Report: Results and Analysis of Questionnaire on Process Management
VerifiedAdded on 2023/06/05
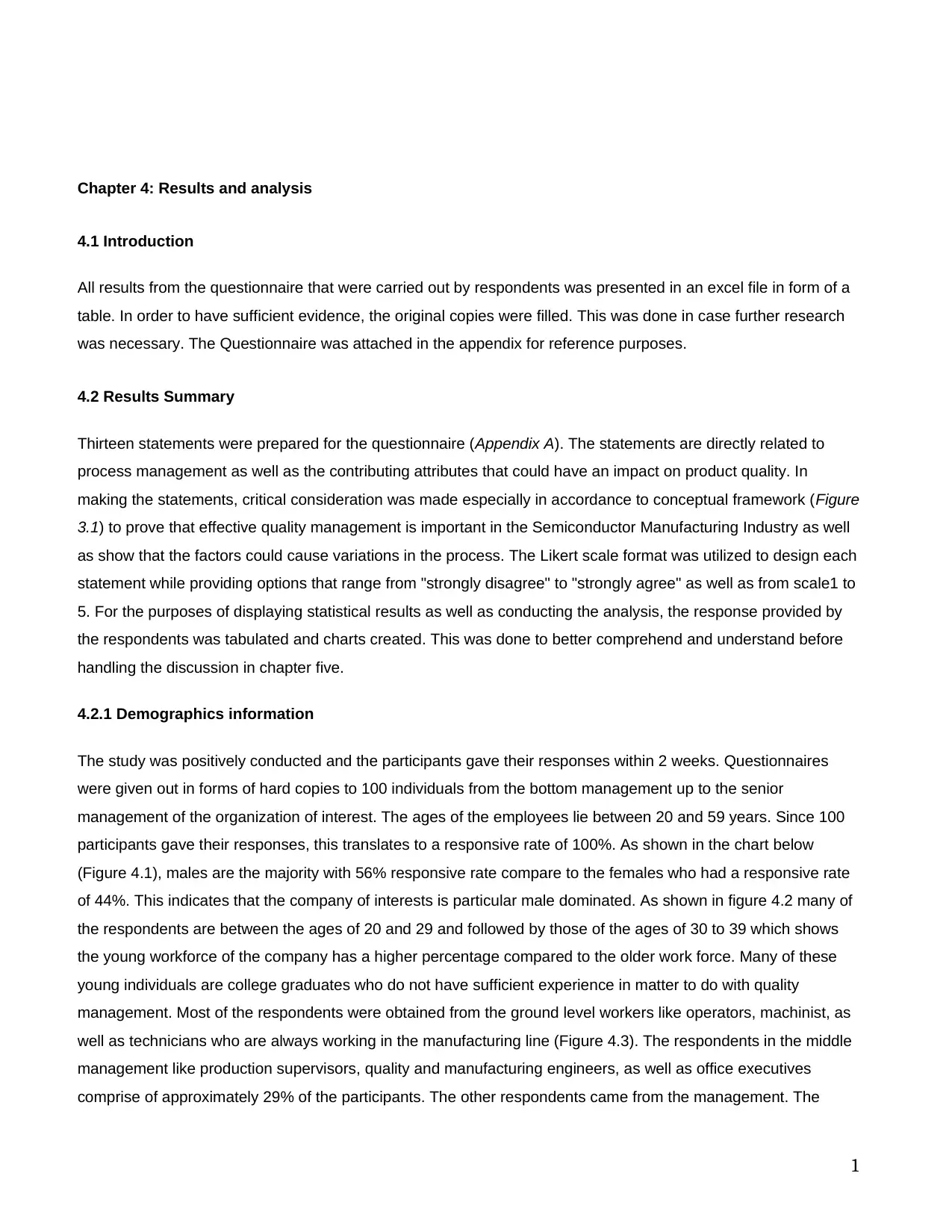
4.1 Introduction
All results from the questionnaire that were carried out by respondents was presented in an excel file in form of a
table. In order to have sufficient evidence, the original copies were filled. This was done in case further research
was necessary. The Questionnaire was attached in the appendix for reference purposes.
4.2 Results Summary
Thirteen statements were prepared for the questionnaire (Appendix A). The statements are directly related to
process management as well as the contributing attributes that could have an impact on product quality. In
making the statements, critical consideration was made especially in accordance to conceptual framework (Figure
3.1) to prove that effective quality management is important in the Semiconductor Manufacturing Industry as well
as show that the factors could cause variations in the process. The Likert scale format was utilized to design each
statement while providing options that range from "strongly disagree" to "strongly agree" as well as from scale1 to
5. For the purposes of displaying statistical results as well as conducting the analysis, the response provided by
the respondents was tabulated and charts created. This was done to better comprehend and understand before
handling the discussion in chapter five.
4.2.1 Demographics information
The study was positively conducted and the participants gave their responses within 2 weeks. Questionnaires
were given out in forms of hard copies to 100 individuals from the bottom management up to the senior
management of the organization of interest. The ages of the employees lie between 20 and 59 years. Since 100
participants gave their responses, this translates to a responsive rate of 100%. As shown in the chart below
(Figure 4.1), males are the majority with 56% responsive rate compare to the females who had a responsive rate
of 44%. This indicates that the company of interests is particular male dominated. As shown in figure 4.2 many of
the respondents are between the ages of 20 and 29 and followed by those of the ages of 30 to 39 which shows
the young workforce of the company has a higher percentage compared to the older work force. Many of these
young individuals are college graduates who do not have sufficient experience in matter to do with quality
management. Most of the respondents were obtained from the ground level workers like operators, machinist, as
well as technicians who are always working in the manufacturing line (Figure 4.3). The respondents in the middle
management like production supervisors, quality and manufacturing engineers, as well as office executives
comprise of approximately 29% of the participants. The other respondents came from the management. The
1
Paraphrase This Document
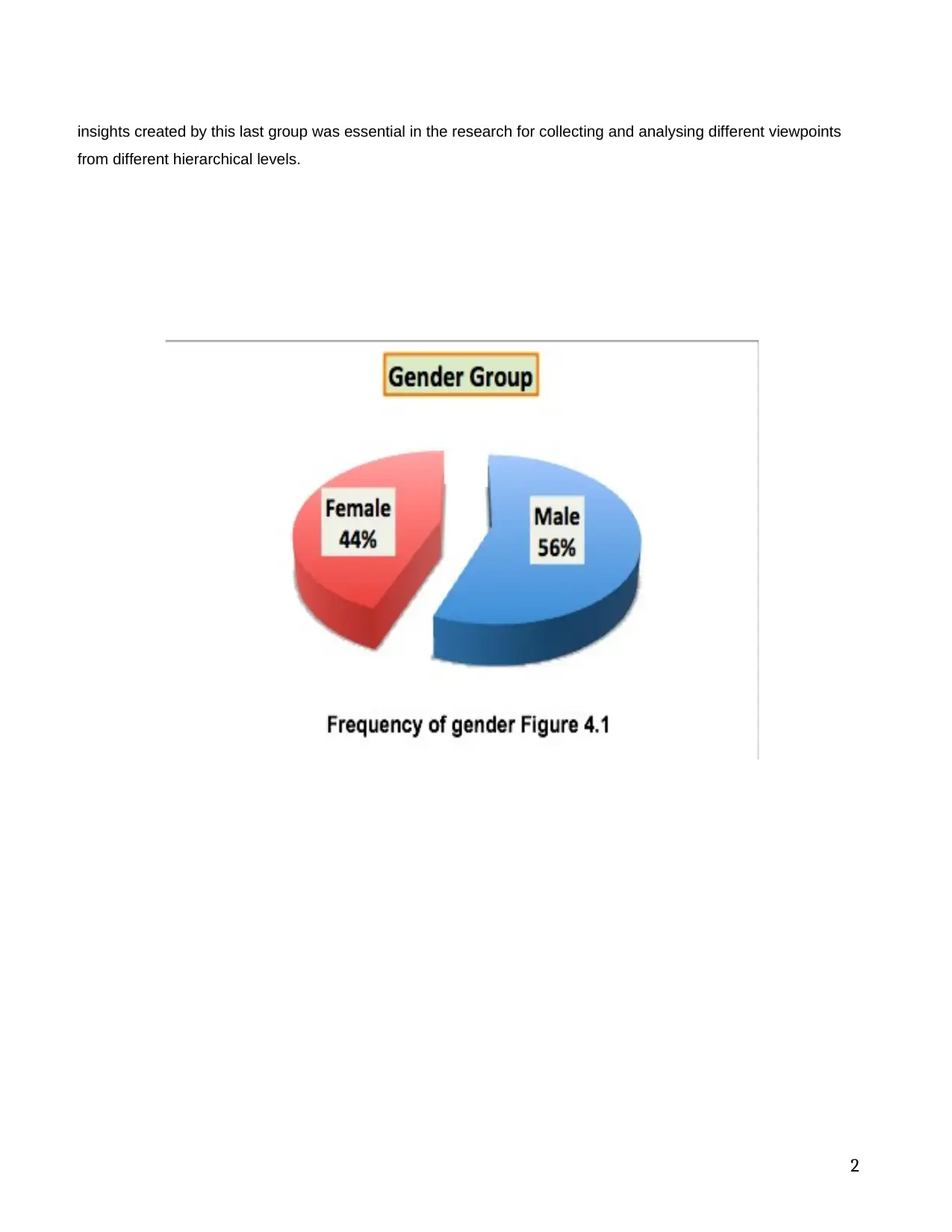
from different hierarchical levels.
2
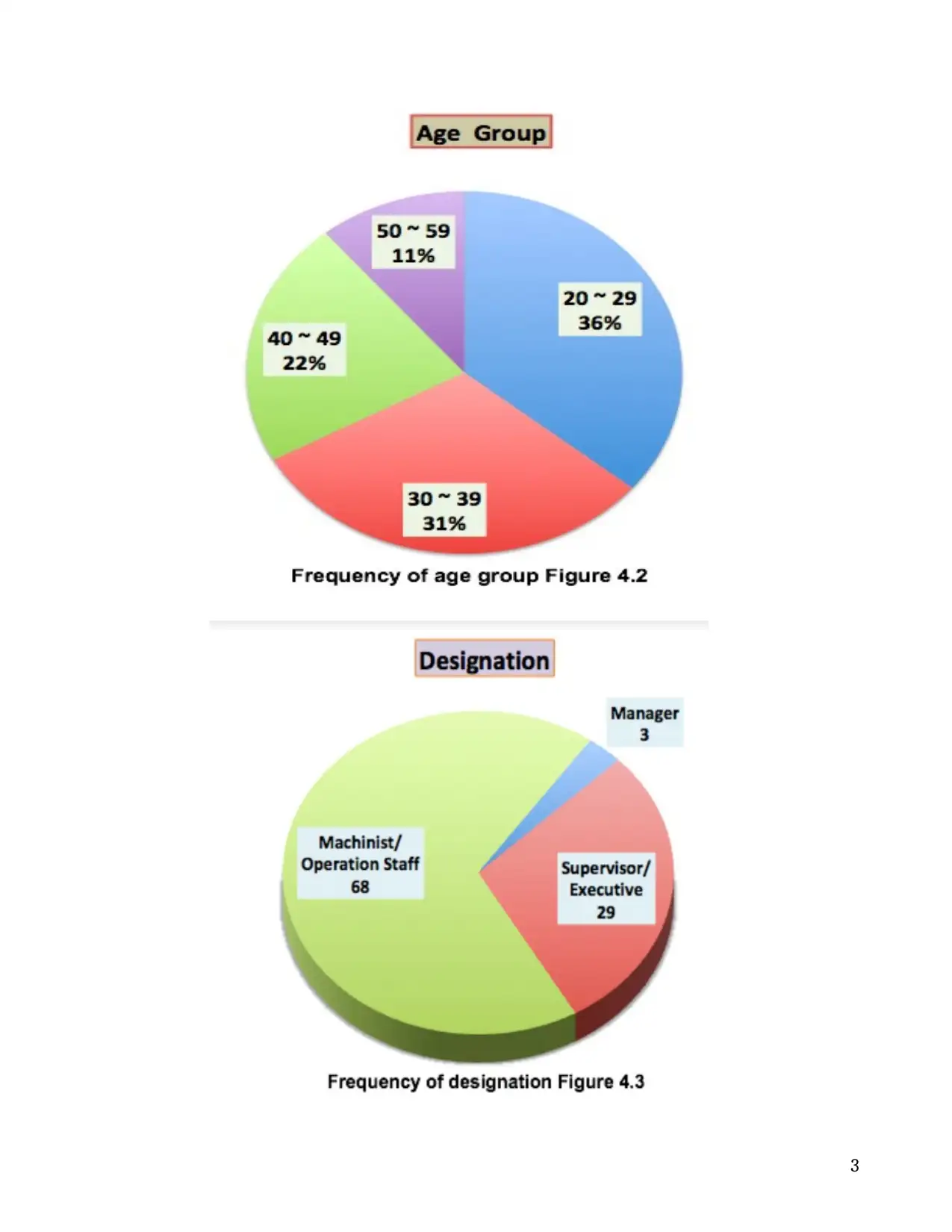
⊘ This is a preview!⊘
Do you want full access?
Subscribe today to unlock all pages.

Trusted by 1+ million students worldwide
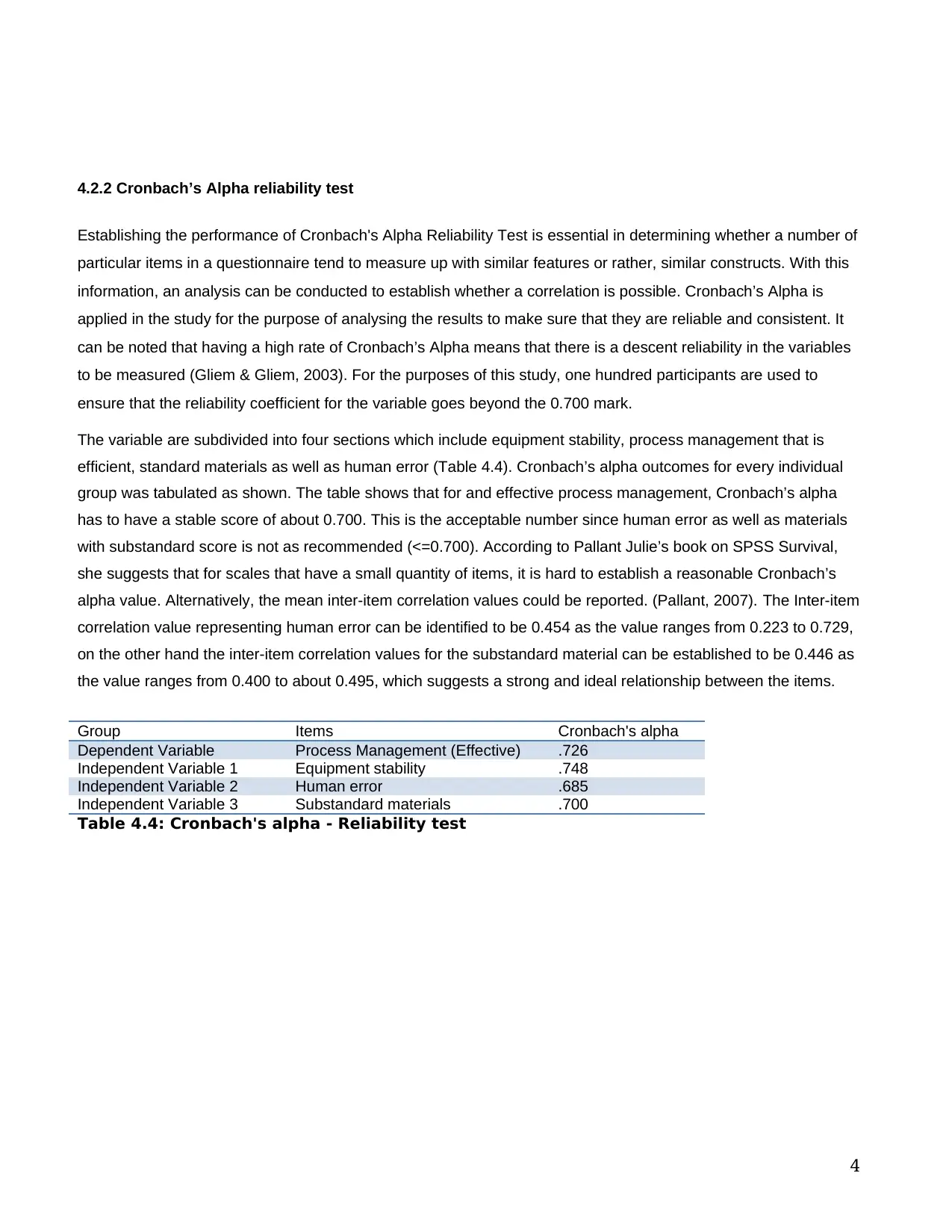
Establishing the performance of Cronbach's Alpha Reliability Test is essential in determining whether a number of
particular items in a questionnaire tend to measure up with similar features or rather, similar constructs. With this
information, an analysis can be conducted to establish whether a correlation is possible. Cronbach’s Alpha is
applied in the study for the purpose of analysing the results to make sure that they are reliable and consistent. It
can be noted that having a high rate of Cronbach’s Alpha means that there is a descent reliability in the variables
to be measured (Gliem & Gliem, 2003). For the purposes of this study, one hundred participants are used to
ensure that the reliability coefficient for the variable goes beyond the 0.700 mark.
The variable are subdivided into four sections which include equipment stability, process management that is
efficient, standard materials as well as human error (Table 4.4). Cronbach’s alpha outcomes for every individual
group was tabulated as shown. The table shows that for and effective process management, Cronbach’s alpha
has to have a stable score of about 0.700. This is the acceptable number since human error as well as materials
with substandard score is not as recommended (<=0.700). According to Pallant Julie’s book on SPSS Survival,
she suggests that for scales that have a small quantity of items, it is hard to establish a reasonable Cronbach’s
alpha value. Alternatively, the mean inter-item correlation values could be reported. (Pallant, 2007). The Inter-item
correlation value representing human error can be identified to be 0.454 as the value ranges from 0.223 to 0.729,
on the other hand the inter-item correlation values for the substandard material can be established to be 0.446 as
the value ranges from 0.400 to about 0.495, which suggests a strong and ideal relationship between the items.
Group Items Cronbach's alpha
Dependent Variable Process Management (Effective) .726
Independent Variable 1 Equipment stability .748
Independent Variable 2 Human error .685
Independent Variable 3 Substandard materials .700
Table 4.4: Cronbach's alpha - Reliability test
4
Paraphrase This Document
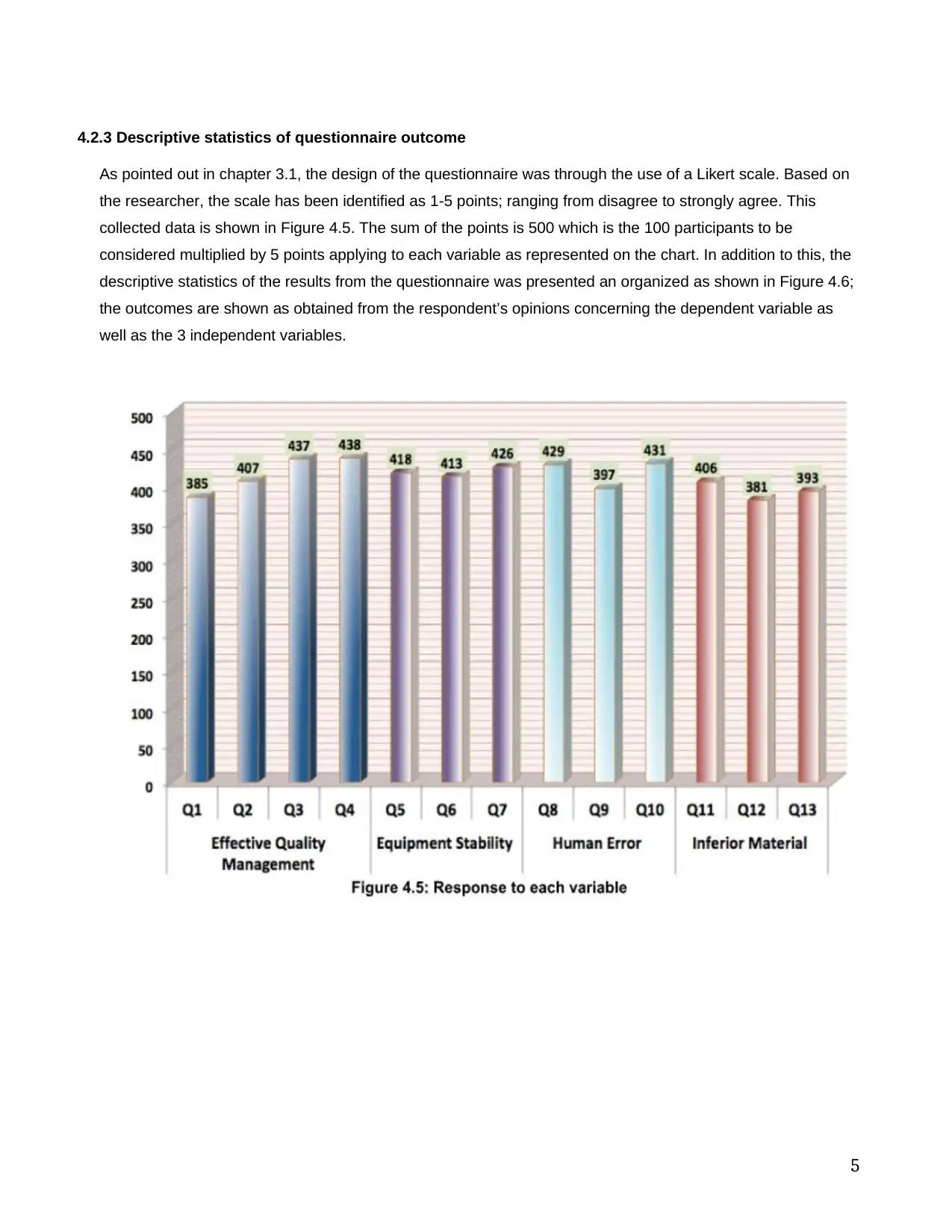
As pointed out in chapter 3.1, the design of the questionnaire was through the use of a Likert scale. Based on
the researcher, the scale has been identified as 1-5 points; ranging from disagree to strongly agree. This
collected data is shown in Figure 4.5. The sum of the points is 500 which is the 100 participants to be
considered multiplied by 5 points applying to each variable as represented on the chart. In addition to this, the
descriptive statistics of the results from the questionnaire was presented an organized as shown in Figure 4.6;
the outcomes are shown as obtained from the respondent’s opinions concerning the dependent variable as
well as the 3 independent variables.
5
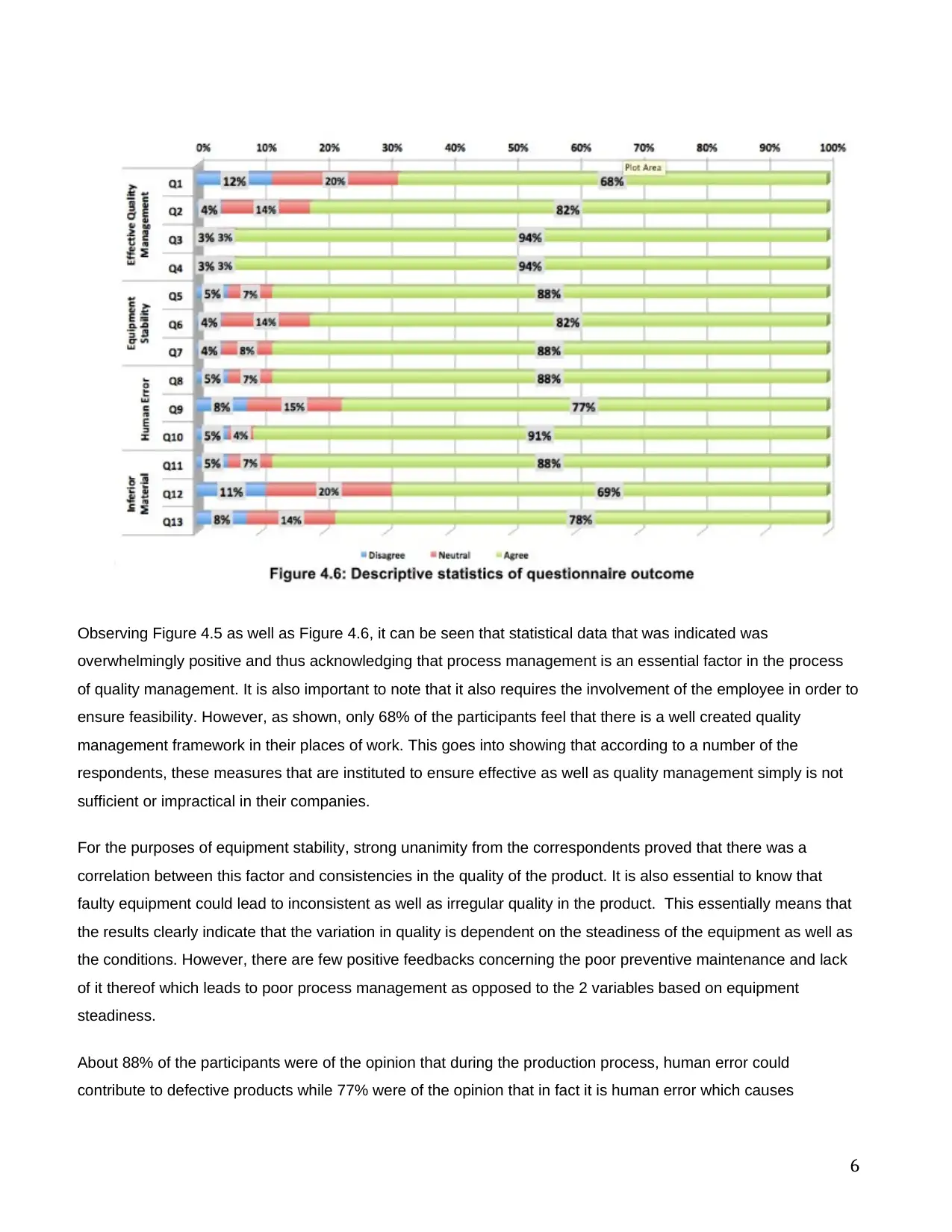
overwhelmingly positive and thus acknowledging that process management is an essential factor in the process
of quality management. It is also important to note that it also requires the involvement of the employee in order to
ensure feasibility. However, as shown, only 68% of the participants feel that there is a well created quality
management framework in their places of work. This goes into showing that according to a number of the
respondents, these measures that are instituted to ensure effective as well as quality management simply is not
sufficient or impractical in their companies.
For the purposes of equipment stability, strong unanimity from the correspondents proved that there was a
correlation between this factor and consistencies in the quality of the product. It is also essential to know that
faulty equipment could lead to inconsistent as well as irregular quality in the product. This essentially means that
the results clearly indicate that the variation in quality is dependent on the steadiness of the equipment as well as
the conditions. However, there are few positive feedbacks concerning the poor preventive maintenance and lack
of it thereof which leads to poor process management as opposed to the 2 variables based on equipment
steadiness.
About 88% of the participants were of the opinion that during the production process, human error could
contribute to defective products while 77% were of the opinion that in fact it is human error which causes
6
⊘ This is a preview!⊘
Do you want full access?
Subscribe today to unlock all pages.

Trusted by 1+ million students worldwide
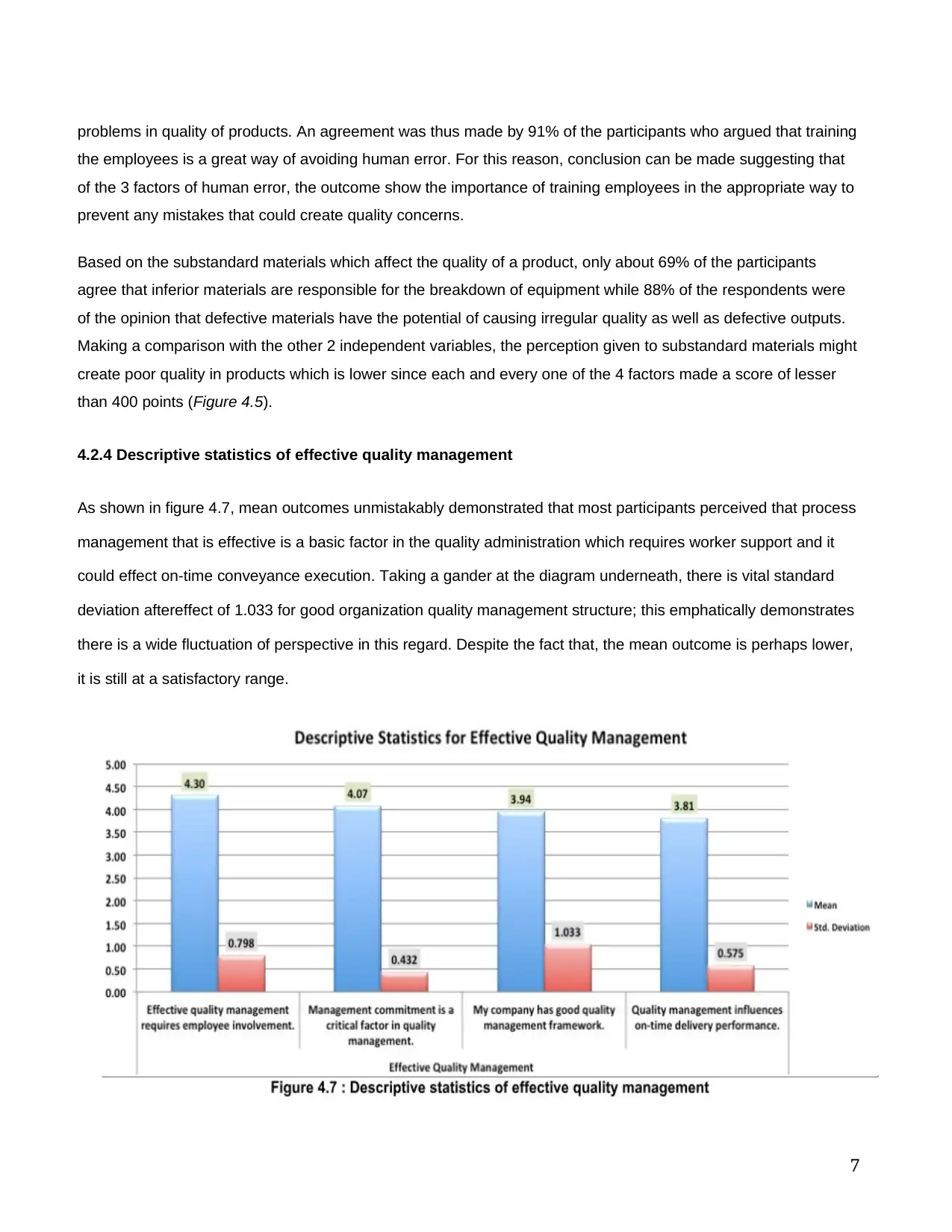
the employees is a great way of avoiding human error. For this reason, conclusion can be made suggesting that
of the 3 factors of human error, the outcome show the importance of training employees in the appropriate way to
prevent any mistakes that could create quality concerns.
Based on the substandard materials which affect the quality of a product, only about 69% of the participants
agree that inferior materials are responsible for the breakdown of equipment while 88% of the respondents were
of the opinion that defective materials have the potential of causing irregular quality as well as defective outputs.
Making a comparison with the other 2 independent variables, the perception given to substandard materials might
create poor quality in products which is lower since each and every one of the 4 factors made a score of lesser
than 400 points (Figure 4.5).
4.2.4 Descriptive statistics of effective quality management
As shown in figure 4.7, mean outcomes unmistakably demonstrated that most participants perceived that process
management that is effective is a basic factor in the quality administration which requires worker support and it
could effect on-time conveyance execution. Taking a gander at the diagram underneath, there is vital standard
deviation aftereffect of 1.033 for good organization quality management structure; this emphatically demonstrates
there is a wide fluctuation of perspective in this regard. Despite the fact that, the mean outcome is perhaps lower,
it is still at a satisfactory range.
7
Paraphrase This Document
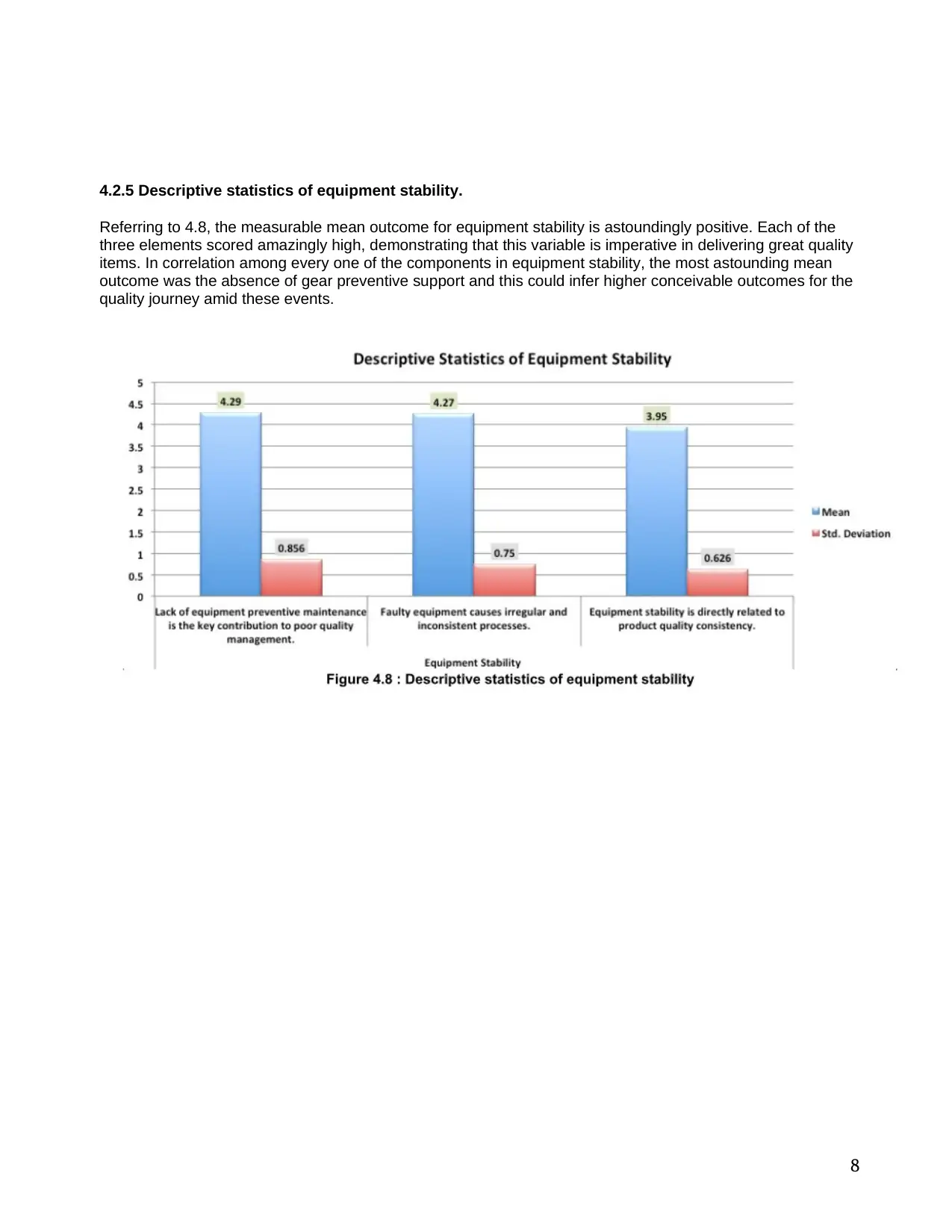
Referring to 4.8, the measurable mean outcome for equipment stability is astoundingly positive. Each of the
three elements scored amazingly high, demonstrating that this variable is imperative in delivering great quality
items. In correlation among every one of the components in equipment stability, the most astounding mean
outcome was the absence of gear preventive support and this could infer higher conceivable outcomes for the
quality journey amid these events.
8
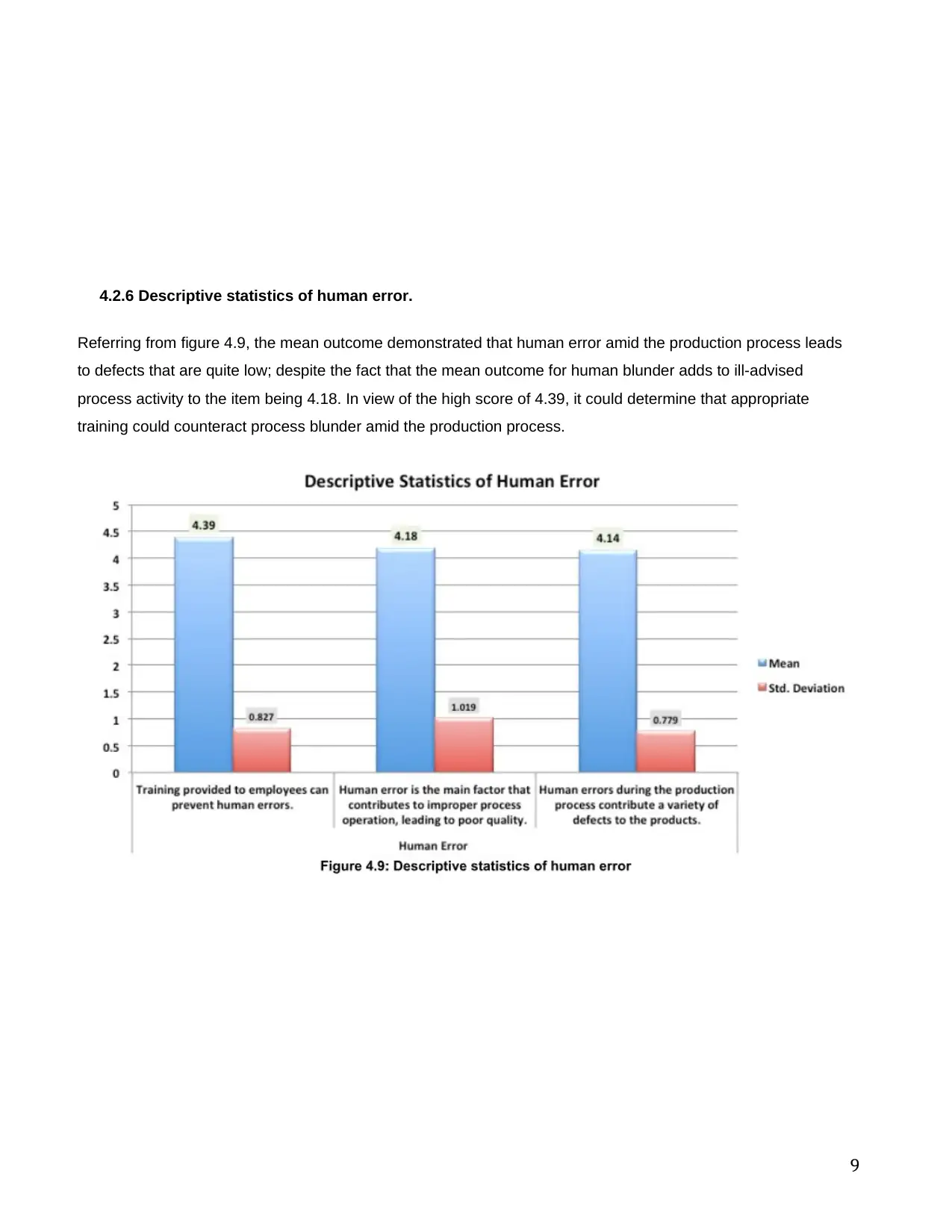
Referring from figure 4.9, the mean outcome demonstrated that human error amid the production process leads
to defects that are quite low; despite the fact that the mean outcome for human blunder adds to ill-advised
process activity to the item being 4.18. In view of the high score of 4.39, it could determine that appropriate
training could counteract process blunder amid the production process.
9
⊘ This is a preview!⊘
Do you want full access?
Subscribe today to unlock all pages.

Trusted by 1+ million students worldwide
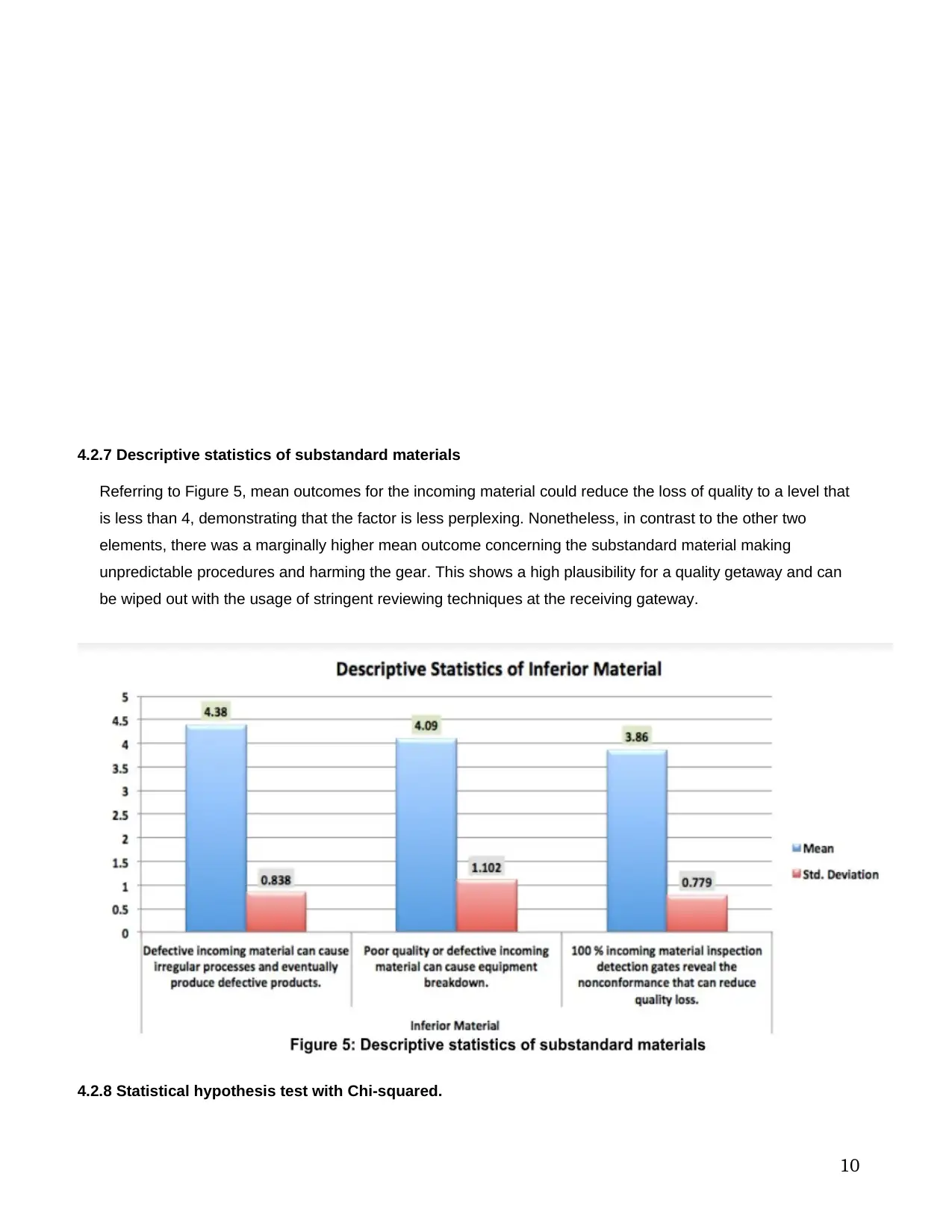
Referring to Figure 5, mean outcomes for the incoming material could reduce the loss of quality to a level that
is less than 4, demonstrating that the factor is less perplexing. Nonetheless, in contrast to the other two
elements, there was a marginally higher mean outcome concerning the substandard material making
unpredictable procedures and harming the gear. This shows a high plausibility for a quality getaway and can
be wiped out with the usage of stringent reviewing techniques at the receiving gateway.
4.2.8 Statistical hypothesis test with Chi-squared.
10
Paraphrase This Document
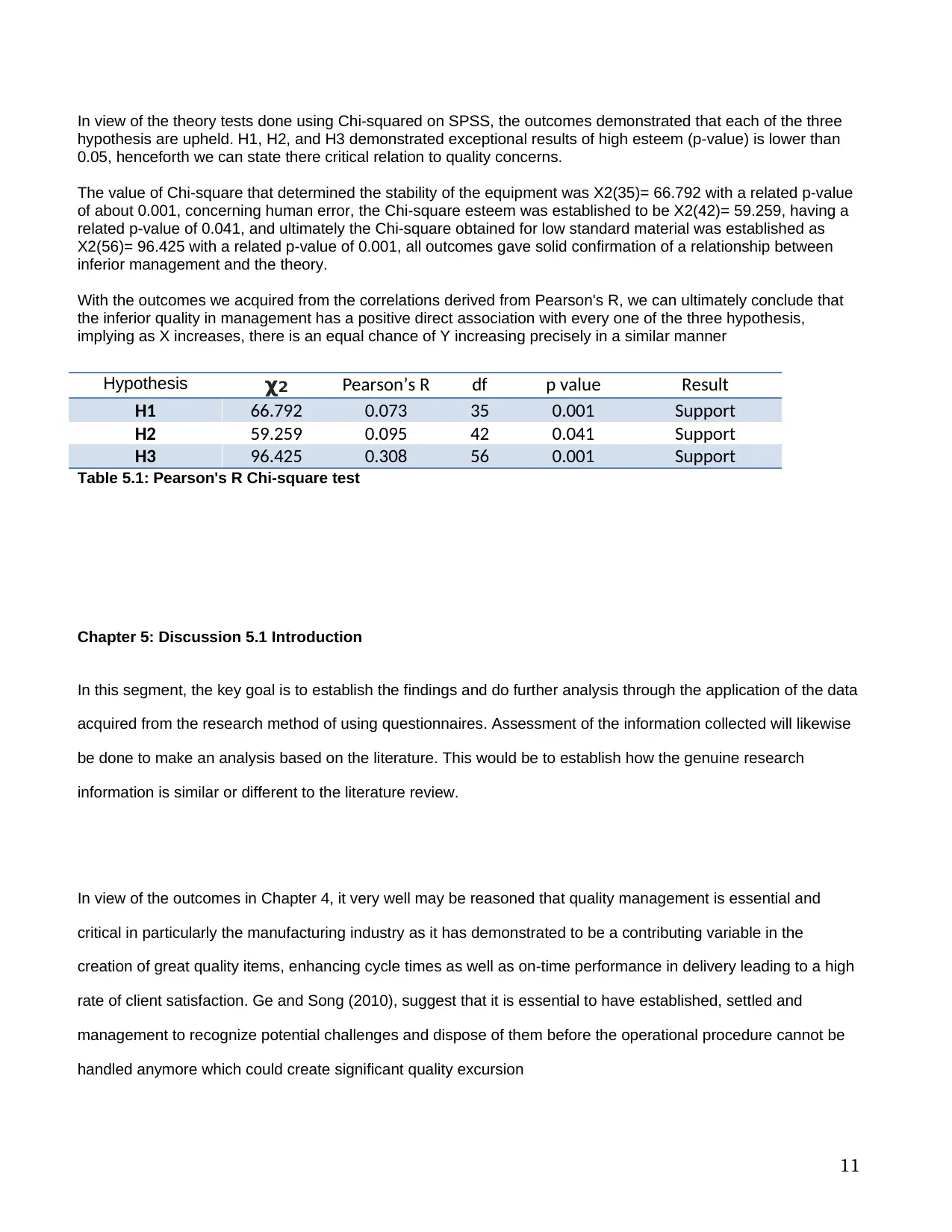
hypothesis are upheld. H1, H2, and H3 demonstrated exceptional results of high esteem (p-value) is lower than
0.05, henceforth we can state there critical relation to quality concerns.
The value of Chi-square that determined the stability of the equipment was X2(35)= 66.792 with a related p-value
of about 0.001, concerning human error, the Chi-square esteem was established to be X2(42)= 59.259, having a
related p-value of 0.041, and ultimately the Chi-square obtained for low standard material was established as
X2(56)= 96.425 with a related p-value of 0.001, all outcomes gave solid confirmation of a relationship between
inferior management and the theory.
With the outcomes we acquired from the correlations derived from Pearson's R, we can ultimately conclude that
the inferior quality in management has a positive direct association with every one of the three hypothesis,
implying as X increases, there is an equal chance of Y increasing precisely in a similar manner
Hypothesis χ2 Pearson’s R df p value Result
H1 66.792 0.073 35 0.001 Support
H2 59.259 0.095 42 0.041 Support
H3 96.425 0.308 56 0.001 Support
Table 5.1: Pearson's R Chi-square test
Chapter 5: Discussion 5.1 Introduction
In this segment, the key goal is to establish the findings and do further analysis through the application of the data
acquired from the research method of using questionnaires. Assessment of the information collected will likewise
be done to make an analysis based on the literature. This would be to establish how the genuine research
information is similar or different to the literature review.
In view of the outcomes in Chapter 4, it very well may be reasoned that quality management is essential and
critical in particularly the manufacturing industry as it has demonstrated to be a contributing variable in the
creation of great quality items, enhancing cycle times as well as on-time performance in delivery leading to a high
rate of client satisfaction. Ge and Song (2010), suggest that it is essential to have established, settled and
management to recognize potential challenges and dispose of them before the operational procedure cannot be
handled anymore which could create significant quality excursion
11
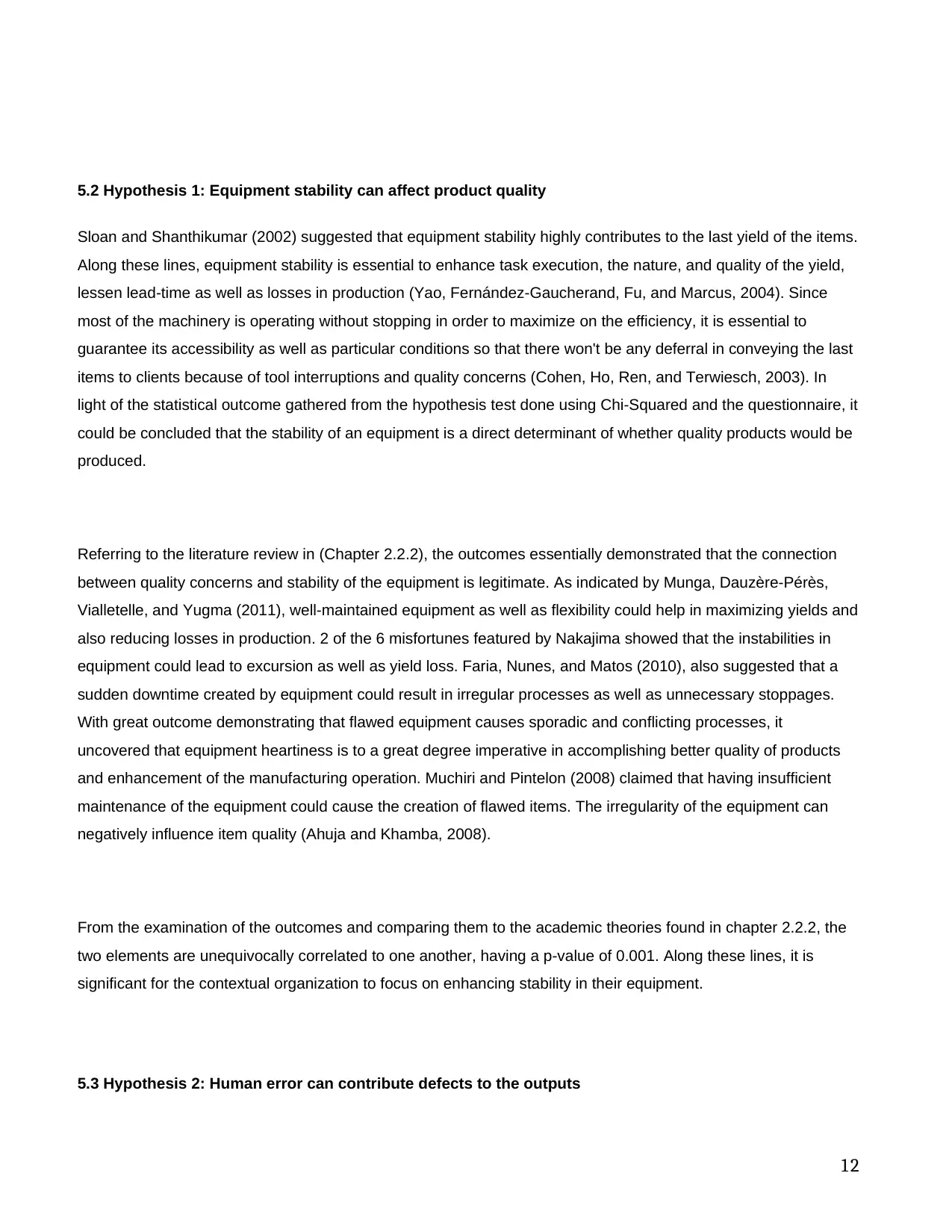
Sloan and Shanthikumar (2002) suggested that equipment stability highly contributes to the last yield of the items.
Along these lines, equipment stability is essential to enhance task execution, the nature, and quality of the yield,
lessen lead-time as well as losses in production (Yao, Fernández-Gaucherand, Fu, and Marcus, 2004). Since
most of the machinery is operating without stopping in order to maximize on the efficiency, it is essential to
guarantee its accessibility as well as particular conditions so that there won't be any deferral in conveying the last
items to clients because of tool interruptions and quality concerns (Cohen, Ho, Ren, and Terwiesch, 2003). In
light of the statistical outcome gathered from the hypothesis test done using Chi-Squared and the questionnaire, it
could be concluded that the stability of an equipment is a direct determinant of whether quality products would be
produced.
Referring to the literature review in (Chapter 2.2.2), the outcomes essentially demonstrated that the connection
between quality concerns and stability of the equipment is legitimate. As indicated by Munga, Dauzère-Pérès,
Vialletelle, and Yugma (2011), well-maintained equipment as well as flexibility could help in maximizing yields and
also reducing losses in production. 2 of the 6 misfortunes featured by Nakajima showed that the instabilities in
equipment could lead to excursion as well as yield loss. Faria, Nunes, and Matos (2010), also suggested that a
sudden downtime created by equipment could result in irregular processes as well as unnecessary stoppages.
With great outcome demonstrating that flawed equipment causes sporadic and conflicting processes, it
uncovered that equipment heartiness is to a great degree imperative in accomplishing better quality of products
and enhancement of the manufacturing operation. Muchiri and Pintelon (2008) claimed that having insufficient
maintenance of the equipment could cause the creation of flawed items. The irregularity of the equipment can
negatively influence item quality (Ahuja and Khamba, 2008).
From the examination of the outcomes and comparing them to the academic theories found in chapter 2.2.2, the
two elements are unequivocally correlated to one another, having a p-value of 0.001. Along these lines, it is
significant for the contextual organization to focus on enhancing stability in their equipment.
5.3 Hypothesis 2: Human error can contribute defects to the outputs
12
⊘ This is a preview!⊘
Do you want full access?
Subscribe today to unlock all pages.

Trusted by 1+ million students worldwide
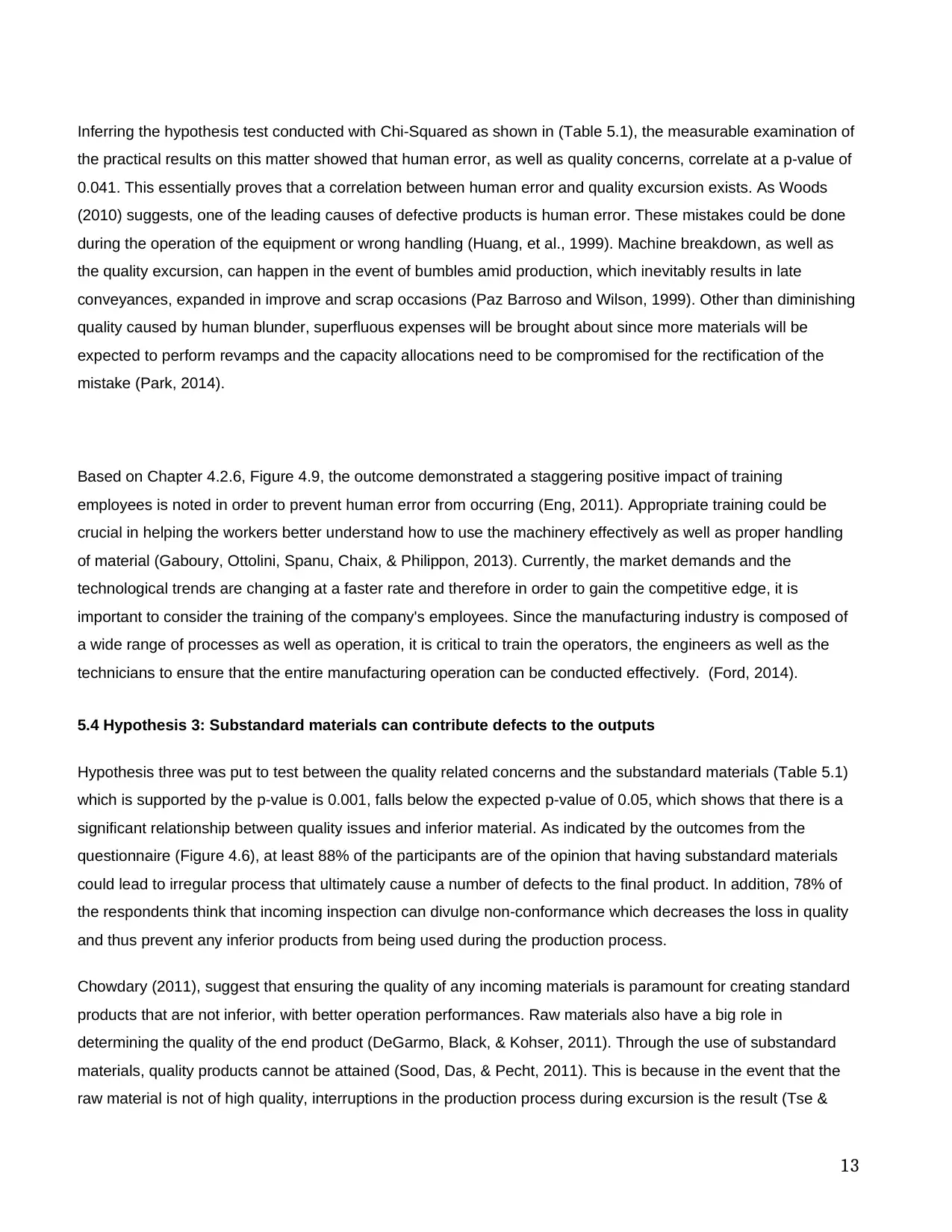
the practical results on this matter showed that human error, as well as quality concerns, correlate at a p-value of
0.041. This essentially proves that a correlation between human error and quality excursion exists. As Woods
(2010) suggests, one of the leading causes of defective products is human error. These mistakes could be done
during the operation of the equipment or wrong handling (Huang, et al., 1999). Machine breakdown, as well as
the quality excursion, can happen in the event of bumbles amid production, which inevitably results in late
conveyances, expanded in improve and scrap occasions (Paz Barroso and Wilson, 1999). Other than diminishing
quality caused by human blunder, superfluous expenses will be brought about since more materials will be
expected to perform revamps and the capacity allocations need to be compromised for the rectification of the
mistake (Park, 2014).
Based on Chapter 4.2.6, Figure 4.9, the outcome demonstrated a staggering positive impact of training
employees is noted in order to prevent human error from occurring (Eng, 2011). Appropriate training could be
crucial in helping the workers better understand how to use the machinery effectively as well as proper handling
of material (Gaboury, Ottolini, Spanu, Chaix, & Philippon, 2013). Currently, the market demands and the
technological trends are changing at a faster rate and therefore in order to gain the competitive edge, it is
important to consider the training of the company's employees. Since the manufacturing industry is composed of
a wide range of processes as well as operation, it is critical to train the operators, the engineers as well as the
technicians to ensure that the entire manufacturing operation can be conducted effectively. (Ford, 2014).
5.4 Hypothesis 3: Substandard materials can contribute defects to the outputs
Hypothesis three was put to test between the quality related concerns and the substandard materials (Table 5.1)
which is supported by the p-value is 0.001, falls below the expected p-value of 0.05, which shows that there is a
significant relationship between quality issues and inferior material. As indicated by the outcomes from the
questionnaire (Figure 4.6), at least 88% of the participants are of the opinion that having substandard materials
could lead to irregular process that ultimately cause a number of defects to the final product. In addition, 78% of
the respondents think that incoming inspection can divulge non-conformance which decreases the loss in quality
and thus prevent any inferior products from being used during the production process.
Chowdary (2011), suggest that ensuring the quality of any incoming materials is paramount for creating standard
products that are not inferior, with better operation performances. Raw materials also have a big role in
determining the quality of the end product (DeGarmo, Black, & Kohser, 2011). Through the use of substandard
materials, quality products cannot be attained (Sood, Das, & Pecht, 2011). This is because in the event that the
raw material is not of high quality, interruptions in the production process during excursion is the result (Tse &
13
Paraphrase This Document
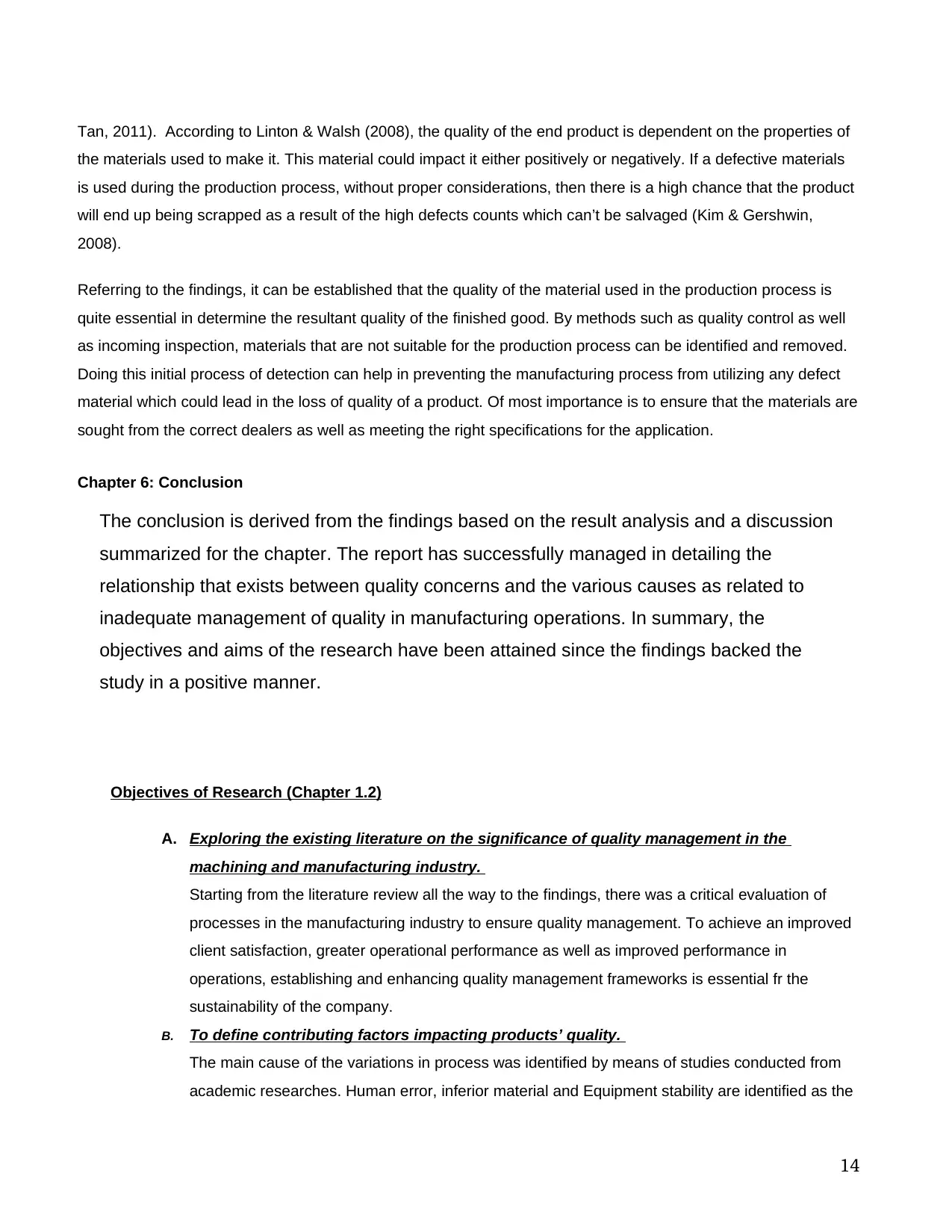
the materials used to make it. This material could impact it either positively or negatively. If a defective materials
is used during the production process, without proper considerations, then there is a high chance that the product
will end up being scrapped as a result of the high defects counts which can’t be salvaged (Kim & Gershwin,
2008).
Referring to the findings, it can be established that the quality of the material used in the production process is
quite essential in determine the resultant quality of the finished good. By methods such as quality control as well
as incoming inspection, materials that are not suitable for the production process can be identified and removed.
Doing this initial process of detection can help in preventing the manufacturing process from utilizing any defect
material which could lead in the loss of quality of a product. Of most importance is to ensure that the materials are
sought from the correct dealers as well as meeting the right specifications for the application.
Chapter 6: Conclusion
The conclusion is derived from the findings based on the result analysis and a discussion
summarized for the chapter. The report has successfully managed in detailing the
relationship that exists between quality concerns and the various causes as related to
inadequate management of quality in manufacturing operations. In summary, the
objectives and aims of the research have been attained since the findings backed the
study in a positive manner.
Objectives of Research (Chapter 1.2)
A. Exploring the existing literature on the significance of quality management in the
machining and manufacturing industry.
Starting from the literature review all the way to the findings, there was a critical evaluation of
processes in the manufacturing industry to ensure quality management. To achieve an improved
client satisfaction, greater operational performance as well as improved performance in
operations, establishing and enhancing quality management frameworks is essential fr the
sustainability of the company.
B. To define contributing factors impacting products’ quality.
The main cause of the variations in process was identified by means of studies conducted from
academic researches. Human error, inferior material and Equipment stability are identified as the
14
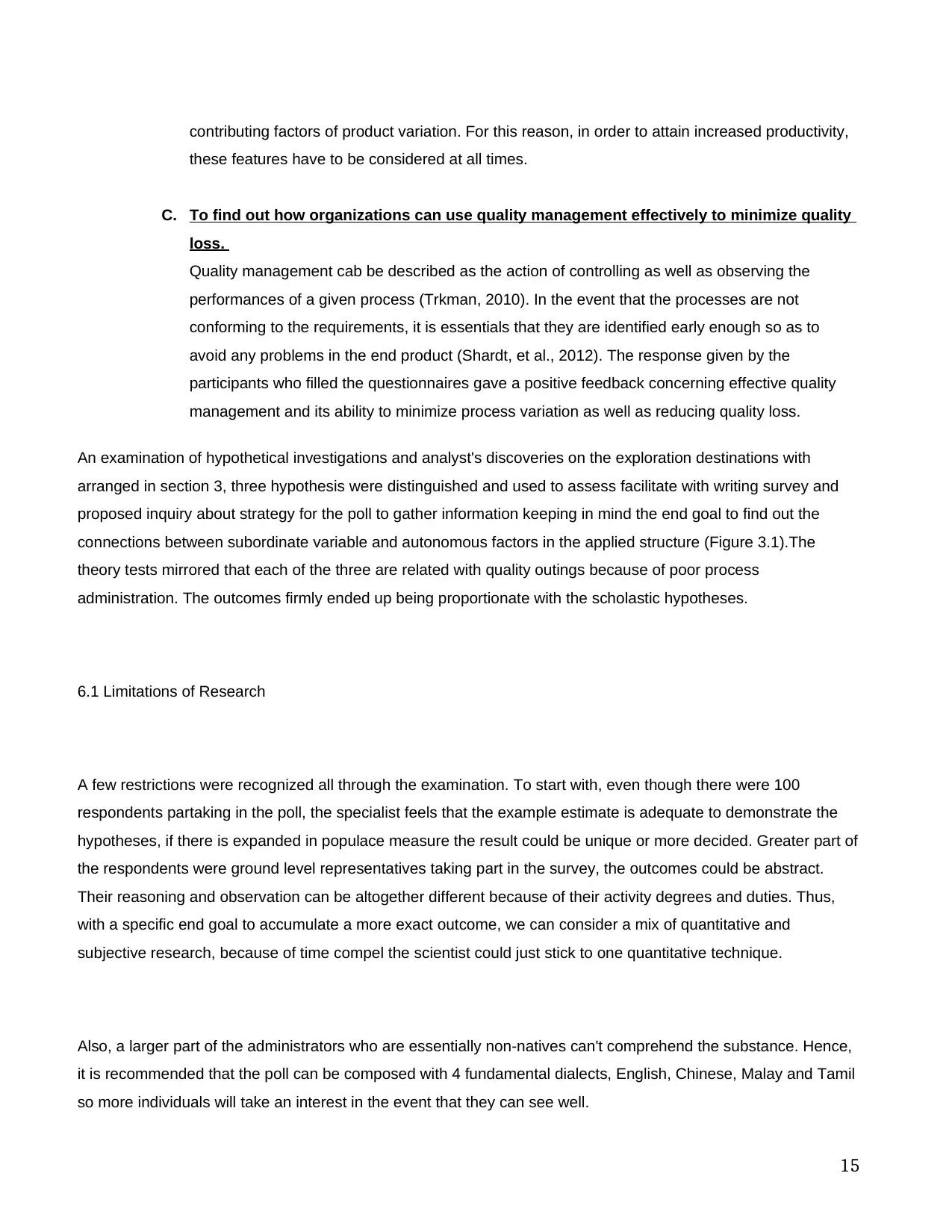
these features have to be considered at all times.
C. To find out how organizations can use quality management effectively to minimize quality
loss.
Quality management cab be described as the action of controlling as well as observing the
performances of a given process (Trkman, 2010). In the event that the processes are not
conforming to the requirements, it is essentials that they are identified early enough so as to
avoid any problems in the end product (Shardt, et al., 2012). The response given by the
participants who filled the questionnaires gave a positive feedback concerning effective quality
management and its ability to minimize process variation as well as reducing quality loss.
An examination of hypothetical investigations and analyst's discoveries on the exploration destinations with
arranged in section 3, three hypothesis were distinguished and used to assess facilitate with writing survey and
proposed inquiry about strategy for the poll to gather information keeping in mind the end goal to find out the
connections between subordinate variable and autonomous factors in the applied structure (Figure 3.1).The
theory tests mirrored that each of the three are related with quality outings because of poor process
administration. The outcomes firmly ended up being proportionate with the scholastic hypotheses.
6.1 Limitations of Research
A few restrictions were recognized all through the examination. To start with, even though there were 100
respondents partaking in the poll, the specialist feels that the example estimate is adequate to demonstrate the
hypotheses, if there is expanded in populace measure the result could be unique or more decided. Greater part of
the respondents were ground level representatives taking part in the survey, the outcomes could be abstract.
Their reasoning and observation can be altogether different because of their activity degrees and duties. Thus,
with a specific end goal to accumulate a more exact outcome, we can consider a mix of quantitative and
subjective research, because of time compel the scientist could just stick to one quantitative technique.
Also, a larger part of the administrators who are essentially non-natives can't comprehend the substance. Hence,
it is recommended that the poll can be composed with 4 fundamental dialects, English, Chinese, Malay and Tamil
so more individuals will take an interest in the event that they can see well.
15
⊘ This is a preview!⊘
Do you want full access?
Subscribe today to unlock all pages.

Trusted by 1+ million students worldwide
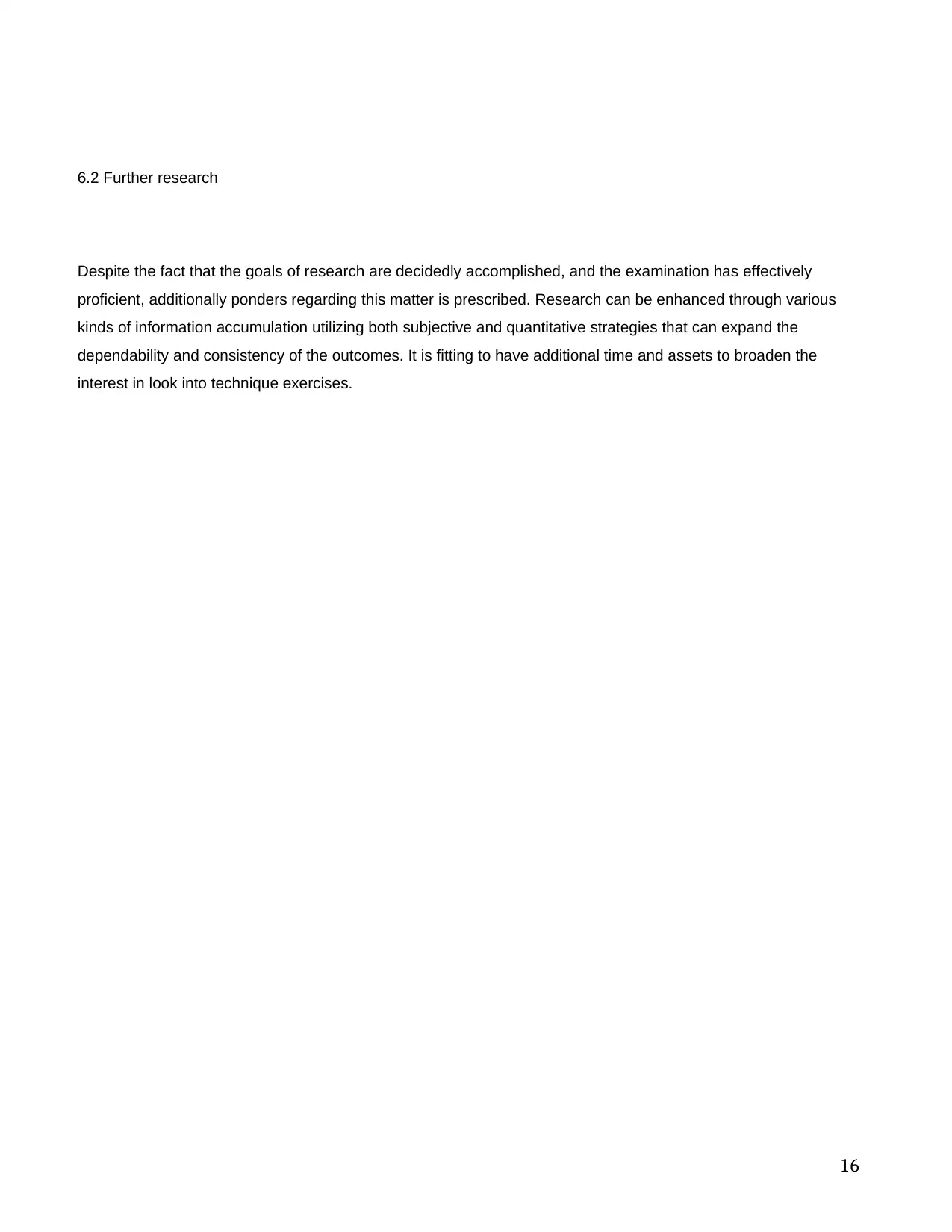
Despite the fact that the goals of research are decidedly accomplished, and the examination has effectively
proficient, additionally ponders regarding this matter is prescribed. Research can be enhanced through various
kinds of information accumulation utilizing both subjective and quantitative strategies that can expand the
dependability and consistency of the outcomes. It is fitting to have additional time and assets to broaden the
interest in look into technique exercises.
16
Paraphrase This Document
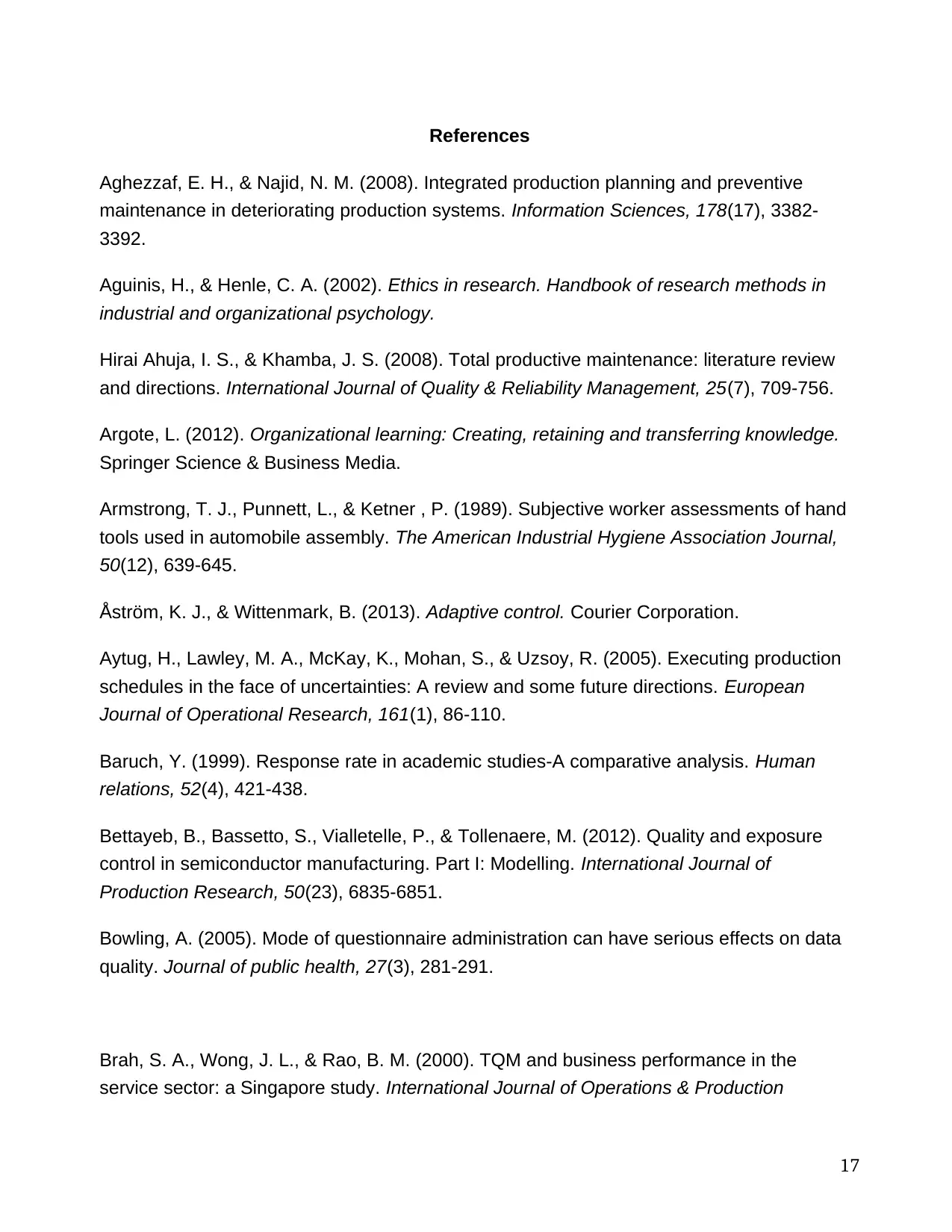
Aghezzaf, E. H., & Najid, N. M. (2008). Integrated production planning and preventive
maintenance in deteriorating production systems. Information Sciences, 178(17), 3382-
3392.
Aguinis, H., & Henle, C. A. (2002). Ethics in research. Handbook of research methods in
industrial and organizational psychology.
Hirai Ahuja, I. S., & Khamba, J. S. (2008). Total productive maintenance: literature review
and directions. International Journal of Quality & Reliability Management, 25(7), 709-756.
Argote, L. (2012). Organizational learning: Creating, retaining and transferring knowledge.
Springer Science & Business Media.
Armstrong, T. J., Punnett, L., & Ketner , P. (1989). Subjective worker assessments of hand
tools used in automobile assembly. The American Industrial Hygiene Association Journal,
50(12), 639-645.
Åström, K. J., & Wittenmark, B. (2013). Adaptive control. Courier Corporation.
Aytug, H., Lawley, M. A., McKay, K., Mohan, S., & Uzsoy, R. (2005). Executing production
schedules in the face of uncertainties: A review and some future directions. European
Journal of Operational Research, 161(1), 86-110.
Baruch, Y. (1999). Response rate in academic studies-A comparative analysis. Human
relations, 52(4), 421-438.
Bettayeb, B., Bassetto, S., Vialletelle, P., & Tollenaere, M. (2012). Quality and exposure
control in semiconductor manufacturing. Part I: Modelling. International Journal of
Production Research, 50(23), 6835-6851.
Bowling, A. (2005). Mode of questionnaire administration can have serious effects on data
quality. Journal of public health, 27(3), 281-291.
Brah, S. A., Wong, J. L., & Rao, B. M. (2000). TQM and business performance in the
service sector: a Singapore study. International Journal of Operations & Production
17
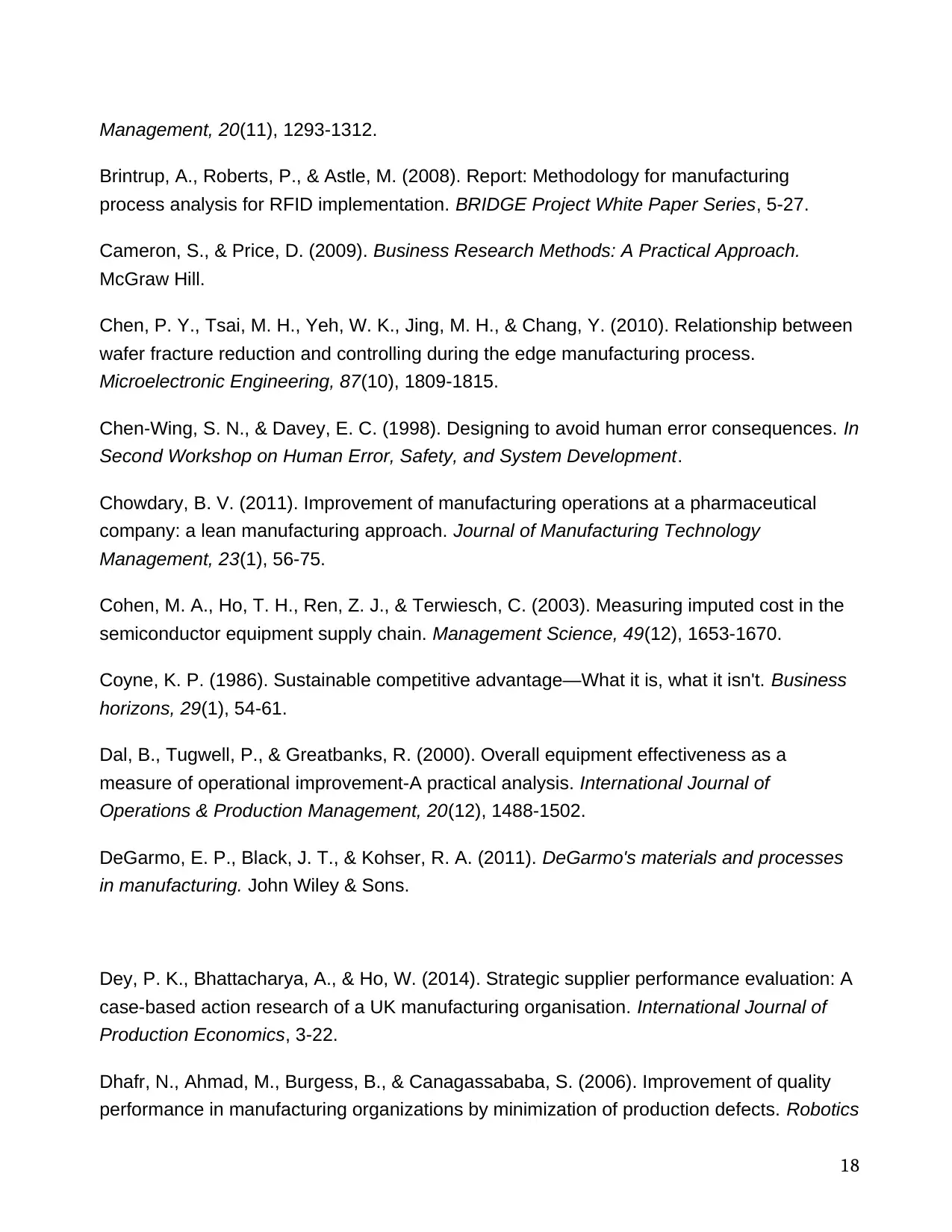
Brintrup, A., Roberts, P., & Astle, M. (2008). Report: Methodology for manufacturing
process analysis for RFID implementation. BRIDGE Project White Paper Series, 5-27.
Cameron, S., & Price, D. (2009). Business Research Methods: A Practical Approach.
McGraw Hill.
Chen, P. Y., Tsai, M. H., Yeh, W. K., Jing, M. H., & Chang, Y. (2010). Relationship between
wafer fracture reduction and controlling during the edge manufacturing process.
Microelectronic Engineering, 87(10), 1809-1815.
Chen-Wing, S. N., & Davey, E. C. (1998). Designing to avoid human error consequences. In
Second Workshop on Human Error, Safety, and System Development.
Chowdary, B. V. (2011). Improvement of manufacturing operations at a pharmaceutical
company: a lean manufacturing approach. Journal of Manufacturing Technology
Management, 23(1), 56-75.
Cohen, M. A., Ho, T. H., Ren, Z. J., & Terwiesch, C. (2003). Measuring imputed cost in the
semiconductor equipment supply chain. Management Science, 49(12), 1653-1670.
Coyne, K. P. (1986). Sustainable competitive advantage—What it is, what it isn't. Business
horizons, 29(1), 54-61.
Dal, B., Tugwell, P., & Greatbanks, R. (2000). Overall equipment effectiveness as a
measure of operational improvement-A practical analysis. International Journal of
Operations & Production Management, 20(12), 1488-1502.
DeGarmo, E. P., Black, J. T., & Kohser, R. A. (2011). DeGarmo's materials and processes
in manufacturing. John Wiley & Sons.
Dey, P. K., Bhattacharya, A., & Ho, W. (2014). Strategic supplier performance evaluation: A
case-based action research of a UK manufacturing organisation. International Journal of
Production Economics, 3-22.
Dhafr, N., Ahmad, M., Burgess, B., & Canagassababa, S. (2006). Improvement of quality
performance in manufacturing organizations by minimization of production defects. Robotics
18
⊘ This is a preview!⊘
Do you want full access?
Subscribe today to unlock all pages.

Trusted by 1+ million students worldwide
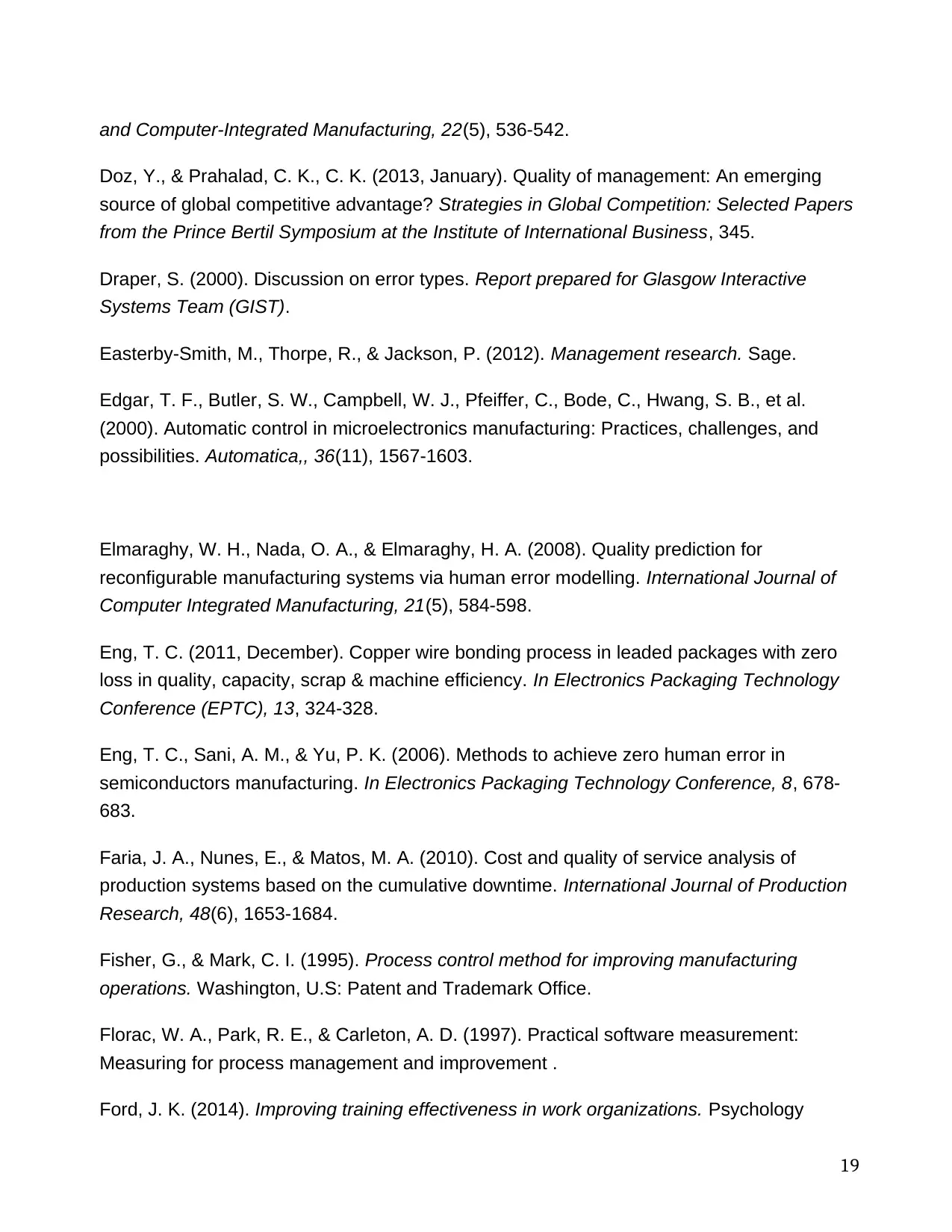
Doz, Y., & Prahalad, C. K., C. K. (2013, January). Quality of management: An emerging
source of global competitive advantage? Strategies in Global Competition: Selected Papers
from the Prince Bertil Symposium at the Institute of International Business, 345.
Draper, S. (2000). Discussion on error types. Report prepared for Glasgow Interactive
Systems Team (GIST).
Easterby-Smith, M., Thorpe, R., & Jackson, P. (2012). Management research. Sage.
Edgar, T. F., Butler, S. W., Campbell, W. J., Pfeiffer, C., Bode, C., Hwang, S. B., et al.
(2000). Automatic control in microelectronics manufacturing: Practices, challenges, and
possibilities. Automatica,, 36(11), 1567-1603.
Elmaraghy, W. H., Nada, O. A., & Elmaraghy, H. A. (2008). Quality prediction for
reconfigurable manufacturing systems via human error modelling. International Journal of
Computer Integrated Manufacturing, 21(5), 584-598.
Eng, T. C. (2011, December). Copper wire bonding process in leaded packages with zero
loss in quality, capacity, scrap & machine efficiency. In Electronics Packaging Technology
Conference (EPTC), 13, 324-328.
Eng, T. C., Sani, A. M., & Yu, P. K. (2006). Methods to achieve zero human error in
semiconductors manufacturing. In Electronics Packaging Technology Conference, 8, 678-
683.
Faria, J. A., Nunes, E., & Matos, M. A. (2010). Cost and quality of service analysis of
production systems based on the cumulative downtime. International Journal of Production
Research, 48(6), 1653-1684.
Fisher, G., & Mark, C. I. (1995). Process control method for improving manufacturing
operations. Washington, U.S: Patent and Trademark Office.
Florac, W. A., Park, R. E., & Carleton, A. D. (1997). Practical software measurement:
Measuring for process management and improvement .
Ford, J. K. (2014). Improving training effectiveness in work organizations. Psychology
19
Paraphrase This Document
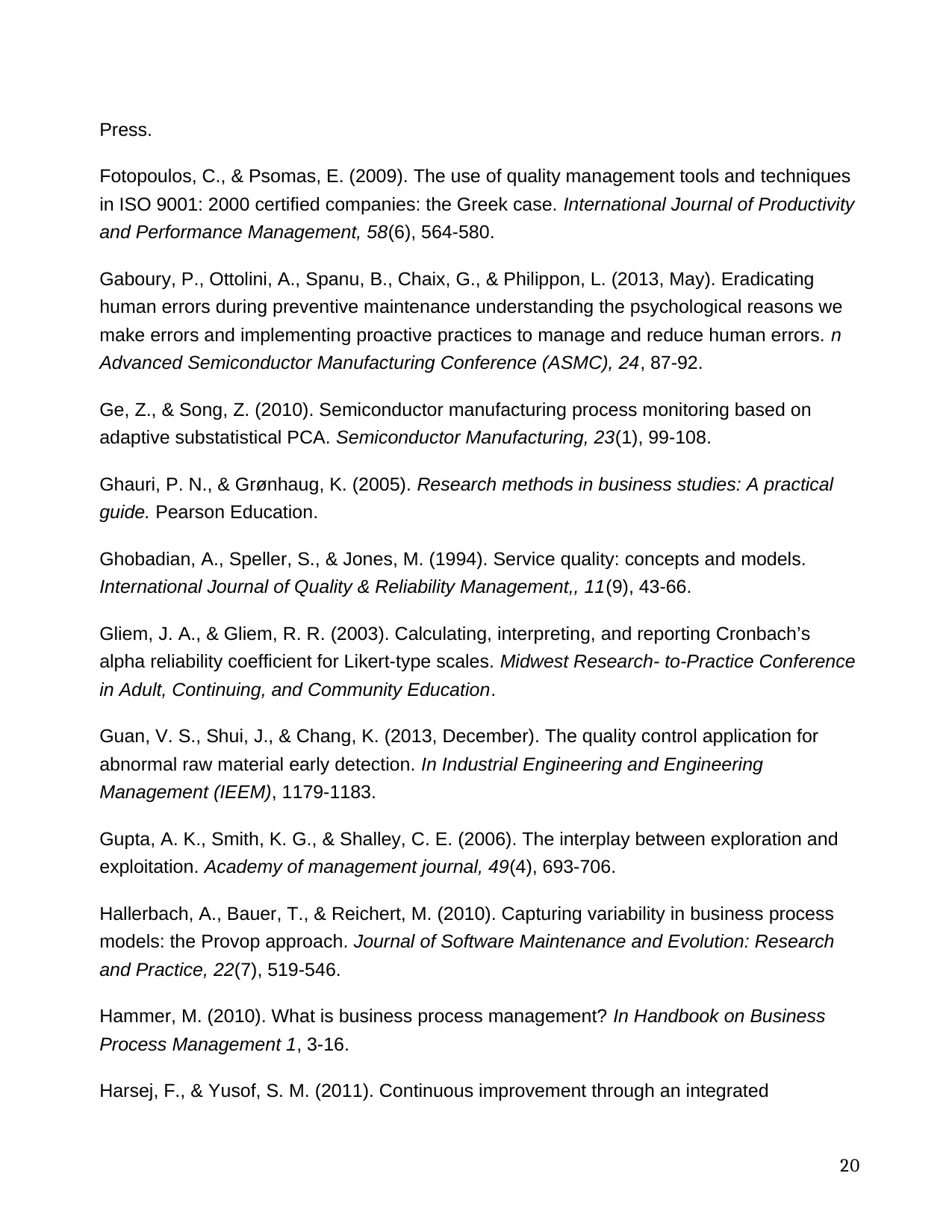
Fotopoulos, C., & Psomas, E. (2009). The use of quality management tools and techniques
in ISO 9001: 2000 certified companies: the Greek case. International Journal of Productivity
and Performance Management, 58(6), 564-580.
Gaboury, P., Ottolini, A., Spanu, B., Chaix, G., & Philippon, L. (2013, May). Eradicating
human errors during preventive maintenance understanding the psychological reasons we
make errors and implementing proactive practices to manage and reduce human errors. n
Advanced Semiconductor Manufacturing Conference (ASMC), 24, 87-92.
Ge, Z., & Song, Z. (2010). Semiconductor manufacturing process monitoring based on
adaptive substatistical PCA. Semiconductor Manufacturing, 23(1), 99-108.
Ghauri, P. N., & Grønhaug, K. (2005). Research methods in business studies: A practical
guide. Pearson Education.
Ghobadian, A., Speller, S., & Jones, M. (1994). Service quality: concepts and models.
International Journal of Quality & Reliability Management,, 11(9), 43-66.
Gliem, J. A., & Gliem, R. R. (2003). Calculating, interpreting, and reporting Cronbach’s
alpha reliability coefficient for Likert-type scales. Midwest Research- to-Practice Conference
in Adult, Continuing, and Community Education.
Guan, V. S., Shui, J., & Chang, K. (2013, December). The quality control application for
abnormal raw material early detection. In Industrial Engineering and Engineering
Management (IEEM), 1179-1183.
Gupta, A. K., Smith, K. G., & Shalley, C. E. (2006). The interplay between exploration and
exploitation. Academy of management journal, 49(4), 693-706.
Hallerbach, A., Bauer, T., & Reichert, M. (2010). Capturing variability in business process
models: the Provop approach. Journal of Software Maintenance and Evolution: Research
and Practice, 22(7), 519-546.
Hammer, M. (2010). What is business process management? In Handbook on Business
Process Management 1, 3-16.
Harsej, F., & Yusof, S. M. (2011). Continuous improvement through an integrated
20

He, Q. P., & Wang, J. (2011). Statistics pattern analysis: A new process monitoring
framework and its application to semiconductor batch processes. AIChE journal, 57(1), 107-
121.
Heng, A., Zhang, S., Tan, A. C., & Mathew, J. (2009). Rotating machinery prognostics:
State of the art, challenges and opportunities. Mechanical Systems and Signal Processing,
23(3), 724-739.
Hollnagel, E. (2004). Barriers and accident prevention. Aldershot: Ashgate.
Hox, J. J., & Boeije, H. R. (2005). Data collection, primary vs. secondary. Encyclopedia of
social measurement, 1, 593-599.
Huang, C. C., Hsu, S. H., Lin, G. L., Hu, S. J., Shen, H. Y., Chu, H. L., et al. (1999).
Operator Error Prevention system of semiconductor foundry manufacturing. (1. I.
Symposium, Ed.) In Semiconductor Manufacturing Conference Proceedings, 285-287.
Iannone, R., & Nenni, M. E. (2013). Managing OEE to Optimize Factory Performance.
INTECH Open Access Publisher.
Introna, V., Giuiusa, A., & Cesarotti, V. (2013). Using Overall Equipment Effectiveness for
Manufacturing System Design . Operations Management, 51-80.
Ismail, A., Ghani, J. A., Ab Rahman, M. N., Deros, B. M., & Haron, C. C. (2014). pplication
of Lean Six Sigma Tools for Cycle Time Reduction in Manufacturing: Case Study in
Biopharmaceutical Industry. Arabian Journal for Science and Engineering, 39(2), 1449-
1463.
Jeston, J., & Nelis, J. (2014). Business process management. Routledge.
Kang, P., Kim, D., Lee, H. J., Doh, S., & Cho, S. (2011). Virtual metrology for run-to-run
control in semiconductor manufacturing . Expert Systems with Applications, 38(3), 2508-
2522.
Kim, J., & Gershwin, S. B. (2008). Analysis of long flow lines with quality and operational
failures. IE Transactions, 40(3), 284-296.
21
⊘ This is a preview!⊘
Do you want full access?
Subscribe today to unlock all pages.

Trusted by 1+ million students worldwide
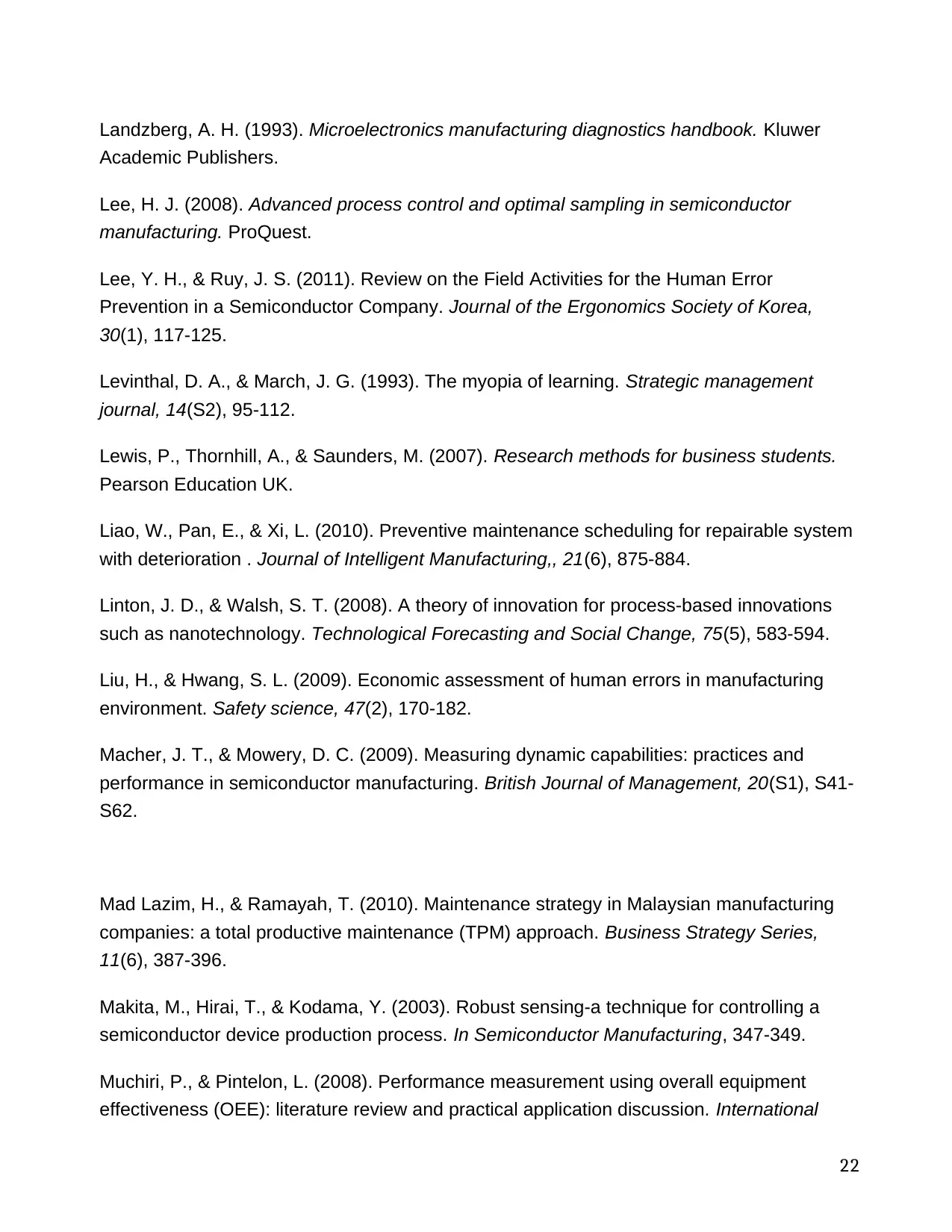
Academic Publishers.
Lee, H. J. (2008). Advanced process control and optimal sampling in semiconductor
manufacturing. ProQuest.
Lee, Y. H., & Ruy, J. S. (2011). Review on the Field Activities for the Human Error
Prevention in a Semiconductor Company. Journal of the Ergonomics Society of Korea,
30(1), 117-125.
Levinthal, D. A., & March, J. G. (1993). The myopia of learning. Strategic management
journal, 14(S2), 95-112.
Lewis, P., Thornhill, A., & Saunders, M. (2007). Research methods for business students.
Pearson Education UK.
Liao, W., Pan, E., & Xi, L. (2010). Preventive maintenance scheduling for repairable system
with deterioration . Journal of Intelligent Manufacturing,, 21(6), 875-884.
Linton, J. D., & Walsh, S. T. (2008). A theory of innovation for process-based innovations
such as nanotechnology. Technological Forecasting and Social Change, 75(5), 583-594.
Liu, H., & Hwang, S. L. (2009). Economic assessment of human errors in manufacturing
environment. Safety science, 47(2), 170-182.
Macher, J. T., & Mowery, D. C. (2009). Measuring dynamic capabilities: practices and
performance in semiconductor manufacturing. British Journal of Management, 20(S1), S41-
S62.
Mad Lazim, H., & Ramayah, T. (2010). Maintenance strategy in Malaysian manufacturing
companies: a total productive maintenance (TPM) approach. Business Strategy Series,
11(6), 387-396.
Makita, M., Hirai, T., & Kodama, Y. (2003). Robust sensing-a technique for controlling a
semiconductor device production process. In Semiconductor Manufacturing, 347-349.
Muchiri, P., & Pintelon, L. (2008). Performance measurement using overall equipment
effectiveness (OEE): literature review and practical application discussion. International
22
Paraphrase This Document
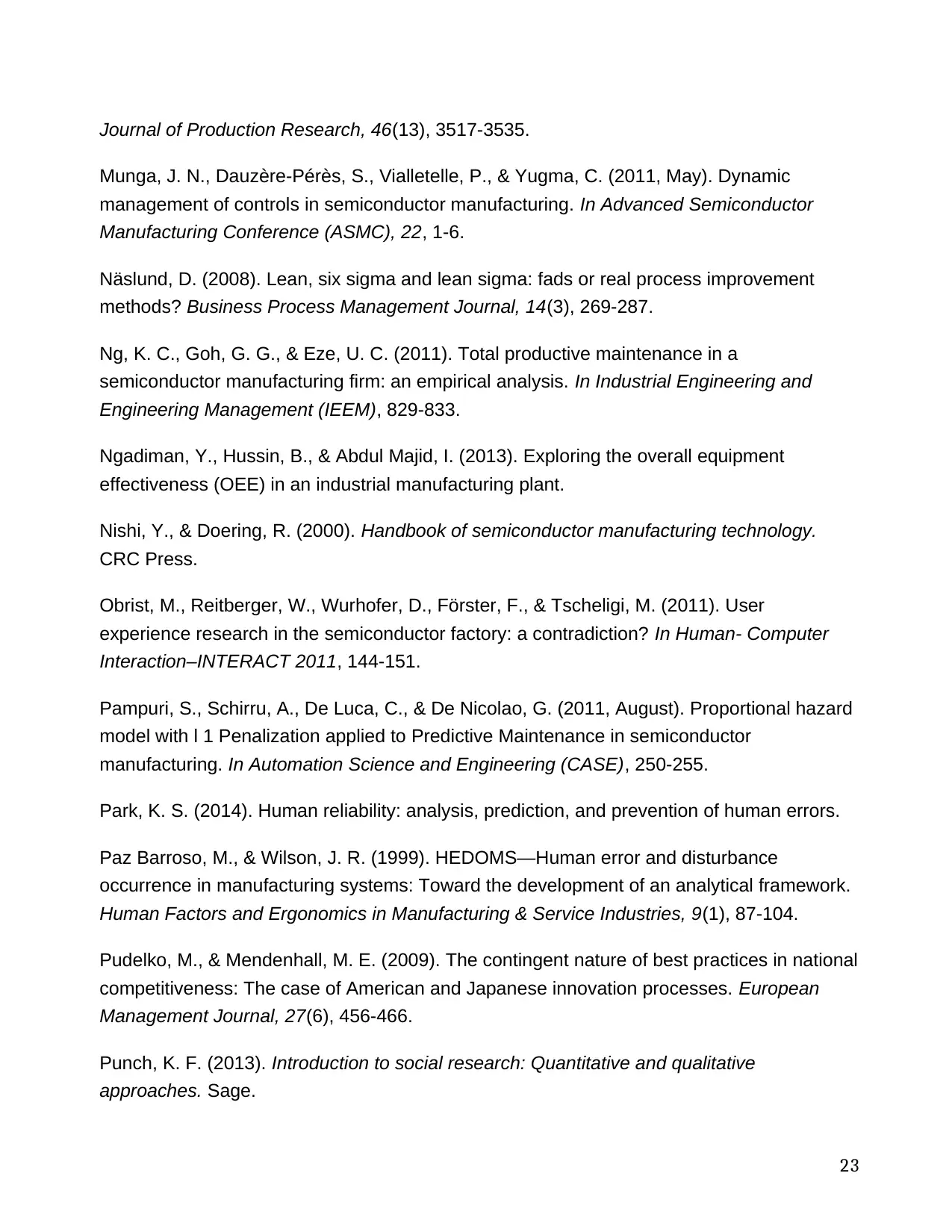
Munga, J. N., Dauzère-Pérès, S., Vialletelle, P., & Yugma, C. (2011, May). Dynamic
management of controls in semiconductor manufacturing. In Advanced Semiconductor
Manufacturing Conference (ASMC), 22, 1-6.
Näslund, D. (2008). Lean, six sigma and lean sigma: fads or real process improvement
methods? Business Process Management Journal, 14(3), 269-287.
Ng, K. C., Goh, G. G., & Eze, U. C. (2011). Total productive maintenance in a
semiconductor manufacturing firm: an empirical analysis. In Industrial Engineering and
Engineering Management (IEEM), 829-833.
Ngadiman, Y., Hussin, B., & Abdul Majid, I. (2013). Exploring the overall equipment
effectiveness (OEE) in an industrial manufacturing plant.
Nishi, Y., & Doering, R. (2000). Handbook of semiconductor manufacturing technology.
CRC Press.
Obrist, M., Reitberger, W., Wurhofer, D., Förster, F., & Tscheligi, M. (2011). User
experience research in the semiconductor factory: a contradiction? In Human- Computer
Interaction–INTERACT 2011, 144-151.
Pampuri, S., Schirru, A., De Luca, C., & De Nicolao, G. (2011, August). Proportional hazard
model with l 1 Penalization applied to Predictive Maintenance in semiconductor
manufacturing. In Automation Science and Engineering (CASE), 250-255.
Park, K. S. (2014). Human reliability: analysis, prediction, and prevention of human errors.
Paz Barroso, M., & Wilson, J. R. (1999). HEDOMS—Human error and disturbance
occurrence in manufacturing systems: Toward the development of an analytical framework.
Human Factors and Ergonomics in Manufacturing & Service Industries, 9(1), 87-104.
Pudelko, M., & Mendenhall, M. E. (2009). The contingent nature of best practices in national
competitiveness: The case of American and Japanese innovation processes. European
Management Journal, 27(6), 456-466.
Punch, K. F. (2013). Introduction to social research: Quantitative and qualitative
approaches. Sage.
23
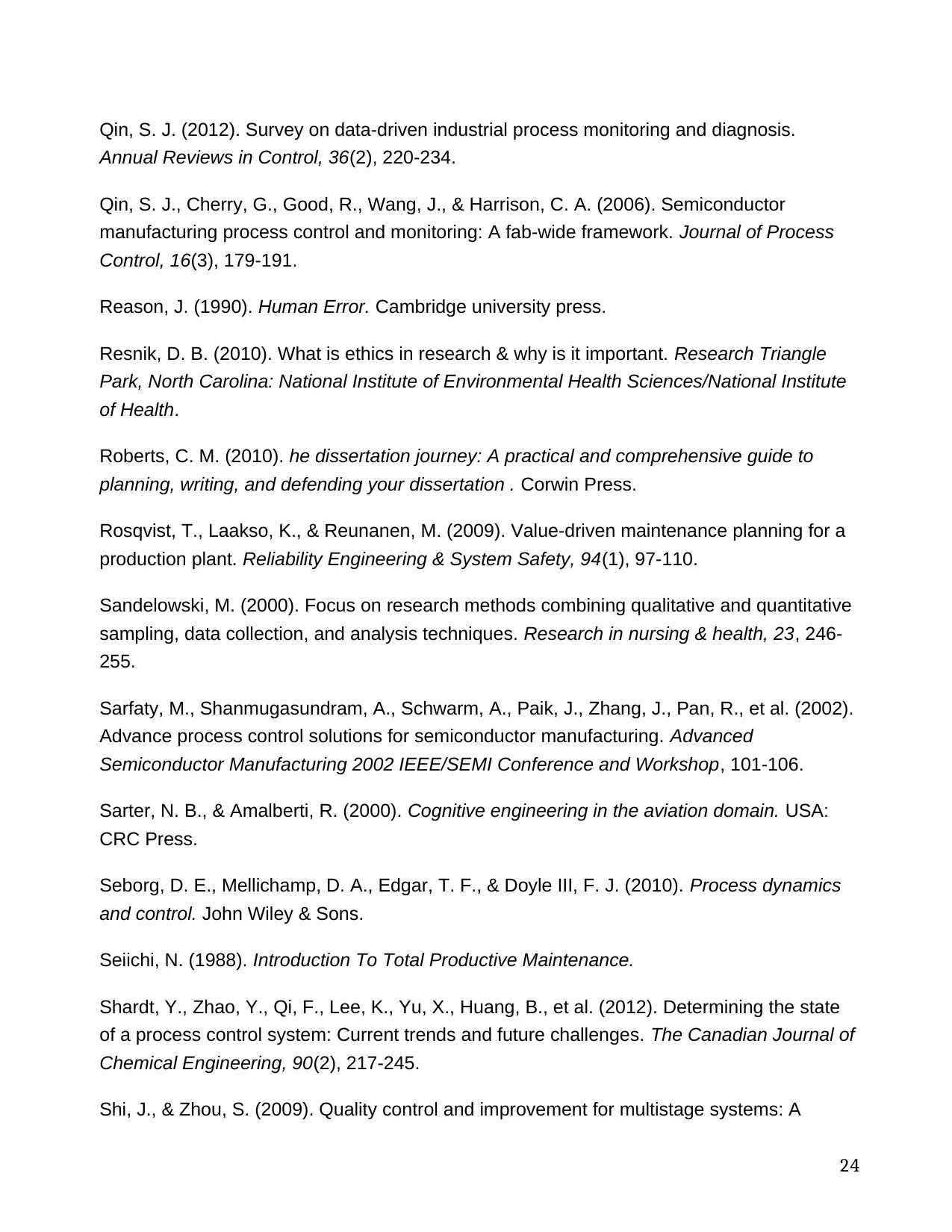
Annual Reviews in Control, 36(2), 220-234.
Qin, S. J., Cherry, G., Good, R., Wang, J., & Harrison, C. A. (2006). Semiconductor
manufacturing process control and monitoring: A fab-wide framework. Journal of Process
Control, 16(3), 179-191.
Reason, J. (1990). Human Error. Cambridge university press.
Resnik, D. B. (2010). What is ethics in research & why is it important. Research Triangle
Park, North Carolina: National Institute of Environmental Health Sciences/National Institute
of Health.
Roberts, C. M. (2010). he dissertation journey: A practical and comprehensive guide to
planning, writing, and defending your dissertation . Corwin Press.
Rosqvist, T., Laakso, K., & Reunanen, M. (2009). Value-driven maintenance planning for a
production plant. Reliability Engineering & System Safety, 94(1), 97-110.
Sandelowski, M. (2000). Focus on research methods combining qualitative and quantitative
sampling, data collection, and analysis techniques. Research in nursing & health, 23, 246-
255.
Sarfaty, M., Shanmugasundram, A., Schwarm, A., Paik, J., Zhang, J., Pan, R., et al. (2002).
Advance process control solutions for semiconductor manufacturing. Advanced
Semiconductor Manufacturing 2002 IEEE/SEMI Conference and Workshop, 101-106.
Sarter, N. B., & Amalberti, R. (2000). Cognitive engineering in the aviation domain. USA:
CRC Press.
Seborg, D. E., Mellichamp, D. A., Edgar, T. F., & Doyle III, F. J. (2010). Process dynamics
and control. John Wiley & Sons.
Seiichi, N. (1988). Introduction To Total Productive Maintenance.
Shardt, Y., Zhao, Y., Qi, F., Lee, K., Yu, X., Huang, B., et al. (2012). Determining the state
of a process control system: Current trends and future challenges. The Canadian Journal of
Chemical Engineering, 90(2), 217-245.
Shi, J., & Zhou, S. (2009). Quality control and improvement for multistage systems: A
24
⊘ This is a preview!⊘
Do you want full access?
Subscribe today to unlock all pages.

Trusted by 1+ million students worldwide
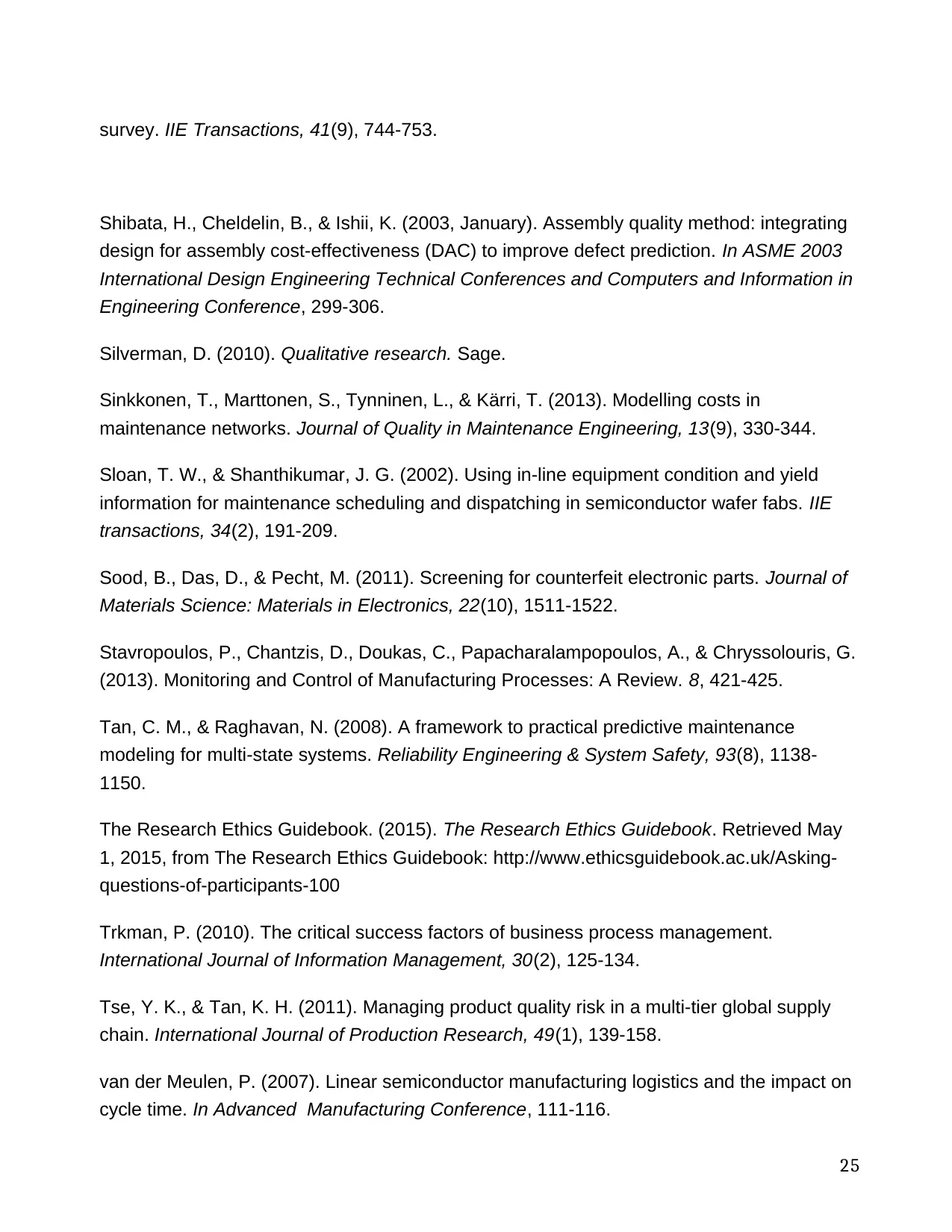
Shibata, H., Cheldelin, B., & Ishii, K. (2003, January). Assembly quality method: integrating
design for assembly cost-effectiveness (DAC) to improve defect prediction. In ASME 2003
International Design Engineering Technical Conferences and Computers and Information in
Engineering Conference, 299-306.
Silverman, D. (2010). Qualitative research. Sage.
Sinkkonen, T., Marttonen, S., Tynninen, L., & Kärri, T. (2013). Modelling costs in
maintenance networks. Journal of Quality in Maintenance Engineering, 13(9), 330-344.
Sloan, T. W., & Shanthikumar, J. G. (2002). Using in-line equipment condition and yield
information for maintenance scheduling and dispatching in semiconductor wafer fabs. IIE
transactions, 34(2), 191-209.
Sood, B., Das, D., & Pecht, M. (2011). Screening for counterfeit electronic parts. Journal of
Materials Science: Materials in Electronics, 22(10), 1511-1522.
Stavropoulos, P., Chantzis, D., Doukas, C., Papacharalampopoulos, A., & Chryssolouris, G.
(2013). Monitoring and Control of Manufacturing Processes: A Review. 8, 421-425.
Tan, C. M., & Raghavan, N. (2008). A framework to practical predictive maintenance
modeling for multi-state systems. Reliability Engineering & System Safety, 93(8), 1138-
1150.
The Research Ethics Guidebook. (2015). The Research Ethics Guidebook. Retrieved May
1, 2015, from The Research Ethics Guidebook: http://www.ethicsguidebook.ac.uk/Asking-
questions-of-participants-100
Trkman, P. (2010). The critical success factors of business process management.
International Journal of Information Management, 30(2), 125-134.
Tse, Y. K., & Tan, K. H. (2011). Managing product quality risk in a multi-tier global supply
chain. International Journal of Production Research, 49(1), 139-158.
van der Meulen, P. (2007). Linear semiconductor manufacturing logistics and the impact on
cycle time. In Advanced Manufacturing Conference, 111-116.
25
Paraphrase This Document
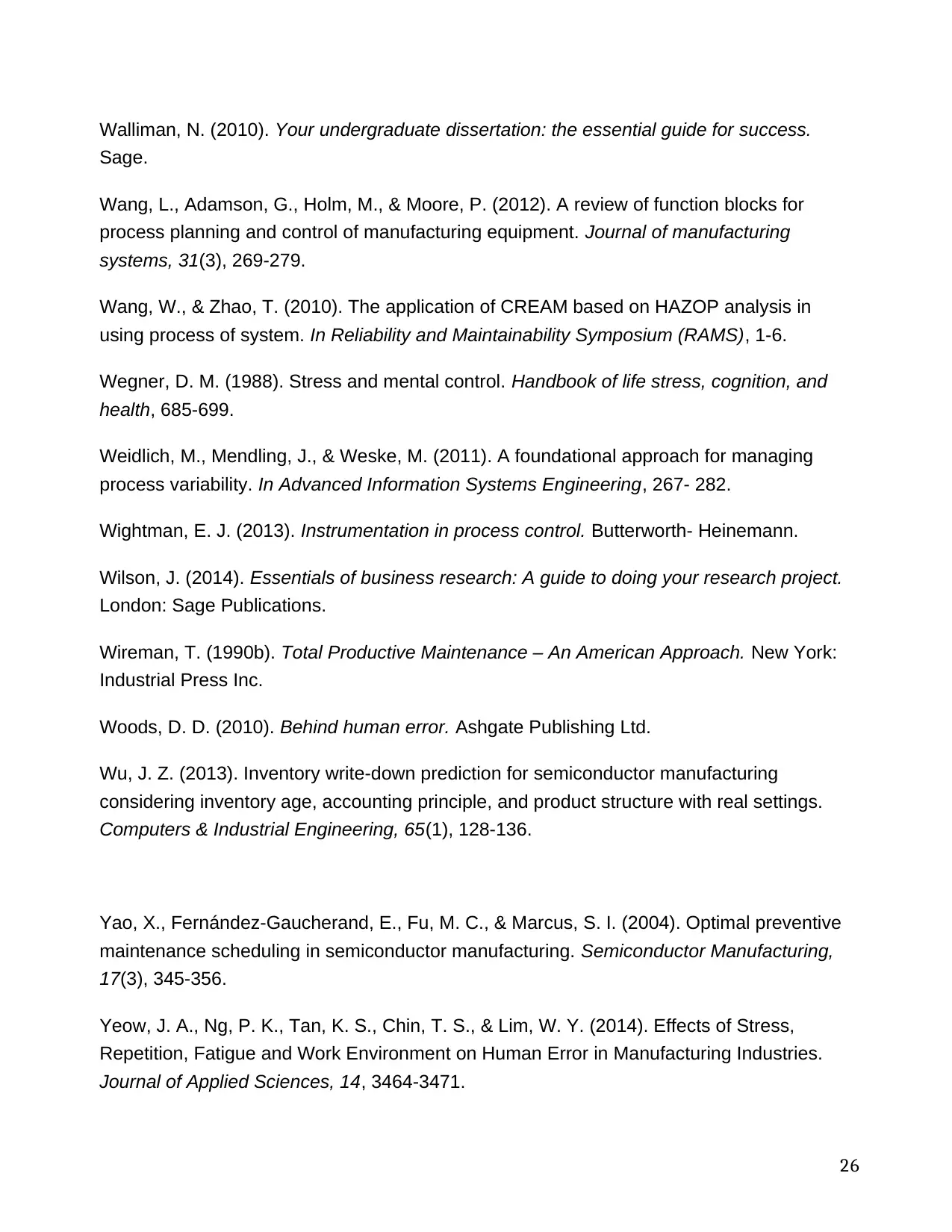
Sage.
Wang, L., Adamson, G., Holm, M., & Moore, P. (2012). A review of function blocks for
process planning and control of manufacturing equipment. Journal of manufacturing
systems, 31(3), 269-279.
Wang, W., & Zhao, T. (2010). The application of CREAM based on HAZOP analysis in
using process of system. In Reliability and Maintainability Symposium (RAMS), 1-6.
Wegner, D. M. (1988). Stress and mental control. Handbook of life stress, cognition, and
health, 685-699.
Weidlich, M., Mendling, J., & Weske, M. (2011). A foundational approach for managing
process variability. In Advanced Information Systems Engineering, 267- 282.
Wightman, E. J. (2013). Instrumentation in process control. Butterworth- Heinemann.
Wilson, J. (2014). Essentials of business research: A guide to doing your research project.
London: Sage Publications.
Wireman, T. (1990b). Total Productive Maintenance – An American Approach. New York:
Industrial Press Inc.
Woods, D. D. (2010). Behind human error. Ashgate Publishing Ltd.
Wu, J. Z. (2013). Inventory write-down prediction for semiconductor manufacturing
considering inventory age, accounting principle, and product structure with real settings.
Computers & Industrial Engineering, 65(1), 128-136.
Yao, X., Fernández-Gaucherand, E., Fu, M. C., & Marcus, S. I. (2004). Optimal preventive
maintenance scheduling in semiconductor manufacturing. Semiconductor Manufacturing,
17(3), 345-356.
Yeow, J. A., Ng, P. K., Tan, K. S., Chin, T. S., & Lim, W. Y. (2014). Effects of Stress,
Repetition, Fatigue and Work Environment on Human Error in Manufacturing Industries.
Journal of Applied Sciences, 14, 3464-3471.
26

allocation: A case in the semiconductor industry. Computers & Industrial Engineering, 55(3),
634-646.
Yusof, S. R. M., & Aspinwall, E. , S. M. (2000). Total quality management implementation
frameworks: comparison and review. 11(3), 281-294.
Zhang, Q., & Hu , K. (2012, August). The study of impacts on long-term storage reliability
caused by IC packages and preventing measurements. In Electronic Packaging Technology
and High Density Packaging (ICEPT-HDP), 13, 1290-1293.
Babbie, E. R. (2004). The practice of social research. Belmont, CA: Thomson/Wadsworth.
Cooper, D., & Schindler, P. (2008). Business research methods. Boston:
McGraw-Hill/Irwin.
Saunders, M., Lewis, P. and Thornhill, A. (2009) Research methods for business students.
5th edn. Italy: Pearson Education
Bryman, A. and Bell, E. (2007) Business research methods. 3rd edn. New York: Oxford
University Press.
Sandelowski, M. (2004) Using Qualitative Research. Qualitative Health Research, 14, 1366-
1386. https://doi.org/10.1177/1049732304269672
Blaikie, N. (2003). Analyzing quantitative data: From description to explanation. Sage.
Collis, J., & Hussey, R. (2013). Business research: A practical guide for undergraduate and
postgraduate students. Palgrave macmillan
Pallant, J. (2007). SPSS survival manual: A step by step guide to data analysis using SPSS
for Windows.
27
⊘ This is a preview!⊘
Do you want full access?
Subscribe today to unlock all pages.

Trusted by 1+ million students worldwide
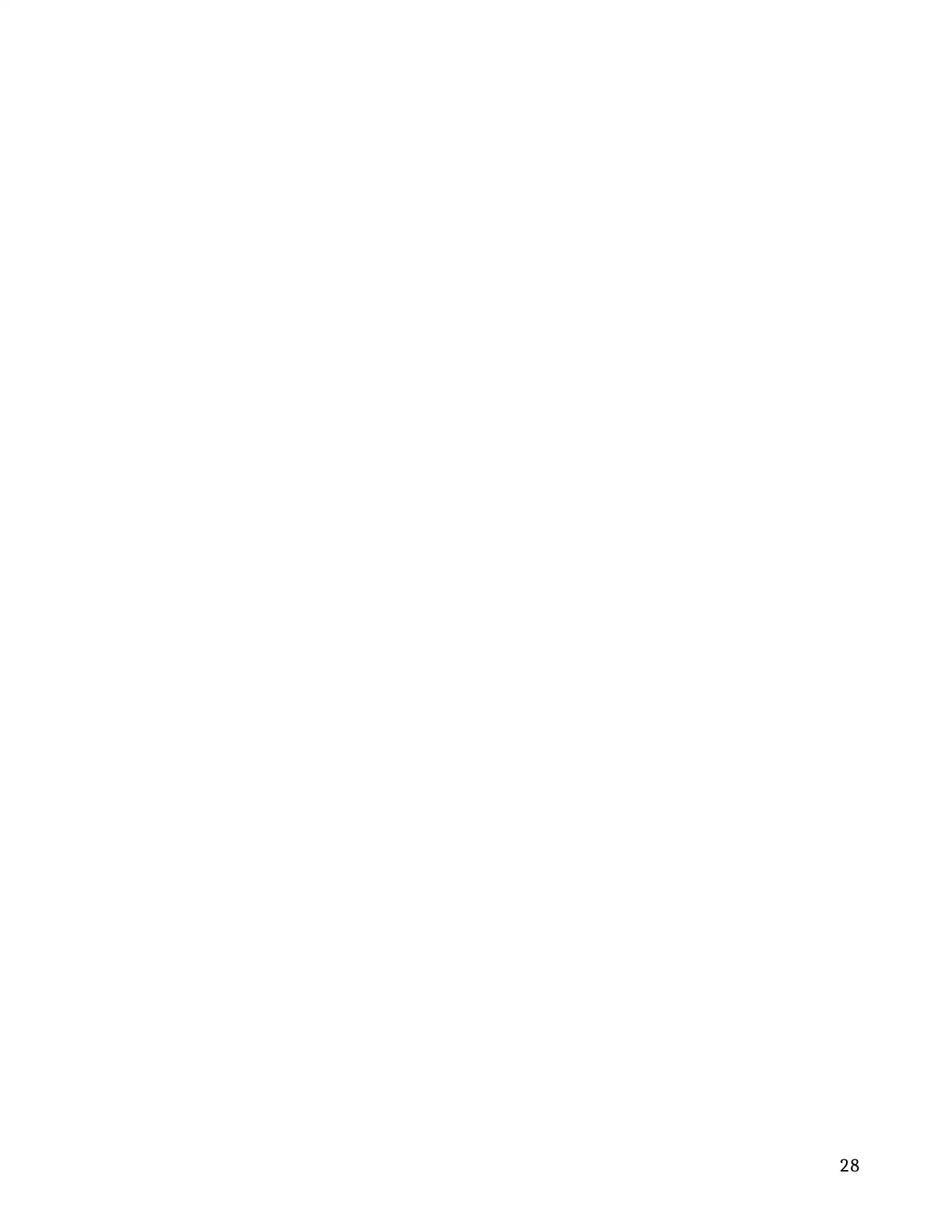
Related Documents

Your All-in-One AI-Powered Toolkit for Academic Success.
+13062052269
info@desklib.com
Available 24*7 on WhatsApp / Email
© 2024 | Zucol Services PVT LTD | All rights reserved.