Strategic Quality Improvement Plan for Quality Tooling Company (QTC)
VerifiedAdded on 2023/06/09
|11
|3703
|325
Report
AI Summary
This report presents a comprehensive quality improvement strategy for Quality Tooling Company (QTC), a firm specializing in engineering tools. Facing increasing globalization and competition, QTC aims to enhance its operations and product quality. The strategy incorporates Total Quality Manag...
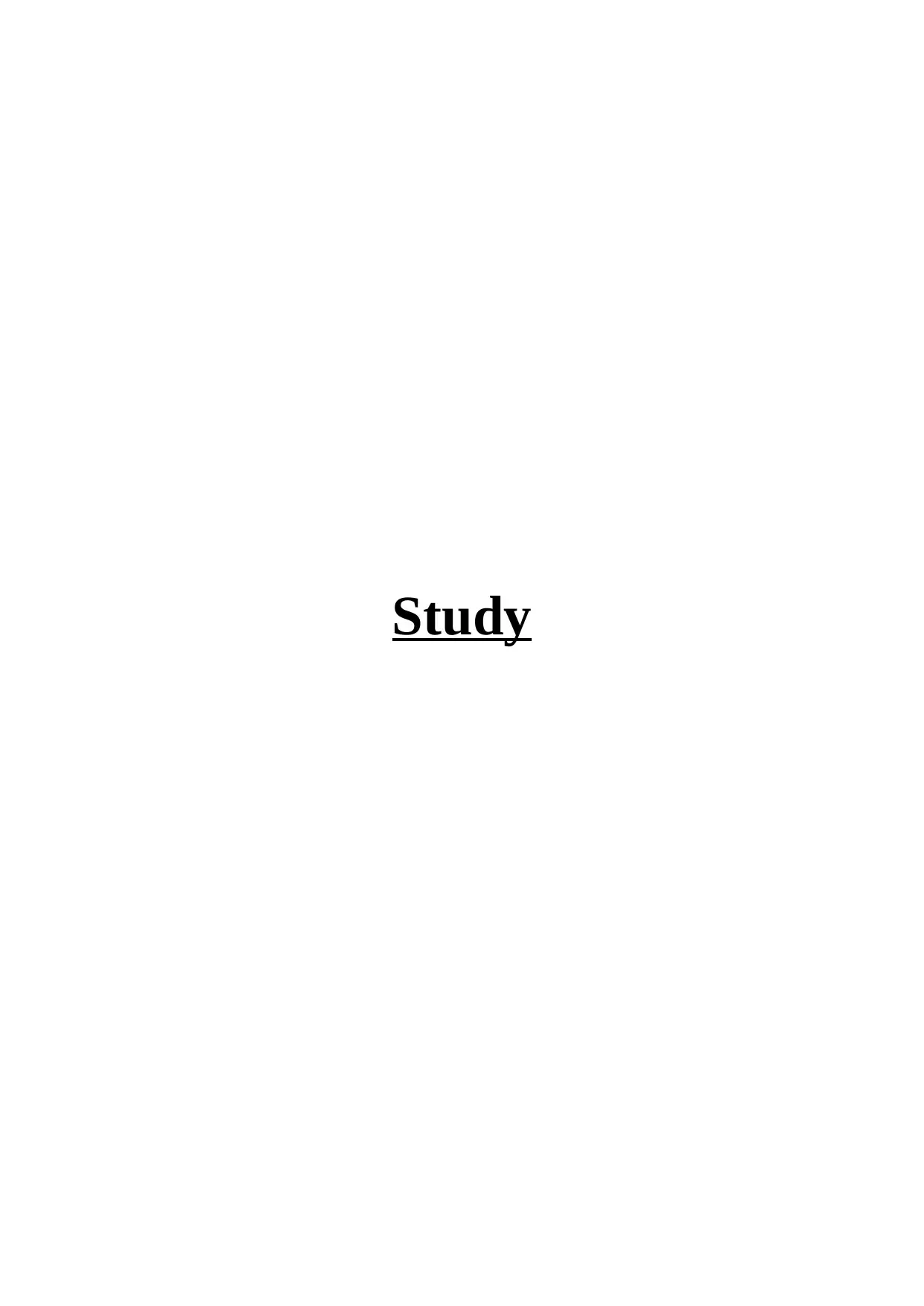
Study
Paraphrase This Document
Need a fresh take? Get an instant paraphrase of this document with our AI Paraphraser
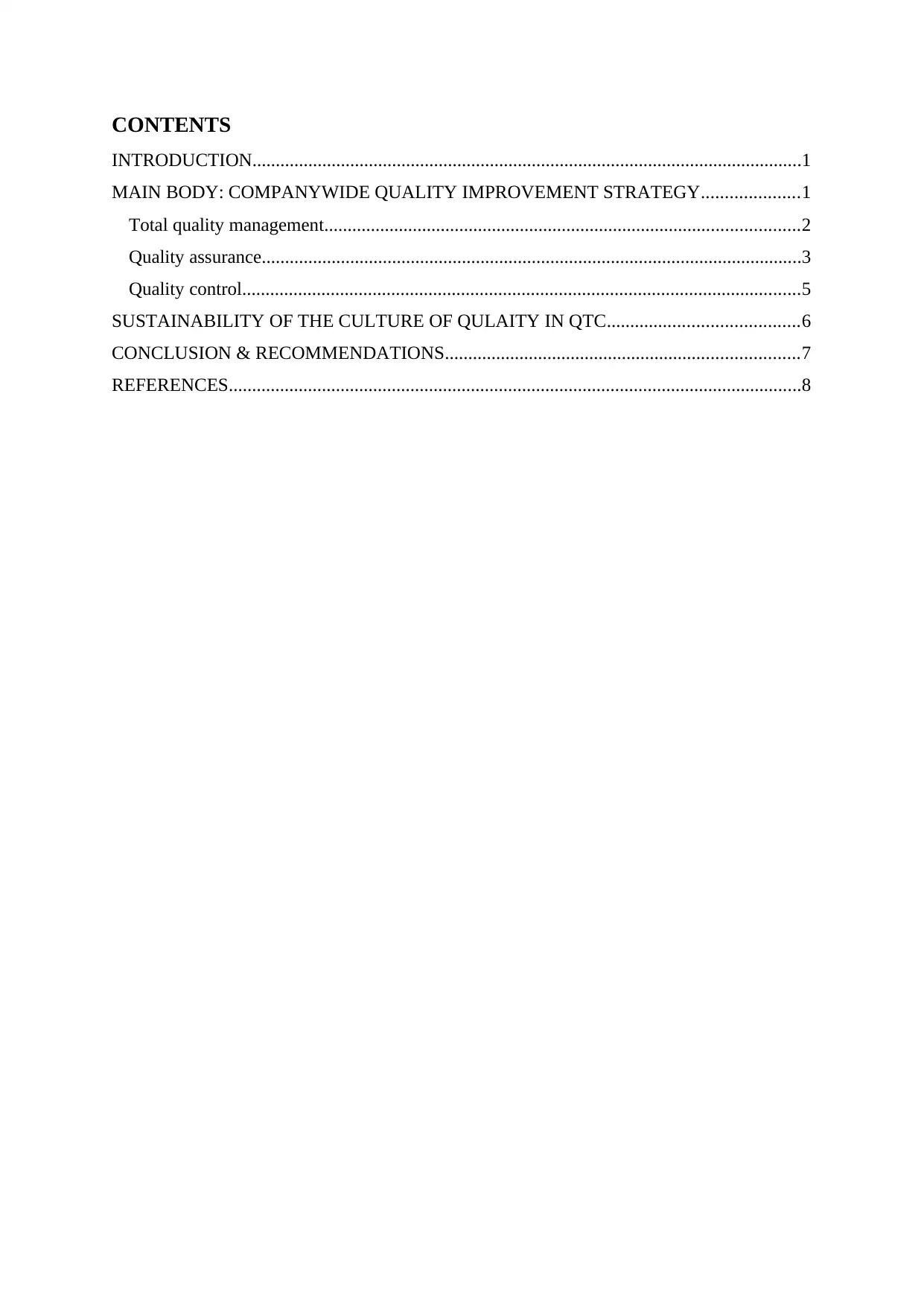
CONTENTS
INTRODUCTION......................................................................................................................1
MAIN BODY: COMPANYWIDE QUALITY IMPROVEMENT STRATEGY.....................1
Total quality management......................................................................................................2
Quality assurance....................................................................................................................3
Quality control........................................................................................................................5
SUSTAINABILITY OF THE CULTURE OF QULAITY IN QTC.........................................6
CONCLUSION & RECOMMENDATIONS............................................................................7
REFERENCES...........................................................................................................................8
INTRODUCTION......................................................................................................................1
MAIN BODY: COMPANYWIDE QUALITY IMPROVEMENT STRATEGY.....................1
Total quality management......................................................................................................2
Quality assurance....................................................................................................................3
Quality control........................................................................................................................5
SUSTAINABILITY OF THE CULTURE OF QULAITY IN QTC.........................................6
CONCLUSION & RECOMMENDATIONS............................................................................7
REFERENCES...........................................................................................................................8
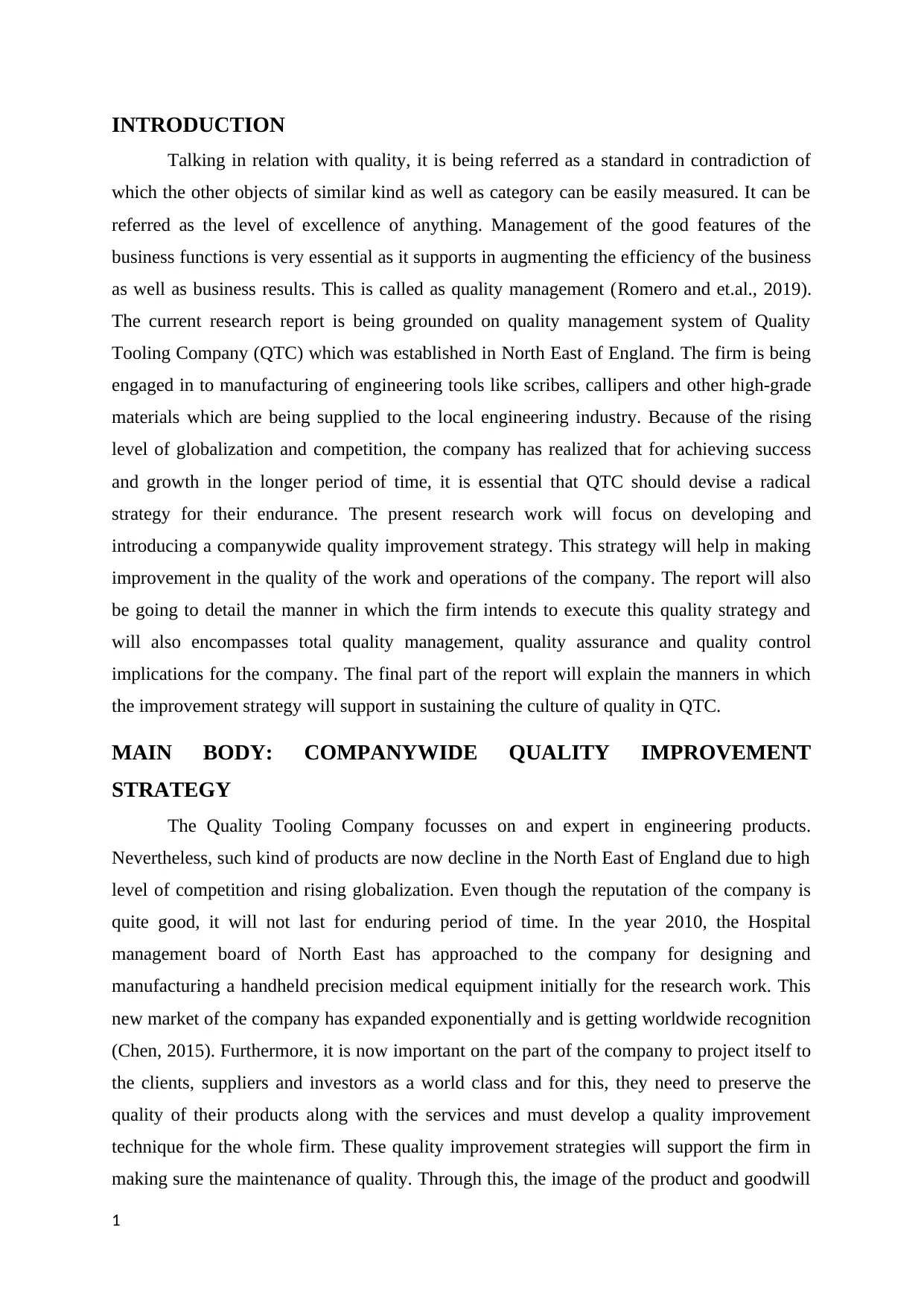
INTRODUCTION
Talking in relation with quality, it is being referred as a standard in contradiction of
which the other objects of similar kind as well as category can be easily measured. It can be
referred as the level of excellence of anything. Management of the good features of the
business functions is very essential as it supports in augmenting the efficiency of the business
as well as business results. This is called as quality management (Romero and et.al., 2019).
The current research report is being grounded on quality management system of Quality
Tooling Company (QTC) which was established in North East of England. The firm is being
engaged in to manufacturing of engineering tools like scribes, callipers and other high-grade
materials which are being supplied to the local engineering industry. Because of the rising
level of globalization and competition, the company has realized that for achieving success
and growth in the longer period of time, it is essential that QTC should devise a radical
strategy for their endurance. The present research work will focus on developing and
introducing a companywide quality improvement strategy. This strategy will help in making
improvement in the quality of the work and operations of the company. The report will also
be going to detail the manner in which the firm intends to execute this quality strategy and
will also encompasses total quality management, quality assurance and quality control
implications for the company. The final part of the report will explain the manners in which
the improvement strategy will support in sustaining the culture of quality in QTC.
MAIN BODY: COMPANYWIDE QUALITY IMPROVEMENT
STRATEGY
The Quality Tooling Company focusses on and expert in engineering products.
Nevertheless, such kind of products are now decline in the North East of England due to high
level of competition and rising globalization. Even though the reputation of the company is
quite good, it will not last for enduring period of time. In the year 2010, the Hospital
management board of North East has approached to the company for designing and
manufacturing a handheld precision medical equipment initially for the research work. This
new market of the company has expanded exponentially and is getting worldwide recognition
(Chen, 2015). Furthermore, it is now important on the part of the company to project itself to
the clients, suppliers and investors as a world class and for this, they need to preserve the
quality of their products along with the services and must develop a quality improvement
technique for the whole firm. These quality improvement strategies will support the firm in
making sure the maintenance of quality. Through this, the image of the product and goodwill
1
Talking in relation with quality, it is being referred as a standard in contradiction of
which the other objects of similar kind as well as category can be easily measured. It can be
referred as the level of excellence of anything. Management of the good features of the
business functions is very essential as it supports in augmenting the efficiency of the business
as well as business results. This is called as quality management (Romero and et.al., 2019).
The current research report is being grounded on quality management system of Quality
Tooling Company (QTC) which was established in North East of England. The firm is being
engaged in to manufacturing of engineering tools like scribes, callipers and other high-grade
materials which are being supplied to the local engineering industry. Because of the rising
level of globalization and competition, the company has realized that for achieving success
and growth in the longer period of time, it is essential that QTC should devise a radical
strategy for their endurance. The present research work will focus on developing and
introducing a companywide quality improvement strategy. This strategy will help in making
improvement in the quality of the work and operations of the company. The report will also
be going to detail the manner in which the firm intends to execute this quality strategy and
will also encompasses total quality management, quality assurance and quality control
implications for the company. The final part of the report will explain the manners in which
the improvement strategy will support in sustaining the culture of quality in QTC.
MAIN BODY: COMPANYWIDE QUALITY IMPROVEMENT
STRATEGY
The Quality Tooling Company focusses on and expert in engineering products.
Nevertheless, such kind of products are now decline in the North East of England due to high
level of competition and rising globalization. Even though the reputation of the company is
quite good, it will not last for enduring period of time. In the year 2010, the Hospital
management board of North East has approached to the company for designing and
manufacturing a handheld precision medical equipment initially for the research work. This
new market of the company has expanded exponentially and is getting worldwide recognition
(Chen, 2015). Furthermore, it is now important on the part of the company to project itself to
the clients, suppliers and investors as a world class and for this, they need to preserve the
quality of their products along with the services and must develop a quality improvement
technique for the whole firm. These quality improvement strategies will support the firm in
making sure the maintenance of quality. Through this, the image of the product and goodwill
1
⊘ This is a preview!⊘
Do you want full access?
Subscribe today to unlock all pages.

Trusted by 1+ million students worldwide
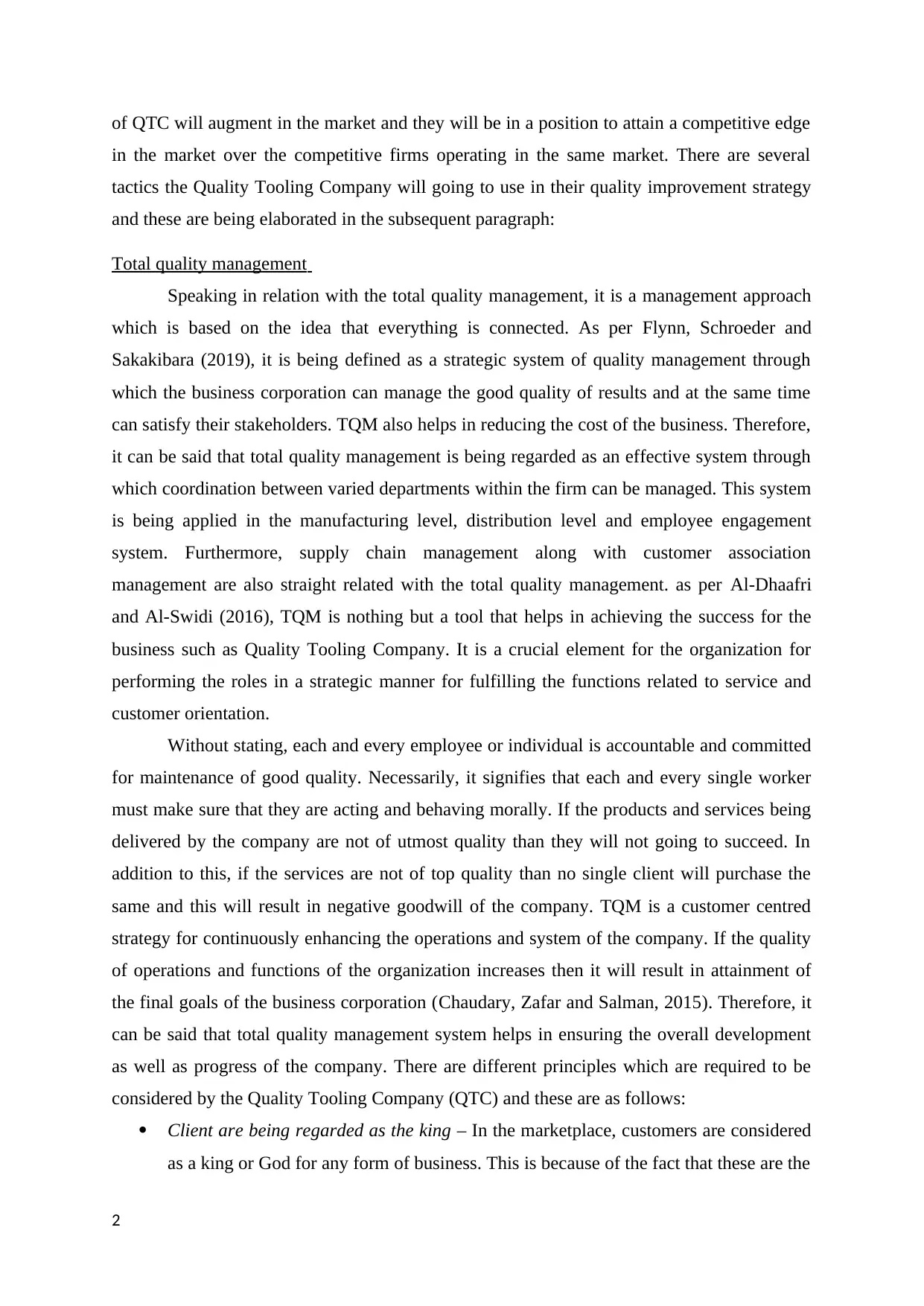
of QTC will augment in the market and they will be in a position to attain a competitive edge
in the market over the competitive firms operating in the same market. There are several
tactics the Quality Tooling Company will going to use in their quality improvement strategy
and these are being elaborated in the subsequent paragraph:
Total quality management
Speaking in relation with the total quality management, it is a management approach
which is based on the idea that everything is connected. As per Flynn, Schroeder and
Sakakibara (2019), it is being defined as a strategic system of quality management through
which the business corporation can manage the good quality of results and at the same time
can satisfy their stakeholders. TQM also helps in reducing the cost of the business. Therefore,
it can be said that total quality management is being regarded as an effective system through
which coordination between varied departments within the firm can be managed. This system
is being applied in the manufacturing level, distribution level and employee engagement
system. Furthermore, supply chain management along with customer association
management are also straight related with the total quality management. as per Al-Dhaafri
and Al-Swidi (2016), TQM is nothing but a tool that helps in achieving the success for the
business such as Quality Tooling Company. It is a crucial element for the organization for
performing the roles in a strategic manner for fulfilling the functions related to service and
customer orientation.
Without stating, each and every employee or individual is accountable and committed
for maintenance of good quality. Necessarily, it signifies that each and every single worker
must make sure that they are acting and behaving morally. If the products and services being
delivered by the company are not of utmost quality than they will not going to succeed. In
addition to this, if the services are not of top quality than no single client will purchase the
same and this will result in negative goodwill of the company. TQM is a customer centred
strategy for continuously enhancing the operations and system of the company. If the quality
of operations and functions of the organization increases then it will result in attainment of
the final goals of the business corporation (Chaudary, Zafar and Salman, 2015). Therefore, it
can be said that total quality management system helps in ensuring the overall development
as well as progress of the company. There are different principles which are required to be
considered by the Quality Tooling Company (QTC) and these are as follows:
Client are being regarded as the king – In the marketplace, customers are considered
as a king or God for any form of business. This is because of the fact that these are the
2
in the market over the competitive firms operating in the same market. There are several
tactics the Quality Tooling Company will going to use in their quality improvement strategy
and these are being elaborated in the subsequent paragraph:
Total quality management
Speaking in relation with the total quality management, it is a management approach
which is based on the idea that everything is connected. As per Flynn, Schroeder and
Sakakibara (2019), it is being defined as a strategic system of quality management through
which the business corporation can manage the good quality of results and at the same time
can satisfy their stakeholders. TQM also helps in reducing the cost of the business. Therefore,
it can be said that total quality management is being regarded as an effective system through
which coordination between varied departments within the firm can be managed. This system
is being applied in the manufacturing level, distribution level and employee engagement
system. Furthermore, supply chain management along with customer association
management are also straight related with the total quality management. as per Al-Dhaafri
and Al-Swidi (2016), TQM is nothing but a tool that helps in achieving the success for the
business such as Quality Tooling Company. It is a crucial element for the organization for
performing the roles in a strategic manner for fulfilling the functions related to service and
customer orientation.
Without stating, each and every employee or individual is accountable and committed
for maintenance of good quality. Necessarily, it signifies that each and every single worker
must make sure that they are acting and behaving morally. If the products and services being
delivered by the company are not of utmost quality than they will not going to succeed. In
addition to this, if the services are not of top quality than no single client will purchase the
same and this will result in negative goodwill of the company. TQM is a customer centred
strategy for continuously enhancing the operations and system of the company. If the quality
of operations and functions of the organization increases then it will result in attainment of
the final goals of the business corporation (Chaudary, Zafar and Salman, 2015). Therefore, it
can be said that total quality management system helps in ensuring the overall development
as well as progress of the company. There are different principles which are required to be
considered by the Quality Tooling Company (QTC) and these are as follows:
Client are being regarded as the king – In the marketplace, customers are considered
as a king or God for any form of business. This is because of the fact that these are the
2
Paraphrase This Document
Need a fresh take? Get an instant paraphrase of this document with our AI Paraphraser
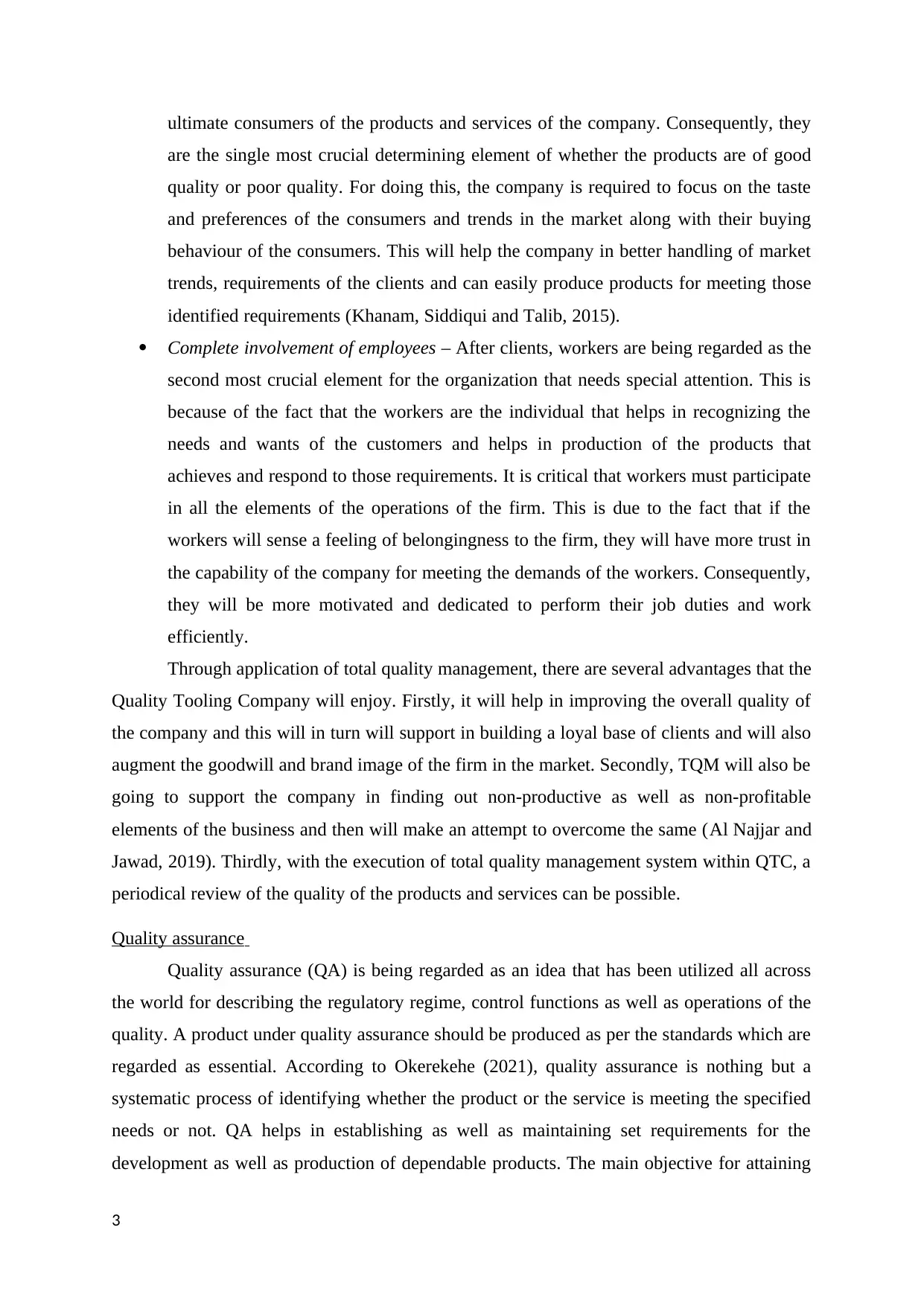
ultimate consumers of the products and services of the company. Consequently, they
are the single most crucial determining element of whether the products are of good
quality or poor quality. For doing this, the company is required to focus on the taste
and preferences of the consumers and trends in the market along with their buying
behaviour of the consumers. This will help the company in better handling of market
trends, requirements of the clients and can easily produce products for meeting those
identified requirements (Khanam, Siddiqui and Talib, 2015).
Complete involvement of employees – After clients, workers are being regarded as the
second most crucial element for the organization that needs special attention. This is
because of the fact that the workers are the individual that helps in recognizing the
needs and wants of the customers and helps in production of the products that
achieves and respond to those requirements. It is critical that workers must participate
in all the elements of the operations of the firm. This is due to the fact that if the
workers will sense a feeling of belongingness to the firm, they will have more trust in
the capability of the company for meeting the demands of the workers. Consequently,
they will be more motivated and dedicated to perform their job duties and work
efficiently.
Through application of total quality management, there are several advantages that the
Quality Tooling Company will enjoy. Firstly, it will help in improving the overall quality of
the company and this will in turn will support in building a loyal base of clients and will also
augment the goodwill and brand image of the firm in the market. Secondly, TQM will also be
going to support the company in finding out non-productive as well as non-profitable
elements of the business and then will make an attempt to overcome the same (Al Najjar and
Jawad, 2019). Thirdly, with the execution of total quality management system within QTC, a
periodical review of the quality of the products and services can be possible.
Quality assurance
Quality assurance (QA) is being regarded as an idea that has been utilized all across
the world for describing the regulatory regime, control functions as well as operations of the
quality. A product under quality assurance should be produced as per the standards which are
regarded as essential. According to Okerekehe (2021), quality assurance is nothing but a
systematic process of identifying whether the product or the service is meeting the specified
needs or not. QA helps in establishing as well as maintaining set requirements for the
development as well as production of dependable products. The main objective for attaining
3
are the single most crucial determining element of whether the products are of good
quality or poor quality. For doing this, the company is required to focus on the taste
and preferences of the consumers and trends in the market along with their buying
behaviour of the consumers. This will help the company in better handling of market
trends, requirements of the clients and can easily produce products for meeting those
identified requirements (Khanam, Siddiqui and Talib, 2015).
Complete involvement of employees – After clients, workers are being regarded as the
second most crucial element for the organization that needs special attention. This is
because of the fact that the workers are the individual that helps in recognizing the
needs and wants of the customers and helps in production of the products that
achieves and respond to those requirements. It is critical that workers must participate
in all the elements of the operations of the firm. This is due to the fact that if the
workers will sense a feeling of belongingness to the firm, they will have more trust in
the capability of the company for meeting the demands of the workers. Consequently,
they will be more motivated and dedicated to perform their job duties and work
efficiently.
Through application of total quality management, there are several advantages that the
Quality Tooling Company will enjoy. Firstly, it will help in improving the overall quality of
the company and this will in turn will support in building a loyal base of clients and will also
augment the goodwill and brand image of the firm in the market. Secondly, TQM will also be
going to support the company in finding out non-productive as well as non-profitable
elements of the business and then will make an attempt to overcome the same (Al Najjar and
Jawad, 2019). Thirdly, with the execution of total quality management system within QTC, a
periodical review of the quality of the products and services can be possible.
Quality assurance
Quality assurance (QA) is being regarded as an idea that has been utilized all across
the world for describing the regulatory regime, control functions as well as operations of the
quality. A product under quality assurance should be produced as per the standards which are
regarded as essential. According to Okerekehe (2021), quality assurance is nothing but a
systematic process of identifying whether the product or the service is meeting the specified
needs or not. QA helps in establishing as well as maintaining set requirements for the
development as well as production of dependable products. The main objective for attaining
3
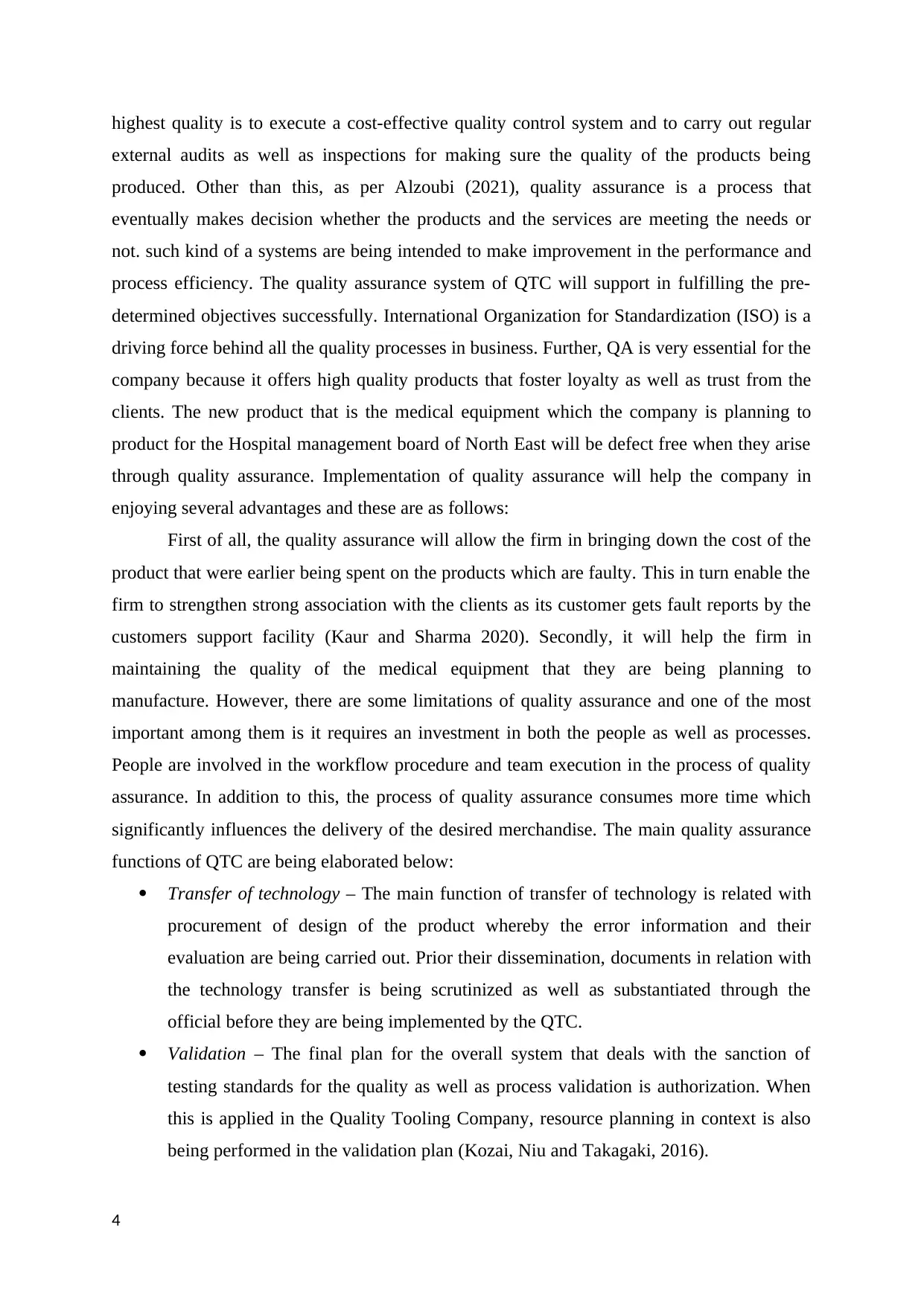
highest quality is to execute a cost-effective quality control system and to carry out regular
external audits as well as inspections for making sure the quality of the products being
produced. Other than this, as per Alzoubi (2021), quality assurance is a process that
eventually makes decision whether the products and the services are meeting the needs or
not. such kind of a systems are being intended to make improvement in the performance and
process efficiency. The quality assurance system of QTC will support in fulfilling the pre-
determined objectives successfully. International Organization for Standardization (ISO) is a
driving force behind all the quality processes in business. Further, QA is very essential for the
company because it offers high quality products that foster loyalty as well as trust from the
clients. The new product that is the medical equipment which the company is planning to
product for the Hospital management board of North East will be defect free when they arise
through quality assurance. Implementation of quality assurance will help the company in
enjoying several advantages and these are as follows:
First of all, the quality assurance will allow the firm in bringing down the cost of the
product that were earlier being spent on the products which are faulty. This in turn enable the
firm to strengthen strong association with the clients as its customer gets fault reports by the
customers support facility (Kaur and Sharma 2020). Secondly, it will help the firm in
maintaining the quality of the medical equipment that they are being planning to
manufacture. However, there are some limitations of quality assurance and one of the most
important among them is it requires an investment in both the people as well as processes.
People are involved in the workflow procedure and team execution in the process of quality
assurance. In addition to this, the process of quality assurance consumes more time which
significantly influences the delivery of the desired merchandise. The main quality assurance
functions of QTC are being elaborated below:
Transfer of technology – The main function of transfer of technology is related with
procurement of design of the product whereby the error information and their
evaluation are being carried out. Prior their dissemination, documents in relation with
the technology transfer is being scrutinized as well as substantiated through the
official before they are being implemented by the QTC.
Validation – The final plan for the overall system that deals with the sanction of
testing standards for the quality as well as process validation is authorization. When
this is applied in the Quality Tooling Company, resource planning in context is also
being performed in the validation plan (Kozai, Niu and Takagaki, 2016).
4
external audits as well as inspections for making sure the quality of the products being
produced. Other than this, as per Alzoubi (2021), quality assurance is a process that
eventually makes decision whether the products and the services are meeting the needs or
not. such kind of a systems are being intended to make improvement in the performance and
process efficiency. The quality assurance system of QTC will support in fulfilling the pre-
determined objectives successfully. International Organization for Standardization (ISO) is a
driving force behind all the quality processes in business. Further, QA is very essential for the
company because it offers high quality products that foster loyalty as well as trust from the
clients. The new product that is the medical equipment which the company is planning to
product for the Hospital management board of North East will be defect free when they arise
through quality assurance. Implementation of quality assurance will help the company in
enjoying several advantages and these are as follows:
First of all, the quality assurance will allow the firm in bringing down the cost of the
product that were earlier being spent on the products which are faulty. This in turn enable the
firm to strengthen strong association with the clients as its customer gets fault reports by the
customers support facility (Kaur and Sharma 2020). Secondly, it will help the firm in
maintaining the quality of the medical equipment that they are being planning to
manufacture. However, there are some limitations of quality assurance and one of the most
important among them is it requires an investment in both the people as well as processes.
People are involved in the workflow procedure and team execution in the process of quality
assurance. In addition to this, the process of quality assurance consumes more time which
significantly influences the delivery of the desired merchandise. The main quality assurance
functions of QTC are being elaborated below:
Transfer of technology – The main function of transfer of technology is related with
procurement of design of the product whereby the error information and their
evaluation are being carried out. Prior their dissemination, documents in relation with
the technology transfer is being scrutinized as well as substantiated through the
official before they are being implemented by the QTC.
Validation – The final plan for the overall system that deals with the sanction of
testing standards for the quality as well as process validation is authorization. When
this is applied in the Quality Tooling Company, resource planning in context is also
being performed in the validation plan (Kozai, Niu and Takagaki, 2016).
4
⊘ This is a preview!⊘
Do you want full access?
Subscribe today to unlock all pages.

Trusted by 1+ million students worldwide
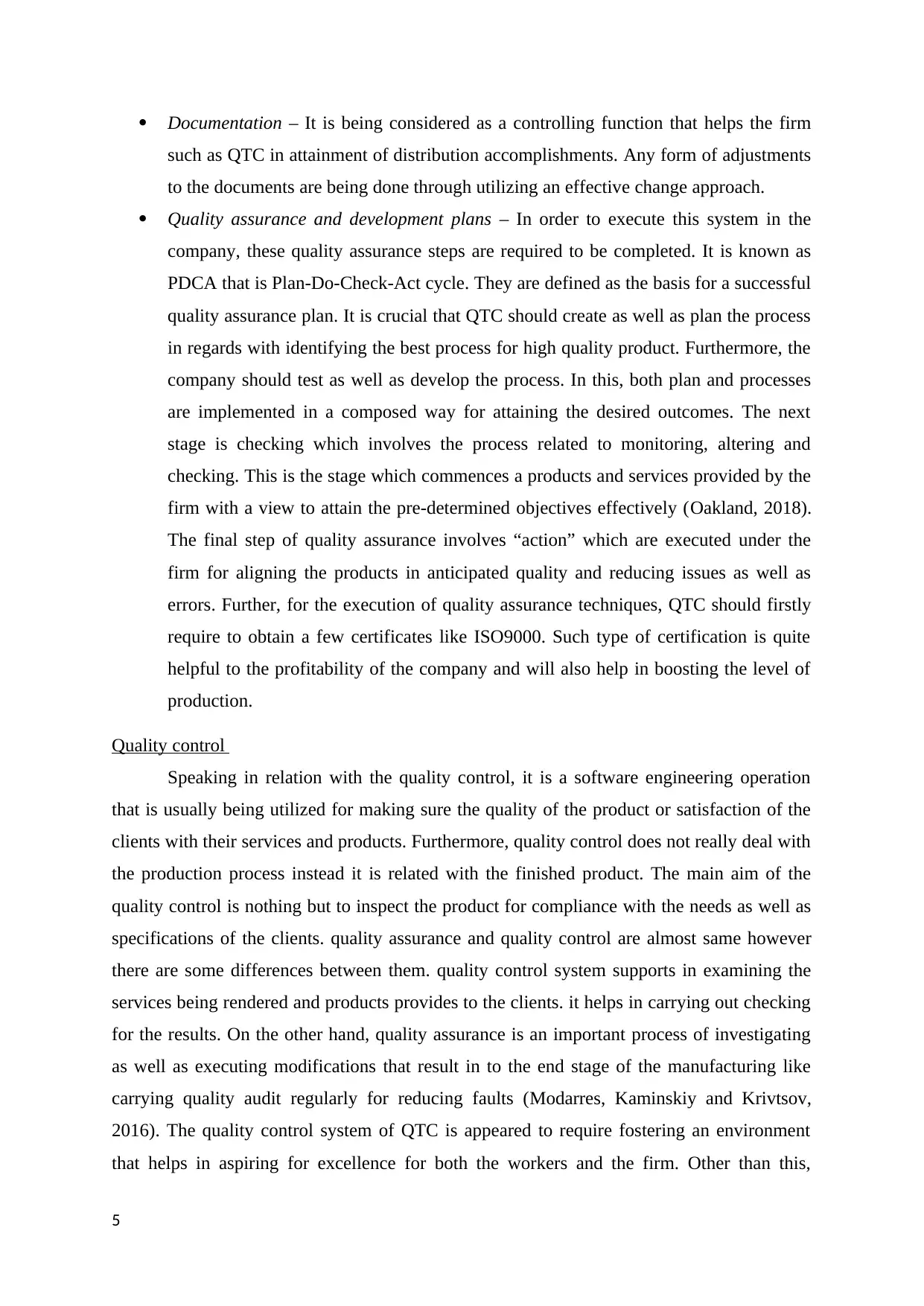
Documentation – It is being considered as a controlling function that helps the firm
such as QTC in attainment of distribution accomplishments. Any form of adjustments
to the documents are being done through utilizing an effective change approach.
Quality assurance and development plans – In order to execute this system in the
company, these quality assurance steps are required to be completed. It is known as
PDCA that is Plan-Do-Check-Act cycle. They are defined as the basis for a successful
quality assurance plan. It is crucial that QTC should create as well as plan the process
in regards with identifying the best process for high quality product. Furthermore, the
company should test as well as develop the process. In this, both plan and processes
are implemented in a composed way for attaining the desired outcomes. The next
stage is checking which involves the process related to monitoring, altering and
checking. This is the stage which commences a products and services provided by the
firm with a view to attain the pre-determined objectives effectively (Oakland, 2018).
The final step of quality assurance involves “action” which are executed under the
firm for aligning the products in anticipated quality and reducing issues as well as
errors. Further, for the execution of quality assurance techniques, QTC should firstly
require to obtain a few certificates like ISO9000. Such type of certification is quite
helpful to the profitability of the company and will also help in boosting the level of
production.
Quality control
Speaking in relation with the quality control, it is a software engineering operation
that is usually being utilized for making sure the quality of the product or satisfaction of the
clients with their services and products. Furthermore, quality control does not really deal with
the production process instead it is related with the finished product. The main aim of the
quality control is nothing but to inspect the product for compliance with the needs as well as
specifications of the clients. quality assurance and quality control are almost same however
there are some differences between them. quality control system supports in examining the
services being rendered and products provides to the clients. it helps in carrying out checking
for the results. On the other hand, quality assurance is an important process of investigating
as well as executing modifications that result in to the end stage of the manufacturing like
carrying quality audit regularly for reducing faults (Modarres, Kaminskiy and Krivtsov,
2016). The quality control system of QTC is appeared to require fostering an environment
that helps in aspiring for excellence for both the workers and the firm. Other than this,
5
such as QTC in attainment of distribution accomplishments. Any form of adjustments
to the documents are being done through utilizing an effective change approach.
Quality assurance and development plans – In order to execute this system in the
company, these quality assurance steps are required to be completed. It is known as
PDCA that is Plan-Do-Check-Act cycle. They are defined as the basis for a successful
quality assurance plan. It is crucial that QTC should create as well as plan the process
in regards with identifying the best process for high quality product. Furthermore, the
company should test as well as develop the process. In this, both plan and processes
are implemented in a composed way for attaining the desired outcomes. The next
stage is checking which involves the process related to monitoring, altering and
checking. This is the stage which commences a products and services provided by the
firm with a view to attain the pre-determined objectives effectively (Oakland, 2018).
The final step of quality assurance involves “action” which are executed under the
firm for aligning the products in anticipated quality and reducing issues as well as
errors. Further, for the execution of quality assurance techniques, QTC should firstly
require to obtain a few certificates like ISO9000. Such type of certification is quite
helpful to the profitability of the company and will also help in boosting the level of
production.
Quality control
Speaking in relation with the quality control, it is a software engineering operation
that is usually being utilized for making sure the quality of the product or satisfaction of the
clients with their services and products. Furthermore, quality control does not really deal with
the production process instead it is related with the finished product. The main aim of the
quality control is nothing but to inspect the product for compliance with the needs as well as
specifications of the clients. quality assurance and quality control are almost same however
there are some differences between them. quality control system supports in examining the
services being rendered and products provides to the clients. it helps in carrying out checking
for the results. On the other hand, quality assurance is an important process of investigating
as well as executing modifications that result in to the end stage of the manufacturing like
carrying quality audit regularly for reducing faults (Modarres, Kaminskiy and Krivtsov,
2016). The quality control system of QTC is appeared to require fostering an environment
that helps in aspiring for excellence for both the workers and the firm. Other than this,
5
Paraphrase This Document
Need a fresh take? Get an instant paraphrase of this document with our AI Paraphraser

learning as well as development training in the firm helps in establishing a standard for
manufacturing quality and testing them for maintenance as well as recognition of
quantitatively important transformations. There are different primary functions which are
being implicated in the quality control system of Quality Tooling Company and these are as
follows:
Testing – This is the basic function of quality control which needs to be implemented
by QTC in their production processes from the beginning to end. With this, the
company will be able to detect errors and faults and can correct them timely.
Monitoring – The next step involves monitoring which should be done in a regular
basis through conducting tests and reviews in order to look for any probable trends in
the quality of products (Kutnjak, Miljenovic and Mirkovic, 2019).
Auditing – The specialists related to quality control performs audits regularly for
controlling the standard of work being implemented within the premises.
Reporting – This is again an important step which involves reporting of any issue
within the quality of the products being found out from monitoring and auditing. By
this, problems can be reviewed effectively by the top management.
SUSTAINABILITY OF THE CULTURE OF QULAITY IN QTC
The culture of the organization is nothing but a set of practices that initiates with the
leadership that comprehended as well as believes the consequences of a standardized
viewpoints and the requirement of the clients for succeeding. Sustenance of quality culture in
Quality Tooling Company is very essential for greater experience of the clients, growth,
development and improvement of the performance (Eslami and et.al., 2019). Quality is being
regarded as the most crucial component that helps in driving the experience of the clients. for
maintaining culture of quality, it is important that QTC should always approach certain
elements in their business and these are:
Motivating employee engagement – For sustainability of quality culture, it is crucial
that the management of QTC should encourage peer involvement in quality
improvement initiatives which will support in development of employee’s interest and
will allow more creativity and innovation.
Maintaining leadership – Leadership is being regarded as a significant element that
helps in motivating workers for maintaining high quality products. Workshops should
be planned for leaders for helping them to remain focussed on the goals of quality
orientation.
6
manufacturing quality and testing them for maintenance as well as recognition of
quantitatively important transformations. There are different primary functions which are
being implicated in the quality control system of Quality Tooling Company and these are as
follows:
Testing – This is the basic function of quality control which needs to be implemented
by QTC in their production processes from the beginning to end. With this, the
company will be able to detect errors and faults and can correct them timely.
Monitoring – The next step involves monitoring which should be done in a regular
basis through conducting tests and reviews in order to look for any probable trends in
the quality of products (Kutnjak, Miljenovic and Mirkovic, 2019).
Auditing – The specialists related to quality control performs audits regularly for
controlling the standard of work being implemented within the premises.
Reporting – This is again an important step which involves reporting of any issue
within the quality of the products being found out from monitoring and auditing. By
this, problems can be reviewed effectively by the top management.
SUSTAINABILITY OF THE CULTURE OF QULAITY IN QTC
The culture of the organization is nothing but a set of practices that initiates with the
leadership that comprehended as well as believes the consequences of a standardized
viewpoints and the requirement of the clients for succeeding. Sustenance of quality culture in
Quality Tooling Company is very essential for greater experience of the clients, growth,
development and improvement of the performance (Eslami and et.al., 2019). Quality is being
regarded as the most crucial component that helps in driving the experience of the clients. for
maintaining culture of quality, it is important that QTC should always approach certain
elements in their business and these are:
Motivating employee engagement – For sustainability of quality culture, it is crucial
that the management of QTC should encourage peer involvement in quality
improvement initiatives which will support in development of employee’s interest and
will allow more creativity and innovation.
Maintaining leadership – Leadership is being regarded as a significant element that
helps in motivating workers for maintaining high quality products. Workshops should
be planned for leaders for helping them to remain focussed on the goals of quality
orientation.
6
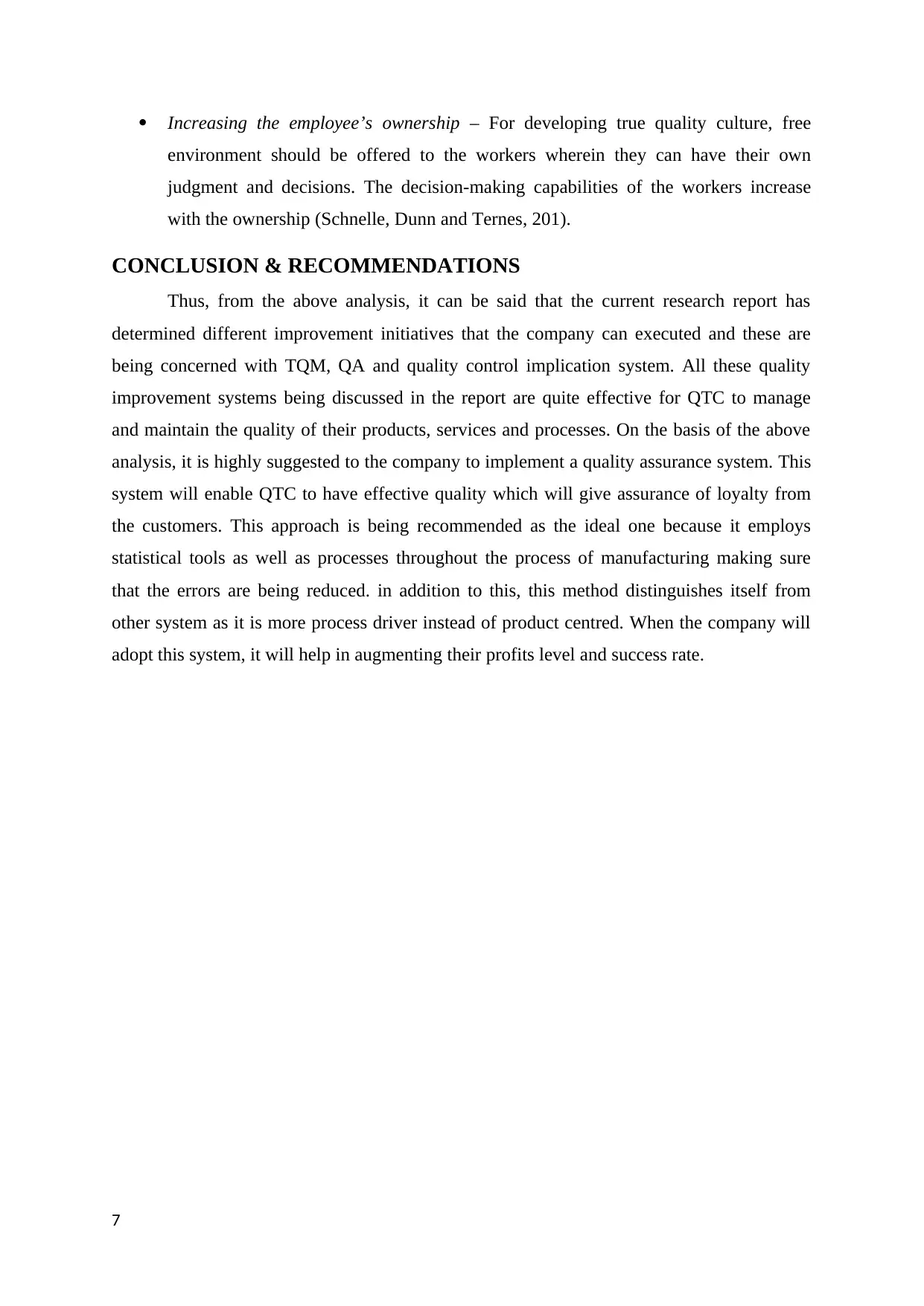
Increasing the employee’s ownership – For developing true quality culture, free
environment should be offered to the workers wherein they can have their own
judgment and decisions. The decision-making capabilities of the workers increase
with the ownership (Schnelle, Dunn and Ternes, 201).
CONCLUSION & RECOMMENDATIONS
Thus, from the above analysis, it can be said that the current research report has
determined different improvement initiatives that the company can executed and these are
being concerned with TQM, QA and quality control implication system. All these quality
improvement systems being discussed in the report are quite effective for QTC to manage
and maintain the quality of their products, services and processes. On the basis of the above
analysis, it is highly suggested to the company to implement a quality assurance system. This
system will enable QTC to have effective quality which will give assurance of loyalty from
the customers. This approach is being recommended as the ideal one because it employs
statistical tools as well as processes throughout the process of manufacturing making sure
that the errors are being reduced. in addition to this, this method distinguishes itself from
other system as it is more process driver instead of product centred. When the company will
adopt this system, it will help in augmenting their profits level and success rate.
7
environment should be offered to the workers wherein they can have their own
judgment and decisions. The decision-making capabilities of the workers increase
with the ownership (Schnelle, Dunn and Ternes, 201).
CONCLUSION & RECOMMENDATIONS
Thus, from the above analysis, it can be said that the current research report has
determined different improvement initiatives that the company can executed and these are
being concerned with TQM, QA and quality control implication system. All these quality
improvement systems being discussed in the report are quite effective for QTC to manage
and maintain the quality of their products, services and processes. On the basis of the above
analysis, it is highly suggested to the company to implement a quality assurance system. This
system will enable QTC to have effective quality which will give assurance of loyalty from
the customers. This approach is being recommended as the ideal one because it employs
statistical tools as well as processes throughout the process of manufacturing making sure
that the errors are being reduced. in addition to this, this method distinguishes itself from
other system as it is more process driver instead of product centred. When the company will
adopt this system, it will help in augmenting their profits level and success rate.
7
⊘ This is a preview!⊘
Do you want full access?
Subscribe today to unlock all pages.

Trusted by 1+ million students worldwide
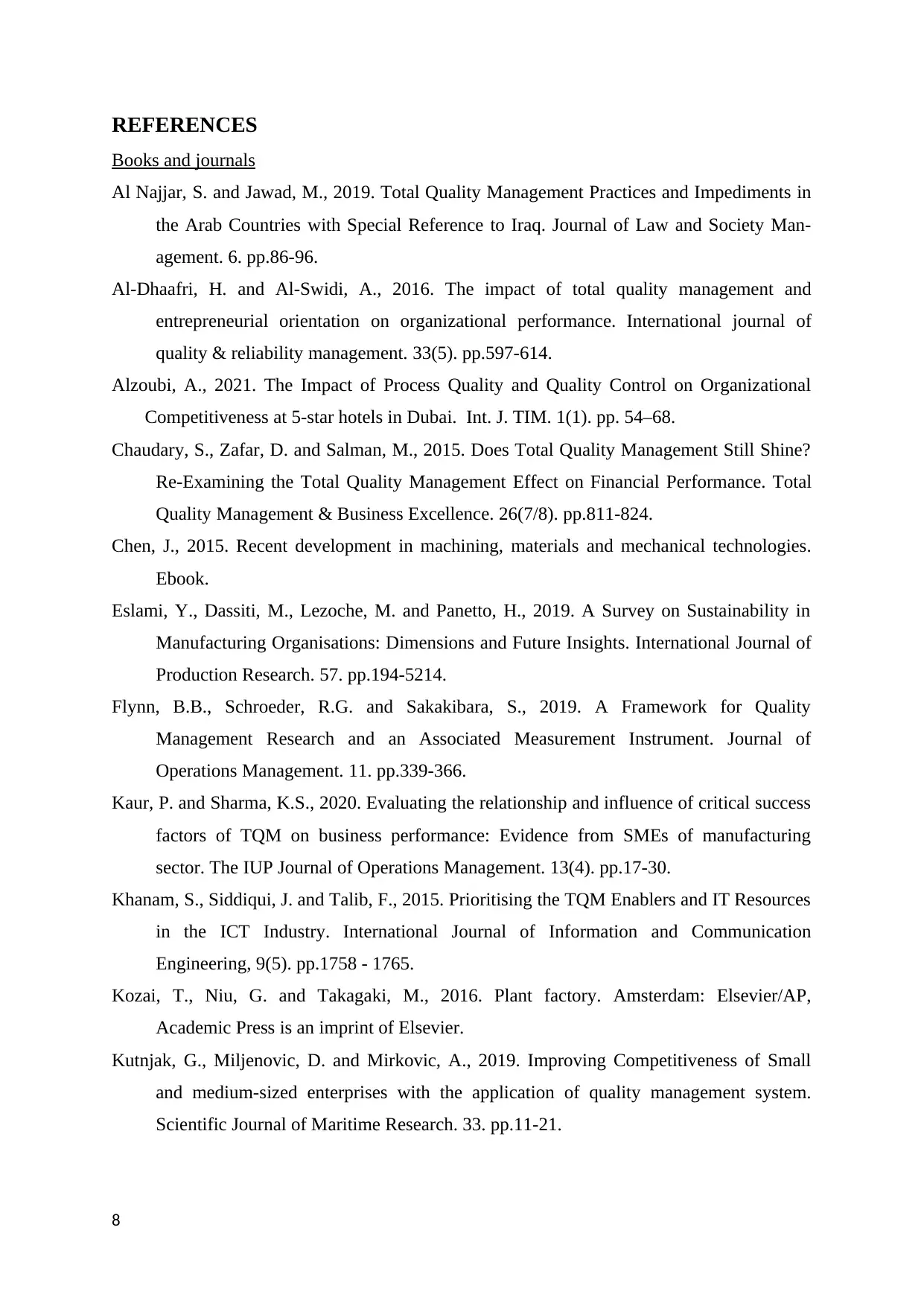
REFERENCES
Books and journals
Al Najjar, S. and Jawad, M., 2019. Total Quality Management Practices and Impediments in
the Arab Countries with Special Reference to Iraq. Journal of Law and Society Man-
agement. 6. pp.86-96.
Al-Dhaafri, H. and Al-Swidi, A., 2016. The impact of total quality management and
entrepreneurial orientation on organizational performance. International journal of
quality & reliability management. 33(5). pp.597-614.
Alzoubi, A., 2021. The Impact of Process Quality and Quality Control on Organizational
Competitiveness at 5-star hotels in Dubai. Int. J. TIM. 1(1). pp. 54–68.
Chaudary, S., Zafar, D. and Salman, M., 2015. Does Total Quality Management Still Shine?
Re-Examining the Total Quality Management Effect on Financial Performance. Total
Quality Management & Business Excellence. 26(7/8). pp.811-824.
Chen, J., 2015. Recent development in machining, materials and mechanical technologies.
Ebook.
Eslami, Y., Dassiti, M., Lezoche, M. and Panetto, H., 2019. A Survey on Sustainability in
Manufacturing Organisations: Dimensions and Future Insights. International Journal of
Production Research. 57. pp.194-5214.
Flynn, B.B., Schroeder, R.G. and Sakakibara, S., 2019. A Framework for Quality
Management Research and an Associated Measurement Instrument. Journal of
Operations Management. 11. pp.339-366.
Kaur, P. and Sharma, K.S., 2020. Evaluating the relationship and influence of critical success
factors of TQM on business performance: Evidence from SMEs of manufacturing
sector. The IUP Journal of Operations Management. 13(4). pp.17-30.
Khanam, S., Siddiqui, J. and Talib, F., 2015. Prioritising the TQM Enablers and IT Resources
in the ICT Industry. International Journal of Information and Communication
Engineering, 9(5). pp.1758 - 1765.
Kozai, T., Niu, G. and Takagaki, M., 2016. Plant factory. Amsterdam: Elsevier/AP,
Academic Press is an imprint of Elsevier.
Kutnjak, G., Miljenovic, D. and Mirkovic, A., 2019. Improving Competitiveness of Small
and medium-sized enterprises with the application of quality management system.
Scientific Journal of Maritime Research. 33. pp.11-21.
8
Books and journals
Al Najjar, S. and Jawad, M., 2019. Total Quality Management Practices and Impediments in
the Arab Countries with Special Reference to Iraq. Journal of Law and Society Man-
agement. 6. pp.86-96.
Al-Dhaafri, H. and Al-Swidi, A., 2016. The impact of total quality management and
entrepreneurial orientation on organizational performance. International journal of
quality & reliability management. 33(5). pp.597-614.
Alzoubi, A., 2021. The Impact of Process Quality and Quality Control on Organizational
Competitiveness at 5-star hotels in Dubai. Int. J. TIM. 1(1). pp. 54–68.
Chaudary, S., Zafar, D. and Salman, M., 2015. Does Total Quality Management Still Shine?
Re-Examining the Total Quality Management Effect on Financial Performance. Total
Quality Management & Business Excellence. 26(7/8). pp.811-824.
Chen, J., 2015. Recent development in machining, materials and mechanical technologies.
Ebook.
Eslami, Y., Dassiti, M., Lezoche, M. and Panetto, H., 2019. A Survey on Sustainability in
Manufacturing Organisations: Dimensions and Future Insights. International Journal of
Production Research. 57. pp.194-5214.
Flynn, B.B., Schroeder, R.G. and Sakakibara, S., 2019. A Framework for Quality
Management Research and an Associated Measurement Instrument. Journal of
Operations Management. 11. pp.339-366.
Kaur, P. and Sharma, K.S., 2020. Evaluating the relationship and influence of critical success
factors of TQM on business performance: Evidence from SMEs of manufacturing
sector. The IUP Journal of Operations Management. 13(4). pp.17-30.
Khanam, S., Siddiqui, J. and Talib, F., 2015. Prioritising the TQM Enablers and IT Resources
in the ICT Industry. International Journal of Information and Communication
Engineering, 9(5). pp.1758 - 1765.
Kozai, T., Niu, G. and Takagaki, M., 2016. Plant factory. Amsterdam: Elsevier/AP,
Academic Press is an imprint of Elsevier.
Kutnjak, G., Miljenovic, D. and Mirkovic, A., 2019. Improving Competitiveness of Small
and medium-sized enterprises with the application of quality management system.
Scientific Journal of Maritime Research. 33. pp.11-21.
8
Paraphrase This Document
Need a fresh take? Get an instant paraphrase of this document with our AI Paraphraser
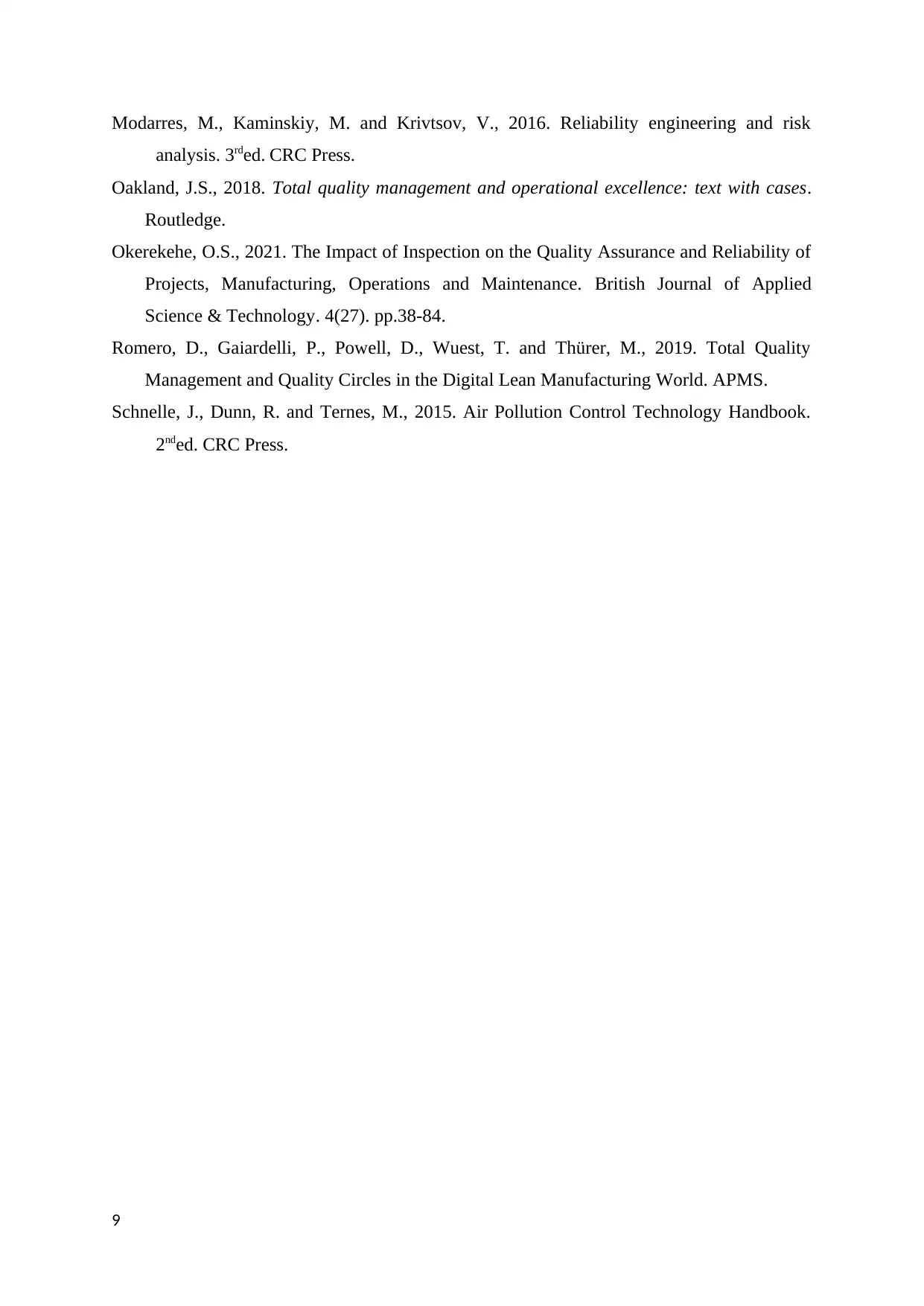
Modarres, M., Kaminskiy, M. and Krivtsov, V., 2016. Reliability engineering and risk
analysis. 3rded. CRC Press.
Oakland, J.S., 2018. Total quality management and operational excellence: text with cases.
Routledge.
Okerekehe, O.S., 2021. The Impact of Inspection on the Quality Assurance and Reliability of
Projects, Manufacturing, Operations and Maintenance. British Journal of Applied
Science & Technology. 4(27). pp.38-84.
Romero, D., Gaiardelli, P., Powell, D., Wuest, T. and Thürer, M., 2019. Total Quality
Management and Quality Circles in the Digital Lean Manufacturing World. APMS.
Schnelle, J., Dunn, R. and Ternes, M., 2015. Air Pollution Control Technology Handbook.
2nded. CRC Press.
9
analysis. 3rded. CRC Press.
Oakland, J.S., 2018. Total quality management and operational excellence: text with cases.
Routledge.
Okerekehe, O.S., 2021. The Impact of Inspection on the Quality Assurance and Reliability of
Projects, Manufacturing, Operations and Maintenance. British Journal of Applied
Science & Technology. 4(27). pp.38-84.
Romero, D., Gaiardelli, P., Powell, D., Wuest, T. and Thürer, M., 2019. Total Quality
Management and Quality Circles in the Digital Lean Manufacturing World. APMS.
Schnelle, J., Dunn, R. and Ternes, M., 2015. Air Pollution Control Technology Handbook.
2nded. CRC Press.
9
1 out of 11
Related Documents

Your All-in-One AI-Powered Toolkit for Academic Success.
+13062052269
info@desklib.com
Available 24*7 on WhatsApp / Email
Unlock your academic potential
© 2024 | Zucol Services PVT LTD | All rights reserved.