PROJ 6002 - Project Planning and Budgeting: Cost & Quality Plan
VerifiedAdded on 2020/12/22
|12
|2352
|267
Report
AI Summary
This report, prepared by Jaime Daza and Mauricio Montoya for PROJ 6002, details a comprehensive cost and quality management plan for a rubber component manufacturing project. It outlines quality objectives, methods, and tools, including deliverables, quality control procedures, and defect escalation protocols. The plan emphasizes the importance of acceptance criteria, technical tests, and customer feedback. The cost management section covers the cost management approach, estimation techniques, budget determination, and roles and responsibilities. The report uses tools such as cost variance, CPI, SPI, and schedule variance for effective cost control and performance measurement. The conclusion highlights the significance of project management tools and techniques in achieving product standards and mitigating project risks, ensuring that project managers select suitable tools. The report is focused on ensuring the project meets quality standards, remains within budget, and delivers the final product according to the client’s expectations.
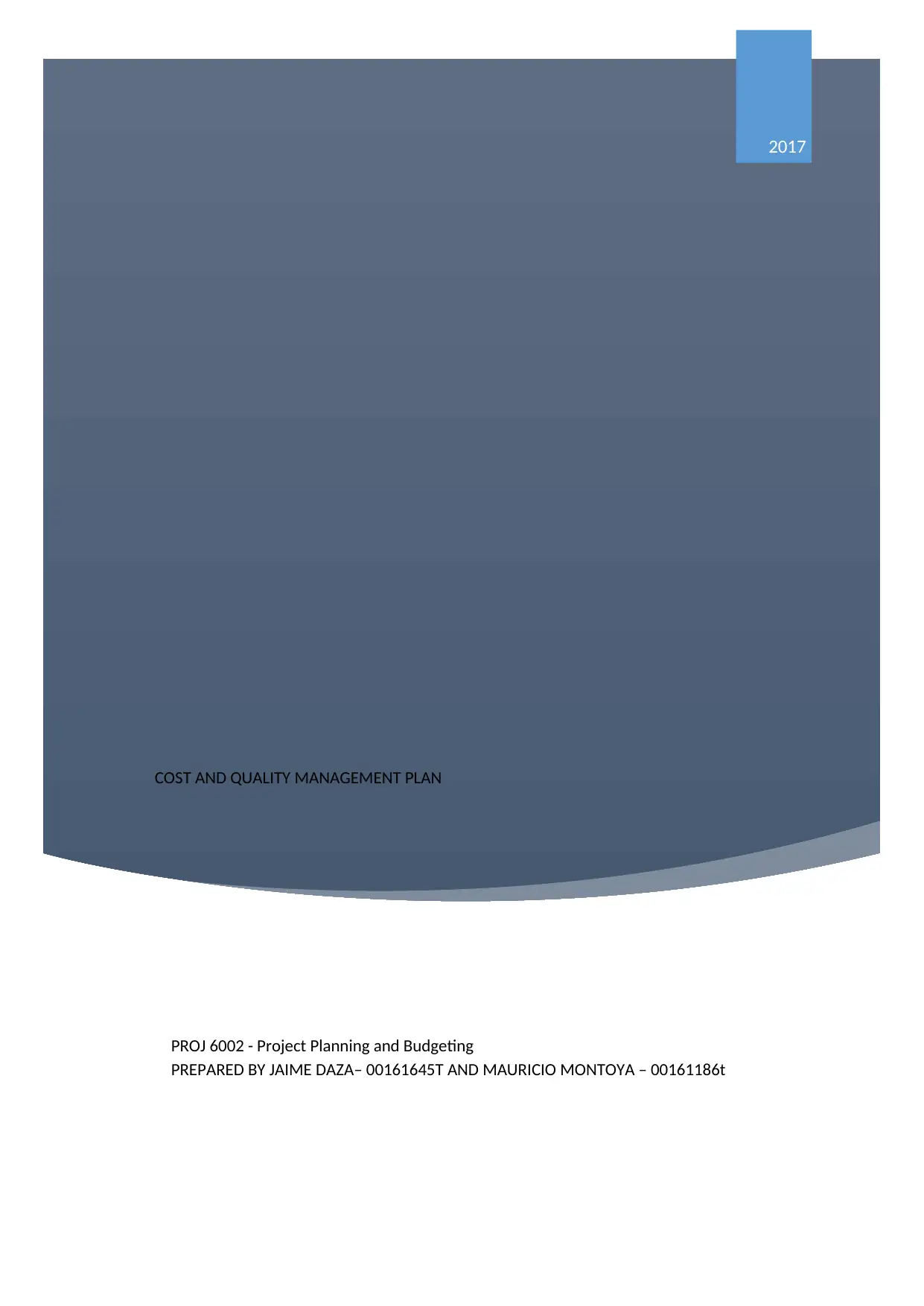
COST AND QUALITY MANAGEMENT PLAN
2017
PROJ 6002 - Project Planning and Budgeting
PREPARED BY JAIME DAZA– 00161645T AND MAURICIO MONTOYA – 00161186t
2017
PROJ 6002 - Project Planning and Budgeting
PREPARED BY JAIME DAZA– 00161645T AND MAURICIO MONTOYA – 00161186t
Paraphrase This Document
Need a fresh take? Get an instant paraphrase of this document with our AI Paraphraser
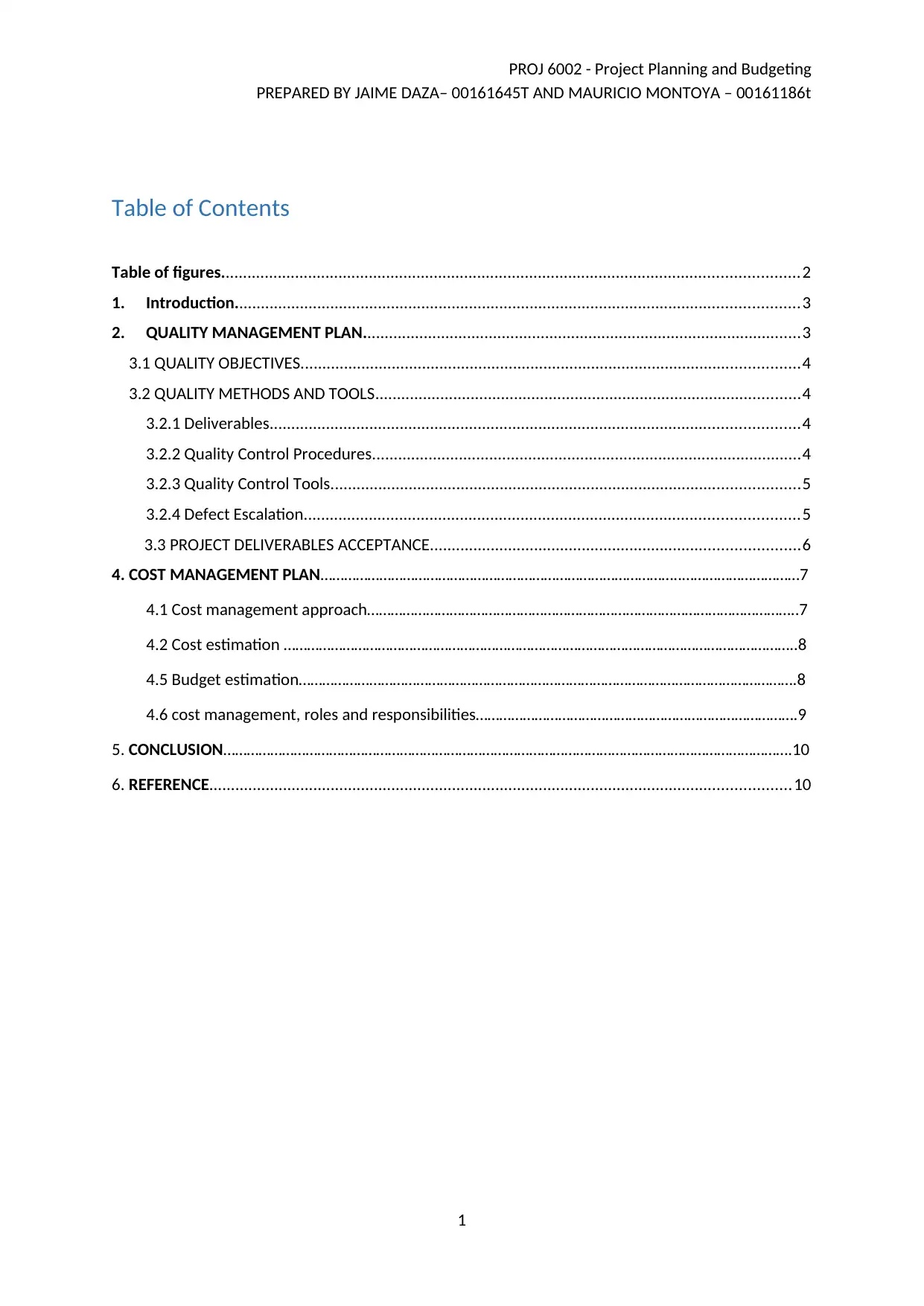
PROJ 6002 - Project Planning and Budgeting
PREPARED BY JAIME DAZA– 00161645T AND MAURICIO MONTOYA – 00161186t
Table of Contents
Table of figures.....................................................................................................................................2
1. Introduction..................................................................................................................................3
2. QUALITY MANAGEMENT PLAN.....................................................................................................3
3.1 QUALITY OBJECTIVES...................................................................................................................4
3.2 QUALITY METHODS AND TOOLS..................................................................................................4
3.2.1 Deliverables..........................................................................................................................4
3.2.2 Quality Control Procedures...................................................................................................4
3.2.3 Quality Control Tools............................................................................................................5
3.2.4 Defect Escalation..................................................................................................................5
3.3 PROJECT DELIVERABLES ACCEPTANCE.....................................................................................6
4. COST MANAGEMENT PLAN………………………………………………………………………………..…………………………7
4.1 Cost management approach………………………………………………………………………………………………..7
4.2 Cost estimation …………………………………………………………………………………………………………………..8
4.5 Budget estimation……………………………………………………………………………………………………………….8
4.6 cost management, roles and responsibilities……………………………………………………………………….9
5. CONCLUSION……………………………………………………………………………………………………………………………….10
6. REFERENCE......................................................................................................................................10
1
PREPARED BY JAIME DAZA– 00161645T AND MAURICIO MONTOYA – 00161186t
Table of Contents
Table of figures.....................................................................................................................................2
1. Introduction..................................................................................................................................3
2. QUALITY MANAGEMENT PLAN.....................................................................................................3
3.1 QUALITY OBJECTIVES...................................................................................................................4
3.2 QUALITY METHODS AND TOOLS..................................................................................................4
3.2.1 Deliverables..........................................................................................................................4
3.2.2 Quality Control Procedures...................................................................................................4
3.2.3 Quality Control Tools............................................................................................................5
3.2.4 Defect Escalation..................................................................................................................5
3.3 PROJECT DELIVERABLES ACCEPTANCE.....................................................................................6
4. COST MANAGEMENT PLAN………………………………………………………………………………..…………………………7
4.1 Cost management approach………………………………………………………………………………………………..7
4.2 Cost estimation …………………………………………………………………………………………………………………..8
4.5 Budget estimation……………………………………………………………………………………………………………….8
4.6 cost management, roles and responsibilities……………………………………………………………………….9
5. CONCLUSION……………………………………………………………………………………………………………………………….10
6. REFERENCE......................................................................................................................................10
1
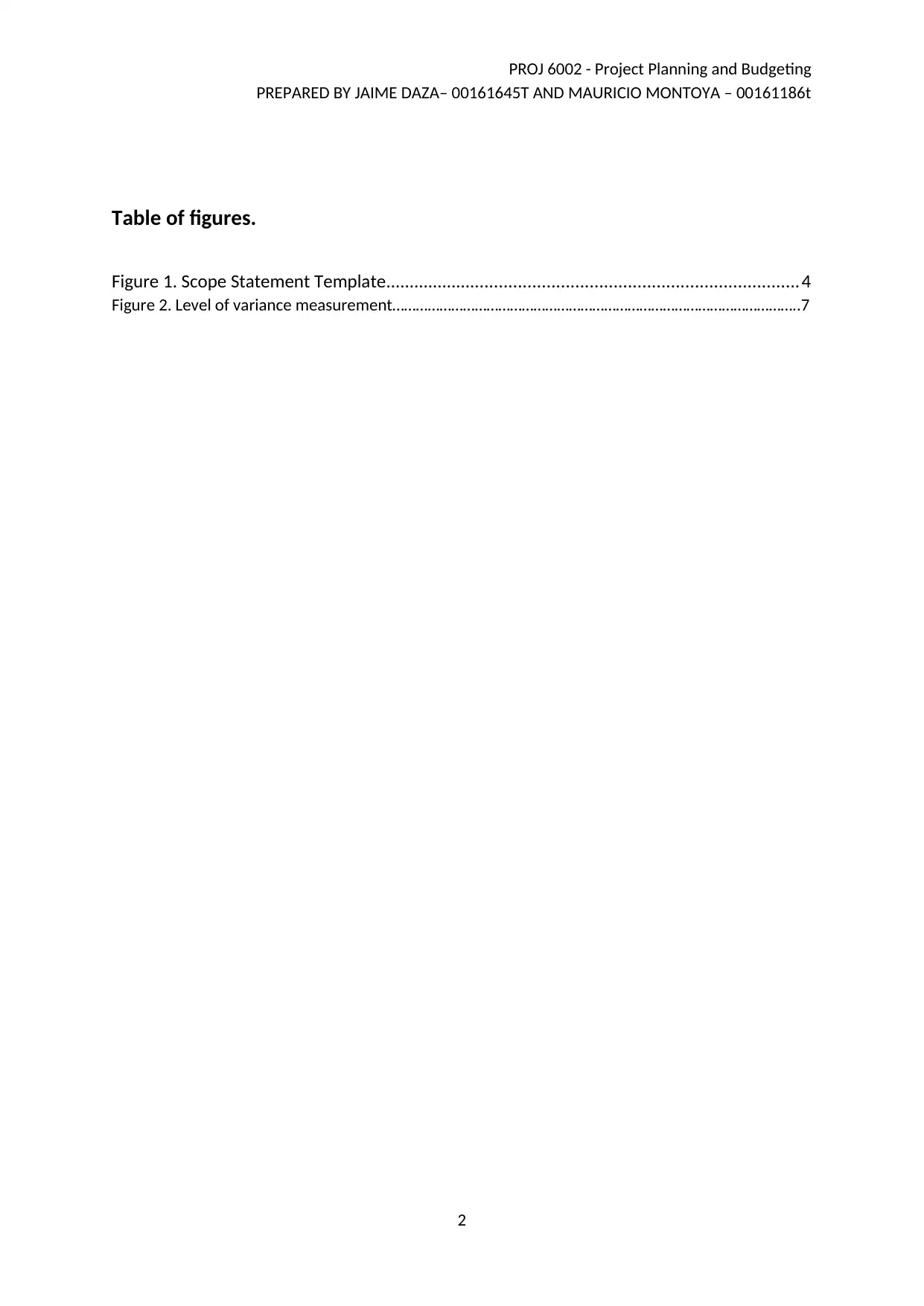
PROJ 6002 - Project Planning and Budgeting
PREPARED BY JAIME DAZA– 00161645T AND MAURICIO MONTOYA – 00161186t
Table of figures.
Figure 1. Scope Statement Template.......................................................................................4
Figure 2. Level of variance measurement…………………………………………………………………………………………..7
2
PREPARED BY JAIME DAZA– 00161645T AND MAURICIO MONTOYA – 00161186t
Table of figures.
Figure 1. Scope Statement Template.......................................................................................4
Figure 2. Level of variance measurement…………………………………………………………………………………………..7
2
⊘ This is a preview!⊘
Do you want full access?
Subscribe today to unlock all pages.

Trusted by 1+ million students worldwide

PROJ 6002 - Project Planning and Budgeting
PREPARED BY JAIME DAZA– 00161645T AND MAURICIO MONTOYA – 00161186t
1. Introduction.
Over the last few decades, cost and quality management and has ensured project objectives
and budget for delivering a product or services effective and efficient. Project managers
need to identify quality and cost requirements for all deliverables process and decide how
to meet them.
Tools and techniques are found widely for project management to be used according with
project requirements. This case study will explain clearly how a rubber project would use
these elements and analyse some potential factors to be successful in cost and quality
requirements.
3
PREPARED BY JAIME DAZA– 00161645T AND MAURICIO MONTOYA – 00161186t
1. Introduction.
Over the last few decades, cost and quality management and has ensured project objectives
and budget for delivering a product or services effective and efficient. Project managers
need to identify quality and cost requirements for all deliverables process and decide how
to meet them.
Tools and techniques are found widely for project management to be used according with
project requirements. This case study will explain clearly how a rubber project would use
these elements and analyse some potential factors to be successful in cost and quality
requirements.
3
Paraphrase This Document
Need a fresh take? Get an instant paraphrase of this document with our AI Paraphraser
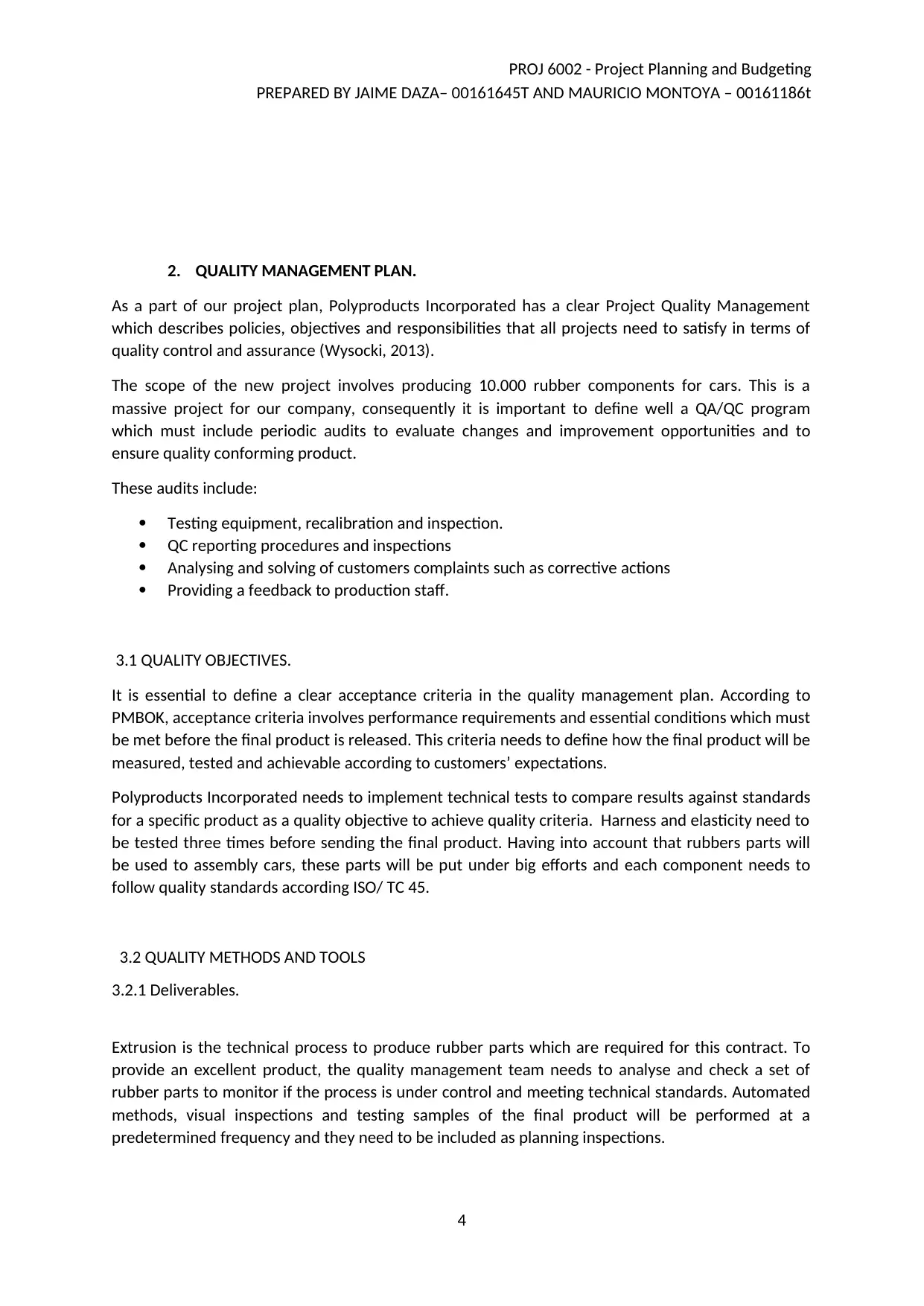
PROJ 6002 - Project Planning and Budgeting
PREPARED BY JAIME DAZA– 00161645T AND MAURICIO MONTOYA – 00161186t
2. QUALITY MANAGEMENT PLAN.
As a part of our project plan, Polyproducts Incorporated has a clear Project Quality Management
which describes policies, objectives and responsibilities that all projects need to satisfy in terms of
quality control and assurance (Wysocki, 2013).
The scope of the new project involves producing 10.000 rubber components for cars. This is a
massive project for our company, consequently it is important to define well a QA/QC program
which must include periodic audits to evaluate changes and improvement opportunities and to
ensure quality conforming product.
These audits include:
Testing equipment, recalibration and inspection.
QC reporting procedures and inspections
Analysing and solving of customers complaints such as corrective actions
Providing a feedback to production staff.
3.1 QUALITY OBJECTIVES.
It is essential to define a clear acceptance criteria in the quality management plan. According to
PMBOK, acceptance criteria involves performance requirements and essential conditions which must
be met before the final product is released. This criteria needs to define how the final product will be
measured, tested and achievable according to customers’ expectations.
Polyproducts Incorporated needs to implement technical tests to compare results against standards
for a specific product as a quality objective to achieve quality criteria. Harness and elasticity need to
be tested three times before sending the final product. Having into account that rubbers parts will
be used to assembly cars, these parts will be put under big efforts and each component needs to
follow quality standards according ISO/ TC 45.
3.2 QUALITY METHODS AND TOOLS
3.2.1 Deliverables.
Extrusion is the technical process to produce rubber parts which are required for this contract. To
provide an excellent product, the quality management team needs to analyse and check a set of
rubber parts to monitor if the process is under control and meeting technical standards. Automated
methods, visual inspections and testing samples of the final product will be performed at a
predetermined frequency and they need to be included as planning inspections.
4
PREPARED BY JAIME DAZA– 00161645T AND MAURICIO MONTOYA – 00161186t
2. QUALITY MANAGEMENT PLAN.
As a part of our project plan, Polyproducts Incorporated has a clear Project Quality Management
which describes policies, objectives and responsibilities that all projects need to satisfy in terms of
quality control and assurance (Wysocki, 2013).
The scope of the new project involves producing 10.000 rubber components for cars. This is a
massive project for our company, consequently it is important to define well a QA/QC program
which must include periodic audits to evaluate changes and improvement opportunities and to
ensure quality conforming product.
These audits include:
Testing equipment, recalibration and inspection.
QC reporting procedures and inspections
Analysing and solving of customers complaints such as corrective actions
Providing a feedback to production staff.
3.1 QUALITY OBJECTIVES.
It is essential to define a clear acceptance criteria in the quality management plan. According to
PMBOK, acceptance criteria involves performance requirements and essential conditions which must
be met before the final product is released. This criteria needs to define how the final product will be
measured, tested and achievable according to customers’ expectations.
Polyproducts Incorporated needs to implement technical tests to compare results against standards
for a specific product as a quality objective to achieve quality criteria. Harness and elasticity need to
be tested three times before sending the final product. Having into account that rubbers parts will
be used to assembly cars, these parts will be put under big efforts and each component needs to
follow quality standards according ISO/ TC 45.
3.2 QUALITY METHODS AND TOOLS
3.2.1 Deliverables.
Extrusion is the technical process to produce rubber parts which are required for this contract. To
provide an excellent product, the quality management team needs to analyse and check a set of
rubber parts to monitor if the process is under control and meeting technical standards. Automated
methods, visual inspections and testing samples of the final product will be performed at a
predetermined frequency and they need to be included as planning inspections.
4
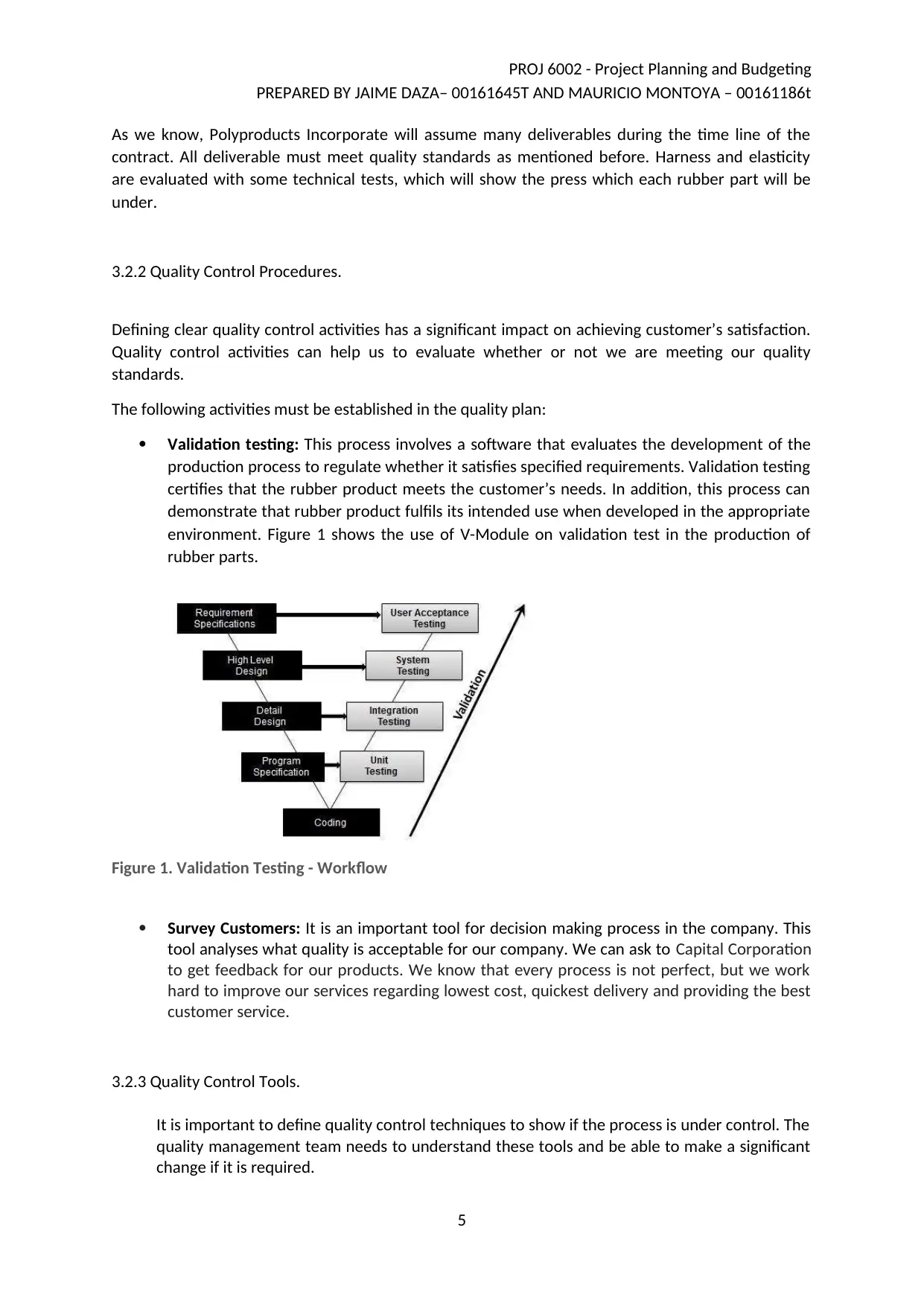
PROJ 6002 - Project Planning and Budgeting
PREPARED BY JAIME DAZA– 00161645T AND MAURICIO MONTOYA – 00161186t
As we know, Polyproducts Incorporate will assume many deliverables during the time line of the
contract. All deliverable must meet quality standards as mentioned before. Harness and elasticity
are evaluated with some technical tests, which will show the press which each rubber part will be
under.
3.2.2 Quality Control Procedures.
Defining clear quality control activities has a significant impact on achieving customer’s satisfaction.
Quality control activities can help us to evaluate whether or not we are meeting our quality
standards.
The following activities must be established in the quality plan:
Validation testing: This process involves a software that evaluates the development of the
production process to regulate whether it satisfies specified requirements. Validation testing
certifies that the rubber product meets the customer’s needs. In addition, this process can
demonstrate that rubber product fulfils its intended use when developed in the appropriate
environment. Figure 1 shows the use of V-Module on validation test in the production of
rubber parts.
Figure 1. Validation Testing - Workflow
Survey Customers: It is an important tool for decision making process in the company. This
tool analyses what quality is acceptable for our company. We can ask to Capital Corporation
to get feedback for our products. We know that every process is not perfect, but we work
hard to improve our services regarding lowest cost, quickest delivery and providing the best
customer service.
3.2.3 Quality Control Tools.
It is important to define quality control techniques to show if the process is under control. The
quality management team needs to understand these tools and be able to make a significant
change if it is required.
5
PREPARED BY JAIME DAZA– 00161645T AND MAURICIO MONTOYA – 00161186t
As we know, Polyproducts Incorporate will assume many deliverables during the time line of the
contract. All deliverable must meet quality standards as mentioned before. Harness and elasticity
are evaluated with some technical tests, which will show the press which each rubber part will be
under.
3.2.2 Quality Control Procedures.
Defining clear quality control activities has a significant impact on achieving customer’s satisfaction.
Quality control activities can help us to evaluate whether or not we are meeting our quality
standards.
The following activities must be established in the quality plan:
Validation testing: This process involves a software that evaluates the development of the
production process to regulate whether it satisfies specified requirements. Validation testing
certifies that the rubber product meets the customer’s needs. In addition, this process can
demonstrate that rubber product fulfils its intended use when developed in the appropriate
environment. Figure 1 shows the use of V-Module on validation test in the production of
rubber parts.
Figure 1. Validation Testing - Workflow
Survey Customers: It is an important tool for decision making process in the company. This
tool analyses what quality is acceptable for our company. We can ask to Capital Corporation
to get feedback for our products. We know that every process is not perfect, but we work
hard to improve our services regarding lowest cost, quickest delivery and providing the best
customer service.
3.2.3 Quality Control Tools.
It is important to define quality control techniques to show if the process is under control. The
quality management team needs to understand these tools and be able to make a significant
change if it is required.
5
⊘ This is a preview!⊘
Do you want full access?
Subscribe today to unlock all pages.

Trusted by 1+ million students worldwide
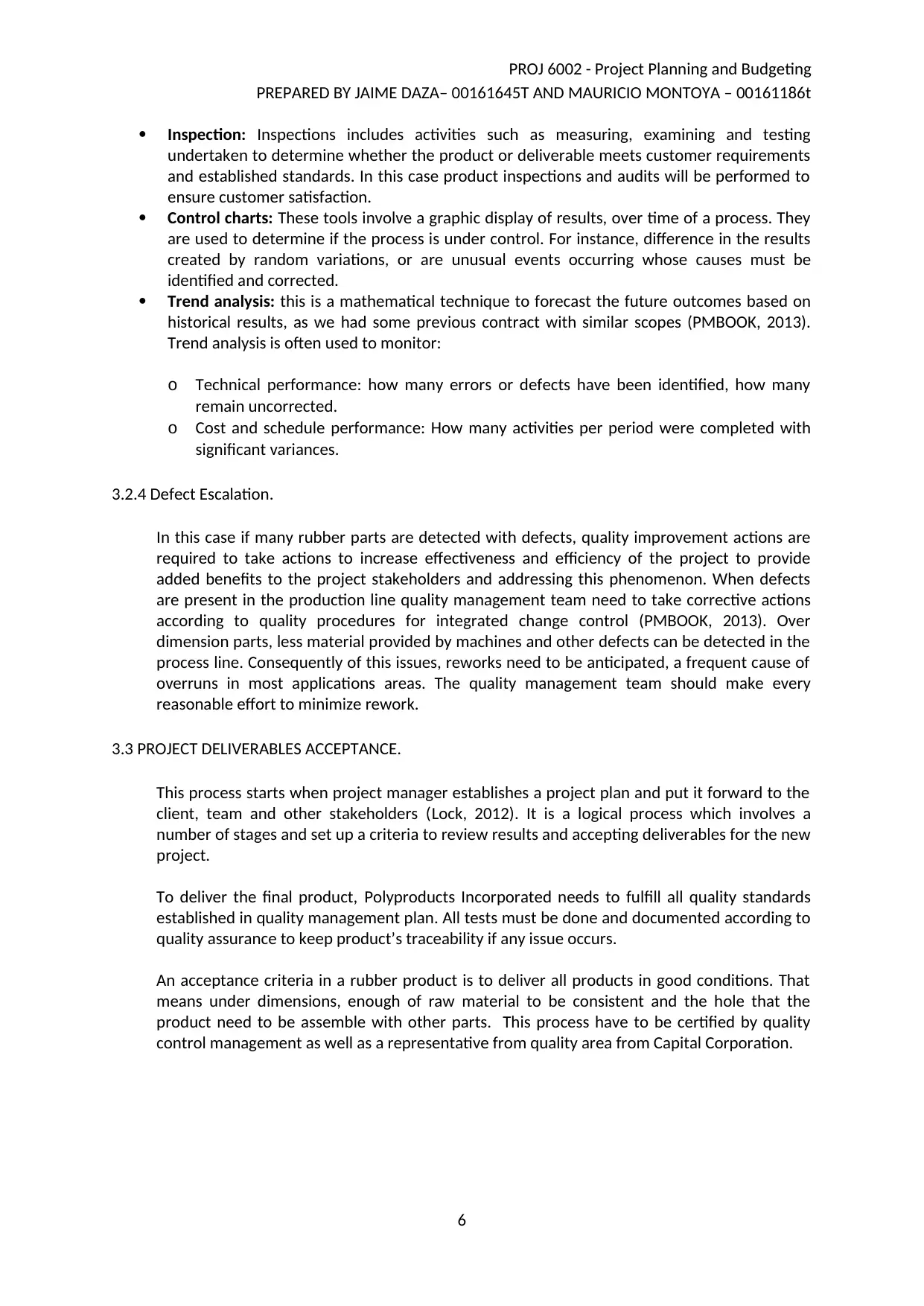
PROJ 6002 - Project Planning and Budgeting
PREPARED BY JAIME DAZA– 00161645T AND MAURICIO MONTOYA – 00161186t
Inspection: Inspections includes activities such as measuring, examining and testing
undertaken to determine whether the product or deliverable meets customer requirements
and established standards. In this case product inspections and audits will be performed to
ensure customer satisfaction.
Control charts: These tools involve a graphic display of results, over time of a process. They
are used to determine if the process is under control. For instance, difference in the results
created by random variations, or are unusual events occurring whose causes must be
identified and corrected.
Trend analysis: this is a mathematical technique to forecast the future outcomes based on
historical results, as we had some previous contract with similar scopes (PMBOOK, 2013).
Trend analysis is often used to monitor:
o Technical performance: how many errors or defects have been identified, how many
remain uncorrected.
o Cost and schedule performance: How many activities per period were completed with
significant variances.
3.2.4 Defect Escalation.
In this case if many rubber parts are detected with defects, quality improvement actions are
required to take actions to increase effectiveness and efficiency of the project to provide
added benefits to the project stakeholders and addressing this phenomenon. When defects
are present in the production line quality management team need to take corrective actions
according to quality procedures for integrated change control (PMBOOK, 2013). Over
dimension parts, less material provided by machines and other defects can be detected in the
process line. Consequently of this issues, reworks need to be anticipated, a frequent cause of
overruns in most applications areas. The quality management team should make every
reasonable effort to minimize rework.
3.3 PROJECT DELIVERABLES ACCEPTANCE.
This process starts when project manager establishes a project plan and put it forward to the
client, team and other stakeholders (Lock, 2012). It is a logical process which involves a
number of stages and set up a criteria to review results and accepting deliverables for the new
project.
To deliver the final product, Polyproducts Incorporated needs to fulfill all quality standards
established in quality management plan. All tests must be done and documented according to
quality assurance to keep product’s traceability if any issue occurs.
An acceptance criteria in a rubber product is to deliver all products in good conditions. That
means under dimensions, enough of raw material to be consistent and the hole that the
product need to be assemble with other parts. This process have to be certified by quality
control management as well as a representative from quality area from Capital Corporation.
6
PREPARED BY JAIME DAZA– 00161645T AND MAURICIO MONTOYA – 00161186t
Inspection: Inspections includes activities such as measuring, examining and testing
undertaken to determine whether the product or deliverable meets customer requirements
and established standards. In this case product inspections and audits will be performed to
ensure customer satisfaction.
Control charts: These tools involve a graphic display of results, over time of a process. They
are used to determine if the process is under control. For instance, difference in the results
created by random variations, or are unusual events occurring whose causes must be
identified and corrected.
Trend analysis: this is a mathematical technique to forecast the future outcomes based on
historical results, as we had some previous contract with similar scopes (PMBOOK, 2013).
Trend analysis is often used to monitor:
o Technical performance: how many errors or defects have been identified, how many
remain uncorrected.
o Cost and schedule performance: How many activities per period were completed with
significant variances.
3.2.4 Defect Escalation.
In this case if many rubber parts are detected with defects, quality improvement actions are
required to take actions to increase effectiveness and efficiency of the project to provide
added benefits to the project stakeholders and addressing this phenomenon. When defects
are present in the production line quality management team need to take corrective actions
according to quality procedures for integrated change control (PMBOOK, 2013). Over
dimension parts, less material provided by machines and other defects can be detected in the
process line. Consequently of this issues, reworks need to be anticipated, a frequent cause of
overruns in most applications areas. The quality management team should make every
reasonable effort to minimize rework.
3.3 PROJECT DELIVERABLES ACCEPTANCE.
This process starts when project manager establishes a project plan and put it forward to the
client, team and other stakeholders (Lock, 2012). It is a logical process which involves a
number of stages and set up a criteria to review results and accepting deliverables for the new
project.
To deliver the final product, Polyproducts Incorporated needs to fulfill all quality standards
established in quality management plan. All tests must be done and documented according to
quality assurance to keep product’s traceability if any issue occurs.
An acceptance criteria in a rubber product is to deliver all products in good conditions. That
means under dimensions, enough of raw material to be consistent and the hole that the
product need to be assemble with other parts. This process have to be certified by quality
control management as well as a representative from quality area from Capital Corporation.
6
Paraphrase This Document
Need a fresh take? Get an instant paraphrase of this document with our AI Paraphraser
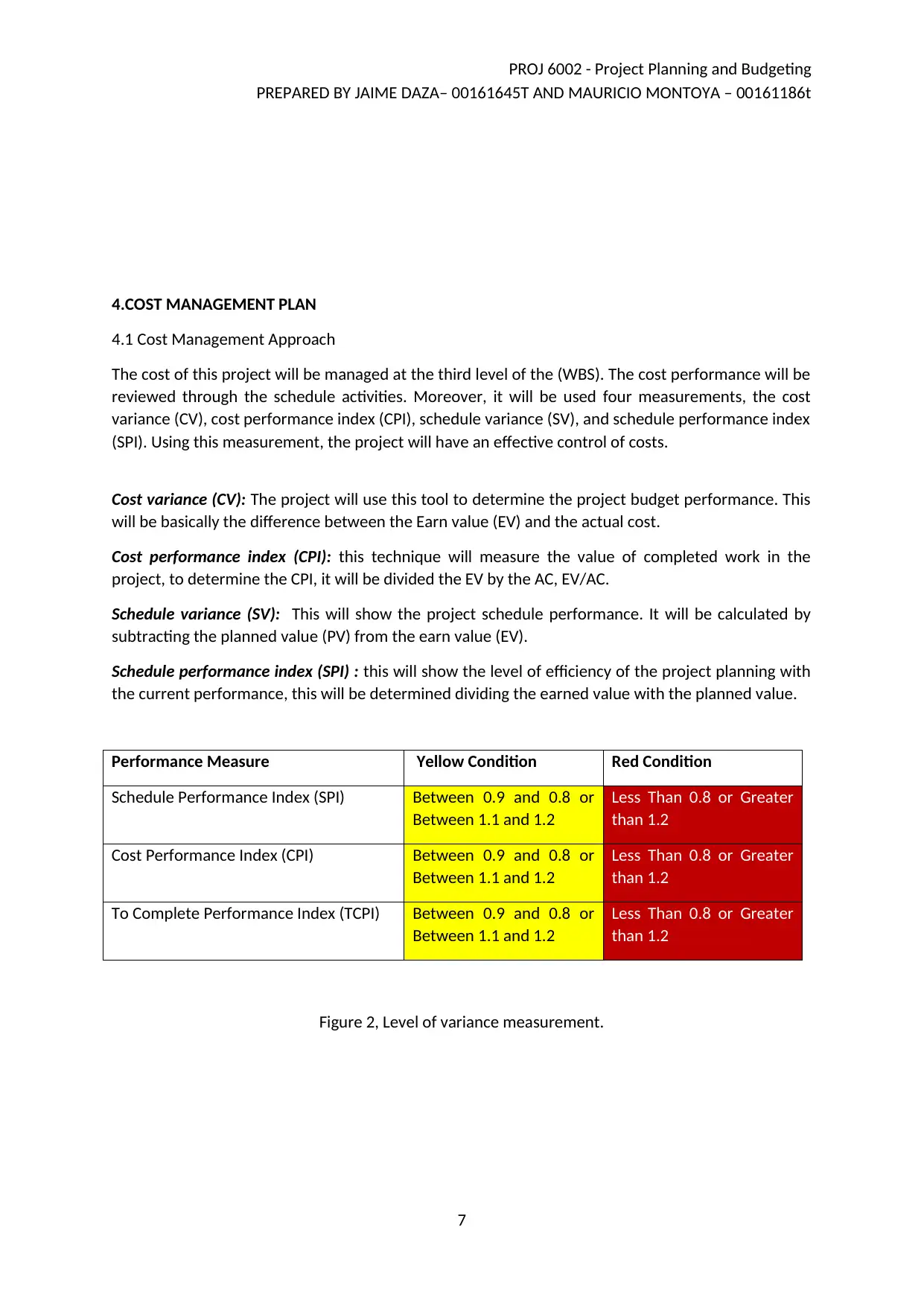
PROJ 6002 - Project Planning and Budgeting
PREPARED BY JAIME DAZA– 00161645T AND MAURICIO MONTOYA – 00161186t
4.COST MANAGEMENT PLAN
4.1 Cost Management Approach
The cost of this project will be managed at the third level of the (WBS). The cost performance will be
reviewed through the schedule activities. Moreover, it will be used four measurements, the cost
variance (CV), cost performance index (CPI), schedule variance (SV), and schedule performance index
(SPI). Using this measurement, the project will have an effective control of costs.
Cost variance (CV): The project will use this tool to determine the project budget performance. This
will be basically the difference between the Earn value (EV) and the actual cost.
Cost performance index (CPI): this technique will measure the value of completed work in the
project, to determine the CPI, it will be divided the EV by the AC, EV/AC.
Schedule variance (SV): This will show the project schedule performance. It will be calculated by
subtracting the planned value (PV) from the earn value (EV).
Schedule performance index (SPI) : this will show the level of efficiency of the project planning with
the current performance, this will be determined dividing the earned value with the planned value.
Figure 2, Level of variance measurement.
7
Performance Measure Yellow Condition Red Condition
Schedule Performance Index (SPI) Between 0.9 and 0.8 or
Between 1.1 and 1.2
Less Than 0.8 or Greater
than 1.2
Cost Performance Index (CPI) Between 0.9 and 0.8 or
Between 1.1 and 1.2
Less Than 0.8 or Greater
than 1.2
To Complete Performance Index (TCPI) Between 0.9 and 0.8 or
Between 1.1 and 1.2
Less Than 0.8 or Greater
than 1.2
PREPARED BY JAIME DAZA– 00161645T AND MAURICIO MONTOYA – 00161186t
4.COST MANAGEMENT PLAN
4.1 Cost Management Approach
The cost of this project will be managed at the third level of the (WBS). The cost performance will be
reviewed through the schedule activities. Moreover, it will be used four measurements, the cost
variance (CV), cost performance index (CPI), schedule variance (SV), and schedule performance index
(SPI). Using this measurement, the project will have an effective control of costs.
Cost variance (CV): The project will use this tool to determine the project budget performance. This
will be basically the difference between the Earn value (EV) and the actual cost.
Cost performance index (CPI): this technique will measure the value of completed work in the
project, to determine the CPI, it will be divided the EV by the AC, EV/AC.
Schedule variance (SV): This will show the project schedule performance. It will be calculated by
subtracting the planned value (PV) from the earn value (EV).
Schedule performance index (SPI) : this will show the level of efficiency of the project planning with
the current performance, this will be determined dividing the earned value with the planned value.
Figure 2, Level of variance measurement.
7
Performance Measure Yellow Condition Red Condition
Schedule Performance Index (SPI) Between 0.9 and 0.8 or
Between 1.1 and 1.2
Less Than 0.8 or Greater
than 1.2
Cost Performance Index (CPI) Between 0.9 and 0.8 or
Between 1.1 and 1.2
Less Than 0.8 or Greater
than 1.2
To Complete Performance Index (TCPI) Between 0.9 and 0.8 or
Between 1.1 and 1.2
Less Than 0.8 or Greater
than 1.2
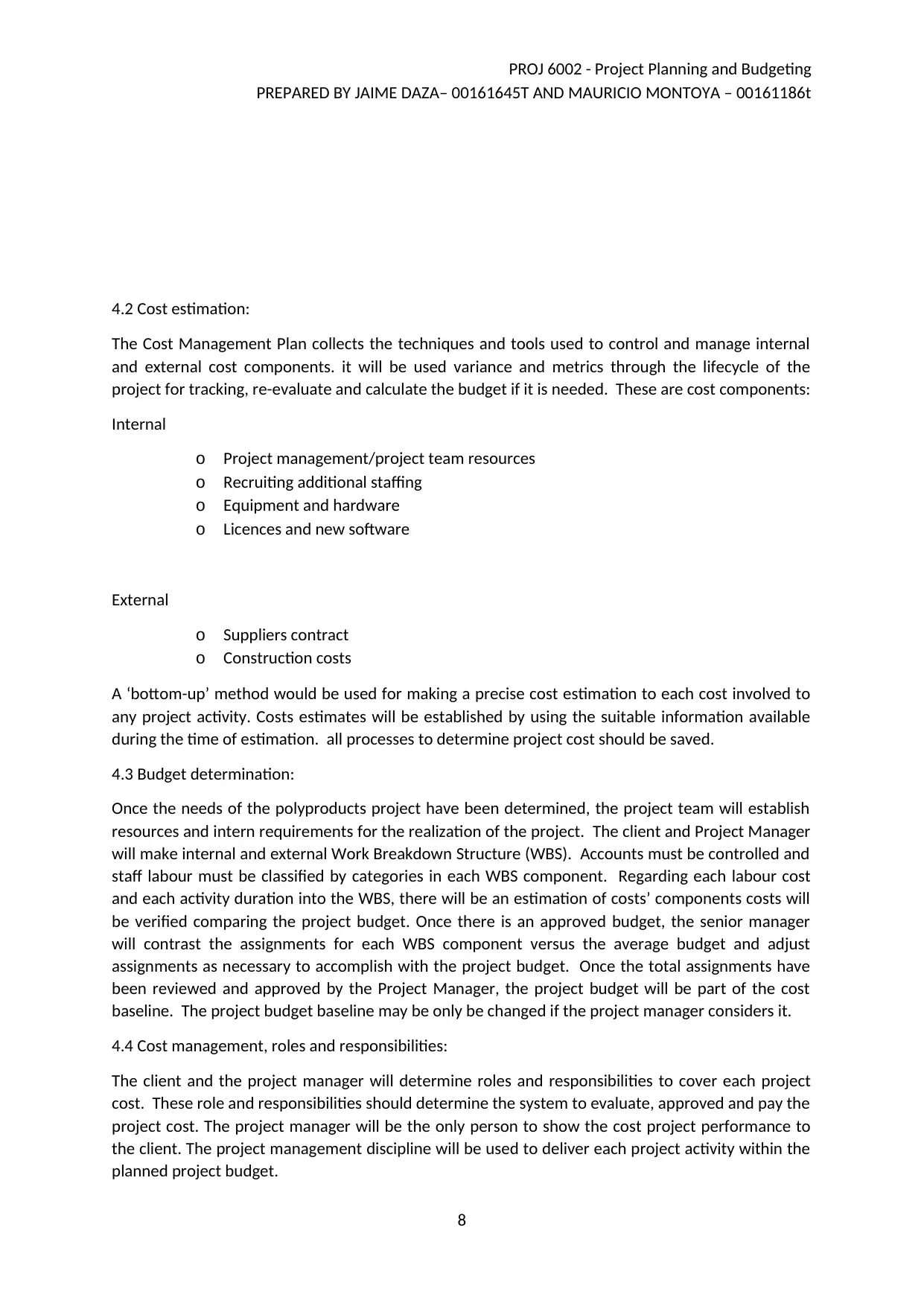
PROJ 6002 - Project Planning and Budgeting
PREPARED BY JAIME DAZA– 00161645T AND MAURICIO MONTOYA – 00161186t
4.2 Cost estimation:
The Cost Management Plan collects the techniques and tools used to control and manage internal
and external cost components. it will be used variance and metrics through the lifecycle of the
project for tracking, re-evaluate and calculate the budget if it is needed. These are cost components:
Internal
o Project management/project team resources
o Recruiting additional staffing
o Equipment and hardware
o Licences and new software
External
o Suppliers contract
o Construction costs
A ‘bottom-up’ method would be used for making a precise cost estimation to each cost involved to
any project activity. Costs estimates will be established by using the suitable information available
during the time of estimation. all processes to determine project cost should be saved.
4.3 Budget determination:
Once the needs of the polyproducts project have been determined, the project team will establish
resources and intern requirements for the realization of the project. The client and Project Manager
will make internal and external Work Breakdown Structure (WBS). Accounts must be controlled and
staff labour must be classified by categories in each WBS component. Regarding each labour cost
and each activity duration into the WBS, there will be an estimation of costs’ components costs will
be verified comparing the project budget. Once there is an approved budget, the senior manager
will contrast the assignments for each WBS component versus the average budget and adjust
assignments as necessary to accomplish with the project budget. Once the total assignments have
been reviewed and approved by the Project Manager, the project budget will be part of the cost
baseline. The project budget baseline may be only be changed if the project manager considers it.
4.4 Cost management, roles and responsibilities:
The client and the project manager will determine roles and responsibilities to cover each project
cost. These role and responsibilities should determine the system to evaluate, approved and pay the
project cost. The project manager will be the only person to show the cost project performance to
the client. The project management discipline will be used to deliver each project activity within the
planned project budget.
8
PREPARED BY JAIME DAZA– 00161645T AND MAURICIO MONTOYA – 00161186t
4.2 Cost estimation:
The Cost Management Plan collects the techniques and tools used to control and manage internal
and external cost components. it will be used variance and metrics through the lifecycle of the
project for tracking, re-evaluate and calculate the budget if it is needed. These are cost components:
Internal
o Project management/project team resources
o Recruiting additional staffing
o Equipment and hardware
o Licences and new software
External
o Suppliers contract
o Construction costs
A ‘bottom-up’ method would be used for making a precise cost estimation to each cost involved to
any project activity. Costs estimates will be established by using the suitable information available
during the time of estimation. all processes to determine project cost should be saved.
4.3 Budget determination:
Once the needs of the polyproducts project have been determined, the project team will establish
resources and intern requirements for the realization of the project. The client and Project Manager
will make internal and external Work Breakdown Structure (WBS). Accounts must be controlled and
staff labour must be classified by categories in each WBS component. Regarding each labour cost
and each activity duration into the WBS, there will be an estimation of costs’ components costs will
be verified comparing the project budget. Once there is an approved budget, the senior manager
will contrast the assignments for each WBS component versus the average budget and adjust
assignments as necessary to accomplish with the project budget. Once the total assignments have
been reviewed and approved by the Project Manager, the project budget will be part of the cost
baseline. The project budget baseline may be only be changed if the project manager considers it.
4.4 Cost management, roles and responsibilities:
The client and the project manager will determine roles and responsibilities to cover each project
cost. These role and responsibilities should determine the system to evaluate, approved and pay the
project cost. The project manager will be the only person to show the cost project performance to
the client. The project management discipline will be used to deliver each project activity within the
planned project budget.
8
⊘ This is a preview!⊘
Do you want full access?
Subscribe today to unlock all pages.

Trusted by 1+ million students worldwide
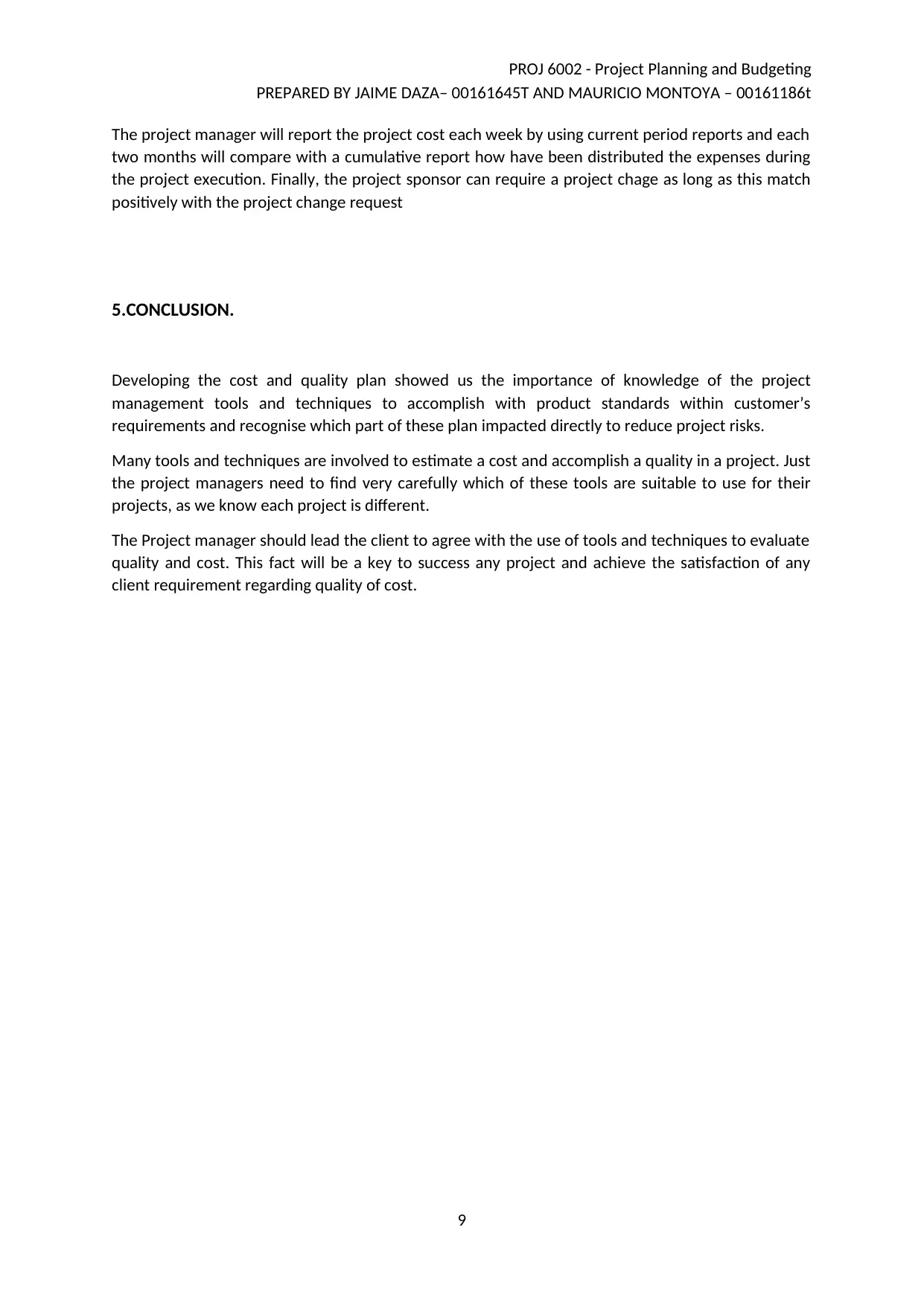
PROJ 6002 - Project Planning and Budgeting
PREPARED BY JAIME DAZA– 00161645T AND MAURICIO MONTOYA – 00161186t
The project manager will report the project cost each week by using current period reports and each
two months will compare with a cumulative report how have been distributed the expenses during
the project execution. Finally, the project sponsor can require a project chage as long as this match
positively with the project change request
5.CONCLUSION.
Developing the cost and quality plan showed us the importance of knowledge of the project
management tools and techniques to accomplish with product standards within customer’s
requirements and recognise which part of these plan impacted directly to reduce project risks.
Many tools and techniques are involved to estimate a cost and accomplish a quality in a project. Just
the project managers need to find very carefully which of these tools are suitable to use for their
projects, as we know each project is different.
The Project manager should lead the client to agree with the use of tools and techniques to evaluate
quality and cost. This fact will be a key to success any project and achieve the satisfaction of any
client requirement regarding quality of cost.
9
PREPARED BY JAIME DAZA– 00161645T AND MAURICIO MONTOYA – 00161186t
The project manager will report the project cost each week by using current period reports and each
two months will compare with a cumulative report how have been distributed the expenses during
the project execution. Finally, the project sponsor can require a project chage as long as this match
positively with the project change request
5.CONCLUSION.
Developing the cost and quality plan showed us the importance of knowledge of the project
management tools and techniques to accomplish with product standards within customer’s
requirements and recognise which part of these plan impacted directly to reduce project risks.
Many tools and techniques are involved to estimate a cost and accomplish a quality in a project. Just
the project managers need to find very carefully which of these tools are suitable to use for their
projects, as we know each project is different.
The Project manager should lead the client to agree with the use of tools and techniques to evaluate
quality and cost. This fact will be a key to success any project and achieve the satisfaction of any
client requirement regarding quality of cost.
9
Paraphrase This Document
Need a fresh take? Get an instant paraphrase of this document with our AI Paraphraser
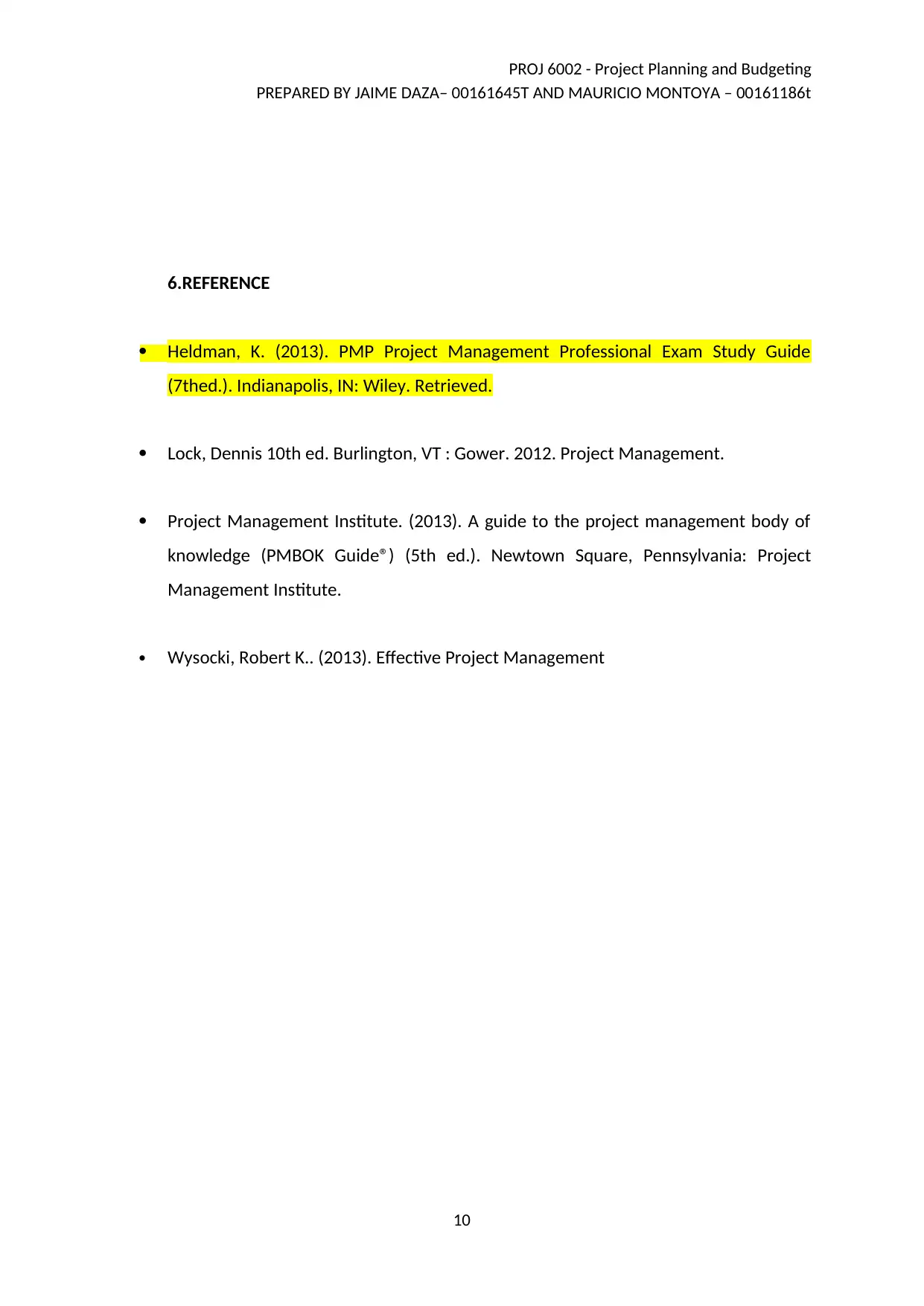
PROJ 6002 - Project Planning and Budgeting
PREPARED BY JAIME DAZA– 00161645T AND MAURICIO MONTOYA – 00161186t
6.REFERENCE
Heldman, K. (2013). PMP Project Management Professional Exam Study Guide
(7thed.). Indianapolis, IN: Wiley. Retrieved.
Lock, Dennis 10th ed. Burlington, VT : Gower. 2012. Project Management.
Project Management Institute. (2013). A guide to the project management body of
knowledge (PMBOK Guide®) (5th ed.). Newtown Square, Pennsylvania: Project
Management Institute.
Wysocki, Robert K.. (2013). Effective Project Management
10
PREPARED BY JAIME DAZA– 00161645T AND MAURICIO MONTOYA – 00161186t
6.REFERENCE
Heldman, K. (2013). PMP Project Management Professional Exam Study Guide
(7thed.). Indianapolis, IN: Wiley. Retrieved.
Lock, Dennis 10th ed. Burlington, VT : Gower. 2012. Project Management.
Project Management Institute. (2013). A guide to the project management body of
knowledge (PMBOK Guide®) (5th ed.). Newtown Square, Pennsylvania: Project
Management Institute.
Wysocki, Robert K.. (2013). Effective Project Management
10
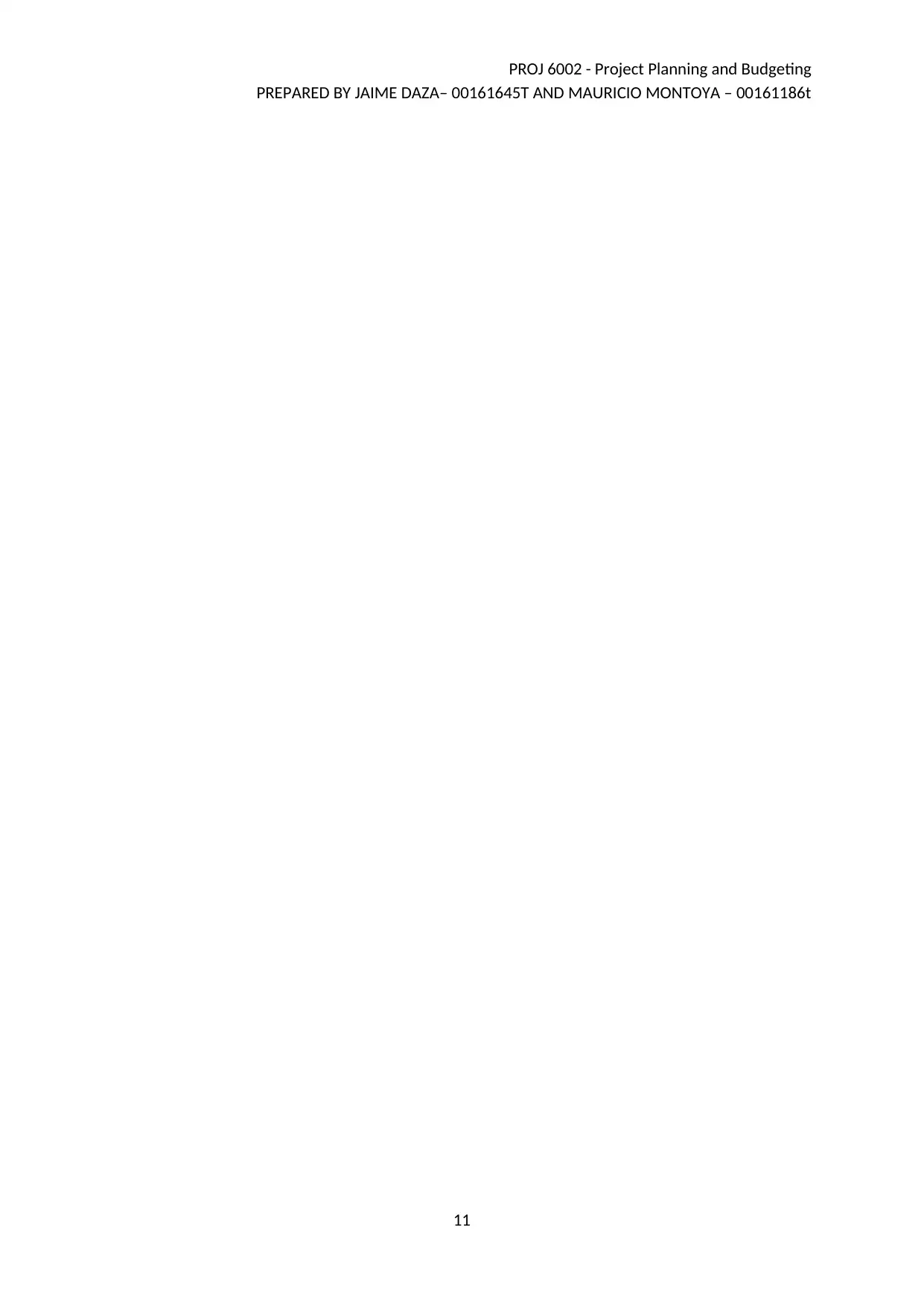
PROJ 6002 - Project Planning and Budgeting
PREPARED BY JAIME DAZA– 00161645T AND MAURICIO MONTOYA – 00161186t
11
PREPARED BY JAIME DAZA– 00161645T AND MAURICIO MONTOYA – 00161186t
11
⊘ This is a preview!⊘
Do you want full access?
Subscribe today to unlock all pages.

Trusted by 1+ million students worldwide
1 out of 12