Quality Planning & Analysis: Refrigerator Design Report - Autumn 2018
VerifiedAdded on 2023/06/11
|35
|7684
|299
Report
AI Summary
This report provides a comprehensive quality planning and analysis of refrigerator design, focusing on customer satisfaction, supplier selection, and statistical process control. It includes stakeholder analysis, customer needs analysis using methods like surveys, focus groups, and ethnographic studies, and Kano analysis to prioritize customer needs. The report translates customer needs into design requirements using QFD and assesses design risks using FMEA. Supplier selection criteria and evaluation methods are detailed, along with the application of statistical process control (SPC) charts for monitoring manufacturing processes. Finally, the report addresses problem-solving using brainstorming, why-why diagrams, check sheets, and Pareto diagrams to identify and resolve issues like power supply failures. The analysis aims to improve refrigerator quality, reliability, and customer satisfaction.
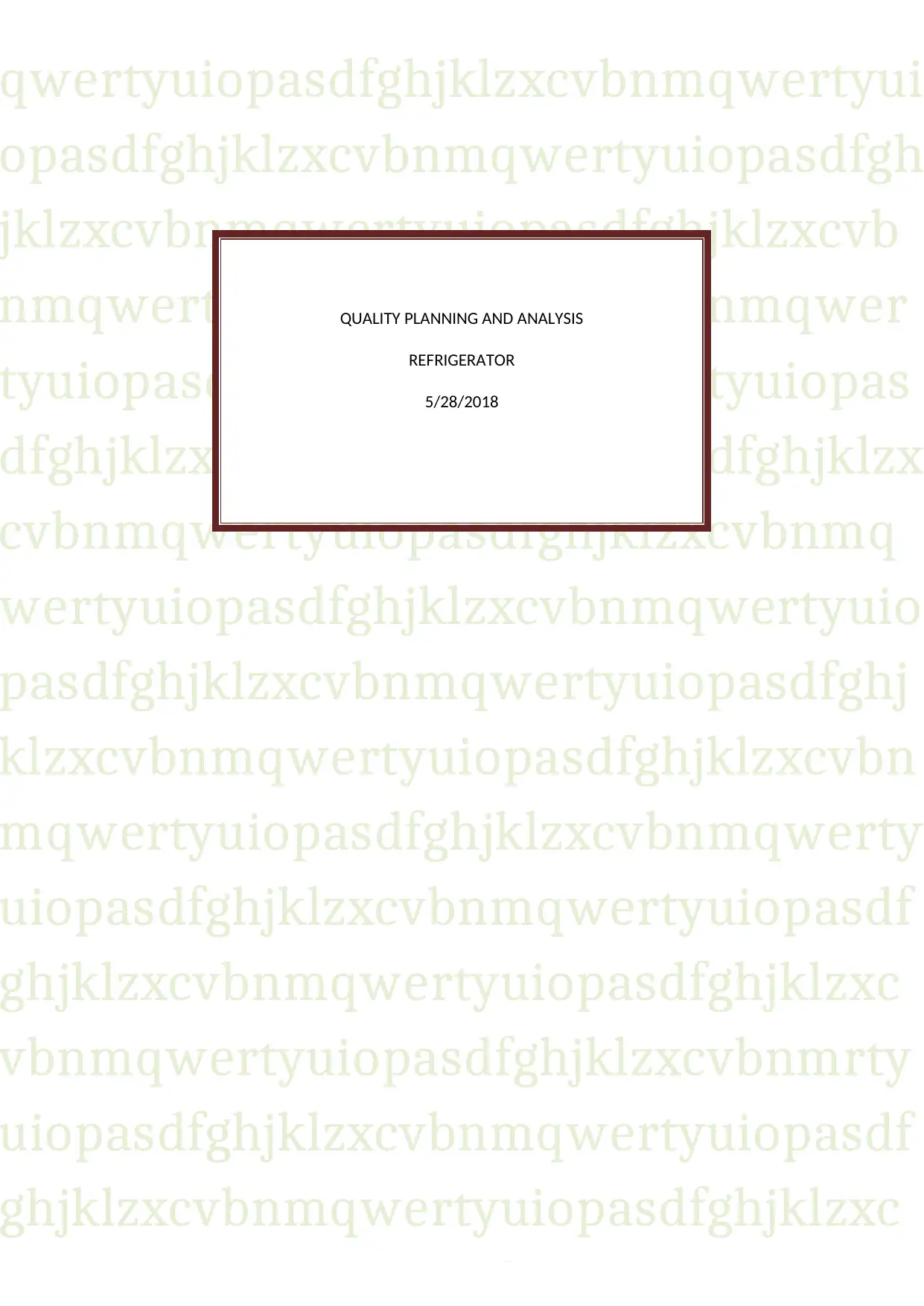
qwertyuiopasdfghjklzxcvbnmqwertyui
opasdfghjklzxcvbnmqwertyuiopasdfgh
jklzxcvbnmqwertyuiopasdfghjklzxcvb
nmqwertyuiopasdfghjklzxcvbnmqwer
tyuiopasdfghjklzxcvbnmqwertyuiopas
dfghjklzxcvbnmqwertyuiopasdfghjklzx
cvbnmqwertyuiopasdfghjklzxcvbnmq
wertyuiopasdfghjklzxcvbnmqwertyuio
pasdfghjklzxcvbnmqwertyuiopasdfghj
klzxcvbnmqwertyuiopasdfghjklzxcvbn
mqwertyuiopasdfghjklzxcvbnmqwerty
uiopasdfghjklzxcvbnmqwertyuiopasdf
ghjklzxcvbnmqwertyuiopasdfghjklzxc
vbnmqwertyuiopasdfghjklzxcvbnmrty
uiopasdfghjklzxcvbnmqwertyuiopasdf
ghjklzxcvbnmqwertyuiopasdfghjklzxc
vbnmqwertyuiopasdfghjklzxcvbnmqw
QUALITY PLANNING AND ANALYSIS
REFRIGERATOR
5/28/2018
opasdfghjklzxcvbnmqwertyuiopasdfgh
jklzxcvbnmqwertyuiopasdfghjklzxcvb
nmqwertyuiopasdfghjklzxcvbnmqwer
tyuiopasdfghjklzxcvbnmqwertyuiopas
dfghjklzxcvbnmqwertyuiopasdfghjklzx
cvbnmqwertyuiopasdfghjklzxcvbnmq
wertyuiopasdfghjklzxcvbnmqwertyuio
pasdfghjklzxcvbnmqwertyuiopasdfghj
klzxcvbnmqwertyuiopasdfghjklzxcvbn
mqwertyuiopasdfghjklzxcvbnmqwerty
uiopasdfghjklzxcvbnmqwertyuiopasdf
ghjklzxcvbnmqwertyuiopasdfghjklzxc
vbnmqwertyuiopasdfghjklzxcvbnmrty
uiopasdfghjklzxcvbnmqwertyuiopasdf
ghjklzxcvbnmqwertyuiopasdfghjklzxc
vbnmqwertyuiopasdfghjklzxcvbnmqw
QUALITY PLANNING AND ANALYSIS
REFRIGERATOR
5/28/2018
Paraphrase This Document
Need a fresh take? Get an instant paraphrase of this document with our AI Paraphraser
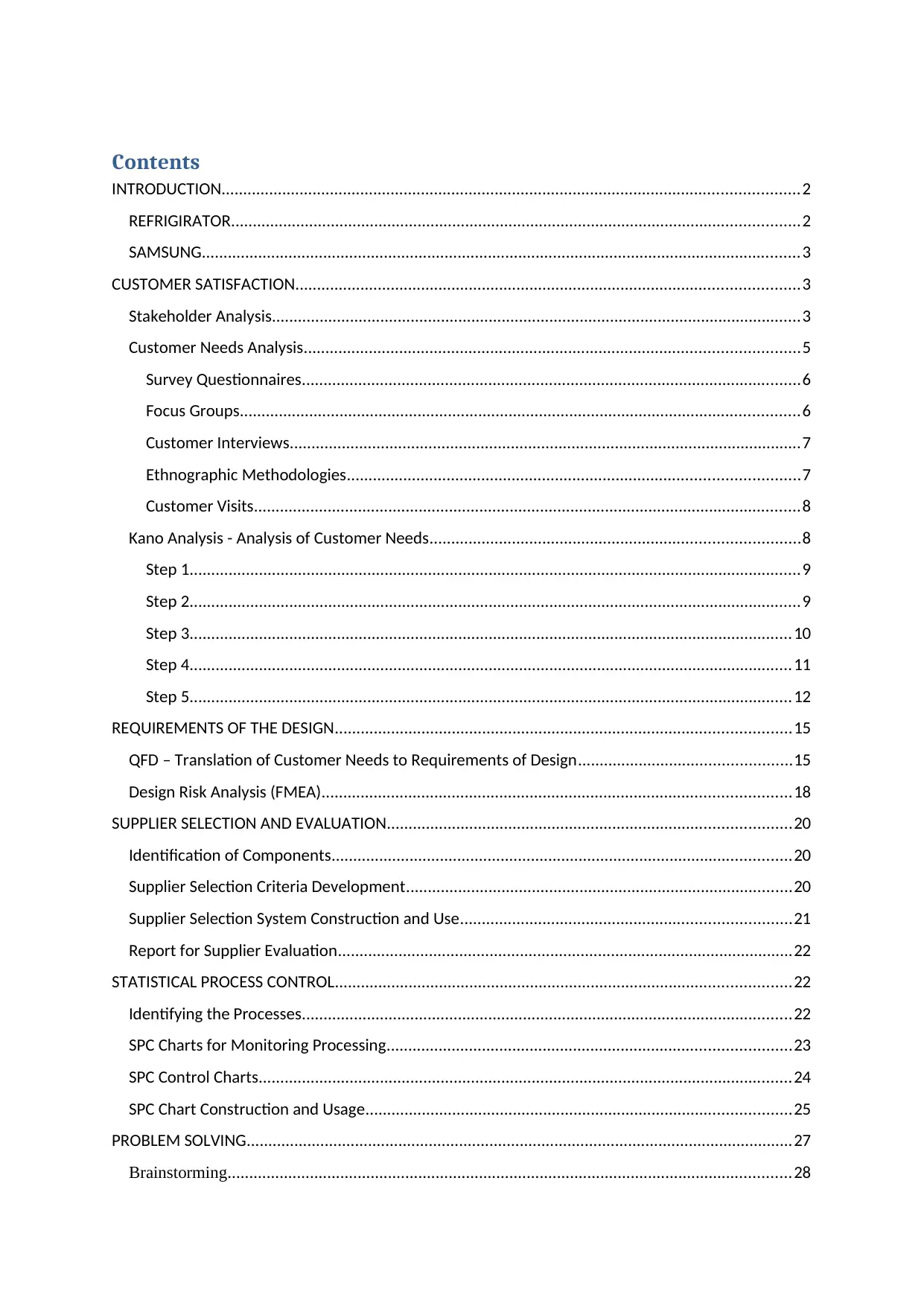
Contents
INTRODUCTION.....................................................................................................................................2
REFRIGIRATOR...................................................................................................................................2
SAMSUNG..........................................................................................................................................3
CUSTOMER SATISFACTION....................................................................................................................3
Stakeholder Analysis..........................................................................................................................3
Customer Needs Analysis..................................................................................................................5
Survey Questionnaires...................................................................................................................6
Focus Groups.................................................................................................................................6
Customer Interviews......................................................................................................................7
Ethnographic Methodologies........................................................................................................7
Customer Visits..............................................................................................................................8
Kano Analysis - Analysis of Customer Needs.....................................................................................8
Step 1.............................................................................................................................................9
Step 2.............................................................................................................................................9
Step 3...........................................................................................................................................10
Step 4...........................................................................................................................................11
Step 5...........................................................................................................................................12
REQUIREMENTS OF THE DESIGN.........................................................................................................15
QFD – Translation of Customer Needs to Requirements of Design.................................................15
Design Risk Analysis (FMEA)............................................................................................................18
SUPPLIER SELECTION AND EVALUATION.............................................................................................20
Identification of Components..........................................................................................................20
Supplier Selection Criteria Development.........................................................................................20
Supplier Selection System Construction and Use............................................................................21
Report for Supplier Evaluation.........................................................................................................22
STATISTICAL PROCESS CONTROL.........................................................................................................22
Identifying the Processes.................................................................................................................22
SPC Charts for Monitoring Processing.............................................................................................23
SPC Control Charts...........................................................................................................................24
SPC Chart Construction and Usage..................................................................................................25
PROBLEM SOLVING..............................................................................................................................27
Brainstorming..................................................................................................................................28
INTRODUCTION.....................................................................................................................................2
REFRIGIRATOR...................................................................................................................................2
SAMSUNG..........................................................................................................................................3
CUSTOMER SATISFACTION....................................................................................................................3
Stakeholder Analysis..........................................................................................................................3
Customer Needs Analysis..................................................................................................................5
Survey Questionnaires...................................................................................................................6
Focus Groups.................................................................................................................................6
Customer Interviews......................................................................................................................7
Ethnographic Methodologies........................................................................................................7
Customer Visits..............................................................................................................................8
Kano Analysis - Analysis of Customer Needs.....................................................................................8
Step 1.............................................................................................................................................9
Step 2.............................................................................................................................................9
Step 3...........................................................................................................................................10
Step 4...........................................................................................................................................11
Step 5...........................................................................................................................................12
REQUIREMENTS OF THE DESIGN.........................................................................................................15
QFD – Translation of Customer Needs to Requirements of Design.................................................15
Design Risk Analysis (FMEA)............................................................................................................18
SUPPLIER SELECTION AND EVALUATION.............................................................................................20
Identification of Components..........................................................................................................20
Supplier Selection Criteria Development.........................................................................................20
Supplier Selection System Construction and Use............................................................................21
Report for Supplier Evaluation.........................................................................................................22
STATISTICAL PROCESS CONTROL.........................................................................................................22
Identifying the Processes.................................................................................................................22
SPC Charts for Monitoring Processing.............................................................................................23
SPC Control Charts...........................................................................................................................24
SPC Chart Construction and Usage..................................................................................................25
PROBLEM SOLVING..............................................................................................................................27
Brainstorming..................................................................................................................................28
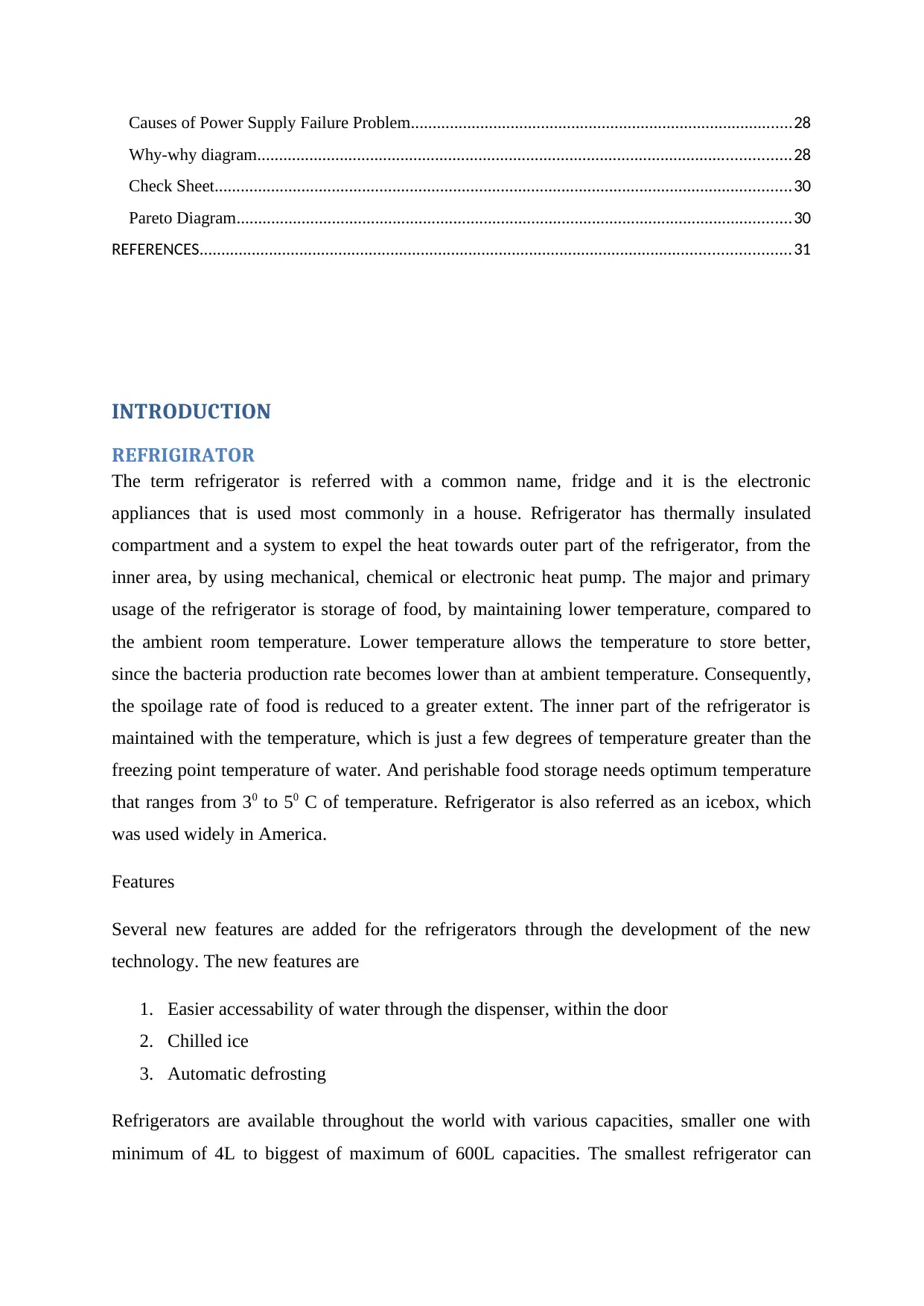
Causes of Power Supply Failure Problem........................................................................................28
Why-why diagram...........................................................................................................................28
Check Sheet.....................................................................................................................................30
Pareto Diagram................................................................................................................................30
REFERENCES........................................................................................................................................31
INTRODUCTION
REFRIGIRATOR
The term refrigerator is referred with a common name, fridge and it is the electronic
appliances that is used most commonly in a house. Refrigerator has thermally insulated
compartment and a system to expel the heat towards outer part of the refrigerator, from the
inner area, by using mechanical, chemical or electronic heat pump. The major and primary
usage of the refrigerator is storage of food, by maintaining lower temperature, compared to
the ambient room temperature. Lower temperature allows the temperature to store better,
since the bacteria production rate becomes lower than at ambient temperature. Consequently,
the spoilage rate of food is reduced to a greater extent. The inner part of the refrigerator is
maintained with the temperature, which is just a few degrees of temperature greater than the
freezing point temperature of water. And perishable food storage needs optimum temperature
that ranges from 30 to 50 C of temperature. Refrigerator is also referred as an icebox, which
was used widely in America.
Features
Several new features are added for the refrigerators through the development of the new
technology. The new features are
1. Easier accessability of water through the dispenser, within the door
2. Chilled ice
3. Automatic defrosting
Refrigerators are available throughout the world with various capacities, smaller one with
minimum of 4L to biggest of maximum of 600L capacities. The smallest refrigerator can
Why-why diagram...........................................................................................................................28
Check Sheet.....................................................................................................................................30
Pareto Diagram................................................................................................................................30
REFERENCES........................................................................................................................................31
INTRODUCTION
REFRIGIRATOR
The term refrigerator is referred with a common name, fridge and it is the electronic
appliances that is used most commonly in a house. Refrigerator has thermally insulated
compartment and a system to expel the heat towards outer part of the refrigerator, from the
inner area, by using mechanical, chemical or electronic heat pump. The major and primary
usage of the refrigerator is storage of food, by maintaining lower temperature, compared to
the ambient room temperature. Lower temperature allows the temperature to store better,
since the bacteria production rate becomes lower than at ambient temperature. Consequently,
the spoilage rate of food is reduced to a greater extent. The inner part of the refrigerator is
maintained with the temperature, which is just a few degrees of temperature greater than the
freezing point temperature of water. And perishable food storage needs optimum temperature
that ranges from 30 to 50 C of temperature. Refrigerator is also referred as an icebox, which
was used widely in America.
Features
Several new features are added for the refrigerators through the development of the new
technology. The new features are
1. Easier accessability of water through the dispenser, within the door
2. Chilled ice
3. Automatic defrosting
Refrigerators are available throughout the world with various capacities, smaller one with
minimum of 4L to biggest of maximum of 600L capacities. The smallest refrigerator can
⊘ This is a preview!⊘
Do you want full access?
Subscribe today to unlock all pages.

Trusted by 1+ million students worldwide
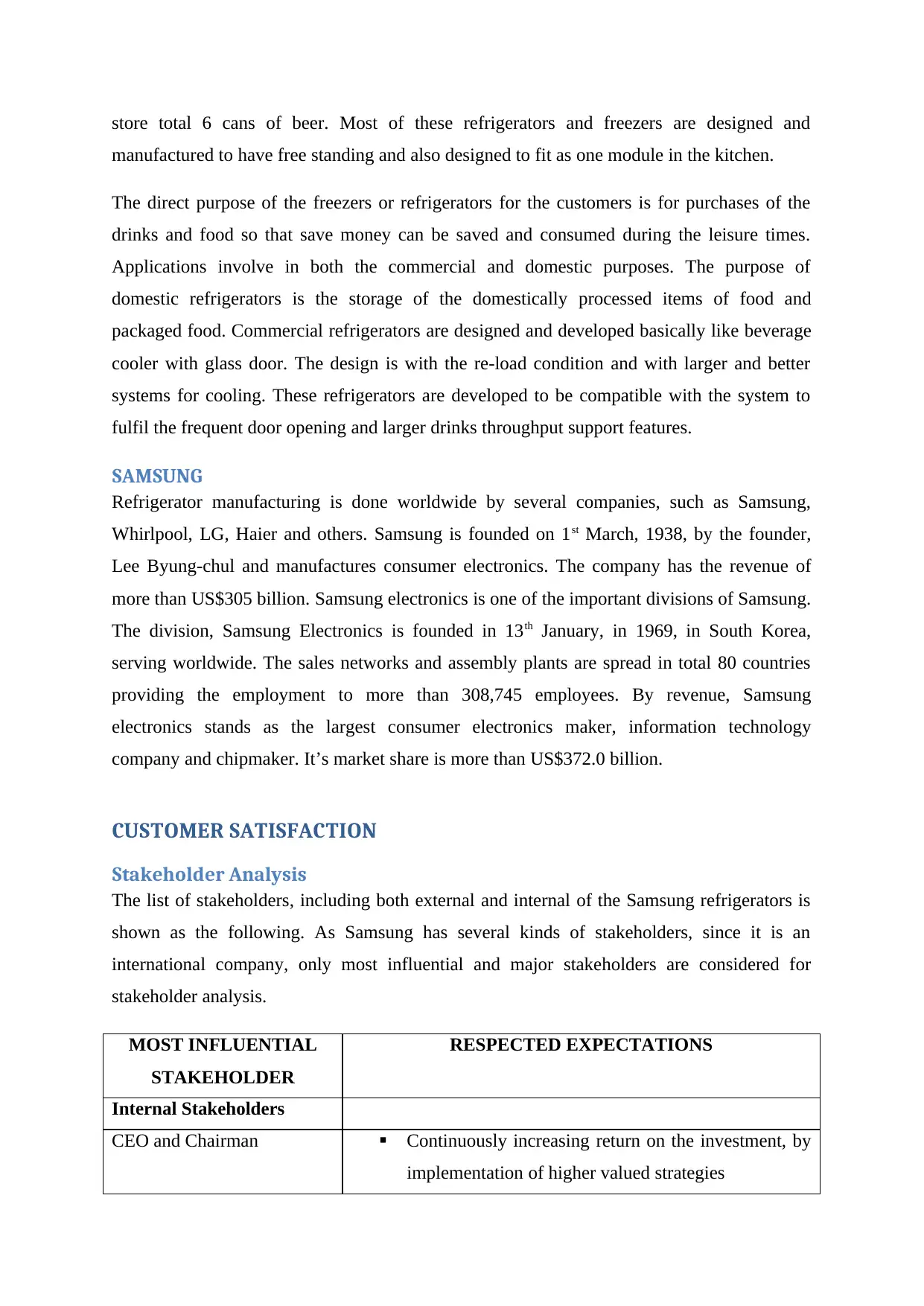
store total 6 cans of beer. Most of these refrigerators and freezers are designed and
manufactured to have free standing and also designed to fit as one module in the kitchen.
The direct purpose of the freezers or refrigerators for the customers is for purchases of the
drinks and food so that save money can be saved and consumed during the leisure times.
Applications involve in both the commercial and domestic purposes. The purpose of
domestic refrigerators is the storage of the domestically processed items of food and
packaged food. Commercial refrigerators are designed and developed basically like beverage
cooler with glass door. The design is with the re-load condition and with larger and better
systems for cooling. These refrigerators are developed to be compatible with the system to
fulfil the frequent door opening and larger drinks throughput support features.
SAMSUNG
Refrigerator manufacturing is done worldwide by several companies, such as Samsung,
Whirlpool, LG, Haier and others. Samsung is founded on 1st March, 1938, by the founder,
Lee Byung-chul and manufactures consumer electronics. The company has the revenue of
more than US$305 billion. Samsung electronics is one of the important divisions of Samsung.
The division, Samsung Electronics is founded in 13th January, in 1969, in South Korea,
serving worldwide. The sales networks and assembly plants are spread in total 80 countries
providing the employment to more than 308,745 employees. By revenue, Samsung
electronics stands as the largest consumer electronics maker, information technology
company and chipmaker. It’s market share is more than US$372.0 billion.
CUSTOMER SATISFACTION
Stakeholder Analysis
The list of stakeholders, including both external and internal of the Samsung refrigerators is
shown as the following. As Samsung has several kinds of stakeholders, since it is an
international company, only most influential and major stakeholders are considered for
stakeholder analysis.
MOST INFLUENTIAL
STAKEHOLDER
RESPECTED EXPECTATIONS
Internal Stakeholders
CEO and Chairman Continuously increasing return on the investment, by
implementation of higher valued strategies
manufactured to have free standing and also designed to fit as one module in the kitchen.
The direct purpose of the freezers or refrigerators for the customers is for purchases of the
drinks and food so that save money can be saved and consumed during the leisure times.
Applications involve in both the commercial and domestic purposes. The purpose of
domestic refrigerators is the storage of the domestically processed items of food and
packaged food. Commercial refrigerators are designed and developed basically like beverage
cooler with glass door. The design is with the re-load condition and with larger and better
systems for cooling. These refrigerators are developed to be compatible with the system to
fulfil the frequent door opening and larger drinks throughput support features.
SAMSUNG
Refrigerator manufacturing is done worldwide by several companies, such as Samsung,
Whirlpool, LG, Haier and others. Samsung is founded on 1st March, 1938, by the founder,
Lee Byung-chul and manufactures consumer electronics. The company has the revenue of
more than US$305 billion. Samsung electronics is one of the important divisions of Samsung.
The division, Samsung Electronics is founded in 13th January, in 1969, in South Korea,
serving worldwide. The sales networks and assembly plants are spread in total 80 countries
providing the employment to more than 308,745 employees. By revenue, Samsung
electronics stands as the largest consumer electronics maker, information technology
company and chipmaker. It’s market share is more than US$372.0 billion.
CUSTOMER SATISFACTION
Stakeholder Analysis
The list of stakeholders, including both external and internal of the Samsung refrigerators is
shown as the following. As Samsung has several kinds of stakeholders, since it is an
international company, only most influential and major stakeholders are considered for
stakeholder analysis.
MOST INFLUENTIAL
STAKEHOLDER
RESPECTED EXPECTATIONS
Internal Stakeholders
CEO and Chairman Continuously increasing return on the investment, by
implementation of higher valued strategies
Paraphrase This Document
Need a fresh take? Get an instant paraphrase of this document with our AI Paraphraser
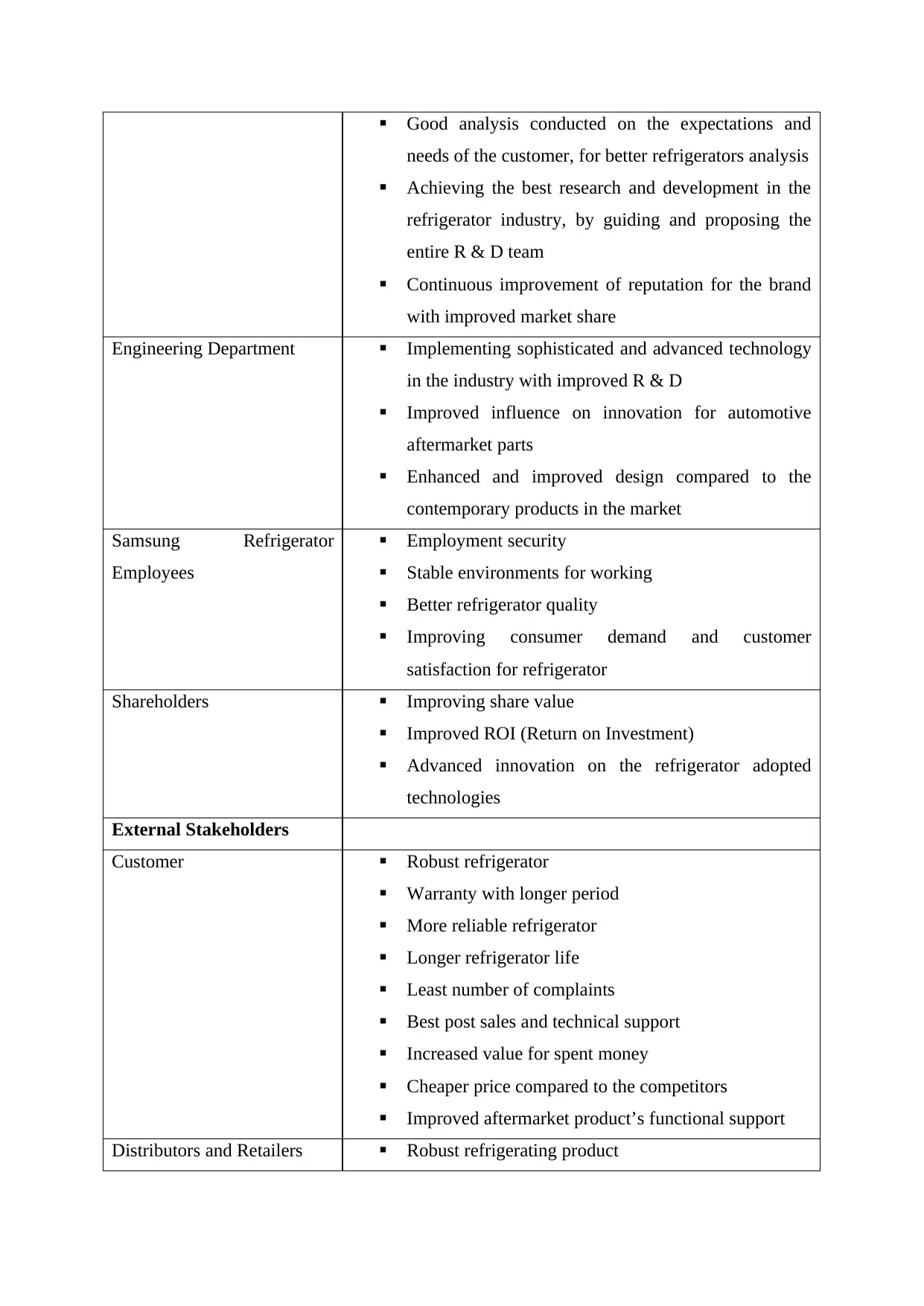
Good analysis conducted on the expectations and
needs of the customer, for better refrigerators analysis
Achieving the best research and development in the
refrigerator industry, by guiding and proposing the
entire R & D team
Continuous improvement of reputation for the brand
with improved market share
Engineering Department Implementing sophisticated and advanced technology
in the industry with improved R & D
Improved influence on innovation for automotive
aftermarket parts
Enhanced and improved design compared to the
contemporary products in the market
Samsung Refrigerator
Employees
Employment security
Stable environments for working
Better refrigerator quality
Improving consumer demand and customer
satisfaction for refrigerator
Shareholders Improving share value
Improved ROI (Return on Investment)
Advanced innovation on the refrigerator adopted
technologies
External Stakeholders
Customer Robust refrigerator
Warranty with longer period
More reliable refrigerator
Longer refrigerator life
Least number of complaints
Best post sales and technical support
Increased value for spent money
Cheaper price compared to the competitors
Improved aftermarket product’s functional support
Distributors and Retailers Robust refrigerating product
needs of the customer, for better refrigerators analysis
Achieving the best research and development in the
refrigerator industry, by guiding and proposing the
entire R & D team
Continuous improvement of reputation for the brand
with improved market share
Engineering Department Implementing sophisticated and advanced technology
in the industry with improved R & D
Improved influence on innovation for automotive
aftermarket parts
Enhanced and improved design compared to the
contemporary products in the market
Samsung Refrigerator
Employees
Employment security
Stable environments for working
Better refrigerator quality
Improving consumer demand and customer
satisfaction for refrigerator
Shareholders Improving share value
Improved ROI (Return on Investment)
Advanced innovation on the refrigerator adopted
technologies
External Stakeholders
Customer Robust refrigerator
Warranty with longer period
More reliable refrigerator
Longer refrigerator life
Least number of complaints
Best post sales and technical support
Increased value for spent money
Cheaper price compared to the competitors
Improved aftermarket product’s functional support
Distributors and Retailers Robust refrigerating product
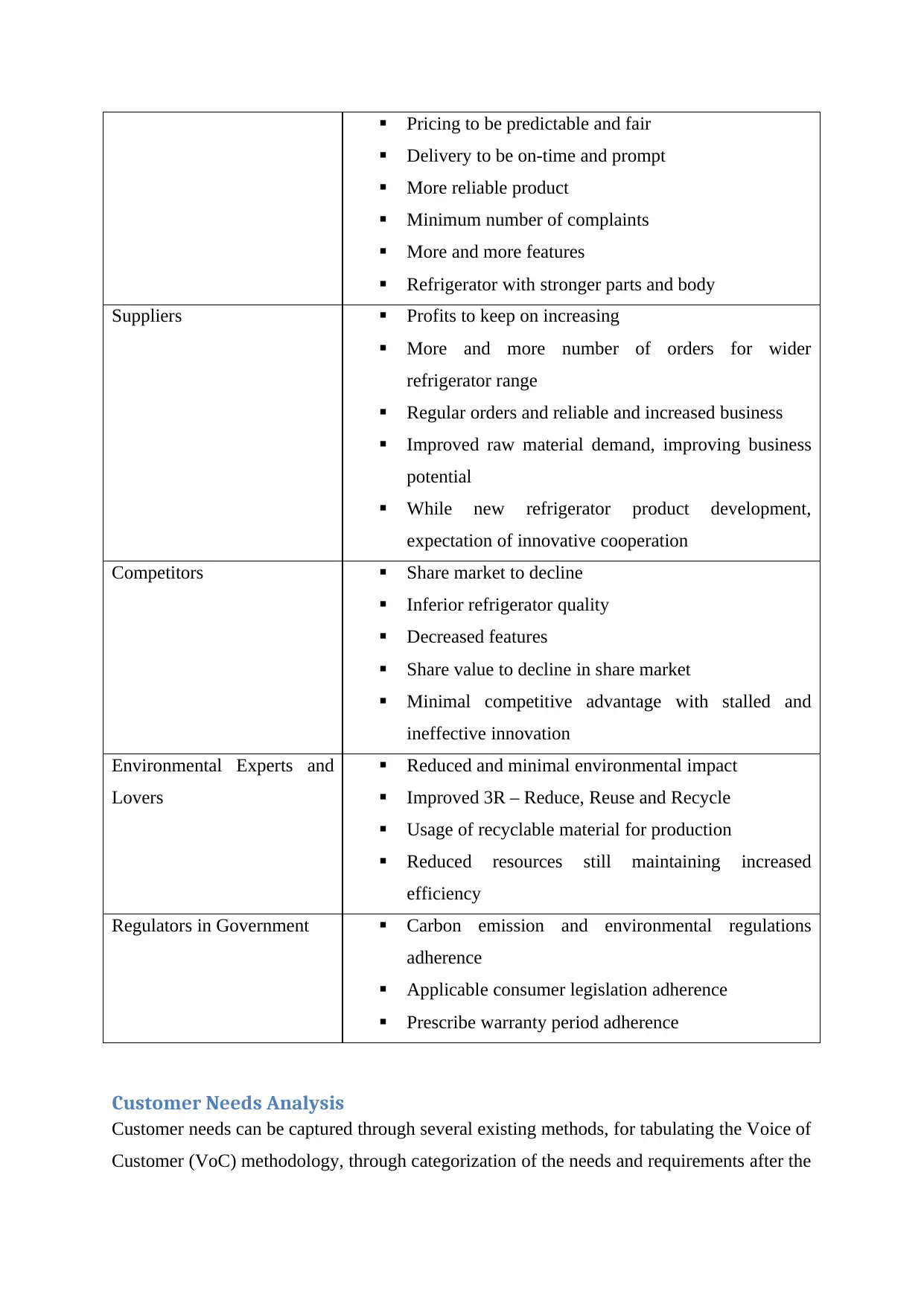
Pricing to be predictable and fair
Delivery to be on-time and prompt
More reliable product
Minimum number of complaints
More and more features
Refrigerator with stronger parts and body
Suppliers Profits to keep on increasing
More and more number of orders for wider
refrigerator range
Regular orders and reliable and increased business
Improved raw material demand, improving business
potential
While new refrigerator product development,
expectation of innovative cooperation
Competitors Share market to decline
Inferior refrigerator quality
Decreased features
Share value to decline in share market
Minimal competitive advantage with stalled and
ineffective innovation
Environmental Experts and
Lovers
Reduced and minimal environmental impact
Improved 3R – Reduce, Reuse and Recycle
Usage of recyclable material for production
Reduced resources still maintaining increased
efficiency
Regulators in Government Carbon emission and environmental regulations
adherence
Applicable consumer legislation adherence
Prescribe warranty period adherence
Customer Needs Analysis
Customer needs can be captured through several existing methods, for tabulating the Voice of
Customer (VoC) methodology, through categorization of the needs and requirements after the
Delivery to be on-time and prompt
More reliable product
Minimum number of complaints
More and more features
Refrigerator with stronger parts and body
Suppliers Profits to keep on increasing
More and more number of orders for wider
refrigerator range
Regular orders and reliable and increased business
Improved raw material demand, improving business
potential
While new refrigerator product development,
expectation of innovative cooperation
Competitors Share market to decline
Inferior refrigerator quality
Decreased features
Share value to decline in share market
Minimal competitive advantage with stalled and
ineffective innovation
Environmental Experts and
Lovers
Reduced and minimal environmental impact
Improved 3R – Reduce, Reuse and Recycle
Usage of recyclable material for production
Reduced resources still maintaining increased
efficiency
Regulators in Government Carbon emission and environmental regulations
adherence
Applicable consumer legislation adherence
Prescribe warranty period adherence
Customer Needs Analysis
Customer needs can be captured through several existing methods, for tabulating the Voice of
Customer (VoC) methodology, through categorization of the needs and requirements after the
⊘ This is a preview!⊘
Do you want full access?
Subscribe today to unlock all pages.

Trusted by 1+ million students worldwide
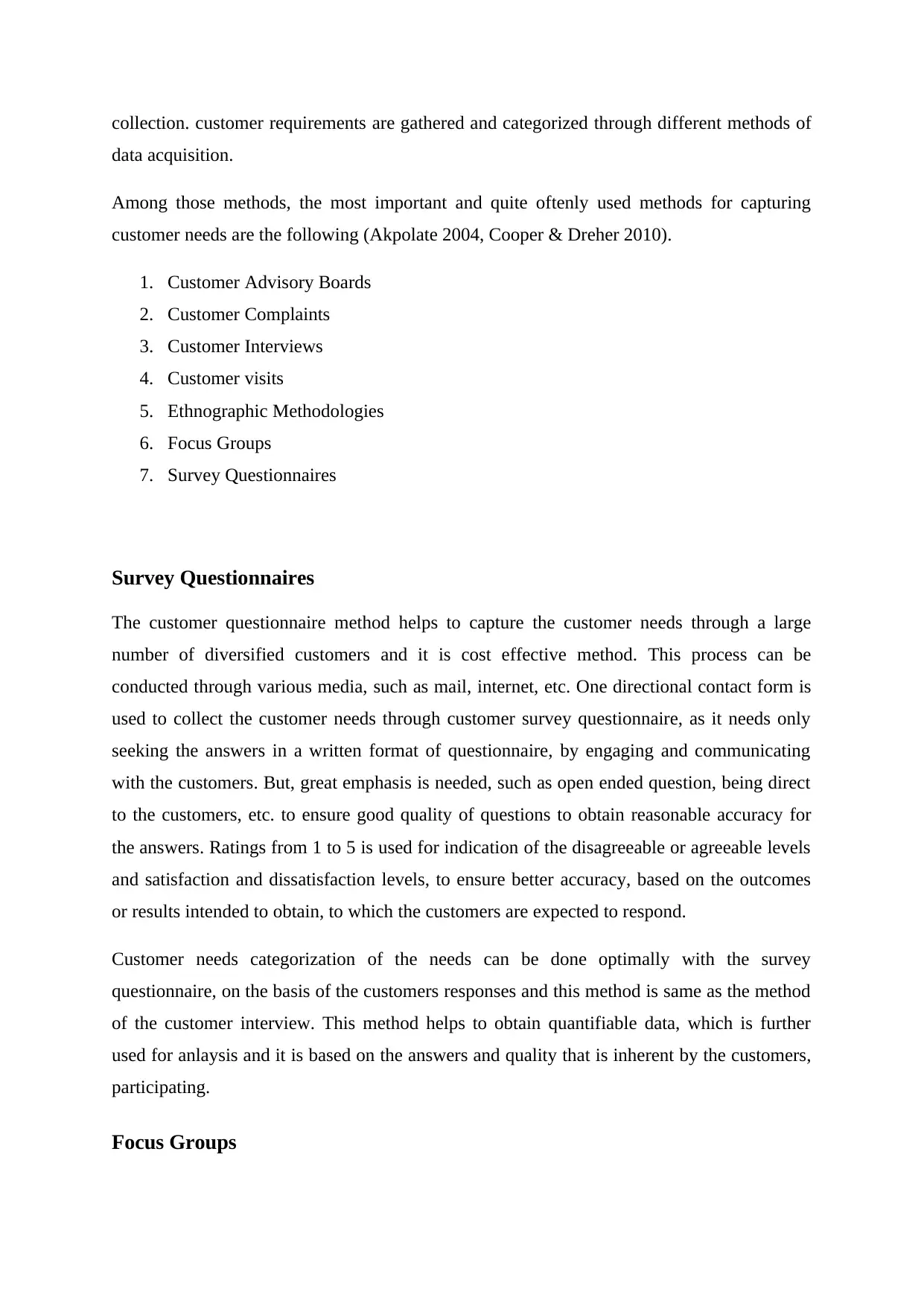
collection. customer requirements are gathered and categorized through different methods of
data acquisition.
Among those methods, the most important and quite oftenly used methods for capturing
customer needs are the following (Akpolate 2004, Cooper & Dreher 2010).
1. Customer Advisory Boards
2. Customer Complaints
3. Customer Interviews
4. Customer visits
5. Ethnographic Methodologies
6. Focus Groups
7. Survey Questionnaires
Survey Questionnaires
The customer questionnaire method helps to capture the customer needs through a large
number of diversified customers and it is cost effective method. This process can be
conducted through various media, such as mail, internet, etc. One directional contact form is
used to collect the customer needs through customer survey questionnaire, as it needs only
seeking the answers in a written format of questionnaire, by engaging and communicating
with the customers. But, great emphasis is needed, such as open ended question, being direct
to the customers, etc. to ensure good quality of questions to obtain reasonable accuracy for
the answers. Ratings from 1 to 5 is used for indication of the disagreeable or agreeable levels
and satisfaction and dissatisfaction levels, to ensure better accuracy, based on the outcomes
or results intended to obtain, to which the customers are expected to respond.
Customer needs categorization of the needs can be done optimally with the survey
questionnaire, on the basis of the customers responses and this method is same as the method
of the customer interview. This method helps to obtain quantifiable data, which is further
used for anlaysis and it is based on the answers and quality that is inherent by the customers,
participating.
Focus Groups
data acquisition.
Among those methods, the most important and quite oftenly used methods for capturing
customer needs are the following (Akpolate 2004, Cooper & Dreher 2010).
1. Customer Advisory Boards
2. Customer Complaints
3. Customer Interviews
4. Customer visits
5. Ethnographic Methodologies
6. Focus Groups
7. Survey Questionnaires
Survey Questionnaires
The customer questionnaire method helps to capture the customer needs through a large
number of diversified customers and it is cost effective method. This process can be
conducted through various media, such as mail, internet, etc. One directional contact form is
used to collect the customer needs through customer survey questionnaire, as it needs only
seeking the answers in a written format of questionnaire, by engaging and communicating
with the customers. But, great emphasis is needed, such as open ended question, being direct
to the customers, etc. to ensure good quality of questions to obtain reasonable accuracy for
the answers. Ratings from 1 to 5 is used for indication of the disagreeable or agreeable levels
and satisfaction and dissatisfaction levels, to ensure better accuracy, based on the outcomes
or results intended to obtain, to which the customers are expected to respond.
Customer needs categorization of the needs can be done optimally with the survey
questionnaire, on the basis of the customers responses and this method is same as the method
of the customer interview. This method helps to obtain quantifiable data, which is further
used for anlaysis and it is based on the answers and quality that is inherent by the customers,
participating.
Focus Groups
Paraphrase This Document
Need a fresh take? Get an instant paraphrase of this document with our AI Paraphraser
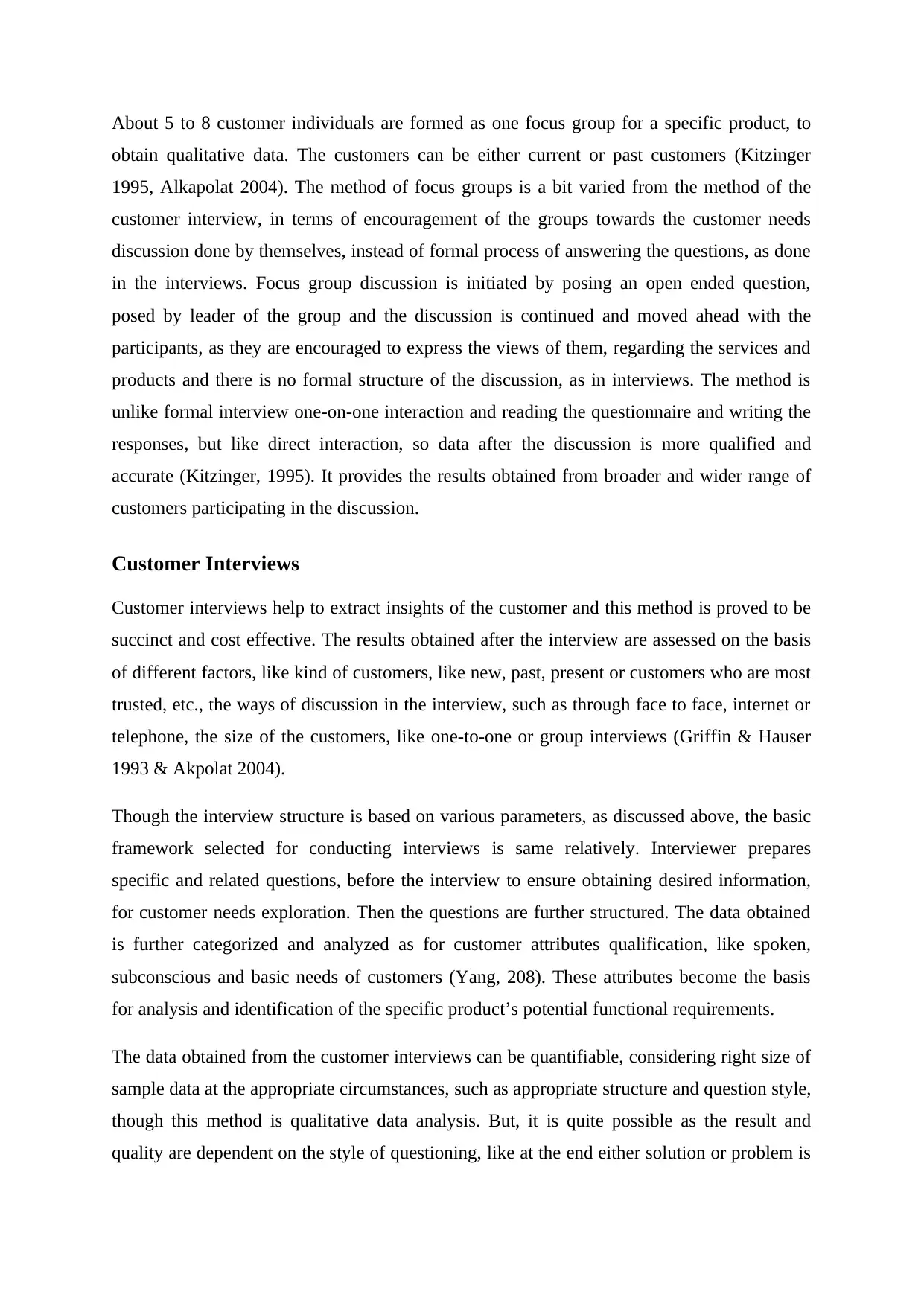
About 5 to 8 customer individuals are formed as one focus group for a specific product, to
obtain qualitative data. The customers can be either current or past customers (Kitzinger
1995, Alkapolat 2004). The method of focus groups is a bit varied from the method of the
customer interview, in terms of encouragement of the groups towards the customer needs
discussion done by themselves, instead of formal process of answering the questions, as done
in the interviews. Focus group discussion is initiated by posing an open ended question,
posed by leader of the group and the discussion is continued and moved ahead with the
participants, as they are encouraged to express the views of them, regarding the services and
products and there is no formal structure of the discussion, as in interviews. The method is
unlike formal interview one-on-one interaction and reading the questionnaire and writing the
responses, but like direct interaction, so data after the discussion is more qualified and
accurate (Kitzinger, 1995). It provides the results obtained from broader and wider range of
customers participating in the discussion.
Customer Interviews
Customer interviews help to extract insights of the customer and this method is proved to be
succinct and cost effective. The results obtained after the interview are assessed on the basis
of different factors, like kind of customers, like new, past, present or customers who are most
trusted, etc., the ways of discussion in the interview, such as through face to face, internet or
telephone, the size of the customers, like one-to-one or group interviews (Griffin & Hauser
1993 & Akpolat 2004).
Though the interview structure is based on various parameters, as discussed above, the basic
framework selected for conducting interviews is same relatively. Interviewer prepares
specific and related questions, before the interview to ensure obtaining desired information,
for customer needs exploration. Then the questions are further structured. The data obtained
is further categorized and analyzed as for customer attributes qualification, like spoken,
subconscious and basic needs of customers (Yang, 208). These attributes become the basis
for analysis and identification of the specific product’s potential functional requirements.
The data obtained from the customer interviews can be quantifiable, considering right size of
sample data at the appropriate circumstances, such as appropriate structure and question style,
though this method is qualitative data analysis. But, it is quite possible as the result and
quality are dependent on the style of questioning, like at the end either solution or problem is
obtain qualitative data. The customers can be either current or past customers (Kitzinger
1995, Alkapolat 2004). The method of focus groups is a bit varied from the method of the
customer interview, in terms of encouragement of the groups towards the customer needs
discussion done by themselves, instead of formal process of answering the questions, as done
in the interviews. Focus group discussion is initiated by posing an open ended question,
posed by leader of the group and the discussion is continued and moved ahead with the
participants, as they are encouraged to express the views of them, regarding the services and
products and there is no formal structure of the discussion, as in interviews. The method is
unlike formal interview one-on-one interaction and reading the questionnaire and writing the
responses, but like direct interaction, so data after the discussion is more qualified and
accurate (Kitzinger, 1995). It provides the results obtained from broader and wider range of
customers participating in the discussion.
Customer Interviews
Customer interviews help to extract insights of the customer and this method is proved to be
succinct and cost effective. The results obtained after the interview are assessed on the basis
of different factors, like kind of customers, like new, past, present or customers who are most
trusted, etc., the ways of discussion in the interview, such as through face to face, internet or
telephone, the size of the customers, like one-to-one or group interviews (Griffin & Hauser
1993 & Akpolat 2004).
Though the interview structure is based on various parameters, as discussed above, the basic
framework selected for conducting interviews is same relatively. Interviewer prepares
specific and related questions, before the interview to ensure obtaining desired information,
for customer needs exploration. Then the questions are further structured. The data obtained
is further categorized and analyzed as for customer attributes qualification, like spoken,
subconscious and basic needs of customers (Yang, 208). These attributes become the basis
for analysis and identification of the specific product’s potential functional requirements.
The data obtained from the customer interviews can be quantifiable, considering right size of
sample data at the appropriate circumstances, such as appropriate structure and question style,
though this method is qualitative data analysis. But, it is quite possible as the result and
quality are dependent on the style of questioning, like at the end either solution or problem is
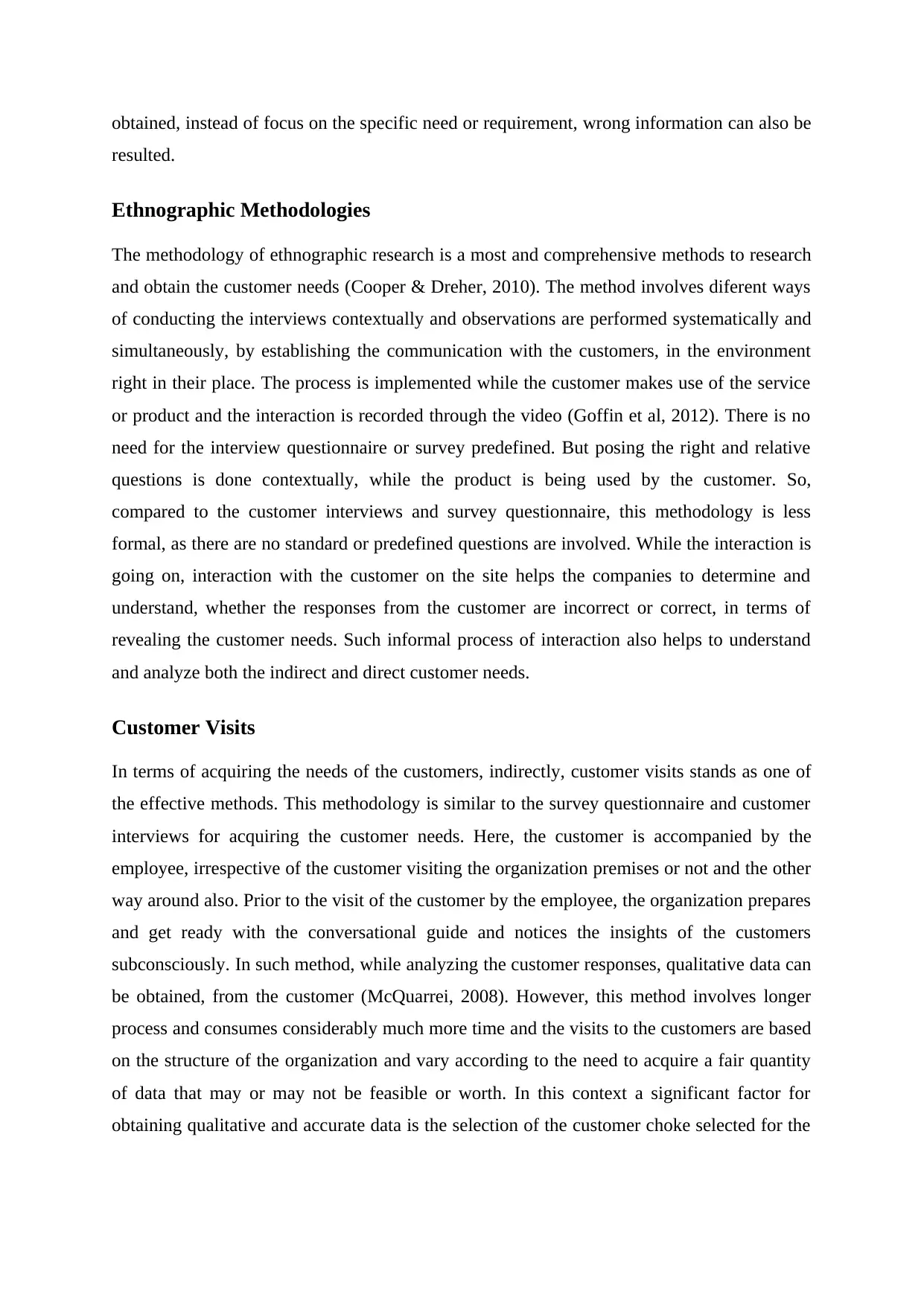
obtained, instead of focus on the specific need or requirement, wrong information can also be
resulted.
Ethnographic Methodologies
The methodology of ethnographic research is a most and comprehensive methods to research
and obtain the customer needs (Cooper & Dreher, 2010). The method involves diferent ways
of conducting the interviews contextually and observations are performed systematically and
simultaneously, by establishing the communication with the customers, in the environment
right in their place. The process is implemented while the customer makes use of the service
or product and the interaction is recorded through the video (Goffin et al, 2012). There is no
need for the interview questionnaire or survey predefined. But posing the right and relative
questions is done contextually, while the product is being used by the customer. So,
compared to the customer interviews and survey questionnaire, this methodology is less
formal, as there are no standard or predefined questions are involved. While the interaction is
going on, interaction with the customer on the site helps the companies to determine and
understand, whether the responses from the customer are incorrect or correct, in terms of
revealing the customer needs. Such informal process of interaction also helps to understand
and analyze both the indirect and direct customer needs.
Customer Visits
In terms of acquiring the needs of the customers, indirectly, customer visits stands as one of
the effective methods. This methodology is similar to the survey questionnaire and customer
interviews for acquiring the customer needs. Here, the customer is accompanied by the
employee, irrespective of the customer visiting the organization premises or not and the other
way around also. Prior to the visit of the customer by the employee, the organization prepares
and get ready with the conversational guide and notices the insights of the customers
subconsciously. In such method, while analyzing the customer responses, qualitative data can
be obtained, from the customer (McQuarrei, 2008). However, this method involves longer
process and consumes considerably much more time and the visits to the customers are based
on the structure of the organization and vary according to the need to acquire a fair quantity
of data that may or may not be feasible or worth. In this context a significant factor for
obtaining qualitative and accurate data is the selection of the customer choke selected for the
resulted.
Ethnographic Methodologies
The methodology of ethnographic research is a most and comprehensive methods to research
and obtain the customer needs (Cooper & Dreher, 2010). The method involves diferent ways
of conducting the interviews contextually and observations are performed systematically and
simultaneously, by establishing the communication with the customers, in the environment
right in their place. The process is implemented while the customer makes use of the service
or product and the interaction is recorded through the video (Goffin et al, 2012). There is no
need for the interview questionnaire or survey predefined. But posing the right and relative
questions is done contextually, while the product is being used by the customer. So,
compared to the customer interviews and survey questionnaire, this methodology is less
formal, as there are no standard or predefined questions are involved. While the interaction is
going on, interaction with the customer on the site helps the companies to determine and
understand, whether the responses from the customer are incorrect or correct, in terms of
revealing the customer needs. Such informal process of interaction also helps to understand
and analyze both the indirect and direct customer needs.
Customer Visits
In terms of acquiring the needs of the customers, indirectly, customer visits stands as one of
the effective methods. This methodology is similar to the survey questionnaire and customer
interviews for acquiring the customer needs. Here, the customer is accompanied by the
employee, irrespective of the customer visiting the organization premises or not and the other
way around also. Prior to the visit of the customer by the employee, the organization prepares
and get ready with the conversational guide and notices the insights of the customers
subconsciously. In such method, while analyzing the customer responses, qualitative data can
be obtained, from the customer (McQuarrei, 2008). However, this method involves longer
process and consumes considerably much more time and the visits to the customers are based
on the structure of the organization and vary according to the need to acquire a fair quantity
of data that may or may not be feasible or worth. In this context a significant factor for
obtaining qualitative and accurate data is the selection of the customer choke selected for the
⊘ This is a preview!⊘
Do you want full access?
Subscribe today to unlock all pages.

Trusted by 1+ million students worldwide
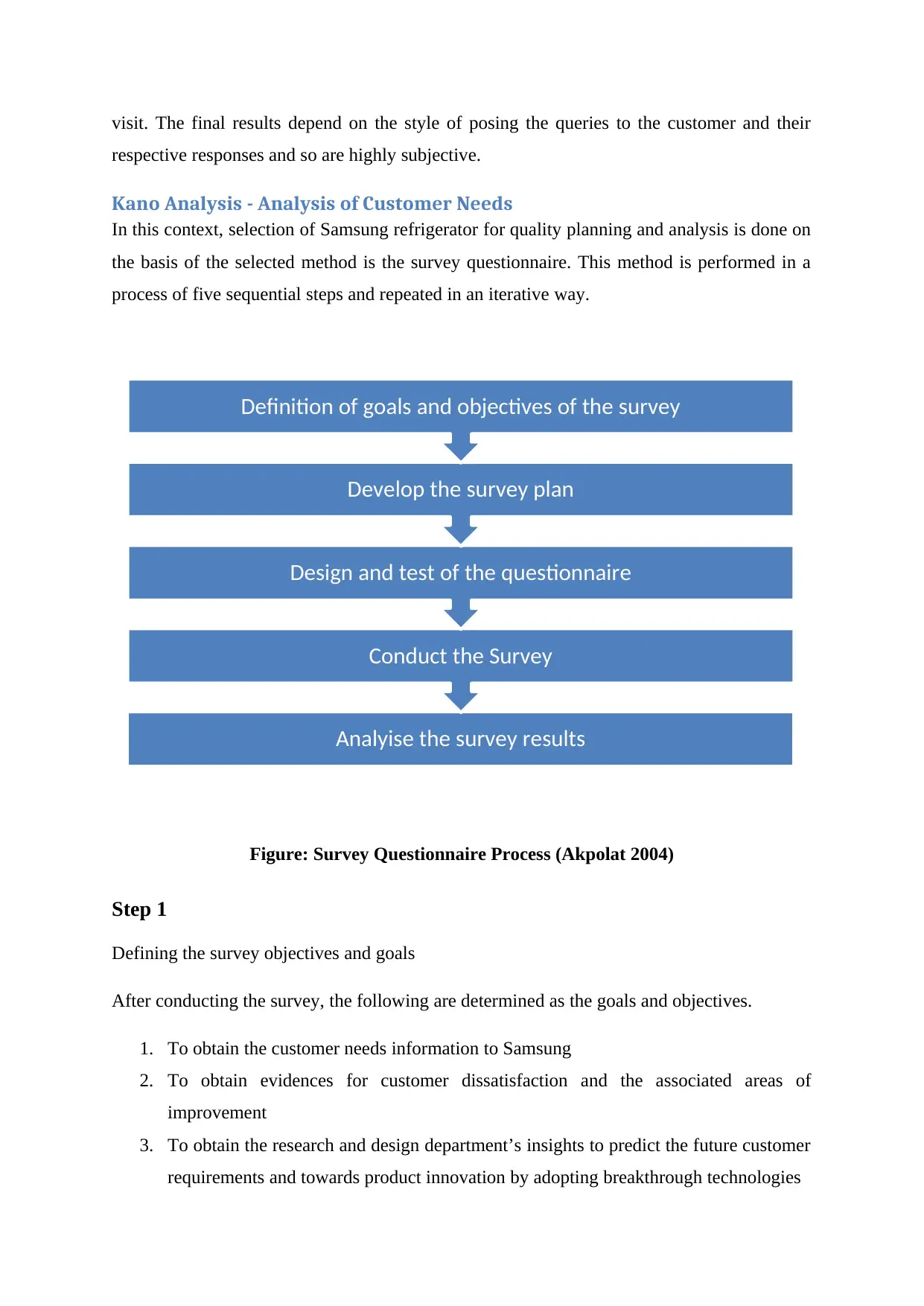
visit. The final results depend on the style of posing the queries to the customer and their
respective responses and so are highly subjective.
Kano Analysis - Analysis of Customer Needs
In this context, selection of Samsung refrigerator for quality planning and analysis is done on
the basis of the selected method is the survey questionnaire. This method is performed in a
process of five sequential steps and repeated in an iterative way.
Figure: Survey Questionnaire Process (Akpolat 2004)
Step 1
Defining the survey objectives and goals
After conducting the survey, the following are determined as the goals and objectives.
1. To obtain the customer needs information to Samsung
2. To obtain evidences for customer dissatisfaction and the associated areas of
improvement
3. To obtain the research and design department’s insights to predict the future customer
requirements and towards product innovation by adopting breakthrough technologies
Analyise the survey results
Conduct the Survey
Design and test of the questionnaire
Develop the survey plan
Definition of goals and objectives of the survey
respective responses and so are highly subjective.
Kano Analysis - Analysis of Customer Needs
In this context, selection of Samsung refrigerator for quality planning and analysis is done on
the basis of the selected method is the survey questionnaire. This method is performed in a
process of five sequential steps and repeated in an iterative way.
Figure: Survey Questionnaire Process (Akpolat 2004)
Step 1
Defining the survey objectives and goals
After conducting the survey, the following are determined as the goals and objectives.
1. To obtain the customer needs information to Samsung
2. To obtain evidences for customer dissatisfaction and the associated areas of
improvement
3. To obtain the research and design department’s insights to predict the future customer
requirements and towards product innovation by adopting breakthrough technologies
Analyise the survey results
Conduct the Survey
Design and test of the questionnaire
Develop the survey plan
Definition of goals and objectives of the survey
Paraphrase This Document
Need a fresh take? Get an instant paraphrase of this document with our AI Paraphraser
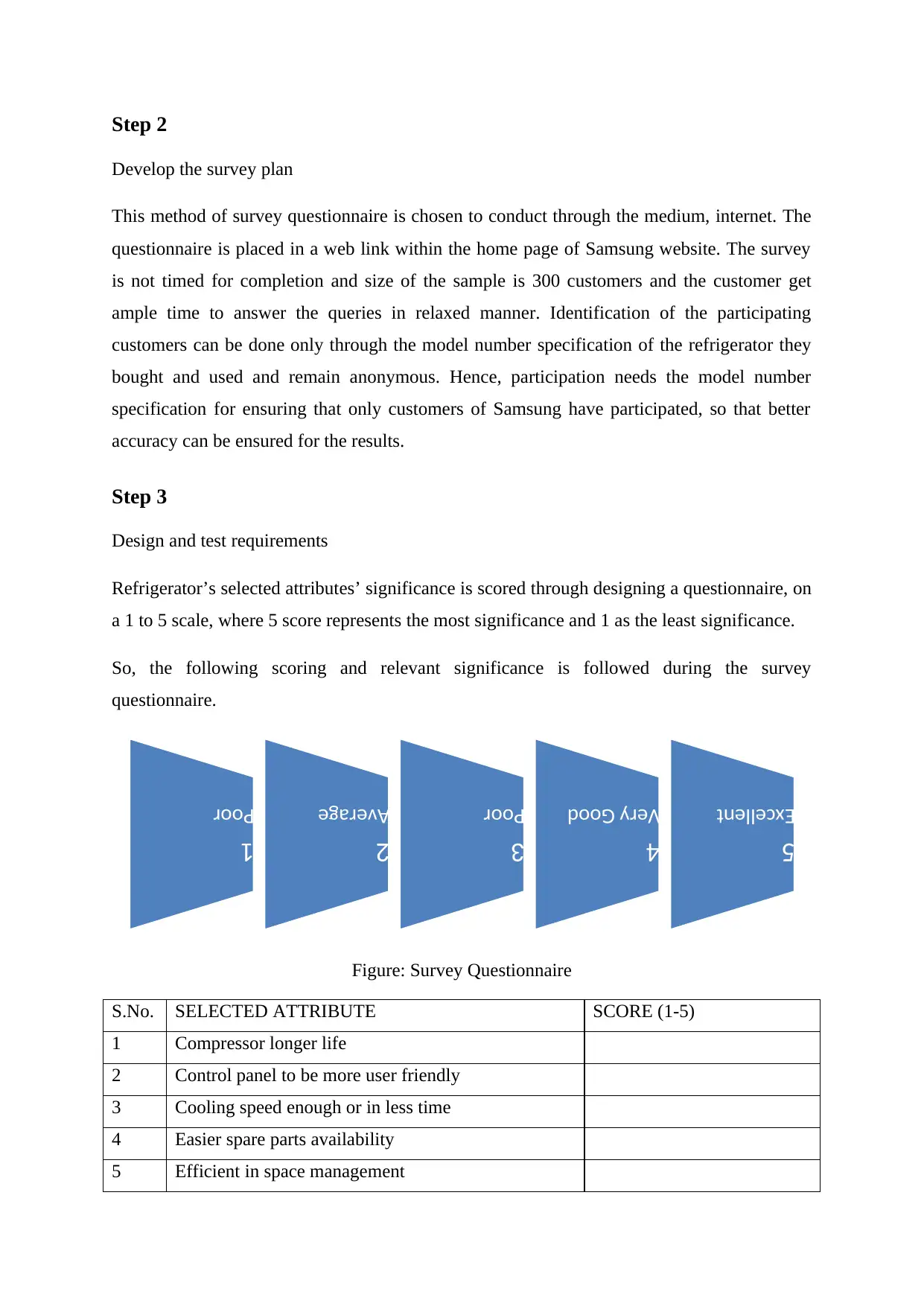
Step 2
Develop the survey plan
This method of survey questionnaire is chosen to conduct through the medium, internet. The
questionnaire is placed in a web link within the home page of Samsung website. The survey
is not timed for completion and size of the sample is 300 customers and the customer get
ample time to answer the queries in relaxed manner. Identification of the participating
customers can be done only through the model number specification of the refrigerator they
bought and used and remain anonymous. Hence, participation needs the model number
specification for ensuring that only customers of Samsung have participated, so that better
accuracy can be ensured for the results.
Step 3
Design and test requirements
Refrigerator’s selected attributes’ significance is scored through designing a questionnaire, on
a 1 to 5 scale, where 5 score represents the most significance and 1 as the least significance.
So, the following scoring and relevant significance is followed during the survey
questionnaire.
Figure: Survey Questionnaire
S.No. SELECTED ATTRIBUTE SCORE (1-5)
1 Compressor longer life
2 Control panel to be more user friendly
3 Cooling speed enough or in less time
4 Easier spare parts availability
5 Efficient in space management
1
Poor
2
Average
3
Poor
4
Very Good
5
Excellent
Develop the survey plan
This method of survey questionnaire is chosen to conduct through the medium, internet. The
questionnaire is placed in a web link within the home page of Samsung website. The survey
is not timed for completion and size of the sample is 300 customers and the customer get
ample time to answer the queries in relaxed manner. Identification of the participating
customers can be done only through the model number specification of the refrigerator they
bought and used and remain anonymous. Hence, participation needs the model number
specification for ensuring that only customers of Samsung have participated, so that better
accuracy can be ensured for the results.
Step 3
Design and test requirements
Refrigerator’s selected attributes’ significance is scored through designing a questionnaire, on
a 1 to 5 scale, where 5 score represents the most significance and 1 as the least significance.
So, the following scoring and relevant significance is followed during the survey
questionnaire.
Figure: Survey Questionnaire
S.No. SELECTED ATTRIBUTE SCORE (1-5)
1 Compressor longer life
2 Control panel to be more user friendly
3 Cooling speed enough or in less time
4 Easier spare parts availability
5 Efficient in space management
1
Poor
2
Average
3
Poor
4
Very Good
5
Excellent
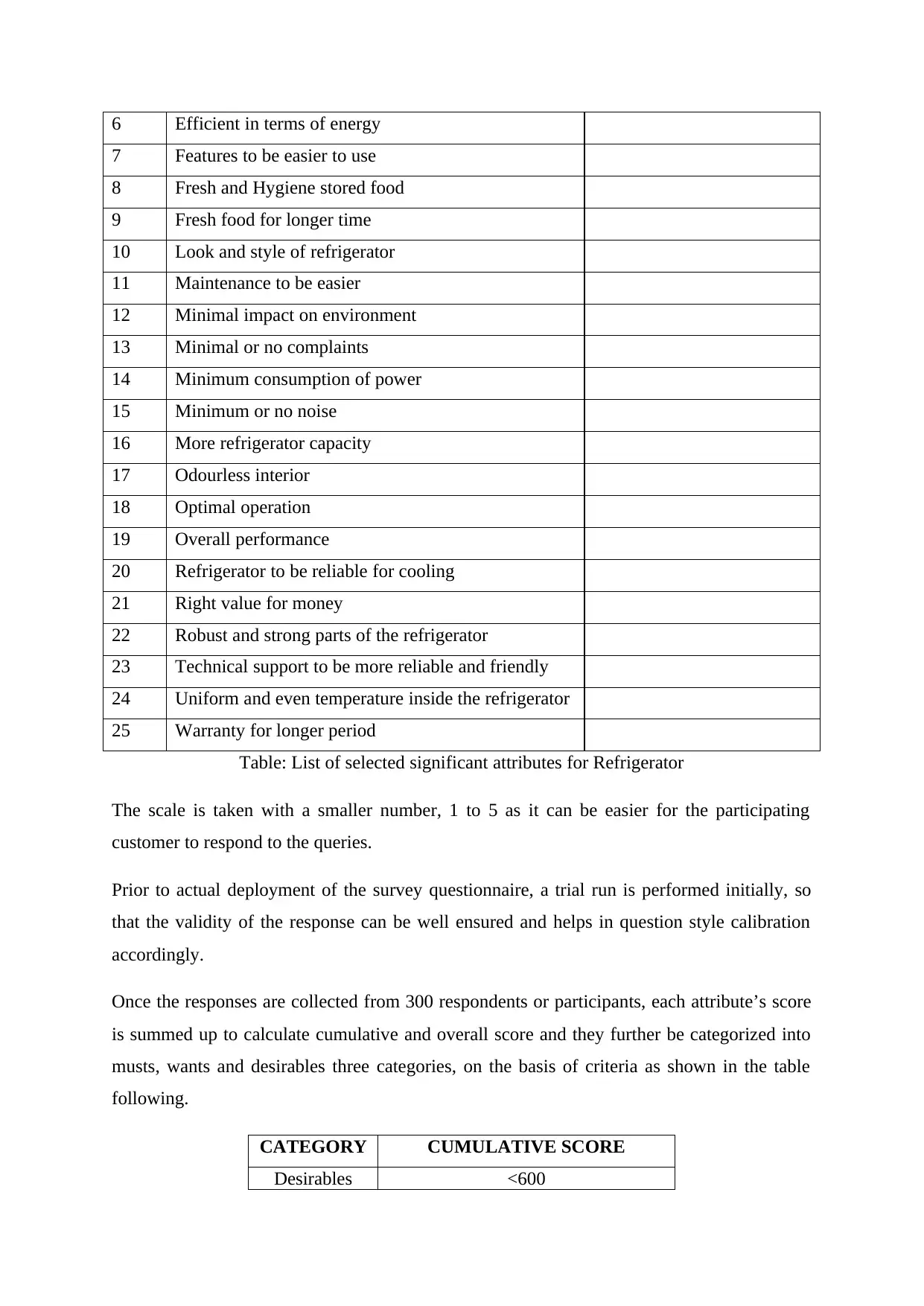
6 Efficient in terms of energy
7 Features to be easier to use
8 Fresh and Hygiene stored food
9 Fresh food for longer time
10 Look and style of refrigerator
11 Maintenance to be easier
12 Minimal impact on environment
13 Minimal or no complaints
14 Minimum consumption of power
15 Minimum or no noise
16 More refrigerator capacity
17 Odourless interior
18 Optimal operation
19 Overall performance
20 Refrigerator to be reliable for cooling
21 Right value for money
22 Robust and strong parts of the refrigerator
23 Technical support to be more reliable and friendly
24 Uniform and even temperature inside the refrigerator
25 Warranty for longer period
Table: List of selected significant attributes for Refrigerator
The scale is taken with a smaller number, 1 to 5 as it can be easier for the participating
customer to respond to the queries.
Prior to actual deployment of the survey questionnaire, a trial run is performed initially, so
that the validity of the response can be well ensured and helps in question style calibration
accordingly.
Once the responses are collected from 300 respondents or participants, each attribute’s score
is summed up to calculate cumulative and overall score and they further be categorized into
musts, wants and desirables three categories, on the basis of criteria as shown in the table
following.
CATEGORY CUMULATIVE SCORE
Desirables <600
7 Features to be easier to use
8 Fresh and Hygiene stored food
9 Fresh food for longer time
10 Look and style of refrigerator
11 Maintenance to be easier
12 Minimal impact on environment
13 Minimal or no complaints
14 Minimum consumption of power
15 Minimum or no noise
16 More refrigerator capacity
17 Odourless interior
18 Optimal operation
19 Overall performance
20 Refrigerator to be reliable for cooling
21 Right value for money
22 Robust and strong parts of the refrigerator
23 Technical support to be more reliable and friendly
24 Uniform and even temperature inside the refrigerator
25 Warranty for longer period
Table: List of selected significant attributes for Refrigerator
The scale is taken with a smaller number, 1 to 5 as it can be easier for the participating
customer to respond to the queries.
Prior to actual deployment of the survey questionnaire, a trial run is performed initially, so
that the validity of the response can be well ensured and helps in question style calibration
accordingly.
Once the responses are collected from 300 respondents or participants, each attribute’s score
is summed up to calculate cumulative and overall score and they further be categorized into
musts, wants and desirables three categories, on the basis of criteria as shown in the table
following.
CATEGORY CUMULATIVE SCORE
Desirables <600
⊘ This is a preview!⊘
Do you want full access?
Subscribe today to unlock all pages.

Trusted by 1+ million students worldwide
1 out of 35