Quality Planning & Analysis: Porcelain Tiles - Stakeholder Report
VerifiedAdded on 2023/06/12
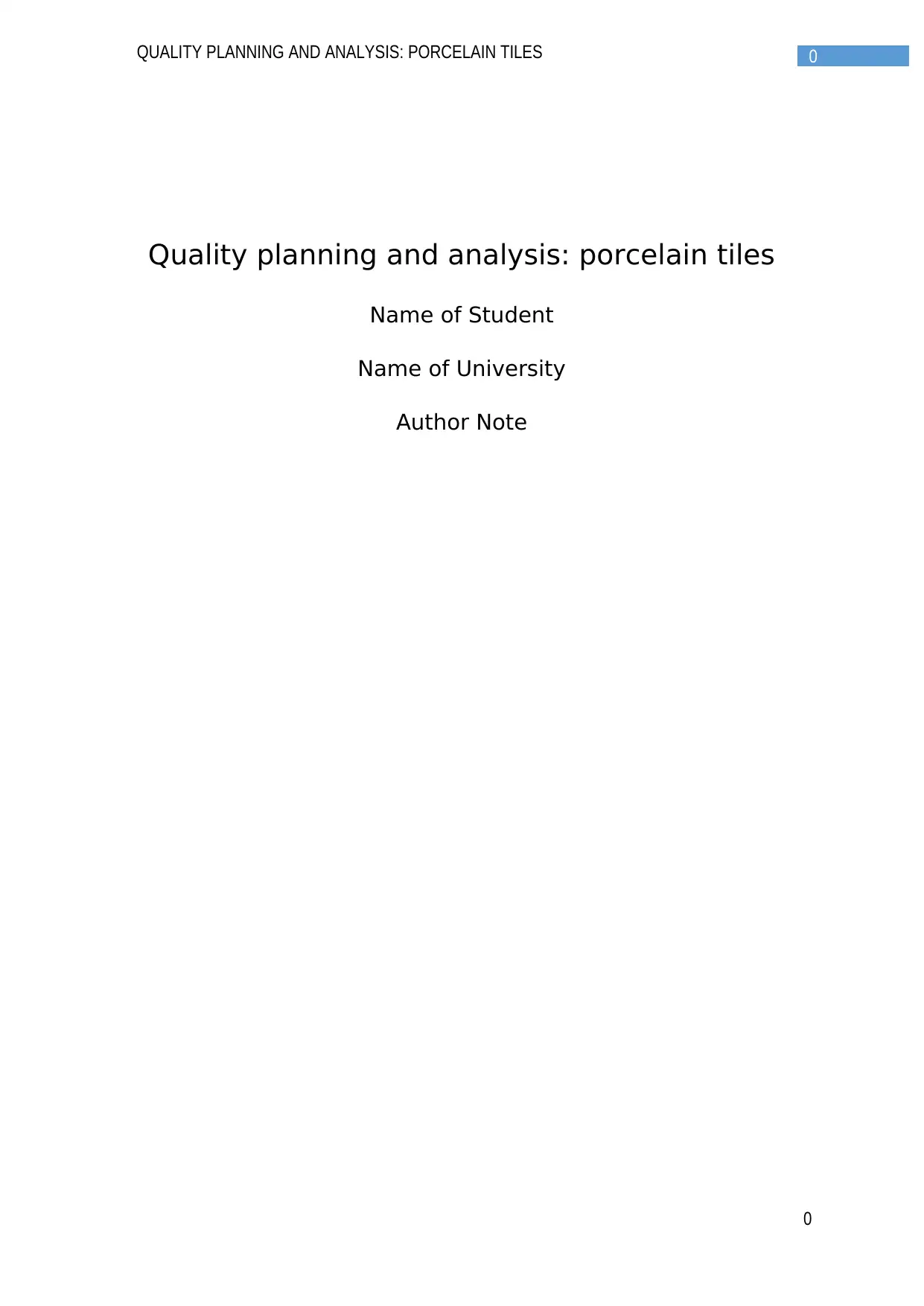
Quality planning and analysis: porcelain tiles
Name of Student
Name of University
Author Note
0
Paraphrase This Document
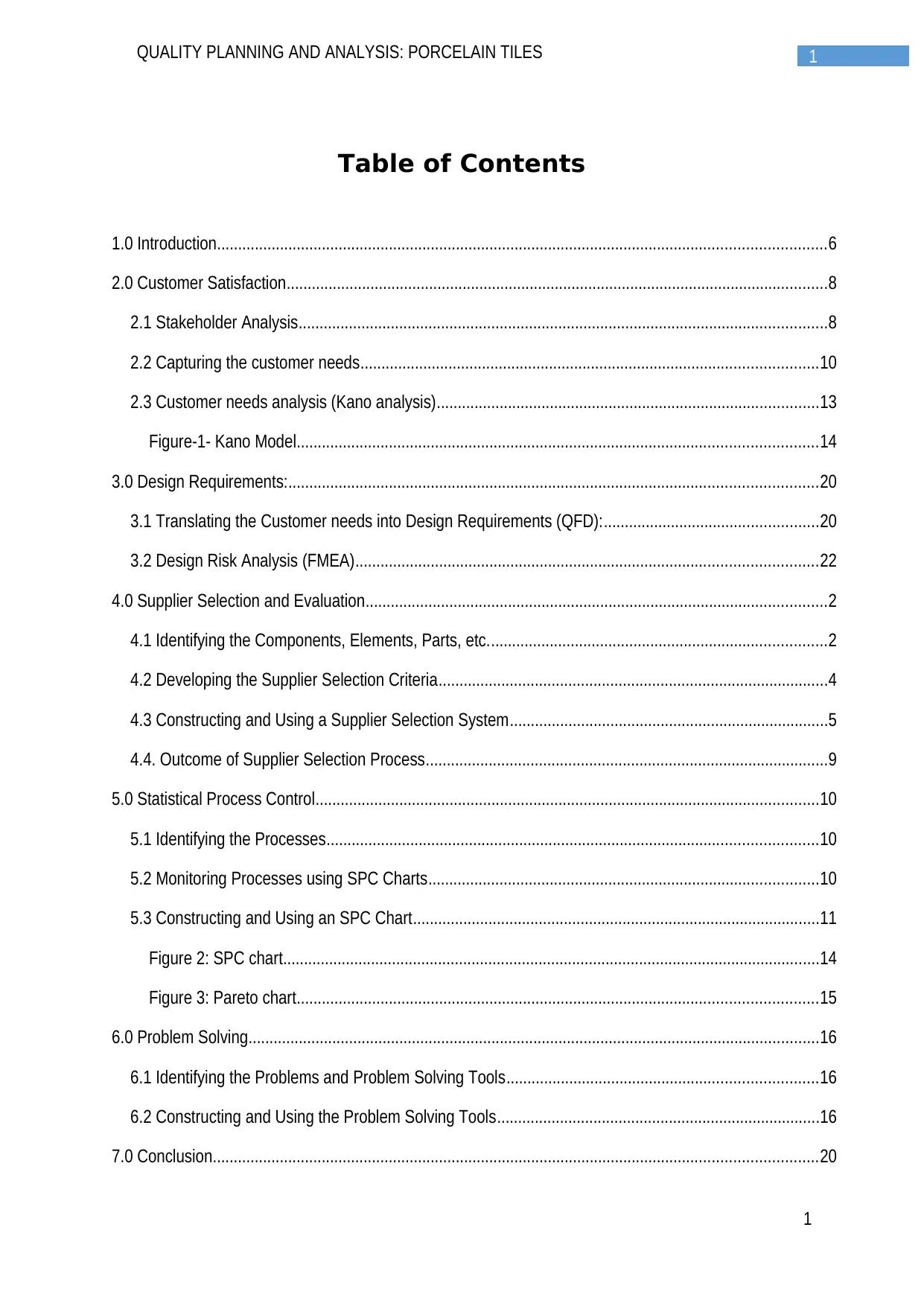
Table of Contents
1.0 Introduction.................................................................................................................................................6
2.0 Customer Satisfaction.................................................................................................................................8
2.1 Stakeholder Analysis..............................................................................................................................8
2.2 Capturing the customer needs.............................................................................................................10
2.3 Customer needs analysis (Kano analysis)...........................................................................................13
Figure-1- Kano Model............................................................................................................................14
3.0 Design Requirements:..............................................................................................................................20
3.1 Translating the Customer needs into Design Requirements (QFD):...................................................20
3.2 Design Risk Analysis (FMEA)..............................................................................................................22
4.0 Supplier Selection and Evaluation..............................................................................................................2
4.1 Identifying the Components, Elements, Parts, etc.................................................................................2
4.2 Developing the Supplier Selection Criteria.............................................................................................4
4.3 Constructing and Using a Supplier Selection System............................................................................5
4.4. Outcome of Supplier Selection Process................................................................................................9
5.0 Statistical Process Control........................................................................................................................10
5.1 Identifying the Processes.....................................................................................................................10
5.2 Monitoring Processes using SPC Charts.............................................................................................10
5.3 Constructing and Using an SPC Chart.................................................................................................11
Figure 2: SPC chart................................................................................................................................14
Figure 3: Pareto chart............................................................................................................................15
6.0 Problem Solving........................................................................................................................................16
6.1 Identifying the Problems and Problem Solving Tools..........................................................................16
6.2 Constructing and Using the Problem Solving Tools.............................................................................16
7.0 Conclusion................................................................................................................................................20
1
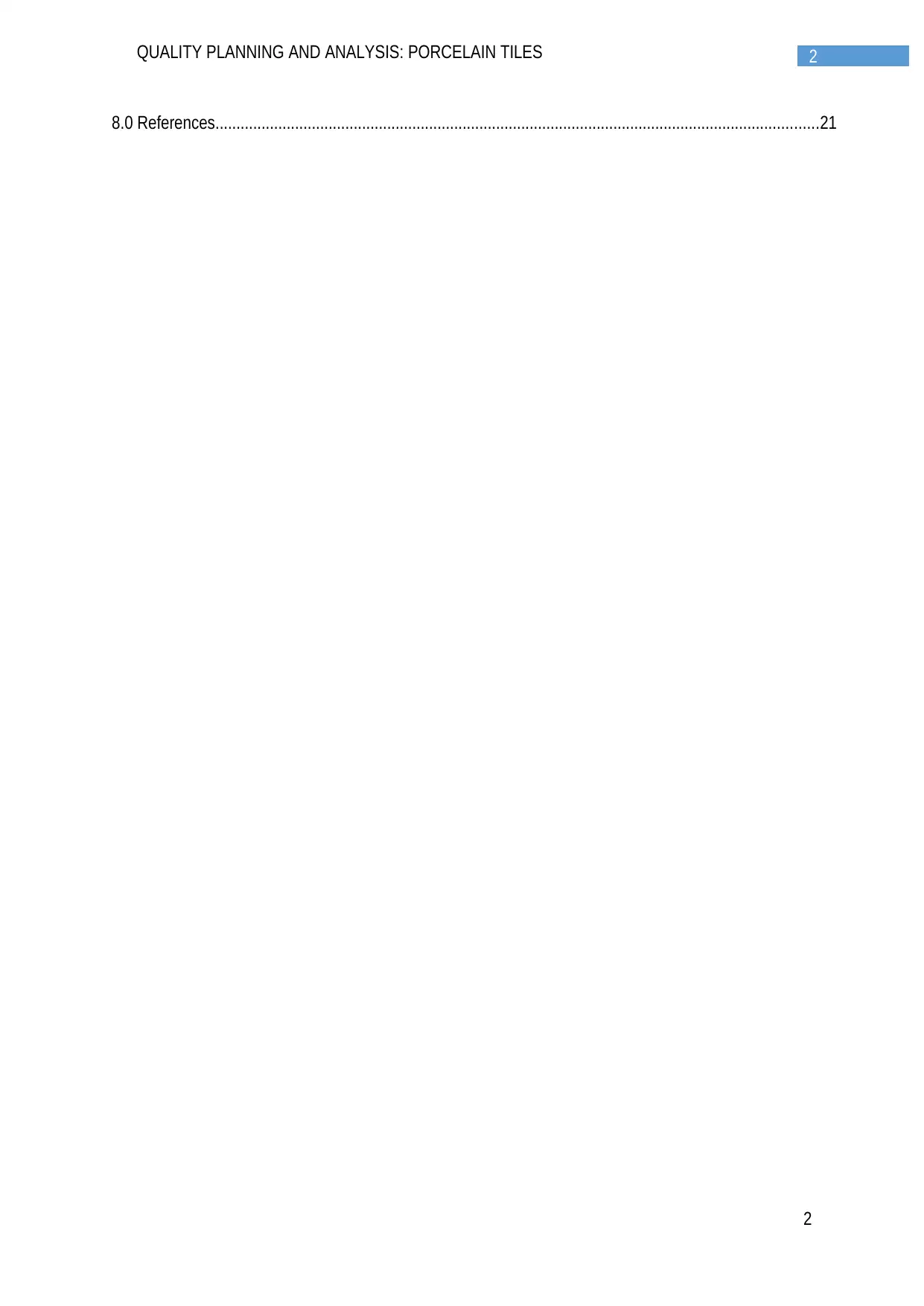
8.0 References................................................................................................................................................21
2
⊘ This is a preview!⊘
Do you want full access?
Subscribe today to unlock all pages.

Trusted by 1+ million students worldwide
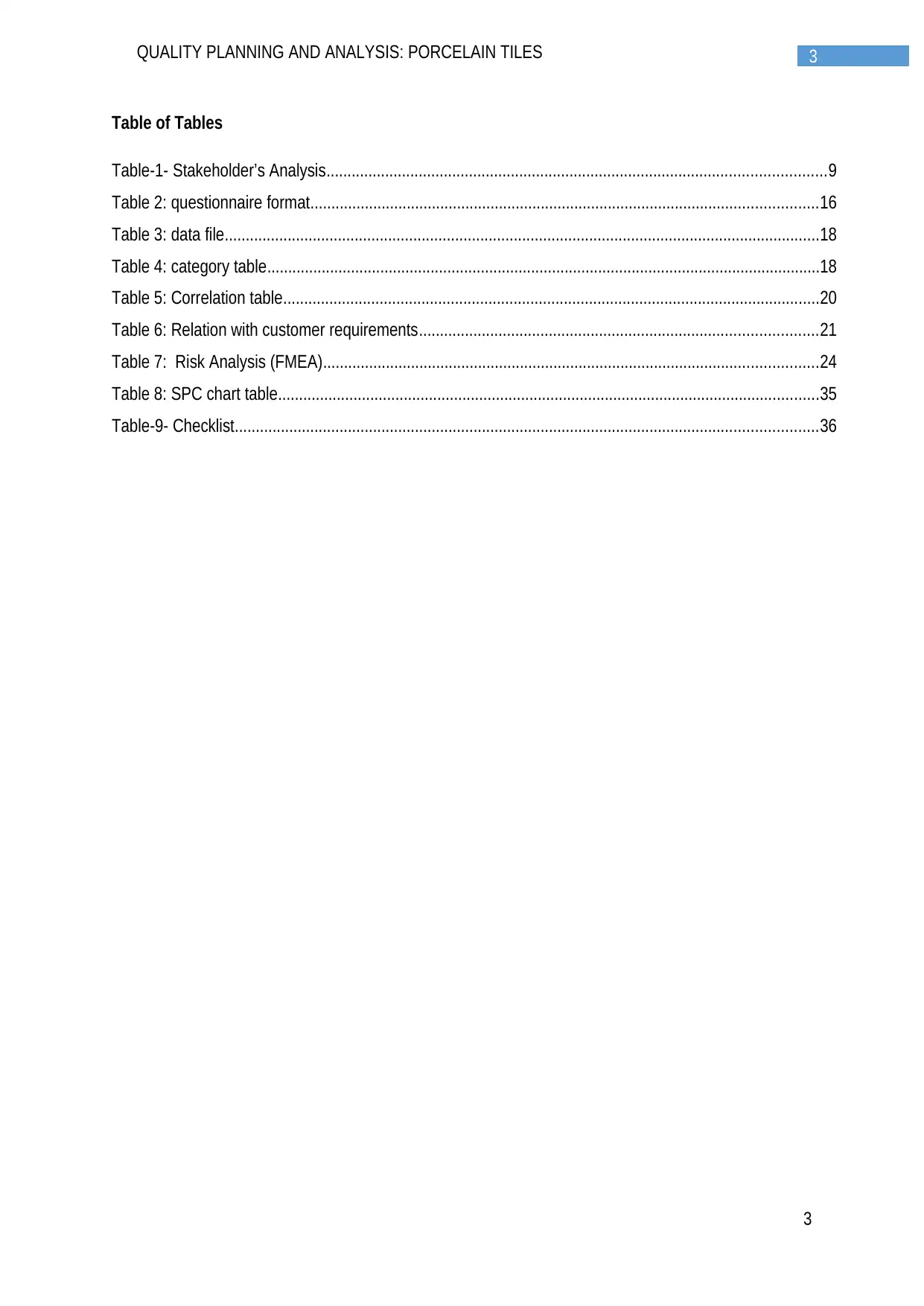
Table of Tables
Table-1- Stakeholder’s Analysis.......................................................................................................................9
Table 2: questionnaire format.........................................................................................................................16
Table 3: data file..............................................................................................................................................18
Table 4: category table....................................................................................................................................18
Table 5: Correlation table................................................................................................................................20
Table 6: Relation with customer requirements...............................................................................................21
Table 7: Risk Analysis (FMEA)......................................................................................................................24
Table 8: SPC chart table.................................................................................................................................35
Table-9- Checklist...........................................................................................................................................36
3
Paraphrase This Document
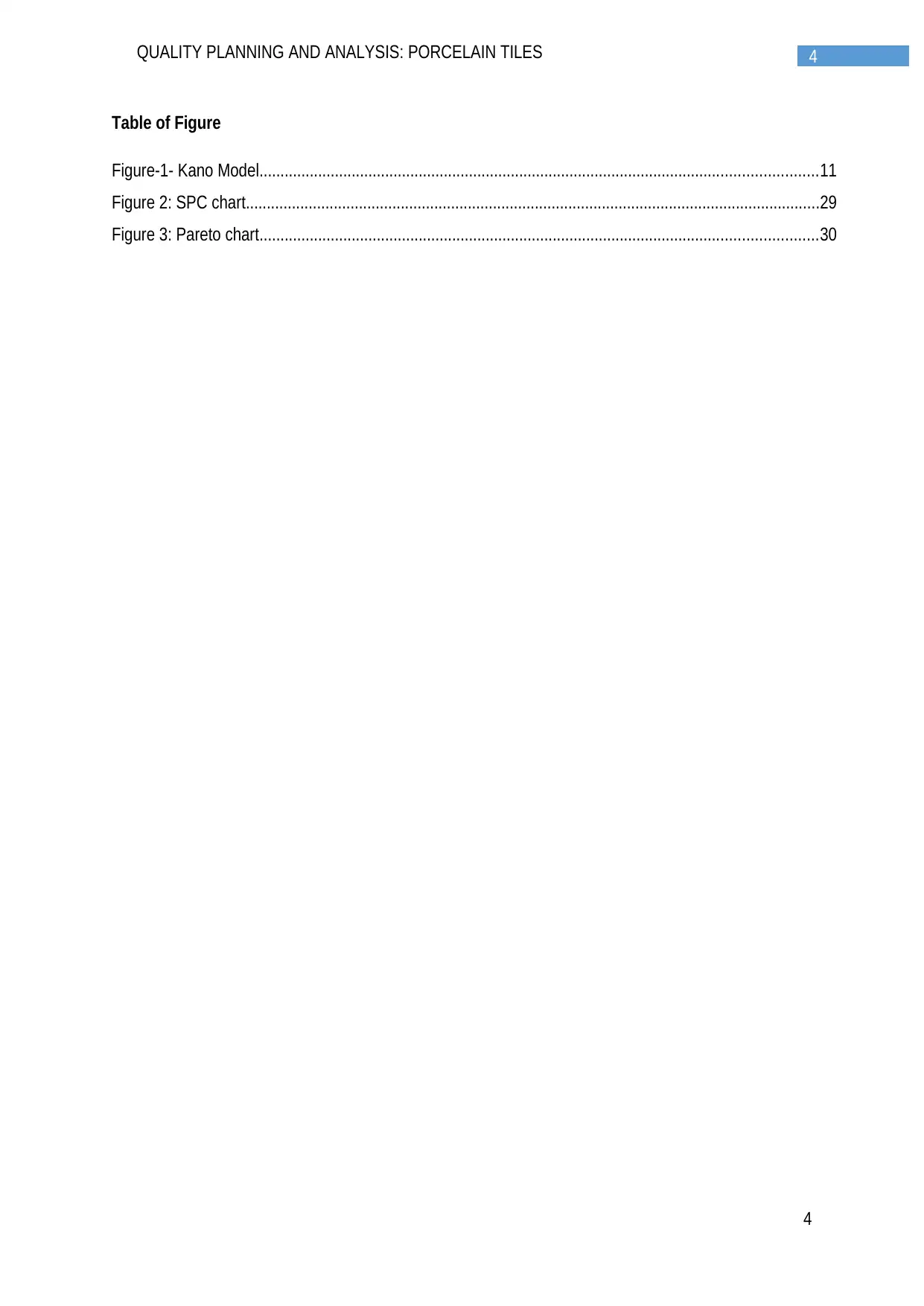
Table of Figure
Figure-1- Kano Model.....................................................................................................................................11
Figure 2: SPC chart.........................................................................................................................................29
Figure 3: Pareto chart.....................................................................................................................................30
4
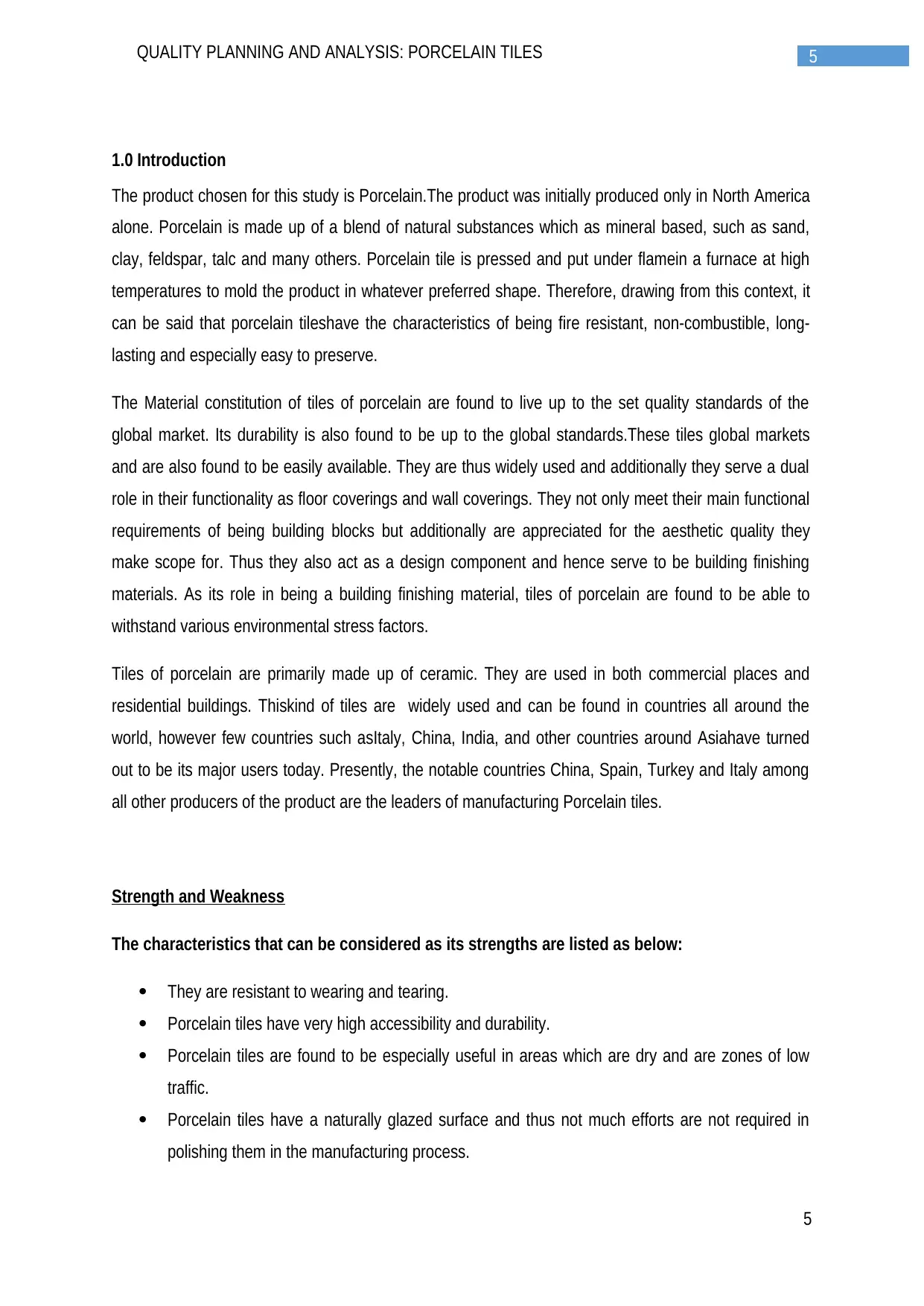
1.0 Introduction
The product chosen for this study is Porcelain.The product was initially produced only in North America
alone. Porcelain is made up of a blend of natural substances which as mineral based, such as sand,
clay, feldspar, talc and many others. Porcelain tile is pressed and put under flamein a furnace at high
temperatures to mold the product in whatever preferred shape. Therefore, drawing from this context, it
can be said that porcelain tileshave the characteristics of being fire resistant, non-combustible, long-
lasting and especially easy to preserve.
The Material constitution of tiles of porcelain are found to live up to the set quality standards of the
global market. Its durability is also found to be up to the global standards.These tiles global markets
and are also found to be easily available. They are thus widely used and additionally they serve a dual
role in their functionality as floor coverings and wall coverings. They not only meet their main functional
requirements of being building blocks but additionally are appreciated for the aesthetic quality they
make scope for. Thus they also act as a design component and hence serve to be building finishing
materials. As its role in being a building finishing material, tiles of porcelain are found to be able to
withstand various environmental stress factors.
Tiles of porcelain are primarily made up of ceramic. They are used in both commercial places and
residential buildings. Thiskind of tiles are widely used and can be found in countries all around the
world, however few countries such asItaly, China, India, and other countries around Asiahave turned
out to be its major users today. Presently, the notable countries China, Spain, Turkey and Italy among
all other producers of the product are the leaders of manufacturing Porcelain tiles.
Strength and Weakness
The characteristics that can be considered as its strengths are listed as below:
They are resistant to wearing and tearing.
Porcelain tiles have very high accessibility and durability.
Porcelain tiles are found to be especially useful in areas which are dry and are zones of low
traffic.
Porcelain tiles have a naturally glazed surface and thus not much efforts are not required in
polishing them in the manufacturing process.
5
⊘ This is a preview!⊘
Do you want full access?
Subscribe today to unlock all pages.

Trusted by 1+ million students worldwide
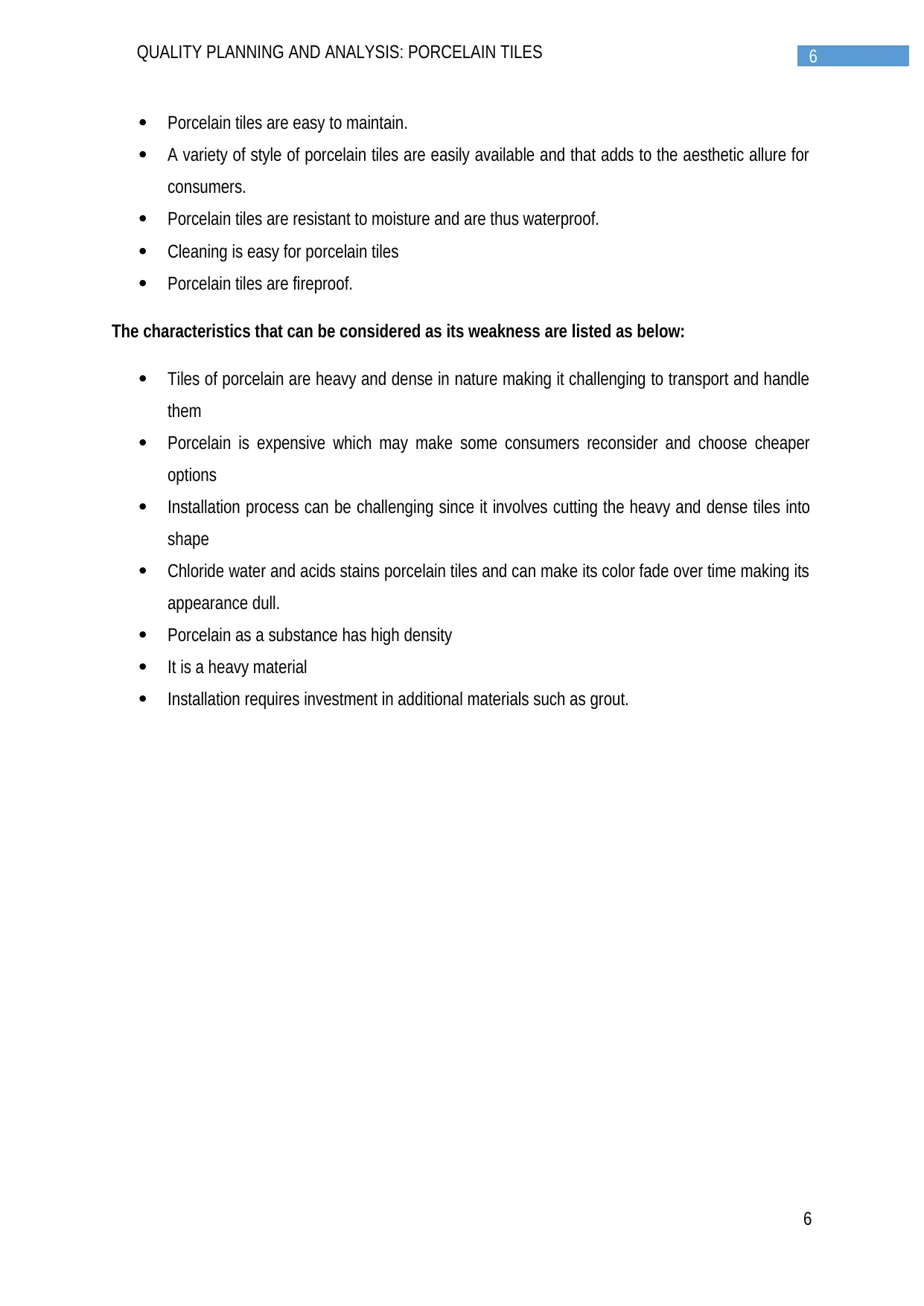
Porcelain tiles are easy to maintain.
A variety of style of porcelain tiles are easily available and that adds to the aesthetic allure for
consumers.
Porcelain tiles are resistant to moisture and are thus waterproof.
Cleaning is easy for porcelain tiles
Porcelain tiles are fireproof.
The characteristics that can be considered as its weakness are listed as below:
Tiles of porcelain are heavy and dense in nature making it challenging to transport and handle
them
Porcelain is expensive which may make some consumers reconsider and choose cheaper
options
Installation process can be challenging since it involves cutting the heavy and dense tiles into
shape
Chloride water and acids stains porcelain tiles and can make its color fade over time making its
appearance dull.
Porcelain as a substance has high density
It is a heavy material
Installation requires investment in additional materials such as grout.
6
Paraphrase This Document
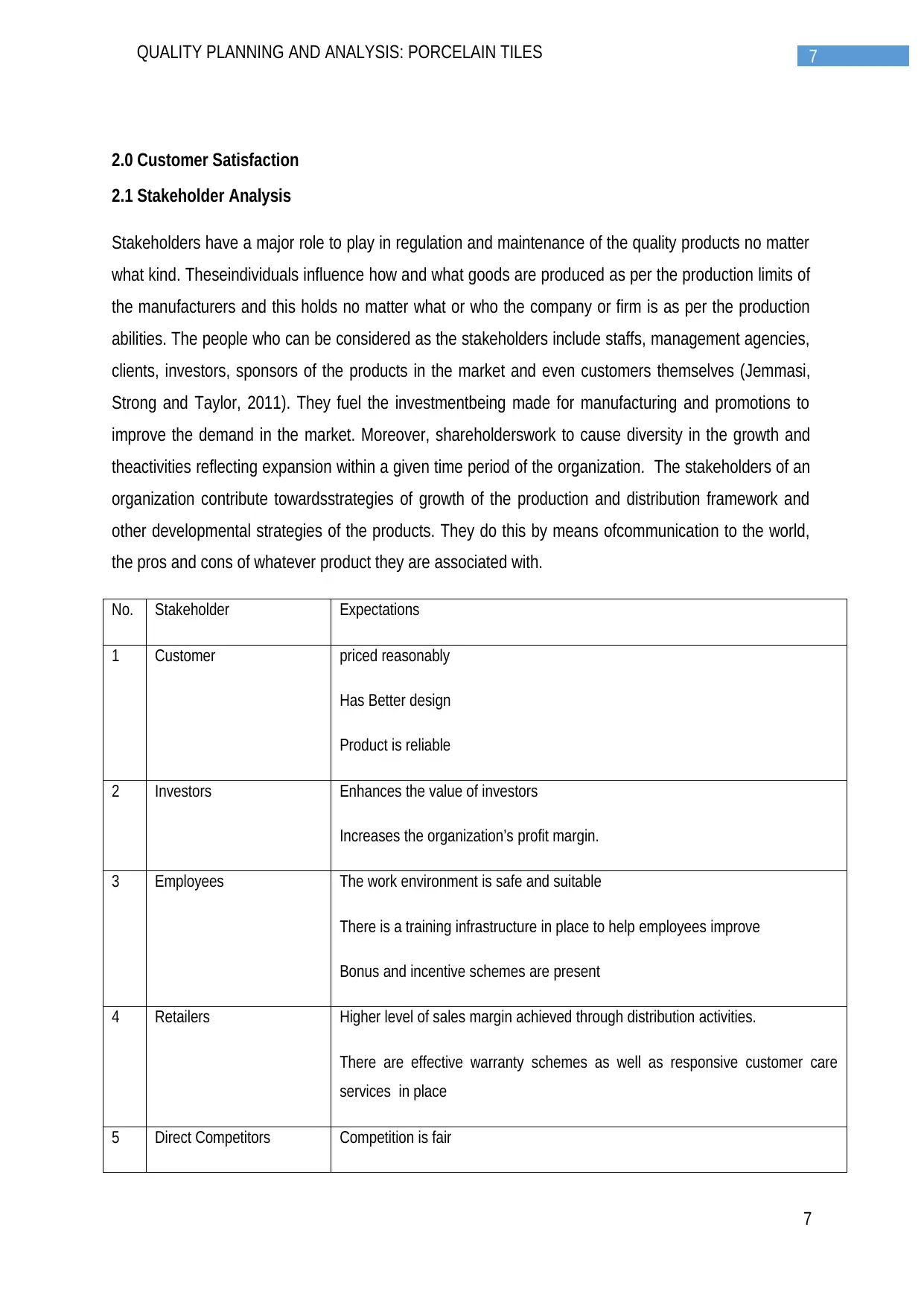
2.0 Customer Satisfaction
2.1 Stakeholder Analysis
Stakeholders have a major role to play in regulation and maintenance of the quality products no matter
what kind. Theseindividuals influence how and what goods are produced as per the production limits of
the manufacturers and this holds no matter what or who the company or firm is as per the production
abilities. The people who can be considered as the stakeholders include staffs, management agencies,
clients, investors, sponsors of the products in the market and even customers themselves (Jemmasi,
Strong and Taylor, 2011). They fuel the investmentbeing made for manufacturing and promotions to
improve the demand in the market. Moreover, shareholderswork to cause diversity in the growth and
theactivities reflecting expansion within a given time period of the organization. The stakeholders of an
organization contribute towardsstrategies of growth of the production and distribution framework and
other developmental strategies of the products. They do this by means ofcommunication to the world,
the pros and cons of whatever product they are associated with.
No. Stakeholder Expectations
1 Customer priced reasonably
Has Better design
Product is reliable
2 Investors Enhances the value of investors
Increases the organization’s profit margin.
3 Employees The work environment is safe and suitable
There is a training infrastructure in place to help employees improve
Bonus and incentive schemes are present
4 Retailers Higher level of sales margin achieved through distribution activities.
There are effective warranty schemes as well as responsive customer care
services in place
5 Direct Competitors Competition is fair
7
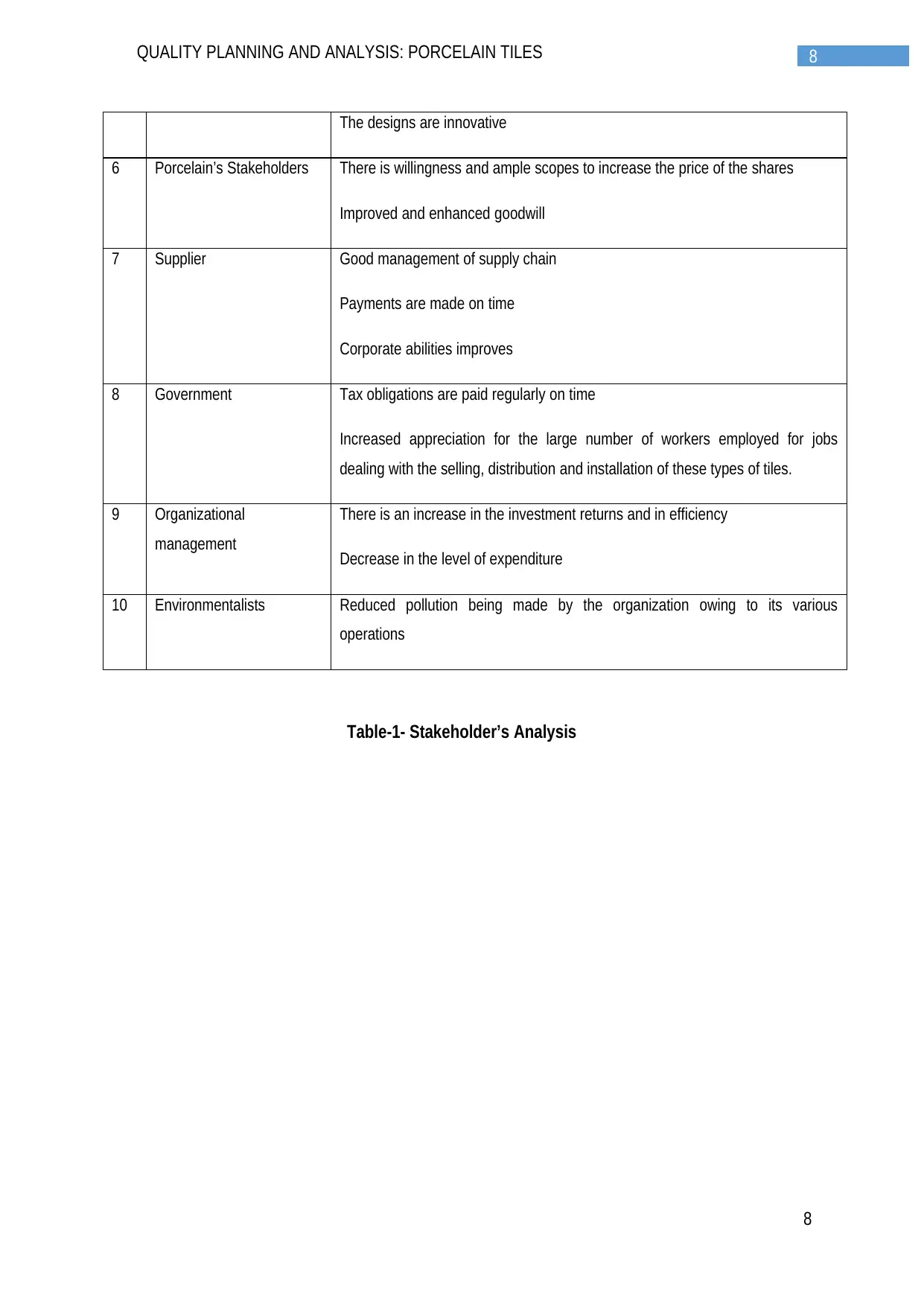
The designs are innovative
6 Porcelain’s Stakeholders There is willingness and ample scopes to increase the price of the shares
Improved and enhanced goodwill
7 Supplier Good management of supply chain
Payments are made on time
Corporate abilities improves
8 Government Tax obligations are paid regularly on time
Increased appreciation for the large number of workers employed for jobs
dealing with the selling, distribution and installation of these types of tiles.
9 Organizational
management
There is an increase in the investment returns and in efficiency
Decrease in the level of expenditure
10 Environmentalists Reduced pollution being made by the organization owing to its various
operations
Table-1- Stakeholder’s Analysis
8
⊘ This is a preview!⊘
Do you want full access?
Subscribe today to unlock all pages.

Trusted by 1+ million students worldwide
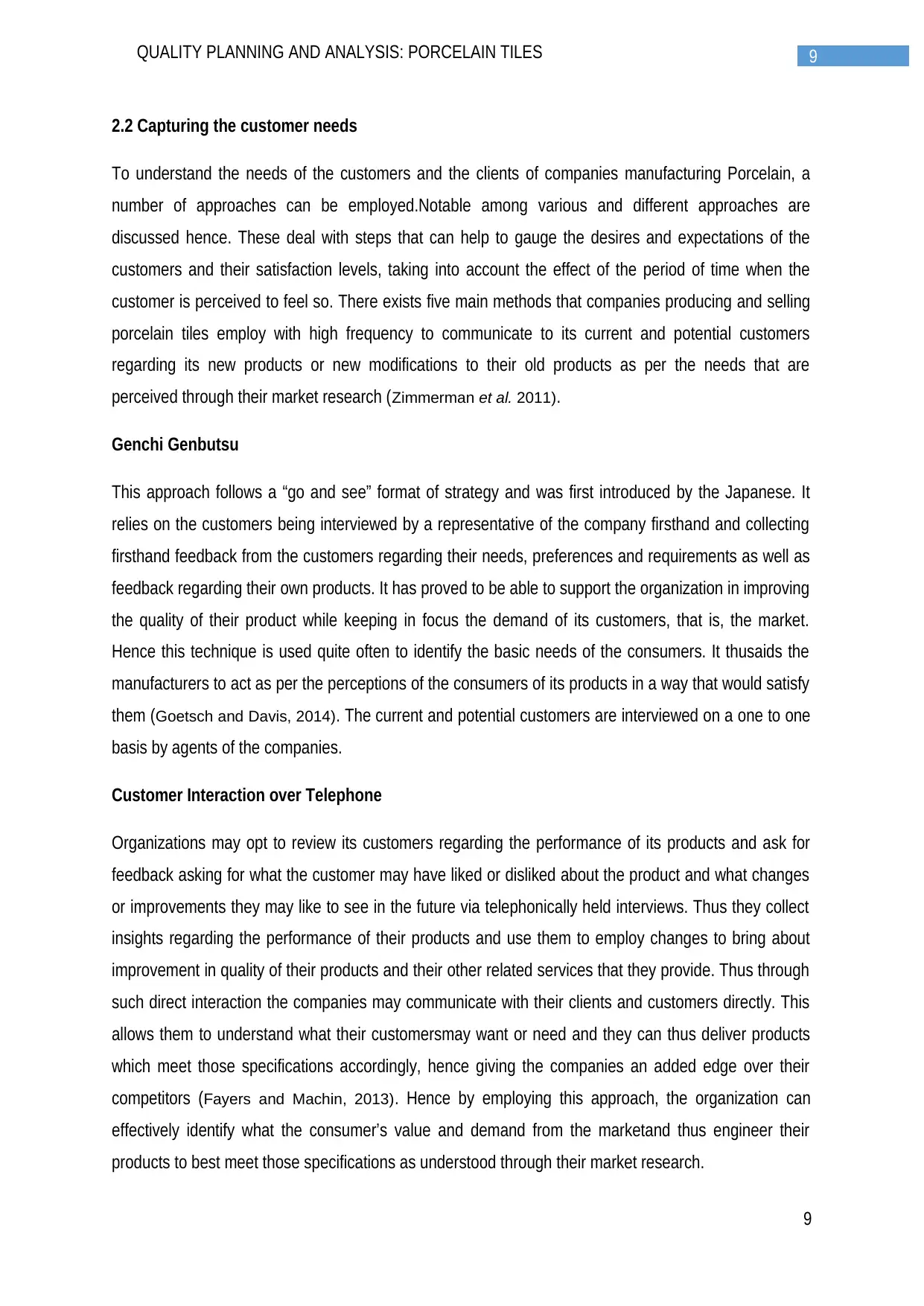
2.2 Capturing the customer needs
To understand the needs of the customers and the clients of companies manufacturing Porcelain, a
number of approaches can be employed.Notable among various and different approaches are
discussed hence. These deal with steps that can help to gauge the desires and expectations of the
customers and their satisfaction levels, taking into account the effect of the period of time when the
customer is perceived to feel so. There exists five main methods that companies producing and selling
porcelain tiles employ with high frequency to communicate to its current and potential customers
regarding its new products or new modifications to their old products as per the needs that are
perceived through their market research (Zimmerman et al. 2011).
Genchi Genbutsu
This approach follows a “go and see” format of strategy and was first introduced by the Japanese. It
relies on the customers being interviewed by a representative of the company firsthand and collecting
firsthand feedback from the customers regarding their needs, preferences and requirements as well as
feedback regarding their own products. It has proved to be able to support the organization in improving
the quality of their product while keeping in focus the demand of its customers, that is, the market.
Hence this technique is used quite often to identify the basic needs of the consumers. It thusaids the
manufacturers to act as per the perceptions of the consumers of its products in a way that would satisfy
them (Goetsch and Davis, 2014). The current and potential customers are interviewed on a one to one
basis by agents of the companies.
Customer Interaction over Telephone
Organizations may opt to review its customers regarding the performance of its products and ask for
feedback asking for what the customer may have liked or disliked about the product and what changes
or improvements they may like to see in the future via telephonically held interviews. Thus they collect
insights regarding the performance of their products and use them to employ changes to bring about
improvement in quality of their products and their other related services that they provide. Thus through
such direct interaction the companies may communicate with their clients and customers directly. This
allows them to understand what their customersmay want or need and they can thus deliver products
which meet those specifications accordingly, hence giving the companies an added edge over their
competitors (Fayers and Machin, 2013). Hence by employing this approach, the organization can
effectively identify what the consumer’s value and demand from the marketand thus engineer their
products to best meet those specifications as understood through their market research.
9
Paraphrase This Document
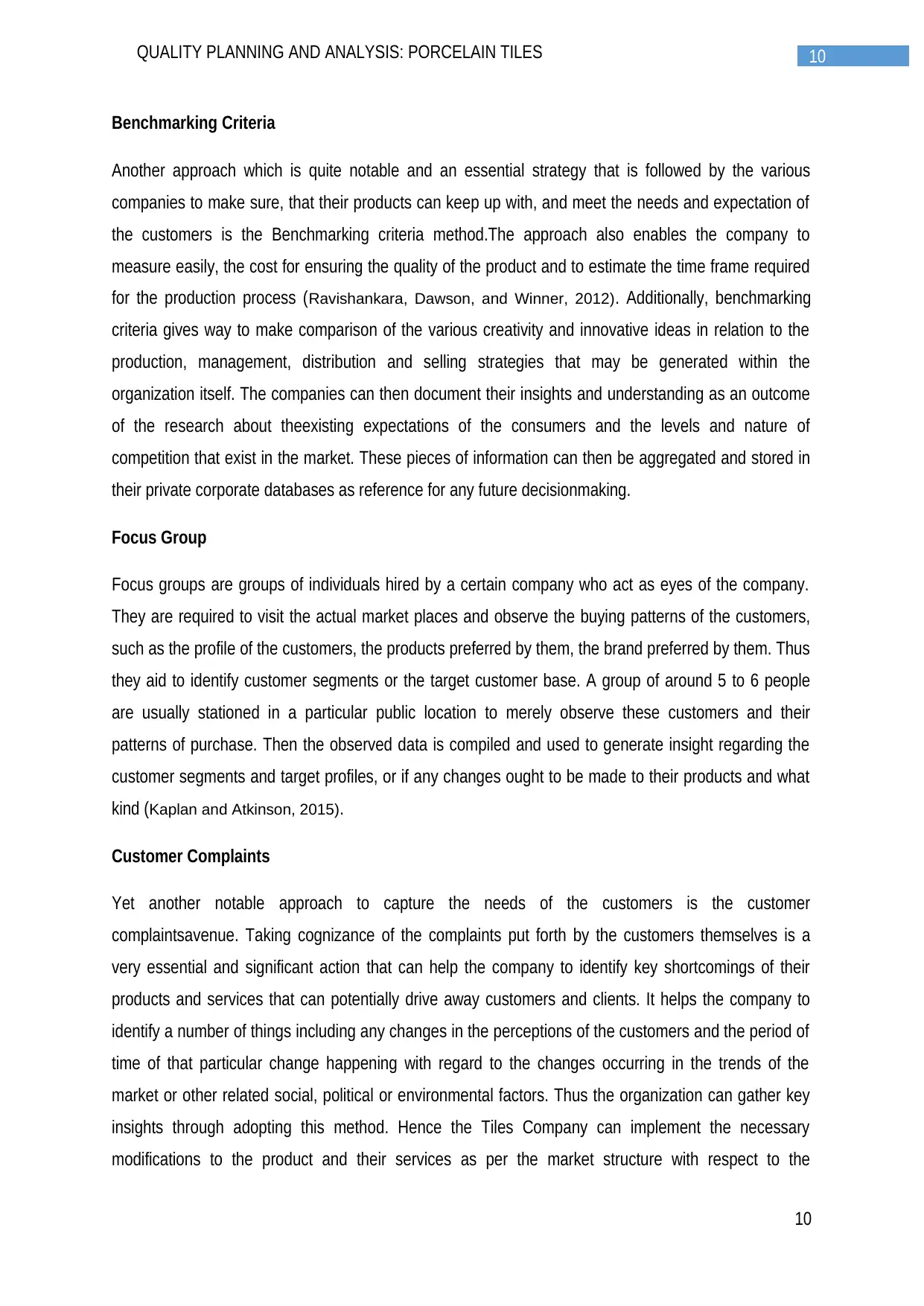
Benchmarking Criteria
Another approach which is quite notable and an essential strategy that is followed by the various
companies to make sure, that their products can keep up with, and meet the needs and expectation of
the customers is the Benchmarking criteria method.The approach also enables the company to
measure easily, the cost for ensuring the quality of the product and to estimate the time frame required
for the production process (Ravishankara, Dawson, and Winner, 2012). Additionally, benchmarking
criteria gives way to make comparison of the various creativity and innovative ideas in relation to the
production, management, distribution and selling strategies that may be generated within the
organization itself. The companies can then document their insights and understanding as an outcome
of the research about theexisting expectations of the consumers and the levels and nature of
competition that exist in the market. These pieces of information can then be aggregated and stored in
their private corporate databases as reference for any future decisionmaking.
Focus Group
Focus groups are groups of individuals hired by a certain company who act as eyes of the company.
They are required to visit the actual market places and observe the buying patterns of the customers,
such as the profile of the customers, the products preferred by them, the brand preferred by them. Thus
they aid to identify customer segments or the target customer base. A group of around 5 to 6 people
are usually stationed in a particular public location to merely observe these customers and their
patterns of purchase. Then the observed data is compiled and used to generate insight regarding the
customer segments and target profiles, or if any changes ought to be made to their products and what
kind (Kaplan and Atkinson, 2015).
Customer Complaints
Yet another notable approach to capture the needs of the customers is the customer
complaintsavenue. Taking cognizance of the complaints put forth by the customers themselves is a
very essential and significant action that can help the company to identify key shortcomings of their
products and services that can potentially drive away customers and clients. It helps the company to
identify a number of things including any changes in the perceptions of the customers and the period of
time of that particular change happening with regard to the changes occurring in the trends of the
market or other related social, political or environmental factors. Thus the organization can gather key
insights through adopting this method. Hence the Tiles Company can implement the necessary
modifications to the product and their services as per the market structure with respect to the
10
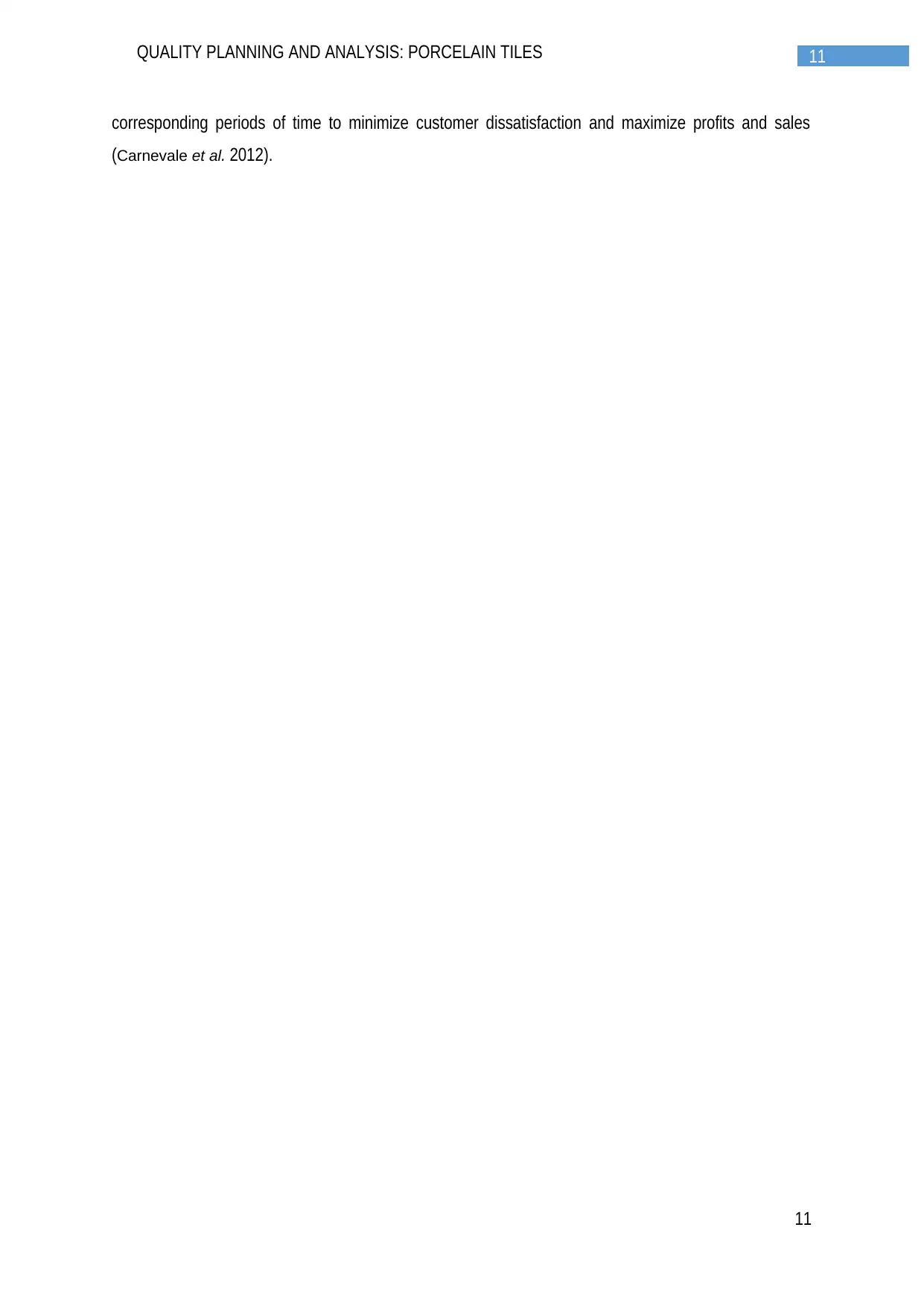
corresponding periods of time to minimize customer dissatisfaction and maximize profits and sales
(Carnevale et al. 2012).
11
⊘ This is a preview!⊘
Do you want full access?
Subscribe today to unlock all pages.

Trusted by 1+ million students worldwide
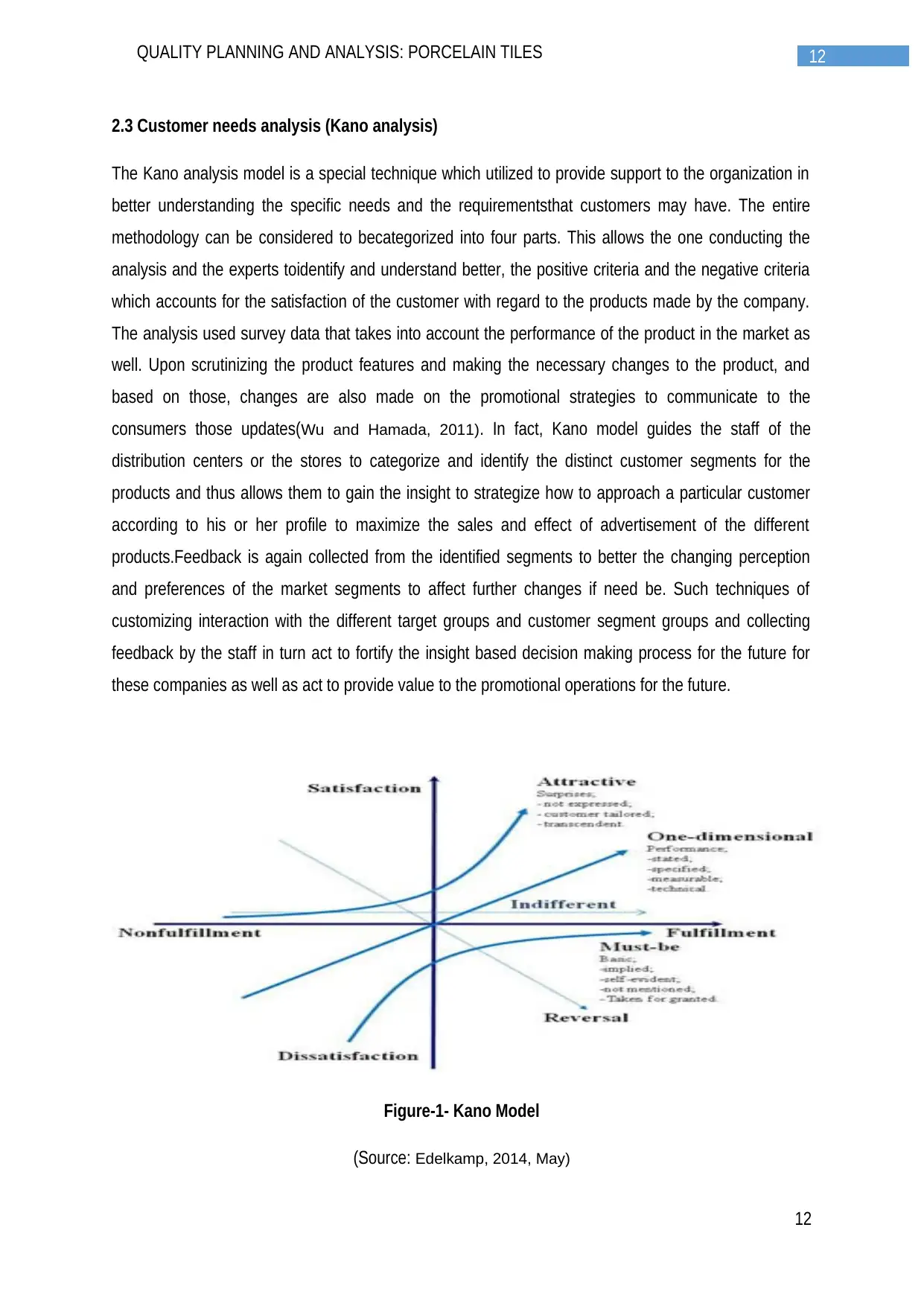
2.3 Customer needs analysis (Kano analysis)
The Kano analysis model is a special technique which utilized to provide support to the organization in
better understanding the specific needs and the requirementsthat customers may have. The entire
methodology can be considered to becategorized into four parts. This allows the one conducting the
analysis and the experts toidentify and understand better, the positive criteria and the negative criteria
which accounts for the satisfaction of the customer with regard to the products made by the company.
The analysis used survey data that takes into account the performance of the product in the market as
well. Upon scrutinizing the product features and making the necessary changes to the product, and
based on those, changes are also made on the promotional strategies to communicate to the
consumers those updates(Wu and Hamada, 2011). In fact, Kano model guides the staff of the
distribution centers or the stores to categorize and identify the distinct customer segments for the
products and thus allows them to gain the insight to strategize how to approach a particular customer
according to his or her profile to maximize the sales and effect of advertisement of the different
products.Feedback is again collected from the identified segments to better the changing perception
and preferences of the market segments to affect further changes if need be. Such techniques of
customizing interaction with the different target groups and customer segment groups and collecting
feedback by the staff in turn act to fortify the insight based decision making process for the future for
these companies as well as act to provide value to the promotional operations for the future.
Figure-1- Kano Model
(Source: Edelkamp, 2014, May)
12
Paraphrase This Document
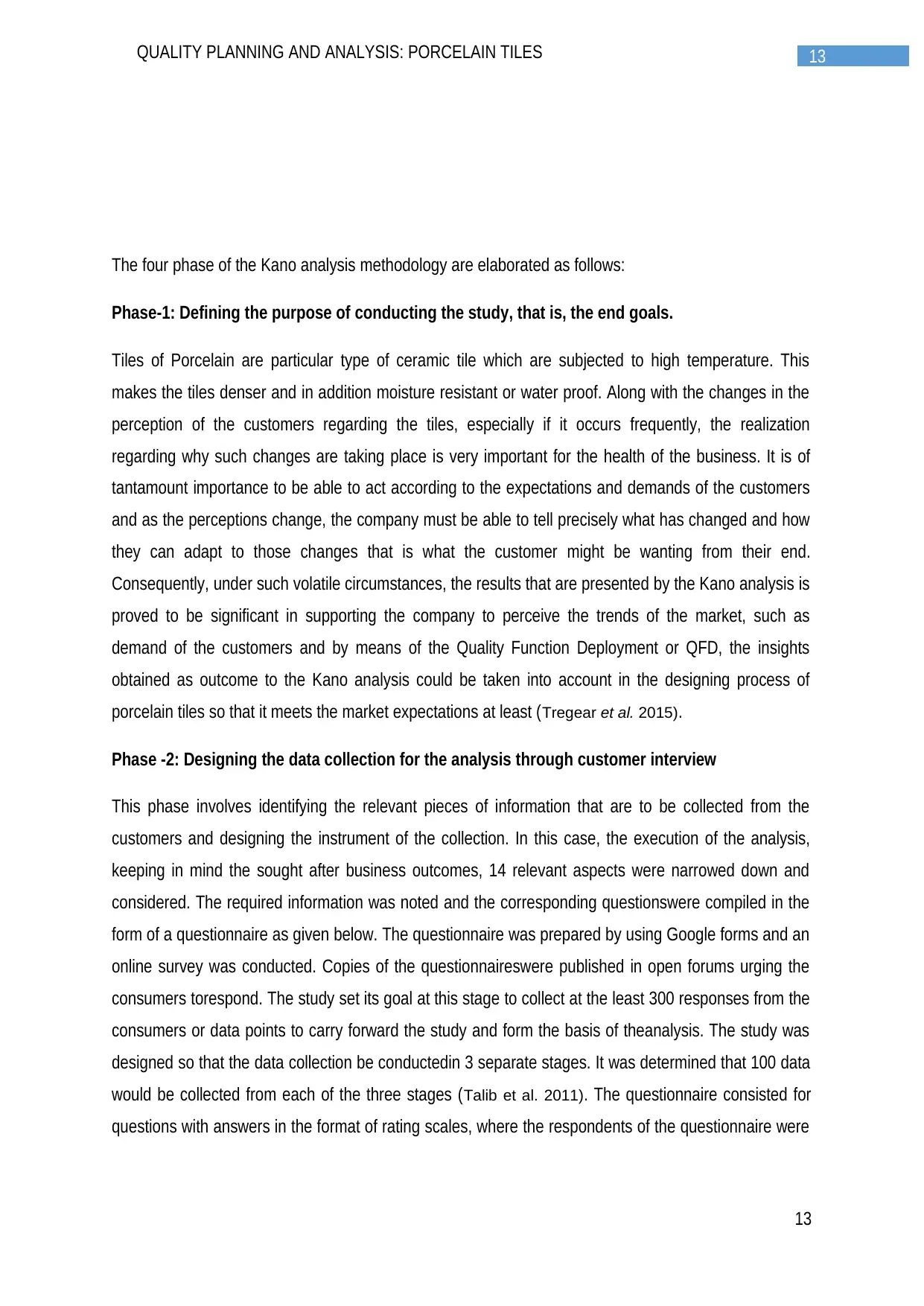
The four phase of the Kano analysis methodology are elaborated as follows:
Phase-1: Defining the purpose of conducting the study, that is, the end goals.
Tiles of Porcelain are particular type of ceramic tile which are subjected to high temperature. This
makes the tiles denser and in addition moisture resistant or water proof. Along with the changes in the
perception of the customers regarding the tiles, especially if it occurs frequently, the realization
regarding why such changes are taking place is very important for the health of the business. It is of
tantamount importance to be able to act according to the expectations and demands of the customers
and as the perceptions change, the company must be able to tell precisely what has changed and how
they can adapt to those changes that is what the customer might be wanting from their end.
Consequently, under such volatile circumstances, the results that are presented by the Kano analysis is
proved to be significant in supporting the company to perceive the trends of the market, such as
demand of the customers and by means of the Quality Function Deployment or QFD, the insights
obtained as outcome to the Kano analysis could be taken into account in the designing process of
porcelain tiles so that it meets the market expectations at least (Tregear et al. 2015).
Phase -2: Designing the data collection for the analysis through customer interview
This phase involves identifying the relevant pieces of information that are to be collected from the
customers and designing the instrument of the collection. In this case, the execution of the analysis,
keeping in mind the sought after business outcomes, 14 relevant aspects were narrowed down and
considered. The required information was noted and the corresponding questionswere compiled in the
form of a questionnaire as given below. The questionnaire was prepared by using Google forms and an
online survey was conducted. Copies of the questionnaireswere published in open forums urging the
consumers torespond. The study set its goal at this stage to collect at the least 300 responses from the
consumers or data points to carry forward the study and form the basis of theanalysis. The study was
designed so that the data collection be conductedin 3 separate stages. It was determined that 100 data
would be collected from each of the three stages (Talib et al. 2011). The questionnaire consisted for
questions with answers in the format of rating scales, where the respondents of the questionnaire were
13
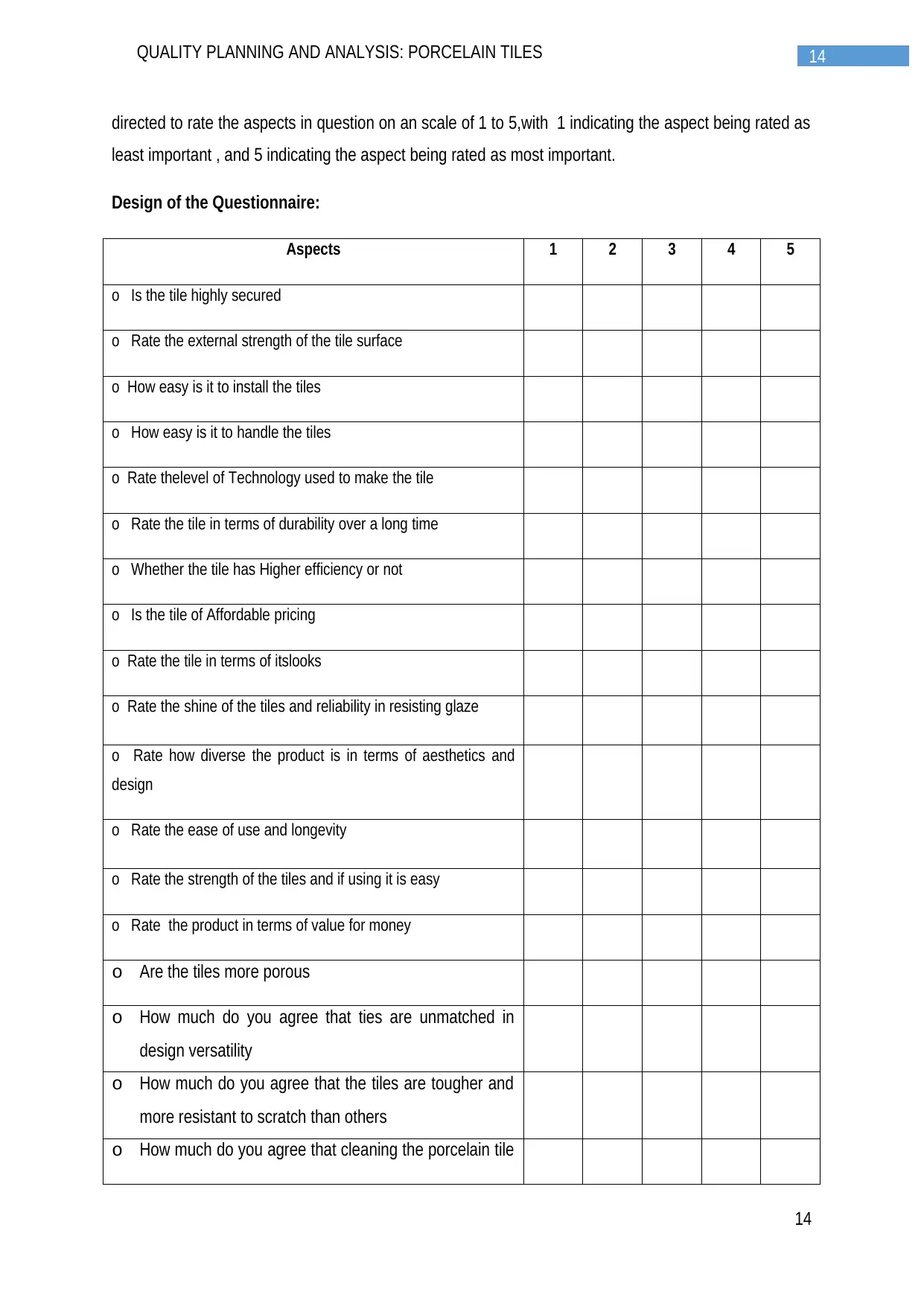
directed to rate the aspects in question on an scale of 1 to 5,with 1 indicating the aspect being rated as
least important , and 5 indicating the aspect being rated as most important.
Design of the Questionnaire:
Aspects 1 2 3 4 5
o Is the tile highly secured
o Rate the external strength of the tile surface
o How easy is it to install the tiles
o How easy is it to handle the tiles
o Rate thelevel of Technology used to make the tile
o Rate the tile in terms of durability over a long time
o Whether the tile has Higher efficiency or not
o Is the tile of Affordable pricing
o Rate the tile in terms of itslooks
o Rate the shine of the tiles and reliability in resisting glaze
o Rate how diverse the product is in terms of aesthetics and
design
o Rate the ease of use and longevity
o Rate the strength of the tiles and if using it is easy
o Rate the product in terms of value for money
o Are the tiles more porous
o How much do you agree that ties are unmatched in
design versatility
o How much do you agree that the tiles are tougher and
more resistant to scratch than others
o How much do you agree that cleaning the porcelain tile
14
⊘ This is a preview!⊘
Do you want full access?
Subscribe today to unlock all pages.

Trusted by 1+ million students worldwide
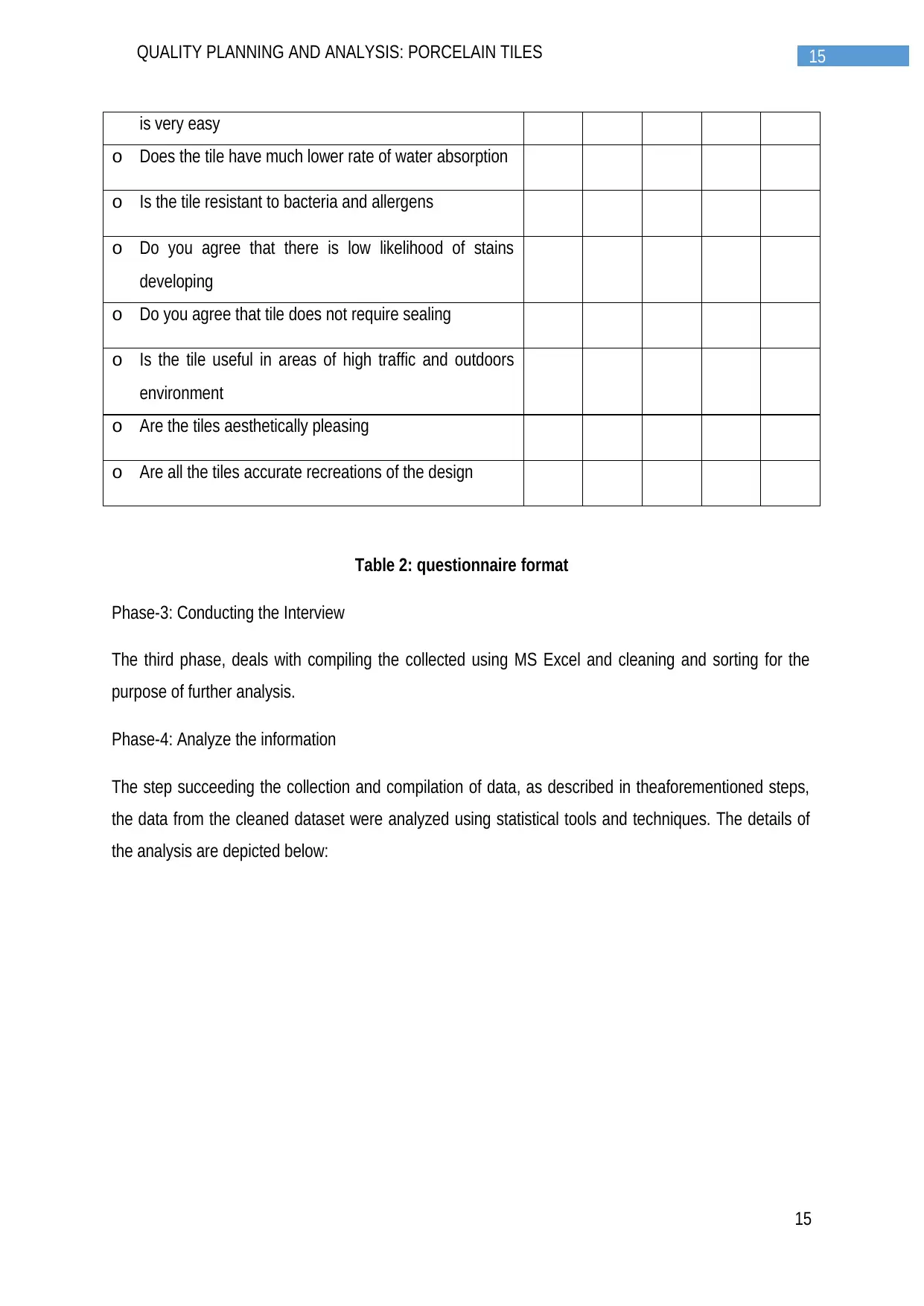
is very easy
o Does the tile have much lower rate of water absorption
o Is the tile resistant to bacteria and allergens
o Do you agree that there is low likelihood of stains
developing
o Do you agree that tile does not require sealing
o Is the tile useful in areas of high traffic and outdoors
environment
o Are the tiles aesthetically pleasing
o Are all the tiles accurate recreations of the design
Table 2: questionnaire format
Phase-3: Conducting the Interview
The third phase, deals with compiling the collected using MS Excel and cleaning and sorting for the
purpose of further analysis.
Phase-4: Analyze the information
The step succeeding the collection and compilation of data, as described in theaforementioned steps,
the data from the cleaned dataset were analyzed using statistical tools and techniques. The details of
the analysis are depicted below:
15
Paraphrase This Document
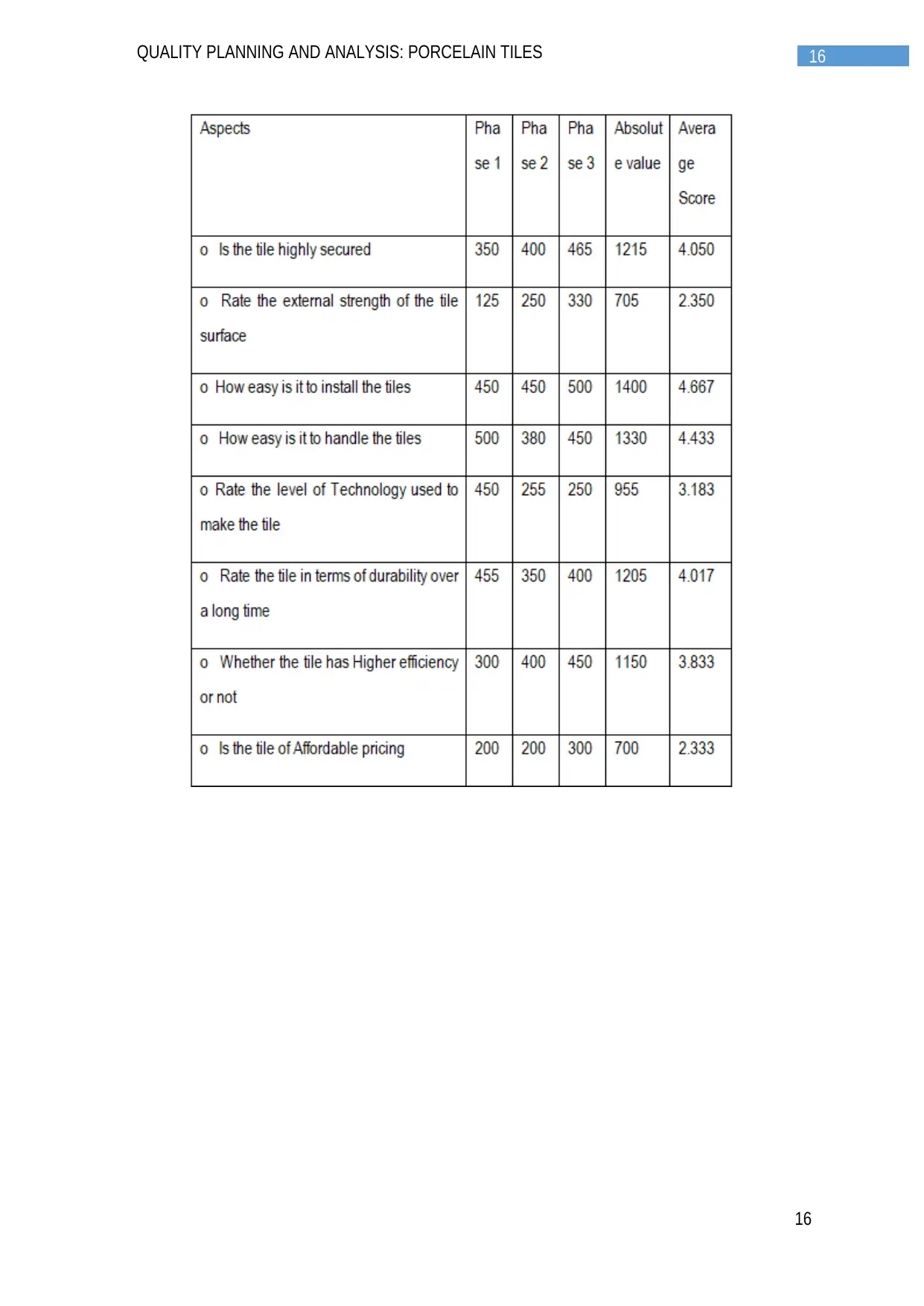
16
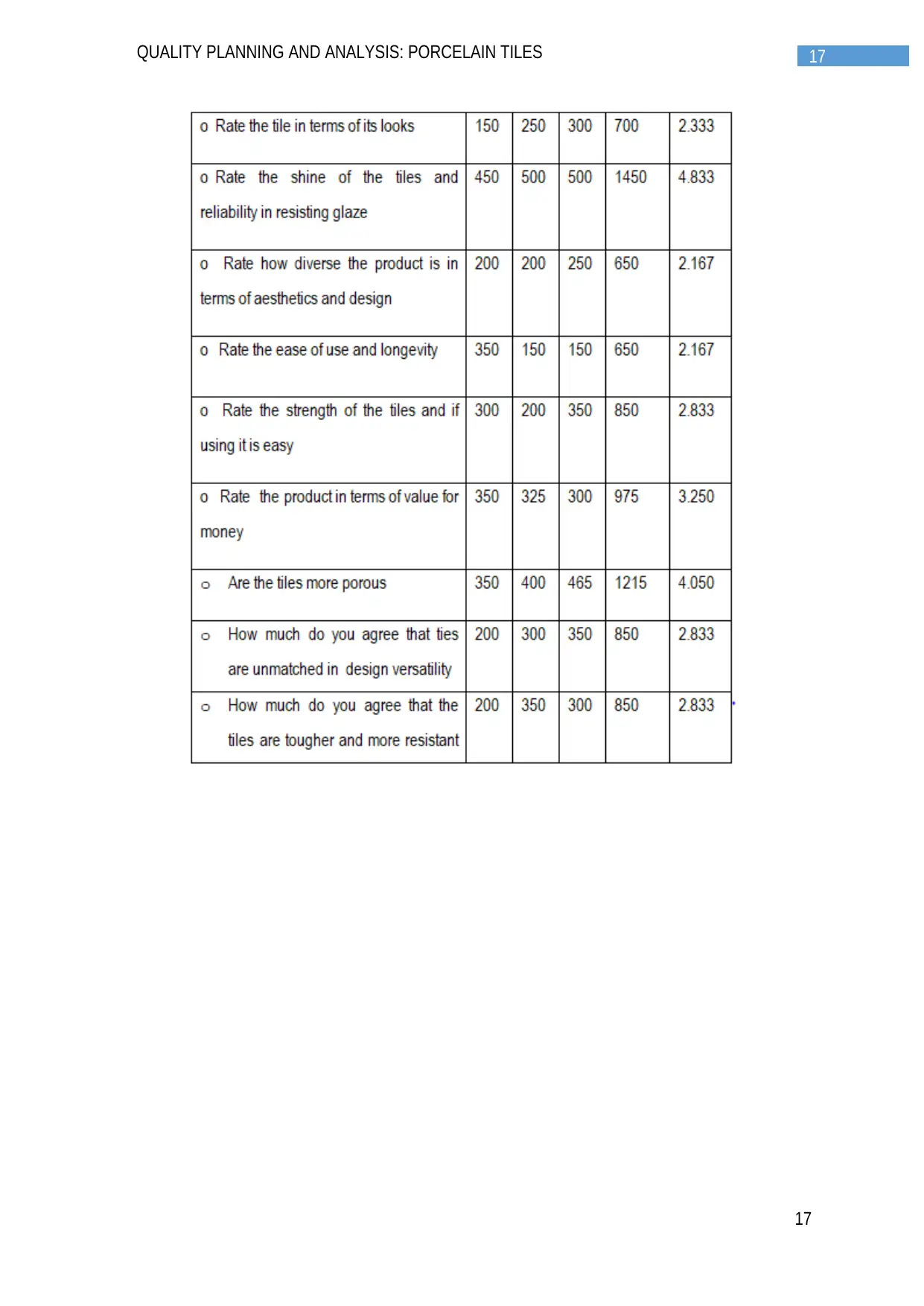
17
⊘ This is a preview!⊘
Do you want full access?
Subscribe today to unlock all pages.

Trusted by 1+ million students worldwide
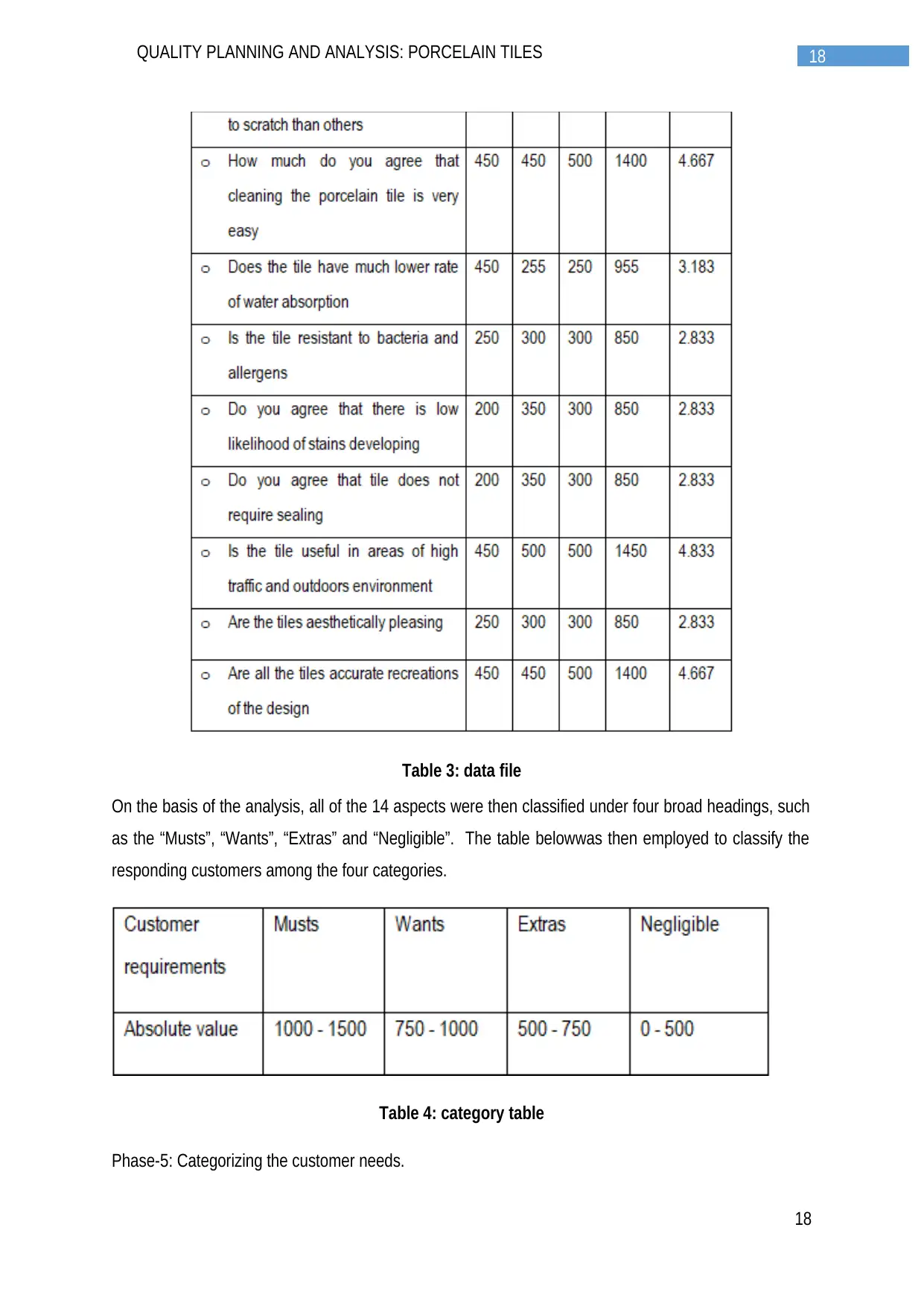
Table 3: data file
On the basis of the analysis, all of the 14 aspects were then classified under four broad headings, such
as the “Musts”, “Wants”, “Extras” and “Negligible”. The table belowwas then employed to classify the
responding customers among the four categories.
Table 4: category table
Phase-5: Categorizing the customer needs.
18
Paraphrase This Document
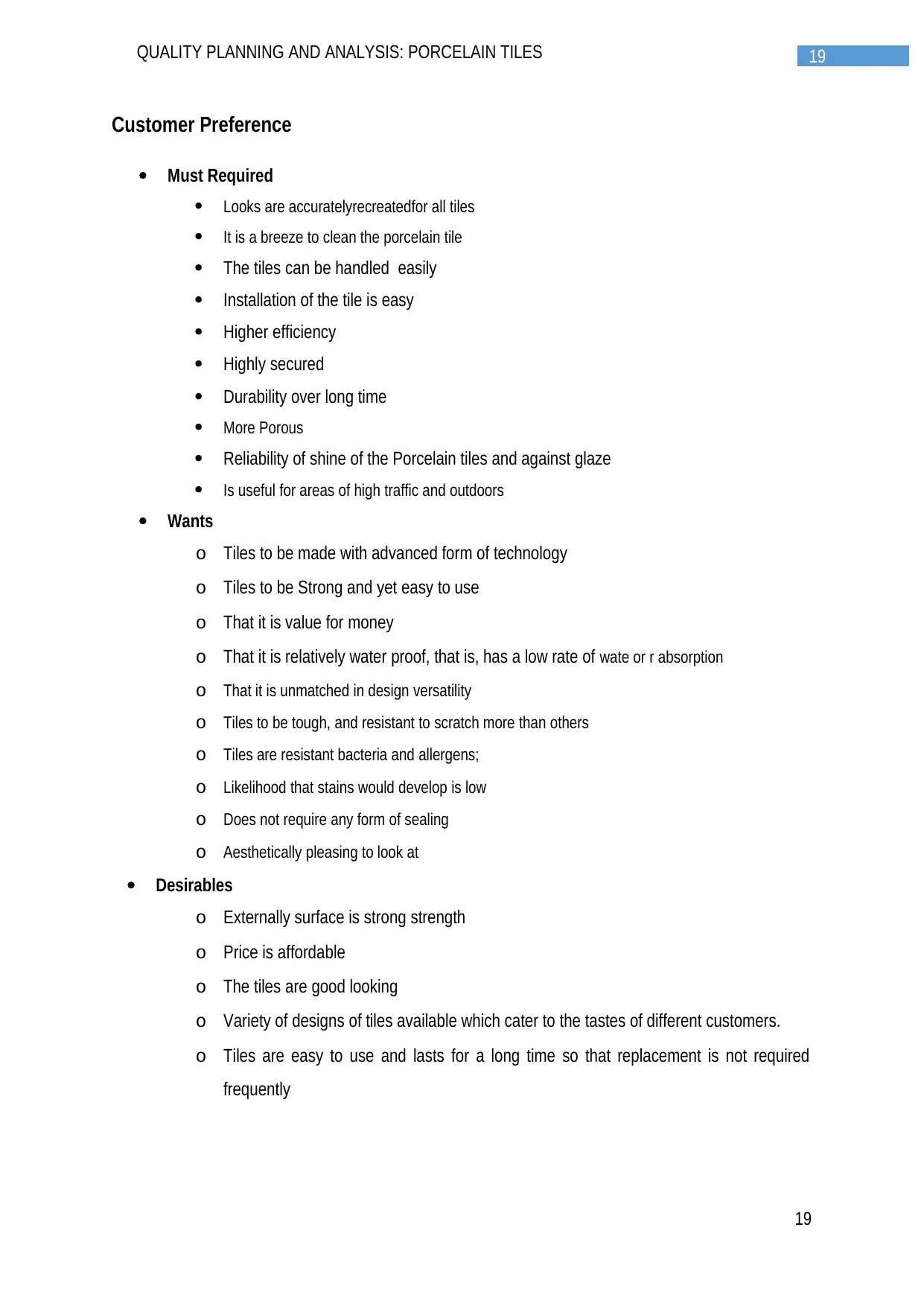
Customer Preference
Must Required
Looks are accuratelyrecreatedfor all tiles
It is a breeze to clean the porcelain tile
The tiles can be handled easily
Installation of the tile is easy
Higher efficiency
Highly secured
Durability over long time
More Porous
Reliability of shine of the Porcelain tiles and against glaze
Is useful for areas of high traffic and outdoors
Wants
o Tiles to be made with advanced form of technology
o Tiles to be Strong and yet easy to use
o That it is value for money
o That it is relatively water proof, that is, has a low rate of wate or r absorption
o That it is unmatched in design versatility
o Tiles to be tough, and resistant to scratch more than others
o Tiles are resistant bacteria and allergens;
o Likelihood that stains would develop is low
o Does not require any form of sealing
o Aesthetically pleasing to look at
Desirables
o Externally surface is strong strength
o Price is affordable
o The tiles are good looking
o Variety of designs of tiles available which cater to the tastes of different customers.
o Tiles are easy to use and lasts for a long time so that replacement is not required
frequently
19
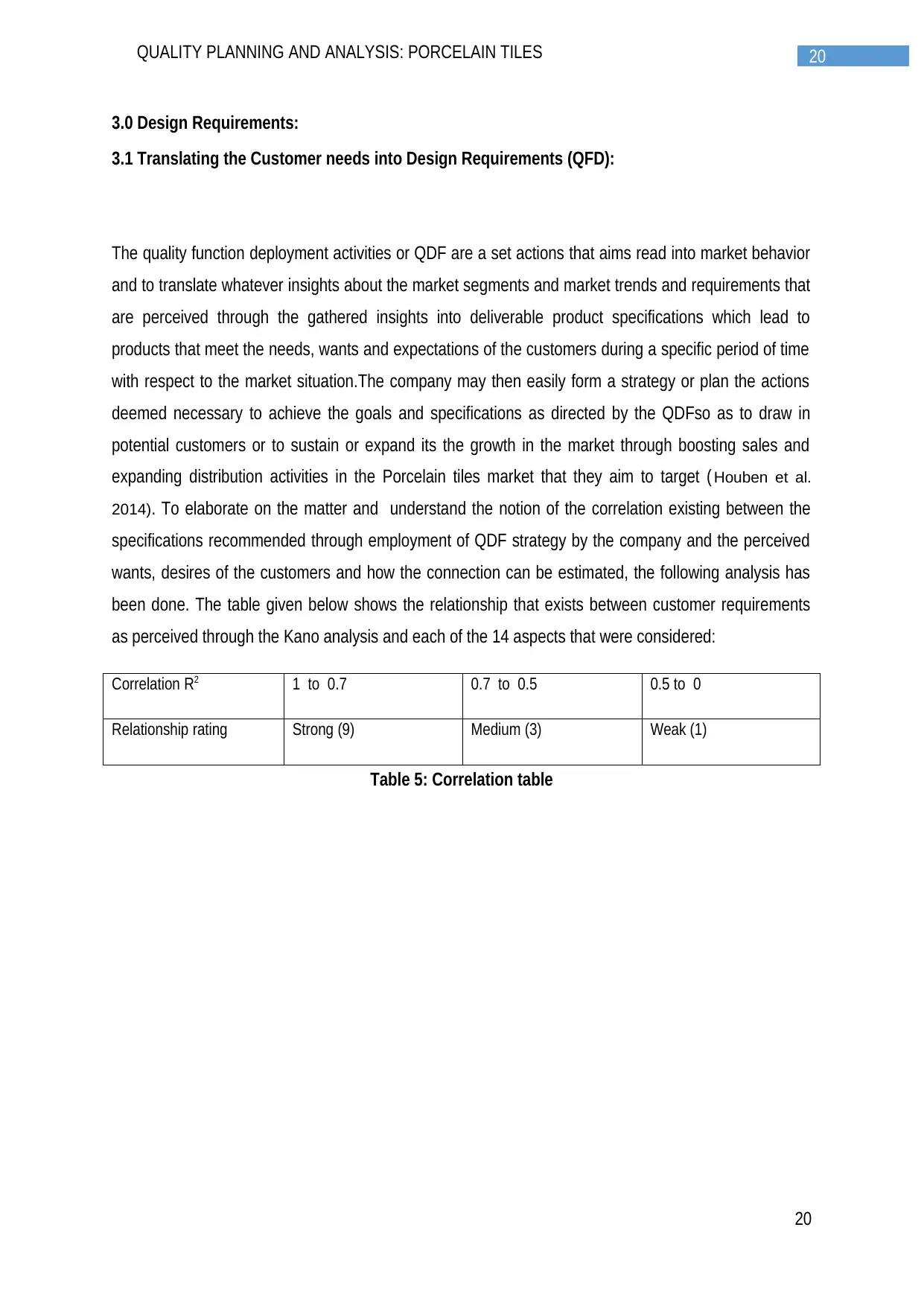
3.0 Design Requirements:
3.1 Translating the Customer needs into Design Requirements (QFD):
The quality function deployment activities or QDF are a set actions that aims read into market behavior
and to translate whatever insights about the market segments and market trends and requirements that
are perceived through the gathered insights into deliverable product specifications which lead to
products that meet the needs, wants and expectations of the customers during a specific period of time
with respect to the market situation.The company may then easily form a strategy or plan the actions
deemed necessary to achieve the goals and specifications as directed by the QDFso as to draw in
potential customers or to sustain or expand its the growth in the market through boosting sales and
expanding distribution activities in the Porcelain tiles market that they aim to target ( Houben et al.
2014). To elaborate on the matter and understand the notion of the correlation existing between the
specifications recommended through employment of QDF strategy by the company and the perceived
wants, desires of the customers and how the connection can be estimated, the following analysis has
been done. The table given below shows the relationship that exists between customer requirements
as perceived through the Kano analysis and each of the 14 aspects that were considered:
Correlation R2 1 to 0.7 0.7 to 0.5 0.5 to 0
Relationship rating Strong (9) Medium (3) Weak (1)
Table 5: Correlation table
20
⊘ This is a preview!⊘
Do you want full access?
Subscribe today to unlock all pages.

Trusted by 1+ million students worldwide
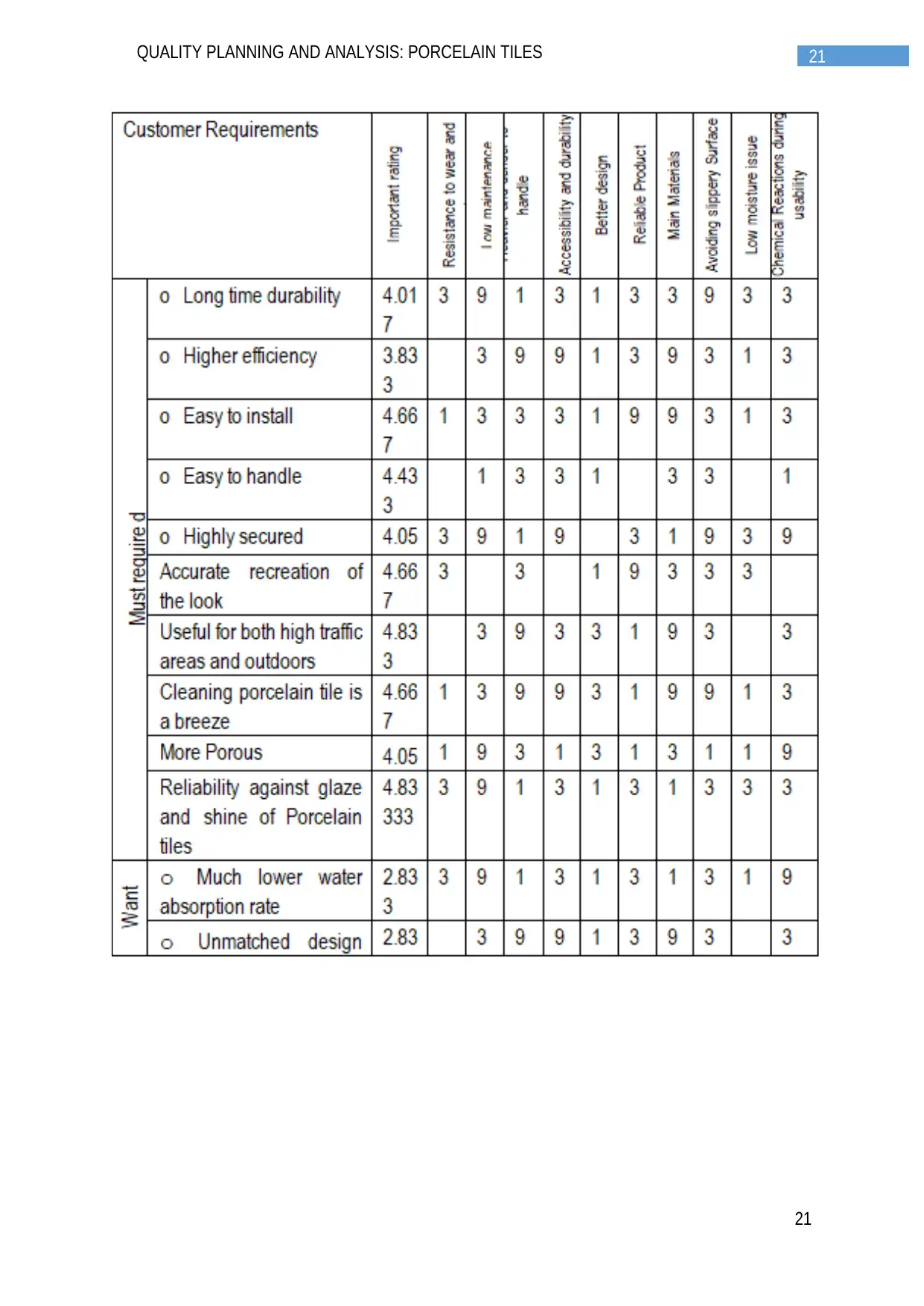
21
Paraphrase This Document

22
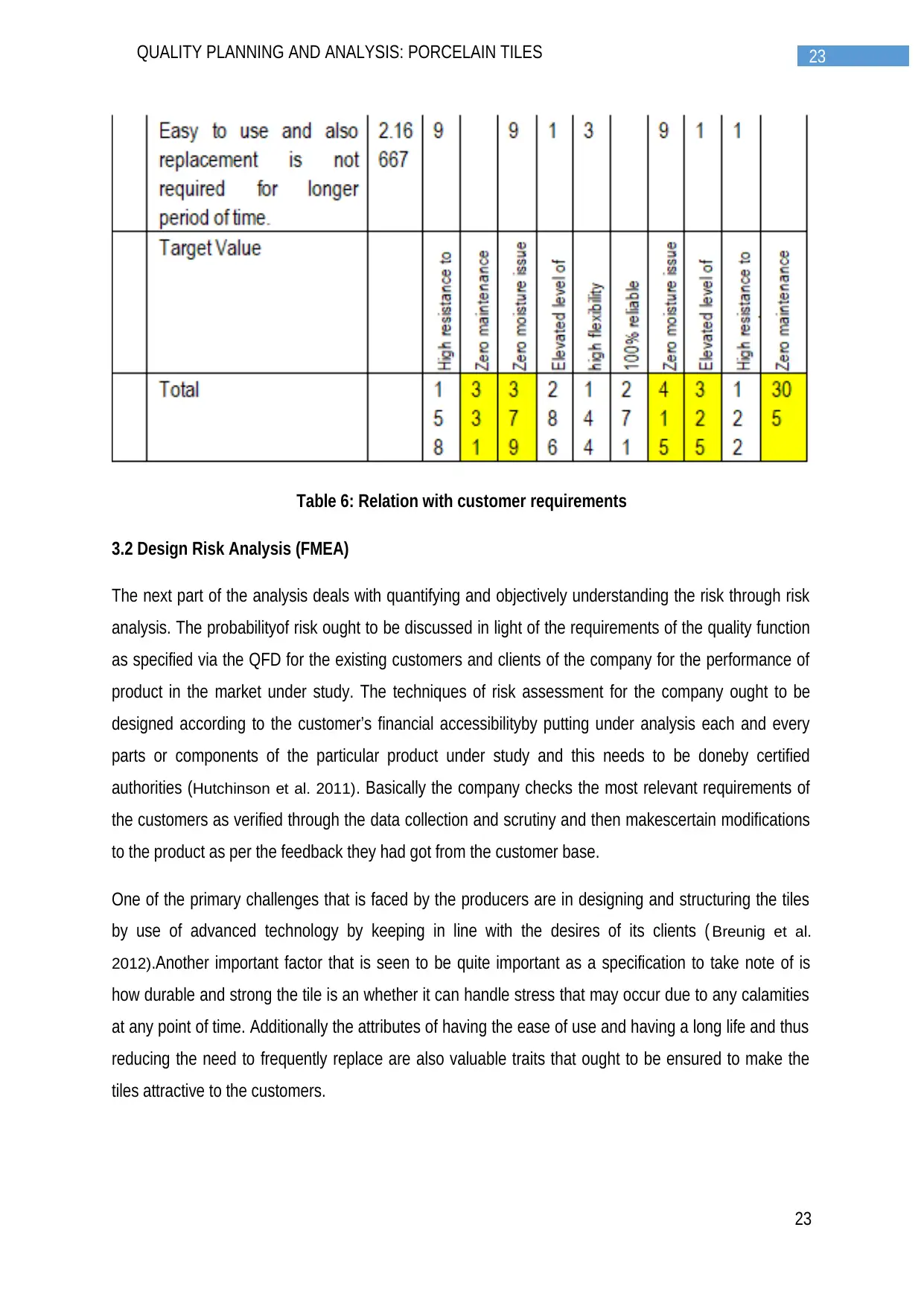
Table 6: Relation with customer requirements
3.2 Design Risk Analysis (FMEA)
The next part of the analysis deals with quantifying and objectively understanding the risk through risk
analysis. The probabilityof risk ought to be discussed in light of the requirements of the quality function
as specified via the QFD for the existing customers and clients of the company for the performance of
product in the market under study. The techniques of risk assessment for the company ought to be
designed according to the customer’s financial accessibilityby putting under analysis each and every
parts or components of the particular product under study and this needs to be doneby certified
authorities (Hutchinson et al. 2011). Basically the company checks the most relevant requirements of
the customers as verified through the data collection and scrutiny and then makescertain modifications
to the product as per the feedback they had got from the customer base.
One of the primary challenges that is faced by the producers are in designing and structuring the tiles
by use of advanced technology by keeping in line with the desires of its clients ( Breunig et al.
2012).Another important factor that is seen to be quite important as a specification to take note of is
how durable and strong the tile is an whether it can handle stress that may occur due to any calamities
at any point of time. Additionally the attributes of having the ease of use and having a long life and thus
reducing the need to frequently replace are also valuable traits that ought to be ensured to make the
tiles attractive to the customers.
23
⊘ This is a preview!⊘
Do you want full access?
Subscribe today to unlock all pages.

Trusted by 1+ million students worldwide
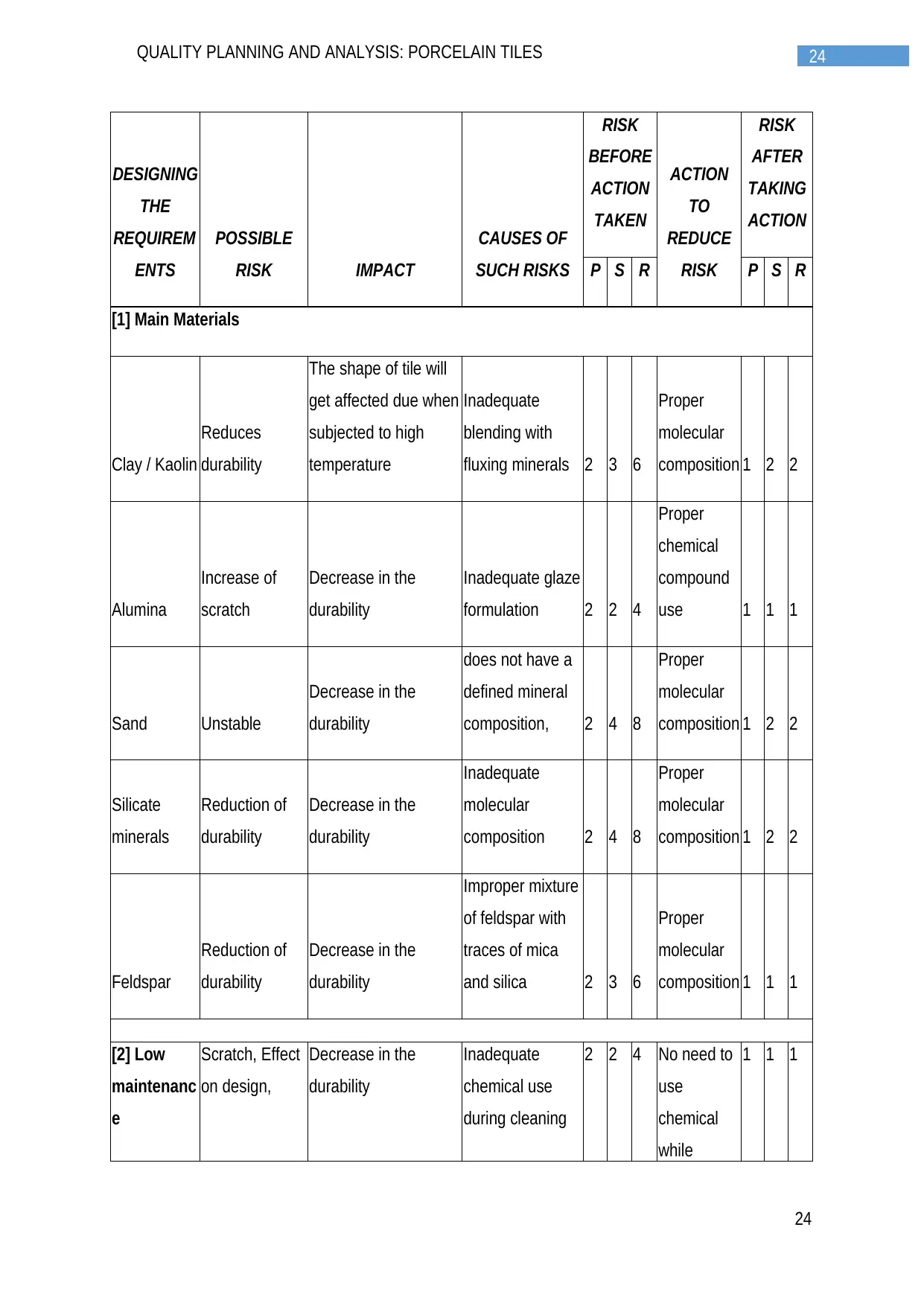
DESIGNING
THE
REQUIREM
ENTS
POSSIBLE
RISK IMPACT
CAUSES OF
SUCH RISKS
RISK
BEFORE
ACTION
TAKEN
ACTION
TO
REDUCE
RISK
RISK
AFTER
TAKING
ACTION
P S R P S R
[1] Main Materials
Clay / Kaolin
Reduces
durability
The shape of tile will
get affected due when
subjected to high
temperature
Inadequate
blending with
fluxing minerals 2 3 6
Proper
molecular
composition 1 2 2
Alumina
Increase of
scratch
Decrease in the
durability
Inadequate glaze
formulation 2 2 4
Proper
chemical
compound
use 1 1 1
Sand Unstable
Decrease in the
durability
does not have a
defined mineral
composition, 2 4 8
Proper
molecular
composition 1 2 2
Silicate
minerals
Reduction of
durability
Decrease in the
durability
Inadequate
molecular
composition 2 4 8
Proper
molecular
composition 1 2 2
Feldspar
Reduction of
durability
Decrease in the
durability
Improper mixture
of feldspar with
traces of mica
and silica 2 3 6
Proper
molecular
composition 1 1 1
[2] Low
maintenanc
e
Scratch, Effect
on design,
Decrease in the
durability
Inadequate
chemical use
during cleaning
2 2 4 No need to
use
chemical
while
1 1 1
24
Paraphrase This Document
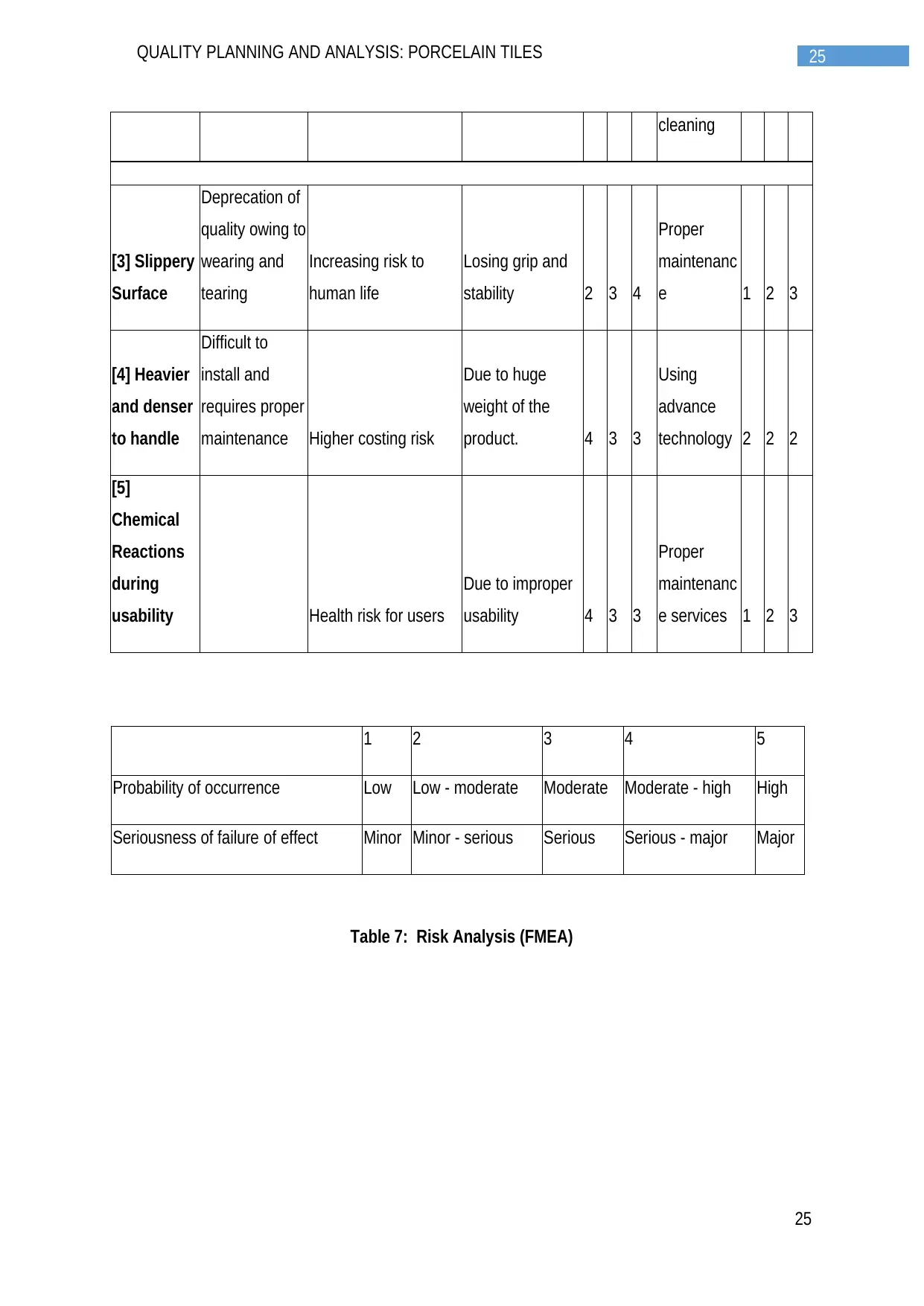
cleaning
[3] Slippery
Surface
Deprecation of
quality owing to
wearing and
tearing
Increasing risk to
human life
Losing grip and
stability 2 3 4
Proper
maintenanc
e 1 2 3
[4] Heavier
and denser
to handle
Difficult to
install and
requires proper
maintenance Higher costing risk
Due to huge
weight of the
product. 4 3 3
Using
advance
technology 2 2 2
[5]
Chemical
Reactions
during
usability Health risk for users
Due to improper
usability 4 3 3
Proper
maintenanc
e services 1 2 3
1 2 3 4 5
Probability of occurrence Low Low - moderate Moderate Moderate - high High
Seriousness of failure of effect Minor Minor - serious Serious Serious - major Major
Table 7: Risk Analysis (FMEA)
25
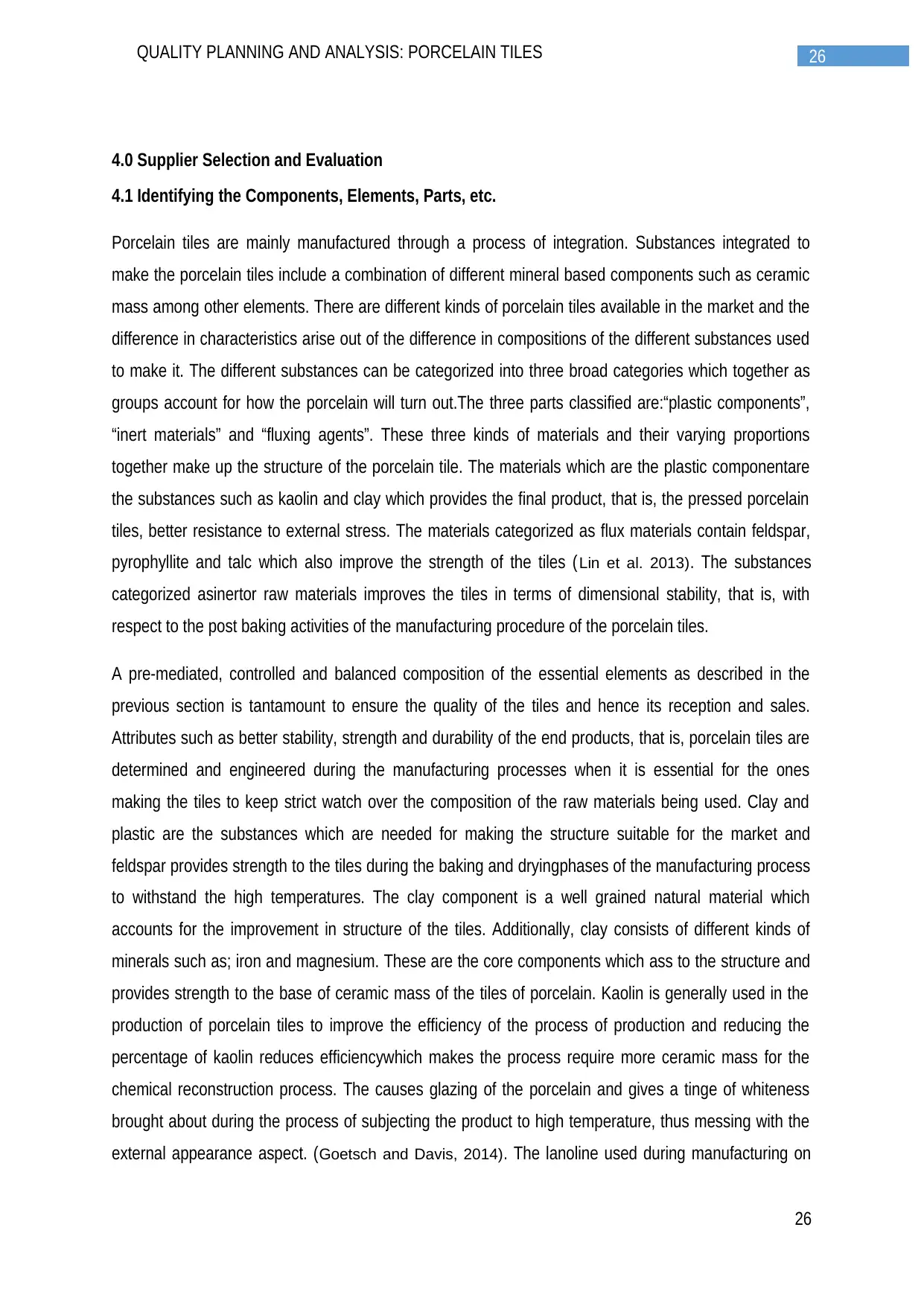
4.0 Supplier Selection and Evaluation
4.1 Identifying the Components, Elements, Parts, etc.
Porcelain tiles are mainly manufactured through a process of integration. Substances integrated to
make the porcelain tiles include a combination of different mineral based components such as ceramic
mass among other elements. There are different kinds of porcelain tiles available in the market and the
difference in characteristics arise out of the difference in compositions of the different substances used
to make it. The different substances can be categorized into three broad categories which together as
groups account for how the porcelain will turn out.The three parts classified are:“plastic components”,
“inert materials” and “fluxing agents”. These three kinds of materials and their varying proportions
together make up the structure of the porcelain tile. The materials which are the plastic componentare
the substances such as kaolin and clay which provides the final product, that is, the pressed porcelain
tiles, better resistance to external stress. The materials categorized as flux materials contain feldspar,
pyrophyllite and talc which also improve the strength of the tiles (Lin et al. 2013). The substances
categorized asinertor raw materials improves the tiles in terms of dimensional stability, that is, with
respect to the post baking activities of the manufacturing procedure of the porcelain tiles.
A pre-mediated, controlled and balanced composition of the essential elements as described in the
previous section is tantamount to ensure the quality of the tiles and hence its reception and sales.
Attributes such as better stability, strength and durability of the end products, that is, porcelain tiles are
determined and engineered during the manufacturing processes when it is essential for the ones
making the tiles to keep strict watch over the composition of the raw materials being used. Clay and
plastic are the substances which are needed for making the structure suitable for the market and
feldspar provides strength to the tiles during the baking and dryingphases of the manufacturing process
to withstand the high temperatures. The clay component is a well grained natural material which
accounts for the improvement in structure of the tiles. Additionally, clay consists of different kinds of
minerals such as; iron and magnesium. These are the core components which ass to the structure and
provides strength to the base of ceramic mass of the tiles of porcelain. Kaolin is generally used in the
production of porcelain tiles to improve the efficiency of the process of production and reducing the
percentage of kaolin reduces efficiencywhich makes the process require more ceramic mass for the
chemical reconstruction process. The causes glazing of the porcelain and gives a tinge of whiteness
brought about during the process of subjecting the product to high temperature, thus messing with the
external appearance aspect. (Goetsch and Davis, 2014). The lanoline used during manufacturing on
26
⊘ This is a preview!⊘
Do you want full access?
Subscribe today to unlock all pages.

Trusted by 1+ million students worldwide
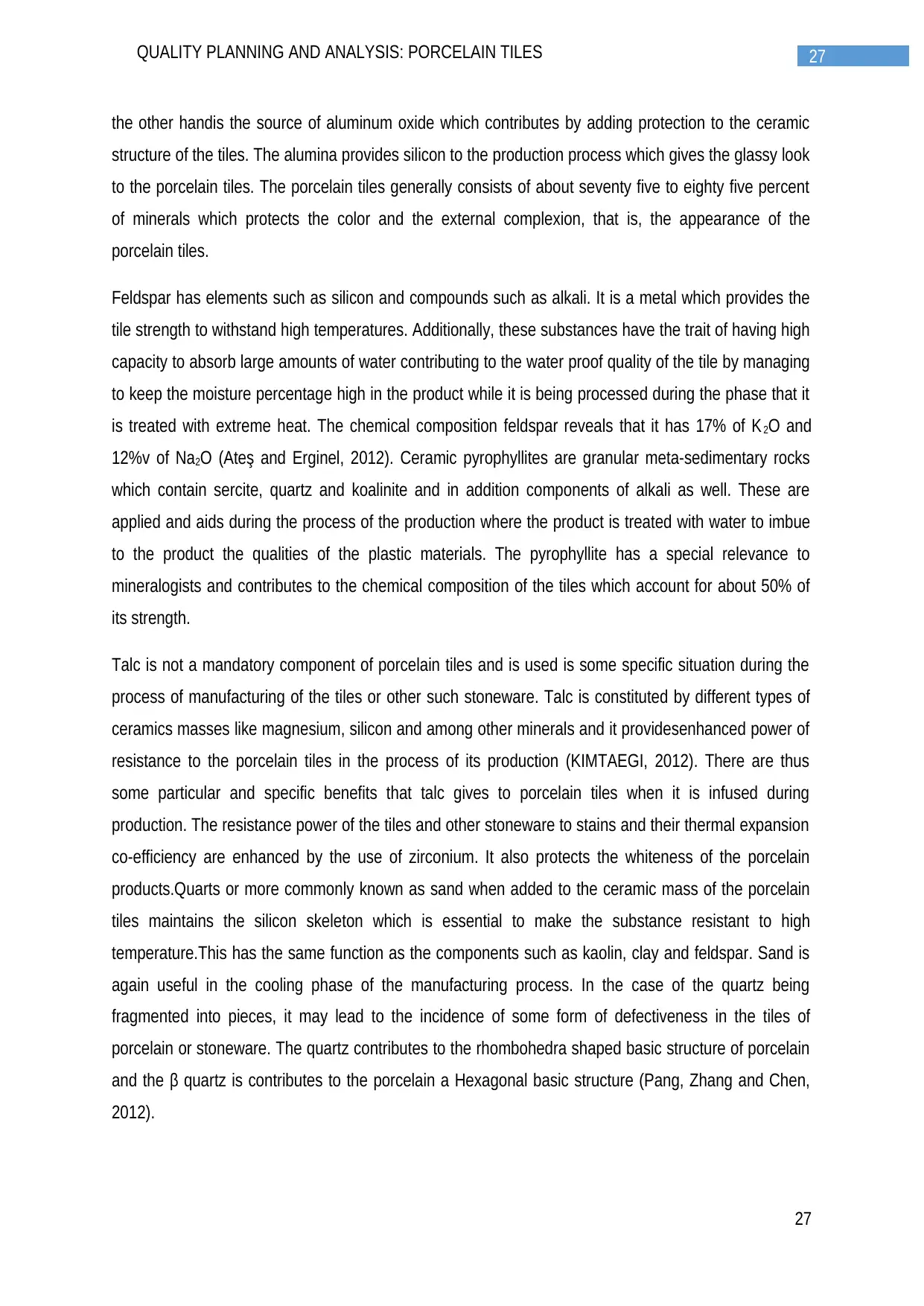
the other handis the source of aluminum oxide which contributes by adding protection to the ceramic
structure of the tiles. The alumina provides silicon to the production process which gives the glassy look
to the porcelain tiles. The porcelain tiles generally consists of about seventy five to eighty five percent
of minerals which protects the color and the external complexion, that is, the appearance of the
porcelain tiles.
Feldspar has elements such as silicon and compounds such as alkali. It is a metal which provides the
tile strength to withstand high temperatures. Additionally, these substances have the trait of having high
capacity to absorb large amounts of water contributing to the water proof quality of the tile by managing
to keep the moisture percentage high in the product while it is being processed during the phase that it
is treated with extreme heat. The chemical composition feldspar reveals that it has 17% of K2O and
12%v of Na2O (Ateş and Erginel, 2012). Ceramic pyrophyllites are granular meta-sedimentary rocks
which contain sercite, quartz and koalinite and in addition components of alkali as well. These are
applied and aids during the process of the production where the product is treated with water to imbue
to the product the qualities of the plastic materials. The pyrophyllite has a special relevance to
mineralogists and contributes to the chemical composition of the tiles which account for about 50% of
its strength.
Talc is not a mandatory component of porcelain tiles and is used is some specific situation during the
process of manufacturing of the tiles or other such stoneware. Talc is constituted by different types of
ceramics masses like magnesium, silicon and among other minerals and it providesenhanced power of
resistance to the porcelain tiles in the process of its production (KIMTAEGI, 2012). There are thus
some particular and specific benefits that talc gives to porcelain tiles when it is infused during
production. The resistance power of the tiles and other stoneware to stains and their thermal expansion
co-efficiency are enhanced by the use of zirconium. It also protects the whiteness of the porcelain
products.Quarts or more commonly known as sand when added to the ceramic mass of the porcelain
tiles maintains the silicon skeleton which is essential to make the substance resistant to high
temperature.This has the same function as the components such as kaolin, clay and feldspar. Sand is
again useful in the cooling phase of the manufacturing process. In the case of the quartz being
fragmented into pieces, it may lead to the incidence of some form of defectiveness in the tiles of
porcelain or stoneware. The quartz contributes to the rhombohedra shaped basic structure of porcelain
and the β quartz is contributes to the porcelain a Hexagonal basic structure (Pang, Zhang and Chen,
2012).
27
Paraphrase This Document
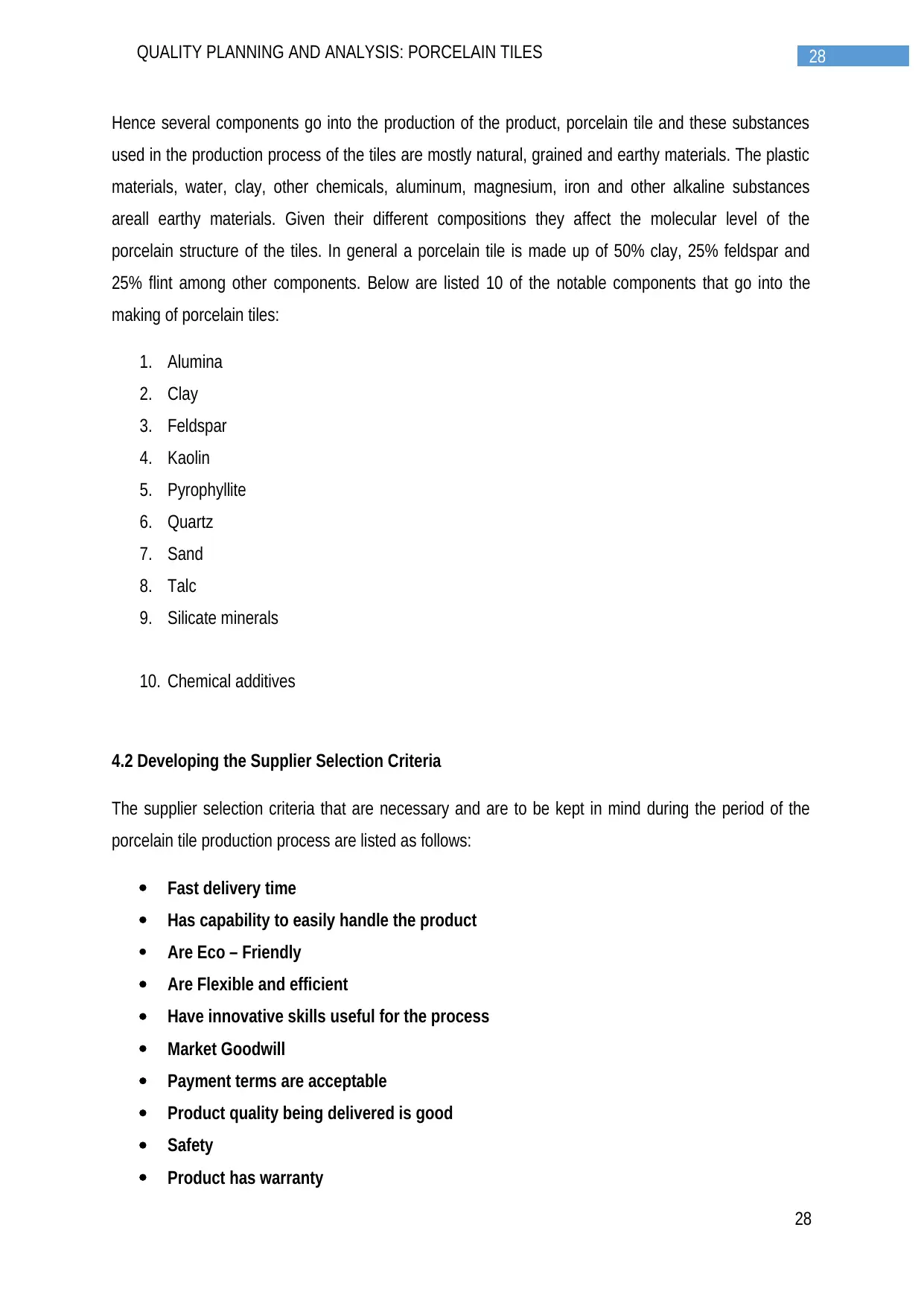
Hence several components go into the production of the product, porcelain tile and these substances
used in the production process of the tiles are mostly natural, grained and earthy materials. The plastic
materials, water, clay, other chemicals, aluminum, magnesium, iron and other alkaline substances
areall earthy materials. Given their different compositions they affect the molecular level of the
porcelain structure of the tiles. In general a porcelain tile is made up of 50% clay, 25% feldspar and
25% flint among other components. Below are listed 10 of the notable components that go into the
making of porcelain tiles:
1. Alumina
2. Clay
3. Feldspar
4. Kaolin
5. Pyrophyllite
6. Quartz
7. Sand
8. Talc
9. Silicate minerals
10. Chemical additives
4.2 Developing the Supplier Selection Criteria
The supplier selection criteria that are necessary and are to be kept in mind during the period of the
porcelain tile production process are listed as follows:
Fast delivery time
Has capability to easily handle the product
Are Eco – Friendly
Are Flexible and efficient
Have innovative skills useful for the process
Market Goodwill
Payment terms are acceptable
Product quality being delivered is good
Safety
Product has warranty
28
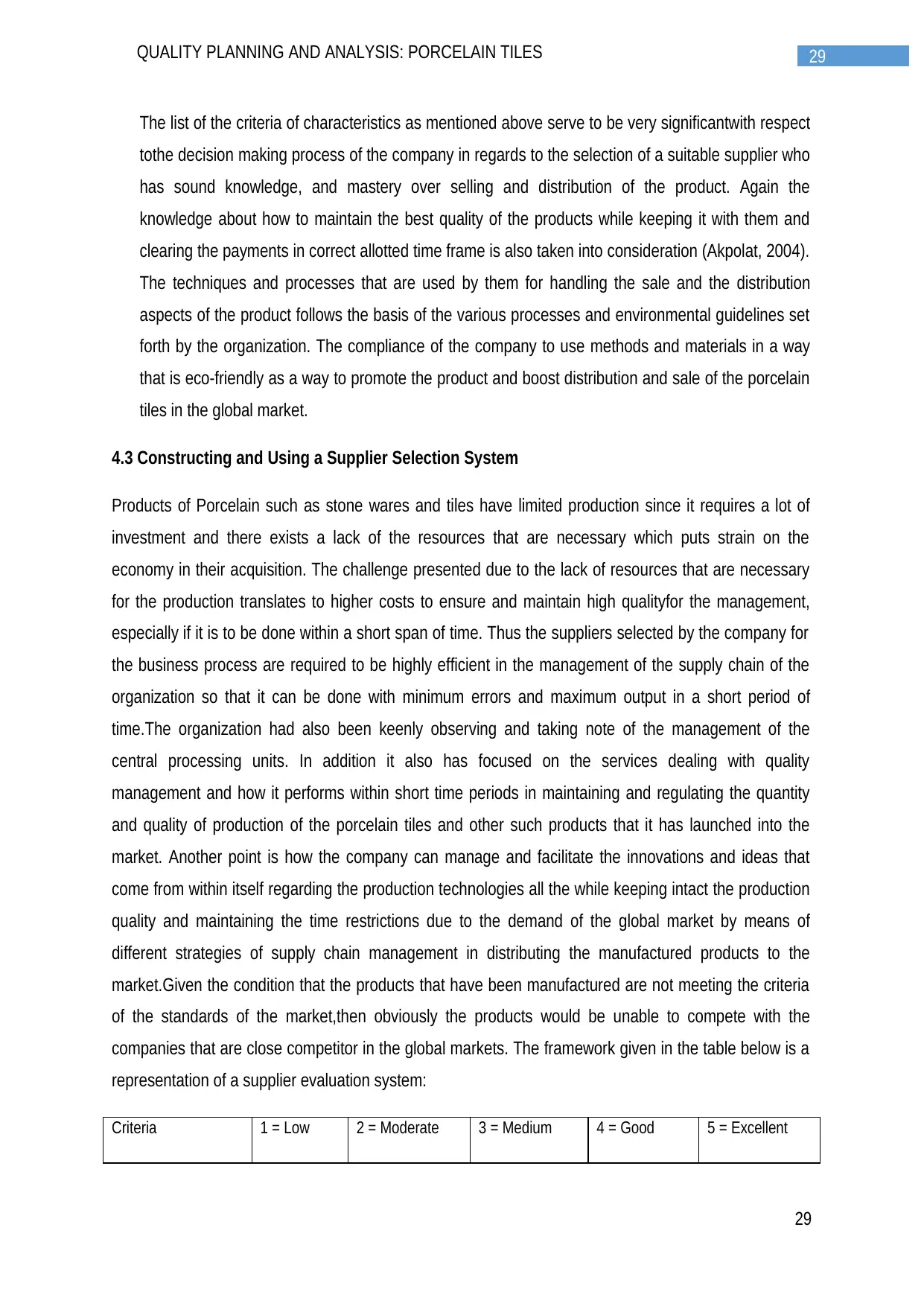
The list of the criteria of characteristics as mentioned above serve to be very significantwith respect
tothe decision making process of the company in regards to the selection of a suitable supplier who
has sound knowledge, and mastery over selling and distribution of the product. Again the
knowledge about how to maintain the best quality of the products while keeping it with them and
clearing the payments in correct allotted time frame is also taken into consideration (Akpolat, 2004).
The techniques and processes that are used by them for handling the sale and the distribution
aspects of the product follows the basis of the various processes and environmental guidelines set
forth by the organization. The compliance of the company to use methods and materials in a way
that is eco-friendly as a way to promote the product and boost distribution and sale of the porcelain
tiles in the global market.
4.3 Constructing and Using a Supplier Selection System
Products of Porcelain such as stone wares and tiles have limited production since it requires a lot of
investment and there exists a lack of the resources that are necessary which puts strain on the
economy in their acquisition. The challenge presented due to the lack of resources that are necessary
for the production translates to higher costs to ensure and maintain high qualityfor the management,
especially if it is to be done within a short span of time. Thus the suppliers selected by the company for
the business process are required to be highly efficient in the management of the supply chain of the
organization so that it can be done with minimum errors and maximum output in a short period of
time.The organization had also been keenly observing and taking note of the management of the
central processing units. In addition it also has focused on the services dealing with quality
management and how it performs within short time periods in maintaining and regulating the quantity
and quality of production of the porcelain tiles and other such products that it has launched into the
market. Another point is how the company can manage and facilitate the innovations and ideas that
come from within itself regarding the production technologies all the while keeping intact the production
quality and maintaining the time restrictions due to the demand of the global market by means of
different strategies of supply chain management in distributing the manufactured products to the
market.Given the condition that the products that have been manufactured are not meeting the criteria
of the standards of the market,then obviously the products would be unable to compete with the
companies that are close competitor in the global markets. The framework given in the table below is a
representation of a supplier evaluation system:
Criteria 1 = Low 2 = Moderate 3 = Medium 4 = Good 5 = Excellent
29
⊘ This is a preview!⊘
Do you want full access?
Subscribe today to unlock all pages.

Trusted by 1+ million students worldwide
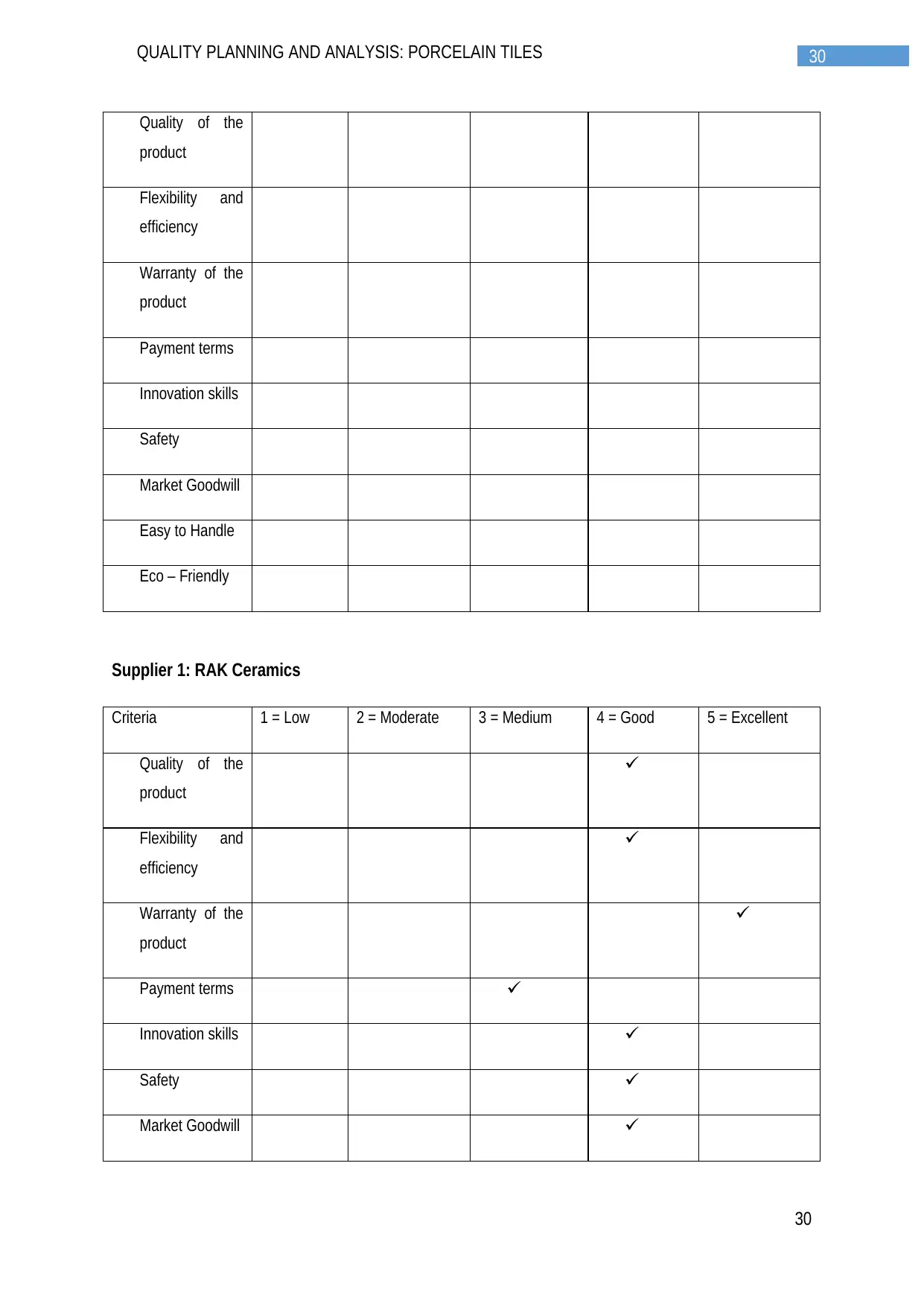
Quality of the
product
Flexibility and
efficiency
Warranty of the
product
Payment terms
Innovation skills
Safety
Market Goodwill
Easy to Handle
Eco – Friendly
Supplier 1: RAK Ceramics
Criteria 1 = Low 2 = Moderate 3 = Medium 4 = Good 5 = Excellent
Quality of the
product
Flexibility and
efficiency
Warranty of the
product
Payment terms
Innovation skills
Safety
Market Goodwill
30
Paraphrase This Document
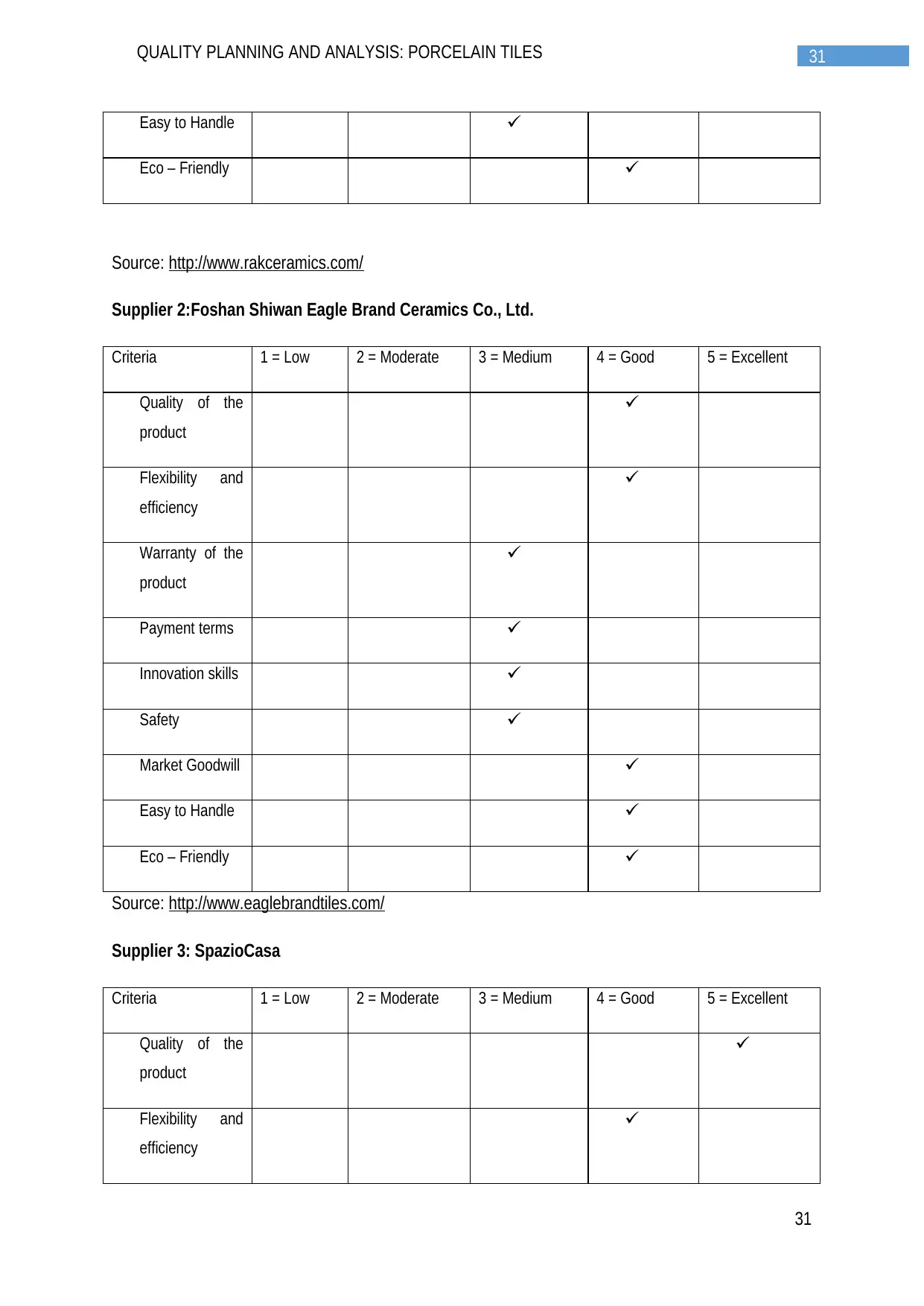
Easy to Handle
Eco – Friendly
Source: http://www.rakceramics.com/
Supplier 2:Foshan Shiwan Eagle Brand Ceramics Co., Ltd.
Criteria 1 = Low 2 = Moderate 3 = Medium 4 = Good 5 = Excellent
Quality of the
product
Flexibility and
efficiency
Warranty of the
product
Payment terms
Innovation skills
Safety
Market Goodwill
Easy to Handle
Eco – Friendly
Source: http://www.eaglebrandtiles.com/
Supplier 3: SpazioCasa
Criteria 1 = Low 2 = Moderate 3 = Medium 4 = Good 5 = Excellent
Quality of the
product
Flexibility and
efficiency
31
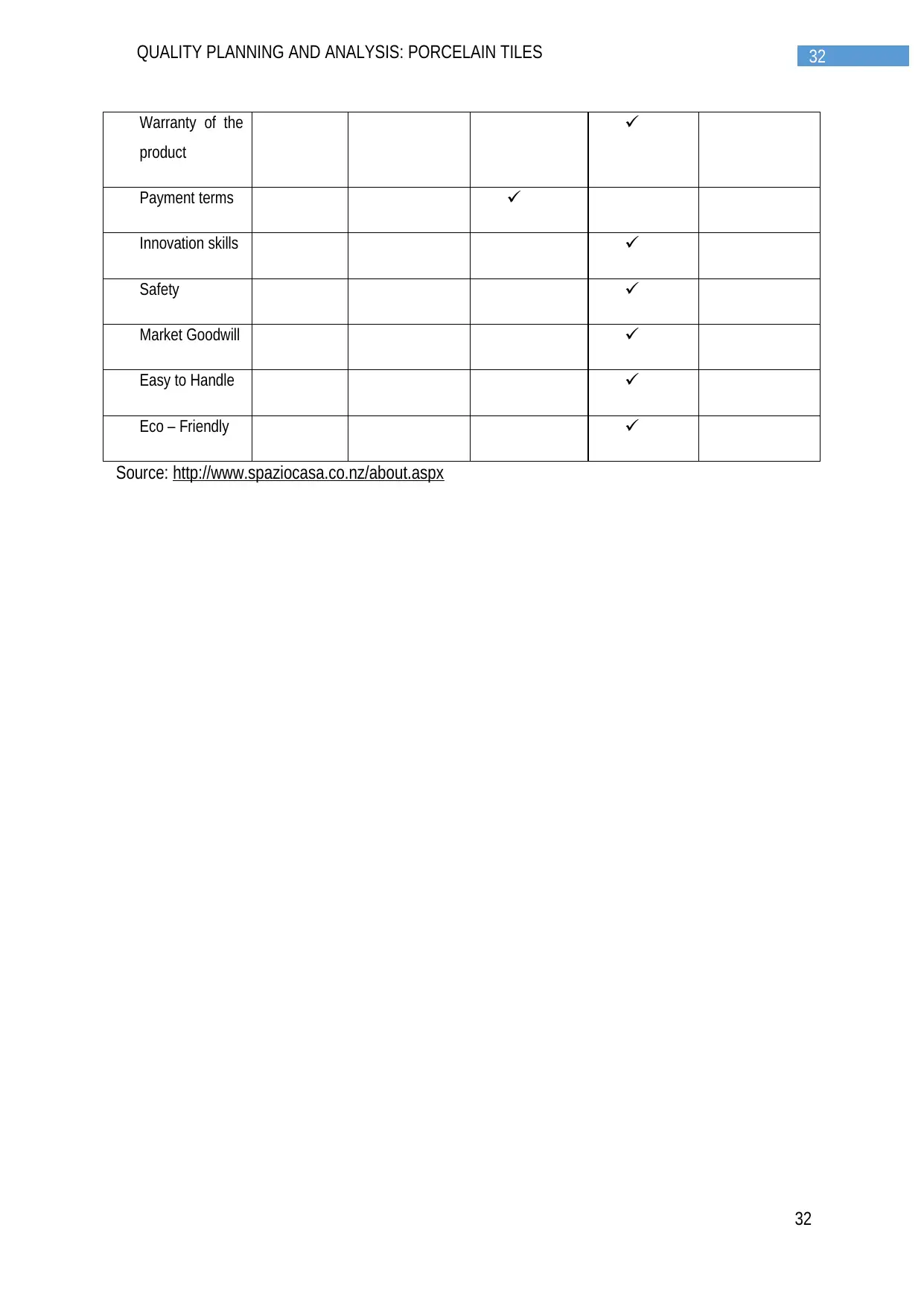
Warranty of the
product
Payment terms
Innovation skills
Safety
Market Goodwill
Easy to Handle
Eco – Friendly
Source: http://www.spaziocasa.co.nz/about.aspx
32
⊘ This is a preview!⊘
Do you want full access?
Subscribe today to unlock all pages.

Trusted by 1+ million students worldwide
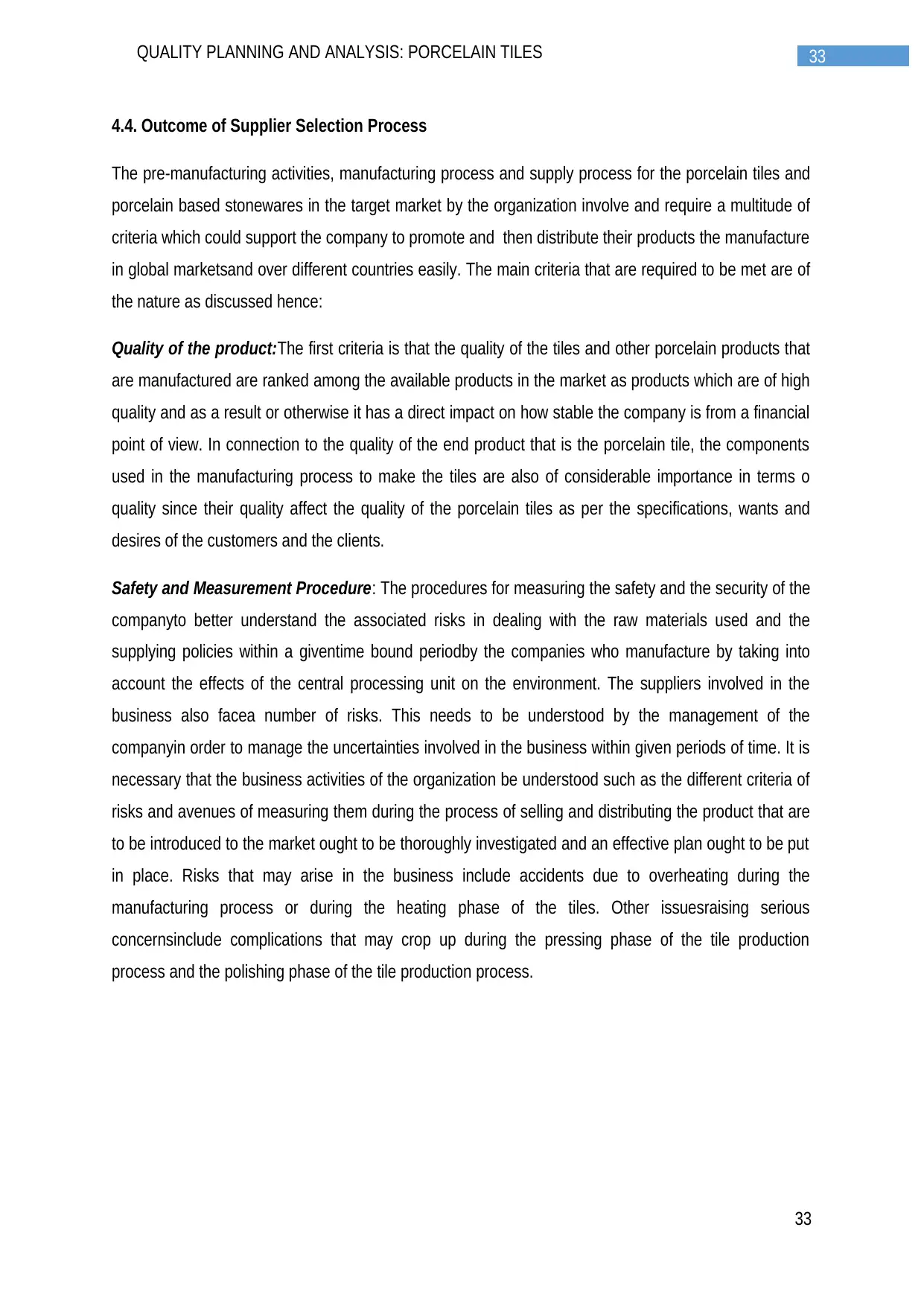
4.4. Outcome of Supplier Selection Process
The pre-manufacturing activities, manufacturing process and supply process for the porcelain tiles and
porcelain based stonewares in the target market by the organization involve and require a multitude of
criteria which could support the company to promote and then distribute their products the manufacture
in global marketsand over different countries easily. The main criteria that are required to be met are of
the nature as discussed hence:
Quality of the product:The first criteria is that the quality of the tiles and other porcelain products that
are manufactured are ranked among the available products in the market as products which are of high
quality and as a result or otherwise it has a direct impact on how stable the company is from a financial
point of view. In connection to the quality of the end product that is the porcelain tile, the components
used in the manufacturing process to make the tiles are also of considerable importance in terms o
quality since their quality affect the quality of the porcelain tiles as per the specifications, wants and
desires of the customers and the clients.
Safety and Measurement Procedure: The procedures for measuring the safety and the security of the
companyto better understand the associated risks in dealing with the raw materials used and the
supplying policies within a giventime bound periodby the companies who manufacture by taking into
account the effects of the central processing unit on the environment. The suppliers involved in the
business also facea number of risks. This needs to be understood by the management of the
companyin order to manage the uncertainties involved in the business within given periods of time. It is
necessary that the business activities of the organization be understood such as the different criteria of
risks and avenues of measuring them during the process of selling and distributing the product that are
to be introduced to the market ought to be thoroughly investigated and an effective plan ought to be put
in place. Risks that may arise in the business include accidents due to overheating during the
manufacturing process or during the heating phase of the tiles. Other issuesraising serious
concernsinclude complications that may crop up during the pressing phase of the tile production
process and the polishing phase of the tile production process.
33
Paraphrase This Document
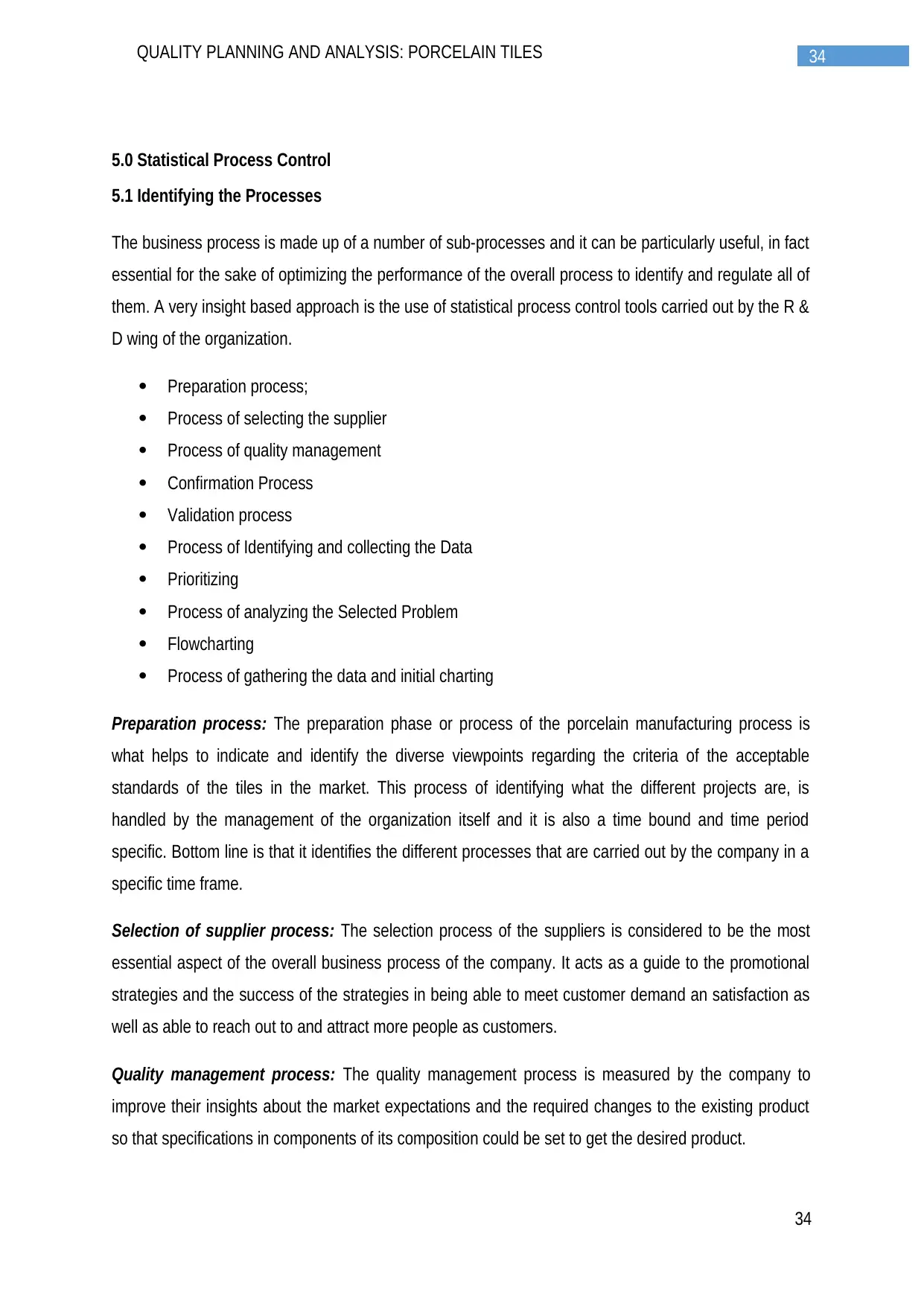
5.0 Statistical Process Control
5.1 Identifying the Processes
The business process is made up of a number of sub-processes and it can be particularly useful, in fact
essential for the sake of optimizing the performance of the overall process to identify and regulate all of
them. A very insight based approach is the use of statistical process control tools carried out by the R &
D wing of the organization.
Preparation process;
Process of selecting the supplier
Process of quality management
Confirmation Process
Validation process
Process of Identifying and collecting the Data
Prioritizing
Process of analyzing the Selected Problem
Flowcharting
Process of gathering the data and initial charting
Preparation process: The preparation phase or process of the porcelain manufacturing process is
what helps to indicate and identify the diverse viewpoints regarding the criteria of the acceptable
standards of the tiles in the market. This process of identifying what the different projects are, is
handled by the management of the organization itself and it is also a time bound and time period
specific. Bottom line is that it identifies the different processes that are carried out by the company in a
specific time frame.
Selection of supplier process: The selection process of the suppliers is considered to be the most
essential aspect of the overall business process of the company. It acts as a guide to the promotional
strategies and the success of the strategies in being able to meet customer demand an satisfaction as
well as able to reach out to and attract more people as customers.
Quality management process: The quality management process is measured by the company to
improve their insights about the market expectations and the required changes to the existing product
so that specifications in components of its composition could be set to get the desired product.
34
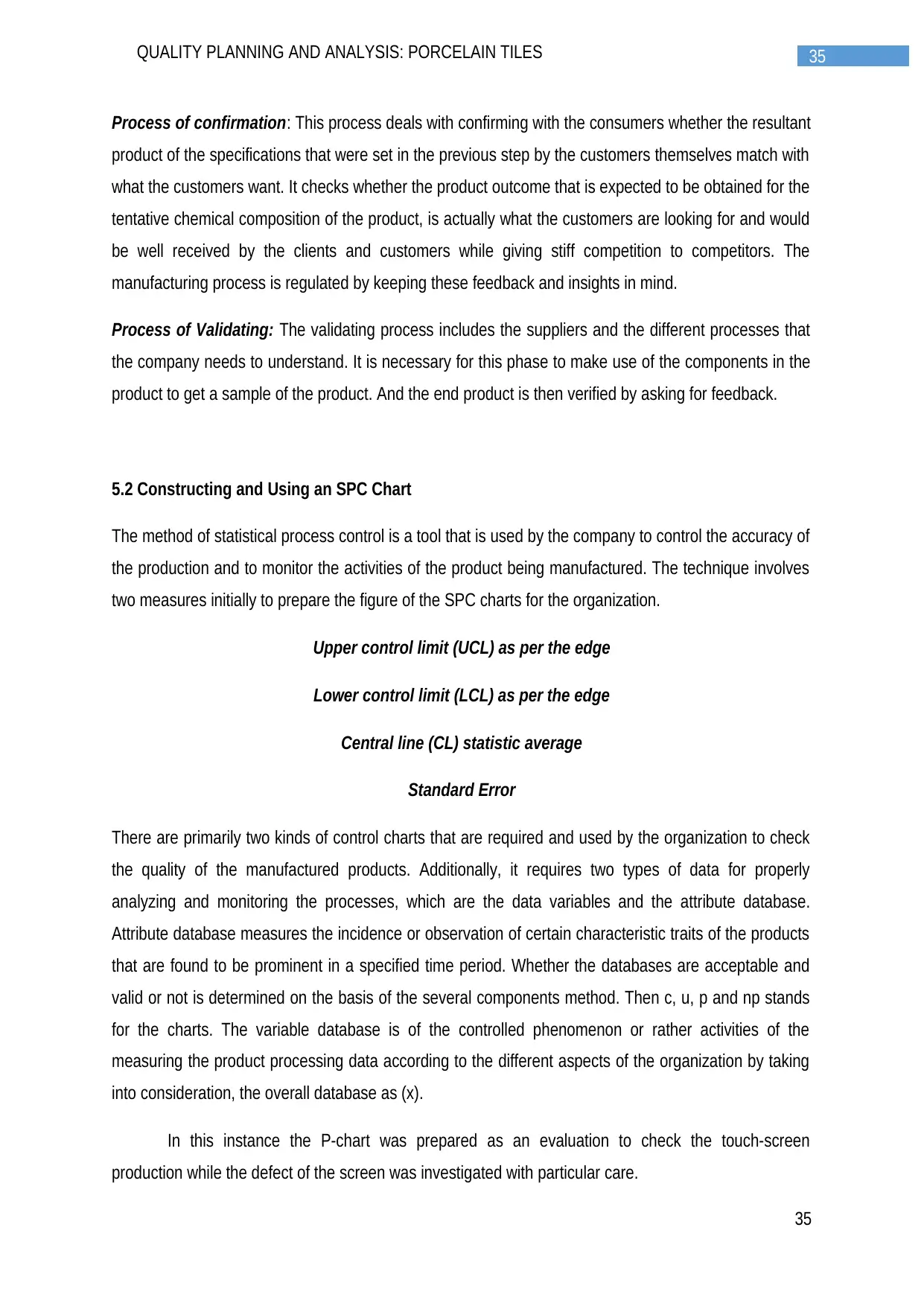
Process of confirmation: This process deals with confirming with the consumers whether the resultant
product of the specifications that were set in the previous step by the customers themselves match with
what the customers want. It checks whether the product outcome that is expected to be obtained for the
tentative chemical composition of the product, is actually what the customers are looking for and would
be well received by the clients and customers while giving stiff competition to competitors. The
manufacturing process is regulated by keeping these feedback and insights in mind.
Process of Validating: The validating process includes the suppliers and the different processes that
the company needs to understand. It is necessary for this phase to make use of the components in the
product to get a sample of the product. And the end product is then verified by asking for feedback.
5.2 Constructing and Using an SPC Chart
The method of statistical process control is a tool that is used by the company to control the accuracy of
the production and to monitor the activities of the product being manufactured. The technique involves
two measures initially to prepare the figure of the SPC charts for the organization.
Upper control limit (UCL) as per the edge
Lower control limit (LCL) as per the edge
Central line (CL) statistic average
Standard Error
There are primarily two kinds of control charts that are required and used by the organization to check
the quality of the manufactured products. Additionally, it requires two types of data for properly
analyzing and monitoring the processes, which are the data variables and the attribute database.
Attribute database measures the incidence or observation of certain characteristic traits of the products
that are found to be prominent in a specified time period. Whether the databases are acceptable and
valid or not is determined on the basis of the several components method. Then c, u, p and np stands
for the charts. The variable database is of the controlled phenomenon or rather activities of the
measuring the product processing data according to the different aspects of the organization by taking
into consideration, the overall database as (x).
In this instance the P-chart was prepared as an evaluation to check the touch-screen
production while the defect of the screen was investigated with particular care.
35
⊘ This is a preview!⊘
Do you want full access?
Subscribe today to unlock all pages.

Trusted by 1+ million students worldwide
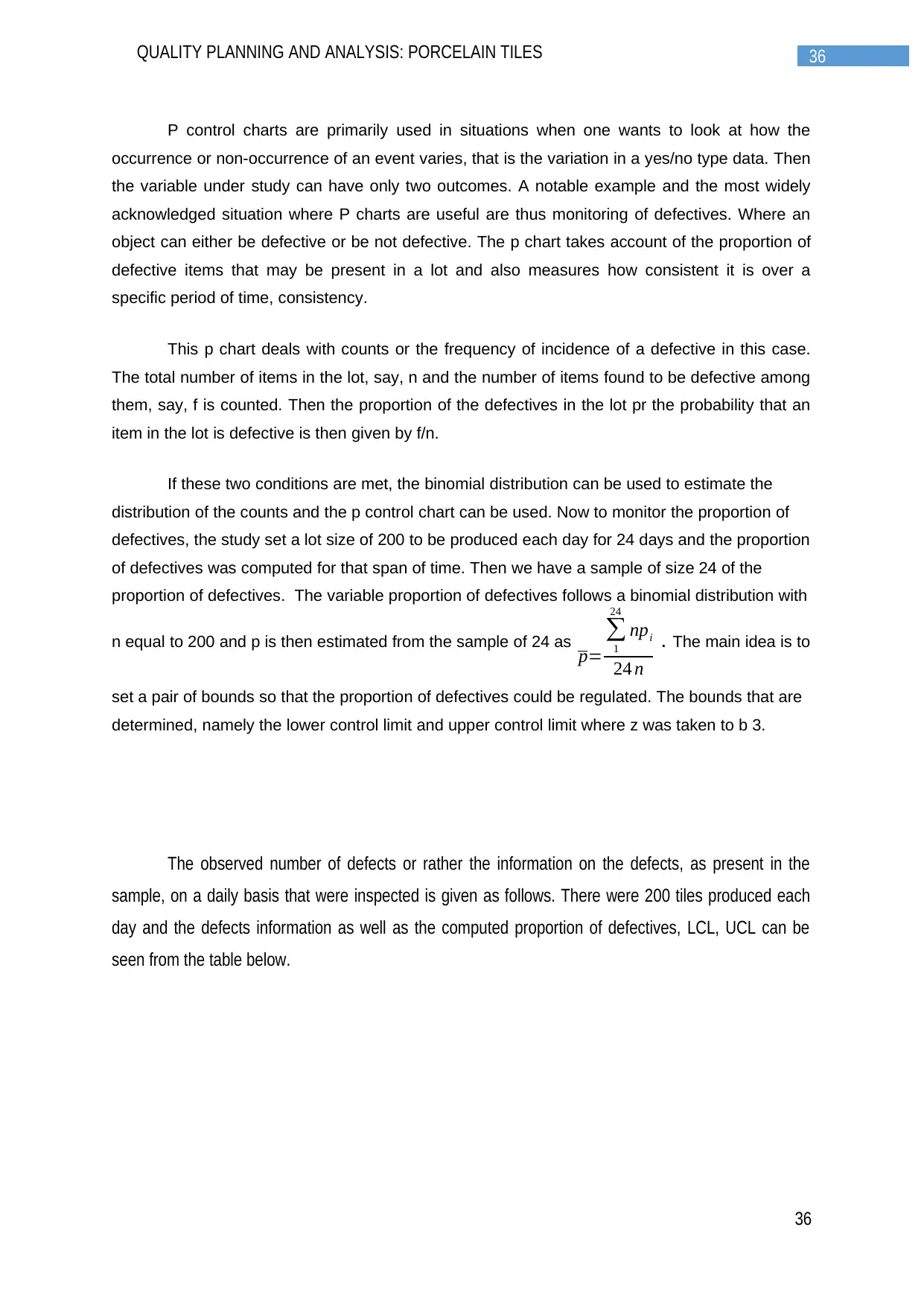
LC
L
p z p p
n
3
1
UC
L
p z p p
n
1
36QUALITY PLANNING AND ANALYSIS: PORCELAIN TILES
P control charts are primarily used in situations when one wants to look at how the
occurrence or non-occurrence of an event varies, that is the variation in a yes/no type data. Then
the variable under study can have only two outcomes. A notable example and the most widely
acknowledged situation where P charts are useful are thus monitoring of defectives. Where an
object can either be defective or be not defective. The p chart takes account of the proportion of
defective items that may be present in a lot and also measures how consistent it is over a
specific period of time, consistency.
This p chart deals with counts or the frequency of incidence of a defective in this case.
The total number of items in the lot, say, n and the number of items found to be defective among
them, say, f is counted. Then the proportion of the defectives in the lot pr the probability that an
item in the lot is defective is then given by f/n.
If these two conditions are met, the binomial distribution can be used to estimate the
distribution of the counts and the p control chart can be used. Now to monitor the proportion of
defectives, the study set a lot size of 200 to be produced each day for 24 days and the proportion
of defectives was computed for that span of time. Then we have a sample of size 24 of the
proportion of defectives. The variable proportion of defectives follows a binomial distribution with
n equal to 200 and p is then estimated from the sample of 24 as p=
∑
1
24
npi
24 n
. The main idea is to
set a pair of bounds so that the proportion of defectives could be regulated. The bounds that are
determined, namely the lower control limit and upper control limit where z was taken to b 3.
The observed number of defects or rather the information on the defects, as present in the
sample, on a daily basis that were inspected is given as follows. There were 200 tiles produced each
day and the defects information as well as the computed proportion of defectives, LCL, UCL can be
seen from the table below.
36
Paraphrase This Document
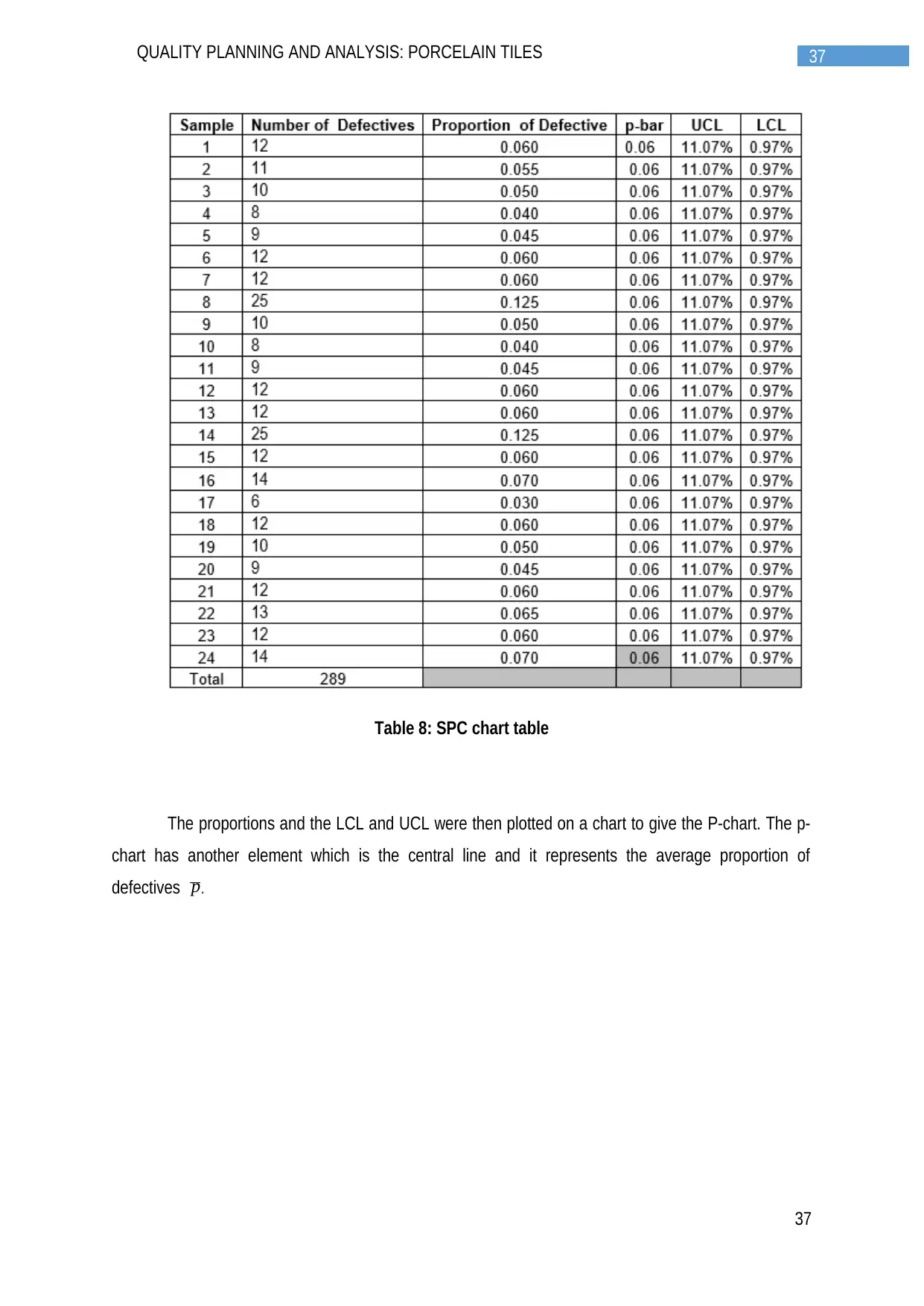
Table 8: SPC chart table
The proportions and the LCL and UCL were then plotted on a chart to give the P-chart. The p-
chart has another element which is the central line and it represents the average proportion of
defectives p.
37
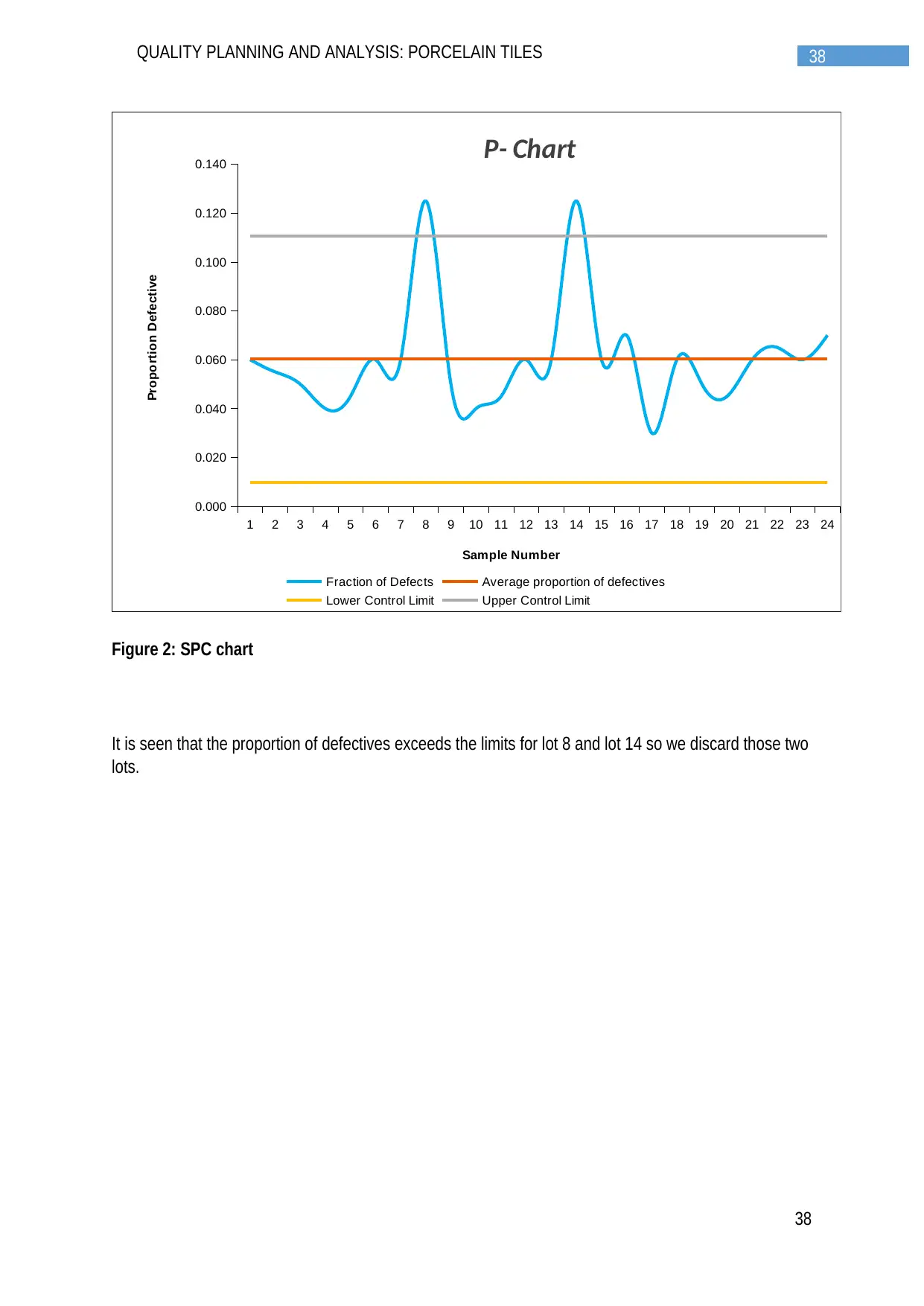
1 2 3 4 5 6 7 8 9 10 11 12 13 14 15 16 17 18 19 20 21 22 23 24
0.000
0.020
0.040
0.060
0.080
0.100
0.120
0.140 P- Chart
Fraction of Defects Average proportion of defectives
Lower Control Limit Upper Control Limit
Sample Number
Proportion Defective
Figure 2: SPC chart
It is seen that the proportion of defectives exceeds the limits for lot 8 and lot 14 so we discard those two
lots.
38
⊘ This is a preview!⊘
Do you want full access?
Subscribe today to unlock all pages.

Trusted by 1+ million students worldwide
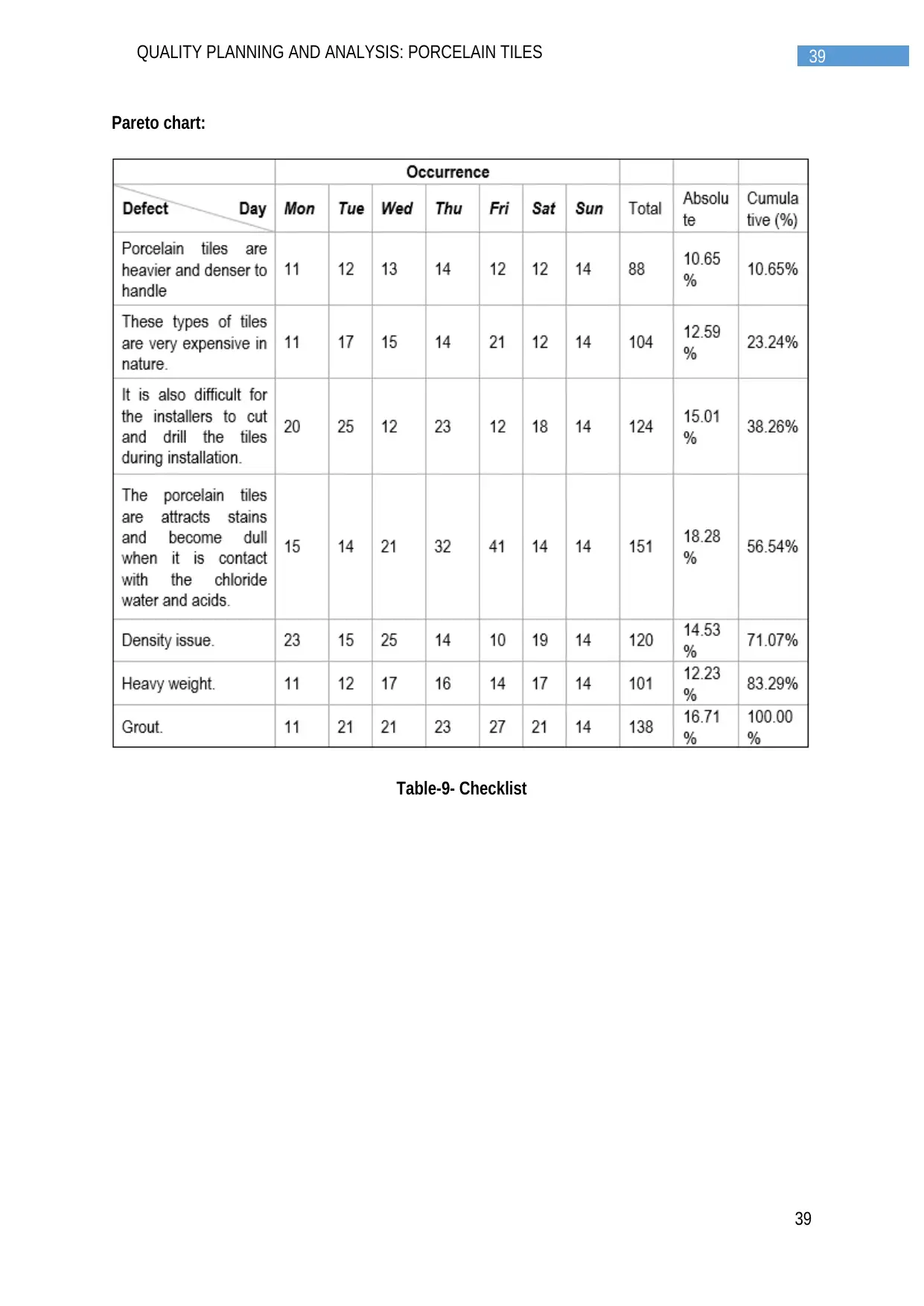
Pareto chart:
Table-9- Checklist
39
Paraphrase This Document

0.00%
20.00%
40.00%
60.00%
80.00%
100.00%
120.00%
0.00%
20.00%
40.00%
60.00%
80.00%
100.00%
120.00%
Pareto Chart for Defects
P rop o rti o n o f O c cu re n ce
Cu m u la ti ve p ro p o rti o n o f o c cu re n ce
Figure 3: Pareto chart
40
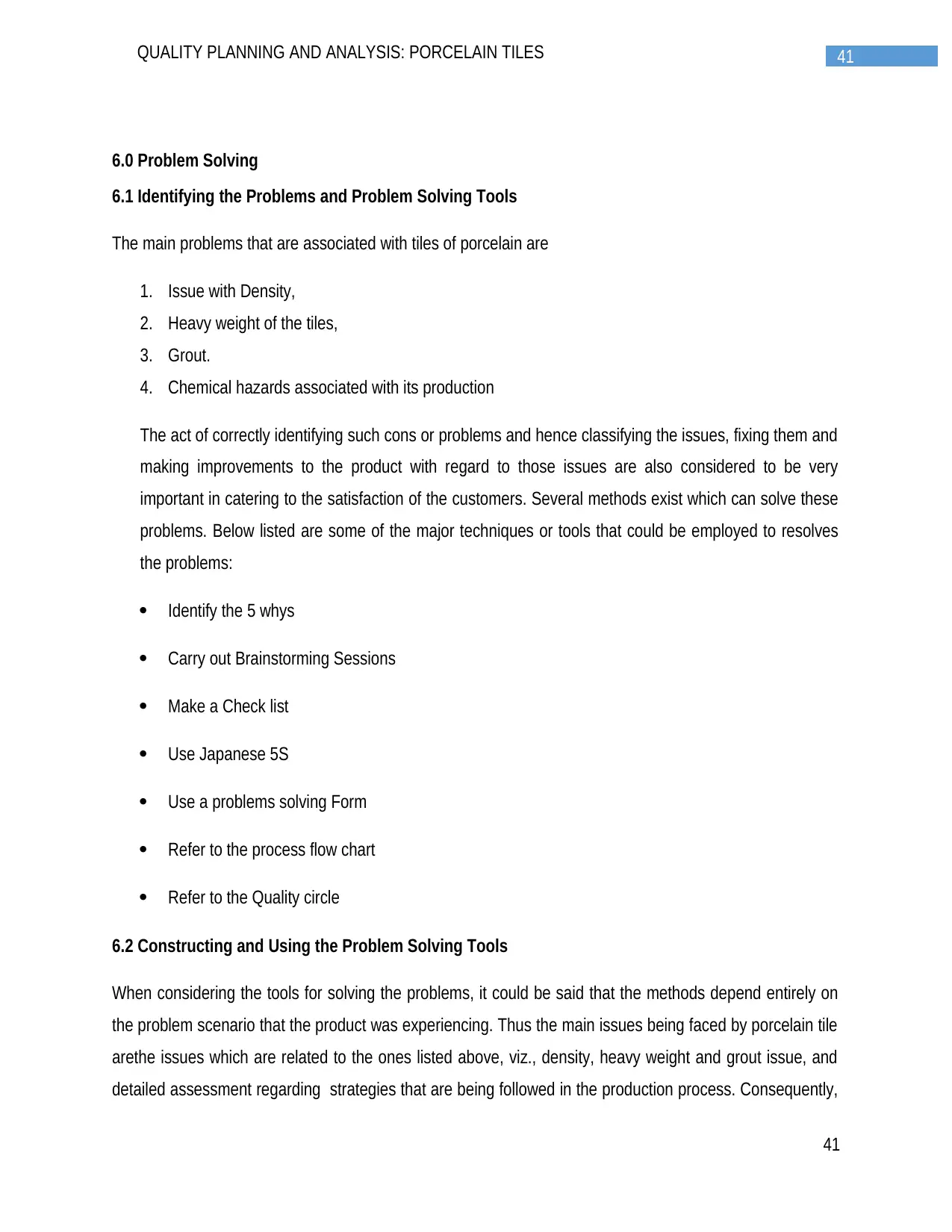
6.0 Problem Solving
6.1 Identifying the Problems and Problem Solving Tools
The main problems that are associated with tiles of porcelain are
1. Issue with Density,
2. Heavy weight of the tiles,
3. Grout.
4. Chemical hazards associated with its production
The act of correctly identifying such cons or problems and hence classifying the issues, fixing them and
making improvements to the product with regard to those issues are also considered to be very
important in catering to the satisfaction of the customers. Several methods exist which can solve these
problems. Below listed are some of the major techniques or tools that could be employed to resolves
the problems:
Identify the 5 whys
Carry out Brainstorming Sessions
Make a Check list
Use Japanese 5S
Use a problems solving Form
Refer to the process flow chart
Refer to the Quality circle
6.2 Constructing and Using the Problem Solving Tools
When considering the tools for solving the problems, it could be said that the methods depend entirely on
the problem scenario that the product was experiencing. Thus the main issues being faced by porcelain tile
arethe issues which are related to the ones listed above, viz., density, heavy weight and grout issue, and
detailed assessment regarding strategies that are being followed in the production process. Consequently,
41
⊘ This is a preview!⊘
Do you want full access?
Subscribe today to unlock all pages.

Trusted by 1+ million students worldwide
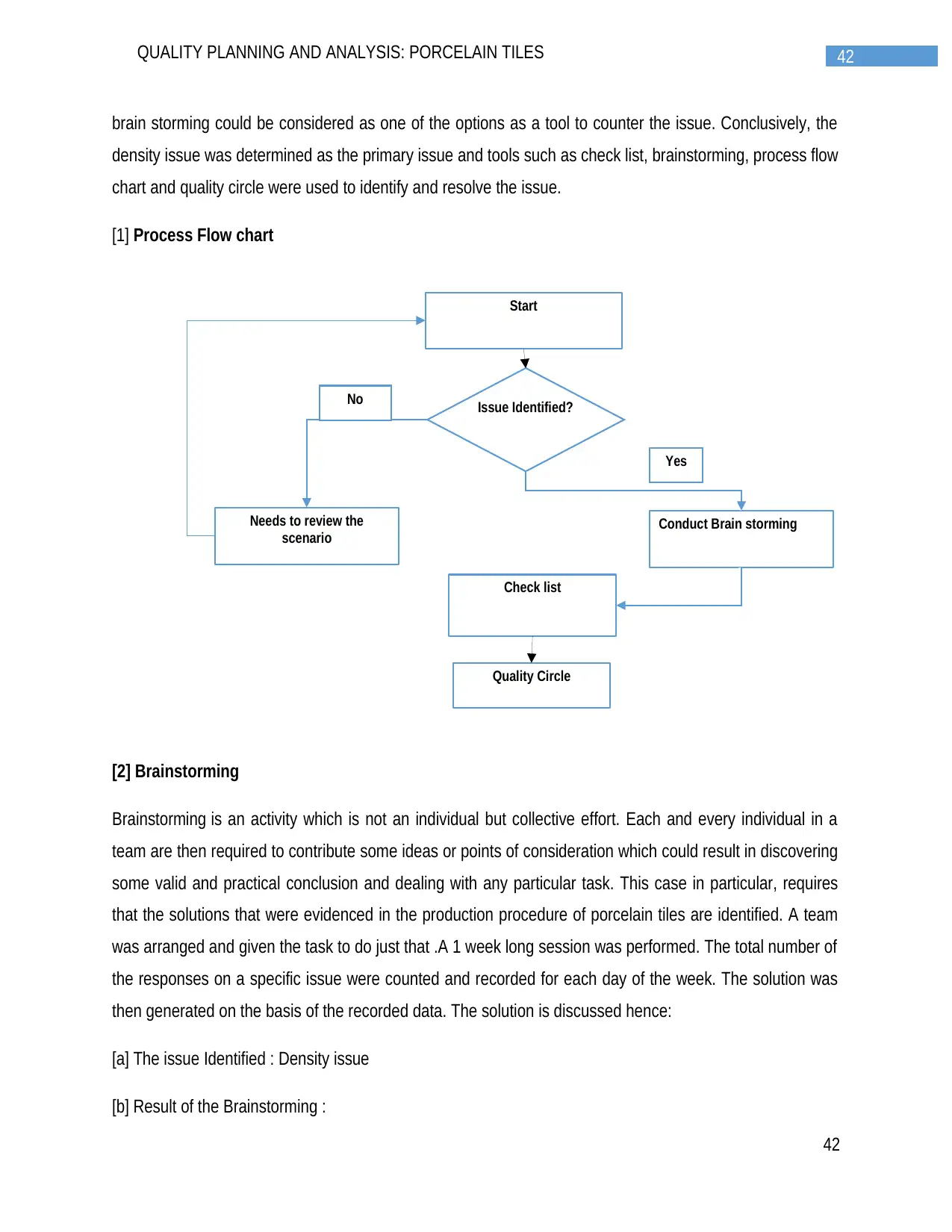
Issue Identified?
Needs to review the
scenario Conduct Brain storming
No
Yes
Check list
Quality Circle
42QUALITY PLANNING AND ANALYSIS: PORCELAIN TILES
brain storming could be considered as one of the options as a tool to counter the issue. Conclusively, the
density issue was determined as the primary issue and tools such as check list, brainstorming, process flow
chart and quality circle were used to identify and resolve the issue.
[1] Process Flow chart
[2] Brainstorming
Brainstorming is an activity which is not an individual but collective effort. Each and every individual in a
team are then required to contribute some ideas or points of consideration which could result in discovering
some valid and practical conclusion and dealing with any particular task. This case in particular, requires
that the solutions that were evidenced in the production procedure of porcelain tiles are identified. A team
was arranged and given the task to do just that .A 1 week long session was performed. The total number of
the responses on a specific issue were counted and recorded for each day of the week. The solution was
then generated on the basis of the recorded data. The solution is discussed hence:
[a] The issue Identified : Density issue
[b] Result of the Brainstorming :
42
Paraphrase This Document
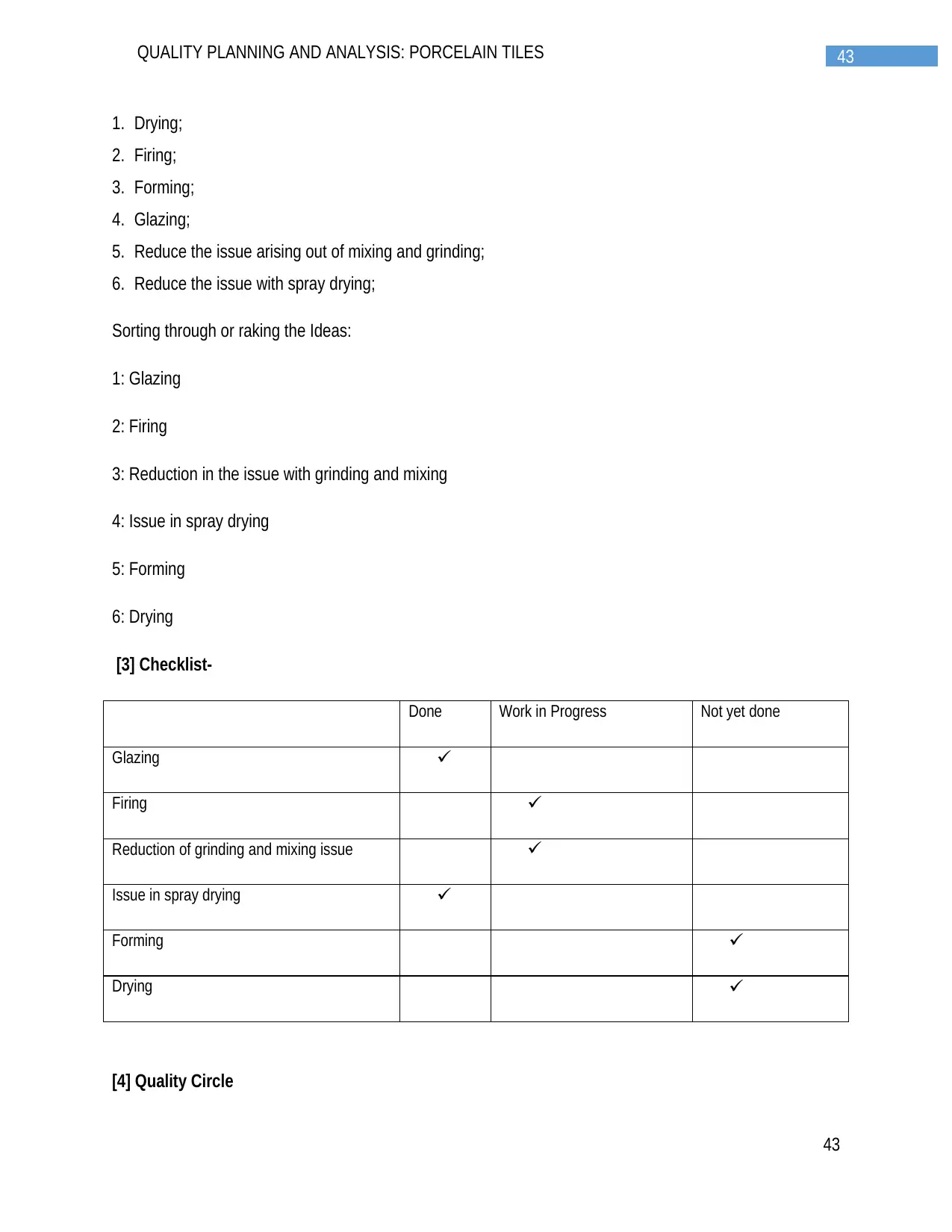
1. Drying;
2. Firing;
3. Forming;
4. Glazing;
5. Reduce the issue arising out of mixing and grinding;
6. Reduce the issue with spray drying;
Sorting through or raking the Ideas:
1: Glazing
2: Firing
3: Reduction in the issue with grinding and mixing
4: Issue in spray drying
5: Forming
6: Drying
[3] Checklist-
Done Work in Progress Not yet done
Glazing
Firing
Reduction of grinding and mixing issue
Issue in spray drying
Forming
Drying
[4] Quality Circle
43
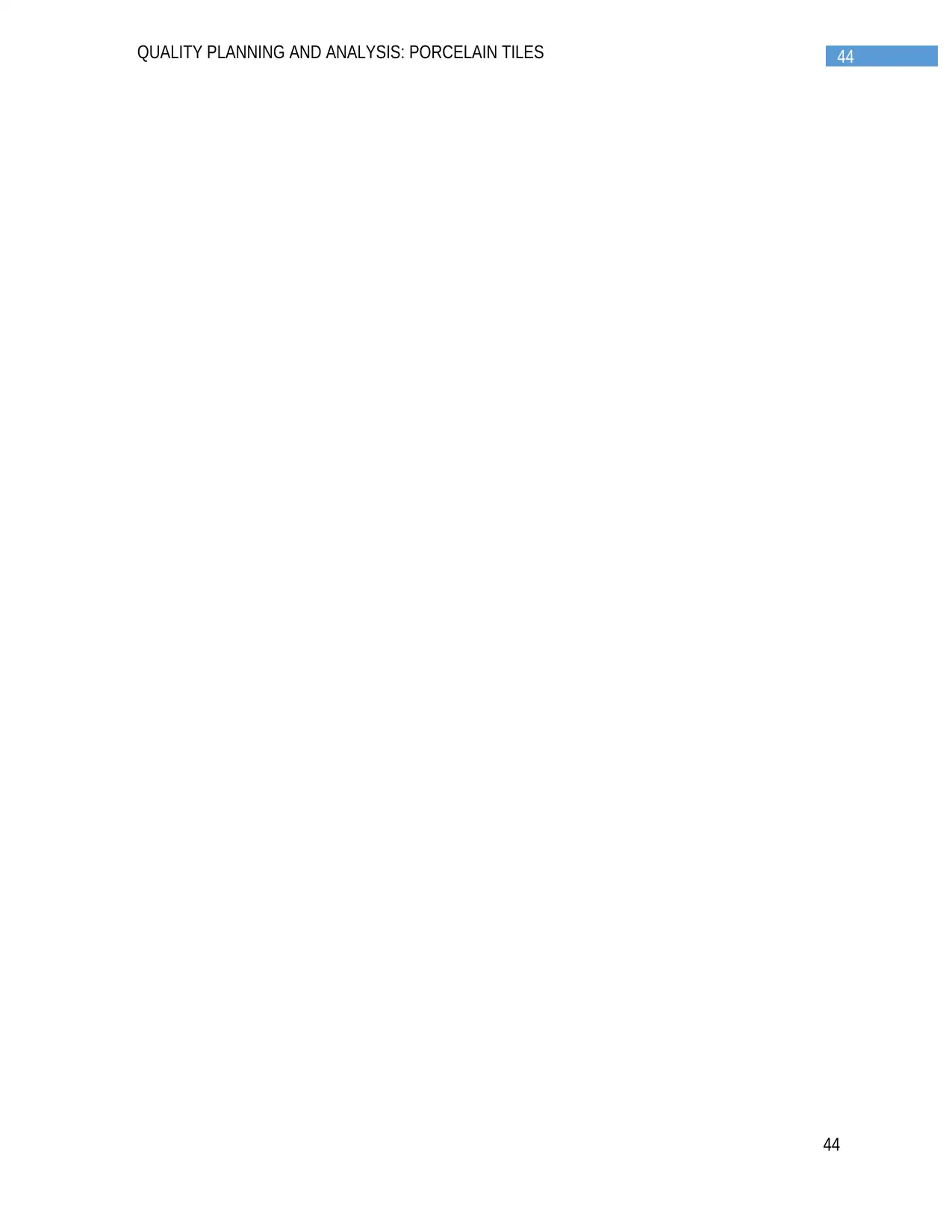
44
⊘ This is a preview!⊘
Do you want full access?
Subscribe today to unlock all pages.

Trusted by 1+ million students worldwide
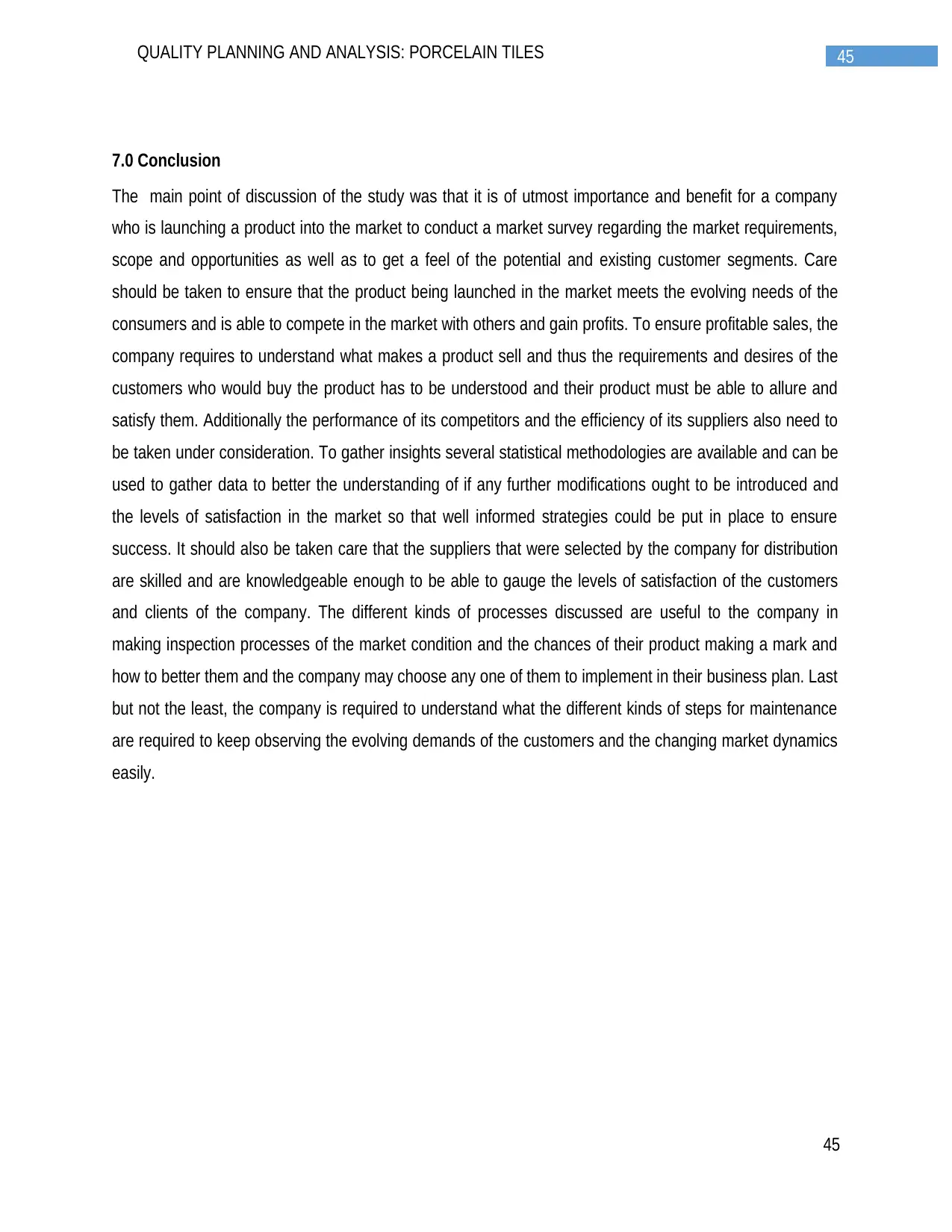
7.0 Conclusion
The main point of discussion of the study was that it is of utmost importance and benefit for a company
who is launching a product into the market to conduct a market survey regarding the market requirements,
scope and opportunities as well as to get a feel of the potential and existing customer segments. Care
should be taken to ensure that the product being launched in the market meets the evolving needs of the
consumers and is able to compete in the market with others and gain profits. To ensure profitable sales, the
company requires to understand what makes a product sell and thus the requirements and desires of the
customers who would buy the product has to be understood and their product must be able to allure and
satisfy them. Additionally the performance of its competitors and the efficiency of its suppliers also need to
be taken under consideration. To gather insights several statistical methodologies are available and can be
used to gather data to better the understanding of if any further modifications ought to be introduced and
the levels of satisfaction in the market so that well informed strategies could be put in place to ensure
success. It should also be taken care that the suppliers that were selected by the company for distribution
are skilled and are knowledgeable enough to be able to gauge the levels of satisfaction of the customers
and clients of the company. The different kinds of processes discussed are useful to the company in
making inspection processes of the market condition and the chances of their product making a mark and
how to better them and the company may choose any one of them to implement in their business plan. Last
but not the least, the company is required to understand what the different kinds of steps for maintenance
are required to keep observing the evolving demands of the customers and the changing market dynamics
easily.
45
Paraphrase This Document
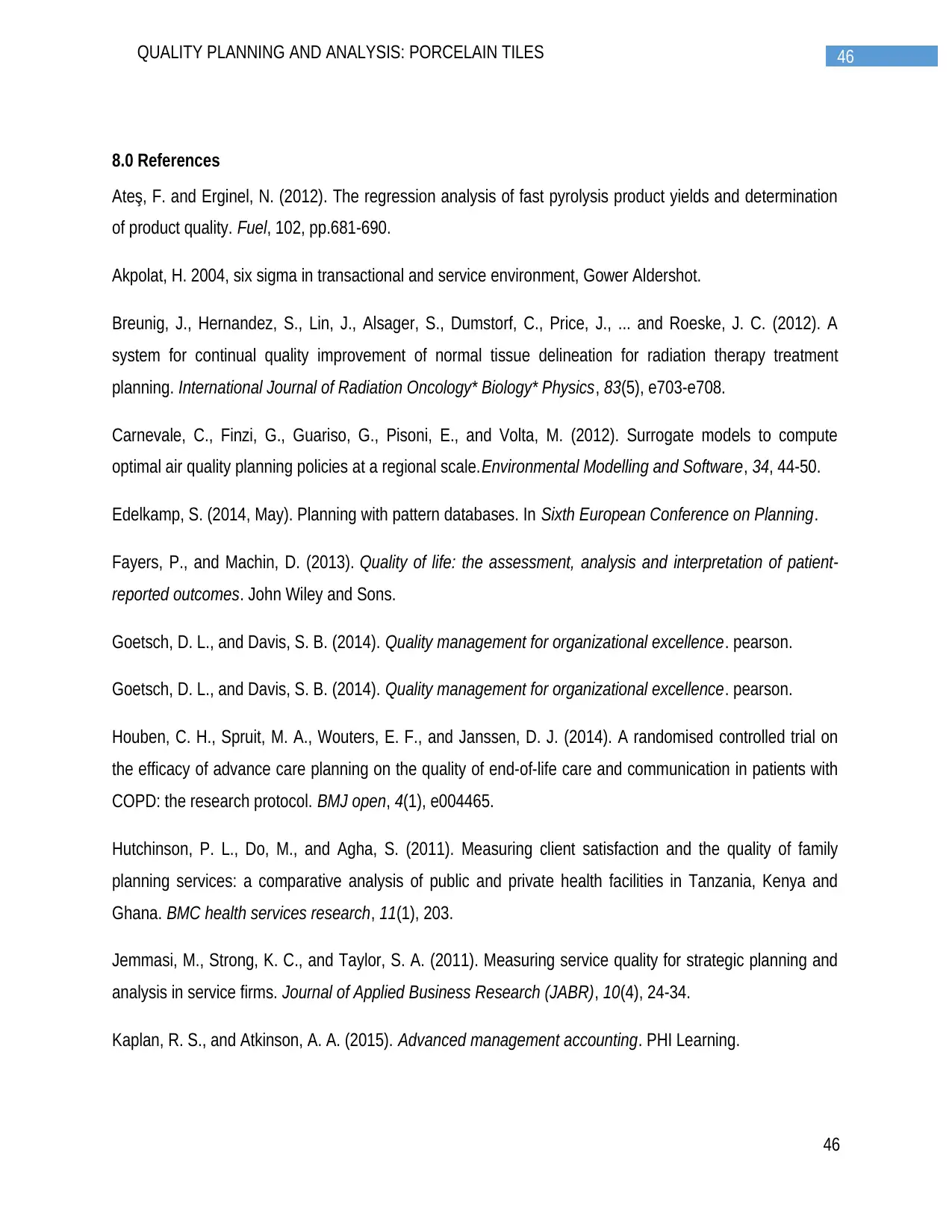
8.0 References
Ateş, F. and Erginel, N. (2012). The regression analysis of fast pyrolysis product yields and determination
of product quality. Fuel, 102, pp.681-690.
Akpolat, H. 2004, six sigma in transactional and service environment, Gower Aldershot.
Breunig, J., Hernandez, S., Lin, J., Alsager, S., Dumstorf, C., Price, J., ... and Roeske, J. C. (2012). A
system for continual quality improvement of normal tissue delineation for radiation therapy treatment
planning. International Journal of Radiation Oncology* Biology* Physics, 83(5), e703-e708.
Carnevale, C., Finzi, G., Guariso, G., Pisoni, E., and Volta, M. (2012). Surrogate models to compute
optimal air quality planning policies at a regional scale.Environmental Modelling and Software, 34, 44-50.
Edelkamp, S. (2014, May). Planning with pattern databases. In Sixth European Conference on Planning.
Fayers, P., and Machin, D. (2013). Quality of life: the assessment, analysis and interpretation of patient-
reported outcomes. John Wiley and Sons.
Goetsch, D. L., and Davis, S. B. (2014). Quality management for organizational excellence. pearson.
Goetsch, D. L., and Davis, S. B. (2014). Quality management for organizational excellence. pearson.
Houben, C. H., Spruit, M. A., Wouters, E. F., and Janssen, D. J. (2014). A randomised controlled trial on
the efficacy of advance care planning on the quality of end-of-life care and communication in patients with
COPD: the research protocol. BMJ open, 4(1), e004465.
Hutchinson, P. L., Do, M., and Agha, S. (2011). Measuring client satisfaction and the quality of family
planning services: a comparative analysis of public and private health facilities in Tanzania, Kenya and
Ghana. BMC health services research, 11(1), 203.
Jemmasi, M., Strong, K. C., and Taylor, S. A. (2011). Measuring service quality for strategic planning and
analysis in service firms. Journal of Applied Business Research (JABR), 10(4), 24-34.
Kaplan, R. S., and Atkinson, A. A. (2015). Advanced management accounting. PHI Learning.
46
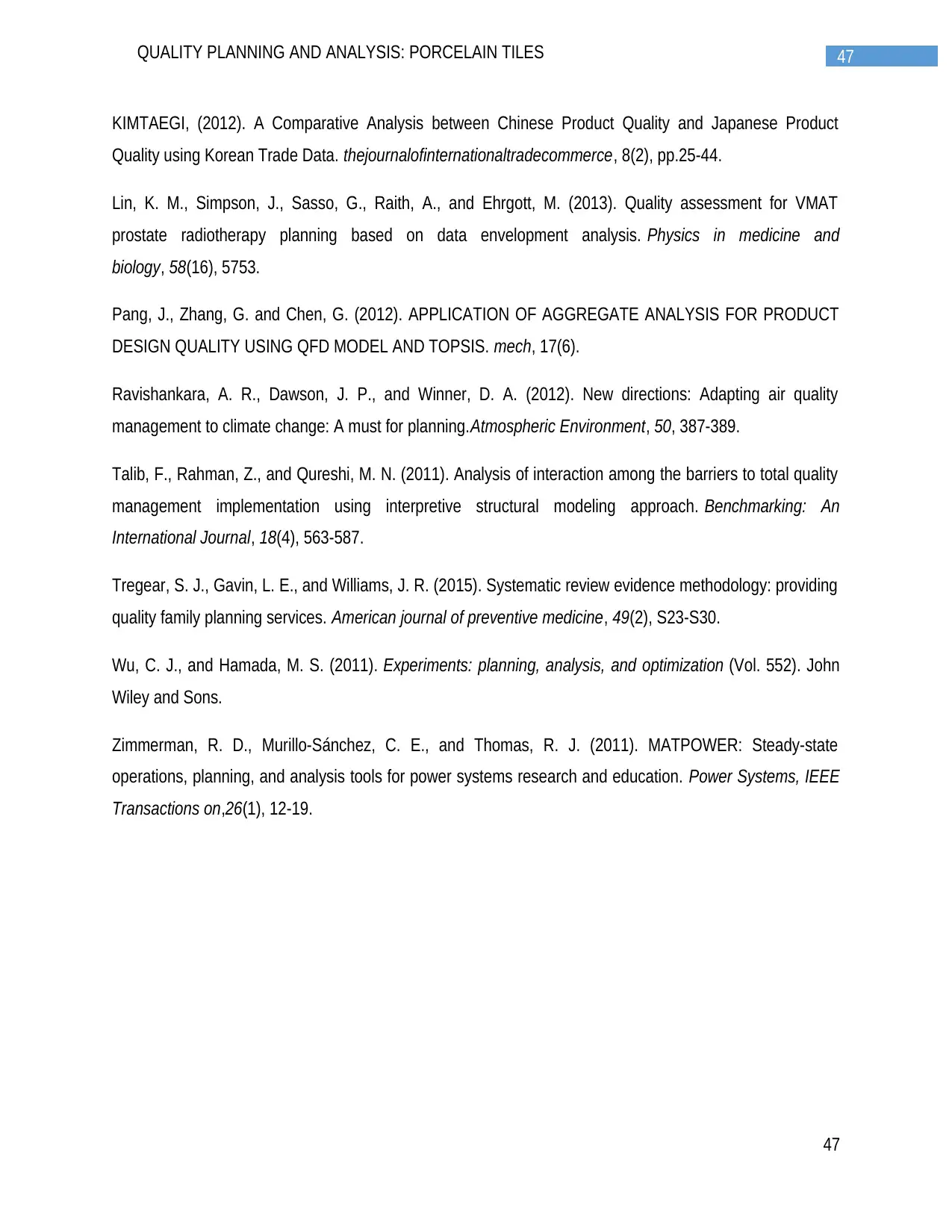
KIMTAEGI, (2012). A Comparative Analysis between Chinese Product Quality and Japanese Product
Quality using Korean Trade Data. thejournalofinternationaltradecommerce, 8(2), pp.25-44.
Lin, K. M., Simpson, J., Sasso, G., Raith, A., and Ehrgott, M. (2013). Quality assessment for VMAT
prostate radiotherapy planning based on data envelopment analysis. Physics in medicine and
biology, 58(16), 5753.
Pang, J., Zhang, G. and Chen, G. (2012). APPLICATION OF AGGREGATE ANALYSIS FOR PRODUCT
DESIGN QUALITY USING QFD MODEL AND TOPSIS. mech, 17(6).
Ravishankara, A. R., Dawson, J. P., and Winner, D. A. (2012). New directions: Adapting air quality
management to climate change: A must for planning.Atmospheric Environment, 50, 387-389.
Talib, F., Rahman, Z., and Qureshi, M. N. (2011). Analysis of interaction among the barriers to total quality
management implementation using interpretive structural modeling approach. Benchmarking: An
International Journal, 18(4), 563-587.
Tregear, S. J., Gavin, L. E., and Williams, J. R. (2015). Systematic review evidence methodology: providing
quality family planning services. American journal of preventive medicine, 49(2), S23-S30.
Wu, C. J., and Hamada, M. S. (2011). Experiments: planning, analysis, and optimization (Vol. 552). John
Wiley and Sons.
Zimmerman, R. D., Murillo-Sánchez, C. E., and Thomas, R. J. (2011). MATPOWER: Steady-state
operations, planning, and analysis tools for power systems research and education. Power Systems, IEEE
Transactions on,26(1), 12-19.
47
⊘ This is a preview!⊘
Do you want full access?
Subscribe today to unlock all pages.

Trusted by 1+ million students worldwide
Related Documents

Your All-in-One AI-Powered Toolkit for Academic Success.
+13062052269
info@desklib.com
Available 24*7 on WhatsApp / Email
© 2024 | Zucol Services PVT LTD | All rights reserved.