Cost Accounting Homework: Financial, Cost, and Profit Analysis
VerifiedAdded on 2020/04/07
|13
|2454
|500
Homework Assignment
AI Summary
This homework assignment solution provides a detailed analysis of various cost accounting problems. It begins with a process costing problem, calculating equivalent units, cost per unit, and the cost of goods transferred out and ending work-in-process inventory. The solution then addresses financial,...
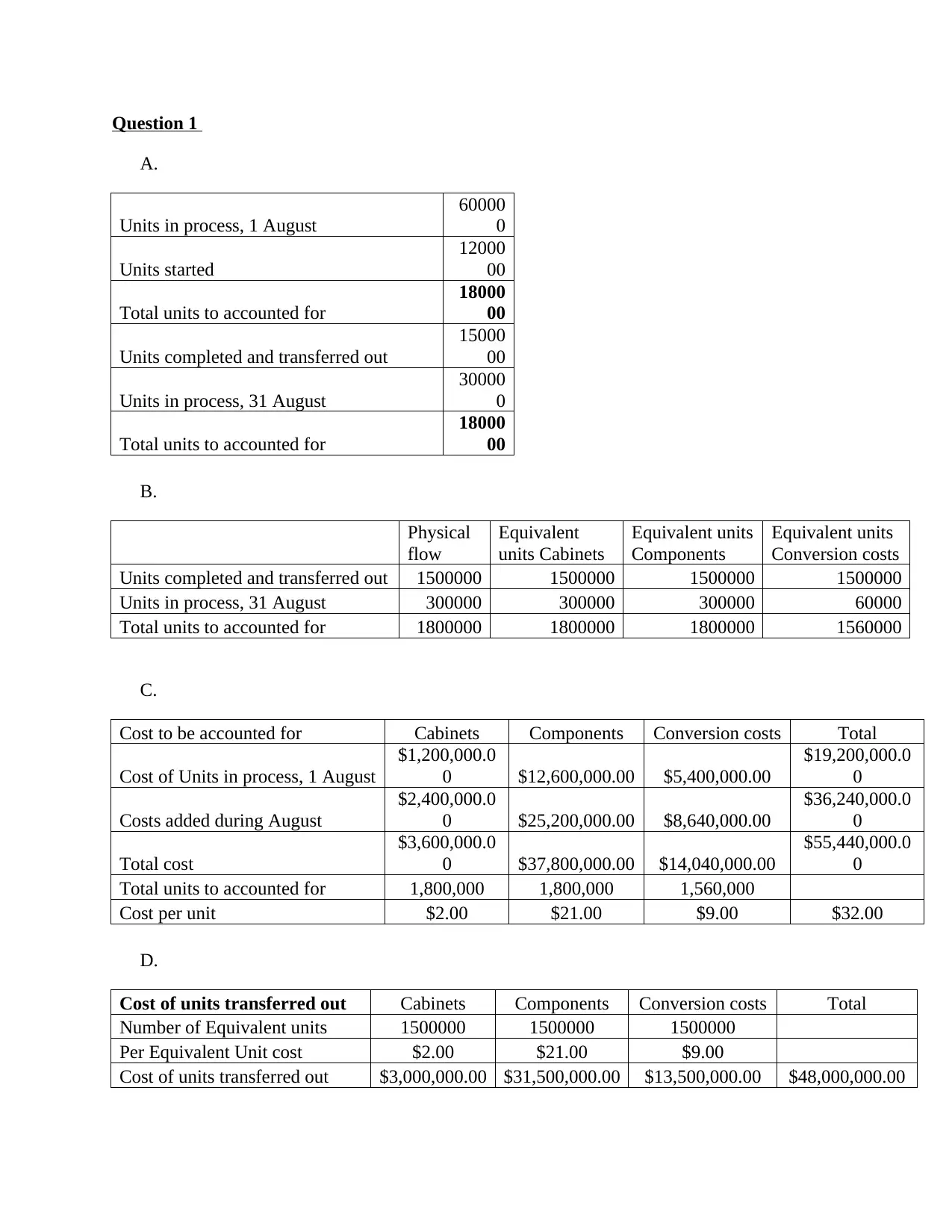
Question 1
A.
Units in process, 1 August
60000
0
Units started
12000
00
Total units to accounted for
18000
00
Units completed and transferred out
15000
00
Units in process, 31 August
30000
0
Total units to accounted for
18000
00
B.
Physical
flow
Equivalent
units Cabinets
Equivalent units
Components
Equivalent units
Conversion costs
Units completed and transferred out 1500000 1500000 1500000 1500000
Units in process, 31 August 300000 300000 300000 60000
Total units to accounted for 1800000 1800000 1800000 1560000
C.
Cost to be accounted for Cabinets Components Conversion costs Total
Cost of Units in process, 1 August
$1,200,000.0
0 $12,600,000.00 $5,400,000.00
$19,200,000.0
0
Costs added during August
$2,400,000.0
0 $25,200,000.00 $8,640,000.00
$36,240,000.0
0
Total cost
$3,600,000.0
0 $37,800,000.00 $14,040,000.00
$55,440,000.0
0
Total units to accounted for 1,800,000 1,800,000 1,560,000
Cost per unit $2.00 $21.00 $9.00 $32.00
D.
Cost of units transferred out Cabinets Components Conversion costs Total
Number of Equivalent units 1500000 1500000 1500000
Per Equivalent Unit cost $2.00 $21.00 $9.00
Cost of units transferred out $3,000,000.00 $31,500,000.00 $13,500,000.00 $48,000,000.00
A.
Units in process, 1 August
60000
0
Units started
12000
00
Total units to accounted for
18000
00
Units completed and transferred out
15000
00
Units in process, 31 August
30000
0
Total units to accounted for
18000
00
B.
Physical
flow
Equivalent
units Cabinets
Equivalent units
Components
Equivalent units
Conversion costs
Units completed and transferred out 1500000 1500000 1500000 1500000
Units in process, 31 August 300000 300000 300000 60000
Total units to accounted for 1800000 1800000 1800000 1560000
C.
Cost to be accounted for Cabinets Components Conversion costs Total
Cost of Units in process, 1 August
$1,200,000.0
0 $12,600,000.00 $5,400,000.00
$19,200,000.0
0
Costs added during August
$2,400,000.0
0 $25,200,000.00 $8,640,000.00
$36,240,000.0
0
Total cost
$3,600,000.0
0 $37,800,000.00 $14,040,000.00
$55,440,000.0
0
Total units to accounted for 1,800,000 1,800,000 1,560,000
Cost per unit $2.00 $21.00 $9.00 $32.00
D.
Cost of units transferred out Cabinets Components Conversion costs Total
Number of Equivalent units 1500000 1500000 1500000
Per Equivalent Unit cost $2.00 $21.00 $9.00
Cost of units transferred out $3,000,000.00 $31,500,000.00 $13,500,000.00 $48,000,000.00
Paraphrase This Document
Need a fresh take? Get an instant paraphrase of this document with our AI Paraphraser
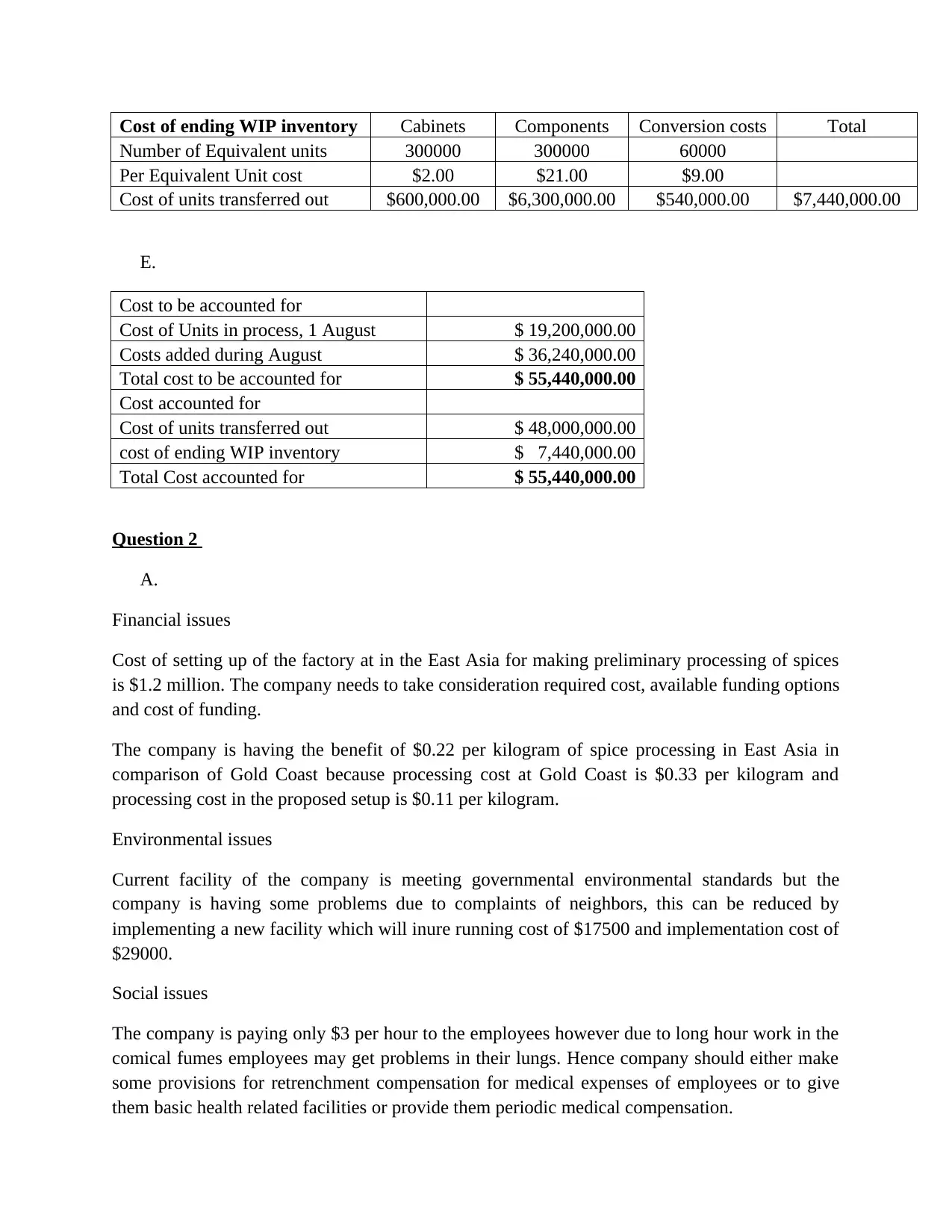
Cost of ending WIP inventory Cabinets Components Conversion costs Total
Number of Equivalent units 300000 300000 60000
Per Equivalent Unit cost $2.00 $21.00 $9.00
Cost of units transferred out $600,000.00 $6,300,000.00 $540,000.00 $7,440,000.00
E.
Cost to be accounted for
Cost of Units in process, 1 August $ 19,200,000.00
Costs added during August $ 36,240,000.00
Total cost to be accounted for $ 55,440,000.00
Cost accounted for
Cost of units transferred out $ 48,000,000.00
cost of ending WIP inventory $ 7,440,000.00
Total Cost accounted for $ 55,440,000.00
Question 2
A.
Financial issues
Cost of setting up of the factory at in the East Asia for making preliminary processing of spices
is $1.2 million. The company needs to take consideration required cost, available funding options
and cost of funding.
The company is having the benefit of $0.22 per kilogram of spice processing in East Asia in
comparison of Gold Coast because processing cost at Gold Coast is $0.33 per kilogram and
processing cost in the proposed setup is $0.11 per kilogram.
Environmental issues
Current facility of the company is meeting governmental environmental standards but the
company is having some problems due to complaints of neighbors, this can be reduced by
implementing a new facility which will inure running cost of $17500 and implementation cost of
$29000.
Social issues
The company is paying only $3 per hour to the employees however due to long hour work in the
comical fumes employees may get problems in their lungs. Hence company should either make
some provisions for retrenchment compensation for medical expenses of employees or to give
them basic health related facilities or provide them periodic medical compensation.
Number of Equivalent units 300000 300000 60000
Per Equivalent Unit cost $2.00 $21.00 $9.00
Cost of units transferred out $600,000.00 $6,300,000.00 $540,000.00 $7,440,000.00
E.
Cost to be accounted for
Cost of Units in process, 1 August $ 19,200,000.00
Costs added during August $ 36,240,000.00
Total cost to be accounted for $ 55,440,000.00
Cost accounted for
Cost of units transferred out $ 48,000,000.00
cost of ending WIP inventory $ 7,440,000.00
Total Cost accounted for $ 55,440,000.00
Question 2
A.
Financial issues
Cost of setting up of the factory at in the East Asia for making preliminary processing of spices
is $1.2 million. The company needs to take consideration required cost, available funding options
and cost of funding.
The company is having the benefit of $0.22 per kilogram of spice processing in East Asia in
comparison of Gold Coast because processing cost at Gold Coast is $0.33 per kilogram and
processing cost in the proposed setup is $0.11 per kilogram.
Environmental issues
Current facility of the company is meeting governmental environmental standards but the
company is having some problems due to complaints of neighbors, this can be reduced by
implementing a new facility which will inure running cost of $17500 and implementation cost of
$29000.
Social issues
The company is paying only $3 per hour to the employees however due to long hour work in the
comical fumes employees may get problems in their lungs. Hence company should either make
some provisions for retrenchment compensation for medical expenses of employees or to give
them basic health related facilities or provide them periodic medical compensation.
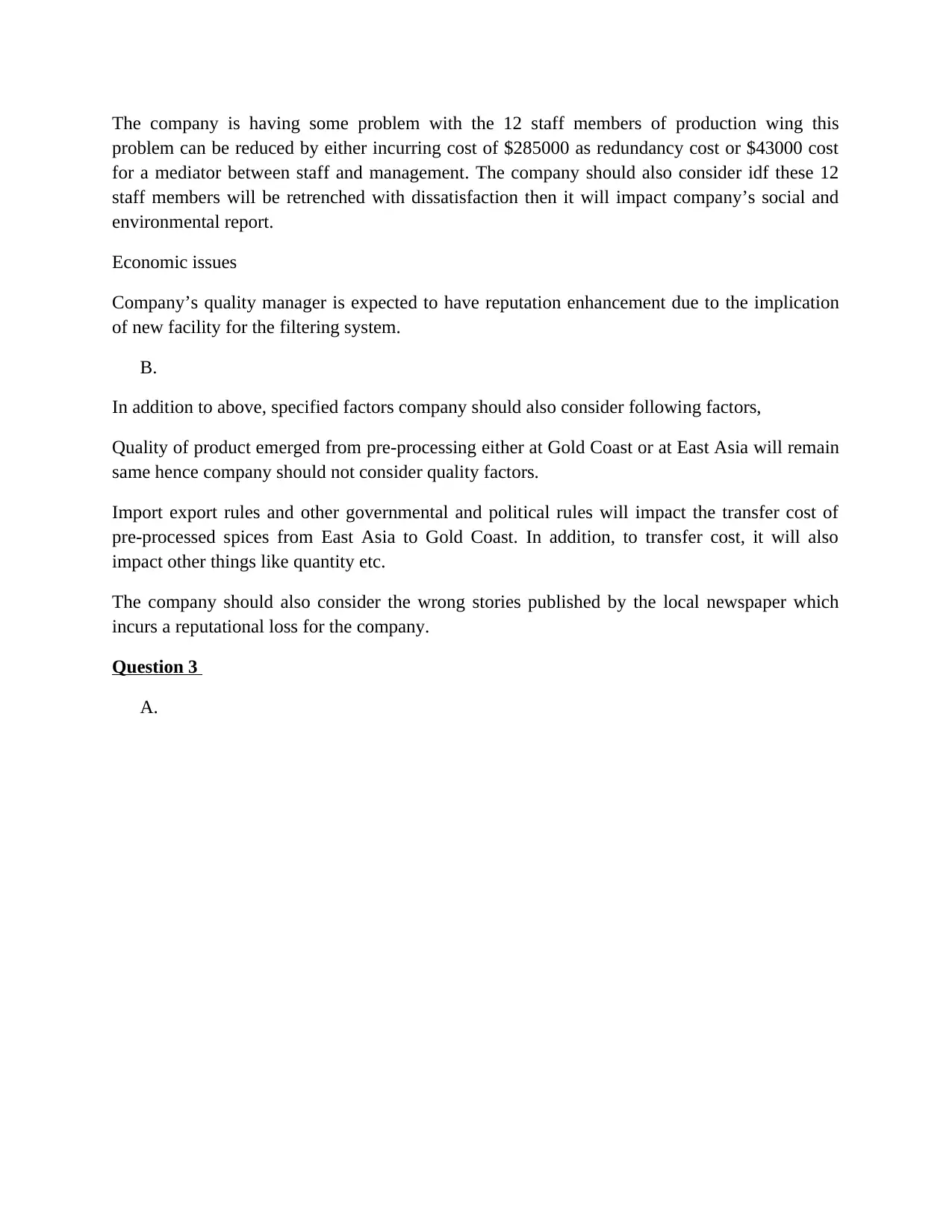
The company is having some problem with the 12 staff members of production wing this
problem can be reduced by either incurring cost of $285000 as redundancy cost or $43000 cost
for a mediator between staff and management. The company should also consider idf these 12
staff members will be retrenched with dissatisfaction then it will impact company’s social and
environmental report.
Economic issues
Company’s quality manager is expected to have reputation enhancement due to the implication
of new facility for the filtering system.
B.
In addition to above, specified factors company should also consider following factors,
Quality of product emerged from pre-processing either at Gold Coast or at East Asia will remain
same hence company should not consider quality factors.
Import export rules and other governmental and political rules will impact the transfer cost of
pre-processed spices from East Asia to Gold Coast. In addition, to transfer cost, it will also
impact other things like quantity etc.
The company should also consider the wrong stories published by the local newspaper which
incurs a reputational loss for the company.
Question 3
A.
problem can be reduced by either incurring cost of $285000 as redundancy cost or $43000 cost
for a mediator between staff and management. The company should also consider idf these 12
staff members will be retrenched with dissatisfaction then it will impact company’s social and
environmental report.
Economic issues
Company’s quality manager is expected to have reputation enhancement due to the implication
of new facility for the filtering system.
B.
In addition to above, specified factors company should also consider following factors,
Quality of product emerged from pre-processing either at Gold Coast or at East Asia will remain
same hence company should not consider quality factors.
Import export rules and other governmental and political rules will impact the transfer cost of
pre-processed spices from East Asia to Gold Coast. In addition, to transfer cost, it will also
impact other things like quantity etc.
The company should also consider the wrong stories published by the local newspaper which
incurs a reputational loss for the company.
Question 3
A.
⊘ This is a preview!⊘
Do you want full access?
Subscribe today to unlock all pages.

Trusted by 1+ million students worldwide
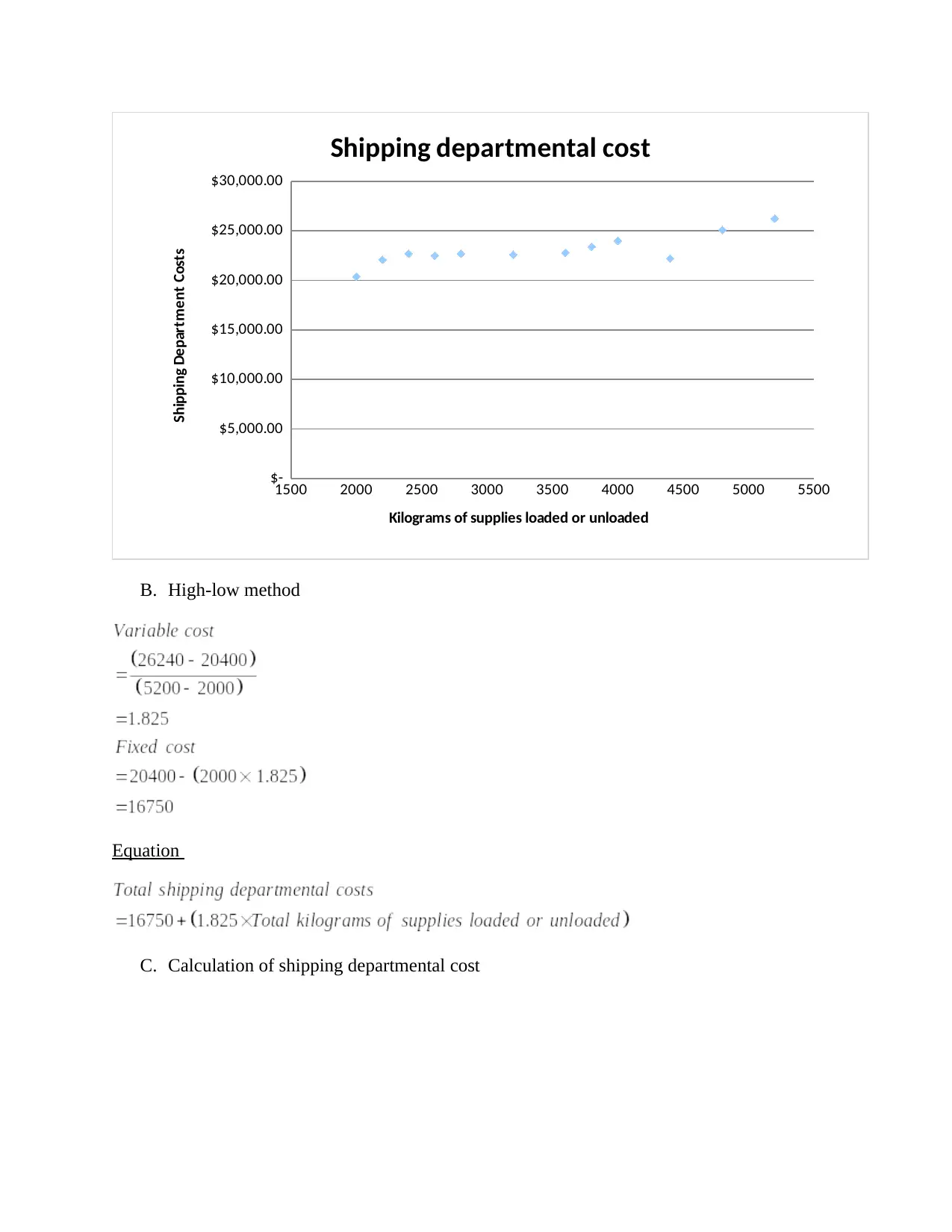
1500 2000 2500 3000 3500 4000 4500 5000 5500
$-
$5,000.00
$10,000.00
$15,000.00
$20,000.00
$25,000.00
$30,000.00
Shipping departmental cost
Kilograms of supplies loaded or unloaded
Shipping Department Costs
B. High-low method
Equation
C. Calculation of shipping departmental cost
$-
$5,000.00
$10,000.00
$15,000.00
$20,000.00
$25,000.00
$30,000.00
Shipping departmental cost
Kilograms of supplies loaded or unloaded
Shipping Department Costs
B. High-low method
Equation
C. Calculation of shipping departmental cost
Paraphrase This Document
Need a fresh take? Get an instant paraphrase of this document with our AI Paraphraser
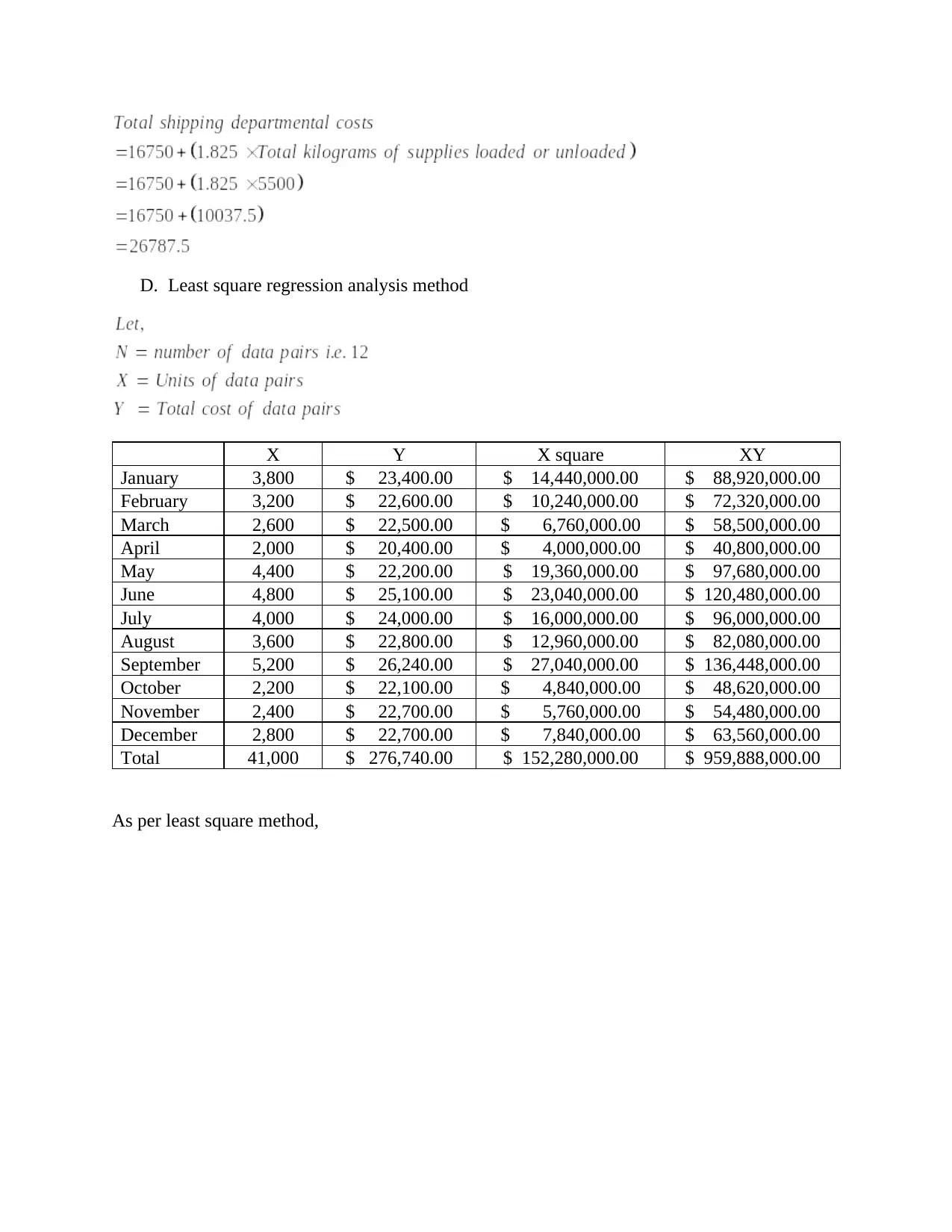
D. Least square regression analysis method
X Y X square XY
January 3,800 $ 23,400.00 $ 14,440,000.00 $ 88,920,000.00
February 3,200 $ 22,600.00 $ 10,240,000.00 $ 72,320,000.00
March 2,600 $ 22,500.00 $ 6,760,000.00 $ 58,500,000.00
April 2,000 $ 20,400.00 $ 4,000,000.00 $ 40,800,000.00
May 4,400 $ 22,200.00 $ 19,360,000.00 $ 97,680,000.00
June 4,800 $ 25,100.00 $ 23,040,000.00 $ 120,480,000.00
July 4,000 $ 24,000.00 $ 16,000,000.00 $ 96,000,000.00
August 3,600 $ 22,800.00 $ 12,960,000.00 $ 82,080,000.00
September 5,200 $ 26,240.00 $ 27,040,000.00 $ 136,448,000.00
October 2,200 $ 22,100.00 $ 4,840,000.00 $ 48,620,000.00
November 2,400 $ 22,700.00 $ 5,760,000.00 $ 54,480,000.00
December 2,800 $ 22,700.00 $ 7,840,000.00 $ 63,560,000.00
Total 41,000 $ 276,740.00 $ 152,280,000.00 $ 959,888,000.00
As per least square method,
X Y X square XY
January 3,800 $ 23,400.00 $ 14,440,000.00 $ 88,920,000.00
February 3,200 $ 22,600.00 $ 10,240,000.00 $ 72,320,000.00
March 2,600 $ 22,500.00 $ 6,760,000.00 $ 58,500,000.00
April 2,000 $ 20,400.00 $ 4,000,000.00 $ 40,800,000.00
May 4,400 $ 22,200.00 $ 19,360,000.00 $ 97,680,000.00
June 4,800 $ 25,100.00 $ 23,040,000.00 $ 120,480,000.00
July 4,000 $ 24,000.00 $ 16,000,000.00 $ 96,000,000.00
August 3,600 $ 22,800.00 $ 12,960,000.00 $ 82,080,000.00
September 5,200 $ 26,240.00 $ 27,040,000.00 $ 136,448,000.00
October 2,200 $ 22,100.00 $ 4,840,000.00 $ 48,620,000.00
November 2,400 $ 22,700.00 $ 5,760,000.00 $ 54,480,000.00
December 2,800 $ 22,700.00 $ 7,840,000.00 $ 63,560,000.00
Total 41,000 $ 276,740.00 $ 152,280,000.00 $ 959,888,000.00
As per least square method,
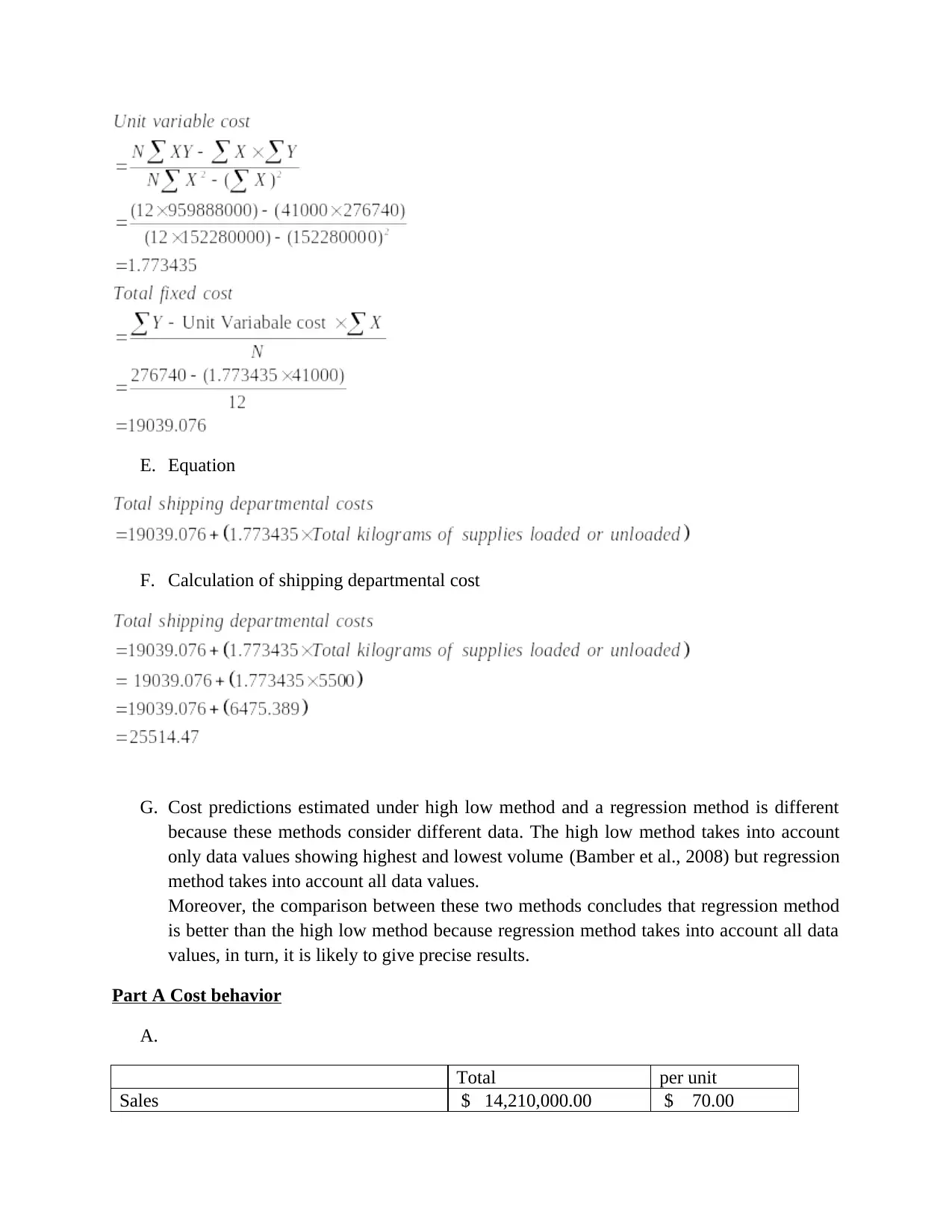
E. Equation
F. Calculation of shipping departmental cost
G. Cost predictions estimated under high low method and a regression method is different
because these methods consider different data. The high low method takes into account
only data values showing highest and lowest volume (Bamber et al., 2008) but regression
method takes into account all data values.
Moreover, the comparison between these two methods concludes that regression method
is better than the high low method because regression method takes into account all data
values, in turn, it is likely to give precise results.
Part A Cost behavior
A.
Total per unit
Sales $ 14,210,000.00 $ 70.00
F. Calculation of shipping departmental cost
G. Cost predictions estimated under high low method and a regression method is different
because these methods consider different data. The high low method takes into account
only data values showing highest and lowest volume (Bamber et al., 2008) but regression
method takes into account all data values.
Moreover, the comparison between these two methods concludes that regression method
is better than the high low method because regression method takes into account all data
values, in turn, it is likely to give precise results.
Part A Cost behavior
A.
Total per unit
Sales $ 14,210,000.00 $ 70.00
⊘ This is a preview!⊘
Do you want full access?
Subscribe today to unlock all pages.

Trusted by 1+ million students worldwide
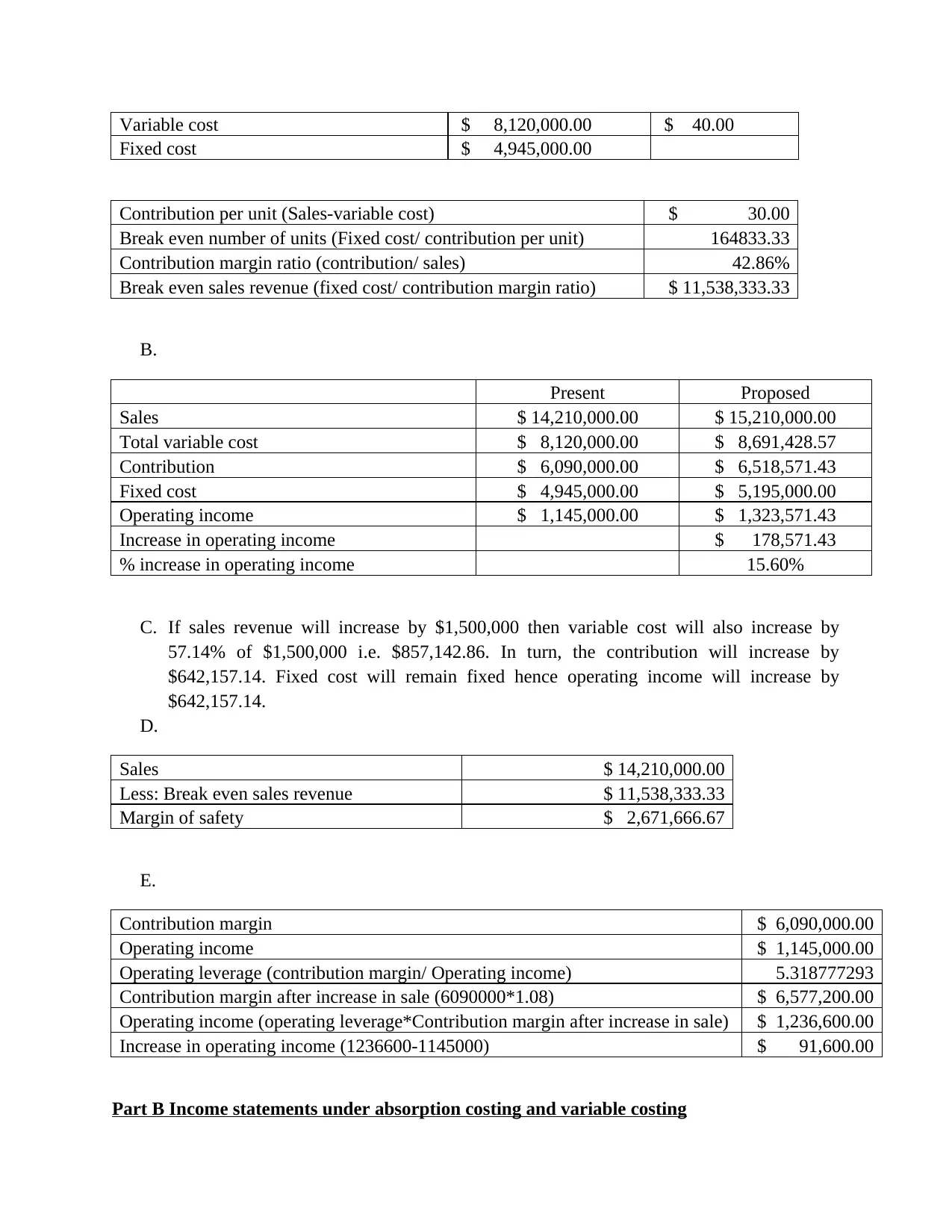
Variable cost $ 8,120,000.00 $ 40.00
Fixed cost $ 4,945,000.00
Contribution per unit (Sales-variable cost) $ 30.00
Break even number of units (Fixed cost/ contribution per unit) 164833.33
Contribution margin ratio (contribution/ sales) 42.86%
Break even sales revenue (fixed cost/ contribution margin ratio) $ 11,538,333.33
B.
Present Proposed
Sales $ 14,210,000.00 $ 15,210,000.00
Total variable cost $ 8,120,000.00 $ 8,691,428.57
Contribution $ 6,090,000.00 $ 6,518,571.43
Fixed cost $ 4,945,000.00 $ 5,195,000.00
Operating income $ 1,145,000.00 $ 1,323,571.43
Increase in operating income $ 178,571.43
% increase in operating income 15.60%
C. If sales revenue will increase by $1,500,000 then variable cost will also increase by
57.14% of $1,500,000 i.e. $857,142.86. In turn, the contribution will increase by
$642,157.14. Fixed cost will remain fixed hence operating income will increase by
$642,157.14.
D.
Sales $ 14,210,000.00
Less: Break even sales revenue $ 11,538,333.33
Margin of safety $ 2,671,666.67
E.
Contribution margin $ 6,090,000.00
Operating income $ 1,145,000.00
Operating leverage (contribution margin/ Operating income) 5.318777293
Contribution margin after increase in sale (6090000*1.08) $ 6,577,200.00
Operating income (operating leverage*Contribution margin after increase in sale) $ 1,236,600.00
Increase in operating income (1236600-1145000) $ 91,600.00
Part B Income statements under absorption costing and variable costing
Fixed cost $ 4,945,000.00
Contribution per unit (Sales-variable cost) $ 30.00
Break even number of units (Fixed cost/ contribution per unit) 164833.33
Contribution margin ratio (contribution/ sales) 42.86%
Break even sales revenue (fixed cost/ contribution margin ratio) $ 11,538,333.33
B.
Present Proposed
Sales $ 14,210,000.00 $ 15,210,000.00
Total variable cost $ 8,120,000.00 $ 8,691,428.57
Contribution $ 6,090,000.00 $ 6,518,571.43
Fixed cost $ 4,945,000.00 $ 5,195,000.00
Operating income $ 1,145,000.00 $ 1,323,571.43
Increase in operating income $ 178,571.43
% increase in operating income 15.60%
C. If sales revenue will increase by $1,500,000 then variable cost will also increase by
57.14% of $1,500,000 i.e. $857,142.86. In turn, the contribution will increase by
$642,157.14. Fixed cost will remain fixed hence operating income will increase by
$642,157.14.
D.
Sales $ 14,210,000.00
Less: Break even sales revenue $ 11,538,333.33
Margin of safety $ 2,671,666.67
E.
Contribution margin $ 6,090,000.00
Operating income $ 1,145,000.00
Operating leverage (contribution margin/ Operating income) 5.318777293
Contribution margin after increase in sale (6090000*1.08) $ 6,577,200.00
Operating income (operating leverage*Contribution margin after increase in sale) $ 1,236,600.00
Increase in operating income (1236600-1145000) $ 91,600.00
Part B Income statements under absorption costing and variable costing
Paraphrase This Document
Need a fresh take? Get an instant paraphrase of this document with our AI Paraphraser

A.
Beginning finished goods Units 8200
Add: Produced finished goods Units 200000
Total 208200
Less: Sold finished goods Units 204300
Ending inventory units 3900
Direct material cost per unit $ 2.85
Direct labor cost per unit $ 1.92
Variable Overhead cost per unit $ 1.60
Fixed Overhead cost per unit (180000/200000) $ 0.90
Total per-unit inventory cost $ 7.27
Ending inventory units 3900
Total per-unit inventory cost $ 7.27
Total cost of ending inventory $ 28,353
B.
Sales (204300*9) $ 1,838,700.00
Less: Cost of goods sold (204300*7.27) $ 1,485,261.00
Gross margin $ 353,439.00
Less: Selling and administration expenses
Fixed Selling and administration expenses $ 96,000.00
Variable Selling and administration expenses (204300*0.9) $ 183,870.00
Operating income $ 73,569.00
C.
Direct material cost per unit $ 2.85
Direct labor cost per unit $ 1.92
Variable Overhead cost per unit $ 1.60
Total per-unit inventory cost $ 6.37
Yes, total per-unit inventory cost under variable costing and under absorption costing is differ
from each other because variable costing approach does not consider the per unit fixed the cost
of production in the per-unit inventory cost but absorption costing approach considers the per
unit fixed the cost of production in the per-unit inventory cost.
Beginning finished goods Units 8200
Add: Produced finished goods Units 200000
Total 208200
Less: Sold finished goods Units 204300
Ending inventory units 3900
Direct material cost per unit $ 2.85
Direct labor cost per unit $ 1.92
Variable Overhead cost per unit $ 1.60
Fixed Overhead cost per unit (180000/200000) $ 0.90
Total per-unit inventory cost $ 7.27
Ending inventory units 3900
Total per-unit inventory cost $ 7.27
Total cost of ending inventory $ 28,353
B.
Sales (204300*9) $ 1,838,700.00
Less: Cost of goods sold (204300*7.27) $ 1,485,261.00
Gross margin $ 353,439.00
Less: Selling and administration expenses
Fixed Selling and administration expenses $ 96,000.00
Variable Selling and administration expenses (204300*0.9) $ 183,870.00
Operating income $ 73,569.00
C.
Direct material cost per unit $ 2.85
Direct labor cost per unit $ 1.92
Variable Overhead cost per unit $ 1.60
Total per-unit inventory cost $ 6.37
Yes, total per-unit inventory cost under variable costing and under absorption costing is differ
from each other because variable costing approach does not consider the per unit fixed the cost
of production in the per-unit inventory cost but absorption costing approach considers the per
unit fixed the cost of production in the per-unit inventory cost.
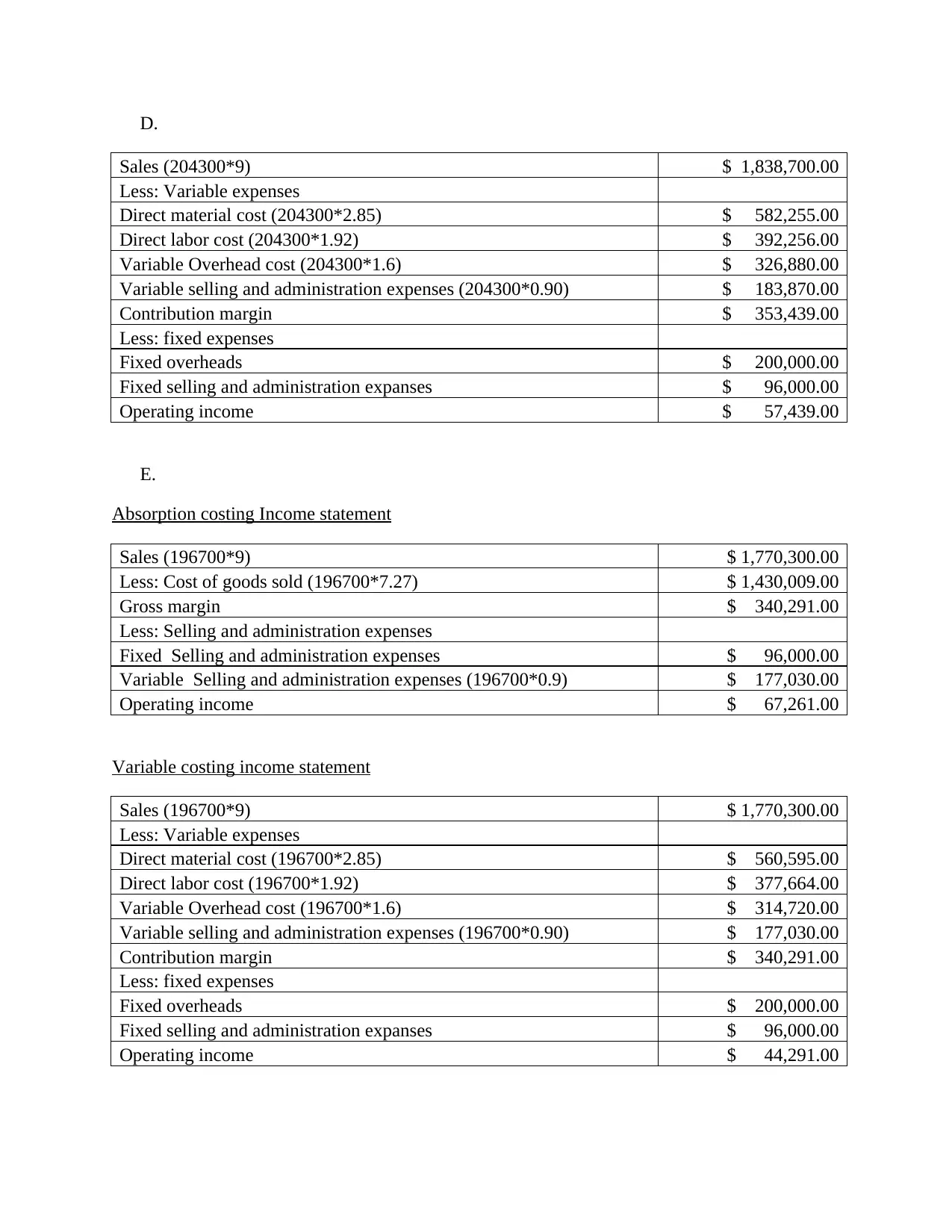
D.
Sales (204300*9) $ 1,838,700.00
Less: Variable expenses
Direct material cost (204300*2.85) $ 582,255.00
Direct labor cost (204300*1.92) $ 392,256.00
Variable Overhead cost (204300*1.6) $ 326,880.00
Variable selling and administration expenses (204300*0.90) $ 183,870.00
Contribution margin $ 353,439.00
Less: fixed expenses
Fixed overheads $ 200,000.00
Fixed selling and administration expanses $ 96,000.00
Operating income $ 57,439.00
E.
Absorption costing Income statement
Sales (196700*9) $ 1,770,300.00
Less: Cost of goods sold (196700*7.27) $ 1,430,009.00
Gross margin $ 340,291.00
Less: Selling and administration expenses
Fixed Selling and administration expenses $ 96,000.00
Variable Selling and administration expenses (196700*0.9) $ 177,030.00
Operating income $ 67,261.00
Variable costing income statement
Sales (196700*9) $ 1,770,300.00
Less: Variable expenses
Direct material cost (196700*2.85) $ 560,595.00
Direct labor cost (196700*1.92) $ 377,664.00
Variable Overhead cost (196700*1.6) $ 314,720.00
Variable selling and administration expenses (196700*0.90) $ 177,030.00
Contribution margin $ 340,291.00
Less: fixed expenses
Fixed overheads $ 200,000.00
Fixed selling and administration expanses $ 96,000.00
Operating income $ 44,291.00
Sales (204300*9) $ 1,838,700.00
Less: Variable expenses
Direct material cost (204300*2.85) $ 582,255.00
Direct labor cost (204300*1.92) $ 392,256.00
Variable Overhead cost (204300*1.6) $ 326,880.00
Variable selling and administration expenses (204300*0.90) $ 183,870.00
Contribution margin $ 353,439.00
Less: fixed expenses
Fixed overheads $ 200,000.00
Fixed selling and administration expanses $ 96,000.00
Operating income $ 57,439.00
E.
Absorption costing Income statement
Sales (196700*9) $ 1,770,300.00
Less: Cost of goods sold (196700*7.27) $ 1,430,009.00
Gross margin $ 340,291.00
Less: Selling and administration expenses
Fixed Selling and administration expenses $ 96,000.00
Variable Selling and administration expenses (196700*0.9) $ 177,030.00
Operating income $ 67,261.00
Variable costing income statement
Sales (196700*9) $ 1,770,300.00
Less: Variable expenses
Direct material cost (196700*2.85) $ 560,595.00
Direct labor cost (196700*1.92) $ 377,664.00
Variable Overhead cost (196700*1.6) $ 314,720.00
Variable selling and administration expenses (196700*0.90) $ 177,030.00
Contribution margin $ 340,291.00
Less: fixed expenses
Fixed overheads $ 200,000.00
Fixed selling and administration expanses $ 96,000.00
Operating income $ 44,291.00
⊘ This is a preview!⊘
Do you want full access?
Subscribe today to unlock all pages.

Trusted by 1+ million students worldwide
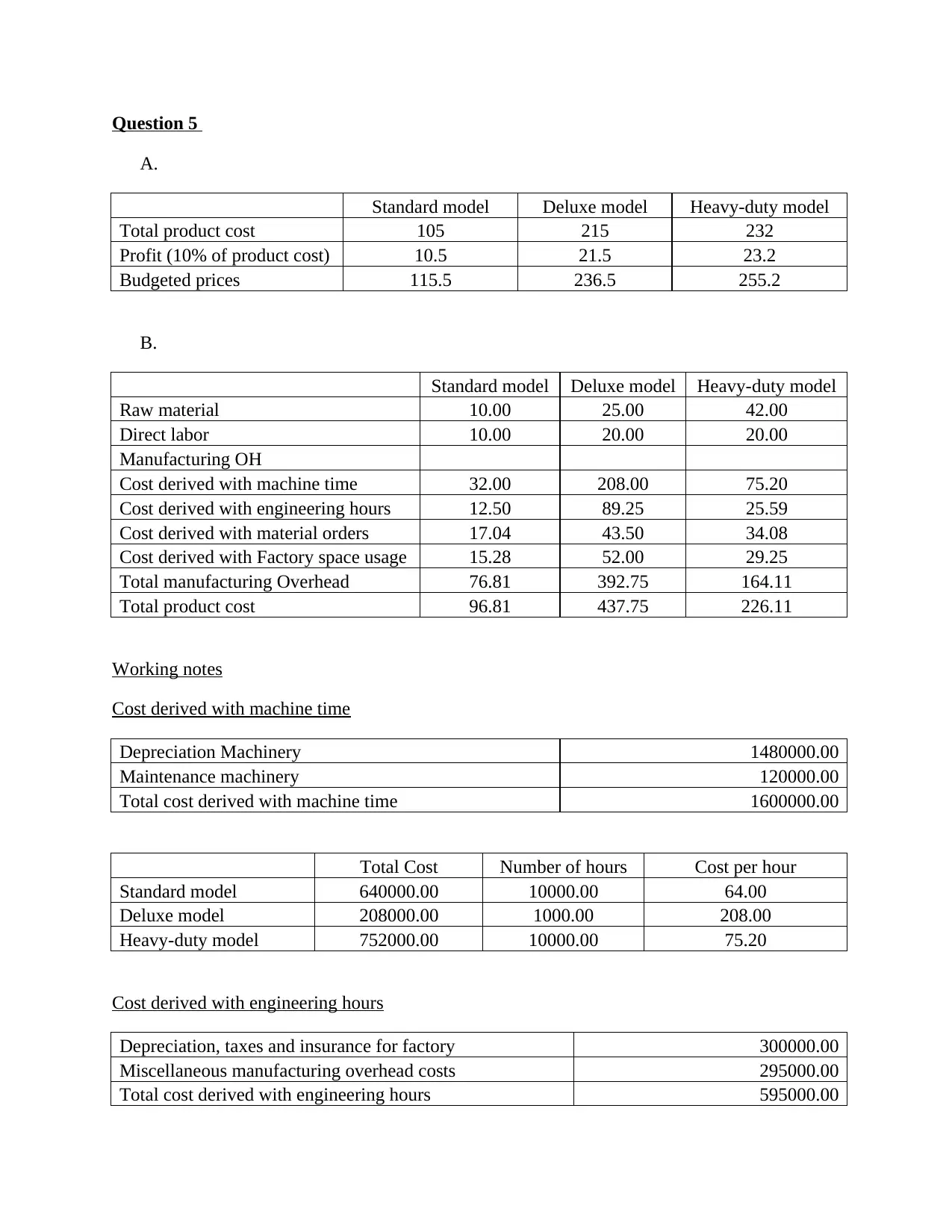
Question 5
A.
Standard model Deluxe model Heavy-duty model
Total product cost 105 215 232
Profit (10% of product cost) 10.5 21.5 23.2
Budgeted prices 115.5 236.5 255.2
B.
Standard model Deluxe model Heavy-duty model
Raw material 10.00 25.00 42.00
Direct labor 10.00 20.00 20.00
Manufacturing OH
Cost derived with machine time 32.00 208.00 75.20
Cost derived with engineering hours 12.50 89.25 25.59
Cost derived with material orders 17.04 43.50 34.08
Cost derived with Factory space usage 15.28 52.00 29.25
Total manufacturing Overhead 76.81 392.75 164.11
Total product cost 96.81 437.75 226.11
Working notes
Cost derived with machine time
Depreciation Machinery 1480000.00
Maintenance machinery 120000.00
Total cost derived with machine time 1600000.00
Total Cost Number of hours Cost per hour
Standard model 640000.00 10000.00 64.00
Deluxe model 208000.00 1000.00 208.00
Heavy-duty model 752000.00 10000.00 75.20
Cost derived with engineering hours
Depreciation, taxes and insurance for factory 300000.00
Miscellaneous manufacturing overhead costs 295000.00
Total cost derived with engineering hours 595000.00
A.
Standard model Deluxe model Heavy-duty model
Total product cost 105 215 232
Profit (10% of product cost) 10.5 21.5 23.2
Budgeted prices 115.5 236.5 255.2
B.
Standard model Deluxe model Heavy-duty model
Raw material 10.00 25.00 42.00
Direct labor 10.00 20.00 20.00
Manufacturing OH
Cost derived with machine time 32.00 208.00 75.20
Cost derived with engineering hours 12.50 89.25 25.59
Cost derived with material orders 17.04 43.50 34.08
Cost derived with Factory space usage 15.28 52.00 29.25
Total manufacturing Overhead 76.81 392.75 164.11
Total product cost 96.81 437.75 226.11
Working notes
Cost derived with machine time
Depreciation Machinery 1480000.00
Maintenance machinery 120000.00
Total cost derived with machine time 1600000.00
Total Cost Number of hours Cost per hour
Standard model 640000.00 10000.00 64.00
Deluxe model 208000.00 1000.00 208.00
Heavy-duty model 752000.00 10000.00 75.20
Cost derived with engineering hours
Depreciation, taxes and insurance for factory 300000.00
Miscellaneous manufacturing overhead costs 295000.00
Total cost derived with engineering hours 595000.00
Paraphrase This Document
Need a fresh take? Get an instant paraphrase of this document with our AI Paraphraser
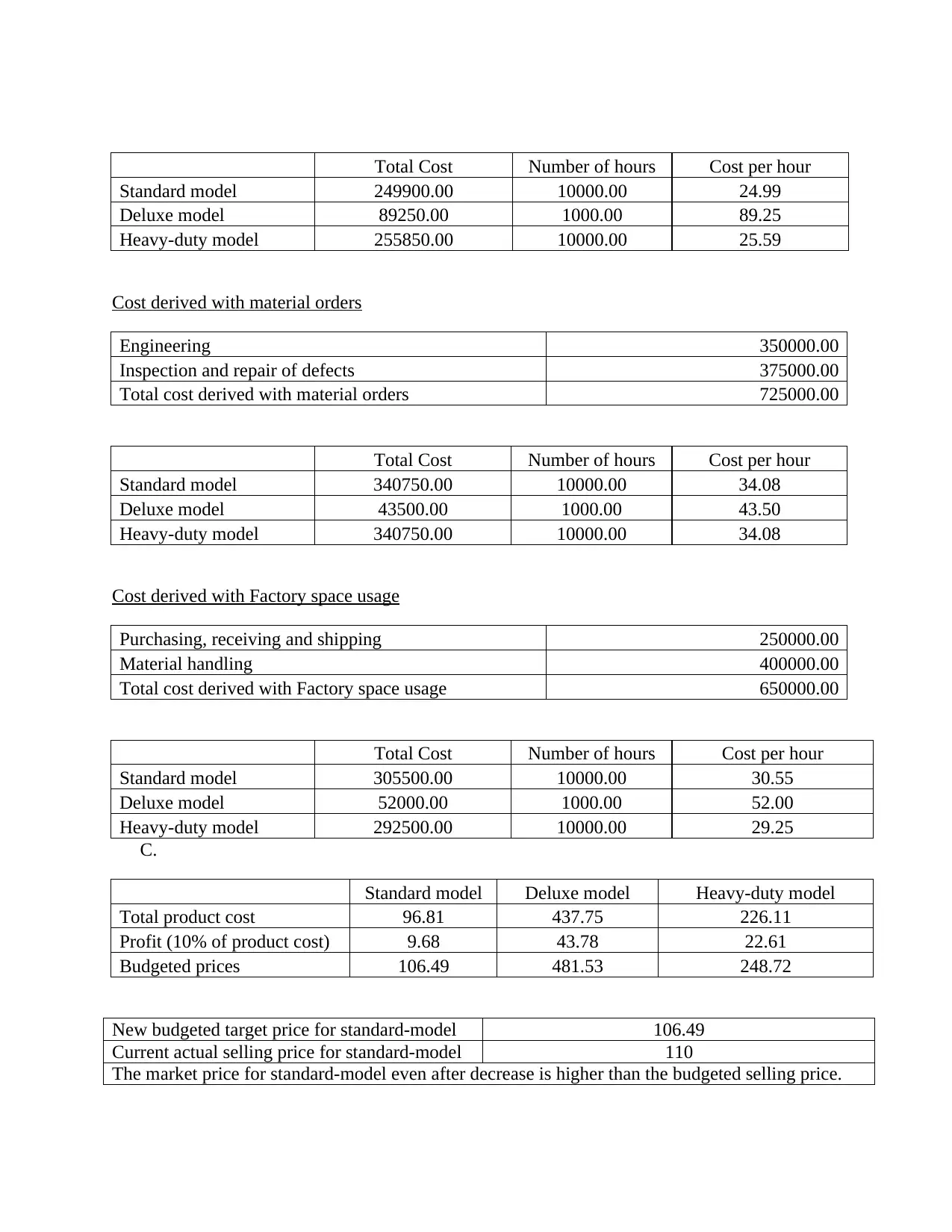
Total Cost Number of hours Cost per hour
Standard model 249900.00 10000.00 24.99
Deluxe model 89250.00 1000.00 89.25
Heavy-duty model 255850.00 10000.00 25.59
Cost derived with material orders
Engineering 350000.00
Inspection and repair of defects 375000.00
Total cost derived with material orders 725000.00
Total Cost Number of hours Cost per hour
Standard model 340750.00 10000.00 34.08
Deluxe model 43500.00 1000.00 43.50
Heavy-duty model 340750.00 10000.00 34.08
Cost derived with Factory space usage
Purchasing, receiving and shipping 250000.00
Material handling 400000.00
Total cost derived with Factory space usage 650000.00
Total Cost Number of hours Cost per hour
Standard model 305500.00 10000.00 30.55
Deluxe model 52000.00 1000.00 52.00
Heavy-duty model 292500.00 10000.00 29.25
C.
Standard model Deluxe model Heavy-duty model
Total product cost 96.81 437.75 226.11
Profit (10% of product cost) 9.68 43.78 22.61
Budgeted prices 106.49 481.53 248.72
New budgeted target price for standard-model 106.49
Current actual selling price for standard-model 110
The market price for standard-model even after decrease is higher than the budgeted selling price.
Standard model 249900.00 10000.00 24.99
Deluxe model 89250.00 1000.00 89.25
Heavy-duty model 255850.00 10000.00 25.59
Cost derived with material orders
Engineering 350000.00
Inspection and repair of defects 375000.00
Total cost derived with material orders 725000.00
Total Cost Number of hours Cost per hour
Standard model 340750.00 10000.00 34.08
Deluxe model 43500.00 1000.00 43.50
Heavy-duty model 340750.00 10000.00 34.08
Cost derived with Factory space usage
Purchasing, receiving and shipping 250000.00
Material handling 400000.00
Total cost derived with Factory space usage 650000.00
Total Cost Number of hours Cost per hour
Standard model 305500.00 10000.00 30.55
Deluxe model 52000.00 1000.00 52.00
Heavy-duty model 292500.00 10000.00 29.25
C.
Standard model Deluxe model Heavy-duty model
Total product cost 96.81 437.75 226.11
Profit (10% of product cost) 9.68 43.78 22.61
Budgeted prices 106.49 481.53 248.72
New budgeted target price for standard-model 106.49
Current actual selling price for standard-model 110
The market price for standard-model even after decrease is higher than the budgeted selling price.
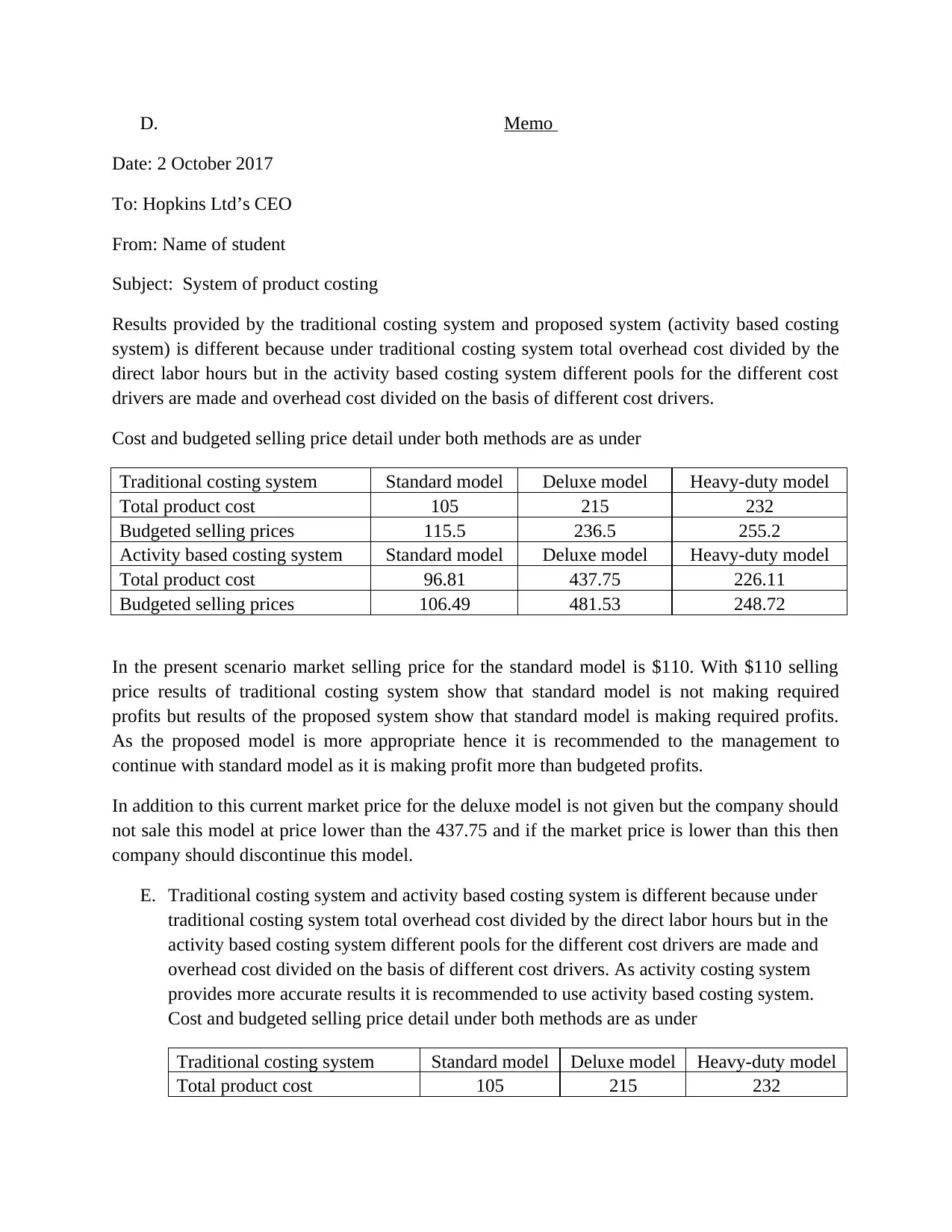
D. Memo
Date: 2 October 2017
To: Hopkins Ltd’s CEO
From: Name of student
Subject: System of product costing
Results provided by the traditional costing system and proposed system (activity based costing
system) is different because under traditional costing system total overhead cost divided by the
direct labor hours but in the activity based costing system different pools for the different cost
drivers are made and overhead cost divided on the basis of different cost drivers.
Cost and budgeted selling price detail under both methods are as under
Traditional costing system Standard model Deluxe model Heavy-duty model
Total product cost 105 215 232
Budgeted selling prices 115.5 236.5 255.2
Activity based costing system Standard model Deluxe model Heavy-duty model
Total product cost 96.81 437.75 226.11
Budgeted selling prices 106.49 481.53 248.72
In the present scenario market selling price for the standard model is $110. With $110 selling
price results of traditional costing system show that standard model is not making required
profits but results of the proposed system show that standard model is making required profits.
As the proposed model is more appropriate hence it is recommended to the management to
continue with standard model as it is making profit more than budgeted profits.
In addition to this current market price for the deluxe model is not given but the company should
not sale this model at price lower than the 437.75 and if the market price is lower than this then
company should discontinue this model.
E. Traditional costing system and activity based costing system is different because under
traditional costing system total overhead cost divided by the direct labor hours but in the
activity based costing system different pools for the different cost drivers are made and
overhead cost divided on the basis of different cost drivers. As activity costing system
provides more accurate results it is recommended to use activity based costing system.
Cost and budgeted selling price detail under both methods are as under
Traditional costing system Standard model Deluxe model Heavy-duty model
Total product cost 105 215 232
Date: 2 October 2017
To: Hopkins Ltd’s CEO
From: Name of student
Subject: System of product costing
Results provided by the traditional costing system and proposed system (activity based costing
system) is different because under traditional costing system total overhead cost divided by the
direct labor hours but in the activity based costing system different pools for the different cost
drivers are made and overhead cost divided on the basis of different cost drivers.
Cost and budgeted selling price detail under both methods are as under
Traditional costing system Standard model Deluxe model Heavy-duty model
Total product cost 105 215 232
Budgeted selling prices 115.5 236.5 255.2
Activity based costing system Standard model Deluxe model Heavy-duty model
Total product cost 96.81 437.75 226.11
Budgeted selling prices 106.49 481.53 248.72
In the present scenario market selling price for the standard model is $110. With $110 selling
price results of traditional costing system show that standard model is not making required
profits but results of the proposed system show that standard model is making required profits.
As the proposed model is more appropriate hence it is recommended to the management to
continue with standard model as it is making profit more than budgeted profits.
In addition to this current market price for the deluxe model is not given but the company should
not sale this model at price lower than the 437.75 and if the market price is lower than this then
company should discontinue this model.
E. Traditional costing system and activity based costing system is different because under
traditional costing system total overhead cost divided by the direct labor hours but in the
activity based costing system different pools for the different cost drivers are made and
overhead cost divided on the basis of different cost drivers. As activity costing system
provides more accurate results it is recommended to use activity based costing system.
Cost and budgeted selling price detail under both methods are as under
Traditional costing system Standard model Deluxe model Heavy-duty model
Total product cost 105 215 232
⊘ This is a preview!⊘
Do you want full access?
Subscribe today to unlock all pages.

Trusted by 1+ million students worldwide
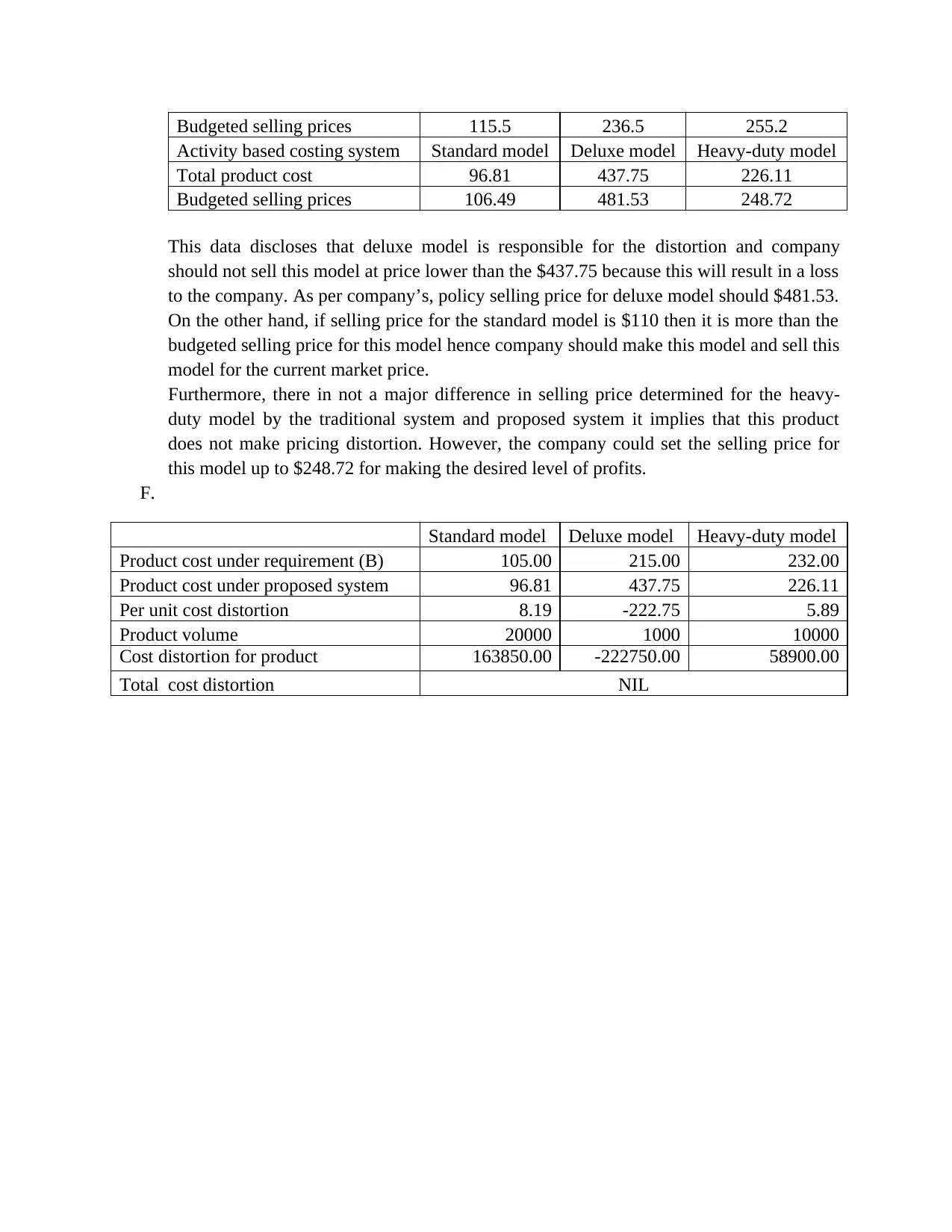
Budgeted selling prices 115.5 236.5 255.2
Activity based costing system Standard model Deluxe model Heavy-duty model
Total product cost 96.81 437.75 226.11
Budgeted selling prices 106.49 481.53 248.72
This data discloses that deluxe model is responsible for the distortion and company
should not sell this model at price lower than the $437.75 because this will result in a loss
to the company. As per company’s, policy selling price for deluxe model should $481.53.
On the other hand, if selling price for the standard model is $110 then it is more than the
budgeted selling price for this model hence company should make this model and sell this
model for the current market price.
Furthermore, there in not a major difference in selling price determined for the heavy-
duty model by the traditional system and proposed system it implies that this product
does not make pricing distortion. However, the company could set the selling price for
this model up to $248.72 for making the desired level of profits.
F.
Standard model Deluxe model Heavy-duty model
Product cost under requirement (B) 105.00 215.00 232.00
Product cost under proposed system 96.81 437.75 226.11
Per unit cost distortion 8.19 -222.75 5.89
Product volume 20000 1000 10000
Cost distortion for product 163850.00 -222750.00 58900.00
Total cost distortion NIL
Activity based costing system Standard model Deluxe model Heavy-duty model
Total product cost 96.81 437.75 226.11
Budgeted selling prices 106.49 481.53 248.72
This data discloses that deluxe model is responsible for the distortion and company
should not sell this model at price lower than the $437.75 because this will result in a loss
to the company. As per company’s, policy selling price for deluxe model should $481.53.
On the other hand, if selling price for the standard model is $110 then it is more than the
budgeted selling price for this model hence company should make this model and sell this
model for the current market price.
Furthermore, there in not a major difference in selling price determined for the heavy-
duty model by the traditional system and proposed system it implies that this product
does not make pricing distortion. However, the company could set the selling price for
this model up to $248.72 for making the desired level of profits.
F.
Standard model Deluxe model Heavy-duty model
Product cost under requirement (B) 105.00 215.00 232.00
Product cost under proposed system 96.81 437.75 226.11
Per unit cost distortion 8.19 -222.75 5.89
Product volume 20000 1000 10000
Cost distortion for product 163850.00 -222750.00 58900.00
Total cost distortion NIL
1 out of 13
Related Documents

Your All-in-One AI-Powered Toolkit for Academic Success.
+13062052269
info@desklib.com
Available 24*7 on WhatsApp / Email
Unlock your academic potential
© 2024 | Zucol Services PVT LTD | All rights reserved.