Process Mapping: Techniques, Benefits, and Waste Reduction
VerifiedAdded on 2023/06/08
|6
|886
|211
AI Summary
This article discusses process mapping, a technique used to identify and analyze the steps required to achieve a desired outcome. It covers the benefits of process mapping, waste reduction strategies, and the seven wastes to avoid. The article includes a case study on making a Big Mac.
Contribute Materials
Your contribution can guide someone’s learning journey. Share your
documents today.
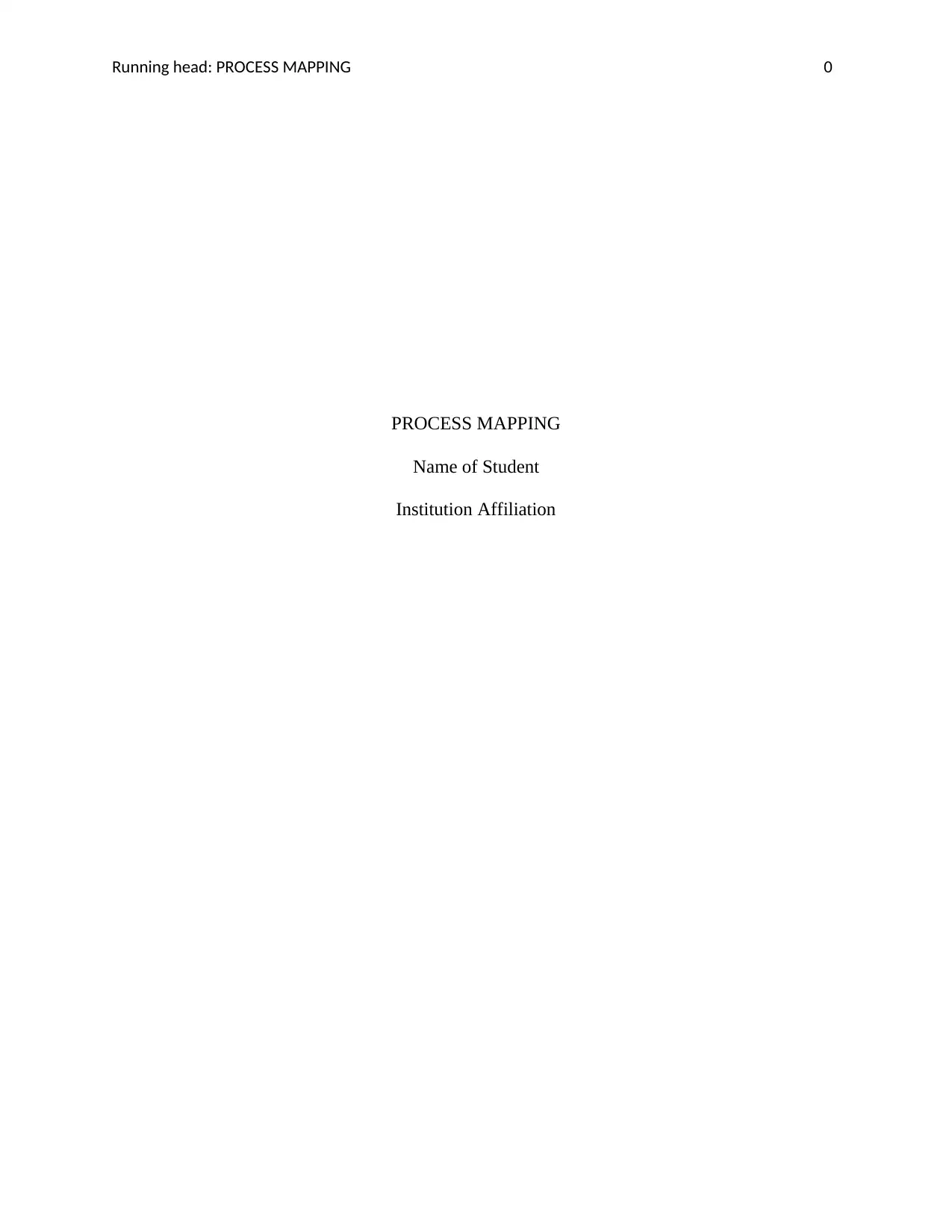
Running head: PROCESS MAPPING 0
PROCESS MAPPING
Name of Student
Institution Affiliation
PROCESS MAPPING
Name of Student
Institution Affiliation
Secure Best Marks with AI Grader
Need help grading? Try our AI Grader for instant feedback on your assignments.
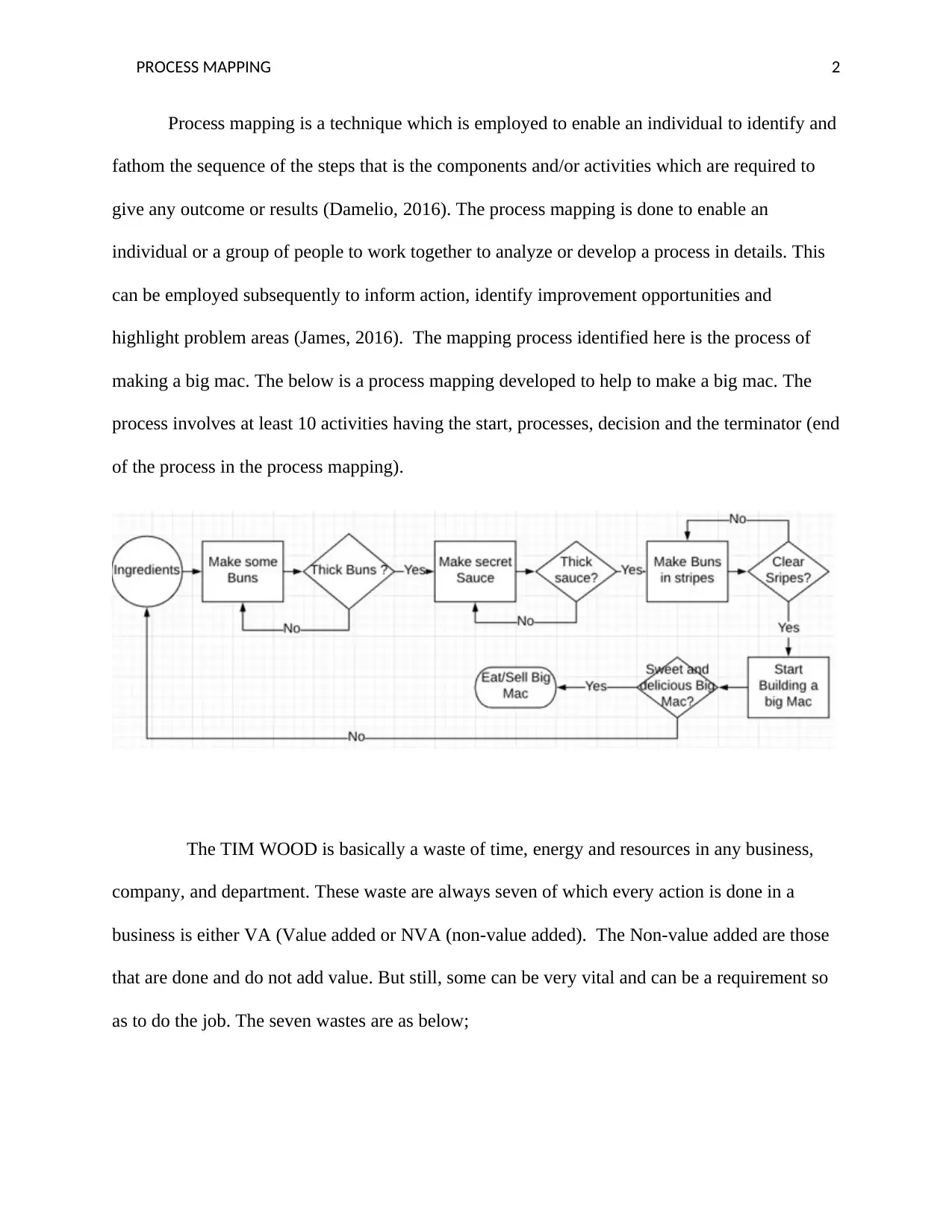
PROCESS MAPPING 2
Process mapping is a technique which is employed to enable an individual to identify and
fathom the sequence of the steps that is the components and/or activities which are required to
give any outcome or results (Damelio, 2016). The process mapping is done to enable an
individual or a group of people to work together to analyze or develop a process in details. This
can be employed subsequently to inform action, identify improvement opportunities and
highlight problem areas (James, 2016). The mapping process identified here is the process of
making a big mac. The below is a process mapping developed to help to make a big mac. The
process involves at least 10 activities having the start, processes, decision and the terminator (end
of the process in the process mapping).
The TIM WOOD is basically a waste of time, energy and resources in any business,
company, and department. These waste are always seven of which every action is done in a
business is either VA (Value added or NVA (non-value added). The Non-value added are those
that are done and do not add value. But still, some can be very vital and can be a requirement so
as to do the job. The seven wastes are as below;
Process mapping is a technique which is employed to enable an individual to identify and
fathom the sequence of the steps that is the components and/or activities which are required to
give any outcome or results (Damelio, 2016). The process mapping is done to enable an
individual or a group of people to work together to analyze or develop a process in details. This
can be employed subsequently to inform action, identify improvement opportunities and
highlight problem areas (James, 2016). The mapping process identified here is the process of
making a big mac. The below is a process mapping developed to help to make a big mac. The
process involves at least 10 activities having the start, processes, decision and the terminator (end
of the process in the process mapping).
The TIM WOOD is basically a waste of time, energy and resources in any business,
company, and department. These waste are always seven of which every action is done in a
business is either VA (Value added or NVA (non-value added). The Non-value added are those
that are done and do not add value. But still, some can be very vital and can be a requirement so
as to do the job. The seven wastes are as below;
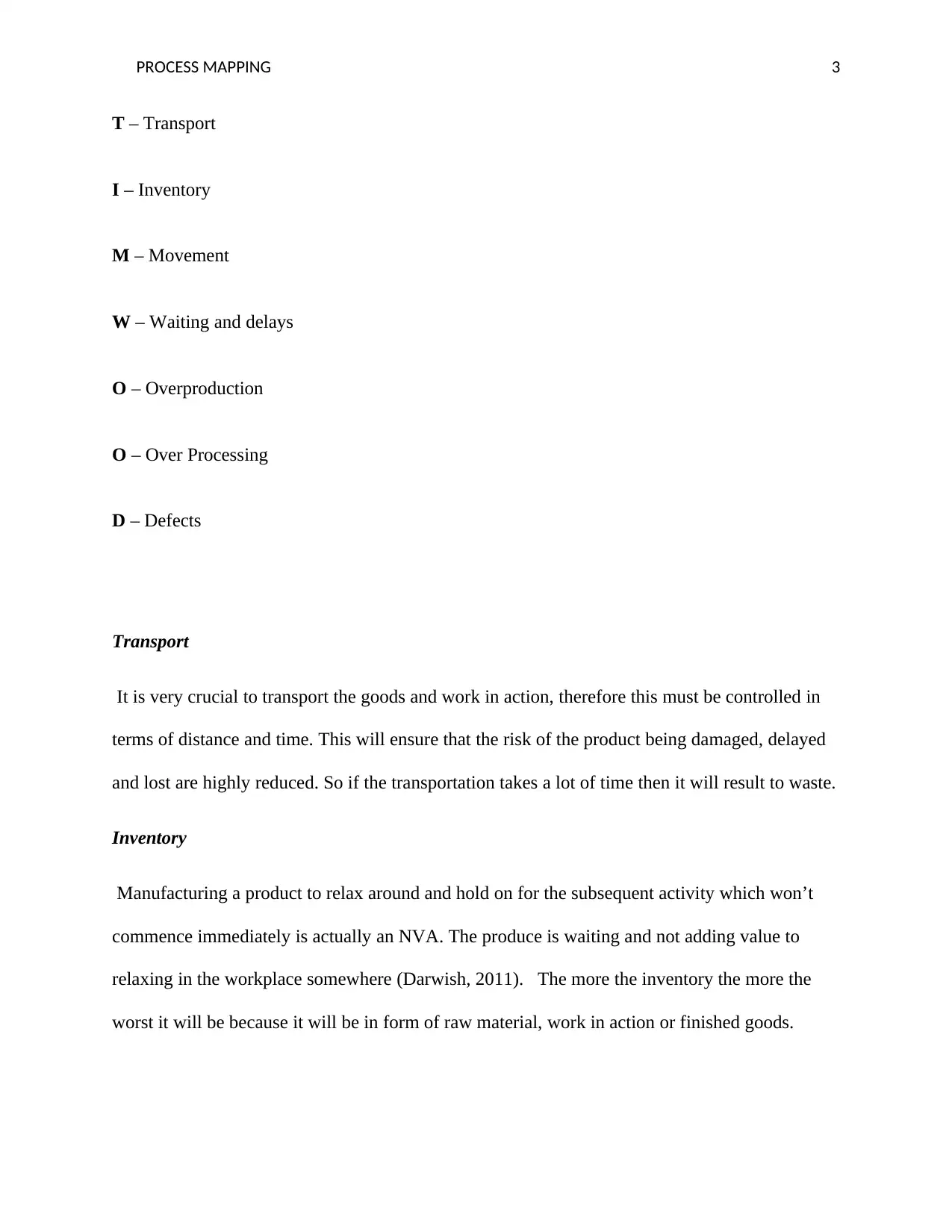
PROCESS MAPPING 3
T – Transport
I – Inventory
M – Movement
W – Waiting and delays
O – Overproduction
O – Over Processing
D – Defects
Transport
It is very crucial to transport the goods and work in action, therefore this must be controlled in
terms of distance and time. This will ensure that the risk of the product being damaged, delayed
and lost are highly reduced. So if the transportation takes a lot of time then it will result to waste.
Inventory
Manufacturing a product to relax around and hold on for the subsequent activity which won’t
commence immediately is actually an NVA. The produce is waiting and not adding value to
relaxing in the workplace somewhere (Darwish, 2011). The more the inventory the more the
worst it will be because it will be in form of raw material, work in action or finished goods.
T – Transport
I – Inventory
M – Movement
W – Waiting and delays
O – Overproduction
O – Over Processing
D – Defects
Transport
It is very crucial to transport the goods and work in action, therefore this must be controlled in
terms of distance and time. This will ensure that the risk of the product being damaged, delayed
and lost are highly reduced. So if the transportation takes a lot of time then it will result to waste.
Inventory
Manufacturing a product to relax around and hold on for the subsequent activity which won’t
commence immediately is actually an NVA. The produce is waiting and not adding value to
relaxing in the workplace somewhere (Darwish, 2011). The more the inventory the more the
worst it will be because it will be in form of raw material, work in action or finished goods.
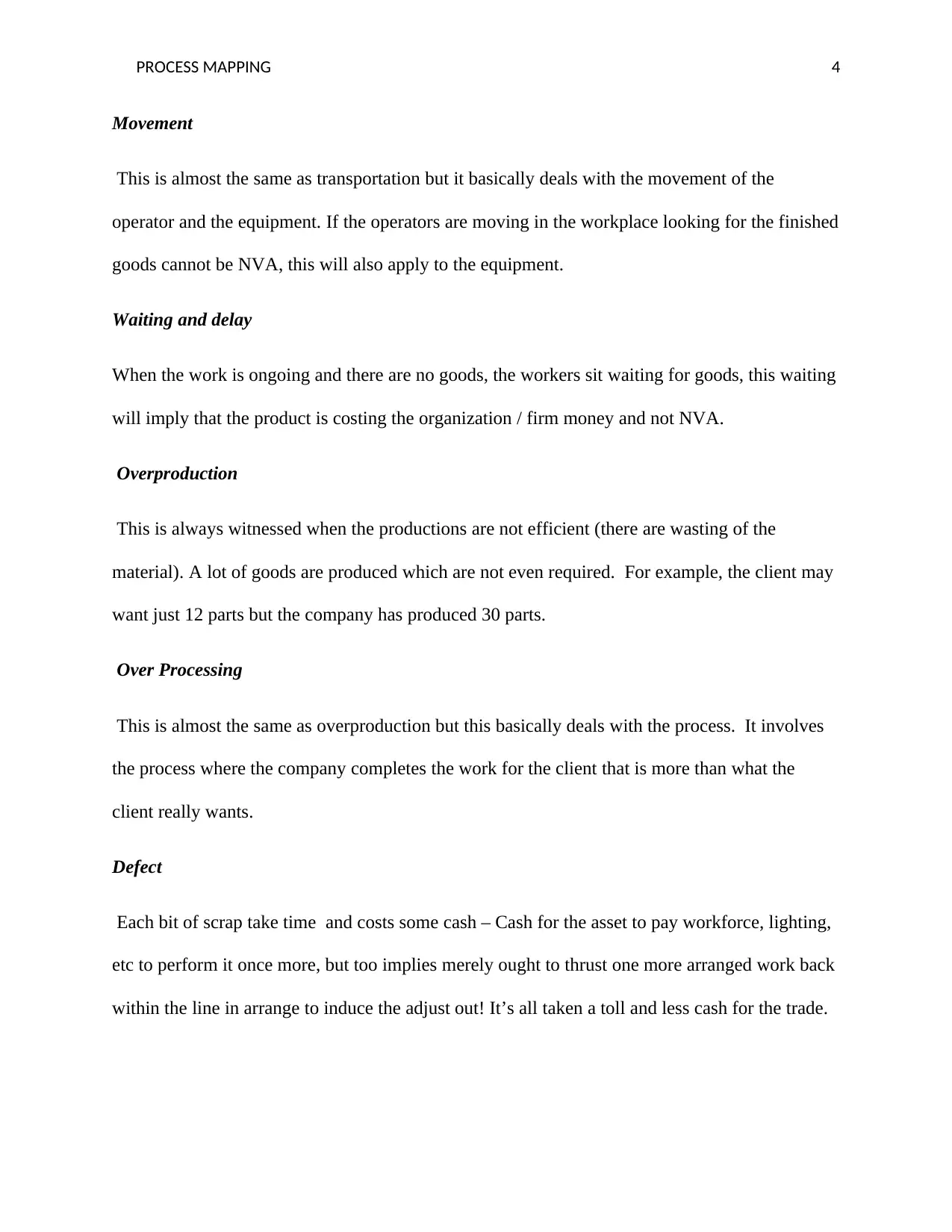
PROCESS MAPPING 4
Movement
This is almost the same as transportation but it basically deals with the movement of the
operator and the equipment. If the operators are moving in the workplace looking for the finished
goods cannot be NVA, this will also apply to the equipment.
Waiting and delay
When the work is ongoing and there are no goods, the workers sit waiting for goods, this waiting
will imply that the product is costing the organization / firm money and not NVA.
Overproduction
This is always witnessed when the productions are not efficient (there are wasting of the
material). A lot of goods are produced which are not even required. For example, the client may
want just 12 parts but the company has produced 30 parts.
Over Processing
This is almost the same as overproduction but this basically deals with the process. It involves
the process where the company completes the work for the client that is more than what the
client really wants.
Defect
Each bit of scrap take time and costs some cash – Cash for the asset to pay workforce, lighting,
etc to perform it once more, but too implies merely ought to thrust one more arranged work back
within the line in arrange to induce the adjust out! It’s all taken a toll and less cash for the trade.
Movement
This is almost the same as transportation but it basically deals with the movement of the
operator and the equipment. If the operators are moving in the workplace looking for the finished
goods cannot be NVA, this will also apply to the equipment.
Waiting and delay
When the work is ongoing and there are no goods, the workers sit waiting for goods, this waiting
will imply that the product is costing the organization / firm money and not NVA.
Overproduction
This is always witnessed when the productions are not efficient (there are wasting of the
material). A lot of goods are produced which are not even required. For example, the client may
want just 12 parts but the company has produced 30 parts.
Over Processing
This is almost the same as overproduction but this basically deals with the process. It involves
the process where the company completes the work for the client that is more than what the
client really wants.
Defect
Each bit of scrap take time and costs some cash – Cash for the asset to pay workforce, lighting,
etc to perform it once more, but too implies merely ought to thrust one more arranged work back
within the line in arrange to induce the adjust out! It’s all taken a toll and less cash for the trade.
Secure Best Marks with AI Grader
Need help grading? Try our AI Grader for instant feedback on your assignments.
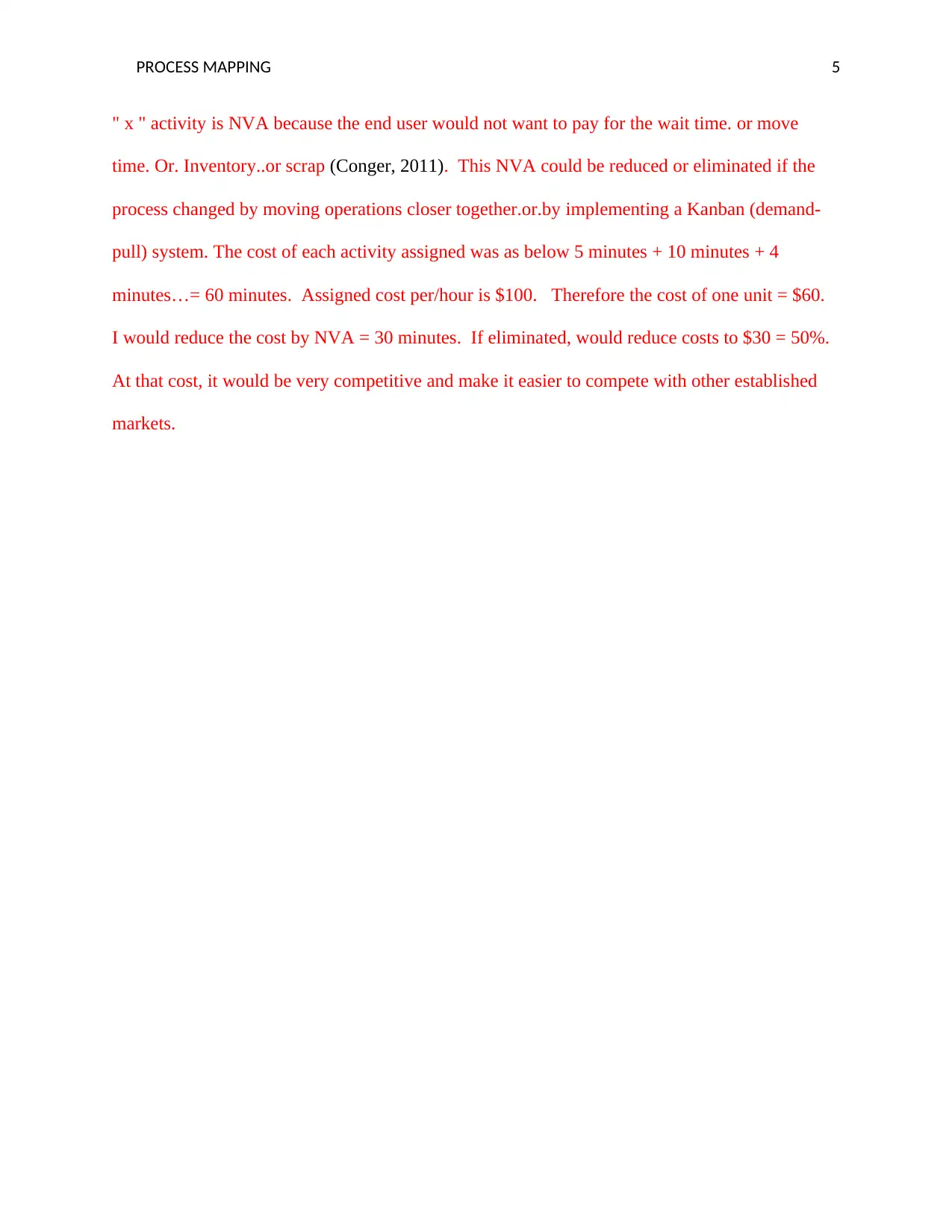
PROCESS MAPPING 5
" x " activity is NVA because the end user would not want to pay for the wait time. or move
time. Or. Inventory..or scrap (Conger, 2011). This NVA could be reduced or eliminated if the
process changed by moving operations closer together.or.by implementing a Kanban (demand-
pull) system. The cost of each activity assigned was as below 5 minutes + 10 minutes + 4
minutes…= 60 minutes. Assigned cost per/hour is $100. Therefore the cost of one unit = $60.
I would reduce the cost by NVA = 30 minutes. If eliminated, would reduce costs to $30 = 50%.
At that cost, it would be very competitive and make it easier to compete with other established
markets.
" x " activity is NVA because the end user would not want to pay for the wait time. or move
time. Or. Inventory..or scrap (Conger, 2011). This NVA could be reduced or eliminated if the
process changed by moving operations closer together.or.by implementing a Kanban (demand-
pull) system. The cost of each activity assigned was as below 5 minutes + 10 minutes + 4
minutes…= 60 minutes. Assigned cost per/hour is $100. Therefore the cost of one unit = $60.
I would reduce the cost by NVA = 30 minutes. If eliminated, would reduce costs to $30 = 50%.
At that cost, it would be very competitive and make it easier to compete with other established
markets.
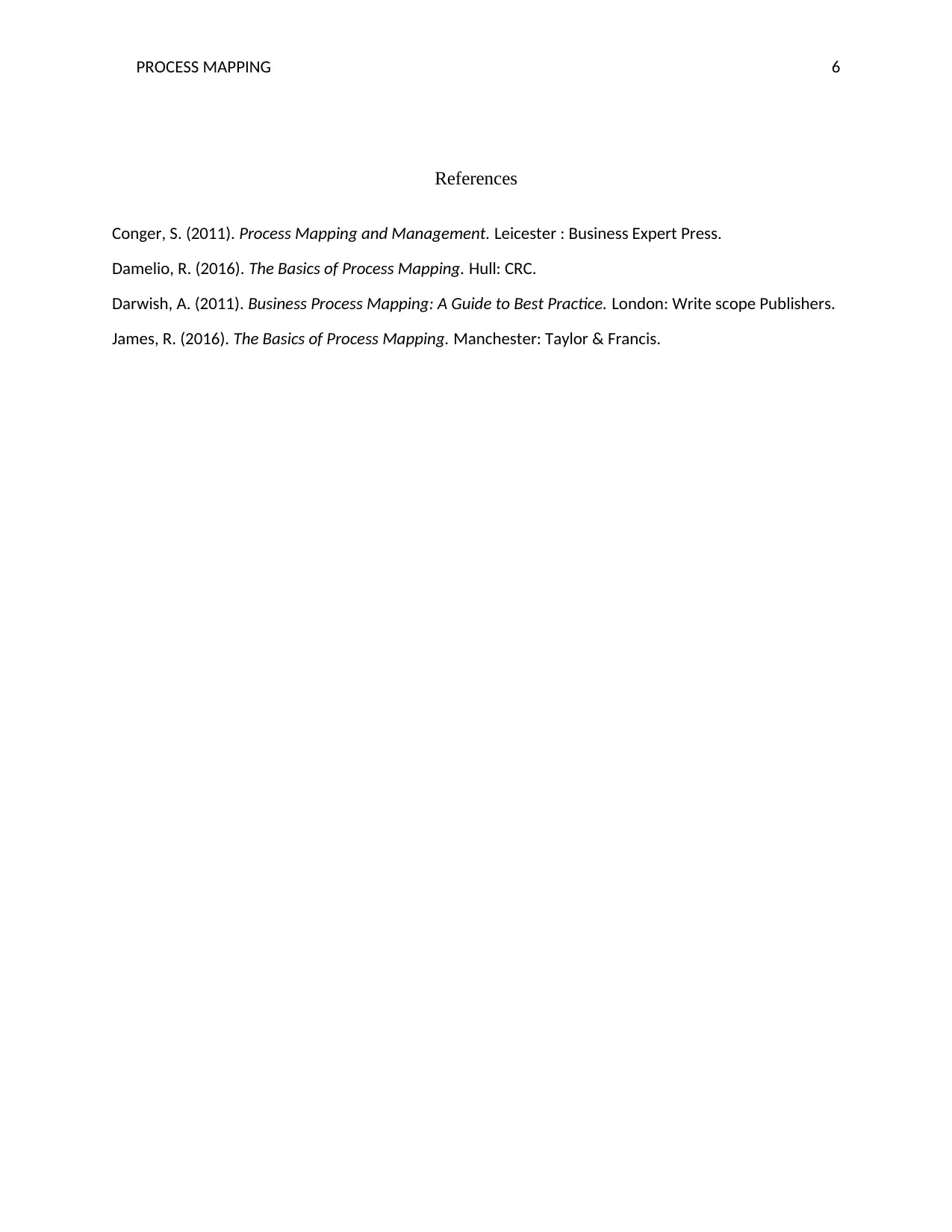
PROCESS MAPPING 6
References
Conger, S. (2011). Process Mapping and Management. Leicester : Business Expert Press.
Damelio, R. (2016). The Basics of Process Mapping. Hull: CRC.
Darwish, A. (2011). Business Process Mapping: A Guide to Best Practice. London: Write scope Publishers.
James, R. (2016). The Basics of Process Mapping. Manchester: Taylor & Francis.
References
Conger, S. (2011). Process Mapping and Management. Leicester : Business Expert Press.
Damelio, R. (2016). The Basics of Process Mapping. Hull: CRC.
Darwish, A. (2011). Business Process Mapping: A Guide to Best Practice. London: Write scope Publishers.
James, R. (2016). The Basics of Process Mapping. Manchester: Taylor & Francis.
1 out of 6
![[object Object]](/_next/image/?url=%2F_next%2Fstatic%2Fmedia%2Flogo.6d15ce61.png&w=640&q=75)
Your All-in-One AI-Powered Toolkit for Academic Success.
+13062052269
info@desklib.com
Available 24*7 on WhatsApp / Email
Unlock your academic potential
© 2024 | Zucol Services PVT LTD | All rights reserved.