Production and Operation Management
VerifiedAdded on  2023/04/20
|9
|1743
|173
AI Summary
This document provides an overview of production and operation management, covering topics such as operational management, NOSA, product planning process, reliability, and demand forecasting. It also discusses independent and dependent demand, pipeline and buffer inventory, carrying costs, JIT, and MRP-II. Additionally, it explores fixed capacity planning and continuous production process. The document concludes with a computation of EOQ and reorder point, as well as a discussion on the operation systems of a business.
Contribute Materials
Your contribution can guide someone’s learning journey. Share your
documents today.
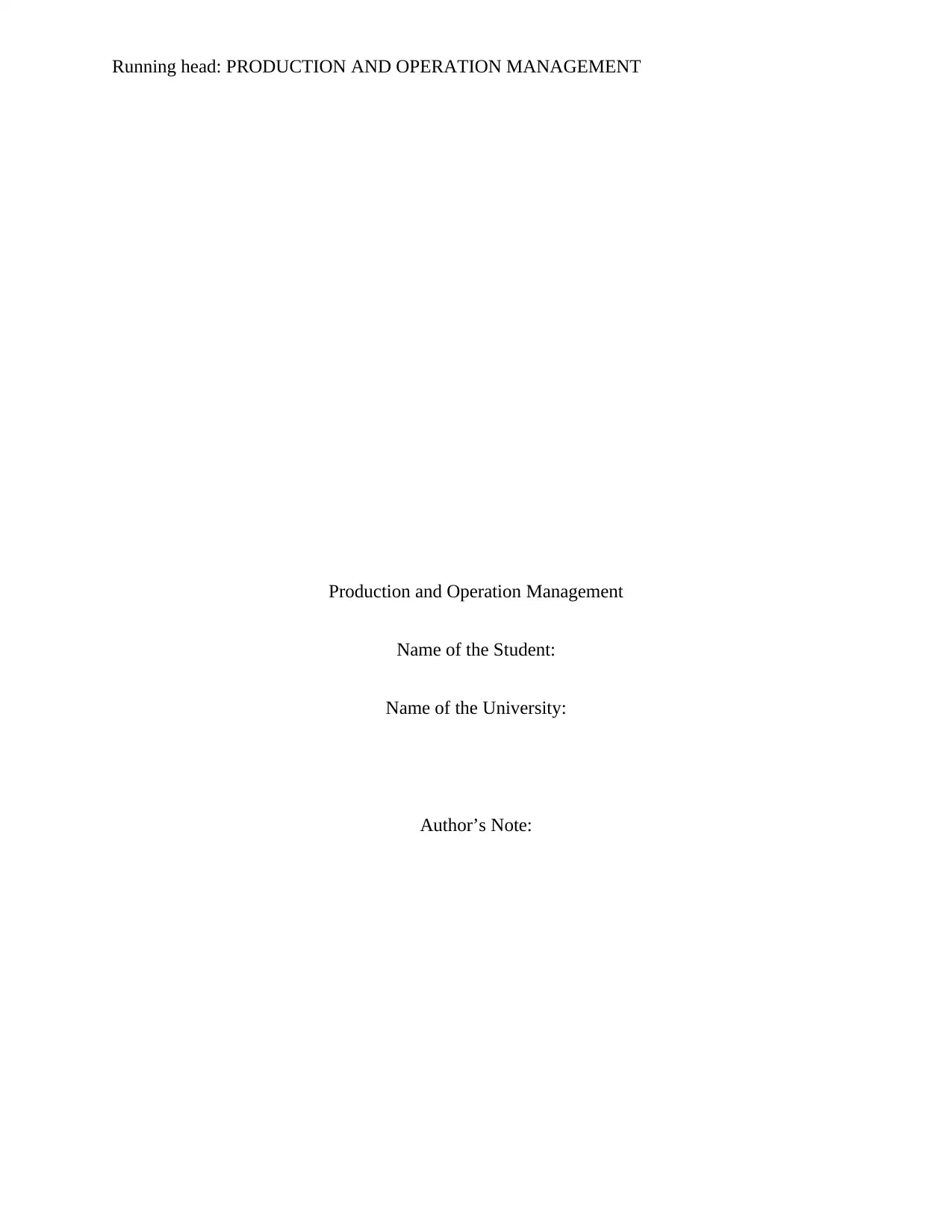
Running head: PRODUCTION AND OPERATION MANAGEMENT
Production and Operation Management
Name of the Student:
Name of the University:
Author’s Note:
Production and Operation Management
Name of the Student:
Name of the University:
Author’s Note:
Secure Best Marks with AI Grader
Need help grading? Try our AI Grader for instant feedback on your assignments.
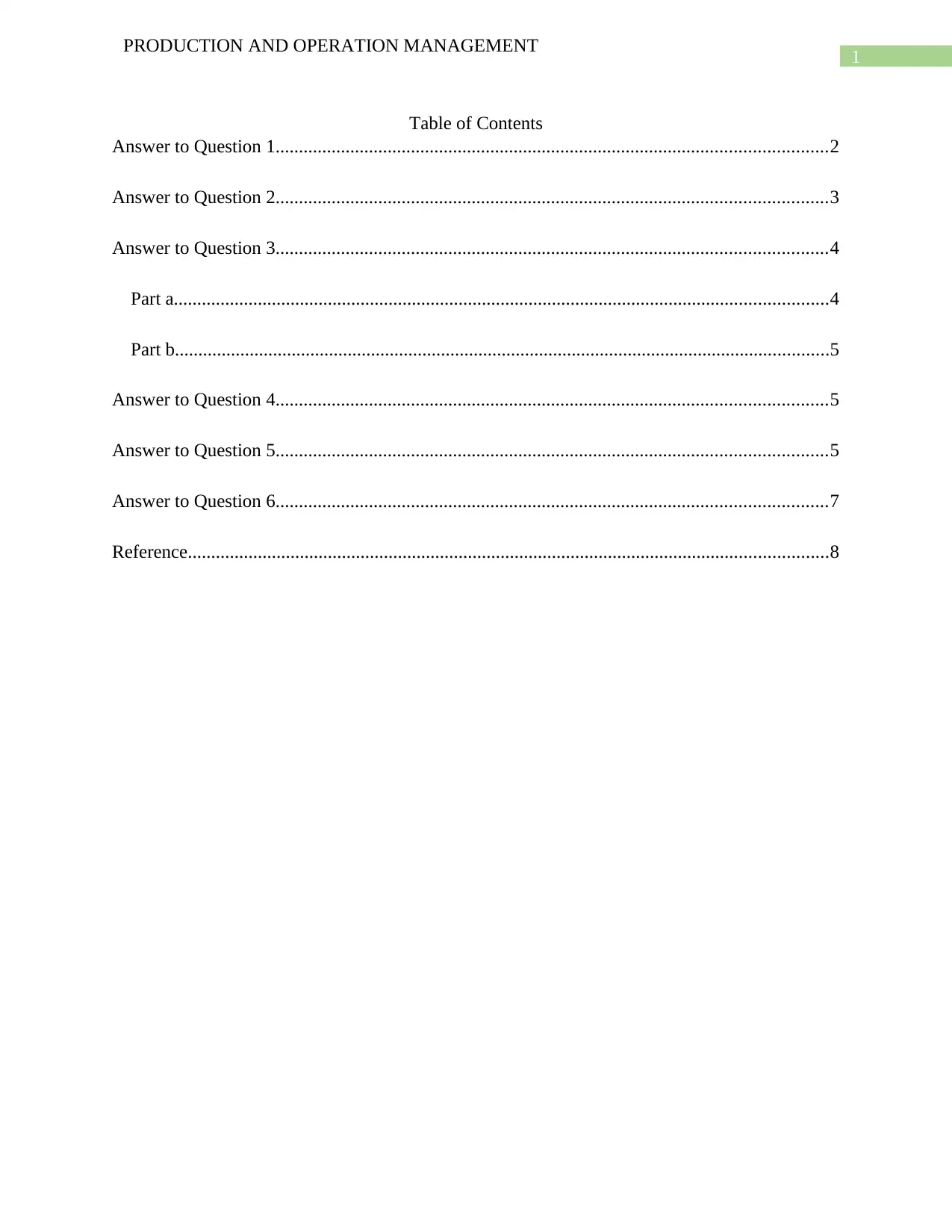
1
PRODUCTION AND OPERATION MANAGEMENT
Table of Contents
Answer to Question 1......................................................................................................................2
Answer to Question 2......................................................................................................................3
Answer to Question 3......................................................................................................................4
Part a............................................................................................................................................4
Part b............................................................................................................................................5
Answer to Question 4......................................................................................................................5
Answer to Question 5......................................................................................................................5
Answer to Question 6......................................................................................................................7
Reference.........................................................................................................................................8
PRODUCTION AND OPERATION MANAGEMENT
Table of Contents
Answer to Question 1......................................................................................................................2
Answer to Question 2......................................................................................................................3
Answer to Question 3......................................................................................................................4
Part a............................................................................................................................................4
Part b............................................................................................................................................5
Answer to Question 4......................................................................................................................5
Answer to Question 5......................................................................................................................5
Answer to Question 6......................................................................................................................7
Reference.........................................................................................................................................8
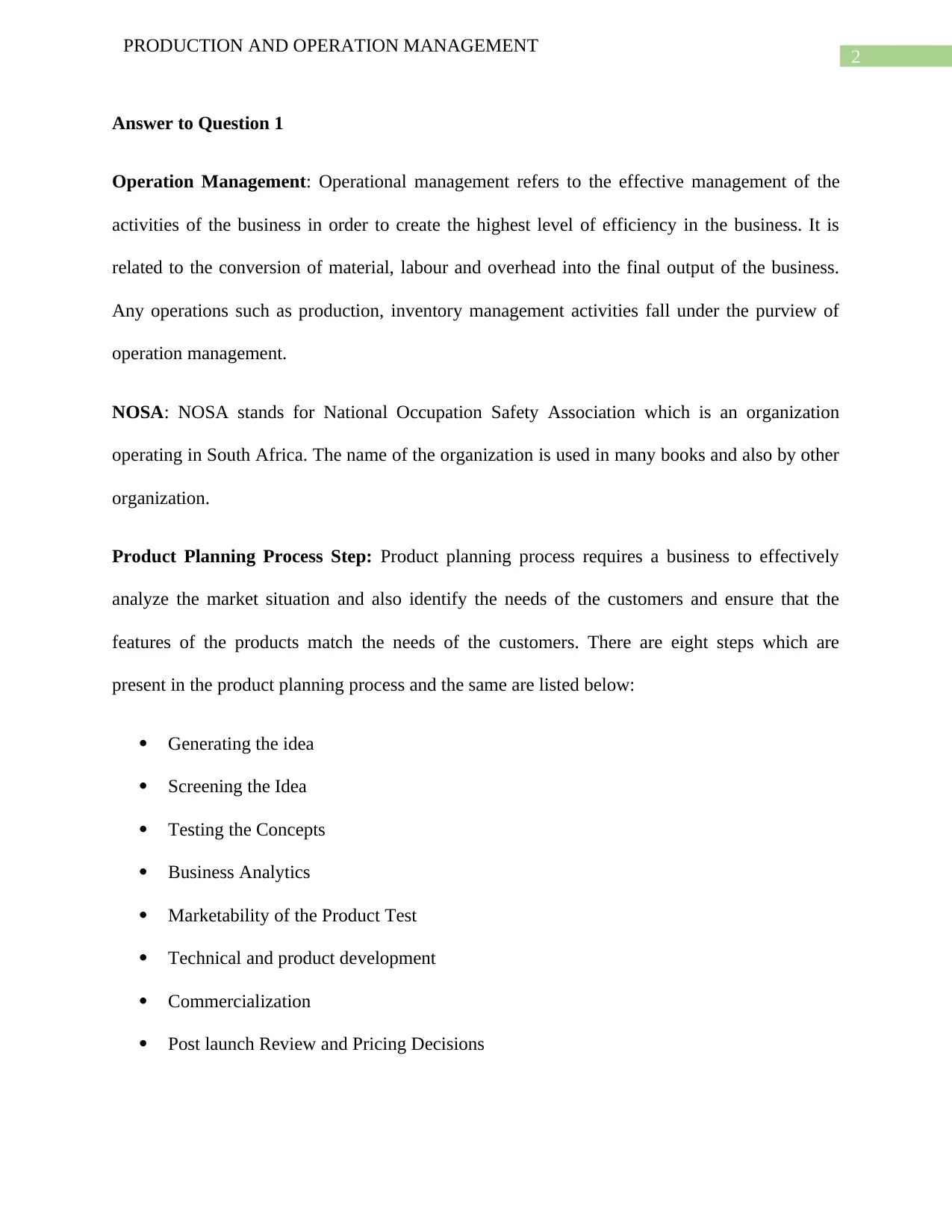
2
PRODUCTION AND OPERATION MANAGEMENT
Answer to Question 1
Operation Management: Operational management refers to the effective management of the
activities of the business in order to create the highest level of efficiency in the business. It is
related to the conversion of material, labour and overhead into the final output of the business.
Any operations such as production, inventory management activities fall under the purview of
operation management.
NOSA: NOSA stands for National Occupation Safety Association which is an organization
operating in South Africa. The name of the organization is used in many books and also by other
organization.
Product Planning Process Step: Product planning process requires a business to effectively
analyze the market situation and also identify the needs of the customers and ensure that the
features of the products match the needs of the customers. There are eight steps which are
present in the product planning process and the same are listed below:
ï‚· Generating the idea
ï‚· Screening the Idea
ï‚· Testing the Concepts
ï‚· Business Analytics
ï‚· Marketability of the Product Test
ï‚· Technical and product development
ï‚· Commercialization
ï‚· Post launch Review and Pricing Decisions
PRODUCTION AND OPERATION MANAGEMENT
Answer to Question 1
Operation Management: Operational management refers to the effective management of the
activities of the business in order to create the highest level of efficiency in the business. It is
related to the conversion of material, labour and overhead into the final output of the business.
Any operations such as production, inventory management activities fall under the purview of
operation management.
NOSA: NOSA stands for National Occupation Safety Association which is an organization
operating in South Africa. The name of the organization is used in many books and also by other
organization.
Product Planning Process Step: Product planning process requires a business to effectively
analyze the market situation and also identify the needs of the customers and ensure that the
features of the products match the needs of the customers. There are eight steps which are
present in the product planning process and the same are listed below:
ï‚· Generating the idea
ï‚· Screening the Idea
ï‚· Testing the Concepts
ï‚· Business Analytics
ï‚· Marketability of the Product Test
ï‚· Technical and product development
ï‚· Commercialization
ï‚· Post launch Review and Pricing Decisions
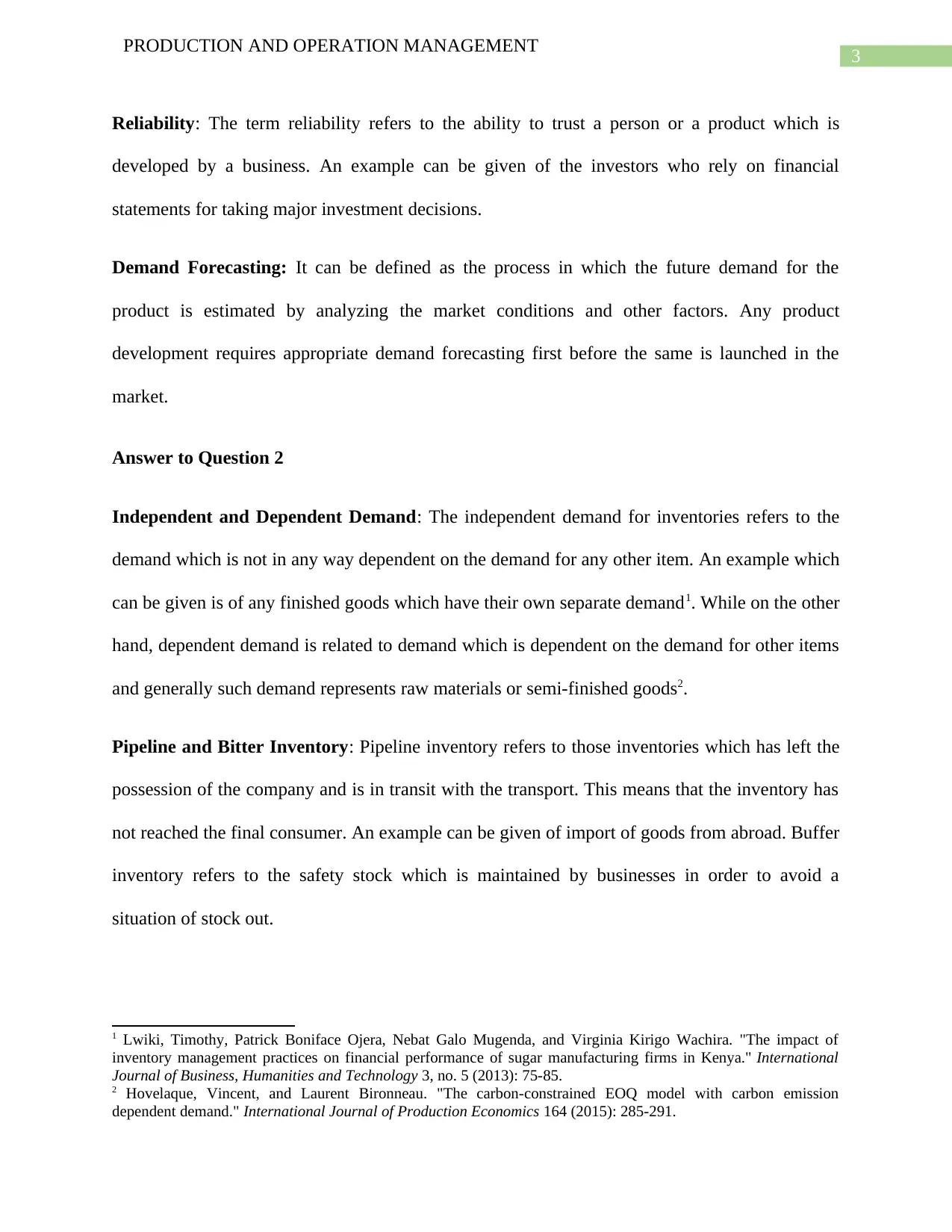
3
PRODUCTION AND OPERATION MANAGEMENT
Reliability: The term reliability refers to the ability to trust a person or a product which is
developed by a business. An example can be given of the investors who rely on financial
statements for taking major investment decisions.
Demand Forecasting: It can be defined as the process in which the future demand for the
product is estimated by analyzing the market conditions and other factors. Any product
development requires appropriate demand forecasting first before the same is launched in the
market.
Answer to Question 2
Independent and Dependent Demand: The independent demand for inventories refers to the
demand which is not in any way dependent on the demand for any other item. An example which
can be given is of any finished goods which have their own separate demand1. While on the other
hand, dependent demand is related to demand which is dependent on the demand for other items
and generally such demand represents raw materials or semi-finished goods2.
Pipeline and Bitter Inventory: Pipeline inventory refers to those inventories which has left the
possession of the company and is in transit with the transport. This means that the inventory has
not reached the final consumer. An example can be given of import of goods from abroad. Buffer
inventory refers to the safety stock which is maintained by businesses in order to avoid a
situation of stock out.
1 Lwiki, Timothy, Patrick Boniface Ojera, Nebat Galo Mugenda, and Virginia Kirigo Wachira. "The impact of
inventory management practices on financial performance of sugar manufacturing firms in Kenya." International
Journal of Business, Humanities and Technology 3, no. 5 (2013): 75-85.
2 Hovelaque, Vincent, and Laurent Bironneau. "The carbon-constrained EOQ model with carbon emission
dependent demand." International Journal of Production Economics 164 (2015): 285-291.
PRODUCTION AND OPERATION MANAGEMENT
Reliability: The term reliability refers to the ability to trust a person or a product which is
developed by a business. An example can be given of the investors who rely on financial
statements for taking major investment decisions.
Demand Forecasting: It can be defined as the process in which the future demand for the
product is estimated by analyzing the market conditions and other factors. Any product
development requires appropriate demand forecasting first before the same is launched in the
market.
Answer to Question 2
Independent and Dependent Demand: The independent demand for inventories refers to the
demand which is not in any way dependent on the demand for any other item. An example which
can be given is of any finished goods which have their own separate demand1. While on the other
hand, dependent demand is related to demand which is dependent on the demand for other items
and generally such demand represents raw materials or semi-finished goods2.
Pipeline and Bitter Inventory: Pipeline inventory refers to those inventories which has left the
possession of the company and is in transit with the transport. This means that the inventory has
not reached the final consumer. An example can be given of import of goods from abroad. Buffer
inventory refers to the safety stock which is maintained by businesses in order to avoid a
situation of stock out.
1 Lwiki, Timothy, Patrick Boniface Ojera, Nebat Galo Mugenda, and Virginia Kirigo Wachira. "The impact of
inventory management practices on financial performance of sugar manufacturing firms in Kenya." International
Journal of Business, Humanities and Technology 3, no. 5 (2013): 75-85.
2 Hovelaque, Vincent, and Laurent Bironneau. "The carbon-constrained EOQ model with carbon emission
dependent demand." International Journal of Production Economics 164 (2015): 285-291.
Secure Best Marks with AI Grader
Need help grading? Try our AI Grader for instant feedback on your assignments.
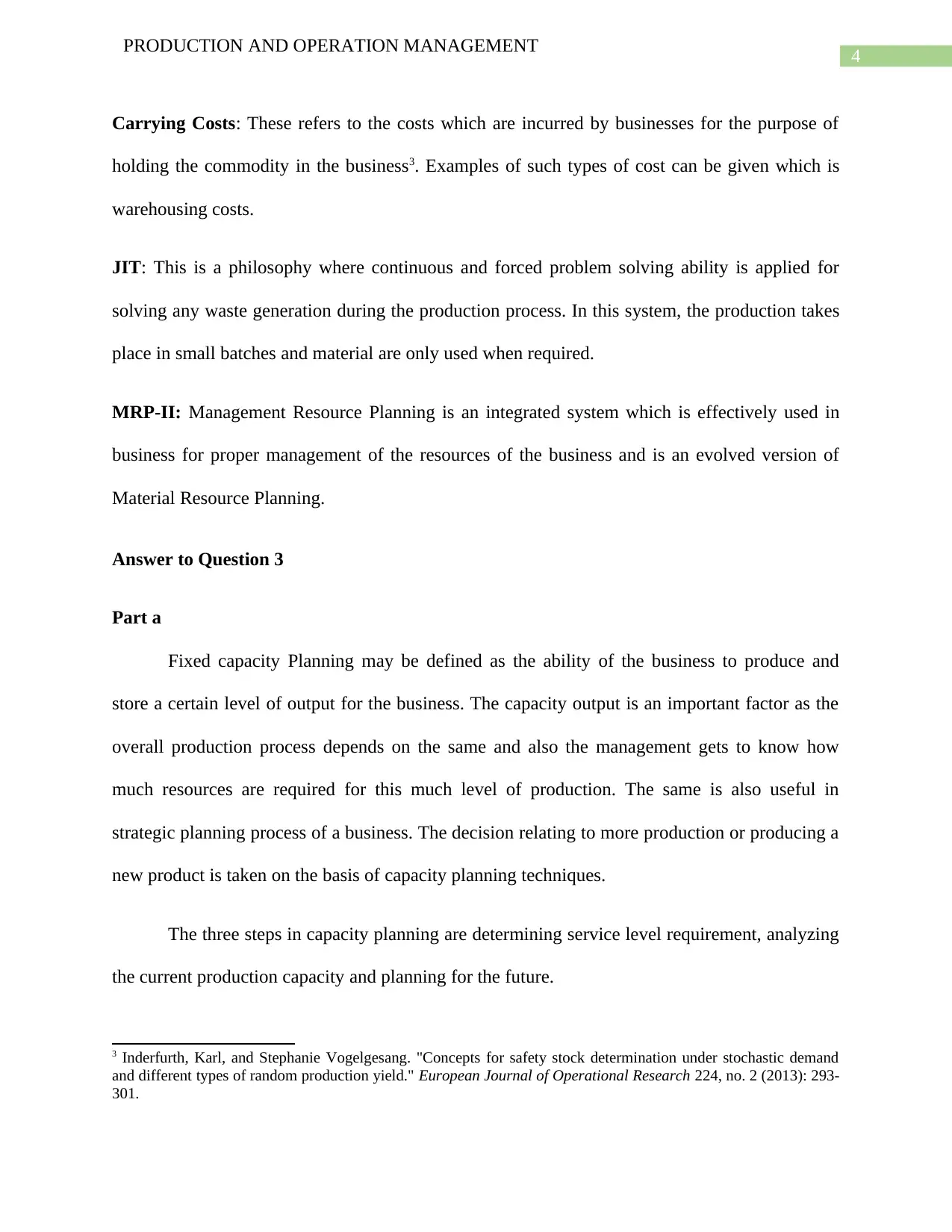
4
PRODUCTION AND OPERATION MANAGEMENT
Carrying Costs: These refers to the costs which are incurred by businesses for the purpose of
holding the commodity in the business3. Examples of such types of cost can be given which is
warehousing costs.
JIT: This is a philosophy where continuous and forced problem solving ability is applied for
solving any waste generation during the production process. In this system, the production takes
place in small batches and material are only used when required.
MRP-II: Management Resource Planning is an integrated system which is effectively used in
business for proper management of the resources of the business and is an evolved version of
Material Resource Planning.
Answer to Question 3
Part a
Fixed capacity Planning may be defined as the ability of the business to produce and
store a certain level of output for the business. The capacity output is an important factor as the
overall production process depends on the same and also the management gets to know how
much resources are required for this much level of production. The same is also useful in
strategic planning process of a business. The decision relating to more production or producing a
new product is taken on the basis of capacity planning techniques.
The three steps in capacity planning are determining service level requirement, analyzing
the current production capacity and planning for the future.
3 Inderfurth, Karl, and Stephanie Vogelgesang. "Concepts for safety stock determination under stochastic demand
and different types of random production yield." European Journal of Operational Research 224, no. 2 (2013): 293-
301.
PRODUCTION AND OPERATION MANAGEMENT
Carrying Costs: These refers to the costs which are incurred by businesses for the purpose of
holding the commodity in the business3. Examples of such types of cost can be given which is
warehousing costs.
JIT: This is a philosophy where continuous and forced problem solving ability is applied for
solving any waste generation during the production process. In this system, the production takes
place in small batches and material are only used when required.
MRP-II: Management Resource Planning is an integrated system which is effectively used in
business for proper management of the resources of the business and is an evolved version of
Material Resource Planning.
Answer to Question 3
Part a
Fixed capacity Planning may be defined as the ability of the business to produce and
store a certain level of output for the business. The capacity output is an important factor as the
overall production process depends on the same and also the management gets to know how
much resources are required for this much level of production. The same is also useful in
strategic planning process of a business. The decision relating to more production or producing a
new product is taken on the basis of capacity planning techniques.
The three steps in capacity planning are determining service level requirement, analyzing
the current production capacity and planning for the future.
3 Inderfurth, Karl, and Stephanie Vogelgesang. "Concepts for safety stock determination under stochastic demand
and different types of random production yield." European Journal of Operational Research 224, no. 2 (2013): 293-
301.
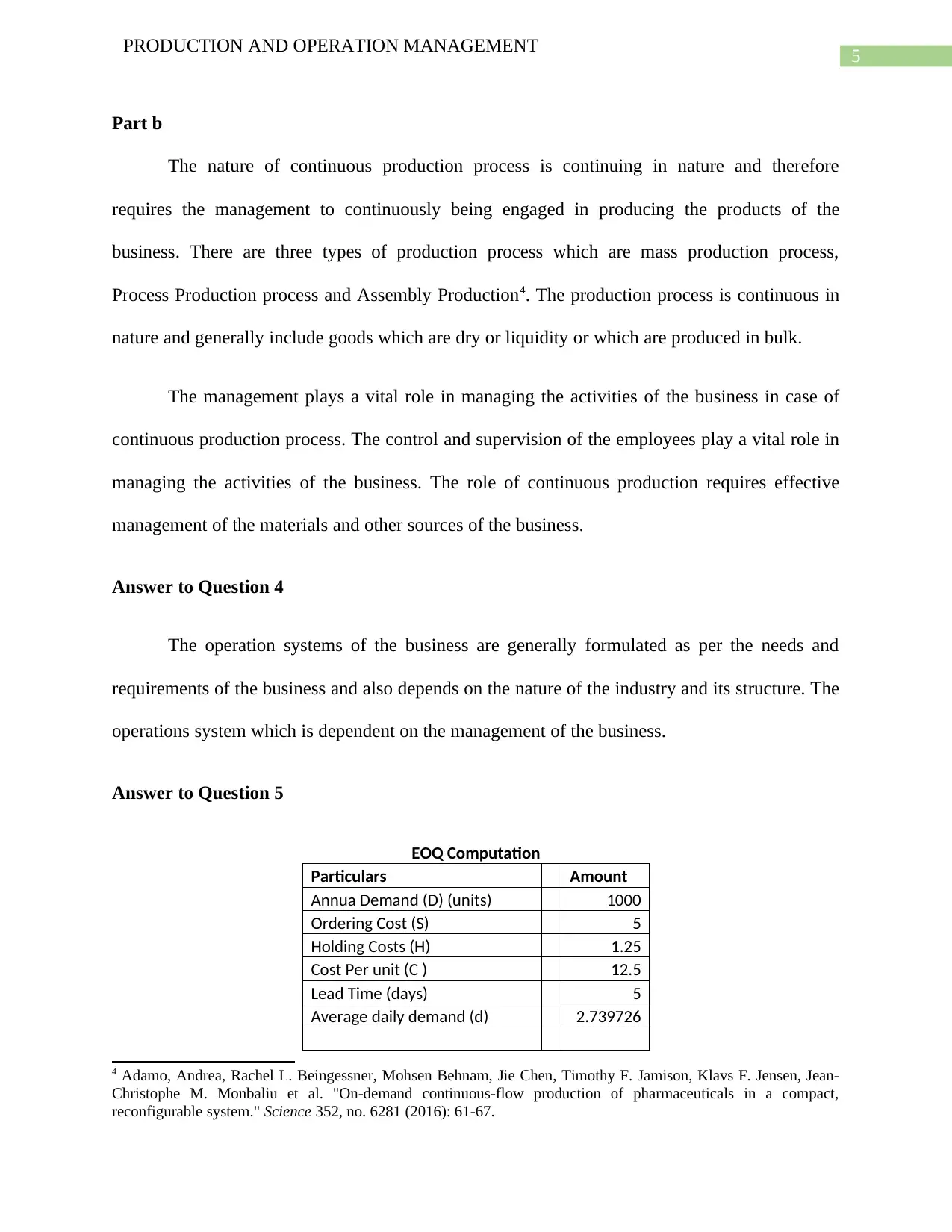
5
PRODUCTION AND OPERATION MANAGEMENT
Part b
The nature of continuous production process is continuing in nature and therefore
requires the management to continuously being engaged in producing the products of the
business. There are three types of production process which are mass production process,
Process Production process and Assembly Production4. The production process is continuous in
nature and generally include goods which are dry or liquidity or which are produced in bulk.
The management plays a vital role in managing the activities of the business in case of
continuous production process. The control and supervision of the employees play a vital role in
managing the activities of the business. The role of continuous production requires effective
management of the materials and other sources of the business.
Answer to Question 4
The operation systems of the business are generally formulated as per the needs and
requirements of the business and also depends on the nature of the industry and its structure. The
operations system which is dependent on the management of the business.
Answer to Question 5
EOQ Computation
Particulars Amount
Annua Demand (D) (units) 1000
Ordering Cost (S) 5
Holding Costs (H) 1.25
Cost Per unit (C ) 12.5
Lead Time (days) 5
Average daily demand (d) 2.739726
4 Adamo, Andrea, Rachel L. Beingessner, Mohsen Behnam, Jie Chen, Timothy F. Jamison, Klavs F. Jensen, Jean-
Christophe M. Monbaliu et al. "On-demand continuous-flow production of pharmaceuticals in a compact,
reconfigurable system." Science 352, no. 6281 (2016): 61-67.
PRODUCTION AND OPERATION MANAGEMENT
Part b
The nature of continuous production process is continuing in nature and therefore
requires the management to continuously being engaged in producing the products of the
business. There are three types of production process which are mass production process,
Process Production process and Assembly Production4. The production process is continuous in
nature and generally include goods which are dry or liquidity or which are produced in bulk.
The management plays a vital role in managing the activities of the business in case of
continuous production process. The control and supervision of the employees play a vital role in
managing the activities of the business. The role of continuous production requires effective
management of the materials and other sources of the business.
Answer to Question 4
The operation systems of the business are generally formulated as per the needs and
requirements of the business and also depends on the nature of the industry and its structure. The
operations system which is dependent on the management of the business.
Answer to Question 5
EOQ Computation
Particulars Amount
Annua Demand (D) (units) 1000
Ordering Cost (S) 5
Holding Costs (H) 1.25
Cost Per unit (C ) 12.5
Lead Time (days) 5
Average daily demand (d) 2.739726
4 Adamo, Andrea, Rachel L. Beingessner, Mohsen Behnam, Jie Chen, Timothy F. Jamison, Klavs F. Jensen, Jean-
Christophe M. Monbaliu et al. "On-demand continuous-flow production of pharmaceuticals in a compact,
reconfigurable system." Science 352, no. 6281 (2016): 61-67.
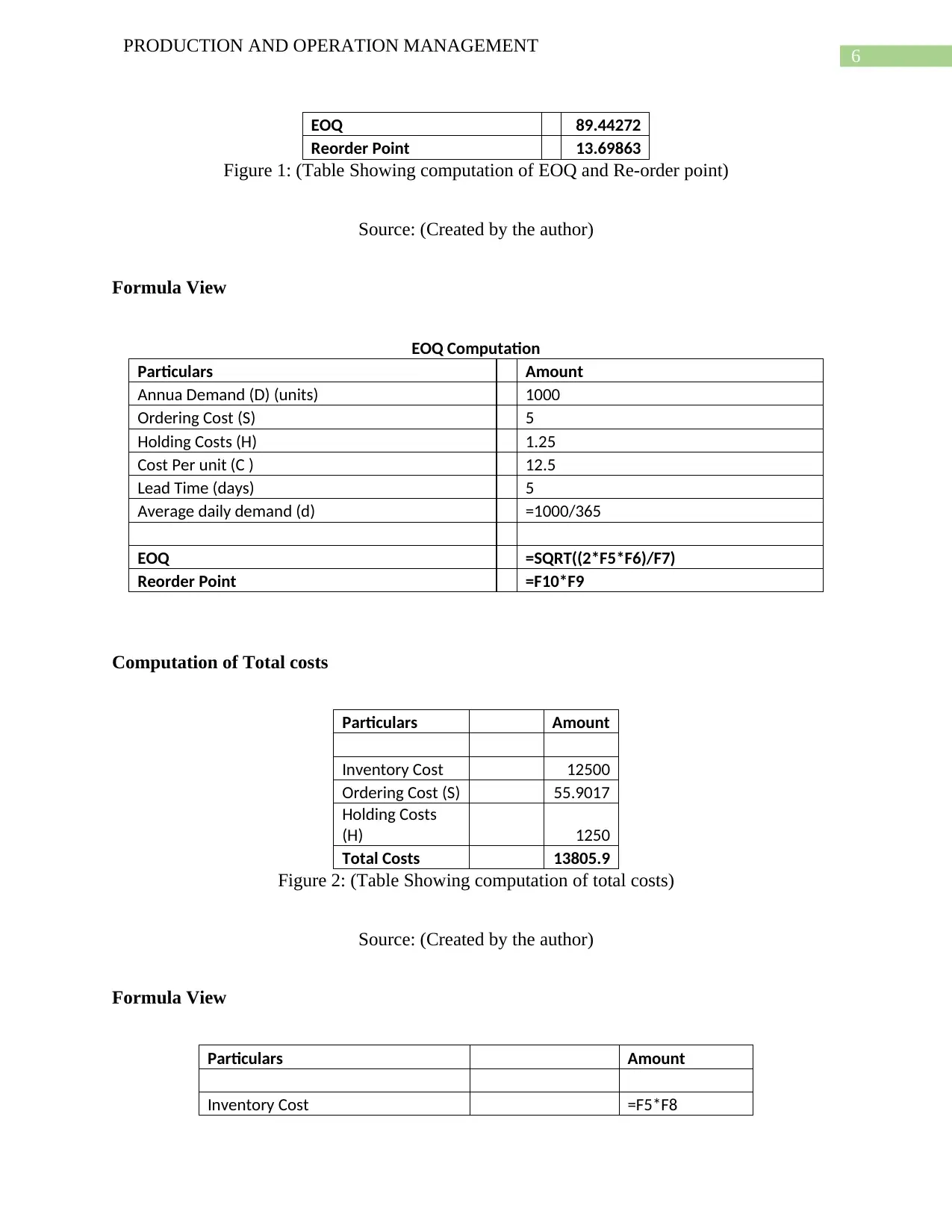
6
PRODUCTION AND OPERATION MANAGEMENT
EOQ 89.44272
Reorder Point 13.69863
Figure 1: (Table Showing computation of EOQ and Re-order point)
Source: (Created by the author)
Formula View
EOQ Computation
Particulars Amount
Annua Demand (D) (units) 1000
Ordering Cost (S) 5
Holding Costs (H) 1.25
Cost Per unit (C ) 12.5
Lead Time (days) 5
Average daily demand (d) =1000/365
EOQ =SQRT((2*F5*F6)/F7)
Reorder Point =F10*F9
Computation of Total costs
Particulars Amount
Inventory Cost 12500
Ordering Cost (S) 55.9017
Holding Costs
(H) 1250
Total Costs 13805.9
Figure 2: (Table Showing computation of total costs)
Source: (Created by the author)
Formula View
Particulars Amount
Inventory Cost =F5*F8
PRODUCTION AND OPERATION MANAGEMENT
EOQ 89.44272
Reorder Point 13.69863
Figure 1: (Table Showing computation of EOQ and Re-order point)
Source: (Created by the author)
Formula View
EOQ Computation
Particulars Amount
Annua Demand (D) (units) 1000
Ordering Cost (S) 5
Holding Costs (H) 1.25
Cost Per unit (C ) 12.5
Lead Time (days) 5
Average daily demand (d) =1000/365
EOQ =SQRT((2*F5*F6)/F7)
Reorder Point =F10*F9
Computation of Total costs
Particulars Amount
Inventory Cost 12500
Ordering Cost (S) 55.9017
Holding Costs
(H) 1250
Total Costs 13805.9
Figure 2: (Table Showing computation of total costs)
Source: (Created by the author)
Formula View
Particulars Amount
Inventory Cost =F5*F8
Paraphrase This Document
Need a fresh take? Get an instant paraphrase of this document with our AI Paraphraser
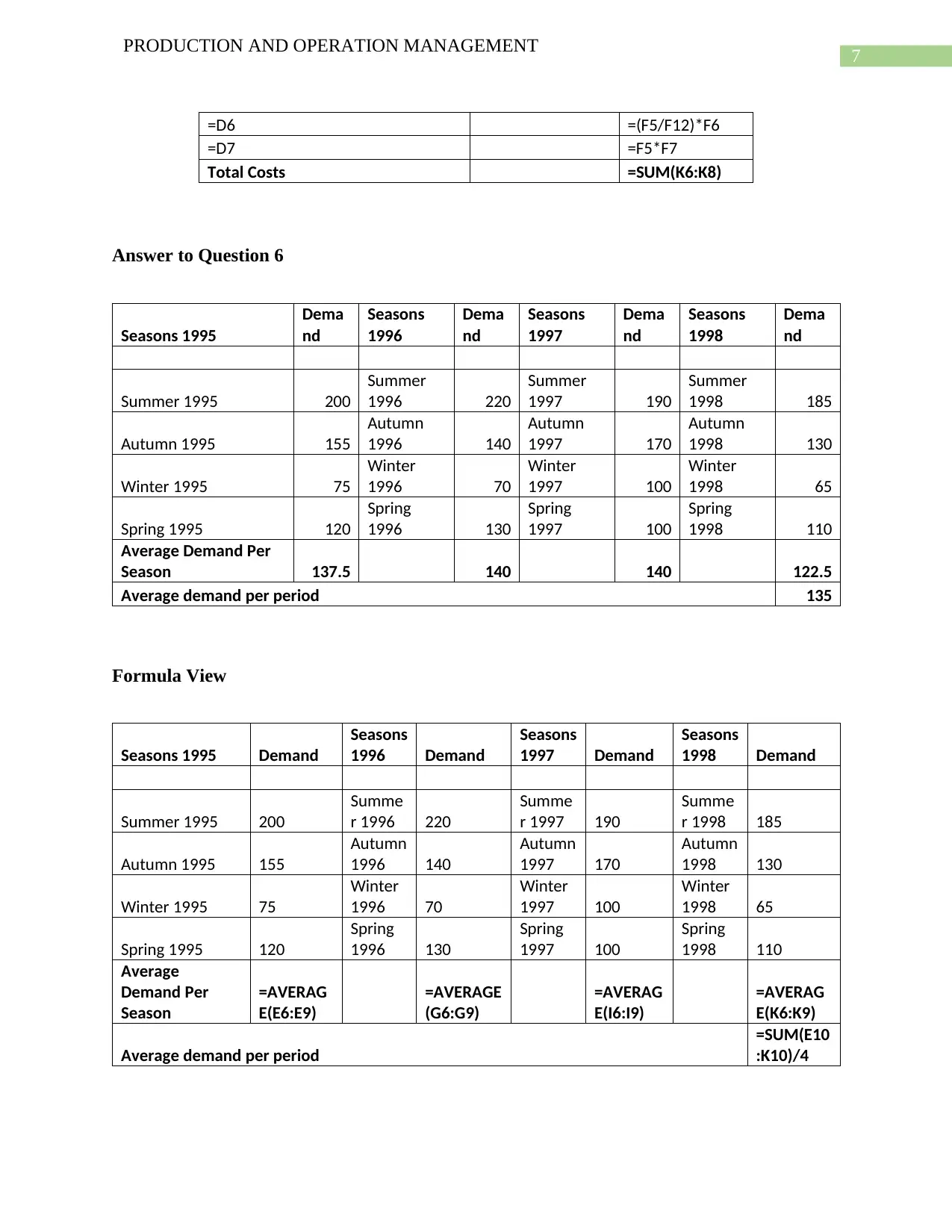
7
PRODUCTION AND OPERATION MANAGEMENT
=D6 =(F5/F12)*F6
=D7 =F5*F7
Total Costs =SUM(K6:K8)
Answer to Question 6
Seasons 1995
Dema
nd
Seasons
1996
Dema
nd
Seasons
1997
Dema
nd
Seasons
1998
Dema
nd
Summer 1995 200
Summer
1996 220
Summer
1997 190
Summer
1998 185
Autumn 1995 155
Autumn
1996 140
Autumn
1997 170
Autumn
1998 130
Winter 1995 75
Winter
1996 70
Winter
1997 100
Winter
1998 65
Spring 1995 120
Spring
1996 130
Spring
1997 100
Spring
1998 110
Average Demand Per
Season 137.5 140 140 122.5
Average demand per period 135
Formula View
Seasons 1995 Demand
Seasons
1996 Demand
Seasons
1997 Demand
Seasons
1998 Demand
Summer 1995 200
Summe
r 1996 220
Summe
r 1997 190
Summe
r 1998 185
Autumn 1995 155
Autumn
1996 140
Autumn
1997 170
Autumn
1998 130
Winter 1995 75
Winter
1996 70
Winter
1997 100
Winter
1998 65
Spring 1995 120
Spring
1996 130
Spring
1997 100
Spring
1998 110
Average
Demand Per
Season
=AVERAG
E(E6:E9)
=AVERAGE
(G6:G9)
=AVERAG
E(I6:I9)
=AVERAG
E(K6:K9)
Average demand per period
=SUM(E10
:K10)/4
PRODUCTION AND OPERATION MANAGEMENT
=D6 =(F5/F12)*F6
=D7 =F5*F7
Total Costs =SUM(K6:K8)
Answer to Question 6
Seasons 1995
Dema
nd
Seasons
1996
Dema
nd
Seasons
1997
Dema
nd
Seasons
1998
Dema
nd
Summer 1995 200
Summer
1996 220
Summer
1997 190
Summer
1998 185
Autumn 1995 155
Autumn
1996 140
Autumn
1997 170
Autumn
1998 130
Winter 1995 75
Winter
1996 70
Winter
1997 100
Winter
1998 65
Spring 1995 120
Spring
1996 130
Spring
1997 100
Spring
1998 110
Average Demand Per
Season 137.5 140 140 122.5
Average demand per period 135
Formula View
Seasons 1995 Demand
Seasons
1996 Demand
Seasons
1997 Demand
Seasons
1998 Demand
Summer 1995 200
Summe
r 1996 220
Summe
r 1997 190
Summe
r 1998 185
Autumn 1995 155
Autumn
1996 140
Autumn
1997 170
Autumn
1998 130
Winter 1995 75
Winter
1996 70
Winter
1997 100
Winter
1998 65
Spring 1995 120
Spring
1996 130
Spring
1997 100
Spring
1998 110
Average
Demand Per
Season
=AVERAG
E(E6:E9)
=AVERAGE
(G6:G9)
=AVERAG
E(I6:I9)
=AVERAG
E(K6:K9)
Average demand per period
=SUM(E10
:K10)/4
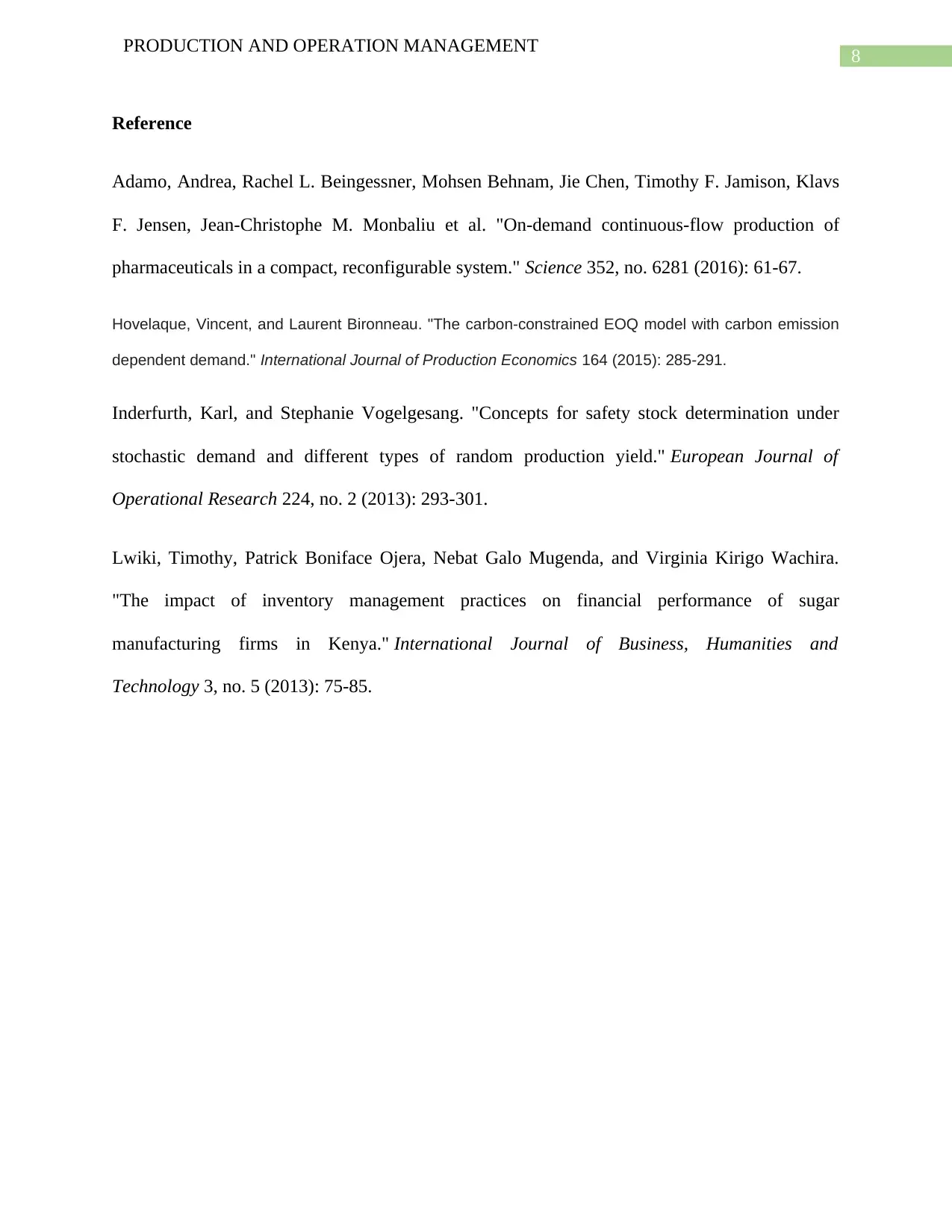
8
PRODUCTION AND OPERATION MANAGEMENT
Reference
Adamo, Andrea, Rachel L. Beingessner, Mohsen Behnam, Jie Chen, Timothy F. Jamison, Klavs
F. Jensen, Jean-Christophe M. Monbaliu et al. "On-demand continuous-flow production of
pharmaceuticals in a compact, reconfigurable system." Science 352, no. 6281 (2016): 61-67.
Hovelaque, Vincent, and Laurent Bironneau. "The carbon-constrained EOQ model with carbon emission
dependent demand." International Journal of Production Economics 164 (2015): 285-291.
Inderfurth, Karl, and Stephanie Vogelgesang. "Concepts for safety stock determination under
stochastic demand and different types of random production yield." European Journal of
Operational Research 224, no. 2 (2013): 293-301.
Lwiki, Timothy, Patrick Boniface Ojera, Nebat Galo Mugenda, and Virginia Kirigo Wachira.
"The impact of inventory management practices on financial performance of sugar
manufacturing firms in Kenya." International Journal of Business, Humanities and
Technology 3, no. 5 (2013): 75-85.
PRODUCTION AND OPERATION MANAGEMENT
Reference
Adamo, Andrea, Rachel L. Beingessner, Mohsen Behnam, Jie Chen, Timothy F. Jamison, Klavs
F. Jensen, Jean-Christophe M. Monbaliu et al. "On-demand continuous-flow production of
pharmaceuticals in a compact, reconfigurable system." Science 352, no. 6281 (2016): 61-67.
Hovelaque, Vincent, and Laurent Bironneau. "The carbon-constrained EOQ model with carbon emission
dependent demand." International Journal of Production Economics 164 (2015): 285-291.
Inderfurth, Karl, and Stephanie Vogelgesang. "Concepts for safety stock determination under
stochastic demand and different types of random production yield." European Journal of
Operational Research 224, no. 2 (2013): 293-301.
Lwiki, Timothy, Patrick Boniface Ojera, Nebat Galo Mugenda, and Virginia Kirigo Wachira.
"The impact of inventory management practices on financial performance of sugar
manufacturing firms in Kenya." International Journal of Business, Humanities and
Technology 3, no. 5 (2013): 75-85.
1 out of 9
Related Documents
![[object Object]](/_next/image/?url=%2F_next%2Fstatic%2Fmedia%2Flogo.6d15ce61.png&w=640&q=75)
Your All-in-One AI-Powered Toolkit for Academic Success.
 +13062052269
info@desklib.com
Available 24*7 on WhatsApp / Email
Unlock your academic potential
© 2024  |  Zucol Services PVT LTD  |  All rights reserved.