Boeing 787 Dreamliner Case Study
VerifiedAdded on 2020/03/13
|12
|2300
|39
AI Summary
This assignment delves into the Boeing 787 Dreamliner case study, examining various aspects of its development and operation. It analyzes the aircraft's supply chain model, including outsourcing strategies and global partnerships. The case also explores the design innovations incorporated into the Dreamliner, such as composite materials and advanced aerodynamics. Furthermore, it investigates the operational challenges faced by Boeing during the Dreamliner's production and delivery phases. The assignment aims to provide a comprehensive understanding of the complexities involved in developing and manufacturing a cutting-edge commercial aircraft.
Contribute Materials
Your contribution can guide someone’s learning journey. Share your
documents today.
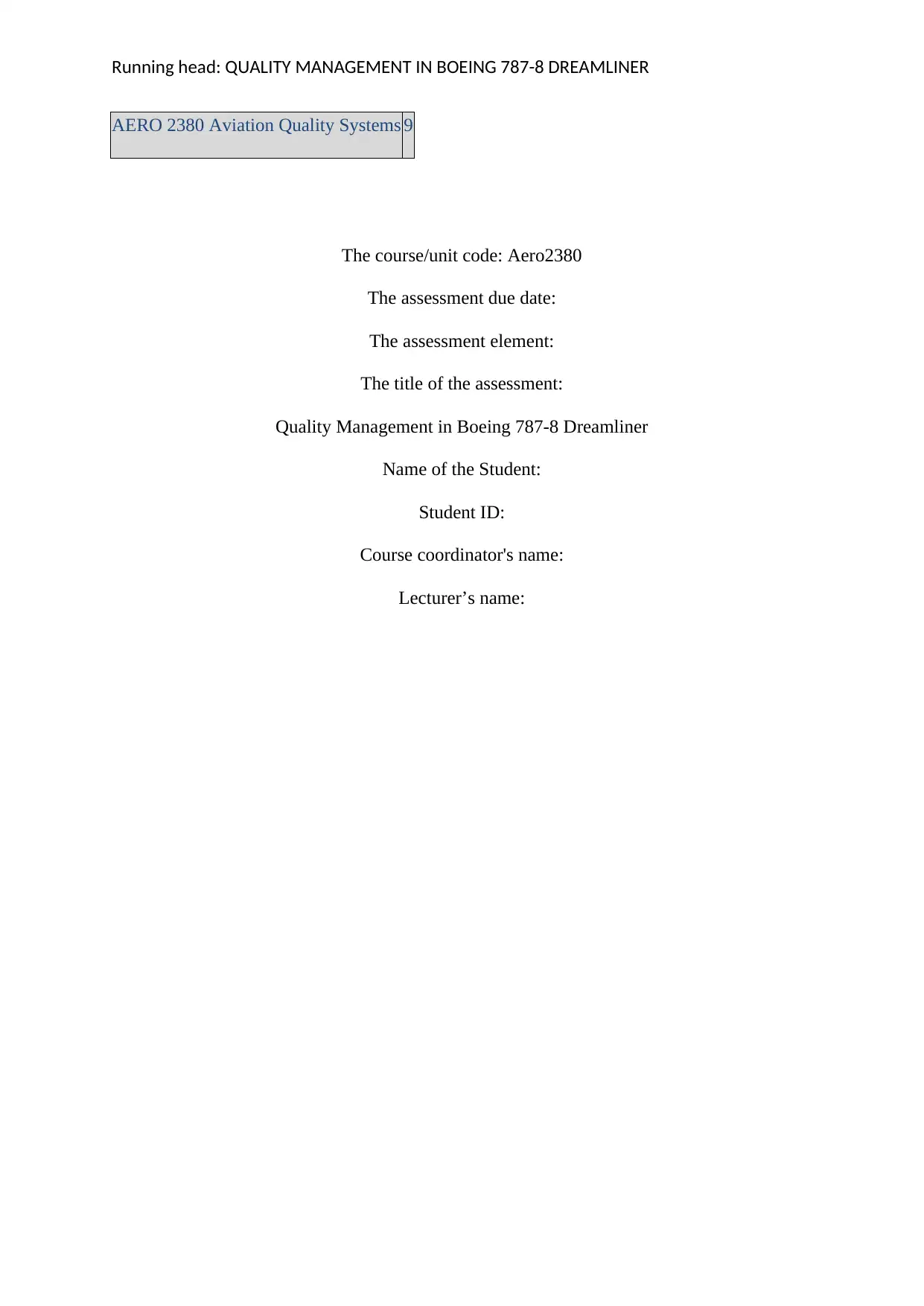
Running head: QUALITY MANAGEMENT IN BOEING 787-8 DREAMLINER
AERO 2380 Aviation Quality Systems 9
The course/unit code: Aero2380
The assessment due date:
The assessment element:
The title of the assessment:
Quality Management in Boeing 787-8 Dreamliner
Name of the Student:
Student ID:
Course coordinator's name:
Lecturer’s name:
AERO 2380 Aviation Quality Systems 9
The course/unit code: Aero2380
The assessment due date:
The assessment element:
The title of the assessment:
Quality Management in Boeing 787-8 Dreamliner
Name of the Student:
Student ID:
Course coordinator's name:
Lecturer’s name:
Secure Best Marks with AI Grader
Need help grading? Try our AI Grader for instant feedback on your assignments.
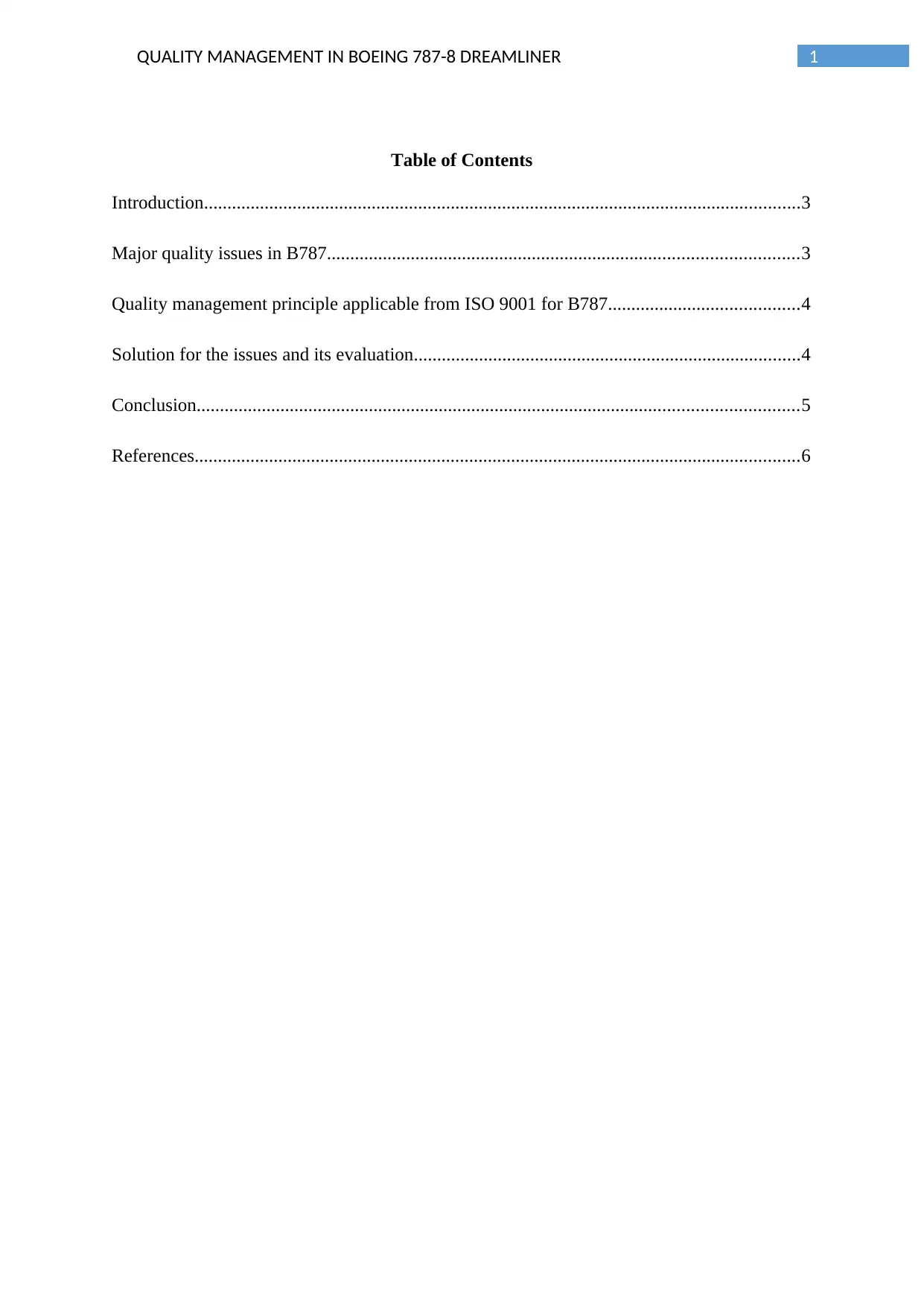
1QUALITY MANAGEMENT IN BOEING 787-8 DREAMLINER
Table of Contents
Introduction................................................................................................................................3
Major quality issues in B787.....................................................................................................3
Quality management principle applicable from ISO 9001 for B787.........................................4
Solution for the issues and its evaluation...................................................................................4
Conclusion.................................................................................................................................5
References..................................................................................................................................6
Table of Contents
Introduction................................................................................................................................3
Major quality issues in B787.....................................................................................................3
Quality management principle applicable from ISO 9001 for B787.........................................4
Solution for the issues and its evaluation...................................................................................4
Conclusion.................................................................................................................................5
References..................................................................................................................................6
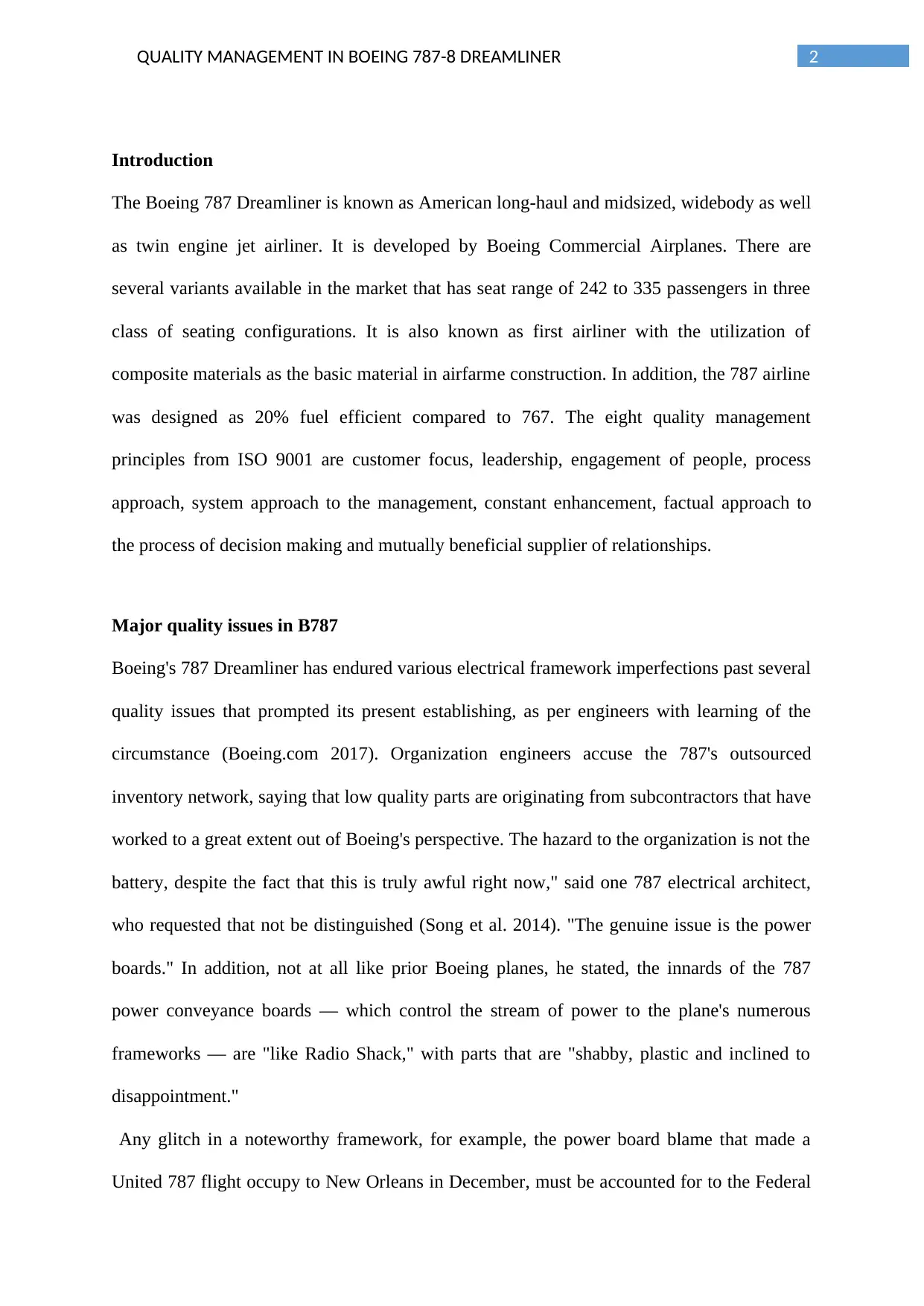
2QUALITY MANAGEMENT IN BOEING 787-8 DREAMLINER
Introduction
The Boeing 787 Dreamliner is known as American long-haul and midsized, widebody as well
as twin engine jet airliner. It is developed by Boeing Commercial Airplanes. There are
several variants available in the market that has seat range of 242 to 335 passengers in three
class of seating configurations. It is also known as first airliner with the utilization of
composite materials as the basic material in airfarme construction. In addition, the 787 airline
was designed as 20% fuel efficient compared to 767. The eight quality management
principles from ISO 9001 are customer focus, leadership, engagement of people, process
approach, system approach to the management, constant enhancement, factual approach to
the process of decision making and mutually beneficial supplier of relationships.
Major quality issues in B787
Boeing's 787 Dreamliner has endured various electrical framework imperfections past several
quality issues that prompted its present establishing, as per engineers with learning of the
circumstance (Boeing.com 2017). Organization engineers accuse the 787's outsourced
inventory network, saying that low quality parts are originating from subcontractors that have
worked to a great extent out of Boeing's perspective. The hazard to the organization is not the
battery, despite the fact that this is truly awful right now," said one 787 electrical architect,
who requested that not be distinguished (Song et al. 2014). "The genuine issue is the power
boards." In addition, not at all like prior Boeing planes, he stated, the innards of the 787
power conveyance boards — which control the stream of power to the plane's numerous
frameworks — are "like Radio Shack," with parts that are "shabby, plastic and inclined to
disappointment."
Any glitch in a noteworthy framework, for example, the power board blame that made a
United 787 flight occupy to New Orleans in December, must be accounted for to the Federal
Introduction
The Boeing 787 Dreamliner is known as American long-haul and midsized, widebody as well
as twin engine jet airliner. It is developed by Boeing Commercial Airplanes. There are
several variants available in the market that has seat range of 242 to 335 passengers in three
class of seating configurations. It is also known as first airliner with the utilization of
composite materials as the basic material in airfarme construction. In addition, the 787 airline
was designed as 20% fuel efficient compared to 767. The eight quality management
principles from ISO 9001 are customer focus, leadership, engagement of people, process
approach, system approach to the management, constant enhancement, factual approach to
the process of decision making and mutually beneficial supplier of relationships.
Major quality issues in B787
Boeing's 787 Dreamliner has endured various electrical framework imperfections past several
quality issues that prompted its present establishing, as per engineers with learning of the
circumstance (Boeing.com 2017). Organization engineers accuse the 787's outsourced
inventory network, saying that low quality parts are originating from subcontractors that have
worked to a great extent out of Boeing's perspective. The hazard to the organization is not the
battery, despite the fact that this is truly awful right now," said one 787 electrical architect,
who requested that not be distinguished (Song et al. 2014). "The genuine issue is the power
boards." In addition, not at all like prior Boeing planes, he stated, the innards of the 787
power conveyance boards — which control the stream of power to the plane's numerous
frameworks — are "like Radio Shack," with parts that are "shabby, plastic and inclined to
disappointment."
Any glitch in a noteworthy framework, for example, the power board blame that made a
United 787 flight occupy to New Orleans in December, must be accounted for to the Federal
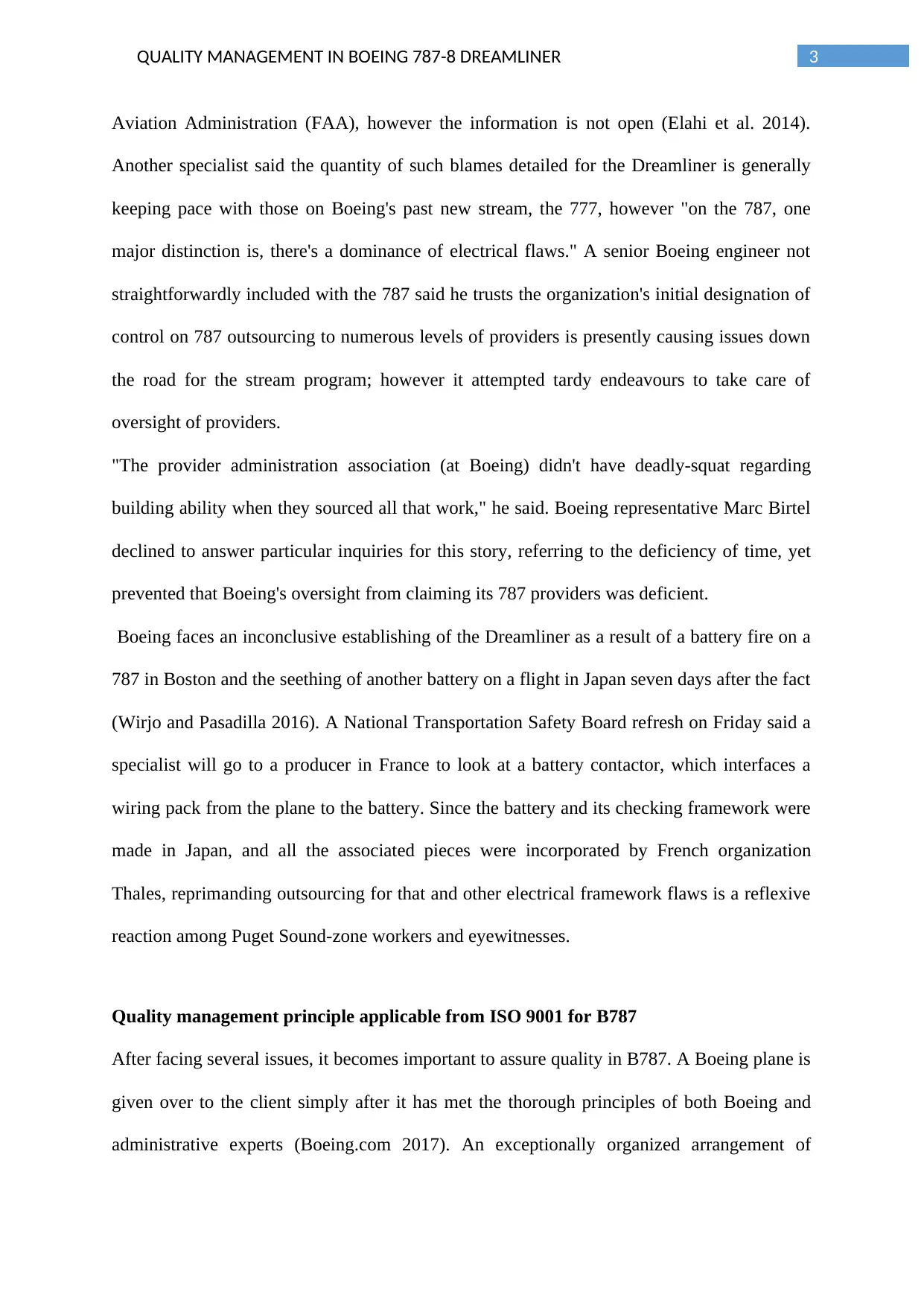
3QUALITY MANAGEMENT IN BOEING 787-8 DREAMLINER
Aviation Administration (FAA), however the information is not open (Elahi et al. 2014).
Another specialist said the quantity of such blames detailed for the Dreamliner is generally
keeping pace with those on Boeing's past new stream, the 777, however "on the 787, one
major distinction is, there's a dominance of electrical flaws." A senior Boeing engineer not
straightforwardly included with the 787 said he trusts the organization's initial designation of
control on 787 outsourcing to numerous levels of providers is presently causing issues down
the road for the stream program; however it attempted tardy endeavours to take care of
oversight of providers.
"The provider administration association (at Boeing) didn't have deadly-squat regarding
building ability when they sourced all that work," he said. Boeing representative Marc Birtel
declined to answer particular inquiries for this story, referring to the deficiency of time, yet
prevented that Boeing's oversight from claiming its 787 providers was deficient.
Boeing faces an inconclusive establishing of the Dreamliner as a result of a battery fire on a
787 in Boston and the seething of another battery on a flight in Japan seven days after the fact
(Wirjo and Pasadilla 2016). A National Transportation Safety Board refresh on Friday said a
specialist will go to a producer in France to look at a battery contactor, which interfaces a
wiring pack from the plane to the battery. Since the battery and its checking framework were
made in Japan, and all the associated pieces were incorporated by French organization
Thales, reprimanding outsourcing for that and other electrical framework flaws is a reflexive
reaction among Puget Sound-zone workers and eyewitnesses.
Quality management principle applicable from ISO 9001 for B787
After facing several issues, it becomes important to assure quality in B787. A Boeing plane is
given over to the client simply after it has met the thorough principles of both Boeing and
administrative experts (Boeing.com 2017). An exceptionally organized arrangement of
Aviation Administration (FAA), however the information is not open (Elahi et al. 2014).
Another specialist said the quantity of such blames detailed for the Dreamliner is generally
keeping pace with those on Boeing's past new stream, the 777, however "on the 787, one
major distinction is, there's a dominance of electrical flaws." A senior Boeing engineer not
straightforwardly included with the 787 said he trusts the organization's initial designation of
control on 787 outsourcing to numerous levels of providers is presently causing issues down
the road for the stream program; however it attempted tardy endeavours to take care of
oversight of providers.
"The provider administration association (at Boeing) didn't have deadly-squat regarding
building ability when they sourced all that work," he said. Boeing representative Marc Birtel
declined to answer particular inquiries for this story, referring to the deficiency of time, yet
prevented that Boeing's oversight from claiming its 787 providers was deficient.
Boeing faces an inconclusive establishing of the Dreamliner as a result of a battery fire on a
787 in Boston and the seething of another battery on a flight in Japan seven days after the fact
(Wirjo and Pasadilla 2016). A National Transportation Safety Board refresh on Friday said a
specialist will go to a producer in France to look at a battery contactor, which interfaces a
wiring pack from the plane to the battery. Since the battery and its checking framework were
made in Japan, and all the associated pieces were incorporated by French organization
Thales, reprimanding outsourcing for that and other electrical framework flaws is a reflexive
reaction among Puget Sound-zone workers and eyewitnesses.
Quality management principle applicable from ISO 9001 for B787
After facing several issues, it becomes important to assure quality in B787. A Boeing plane is
given over to the client simply after it has met the thorough principles of both Boeing and
administrative experts (Boeing.com 2017). An exceptionally organized arrangement of
Secure Best Marks with AI Grader
Need help grading? Try our AI Grader for instant feedback on your assignments.
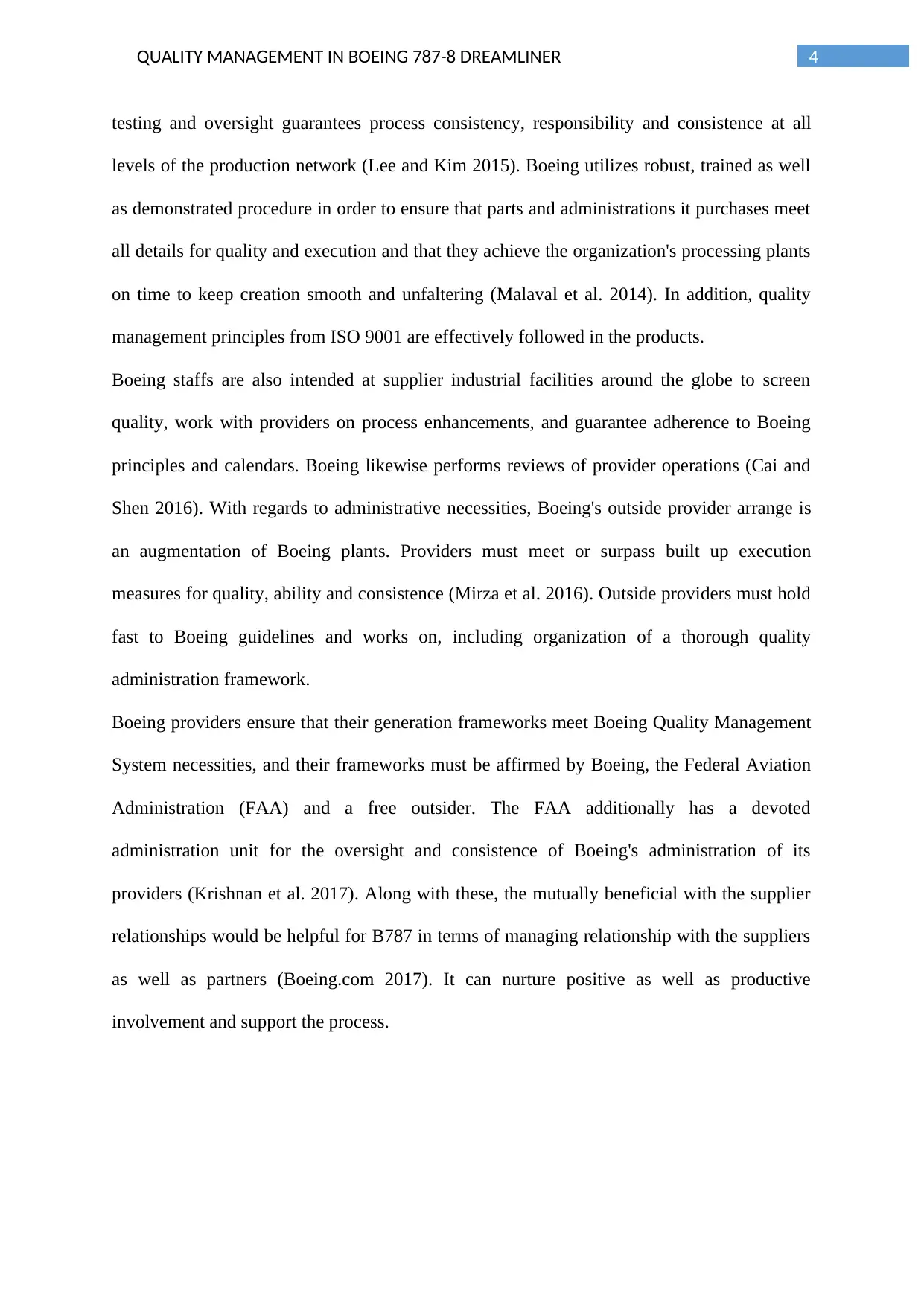
4QUALITY MANAGEMENT IN BOEING 787-8 DREAMLINER
testing and oversight guarantees process consistency, responsibility and consistence at all
levels of the production network (Lee and Kim 2015). Boeing utilizes robust, trained as well
as demonstrated procedure in order to ensure that parts and administrations it purchases meet
all details for quality and execution and that they achieve the organization's processing plants
on time to keep creation smooth and unfaltering (Malaval et al. 2014). In addition, quality
management principles from ISO 9001 are effectively followed in the products.
Boeing staffs are also intended at supplier industrial facilities around the globe to screen
quality, work with providers on process enhancements, and guarantee adherence to Boeing
principles and calendars. Boeing likewise performs reviews of provider operations (Cai and
Shen 2016). With regards to administrative necessities, Boeing's outside provider arrange is
an augmentation of Boeing plants. Providers must meet or surpass built up execution
measures for quality, ability and consistence (Mirza et al. 2016). Outside providers must hold
fast to Boeing guidelines and works on, including organization of a thorough quality
administration framework.
Boeing providers ensure that their generation frameworks meet Boeing Quality Management
System necessities, and their frameworks must be affirmed by Boeing, the Federal Aviation
Administration (FAA) and a free outsider. The FAA additionally has a devoted
administration unit for the oversight and consistence of Boeing's administration of its
providers (Krishnan et al. 2017). Along with these, the mutually beneficial with the supplier
relationships would be helpful for B787 in terms of managing relationship with the suppliers
as well as partners (Boeing.com 2017). It can nurture positive as well as productive
involvement and support the process.
testing and oversight guarantees process consistency, responsibility and consistence at all
levels of the production network (Lee and Kim 2015). Boeing utilizes robust, trained as well
as demonstrated procedure in order to ensure that parts and administrations it purchases meet
all details for quality and execution and that they achieve the organization's processing plants
on time to keep creation smooth and unfaltering (Malaval et al. 2014). In addition, quality
management principles from ISO 9001 are effectively followed in the products.
Boeing staffs are also intended at supplier industrial facilities around the globe to screen
quality, work with providers on process enhancements, and guarantee adherence to Boeing
principles and calendars. Boeing likewise performs reviews of provider operations (Cai and
Shen 2016). With regards to administrative necessities, Boeing's outside provider arrange is
an augmentation of Boeing plants. Providers must meet or surpass built up execution
measures for quality, ability and consistence (Mirza et al. 2016). Outside providers must hold
fast to Boeing guidelines and works on, including organization of a thorough quality
administration framework.
Boeing providers ensure that their generation frameworks meet Boeing Quality Management
System necessities, and their frameworks must be affirmed by Boeing, the Federal Aviation
Administration (FAA) and a free outsider. The FAA additionally has a devoted
administration unit for the oversight and consistence of Boeing's administration of its
providers (Krishnan et al. 2017). Along with these, the mutually beneficial with the supplier
relationships would be helpful for B787 in terms of managing relationship with the suppliers
as well as partners (Boeing.com 2017). It can nurture positive as well as productive
involvement and support the process.
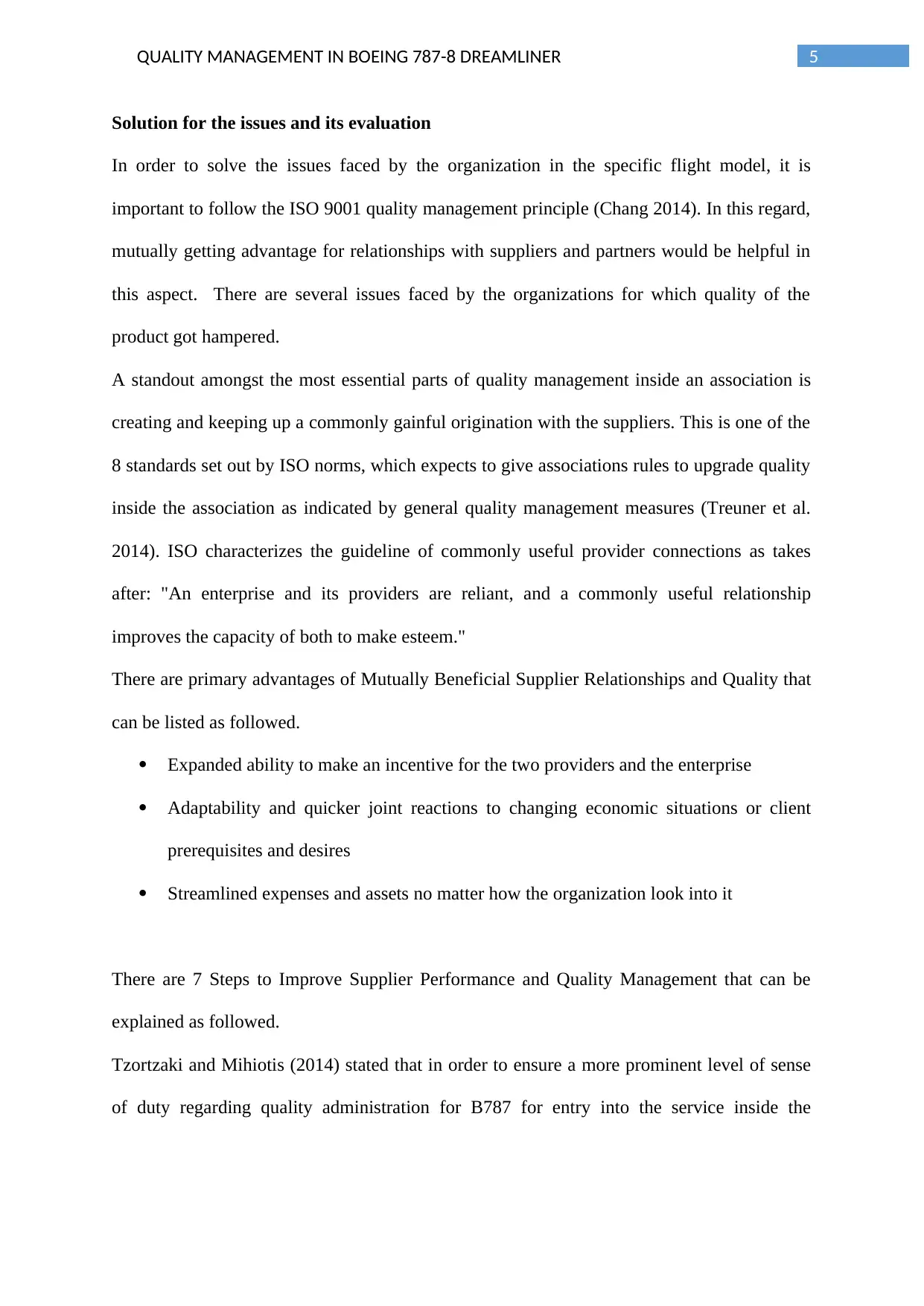
5QUALITY MANAGEMENT IN BOEING 787-8 DREAMLINER
Solution for the issues and its evaluation
In order to solve the issues faced by the organization in the specific flight model, it is
important to follow the ISO 9001 quality management principle (Chang 2014). In this regard,
mutually getting advantage for relationships with suppliers and partners would be helpful in
this aspect. There are several issues faced by the organizations for which quality of the
product got hampered.
A standout amongst the most essential parts of quality management inside an association is
creating and keeping up a commonly gainful origination with the suppliers. This is one of the
8 standards set out by ISO norms, which expects to give associations rules to upgrade quality
inside the association as indicated by general quality management measures (Treuner et al.
2014). ISO characterizes the guideline of commonly useful provider connections as takes
after: "An enterprise and its providers are reliant, and a commonly useful relationship
improves the capacity of both to make esteem."
There are primary advantages of Mutually Beneficial Supplier Relationships and Quality that
can be listed as followed.
Expanded ability to make an incentive for the two providers and the enterprise
Adaptability and quicker joint reactions to changing economic situations or client
prerequisites and desires
Streamlined expenses and assets no matter how the organization look into it
There are 7 Steps to Improve Supplier Performance and Quality Management that can be
explained as followed.
Tzortzaki and Mihiotis (2014) stated that in order to ensure a more prominent level of sense
of duty regarding quality administration for B787 for entry into the service inside the
Solution for the issues and its evaluation
In order to solve the issues faced by the organization in the specific flight model, it is
important to follow the ISO 9001 quality management principle (Chang 2014). In this regard,
mutually getting advantage for relationships with suppliers and partners would be helpful in
this aspect. There are several issues faced by the organizations for which quality of the
product got hampered.
A standout amongst the most essential parts of quality management inside an association is
creating and keeping up a commonly gainful origination with the suppliers. This is one of the
8 standards set out by ISO norms, which expects to give associations rules to upgrade quality
inside the association as indicated by general quality management measures (Treuner et al.
2014). ISO characterizes the guideline of commonly useful provider connections as takes
after: "An enterprise and its providers are reliant, and a commonly useful relationship
improves the capacity of both to make esteem."
There are primary advantages of Mutually Beneficial Supplier Relationships and Quality that
can be listed as followed.
Expanded ability to make an incentive for the two providers and the enterprise
Adaptability and quicker joint reactions to changing economic situations or client
prerequisites and desires
Streamlined expenses and assets no matter how the organization look into it
There are 7 Steps to Improve Supplier Performance and Quality Management that can be
explained as followed.
Tzortzaki and Mihiotis (2014) stated that in order to ensure a more prominent level of sense
of duty regarding quality administration for B787 for entry into the service inside the
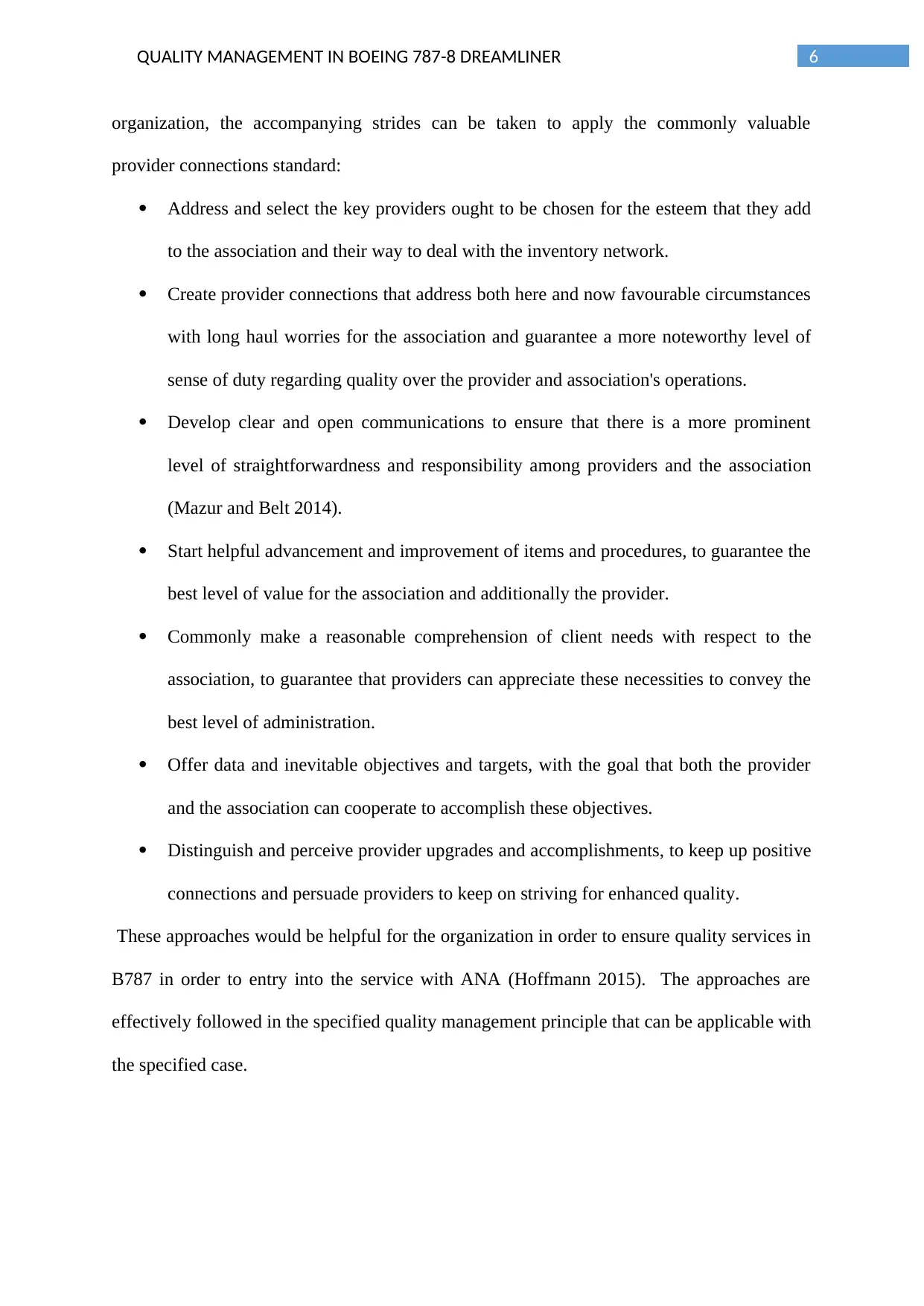
6QUALITY MANAGEMENT IN BOEING 787-8 DREAMLINER
organization, the accompanying strides can be taken to apply the commonly valuable
provider connections standard:
Address and select the key providers ought to be chosen for the esteem that they add
to the association and their way to deal with the inventory network.
Create provider connections that address both here and now favourable circumstances
with long haul worries for the association and guarantee a more noteworthy level of
sense of duty regarding quality over the provider and association's operations.
Develop clear and open communications to ensure that there is a more prominent
level of straightforwardness and responsibility among providers and the association
(Mazur and Belt 2014).
Start helpful advancement and improvement of items and procedures, to guarantee the
best level of value for the association and additionally the provider.
Commonly make a reasonable comprehension of client needs with respect to the
association, to guarantee that providers can appreciate these necessities to convey the
best level of administration.
Offer data and inevitable objectives and targets, with the goal that both the provider
and the association can cooperate to accomplish these objectives.
Distinguish and perceive provider upgrades and accomplishments, to keep up positive
connections and persuade providers to keep on striving for enhanced quality.
These approaches would be helpful for the organization in order to ensure quality services in
B787 in order to entry into the service with ANA (Hoffmann 2015). The approaches are
effectively followed in the specified quality management principle that can be applicable with
the specified case.
organization, the accompanying strides can be taken to apply the commonly valuable
provider connections standard:
Address and select the key providers ought to be chosen for the esteem that they add
to the association and their way to deal with the inventory network.
Create provider connections that address both here and now favourable circumstances
with long haul worries for the association and guarantee a more noteworthy level of
sense of duty regarding quality over the provider and association's operations.
Develop clear and open communications to ensure that there is a more prominent
level of straightforwardness and responsibility among providers and the association
(Mazur and Belt 2014).
Start helpful advancement and improvement of items and procedures, to guarantee the
best level of value for the association and additionally the provider.
Commonly make a reasonable comprehension of client needs with respect to the
association, to guarantee that providers can appreciate these necessities to convey the
best level of administration.
Offer data and inevitable objectives and targets, with the goal that both the provider
and the association can cooperate to accomplish these objectives.
Distinguish and perceive provider upgrades and accomplishments, to keep up positive
connections and persuade providers to keep on striving for enhanced quality.
These approaches would be helpful for the organization in order to ensure quality services in
B787 in order to entry into the service with ANA (Hoffmann 2015). The approaches are
effectively followed in the specified quality management principle that can be applicable with
the specified case.
Paraphrase This Document
Need a fresh take? Get an instant paraphrase of this document with our AI Paraphraser
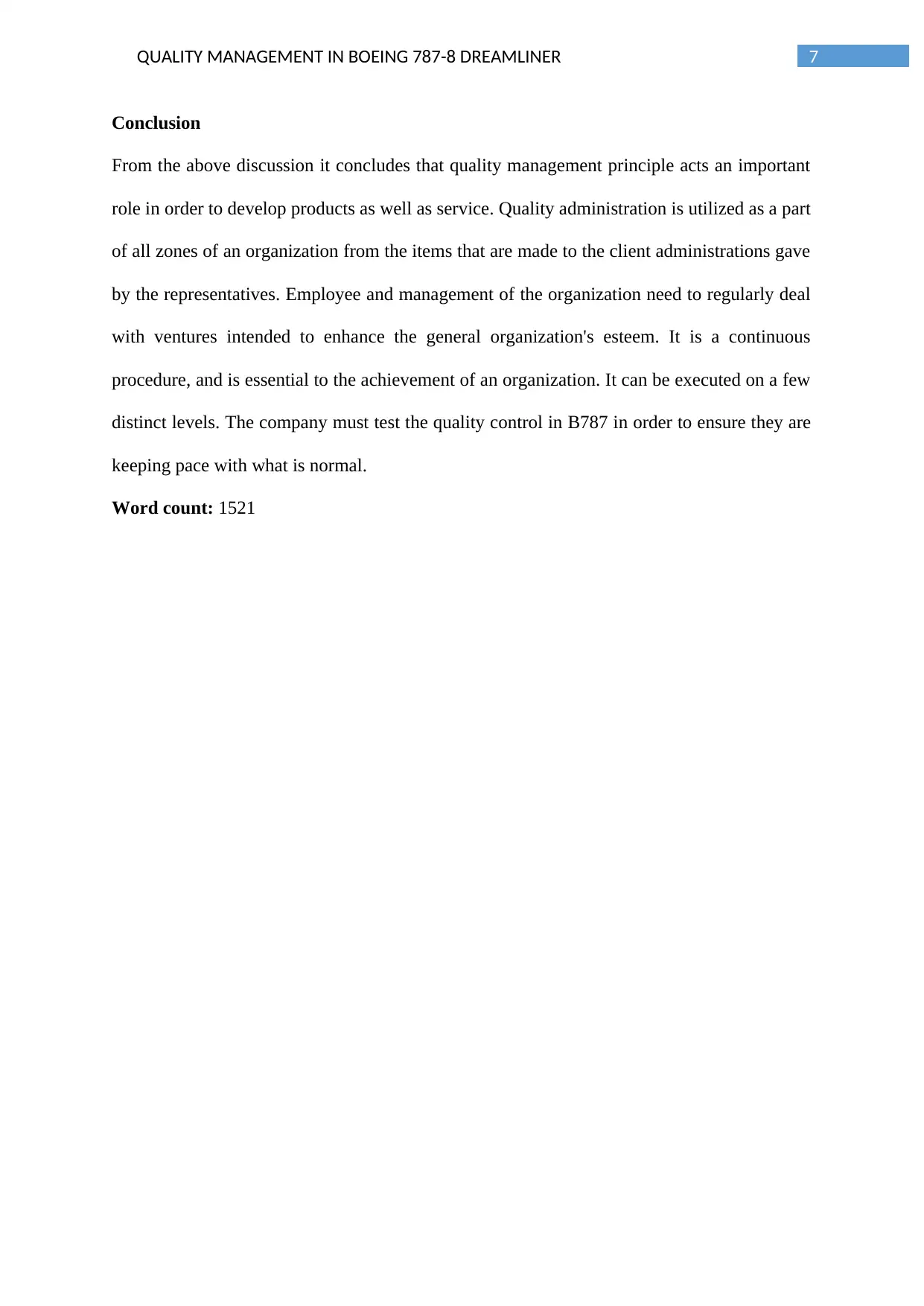
7QUALITY MANAGEMENT IN BOEING 787-8 DREAMLINER
Conclusion
From the above discussion it concludes that quality management principle acts an important
role in order to develop products as well as service. Quality administration is utilized as a part
of all zones of an organization from the items that are made to the client administrations gave
by the representatives. Employee and management of the organization need to regularly deal
with ventures intended to enhance the general organization's esteem. It is a continuous
procedure, and is essential to the achievement of an organization. It can be executed on a few
distinct levels. The company must test the quality control in B787 in order to ensure they are
keeping pace with what is normal.
Word count: 1521
Conclusion
From the above discussion it concludes that quality management principle acts an important
role in order to develop products as well as service. Quality administration is utilized as a part
of all zones of an organization from the items that are made to the client administrations gave
by the representatives. Employee and management of the organization need to regularly deal
with ventures intended to enhance the general organization's esteem. It is a continuous
procedure, and is essential to the achievement of an organization. It can be executed on a few
distinct levels. The company must test the quality control in B787 in order to ensure they are
keeping pace with what is normal.
Word count: 1521
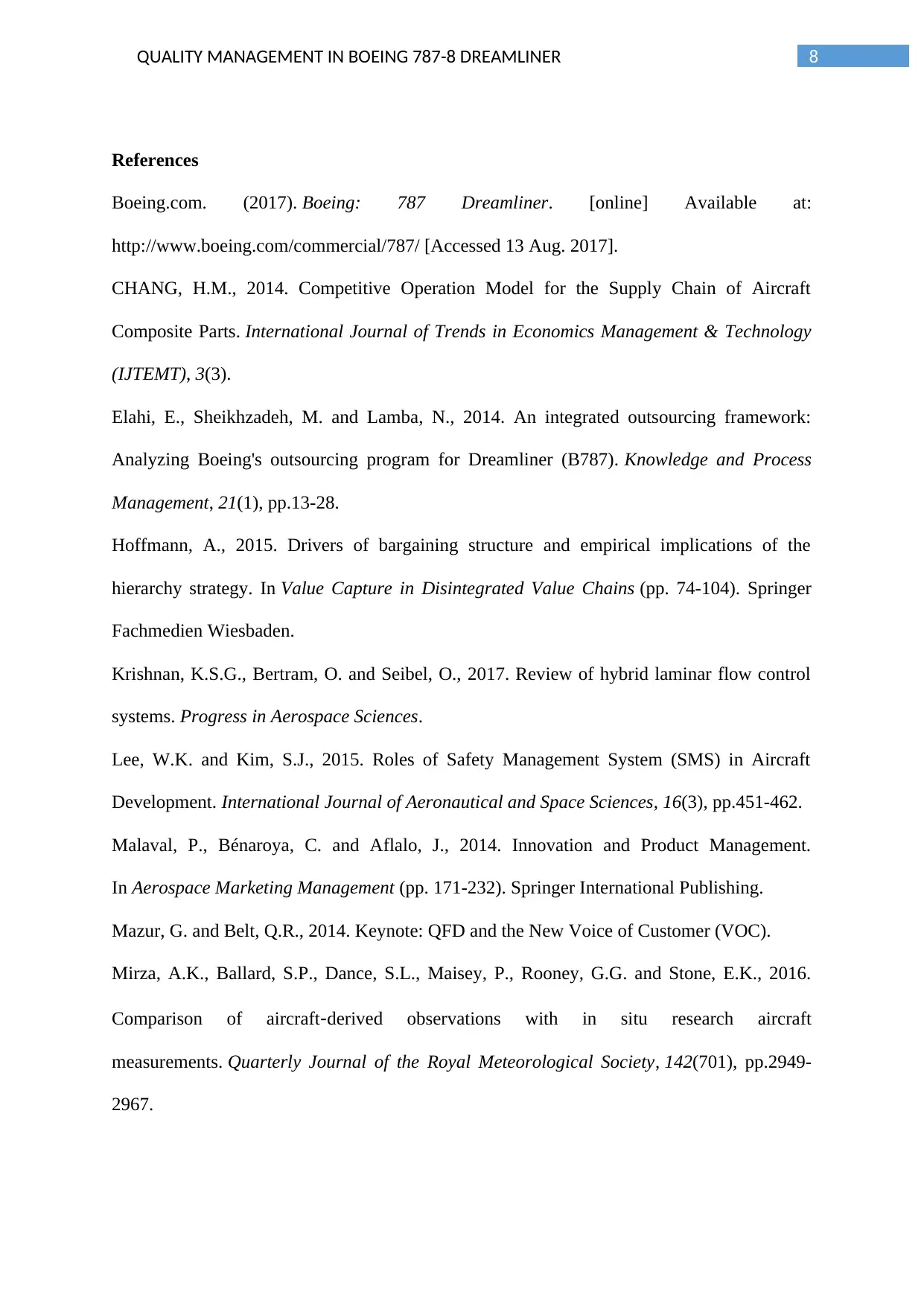
8QUALITY MANAGEMENT IN BOEING 787-8 DREAMLINER
References
Boeing.com. (2017). Boeing: 787 Dreamliner. [online] Available at:
http://www.boeing.com/commercial/787/ [Accessed 13 Aug. 2017].
CHANG, H.M., 2014. Competitive Operation Model for the Supply Chain of Aircraft
Composite Parts. International Journal of Trends in Economics Management & Technology
(IJTEMT), 3(3).
Elahi, E., Sheikhzadeh, M. and Lamba, N., 2014. An integrated outsourcing framework:
Analyzing Boeing's outsourcing program for Dreamliner (B787). Knowledge and Process
Management, 21(1), pp.13-28.
Hoffmann, A., 2015. Drivers of bargaining structure and empirical implications of the
hierarchy strategy. In Value Capture in Disintegrated Value Chains (pp. 74-104). Springer
Fachmedien Wiesbaden.
Krishnan, K.S.G., Bertram, O. and Seibel, O., 2017. Review of hybrid laminar flow control
systems. Progress in Aerospace Sciences.
Lee, W.K. and Kim, S.J., 2015. Roles of Safety Management System (SMS) in Aircraft
Development. International Journal of Aeronautical and Space Sciences, 16(3), pp.451-462.
Malaval, P., Bénaroya, C. and Aflalo, J., 2014. Innovation and Product Management.
In Aerospace Marketing Management (pp. 171-232). Springer International Publishing.
Mazur, G. and Belt, Q.R., 2014. Keynote: QFD and the New Voice of Customer (VOC).
Mirza, A.K., Ballard, S.P., Dance, S.L., Maisey, P., Rooney, G.G. and Stone, E.K., 2016.
Comparison of aircraft‐derived observations with in situ research aircraft
measurements. Quarterly Journal of the Royal Meteorological Society, 142(701), pp.2949-
2967.
References
Boeing.com. (2017). Boeing: 787 Dreamliner. [online] Available at:
http://www.boeing.com/commercial/787/ [Accessed 13 Aug. 2017].
CHANG, H.M., 2014. Competitive Operation Model for the Supply Chain of Aircraft
Composite Parts. International Journal of Trends in Economics Management & Technology
(IJTEMT), 3(3).
Elahi, E., Sheikhzadeh, M. and Lamba, N., 2014. An integrated outsourcing framework:
Analyzing Boeing's outsourcing program for Dreamliner (B787). Knowledge and Process
Management, 21(1), pp.13-28.
Hoffmann, A., 2015. Drivers of bargaining structure and empirical implications of the
hierarchy strategy. In Value Capture in Disintegrated Value Chains (pp. 74-104). Springer
Fachmedien Wiesbaden.
Krishnan, K.S.G., Bertram, O. and Seibel, O., 2017. Review of hybrid laminar flow control
systems. Progress in Aerospace Sciences.
Lee, W.K. and Kim, S.J., 2015. Roles of Safety Management System (SMS) in Aircraft
Development. International Journal of Aeronautical and Space Sciences, 16(3), pp.451-462.
Malaval, P., Bénaroya, C. and Aflalo, J., 2014. Innovation and Product Management.
In Aerospace Marketing Management (pp. 171-232). Springer International Publishing.
Mazur, G. and Belt, Q.R., 2014. Keynote: QFD and the New Voice of Customer (VOC).
Mirza, A.K., Ballard, S.P., Dance, S.L., Maisey, P., Rooney, G.G. and Stone, E.K., 2016.
Comparison of aircraft‐derived observations with in situ research aircraft
measurements. Quarterly Journal of the Royal Meteorological Society, 142(701), pp.2949-
2967.
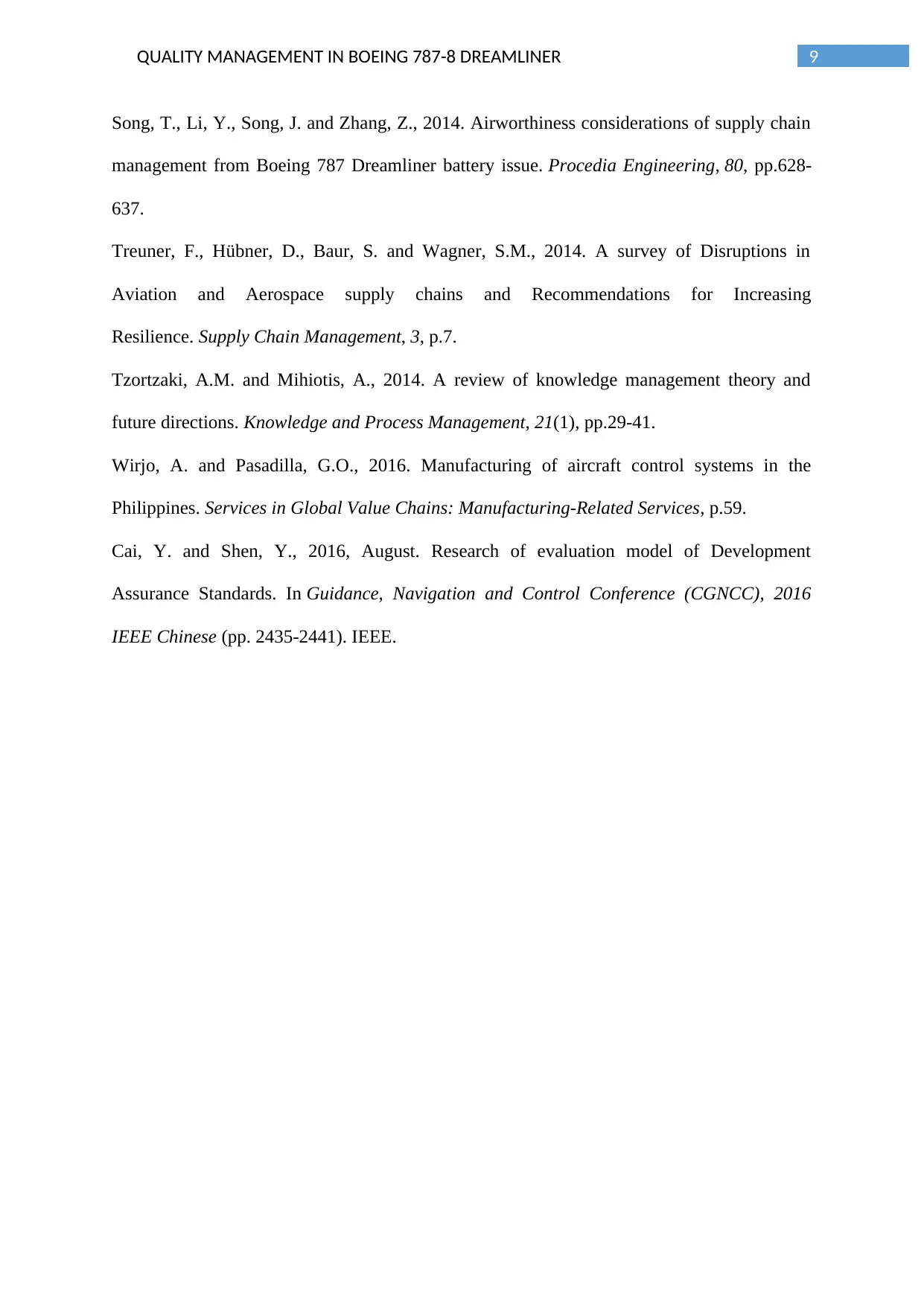
9QUALITY MANAGEMENT IN BOEING 787-8 DREAMLINER
Song, T., Li, Y., Song, J. and Zhang, Z., 2014. Airworthiness considerations of supply chain
management from Boeing 787 Dreamliner battery issue. Procedia Engineering, 80, pp.628-
637.
Treuner, F., Hübner, D., Baur, S. and Wagner, S.M., 2014. A survey of Disruptions in
Aviation and Aerospace supply chains and Recommendations for Increasing
Resilience. Supply Chain Management, 3, p.7.
Tzortzaki, A.M. and Mihiotis, A., 2014. A review of knowledge management theory and
future directions. Knowledge and Process Management, 21(1), pp.29-41.
Wirjo, A. and Pasadilla, G.O., 2016. Manufacturing of aircraft control systems in the
Philippines. Services in Global Value Chains: Manufacturing-Related Services, p.59.
Cai, Y. and Shen, Y., 2016, August. Research of evaluation model of Development
Assurance Standards. In Guidance, Navigation and Control Conference (CGNCC), 2016
IEEE Chinese (pp. 2435-2441). IEEE.
Song, T., Li, Y., Song, J. and Zhang, Z., 2014. Airworthiness considerations of supply chain
management from Boeing 787 Dreamliner battery issue. Procedia Engineering, 80, pp.628-
637.
Treuner, F., Hübner, D., Baur, S. and Wagner, S.M., 2014. A survey of Disruptions in
Aviation and Aerospace supply chains and Recommendations for Increasing
Resilience. Supply Chain Management, 3, p.7.
Tzortzaki, A.M. and Mihiotis, A., 2014. A review of knowledge management theory and
future directions. Knowledge and Process Management, 21(1), pp.29-41.
Wirjo, A. and Pasadilla, G.O., 2016. Manufacturing of aircraft control systems in the
Philippines. Services in Global Value Chains: Manufacturing-Related Services, p.59.
Cai, Y. and Shen, Y., 2016, August. Research of evaluation model of Development
Assurance Standards. In Guidance, Navigation and Control Conference (CGNCC), 2016
IEEE Chinese (pp. 2435-2441). IEEE.
Secure Best Marks with AI Grader
Need help grading? Try our AI Grader for instant feedback on your assignments.
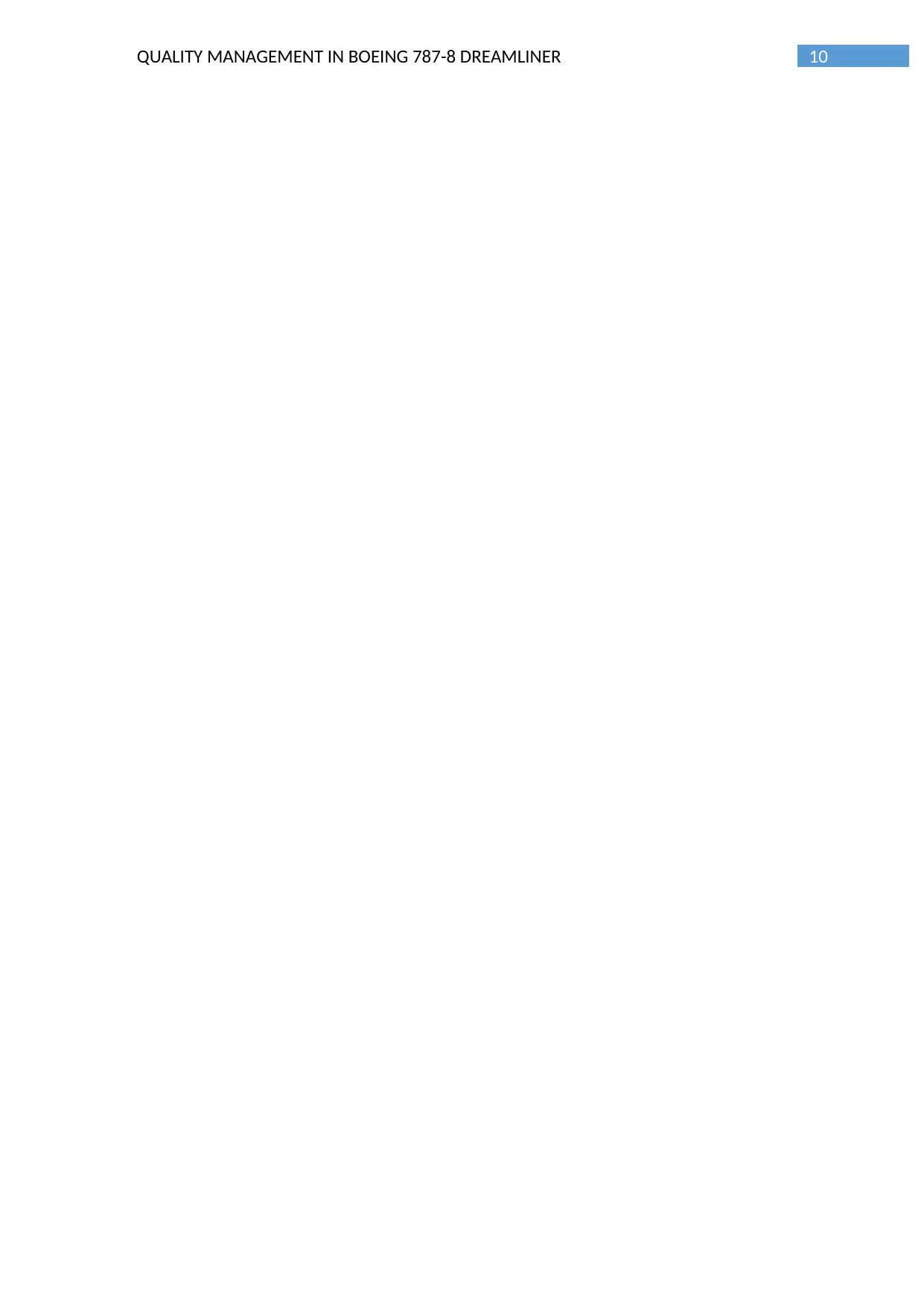
10QUALITY MANAGEMENT IN BOEING 787-8 DREAMLINER
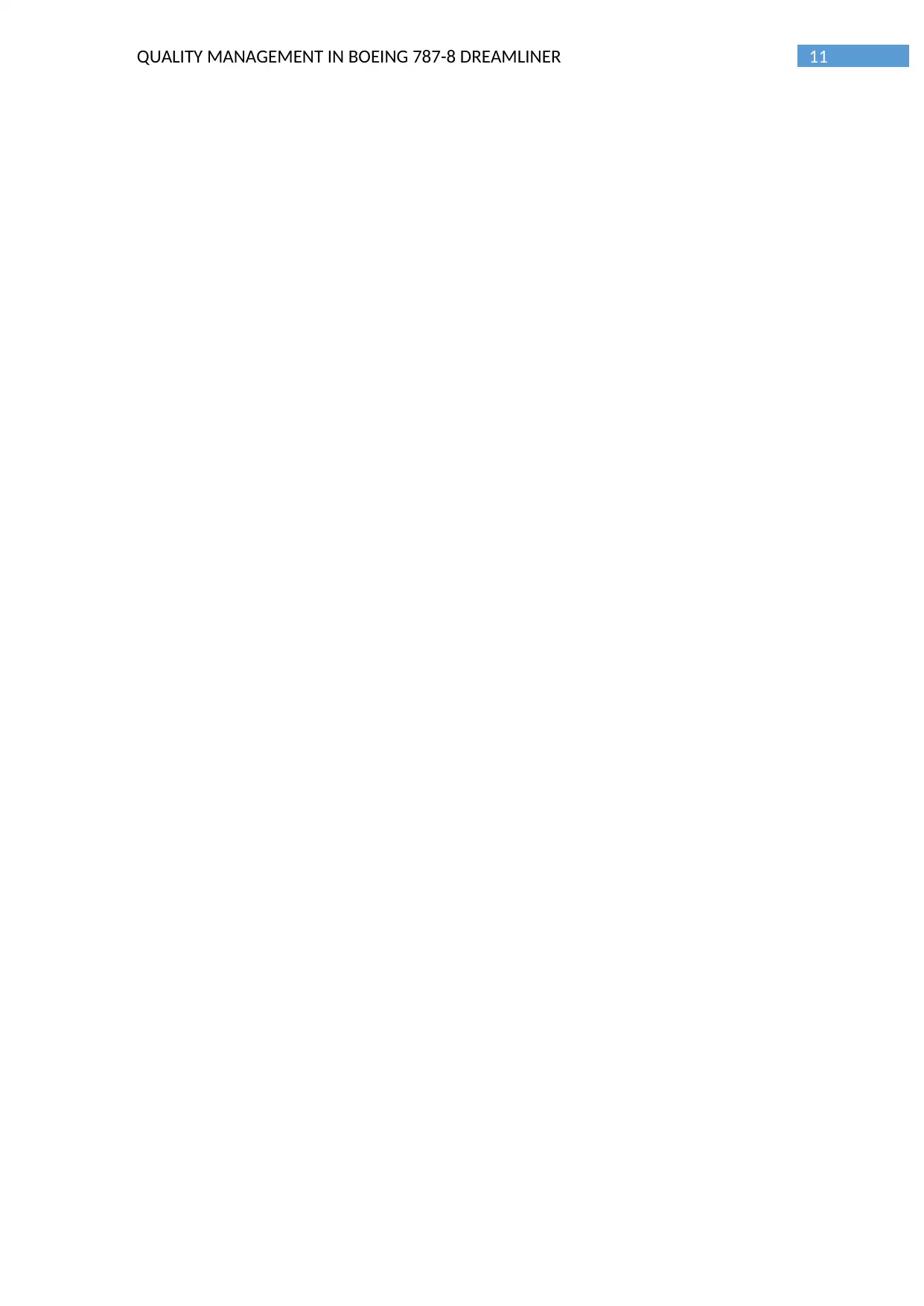
11QUALITY MANAGEMENT IN BOEING 787-8 DREAMLINER
1 out of 12
![[object Object]](/_next/image/?url=%2F_next%2Fstatic%2Fmedia%2Flogo.6d15ce61.png&w=640&q=75)
Your All-in-One AI-Powered Toolkit for Academic Success.
+13062052269
info@desklib.com
Available 24*7 on WhatsApp / Email
Unlock your academic potential
© 2024 | Zucol Services PVT LTD | All rights reserved.