
complete within 3 months. First I acquired necessary resources including additional national
technical staff and unskilled manpower. With the collaboration of other project staff, I lead
the team for the investigation. I supervised, trained and performed with my team in first
50km by sampling the existing subgrade material every 2-5 km interval and locating barrow
areas beside the road corridor. Then I closely supervised the material testing at UNOPS
Yambio site office and ensured that proctor, CBR and Sieve analysis of these sample was
performed regularly. Moreover, I identified the sensitive part of road stretch using test result
and topography of the location. I performed Dynamic Cone Penetration test (DCPT) at these
locations and analysed these data with the direction of project manager. To meet the time line
of the project, I got special approval from my project manager to work on Weekends and for
21
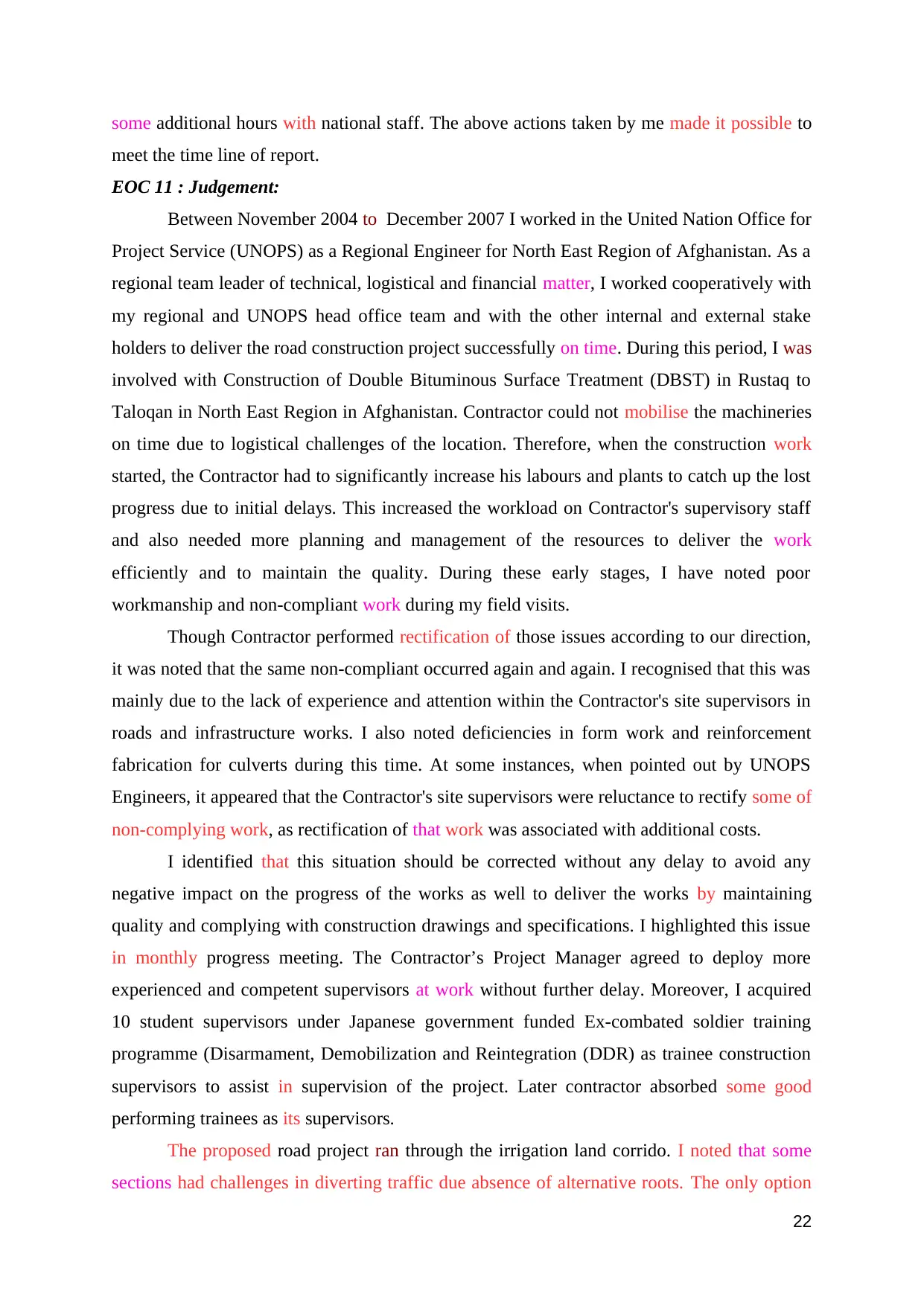
some additional hours with national staff. The above actions taken by me made it possible to
meet the time line of report.
EOC 11 : Judgement:
Between November 2004 to December 2007 I worked in the United Nation Office for
Project Service (UNOPS) as a Regional Engineer for North East Region of Afghanistan. As a
regional team leader of technical, logistical and financial matter, I worked cooperatively with
my regional and UNOPS head office team and with the other internal and external stake
holders to deliver the road construction project successfully on time. During this period, I was
involved with Construction of Double Bituminous Surface Treatment (DBST) in Rustaq to
Taloqan in North East Region in Afghanistan. Contractor could not mobilise the machineries
on time due to logistical challenges of the location. Therefore, when the construction work
started, the Contractor had to significantly increase his labours and plants to catch up the lost
progress due to initial delays. This increased the workload on Contractor's supervisory staff
and also needed more planning and management of the resources to deliver the work
efficiently and to maintain the quality. During these early stages, I have noted poor
workmanship and non-compliant work during my field visits.
Though Contractor performed rectification of those issues according to our direction,
it was noted that the same non-compliant occurred again and again. I recognised that this was
mainly due to the lack of experience and attention within the Contractor's site supervisors in
roads and infrastructure works. I also noted deficiencies in form work and reinforcement
fabrication for culverts during this time. At some instances, when pointed out by UNOPS
Engineers, it appeared that the Contractor's site supervisors were reluctance to rectify some of
non-complying work, as rectification of that work was associated with additional costs.
I identified that this situation should be corrected without any delay to avoid any
negative impact on the progress of the works as well to deliver the works by maintaining
quality and complying with construction drawings and specifications. I highlighted this issue
in monthly progress meeting. The Contractor’s Project Manager agreed to deploy more
experienced and competent supervisors at work without further delay. Moreover, I acquired
10 student supervisors under Japanese government funded Ex-combated soldier training
programme (Disarmament, Demobilization and Reintegration (DDR) as trainee construction
supervisors to assist in supervision of the project. Later contractor absorbed some good
performing trainees as its supervisors.
The proposed road project ran through the irrigation land corrido. I noted that some
sections had challenges in diverting traffic due absence of alternative roots. The only option
22
meet the time line of report.
EOC 11 : Judgement:
Between November 2004 to December 2007 I worked in the United Nation Office for
Project Service (UNOPS) as a Regional Engineer for North East Region of Afghanistan. As a
regional team leader of technical, logistical and financial matter, I worked cooperatively with
my regional and UNOPS head office team and with the other internal and external stake
holders to deliver the road construction project successfully on time. During this period, I was
involved with Construction of Double Bituminous Surface Treatment (DBST) in Rustaq to
Taloqan in North East Region in Afghanistan. Contractor could not mobilise the machineries
on time due to logistical challenges of the location. Therefore, when the construction work
started, the Contractor had to significantly increase his labours and plants to catch up the lost
progress due to initial delays. This increased the workload on Contractor's supervisory staff
and also needed more planning and management of the resources to deliver the work
efficiently and to maintain the quality. During these early stages, I have noted poor
workmanship and non-compliant work during my field visits.
Though Contractor performed rectification of those issues according to our direction,
it was noted that the same non-compliant occurred again and again. I recognised that this was
mainly due to the lack of experience and attention within the Contractor's site supervisors in
roads and infrastructure works. I also noted deficiencies in form work and reinforcement
fabrication for culverts during this time. At some instances, when pointed out by UNOPS
Engineers, it appeared that the Contractor's site supervisors were reluctance to rectify some of
non-complying work, as rectification of that work was associated with additional costs.
I identified that this situation should be corrected without any delay to avoid any
negative impact on the progress of the works as well to deliver the works by maintaining
quality and complying with construction drawings and specifications. I highlighted this issue
in monthly progress meeting. The Contractor’s Project Manager agreed to deploy more
experienced and competent supervisors at work without further delay. Moreover, I acquired
10 student supervisors under Japanese government funded Ex-combated soldier training
programme (Disarmament, Demobilization and Reintegration (DDR) as trainee construction
supervisors to assist in supervision of the project. Later contractor absorbed some good
performing trainees as its supervisors.
The proposed road project ran through the irrigation land corrido. I noted that some
sections had challenges in diverting traffic due absence of alternative roots. The only option
22
Secure Best Marks with AI Grader
Need help grading? Try our AI Grader for instant feedback on your assignments.
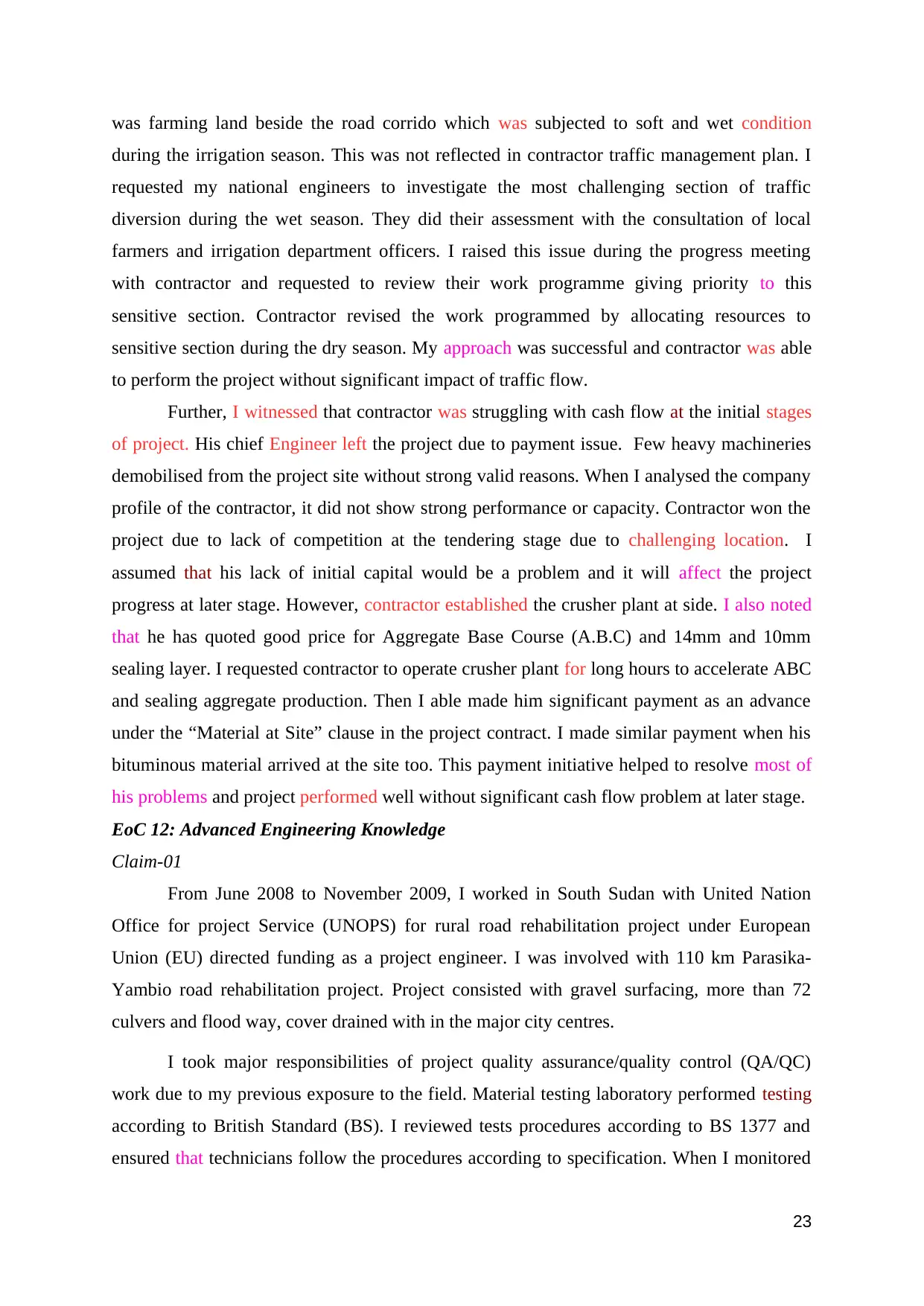
was farming land beside the road corrido which was subjected to soft and wet condition
during the irrigation season. This was not reflected in contractor traffic management plan. I
requested my national engineers to investigate the most challenging section of traffic
diversion during the wet season. They did their assessment with the consultation of local
farmers and irrigation department officers. I raised this issue during the progress meeting
with contractor and requested to review their work programme giving priority to this
sensitive section. Contractor revised the work programmed by allocating resources to
sensitive section during the dry season. My approach was successful and contractor was able
to perform the project without significant impact of traffic flow.
Further, I witnessed that contractor was struggling with cash flow at the initial stages
of project. His chief Engineer left the project due to payment issue. Few heavy machineries
demobilised from the project site without strong valid reasons. When I analysed the company
profile of the contractor, it did not show strong performance or capacity. Contractor won the
project due to lack of competition at the tendering stage due to challenging location. I
assumed that his lack of initial capital would be a problem and it will affect the project
progress at later stage. However, contractor established the crusher plant at side. I also noted
that he has quoted good price for Aggregate Base Course (A.B.C) and 14mm and 10mm
sealing layer. I requested contractor to operate crusher plant for long hours to accelerate ABC
and sealing aggregate production. Then I able made him significant payment as an advance
under the “Material at Site” clause in the project contract. I made similar payment when his
bituminous material arrived at the site too. This payment initiative helped to resolve most of
his problems and project performed well without significant cash flow problem at later stage.
EoC 12: Advanced Engineering Knowledge
Claim-01
From June 2008 to November 2009, I worked in South Sudan with United Nation
Office for project Service (UNOPS) for rural road rehabilitation project under European
Union (EU) directed funding as a project engineer. I was involved with 110 km Parasika-
Yambio road rehabilitation project. Project consisted with gravel surfacing, more than 72
culvers and flood way, cover drained with in the major city centres.
I took major responsibilities of project quality assurance/quality control (QA/QC)
work due to my previous exposure to the field. Material testing laboratory performed testing
according to British Standard (BS). I reviewed tests procedures according to BS 1377 and
ensured that technicians follow the procedures according to specification. When I monitored
23
during the irrigation season. This was not reflected in contractor traffic management plan. I
requested my national engineers to investigate the most challenging section of traffic
diversion during the wet season. They did their assessment with the consultation of local
farmers and irrigation department officers. I raised this issue during the progress meeting
with contractor and requested to review their work programme giving priority to this
sensitive section. Contractor revised the work programmed by allocating resources to
sensitive section during the dry season. My approach was successful and contractor was able
to perform the project without significant impact of traffic flow.
Further, I witnessed that contractor was struggling with cash flow at the initial stages
of project. His chief Engineer left the project due to payment issue. Few heavy machineries
demobilised from the project site without strong valid reasons. When I analysed the company
profile of the contractor, it did not show strong performance or capacity. Contractor won the
project due to lack of competition at the tendering stage due to challenging location. I
assumed that his lack of initial capital would be a problem and it will affect the project
progress at later stage. However, contractor established the crusher plant at side. I also noted
that he has quoted good price for Aggregate Base Course (A.B.C) and 14mm and 10mm
sealing layer. I requested contractor to operate crusher plant for long hours to accelerate ABC
and sealing aggregate production. Then I able made him significant payment as an advance
under the “Material at Site” clause in the project contract. I made similar payment when his
bituminous material arrived at the site too. This payment initiative helped to resolve most of
his problems and project performed well without significant cash flow problem at later stage.
EoC 12: Advanced Engineering Knowledge
Claim-01
From June 2008 to November 2009, I worked in South Sudan with United Nation
Office for project Service (UNOPS) for rural road rehabilitation project under European
Union (EU) directed funding as a project engineer. I was involved with 110 km Parasika-
Yambio road rehabilitation project. Project consisted with gravel surfacing, more than 72
culvers and flood way, cover drained with in the major city centres.
I took major responsibilities of project quality assurance/quality control (QA/QC)
work due to my previous exposure to the field. Material testing laboratory performed testing
according to British Standard (BS). I reviewed tests procedures according to BS 1377 and
ensured that technicians follow the procedures according to specification. When I monitored
23
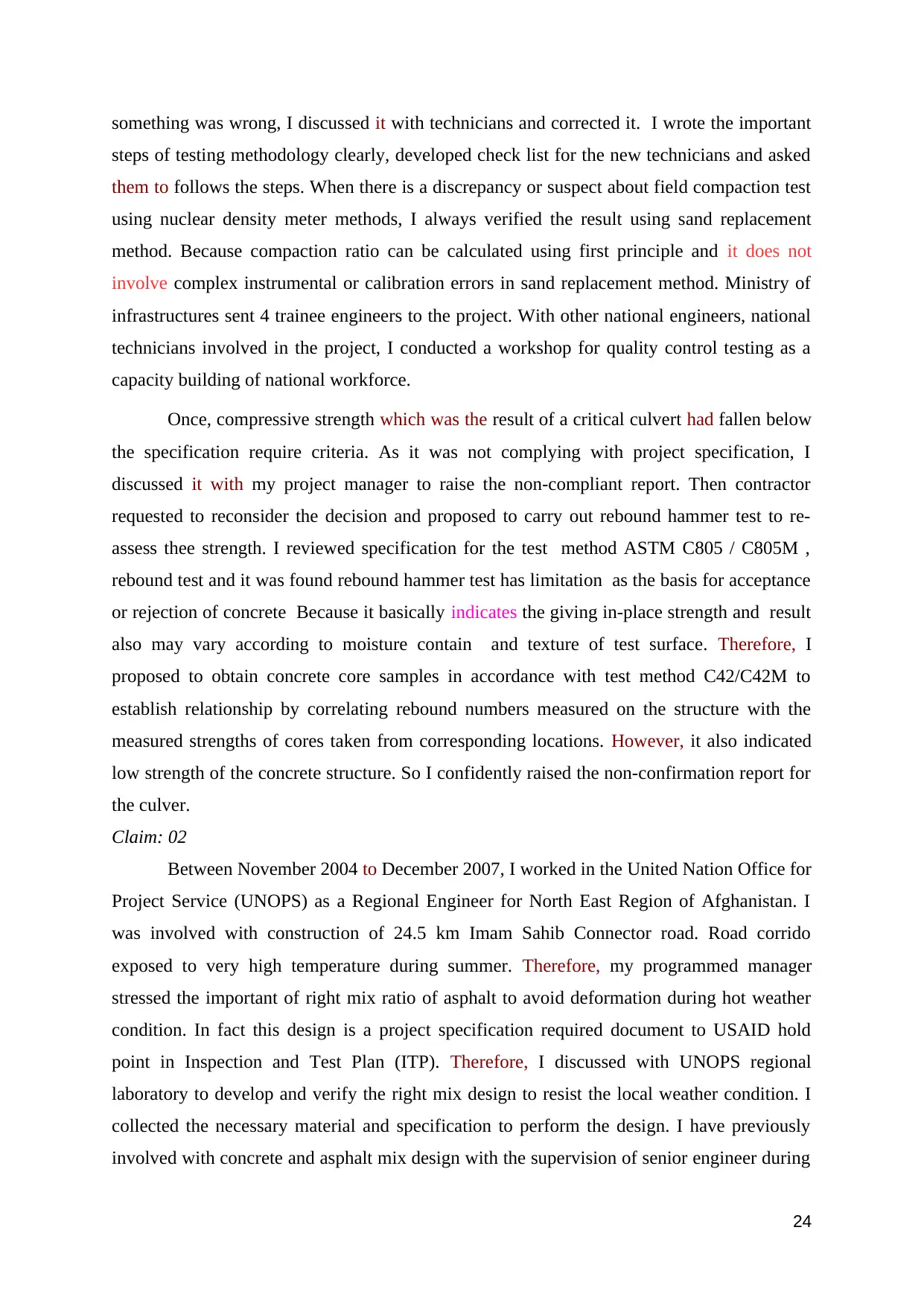
something was wrong, I discussed it with technicians and corrected it. I wrote the important
steps of testing methodology clearly, developed check list for the new technicians and asked
them to follows the steps. When there is a discrepancy or suspect about field compaction test
using nuclear density meter methods, I always verified the result using sand replacement
method. Because compaction ratio can be calculated using first principle and it does not
involve complex instrumental or calibration errors in sand replacement method. Ministry of
infrastructures sent 4 trainee engineers to the project. With other national engineers, national
technicians involved in the project, I conducted a workshop for quality control testing as a
capacity building of national workforce.
Once, compressive strength which was the result of a critical culvert had fallen below
the specification require criteria. As it was not complying with project specification, I
discussed it with my project manager to raise the non-compliant report. Then contractor
requested to reconsider the decision and proposed to carry out rebound hammer test to re-
assess thee strength. I reviewed specification for the test method ASTM C805 / C805M ,
rebound test and it was found rebound hammer test has limitation as the basis for acceptance
or rejection of concrete Because it basically indicates the giving in-place strength and result
also may vary according to moisture contain and texture of test surface. Therefore, I
proposed to obtain concrete core samples in accordance with test method C42/C42M to
establish relationship by correlating rebound numbers measured on the structure with the
measured strengths of cores taken from corresponding locations. However, it also indicated
low strength of the concrete structure. So I confidently raised the non-confirmation report for
the culver.
Claim: 02
Between November 2004 to December 2007, I worked in the United Nation Office for
Project Service (UNOPS) as a Regional Engineer for North East Region of Afghanistan. I
was involved with construction of 24.5 km Imam Sahib Connector road. Road corrido
exposed to very high temperature during summer. Therefore, my programmed manager
stressed the important of right mix ratio of asphalt to avoid deformation during hot weather
condition. In fact this design is a project specification required document to USAID hold
point in Inspection and Test Plan (ITP). Therefore, I discussed with UNOPS regional
laboratory to develop and verify the right mix design to resist the local weather condition. I
collected the necessary material and specification to perform the design. I have previously
involved with concrete and asphalt mix design with the supervision of senior engineer during
24
steps of testing methodology clearly, developed check list for the new technicians and asked
them to follows the steps. When there is a discrepancy or suspect about field compaction test
using nuclear density meter methods, I always verified the result using sand replacement
method. Because compaction ratio can be calculated using first principle and it does not
involve complex instrumental or calibration errors in sand replacement method. Ministry of
infrastructures sent 4 trainee engineers to the project. With other national engineers, national
technicians involved in the project, I conducted a workshop for quality control testing as a
capacity building of national workforce.
Once, compressive strength which was the result of a critical culvert had fallen below
the specification require criteria. As it was not complying with project specification, I
discussed it with my project manager to raise the non-compliant report. Then contractor
requested to reconsider the decision and proposed to carry out rebound hammer test to re-
assess thee strength. I reviewed specification for the test method ASTM C805 / C805M ,
rebound test and it was found rebound hammer test has limitation as the basis for acceptance
or rejection of concrete Because it basically indicates the giving in-place strength and result
also may vary according to moisture contain and texture of test surface. Therefore, I
proposed to obtain concrete core samples in accordance with test method C42/C42M to
establish relationship by correlating rebound numbers measured on the structure with the
measured strengths of cores taken from corresponding locations. However, it also indicated
low strength of the concrete structure. So I confidently raised the non-confirmation report for
the culver.
Claim: 02
Between November 2004 to December 2007, I worked in the United Nation Office for
Project Service (UNOPS) as a Regional Engineer for North East Region of Afghanistan. I
was involved with construction of 24.5 km Imam Sahib Connector road. Road corrido
exposed to very high temperature during summer. Therefore, my programmed manager
stressed the important of right mix ratio of asphalt to avoid deformation during hot weather
condition. In fact this design is a project specification required document to USAID hold
point in Inspection and Test Plan (ITP). Therefore, I discussed with UNOPS regional
laboratory to develop and verify the right mix design to resist the local weather condition. I
collected the necessary material and specification to perform the design. I have previously
involved with concrete and asphalt mix design with the supervision of senior engineer during
24
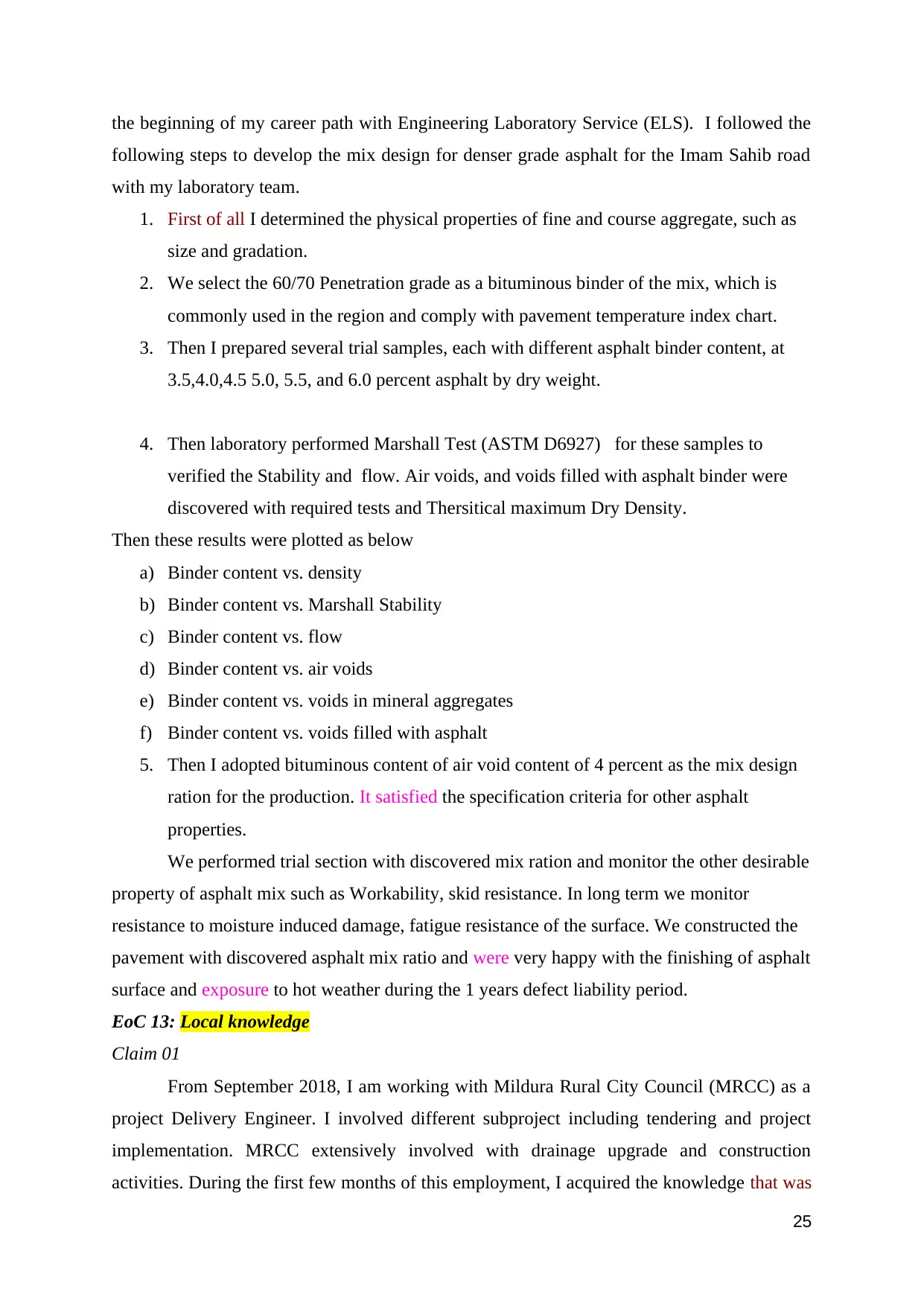
the beginning of my career path with Engineering Laboratory Service (ELS). I followed the
following steps to develop the mix design for denser grade asphalt for the Imam Sahib road
with my laboratory team.
1. First of all I determined the physical properties of fine and course aggregate, such as
size and gradation.
2. We select the 60/70 Penetration grade as a bituminous binder of the mix, which is
commonly used in the region and comply with pavement temperature index chart.
3. Then I prepared several trial samples, each with different asphalt binder content, at
3.5,4.0,4.5 5.0, 5.5, and 6.0 percent asphalt by dry weight.
4. Then laboratory performed Marshall Test (ASTM D6927) for these samples to
verified the Stability and flow. Air voids, and voids filled with asphalt binder were
discovered with required tests and Thersitical maximum Dry Density.
Then these results were plotted as below
a) Binder content vs. density
b) Binder content vs. Marshall Stability
c) Binder content vs. flow
d) Binder content vs. air voids
e) Binder content vs. voids in mineral aggregates
f) Binder content vs. voids filled with asphalt
5. Then I adopted bituminous content of air void content of 4 percent as the mix design
ration for the production. It satisfied the specification criteria for other asphalt
properties.
We performed trial section with discovered mix ration and monitor the other desirable
property of asphalt mix such as Workability, skid resistance. In long term we monitor
resistance to moisture induced damage, fatigue resistance of the surface. We constructed the
pavement with discovered asphalt mix ratio and were very happy with the finishing of asphalt
surface and exposure to hot weather during the 1 years defect liability period.
EoC 13: Local knowledge
Claim 01
From September 2018, I am working with Mildura Rural City Council (MRCC) as a
project Delivery Engineer. I involved different subproject including tendering and project
implementation. MRCC extensively involved with drainage upgrade and construction
activities. During the first few months of this employment, I acquired the knowledge that was
25
following steps to develop the mix design for denser grade asphalt for the Imam Sahib road
with my laboratory team.
1. First of all I determined the physical properties of fine and course aggregate, such as
size and gradation.
2. We select the 60/70 Penetration grade as a bituminous binder of the mix, which is
commonly used in the region and comply with pavement temperature index chart.
3. Then I prepared several trial samples, each with different asphalt binder content, at
3.5,4.0,4.5 5.0, 5.5, and 6.0 percent asphalt by dry weight.
4. Then laboratory performed Marshall Test (ASTM D6927) for these samples to
verified the Stability and flow. Air voids, and voids filled with asphalt binder were
discovered with required tests and Thersitical maximum Dry Density.
Then these results were plotted as below
a) Binder content vs. density
b) Binder content vs. Marshall Stability
c) Binder content vs. flow
d) Binder content vs. air voids
e) Binder content vs. voids in mineral aggregates
f) Binder content vs. voids filled with asphalt
5. Then I adopted bituminous content of air void content of 4 percent as the mix design
ration for the production. It satisfied the specification criteria for other asphalt
properties.
We performed trial section with discovered mix ration and monitor the other desirable
property of asphalt mix such as Workability, skid resistance. In long term we monitor
resistance to moisture induced damage, fatigue resistance of the surface. We constructed the
pavement with discovered asphalt mix ratio and were very happy with the finishing of asphalt
surface and exposure to hot weather during the 1 years defect liability period.
EoC 13: Local knowledge
Claim 01
From September 2018, I am working with Mildura Rural City Council (MRCC) as a
project Delivery Engineer. I involved different subproject including tendering and project
implementation. MRCC extensively involved with drainage upgrade and construction
activities. During the first few months of this employment, I acquired the knowledge that was
25
Paraphrase This Document
Need a fresh take? Get an instant paraphrase of this document with our AI Paraphraser
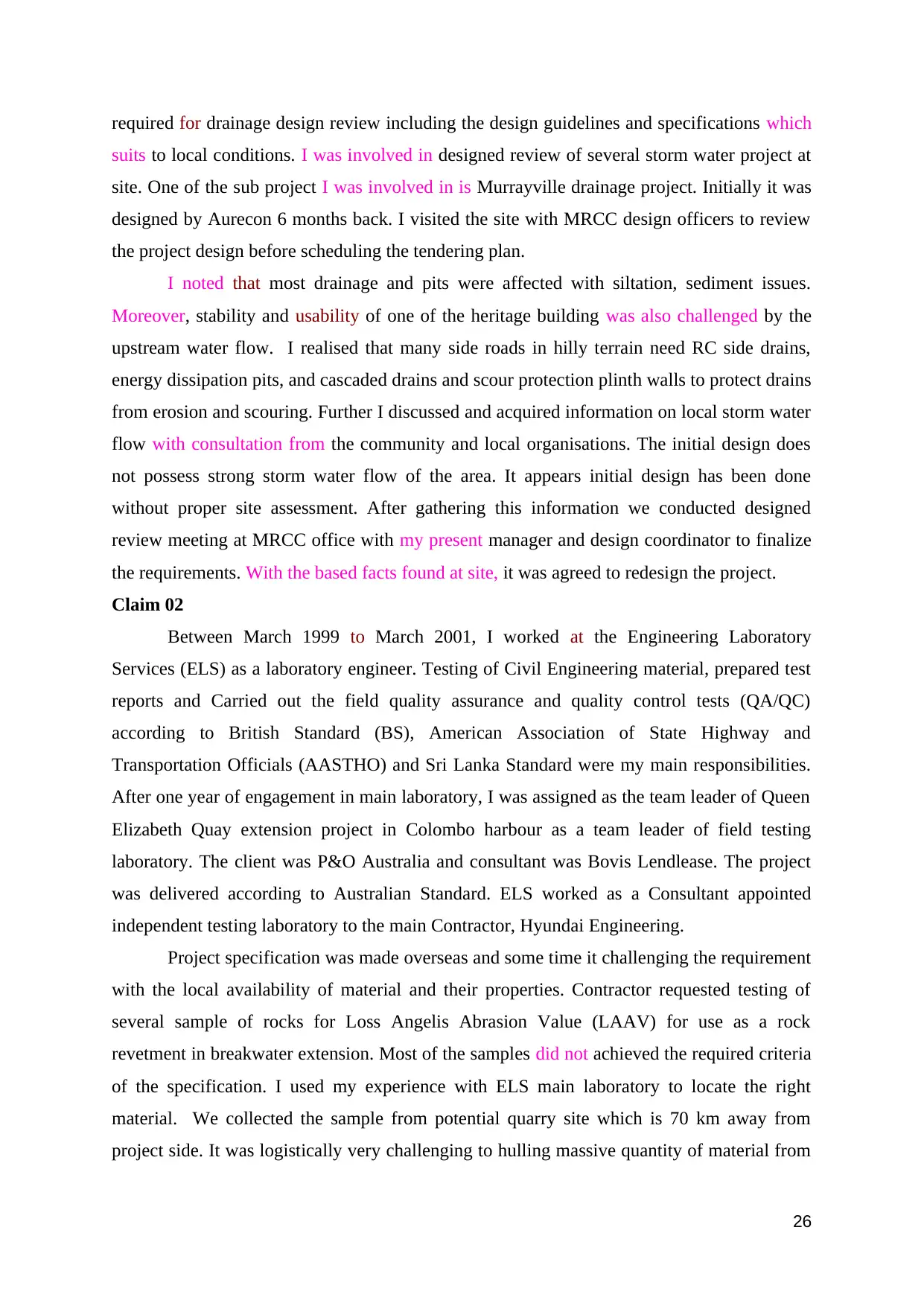
required for drainage design review including the design guidelines and specifications which
suits to local conditions. I was involved in designed review of several storm water project at
site. One of the sub project I was involved in is Murrayville drainage project. Initially it was
designed by Aurecon 6 months back. I visited the site with MRCC design officers to review
the project design before scheduling the tendering plan.
I noted that most drainage and pits were affected with siltation, sediment issues.
Moreover, stability and usability of one of the heritage building was also challenged by the
upstream water flow. I realised that many side roads in hilly terrain need RC side drains,
energy dissipation pits, and cascaded drains and scour protection plinth walls to protect drains
from erosion and scouring. Further I discussed and acquired information on local storm water
flow with consultation from the community and local organisations. The initial design does
not possess strong storm water flow of the area. It appears initial design has been done
without proper site assessment. After gathering this information we conducted designed
review meeting at MRCC office with my present manager and design coordinator to finalize
the requirements. With the based facts found at site, it was agreed to redesign the project.
Claim 02
Between March 1999 to March 2001, I worked at the Engineering Laboratory
Services (ELS) as a laboratory engineer. Testing of Civil Engineering material, prepared test
reports and Carried out the field quality assurance and quality control tests (QA/QC)
according to British Standard (BS), American Association of State Highway and
Transportation Officials (AASTHO) and Sri Lanka Standard were my main responsibilities.
After one year of engagement in main laboratory, I was assigned as the team leader of Queen
Elizabeth Quay extension project in Colombo harbour as a team leader of field testing
laboratory. The client was P&O Australia and consultant was Bovis Lendlease. The project
was delivered according to Australian Standard. ELS worked as a Consultant appointed
independent testing laboratory to the main Contractor, Hyundai Engineering.
Project specification was made overseas and some time it challenging the requirement
with the local availability of material and their properties. Contractor requested testing of
several sample of rocks for Loss Angelis Abrasion Value (LAAV) for use as a rock
revetment in breakwater extension. Most of the samples did not achieved the required criteria
of the specification. I used my experience with ELS main laboratory to locate the right
material. We collected the sample from potential quarry site which is 70 km away from
project side. It was logistically very challenging to hulling massive quantity of material from
26
suits to local conditions. I was involved in designed review of several storm water project at
site. One of the sub project I was involved in is Murrayville drainage project. Initially it was
designed by Aurecon 6 months back. I visited the site with MRCC design officers to review
the project design before scheduling the tendering plan.
I noted that most drainage and pits were affected with siltation, sediment issues.
Moreover, stability and usability of one of the heritage building was also challenged by the
upstream water flow. I realised that many side roads in hilly terrain need RC side drains,
energy dissipation pits, and cascaded drains and scour protection plinth walls to protect drains
from erosion and scouring. Further I discussed and acquired information on local storm water
flow with consultation from the community and local organisations. The initial design does
not possess strong storm water flow of the area. It appears initial design has been done
without proper site assessment. After gathering this information we conducted designed
review meeting at MRCC office with my present manager and design coordinator to finalize
the requirements. With the based facts found at site, it was agreed to redesign the project.
Claim 02
Between March 1999 to March 2001, I worked at the Engineering Laboratory
Services (ELS) as a laboratory engineer. Testing of Civil Engineering material, prepared test
reports and Carried out the field quality assurance and quality control tests (QA/QC)
according to British Standard (BS), American Association of State Highway and
Transportation Officials (AASTHO) and Sri Lanka Standard were my main responsibilities.
After one year of engagement in main laboratory, I was assigned as the team leader of Queen
Elizabeth Quay extension project in Colombo harbour as a team leader of field testing
laboratory. The client was P&O Australia and consultant was Bovis Lendlease. The project
was delivered according to Australian Standard. ELS worked as a Consultant appointed
independent testing laboratory to the main Contractor, Hyundai Engineering.
Project specification was made overseas and some time it challenging the requirement
with the local availability of material and their properties. Contractor requested testing of
several sample of rocks for Loss Angelis Abrasion Value (LAAV) for use as a rock
revetment in breakwater extension. Most of the samples did not achieved the required criteria
of the specification. I used my experience with ELS main laboratory to locate the right
material. We collected the sample from potential quarry site which is 70 km away from
project side. It was logistically very challenging to hulling massive quantity of material from
26
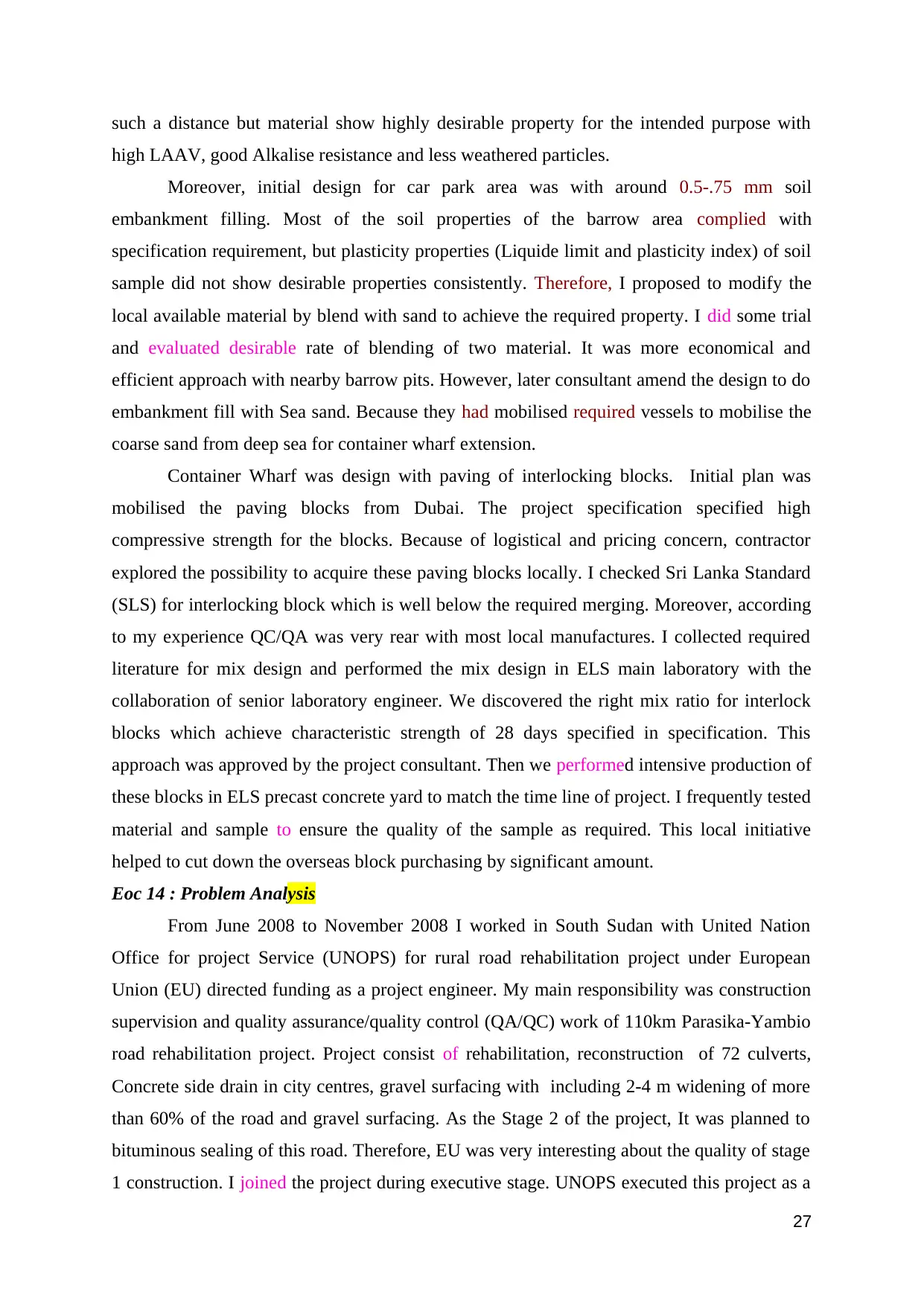
such a distance but material show highly desirable property for the intended purpose with
high LAAV, good Alkalise resistance and less weathered particles.
Moreover, initial design for car park area was with around 0.5-.75 mm soil
embankment filling. Most of the soil properties of the barrow area complied with
specification requirement, but plasticity properties (Liquide limit and plasticity index) of soil
sample did not show desirable properties consistently. Therefore, I proposed to modify the
local available material by blend with sand to achieve the required property. I did some trial
and evaluated desirable rate of blending of two material. It was more economical and
efficient approach with nearby barrow pits. However, later consultant amend the design to do
embankment fill with Sea sand. Because they had mobilised required vessels to mobilise the
coarse sand from deep sea for container wharf extension.
Container Wharf was design with paving of interlocking blocks. Initial plan was
mobilised the paving blocks from Dubai. The project specification specified high
compressive strength for the blocks. Because of logistical and pricing concern, contractor
explored the possibility to acquire these paving blocks locally. I checked Sri Lanka Standard
(SLS) for interlocking block which is well below the required merging. Moreover, according
to my experience QC/QA was very rear with most local manufactures. I collected required
literature for mix design and performed the mix design in ELS main laboratory with the
collaboration of senior laboratory engineer. We discovered the right mix ratio for interlock
blocks which achieve characteristic strength of 28 days specified in specification. This
approach was approved by the project consultant. Then we performed intensive production of
these blocks in ELS precast concrete yard to match the time line of project. I frequently tested
material and sample to ensure the quality of the sample as required. This local initiative
helped to cut down the overseas block purchasing by significant amount.
Eoc 14 : Problem Analysis
From June 2008 to November 2008 I worked in South Sudan with United Nation
Office for project Service (UNOPS) for rural road rehabilitation project under European
Union (EU) directed funding as a project engineer. My main responsibility was construction
supervision and quality assurance/quality control (QA/QC) work of 110km Parasika-Yambio
road rehabilitation project. Project consist of rehabilitation, reconstruction of 72 culverts,
Concrete side drain in city centres, gravel surfacing with including 2-4 m widening of more
than 60% of the road and gravel surfacing. As the Stage 2 of the project, It was planned to
bituminous sealing of this road. Therefore, EU was very interesting about the quality of stage
1 construction. I joined the project during executive stage. UNOPS executed this project as a
27
high LAAV, good Alkalise resistance and less weathered particles.
Moreover, initial design for car park area was with around 0.5-.75 mm soil
embankment filling. Most of the soil properties of the barrow area complied with
specification requirement, but plasticity properties (Liquide limit and plasticity index) of soil
sample did not show desirable properties consistently. Therefore, I proposed to modify the
local available material by blend with sand to achieve the required property. I did some trial
and evaluated desirable rate of blending of two material. It was more economical and
efficient approach with nearby barrow pits. However, later consultant amend the design to do
embankment fill with Sea sand. Because they had mobilised required vessels to mobilise the
coarse sand from deep sea for container wharf extension.
Container Wharf was design with paving of interlocking blocks. Initial plan was
mobilised the paving blocks from Dubai. The project specification specified high
compressive strength for the blocks. Because of logistical and pricing concern, contractor
explored the possibility to acquire these paving blocks locally. I checked Sri Lanka Standard
(SLS) for interlocking block which is well below the required merging. Moreover, according
to my experience QC/QA was very rear with most local manufactures. I collected required
literature for mix design and performed the mix design in ELS main laboratory with the
collaboration of senior laboratory engineer. We discovered the right mix ratio for interlock
blocks which achieve characteristic strength of 28 days specified in specification. This
approach was approved by the project consultant. Then we performed intensive production of
these blocks in ELS precast concrete yard to match the time line of project. I frequently tested
material and sample to ensure the quality of the sample as required. This local initiative
helped to cut down the overseas block purchasing by significant amount.
Eoc 14 : Problem Analysis
From June 2008 to November 2008 I worked in South Sudan with United Nation
Office for project Service (UNOPS) for rural road rehabilitation project under European
Union (EU) directed funding as a project engineer. My main responsibility was construction
supervision and quality assurance/quality control (QA/QC) work of 110km Parasika-Yambio
road rehabilitation project. Project consist of rehabilitation, reconstruction of 72 culverts,
Concrete side drain in city centres, gravel surfacing with including 2-4 m widening of more
than 60% of the road and gravel surfacing. As the Stage 2 of the project, It was planned to
bituminous sealing of this road. Therefore, EU was very interesting about the quality of stage
1 construction. I joined the project during executive stage. UNOPS executed this project as a
27
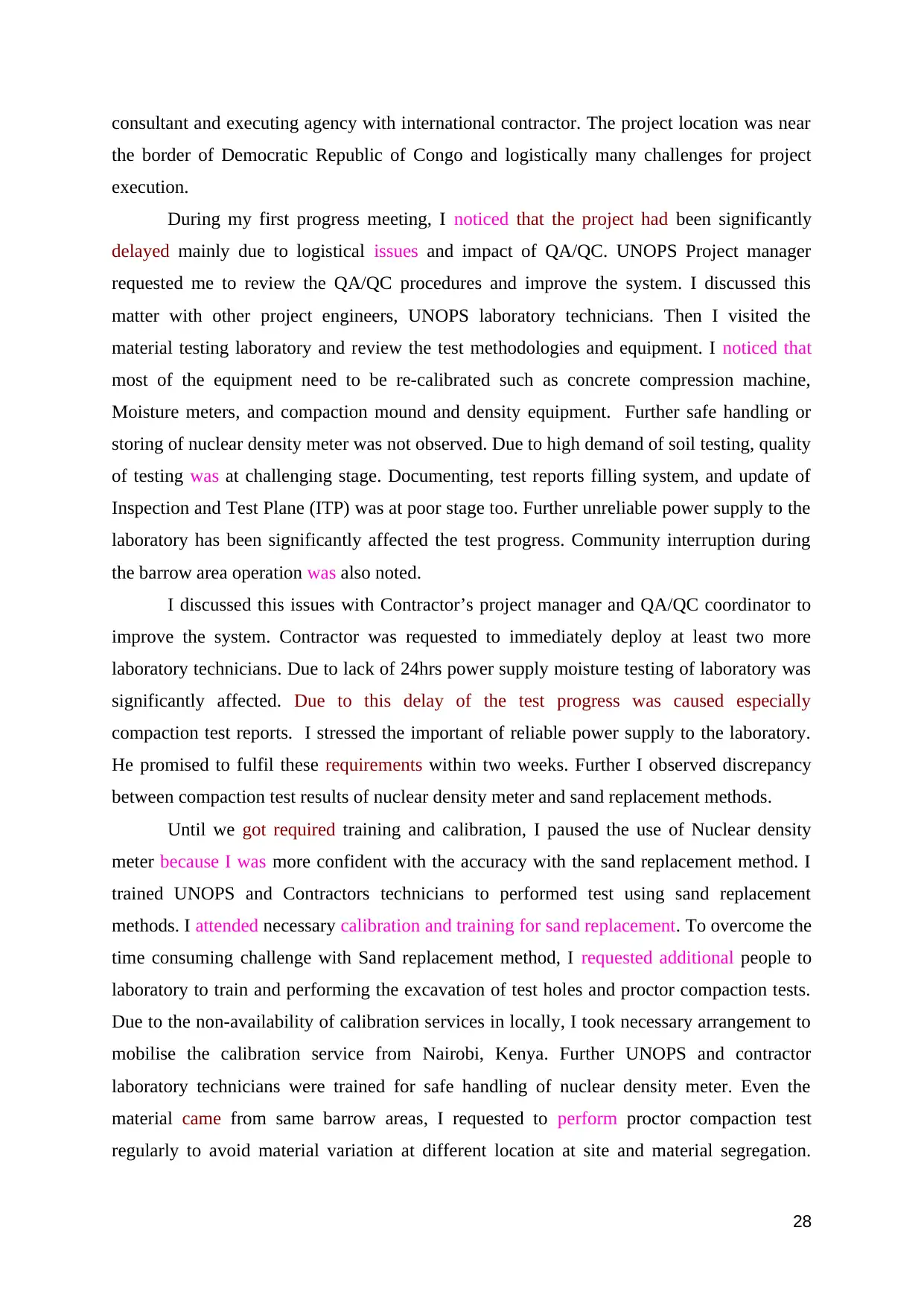
consultant and executing agency with international contractor. The project location was near
the border of Democratic Republic of Congo and logistically many challenges for project
execution.
During my first progress meeting, I noticed that the project had been significantly
delayed mainly due to logistical issues and impact of QA/QC. UNOPS Project manager
requested me to review the QA/QC procedures and improve the system. I discussed this
matter with other project engineers, UNOPS laboratory technicians. Then I visited the
material testing laboratory and review the test methodologies and equipment. I noticed that
most of the equipment need to be re-calibrated such as concrete compression machine,
Moisture meters, and compaction mound and density equipment. Further safe handling or
storing of nuclear density meter was not observed. Due to high demand of soil testing, quality
of testing was at challenging stage. Documenting, test reports filling system, and update of
Inspection and Test Plane (ITP) was at poor stage too. Further unreliable power supply to the
laboratory has been significantly affected the test progress. Community interruption during
the barrow area operation was also noted.
I discussed this issues with Contractor’s project manager and QA/QC coordinator to
improve the system. Contractor was requested to immediately deploy at least two more
laboratory technicians. Due to lack of 24hrs power supply moisture testing of laboratory was
significantly affected. Due to this delay of the test progress was caused especially
compaction test reports. I stressed the important of reliable power supply to the laboratory.
He promised to fulfil these requirements within two weeks. Further I observed discrepancy
between compaction test results of nuclear density meter and sand replacement methods.
Until we got required training and calibration, I paused the use of Nuclear density
meter because I was more confident with the accuracy with the sand replacement method. I
trained UNOPS and Contractors technicians to performed test using sand replacement
methods. I attended necessary calibration and training for sand replacement. To overcome the
time consuming challenge with Sand replacement method, I requested additional people to
laboratory to train and performing the excavation of test holes and proctor compaction tests.
Due to the non-availability of calibration services in locally, I took necessary arrangement to
mobilise the calibration service from Nairobi, Kenya. Further UNOPS and contractor
laboratory technicians were trained for safe handling of nuclear density meter. Even the
material came from same barrow areas, I requested to perform proctor compaction test
regularly to avoid material variation at different location at site and material segregation.
28
the border of Democratic Republic of Congo and logistically many challenges for project
execution.
During my first progress meeting, I noticed that the project had been significantly
delayed mainly due to logistical issues and impact of QA/QC. UNOPS Project manager
requested me to review the QA/QC procedures and improve the system. I discussed this
matter with other project engineers, UNOPS laboratory technicians. Then I visited the
material testing laboratory and review the test methodologies and equipment. I noticed that
most of the equipment need to be re-calibrated such as concrete compression machine,
Moisture meters, and compaction mound and density equipment. Further safe handling or
storing of nuclear density meter was not observed. Due to high demand of soil testing, quality
of testing was at challenging stage. Documenting, test reports filling system, and update of
Inspection and Test Plane (ITP) was at poor stage too. Further unreliable power supply to the
laboratory has been significantly affected the test progress. Community interruption during
the barrow area operation was also noted.
I discussed this issues with Contractor’s project manager and QA/QC coordinator to
improve the system. Contractor was requested to immediately deploy at least two more
laboratory technicians. Due to lack of 24hrs power supply moisture testing of laboratory was
significantly affected. Due to this delay of the test progress was caused especially
compaction test reports. I stressed the important of reliable power supply to the laboratory.
He promised to fulfil these requirements within two weeks. Further I observed discrepancy
between compaction test results of nuclear density meter and sand replacement methods.
Until we got required training and calibration, I paused the use of Nuclear density
meter because I was more confident with the accuracy with the sand replacement method. I
trained UNOPS and Contractors technicians to performed test using sand replacement
methods. I attended necessary calibration and training for sand replacement. To overcome the
time consuming challenge with Sand replacement method, I requested additional people to
laboratory to train and performing the excavation of test holes and proctor compaction tests.
Due to the non-availability of calibration services in locally, I took necessary arrangement to
mobilise the calibration service from Nairobi, Kenya. Further UNOPS and contractor
laboratory technicians were trained for safe handling of nuclear density meter. Even the
material came from same barrow areas, I requested to perform proctor compaction test
regularly to avoid material variation at different location at site and material segregation.
28
Secure Best Marks with AI Grader
Need help grading? Try our AI Grader for instant feedback on your assignments.
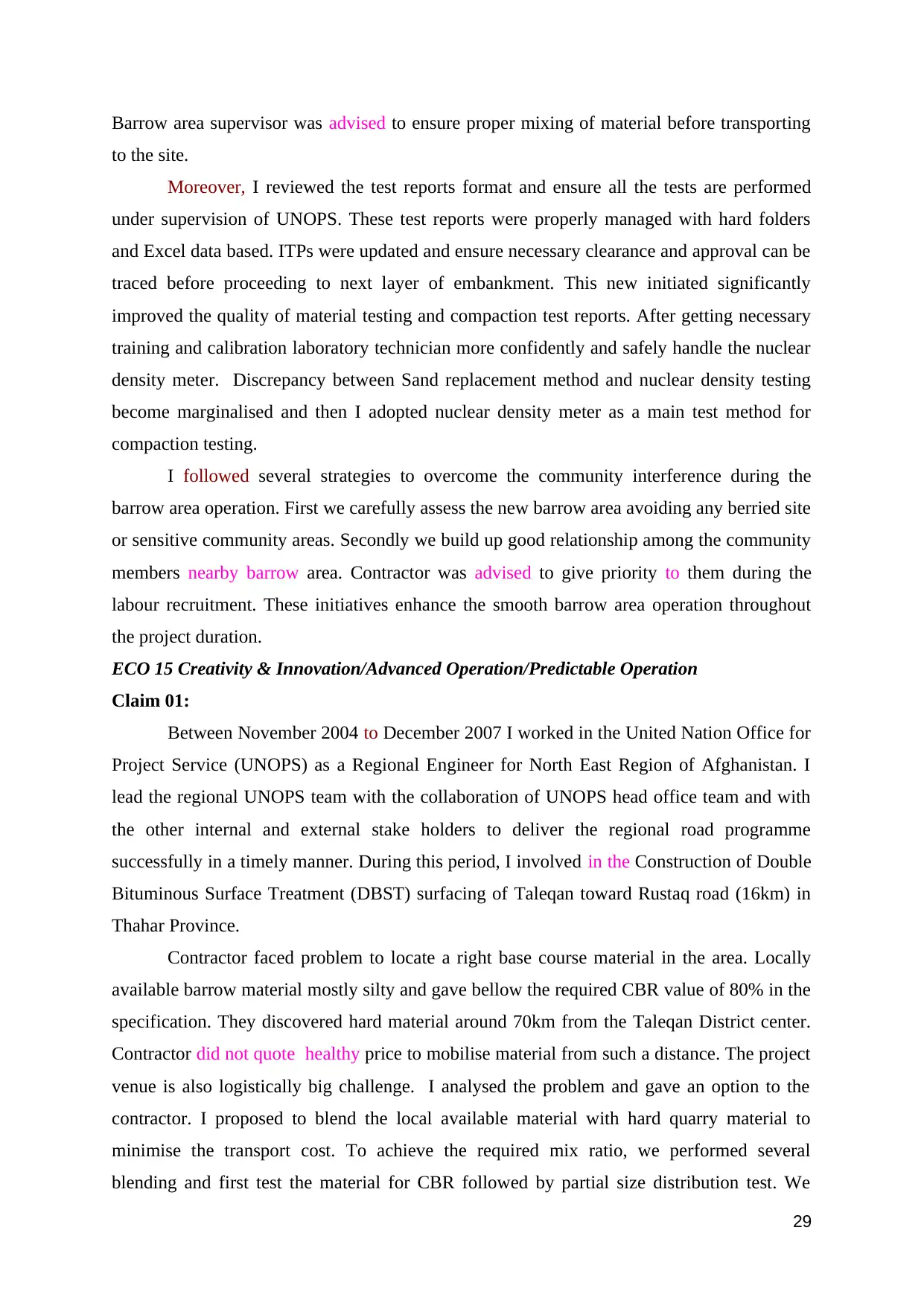
Barrow area supervisor was advised to ensure proper mixing of material before transporting
to the site.
Moreover, I reviewed the test reports format and ensure all the tests are performed
under supervision of UNOPS. These test reports were properly managed with hard folders
and Excel data based. ITPs were updated and ensure necessary clearance and approval can be
traced before proceeding to next layer of embankment. This new initiated significantly
improved the quality of material testing and compaction test reports. After getting necessary
training and calibration laboratory technician more confidently and safely handle the nuclear
density meter. Discrepancy between Sand replacement method and nuclear density testing
become marginalised and then I adopted nuclear density meter as a main test method for
compaction testing.
I followed several strategies to overcome the community interference during the
barrow area operation. First we carefully assess the new barrow area avoiding any berried site
or sensitive community areas. Secondly we build up good relationship among the community
members nearby barrow area. Contractor was advised to give priority to them during the
labour recruitment. These initiatives enhance the smooth barrow area operation throughout
the project duration.
ECO 15 Creativity & Innovation/Advanced Operation/Predictable Operation
Claim 01:
Between November 2004 to December 2007 I worked in the United Nation Office for
Project Service (UNOPS) as a Regional Engineer for North East Region of Afghanistan. I
lead the regional UNOPS team with the collaboration of UNOPS head office team and with
the other internal and external stake holders to deliver the regional road programme
successfully in a timely manner. During this period, I involved in the Construction of Double
Bituminous Surface Treatment (DBST) surfacing of Taleqan toward Rustaq road (16km) in
Thahar Province.
Contractor faced problem to locate a right base course material in the area. Locally
available barrow material mostly silty and gave bellow the required CBR value of 80% in the
specification. They discovered hard material around 70km from the Taleqan District center.
Contractor did not quote healthy price to mobilise material from such a distance. The project
venue is also logistically big challenge. I analysed the problem and gave an option to the
contractor. I proposed to blend the local available material with hard quarry material to
minimise the transport cost. To achieve the required mix ratio, we performed several
blending and first test the material for CBR followed by partial size distribution test. We
29
to the site.
Moreover, I reviewed the test reports format and ensure all the tests are performed
under supervision of UNOPS. These test reports were properly managed with hard folders
and Excel data based. ITPs were updated and ensure necessary clearance and approval can be
traced before proceeding to next layer of embankment. This new initiated significantly
improved the quality of material testing and compaction test reports. After getting necessary
training and calibration laboratory technician more confidently and safely handle the nuclear
density meter. Discrepancy between Sand replacement method and nuclear density testing
become marginalised and then I adopted nuclear density meter as a main test method for
compaction testing.
I followed several strategies to overcome the community interference during the
barrow area operation. First we carefully assess the new barrow area avoiding any berried site
or sensitive community areas. Secondly we build up good relationship among the community
members nearby barrow area. Contractor was advised to give priority to them during the
labour recruitment. These initiatives enhance the smooth barrow area operation throughout
the project duration.
ECO 15 Creativity & Innovation/Advanced Operation/Predictable Operation
Claim 01:
Between November 2004 to December 2007 I worked in the United Nation Office for
Project Service (UNOPS) as a Regional Engineer for North East Region of Afghanistan. I
lead the regional UNOPS team with the collaboration of UNOPS head office team and with
the other internal and external stake holders to deliver the regional road programme
successfully in a timely manner. During this period, I involved in the Construction of Double
Bituminous Surface Treatment (DBST) surfacing of Taleqan toward Rustaq road (16km) in
Thahar Province.
Contractor faced problem to locate a right base course material in the area. Locally
available barrow material mostly silty and gave bellow the required CBR value of 80% in the
specification. They discovered hard material around 70km from the Taleqan District center.
Contractor did not quote healthy price to mobilise material from such a distance. The project
venue is also logistically big challenge. I analysed the problem and gave an option to the
contractor. I proposed to blend the local available material with hard quarry material to
minimise the transport cost. To achieve the required mix ratio, we performed several
blending and first test the material for CBR followed by partial size distribution test. We
29
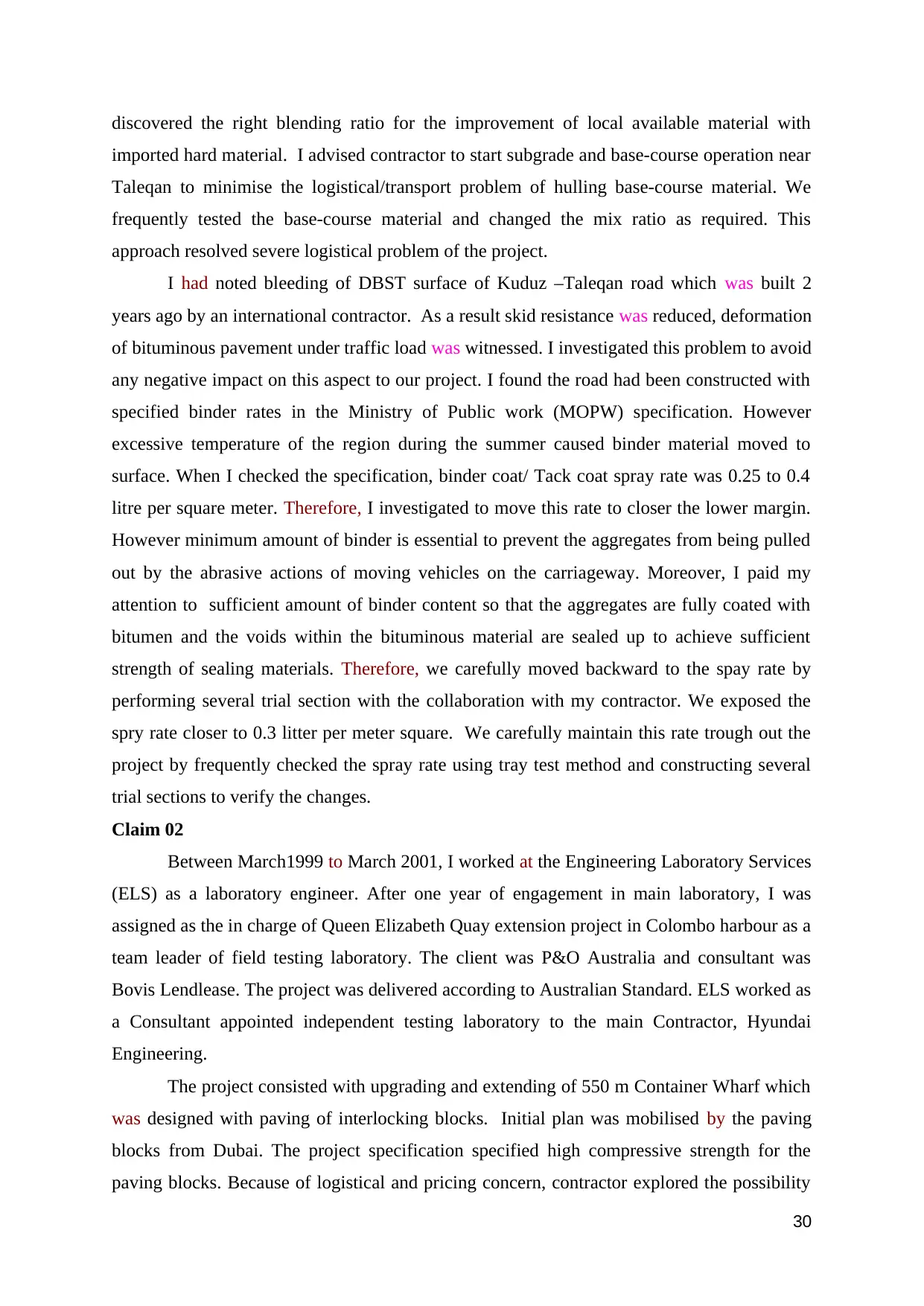
discovered the right blending ratio for the improvement of local available material with
imported hard material. I advised contractor to start subgrade and base-course operation near
Taleqan to minimise the logistical/transport problem of hulling base-course material. We
frequently tested the base-course material and changed the mix ratio as required. This
approach resolved severe logistical problem of the project.
I had noted bleeding of DBST surface of Kuduz –Taleqan road which was built 2
years ago by an international contractor. As a result skid resistance was reduced, deformation
of bituminous pavement under traffic load was witnessed. I investigated this problem to avoid
any negative impact on this aspect to our project. I found the road had been constructed with
specified binder rates in the Ministry of Public work (MOPW) specification. However
excessive temperature of the region during the summer caused binder material moved to
surface. When I checked the specification, binder coat/ Tack coat spray rate was 0.25 to 0.4
litre per square meter. Therefore, I investigated to move this rate to closer the lower margin.
However minimum amount of binder is essential to prevent the aggregates from being pulled
out by the abrasive actions of moving vehicles on the carriageway. Moreover, I paid my
attention to sufficient amount of binder content so that the aggregates are fully coated with
bitumen and the voids within the bituminous material are sealed up to achieve sufficient
strength of sealing materials. Therefore, we carefully moved backward to the spay rate by
performing several trial section with the collaboration with my contractor. We exposed the
spry rate closer to 0.3 litter per meter square. We carefully maintain this rate trough out the
project by frequently checked the spray rate using tray test method and constructing several
trial sections to verify the changes.
Claim 02
Between March1999 to March 2001, I worked at the Engineering Laboratory Services
(ELS) as a laboratory engineer. After one year of engagement in main laboratory, I was
assigned as the in charge of Queen Elizabeth Quay extension project in Colombo harbour as a
team leader of field testing laboratory. The client was P&O Australia and consultant was
Bovis Lendlease. The project was delivered according to Australian Standard. ELS worked as
a Consultant appointed independent testing laboratory to the main Contractor, Hyundai
Engineering.
The project consisted with upgrading and extending of 550 m Container Wharf which
was designed with paving of interlocking blocks. Initial plan was mobilised by the paving
blocks from Dubai. The project specification specified high compressive strength for the
paving blocks. Because of logistical and pricing concern, contractor explored the possibility
30
imported hard material. I advised contractor to start subgrade and base-course operation near
Taleqan to minimise the logistical/transport problem of hulling base-course material. We
frequently tested the base-course material and changed the mix ratio as required. This
approach resolved severe logistical problem of the project.
I had noted bleeding of DBST surface of Kuduz –Taleqan road which was built 2
years ago by an international contractor. As a result skid resistance was reduced, deformation
of bituminous pavement under traffic load was witnessed. I investigated this problem to avoid
any negative impact on this aspect to our project. I found the road had been constructed with
specified binder rates in the Ministry of Public work (MOPW) specification. However
excessive temperature of the region during the summer caused binder material moved to
surface. When I checked the specification, binder coat/ Tack coat spray rate was 0.25 to 0.4
litre per square meter. Therefore, I investigated to move this rate to closer the lower margin.
However minimum amount of binder is essential to prevent the aggregates from being pulled
out by the abrasive actions of moving vehicles on the carriageway. Moreover, I paid my
attention to sufficient amount of binder content so that the aggregates are fully coated with
bitumen and the voids within the bituminous material are sealed up to achieve sufficient
strength of sealing materials. Therefore, we carefully moved backward to the spay rate by
performing several trial section with the collaboration with my contractor. We exposed the
spry rate closer to 0.3 litter per meter square. We carefully maintain this rate trough out the
project by frequently checked the spray rate using tray test method and constructing several
trial sections to verify the changes.
Claim 02
Between March1999 to March 2001, I worked at the Engineering Laboratory Services
(ELS) as a laboratory engineer. After one year of engagement in main laboratory, I was
assigned as the in charge of Queen Elizabeth Quay extension project in Colombo harbour as a
team leader of field testing laboratory. The client was P&O Australia and consultant was
Bovis Lendlease. The project was delivered according to Australian Standard. ELS worked as
a Consultant appointed independent testing laboratory to the main Contractor, Hyundai
Engineering.
The project consisted with upgrading and extending of 550 m Container Wharf which
was designed with paving of interlocking blocks. Initial plan was mobilised by the paving
blocks from Dubai. The project specification specified high compressive strength for the
paving blocks. Because of logistical and pricing concern, contractor explored the possibility
30
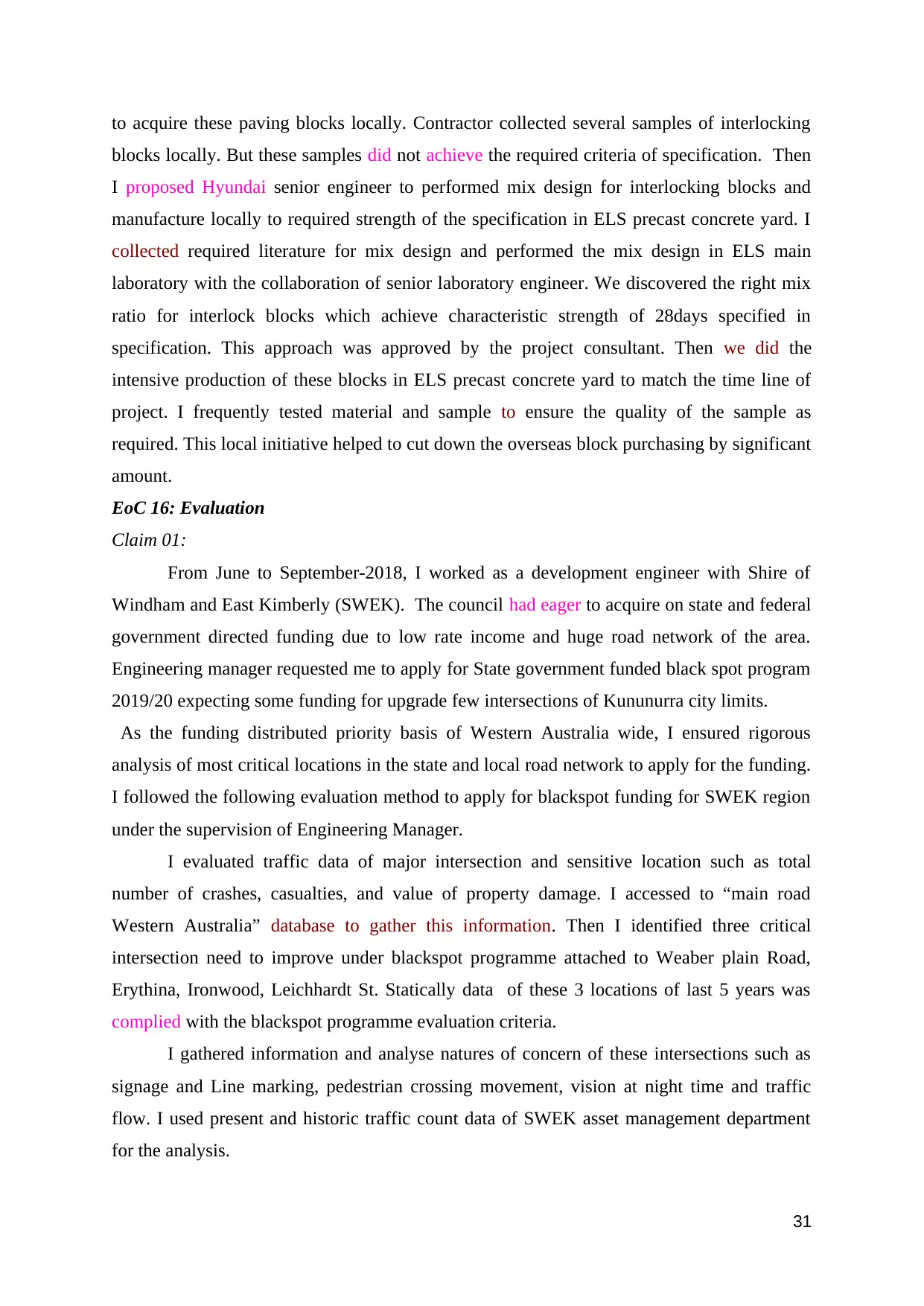
to acquire these paving blocks locally. Contractor collected several samples of interlocking
blocks locally. But these samples did not achieve the required criteria of specification. Then
I proposed Hyundai senior engineer to performed mix design for interlocking blocks and
manufacture locally to required strength of the specification in ELS precast concrete yard. I
collected required literature for mix design and performed the mix design in ELS main
laboratory with the collaboration of senior laboratory engineer. We discovered the right mix
ratio for interlock blocks which achieve characteristic strength of 28days specified in
specification. This approach was approved by the project consultant. Then we did the
intensive production of these blocks in ELS precast concrete yard to match the time line of
project. I frequently tested material and sample to ensure the quality of the sample as
required. This local initiative helped to cut down the overseas block purchasing by significant
amount.
EoC 16: Evaluation
Claim 01:
From June to September-2018, I worked as a development engineer with Shire of
Windham and East Kimberly (SWEK). The council had eager to acquire on state and federal
government directed funding due to low rate income and huge road network of the area.
Engineering manager requested me to apply for State government funded black spot program
2019/20 expecting some funding for upgrade few intersections of Kununurra city limits.
As the funding distributed priority basis of Western Australia wide, I ensured rigorous
analysis of most critical locations in the state and local road network to apply for the funding.
I followed the following evaluation method to apply for blackspot funding for SWEK region
under the supervision of Engineering Manager.
I evaluated traffic data of major intersection and sensitive location such as total
number of crashes, casualties, and value of property damage. I accessed to “main road
Western Australia” database to gather this information. Then I identified three critical
intersection need to improve under blackspot programme attached to Weaber plain Road,
Erythina, Ironwood, Leichhardt St. Statically data of these 3 locations of last 5 years was
complied with the blackspot programme evaluation criteria.
I gathered information and analyse natures of concern of these intersections such as
signage and Line marking, pedestrian crossing movement, vision at night time and traffic
flow. I used present and historic traffic count data of SWEK asset management department
for the analysis.
31
blocks locally. But these samples did not achieve the required criteria of specification. Then
I proposed Hyundai senior engineer to performed mix design for interlocking blocks and
manufacture locally to required strength of the specification in ELS precast concrete yard. I
collected required literature for mix design and performed the mix design in ELS main
laboratory with the collaboration of senior laboratory engineer. We discovered the right mix
ratio for interlock blocks which achieve characteristic strength of 28days specified in
specification. This approach was approved by the project consultant. Then we did the
intensive production of these blocks in ELS precast concrete yard to match the time line of
project. I frequently tested material and sample to ensure the quality of the sample as
required. This local initiative helped to cut down the overseas block purchasing by significant
amount.
EoC 16: Evaluation
Claim 01:
From June to September-2018, I worked as a development engineer with Shire of
Windham and East Kimberly (SWEK). The council had eager to acquire on state and federal
government directed funding due to low rate income and huge road network of the area.
Engineering manager requested me to apply for State government funded black spot program
2019/20 expecting some funding for upgrade few intersections of Kununurra city limits.
As the funding distributed priority basis of Western Australia wide, I ensured rigorous
analysis of most critical locations in the state and local road network to apply for the funding.
I followed the following evaluation method to apply for blackspot funding for SWEK region
under the supervision of Engineering Manager.
I evaluated traffic data of major intersection and sensitive location such as total
number of crashes, casualties, and value of property damage. I accessed to “main road
Western Australia” database to gather this information. Then I identified three critical
intersection need to improve under blackspot programme attached to Weaber plain Road,
Erythina, Ironwood, Leichhardt St. Statically data of these 3 locations of last 5 years was
complied with the blackspot programme evaluation criteria.
I gathered information and analyse natures of concern of these intersections such as
signage and Line marking, pedestrian crossing movement, vision at night time and traffic
flow. I used present and historic traffic count data of SWEK asset management department
for the analysis.
31
Paraphrase This Document
Need a fresh take? Get an instant paraphrase of this document with our AI Paraphraser
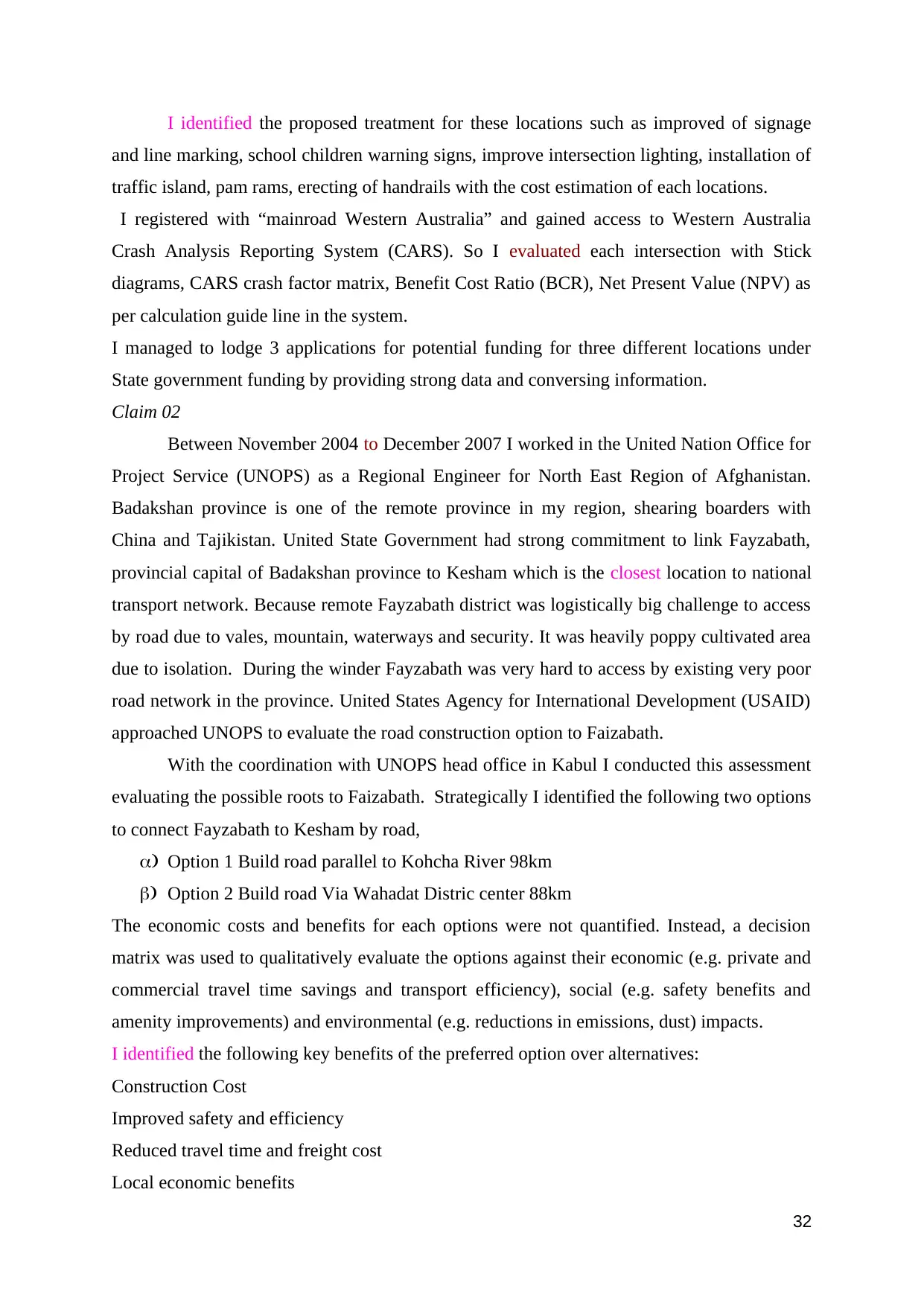
I identified the proposed treatment for these locations such as improved of signage
and line marking, school children warning signs, improve intersection lighting, installation of
traffic island, pam rams, erecting of handrails with the cost estimation of each locations.
I registered with “mainroad Western Australia” and gained access to Western Australia
Crash Analysis Reporting System (CARS). So I evaluated each intersection with Stick
diagrams, CARS crash factor matrix, Benefit Cost Ratio (BCR), Net Present Value (NPV) as
per calculation guide line in the system.
I managed to lodge 3 applications for potential funding for three different locations under
State government funding by providing strong data and conversing information.
Claim 02
Between November 2004 to December 2007 I worked in the United Nation Office for
Project Service (UNOPS) as a Regional Engineer for North East Region of Afghanistan.
Badakshan province is one of the remote province in my region, shearing boarders with
China and Tajikistan. United State Government had strong commitment to link Fayzabath,
provincial capital of Badakshan province to Kesham which is the closest location to national
transport network. Because remote Fayzabath district was logistically big challenge to access
by road due to vales, mountain, waterways and security. It was heavily poppy cultivated area
due to isolation. During the winder Fayzabath was very hard to access by existing very poor
road network in the province. United States Agency for International Development (USAID)
approached UNOPS to evaluate the road construction option to Faizabath.
With the coordination with UNOPS head office in Kabul I conducted this assessment
evaluating the possible roots to Faizabath. Strategically I identified the following two options
to connect Fayzabath to Kesham by road,
a) Option 1 Build road parallel to Kohcha River 98km
b) Option 2 Build road Via Wahadat Distric center 88km
The economic costs and benefits for each options were not quantified. Instead, a decision
matrix was used to qualitatively evaluate the options against their economic (e.g. private and
commercial travel time savings and transport efficiency), social (e.g. safety benefits and
amenity improvements) and environmental (e.g. reductions in emissions, dust) impacts.
I identified the following key benefits of the preferred option over alternatives:
Construction Cost
Improved safety and efficiency
Reduced travel time and freight cost
Local economic benefits
32
and line marking, school children warning signs, improve intersection lighting, installation of
traffic island, pam rams, erecting of handrails with the cost estimation of each locations.
I registered with “mainroad Western Australia” and gained access to Western Australia
Crash Analysis Reporting System (CARS). So I evaluated each intersection with Stick
diagrams, CARS crash factor matrix, Benefit Cost Ratio (BCR), Net Present Value (NPV) as
per calculation guide line in the system.
I managed to lodge 3 applications for potential funding for three different locations under
State government funding by providing strong data and conversing information.
Claim 02
Between November 2004 to December 2007 I worked in the United Nation Office for
Project Service (UNOPS) as a Regional Engineer for North East Region of Afghanistan.
Badakshan province is one of the remote province in my region, shearing boarders with
China and Tajikistan. United State Government had strong commitment to link Fayzabath,
provincial capital of Badakshan province to Kesham which is the closest location to national
transport network. Because remote Fayzabath district was logistically big challenge to access
by road due to vales, mountain, waterways and security. It was heavily poppy cultivated area
due to isolation. During the winder Fayzabath was very hard to access by existing very poor
road network in the province. United States Agency for International Development (USAID)
approached UNOPS to evaluate the road construction option to Faizabath.
With the coordination with UNOPS head office in Kabul I conducted this assessment
evaluating the possible roots to Faizabath. Strategically I identified the following two options
to connect Fayzabath to Kesham by road,
a) Option 1 Build road parallel to Kohcha River 98km
b) Option 2 Build road Via Wahadat Distric center 88km
The economic costs and benefits for each options were not quantified. Instead, a decision
matrix was used to qualitatively evaluate the options against their economic (e.g. private and
commercial travel time savings and transport efficiency), social (e.g. safety benefits and
amenity improvements) and environmental (e.g. reductions in emissions, dust) impacts.
I identified the following key benefits of the preferred option over alternatives:
Construction Cost
Improved safety and efficiency
Reduced travel time and freight cost
Local economic benefits
32
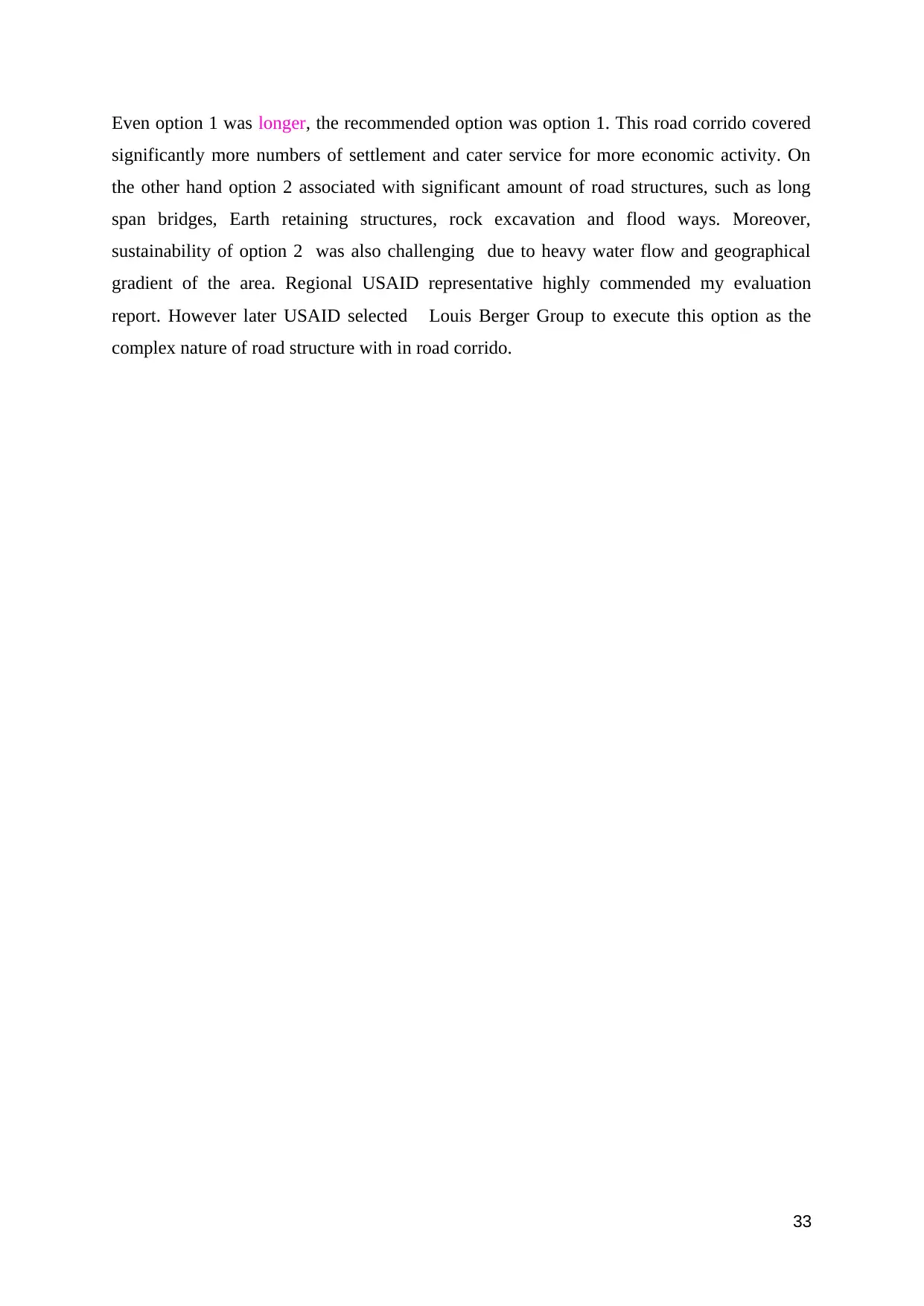
Even option 1 was longer, the recommended option was option 1. This road corrido covered
significantly more numbers of settlement and cater service for more economic activity. On
the other hand option 2 associated with significant amount of road structures, such as long
span bridges, Earth retaining structures, rock excavation and flood ways. Moreover,
sustainability of option 2 was also challenging due to heavy water flow and geographical
gradient of the area. Regional USAID representative highly commended my evaluation
report. However later USAID selected Louis Berger Group to execute this option as the
complex nature of road structure with in road corrido.
33
significantly more numbers of settlement and cater service for more economic activity. On
the other hand option 2 associated with significant amount of road structures, such as long
span bridges, Earth retaining structures, rock excavation and flood ways. Moreover,
sustainability of option 2 was also challenging due to heavy water flow and geographical
gradient of the area. Regional USAID representative highly commended my evaluation
report. However later USAID selected Louis Berger Group to execute this option as the
complex nature of road structure with in road corrido.
33
1 out of 33
![[object Object]](/_next/image/?url=%2F_next%2Fstatic%2Fmedia%2Flogo.6d15ce61.png&w=640&q=75)
Your All-in-One AI-Powered Toolkit for Academic Success.
+13062052269
info@desklib.com
Available 24*7 on WhatsApp / Email
Unlock your academic potential
© 2024 | Zucol Services PVT LTD | All rights reserved.