Productivity Concepts and Measures | Assignment
VerifiedAdded on 2022/09/09
|7
|1792
|16
AI Summary
Contribute Materials
Your contribution can guide someone’s learning journey. Share your
documents today.
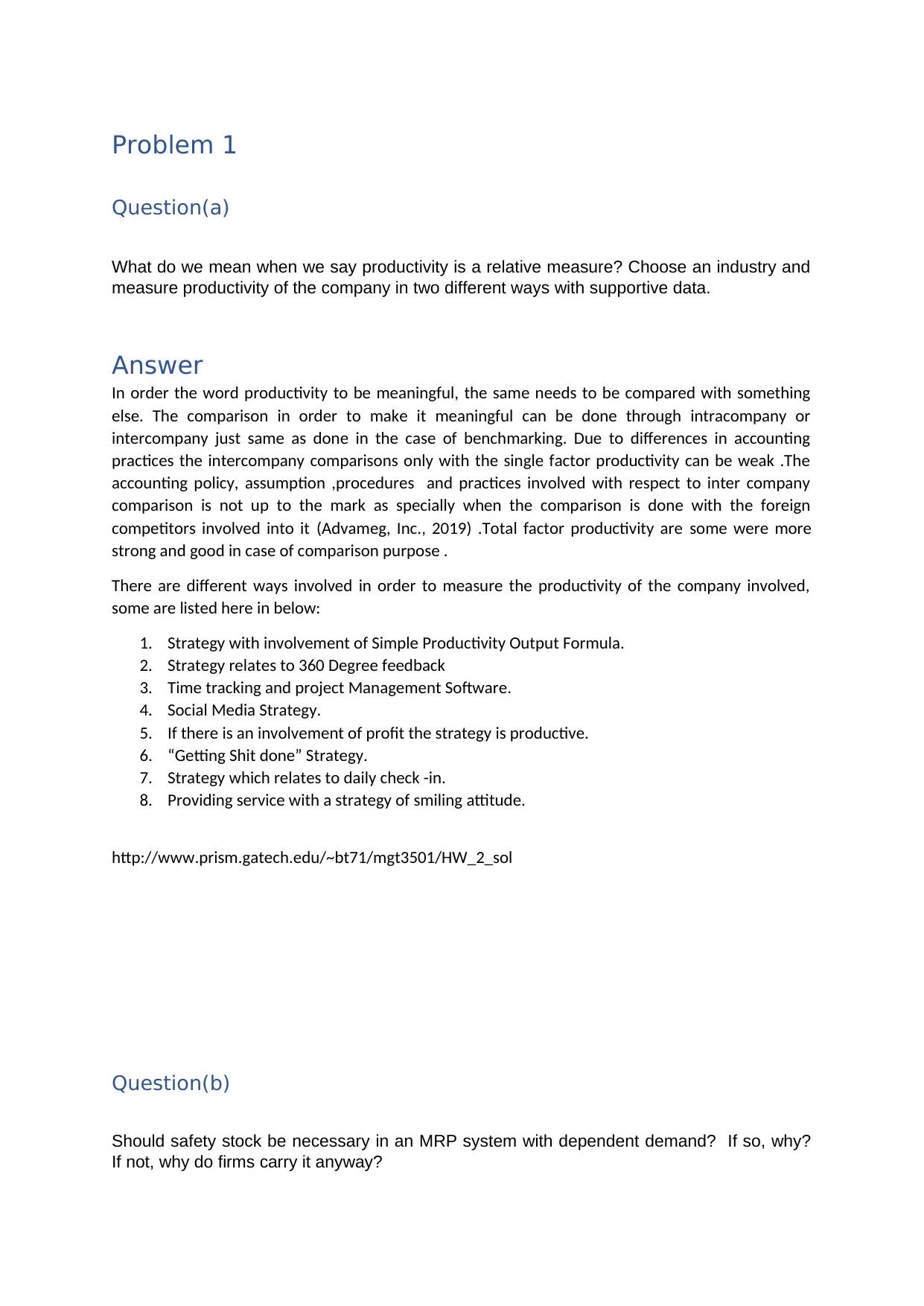
Problem 1
Question(a)
What do we mean when we say productivity is a relative measure? Choose an industry and
measure productivity of the company in two different ways with supportive data.
Answer
In order the word productivity to be meaningful, the same needs to be compared with something
else. The comparison in order to make it meaningful can be done through intracompany or
intercompany just same as done in the case of benchmarking. Due to differences in accounting
practices the intercompany comparisons only with the single factor productivity can be weak .The
accounting policy, assumption ,procedures and practices involved with respect to inter company
comparison is not up to the mark as specially when the comparison is done with the foreign
competitors involved into it (Advameg, Inc., 2019) .Total factor productivity are some were more
strong and good in case of comparison purpose .
There are different ways involved in order to measure the productivity of the company involved,
some are listed here in below:
1. Strategy with involvement of Simple Productivity Output Formula.
2. Strategy relates to 360 Degree feedback
3. Time tracking and project Management Software.
4. Social Media Strategy.
5. If there is an involvement of profit the strategy is productive.
6. “Getting Shit done” Strategy.
7. Strategy which relates to daily check -in.
8. Providing service with a strategy of smiling attitude.
http://www.prism.gatech.edu/~bt71/mgt3501/HW_2_sol
Question(b)
Should safety stock be necessary in an MRP system with dependent demand? If so, why?
If not, why do firms carry it anyway?
Question(a)
What do we mean when we say productivity is a relative measure? Choose an industry and
measure productivity of the company in two different ways with supportive data.
Answer
In order the word productivity to be meaningful, the same needs to be compared with something
else. The comparison in order to make it meaningful can be done through intracompany or
intercompany just same as done in the case of benchmarking. Due to differences in accounting
practices the intercompany comparisons only with the single factor productivity can be weak .The
accounting policy, assumption ,procedures and practices involved with respect to inter company
comparison is not up to the mark as specially when the comparison is done with the foreign
competitors involved into it (Advameg, Inc., 2019) .Total factor productivity are some were more
strong and good in case of comparison purpose .
There are different ways involved in order to measure the productivity of the company involved,
some are listed here in below:
1. Strategy with involvement of Simple Productivity Output Formula.
2. Strategy relates to 360 Degree feedback
3. Time tracking and project Management Software.
4. Social Media Strategy.
5. If there is an involvement of profit the strategy is productive.
6. “Getting Shit done” Strategy.
7. Strategy which relates to daily check -in.
8. Providing service with a strategy of smiling attitude.
http://www.prism.gatech.edu/~bt71/mgt3501/HW_2_sol
Question(b)
Should safety stock be necessary in an MRP system with dependent demand? If so, why?
If not, why do firms carry it anyway?
Secure Best Marks with AI Grader
Need help grading? Try our AI Grader for instant feedback on your assignments.
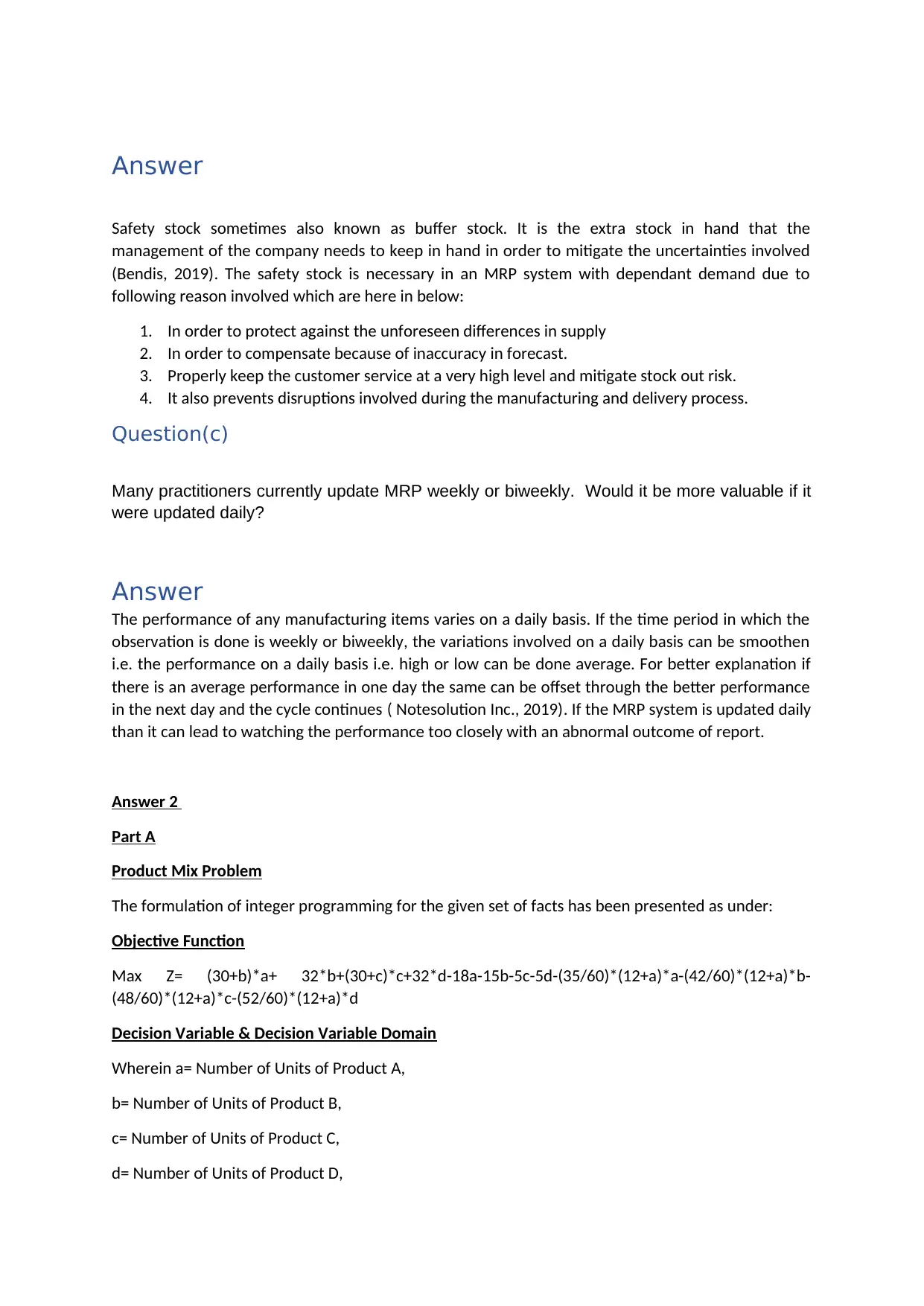
Answer
Safety stock sometimes also known as buffer stock. It is the extra stock in hand that the
management of the company needs to keep in hand in order to mitigate the uncertainties involved
(Bendis, 2019). The safety stock is necessary in an MRP system with dependant demand due to
following reason involved which are here in below:
1. In order to protect against the unforeseen differences in supply
2. In order to compensate because of inaccuracy in forecast.
3. Properly keep the customer service at a very high level and mitigate stock out risk.
4. It also prevents disruptions involved during the manufacturing and delivery process.
Question(c)
Many practitioners currently update MRP weekly or biweekly. Would it be more valuable if it
were updated daily?
Answer
The performance of any manufacturing items varies on a daily basis. If the time period in which the
observation is done is weekly or biweekly, the variations involved on a daily basis can be smoothen
i.e. the performance on a daily basis i.e. high or low can be done average. For better explanation if
there is an average performance in one day the same can be offset through the better performance
in the next day and the cycle continues ( Notesolution Inc., 2019). If the MRP system is updated daily
than it can lead to watching the performance too closely with an abnormal outcome of report.
Answer 2
Part A
Product Mix Problem
The formulation of integer programming for the given set of facts has been presented as under:
Objective Function
Max Z= (30+b)*a+ 32*b+(30+c)*c+32*d-18a-15b-5c-5d-(35/60)*(12+a)*a-(42/60)*(12+a)*b-
(48/60)*(12+a)*c-(52/60)*(12+a)*d
Decision Variable & Decision Variable Domain
Wherein a= Number of Units of Product A,
b= Number of Units of Product B,
c= Number of Units of Product C,
d= Number of Units of Product D,
Safety stock sometimes also known as buffer stock. It is the extra stock in hand that the
management of the company needs to keep in hand in order to mitigate the uncertainties involved
(Bendis, 2019). The safety stock is necessary in an MRP system with dependant demand due to
following reason involved which are here in below:
1. In order to protect against the unforeseen differences in supply
2. In order to compensate because of inaccuracy in forecast.
3. Properly keep the customer service at a very high level and mitigate stock out risk.
4. It also prevents disruptions involved during the manufacturing and delivery process.
Question(c)
Many practitioners currently update MRP weekly or biweekly. Would it be more valuable if it
were updated daily?
Answer
The performance of any manufacturing items varies on a daily basis. If the time period in which the
observation is done is weekly or biweekly, the variations involved on a daily basis can be smoothen
i.e. the performance on a daily basis i.e. high or low can be done average. For better explanation if
there is an average performance in one day the same can be offset through the better performance
in the next day and the cycle continues ( Notesolution Inc., 2019). If the MRP system is updated daily
than it can lead to watching the performance too closely with an abnormal outcome of report.
Answer 2
Part A
Product Mix Problem
The formulation of integer programming for the given set of facts has been presented as under:
Objective Function
Max Z= (30+b)*a+ 32*b+(30+c)*c+32*d-18a-15b-5c-5d-(35/60)*(12+a)*a-(42/60)*(12+a)*b-
(48/60)*(12+a)*c-(52/60)*(12+a)*d
Decision Variable & Decision Variable Domain
Wherein a= Number of Units of Product A,
b= Number of Units of Product B,
c= Number of Units of Product C,
d= Number of Units of Product D,
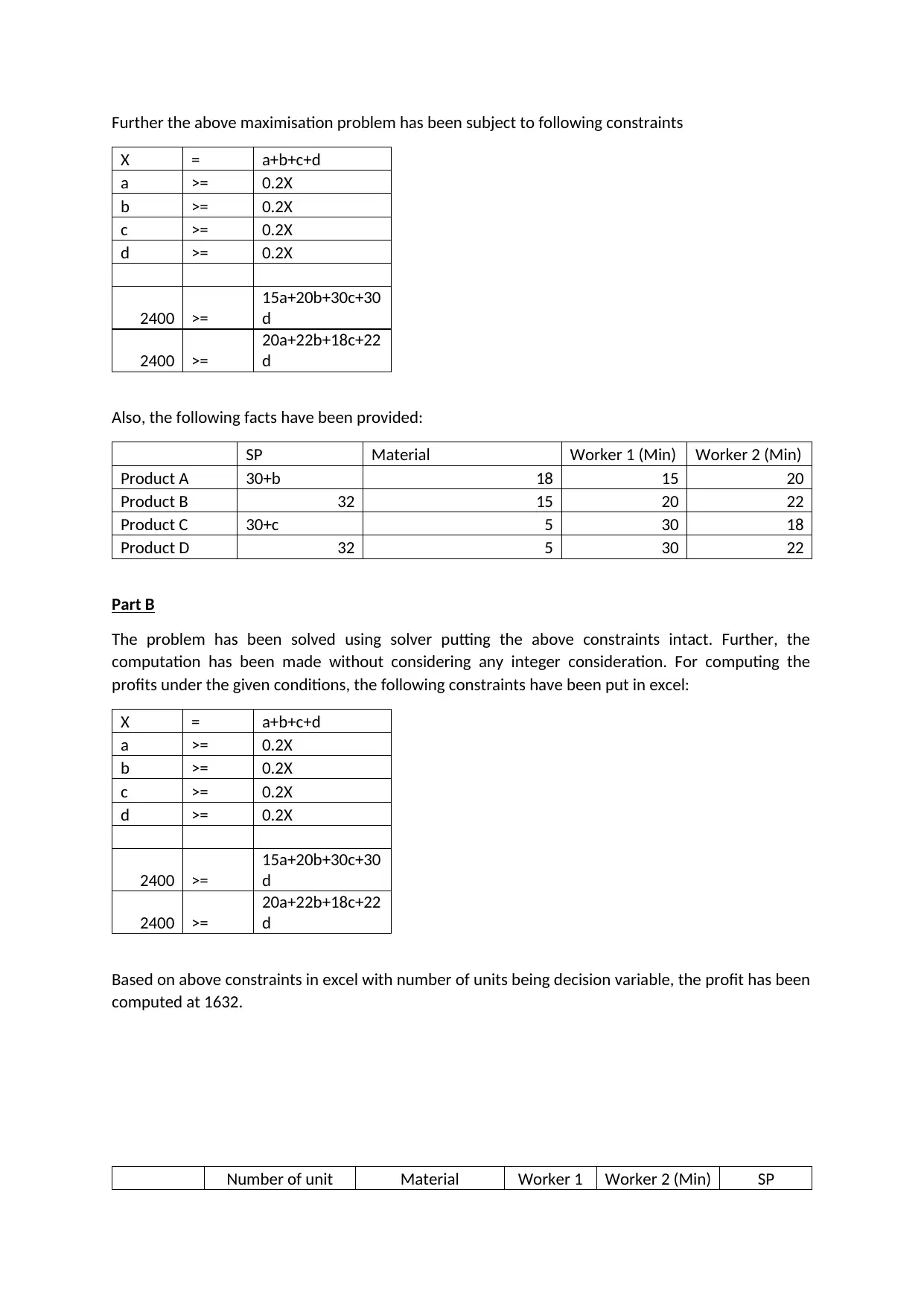
Further the above maximisation problem has been subject to following constraints
X = a+b+c+d
a >= 0.2X
b >= 0.2X
c >= 0.2X
d >= 0.2X
2400 >=
15a+20b+30c+30
d
2400 >=
20a+22b+18c+22
d
Also, the following facts have been provided:
SP Material Worker 1 (Min) Worker 2 (Min)
Product A 30+b 18 15 20
Product B 32 15 20 22
Product C 30+c 5 30 18
Product D 32 5 30 22
Part B
The problem has been solved using solver putting the above constraints intact. Further, the
computation has been made without considering any integer consideration. For computing the
profits under the given conditions, the following constraints have been put in excel:
X = a+b+c+d
a >= 0.2X
b >= 0.2X
c >= 0.2X
d >= 0.2X
2400 >=
15a+20b+30c+30
d
2400 >=
20a+22b+18c+22
d
Based on above constraints in excel with number of units being decision variable, the profit has been
computed at 1632.
Number of unit Material Worker 1 Worker 2 (Min) SP
X = a+b+c+d
a >= 0.2X
b >= 0.2X
c >= 0.2X
d >= 0.2X
2400 >=
15a+20b+30c+30
d
2400 >=
20a+22b+18c+22
d
Also, the following facts have been provided:
SP Material Worker 1 (Min) Worker 2 (Min)
Product A 30+b 18 15 20
Product B 32 15 20 22
Product C 30+c 5 30 18
Product D 32 5 30 22
Part B
The problem has been solved using solver putting the above constraints intact. Further, the
computation has been made without considering any integer consideration. For computing the
profits under the given conditions, the following constraints have been put in excel:
X = a+b+c+d
a >= 0.2X
b >= 0.2X
c >= 0.2X
d >= 0.2X
2400 >=
15a+20b+30c+30
d
2400 >=
20a+22b+18c+22
d
Based on above constraints in excel with number of units being decision variable, the profit has been
computed at 1632.
Number of unit Material Worker 1 Worker 2 (Min) SP
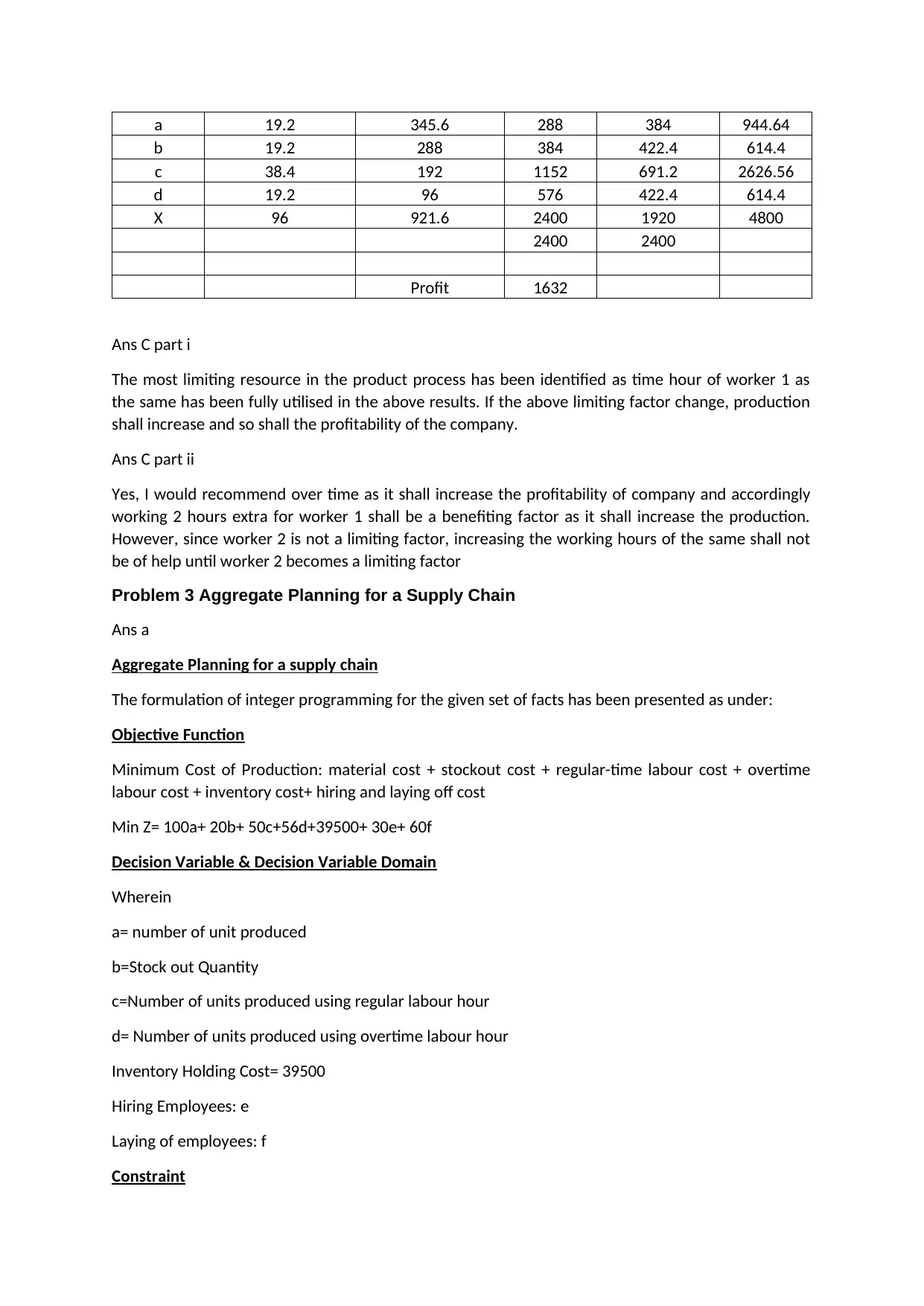
a 19.2 345.6 288 384 944.64
b 19.2 288 384 422.4 614.4
c 38.4 192 1152 691.2 2626.56
d 19.2 96 576 422.4 614.4
X 96 921.6 2400 1920 4800
2400 2400
Profit 1632
Ans C part i
The most limiting resource in the product process has been identified as time hour of worker 1 as
the same has been fully utilised in the above results. If the above limiting factor change, production
shall increase and so shall the profitability of the company.
Ans C part ii
Yes, I would recommend over time as it shall increase the profitability of company and accordingly
working 2 hours extra for worker 1 shall be a benefiting factor as it shall increase the production.
However, since worker 2 is not a limiting factor, increasing the working hours of the same shall not
be of help until worker 2 becomes a limiting factor
Problem 3 Aggregate Planning for a Supply Chain
Ans a
Aggregate Planning for a supply chain
The formulation of integer programming for the given set of facts has been presented as under:
Objective Function
Minimum Cost of Production: material cost + stockout cost + regular-time labour cost + overtime
labour cost + inventory cost+ hiring and laying off cost
Min Z= 100a+ 20b+ 50c+56d+39500+ 30e+ 60f
Decision Variable & Decision Variable Domain
Wherein
a= number of unit produced
b=Stock out Quantity
c=Number of units produced using regular labour hour
d= Number of units produced using overtime labour hour
Inventory Holding Cost= 39500
Hiring Employees: e
Laying of employees: f
Constraint
b 19.2 288 384 422.4 614.4
c 38.4 192 1152 691.2 2626.56
d 19.2 96 576 422.4 614.4
X 96 921.6 2400 1920 4800
2400 2400
Profit 1632
Ans C part i
The most limiting resource in the product process has been identified as time hour of worker 1 as
the same has been fully utilised in the above results. If the above limiting factor change, production
shall increase and so shall the profitability of the company.
Ans C part ii
Yes, I would recommend over time as it shall increase the profitability of company and accordingly
working 2 hours extra for worker 1 shall be a benefiting factor as it shall increase the production.
However, since worker 2 is not a limiting factor, increasing the working hours of the same shall not
be of help until worker 2 becomes a limiting factor
Problem 3 Aggregate Planning for a Supply Chain
Ans a
Aggregate Planning for a supply chain
The formulation of integer programming for the given set of facts has been presented as under:
Objective Function
Minimum Cost of Production: material cost + stockout cost + regular-time labour cost + overtime
labour cost + inventory cost+ hiring and laying off cost
Min Z= 100a+ 20b+ 50c+56d+39500+ 30e+ 60f
Decision Variable & Decision Variable Domain
Wherein
a= number of unit produced
b=Stock out Quantity
c=Number of units produced using regular labour hour
d= Number of units produced using overtime labour hour
Inventory Holding Cost= 39500
Hiring Employees: e
Laying of employees: f
Constraint
Secure Best Marks with AI Grader
Need help grading? Try our AI Grader for instant feedback on your assignments.
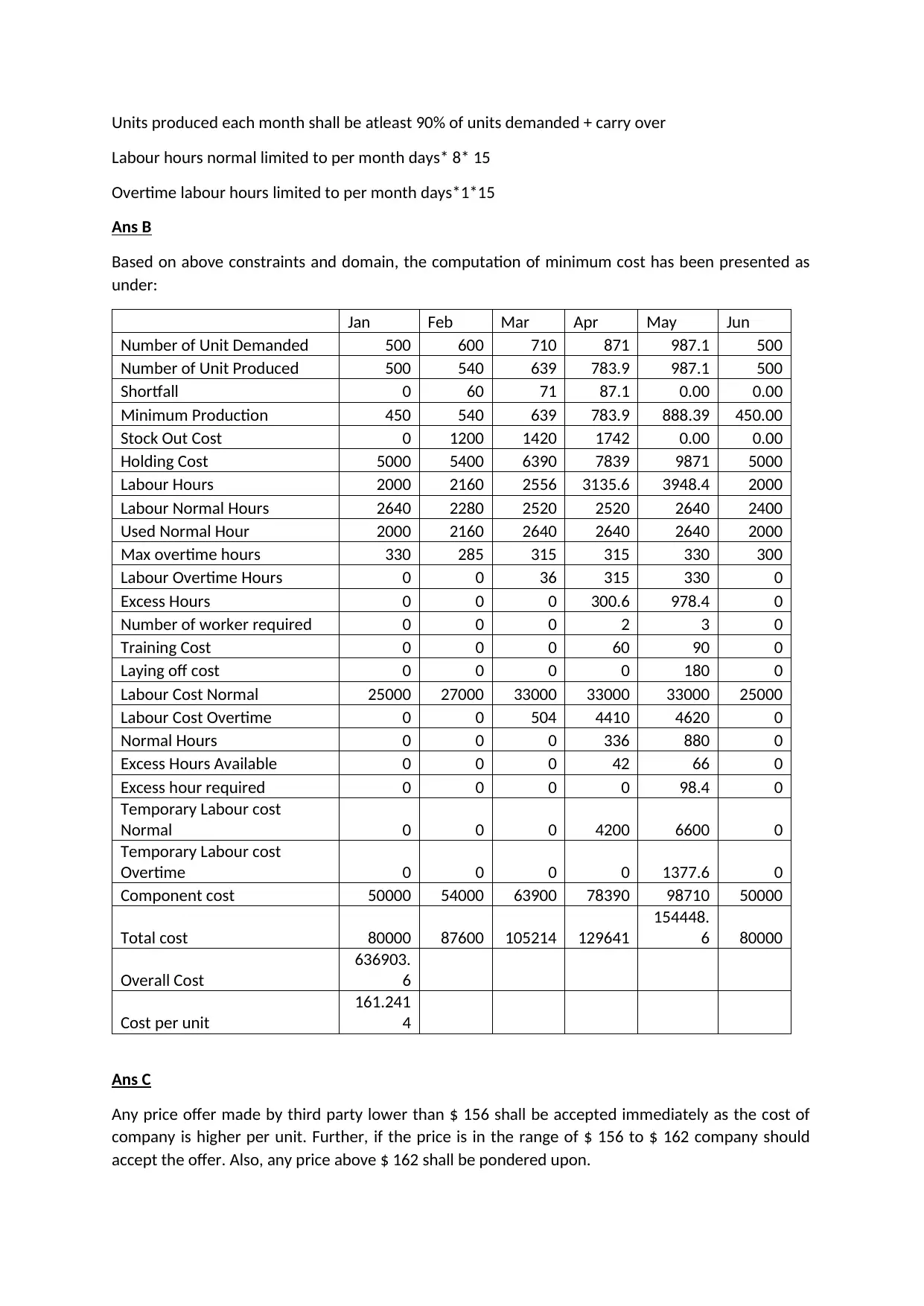
Units produced each month shall be atleast 90% of units demanded + carry over
Labour hours normal limited to per month days* 8* 15
Overtime labour hours limited to per month days*1*15
Ans B
Based on above constraints and domain, the computation of minimum cost has been presented as
under:
Jan Feb Mar Apr May Jun
Number of Unit Demanded 500 600 710 871 987.1 500
Number of Unit Produced 500 540 639 783.9 987.1 500
Shortfall 0 60 71 87.1 0.00 0.00
Minimum Production 450 540 639 783.9 888.39 450.00
Stock Out Cost 0 1200 1420 1742 0.00 0.00
Holding Cost 5000 5400 6390 7839 9871 5000
Labour Hours 2000 2160 2556 3135.6 3948.4 2000
Labour Normal Hours 2640 2280 2520 2520 2640 2400
Used Normal Hour 2000 2160 2640 2640 2640 2000
Max overtime hours 330 285 315 315 330 300
Labour Overtime Hours 0 0 36 315 330 0
Excess Hours 0 0 0 300.6 978.4 0
Number of worker required 0 0 0 2 3 0
Training Cost 0 0 0 60 90 0
Laying off cost 0 0 0 0 180 0
Labour Cost Normal 25000 27000 33000 33000 33000 25000
Labour Cost Overtime 0 0 504 4410 4620 0
Normal Hours 0 0 0 336 880 0
Excess Hours Available 0 0 0 42 66 0
Excess hour required 0 0 0 0 98.4 0
Temporary Labour cost
Normal 0 0 0 4200 6600 0
Temporary Labour cost
Overtime 0 0 0 0 1377.6 0
Component cost 50000 54000 63900 78390 98710 50000
Total cost 80000 87600 105214 129641
154448.
6 80000
Overall Cost
636903.
6
Cost per unit
161.241
4
Ans C
Any price offer made by third party lower than $ 156 shall be accepted immediately as the cost of
company is higher per unit. Further, if the price is in the range of $ 156 to $ 162 company should
accept the offer. Also, any price above $ 162 shall be pondered upon.
Labour hours normal limited to per month days* 8* 15
Overtime labour hours limited to per month days*1*15
Ans B
Based on above constraints and domain, the computation of minimum cost has been presented as
under:
Jan Feb Mar Apr May Jun
Number of Unit Demanded 500 600 710 871 987.1 500
Number of Unit Produced 500 540 639 783.9 987.1 500
Shortfall 0 60 71 87.1 0.00 0.00
Minimum Production 450 540 639 783.9 888.39 450.00
Stock Out Cost 0 1200 1420 1742 0.00 0.00
Holding Cost 5000 5400 6390 7839 9871 5000
Labour Hours 2000 2160 2556 3135.6 3948.4 2000
Labour Normal Hours 2640 2280 2520 2520 2640 2400
Used Normal Hour 2000 2160 2640 2640 2640 2000
Max overtime hours 330 285 315 315 330 300
Labour Overtime Hours 0 0 36 315 330 0
Excess Hours 0 0 0 300.6 978.4 0
Number of worker required 0 0 0 2 3 0
Training Cost 0 0 0 60 90 0
Laying off cost 0 0 0 0 180 0
Labour Cost Normal 25000 27000 33000 33000 33000 25000
Labour Cost Overtime 0 0 504 4410 4620 0
Normal Hours 0 0 0 336 880 0
Excess Hours Available 0 0 0 42 66 0
Excess hour required 0 0 0 0 98.4 0
Temporary Labour cost
Normal 0 0 0 4200 6600 0
Temporary Labour cost
Overtime 0 0 0 0 1377.6 0
Component cost 50000 54000 63900 78390 98710 50000
Total cost 80000 87600 105214 129641
154448.
6 80000
Overall Cost
636903.
6
Cost per unit
161.241
4
Ans C
Any price offer made by third party lower than $ 156 shall be accepted immediately as the cost of
company is higher per unit. Further, if the price is in the range of $ 156 to $ 162 company should
accept the offer. Also, any price above $ 162 shall be pondered upon.
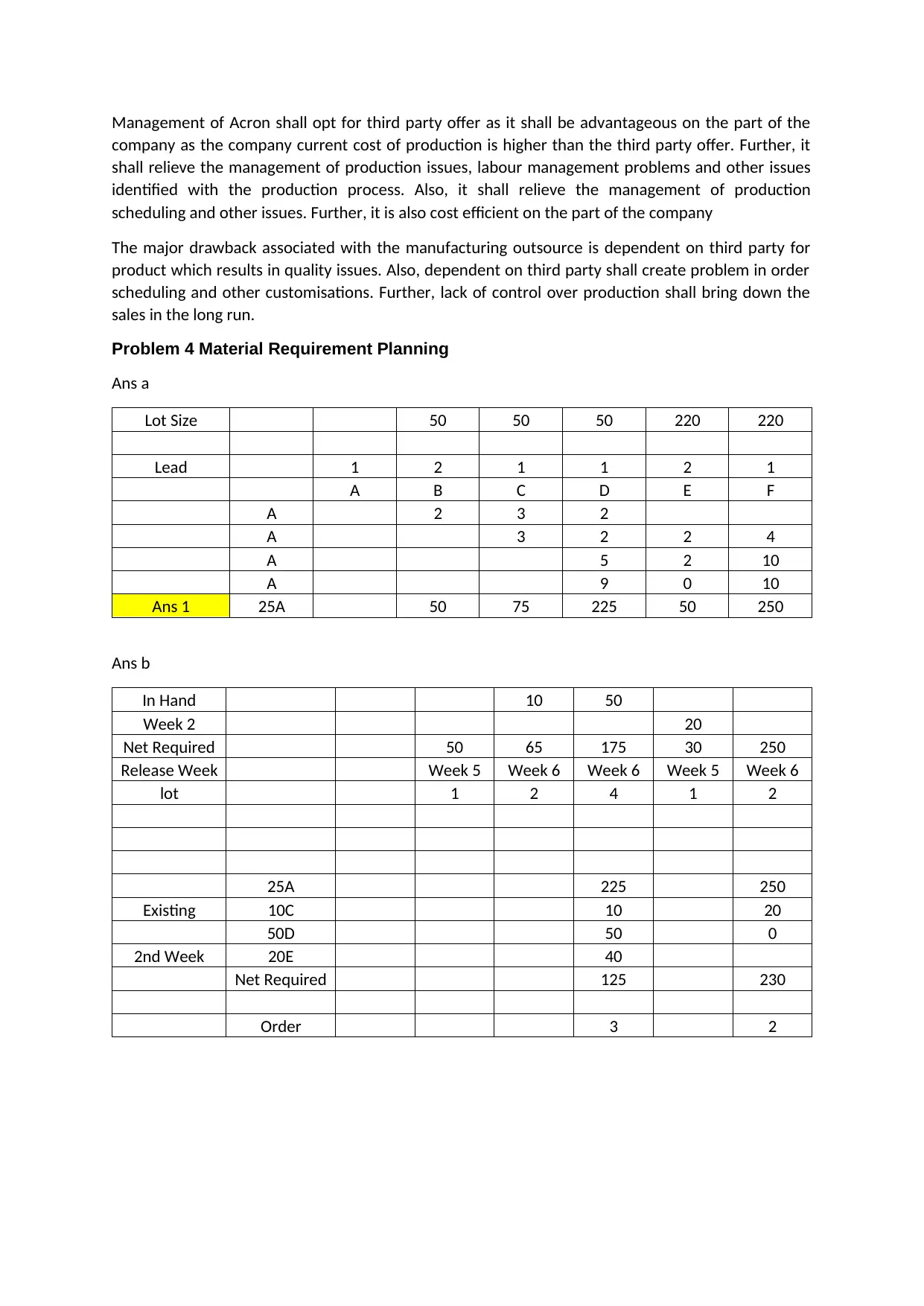
Management of Acron shall opt for third party offer as it shall be advantageous on the part of the
company as the company current cost of production is higher than the third party offer. Further, it
shall relieve the management of production issues, labour management problems and other issues
identified with the production process. Also, it shall relieve the management of production
scheduling and other issues. Further, it is also cost efficient on the part of the company
The major drawback associated with the manufacturing outsource is dependent on third party for
product which results in quality issues. Also, dependent on third party shall create problem in order
scheduling and other customisations. Further, lack of control over production shall bring down the
sales in the long run.
Problem 4 Material Requirement Planning
Ans a
Lot Size 50 50 50 220 220
Lead 1 2 1 1 2 1
A B C D E F
A 2 3 2
A 3 2 2 4
A 5 2 10
A 9 0 10
Ans 1 25A 50 75 225 50 250
Ans b
In Hand 10 50
Week 2 20
Net Required 50 65 175 30 250
Release Week Week 5 Week 6 Week 6 Week 5 Week 6
lot 1 2 4 1 2
25A 225 250
Existing 10C 10 20
50D 50 0
2nd Week 20E 40
Net Required 125 230
Order 3 2
company as the company current cost of production is higher than the third party offer. Further, it
shall relieve the management of production issues, labour management problems and other issues
identified with the production process. Also, it shall relieve the management of production
scheduling and other issues. Further, it is also cost efficient on the part of the company
The major drawback associated with the manufacturing outsource is dependent on third party for
product which results in quality issues. Also, dependent on third party shall create problem in order
scheduling and other customisations. Further, lack of control over production shall bring down the
sales in the long run.
Problem 4 Material Requirement Planning
Ans a
Lot Size 50 50 50 220 220
Lead 1 2 1 1 2 1
A B C D E F
A 2 3 2
A 3 2 2 4
A 5 2 10
A 9 0 10
Ans 1 25A 50 75 225 50 250
Ans b
In Hand 10 50
Week 2 20
Net Required 50 65 175 30 250
Release Week Week 5 Week 6 Week 6 Week 5 Week 6
lot 1 2 4 1 2
25A 225 250
Existing 10C 10 20
50D 50 0
2nd Week 20E 40
Net Required 125 230
Order 3 2
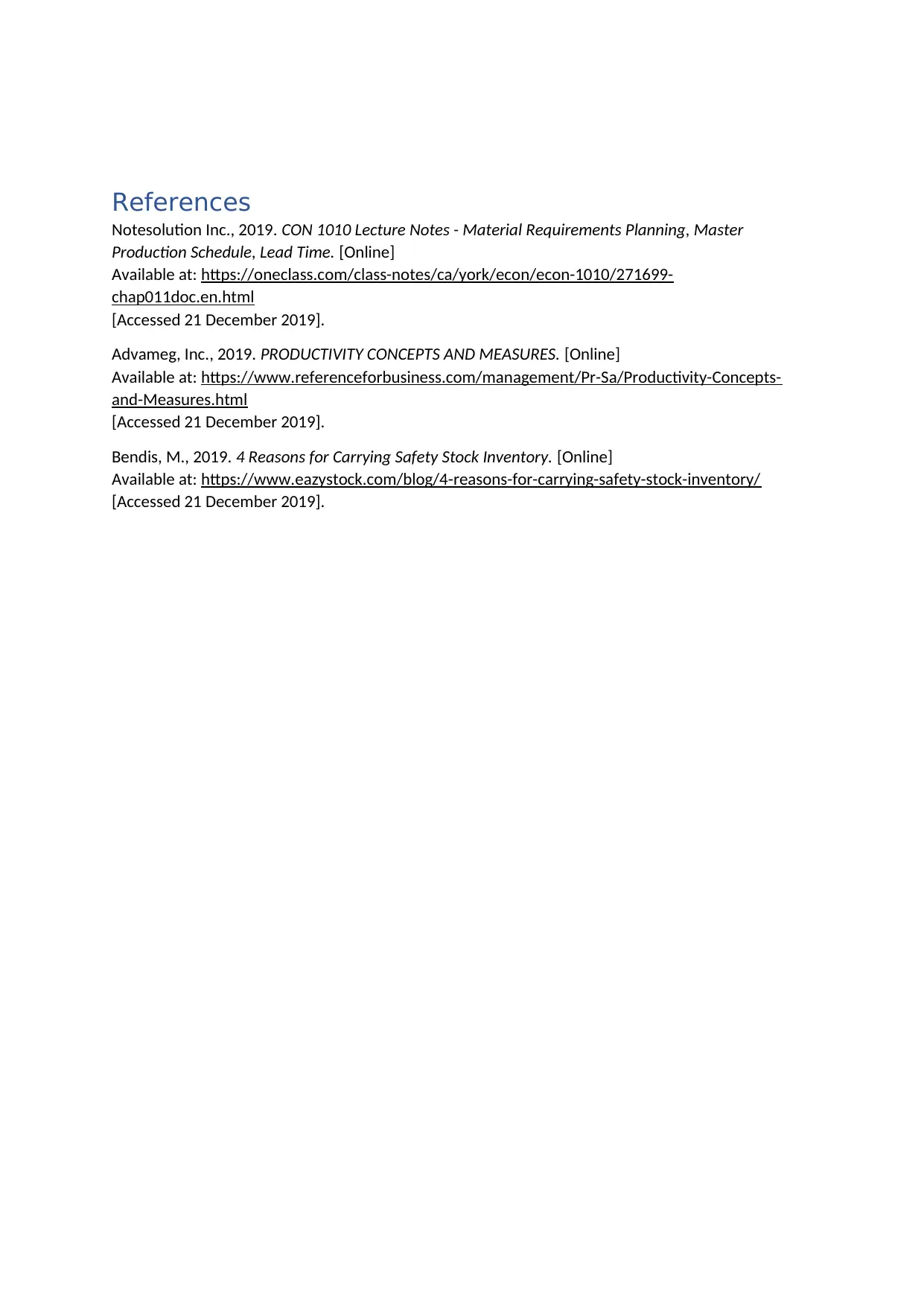
References
Notesolution Inc., 2019. CON 1010 Lecture Notes - Material Requirements Planning, Master
Production Schedule, Lead Time. [Online]
Available at: https://oneclass.com/class-notes/ca/york/econ/econ-1010/271699-
chap011doc.en.html
[Accessed 21 December 2019].
Advameg, Inc., 2019. PRODUCTIVITY CONCEPTS AND MEASURES. [Online]
Available at: https://www.referenceforbusiness.com/management/Pr-Sa/Productivity-Concepts-
and-Measures.html
[Accessed 21 December 2019].
Bendis, M., 2019. 4 Reasons for Carrying Safety Stock Inventory. [Online]
Available at: https://www.eazystock.com/blog/4-reasons-for-carrying-safety-stock-inventory/
[Accessed 21 December 2019].
Notesolution Inc., 2019. CON 1010 Lecture Notes - Material Requirements Planning, Master
Production Schedule, Lead Time. [Online]
Available at: https://oneclass.com/class-notes/ca/york/econ/econ-1010/271699-
chap011doc.en.html
[Accessed 21 December 2019].
Advameg, Inc., 2019. PRODUCTIVITY CONCEPTS AND MEASURES. [Online]
Available at: https://www.referenceforbusiness.com/management/Pr-Sa/Productivity-Concepts-
and-Measures.html
[Accessed 21 December 2019].
Bendis, M., 2019. 4 Reasons for Carrying Safety Stock Inventory. [Online]
Available at: https://www.eazystock.com/blog/4-reasons-for-carrying-safety-stock-inventory/
[Accessed 21 December 2019].
1 out of 7
![[object Object]](/_next/image/?url=%2F_next%2Fstatic%2Fmedia%2Flogo.6d15ce61.png&w=640&q=75)
Your All-in-One AI-Powered Toolkit for Academic Success.
+13062052269
info@desklib.com
Available 24*7 on WhatsApp / Email
Unlock your academic potential
© 2024 | Zucol Services PVT LTD | All rights reserved.