Operations Management : Productivity is a Relative Measure
VerifiedAdded on 2022/08/31
|8
|1972
|22
AI Summary
Contribute Materials
Your contribution can guide someone’s learning journey. Share your
documents today.
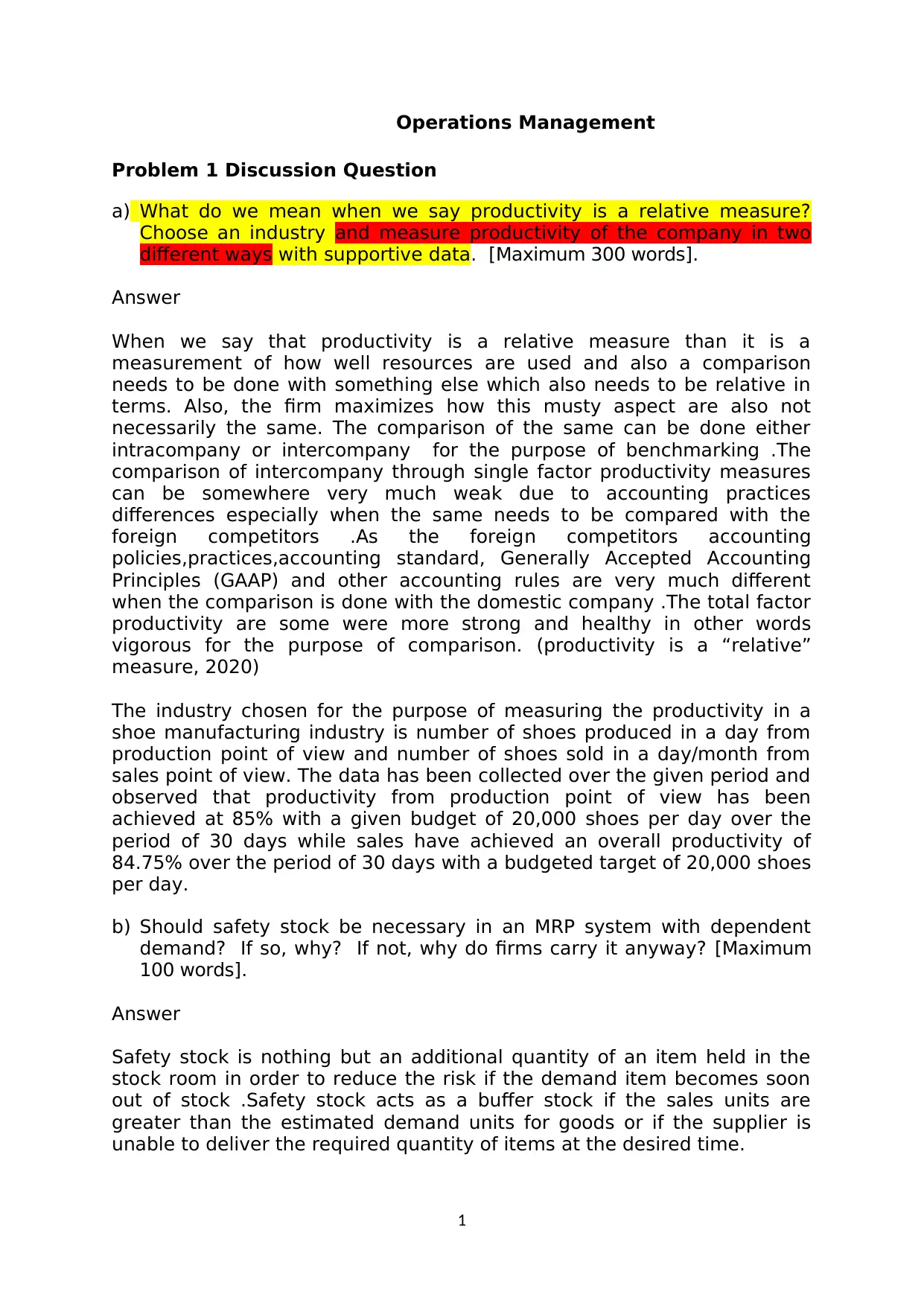
Operations Management
Problem 1 Discussion Question
a) What do we mean when we say productivity is a relative measure?
Choose an industry and measure productivity of the company in two
different ways with supportive data. [Maximum 300 words].
Answer
When we say that productivity is a relative measure than it is a
measurement of how well resources are used and also a comparison
needs to be done with something else which also needs to be relative in
terms. Also, the firm maximizes how this musty aspect are also not
necessarily the same. The comparison of the same can be done either
intracompany or intercompany for the purpose of benchmarking .The
comparison of intercompany through single factor productivity measures
can be somewhere very much weak due to accounting practices
differences especially when the same needs to be compared with the
foreign competitors .As the foreign competitors accounting
policies,practices,accounting standard, Generally Accepted Accounting
Principles (GAAP) and other accounting rules are very much different
when the comparison is done with the domestic company .The total factor
productivity are some were more strong and healthy in other words
vigorous for the purpose of comparison. (productivity is a “relative”
measure, 2020)
The industry chosen for the purpose of measuring the productivity in a
shoe manufacturing industry is number of shoes produced in a day from
production point of view and number of shoes sold in a day/month from
sales point of view. The data has been collected over the given period and
observed that productivity from production point of view has been
achieved at 85% with a given budget of 20,000 shoes per day over the
period of 30 days while sales have achieved an overall productivity of
84.75% over the period of 30 days with a budgeted target of 20,000 shoes
per day.
b) Should safety stock be necessary in an MRP system with dependent
demand? If so, why? If not, why do firms carry it anyway? [Maximum
100 words].
Answer
Safety stock is nothing but an additional quantity of an item held in the
stock room in order to reduce the risk if the demand item becomes soon
out of stock .Safety stock acts as a buffer stock if the sales units are
greater than the estimated demand units for goods or if the supplier is
unable to deliver the required quantity of items at the desired time.
1
Problem 1 Discussion Question
a) What do we mean when we say productivity is a relative measure?
Choose an industry and measure productivity of the company in two
different ways with supportive data. [Maximum 300 words].
Answer
When we say that productivity is a relative measure than it is a
measurement of how well resources are used and also a comparison
needs to be done with something else which also needs to be relative in
terms. Also, the firm maximizes how this musty aspect are also not
necessarily the same. The comparison of the same can be done either
intracompany or intercompany for the purpose of benchmarking .The
comparison of intercompany through single factor productivity measures
can be somewhere very much weak due to accounting practices
differences especially when the same needs to be compared with the
foreign competitors .As the foreign competitors accounting
policies,practices,accounting standard, Generally Accepted Accounting
Principles (GAAP) and other accounting rules are very much different
when the comparison is done with the domestic company .The total factor
productivity are some were more strong and healthy in other words
vigorous for the purpose of comparison. (productivity is a “relative”
measure, 2020)
The industry chosen for the purpose of measuring the productivity in a
shoe manufacturing industry is number of shoes produced in a day from
production point of view and number of shoes sold in a day/month from
sales point of view. The data has been collected over the given period and
observed that productivity from production point of view has been
achieved at 85% with a given budget of 20,000 shoes per day over the
period of 30 days while sales have achieved an overall productivity of
84.75% over the period of 30 days with a budgeted target of 20,000 shoes
per day.
b) Should safety stock be necessary in an MRP system with dependent
demand? If so, why? If not, why do firms carry it anyway? [Maximum
100 words].
Answer
Safety stock is nothing but an additional quantity of an item held in the
stock room in order to reduce the risk if the demand item becomes soon
out of stock .Safety stock acts as a buffer stock if the sales units are
greater than the estimated demand units for goods or if the supplier is
unable to deliver the required quantity of items at the desired time.
1
Secure Best Marks with AI Grader
Need help grading? Try our AI Grader for instant feedback on your assignments.
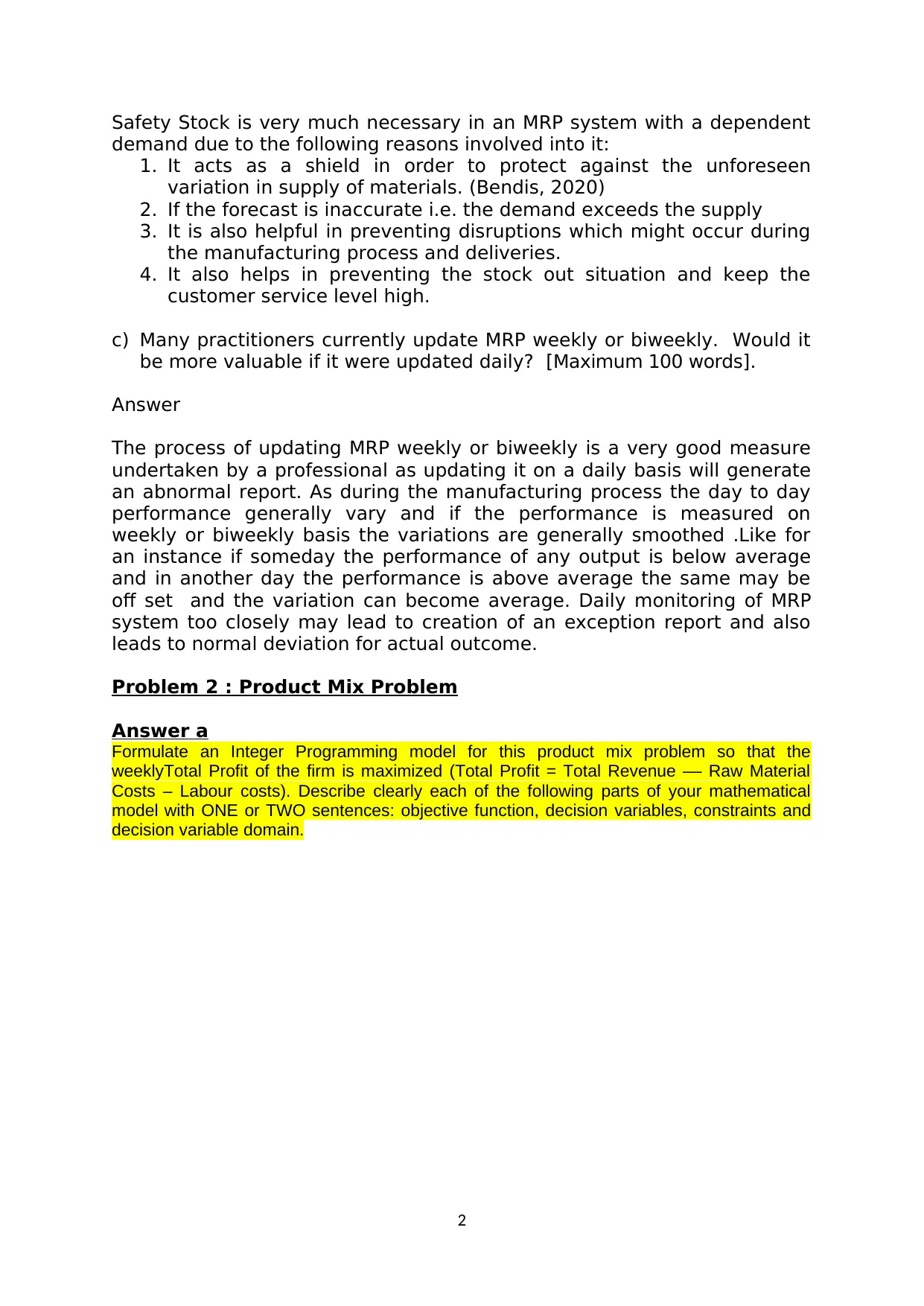
Safety Stock is very much necessary in an MRP system with a dependent
demand due to the following reasons involved into it:
1. It acts as a shield in order to protect against the unforeseen
variation in supply of materials. (Bendis, 2020)
2. If the forecast is inaccurate i.e. the demand exceeds the supply
3. It is also helpful in preventing disruptions which might occur during
the manufacturing process and deliveries.
4. It also helps in preventing the stock out situation and keep the
customer service level high.
c) Many practitioners currently update MRP weekly or biweekly. Would it
be more valuable if it were updated daily? [Maximum 100 words].
Answer
The process of updating MRP weekly or biweekly is a very good measure
undertaken by a professional as updating it on a daily basis will generate
an abnormal report. As during the manufacturing process the day to day
performance generally vary and if the performance is measured on
weekly or biweekly basis the variations are generally smoothed .Like for
an instance if someday the performance of any output is below average
and in another day the performance is above average the same may be
off set and the variation can become average. Daily monitoring of MRP
system too closely may lead to creation of an exception report and also
leads to normal deviation for actual outcome.
Problem 2 : Product Mix Problem
Answer a
Formulate an Integer Programming model for this product mix problem so that the
weeklyTotal Profit of the firm is maximized (Total Profit = Total Revenue –– Raw Material
Costs – Labour costs). Describe clearly each of the following parts of your mathematical
model with ONE or TWO sentences: objective function, decision variables, constraints and
decision variable domain.
2
demand due to the following reasons involved into it:
1. It acts as a shield in order to protect against the unforeseen
variation in supply of materials. (Bendis, 2020)
2. If the forecast is inaccurate i.e. the demand exceeds the supply
3. It is also helpful in preventing disruptions which might occur during
the manufacturing process and deliveries.
4. It also helps in preventing the stock out situation and keep the
customer service level high.
c) Many practitioners currently update MRP weekly or biweekly. Would it
be more valuable if it were updated daily? [Maximum 100 words].
Answer
The process of updating MRP weekly or biweekly is a very good measure
undertaken by a professional as updating it on a daily basis will generate
an abnormal report. As during the manufacturing process the day to day
performance generally vary and if the performance is measured on
weekly or biweekly basis the variations are generally smoothed .Like for
an instance if someday the performance of any output is below average
and in another day the performance is above average the same may be
off set and the variation can become average. Daily monitoring of MRP
system too closely may lead to creation of an exception report and also
leads to normal deviation for actual outcome.
Problem 2 : Product Mix Problem
Answer a
Formulate an Integer Programming model for this product mix problem so that the
weeklyTotal Profit of the firm is maximized (Total Profit = Total Revenue –– Raw Material
Costs – Labour costs). Describe clearly each of the following parts of your mathematical
model with ONE or TWO sentences: objective function, decision variables, constraints and
decision variable domain.
2
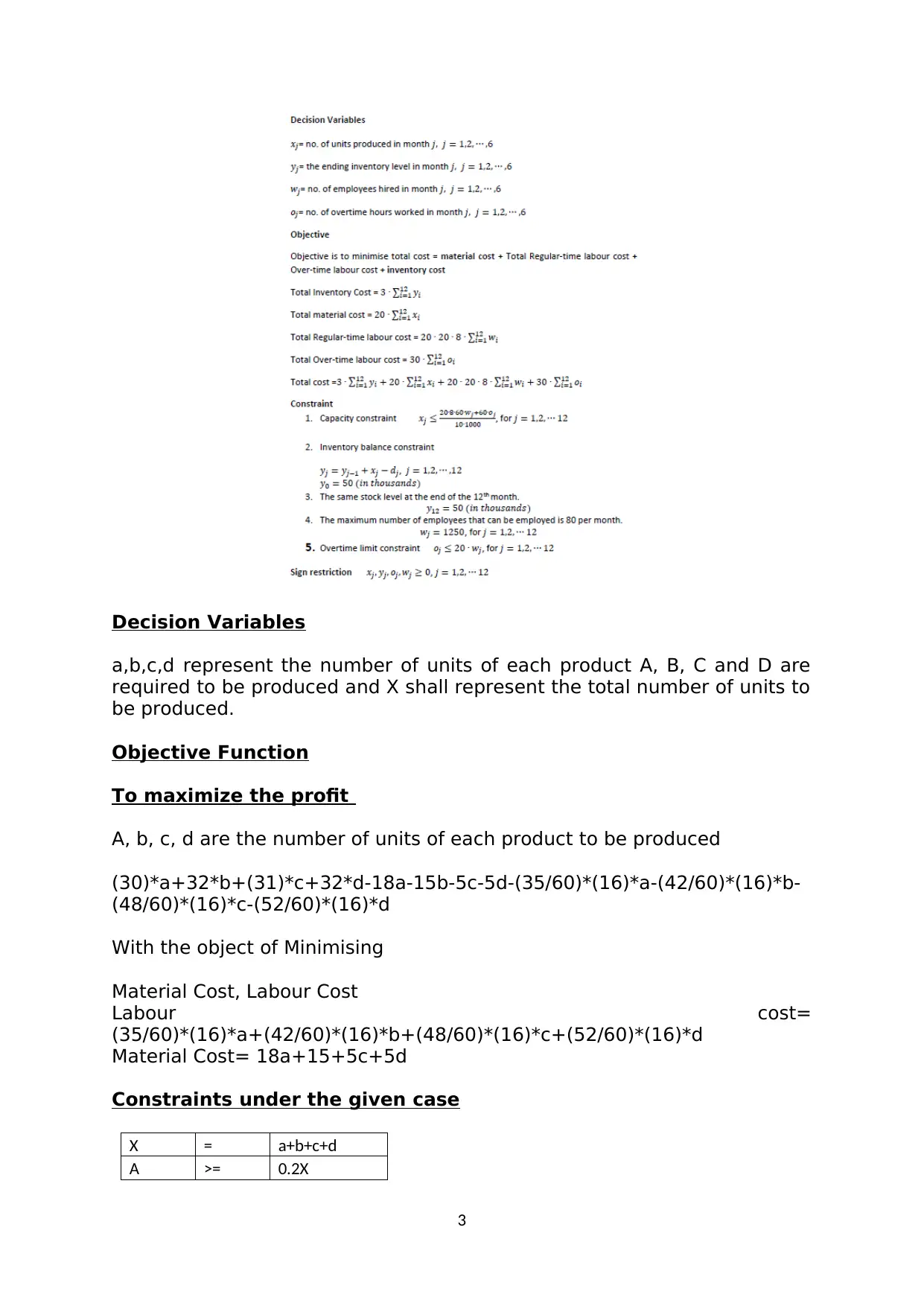
Decision Variables
a,b,c,d represent the number of units of each product A, B, C and D are
required to be produced and X shall represent the total number of units to
be produced.
Objective Function
To maximize the profit
A, b, c, d are the number of units of each product to be produced
(30)*a+32*b+(31)*c+32*d-18a-15b-5c-5d-(35/60)*(16)*a-(42/60)*(16)*b-
(48/60)*(16)*c-(52/60)*(16)*d
With the object of Minimising
Material Cost, Labour Cost
Labour cost=
(35/60)*(16)*a+(42/60)*(16)*b+(48/60)*(16)*c+(52/60)*(16)*d
Material Cost= 18a+15+5c+5d
Constraints under the given case
X = a+b+c+d
A >= 0.2X
3
a,b,c,d represent the number of units of each product A, B, C and D are
required to be produced and X shall represent the total number of units to
be produced.
Objective Function
To maximize the profit
A, b, c, d are the number of units of each product to be produced
(30)*a+32*b+(31)*c+32*d-18a-15b-5c-5d-(35/60)*(16)*a-(42/60)*(16)*b-
(48/60)*(16)*c-(52/60)*(16)*d
With the object of Minimising
Material Cost, Labour Cost
Labour cost=
(35/60)*(16)*a+(42/60)*(16)*b+(48/60)*(16)*c+(52/60)*(16)*d
Material Cost= 18a+15+5c+5d
Constraints under the given case
X = a+b+c+d
A >= 0.2X
3
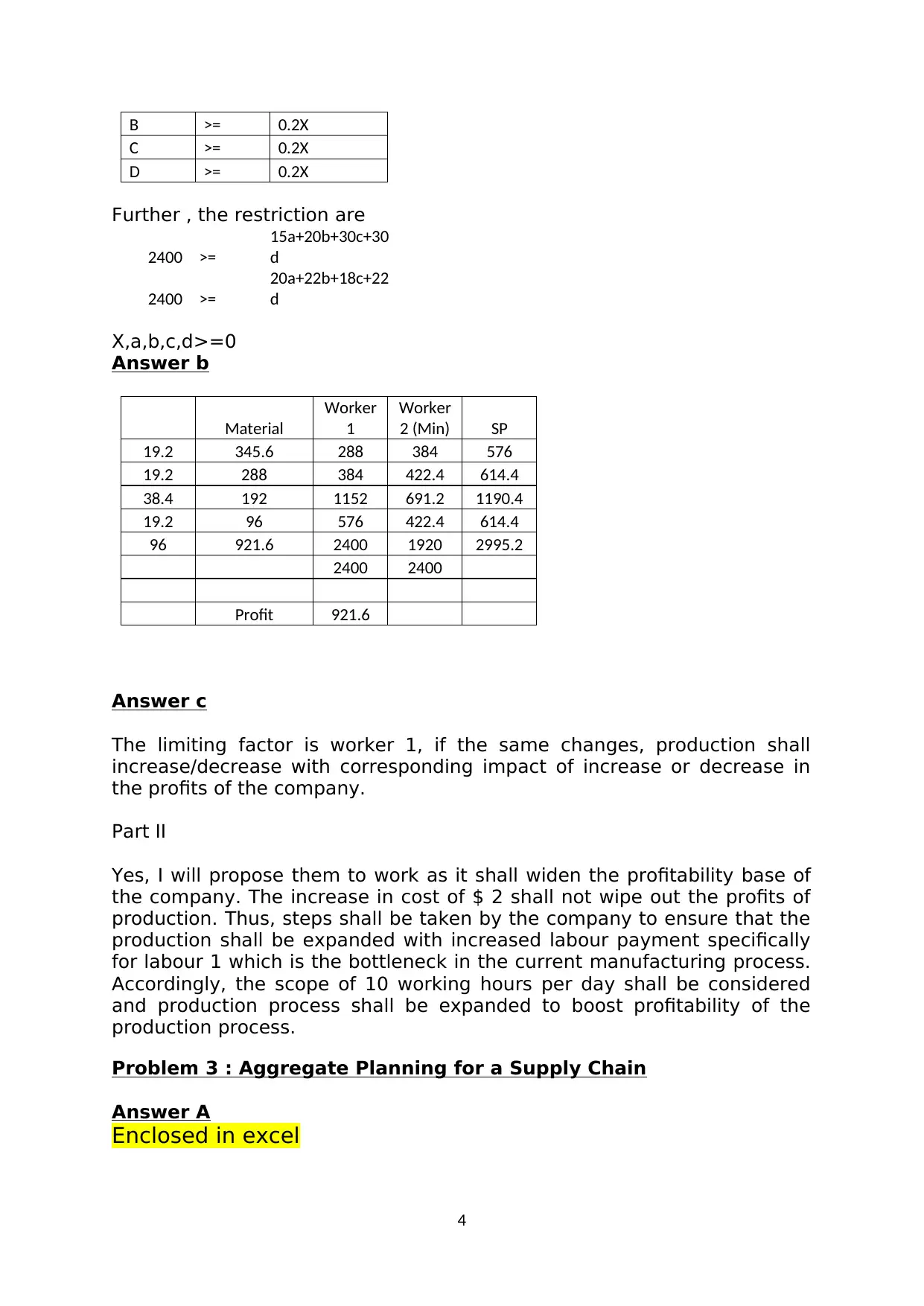
B >= 0.2X
C >= 0.2X
D >= 0.2X
Further , the restriction are
2400 >=
15a+20b+30c+30
d
2400 >=
20a+22b+18c+22
d
X,a,b,c,d>=0
Answer b
Material
Worker
1
Worker
2 (Min) SP
19.2 345.6 288 384 576
19.2 288 384 422.4 614.4
38.4 192 1152 691.2 1190.4
19.2 96 576 422.4 614.4
96 921.6 2400 1920 2995.2
2400 2400
Profit 921.6
Answer c
The limiting factor is worker 1, if the same changes, production shall
increase/decrease with corresponding impact of increase or decrease in
the profits of the company.
Part II
Yes, I will propose them to work as it shall widen the profitability base of
the company. The increase in cost of $ 2 shall not wipe out the profits of
production. Thus, steps shall be taken by the company to ensure that the
production shall be expanded with increased labour payment specifically
for labour 1 which is the bottleneck in the current manufacturing process.
Accordingly, the scope of 10 working hours per day shall be considered
and production process shall be expanded to boost profitability of the
production process.
Problem 3 : Aggregate Planning for a Supply Chain
Answer A
Enclosed in excel
4
C >= 0.2X
D >= 0.2X
Further , the restriction are
2400 >=
15a+20b+30c+30
d
2400 >=
20a+22b+18c+22
d
X,a,b,c,d>=0
Answer b
Material
Worker
1
Worker
2 (Min) SP
19.2 345.6 288 384 576
19.2 288 384 422.4 614.4
38.4 192 1152 691.2 1190.4
19.2 96 576 422.4 614.4
96 921.6 2400 1920 2995.2
2400 2400
Profit 921.6
Answer c
The limiting factor is worker 1, if the same changes, production shall
increase/decrease with corresponding impact of increase or decrease in
the profits of the company.
Part II
Yes, I will propose them to work as it shall widen the profitability base of
the company. The increase in cost of $ 2 shall not wipe out the profits of
production. Thus, steps shall be taken by the company to ensure that the
production shall be expanded with increased labour payment specifically
for labour 1 which is the bottleneck in the current manufacturing process.
Accordingly, the scope of 10 working hours per day shall be considered
and production process shall be expanded to boost profitability of the
production process.
Problem 3 : Aggregate Planning for a Supply Chain
Answer A
Enclosed in excel
4
Secure Best Marks with AI Grader
Need help grading? Try our AI Grader for instant feedback on your assignments.
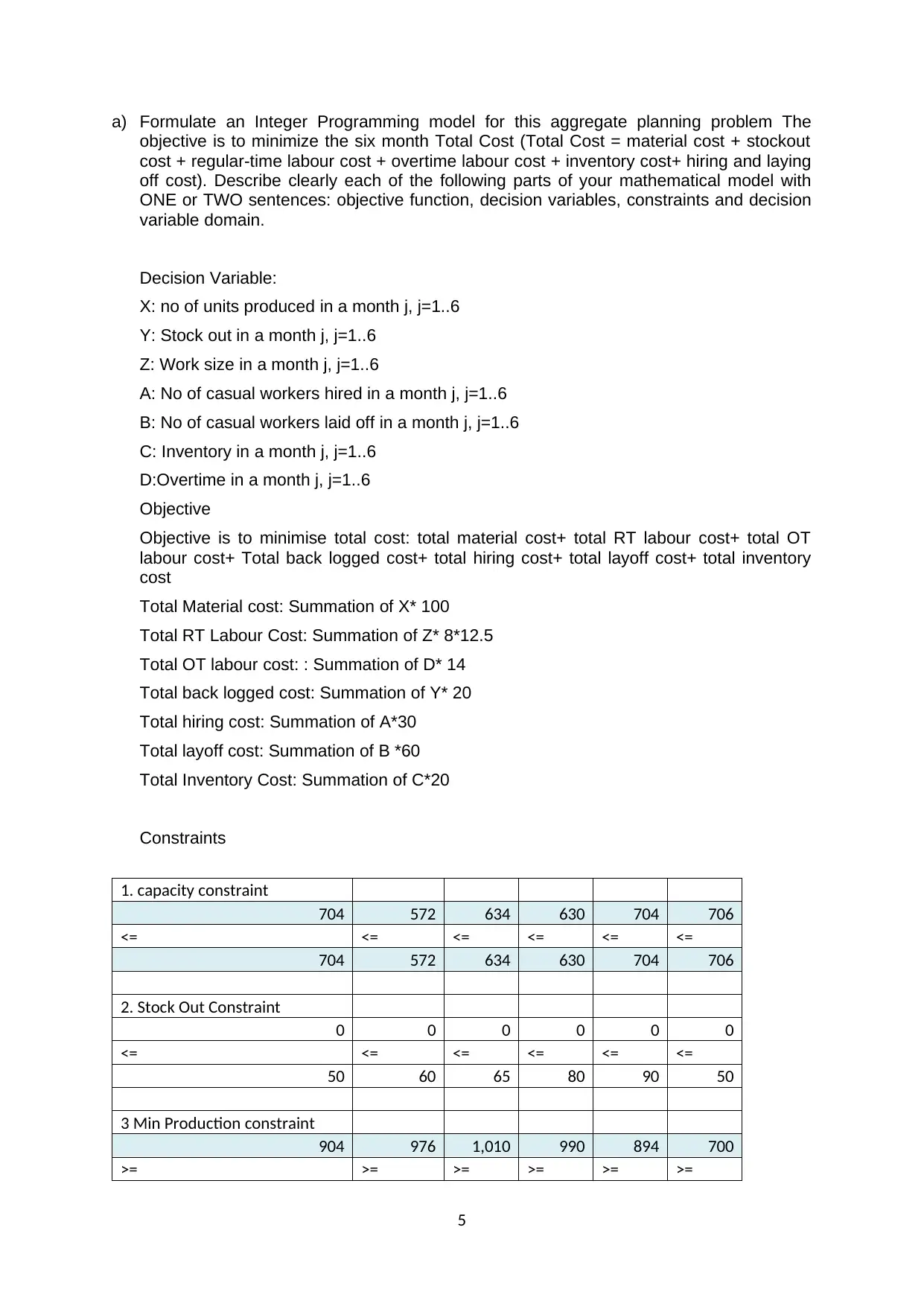
a) Formulate an Integer Programming model for this aggregate planning problem The
objective is to minimize the six month Total Cost (Total Cost = material cost + stockout
cost + regular-time labour cost + overtime labour cost + inventory cost+ hiring and laying
off cost). Describe clearly each of the following parts of your mathematical model with
ONE or TWO sentences: objective function, decision variables, constraints and decision
variable domain.
Decision Variable:
X: no of units produced in a month j, j=1..6
Y: Stock out in a month j, j=1..6
Z: Work size in a month j, j=1..6
A: No of casual workers hired in a month j, j=1..6
B: No of casual workers laid off in a month j, j=1..6
C: Inventory in a month j, j=1..6
D:Overtime in a month j, j=1..6
Objective
Objective is to minimise total cost: total material cost+ total RT labour cost+ total OT
labour cost+ Total back logged cost+ total hiring cost+ total layoff cost+ total inventory
cost
Total Material cost: Summation of X* 100
Total RT Labour Cost: Summation of Z* 8*12.5
Total OT labour cost: : Summation of D* 14
Total back logged cost: Summation of Y* 20
Total hiring cost: Summation of A*30
Total layoff cost: Summation of B *60
Total Inventory Cost: Summation of C*20
Constraints
1. capacity constraint
704 572 634 630 704 706
<= <= <= <= <= <=
704 572 634 630 704 706
2. Stock Out Constraint
0 0 0 0 0 0
<= <= <= <= <= <=
50 60 65 80 90 50
3 Min Production constraint
904 976 1,010 990 894 700
>= >= >= >= >= >=
5
objective is to minimize the six month Total Cost (Total Cost = material cost + stockout
cost + regular-time labour cost + overtime labour cost + inventory cost+ hiring and laying
off cost). Describe clearly each of the following parts of your mathematical model with
ONE or TWO sentences: objective function, decision variables, constraints and decision
variable domain.
Decision Variable:
X: no of units produced in a month j, j=1..6
Y: Stock out in a month j, j=1..6
Z: Work size in a month j, j=1..6
A: No of casual workers hired in a month j, j=1..6
B: No of casual workers laid off in a month j, j=1..6
C: Inventory in a month j, j=1..6
D:Overtime in a month j, j=1..6
Objective
Objective is to minimise total cost: total material cost+ total RT labour cost+ total OT
labour cost+ Total back logged cost+ total hiring cost+ total layoff cost+ total inventory
cost
Total Material cost: Summation of X* 100
Total RT Labour Cost: Summation of Z* 8*12.5
Total OT labour cost: : Summation of D* 14
Total back logged cost: Summation of Y* 20
Total hiring cost: Summation of A*30
Total layoff cost: Summation of B *60
Total Inventory Cost: Summation of C*20
Constraints
1. capacity constraint
704 572 634 630 704 706
<= <= <= <= <= <=
704 572 634 630 704 706
2. Stock Out Constraint
0 0 0 0 0 0
<= <= <= <= <= <=
50 60 65 80 90 50
3 Min Production constraint
904 976 1,010 990 894 700
>= >= >= >= >= >=
5
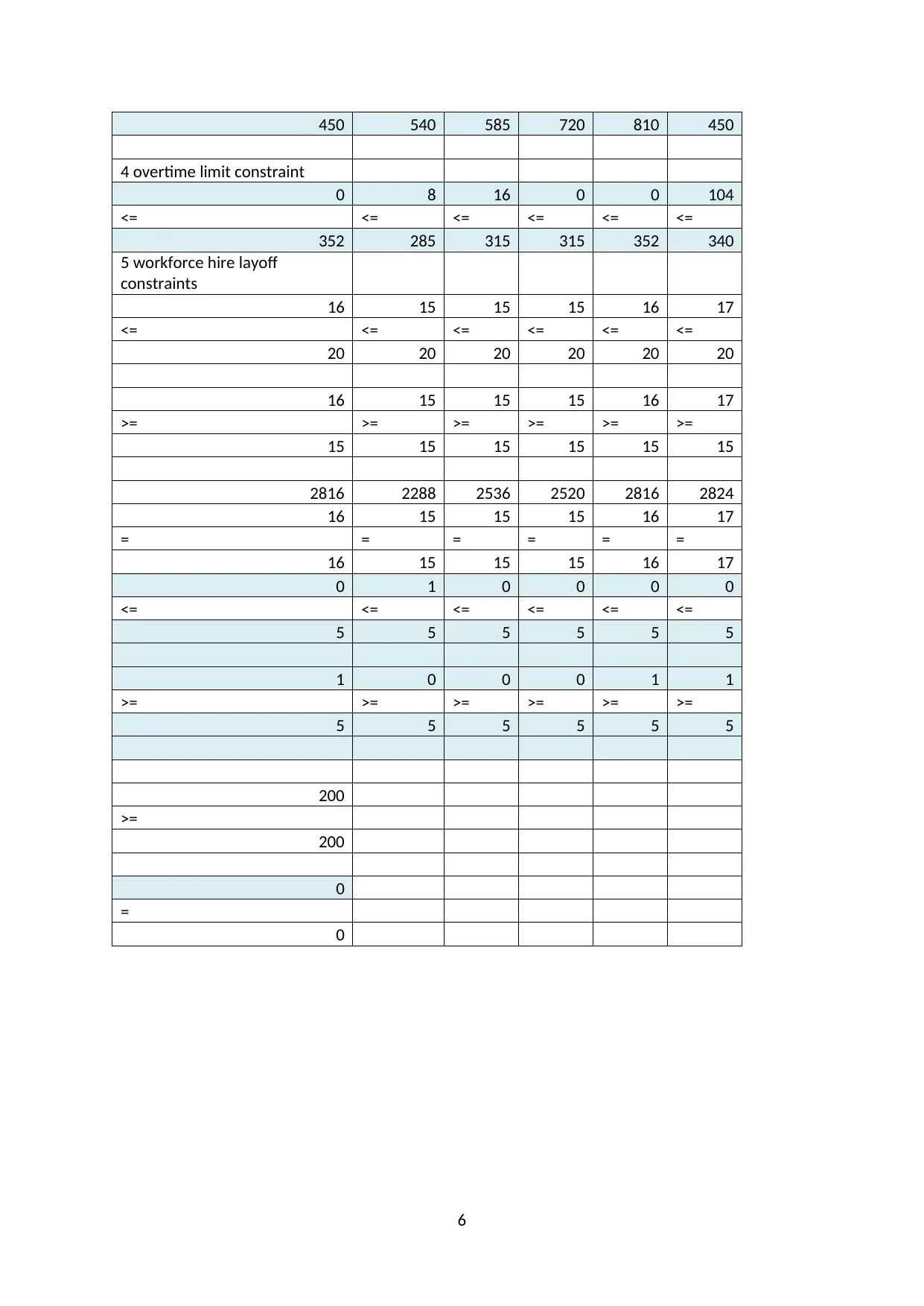
450 540 585 720 810 450
4 overtime limit constraint
0 8 16 0 0 104
<= <= <= <= <= <=
352 285 315 315 352 340
5 workforce hire layoff
constraints
16 15 15 15 16 17
<= <= <= <= <= <=
20 20 20 20 20 20
16 15 15 15 16 17
>= >= >= >= >= >=
15 15 15 15 15 15
2816 2288 2536 2520 2816 2824
16 15 15 15 16 17
= = = = = =
16 15 15 15 16 17
0 1 0 0 0 0
<= <= <= <= <= <=
5 5 5 5 5 5
1 0 0 0 1 1
>= >= >= >= >= >=
5 5 5 5 5 5
200
>=
200
0
=
0
6
4 overtime limit constraint
0 8 16 0 0 104
<= <= <= <= <= <=
352 285 315 315 352 340
5 workforce hire layoff
constraints
16 15 15 15 16 17
<= <= <= <= <= <=
20 20 20 20 20 20
16 15 15 15 16 17
>= >= >= >= >= >=
15 15 15 15 15 15
2816 2288 2536 2520 2816 2824
16 15 15 15 16 17
= = = = = =
16 15 15 15 16 17
0 1 0 0 0 0
<= <= <= <= <= <=
5 5 5 5 5 5
1 0 0 0 1 1
>= >= >= >= >= >=
5 5 5 5 5 5
200
>=
200
0
=
0
6
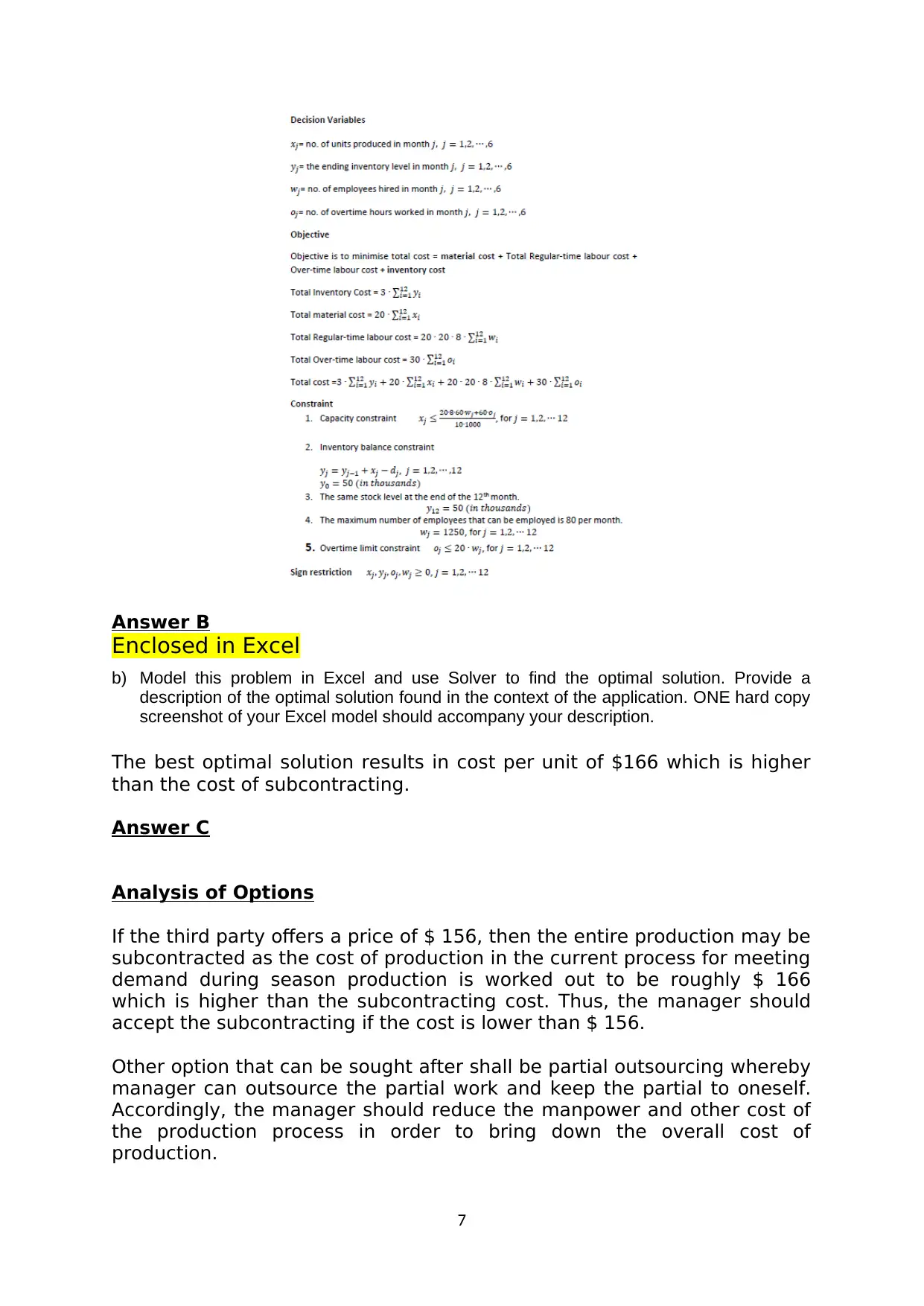
Answer B
Enclosed in Excel
b) Model this problem in Excel and use Solver to find the optimal solution. Provide a
description of the optimal solution found in the context of the application. ONE hard copy
screenshot of your Excel model should accompany your description.
The best optimal solution results in cost per unit of $166 which is higher
than the cost of subcontracting.
Answer C
Analysis of Options
If the third party offers a price of $ 156, then the entire production may be
subcontracted as the cost of production in the current process for meeting
demand during season production is worked out to be roughly $ 166
which is higher than the subcontracting cost. Thus, the manager should
accept the subcontracting if the cost is lower than $ 156.
Other option that can be sought after shall be partial outsourcing whereby
manager can outsource the partial work and keep the partial to oneself.
Accordingly, the manager should reduce the manpower and other cost of
the production process in order to bring down the overall cost of
production.
7
Enclosed in Excel
b) Model this problem in Excel and use Solver to find the optimal solution. Provide a
description of the optimal solution found in the context of the application. ONE hard copy
screenshot of your Excel model should accompany your description.
The best optimal solution results in cost per unit of $166 which is higher
than the cost of subcontracting.
Answer C
Analysis of Options
If the third party offers a price of $ 156, then the entire production may be
subcontracted as the cost of production in the current process for meeting
demand during season production is worked out to be roughly $ 166
which is higher than the subcontracting cost. Thus, the manager should
accept the subcontracting if the cost is lower than $ 156.
Other option that can be sought after shall be partial outsourcing whereby
manager can outsource the partial work and keep the partial to oneself.
Accordingly, the manager should reduce the manpower and other cost of
the production process in order to bring down the overall cost of
production.
7
Paraphrase This Document
Need a fresh take? Get an instant paraphrase of this document with our AI Paraphraser
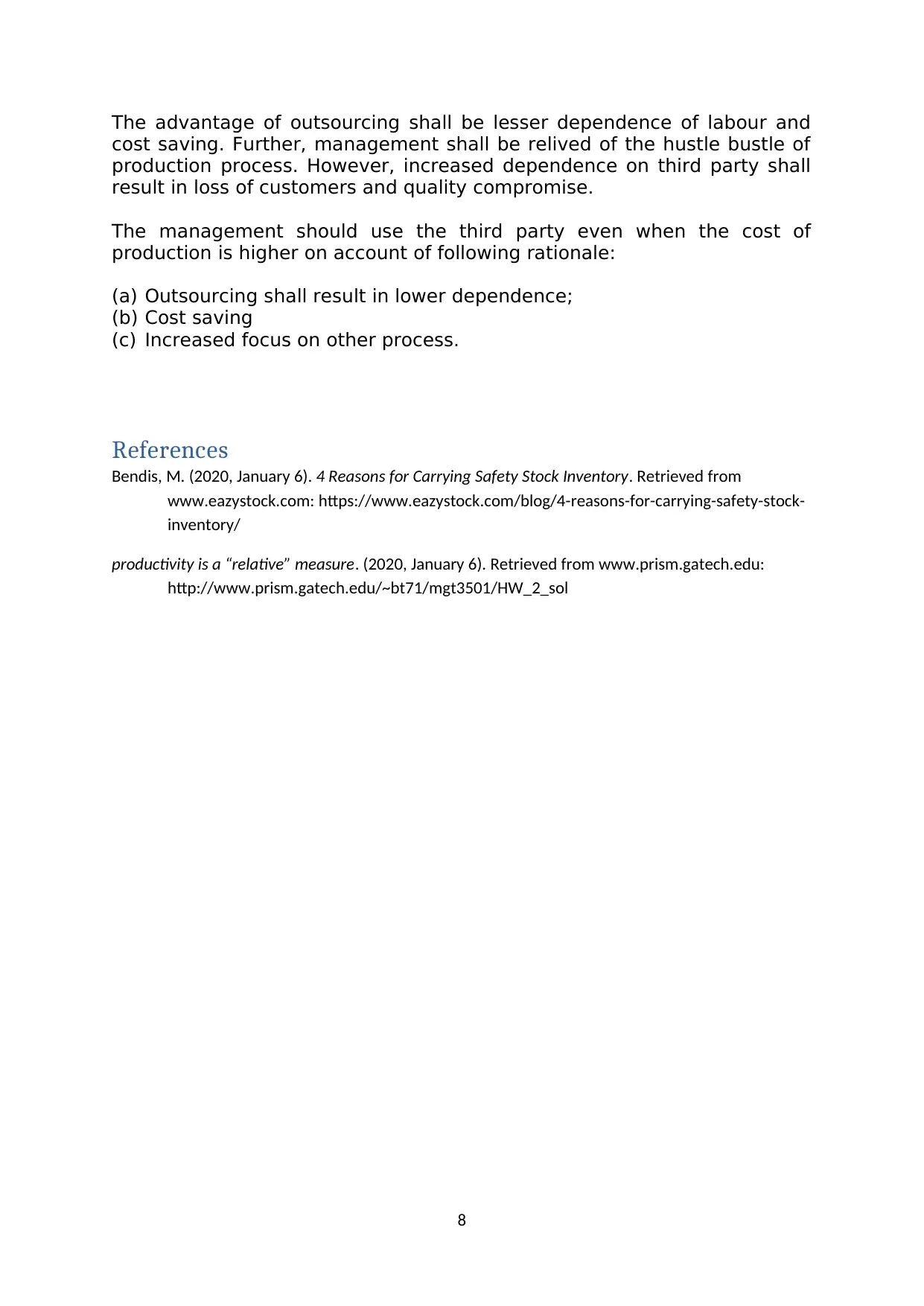
The advantage of outsourcing shall be lesser dependence of labour and
cost saving. Further, management shall be relived of the hustle bustle of
production process. However, increased dependence on third party shall
result in loss of customers and quality compromise.
The management should use the third party even when the cost of
production is higher on account of following rationale:
(a) Outsourcing shall result in lower dependence;
(b) Cost saving
(c) Increased focus on other process.
References
Bendis, M. (2020, January 6). 4 Reasons for Carrying Safety Stock Inventory. Retrieved from
www.eazystock.com: https://www.eazystock.com/blog/4-reasons-for-carrying-safety-stock-
inventory/
productivity is a “relative” measure. (2020, January 6). Retrieved from www.prism.gatech.edu:
http://www.prism.gatech.edu/~bt71/mgt3501/HW_2_sol
8
cost saving. Further, management shall be relived of the hustle bustle of
production process. However, increased dependence on third party shall
result in loss of customers and quality compromise.
The management should use the third party even when the cost of
production is higher on account of following rationale:
(a) Outsourcing shall result in lower dependence;
(b) Cost saving
(c) Increased focus on other process.
References
Bendis, M. (2020, January 6). 4 Reasons for Carrying Safety Stock Inventory. Retrieved from
www.eazystock.com: https://www.eazystock.com/blog/4-reasons-for-carrying-safety-stock-
inventory/
productivity is a “relative” measure. (2020, January 6). Retrieved from www.prism.gatech.edu:
http://www.prism.gatech.edu/~bt71/mgt3501/HW_2_sol
8
1 out of 8
![[object Object]](/_next/image/?url=%2F_next%2Fstatic%2Fmedia%2Flogo.6d15ce61.png&w=640&q=75)
Your All-in-One AI-Powered Toolkit for Academic Success.
+13062052269
info@desklib.com
Available 24*7 on WhatsApp / Email
Unlock your academic potential
© 2024 | Zucol Services PVT LTD | All rights reserved.